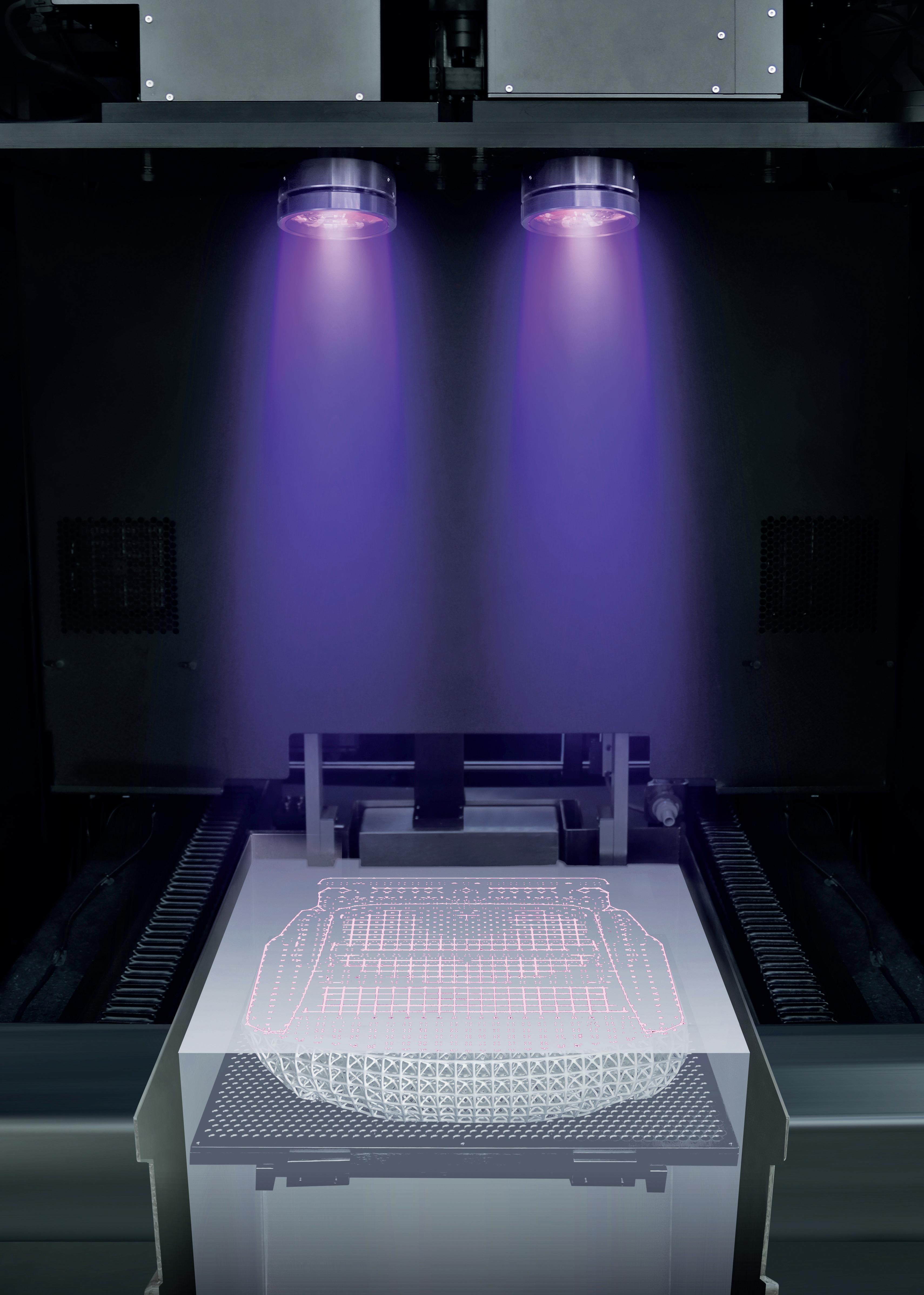
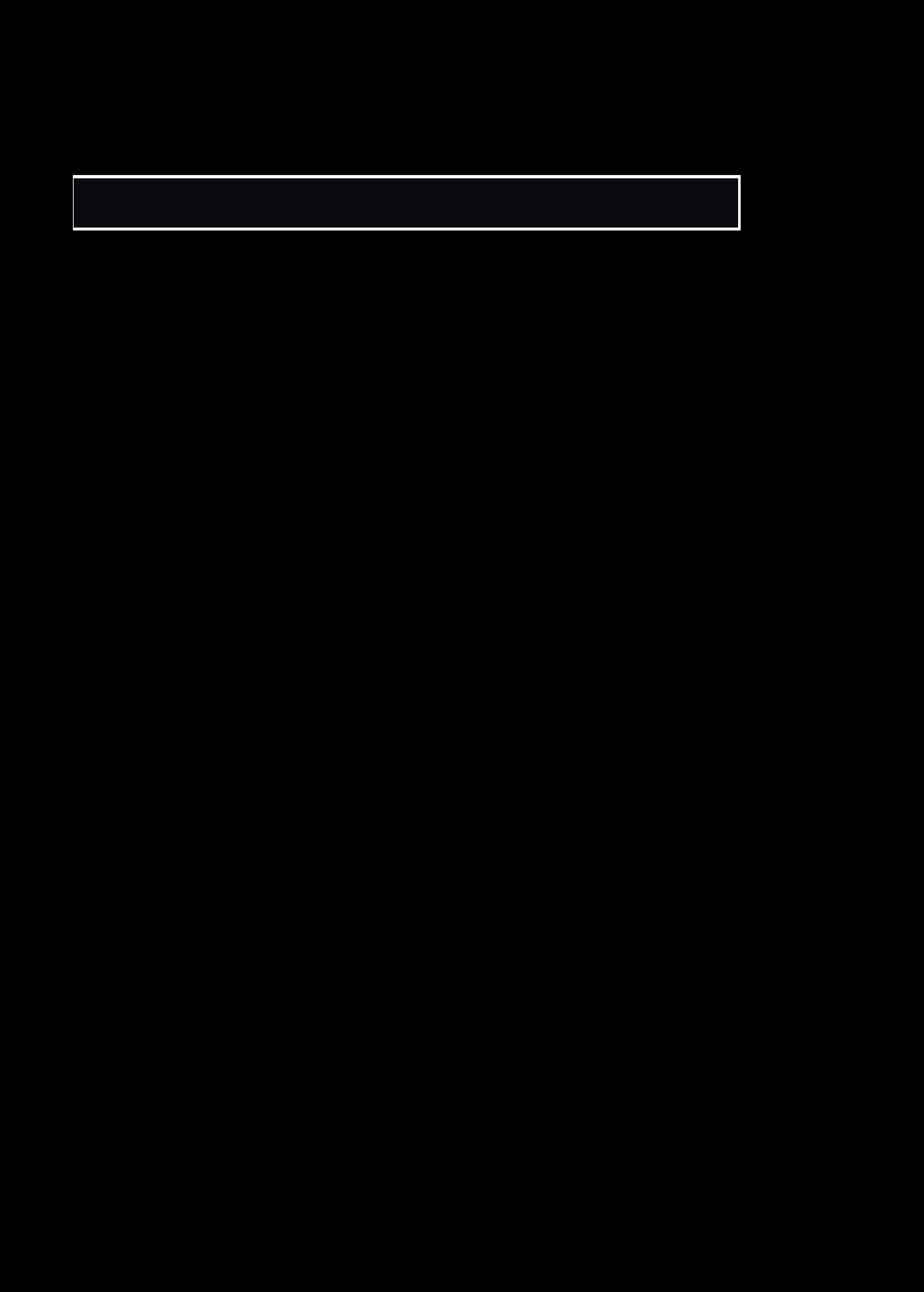
Nicky Martin e: nicky.martin@rapidnews.com t: + 44 1244 952 365
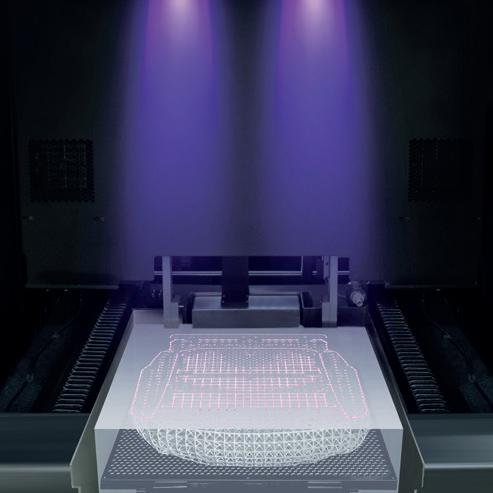
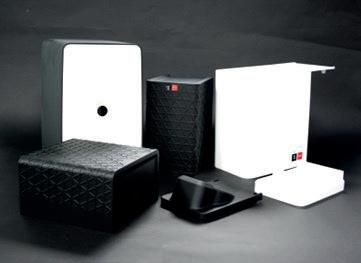
SALES EXECUTIVE TCT PORTFOLIO
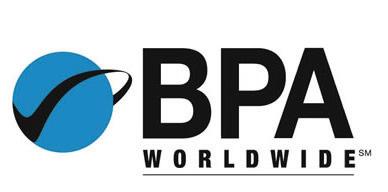
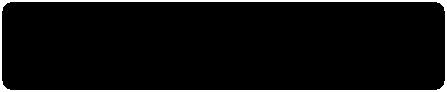
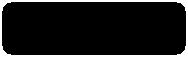
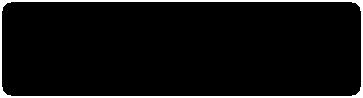
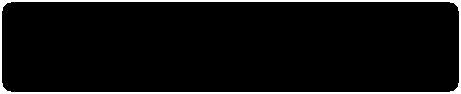
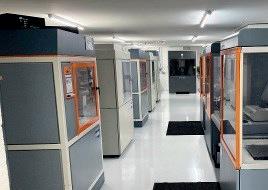
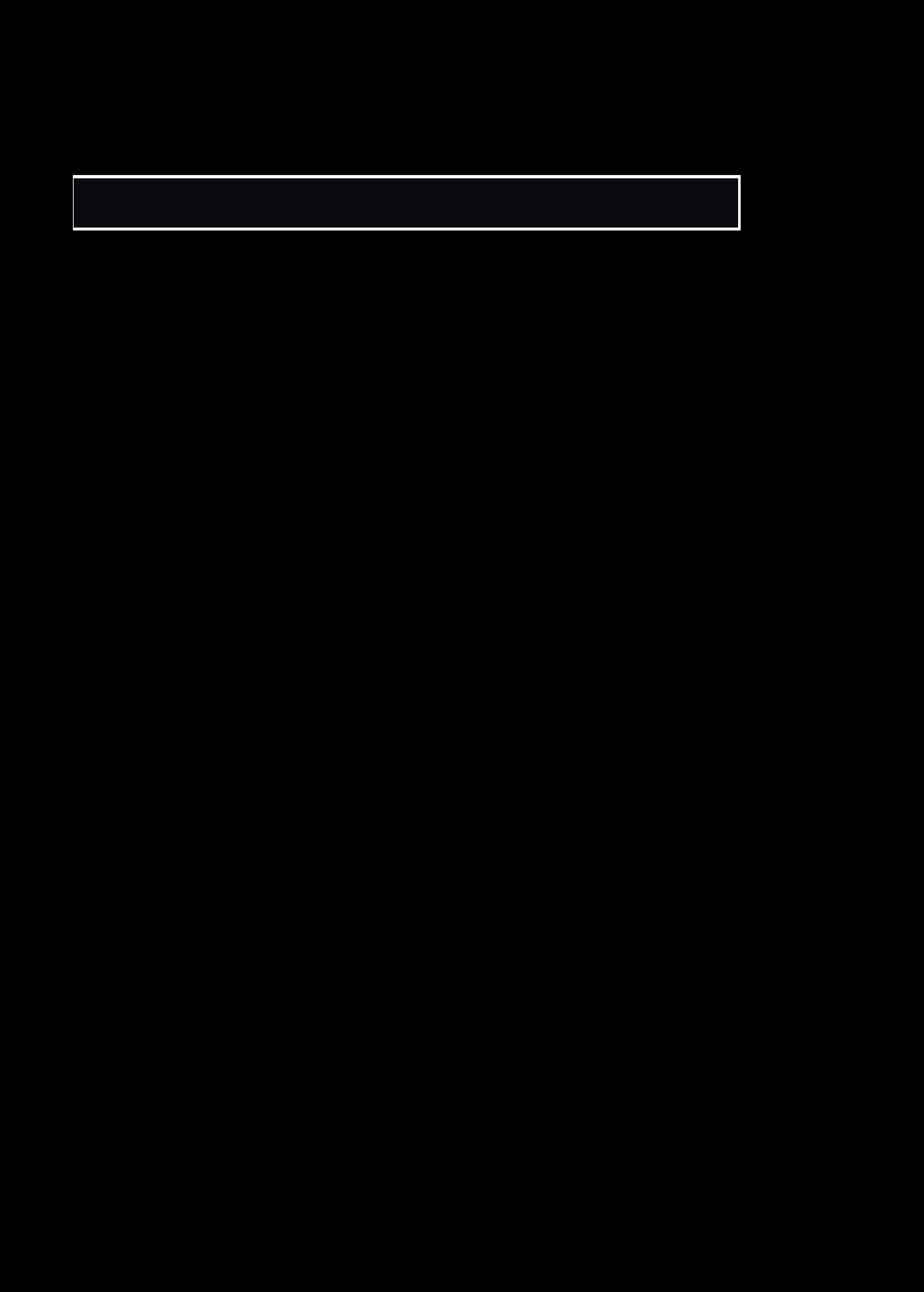
andrew.cooper@rapidnews.com
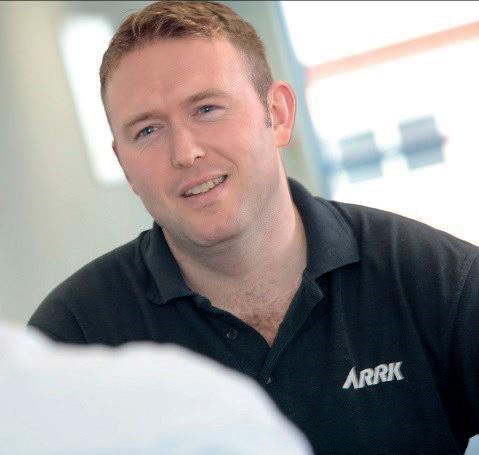
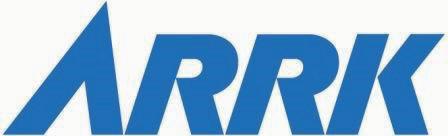
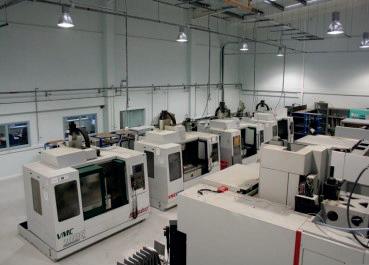
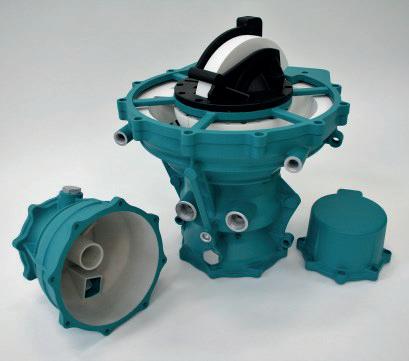
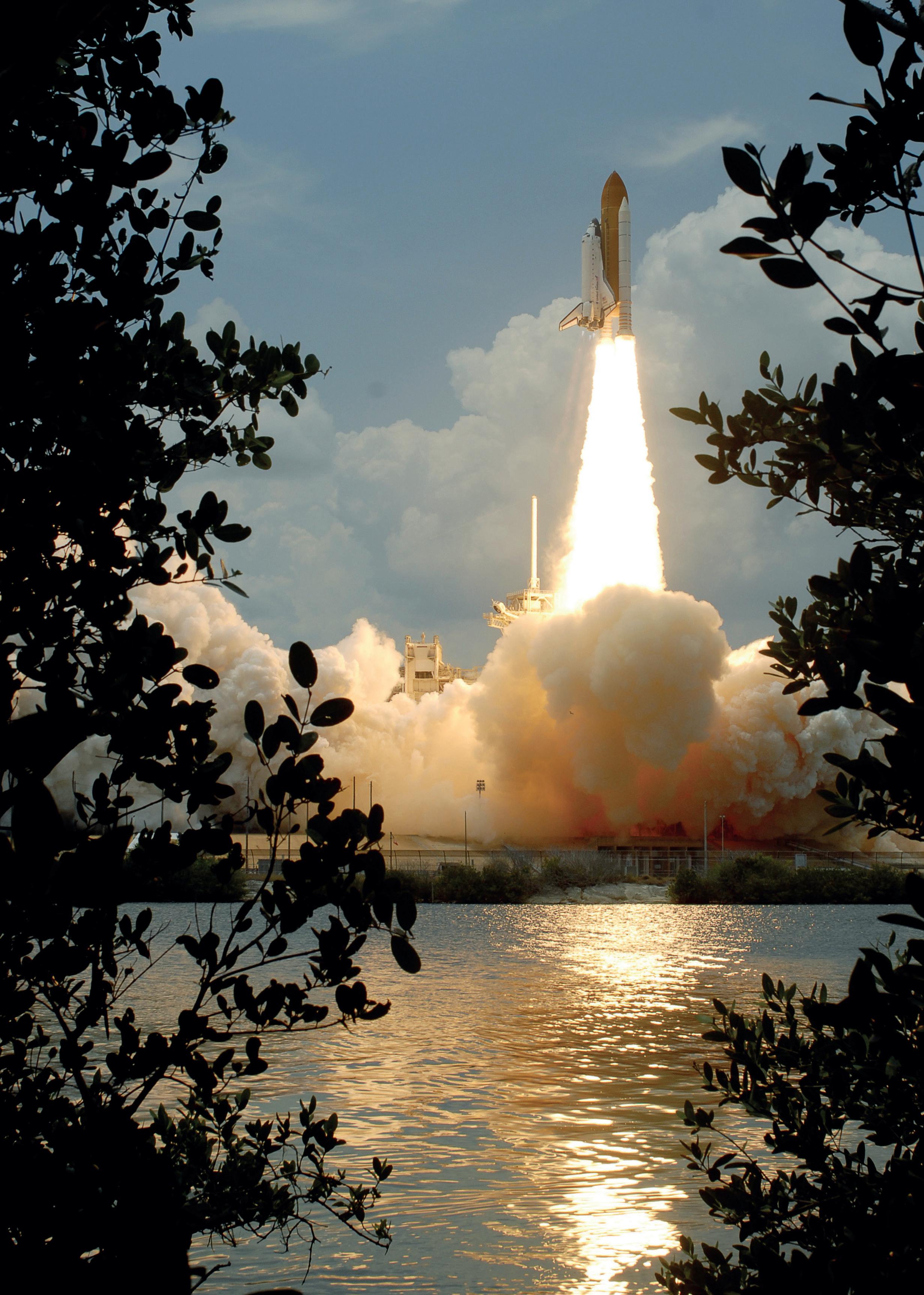
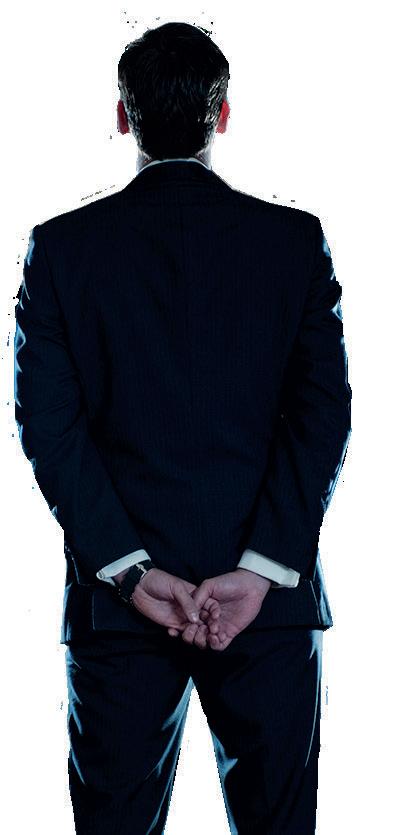
Nicky Martin e: nicky.martin@rapidnews.com t: + 44 1244 952 365
SALES EXECUTIVE TCT PORTFOLIO
andrew.cooper@rapidnews.com
It was nice while it lasted but after an unusually hot summer, the familiar sound of rain against the office window, which seems to have appeared overnight to stubbornly uphold the stereotype of a grey and wet United Kingdom, feels about right.
The good news, however, is that with this rapid autumnal shift comes the second round of annual events for the additive manufacturing industry (AM). As I write this letter, our Senior Content Producer Sam Davies is likely on his second in-flight movie somewhere above the Atlantic by now as he makes his way back from a busy week at the International Manufacturing Technology Show in Chicago. HP, Nexa3D and a handful of other AM companies chose to launch long-awaited production-oriented hardware at the event (you can hear all about it on a recent episode of our Additive Insight podcast) which speaks volumes about those player’s ambitions in the wider manufacturing landscape and provides us with a glimpse at what we can expect from exhibition floors and conference theatres over the coming months. For many of us, the next port of call will be Formnext and the adjacent TCT Conference @ Formnext, for which we recently unveiled a stacked line-up of speakers from PepsiCo to Jack Wolfskin, Honda to Boeing. Tickets are now on sale at tctconferenceformnext.com.
But, onto this issue. It seems only fitting to mark the start of the school year with our Research & Academia feature, which includes the latest AM findings coming out
of the University of Cambridge and numerous U.S. institutions alongside a candid conversation between lecturer and student on the culture of AM in academia.
There’s change happening at AMUK too, the UK’s AM association, which relaunches this October and shared details with TCT about its renewed ambitions to put the UK on the AM map (page 19).
There are, of course, other shifts that take their time. Two years ago, when Sam and I mapped out the features we wanted to tackle inside this magazine, we chose diversity as a key industry challenge. For this issue, Sam collates conversations from a number of AM professionals about the experiences of Black people and people of colour in AM. It’s an important read and can be found on page 28.
Elsewhere we have interviews with Divergent (p. 11), Volkswagen (p. 17) and Alstom (p. 15), explorations of new material formulations (p. 23), ceramics (p. 21) and copper (p. 27) in our materials feature, and an expert column on the importance of the sometimes misunderstood subject of DfAM (p. 42).
Enjoy the issue.
P.S. I recently joined Women in 3D Printing as a UK ambassador. There are numerous chapters dotted around the UK, open to all, and I encourage you to support activities in your local area. If that’s Chester, get in touch! laura.griffiths@rapidnews.com
Sam Davies speaks to Divergent CEO Kevin Czinger about supplying additive manufacturing solutions to automotive brands like Aston Martin.
A FOOT IN THE DOOR Alstom and Replique discuss their collaboration after the additive manufacture of a series of doorstopper components.
A WIN-WIN Volkswagen and Additive Industries on their TCT Award-winning VW Tiguan tooling nozzle collaboration.
Laura speaks to Lithoz about how its new LIS technology is opening up applications in dark ceramics.
IN WITH THE NEW Sam explores the demand for novel material formulations in additive.
Oliver Johnson speaks to Ursa Major about the complexities of copper for AM applications in space.
Douglas Brion and Sebastian Pattinson from University of Cambridge on developing intelligent 3D printers that quickly detect and correct errors.
RESEARCH ROUND-UP Oli spotlights some of the latest AM research coming out of universities.
IF TRUTH BE TOLD A focus on the experiences of Black people & people of colour in the 3D printing industry.
Within the complex field of 3D printing technologies, Digital Light Processing or DLP is easily one of the most simple, mature, and popular methods available for polymer parts manufacturing.
DLP harnesses the power of light from an area-wide projector to cure photosensitive liquid resins into parts layer by layer, one quick flash at a time — delivering smooth, accurate parts in a fraction of the time of laser-based stereolithography, or SLA, which must draw out part designs individually.
Over its 20-plus years of existence the DLP process has largely been executed in the same way: a video projector is stationed below a vat of photosensitive resin, and print jobs are built as a job advances vertically out of the vat attached to a build plate. While the field has enjoyed many advancements, most have been incremental in nature and focused on limiting the detrimental separation forces inherent to building parts bottom-up.
As global manufacturers begin to utilise 3D printing for the production of functional end-use parts, there is a requirement to print larger batch sizes, bigger parts and engineered polymers. These requirements shine the spotlight on the limitations of bottom-up DLP.
For one, there’s a limit to how many parts and how much weight can be suspended vertically from a build plate when printing with a bottom-up projector. More importantly, this printing approach forces serious constraints on the types of resins that can be used. Because the resin in the bottom-up DLP printing approach must flow back under the build plate easily and quickly during recoating, it must be a relatively low viscosity. This ultimately limits the final material properties the
resin can deliver, or requires two-part resins that must be mixed together then quickly printed before they spoil.
The fact that the market has not yet produced a robust approach for top-down DLP printers is interesting given that SLA 3D printers, the precursor process to DLP, have long offered a healthy commercial market for both bottom-up and top-down designs. Bottom-up styles are often featured in more affordable desktop units while industrial models often deploy the top-down approach.
Now, ETEC is embarking on this more industrial approach to DLP with the Xtreme 8K. Aside from holding the distinction as the world’s largest production-grade DLP printer, the Xtreme 8K is also one of the industry’s only top-down DLP printers — two features that are, as it turns out, highly interconnected. Most importantly to users, it provides an extremely large build area and better material properties without sacrificing surface quality and part accuracy.
This cutting-edge DLP machine, first revealed in 2021, features two industrial overhead projectors stationed above the resin vat. This allows the Xtreme 8K to offer the largest DLP build area — 166,950 mm2 (450 x 371 x 399 mm) — among commerciallyavailable, production-grade DLP printers. Additionally, two intense and direct light sources that don’t have to penetrate through a vat film or tray enable new materials with higher energy requirements for curing.
This innovative machine design has unlocked the ability to produce large parts and manufacture in high-volumes with DLP 3D printing as well as process new materials that directly compete with thermoplastics used in traditional plastic injection moulding.
Many of the initial low-viscosity photopolymer resins used in vat photopolymerisation – whether DLP or SLA – were derived from the protective coatings industry, where they were applied in ultra-thin layers and then cured with UV lights.
During curing, the materials are crosslinked, or chemically bonded to form a polymer. While these early photopolymer resins rapidly cure and offer good surface finish, they tend to be brittle and prone to cracking and shattering, offering poor impact resistance and little of the toughness and resilience needed to compete with today’s traditionally manufactured plastics. Their performance also tends to degrade over time or as parts are exposed to light and hot or cold temperatures.
For decades, the field of polymer AM has been working to enhance the material properties to overcome these hurdles and deliver more resilient, elastomeric properties.
In a DLP market segment dominated by bottom-up 3D printers, ETEC delivers an industrial top-down printer that is changing the game with part size, throughput, and allnew material properties.SHOWN: ETR 90 PRINTED DUCT
DuraChain is a new category of materials invented by Adaptive3D, a subsidiary of Desktop Metal, to solve these problems. Adaptive3D developed a proprietary and unique blend of materials that takes advantage of a specific chemical reaction process, called Photo Polymerization-Induced Phase Separation, or Photo PIPS, to deliver all-new material properties in DLP.
When exposed to light during DLP printing, DuraChain photopolymer resins phase separate at the nano level as they cure into a resilient, highperformance network much like legacy two-part material systems that have a shorter pot life. One of the challenges in printing these materials is that they contain high-viscosity base oligomers — similar to honey or molasses — and miscible monomers that would not be easy to process on bottom-up DLP systems, which require more free-flowing resins.
Ultimately, this groundbreaking portfolio of photo-elastomers is finally delivering the tough and resilient properties that the market requires — with high tear strength, elongation, and toughness. What’s more, this unique approach is delivered in a one-part, pot-stable chemistry. Because these materials are so viscous they currently require a top-down DLP printer for processing.
Today, DuraChain resins, which includes all the materials listed below, are printable exclusively on the ETEC Xtreme 8K:
Elastic ToughRubber 90 (ETR 90)
– The toughest AM elastomer on the market. ETR 90 can already be found in parts and products that are sold on store shelves. It is perfect for shoe midsoles and heel cups, seals, door boots, bellows, foam-like lattice structures and impact parts.
Elastic ToughRubber 70 (ETR 70)
– A softer, stretchier ToughRubber useful when printing resolution limits of individual struts and minimum feature sizes do not allow ETR 90 to achieve the requisite soft feel via microarchitecture alone.
Soft ToughRubber (STR)
– Designed for functional prototypes of audio earbuds, wearable electronics, and anatomical medical models, Soft ToughRubber (STR) delivers a silicone feel and mechanical properties with the resolution and surface finish that DLP printing provides.
FreeFoam – A new family of photopolymer resins containing a heat-activated foaming agent. After printing a design in FreeFoam, the part is expanded during foaming in an oven, creating a closed-cell foam with tight dimensional accuracy, and customizable for a variety of Shore A hardness values.
“Groundbreaking portfolio of photoelastomers.”
Inside the factory of an electric vehicle (EV) battery design and manufacturing company, Kevin Czinger is making some calculations.
The manufacture of these lithium-ion phosphate battery cells at Coda’s facility in China relies heavily on coal-fired power. And because of that, ‘well over' 200 kilogrammes (kg) of Co2 per kilowatt hour (kWh) is being produced in battery manufacture. At this time, kg of Co2 per kWh is the most important metric on Czinger’s mind and the cogs whirring in his head only intensify as he does the workings out to reveal that these batteries and EVs aren’t having enough impact.
“Say you take the low end of that range, 200 kilogrammes of Co2 emitted per kilowatt hour, you don’t take into account extractive emissions or any of these other things, you’re just looking at the cell factory itself – 200 times 90-kilowatt hour [for a] Tesla is 18,000 kilogrammes of Co2 emitted in the manufacture of the battery before the car is ever charged,” Czinger explains. “In comparison, a Toyota Camry driven for 80,000 miles emits, through tailpipe exhaust, 16,000 kilogrammes of Co2. I looked at that and said, ‘you fool – you think
that you’re having a positive impact, but you’re only going to have a positive impact if you look at the entire system.’”
So, he has. Coda Automotive and the Miles Electric Vehicles business Czinger was previously involved with are no longer functioning, but rather than pursue ambitions as an OEM of EVs, he has taken a step sideways.
Post Coda, Czinger educated himself on lifecycle assessments, figuring only a holistic approach would return the energy emission reduction that is required in an era of climate emergency. He also came to realise that the way automotive structures are manufactured, and the costs required to do so, need optimising – particularly as EVs, hybrid cars and internal combustion engine vehicles (and all the tooling and fixturing to come with them) continue to emerge.
“The amortisation period, the competition, the driving down of values, you’re looking and saying, ‘this is environmentally and economically broken,’” Czinger says.
If you recognise Czinger’s name, you’ll know that his answer to this ‘broken’ system was to establish Divergent Technologies. In doing so, Czinger and his team developed the Divergent Adaptive Production System (DAPS) to ‘digitise and dematerialise’ automotive production and provide the technical competency for the company, in time, to become a Tier One supplier to the automotive industry. After Aston Martin’s launch of the DBR22 in August – which features an additively manufactured rear subframe – that time is now.
DAPS is certified against ISO 9001:2015; ISO 14001; AS 9100D; and IATF 16949:2016 standards and is comprised of generative design, additive manufacturing, and automated assembly. The combination of these three elements, Divergent believes, will ‘massively expand the design space’ with humans setting the requirements and the software optimising the structure to Pareto efficiency.
Key to the development of DAPS is a collaboration with SLM Solutions commencing in 2017. As Czinger surveyed the market for a fabrication tool that aligned with his vision, he saw
“We have to be prepared to invent everything.”SHOWN: ASTON MARTIN DBR22 WORDS: SAM DAVIES
in 3D printing a ‘half invented industry’ where the printers were ‘way too slow and way too expensive.’ He recognised the potential though and convinced former SLM Solutions Chairman Hans Ihde to work with Divergent to jointly develop a 12-laser machine. Thus, the NXG XII 600 was ‘specced’ to fit the cost and rate structure of DAPS, and has now been used by Divergent for two and a half years. By the end of 2022, Divergent will have six of the machines installed, supplementing other AM technology that the company is choosing not to disclose.
What Divergent is willing to talk about, however, is how its DAPS workflow works. Its engineers start by understanding the static stiffness targets of a structure, then the typical load cases it will be exposed to, then what its boundary conditions are, then its crash requirements, durability requirements and dynamic stiffness response requirements. This information is the input for the Divergent design algorithm, which is where the company enters the concept phase. Here, Divergent gives the OEM ‘optionality’ to, for example, reduce stiffness in a certain area of the structure to reduce mass. After the concept phase comes the detailed design phase, and after that, it’s time to print the part.
“One of the many, many benefits is that those first units that we print,” Cooper Keller, Divergent’s VP, Program Management and Production Operations, explains, “are printed with production processes, production machines, production materials. So, if there are no design changes required through the rest of the programme, that is production validation.”
Divergent has had last-minute changes requested – ‘major revisions of structures’ – but instead of 12 months to scrap the part, cast the moulds and stamp the tools, it needs only to be a delay of three weeks to get the next iteration additively manufactured. The company has also seen the value in being able to validate these structures against real-world requirements in-house. Its facility not only includes the DAPS system, but also MTS multi-actuator durability rigs, a crash tower with high-speed cameras, a full materials lab, thermal testing, corrosion testing and environmental testing.
The 230 engineers and scientists in the Divergent facility are also encouraged to take inspiration from Kelly Johnson, who ran Lockheed Martin’s Skunk Works operations some 60 years ago.
“They built the SR 71 Blackbird in 20 months, and they did that with 135 engineers,” Czinger says. “Here, Kelly Johnson said, ‘when we built that, everything had to be invented.’ I wouldn’t say we’ve invented everything across those three different subsystems [generative design, AM, robotic assembly], but we have to be prepared to invent everything.”
To back those words up: Divergent has 530 patent filings and patents issued across DAPS, from software to materials to machines to optics. That five years of intense R&D has caught the eye of eight automotive OEMs, most of them within the top ten major OEM groups in the world,
and one of them Aston Martin. For Aston Martin, Divergent has additively manufactured the DBR22’s rear subframe in multiple titanium pieces which are then bonded together. Though details are scant and Divergent isn’t forthcoming, Aston Martin says there was a significant weight saving with no reduction in stiffness.
Divergent is going to continue supplying Aston Martin with structures for existing and future vehicle models, while parts for multiple other brands have gone through full durability and crash testing. These programmes include structures for vehicle models that are in the volumes of dozens to those in the volumes of tens of thousands – Divergent is aiming to be ready for the latter by 2025. Czinger also says the company is working on aerospace and defence programmes.
The company believes it can achieve such volumes because of the savings made in engineering and assembly, plus the capabilities of its generative design software. But it also knows that it has to.
“Right now, we have a built world around us which is environmentally and economically and socially unsustainable. And we need to use technology in a very intentional way,” Czinger says. “We’ve gone quickly from a billion to eight billion people over a 100year period or so. We cannot use analogue processes that consume more and more material and energy and capital – we need to use our technologies to create super-efficient systems that mirror what an Alpine Meadow does. What does an Alpine Meadow do? It uses evolution in an environment where there is incredible competition for material
and energy to create a fully optimised structure. I think that is critical to our survival. We’re destroying ourselves, we’re destroying the planet, and we’ve got to create a stable economic, environmental and community system.”
So that’s the motivation, but where is the inspiration? Czinger talks about a combination of ten-printer fleets plus a 22 x 22 metre assembly module in the near term while hinting at a future where its DAPS might lean on 100, 500, or even 1,000 printers to produce structures for the world’s biggest automotive OEMs. But can it be done?
“What we’re doing is much more complex but if you look at the CNC machines of 2005/2006 – pre-Apple and Foxconn using them to manufacture microelectronics – after that, you saw a scale up from tens of machines to, [at] Foxconn, 150,000 lights out machines,” Czinger says. “Do you think they were thinking in 2005, ‘there are ten machines here now [but] we’re going to have 150,000 lights out automated [in the future]?’ I’m not trying to do this to create any kind of hype. I’m 63 years old, I’ve made money, I don’t need any of that. This is, here’s a chance to digitise and de-materialise that built world if you try to make it happen.”
Alstom and Replique discuss their collaboration after the additive manufacture of a series of doorstopper components.
ten parts able to be printed per build. The parts were then sintered and debinded in a total postprocessing time of around five hours. Alstom then carried out the required qualification process, which included static testing, to assure themselves that the part was in line with its quality standards and could feasibly fulfil its function over the entire service life of the train. From beginning to end, the delivery of the parts was completed within six weeks.
But Alstom and Replique might not be done yet.
Additive manufacturing (AM) is now a key part of our supply chain,” the 3D Printing Hub Manager of Alstom Transport Deutschland GmbH noted this summer.
After working with AM for several years, it was gratifying that Alstom could say that.
In June, Alstom revealed a series of doorstopper components had been produced with the BASF Ultrafuse 316L material on Ultimaker and BCN3D extrusion printers. It followed an earlier application of 3D printing by the French rolling stock manufacturer for spare parts, which included the 3D printing of a dozen rubber drainage plugs to seal the holes in tram headlights.
The doorstopper parts are deployed within the partition door between the first- and second-class carriages of a train and are required to be durable – to last the service life of the train – and to have aesthetic qualities – since it is visible to passengers. To deliver the parts, Alstom turned to Replique.
“This doorstopper was made of sheet metal in the past and we thought to buy sheet metal, to laser it, to bend it, to weld it, to shot blast it, and then to paint it, that’s a complex manufacturing [process],” explained Dr. Uwe Jurdeczka, Senior Expert, AM at Alstom. “What about 3D printing? We looked around at who will be able to provide quality, material, experience and all the service around [the part]. That’s [when] we made contact with Replique.”
Replique is a service provider which harnesses a fully encrypted 3D printing
platform to deliver functional end-use parts. The venture of the internal incubator programme of BASF arised from BASF’s Digital Transformation initiative and has built a network of partners that gives its users access to polymer, metal and composite AM. Though Replique’s materials collaborators include more than just BASF, it deemed its Ultrafuse 316L the best material for the job when Alstom reached out.
“We wanted to have the best price, performance and quality combination, so that was why we selected [FDM and the Ultrafuse 316L],” Replique CEO Max Siebert said. “[Using Ultrafuse 316L] was quite a nice solution, fitting very nicely because, sizewise, it’s still able to be manufactured in the filament process and, cost-wise, it turned out to be superior to an SLM process. In close collaboration with Alstom, we optimised a little bit the design and we found the right manufacturing parameters later on for the serial process. Then, the part has been produced, and we sent it over to Alstom for qualification and first article inspection.”
Using FDM, Replique delivered 50 parts to Alstom – including prototypes – with up to
With Alstom’s international footprint and Replique’s growing decentralised manufacturing network, there may be scope for further collaboration. Decentralised manufacturing, per Alstom Additive Manufacturing Programme Manager Aurelien Fussel, is the ‘golden target’ for all industrial companies, though he believes this is more a long-term goal than a short-term one. As such, there is still work to do.
Alstom still wants to see improvements to AM before it rolls the technology out to the extent it believes it can, while factory audits on Replique partner factories would also need to be carried out. But, after the doorstopper success, there is a will to see it come to fruition.
“I propose an exercise of putting [Replique] in our shoes,” Fussel added. “Our customer could ask to audit or visit the place where the parts are manufactured. If we qualify a site of Replique, it should be followed, known and auditable. This will not be negotiable. It is because when you put yourself in the shoes of our customer, you understand that it’s quality first.”
“It is important to understand the meaning of quality from the customer’s perspective,” Siebert finished. “That is why we regularly visit our partners to ensure high quality of our print farm network, but also from a technical perspective we want to ensure repeatable quality. If some parts have to be replaced, we need to be able to achieve the same quality five years later, ten years later. We can ensure this by locking production parameters, technology and materials for parts produced anywhere worldwide. We also have a quality documentation module on the platform, recording quality parameters of the used machines and produced parts before sending it out, enabling tracing of single parts in all quality aspects.”
WORDS: LAURA
GRIFFITHSIt’s not a first for Additive Industries, nor Volkswagen, but as this year’s recipients of the TCT Transport Application Award, the double TCT Award-winning collaborators demonstrate how oftentimes, it’s the low hanging fruit that stands to yield the biggest gains when it comes to deploying additive manufacturing (AM) for automotive.
Having already taken home awards for their own projects in respective automotive and industrial applications, the two recently came together to reimagine a tooling nozzle used for the automated deposition of a rope in the chassis flange of the VW Tiguan, which helps prevent corrosion. The original design was machined in two parts in an expensive titanium alloy and welded together. Working with the Dutch metal 3D printing company’s Additive Studios consulting services, Volkswagen deployed Additive Industries’ MetalFAB metal 3D printer to manufacture a new design which achieved a huge 650% cost reduction against conventionally manufactured nozzles.
“We follow two main targets,” Oliver Pohl, Head of Additive Manufacturing at Volkswagen, told TCT. “On the one hand we try to use as less supports as possible and we try during the iteration to find the best orientation to reach the quality targets of the nozzle outlet. On the other hand, we had the challenge to reach the quality of the produced PVC rope in the production. Also, the optimal fluid flow in the internal channel, we have [to pay] attention to.”
The parts were printed internally at Volkswagen where a single build on the four-laser configuration of Additive Industries’ modular MetalFAB system can produce 48 nozzles in just 15 hours. Optimised for additive, the nozzle was able to be manufactured as a single component in a cheaper material, 316L vs the traditionally used Ti-alloy, while achieving the same mechanical performance. The consolidation of parts meant postprocessing was minimal due to the removal of previously necessarily milling and heat treatment steps, while the switch
to additive also meant less material usage and no excess machining chips.
Martina Riccio, Process and Application Development Manager at Additive Industries, explained: “The cost reduction is thanks to a combination of factors such as the use of a cheaper material (316L vs Ti-alloys), to less material usage, no machining chips, to part consolidation, and the removal of different manufacturing steps [such as] machining, welding, etc. The overall cost reduction has a huge impact since more than 1,000 nozzles per year are needed per VW vehicle.”
Those volumes are significant. While metal AM applications in the automotive space have been typically reserved for luxury brands and racing teams, like Sauber Technologies and Alfa Romeo Racing which Additive Industries has been working with since 2017, this part serves as a proof point for the viability of metal AM in the mass production environment of a mainstream passenger vehicle. What’s more, the company believes the success of this application will inspire the rapid development and
manufacture of other new, optimised nozzle geometries, which are different for each car model. Volkswagen confirms, based on this experience, these additive alternatives can be rolled out to replace their conventional counterparts, and while not all applications will experience benefits of this magnitude, Pohl estimates further applications could lead to typical cost reductions of at least half that of traditional components.
Riccio added: “The tooling nozzle is an interesting business case which can be used for demonstrating the benefits on metal AM where awareness is still limited. This project shows how manufacturers can think differently for achieving metal AM benefits. A simple tooling component, if adequately redesigned and when part consolidation is applied, can be a perfect use of metal AM for cost and lead time reduction.”
WATCH THIS SPACE: Submissions for TCT Awards 2023 open soon at tctawards.com
The industry responded favourably, with around 100 companies signing up for the body. Such has been the show of support, it is clear the industry is keen on having a professional trade association representing its interests. The relaunch signifies a new beginning for AMUK as it prepares to morph into a full association capable of supporting its members and making additive and 3D printing technology mainstream in both its use and adoption.
TCT: What’s AMUK’s mission today and why is now the right time to make it happen?
TCT: AMUK launched back in 2014, initially government-backed and is now part of the MTA family. What’s been happening in that time? Why the relaunch?
JD: AMUK was originally established in 2014 by the Manufacturing Technology Centre (MTC) as a collective industry body to lobby government for improved funding to advance the development of additive and 3D printing technology. The body also sought support to drive forward the UK’s national additive manufacturing strategy.
By 2019 the MTC felt it had achieved its goals and felt AMUK needed to morph into more than just a lobbying body to help push the sector forward. Discussions with the MTC concluded that AMUK would be a better fit alongside the current Manufacturing Technologies Association’s membership. Therefore, in 2020, the MTA took over responsibility for AMUK.
The MTA’s plans for the integration of AMUK stalled during the COVID-19 pandemic but in the lead up to MACH 2022, the association decided to revisit its plans see if there was interest from industry for a dedicated trade association which could lobby for the additive and 3D printing eco-system in the UK.
JD: AMUK’s mission is to establish the UK as a world leader in the development, adoption and use of additive manufacturing and 3D printing. It wants to create the eco-system where additive manufacturing can take its rightful place among the UK’s manufacturing technologies and thrive. It will also be working to create the conditions whereby the UK is seen as a world class hub for companies looking to undertake innovative R&D in additive and 3D printing, as well as finding collaborators and partners for any of their projects.
The UK has long been recognised as a world leader in R&D, but we often fail to take advantage of this and miss out on opportunities to commercialise new products and services. We are hoping that by bringing the additive and 3D printing community into the mainstream, we can leverage our strengths in R&D and establish the UK as a global centre of excellence for this exciting technology.
TCT: What’s AMUK’s view on the current AM opportunity for the UK?
JD: We see great opportunities for AM in the UK. The UK is the ninth largest manufacturing country in the world, with world-leading
engineering sectors such as automotive and aerospace. AM has the potential revolutionise these industries in terms of increased design freedom, opportunities for customisation, faster product development cycles and, in some circumstances, the ability to manufacture at the point of need.
If AM can be adopted, utilised and the benefits realised by the manufacturing supply chains that underpin our world leading engineering sectors, then there are opportunities for the UK to take the lead on the design, development, and production of the next generation of complex components and systems which these sectors will increasingly require.
TCT: …And the challenges?
JD: Sadly, there are challenges, and these cannot be resolved overnight. They require constant effort over time and must be backed by investment and skills development. Also, there needs to be a concerted plan to educate people on the breadth of the technology and what it is capable of achieving. Set against such a complex landscape, change may not be as rapid as hoped. The best way to put all these things into perspective is to look at how an established manufacturing technology,
such as machine tools, has evolved. Machine tools have been around for more than a century and industry is very knowledgeable on what they can and can’t do.
In comparison, AM, although first invented back in the 1980s, has only really become a mainstream manufacturing technology in the last ten years, therefore there is little recognition of what it does and what it is capable of achieving. Sadly, this means there is also a shortage of skilled professionals which companies can employ to help them take advantage of the technology. Furthermore, there are a multitude of techniques for AM, all of which require specific knowledge or skills, and can make the AM technology landscape increasingly complex.
At AMUK, we are aiming to address these areas to ensure the UK is not a laggard with the technology and is instead, one of the trendsetters.
TCT: Back in 2017, the UK Government’s 255-page Industrial Strategy included just a single mention of AM. With the recent launch of initiatives such as AM Forward in the US, should the UK government be paying closer attention to the technology?
JD: In short, yes. In other industrialised countries', such as the United States, governments have been quicker to realise the opportunities offered by AM. In the US, AM Forward is a strategy that recognises the potential for Additive technology to play a critical role in resolving reshoring and protecting supply chains. The sooner the UK government realises this, and fully appreciates what AM is capable of doing for UK industry, then the faster we will see a more conducive environment in which AM in the UK can flourish. This is something for which AMUK will be campaigning.
TCT: Tell us how members can benefit from joining AMUK.
JD: In October, at the official relaunch of AMUK, we will announce the list
of services AMUK members will be offered, along with the tangible benefits membership of such a body brings.
Initially, these will be focused on three critical areas:
• Business Support – HR and Legal support, Training, and Networking
• Business Intelligence – Market Data, Technology Trends, and Funding Information
• Business Promotion – Trade Shows, International Pavilions, and e-Newsletters
As AMUK has been restarted from a blank sheet of paper, we’ve had a real opportunity to develop the services critical to establishing a successful AM eco-system in the UK. The services we are looking to offer have been developed following conversations with AMUK members, and we therefore hope these will help raise the profile of companies working with AM, allow them to do more business and push the whole sector forward.
TCT: Following October’s relaunch, what are AMUK’s next steps? How does the UK keep its AM momentum going?
JD: Following the relaunch, we are going to be looking at refining the services that we offer still further. We want AMUK to best serve the industry’s needs, so will be looking for feedback on what members think we should be doing so we can make any necessary changes.
In terms of maintaining momentum, we are engaging with industry stakeholders - both nationally and internationally - to see how we can collaborate for the benefit of the AM community in the UK. We will also be scoping out our softer services, which include things like supporting the talent pathway, getting government support and influencing standards.
“AMUK’s mission is to establish the UK as a world leader in the development, adoption and use of AM.”
When TCT met with Dr Johannes Homa to mark the 10th anniversary of Lithoz, the CEO recalled the ceramics 3D printing company’s early days. Homa, along with Lithoz CTO Dr. Johannes Benedikt, both university students at the time, had a gut feeling that there would be similar demand for additive manufacturing (AM) production capabilities in ceramics as there was for plastics and metals, if they could just develop the right solution.
Over that decade, Lithoz has successfully built and commercialised its Lithography-based Ceramic Manufacturing technology, and earned customers across demanding sectors from aerospace to medical, many of which have adopted multiple of its CeraFab systems – the biggest customer fleet will soon consist of 25 machines. Now, with the launch of its latest technology, Lithoz is once again going with its gut having established itself as a leader with its LCM technology as a tool for digital mass production, and listening to the market to step into an, as yet, underserved area.
“It was clear for us that there was this opportunity in the ceramic field, and the opportunity was simply having bigger parts and full densities,” Isabel Potestio, Director Sales & Marketing at Lithoz, told TCT. “Binder jetting is interesting for bigger parts but not when it comes to high density, and those densities really make a big difference in the kinds of applications you can access.”
The answer, Lithoz believes, is LaserInduced Slipcasting (LIS), a new process that specifically addresses those needs through a larger build volume and water-based suspensions with very low organic binder contents to manufacture thick-walled, fully dense parts in oxide and non-oxide ceramics with no debinding needed.
“The reason you can use different kinds of materials is at the heart of the LIS technology,” Potestio explained. “The technology uses a laser to evaporate water from a water-based slurry. As LIS is a heat-based process rather than light-based, the colour of the ceramic material makes no difference to the results.”
The new material capabilities afforded by this approach allow users to finally tap into dark
ceramics including silicone carbide, “the king of ceramic materials,” as Potestio describes, due to its rapid cooling, high strength, heat, oxidation and wear resistance, and weight efficiency. But, it is notoriously difficult to additively manufacture. These properties, in addition to virtually no thermal expansion, have caught the eye of users in aerospace, semiconductor and heavy industries where dark ceramics can be used to meet demands for high hardness, density and chemical resistance and are able to withstand extreme temperatures above 3,000°C.
The LIS technology onboard the CeraMax Vario V900, with its 250 x 250 x 290 mm build area and ability to apply up to 1,000μm slurry per layer in under a minute, has been described as an ‘ideal technological entry point’ to ceramic 3D printing. Slipcasting is already widely used and understood in ceramics but limited in design complexity, while Lithoz says LIS parts, made using a wide range of familiar materials,
can be easily reintroduced into the traditional ceramic workflow.
“The development of materials is very easy because there is no real chemistry knowledge needed,” said Potestio on LIS ability to process standard ceramic mateials already used by industry today due to the lack of binder content. “An industry that is used to working with its own powder can basically take the material they were already using, put it in the machine and work with it. This really helps lower the barrier.”
Having formally unveiled the machine at ceramitec in June, it’s still early days but Lithoz confirms several LIS systems are already being installed and operated by partners such as QEP3D and Alumina Systems.
“We’re constantly getting requests from the industry because there is no other solution right now on the market [for creating] thick-walled, fully dense ceramic parts, and at the same time, processing dark ceramics,” Potestio concluded. “We were expecting this kind of response but it’s been really nice to see your expectations paid off. Everything looks quite simple sometimes but there’s hard work behind it and that’s really satisfying to see the market react positively to it.”
Sam Davies speaks to several AM experts on the need for new and novel materials formulations.
If you could have any material, what would it be? If you could do anything with materials and 3D printing, what would you do?”
These are the questions metal additive manufacturing (AM) alloy developer Elementum 3D has been asking. Not as a fun hypothetical during the lunch hour, but in hundreds of conversations with its customers.
It is music to the ears of Eliana Fu and Melanie Lang, two recent Additive Insight podcast guests.
“My question is, why are we using materials that were developed 70+ years ago, when we could be using new materials developed specifically for AM?” the former told TCT after her appearance on the podcast.
“I think we are limiting ourselves right now to a set of materials that have been around for decades if not centuries,” offered the latter.
Fu and Lang aren’t alone in yearning for such developments, and neither is Elementum 3D in working to provide them.
In Uppsala, Sweden, VBN Components has developed a so-far five-strong portfolio of Vibenite metals, all of which exhibit high carbon content to achieve extreme wear resistance. Because of this high carbon content, the materials are difficult to machine, forge and roll. They are, however, 3D printable and the Vibenite 290 material is believed to be the world’s hardest steel with a Rockwell hardness measurement of 72.
Over in Chaska, Minnesota, Jabil this year commercialised its patentpending PK 5000 material, based on a polyketone resin that is made from carbon monoxide and is said to boast high impact strength, high abrasion resistance and improved elongation compared to existing Nylon materials.
Back in the metals sphere, NASA has developed the high-conductivity and high-strength GRCop 42 copperchrome-niobium alloy, developed for harsh environments specific to regeneratively-cooled combustion chambers and nozzles with good oxidation resistance.
Here lies one of the key motivations for developing new materials formulations. To design the material and its characteristics for a specific process and a specific application.
“We’re seeing people that now move to the concept of ‘what if we looked at an alloy that was designed for 3D printing, not just to make it printable, but to make it widely available and better than you could possibly do without printing,” says Jacob Nuechterlein, CEO of Elementum 3D, who supported NASA in the development of GRCop 42. “That’s exciting, as a metallurgist, to be able to go into the wild of brand-new materials and brand-new alloys.”
“Let’s get to a point where we can talk about what the part needs to do and what the part needs to perform and then go backwards and make that your requirement,” Lang noted.
For those tinkering with chemical formulations, these are important considerations to make. As Fu explained, the materials formulations that make it out of the lab and into the real world have several things in common: a manufacturing technique that can process it, an application that demands its properties, and an idea of what you do with the part after it’s been used.
“If you don’t have a process to make it, you can have a Noble Prize-winning chemistry but if it can’t be made in real life, it’s not going to go anywhere,” she said. “I’ve seen so many great ideas just come to a halt because there’s no end use, there’s no secondary market, there’s no way to handle the turning scrap, and there’s no recycling method.”
Fu believes it takes a community-led effort to bring new materials to fruition, citing some of the work being carried out by the ASTM F42 Committee as a positive. There may also be a requirement for risk and revenue sharing, whereby potential end-users team with the material developers to qualify new formulations against
existing or new applications in exchange for discounted rates or a cut of the profits.
Covestro Additive Manufacturing has several models in place for how such an arrangement might work. After its merger with Stratasys is closed, the company will be able to have instant access to the hardware it has previously had to strike partnership agreements for, while the company will also make deals whereby commitments are made to buy material upfront, as well as others where the manufacturer can decide at a later date whether the project is worth pursuing further after laying down a monetary deposit. There are also many instances where exclusivity is given to a single manufacturer.
Whatever the journey for a new formulation, most agree it is paramount that an application is top of mind when it is being developed. You need to be solving a problem somewhere for someone, and ideally you know where and for who. Hugo da Silva, the VP of Covestro Additive Manufacturing, noted that the dental and medical markets will bring much opportunity for new chemistries, because of the demand for personalised goods. He also noted that entirely new applications will open the door for novel formulations, again citing an example in dental.
“Dental aligners didn’t exist in the past, and then they start making moulds to do dental aligners, but that mould in that process was new,” he said. “Now, all the companies are trying to print a direct printed dental aligner. It’s also a new application – there are no references out there. When you get applications [where] there are no references, it makes it much easier.”
Covestro AM, da Silva told TCT, is currently working on multiple materials that are tailored to applications in the medical, dental, and industrial sectors, with commercial launches anticipated in the not-too-distant future. It is likely that these are being brought to market via
one of the risk and revenue sharing models detailed above. Yet, while having applications and customers in mind go a long way to overcoming the many hurdles involved with new materials development, there are still plenty of other elements to consider.
These include identifying potential secondary products where the material properties can be applied – in cases where there is no exclusivity – and also developing supply chains that make economic and environmental sense. Manufacturers that are moving away from familiar materials might also need to be educated and persuaded that this new grade can match or better the performance of the existing one, while also matching or bettering the cost, which raises another consideration. This becomes complex because with 3D printing there is likely to be less material used to make the part, there are no tooling costs, the engineering time that is factored in is different, and, in theory, the way spare parts might be handled will also change – hence, the cost modelling, in addition to the material, may be new to the end user.
The introduction of new materials, then, is not without its challenges. There is also the fact that materials are, in essence, brands that are
trusted to carry out the job and there is decades’ worth of data points to back up their capabilities. To compete with a tried and trusted PEEK or 316L takes a lot of testing, a lot of data and a lot of time. But it all comes back to solving problems. If you can do that, the manufacturers will be interested, and there are benefits to be had all round.
“We are trying to take problems in additive, materials and production parts, and come up with solutions,” Matt Torosian, Director of Product Management at Jabil Additive, said at RAPID + TCT.
“When you do that, it’s not hard to switch people at all. It’s much harder to take something out there and say, ‘here’s a me too, why don’t you use this?’ Then you’re in a price game that downward spirals to nothing.”
The best approach, for Jabil and others, is to address market problems – of which there are many – with novel solutions. Yes, there is an extensive workload required to bring those solutions to fruition, but the end results are worth it. What’s more, 3D printing technology is perhaps best placed to provide many of the answers.
“AM is re-inventing material development,” Ulrik Beste, CTO at VBN Components, said. “When you’re using additive manufacturing, you don’t have this production constraint that we talk about, and you also have a very high yield in your process, and you can print it near net shape. When you have a high yield, then you can also choose much more expensive elements that hopefully will result in a fantastic property. You have an enormous opportunity here by thinking outside of the box.”
“Instead of looking at what’s possible to make by, say, casting or forging, it is becoming possible to look at what you would like to have, which is not something people have been able to do before,” Pär Arumskog, Field Application and Development Engineer at VBN Components, finished. “Now, you can imagine your ideal material and you can probably find a way to produce it. And that really wasn’t possible.”
“You have an enormous opportunity here by thinking outside of the box.”
Ursa Major recently delivered its first copper-based 3D printed engine components. The combustion chambers were created in the company’s Advanced Manufacturing Lab in Youngstown, Ohio, which began producing and delivering various other rocket engine parts in May of this year.
Speaking to TCT, Thomas Pomorski, Additive Manufacturing Development Engineer for Ursa Major, said: “Our additive manufacturing team is tasked with advancing 3D printing processes for working with metal alloys like copper. They use a large format laser powder bed fusion 3D printer that is designed to work with metal alloys.
“The builds using copper powder feedstock can take up to a week to complete. After some additional processing, including heat treatment and bead blasting, the part is shipped out to our Berthoud, Colorado facility for final machining, inspection, and proof testing. Finally, the chamber is installed on an engine and tested for space launch and hypersonic applications.”
Copper traditionally presents difficulties when used in additive manufacturing due to its highly conductive nature. Pomorski spoke about how Ursa Major attempted to tackle such challenges: “The learnings from our research and development facility are helping to mature the knowledge in the industry around this type of 3D printing. We work with a specific copper alloy that is optimised for additive manufacturing.”
Elaborating on some of the issues Ursa Major is tackling in the industry through its developments in copper, Pomorski said: “The existing copper alloy supply chain is limited, which leads to long lead times for turning around a needed revision when producing and procuring parts by traditional manufacturing methods. Thanks to 3D printing, Ursa Major is able to compress the production and delivery cycle for its copper-based 3D printed rocket engine combustion chambers to one month, compared to a minimum of six months using traditional manufacturing processes.”
Emphasising the importance of additive manufacturing to Ursa Major, Pomorski continued: “3D printing is one of the reasons why Ursa Major exists as a company today because it allows us to iterate designs quickly and cost effectively. In the early days of Ursa Major, 3D printing allowed a handful of engineers to design, build, and test a pump-fed oxygen-rich staged combustion engine.”
Ursa Major is the only privately funded company in the US that has a sole focus on rocket propulsion. The company has ambitions to speed up the rocket engine production process in an attempt to relieve restricted access to space and hypersonics testing in the US.
Pomorski shared how he envisions AM will impact the space exploration supply chain: “There is a new hardware rich mentality in the aerospace industry, and this is only possible due to additive manufacturing.
It allows Ursa Major to speed up engine production and apply improvements gleaned from testing in real time, lowering costs and speeding through the development cycle.”
Additive manufacturing is used in all three Ursa Major rocket engine programmes: the Hadley, a 5,000 pound thrust, oxygen-rich staged combustion engine used in small launch and hypersonics; Ripley, a 50,000
pound thrust engine; and the recently announced Arroway, a 200,000 pound thrust engine designed for medium and heavy launch.
Ursa Major is scheduled to deliver 30 rocket engines in total by the end of the year. Speaking about the frequency with which Ursa Major can deliver for its customers, Pomorski concluded: “3D printing lets Ursa Major bring highperforming rocket propulsion to market for its customers in months, not years. Once in production, Ursa Major can build about two engines in a week. In fact, we were recently able to deliver three engines in one week.”
“3D
is one of the reasons why Ursa Major exists.”SHOWN: URSA MAJOR ENGINE DURING TESTING SHOWN: THE FACILITY IS BASED IN THE YOUNGSTOWN BUSINESS INCUBATOR
No. Not really. Absolutely not. These were the pointed answers to a pointed question: Would you consider the additive manufacturing (AM) industry a safe and welcoming space for Black people and people of colour?
This question was not part of an in-depth survey, nor does this article rely heavily on statistics. Instead, it brings forth the personal accounts of a select few people who have worked in the industry for several years and were willing to share their experiences. Because, while we could ask this question to every Black person and person of colour in the industry, that even one single person could feel this way about their professional environment is reason enough for a conversation to be had.
During his interview for this feature, Vivek Krishnamurthy paused to caveat that everything he had said and was about to say should be framed in the context that he loves the AM industry – several others expressed similar feelings. He feels very grateful towards AM since it is the place in which he finally realised what he wanted to do with his career. Today, he is the Sr. Business Development Manager at Sakuu, but he has worked in 3D printing for several other leading brands and enjoyed those eight years – for the most part.
“I only want to bring these things to light because I love this industry and I care about it,” Krishnamurthy told TCT. “I want people younger than me to have a better experience.”
Krishnamurthy is a first-generation American, born and raised in the Northeast US. At various points of his personal and professional life he feels he has been made to feel like an outsider. During his time in the AM industry, some peers have refused to attempt to pronounce his surname, asked him where he is ‘really’ from and what his nationality is.
But none of that has shaken his pride in being an American nor distorted his perception of the value that he, and those with similar backgrounds to him, bring to the country he calls home.
“Immigration is the backbone of the Western World,” he said. “It’s what helped push entire economies forward; the dream of having a better life. My father came to the US in the mid-60s with nothing but six dollars in his pocket and a dream. His contributions to science are immeasurable and I am his legacy. That’s what I believe immigration should be associated with in my opinion.”
“We are working on the most cuttingedge technology,” SJ Jones, a metal AM engineer, said in their assessment of diversity, equity, and inclusion (DE&I) in AM. “We’re probably one of the technologies that are as close to magic as we’re ever going to get. So, when you have that much power, you have a responsibility to all groups and to all people.”
“Having perspectives from different areas of the world helps connect parts of the world that otherwise may not connect,” Krishnamurthy added. “It is my belief that collaboration fosters the exchange of ideas and the formulation of newer and better ones. So, when you add in people coming from diverse backgrounds, there is a multiplier effect.”
The same can be said of people of different genders, race, and socioeconomic backgrounds – anyone who might think differently and bring alternative perspectives. And where better to share the ideas born from that different lived experience than in formal team meetings? Except, this is another setting where people are made to feel like they can’t be their true selves. SJ says they often find themselves holding back on emotion or passion in meetings, so as not to be judged against the ‘angry black woman’ stereotype – a source of much frustration for Lisa
Block, the most recent addition to Women in 3D Printing’s Board.
“Meetings are where the passion should be, meetings are where we express the ideas that further the company,” Block said. “But I don’t think we should detract from everyone feeling that they can express their true feelings in a meeting without consequence, and we have not gotten to that place just yet. There is a perception that if a black woman elevates her voice at all, if she does not agree with you, that she’s confrontational, she’s being argumentative. Well, she may just be telling you the truth about something, and you’re not prepared to hear it. That’s a real reality of our time now. We’ve got a whole lot of truth that we’re not prepared to hear, we’re not prepared to deal with. It’s like, I want you to be seen, I want you to feel accepted, but don’t be transparent about your experiences because that says something about me and I’m not ready to deal with me.”
“It’s got to get worse before it gets better,” Jones emphasised, “because people who were doing wrong or people who are creating these toxic spaces are not just going to wake up tomorrow and be like, ‘oh my God, I was toxic, I’m so sorry.’ That’s not going to happen. People will go kicking and screaming into the truth.”
“When we innovate, we do things a specific way until technology proceeds us and says, ‘there’s something better, there’s a bigger way to do this,’ and then we evolve,” Block added. “But humanity has not made that evolution possible. We are so upset that the authority figures in our lives possibly could not have informed us in the correct way that we say to go against them is to go against who I am, and I can’t do that. If I had any problem with race or gender or creed or anything like that, it would be that it’s the only environment in which we’re willing to operate on absolutely archaic technology. It’s the only area of our life we’re willing to stop advancing.”
While changes to the culture won’t happen overnight, and to some extent are out of the control of those speaking passionately about the experiences of Black people and people
of colour in industries such as AM, there are efforts that can be made and are being made.
In August, the Greater Than Tech (GTT) initiative set up by Jasmine LeFlore and Dr Brittany Wheeler coordinated a ‘Girl Meets Additive Manufacturing’ programme, which was designed to expose underserved high school students to a blend of engineering and business. During the four-day workshop, the students were taught how to use CAD, learned about the costs associated with AM versus traditional manufacturing, and were tasked with pitching their designs. They also took in presentations from industry experts and participated in a facility tour of a GTT partner organisation.
The intention of GTT’s ‘Girl Meets…’ programmes are to ‘make the uncommon common' by introducing young women of colour to STEM and entrepreneurship, emphasising that careers in these fields are possible. Partnerships with the likes of Collins Aerospace, where there may be future apprenticeship opportunities, will go some way to providing a pathway for students to become engineers and business leaders.
But right now, there isn’t a clear enough route for people of certain backgrounds to make it, and LeFlore has ideas as to why.
“I think a lot of opportunities come into play based on, I’ll say, affinity bias, where if you’re familiar to me and you remind me of myself, I’m more likely to give you an opportunity than someone else,” she said. “This is something that plays out often in the workplace […] and I think if we have more leaders who understand the journey of what it’s like being a woman in STEM or a woman of colour in STEM, so on and so forth, we will be able to have better equitable opportunities because everyone isn’t able to start with the same tools to learn. The more we realise and recognise that, the [more] we will have people get into positions of power and being decision-makers to help others.”
GTT is not alone in contributing to these efforts, with several other organisations working to give young people access to STEM education, specifically targeting underserved communities and occasionally focusing on AM. There are also those like Women in 3D Printing and Black Women in Science and Engineering (BWISE) which allow underrepresented groups to connect and network, while the annual TIPE Conference platforms a diverse range of speakers in AM. Xometry, meanwhile, has established a scholarship scheme with Howard University, a Historically Black College and University.
“When you have that much power, you have a responsibility to all groups and to all people.”
Open
But for all these efforts, there are still barriers to break down from within AM. Left out, excluded, and unwelcome is how Black people and people of colour in this industry often feel. Some can’t help but feel isolated when they walk a trade show floor, others feel marginalised because their parents are immigrants, and there have been instances where people are confronted with surprise when they deliver their words in ‘well-spoken’ English.
Whether it’s outright discrimination, veiled racism or cases of ignorance, there is enough hostility and ostracism to make people – who are sufficiently qualified and care just as much as anyone else about additive – feel like they don’t belong. It is one thing to build the pipeline, but it is another to foster a culture that maintains a diverse range of talent. Some fear AM, like other STEM industries, isn’t doing that well enough.
Detoxifying spaces within AM is the responsibility of each of us occupying a position in the industry. Like any other, this industry’s culture is made up of the thousands of individual attitudes and values each person brings to the table, with simple actions like including colleagues in conversations and not making crude jokes at their expense going a long way to making people feel welcome.
Addressing such behaviour is not a big ask but is of big significance. To varying degrees, everybody working within AM believes the technology has vast potential. But to reach that potential, studies would suggest a need for input from a broad range of perspectives.
“AM, even as a concept, is so beautiful,” Mina Lee, Manager of People and Culture at MakerBot, said. “You’re literally making something by adding layers and layers and layers until it’s this final product.
And I think
having that diversity and inclusion and having diverse voices should also be in that DNA. You’re layering people’s experiences. You hear all the time about how lack of diversity in test groups leads to very racially complicated things, so you see these gaps that end up making a product in tech that is not inclusive. You decrease the amount of disparity by increasing the levels of diversity and diverse thought and diverse experiences. Having that adds more to the innovation and will only propel us to the future in creating incredibly innovative technologies.”
“A lot of start-ups fail because of the founding team because there’s no dissonance, there’s no diversity of thought, whether that’s background or race, things that make people different,” Makelab CEO Christina Perla analogised. “You see companies go down because every single founder came through the exact same school at the same time. In fact, they were roommates. That can be problematic because you fall into that level of comfort. And comfort can be a killer of a lot of things, including culture. It’s something you always need to stay on top of and be cognisant of, you always need to make an effort towards it. It’s more about the actions you don’t take rather than the actions you do take. The key to a successful future of this industry [is] diversity of thought. We just need it.”
In her role as Manager of People and Culture at MakerBot, it is within Lee’s remit to source talent to come and work with MakerBot. She accepts committing to providing a diverse range of people with the opportunity to work for a technology brand such as MakerBot requires a lot of time and bandwidth, but she does believe there are smart ways to factor in this requirement when recruiting. Lee uses a saved search on LinkedIn which presents alumni from HBCUs and women's universities when she is struggling to
find diverse talent on an unfiltered LinkedIn search. Perla, meanwhile, is seeing the value of looking outside of the AM space in MakeLab’s search for a new member of its leadership team. While CVs have come in from fellow 3D printing brands, she is finding a more diverse pool of talent – and potentially thought – in the managers serving tech conglomerates and food and beverage franchises.
Internally at MakerBot, Lee is committed to outlining career pathing and career development for all employees, but the same opportunity needs applying to everyone everywhere. Krishnamurthy, Jones, Block, LeFlore, Lee, and Perla all share a passion to usher in a more diverse cohort and see them thrive with less of the prejudice, exclusion, and discrimination that they know exists. They do so because they care – about people and about this industry.
“We are in an industry where we are constantly looking at our numbers – how we can satisfy investors, how we can make sure we’re profitable, how we can make sure that we’re here to stay,” Block finished. “And the truth of the matter is, I think we’ve been looking at the wrong thing. All the money will come when we care as much about humanity as we care about financial gain.
“At the moment we care about people to the degree that we care about money, we will see additive explode. But we have facilitated environments where, just because people are talented, they don’t have to be appropriate, they don’t have to be inclusive, they don’t have to be kind.”
Earlier this year, Erin Walsh [EW] – a University of Glasgow medical student who previously carried out PhD research in the manufacturing of pharmaceuticals – sat down with University of Sheffield Mechanical Engineering Senior Lecturer Candice Majewski [CM] at the request of TCT.
The pair met online while Walsh was working on her PhD. Through that PhD, Walsh was exploring the integration of design features into a pharmaceutical tablet, which introduced her to 3D printing technology. In need of some guidance, she reached out to Majewski, who has worked with 3D printing materials and processes throughout her career in academia.
With the PhD now complete and Walsh now pursuing an undergraduate degree in the Medical field, they reconvened to share their insights on the additive manufacturing research landscape, including the culture of competitiveness and the need for more collaboration.
EW: I think it's critical that anything that you think can add value that you share, and that you share openly. Particularly with technologies that are new and upcoming people can be a little bit protective of sharing, when you're doing literature reviews, what really becomes apparent is everyone wants to share the shiny things that work, nobody will say here's the 1,000 things that we've tried in the meantime that didn't work. And by sharing those things that didn't work, those are still learnings. And that saves a lot of time for the rest of the community to say, ‘we tried that, it didn't work, this is what we learned from it.’
If someone was to publish everything that they had tried that didn't work and what they had learned
from that, I think that adds more value to the community and to the technology and what we know about it than just what did work.
I always have seen that it feels as if it's my responsibility as a researcher, to not just share the successes and it's something that is made more challenging by the academic culture.
CM: I completely agree. It is part of the academic environment that I think people become perhaps scared to admit they've made mistakes. Because we think of something that doesn't work as a mistake, but if you had a good hypothesis, you test it and it doesn't work, that's not a mistake. Sometimes good ideas don't work. You learn from that, and you say, ‘okay, why did that not work?’
Now that I'm leading a group of researchers, I feel that is really important because if I don't admit to mistakes, and if I just pretend like everything's always perfect, then all those people who are coming through the system, that's all they're exposed to. I think it's important for the community to understand what's been tried and hopefully save time in the long term, but it's on all of us to make it clear that science is about trying stuff.
EW: If you were to try and name all the different subtypes of AM, you'd be here all day and it feels as if what we've done is we've went really broad, but what's missing is still some of that fundamental understanding. So, for example, I was working with liquids, so rheology is not something that's been hugely studied for liquid photopolymers but makes a huge difference to things like print quality. And that's a core chemical property. Because it's been such an explosive interest in this technology, it feels as we've almost missed that really; the lowest tier basic understanding. And it's something that people then don't study when they publish about things. So, you’re then trying to go out and looking at the research out there, and there's nothing there, which is a real challenge because that kind of study takes time. And it's the kind of study that you just need somebody to do once and do properly and share and then we're not all having to do it, but it seems as if that's an afterthought for some of these technologies.
CM: I think you're right, Erin, we have missed a lot of that fundamental understanding. Because there's always this rush to be the first to get this out there, and let's get it known, and then almost backtrack to figure out how it actually works.
I think we [also] have a real challenge in terms of people. We have a real issue with early career people, there's been a lot all over the news and with the ongoing strikes and stuff about precarity in academia. It is so difficult for someone to make each career jump. You might do a PhD but that doesn't mean there's a guarantee of a postdoc position straight afterwards. And if you're a postdoc who wants to make a jump into being an academic, you get so many applications for every academic position. Again, there's so much competition there, it's becoming very difficult. Even if you get that postdoc position, you aren't guaranteed the next one. There’s this ongoing process of until you've got that permanent possession, you're always like, what's next? I've got a contract for two years, so what am I doing after that? Regardless of your situation, that's really difficult, like, can I buy a house? Can I settle down? Because of that, we lose really good people, and we lose that continuity of people.
On a positive note, there's a lot more people doing research. There's a broader range of research going on. And I think that is important because if you've got still relatively new technologies, you need to keep figuring out where the boundaries are and what we can do. I think that diversity of research can be a really good thing. We have got a lot of areas of overlap where lots of different people are working on the same thing and that has led to what I would say is a very negative competitiveness in some cases because you have two options, you say, oh this Erin person is doing some cool research that's similar to mine, I could get in touch and see if we can work together or I can say, ‘well, what I need to do is keep everything quiet.’
We definitely have more women than we did. There's a Women in 3D Printing network and all that kind of stuff. I think what we need to do next is say, who else are we missing? We still see a lot of very white panels.
That's an ongoing thing. We have issues, especially on the experimental side, for example, with disabled people. So how do we accommodate disabled people in a way that they can do these jobs that they can be really good at? Someone said once, they were fed up with always being put on computer-based projects because there was an assumption that they couldn't do experimental work. I think we're still combating a lot of those things that we don't yet know how to fix. So, I think we have more work to do there. But we're heading in the right direction.
EW: The really critical one for me is collaboration, and that is entirely cultural, but it's something that we need to instil from undergrad. We are bringing young individuals into the world of education and academia, we are training them to be hyper competitive, to be overprotective, but it's not helping us to grow and to learn as a wider community. It is a bottleneck in terms of the amount of people that will do an undergrad, that will do a postgrad and will go on to postdoc and academia, we're filtering. And there are major issues within even that filtering process with diversity and equality. But by just filtering in that way, we are losing value. Every time you go up a level, it becomes more competitive and what you're doing is you're honing what you've taught that individual, what you've trained them to be,
and then you get less and less and less communication the further up you go.
PhD students are far more willing to ask for help and to reach out the same way that I did to Candice. If I had been at academic level, that wouldn't have been as simple. I think that would have been less culturally normal. And it's almost as if the minorities in this society and this kind of culture are having to create things like Women in 3D Printing, which is phenomenal, but why do we need it? We've [also] got other groups that are not shown in the same way that they should be. We need that diversity but it's about keeping that momentum and driving it forward. And really, I think it needs to start from the bottom. By starting from the bottom and changing the culture that we have in academia, that will also spill over into industry because of your undergrads, if you teach it then a lot of those undergrads are going to go into industry. You’ve got to start there so that you get this collaborative approach across both.
Having also come from EPSRC Future Manufacturing hub, I've seen the benefit of having academia and industry work side by side. But it shouldn't have to be this fancy grant to encourage that, we shouldn't be having to have really competitive grants that are paying us a lot of money just to try and put these together, it should be becoming a standard.
[Editor: The discussion has been edited for brevity and clarity].
“If you've got still relatively new technologies, you need to keep figuring out where the boundaries are.”
The world’s largest production-grade
Largest production-grade DLP 3D printer in the world with high-power projectors and array technology to enable area-wide printing without sacrificing resolution or repeatability
Faster print speeds with industrialgrade projectors with custom optics to minimize power loss for fast polymerization times and high throughput in a large build volume
Top-down digital light processing (DLP) requires fewer supports, eliminates failure due to separation forces, and patented pixel tuning provides high-quality surface finishes
Leverages long-chain polymer chemistry to create fully-isotropic, stable, strong end-use parts without the bottlenecks of traditional injection molding production
With wide material compatibility, to produce elastomers, rubbers, hard plastics, and high-temperature plastics, including from trusted brands such as Loctite® and Adaptive3D
Supports highly vicious resins that provide superior part properties, including proprietary DuraChain™ resins, an all-new category of durable one-pot photopolymers
ETEC Xtreme 8K with a 450 x 371 x 399 mm / 17.7 x 14.6 x 15.7 in build envelope
While additive manufacturing processes provide unique opportunities, they are generally complex and slow. This leads to many ways for things to go wrong and makes it costly when they do. Typical errors range from small geometrical inaccuracies or mechanical weakness to complete build failures.
Usually, a skilled worker observes the process to prevent or correct errors. The worker needs to recognise an error, stop the print, remove the part, and make a judgement on how to adjust settings for a new part. Workers need training to carry out this task as well as time to gain experience when working with new printers or materials. Even so, a human cannot constantly watch multiple printers at the same time, especially not for very long prints. Nor can a human correct printer settings in real-time. And there are common errors, such as warping, where it is often unclear how to update settings to prevent future occurrences.
This has motivated a lot of work in integrating sensors into additive manufacturing systems to automatically detect errors. This has included acoustic, inertial and current sensors, but camerabased approaches are most widely adopted given their versatility and data-richness. Coupling cameras to traditional computer vision approaches has been successful in explicitly detecting specific errors in parts and 3D printing systems for which they have been calibrated. But it is very difficult
to handcraft algorithms that work for different errors, parts, printers, materials and printing setups.
Machine learning, particularly deep learning, approaches have shown unprecedented performance in many applications including vision. This has led to several recent examples of applying machine learning to detecting errors in additive processes, but usually still only in a single part and for a single type of error. The greatest potential advantage of machine learning though, to enable robust error detection and correction that works across different parts, materials and printers, remains unexplored.
In work recently published open-access in Nature Communications, we made intelligent 3D printers that can rapidly detect and correct errors, even in new parts, materials and printing systems., via learning from other printers. We did this by developing a machine learning algorithm that can both detect and correct diverse errors in real-time, and can be easily added to new or existing machines to enhance their capabilities. The algorithm was trained by showing it approximately 950,000 images taken from a printheadmounted camera during the printing of 192 different parts. Every image was labelled with relevant printer settings, for example the temperature of the nozzle and the flow rate of material from the nozzle. The algorithm was also shown how far those settings were from appropriate values. This combination enabled the algorithm to
learn not just when things go wrong, but also how to fix it when they do, just by looking at an image of the process.
During the training phase, the algorithm was only shown images from a single type of FFF 3D printer using PLA polymer. But the algorithm was able to correct errors in different polymers and even unfamiliar systems such as direct ink write ketchup and mayonnaise. This suggests that the algorithm is able to pick up features that are general to extrusion 3D printing.
A future system could significantly improve the productivity and reliability of additive manufacturing in general, leading to new markets including in safety-critical applications. We are commercialising this technology through Matta, a spin-out. We are especially interested in developing learning systems to prevent errors in high-value parts including in the aerospace, automotive and energy sectors. The loss in machine time, energy, material and from discovering an error during final inspection in such applications would amplify the benefits from our learning approach.
The potential for machine learning technologies in additive manufacturing is vast and we are only scratching the surface of what it is capable of. Given machine learning’s increasing power, accessibility and the need for better solutions to complex manufacturing challenges, machine learning is poised to play a key role in driving additive manufacturing to ever greater heights.
Researchers at Universty of Massachusetts Amherst (UMass) and Georgia Tech developed a 3D printed, dual-phase, nanostructured, highentropy alloy that they say exceeds the strength and ductility of other AM materials.
MIT alone has seen a handful of 3D printing developments over the last few months. A new programmable 3D printed material that can sense its surroundings, 3D printed sensors for satellites, and using artificial intelligence to correct AM errors in real time.
In late July, MIT announced that a team of researchers had created the “first completely digitally manufactured plasma sensors” for orbiting spacecraft. The sensors are known as retarding potential analysers (RPAs) and are used by satellites to determine the chemical composition and ion energy distribution of the atmosphere.
Researchers at MIT also trained a machine-learning model to monitor and adjust the 3D printing process to correct errors in real time. The scientists used artificial intelligence to develop a system which uses computer vision to watch the manufacturing process and correct the errors in how it handles the material.
High entropy alloys (HEAs) are comprised of five or more elements and allow for the creation of near unlimited numbers of combinations for alloy design. The researchers combined an HEA with laser powder bed fusion technology during the development of the new material.
rise to ultrahigh strength and enhanced ductility, which is uncommon.
Researchers at Pennsylvania State University have made a potential breakthrough in biomaterials. A team developed a novel nanoengineered granular hydrogel bioink that makes use of self-assembling nanoparticles and hydrogel microparticles, or microgels.
Researchers at Washington State University have combined a small amount of simulated crushed Martian rock with a titanium alloy, to create a strong highperformance material. The team who took part in the research hope that the process could one day be used on Mars to produce tools or rocket parts.
The team created parts with as little as 5% Martian regolith, a black powdery substance that mimics the material found on the surface of the red planet,
all the way up to 100%. The 5% regolith parts were strong, and even had better properties than just the titanium alloy, but the 100% parts were brittle and cracked easily. However, researchers did determine that high-Martian content materials would be useful for making coatings to protect equipment from rust or radiation damage.
The main benefits that could be achieved from using this 3D printing process would be found in weight and cost savings. The authors of the study noted that it costs NASA 54,000 USD for a space shuttle to put just one kilogramme of payload into Earth orbit.
A big problem that has been present in the past when developing bioinks is having high fidelity whilst not compromising porosity. Penn State researchers approached this by increasing the stickiness of microgels to each other. The way the microgels cling together removes the need for them to be tightly packed, preserving microscale pores.
The researchers plan to explore how the newly nanoengineered bioink can be further applied for tissue engineering and regeneration, models of organs and possibly insitu 3D bioprinting of organs (the direct printing of bioinks to create or repair at a defect site).
Design for Additive Manufacturing (DfAM) is not a new discipline but recently there has been more focus on this vital, yet sometimes vague, subject.
I am a member of the UK DfAM Network steering committee, established at the end of 2020. I suspect that the network has been one driver of this renewed focus on DfAM with a series of application specific workshops attracting international speakers and audiences online and in-person. This work has opened my eyes to the breadth and depth of DfAM expertise both within the UK and globally.
I have also become aware that within the AM community, there is a strain of ambivalence, verging on hostility, towards the discipline of DfAM. I have heard opinions from AM practitioners and educators that I deeply admire, that they find DfAM esoteric, effete (an effete choice of vocabulary!) and an unhelpful mystification of what is fundamentally traditional designing. Stronger opinion was expressed in a recent instalment of Duann Scott’s excellent DfAM Substack series that tried to nail down a definition of DfAM from a group of experts. One of them stating that advocates of DfAM deliberately mystify this design practice to excuse AM’s limitations and elevate their status within the AM industry.
I do have a certain sympathy with this view, having had to pick up the pieces after a “guru” has led clients down a blind alley.
However, dismissing the constantly evolving design understanding of a relatively new manufacturing technology is foolhardy. This understanding has been hard earned through trial and error by thousands of designers and rejecting this knowhow condemns anyone exploring AM to waste time reinventing the wheel.
It is uncool to talk about design rules for AM when for so long it has been associated with the fantasy of “total design freedom.” It certainly offers the possibility to manifest new geometries but that alone is technical shape making. DfAM is not only about how thick or thin, large or small you can print with a different technologies. That is printability. Imperative for sure, but just the start of DfAM.
My definition of DfAM is straightforward. First select the appropriate AM technology and material applicable to you and your project. Then absorb a series of principles and lessons belonging to that technology. Finally, apply that to designing something that functions and is valuable enough to manufacture. Many regard DfAM as the use of optimisation software, generative design and parametrics. All of these should augment this basic
DfAM grounding; the Klingon aesthetic is sexy, but it doesn’t automatically make a part valuable.
This approach is what promotes widest AM adoption. Where adoption is simply procuring AM parts, never purchasing AM hardware (sorry salesfriends). When using AM is commercially viable, you’ll do it again. Then one gains the confidence to explore more technologies and eventually buy hardware if it really makes sense.
Let us review a simplified sequence of the development of AM (with clear overlaps) over the years:
1. Hardware and Materials Development: AM starts with the evolution of the different hardware technologies and materials that we have today.
2. AM Software Development: This took a step back in the production sequence. It was identified that to realise the potential of AM, designers first required the tools to produce the geometries that were now possible and file fixing automation to make files print ready and more reliable to produce.
3. Post-Processing, Finishing, Production Automation and Qualification: Focus then turned to the end of the production sequence, accelerating postprocessing, improving the quality of finishes available, integration and automation in a manufacturing environment and certification standards.
With tools, technologies, quality and productivity being firmly established, I hope that a new attention on DfAM heralds a fourth stage of development focus placed at the very start of the production sequence.
From here, when the lessons are clearly disseminated, they can be absorbed by new and existing users alike, to improve the output
of AM. Many of the advances in AM that open new applications and markets are the result of informed DfAM, making all of AM’s systems look better.
Better designed AM parts have optimal productivity, print reliably, are consistently post processed, function and can include beneficial performance. Crucially, they commercially stack up.
Some believe that DfAM is simply Design for Manufacturability (DfM.) Just because you can manufacture something with AM does not mean that it is worth manufacturing. This is what DfAM aims to resolve.
Looking ahead, I hope that DfAM does merge into DfM as future generations of designers properly select AM as second nature. When that day dawns, DfAM will have completed its job.