
14 minute read
Gewinnung des Solling-Sandsteins
Die Verwendung von Steinen beim Bauen von Häusern, Kirchen oder anderen Bauwerken ging Hand in Hand mit der Verbesserung der Werkzeuge — vom Stein über Bronze und Eisen zum Stahl. Die Bearbeitungsmethoden der Steinmetze sind jedoch schon frühzeitig so vollkommen gewesen, dass sich die bis ins letzte Jahrhundert üblichen Arbeitsmethoden nicht wesentlich von denen unserer frühgeschichtlichen Vorfahren unterschieden. Erst durch die Einführung von motorengetriebenen Maschinen in diesem Jahrhundert wurde die Gewinnung und Bearbeitung der Natursteine grundlegend verändert; vor allem bei der Weiterverarbeitung ist jedoch geschickte Handarbeit nach wie vor sehr wichtig.
Am Anfang stand der Kummer
Advertisement
Die Gewinnung des Sandsteines war von jeher eine schwierige und kräftezehrende Arbeit, die viele gesundheitliche Gefahren mit sich brachte. Bis in die heutige Zeit hinein ist der Abbau und die Weiterverarbeitung des Sandsteins schwere Knochenarbeit, verbunden mit großem handwerklichem Können.
Mit dem Abbau des Gesteins wird am oberen Ende der Lagerstätte begonnen; bis in über 30 Meter Tiefe wird diese dann terrassenförmig nach unten ausgebeutet. Zunächst muss jedoch das aufliegende Material, der sogenannte Abraum oder Kummer, weggeschafft werden. Meist im Winter, durch neue, noch ungelernte Kräfte und in früherer Zeit auch durch Frauen. In Handarbeit — mit Hacke und Schaufel, Brecheisen und Spitzhacke — wurde die aufgelagerte Erde und weiche Verwitterungskruste einfach zur Seite auf Halde geworfen, ebenso wie das später während der eigentlichen Gesteinsgewinnung anfallende, nicht geeignete Material. Um die Steinbrüche herum bilden sich daher nach und nach riesige, hochgetürmte Abraumhalden, die eine Hügellandschaft bilden.
Die eigentliche Steingewinnung wurde von erfahrenen Steinbrechern und den Steinhauern oder Fertigmachern ausgeführt. Ihnen fiel eine doppelte Aufgabe zu: Die Gewinnung des Rohmaterials und dessen erste Aufarbeitung zu Quadern. Auch sie waren meist ungelernt, die auszuführenden Arbeiten im Steinbruch guckte man sich von den anderen ab. Wer einige Jahre dabei war, hatte sich alle wichtigen Handgriffe angeeignet. Anders war es bei den Steinmetzen: Sie sind schon seit dem frühen
Steinbruch bei Arholzen Oben: Keilsprengung mit dem Hammer
Abraumhalde bei Arholzen
Mittelalter zunftmäßig organisiert. Die Ausbildung in den Betrieben ist eine der ältesten und längsten im Handwerk, bis zu fünf Jahre musste man lernen. Heute benötigen die Lehrlinge drei Jahre, um Steinmetzgeselle zu werden.
Die Methoden der Gewinnung
Das Material wurde meist durch Keilsprengung des Gesteins gewonnen. Bei festerem Gestein wurden Buchenoder Eichenholzkeile genommen. Mit
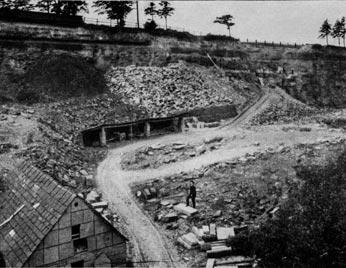
Hammer und Meißel trieben die Steinbrecher in kleineren Abständen Löcher in die senkrecht zerklüfteten Felsspalten, in die die trockenen Holzkeile hineingesteckt wurden. Mit Wasser befeuchtet, dehnten sich die Hölzer aus und sprengten den Sandsteinblock aus dem Fels. Rohblöcke, mit einem Maß von zwei bis drei Kubikmetern entstanden. Durch im Gestein vorhandene senkrechte Spalten war es möglich, große rissfreie, von geraden Flächen und rechten Winkeln begrenzte Quader zu gewinnen. Das horizontal geschichtete, etwas weichere Material wurde in knochenharter Arbeit mit Brecheisen aus der Wand gelöst.
Bei Versuchen mit Sprengungen durch Schwarzpulver oder ähnlichem litt die Qualität der Steine, wie Erich Henke, ein Bauunternehmer aus Bodenfelde berichtet: „Das Sprengen hat sich in unseren Sandsteinbrüchen nicht bewährt, denn der Stein kriegte doch was mit. Einen leichten Sprung meistens. Der Steinhauer machte dann den Stein zurecht und letzten Endes fiel er ihm auseinander. Dann war die ganze Arbeit umsonst gewesen.“
Waren die Blöcke losgebrochen, wurden sie von den Fertigmachern mit kleinen, eisernen Keilen zu Platten oder Steinen nach beliebiger Dicke und Größe geschlagen. Meist arbeiteten ein Steinbrecher und ein Fertigmacher im Gruppenakkord zusammen. Der Brecher mußte neben großer körperlicher Kraft auch einen geübten Blick für das geeignete Gestein haben. Warf er dem Steinhauer schlechtes Material hin, war der Verdienst gering.
Blick in den Steinbruch „Grosse Winterseite“ der „Administration der Sollinger Steinbrüche“ (Foto um 1915)
Beim einfachen Bossieren werden die Steine in den sogenannten roh behauenen oder auch gespitzten Zustand gebracht. Nach und nach wird unter Anwendung von
Richtscheit und Winkeleisen sowie Hammer (unten rechts) und Meißel der Stein in die gewünschte Größe und Form gebracht. Die Steine sind rechtwinklig geschlagen und die Sichtflächen werden nicht mehr extra bearbeitet, höchstens größere Unebenheiten werden beseitigt. Die einfallsreichsten Bezeichnungen, wie Klöpfel, Klüppel oder sogar Knüppel hat der runde Holzhammer mit dem kurzem Stiel (großes Foto), der mit den verschiedenen Schlageisen (Meißeln, Bild oben links) zu den wichtigsten Werkzeugen der Steinmetze gehört. Beim Bossieren schlägt der Steinmetz mit dem Klöpfel und Meißel die gewünschte Größe und Form des Steines. Die Weiterverarbeitung erfolgt häufig durch das „Kröneln“ oder das „Scharrieren“ des Steines. Beim Kröneln wird der Stein etwas geglättet. Mit beiden Händen wird der sieben bis acht Pfund wiegende Krönel (Bild mitte rechts) durch hohen Kraftaufwand in schräger Richtung gegen den Stein geführt. 12 bis 15 kleine Meißel sitzen fest eingeklemmt in einem Längsschnitt im Eisen und bilden den Krönel. Diese große Anzahl an beiden Seiten kantig zugespitzter Stahlmeißel wirkt dabei gleichzeitig auf den Stein ein. Ein gekrönelter Stein weist an seiner Sichtfläche nur noch kleinere Unebenheiten von höchstens einen halben Zentimeter auf.
Durch Klöpfel und Scharriereisen, das eine etwa zwölf Zentimeter breite Schneide hat, erhält die Oberfläche des Steines parallele Riefen. Die Sandsteine wurden vorwiegend scharriert verwendet.
Klöpfel, Klüppel oder Knüppel
Die Steinhauer — heute meist als Steinmetze bezeichnet — hatten die Aufgabe, aus den gebrochenen, rohen Blöcken Steine von genauen Abmessungen und gewünschter Form herzustellen. Unendlich lang erscheint die Liste der vom Steinmetz angefertigten Dinge aus Sandstein: Fenster- und Türgewände, Treppenstufen, Gesimse, Säulen, Sockel,
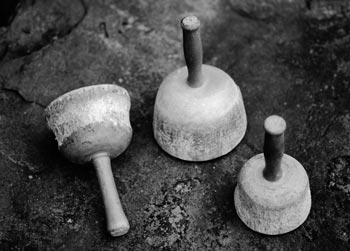
Schwellen, Pfeiler, verschiedene Plattenund Mauersteine sowie Hohlwaren wie Tröge, Brunnen und Futterkrippen, Rinnsteine, Gossen, Spülsteine, Grabsteine und -denkmäler und vieles andere.
Heutzutage haben kostengünstige, gleichförmige Industrieprodukte nahezu alle diese von Hand gefertigten Dinge ersetzt.
Mit großem Geschick mussten die Steinmetze Steine mit scharfen oder runden Kanten, ebenen und angerauten Flächen sowie profilierte oder ornamentale Bauteile aus den rechteckigen Quadern herausarbeiten. Auf Böcken aus
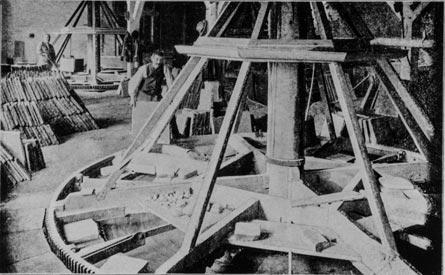
Fichtenholz, auf denen eine dicke Steinplatte lag, haben die Steinmetze den ganzen Tag lang im Stehen die Rohsteine „fertig gemacht“.
Sehr unterschiedlich ist die Intensität der Bearbeitung der Rohblöcke. Je nach Verwendung geht es vom einfachen „Bossieren“ der Steine über das „Kröneln“ und „Scharrieren“ (siehe Werkzeuge Seite 41) bis hin zu sehr aufwendigen Verzierungen durch geometrische Muster. Mit den unterschiedlichen Bearbeitungsmethoden erhält der plattig auftretende Solling-Sandstein verschiedene Oberflächen.
Mit der Einführung von Maschinen und Presslufthämmern veränderten sich bis heute viele dieser Tätigkeiten. Doch langwierige Handarbeit, die auch heute noch die Arbeit überwiegend bestimmt, ist teuer und für viele nicht bezahlbar. Daher haben die anspruchsvollen Produkte ihre Bedeutung auf dem Markt verloren.
In den Schleifmühlen
Die vorbearbeiteten Steine wurden — je nach Verwendung — einem Schleifoder Politurprozess unterzogen. Meist waren es die Dehl- und Legesteine, die schon seit dem 16. Jahrhundert in Steinschleifmühlen maschinell bearbeitet wurden. Voraussetzung für das Betreiben einer Schleifmühle war eine günstige Verkehrslage und Wasser als Antriebsmittel. „Der Mechansimus der Schleifmühlen war sehr einfach. Ein vom Wasser getriebenes Kammrad bewegte eine Maschine, welche ungefähr die Gestalt einer umgekehrten Garnwinde hatte, worin die Steine so eingeklammert wurden, daß sie sich auf einer zweiten Lage Steine, auf denen sich die Maschine ziemlich geschwinde umdrehte, rieben, so daß also ein Stein den anderen schliff.
Schleifmühle der „Administration der Sollinger Steinbrüche“ in Holzminden (Foto um 1915)
Ein Kasten, welcher Sand dazwischenstreute, und eine Röhre durch welche Wasser zugeleitet wurde, vervollständigten den einfachen Mechanismus dieser Mühlen.“ (Holzmindisches Wochenblatt, 1790; aus Tacke, 1941) Heute verrichtet eine moderne Wandarmschleifmaschine mit einem Schleifkopf, der mit Diamantsplittern besetzt ist, die Arbeit.
Der gute Blick für den Stein
Erst nach zwei bis drei Jahren Erfahrung im Steinbruch beherrschte ein Arbeiter die schwierige Technik des Lösens und der Aufarbeitung des Gesteines. Einen guten Blick für den Stein mussten die Pflasterstein macher zur Herstellung von quadratischen, gleich großen Steinen haben. Ihr einziges Werkzeug war der Schellhammer oder die Fläche (Foto Seite 41 oben rechts), weder Schablone noch Richtmaß hatten sie zur Verfügung. Es entstanden äußerst gleichmäßig behauene Mosaiksteine, mit denen die meisten Straßenzüge der Dörfer aber auch die Bauernhöfe der Gegend gepflastert waren. Heute finden Sie dieses Kopfsteinpflaster noch fragmentarisch auf alten Höfen oder — wieder modern geworden — in den Fußgängerzonen der Städte. Mit Hilfe des Hammers mit zwei gleichen, zu beiden Seiten liegenden, schmalen abgerundeten Schneiden, wurden im Akkord die würfelförmigen Steine angefertigt. Mit voller Wucht wurde der Schellhammer gegen den Stein getrieben, um durch das Abspalten kleiner Stücke die gewünschte Form zu erhalten.
Das „Schicksal“ gegen Regen
In den Steinbrüchen herrschten bis in die Nachkriegszeit hinein katastrophale Arbeitsbedingungen. Es fehlte meist jeglicher Schutz vor Unfällen, Berufskrankheiten oder der Witterung. So standen in den wenigsten Brüchen offene Arbeitshütten oder gar Aufenthaltsräume, um sich vor Kälte, Nässe, Wind oder Hitze zu schützen. Walter Helling, ein ehemaliger Steinbrucharbeiter berichtet in dem Buch „Bouen uppen Dörpe“, 1986: „Viele haben sich die Gesundheit kaputtgemacht, weil sie bei
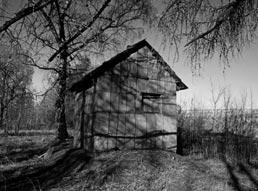
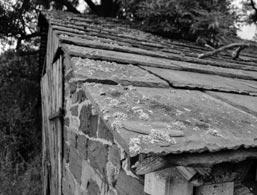
Hütte imn einem Steinbruch bei Arholzen
Sandsteindach einer Feldscheune bei Holzminden
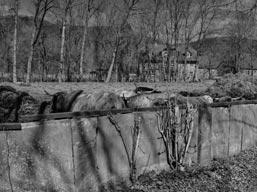
Weidezaun aus Sandsteinplatten in Forst
Regen weitergearbeitet haben. Manchmal hatten wir auch ,Schicksal’. Da waren ein paar Pfähle in den Boden gerammt, ein Dach drüber zum Unterstellen. Damit man auch bei Regen behauen konnte. Sehen Sie, das war ,Schicksal’. Man war dadurch nicht so vom Wetter abhängig.“
Die manchmal auch außerhalb der Brüche liegenden Steinmetzbetriebe
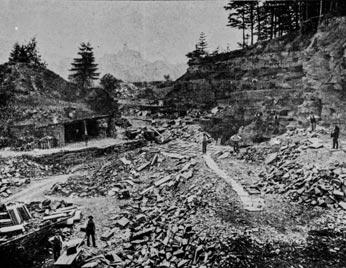
waren meist mit Arbeitshütten ausgestattet. Für die Zahl der dort beschäftigten Arbeiter waren sie jedoch viel zu klein, vor allem zu niedrig. Wegen der niedrigen Höhe und einer fehlenden Belüftung der Hütten mussten die Arbeiter den Steinstaub einatmen und die räumliche Enge in den Hütten führte zu Arbeitsunfällen: Zum Beispiel wurde durch abspringendes Gestein der daneben stehende Arbeiter verletzt. Augenverletzungen waren alltäglich, da Schutzbrillen nicht verfügbar waren oder nicht genutzt wurden. Zudem gab es häufig zu wenig Werkzeug im Bruch, das vorhandene befand sich meist in einem äußerst schlechten Zustand.
Im Winter, durch den Frost gehindert, konnte meist lediglich abgekummert werden. Das Lösen des Gesteins war zu gefährlich, da es bei Fost riss.
Um die Jahrhundertwende waren die Löhne vergleichsweise so gering, dass die Weiterverarbeitung so lange wie möglich in die kalte Jahreszeit hinausgezögert wurde, wie A. Rosenthal in „Bouen uppen Dörpe“, 1986, berichtete: „Wenn das Wetter einigermaßen war, sind sie in den Steinbruch. (...) Mein Vater ist bei Schnee schon hingewesen und hat gearbeitet. Ich weiß, daß er zwei Strohsäcke hatte. Dann hat er die Füße in einem Strohsack gehabt und ein Strohpolster im Rücken. Er mußte zur Arbeit gehen, wenn es irgend ging, weil er ja sonst nichts verdiente. (...) Meine Mutter hat Handschuhe für meinen Vater geschnitten und genäht von alten Hosen. (...)“.
Arbeitshütte im Steinbruch „Kleine Winterseite“ im Hooptal. Im Hintergrund: Kloster Amelungsborn (Foto um 1915) Gegenüberliegende Seite: Verschiedene Produkte aus Sandstein
Die Steinbrecher sind alle nicht alt geworden
Die schlechten Arbeitsverhältnisse sowie die schwere körperliche Arbeit führten zu chronischen Krankheiten. Daneben ist der sich bei der Arbeit bildende Quarzstaub am schlimmsten einzuschätzen. „Der Hauptfeind der Gesundheit der Steinbrecher ist der während des Arbeitsprozesses sich entwickelnde Staub. Die spezifische Ursache für die häufigen Krankheiten ist in dem Umstande zu suchen, daß der Steinarbeiter fortgesetzt, jedenfalls aber zu lange in einer von feinem, scharfem, spitzigem Steinstaub erfüllten Atmosphäre zubringen muß. Die Annahme, daß durch die Einathmung von Luft, die Staubtheile in größerer Menge enthält, Affektionen der Respirationsorgane vom einfachen Katarrh bis zur Lungenschwindsucht entstehen können, ist so alt, so weit verbreitet, daß man darüber zu sprechen kaum mehr nöthig hat. Ganz besonders aber schädlich ist der Stein-
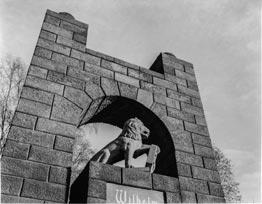
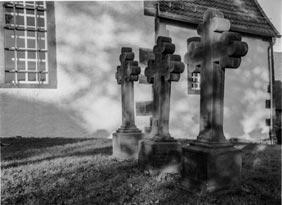
An den ehemaligen „braunschweigischen Weserdistrict“ erinnert das Denkmal für den braunschweigischen Herzog Wilhelm (1806 - 1884) auf dem Weinberg oberhalb von Rühle
Grabkreuze vor der Kirche in Mackensen
Bilder außen: Den Sockel dieses Denkmales einer Kräuterfrau in Stadtoldendorf ziert ein Satz von Wilhelm Raabe: „Es ist viel schönes Licht in der Welt“
Hugenottenturm bei Karlshafen
Löwenbrunnen mit Stadtwappen am Markt in Stadtoldendorf
staub. (...) Daher ist wohl der Sandstein als der gefährlichste zu erachten. (...) tausendfältige Beobachtungen thun immer auf’s Neue dar, daß auch die allerkräftigsten Personen nach langjähriger Beschäftigung im Steinhauerberufe der verhängnisvollen Einwirkung des scharfen Steinstaubes nicht entgehen, und zwischen jüngeren und älteren, schwächeren und kräftigeren Individuen nur der Unterschied obwaltet, daß die einen früher, die anderen später ihrem Schicksal verfallen.“ (Calwer, R. 1901)
Die durchschnittliche Lebenserwartung eines Steinbrucharbeiters betrug, vor allem aufgrund der zahlreichen Atemwegserkrankungen, die bis zur Tuberkulose reichten, nicht mehr als 40 Jahre. Besonders die Pflastersteinmacher litten unter der starken Einwirkung des Quarzstaubes, da sie während der Bearbeitung der Steine saßen. Die tief gebeugte Haltung direkt über der Quelle der Staubentwicklung führte schon frühzeitig zu einer Staublunge. Die Pflastersteinmacher hatten die geringste Lebenserwartung unter den Steinhauern.
Um den Staub herunterzuspülen, bekamen die Steinarbeiter täglich bis zu einem halben Liter Schnaps zugeteilt. In der Nähe von Steinbrüchen gab es deshalb immer Bier und Schnaps zu kaufen. Der überhöhte Alkoholgenuss forderte natürlich auch seine Opfer.
Ständig dem Wetter und damit auch Kälte und Feuchtigkeit schutzlos ausgesetzt, kamen bei vielen Steinarbeitern rheumatische Beschwerden dazu. Lange Arbeitswege von bis zu drei Stunden, verbunden mit Arbeitszeiten von 14 Stunden (im Sommer) im Akkord schwächten die Arbeiter zusätzlich. Aus einer Ende des 19. Jahrhunderts veröffentlichten Statistik geht hervor, dass ein Steinarbeiter die sichere Erwartung hatte, alle zwei bis zweieinhalb Jahre zu erkranken. Alle Steinarbeiter wurden deshalb aus den damals üblichen Krankenkassen ausgeschlossen.
Heute sind die allgemeinen Arbeitsbedingungen durch den Einsatz von Presslufthämmern etwas verbessert. Immer noch wird allerdings von Hand gearbeitet und die Gesundheitsgefahr durch den, von den modernen Maschinen verursachten, viel feineren Quarzstaub besteht weiter.
Oben: Kriegerdenkmal für die Opfer des Ersten Weltkrieges in Holzminden
Grabstein aus dem frühen 18. Jahrhundert in Schönhagen
Das typische Ornament in der späten Weserrenaissance ist der Kerbschnitt-Bossenstein. Seine Verwendung können Sie am Schloss Bevern in den verschiedensten Varianten bewundern.
Ein Vorfahr des berühmten Lügenbarons von Münchhausen begann im Jahre 1603 den Bau eines der schönsten und interessantesten Weserrenaissance-Bauten. Nach neunjähriger Bauzeit war Schloss Bevern im gleichnamigen Ort Bevern als Vierflügel-Anlage mit umlaufendem Graben, Zugbrücke und 14 Wirtschaftsgebäuden fertig. Im Laufe der nächsten Jahrhunderte wurde das Schloss ständig verändert, umgestaltet und unterschiedlich genutzt. Vom ehemaligen Edelsitz der Münchhausens über ein herzogliches Jagdschloss, Pensionärswohnsitz, Schule, Kaserne und Möbellager präsentiert es sich heute als kulturelles Zentrum für die Region.
Gleich Perlen an einer Schnur reihen sich entlang der Weser die Schlösser und bedeutenden Bauwerke der Weserrenaissance. B. Niemeyer schreibt in „Die Weserrenaissance“, 1964: „Zur Zeit der Renaissance (1585-1615) tritt die Zierweise des Kerbschnittes im Wesergebiet so stark auf, daß sie als typisches Dekorationsmittel charakteristisch für eine ganze Baugruppe wird und geradezu als stilistisches Wahrzeichen für sie betrachtet werden kann.“ Das Muster des KerbDie Bilder auf dieser Doppelseite zeigen Schloss Bevern.
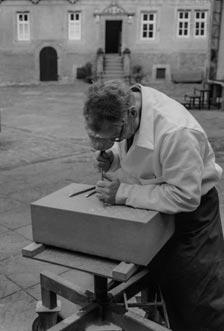
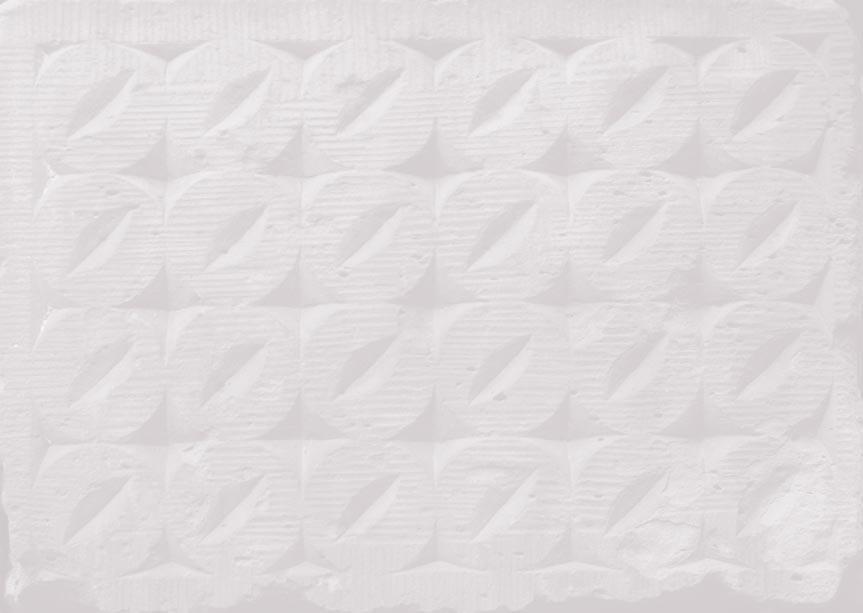
schnitt-Bossensteines ist jedoch keine kreative künstlerische Arbeit, sondern eher ein streng geometrisches, aus zahlreichen exakten Zirkelschlägen entwickeltes einheitliches Ornament. H. Kreft und J. Soenke berichten in „Die Weserrenaissance“, 1964: „Der Kerbschnitt-Bossen stein ist kein anspruchsvolles Kunstwerk, sondern gleichsam ein naives Volkslied, bei dem der sich endlos wiederholende, manchmal monotone Refrain, den alle mitsingen können, das Wichtigste ist: ein Lied der Steinhauer. (...) Doch wenn die Bossensteine im einzelnen auch nur simple Geschöpfe des Zirkels und des Lineals sind, in der
Steinmetz Gerhard Mitzkatbei der Arbeit an einem Kerbschnitt-Bossenstein
Gesamtheit stellen sie sich uns als ein phantastisches Spiel mit dem Sandstein dar, das für unsere Landschaft ebenso kennzeichnend ist, (...) “.
Der Anfang der Verwendung des Ornaments wird um 1560 am Schloss Uslar in der Form von Zweiecken gemacht. Danach taucht der KerbschnittBossenstein nach und nach an vielen bedeutenden Bauwerken der Weserrenaissance auf. Zunächst vorwiegend nur vertikal zur Belebung der Portale angeordnet, wird bei der Hämelschenburg (gebaut 1588/99) erstmals der Kerbschnitt-Bossenstein durch Reihen von Zierquadern über die gesamte Fassade hinweg als Mittel zur gleichmäßigen Flächengestaltung eingesetzt.
Bei Schloss Bevern sind die Fassaden verputzt, es sind jedoch fast ausnahmslos alle horizontalen und vertikalen Elemente mit Kerbschnitt-Bossensteinen verziert. Selbst bei den Rahmen und Pfosten von Fenstern oder der Eckquadrierung der Türme können Sie eine Kette von Kerbschnitt-Bossensteinen entdecken. Der vielseitigen Verwendung der Muster sind scheinbar keine Grenzen gesetzt. Wenn Sie das Auge aufmerksam über die Anlage gleiten lassen, entdecken Sie eine wahre Musterkollektion von Kerbschnitt-Bossensteinen. Das Faszinierende daran ist die Tatsache, dass alle Muster auf streng geometrisch aneinander gereihten Halbkreisen beruhen. Trotz
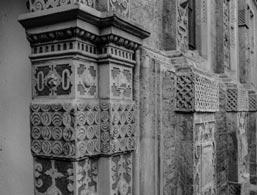
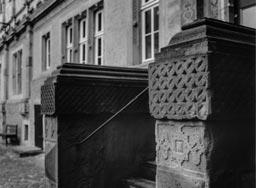
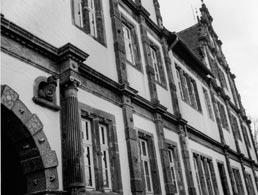
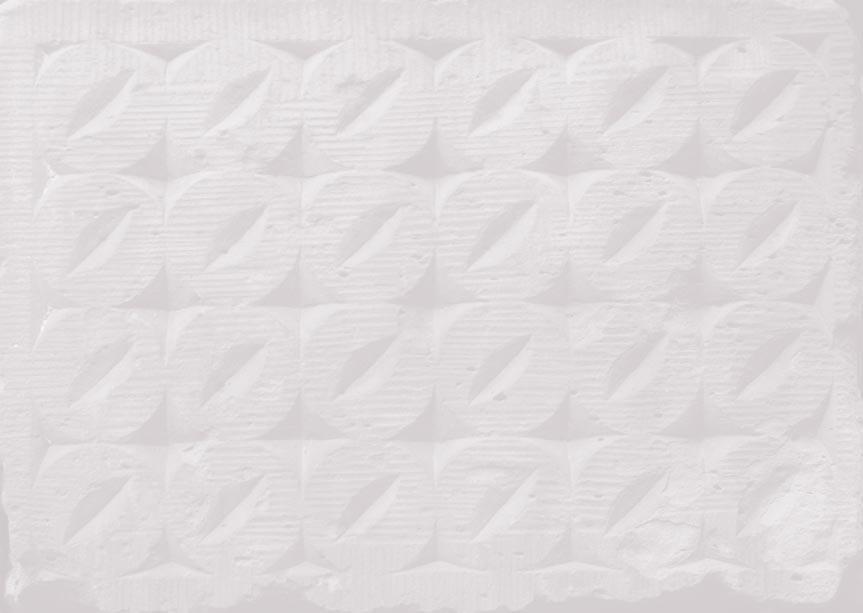
der Reduzierung auf die Kreisform, ist eine Vielzahl von Mustern möglich. Sie reichen von einfachen Zweiecken bis hin zu Sternen- und Blumenmustern. Je nach Sonneneinstrahlung werfen die fünf bis zehn Millimeter tief gearbeiteten Halbkreise unterschiedliche Schatten.Treten Sie näher an die Verzierungen heran, werden Sie feststellen, daß Sie die Ornamente in verschiedener Weise wahrnehmen können. Einer optischen Täuschung gleich, verschwimmt plötzlich die betrachtete Blumenverzierung und erscheint Ihnen jetzt als Karomuster. Wenige Sekunden später tauchen wieder die Blumen auf.
Die Ausführung des Kerbschnitt-Bossensteins ist sehr langwierig. Schlag um Schlag haut der Steinmetz die regelmäßigen Halbkreise in den weichen Sandstein. Mit viel Geduld entsteht so nach und nach die gewünschte Verzierung. Auf die Frage, ob man bei der langwierigen und mühevollen Arbeit nicht ungeduldig wird, antwortet der Steinmetzmeister Gerhard Mitzkat: „Das hat der Steinmetz ja gelernt, dass er Geduld haben muß — für den Steinmetz gibt es mühevollere Arbeiten. Das ist nicht schwierig. Vielleicht ist es bei denen, die heute das Steinmetzhandwerk mit Hilfe moderner Maschinen erlernen, anders: Dadurch verlieren die Jungen die Fähigkeit, Geduld zu haben.“
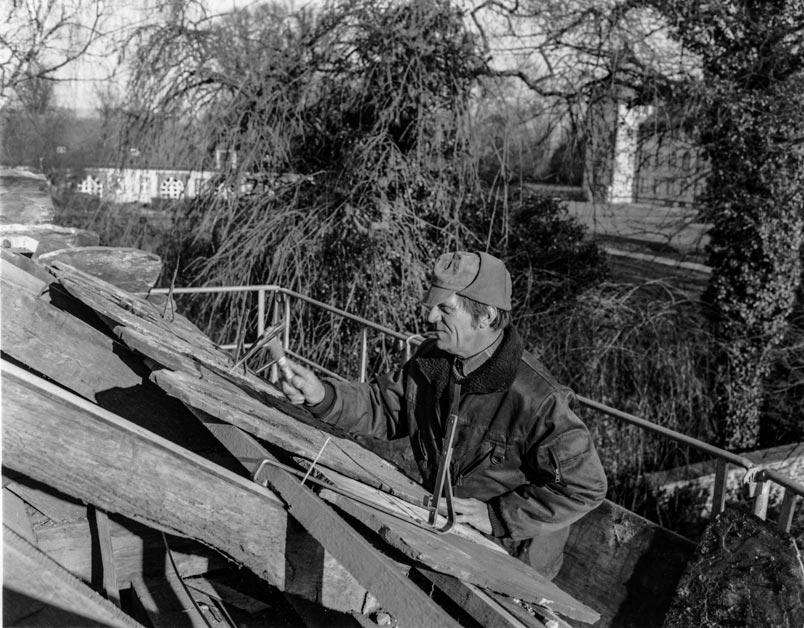