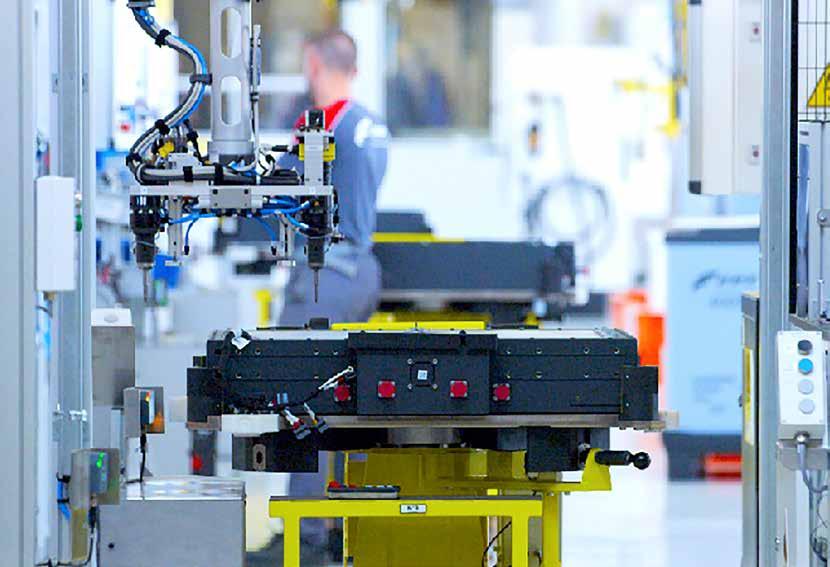
3 minute read
Batterie: il cuore del veicolo
Come nasce una Il cuore di ogni veicolo elettrico è la batteria: accumula l’energia e successivamente la trasmette al motore. Ma come si costruisce? Ecco tutti i passaggi necessari, dalle materie prime fino all’installazione nel telaio di Luca Gaier batteria

Advertisement
Il componente più importante di ogni veicolo elettrica? Si sa, è la batteria! Ha il compito di accumulare l’energia necessaria al movimento e di fornirla al motore. Ciò che si sa meno è come è fatta, come si costruisce e come si installa nel veicolo. Partiamo dall’inizio: i quattro minerali principali che costituiscono ogni batteria sono litio, nichel, manganese e cobalto (Li, Ni, Mn e Co). “Dopo l’estrazione subiscono un trattamento chimico da cui si ottiene il materiale attivo, le cui reazioni chimiche permettono di stoccare e rilasciare energia” spiega Francesc Sabaté, Responsabile del Test Center Energy (TCE), il centro di Ricerca e Sviluppo per le batterie di SEAT S.A., unico nel suo genere nell’Europa meridionale.
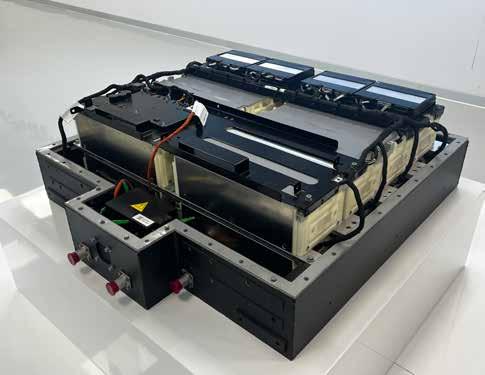
IL CUORE DELLE BATTERIE: GLI ELETTRODI
Il materiale attivo è utilizzato per creare gli elettrodi, cioè gli elementi che immagazzinano effettivamente l’energia e che si trovano all’interno delle celle, ovvero le unità minime di accumulo di energia. Al loro interno c’è un elettrodo positivo (anodo) e un elettrodo negativo (catodo) che sono raggruppati insieme con un separatore che impedisce il contatto tra di loro. Questi elettrodi sono responsabili del trasferimento dell’energia e ogni cella ha una tensione di
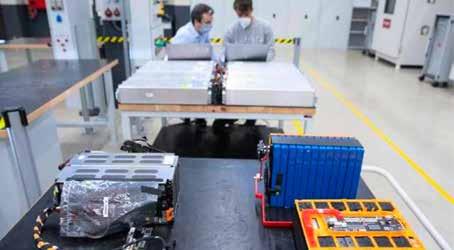
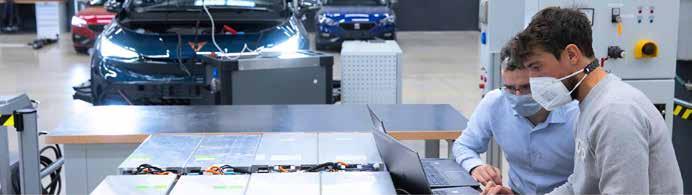
3,7 volt – quanto basta per alimentare una torcia LED. Per muovere un’auto elettrica, invece, servono circa 400 volt; quindi, è necessario collegare un gran numero di celle in una disposizione in serie. Sono questi gruppi di celle che formano il famoso pacco batteria. Le celle, infatti, vengono interconnesse tra loro e quindi assemblate in gruppi di moduli. La somma dei moduli forma il pacco batteria. Ogni modulo è collegato agli altri attraverso i connettori, per garantire sia il flusso di energia
TEST CENTER ENERGY
Per garantire qualità e prestazioni, le batterie vanno testate simulando ogni tipo di condizione. SEAT S.A. esegue questi test nel pionieristico Test Center Energy, dove ogni anno vengono eseguiti fino a 6.000 test completi del sistema ad alta tensione e le batterie sono sottoposte a una media di 17.500 ore di prove e simulazioni. È una struttura che si sviluppa su una superficie di 1.500 metri quadrati, operativa 24 ore su 24, 7 giorni su 7; qui si conducono anche test climatici con escursioni termiche fino a 80° C. Le batterie, dunque, vengono spinte al limite per garantire prestazioni adeguate in ogni circostanza. Fonte: SEAT S.A. che la comunicazione tra la centralina elettronica del veicolo (BMCe) e le schede elettroniche che monitorano lo stato delle singole celle (CMC). “Non resta che aggiungere il sistema di raffreddamento e l’involucro, dopodiché la batteria è pronta per essere installata nel veicolo” prosegue Sabaté.
FPT PUNTA SULL’ALTA TECNOLOGIA
Il 18 ottobre FPT Industrial, il brand globale di Iveco Group per i sistemi di propulsione, ha inaugurato il nuovo stabilimento ePowertrain interamente dedicato alla produzione della gamma elettrica del marchio, che comprende assali elettrici, central drive e pacchi batteria per veicoli commerciali leggeri, minibus e autobus. Il nuovo stabilimento ePowertrain, dedicato all’elettrificazione, è integrato nell’area FPT Industrial di Stura, vicino al testing e agli impianti per la produzione di motori a combustione interna, trasmissioni e assali, con evidenti vantaggi in termini di sinergie industriali. A pieno regime produrrà 20.000 pacchi batteria all’anno. La caratteristica di questo impianto, e quindi del sistema di produzione delle batterie, è l’introduzione di innovazioni rilevanti nelle linee di produzione con una forte collaborazione uomo-macchina grazie alle tecnologie Industry 4.0 adottate in tutte le aree, che consentono la raccolta e l’analisi automatica di tutti i dati indispensabili per monitorare e migliorare la sicurezza, la qualità e la produttività. Tutti i processi produttivi si basano su magazzini altamente automatizzati per la gestione dei componenti e si sviluppano attraverso stazioni di assemblaggio a controllo elettronico. Le tecnologie di ultima generazione adottate includono la realtà aumentata e virtuale, che riduce i tempi di progettazione delle linee di produzione simulando il risultato operativo prima dell’installazione fisica, la stampa 3D e i sistemi “Smart Observer” basati su sensori intelligenti, scanner 3D per misurazioni di qualità metrologica, simulatori di realtà 3D e robot collaborativi. I controlli di qualità in cloud consentono di individuare immediatamente i problemi, mentre quelli di fine linea certificano la conformità del prodotto in termini di configurazione, prestazioni e sicurezza.#