ABB: Insight from connected motors boosts mill efficiency
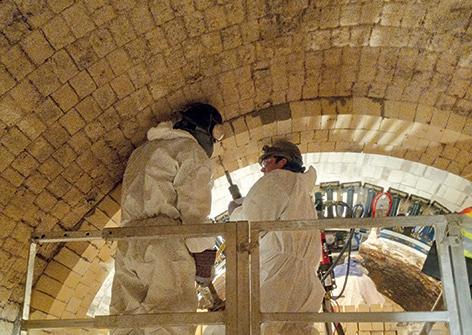
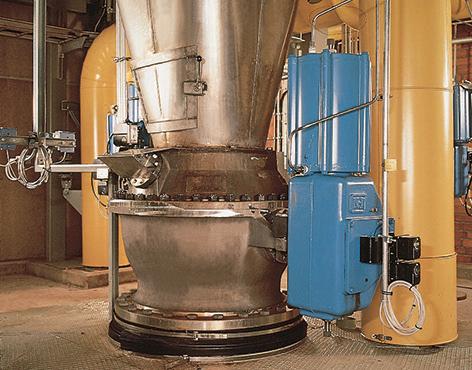
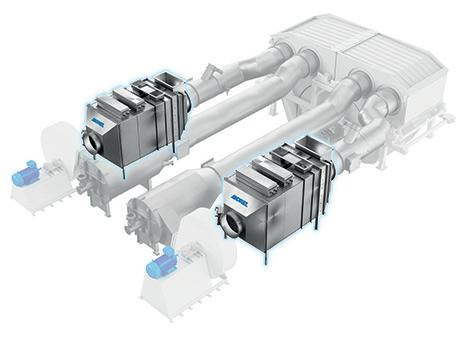

Bearing in mind environmental sustainability and the cost of energy, Prime Dry Hood E uses the same air system as gas- or steam-heated hoods, but with electric heaters replacing gas burners or steam heaters. The result is a system capable of achieving air temperatures of 400 - 450°C while increasing energy efficiency and reducing carbon dioxide emissions. To optimize energy cost and
energy security, a hybrid system is feasible. This can switch between gas and electric heating for hood air and enables a mill to select the fuel source which is most suitable for prevailing climatic conditions, the time of day, or changing tariffs for gas and electricity over a 24-hour period. For further information, please contact us at tissue@andritz.com
elcome to the July-August issue of Pulp Paper & Logistics, which includes much about process control and conditioning monitoring. Which is appropriate because, as I write this, the news is being dominated by the heat wave in Europe. Reservoirs are at dangerously low levels, and water supply and its use is inevitably coming under even tighter scrutiny.
As an industry, water plays a key role in the production of pulp and paper and as supplies come under threat there is an increasing need to recover and recycle it. With the drive to net zero emissions, mills are looking to reduce the consumption of both chemicals and water while reducing both industrial emissions and waste.
Reducing fresh water consumption can be achieved through process optimisation, advanced water treatment filtration systems and the reuse of process water. However depending on the product being manufactured the entire mill’s water consumption may have to be evaluated, from start to finish to establish the correct course of action.
In our next issue, for September-October, we will be previewing the MIAC 2023 show in Lucca, Italy; tissue production and processing; raw materials; chemicals; and additives. Submissions should be with us no later than 19 September.
Vol. 14 Issue No. 79,
July/August 2023
ISSN 2045-8622 (PRINT)
PUBLISHER & EDITORIAL DIRECTOR
Vince Maynard
Tralee, Hillcrest Road, Edenbridge, Kent, TN8 6JS, UK
Tel: +44 (0) 1732 505724
Mobile: +44 (0) 7747 002286
Email: pulppaperlogistics@virginmedia.com
CONSULTANT EDITOR
David Young
Tel: +44 (0) 1737 551687
Mobile: +44 (0) 7785 796826
EDITOR
John Nutting
Email: johnnutting47@gmail.com
REGIONAL REPRESENTATIVE
Einar Johansson
Tel: +46 8 540 255 15
Mobile: 0046 70 234 80 85
Email: einar.lennart@gmail.com
PRODUCTION
Anthony Wiffen
ASTAC Business Publishing Ltd
Tel: +44 (0) 1460 261011
Mobile: +44 (0) 7557 280 769
Email: anton_print_1@mac.com
PRINTER
Brown Knight and Truscott
Tunbridge Wells, Kent, TN2 3BW
United Kingdom
Tel: +44 (0)1892 511678
Swedish pulp and paper giant Stora Enso is planning to make itself leaner and more competitive with a number of restructuring plans for its operations and management.
The plans are aimed at improving profitability and focusing on growth markets, but will also mean thousands of job losses, which is why the process won’t start until negotiations with staff have been concluded.
The plans involve the closure of Stora Enso’s Sunila pulp mill in Finland, the De Hoop containerboard site in the Netherlands, one containerboard line at its Ostrołęka site in Poland, and the Näpi sawmill in Estonia, all with the loss of 600 employees.
To reduce and reorganise its group management there will be a planned reduction in employees. Some 1,300 are within the scope of the group function negotiations, with a planned reduction of about 300.
Stora Enso has recently completed most of the change negotiations in its Packaging Materials division with a reduction of around 250 jobs
in its management and support functions.
Although the changes are expected to cut annual sales by about €380 million, or about 3.3 percent of last year’s sales of €11.7 billion, yearly earnings before interest and tax are expected to increase by €110m. In the 2022 results, operational ebit was €1.9bn. The cost of restructuring could be up to €190m.
Annica Bresky, chief executive of Stora Enso, said: “These measures are of course very difficult and would not be proposed unless it
was absolutely necessary for our long-term competitiveness.
“We are at a critical juncture in our strategy advancement, and to further our market position an increased focus on capital allocation and decentralised empowerment is needed. This sadly means that assets suffering from challenged profitability would need to be closed, in combination with a more streamlined headquarter organisation.
“Through these actions we would be able to continue to deliver strategic growth from a more resilient and cost-efficient
business platform, better equipped to support the longterm growing demand for Stora Enso’s renewable products.”
● Stora Enso has opened a corrugated packaging plant at De Lier in the Netherlands. Expansion at the site, part of the recently-acquired De Jong Packaging group, adds a new, second factory and the equipping of the facility with two new corrugators to augment the existing two. As a result of the expansion, the site is now said to be the largest and most modern corrugated packaging facility in Europe.
Speciality chemicals supplier to the pulp and paper industry, Solenis has completed the US$4.6 billion acquisition of Diversey Holdings, a leading provider of hygiene, infection prevention and cleaning products and technology.
Based in Wilmington, Delaware, Solenis was acquired
by Platinum Equity in 2021. Bain Capital, the majority shareholder of Diversey, will hold a minority stake in Solenis as a result of this transaction.
Commenting on the sale chief executive of Solenis John Panichella commented: “This merger makes Solenis a more diversified company with
significantly increased scale, broader global reach and the ability to offer a ‘one-stop shop’ suite of solutions that meet customer demand and address water management, cleaning and hygiene issues on a global basis.
“Together, we have a foundation from which we can
continue to leverage our strong customer partnerships, leadingedge innovations and valueadded services to propel Solenis’ aggressive growth trajectory. With continued support from Platinum Equity, we are confident that we will maximise the promising opportunities ahead.”
US-based machine clothing and aerospace engineer
Albany International has agreed to acquire privatelyheld Heimbach Group, the German-based global supplier of paper machine clothing, in a cash deal valued at €153 million.
The deal, which is expected to close in the second half of 2023, will expand Albany’s global footprint and enable further expansion of Heimbach’s product range and reach.
Based in Rochester, New Hampshire, Albany International has 23 facilities in 11 countries, 4,200 employees and annual sales of more than US$1 billion. It says its Machine Clothing division is the world’s leading producer of custom-designed, consumable belts essential for the manufacture of all grades of paper products.
“The acquisition of Heimbach is an exciting opportunity to create significant value for our shareholders as well as for our customers as the partner of choice,” said Bill Higgins, chief executive of Albany, who in March said he plans to retire.
“With Heimbach, we gain increased scale and
complementary technology, while broadening our geographic footprint to efficiently serve markets in Europe and Asia. This transaction also provides an opportunity to leverage Albany’s expertise to drive meaningful margin expansion in Heimbach’s operations and cash flows that can be reinvested in high-growth areas of the company. We look forward to working with the Heimbach team and welcoming them to Albany.”
With headquarters at Düren in Germany, Heimbach is a supplier of paper machine clothing for the production of all grades of paper and cardboard on all machine types, with a history going back more than two centuries. It has nine manufacturing sites: in Germany, China, Spain, Switzerland, the United Kingdom, Belgium and Italy, and sales in 2022 of €161m ($178m).
Marco Esper, chief executive of Heimbach Group, said: “In Albany International, we found a like-minded partner who shares our commitment to best-in-class customer service and advancing modern paper production. Together, we will leverage our collective product and technology portfolios to become an even
better provider to our customers. I am incredibly proud of everything that Heimbach and our team have accomplished and look forward to working closely with Albany’s leadership to reach even greater success.”
Daniel Halftermeyer, president of Albany’s Machine Clothing business, added: “Heimbach is a solid addition to our company,” said. “Their operations are an excellent complement to Albany’s existing network of forwarddeployed manufacturing assets. Together, we look forward to providing our customers with even more value in terms of logistics, delivery capability, advice and service quality.”
In a release Albany International
● Saica Group has agreed with the Taschetti family to acquire a minority share in their two corrugated ADDA Ondulati plants in Annone di Brianza and Pietrasanta in Italy. The plants had combined sales of €105 million in 2022.
“This operation is a step forward as it allows us to expand our footprint within the Southern European markets for corrugated board, in this case, by acquiring minority shares of plants in Italy. It is a great opportunity to increase Saica ́s value proposition of sustainable
said that Heimbach’s strength in central European markets is an excellent fit with Albany’s northern European presence. Heimbach also brings additional production capacity in Asia, enhancing Albany’s ability to serve clients throughout the region. Heimbach brings complementary technology, said Albany: “In addition to its broad offerings in paper machine clothing, Heimbach brings technologies that support Albany’s differentiation and ability to provide customers with optimized, application-specific solutions.”
● Heimbach’s approach to optimum felt conditioning: see pages 18-21
packaging solutions for our customers” said Ramon Alejandro, president of Saica Group.
● Saica Pack has installed a fully automatic vertical storage system for corrugated board, installed by Duro Felguera Logistic Systems. The project has been developed for the new corrugated cardboard packaging facility in Livingston, Scotland. It is the first project that Duro Felguera has delivered in the United Kingdom.
UPM inaugurated its Paso de los Toros pulp mill in Central Uruguay in June with an event attended by the President of Uruguay Luis Lacalle Pou, several ministers and representatives of other stakeholders who have helped with the pulp and paper maker’s growth project in the country.
UPM chairman Henrik Ehrnrooth highlighted the consistent development of the sustainable Uruguayan forest industry and UPM’s operations in the country: “A key milestone for the Uruguayan forest industry was the Forestry Law which was enacted in 1987. The aim of this law was to diversify the country’s industrial portfolio,
ensuring sustainable land-use and protecting its natural forests. We can all see how well it has succeeded in all these goals and created a strong new export industry in Uruguay, sustainably.
“Today we celebrate UPM’s largest investment in our 150-year history. UPM’s first eucalyptus seedlings were planted in 1990. The path from then until today has been a great cooperation between authorities, UPM and its partners. The results of this cooperation will serve the interests of Uruguay and its people as well as UPM for decades to come.”
After four years of construction in Durazno, and despite the pandemic, the Paso de los Toros pulp mill was started up in April 2023 with the first pulp delivery
to customers following a month later. UPM’s third tree nursery in Sarandí del Yí started operating in the summer of 2022, and the new pulp terminal in Montevideo in October the same year. The total investment of US$3.47 billion covers the pulp mill and the port terminal as well as the local infrastructure in Paso de los Toros.
UPM’s new mill has annual capacity for 2.1 million tonnes of
Mondi is to acquire the Hinton Pulp mill in Alberta, Canada, from West Fraser Timber for US$5 million to support its growth in the North America paper bags business. As part of the transaction, Mondi will partner with West Fraser to access local, high-quality fibre from a wellestablished wood source.
With annual pulp capacity for 250,000 tonnes, the Hinton mill is to be expanded by Mondi with an investment of €400 million including a new kraft paper machine producing 200,000 tonnes a year, with start-up expected in 2027.
Both moves will fully integrate operations in the Americas and
enable Mondi to secure the longterm supply of high quality, cost competitive kraft paper into its network of 10 paper bag plants in the region, better positioning Mondi to support the growing market demand for industrial and mailer bags.
Commenting on the acquisition,
chief executive of Mondi Group Andrew King, said: “Strategically, we are focused on investing to support the growing market demand for our sustainable packaging products, while delivering attractive mid-teen returns through cycle.
“The acquisition of Hinton is an
eucalyptus pulp. With an increase of more than 50 percent in UPM’s current pulp capacity, the investment has had a significant impact on Uruguay’s economy.
The pulp maker’s value chain includes eucalyptus plantation operations, the Fray Bentos and Paso de los Toros pulp mills and related logistics, creating 7,000 direct and 10,000 indirect jobs in Uruguay.
excellent opportunity for us to secure locally-produced kraft paper for our bags customers, helping to meet the current and anticipated future growth in demand for industrial and mailer bags in the Americas. This acquisition will also enable us to further strengthen our position as the global market leader in the production of kraft paper and paper bags.
“We are delighted to be making this investment in Canada and look forward to working with Hinton colleagues, West Fraser as a long-term partner, and other local stakeholders towards improving the mill’s environmental footprint and securing its sustainable future.”
Holmen Iggesund’s Workington mill in the UK has again been awarded the EcoVadis Platinum sustainability rating – placing the mill in the top 1 percent of more than 30,000 companies assessed.
Ulf Lofgren, managing director of the Workington mill, commented on the award, saying: “As a producer of Incada, a high-quality paperboard, we are delighted to excel on the environment and climate aspects of the assessment. We are very pleased that our work relating to our wider business practices in
areas such as employment, ethics and procurement are also scoring exceptionally well.”
EcoVadis is an international assessment agency that evaluates the sustainability performance of companies. In 2022, EcoVadis conducted around 30,000 assessments of companies in more than 200 sectors in 160 countries.
“We joined EcoVadis because we believe in transparency and were looking for ways to share our sustainability performance with customers and stakeholders, who also regard this as essential,” says Johan Granås, sustainability
director at Holmen Iggesund.
“Climate change is the biggest challenge of our time, and we want our customers to trust that we will supply them with the highest standard of sustainable packaging material. We need to seriously consider all aspects of
sustainability, including transparent and comprehensive reporting.”
Located in Cumbria, the Workington mill is powered entirely by fossil-carbon-free bioenergy. It is the third time the Workington mill has received the Platinum rating, each year increasing its overall score through dedicated teamwork and continuous improvements.
Holmen Iggesund is part of the Swedish forest industry group Holmen, which has been listed as one of the world’s 100 most sustainable companies on various sustainability indices several times in the past decade.
Körber’s tissue business is being acquired by Valmet in a move that is described as a “good strategic fit”. The value of the deal between the German group and the Finnish engineering giant was not revealed.
In a statement, Körber, a fullyintegrated global provider of advanced technologies for the tissue industry, said the move would continue its successful evolution towards [being] a leading player.
Stephan Seifert, chief executive of the Körber Group, commented: “This is an excellent opportunity to form a unique tissue player and set the course for the future. The complementary positioning as well as the shared entrepreneurial mindset and clear customer focus contribute to the best conditions for a successful joint growth
trajectory.
“Our Business Area Tissue will be able to further expand its potential, offering, and reach with Valmet as its new committed owner, who will accelerate our efforts to date. At the same time, Körber continues and stays fully dedicated to strengthen its other Business Areas and pursue its organic and inorganic growth strategy.”
Commenting on the deal, chief executive of Valmet Pasi Laine, said: “The combination of Valmet’s current tissue making technologies, services and automation offering and the acquired tissue converting offering and competences is a good strategic fit and forms a strong basis to create new business opportunities and serve our customers even better. We are happy and proud to warmly
welcome all the new colleagues from Körber’s Business Area Tissue to become part of Valmet.”
Körber will remain a partner with Valmet and the tissue industry, through offerings in its other areas, such as palletisers from the supply chain business. With its ventures like FactoryPal, Körber will further advance its strong stance in digital systems for manufacturing efficiency in the tissue industry.
Körber said that its tissue business is in an excellent position with the industry’s most comprehensive portfolio of tissue technology to support customers across the value chain of tissue converting and packaging – from roll to fold, from converting to packaging. Its technologies, products, and digital services complement Valmet’s competencies and
With the continued decline in demand for graphic papers, UPM Communication Papers is planning to permanently close its Plattling mill in Germany, reducing its uncoated and coated publication paper capacity by 595,000 tonnes a year in Europe.
UPM says the plans are a continuation of necessary steps to ensure competitiveness of its operations and align its graphic paper capacity to demand.
The mill has two paper machines with capacity to make 380,000 tonnes of uncoated publication paper and 215,000 tonnes of coated publication
paper.
Massimo Reynaudo, executive vice president at UPM Communication Papers, explained the plans: “Mature graphic paper markets require continuous and relentless efforts to ensure cost competitive operations that also meet the future customer demand. UPM is committed to leading our business in a responsible manner. We respect the interests of both our workforce and our customers and consider them a central part of our plans. We recognise that [the] announcement is very difficult news for our employees
in Plattling. Together with the employee representatives, we will seek responsible solutions for our personnel and enter directly into a fair dialogue.”
Restructuring charges will cost €122 million, resulting in annual fixed-cost savings of €60m.
At the same time, UPM Communication Papers is planning temporary layoffs in Finland. Decisions on the continuation of the possible temporary layoffs in the four mills will be taken after the consultations have been concluded. Around 1,100 employees are covered by the consultations.
current portfolio of tissue-making technologies, services, and automation.
Oswaldo Cruz, chief executive of Körber Business Area Tissue, added: “Valmet has profound market expertise, a strong customer focus, and extensive experience in integrating additional competencies. We are very pleased that in Valmet, we have found the ideal future partner for our employees, customers, and suppliers to leverage the full potential of our tissue business.”
● With a joint investment of around €29 million from Stora Enso and Tetra Pak, a recycling line for post-consumer beverage cartons has started up at Ostrołęka in Poland. Stora Enso has installed a repulping line that will recover carton fibres, while Tetra Pak and Plastigram have a new line with the potential to triple the annual recycling capacity of beverage cartons in the country to 75,000 tonnes, enough for the total volume of beverage cartons sold in Poland, as well as additional volumes from neighbouring countries, including the Czech Republic, Hungary, Slovakia, Latvia, Estonia and Lithuania.
Irish-based packaging provider Zeus Group has acquired two more companies: Cima Paper Spa in Italy and NIPS Ordnungssysteme GmbH in Germany. The value of the deals were not revealed.
With annual sales of €65 million, Cima Paper was established in 1870 and has since grown into one of Europe’s leading convertors of paper and board for the packaging sector.
Zeus said that the acquisition will leverage Cima Paper’s scale, expertise and resources into existing and future supply chains, enhancing its current manufacturing capability, streamlining existing Italian operations and expanding Cima’s geographical reach across Europe.
“We are thrilled to welcome Cima Paper to the Zeus Group family,” said Keith Ockenden, chief executive of Zeus Group. “With a long-standing tradition in the industry, Cima Paper aligns
perfectly with Zeus Group’s vertically-integrated strategy, optimising supply chains and delivering enhanced value across our finished products, particularly within the manufacturing, food and retail packaging sectors.”
Based in Regensburg, Germany, near Munich, NIPS Ordnungssysteme (NIPS) has more than four decades of industry experience serving more than 11 countries in Europe. NIPS delivers high-quality packaging to
various sectors, including retail, manufacturing, and logistics. Commenting on the NIPS deal, Ockenden said: “We are excited to welcome NIPS to the Zeus Group family. This strategic acquisition allows us to expand our capabilities in the German packaging industry. The addition of the NIPS business complements our existing industrial and food packaging offering and pushes revenues from our mainland Europe businesses
close to €200m.”
NIPS will continue to operate autonomously within Zeus Group, preserving its brand identity, existing customer relationships, and partnerships. The integration of NIPS into Zeus Group’s extensive network is expected to foster collaboration and knowledge sharing, driving synergies and accelerating growth opportunities.
“NIPS is thrilled to become a part of Zeus Group,” said Matthias Röder, founder and managing director of NIPS. “The acquisition will provide us with access to enhanced resources, global reach, and an extensive customer base. Together, we will strengthen our position in the market and continue to deliver exceptional packaging solutions that meet and exceed our customers’ expectations.”
Earlier, Zeus acquired Northern Ireland business, James Hamilton Group, which has annual sales of around €18m.
Smurfit Kappa has inaugurated a new integrated corrugated mill in Rabat, Morocco, its first operation in North Africa.
The paper maker says that Morocco offers an exciting opportunity, with the OECD forecasting a 3.5 percent growth rate in 2023 and 3.7 percent in 2024. The country’s location enables Smurfit Kappa to serve both the local market and wider regions in Africa.
The group has invested more than €35 million in the 25,000 sqm facility, which was completed from ground-breaking to operation in seven months.
Providing 400 direct and indirect jobs, the business will serve domestic Moroccan customers and global companies across a range of sectors: industrial, agricultural, FMCG, automotive, pharma and ceramics. It also features the newest Experience Centres, part of a network of more than 30 centres worldwide, which showcase the latest innovations in packaging.
Almost 1,500 solar panels will power the plant, making it Morocco’s first packaging facility which is supplied by green energy, saving 55 percent of electricity and 900 tonnes of carbon dioxide
emissions per year. The innovative packaging plant also has a purification and water treatment system that halves consumption.
Tony Smurfit, group chief executive, said: “Our first
corrugated operation in North Africa is an exciting step for Smurfit Kappa and we’re delighted to unveil our state-ofthe-art Moroccan facility. We continue to innovate and give our customers a great product in a sustainable way.
“We’re combining our global scale and expertise with our local team’s best-in-class knowledge to provide the best service to our customers. Morocco’s geographical location complements our operations in Europe and adds to our global footprint, which is a competitive advantage.”
The industrial crane service operations of Norway’s Munck Cranes AS, have been acquired by Finland’s Konecranes, giving it access to new customers and a large installed base of Munck’s industrial cranes on the domestic market and elsewhere in Europe.
Munck Cranes AS is a industrial crane and crane service provider with international component export operations. For almost 100 years, Munck Cranes has served a variety of customers including pulp and paper mills, steel mills, metal service centres and hydro-electric power plants.
Munck Cranes AS entered into bankruptcy proceedings in late May and Konecranes recently acquired the industrial crane service operations from the bankruptcy estate.
In a statement Konecranes said that most recently, the annual net sales of the acquired crane service business have totalled around €8-10 million and the industrial crane service business has been clearly profitable. This acquisition gives Konecranes access to a
Konecranes has expanded its business in Norway
large installed base of Munck’s industrial cranes, and access to new customers and growth opportunities for its Industrial Service and Equipment business area. The business acquired has been run by some 40 employees throughout Norway, operating in four regional teams.
“We welcome our Munck Cranes colleagues to Konecranes and look forward to working together to develop and expand operations in the Nordic region
and beyond,” said Tomas Myntti, senior vice president in the EMEA region for Industrial Service and Equipment at Konecranes. In a recent change in management, Topi Tiitola, senior vice president for Integration and Project Management, decided to leave Konecranes to pursue other opportunities. He left Konecranes Leadership Team in July, but will continue to be employed by Konecranes until January 2024, ensuring smooth
handover of his duties.
“I want to thank Topi Tiitola for his contribution to Konecranes’ Leadership Team and the company overall over the past years. I warmly wish Topi all the best in his future endeavors,” said Anders Svensson, chief executive of Konecranes, which in its most recent half-yearly results had global sales of €913 million, up by 16 percent year on year.
More information from www. Konecranes.com
UPM has agreed to sell the ASK Kinsau recovered paper sorting plant in Germany to Fisel Holding, a recovered logistics and municipal waste disposal company.
The value of the sale, which includes the site and buildings, was not disclosed. All employees
of ASK Kinsau will be transferred to the new owner.
Marco Kulterer, responsible for RCP Supply Chain & Operations at UPM Sourcing, said: “We are pleased, having found a long-term oriented and innovative buyer for the Kinsau site. The Fisel Group has a high level of expertise in handling
recovered paper. As an integral part of this recycling company the sorting facilities could be better developed and optimised.”
Managing director of ASK, Matthias Fisel, added: “ASK Kinsau will remain an important site for sorting and processing further recovered paper in Bavaria. We
plan to invest in the sorting plant and the site in near future, as well as to improve the logistical capabilities on site. We are pleased to welcome the longserving and competent employees to our company and look forward to the future with optimism together with them.”
Asurvey by ABB in March 2023 found that 92 percent of business leaders around the world see rising energy costs as a threat to competitiveness. High energy prices over the past year have put pressure on businesses to make hard decisions on how to allocate budgets. Many leaders have accepted lower profitability, while others are cutting back on people, marketing and infrastructure.
The energy crisis could also delay the achievement of Net Zero targets. Of the respondents that reported, 58 percent said
that the energy crisis will delay their decarbonisation plans by up to five years. In addition, 61 percent stated that reducing energy costs is a top priority, while only 40 percent said the same for decarbonisation.
As a technique with potential to cut both operational costs and carbon dioxide (CO2) emissions, energy efficiency has huge potential. This is particularly true for the efficiency of motor-driven systems.
More than 45 percent of all electricity produced today is consumed by industrial electric motors – and that is set to double by 2040. This transition will place greater demand on electricity resources, which is likely to keep prices high.
In this environment, energy efficiency is perhaps the best opportunity available for industrial businesses like pulp and paper mills that want to reduce their CO2 emissions in line with Net
Zero targets while also cutting operational expenditure (OPEX) by reducing energy demand.
By improving the efficiency of a mill’s electric motors and variable speed drives, an operator’s investment in energy efficiency can pay for itself – an effect that becomes stronger when energy prices are high.
However, the challenge is knowing where to target this investment. A typical pulp and paper mill might have a fleet of
hundreds of motors, each of which has a unique set of operating parameters and loading patterns.
Traditionally, operators have used energy audits to find these opportunities. During a traditional audit, an expert will visit to gather data manually before analysing it and providing recommendations that show the
return on investment of taking actions. These tend to be used to gain deep insight into the largest motors on the critical line.
New developments in technology are now overcoming this barrier. Today, it’s possible for a mill’s own operators to deploy digital data-gathering through connected motors and variable speed drives (VSDs). A service expert can review this data remotely without necessarily having to travel to site. With this digital approach, it’s possible to extend a digital energy efficiency appraisal to cover many more motors, potentially even entire fleets. It has a secondary benefit of reducing CO2 emissions related to travel.
Analysis of the data from an energy efficiency perspective can show which motors are operating far from their peak efficiency and – crucially – how much energy is wasted. The expert can then identify potential actions to resolve this, and the costs of these. For example, they might suggest adjusting operational parameters so that the motor only operates when it can do so efficiently. Alternatively, they could recommend adding a VSD
to a fixed speed motor. A further option is to modernise an entire electric drivetrain, made up of a motor and VSD, to premium efficiency technology and sending the time-served system to be recycled.
Similar data from connected motors can also be analysed to provide insight into motor condition, performance and health. Plant managers can use this as the basis of a conditionbased maintenance strategy that minimises unplanned downtime by identifying and resolving issues before they happen.
Two pulp and paper mills in Sweden are at the forefront of the digital approach and are using digital energy audits to reduce energy consumption and cut emissions.
enables SCA Group to target 50 GWh annual savings SCA Group’s kraft paper mill at Munksund in north east Sweden produces 400,000 tonnes of packaging per year and has a strong focus on sustainability. It uses bioenergy to generate most of its electricity and this has enabled it to become 95 percent fossil-fuel-free. However, its managers saw an opportunity to save more energy by targeting the 2,400 electric motors that drive its processes.
Anders Kyösti, the site’s technical manager, said: “Our objective is to improve energy efficiency through enhancements of at least 50 GWh per year based on the company’s energy consumption in 2020. Electrical motors account for a large part of our electricity consumption. Given higher energy prices and the trend towards electrification, optimising energy use will become even more important in the future.”
Motor data is gathered and uploaded directly to the cloud, where it is accessed at regular intervals by an ABB energy efficiency experts. They evaluate the energy consumed by individual motors and compare it with the work done. The experts provide a regular report with recommendations on actions, as well as their cost and the return on investment that can be achieved.
This provides evidence for SCA to prioritise investments in upgrading motors, adding VSDs or changing the operating regime to save energy. The advantage of carrying out this review periodically is that as the cost of energy changes, so does the payback period. Therefore, when energy prices are high, the operator can achieve savings by acting quickly.
SCA’s team is also looking at data from the same source to understand and improve the reliability and availability of its machines under a conditionmonitoring strategy. This enables it to carry out predictive maintenance and optimise its operations.
A further benefit of monitoring and evaluating energy efficiency is the sustainable recycling of motors that have been replaced by modern high-efficiency models. By separating old motors into their component materials, ABB’s recycling partner in the Nordics, Stena Recycling, can recover high-value copper and iron. This can then be recycled for use in new products in a circular process that reduces CO2 emissions and water compared with using virgin materials.
Waggeryd Cell in southern Sweden is another example of
a mill that is identifying energy efficiency savings as a secondary benefit to using condition monitoring. The mill produces 190,000 tonnes of bleached chemi-thermo-mechanical pulp (BCTMP) per year for production of paperboard, tissue, printing paper and writing paper using wood chips from its parent company ATA Group, a major producer of sawn timber. Its mill is one of the most modern and efficient BCTMP mills in the world. To build on this, Waggeryd decided to connect its motors to the cloud with the goal of gaining continuous insight and deep knowledge about the equipment serving its critical line. To achieve this, it is gathering data from around 100 critical motors out of a total installed base of 450 motors.
As well as providing insight into the performance and condition of motors to support Waggeryd’s maintenance planning, the data has also identified energy-saving opportunities. An initial report in
early 2022 identified 10 motors with low operating efficiency, as well as others that are oversized (and therefore underutilised).
Using this insight, Waggeryd decided to prioritise upgrade of six of these motors. This shows how the data-driven approach can be
used to pinpoint energy savings that could be hard to identify in other ways.
Andreas Råvik, mill manager at Waggeryd Cell, said: “We have improved our energy efficiency by working with ABB. By using their energy reports, we can identify
assets like incorrectly dimensioned motors, or old motors with poor efficiency, and replace them.”
Although some of its early adopters come from the Nordic pulp and paper industries, this new breed of digital powertrain service can be applied to any industry, anywhere.
It is a potential solution to operators that are under pressure to make the best possible use of energy resources. Digital energy efficiency audits, which are sometimes also known as appraisals, can help by pinpointing the precise location of potential energy savings in mills and other sites.
Ultimately, as a new-generation service that sits alongside remote condition monitoring, digital energy audit services can help pulp and paper mills to cut energy consumption and target investment where they can get the most benefit.
More information from: new.abb. com/service/motion/data-andadvisory-services/energy-appraisal
Your paper machine certainly has a lot of potential, it‘s a question of getting it out: Start up faster, dewater more and run your clothing for longer - with our New-Tech fabrics you can increase performance and cost efficiency. Are you looking for process optimisation? Our experts can support you in reaching your goals with a combination of high-tech equipment and know-how. Learn more at:
www.heimbach.com
The range of valves that offer flow control options for the pulp, paper, board and tissue industry is immense.
and paper industry management at Valmet’s
line, delves into the details of its scope
Valves play a vital part in pulp, paper, board and tissue production. As efficiency, reliability, sustainability, safety and profitability demands on processes have grown over time, the valve technologies have also developed immensely. Valmet is an active participant in driving modern flow control solutions forward to best serve its customers.
The role of valves as a part of the process is important in many ways. While accurate flow control has a direct impact on the quality of the end products, perhaps more importantly the right valve selection can significantly help improve the
efficiency and sustainability of the process itself. This of course also means creating savings and lowering overall costs. Valves, especially when paired with intelligent control and increased levels of automation, can make a real difference.
Valmet today is in a unique position after the addition of flow control solutions to its overall offering. With the industry’s strongest valve portfolio complementing Valmet’s process technology, advanced automation and expert service offering, we can truly provide customers with added value that far surpasses what any other supplier can offer today – all from one reliable source.
director
Valves may not be thought of as central components of the process, but there are literally thousands of valves involved in the journey from wood to pulp to finished end product.
Today, still more than 75 percent of the world’s pulp passes through at least one of our valves during production. More than 60 years in the service of the pulp and paper industries may also have a lot to do with it. Also, our offering of world-renowned valve solutions from trademarked product brands such as Neles, Jamesbury, Neles Easyflow, Stonel, Valvcon and Flowrox enjoys a strong reputation of quality, accuracy, safety and reliability.
We have always taken pride in our position as an industry trailblazer when it comes to valve technologies used in the pulp, paper, board and tissue processes. Our flow control portfolio consists of all the typical valves for control and on-off use, including ball, butterfly and segment valves. Additionally, our industry-leading offering also includes a wide range of accessories, intelligent devices and software products, all engineered to meet each individual pulp or paper mill’s needs and challenges.
Innovation has always been a key driver for product development. There are many pulp and paper-
specific flow control products in use today, that have their origins on our desks. Such innovations over the years have included the capping valve for batch cooking, a high-consistency valve for bleaching, a valve for basis weight control, ceramic ball valves for erosive applications as well as a host of intelligent valve controllers, to name a few.
Every day, I see first-hand how our industry-leading valve solutions are helping improve business performance in mills around the world. Our solutions are helping customers maximise process efficiency, availability and performance, all while improving the safety and reliability across the lifecycle of the entire mill.
The rising cost and growing scarcity of both raw materials and energy will continue to drive the need for improving process performance and efficiency in the future. Also, we have seen that despite what many thought, the pulp, paper, board and tissue
segment has grown steadily, and will continue to grow.
The reduction in demand for printing and writing paper in this digital era has not stopped the growth in demand for other pulp-based products. If anything, this more environmentallyconscious society we live in has driven the demand for non-plastic alternatives for many traditional products from packaging materials to drinking straws. We are even seeing the emergence of new pulp-based textile fibres.
So, while the basic functions of valves in different parts of the papermaking process may have stayed largely unchanged over time, the growing demands related to efficiency, profitability, safety, reliability and sustainability have been active drivers for product development and R&D. Our improved globe valve
continues to deliver excellent control performance in highpressure applications such as boilers in operation at mill power plants. At the same time, our latest versatile butterfly valves are proving to be an optimum solution for a host of end uses thanks to their modular yet robust and reliable design and construction.
The continuing developments in digitalisation, automation and networking of smart devices have been one of the biggest gamechangers in industry as a whole. This is also true in the pulp, paper,
board and tissue industries. The virtually real-time control and monitoring capabilities that come with smart devices such as our NDX valve controllers are the modern way to ensure process quality and performance. With seamless connectivity and compatibility with Valmet’s vast automation offering, the customer benefits are further amplified.
Predictive maintenance is the best way to avoid problems and ensure reliability and optimised process uptime. It is made possible by accurate real time data used to fine tune a predictive maintenance plan based on decades of application knowledge, service experience and statistical analysis of service records. The latest development in further integrating intelligence to improve service planning, the Valmet Industrial Internet (VII), will be made available to the first customers this year.
It’s about much more than just data on current valve performance. It incorporates our vast installed base data, decades of service experience, diagnostics, device service history and current performance. So basically, everything you need to plan service and maintenance operations on a device and mill level.
I also emphasis that the ability
to harness our long-running pulp and paper industry experience and understanding to ensure the best available services anywhere in the world, puts Valmet in a strong position. We combine the latest technologies with the strongest industry experience to provide our customers a level of service that gives them a measurable competitive edge in business.
Valmet’s state-of-the-art valve production facilities around the world, and our convenientlyplaced service centres, ensure that we can provide the best in both products and services to customers worldwide. Flow control solutions and a wide range of lifecycle services are provided for both greenfield projects and the many conversion projects from paper to board production.
Our Flow Control Business Line is partnered with existing mills all across the globe. At the same time, we are happy to see so many new mill projects starting up – not just across Northern and Central Europe, but also in the Americas and across China and Asia Pacific.
Just this year, we delivered more than 3,000 individual valves to Metsä Group’s new bioproduct mill project in Kemi, Finland. To help collect performance data and optimise future valve service and maintenance operations a majority of the delivered valves were fitted with our intelligent valve controllers.
We are thrilled about being a part of projects like this. With the continued demand for pulp, the shift from paper to board and tissue and the emergence of new innovative pulp-based products, this is an exciting industry that we want to be a part of developing and serving.
As tissue mills try to optimise their energy consumption with sustainability as a priority, the launch by Andritz of a hood air heating system using electrical energy is very timely.
Marco Cattani and George Nowakowski reportFrom environmental considerations to the basic economics of running any energyintensive process, there are today many reasons for tissue mills to examine their energy strategy. Add in the uncertainty over gas supply created by the current geopolitical situation and the case for electricity becomes very compelling.
This is particularly the case in
any location where wind and sun are in plentiful supply. There is a growing list of mills which source electrical energy, at least in part, from renewables. In Europe and the USA, there is tax to pay on emissions, including carbon dioxide, which provides a further incentive to use electricallypowered systems, particularly if the power is sourced from renewables rather than fossil fuels. Government subsidies on
renewable energy are another factor in the equation.
In this context, Andritz has taken a wealth of knowledge regarding electrical heating, in the drying of spunbond materials for nonwovens in some of their installations and applied it to hood air systems for tissue machines. The result is the PrimeDry Hood E, which uses the same air system as gas- or steam-heated hoods, but with electric heaters replacing
offering flexibility in operation
gas burners or steam heaters. The result is a system capable of achieving air temperatures of between 400 and 450 deg C.
Compared with, for instance, gas-heated systems, PrimeDry Hood E increases energy efficiency for the hood drying system by up to 4 percent. Electrical heating is more efficient because a conventional gas burner requires
heating of both the combustion air and drying air for the burner to function, while electrical heating does not require combustion air. And in theory at least, 100 percent of electrical energy is converted into thermal energy. Compared to steam-heated systems, the PrimeDry Hood E can increase production through its capability to achieve elevated temperatures.
Electrical heating offers the further advantage that no combustion residuals are emitted to the air. Overall, tissue
machines can expect a reduction in carbon dioxide emissions of approximately 70 percent compared to a conventional gas-heated system. In many parts of the world, Europe and the USA included, mills pay tax on emissions to the atmosphere, so there is a clear economic argument for electric heating as well.
The potential for lower availability compared with gasheated air systems is mitigated by the use of filters with automatic cleaning in case of low temperatures, as is already implemented with steam-heated hoods.
There are two types of electric heaters available from Andritz: the Corner Type and the In-Line Type. In performance there is no difference, but each format is suited for a particular mill layout and recommended on a caseby-case basis. Electrical heating comprises the main body of the electrical resistor, a terminal box and control panel, the placement of which is flexible.
While the application of electric heating for hood air in tissue production is new, electrical heating in industrial contexts where drying is involved is not.
So, it has the benefits of being proven technology – for instance in some Andritz nonwovens installations. It also means that there are existing design solutions to manage specific situations, such as where there is the potential for seismic activity.
The electrical heater has been specifically designed with least disruptive maintenance in mind. The standard system enables easy removal of both top/bottom and laterally affixed resistors by unbolting them from the plates. Andritz proposes an even more convenient solution, in which the heating elements can be removed in bundles from the duct heater rather than having to extract the whole duct heater installation. Through a minor modification of the duct heater design, this refinement facilitates maintenance of a single heating bundle while the tissue machine continues to operate at a lower capacity, rather than being shut down completely.
Electrical heating is a positive addition to Andritz ’s portfolio in a changing world. It is not
going to suit every situation, but its flexibility makes it widely applicable. Renewable energy sources might not be available 24/7, but a hybrid system which can switch between gas and electric heating for hood air enables a mill to switch the fuel source, which is most suitable for prevailing climatic conditions, time of day, or even changing tariffs for gas and electricity over a 24-hour period. It is a question both of optimising energy cost and security. And if drying capacity is a limiting factor in any tissuemaking scenario, the addition of electrical heating can increase capacity.
As a new application of a tried and tested technology, there is minimal technical risk to the user. PrimeDry Hood E is equally suitable for dry-crepe tissue production as for textured or structured (TAD) tissue machines. With zero carbon dioxide emissions from combustion, there is also a benefit to the final product’s eco credentials. This will appeal to the consumer and therefore the retailer. A genuine marketing opportunity born out of technology – and based on hot air.
Generally speaking, conditioning starts with a high pressure shower. If necessary, this is followed by an edge shower. This should then be followed by a low pressure shower and a Uhle box. This order should be strictly adhered to. With this setup, the felt surface is adequately lubricated before coming into contact with the aggressive ceramic coatings of the Uhle box covers. All these elements generally interact with the paper side of the felt.
Dirt, fines and fillers are introduced into the process through the paper stock, which can subsequently lead to compaction of the felt. This can result in diminished dewatering over the lifetime of the felt. Numerous settings must be taken into account to ensure that mechanical felt cleaning is effective. The more precisely this is carried out, the more efficient the felt performance.
The basic objective is the removal of dirt and deposits from the
inside of the felt in a continuous and balanced manner. This needs to be done over the entire length and width of the clothing. It is important to ensure that every square centimetre of the felt is cleaned equally well. If this is not done, it is likely that there will be different levels of contamination and, therefore, different levels of felt compaction. This can then lead to cross-profile variations in the felt and paper, or can incur locally increased wear. And, last but by no means least, to premature removals.
The needle jet
There are several key factors in the correct operation of a highpressure shower pipe. Two of them are particularly important to pay attention to:
l The high-pressure needle jet must always be laminar. This is the only way to ensure that the full energy of the jet reaches the felt surface. A turbulent jet that is inclined to break up before reaching the felt will lose energy and therefore be unable to apply its full cleaning power (the differences are shown in Figures 1a and 1b).
l Heimbach also recommends that a distance of 100mm from the shower nozzle outlet to
the felt surface is respected. Heimbach has had good experiences when the needle jet works at a 90-degree angle to the press felt.
The nozzles
All nozzles need to be in perfect condition to ensure that the felt is evenly cleaned across its full width. They must not be either polluted or clogged (see Figure 2). Unfortunately, this is often not the case in practice. Accordingly, felts are frequently encountered in the most varied degrees of contamination (See Figure 3). The distance between individual nozzles should ideally be between 100 and 150mm. The exact distance depends on the required cleaning intensity in the respective felt position. This leads on to another important aspect of felt conditioning: the correct oscillation of the highpressure shower pipe. In order to reach every single point of the felt with a thin needle jet,
Felt conditioning plays a key role in the increased production efficiency. Clothing expert Heimbach often notices that this issue does not always receive the attention that it deserves. PPL reportsFigure 1a - laminar jet Figure 1b - Turbulent jet
the high-pressure shower must constantly traverse across the width. For the most homogenous deep clean to be effective, a single or multiple of the nozzle spacing should be selected as the stroke.
As for nozzle quality, two further questions arise: What should be the optimum diameter? How high should the pressure applied reach? For some years now, the trend has been towards smaller-diameter nozzles. They certainly offer better cleaning – provided they do not become prematurely clogged due to poor water quality. Diameters between 0.7 and 0.9mm are common today.
Central to the service life of the shower nozzles is the quality of water in use. Heimbach advises fresh water or alternatively superclear filtrate. The aim is always to keep the amount of suspended particles introduced into the system in the water as low as possible. Otherwise, there is a risk that nozzles can become clogged or nozzle filters polluted.
The higher the pressure, the more the stress on the felt surface. Of course, finer fibres will have less resistance than coarser ones. Overall, the felt should be treated
under moderate pressure (up to 10 bar) over the first few days with the intensity then increased over clothing lifetime. For continuous HP cleaning, 25 bar should be regarded as the upper limit. For short periods, around 30 bar can be acceptable.
The specifications as outlined should not, however, be set in stone. This is because newlydeveloped ultra-high pressure shower systems now promise new opportunities. We have seen numerous positive results on packaging grades when using units with a nozzle diameter of 0.25mm
and a pressure of 50 to 160 bar. This has not led to any noticeable decrease in felt wear, but has provided positive results in terms of cleaning – and fresh water consumption.
With its fan nozzles, a lowpressure shower will introduce large quantities of water to the felt. This keeps the felt moisturised throughout and provides a potent lubricating effect before the Uhle box.
For ideal low-pressure spray shower operation, we recommend
that the following parameters are respected: Water should be applied from all fan nozzles with a slightly overlapping jet at a distance of 100 up to 150 mm maximum from the felt surface and at a slightly inclined angle to the direction of felt travel. If water is applied unevenly (See Figures 4 and 5), trouble can develop quite rapidly. Firstly, moisture fluctuations will occur in the felt, which will be reflected in damp and dry areas (See Figure 6). The irregularities can be quickly picked up by measuring water content, or in many cases can be seen by the naked eye.
Wet/dry streaks such as these in the felt rapidly transfer to the sheet, leading to irregular cross direction moisture profiles.
The graphic (shown in Figure 7) illustrates the importance of an overlap of fan jets. Either no
overlap, or too much, will cause irregularities in cross machine profiles.
Dry streaks can, in some cases,
lead directly to increased felt wear (as shown in Figures 8 and 9). This is due to a lack of lubrication and the resulting increased friction over the Uhle box cover. This then can be a cause of premature felt removal. Unlike the highpressure shower, the low-pressure version does not oscillate. Clear filtrate water is generally used to pressurise the fan nozzles with water.
Uhle boxes have the added task of indirectly dewatering the sheet by means of the press felts. Using vacuum, some of the water transported in the clothing is sucked away by the units. This means high stress for the felt, as it is in permanent contact with the Uhle box due to the set vacuum. It should also be noted that this happens at speeds up to 2,000 metres per minute. In this case, contact also means friction, which not infrequently leads to loss of batt from the felt.
With the Uhle box, there is always a risk of adjustment errors which could cause the
press felt to suffer premature wear, causing early removal from the paper machine.
In one case, a felt suffered premature removal, as the whole of the fibre batt had been removed in the edge area (shown in Figure 10). This was due to incorrect setting and positioning of the edge deckles (shown in Figure 11).
These should ideally be aligned with the plastic or ceramic blades of the Uhle box. Otherwise, the felt rubs permanently against the edge of the raised deckles and as a result continuously wears away the fibre batt.
Heimbach often observes that edge deckles are not optimally set. Just as with the low-pressure shower units, a deficiency like this can lead to uneven moisture – this time in the sensitive edge area of the press felt (see Figure 12). This can become very critical where seam felts are concerned: Such fluctuations put a lot of stress on the MD yarns and seam loops. As a result there will be risk of seam opening.
There is no rule of thumb for the correct vacuum in a Uhle box. It can be stated, however, that
higher vacuums generally lead to higher felt wear. This is one of the main reasons why Heimbach clearly favours nip dewatering at medium and high speeds. In these cases, it is possible to run with a substantially reduced vacuum or even to completely dispense with Uhle boxes. This
reduces felt wear but also saves energy.
It is important to ensure that nothing is deposited on the Uhle box cover that could lead to melt marks in the press felt. Worn or sharp edged covers must be replaced as they can have a negative impact on felt service life.
Slotted covers remain the standard here. It is however true that drilled covers have become more popular. The clothing expert Heimbach certainly sees the benefits of this cover design type: be it through reduced felt wear or improved profiles of felt and sheet.
More information from www. heimbach.com
Lime kilns play a vital role in pulp and paper mills as they convert calcium carbonate (a by-product of the pulping process) to calcium oxide (lime). The lime returns back to the pulping process, completing the loop used by mills in the Kraft-pulping process.
The mills rely on functioning, quality refractory to keep the plant up and running. The worst nightmare for these operations is unplanned downtime and maintenance. One shutdown can cost mills thousands of dollars a day in lost production, especially for a facility that is producing more than 300,000 tons of pulp and paper per year.
One mill in Terrace Bay, Ontario, faced a refractory failure just one year after a fresh installation. The mill had an assessment completed which identified the problem as poor installation and inferior bricks.
To combat this, the pulp and paper mill reached out to a man known for his quality bricking installations: John Taylor, founder and president of Kingston Refractory Services (KRS). Taylor and his team knew they needed to do the job right. And the best way to do that is to use the most effective equipment, which is why they rented, and ultimately
purchased, a bricking machine from Bricking Solutions.
When looking for a new contractor to install refractory brick, the pulp and paper mill’s
management knew it needed someone who’s been in the business for a long time with a reputation for quality work. Taylor was just the man. He worked as a brick layer with the brick layer’s union out of Kingston before
starting his own company. When he had the opportunity to do a refractory brick installation for a large cement facility in 2008, he and his wife, Laurie, worked together to start their own company: Kingston Refractory Services (KRS).
KRS provides refractory engineering, demolition, installation, clean up, anchor removal and more. They primarily service the southern Ontario region of Canada with a few customers in northern Ontario. Most of the facilities they work with own their own custom bricking machines for refractory installation. This is where Taylor and his team were first introduced to Bricking Solutions, which left an impression on a man who is known for his commitment to his team’s safety.
Andrew Wojciechowski, director of operations for Kingston Refractory Service’s subsidiary branch, Réfractaire Québec, explained, “John is adamant about safety in the field. It is the number-one priority for us and always has been. KRS is going on six years without any kind of safety-related incident. We’ve even stopped working before when an installation became unsafe just to reassess our methods.”
Taylor found that bricking machines provided the safest and highest-performing installations
When the refractory in kilns used in pulp and paper mills needs to be replaced, bricking machines provided the safest and highest-performing option, explains Heather Harding*The Kingston Refractory crew is able to install the bricking machine in just 60 to 90 minutes, whereas other methods take between six to eight hours to set up
in the business. For the first installation with the pulp and paper mill, he decided to rent a Bricking Solutions EZ Flexx50 bricking machine.
The first step of the pulp and paper mill installation came in a single kiln rebricking. Taylor and his crew decided to rent a bricking machine for the process. The EZ Flexx50 bricking machine is capable of bricking 9.8- to 13-foot (3-to-4m) interior diameter kilns and has a 6,600-pound (3,000 kg) load capacity with a 12-foot (3.65m) work platform. Made of 6061-T6 aircraft-grade aluminium, the structure is as strong as steel but weighs two-thirds less. Their crew can install the bricking machine in just 60 to 90 minutes whereas other methods take between six to eight hours to set up.
The previous installation used the pogo stick method, one of the oldest systems for bricking installation. This method suites all brick shapes but, unfortunately, setup time can take as long as a day in larger kilns. It uses a fabricated wooden arch that sits on a platform and uses spring loaded rods – pogo sticks – to push the bricks against the kiln shell to hold them in place. This approach limits installers to just one course at a time to ensure the jig doesn’t collapse. Because one pogo stick is required for each brick, and must be individually set and retracted, installation time is extended. There also isn’t a standard platform available to facilitate the bricking procedure and no international design or safety standards. This installation method is also very hard on the bodies of the crew because it requires a lot of above-height work. Workers
are required to set up each individual pogo stick and hold the bricking in place as they go, risking worker fatigue. A group of skilled workers using a bricking machine can complete a project twice as quickly as they could with another method. The pneumatic ring of the bricking machine holds the bricks against the shell of the kiln instead of relying on crew members to do so manually. The most challenging feature of the kiln in the pulp and paper mill came in the dual layer installation. This type of installation requires two layers of brick, first a layer of insulation brick mortared together and, second, a layer of hot face brick. The bricking machine
significantly improved the efficiency of the installation team because the arch could easily be adjusted to fit the second ring of brick instead of requiring a change of pogo sticks that the previous method required. The bricking machine’s arches hold each brick firmly against the kiln shell to reduce the risk of sagging. This properly aligns the brickwork and fights against catastrophic failure, which is what the pulp and paper mill experienced with the last installation.
“Both the plant and our team were extremely satisfied with the result of the project with the use of the Bricking Solutions bricking machine,” Wojciechowski
said. “Being able to use the bricking machine for the plant allowed the customer to see the technology and experience the results in real-time.”
The increased efficiency of the bricking machine alongside the extended lifespan of the refractory brick impressed the pulp and paper mill’s management so much that they invited KRS back to do a full shutdown at the facility. To complete the shutdown, KRS decided to purchase an EZ Flexx50 bricking machine of their own. It gave them the opportunity to complete the rebricking of the kiln and offer more options to clients who may not own their own machine.
John Taylor and the KRS team always want to build a partnership with their clients for the long-term. The full rebricking job was completed ahead of time and under budget with the use of the newly-purchased Bricking Solutions bricking machine.
The mill was extremely satisfied with the results of the installation and the quality of the refractory brick lining, especially when they found that the refractory lifespan was stretched to an impressive three years. The pulp and paper mill reached out to KRS to work with them for the next refractory installation project that they’ll be completing soon.
* Heather Harding is the managing director of Bricking Solutions, a world leader in kiln refractory installations. More information from Bricking Solutions Inc, 1144 Village Way, Monroe, Washington 98272, USA. Tel: 1 360 799 4767.
Website: www.brickingsolutions. com
The L&W Bursting Strength Tester from ABB has been enhanced with new features that are said to deliver quicker, easier and more reliable operatorindependent testing.
Unlike previous versions, which take longer with more manual effort, the new tester gets faster results.
Bursting strength is an important material property that impacts product performance in paper making, converting and end-use operations.
Also said to be reliable and easy-to-use, the updated tester includes a large touchscreen, userfriendly interface and increased digitalisation to deliver accurate, reliable and repeatable bursting
strength results. It also features a fast-testing sequence, safe and ergonomic operation and operator-independent results.
Specific features include: an integrated strip feeder and diaphragm stiffness compensated results; an embedded graphical
presentation of the pressure curve within the instrument displaying the elastic tendency of the sample; and modern digital and safety features in one instrument.
The latest model can also be integrated with other ABB products such as the L&W Lab Management
The latest version of ABB’s Automation Software Maintenance (ASM) lifecycle management program has been launched to cover the software related to Paper Machine Drives (PMC800) and Pulp and Paper Process Control Library (PPLib800xA).
It is an extension of ABB’s ASM program, and complements the Quality Control System (QCS) that was introduced in January 2023.
The basis of all ASM programs is to offer a tiered subscription service that enables system evolution from older versions to the latest and/or provide on-demand access to regular software updates that include incremental improvements, patches and new features.
This proactive system management helps pulp, paper,
packaging and tissue mills to maximise their system investment and reduce maintenance and support costs.
ASM tiered subscription options open up the features available as mills go through the upgrade process. Maintain Plus provides customers with access to incremental updates for PPLib800xA and PM Drives containing fixes and enhancements, meaning mill operators can benefit from new or improved features, as well as keep pace with important cyber security updates. Maintain & Evolve includes all the benefits of the Maintain Plus level, with the added ability to upgrade from an older legacy system version to the latest and between system generations.
The program also gives users of both PPLib800xA and PM Drives access to the myABB business portal for program management and premium system documentation, helping keep process control software up to date.
With PM Drives ASM, mill operators can benefit from free licenses to ABB’s newest drives software applications such as Datalogger and PM Drives Performance – allowing them to leverage data for more predictive maintenance and troubleshooting –as well as machine control safety.
With PPLib800xA ASM, the subscription enables an improved human-machine interface (HMI) experience and access to the PPSupport tool, a .Net stand-alone application that detects unintended
System (LMS), which provides connectivity to the full Quality Data Management and Manufacturing Execution System (MES), enabling greater visibility of quality data across the mill and enterprise.
“Pulp and paper mill customers that transition to ABB’s newgeneration L&W Bursting Strength Tester can look forward to the same long lifecycle as other instruments from the L&W product portfolio as well as the benefits with the new technology and digital possibilities,” says Ghazal Amar, global product manager for paper testing equipment at ABB. “Connectivity to digital lab management systems like ABB’s L&W LMS automates reporting and enables mills to do more in less time.”
changes and aids system engineers in migrating the existing process application libraries to the latest version.
“ABB’s ASM lifecycle management program has been expanded to offer proactive mill operators even better support for their pulp and paper-specific software, allowing them to better manage and predict total cost of ownership,” said Shankar Singh, global product line manager for drives and automationin ABB‘s pulp and paper business.
“Customers can unlock new features for improved troubleshooting and advanced performance, while at the same time keeping their system software up to date.”
Holmen Iggesund Paperboard has ordered two wash presses from Valmet for its Iggesund Mill in Sweden, with start-up scheduled for October 2024.
Valmet will supply two TRPE-940 TwinRoll wash presses including process piping, mechanical erection, basic engineering, commissioning, start-up, process support and advisory services.
Valmet also continues to support Holmen Iggesund to maximise reliability and optimise the performance of the fibreline and cooking with a three-year performance agreement. The agreement covers continuous support and collaboration for operation and process evaluations, on-site services, and reports. It also includes customer support
from Valmet’s global network of experts through Valmet Performance Center and various Industrial Internet services.
“We are happy to cooperate with Holmen once again and deliver two additional Valmet
TwinRoll wash presses to their mill in Iggesund. The wash presses will help them improve the efficiency of the hardwood bleach plant,” says Mikael Gustafsson, senior sales manager for Fiberline in the pulp and
energy business at Valmet. Holmen’s mill at Iggesund is a fully-integrated pulp and paperboard plant producing solid bleach board made from virgin fibres sourced from the forestry operations of Holmen Forest.
Chinese paper maker Huawon successfully started up the new PM16 line at its Ma’anshan mill in Anhui Province in June, producing, it is said, high-quality, environmentally-friendly décor base paper.
Key components of the line supplied by Voith include a BlueLine stock preparation system for virgin fibre, WEP, headbox, DuoShake DG and calender. As Huawon’s fifth follow-up order with Voith, the line is said to represent the transfer of knowledge from past projects, enabling the design to be optimised.
Commenting on the startup, chairman of Huawon Dou Zhengliang said: “The successful
start-up of PM16 has once again proven the reliable quality of Voith equipment and raises Huawon’s production capacity and scale to a new level. I would like to thank the employees of both companies for their trustful cooperation. Voith is a global technical leader in the field of speciality papers and has a wealth of experience. We will deepen cooperation with Voith and jointly develop new markets for speciality papers.”
Lin Carlos, vice president of order execution and manufacturing at Voith Paper Asia, added: “Huawon has achieved remarkable success in the field of décor papers with
its outstanding innovation, excellent quality standards and first-class customer service.
“I would like to thank all the professionals for their contribution to this endeavour. We are confident that we can achieve more great successes together in the future and help Huawon become a leading national brand for world-class décor base papers.”
Hangzhou Huawang Industrial Group, based in the Science and Technology city of Lin’an Economic Development Zone, in Zhejiang Province, increased its sales volume of decorative papers by 12.3 percent last year to 227,400 tons.
What is described as a complex and highly technological rebuild of Hiang Seng Fibre Container’s PM5 line at its Bangkok mill in Thailand will be carried out by A.Celli/PMT.
The Italian engineers will rebuild the PM5 headbox, converting it from single to double-layer with the aim of improving the testliner printability. The intervention, scheduled for the first quarter of 2024, will also increase the flexibility of the lines to make the best use of the different furnishes.
Sarunyou Tejavibulya, owner
and managing director of Hiang Seng, says: “I’ve worked with
PMT for a long time, and their service has always been great.
South Africa’s Mpact Operations is to have a pulping line upgraded by Andritz at its Mkhondo Paper Mill in Mpumalanga.
The upgrade will increase the line’s capacity and improve the paper’s strength properties, helping the customer respond to the strong domestic and international demand for highquality sustainable packing solutions.
Brian Smith, project director at Mpact explained: “With the technological solution proposed by Andritz, we can increase our mill’s performance and make our production more sustainable at the same time. In addition, we get everything from a single source –three good reasons for choosing Andritz as a partner.”
Andritz will upgrade the whole neutral sulphite semi-chemical pulping (NSSC) line, which processes eucalyptus and pine to provide fluting and linerboard for the production of containerboard. The comprehensive Andritz system comprises key equipment for the wood processing, cooking, washing and refining sections to increase the line’s capacity from 225 bdmt/d to 365 bdmt/d and at the same time enhance product quality.
● A new chipping line will provide better chip size distribution to secure a homogenous cooking result with minimal amounts of fines for improved material efficiency.
● The conversion of the cooking system will maximise fibre
quality and pulp cleanliness.
● The use of clean condensate to generate fresh steam for chip pre-steaming will provide clear environmental benefits in terms of fresh-water usage and primary steam utilisation.
● Excellent washing results with the new generation Compact Press technology will lead to high humidity resistance of the product.
● Andritz TwinFlo Prime refiners will optimise the fibre quality prior to washing and thus the product quality. Using waterlubricated bearing technology, the latest LC refiner allows a more environmentally-friendly operation.
● An Andritz PrimeFilter D will ensure superior preparation of
When I heard that they were now member of the A.Celli Group, I was excited to see what they could do. I have to say, the solution they proposed was exactly what we needed to improve the quality of our testliner. I know I can count on A.Celli to continue to improve Hiang Seng’s performance.”
Established in its present form in 1968, Hiang Seng Fibre Container produces a wide range of paper and corrugated products. It is one of the largest integrated paper and packaging manufacturers in Thailand, supplying about 30 percent of the domestic market.
clear and super clear filtrate. Andritz will also provide supervision over the erection, commissioning, and start-up as well as the training of the operating personnel. Start-up of the upgraded line is scheduled for the first half of 2025.
The upgrade to the pulping line is part of the bigger mill upgrade project which Mpact announced in December 2022 with the approval of a SAR1.2 billion (€60 million) capital investment project at its Mkhondo Paper Mill. It forms part of Mpact’s portfolio optimisation and strategically positions the mill to meet the increasing demand for high quality, sustainable, fresh produce packaging solutions driven by robust growth in the South African export fruit sector.
In Sweden, SCA reports that it is successfully using Voith’s digital and automation systems to optimise the production efficiency of the new XcelLine paper machine at its Obbola mill.
The PM2 line, said to be the world’s largest of its type annually producing 725,000 tons of kraftliner with basis weights between 100 and 200 gsm, was commissioned by the full-line supplier last year. It has a wire width of 10.2 metres and a design speed of up to 1,400 metres per minute.
“The journey for SCA and Voith together has only just begun,” says Gustaf Nygren, manager of the Obbola mill. “We have a long-term partnership in place with the target of reaching the common vision of PM2 in Obbola becoming the new reference for safety, efficiency and digitalisation.”
To achieve its goals, SCA is using more than 10 innovative digitalisation and automation systems throughout the machine, all from Voith’s Papermaking 4.0 portfolio, and its BTG subsidiary.
Typically, the OnEfficiency family helps increase line efficiency and stabilise product and process quality. The improved efficiency reportedly also contributes to more sustainable and resourcesaving paper production. SCA uses applications from the OnCare family to monitor productivity and to quickly take optimisation measures.
Machine availability is further increased by digital services such as the OnCall.Video remote maintenance service. The digital
portfolio is made available on Voith’s IIoT dataPARC cloud platform, which features the highest security standards.
“With the PM2, we will take our next steps in the digitalisation journey. The applications provided by Voith will help us to monitor the process and make the right decisions,” says Niclas Ahnmark, paper mill manager at SCA.
SCA has also signed a longterm service agreement with Voith subsidiary BTG for process control. BTG’s Lifecycle programme
ensures optimum consistency and control with the use of preventive maintenance for all of the consistency sensors, including regular calibration and routine checks. BTG Field Service Engineers assist in the planning, implementation and coordination of the various maintenance services, maximising machine uptime and stability while maintaining SCA’s high safety standards.
The collaboration with SCA is long-term and is particularly evident through the Efficiency Partnership. Throughout the process, the teams work closely together to ensure that the systems are used at the optimum.
Stephan Sicking, vice president of sales for the EMEA region at Voith Paper, explains: “As part of a digitalisation roadmap, we have defined common goals and KPIs in a cross-functional team, developed a customised concept and are now providing support for successive installation and employee training. Already, the benefits from this collaborative approach are clearly demonstrated.”
A paper rewinder supplied to Artic Paper’s Kostrzyn mill in Poland by A.Celli has been started up in record time.
The E-Wind P80 rewinder’s installation, commissioning and start up took just 22 days.
The rewinder has since been used with what are “great results” to produce uncoated wood-free paper reels with basis weight from 38 to 170 gsm and width of 1,800 mm, and at a design speed of 1,500 metres
per minute.
Michal Jarczynski, chief executive of Arctic Paper, says:
“We are very happy with the work done by A.Celli, both for the rewinder itself and for the very short time between installation and start-up. Performance are also in line with expectations. I can confidently say that A.Celli’s solutions quality is top-notch.”
Arctic Paper Kostrzyn, part of Arctic Paper SA Group, is the largest producer of paper for offset printing in Poland with a capacity of 315,000 tonnes per year. Under the brand name Amber the mill produces uncoated wood-free paper for general printing of books, brochures and documents, as well as modern papers for highspeed inkjet printing.
Stora Enso has ordered sectional drive systems from ABB for its Oulu mill in northern Finland, where a former paper line will be converted into a consumer board line for folding box board and coated unbleached kraft.
In 2021, when Stora Enso converted its first machine from paper to kraftliner at the Oulu site, ABB supplied a comprehensive drive system package. Now, with the second line conversion the annual capacity at the site will increase by 750,000 tonnes, reaching 1.2 million tonnes of
board once the new machine comes online.
The order for the new project includes liquid- and air-cooled
Norske Skog Skogn has ordered a thermo-mechanical pulping (TMP) line for its Levanger newsprint mill in Norway from Andritz.
The project combines pre-used and new equipment to provide a customised package that precisely fits the local conditions, said Andritz
The new line will enable Norske Skog Skogn to change its raw material mix and thereby reduce variable costs and the environmental impact of its operations, in particular NOx emissions, fossil-based carbon dioxide emissions, and landfilled waste.
Managing director of Norske Skog Skogn AS, Håvard Busklein commented: “With this investment, we are taking an important step in securing Norske Skog Skogn’s longterm competitiveness, and
we will further improve our environmental performance.
“We wanted a solution that would make the best possible use of the available space and existing equipment. The Andritz team offered us a smartly-engineered solution that precisely meets our needs.”
The new line will have the capacity to produce 100,000 tons of thermomechanical pulp per year and is scheduled to start operating in the first half of 2024. A number of pre-used machines will be refurbished and upgraded and combined with new equipment.
The order includes a new TF58 LC refiner; refurbishment of the pre-treatment equipment; a pre-used first-stage refiner with an Andritz control system; and refurbishment of a RGP65 secondary stage refiner.
ACS880 Multidrives and motors for the board production line, a PMC800 Drive Control System –based on ABB’s latest automation technology – and a machine directive-compliant Safety PLC for the sectional drives system.
“We’re excited
to be supporting the Oulu mill on such an important project, one that also aligns closely to the company’s sustainability commitments,” said Niko Lahtinen, who manages paper machine drives within the process industries segment at ABB. “Our earlier experience with Stora Enso – particularly around drive systems and drive controls – coupled with our consultative expertise are a good starting point for the project. We are thrilled with the trust and value Stora Enso has placed in our approach and solutions.”
Production on the newly converted machine is expected to start during 2025.
Tetra Pak South East Asia in Singapore has ordered a system for the recycling of used beverage cartons (UBC) from Andritz.
The equipment will be installed in the board production mill operated by Dong Tien Binh Duong Paper Co located in Ben Cat Town, Binh Duong Province, Vietnam. Start-up is scheduled in mid 2023.
The stock preparation line will
feature two new products from Andritz ’s Prime product line including a PrimeFFD BT pulper with capacity to process 50 tons a day and turn the cartons into highquality fibres while separating aluminium foil.
Tetra Pak has been working with Don Tien, focusing on the collection and recycling of beverage cartons.
DS Smith has ordered a complete stock preparation line and a reject treatment system for its Porcari mill in Italy from Andritz.
The line, which will produce stock for packaging papers from 100 percent recycled paper, will also include what is said to be Europe’s largest FibreFlow drum pulper.
The equipment provided by Andritz will be used with a new paper machine, due to start up mid-2025, which will provide a range of paper grades for the fmcg and e-commerce sectors serviced by DS Smith.
Stefano Andreotti, project manager at DS Smith, says: “The new equipment from Andritz, as well as helping us to recover more water, will help us capture, clean and use fibres that would normally get rejected in the paper making process, so they can be once again used in our
recycling loops.”
The new stock preparation line will have a design capacity of 1,650 bdmt per day and process various types of raw material, such as old corrugated containers, mixed papers and board as well as
new shavings of corrugated board. The system includes a number of technological highlights:
● A FibreFlow drum pulper with a pulping zone diameter of 4.5m and a total drum length of 50m – the largest of this type
in Europe – for gentle pulping of the raw material mix and efficient removal of coarse contaminants
● Nine PrimeScreen X screens with state-of-the-art rotor design providing high screening efficiency at low energy consumption and superior stock quality
● Two PrimeFilter D filters to handle higher feed consistencies and higher-freeness pulp, even in the most demanding applications.
The reject treatment system, capable of handling 135 bdmt per day, will comprise a ADuro C shredder as well as ReCo reject compactors to process the rejects from pulping and coarse screening in the most efficient way, says Andritz
The order also contains basic and detail engineering, installation and supervision, commissioning, and operator training.
The idled PM3 paper machine at the Steyrermühl mill in Austria, which will be acquired by Heinzel at the beginning of 2024, is being converted by Andritz to produce kraft papers for flexible packaging.
The machine previously produced graphic paper for UPM. After being converted the paper machine, to be called PM6, will annually produce up to 150,000 tons of brown and white lowbasis-weight kraft paper that will be sold under the Heinzel Group’s StarKraft brand. The paper will be used for shopping bags, pouches,
and other flexible packaging products.
Werner Hartmann, operations chief of Heinzel Pöls, says: “With this investment, StarKraft will
become one of the world’s leading brands for bleached and unbleached kraft paper. Andritz PrimeLine technology is already successfully operating at our Pöls
and Laakirchen mills. The current rebuild by Andritz will help us expand our product portfolio for sustainable packaging.”
The PM6 at Steyrermühl will use an innovative gap forming design to produce bleached and unbleached calendered kraft paper grades. It is based on a unique headbox and shoe-blade gap-former combination. Together with an Andritz PrimePress X shoe press and an upgrade of the existing steam and condensate system, Andritz says it will achieve significant energy savings while producing high-quality end products.
Ahigh-capacity winder has been ordered by Gascogne Papier in France for its mill at Mimizan.
Supplied by Valmet, the winder will be used on the mill’s PM7 line with start-up scheduled for 2025.
“This winder will be a key contributor to the top-level quality of our future papers, which will reinforce the current positioning of Gascogne Papier as a world-leading kraft paper producer,” says industrial director Régis Laffont.
The order includes a high-
capacity OptiWin two-drum compact winder that is said to offer a wide production range of widths and diameters of shipping rolls, and is equipped with proactive dual spreading.
The winder is also equipped with automated butt-joint splicing to achieve high-capacity targets specified by the customer. Valmet will provide a wide site service for easier project handling, maintenance master data, a Slitter Management Program, a spare parts package, and Industrial Internet solutions, such as Valmet Winder Diagnostics.
Infinya Containerboard in Israel has ordered a complete OCC line including a reject treatment system from Andritz for its recycled paper mill at Hadera.
The OCC line will have a capacity for 1,080 bdmt per day and will use mixed old corrugated containers as raw material to produce highquality fluting and testliner for the domestic market.
The key equipment includes the complete stock preparation line with a FibreFlow drum pulping system for gentle slushing and removal of contaminants at minimum fibre loss.
Andritz will install a number of its Prime stock preparation products, such as PrimeScreen X screens for screening and fractionation with energy consumption. A PrimeFilter D disc filter with an advanced feed system will enable higher productivity and
operation at reduced energy costs.
The new reject treatment system will be equipped with an ADuro C shredder for coarse shredding and ReCo reject compactors for dewatering the rejects to highest possible dry contents. The new OCC line will be equipped with an Andritz distributed control system and motor control centre, to ensure optimum plant performance.
Andritz will also provide field instruments, the basic and detail engineering, supervision of installation, commissioning and start-up service as well as the operator training. Start-up is planned for the third quarter of 2024. Infinya, established in 1953, is the largest packaging and recycling company in Israel. The company specialises in recycling, cardboard paper production and packaging production.
PM7 produces natural machineglazed and sack kraft paper grades with a design speed of 1,300 metres per minute and a daily capacity of 450 tons. The new winder will handle parent rolls with a width of 6,870 mm and a diameter of 3,200 mm.
Gascogne Papier is one of the four businesses of Groupe Gascogne, which was founded in
1925 in the Landes area of south west France. Gascogne Papier offers a wide range of natural, technical, and innovative papers for packaging and industry, and is a leader in natural unbleached kraft paper. Mimizan is an integrated pulp and paper mill that annually produces 150,000 tons on four paper machines and one coating machine.
A black liquor evaporation plant is being supplied by Andritz to Hyogo Pulp Industries, the Japanese unbleached kraft pulp producer, to replace the mill’s two existing evaporation lines. The plant will evaporate water from the black liquor, a byproduct of the kraft process, so that it can be burned efficiently in the mill’s recovery boiler.
“Andritz ’s technology will help us to eliminate existing bottlenecks in production, and it will support us in our recycling-oriented operations,” said Naoki Ikawa, representative executive director at Hyogo Pulp Industries.
Andritz will supply a six-effect evaporation plant equipped with the latest lamella technology
ensuring resistance to scaling. It includes an integrated stripping plant for energy-efficient cleaning of the foul condensate to produce clean secondary condensate, which will replace fresh water in other sections of the mill.
Start-up is scheduled for the second quarter of 2025. As part of its investments to improve sustainability, Hyogo Pulp Industries previously ordered an Andritz DD Washer and polishing filters for polysulfide cooking.
Founded in 1955, Hyogo Pulp Industries yearly produces about 200,000 tons of unbleached softwood pulp for customers in Japan and south east Asia, along with ‘green’ electricity generated from biomass.
Jérôme Porlier has been appointed as president and operations chief at the Specialty Products Group of Canadian paper packaging and tissue manufacture Cascades.
Porlier succeeds Luc Langevin, who after more than 12 years as the head of SPG is working towards retirement. Langevin will continue to be responsible for Cascades Recovery+ and will offer his experience and advice to various other Cascades corporate departments.
He has been part of the Cascades’ team for more than 10 years, joining the company as succession plant manager for the Tissue Group
in 2012, taking responsibility for the Candiac mill. Less than two years later, he was promoted to manager of the Granby mill, before again being promoted to Tissue Group General Manager in 2016.
In 2019, Porlier joined the Cascade’s Specialty Products Group, where he evolved as vice president of operations of the packaging sector.
“Jérôme has already made a major contribution to SPG’s operational performance, notably by implementing several investment projects leading to the group’s modernisation, automation and growth in its chosen markets,” said Mario Plourde, chief executive
of Cascades.
“Not only does he have the energy and leadership, but also the vision necessary to ensure that the business continues to progress as a leader in eco-responsible packaging, to be customer-focused where quality and operational excellence are key, and to emphasize innovation and talent development.”
Commenting on Langevin’s career, Plourde said: “Luc is a team player who has left his mark on Cascades through his deep commitment to our corporate values, his courage, his vision and his pursuit of excellence.
“His legacy is apparent in the
Paul Clarke has been appointed as managing director of DS Smith’s UK and Ireland packaging division. Formerly operations director, Clarke will be improving collaborative structures across DS Smith, unlocking value across its end-to-end supply chain, said DS Smith.
Commenting on his appointment, Clarke said: “I’m delighted to be appointed to this new role and for the opportunity to contribute to spearheading DS Smith’s agenda on our commitment to developing and redefining packaging solutions for customers globally and a focus on sustainable ventures and innovation.
“We have a highly engaged community of talented employees within DS Smith; my priority first and foremost is to ensure we continue to build a healthy, safe and inclusive environment for all. Our people are our best asset;
together we have had to be more resilient than ever in recent years as we help our customers navigate a challenging economic environment.
“As a FTSE 100 sustainable business working with the world’s largest multi-national FMCGs and manufacturers, we are exposed to trends in retail, e-commerce, digital and supply chain, and our focus is firmly on innovating packaging solutions that will support both current customers and consumers
as well as pave the path ahead for future generations.
“We need to close the loop through better design, protect the environment by making the most of every fibre, and reduce waste and resources through circular appointments and careful strategic delivery of each and every new product.”
Professor Niko DeMartini has been appointed as director of the Pulp & Paper Centre at the University of Toronto, with a term of three years until June 2026.
Commenting on DeMartini’s appointment, Prof Ramin Farnood, chair of the Department of Chemical Engineering & Applied Chemistry, said: “In his new role
success that this business group has had in growing in its chosen markets its resolute focus on innovation, and that it is solidly equipped to meet the challenges presented by our industry while remaining a model in terms of the circular economy.”
Langevin’s career with Cascades began in 1995. As a graduate engineer, he joined the company as a plant manager. He rose to become operations chief of SPG in 2011.
as Director, PPC, Niko will be focusing on fostering research partnership opportunities with industry, government agencies, NGOs, and research institutions, as well as facilitating the creation and launch of multi-researcher university-industry consortia and collaborative research initiatives to stimulate research and support teaching in pulp and paper science and engineering.”
Improve your press section efficiency! SmartScan™ contactless sensor accurately measures paper web dryness after the press section 24 hours a day, 7 days a week. Using a proprietary microwave technology, it is developed to overcome the typical limits of the NIR (near-infrared) sensors.
SmartScan™ is available both for fixed point positions or traversing web scan To save hundred of thousands of Euros in energy costs, stop collecting samples, choose the safe accuracy of SmartScan™ technology.
If you need a versatile solution to better manage your software lifecycle, look no further than Automation Software Maintenance (ASM). ABB’s newest lifecycle management program removes the complexity and cost of accessing new software releases and features, corrections and enhancements between major system upgrades. ASM is available for DCS, QCS, Paper Machine Drives and Pulp and Paper Process Control Library.
Learn more: abb.com/pulpandpaper