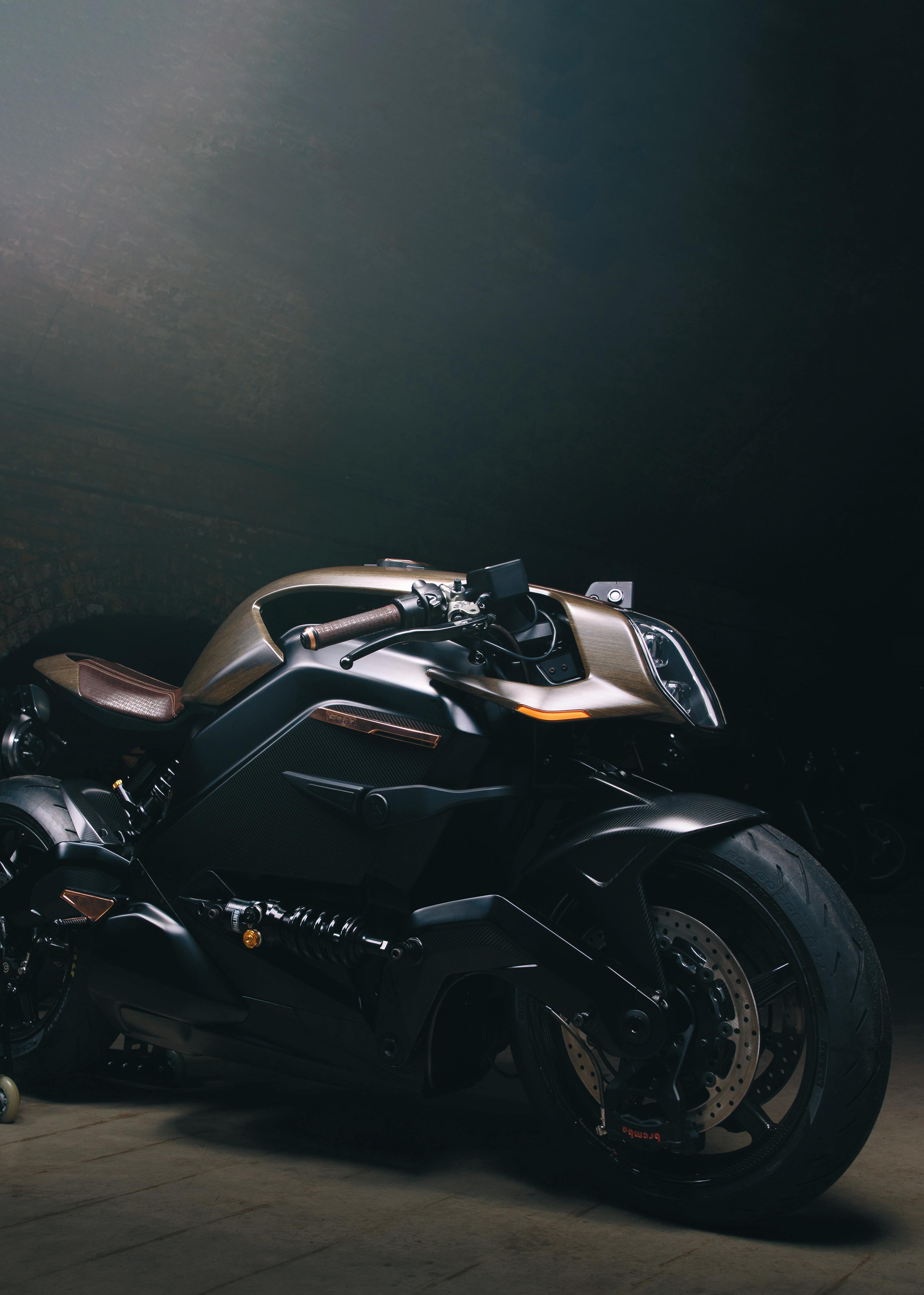
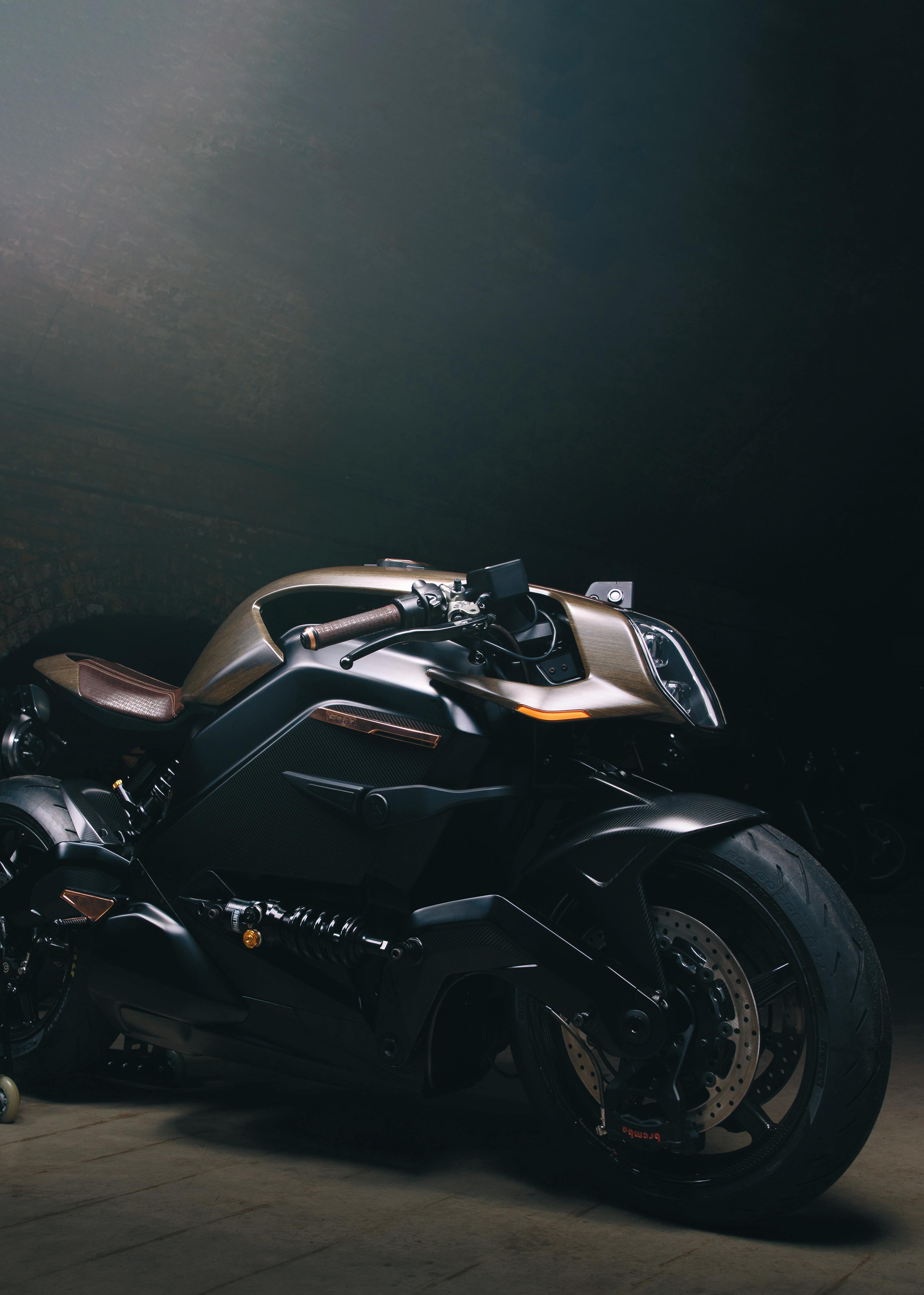
Automate SOLIDWORKS manufacturing processes & sell digitally using DriveWorks
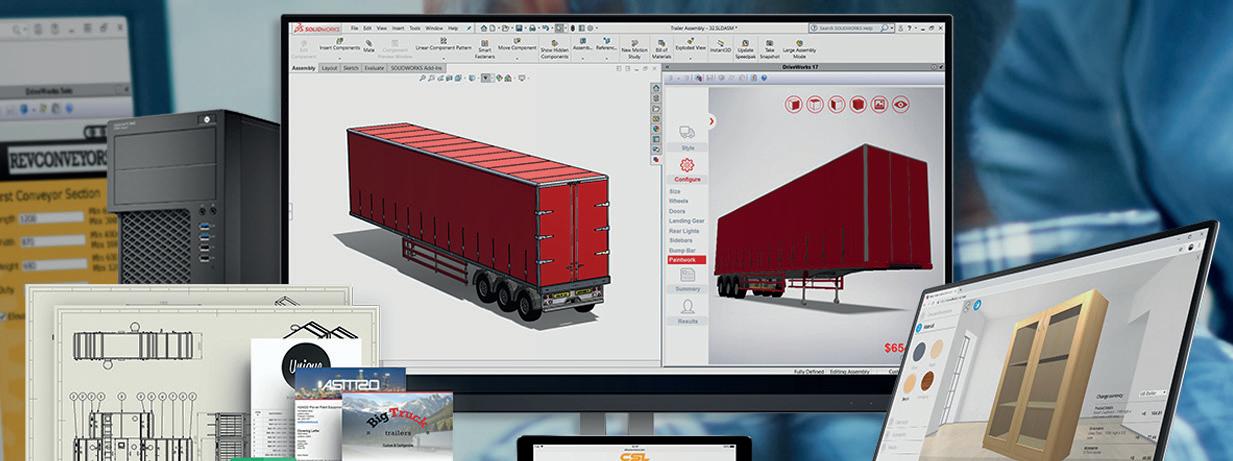
DriveWorks is flexible and scalable. Start for free, upgrade anytime. DriveWorksXpress is included free inside SOLIDWORKS or start your free 30 day trial of DriveWorks Solo.
30DAY FREETRIAL
DriveWorks Solo
SOLIDWORKS® part, assembly and drawing automation add-in
DriveWorksXpress
Entry level design automation software included free inside SOLIDWORKS®
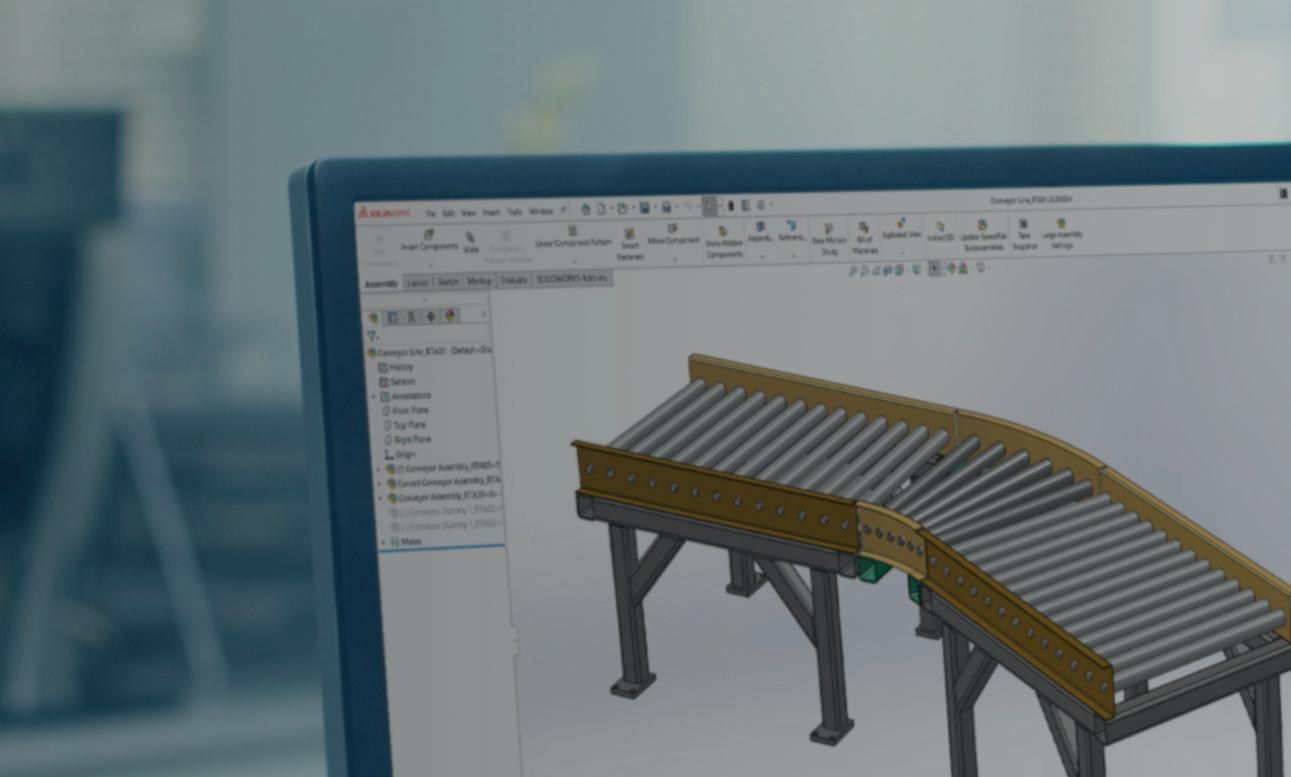
Entry level SOLIDWORKS part and assembly automation
Create a drawing for each part and assembly
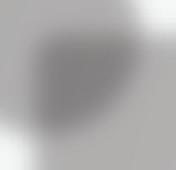
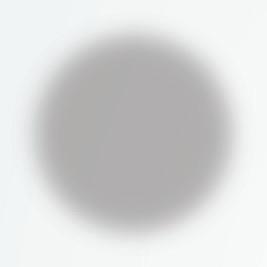
Find under the SOLIDWORKS tools menu

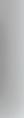

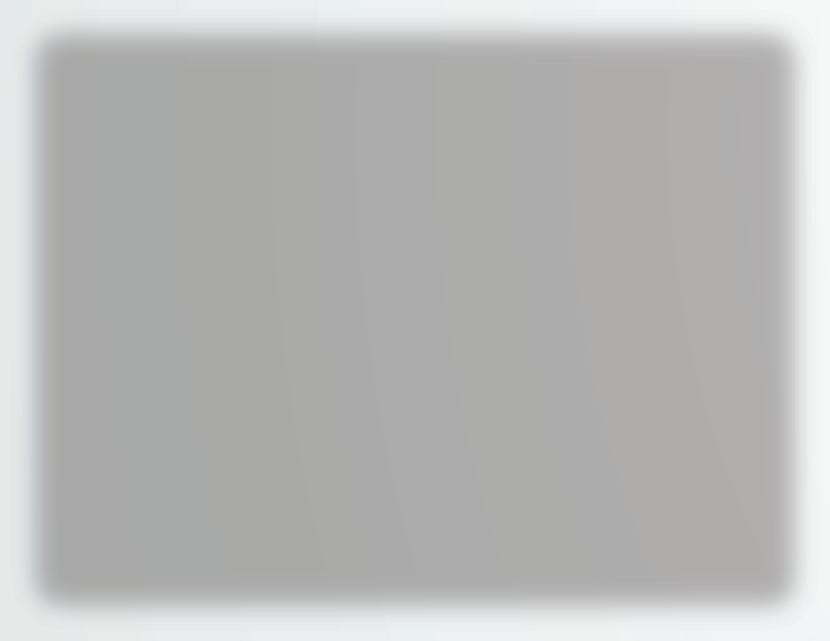
Automate SOLIDWORKS parts, assemblies and drawings
Generate production ready drawings, BOMs & quote documents automatically
Enter product specifications and preview designs inside SOLIDWORKS
Free online technical learning resources, sample projects and help file
Sold and supported by your local SOLIDWORKS reseller
One time setup
Set up once and run again and again. No need for complex SOLIDWORKS macros, design tables or configurations.

Save time & innovate more Automate repetitive SOLIDWORKS tasks and free up engineers to focus on product innovation and development.
Eliminate errors DriveWorks rules based SOLIDWORKS automation eliminates errors and expensive, time-consuming design changes.
DriveWorks Pro
Modular SOLIDWORKS® automation & online product configurator software

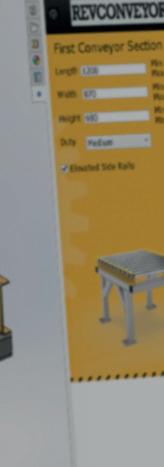
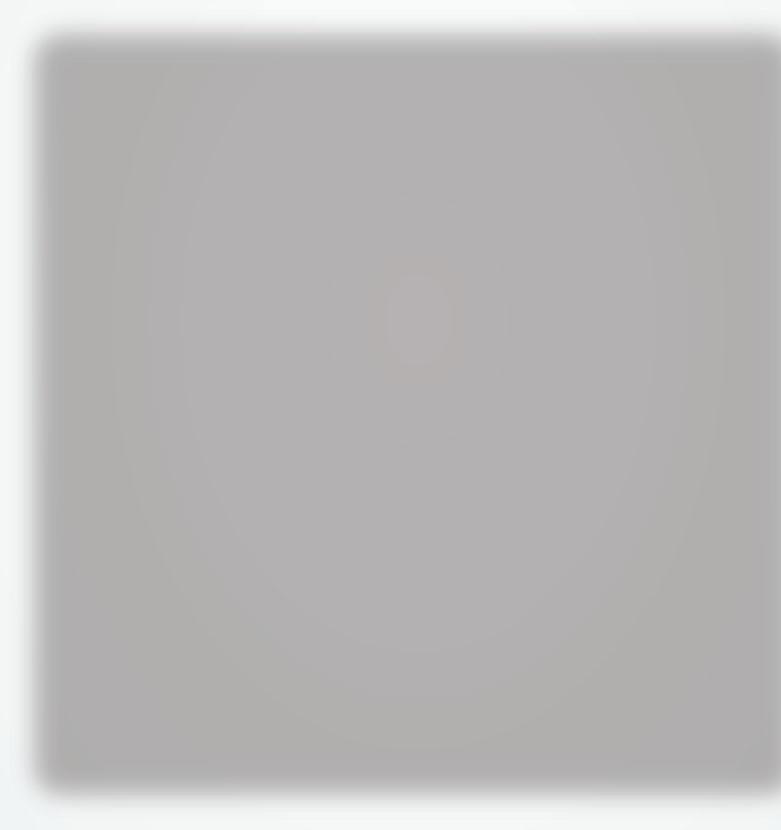
Complete SOLIDWORKS part, assembly and drawing automation
Automatically generate manufacturing and sales documents
Configure order specific designs in a browser on desktop, mobile or tablet


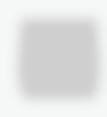
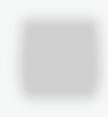
Show configurable design details with interactive 3D previews
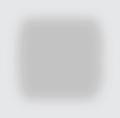
Integrate with SOLIDWORKS PDM, CRM, ERP, CAM and other company systems


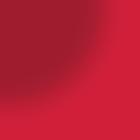
Scalable and flexible licensing options
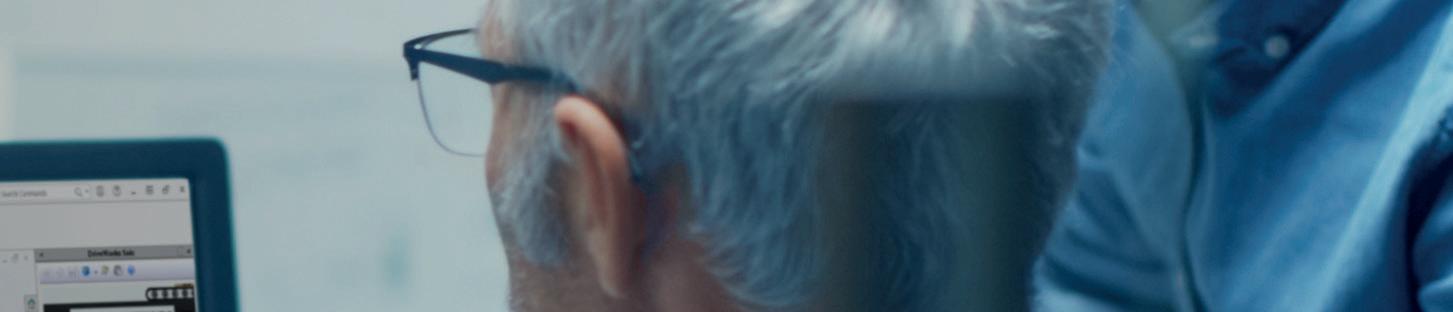
Sold and supported by your local SOLIDWORKS reseller
Connect sales & manufacturing
Validation ensures you only offer products that can be manufactured, eliminating errors and boosting quality.

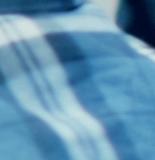
Integrate with other systems DriveWorks Pro can integrate with other company systems, helping you work more efficiently and effectively.
Intelligent guided selling
Ensure your sales teams / dealers configure the ideal solution every time with intelligent rules-based guided selling.
EDITORIAL
Editor
Stephen Holmes stephen@x3dmedia.com +44 (0)20 3384 5297
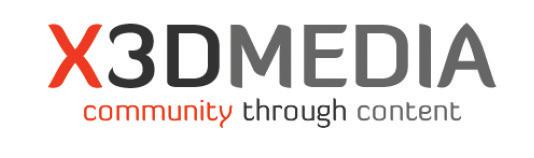
Managing Editor
Greg Corke
greg@x3dmedia.com +44 (0)20 3355 7312
Staff Writer
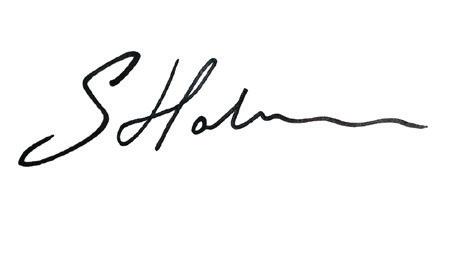
Claudia Schergna claudia@x3dmedia.com
Consulting Editor
Jessica Twentyman jtwentyman@gmail.com
+44 (0)20 7913 0919
Consulting Editor
Martyn Day martyn@x3dmedia.com
+44 (0)7525 701 542
DESIGN/PRODUCTION
Design/Production
Greg Corke greg@x3dmedia.com +44 (0)20 3355 7312

ADVERTISING
Group Media Director
Tony Baksh tony@x3dmedia.com +44 (0)20 3355 7313
Deputy Advertising Manager

Steve King steve@x3dmedia.com +44 (0)20 3355 7314
US Sales Director Denise Greaves denise@x3dmedia.com +1 857 400 7713
SUBSCRIPTIONS
Circulation Manager
Alan Cleveland alan@x3dmedia.com +44 (0)20 3355 7311
ACCOUNTS
Accounts Manager Charlotte Taibi charlotte@x3dmedia.com
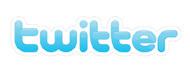
Financial Controller Samantha Todescato-Rutland sam@chalfen.com
ABOUT
DEVELOP3D is published by
X3DMedia 19 Leyden Street London E1 7LE, UK T. +44 (0)20 3355 7310 F. +44 (0)20 3355 7319
© 2022 X3DMedia Ltd
All
It doesn’t seem a moment since the last great economic crisis was upon us, yet here we are, getting ready to go another round in the face of adversity and the unknown.
After over a decade of uncertainty we’d hope that your workflow is as honed as a French Revolutionary guillotine, but with the ever-changing nature of technology and the role that it plays in our industry, moments like these are still a time to consider where your process could be even more lean.
Which leads us on to DEVELOP3D LIVE, which will open its doors on Tuesday 1 November (following a hiatus enforced by the previous great crisis – remember that?!), an event that will contain so much technology, exciting innovation and positivity around our sector that you’d be a fool to miss out. For those of you reading this outside of UK shores, there’ll be the chance to watch the mainstage action online, so remember to register your interest at develop3dlive.com.
Aside from a full event preview [see page 48], this issue of the magazine keeps us moving forward at pace – helped in no small amount by ARC Motorcycles. A spin-out from Jaguar Land Rover, with its electric motorcycle design, the company has created one of the most desirable forms of sustainable transport we’ve seen yet.
Elsewhere, we bring you a roundup of handheld 3D scanners to keep you abreast of what’s happening in the field of reverse engineering, where these nifty and increasingly versatile pieces of kit are entering a golden age of price and performance.
It’s exactly these kinds of developments that you’ll have the chance to get handson with at DEVELOP3D LIVE, as well as learning how others are incorporating them in ways that might inspire you.
Looking forward to seeing you all in person in Sheffield on 1 November!
Stephen Holmes Editor, DEVELOP3D Magazine, @swearstoomuch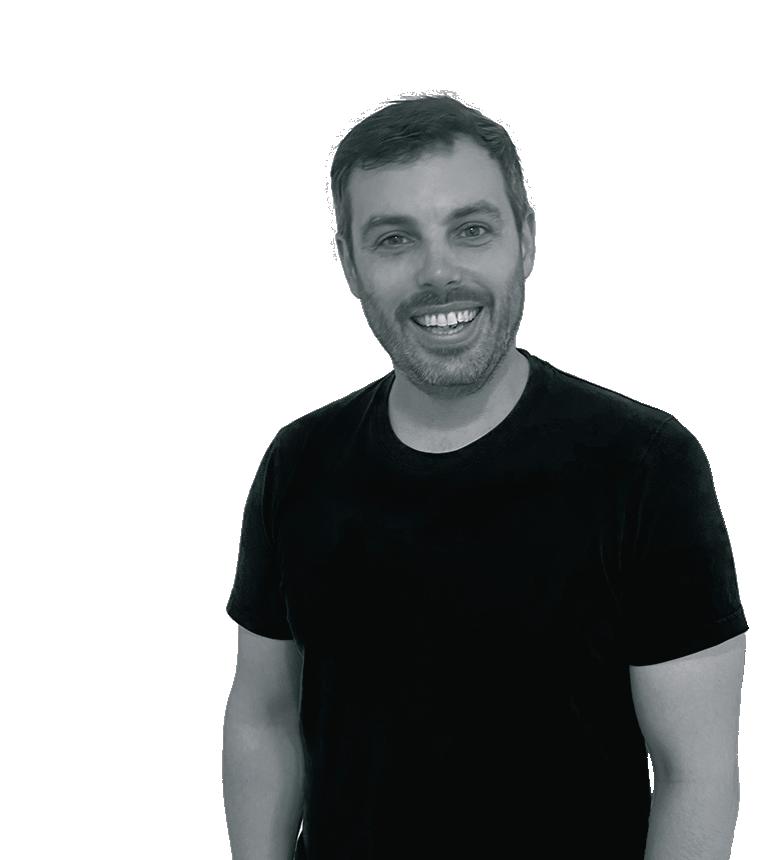
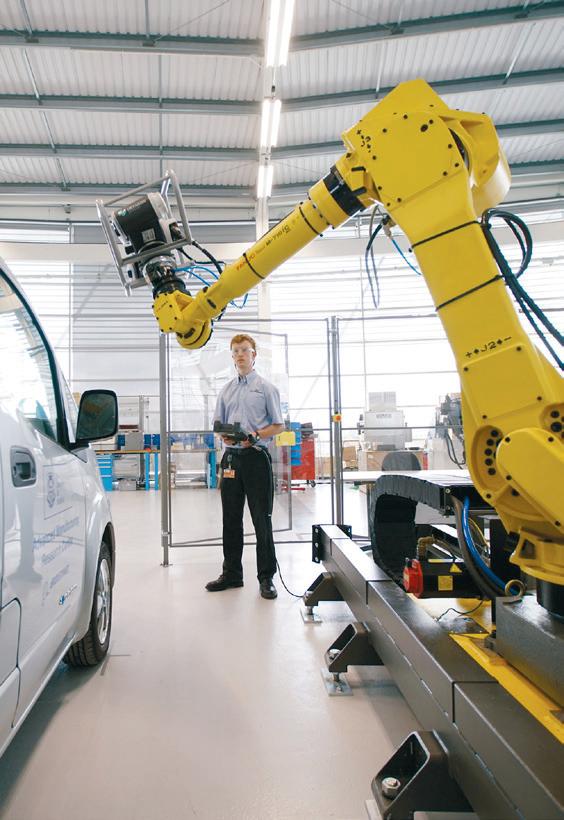
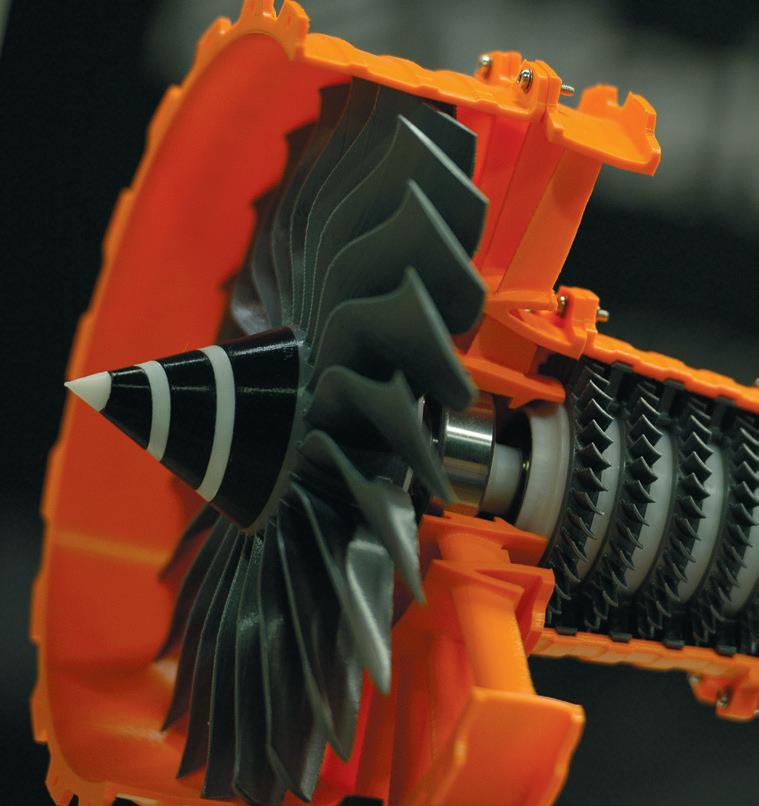
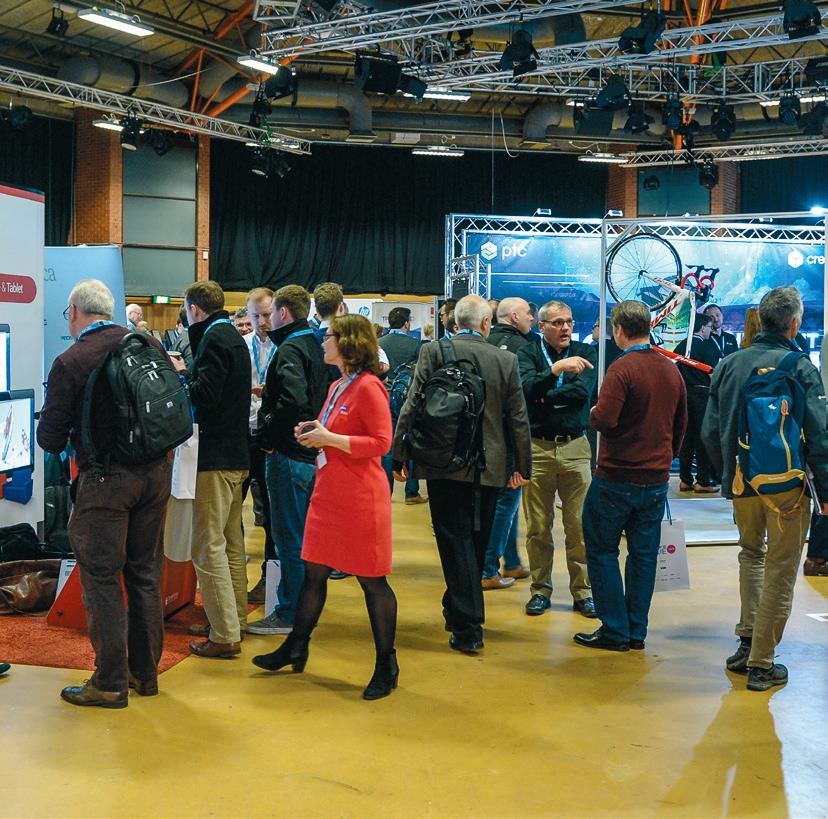

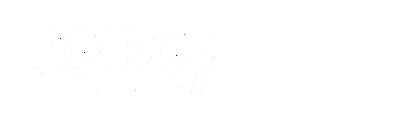

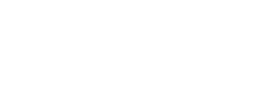

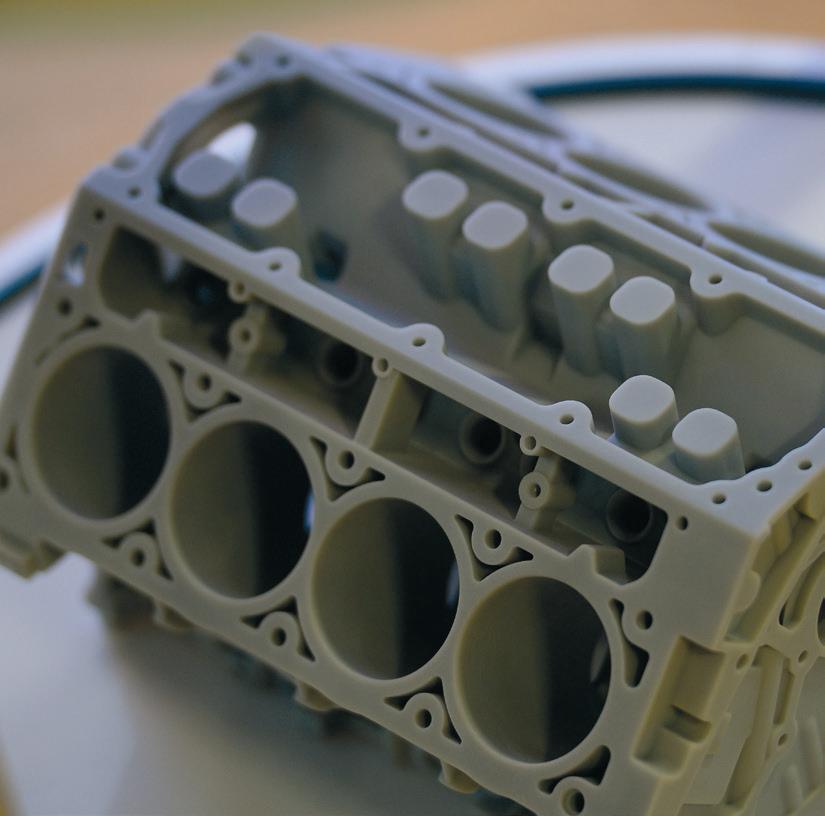

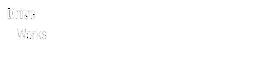


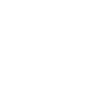
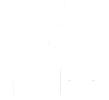
NEWS
Autodesk puts Fusion 360 in a browser, Desktop Metal optimises sheet metal forming, HP stakes claim in supply chain with metal 3D printer + lots more
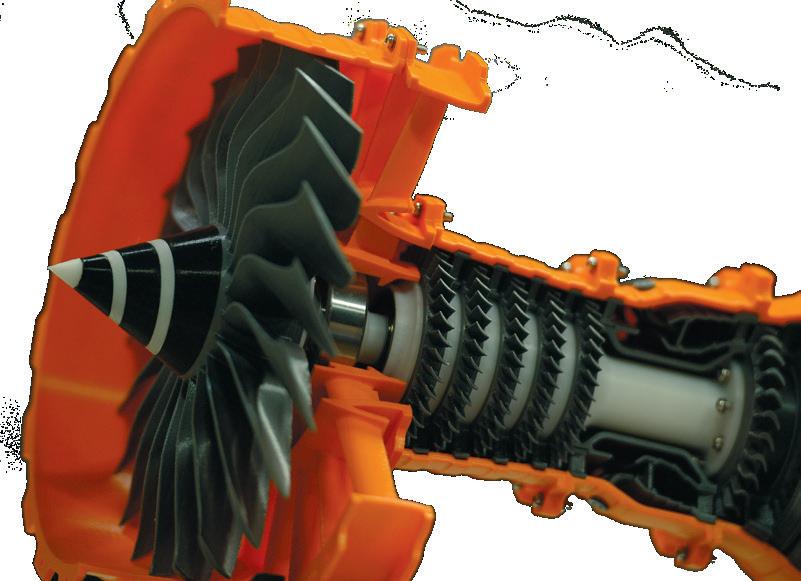
WORKSTATION NEWS
Nvidia enhances viz workflows with RTX 6000, AMD boosts 3D graphics performance in Solidworks, Intel gets first discrete Arc Pro GPU win + lots more
COMMENT
SJ on why diversity in product design is critical Matt Batchelor on the disconnect of 3D printing
FEATURES
Visual Design Guide: Sennheiser Momentum
STORY The all-electric Arc Vector motorcycle Best 3D scanners for the design studio

Autodesk University - a new era of cloud with Fusion Kalkhoff 3D prints aluminium bike frame prototype Design for additive manufacturing (DFAM)
DEVELOP3D LIVE
We preview the inspirational presentations in our multistream conference and the cutting edge technologies on the exhibition show floor at 2022’s must attend event
THE LAST WORD
Holmes
how the need for both digital
works in the fluid
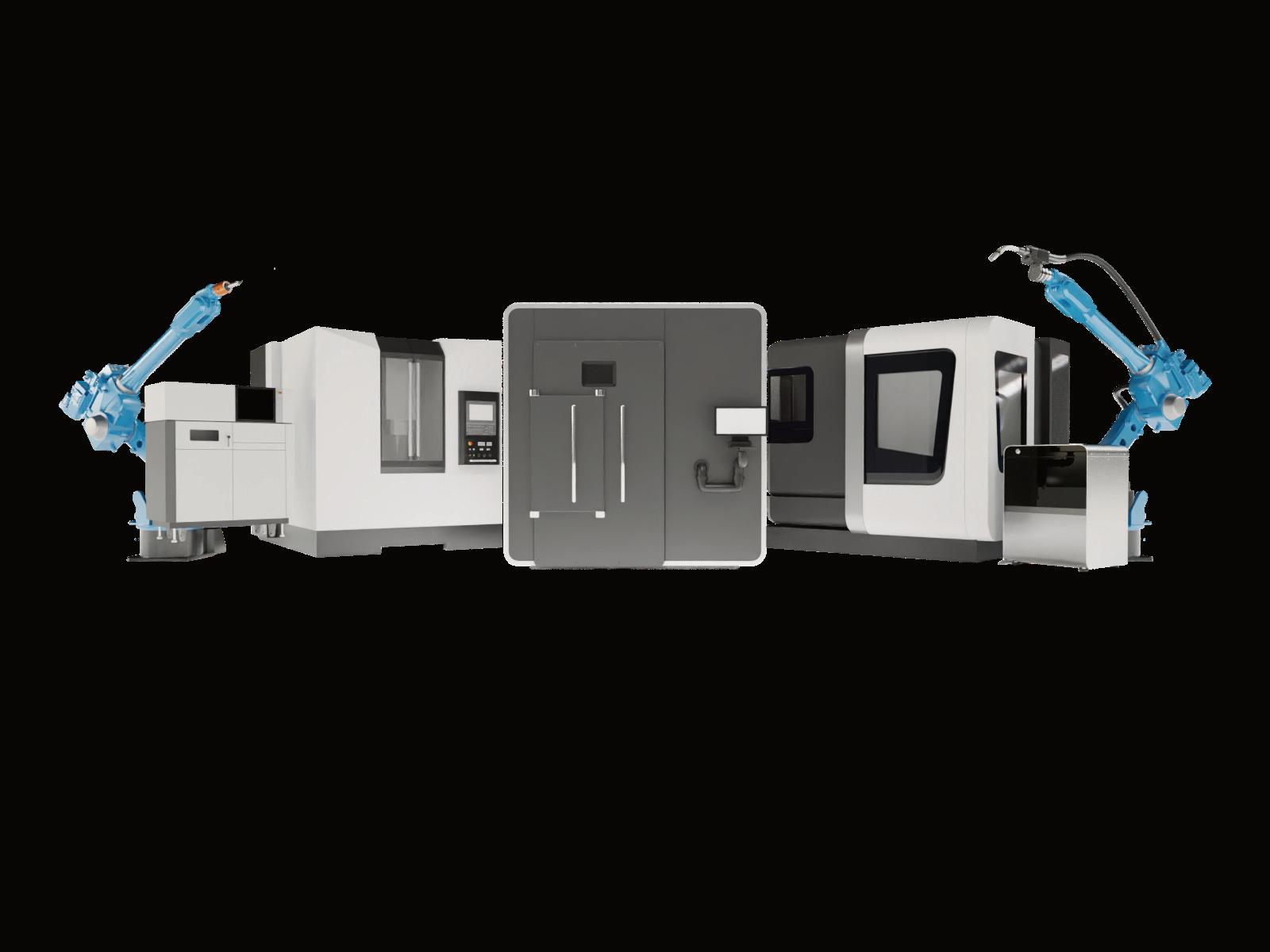
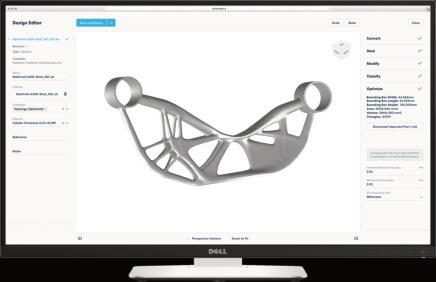

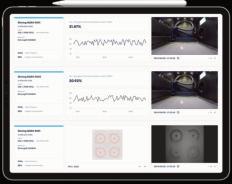


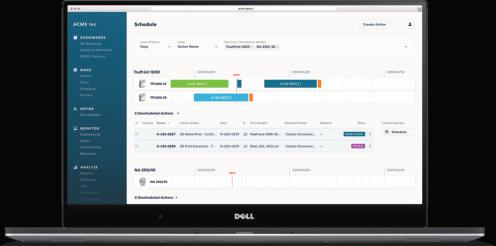
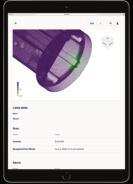


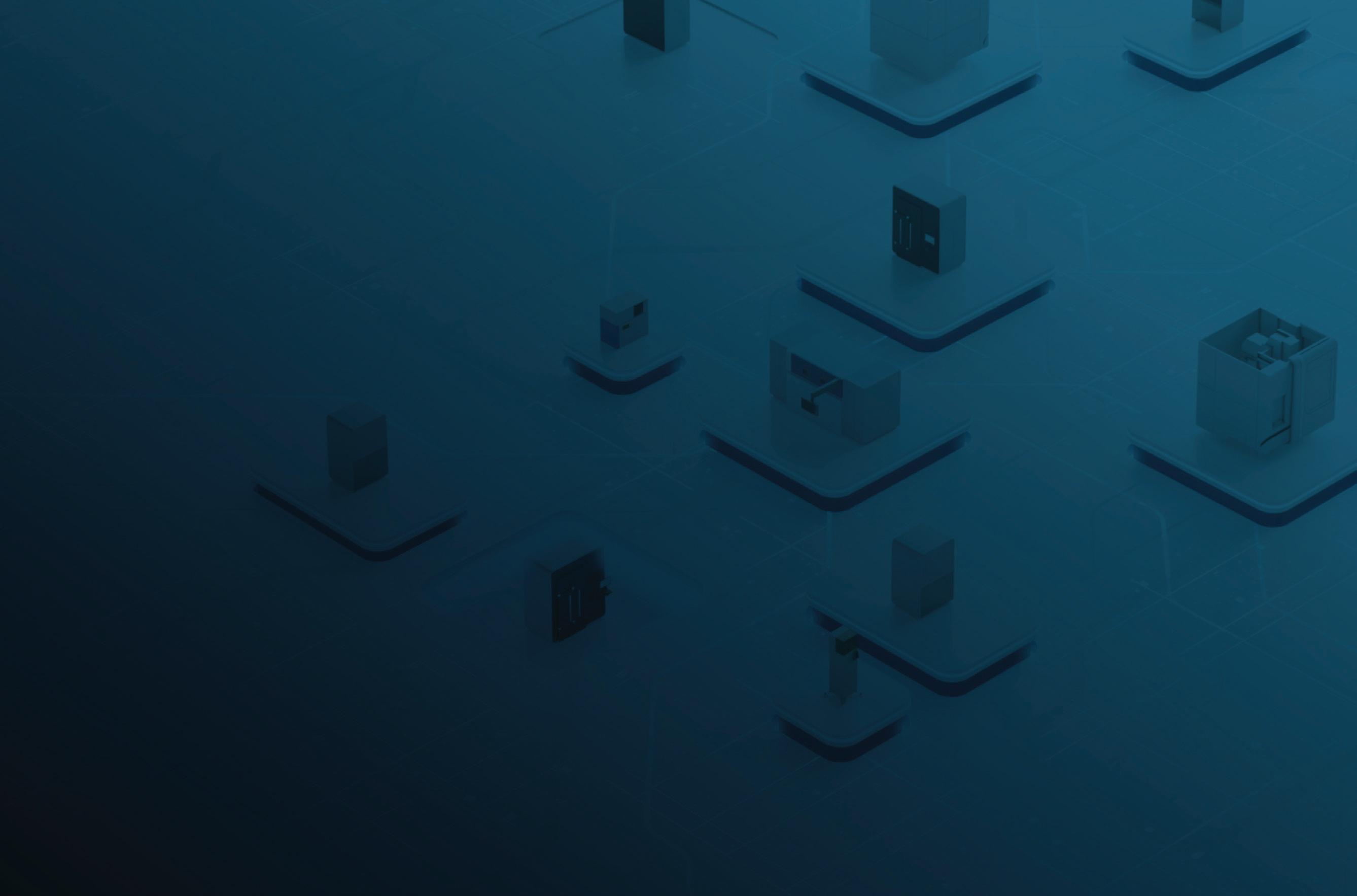
AUTODESK UNVEILS BROWSER-BASED FUSION 360 AND ADDS NEW EXTENSIONS
Autodesk has increased online browser-based access to Fusion 360 for commercial subscribers, moving the company closer to its vision of ‘data and device independence’, it has announced in New Orleans at Autodesk University 2022.
“Fusion running in a browser will run on anything. Anytime. Anywhere,” said Jeff Kinder, executive VP of product development and manufacturing solutions, Autodesk, citing that the pandemic has highlighted the value of having access to software tools and data anywhere.
“Countless people come together to design, make, supply, market, sell, and deliver every product. Each role needs timely, relevant access to project data to provide input or track changes that could impact their work. Opening online access to Fusion moves Autodesk closer to our vision of data and device independence, meeting the needs of our customers now and into the future,” Kinder added.
New Autodesk Fusion 360 extensions powered by Ansys and ModuleWorks were also announced to advance electronic product design and manufacturing capabilities.
Signal Integrity Extension, powered by Ansys, will provide useful insights about printed circuit board (PCB) signal quality as a part of the board design process. It aims to give PCB designers insights into design impacts of electromagnetics on product performance, enabling them to identify and resolve issues directly within Fusion 360.
Advanced toolpath creation algorithms from ModuleWorks have also been revealed for the software’s Machining Extension, with enhanced 5-axis machining and other complex manufacturing workflows originally from Autodesk PowerMill added.
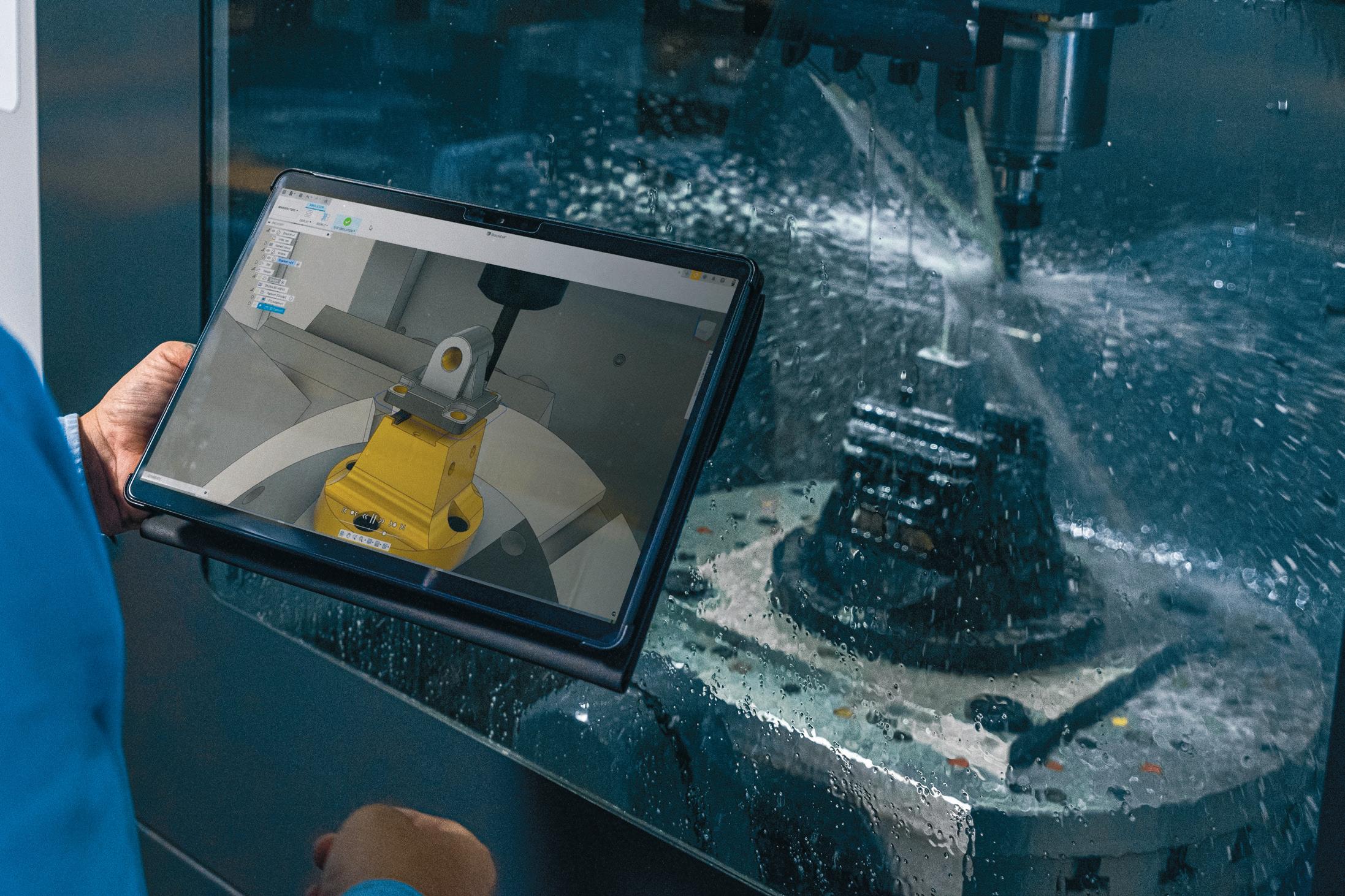
Autodesk says that the new capabilities will generate higher-performance, collision-free toolpaths for efficient multiaxis milling.
The first advanced strategies include new rotary pocket, rotary contour, and
automatic multi-axis deburring.
Elsewhere, a partnership with Makersite, an environmental supply chain AI and data management company, was announced to bring eco insights to early-stage design for better sustainable product and production decisions at scale.
Makersite’s environmental impact and cost data will be combined with Fusion 360’s product design data, with a new plug-in enabling users to have Makersite ‘instantly calculate’ the environmental and cost impacts of a product or component design based on its structure, materials, and weight.
Designers will get back recommendations regarding expected costs and alternative materials that are based on their organisation’s own material masters and procurement data to provide real-time environmental transparency. www.autodesk.com/fusion360
Meanwhile, turn to page 40 for more news from Autodesk University 2022
Fusion in a browser is designed to provide users from the design office to the shop floor access to Fusion on tablets and other devices
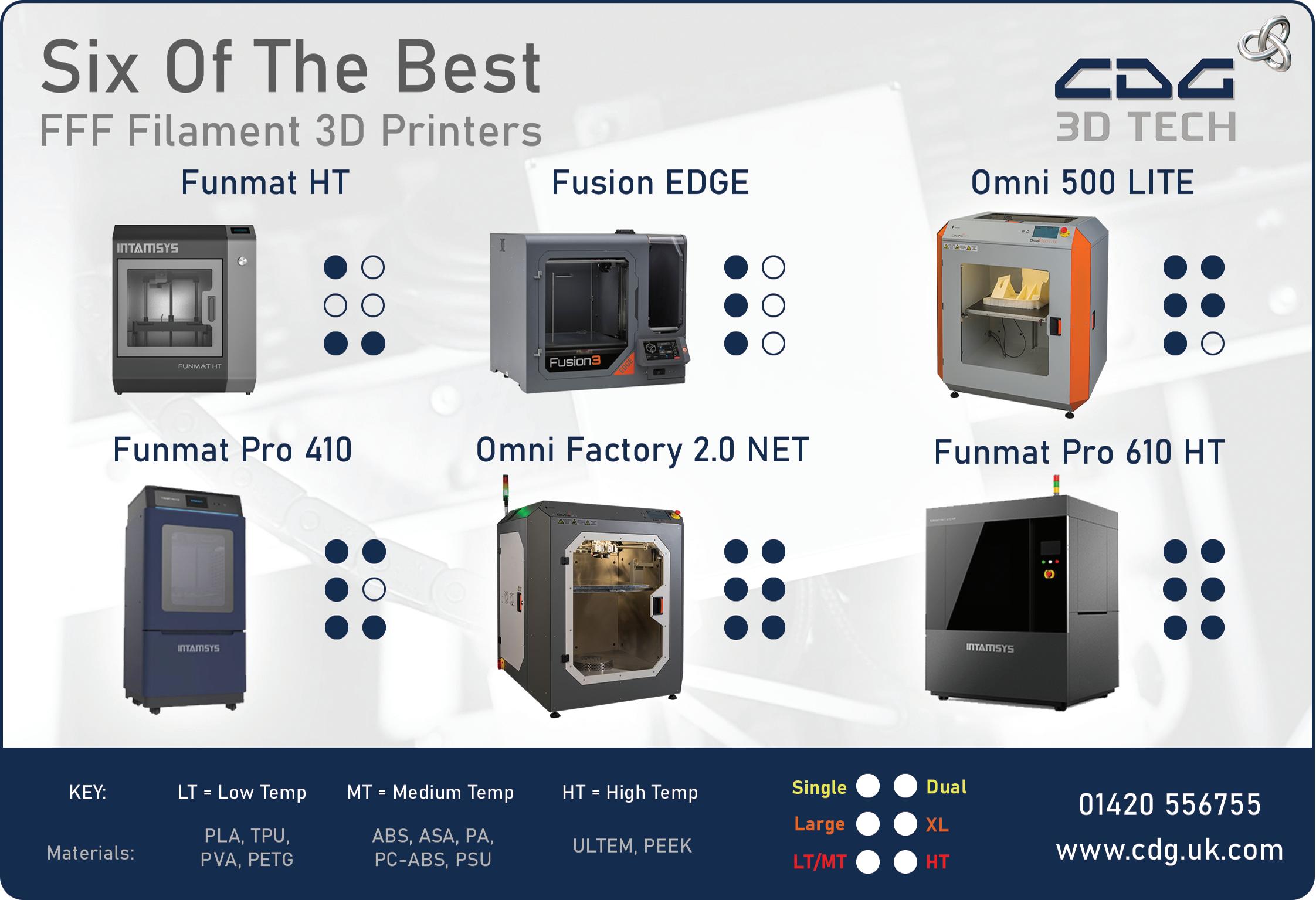

FIGUR G15 LAUNCHED FOR SHEET METAL FORMING
Figur G15, a system for shaping standard sheet metal on demand directly from a digital design file, has been launched by Desktop Metal – requiring no custom stamping tools, moulds, dies, or presses.
Desktop Metal says that Figur’s patentpending Digital Sheet-Forming (DSF) technology begins with easy-to-use software that creates a toolpath for a ceramic tool on an XY gantry to shape sheet metal with up to 2,000 lbs of force.
Precision is said to be maintained by the proprietary build box design that reduces force distribution across the sheet during the build. The company says that DSF
parts have a high quality surface finish straight off the machine with little to no post finishing required.
The Figur G15 launch model has an XY forming area of 1,450 x 1,000mm and can process forms up to 400mm in the Z direction. A wide variety of metals and sheet thicknesses can also be processed, including steel and aluminium.
The technology is claimed to be capable of producing parts such as a common automotive exhaust muffler – which would traditionally require the purchase of a $150,000 die with a three month lead time and a quantity of 1,000 parts, at around $160 cost per part, including materials. www.desktopmetal.com
Desktop Metal says DSF parts have a high quality surface finish straight off the machine with little to no post finishing required
Altair launches Simulation 2022.1
Altair has released Simulation 2022.1, which is designed to allow users to apply simulation earlier in design processes to reduce errors, increase efficiency, reduce costs and enable sustainable lifecycles.
Simulation 2022.1 brings a variety of updates designed to bolster Altair’s sustainable product design capabilities. According to Altair, updates to Altair Material Data Center, OptiStruct, Multiscale Designer, HyperWorks, and SimLab will help companies meet their lightweighting objectives, design requirements, budget constraints, and regulatory requirements. www.altair.com
Nikon in takeover of SLM Solutions
Nikon and SLM Solutions have announced the former’s investment agreement that, if approved, would see a public takeover offer of €622m of SLM Solutions.
SLM Solutions and its wide range of integrated metal additive manufacturing solutions has played a prominent role in the advancement of 3D printing end use parts, with its portfolio of technologies capped by the giant 12 laser NXG XII 600 system, capable of build rates of up to 1,000 ccm/h in its 600 x 600 x 600mm build chamber. www.slm-solutions.com
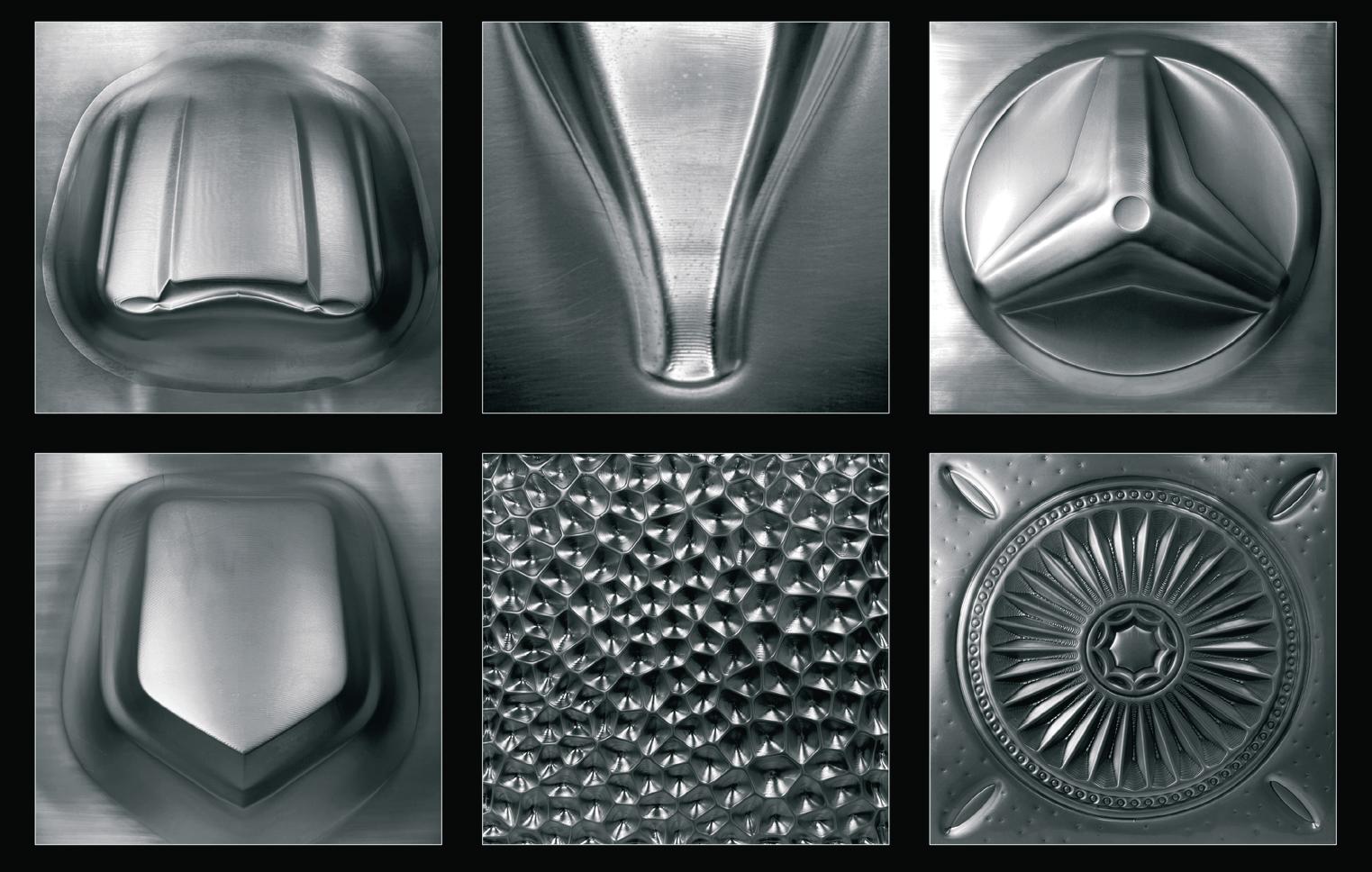
Carbon expands software with ParaMatters
Carbon has acquired ParaMatters and its generative design software as it looks to expand its software offering to allow optimised designs for additive manufacturing.
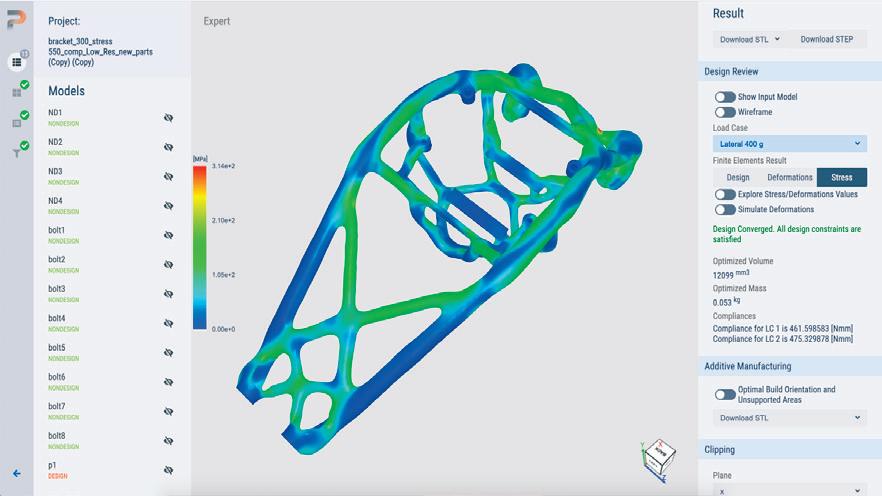
Initially focused on providing latticed parts, Carbon’s Design Engine software platform will be broadened with the acquisition, allowing it to include topology optimisation as well as incorporating a wide variety of materials and production systems beyond Carbon’s own hardware.
Craig Carlson, Carbon CTO and office of the CEO member, said of the announcement that software is ‘the backbone of our idea-to-production platform’ and that generative design capabilities from ParaMatters are a key expansion for Carbon’s design software.
“We recognise the critical role software design tools play in our customers’ digital transformation. For far too long, designers have settled for software design tools that adhere to the limitations of traditional manufacturing,” said Phil DeSimone, cofounder, office of the CEO at Carbon. www.carbon3d.com
Tech Soft 3D to bolster rendering
Tech Soft 3D has acquired Redway3D as it looks to expand its visualisation portfolio of SDKs to provide photorealistic and advanced real-time rendering capabilities.
Tech Soft 3D says that Redway3D's software component Redsdk complements its existing solution, Hoops Visualize, through its strong focus on raytracingbased photorealistic rendering and its game-engine approach to advanced real-time visualisation. Hoops Visualize is an engineering-focused graphics library and SDK for rendering 3D CAD models on desktop, mobile and AR/VR devices, and relied on by companies such as Hexagon, Ansys, Solidworks, Autodesk and more. www.techsoft3d.com
HP STAKES CLAIM IN SUPPLY CHAIN WITH METAL JET S100
The new Metal Jet S100 from HP has been unveiled as the brand’s first commercially available metals AM system, taking the company and its printhead technology to the next level with binder jetted metals in a 'user friendly, scalable set-up'.
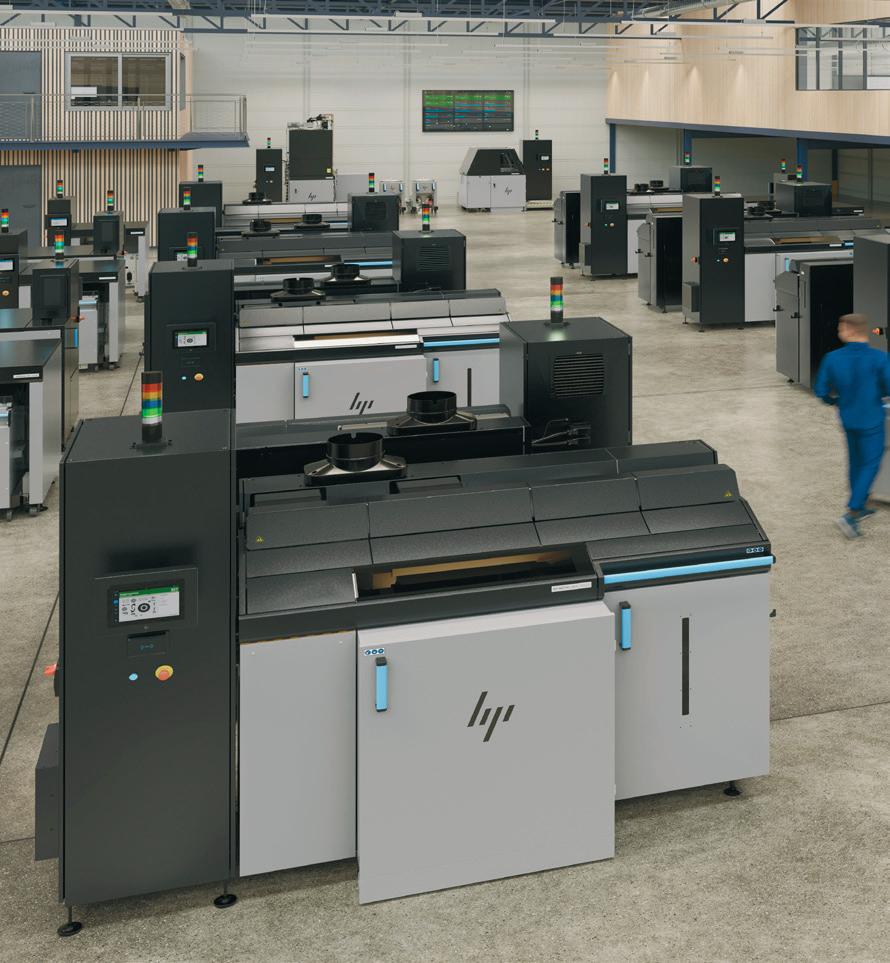
In development since 2018, at launch, the Metal Jet S100 has two ‘characterised’ stainless steel materials, 316L and 17-4PH, but the scope is there for more in reaction to customer interest as the full system –including powder prep and management, 3D printer, curing station and powder removal – looks to be introduced into existing manufacturing supply chains for end use parts.
HP claims its advantages over existing technologies are to be found in elements drawn from its long experience in 2D printing – namely its Thermal Inkjet printheads and its leverage of IP around Latex, the long chain polymer used as a binder material in the process.
Binder jetting using the Metal Jet S100 is billed by HP as being 'ten-times more productive' than SLS methods, a vague statistic, but one that comes with some factors to back it up – there’s no need for inert gasses, hazmat suits, or high-power lasers. With production compartmentalised into individual build chambers, much like its polymer systems, there is potential for further automation, while parts can be sintered in an existing oven.
The fast swapping out of printheads is a less complicated process to changing lasers, while HP says that the Metal Jet S100 comes with some of its most advance printer software, to help manage
efficiency, scalability and also predictive system maintenance to keep on top of those printhead swaps.
Services from HP will also include this to help users identify, optimise, and accelerate designs and applications, while onboarding and maintenance services will be launched to help deploy, scale and maintain OEE for Metal Jet factories.
A launch case study features the Metal Jet S100’s use by GKN to build a new filter used on Schneider Electric’s NSX breaker, which could not be achieved with conventional industrial manufacturing capabilities due to the shape and material complexity.
www.hp.com
PTC Onshape invests in cloud-native CAM
PTC has acquired cloud-native CAM solution CloudMilling, allowing it to add ‘accessible from anywhere on any device’ CAM functionality to its Onshape platform.
Like Onshape, CloudMilling was designed for the cloud, while offering familiar features for machinists and engineers, including 2-axis and 5-axis toolpaths capable of being generated ‘in a matter of seconds’; a fully integrated tool library that keeps track across all workspaces; and real-time visualisation capabilities for following tool paths, tracking stock changes, and verifying material removal.
By being on the Cloud, CloudMilling says its workspaces can handle hundreds of parts simultaneously, each with their own job and related operations – potentially allowing users to machine an entire car
and all of its individual components in a single workspace.
Meanwhile, PTC has introduced Onshape-Arena Connection, which connects its cloud-native Onshape product development and Arena product lifecycle management (PLM) solutions. www.beta-cae.com
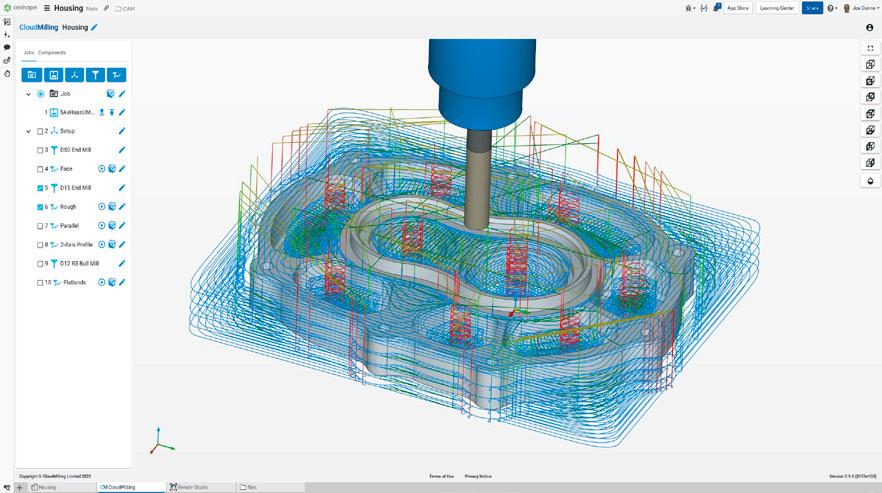
CloudMilling says its workspaces can handle hundreds of parts simultaneously
ROUND UP
Open Design Alliance (ODA) has announced a new initiative to develop a MCAD SDK, an open exchange framework for 3D CAD to provide access to all major proprietary 3D CAD formats including Dassault Systèmes Solidworks and Catia, Siemens Solid Edge, PTC Creo and more www.opendesign.com
Altair has acquired RapidMiner’s low-code platform to help develop production-scale data pipelines and machine learning models. It will be integrated within Altair's existing tools, such as Altair Knowledge Studio, Altair SmartWorks, and Altair SLC www.rapidminer.com
LimitState:Fix 4.0 has been announced for 3D model mesh repair, adding new features for faster repairs, splitting shells into multiple parts, and more batch uses. The software, which 'automatically heals' 3D mesh files for print or other end use applications, utilises Polygonica mesh processing technology www.limitstate.com/fix
The Bantam Tools Explorer
CNC milling machine has landed in a package that weighs around 23kg, and has been designed with power and portability in mind. It boasts a durable exoskeleton, the ability to run on battery power, and can be transported in a pelican case www.bantamtools.com
AMD has updated AMD Radeon ProRender for Autodesk Inventor, for handling reviewing, editing, lighting, material editing, and final rendering of Inventor assemblies, all enabled with Pixar’s USD as well as MaterialX technologies. It works with all different brands of GPUs www.amd.com
NVIDIA RTX 6000 GPU DELIVERS BOOST FOR BOTH VISUALISATION AND SIMULATION
» High-end workstation GPU not only boasts more powerful hardware, but promises to boost performance further by changing the way viewports and scenes are rendered
Huang made no reference to how DLSS 3 might benefit professional 3D applications. But while DLSS 2 was used mainly in GPUlimited viz applications such as Enscape and Autodesk VRED, we wonder if DLSS 3 might deliver big performance gains for 3D CAD, which tends to be CPU-limited.
Nvidia has launched the Nvidia RTX 6000, a high-end workstation GPU built on the company’s new 'Ada Lovelace' architecture.
The RTX 6000 is said to deliver up to two to four times the performance of the previous generation ‘Ampere’ RTX A6000 and promises to deliver big advances in real-time rendering, graphics, AI and compute, including simulation.
The RTX 6000 is a dual-slot card with 48GB of GDDR6 memory (with ECC), a max power consumption of 300W and support for PCIe Gen 4.
The GPU offers all the generational improvements you’d expect from a new architecture – third-gen RT Cores for ray tracing, fourth-gen Tensor Cores for AI compute, and next-gen CUDA cores for graphics and simulation – but there are also significant changes in the way the GPU carries out calculations to increase performance in graphics workflows.
One of these is Nvidia Deep Learning Super Sampling 3 (DLSS). DLSS has been around for several years and, with the RTX 6000, is now on its third generation. It uses deep learning-based upscaling techniques, where frames are rendered at a lower resolution and the GPU’s ‘AI’ Tensor cores are then used to predict what a high-res frame would look like.
With Nvidia’s previous generation ‘Ampere’ GPUs, DLSS 2 took a lowresolution current frame and the highresolution previous frame to predict, on a pixel-by-pixel basis, what a high-resolution current frame would look like.
With DLSS 3, the AI generates entirely new frames, rather than just pixels. It processes the new frame, and the prior frame, to discover how the scene is changing, then generates entirely new frames without having to process the graphics pipeline.
According to Nvidia CEO Jensen Huang, this approach means DLSS 3 will benefit both GPU and CPU limited games.
The RTX 6000 also supports Shader Execution Reordering (SER). Huang explained that GPUs are most efficient when processing similar work at the same time. However, with ray tracing, rays bounce in different directions and intersect surfaces of various types. According to Huang, this can lead to different threads processing different shaders or accessing memory that is hard to coalesce or cache.
With SER, the RTX 6000 dynamically reorganises its workload, so similar shaders are processed together. According to Nvidia, SER can deliver a two to three times speed-up for ray tracing and a frame rate increase of up to 25%. The company did not announce which applications will take advantage of this technology.
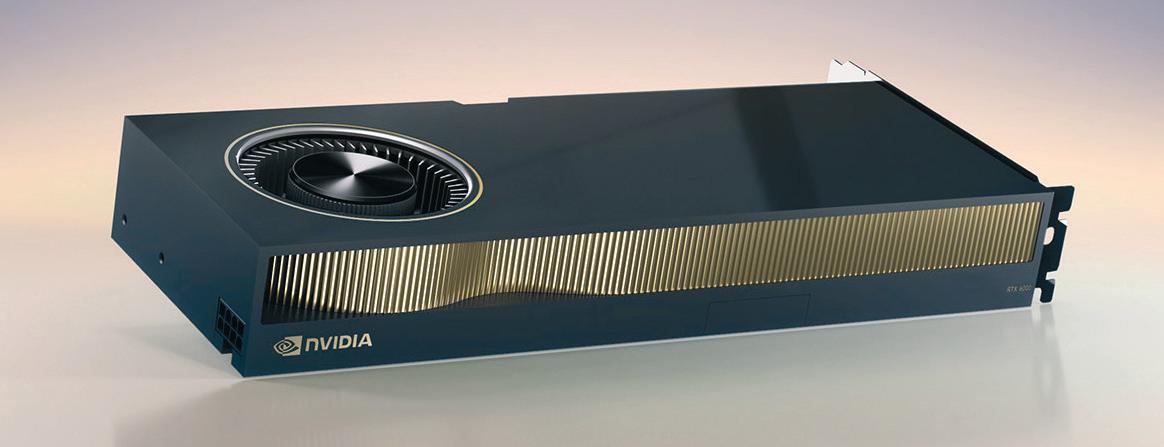
Nvidia also explained how the new GPU can benefit simulation, demonstrating computational fluid dynamics (CFD) examples in Ansys Discovery and Ansys Fluent. It highlighted how, with the RTX 6000’s 48GB of memory, designers can increase the fidelity of the solver to perform more accurate simulations and still obtain the results in near real time. www.nvidia.com/RTX
AMD boosts 3D performance in Solidworks and other OpenGL apps
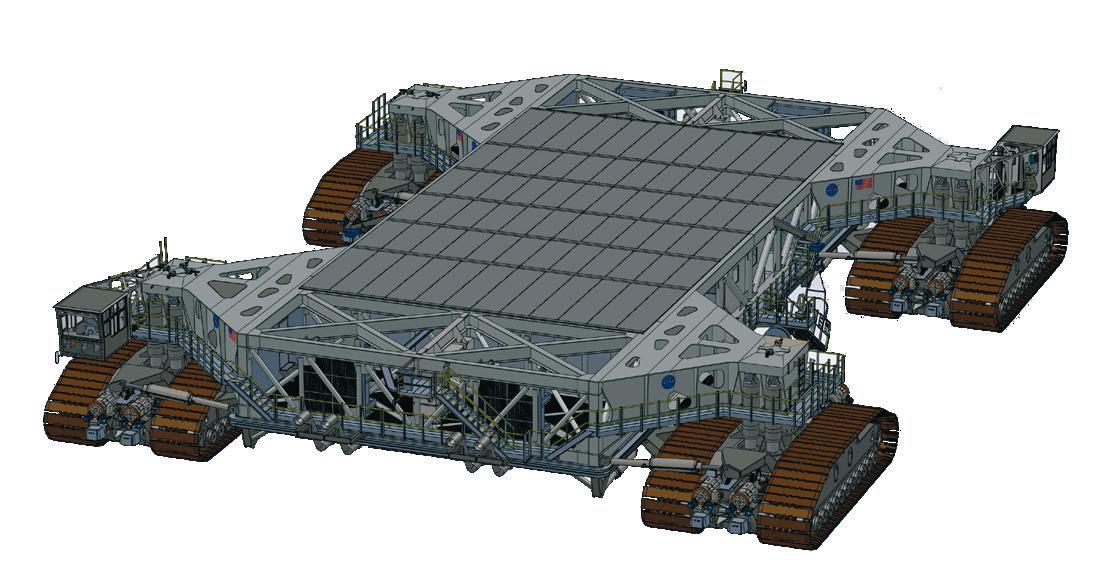
AMD has launched a new professional graphics driver that is said to provide a major performance uplift in CAD and other 3D applications that rely on the OpenGL graphics API. This includes Dassault Systemes Solidworks, Autodesk Maya, Trimble SketchUp and McNeel Rhino.
The re-architected driver (AMD Software: Pro Edition 22.Q3) works with current generation and older generation Radeon Pro GPUs.
AMD has released performance figures that show gains ranging from 0% to 76% in the SPECviewperf 2020 benchmark.
Initial testing in DEVELOP3D's labs demonstrate performance gains can be even higher — close to 300% faster in
visualisation software Autodesk VRED Professional 2023 and over 200% faster in Solidworks 2022. However, our testing
applications, when using large assemblies that do not fit entirely into GPU memory, or with particularly old GPUs such as the Radeon Pro WX 5100, which was released in 2016.
WHAT DEVELOP3D THINKS
It’s good to see AMD innovating in an area that can potentially bring huge benefits to users of 3D CAD. OpenGL might not be the future of graphics APIs, but it’s still used extensively in many 3D applications. Getting more out of your computer hardware for free is always a good thing, but it’s perhaps those with ageing graphics cards that can benefit most here.
While our tests show that the Radeon Pro WX 5100 slows down in Solidworks when using the new driver, AMD’s previous generation Radeon Pro W5500 gets a new lease of life, which in certain workflows, could deliver a big boost in productivity.
We will be testing out the new Q3.22 driver extensively in the Workstation Special Report in the next edition of DEVELOP3D.
INTEL GETS FIRST DISCRETE ARC PRO GPU WIN WITH LENOVO Automotive giants test Nvidia
OVX GPU systems
Lenovo has become the first major workstation vendor to offer a discrete Intel professional GPU in a mobile workstation.
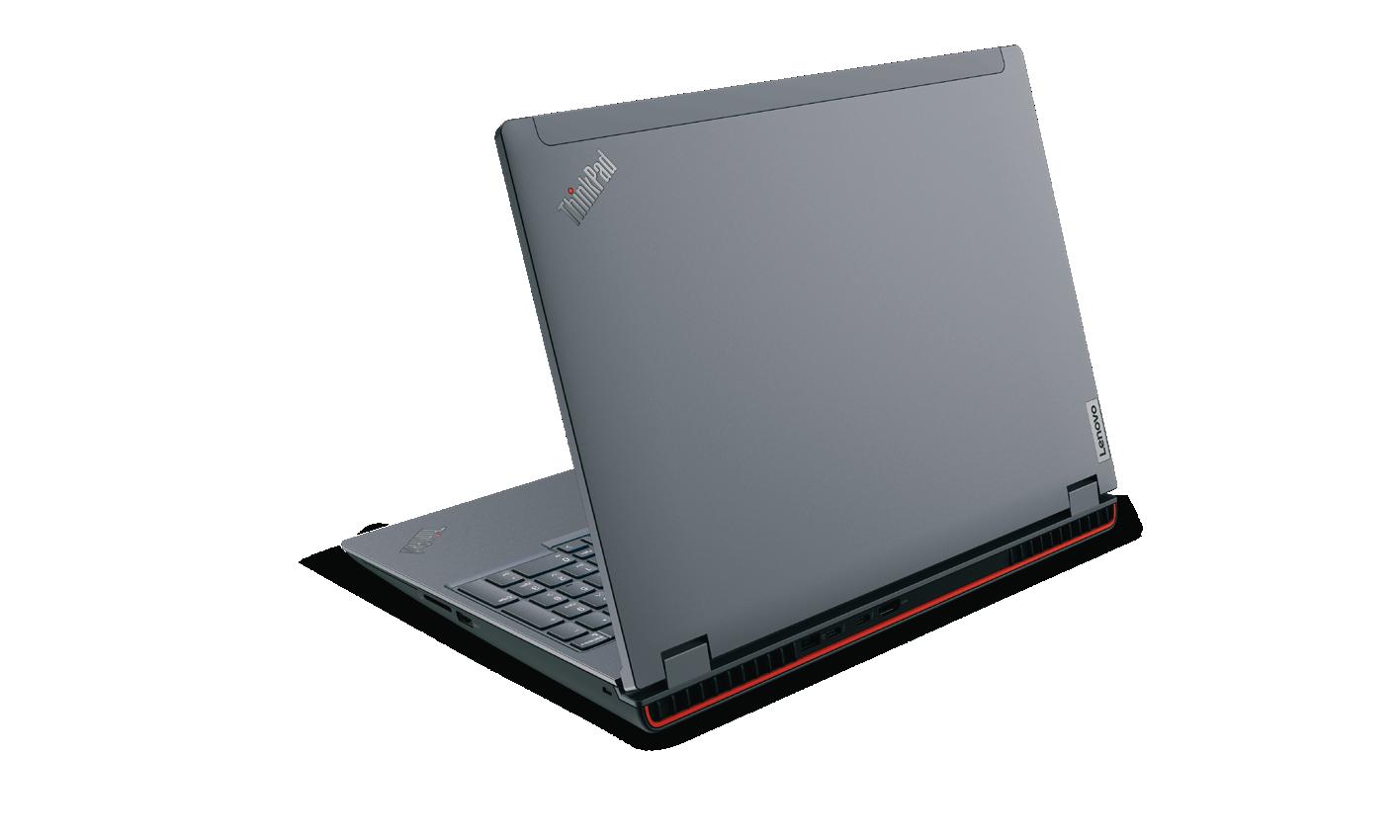
The Lenovo ThinkPad P16 Gen 1 can now be configured with the Intel Arc Pro A30M (4GB), as an alternative to the standard Nvidia options, which range from the Nvidia RTX A1000 (4GB) up to the Nvidia RTX A5500 (16GB).
The Intel Arc Pro A30M is an entry-level pro GPU, and is part of Intel’s much-anticipated entry to the world of discrete workstation graphics.
By offering the GPU in the powerful ThinkPad P16, it should give prospective buyers more choice for less demanding 2D and 3D workflows, such as CAD and BIM.
The Intel Arc Pro A30M also includes hardware-accelerated ray tracing and hardware-assisted AI (XeSS). On paper, this should make it suitable for ray trace rendering in applications that support Microsoft DX12/DXR, and ray tracing using the Vulkan API. However, those who take design visualisation seriously will likely
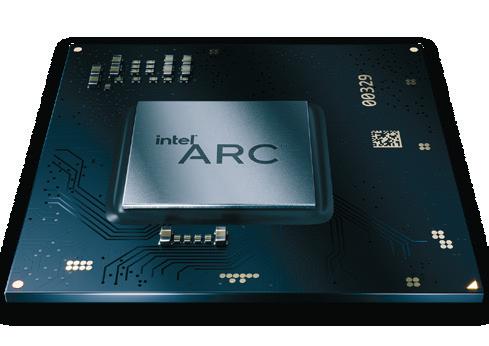
be better served by one of the higher-end Nvidia RTX GPUs.
For less demanding users, the Intel Arc Pro A30M GPU does offer considerable cost savings.
On Lenovo’s UK website, configuring the ThinkPad P16 with the Intel GPU instead of the lowest cost Nvidia option – the Nvidia RTX A1000 (4GB) – will shave £183 off the price of the laptop.
Selecting it in place of the Nvidia RTX A2000 (8GB) will save £413.
This is a significant first step for Intel as it looks to take on Nvidia and AMD, which both have a strong pedigree in workstation GPUs.
We have yet to hear news of any major workstation vendor offering Intel’s desktop pro GPUs – the Intel Arc Pro A40 and Intel Arc Pro A50. However, with 13th Gen Intel Core ‘Raptor Lake’ CPUs rumoured to launch in Q4 2022, any announcements could coincide with the new desktop workstations that will certainly follow. www.intel.com/ arcprographics
HP display boasts deeper and richer blacks
HP has introduced the HP Z32k G3 4K USB-C display with IPS Black Panel, a technology that offers double the contrast ratio of a traditional IPS panel for “deeper and richer” blacks.
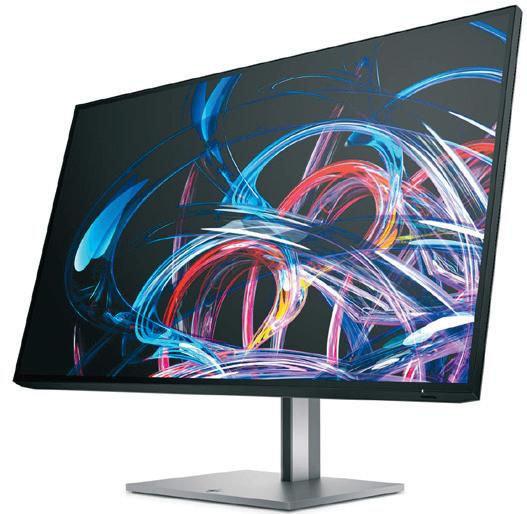
The 31.5-inch 4K display is said to offer ‘ultimate colour accuracy’ with support for 100% of the sRGB colour gamut and 98% of DCI-P3. According to HP, it allows users to experience anything from CAD drawings to product renders in tangible, lifelike detail.
Beyond image quality, the HP Z32k G3 4K USB-C display also offers several practical features.
Through a single Thunderbolt
4 connection, the display drives 4K resolution at 60Hz, supports daisy chaining for a second 4K monitor without a dock, as well as high-speed data and internet — all while charging a device up to 100W.
‘Single power on’ allows users to turn on their workstation by simply pressing the power button on the bottom right of the display. “You no longer need to open the laptop and hunt for the power button,” says HP’s Aaron Slessinger.
KVM switch allows easy switching between two workstations – a laptop and a desktop, for example.
Users can also save space by attaching a HP Z2 Mini Workstation at the rear. www.hp.com
The HP Z32k G3 4K USB-C display offers double the contrast ratio of a typical IPS panel
B
MW Group and Jaguar Land Rover will be among the first companies to test second generation Nvidia OVX systems with Nvidia L40 GPUs, designed to power large-scale Omniverse digital twins.
“Planning our factories of the future starts with building state-of-the-art digital twins using Nvidia Omniverse,” said Jürgen Wittmann, head of innovation and virtual production at BMW Group. “Using Nvidia OVX systems to run our digital twin workloads will provide the performance and scale needed to develop large-scale photorealistic models of our factories and conduct true-to-reality simulations that will transform our manufacturing, design and production processes.”
“Nvidia OVX and Drive Sim deliver a powerful platform that enables us to simulate a wide range of real-world driving scenarios to safely and efficiently test our next generation of connected and autonomous vehicles as well as to recreate the customer journey to demonstrate vehicle features and functions,” said Alex Heslop, director of electrical, electronic and software engineering at Jaguar Land Rover.
“Using this technology to generate large volumes of high-fidelity, physically accurate scenarios in a scalable, cost-efficient manner will accelerate our progress towards our goal of a future with zero accidents and less congestion.”
Second-generation Nvidia OVX systems will be available from Inspur, Lenovo and Supermicro by early 2023.
Samsung 990 Pro SSD launches
Samsung has announced the SSD 990 Pro, a new highperformance PCIe 4.0 NVMe SSD designed for desktop and mobile workstations.

Samsung claims the M.2 form factor SSD offers the highest speed currently available from the PCIe 4.0 interface.
to the 980 Pro it replaces, the 990 Pro is said to deliver faster sequential read and write speeds and even bigger gains in random read/write performance.
AMD RYZEN 7000 SERIES CPUS LAUNCH WITH BOOST FOR CAD AND RENDERING
» ‘Zen 4’ CPUs feature a 5.7 GHz boost frequency and a significant Instructions Per Clock (IPC) increase, compared to AMD's previous generation ‘Zen 3’ architecture
AMD has launched the Ryzen 7000 Series, a new family of desktop processors based on its 5nm ‘Zen 4’ architecture. This includes the flagship 16-core Ryzen 9 7950X, which AMD claims is the fastest desktop CPU in the world, featuring a 5.7 GHz boost frequency and a significant Instructions Per Clock (IPC) increase, compared to its previous generation ‘Zen 3’ architecture.
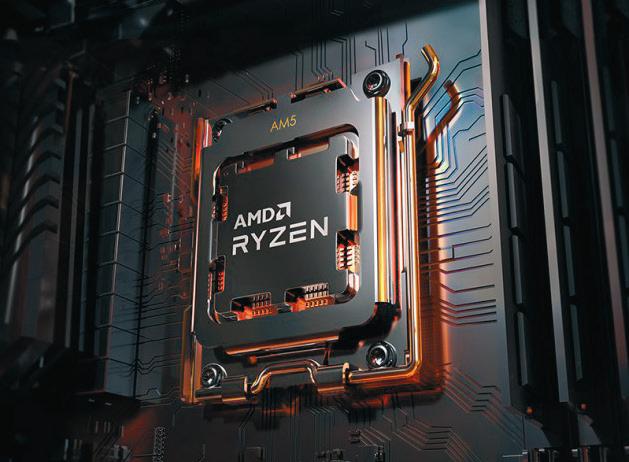
According to AMD, the Ryzen 7000 Series will outperform 12th Gen Intel Core processors in both single-threaded workflows (which is important for CAD and BIM) and multi-threaded workflows, such as ray trace rendering.
In V-Ray Render, for example, AMD claims the Ryzen 9 7950X offers 62% more performance than the Intel Core i9-12900K, Intel’s current flagship mainstream CPU which has 8 Performance cores and 8 Efficient Cores. Performance gains in other rendering benchmarks are smaller, with Cinebench R23 NT quoted at 41% and Blender Render at 36%. However, with 13th Gen Intel Core ‘Raptor Lake’
CPUs just launching now (see below), AMD will soon face increased competition.
AMD’s Ryzen 7000 Series also marks a significant improvement over AMD’s previous generation ‘Zen 3’ Ryzen 5000 Series. Compared to the Ryzen 9 5950X, the Ryzen 9 7950X boasts a single-core performance improvement of up to 29% and up to 48% more performance when rendering in V-Ray and Cinebench R23 nT.
The Ryzen 7000 Series also offers “leadership energy efficiency”, claims AMD. The company states that the Ryzen 9 7950X is up to 47% more energy efficient than the Intel Core i9-12900K when ray trace rendering in the Chaos V-Ray Benchmark.
With a TDP of 170W, the Ryzen 9 7950X is more power-hungry than the 105W Ryzen 9 5950X it replaces. However, the 7950X wins out in performance per watt. It delivers the same performance as the 5950X, while using up to 62% less power, says AMD.
The Ryzen 7000 Series also marks the launch of the new Socket AM5 platform, which features dual-channel DDR5 memory and support for PCIe 5.0,
including next-generation SSDs.
There are currently four models in the AMD Ryzen 7000 Series – the 16-core Ryzen 9 7950X, 12-core Ryzen 9 7900X, 8-core Ryzen 7 7700X and 6-core Ryzen 5 7600X. The lower-core count CPUs, which are perhaps best suited to entry-level CAD and BIM workflows, also have slightly lower boost frequencies than the higher core count models.
www.amd.com/ryzen
Intel unveils 13th Gen Intel Core CPUs to set up battle with AMD
Intel has announced its 13th Gen Intel Core processor family, led by the Intel Core i9-13900K, which features 24 cores and a max turbo frequency of 5.8 GHz. The new ‘Raptor Lake’ CPUs will be available in desktop workstations later this year and will go head-to-head with the new AMD Ryzen 7000 Series, competing on a range of workflows from CAD and BIM to rendering and simulation.
13th Gen Intel Core processors pick up where 12th Gen Intel Core left off, with a hybrid architecture that features two different types of cores: Performancecores (P-cores) for primary tasks and slower Efficient-cores (E-cores). Workloads are split ‘intelligently’ using Intel’s Thread Director.
The big difference with 13th Gen Intel Core is that it has more E-cores than its predecessor. The flagship Intel Core i913900K, for example, has 16, double that of the Core i9-12900K. This should deliver a big performance lift in multi-threaded workflows such as rendering - as much as 41% faster, according to Intel.
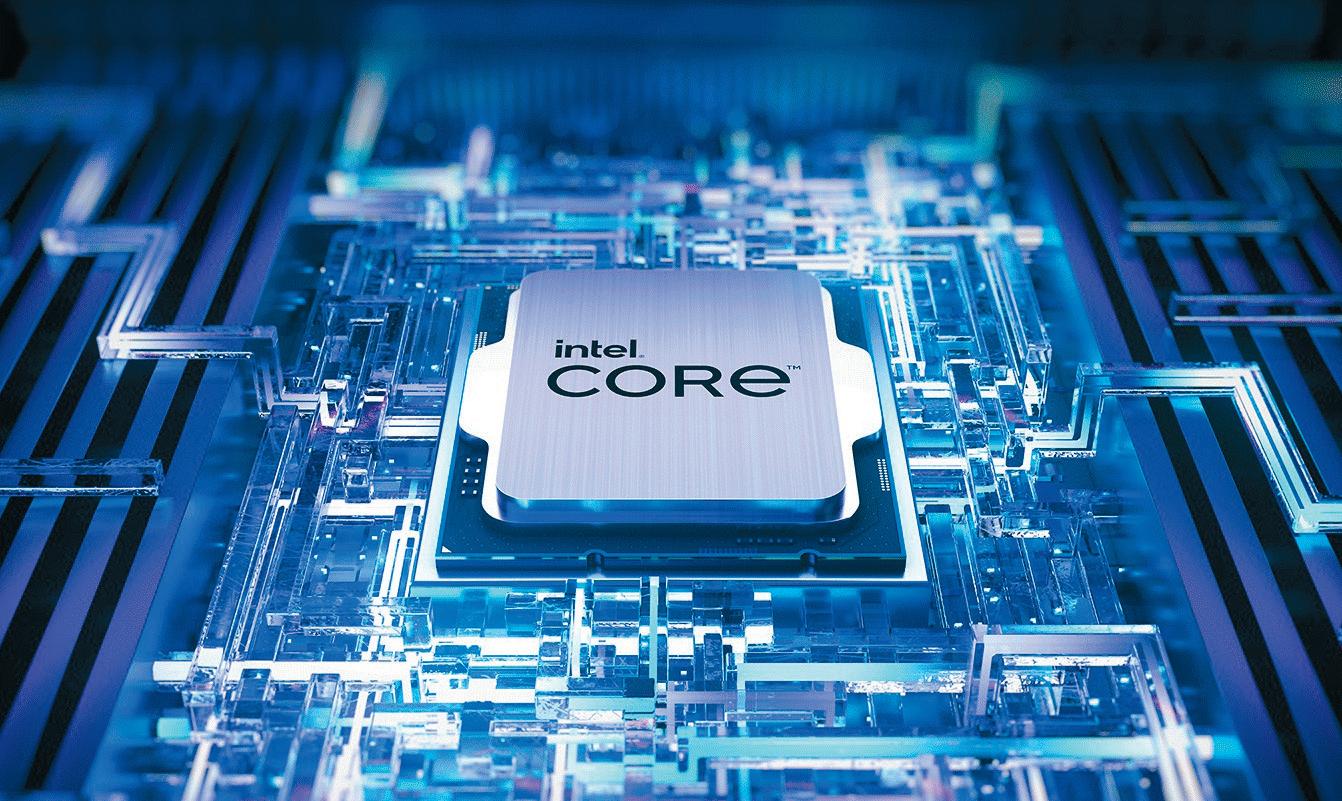
Of course, the P-cores have also been
enhanced and while their number remains the same (a total of eight in the Core i913900K), Intel says users can expect up to 15% better single-threaded performance compared to the previous generation. While the spotlight is on the flagship Core i9-13900K, Intel has launched six 13th Gen Intel Core processors – three with integrated graphics and three without. The Core i7-13700K and Core i513600K could be of more interest to price conscious architects and engineers with predominantly single threaded workflows, such as CAD and BIM.
WHAT DEVELOP3D THINKS
This is an incredibly exciting time for mainstream computer processors, with Intel and AMD both launching new architectures within weeks of each other. In recent years, AMD has certainly had a significant advantage for ray-trace rendering, but we now expect Intel to compete much more strongly in multithreaded workflows, as it did already in single threaded workflows like CAD.
Of course, when it comes to workstations, customers don’t always get a choice, with many large manufacturing firms being tied to procuring IT only from major manufacturers.
While we expect both 13th Gen Intel Core and AMD Ryzen 7000 Series workstations to be widely available from custom system builders like Scan, BOXX, Armari and Workstation Specialists, we still expect Intel to dominate among the tier ones. To date, Lenovo is the only one out of HP, Dell and Fujitsu to offer an AMD Ryzen processor in a mainstream workstation. Whether Ryzen 7000 becomes the catalyst for others to follow suit remains to be seen.
Begins
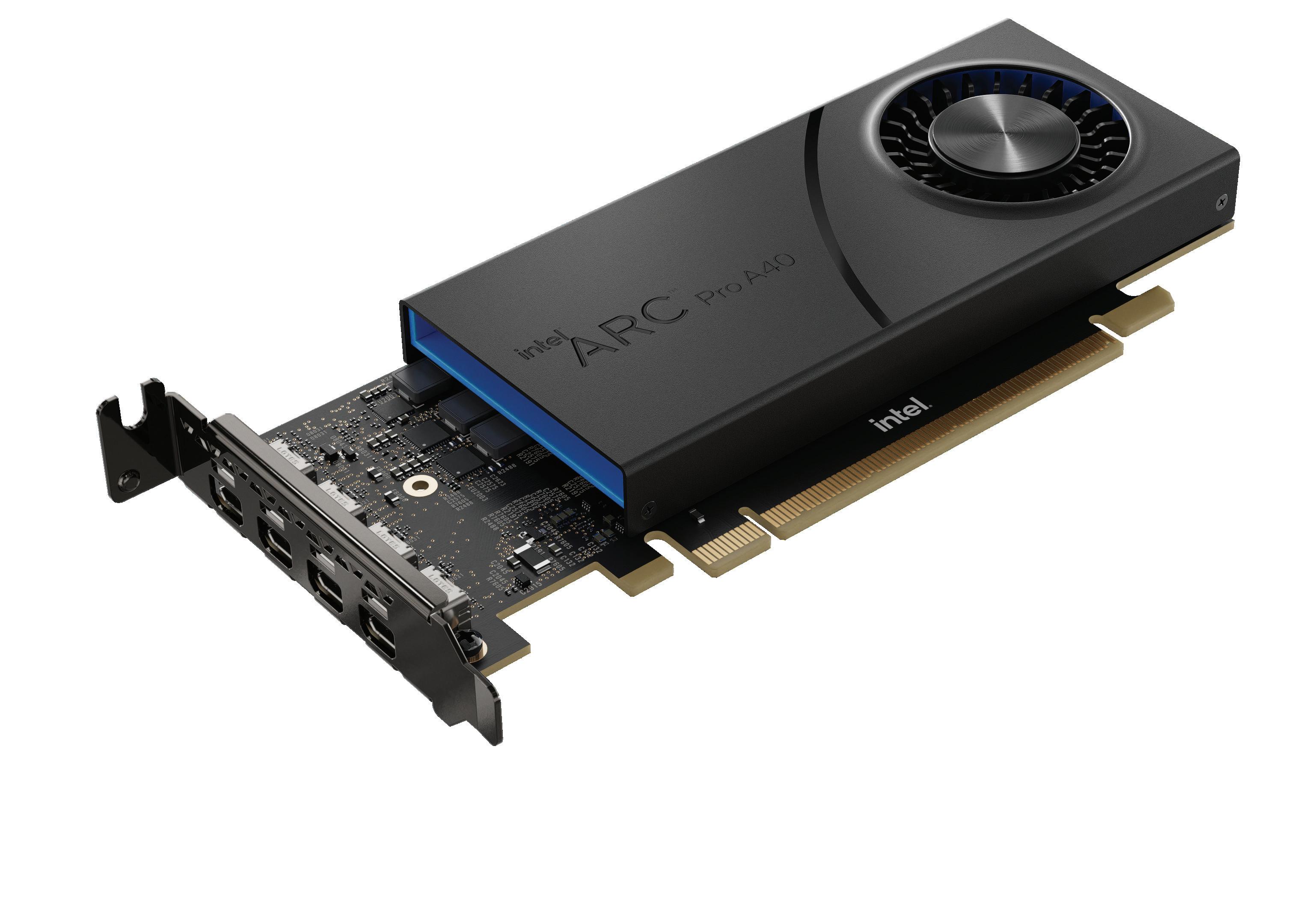
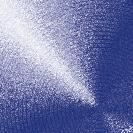

Diversity in product design can be a matter of life or death. As our columnist
SJ recounts, her recent experience with a pulse oximeter drives home the point that a lack of inclusive thinking can have devastating consequences
Diversity, equity, and inclusion – or DEI. Convenient lip service paid by companies and industries to show that they care about employees and customers. But does it really matter for design? I mean, diversity of thought always makes for better products, sure — but is it ever going to be important enough to be life or death?
I’m positive it is. “Yes, I’m positive” – the three most overused words since the 2020 outbreak of the Covid pandemic.
With shaky hands, I turned to my wife and showed her the tiny little rectangle with the two lines that matched hers.
We both had Covid. We both had underlying conditions. And we were both black, which makes us statistically twice as likely to be hospitalised with Covid, according to the Mayo Clinic.
As I lay there, barely able to pull air into my lungs, my wife’s hands shook as she struggled to fit the pulse oximeter onto my finger. “I can’t take you to the hospital for COVID treatment unless your oxygen reads less than 93%,” she mumbled.
A bunch of expletives flew from her lips as she took it off one finger and placed it onto another, over and over, trying to find a reading. There was none.
She took the device off my hand and tried it on hers – 99%. It worked, just not for me. A sob choked out of her lips as she whispered, “It’s not fair.”
My wife has always had complicated feelings about her biracial heritage. Hovering somewhere between not quite dark enough to be ‘black’, and not quite pale enough to pass for ‘white’, her identity and origin are always questioned whenever she enters a room.
How many drops of blood does it take to be considered black? For our marriage, it never mattered. But as I lay there, barely able to breathe, unable to obtain a pulse ox reading, we both felt the immense distance, this chasm between us – all down to nary but a few drops of blood separating us.
ONE SIZE DOESN’T FIT ALL
Pulse oximeters were widely adopted in standard medical practice in the late 1980s.
They are a non-invasive way to measure oxygen, using light absorption. The LED in the device sends light through the patient’s finger and then calculates their oxygenation, by figuring out how much of the light was absorbed by haemoglobin in the blood.
For people with darker skin – especially those of Black, Asian and Hispanic descent – skin pigmentation also absorbs this light, resulting in inaccurate readings.
For these patients, incorrect readings (which often report oxygen levels as being higher than they actually are) have prevented them from receiving critical oxygen support in Covid wards.
Many people have died as a result of this systemic exclusion. All because the original design of the device was tested on primarily white patients. And that comes as no surprise when you consider that the desegregation of the US-wide hospital system didn’t pass until 1964.
So, as I lay there listening to my lungs rattling against my ribcage, my blood ran cold not from lack of oxygen, but from the knowledge that it was a lack of diversity – of DEI – that could inevitably bring about my downfall.
I thought of all the social media posts I’d been bombarded with over the past two years. All of it sounding like lip service, because I know and deeply understand how slowly mindsets shift. The pulse ox was designed when civil rights was in its infancy – and this is just one example of 50 years of systemic inequality having the potential to literally kill someone. But in this case, not just anyone. Me.
DIVERSITY MATTERS
It’s DEI or die, right? As a black, gay, nonbinary person, I have many intersections when navigating predominantly white engineering spaces. And I’m often reminded that when one considers diversity, it is about so much more than skin color. There’s the diversity of gender – not just men and
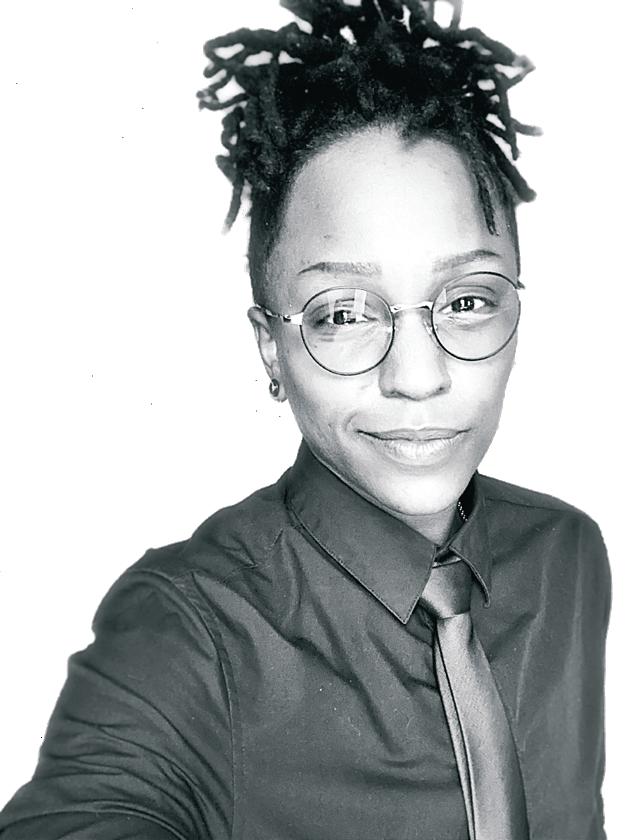
women, but non-binary and trans humans as well. Additionally, there’s diversity of mind –also called neurodivergence – which includes members of our communities struggling to disguise their autism, their ADHD. You can’t forget that one coworker who always has the answers to every problem but can’t seem to figure out how to convert a word doc to a PDF – that may be diversity of age. Finally, I’d also like to bring attention to our colleagues with disabilities, because making and creating spaces that are accessible make them safer and better for all.
All of this diversity gives us a magnanimous, wide-ranging horizon as we go forward creating new companies and new technologies. I think of the excitement sparked by the first iPod; the grimace (but also curiousity) generated by the Croc sandal; and the wonder that the first VR headsets sparked.
Those designs were novel and exciting –first-of-their-kind wonders that left us all hungering and hopeful for more. But, in my opinion, the single greatest attribute of a design that is determined to make an impact is that it is inclusive. For everyone and anyone at all intersections – no matter our race, gender, body shape or size, disability, age, neurodivergence or any combination thereof.
When it comes to engineering design, DEI is truly life or death. We are shaped by our environment – impacted by our diverse intersections – and this in turn shapes the products we produce.
Some would argue that recognising the physical or mental differences between us is in itself discriminatory, but not recognising and appreciating what makes each of us unique can have drastic consequences down to the healthcare we are given, on how we navigate the world.
ABOUT THE AUTHOR: Contributor SJ is a metal additive engineer, aka THEE Hottie of Metal Printing. SJ’s work involves providing additive manufacturing solutions and #3dprinting of metal parts to help create a decarbonised world.
Not recognising what makes each of us unique can have a drastic impact on how we navigate the world
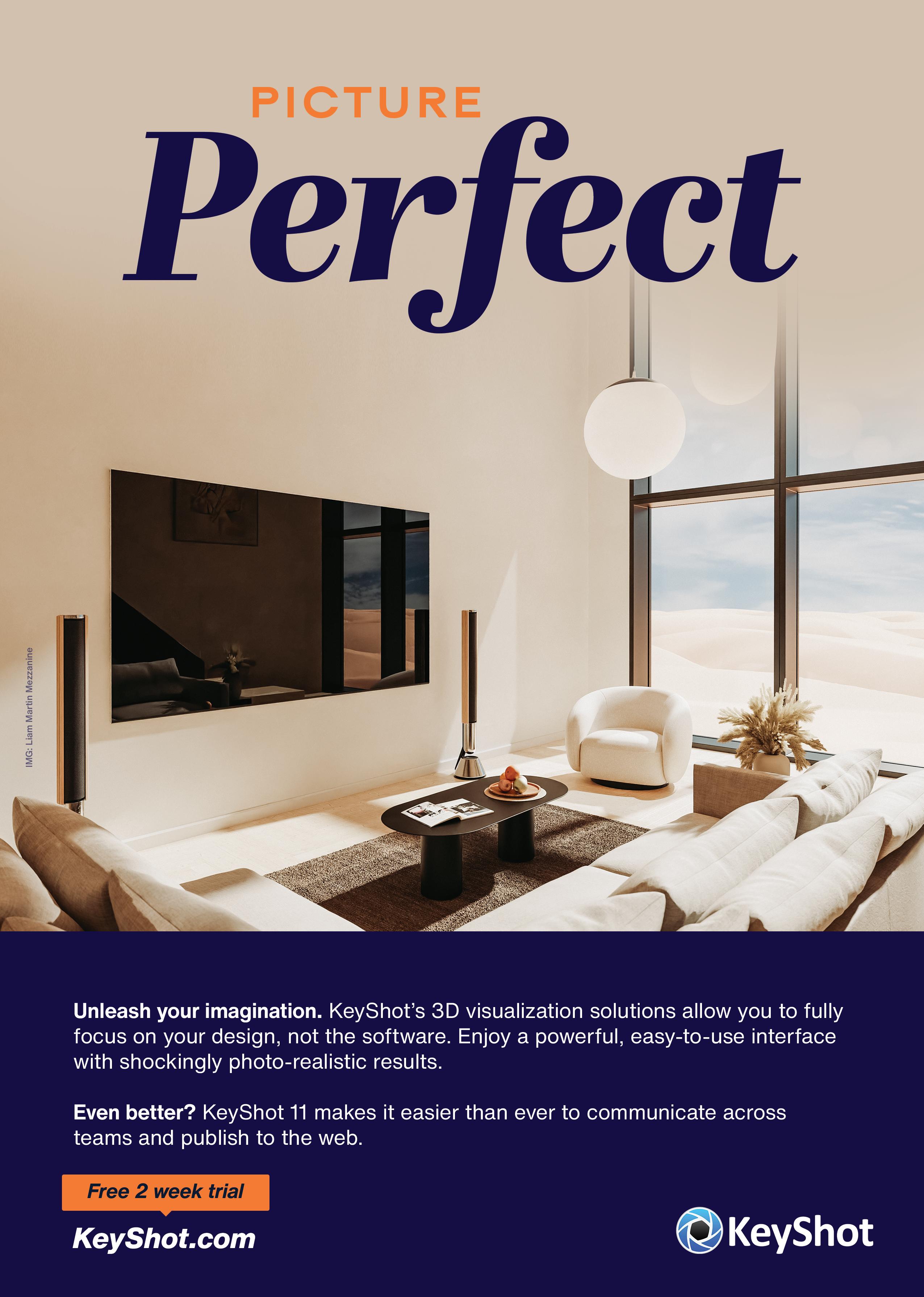

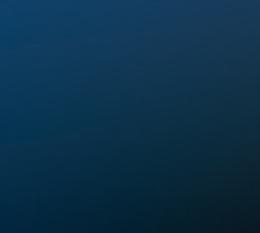

The means of manufacture has always had bearing on design, writes Matt Batchelor. For all its benefits in prototyping, 3D printing can disconnect designers from the end process and its overall impact
For most of my career, there has been pressure to prototype digitally, driven by desire to cut time to market and R&D expenditure.
When I worked at Fiat, a new virtual reality (VR) cave, bought for a rumoured sixdigits in 2007/8, was still only as expensive as one of tens of prototype tractors built for mechanical testing. But in most cases physical prototypes crept back in, either to test hard-to-model jobs like harness and hose routing, or else to enable us to mock things up in cardboard, full-size, as real ‘rapid prototypes’.
In the broader industry, the twentieth century succession of design-isms gave way to the generic organic-ergonomic-smoothgoodgrips-sex-toy-potato school of styling, made possible by the wide adoption of CAD/CAM and the move towards making everything in lightweight, low-maintenance, no-finishing-ops injection-moulded plastic, typically in low-wage countries.
Somewhere along the way, it seems, many of us forgot the link between material, process and form that made many classic industrial designs elegant, appropriate and, crucially for a mass-produced product, efficient to make.
You couldn’t produce the Blueberry G3 iMac in anything other than injectionmoulded plastics, in the same way as if you started to make a car front wing with a sheet of aluminium and an English roller, it would come out looking like an E-type or Ferrari 250.
A handsome iron casting, drop forging, ceramic insulator or hardwood table leg can only ever look like what it is, by letting it be what the material and process will permit.
A REFRESHING CHANGE
Fast-forward to 2022, and it was refreshing to walk around the New Designers this year, looking at tables full of FDM prototypes.
Low-cost, reliable FDM machines and maybe the end of ‘digital’ being a novelty means that cost and lack of workshop
machinery are no longer a barrier to a designer making quite a sophisticated ‘looks-like’ or ‘works-like’ model. The trouble is that these are rarely ‘made-like’ models; but why is that a problem?
On a minor level, things like lesscontrolled tolerancing, shrinkage, warpage and non-precision surface finishes compared to moulded or machined parts mean that even with state-of-the-art bureau machines, we’ve often had to debug the AM prototyping process before we debug the design.
The real problem is that design is not just the shape of an object, or even just its physical properties. In the design and engineering professions, we know about anthropogenic climate change, the many impacts of resource extraction, processing and disposal, and the impossibility of infinite consumption on a demonstrably finite lump of rock.
As a result, there is a consensus that we should be responsible for at least minimising or even eliminating the impact of the things around us.
I’ve heard it said that 95% of the cost of an object is determined in the first 5% of the design process. I would argue that the same is true of the broader resource cost of that object in its existence, use and eventual disposal.
INFORMATION LOSS
In the prototyping phase, 3D printers need an explicitly defined 3D shape to print, which means we lose some information about the material and the energy needed to turn it into an object.
Standing in an iron foundry, the enormous amount of thermal energy going into melting the iron is obvious. But then the complexity of shape that sand casting provides allows objects to be made more efficiently of one or several castings — rather than, say, a complex welded assembly or machining job.
Extrusions are an amazingly efficient way to get a complex functional cross-section,
provided that complexity can be in two dimensions.
Many early cultures independently learned how wood can be split, steam-bent and shaped to make high-performance sailing ships. A Viking ship on a close reach looks a thousand years more advanced in its speed and efficiency than a Maersk E-Class forcing its way through the water.
At Instrument, we’re working on a sustainability concept that involves some very involved metal forming to replace plastics.
And while our SLA printer has let us iterate a forming process very quickly by printing tool inserts, we could not make any progress if we weren’t working on a material of the right grade and gauge to make sure it all works in practice. By prototyping the process as well as the part, you naturally tend to design for the minimum of wasted material, energy or complexity; which details work and which can be forgotten.
It may be financially convenient to have a little shape-it-all box in the corner, but if we are to meet the ultimate design requirement of not making ourselves extinct, we need to think carefully about which design tools we use and when.
3D printing is amazing, but I sometimes worry that it belongs to the bad old ways.
ABOUT THE AUTHOR: Matt Batchelor is an industrial and engineering designer, and co-owner of Instrument Industries, a London-based design and manufacturing firm. He tolerates the company’s SLA machine, but wishes it was a Bridgeport.
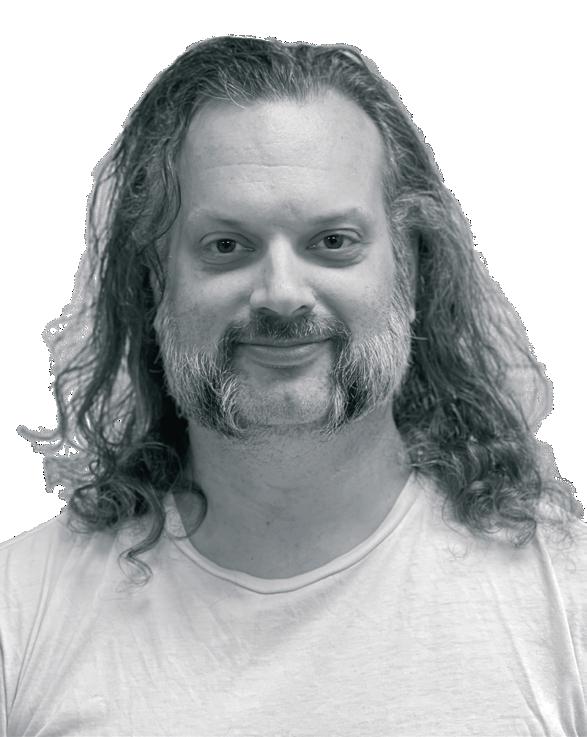
If we are to meet the ultimate design requirement of making sure that humans can continue to live without causing our own extinction, we need to be careful about the tools we use and when we use them
VISUAL DESIGN GUIDE SENNHEISER MOMENTUM 4
Focusing on sound quality, comfort and ease of use, the new Sennheiser Momentum 4 wireless headphones deliver an array of new technologies, neatly packaged in a minimalist lightweight design

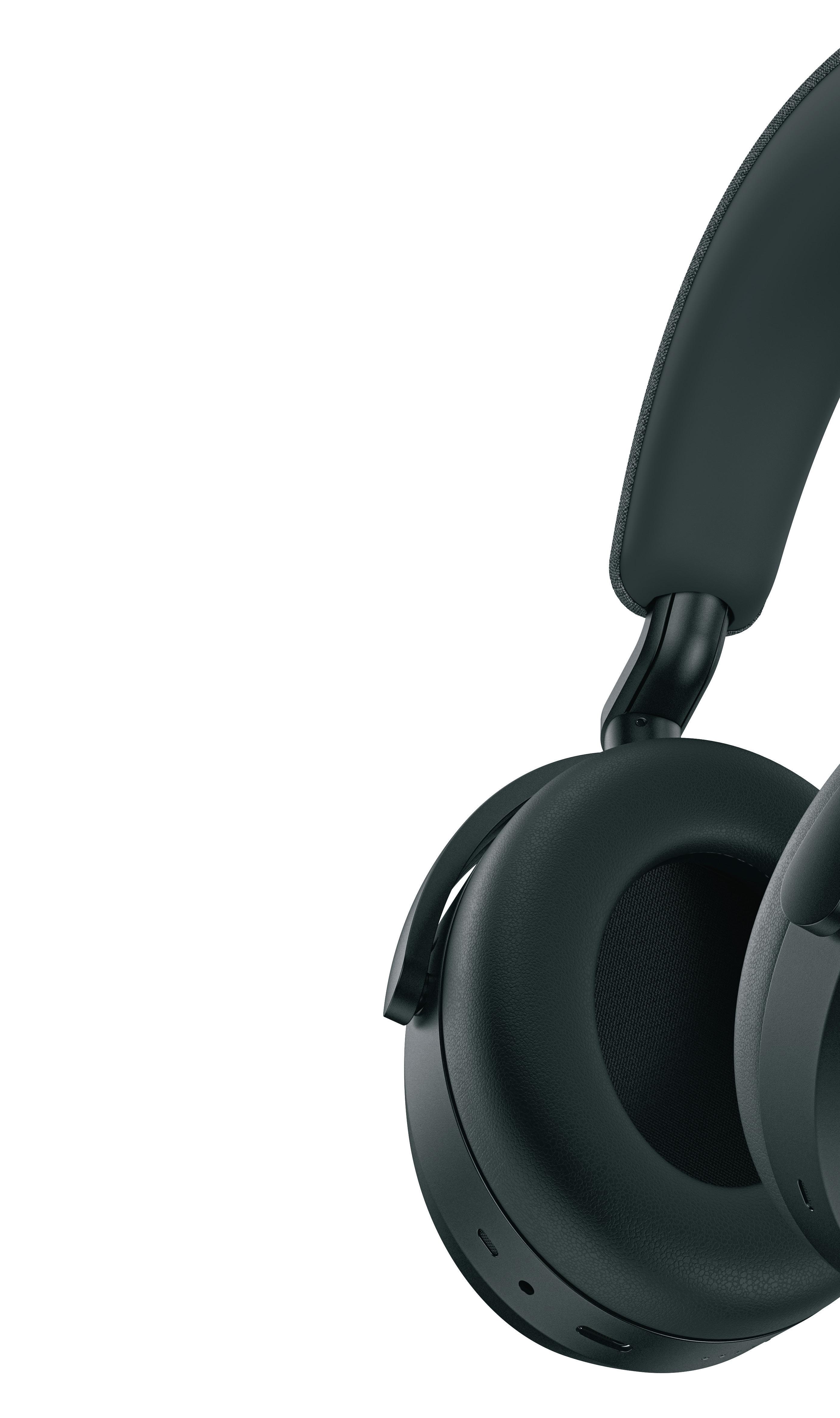
INVISIBLE MOVEMENT
A rotary axis above the clamp holding the ear cups is cylindrical in shape, allowing the slider to disappear into the headband. In this way, a uniform profile is maintained, regardless of how the user modifies the headband’s length or rotates the ear cups
SOFT AS CLOUDS
Cushioned ear pads ensure long-lasting comfort. The low-friction hinge mechanism adjusts to give a great fit without placing excess pressure on the head
UNLIMITED LISTENING
LED lights display battery level. Should the battery run out, typically after some 60 hours of use, an audio cable is provided for wired listening
ALL ABOUT BALANCE
The dent in the centre of the headband is intended to account for users sensitive to pressure on the top of their head, with the design ensuring even weight distribution
FULL IMMERSION
The headphones feature dual sets of outer and inner noise cancellation microphones, helping to keep out unwanted sound

PRICE AND AVAILABILITY Momentum 4 is available from Sennheiser, RRP £299.99 www.sennheiser.com

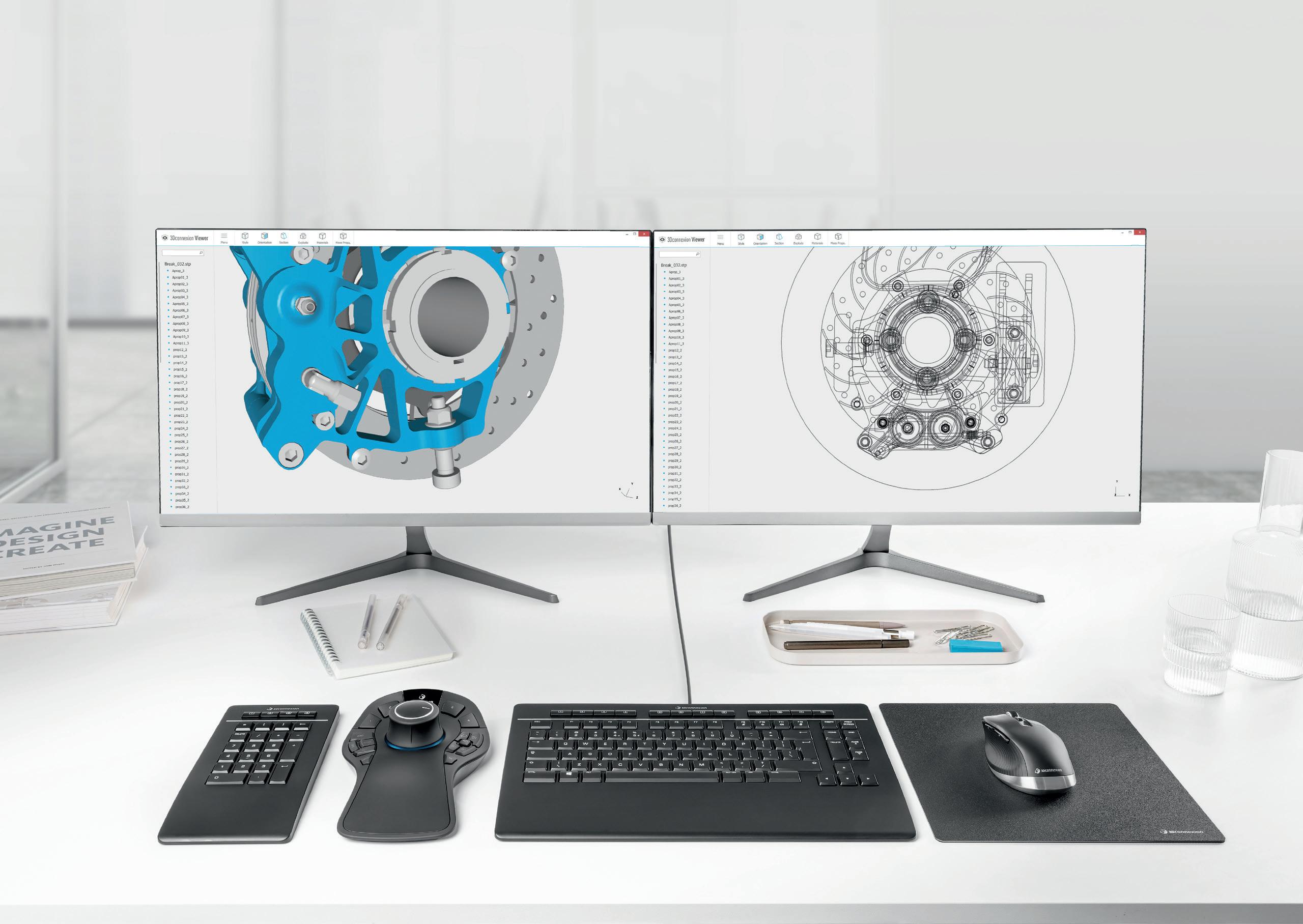
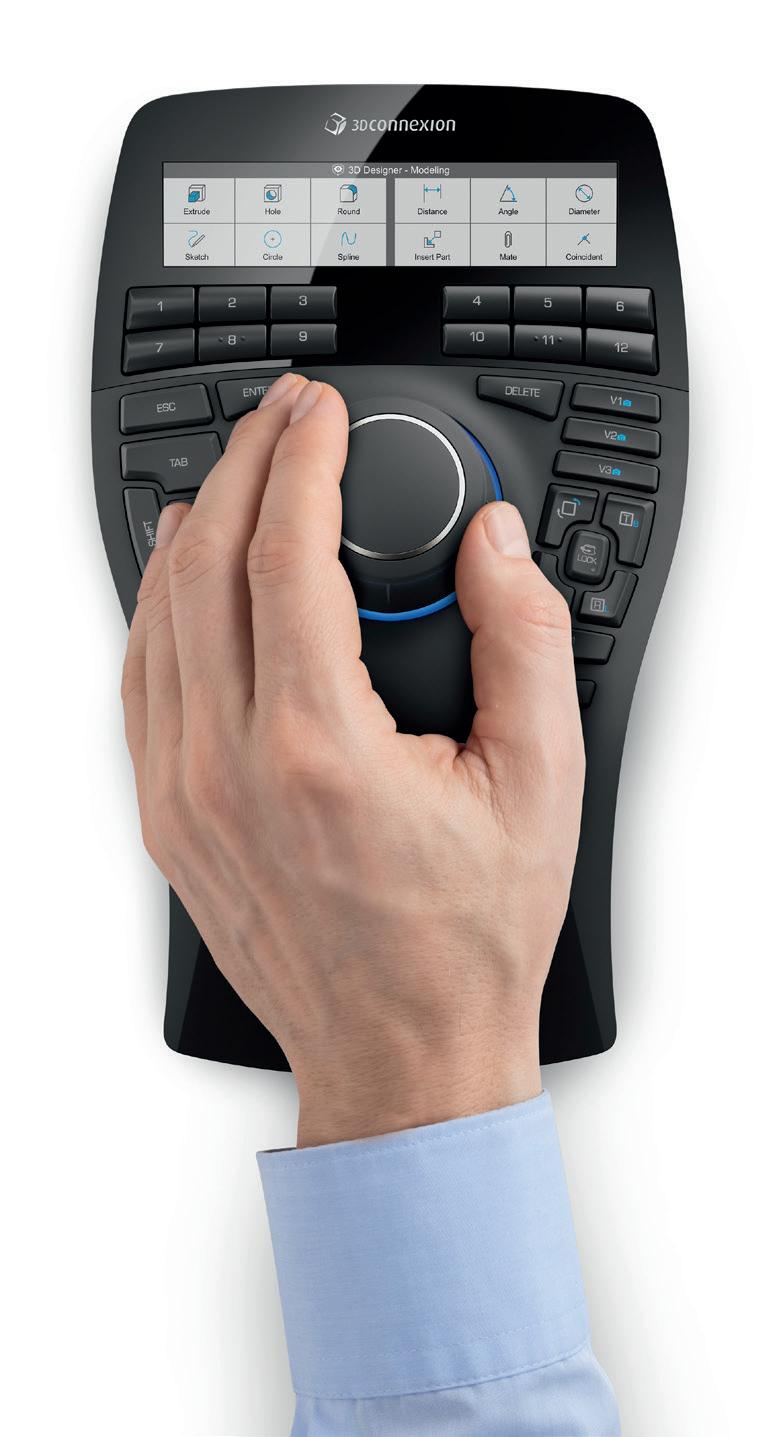
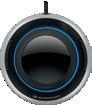
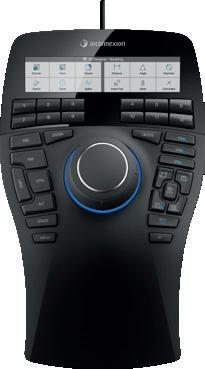
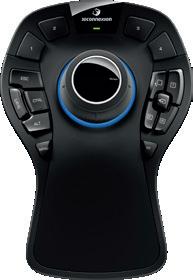

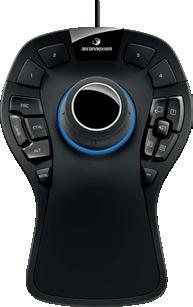
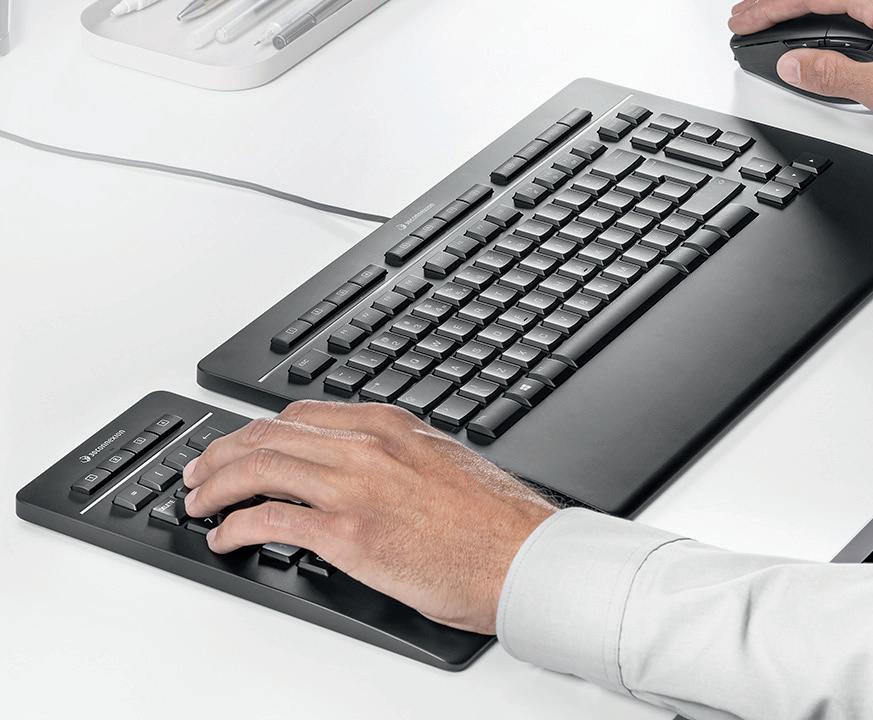
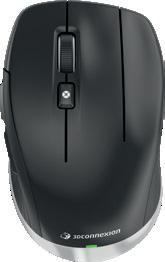

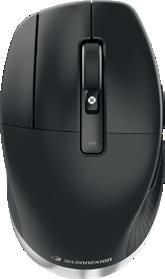
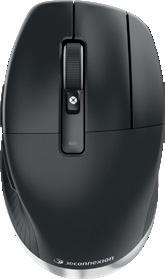
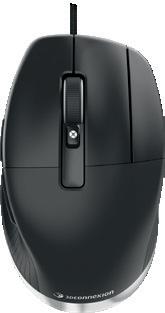
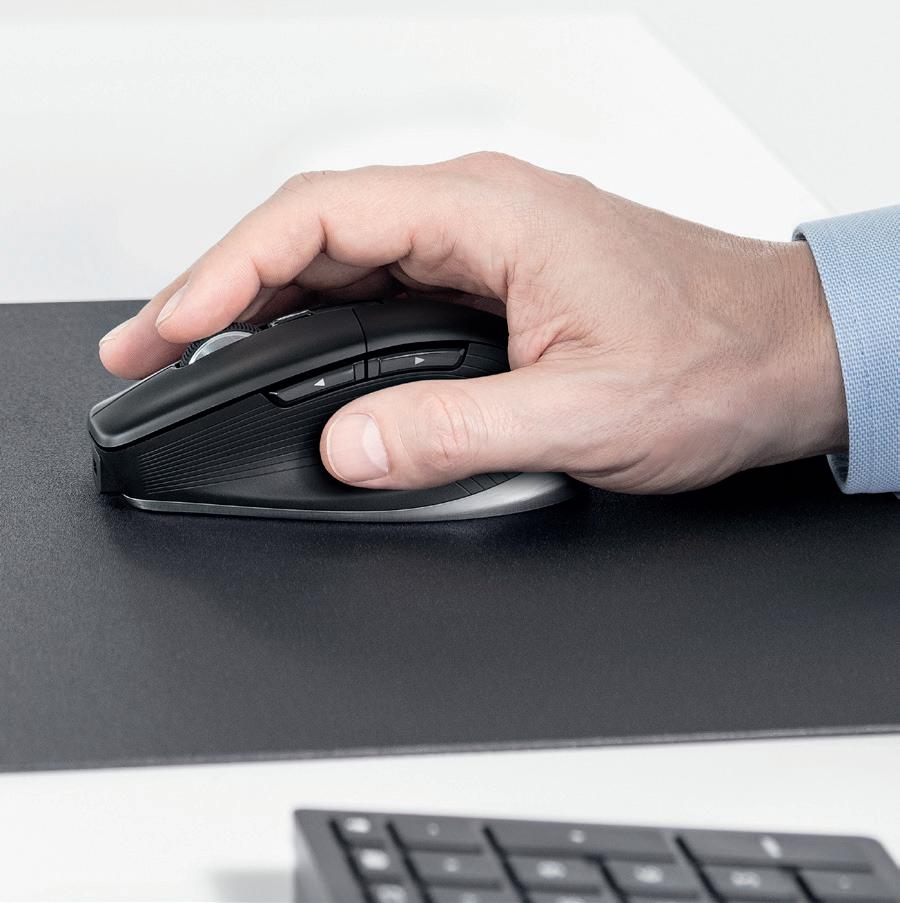

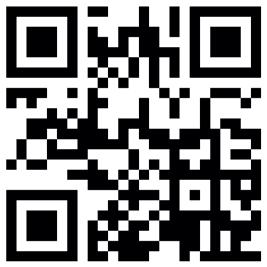
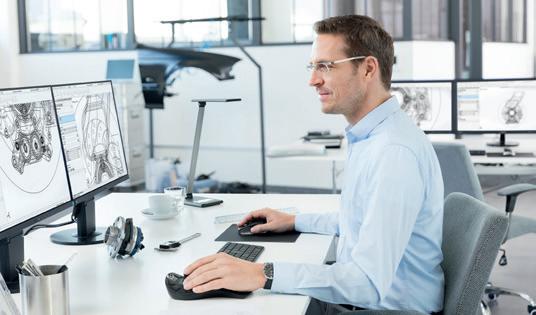
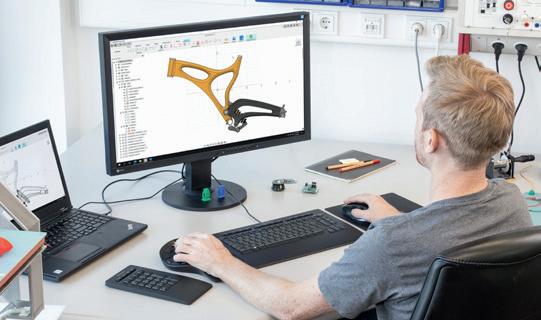
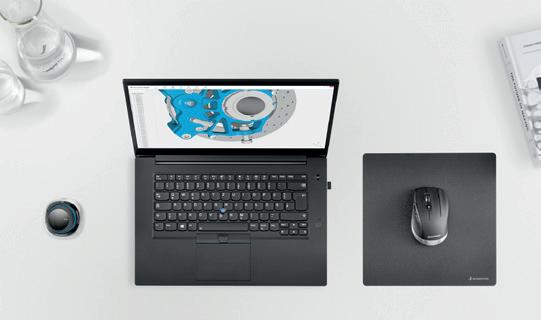
DREAMMACHINE
» Inspired by cafe racers and electric violins, the Arc Vector promises a truly unique experience for motorcycle enthusiasts looking for a high-end, all-electric ride. DEVELOP3D went behind the scenes to hear about the motorcycle’s design from Arc Vehicles CEO Mark Truman

MACHINE
Every Arc Vector is handcrafted in the UK to the individual owner’s requirements

It takes a very special motorbike to impress former British Superbike Championship runnerup and MotoGP rider James Ellison. In the Arc Vector, it looks like he has found that bike.
Over the summer of 2022, Ellison has been working with the team at Arc Vehicles, a spin-off from automotive company Jaguar Land Rover (JLR), to finesse the final spring and damper settings on the Vector’s innovative suspension system.
He certainly enjoyed the experience. “The way the machine carves up corners is incredible. Vector is definitely big on ‘grin factor’,” he says. “It’s just so different to anything else you will ride. I’ve been really surprised by the agility. The bike changes direction like a much smaller bike due to the steep steering angle it can run. This means the bike can be flicked from side to side with little effort.”
That glowing praise is all the more striking when you consider that the Arc Vector is the world’s first fully electric neo-cafe racer. And the team that designed it, led by Arc CEO Mark Truman, is no less infatuated with their creation.
Truman, a self-confessed motorcycle fanatic, regularly takes the bike out himself and jumped at the chance to ride alongside Ellison, to hone the final settings before the Vector goes into production. “Riding the Vector alongside James has been fantastic,” he says. “His perception and feeling for the slightest change to the settings are second to none and his experience goes without saying.”
CAFE RACERS AND ELECTRIC VIOLINS
Arc Vehicles was spun out of JLR in 2017. Truman, who previously led JLR’s White Space innovation team, developed an electric motorbike prototype during his time there. Management were so excited by the idea, that they happily gave their backing to the spin-out and to Truman’s ambition to build a market leader in electric recreational vehicles.
What Truman and his team also have is the freedom to work from first principles. “We’re very lucky in that our products are more at the premium end of the market, so that means we are able to deliver a vehicle from scratch each time and develop innovative products that really break the mould, rather than working from carry-over content from previous vehicles to save time and costs,” he says.
“So we can go right back to basics: ‘What are the use cases here? What would be the perfect product to fit those use cases?’ From there, we try to work in a way that is as unrestrained as possible, carrying that concept right through into production so that the final product is very much a representation of the idea we had right at the start of the project.”
So what was that idea for the Arc Vector? The answer is two-fold. First, the team wanted to create a very futuristic motorcycle, with retro flourishes. “We were thinking in terms of how a cafe racer would look, if the term ‘cafe racer’ was first coined ten years from now,” Truman says.
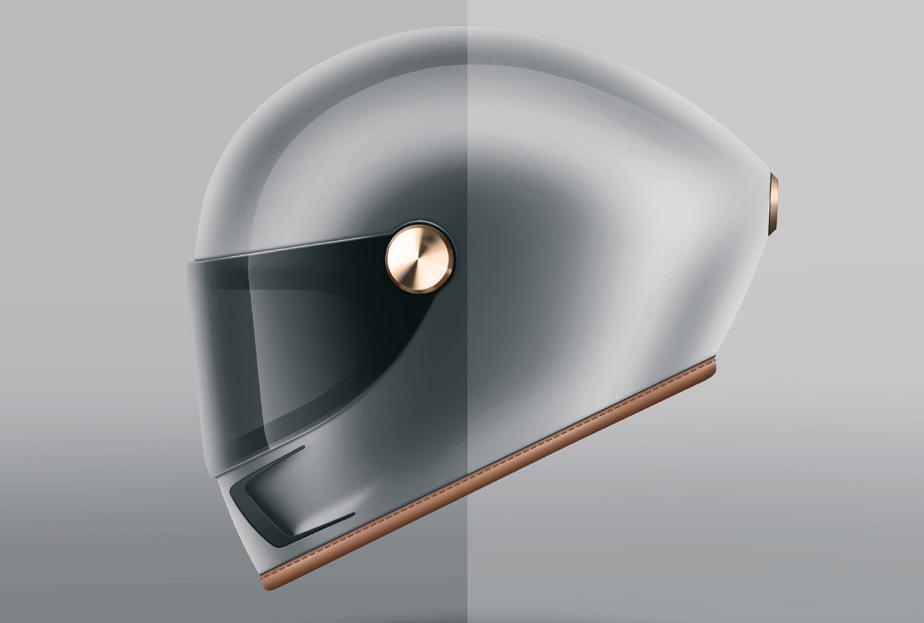
Second, they were inspired by the appearance of electric violins. “We found some beautiful pictures of instruments that had everything in place that they needed to make a beautiful sound, but where anything that wasn’t required had been taken away. We thought they were stunning and that seemed a really nice philosophy for our product, as well as other products from us in the future.”
To take these eclectic concepts to a production-ready product, the initial ideation process at Arc is very manual, but quickly moves into PTC Creo for 3D CAD. Arc has used PTC Creo since Day One of its existence, supported by Cambridge-based Root Solutions, part of the worldwide PDSVision group and PTC’s longest standing Platinum Partner in the UK.
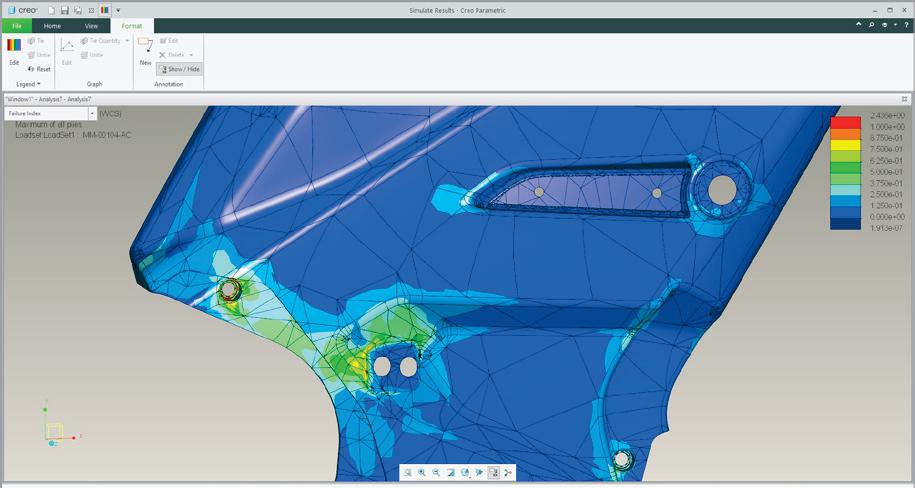
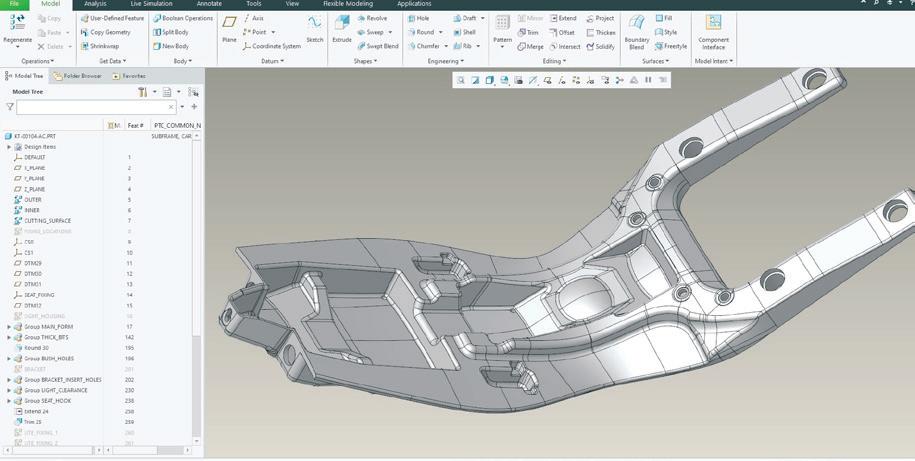
Initial ideation involves a lot of “whiteboards, blackboards, Post-it notes and mind maps”, says Truman, then 2D sketches, Illustrator, Photoshop and so on. A lot of 3D printing goes on, too, in an effort to move away from the traditional clay modelling processes typically associated with designing this kind of product. Rapid prototyping using 3D printing, Truman explains, makes it easier for designers and engineers to be working concurrently.
But work in Creo starts early, he says. “We’ll have designers working on surfacing in Creo and engineers using it to work on parts pretty early on, figuring out how parts will fix to the product, how we get that quality right, the gapping right and so on. We want to be thinking about all of that as early and as upfront as we possibly can.”
He and his team wanted to avoid a situation where designers create something and then throw it over the fence to engineers, who then have to try to make it work.
‘‘
We try to work in a way that is as unrestrained as possible, so that the final product very much represents the idea that we had right at the start of the project ’’
The

“That often results in a very argumentative process. The designer gets engineering back that isn’t quite the same as what they designed. Or engineers get stuck with trying to figure out something that’s just not possible or that’s going to be too expensive to achieve.”
Collaboration tools in Creo support that process, helping designers and engineers to share ideas easily and keeping all relevant, up-to-date information in one software package. The team at Arc is also using Creo’s generative design and design for additive manufacturing (DfAM) capabilities more and more, he says. They’ve given the team the ability to think more creatively and to assess manufacturing methods based on different attributes such as cost or weight, he says.
“We do a lot of reverse engineering on our early prototypes, to decide how we could create individual parts better. When you first set out, you’re probably not as concerned about costs, but when you start getting to the end of the process, you can really start to understand how much things might cost and then make changes,” he explains.
“So at that point, there’s a lot of scanning that goes on of those initial parts and then reverse-engineering the CAD that we’ve created, with reference to generative design, which informs us of improvements we might make. It’s fantastic to have that ability to revisit and refine with a high degree of accuracy.”
Since around 50% of the manufacture of the Arc Vector
is outsourced to specialists, these collaborative features are also a help in working with suppliers. “Obviously we don’t really share the full bike with anybody in the outside world, but Creo helps us to share relevant 3D CAD information and drawings with the companies we work with.
ACCELERATING INNOVATION
All this has led to a final design that can boast some truly innovative features. The Arc Vector utilises a carbon front-swing arm and hub centre steering, resulting in a bike that feels similar to one that uses front forks, but offers increased stiffness and the ability to run on steeper steering angles. With hub centre steering, for example, the Vector runs a 20-degree rake angle.
The company is also looking to get great feedback from 10 customers who will participate in a programme to help develop the Arc’s human-machine interface (HMI) system. Each participant will receive an Angel Edition (AE) Vector motorcycle and engage with a testing programme to try out prototype versions of the HMI system on tracks in the UK and US. Their direct feedback will be incorporated into the system until it is ready for the open road. According to Truman, it’s not just the “ultimate peek behind the curtain” for participants, but also a way to create a system that will boost enjoyment and safety of the product for future owners.
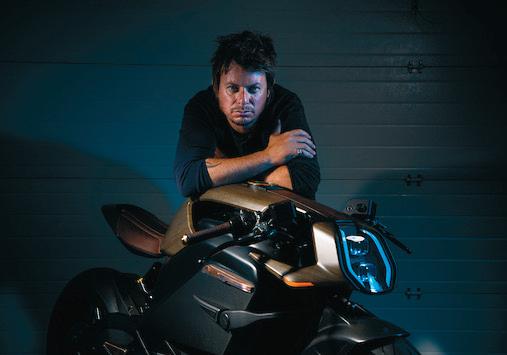
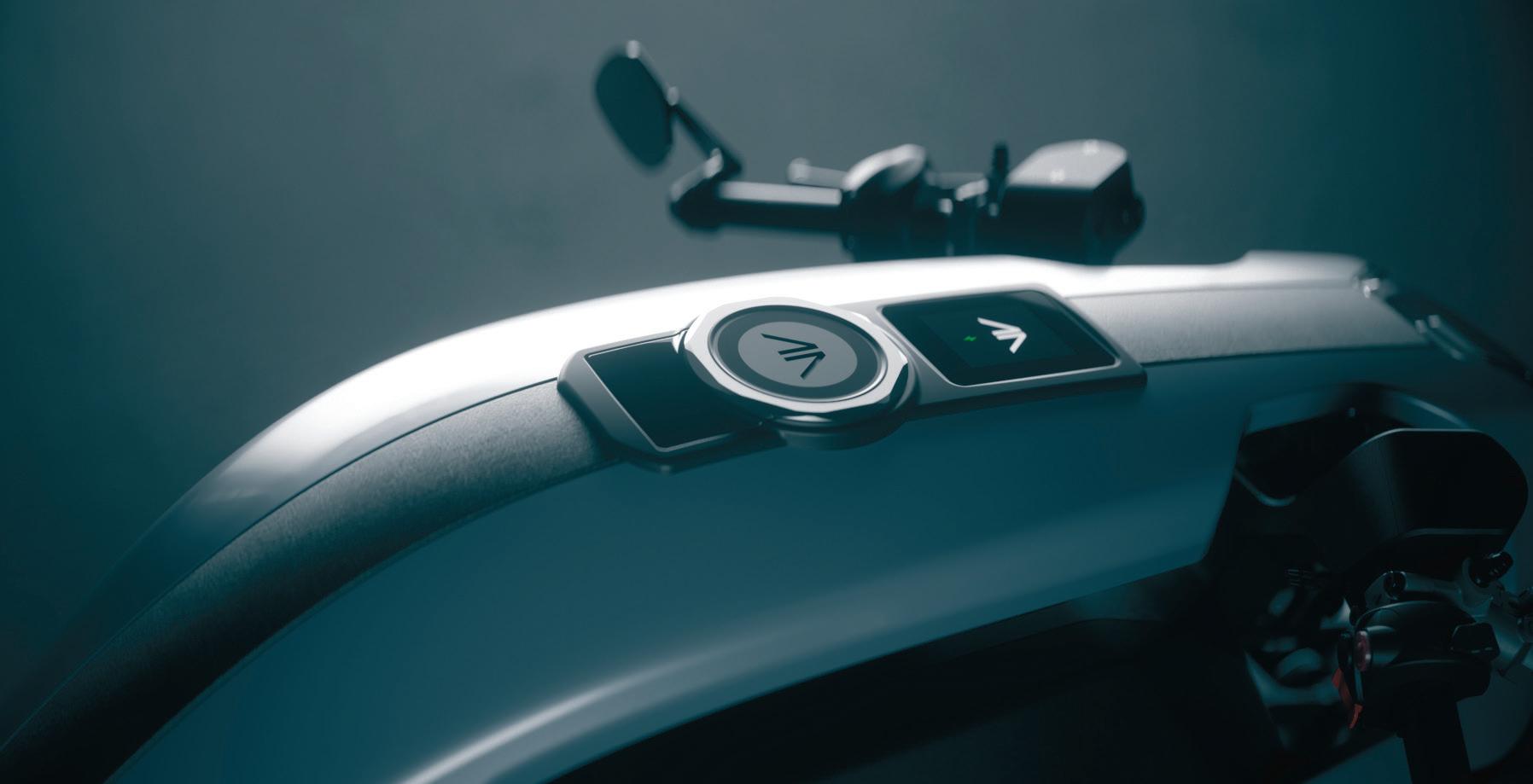
And since this is a premium product, those owners are given extensive opportunities to customise their Vector, resulting in a vehicle that is truly bespoke. Invited to Arc’s commissioning suite at its Coventry headquarters, they can choose between a wide range of finishes and extra features.
On top of this, an augmented reality (AR) experience will enable them to ‘see’ their Vector, parked in their own garage or on their front drive, both before and after those bespoke touches are added. This AR application was developed for Arc by Root Solutions.
“We are putting all our best creative thinking into ensuring that buying, owning and riding an Arc Vector will be a truly unique experience for owners — something very special indeed,” Truman promises.

BEST 3D SCANNERS forthe DESIGN STUDIO
» Buyer beware: choosing the right 3D scanner can be hard. There are lots of models available, at lots of price points. Performance varies widely, as does suitability for specific use cases. Claudia Schergna takes a look at some of the best of the bunch, with the needs of product designers firmly in mind
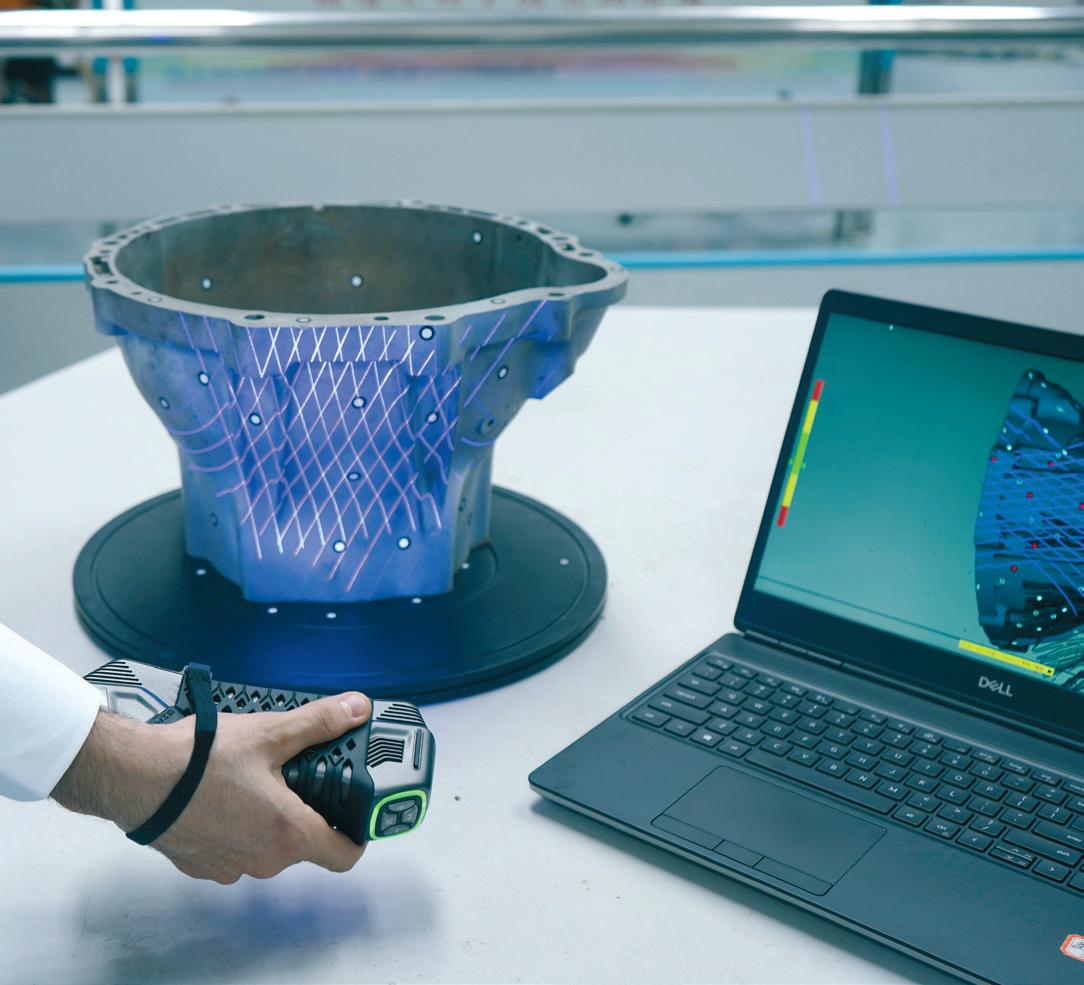

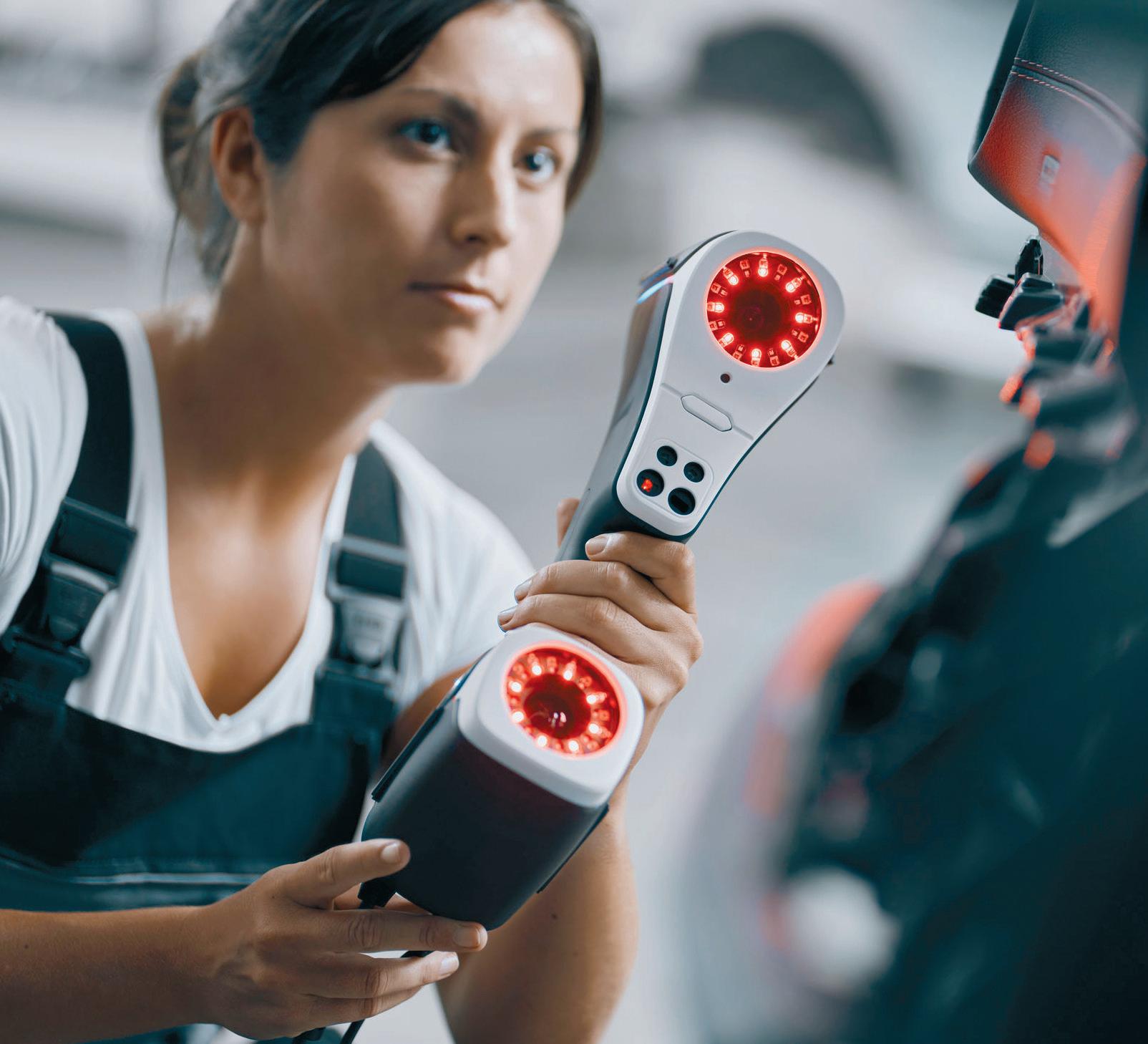
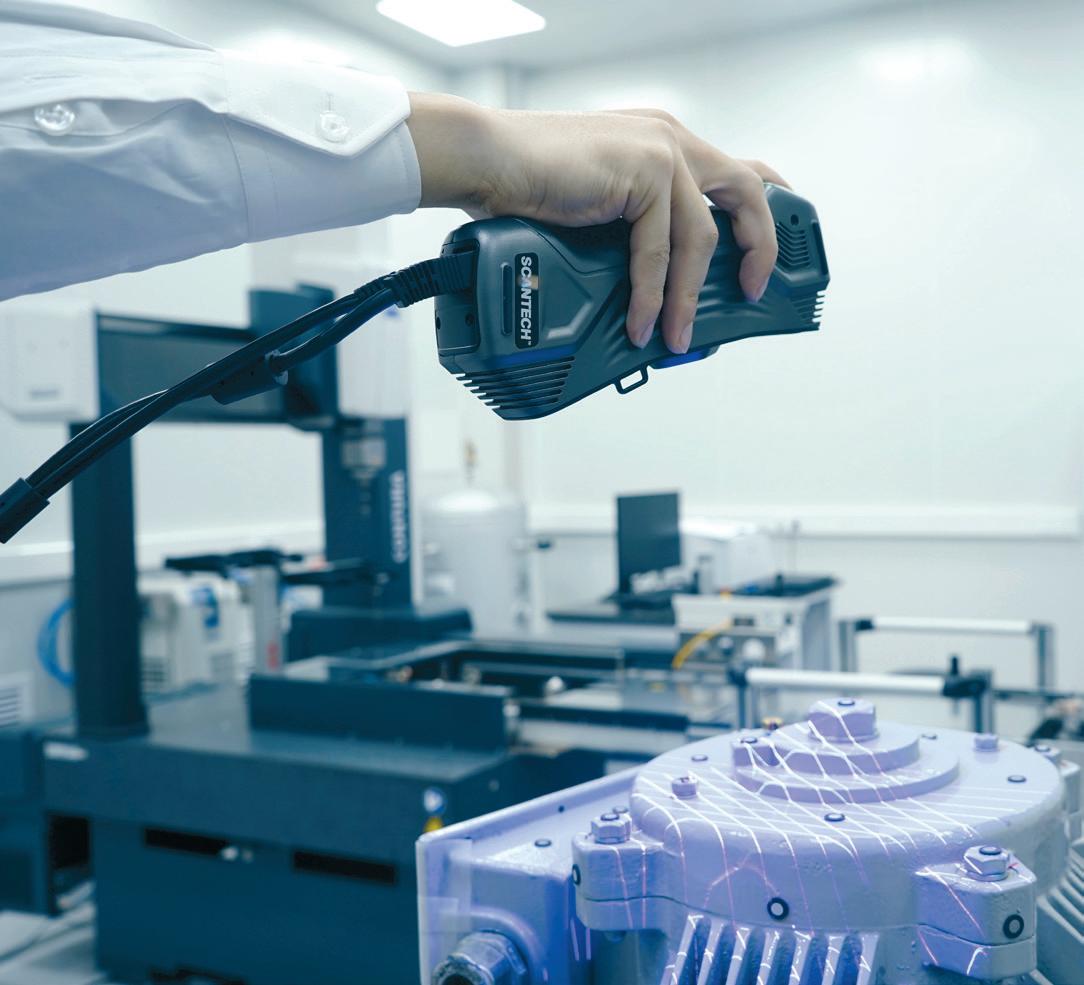
EINSCAN PROHD SHINING 3D
The EinScan proHD is a versatile, accessible physical form capture technology. With a weight of 1.13kg, it can be operated with a single hand, or combined with a dedicated tripod. The device offers two sub-modes: Rapid and HD, with the former providing faster scanning, and the latter providing a higher level of detail. Thanks to this device’s structured light projection technology, it is capable of scanning dark and casting metal surfaces at 3,000,000 points/second.

The transformative impact that 3D scanners have had on manufacturing and design in recent years can’t be overstated. Whether they use light, laser or photogrammetry, these devices offer a serious helping hand when it comes to reverse engineering and rapid prototyping tasks. Along the way, they have revolutionised workflows.
But these days, you don’t need to work for a major design consultancy or multinational engineering giant to have access to some outstanding 3D scanning technology. The technology has gone mass-market, and there are now options to suit every budget.
The huge variety can make it really challenging to choose the right tool for your trade. Here, we’ve showcased some of the best models on the market, taking into consideration such features as accuracy, resolution, ease of use, weight and price-performance ratio.
2
FREESTYLE 2 FARO
Originally developed for forensic investigators and crime scene documentation, features of Freestyle 2 also make it useful for product development. The scanner’s infrared laser projects a 100 x 100 grid of invisible dots onto the target and is interpreted by two cameras built into the T-shaped casing of the device. It performs strongly both indoors and outdoors, including in overcast conditions and complete darkness.

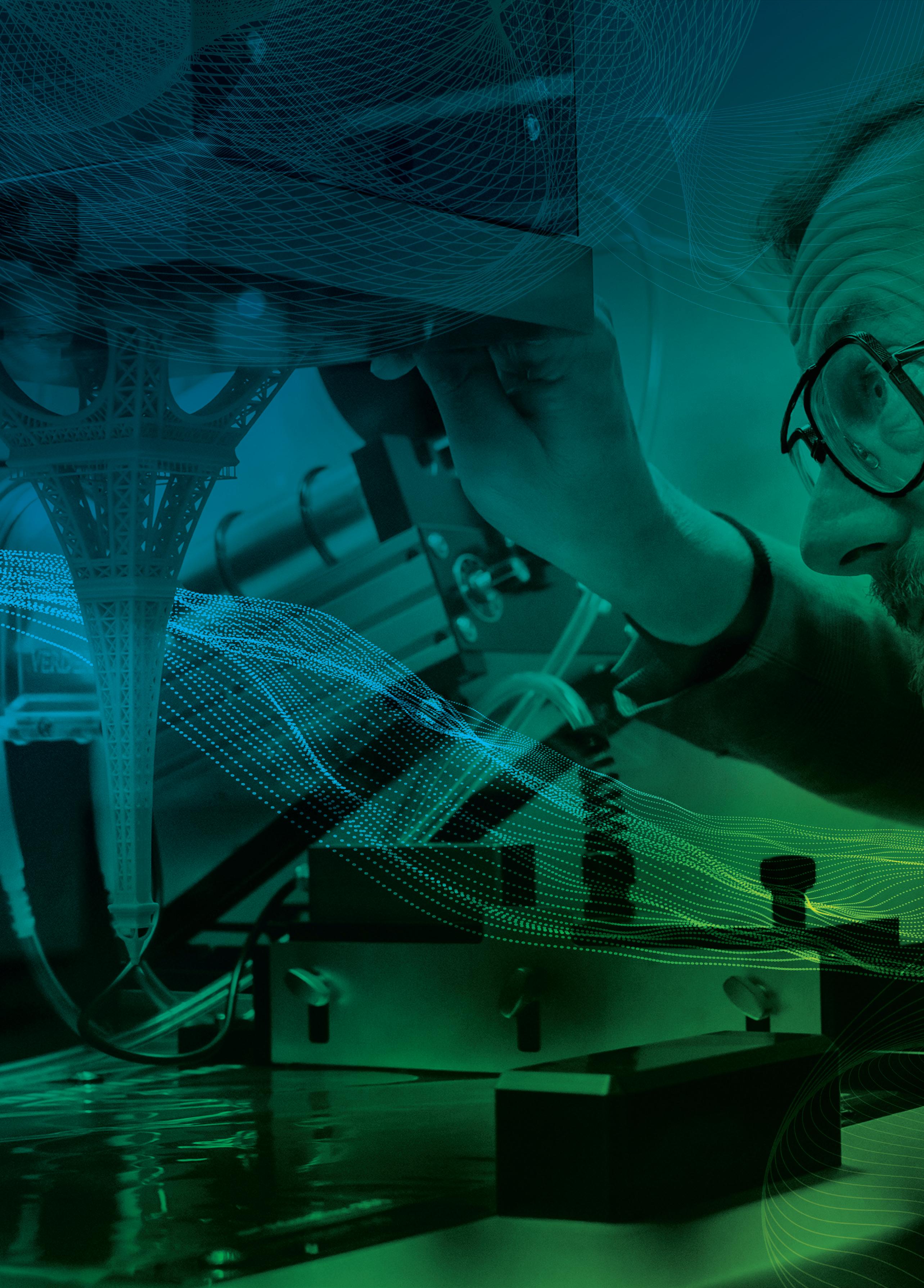
POLYGA H3 POLYGA
Powered by two industrial-grade cameras at a high speed of 700 frames per second, the Polyga H3 can scan up to 1.5 million points per scan using a structured light technology. Marketed as Polyga’s first ‘point and shoot’ system, it doesn’t require calibration. The H3 is powered by LMI Technologies’ FlexScan3D, the same 3D scanning software that all Polyga’s stationary 3D scanners run on.
4
KSCAN MAGIC SCANTECH
Released in 2021, this handheld unit features a built-in photogrammetry capability, 22 crossed blue lasers, a single laser for deep pockets, 7 parallel lines for fine detail scanning on small parts, and 12 infrared parallel lasers specifically aimed at large parts.
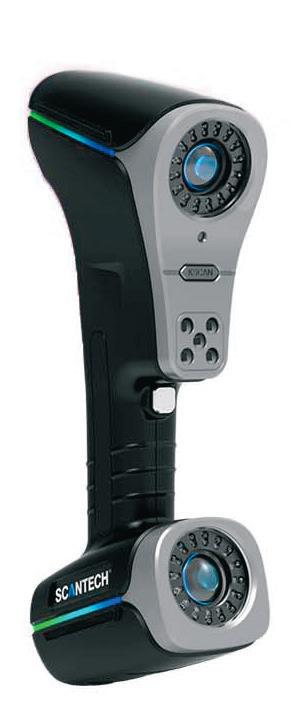
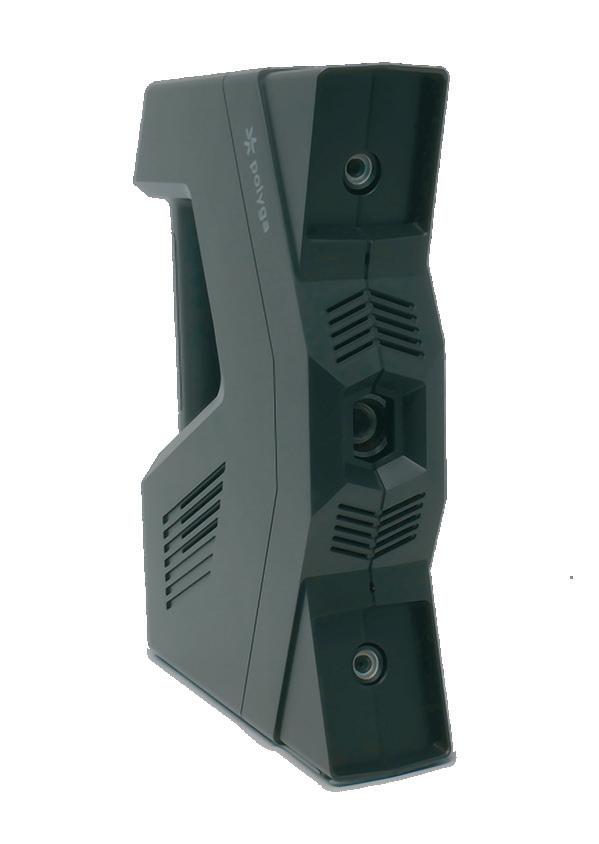
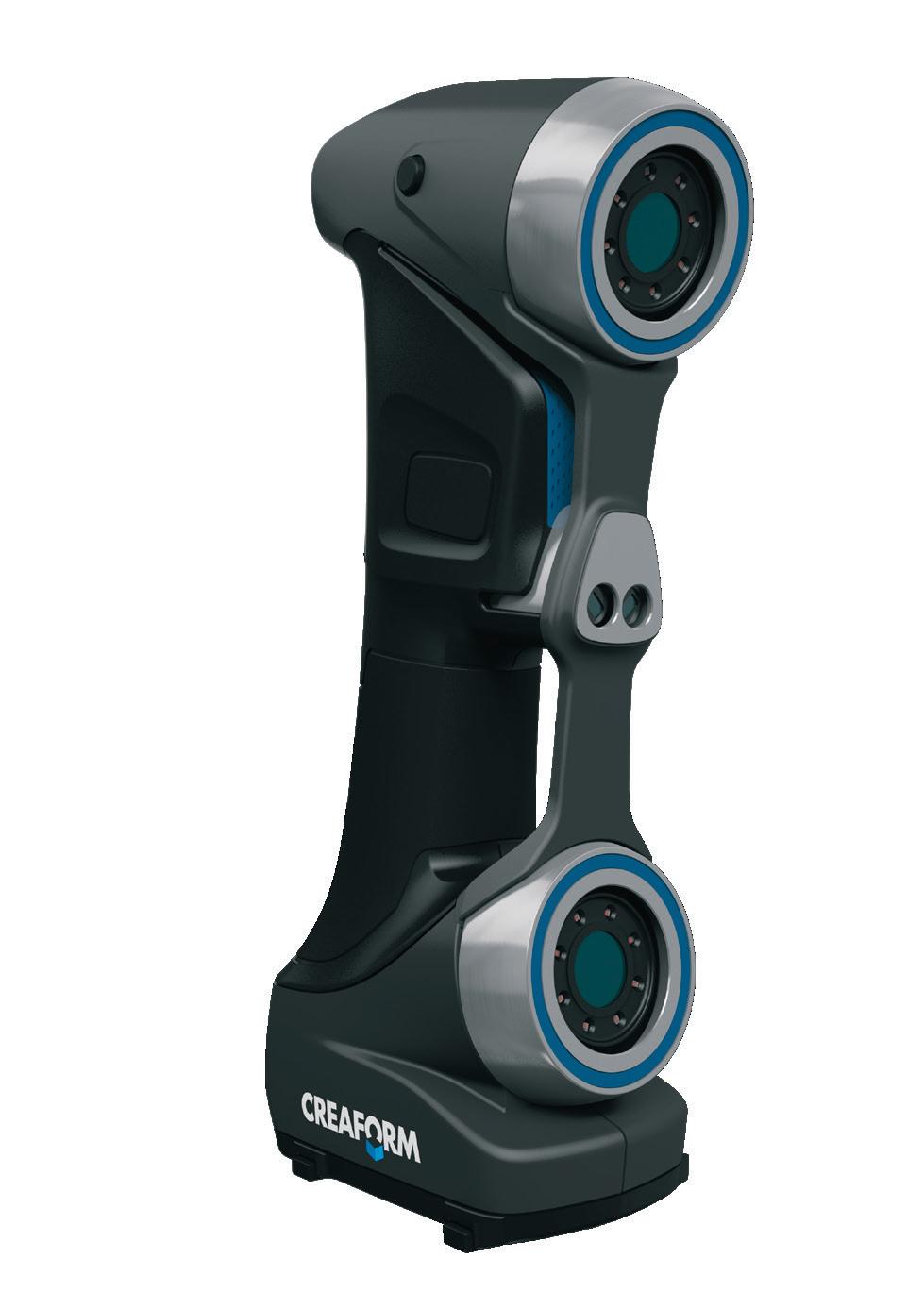
KScan Magic can be fitted with a portable CMM probe, with point repeatability of 0.03mm, allowing users to measure holes, hidden points and hard-to-access features.
5
HANDYSCAN 3D SILVER SERIES CREAFORM
The HandySCAN Silver Series comes in two models: the 307 and the 700. The 307 offers accuracy down to 0.04mm and a resolution of 0.1 mm. The 700 offers accuracy down to 0.03mm and resolution of 0.05mm.
HandyScan 3D Silver features seven red laser crosses, which allow scanning in most light situations and of most materials, including dark and reflective ones. Thanks to in-built optical reflectors, it can triangulate positions, so there is no need for external tracking or targets.
GO!SCAN SPARK 3D CREAFORM
Go!Scan is Creaform’s top product in the category of handheld scanners aimed at professional users. The ergonomic design features four inline cameras for faster 3D scanning and colour acquisition. Dynamic referencing technology allows users to hold an object with positioning targets on it and move it around during scanning. Files are captured using 99 white-light scanning lines.
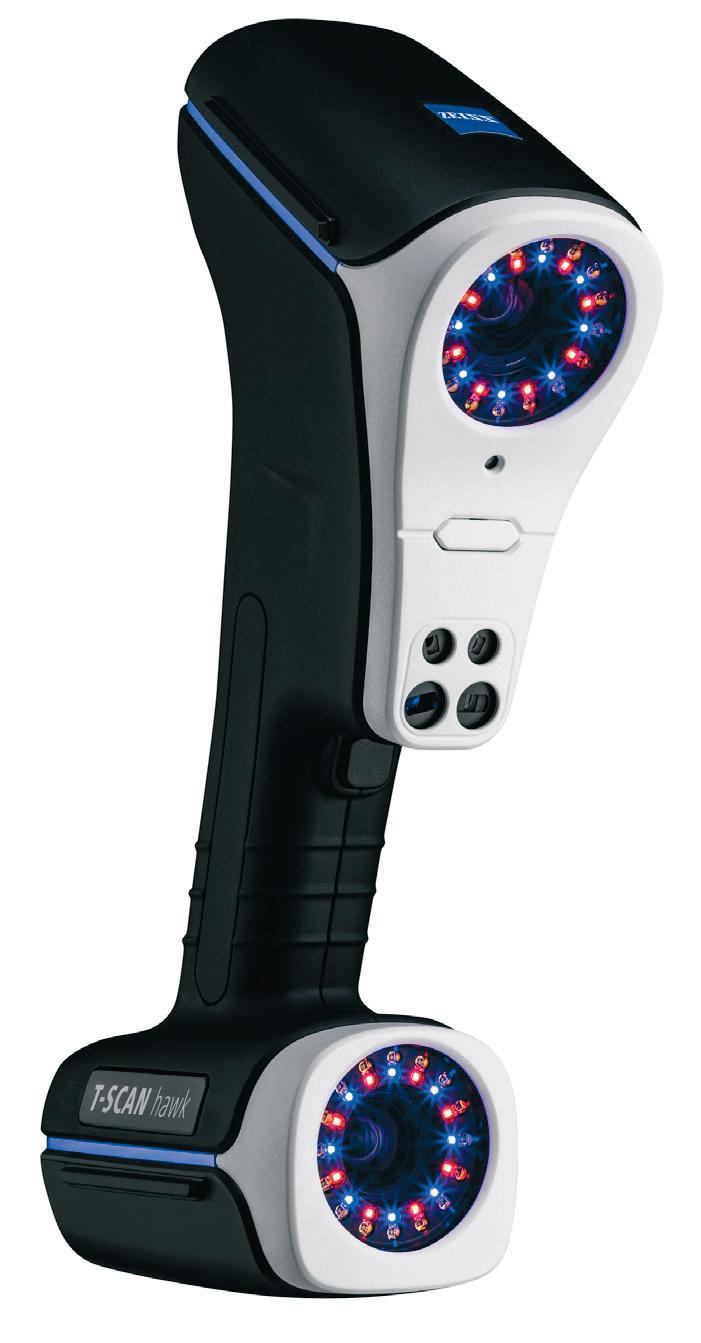
7
HANDYSCAN 3D BLACK SERIES CREAFORM
HandyScan 3D Black Series scanners use a laser triangulation technology with nine blue lasers in the standard model and 11 in the elite model. Weighing a featherweight 940g, the scanners have a resolution of 0.025mm. Like the Go!Scan Spark, they come equipped with Creaform’s own VXelements software to produce CAD-ready data.
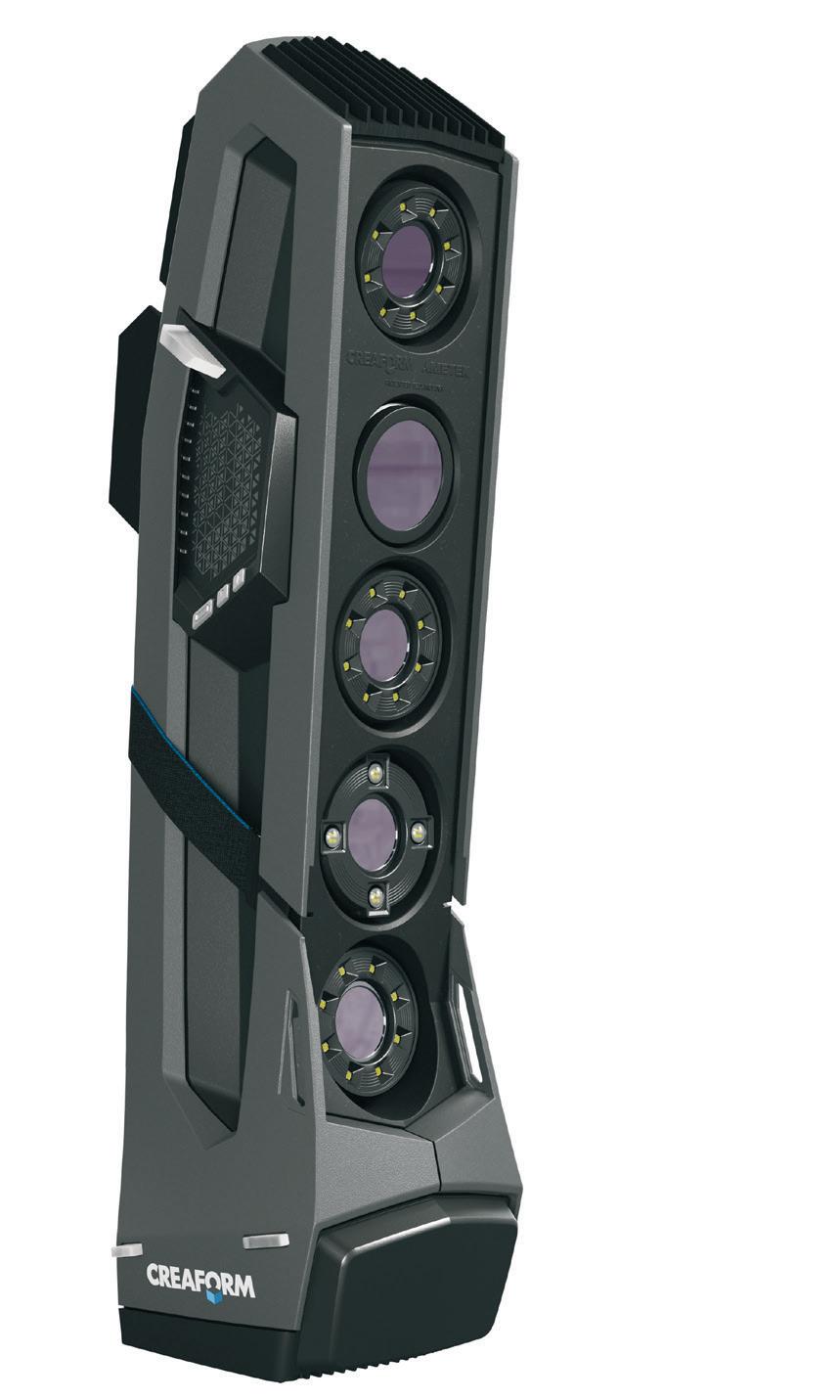
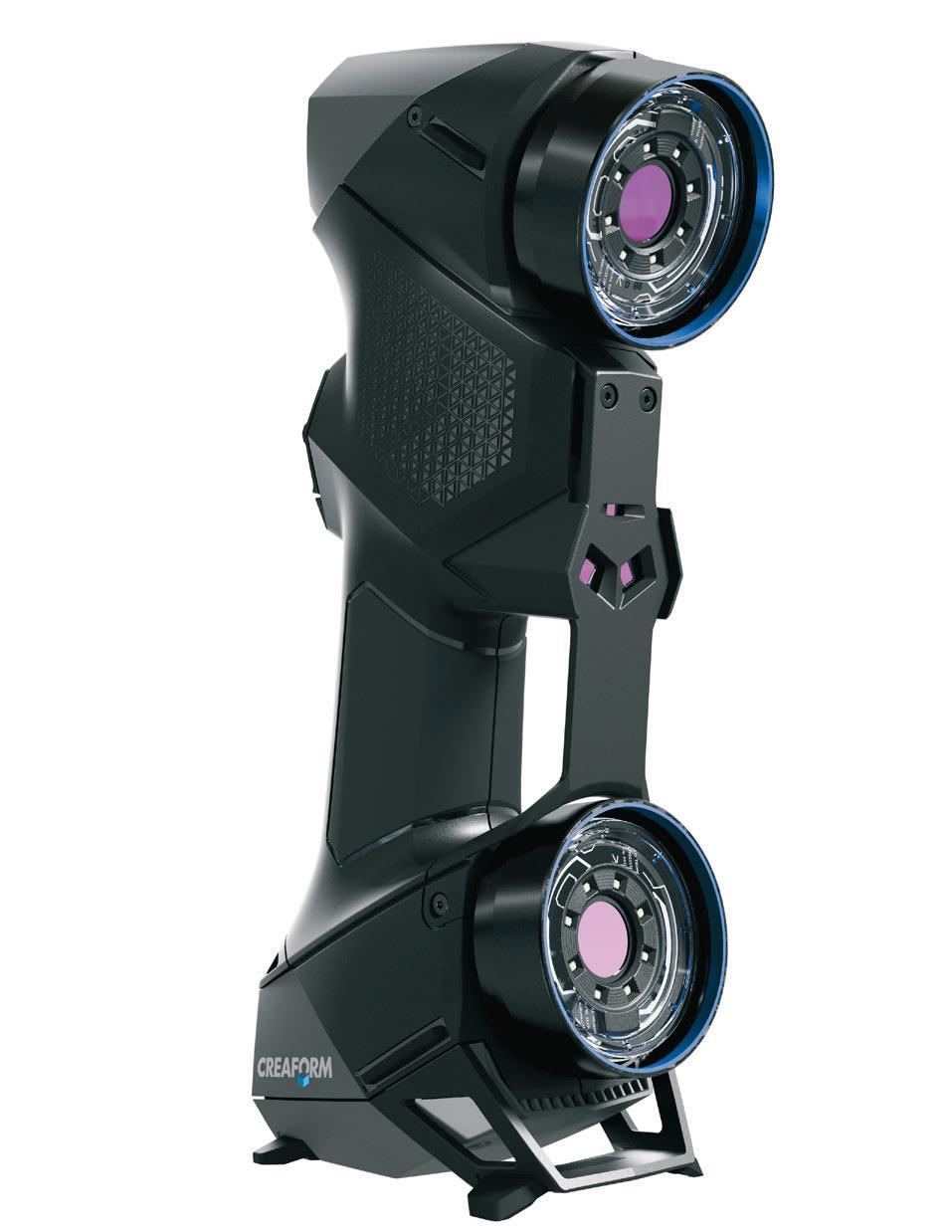
T-SCAN HAWK ZEISS
For users with a more generous budget, T-Scan Hawk by Zeiss offers an advanced laser triangulation system and high accuracy. It works on dark and reflective surfaces and even deep pockets. It has 3 scanning modes: red crosses mode, for scanning large sections; single red line mode, when the scan requires precision (good for hard-to-reach areas); and finally, blue lines mode, for scanning dark, shiny or reflective surfaces.
“
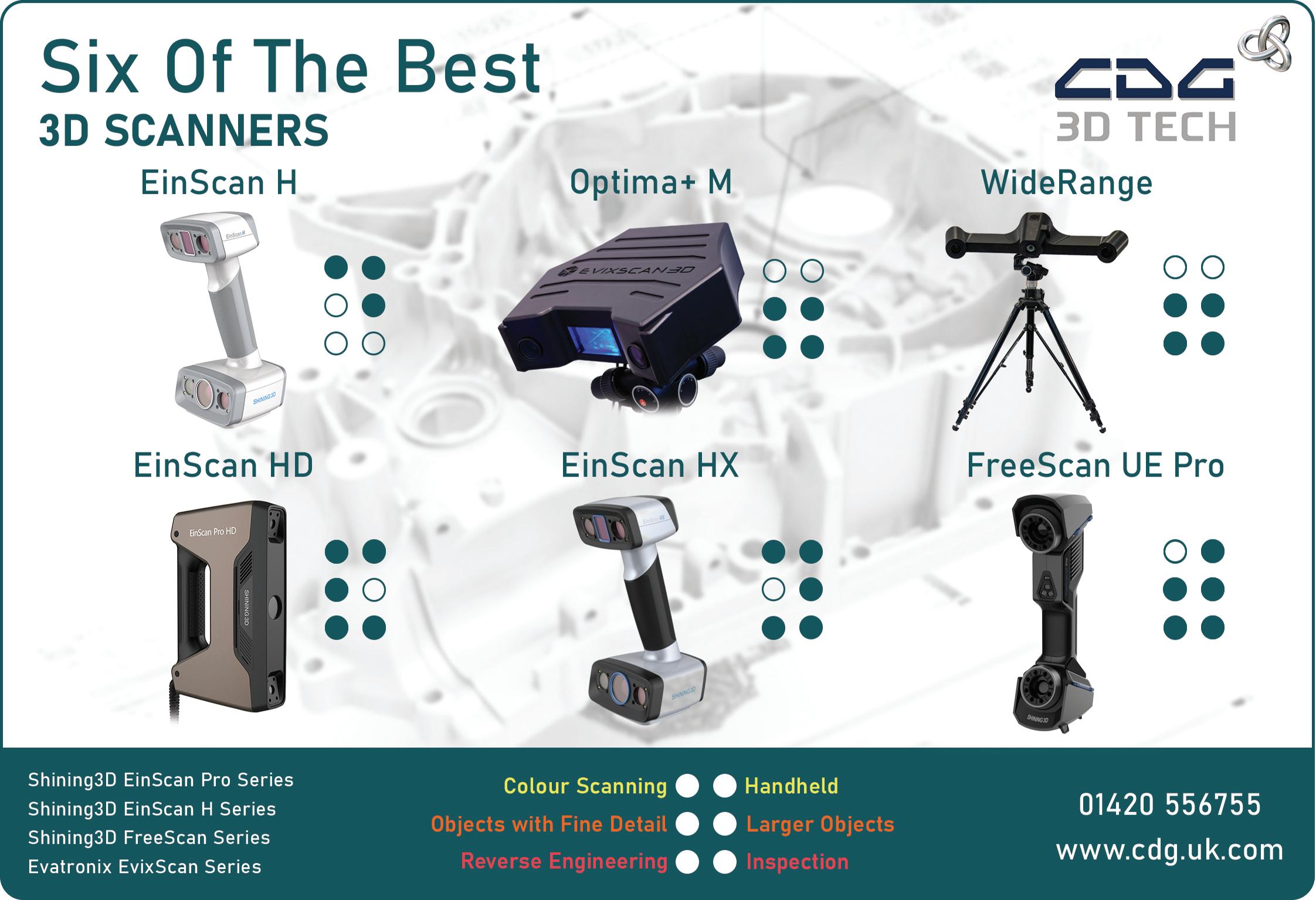

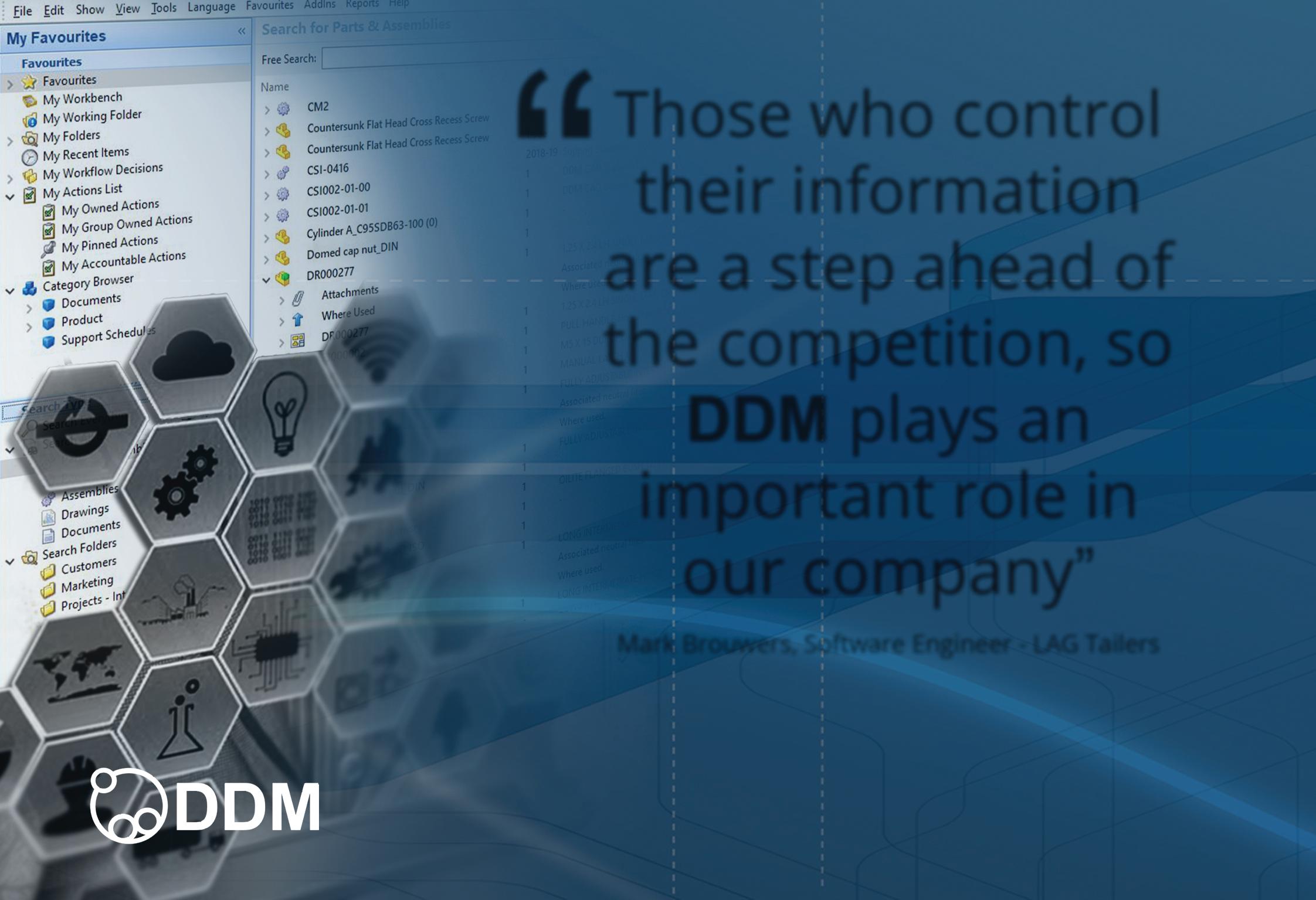
LEO ARTEC
With its 5.5-inch touchscreen, Leo enables a user to monitor a scan as they go, with no need for a computer. The device uses vertical-cavity surface-emitting laser (VCSEL) structured light, which works well even in low lighting conditions.
Hybrid geometry and texture tracking allows users to scan without targets. On the downside, it is amongst the heaviest handheld scanners on the market, weighing in at 2.6 kg.
KIRI ENGINE KIRI INNOVATION
An app rather than a 3D scanner, Kiri Engine still deserves a spot on this list. Available for both Android and iOS, Kiri can scan any 3D object and turn the data into printable files.
The app is based on photogrammetry and its AI algorithms reconstruct an object in 3D based on photos. The app has a free and a premium (paid) version. Kiri does not come equipped with modelling software.
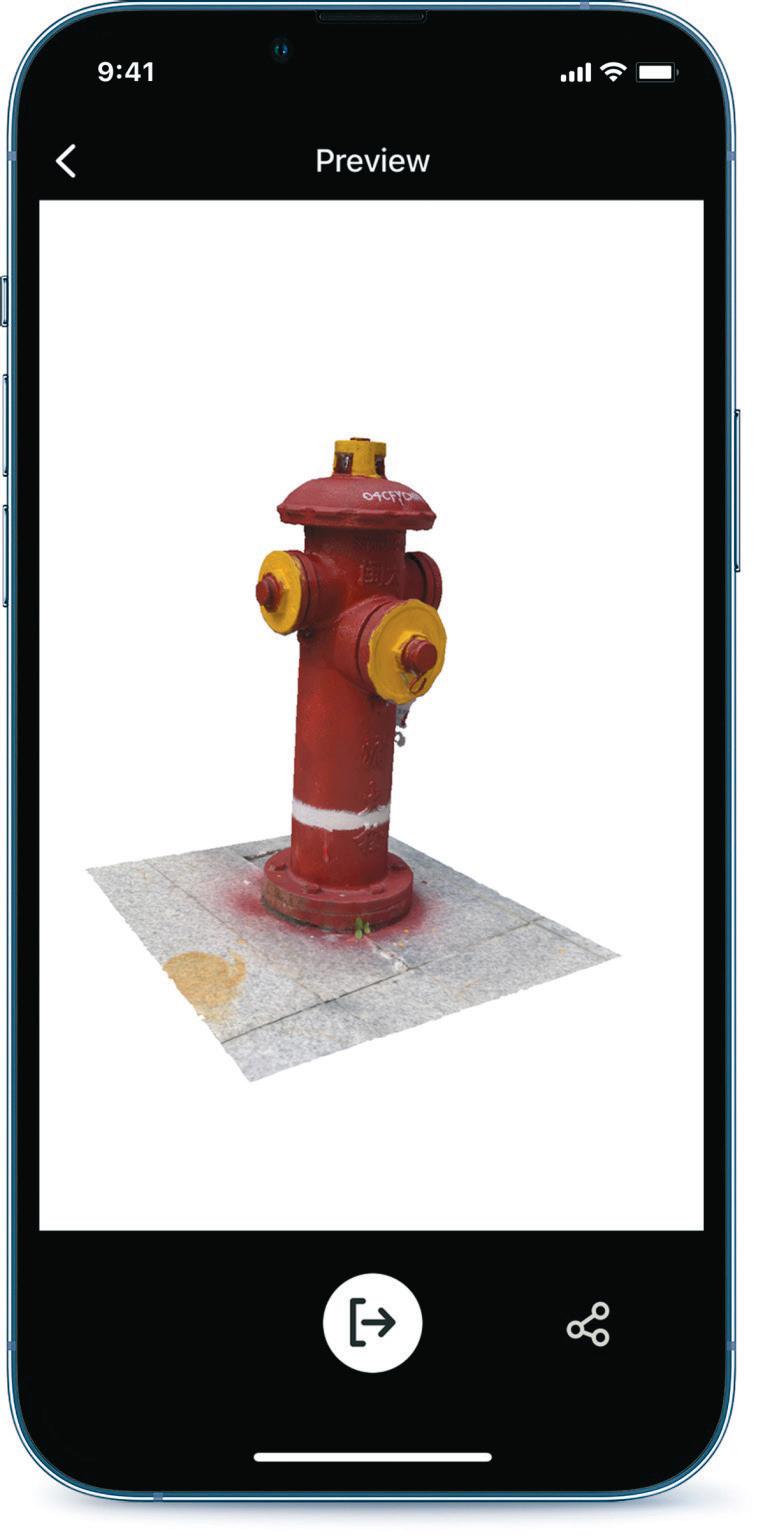
SIMSCAN SCANTECH
Marketed as the only hand-sized 3D scanner on the market, SimScan weighs under a half-kilo — just 570g, to be precise. Released in 2021, it uses eleven crossed blue lasers, offers accuracy to 0.02 mm and can scan in three different modes. These are ultra-fast scanning, hyperfine scanning and deep hole scanning. While the device features an impressive acquisition speed of up to 2,020,000 points/second, it is not able to scan textures or colours.


EINSCAN HX SHINING 3D

With a reputation for affordability, Shining 3D aims to bring physical form capture technology to the mass market. Its EinScan HX offers both a rapid mode and a laser scanning mode. The former uses structured light technology and allows the user to capture data quickly without registration targets. The latter offers higher resolution and volumetric accuracy, but a slower scanning process that relies on targets. Users can also opt for a hybrid approach which combines elements of both modes.
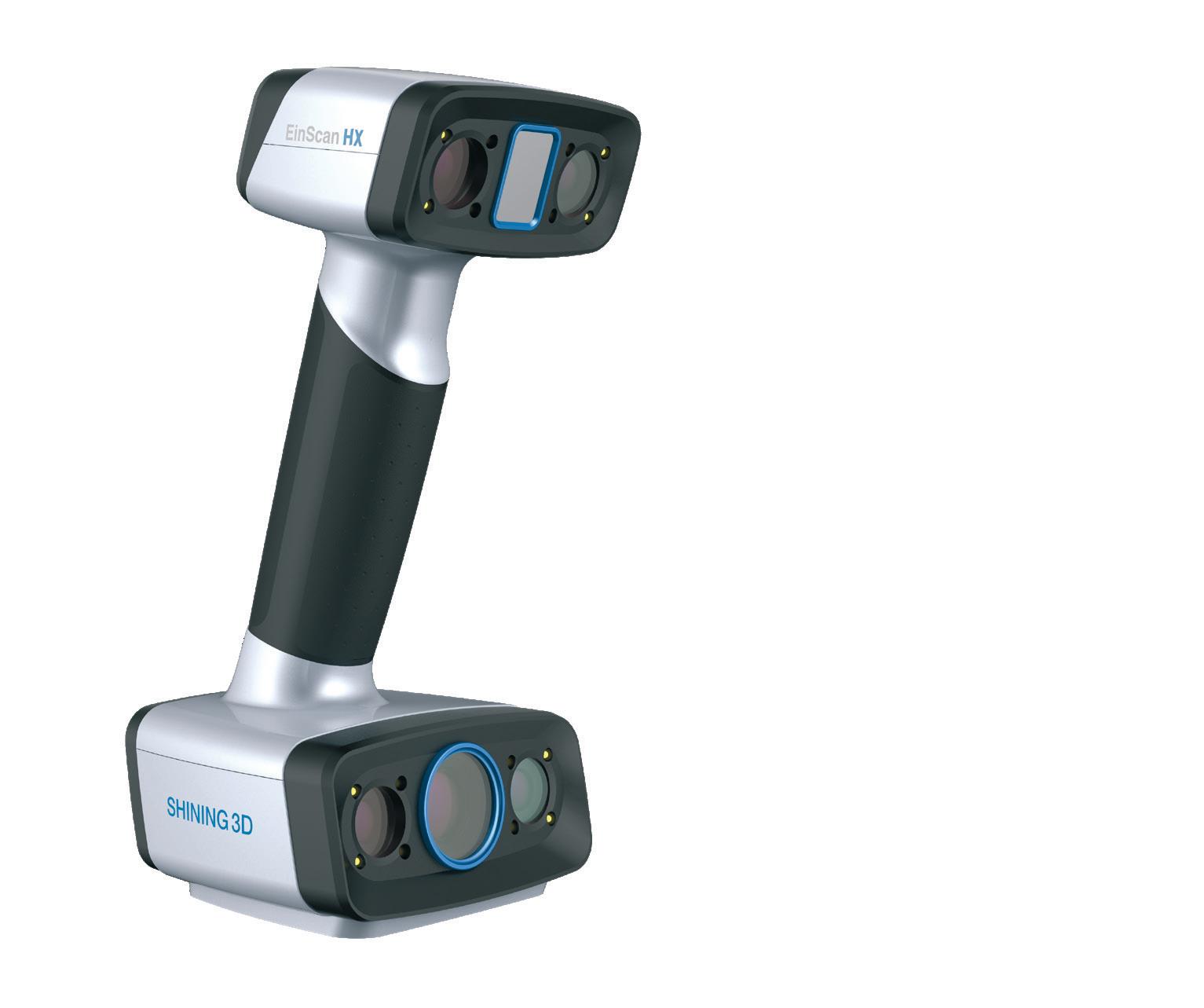
12
LEICA BLK2GO LEICA
Very much a premium model, the Leica BLK2GO can digitally capture space with no interruption. Easy to manoeuvre and lightweight at 775g, it features a 12-megapixel detail camera, plus three panoramic cameras for navigation. It is operated by a single-button operation system and can be wirelessly linked with a Leica iPhone app, so that the user can see the data it gathers in real time, in both 2D and 3D.
PEEL 3D
Originally aimed at hobbyists and creatives, the third generation of Peel 3D is suitable for more professional reverse engineering applications. With its slick LCD screen, it can also be used as a distance meter, enabling the user to easily scan without looking at their computer. Recognisable vibration patterns guide the user around narrow and hard-to-reach places without a direct line-of-sight, giving them real-time feedback.
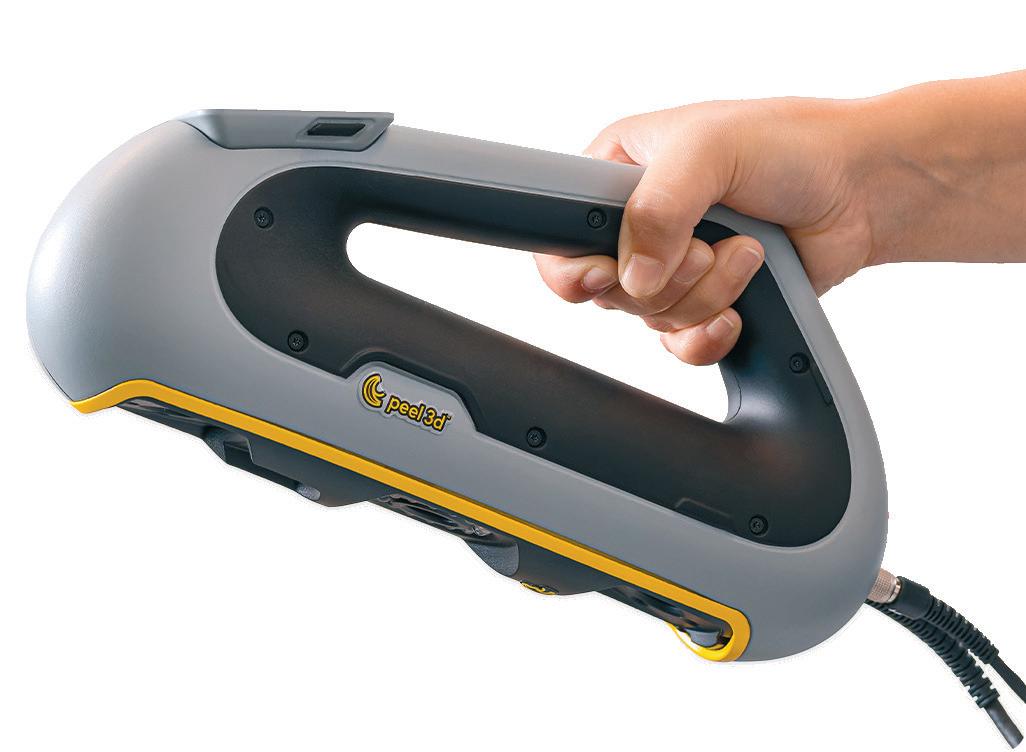
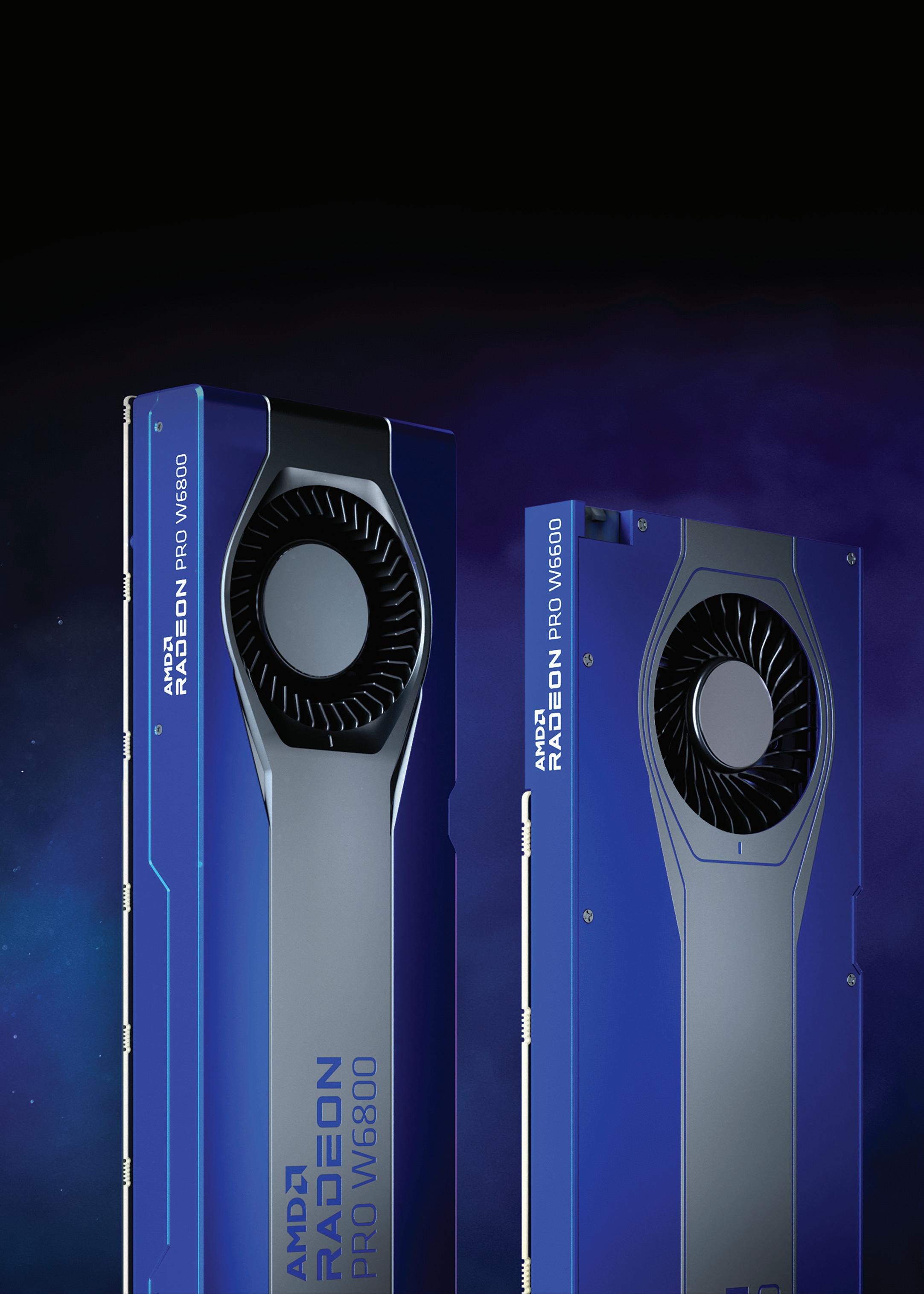
SMART PERFORMANCE. SMART PAIRING
the ultimate software
a gigantic
of lightning-fast
up to 6
wrapped
RDNA™
which is the

AUTODESK REACHES FOR THE CLOUD
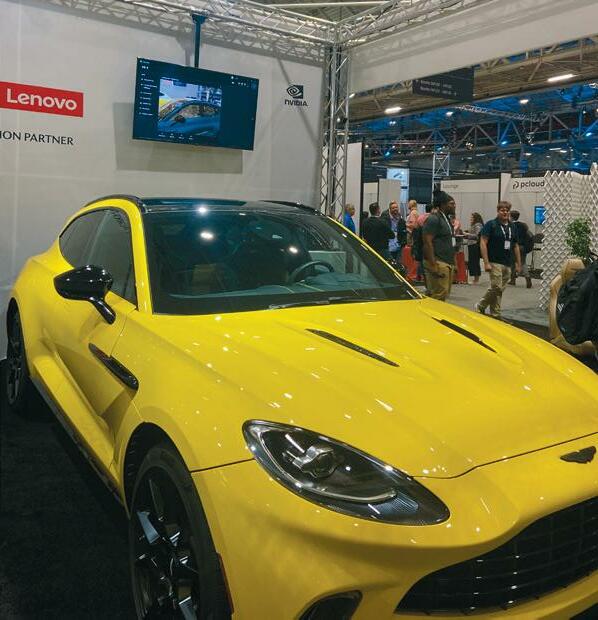
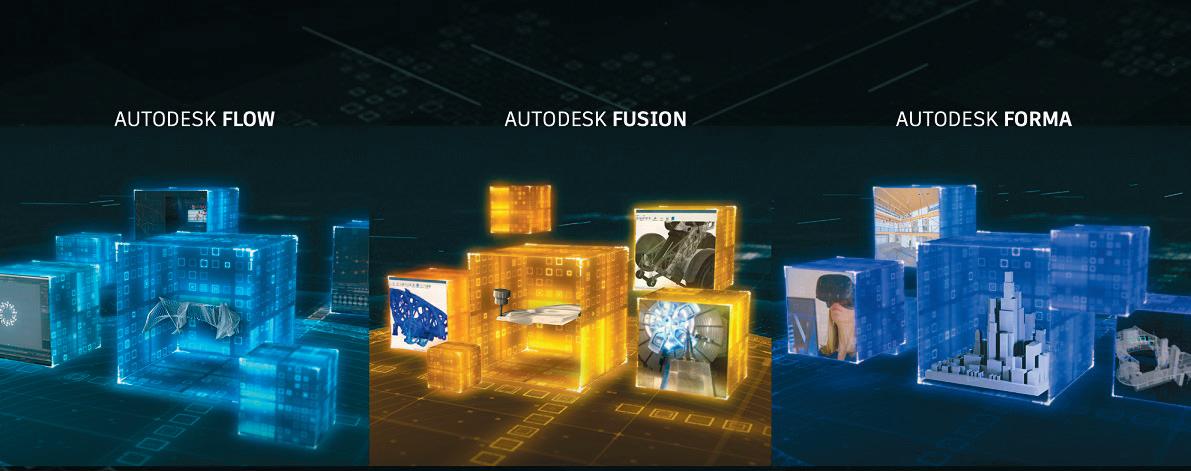
After a three-year hiatus, Autodesk University is finally back in person to get users up to speed on all the latest updates to its widely used software, to exchange feedback, and to discuss how to address the challenges of our time, as Claudia Schergna reports
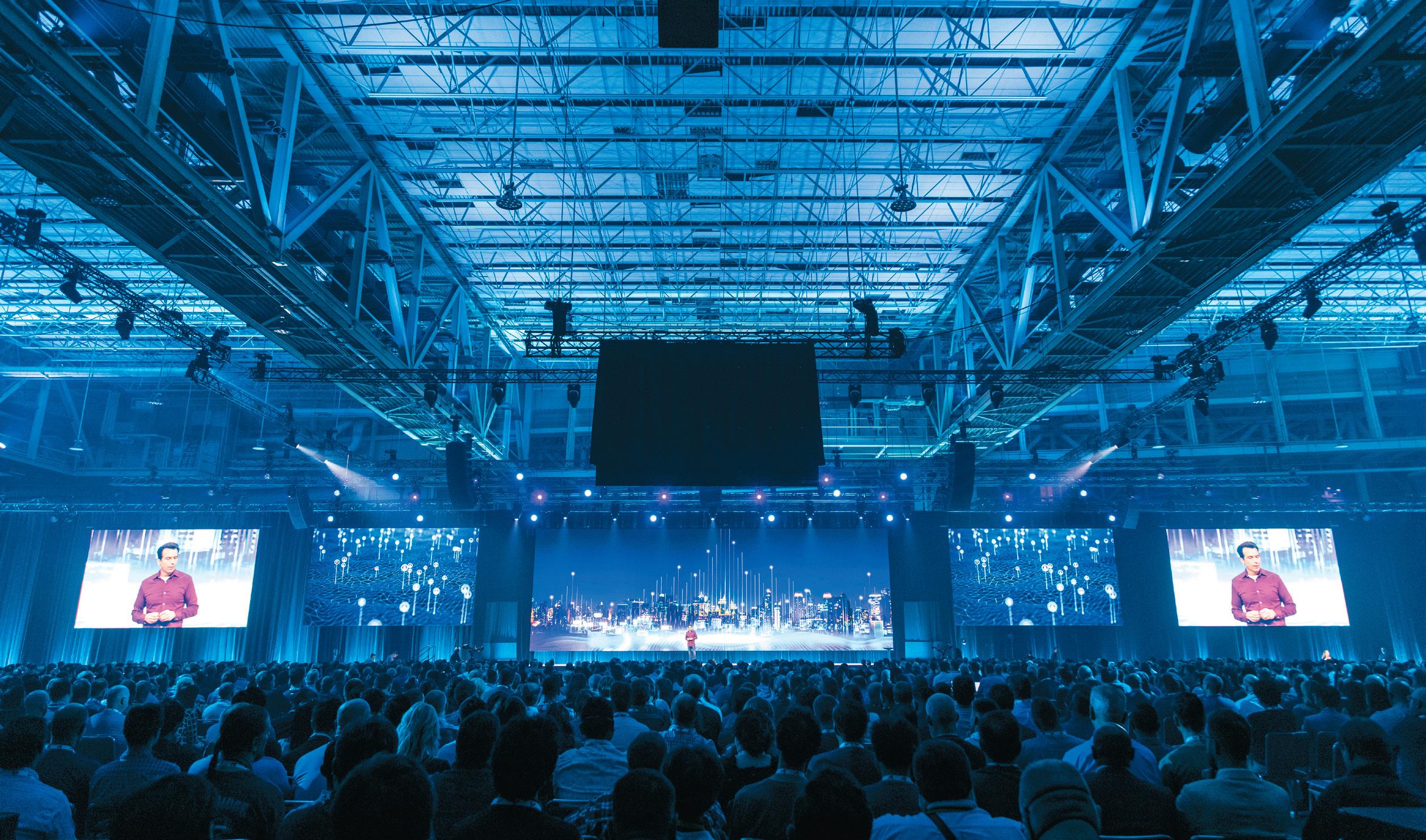
Flexible, device independent, connected: these were the buzzwords of Autodesk 2022. During the first in-person event since the pandemic, designers and engineers from around the world had a chance to find out about Autodesk’s plan to fully embrace the cloud. The software giant aims to facilitate the growing demand for tools to keep remote teams always connected, and to make sure everyone in the supply chain has access to the data they need precisely when they need it.
The aim is to reduce production times, save resources, facilitate the connection between team members and democratise tools, making them accessible on any device.
Another big theme for the three-day event, with the approach of Hurricane Ian towards US shores making it seem ever more urgent, was sustainability.
Autodesk’s big eco announcement was its collaboration with Makersite to develop a plug-in for Fusion 360, which aims to provide designers with the sustainability data they need at any step of the design process.
Makersite is a software company that develops data management tools for the global manufacturing industry, empowering companies to manage product sustainability, cost, and compliance.
Thanks to the plug-in, currently in the trial phase, designers should be able to visualise the environmental impact of every single iteration they make to the project and be provided with options to help them meet cost and emission targets, taking into consideration the entire product lifecycle.
The plug-in has been tested by the British company Pembree Pedals. Its founder Phil Law, joined by Makersite CEO Neil D’Souza and Autodesk sustainability strategy manager Zoé Bezpalko, presented a demo of how it has helped the bicycle part manufacturer develop pedals that are as sustainable as they can possibly be, while at a reasonable cost.
Meanwhile, on the exhibition floor, attendees could try on some of the latest AR, VR and XR technologies, starting with a Varjo headset powered by a Lenovo ThinkStation workstation that attendees could test on a gleaming yellow Aston Martin. Parked next to the physical car, at the very entrance of the exhibition floor, was standing its incredibly realistic digital twin in XR.
Further down the exhibition, Faro was inviting visitors to try its newest 3D scanners, including Faro’s Freestyle 2 (featured in our handheld 3D scanner round up on page 30) and Focus Premium.
In the ‘Factory’ area of the exhibition, Autodesk offered a live demo of how a VR headset can help teams collaborate from their remote locations.
THE KEYNOTES
Welcomed by music and dance performances, in proper New Orleans style, the keynote session brought everyone together in the main hall to officially announce what was already in the air.
Autodesk CEO Andrew Anagnost started by thanking all attendees and the city of New Orleans, talking about
its troubled history and historical resilience.
The first guest was Meagan William, Urban Water program manager for the city of New Orleans. William, a New Orleans native, was 16 when Katrina happened and clearly remembers the devastation that it brought to her city. Her job aims to safeguard and protect new generations from issues caused by climate change and the rise of sea levels.
Andrew Anagnost took back the microphone to talk about one of the biggest problems that design, engineering, and architecture teams all around the world face daily: dysconnectivity and lost-in-translation data. These are issues that Autodesk is looking to resolve by introducing three industry clouds: Autodesk Fusion (for design and manufacturing) Autodesk Forma (for architecture, engineering and construction) and Autodesk Flow (for media and entertainment).
Given the multitude of industries Autodesk users work within, the keynote sessions were split into three parts.
For manufacuring, Jeff Kinder, Autodesk executive VP of product development and manufacturing solutions, took the stage with some exciting news about Fusion 360.
Besides the Autodesk Fusion cloud offering, Kinder announced new Fusion 360 extensions powered by Ansys and ModuleWorks, which aim to unlock advanced product design and manufacturing capabilities.
The integration of Ansys simulation technology looks to provide useful insights about printed circuit board (PCB) signal quality as part of the board design process, while the collaboration with ModuleWorks should offer new capabilities to Fusion’s Machining Extension, to generate higher-performance, collision-free toolpaths for efficient multi-axis milling.
It seemed that all the updates on Fusion 360 are part of a bigger move that aims to build out a complete platform, able to connect all phases of the process, from design to make, going through CAD, CAM, simulation, and rendering, while being device-independent, always connected to other users and applications or, as Kinder defined it, a “click-to-make” tool.
THE JOURNEY TO THE CLOUD
During the media Q&A, Anagnost addressed journalists and analysts, curious to know what the future holds, the purpose of developing three different industry clouds, and how Autodesk is working to make its cloud offering accessible from any location across the globe.
As Anagnost explained, not all of these questions have a definitive answer yet, as the recent announcements are only the beginning of a bigger strategy, which will see more tools connected not only in the cloud but into one single piece of software.
While we might have to wait a little longer to see the final results of this ambitious move, there was plenty to take away from New Orleans, with the chance to be in-person among an international community of users talking positively about how the industry can tackle the world’s most pressing issues. www.autodesk.com/autodesk-university
● 1 Autodesk CEO, Andrew Anagnost, addresses the masses in his keynote
● 2 As part of its new Autodesk Platform, Autodesk introduced three industry clouds at Autodesk University: Fusion, Forma, and Flow
● 3 On the show floor, Lenovo used XR to showcase a gleaming yellow virtual Aston Martin DBX alongside the real one
‘‘
The software giant aims to facilitate the growing demand for tools to keep remote teams always connected, and to make sure everyone in the supply chain has access to the data they need precisely when they need it ’’
IN THE FRAME
Kalkhoff’s efforts to accelerate physical prototyping for its bicycle frame looked to have hit a rut, until Materialise got them back on track. Stephen Holmes reports on how the company 3D printed an aluminium prototype in record time
With over 100 years of experience, Kalkhoff knows how to build a bike that goes the distance. But even the German manufacturer is impressed with the speed at which its latest e-bike moved from concept to physical prototype testing.
It can take years to ready a bike for production, with product development for any new Kalkhoff product always a balancing act. Designers need to maintain the unique geometry now synonymous with the visual identity of Kalkhoff e-bikes, while also considering functional ability and the necessary components for the design.
The company strives for its bikes to be comfortable, agile and reliable, giving every customer a smooth and
enjoyable riding experience. To achieve this, the company tests each bike’s frame well beyond the industry standard.
Usually, a bike frame must pass loads of up to 150 kg. In comparison, Kalkhoff’s frames are pushed to tolerate loads of around 170 kg. “Our business prides itself on providing our customers with the opportunity to cycle freely without limitations,” says Kalkhoff industrial designer Rik Maes. “Cycling should reflect our company motto: ‘Kalkhoff moves you everywhere,’” he says.
For prototyping to begin, rideable models must be first produced – an expensive and time-consuming process that requires tooling to be cut, and which cannot be undertaken with plastic form models.

With this obstacle in mind, Kalkhoff contacted its polymer additive manufacturing supplier Materialise, to discuss a potential solution through metals 3D printing.
● 1 Materialise Magics was used to segment the bike frame for 3D printing, optimising the build process
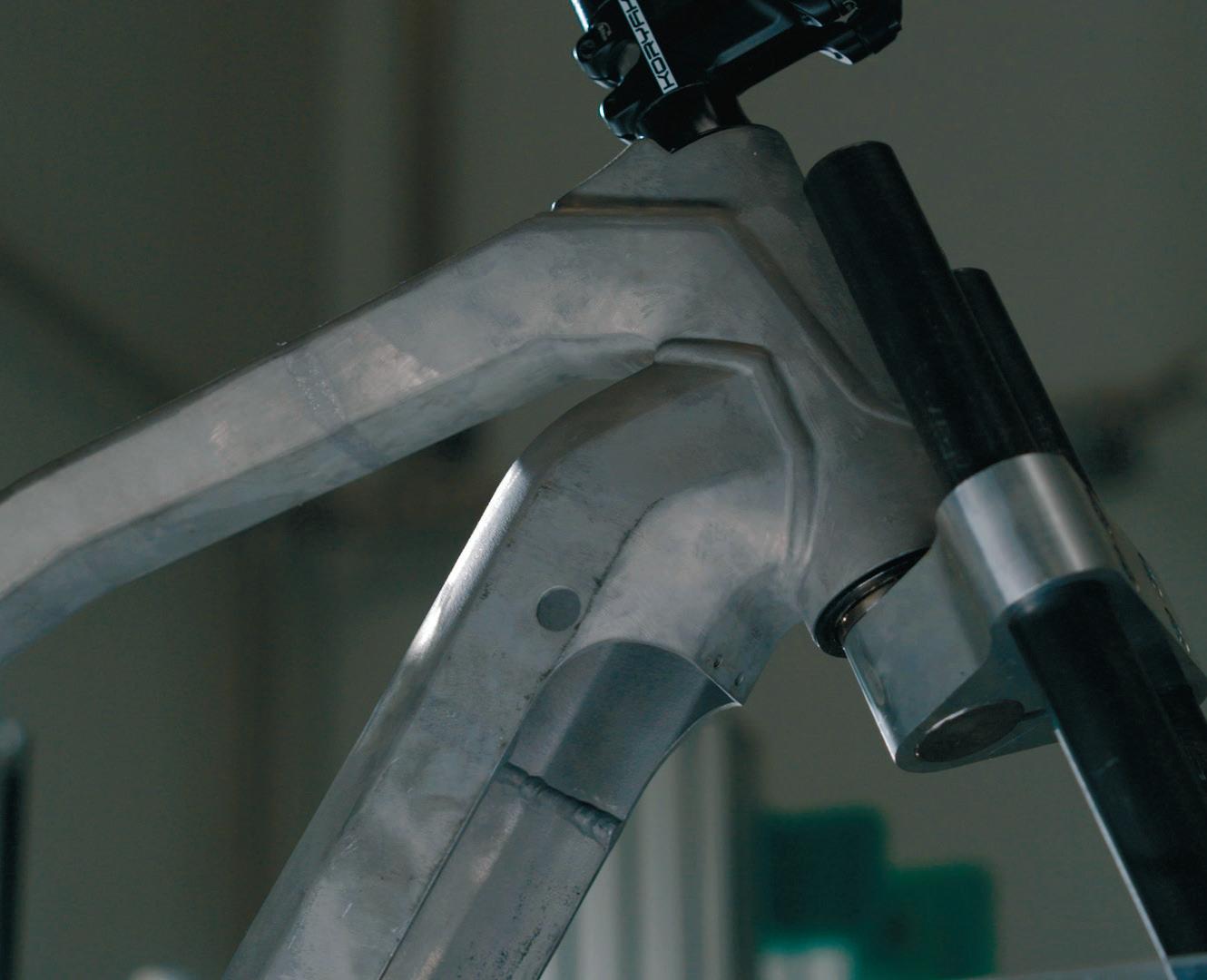

● 2 The 3D-printed aluminium parts were precisely welded together and heattreated to form a complete frame
● 3 Once kitted out with wheels and fittings, Kalkhoff’s frames are pushed to tolerate test loads of around 170kg
METAL HEADS
With Materialise’s Metal Competence Center (MCC) for 3D printing located in Bremen, close to Kalkhoff’s headquarters in Cloppenburg, the teams met to begin optimising the bike’s design for additive manufacturing in aluminium.
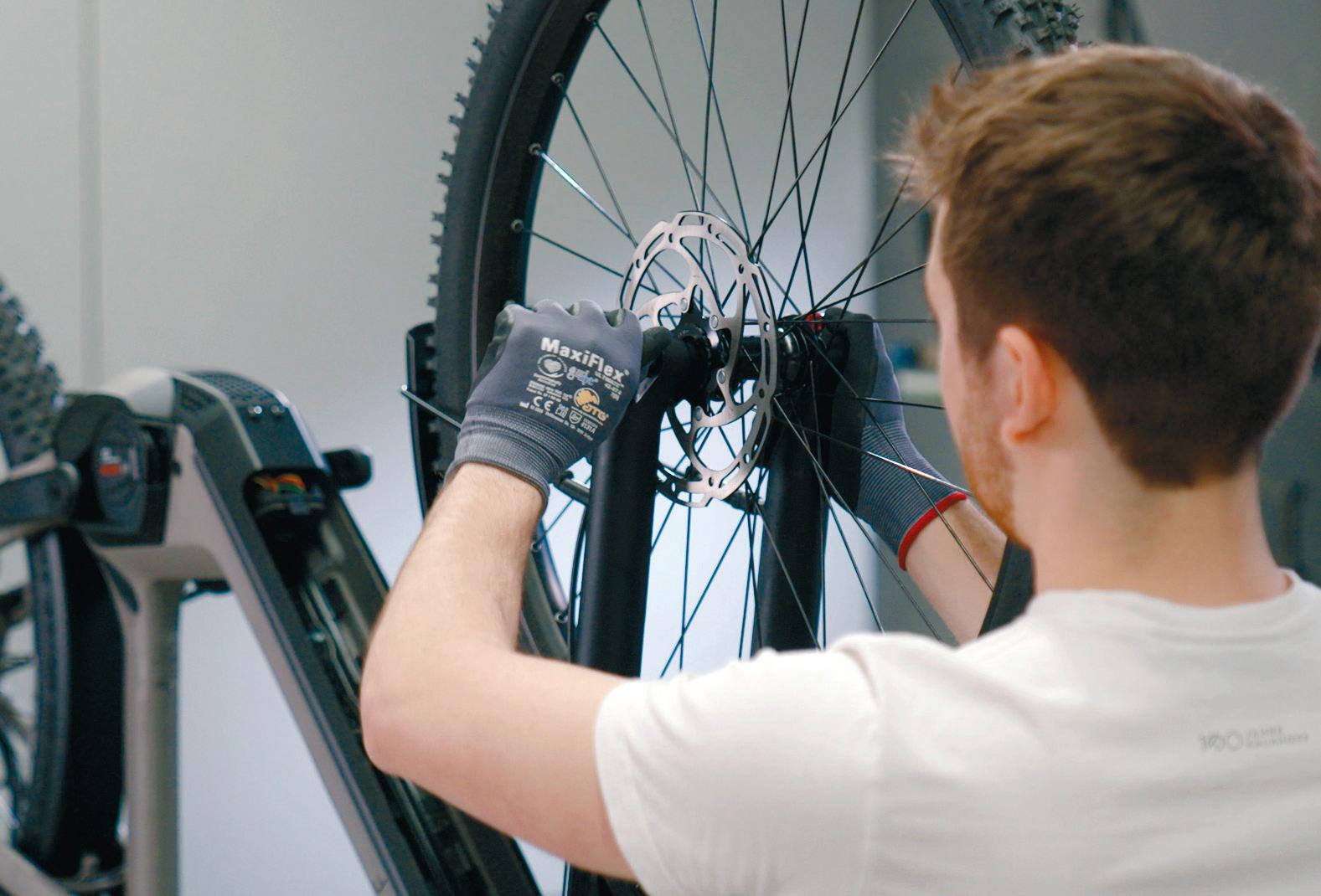
With the maximum part size for Materialise’s SLS 3D printers set at 500 x 280 x 315mm, building the full frame as a single piece was not an option, so the first step was to convert the 3D CAD model of the bike into printable sections.
The optimal segmentation of the design was determined in Materialise Magics, positioning the cuts on the frame to consider existing loads to avoid peak stress in the welded joints and ensuring that an entire bicycle frame would fit into the 3D printer’s build chamber.
Optimising the build strategy also helped to reduce machine time and post processing efforts. Once the joining segments were defined, the end segments were redesigned in CAD to create a better welded surface once printed.
Welding and testing was performed by Seefried, a company specialising in small series welding and located near the MCC. ACTech, a Materialise-owned specialist in metallurgy and low volume production took care of heattreating the welded frame, performing this task via two processes — solution annealing and artificial ageing.
While components were being printed, the simulation for the welding and heat treatment of the frame was run simultaneously using the 3D CAD data, helping streamline the process even further.
“Situations like this and moments such as after the annealing stage that require real-time measurements
of the frame with millimetre-accurate geometry are not possible without close cooperation and the expertise of all those involved,” explains Michael Röhner, product manager metal 3D Printing at ACTech.
EXPECTATIONS SURPASSED
Typically, the complete development of a bike takes between two and two-and-a-half years. By using metal 3D printing and the expert know-how at Materialise, the whole prototype frame was delivered in six weeks from start to finish — an overall saving of three months in the development phase.
“Metal 3D printing has surpassed our expectations,” states Maes. “We can make changes at short notice, because no tools or moulds were specifically needed to be built for this model. In the development phase or the ‘engineering design freeze,’ we will have mobile design prototypes where we can test all the selected parts. This has never been possible!”
Additionally, producing the frames with local partners meant Kalkhoff could save time, get the test results faster and feed any changes back into the design without worrying about long transportation waits from Asian suppliers.
“That’s a good thing for us, as we’re first to market with innovative bikes for our customers!” concludes Maes.
Once testing is complete, the test bikes go on to fulfil other purposes. For example, new designs are available for showcasing at marketing events and for test rides long before the production models reach the market. The process also acts as an exploratory step towards more sustainable future production methods that will help shape the next century of Kalkhoff’s designs.
‘‘
Metal 3D printing has surpassed our expectations. We can make changes at short notice, because no tools or moulds were specifically needed to be built for this model ’’
DESIGN FOR PROCESS
A lack of focus on design for additive manufacturing means 3D printing fails to achieve its full potential. But DFAM doesn’t have to be intimidating, writes Nick Sondej. It’s just another everyday engineering workflow — and one that’s likely more familiar than you might think
Let’s face it: at one time or another, we’ve all probably hit a stumbling block in our design process and thought, “Screw it. Let’s just 3D print it and find out what happens!” I know I have.
The problem is that, far too often, we do this without first tailoring the design to the printing process. Disappointment soon follows, when printed parts break or fail to perform as expected. As a result, 3D printing’s reputation and use as a serious engineering tool suffers.
But good engineering demands both creative experimentation and detailed analytical design. So taking healthy risks and prototyping with uncertainty is a necessary part of the engineering process and 3D printing makes it easy to create a diverse array of part geometries that would challenge the capabilities of other, more traditional methods.
However, 3D printing is just another manufacturing process — or to be more specific, another family of manufacturing processes. If you want to get the most out of your chosen variety of AM, you’re going to have to intentionally design for it. What’s more, this thinking needs to be factored in even at the prototyping stage if you want to rely on 3D printing as a powerful tool at your side.
FALSE STARTS AND HISTORICAL BAGGAGE
It’s no secret that the additive industry’s early days were characterised by unrealistic hype, and we’re still paying for it today. “A 3D printer in every home,” we were told, and, “You can 3D print anything.”
While many 3D printer manufacturers have since seen the light and pivoted towards highlighting intentional DFAM (design for additive manufacturing) and targeted best-fit applications of 3D printing, the echoes of this previous mindset still persist among vendors and users alike.
As engineers and designers, we’d be ridiculed if we
tried to “just injection-mould it”, or “just machine it” on a project, without first considering both the technical and economic requirements of the parts under discussion, as well as the capabilities of the chosen manufacturing process. Typically, once that manufacturing process is selected, we then proceed through an organised design process, in order to
ensure that the final component or assembly is designed specifically with the capabilities and limitations of that technology in mind. For example, you might design CNC-machined pockets with corner radii larger than a chosen end mill radius; or injection-mould components with consistent wall thicknesses to avoid warpage during shrinking.
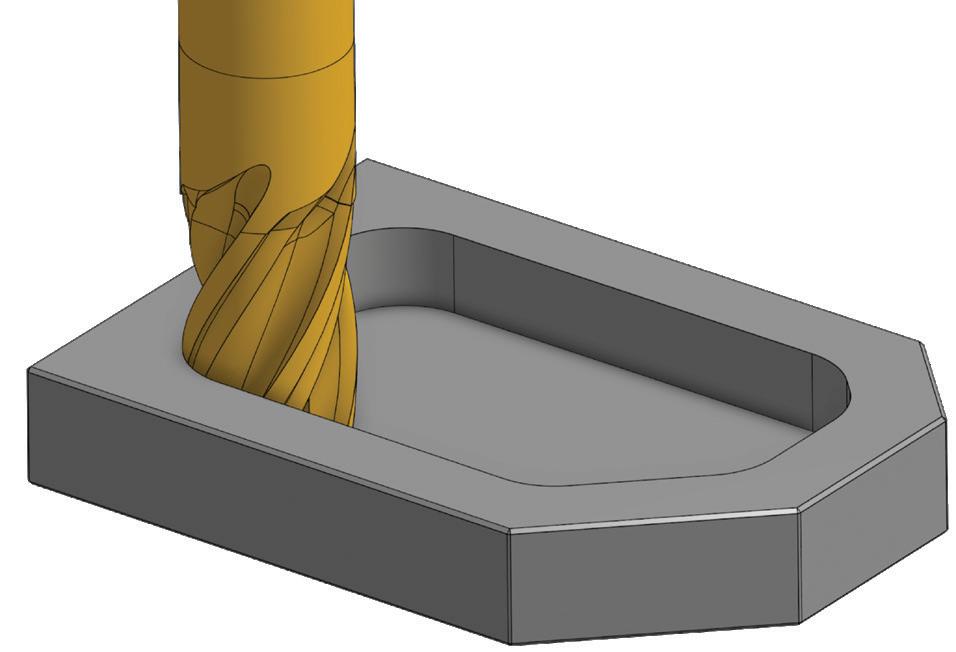
But when it comes to 3D printing, this conventional design for manufacturing wisdom tends to get thrown out the window. Instead, the 3D printer gets treated as a ‘magic box’, capable of printing anything. When poorly optimised designs fail, the tool takes the blame and 3D printing is viewed as unreliable.
The good news is that driving successful 3D printed applications by designing intentionally for your printing technology, is simply designing for a different manufacturing process. It’s straightforward to integrate DFAM into your existing engineering design work as an addition to your array of existing tools. Here’s how that would work, step by step:
1. Uncover the root cause of the challenge you’re trying to solve
2. Identify the economic and functional requirements of potential solutions
3. Choose a specific manufacturing process, AM or otherwise, that can likely meet these requirements
‘‘ If you want to get the most out of your chosen variety of AM, you’re going to have to intentionally design for it ’’
4. Start designing a solution to meet your particular requirements
5. As the design progresses, begin to tailor your design to the chosen manufacturing process
6. Build (via AM or traditional manufacturing) your prototype design
7. Test component(s) and measure performance against desired operation
8. Repeat until a solution is achieved, changing manufacturing processes if necessary
You’re probably realising that this isn’t rocket science. You may even be wondering if I’m wasting your time. I’m not, but you’re right about the first part. DFAM doesn’t have to be complicated, and this workflow is probably similar to how you’re already designing for other manufacturing processes today.
There are two important points to be made about this workflow. First, it takes an integrated approach to 3D printing, adding it to your toolset, without replacing existing tools or encouraging you to view projects only through an additive lens. The world of engineering is large and full of diverse challenges, and you should choose the right tool for the right job.
Secondly, regarding Step #5, you need to consider that 3D printing is not a monolith, but instead an entire family of different technologies, each of which has its own subset of design guidelines and best practices.
There are some similarities among these technologies; for example, 3D printers generally build parts one layer at a time. But even within that 3D printing process characteristic, some processes build layers upwards and others – notably stereolithography (SLA) or some flavours of digital light processing (DLP) – build downwards. Gravity has a very different effect on these processes, and the design of features like cantilevered overhangs must be approached differently based on the target AM process.
WHERE DO WE GO FROM HERE?
Everything you need to know about designing for a specific 3D printing process could occupy several dozen articles. (And I should know, because I built an entire course around the topic at my previous company.)
But in more general terms, there’s an easy set of starting points to improve your DFAM techniques.
First, identify the type of 3D printer you have access to and learn how it builds a part, as well as the physics behind the process it uses (for example, FDM, SLA, SLS, DMLS, and so on). This helps you understand what kind of performance is realistic from the process.
The manufacturer’s website is often a great source for tutorial literature on designing for their process, as well as offering design guides that often detail the geometric limits of the technology, such as minimum feature sizes in different axii. These will help you understand what you can’t do with the technology, but not the full
● 1 Every manufacturing process has its limitations. For example, machining cannot produce a pocket with corner radii smaller than the radius of the endmill
● 2 This 3D-printed CNC tube bending die was designed to incorporate cheap off-the-shelf hardware to add significant strength where the part has reduced strength due to limitations of the 3D printing process (Credit: Markforged)
extent of what you can achieve, so don’t limit yourself to only what the supplier showcases.
Second, understand the materials you have available. Data sheets will enable you to compare them to the materials you currently use. Print some test parts and deliberately try to break them, in order to get a real feel for their mechanical properties and performance.
As always, best design techniques are learned by solving an actual problem, not as a theoretical exercise. Have a real project, and search for user groups, design tips and learning materials from others using the same types of printing to do real engineering and design work. Get advice and feedback from your colleagues, as well as external peers using the same technologies.
Finally, remember that 3D printing isn’t your only tool, and that you can often use off-the-shelf components or other traditionally manufactured parts to add capabilities to an assembly, just like you do with any other engineering project.
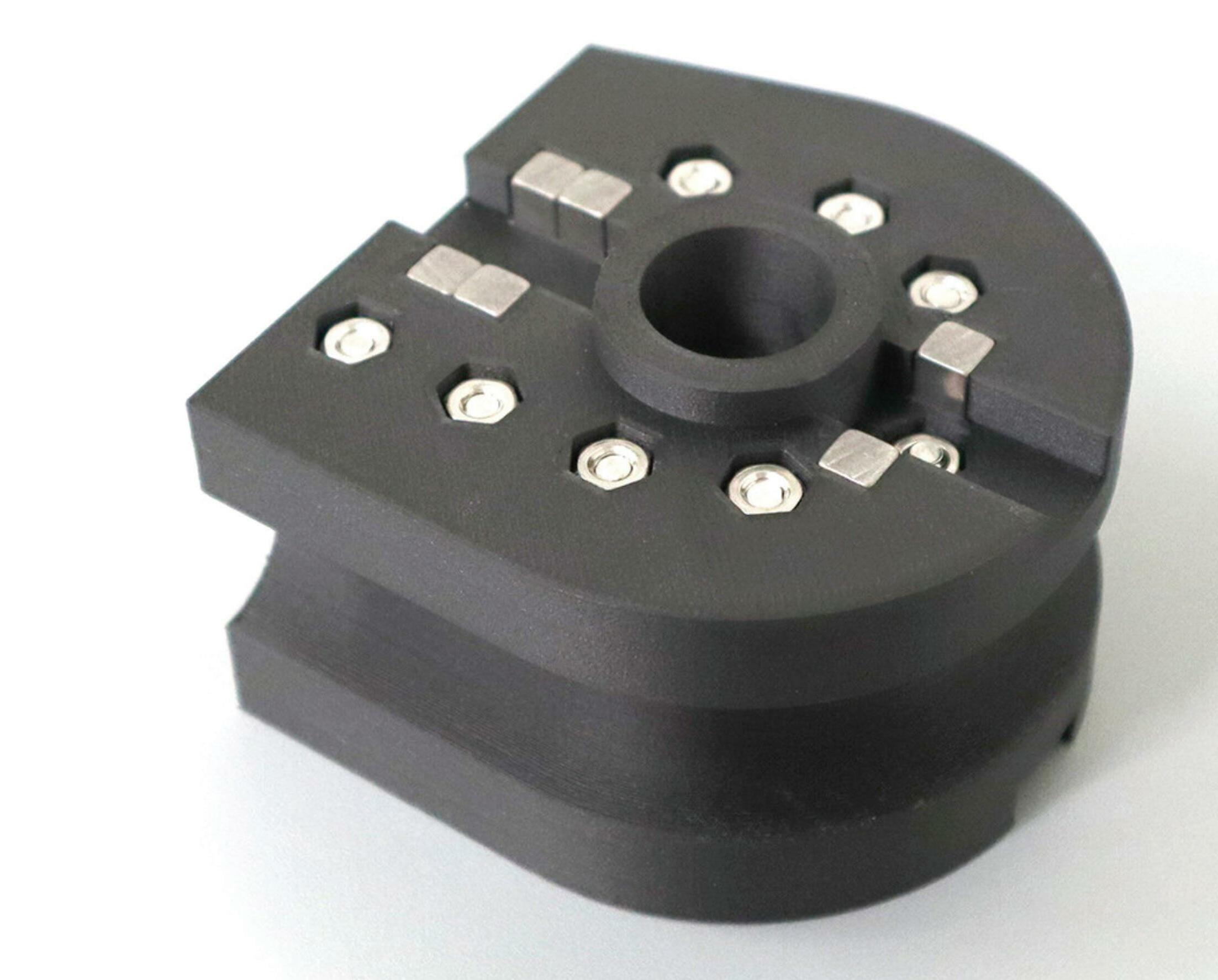
You won’t become an expert overnight, but you will begin to solve more complex engineering problems with less time and effort, ones that fluidly incorporate clever 3D-printed designs. And maybe, when you think about it, that’s the real magic at work here.
ABOUT THE AUTHOR Nick Sondej is a mechanical engineer and the Founder & Principal of Matti Group, an engineering services firm with a focus on using advanced technologies to help clients solve technical and business challenges. Previously he was an early employee at Markforged, spending nearly a decade leading the development of an engineering first-principles approach to 3D printing application development, and building the Markforged University additive training curriculum. In his spare time he cooks well, cycles long, and surfs poorly, all with a side order of particularly dumb jokes.
GO FAST CAMPERS TURNS TRUCKS INTO TENTS WITH AUTODESK FUSION 360

A look inside how the Go Fast Campers team designs and manufactures truck-top campers — from 3D modelling to robotic automation.
For years, Wiley Davis made many treks to Baja, Mexico. Packing up 4x4 trucks with motorcycles, bikes, and surfboards, he and his buddies would head south from Montana for off-road adventures and remote, surfside camping.
Davis loved these trips except for one part — the sleeping accommodations. At 6’4”, he simply doesn’t fit in the back of most truck beds. He’d already founded a couple of small businesses designing and manufacturing gadgets and offroad parts. Now, it was time to solve the Baja bed problem.
Go Fast Campers is born
“About four years ago, I was sketching a way to do a truck topper shell that I could actually sleep in comfortably,” Davis says. “At the same time, I
Image courtesy of Go Fast Campers
wanted to find something that would force me to learn how to work on a more complicated project with a lot more people.”
Back home in Montana at his shop, Davis teamed up with a fabricator next door who worked on large expedition vehicles. Within a year, Go Fast Campers was born. Their debut product was a one-of-akind, truck-top camper, which was manufactured in a small, rented shop space. “We had to turn it sideways to get it out the door,” Davis says.
Now, they’ve moved into a much larger manufacturing space and grown from three people to more than 70 employees. And it’s all thanks to the commitment to thoughtful design, quality, innovative manufacturing techniques — and just being good people. GFC is exceptionally transparent on its website, from a detailed look
Image courtesy of Go Fast Campers
into its manufacturing process to visible salaries. “We pay [our employees] the highest starting wage of any manufacturer in the area, if not the state,” reads the GFC site.
The GFC Platform Camper
Go Fast Campers’ products are all designed and manufactured in the United States. The campers are minimalist in their look but rich in details, features, and durability.
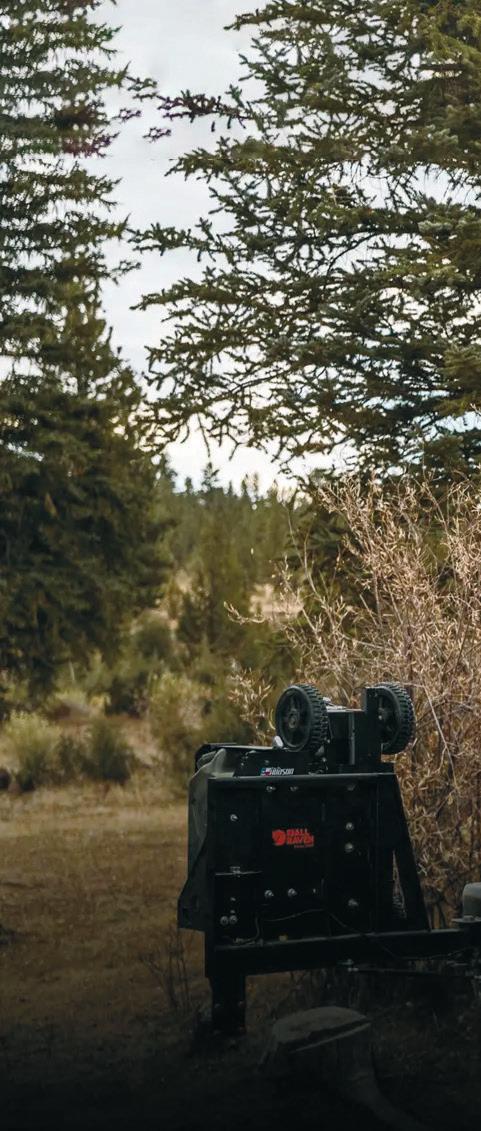
The GFC Platform Camper is the flagship product, featuring the “pop-top magic” for effortless camping. According to the company, it’s a Swiss watch masquerading as a truck topper with obsessive attention to detail, down to the hinges and latches. “Nothing on a GFC is an afterthought,” states the GFC website.
They also offer a chase frame for the truck bed and a rooftop tent, which is essentially the upper version of the platform camper.
“Everything is made out of metal with the exception of obviously the fabric inside the cushions and the honeycomb composite roof and floor panels,” Davis says. “Many of these things would have been made with wood, glue, staples, and stuff that will rot. With our campers, you take the cushions out, you open them up, and you can literally hose them inside and out. It’s not going to hurt anything.
It’s very different, and people really like it.”
Best of all? Even 6’4” Davis can get a comfortable night’s sleep.
Manufacturing 140 Versions of a Product
Innovating, designing, and manufacturing three core products is already an impressive feat. But when it comes to providing the campers for individual vehicles, it gets complicated because every truck model is different. Go Fast Camper’s products are customized with parts for over 140 unique truck models. That takes a lot of CAM—and Autodesk Fusion 360 is their chosen platform for all of it.
“Because we were using Fusion 360 for CAM and generating so many parts, we switched to using completely Fusion 360 even on the modelling side,” Davis says. “The parametric modelling in Fusion 360 is to the point where we can use it for whatever we need. Not having to reimport models and regen or redo all the CAM for every model change saves us a ton of time.”
Bringing Automation Into the Mix
For Go Fast Campers, there isn’t a debate about automation. Robotics is an essential part of the business. From the beginning, robots were integral to the design process. The company has a few Universal Robots robot arms in action on the shop floor.
“Robotics is what allows us to have lots of parts and
really nice, small, machined aluminium parts instead of something moulded out of plastic,” Davis says.
With over 600 parts in one camper, that’s an intensive manufacturing effort — especially for a small business. One person runs five automated machining cells, and they can change parts in under five minutes.
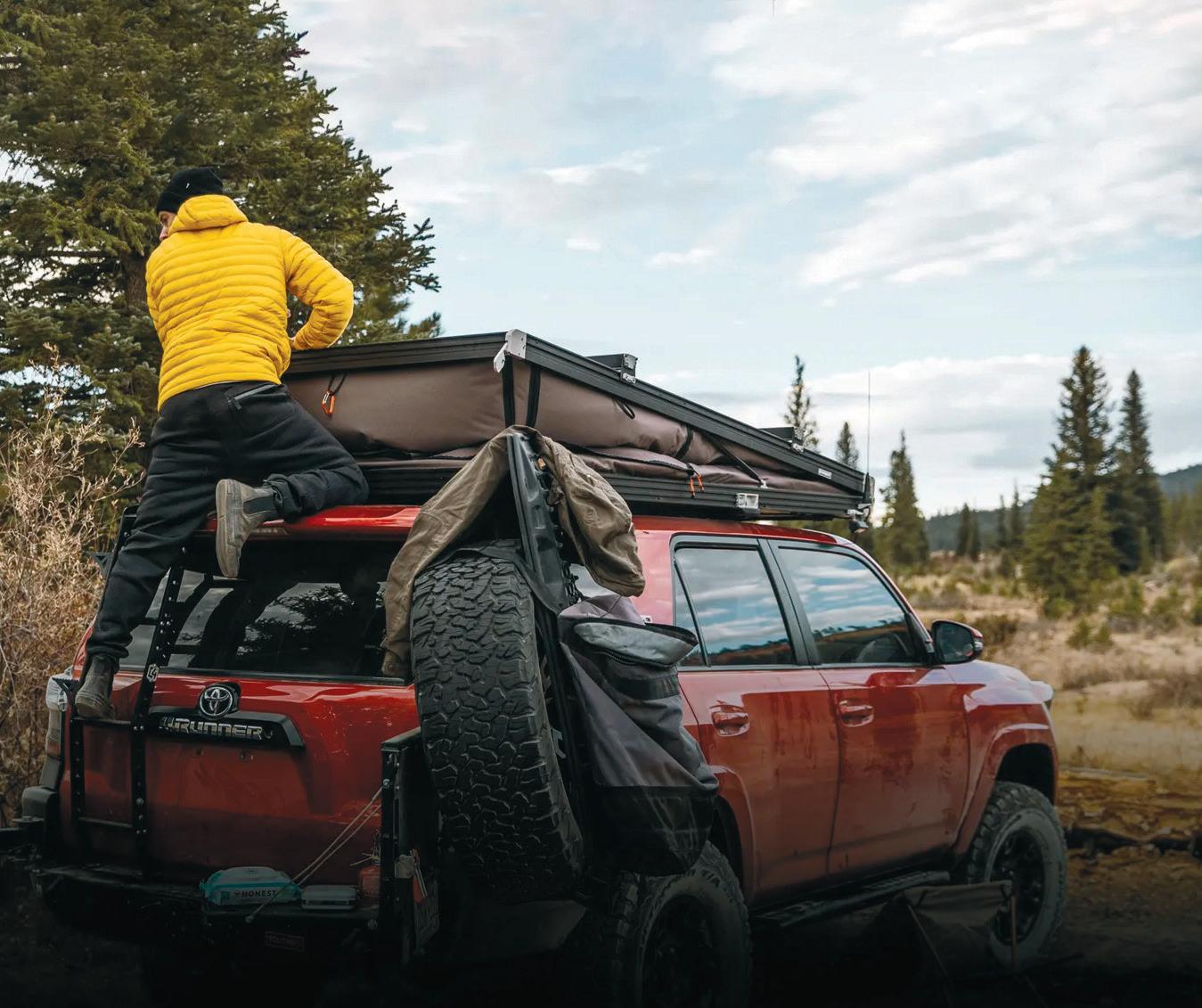
“Without the robots, we wouldn’t be able to do it,” Davis says. “We’d have so many people standing at machines all day putting parts in and out of machines. These campers would cost twice as much, and it wouldn’t be a viable product at that point.”
The combination of Fusion 360, the Fusion 360 Machining Extension, Haas Automation machines, and robotic arms makes automation increasingly accessible for manufacturing companies of any size.
“With Fusion 360 for our production process and CAM, we essentially have the entire robot system modelled in there,” Davis says. “When we program a new part in Fusion 360, it’s all systematized around a template. You can program a part, and no one has to re-indicate or set up a machine differently. You just program the part machine and the job and run it.”
Learn more about Fusion 360 here: https://www.autodesk.com/products/fusion-360/
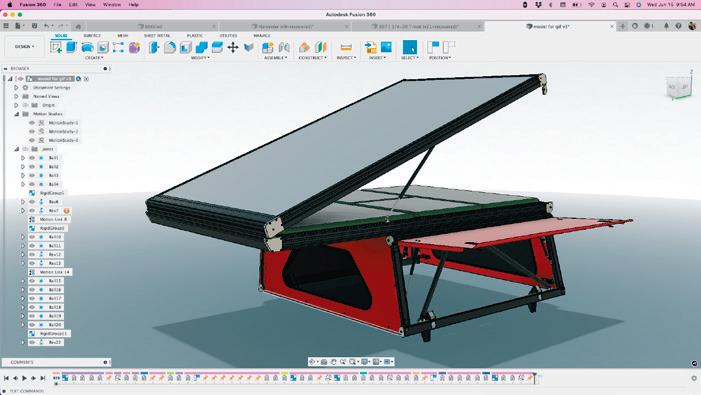
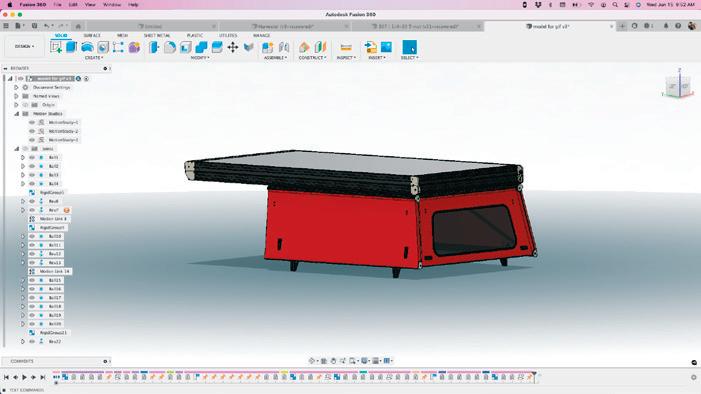

DEVELOP3D LIVE 2022 PREVIEW
We never stop learning. Up to and including our last day on this floating rock we stand the chance of uncovering something completely unbeknown to us.
Designers and engineers are by their nature some of the most curious individuals, intent on learning about people, processes and problems that were not even in their purview moments earlier. While DEVELOP3D LIVE is an event where the latest technology affecting product development comes to the fore, I’ve often seen it more as a place for the curious to meet and engage.
If, for example, automotive designers spent their time surrounded by presentations solely about car design, then you would expect that a) those presentations would grow dull, and b) they would be missing out on so many exciting new developments and ideas in other sectors.
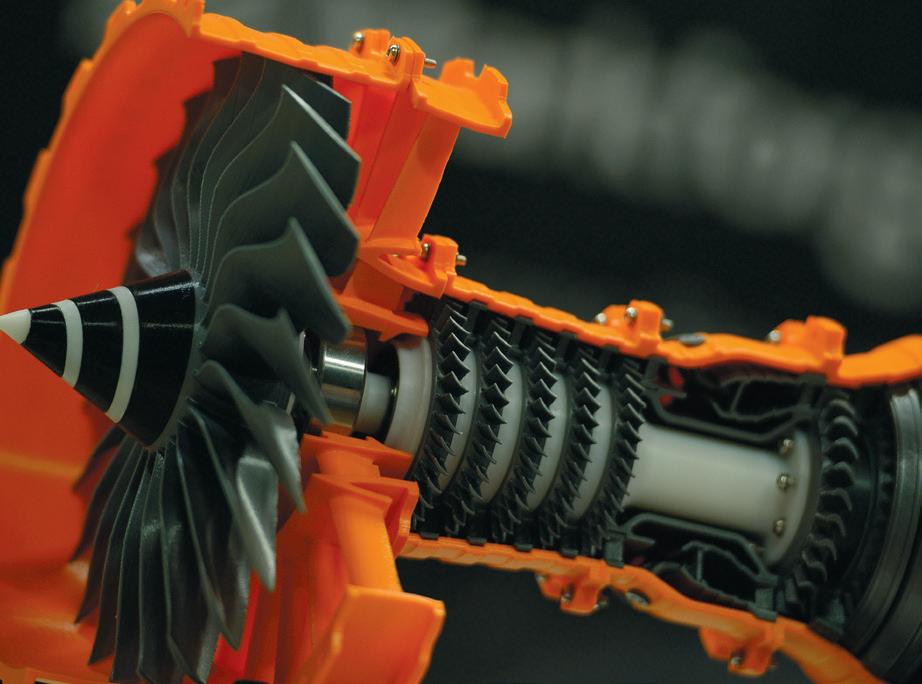
In the years we’ve been running the event I’ve learned from attendees – designers and engineers – how they have gone away with a key piece of knowledge they could adopt into their workflow from an industry very different to their own – whether from a presentation, or a chance meeting with another delegate.
Our conference program for 2022 stands to draw as diverse a crowd as always. Vital Auto will showcase an exciting blend of technologies as it explains its role in cutting edge automotive prototyping with a blend of physical and digital tools. Also on the Main Stage, Ocado Technology will lift the lid on the company’s 600 Series robot, built to enable the next generation of grocery fulfilment centres using a radical, additive-first approach to robotics hardware development.
And those are just the start. Elsewhere we have presentations from the established 3D design software vendors at the heart of all our workflows, each one giving an insight into the direction of their tools and the challenges of users that they’re working to overcome.
We have new perspectives on tackling challenges for start-ups, with an expert panel, plus some companies that will explain how they’ve managed to cultivate and scale their ideas.
With manufacturing technologies offering new and better ways to produce products than ever before, we’ve enlisted a panel of experts across hardware and software to give you the inside line on how processes and machinery will evolve, and how this technology can feed back into the earliest stages of the development process to give you the edge over competitors.
There’s also a track devoted to wide range of designers showcasing topics as diverse as how to best adopt more sustainable materials, through to the impact that AI will have on your design process.
Check out the highlights over the next few pages, with many more speakers at www.develop3dlive.com/speakers
And let’s not forget the exhibition, showcasing a whole smorgasbord of technologies from CAD, generative design, topology optimisation, additive manufacturing, AI and 3D printing, to workstations, design viz, VR/AR, simulation, data management, 3D scanning, tolerance analysis and lots, lots more. See pages 54-64
We hope to see you on 1 November in Sheffield. Never stop learning.
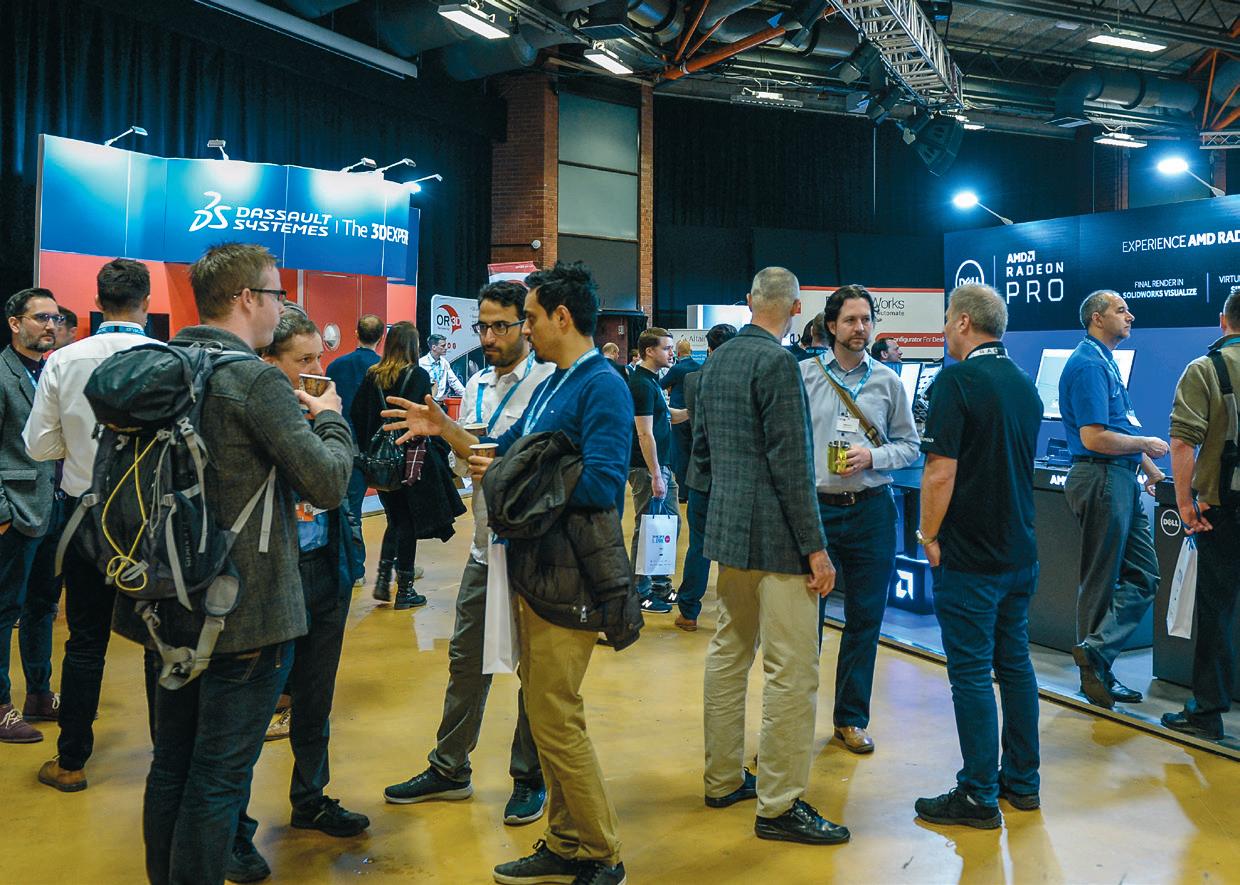
Ocado’s
manufacturing
COMBINING ADDITIVE MANUFACTURING AND AGILE METHODOLOGIES FOR RAPID ROBOTICS INNOVATION MATT WHELAN, OCADO
Matt Whelan, Head of Engineering for Ocado Technology’s 600 Series bot, will be lifting the lid on the company’s radical additive-first approach to robotics hardware development. This novel design process, which puts additive at the centre and draws inspiration from the world of agile software development, allowed the team to create the world’s lightest and most efficient grocery fulfilment bot.
Matt Whelan, Head of Engineering for Ocado Technology’s 600 Series bot
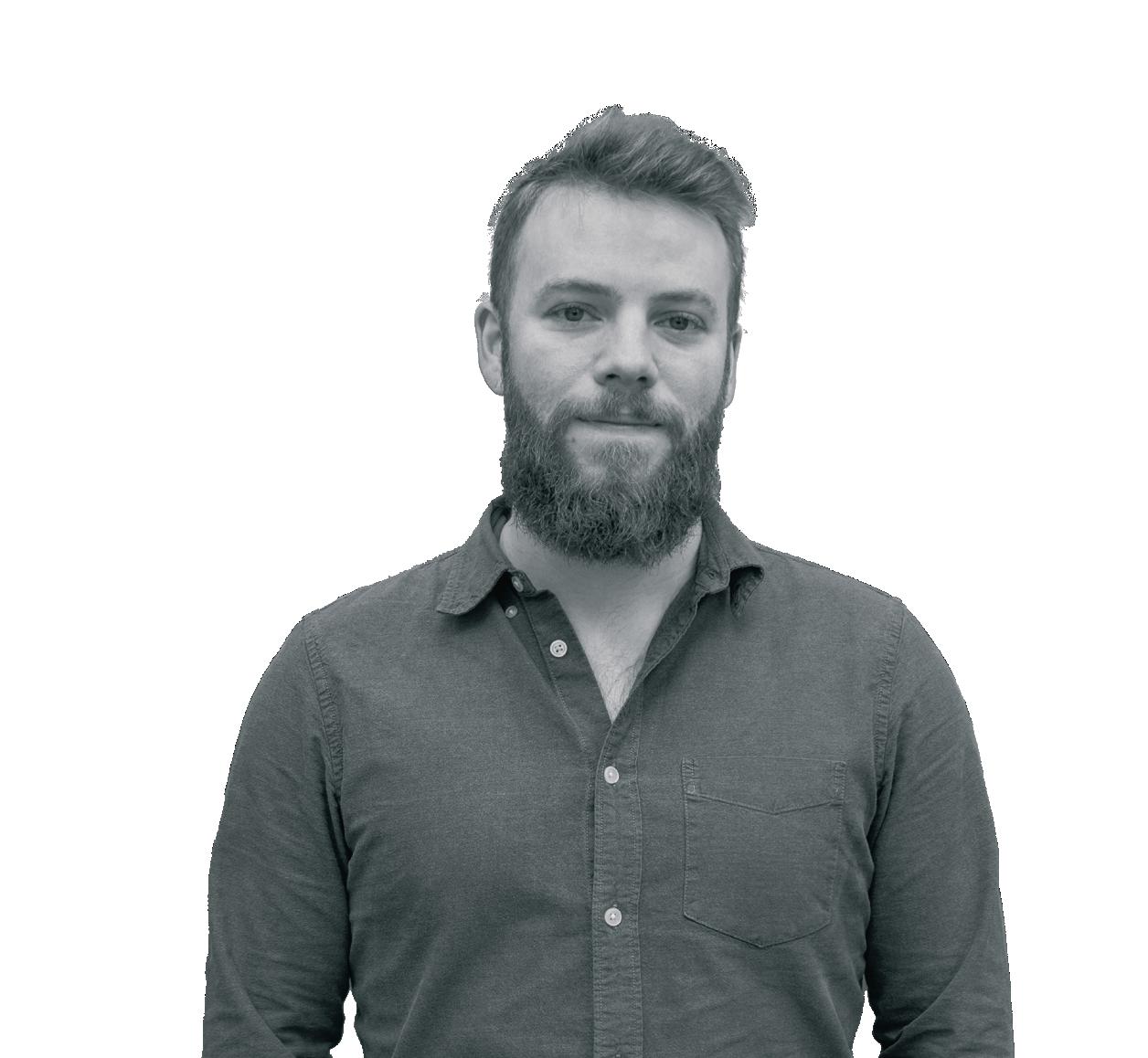

optimisation
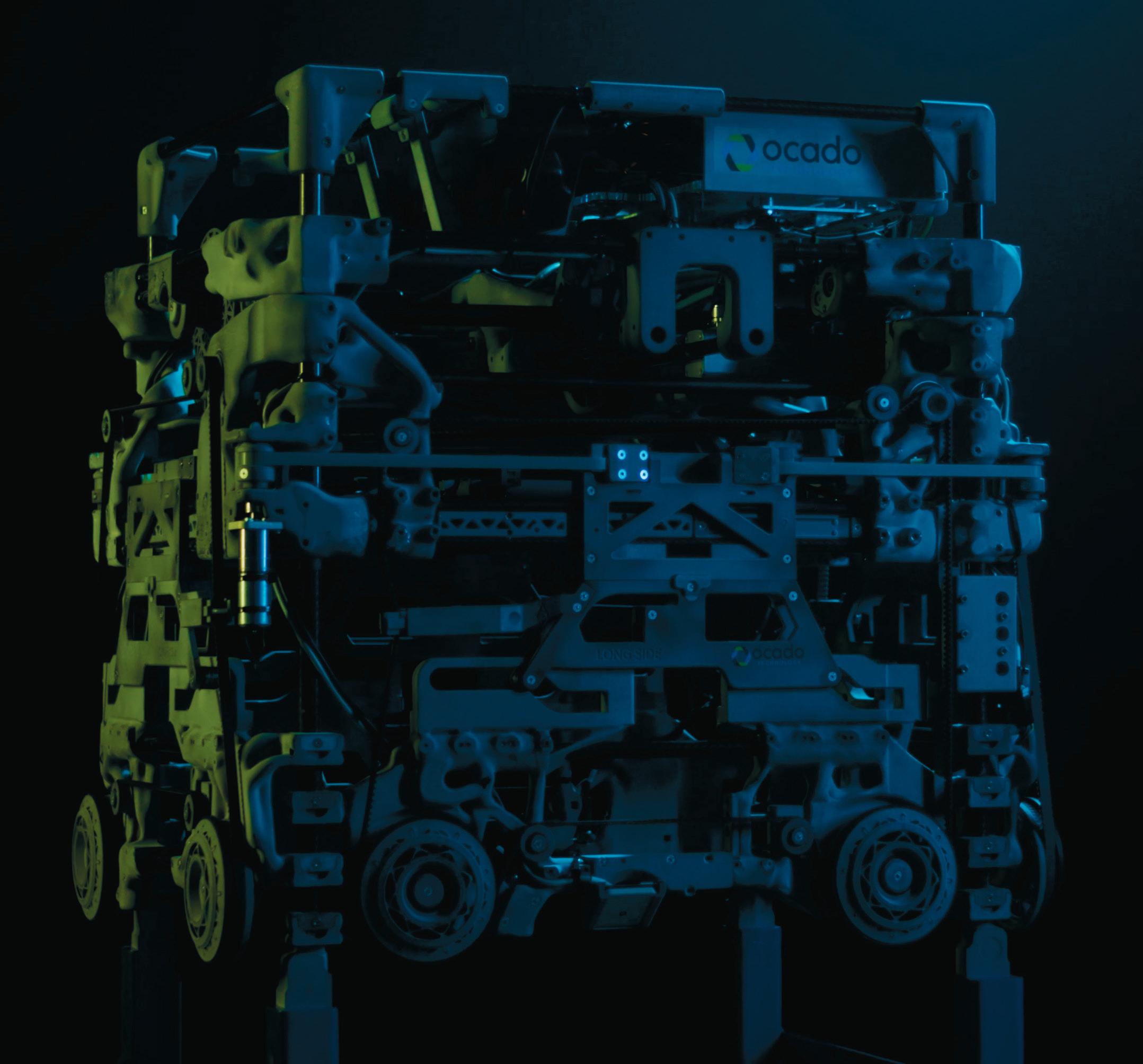
team
NEW TECH SHOWCASE AMD // ZEA FLOW ENGINEERING
AMD's Rob Jamieson will present a new graphics driver for Radeon Pro GPUs that promises to boost 3D performance in Solidworks and other OpenGL CAD software (see page 12).
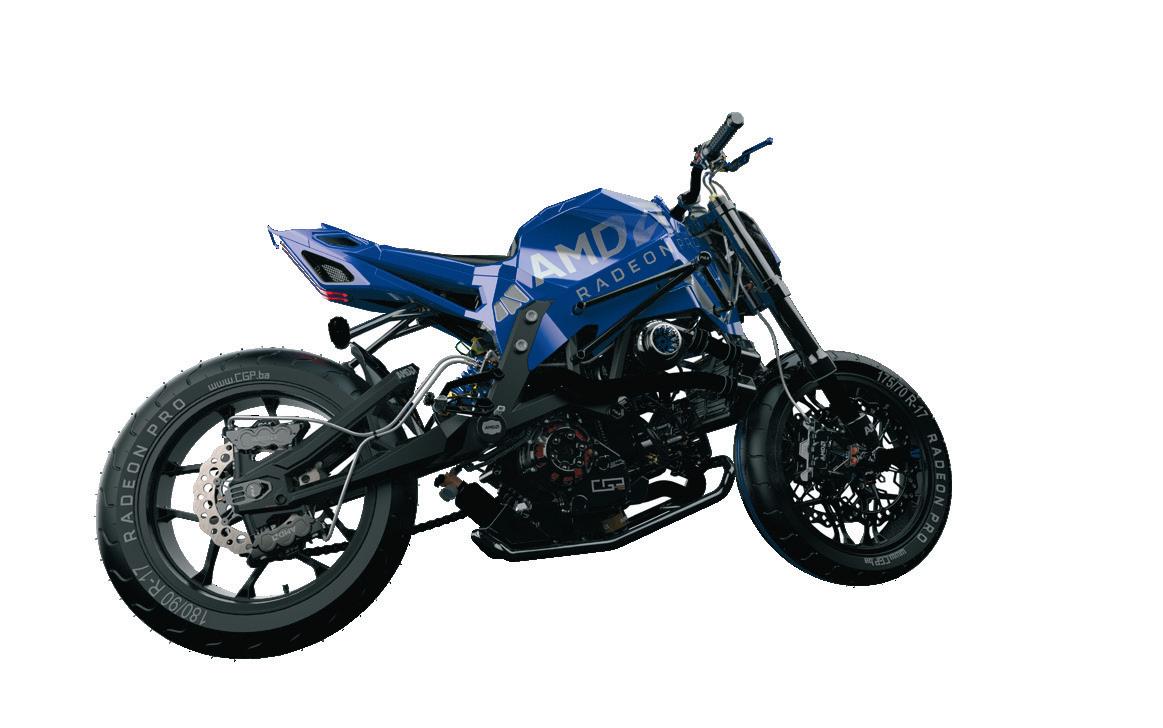
Michael Smith & Philip Taylor, CEO & CTO of Zea will bust the top three myths holding back 3D technical product documentation.
Pari Singh of Flow Engineering will showcase a new collaboration tool for streamlining team engineering processes from requirements, to modelling, to verification.
SUSTAINABLE MATERIALS: A STEP IN THE RIGHT DIRECTION CHARLOTTE JONES CALLUM
As the circular economy becomes central to future design, and sustainability at the core of future materials choices, Charlotte will discuss how design and engineering
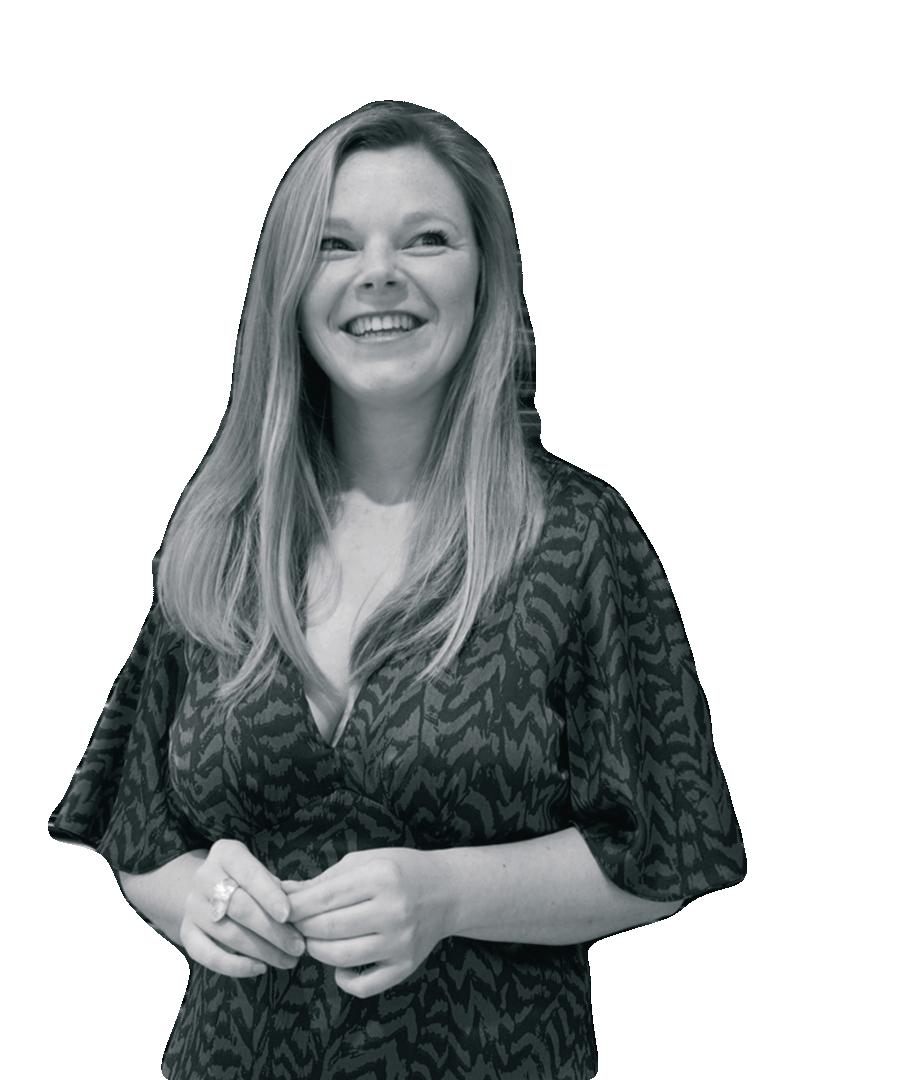
WHAT’S NEXT FOR DESIGN SOFTWARE?
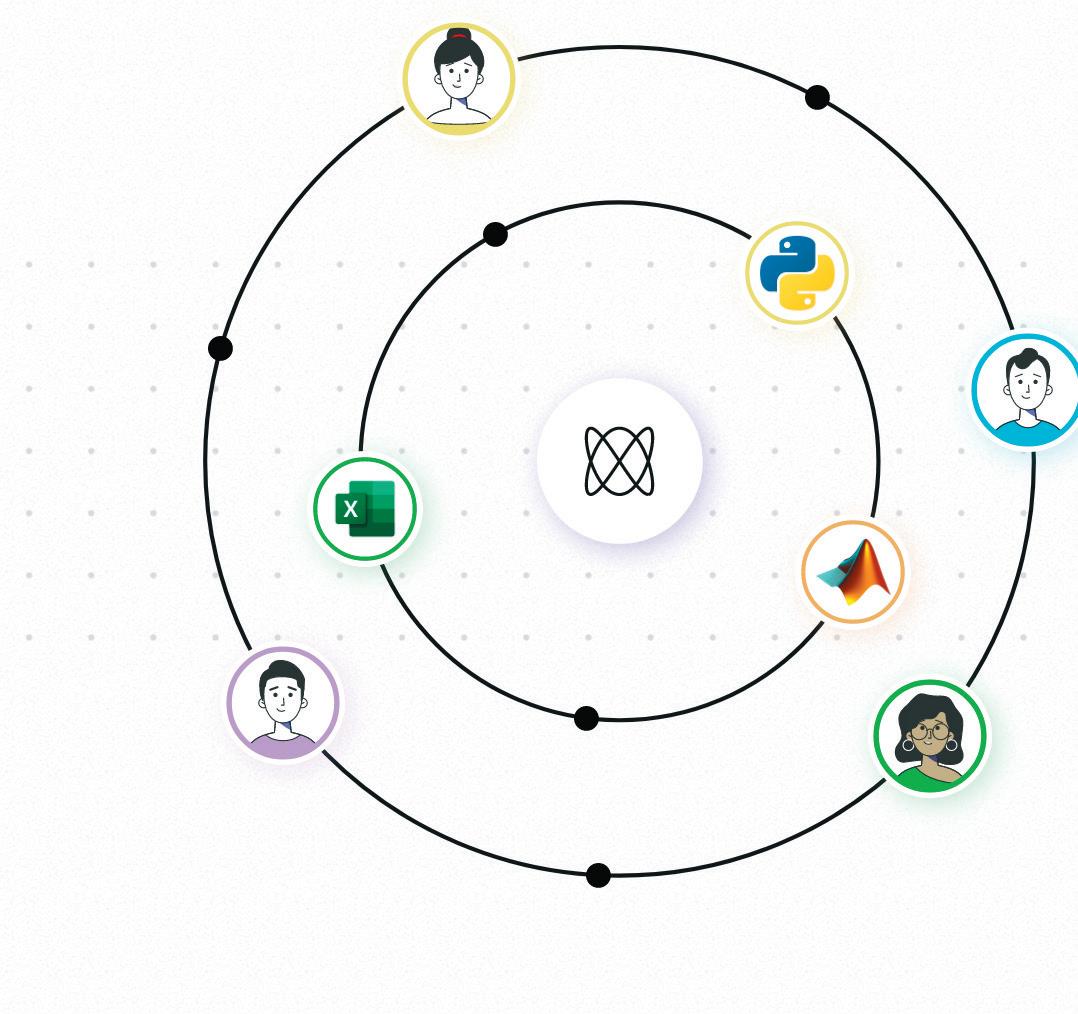
Featuring Altair, Autodesk, Dassault Systèmes, nTopology, PTC, & Siemens. Some of the leading figures from the biggest industry brands are taking to the main stage for back to back presentations that will give a glimpse into what is coming next. Focussing on industry trends, real life user cases, and the abilities of next generation hardware, attendees will attain an understanding of where some of their core workflow tools are heading.
Making his first appearance at DEVELOP3D LIVE is new Solidworks CEO Manish Kumar (pictured).
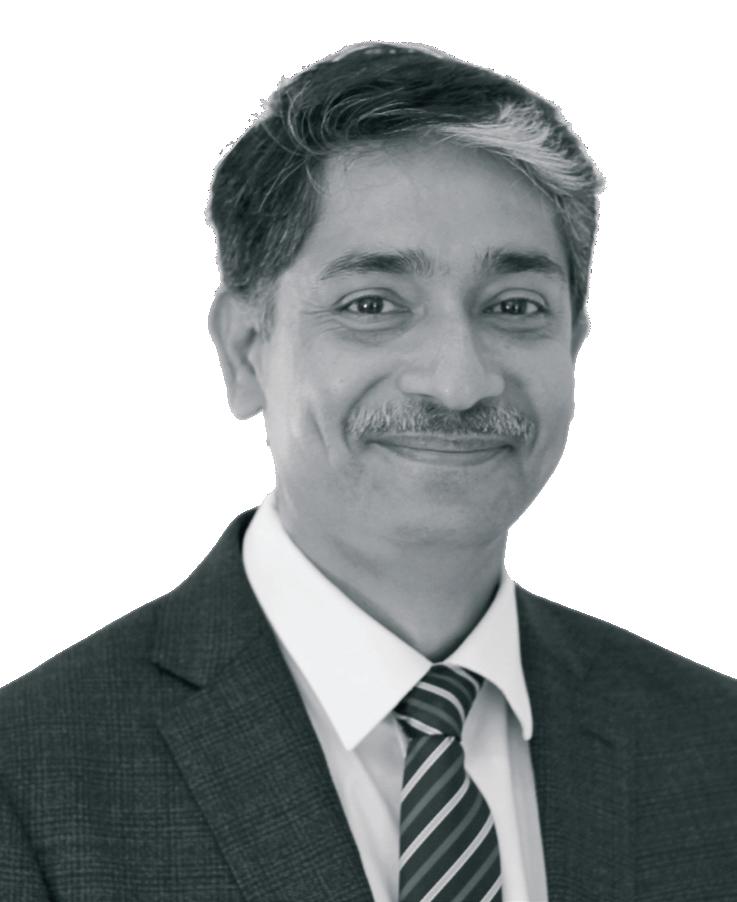
BAC MONO IAN BRIGGS
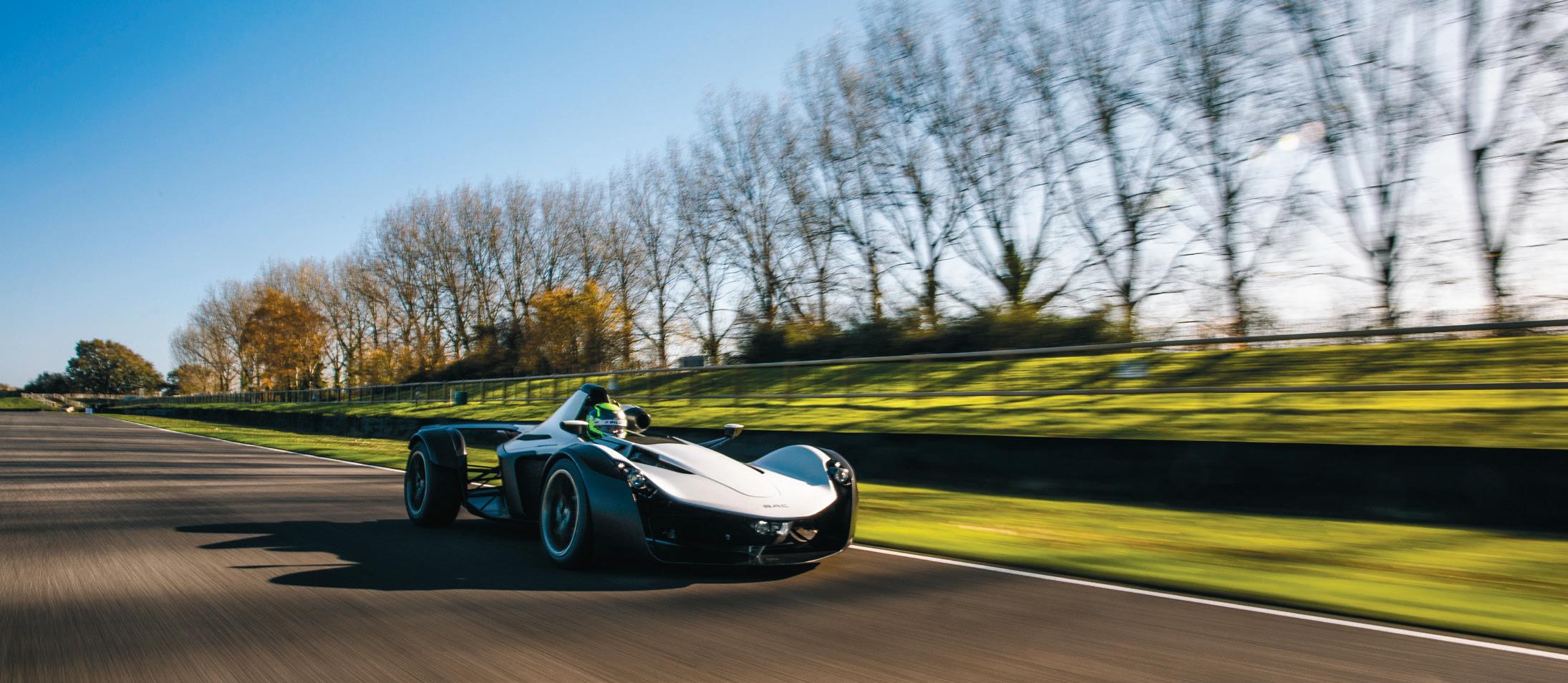
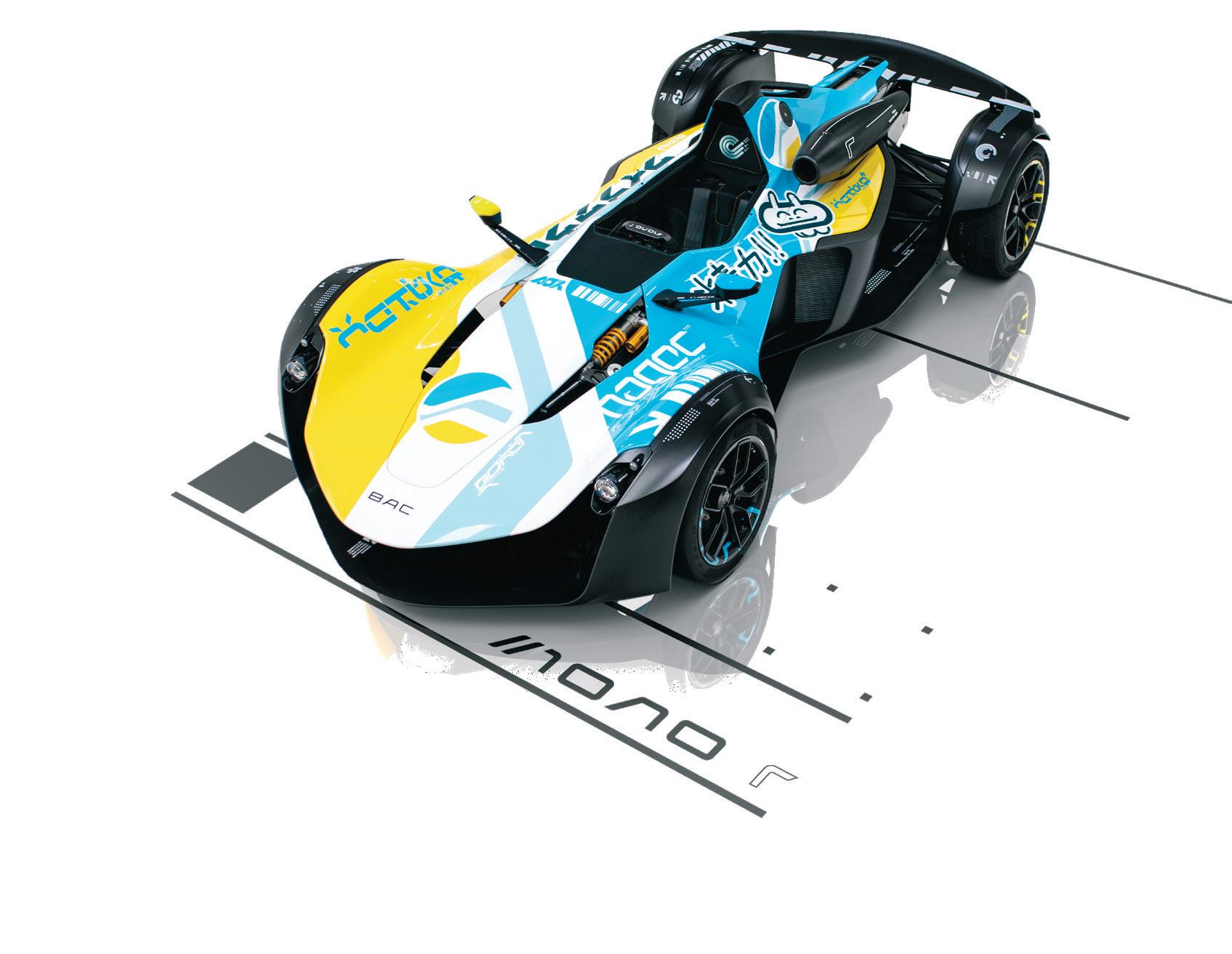
The audience will need to buckle-up as founder and design director Ian Briggs will give attendees an insight into the design and engineering process of the British company’s latest road legal, track-honed car, the BAC Mono R. This incredible machine fits a new mould of automotive market that is being crafted for those passionate about driving. The development process is just as fast-paced, bringing together generative design, customisation, additive manufacturing and more in order to create a pure driving experience.
STARTUPS PANEL DISCUSSION
The post lockdown world is now full of hardware start-ups looking to break through with their products. At DEVELOP3D LIVE we have assembled an experienced panel that will look at the methods, programs, and technologies that enable product ideas to grow from an initial spark, into a fullblown go-to-market product. The panel will consist of start-ups that have been there and done it already; experts from the fields of legal, financial guidance, crowd funding and accelerator programs, and much more. Bring your own questions and leave inspired!
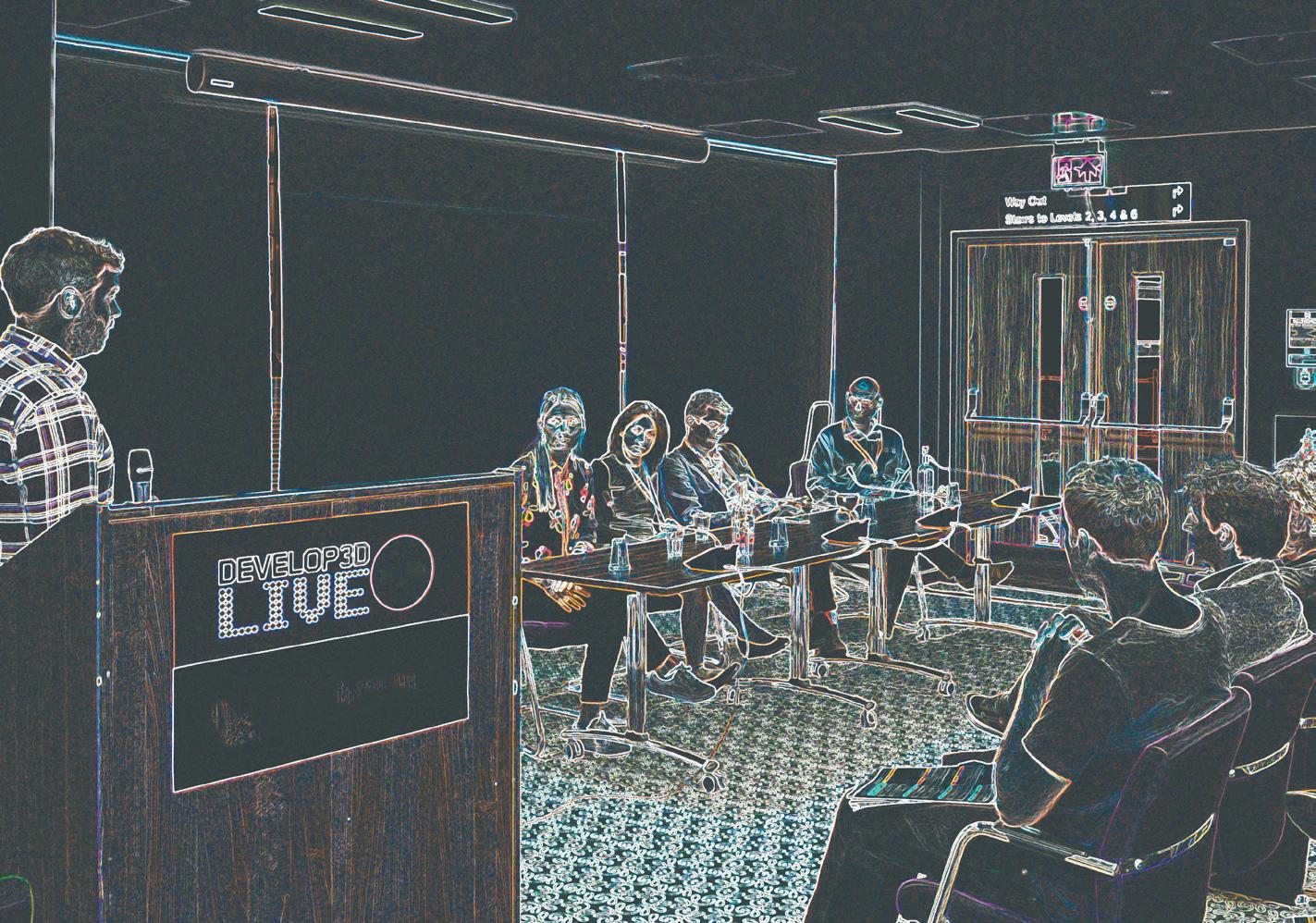
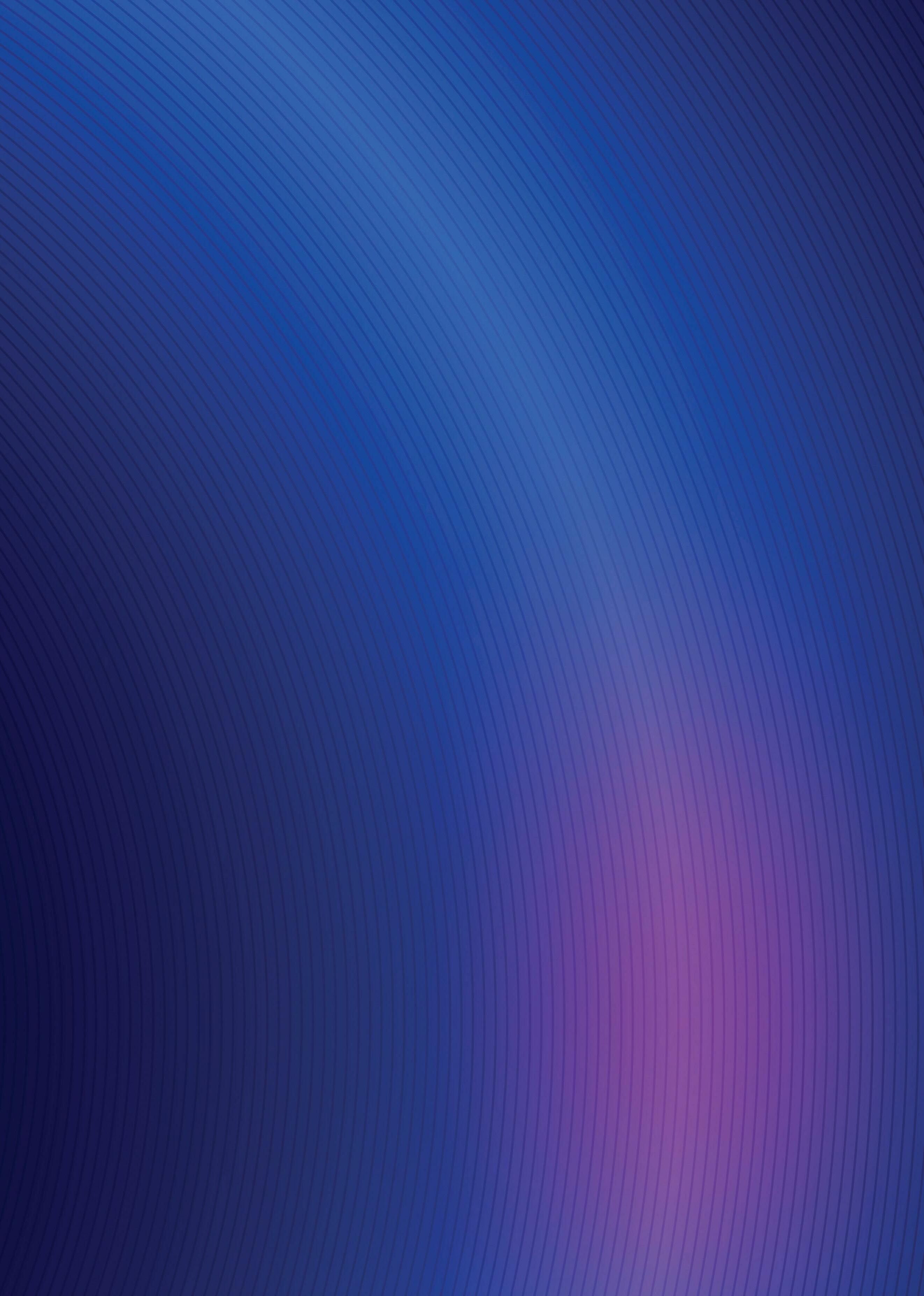
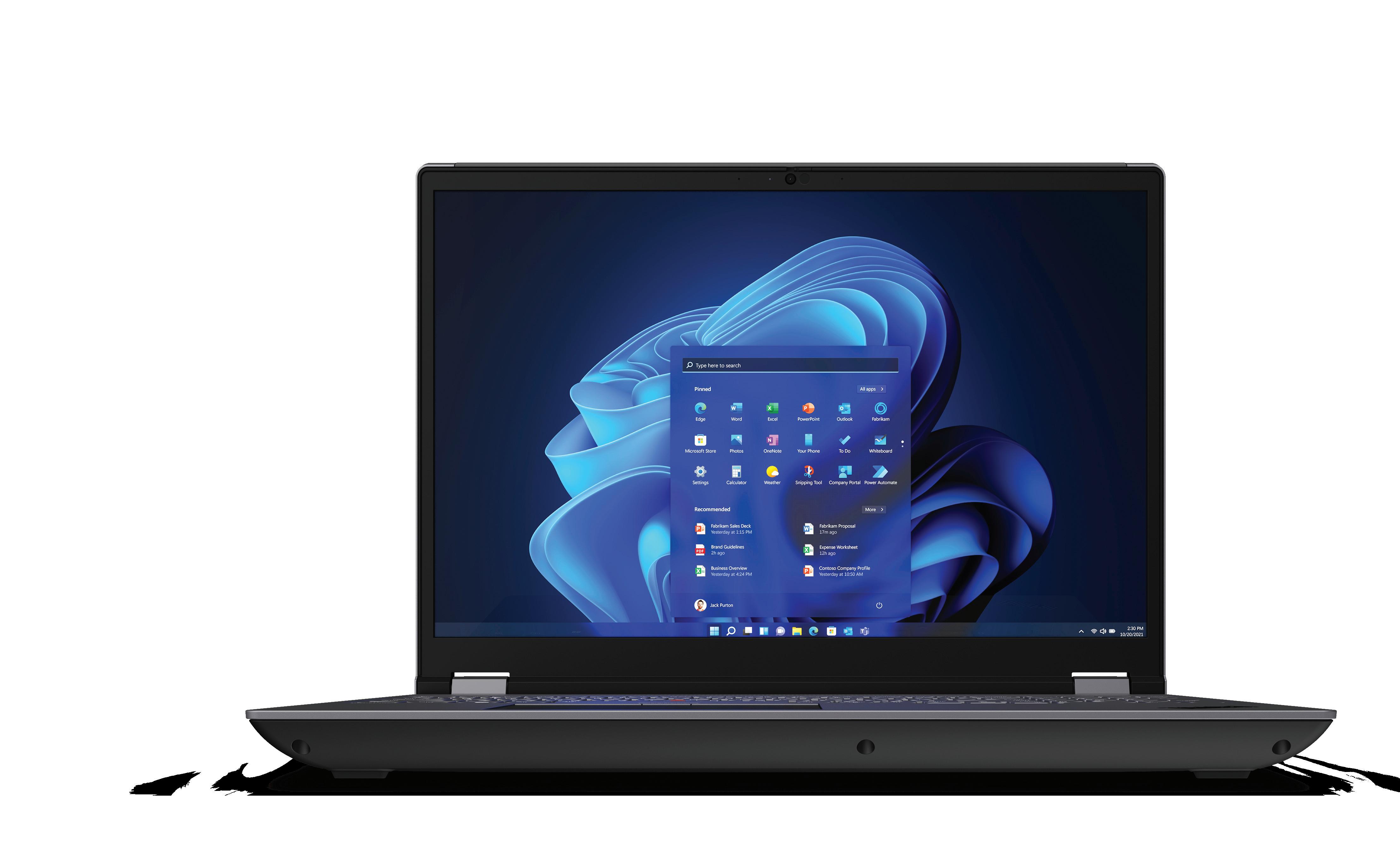

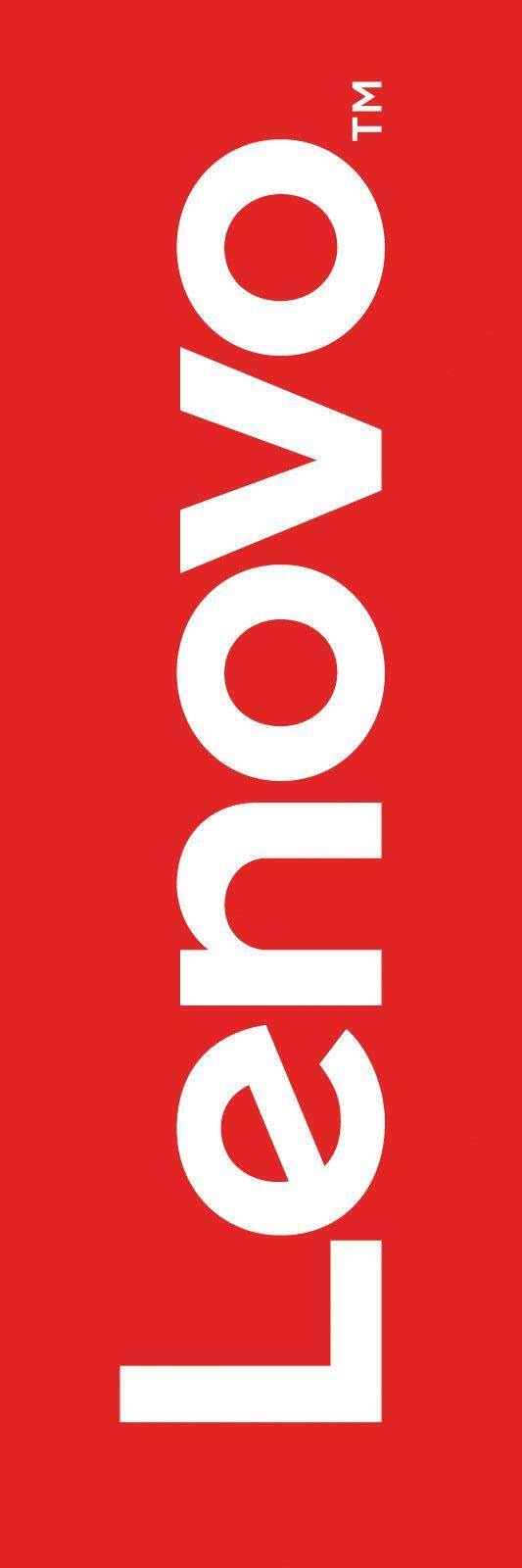
HOW VISIONS OF FUTURE PRODUCTS COME TO LIFE IN AUTOMOTIVE SHAY MORADI & PAUL HEYS VITAL AUTO

At Vital Auto, Paul and Shay operate at the intersection between analogue and digital. Collectively they are responsible for creating new systems, new tools and producing innovative interfaces and creative strategies that impact consumer experience from end to end. They will explore blending physical and digital prototyping to provide designers with opportunities to enhance their products
From
DIGITAL MANUFACTURING PANEL DISCUSSION
Up your game for more agile production
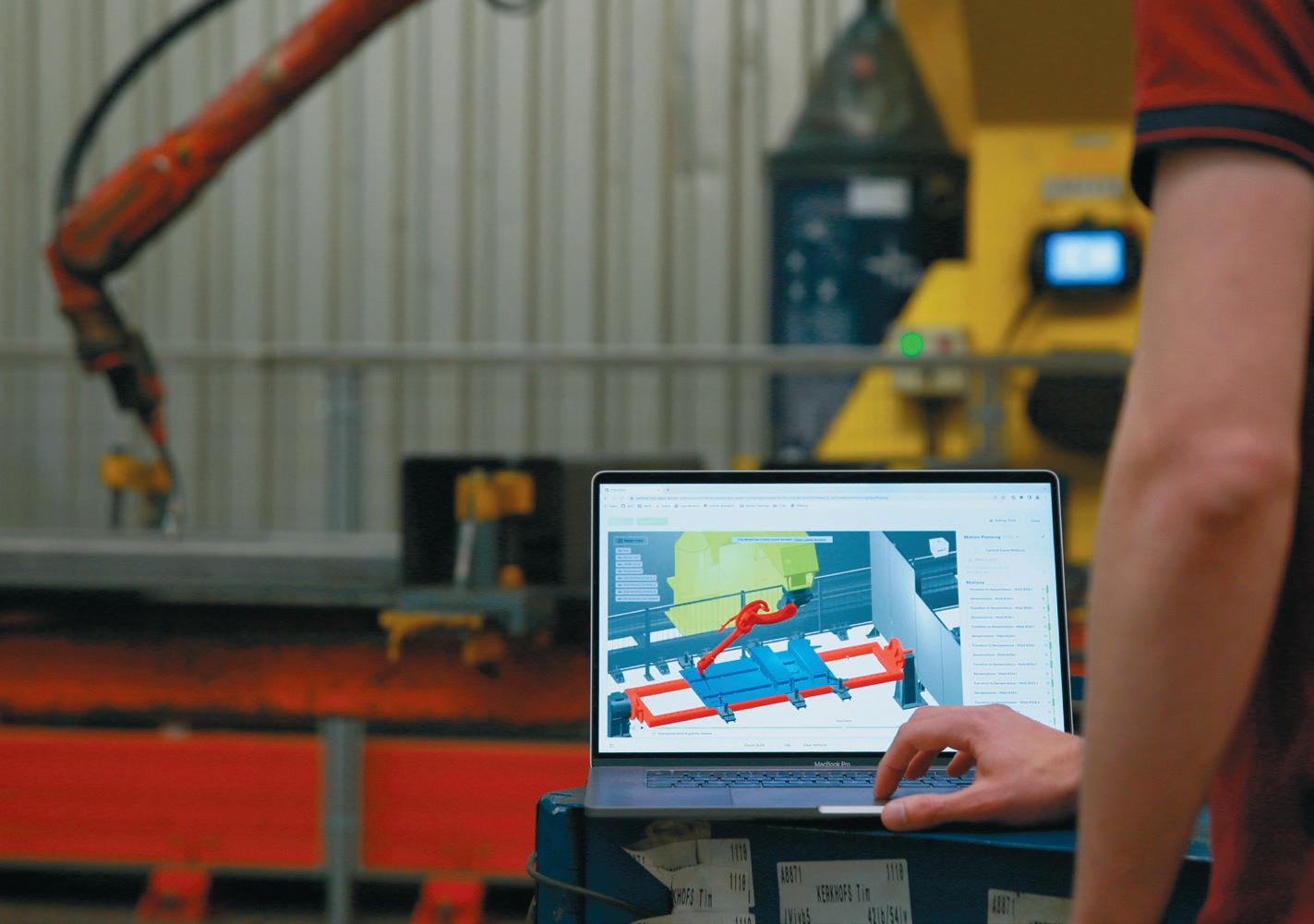
Manufacturing and production methods have been thrown into the spotlight recently by pandemic and war. The most agile have jumped ahead from the competition, while others are still looking to make their manufacturing more flexible, reshore some elements, or drive for more sustainable practises. We bring you a panel full of experience – from software to hardware – to help you make the next leap. Experts will lend opinions on optimising workflows for equipment you already own, to the very latest kit to accelerate your business.

3DCONNEXION
STAND A4
3Dconnexion is a provider of awardwinning devices for 3D design and visualisation professionals. 3Dconnexion mice are designed to provide a more intuitive and natural way to interact with 3D content and support today's most popular and powerful mechanical engineering and other 3D applications.
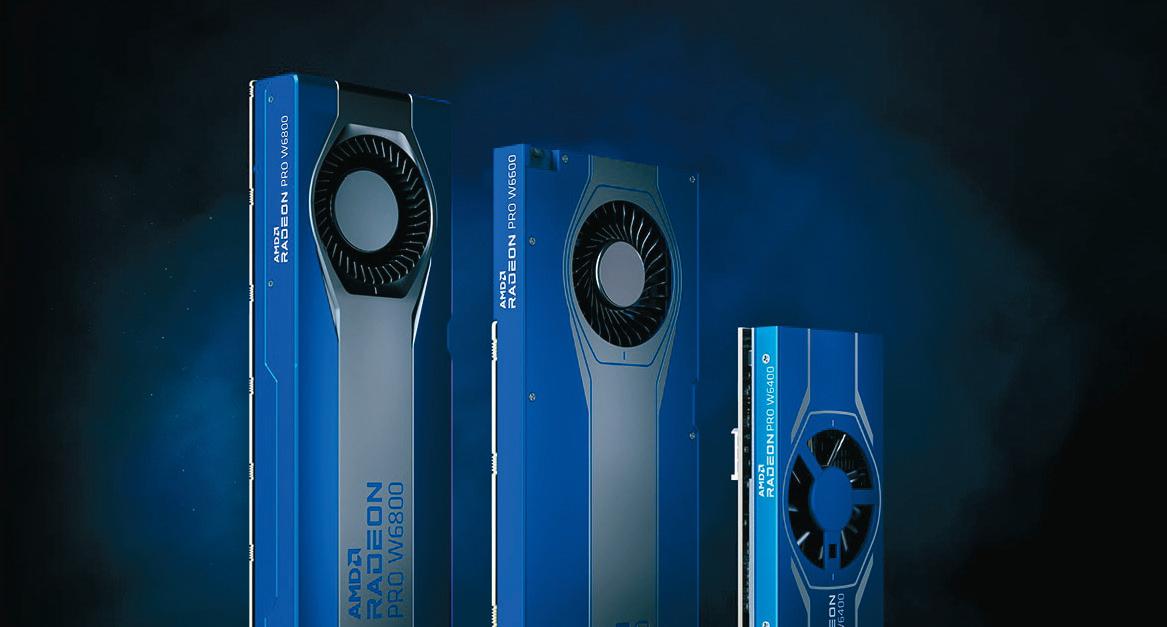
From its SpaceMouse 3D mice to the CadMouse, 3Dconnexion products are said to provide a superior way for CAD professionals to interact with and experience the digital world.
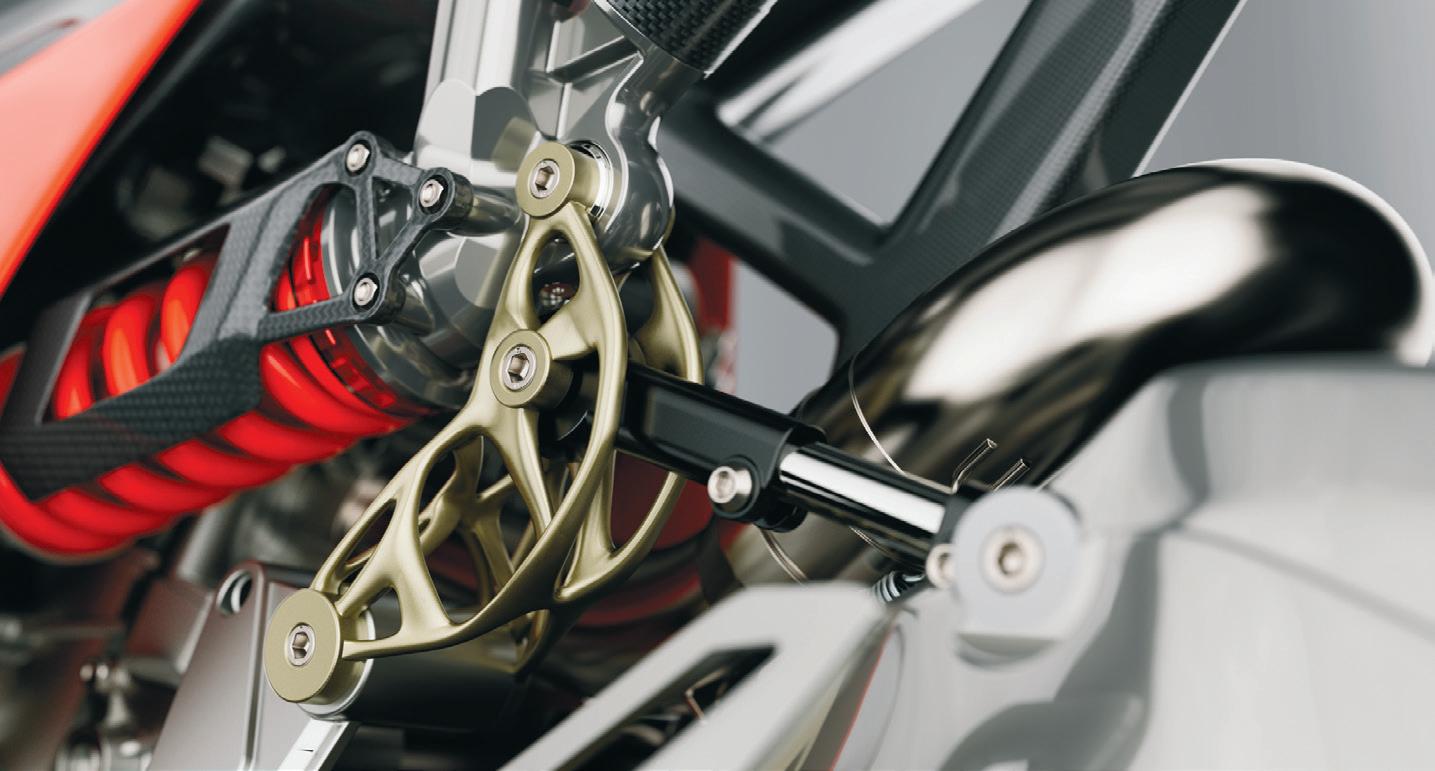
With a SpaceMouse, users have the ability to simultaneously pan, zoom and rotate models while the regular mouse stays in its regular place. www.3dconnexion.co.uk
ALTAIR STAND A7/A8
Altair provides software and cloud solutions in simulation, high-performance computing (HPC), data analytics, and artificial intelligence (AI). Altair’s simulation-driven design approach to product development, where simulation technologies are used early in the development process, enables designers, design engineers and simulation specialists to make more informed design decisions earlier, reducing the need for repeated design iterations and extensive prototype testing.
Altair Inspire helps users to create designs that achieve better performance and manufacturability, and SimSolid is a ‘revolutionary structural analysis solution.'
3DPRINTUK STAND A34
Focused on production runs, 3DPRINTUK bridges the gap between additive manufacture and injection moulding for plastic items. According to the company, the viability of using SLS as an alternative to injection moulding kicks in with smaller items; there are no set-up fees only a unit cost, so for small parts with volumes of up to 10,000 units, it’s a ‘no brainer'. The more complex the part, the higher the viability as tooling costs increase.
3DPRINTUK focuses on low to mid volume batch production using in house SLS printers. CAD files can be uploaded for an immediate quote or the Pricing Estimator App used to get a cost for printing your part. www.3dprint-uk.co.uk
ADDITIVE-X
STAND A24
Additive-X has 30+ years of experience in building relationships and knowledge bases with the best manufacturers. The company doesn't just sell 3D printers, it provides ‘best-in-class' additive manufacturing solutions with full certified technical support, training, and brand specialists.
Additive-X offers impartial advice on the wide range of technology it offers and its technical support, sales and customer service teams have developed a wealth of experience in many industries.
The company is an authorised reseller and trusted partner of Formlabs, Lynxter, Markforged, 3DGence, Ultimaker, BCN3D, Builder, AMT & Mayku.
AMD STAND A40/A41
For more than 50 years AMD has driven innovation in high-performance computing, graphics and visualisation technologies. Billions of people, leading Fortune 500 businesses and cutting-edge scientific research institutions around the world rely on AMD technology daily to improve how they live, work and play. AMD employees are focused on building leadership highperformance and adaptive products that push the boundaries of what is possible.
AUTODESK VIRTUAL SPONSOR
Autodesk makes software for people who make things and helps people imagine, design and create a better world. The company's manufacturing software helps you machine, print, inspect, and fabricate better quality parts, faster. Manufacturing solutions for CAM, additive and composites can help you manufacture large moulds, automate machining, integrate design with manufacturing, and much more.
Autodesk says that with its manufacturing expertise, you are able to automate, optimise and connect all your manufacturing processes. The company's Cloud-Connected Manufacturing allows you to collaborate and manufacture ‘anytime, anywhere.'
BOSTON MICRO FABRICATION
STAND A48
Boston Micro Fabrication (BMF) specialises in micro-scale precision 3D printing.
The company’s microArch 3D printing system uses a proprietary approach to 3D printing called PμSL that leverages light. It enables the technology to produce what BMF describes as the industry’s most accurate and precise high-resolution prints at an imperceptibly small scale for commercial manufacturers.
BMF states that the technology represents a true industry breakthrough by empowering product manufacturers to capitalise on the benefits of 3D printing without sacrificing quality or scale.

BMF has offices in Singapore, Boston, Shenzhen and Tokyo.
BOXERSOLUTIONS
STAND A26
BOXERsolutions' aim is to exploit the power of digital geometry.
BOXERgeom’s Digital Geometry kernel supports voxel-based AI and Machine Learning, and can help digitalise workflows to support ‘innovative design', Digital Twins & MRO and Design optimisation freed from the constraints of BREP NURBS.
BOXERmesh is a fully parallel mesh generation program for creating bodyfitted, CFD-style unstructured grids around complex 3D geometry, for use in standard commercial and open-source CFD solvers.
BOXERsolutions has a background in aerospace, turbomachinery and combustion.
CIMPA STAND A35
CIMPA, a specialist in PLM (Product Lifecycle Management) services and a subsidiary of Sopra Steria, provides end-to-end services in consulting, information systems integration, business processes and support.
CIMPA guides and supports its clients in their digital transformation, in various industries such as aerospace, defence, transportation and energy.
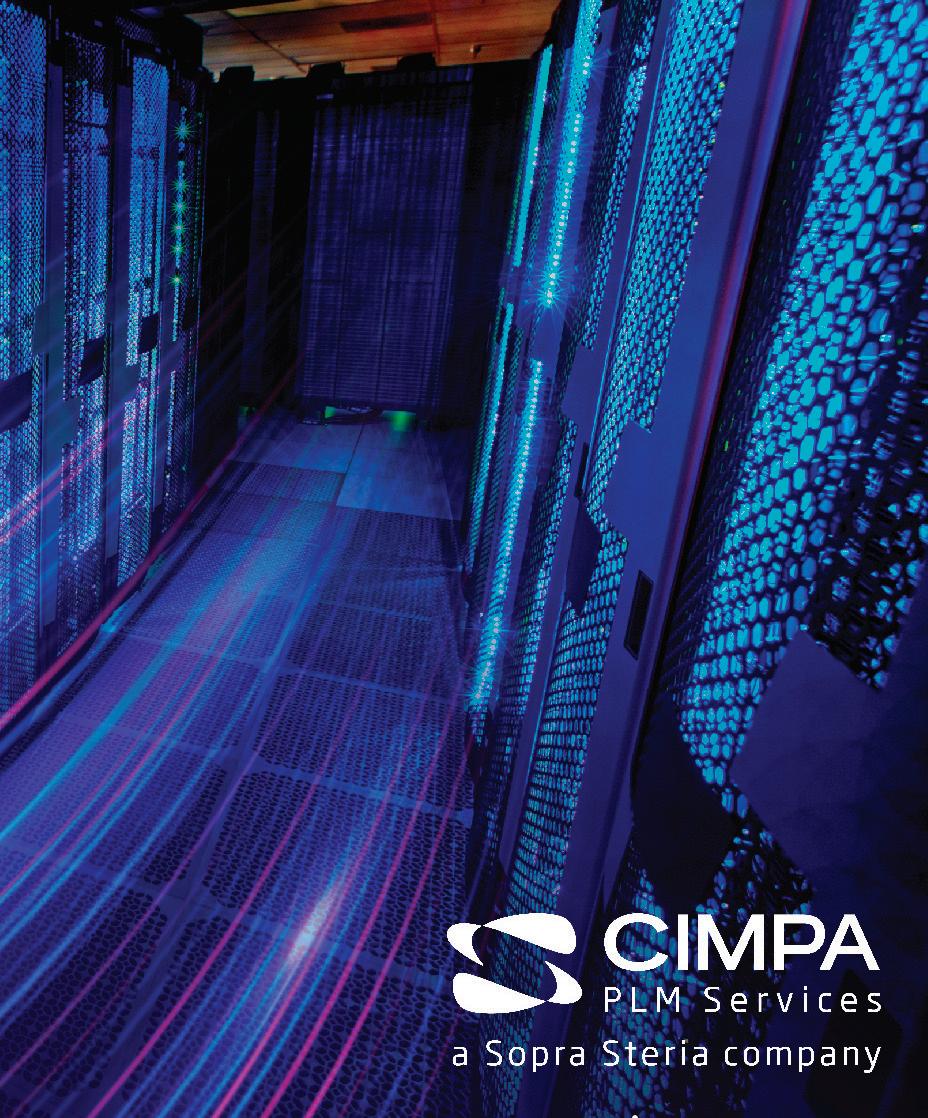
According to the company, its added value lies in its ability to meet the strategic and operational challenges of its clients.
CIMPA has over 1,400 employees in Europe.
BRONZE SPONSOR
CONCURRENT DESIGN GROUP (CDG) STAND B60
CDG is a leading supplier of 3D printers, 3D scanners and 3D software. With 3D Systems it offers the Figure-4 Standalone and Modular DLP printers and others. It also supplies 3D printers from Intamsys, Omni3D, Sinterit, as well as the Fusion EDGE and Zmorph i500.
CDG supplies Einscan, Freescan UE Pro and Evatronix 3D scanners. The company's software solutions include Geomagic Essentials, Wrap and Design X for reverse engineering and scan-to-CAD and Control X for inspection; Geomagic Freeform for voxel-based digital clay modelling; and Cimatron for CAD/CAM, tool design and manufacture, and conformal cooling.
CORREVATE STAND A22
Correvate is the developer of Vercator, which is billed as the most efficient cloud platform to process point cloud data.
Vercator enables a desktop software like experience in a browser, all backed up by the cloud with clusters of computers to quickly process point cloud data as it scales.
The software offers automatic registration and segmentation from the cloud backed by AI, with the associated benefits of access, security and speed.
The company's ambition is to evolve the Vercator platform further with additional tools from both Correvate and third-party suppliers, adding a suite of capabilities and features which deliver cost efficient improvements to its users.
DRIVEWORKS STAND A46
DriveWorks offers Design Automation and CPQ configurator software. It is used by manufacturing multi-nationals and SMEs across many different industries to:
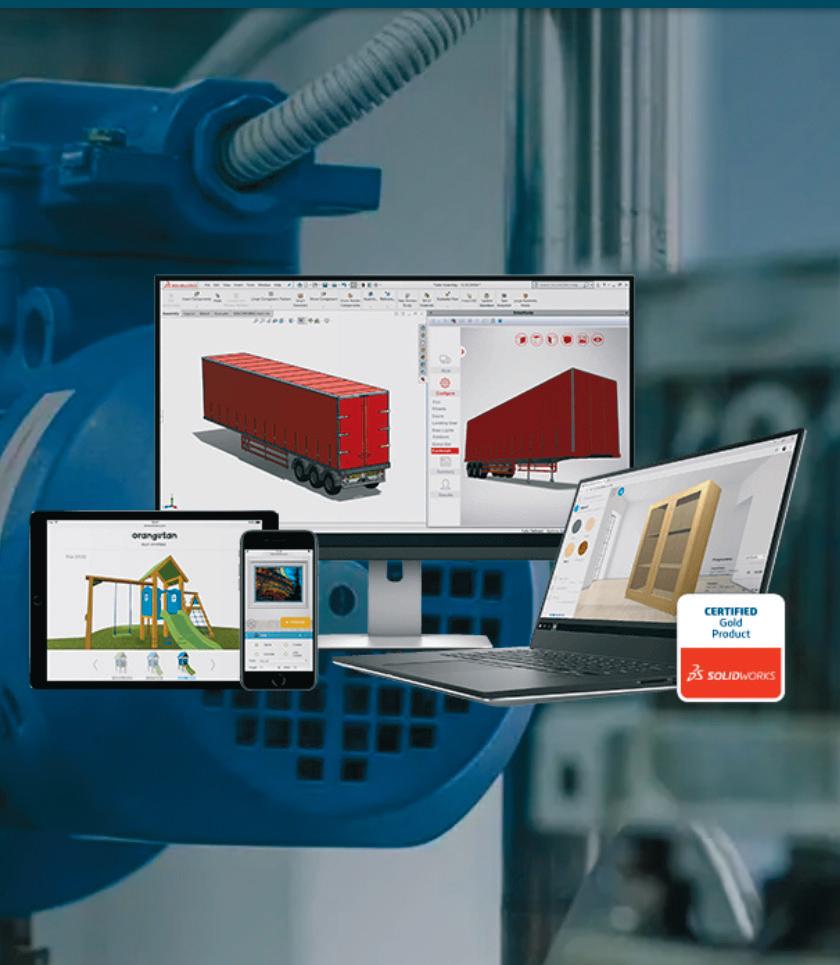
• Configure custom products on any device
• Respond quickly to sales enquiries
• Generate more custom orders
• Win more business
• Enhance product quality
• Reduce repetitive tasks
The software can be used for 3D printing or traditional manufacturing methods. It can automatically generate manufacturing drawings, 3D models, and sales documents (including quotes).
FRAME
STANDS A42/A43
Frame is an industry-leading hybrid and multicloud Desktop as a Service (DaaS) solution that enables customers to deliver virtual apps and desktops hosted in public cloud (AWS, Microsoft Azure, and Google Cloud Platform) and on-premises on Nutanix AHV – all managed from a single control plane.
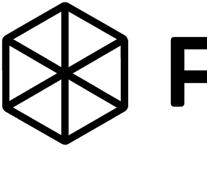
Users can access their Windows or Linux apps and desktops from the convenience of their browser, no client or plug-in needed, on any device anywhere. This includes graphicsintensive, high-fidelity, multimedia, and 2D/3D design apps.
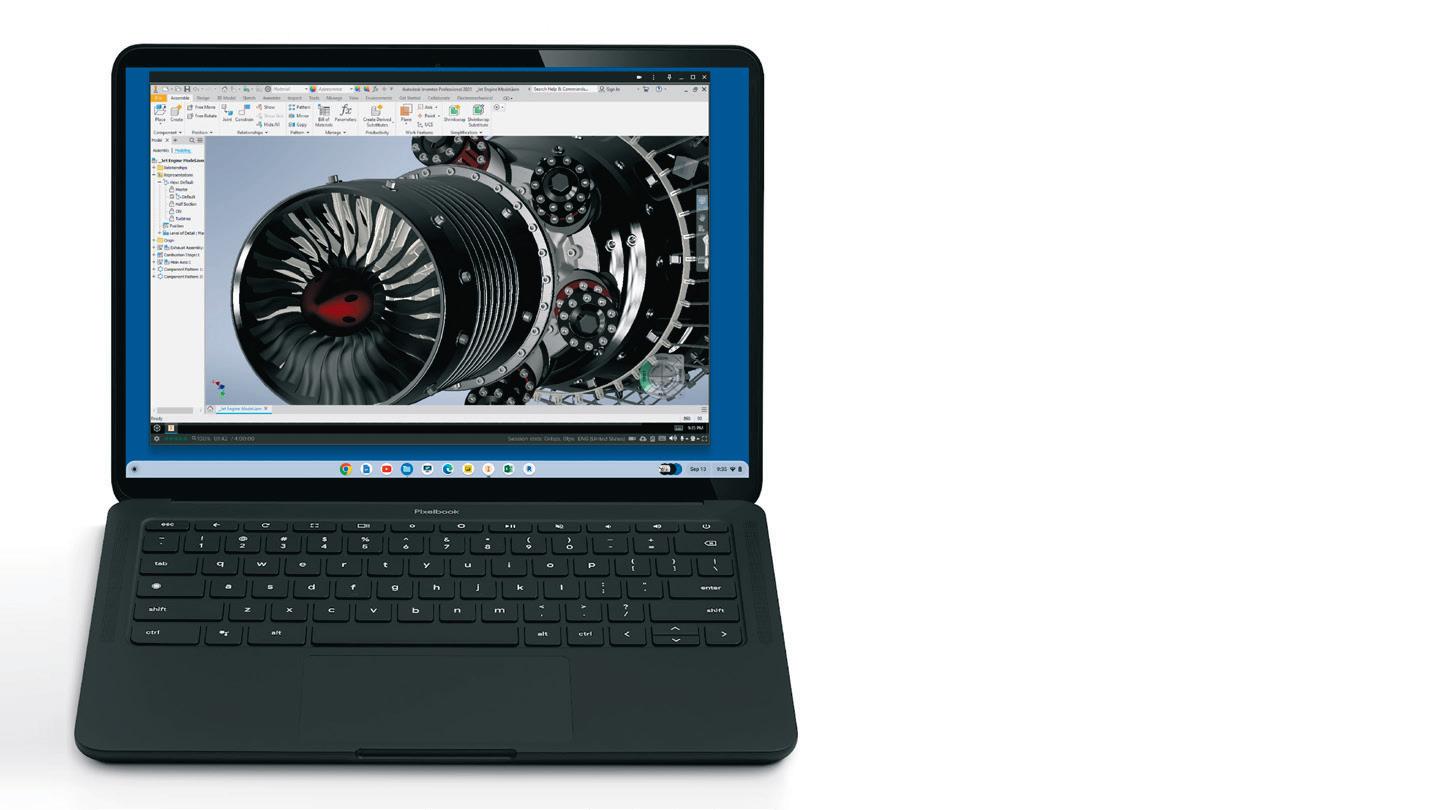
The company invites you to embrace the new world of hybrid work, powered by Frame. www.nutanix.com/products/frame
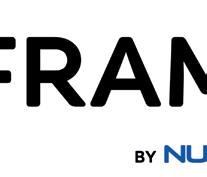
EUROPAC 3D STAND B58
Europac3D is a leading UK supplier of 3D scanning and printing equipment.
The company offers Kreon and Solutionix scanners and Artec handheld scanners, and 3D scanning software for reverse engineering and inspection, featuring Geomagic Design X for complex scan to CAD projects.

Europac3D is also a Uniontech 3D printers specialist, offering ‘high quality', large volume resin additive manufacturing machines and a comprehensive range of open source materials.
Europac3D also offers a bureau service from 3D digital capture of objects through to 3D print service including production parts in PA12 and PA11 Nylon. www.europac3d.com
BRONZE SPONSOR









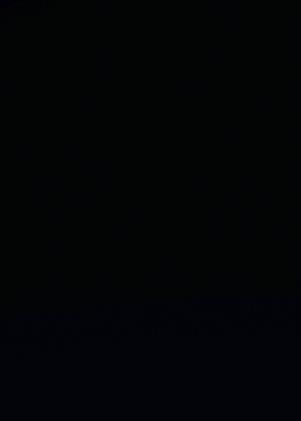
HYBRID SERVICES STAND B51
Hybrid Services is the exclusive distributor in the UK and Ireland for Japanese technology manufacturer, Mimaki.
With a product portfolio that encompasses almost the entire digital 2D print sector, Mimaki brings its many decades of innovation to 3D print with a range of full colour 3D printers.
According to Hybrid, Mimaki’s latest full colour 3D printer offers new levels of creativity, accurate reproduction of up to 10,000,00 colours and precise detail — with a sub £35k price point.
Hybrid will have a variety of samples on its stand at DEVELOP3D Live that demonstrate Mimaki’s breadth of full colour 3D printing capabilities. www.hybridservices.co.uk
ITI – INTERNATIONAL TECHNEGROUP

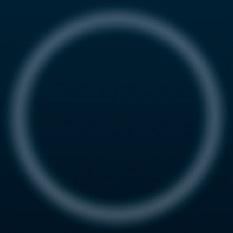

STAND A21
ITI is a leader in the development and delivery of interoperability solutions for CAD/CAM/CAE/PDM. Since 1985 ITI has partnered with leading PLM system vendors to assemble what it describes as an unparalleled suite of software products and related services – all aimed at eliminating non-value-added time and costs associated with reusing product data and maintaining data integrity and value.
ITI’s solutions include: CADfix, for 3D CAD model translation, repair, healing, defeaturing, and simplification; Proficiency, for feature-based CAD conversion; and CADIQ, for identifying model-based design data quality issues. www.iti-global.com
INNEO STAND A28
INNEO Solutions is a partner for product development and digital reality, providing solutions for over 4,000 companies.





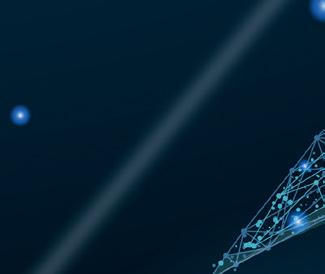

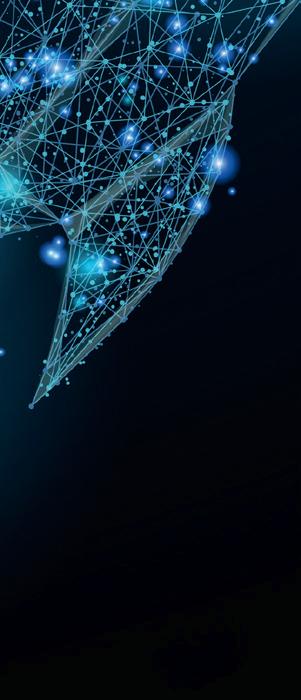
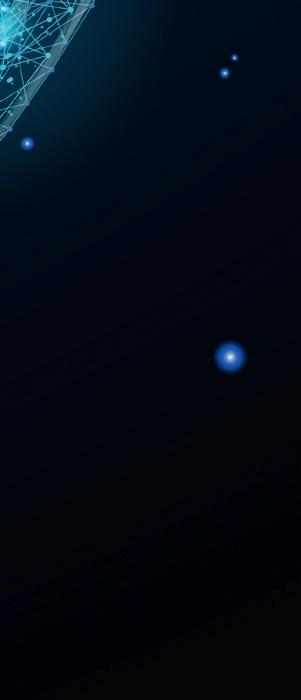
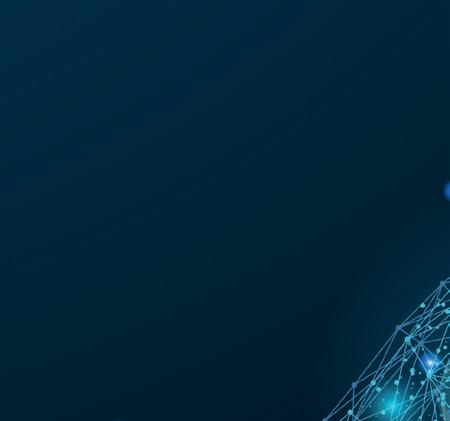

THE ART OF THE POSSIBLE
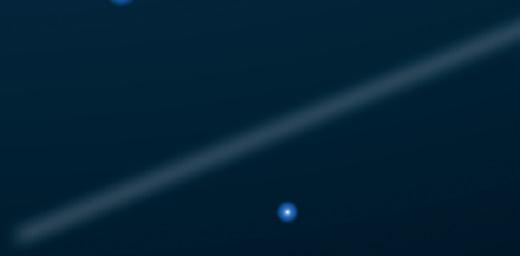
According to the company, it will take the time to understand your business to help you choose the right tools to make your digital journey a reality.

Your innovation – powered by INNEO Your Digital Transformation Business Partners
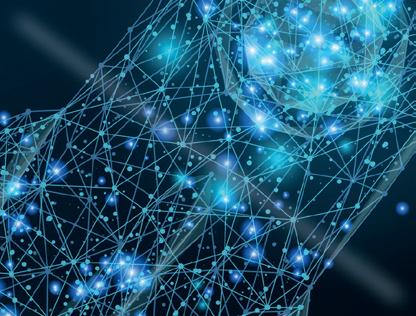
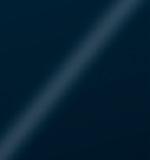
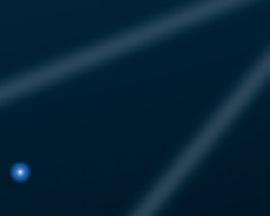



As a PTC Platinum Partner and KeyShot Platinum Reseller, INNEO Solutions offers solutions for CAD, PDM, PLM, IOT, visualisation, CGI and IT. Whether you need application-specific software or services, implementation or customised training and consulting, INNEO states that it will help you achieve a quick and lasting return on your investment. www.inneo.co.uk
VISIT US AT DEVELOP 3D LIVE – STAND A28


KENESTO
STAND B50
Kenesto is a secure cloud-based Document Management and Workflow Platform designed for teams and technology providers, with project management applications in mind.
The developers explain that Kenesto requires no setup, provides unlimited storage, mobile access and reliability with real-time access to field data. Users collaborate directly on master files with suppliers using virtual local drives. www.kenesto.com
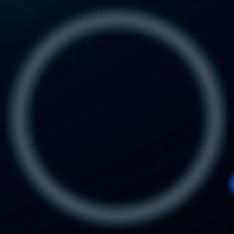
LENOVO
STAND A40/A41
Lenovo, known for product innovation, performance and reliability, offers the complete portfolio of mobile and desktop workstations, with its ThinkPad and ThinkStation solutions. These highperformance workstations are designed to not just meet, but exceed expectations; combining maximum performance with outright platform reliability.
Pushing beyond the hardware, Lenovo strives to support the people behind the systems, to foster relationships and improve the industry overall. This includes supporting creative thinkers and enabling them with the latest technology to explore the possibilities.
LUXION STAND A49
Luxion is a developer of advanced 3D rendering, animation and lighting technology and the maker of KeyShot, which aims to break down the complexity of creating photographic images of 3D models. The real-time ray tracing application uses a physically correct render engine based on scientifically accurate material representation and global illumination.
KeyShot is built around the visualisation workflow allowing users to easily change materials, create advanced lighting scenarios and adjust cameras interactively, in real-time. It offers direct import for every major 3D file format, and support for both Mac and PC.

BRONZE SPONSOR
MEASUREMENT SOLUTIONS LIMITED (MSL) STAND A33
MSL has over 24 years’ experience, supplying UK Industry with measuring equipment and Creaform scanning solutions. It brings engineering experience to metrology, combining tools and software from leading manufacturers to create integrated systems for your workflows.
MSL offers high-quality 3D scanning, 3D software and 3D metrology for end-toend design, manufacture and inspection solutions and services to improve manufacturing processes.
Creaform scan data can be imported into nTopology for lightweighting, optimisation, modification for additive manufacturing and other operations.

NTOPOLOGY VIRTUAL SPONSOR
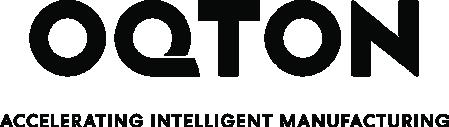
nTopology is a next-generation design software built from the ground up to enable engineers to take full advantage of the design freedom of additive manufacturing.
According to the company, nTopology’s, core technologies make it fundamentally different to any other engineering design software currently on the market.
BRONZE SPONSOR
OPEN BOUNDARIES
STAND A1
Open Boundaries states that it delivers great user experiences and simplifies creatives' lives, making astute users more efficient and versatile using Cloud technology.
The company's Managed Cloud Graphics Workstation subscription enables individuals or teams to have instant access to 3D graphics workstations 24/7/365, providing assurance and peace of mind.
Choose between different Cloud Workstations subscriptions, which are cost effective, scalable and flexible 3D graphics solutions.
OQTON STAND A25
The Geomagic Suite, developed by Oqton, delivers a complete reverse engineering, design, and inspection software solution that is said to unify engineering and production to accelerate intelligent manufacturing. Serving industries include aerospace, dental, automotive, and more, Geomagic Freeform is a 3D design tool combined with touch-based haptic devices, that is designed to transform traditional handcraftsmanship into organic, digital design for custom manufacturing. Geomagic Design X allows users to reverse-engineer physical parts into digital parametric CAD models with a tool that combines history-based CAD with 3D scan data processing.
www.oqton.com
OR3D
STAND A9
OR3D specialises in providing 3D solutions and, as the UK’s largest Geomagic partner for hardware and software, the company states that it is well placed to offer the right solution.
OR3D offers a range of laser scanning equipment that covers long range scanning to non-destructive testing with CT machines. For high precision manufacturing and engineering, the company highlights the capabilities of sub millimetre accurate scanners and laser trackers from API.

Using Geomagic Design X, OR3D can demonstrate complete scan-to-CAD workflows, including the creation of native parametric CAD models in Solidworks, Inventor, NX, Creo and Catia.
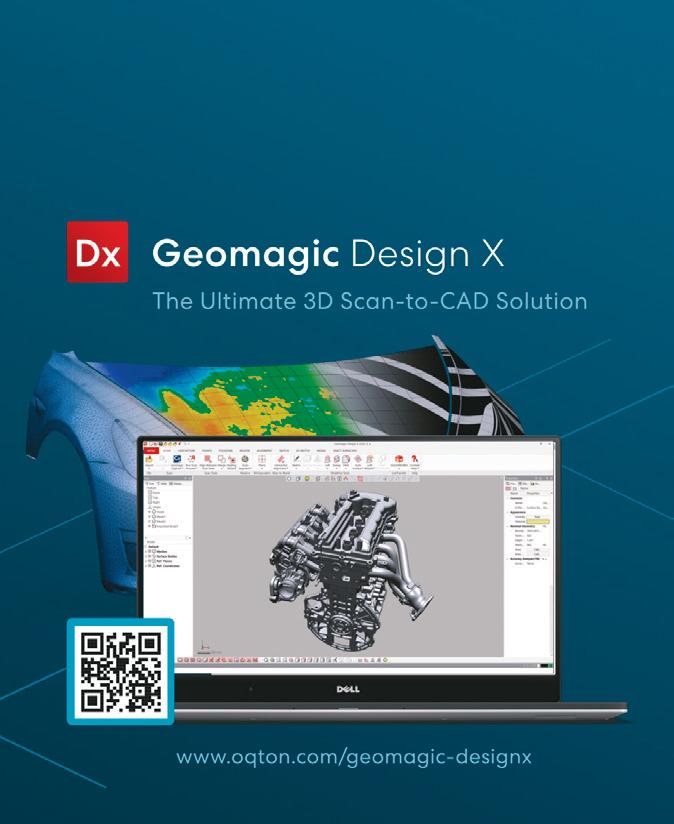
ORIGIN ENGINEERING
SOLUTIONS
STAND A18
Origin Engineering is a software VAR focused on design and simulation for the manufacturing industry. The company believes that utilising simulation early in the product development process provides opportunities for organisations to speed up product development, reduce costs and improve the quality of products being manufactured.
Origin Engineering works alongside Altair and its Inspire product portfolio, which allows manufacturing engineers to simulate various manufacturing processes to eliminate defects and failed production runs through its ‘intuitive interface and simple workflows'.
PNY STAND A23
For over 30 years and thanks to strong partnerships with technology innovation companies such as Nvidia, PNY says it represents a real success story of a company leading the EMEA graphics, HPC and AI computing market.
Providing engineers, researchers and visualisation clients with ‘cutting-edge' Nvidia Quadro, Nvidia Tesla and Nvidia DGX solutions, PNY says it understands the needs of its clients, offering professional technical support and a constant commitment to customer satisfaction.
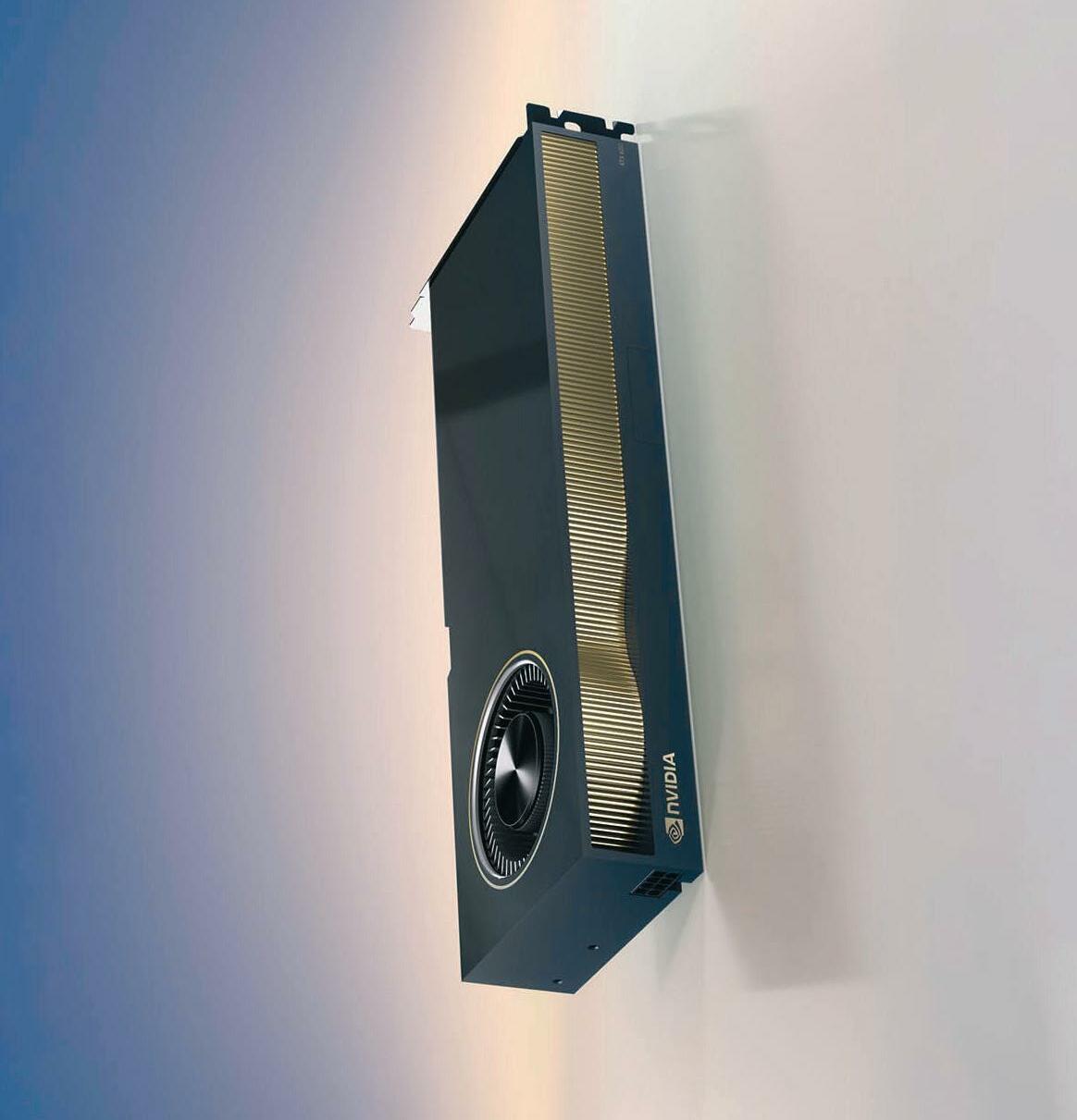
PNY offers a full spectrum of GPUs and SSDs but also complete servers for compute, storage and network certified for all VDI, HPC and AI environments. www.pny.eu/en
PTC STAND A36/A37
PTC offers a variety of innovative CAD solutions for the engineering community, including Creo and Onshape.
According to the company, Creo continues to advance the state of the art in CAD technology, with emerging technologies that are fully integrated into the Creo design environment. Meanwhile, PTC adds that cloud-native Onshape is ‘revolutionising the CAD industry' by enabling companies to connect, collaborate, and create better products. www.ptc.com/product/creo
ROLAND DG STAND A12
Roland DG offers advanced 3D milling technology, developed under its DGSHAPE brand. This includes the MDX-50 benchtop CNC mill and monoFab SRM-20 desktop milling machine.
The MDX-50 combines ‘precise, automated milling and unmatched ease-of-use.’ Roland says it is an ideal solution for short-runs and prototypes, reducing operation time and simplifying production, so users of all abilities can mill functional parts with incredible quality on a wide range of materials.
The SRM-20 is a small milling machine for the production of realistic parts and prototypes. Roland says it offers powerful functionality at an affordable price. www.rolanddg.co.uk
BRONZE SPONSOR
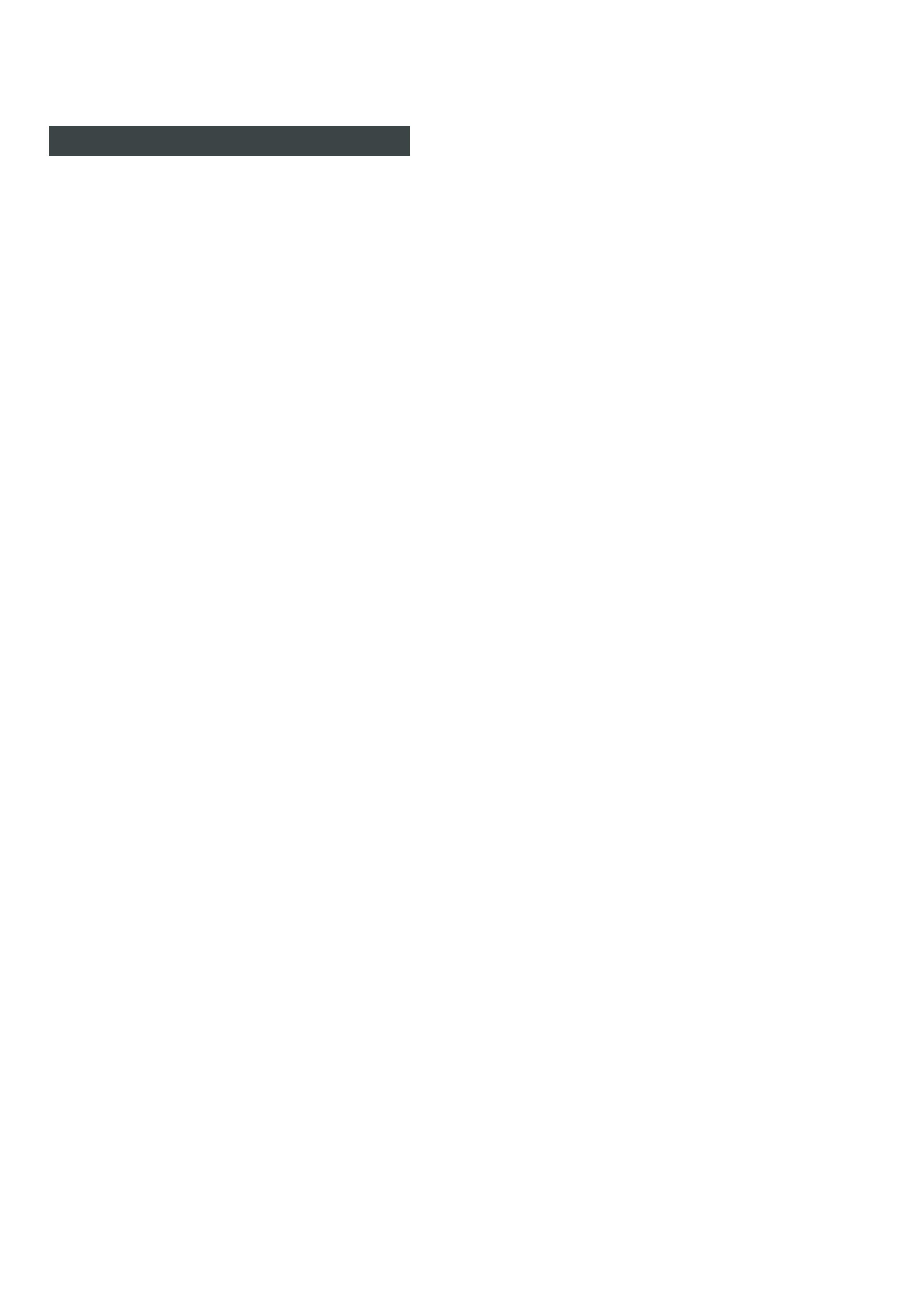
MachineWorks Ltd, the developer of Polygonica, has been providing advanced 3D software engines to manufacturers and engineering software developers since 1994.
Polygonica is an engine for polygon-mesh modelling and is widely used in a range of markets, including CAD, CAM, CAE, and AM, along with medical, dental, EDA, metrology, AEC, construction, mining, and other large capital asset industries.
MachineWorks is a toolkit for CNC simulation and verification and is supplied embedded within a wide range of brands from major machine tools and CNC controller manufacturers and CAM www.machineworks.com | www.polygonica.com
SHAPR3D VIRTUAL SPONSOR
Shapr3D is on a mission to reinvent the CAD industry that got stuck in the past. According to the developers, the CAD software allows you to design where and what you want to design, not where and what your CAD tool dictates. Wherever your workflow takes you, Shapr3D can go with you. Go from sketching to manufacture—with full functionality across Windows PCs and tablets, Macs, and iPads—make your design flow. www.shapr3d.com
SIEMENS DIGITAL INDUSTRIES SOFTWARE STAND A5/A6
Siemens Digital Industries Software says it is bringing the solutions of tomorrow to its customers today. The company invites delegates to learn more about the value of the digital enterprise that enables customers to create better, more innovative products, faster.
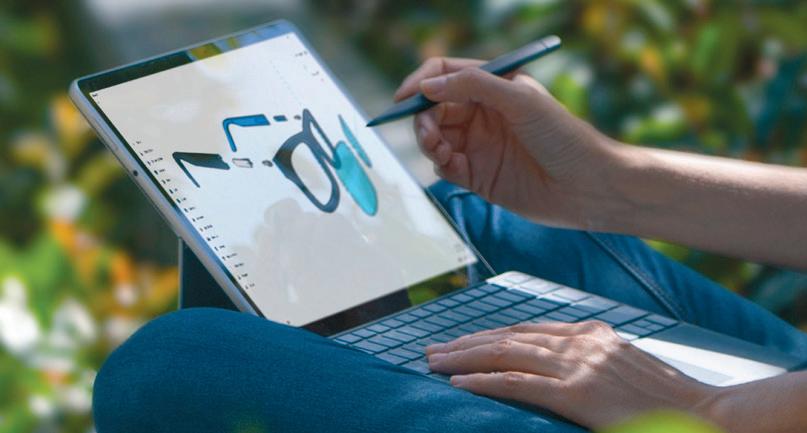
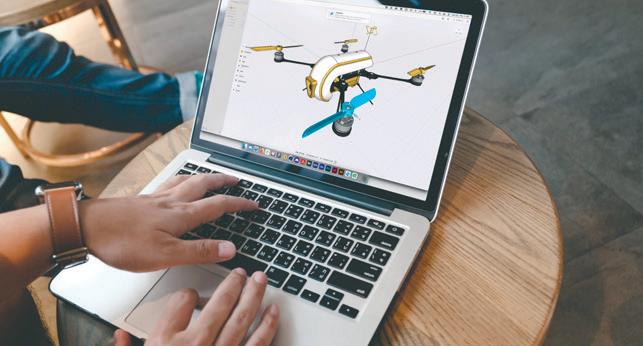
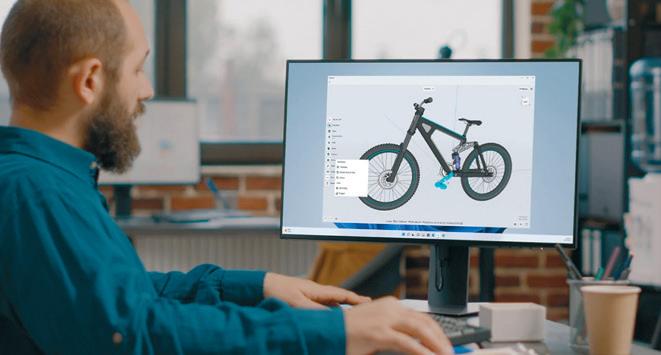
Siemens offers an integrated portfolio of software and services that helps companies become digital enterprises through technologies that integrate solutions for PLM, Electronic Design Automation (EDA), Application Lifecycle Management (ALM), Manufacturing Operations Management (MOM), Embedded Software and Internet of Things (IoT), and much more. www.siemens.com/plm
SIGMETRIX
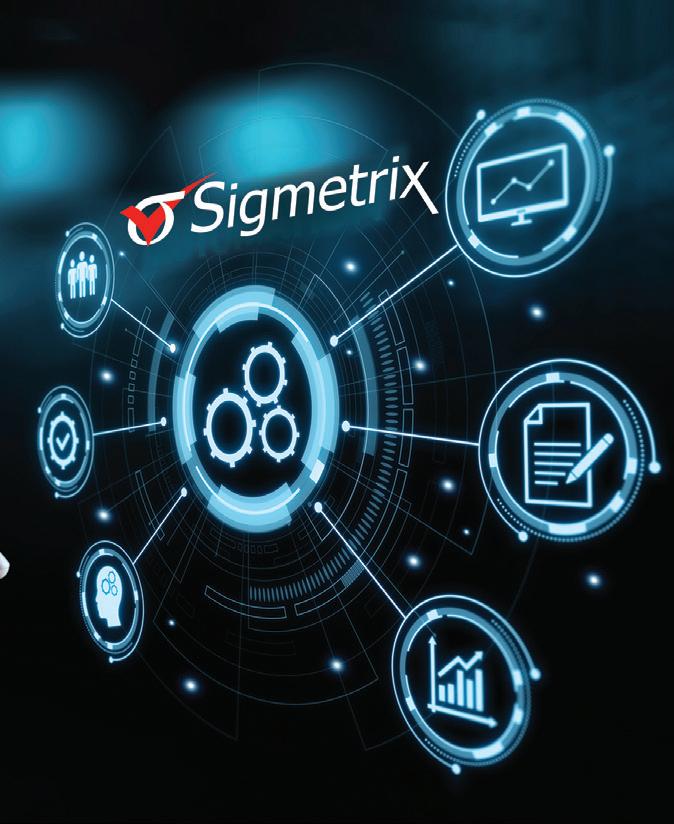
STAND A27
Sigmetrix has been helping companies produce better products for over 20 years through a combination of software solutions, training, and consulting services that focus on managing the impact of mechanical variation. These solutions enable collaborative decisions between design, manufacturing, and inspection.
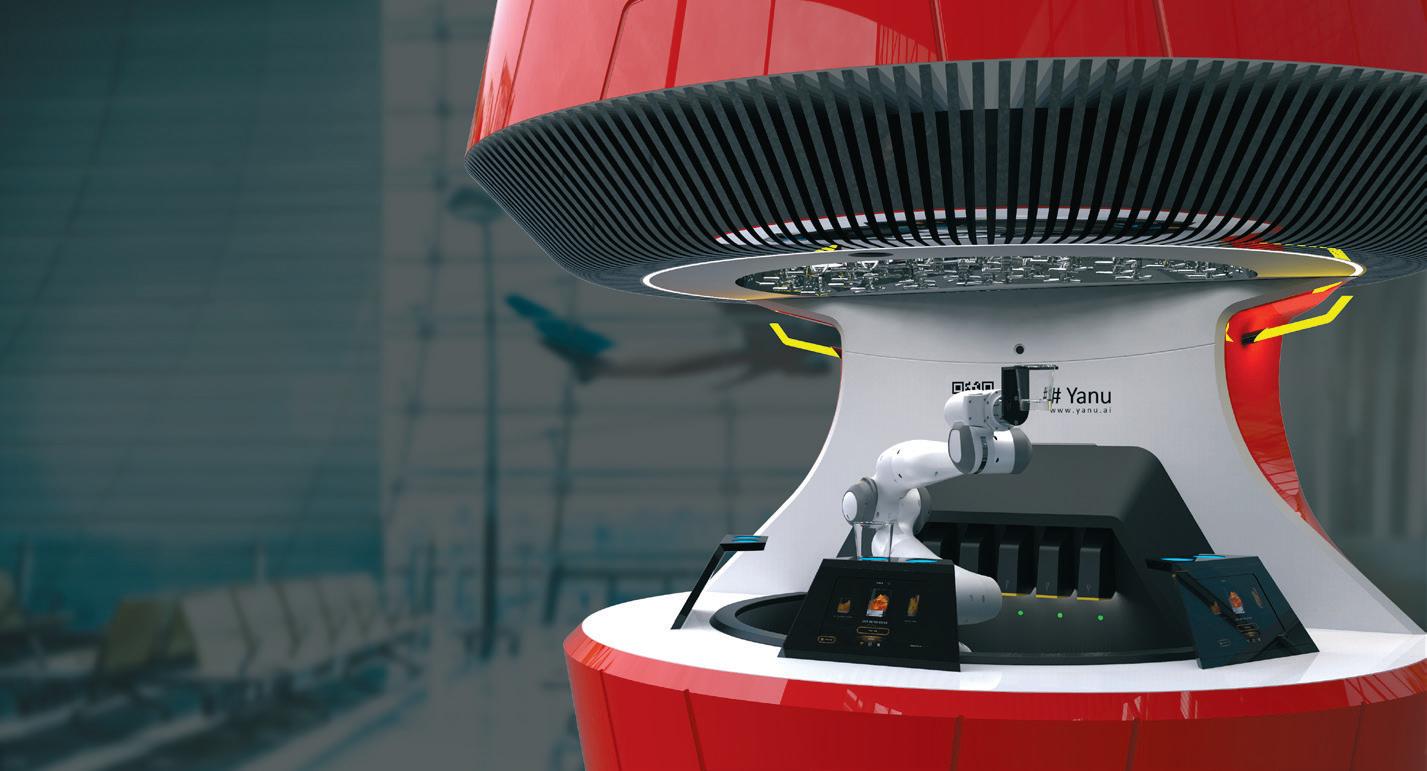
Products include CETOL 6, a fullyintegrated 3D tolerance analysis solution that enables designers and engineers to understand the impact of part and assembly variation on the fit and performance of their products; EZtol, a 1D analysis tool; and GD&T Advisor, an interactive tool that provides guidance on the correct application of GD&T on models.

SOLID PEOPLE
STAND A44
Solid People is a specialist CAD recruitment agency offering both permanent and contract recruitment services to a wide range of clients.With over ten years of experience, the agency states that it really understands the industry and knows how to find well matched designers. Its consultants all come from a design background.
Solid People explains that it won’t bombard clients with irrelevant CVs. It fully screens all candidates, uses its knowhow to assess their skills, and only puts forward those who would be the best fit for a client's team.
Solid People wants to meet companies looking for designers, or designers looking for their next career move. www.solidpeople.co.uk
SOLID SOLUTIONS
STAND A19
Founded in 1998, Solid Solutions has amassed over 20 years of experience in delivering ‘best-in-class' services and solutions. Having become the leading provider of Solidworks throughout the UK and Ireland, Solid Solutions has grown through several strategic partnerships and acquisitions, forming the Solid Solutions Group. 2021 saw the formation of the Solid Solutions Business Transformation Team, expanding its services beyond Solidworks, into the wider Dassault Systèmes portfolio.
In June 2022, TriMech acquired the Solid Solutions Group, bringing together hundreds of talented people across four countries, and expanding its support. www.solidsolutions.co.uk
SOLID PRINT3D
STAND A20
Solid Print3D is part of the Solid Solutions Group. With experts for every area of ‘3D', from scanning, CAD, CAM, simulation, PLM, 3D printing & CNC, its goal is to help you reinvent manufacturing.
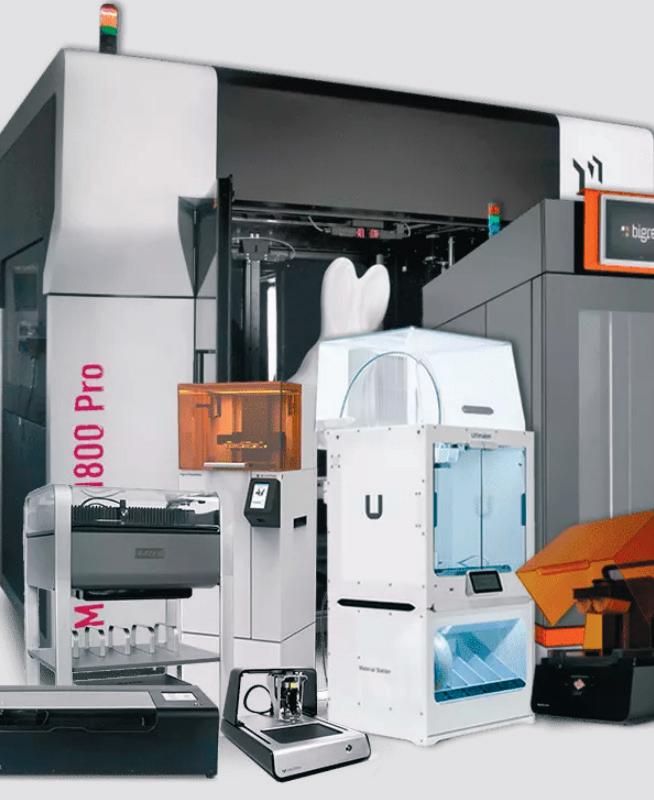
Solid Print3D will show that production 3D printing is no longer expensive, difficult to use or reserved only for specialists in OEMs.
For reverse engineering, it will show how 3D scanning has never been more accessible. With the ability to get information into a CAD system fast, engineers have new ways of capturing data.
Products include the Formlabs Fuse 1 compact SLS 3D printer, and the Peel 3D handheld 3D scanner. www.solidprint3d.co.uk
BRONZE SPONSOR
SOLIDWORKS
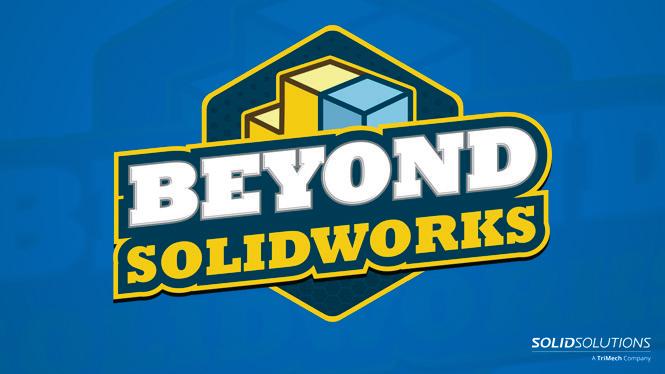
VIRTUAL SPONSOR
SolidWorks, a Dassault Systèmes brand, offers complete 3D software tools that let you create, simulate, publish, and manage your data. The company states that its products are easy to learn and use, and work together to help you design products better, faster, and more cost-effectively. It adds that the Solidworks focus on ease-of-use allows more engineers, designers and other technology professionals than ever before to take advantage of 3D in bringing their designs to life.
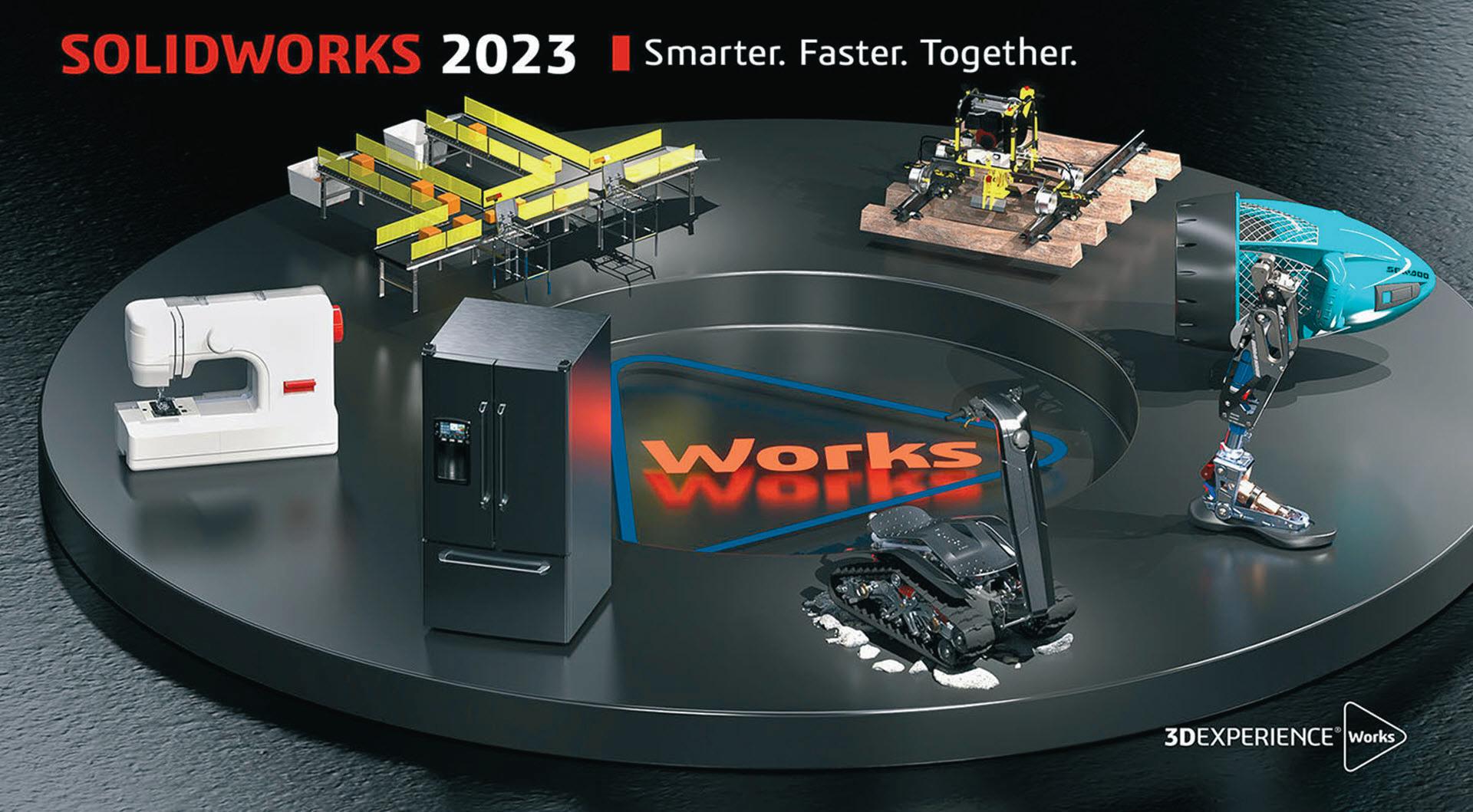
SYMETRI
know that connecting Design and Manufacturing can challenging - Symetri supports many businesses with aspect of their design and manufacturing processes
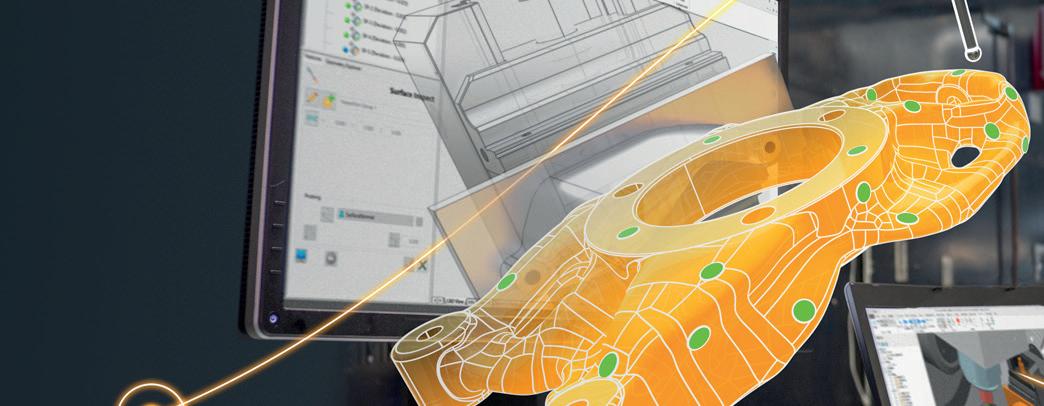
SYSTEMACTIVE STAND A47
Design
Machining
BRONZE SPONSOR
Manufacture
T3DMC STAND B52
on Stand A29 to discuss how we could help you to add into your business.
info@symetri.co.uk +44 345 370 1500
SystemActive is one of the UK’s leading workstation hardware and immersive solution providers. The company is a HP and Lenovo Platinum Partner, and Nvidia preferred solution provider with specialisations in workstations and highend compute in all.
The company will be showcasing the Varjo XR-3, the photorealistic mixed reality headset. It is a mixed reality developer device for engineers, researchers and industrial designers who are ‘pioneering a new reality'. With photorealistic visual fidelity, ultra-low latency and integrated eye tracking, SystemActive states that the XR-3 is the only device capable of truly blending virtual with reality. www.systemactive.co.uk
THEOREM SOLUTIONS
STAND A13/A14
Theorem Solutions’ range of use-case focused solutions are based off years of experience in optimising 3D CAD data. This includes Theorem-XR, which enables engineering and manufacturing organisations to utilise their existing 3D assets on Augmented (AR), Mixed (MR), or Virtual Reality (VR) devices.
The Theorem-XR suite allows engineers and designers to visualise their 3D data in context. Teams can collaborate, both remotely and locally, working together in a single session in both MR and VR. Theorem-XR's Visualization Pipeline is used for ‘efficient and automated' processing of 3D CAD and visualisation data.

Additive
Data
Inspection
The 3D Measurement Company (T3DMC) is an engineering solutions provider of 3D measurement, quality & inspection and reverse engineering services. It is also the exclusive UK distributor of a range of affordable, handheld and portable 3D scanners suitable for a wide range of industrial applications.
T3DMC states that it can support your design and manufacturing needs through its 3D scanning & measurement services, on site or at its facility. The company explains that its scanning services combine ‘market leading' metrology equipment with a comprehensive range of software solutions to offer inspection and design solutions for the most complex of challenges. www.t3dmc.com
TOTAL MATERIA AG STAND B59
Total Materia AG is dedicated to collecting, connecting, and managing materials information. Since 1999, when Key to Metals AG founded the solution, a team of materials engineers have collated commercial materials properties and developed a taxonomy, properties and integrations that support multiple engineering roles and scenarios within engineering, quality, simulation, compliance, sustainability, manufacturing and, of course, materials.
VIRTUAL INTERCONNECT STAND A32
Virtual Interconnect is an engineering consultancy and a PTC Gold Technology Partner, specialising in the design of complex routed systems encompassing wire harnesses and hydraulic/piping installations for the industrial, automotive, military and aerospace markets.
The company aims to reduce your risks and improve your products’ time to market through three services: ‘Project', where its engineers work as a remote design team to aid the development of your solution; ‘Process', to help enhance your current wire harness design process; and ‘Product', where its software design team provides general-purpose solutions for wire harness and electrical design.
UNIVERSITY OF SHEFFIELD - FACULTY OF ENGINEERING STAND B55/B56
This stand will showcase various projects from the University of Sheffield’s Faculty of Engineering, whose vision is to deliver life-enhancing research, innovation and education that not only transforms the lives of its graduates, but shapes the world we live in. The faculty believes the best way to achieve this is by fostering an ambitious, inclusive, collaborative community.
WORKSTATION SPECIALISTS
STAND A15
Workstation Specialists is an awardwinning workstation and server solutions manufacturer. The UK company designs and manufactures high-performance computing solutions for industries such as 3D CAD, visual effects and others.
Workstation Specialists works with clients on a consultancy approach believing that there is no one size fits all solution to workstation/server technologies, and that tailoring hardware specifically for each client is essential in order to achieve best in class performance and value for money.
Products include professional desktops and laptop-based workstations, plus deskside and rackmount server solutions.
ZEA STAND B57
Manufacturers want to maximise the value of using their products to their customers. However, as Zea points out, they fall short of that value proposition when a product breaks down and isn’t adequately supported.
Zea envisions the day when a fully documented digital twin becomes the new baseline for product support. The company is mapping a path towards this vision with a novel 3D digital experience platform that saves content authoring time and improves customer experience.
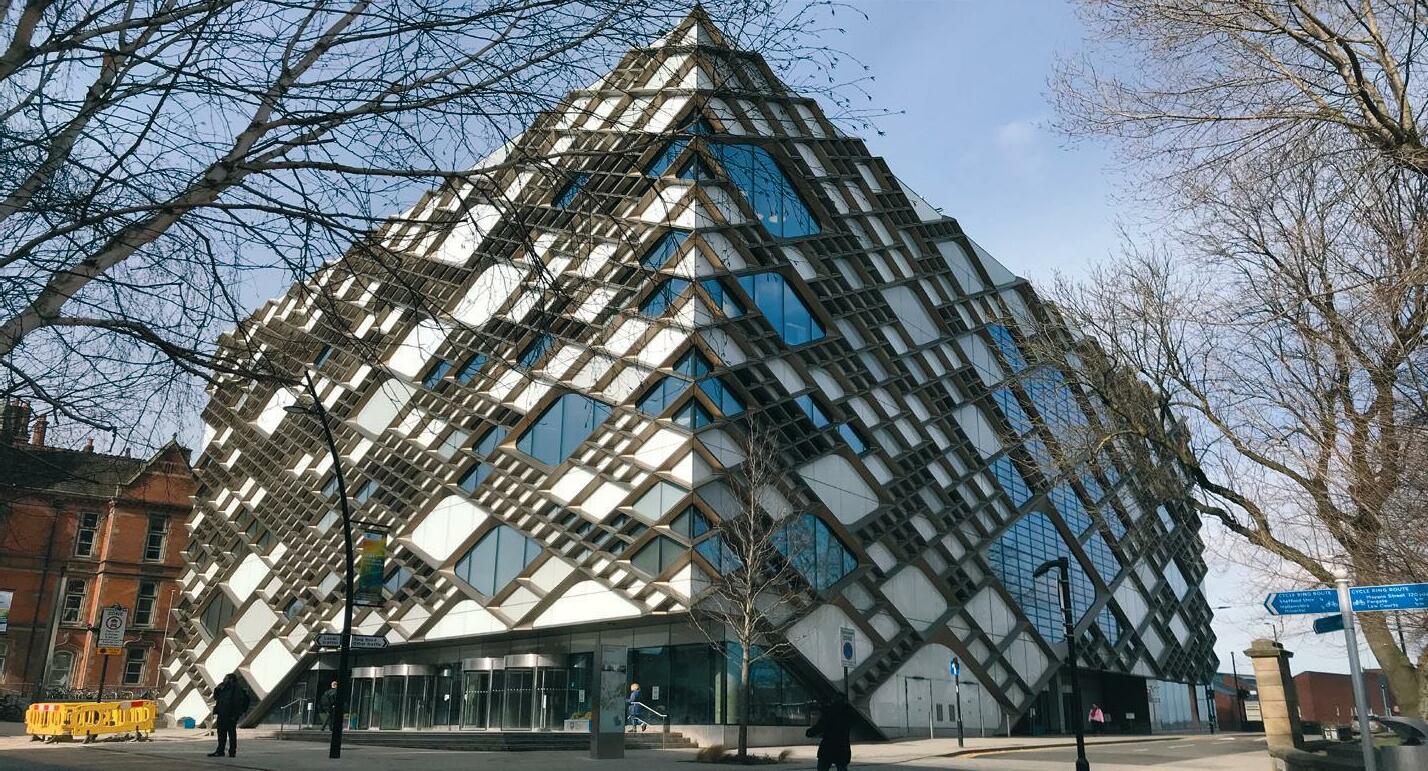
13-15, 2023 DENVER, CO - USA geo-week.com
Accomplish a year’s worth of geospatial business in just one week by attending Geo Week 2023
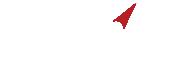
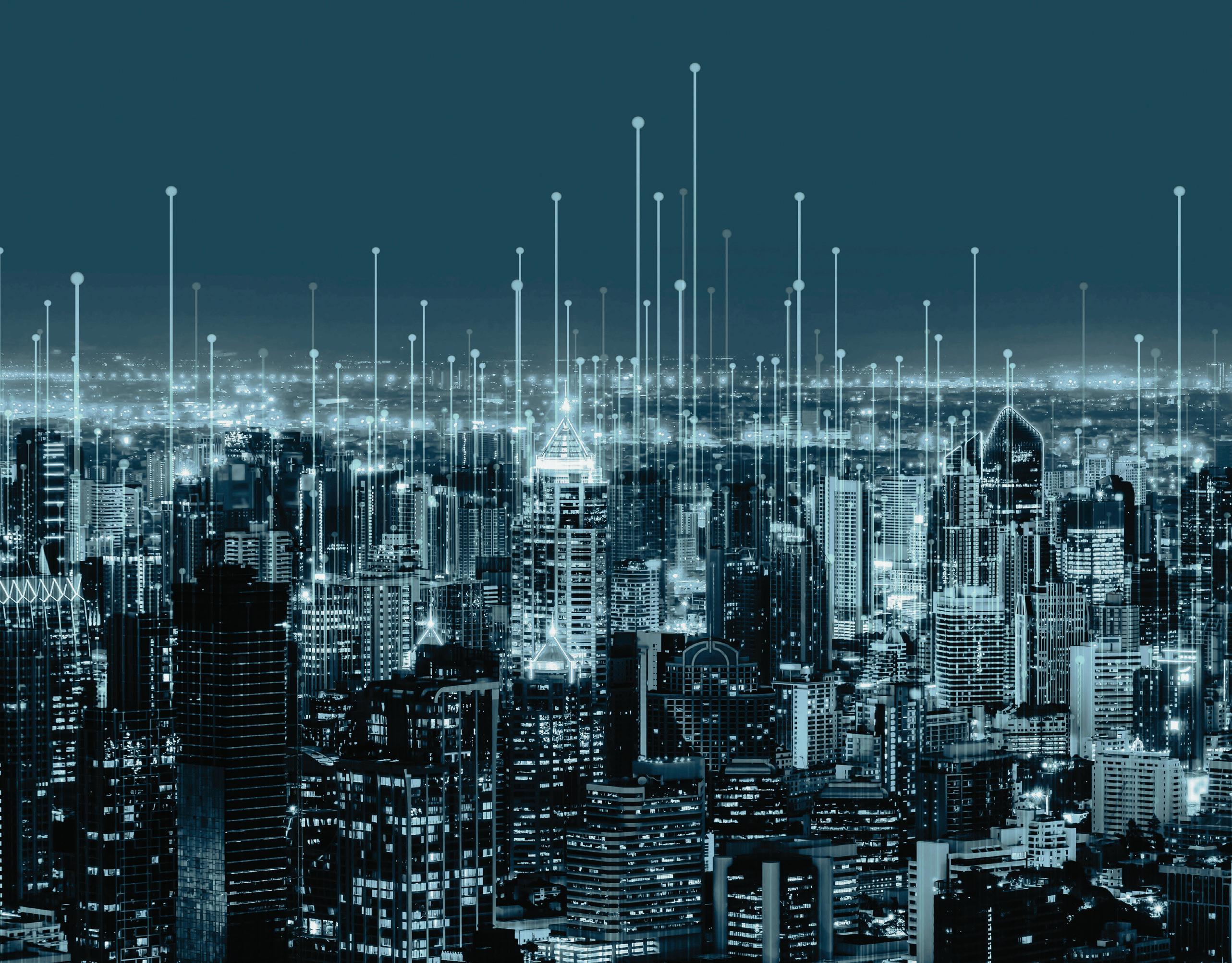
Imagine a single powerhouse event that champions the coming together of geospatial technologies and the built environment. Where professionals from a range of disciplines network and gain insight into the increasing confluence of their worlds. Where cuttingedge technology offers new possibilities, improved efficiencies, and better outcomes. And where education opens the door to the future just ahead.
Use code SAVE100 for $100 off a conference pass or a FREE exhibit hall pass.

more! geo-week.com
by
Veteran home worker Stephen Holmes has watched the shift to ‘hybrid’ working with intrigue, as he tries to imagine how the need for both digital design and physical prototypes can work in more fluid systems
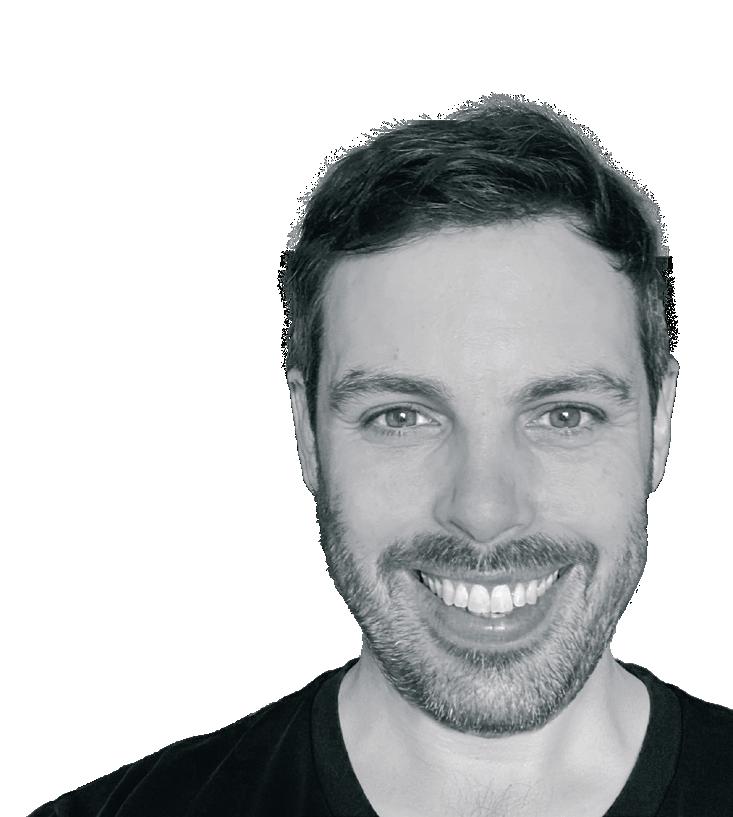
Getting things delivered to the house during daylight hours often leads to queries around ‘are you working from home?’ – the alternative being that I look somewhat freshfaced for a retiree taking receipt of his doorstep groceries at this time of day.
It was during such an interaction this week that the delivery driver squeezed in the extra question of “is that a Covid thing?”, to which I proudly replied that I’m actually a decade-long veteran of the home working fraternity. The Pyjama Brigade. Team Daytime Telly. The Anti-Pret.
Yet the Covid thing means that our ranks have been bolstered. Spare bedrooms have been transformed, garages converted and flags resolutely planted on coffee shop tables nearest the sole working power outlet.
The UK’s lockdown showcased this: We know from your subscriptions to DEVELOP3D that many of you moved your deliveries to residential properties, and while some have shifted back, many of you are likely reading this on the very short commute from where you woke up this morning.
Designers I’ve spoken with moved their work set-ups home – hardware, software and even workshop equipment. I doubt there were many trying to load a Bridgeport into the back of a taxi, but hundreds of you picked up the office 3D printers and wheeled laser cutters home. We know that while this enabled projects to continue, and businesses to keep the lights on, it had another effect. Many of you used the time while furloughed to develop personal projects, some benefitting the companies you work for, others fulfilling a lifelong dream of setting up a product-based
business or design studio of your own. During this period the registration of new companies went through the roof.
It has changed the way we work, even if you’re sat back in a familiar office cubicle full time. The greater emphasis on less rigid working set-ups elsewhere means you’re more likely to jump on a Teams call than head out to a meeting. The software we use is accelerating us in the direction of the cloud, and collaboration is the buzzword among companies.
Whether you’re working with someone four seats or four time zones away, there are means now to meaningfully collaborate – some are better than others, and I’m sure you’re all finding out which work best for your teams and stakeholders.
The C word is big business. Adobe has just dropped $20 billion on Figma, a product that, at first glance, might look a little like a toolset it already owns. Yet at its own admission, Figma was ‘purposebuilt for collaboration’.
Slack, Microsoft Teams, Google Chat – all of these have been picked-up by design teams dispersed by Covid but are now deeply ingrained even though we’re able to be back together.
But where does this leave us? I’m not writing this at the behest of a new sponsorship from Greggs aimed at getting us all back into the office [my offer is still on the table], but creative people have some of their best ideas in conversation. I’ve seen first-hand problems being solved and new solutions imagined in person.
Yet, in a world where the cost of workshop kit has fallen, leading to more in-house technologies like 3D printing, and the importance of physical prototyping grown, as part of an iterative design
workflow, how is this new hybrid reality going to look?
Many of you would rather endure another lockdown Zoom quiz with your drunken aunt and xenophobe uncle than approach the current crop of mixed reality solutions, which while amazing for top tier automotive companies to get around for design reviews, are still a luxury for the majority.
Desktop 3D printers have come a long way in recent history, with something available for every need, but the option of sharing a file to be 3D printed on the other side of the world still relies on a lot of manual setup to gain perfect results. An umbrella issue over all of this is that security around sharing files between stakeholders is still mired in permissions issues and distrust.
New softwares are in the pipeline to help bridge this – a few of which you can get an early glimpse of at DEVELOP3D LIVE on 1 November [see page 48] – but until then it might be a case of more knocks at the door and parcels being delivered, as model shops and 3D printing bureaux combine with couriers to deliver more physical prototypes the old fashioned way. At least you’ll get a chat with the delivery driver.
Stephen likes his meat pies as much as the next person, but appreciates there are more benefits to working in a office than ready access to hot pastry delights
IN TOUCH: If you took some serious hardware home during lockdown then please get in touch, as Stephen would like nothing more than to hear about how and what you snuck out the door and whether it was returned (eBay suggests some of it
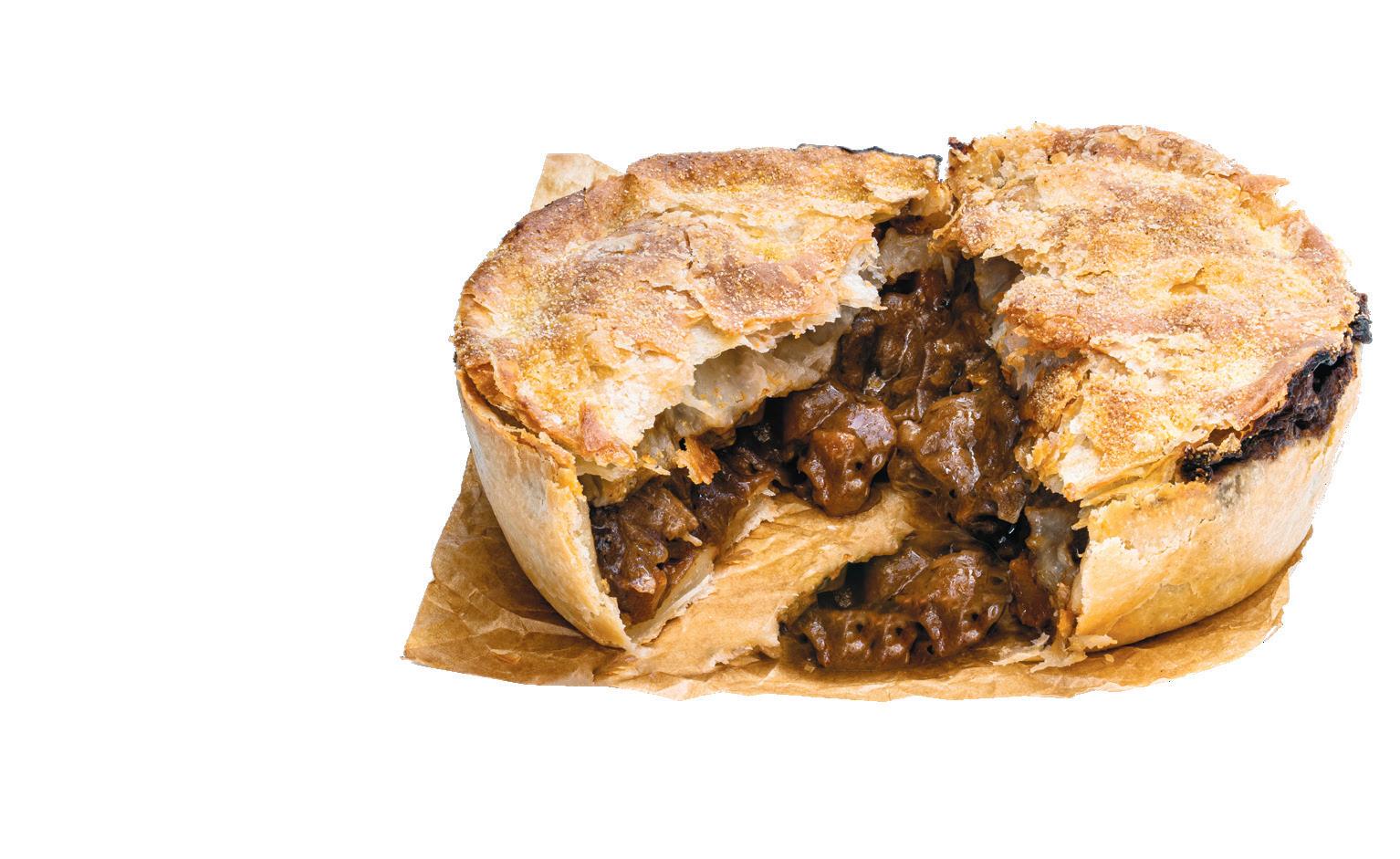
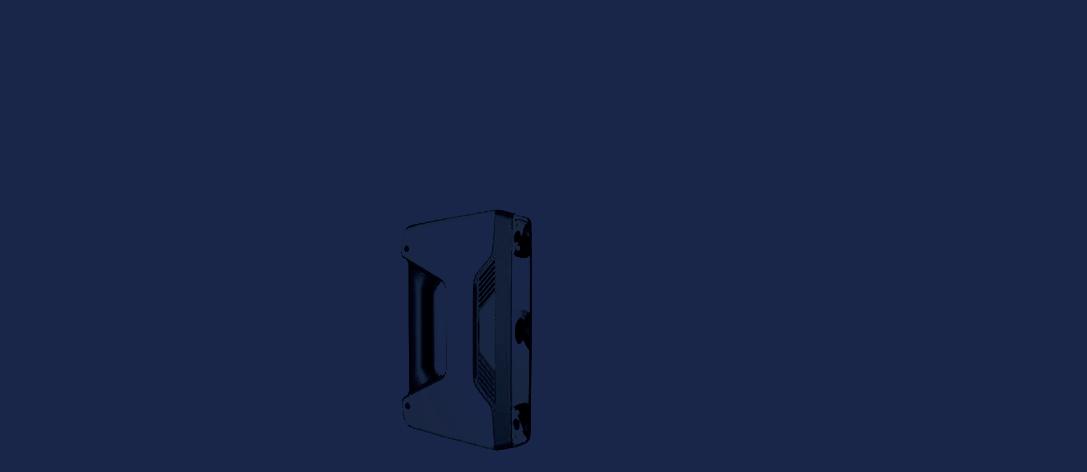
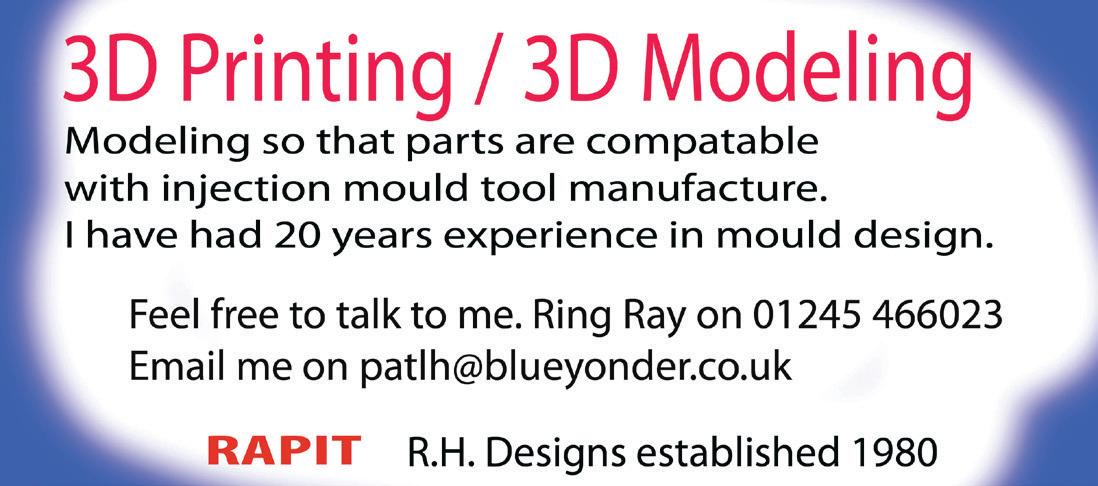


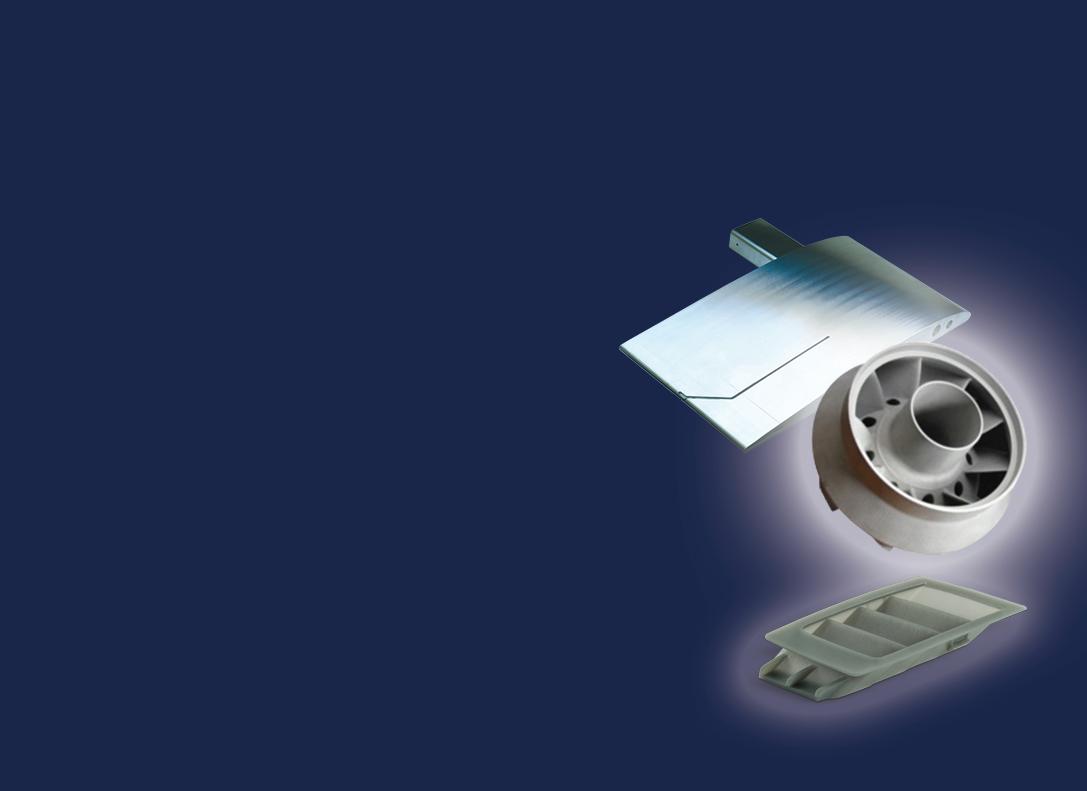
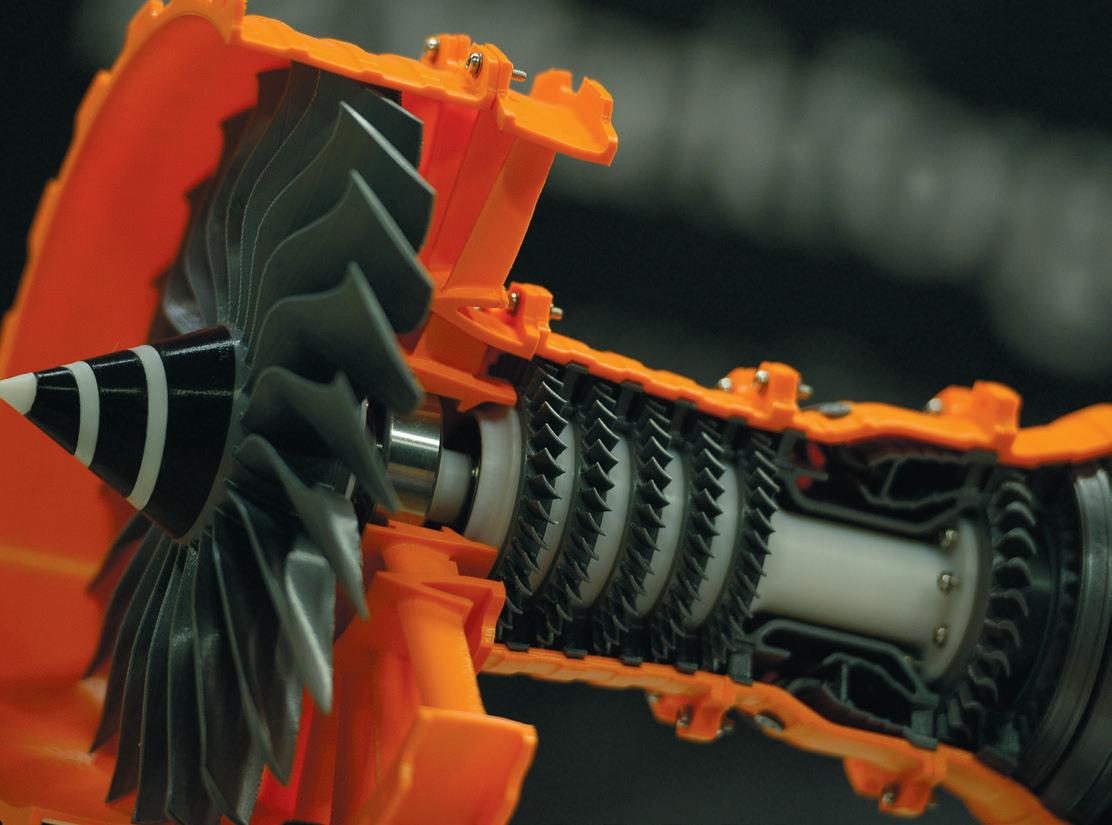

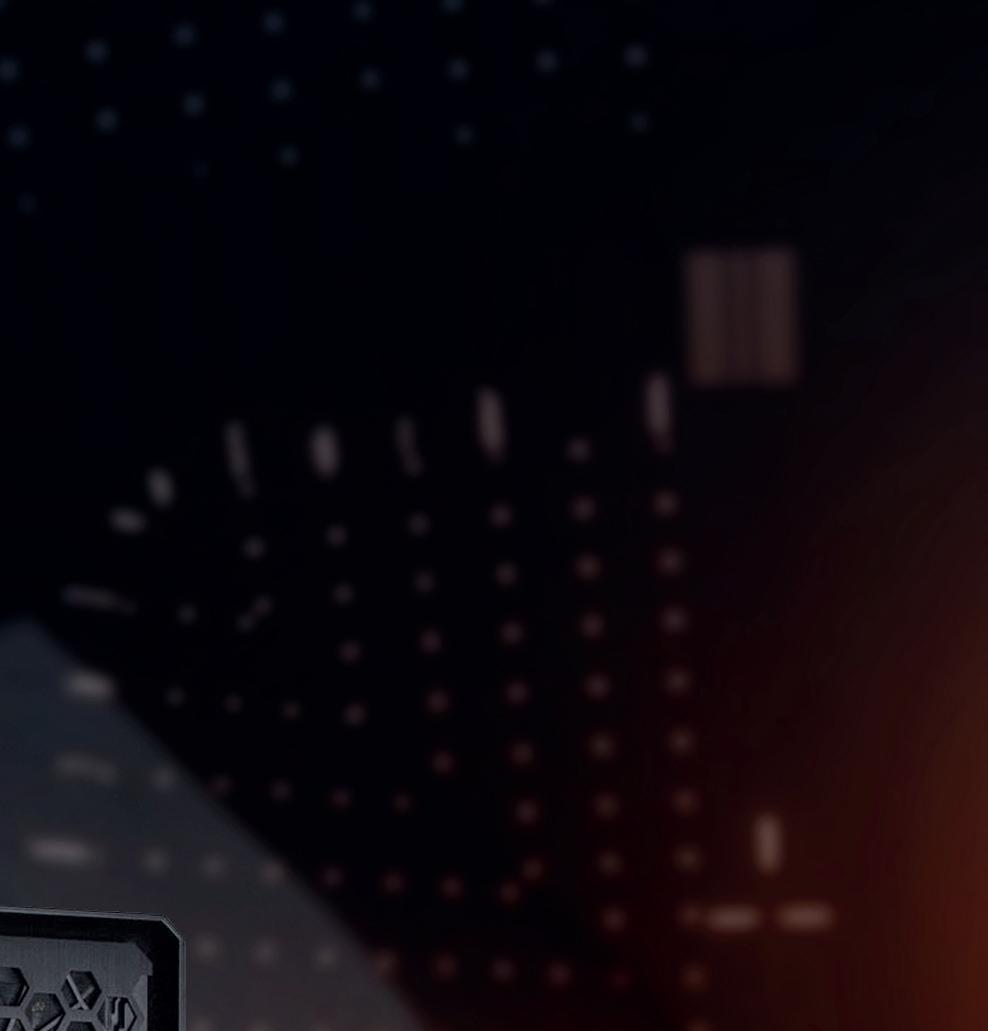
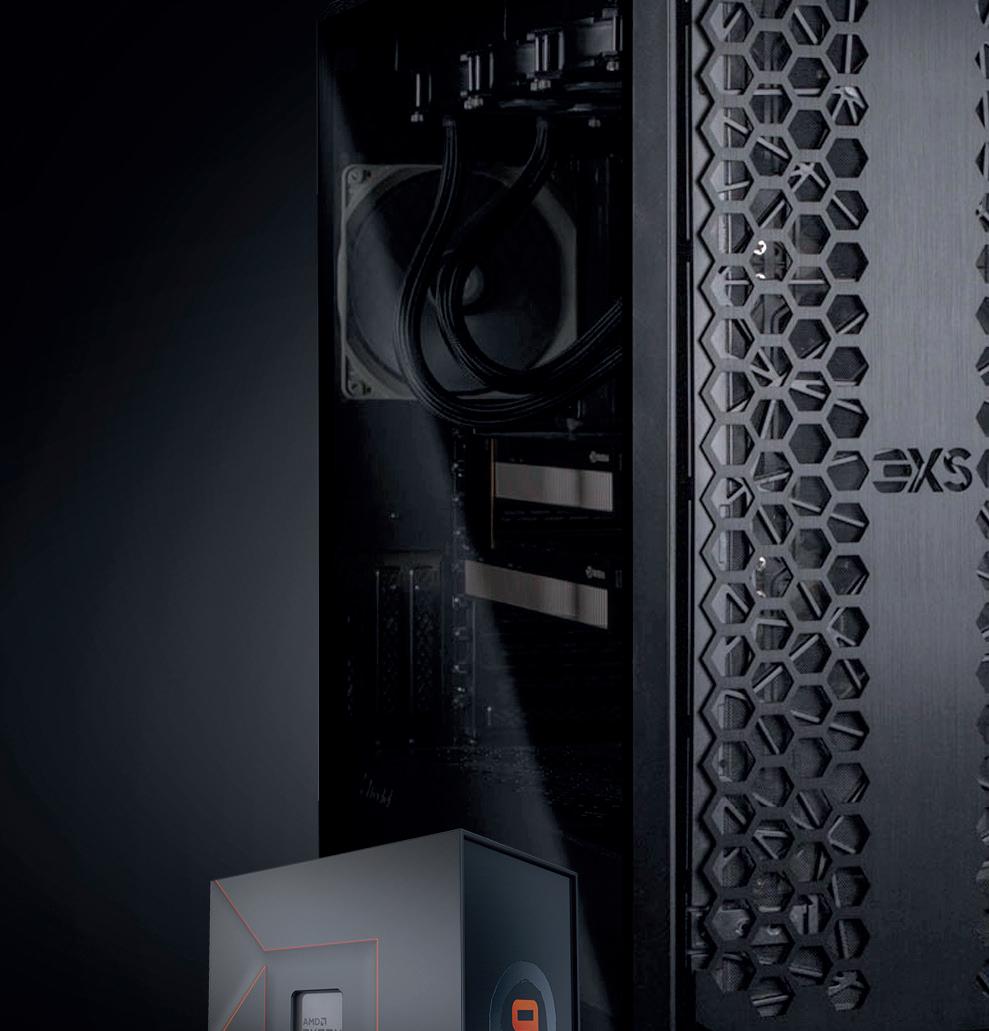

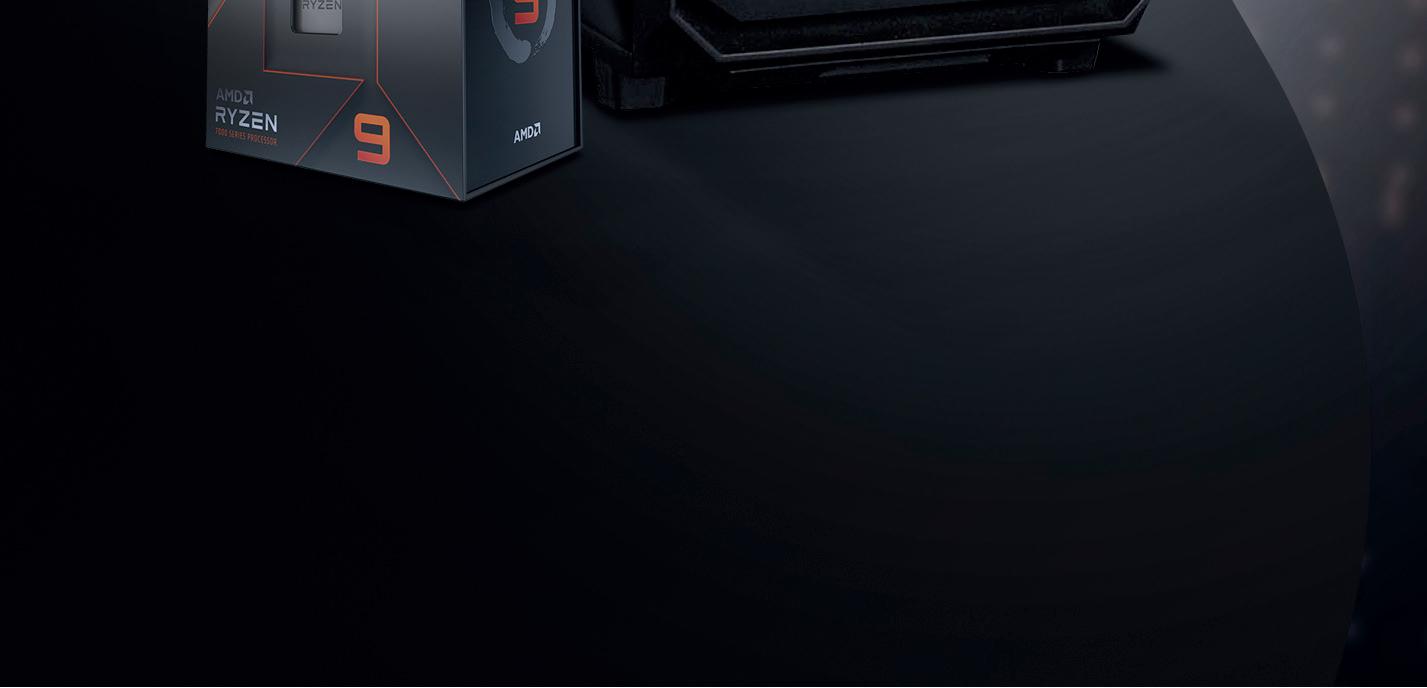
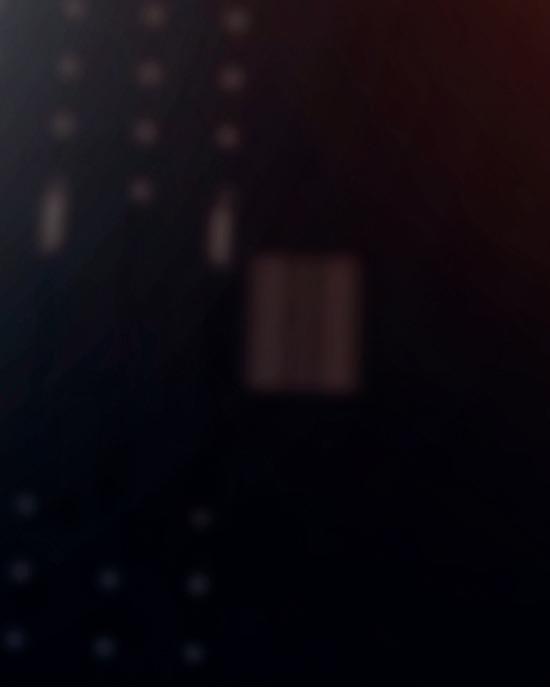

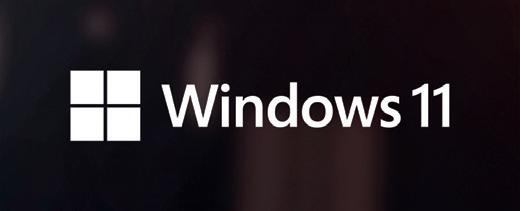