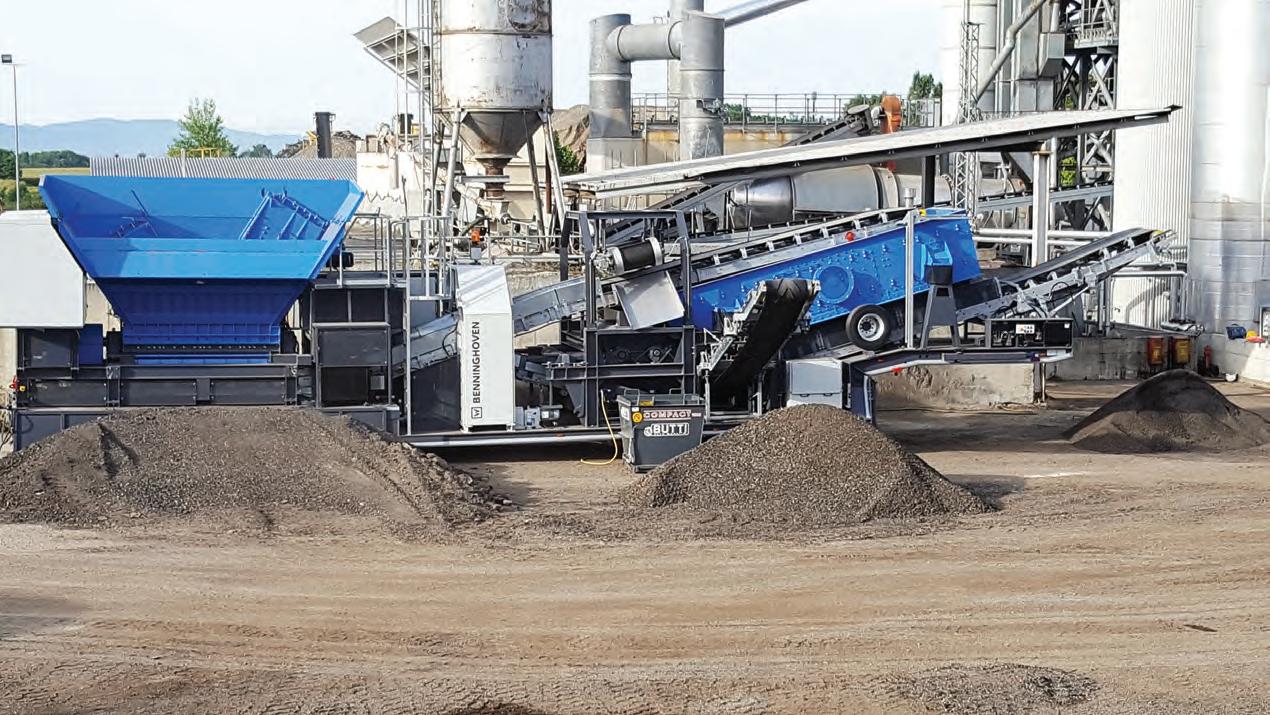
8 minute read
Una vera industria del conglomerato
asfalti&bitumi
UNA VERA INDUSTRIA
Advertisement
DEL CONGLOMERATO
IL FORTE IMPULSO CHE LA SOCIETÀ BITUX HA VOLUTO DARE AL SUO SETTORE STRADALE SI È TRADOTTO NELL’ACQUISIZIONE DEL NUOVO IMPIANTO PER LA PRODUZIONE DI CONGLOMERATI BITUMINOSI BENNINGHOVEN BA 5000
La forte crescita di lavori, la necessità di garantire la massima qualità del prodotto finito anche con alte percentuali di fresato, la richiesta di prodotti sempre più innovativi, la necessità di garantire il massimo rispetto dell’ambiente: tutto questo si è concretizzato con la decisione, da parte della Società Bitux SpA, di acquistare il nuovo impianto Benninghoven Competence BA 5000.
IL NUOVO IMPIANTO BENNINGHOVEN COMPETENCE BA 5000
Questo impianto è il risultato di un lungo studio del mercato e dalla analisi di quanto poteva essere offerto: la potenzialità di 400 t/ora ha convinto il Titolare della Bitux SpA - Sig. Luigino Valle - a cambiare completamente il modo di produrre il conglomerato e a riorganizzare la propria Società dal punto di vista della produzione del conglomerato bituminoso. In realtà, l’Azienda aveva iniziato l’analisi dei possibili miglioramenti e delle ottimizzazioni realizzabili nel ciclo produttivo dalla lavorazione del fresato già da oltre un anno: la visita di vari cantieri italiani ed esteri aveva chiaramente mostrato la corretta direzione. Innanzitutto, la necessità di avere il giusto spazio a disposizione per uno stoccaggio differenziato del materiale fresato a seconda della provenienza e della qualità dei materiali; a seconda del tipo di aggregati, della curva granulometrica, del tipo di bitume presenti nel materiale da riciclare, si provvede a suddividere il materiale riciclato in maniera differenziata.


2. L’impianto Benninghoven Competence BA 5000

3. Il cilindro essiccatore e il sistema di gestione delle aspirazioni IMPIANTI PER CONGLOMERATI
Per riuscire a gestire questa prima fase di lavorazione nella maniera corretta è stato comprato un terreno adiacente al cantiere e di conseguenza tutto il materiale proveniente dalla fresatura viene depositato in aree asfaltate e ben differenziate; successivamente il materiale stesso viene lavorato da un granulatore Benninghoven MBRG 2000-2 in modo da creare diversi cumuli coperti di materiale selezionato che viene attentamente controllato e verificato all’interno del laboratorio della Società. Avendo una perfetta conoscenza della qualità dei vari cumuli di fresato, è così molto più semplice riuscire a garantire la massima qualità del prodotto finito anche con percentuali più elevate di fresato riutilizzato nella produzione del conglomerato bituminoso; la copertura degli stessi garantisce inoltre una riduzione dei consumi e delle conseguenti emissioni in atmosfera. In particolare, una caratteristica sostanziale del granulatore MBRG 2000-2 è quella di disgregare il materiale fresato senza rompere gli aggregati e, di conseguenza, la curva granulometrica del materiale di partenza viene rispettata senza il problema di dover gestire una quantità elevata di fini; quindi, pur aumentando la quantità di materiale fresato nelle formule di produzione, si ha la tranquillità di produrre un conglomerato non troppo rigido e nel pieno rispetto dei capitolati prestazionali. Altra caratteristica fondamentale del granulatore è quella di poter gestire la lavorazione di placche di conglomerato provenienti dalla demolizione delle strade; la dimensione gestibile raggiunge anche i 1.500 mm senza la necessità di dover utilizzare escavatori o mulini frantumatori. Il tutto viene gestito semplicemente dalla pala caricatrice e dal granulatore stesso con due stadi di granulazione; in tal modo, l’efficienza della lavorazione viene massimizzata ed i costi di trattamento del materiale fresato raggiungono i minimi possibili.
LA PRODUZIONE CON ALTE PERCENTUALI DI FRESATO
La corretta preselezione e lavorazione del fresato consente veramente di ottenere la “materia prima seconda” con la giusta qualità in modo da poter produrre conglomerati altamente prestazionali anche con l’utilizzo di alte percentuali di materiale fresato. La seconda fase dello studio si è concentrata sull’impianto: con i volumi di produzione in gioco era essenziale riuscire a produrre altissime quantità di conglomerato, gestire numerose ricette per alimentare nel modo corretto i diversi cantieri, evitare che i camion dovessero attendere troppo tempo in cantiere prima di essere caricati e di conseguenza ottimizzare l’efficienza delle varie squadre di stesa, sia proprie, sia dei diversi clienti che si riforniscono presso l’impianto. Il Sig. Luigino Valle ha avuto subito le idee chiare e, ben conoscendo i punti da migliorare relativi all’efficienza del proprio ciclo produttivo, ha immediatamente focalizzato la propria attenzione sull’impianto top di gamma nella produzione della Benninghoven; il vero salto di qualità poteva essere fatto solamente con un cambio radicale nel modo di lavorare, sia qualitativo, sia quantitativo. Gli input che sono stati dati erano chiari: • qualità del prodotto finito con la conseguente necessità di vagliare nel modo migliore la maggiore quantità degli aggregati e la possibilità di utilizzare il vaglio per ricontrollare gli inerti anche quando si utilizza il fresato; • flessibilità nella produzione, nei cambi di formula e nella possibilità di produrre qualsiasi tipo di conglomerato, dai più tradizionali, ai più innovativi (tiepidi, freddi, con additivi, polimeri, fibre, ecc.); • altissime capacità di stoccaggio del prodotto finito; • poter utilizzare fresato alle massime percentuali attualmente gestibili in Italia ed essere già pronti per il futuro per l’eventuale aggiunta del tamburo parallelo in modo da raggiungere altissime percentuali di utilizzo, non appena i Capitolati lo permetteranno. A seguito di diverse visite a cantieri esistenti, la scelta è ricaduta sull’impianto BA 5000 che permette di gestire produzioni elevatissime, fino a 400 t/ora. 4. Il granulatore per materiale fresato Benninghoven MBRG 2000-2
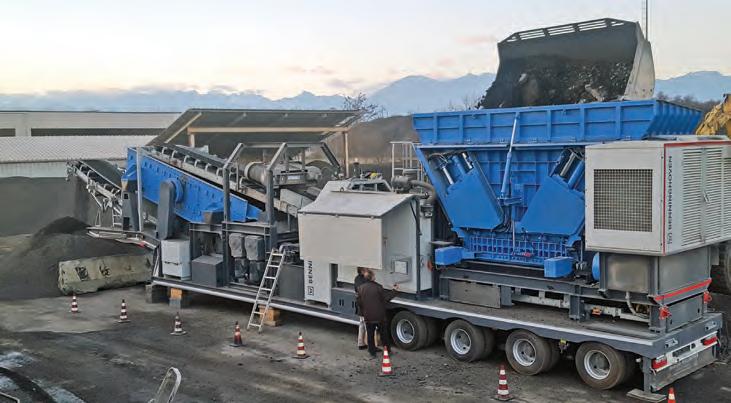
asfalti &bitumi

5. Il bruciatore brevettato per la gestione di emissioni diffuse
GLI ELEMENTI PRINCIPALI DELL’IMPIANTO BA 5000
Altre caratteristiche sostanziali sono il vaglio riselezionatore a sei selezioni con una superficie vagliante di oltre 52 m2 e delle tramogge sotto vaglio maggiorate con una capacità complessiva di materiale caldo selezionato di 270 t: in questo modo si ha il massimo controllo della curva granulometrica del prodotto finito, una flessibilità ineguagliabile nel gestire i cambi formula e la possibilità di minimizzare gli start/stop dell’impianto legati ad eventuali produzioni non programmate e gestire in maniera ottimale i clienti che si presentano all’impianto senza aver preventivamente avvisato. Il mescolatore maggiorato a 5 t garantisce la possibilità di produrre in pochi minuti il conglomerato necessario per riempire i camion; inoltre, consente di allungare il tempo di mescolazione (nel caso di dover utilizzare additivi, fibre, alte percentuali di fresato) senza “pesare” troppo sulla produzione oraria dell’impianto stesso. I sili deposito del prodotti finito (quattro scomparti da 80 t cadauno) consentono di preparare oltre dieci bilici di materiale già pronto e di conseguenza alimentare con la massima velocità i camion in cantiere. Tutta la sezione sili deposito, navetta di alimentazione dei sili, modulo di dosaggi e mescolazione sono chiusi e tenuti in depressione; in tal modo, l’impianto consente di garantire il massimo rispetto ambientale riducendo rumori, polverosità, dispersioni termiche, emissioni diffuse in atmosfera. In particolare, quest’ultimo argomento è stato curato nel miglior modo possibile ed il bruciatore dell’impianto è stato previsto con un kit brevettato per poter gestire le emissioni diffuse che vengono aspirate e convogliate al bruciatore stesso in modo da poterle “bruciare” all’interno del cilindro essiccatore; in tal modo le eventuali particelle oleose “sospese” nei vapori che si sviluppano al momento dello scarico del conglomerato vengono captate, bruciate e di conseguenza l’impatto dell’impianto verso l’ambiente circostante è sicuramente ottimizzato. Logicamente, per gestire al meglio questa delicata operazione, il bruciatore è gestito da un PLC dedicato che permette di controllare i rapporti aria-combustibile tenendo in considerazione sia l’aria primaria (proveniente dalla ventola principale del bruciatore controllata da inverter), sia l’aria secondaria (proveniente dalla ventola che aspira le emissioni diffuse); inoltre il PLC stesso permette di utilizzare in alternativa come combustibile sia il gas metano, sia il GPL.
ATTENZIONE E RISPETTO PER L’AMBIENTE
L’elevata attenzione che Bitux ha posto sul rispetto ambientale si è tradotta anche nella possibilità di produrre sia conglomerati tiepidi (con l’utilizzo del bitume schiumato) sia riciclato a freddo (con l’utilizzo dell’emulsione), in modo da minimizzare i consumi energetici e le conseguenti emissioni in atmosfera. Sempre in questa direzione, si è scelta la tecnologia brevettata di utilizzo del fresato Multivariable System che permette di raggiungere alte percentuali senza utilizzare l’anello di riciclaggio, con tutte le problematiche che lo stesso comporta dal punto di vista, odori, emissioni, manutenzioni; l’impianto è già predisposto (con parte della struttura metallica necessaria) per un successivo completamento con il tamburo parallelo con generatore di aria calda; soluzione che permette il raggiungimento di percentuali di utilizzo del fresato anche superiori al 90%, nel pieno rispetto delle emissioni in atmosfera. Anche tutte le cisterne per il deposito del bitume e dell’emulsione sono state previste con riscaldamento elettrico e con coibentazioni maggiorate in modo da evitare la caldaia (con le relative emissioni in atmosfera) e l’olio diatermico (con i conseguenti rischi di utilizzo di fluido ad alta temperatura); in questo modo i consumi per mantenere caldo il bitume sono stati ottimizzati e inoltre gli sfiati delle cisterne sono stati raccolti in un unico punto e gestiti con un “separatore” in modo da minimizzare “l’odorosità” che talvolta può dare fastidio al vicinato. Il grande sforzo finanziario che la Bitux ha dovuto sostenere per poter realizzare questo importante progetto verrà sicuramente ricompensato con un aumento della efficienza complessiva della Società, con una riduzione dei costi di produzione e un contemporaneo aumento della qualità del prodotto finito. n
(1) Ingegnere, Product Manager di Benninghoven (Wirtgen Group)
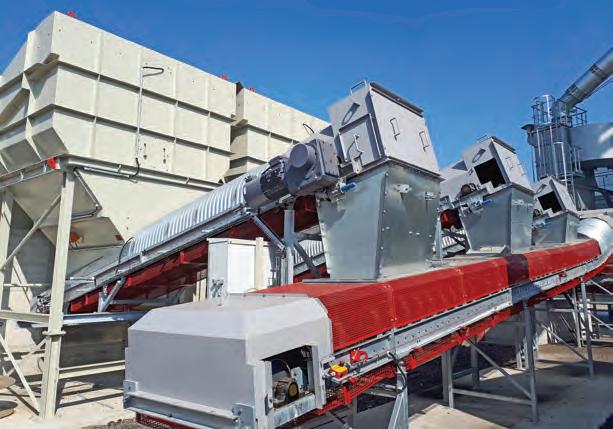
6. Il gruppo dosaggio a tre selezioni di fresato