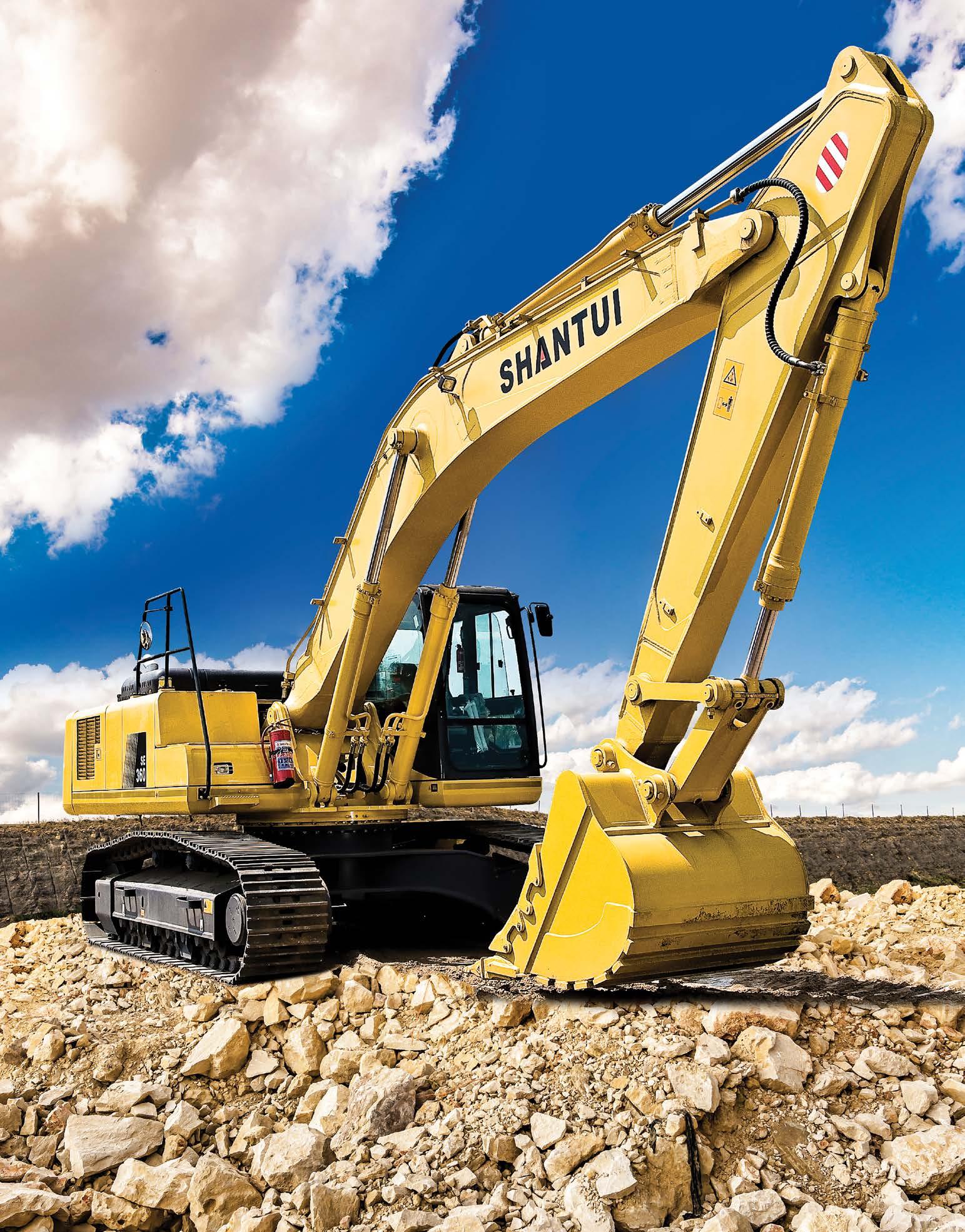

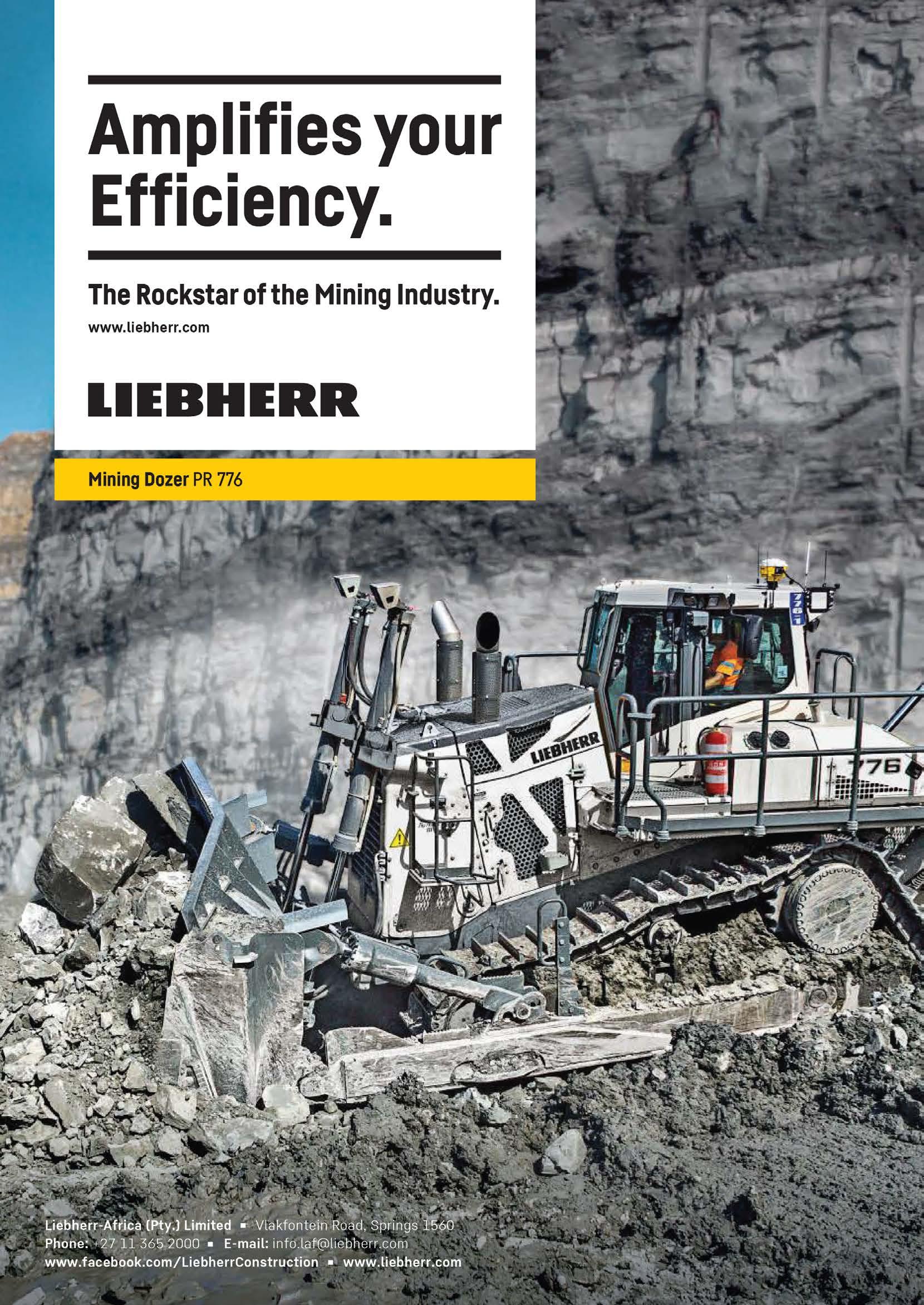
The ‘strength in numbers’ idiom should be an indispensable guide for all industries that seek to drive collaborative success. This is chiefly true for the extractive industry, particularly the quarrying sector which, in my view, needs to speak with one voice to better engage with policymakers, and to give a voice to companies, big or small.
The complex nature of the mining sector consequently involves many different laws and institutions, compounded by challenges involving both gaps in legislation and its implementation. It is therefore imperative for the industry to find better ways to engage with policymakers in order to influence sustainable development.
I am particularly impressed by ASPASA’s stance when it comes to collaboration. In my recent one-on-one with Letisha van den Berg, the new director of the surface mining industry association, she reiterated the importance of collaboration to drive the industry forward. During her first two months in charge, one of her key priorities has been to maximise collaboration with other industry bodies.
She reckons that if the industry is to successfully engage policymakers, it needs to have a collective voice. If there are a lot of disjointed voices, every single association or company will go to government with a different request despite having similar issues. Bringing those voices together makes the message stronger, clearer and more likely to succeed.
the industry insists that it should be from the muckpile. ASPASA is exploring ways to join forces with other industry bodies on this battle. If successful, that will offer key economic benefits for the industry.
To succeed in such complex legal challenges, mining industry bodies should build strong alliances with one another. By banding together, the industry definitely commands a stronger voice and has decidedly more influence. Collective lobbying and government relations efforts are areas where collaboration is particularly crucial. Alone the voice of a single association or a company will have less impact, but together the industry is able to get the attention of key policymakers. Apart from government liaison, collaboration can play a crucial role in advancing training. We would all agree that the industry should be investing more time and resources in skills development. Based on this understanding, ASPASA and the Institute of Quarrying have reached an agreement to pull resources together to advance industry training.
Skills development is an area of critical importance for both organisations. They acknowledge that the current skills shortage, exacerbated by the brain drain, is a major challenge, not only for the quarrying industry, but for the mining sector at large. This is particularly hostile to business growth.
Email:
munesu@quarryingafrica.com
A case in point is the royalties dispute with the South African Revenue Services (SARS). Over the years, payment of royalties has been a hotly contested issue among quarry owners and operators as to where the value of a mined product needs to be determined in order to calculate exact payments.
The industry’s dispute with SARS exists over the first point of sale at which the value of royalties needs to be calculated. The ‘taxman’ argues that royalties should be calculated from the stockpile, while
In addition, collaboration plays a crucial role in the development of consistent best practice and standards for the industry. Some of the benefits of adopting voluntary best practices and standards include data sharing, streamlined systems and processes, and increased operational efficiencies. More importantly, it translates into unparalleled health and safety standards, thus driving the industry’s quest for zero harm.
In my view, for companies that do not have a compliance budget yet, associations can help because they can amplify smaller voices higher up the chain. That allows them to tap into the collective voice of the industry. a
Publishing Editor: Munesu Shoko
Sub Editor: Glynnis Koch
Admin: Linda T. Chisi
Design: Kudzo Mzire Maputire
Web Manager: Thina Bhebhe
Quarrying Africa is the information hub for the sub-Saharan African quarrying sector. It is a valued reference tool positioned as a must-read for the broader spectrum of the aggregates value chain, from quarry operators and aggregate retailers, to concrete and cement producers, mining contractors, aggregate haulage companies and the supply chain at large.
Quarrying Africa, published by DueNorth Media Africa, makes constant effort to ensure that content is accurate before publication. The views expressed in the articles reflect the source(s) opinions and are not necessarily the views of the publisher and editor.
The opinions, beliefs and viewpoints expressed by the various thought leaders and contributors do not necessarily reflect the opinions, beliefs and viewpoints of the Quarrying Africa team.
Quarrying Africa prides itself on the educational content published via www.quarryingafrica.com and in Quarrying Africa magazine in print. We believe knowledge is power, which is why we strive to cover topics that affect the quarrying value chain at large.
Printed by:
Contact Information
Email: munesu@quarryingafrica.com
Cell: +27 (0)73 052 4335
Amid rising costs of operation in a low growth environment, quarry owners should re-evaluate their procurement strategies. This is the view of Marcus du Toit, Equipment Sales manager at Handax Machinery, the Shantui distributor in southern Africa, who stresses that, now more than ever, fleet owners must emphasise price competitiveness, coupled with quality, sufficient functionality, reliability and sound backup support, in order to achieve a quick and high return on investment (ROI), writes Munesu Shoko.
Buying heavy equipment for quarrying operations represents a significant capital investment. Given that quarrying is a capitalintensive business with razor-thin margins, quarry owners should therefore make informed decisions when it is time to replace or expand their fleets of yellow metal equipment. According to Du Toit, ROI should be at the centre of every procurement decision when it comes to mission-critical and big-ticket purchases such as earthmoving equipment.
For Du Toit, it is about finding the balance between quality and cost. “It is about procuring equipment with the reliability and availability needed to execute the required work as efficiently and safely as possible. The balance between quality and price must be a key consideration in every procurement decision and that is where brands such as Shantui offer great value,” he says.
Buying heavy equipment for quarrying operations represents a significant capital investment
Given that quarrying is a capital-intensive business with razor-thin margins, quarry owners should therefore make informed decisions when it is time to replace or expand their fleets of yellow metal equipment
Return on investment should be at the centre of every procurement decision when it comes to mission-critical and big-ticket purchases such as earthmoving equipment
In the decision-making process, one of the critical considerations should be the ability to source all of the end user’s equipment needs from a single supplier
Once dismissed as low-end ‘upstarts’, Chinese equipment brands have built up their capabilities and now compete head-to-head with multinational companies across many global markets. The ascent of these products has been fuelled in part by the rise of the ‘value’ market in rapidly developing economies, where customers have boosted demand for ‘good enough’ products that emphasise price competitiveness and sufficient functionality rather than supporting the most advanced technologies.
Customers, says Du Toit, are becoming more open-minded about trying non-premium products in search of the right balance between cost and productivity. Consequently, the trend has given rise to a global shift towards competitively priced yellow metal equipment solutions, better known as value brands.
In fact, available industry statistics show that value brands currently constitute about 80% of
its productive and efficient
global construction machine sales. However, this is more prevalent in developing markets. To give context, Chinese brands now have a 60% share of the African wheel loader market.
This, says Du Toit, is a clear indication that nonsophisticated offerings are evolving. “Innovation is traditionally defined by sophisticated technologies, but in these challenging economic conditions, it shouldn’t always be the case. Some of the best ideas, especially in today’s designs of yellow metal equipment, are very simple, based on a clear and deep understanding of customers’ needs – finding balance between price and productivity,” he says.
Quarrying customers seeking a quick and high return on their equipment investments can take advantage of Shantui’s extensive excavator, dozer, grader and wheel loader ranges. “Our competitive edge is that these offerings are affordable and are built to last. Coupled with a growing support footprint, the resale value of the units is incredibly competitive,” says Du Toit.
Since its arrival in the southern African market back in 2007, the Chinese maker has particularly proved its mettle in the dozer market which has traditionally been dominated by premium OEMs. In fact, Shantui is a force to be reckoned with in the global dozer market. With a whopping 60% share of its domestic Chinese dozer market, the company holds a 15-20% share of the global dozer market, confirms Du Toit.
In 2010, Shantui went on to become the largest producer by volume of bulldozers globally, making over 10 000 units that year, thus representing two in five crawler-type dozers produced in the world. Currently, the company produces in excess of 15 000 units a year. Apart from dozers, over the years Shantui has grown
its excavator and wheel loader market share, both locally and in the global market, further reinforcing its competitiveness in the global earthmoving equipment market.
“Locally, our market share continues to grow at a rapid pace. Key to the growth of the product are the competitiveness of our pricing, quality of machinery and aftermarket support,” says Du Toit.
To further boost its aftermarket regime, Handax Machinery will embark on an aggressive rollout of service dealerships in the next 24 months. These will be established across South Africa and neighbouring countries, including Namibia, Botswana and Zimbabwe, as well as Zambia and the DRC.
“In addition, we will continue to increase our stock holding of machines and parts across our dealer network and at the head office. Shantui will become a brand for the smart, the visionaries who know that ROI is what makes their business work, thus offering customers the value that works,” he says.
In the decision-making process, Du Toit says one of the critical considerations should be the ability to source all of the end user’s equipment needs from a single supplier. One of Shantui’s key strengths is the ability to offer a total yellow metal solution from one stable, all the way from graders and bulldozers to wheel loaders and excavators.
“It’s much simpler in the long run to deal with a single equipment provider. Having to purchase equipment that drives your business from different suppliers and being serviced by all the different dealers can be time-consuming and costly. Working with an established supplier means you will have access to reliable support, as well as the parts and equipment you depend on for maximum uptime,” concludes Du Toit. a
I started out as an admin clerk at an operation in KwaZuluNatal. In this role, I was more of a ‘jack of all trades’, which exposed me to the various functions on site, all the way from technical and plant maintenance to cost management, and everything in between.
Having taken the reins as the new director of ASPASA at the start of the year, Letisha van den Berg has hit the ground running, with a number of initiatives already in place to help deal with some of the pressing matters facing the industry. In a one-on-one with Quarrying Africa, she reiterates her commitment to ‘give a voice’ to small-scale miners. By Munesu Shoko.
Quarries and other small-scale miners play a crucial role in the development of any economy. As well as providing essential construction materials, these operations stimulate local communities through investment and by providing jobs. Yet, in South Africa, they are currently faced with a number of challenges that threaten their existence. The lack of meaningful infrastructure investment in the past 10 years has in particular presented a major economic hurdle for the industry.
In addition to tough economic challenges, small-scale miners have to grapple with their legislative obligations. Compliance by its very nature costs money, and a lot of it, which is why Van den Berg has set her sights on providing small-scale
miners with cost-effective solutions to comply.
Her passion for the small-scale mining industry is not only rooted in her 25-year experience in the quarrying industry, but also in the fact that she kick-started her decorated career at a small AfriSam (then Alpha Cement) aggregate and readymix operation back in 1998.
“I started out as an admin clerk at an operation in KwaZulu-Natal. In this role, I was more of a ‘jack of all trades’, which exposed me to the various functions on site, all the way from technical and plant maintenance to cost management, and everything in between,” she says. “Managing costs for such a small operation was particularly critical, and we successfully found ways to comply within our limited means. That’s where my passion for small-scale miners stems from because I have firsthand experience of how things work in their world.”
However, from the onset, Van den Berg had a great passion for health and safety. In 2003, she moved to AfriSam’s Verulam Quarry, where she was granted her wish to focus on health and safety, and the rest is history. Two years later, she was appointed AfriSam’s regional safety practitioner for KwaZulu-Natal, before she assumed the role of group health and safety manager for the company’s Construction Materials Division in 2010.
After 17 years at AfriSam, she moved to Afrimat in 2017, where she was appointed group health and safety executive, a role she held until her recent appointment as the director of ASPASA in January this year.
Leveraging her wealth of health and safety management experience, Van den Berg is determined to further accelerate the industry’s drive for zero harm. While ASPASA members have achieved a remarkable seven-year fatality-free feat, she believes that a lot more can be done to eliminate accidents and injuries on sites.
“We cannot deny the fact that our industry works in a potentially dangerous environment. However, having been in the industry for so long, I understand the reasons behind some of the injuries we still record at our member operations. One of my immediate objectives is to find ways to curb these injuries, which is key to our quest to achieve zero harm,” she says.
On the health and safety front, Van den Berg’s tenure at ASPASA coincides with the recent
gazetting of the Collision Avoidance Systems (CAS) regulations by the Department of Mineral Resources and Energy (DMRE).
During the Zero Harm Forum of the Minerals Council South Africa (MINCOSA) in October 2022, the chief inspector of mines (CIOM) expressed his concerns about trackless mobile machinery (TMM)- related fatalities and the slow implementation of collision avoidance systems. He consequently requested for the technology readiness date of December 2023 to be pushed forward to January 2023. At the Mine Health Safety Council summit last year, organised labour also advocated for early technology implementation.
In late 2022, MINCOSA met with the TMM technical team and offered reasons why this was not practical. However, the 17 TMM-related fatalities at both surface and underground operations did not help the industry’s case, says Van den Berg. On December 6, 2022, the Minister of Mineral Resources and Energy subsequently signed an order for sub-regulations 8.10.1.2 (b) and 8.10.2.1 (b) in Chapter 8 of the Mine Health and Safety Act, 1996, to come into force.
However, advises Van den Berg, operations can ask for exemption from all or part of the requirements of the Act. The Act gives provision
Leveraging her wealth of health and safety management experience, new director of ASPASA, Letisha Van den Berg, is determined to further accelerate the industry’s drive for zero harm
Under Van den Berg’s leadership, ASPASA will further cast the spotlight on environmental compliance
To help ease the burden of economic challenges, Van den Berg has implemented a levy structure change
To help the industry close the skills gap, ASPASA has taken a decision to work closely with the Institute of Quarrying Southern Africa
that mines may request an exemption from the Minister. If satisfied that the employer has consulted appropriately with the affected employees or their representatives, the Minister may exempt the employer from any or all of the provisions of the Act or from a notice or instruction under this Act.
indicated that they are waiting for the head office to give guidance. We are of the view that the department must first determine how this legislation will be enforced,” she says.
Another option is to engage with OEMs on the technology, its availability and warranties. Mines can also apply for an exemption from the requirements of the Act.
On
“If any mine owner decides to go the exemption route, firstly it is important to explain how they are going to manage the ‘significant risk’ on site – that is principal,” she says. “Then they also need to provide the basis or references upon which past and future CPS ecosystems are based on. These include traffic management processes, TMM fleet size, competencies of operators and an explanation of their environment (production throughput, blasting frequency, tonnes moved and employee complement).”
“The motivation for exemption can also include issues such as skills shortage and the prohibitive costs of installing CAS systems at small surface mining operations. The motivation, however, should be based on how the operation is going to reduce significant risk, citing tasks that have been completed to date and those in the process of being implemented,” she adds.
Based on feedback from multiple industry stakeholders and those in the legal field, ASPASA has determined several options for its members. “Firstly, members can engage with the DMRE regarding the way forward in their respective regions. We have already spoken to the DMRE in various regions, and some have indicated that there is a three-month window for implementation, as with any other Code of Practice that is gazetted,” she says. “Others have
6,
“Operations should use this time to reassess their risk-based approach and confirm that no CAS installation is required as reasonably practicable measures have been implemented and no significant risk to persons exists in terms of diesel/diesel collisions. It is also critical to keep documented proof of the process to present to the DMRE if required,” says Van den Berg.
Under Van den Berg’s leadership, ASPASA will further cast the spotlight on environmental compliance, which in her view will grow in importance to even surpass safety in the near future. “We cannot deny the growing focus on Environmental, Social and Governance (ESG) in the mining sector. It is, however, still a concept that fits into the global environmental plan, but not everything has been legislated yet, but one can see that it’s coming,” she says.
The lack of environmental compliance, she says, can have dire consequences for operations.
“Remember it is one of the key aspects that can lead to the revoking of a mining licence. In my view, it is as important as safety management, but not everybody understands that. To provide context, there are mining CEOs who are in jail and
Over the years, payment of royalties has been a hotly contested issue among quarry owners and operators as to where the value of a mined product needs to be determined in order to calculate exact payments.
some who have paid up to R5-million fines related to the environment.”
One of Van den Berg’s first initiatives in December 2022, well before she even officially started her tenure, was to run a survey to gauge ASPASA members’ sentiment on the growing importance of environmental compliance.
“They all rated their safety and environmental audits highly, but have also asked the association to close some compliance gaps. We will compile all the gaps and see how we can support our members,” she says.
Owing to South Africa’s poor economic performance and a struggling construction industry, the quarrying sector has been under severe pressure over the past few years. “We cannot downplay the economic situation and its impact on our members,” she says. “As an association, we have looked at various ways to help small surface mines to comply in a cost-effective manner.”
To help ease the burden of economic challenges, Van den Berg has implemented a levy structure change, which at the time of writing, was awaiting approval by the association’s management committee (MANCOM).
“As we continue to identify a few roofs that we can take off to unlock further cost benefits for our members, we believe this new levy structure will be a welcome relief for an industry that is reeling from the current economic burden,” she says.
Another key focus area for Van den Berg and her team is the issue of royalties. Over the years, payment of royalties has been a hotly contested issue among quarry owners and operators as to where the value of a mined product needs to be determined in order to calculate exact payments.
The industry’s dispute with the South African Revenue Services (SARS) exists over the first point of sale at which the value of royalties needs to be calculated. The ‘taxman’ argues that royalties
should be calculated from the stockpile, while the industry insists that it should be from the muckpile.
“We are busy exploring ways to join forces with other industry bodies on the royalties battle. If successful, that will offer another economic benefit for our members,” she adds.
Skills development is another area of critical importance for Van den Berg. She acknowledges that the current skills shortage, exacerbated by the brain drain, is a major challenge, not only for the quarrying industry, but for the mining sector at large. This is particularly hostile to business growth.
To help the industry close the skills gap, ASPASA has taken a decision to work closely with the Institute of Quarrying Southern Africa (IQSA).
“One of the first decisions we made was to re-establish our collaboration with IQSA. We are handing over the whole training leg of our service wheel to IQSA. We are therefore looking for a young, dynamic professional to run the training department. We are also looking at starting a mentorship programme. I believe we have some brilliant people within ASPASA who can drive this forward,” she says.
To further enable action on the ground, ASPASA is creating a new level within its setup. Traditionally, there has been the MANCOM and the director. “We are bringing in a new level called Steercom, which is basically a regional chairperson per region,” she says.
In addition, the association has reviewed its service wheel, based on the survey Van den Berg conducted in December. This, she says, will help realign the association’s service offering with industry needs. “We have hit the ground running, with a couple of initiatives already achieved since the start of the year. We look forward to further providing immense value for our members,” concludes Van den Berg. a
Following years of a protracted downturn and successive waves of adversity in recent times, is the South African construction sector in for a breath of fresh air in 2023? In a one-on-one with Quarrying Africa, Elsie Snyman, CEO of Industry Insight, unpacks the state of affairs, the outlook of the industry this year and some trends that are likely to shape the sector in 2023. By Munesu Shoko.
The construction industry has been in decline since 2014, with 2013 being the last year to record any noteworthy growth (6,7%)
Global economic growth is projected at only 3% in 2023, with the local South African economy unlikely to breach a 1% growth rate
The growing contribution of the private sector in economic infrastructure is expected to have a positive impact on the construction industry in 2023
The estimated value of civil projects out to tender increased by 30% in 2022, and could support investment growth in 2023, coming off a low base
As of October 2022, the industry recorded about R251billion worth of high-impact projects that were announced during the year
According to the South African Reserve Bank, the private sector invested close to R120-billion in construction works (typically economic infrastructure) over the three-year period 2019 - 2021
Formal employment in the construction sector fell by 5% on average during the first three quarters of 2022, according to Stats SA’s quarterly employment survey.
From enjoying a surge in infrastructure development in the run up to the 2010 Soccer World Cup, chalking up billions of rands in government infrastructure spending, the South African construction industry has suffered a change of fortune in the last decade. Besides the pandemic, the slower growth comes amid a standstill in infrastructure project flows on the back of reduced government spending.
The construction industry, says Snyman, has been in decline since 2014, with 2013 being the last year to record any noteworthy growth (6,7%). Since then, the industry has declined by an average of 3% per annum, barring the 17% pandemic-influenced drop in 2020.
“The local construction sector is battered; even following the dismal performance in 2020, investment still declined by a further 3,6% in 2021. The trend continued into 2022, with a 6% decline during the first three quarters of the year, influenced by a sharp double-digit decline in investment in non-residential buildings and close to a 10% drop in construction works. However, investment in housing increased by 8,5% in 2021, off the back of a solid real estate market, supported by a lower interest rate environment and the rally in the DIY market at the time,” says Snyman.
Growth, she says, however, slowed to 0,7% for the three quarters in 2022 as higher lending rates cooled down demand for DIY spending.
Formal employment in the construction
sector fell by 5% on average during the first three quarters of 2022, according to Stats SA’s quarterly employment survey, showing the sharpest decline compared to the other economic sectors. This, she says, confirms how the construction sector is bearing the brunt of the current economic catastrophe.
So, what can the industry expect in 2023? It is important to note that global economic growth is projected at only 3% in 2023, with the local South African economy unlikely to breach a 1% growth rate.
“The outlook for 2023 is a mixed bag of optimism and realistic expectations. Lack of infrastructure investment by the public sector has finally caught up, adding significant strain to the local economy, affecting every fibre of economic sustainability, thus slashing hopes for an economic recovery,” says Snyman. Government, she adds, simply cannot continue on the path of disinvestment. With the 2024 elections around the corner, it will face serious repercussions at the polls if there is no sign of serious re-commitment to improving the state of infrastructure in the country. In its October 2022 Medium-Term Budget Policy Statement, the Ministry of Finance alluded to the urgent need for infrastructure investment. On the back of this acceptance of defeat, government is finally opening investment corridors for the private sector.
The growing contribution of the private sector in economic infrastructure is expected to have a positive impact on the construction industry in 2023. As existing infrastructure continues to collapse, says Snyman, government has finally realised that it cannot do it alone.
In its recent report, Industry Insight notes that the lack of involvement by the private sector in critical economic infrastructure development has been highlighted as a major constraint for investment and economic growth. Over the years, government has maintained its stronghold on the supply of energy, rail and water resources, despite failing dismally to maintain these assets. Until it no longer had a choice.
According to the South African Reserve Bank, the private sector invested close to R120-billion in construction works (typically economic infrastructure) over the three-year period 20192021, increasing its contribution to an average of 24% compared to a 20-year average of only 10%.
“For the first time we are seeing a more earnest approach by government to include the private sector in economic infrastructure development, and we hope that the renewable energy sector is just the beginning,” says Snyman. “There is still a long way to go, and we do not expect a quick turnaround in the construction sector, but at best we hope that the rate of decline will start to stabilise with some (albeit limited) growth prospects over the next three years.”
The estimated value of civil projects out to tender increased by 30% in 2022, and could support investment growth in 2023, coming off a low base, she says. Tender activity in terms of the number of projects out to tender, remains depressed (down 19% year-on-year in 2022) meaning there are fewer but higher value projects out to tender.
“This should offer some reprieve to the larger contractors, but as we have seen in recent times, these projects don’t always benefit local contractors. A case in point is SANRAL’s recent awarding of multibillion rand projects to Chinese contractors,” she says.
As of October 2022, the industry recorded about R251-billion worth of high-impact projects that were announced during the year. This includes the R75-billion green hydrogen project announced in January 2022. Projects announced during last year were by far dominated by the renewable energy sector, followed by mixed-use developments.
“There is some capex coming out of the mining sector – given the improved performance in that industry – that will benefit the construction industry. The challenge with these projects is the lengthy timelines associated with the multibillion-rand projects,” she says.
The gradual decline in investment by the general government and state-owned enterprises SOE’s have created a significant infrastructure deficit that has now reached a critical point.
The contribution by the private sector in typically public sector dominated infrastructure has already grown to more than 20% in the last three years.
Snyman adds that the bulk of the high value projects announced in 2021 was dominated by the industrial sector and some of the largescale developments have since come off stream. Industrial construction activity remains strong, and this is probably the only sector in the commercial sector that is showing any potential for growth.
Snyman notes that spending budgetary allocations remains a serious challenge, particularly within local government. It will therefore be critical to ensure that local governments, including Metropolitan areas, have the necessary capacity to plan and implement the necessary infrastructure programmes. The construction industry, she adds, has also had to endure a significant increase in risk over the past few years, while having to deal with near record low profitability levels. “This is simply not sustainable, and we hope that the sector will receive higher levels of government support to mitigate some of these risks, particularly when it comes to extortion by the so called ‘business forums’ that are doing nothing else but promoting criminal behaviour,” concludes Snyman. a
Ahead of the 52nd Institute of Quarrying Southern Africa (IQSA) annual conference, chairman Jeremy Hunter-Smith tells Quarrying Africa that this year’s event will cast the spotlight on the importance of collaboration to drive the industry forward. Other key focus areas will include skills development and networking opportunities for young members. By Munesu Shoko.
Having officially taken the reins as chairman of IQSA at last year’s conference, Hunter-Smith says one of his immediate tasks was to understand and re-evaluate IQSA’s offering to its members and the role it plays in the industry at large, as well as to assess where the association was and where it needed to be.
IQSA, he says, is an industry association that is based on membership for individuals who are passionate about the quarrying industry – those who have made it their career for many years (bringing years of experience across various operations, big and small) and those who want to make it a career path and become the next industry leaders.
“My key focus areas during the first year have been training, networking and the Young Members Network. In terms of training, we have been working hard to create a network of quality service providers that can make a difference to our members, by offering quality, endorsed training,” he says.
Under the leadership of Hunter-Smith, IQSA has also focused its efforts on creating a platform for suppliers to engage with the industry, allowing the supply chain to showcase new products and technology.
“Under the Young Members Network, we have illustrated the opportunity for our young members to tap into the global network within our industry. The idea is to highlight the scope of our industry and its importance to the global economy. Without quarrying, there is no development; aggregates are the ‘foundation’ to any new development,” says Hunter-Smith.
Commenting on some key focus areas for this year’s IQSA conference – which will take place on 13 and 14 April 2023 at Premier Hotel, Umhlanga –Hunter-Smith says there is a need to highlight the importance of collaboration with other industry bodies to unlock training opportunities for young members.
My key focus areas during the first year have been training, networking and the Young Members Network. In terms of training, we have been working hard to create a network of quality service providers that can make a difference to our members, by offering quality, endorsed training.
Jeremy Hunter-Smith, chairman of the Institute of Quarrying Southern AfricaOne such collaboration is with ASPASA, the leading surface mining industry association. “Since the appointment of Letisha van den Berg as the new director of ASPASA, we have been working together to make sure we serve the industry. By working towards common goals, we can make a difference to it. We are collaborating with ASPASA to ensure that we offer the right training to the industry,” says Hunter-Smith.
“Letisha and I have a passion to grow the young membership within the industry. ASPASA has successfully introduced a virtual young professionals meeting that will be held three times a year. On the eve of the conference, we have traditionally hosted a young members’ dinner for the young members to interact and get to know one another. This year we are reintroducing it, and I would like to invite any willing candidates to attend and network with tomorrow’s industry leaders,” he adds.
As part of the collaboration efforts, members will have an opportunity to interact with leading original equipment manufacturer (OEM) suppliers, ask questions and engage with
This year’s IQSA conference – which will take place on 13 and 14 April 2023 at Premier Hotel, Umhlanga – will highlight the importance of collaboration
IQSA is collaborating with ASPASA to ensure that it offers the right training to the industry
The IQ Academy Select training was implemented as a cost-effective means to acquire CPD points through internationally recognised training institutions
As part of the collaboration efforts, members will have an opportunity to interact with leading original equipment manufacturer suppliers
specialists to get a better understanding of the products and solutions available in the market.
As always, IQSA has also sourced technical papers to create awareness of leading practices and techniques in the industry. This will be complemented by an industry awards dinner where top achievers are recognised for their commitment to making a difference to the industry. Other key topics of discussion will include women in mining, as well as environmental, health and safety compliance.
Last year, IQSA highlighted the industry’s need to focus on skills development to respond to an ever-changing business and operational environment. To this end, the association used the event to launch the IQ Academy Select.
Globally, the Institute of Quarrying focuses on the Continuing Professional Development (CPD) of its members. This is a means of recording a members’ commitment to continually improve their skills sets.
As engineering professionals, members are required to accumulate 25 CPD points over five years with a minimum of three per year. The IQ Academy Select training was implemented as a cost-effective means to acquire CPD points through internationally recognised training institutions.
“Training is key to ensuring that we close the skills gap, hence the collaboration with ASPASA to understand the training needs within our industry. Together we can address those needs through quality, endorsed training,” concludes Hunter-Smith. a
The importance of maintaining heating, ventilation and air conditioning (HVAC) systems on mobile mining equipment cannot be stressed enough. Leading HVAC specialist Booyco Engineering maintains that systems that operate optimally and consistently ensure the safety and wellbeing of operators, which has a knockon effect on efficiency and productivity on site. By
In the mining and quarrying industry, it is vital for HVAC systems on mobile equipment such as dump trucks, excavators, dozers and drill rigs to be fully functional at all times to maintain safe working environments for operators. This is the view of Grant Miller, executive director at Booyco Engineering, who stresses that if HVAC systems are not in good working order, operators are subjected to unsafe working conditions, which has a ripple effect on both
safety and productivity.
Munesu Shoko.“In extreme heat conditions, for example, there is potential that the operator can pass out due to heatstroke and heat exhaustion, which could endanger not only the operator but everyone on site. This also has an adverse effect on productivity,” says Miller.
Brenton Spies, MD of Booyco Engineering, says that most local quarries and opencast mines are typically located in areas that experience extremely scorching summer conditions and awfully cold
With a track record spanning over 37 years, Booyco Engineering has cut its teeth across a number of demanding sectors, including military, rail and mining
Booyco Engineering has been supplying and maintaining HVAC systems in mining for the past 20 years, during which time it has been offering its man-on-site service
In the mining and quarrying industry, it is vital for HVAC systems on mobile equipment such as dump trucks, excavators, dozers and drill rigs to be fully functional at all times to maintain safe working environments for operators
It is critical that the HVAC system is designed for the operation’s climatic conditions
Equally important is a stringent maintenance regime for these HVAC systems to function properly
For over three decades, Booyco Engineering has been designing, manufacturing and maintaining HVAC systems for customers in the railways, defence and mining industries
“It is therefore important to ensure that the HVAC systems are specifically designed for the operating environment. Failure to do that, they may not provide the appropriate cooling or filtration,” he says.
winter periods. These extreme temperatures affect the wellbeing of operators and should therefore be mitigated through the use of consistently functional HVAC systems.
“A typical yellow metal hauler’s cabin is tantamount to a glass box. If, for example, you are operating in hot climates of about 40°C without any ventilation, temperatures in the cabin can rise to as high as 65 - 70°C in as little as 30 minutes, which is life threatening. It is therefore important to ensure that HVAC systems are in good working order at all times,” says Spies.
According to Spies, there are two important things to take note of when it comes to HVAC systems. Firstly, he says, it is critical that the system is designed for the operation’s climatic conditions. Consequently, different sites will have different requirements.
Secondly, adds Spies, it is also critical to maintain a stringent maintenance regime for these HVAC systems to function properly. “It is important to have the right equipment for the right environment, which is then maintained regularly to ensure that it works optimally. HVAC systems that are not properly maintained can force a production halt, which can be expensive for quarries and mines through lost production and hours of unplanned downtime,” says Spies.
Very often, he adds, HVAC systems are treated as an afterthought and are not afforded the necessary maintenance attention as long as they are still working. The thought process, says Spies, is that if it stops working, one can open the window, which in many mining conditions is a heath hazard due to the exposure to silica dust and other harmful fumes.
Long-term cumulative exposure to silica dust is likely to develop into serious health issues such as silicosis, silico-tuberculosis, pulmonary tuberculosis, obstructive airways disease and occupational asthma, among others.
“Having a safe working environment is equally important to having personal protective equipment (PPE). There is a greater focus on PPE, which is understandable, but providing an operator with a safe and comfortable working environment is just as essential as making sure that they are wearing a hard hat or their safety boots,” says Spies.
“Heat and body stress is defined as a category A safety hazard and drivers and heavy machine operators are therefore entitled to stop work if the HVAC system is not functioning properly,” says Spies.
According to Spies, the need for a safe working environment is being compelled in the South African mining landscape. Modern health and safety laws in South Africa are very demanding and operators are entitled to stop work if ambient temperatures in the cab are too high or, for that matter, too low.
decades, the company has been designing, manufacturing and maintaining HVAC systems for customers in the railway, defence and mining industries.
“South Africa is, to a large extent, at the forefront of stringent health and safety laws. One of the reasons for this is because of the higher number of fatalities than in most other mining destinations in the world. Consequently, there is a huge focus by the regulator, the Department of Mineral Resources and Energy (DMRE), to ensure safe mining conditions and keeping workers alive,” he says.
Working with an experienced HVAC service provider is also a must for mines and quarries to ensure that the systems are well looked after and always perform optimally. With a track record spanning over 37 years, Booyco Engineering has cut its teeth across a number of demanding sectors. For over three
“We started in the military, where we designed systems for military vehicles operating in highvibration conditions. From there we expanded into the rail sector and eventually into mining,” explains Miller. “We initially designed bespoke systems for customers’ specific needs, which we still do today. However, from the 37 years of experience, we now know what works in certain conditions. We have therefore leveraged that experience to design standard units that can be deployed across multiple vehicles, thus shortening lead times for customers and making installation simpler.”
Booyco Engineering has been supplying and maintaining HVAC systems in mining for the past 20 years, during which time it has been offering its man-on-site service. The company still has units operating in these harsh conditions even after two decades, owing to the ruggedness and fit-for-purpose design of the units, as well as the complementary maintenance regime offered by the company.
“If a mine or quarry buys HVAC systems from us and also signs up for a man-on-site contract, we offer a five-year warranty. That’s how much trust we have in our design and manufacturing capabilities,” concludes Spies. a
The importance of maintaining heating, ventilation and air conditioning systems on mobile mining equipment cannot be stressed enough.Brenton Spies, MD of Booyco Engineering (left), and Grant Miller, executive director at Booyco Engineering.
In the quest for zero harm, ASPASA members continue to maintain high levels of health and safety standards. With an average score of 88,91% in the annual 2022 ISHE Audit, members of the surface mining industry association have once again demonstrated total commitment to the health and safety of their employees, a key factor behind ASPASA’s sevenyear run with no fatalities at member operations. By
Munesu Shoko.The importance of appropriate health and safety compliance at quarry sites cannot be reiterated enough. This is the view of ASPASA ISHE auditor Marius van Deventer, who tells Quarrying Africa that quarry operators therefore need to ensure high levels of compliance to ensure that they are better equipped to manage risks to health and safety
With an average score of 88,91% in the annual 2022 ISHE Audit, members of ASPASA have once again demonstrated total commitment to the industry’s quest for zero harm
For the second year running, Afrimat’s Free State-based Qwa Qwa Quarry was the Top Performer, with a score of 97,25%
Midmar Quarry was the overall runnerup for the second consecutive year with a 95,72% score, cementing its position as the Top Independent Performer in the process
Compliance to legal requirements, and setting of own standards and procedures, remain high throughout the industry
Audit scores
Showplace Status (95%+) 14 operations
5 Shield Status (90-95%) 38 operations
4 Shield Status (80-90%) 25 operations
3 Shield Status (70-80%) 6 operations
2 Shield Status (60-70%) 1 operation
1 Shield Status (50-60%) 0 operations
Less than 50% 1 operation
The audit outcomes of 2022 have once again shown that ASPASA members are fully committed to the health and safety of their employees and all stakeholders affected by their operations.
with regard to their operations. With this in mind, the health and safety performances of ASPASA members have always been of a high standard, and 2022 was no different. “The audit outcomes of 2022 have once again shown that ASPASA members are fully committed to the health and safety of their employees and all stakeholders affected by their operations,” says Van Deventer.
A total of 85 operations participated in the 2022 audit, compared to 69 the previous year, achieving an average score of 88,91%, with the highest being 97,25% and the lowest of 37,5%.
Testimony to the high level of compliance, 60% of the audited operations achieved scores of above 90%. A total of 14 operations achieved Showplace Status (95% +), while 38 attained 5 Shield Status (90-95%) and some 25 operations achieved 4 Shield Status (80-90%).
For the second year running, Afrimat’s Free State-based Qwa Qwa Quarry was the Top Performer, with a score of 97,25%. Midmar Quarry was the overall runner-up for the second consecutive year, cementing its position as the Top Independent Performer in the process.
“Other quarries should learn from these two operations, not only in maintaining leading practices and achieving top health and safety performances, but also in sustaining the high standards on a consistent basis,” says Van Deventer.
While there were a few issues of concern highlighted in the audit findings, Van Deventer is encouraged by the overall positives. For example, he says, high health and safety conditions were sustained and maintained throughout the industry, under very difficult operating conditions. Employees are better informed about the requirements of safe working conditions. Consequently, no fatalities were recorded for the auditing period.
“We also noted a general improvement in the compliance with machine guarding requirements. This had been highlighted as an area which required greater attention in the 2021
audit. In addition, some operations made some much-needed modifications and improvements to their crushing and screening plants to further improve their health and safety standards,” explains Van Deventer.
On another positive note, mine development activities were made according to mine planning guidelines and no serious incidents of mine failure were recorded during the audit period. Overall, Van Deventer says compliance with legal requirements, and setting of own standards and procedures, remain high throughout the industry. However, this does not safeguard operations against accidents or incidents and findings from the Department of Mineral Resources and Energy (DMRE) inspectors. Consistent compliance on a day-to-day basis therefore needs to be prioritised.
“Feedback received from audited operations is encouraging and there is a consistent feeling in the industry that the audit process does add significant value to every operation, thus contributing to the health and safety of employees and the industry’s quest to achieve zero harm,” says Van Deventer.
For the industry to continue achieving high levels of health and safety performance, Van Deventer says the sharing of information is crucial. He is encouraged by quarry managers’ eagerness to learn from each other to improve their audit scores and health and safety compliance at large.
“As an association, we call upon all members to
continue sharing their leading practices with the rest of the ASPASA member base to ensure high levels of health and safety performances at an industry level,” he says.
While the industry achieved high scores on average, the 2022 audit also highlighted several areas which require the industry’s immediate attention. More importantly, there were too many lost time injuries (LTIs), disabling injuries and reportable injuries recorded during the audit period. The industry has also been called on to improve the identification of risks and/ or non-compliances, as well as own inspections and machine pre-start inspections.
“For the 2023 audit, we have highlighted the need for operations to focus on the full implementation of effective Traffic Management Plans. There is also a need to improve trackless mobile machinery (TMM) prestart checklists’ hazard classification. Operations should also prioritise housekeeping in plants to reduce dust exposure while machinery is running,” he says.
In addition, Van Deventer says operations should pay attention to accident/incident investigations to establish root causes of incidents and accidents on site.
“However, the results of the 2022 ISHE Audit are of an extremely high standard. Participating members should all be commended for their exceptional commitment to the quest for zero harm. We are confident that the recommendations noted in the 2022 audit will be executed in the 2023 audit, to ensure that ASPASA members maintain their top health and safety standards,” concludes Van Deventer. a
As the increasing discrepancy between the need for manufactured sand in society and the scarcity of water hits home, water management systems have become a must-have for sand producers to comply with environmental regulations. By Munesu Shoko .
That sand is one of the most important materials in the modern world is no overstatement. In fact, it is the second largest natural resource by volume after water and accounts for the largest volume of solid material extracted globally.
In a one-on-one with Quarrying Africa , Ruchin Garg, regional manager, Middle East & Africa at CDE, says the world is on
track to be a planet of nearly 10-billion people by 2050. In addition, about 70% of the world’s population will live in urban areas by 2050. Shifting consumption patterns, growing populations, increasing urbanisation and infrastructure development have accelerated the demand for sand three-fold over the last two decades. The world now needs 50-billion tonnes per year (tpy), an average of 18 kg per person per day.
90%
CDE’s AquaCycle thickener minimises costly water consumption by ensuring up to 90% of the process water is recycled for immediate recirculation
the profitability of their operations by minimising the consumption of costly water resources.”
Shifting consumption patterns, growing populations, increasing urbanisation and infrastructure development have accelerated the demand for sand three-fold over the last two decades
Innovations in the washing sector and the continued advancement of CDE’s pioneering wet processing solutions are supporting quarry operators and materials processors alike to overcome the challenges stemming from water management – cost-based, efficient, sustainable and regulatory
Delivering competitive advantages to its customers, CDE’s AquaCycle thickener accelerates return on investment by maximising production efficiency, minimising the loss of valuable fines and reducing water and energy costs
Every aspect of the CDE design is carefully considered so that the system is responsive to the site-specific needs
Yet, according to some forecasts, buildable sand may run out as early as the first half of this century. According to a United Nations report, the world has been exceeding easily available sand resources at a growing rate for decades, spending the sand ‘budget’ faster than the sand that can be produced responsibly.
Sand has traditionally been obtained from natural sources such as rivers and coastlines. However, new regulations have been enacted to protect these sources. In many cases, sourcing sand from riverbanks and shorelines has been outlawed completely because of the dire environmental consequences such as erosion in rivers and coastlines, as well as changes in the water’s PH levels. Consequently,
“Developing technological solutions to tackle these mounting challenges is paramount for many materials processors seeking to boostRuchin Garg, regional manager, Middle East & Africa at CDE
notes Garg, illegal sand extraction has in fact become a major transactional crime, just behind drug trafficking and counterfeiting.
As the scarcity of natural sand becomes a reality, the industry has been forced to adopt a suitable and sustainable alternative fine aggregate. Manufactured sand has therefore proven to be the most economical and ecological alternative. Yet, wet processing, a crucial part of sand production, has its own challenges due to the documented global water shortages.
“Water is indispensable. Essential for life, water is vital for economies and climate regulation. It is of utmost importance, therefore, that our water resources be protected – even regulated. The mining, quarrying, manufacturing and construction sectors accounted for 10,6% of total water use in Europe in 2017 and the industry compounds water scarcity, water efficiency and wastewater management challenges the world over. All corners of the globe are facing unique challenges,” says Garg.
Continued innovations in wet processing technology are helping the industry meet the rising demand for manufactured sand, while using water sparingly, thus overcoming water management challenges.
While laws governing water vary around the world, Garg says it is a resource that is absolutely essential to the extractive industries and is therefore increasingly under the water management microscope.
“Innovations in the washing sector and the continued advancement of CDE’s pioneering wet processing solutions are, however, supporting quarry operators and materials processors alike in order to overcome the challenges stemming from water management – cost-based, efficient, sustainable and regulatory,” says Garg.
CDE consistently invests in research and development with the aim of enhancing the capabilities of its premier water recycling and management equipment. At the forefront of its water recycling systems is the AquaCycle™ thickener, a single, compact and user-friendly unit that can be applied to high and low tonnages across many markets.
Delivering competitive advantages to its customers, CDE’s AquaCycle thickener accelerates return on investment by maximising production efficiency, minimising the loss of valuable fines and reducing water and energy costs.
An alternative to water extraction and the costly process of pumping water to the plant, CDE’s AquaCycle thickener is a highly efficient water management solution that minimises costly water consumption by ensuring up to 90% of the process water is recycled for immediate recirculation.
“In the past, it was not possible to turn the fine crushing waste into a quality product, as the technology at the time did not offer the precision needed to produce a reliable and homogeneous artificial sand from the fine crushing waste,” says Garg. “Such technology was realised in the new CDE Combo™ – a complete solution to both the ever-increasing demand for fine minerals and the everdecreasing use of natural resources.”
The CDE Combo can be moved around, making it ideal for quarry fines. It can process spoil at one location and then be moved to another. Additional important advantages of the Combo unit are the integrated water supply and recirculation systems.
Though water recycling may seem simple in theory, it is, in practice, much more complex. Water thickeners are not born equal and their efficiency is the result of years of dedicated research, development and refinement.
Every aspect of the CDE design is carefully considered so that the system is responsive to the site-specific needs.
“All CDE equipment is designed to allow plug-and-play operation, it is pre-wired and pre-tested before despatch, designed for rapid assembly and set up and can start processing material within days of arrival on site. These design considerations and factory acceptance tests significantly reduce installation time and accelerate return on investment,” says Garg.
Return on investment with a CDE AquaCycle thickener is typically achieved in just six to nine months.
CDE’s modular wet processing equipment can contribute to the easing of water scarcity issues arising from the materials processing industry’s consumption of water resources, greatly improve water efficiency and better wastewater management practices.
“Developing technological solutions to tackle these mounting challenges is paramount for many materials processors seeking to boost the profitability of their operations by minimising the consumption of costly water resources,” he says.
Over the years, CDE technology has been deployed on several African sites with great success. The partnership between CDE Global and Estim Construction in Dar es Salaam was a particularly exciting breakthrough in the African market.
Estim Construction’s dedication to excellence and innovation mirrors the CDE work ethos, so developing the most efficient sand washing solution was a gratifying process resulting in a product that surpassed Estim Construction’s expectations.
To ensure that Estim Construction had complete ownership of its operation, a CDE engineer trained an Estim Construction operator to oversee the installation and take actions based on the changing characteristics
of the feed material. The plant is fed 50 tonnes per hour (tph) to produce 40 tph of final quality washed sand. Waste and water from the EvoWash report to the AquaCycle highrate thickener so that up to 90% of the water is recycled and reused. The concentrated fines are flushed out, resulting in minimal water to replenish the water tanks.
Founded in 2011, Mission Point Mining (MPM) is now a major player in the South African sand production industry and employs 30 people on its mining site in Sasolburg. “Since we replaced our bucket wheel with a CDE turnkey plant, we have witnessed a significant increase in the quality of our product and a no less significant decrease in our water consumption, so switching to CDE technology has proven to be the smart choice. With the EvoWash and Aquacycle working in tandem, the quality of our washed product is much better and much drier than any other producers’ in the region,” says MPM’s Johann Pretorius. Since MPM switched to the CDE cyclone and water recycling technology, demand for its products has grown to the point that the company is now expanding its business and exploring the best value for money solutions to increase sand production.
According to Garg, water management systems are becoming a must-have for mine and quarry operations to comply with environmental regulations. Matters concerning the protection of finite resources on the planet will only become more prevalent, too.
“At CDE we see the solution increasingly pointing towards manufactured sand – it is in more demand as natural sand sources deplete, there is value in quarry waste/fines and it is predicted that the use of manufactured sand by the construction market will overtake the use of natural sand by 2026,” concludes Garg. a
Water management systems are becoming a must-have for mine and quarry operations to comply with environmental regulations.
To help the industry achieve its zero harm targets, Volvo Construction Equipment has launched its Collision Mitigation System for wheel loaders. The automatic braking system supports operator response and helps reduce the risk or consequences of collision when working in reverse. By Munesu Shoko.
40-50%
Given that wheel loaders spend an average of 40-50% of their operating time being driven in reverse, Volvo Construction Equipment believes that the Collision Mitigation System is a valuable tool to boost jobsite safety
The braking action has a duration of 2-3 seconds, which effectively slows down the machine while prompting the operator to pay attention and take control
Given that wheel loaders spend an average of 40-50% of their operating time being driven in reverse, Volvo Construction Equipment (Volvo CE) believes that the Collision Mitigation System is a valuable tool to boost jobsite safety.
The system – said to be the first of its kind developed inhouse by an original equipment manufacturer – assists operators while working in reverse and automatically applies service brakes when the wheel loader approaches any obstacle, alerting the operator to take further action.
In a one-on-one with Quarrying Africa , Anteneh Gebremeskel, GPE product manager at Volvo CE, says while not designed to ever
replace safe operator behaviour, the Collision Mitigation System is a smart tool to further enhance jobsite safety – a central focus and core value for Volvo since the company’s inception.
“Safety, quality and environmental care are our core values as a company and the cornerstones of our product development. We have a vision for zero accidents, so we build safety into every design element and work tirelessly to develop intelligent solutions that will not only mitigate the consequences of accidents but strive to avoid them altogether,” says Gebremeskel. “The new Collision Mitigation System for wheel loaders is an example of one such solution. It will help both experienced and novice operators
While not designed to ever replace safe operator behaviour, the Collision Mitigation System is a smart tool to further enhance jobsite safety.
KEY POINTS
Volvo Construction Equipment has launched its Collision Mitigation System for wheel loaders
The automatic braking system supports operator response and helps reduce the risk or consequences of collision when working in reverse
The new Volvo Collision Mitigation System comes with smart software that detects slopes or objects present at the moment of driving past them forwards, so as not to mistakenly consider them as an object of collision risk while reversing in the same direction
The Collision Mitigation System is a factoryfit option currently available for the Volvo H-series wheel loader range, namely the L150H, L180H, L220H, L260H and L200H High Lift models, in the Middle East and Africa
“
The system is open for sales on models
L150H to L260H in Africa, which represents a broad section of our wheel loader range. These models are part of the H-Series, which has all the enabling features for the system.
to improve safety on site.”
From a market perspective, Volvo CE has seen high demand for such safety features in Africa and elsewhere in the world. For quarrying and mining operations, says Gebremeskel, stringent safety regulations have become the order of the day to protect workers in such particularly hazardous working environments.
“South Africa is a good example of a market that is setting higher demands for safety technology such as Collision Mitigation Systems,” says Gebremeskel.
The Collision Mitigation System is a factory-fit option currently available for the Volvo H-series wheel loader range, namely the L150H, L180H, L220H, L260H and L200H High Lift models, in the Middle East and Africa. Currently, the system is only available to order on new machines from the factory. A retrofit kit is not available yet, but Gebremeskel tells Quarrying Africa that it will come in the future.
“The system is open for sales on models L150H to L260H in Africa, which represents a broad section of our wheel loader range. These models are part of the H-Series, which has all the enabling features for the system,”
explains Gebremeskel.
However, the system is not available on smaller models, as these form part of the F-Series, which lacks some of the enabling features required, including Volvo Co-Pilot. At the other end of the size scale, the Collision Mitigation System is yet to be developed for Volvo CE’s biggest wheel loader, the L350H.
“The Collision Mitigation System is an ongoing development. The reason we started with wheel loaders is the fact that the enabling components are readily available on these machines.
These include the radar detection system, the Volvo CoPilot and the Reverse By Braking (RBB) valve,” says Gebremeskel.
“The Collision Mitigation System is yet to be developed for haulers, but in the meantime, we are partnering with thirdparty suppliers to offer a proximity detection system for haulers. We would encourage any customers interested to discuss the opportunities available for such systems with their local Volvo dealer,” he adds.
The system works by identifying when there is a risk of collision and responding by automatically activating the brakes for 2-3 seconds to slow the machine down prior to
impact or bring it to a stop to avoid it. This initiation of the braking alerts the operator to intervene.
“Functioning only when the wheel loader is in reverse and driving at speeds of between 3-15 km/h, no matter what gear it is in, it serves as a facilitator to jobsite safety. However, even assistance systems like this cannot eliminate accidents, which is why Volvo CE always advocates for safe operator driving behaviour,” he says.
The new Volvo Collision Mitigation System comes with smart software that detects slopes or objects present at the moment of driving past them forwards, so as not to mistakenly consider them as an object of collision risk while reversing in the same direction. This enables the system to work with little disturbance while stockpiling or driving close to walls, for example.
eliminating accidents – and therefore improving jobsite safety for everyone – but also reducing any unplanned interruptions that can be incurred during those avoidable knocks and bumps.
3-15
“This safety feature supports the operator before a potential collision incident by releasing an audible warning along with a visual warning on the Volvo Co-Pilot screen and, at the same time, applying the service brakes automatically in the event of object detection within the range,” explains Gebremeskel.
“The system is always active when the machine starts, but it is possible to temporarily deactivate. If manually deactivated, the system will automatically activate again after a 90-minute time lapse. It is designed to detect both stationary and moving objects,” explains Gebremeskel.
With this new system, he adds, customers are moving a step closer to not only
The braking action has a duration of 2-3 seconds, which effectively slows down the machine while prompting the operator to pay attention and take control. The operator still has full responsibility for the machine. The system works when gears are engaged or when the operator is coasting backwards in neutral.
“Requiring a Radar Detect System to be fitted, it works as an additional system to the existing wide range of features, options and site services provided by Volvo CE for its line of wheel loaders, all of which have been designed to elevate jobsite safety and minimise unplanned interruptions,” concludes Gebremeskel. a
Key
The DF514 has proven over the years to be one of the most robust and reliable compact scalping screens available on the market. Fully equipped with a 4,27 x 1,52 m double deck screenbox, the machine has one of the longest screen boxes in the compact screening segment.
27 000 kg
The machine weighs in at 27 000 kg in an apron feeder configuration, about 7 000 kg less than the larger DF518 model
KEY POINTS
Having initially launched the larger DF518 scalping screen, Vermeer Equipment Suppliers is bringing the compact Anaconda DF514 model to the local market
The first machine is expected to arrive during the second half of the year
With its compact nature, the DF514 fits the bill for entry level and mid-level contractor markets
The machine comes with either a belt or apron feeder, depending on customer preference
Amid increased demand for compact scalping screens, largely driven by the contractor fraternity, Vermeer Equipment Suppliers is introducing the Anaconda DF514 tracked mobile scalping screen to the local market. Capable of processing tonnages of up to 375 tonnes per hour (tph), the machine packs a punch across applications, writes Munesu Shoko.
Having initially launched the larger DF518 scalping screen, Vermeer Equipment Suppliers, the authorised distributor of the Anaconda crushing and screening range in sub-Sahara Africa, is bringing a compact model to the local market. In a one-on-one with Quarrying Africa , sales manager Shaun O’Toole says the first unit of this compact model will arrive during the second half of the year. Capable of processing up to 375 tph
depending on the application, the DF514 fits the bill for entry level and mid-level contractor markets. Its ability to be deployed across applications, including recycling, quarrying and coal processing, among others, ticks the much-needed versatility box for this group of customers.
According to O’Toole, the DF514 is globally one of the most popular Anaconda screens. “The DF514 has proven over the years to be one of the most robust and reliable compact scalping screens available on the market. Fully equipped with a 4,27 x 1,52 m double deck screenbox, the machine has one of the longest screen boxes in the compact screening segment,” he says. “It comes with either a belt or apron feeder, depending on customer preference. However, we highly recommend the apron feeder option for our local customers.”
Apart from its versatility, the DF514 offers contractors greater value for money. Its compact size means it is easy to transport between jobsites, making it easy for nomadic contractors to move from one job to another. With dimensions of 13,6 m length x 3 m width x 3,4 m height, the machine fits the bill for sites where space is at a premium. Set-up is simple and the machine can be up and running within 20 minutes of delivery. Commissioning is made easy by the hydraulic controls designed to position and guide all the conveyors and screen box.
“The machine weighs in at 27 000 kg in an apron feeder configuration, about 7 000 kg less than the larger DF518 model. Yet it is still
capable of producing the same tonnages of up to 375 tph. This means that customers can still achieve the same production capacity with a much smaller machine which is easy to transport, comes at a much lower price point and is efficient to run. This, we believe, will be a key selling point for the DF514,” he says.
When it comes to uptime, the unit has hydraulic folding hopper sides as standard, a hydraulic screen angle adjustable from 15-19°, a hydraulic screenbox raise/lower for ease of mesh change, and wired remote as standard; (radio remote is optional).
All the service points of the machine are easily accessible. There is no need to strip the machine to reach certain components, thus service-related downtime is minimal. It is an easy machine to use and service; it’s a simple screen with no complicated electronics.
“The Anaconda product is robust, yet easy to operate and service, which is key for African contractors who often find themselves operating in remote locations,” he says. “On close inspection, one can see the attention to detail with little things such as collars around the clamp bar bolt heads to make change-out easier – something that operators in the field will appreciate.”
Following the arrival of the first Anaconda machines last year, O’Toole says the brand is gaining much-needed traction in the local market. Two machines, a J12 jaw crusher and a DF518 scalping screen, are currently hard at work in a coal application, and have performed beyond expectations to date.
“Thus far, the coal industry has shown great interest in these particular products. We have had several enquiries already, and judging from the attention given to date, we are confident that we will be able to deliver more machines this year,” he says. “With the arrival of the DF514, we are even more confident that the range will garner more interest in the market.”
A good product, says O’Toole, is only as good its service. Backup support is the most important consideration in this industry, especially given the importance of machine uptime in the contracting fraternity. “Contractors need to maximise uptime to be able to earn money,” he says.
“Our track record when it comes to the provision of parts and services speaks for itself. Vermeer Equipment Suppliers has established itself for the past 20 years as a reliable partner with strong relationship building and dedication to its customers,” concludes O’Toole. a
In order to operate profitably, principal parameters in the quarrying and mining space are productivity, efficiency and safety. Over the years, Bell Equipment has responded to this need with a range of technological advancements designed to improve the performance of its articulated dump trucks (ADTs). By Munesu Shoko.
The ADT market has seen several technological advancements in recent years. According to Jeremiah Mokhomo, ADT product manager at Bell Equipment, some of the key technological advances that have come to market include telematics, efficient engines and improved safety features.
In 2003 Bell Equipment launched Fleetm@tic ® to become the first heavy original equipment manufacturer to offer its customers a fully global remote fleet management system with pole-topole coverage.
“ADTs are now equipped with telematics systems that provide realtime information on the location, speed and utilisation of the truck. This helps fleet managers to optimise the use of their assets and reduce operating costs. Bell ADTs are fitted with our proprietary Fleetm@tic system, which offers real time tracking,” says Mokhomo.
In addition, manufacturers have developed engines that are more fuelefficient and environmentally friendly, helping fleet owners to not only run profitable operations, but also to reduce the carbon (CO2) footprint of their trucks. To provide context, he says, all large Bell ADTs can operate on hydro-treated vegetable oil (HVO) without needing dilution with diesel or impacting on engine service intervals. HVO can reduce CO2 by up to 90%.
Improved transmission software such as Allison’s FuelSense 2.0 used in Bell machines is key to improved fuel efficiency. The technology uses DynActive Shifting to provide an infinitely variable combination of shift points, thus improving fuel economy by 6% beyond the original FuelSense.
“Given the criticality of running safe operations, ADTs are now equipped with a range of safety features, including cameras, proximity sensors and collision avoidance systems, which help to improve
ADTs are now equipped with telematics systems that provide real-time information on the location, speed and utilisation of the truck
Given the criticality of running safe operations, ADTs are now equipped with a range of safety features, including cameras, proximity sensors and collision avoidance systems, which help to improve visibility and prevent accidents
Bell ADTs are designed to be platform-agnostic to allow them to be fitted with the autonomous system of the customer’s choice
With the increasing focus on sustainability and reduction of carbon emissions, the market is likely to see an increased demand for hydrogen-powered ADTs in the future
visibility and prevent accidents. Bell ADTs come with onboard weighing and angle sensors, which help to refine our downhill descent system, Hill Assist, and safe tipping,” explains Mokhomo.
With autonomy fast becoming a necessity, Bell ADTs are designed to be platform-agnostic to allow them to be fitted with the autonomous system of the customer’s choice. The company has already completed a proof of concept with Pronto in the US and xtonomy in Europe. The machines use the
With the increasing focus on sustainability and reduction of carbon emissions, we are likely to see an increased demand for hydrogenpowered ADTs in the future.
Jeremiah Mokhomo, ADT product manager at Bell Equipment
standard cab, which makes it easy for customers to move the machine to different sites with different systems, or even return to a standard truck when an autonomous contract ends.
Driving ADT efficiency has been one of the key design focus areas for all manufacturers. To meet the principal need of efficient operation, Bell has cast the spotlight on engine technology. “Bell uses advanced engine technology that combines high power output with low fuel consumption to deliver improved efficiency. The engines are designed to operate at optimal RPMs, thereby reducing fuel consumption and emissions,” he says.
The company’s weight-optimised design ensures no fuel is used to move unnecessary structural deadweight. Automated functions such as i-Tip automated tipping and operator-selected speed control reduce cycle times and allow operators to concentrate on productivity. Standard onboard weighing allows operators to consistently achieve the targeted payloads while production managers and owners can track production.
In addition, Bell Equipment’s telematics system provides real-time information on the performance and efficiency of the truck. This helps fleet managers to identify areas where
The Bell ADT Versatruck provides mining and quarrying operations with high levels of flexibility and efficiency.
The Bell ADT Versatrucks have become a major player in the mining industry due to their versatility and range of features that make them well-suited for the demanding conditions of the industry. With their ability to operate as water tankers, diesel trucks and service trucks, the Bell ADT Versatruck provides mining and quarrying operations with high levels of flexibility and efficiency.
The in-cab-operated water tankers, in particular, provide mining operations with an efficient way to manage water resources, and the diesel and service trucks provide the support and resources that are necessary to keep mining operations running smoothly. With their powerful engines, advanced material handling capabilities, and improved safety features, the Bell ADT Versatrucks are helping to improve productivity and efficiency in the mining industry.
improvements can be made and thus optimise the use of the asset.
In the quarrying and mining space, increased productivity is a critical requirement, stresses Mokhomo. Bell has responded to this need with a range of technological enhancements designed to improve the productivity of its ADTs. One of the key enhancements is the innovative prognostic capability which has been programmed into the trucks, allowing for identification of issues before they result in costly downtime.
“Full diagnostic capability and a significant increase in vehicle system sensors allows for quick identification of any problems through the easy-to-use colour display,” he says.
In addition, Fleetm@tic desktop control allows customers to keep an eye on their machines and receive alerts on a wide range of parameters. Daily fluid checks can be done quickly from inside the cab while vehicle sensors keep an eye on systems during operation.
Wet disk braking, standard on trucks from the B30E and larger, means no lost time for service brake pad replacement – even in the muddiest conditions, thus ensuring high truck uptime. Automatic greasing, available on all models, and comprehensive lubrication charts, ensure preventative maintenance is not compromised. High levels of access to all components ensures any repairs are carried out in the shortest possible time, thus increasing machine availability.
Commenting on the future of the ADT, Mokhomo says the product segment is constantly evolving, and new technological trends will continue to emerge all the time.
“With the increasing focus on sustainability and reduction of carbon emissions, we are likely to see an increased demand for hydrogen-powered ADTs in the future,” he says.
Autonomous operation, he adds, is becoming increasingly popular across many industries, and the ADT market is no exception. “We are likely to see an increase in the number of ADTs that are capable of performing tasks without human intervention, improving efficiency and reducing operating costs. Bell is already active in this space, making our ADTs among the most advanced in the market today,” says Mokhomo. Telematics systems, he adds, are becoming more sophisticated, providing real-time information on the performance and efficiency of the truck. “In the future, we are likely to see the development of predictive analytics and machine-learning capabilities that will help fleet managers to further optimise their assets and reduce operating costs,” he says. a
With the current economic situation, it is more important than ever to reduce costs and achieve the lowest total cost of ownership possible. Rokbak’s senior product manager, Scott Pollock, explains how the company is helping customers achieve this.
Rokbak’s fuel-efficient drivetrains deliver powerful performance and meet worldwide emission standards with low cost of operation and low environmental impact.
Fuel consumption is the biggest cost of operating a machine.
The Rokbak RA30 and RA40 EU Stage V engines produce a fuel consumption saving of up to 7%, when compared to the previous EU Stage IV engines. This means lower operating costs and less impact on the environment. The RA30 EPA Tier 4 Final machines also achieved a fuel saving of up to 5% when the latest eight-speed transmission was introduced.
A key feature towards increasing productivity and reliability for the customer is the engine air intake filter. Within the dry-type, twostage aspirated air cleaner, this small suction draws out major contaminates, extending the time between maintenance intervals, lowering total cost of ownership and potentially increasing machine life cycle.
Rokbak’s Haul Track telematics system helps machine owners to reduce total cost of ownership (TCO) by keeping an eye on everything from fuel consumption and machine usage to issues that, if neglected, could lead to repairs or unplanned downtime.
The system enables you to remotely monitor your machine to manage performance, plan preventative maintenance, proactively control production and track the condition of your hauler. By taking a deep dive into a variety of software parameters – such as
travel speed, fuel consumption, temperatures and pressures –owners can look for patterns and identify improvement areas that can reduce TCO.
Haul Track connects to the onboard weighing (OBW) system, so any under or overloading can be easily identified and used to help educate operators in correct machine usage. 2022 saw the re-introduction of improved fault alerts, with improved maintenance alerts being reintroduced shortly. These not only notify the dealer of upcoming service intervals, but also provide a list of required parts for that specific task – enabling faster servicing and greater machine uptime.
Both Rokbak articulated haulers are installed with hydraulic system magnetic suction filters, which reduce the risk of contaminants entering the hydraulic system, saving on disposable maintenance materials and maximising productive uptime through cleaner systems and prolonged component life.
The RA30 and RA40 both adopt modern hydraulic fluids that maximise time between maintenance periods to 4 000 hours. The RA40’s transmission has high-performance fluid and up to 6 000 hours between service intervals, while the RA30’s long-life transmission fluid supports 4 000 hours between oil maintenance intervals. As a result, customers can achieve increased productivity and uptime, as well as low cost per tonne.
Rokbak has created the ideal ergonomic environment for the articulated hauler operator to work
within. Operators can have a huge influence on TCO. A happy operator is a productive operator, and the more your machines move the more you earn.
Spacious, pressurised cabs have been designed to avoid fatigue and be highly comfortable – with low noise, an active air suspension operator’s seat with adjustable arm rests, cushioned steering, and high-capacity heating and airconditioning.
The RA30 is equipped with true independent front suspension as standard, further enhancing operator comfort and enabling excellent traction control and maximum productivity, even in challenging conditions. a
Unit operations such as loading and hauling are major variables in any quarry’s total cost equation. The utilisation of innovative technologies is therefore important for the industry to be cost-effective. In order to improve hauling efficiency, productivity and safety, Volvo Construction Equipment has rapidly adopted technology in all forms, placing its articulated haulers at the cutting edge, writes Munesu Shoko.
12 kg
Shell has installed a state-ofthe-art hydrogen refuelling station at the Volvo CE test track in Braås, Sweden, which can refuel the HX04 with 12 kg of hydrogen in around 7,5 minutes, enabling it to operate for approximately four hours.
The articulated dump truck (ADT) market has seen several technological advancements in recent years. Since the inception of its ‘Gravel Charlie’ in 1966, said to be the first ever ADT to be made, Volvo Construction Equipment (Volvo CE) has established over decades a solid reputation for evolving machines that place innovation at the centre of their development. The primary aim in doing this is to provide hauling solutions which help to overcome project time and cost constraints.
According to GPE product manager at Volvo CE, Anteneh Gebremeskel, the company’s articulated dump truck, invented back in 1966 and known as the famous 10-t payload DR631,
10%
Hill Assist is a Volvo CE feature which contributes to greater safety by holding the hauler in place when working on uphill slopes of 10% or greater without the need to engage the parking brake
24/7
To maximise uptime, Volvo CE offers a 24/7 remote machine monitoring and a weekly fleet utilisation reporting service called ActiveCare
or ‘Gravel Charlie’, has paved the way for generation-after-generation of hauler innovation. “Our focus on new technologies has enabled us to retain a leading position in the global market,” he says.
Some of the recent technologies that the company has brought to market include Connected Map, Cruise Control & Downhill Speed Control, Hill Assist, Terrain Memory, Dump Support System and the Tyre Pressure Monitoring System. These features cast the spotlight on hauling safety, thus helping reduce global safety incidents related to trackless mobile machinery (TMM).
Part of Volvo Co-Pilot with Haul Assist, Connected Map informs the operator of the location of other machines and personnel on site, reducing congestion and improving safety. It also issues speed limit notifications when necessary to remind operators to keep to the recommended speed for safer operation.
Cruise Control & Downhill Speed Control are important features for safety and operator comfort. The operator can set and adjust the Cruise Control to maintain a constant travel
Volvo CE’s first articulated dump truck, invented back in 1966 and known as the famous 10-t payload DR631, or ‘Gravel Charlie’, has paved the way for generation-after-generation of hauler innovation
As part of Volvo Co-Pilot with Haul Assist, Connected Map informs the operator of the location of other machines and personnel on site, reducing congestion and improving safety
The introduction of the largest production articulated hauler with automatic 6x4 and 6x6 configuration, the 55-t capacity Volvo A60H, has made a particular difference to productivity in the quarrying and mining space
In the immediate future, customers in Africa should look forward to seeing Volvo Co-Pilot with Haul Assist on their new machines, including On-Board Weighing and other valuable features
Productivity is obviously more than just payload capacity and hauling speed. There are numerous factors that influence productivity, including uptime, fleet composition and site layout, amongst others.
Anteneh Gebremeskel, GPE product manager at Volvo CE
speed for smoother and more efficient hauling. “When travelling downhill, the Downhill Speed Control enables operators to maintain their control and speed for greater safety, comfort and productivity in all conditions,” explains Gebremeskel.
Hill Assist is a Volvo CE feature which contributes to greater safety by holding the hauler in place when working on uphill slopes of 10% or greater without the need to engage the parking brake. It automatically activates when arriving at a complete stop on a hill and is disengaged when the operator accelerates.
“Part of the intelligent Volvo drivetrain, Terrain Memory identifies and remembers slippery road segments that cause the automatic traction control (ATC) to engage and disengage frequently and keeps the ATC engaged to optimise traction control and off-road mobility,” he explains. He points out that Volvo CE’s CareTrack telematics system is required for this feature to function.
Dump Support System also contributes to greater safety by allowing the operator to see the percentage side inclination of the truck and sets allowable parameters for safe dumping operations. The tipping lever has automatic hold in the lowering position, which provides precise control for faster cycle times.
As part of Volvo Co-Pilot with Haul Assist, the Tyre Pressure Monitoring System gives operators an instant and safe indication that tyres are functioning within the correct parameters, thus enhancing safety, machine availability and lower total cost of ownership (TCO).
“Via the 10-inch touchscreen Volvo Co-Pilot display in the cab, operators can see real-time information on tyre pressure and temperature, both as nominal values and percentages.
They also receive visual alerts if there are inconsistencies in pressure or temperature, indicating they should keep certain tyres under observation and, if the inconsistencies have worsened, signalling it is time to take action,” says Gebremeskel.
The importance of efficiency in hauling cannot be reiterated enough. Volvo CE has over the years brought to market some technological advancements that speak directly to better running efficiency of its ADTs.
Volvo articulated haulers’ excellent traction on slopes and in slippery conditions means that operators can maintain fast cycle times, getting the job done efficiently. Cruise Control and Downhill Speed Control also play a role in this respect.
Volvo’s Reverse by Braking (RBB) and OptiShift are key to maintaining high fuel efficiency when stopping and starting and changing directions. RBB slows the machine when the operator wants to change direction, by reducing engine rpm and automatically applying the service brakes.
“Among the newer features, Haul Assist OnBoard Weighing is important for efficiency as it ensures the hauler is optimally loaded at each cycle to move more material in fewer cycles,” he says. “Connected Map also ensures operators are taking the most efficient route thus avoiding delays caused by traffic, improving cycle times and fuel consumption.”
Many of the features that improve efficiency, safety and operator convenience also contribute to greater productivity, because if operators are reducing the time taken to get
the job done, they can do more within their shifts.
“However, the introduction of the largest production articulated hauler with automatic 6x4 and 6x6 configuration, the 55-tonne (t) capacity Volvo A60H, has made a particular difference to productivity in the quarrying and mining space,” says Gebremeskel. “It enabled a 40% payload increase on the popular A40G, helping operators to move more tonnes per hour, while offering a more flexible alternative to rigid haulers in this class size.”
In fact, Gebremeskel has seen a trend where customers are replacing rigid haulers with the A60H as its off-road capabilities on steep gradients and in slippery conditions enable safe and productive operation throughout the rainy seasons.
“Productivity is obviously more than just payload capacity and hauling speed. There are numerous factors that influence productivity, including uptime, fleet composition and site layout, amongst others,” he says.
“To maximise uptime, we offer a 24/7 remote machine-monitoring and a weekly fleet utilisation reporting service called ActiveCare. With ActiveCare, CareTrack telematics data is managed on behalf of the customer. Volvo and the local dealer provide remote diagnosis and become aware of problems before they occur,” says Gebremeskel.
These activities, he adds, takes the burden of monitoring and initial diagnosis off the customer, who is notified only when specific action is necessary. From the customer’s perspective, issues are resolved proactively and seamlessly with their local dealer before they have the chance to develop into serious and expensive problems – and uptime is maintained.
reducing congestion and improving safety.
Another key Volvo service that improves productivity is Site Simulation. This consultancy service models and calculates the optimum flow of production over an entire site. By inputting the density of the material, distances and topography of the site, a Volvo consultant can recommend the ideal number and capacity of machines, as well as the optimum speed and routes operators should drive, based on the tonnes per hour and the cost per tonne.
“This helps to eliminate unnecessary waste and waiting and get the job done in an efficient and productive manner. Site studies such as this are regularly carried out in the mining industry, but Volvo CE is unique in its ability to offer comprehensive simulations for small- and medium-sized sites too,” he says.
Autonomy is no longer a concept in ADTs. Several OEMs have already made significant headway in this area.
“Autonomy is an enormously complex challenge. Our approach has been to start small, in a tightly confined environment with a limited number of variables and build on our success over time,” says Gebremeskel.
Quarries, he adds, are the perfect place to start as they are highly regulated and contained environments with clearly defined load-anddump locations over generally short, simple repetitive circuits that can be separated out from other processes on site. A case in point is Volvo CE’s Electric Site project, where the company tested its autonomous battery-electric load carrier concept at a quarry in Sweden in 2018.
“The next step could be underground mining and tunnel applications since autonomous machines work just as well in the dark as in the
light and it would be good to remove people as far as possible from such hazardous locations. From there, we could focus on large earthmoving projects that are still contained but have more variables to cope with, as our technology becomes more embedded over time,” he says.
However, Gebremeskel stresses that any move to autonomous machines would not simply be a case of replacing a machine with an operator to one without. Autonomous machines require a new way of looking at the entire operation and prompt the development of a total solution to manage the full automated transport process.
In 2020, Volvo Group launched a new entity, Volvo Autonomous Solutions (VAS), to develop and commercialise autonomous transport solutions for the entire group. This team can focus on challenges outside of Volvo CE’s usual areas of expertise and which may be common to other Volvo business areas – namely the supporting infrastructure, control towers, repair and maintenance, virtual drivers and even running the operations if required.
VAS now offers the Tara system, which includes the fully automated Volvo TA15 battery-electric dumper, a virtual driver and support with all the necessary site infrastructure, as a complete automation solution for quarries. Improved process optimisation, lower energy consumption and greater safety are just three of the many benefits.
Looking to the future, Gebremeskel says apart from battery-electric solutions, Volvo CE is also exploring the potential of electrification through hydrogen fuel cell technology. Last year, the company reached an important milestone with the testing of a world-first emission-free hydrogen fuel cell articulated
hauler prototype, the Volvo HX04.
Fuel cells work by combining hydrogen with oxygen and the resulting chemical reaction produces electricity to power the machine. The only emission is water vapour.
“While an early prototype, the HX04 will give valuable insights into the opportunities of hydrogen in the energy transformation scheme alongside battery-electric solutions,” he says.
Infrastructure for hydrogen is still in development, which means refuelling the Volvo HX04 is an important aspect to solve within the project. Shell has installed a state-of-theart hydrogen refuelling station at the Volvo CE test track in Braås, Sweden, which can refuel the HX04 with 12 kg of hydrogen in around 7,5 minutes, enabling it to operate for approximately four hours.
“In the immediate future, however, customers in Africa should look forward to seeing Volvo Co-Pilot with Haul Assist on their new machines, including On-Board Weighing and other valuable features. Volvo Co-Pilot builds on all benefits of the Volvo transmission and drivetrain to deliver new levels of safety, efficiency and productivity,” says Gebremeskel.
On-Board Weighing, in particular, helps eliminate dangerous overloading, and to improving safety and decreasing unnecessary fuel consumption and wear to the hauler. The system provides real-time payload information to the screen in the cab and uses external lights as a visual guide for the operator of the loading unit as to when the nominal load has been reached. It also enables remote monitoring of productivity.
“We will continue to develop Volvo Co-Pilot with Haul Assist as a platform for further services in the future, so watch this space,” concludes Gebremeskel. a
There are many issues to consider when specifying the most appropriate conveyor belt cleaner, not the least of which is maintaining proper tension to achieve optimal cleaning performance without introducing any related problems.
Inadequate tensioning causes carryback to cling to the belt and spill along its path, piling up under the conveyor and emitting excessive dust. This requires extra labour for clean-up and can affect air quality. Over-tensioning leads to friction damage to the carrying side of the belt, premature blade wear and potential splice damage. Both scenarios contribute to unsafe work conditions and raise the cost of operation.
“There are two basic approaches to applying tension to the belt cleaner: linear and rotary,” says Dave Mueller, Conveyor Products manager at Martin Engineering. “The blade’s cleaning
position and angle of approach to the belt often dictate whether a linear or rotary tensioner is used.”
The Conveyor Equipment Manufacturers Association (CEMA) defines the cleaning positions as primary, secondary, or tertiary. Primary cleaners typically function with a ‘peeling’ action, while secondary and tertiary cleaners are usually scrapers. Belt cleaners mounted in the primary position generally employ a rotary style tensioner, while most units mounted in the secondary or tertiary positions use linear style tensioners.
In most cases, belt tensioners have to be monitored and adjusted manually so
that they can maintain both optimum pressure and carryback removal. Estimating when blades need changing is often a ‘guessing game’ which, if left too long, may lead to unnecessary complications.
“Linear tensioners are most often applied where the compensation for wear is required in small increments, such as with hard metaltipped cleaners located in the secondary cleaning position or with brush cleaners,” Mueller says.
The simple design of linear tensioners often allows just one setting for full blade wear. Further, these tensioners can accommodate actuator deflection for accurate adjustment of cleaning pressure, delivering the ability to accommodate uneven mounting positions or asymmetrical blade wear.
The required tensioning forces can be applied by springs, hydraulic or pneumatic cylinders, electric actuators or from torque stored in an elastomeric element. Rotary tensioners like the Martin Twist Tensioner are often used with urethane blades, where the change in blade height and thickness as it wears is significant.
Rotary designs tend to be compact and, in most cases, the actuator(s) can be mounted at any orientation, which provides options
for installing the belt cleaner in the optimum position.
Air tensioners use the resilience of a pneumatic cylinder to cushion impact. The tensioners can use Martin’s Air Connection Kit to plug them directly into an existing air system, allowing for a more streamlined installation process.
Spring tensioners maintain efficient belt cleaning with a rugged coil spring. The Martin XHD Spring Tensioners deliver effective cleaning while cushioning splice shock to prevent damage, well suited for tensioning heavy duty belt cleaners while standing up to tough conditions.
Dual tensioning is recommended for belt cleaners installed on belts wider than 1 200 mm. However, dual tensioning does not change the fact that regular adjustment is required to maintain suitable cleaning pressure on the belt, which is where Martin’s N2 Smart Technology comes into play.
Martin Engineering’s smart technology platform includes the company’s patented N2 Position Indicator to monitor primary cleaner blade wear and inform operators when the blade needs changing. The system uses a cellular gateway that relays data to the cloud and then to the user, delivering actionable information in real time.
The N2 PI and Smart Device Manager App ease the burden on managers and workers so they can focus their attention on other critical details of the operation. Precise tensioning and improved belt cleaning reduce the volume of dust and spillage from carryback, improving workplace conditions and decreasing the labour needed to maintain and clean around the discharge zone. While manufacturers continue to improve belt cleaner effectiveness, it has become clear that there is no single or ideal solution for belt cleaning and tensioner selection. Safety of personnel and the belt itself is the primary consideration when selecting a tensioner. Ease of inspection and maintenance is critical for belt cleaner effectiveness, so the tensioner must allow quick and safe service. Martin Engineering offers the services and tensioning products that are necessary to meet the multifaceted demands of belt cleaning. a
In our business, we are in the unique position where we get to spend time at countless sites, working with drillers and blasters during the planning, preparation and execution of blasts. Our time spent on sites is mostly on blast day, where the pressure is on to charge, stem, tie-up and set off the blast.
By Eugene Preis, MD of ERG Industrial.Across many sites, I have observed several impactful good practices relating to blast execution. The list is not meant to be exhaustive, but rather a representation of the most prominent good practices that I have learned.
Charging: Although overcharged holes look spectacular in footage, they have an adverse impact on fragmentation and greatly increase the probability of flyrock. Fixing overcharged holes can be a tedious and laborious task, and oftentimes I have seen that the right tool for the job is not available on site. Having a tool available that can safely remove
explosives from blastholes is valuable. In many cases the explosives provider has such a tool, but I would recommend that a spare ‘in-house’ solution be available as a Plan B.
The extra effort put into fixing overcharged holes will be rewarded in the blast result that you achieve. In an ideal world, each hole would be charged exactly as per the design. In reality, quality assurance (for example, explosives removal tool) and quality control (for example, stemming checks) measures should be in place to get as close to the design as possible. Stemming: I always say that energy is lazy – it will take the path of least resistance. And in the case of blasting, this is mostly up and out of the blastholes. But not if your stemming practices
KEY POINTS
Although overcharged holes look spectacular in footage, they have an adverse impact on fragmentation and greatly increase the probability of flyrock
Good stemming practice is probably one of the most underrated activities in blasting
Drilling of blastholes is an expensive activity, and blastholes should be protected once they have been drilled
Factors such as block geometry, geology, rock characteristics and on-site conditions should be considered when designing blasts
It is recommended to film blasts to capture the necessary data to inform post-blast analysis.
are up to standard.
Good stemming practice is probably one of the most underrated activities in blasting. There is immense value in ‘doing stemming right’. The more robust the stopping power in your holes, the more the energy that will be channelled towards breaking your rock mass.
In many cases, aggregate beats drill chippings every day. Using aggregate is not always possible due to costs or availability, especially on the more remote mining sites. Drill chippings are the second choice and, depending on the characteristics and size of the chippings, the effectiveness can pale in comparison to aggregate.
Re-drilling is a ‘swear word’ in mining. A lot of re-drills are simply due to unfortunate geology and rock characteristics. Others are mostly avoidable by ensuring that blastholes are properly protected.
Apart from re-drilling, not protecting your holes from potential debris falling in can lead to a blocked hole, causing a range of other problems. And possibly another re-drill or short hole if you cannot fix the problem.
Create that stopping power with appropriate stemming, even if it costs more. You will thank yourself later when you see the difference in blast outcomes.
Drilling of blastholes is an expensive activity, and blastholes should be protected once they have been drilled. Mining is a rough environment, and there are a lot of things that can happen to a blasthole before being charged that can have a negative impact (both in terms of cost and blast performance).
A final point on protecting blastholes – they need to be protected after charging and before stemming as well. My experience on sites is that most of the debris gets into holes during this window period. I have personally spent hours trying to dislodge rocks that fell into holes after charging, with limited success. The consequence of this is then a hole that cannot be properly stemmed and loses large amounts of energy, and in certain cases a great increase in the risk of flyrock.
At each new site that we spend some time at, I always ask about the blast design. Based on the results that we have seen, a dynamic approach to blast design seems to yield the best results. Each blasting block/area is unique
and should be treated as such. Factors such as block geometry, geology, rock characteristics and on-site conditions should be considered when designing blasts.
Machines in mining break frequently, and that is a reality. Conditions are tough. We have the power to reduce the number of unexpected breakdowns by doing preventative maintenance.
It is Murphy’s law that a critical piece of equipment will break when needed most on a blast block. I have seen this many times, and this is something that can actively be mitigated through diligent preventative maintenance.
For each blast that we participate in, we always have a drone (or two drones), filming at 240 frames per second. This basically gives us visibility on every 4 milliseconds of the blast. For postblast analysis, this is absolute gold. Even if you are filming your blasts with a standard camera or a cellphone camera, seriously consider investing in an entrylevel drone to film your blast. The learnings from this will quickly pay back your investment. We often see things that would have never been possible with the naked eye or with a standard camera.
Blasts happen very quickly. Too quick for our eyes to really understand what is going on. On a biological level, our eyes are just not capable of capturing super-fast visual changes accurately. What happens is that we see only fragments of the truth, and our brains fill in the blanks.
The human eye can see between 30-60 frames per second. An entry-level drone can see at 240 frames per second at a resolution of 1080 p.
want art, respect the artist! Quality almost always beats quantity with blasting. In the mining world there are always production pressures and tight schedules. The one area that should not be rushed is drilling and blasting. The activities should be both effective and efficient, and this is not always possible when time is constrained. Ever heard the saying ‘you can’t rush a good thing’? Good blasting is art, and blasters are the artists. We expect excellent results every time from blasters, but we almost never provide them with the environment to be both effective and efficient. Want art? Give the artist their tools and their time, and you will get it. a
Aggregate and mining producers rely on their equipment to keep operations running smoothly. Productivity and profits depend not only on maintaining high efficiency, but preventing disruptive downtime that costs producers money every minute the screening plant is not functioning. By Lars Bräunling, MAJOR director of product technology.
Screen boxes and screen media in particular take on a lot of dayto-day stress and must be well maintained to prevent unexpected breakdowns. Adhering to regular service intervals is necessary, but can only go so far in anticipating the maintenance needs of your equipment.
And even if vibrating screens are functioning, it might not be at maximum efficiency. Productivity lost from underperforming equipment can be an unidentified burden on an aggregate or mining operation’s profitability.
Producers can use vibration analysis technology to get the information they need to prevent unforeseen breakdowns, as well as optimise their vibrating screens for maximum performance. As a result, vibration analysis tools are the easiest way to get started and get basic information quickly. Here is how:
Greater productivity: Vibration analysis technology gathers data on your screen box by measuring parameters such as g-force, stroke, rpm, orbit – even lateral movement, a measurement not offered by many alternative vibration analysis systems.
This valuable data can give producers the information they need to fine tune their machine for optimum productivity. It can even help prevent costly breakdowns.
Improved machine longevity: Aggregate and mining producers are well aware the abuse a screen box sees in a normal workday. These operations invest a lot of resources in choosing, integrating and maintaining their equipment, so protecting that investment is of the utmost importance.
Vibration analysis gives screening plant managers the information necessary to fine tune and properly maintain the equipment. It helps find issues that would often go undetected, such as a weakened springs on the side plate, and lead to significant damage to the machine.
Shutdown-free measurement: Certain
Vibration analysis technology provides producers the information they need to prevent unforeseen breakdowns, as well as optimise their vibrating screens for maximum performance.
vibration analysis tools offer the ability to collect data without shutting down the equipment. Stealing nothing from the day’s production, these types of vibration analysis tools use a sensor positioned on the screen box and conduct tests as the machine operates. Immediate results: While some vibration analysis tools may take up to a day to send test results, others offer immediate insight into the equipment’s performance. Certain manufacturers offer a vibration analysis app to allow operators to view results within minutes.
Producers can use the information gathered by vibration analysis tools to determine whether a more in-depth analysis is needed. If questions come up or further analysis is needed, it’s best to work with a trusted manufacturer to analyse test results and maximise productivity. a
According to SRK Consulting principal consultant Fiona Sutton, water stewardship is coming to the fore in ESG reporting –with ESG itself also still evolving a consistent framework that is broadly recognised by the investment community.
“In the most recent EY Global Institutional Investor Survey, for instance, it is argued that the reporting of ESG performance needs to be measured against a set of globally consistent standards – which could become a mandatory requirement,” says Sutton. “With water management ranked by EY as the number one ESG risk in mining, and with ESG itself being the top risk for the second year running, there is some urgency for mining companies to assess water risk in terms of a credible framework.”
She points out that water stewardship and biodiversity (the latter ranked eighth in EY’s 2023 risks) are fast becoming urgent priorities. Factors putting pressure on water resources include population growth, shifts toward more meat-based diets, climate change and other challenges. The world’s water is increasingly becoming degraded in quality, she explains, increasing the cost of treatment, and also threatening human and ecosystem health. Furthermore, the physical availability of freshwater resources does not guarantee that a safe, affordable water supply is available to all.
“The growing significance of water management within ESG strategy means that more rigorous
reporting will be demanded by mining company stakeholders,” she says. “Better water reporting will also be necessary to access capital and to secure a license to operate.”
More detailed water management reporting will in turn require more trustworthy and useful ESG data, including information related to relevant financial and social impact risks.
“An effective response to these risks can be rooted in the concept of water stewardship, which provides a process for companies to work collaboratively with other partners to manage shared water resources,” she says. “In this way, water stewardship can be an important component to mitigating corporate water risk and facilitating business growth.”
SRK Consulting MD Andrew van Zyl, affirms the critical importance of water risk on the mining agenda –and the importance of global best practice tools like the International Water Stewardship Standard from the Alliance for Water Stewardship (AWS).
“Assurance is a key facet in increasing trust in the quality and accuracy of sustainability information,” says Van Zyl. “The AWS Standard offers a credible and globally applicable framework for major water users to understand their own water use and impacts with practical guidance on how to effectively manage these impacts.”
SRK associate partner and principal environmental geologist Lindsay
Shand highlights the practical value of the AWS standard.
“The principles of water stewardship are drawn from high level environmental imperatives,” says Shand, “However, they also give water users a more practical framework from which to tackle their issues of water quantity and quality.”
Applying the International Water Stewardship Standard, explains Sutton, means a more effective evaluation of water use. It guides companies in disclosing aspects such as water governance, metrics, site risks, catchment risks, quality targets, strategies and performance.
“Another way that the AWS standard reinforces – rather than duplicates – existing systems and processes in mining companies, is that it aligns with other reporting frameworks that they might use,” she points out. a
As a vital aspect of environmental, social and governance (ESG) risk, water management should take priority for every mining operation. SRK Consulting highlights that the mining sector will increasingly need to report its waterrelated performance in terms of credible global standards.
Weak economic conditions in construction have led contractors to find new ways of surviving, but some of these strategies could undermine the longevity of roads and buildings, says AfriSam Construction Materials executive Avi Bhoora.
“On the aggregates side, we find that the call for ‘brown’ material – as opposed to the highvalue ‘blue’ material like quartzite, tillite and dolomite – is rising,” he says. “While some brown materials can be modified by additives, they cannot match the quality of competent rock.”
In the past, G1 aggregate was the main base course for roads, with G2 as the sub-base, and G4 and G5 used for the selected layers. Bhoora says that recently there are efforts to substitute these, using products with names like G4A or G4A Special, for instance. Specifications are being adapted possibly because of cost pressure, but have not yet stood the test of time.
“During my 40 years in construction, I have been involved in projects building roads that have outlasted their expected 25-year lifespan by a decade or more,” says Bhoora. “It is uncertain whether the new specifications will be as effective, especially with the much heavier loads on our roads today. My personal view is that going this route might be short sighted in the long run.”
In terms of the readymix market, he says the average strength of concrete supplied has been gradually declining. AfriSam has long been known in the sector as a specialist in high strength products for demanding applications like high-rise buildings – with concrete strengths up to 100 MPa for high-rise projects.
“There are fewer projects like this currently, but there are also signs of users ‘buying down’ when it comes to readymix,” he says. “Whereas 35 MPa was the average strength we supplied until recently, that average is now closer to 28 MPa. This is concerning, as skimping on concrete strength is certain to have long term consequences for buildings’ longevity.”
He notes that there is still insufficient work entering the project pipeline, holding back the potential of the construction sector to create jobs and build valuable infrastructure. Contractors and their supply chain remain under pressure, with low margins leading to the demise of amalgamation of important industry bodies. a