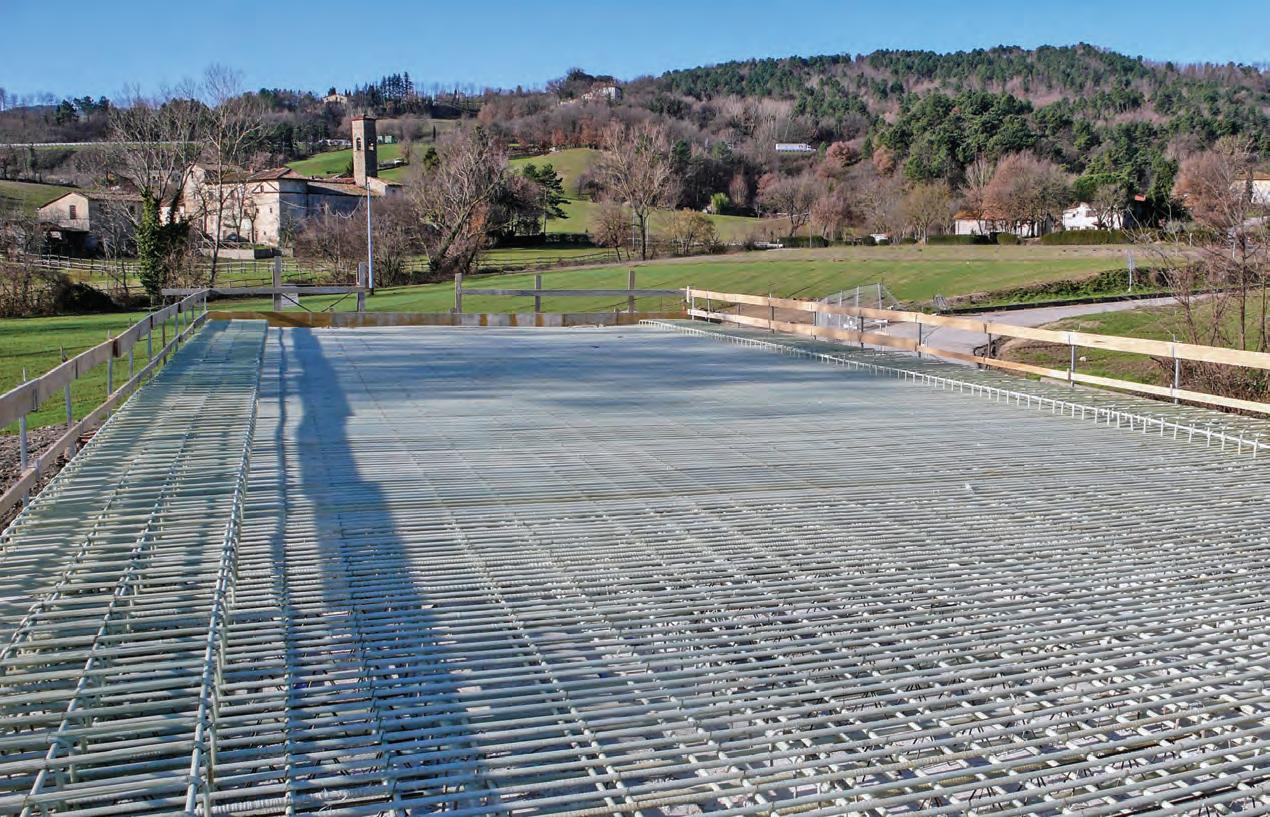
11 minute read
I compositi in fibra di vetro per la durabilità delle infrastrutture
Ugo Dibennardo(1), Paolo Mannella(2) materiali&inerti
I COMPOSITI IN FIBRA DI VETRO
Advertisement
PER LA DURABILITÀ DELLE INFRASTRUTTURE
Uno dei problemi che maggiormente influenzano la durabilità delle strutture in calcestruzzo armato, riducendone la vita utile, è rappresentato dalla corrosione delle armature metalliche. Al riguardo, occorre ricordare che l’acciaio - una volta annegato nel calcestruzzo - si trova protetto dalla corrosione fintanto che il calcestruzzo stesso è caratterizzato da un valore dell’alcalinità compreso tra pH 12 e pH 14. Nelle fasi iniziali di realizzazione di un elemento strutturale in c.a., sull’acciaio costituente le armature metalliche si forma un sottilissimo film passivante (formato da ossidi dello spessore di pochi strati molecolari) che protegge l’armatura metallica e rende praticamente impossibile la corrosione. Col passare del tempo, tuttavia, l’alcalinità del calcestruzzo viene neutralizzata dall’anidride carbonica proveniente dall’esterno che, lentamente, determina il fenomeno della carbonatazione del calcestruzzo. Tale fenomeno non è di per sé dannoso per il calcestruzzo, anzi ne aumenta le caratteristiche di resistenza meccanica a compressione, ma induce la riduzione dell’alcalinità del calcestruzzo, fino a raggiungere valori compresi tra pH 9 e pH 11. Al di sotto del valore di pH 11,5, il film protettivo passivante che avvolge le barre di armatura metallica si dissolve e, in presenza di acqua e ossigeno, inizia la corrosione dell’armatura in acciaio. Tale fenomeno è aggravato dalla presenza di cloruri che troviamo nei sali disgelanti utilizzati nel periodo invernale sui ponti e sui viadotti situati in aree montane e che pure sono presenti nell’atmosfera in prossimità del mare, a distanza inferiore ai 500 m dalla linea costiera, il cosiddetto aerosol marino. La corrosione dell’acciaio presente negli elementi strutturali in c.a., inoltre, può essere innescata da correnti galvaniche che si determinano nelle vicinanze di linee elettriche aeree e cavidotti ad alta tensione. Spesso, al fine di aumentare la durabilità di un opera in c.a., si sceglie di aumentare il valore del copriferro a protezione dell’armatura metallica; tale scelta, tuttavia, in caso di non corretta realizzazione e armatura dello spessore di copriferro - necessaria quando questo assume valori superiori ai 5 cm - può determinare la rapida insorgenza di fessurazioni con i danni conseguenti. La corrosione delle armature metalliche produce ossido di ferro che causa il rigonfiamento delle barre; tale aumento di volume induce fessurazioni nel calcestruzzo, perdita di aderenza ed espulsione del copriferro. Il risultato finale del fenomeno di carbonatazione del calcestruzzo e della successiva ossidazione delle barre di armatura è ben noto a tutti e può essere bene esemplificato dalle immagini che seguono (Figure 2 e 3).
1.
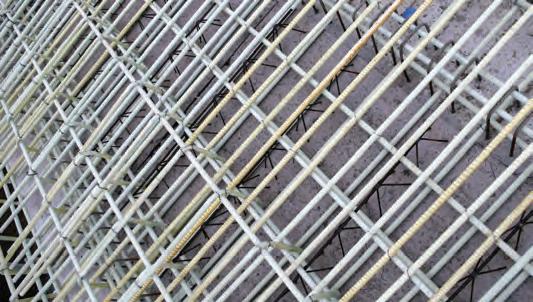
materiali &inerti

2. Il degrado dell’armatura metallica in corrispondenza di giunto
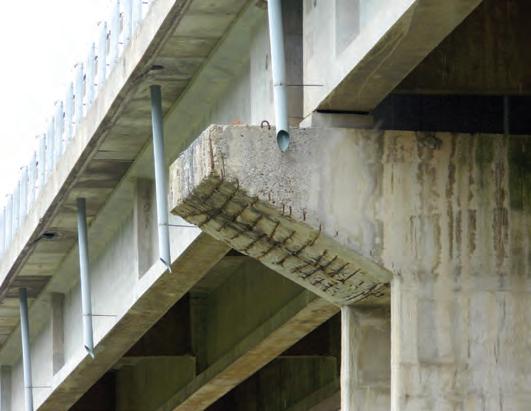
3. Il degrado dell’armatura metallica di pulvino
L’impatto estetico prodotto da tale fenomeno è assolutamente negativo e sembra richiamare a opere abbandonate e non curate. Per contrastare tale fenomeno, che rappresenta la causa principale di degrado delle opere in calcestruzzo armato presenti sulla rete in gestione, ANAS si sta adoperando con ingenti investimenti - assentiti nell’ambito del Contratto di Programma 2016-2020 - che mirano alla tutela del patrimonio esistente e all’allungamento della vita utile di ponti e viadotti. In tale ambito, l’attività principale avviata consiste nel ripristino corticale delle opere in c.a. che deve essere eseguito mediante la pedissequa applicazione di progetti tipologici appositamente redatti e inviati a i tutti i Progettisti ANAS; tali progetti sono anche disponibili sul sito aziendale. Sempre al fine di contrastare la corrosione e i suoi effetti, è in fase di svolgimento una gara per l’Accordo Quadro dell’importo di 20 milioni di Euro per la protezione catodica galvanica delle opere in c.a.. Con questo strumento, ANAS - per la prima volta - intende applicare in maniera estesa tale tecnica di protezione delle barre metalliche di armatura presenti negli elementi strutturali più importanti di un selezionato numero di ponti e viadotti.
LE BARRE IN VETRORESINA
Il tema della protezione degli elementi strutturali in c.a., come si vede, è al centro delle attività di ANAS; a tale riguardo, una interessante “novità” che si ritiene debba essere studiata accuratamente per valutarne l’impiego è quella costituita dall’utilizzo di barre in vetroresina per l’armatura delle parti di opera oggetto di ripristino strutturale. Le barre in vetroresina sono realizzate con fibre continue di vetro ECR, che vengono impregnate con resine termoindurenti di vinilestere e successivamente polimerizzate. Il processo di polimerizzazione è irreversibile: a differenza delle resine termoplastiche, una volta polimerizzate queste barre diventano chimicamente stabili e non possono più essere modificate. Non è possibile ad esempio la piegatura delle stesse in cantiere, ma la loro forma e dimensione deve essere ottenuta durante il processo produttivo, prima della loro completa polimerizzazione. Le armature in vetroresina, composte da resina di vinilestere e vetro “ECR”, hanno un comportamento completamente diverso e in un certo senso opposto a quello delle barre metalliche: esse non sono aggredite dalla corrosione e, al contrario delle barre metalliche, “soffrono” di più in ambiente alcalino mentre sono completamente inerti in ambienti acidi o neutri. Ciò significa che, con il passare del tempo e il progredire della carbonatazione del calcestruzzo, che come abbiamo visto normalmente costituisce un problema, la durabilità del rinforzo armato con barre in vetroresina si incrementa. Per quanto riguarda la corrosione galvanica, con la vetroresina questa non si determina in nessuna circostanza in quanto il materiale è completamente isolante e insensibile a campi elettrici e onde elettromagnetiche; non sono necessari, quindi, interventi di messa a terra o protezioni con anodi sacrificali. In cantiere possono essere maneggiate e legate con gli stessi accorgimenti e metodi utilizzati per le barre in acciaio, con il vantaggio di pesare molto meno rispetto alle barre di acciaio. La loro densità, infatti, è pari a circa 1.900 kg per metro cubo, a fronte dei 7.850 kg per metro cubo dell’acciaio. In merito alle caratteristiche meccaniche delle armature in GFRP, occorre considerare che la loro resistenza a trazione è molto elevata: da 600 a oltre 1.000 MPa; il loro modulo elastico è, invece, inferiore a quello dell’acciaio e risulta compreso tra i 40 e 50 GPa. Le barre in vetroresina hanno un comportamento a trazione elastico fino alla rottura e, a differenza delle barre in acciaio, non presentano il fenomeno dello snervamento e sono, pertanto, in grado di riassorbire completamente le deformazioni dovute a carichi temporanei. Dal punto di vista progettuale, bisogna sempre considerare tale differenza di comportamento; i principi essenziali per sfruttare al meglio tale materiale sono di seguito sinteticamente illustrati. In un progetto di tipo tradizionale, dove viene impiegato calcestruzzo armato con barre in acciaio, viene definita la quantità di acciaio dell’armatura, in modo tale che l’acciaio risulti essere l’elemento debole della struttura. In questa situazione, le barre in acciaio si allungano per snervamento, segnalando così, la prossima rottura dell’elemento in calcestruzzo. Diversamente, impiegando delle barre in GFRP, il numero di barre da utilizzare si calcola in modo che la parte resistente più debole sia costituita dal calcestruzzo.
COMPOSITI PER INFRASTRUTTURE
Sarà questo che, collassando, segnalerà la crisi, lasciando peraltro ancora un notevole margine alla capacità di trazione dell’armatura in GFRP. A causa del modulo di elasticità delle barre in vetroresina, in fase di progetto vanno considerate la deformazione e la larghezza delle fessurazioni. L’elevata deformazione e la larghezza delle fessurazioni forniranno ulteriori segnali di rottura prima del cedimento per compressione del calcestruzzo; molto spesso saranno proprio la deformazione e larghezza delle fessurazioni i limiti di progetto. Al fine di valutare il comportamento delle barre in vetrore-
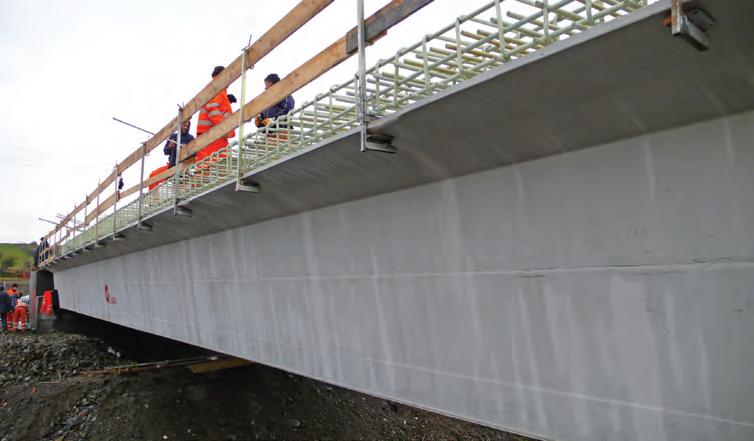
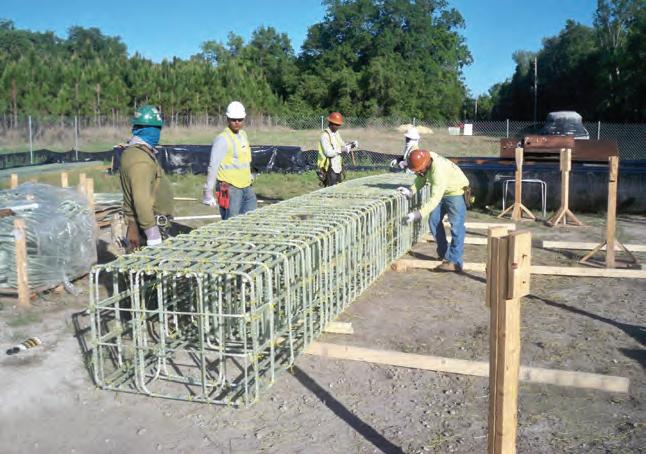
4A, 4B, 4C e 4D. I lavori di rifacimento del ponte sul fiume Halls in Florida (a cura del FDOT Florida Department of Transportation) sina, a livello internazionale sono stati condotti molti studi il più importante dei quali certamente è quello realizzato nel 2005 congiuntamente in Canada e negli Stati uniti. In tale studio sono stati prelevati - per carotaggio - campioni di armatura in vetroresina, dai deck di cinque differenti ponti, realizzati sperimentalmente circa dieci anni prima, usando come armatura barre composte da “vetro E” e “resina di vinilestere”. Tali campioni sono stati inviati in differenti laboratori universitari in Canada e negli Stati Uniti e sottoposti ad approfonditi esami fisico-chimici, a seguito dei quali è stato appurato che le barre di armatura in vetroresina non avevano subito alcun degrado apprezzabile, nessun cambiamento di sezione né deterioramento delle fibre impiegate. La continua e pressante richiesta da parte delle Autorità nel settore delle infrastrutture di garantire una maggiore durabilità dell’opera, una ridotta manutenzione e non ultima la richiesta di rispondere alle istanze internazionali di riduzione delle emissioni di CO2 hanno spinto gli Enti e i Rappresentanti del mondo scientifico e normativo a definire Norme e raccomandazioni per l’utilizzo di armature in GFRP che, in effetti, sono in grado di rispondere a tutte queste importanti istanze.

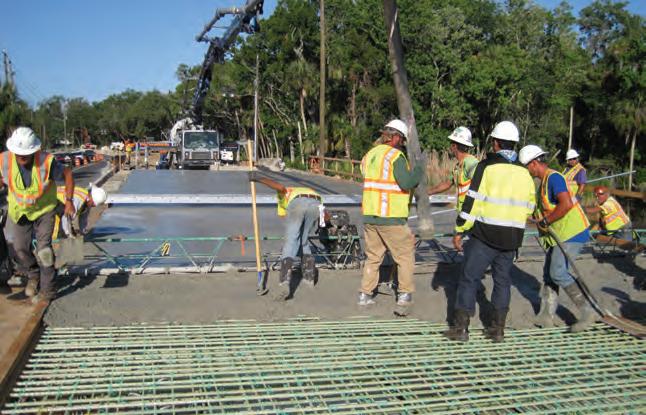
materiali &inerti
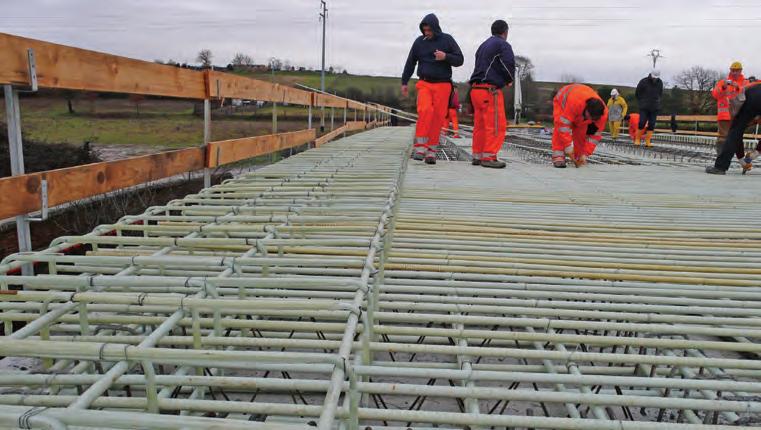

5A e 5B. Un particolare della posa dell’armatura RWB-A in GFRP della soletta del ponte sul fiume Halls
IL PROBLEMA NORMATIVO E LO SCENARIO INTERNAZIONALE
In Canada l’uso della vetroresina per la realizzazione di solette da ponte è ormai diffuso e regolato da una apposita Normativa, la CSA S-806 del 2012, già alla seconda edizione. Anche negli Stati Uniti esistono linee guida consolidate, giunte alla seconda edizione (ACI 440-1R del 2015); inoltre, nel corso del 2018 in Florida è stato realizzato il primo ponte in calcestruzzo totalmente armato con materiali compositi, dalle pile alle travi e alle solette. In Europa, invece, dal punto di vista normativo, esiste solo il Bollettino FIB n. 40 che però non può essere utilizzato per la progettazione. Da questo punto di vista, il nostro Paese è in una condizione migliore rispetto al resto d’Europa grazie al lavoro svolto dal CNR e al documento CNR DT-203 del 2006 (Istruzioni per la progettazione, l’esecuzione e il controllo di strutture di calcestruzzo armato con barre di materiale composito fibrorinforzato). Tali linee guida, tuttavia, non sono state ancora recepite dal Ministero delle Infrastrutture e dei Trasporti e risulta difficoltoso ottenere il Certificato di idoneità tecnica (CIT) necessario per i diversi impieghi che si volessero fare delle barre in fibra di vetro. Si ritiene, invece, che l’utilizzo di tale materiale nei ripristini strutturali delle opere d’arte possa offrire considerevoli vantaggi.
ESEMPI DI CONCRETO UTILIZZO
I compositi in vetroresina sono utilizzati abitualmente in Canada, proprio per la loro resistenza agli agenti atmosferici prevalentemente nella realizzazione di solette, cordoli e barriere da ponte. Nel corso del 2018, in Florida (a Tampa), si è conclusa la costruzione del primo ponte stradale in calcestruzzo, (“Halls river Bridge”) totalmente rinforzato (pile, travi, solette e cordoli) con barre in fibra di vetro. Il progetto, finanziato dalla Federal Highway Administration, ha lo scopo di promuovere l’utilizzo estensivo dei compositi nelle infrastrutture, in modo da ridurre il costo della manutenzione. Nell’ambito di questa realizzazione, è stata inserita anche parte della sperimentazione Seacon con lo scopo di dimostrare la possibilità di utilizzare acqua di mare e aggregati contaminati da sali per la produzione di calcestruzzo eco-sostenibile, rinforzato con armature non corrodibili. Il Progetto sperimentale, guidato dall’università di Miami e dal Politecnico di Milano, è finanziato dal programma di ricerche europeo Infravation, che comprende partner industriali americani e italiani. Le possibilità di utilizzo dei compositi nell’ambito degli interventi ANAS sono molteplici sia per quanto riguarda la realizzazione di nuove opere, sia nel settore dei ripristini strutturali delle opere esistenti aggredite dalla corrosione. Ad esempio, nel ripristino delle gallerie, reti in vetroresina possono essere vantaggiosamente impiegate per il rinforzo delle riparazioni del rivestimento e per la realizzazione di drenaggi, in calotta o nei piedritti dove, anche in presenza di forti venute d’acqua, non presentano i problemi di ossidazione e rigonfiamento tipici dei rinforzi in acciaio. In ponti e viadotti, grazie anche alla loro leggerezza e alla possibilità di essere realizzati con forme e dimensioni particolari anche in piccole serie, possono essere utilizzati per il reintegro e/o incremento di armature in acciaio ormai corrose in pile, pulvini, velette e cordoli. Una ulteriore applicazione può essere quella di ripristinare le armature ormai scoperte delle pile dei ponti aggiungendo una gabbia esterna leggera e non corrodibile realizzata con barre e staffe aperte ganciate. Occorre, infine, considerare che l’utilizzo delle barre realizzate con compositi in fibra di vetro permette di ottenere un’ottima performance ambientale nella valutazione del ciclo di vita (LCA, Life Cycle Assessment) con un impatto sull’ambiente molto minore rispetto all’acciaio. Proprio per dare concreta applicazione a questi possibili e vantaggiosi interventi, ANAS sta preparando appositi progetti tipologici, da poter impiegare per il ripristino di tali situazioni di degrado molto diffuso. n
(1) Ingegnere, Direttore Operation e Coordinamento Territoriale di ANAS SpA (2) Ingegnere, Direzione Operation e Coordinamento Territoriale - Ufficio Ponti Viadotti e Gallerie - Responsabile Centro-Sud di ANAS SpA