ANTIFRAGILE GLASS
edited by Maria Antonia Barucco, Elti Cattaruzza, Rosa ChiesaANTIFRAGILE GLASS
supported by
Antifragile Glass edited by Maria Antonia Barucco, Elti Cattaruzza, Rosa Chiesa
Printed version ISBN 979-12-5953-034-9 Digital version ISBN 979-12-5953-096-7
This publication is an Open Access Gold book. The publication file is freely downloadable from the Anteferma Open Books platform (https://www.anteferma.it/aob/index.php/antefermaopenbooks/index)
Anteferma Open Books is the platform for publishing research volumes, respecting ethical and qualitative standards and the provision of open access content.
Book design Margherita Ferrari
Editorial board Emilio Antoniol, Rosaria Revellini
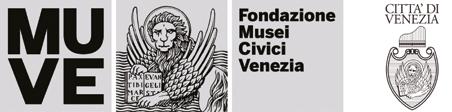
Publisher Anteferma Edizioni Srl via Asolo 12, Conegliano, TV edizioni@anteferma.it
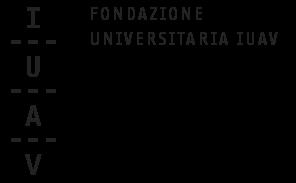
First Edition November 2022
Copyright
This book is published under a Creative Commons license Attribution - Non Commercial - Share Alike 4.0 International
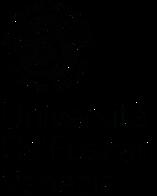
ANTIFRAGILE GLASS
This volume collects proceedings from the ANTIFRAGILE GLASS Conference - Venice November 18th, 2022
PROMOTED BY Università Iuav di Venezia, Università Ca’ Foscari Venezia, MUVE Fondazione Musei Civici Venezia
SUPPORTED BY Fondazione Universitaria Iuav, Regione Veneto, OFFICINA*, Anteferma, Rehub
PARTNERSHIPS
SITdA Società Italiana della Tecnologia dell’Architettura, International Year of Glass 2022, Promovetro Murano, Future Cities Research Hub, CoReVe, Consorzio Nazionale Imballaggi, Confindustria Venezia Area Metropolitana di Venezia e Rovigo
SCIENTIFIC COMMITTEE
Michele Back Università Ca’ Foscari Venezia; Laura Badalucco Università Iuav di Venezia; Adolfo Francesco Lucio Baratta Università degli Studi Roma Tre; MariaAntonia Barucco (chair) Università Iuav di Venezia; Paola Boarin University of Auckland; Laura Calcagnini Università degli Studi Roma Tre; Andrea Campioli Politecnico di Milano; Elti Cattaruzza (chair) Università Ca’ Foscari Venezia; Cristiana Cellucci Università Iuav di Venezia; Rosa Chiesa (chair) Università Iuav di Venezia; Massimiliano Condotta Università Iuav di Venezia; Alessio Franconi Brunel University London; Elena Giacomello Università Iuav di Venezia; Francesco Gonella Università Ca’ Foscari Venezia; Monica Lavagna Politecnico di Milano; Ligia Moretto Università Ca’ Foscari Venezia; Giovanni Mucelli Università Iuav di Venezia; Serena Panighello Stevanato Group Lab Analytics; Augusto Panini Fondazione Musei Civici di Venezia; Barbara Pasa Università Iuav di Venezia; Alberto Quaranta Università di Trento; Raimonda Riccini Università Iuav di Venezia; Massimo Rossetti Università Iuav di Venezia; Chiara Squarcina (chair) Fondazione Musei Civici di Venezia; Setsuhisa Tanabe Kyoto University; Valeria Tatano Università Iuav di Venezia; Maria Chiara Tosi Università Iuav di Venezia; Dario Trabucco Università Iuav di Venezia; Enrico Trave Università Ca’ Foscari Venezia; Arianna Traviglia Centre for Cultural Heritage Technology dell’Istituto Italiano di Tecnologia.
ORGANIZING COMMITTEE
Emilio Antoniol Anteferma Edizioni, Università Iuav di Venezia; Margherita Ferrari Anteferma Edizioni, Università Iuav di Venezia; Pietroluigi Genovesi MUVE; Rosaria Revellini Università Iuav di Venezia; Matteo Silverio Rehub.
ORGANIZING SECRETARIAT
Letizia Goretti BnF Parigi; Marta Possiedi Università Iuav di Venezia; Daniela Fontana Fondazione Universitaria Iuav; Chiara Pagani Fondazione Universitaria Iuav.
ANTIFRAGILE GLASS
MARIA ANTONIA BARUCCO, ELTI CATTARUZZA, ROSA CHIESAThe year 2022 is the International Year of Glass, established by the United Nations with Resolution 75/279. Università Iuav di Venezia, Università Ca’ Foscari Venezia and the Fondazione dei Musei Civici Veneziani are celebrating 2022 with ANTIFRAGILE GLASS: a conference, an exhibition and a publication, but also, and most of all, a celebration of a material, an ancient art form and an industry in constant evolution.
The objective of the UN is to highlight glass technologies and their potential contribution to addressing the challenges of sustainable development and inclusive societies. With this in mind, ANTIFRAGILE GLASS examines the past and future of glass, so that those who work and study this material can continue to ensure that crises are, to all intents and purposes, new starting points for bold innovations.
For many years, Università Iuav di Venezia, Università Ca’ Foscari Venezia and the Fondazione dei Musei Civici Veneziani have been involved in training, research and promotion of the history and innovation of glass. The year 2022 was therefore chosen as the ideal time to establish potential partnerships, to structure the dialogue between the region and academia with new guidelines, to challenge young people to imagine the future, to learn from the past and to describe the current state of the art.
The ANTIFRAGILE GLASS programme was designed to promote opportunities for exchange, interaction and discussion. Developed during a period between the initial resumption of collective life and the outbreak of the war in Ukraine, it is therefore a proudly optimistic, broad and challenging programme. ANTIFRAGILE GLASS is an opportunity for discussion, to envision the future of glass, to meet and discuss the need to respond to crises and work on new projects. ANTIFRAGILE GLASS is an opportunity to reaffirm the interest in continuing, renewing or reinventing the aptitude for innovation that craftspeople, manufacturers and researchers share.
Even the title, ANTIFRAGILE GLASS, affirms these objectives. Nassim Nicholas Taleb has proposed using the adjective “antifragile” to describe a new worldview; indeed, this very adjective is the title of his acclaimed book, published in 2012, in which he emphasises the difference between resilience and antifragility. Those who are resilient stand the test of time and retain their structure, their choices and their goals. Those who are antifragile change over time and with time grow, transform, evolve or regress in alternating phases; this renders them consistent with the present day and often innovative. Research, culture, and glass are antifragile. Antifragile is the property of remaining strong during the fluctuations between authority and checks and balances. Antifragile is the ability to develop new ways of thinking and new products in the constantly changing human, economic, and political environment. Antifragile has a stubborn, challenging and revolutionary character. Antifragile is an attitude that becomes stronger in adversity. The city of Venice must also, now more than ever, persists in becoming fully antifragile.
ANTIFRAGILE GLASS enters into a dialogue with this definition and provides evidence that, throughout history, glass has faced challenges, crises, and innovations by transforming technologies, processes, production methods, shapes and designs, while continuing to enhance the characteristics of the material. Glassmakers, innovators, scientists, artists, entrepreneurs and designers have studied and worked with this material; one that has accompanied mankind in the development of new products since the very dawn of civilisation. The material, its design and its technologies are transformed by fulfilling different functions, affirming some of its characteristics and modifying others, adapting to changing contexts and demonstrating a capacity for innovation.
The history of Murano glass is such an example of antifragility. Many crises have affected this art form; they have exhausted and renewed it, put it to the test, overcome and strengthened it. Antique glass more than a thousand years old is very different to the glass that is created in the kilns of Murano today, but between these two manifestations there exists a strong historical and cultural bond. An antifragile, stubborn, and tenacious culture, in as much as it is willing to rise to the challenge of learning the new and from the new. The characteristics that can be observed in a small but highly-valued geographical area – the island of Murano – are also recognisable in academic research, in science, in art-historical and archival research, in design skills, in business culture, and in the skills of the artists and designers who work with glass. It is for this very reason that glass is antifragile.
And to draw the attention of young people to these issues, to invite them to describe their vision for the future of glass and to emphasise the value of shared work, we organised a residential interdisciplinary workshop entitled VETRO FUTURO, which took the form of a hackathon. Strongly endorsed by Università Ca’ Foscari Venezia and organised by Università Iuav di Venezia, VETRO FUTURO was included in the programme of The Italian Glass Weeks 2022. This volume of proceedings presents the outcomes in the form of three posters, material produced by twelve master’s degree students from the two Venetian universities. What clearly emerges from these papers is the extraordinary ability of these students to reframe the issues we face as starting points for recognising that these problems represent opportunities and new challenges. With this approach, everything can be reevaluated. With muraNEWABLE, the energy supply issue that is affecting Murano becomes an opportunity to rethink energy sources for sustaining a large territory, while poroVE suggests the recycling of waste glass to exploit its chemical and physical characteristics in order to address the complex problems of drinking water pollution and microplastics; finally, wearGLASS proposes the technology transfer of innovations to the fashion industry, which could enable even the most underused waste (such as discarded plate glass from buildings) to be exploited. In this context, Murano and Venice serve as a laboratory of ideas and a hotbed of experimentation, land and culture: ingenuity and willingness to work together are the qualities that the students lend to the universities they attend and to the proposed outreach to local companies. The
editors of this volume aim to seize this momentum in order to work on glass with an increasingly international, collaborative and inclusive outlook.
A call for papers, an exhibition, a workshop and a publication, but, above all, a place for dialogue: all this serves as an important reminder that we cannot be antifragile alone. Antifragility is a quality that can only be developed through a network of connections and bonds that, although in constant flux, recognise the value of antifragility, and support and benefit from it. When one node or connection in the network fails, others make up for this and develop new skills and aptitudes. Every failure, as well as being the actualisation of a crisis, is an impetus for fresh growth. ANTIFRAGILE GLASS is the result of a working method based on collaboration between many people.
For the support given to this work, sincere and grateful thanks are due to the organisations that supported it: Fondazione Iuav, Anteferma Edizioni, the OFFICINA* cultural association and the Regione del Veneto. Without these partners, ANTIFRAGILE GLASS would not be antifragile at all and would lack courage, perseverance and substance. Furthermore, we should not forget the sponsoring bodies, who believed in the value of a wide-ranging and complex project and encouraged its dissemination:
• Italian Committee of IYOG2022 – International Year Of Glass 2022
• CONAI – National Packaging Consortium
• Confindustria Venezia – Metropolitan Area of Venice and Rovigo
• Consorzio Promovetro di Murano
• COREVE – Consorzio Recupero Vetro
• Future Cities Research Hub, School of Architecture and Planning, Waipapa Taumata Rau – University of Auckland
• SITdA – Italian Society of Architectural Technology
The visual identity and, in particular, the logo of ANTIFRAGILE GLASS expresses this variety and diversity in its network of stakeholders: the atoms that make up the tetrahedron structure of silica draw a pattern and constitute the main “ingredients” in the “recipes” of the ordinary glass that is all around us. Silica atoms and three backgrounds, to highlight the three lenses through which we have chosen to investigate glass: science, architecture and design. These are just three among many other potential approaches, questions, perspectives and insights – the first three, and not the only three, points of view that Università Iuav di Venezia, Università Ca’ Foscari Venezia and the Fondazione dei Musei Civici Veneziani want to address.
ANTIFRAGILE GLASS is a set of research, teaching and third mission activities that has actively involved teachers and students in a dialogue with the historical, industrial and artistic activity of Venice, the glass capital of yesterday and tomorrow. Both the title and the logo representing the event express the hope that this opportunity for work, discussion and meetings will enable a varied and complex series of activities to be launched to support and enhance the present and possible future of a material that is as innovative as it is ancient.
TABLE OF CONTENTS
13. Glass and Science
ELTI CATTARUZZA
17. Glass and Architecture MARIA ANTONIA BARUCCO
21. Glass and Design
ROSA CHIESA
24. How the technological advancement of glazing changes cities’ identity: the example of Dubai CHIARA SCANAGATTA
34. Systemic reuse models for sustainable glass packaging design and innovation CRISTINA MARINO, PAOLO M. TAMBORRINI, LAURA MIOTTO, GIULIA FERRONATO
44. Fragile Business: Libbey-Owens-Ford and the impact of the 1970s energy crisis on the american glass industry GIORGIO MARFELLA
54. POSTER Use of waste glass as aggregate for cementitious mortars
JACOPO DONNINI, ANGELO MONTENERO, L. DAVID PYE, VALERIA CORINALDESI
56. Glass on stage. The woman of fire Marietta Barovier MASSIMILIANO CIAMMAICHELLA
66. Insights into LCA and EPD environmental impacts data related to glass products for windows
ANNA DALLA VALLE, MONICA LAVAGNA, ANDREA CAMPIOLI
76. The “beautiful scraps” a precious resource ERIKA COCCATO, LAURA BADALUCCO
86. POSTER Ancient glass alteration and advancement in active conservation strategies
GIULIA FRANCESCHIN, ROBERTA ZANINI, STEFANO CENTENARO
88. Authorship in Glass Design in Portugal- Four Cycles: from 50´s to Contemporaneity
CLÁUDIA PEDRO SANTOS
98. MURANO PIXEL. An experimental and shared research
MARIA ANTONIA BARUCCO, ELTI CATTARUZZA, MATTEO SILVERIO
108. From industrial float glass to collectible design: the functional light sculptures Baracche, project by artist Paolo Gonzato
BEATRICE BIANCO, MARINELLA FERRARA
118. POSTER Physico-chemical and morphological characterization of inner surfaces of glass pharmaceutical vials
GIOVANNA PINTORI, SERENA PANIGHELLO
120. (E)merging layers in Venice. The potential of one landscape and single raw material
MAXIMILIANO ROMERO, ANNA LORENS
130. Air, light, and liquid in motion: blurred transparency of the Glass pavilion in Toledo
AKI ISHIDA
140. POSTER Glass-making workshop: fostering new design practices
SOFIA CRETAIO, CRISTINA MARINO, JOSEAN GARCIA DIAZ, PAOLO TAMBORRINI
142. Glass Future Lab. Murano glass production and digital manufacturing: possible relationships in a future scenario
ROSA CHIESA, RICCARDO BERRONE, LUCA COPPOLA
150. Innovation scenarios in the glass industry in Europe
LUCA TRULLI
160. POSTER XPS characterization of plasma-activated surfaces. A possible benefit for glass bonding
ANNE TALNEAU, CHRISTOPHE CARDINAUD
162. Technology hybridization for multi-performance variable glazing
CRISTIANA CELLUCCI, BENEDETTA MARRADI
172. Glass and light. Suspension lamp design in Italy between 1930 and 1969 in the magazines
FEDERICA DAL FALCO, RAISSA D’UFFIZI
184. POSTER Guaranteeing the authenticity of VENINI Murano glass
ELENA TESSER, FABRIZIO ANTONELLI
186. Apparent divide. An observation of the handmade and the machine-made through the work of Laura de Santillana LAURA PANCHAUD
196. Digital manufacturing for Murano glass OMRI REVESZ
206. POSTER VETRO FUTURO muraNEWABLE: from the needs of glass comes a new energetic opportunity GIULIA CAZZADOR, GIANMARCO GNOATO, DANIELE VENDRAME, SOFIA ZANANDREA
208. POSTER VETRO FUTURO poroVE: the fluid value of the waste CHIARA GHIDINI, SARA LABIDI, IRENE MARTIN, ILENIA PESSOTTO
210. POSTER VETRO FUTURO wearGLASS: from waste to resource for wearable GIULIA DA PIAN, SERENA DE CONTI,NICOLA MASSIMI, MICHELE MESCOLIN
GLASS AND SCIENCE
ELTI CATTARUZZA
Glass is an extraordinarily distinctive material. Its uniqueness is recognised by ordinary people, who value its colour and luminosity in everyday objects such as glassware and in the most sought-after items such as glass beads (included on the UNESCO List of the Intangible Cultural Heritage of Humanity since 2020), but also by scientists who understand and explore its innermost patterns of behaviour, discovering that it flouts the usual rules that other common materials, such as metals, follow. Glass is in the transparent cup we can use to drink a fantastic vintage red wine, capable of making us fly over Mount Parnassus... but that cup is made of a material with devilish properties. A material considered fragile? This is just a small aspect of its existence. That same material can make our daily lives better, thanks to its features explored in smart windows, in optical fibres, in the flexible glass of some now commonly used devices, and in bioglass, which are bioactive glass materials that are capable of stimulating bone regeneration... This is why we prefer to think of it – in a way that is more inclusive of all its distinctive features – as an antifragile, enduring material that persists, undaunted, in remaining mysterious, complex, multifaceted, elusive and perennial. Its properties are never hic et nunc, because they depend on its history, on the chronology of the thermal processes that led it to become an object, on the atmospheres it went through in its creative labour. And will the form it has now taken really be the final one, for a material that can always prove to be as divine as it is infernal? Or is it just our desire as humans to demand it to be eternal, static, as if it were a cornerstone of our ability to conquer matter? Glass can often provide answers, but above all it raises endless questions that transcend science by meeting art, that go beyond mere utility by enchanting and rousing the senses. It is no coincidence that the poet Wisłava Szymborska, winner of the Nobel Prize for Literature in 1996, once wrote about a man who “built himself a glass violin because he wanted to see the music”.
The history of glass is a continuous crossing of boundaries between magic and science, utility and art, transparency and colour. In a famous scientific article published in 2016, entitled Welcome to the Glass Age, two famous researchers floated the idea of declaring the current century the Age of Glass. We can hardly blame them, if we consider that in recent years some 7,000 scientific articles containing the word glass are published every year, and more than 25,000 a year on the topic of glass. Moreover, it is not surprising that the United Nations decided to celebrate this material by declaring 2022 the International Year of Glass. And just to recall a historical fact, it was right here in Venice that the great scientist Galileo Galilei was invited on 25 August 1609 to present to the Doge and the Venetian aristocrats a new instrument that he had perfected as no one had ever been able to do before. It was an instrument containing glass lenses whose creation he himself had patiently and skilfully overseen at every stage, from the search for optimal transparency of the material to the perfection of the curvature of the surfaces, which he polished with his own hands, cooperating on all these aspects with the master glassmakers of the island of Murano. We are talking about the telescope – an ancient example of how glass allows us to “see far”. Staying on the subject of devilishness, the great Wolfgang Pauli, Nobel Prize winner for Physics in 1945, once said that “the surfaces were invented by the devil”. Thinking about the surface of a solid, the atoms that compose it are the boundary between one world and another, a door to be passed through to access new possibilities, the development of physical and chemical rules that are amplified in the ambiguity of the boundary atoms. Similarly in the case of glass, such as the most widely used type of glass (sodium-calciumsilicate glass), which is used in a variety of applications such as materials for screens, pharmaceutical containers, photovoltaic systems and so on, it is important to have investigation techniques that enable the study and analysis of its surface, allowing light to be shed on highly complex phenomena relating to the reactivity between its surface atoms and those of the surrounding environment. These interactions can lead to alterations in surface chemistry and structure, internal structural connectivity, the ratio of bridging and non-bridging oxygen, corrosion resistance, leaching of modifier elements, adsorption, wetting and hydrophobicity. The use of appropriate analysis techniques, capable of investigating the boundary atoms between the solid and the surrounding environment (techniques with sampling depths that can vary from a few atomic layers up to several microns), allows us to understand the condition of the glass surface, thus making it possible to plan conservation or protective treatments and to verify their actual effectiveness over time. This applies, for example, to artistic glass for the purpose of studying and preventing/slowing down its degradation, or to glass that comes into contact with liquid solutions (such as in the pharmaceutical field, food industry, etc.) with regard to the potential release of atoms into the solution.
Glass has countless lives, because it is a highly recyclable and reusable material. Europe is aiming to reach a glass recycling rate of 75% by 2030. Italy has already surpassed this target ahead of schedule, reaching a glass recycling rate of 79% in 2020. But the many facets of glass – its antifragility –enable it to be easily and almost directly reused even as an additive material in many areas of the building industry, or even to become the centrepiece of objects of design if the scraps come from highly distinctive and unique manufacturers, such as the Murano glassworks. Here, even scraps – not remelted but transformed into new objects – retain the history and beauty of the places and artefacts from which they originate, transmit the poetry and wisdom of centuries of craftsmanship and knowledge handed down through the generations. These distinctive features should not be lost, neither on the scraps nor on the originals, but rather safeguarded and protected. Recycling, repurposing, reusing: these words should have increasing resonance in the case of glass too, given that the manufacture of an object from scratch –i.e. produced from the usual raw materials, including silica sand – requires approximately three times as much energy as that produced by recycling glass fragments and powder. The simple initial melting of silica sand, due to the high temperature required, consumes about 25% more energy than the melting of preformed glass... It is needless yet self-evident to emphasise today, in the current geopolitical situation, the importance of energy savings in the various stages of the production of a material. In 2017, so quite some time ago now, a scientific article entitled “Venice artistic glass: Linking art, chemistry and environment – A comprehensive emergy analysis”, which featured an “emergy” analysis of the annual production of artistic glass by an averagesized Murano glassworks (an analysis that quantitatively considers and evaluates both the economic and environmental aspects of the entire process of making the glass artefact), highlighted how dangerously dependent its overall economy was on traditional energy sources, for which economic and social factors are extremely critical and cannot be controlled from within the system. Ipse dixit? Unfortunately, reality. Even for glass, therefore, we need education geared towards fully enhancing and understanding it in a broader sense, so as to embrace the concept of synergy between aesthetic possibilities and functional opportunities. Cross-pollinating, reinterpreting, experimenting: glass science and industrial technology that confronts and merges with the manual art of those who know how to make unique artefacts, with a view to innovation that must not disregard the preservation of ancient craftsmanship, making each approach increasingly sustainable and suited to a society in a constant state of flux. This, perhaps, is the new paradigm of glass.
GLASS AND ARCHITECTURE
MARIA ANTONIA BARUCCO
The cultural aspects of the project cross fields and touch upon different areas, and the work of the innovators transforms what is experimental research into practical and valuable innovation. The contributions presented here describe glass technology and its connections with various fields and take stock of the relationship between business, experimentation and research; processes and products useful for the near future; and projects and products that have marked the development of glass technology.
The papers describe a form of architectural design that is closely linked to materials and is shaped by the history and culture of people, territories and companies: the balance between history and innovation; the cultural references and the character that a technology can help to anchor in the design of places; the strong connection between production and economies, between designs and needs, between thought and technique. At the same time, the nexus between the study of a material and architectural design is technology.
The entire call for papers of ANTIFRAGILE GLASS is strongly linked to the themes of science and technology, but there are profound and manifold cross-references to the humanities, history and environmental awareness, which affects every field of research as well as representing a real and pressing shared need.
ANTIFRAGILE GLASS has its roots in the Venetian lagoon and the factories of Murano: places where the boundary between art, myth, technology and production becomes so blurred that it loses its meaning. Art and technology blend like glass in furnaces and become unique objects in the hands of master glassmakers. And the production of glass that is both industrial and artisanal is in itself mythical, known the world over for its alternating fortunes, discoveries and innovations as well as for the unique beauty of its creations.
Thus, the ANTIFRAGILE GLASS call for papers is open to the framework in which technology is the dominant element, which makes explicit the aim of
keeping the industry running. ANTIFRAGILE GLASS also addresses the myth – everything that glass has conveyed since the dawn of time, and which has nothing to do with the mechanisms and supply chains to which it belongs or to which it is accountable for its choices.
Reading the papers reveals how technology connects these two opposing visions. Architectural design is the field of application and articulation of the historical, scientific, cultural and experimental analyses; the conference, the exhibition and this publication offer those who responded to the call for papers a useful forum for discussion.
Writing a preface to these papers means emphasising different points of view and shared roots. It also means interpreting a discourse and helping to recognise the considerable interest there is in working in the context of boundaries, between technology and myth of glass in the past, the present and the near future.
This future is certainly influenced by the issue of energy, which will drive major choices in both the design of glass products and the design of glass production processes.
On the first aspect, which is almost completely unexplored, Campioli, Dalla Valle and Lavagna focus on research that is both promising in terms of its findings and highly relevant to the construction sector: they offer an analysis of LCA and EPD environmental impact data related to glass products for windows. The paper defines a number of principles that are fundamental to the development of research on these issues: “identifying reference values, verifying any differences between the internationally recognised datasets and the data of producers, and disclosing the percentage increase that results from the various types of glass processing”. The issue of embodied energy and waste reduction in production are themes that also recur in different contexts: Barucco, Cattaruzza and Silverio analyse production and waste in Murano glassworks through the lens of the circular economy. And it is to this research and the provocative nature of the proposed theme that we effectively owe the triggering of a series of interests and dialogues that have taken shape in the organisation of ANTIFRAGILE GLASS.
The highly energy-intensive glass manufacturing industries are a key focus of attention in the energy cost debate that has dominated discussions in recent months. However, for some time now, these industries have been committed to understanding how they can innovate and evolve production systems that use energy from fossil fuels. Trulli offers a historical reading of the manufacturing processes and innovations developed in Europe, but with a global outlook. Marfella presents an accurate and compelling analysis of a business that he defines as “fragile” and describes the Impact of the 1970s Energy Crisis on the American Glass Industry. Marfella illustrates “the vital relationship of the glass industry with the global economics of energy and its business repercussions for the development of architectural products with better environmental performance”.
But glass is more than just production, energy and industry: the boundary between magic and concreteness that characterises working and designing with glass is aptly described by Ishida. Her paper highlights meticulously crafted details of the Glass Pavilion built in Toledo (the American city of glass) by SANAA: “When glass is experienced in motion under changing light, the perception of it is not simply as transparent but is a specific kind of transparency that can be called blurred. A mix of mechanical and structural engineering, light design and sensibility make magic the architecture described and its description”.
And undoubtedly the values of glass in architecture and its meanings profoundly influence design choices: Scannagatta describes “how the technological advancement of glazing changes cities’ identity”. The example of Dubai is certainly one of the most stunning in the world and the contribution published here “analyses how the technical advancement of glass façades can change the skyline of cities through the example of Dubai”. Cellucci and Marradi cast their gaze towards an even more distant horizon: “technology hybridisation should aim at multi-performance variable glazing. The authors describe the trend in which sheets of glass become a variable multi-performance system with the aim of creating highly usable and accessible products. The cross-pollination of creative forms, adaptive façades and new uses of glass are stressed in this paper”.
In this context, Venice is once again an example. It was an example at the beginning of this discussion on glass technology, when the energy, technical and analytical aspects of environmental sustainability assessments were addressed. It was also (and perhaps above all) an example in its conclusion, in developing a linguistic experiment that allows architectural design to appropriate what is usually considered waste but which can become the material that enhances an object, a space and a place. The projects described by Romero and Lorens have the merit of transforming an emergency into cultural signs capable of enhancing places that are in themselves emblematic, enriching them with a range of profound meanings and renewed environmental awareness. This is thanks to the ability that a design workshop develops in designing and offering products that translate contemporary values into designs, forms and objects that determine the architecture of places. The set of papers presented in this section proves that talking about glass using Venice as a catalyst for ideas around the future means creating a short circuit between technology and myth. Working on ANTIFRAGILE GLASS meant placing ourselves in this context, accepting and welcoming new ways of thinking. Venice is a place that may also be difficult but is certainly unique (as well as magnificent). A place to develop new ideas, stimulate supply chains and nurture myths: ancient and recent, of history, innovation and development. A place that is not a territorial boundary but an amplifier of similarities and different ideas; a place where new approaches to technology can be developed and goals to aspire to can be set, including having the courage to propose visions that are as extraordinary and revolutionary as the myths of its past.
GLASS AND DESIGN
ROSA CHIESA
The design and culture of the project, understood in its most inclusive sense, is of course also based on our relationship with materials, as Laura Tripaldi (2020) reminds us: “because the materials we use are not passive objects, but, on the contrary, are determined by our socio-cultural life and in turn determine our relationship with the world, forming what is usually called material culture: a culture that is structured around the invention, production and use of the materials that surround us”.
How, then, can we not reflect on our relationship with a material as ancient and enduring as glass? But above all, how can we ignore its intrinsic capacity to be antifragile, to reshape its configurations according to its state (liquid, solid) and, at the same time, metaphorically reconfigure itself to cope with moments of crisis?
The highly interdisciplinary approach of the ANTIFRAGILE GLASS call for papers thus represents a meeting place between the project themes –investigated through architecture and design – those more appropriately pertaining to science and technology, and the “humanities”, understood here as wide-ranging historical disciplines that push the boundaries of reflection on the future, starting from the past.
Talking about glass as a “cultural” material, with which our history has been built through the design of artistic and architectural artefacts and utilitarian objects, without forgetting the field of science, therefore means dwelling in those places of intersection between liminal areas, which share both the use of a material – glass – and its ability to shape the technologies we use to mould it. This is how historical analysis, scientific research and experiments into processes and applications take on new cultural significance – in dialogue between history and design, and between technologies, innovation, successes and failures.
The design of glass artefacts (artistic and industrial) as well as the modernisation of glass production processes will, in the future (and even now), have to deal with changes in the energy supply and the unavoidable steps towards a transition to more sustainable systems.
The meeting points and cross-disciplinary sharing thus help to map out a structural network of tense relationships between history and innovation, which – as is the case with materials subject to hysteresis phenomena, i.e. those that change their behaviour to a stimulus on the basis of their previous history (Tripaldi, 2020) – will prove to be fundamental in renewing the entire glass industry.
To simplify reading – but without wishing in any way to detract from the originality of each contribution – the papers have been grouped thematically in the following summary.
The “magic” of glass, a simple and constantly evolving material, especially that associated with blown glass and the island of Murano, is recognised around the world. An initial founding contribution by Massimiliano Ciammaichella, Glass on Stage. The Woman of Fire Marietta Barovier, helps to define the historical frame of reference of the themes progressively proposed, highlighting precisely the narrative linked to the events surrounding the manufacture of glass beads, but at the same time emphasising a highly topical theme, that of female entrepreneurship in 15th century Murano through the pioneering figure of Marietta Barovier. What emerges is a compelling dialogue between the past and the future, which uses theatre as the vehicle to convey a contemporary story.
Resilience, understood as “balance between tradition and innovation, to the transformations in various contexts under the banner of the craftsmanship and elegance of glass design”, is the key theme of the historical overview presented by Federica Dal Falco and Raissa D’Uffizi in Glass and light. Suspension lamp design in Italy between 1930 and 1969 in the magazines, recounts the evolution of glass light fittings between the early 1930s and the mid-1960s, focusing in particular on pendant lamps. The rigorous methodology of historical investigation, conducted through the analysis of magazines, highlights the implications, not only in terms of form, that glass had with the technological evolution of other materials.
The systematisation of historical knowledge about the authorial production of Portuguese glass, in the period from 1950 to the present day, is the main focus of the paper proposed by Claudia Pedro, Authorship in Glass Design in Portugal –Four Cycles: from the ‘50s to the Present. The complex theme of the relationship between art and design emerges between the lines of the contribution that addresses the issue of glass design authorship, investigated in the Marinha Grande cluster in Portugal.
By contrast, it is the innovative work of artist/designer Laura de Santillana that serves as an opportunity for Laura Panchaud, in her paper Apparent divide –An observation of the handmade and the machine-made through the work of Laura de Santillana, to focus on the apparent opposition between the “handmade” and the “machine-made” within the Murano and international glassmaking tradition. Exploring a new production process, “slumping” glass, and its many possible applications, the discussion leads into broader considerations on training and the often “crystallised” roles in the traditional glassmaking process.
Another important theme – that of the relationship between design and craftsmanship – is addressed by the essay From industrial float glass to collectible
design light sculpture: the case of Baracche project by artist Paolo Gonzato by Maria Rita Ferrara and Beatrice Bianco. The central focus is “the intersection of the industrial and standardised material of float glass, and artist Paolo Gonzato’s creative approach to this material in creating unique lightweight glass sculptures” in a novel use of the material, commonly used for construction purposes, that is becoming “promising in the perspective of the development of creative industries and economies in Italy”.
In Systemic reuse models for sustainable glass packaging design and innovation, Marino, Tamborrini, Miotto and Ferronato take stock of the Italian glass packaging industry, a strategic sector for Italy. Indicating some possible strategies that could be implemented to initiate a sustainable transition and reduce environmental impact, the contribution focuses on the topic of reuse and, ultimately, the search for innovative solutions aimed at creating a “systemic business”. Again, the theme of the potential of waste and the role of the designer as a promoter of innovation on a systemic level is the focus of The “beautiful scraps” a precious resource, curated by Erika Coccato and Laura Badalucco.
Finally, two contributions share a pursuit of integrating digital technologies with the traditional production process of glass artefacts.
In Digital manufacturing for Murano glass, Omri Revesz focuses on an experiment – Islands – which reveals original and expressive results on the use of traditional murrine through the development of an innovative production technique, giving rise to a kind of digital craftsmanship under the banner of the fruitful combination of digital and manual.
Glass Future Lab. Murano glass production and digital manufacturing: possible relationships in a future scenario by Chiesa, Berrone and Coppola, proposes a reflection on the topic of the possibilities of integrating digital fabrication into the traditional process of producing glass artefacts. Imagining new ways of hybridising production processes, once again, certainly means solving or facilitating certain technical aspects and producing new aesthetic results, but at the same time, it means envisioning a future for the glass industry that stems from continuity with its valuable historical heritage.
Albeit with some simplifications, what emerges from the papers presented in the design section yields a wealth of stimulating nuances for research around the theme of glass investigated from a design perspective. From history – an essential discipline that always plays an active role in foreshadowing future scenarios – to thematic nodes such as the redefinition of glass production, long disputed between art, craftsmanship and design, and that perhaps the prospect of encountering new technologies may help to resolve, by opening up new paths instead of building increasingly insurmountable barriers.
Finally, the issue of the transition to a sustainable structure – inseparable from digital – is key to supporting all research that looks to the future of the industry and will be fundamental in providing, as always, new lifeblood to the glass industry, which even today is challenging the economic crisis with its eternal antifragility.
How the technological advancement of glazing changes cities’ identity: the example of Dubai
CHIARA SCANAGATTAAGlazing technological advancements changed the language used in architecture all over the world, and they defined the development of some cities. The present contribution wants to analyze how the technical advancement of glass façades can change the skyline of cities through the example of Dubai. The first part of the paper studies the scenario and the state of the art of architectural glass, by considering how its use as an architectural element changes buildings’ aesthetics. The second part focuses on the development of Dubai from the 1990s through the analysis of iconic buildings such as the Burj Al Arab and the Burj Khalifa. Conclusions then comment on how technological advancements of glazing changed the way buildings are designed, and how that influences cities’ heterogeneity.
KEYWORDS: ARCHITECTURAL GLASS AESTHETIC, DUBAI’S SKYLINE, GLAZING TECHNOLOGICAL ADVANCEMENTS
Introduction
In recent decades glass has increasingly become a major player in architecture, moving from its traditional use on windows to its use as a structural component in iconic buildings such as New York’s Apple Store on the 5th Ave. This change in how architects use glass was possible due to important technological advancements that allowed to improve its strength.
The opportunities given by new glazing technologies such as curtain walls allowed architects to have greater freedom in terms of architectural language, making it possible to split structural boundaries from exterior appearances. But this was not the only aspect that allowed a wider spread of glass with different applications in architecture.
Due to climatic changes, more focus is put on energy-saving solutions, and all building sectors have focused on the goal of having better materials and construction systems to reduce energy consumption. In the glass sector, new advancements in terms of glass coating permitted to reach higher levels of UV radiation blocking and of heating control. These new coated glasses allowed to make extensive use of glass in areas with important climate fluctuations and with extreme temperatures, where traditionally glass was not used due to its low insulation performance. On the other hand, the possibility of having curtain wall façades even in climatically adverse areas, completely changed the design process of new buildings, to the point of erasing traditional construction techniques that characterized the different areas.
An impressive example of this evolution of the architectural language based on the wider use of glass is desertic areas, where climate fluctuations are extreme throughout the whole year and architecture saw a complete change of stylistic language. The most known example is that of Dubai with its change from traditional Arabic architecture to curtain walls skyscrapers that sometimes have no link to tradition.
This paper, based on these preliminary remarks, wants to investigate how glazing’s technological advancements modified and modify buildings’ architectural language, and how this influences cities’ identity. To analyze such changes the city of Dubai is used as case study, since its new development took place in the past thirty years, and it followed different architectural trends creating a unique city in the Arab world.
Literature review
Glazing technological advancements
The development of what we nowadays know as architectural glass started in the 1950s with the introduction of the float glass production process, which allowed the mass production of a flat, high-quality, and transparent material (Savić et al., 2013). After the development of the float process,
technological advancement for glazing was aimed at maximizing three characteristics: the ability to transmit light, the capacity to block heat, and safety issues. Indeed, apart from esthetic criteria, contemporary structures – and the materials used for their building – must meet several criteria. As Savić et al. (2013, p. 35) remember, “regardless of it being used for windows, façade or interior partitions, glass connects the space, improves the quality of space, transmits sufficient light, and the contemporary types of glass may contribute to energy saving [since] it is known that energy saving is one of the most important architectonic challenges of our age”.
Due to the energy savings needs, that represented a hot topic in the past decades, the development of glazing allowed the transition from monolithic glasses to multi-cavity insulating glass units, that can be integrated with different treatments and interlayered films which contribute to energy saving and indoor comfort. Parallel to this, efforts were also made to develop the aesthetic aspects of glazing, moving from treatments that varied the coloring of the glass to colorless glass with outstanding performance.
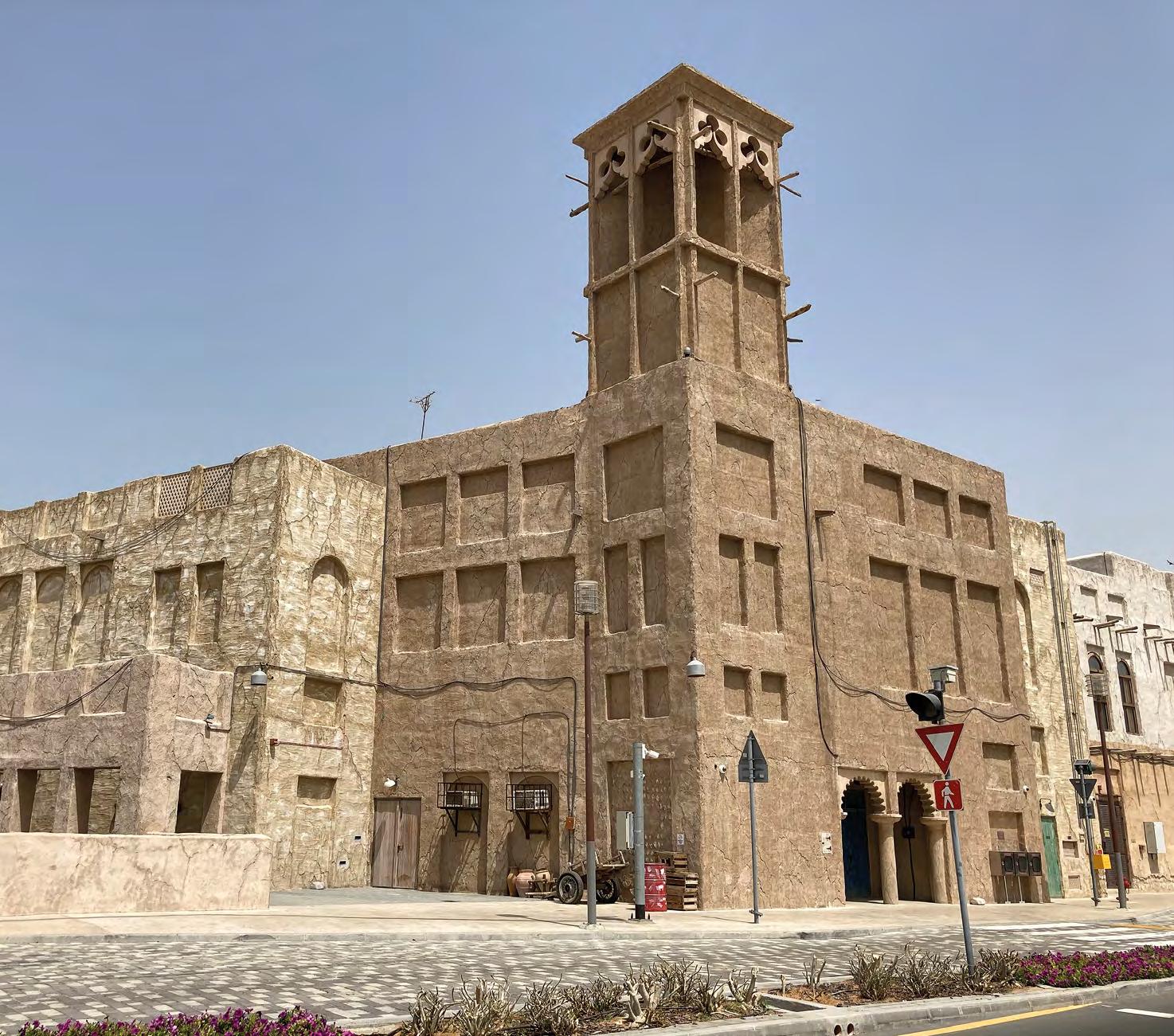
Modern architectural glazing usually combines laminated glasses and multi-cavity insulating glass units, allowing for improved performance. By doing so, it is possible to choose which characteristics are needed. Glass plies can be thermally toughened, annealed, heat-strengthened, or different types of glass can be combined in a single laminated glass, and the number of glass plies and the requirements for the interlayer depend on the application of the glass component (Musgraves et al., 2019). The presence of polymeric interlayers also allows to contain the thickness compared to monolithic glasses. The clarity characteristic was gone lost in the initial advancements aimed at improving glass’ energy-saving characteristics, but modern processes also allowed the optimization of transparent façades, curtainwalls, and commercial windows, by improving the visible light transmittance1 .
As abovementioned numerous processes and technologies can be applied to float glass today to meet different needs, and this allows for glass to now play an important role in architecture. Indeed, as Wiederhorn and Clarke (2022, p. 561) said, “recent decades have seen growing and widespread adoption of glass as an architectural material that can be used not only in window panes [since] glass has enabled architects to expand their visions of buildings, using light and space to create wonderful new designs”. Such achievement was possible thanks to many advancements in glazing technologies and to a better understanding of how glass works when applied for uses other than windows.
Architectural glass’ language
Glass became a predominant material in the definition of architectural language since the beginning of the twentieth Century with the spread of skyscrapers. An example is that of Mies van der Rohe’s skyscrapers in Chicago, with their recognizable dark skins. Later, over the last two decades of the twentieth Century, architects emphasized the tall building’s form and façade, by stressing the height aspect and mixing materials. Starting from the twenty-first Century, glass is becoming almost the only visible material on tall buildings’ façades, defining new languages by using its different treatments and characteristics. As Al-Kodmany (2013, p. 26) announced nearly ten years ago “these tall buildings are notable for their shape, lightness, transparency, and reflectivity”. There is then a return to the idea of skyscrapers from the 1960s, but the language proposed by new ones becomes completely different due to the lighter and reflective surfaces that are now proposed, which express lightness in opposition to the dark solid surface of the 1960s ones (Al-Kodmany, 2013).
1 Vitro Architectural Glass, Starphire® Glass for Exteriors. More information at: https://www.vitroglazings. com/products/low-iron-glass/starphire-ultra-clear-glass/exterior-starphire-glass/ (last accessed July 2022).
The use of color becomes important for glass skins as well since now it is possible to choose façade finishings freely from the technical characteristics that are required from glass. Since color has an important role in the visual perception of buildings’ exteriors, architects can choose how to use it to further define a building. By doing so, it is possible to add an aesthetical effect to glass architectural façades. Color then gains two uses: symbolic and functional. The first is to get the impression that the color gives about the form of the building, and the second allows to reach the best integration between form and structure based on the used color (Osman Bakr, 2019), and this is particularly important for glass façades since they can be no more linked to the structure’s shape.
At the same time, the lightness and luminosity of new skyscrapers are reshaping most cities’ skylines, as they define the city’s identity at urban scale. In this sense, the technological evolution of glazing that led to curtain wall cladding, allowed architects to stretch the rules applied to tall buildings in the past, moving to the idea that such iconic buildings can become sculptures with their skin detached from the structural form (Al-Kodmany, 2013).
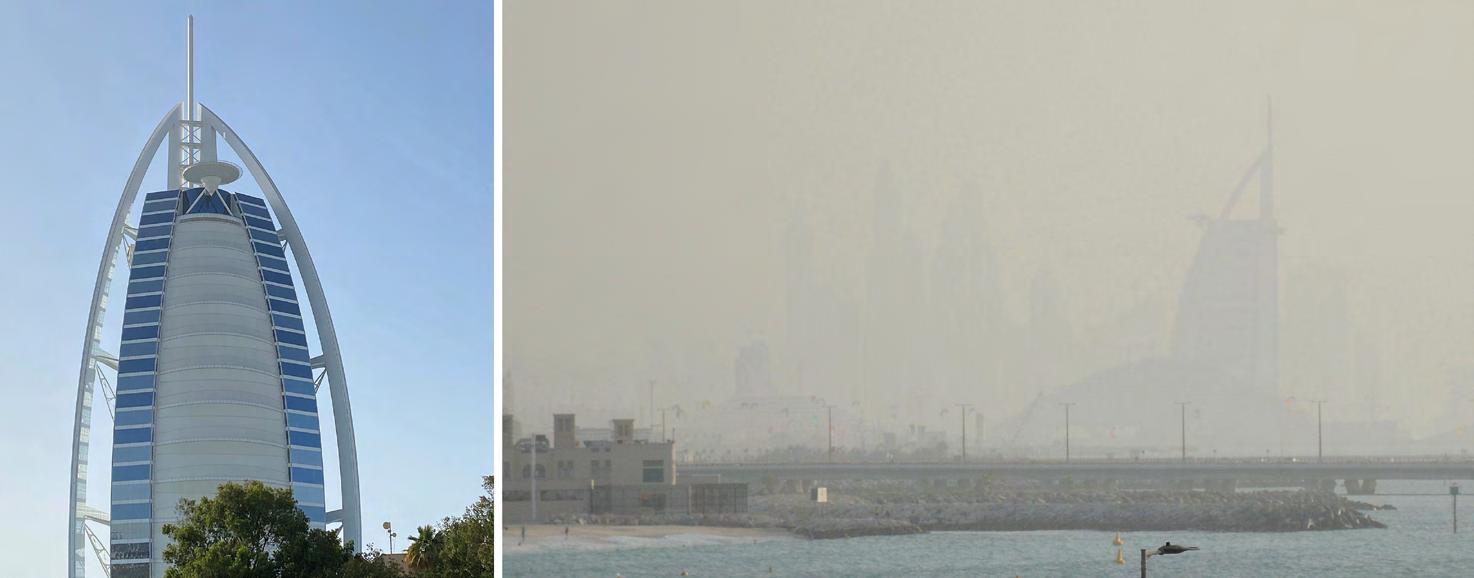
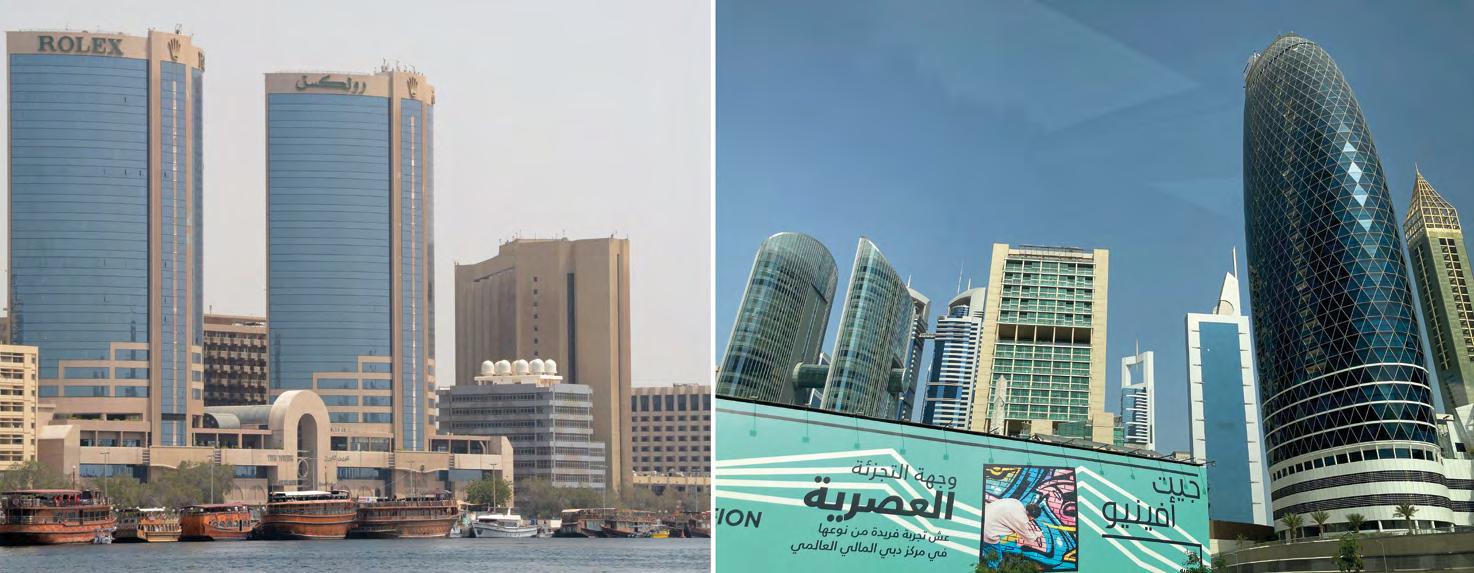
Open questions on glass aesthetic and its environmental contribution
The evolution of the architectural language of glass has always been linked with its technological advancements because, even if it was mostly appreciated for its aesthetics, environmental concerns have been a hot topic in past decades (Ritchie, 2004). This means that glazing technological advancement towards energy-saving solutions was mandatory, otherwise it wouldn’t be able to meet current regulations.
But questions arise on future implementations of glass in architecture both from an aesthetical and a technical point of view. Based on what was studied in the past, it is important to understand how glazing’s technological advancements will modify the architectural language of buildings and cities, given the enormous changes that have already been triggered. And considering the big push there is toward issues related to sustainability, how can glass façades be implemented to face the demand for nearly-zeroenergy buildings in areas with adverse climatic conditions.
Dubai is the perfect example of how a city skyline changed following the trends and advancements of glass, and where adverse climate conditions call for always updated energy-saving solutions to reduce cooling demands. Starting from the analysis of the development of modern Dubai, some considerations on how architectural glass will further change cities will be made.
Dubai’s identity evolution through its façades
Modern Dubai is completely different from both its historic area and its first phase of development in the 1990s. Traditional buildings’ architectural features were aimed at facing the desertic climate and included few façade openings, windcatchers for natural ventilation and cooling of the interiors, and façade colors that recalled the environment (Figure 1). Today none of these characteristics are visible in new constructions since modern buildings make great use of glass façades and HVAC systems.
Dubai’s development as skyscrapers’ capital began in the early 1990s, and it started with the construction that were influenced by Chinese skyscrapers. These buildings presented external claddings made of stones resembling desert tones and glazing with a specific gradation of blue that was due to the polymeric interlayers added to glasses to block UV radiations and heating. Architectural choices were thus extremely constrained by the technical properties of glass, which was mainly used to add the necessary glazing since polymeric interlayers for solar radiation and heat control were not that performing. Furthermore, when possible, the glazing was placed in a rearward position, or even inside loggias to reduce direct radiation.
With further improvements in glass treatments and coatings, it was then possible to change the used architectural language by using wider glazing and less stone or similar claddings. But this change in the used language,
combined with an absence of regulation on the typological characters to be used, led to a skyline development based on the research of the most iconic building (Figure 2).
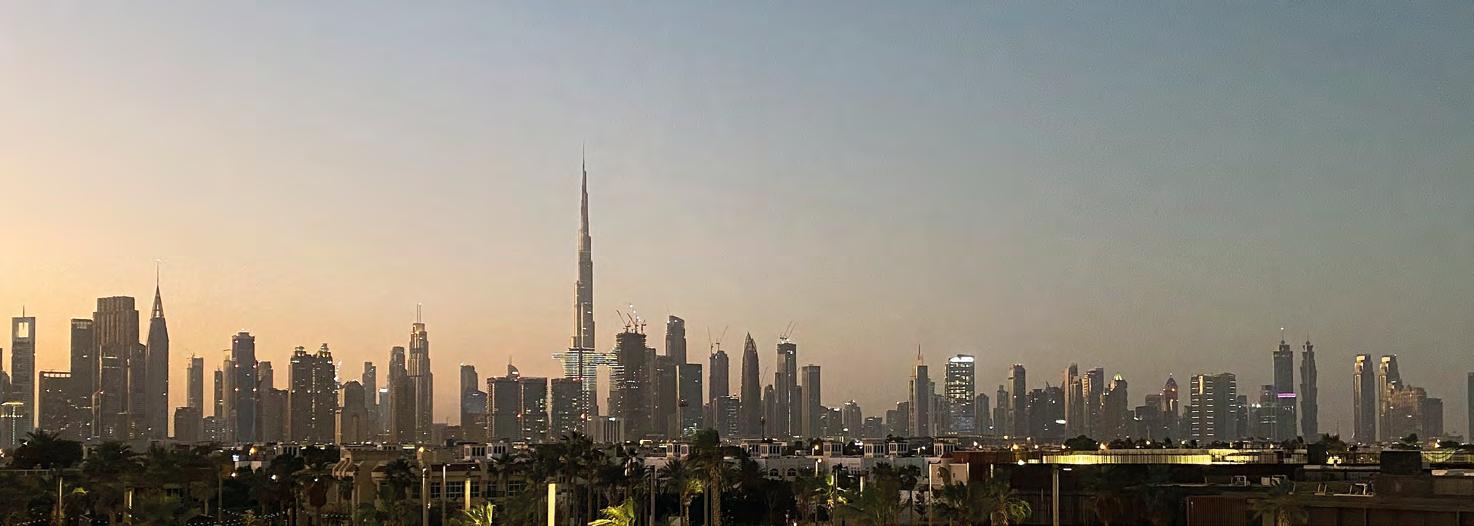
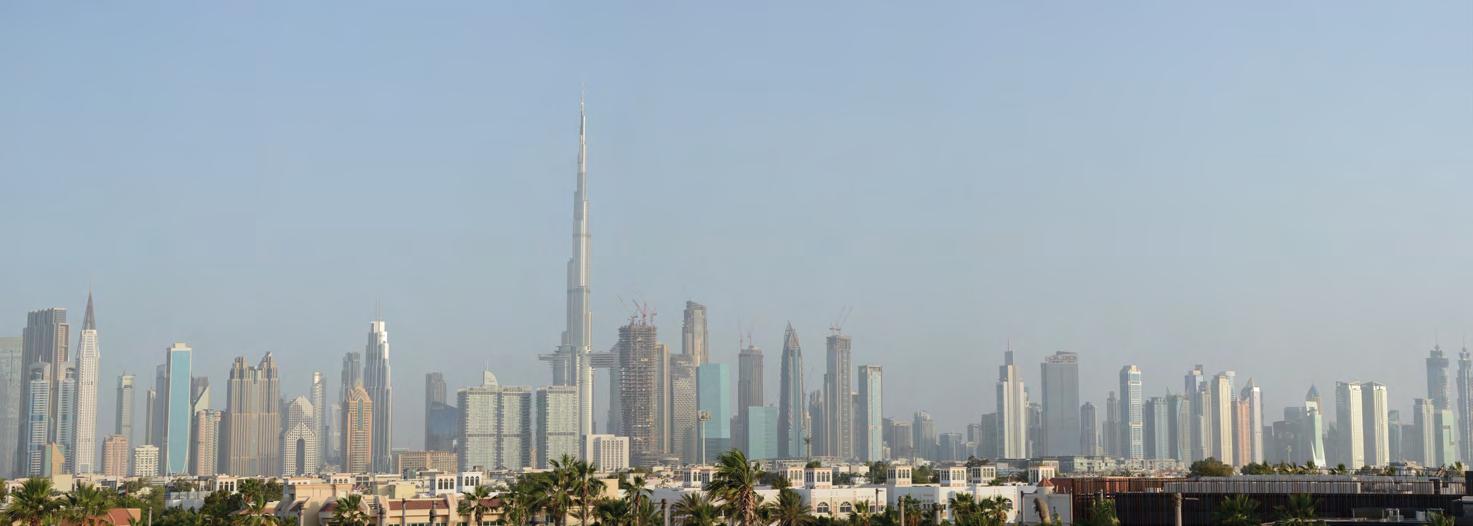
The game-changer for Dubai’s skyscraper development was the Burj Al-Arab (Figure 3) since it is notable for several complex engineering and construction features that were firstly applied at the time. The building has a V-shaped floor plan, with two façades completely glazed, and one that is covered with two layers of architectural fabric (a PTFE-coated glass fiber fabric), separated by 60 cm to filter out excessive heat and sunlight (Design Buildings, 2022).
The membranous façade covers the 18-stories hall and filters UV radiations, and it appears as opposed to the other glass façades of the building where the different glass tones are used to define the aesthetic of the building itself. The use of different glass colors – obtained with polymeric interlayer that ensures solar and heat control – contrast with the plain white of the steel structures and atrium membrane, creating a specific language that characterizes the building and that was a novelty for the skyline when it was built. Moreover, the color choice for the glasses emphasizes the height and “sailing” shape of the building itself.
As plenty of building sites begins in Dubai, it is possible to see how recent skyscrapers now are more influenced by European and North American architectures rather than Chinese and Asian ones, since Dubai has commercial exchanges shifted to the West (Figure 4). This results in a preference for curtain wall façades (e.g., Burj Khalifa) and wider neutral color windows (e.g., Etihad Museum). The extensive use of glazing then raises the abovementioned technical issues of maintenance and climate control, which can be analyzed through the example of the most “extreme” skyscraper: the Burj Khalifa.
Burj Khalifa’s curtain wall is the quintessential evolution of skyscrapers and glass façades in Dubai, and various technological gimmicks were used to allow its realization. Hereby the façade aspects are considered to explain why technological advancements in glazing were essential for its development.
The Burj Khalifa’s design was inspired by the form of the Spider Lily, a regional desert flower, that was used in the definition of the building’s outline. Due to the shape of floor plans, and the extreme wanted height, technical issues concerning winds, solar exposure, and climate control arose.
The height development of the building was therefore shaped to counteract wind thrusts, but a great deal of technical work was done on the façades as the aim was of creating a curtain wall cladding that emphasized the verticality of the building while keeping high-security standards to avoid glass panels detaching due to the extreme wind. Furthermore, architects and engineers needed to study solutions to control solar gain and the amount of heat coming from this broad glass façade surface. The solution adopted to help disperse sunlight was that of a curved curtain wall (Al-Kodmany, 2013; Fink Shapiro, 2010) but, since curved glass was cost-intensive, the rounded effect was achieved with flat panels with angled joints hidden behind the aluminum vertical fins (Figure 6). To emphasize the building’s verticality, and to reduce the possible amount of sand deposited on horizontal elements, structural silicone glazing technology was used to seal the superimposed glasses (Weismantle et al., 2007). This technique has made it possible to have a fully glassed façade, without any other framing visible from the exterior.
The used glasses are coated and have specific characteristics of high selectivity for solar protection2 and with a reflective appearance3. In addition, a neutral-looking finish was chosen to have an unfiltered view of the outdoor environment, and this colorless characteristic of the glasses from the indoor was quite a novelty at the time of building.
2 Guardian Glass, SunGuard® SuperNeutral SN 50 T. More information at: https://www.guardianglass.com/ ap/en/our-glass/sunguard-superneutral/sn-50-t (last accessed May 2022).
3 Guardian Glass, SunGuard® High Durable Silver 20. More informatio at: https://www.guardianglass.com/eu/ en/our-glass/sunguard-high-durable/silver-20 (last accessed May 2022).
Conclusions
Dubai’s example shows how technological advancements in architectural glass enhance infinite possibilities for architects, that can choose freely how to design tall buildings.
This improvement of glazing characteristics also allows to better face the requests for indoor comfort considering the restraints given by the need to reduce energy consumption. This is possible because coated glasses used for curtain walls can now contribute by reducing solar radiations while keeping a clearer view from the inside, and by having higher heat control capacities, with a consequent reduction of HVAC systems use. However, there are also some downsides. Despite having higher indoor comfort performances with less aesthetic boundaries, maintenance requests and costs raised (e.g., cleaning all Burj Khalifa’s façades requires up to 4 months of manual work), and now almost breaks even with the benefits of reduced energy demand.
Despite this, tall buildings are now considered sustainable from an energysaving point of view (this is possible if the construction phase, with its use of non-renewable materials, e.g., sand used for construction is of marine origin, it is not considered when evaluating the environmental impact of buildings).
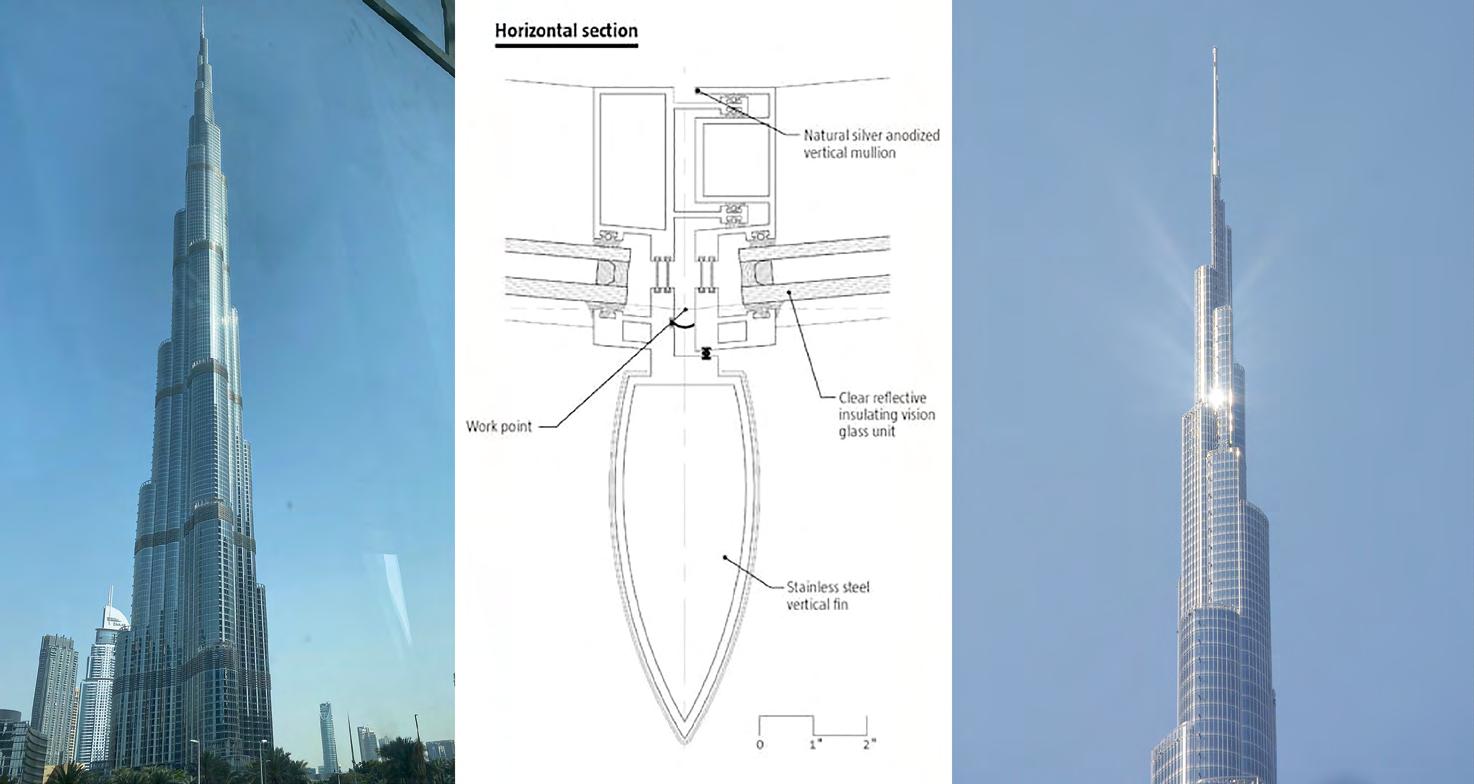
Besides, architectural glass has a higher impact on changing cities’ identity if compared with other materials. In this sense, Dubai is an example of how glass can change a city, as it changed and was defined starting from “small” glass buildings and recently it has been defined by its megastructures (Figure 5).
Cities are losing more and more of their traditional language, arriving at the extreme where some European buildings look more “Arabic” (e.g., Jean
Nouvel’s Arabic World Institute in Paris) than the ones built in Dubai. This results in an absence of a distinctive architectural language, that creates a crowded skyline where the watchword is: the bigger the better.
Glass is then just an example of how even small technological advancements can change the way buildings are designed and how the identity of cities is perceived.
References
Al-Kodmany, K. (2013). The Visual Integration of Tall Buildings: New Technologies and the City Skyline. Journal of Urban Tech nology, n. 20 (2). London: Routledge, pp. 25-44.
Design Buildings (2022). Burj al-Arab, Dubai (online). In https://www.designingbuildings.co.uk/wiki/Burj_al_Arab,_Dubai (last accessed August 2022).
Fink Shapiro, G. (2010). Detail: Burj Khalifa Curtain Wall (online). In https://www.architectmagazine.com/technology/architec tural-detail/detail-burj-khalifa-curtain-wall_o (last accessed June 2022).
Musgraves, J. D., Hu, J., Calvez, L. (2019). Springer Handbook of Glass. Cham: Springer Nature Switzerland.
Osman Bakr, A. (2019). The Aesthetics of Color in Architecture Glass Facade. Journal of Applied Art and Science. Damietta: Damietta University, pp. 1-16.
Ritchie, I. (2004). Aesthetics in Glass Structures. Structural Engineering International, n. 14 (2). London: Taylor & Francis, pp.73-75. Savić, J., Durić-Mijović, D., Bogdanović, V. (2013). Architectural Glass: Types, Performance and Legislation. Facta Universitatis –series: Architecture and Civil Engineering, n. 11 (1). Niš: University of Niš, pp. 35-45.
Weismantle, P. A., Smith, G. L., Sheriff, M. (2007). Burj Dubai: an Architectural Technical Design Case Study. The Structural De sign of Tall and Special Buildings, n. 16(4). New York City: John Wiley & Sons, Inc, pp. 335-360.
Wiederhorn, S. M., Clarke, D. R. (2022). Architectural Glass. Annual Review of Materials Research, n. 52 (1). San Mateo: Annual Reviews, pp. 561-592.
Systemic reuse models for sustainable glass packaging design and innovation
CRISTINA MARINOA, PAOLO M. TAMBORRINIA,B, LAURA MIOTTOC, GIULIA FERRONATOCThe Italian glass packaging industry is in first place in Europe with 21.3% of production value. It has 14 companies with 39 factories, 7,800 employees and a growing annual turnover of 2.4 billion euros. This trend of production preserves, on the one hand, a good synergy concerning the recycling process, but at the same time, it needs to reduce environmental impacts through reuse practices.
This research and analysis work was carried out in collaboration with a company that designs and produces glass packaging, focusing on and evaluating the current reuse and returnable-empty models, outlining the opportunities for a transition towards systemic business that stimulates innovation in new sectors. Subsequently, through a researchthrough-design approach, a second concept phase defines which guidelines to design packaging within returnable vacuum systems in new sectors and which strategies are feasible to start a transition.
A Department of Architecture and Design, Politecnico di Torino, Italy.
B Department of Engineering and Architecture, University of Parma, Italy.
C Marketing and Communication, Verallia, Italy.
KEYWORDS: PACKAGING DESIGN, SYSTEMIC APPROACH, REUSE MODEL
Introduction
The Italian glass packaging industry is today in first place in Europe with 21.3% of production value. It has 14 companies with 39 factories, 7,800 employees and an annual turnover of 2.4 billion euros. The growing trend reported by sector association studies (Feve and Weber Shandwick, 2020) predicts an increase of over 500 jobs between 2020 and 2024, with a production of 500,000 tonnes of glass packaging. This continuously increasing production as early as 2019 indicates virtuous glass-environment ‘synergies’. Indeed, data published by the Close the Glass Loop platform (Feve, 2019) confirm that glass collection and recycling increased in 2019 to an average rate of 78%, up 2% from the previous year’s results. These figures, encouraging for the multi-stakeholder platform that has set itself the goal of achieving a 90% post-consumer glass container collection target by 2030, ensure that a large proportion of packaging glass is correctly recycled in the glass production cycle.
This industry overview shows how, over the years, the environmental footprint of this material has been increasingly reduced, so much so that 85% of Italian consumers consider it the best packaging (Feve, 2019). Compared to 40 years ago, producing bottles and jars has reduced energy requirements by 50% and emissions by 70%. The recycling rate for glass reached 76.3% in 2018 (+6.6% compared to the previous year). Thanks to recycling in 2018, 3,395,000 tons of virgin raw materials, 320,000 tons of energy, and 2,082,000 tons of CO2 were saved. In 2018, 85.9% of households sorted glass (10 years earlier, it was just over 50%). Bottles and jars then underwent a drastic ‘slimming down’: a bottle of sparkling wine since the 1990s, for example, has decreased in weight by 18%, a jar of baby food by 13% and an oil bottle by 12.2%.
Glass is the only material that meets the definition of a ‘permanent’ (Larsen et al., 2009). This is because:
• it maintains its chemical and physical features unaltered over time;
• collection systems are centralized for an effective recycling, treatment and reuse strategy; and
• reuse is permitted an infinite number of times.
This virtuous process thus saves energy for production from virgin materials, reduces the impact of glass on the environment and creates new entrepreneurship (Cocking, 2003).
Nonetheless, although the glass industry, and the glass packaging industry in particular, already applies circular economy principles (e.g. with water and minor with beer packaging), not all product categories are currently in these processes, and the circular economy approach is sometimes limiting concerning the urge to close the process on itself.
In particular, the circular economy applied to glass is strictly linked to the manufacture of products and the concept of the life cycle of industrial
processes (Verallia, 2022). Instead, this research uses Systemic Design as a methodological approach (Barbero and Tamborrini, 2015). An innovative design practice developed to apply design knowledge to systemic problems with the aims of co-designing products, systems, and policies for better and sustainable services (Jones, 2014).
Systemic design methods and principles enable the human-centred design of complex, multi-system and multi-stakeholder services and programmes by connecting different cycles and creating open systems sustained by relationships and connections between local realities.
With this approach, the main aim of this research and analysis work carried out in collaboration with a company that designs and produces glass packaging is to focus on and evaluate the current reuse and returnableempty models, outlining the opportunities for a transition towards systemic business that stimulate innovation in new sectors1. Subsequently, through a research-through-design approach, a second development phase defines which guidelines to design packaging within returnable vacuum systems in new sectors and which strategies are feasible to start a transition.
Methodology
For future sustainability, it is necessary to understand the different and complex challenges surrounding glass reuse: from changing consumer behaviour to product design trends, from logistics for glass collection and cleaning to the development of new business models within the different political contexts of the target markets. This investigation, thus guided by a two-track approach, on the one hand, systematises research for means to reduce emissions through alternative business models and, on the other, identifies the most compelling features and practices to reuse glass packaging.
The broad inquiry subject, including different product categories and production formats, underwent the first skimming through selecting some product categories. The selection was made by taking into consideration both qualitative aspects for which product categories not yet involved in returnable vacuum systems were preferred, and quantitative aspects that, concerning the identified category, considered the possible collection volumes and a balance between revenues and investments about the business model, at first linear, then systemic.
The theoretical framework, considering the complexity of the topic, is based
1 This research work was conducted within the Design 1 laboratory of the Master Eco Packaging Design – Systemic Innovation Design for the packaging project of the Politecnico di Torino in collaboration with Verallia. The Master is a one-year training course that deals in an interdisciplinary way with the strategic and project aspects of design, communication and sustainability for the packaging project in collaboration with Fondazione Carta Etica. The students involved in the research were: Marta Caruso, Marika Baresi, Anna Rita Asaro, Irene Rubino, Ginevra Grisotto, Margherita Viràg Sartori, Natalia Cito, Andrea Guidi, Ruben Faraci, Elisabetta Sechi, Maria Chiara Tortia.
FERRONATOon a “mixed” approach. It proposes the use in the first instance of an analysis of current models and, in the second phase, a research-through-design approach aimed at defining design guidelines for reusing glass packaging.
In order to explore a business model for reuse, it was necessary to know in-depth the challenges and characteristics of the main stakeholders in the supply chain. Therefore, the basic research integrated concepts, experiences, and interventions not only from the glass packaging design field but also from the business sector, whose models are examined in the analysis. For this reason, we involved several brands that accompanied the research project and returned a helpful transdisciplinary approach to thinking in terms of open systems. Specifically, the stakeholders that have been involved were: an online shopping brand, a food delivery service, a mineral water brand, a producer of food packaging caps, an organic supermarket chain and a producer of food packaging labels.
This transversal involvement of several realities was fundamental to treating the individual production systems as complex ones with complementary and symbiotic activities rather than disconnected entities. In this way, the research process could benefit from sharing resources, knowhow and technological skills.
The second part, dedicated to applied research where concept
Fig. 01 Example of the linear model analysis of the wine q-commerce system. Courtesy of the authors
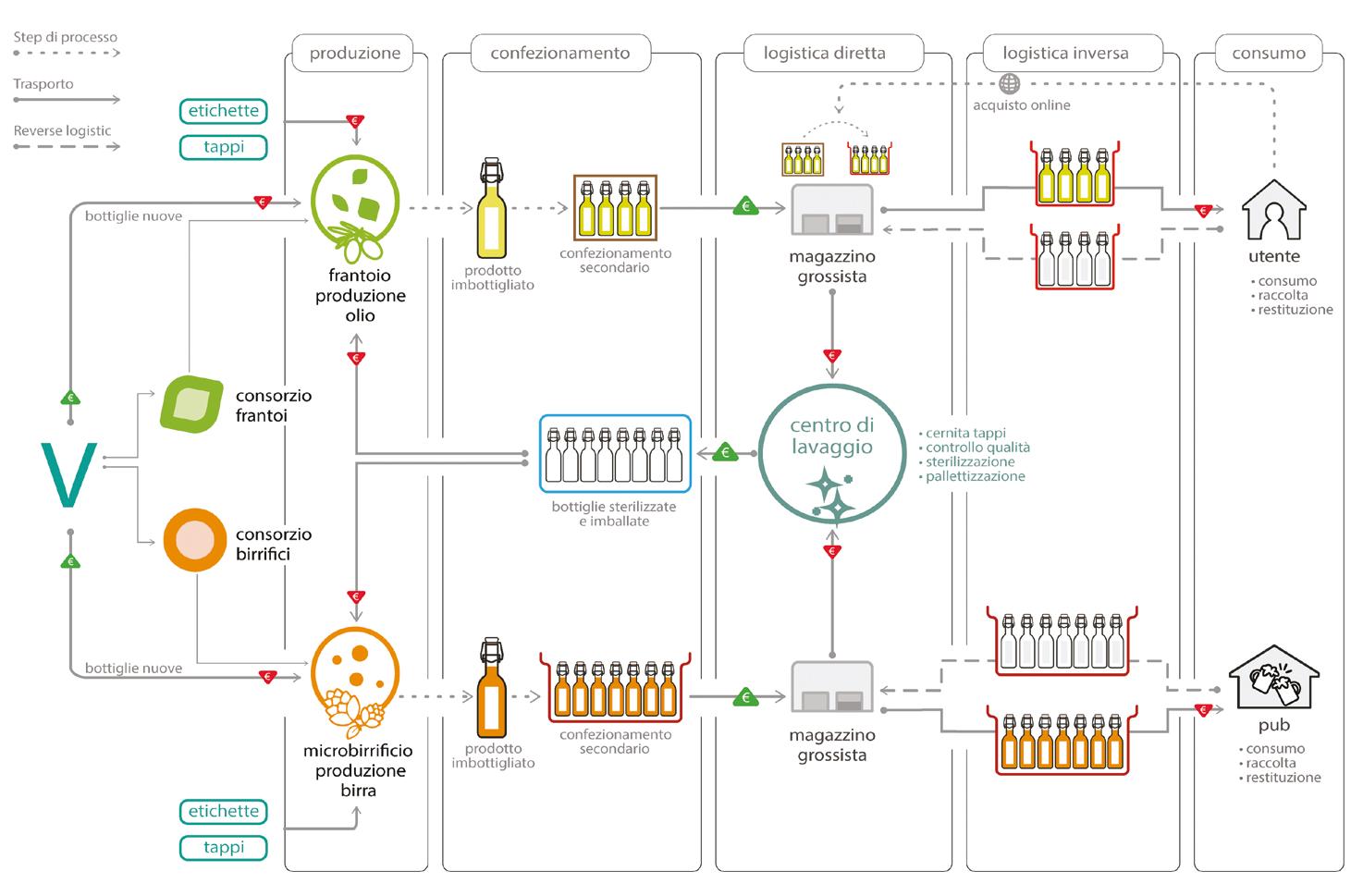
development took place, was supported, and verified by the glass packaging company, which provided feedback on the prototypes’ suitability concerning innovative business models.
Therefore, the research methods involved the analysis of several case studies divided into the following categories: large-scale retail purchasing models, large-scale retail distribution platforms, traditional e-commerce and quick commerce, and proximity commerce.
Then, four innovative business models were developed, each assuming a specific product category. Bottles of oil, beer, wine, fruit juices and jars for jam and ready-to-eat products were analyzed. A user with different needs was traced back to each product category to define better the aesthetic-functional characteristics of both the model and the product under consideration. Following the validation phases by the experts, the data collected were synthesized into some guidelines for the design of glass packaging capable of adapting to the returnable vacuum models.
Analysis of existing business models
The first part of the research provides a basic description of the functioning of the different models and distinguishing implementation issues. The models analysed fall within the following categories: retail purchasing models, retail distribution platforms, traditional e-commerce, quick commerce and proximity commerce (Barbero and Pereno, 2020).
The analysis summarised in Table 1 shows that each model has peculiarities concerning timing and supply. The transport systems and logistics platforms differ mainly in the distribution over the territory and the size of the warehouses. If storage and timing are two factors that specifically impact the user experience, transport systems, handling dynamics, and the need for large or small warehouses are critical points for the design of returnable collection systems.
Figure 1 exemplifies a scheme for analysing the linear system of a quick commerce model, highlighting critical points. All the other models were investigated using the same method; the results of the comparative analysis are summarized in Table 2.
Recurring criticalities include the premature disposal of glass packaging, often still intact, and the over-packaging of the product for further protection. On the other hand, opportunities enclose leveraging local relationships, exploiting empty trips by riders, warehouses and points of sale throughout the territory to facilitate collection operations on the one hand, and container storage on the other.
However, a gap in the analysis was found in the lack or reduced availability of external washing and sterilisation services. The latter would represent a costly investment for companies to start an internal returnable vacuum cycle but also a pivotal point to establish new entrepreneurship around reusing glass packaging.
FERRONATOTraditional Commerce E-commerce Quick commerce Proximity commerce
Time to shop Self-service 2-3 day delivery Less than 1h delivery Reservation of grocery
Offer Wide offer Limited offer Small offer Small offer
Transport Private vehicles Road transport Bike transport Private vehicles
Support platform Superstore Mega warehouses Warehouse / local stores Local stores
Tab. 01 Business Model Analysis categories.
Designing innovative business models for glass packaging reuse
The second part focuses on packaging reuse solutions in business-toconsumer (B2C) and business-to-business (B2B) applications. Both design directions have been retained because, although there are many opportunities for reuse in business-to-business (B2B) applications, the latter are generally better understood and adopted at scale. Therefore, part of the research aimed to identify sectors that do not currently adopt reuse models, which could also open up to reuse models, especially to consumers.
For this reason, before conceptualising a functional reuse model for the glass packaging industry, a case study review was interposed on currently advantageous reuse models, both environmentally and economically. Such models, classified in the Ellen MacArthur Foundation’s Reuse report (2019), can be categorised as:
• Refill at home: where users refill their reusable packaging at home;
• Refill on the go: where users refill their reusable containers away from home (e.g.at, an in-store dispensing system);
• Return from home: packaging is picked up from home by a pick-up service (e.g. by a logistics company);
• Return on the go: users return the packaging at a store or drop-off point (e.g. in a deposit return machine or mailbox).
Based on the analysis of the case studies, some of the strategies identified appear to be ill-suited to the world of glass packaging, so it was decided to opt for door-to-door and out-of-home return models. A door-to-door collection is an option that, although it can overcome certain limitations, as far as recycling is concerned, from a system perspective, is more costly due to the weight of the product itself and the emissions generated during transport. However, it becomes disadvantageous if collection volumes are not high and the consumption of specific product categories infrequent.
The analysis, therefore, led to the exclusion of product categories with sporadic consumption and instead to a preference for local productions, with low volumes but high networking potential in the local area, and categories that cannot do without glass packaging at present.
An example of a new business model which comes from the intuition to systematise similar packaging is the ‘Elis’ project, which is based precisely on the creation of added value through the collaboration of existing and geographically close players. The project proposes the development of a new range of hybrid bottles. Also, it connects oil mills and microbreweries that, despite being realities of limited size and production scale, are born with the concrete intention of being sustainable and therefore need suitable containers to communicate their mission.
The design of this model is aimed at both B2C and B2B users. This way, the system can optimise the delivery trip for vacuum collection by consumers and companies by fitting both consumption times and collection volumes.
Similar projects also targeted small local producers in the concept phase by leveraging proximity commerce as a collection point. Other projects, referring to wine or ready-to-eat products, have optimised the reduced volumes of collected packaging by redistributing it to micro and mediumsized enterprises that do not need large orders and can quickly source from third parties.
Finally, some reflections concerning the conceptualisation of new models emerge about the colouring of glass packaging produced mainly in three colours: clear, green and amber. Undoubtedly, although mixed scrap can only be used for the production of green glass, the production of clear or flint glass and, to a lesser extent, amber glass requires a scrap of the same colour. Therefore, mixed colours can lead to overcapacity for green glass furnaces (Testa et. al, 2017), and the collection of the products should take place in a differentiated manner. This point, in particular, meant that colour was a characteristic feature of packaging explicitly designed for inclusion in unique returnable vacuum models at the expense of clear glass.
Logistics Criticalities User Criticalities
Commerce Lack of door-to-door pick-up; packaging management delegated to the municipality
Autonomous time and vehicles for grocery shopping, fatigue; storage space needs
Opportunities
In-store collection possibilities, user incentives, warehouse space, suppliers network
E-commerce Excessive consumption during transport Delivery/collection booking Multiple productions/ systems connection on territory
Q-commerce Rider’s empty trips Unclear disposal process Take advantage of empty trips and warehouse points
Packaging features Premature recycling of an undamaged packaging, risk of breakage during handling
Use of bubble plastic wrap, overpackaging and frustration
Tab. 02 Criticalities and Opportunities of Linear Business Model.
MARINO, P.M. TAMBORRINI , MIOTTO, G. FERRONATOStackability, adaptability to multiple production systems, standardization
Guidelines for designing returnable glass packaging
The study outlines the following guidelines concerning the design of glass packaging for the returnable vacuum:
• Standardisation: although standardisation is often interpreted as a flattening of the creativity and uniqueness of the individual product, in the context of returnable packaging, standardising the aestheticfunctional characteristics means making the system adaptive to multiple business and production systems.
• Communication of sustainability: the transparency of glass, a characteristic that has long remained attributable solely to this material, is a fundamental value category in returnable packaging: communication of the sustainability and quality of the product contained in glass packaging is often attributed to this hygienic-functional, and aesthetic-emotional parameter. In this specific case, however, the systems designed wanted to focus on the characteristics of dark glass: more recyclable, less treated, this glass is more in keeping with the sustainability characteristics not only of the product but of the entire system. A second way to communicate the system’s sustainability is also through the label. Strategies of this type have highlighted the need for labels that are not intrusive to the packaging but can also enhance the multi-cyclic packaging system through the materials used.
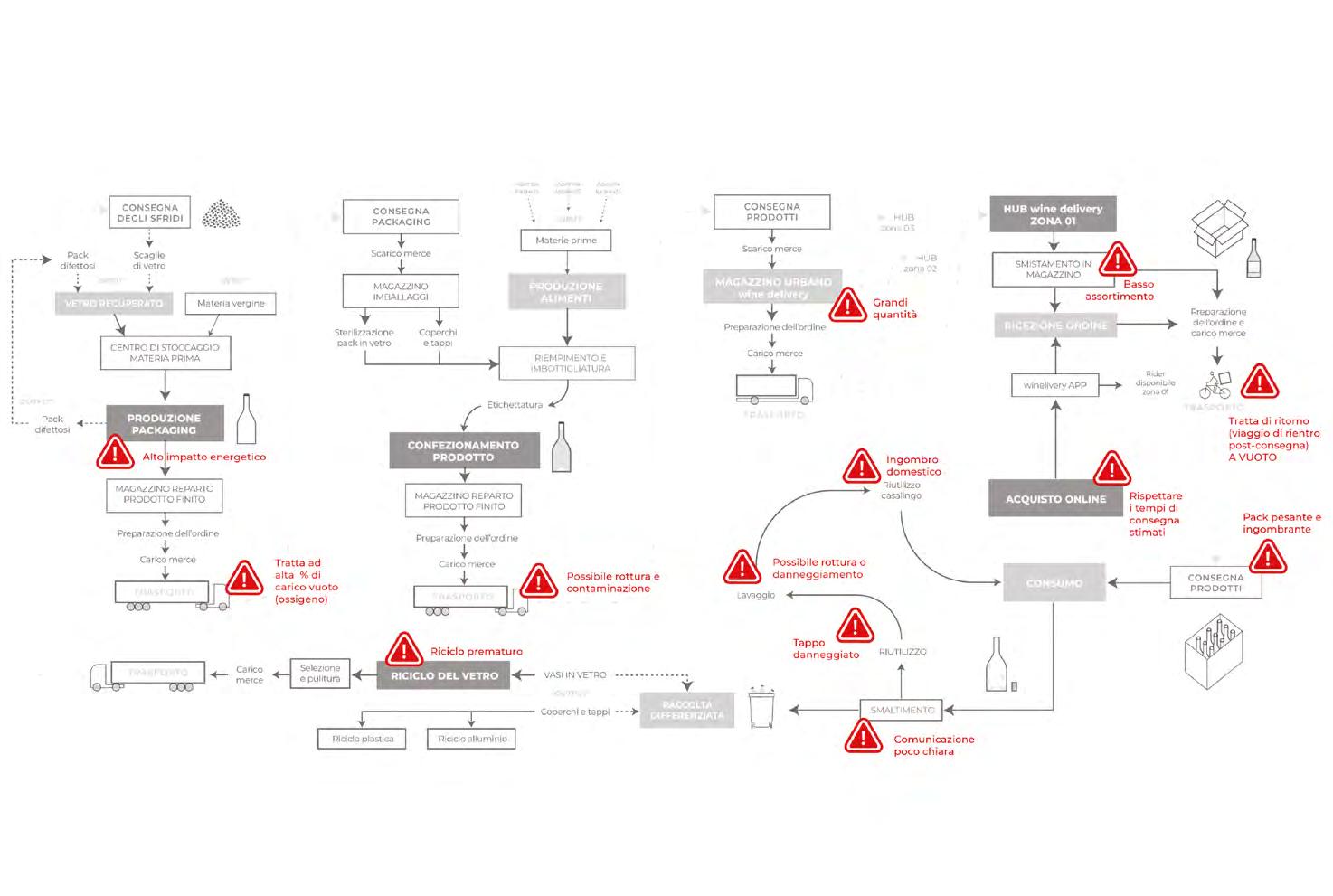
• Stackability and optimisation of transport: the concepts developed also focused on the formal characteristics of the packaging in terms of both weight and volume. In addition, jars and entire product families were designed to be stackable and facilitate transport operations in quick commerce systems and crates. The latter is suggested to be equipped with intelligent systems for monitoring returnable cycles. These guidelines, drawn up for the reuse of glass packaging, allow for specific improvements to the product as a result of a systemic analysis that addresses future needs by adopting sustainability criteria throughout a product’s life cycle, from conception through transport to final disposal; considering the needs of the product at all stages of the process and the co-responsibility of all the players involved in the system. A system that is made up and has to consider manufacturers, packaging converters, user companies, associations and consortia, etc., and who must not forget the end-users who play a decisive role in the purchasing, consumption and postconsumption phases. In this way, the packaging results from an integrated set of choices made by the plurality of actors, each of which plays a specific -direct or indirect- role in its definition.
Conclusion
To conclude, this research project, which applies the systemic approach to the glass packaging sector to study innovative business models based on reuse, has shown how tangible effects on the product exist if the entire design process is structured following a holistic approach. The range of products designed responds to specific needs that do not derive from market research or the requirements of a single sector but address the real needs that have emerged from the paradigm shift they apply in an interconnected manner. The project activates systemic value chains thanks to an in-depth multistakeholder analysis that integrates different actors and sectors, enhancing local production and connecting the actors of a territory, standardising where necessary the product but considering the reality of local needs to activate returnable vacuum strategies. In this way, the research shows that there is a space to open up different scenarios, not only at the system level but also at the product design level, which must prepare itself to respond to sustainability challenges, sometimes going beyond traditional aestheticformal characteristics. The project then highlights the scalability of the multilevel approach to the glass packaging industry. It proposes to open up to other product and production categories to implement the value chain.
FERRONATOReferences
Barbero, S., Pereno, A. (2020). Packaging Design in the Digital Age: A systemic approach to e-commerce. Milano: FrancoAngeli.
Barbero, S., Tamborrini, P. (2015). Systemic Design goes between disciplines for sustainability in food processes and cultures. In AA. VV. (ed.), Sustainable Food Planning Conference. Torino: Proceedings of the 7th International Aesop, pp. 7-9.
Cocking, R. (2003). The challenge for glass recycling. In Sustainable waste management. London: Proceedings of the interna tional symposium held at the University of Scotland Dundee, pp. 73-78.
Ellen MacArthur Foundation (2019). Reuse – rethinking packaging (online). In https://ellenmacarthurfoundation.org/reuse-re thinking-packaging (last accessed August 2022).
Feve (2019). Record collection of glass containers for recycling hits 78% in the EU (online). In https://feve.org/glass_recycling_ stats_2019/ (last accessed August 2022).
Feve and Weber Shandwick (2020). Packaging & Recycling survey (online). In: https://content.presspage.com/uploads/1081/ feve-packagingrecycling-finalreport-commsapril2020.pdf?10000 (last accessed August 2022).
Jones, P. H. (2014). Systemic design principles for complex social systems. In Metcalf, G. (ed.), Social systems and design. Trans lational Systems Sciences, vol 1. Tokyo: Springer, pp. 91-128.
Larsen, A. W., Merrild, H., Christensen, T. H. (2009). Recycling of glass: accounting of greenhouse gases and global warming contributions. Waste Management & Research, 27 (8), pp. 754-762.
Testa, M., Malandrino, O., Sessa, M. R., Supino, S., Sica, D. (2017). Long-term sustainability from the perspective of cullet recy cling in the container glass industry: Evidence from Italy. Sustainability, 9 (10), 1752.
Verallia (2022). Reimagining reuse for the circular economy of glass. Stakeholder Perspectives Series (online). In https://www. verallia.com/wp-content/uploads/2022/03/VERALLIA_WHITE-BOOK_EN_march2022.pdf (last accessed August 2022).
Fragile Business: Libbey-Owens-Ford and the impact of the 1970s energy crisis on the american glass industry
GIORGIO MARFELLAAThe energy crisis of the 1970s had devastating economic effects on the modern glass industry, yet it accelerated the development and distribution of more energyefficient architectural glass products. The case of the US manufacturing company Libbey-Owens-Ford illustrates the vital relationship of the glass industry with the global economics of energy and its business repercussions for the development of architectural products with better environmental performance.
A Faculty of Architecture, Building and Planning, University of Melbourne, Australia.
KEYWORDS: GLASS MANUFACTURING, OIL CRISIS, ARCHITECTURAL GLASS PRODUCTS
Introduction
Glass manufacturing is a technically complex and capital-intensive business. The science and know-how of glass are sophisticated and fascinating, making its history an ideal terrain for studying the interactions of architectural design with the economics of industrial production and the explanation of the processes of innovation with building materials.
Glass is also somewhat indispensable in our daily lives, and it is a very fuelintensive and energy-dependent material. Glass manufacturing has always had to rely on an extraordinary expenditure of limited resources, and glass products, especially those for architectural applications, are intimately linked to the environmental performance of human habitats.
The relationship of glass with energy has important implications for its historical development and calls in question the future of its manufacturing industry. There are pressing calls to reconsider how glass is used – and sometimes abused – in architecture and opening avenues for an academic renaissance of critical studies on glass in the built environment.
The history of glass in architecture has an authoritative scholarly precedent (McGrath and Frost, 1961), and there is a nascent interest in the historical relationship of its manufacturing developments with technological innovation and architectural design. Some recent scholarly examples have focused on the modern period, showing the socio-economic facets of new glass products and their important role in commercial and residential developments in America (Esperdy, 2008), or as an instrument of scientific experimentation in the hands of the European avant-garde (Urbano Gutierrez, 2013). These contributions offer alternative lines of thought to the more mainstream, and rather pessimistic views of architectural historiography, which tends to liquidate the critique on glass in modern architecture under pejorative assumptions or the stylistic label of the International Style.
The purpose of this paper it to emphasise the delicate nexus of the glass manufacturing industry with the economics of global energy consumption. The fragility of this nexus can be understood by studying the effects of the energy crisis of the 1970s and the ensuing inflationary economic repercussions that spread from that crisis on a global scale. The two Oil Crises of the 1970s, the first one in 1973 and the second in 1979, had major adverse effects on the global industrial economy (Yergin, 2012). For one of the biggest American industrial manufacturers of the twentieth Century in the world, glass maker Libbey-Owens-Ford (LOF), the effects were as severe as to cause rapid business decline, albeit by managing to avoid bankruptcy by being acquired by another large glass manufacturer.
Looking retrospectively at LOF’s annual reports to its shareholders from 1945 until the demise of the company in 1982, the fallacy of some US industrial corporate models that were pervasive in the second half of the
Century becomes apparent. The long-term fragility of business models that sought over-diversification at the expense of research and development is evident in the case of a glass company that was confronted by global changes sparked by an energy crisis. The case of LOF is significant for the history of modern glass manufacturing, and useful to derive insight and observations into the likely risks and challenges faced by all glass manufacturers in times of energy crisis and high inflation.
Libbey-Owens-Ford and the post WWII American glass industry
Libbey-Owens-Ford (LOF) was founded in 1930 by the merging of two major US glass companies located in Toledo, Ohio, a city with a long tradition of glass manufacturing due the local availability of sand and natural gas deposits (Floyd, 2015).
One side of the company, originated from the Libbey Glass company established in 1888 by Edward D. Libbey. Libbey subsequently incorporated the Mike Owens’ Bottle Machine, the company of the inventor of the first mechanical bottle blowing apparatus. In the 1910s, Libbey and Owens entered the flat sheet glass manufacturing business after the acquisition of the Colburn’s continuous horizontally drawn glass production method, a precursor of the modern manufacturing method that would be perfected years later by Pilkington with the float glass method.
The other side of the company is linked to the glass manufacturing tradition of Edward Ford, one of the original founders of the Pittsburgh Plate Glass Company (PPG). Ford left PPG in 1896 to setup company in Rossford, near Toledo. By the 1920s, the Edward Ford Plate Glass Company was one of the principal producers of polished plate glass in America and in 1930, in order to meet the extraordinary expenditures required for implementing polished plate glass production, the two companies of Ford and Libbey-Owens joined forces becoming the Libbey-Owens-Ford Glass Company.
LOF grew rapidly, becoming with their Pennsylvanian rival, PPG, one of the two largest producers of glass in America, and a major producer in the world. The company’s growth was aided by the sudden expansion of the American automobile industry, and the company’s ability to strike an exclusive deal of supply of automotive glass with General Motors. Equally important for LOF was an intelligent strategy of acquisition of patents and investments in research development, which put the company at the forefront of product innovations, such as Thermopane, the first commercialized insulated glass units (Leslie, 2018). LOF’s capacity to innovate with commercially viable products was strengthened by the large size of the company, and the marketing ability and pervasiveness of a nationwide network of distributors. The innovative capacity and culture of LOF became a valuable national resource of the industrial war effort during WWII, when the company converted the best part
of its operations to the production of components for military applications.
After WWII, the massive expansion of the US car industry, fueled a growing demand for car windshields of a larger size, helping glass manufacturers in the reconversion of their production lines from military to civil purpose. Larger car windshields appealed the growing market of the American 2-family car and were made technically possible by advancements with laminated glass production, which responded to higher safety standards, and skills in the making of bent glass developed at LOF during WWII for the manufacturing of military aircraft canopies (Marfella, 2019).
By the end of the 1950s, the US domestic demand of glass had created a duopoly dominated by PPG and LOF with the Toledo’s company holding a competitive advantage as the largest automotive supplier of the country.

LOF’s economic prosperity of the post-WWII period began to wither in the early 1960s, when the long-term contract for the exclusive supply to General Motors expired. While the company continued to be profitable, earnings alternated between negative and positive results. Moreover, LOF began facing increasing competition from foreign imports from Europe and Japan. Pressure from foreign supplies was in part due to ‘dumping’ of lower quality glass products in the US domestic market, but ultimately LOF began losing competitive advantage due to the international liberalization of US markets, against which the company had lobbied strongly against tariff elimination
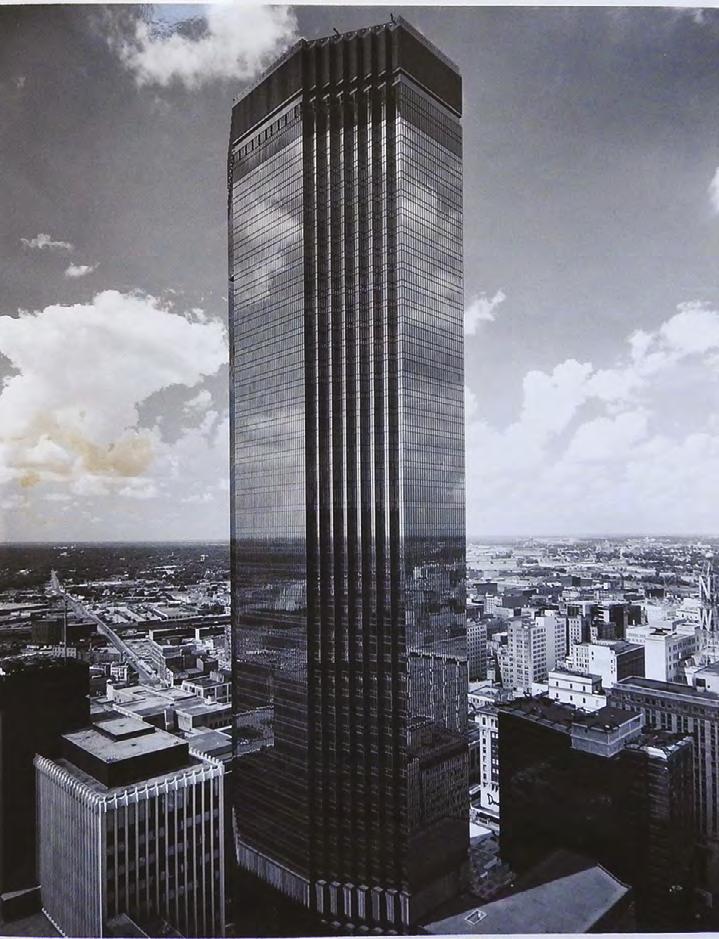
policies implemented by the Kennedy’s administration (LOF, 1961; LOF, 1962).
Making matters worse, American glass manufacturers were handicapped by the strategic advantage gained by British manufacturer Pilkington with the successful implementation of the float glass method of production. Float glass manufacturing, by eliminating the costly and laborious process of mechanical polishing needed to obtain flat glass surfaces, caused the large-scale massproducing manufacturing plants of the American glass makers to become superseded. To avert the risk of being priced out by the more efficient float method, both PPG and LOF took immediate steps to become licensee of the Pilkington’s patent, investing extraordinarily in the conversion or expansion of their plants to adopt the new technology.
To counteract these foreign competitive pressures, LOF began a strategy of foreign investments. The most ambitious of these was in 1962 when LOF acquired one third ownership with two Italian companies in the establishment of Societá Italiana Vetro (SIV). Defying LOF’s hopes of breaking through the European market by feeding the Italian industrial miracle, SIV entered the full production stage in 1966, but struggled to become profitable. On 12 December 1967, an unprecedentedly heavy storm hit the Adriatic Coast in Italy, causing severe damage to SIV facilities. The event forced LOF to ship substantial quantities of plate glass to Italy to meet automotive order commitments of their co-owned subsidiary. In 1970 despite registering signs of growth with rising volumes of sales in the European car market, SIV was still an investment at loss for the American partner, and a year later LOF sold its share of the Italian company, abandoning thereon plans to disrupt the European market.
Despite recording substantial increases in sales, by the end of the 1960s, LOF’s glass share in the domestic market had reached the plateau of a ‘stabletech’ company (Chandler, 1994). The company was a reputable, successful, and profitable enterprise of the American manufacturing industry. Yet, in the eyes of a new generation of executives that took hold of the company in 1967, LOF did not provide the return on investment that they thought it should.
At the root of the relatively sluggish financial performance of the company, there was the capital-intensive nature of the glass industry. In the 1960s, US glass industry wages were estimated at 26.5% of the total value of gross sales, as opposed to the 15% share estimated for manufacturing workers as a whole. In 1968, glass operations at LOF required $27,000 of investment per employee, compared to the average $14,000 per employee of the 500 US largest industrial companies of the time (LOF, 1968). The capital-intensive crunch imposed by high labour costs, could be alleviated by the introduction of float lines, but these required the significant one-off costs imposed by the conversion of manufacturing processes from the obsolete sheet plate production.
In the effort to seek higher returns for their shareholders, LOF committed to a major program of acquisitions with the scope of diversifying from the
glass business. In the process, the new leadership revamped substantially the organisation setting new corporate objectives. LOF abandoned the productbased development and distribution model of their sales team and set to adopt a so-called ‘market-oriented’ structure. This meant an overhaul of the existing sales force with the objective of specializing distributions by markets, and not by product followed, with success, by the company in the past. The marketing approach put at the forefront strategies to achieve market penetration and better price points, creating sales specialists and managers who were asked to focus and report ‘exclusively’ on their markets.
Significantly, in 1968, the company decided to remove the word ‘Glass’ from the LOF shield and logo. From therein LOF embarked in an aggressive strategy of corporate diversification, starting with the acquisition of Aeroquip, a rapidly growing supplier of fluid power components for the automotive and aeronautical industry.
The effects of the 1970s energy crisis on LOF Glass
In spite of the corporate remodeling and changes of strategies of the late 1960s, the following decade did not open in an auspicial way for LOF’s shareholders. In 1970, a nationwide recession and long periods of industrial unrest led to poor sales and earnings. LOF’s executives had to cut personnel and dividends and recur to a significant increase in bank borrowings (LOF, 1970). After a short-lived rebound, the destabilizing consequences caused by the First Oil Crisis began to unfold in 1973. As inflation began to rise due to higher petrol prices, LOF felt the brunt of depreciation on major investments in manufacturing equipment that were necessary for the implementation of the float process. The financial impact was registered above all in 1974, when LOF recorded lower sales in all its sectors and profits slumped by 50% from the previous year.
In the mid-1970s, the economic situation of LOF improved, but only temporarily. Sales passed the 1-billion-dollar threshold in 1978, but alternating profit results, and a declining, or at best fluctuating performance of the glass division lingered on. From time to time, the scarce profitability of glass making depended on external occasional factors, such as losses of productivity due to cold-weather or industrial unrest. Other factors were an inevitable part of the business of large-scale glass manufacturing. Such was the case of heavy start-up costs required for setting up construction to satisfy new automotive models and decreasing levels of demand due to 1970s car design trends that preferred smaller car sizes and windshield areas.
However, LOF’s economies of scale, and the benefits of advanced research and development efforts undertaken in the early 1960s, allowed the company to mitigate the adverse effects of the crisis. The successful release of a new suite of glass products able to provide higher environmental performance, namely reflective glass, became critical to allow economic survival.
Since the end of WWII, LOF had started research and development with vacuum-applied metallic coating on glass, converting ideas developed for hightech military products for optical and electronic applications into experiments for commercial products. In 1964, LOF’s product engineering team announced the reaching of a ‘breakthrough’ in the glass filming field, which consisted of the development of a system of reflective coating utilizing vapor deposition, pyrolithic decomposition and evaporation of metal deposits (LOF, 1964).
Construction of a pilot plant to perfect the technology commenced soon after, with work and investments flowing into the technology, and preparing for the establishment of a continuous production line for reflective glass. The technology was bound to render obsolete the time-consuming and less energy-efficient processes of tinted heat-absorbing glass. These advances led to the release of the first reflective product line, Vari-Tran coated glass in 1967, which LOF made available also for use in conjunction with their insulated glass product line, Thermopane.
In 1971, Vari-Tran was the leading and most innovative glass product produced by LOF. The reflective coating could be applied to sheets of glass as large as 10x12 feet, using a semi-continuous deposition of metallic coatings. Glass was fed through a series of vacuum chambers used to lower the boiling point of the metals applied to the surface of glass. The resulting film was extremely thin, allowing visible light transmittance while reflecting a considerable amount of solar energy. LOF’s reflective glass product lines quickly expanded with more than fifty versions of the product available, combining reflective coatings with clear glass or heat-absorbing tinted glass in grey, blue, bronze, silver, or gold colors (LOF, 1971).
The mirror-like product soon began to attract interest among American architects. The Adoption of reflective glass was encouraged also by legislative changes, like the Model Code 90-75 prepared by American Society of Heating, Refrigeration and Air Conditioning Engineers (ASHRAE). The first building typology to exploit the benefits of reflective glass were especially office buildings, where the economics of building operations married conveniently with the mirror-like appeal of rising post-modern aesthetics. Among the earliest examples of the new architectural genre, LOS supplied glass to small office towers, like the Detroit Northern Savings Banks in Hancock, Michigan, and notorious city landmarks alike, like the Investors Diversified Services (IDS) Tower in Minneapolis and the Pennzoil Center in Houston.
LOF had managed to weather the storm of the First Oil Crisis in virtue of the successful marketing of a product innovation, reflective glass, that responded timely to the energy conservation needs of the times. But the company could not survive the pressures induced by the sudden oncoming of a second crisis. In 1979, a Second Oil Crisis created further adverse market conditions, turning LOF’s glass operations, for the first time in its history, into an unprofitable business. In 1980, the glass division incurred a $6.2 million
loss due to the simultaneous fall of demand in the automotive and residential markets. In the following year, the US automotive and housing construction markets hit their 20-year and 35-year lows, respectively, defying LOF’s hopes of recovery in the glass market (LOF, 1980).
LOF Glass, as a result, continued to decline sharply, losing $14 million in one year. The performance of the glass division of the business was in stark contrast with the profitable subsidiary divisions of fluid power equipment and plastics that LOF incorporated following financial diversification strategies (LOF, 1981).
In 1983 LOF issued the last annual report to its shareholders. The report described the previous year as one of change, announcing the group intent to become a ‘stronger marketing company’ (LOF, 1982). In December 1982, Pilkington had purchased a third of LOF’s equity in Wall Street. The company announced a ‘technical assistance program’ with Pilkington, accepting de facto to turn its Glass Division into a subsidiary of the British glass manufacturer. Cuts to the glass department, and the profitable earnings of LOF’s subsidiaries active in other sectors, had minimized the damage for shareholders, attracting a most reputable rescuing partner. Financial bankruptcy was averted by corporate diversification, but the American industry had lost one of its most important and globally influential glass companies.
Discussion
The case of Libbey-Owens-Ford illustrates the far-reaching effects on the business of glass making that can be triggered by inflation and global disruptions to the markets of energy supply. The dynamics that led to LOF’s demise are significantly instructive because they show the vulnerability to energy-related fluctuations of one of the largest glass producers of the twentieth Century. The vicissitudes of a single glass manufacturer should not induce to apply a general parallel with the history of the modern glass industry as a whole. Nevertheless, LOF’s scale and global interconnectedness allow some provisional observations subject to further scrutiny and broadening of the investigation.
The commercial success of glass products depends on the vital imperative to embark on continuous research and development projects with a long-term horizon. Continuous investments in innovation are considerable undertakings for companies engaged in a high-risk industry with capital-intensive operations. But for leading glass manufacturers, the commitment to innovation is an imperative, not optional. The fruits of research and development can be critical to offset periods of crisis, like reflective glass did for LOF, whilst detracting resources and efforts from research and development can quickly lead to economic decline and extinction.
Continuous product development is critical for gaining or keeping a competitive advantage in the two most important markets of glass,
the automotive and construction industries. Glass is indispensable for manufacturing vehicles and constructing buildings. Nevertheless, ongoing glass product developments and innovations maintain a fundamental role in these two industries. The absence of alternative materials available to substitute glass does not override the need for constant technological advancements. The performance of glass products informs critical design decisions related to human safety and energy consumption. When economic and social demands on buildings’ operation and life cycle become more pressing, as they were in the 1970s and are in the present, the commercial success, or survival, of glass products is strongly correlated to the innovative imperative of demonstrating growing performance outcomes.
Finally, corporate diversification strategies, like those implemented by US industrial manufacturers in the second half of the twentieth Century, can be a double-edged sword. On the one hand, when strategies succeed, diversification can offset potential losses arising from risks inherent to the complex nature
Fig. 02 LOF profits, 1945-1982 ($US million adjusted for inflation, 1982 = 100).

Fig. 03 LOF net sales, 1945-1982 ($US million adjusted for inflation, 1982 = 100).
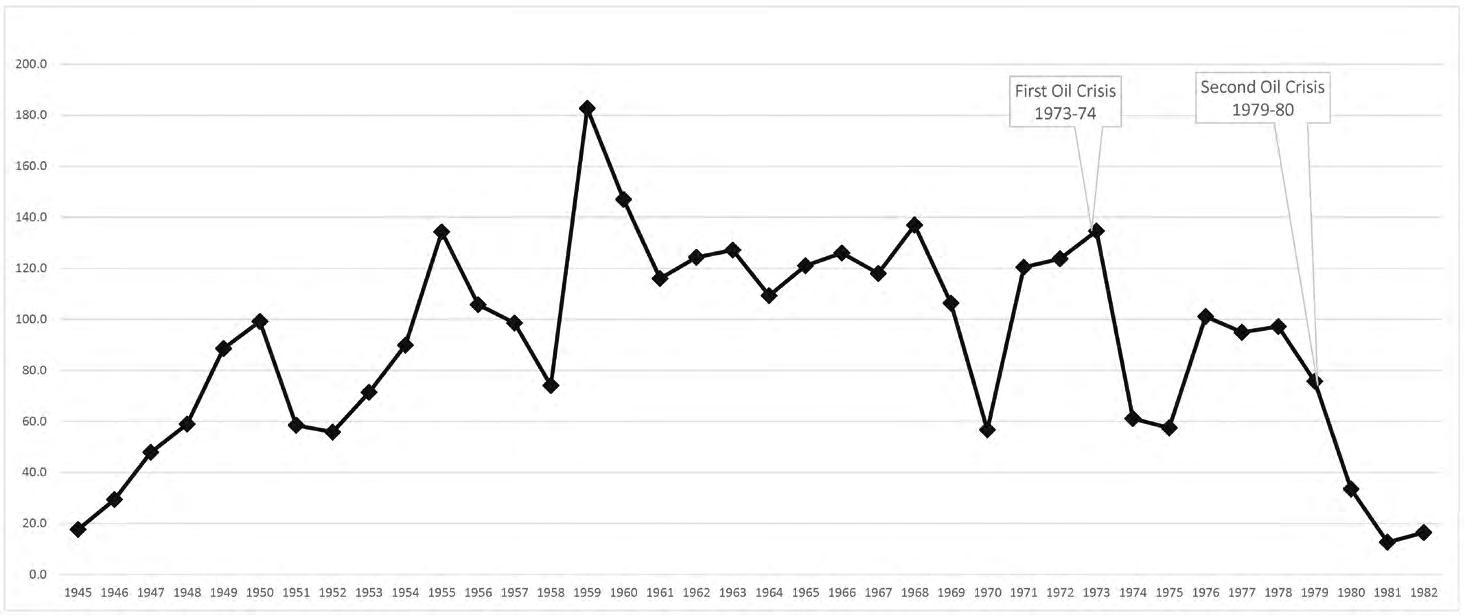
of glassmaking. On the other hand, when diversification is too widespread in a horizontal sense, reaching out to sectors unrelated to glass, and, even worse, when diversification is achieved per se as a mere financial strategy for corporate survival, then diversification can bring the adverse effects of waning know-how and diverting resources from the strategic imperative to innovate.
Conclusion
The energy crisis, as a paradox, gave LOF market growth opportunities with ‘high performance’ glass products. The company had already invested significant efforts prior to the Oil crisis to promote economic benefits for operating costs of air conditioning. The reflective skyscraper was the most notable building type with glass supplied by LOF in the 1970s, as the energy crisis created higher demand for high performance glass, which the reflective coatings applied on float glass products could provide outperforming by far glass products of the previous generation.
Glassmaking is a capital and energy-intensive endeavor, ergo, a potentially fragile business. Like the fragility of the material can be overcome by knowhow with tempering or chemical strengthening, so its industry can acquire strength and resilience through innovation. Economic resilience depends however on the capacity of producers of glass to never lose sight of the specific know-how of their industry and to invest with a long-term horizon by continuously striving to improve the efficiency of its manufacturing methods and the environmental performance of products.
References
Chandler, A.D. (1994). The competitive performance of U.S. industrial enterprises since the Second World War. The Business History Review, n. 68 (1). The President and Fellows of Harvard College, pp. 1-72.
Esperdy, G. (2008). Modernizing Main Street: Architecture and Consumer Culture in the New Deal. Chicago: University of Chicago. Floyd, B. (2015). The Glass City: Toledo and the Industry that Built It. Ann Arbor: University of Michigan Press. Leslie, T. (2018). “Insulation with Vision”: the development of insulated glazing, 1930-1980. APT Bulletin: the Journal of Preser vation Technology, n. 49 (5). Association for Preservation Technology International (APT), pp. 23-32.
LOF (Libbey-Owens-Ford). Libbey-Owens-Ford Annual Reports (1916-1982). Libbey-Owens-Ford Glass Company Archives. Ward M. Canaday Center for Special Collections. University of Toledo, Ohio.
Marfella, G. (2019). Behind the shield: glass as vehicle of technology transfer from the automotive industry to the International Style. In Edquist, H., Stitt, H. (ed.), Autopia: the Car and the Modern City. Proceedings of the 3rd Annual Conference of Automotive Historians Australia, pp. 1-18.
McGrath, R., Frost, A. C. (1961). Glass in Architecture and Decoration. London: The architectural Press.
Urbano Gutiérrez, R. (2013). Le pan de verre scientifique: Le Corbusier and the Saint-Gobain Glass Laboratory experiments (1931-32). Arq-architectural Research Quarterly, n. 17 (1). Cambridge University Press, pp. 63-72.
Yergin, D. (2012). The Prize: the Epic Quest for Oil, Money and Power. New York-London-Toronto-Sydney: Free Press.
Use of waste glass as aggregate for cementitious mortars
JACOPO DONNINIA, ANGELO MONTENEROB, L. DAVID PYEC, VALERIA CORINALDESIAThe possibility of incorporating recycled glass into cementitious inorganic matrices is certainly of great interest. Nowadays, this kind of reuse is still not common due to the risk of alkali–silica reaction (ASR) between alkalis of cement and silica of the waste glass. This expansive reaction can cause great problems of cracking and, consequently, it can be extremely deleterious for the mortar durability.
This work aims at evaluating the influence of both size and color of recycled glass coming from post-consumer domestic containers on the mechanical properties and durability of recycled glass mortars. The attention is focused on both the mechanical behavior, studied by means of bending and compression tests, as well as durability, investigated by means of accelerated aging tests for evaluating the tendency to expand under alkaline environment due to alkali-silica reactions.
Results of this research showed that the use of clear glass cullet in substitution of sand was detrimental due to the very high ASR expansion, and consequent mortar cracking. On the contrary, no evidence of ASR expansion was detected when either amber or green colored glass were used. The use of glass powder in substitution of sand proved to be very interesting and allowed to reach almost the same mechanical performances of those of the reference mortar, with a considerable saving on raw materials. This is due to the fineness of glass powder and its strong pozzolanic effect, which can improve the mechanical properties of cementitious mortars, especially at long ages.
A Department of Materials, Environmental Sciences and Urban Planning (SIMAU), Polytechnic University of Marche, Ancona, Italy.
B Department of Chemistry, Università di Parma, Parma, Italy.
C Alfred University, SUNY College of Ceramics, Alfred, NY, USA.
KEYWORDS: WASTE GLASS, RECYCLING, CEMENT
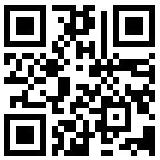
Fig. 01 Expansions vs. time of exposure to 1 N solution of NaOH at 80°C.

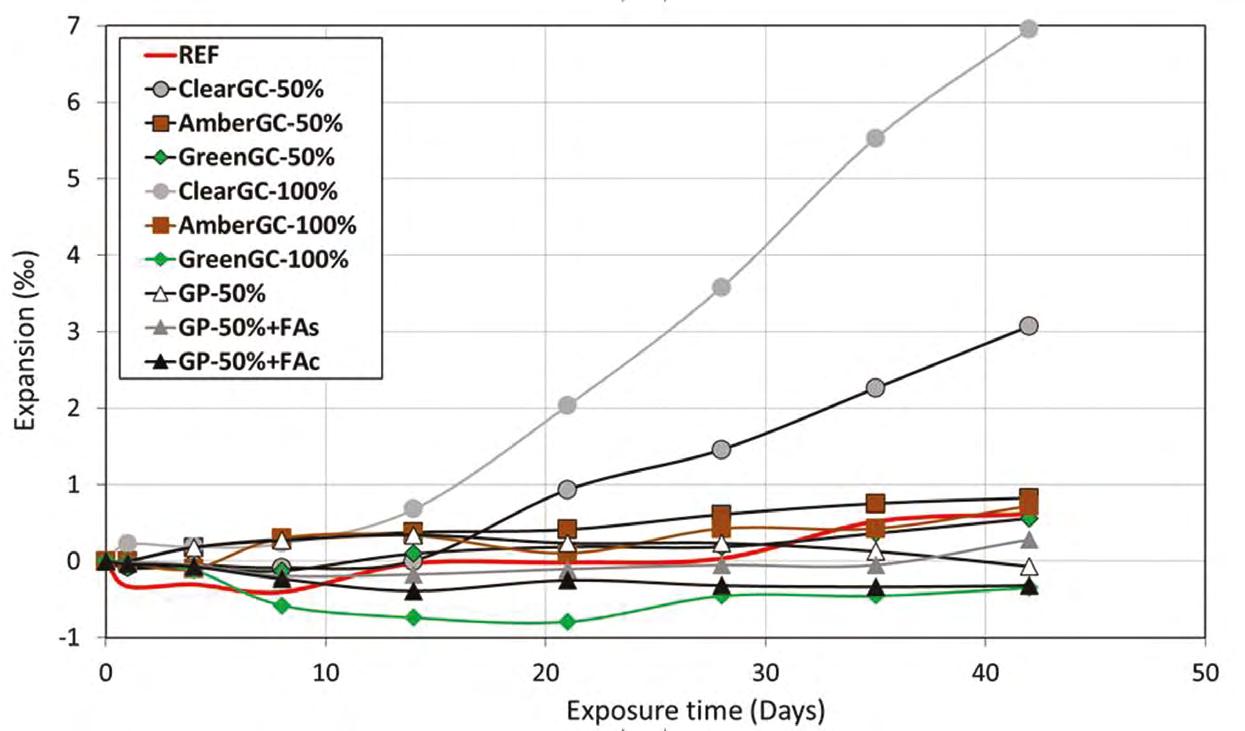
Glass on stage. The woman of fire Marietta Barovier
MASSIMILIANO CIAMMAICHELLAA
Starting from an attentive historical recognition of glass manufacture, the paper traces the salient stages of female entrepreneurship in fifteenth Century Murano, focusing on the pioneering figure of Marietta Barovier.
The theatrical production, dedicated to her, updates her cultural fundament, knowledges, actions, and life, through a performance in constant dialogue between past and present, in which the stage setting is made up of morphing videos that continuously shape the glass matter.
This experience is part of candidacy dossier for the venetian pearls as UNESCO intangible heritage, to help raise awareness and spread the transmission of know-how, the dissemination of which here is confronted with the theatre democratic space.
A Department of Architecture and Arts, Università Iuav di Venezia, Venice.
KEYWORDS: DIGITAL SET DESIGN, THEATER, ROSETTA BEAD
Introduction
In the Serenissima history, the fifteenth Century was undoubtedly a Century of fundamental cultural and productive changes that relaunching Murano as undisputed innovation capital in the glassmaking art that began to be such in its transition from mass production, for purely utilitarian purposes, to elite production, aimed at a public that appreciates the aesthetic value and the workmanship finesse. Proof of this is the confirmation decreed in 1441 of the Fiolèr1 professional figure substitution – documented in the thirteenth Century Capitolare – with that of the glass worker, described in the statute of “Mariegola dell’Arte dei Verierieri da Muran” (Gasparetto, 1988).
In this period, the intervention areas ranged from the construction of large architectural stained-glass windows, as for example happen in the SS. Giovanni e Paolo church in Venice, to the crystal mirrors experimentation, to the empirical and alchemic reworking of tricks, searching for alternative formulas in the coloring of increasingly transparent and homogeneous surfaces, on which further decorations made of enamel paint could be applied.
The raw materials were silica sand, obtained from the hot grinding of quartzrich pebbles, the most valuable of which came from the Ticino River; then coloring pigments or decoloring agents were added, and finally, melting agent, commonly known as Allume catino2: an ash with a high sodium content derivatives from the combustion of littoral plants. The most popular was Syriac (Zecchin, 1997).
Glassworks were generally equipped with three furnaces. The first, also known as the Calchera3, had only one chamber and was assigned to melting the above-described components, to produce the Fritta4, a raw and dense glass with impurities, which was undergo cooling and shattering processes in order to be recast in the second furnace, inside crucibles; it was then poured into the water several times to free it of residual impurities.
Subsequently, blocks for working were produced whose malleable plasticity allowed the extraction of portions to be shaped with blow pipes, tools for cutting and bending. Once the final shape was achieved, it was placed back in the third furnace for work completion (Marascutto and Steiner, 1991).
In this complex sequential procedure, played out on the limits of a challenge between rule and its refinement, alchemical practices were perpetuated to generate artifacts influenced by the tinkling aesthetics, traceable to the durability logics of a fragile and light malleable material.
1 Fiolèr or Fiolaro: Dialect term derived by “fiola”, a narrow-necked liquid vessel.
2 Allume catino: commercial potash or potash sub-carbonate, in Murano furnaces its processing involved alchemical purification of soda ashes.
3 Calchera: oven with two overlapping chambers. In the lower one, named Castra, firewood was placed, and in the upper one, Fritta was prepared.
4 Fritta: silica and melting agent are mixed at the bottom of the Calchera, forming a kind of crumbly, shapeless mound. It constitutes the first phase of the actual fusion.
Glass Innovation and Renaissance
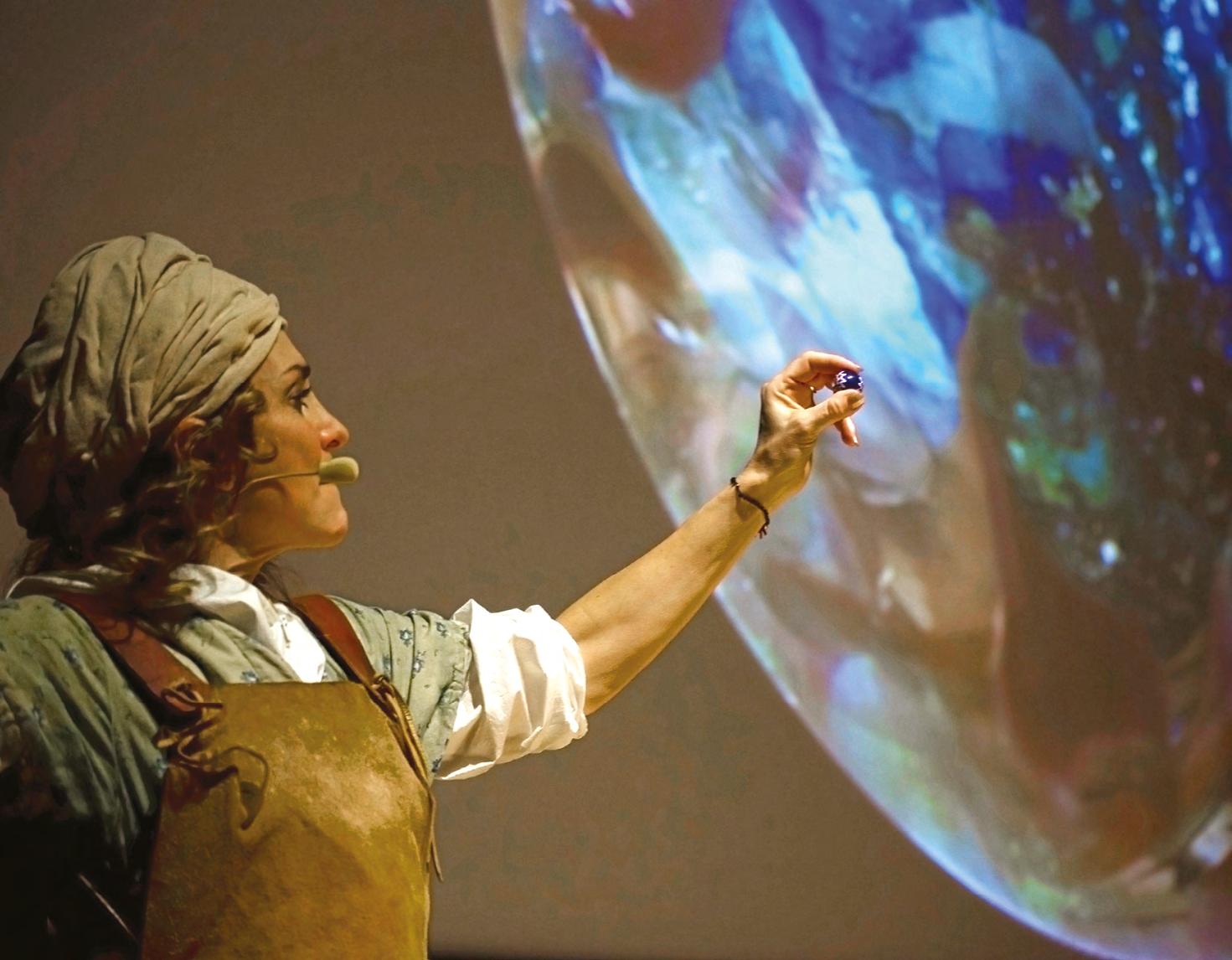
Among the most important protagonists of the fifteenth Century scene, Angelo Barovier is the one who certainly made significant innovations in the field of glassmaking.
As member of one of the historic families of glassmakers, active in Murano since the thirteenth Century, he was trained in the school of San Giovanni Elemosinaro in Rialto, with the mentor, philosopher, and mathematician Paolo dalla Pergola. We learn this from a manuscript document, collected and published by Emmanuele Antonio Cicogna, in which it is stated that the master gave lessons to an “egregium ex primariis Muriani Angelum nominee” (Cicogna, 1853, p. 467), especially regarding the compositions and secrets of glass coloring.
Other statements see him as a protagonist in the ideal city of Sforzinda design, described by Antonio di Pietro Averlino, the Filarete – in his Trattato di architettura composed between 1451 and 1458 – as a sculptor and goldsmith in the service of Milan duke, whose palace and throne were to be decorated by Barovier with inlays of finest glass.
This shows how this ability to experiment with new compositions, aimed at the invention of crystalline glass, owes it precisely to Angelo Barovier to have exported outside the island first, and later to the world, prestigious products that kicked off the Renaissance of the art of glassmaking, thanks to the success of Lattimo and Calcedonio (Zecchin, 1987, II).
The first was milky white, imitating Chinese porcelain, and was obtained by opacifying crystal with lime of lead and tin. Calcedonio glass, on the other hand, recalled the veining of agate, onyx, and other gemstones by adding a combination of metallic compounds, such as silver salts, to the mixture. In fact, the term Lattimo already appeared in some Murano papers from 1420, but in 1452 Barovier in his furnace had succeeded in producing a transparent glass, immediately named Crystal, earning from the Signoria the concession to work it even during the period of the year when inactivity was imposed on the island’s furnaces, from mid-August to the end of October (Zecchin, 1976).
The success of crystal, however, was surely the result of empirical research whose purpose was not so much related to a nostalgic return to the fashion of colorless transparency, already produced since the Middle Ages, but rather to the nullification of impurities and imperfections, mainly due to the melting agent and soda ash that compromised the homogeneity effects of glass (Barovier Mentasti, 1982). In general, all these inventions were protected by short-lived patents and at the special request of the glass makers, to secure their economic interests, and then disseminated to other Murano furnaces after an appropriate period of time.
Actualization of Glass Beads
The protagonist of these events died at the age of 55 in 1460, leaving tangible evidence of his work that receives his surname: the Barovier Cup made of blown glass, painted with polychrome fused enamels, and dated c. 1460, now housed at the Murano Glass Museum.
The inheritance of the family business then passed to the six sons, among whom Marino stands out for his positions as Gastaldo of the glassmakers’ art in 1468 and 1482; then there is Giovanni, who manages the furnaces together with Maria, known as Marietta, who guards the secrets of her father’s craft in a special notebook he gave her and from which she draws ideas for glass compositions and colorations (Cicogna, 1853).
Not much is known about her, but she probably was born in 1431 because her mother Apollonia, in a notarial deed perhaps signed before childbirth, leaves her an inheritance of 70 ducats as a dowry for her future marriage. However, she will never marry, this seems to suggest a definite choice in devoting herself to her passion for her work and claiming a form of social redemption that sees, at last, a woman at the direction of enterprises made up exclusively of men.
Moreover, her active role as an entrepreneur is also documented by the deeds of Murano’s Podestà Francesco Dolfin, dated July 26, 1487, which declare her directing the production of enamel-painted glass, because Doge Agostino Barbarigo granted her the opening of a Muffola, a small furnace used for annealing enamels (Levi, 1895).
Other traces of her existence are dated to May 4, 1496, the day on which the inventory of unsold products from the Barovier brothers’ furnaces was drawn up, among which appear artifacts in non-blown glass and the famous Rosetta bead, of his own invention (Zecchin, 1987, II).
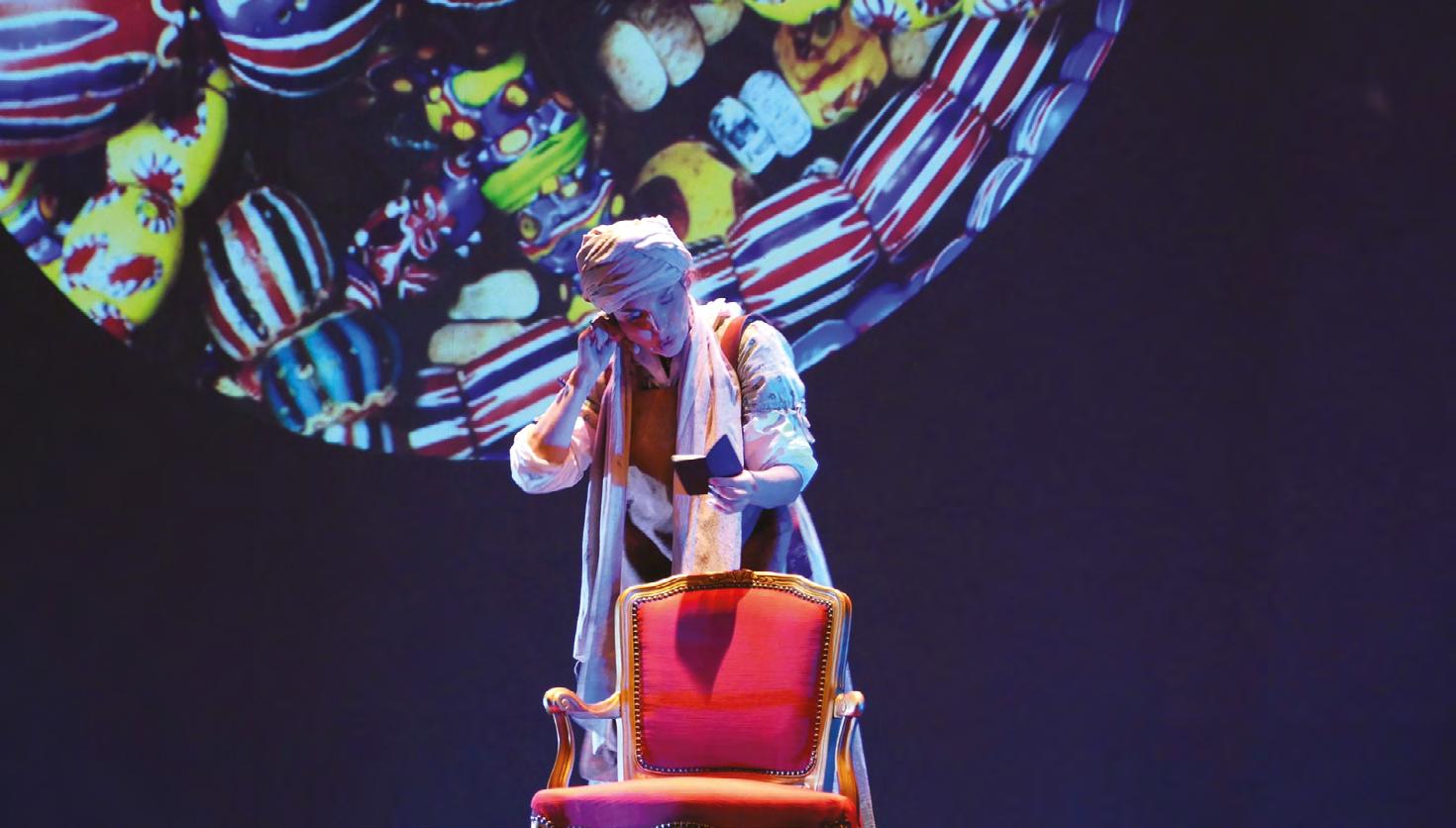
According to the dates given in the documents that have come down to us, at least for the Century in which she lived, the long-lived and eclectic Marietta would have worked on the Rosetta beads production in the small furnace she opened in 1487, although the term already appears in some documents dating back to 1480; in any case the 1496’s inventory refers to the Oldani, which are
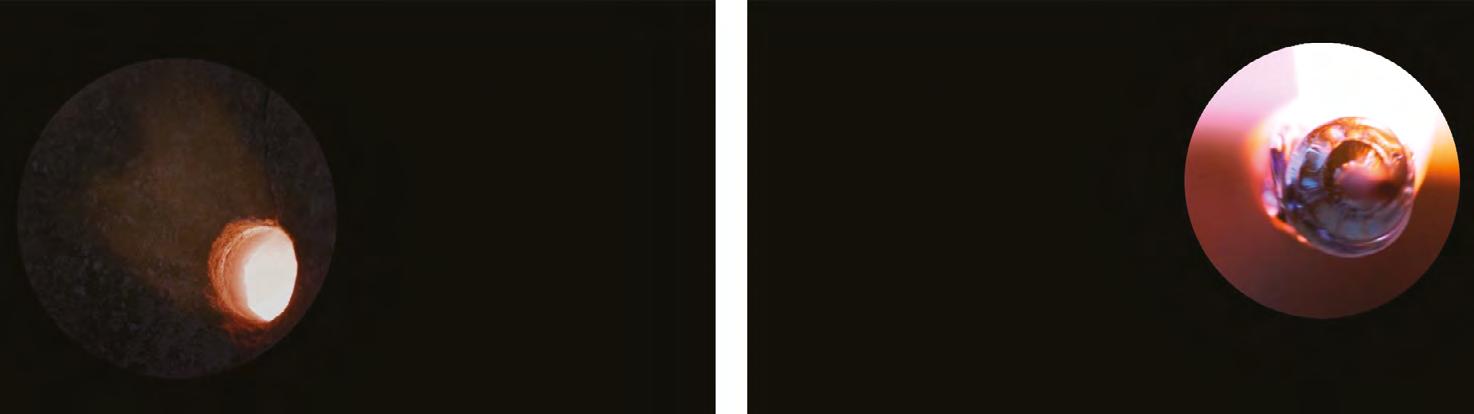
ellipsoidal beads very similar to those still in production today. To make them, a pierced rod contains six layers of colored glass alternating on blue, white, and red in forming five concentric starry, twelve-pointed prisms (Sarpellon, 2003).
The process requires the labor of four or five people and begins with a metal rod being heated by a Servente inside a furnace with three crucibles, containing the colors described above.
First, the white dough is taken to be rolled around the rod on an iron plate until the cylindrical shape is obtained, then the Scagnèr intervenes by holding a pair of pliers in making a hole along the cylinder axis, which is immediately plunged into the crucible where the blue glass is, so as to form a light layer around the white. The dough retains a workable consistency as it is placed in a mold whose section has the characteristic star profile, and this procedure is repeated three more times, alternating the same number of colors, until the last cobalt blue glass covering is rolled, returning to the primary cylindrical shape. At this point the Scagnèr grabs a second iron rod and applies it to the opposite end of the first, delivering them both on the hands of two Tiradori who walk in opposite directions in extending the cylinder until the wanted diameter is reached, and then let the glass rods, cut about a meter long, cool on wooden boards (Moretti, 2005).
Among the most complex steps, grinding, which in Marietta’s time was done by hand, is a long process of abrasion and polishing designed to give the bead its characteristic ellipsoid shape, making it world-famous in becoming exchange currency. Between truth and legend, in fact, Christopher Columbus is believed to have given Rosetta beads to the American Indians, but it is certain that these were found in India by Vasco de Gama in 1497, in Peru and especially in Africa (Bertagnolli et al., 1991).
The Woman of Fire Marietta Barovier
The outcomes of the research, summarized so far, have flowed into the dramaturgical writing of the play La Donna del Fuoco Marietta Barovier. Pioniera delle perle veneziane5, which tells the story of this inventor, businesswoman, and active protagonist of innovation in the art of glass (Figure 01).
In a constant dialogue between past and present, the social and productive dynamics of the Murano furnaces are interwoven, paying particular attention to the raw materials and manufacturing processes of yesterday and today: experiments and practices to which Marietta Barovier, undoubtedly, has dedicated much of her life.
5 Production: Arte-Mide, direction and dramaturgy: Massimo Navone, acting conception and interpretation: Chiarastella Seravalle, music and singing: Rachele Colombo, scenic and video staging: Massimiliano Ciammaichella, costume consulting: Carlos Tieppo. The play premiered at the Goldoni Theater in Venice on September 12, 2021, as the final event of The Venice Glass Week fifth edition. The play was also produced thanks to close collaboration with the Glass Bead Art Committee, which is responsible for the glass beads candidacy as a UNESCO intangible heritage.
Thus, guided by the words of an actress – and the musical compositions of a singer with whom she interacts – the spectator is empathetically introduced to the discovery of the alchemical and fascinating world of beads creation, starting with the origins of the elements of which it consists.
The narrative register is confronted with video appearances, variously positioned in the background scenic backdrop, which interact with the dynamics of a diachronic and synchronic becoming. They are enclosed within circular windows to emphasize the images and sounds of the primary element of fire, unveiled through the narrow opening of the mouth of a Murano furnace and captured on video, in its perpetual motion of preparation for the ritual of a work that repeats itself every day and in the rotational movements of the rod with which the fluid mass of glass is begun to be shaped (Figure 02).
But the reference to the geometric figure of the circumference is also meant to be a tribute to the bead, the undisputed protagonist of the performance, and to the profession of beadmakers today. Thus, some photographs, portraying the working processes of Muriel Balensi’s works, are re-elaborated with morphing techniques, to reproduce in video the complexity and magic of formal combinations that are enclosed in the universe of colors of the precious spheres.
Generally, morphing applied to two-dimensional figures is that deformation technique created on a sequence of animated images, showing the gradual transition from an initial figure to its transformation, achieved by the warping 6 .
In this case, it is a matter of defining a topological correspondence between pairs of photographs, given by the interpolation of recognizable homologous points in both; therefore, the transformations between the source and target images are recorded in video sequences that reveal their effects (Figure 03 to 05).
The only elements of stage decor are a metal frame and a mirror beside which is placed a costume, the one that actress Chiarastella Seravalle wears when she takes us back to fifteenth Century Murano in playing the role of Marietta Barovier. Although not much is known about her private life, she is known to be involved in the industrial espionage case with Giorgio di Pietro, nicknamed Ballarin 7 because of his limping gait.
This Dalmatian laborer was already serving the family furnaces in 1481, because a complaint against Giovanni, son of Angelo Barovier, had been filed for contravening the rule not to hire foreign staff in glassmaking. Yet, chronicles attest that Ballarin himself had stolen the precious book with
6 Warping: distortion by deformation.
7 Ballarin: by Venetian dialect translates to “dancer”.
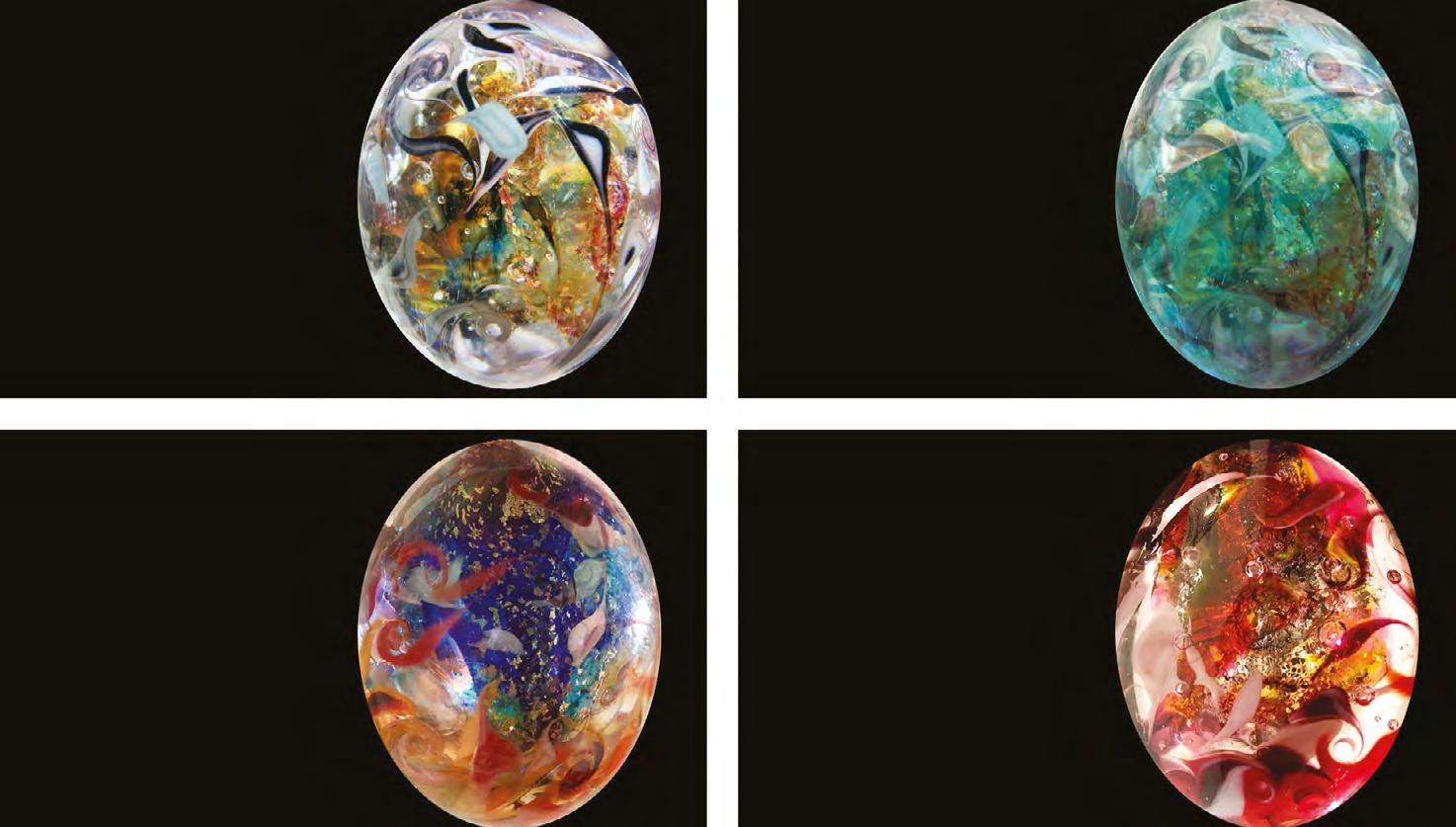
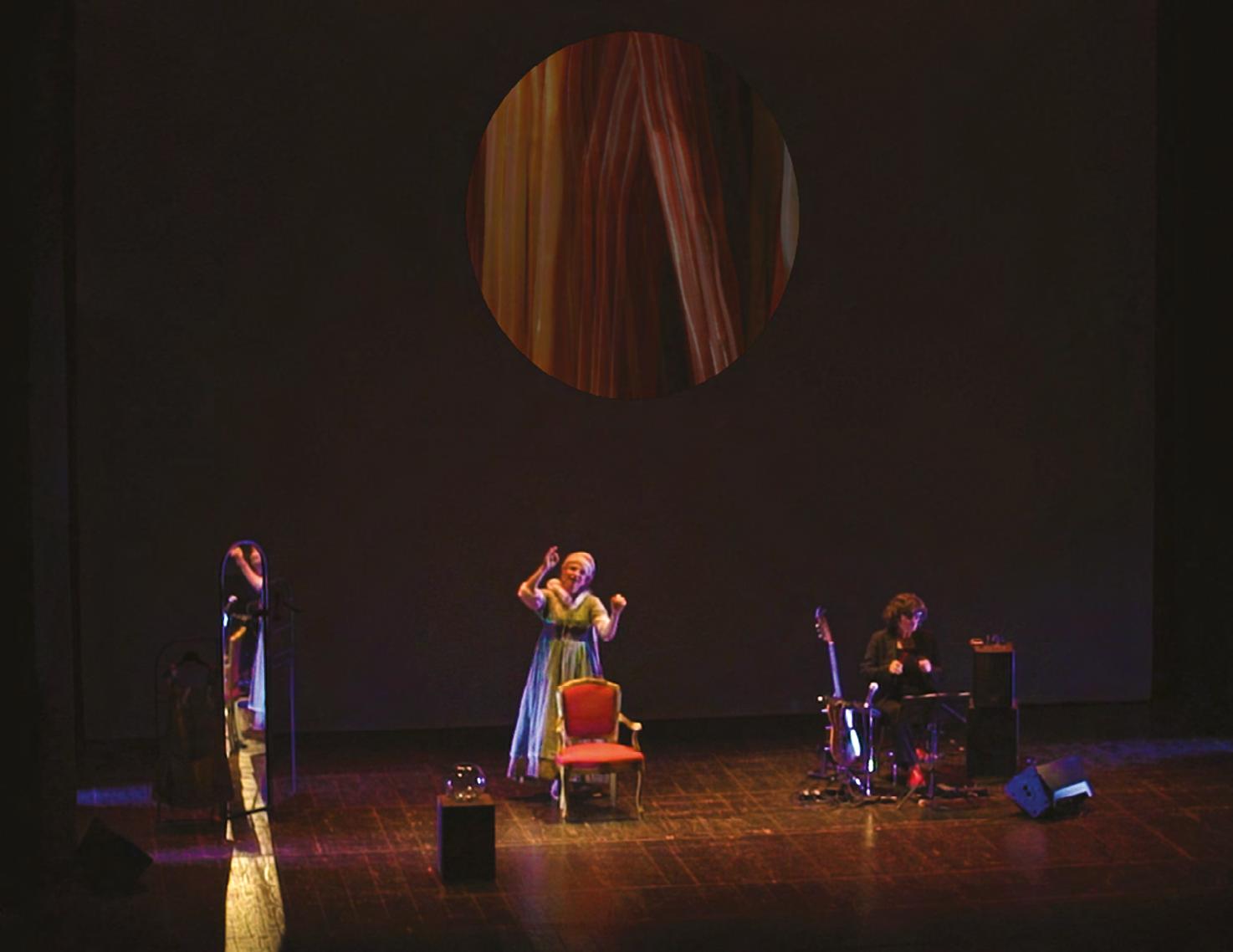
Marietta’s notes and recipes, copied them, and in the same year opened a furnace in Venice, which was forbidden because a decree of 1291 ordered all existing ones to demolish and forbade the construction of new ones. The Serenissima, therefore, avoided any risk of fire and transferred all production to Murano.
This time, instead of defending him, it was Giovanni Barovier who denounced Ballarin, who was arrested and immediately released on bail paid by glassmaker Alvise Trevisan. In any case, in 1492 he opened a furnace in Murano, and in the years 1503-1504 he was honored with the title the glass art Gastaldo (Zecchin, 1987, I).
With the Split native, Marietta continued to have worked relations, despite the misadventures and betrayal of trust in having the precious recipes stolen from her (Marzo Magno, 2017). The spectacle limits itself to the telling of these events, without drawing any conclusions about possible love affairs, as is evident from reading the novel: Marietta. A Maid of Venice (Crawford, 1901).
Conclusions
The performance concludes with a tribute to the extraordinary talent of Marietta Barovier, the first woman who was allowed to open her own furnace and where, in all likelihood, she invented a small artifact that holds secrets and mysteries, concealed even in its same name: Rosetta .
To corroborate the hypothesis that it had an Egyptian origin, some Egyptologists have associated the name with the city that lies at the mouth of the Nile, but this theory is completely wrong, because the Rosetta origin, as seen, lies in the Barovier family furnaces in Murano.
Americans, however, also use other denominations such as, for example, Star beads or Chevron (Moretti, 2005), and it seems that the latter term was introduced by antiquarian John Brent, in his essay: On glass beads with a chevron pattern (Brent, 1880).
But perhaps the little rose contained other meanings: desert rose, mystical rose, rose cross, rose of life. Alchemies and suppositions that probably contributed to the fortune of this ingenious creation in feeding the earnings of merchants and takings of the Serenissima. An object that, even before becoming body adornment, was used as purchasing currency.
Stories and legends related to this bead multiply, crossing over several centuries to the most distant places on Earth, tangible evidence of the value of a woman who dedicated her life to her passion: the art of glass beads.
In conclusion, antifragility here insists on the fluid material to be worked, the glass, and the invention and strength of a Renaissance pioneer, a woman with a history to be rediscovered.
References
Barovier Mentasti, R. (1982). Il vetro veneziano. Milano: Electa. Bertagnolli, E., Sega, M. T., Urbani De Gheltof, R. (1991). Perle veneziane. Venezia: Consorzio Venezia Perle. Brent, J. (1880). On Glass Beads with a Chevron Pattern. Archaeologia, n. 45, pp. 297-308. Cicogna, E. A. (1853). Delle inscrizioni veneziane. Vol. 6. Venezia: Tipografia Andreola. Crawford, F. M. (1901). Marietta. A Maid of Venice. New York: MacMillan. Gasparetto, A. (1988). Dalla realtà archeologica a quella contemporanea. In Barovier Mentasti, R., Dorigato, A., Gasparetto, A., Toninato, T. (ed.), Mille anni di arte del vetro a Venezia. Venezia: Albrizzi, pp. 15-38. Levi, C. A. (1895). L’arte del vetro in Murano nel Rinascimento e i Barroviero. Venezia: Ferrari. Marascutto, P. B., Stainer, M. (1991). Perle veneziane. Verona: Nuove Edizioni Dolomiti. Marzo Magno, A. (2017). Serenissime. Le donne illustri di Venezia dal medioevo a oggi. Pordenone: Biblioteca dell’immagine. Moretti, G. (2005). La Rosetta. Storia e tecnologia della perla di vetro veneziana più conosciuta al mondo. Rivista della Stazione Sperimentale del Vetro, n. 1, pp. 27-39.
Sarpellon, G. (2003). Perle e murrine veneziane. Albignasego: Print House.
Zecchin, L. (1987). Vetro e vetrai di Murano. Studi sulla storia del vetro. Vol. 3. Venezia: Arsenale. Zecchin, L. (1976). Lattimo nelle scritture muranesi del XV e del XVI secolo. Rivista della Stazione Sperimentale del Vetro, n. 3, pp. 115-118.
Zecchin, P. (1997). I fondenti dei vetrai muranesi. I parte: l’allume catino. Rivista della Stazione Sperimentale del Vetro, n. 27, pp. 41-54.
Insights into LCA and EPD environmental impacts data related to glass products for windows
ANNA DALLA VALLEA, MONICA LAVAGNAA, ANDREA CAMPIOLIAIn construction sector, glass products are widely used for the most varied purposes. Windows are however the main application field, crucial for guaranteeing the performance of building envelope as well as for ensuring the well-being of users, emphasizing the potential strategic role of glass in promoting sustainable development initiatives across multiple stakeholders.
In this perspective, the paper focuses on the environmental impacts of the principal glass products for windows, providing an overview of the Life Cycle Assessment-based data retrieved from different sources, including EPD certifications and LCA database. The aim is to give insights into the environmental impacts of glass supply chain, to identify reference values (range minimum-maximum), to verify any differences between the internationally recognized datasets and the data of producers, to disclose the percentage increase that results from the various glass processing.
The presented results are an integral part of Arcadia project, “Life cycle approach in public contracts and Italian LCA database for the efficient use of resources”, constituting in particular the preliminary analysis for the development of the representative datasets of the glass supply chain at national scale.
A Department of Architecture, Built environment and Construction engineering, Politecnico di Milano, Italy.
KEYWORDS: GLASS PRODUCTS, ENVIRONMENTAL IMPACTS, LIFE CYCLE ASSESSMENT
Introduction
From an environmental point of view, the glass industry has a twin distinction. On one hand, it constitutes a highly energy-intensive activity (Martini et al., 2021), requiring the use of high-temperature furnaces for the melting and forming processes, unlike other sectors in a constant and continuous way throughout the year (stops occur only for extraordinary maintenance or end-of-life). On the other hand, it has enormous potential for supporting the transition to the circular economy, as permanent material potentially fully recyclable, that can be melted, reproduced and used countless times without losing its properties and without needing additives or reagents (Scalet et al., 2013). This duality destines glass to play a role of particular interest, by identifying its possible energy efficiency interventions and specific technological solutions (Martini et al., 2021) and by defining its new frontiers to contribute to a zero-emission Europe (Glass for Europe, 2019).
The environmental impact of glass is especially critical in the construction sector, which represents its main field of application (80% of total production), followed by automotive and solar sectors (Glass for Europe, 2021). In particular, after the 2020 crisis, in Italy the provision of incentives and the revival of investments in the construction sector contributed to a swift recovery of glass market (Assovetro, 2021), giving it a strategic importance for promoting sustainable development initiatives across multiple stakeholders. The glass supply chain is in fact one of the 15 national supply chains represented in the near future within the Italian LCA (Life Cycle Assessment) database, currently ongoing as part of Arcadia project. Funded by Agenzia di Coesione Territoriale (PON-governance and institutional capacity 2014-2020), Arcadia project focuses on “Life cycle approach in public contracts and Italian LCA database for the efficient use of resources”. The definition of welldocumented LCA datasets as national reference values, in this instance for the glass supply chain, has multiple purposes. Firstly, to stimulate production companies to improve their products, limiting energy consumption and emissions through the application of eco-innovation tools (e.g. EPD – Environmental Product Declaration and product eco-design). Secondly, to support Public Administrations in promoting LCA-based policies and measures concerning land-use planning and management as well as green public contracts. Last but not least, to provide national datasets available to research bodies and universities for teaching and research activities.
In this context, the research group LifeCycleTEAM of the ABC Department of Politecnico di Milano is in charge of developing the datasets for the glass products for windows. The paper shows the results of the preliminary analysis conducted in the field of environmental sustainability for the development of the representative glass datasets to be included in the Italian LCA database proposed by Arcadia project. This is a detailed and systematic review of the LCA-based environmental profiles of glass products now available on the market, collected from different sources: both EPD certifications and datasets specifically from Ecoinvent, an internationally established database. Objective of the paper is therefore to offer an overview of the
environmental information of glass supply chain, to identify a range of reference values (between minimum and maximum), to verify if Ecoinvent database is still valid or if there is a significant deviation from data of producers, to disclose the percentage increase that currently derives from the various glass processing.
Environmental data collection of representative glass products
The construction sector is characterized by the use of a wide range of glass products that, although different in function, performance and final appearance, entirely derive from flat glass, commonly called “float glass”, recalling the production process (float bath). Starting from float glass, the most representative processes at national level concern the deposition of coatings, the tempering and stratification, from which various types of monolithic glass pane are obtained and then assembled together to create high performance windows and transparent envelope solutions. The object of study are therefore the following representative products: float glass (FG), coated float glass (CFG), toughened safety glass (TSG), laminated safety glass (LSG) and insulated glass units (IGU), both double glazing (IGUd) and triple glazing (IGUt).
For each product at issue, the today available EPDs have been collected from the main EPD platforms, including Environdec, EcoPlatform, INIES, IBU-epd, EPD Italy, as well as from the database embedded within the user-friendly LCA tools for designers, such as OneClick LCA. Note that in this way, the surveyed EPDs refer to different Program Operators, ranging from International EPD System, ift Rosenheim, FDES, ASTM International and IBU. Nevertheless, after a first sweeping investigation, the EPDs to be further explored have been selected, preferring those developed in European context and, only in case of lack of data, referred to foreign contexts (USA and Saudi Arabia). Furthermore, the EPDs of glass products subjected to specific surface treatments (e.g. acid etching) and the EPDs developed in compliance with the new LCA rules (EN 15804:2012+A2:2019) have been eliminated, opting for basic processes and the widely adopted EPD standard (EN 15804:2012+A1:2013). By now it is worth mentioning that most glass EPDs are related to average data based on different production plants, thus determining for a specific glass producer the average environmental profiles within a specific application context (e.g. EU average).
The environmental profiles of the selected EPDs have been thus systematized and analyzed, focusing in particular on A1-A3 phases, relative to the upstream processes (procurement of raw materials and transport to manufacturing plant) and core processes (glass production and subsequent processing, even when performed at different factories). The downstream phases have been currently omitted as subject to higher degree of uncertainty and strongly determined by the underlying assumptions. Where EPDs contain a range of reference products, the environmental information is set out for specific product considered representative of the current glass market offerings. In this way, the typical thickness for the different glass products
is: 4 mm for float glass (10 kg/m2), 3 mm for coated and toughened glass (7.5 kg/m2), 7.5 mm for laminated glass (17.1 kg/m2). On the other hand, the following standard glass-cavity measures have been considered for insulated glass units: 4-16-4 for double glazing (about 20 kg/m2) and 4-14-4-14-4 for triple glazing (about 30 kg/m2). Subsequently, in order to ensure comparability of results among the different glass products, the environmental impacts of float glass and processed glasses (CFG, TSG and LSG) have been converted to 1 mm thick of 1 m2 of glass, with the aim of verifying the percentage increase due to the different processes.
In parallel with the collection and analysis of the EPD-sourced data, the environmental profiles of glass have been explored into Ecoinvent, the LCI database established at international level and contained in the main LCA software for experts (SimaPro and GaBi). Specifically, it includes the environmental information (datasets) only for a limited range of glass products: uncoated flat glass (FG), coated flat glass (CFG), double glazing (IGUd) and triple glazing (IGUt). Therefore, the datasets of both toughened safety glass and laminated safety glass are not present in Ecoinvent (LSG is actually embodied as additional component of double glazing dataset). It should be noted that in Ecoinvent glass datasets are expressed in kg, requiring therefore their transformation according to the functional unit considered in the study, namely 1 m2 of glass pane, considering weights equal to the representative products derived from the EPD survey. As regards insulated glass unit datasets, Ecoinvent already defines them per 1 m2. also specifying the relative transmittance: U <1.1 W/m2K for double glazing and U <0.5 W/m2K for triple glazing.
Following the systematic analysis of glass environmental profiles, both from EPD and Ecoinvent, results are shown by means of bar charts, not intended for statistical purposes but only to describe the range of the reference sample, to identify for each glass product the average impacts from the selected EPDs and the relative deviation from Ecoinvent datasets, as well as the impact percentage of increase associated with the processes in question. To this end, the investigation has been confined to the most significant indicators, namely: Global Warming Potential (GWP); Acidification Potential (AP); Eutrophication Potential (EP); Total use of Primary Energy resources, as sum of Renewable (PERT) and Not Renewable (PENRT), described in detail in the following paragraphs.
Focus on Global Warming Potential (GWP) impacts
From the analysis of the main EPDs currently available on the market, it emerges how GWP impacts of float glass ranges from 2.20 kgCO2eq to 3.25 kgCO2eq, placing the average value (2.75 kgCO2eq) above that set by Ecoinvent dataset “uncoated flat glass” (2.43 kgCO2eq), which is lower than -12%. The offset between the average EPD value and Ecoinvent data becomes even more pronounced in the case of coated glass, in which the average GWP value at 3.93 kgCO2eq is 34% higher than Ecoinvent dataset “coated flat glass” (2.61 kgCO2eq). GWP impacts varies from 3.46 kgCO2eq to 5.70 kgCO2eq in the event of toughened glass and from 6.53 kgCO2eq to 7.93 kgCO2eq when laminated
safety glass are produced. It is important to underline that the comparison among the different glass products refers to different glass manufacturers, so single values cannot be directly compared (e.g. the minimum value of coated glass exactly correspond to the minimum of toughened glass, seeming to imply equal impacts in terms of GWP during the production phase, but this is because the different impact of glass production related to different manufacturing plant). Note that Ecoinvent database does not currently include datasets for TSG and LSG processing to be used for comparison.
By comparing each other the GWP impacts of the different processed glasses, it is possible to disclose the percentage increase associated with each processing, starting from the float glass that corresponds to the reference base product. Considering the average EPD value of float glass at 2.75 kgCO2eq, the production of coated glass (3.93 kgCO2eq) entails an increase in impacts of 43%, reaching 66% in the case of toughened glass (4.58 kgCO2eq) and up to 163% for laminated glass (7.23 kgCO2eq). Instead, regarding GWP impacts available in Ecoinvent, coated glass (2.61 kgCO2eq) results in an increase of only 7% compared to uncoated float glass (2.43 kgCO2eq), narrowing the gap detected by surveying EPDs.
Moving from processed glasses to their assembly, the average EPD-sourced values of insulated glass units are more aligned with those of Ecoinvent, the latter always slightly lower. In the case of double glazing, the GWP impacts declared by producers in the EPDs ranges from 31.1 kgCO2eq to 39.2 kgCO2eq, whose average (35.5 kgCO2eq) is higher than 7% of the impacts by Ecoinvent (32.9 kgCO2eq). On the other hand, in the case of triple glazing, the Ecoinventsourced GWP (53.5 kgCO2eq) is only 2% lower than the average of EPD impacts (54.7 kgCO2eq) which vary from 49.6 kgCO2eq to 59.7 kgCO2eq. Here, the existing GWP deviation between double and triple glazing is fairly uniform between EPD averages and Ecoinvent values. In particular, in compliance with the average EPD impacts, the creation of triple glazing implies an increase in GWP impacts equal to 54% compared to double glazing, while to 63% considering the Ecoinvent datasets.
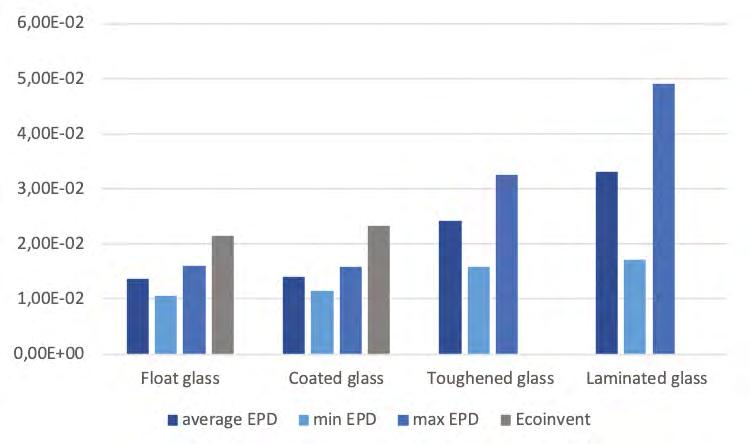
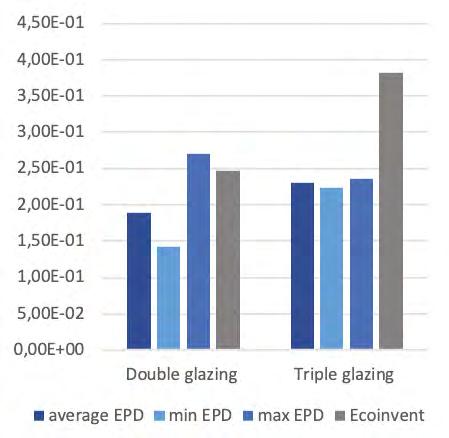
Fig. 01 GWP impacts [kgCO2eq/m2] of the different processed glass per 1 mm thick (sx) and of insulated glass units per 4-16-4 for double glazing and per 4-14-4-14-4 for triple glazing (dx).
A. CAMPIOLIFocus on Acidification Potential (AP) impacts
Concerning the impacts related to Acidification Potential of land and water, according to the analysis of existing EPDs, float glass is around 1.36E-02 kgSO2eq, now lower than that of Ecoinvent (2.15E-02 kgSO2eq) which appears to be +58%. The same variation in impacts, gradually rising (66%), is also found in the case of coated glass, in which the average EPD value (1.41E-02 kgSO2eq) is advantageous (lower) compared to the AP impacts of Ecoinvent dataset (2.33E-02 kgSO2eq). AP impacts show an average of about 2.42E-02 kgSO2eq for toughened glass and 3.32E-02 kgSO2eq for laminated glass, which however derive from a wide range of values, since the maximum more than double the minimum. Moreover, note that in both cases the minimum EPD value is approximately equally by toughened and laminated glass, referring however to different manufacturing plants.
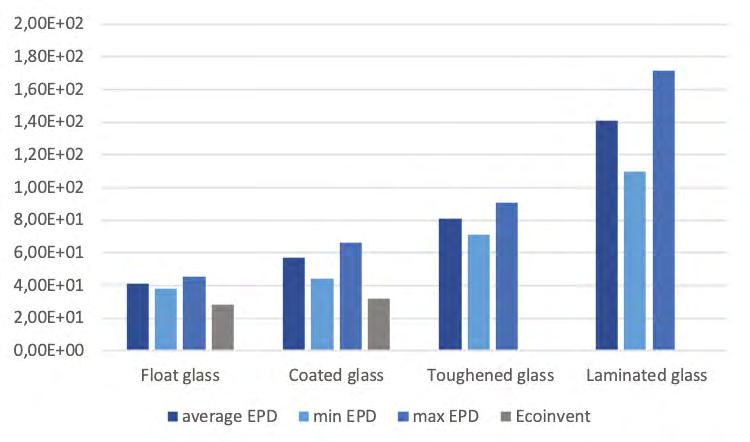
From the calculation of the percentage variation between the different glass products, it points out that compared to average AP impacts of float glass (1.36E-02 kgSO2eq), there is an increase respectively of 3% for coated glass (1.41E-02 kgSO2eq), 78% for toughened glass (2.42E-02 kgSO2eq) and 143% for laminated glass (3.32E-02 kgSO2eq). This is accounting the impacts specified within the EPDs and mostly confirmed by the available Ecoinvent impacts, where coated flat glass (2.33E-02 kgSO2eq) increases by 9% the emissions of float glass (2.15E-02 kgSO2eq), resulting therefore very similar to each other.
AP impacts of insulated glass units widely oscillate in the case of double glazing EPDs, in which maximum is nearly twice the minimum value, by contrast they fluctuate in a relatively narrow range in the triple glazing EPDs, with a variation of only 5%. Considering all collected EPDs, the average value is 1.88E-01 kgSO2eq for double glazing and 2.30E-01 kgSO2eq for triple glazing. They are both lower than the impacts of Ecoinvent datasets, which result in an increase of 31% for IGUd (2.47E-01 kgSO2eq) and of 66% for IGUt (3.81E01 kgSO2eq). Here, the percentage increase of impacts between double and triple glazing is 22% considering the EPD averages, increased up to 54% when embracing Ecoinvent datasets.
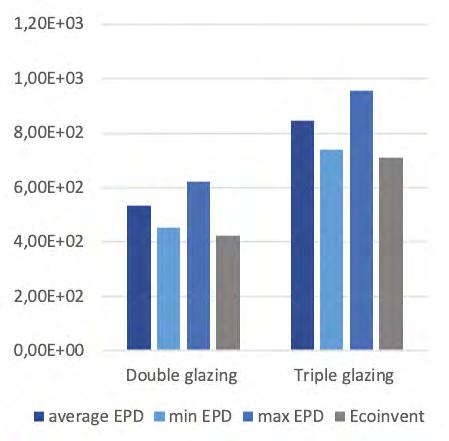
Focus on Eutrophication Potential (EP) impacts
From the analyzes conducted on Eutrophication potential of glass, there is a trend reversal in the sense that EP impacts appear higher for float glass compared to all those of coated, toughened and laminated glasses. It must be kept in mind that the impacts of processed glass (CFG, TSG, LSG) include both the impacts associated with the production of float glass and the ones relating to the subsequent processing. In this way, it seems that the treatment processes allow to reduce the EP impacts of glass production, but always taking into consideration that impacts refers to different manufacturing plants with distinguishing features of the production process. Anyhow, the EPD-sourced impact of float glass ranges from 1.49E-03 kgPO43-eq to 4.55E-03 kgPO43-eq, gaining an average of 3.01E-03 kgPO43-eq. This shows a significant variation in EP impacts of float glass (about 67%), which is also confirmed by the processed glass from EPDs, with range of 53% for coated glass, 63% for toughened glass and 70% for laminated glass. Compared to EPD average values, if the impacts of Ecoinvent datasets are advantageous (lower) by 9% for float glass (2.74E-03 kgPO43-eq), they turn out to be disadvantageous (higher) at 98% in the case of coated glass (3.31E-03 kgPO43eq). However, unlike EPD data, it is important to stress that in Ecoinvent the EP impacts of float glass are lower than those of coated glass.
In light of this, it is not possible to make comparison between float glass and processed glasses. Accordingly, taking as reference point the average EPD impacts of coated glass (1.67E-03 kgPO43-eq), a 16% increase in impacts is disclosed for toughened glass production (1.94E-03 kgPO43-eq) and up to 65% for laminated glass (2.67E-03 kgPO43-eq). Instead, by calculating the difference between float glass (2.74E-03 kgPO43-eq) and coated glass (3.31E-03 kgPO43-eq) set by Ecoinvent datasets, the EP percentage change amounts to about 21%.
As regards the double glazing, the variation between the minimum and maximum EP impacts retrieved from EPDs of both double and triple glazing is around 44%, obtaining as average value 2.88E-02 kgPO43-eq for IGUd and 4.57E02 kgPO43-eq for IGUt. Compared to these, the impacts from Ecoinvent are significantly higher in both cases, with a difference in EP impacts equal to 71% in
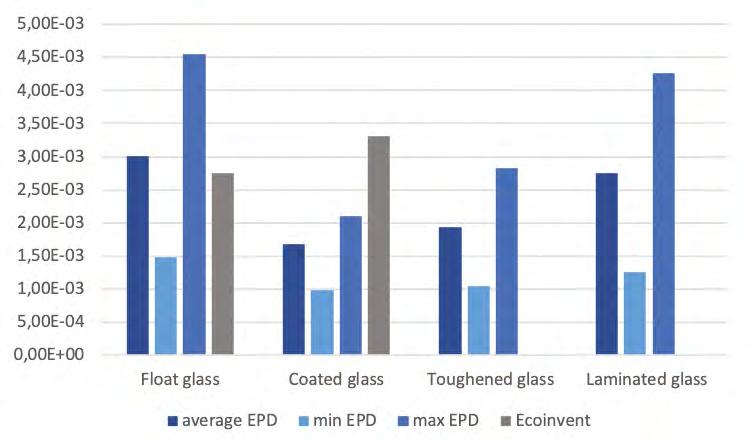

double glazing (4.94E-02 kgPO43-eq) and 81% in triple glazing (8.28E-02 kgPO43eq). Although Ecoinvent data turns out to be more disadvantageous (higher) than those from EPD, the percentage increase in impacts is similar between the two. If considering the EPD averages, the production of insulated glass units with triple glazing involves a 58% increase in EP impacts compared to double glazing, this percentage reaches 68% when referred to Ecoinvent impacts.
Focus on Total use of Primary Energy Resources (PERT+PENRT) impacts
By deepening the total use of renewable and not renewable primary energy resources, the range between minimum and maximum values disclosed by EPDs appears more restrained, limited to 16% in float glass, raised to 34% in coated glass, to 22% in toughened glass and to 36% in laminated glass. However, the relative average impacts come in sequence, starting from 41 MJ for the production of float glass to about 57 MJ, 80 MJ and 141 MJ for the production of processed glass (CFG, TSG, LSG respectively). By comparing the different glass products embedded in Ecoinvent, it emerges that the datasets show more advantageous (lower) energy impacts both in the case of float glass, with total value at around 28 MJ (reduction of -30% compared to average EPD) and of coated glass equal to 32 MJ (-44% reduction).
In this context, it is possible to point out how the total use of primary energy resources with respect to the average EPD value of float glass (41 MJ) is increased up to 39% for the manufacturing of coated glass, 96% for toughened glass and 243% for laminated glass. This percentage variation is significantly reduced in the energy values available in Ecoinvent, where the production of coated glass (32 MJ) leads to an increase by only 11% from float glass (28 MJ).
Energy consumption from both renewable and non-renewable sources is greatly extended for the production of double glazing, reaching average EPD impacts of 489 MJ for double glazing and 848 MJ for triple glazing. In both, the variation between minimum and maximum values is around 25%. Furthermore, as happens for the different glass products, Ecoinvent impacts appear to be slightly lower than those of EPD, showing a reduction of -13% in double glazing (425 MJ) and -16% in triple glazing (711 MJ). It follows that the percentage increase in the impacts of triple
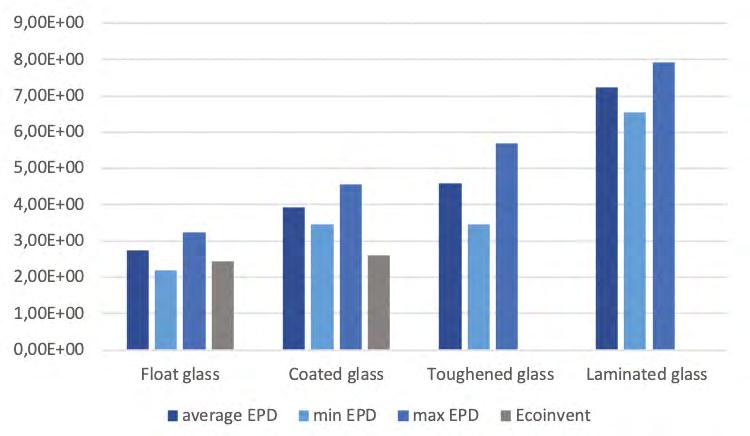
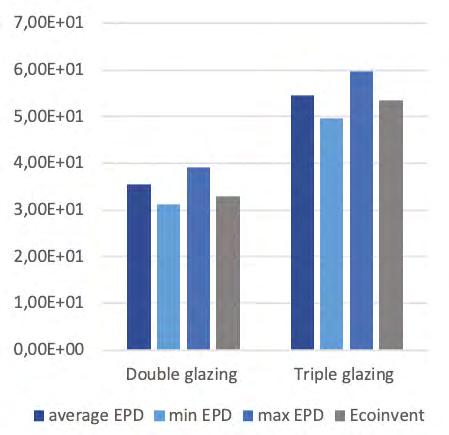
glazing from double glazing is almost aligned between average EPD values, in which it is at 73%, and between Ecoinvent impacts, where it is slightly reduced to 67%.
Conclusions
The in-depth review of the environmental data currently available for the glass industry emphasizes a significant variability of impacts depending on the source, including EPD certifications and Ecoinvent datasets. This places the attention on the importance of a continuous updating of environmental data, to not make them become obsolete but rather to grasp the technological evolution and progress over time. Moreover, only the provision of the metadata behind the LCA studies can evidence what causes the data deviations from different producers of each specific glass product, as well as the percentage increases that emerge for each processing. For this reason, the goal of Arcadia project, namely the definition of updated reference values for the Italian glass industry, turns out to be a challenging task.
To start solving the gap, the research team is currently looking into the inventory data, on one hand, underlying the LCA studies aimed at EPD certification and, on the other, at the development of LCI datasets. However, while Ecoinvent makes available the inventory in a transparent manner and therefore allows users to identify not only quantitative data (foreground system) but also environmental data (background system), EPDs generally omit this information, as they are not currently mandatory to declare. Despite this, some EPDs disclose a summary table of the input materials and the relative quantities in mass percentage on the final product. This enables a preliminary comparison between the quantitative inventory data considered in the EPDs versus Ecoinvent datasets, highlighting the main differences. In particular, concerning float glass, a different percentage is found for forming materials (silica sand and potentially external cullet) and intermediate materials (sodium carbonate, dolomite, limestone, feldspar, sodium sulphate). Based on 100% of float glass, in Ecoinvent silica sand is at 48%, whereas in EPD the average value of forming materials is around 60%. With regard to coated glass, it is important to define the metal oxides used for coating. Moreover, for insulated glass units, discrepancies emerge between double glazing and triple glazing. In Ecoinvent the double-glazing impacts are calculated considering a share of 90% of float glass, while in some EPDs the amount of glass reaches up to 97% of the total mass. In addition, the cavity of double glazing is accounted as argon filled in Ecoinvent, in line with most EPDs, except some that declare various gases, including dehydrated air, argon, krypton or xenon. Instead, in the case of triple glazing, the percentage of glass is aligned between EPDs and Ecoinvent inventories, resulting at 95% of the total mass. Here, a discrepancy is detected for the filling gas, since Ecoinvent dataset of triple glass includes krypton, unlike the majority of EPDs that consider insulated glass units as argon filled. Even here, however, there are EPDs that refer to the wide range of possible gasses.
The identification of the representative products – in terms of composition, process, technologies, techniques, thickness and, in the case of insulated glass
A. CAMPIOLIunits, the arrangement between glass panes and filling gas – is closely linked to the inventory topic. However, this requires the support of glass trade associations and producers active in Italy and their willingness to collaborate, not only to identify the representative products, but also to solve the open issues in the field of environmental impacts, as outlined in previous paragraphs. They are surely sensitive data, but equally crucial for defining the environmental profile derived from the production and processing of glass in the national context. Given the need for clarity on the environmental sustainability of glass, the development of Arcadia project could also be for the principal stakeholders and in general for the glass industry an opportunity for discussion not to be missed but rather to be exploited to the maximum in order to define conscious and shared reference impacts at Italian level. In the near future, the solved issues could be then introduced at European scale to offer aware environmental data and orient glass industry with a view to sustainability.
References
AGC Glass Europe (2018). EPD PLANIBEL (Clear, Clearlite, Clearvision, Linea Azzurra, Coloured). FDES INIES.
AGC Glass Europe (2019). EPD Low-e/solar control double glazing units. FDES INIES.
AGC Glass Europe (2019). EPD Triple glazing units. FDES INIES.
AGC Glass Europe (2020). EPD Solar control magnetron coated glass (ipasol, Stopray). FDES INIES.
Arcadia Project (2019). Approccio ciclo di vita nei contratti pubblici e banca dati italiana LCA per l’uso efficiente delle risorse (on line). In http://bancadatiitalianalca.enea.it (last accessed June 2022).
Assovetro (2021). Quarta edizione dell’Osservatorio sulla trasformazione del vetro piano. Rassegna stampa (online). In www. assovetro.it/wp-content/uploads/2021/12/RASSEGNA-OSSERVATORIO-VETRO-PIANO-2021.pdf (last accessed June 2022).
Astisglass SL (2020). EPD Insulating glass unit Guardian Sun. Kiwa BCS Öko-Garantie GmbH.
Cardinal Glass Industries (2020). EPD Laminated glass products. ASTM International.
Cardinal Glass Industries (2020). EPD Processed glass products. ASTM International.
Ecoinvent (2019). Flat glass, coated {RER}| production | Cut-off, U. Dataset Ecoinvent v.3.6. Ecoinvent (2019). Flat glass, uncoated {RER}| production | Cut-off, U. Dataset Ecoinvent v.3.6. Ecoinvent (2019). Glazing, double, U<1.1 W/m2K {RER}| production | Cut-off, U. Dataset Ecoinvent v.3.6. Ecoinvent (2019). Glazing, double, U<1.1 W/m2K, laminated safety glass {RER}| production | Cut-off, U. Dataset Ecoinvent v.3.6. Ecoinvent (2019). Glazing, triple, U<0.5 W/m2K {RER}| production | Cut-off, U. Dataset Ecoinvent v.3.6.
EN 15804:2012+A1:2013 (2014). Sustainability of construction works — Environmental product declarations — Core rules for the product category of construction products
EN 15804:2012+A2:2019 (2020). Sustainability of construction works – Environmental product declarations – Core rules for the product category of construction products
Euroglas SA (2020). EPD Clear float glass. FDES INIES.
Glass for Europe (2019). 2050: il vetro piano nell’Europa a emissioni zero. Innescare un ciclo virtuoso di decarbonizzazione (online). In www.glassforeurope.com/wp-content/uploads/2020/10/Decarb_broch_ITALIAN_for_WEB.pdf (last accessed June 2022).
Glass for Europe (2021). Key data of Europe’s flat glass sector (online). In www.glassforeurope.com/the-sector/key-data/ (last accessed June 2022).
Martini, C., Martini, F., Salvio, M., Toro, C. (2021). Quaderni dell’efficienza energetica: vetro. Enea (online). In www.pubblicazioni. enea.it/component/jdownloads/?task=download.send&id=451&catid=3&m=0&Itemid=101 (last accessed June 2022).
Pilkington IGP (2017). EPD Flat glass, toughened safety glass and laminated safety glass. ift Rosenheim GmbH.
Saint-Gobain Glass Industry (2016). EPD SGG DIAMANT Extra clear low-iron glass. International EPD System.
Saint-Gobain Glass Industry (2016). EPD SGG PLANICLEAR Clear float glass. International EPD System.
Saint-Gobain Glass Solutions (2016). EPD CLIMAPLUS/CLIMALIT PLUS High performance double glazing. International EPD System. Saint-Gobain Glass Solutions (2016). EPD CLIMATOP High performance triple glazing. International EPD System. Scalet, B.M., Garcia Muñoz, M., Sissa, A.Q., Roudier, S., Delgado Sancho, L. (2013). Best Available Techniques (BAT) Reference Document for the Manufacture of Glass. European Commission, Joint Research Centre (online). In op.europa.eu/it/publica tion-detail/-/publication/ff8a3955-d0d0-46f5-8a15-4b638896cb56 (last accessed June 2022).
Trakya Cam Sanayii A.Ş. (2017). EPD Clear Laminated Glass. Institut Bauen und Umwelt e.V.
The “beautiful scraps” a precious resource
ERIKA COCCATOA, LAURA BADALUCCOAThis work focuses on the study and potential of artistic glass production waste, called cocciame, which highlights the importance of the role of the designer as a promoter of innovation at the system level. This research, developed in the years 2018/2019 and discussed as a master’s degree thesis of the writer Coccato, investigates how the concept of industrial symbiosis can be applied to the recovery and enhancement of artistic glass production waste, thinking about the creation of a synergistic network within the Veneto’s region, with the use of a model that can be replicated and modulated in other areas. It also emphasizes the importance of guided experimentation with the material and the sharing of resources and results in an online space with a view to continuous improvement. For the innovative and systemic approach to the recovery of cocciame that can potentially generate new job opportunities in the Venetian territory, the degree thesis was awarded the first prize in November 2019 at the third edition of the Laudato Si competition.
A Università Iuav di Venezia, Venice.
KEYWORDS: DESIGN, SYMBIOSIS, UPCYCLING
Introduction
The discussions concerning the limit of resources and the importance of their safeguard have been present in the European agendas for several years and have been highlighted also in the CEAP 2.0 (European Commission, 2020). It’s therefore of fundamental importance to think about these issues from a circular perspective. Paying attention not only to the consumption of the upstream resources but also to the product’s end of life and their material’s recovery. In conjunction with this situation, the knowledge by institutions and professionals on the potential of the circular economy is essential. The circular economy “defines a regenerative and reconstitutive industrial system, in terms of both ends and means. We take the concept of the end of life of the product and replace it with that of eternal ‘resurrection and transformation’ [...] enhancing each component in a closed, efficient cycle” (Bompan and Brambilla, 2021, p. 72). Briefly, the circular economy consists in using raw materials from renewable or renewed sources, in which the design and the production are structured according to specific quality standards and to move towards a performance economy. The design of those products respects and cooperates with the environment; these paths are also designed to give a purpose for the end of life of the product in question. Within the circular economy, it is possible to identify different action strategies that intervene at different times in the product life cycle; to address the same time: the scarcity of resources and curb the increase in waste and scraps, it is possible to turn attention to industrial symbiosis. The symbiosis arises from the need to create a connection between companies, to generate a virtuous system for the recovery of waste, capable of creating economic and environmental benefits for those involved. According to the definition established by ENEA “By industrial symbiosis we mean the exchange of resources between two or more dissimilar industries, meaning by ‘resources’ not only materials (by-products or waste) but also energy waste, services, expertise” (Cutaia and Morabito, 2012, p. 44). The structured system, therefore, allows two or more entities to give each other a mutual advantage thanks to a close collaboration regarding some aspects related to production.
This type of reasoning, apparently far from the sphere of glass, is in fact very appropriate. Although glass is a virtually eternal material (Gisotti, 2017), this can only be considered true for some of its types. The characteristics of the glass change according to the chemical composition and are a potential vehicle for end-of-life problems. If for industrial glass, called short glass, we do not encounter particular problems in recovering or reusing the material, the same cannot be said of artistic glass. This type of glass, called long glass or soft glass due to its ability to be processed out of the oven for a longer time than industrial glass, presents numerous difficulties for its recovery at the end of its life. Due to a higher percentage of sodium carbonate in the
mixture, it is impossible to combine this glass with industrial glass, as this would generate structural problems in the printed object. Another important aspect is the range of colours present in artistic glass. This variety of choices makes it possible to create beautiful and visually complex objects, however, the oxides used are often incompatible with each other and they generate breaks and cracks when fused. The production waste of artistic glass, called cocciame, is usually destined for a strong downcycling1 process which leads them to be finely shredded to be used as a material in the road substrate, a waste and a significant loss of value for what turns out to be a precious waste thanks to its aesthetic properties. From these premises arises the need to explore the possibility of applying the concept of industrial symbiosis to the recovery and enhancement of artistic glass waste, generating a path that brings value creating an upcycle path and pushes an alternative reflection for the end of life of this material.
A symbiosis for the artistic glass
The first step to implement an upcycle system for artistic glass, where for the upcycle, we intend “an industrial process that uses waste for products of higher value [...]” (Bompan and Brambilla, 2021, p. 178), but following the example of the industrial symbiosis, was to determine what were the basis for creating a valid path for its recovery. Applying the concept of upcycling to this strategy means following the perspective where this practice isn’t conceived as a simple system of recycling and recovery materials, but above all, as a process within a specific design thought, in which the recovery of large quantities of waste material and the product’s end-oflife are implemented and at the end of their journey, will be reprocessed. This way of acting will make the potential waste material go up the value chain, obtaining not only first-second materials but above all some highperformance products. Studying the proposals made so far, about creating a valid path for the recovery of the artistic glass waste, emerged a discussion regarding the creation of a cocciame collection and sorting centred on the island of Murano, which was then set aside due to the unfavourable result of the cost-benefit analysis and also in light of the fact that in recent years most of the Murano glass industry, due to the high management costs, has decided to move its production to the mainland (City council of Venice IX Commission, July 2016).
From these premises, the consideration of the creation of a single collection center was born, analysis and sorting in an area that can be reached both by land and by water. Two points that meet these requirements have therefore
1 Downcycle: to use waste material or old or used objects to make a product of lower value than the original material or object. Cambridge Dictionary.
been hypothetically taken into consideration in the venetian area. The first is in the area of Punta San Giuliano, the second in the industrial area of the city of Marghera. These two areas would allow not only the approach by land and water but would also be free from the architectural and landscape constraints that limit new constructions on the island (A.Tosi, 2004; Venice Today, 2016).
To facilitate and optimize the recovery of artistic glass waste, the most important aspect is the subdivision of the cocciame to ensure its reintegration into other production cycles. In this regard, we wanted to outline a mechanized subdivision by main geometries and colours, then further refined through a manual step. The selection is to be considered possible only after having guaranteed the safety of the waste. To certify that the cocciame can be used for other productions, as a recovery material or that it doesn’t represent a danger to the environment, a composition test called the elution test or eluate test must be carried out at the chemistry level of the material by a verified issuing body, according to the UNI EN ISO 17294-2:20162. This test will allow it to be catalogued under the EER code (European Waste List) 10.11.12, or as non-hazardous waste (Council Directive 91/689/EEC).
Types of cocciame and the recovery chain
After carrying out a period of on-site observation at the Ballarin glass factory in Murano, it was possible to determine a certain hierarchy of shapes within the cocciame, due to the processing techniques typical of artistic glass, which also deeply characterize the waste produced. Producing objects of different natures, different types of wastes are created; those can be differentiated according to the type of processing to, which the material is subjected.
One of the main techniques for the realization of Murano’s artistic glass is blowing. Thanks to these techniques, one scrap piece commonly found, is the waste resulting from the detachment of the processing residue from the blowing tube, which once reached the breaking temperature, generates a high-pitched sound like a rattle, produced by its rapid contact cooling with the air. This type of element is often of a semi-cylindrical shape, chipped and not complete (called collar). Another type of waste originated from the necessity of passing a vessel from one blowing tube to the other, has a drop shape and often undergoes breakage. An additional scrap, represented by a long wavy strip of material, is produced during the final stage of a vases processing is given by the edge cutting, where the glass excess is cut off. In addition to these wastes made during processing, it’s possible to find scraps deriving from processing errors and broken pieces. Finally, we can find several incomplete glass rods, discarded because they are deemed
unsuitable for processing, also to avoid basic defects in the material, it’s a habit to cut the beginning and the end of the glass rods. From these premises then the choice of applying a selection of the waste to be used for recovery is based on its geometry. Five categories were identified, and each was assigned a name (Figure 01):
• The glass rods. Waste parts of the glass rods
• Offset of the edge crop. Pieces derived precisely from the cutting of the edge of cups and vases or
• finished pieces destroyed
• Collars. Material made by detaching the glass from the blowpipe with a typically hollow cylindrical shape
• Full glass. Derived from cuts of the excess material in a product or the joining of several parts
• Irregular forms. In which all the other components that cannot otherwise be catalogued are gathered.
Selecting the elements and diversifying them by colour and geometric conformation allows not only to give a better-intended use to the waste but also to make their reintroduction into different production cycles practical. In the route diagram (Figure 02) it’s possible to note the various hypotheses of the use of the recovered material. In the first case, an attempt is made to reintegrate the newly recovered material as a secondary raw material,
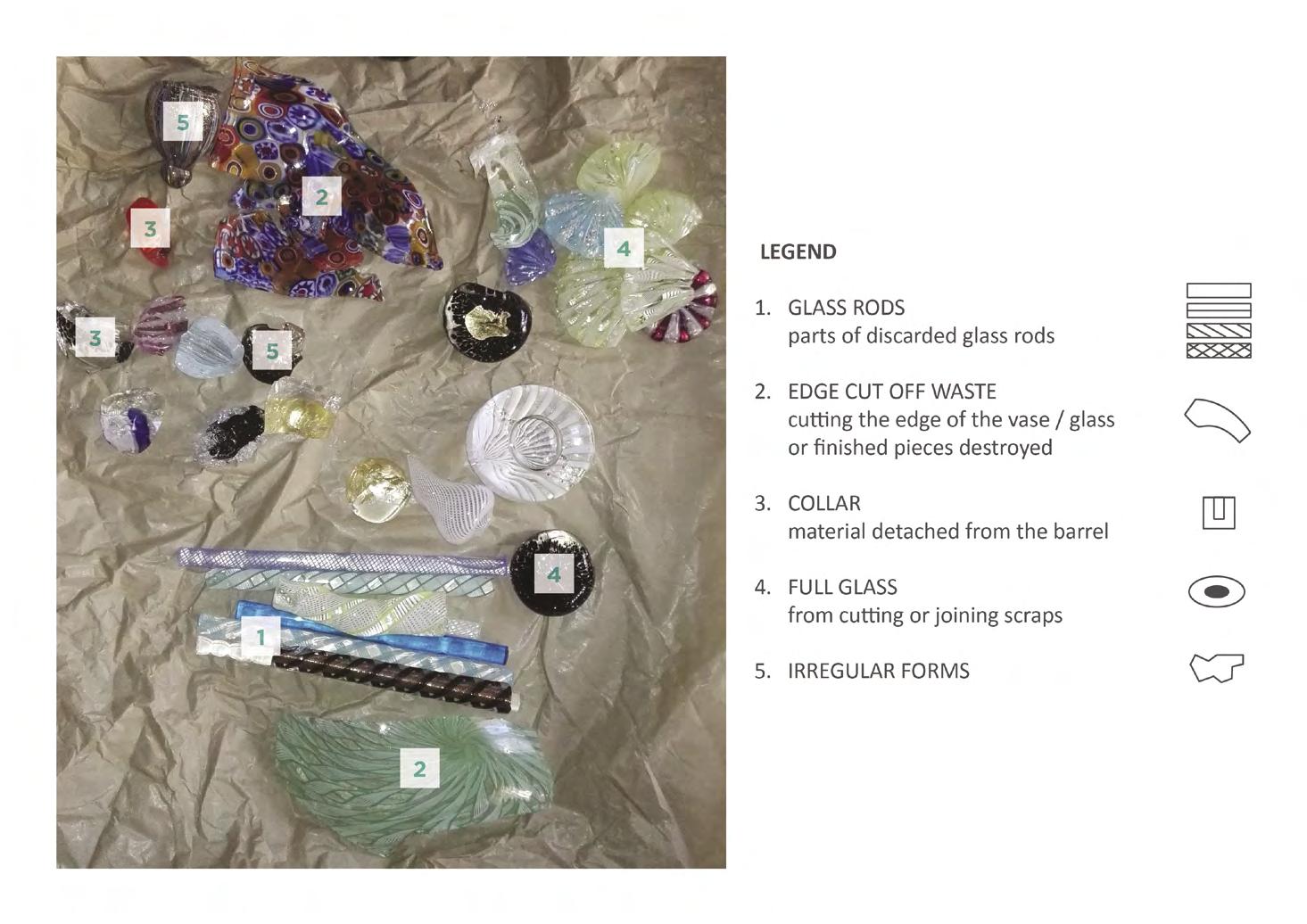
which after being reduced to grit, could be reintroduced into the production cycle, partially replacing the virgin raw material, reducing the amount of raw material and costs. The second path follows the current downcycling scheme. Undersized parts, small-caliber grits, splinters and sands would still be destined for this path already outlined. The last hypothesis of recovery and reintegration represents a complex, but significant path from the point of view of investigating the future of these waste. In the sorting center described above, once the sorting has been carried out, the material directed to the upcycling supply chains would continue towards its new intended use as a secondary raw material to be reintroduced into production.
The purpose of this system, as already reported, is to exploit the aesthetic potential of waste but also to hypothesize different ways to reuse and recover the maximum possible amount of product from an upcycling perspective. When the cocciame has been divided, the output obtained is represented by materials with a defined geometric shape and materials with mixed shapes. A subdivision following the rules previously explained would allow the destination to different uses of the material in question or to reflect on the experimentation with cocciame in a more defined way. At this point, it’s of fundamental importance to be able to guarantee the scientificity of the experimental process. In this sense is essential to provide the experimenter, be it a designer, a professional or otherwise, with adequate tools.
Fig. 02 The symbiosis system. The schematic representation of the system of synergies that would be created rethinking the process as a circular recovery path, with the transport system scheme and after the sorting process of the artistic glass’s waste. E. Coccato

The experimental factor
Design as a catalyst for innovation wants to act as a means to stimulate the creation of new transversal solutions that put designers, producers and researchers in communication. In order to allow the various professionals to communicate using a common language and therefore favor the development of shareable and scientifically valid research on the use of cocciame, post-selection, three targeted tools have been formulated, each with its own peculiarities to be used in the realization of the samples. test with hot working. This approach aims to highlight the potential of the material and to clarify the best techniques and combinations to be used for introduction into serial and industrial production. Below are the three tools that present a physical part and a virtual part accessible from an opensource online platform connected to the project.
The sample book
The first requirement was to structure a catalogue of the samples to understand the use of the cocciame and to give the opportunity to accurately record the results obtained during the experimentation sessions; a system useful for codified and repeatable dissemination of knowledge, for anyone who wants to enter the research context. The card contains all the information useful for understanding the nature of the specimen made, the tools used, the material and quantity, the colours selected, the time and place, the oven temperature, and the time (Figure 03 and 04).
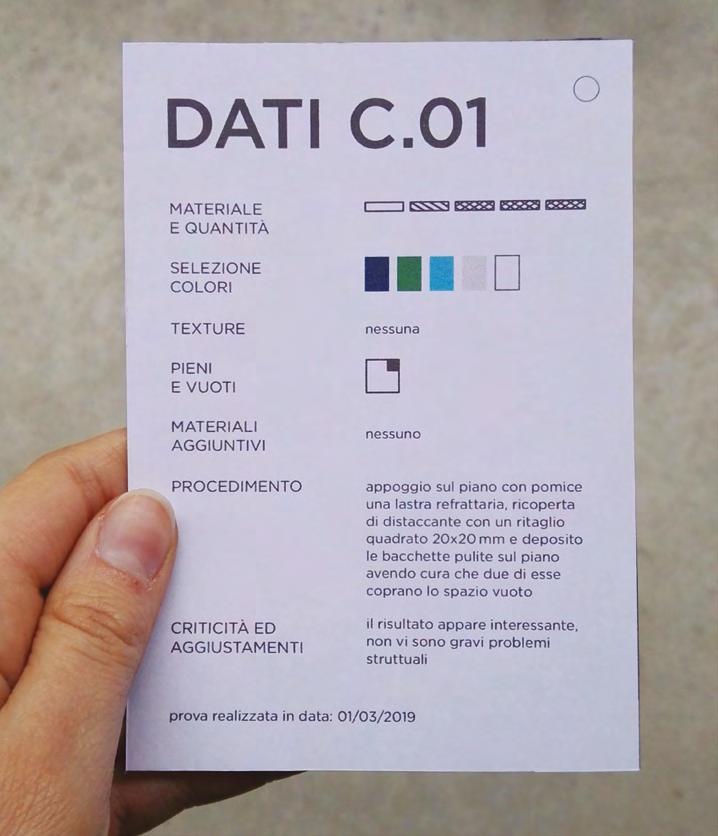
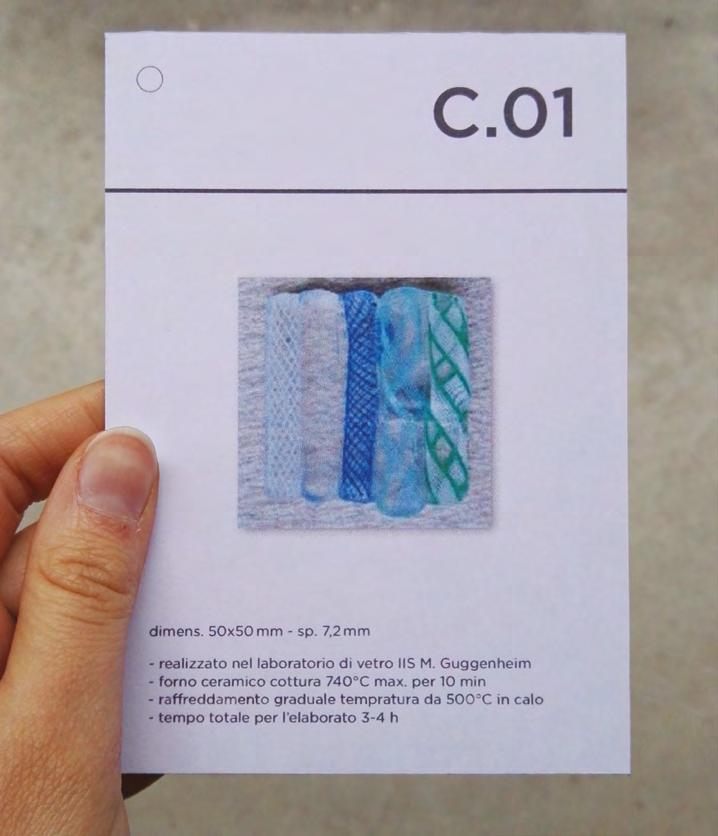
Fig. 03 Samples. Front: name encoding; technical info; information about the experimentation place. E. Coccato
Fig. 04 Samples. Back: specific information about the sample; more accurate indications to replicate the sample. E. Coccato
Fig. 05 Comparative table. The table indicates with white (higher than 50%), grey (50%) and black (lower than 50%) the 1-1 compatibility between colours of different ranges and it is possible to identify it by moving the cursors specially created to highlight the point concerned by the search. While at the top, above the colours description, the green, yellow and reds signs represent the co-compatibility with the other colours of the same range. E. Coccato
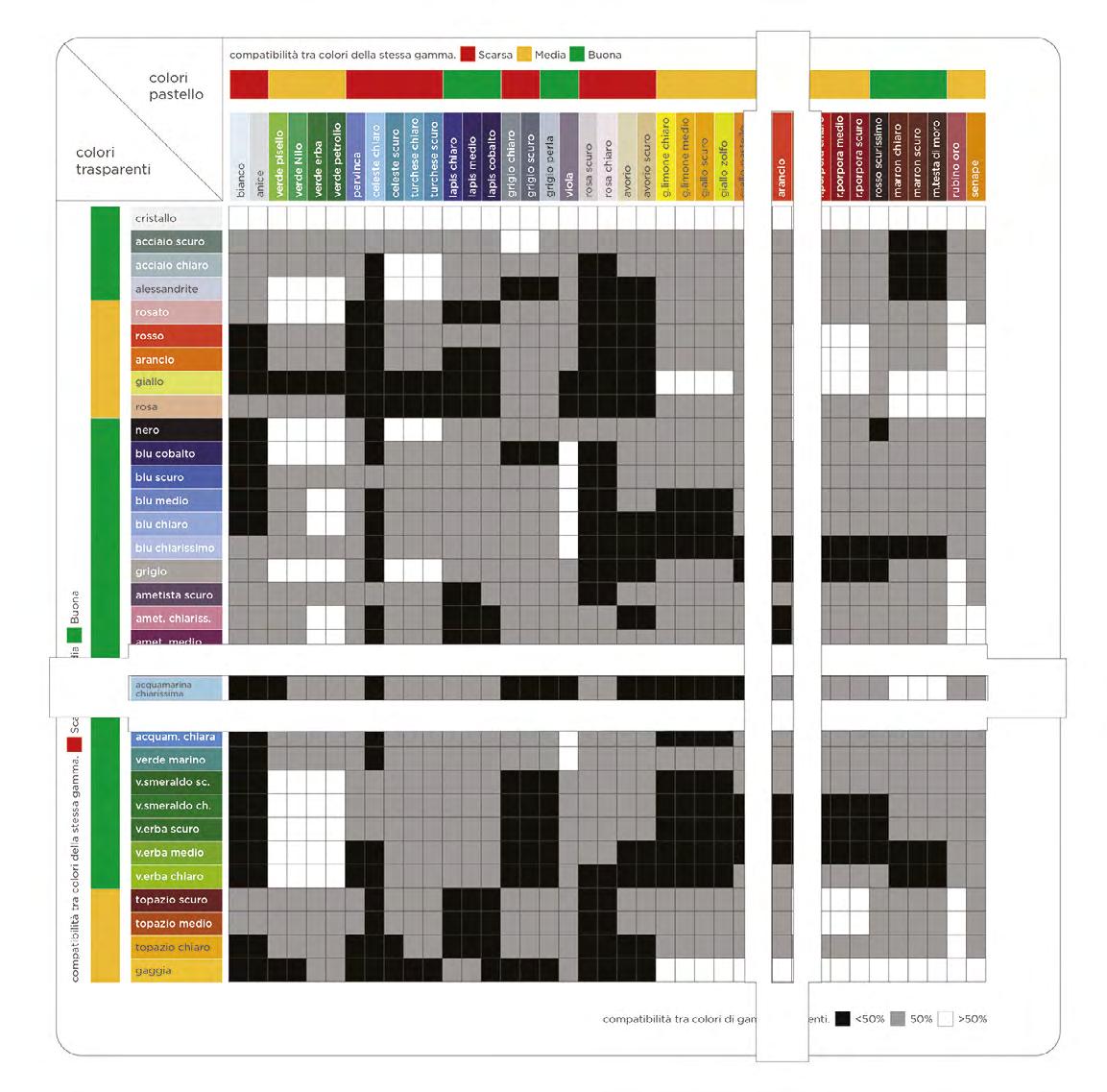
Comparative table
The second working tool was developed to study the combination and compatibility between colours at a chemical level, with particular attention to the response in the melting and cooling phases because, as previously reported, this is a critical point in the recovery of this precious waste. The table present a 1-1 comparison between colours from the transparent range and colours from the pastel range, which can be expanded in the future with the addition of colour scales: alabaster, opalescent, and special; it has been structured in such a way that there is a clear and legible univocal relationship between colours of two different categories and that at the same time allows reading the compatibility between colours of the same range. In the online version, the compatibility information provided can also be enriched with observations by the researcher that emerge as curtains on the selected boxes. This tool is of fundamental importance to provide information on colour compatibility and to allow the researcher or designer to make an informed choice regarding the creation of colour mixes both of the same range and between different ranges (Figure 05).
Textures
The third and last tool consists of a small selection of simple, editable and modular textures thanks to a frame similar to that of movable type printing, which can be created in 3D printing by downloading and modifying the models from the prepared platform. Applicable to the production of textured glass molds.
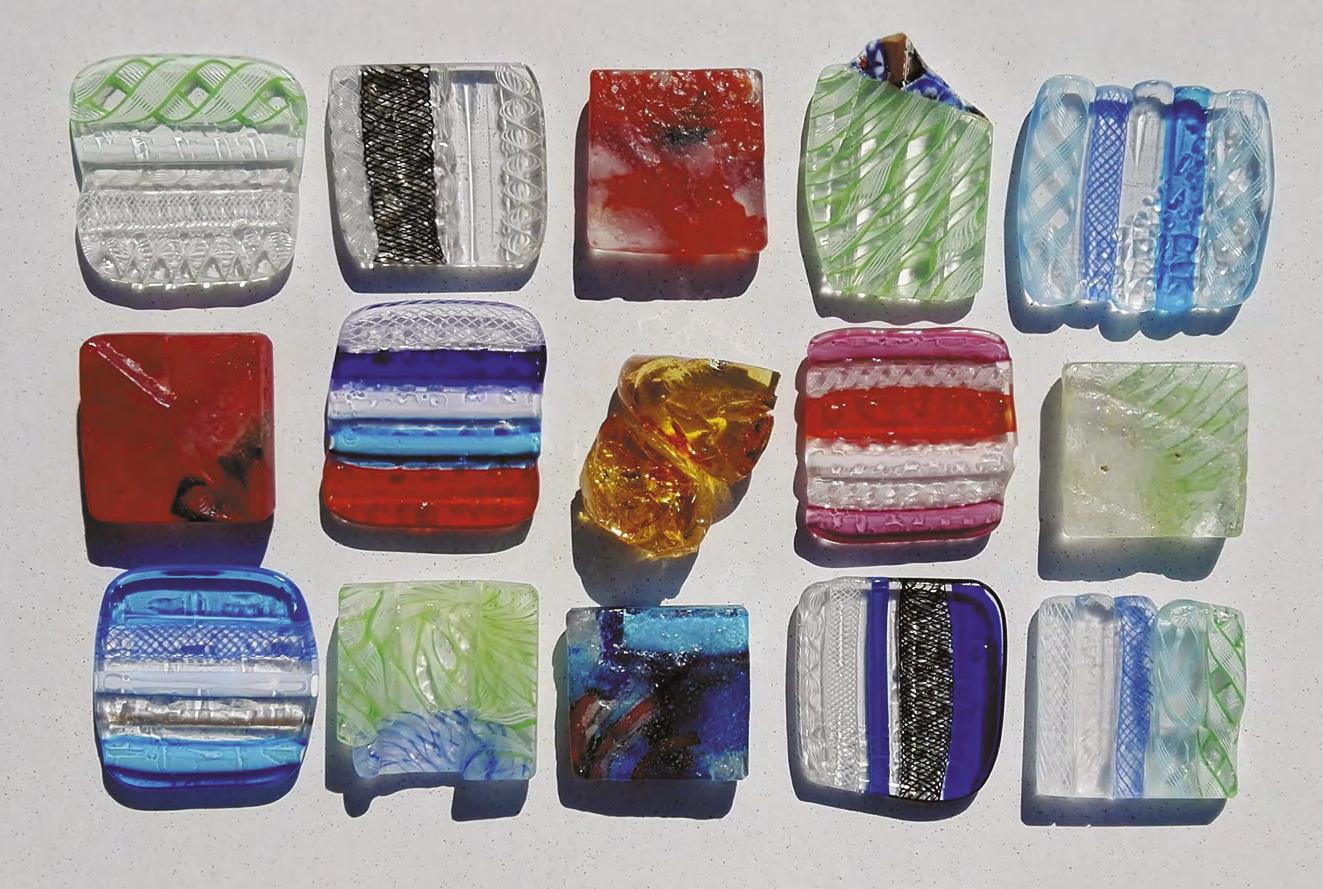
With the use of these tools and the collaboration of the glass master Giuliano Ballarin and the glass professor of I.I.S. M. Guggenheim Jacopo Gioli, it was possible to create a physical sample to verify on a practical level the use of the aforementioned strategies and tools (Figure 06).
Conclusions
The working method discussed in this paper has been set up to operate extensively and for a long time, even in geographically distant areas, as it allows for research and experimentation while maintaining a constant methodology and tools, as well as allowing the continuous expansion and updating of information. Although today the creation of a physical place intended for the recovery, sorting and experimentation with the waste of art glass is not realistic, nothing prevents this hypothesis from becoming a reality in the future, given the potential of the subject investigated. The
research presented is intended as a starting point to start a reflection on the study of the unexpressed potential of this precious waste, stimulating the application of the strategies of the circular economy and design to the study of possible innovative solutions that think about the recovery and enhancement of system-wide material. The hope of the research developed is to create a valid path for guided experimentation with the material, which allows for to structure of recovery strategies even on a large scale, as well as allowing the collection of reasoned and shareable data. As already reported, this research work has also given rise to a thesis, which, precisely because of its potential to generate value in and for the territory, was awarded the first prize at the Laudato Si 2019 competition entitled “Work is a common good”. An acknowledgement by the institutions makes us understand how important it can be to imagine different scenarios for the future of this beautiful waste, putting different actors in synergy and acting from a systemic point of view in the recovery and enhancement of this material.
References
Bompan, E., Brambilla, I. N., (2021). Che cos’è l’economia circolare. Milano: Edizioni Ambiente. Consiglio Comunale Venezia IX Commissione. (2016). Verbale della seduta del 18-07-2016 ore 14:30, Città di Venezia, pp. 3 (online). In http://consigliocomunale.comune.venezia.it/?pag=atti_verb_268 (last accessed May 2022).
Council Directive. (1991). On hazardous waste (91/689/EEC) (OJ L 377, 31.12.1991, p. 20) (online). In https://eur-lex.europa.eu/ legal-content/EN/TXT/PDF/?uri=CELEX:01991L0689-20081212&from=IT (last accessed May 2022).
Cutaia, L., Morabito, R., (2012). Ruolo della Simbiosi industriale per la green economy. Uno strumento innovativo per la chi usura dei cicli delle risorse. Energia, Ambiente e Innovazione. Speciale Verso la green economy: strategie, approcci e opportunità tecnologiche, n. 1. Viterbo: ENEA, pp. 44-49.
Gisotti, M. (2017). Vetro. In Pellizzari, A., Genovesi E. (ed.), Neomateriali nell’economia circolare. Milano: Edizioni Ambiente, pp. 160-163.
European Commission, Directorate-General for Environment. (2020). A new Circular Economy Action Plan. For a cleaner and more competitive Europe. COM(2020) 98 final (online). In https://www.eea.europa.eu/policy-documents/com-2020-98final-a (last accessed August 2022).
Standard UNI EN ISO 17294-2:2016. (2016). Water quality – Application of inductively coupled plasma mass spectrometry (ICPMS) – Part 2: Determination of selected elements including uranium isotopes
Tosi, A. (2004). Murano e il distretto del vetro: aspetti socio-economici. Quaderni. Documenti sulla manutenzione urbana di Venezia, n. 19. Venezia: Insula, pp. 13-19.
Venezia Today. (2016). Un impianto per il recupero del vetro: l’idea per far uscire Murano dalla crisi (online). In https://www. veneziatoday.it/cronaca/vetro-murano-confindustria-ministero.html (last accessed May 2022).
Ancient glass alteration and advancement in active conservation strategies
GIULIA FRANCESCHINA, ROBERTA ZANINIA,B, STEFANO CENTENAROA,BGlass finds application in multiple domains, from the technological field to the artistic one. The study of its durability is central to determinig its potential as a recyclabe and sustainable material capable of replacing several dangerous and polluting constituents such as plastics, particularly in the upcoming era of circular economy.
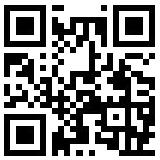
Because of the thermodynamic properties of this material and its high variety of compositions, the evaluation of glass durability and alteration mechanisms remains a challenge. In this work we propose a complete strategy to approach the problem of glass corrosion and stabilization. Combining the results of the macroscopic characterization of archeological glass samples and artificially aged mock-ups, we define a novel silica-based formulation for the consolidation and protection of ancient glass.
A Center for Cultural Heritage Technology - IIT, via Torino, 155, Venezia Mestre, Italy. B Università Ca’ Foscari, Venezia, Italy.
KEYWORDS: WASTE GLASS, RECYCLING, CEMENT
Fig. 01 Three archeological glass samples affected by different types of glass degradation (bottom), list of atmospheric agents rappresented by icons: temperature, water, pollutions, time (top).
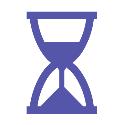

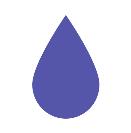
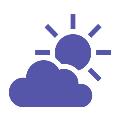

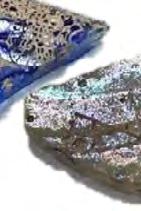

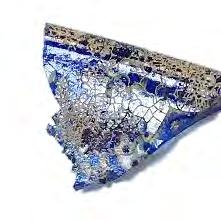
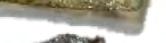


Fig. 02 From the left to the right: protons are not strong enough to break Si-O-Si bonds, promoting the alkalys and alkaline earth ions leaching; hydroxide ions are strong enough to break Si-O-Si bonds; hydroxide ions cause the dissolution of the silica network.

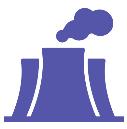
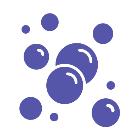
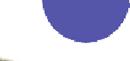


Authorship in Glass Design in Portugal- Four Cycles: from 50´s to Contemporaneity
CLÁUDIA PEDRO SANTOSAThis study consolidates scattered information, complementing the knowledge of the history of glass design in Portugal, from 1950 to now, focusing on authorship in glass design, integrating the profiles of professionals who developed product for Portuguese companies.Most of them closed at the beginning of this century. In the Marinha Grande Cluster, where many of these manufactures were installed, the consequences have been devastating from a social and economic point of view. Our study is a contribution to make the historiography of an intellectual and technical production of a knowledge with more than two and a half centuries in this territory, by transforming matter into products with an identity, that means an antifragile cultural heritage, between history, art and design.
KEYWORDS: GLASS, DESIGN, PORTUGAL
Introduction
Glass has been subject of numerous scientific studies: archaeological, industrial (history andproduction), architectural and construction, from the point of view of engineering materials (perspectives of chemistry and physics), techniques and technologies, production, arts and also product design. About the history of design in Portugal, there is a lack of instalment studies, so our research aims to be a significant contribution to the development of historiographic projects on glass. Thus, we have arisen the opportunity to deepen our knowledge of glass in the Portuguese context, within the framework of this project. This research, Authorship in glass design in Portugal, as the title indicates, focused essentially on the study and contextualization of the life and work of the designers who acted in the scenario of the glass industry in Portugal since the second half of the twentieth century, until now. It was our objective to study, treat and map the authorship in glass design in Portugal, in the second half of the twentieth Century, in order to be known designers, their performance in the glass industry in Portugal and the products they developed.
Four cycles of portuguese glass design
The national glass industryrevealed an intense activity throughout the second half of the twentieth Century, a situation that had repercussions on product design and to some extent was a consequence of the scientific appropriation of this project area in the Portuguese business. Until the mid1970s, glass design was a territory explored by several creative professionals: artisans, artists, plastic artists, designers, architects and, later, by designers, after the first higher courses in design emerged, namely at the Institute of Visual Arts and Design – IADE, ESBAL – Escola Superior de Belas-Artes in Lisbon, ESBAP – Escola Superior de Belas-Artes do Porto and the National Society of Fine Arts – SNBA (Santos, 2015). Glass, due to its physical-chemical properties, as a material, the multiplicity of aesthetic aspects it can offer and the variety of processes, technologies and techniques that can be experienced in it, has always been a matter that all artists and creatives of material culture and in the area of product development wanted to explore. By necessity or by desire, this “matter of invention” (Manzini,1986), of a unique plasticity, offers applications in distinct areas as architecture, engineering, civil and shipbuilding, the automotive industry, optics, some packaging typologies such as bottles and flasks, laboratories, telecommunications, pharmaceutical, applied arts, sculpture and design. In design practice, glass can be explored under an industrial, semi-industrial, handmade or artistic aspect. In the industrial and semi-industrial context, however, there has always been a need, not only to meet project requirements, articulating form
and function, but by social and identity circumstances, among others, there has been a need for, for example, a glass of water to be more than a mere functional container, which leads us to mouth-watering and thus to reach territories of the fine arts, utilitarian arts, decorative arts and crafts with enlarged meanings. In the history of design in Portugal and specifically in the present study, we found that in the chronology covered by this research, in the 1950s and 1960s, there were already forays into the design of glass products, with an authorial aspect.
1st Cycle
From this 1st Cycle of designers, we identify 34 important figures of the national scene, such as Thomaz de Mello (Tom), who triedan introduction of a new aesthetics in the glass industry in Portugal or Bernardo Marques andJorge Barradas who represented drawings or prints with folk themes produced by the factory Companhia Industrial Portuguesa – CIP.Authors like Abel Agostinho, Alice Jorge, Júlio Pomar, Carmo Valente, Maria Helena Matos, Eduardo Afonso Dias, Eduardo Marinho, GéraldGulotta, José Aurélio, Armando Melo among many others who we found, produced the main work of this 1st Cycle of glass designers in Portugal with the meaning of unite industry and arts. However, and after the international oil crisis (1973), which the country also felt, and the social disturbance immediately after 25thaprilof 1974, the Portuguese glass industry, which had ended in its 1st Cycle – with special visibility in the and 2nd Exhibitions of Portuguese Design (1971-73)and in the International Exhibition of Manual Glasswork (1972) – entered into stagnation, which lasted until the mid-1980s (Constantino, 1969).
2nd Cycle
During this period, there was almost no orders for a glass product project by the factories. Fábrica-Escola Irmãos Stephens – FEIS, still intent on bringing art and industry closer together and fostering the artistic aspect in glass production, invited in this decade several glass specialists to disseminate technical knowledge in glasswork, having attributed itself to the 2nd Glass Design Cycle in Portugal the editions of the Young Designer Competition in 1985, by Centro Português do Design – CPD where glass was a material experienced by designers in the Portuguese industry. In 1988, the renowned American glass artist Dale-Chiuly came to Portugal to organize his exhibition at the CalousteGulbenkian Foundation – FCG and hold a workshop at FEIS. The aim was not to develop a product for industry, nor large series, i.e.with the exclusive intervention of the machine and with an underlying aesthetic component, but rather to give rise to creative discourses, in which the authors re-wrote themselves in their projects, arousing the complicity of urban audiences, speaking of themselves and transposing themselves to the matter, for the forms, responding to functions, using the techniques
Fig 01 Jars and solitaire. Design by Carmo Valente. Cristal. FábricaEscolaIrmãos Stephens - FEIS, 1960.
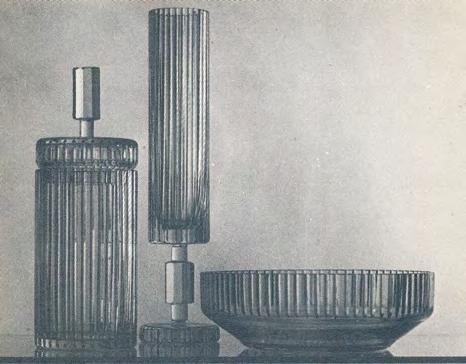
Fig 02 Solitaire, bowl and jars. Glass. Design by Maria Helena Matos. Blowed glass, moulded, chiseled whith metal wheel and polish at acid, 1960.

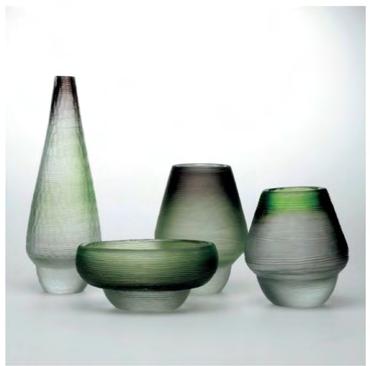
Fig 03 Pieces of de table set II CENTENÁRIO. Design by Maria Helena Matos. Cristal. Fábrica Escola Irmãos Stephens – FEIS. Blowed-molded and lapidated cristal, 1969.
Fig 04 Set of glasses AQUA. Design by Eduardo Afonso Dias. Glass. Crisal Glass. Automatic blowed glass, 1973.

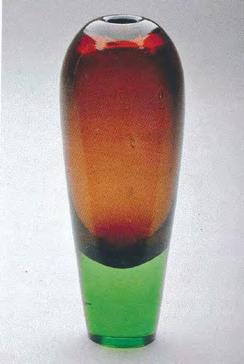
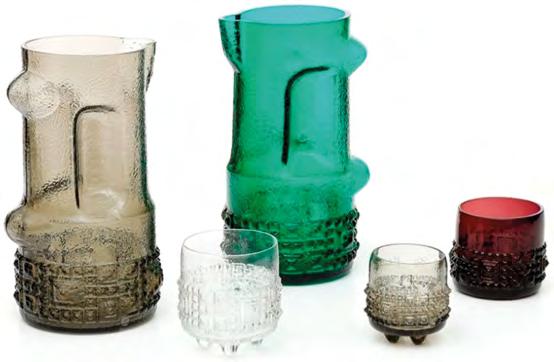
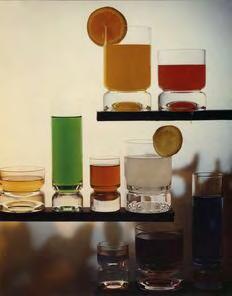
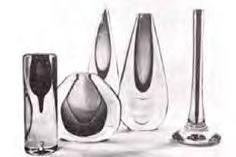
Fig 05 Jugs and glasses ORION. Design by José Eduardo Marinho. Glass. Fábrica Escola Irmãos Stephens, 1971.
Fig 06 SATURNO Lamp. Design by Margarida de Ávila. Glass. Ivima, 1971.

Fig 07 Jar. Design by Alice Jorge. Glass. FábricaEscolaIrmãos Stephens, 1956.
Fig 08 Set of glasses CHROMATICS. Design by Gerald Gulotta. Glass. Crisal, 1971.
Fig 09 Ashtrays/bowls A-12-G. Design by Ascenso Belmonte. Glass. Ivima, 1960.
Fig 10 Two polyvalent pieces: bowl and dish. Prize Fundo de FomentoExportação at International Competition of Manual Glasswork. Design by Vitor Manaças. Glass. Fábrica Escola Irmãos Stephens, 1972.
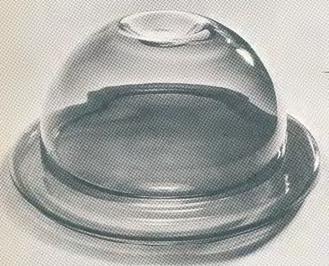
and processes with which they most identified. In a word, freed from the constraints imposed by industry and the tyranny of markets. These pieces, in limited editions, had higher costs and rivalled works of art. Influences of European and contemporary glass production, namely Murano (Italy), Loraine (France), Bohemia, Scandinavia and Eastern countries began to be known in Portugal, sum in an aura of prestige that lacked the national production: the old custom of valuing “foreign junk” – as well saw the author of Repensar Portugal (Antunes, 2006), combined with the belief in the advantages of counterfeiting, facilitated by the visits of entrepreneurs to the reference fairs of glassware and tableware in Europe, enhanced by an unfavourable national conjuncture, make up the sad reality of the national glassware industry. It was then that, along with the international outbreak of author design, Portuguese designers began in the edition of limited series, in parallel with what was already being done in Europe and in the world: with the creation of Studio Alchimia in 1976 or the Memphis Group in 1981, founded by Ettore Sottsass in Milan. Names like Niza Falcão, João Camacho, Eliane Marques or Isabel Dâmaso are part of this cycle. The Memphis group criticized the evolution of the shape of objects only in relation to their function, not subscribing to the indifference by their aesthetic function and symbolic function. Sottsass believed in the search for the identity of objects, from the most provocative, through playful, eccentric and even merely decorative. The aim was to instigate the meaning of products and open new paths to design. In Portugal, in the late 1980s, the Ex-Machina Group formed by young designers Paulo Parra, José Viana and Raúl Cunca emerged in the late 1980s, and in the 1990s, there was a 3rd Cycle of Glass Design, when the IN-FUSÃO factory launched project briefings to designers, having had the participation of Paulo Parra, with his Aqua Chair (CPD-Centro Portuguese do Design, 2000) and Raúl Cunca (Cunha, 2019), with The Scirocco Container, already in an author’s project context. Given the difficulties of dialogue between designers and industry – it is not important to take blame now – and the recent training offer of designers, these young professionals began to partner in glass studios, developing and producing their pieces, also responding to the reduced permeability of the national industry for experimentation. However, most of these pieces, even those that could have longer series, failed to capitalize on their transformative potential, so little designers were with proper distribution and marketing techniques to put their products on the market. Thus, many pieces were only in prototype or were edited in small series.
3rd Cycle
It was notorious, on the part of the glass industry, the attempt to revitalize the sector, which was located mainly in the area of Marinha Grande – where VITROCRISTAL ACE was created in 1994 – and in Oliveira de Azeméis, where
the Centro Vidreiro do Norte de Portugal was installed. Through the use of several strategies, one of them was design – either by the initiative of designers in solo or multi-author projects – as did Marco Sousa Santos (Santos, 2012), through Protodesign, with the project SWR – Sweet Revolution in 1999 (using the blown mould rotated as a semi-industrial basic process of product development), or the Project Sangue Branco (whose main concept was from pre-existing laboratory glassware, and exploring their systematic nature, developing lighting objects) – or, either on the initiative of some companies – such as Atlantis factory, through PROJECT 01 in 1999/2000 (Best of 180 Design Products Portuguese, 2003) and Think-Thank (Santos, 2001). This company has submitted invitations to renowned Portuguese and foreign designers to develop glass product collections for everyday use, with unusual approaches to material and design.
In the late 1990s, the demarcated region of Marinha Grande glass was implemented, as if a cluster were treated. RVMG – Região do Vidro da Marinha Grande, with the MGlassbrand, has associated national companies in the sector, following a market strategy towards the active integration of young designers in product development, with the purpose of competing with the main European glass cores, affirming the national glass production. However, few glass processing companies turned the Century without serious financial problems. We note that we have seen the fact that some designers have acted in more than one cycle, since their activity is transversal over time. We highlight the name of the architect Álvaro Siza Vieira who is contemporary in the age to the designers of the 1st Cycle, began the editing of glass objects in 1975, having been inserted in the 2nd Cycle of Glass Design in Portugal, continued to edit glass pieces in the chronology of the 3rd Cycle and these days are still edited in glass series of his own.
4th Cycle
We found an opportunity for research in the study of glass design authors in Portugal in the first two decades of the 21st Century (2000-2020), as they emerge like an extension of the time period covered by our current research and that we are aware that there are works of designers/authors to historiograph, according to a summary mapping that we carried out, as well as the existence of scattered bibliography to be consulted. There is a new wave of designers/authors of glass design in Portugal, whose performance has taken place in the last two decades. One of the projects is Glass Care (Almeida, 2020) carried out by the Gallery Off Portugal, and in agreement with VÍCARA, an author design editor and publisher, based in Caldas da Rainha and CENCAL1, in Marinha Grande, having as one of the mentors, Paulo Sellmayer product designer, including glass products. In this event,
Fig. 11 ÁGUA Chair. Design by Paulo Parra. Glass. Molded by slumping technique. In-fusão, 1998.
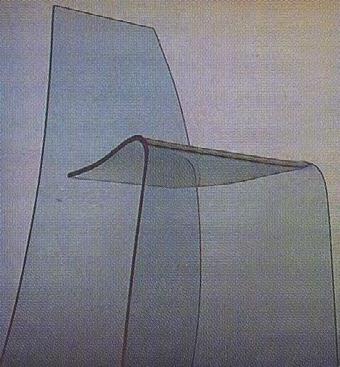
Fig. 12 SIROCO Container. Design by Raúl Cunca.Glass. Molded by floating/slumping technique. In-fusão, 1998.
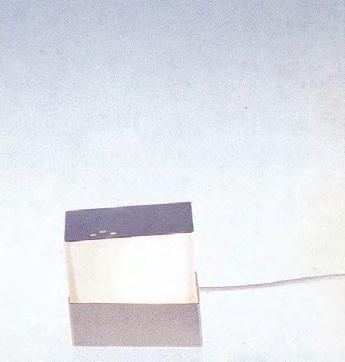
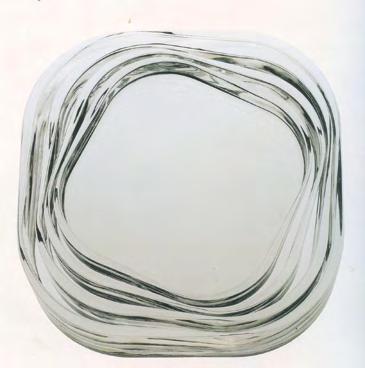
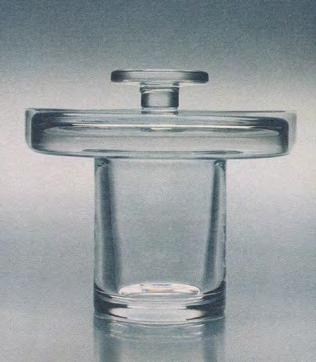
Fig. 13 Glasses bowls/flutes. Design by Eliane Marques. Cristal. ATLANTIS – Cristais de Alcobaça, 1998.
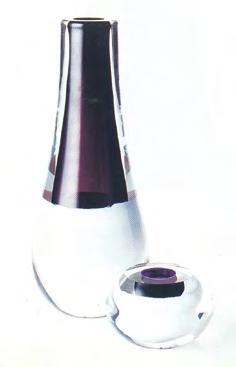
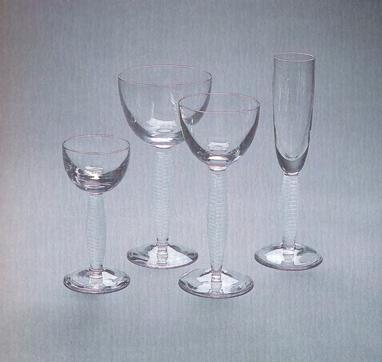

Fig. 14 Container and centerpiece PROJECT 01. Design by Hugo Amado. Cristal. Vista Alegre Atlantis, 2000.
Fig. 15 Set of bowls- PROJECT 01. Design by Filipe Alarcão. Cristal. Vista Alegre Atlantis – VAA, 2001.
Fig. 16 Jar and glasses. STANDARDS MGlass. Design by Fernando Brízio. Glass. Canividro, 2001.
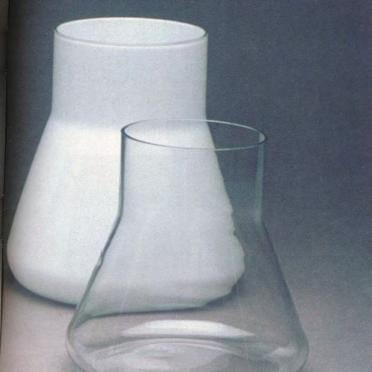
Fig. 17 Jarras 2,3,4. Design by Architect Álvaro Siza Vieira. Glass. MSI, 1996.
Fig. 18 Ashtrays HAVANA. Design by Architect Siza Vieira. Glass, MSI.
Fig. 19 Set of vases and bowls BUBBLES COLLECTION. Design by Paula Lomelino. Glass. Vetricormglass, 2000.
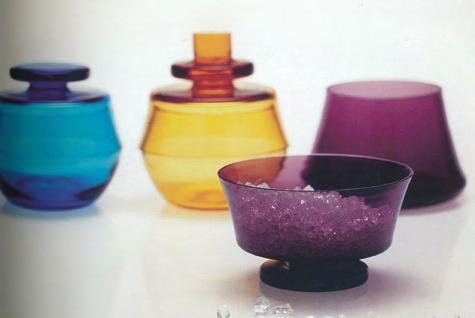
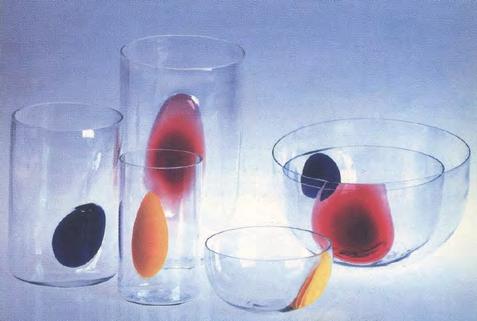
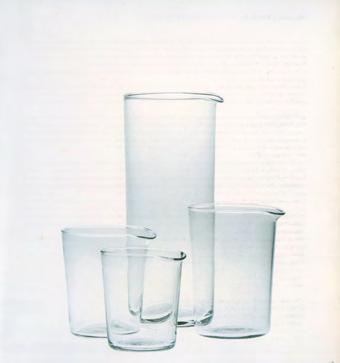
Fig. 20 Set of bottle and glasses FUNNY TOUCH. Design by Ana Flôrand Carla Mendes. Glass. Marividrosmglass, 2000.
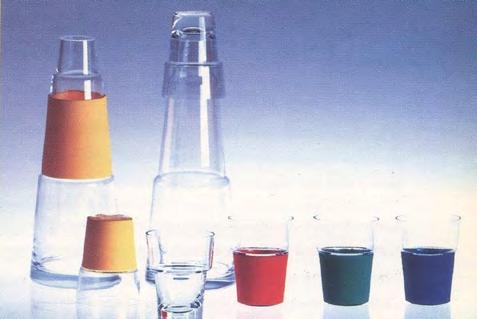
Fig. 21 Bowls/containers REVERSE COLLECTION mglass. Design by Cláudia Pacheco. Glass. IVIMAmglass, 2002.
Fig. 22 Vases MANHATTAN TOWERS. Design by Margarida Garcia. Glass blowed into metal. Marividrosmglass, 2000.
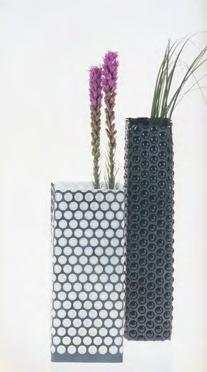
Fig. 23 Jars, vases, bowls and Solitaires REVERSE. Design by Cláudia Pacheco, Margarida Garcia e Paula Marques. Vidro. IVIMAmglass, 2000.
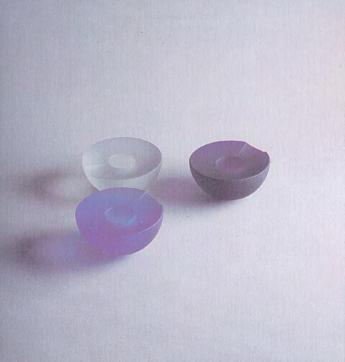
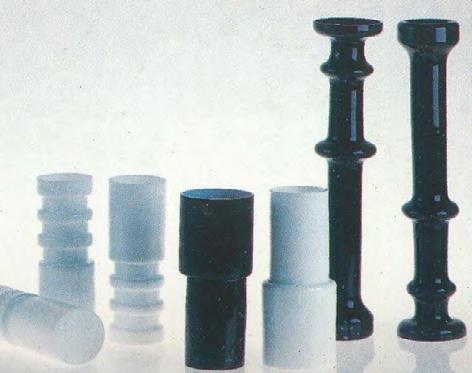
Fig. 24 HYBRIS Jar/vase. Design by Alda Tomás. Ecologic glass. Jasmim/Vicrimagmglass, 2000.
Fig. 25 Lampstand GLASS AN IRON BLOCK. Design by David Matos. Glass. Tosel/Tovilmglass, 2000.
we could know the projects of Samuel Reis, an emerging Portuguese young designer who is inspired by nature as we can see in the CERNE collection (Silva, 2015), whose connection with the conceptions of Scandinavian glass (Design: The Definitive Visual History, 2015), we cannot fail to do and we also considered as an incentive for study and research, the work of designer Vitor Agostinho, which we have classified as integrated into the 3th Cycle of Glass Designers in our work, although he continues to design and develop glass products, as it´s the case with his project Mutants Moulds and the Polyhedron collection. In this sense, we recommend the development of dissemination and awareness-raising actions, identical to the afore mentioned ones, on the social and economic importance of preserving and promoting the development of the glass industry in Portugal. In this new century, we found multi-author glass design projects that emerged in Portugal, as was the case of White Blood created by designer Marco Sousa Santos (Santos, 2012), or Standards projects (Bártolo, 2014) Workshop 25 cl or Women in Glass for Mglass.
Conclusion
With this work, we sought to contribute to the consolidation of the histography of design in Portugal mapping design authorships and Portuguese glass. We believe that in order to act in the present and prepare for the near future, it is necessary to know the past. In this sense, through a scientific method based on direct observation, questionnaires and interviews carried out, we mapped a set of authors and their projects, in order to categorize and group them into four chronological cycles characterized by techniques,period of glass product development. Factors such as competition from glass from eastern European countries (at lower costs), the implementation of large areas (which sell European glass and offer quality products at reduced costs), the lack of formal, conceptual and aesthetic identity ofPortuguese glass, the high energy costs in Portugal (gas and electricity), the absence of recognition of design as a projective discipline by most. Portuguese entrepreneurs, the meager recognition of the work of glass masters and workers, the unsatisfactory working conditions, with harmful effects on health and their low salary remuneration, the resistance to the industrialization of a sector with a very strong artisanal tradition, the lack of project culture, the scarcity of good communication between entrepreneurs, designers and glassware, the difficulty in predicting trends and developing products beyond the most routine horizon are some of the multiple factors portrayed throughout this work and which undertake the current destruction of a significant part of the industrial fabric of glass in our territory in the first two decades of the 21st Century. There will be a place for the author’s design, and this is certainly one of the key paths to follow, so that we can see a
possible plan of revitalization of the Portuguese glass industry assured. At the conclusion of our study, we found that only the companies that were able to adapt, applying design strategies or those that bet on investing in the development of high consumption products, were able to survive – such as the processors/producers of packaging glass (automatic domestic glass, bottlery), glass for scientific, optical, civil construction, components for the automotive industry and for electricity producers. With regard to the general objectives that we set at the beginning of our work and which consisted of knowing and making known in glass design in Portugal, from 1950 to now, we consider that we met the objectives envisaged, although we were already aware of some authors of the 1st , 2nd and 3rd Cycles of Glass Design in national territory, we have come now and at the end of our research, amplify and consolidate our knowledge on the subject and map it, so that we can easily make it known to those who are interested in deepening these contents. As for the specific objectives of this research, these were initially based on the mapping of design and glass authorship in Portugal, as well as on compulsion of scattered information, preserving and rescuing from oblivion a unique material and cultural heritage, conceived by the particular and multifaceted authorship in Glass Design since the second half of the twentieth century in Portugal, until now. Thus, we understand that this planning was carried out by us designed, and we produce theoretical information complemented by graphic and visual information that helps to know the authorships in glass design in Portugal that allows more immediate interpretation of the context of the historiography of glass design, in the 2nd half of the twentieth century until now in Portugal, as well as the current and subsequent theoretical production, thus preserving the material and cultural heritage of Portuguese glass design. We consider that the mapping and study of authorship in glass design in Portugal, from 1950 to nowadays, is a fundamental contribution to knowledge and particularly to the Portuguese History of Design. We leave open the suggestion that one of the possibilities of re-industrialization of the glass sector could be the association of companies of the Table Row, to develop new products, including glass with other materials, which combines tradition with innovation and high added value, in which it could be the designers to develop an awareness campaign, to these companies, for this need that could be of common interest.
References
Almeida, T. (2020). Design Glass Objects: The Portuguese Panorama. Arts, 9, p. 79.
Bártolo, J. (2014). Pequena Históriadas Exposições de Design em Portugal (ca. 1990-2010). Lisboa: Ed. Camões. Best of 180 Produtos de Design Português (2003). CPD-Cent. Lisboa, Portugal: CPD - Centro Português do Design.
Carvalho, P. (2019). Pop & Tutti Frutti: O Vidro Em Portugal Nos Anos 60 et 70: Colecção Pedro Moura Carvalho: Portuguese Glass in the 60s et 70s: Pedro Moura Carvalho Collection. Marinha Grande Portugal: Museu do Vidro.
Constantino, J. (1969). Algumas Considerações Sobre a 1a Exposição de Design Português. Lisboa: Binário.
Costa, D., Martins, J.P.(2003). Manual de Referênciapara o Design no Sector da Cristalariada Marinha Grande. Edited by Atelier Daciano da Costa Arquitectura e Design.
Coutinho, B., Souto, M.H. (2017). Ensaio Para UmArquivo: O Tempo e a Palavra: Design Em Portugal (1960-1974) = Rehears al for an Archive: Time and Word: Design in Portugal (1960-1974). Lisboa: CML MUDE - Museo do Design e da Moda Colecção Francisco Capelo.
CPD-Centro Português do Design, (ed.) (2000). O Tempo Do Design: Anuário 2000 - Ano Oito - N. º21/22. Lisboa Portugal: CPD-Centro Português do Design.
Cunha, R. (2019). Raul Cunca: Design Para a Vida= Design for Life. Castelo Branco: CâmaraMunicipal de Castelo Branco. Dias, E., Pinto, C. (2014). O design possível: 50 anos de profissão / Eduardo Afonso Dias. Lisboa: MUDE - Museu do Design e da Moda.
Exposiçāo Vidro Manual (1972). Hand-Made Glass Exhibition = HandglassAusstellung = Exposition Verre-Main. Lisboa: Grémio Nacional da Indústra Vidreira. Frederico, D. (2007). Os Trabalhos de Alda Tomás. Suplemento Ípsilondo Jornal PÚBLICO de 03.08.2007.
Instituto Nacional de Investigação Industrial (1973). Catálogo da 2a Exposição de Design Português. Lisboa: Imprimarte S.A.R.L. Instituto Nacional de Investigação Industrial (1971). Catálogo da 1a Exposição de Design Português. Lisboa: Imprimarte S.A.R.L. Matos, M. (1959). Exposição de Vidros M. Helena Matos. Lisboa: S.N.I. Santos, R. (2015). Design português. Vila do Conde: Verso da História. Santos, R. (2014). Históriado Design em Portugal entre 1974-2010. CAMÕES: Revista de Letras e CulturasLusófonas, n. 23, pp. 37-50. Santos, R. (2004). Vidro e Cristal Portugueses Contemporâneos. Lisboa: Arte Teoria. Santos, R. (2001). Vidros e Design: Carmo Valente. Arte Ibérica. Lisboa: Editora Arrábida. Santos, R. (1995). Design e Decoração: 1900-1994. Históriada Arte Portuguesa (Dir. Paulo Pereira), Círculo deLeitores, pp. 492-498. Silva, S. (1983). Design & Circunstância: Conformismo & Subversão. Arquitectura. Lisboa.
MURANO PIXEL. An experimental and shared research
MARIA ANTONIA BARUCCOA, ELTI CATTARUZZAB, MATTEO SILVERIOCThe paper describes the motivation, approach and working methodology of a research project financed with POR FSE funds by the Veneto Region. The research involved two universities (Università Iuav di Venezia and Università Ca’ Foscari Venezia), three glassworks in Murano, two network partners (Anteferma Edizioni and WASP) dedicated to innovation and the dissemination of innovation, and three young researchers. A network of professional figures, production realities and interlocutors developed around the figures institutionally involved in the project. These collaborations arose from the desire to share knowledge, production skills and experimentation. Moreover, the research was not limited to Murano but opened up this territory to international debate. This paper proposes the Venice Lagoon as a case study to develop research dedicated to the recycling of materials towards an increasingly comprehensive and complex approach. This is a challenge. The short circuit between the vitality of artisan work and research activity must be triggered.
A Department of Architecture and Arts, Iuav University of Venice, Venice.
B Department of Molecular Sciences and Nanosystems, Ca’ Foscari University of Venice, Venice.
C Co-Founder rehub (Iuav Spinoff) Italy, Murano Venice.
KEYWORDS: CIRCULAR ECONOMY, UPCYCLING, EXPERIMENT
Introduction
Murano and its glass, between art, craft and industry, are part of the lagoon ecosystem: economic weight, historical value, excellence at an international level, a cultural trait of a territory and more. A series of criticalities accumulated over time, before the health emergency and the current international crisis, have undermined the functioning of the dynamics that have characterized work in the furnace over the last hundred (and more) years, dynamics that today seem to be more than suspended, shattered.
Murano glass is a famous Venetian craft product that has long been the subject of study and research aimed at giving it new beauty, variety and value. For this reason, Venetian glass is a challenging topic and it is possible to devise a policy that uses digital technology to overcome the limitation of activities within local processes (Vettore, 2019).
The research addressed these critical issues and challenges by analyzing and planning the reuse of Murano glass waste. This was done starting from a description of the state of affairs and production processes characterizing Murano. In addition, the island’s strong craftsmanship vocation and the capacity for experimentation of the master glassmakers were emphasized.
The research1 made it possible to bring the challenge of the digital closer to the craft and artistic work of the Master Glassmakers. To do this, the digital was defined as much more than a computer or a machine: the digital component of the craftwork was interpreted as the grandiosity of connections made available to develop projects and studies in which experimentation prevails over realized design (Antoniol and Barucco, 2020). The research took the opportunity to experiment and work in the furnace, finding support from three master glassmakers, and dialoguing with Venetian figures and institutions. The research fellows worked in the furnaces of Murano and in the chemistry laboratory of Ca’ Foscari. The research fellows also built contacts with other industrial and industrious realities in the field of experimentation in order to test and prove the new recycling of Murano glass.
The greatest complexities in the development of research are due to the historical period of extreme complexity. These complexities are accentuated by the superficial perception of Murano and the art of glassmaking as realities focused on and immobilized in their own history and tradition. Nothing could be more false. The history and tradition of Murano glass describe first and foremost creativity and experimentation, collaboration and competition between masters, and glassworks striving for the new. To
1 Il progetto circolare del vetro artistico di Murano: come gli scarti divengono risorse per l’industria artigiana 4.0. Codice Progetto 2122-0001-1463-2019. Programma Operativo Regionale Fondo Sociale Europeo 20142020 – Obiettivo generale “Investimenti in favore della crescita e l’Occupazione – Reg. 1304/2013 – Asse I Occupabilità – “Le Strategie regionali per il sistema universitario – Innovazione e ricerca per un Veneto più competitivo” – Delibera della Giunta Regionale n. 1463 dell’8 ottobre 2019.
cope with the crisis, research has been imagined and developed as a meeting place for skills, inspirations and craftsmen. Research offered and still offers knowledge for experimentation, innovators and researchers. Research asserts its role through interdisciplinarity2, the analysis of production processes and the proposal of new circular dynamics for the reuse of waste. Research is made up of many experiments, information and communications developed by very young researchers3. Through an analysis of the opportunities related to the complexity and particularity of the field of investigation, the research proposes a new articulation of the guiding principles of the circular economy, emphasizing the value of experimentation in extreme contexts in order to be able to draw useful generalizations for more widely shared progress.
Moreover, at a time of extreme economic and social hardship, when the Murano furnaces are dying out, practical and theoretical research, experimentation and study have combined in a frenzy that deserves to be highlighted. Some glass masters have opened their doors to researchers and experimented with glass processing and manipulation techniques that do not exclude digital fabrication and additive technologies. Research has probed
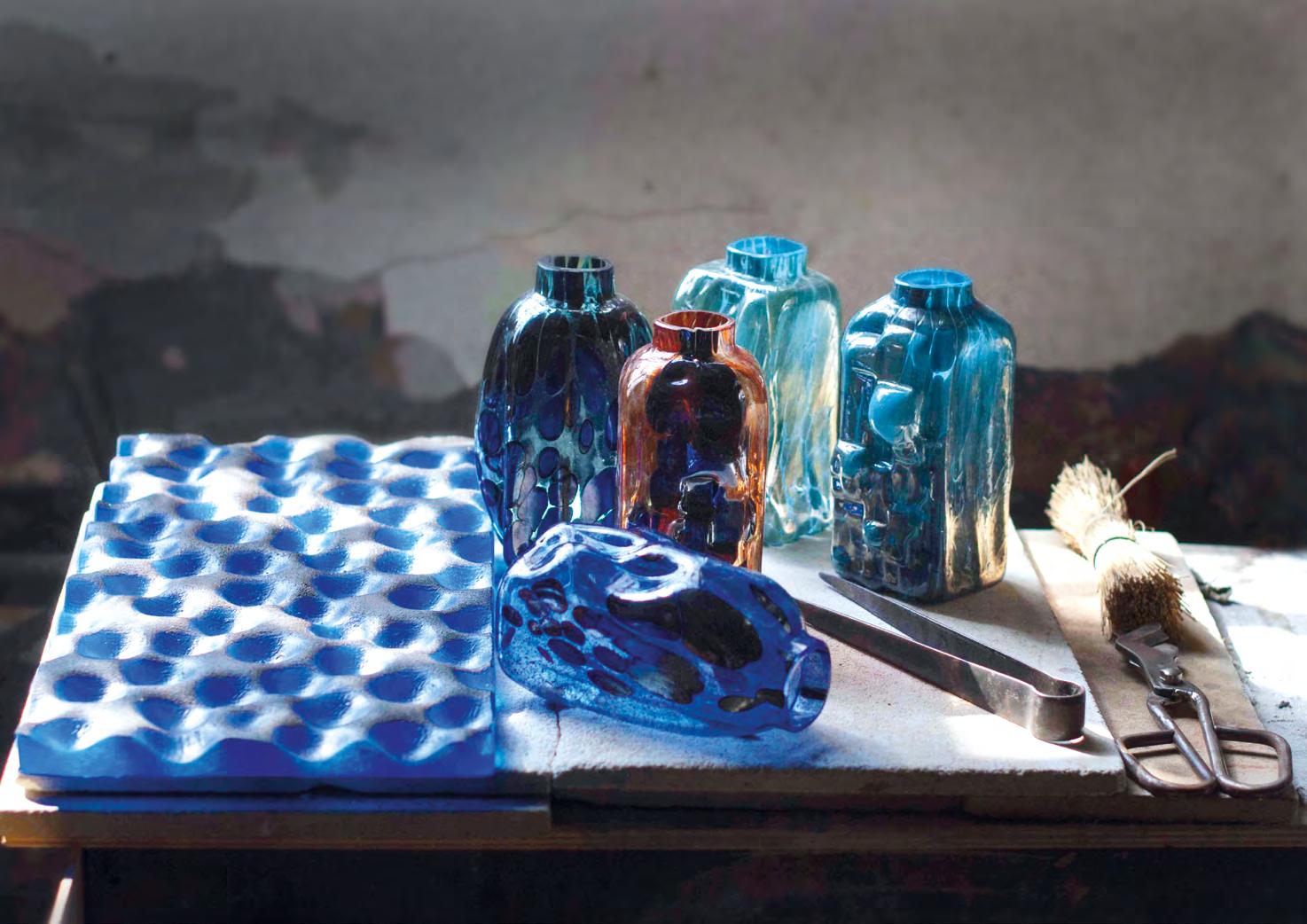
2 The scientific directors of the research are Maria Antonia Barucco (Associate Professor, Architectural Technology ICAR/12) and Elti Cattaruzza (Full Professor, Experimental Physics FIS/01).
3 Paola Careno, Stefano Centenaro, Filippo De Benedetti.
new markets for Murano glass and imagined new declinations of the definition of Master Glassmaker and new life cycles for what is considered waste.
Research responds to the severe crisis with a discipline of work based on flexibility and by exploring an astonishing wealth of usually hidden knowledge and arts. The boundaries between disciplinary areas and sectors are overcome. The research investigates the dynamics of a production and a territory that are related to each other as an ecosystem. Unfortunately, today these dynamics are almost immobile. Murano glass is the result of ancient traditions that are still alive thanks to the work in the furnace, which is made up of attempts, challenges and experimentation shared by several craftsmen. This drives research and awareness that saving raw materials, recycling waste and making the supply chain more efficient are fundamental. Missing the opportunity to innovate, avoiding dialogue with multiple fields of study and denying the directions of Industry 4.0, stopping research as well as shutting down many (too many) furnaces means precluding Murano from the possibility of facing the developments of the 21st Century with quality.
Breakdowns
If inconstancy is the humus for the emergence of communities (Putnam, 1993), it is also the foundation of all innovation and invention. If a network of relationships connects people, skills and interests, if this network has an instrumental character, it can survive all kinds of disruptions because when one node or link is unraveled, others that are different or similar will take their place. The inconstancy of the network and its transformations over time are not a problem; on the contrary, they are the hallmark of a community, which in this way becomes antifragile (Taleb, 2013). The instrumental character, the goal of achieving something, keeps the network alive in its complexity even when its components are missing. And the something that is achieved by virtue of such a system of relationships benefits all those who make up the network and has a value that is greater than the sum of the values perceived by individuals because it is made up of the connections and stories woven from the vicissitudes of which inconstancy is made.
Murano glassmaking has an antifragile history that is not one of gradual growth but is made up of a series of ruptures and crises through which a community, an island of glass, builds its identity. Around the year 1000, glass was already being made in Venice with identifiable techniques and results; it was the growing complexities and fluctuating fortunes of the glass industry that gradually established its presence on an international level. The profound crisis following the plague of 1630 and the Bohemian glass boom are perhaps the most famous crises: Murano resurrected and affirmed its value by displaying new complexities and virtuosity in glassmaking. The postwar period also profoundly marked Murano: of that time we remember the
experiments conducted with architects and designers as well as the ancient techniques studied, tested and re-proposed to become a characteristic feature of the glassworks that are still internationally renowned today. Hybridities, exchanges and currents of study, work, information and experimentation are being severely tested even at the beginning of the 21st Century: surveys by the Promovetro Consortium report on the crisis, the reduction of employees and the fragmentation of large companies into small family businesses (Centro Studi Sintesi, 2015). It is not difficult to find a connection between these trends and the economic crisis of 2008, which caused the decrease in purchasing power of many customers (Centro Studi Sintesi, 2015). Added to this is the pandemic and insane island status that has imposed on Murano (and Venice as a whole, as on many other cities around the world) an absolute isolation to mitigate which the power of the internet can only offer some remedy and, in a few lucky cases, open some doors to future prospects.
Moreover, the excellence and particularity of the workmanship performed in Murano do not escape the evolution of workplace safety and pollution regulations: in 2001 the toxicity of siribites was recognised (ECHA, 2021a), in 2014 the use of diarsenic trioxide was banned, and in 2018 the use of cadmium was banned (ECHA, 2021b). Three constraints have led to the discontinuation of processes that characterize Murano glass: it is no longer possible to produce glass beads, it becomes more difficult to produce opaline glass, and it is no longer possible to reproduce the chromatic richness of warm-coloured glass and the uniqueness of the ruby-red color.
Despite all this or, more correctly, precisely because all this has happened and is happening, Murano designs and experiments to amaze again. The shift from industrial (capital-dominated) to digital (information-dominated) modes of production demands a radical change in the relationship between the production system and knowledge (Vettore, 2019). This transformation also involves (or overwhelms) small industries and workshops in Murano. Moreover, the aforementioned environmental constraints together with new socio-economic dynamics are pushing towards a renewal of the systemic structure of artistic glass production. But in a world rooted in tradition, it is not easy to make room for new and increasingly indispensable concepts, such as the emergence accounting method to assess the environmental sustainability of Murano furnaces in the production of colored glass (“Emergy” Accounting method) (Spagnolo et al., 2018).
The information and easiness in managing the flow of communication between distant places creates a series of short circuits and consequent wonderful sparks of experimental craftsmanship. Murano is connected with external glass industries (which until a few decades ago were only considered competitors), and promotes international events that attract operators from all over the world. An example of this is The Venice Glass Week, an international festival organized by Promovetro, Consorzio di tutela del Vetro
A. BARUCCO, CATTARUZZA, M. SILVERIOartistico di Murano, Fondazione Cini, Fondazione Musei Civici di Venezia and Istituto Veneto di Scienze Lettere ed Arti. Since 2017, The Venice Glass Week has brought new life and energy and offered pretexts for transgressing the practices of established production processes. At the first edition, a group of young designers promoted a “new technology education” (Silverio and Frison, 2017) during which six master glassmakers were joined by six designers with skills in 3D modeling and the use of digital fabrication tools. Three months of experimentation produced works, aroused the interest of many and won important awards.
The AUTONOMA 2020 award was won by the Touch-Me collection (Silverio+Bullo), which is the result of research aimed at subverting the perception of glass. The glass objects in this collection can be continuously transformed and manipulated. The glass used for Touch-Me is waste from other productions and the various glass parts are connected by a polymer matrix. They are fully reversible objects, designed under the banner of the circular economy.
Also ‘Vi – The divine chandelier’ by Maestro Fabio Fornasier is a work dedicated to the reuse of glass waste: he forged a bottle-green chandelier by reusing 180 Franciacorta wine bottles during a performance organized by the Lombardy Wine Consortium.
The prototypes realized during the POR FSE research were inspired by these examples. They are all realizations that try to combine tradition and innovation and that propose the reuse of glass scraps to develop new products, even for sectors other than those that are the normal reference for Murano art glass companies (Barucco et al., 2022). The continuous and mutual training of specialists is the main tool to develop these innovations, equally important is the trust between the people involved and the sharing of knowledge.
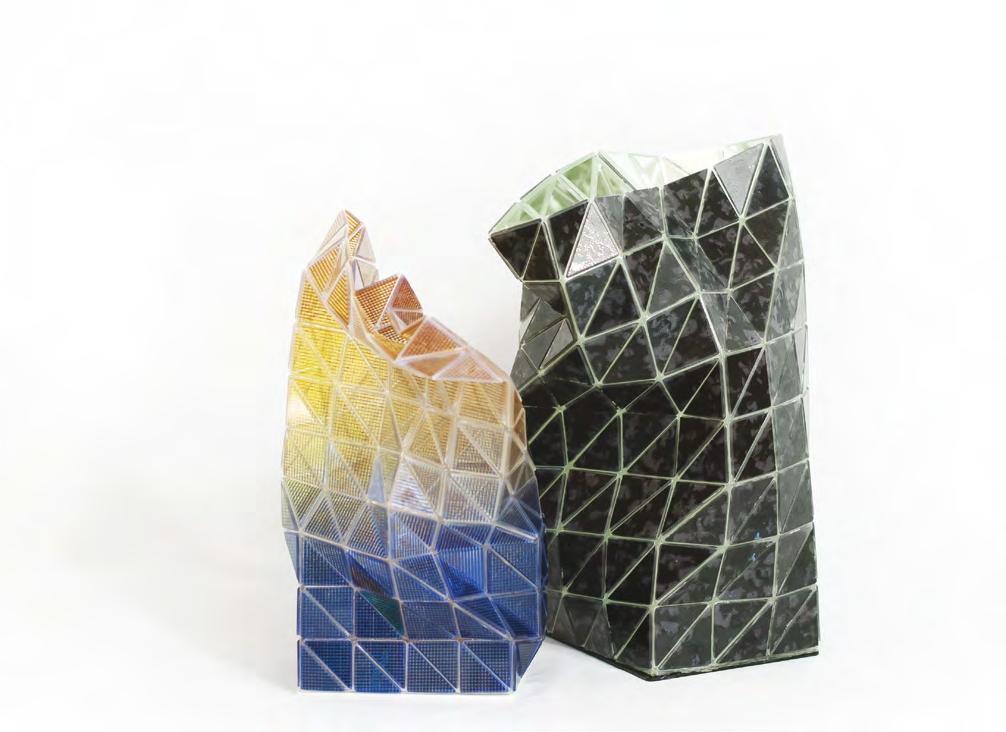
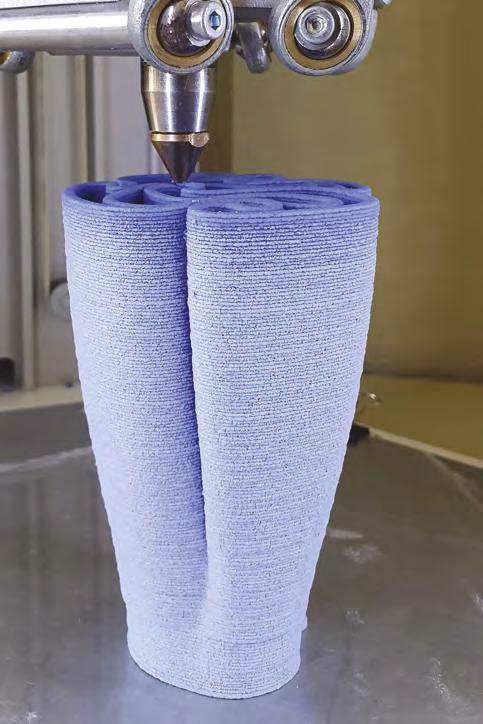
Fig. 02 Vero2. M. Silverio, rehub.
Fig. 03 Touch me. M. Silverio, S. Bullo
Continuity
The second lives of what is generally regarded as waste can be categorized according to the quantity and type of waste materials as well as possible regeneration, valorisation, recycling or reuse. In line with this assumption, the Ellen MacArthur Foundation describes and subdivides materials into four categories:
• old glories. Materials that are easily recoverable and have a good level of recyclability. These are materials that have already undergone recycling routes but often have the disadvantage of losing quality. Example: paper;
• materials with high potential. They are available in large quantities but lack systematic solutions for their recycling. Example: polymers, recycling changes their quality and purity;
• diamonds in the rough. Materials with great potential but with life cycles that have not yet been fully exploited. Example: by-products of manufacturing processes await technological innovations for their reuse;
• future successes, such as materials with very long use cycles or biobased materials: these are materials that can improve productivity.
The research described in this paper makes its contribution to this organization by proposing a fifth category of materials:
• case studies. Cycles and recycling that are exemplary but cannot handle large amounts of waste or that do not solve problems related to high pollution levels.
Murano glass is a challenging material, for which no one demands recycling, also because it is the output of ancient craftsmanship and linked to the creation of works of art of world-class excellence. Like Murano glass, other challenging materials exist and often have the merit of representing the antifragile character of the communities in which they are produced or used and/ or discarded. Marble dust from the Carrara quarries is being experimented with in the textile industry. Part of the surplus milk produced in Italy becomes cloth. Rice chaff from the Novara and Vercelli plains is used in construction with great success. This list of case studies does not break down large levels of pollution or massive amounts of waste. The value of all these experiments is not measured by quantities. Certainly they are man-hours, they are machines, they are research, they are enterprise, work and satisfaction, but above all they are examples. Examples of an inventiveness capable of demonstrating that everything can be rethought from a circular economy perspective.
It is often wrongly implied that there are exceptions to circular economy schemes. But a paradigm shift will only be possible if everyone is involved in the new and future dynamics of material circularity. To dispel any doubts, some research must be devoted to clearly recognisable challenges. The examples confront the history, art and tradition of emblematic contexts. They are materials that must be described because all products and processes must work together to meet the challenges of sustainability.
A. BARUCCO, CATTARUZZA, M. SILVERIOTranslation
The research described attempts to bring together study and knowledge, research and art. On the one hand the tradition and culture of glassmaking, on the other an interpretation of a famous definition of circular economy. Blown glass, lume working and leaded glass are ancient processes and the language describing their practices, intentions and outcomes is also ancient. A very different language from that of scientific research. A very different language also from the communications and slogans that speak to the world about sustainability. This research work is also made up of patient translation of specialized languages and translation of the results of the work into useful communications for a wide audience.
The research measures quantitative, qualitative and descriptive variables to assess waste in art glass. The research highlights some aspects of the contingency in order to develop an environmental policy that is consistent with the international landscape and, at the same time, able to offer a new contribution and a different point of view. The research analyzed the production of three glassworks4 producing stained glass, beads and blown glass. Discards were collected and processing was surveyed for two months. Production activity standards were recorded in order to produce analyses and abstractions useful to produce data describing one year’s activity.
A first datum is the ratio of the quantity of waste glass in relation to the quantity of glass produced (glass useful to be put on sale): 50% of the glass that is processed is discarded. The glass masters had never considered this comparison and did not think of discarding so much glass. There are no periodic measurements of the scraps of Murano glass, but there are heaps of scraps, beautiful and colorful masses of material. This material has an initial cost when it is purchased from glass factories in the form of cotisso, rods or glass plates; it has a very high processing cost because it is subjected to complex transformations by highly specialized hands; it has a considerable disposal cost because it is practically impossible to divide the waste by color.
Thanks to the available data and to the count of the glassworks in Murano, the quantities and types of waste collected have been multiplied and generalized. Each year Murano produces 392 cubic meters of waste glass in various forms: glass drops, bites of rods, broken beads, portions of plates, rolled glass, rollers, glass powder, and generic blown glass processing scraps. A useful measure to understand the total volume of waste glass is its translation into a typical Murano product: 392 cubic meters of glass can allow the creation of 31,250,000 glass goblets. Equally effective is measuring the work required to transport the waste glass. Murano is connected to the mainland only by
4 Vetrate Artistiche Murano (master glassmaker: Stefano Bullo), Costantini Glassbeads (master glassmaker: Alessandro Moretti), Nicola Moretti Snc (master glassmakers: Alberto Moretti and Nicola Moretti).
boats: 392 cubic meters of glass must be moved from Murano to the landfill with 91 fully loaded 11-ton boats.
A range of possible uses for waste glass is identified through the organization of a list of case studies and experiments. A product or prototype can only be included in this list if it enhances the value of waste glass: it must characterize the final product, it must be qualitatively appreciable and it must be descriptive of the product itself. This requirement stems from the desire to valorise Murano glass waste. Some scraps, with their particular colors and shapes, tell of complex and unique workmanship. Other scraps are unique because they are the result of processing that is no longer done (and probably never will be done again): this is the case of the small beads of conteria that do not have a hole in them, that cannot be sold as pearls, and that are discarded and awaiting new uses, and are now closed in sacks and crates and in storage.
Murano glass scraps are very characteristic, they are the result of workmanship and craftsmanship, they contain a small part of a great story. In an era destined to build a future by virtue of the circular economy, these scraps can take part in a history made of prototypes and, perhaps in the near future, even new products of refined quality.
Enhancement
The research, following the path described, becomes a place for the development of a community dedicated to innovation, invention, and making and remaking with the cycles and recycling of art glass. Not only that, this research work is ‘resonant’ (Antoniol and Barucco, 2020): it has increased the intensity and quality of the relationships and exchanges between the subjects involved.
In order not to miss the confrontation with the material culture of Murano, the team of researchers worked in the glassworks as apprentice craftsmen. The glassmakers’ knowledge was hybridized with theoretical study, data analysis and chemical, mechanical and physical analyses carried out in the laboratories of the Iuav and Ca’ Foscari universities.
Among the innovations with which research has been confronted, one in particular is today fulfilling its most flattering promises. VERO2 is a process for manipulating Murano glass waste developed by Matteo Silverio. The waste becomes new raw material: a malleable paste that can be cold extruded using a fluid-dense 3D printer. With this process it is possible to produce new objects that, after a brief passage in the oven (at a temperature of around 700°C), sinter and lose the non-glassy part of the initial compound. The end result is 100% Murano glass.
This new technique for manipulating glass does not aim to replace the work of the master craftsman but seeks to enrich it with new features, first and foremost the reuse of waste. 3D printing also makes it possible to create objects with complex geometries, which are impossible to achieve
A. BARUCCO, E. CATTARUZZA, M. SILVERIOwith traditional glass making techniques. For example, with this process, it is possible to create decorations that can be applied to the artifacts of master glassmakers, because they are made of the same raw material. VERO2 is therefore not only a new way of producing objects with a view to the circular economy, but also and above all a new tool at the disposal of Murano’s master glassmakers.
VERO2 started out as an experimental process and is now the knowhow behind rehub, the innovative start-up founded by Silverio that recently became an IUAV spin-off. After a year of research to optimize the process, a printer was designed and built with an ad hoc extruder: a patent application was filed for these inventions in May 2022. The extrudable glass paste, on the other hand, is covered by trade secrets.
Research, experimentation, dialogue between different skills and in-depth knowledge of the material once again prove to be a bridge between the past and the future (www.rehubstudio.com), a tool to make the art of glassmaking astonishing, once again and even more so than before.
References
Antoniol, E., Barucco, M. A. (2020). Tecnologia risonante. In Barucco, M. A., Bulegato, F., Vaccari, A., Remanufacturing Italy. L’Italia nell’epoca della postproduzione. Milano: Mimesis, pp. Xx-yy.
Barucco, M. A., Cattaruzza, E., Careno, P., Centenaro, S., De Benedetti, F. (2022). Murano Pixel. Economia circolare per gli scarti del vetro artistico. Conegliano: Anteferma.
Centro Studi Sintesi (2015). Murano: un’economia fragile? I numeri, le problematiche, le prospettive (online). In https://www. dl.camcom.it/script.aspx?PRISMABIN=1&objectid=c961081f6b594fcd85ae11445acbf6d5 (last accessed August 2022).
ECHA (2021a). Substance Infocard: Cadmium Sulphide (online). In https://echa.europa.eu/it/substance-information/-/substan ceinfo/100.013.771 (last accessed August 2022)
ECHA (2021b). Substance Infocard: Diarsenic Trioxide (online). In https://echa.europa.eu/it/substance-information/-/substan ceinfo/100.014.075 (last accessed August 2022)
Putnam, D. R. (1993). Making Democracy Work: Civic Traditions in Modern Italy. Princeton: Princeton University Press. Silverio, M., Frison, D. (2017). Glass Matters. Catalogo 2017. Conegliano: Incipit Editore. Spagnolo, S., Gonella, F., Viglia, S., Ulgiati, S. (2018). Venice artistic glass: Linking art, chemistry and environment – A compre hensive emergy analysis. Journal of Cleaner Production, 171, pp. 1638-1649. Taleb, N. N. (2013). Antifragile. Prosperare nel disordine. Milano: Il Saggiatore. Vettore, E. (ed.) (2019). Ariffaraffa. Venezia, quel che resta del Centro storico e del suo Artigianato. Venezia: La Toletta.
From industrial float glass to collectible design: the functional light sculptures Baracche, project by artist Paolo Gonzato
BEATRICE BIANCOA, MARINELLA FERRARABIn the panorama of the today Expanded Design, the connection design-craft, is promising in the perspective of the development of Creative Industries and economies in Italy. This paper brings the direct experience of intersection between the industrial and standardised material float glass, the creative approach of artist Paolo Gonzato on this material to create unique light glass sculptures and all the process related to them. It will encompass the qualities of the glass and the specific production process that characterize it, with the possibilities related to its functional features. It will investigate the phenomenon of the creative process that sees the transformation of such material from an architectural –construction element to a unique artwork, realised in a craft environment.
A IED Turin, Italy.
B Politecnico di Milano, Italy.
KEYWORDS: COLLECTIBLE DESIGN, INDUSTRIAL MATERIAL, FLOAT GLASS
Introducing the material
The making process of float glass is an example of industrial and large-scale production. Invented in the ‘50 by Alastair Pilkington and Kenneth Bickerstaff in England, the aim was to obtain flat or smooth sheets of glass without resorting to costly operations to remove abrasions (Pilkington, 1969).
This radical technological change was quickly adopted by the plate glass industry, where it eliminated the labor-and cost-intensive grinding and polishing production phases. Sheet glass was a cheaper product, and its manufacturing process did not require as huge capital investments as were needed in the plate glass industry. However, float glass gradually entered the sheet glass markets as well and finally the float glass process replaced the existing drawing methods (Uusitalo, 2014).
Pilkington’s discovery of float glass forced other glass manufacturers in the ‘60 to switch production techniques almost overnight and the high cost of installing new plant meant that only larger, cash rich organizations could survive. The result has been to increase the concentration of manufacturing power within a small group of companies operating out of the UK, France, Japan, and the US (Taylor, 1979).
Even though the production of flat glass is one of industrial processes at higher temperatures, it represents only 0.65% of emissions industrial CO2 of the EU16 (Glass for Europe 2020), with a 100% recyclable material.
In Italy most of the distributed float glass comes from St. Gobain and Pilkington, as major glass producers in Europe.
The process
The main components used for the manufacture of “Float” glass are, Silica sand (73%), Calcium Carbonate (9%), Sodium Sulphate (13%).
Once dosed and mixed, a certain mass is added to these components of recycled glass, in fragments, to reduce the gas consumption of the furnaces of Merger. The mixture of raw materials, properly dosed in a silo, passes on a conveyor belt and is fed into a five-sided melting furnace chambers where it is brought to a temperature of about 1,200° C.
At the exit from the melting furnace the mass of molten glass is brought to float on the surface of a molten tin bath, at a temperature of about 1,000° C The glass which at this temperature is very viscous and the tin which instead is very fluid do not mix and the contact surface between the two elements is perfectly flat and smooth.
The glass thus forms a “ribbon” of 3.21 m in width with a thickness that it can vary from 3 to 19 mm. The glass leaves the tin bath at a temperature of about 600° C and enters, now in the solid state, in an annealing chamber passing on a series of rollers. This step of the manufacturing process serves
to change the voltages internal allowing that the glass ribbon, made flat, can be cut into plates without problems the two surfaces of the glass ribbon are perfectly smooth and shiny and not need no further finishing.
At the end of the cooling phase, the glass strip is subjected to a series of very strict controls; then it is washed and dried at this point it is cut into “Cast Plates” having dimensions of 3.21 x 6 m (Ferreira Nascimento, 2014).
Brief colouring elements
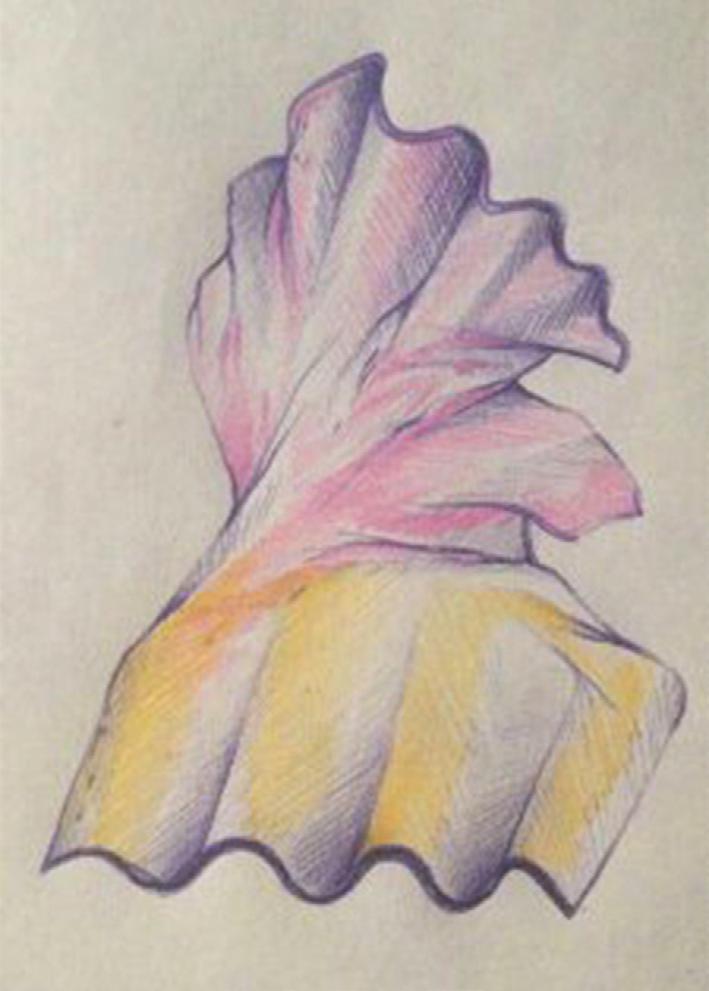
During the process the glass can be treated with minerals and metals like chromium or copper, to give colours to the dough. Iron is one of the most used metals, producing several shades of green – depending on the iron concentration and ion ratio, ultraviolet control, and infrared transmission. Amber colouring is normally used to prevent ultraviolet damages of the contents and is the result of an iron-sulphur chromophore. Highly oxidized glass is an unpleasant yellow green.
Metallic colloids (Au, Cu) dispersed in glasses are the primary source of red glasses. Silver colloids produce a variety of yellow to brown colours. Colloidally coloured glasses have been produced for around 2000 years for art objects and are still routinely used by glassblowers and other glass artists. Other metallic colloids produce either grey to black (Pb, Co, Ni, In, Bi) or brown to black (As, Sb) glasses.

Since the invention of the Pilkington float glass process in the ‘50 enabled the production of float glass with standardized quality, architects and engineers have pushed glass technology for maximizing size and transparency, nurturing a building culture of minimal material presence and maximal transparency in the glass. Meanwhile, multi-coloured glass has been rarely implemented in construction and so in the float process. This is due to the labor intensiveness of the manual crafting process, which results in high costs and non-standardized quality, and the lack of automated methods for manufacturing polychromatic glass at the construction scale. (Giesecke et al., 2022).
From functional needs to aesthetic fruition: the work of Paolo Gonzato on float glass
In 2016 Camp Design Gallery, Italian collectible design gallery based in Milan, founded by me and my former associate Valentina Lucio, participated to the former design fair Operae in Turin, where the gallery was invited to the program Piemonte Handmade. The aim of the program was to connect the figure of the gallery, an invited artist or designer, and a well-known artisan in the productive network of the Turin area.
Paolo Gonzato, Milanese artist, was invited to work with an assigned industrial glass artisan called Cristal King. It was the first time that the artist was called to work such material.
He took confidence with the different types of glasses like the cathedral type or the float glass and the techniques that the artisans use to work it: mostly cuts and assemblage and the thermos-forming through industrial ovens. After several experiences, the option was to use the float glass, thanks to its resistance properties and the possibility to thermos-sculpting it.
The formal and aesthetic research of Paolo Gonzato lies on the contemplation and crystallisation of leftovers and borders, forgotten objects and poor materials. Travelling from Milan to Turin gave the artist the possibility to observe the borders of the cities and notably the metal shacks. Moreover, the industrial environment of the artisan’s factory, gave to the artist the impulse to use exclusively industrial materials for the creation of unique pieces of collectible design: a lightened glass sculpture.
The conceptual process
As aforementioned, Paolo Gonzato’s research is part of an active and daily aesthetic, of collecting and manipulating objects of common use if not waste, exercising an Aesthetic of Existence, as defined by Michel Foucault (1998, p. 27), where “the action of self-creation takes place through the exercise of criticism and care”, in the search for a balance and one’s own order in the world, which
seems to work even in marginal contexts (Lunghi and Trasforini, 2010). In this context Gonzato develops his aesthetic of the forgotten, that includes physical and mental margins, leftovers, to give dignity and beauty to what is voluntary not seen and retained by society. Like Bell Hooks, that defined “aesthetics of existence”, the ability to experience beauty as a form of resistance to social marginalization and the impoverishment of the spirit (1998).
The following text has been written by Damiano Gullì, Art and Public Program Curator at the Triennale Milano, invited by the artist and the gallery to summarise the Baracche project in the occasion of the second solo show displayed at Camp Design Gallery in September 2020.
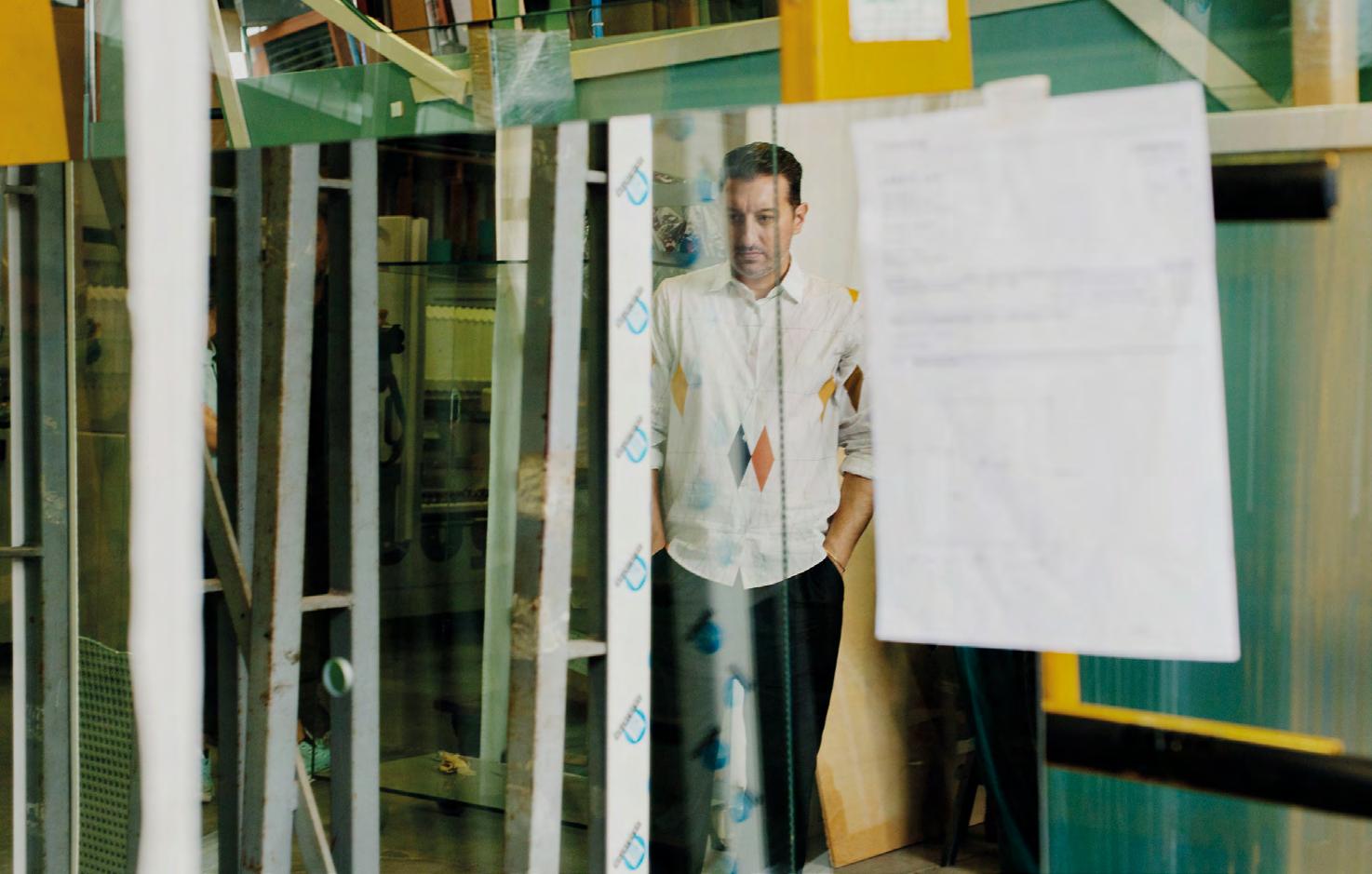
“baracca s. f. [from Catalan barraca (probably pre-Roman voice), through the Spanish]. – 1. Tem¬porary construction, general of wood with metal sheet or asbestos cover, for sheltering people or goods.
In 1906 Giuseppe Ungaretti met Enrico Pea, poet, writer, dramatist, and theatrical impresario, who recently moved to Egypt, with whom gave life to the Baracca Rossa, a marble and timber warehouse that soon became the venue for meetings for an archists and socialists. But not only. Here Ungaretti had the opportunity to get in touch with several intellectuals and writers from all over the world, essential for his educational enrichment.
The cabin is therefore a physical place and at the same time a metaphor for a relational and cre¬ative process poised between anarchy and control, poetry, and rationality. But still with hum¬ble, precarious roots, marked by transience.
Unlike the hut-sophisticated machine-à-habiter (think of Le Cabanon by Le Corbusier), an intellectual shelter, an ideal existenzminimum – the hut conceals, not too subtly, the prodromes of imperfection, imbalance, fragility.
When in 2016 Paolo Gonzato designed the first series of Baracche as part of Operae in Turin – a brilliant dialogue between the designer, Camp Design Gallery in Milan, and the artisan know-how of the Turin glass factory Cristal King – he had a very specific vision in mind: “Instant ar¬chitecture”, “bric-à-brac constructions”.
By carrying out an operation of appropriation and decontextualization (sometimes forcing the technical-executive limits) Gonzato isolates a part of the whole – the corrugated sheet metal constituting the roof of the hut – creating it a luminous body, changing its axis and inclination, making it sculptural. He monumentalizes, ennobles, transforms, and dramatizes scraps and preexisting fragments, initially poor, and translates them into precious glass. This action of recovery, transformation, and transmutation of materials whether paper, ceramic, marble, or glass, in fact – is recurrent in Gonzato’s practice, already evident in one of his first works in 2001, part of the series The Sound of Ego: a bale of hay wrapped in a hot pink satin ribbon. Is it a sculpture of a poor nature in salsa camp? A seat reminding the Straw Chair by Alessandro Mendini from 1975? An ironic fake Christo packaging? Glamor that envelops the bucolic, high and low merge. Cheap and chic, one might say, to take up the name of the famous perfume – almost a claim – by Moschino, surely one of the references of the artist and de- signer for the subversive design approach. Gonzato plays and slides between disciplines and techniques – from art to fashion to design, from painting to installation – while maintaining constant rigor and consistency. He assimilates and makes his own from the lessons of some Italian Masters, whom he loved, also elusive to rigid categorizations and disciplinary hierarchies. In his works the Pontian decoration echoes – and how not to think of the lozenge, an element taken from the costume of Arlecchino, reiterated in numerous paintings and collages by Gonzato – the charm of Pesce’s imperfection, the anthropology of Mendini’s objects, Munari’s aleatory nature, Sot¬tsass’s eroticism and sacredness.
With his Baracche Gonzato outlines an aesthetic of precariousness, marginality – “a smoothie of brutalism and mall ruins, Baracche is the semantic reduction from a house to a caricature”, in the artist’s words that can be placed in an open path from the simulacra of construction sites of the installation L’isola delle rose of 2012 or Achtung! Frisch Gestrichen of 2015. A fascination for ruin and transient that is also found in the recent studies on Giambattista Piranesi merged into the Pastiche series of ceramics of 2020.
With his new Baracche, Gonzato resumes and expands previous research, coming to deal with the type of chandelier to re- semantize it in a goliardic and grotesque key.
Finally, I like to think of a vernacular regional connotation of the expression
“fare shack”, which means “partying”, but also “making noise, confusion”. It is the perfect translation of Gonzato’s work. The chaotic joy of designing.” Damiano Gullì (curatorail text for Baracche 2020, Camp Design Gallery).
Reception, public and market
Since its first show at Operae 2016, the Baracche project received a vivid welcome from the public and the design press. This brought to realise an entire solo show of Paolo Gonzato’s Baracche collections in January 2017 and a second one in September 2020, both at Camp Design Gallery. Moreover, Baracche has been shown in Paris, during the Paris Design week 2020 and at Collectible Design Fair in Brussels both in 2018 and 2020. Among the two collections several commissioned pieces have been created during these years, thanks to the craft approach of the project where every piece is entirely hand made and unique in shape. The reference markets are the collectible design field and the high-end craft market which is composed by a strong niche of private collectors, architects, and interior design studios, on national and international scale.
Craft and handmade design projects like Baracche concern to the collectible design and luxury market as they can provide work and beneficial specialization in the craft sector. Italy has an important craft network to rely on and able to absorb experimental approaches, as we will see in the next paragraph.
Behind the design work
The process for the creation of such piece involves several professional figures that accompany the artist:
• The gallery project manager, that coordinates the artist and the artisans with timing and calendars.
• The glass supplier (a company can’t directly buy glass from the wholesale chain, there’s the distributor that intermediates for it).
• The glass artisan that assists the artist during the preparation of the sculpture.
• The led and transformer supplier.
• The smith that works industrial reinforcing bars as hanging custom prong that holds the glass sculpture.
• The electrician that instal the led and its transformer.
• The crate supplier for national and international transports.
• The shipping companies for the work destination. Emanuele Quinz opens is text Contro l’Oggetto (2020) with a peculiar observation: in Italy there is not only a great tradition of design, but also a great tradition of design definitions. One of the most triggering ones is
certainly that of Maldonado explained in his fundamental essay Disegno Industriale: un riesame (1976), where design is seen as a social practice, and in Italy this connection is particularly strong.
The network of the creative industries is often composed by small and medium-sized enterprises (SMEs), a fundamental element of the Italian productive system. In the panorama of the today Expanded Design, the connection design–craft, as well as contemporary crafting and making modalities, is promising in the perspective of the development of Creative Industries and economies in Italy and abroad. Specifically, Italy is a good example where the collaboration between designers and craftsmen has a solid heritage with successful production innovations (Branzi, 2015). Design, artisanal skills, and industrial manufacture have a tradition of strong connections that brought important profitable achievements with as well a profound contribution in the construction of the Italian contemporary production identity better known as Made in Italy. In these circumstances, in the 70s and 80s experimental practices redefined the role of design, “marking the passage from design as a tool for the industry to a process of collective and social creativity” (Ferrara and Ban, 2022).
For these reasons, Italy plays internationally a key role thanks to the highlevel artisanal tradition and well-known materials that are now branded such as Carrara marble or Murano glass (Micelli, 2011). International artists and designers come all over the world for the production in Italy, and Italian artists and designers benefit from such a rich tradition in manufacturing too. The red thread that runs through the successful Made in Italy is still today the craftsmanship, a trait of Italian culture (Midal, 2019). However, within this flourishing artisanal tradition there is a well-defined threat which is the lack of technological innovation of the artisanal Italian network to keep up with digital tools (Micelli, 2016).
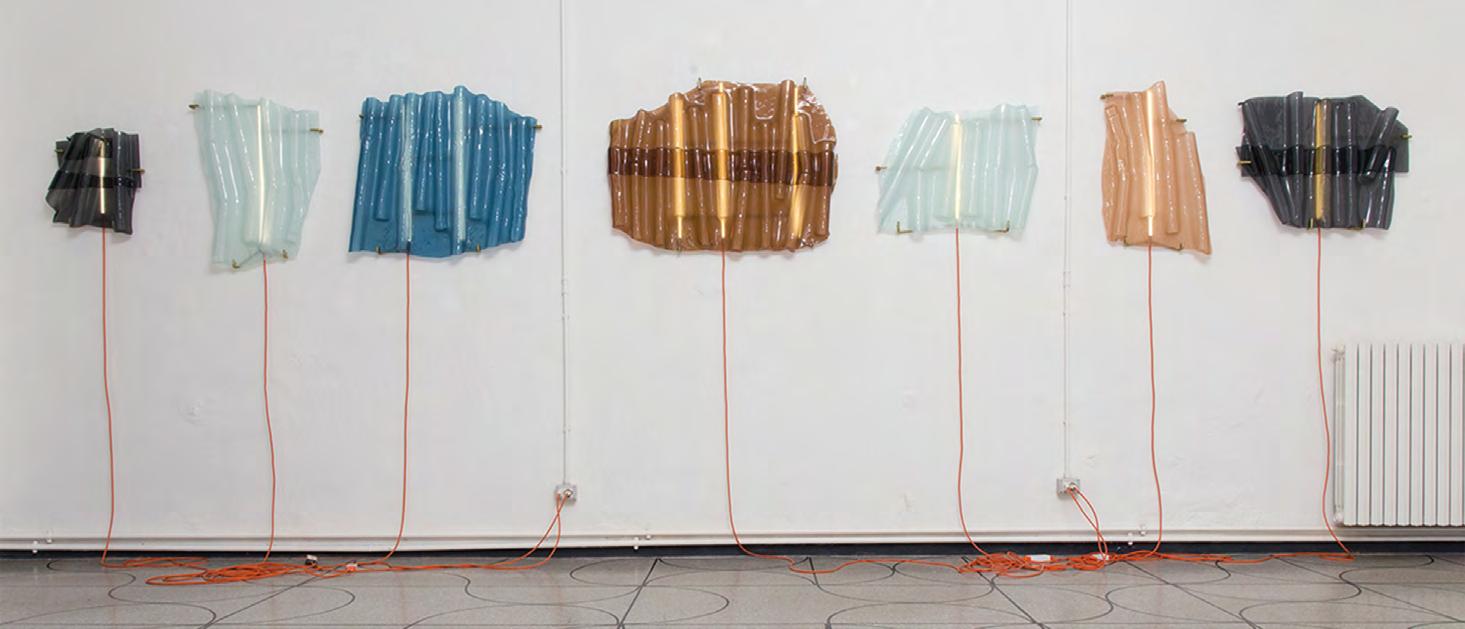
Thanks to new technologies and innovative approaches, craftsmanship developed on different paths of contemporary design. As Margolin stated (1989), with the recognition of design’s wider role in society, we started to make a place for design discourse within the larger debate about social and economic theories, notably those that centre on cultural transitions and sustainable productive development. As well, it is fundamental to consider the development of cultural identity through design practices and methods, traditional craftsmanship and productive process, with the valorisation of crafts practices to be functional for the rise of the creative economies and for the social organization of making (Sennet, 2008).
Conclusions
This paper wanted to tell a story as many can be found in the Italian field of the creative industries associated to the craft network.
In this case it has been underlined the intersections from the massively produced and standardised process of a material such as the float glass and the uniqueness of the final works realised by artist Paolo Gonzato. Bringing the material beyond the standard is what a good artist does.
What made Paolo Gonzato’s artistic process interesting was his capacity to explore contexts and situations in an original way, suggesting ideas and results to a material that has been rarely explored to express emotions and feelings. This ability to find innovative meanings to the material is the outcome of a continuous exercise of deepen knowledge associated to open mindedness to diversity and new perspectives. Thanks to the material approach, the artist had fundamental confrontations with the craft knowledge of uses and manipulation of the material itself, where its direct contact triggers solutions and possibilities. This free approach has been helped by the flexible craft network that Italy offers: small and medium enterprises that are opened to experience and test the process to realise a final work that normally wouldn’t have seen the light.
In this context the project can be analysed as a design experience of social, cultural, and economic mediation with groups of actors that interact within a situated process, as Maffei pointed (2010). Each design experience is unique and therefore not generalizable, it is built thanks to conditions such as shared knowledge, resources, local practices, and experiences of the actors involved. With this heritage the final product of the design experience, unfolds various layers of interaction with abstract subjects such as context, politics, cultural development, and intersectionality (Biggs, 2002). The project becomes a medium of cognitive contexts, conventions, and outcomes in the reality the designers and artists are immersed in1 .
1 Author Contribution: Conceptualization, Beatrice Bianco and Marinella Ferrara; writing—original draft preparation, Beatrice Bianco; review and editing, Beatrice Bianco, Marinella Ferrara. Project Contributions: Paolo Gonzato, Beatrice Bianco. Funding: This project was funded by Camp Design Gallery.
References
Biggs, M. (2002). The role of the artefact in art and design research. International Journal of Design Sciences and Technology, vol. 10, n. 2, pp. 19-24.
Branzi, A (2015). Introduzione al design italiano. Una modernità incompleta. Milan: Baldini & Castoldi. Ferrara, M., Ban, S. (2022). Women and Maker Cultures. The Relevance of Technological Appropriation from History to Current Phenomena. In Oksala, T., Orel, T., Mutanen, A., Friman, M., Lamberg, J., Hintsa M. (ed.), Craft, Technology and Design. Hämeenlinna: JULKAISIJA – Häme University of Applied Sciences, pp. 168-197.
Ferreira Nascimento, M. L. (2014). Brief history of the flat glass patent. Sixty years of the float process. In List, J. (ed.), World Patent Information, vol. 38. Amsterdam: Elsevier, pp. 50-56.
Foucault, M. (1998). Estetica dell’esistenza, etica, politica. In Pandolfi, A., Revel, J., Dal Lago, A. (ed.), Dicts and Ecrits (first published in 1994).
Giesecke, R., Clemente, R., Mitropoulou, I., Skevaki, E., Thiago Peterhan, C., Dillenburger, B. (2022). Beyond transparency: ar chitectural application of robotically fabricated polychromatic float glass. In Brell Cockan, S. (ed.), Construction Robotics. Berlin: Springer. DOI: 10.1007/s41693-022-00071-6
Hooks, B. (1998). Elogio del margine. Razza, sesso e mercato culturale. Milano: Feltrinelli. Lunghi, C., Trasforini, M. A. (2010). La precarietà degli oggetti. Estetica e povertà. Roma: Donizelli. Maffei, S. (2010). Il progetto è una pratica clinica. La prospettiva del design. In Fabbri, T. M. (ed.), L’Organizzazione: Concetti e Metodi. Rome: Carocci, pp. 265-282.
Maldonado, T. (1976). Disegno Industriale: un riesame. Milano: Feltrinelli. Margolin, V. (1989). Design Discourse: history, theory, criticism. Chicago: University of Chicago Press. Micelli, S. (2011). Futuro artigiano. L’innovazione nelle mani degli italiani. Venezia: Marisilio. Micelli, S. (2016). Fare è innovare. Il nuovo lavoro artigiano. Bologna: Il Mulino. Midal, A. (2019). Design by Accident: For a New History of Design. Berlin: Sternberg Press. Pilkington, L. A. B. (1969). Review lecture: the float glass process. Proceedings of the Royal Society of London, vol. 314, n. 1516, pp. 1-25.
Quinz, E. (2020). Contro l’oggetto. Conversazioni sul design. Macerata: Quodlibet. Sennet, R. (2008). The craftsman. New Haven, London: Yale University Press. Taylor, A. (1979). Pilkington out to crack new markets. Financial Times Uusitalo, O. (2014). Float Glass Innovation in the Flat Glass Industry. New York: Springer.
Physico-chemical and morphological characterization of inner surfaces of glass pharmaceutical vials
GIOVANNA PINTORIA, SERENA PANIGHELLOBThe chemical composition of the glass surface is influenced by various interactions which occur on the uppermost atomic layers. On the other hand, the surface properties of glass containers are greatly influenced by the forming process and they are not simply determined by the bulk composition. The investigation of elemental and phase composition of glass surfaces in dependence on their physical and chemical history is thus crucial to understand the reactions of glass surfaces with gases, solutions, coatings, and environmental media. In this study, X-ray photoelectron spectroscopy (XPS) and time-offlight secondary ion mass spectrometry (ToF-SIMS) are applied to investigate compositional changes on the inner surface of glass vials for pharmaceutical use. XPS was successfully applied for qualitative as well as for quantitative investigations. ToFSIMS provided information on the molecular composition of the topmost area of the inner surface of the containers, characterized by structures and inhomogeneities created during the vial forming process and observed by scanning electron microscopy (SEM) micrographs.
The purpose of this study is to provide useful information needed to prevent or mitigate issues encountered in the production of containers for pharmaceutical use. The combination of topological and chemical information provides unique insights into surface processes, which can be used to reduce surface/ drug product interactions.
A Ca’ Foscari University of Venice, Venice, Italy. B Technology excellence center, Stevanato Group, Italy.
KEYWORDS: BOROSILICATE GLASS, TOPOGRAPHY, GLASS TUBING
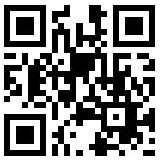
Fig. 01 SEM micrographs of the inner surface of (a) glass tubing, and (b) at 2.5 mm from vial bottom after the forming process. Courtesy of SG Technology Excellence Center
Fig. 02 ToF-SIMS images of inner surface of wall near bottom of the vial after the forming process.
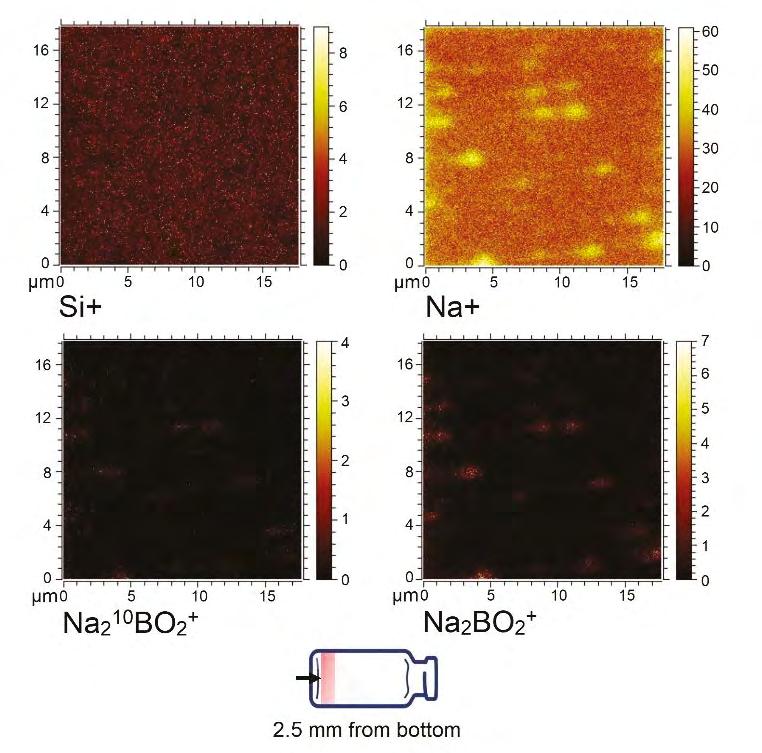
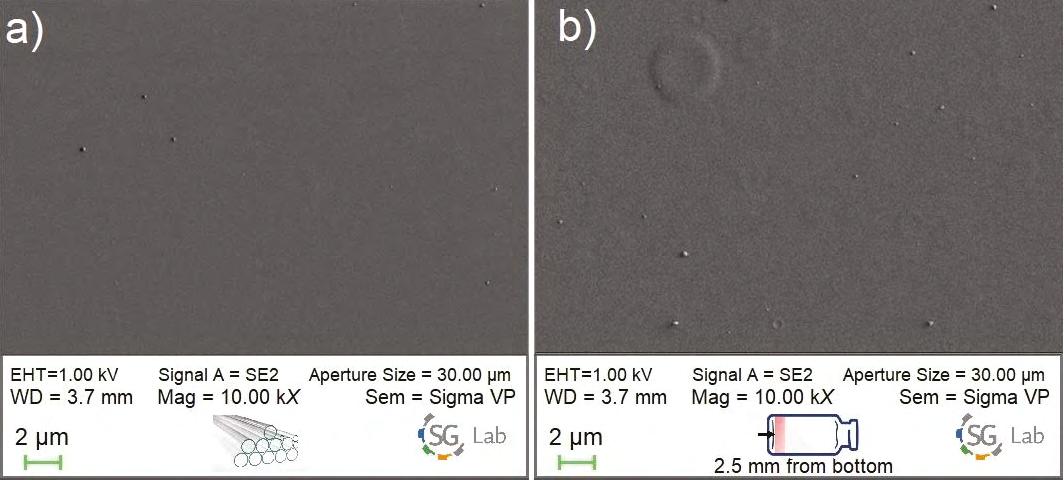
(E)merging layers in Venice. The potential of one landscape and single raw material
MAXIMILIANO ROMEROA, ANNA LORENSB“The difference between past and present [...] is reflected in the fact that the past is experienced now. […] The individual layers of the city are those which uncovered appear as the indigenous and eternal substance of life, the unchanging pattern” (Rossi, 1984, p. 56).
We always come across something, never nothing. Each place has its atmosphere and history. It is often magnificent and intense; other times, it may be initially elusive. But if we keep listening, sooner or later, every place will start talking. The place always dictates the result; we never try to impose something not rooted in it. In this way, we discover, interpret and add new stories to what already exists. Architecture always refers to nature even when nature is not noticeable. Present paper analyses, through the description of a didactic activity, the concept of Fragility at different layers, environmental, material, and relational. Based on a diverse design approach exemplified by the results of each team of workshop participants, he argues that glass is a resilient material, and this characteristic transforms its superficial fragility into innovative antifragility.
A Department of Design, Università Iuav di Venezia, Venice, Italy.
B Division of Design and Theory of Architecture and Product Design, Faculty of Architecture, Warsaw University of Technology, Warsaw, Poland.
KEYWORDS: ARCHITECTURE AND DESIGN, SUSTAINABILITY, NEW TECHNOLOGY
Introduction
Concerning its aesthetics, architecture and design find in the glass a method to achieve a sense of emptiness, absence, and pristine surfaces, both in the solid and in the properties of the material itself. In contemporary reality, on the other hand, there is an increasing need for an object to be resistant to changing conditions (both environmental and functional).
A building designed as a flawless sculpture no longer represents an ideal and timeless architecture. In line with the doctrine of circular economy, adaptability becomes necessary when defining basic guidelines for building design or finding ways to transform buildings. Demolishing and building from scratch are the least economical of the approaches. It is not a question of making sense of the space but of guaranteeing it for appropriate (variable!) functions that come to the fore in sustainable design. At the same time, buildings should benefit from the forces of nature (cooperating with wind and water) and be resilient to manifestations of ecological disaster – e.g., windstorms or seismic shocks. Thus, referring to the aspect of the fragility of glass, and thus the low susceptibility of glass façades to change, a significant influence on the flexibility (by definition of a rigid material) is the design of an appropriate structure that secures the material while maintaining its aesthetic qualities.
(Anti)Fragility
Early twentieth-Century modernism in architecture, the trend of minimalist manifest forms, treated glass as a material that contradicts and distracts from the underlying understanding of Heidegger’s premises for defining the architecture, namely- giving shelter.
In modernism, glass fostered an interpenetration of designed forms with the natural environment and a sense of openness to space. It was a way of avoiding adding superfluous masses by making them invisible. The perfection of form dominated its adaptability, for although the Bauhaus theory glorified the flexibility of use, any modification to a calculated, planned, and proportioned shape, from the point of view of the material’s properties (glass), exposes the fragility of beautiful transparent screens.
The aspect of perfection, which blocks adaptability, was pointed out by Lesang Dikgole when he wrote that “perfect shape introduces perfect fragility” (Dikgole, 2018). Any potential change of the designed volume in ideal proportions initially from the point of view of the designer’s vision (taking away a few centimeters from its height, reconstruction for a change of function, or adaptation to other needs) reveals the fragility of the material and prevents its flexibility.
A fascinating example, which symbolically can be taken as an expression
of irony towards the conditions, function, and context vs. aesthetics, is Prada Aoyama in Tokyo. Glass itself as a material is used here as in the scale of product design. In this case, the building is, as it were (and according to its commercial function), a ‘packaging for products’. Through such a partition, the contents can be shown based on transparency as an entire property of Glass. It is worth alluding to another scale, that of products precisely, to make this fantastic aesthetic property of Glass as a setting visible.
The incredible potential lies in the transparency of the glass. Transparency in architecture offers a view. In design:
• it presents content and protects that content. The fragility of glass is therefore not so important here because the potential becomes the fact that the user knows how to use specific shapes, vessels, and flacons. What’s more
• the fragility and delicacy of glass make us handle the vessel more delicately and focus our attention on other senses.
“The Amalfi type – one of the most common “counter glasses in industrial production – and a classic tulip-shaped glass together so that even a simple wine may be presented and tasted at its best. And so, in this new shape, the glass cup becomes wider, and the rim narrows to emphasize colors and aromas. And the blow top blends with a solid base which welcomes opaque grindings and reveals the artisan’s touch” (Martinelli and Venezia, 2022).

This is how the Oste project by Carolina Martinelli and Vittorio Venezia (Martinelli Venezia) is characterized Glass, then is the setting for the content1 . The design aesthetic promotes the sensory experience of tasting wine and looking at it in a feasting arrangement. Just as in product design, we acquire a collector’s item, where the nobility of the material offers a ritual not only visually but also related to smell, touch or taste.
In the case of Prada’s architectural design – the transparency of the glass works both ways, depending on the user’s perspective. Glass – synonymous with nobility and luxury (also due to its natural delicacy), became the

primary façade filler material of the Prada flagship store. Since the task was to develop a flagship store in Tokyo, in a cramped development, without the possibility of taking advantage of extensive views from the interior or displaying the product from different angles, they designed the building like a product package, inserted and crumpled according to the conditions of the plot. The glass provides an outer shell, compared in the literature to the contact lens of the pupil of the eye, changing the angle of vision and creating an illusion; in this scale of application somewhat in pop culture expression.
However, the plot is exposed to seismic shocks; the glass material is protected by a structure placed on a suitable base. Although structural engineering experts accuse the project of being shaped more by aesthetic considerations than by the overall system’s efficiency, it is noteworthy for the groundbreaking (now over 20 years old) design of the façade. It is a selfsupporting structure, and a grid for the glazing and the aspect of the fragility of the material is irrelevant in this modulated arrangement.
Research conditions of a plot intended for an object with a specific function allow this material to be protected as design intention. Given the interdisciplinary boundaries of architecture, similar design treatments are applied on a smaller scale. The material’s formation, texture, and function in an appropriate aesthetic setting that refers to certain traditions mean that the user treated glass with more outstanding care due to its fragile and sensitive nature.
Thus was Lorenzo Damiani’s design for Allatua, a Murano glass beer mug presented in an exhibition curated by Elisa Testori at Punta Conterie on Murano2. The glass of the cup is banded with a specially designed clamp supporting a wooden cube. In a toasting gesture, these cubes are placed opposite each other on the two tankards in those places. The designer draws attention to the value of glass by depriving the motion of clinking the tankards of the characteristic sound that usually accompanies the successive breaking of fragile glass. He juxtaposes the pop culture clumsy feasting gesture with the nobility of Murano glass and the values contained in the material, the ritual of coming together, and attentiveness.
“A beer mug that plays on the one hand with the idea habits and rituals that identify the classic Bavarian mug (this is the shape of the stein – author’s note) and the precious and extremely delicate Murano artifacts on the other. Allatua is an ironic project that encourages the typical thunderous Prosit! gesture but with an adequate measure of protection for the glass: a customized bumper, distinctly Venetian, made with bricole3 wood offered by the lagoon and patiently handcrafted” (2022 Damiani exhibition).
Such respect for the material can paradoxically affect its durability
(antifragility). Noteworthy, the glass, apart from being fragile, is also – on the contrary – very resistant to the passage of time, and the differences resulting from the randomness of the material’s behavior in processing lend a singular, collectible character. From an environmental and sustainability point of view, leaving a product in circulation for as long as possible and designing it so that the object gains in value over time is the most ecological approach. At the same time, the time of use creates valuable stories around the thing and creates a specific message to the user – respect the material, protect it, care for it, and create a new definition of heritage.
The workshop, curated by Prof Maximiliano Romero and co-led as a guest at Università Iuav di Venezia by Prof. Anna Lorens (hereafter co-authors of this article), was born out of the need to prove that landscape heritage and material (glass) are antifragile.
On field research
In the Venetian lagoon, glass has been an important commercial resource for many years. The Murano glass factory is recognized all over the world for the quality of its production, but at the same time it has an important impact on the fragile lagoon environment.
The glassworks of Murano have been, and still are, one of the causes of environmental pollution of the Venetian Lagoon, primarily via atmospheric
Fig. 03 “Glass cemetery”, R. Tremazi
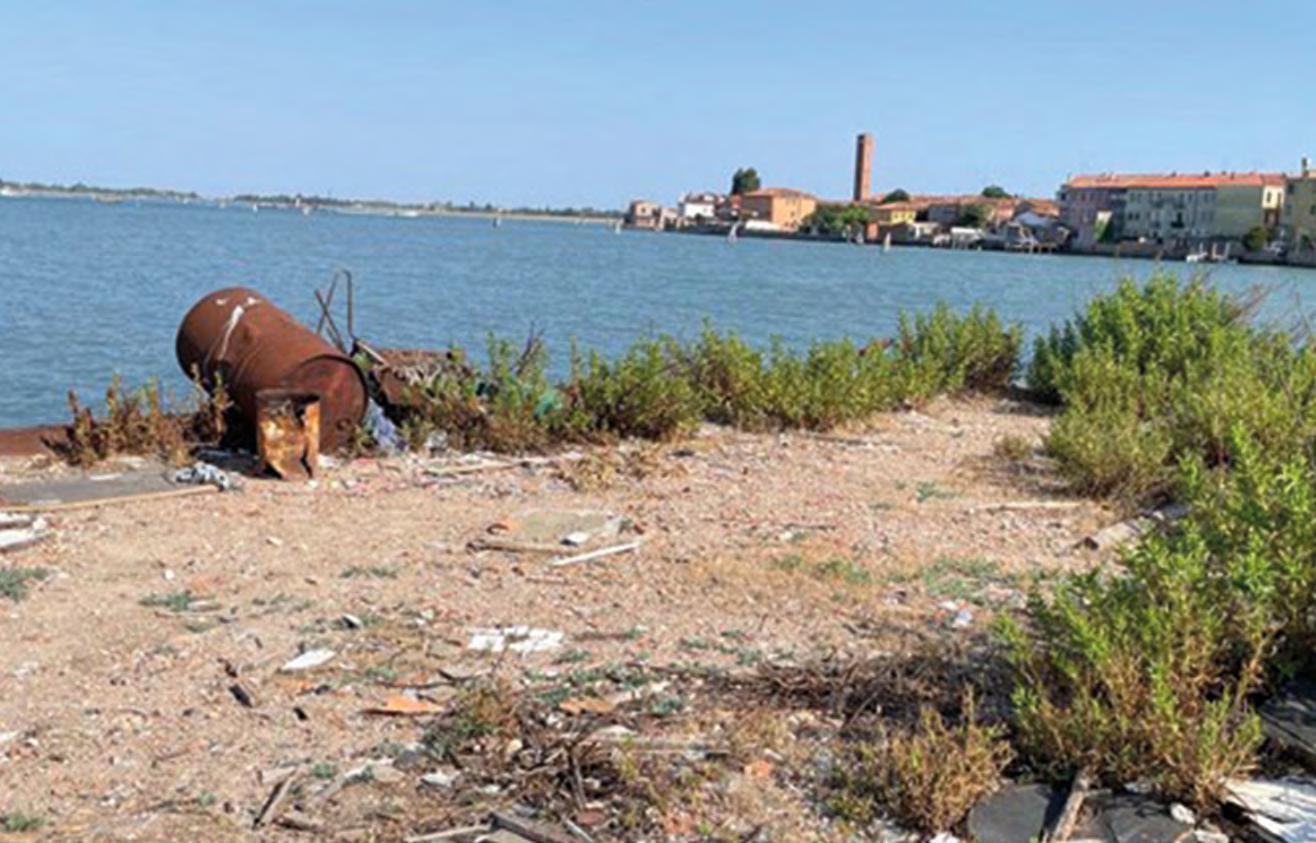
VENICE.
emissions but also as a result of effluent discharges and disposal of solid waste. A preliminary ecological audit of Murano’s glassworks in 1999 indicated that the local entrepreneurs see adopting environmental management systems and pollution-prevention/reduction measures as a significant burden. The main reasons are:
• the costs that must be borne;
• the complexities of Italian legislation and regulation;
• the relatively small size of the majority of the units operating on this island.
Pollution-control and waste-minimization strategies are slowly being implemented due to regulatory pressures (Giusti and Polo, 2002).
With the aim of feeling the impact of the glass industry in the lagoon environment, the workshop participants visited not only the glassworks, but also the closest areas. The student’s group visited the area north of Murano Island, on the landfill unofficially known as “Glass cemetery” because, in the past decades, the site was used illegally for glass production waste recovery. The ground of a section of the island is made up of layers of waste glass – a testimony to the heritage of this craft.
Expert’s support
For the realization of the activity, some glass experts, both in their workshops or factories and online.
Mr. Matteo Silverio presents online his expertise in 3D printing technologies for glass powder. Silverio’s innovative technology is based on a substance developed by himself that gluconate glass powder can be deposited through a CNC-controlled extruder. This additive manufacturing process allows the production of pieces created by CAD software. The technology of arch. Silverio is reflected in particular projects.
Nicola Moretti introduces us to processing and creating glass molds (hot glass molding, them breaking, glass blowing), the parameters and equipment, and the craftsman’s involvement in shaping the individual molds.
He also provided a lot of valuable practical information related to the ins and outs of the technology, especially concerning the coloring of the glass material and the impossibility of combining dyes – as the essential ingredient testifying to the uniqueness of a product made in a particular workshop.
Simone Cenedese explained how a glass manufacturer works on a larger scale and how new concepts and prototyping are implemented in a much larger-scale plant. In addition the creation of traditional Murano chandeliers, the bending of glass molds, and the potential inherent in thermally transformed glass molding had been shown. Teams had the opportunity to discuss glass fusing, decorating, and polishing options.
Group 1_ W.W.V. (Waste. Wall. Venice)4
“A person with a pattern language does not need to be an expert. The expertise is in the language. He/she can contribute to planning and design because they know relevant patterns, how to combine them, and how the particular piece fits into the larger whole” (Alexander et al., 1977, p. 18).
The selected area where it was decided to work, is located in the northeastern part of the landfill. It is located at the most extreme point of Sacca S. Mattia, a place now a waste repository of all kinds. The main reason this area has been chosen is its strong visibility from the sea and the shore of the island of Murano.
The goal is to redevelop the area, using waste materials and through the project, involve the community and encourage interaction between the inhabitants of the island.
This process of shaping the design process essentially resumes what the most specific character of the identified area is. The central premise of the idea was to revitalize the area by creatively retraining it and making it easily recognizable and identifiable to users. The process involved redefining (deforming and forming the shape of the traditional brick), creating a new organic and modular object allowing for easy, intuitive combinations of different modules, making it possible to create new configurations and unique shapes with functional characteristics – from seating to small-scale architecture – partitioning (Figure 04). The idea is based on a reference to local communities, both in the glass ‘brick’ production process and in the strategy of building objects from it according to demand.
Group 2_ Furniture of the Landscape5
“Memory’s images, once they are fixed in words, are erased,” Polo said. “Perhaps I am afraid of losing Venice all at once, if I speak of it, or perhaps, speaking of other cities, I have already lost it, little by little” (Italo Calvino, 1978, p. 87).
The project is based on the values embodied in the site’s history and aims to link the material (manufacturing waste) to the unique character of Murano terrain vague. The function of the urban furniture/object is to generate interaction among users, a place to rest and reflect. The design intention was to reflect the historical tradition of glass production in Murano. Accordingly, the chair was made from damaged crucibles (Figure 05), used in the furnace supply chain. The project’s authors saw extraordinary potential in the aesthetic appeal of the waste from production – a crucible covered
4 Ferrulli F., Melato F., Tremazzi R. (students from Iuav Venezia), Krzysiek K. (student from WUoT Warsaw).
5 Coriele F., D’Amato S., Mescolin M. (students from Iuav Venezia), Wyszynski K. (stud. WUoT Warsaw).
with layers of glass. “Layeredness” – both contained in the landscape (the observation that the “Glass Cemetery” is somehow made of glass material accumulated over the years) but also in the object itself, covered with layers of glass in the production process.
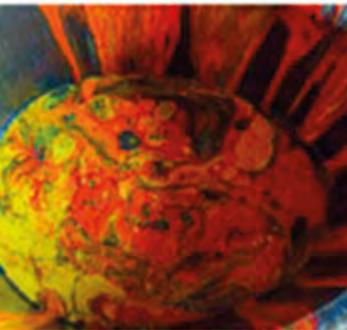
This juxtaposition became the basis of the project idea. It became the designer’s role to search for the ideal ‘cut’ and to counteract the fragility of the glass in the cutting process and technology, to give a completely new value to the crucibles. The final representation of the thoughts and observations is an object meant to reproduce a specific situation: a chair seems to be the most appropriate solution. The design also intends to reflect the history of glass production in Murano. Accordingly, making the chair from damaged crucibles used in the furnace supply chain. This is shown in the drawings and diagrams.
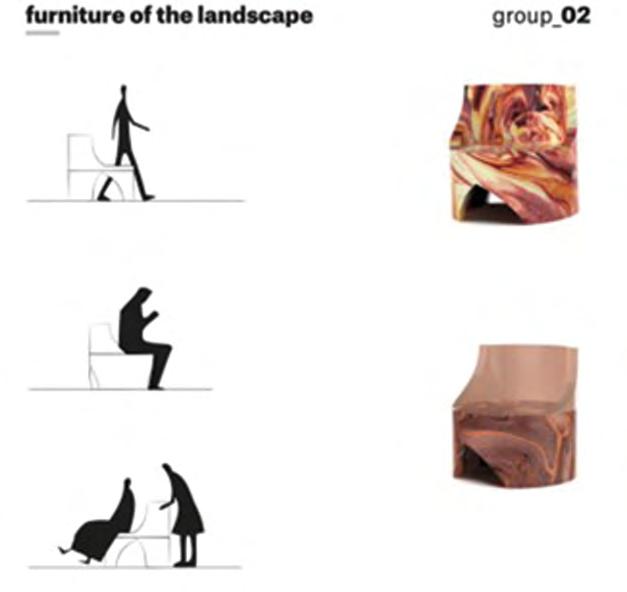
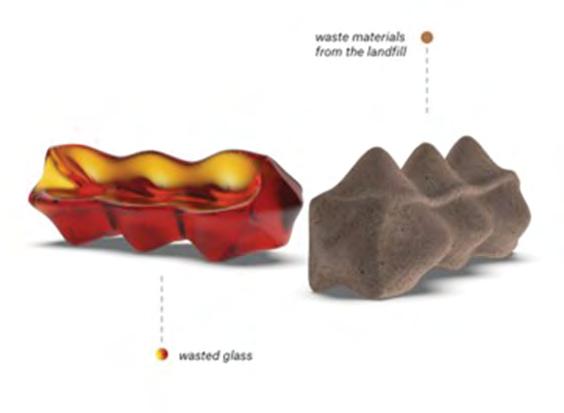
Group 3_Landleidoscope6
The project’s idea was based on observing the constraints and limitations in designing an object out of the material glass. One of the main observations made during a site visit to the Moretti glass manufactory was that specific colors of glass are a manufacturer’s secret and cannot technically be combined except by glue. The defragmentation of the colors of the glass elements became a method of proving that it is possible, through design, to achieve the combination or overlapping of colors differently – namely spatially. The designers observed that the characteristic feature of this place is the feeling of separation – physical – water from land, permanent from temporary, but also symbolic – break from the tourist hustle and bustle, a sense of alienation, ‘defragmentation’.
Small scale architectural forms – a kind of glass tepee – have been created, referring to creating a sub-space in the open area for the user. Thanks to the stained-glass method, the structure, like a colored patchwork, allows us to achieve the effect we can observe in a kaleidoscope – the superimposition of colors and shapes.
Results and conclusion7
The workshop lasted only five days, including two days for study visits to Murano island: the pot and two factories. Participants also had two lectures from Prof. Lorens and Prof. Silverio. A complexity/richness of the activity was the participation of 3 students from Warsaw University of Technology (one for each group). As a result, only a few hours have been used by students to produce results. Described activity was, since the beginning, conceived as a test to be improved.
The experimental workshop showed that research should be based on following the material processing, recognizing the technology and technological possibilities. We made scale prototypes at Iuav in the laboratory using a 3d printer from the plastic filament to identify form and shape specificity. The workshop attempted to prove the potential for innovation in the use (redefinition) of glass in design practice. The goal was to fluctuate the material characteristics (fragility and potential for recovery) with dedication (landscape). The fragility of glass can be a technological potential (in the sense of physical property) and aesthetic/symbolic. In line with the doctrine
6 Grossa E., Calamante M., Solofrano L. (students from Iuav Venezia), Barnaś A. (student from WUoT Warsaw).
7 Authors want to thanks students for their participation, and in particular to Lucrezia Solofrano and Fabio Ferrulli for the collaboration into organizing the WS, Prof. Rosa Chiesa for her scientific support, Mr. Matteo Silverio, Mr. Luca Nichetto and Mr. Dario Stellon for organizing Murano Glass Producers visits, Simone Cenedese and Nicola Moretti for to received us in their workshops and give us the opportunity of to know in details their technical and philosophical approach to the Murano Glass.
of sustainability, the material is perfectly suitable for reuse:
• from waste glass using the printing technology developed and patented by Matteo Silverio as well as according to traditional Murano craft techniques (Group no. 1);
• based on the potential of the object’s form, which is both a matrix and consequently a waste product to give it a new lease of life in line with circularity Furniture of the Landscape (Group no. 2);
• the potential of the degraded landscape- terrain vague of the “Glass Cemetery” (Group no. 3).
All the results have been finally presented in a small exhibition, and participants described their experiences to the general public. From the participant’s point of view, visiting the landscape and factories was very inspiring, and all of them appreciated the international composition of the teams.
References
Alexander, C., Ishikawa, S., Silverstein, M. (1977). A Pattern Language: towns, buildings, construction. New York: Oxford Uni versity Press.
Calvino, I. (1978). Invisible Cities HMH Books; Bilingual.
Dikgole, L. (2018). Bauhaus fragility: an assessment of architecture in buildings and information systems (online). In: https:// vincentlesang.medium.com/bauhaus-fragility-an-assessment-of-architecture-in-buildings-and-information-sys tems-4e0b5533d2b3
Giusti, L., Polo, M.C. (2002). A review of the glass making industry of Murano (Venice, Italy) under an environmental perspec tive. Environmental Management and Health, vol. 13, n. 1, pp. 40-54.
Rossi, A. (1984). The Architecture of the City. Boston: The MIT Press.
Testori, E. (2022). Forme del Bere - Exhibition. Galleria Art Galerie, Puntaconterier, Murano.
Air, light, and liquid in motion: blurred transparency of the Glass pavilion in Toledo
AKI ISHIDAAIn architecture, when glass is experienced in motion under changing light, the perception of it is not simply as transparent but is a specific kind of transparency that can be called blurred. As new technologies in glassmaking and engineering expand the range of effects and performance of clear glass, its transparency becomes increasingly multivalent and complex, making nuanced differences difficult to perceive. Toledo’s Glass Pavilion exemplifies these blurred transparencies, which result from several mutually dependent factors: innovative approaches to mechanical and structural engineering, balancing of light coming from multiple sources and directions, and an unusual spatial organization of glass-enclosed air plenums and rooms to create radical programmatic adjacencies and complex array of reflections.
A Virginia Tech School of Architecture + Design, USA.
KEYWORDS: TRANSPARENCY, GLASS ARCHITECTURE, SANAA
Introduction
The Glass Pavilion (2006) at the Toledo Museum of Art, designed by Kazuyo Sejima and Ryue Nishizawa of SANAA, presents a novel kind of transparency that results from layering of curved glass with volumes of air. Built with clear glass as the primary exterior walls and interior partitions, the Pavilion is simultaneously opaque and transparent in its construction and spatial organization. It is opaque in its concealment of steel structure which supports the transparent ribbons of massive glass. At the same time, it is remarkably transparent in exposing elements of architecture that are typically hidden from view, notably the glass plenum through which air circulates. Historically, glass and air have been intimately linked since the pre-industrial production of glass, in which exhalation of air from human lungs transformed molten glass into cylinders, which were then cut and flattened into sheets. Like the visual effects seen on blown glass, Toledo Glass Pavilion’s transparency is soft, watery, and intimately airy–in contrast to the hard, cold, machine-made impression often associated with glass. This softness is further underscored by its play of layered reflections seen on the surfaces of curved glass (Figure 1).
The Glass Pavilion is a carefully calibrated instrument of light, shadow, and reflection. Although clear glass is the predominant material, the building differs from the see-through transparency of modernism described as shadow-less glass box in Ludwig Hilberseimer’s 1929 essay Glasarchitektur. He writes that the Crystal Palace built in 1850 to 1851 “obliterated the old opposition of light and shadow, which had formed the properties of past architecture. It made a space of evenly distributed brightness; it created a room of shadowless light” (Hilberseimer, 1995, pp. 9-10). The Pavilion is also distinguished from the diffused, shadowy luminosity of translucent glass buildings that became widespread in the late 1990s following PostModernism. In contrast, the use of curved, massive monolithic glass in the Pavilion leads to an intensified transparency in which a clear material gives mutable readings that range from apparent depth to near-opacity.
In architecture, when glass is experienced in motion under changing light, the perception of it is not simply as transparent but is a specific kind of transparency that can be called blurred. As new technologies in glassmaking and engineering expand the range of effects and performance of clear glass, its transparency becomes increasingly multivalent and complex, making nuanced differences difficult to perceive. Toledo’s Glass Pavilion exemplifies these blurred transparencies, which result from several mutually dependent factors: innovative approaches to mechanical and structural engineering, balancing of light coming from multiple sources and directions, and an unusual spatial organization of glass-enclosed air plenums and rooms to create radical programmatic adjacencies and complex array of reflections.
Glass bubbles drawn with a brush
Each individual room in the Pavilion is enclosed by a curving wall of lowiron, monolithic laminated glass panels three-quarters of an inch thick. “Our concept is to wrap each program [element] with a curved line drawn by a single stroke of [the] brush,” writes SANAA’s principal Ryue Nishizawa (Sejima et al., 2011, p. 23). The program elements include exhibition rooms for glass crafts, multi-purpose room, open-air courtyards, storage, and hot glass demonstration shops. In order to keep the main floor free of visual obstructions as much as possible, the mechanical rooms are located in the basement, and the cooling towers and pumps are off-site in a separate building (Lane, 2006). On the main floor, enclosing all bubble-like rooms is an exterior envelope of the same glass but at a greater thickness of one inch. Interior glass rooms float within the exterior envelope’s continuous glass skin, separated from each other by a thirty-inch air cavity (Figures 2). This zone of air mitigates temperature differences between the outdoor and the conditioned indoor spaces, as well as between the galleries and the shops with glass kilns. Normally, this temperature control is served by the air cavity found in standard double-glass facades, or the mechanical shafts and spaces concealed in opaque stud walls. This transparent cavity flows like
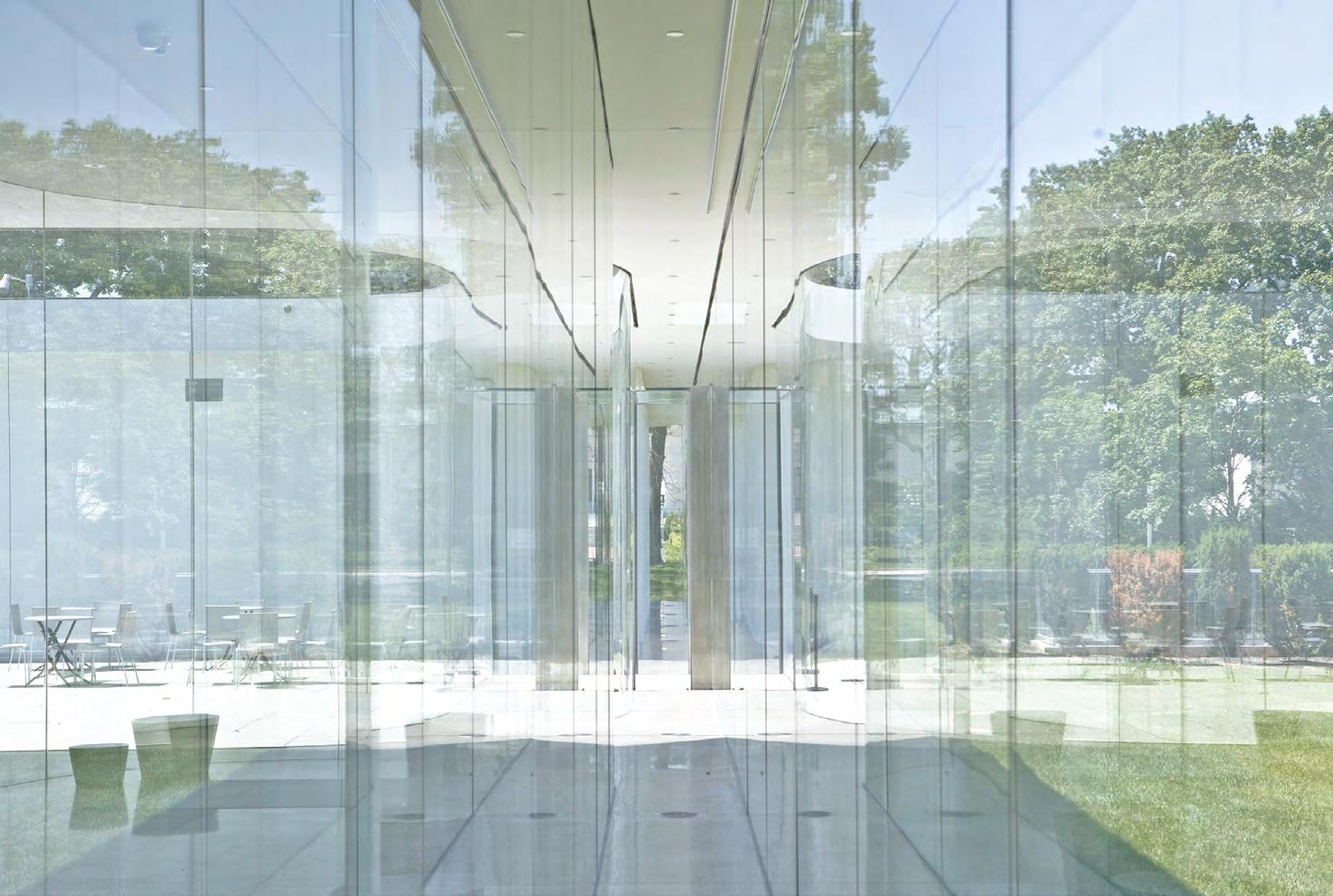
water through the building to make a contiguous air cushion, expanding and contracting as it turns rounded corners while maintaining a minimum egress clearance for people to pass through for maintenance.
Each of the 360 glass panels, measuring thirteen and one-half feet tall and weighing 1,300 to 1,500 pounds (Levine, 2012), were manufactured in Pilkington’s factory in Germany. They were shipped to Shenzhen, China where they were slumped (a process of shaping glass panels over mold at high temperature) and laminated with polyvinyl butyral (PVB) interlayer to fabricate the thick monolithic panels (Ra, 2017). Visible materials and structures other than glass are made inconspicuous. Slender steel columns of three and one-half inch to four and one-quarter inch diameter support spans as long as sixty feet and hold up a shallow roof of two-feet deep (Nordenson and Schneider, 2016). The bottom of the glass wall panels rests on recessed tracks in the concrete floor and are held in place laterally by another track concealed in the ceiling (Ra, 2017). The roof is designed to float over the glass and never bear on the glass panels (Oki, 2017).
At vertical joints, translucent structural silicone holds two sheets of glass together, which eliminates vertical mullions or channels. Since the glass panels are monolithic and not insulated glass units, the glass walls appear continuous and ribbon-like (Ra, 2017). The curved glass panels appear neither completely transparent nor opaque. The viewer sees the interior and exterior simultaneously, layered with reflections of the nearby trees, cars, and houses, overlapping them with the objects and world beyond and before the glass walls.
Whereas museums normally depend on opaque walls to exhibit artifacts, SANAA fittingly maximized transparency in a museum which exhibits glass objects and processes. The all-glass foyer physically separates, yet visually connects, the hot lab from the gallery; without this transparent thermal buffer, these two spaces with highly varied needs for temperature, moisture, and acoustic normally could not be next to each other unless separated by insulated opaque walls. From the glass-wrapped foyer between gallery and hot lab, a visitor can view glass sculptures and vessels, against, in the background, the molten glass shaped into solid objects in the adjacent hot lab (Figure 3). Multiple states of glass appear simultaneously superimposed upon each other, through a plan that situates thick monolithic glass in a radical configuration. The superimposition is also temporal. Glass objects spanning a period of 4,000 year, from a Mesopotamian glass bowl to Libby Glass Company’s punch bowls are viewed in a fluid transition from one enclosure to another.
Nishizawa’s remark that they enclosed each program with a single brush stroke suggests a space different from one drawn with a pen. Like western watercolor paintings, Japanese calligraphy and brush painting–sumi-e–achieves tonality by varying ink density with water. Less ink and more water
are used for faint or distant scenes, and the strokes are layered to depict depth. Moreover, unlike a pen with uniform line width, a brush stroke varies in width and transparency depending on the pressure place on the brush and the angle at which the brush glides across the paper. Like a brush stroke, the air cavity that surrounds each bubble-like enclosure in Toledo is contiguous and varied in width. Similar to multiple superimposed watery brush strokes with a faint hint of ink, transparent glass sheets suggest depth and even opacity when seen through multiple layers, creating a mutable palimpsest of images.
Engineering glass transparency
The Glass Pavilion took an exceptionally integrative approach to climate control in a nearly all-glass building, a type that is notoriously difficult to cool and heat efficiently. Questions of heating and cooling glass building challenged modern architects from the early days of glass buildings. Bruno Taut’s Glass Pavilion in Cologne and Paul Scheerbart’s book Glassarchitektur, both dated 1914, foreshadowed a future in glass buildings with double-glazed walls, including their capacity to solve glass’s critical weakness, thermal transfer. Like Taut, Scheerbart carried the conviction that technology was “the formative agent of the current culture” (Ersoy, 2015, p. 156). Tuat and Scheerbart similarly saw the need to experiment with glass architecture enabled by iron structure. In Scheerbart’s prophetic 1914 book Glasarchitektur, he contemplated double glass, looking far ahead of his time to speculate what glass architecture could be. He wrote, “As air is one of the worst conductors of heat, the double glass wall is an essential condition for all glass architecture. The walls can be a meter apart–or have an even greater space between” (Scheerbart, 1972, p. 42). Taut and Scheerbart’s imagination of two sheets of glass spaced about a meter apart bears a notable resemblance to the thirty-inch air space at the Toledo Glass Pavilion.
SANAA worked with Transsolar, a climate engineering firm founded in Stuttgart, Germany. Transsolar’s climate control strategies contributed a kind of material transparency unique to this program and geographic location. The Pavilion consists of three energy zones (Figure 4): the perimeter buffer zone, the hot glass demonstration areas, and the galleries with individual climate control requirements (Moe, 2008). The perimeter zone mediates spaces with variable climatic needs. Hydronic radiant heating and cooling in the floor and ceiling tempers the air in the first zone. This moderates the difference in temperatures between the indoor and outdoor glass surfaces, which in turn prevents condensation on the glass in both hot and cold weathers. Furthermore, the hot air generated in the hot glass demonstration spaces are recovered and re-directed through a hydronic floor slab in
order to heat other spaces in the building. The building redirects cool air collected from the galleries to cool the hot glass demonstration zone (Moe, 2008). Na Min Mike Ra of Front, the glass consultants on this building, notes recirculating the heat from the hot shop furnace, which is kept on 24/7, made an all-glass building possible in the cold climate of Toledo. Otherwise, the heating cost would have been prohibitively expensive (Ra, 2017).
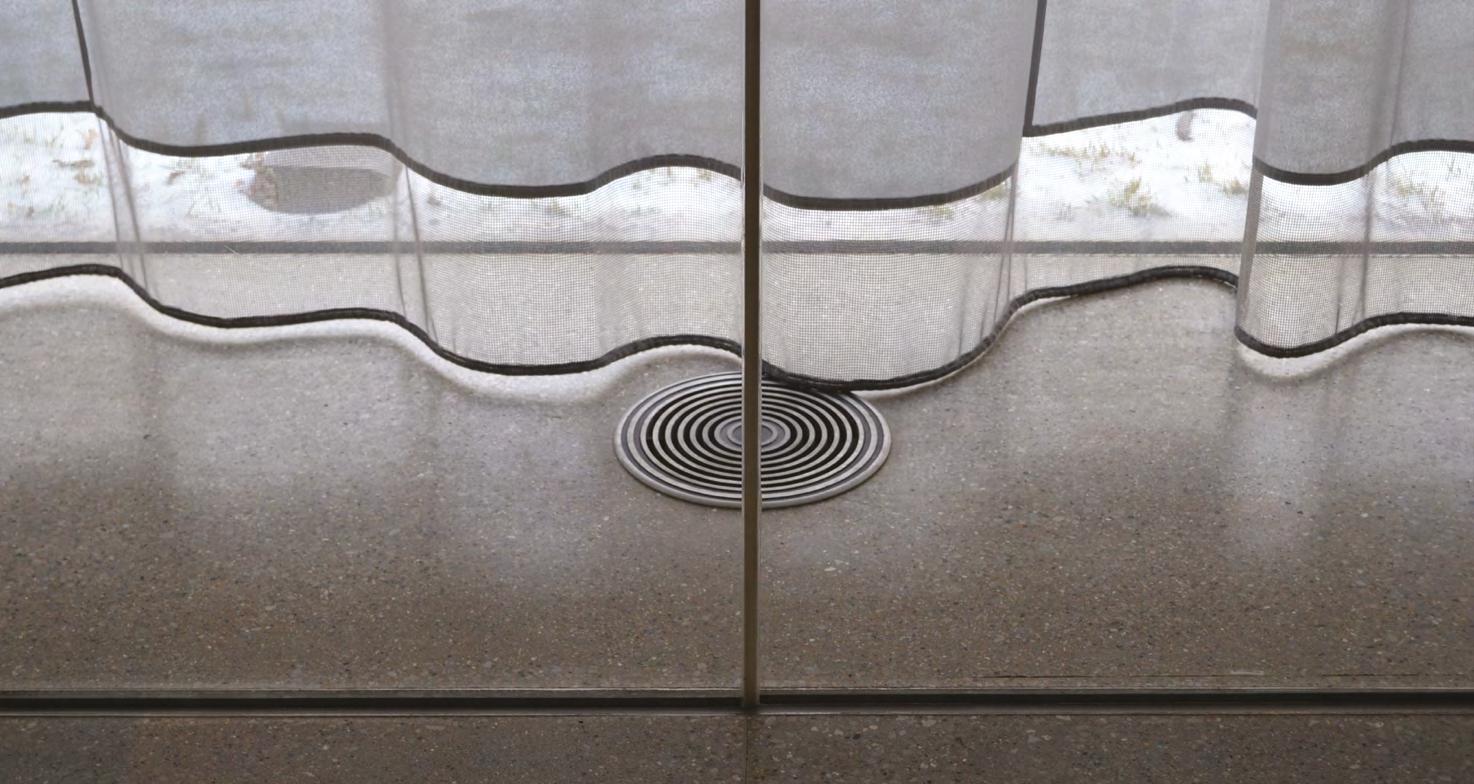
SANAA’s design process treats engineering with equal importance as the other aspects of design. The design team regards technical matters, including the details that guide the construction process and placement of columns relative to the glass, as an integral aspect of visual appearance. The girders and joints, ductwork, and plumbing pipes reside within the twofoot depth of the roof. Vertical runs for the pipes and ducts are housed in the full-height opaque walls. As with many of SANAA’s buildings, such as the Naoshima Ferry Terminal (2006), with ultra-slender columns, these opaque walls must also accommodate lateral bracing. The slender columns are mostly solid steel, but some are hollow to run infrastructure and rainwater between the roof and floor (Nordenson and Schneider, 2016).
SANAA’s buildings are a feat of mechanical and structural engineering. They appear deceptively simple and a-tectonic by comparison to the structural expressions of Peter Rice, Jörg Schlaich, or Norman Foster. In SANAA’s work, the visible structure is minimized so the atmospheric effects become foregrounded. In their essay “Ocean of Air”, Cristina Diaz Moreno and Efren Garcia Grinda describe this phenomenon as “intensified perception in which the process of minimizing the object’s main features (form, materials, size) takes priority over those usually regarded as secondary” (Diaz Moreno and Garcia Grinda, 2004, p. 37).
Glass details and material finishes
At Toledo, SANAA took great care to make the glass construction details unobtrusive while amplifying its spatial effects. This was done through treatment of seams, specification of glass, edge finish, and strategic placement of joints relative to the columns. Exposed glass edges in contemporary buildings are often highly polished to make them prismatic, then arissed (chamfered by sixteenth of an inch). At Toledo, the edges at silicone joints were ground smooth but left unpolished (Ra, 2017) to draw the eye not to the material edges but to the effects on the expansive surfaces. The architects specified low-iron glass was to minimize the green tint of standard glass, and carefully tuned the reflective finishes (Oki, 2017). Even though the architects were interested in reflecting the site context on the glass walls, the effects differ from those of Two-Way Mirror by Dan Graham, for example. Oki recalled they considered coating the glass to reduce reflections but not to increase them. Furthermore, reflective metal finishes are minimized in the building. The slender steel columns and light fixtures are finished in matte white. Exposed metals are limited to the stainless-steel frames at the glass doors and the guardrails around exhibited objects, where the shine is reduced with a matte, directional brushed finish (Oki, 2017). The occasional slender columns of only 3.5 or 4.25-inch diameter are purposely placed off the regular 8’ x 8’ grid so that the curved glass and its optical effects, not the column grid, take priority (Nordenson and Schneider, 2016).
Balance of light and transparency
Sejima and Nishizawa’s presumably do not begin design with specific optical effects of the building. In speaking of their acrylic wall installation of 2011 at the Barcelona Pavilion, they said, “We try not to select options for which we can already imagine the outcome,” an attitude which Beatriz Colomina calls “an architecture of deliberately unclear vision” (Colomina, 2010, p. 29). On the one hand, SANAA’s project architect Toshihiro Oki affirms this was the case in Toledo. On the other, the building is an exquisite lens carefully and deliberately calibrated for optical effects. He says, “Glass has the ability to reflect the seasons, the colors, and the sky. That gives a different kind of atmosphere on any given day or season…That possibility is what they (Sejima and Nishizawa) were interested in. But that’s the unknown in a way…You have an idea, but until you see it built, you don’t know for sure” (Oki, 2017). On the one hand, effects are unknown, but on the other, the Pavilion is marked by precision and discipline characteristic of SANAA. The effects are not accidental.
The architects introduced ways to balance the light levels between inside and outside. At nighttime when electric light makes the interior brighter
than the exterior, the vision of those inside the museum is dominated by the reflections of themselves and the interior objects. To counter this, the surrounding landscape is made artificially brighter to balance the light levels inside and out. This neutralizes the extreme differences and makes the glass appear less visible. Lighting the landscape from light poles reduced the interior reflections on the glass. Lighting designer Richard Kelly mastered this technique at Johnson’s Glass House, where the interior appears to be surrounded by walls of trees washed in spotlights (Drexler, 1993). By making the exterior brighter than the interior, a viewer inside can see through the glass without reflections obstructing the view. However, at Toledo, there are not sufficient vertical surfaces outside on which to project the light; the existing trees were too tall to be eye-level with people inside. Consequently, the interior appears brighter and more visible at night than during the day (Oki, 2017). The flickers of bright reflection spots on the glass play with the eyes to insinuate that there may be more glass rooms beyond a glass room, or perhaps it is a reflection of another.
In the daytime, the light in courtyards provides additional natural illumination for the interior to balance out the light levels. Oki also noted that a high contrast of light levels and constant views of reflections throughout the museum fatigue the eyes. The quiet, day-lit courtyards offer relief from the effects seen on glass (Oki, 2017). The natural light from the courts is filtered by curtains, which are coated with reflective aluminium flakes on the
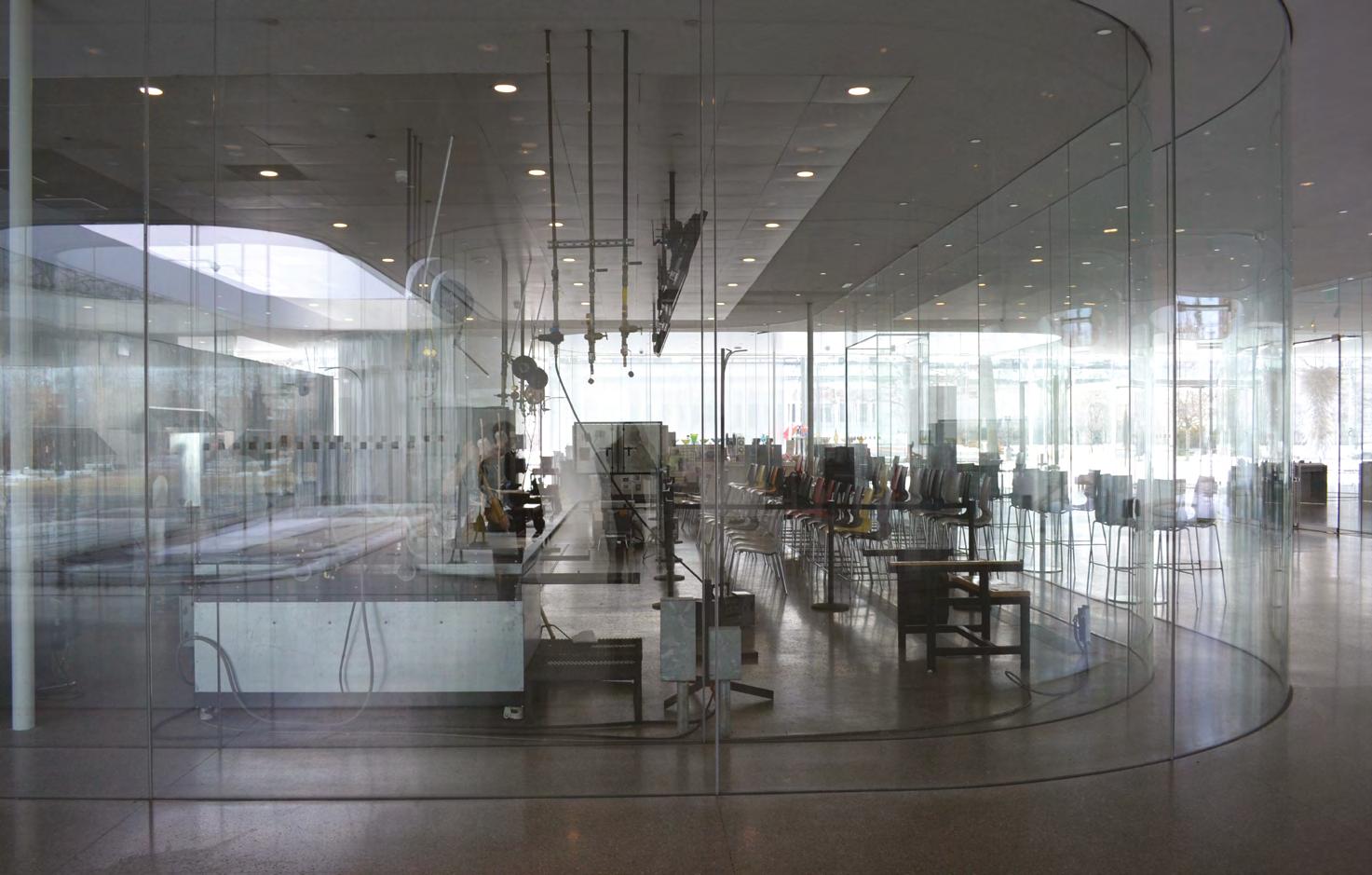
exterior surface to both minimize solar gain and filter visible light. This effect amplifies the diaphanous qualities of the interior (Moe, 2008). The moveable curtains of the Toledo Pavilion respond to the varied light in building at different times of the year and day. Likewise, the transparency of glass fluctuates with the season, the diurnal cycle, and the observer’s position in relation to glass walls.
Clear glass intensified
Observing the glass at the Toledo Glass Pavilion uncover complex and intensified effects, as well as metaphysical readings of transparency. In the Pavilion, a curious organization of rooms in plan and material organization is coalesced with skilful lamination and bending of glass and a daring approach to structural and mechanical engineering. It couples technical innovations with SANAA’s intent to foreground the atmospheric effects over the structure by disrupting the conventional hierarchies between structure and partition,
Fig. 04 Plan color coded to indicate three energy zones: perimeter buffer zone (light gray), hot glass demonstration area (dark gray), and galleries with individual climate control requirements (white). Plan courtesy of SANAA with color coding by author, 2006.
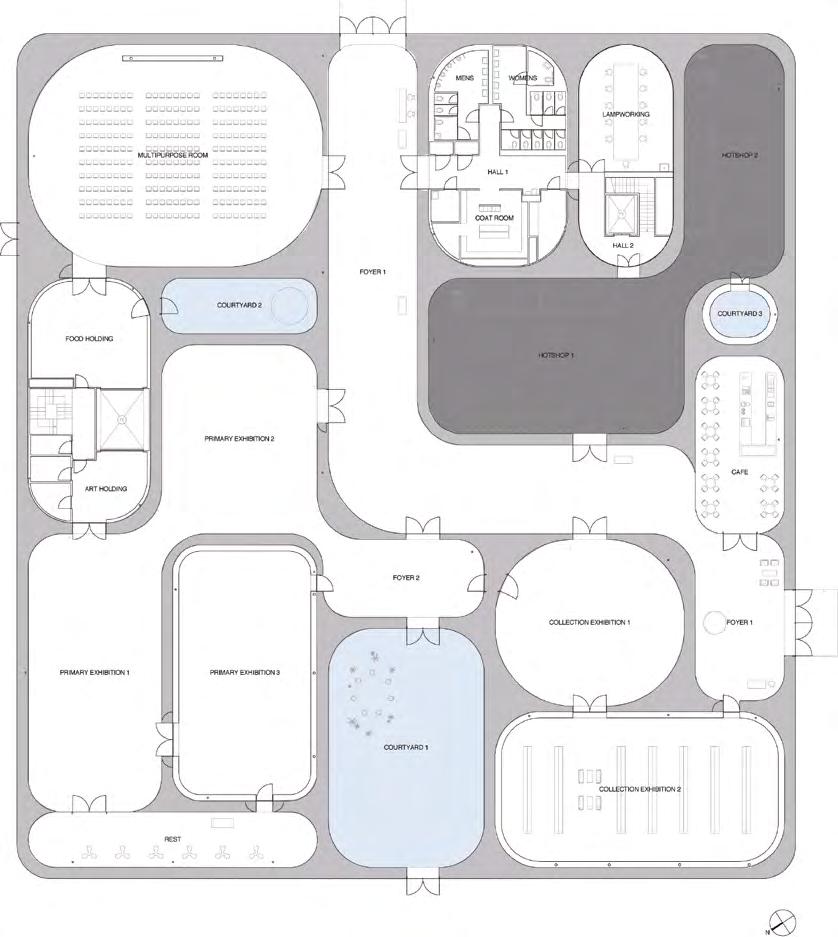
and concealment and exposure. From this approach emerges a different kind of intensified transparency of crystal-clear glass. In the design process, the architects discovered unanticipated programmatic adjacencies afforded by transparent glass. Bubble-like glass rooms are connected to yet isolated from each other by an interstitial airspace typically concealed in an opaque poche. The air cavity appears to fluctuate in opacity and thickness, like a stroke of a brush. The effect is soft, fluid, and watery, evoking return of glass to its non-rigid, liquid state, cushioned by air. The building is disciplined and precise in its execution, yet dynamic in sensual, intangible effects. In and around the pavilion, the glass continuously presents views of deep spaces beyond overlaid with reflections of locations far and near, through quick and slow motions. SANAA’s spatial organization of program, materials and light, combined with blurring of opaque-transparent hierarchy in structural and mechanical systems, result in a complex, intensified space of perception and a novel interpretation dynamic glass transparency.
References
Colomina, B. (2010). Undisturbed. In Costa, X. (ed.), SANAA: Kazuyo Sejima, Ryue Nishizawa. Barcelona: Actar, pp. 18-29. Diaz Moreno, C., Garcia Grinda, E. (2004). Ocean of Air. El Croquis. SANAA Sejima Nishizawa 1998-2004. Madrid: El Croquis, pp. 26-39.
Drexler, A. (1993). The Architecture Opaque and Transparent. In Kipnis, J., Whitney, D. (ed.), Philip Johnson: The Glass House. New York: Pantheon, pp. 2-7.
Ersoy, U. (2015). Glass, as Light as Air, as Deep as Water. In Mindrup, M. (ed.), Material Imagination: Reveries on Architecture and Matter. Burlington: Ashgate, pp. 155-167.
Hilberseimer, L. (1995). Quoted. In Riley, T. (ed.), Light Construction. New York: Museum of Modern Art, 2004, pp. xx-yy Lane, T. (2006). Polishing the Glass Pavilion (online). In http://www.toledoblade.com/Art/2006/06/04/Polishing-the-Glass-Pa vilion.html (last accessed June 2022).
Levine, S. L. (2012). Glass Pavilion (online). In https://sah-archipedia.org/buildings/OH-01-095-0097 (last accessed June 2022). Moe, K. (2008). Integrated Design in Contemporary Architecture. New York: Princeton Architectural Press. Nordenson, G., Schneider, B. (2016). Toledo Museum of Art Glass Pavilion. Structure Magazine (online). In http://www.struc turemag.org/wp-content/uploads/2014/08/D-Spotlight-Nordenson-Feb-091.pdf (last accessed June 2022).
Oki, T. (2017). Phone interview by author to Oki, T. (January 8, 2017). Former project architect at SANAA on the Glass Pavilion at the Toledo Museum of Art.
Ra, N.M. (2017). Phone interview by author to Ra, N.M. (March 27, 2017). Principal in charge of the Glass Pavilion at glass consulting firm FRONT.
Scheerbart, P. (1972). Glass architecture. In Sharp, D. (ed.), Glass architecture, by Paul Scheerbart; and Alpine architecture, by Bruno Taut. New York: Praeger, pp. xx-yy. Sejima, K., Futagawa, Y., Nishizawa, R. (2011). Kazuyo Sejima, Ryue Nishizawa 2006-2011. Tokyo: ADA Edita.
Glass-making workshop: fostering new design practices
Bringing future designers closer to the professional world requires the right balance of theoretical and practical activities; parallel to the traditional ateliers offered in design schools, some institutions are experimenting with different educational models, such as workshops. Contaminating, reinterpreting and experimenting are the keywords behind this activity, carried out in the Politecnico di Torino, in which glass has been one of the protagonists as a material with strong socio-cultural connotations. Because of its increasing application in technological fields, glass’s artisanal identity is getting weaker and requires a shift of focus from technological innovations to social innovations. Therefore, the week-long workshop “Il soffio di vetro”, offers the chance to envision glass as the meeting point between the knowledge of a local glass master and the design-creative skills of students. The experimental approach offered during the workshop enables students to understand the synergy between the glass’s aesthetic possibilities and functional constraints. It also helps define a more substantial value of sustainability in the relationship between university and craftsmanship.
The workshop’s goal is not to create a perfect final product but to bring students to understand the process and review it in a logic of innovation. It also helps to foster sustainable and creative approaches where the relationship between the designer and the material is direct, personal and supported by the local know-how.
A Polytechnic of Turin.
B Joga Glass.
C University of Parma.
KEYWORDS: WORKSHOP, GLASS MAKING, EXPERIENTAL LEARNING
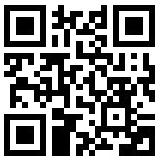
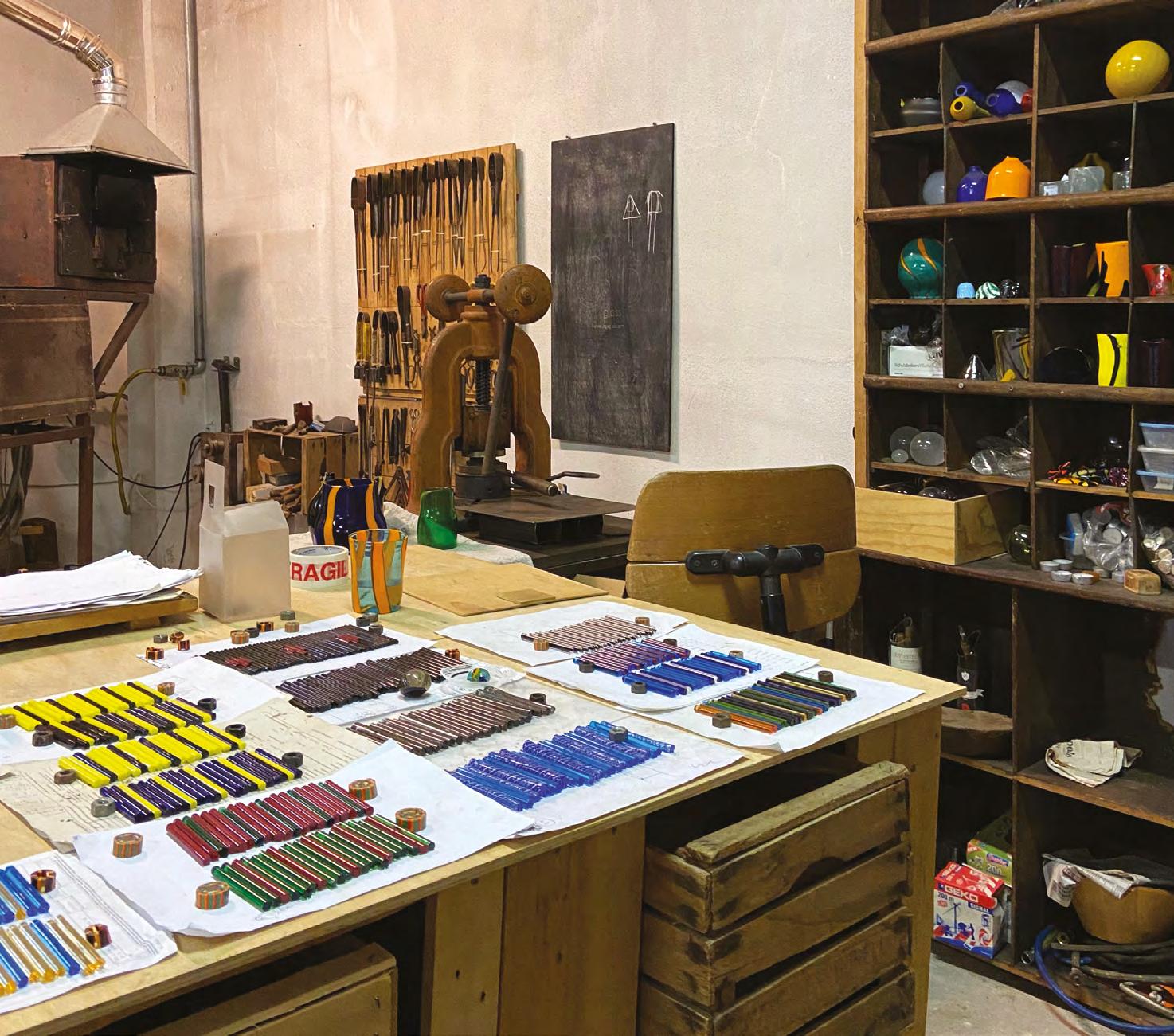

Glass Future Lab. Murano glass production and digital manufacturing: possible relationships in a future scenario
ROSA CHIESAA, RICCARDO BERRONEB, LUCA COPPOLACStarting from the Glass Future Lab project (Glass Week 2021), the contribution proposes a reflection on the theme of the possibilities of intervention in the traditional process of manufacturing glass artefacts. The aid of digital manufacturing is taken into consideration in order to respond to the needs of the production economy, to facilitate certain assembly phases and to accommodate the increasingly stringent demand for product customisation.
The project reversing some of the processing phases, opens up a series of important considerations, some related to the opportunity, even conceptual, of combining glass and plastic material – in a sort of unprecedented counterpoint – others of broader scope, around the future of a glass sector, the art glass sector, which suffers from historical and inherent immobility. Imagining new ways to hybridise production processes therefore means, beyond the purely technical aspect, thinking about training projects aimed at creating new professionals to be included as professional figures in the sector and dreaming of a future that stems from continuity with the sector’s historical legacy and its topicality.
A Department of Design, Università Iuav di Venezia, Venice, Italy.
B Faculty of Design and Art, Free University of Bozen-Bolzano, Bolzano, Italy.
C School of Architecture and Design, University of Camerino, Ascoli Piceno, Italy.
KEYWORDS: DIGITAL MANUFACTURING, FLEXIBILITY, 3D PRINTING
Design practice: intervening in the process
Intervening in the traditional process of designing and producing artefacts is a theme repeatedly addressed in the field of design, since it is precisely in these phases that the contribution of technical and conceptual innovation takes place, which opens up new results-products that are also innovative from an aesthetic point of view.
Intervening in the process does not have an unambiguous meaning, especially when this intervention concerns the hybridisation of techniques or the introduction of unprecedented gestures that pertain to purely artisanal areas. An original combination of craftsmanship and design is linked, for example, to the well-known reflection on the ‘variegated series’, explored by Gaetano Pesce1 (who also uses materials other than glass) in his experiments or by Rei Kawakubo, who has emphasised, in fashion design – among many conceptual dualities – the tension between the concepts of seriality and unique work, between standardisation and customisation, reflecting on the potential of the random but planned intervention that can give uniqueness to a mass-produced item (Bolton, 2018). Certainly also historically, the same theme was addressed in the specific field of Murano glass, which will be the subject of the contribution here, when Sergio Asti designed the Marco vase (Cappa, 1989), made by Salviati in 1961, winner of the Compasso d’Oro in 1962. Beyond the mere formal definition of the object, the project acts on the process –- with a hot intervention – considering the natural propensity of glass to assume natural ‘random’ configurations due to weight and gravity. In this case, it is a design that respects the specific nature of the material and its variable behaviour within the process.
If these examples can be useful to clarify one of the interpretations of intervening in the manufacturing process, the project that will be exhibited here investigates a further meaning of this intervention, introducing digital manufacturing within the process, but always moving in the direction of managing the dichotomy between standardised object and customised work (Antonucci, 2016).
History and recent events
The reference context in which to read the novelty of the Glass Future Lab project proposal, and its potential developments, is certainly linked to the evolution or static nature of the way glass is designed and produced today, to the consequent commercial implications and, more generally, to the urgent question of the future of the Murano glass sector.
For years now, the Murano glass manufacturing industry as a whole has
1 For more on the subject of the variegated series, a theme that is also much explored in art, see the volumes by Carlo Martino and Anty Pansera in the bibliography.
been experiencing a slow decline, partly due to mechanisms that are difficult to counter locally, globalisation and delocalisation processes, increasingly high production costs, the economic crisis, and the systematic reduction of reference product sectors, which have cyclically characterised the history of the glass sector, as can be seen from the rich literature on traditional glassmaking and the specific surveys on the sector and the artistic glass district carried out in more recent years (Chiesa, 2019).

The scarcity of economic resources available to nurture a pathway built on research and development, the lack of dialogue with institutions (now fortunately initiated with the successful Glass Week event) and a poor understanding of the changed socio-economic conditions on the island have led, together with the effect of the COVID-19 pandemic, to a violent acceleration of the crisis in the glass industry, leaving all the problems and contradictions that have characterised recent decades to emerge abruptly.
While it is certainly true that the very recent energy crisis – as in the 1970s –is at the root of the worsening/closure of many local activities, and that, more generally, the environmental problem is becoming more and more pressing (considering that Murano glass is not recyclable) it is, in our opinion, legitimate to envisage a future for the Murano glass industry that envisages multiple responses, as multiple is the configuration of the industry.
BERRONE,Project: the premises
As designers with the AUT Design Collective group, founded in 2011 by Riccardo Berrone, Luca Coppola and Federico Bovara, we have tried over the years to come up with answers based on our background and skills, placing our research within that area of intervention represented by the relationship between design and mouth glass production.
In some ways, Murano is a sector with similar characteristics to other Italian production districts understood “as the natural offspring of a tradition of craftsmanship”: the high manual skill of its operators, a savoir faire rooted in the past, a specific geolocation, a fruitful link, recognisable and celebrated even today, with a certain way of conceiving design.
The design reflection has therefore focused on the redefinition of the relationship between design and production of Murano glass, an emblematic area of a relationship between the world of design and the world of ‘standardised’ artisan production which, especially in Italy, has given rise to happy examples of Made in Italy excellence.
Thanks also to the experience gained over the years within this sector, for example in the long collaboration with the Salviati company2, we have repeatedly posed the question of “where to intervene”, at what level is it permissible and possible to intervene in the phases of a production process without distorting it, but by planning punctual, circumscribed interventions that aim, if not to innovate, at least to propose a sustainable alternative to the state of the art.
Glass Future Lab
Presented at the Fondaco dei Tedeschi on the occasion of Glass Week 2021, the project Glass Future Lab starts out from a consideration of a peculiarity of mouth-blown glass production: its flexibility, understood on the one hand as a characteristic that the designer must traditionally possess in order to share the realisation of his project with an interpreter (the master), but flexibility also in relation to the material glass, which must first be known and ‘indulged’ in its nature, as Semper suggested.
The process imagined with Glass Future Lab, which envisages the use of digital manufacturing, is economically very costly and not advantageous when applied to large production batches, but is instead interesting when production numbers become smaller and customisation a necessity.
In the realisation of complex projects, e.g. the production of a lighting system consisting of several glass components of different shapes, connected together, the difficulty to be overcome lies not so much – or not only – in the
2 More at: https://98800.org/ (last accessed September 2022).
realisation of the glass mould, but above all, in being able to ‘force’ it to conform to standardised joint elements prescribed by stringent safety standards.
The risk of starting a production process that proceeds by trial and error (the possibility of testing is reduced by economic reasons) with the aim of refining the moulds until they fit perfectly into the joint, brings with it a high percentage of unplanned waste, which translates into a significant increase in costs, and equally into the production of non-recyclable waste (Murano glass waste is classified as ‘special waste’) (Coreve, 2021).
The reflection around the theme of the possibilities of intervention in the traditional process of glass manufacturing led us to think of digital manufacturing as a solution to get out of some impasses:
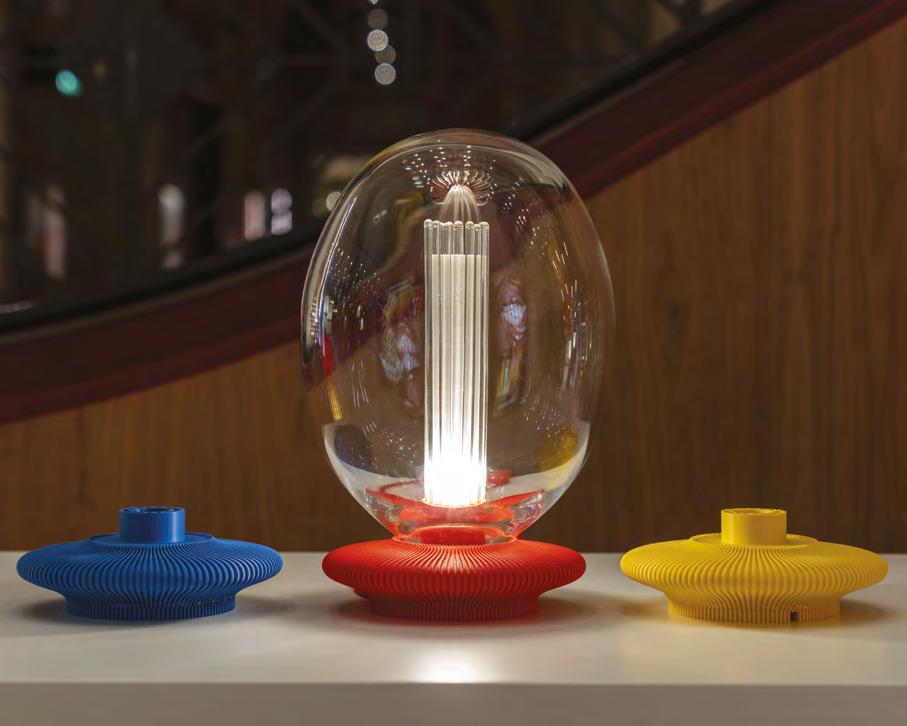
• accommodating the low propensity of the Murano masters towards serial production;
• address production economy requirements (to reduce waste, albeit relatively small numbers);
• facilitate certain assembly phases;
• respond to the increasingly stringent demand for customisation of products.
The project, which finds an indispensable support in digital manufacturing, stands at a great distance from the world of Murano but, paradoxically, shares with this traditional mode of production precisely the theme of flexibility. Digital manufacturing – be it 3D scanning, 3D printing, laser cutting, CNC machining, etc. – allows almost infinite customisation. What’s more, it totally frees the production process from any idea of standards, putting the completion of the variation back into the hands of the designer, or the person making the digital model.
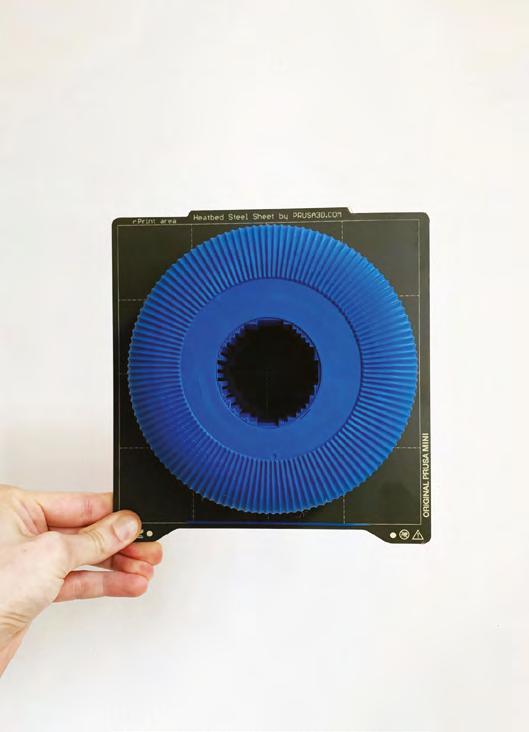
Our design proposal therefore introduces a reversal of perspective and production phases: contrary to what is usually the case, it is no longer the glass (hence production) that has to adapt to a previously defined project, but it is the project that, once production is closed (and the glass artefact with its imperfections is obtained), flexibly develops every detail and subsequently designs and starts the production of subordinate components (Figure 02).
Returning to the previous example of the lighting system, given an outline design, in a first phase the production of the glass components is started, leaving the master the possibility to move comfortably with respect to the variation/imperfection inherent with handcrafted production.
In a second phase, the glass elements are digitally scanned to obtain threedimensional models that can be worked on with the 3D printer. By analysing the three-dimensional models, it will be possible to measure the thicknesses (not always regular) of the individual elements in order to define the exact design of the joint or other subordinate elements that will be produced using digital manufacturing and facilitate the assembly phase.
In this way, by reversing the traditional processing and assembly phases, the original design is realised through the support of digital technology, minimising the margin of error and glass waste (Figure 03).
A process such as the one just described, being flexible, easily responds to the demand for customisation that is increasingly becoming a distinctive feature of exclusive projects, conceptually crossing the evolution of contemporary design towards forms increasingly hybridised with art and the unique piece (Figure 04 and 05).

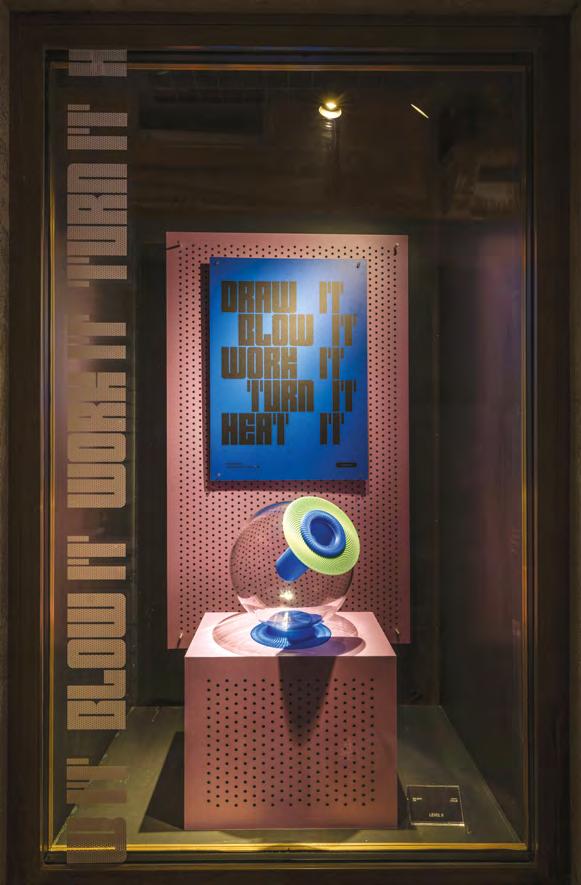
Conclusion
The Glass Future Lab project, which was also accompanied during its official presentation by a discussion-reflection on the future of glass, and which thus sets itself the goal of rethinking the production process by reversing certain processing stages, opens up at the same time to a series of important considerations that we can summarise here (Barovier Mentasti, 1982; Barovier,1999; Deboni, 1996; Dorigato, 1984; Gasparetto, 1958; Mariacher, 1954):
• a first theme concerns the semiotic and aesthetic significance of the coupling of glass and plastic material (the joints made in 3D in the example);
• what may sound like ‘heresy’ to some, may instead reveal itself (as experimentation in fashion design teaches us) to be a daring path with as yet unknown results.
Similarly, the topic of hybridising production processes, particularly the traditional glassblowing process with that of digital manufacturing, can potentially open up new avenues to respond more sustainably to market demands.
A third consideration, of central importance, concerns the opportunity offered by these new hybrid approaches to overcome the traditional separation between ‘handmade’ and ‘machine-made’ by placing this notion in the contemporary context and opening up the classical dual relationship between designer and performer to the formation of new professional figures, from the technical operator to the digital craftsman who can interact with masters and designers (Micelli, 2016).
Naturally, these observations are part of the broader scenario of reflection on the future of a sector, that of artistic glass, which suffers from a historical and inherent immobility and is going through a deep crisis, but which has always found the strength to historically regenerate itself and to ‘revive’, to show itself antifragile.
References
Antonucci, R. (2016). Arte e/o design. Milano, Udine: Mimesis.
Barovier Mentasti, R. (1982). Mille anni di arte del vetro a Venezia. Catalogo mostra Palazzo Ducale Museo Correr, 24 luglio- 24 ottobre 1982. Venezia: Albrizzi.
Barovier, M. (1999). Il vetro a Venezia. Milano: Federico Motta.
Becattini, G. (1998). Distretti industriali e made in Italy. Le basi socioculturali del nostro sviluppo economico. Torino: Bollati Boringhieri.
Bolton, A. (2017). Rei Kawakubo Comme des Garçons: Art of the In-Between. New York: The Metropolitan Museum of Art. Cappa, M. (1989). L’Europe de l’art verrier, des precurseurs de l’art nouveau à l’art actuelle 1850-1990. Bruxelles: Mardaga. Chiesa, R. (2019). Carlo Moretti: vetro e design. Venezia: Marsilio.
Coreve, il Consorzio nazionale per riciclo e recupero di imballaggio in vetro (2021). Rapporto 2021 su raccolta e riciclo del vetro (online). In: https://coreve.it/rapporto-2021-su-raccolta-e-riciclo-del-vetro/ Deboni, F. (1996). Murano 900: vetri e vetrai. Milano: Bocca. Dorigato, A. (1984). Storia del vetro (ed. italiana). Novara: De Agostini. Gasparetto, A. (1958). Il vetro di Murano dalle origini ad oggi. Venezia: Neri Pozza. Mariacher, G. (ed.) (1954). L’arte del vetro. Milano: Arnoldo Mondadori.
Martino, C. (2007). Gaetano Pesce. Materia e differenza. Venezia: Marsilio. Micelli, S. (2016). Fare è innovare. Il nuovo lavoro artigiano. Bologna: Il Mulino. Pansera, A. (2013). Bracciodiferro. Gaetano Pesce-Alessandro Mendini 1971-1975. Catalogo della mostra (Milano, 4-14 aprile 2013). Milano: Silvana Editoriale.
Innovation scenarios in the glass industry in Europe
LUCA TRULLIAThe following article is part of broader doctoral research conducted by the author, concerning innovation and technologies developed in the glass sector.
Thus far, glass is one of the most widely used materials in the construction field. The extent of the use of this material is related to the innovations that have transformed the glass industry throughout history, from the industrial process to the final product.
The proposed paper aims to retrace past and present innovations through the acknowledgment of contemporary demands with a view to possible future developments of glass, by analysing the current sectoral targets and the critical issues that claim for the development of new models, to reduce the environmental impact of the entire glass life cycle.
A Department of Architecture, Roma Tre University, Italy.
KEYWORDS: GLASS, RECYCLE, INNOVATION
The birth of glass: first applications and processing techniques
The historical reconstruction of the evolution and use of glass by man in architecture is an articulated path that goes beyond the discovery of the material itself and involves, throughout history, investments in research and development, political-strategic decisions, stories of innovation, and the evolution of architectural movements. The origins of this material, as reported by Plinius the Elder (23-79 A.D.) in his encyclopaedic text Naturalis Historia (77-78 A.D.), are due to “natrum” traders who, lighting a makeshift fire on the banks of the Belo River, in Syria, melted its silty sand with the blocks of natrum, generating the release of the first glassy mixture and tracing the origins of this discovery back to a fortuitous case. Since its discovery as a precious material derived from a fusion process, but even earlier as a material of volcanic origin such as obsidian, the use of glass was an elitist prerogative of higher social classes. The first processing techniques can be traced back to the 3rd Century B.C., when Syrian artisans, by introducing the glass-blowing system using an hollow pipe, began to understand the various possible transformation processes of the glass mass, expanding its diffusion to a broader segment of the population (Baratta, 2020). The first process innovations can be dated to the first centuries A.D., when the Romans, by modifying the composition of the vitreous mixture with the addition of oxides, enhanced the transparency of the material, increasing its possible uses. The use of glass achieved resounding success among the Romans, who often used it for mosaics, experimenting with various systems of coloring and discoloration as well as with production, by using the first examples of casting. The first architectural uses of glass can be found in the villas of Pompeii and Herculaneum on wooden frames with limited dimensions of 30 x 50 cm and a thickness of 3 to 6 cm (Schittich et al., 1999). The Roman artistry and use of this material were so relevant to be spread even beyond the Alps. In the Middle Ages, the first guilds were born to guarantee the secrecy of glass processing techniques. In 1291, Venice placed the production and processing of glass on the island of Murano, which became the most important centre in the world between the 15th and 17th centuries. During the Middle Ages, further production centres were born in Italy between Tuscany and Liguria, and new manufacturing methods were developed employing ball-blowing and cylinder-blowing. During these centuries, the production techniques of the various master glassmakers began to have a European spread. The Manufacture Royale des glaces à miroirs was born in the small town of Saint-Gobain (FR) in October 1665, at the behest of King Louis XIV and on the initiative of the finance minister J.B. Colbert, to weaken the Venetian domination of glass. This fact guaranteed financier Nicolas Dunoyer and his partners protections and renewable tax exemptions for twenty years for the production of mirrors. (Saint-Gobain, 2022). Developments in processing
techniques, such as that of casting evolved in 1687 by the Frenchman Perrot, extended the boundaries of glass production to other countries. This material, although still very expensive, began to spread in various countries such as England and Germany, subsequently extending into non-European states such as Ohio (USA), becoming, from the latter half of the 19th Century, an increasingly central element in daily life also thanks to the first worldwide events and earliest systems of industrialization.
The innovations of the twentieth Century
The product and process innovations that characterized the 20th Century have allowed a real breakthrough in the production system of flat glass and its applications in the architectural field. New production systems and new plants for secondary processing have expanded the spread of its use on a global scale, by improving the quality of the product and its properties, contributing to the development of new technologies.
The most important process innovation is certainly the one made by Sir Alastair Pilkington in 1952. The actual innovation introduced by Pilkington, which still represents the modern flat glass production system, consisted in making the vitreous mixture float on a 7 cm thick molten tin bath, after the phases of melting, refining, rest, and conditioning. This advancement allowed the glass mixture to obtain two perfectly coplanar faces of the final slab, the lower one obtained from contact with the tin and the upper one due to the effect of gravity and heat. This system has completely transformed the flat glass supply chain by increasing the quality of the final product, allowing the elimination of further processing aimed at obtaining greater transparency and guaranteeing a significant increase in the size of the plates produced, reaching 6 x 3.21 m. Through the introduction of this new glass production system, there is a shift in the design approach to this material, allowing the creation of works that were previously unrealizable due to the absence of this technology.
The fragility and the quality of the final product have always been two crucial aspects of this material. Before the system introduced by Pilkington and called “float glass”, the production of flat glass, and hence its possible applications, were strongly conditioned by the dimensions of the glass itself and by the subsequent processing necessary to obtain a high-quality product. From the second half of the 18th Century, thanks to the first major global events, glass began to arouse the interest of designers and beyond. Among the most iconic uses of glass in the 19th Century, the Crystal Palace is certainly its maximum expression. Made for the Great Exhibition held in London in 1851, this glass building was designed by Joseph Paxton in collaboration with the engineer Charles Fox and was meant to host the event. The importance of this exhibition, being the first in history, prompted the designer to create a
90,000-square meters building, entirely made of steel and glass. The success of this project, besides Paxton’s great capability, was possible thanks to the product and process innovations that the brothers Robert Lucas (1782-1865) and William Chance (1788-1856), of the Chance Brothers Company, brought to their manufacturing system to make the glass of the Crystal Palace.

The London Great Exhibition of 1851 marked the introduction of new building typologies, these being an expression of the development of new technologies, the change of cities, and the way citizens established relations with them. By responding to a new need induced by new trades and manufacturing systems, the industrialization of the city had been a driving force for its development. In these new structures, such as stations, factories, and large pavilions, glass played a central role in the natural lighting of the spaces. The spread of the use of this material, subsequently to the Great Exhibition, profoundly marked the entire 20th Century, characterizing the language of the Modern Movement which gave the glass a strong expressive feature.
The first thirty years of the 20th Century are indeed characterized by two of the most important product innovations made with this material: laminated glass and tempered glass. These techniques, by improving the safety of its application and increasing its mechanical strength, have allowed the use of glass in solutions previously not feasible, with the consequent development of new technologies. The laminated glass, patented in 1903, has been formulated by the French chemist Edouard Benedictus (1878 – 1930), who understood the potential of the interposition of a plastic layer between the
glasses to seal post-break fragments after a laboratory accident. The first uses of this new technology saw the automotive sector as the leading one, which employed it for the replacement of windshields, previously made of annealed glasses, and only later in the building trades. The second product innovation is the one made by the French company Saint-Gobain which, in 1929, began producing safety glasses through the tempering process (Schittich et al., 1999). These two pivot innovations have increased the use of glass in architecture, paving the way for its use as an element for curtain walls or structural glazing, which still uses these two types of glass.
Innovation processes, whether they regard the product or the process, are actions that often respond to an exogenous need induced by the global market. Following the energy crisis of 1973, the approaches to design and particularly the attention to technology, have led to product and process innovations aimed at increasing the performance of products. Within this context, which closely links the economy to the building trade, low-emissivity glass has been developed through incremental innovation. This type of glass is obtained by placing a metallic deposit on one of the two surfaces of the glass. This specific procedure can be carried out during the production of flat glass, through a pyrolysis process, or subsequently through a process called Magnetron Sputtering Deposition (Baratta, 2020). The latter, carried out after the production of the glass sheet, is the most used method to produce lowemission glasses for double-glazing.
These innovations, which characterized the glass sector in the 20th Century, have allowed the spread and use of this material, allowing it to be one of the most used in the building trade due to its qualities and characteristics. The importance and employment of this material are likely to constitute about 50% of the envelope of a building, rising to higher percentages in solutions where the envelope is completely entrusted to technologies that employ this material (Trulli, 2021).
Research and development: new technological solutions using glass
The overall framework of flat glass production is composed of more than 500 furnaces with a production of over 100 million tons and a market of above 270 billion dollars in 2021 (Grand View Research, 2021).
The distribution of the production sites sees the Asian continent as the leading one, gathering about half of the worldwide plants, far more than the 48 plants dependent on the ETS, which are located in Europe (Glass for Europe, 2020), producing over 10 million tons of flat glass every year with a turnover of more than 15 billion euros. Alongside the large numbers of turnover and production, the glass sector is one of the ones with the greatest investments in research and development. In Italy alone, approximately 300 million euros were invested in plants in 2018, keeping an active focus on its updating and possible innovations (Assovetro, 2020). Over the last decades,
these huge investments in product, process, and proceeding innovation have led to increasingly performing products, capable of responding to the performance needs dictated by the market.
At the end of the seventies of the 20th Century, many architects began to develop theories on the adaptability of the envelope in response to different climatic conditions. Among the many, Richard Rogers, one of the leading exponents of the hi-tech current, argues that “the skin of the building must be like a chameleon”, that is a skin capable of adapting to different needs (Stevens, 1980, p. 705). In this context began reflections and experimentations on materials capable of changing their performance or appearance, while conditioning the indoor comfort. Among the leading products developed in this direction, chromogenic glasses have contributed to the “chameleon transformation” of a building. Over the last 20 years, following the low-emissive, selective, or reflective solutions, these types of glasses have increasingly seen their use in architectural solutions (Andreotti, 2009). Among the first ones to understand the potential of these materials were Carl Lambert and Claes-Goran Granqvist, who, during the International Congress of Optical Science and Engineering held in Hamburg in 1988, underlined the importance of these materials for their ability to regulate energy flows in the possible applications in doors and windows and envelopes (Lampert and Granqvis, 1990).
These types of glasses can be distinguished between two macro families, based on the activation system. The first, which concerns thermochromic and photochromic glasses, does not need electrical activation and can selfregulate according to the temperature and intensity of the light. The second type is that of electrochromic glasses, which change their state of transparency through an electrical impulse that intervenes on the electrochromic film.
Over the last three decades, the greater energetic efficiency required from the building heritage has characterized many technological areas,
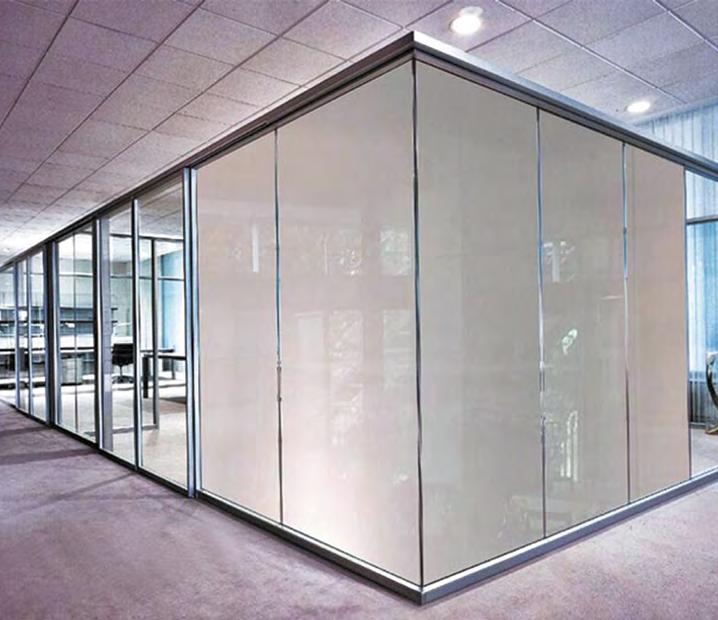
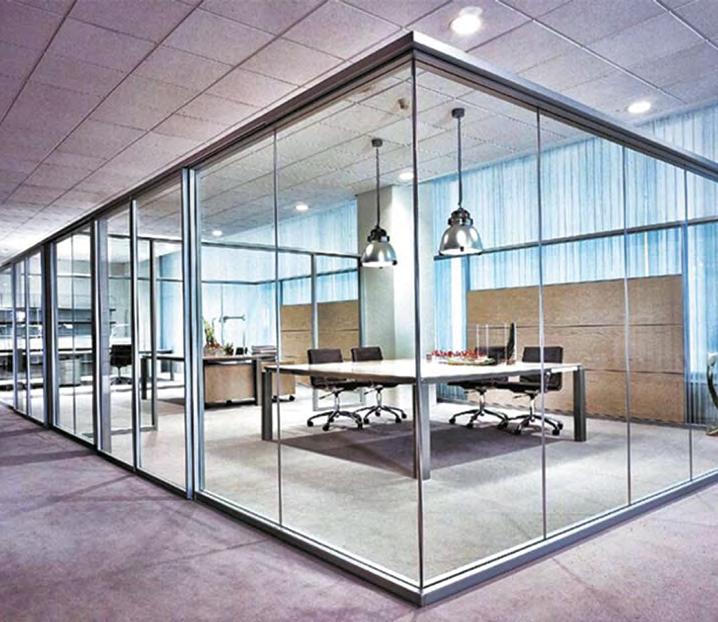
encouraging research towards the development of new and increasingly efficient materials. This research, which in some cases has seen the technology transfer from other industries such as the aerospace one, has now led to high-performance technologies. In the glass sector, this need has led to the development of products that see the combination of previously described technologies, such as double glazing with lowemission glasses, and phase-changing materials (PCM). This product innovation is achieved by placing PCMs, like the most common paraffin, within the space left between the two or more glasses. These phasechanging materials, manage to modify their state with the variation of the temperature and can accumulate and release thermal energy, achieving excellent performance in environments where the temperatures and their variations are very large. The diffusion of these glasses on a large scale in the architectural field is currently seeing its first uses but, even today, the high cost of these technologies affects their usage.
Among some of the most recent developments are the experiments for the production of vacuum glasses. The innovation introduced for these glasses exploits the principle of double-glazing but reduces its overall thickness. The substantial difference between double-glazing and vacuum glass is that, in the first case, the glasses are separated by a “duct” sealed on the perimeter in different types of materials, and in the space generated by this duct is placed a gas, generally argon or krypton. These double-glazing units, used in all modern windows with double or triple-glazing solutions, can reach up to an overall thickness of 45-50 mm to obtain good transmittance characteristics. The innovation introduced by vacuum glasses is the elimination of this space between the glasses, reducing it to thicknesses equal to fractions of a millimetre. This glass, which currently has an overall thickness of 6.2, 8.2, and 10.2 mm, is comparable in thickness to a single glass used in double glazing.
The difference is that within this glass thickness of 6.2 mm, made with two glasses of 3 mm, there is a space of 0.2 mm placed under vacuum. This space, even if smaller than a millimetre, can give these “single” glasses high thermal characteristics, with a transmittance that can even reach Ug = 0.7 W/m2K for thicknesses of 10.2 mm (Pilkington, 2022). The advantages that this product innovation has introduced are several, from the total weight reduction of a single window, with a consequent saving of material, to the application of these glasses in contexts of historical and cultural value. This technology, which has been used for years in Japan, must deal with some of its great limitations that have not been promptly settled. Currently, low-emissivity vacuum glasses can reach a maximum production size of 150 x 250 cm, restricting the possible uses in large solutions with wider frames. Further critical issues, which have to be solved, are the presence between the two glasses of small spacers that are not perfectly transparent but are necessary
in order to avoid contact of the two plates when these are placed under a vacuum, and the currently still very high cost, compared to the ongoing technologies.
The European goals: engine for an ecological transition
Among the goals imposed by the European Union for the reduction of 55% of greenhouse gases by 2030, to become the first climate-neutral continent in 2050 (European Commission, 2021), glass plays a leading role. According to the report drawn up by the Building Performance Institute Europe, the condition of about 75% of buildings in Europe is inefficient from an energetic point of view, and measures will be required in more than 90% of the buildings to reach the 2050 goals (BPIE, 2017). These measures will necessarily intervene on the envelopes of the buildings themselves, affecting all the transparent parts that are now inefficient. According to an estimate conducted by the European Commission, the average performance of windows and doors in Europe is equivalent to Uw 3.4 W/m2K (Glass for Europe, 2020), still far from the values returned by the most recent product innovations for these technologies. The interventions, necessary for this energy efficiency, will trigger a total or partial replacement of the current doors and windows, returning an enormous amount of materials destined for recycling. The glass recycling system is among the most active and efficient in Europe. In 2019, according to the European Container Glass Federation (FEVE), the average rate of hollow glass collection for recycling in Europe reached 78% of the total (FEVE, 2021). These percentages, because of the 2030 European goals, aim to reach 90% of the total weight of products placed on the market, thanks to the expansion of the network of stakeholders involved in the recycling process. The quantity of glass produced in Europe, in the year 2020, exceeded 35 million tons. Of this amount, about 22 million tons are hollow glasses, such as containers and bottles, and just under 11 million are flat glasses, with the residual quantity addressed to the market of domestic glass, wool, and rows (Glass Alliance Europe, 2022). The percentage data related to the glass recycling rate in Europe, as previously reported, only consider the recycling of hollow glass, returning a strong interest in recycling but giving an inaccurate view of the amount of recycled flat glass. Flat glass, unlike hollow glass, poses greater difficulties in recycling due to the high quality required by aspects such as transparency.
The presence of polymeric layers, such as polyvinyl butyral, or silicone materials, makes its recycling for reuse as a secondary raw material a process that is still developing. Another aspect that differentiates hollow glass from flat glass is the duration and permanence time of the two different products, as the flat glass used for windows has a life cycle of about 20-30 years before being removed and destined for a recycling process.
Conclusion
Investments in research and development in this sector have led, over the years, to increasingly performing products with a view to energy and material saving.
The European green deal, with its targeted goals, will be the main engine for a gradual efficiency improvement of the present buildings (European Commission, 2018), with the replacement of millions of tons of glass that will necessarily have to be put into a recycling process. These aspects, closely linked to each other, must aim at the development of two main aspects:
• the increase of the recycling procedure of flat glass with process innovations aimed at eliminating polluting materials and reusing it as a secondary raw material, increasing the percentages of reuse in the production process, currently between 25% and 40%, with a consequent reduction of extractions for the supply of raw materials;
• the encouragement in the use of high-performance technologies such as vacuum glasses, phase-change glasses, and chromogenic glasses, contributing to the enhancement and further development of these and normalisation of costs for use.
The replacement of doors and windows with new products suited to the new needs as well as the recycling of outdated materials will be just two of the strategies the glass supply chain will need to pursue in order to contribute to the achievement of European goals. Considering Europe, current flat glass production systems affect 0.65% of the CO2 industrial emissions: a very low percentage, which can be further reduced.
In Italy, the Divina project was born in 2021, which sees the collaboration of public and private bodies to reduce CO2 emissions through the use of a hydrogen-natural gas mix for the production of glass (SNAM, 2021). This process innovation, even if at the beginning, has opened a way toward the possible future uses of new energy sources for a lower environmental impact. This “circular” system, besides reaching the goal of making the glass production process, its use, and recycling a closed system, would certainly be a driving force for the economy in the construction sector, dragging further interventions aimed at improving the efficiency of envelopes towards buildings with ever lower emissions. Only in Italy, according to what was reported by the National Union of Metallic Construction Industries of the Envelope and Windows (UNICMI) based on Istat data, in 2021 the sector of doors and windows and curtain walls for both residential and non-residential buildings, has generated demand for equal to € 5.2 billion.
Further future developments of glass extend beyond its classic known uses, thanks to research conducted by institutes and academics concerning the use of recycled glass as a replacement for fine aggregates in mortars and concretes. In the last decade, research such as those conducted by professors Luigi Mollo and Rosa Agliata of the University of Campania “Luigi Vanvitelli” on
the use of recycled glass as a substitute for fine aggregates in mortars, has shown how this new design mix exceeded the mechanical requirements of the NTC 2008 (Mollo and Agliata, 2015).
The evolution that this material has had throughout history, with its countless technological and scientific innovations, leads today to materials and technologies with very high performance used in various sectors in addition to construction. Millions of euros in annual investments show how much attention is paid to this sector, which daily improves its products and processes in an incremental perspective for its performance and reduction for the environmental impact.
References
Andreotti, G. (2009). Il vetro. In Sinopoli, N., Tatano, V. (ed.), Sulle tracce dell’innovazione: tra tecniche e architettura. Milano: Franco Angeli, pp. 175-186.
Assovetro (2020). Rapporto di sostenibilità 2020 (online). In https://www.assovetro.it/wp-content/uploads/2020/02/re port-completo-low-min2.pdf (last accessed August 2022).
Baratta, A. F. L. (2020). Materiali per l’architettura. Napoli: Clean.
Building Performance Institute Europe – BPIE (2017). State of the building stock (online). In https://www.bpie.eu/wp-content/ uploads/2017/12/State-of-the-building-stock-briefing_Dic6.pdf (last accessed August 2022).
European Commission (2018). A Clean Planet for all: A European strategic long-term vision for a prosperous, modern, competitive and climate neutral economy (online). In https://eur-lex.europa.eu/legal-content/EN/TXT/?uri=CELEX %3A52018DC0773 (last accessed August 2022).
European Commission (2021). Green Deal europeo: La Commissione propone di trasformare l’economia e la società dell’UE al fine di concretizzare le ambizioni in materia di clima (online). In www.ec.europa.eu/commission/presscorner/detail/it/ ip_21_3541 (last accessed May 2022).
FEVE (2021). La raccolta record di contenitori di vetro per il riciclaggio raggiunge il 78% nell’UE (online). In https://www.federv ini.it/studi-e-ricerche-cat/3860-ricerca-bottiglie-in-vetro-piu-sostenibili-del-bag-in-box (last accessed May 2022).
Glass Alliance Europe (2022). GAE Glass Production (online). In www.glassallianceeurope.eu/images/cont/gae-glass-produc tion-2021_file.pdf (last accessed May 2022).
Glass for Europe (2020). 2050. Il vetro piano nell’Europa a emissioni zero (online). In https://glassforeurope.com/wp-content/ uploads/2020/10/Decarb_broch_ITALIAN_for_WEB.pdf (last accessed May 2022).
Grand View Research (2021). Flat glass market size & share report, 2022-2030 (online). In www.grandviewresearch.com/indus try-analysis/global-flat-glass-market# (last accessed May 2022).
Lampert, C. M., Granqvist, C. G. (1990). Large-area chromogenics: Materials and devices for transmittance control. Volume IS 4. United States.
Mollo, L., Agliata, R. (2015). Il rottame di vetro: da rifiuto a risorsa. In Baratta, A. F. L., Catalano, A. (ed.), Il riciclaggio come pratica virtuosa per il progetto sostenibile. Pisa: ETS, pp.158-171.
Pilkington (2022). Pilkington Spacia (online). In https://www.pilkington.com/it-it/it/prodotti/categorie-prodotti/isolamen to-termico/pilkington-spacia (last accessed May 2022).
Saint-Gobain (2022). 1655: Louis XIV fonde la Manifacture royale des glaces à miroirs à l’instigation de son ministre Colbert (online). In https://archives.saint-gobain.com/ressource/xviie/1665/1665-louis-xiv-fonde-la-manufacture-royale-desglaces-miroirs-linstigation-de (last accessed May 2022).
Schittich, C., Staib, G., Sobek, W., Schuler, M., Balkow, D. (1999). Atlante del vetro. Torino: Utet. Snam (2021). Idrogeno: avviato progetto italiano per la decarbonizzazione dell’industria del vetro (online). In www.snam.it/ export/sites/snam-rp/repository/file/Media/Comunicati_stampa/2021/CS-Divina_RINA_Snam_BORMIOLI.pdf (last ac cessed May 2022).
Stevens, T. (1980). Putting the tech into architecture. New scientist, vol. 88, No 1231. London: Reed Business Information Ltd, pp. 704-706. Trulli, L. (2021). Il riciclaggio come propulsore innovativo nel settore produttivo del vetro. In Baratta, A. F. L. (ed.), PRE|FREE – UP|DOWN – RE|CYCLE Traditional solutions and innovative technologies for the end of waste, 4th International Confer ence. Conegliano: Anteferma, pp.182-193.
XPS characterization of plasma-activated surfaces. A possible benefit for glass bonding
ANNE TALNEAUA, CHRISTOPHE CARDINAUDBDirect bonding of glass without any adhesive or additional material is increasingly used in terrestrial and spatial optical manufacturing. N2- plasma is reported for enhance bonding on Silicon for SOI layers, Germanium, garnet, SiCN. The main reason proposed is the surface activation by N2-plasma, generating dangling bonds which increase the van der Walls interactions. Authors have investigated the surface-dipole generation by XPS on Si surfaces and identified modified binding energies. We here investigate by XPS the role of N2-plasma on Si surface. Two measurements are performed: the first one in-situ within the plasma chamber after plasma exposure, the second one after putting the surface to air thus mimicking what happens when surfaces are brought into contact outside the plasma chamber.
We present the evolution of the Si2p binding energy. It is reduced after N2-plasma exposure and increases after the sample being vented to air. Nevertheless, a reduced binding energy remains.
We propose that this reduction is the signature of a dipole surface formation, which increases van der Waals interaction, thus improving the bonding procedure. This electrical contribution could be complementary to the chemical contribution related to dangling bonds. This expertise on surface plasma-activation is ongoing to identify the impact of plasma on glass surfaces. A potential benefit is expected for finely adjusting annealing parameters of the glass bonding process.
A CNRS-C2N, F- Palaiseau.
B CNRS-Institut des matériaux Jean Rouxel F- Nantes.
KEYWORDS: SURFACE ACTIVATION, PLASMA-ASSISTED BONDING, XPS IN-SITU ANALYSIS
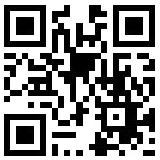

Technology hybridization for multi-performance variable glazing
CRISTIANA CELLUCCIA, BENEDETTA MARRADIBThe current tendency of contemporary architecture to consider the glass surface as an “interface” between two environments in which a constant exchange takes place “between two substances placed in contact” takes place finds in the glazed elements in the building envelope a vehicle for process and product innovation, both characterized by a focus on forms of contamination/interaction of techniques and materials. These innovations have led both to an improvement of fixed performance products –insulating and laminated glass, absorbing and reflective, selective, low-emissivity – and to an increase of variable performance glazing – transparent aerogels, electrochromic, thermochromic, illuminating, solar electric-generating, etc. The result is the tendency of glass sheets to become a variable multi-performance system that aims to create highly usable and accessible products, with the involvement of sense organs and contamination of creative forms; and to the creation of adaptive facades, which is understood as adaptive to environmental conditions as well as to the user inside. The paper traces the main product and process innovation trajectories of glass panes.
A Department of Architecture and Arts, Università Iuav di Venezia, Venice, Italy.
B School of Engineering, University of Pisa, Pisa, Italy.
KEYWORDS: HYBRIDIZATION, DYNAMIC GLAZING, MULTI-PERFORMANCE
Introduction
The modern production process has deeply modified the traditional ways of manufacturing by transforming the relationship between the mankind and the means of production, and consequently between the mankind itself and the products, making it possible to foresee and realize almost unlimited quantities of objects at the same time (Nardi, 1979; Losasso, 1991). This capacity for technical reproducibility can be read, in the field of glazing manufacturing process, in a multiple variability of “glass as a product”, due to the transformative capacities that modern technology is able to apply to materials and to interactive features, through the continuous upgrade of its tools.
The current tendency of contemporary architecture to consider the glass surface as an “interface” between two environments in which a constant exchange takes place “between two substances placed in contact”: in this perspective, the application of glazed elements in the building envelope plays a significant role, as an expression of the transition between interior and exterior, private and public spheres, but also increasingly as a vehicle for process and product innovation, both characterized by a focus on forms of contamination/interaction (Campioli, 1993; La Creta and Truppi, 1994).
The first innovation involves the contamination of the glazing manufacturing process with other industrial fields, such as applied chemistry, physics and electrical engineering, which paved the way for adaptive systems capable of responding to multiple and different demands. Such “intelligent components” vary their appearance as a result of interaction with users and/or the surrounding environment (User-centered and EnvironmentCentered Approach), spreading new perspectives from both functional and communicative points of view.
The second innovation concerns the mixing of materials (glass, plastic, metal, and even concrete or wood) and the overcoming of the typical distinction between the portion of the window through which you can look through and the portion that prevents the sunlight and the view. This separation is increasingly being replaced by integrated solutions, or enhanced with additional functions that improve interior acoustics, harvest electrical or thermal energy, or serve as information media for multimedia facades (LED digital strip, electrically generated glass) to lightweight translucent structural solutions (Glass fiber dipped in resin and Glass tubing used as partitions) (Koster, 2004) (Figure 01).
Therefore, this evolution/interaction of techniques and materials has led both to an improvement of fixed performance products – insulating and laminated glass, absorbing and reflective, selective, low-emissivity –and to an increase of variable performance glazing – transparent aerogels, electrochromic, thermochromic, illuminating, solar electric-generating, etc. This results in a tendency for the glass panes to become a variable multi-
performance system, characterized by a strong interactive component that aims at creating highly usable and accessible products, with the involvement of sense organs and the contamination of creative forms. Glass surfaces embody, today, new values that add to those already experienced by architects, artists, builders and end-users over the past decades, becoming a sort of great “Duchampian glass” through which to look beyond but on which, also, to dwell in order to appreciate what appears on its surface (Maspoli et al., 2012; Dall’Olio, 1997).
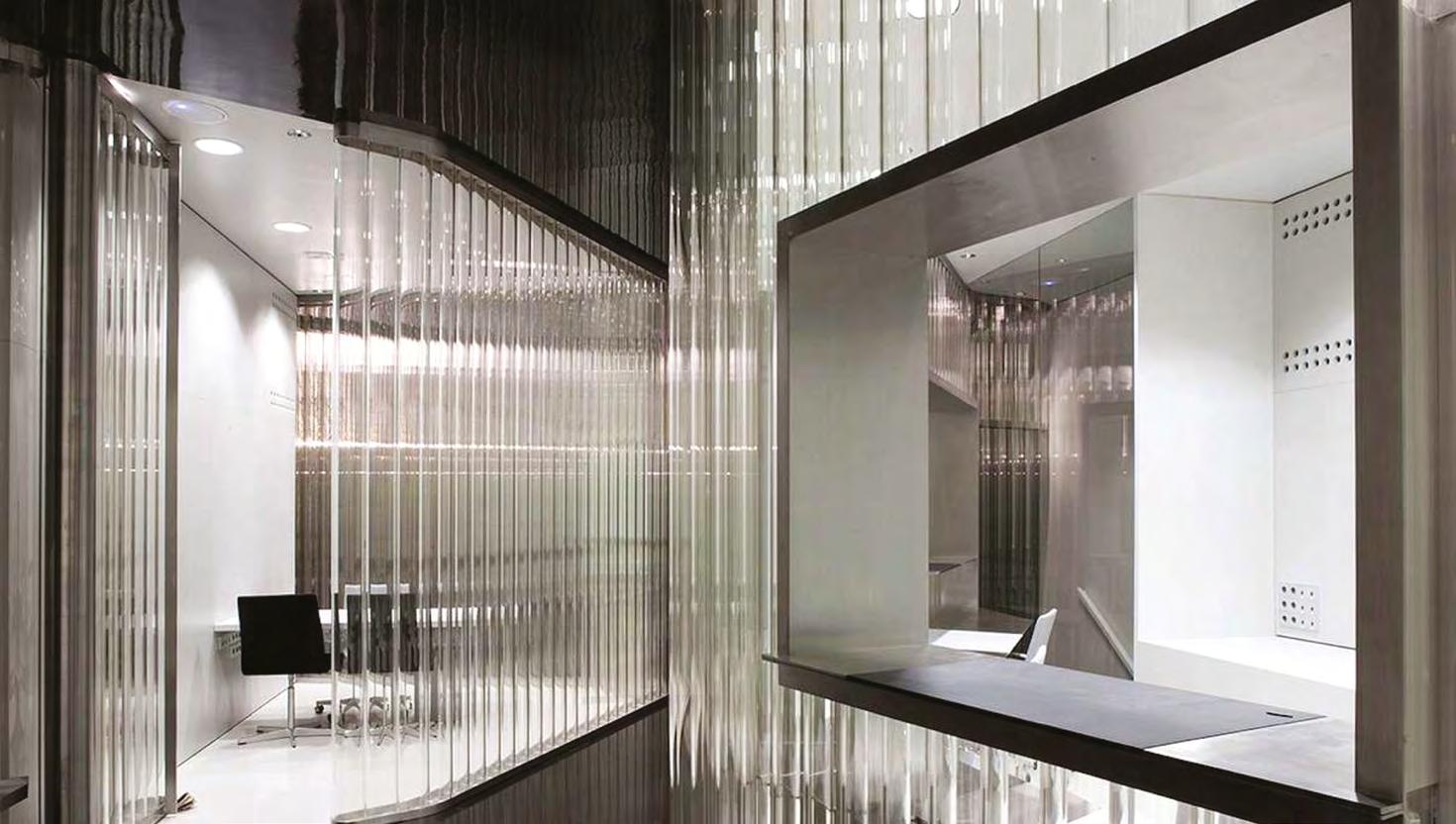
Main perspectives in technical innovation
The introduction of new manufacturing techniques with high technological content (i.e. float glass), the improvements for the installation of glazing panels (optimized silicones, thermal break systems, open joint, profile extrusion etc.) and, finally, the search for transparency and daylight enhancement as architectural issues have affected the development of building components, spreading the variety of products and leading to high levels of expressiveness (Sinopoli and Tatano, 2002).
The common ground of this novel approach consists of a focus on the interface between technology and architectural language, environment and industrial innovation, building construction process and architectural design, in the awareness that a specific design solution involves several implications regarding materials and components, both from the morphological and technological-performance aspects. This hiatus between semantic and technical function has characterized the most important innovations on the
production/application of glazed panels and the development of the related technical features: from transparent/translucent to interactive/selective; from small and thick to thin, large and durable.
Due to its high degree of transparency, durability and versatility in various contexts, glass is still the most widely used material when “viewing through” is required. Innovations in this field, which concern the possibility of increasing the standard transparency value of 92 percent up to 98 percent by drastically reducing reflectance (anti-reflective glass), find application in the enhancement of cultural heritage to avoid interference with the perception of an object (i.e. work of art) or a sensitive environment (i.e. historic center of a city).
In the field of safety, recent technological research trends are oriented towards the development of glazed elements capable of assuring the safety of people both as the ability of the sheet to withstand impact and the nonproduction of sharp splinters in the event of sheet breakage.
In addition, at present, hybridization of architectural surfaces (i.e. Switchable Glass) is one of the latest achievements, with the introduction of components as follows:
• Smart technologies (Interactive System, Energy Plus System, Smart System) in use for media communication and light enhancement as urban screens. LED and low-consumption light sources belong to this category, up to the realization of perceptually and kinematically dynamic surfaces. Some example are the translucent methacrylate envelope designed by Peter Cook and Colin Fournier for the Graz Museum in Austria, on which, thanks to a computerized control, it is possible to remotely adjust both the intensity of the circular fluorescent lights and the vision of movies/videos through projectors placed in the gap between the two façade systems; the facade of the headquarters of the Dutch telecommunications company KPN Telecom by Renzo Piano, in Rotterdam; or Jean Nouvel’s Galleries Lefayette in Berlin.
• Smart materials equipped with high-performance and low-power consumption (integration in glass panes of dichroic, photovoltaic, chromogenic films) up to shape memory materials (Shape Memory Alloy) or variable behavior materials, capable of varying their transmission of solar radiation according to environmental conditions automatically and/or by manual control. These innovations result in selective glass, capable of selecting light radiation; holographic, capable of passing visible waves and reflecting thermal ones invisible to the human eye; electrodynamic, capable of varying transmission with an electrical pulse; and thermodynamic, capable of varying coloration and thus absorption as temperature increases. Both the intensity of the opacification and the switching temperature can be customized during the manufacture of the glass, adhering to a wide range of products suitable for different needs and functions.
From the above considerations, it appears that from standardized products and manufacturing processes there has been a progressive trend in expanding standardization to a variable number of types of the same object. This is clear, for instance, in the evolution of glass lamination processes, which, starting from simple deposits between laminated glazing, have allowed the application of fabrics (Allianz Headquarters Zurich), wire mesh, reeds or wood veneers, and LEDs with transparent electrical wiring not visible to the human eye, capable of transforming the glass panel into a lighting fixture or multimedia screen (Lévy, 1994; Galimberti, 1999) (Figure 02).
In addition, glazed panels have evolved towards increasingly lightweight/ thin and mechanically resistant systems. High-strength, chemically toughened glass sheet, which can be produced as thin as 0.5 mm, are used nowadays for smartphones, tablets or photovoltaic modules, but there are no effective obstacles for future architectural applications. Unlike thermally toughened glass, chemically toughened panes are not heated, but are soaked in a salt bath, in which, an ion exchange process “hardens” the most superficial layer. This process not only makes the sheet more resistant to scratching and breakage, but also results in easier shaping in curves with small radii, less weight per unit area (useful for reducing the considerable weight of 4mm sheets used in triple-glazing systems), and simplified installation procedures (with the possibility of reducing the size of the window system components).
In addition to improvements in thickness, the increase of maximum size of the glazed sheets is also evolving. Following the Crystal Palace in London, the first large exhibition building, with approximately three hundred thousand
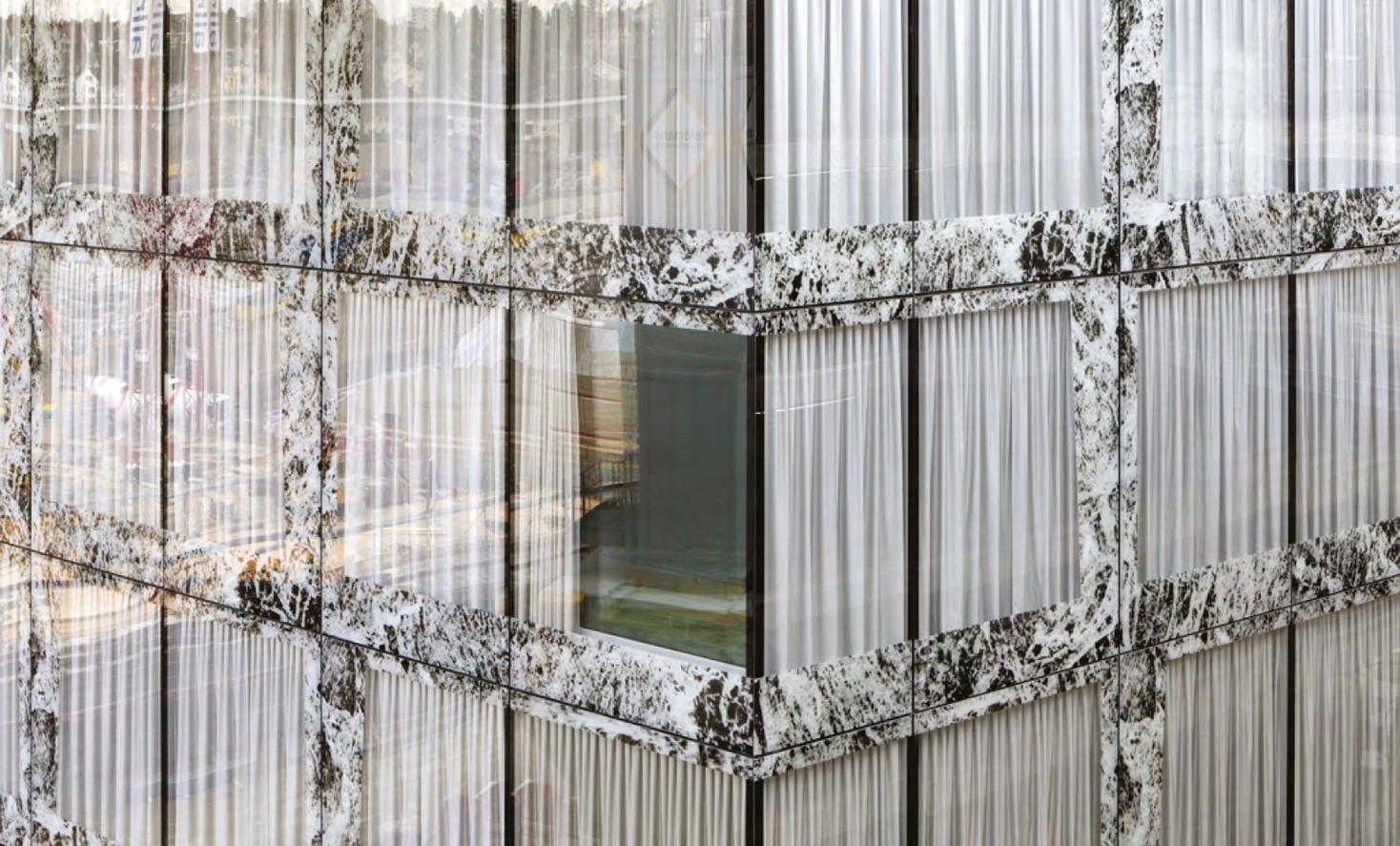
sheets of glass measuring 122x25 cm, the spread of large glass structures originated in the ‘80s from a new generation of architects (RFR, Perrault, Nouvel, Herzog and Meuron), who exploited the potential and the ability of tempered glass to maintain its integrity despite the holes located near the edges of the sheets, that allowed the suspension of the panes by bolts.
Nowadays, the maximum sizes in which laminated safety glass can be produced is amazing. The high demand for large sheets (with max dimensions 18.00 x 3.21 m) pushed to a renewal of the manufacturing process (i.e. the equipment for lamination, the furnaces for obtaining pre-stressed tempered glass) in order to make production more efficient and faster. Within a few years, this led from the glass skin of the Louvre in Lens, which Sanaa proportioned based on the largest available size, to the 10-m slabs used by Foster for the facade and roof of the Apple Store in New York City (Figure 03).
Dynamic products towards a User-Centered approach in glass façade design
For centuries, the main functionality of glass elements in façades has been to meet three principal requirements: to let in daylight, to grant a direct view of the immediate surroundings and, at the same time, to provide protection against wind and rain. The use of glass in architectural applications, especially in façades, has spread recently, in order to meet the current trends of lightness, robustness and energy efficiency.
Moreover, today the façade is one of the most complex parts of a building, which involves an integration among the load-bearing structure, building services, building physics and, not least, different architectural languages. Glass has a fundamental impact on the aesthetics of a building, as well as on the wellbeing of building occupants, mainly due to the transmission of light and the reduction of glare; glazed envelopes performance has a determinant influence on the space heating, cooling and lighting in buildings.
In this framework, the “future” design of transparent enclosures is closely related to a User-Centered approach in terms of user-specific functionalities and design features: a new understanding of adaptive facades is formulated, which is understood as adaptive to environmental conditions as well as to the user inside.
Novel products have been recently developed as kinetic elements of the building envelope, which can provide improved thermohygrometric and visual comfort inside buildings, depending on the intended use (residential, healthcare, school, office etc.). They are the outcomes of technological innovations in heat treatment processes, bending techniques, laminating materials and high strength connections (Wilson, 2010; Henriksen, 2013).
The most innovative technological products, now available on the market, are: LCD glass, heated glass, and electrochromic glass.
LCD panel is a laminated glass composed of two extra-clear glasses with an LCD liquid crystal film applied between two sheets of EVA or PVB. The active liquid crystal film is composed of two technical PET sheets coated with a transparent conducting deposit and assembled together with an extra-thin liquid crystal deposit. In the off position, the liquid crystals are not aligned: the glazing is therefore translucent. Its frosted appearance allows light to pass through without allowing vision. In the on position, the liquid crystals, stressed by the current, are aligned: the panel then instantly becomes transparent. This technology is suitable for use outdoors as well as indoors when increased levels of privacy are needed.
Heated glass uses an energy-efficient coating consisting of metal oxides, which acts as a protection from the cold, and improving thermal, visual and health-related comfort. Now, thanks to laser treatment of the conductive coating, the new generation of heated glass operates without the need for a transformer: single glass panels are directly connected to the power supply, like a standard electric radiator. The heated glass is available in double-glazed or triple-glazed IGUs and as laminated safety glass. It can be incorporated invisibly into window frames, glazing and greenhouses, either as a standard insulating window or as a heating system: it emits heat indoors or outdoors and can be used as a heating system (main or additional), preventing condensation and even being able to melt snow. The heat is radiated in a straight line, providing particularly comfortable heating that does not dry out the air inside rooms. In
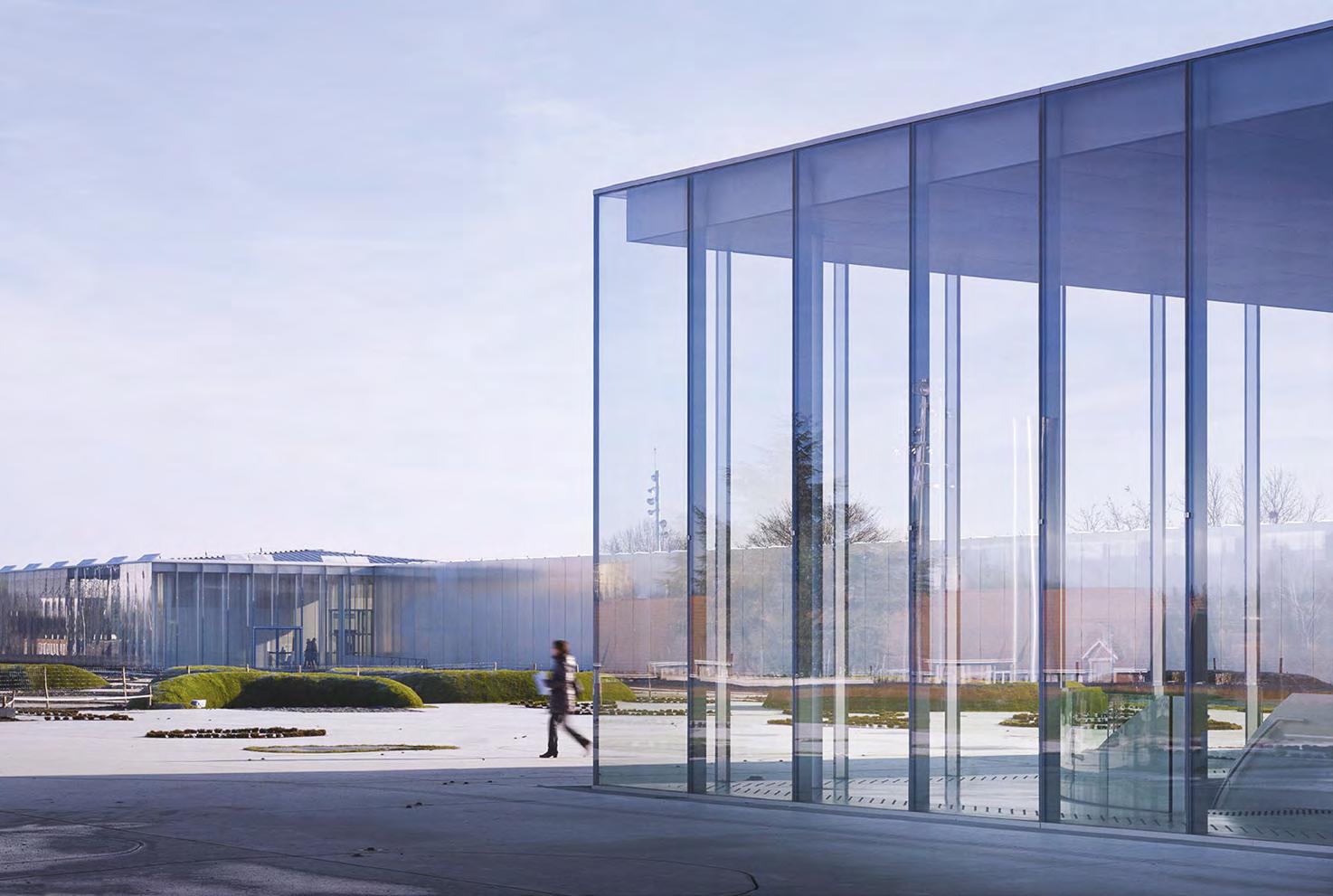
fact, the cooling sensation of surfaces is reduced, thus optimizing the utilization of all living spaces.
Electrochromic (EC) glass panes can change light transmission properties in response to voltage and thus allow control over the amount of light and heat passing through. The electrochromic material changes its opacity, from a colored, translucent (usually blue) to a transparent state. The electrochromic glazing consists of a thin solid electrochromic film (electrolyte) which is sandwiched between two layers of glass. When an electric voltage is applied, an electrochemical reaction triggers the migration of ions from one electrode to the other one, causing a change in the color of the glass, from clear to dark. Darkening occurs from the edges, moving inward, and is a slow process, ranging from many seconds to several minutes depending on window size. Once the change has been affected, no electricity is needed for maintaining the particular shade which has been reached: the system stores a sort of inner “memory” because the electrolyte has a low electronic conductivity. To go back to the previous the conditions of transparency, the polarity must be reversed, allowing cations to leave the electrode and migrate to the counter electrode. Electrochromic devices can considerably decrease the light transmission and can allow control over the amount of light and heat passing through a glass façade, by modulating the potential difference (Figure 04).
Durability in electrochromic glazing is a current issue with having to cope with large number of switching cycle s to survive a reasonable life-time of 5-10 years: the warranty provided by the manufacturer is about 5 years. In addition, the incidence of labor for installation is 15-20% more than traditional glasses.
Architecture and building technology have been evolving fast in the last few decades and previous visions have now become a feasible reality. As a significant element of the overall building energy performance, there is an increasing use of multi-layered and multifunctional glazing systems than can actively adapt to occurring weather condition by changing their own properties (Henriksen, 2013).
The advantages of these applications are multiple and flexible in a huge variety of contexts: by using smart glasses, you can very easily and quickly change filter sight and light on demand, with the preservation of a high level of privacy. Although most business offices and rooms use switches or buttons to filter sight and light, a remote control and a mobile app can also be used to manage it. Adaptive glass can serve as a projection screen.
The possibility of varying thermal and light characteristics, such as solar factor, light transmission factor etc., can be the key to achieving considerable energy savings by reducing heat loss in winter and blocking UV rays in summer.
However, these elements must be dealt with in a balanced and conscious way from the earliest design stages. Buildings with huge glass façades can be energy-efficient, improving the performance of the envelope and the occupant comfort, but not all glass envelopes built in the last years perform well: in many cases HVAC systems have to compensate the overheating during the summer
and heat losses in winter time, therefore energy consumption badly exceeds the intended energy savings. Then, the same technological solutions cannot be taken uncritically as they need to adapt to different climates, orientations, building functions.
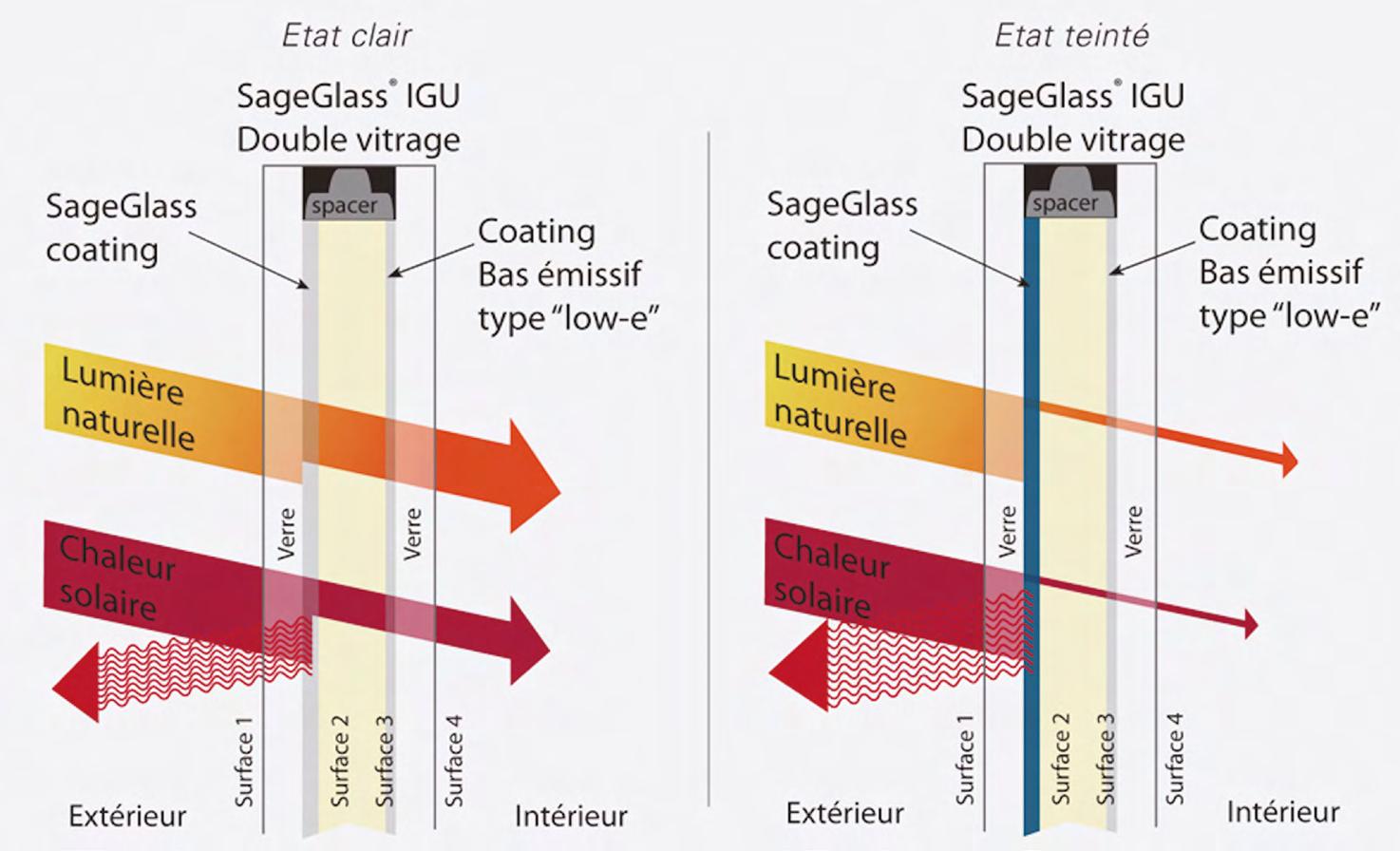
A virtuous example is the two-story atrium at Chabot College Student Service Center in Hayward, California, which has been glazed with EC glass: in this case, the use of EC glass has been integrated with a HVAC free, natural ventilation system, implementing a novel air-cooling strategy. The temperature of the atrium is controlled by radiant heating and cooling in the concrete slab, combined with roof and ceiling air scoops to enhance natural air flows. Implementation of EC glass gave sufficient range of solar control, so a fully glazed South and West facing atrium have been maintained (Paladino & Company, 2010).
Another critical issue at present is the high cost of these products and the difficulties associated with installation, which must be done by qualified personnel. In addition, these technologies operate only through the use of electricity and therefore result in increased electricity consumption.
In future years, however, it is assumed that these aspects can be managed in a more optimized manner, and production costs will be reduced due to technological progress. Indeed, the perspective is that, in case of dynamic glass intended for building envelopes, the actual quest is for variable transparency, durability, energy savings, ease of maintenance: these issues shall be taken into account as stringent design requirements, in order to enable the creation of energy-efficient and comfortable space in response both to the exterior environment and the needs of the building’s occupants.
Conclusions
The future of glass still has many possibilities for innovation, the industry has tried to improve the performance of this material from every point of view as an answer to a demand for “reliability” and “adaptability”.
The first led to the development of interesting design and product experiments, going as far as the recent invention of ultra-thin glasses with a thickness of up to 25 µm to be used in OLED applications (such as the one patented by Schott AG); of glasses integrated with nanotechnology, considered the technology of the twentyfirst Century, which in addition to adding additives to the composition of the glass to improve the strength characteristics, allow for the manipulation of its molecular structure to improve even the less positive properties of the material, up to become a building material, comparable in reliability to metals.
The second refers to materials capable of changing their conformation to external conditions and adapting to the specific needs of users. The latest innovations are the experimentation of ultra-strong honeycomb armored glass used in flooring (Solar Roadways) which, in addition to supporting up to 1,500 t of weight and providing information to users via luminous signs (road signs, dangerous conditions, etc.) they produce electricity (for one charge on a kilometer of road they supply energy to 1,000 homes); of self-cleaning glass capable of recovering daylight and then putting it back into service on request in the form of heat (Center for Materials Science & Engineering of MIT), or perhaps, in the future, of new products that will allow them to be waterproof but at the same time breathable.
References
Campioli, A. (1993). Il contesto del progetto. Il costruire contemporaneo tra sperimentalismo high-tech e diffusione delle tecnol ogie industriali. Milano: Franco Angeli.
Dall’Olio, L. (1997). Arte e Architettura: nuove corrispondenze. Torino: Testo & Immagine.
Galimberti, U. (1999). Psiche e Techne. L’uomo nell’era della tecnica. Milano: Mondolibri. Henriksen, T. (2013). The future of the glass industry. Glass Performance Days (GPD). Tampere: Proceedings of the 2013, pp. 2284-2288.
Koster, H. (2004). Dynamic daylighting architecture: basics, systems, project. Basel, Boston, Berlin: Birkhauser. La Creta, R., Truppi, C. (1994). L’architetto tra tecnologia e progetto. Milano: Franco Angeli. Lévy, P. (1994). L’intelligence collective. Pour une anthropologie du cyberespace. Paris: La Découverte.
Losasso, M. (1991). Architettura: tecnologia e complessità. Napoli: Clean. Maspoli, R., Saccomandi, M., Besser, Y. (2012). Vetri immagine&innovazione: il vetro come espressione creativa nella riqualifi cazione delle architetture post-industriali. Genova: De Ferrari. Nardi, G. (1979). Tecnologia dell’architettura e industrializzazione nell’edilizia. Milano: Franco Angeli. Paladino & Company (2010). Performance Assessment of Electrochromic coatings and control scenarios (online). In https:// www.sageglass.com/sites/default/files/whitepaper_final.pdf (last accessed August 2022). Sinopoli, N., Tatano, V. (2002). Sulle tracce dell’innovazione. Tra tecniche e architettura. Milano: Franco Angeli. Wilson, A. (2010). It’s time to rethink the all-glass building (online). In https://www.buildinggreen.com/blog/its-time-rethinkall-glass-building (last accessed August 2022).
Glass and light. Suspension lamp design in Italy between 1930 and 1969 in the magazines
FEDERICA DAL FALCOA, RAISSA D’UFFIZIBConsistent with the theme of the antifragility of glass, understood as the material’s ability to cope with crises by developing innovations, the contribution proposes a reconstruction between the early 1930s and the mid-1960s of the evolution of a particular category of lighting fixtures: glass pendant lamps. The methodology adopted refers to evolutionary theses applied to families of objects, in which the “archetypes” are transformed while maintaining their matrix in the scenario contemporary to them. The research is carried out using the typological method aimed at modern design studies, through the perusal of some of the leading design and architecture magazines. The result is a jigsaw puzzle of types that, in addition to its documentary and aesthetic value, demonstrates its resilience by adapting, in a balance between tradition and innovation, to the transformations of different contexts in the sign of the mastery and elegance of glass design.
A Associate Professor in Design, PDTA Department, Sapienza University of Rome
B PhD student, PDTA Department, Sapienza University of Rome
KEYWORDS: PENDANT LAMPS, MAGAZINE STUDIES, HISTORY OF DESIGN
Material heritages: testimonial objects with civilisation value
In the last Century, glass products underwent a radical transformation due to the introduction of new glass materials, figurative registers and technologies in keeping with the languages of modernity. In this sector, historical events and wartime crises were the driving force behind complex innovations in both architectural elements and the most diverse types of objects. With an oxymoron, the characteristic fragility of glass is juxtaposed with its opposite meaning, understood as the material’s ability to be resilient and respond to change over time, anticipating new lifestyles. The contribution proposes a reconstruction of the evolution of the typology of hanging lamps made by the most important glass companies between the 1930s and the 1960s. The methodological reference is the studies inherent to archaeological sciences, which have clarified how cities, architecture, landscapes and objects have always been an expression of man’s knowledge in relation to a time and a place. In this sense, finds from the past are documents in which we can read our evolution related to social and anthropological aspects (Manacorda, 2004, 4).
This approach was extended to urban research and 20th Century architecture several decades ago, with less attention paid to the object systems of modernity. In contrast to buildings, things constitute a light and mobile stratification, they travel geographically and in time, transmitting signals from the past, but they must be considered as “material evidence with the value of civilization” (Atti Commissione Franceschini, 1967). Many objects disappear, become antiquated, only to be reborn upon their discovery. In this sense, design can be studied by analysing the development of categories of artefacts, according to evolutionary lines that identify birth, expansion, saturation, up to decay. It is a matter of classifying complex ramifications in which the “archetypes” maintain their matrix, while transforming themselves through technological experimentation and new languages that place them in their contemporary scenario (Branzi, 2007). In the history of decorative and industrial arts styles, a first step is to identify copying and inheritance: these are the gradual, sometimes involuntary transformations resulting from small changes introduced at each stage. Through experimentation, testing and the running behaviour of materials, a process of technological improvement takes place in which certain solutions tend to endure by becoming models (Steadman, 1979). The concept of evolution of objects was advanced in the early 1940s by Carlo Emilio Rava in the pages of Domus comparing antique and modern furniture in relation to their functionality, main components and rationality of assembly. These are representative examples of constant evolutionary lines, denoting the transition from antique to modern in relation to new materials and production processes.
What method and what tools can be used to classify the objects of modernity? In archaeology, associable types constitute what Gordon Childe called the Archaeological Record (Childe, 1956, p.9). These are “things” whose
characteristics originate renewable groups with reference to the “typological method” that Oscar Monteliussystematised in the second half of the 19th Century in relation to evolutionary theories (Manacorda, 2004, p. 59). This methodology, which identifies and classifies archaeological artefacts into groups, can be extended to the objects of modernity by ordering objects from one historical period with the same characteristics.
But how do you “dig” to reconstruct the evolution of pendant lamps? The investigation was conducted by perusing some of the most important magazines in the sector during the period in question (Domus, Casabella, Casa Novità, Ottagono, Lo Stile nella casa e nell’arredamento) and selecting specialised articles, advertising inserts, photographs and captions. The result is a typological repertoire of modernity, where the forms and workings of glass present elements of continuity linked to tradition and evolutionary leaps indicative of more radical innovations. These are forms of glass that reflect the taste and style of the different decades, according to a broad meaning of the term, well expressed by Giò Ponti, as the relationship between art and life and therefore the expression of a particular climate (Ponti, 1941, pp. 11-12). The picture that follows gives us fragments of modernity, which in addition to their documentary and aesthetic value, signal places, environments and interactions, lifestyles of the past, and are bearers of a heritage of memories that are not only material. The hanging lamp typology contributes to the narration of glass, understood as a resilient and innovative material, transformed into objects with poetic features by the mastery of designers and companies of excellence. Types of light that, because of their central location in the environment, illuminate stories and memories of people and families who, in the domestic habitat and beyond, have used them throughout their lives.
The evolution of pendant lamps followed the emergence of Italian rationalist architecture from the early 1930s onwards, before moving towards freer and more organic solutions after the war. These objects are representative of Italian creativity that constitute the prodromes of Made in Italy and correspond to the three key concepts of design culture set out by Giò Ponti in his autobiography (Ponti, 1957, p. 81). The first is a praise of the fantasy of precision, which allows an artefact to be conceived in an exact manner so that the smallest detail corresponds to the whole. The second concerns colour, which must correspond to the chromatic qualities of the materials chosen, while the third reflection focuses on the test of time, that is, the importance of durability associated with the formal and material qualities of architecture and objects.
As is well known, since 1935 the Italian political context of the twenty-year fascist period, with the sanctions imposed by the League of Nations due to the
D’UFFIZIThe 1930s and 1940s. Types between rationality and fantasy of precisions
aggression against Ethiopia, was characterised by economic autarchy applied to all productive sectors. The exploitation of national and colonial raw materials was matched by experimentation with innovative materials, or substitutes as an alternative to the missing resources, with products for architecture, design and fashion (Dal Falco, 2014). And glass, derived from the processing of siliceous sands found in Italy, was considered among the “autarkic materials par excellence”. In fact, there were numerous innovations in the sector: safety crystals, translucent diffusers for glass-cement structures, glass fibres and opaline coatings, which with their lightness, transparency and luminosity asserted themselves as vectors of a new spatial concept (Dal Falco, 2017a, pp. 278-285).
In the lighting sector, the new types of lamps made of ground glass and crystal, paste worked, engraved, coupled with metals, constituted a relevant field of experimentation linked to those principles of modernity already affirmed since the early 1920s especially in France and in the Bauhaus first in Weimar and then in Dessau. In particular, in the category of pendant lamps, the selection made through the perusal of specialised journals can be ascribed to the following types: canopy lamps, globe lamps, arm lamps and lanterns. In general, the research on shapes is marked by essentiality, with a material mix that reflects the specificity of Italian design culture, straddling craftsmanship and industrial production.
The qualities of the glass, the parabolic or conical shapes of the reflectors, the translucent surfaces and indirect lights, the white, coloured etched or satinfinished sheets, the coupling with bronze or light alloy castings, are indications of a strong dynamism in the sector, with refined and innovative products. Already at the end of the 1920s, Carlo Clerici makes it clear how, referring to flame candelabra, artificial lighting is no longer a furniture item, but by integrating itself into the environment structures the space. Furthermore, the issue of lighting technology entails a renewal of the professional profile of the architect, whose role is likened to that of the director who operates considering different specialist skills (Clerici, 1928, pp. 44-46).
The aesthetic aspect of glass lamps, considered as objects that contribute to the harmony of the habitat, was the underlying theme of the 5th Milan Triennale of 1933. Examples of this are the “calotte” and “arm” type, such as the oval “laguna” glass lamp with rosy cup and golden leaves by Venini (Domus, 67, p. 381; Domus, 94, p. 18) and the ten-light chandelier in embossed crystal and copper parts (Domus, 67, p. 381) (Figure 1). Against these figurative themes, there was no lack of objects with rigorous lines of rationalist inspiration, with plays on geometry and light, such as the lamps by Franco Albini for Biancardi and Jordan “suitable for extremist environments, to tie in with the clarity of crystal and steel furniture” (Domus, 69, p. 500) (Figure 2).
Three years later, at the VI Triennale, ceiling lamps combined full geometric shapes with the minute and refined workmanship of crystal (Domus, 103, pp.
32-33) (Figure 3). A significant variant for the domestic environment is the upand-down type for the desk or with a rigid metal tige, which from the early 1930s was to be the subject of experiments on luminous efficiency (Domus, 78, p. 37) (Figures 4), with results of the highest level if the design is entrusted to Pietro Chiesa for Fontana Arte (Domus, 122, p. 25) (Figure 5) and at the end of the 1940s, when this typology will be considered a classic by its creator (Domus, 234, p. 35) (Figure 6). Or when it is Fontana Arte itself that innovates the genre with a cup in white lacquered crystal on the outside, inside which the lenses of the lower surface are ground transparent or mirrored (Domus, 158, p. 52) (Figure 7).
Another type is that of chandeliers with metal stems and bulbs. Such as the solutions designed by Professor Kalmar for Scaglia, in white metal with twentyfour flames and dome-shaped lampshades in frosted glass, or in brass in the shape of a sunburst. Guglielmo Ulrich’s lamps, also for Scaglia, consisted of thin brass or curved metal beams (Domus, 126, p. 52) (Figure 8), while Gino Sarfatti’s design reinterpreted this type with essentiality by using a simple curved ringshaped tube onto which lampholders and bulbs were grafted, all supported by electrical cords (Domus, 151, p. 89) (Figure 9).
Another genre is the “lanterna” chandelier, rational version of traditional shapes recalling mediaeval types, sometimes with oriental elements, always made with accurate plate treatments. There are numerous examples in the pages of Domus, from the more sophisticated types with ground and engraved crystal for Venini, (Domus, 135, p. 78) (Figure 10), to the shaped and groundplatesdesigned by Pietro Chiesa for Fontana Arte (Domus, 147, p. 52) (Figure 11). An example reflecting the integration of lighting body and architectural space is the large suspension in the atrium of the Rector’s Office of the University City of Rome. Composed of two spherical caps and an inverted truncated cone made of glass with alternating transparent and sandblasted stripes, the lantern was made by Fontana Arte at the invitation of Marcello Piacentini, who had already been appointed “General Director and Chief Architect” of the new university complex by Mussolini in 1932. Costing 9,000 lire, the lamp was probably designed by Pietro Chiesa, although there are no documents attesting to its authorship (Dal Falco, 2017b, 40) (Figure 12). Finally, the milk-white glass globes with and without aluminiumtige, for communal areas, corridors, toilets and bathrooms, helped to define the aesthetics of modernity, finding in design a free and light space for experimentation. In the following twenty years, the dome, globe and arm types would evolve with morphologies and workmanships more related to industry, while the lantern design would move towards decadence to be revived in the contemporary world with a different vision of their use.
The 1950s and 1960s. The synthesis of forms
In 1949, Pietro Chiesa died, Giò Ponti celebrated him in Domus in “L’opera di Pietro Chiesa” (1949) where he recalled his luminous artefacts for Fontana
D’UFFIZIArte as an expression of “miraculous Italian quality” and an “excellence of execution never surpassed” (p. 34). The binomial between Pietro Chiesa and Fontana Arte seems to be the point of perfection in the production of glass pendant lamps between the 1930s and 1940s, where a constructive balance of glass is configured (Pagano, 1936, p. 10), through a “perfect taste and masterly experience” (Domus, 147, p. 52). Starting from the Second World War, during the years of reconstruction, “The new taste, the new needs, the new poetics of the interior first dreamed of and then demanded and aroused, in the vast and ductile range of its current possibilities, the glass technique” (Pica, 1949, p. 26). Considering Pietro Chiesa’s work as the forerunner of a modern taste (Domus, 252, p. 60), in the 1950s and 1960s, the design of glass pendant lamps developed into a phase of experimentation, in which forms were simplified through a synthesis procedure in line with industrial style. A break with tradition is evidenced through the exaltation of pure forms, the alteration of colours, the raw display of industrial elements, and the combination or replacement of glass with other materials such as metal or plastic.Through the perusal of trade journals, a number of recurring characteristics emerged which made it possible to categorize similar types of glass pendant lamps. The first recurring feature is the spherical shape, which includes, among the most emblematic examples, the LS1 model designed by Luigi Caccia Dominioni (Domus, 297, p. 26) (Figure 13) and the LS2 model designed by Ignazio Gardella (Domus, 313, p. 60) (Figure 14). Both products are characterised by a round glass shape, a clear reference to the circular image of the moon, the night light source par excellence. The sphere becomes the perfect form through which the purity of the volume is extreme, and the condition of absolute balance is manifested.In 1960, VicoMagistretti also designed the “Omega” pendant lamp for Artemide (Domus, 382, p. 51) (Figure 15), with a matt nickel-plated brass cable, opaline glass globe and frosted glass inner diffuser. The geometric form is “broken down, sectioned, intersected until the final shape is obtained”, resulting in a sphere section (Ottagono, 1, p. 55). Even Gino Sarfatti, a lamp designer since 1936 always in search of new forms and techniques for lighting (Rosselli, 1953, p. 59), collaborated with Arteluce to counter the classical tradition of “curly, neo-liberal chandeliers” (Casa Novità, 1, p. 23) (Figure 16). Sarfatti worked by reduction to obtain a spherical shape, “perfect, pure and with something magical”, creating “metal and crystal spheres, clusters of festive, Christmas and adjustable spheres, spherical joints [...] More than lamps, they were characters destined to give a physiognomy and a flavour to our homes, to transform the simple operation of turning the switch into a meeting with an old friend” (Baldini, 1961, p. 25). This type of hanging lamp determines that spatial balance in home interiors that Piero Della Francesca also reconstructed in the Pala di Brera (1472-1474), where an egg, uniformly lit, is the central point of space and symbol of life.
Canopy lamps are also a frequent type in which the circular shape is partially subtracted to create a modern profile. Franco Albini and Franca Helg designed
Fig. 01 Ten-light chandelier with ashlar crystal bowl and copper metal parts, Domus, 1933, 67, p. 381.
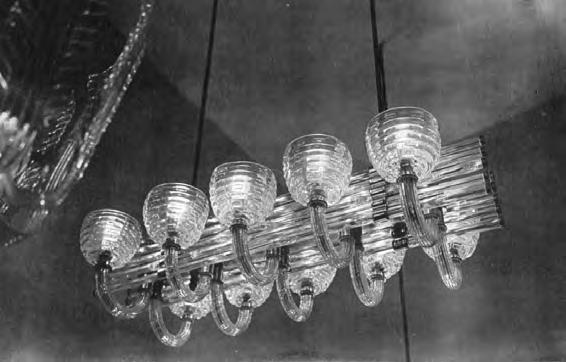
Fig. 02 Chandelier designed by Franco Albini for Biancardi and Jordan, Domus, 1933, 69, p. 500.
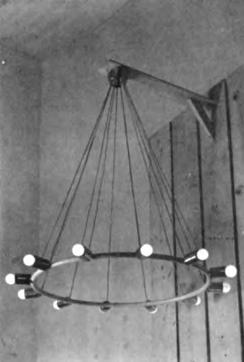
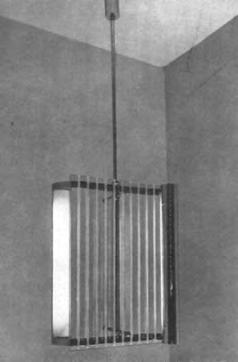
Fig. 03 Murano glass ceiling chandelier by Venini, Domus, 1936, 103, p. 33.
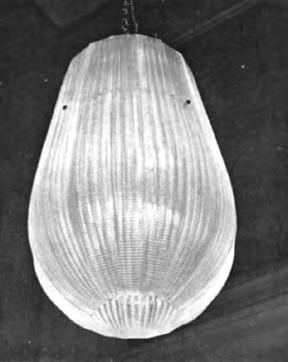
Fig. 04 Pendant chandelier designed by Pietro Chiesa for Fontana, Domus, 1934, 78, p. 37.
Fig. 05 Pendant lamp designed by Pietro Chiesa for Fontana Arte, Domus, 1938, 122,p. 25.
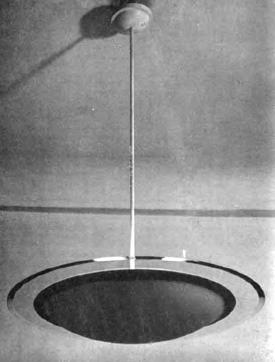
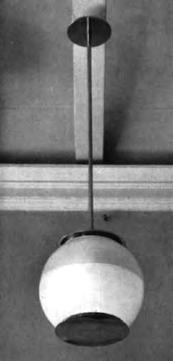
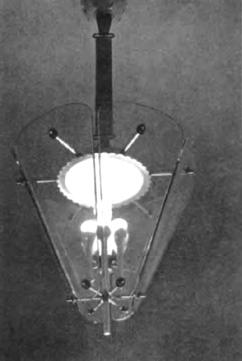

Fig. 06 Reflected light chandelier with white lacquered metal cap and molta crystal disc, designed by Pietro Chiesa for Fontana Arte, Domus, 1949, 234, p. 35.
Fig. 07 Chandelier with crystal bowl externally lacquered in white by Fontana Arte, Domus, 1941, 158,p. 52.
Fig. 08 Lamps designed by Guglielmo Ulrich for Scaglia with bundle of brass stems, Domus, 1938, 126,p.52.
Fig. 09 Chandelier by Gino Sarfatti for Artemide, Domus, 1940, 151, p. 89.

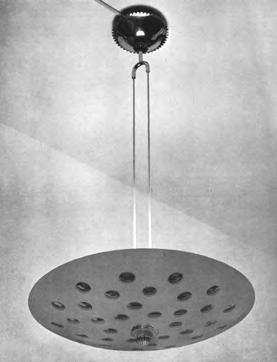
Fig. 10 Shaped, ground and engraved rough crystal chandelier with metal frame, Domus, 1939, 135, p. 78.
Fig. 11 Lantern-shaped metal-frame chandelier with six shaped and ground clear crystals, Domus, 1940, 147, p. 52.
Fig. 12 The lantern in the Rectorate atrium. In La Città Universitaria di Roma, Architettura, special number, XIV, 1935.
Fig. 13 Azucena ceilinglamp by Luigi Caccia Dominioni, Domus, 1954, 297, p. 26.

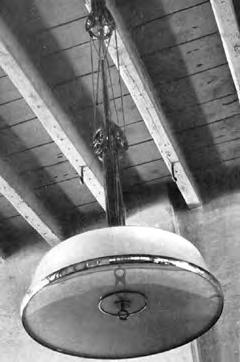
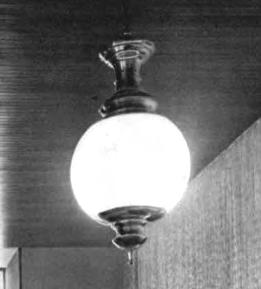
Fig. 14 Lamp designed by Ignazio Gardella for Azucena, Domus, 1955, 313, p. 60.
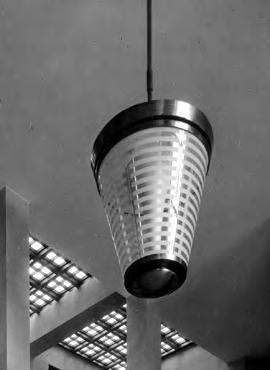
Fig. 15 “Omega” pendant lamp by Vico Magistretti for Artemide, Domus, 1961, 382, p. 51.
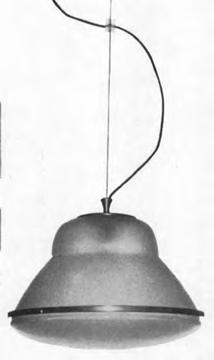
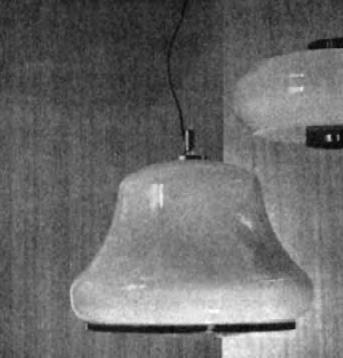
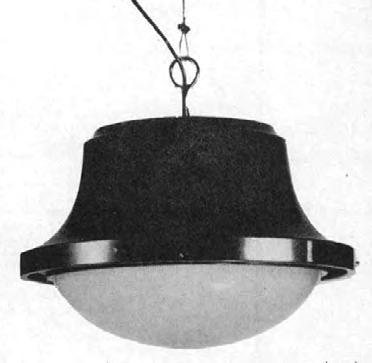
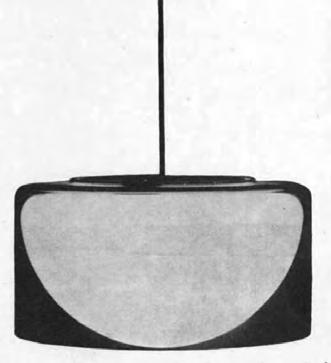

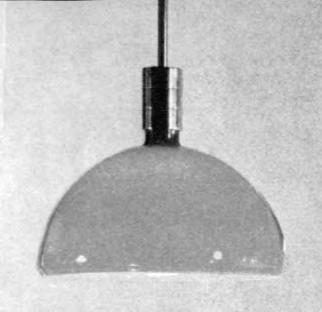

Fig. 16 Chandelier mod.2097 by Gino Sarfatti for Arteluce, Casa Novità, 1961, 1, p. 23.
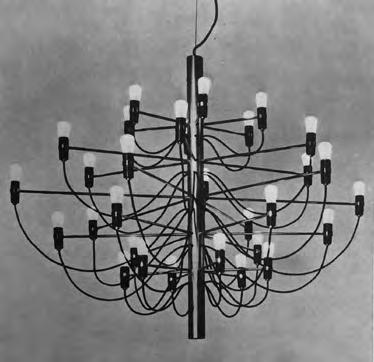
Fig. 17 Suspension lamp model “AM-AS” designed by Franco Albini and Franca Helg for Sirrah, Domus, 1969, 478,Advertising Sirrah.
Fig. 18 “Black and White” lamp by Achille and Pier Giacomo Castiglioni for Flos, photograph by Giorgio Casali, Domus, 1965, 426, p. 31.
Fig. 19 Glass pendant lamps designed by LiisiMeronen Beckmann and produced by the Vistosi glassworks in Murano, Domus, 1966, 435, p. 38.
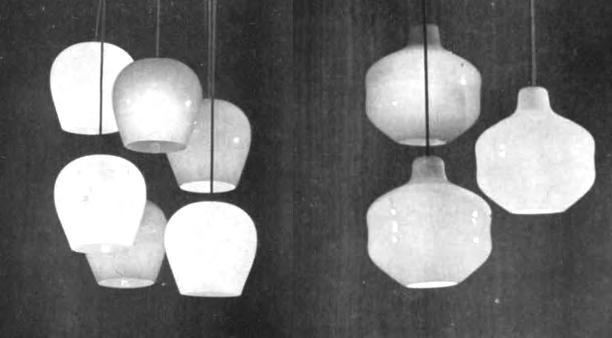
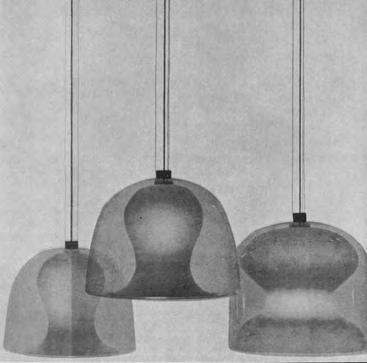
Fig. 20 Suspension lamp by Lumenform with white glass inner envelope and grey or light blue transparent glass outer envelope, Domus, 1964, 411, p. d/195.
Fig. 21 “Tau” model lamp by Sergio Mazza for Artemide in matt nickel-plated brass, aluminium reflector and crystal bowl, Domus, 1963, 399, p. d/108.
Fig. 22 White translucent glass pendant lamp by Martinelli, Domus, 1963, 403,p. d/141.
Fig. 23 Suspension lamp by O-Luce consisting of two frosted glass bowls joined by a polished brass ring, Domus, 1963, 409, p. d/180.
Fig. 24 Lampsproduced by Venini in collaboration with Massimo Vignelli, Domus, 1956, 316, Rassegna Domus.
the “AM/AS” model for Sirrah (Domus, 478) (Figure 17) which featured the opaline glass sphere in its semi-circular version. Achille and Pier Giacomo Castiglioni, who were often involved in the design of lighting fixtures, produced the “Black and White” pendant lamp for the company Flos around 1965, a product that allowed the light to be directed from concentrated to diffused (Domus, 426, pp. 29-33) (Figure 18); the shape of the fixture derives from the superimposition of two cups, the first in smaller aluminium, which reflects the light, and the second in opaline glass, which emits the light instead (Ottagono, 1, pp. 77). The glass pendant lamps designed by LiisiMeronen Beckmann and produced by the Vistosi glassworks in Murano (Figure 19) are also of interesting plasticity. They each consist of two glass shapes, one transparent inserted in the other coloured, which generate a play of transparencies (Domus, 435, p. 38). Or the pendant lamp by Lumenform (Figure 20) which has an upside-down white glass dome as its central core, covered by a rectangular volume in grey or light blue transparent glass which allows a glimpse of the inner dome, with a white inner envelope and outer covering (Domus, 411, p. d/195).
Sometimes the dome evolves through more blunted appearances and elements removed from the original spherical shape, as in the case of the “Tau” model designed by Sergio Mazza for Artemide (Figure 21) in matt nickel-plated brass, with a dark brown aluminium reflector and crystal bowl. The name, in assonance with the subtracted form of the Greek tau that characterises its lines, refers to that symmetrical and circular balance typical of pendant lamps (Domus, 399, p. d/108). In the case of Martinelli’s white translucent glass pendant lamp (Figure 22) the bevelled cap conceals the internal components through the opacity of the glass (Domus, 403, p. d/141) highlighting a “constant search for the application of evolved technical solutions, combined with the study of geometric forms” (Martinelli, 2018, p. 52). While in O-Luce’s pendant lamp (Figure 23), the two frosted glass cups are joined by a polished brass ring (Domus, 409, p. d/180).
A third typology identified is that of the organic and changeable form. Massimo Vignelli in collaboration with Venini produced a series of pendant lamps in a variety of shapes and colours including sapphire red, sulphur, tea powder, green, white, sky blue and pink (Figure 24). These pendant lamps, produced in Murano with simple shapes but all different and distinctive, are outlined with soft, sinuous curved lines, creating an unusual visual vibration (Domus, 316). Like Vignelli for Venini, the experimentation of architects and designers is manifested in their collaboration with companies, through the design of signature pendant lamps; there are many personalities who associate their signature with recurring production realities, as in the case of Gaetano Sciolari for Stilnovo, Flavio Poli for SegusoVetrid’Arte, Tito Agnoli for O-Luce, and Alessandro Pianon for Vistosi. Drawing a general picture, in the 1950s, historical companies rooted in the Murano reality, such as Seguso (1397), Salviati (1859), Borovier&Toso (1880), Vistosi (1945) continued their activity producing more traditional artefacts that were less suitable for industrial production.
D’UFFIZIOn the contrary, alongside the products of Fontana Arte (1932) and Arteluce (1939), more modern realities such as O-Luce (1945), Stilnovo (1946), Mazzega (1946), Azucena (1947) and Martinelli (1950), Artemide (1959), Flos (1962) and LumenForm (1961), Sirrah (1968) were born with the reconstruction.
Towards contamination with new plastics
The glass pendant lamp, in the new industrial product culture, gradually abandoned its ornamental and classical nature, declaring itself on the contrary a humble, punctual and essential element in the modern space. In this period, artefacts simplified in form, clearly moving away from a lavish style and towards a more rational taste. Companies in the lighting sector produced numerous models of lamps, each of which, however, came in different types (pendant, table, floor and wall lamps) in order to offer similar solutions in the same environment and facilitate the stylistic homogenization of the modern home, a process which was widespread in this period.
The most significant innovation of these years, however, lies in a gradual but essential change in the history of glass pendant lamps. Glass, which had always been the preferred material in the design of these lighting fixtures, was progressively replaced in the production of lamps by other materials such as plastic or aluminium; these materials were less expensive, and more suitable for industrial and multiple production, and more prone to experimentation with new forms.
In particular, plastic materials make it possible to equal properties very close to those of glass such as transparency or colour variations or light transmission quality, and to solve more problematic aspects such as fragility, durability or heaviness. Glass therefore becomes plexiglass in the “Alvise” hanging lamp designed by Luigi Massoni for D. H. Guzzini (Domus, 453, p. d/392), or in methacrylate as in the case of the spherical pendant lamp designed for Kartell by the architect Luigi Bandini Buti (Domus, 456, p. d/401) and renews its anatomical structure, generating new abstract forms, as in the lamps “Taraxacum” and “Viscontea” by the Castiglioni brothers in coccon for Flos (Domus, 411, p. d/193).
The future of new materials and the fruitful experimentation in the design of pendant lamps undoubtedly opened up new scenarios for the lighting industry, which went from being mostly exclusively characterised by glass production, to being continued with new materials, where the glass element only exists to a small extent. From the 1960s onwards, glass seemed to become a material for elitist production, circumscribing its use mostly in handicrafts and more traditional forms. Gradually, glass production was limited to the Venetian lagoon, and products from the Murano glassworks became increasingly exclusive, sought-after and high-priced; the manufacture of pendant lighting fixtures was thus updated over time, first through a formal innovation of synthesis, and then through the use of materials other than glass. More generally, the narrative
of glass pendant lamps as a specific furniture product was always rather fragmentary and unspecific between the 1950s and 1960s. The descriptive space dedicated within design magazines can in fact be grouped into two types of narrative. The first is that which sees the product inserted within a setting, in which an in-depth analysis of the lamp rarely appears, except to provide the name of the manufacturer. The second case, on the other hand, proposes the product within reviews dedicated to lighting, with brief descriptions of the object (name of the company, the architects or designers who conceived the project, materials used, year of production and costs), which are too concise to trace an exhaustive history of glass pendant lamps.
The research managed to highlight certain formal specificities and trace changing trends over time with respect to characters, forms and materials. Glass was the preferred material in the design of pendant lamps between the 1930s and 1940s; experimented with in its countless formal and aesthetic possibilities in the 1950s, and joined in production, or perhaps overtaken, by new materials in the 1960s. We can say, that glass has undertaken an articulated but rather circular path, from the appropriation of Murano techniques outside its geographical area of origin, to the exclusive reintegration of history into its native boundaries: the design of glass pendant lamps has migrated outside its original borders, to finally return to the places of its tradition.
References
Atti Commissione Franceschini (1967). Atti Commissione Franceschini, relativa ai beni immobili e loro pertinenzecomprensive dell’arredamento (online). In http://www.icar.beniculturali.it/biblio/pdf/Studi/franceschini.pdf (last accessed August 2022).
Baldini, R. (1961). I personaggi di Sarfatti. Casa Novità, 1, pp. 21-25.
Branzi, A. (ed.) (2007). Capire il design. Firenze: Giunti editore. Casa Novità, 1, (1961). I personaggi di Sarfatti, pp. 21-25.
Childe, V. G. (1956). A Short Introduction to Archeology. London: Collier Books. Clerici, C. (1928). Architetture moderne e illuminazione. Domus, 5, pp. 32-33.
Dal Falco, F. (2014). Prodotti autarchici. 1930-1945. Architettura, design, moda. Studi sulla cultura del progetto per la tutela dei beni culturali. Roma: Rdesignpress.
Dal Falco, F. (2017a). Vetro. Prodotto e applicazioni. Autori e opere. In L. Cupelloni (Ed.), Materiali del Moderno. Campo, tempi e modi del progetto di riqualificazione, pp. 278-285. Roma: Gangemi editore.
Dal Falco, F. (2017b). Il Design della Città universitaria di Roma paradigma del progetto integrale della modernità italiana, Palladio, pp. 35-44.
Domus, 67, (1933). I vetri d’arte italiana alla Triennale, pp. 380-381.
Domus, 69, (1933). L’arte moderna nel vetro e nella illuminazione, p. 500.
Domus, 78, (1934). Due nuove lampade ideate da Pietro Chiesa, p. 37.
Domus, 94, (1935). Caratteri di alcuni arredamenti, p.18.
Domus, 103, (1936). Venini-Murano. Tre lampadari a soffitto in cristallo variamente lavorato, pp. 32-33.
Domus, 122, (1938). Non arredare, ma “circondarci” di quanto ci occorre e ci piace, pp. 24-25.
Domus, 126, (1938). La luce nella casa, pp. 126, 52.
Domus, 135, (1939). Documenti delle produzioni italiane. Cinque lampade, p. 78.
Domus, 147, (1940). Il prodotto italiano deve essere indice di alta qualità, p. 52.
LIGHT.
Domus, 151, (1940). Una serie ingegnosa e pratica di apparecchi di illuminazione, pp. 88-89. Domus, 158, (1941). Nella vostra casa abbiate l’orgoglio di avere prodotti italiani, p. 52.
Domus, 234, (1949). I classici di Pietro Chiesa, p. 35. Domus, 252, (1950). Rassegna. Le lampade, p. 60.
Domus, 297, (1954). A Napoli. Roberto Mango architetto, p. 26. Domus, 313, (1955). Tre versioni di una lampada, p. 60.
Domus, 316, (1956). Rassegna Domus. Domus, 382, (1961). Due nuove lampade. Vico Magistretti architetto, p. 51.
Domus, 399, (1963). Domus per chi deve scegliere lampade di serie. Produzione Studio Artemide, p. d/108. Domus, 403, (1963). Domus per chi deve scegliere lampade di serie. Produzione Martinelli Luce, p. d/141
Domus, 409, (1963). Domus per chi deve scegliere lampade di serie. Lampade Produzione O-Luce, p. d/180. Domus, 411, (1964). Domus per chi deve scegliere lampade in serie. Lampade produzione Flos, p. d/193.
Domus, 411, (1964). Domus per chi deve scegliere lampade in serie. Lampade produzione Lumenform, p. d/195. Domus, 426, (1965). La casa abitata. Achille e Pier Giacomo Castiglioni: stanza da pranzo, pp. 29-33.
Domus, 435, (1966). Lampade, p. 38.
Domus, 453, (1967).Domus per chi deve scegliere lampade in serie. Lampade in plexiglas, produzione D. H. Guzzini, p. d/392. Domus, 456, (1967). Domus per chi deve scegliere lampade diverse. Lampade produzione Kartell, p. d/401.
Manacorda, D. (2004). Prima lezione di archeologia. Roma-Bari: Laterza editore. Martinelli, E. (2018). Funzione ed estetica. Le prime lampade di Elio Martinelli. In Martinelli, E. (ed.), Elio Martinelli e la luce Milano: Electa.
Ottagono, 1, (1966). Coerenza nel design di Vico Magistretti, p. 55.
Ottagono, 1, (1966). Lampada a due luci, pp. 70-77.
Pagano, G. (1936). Un famoso binomio. Pietro Chiesa: la vetrina di Fontana Arte alla Triennale. Domus, 104, p. 10. Pica, A. (1949). Il cristallo nell’arredamento. Domus, 238, pp. 26-29. Ponti, G. (1941). Lo Stile nella casa e nell’arredamento, 1, pp. 11-12.
Ponti, G. (1949). L’opera di Pietro Chiesa. Domus, 234, pp. 32-49. Ponti, G. (1957). Amate l’architettura. Genova: Società editrice Vitali e Ghianda.
Rava, C. E. (1942). Funzionale antico e nuovo VII. Domus, 179, pp. 480-482. Rava, C. E. (1943). Funzionale antico e nuovo VIII. Domus, 185, pp. 220-222. Rosselli, A. (1953). Nuove lampade Arteluce. Disegno per l’industria. Domus, 289, pp. 59-61. Steadman, P. (1979). The evolution of designs. Cambridge: Cambridge University Press.
Guaranteeing the authenticity of VENINI Murano glass
ELENA TESSERA, FABRIZIO ANTONELLIAThe Murano glass is universally considered one of the most prestigious glass in the world. What makes it so special? The ancient tradition, the high quality craftsmanship and the technological and artistic skills and know-how of glassmakers. Despite the continuous and massive increase in counterfeit products that have been trying to imitate the expertise of the Murano masters for years, Murano has managed to reinvent itself, maintaining both the monopoly on glass quality and development or refinement of techniques for centuries. The study described in the poster, has two main goals: the creation of a solid database of both the total chemical composition and the concentration ranges of the main discriminant chemical elements; the preservation and promotion the authenticity of Murano glass.
A LAMA–Laboratory for Analyzing Materials of Ancient origin at Università Iuav di Venezia, Italy.
KEYWORDS: MURANO GLASS, COMPOSITIONAL DATABASE, PXRF
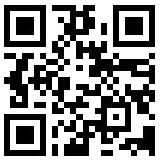

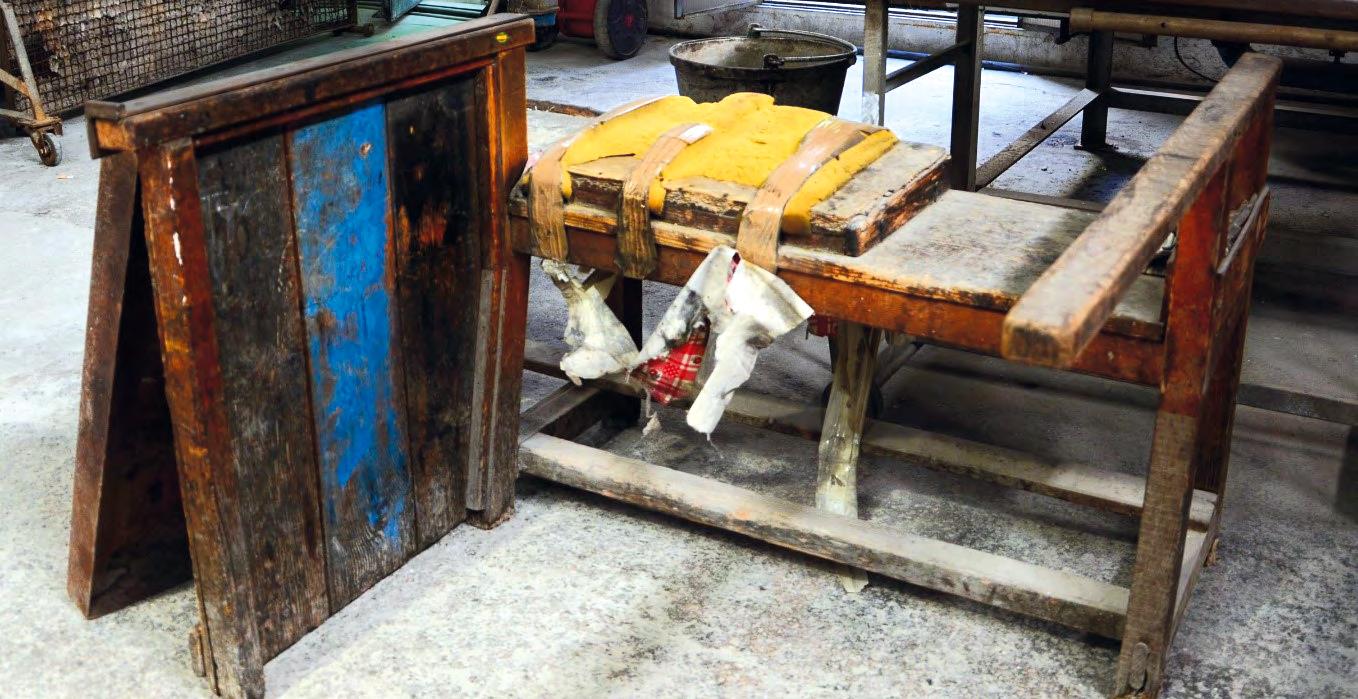
Apparent divide. An observation of the handmade and the machine-made through the work of Laura de Santillana
LAURA PANCHAUDThis paper examines the apparent opposition between the handmade and the machine-made through the work of artist Laura de Santillana (1955-2019). Departing from her work as a designer, she developed a distinctive and innovative practice, creating works in Murano, in the US and, after 2013, in the Czech Republic. Her Czech work marked a turning point in her career, exploring a new production process: “slumping” glass. While in Murano her works were handblown and shaped by a master glassmaker. In The Czech Republic this “hand” was replaced by a “machine”, and the glassmaker by an engineer. These separate locations become representative of the two poles of “manual production” and “industrial production”. This case study explores this shift, and the differences between both ways of making, by examining de Santillana’s working process and oeuvre. In oscillating continuously between both worlds her work offers a way to bridge the apparent divide.
KEYWORDS: LAURA DE SANTILLANA, PRODUCTION PROCESS, GLASSMAKING
Introduction
The apparent divide between the handmade and the machine-made
The work of Laura de Santillana (LdS) is an interesting case within which to consider the utility of the binary divisions of machine-made and handmade, industrial and craft. The machine and the human hand represent contradictory values. This becomes a particularly interesting question in the field of glassmaking, where these categories seem especially persistent. The master glassmaker in Murano shapes his object by working freehand without the aid of technology. It takes years of experience to gain mastery of the necessary skills. Even though a particular process might be repeated, every object that results remains unique, carrying the trace of the maker’s hand. The idea of the machine-made, a process that ideally results in perfect replication, seems diametrically opposed to this model of production. The work of Laura de Santillana, however, meanders between these two poles, dissolving this opposition. Close study of her working processes throws the utility of these distinctions into question, especially in the field of glassmaking.
Laura de Santillana’s formative years
De Santillana’s training and background are important in understanding her work. Born in Venice, she was the granddaughter of Paolo Venini, founder of the Venini glassworks in Murano, which after his death was taken over by Laura’s father Ludovico Diaz de Santillana. She grew up in this environment and joined the family business as a designer in 1975 after training in graphic design with Lella and Massimo Vignelli in New York. From 1989 to 1993 Laura de Santillana was the creative director of EOS, a new glass brand that was founded by the Santillana-Venini family following their ouster from the Venini company in 1986. For a few years she worked as an independent designer for companies such as Rosenthal, Arcade, Salviati and private commissions. After these first experiences as a designer she decided to take an artistic path and subsequently worked as a designer only on rare occasions.
Everything de Santillana learned in these formative years would manifest itself in her artistic practice. She developed a deep understanding of the material of glass and how to manipulate it. Spending every day within the Venini factory she was immersed in all the facets of that business – the evolution of a design from the first prototype to the finalized object that must fulfill the highest standards. Every object had to be perfect in terms of shape, proportions and colour, and underwent a very strict quality control check before leaving the factory. The company culture placed an enormous importance to the on-going experimentation process between the designer and the maker which led to innovations that were the company’s calling cards, and which were revealed with fanfare during tradefairs. Working by her father’s side, she oversaw numerous talented designers who came to
work at the factory and helped to adjust their projects to the specific material requirements of glassmaking. During these years she learned everything about colors, which at Venini held a particular importance, as well as how to navigate the relationship with a master glassmaker. This rich and varied experience in glassmaking enabled her to become an exacting partner in the design process, but one who also understood how much the work relied on the knowledge and mastery of the maker. During her artistic career she would eventually work exclusively with one master glassmaker with whom she established a unique relationship over the course of 20 years of collaboration.
During her time at Venini and EOS, numerous designs by Laura de Santillana went into production, proof of her capacity to create objects in glass that were suited for industrial production and are in line with the industrial object. The case of glassblowing is particular, because even the industrial object is unique, forcing de Santillana to consider material variation in her designs and how factors such as economy affect the end result. This idea of reproduction and repetition gives rise to LdS’ philosophy of the object in a state of repetition, an idea that will become one of the key aspects of her artistic practice.
In an interview conducted by her partner, Gianlugi Calderone, who is a filmmaker, de Santillana names three men who have had a significant influence on her (Calderone and De Santillana, 2009). The first is her father Ludovico Diaz de Santillana, an architect. The second is her grandfather, Giorgio de Santillana, a scientist-philosopher who worked as a professor at the Massachusetts Institute of Technology. From him she acquired the need to measure and the impulse to create order to gain analytic understanding. The third is the designer Massimo Vignelli, who taught de Santillana the discipline of precision (De Santillana and Bethenod, 2014). It is interesting to see LdS synthesize these three professions of architect, scientist, and designer as we begin to look at her artistic practice.
Laura de Santillana’s artistic practice
This background surely gave rise to Santillana’s preoccupation with the idea of industrial production as a repeated process that nonetheless resulted in a unique piece, the work of art. In 1999, a flat shape appeared in her work, resulting from the compression of a bubble of glass. She repeated this process over and over, creating a series that at first seem like an endless repetition of the same form, yet in which every piece is unique at a closer look (Figure 01 and 02). Recognizing the endless possibilities held by this object, it would become the iconic form of LdS’s work, giving her enormous freedom to experiment. This flattened form acted almost like a canvas that permitted de Santillana to investigate colour, techniques or the simple gesture of cutting open the hot glass.
It is through repetition that de Santillana conducted her research. In the same documentary (Calderone, 2019) she explains that she is more interested
Fig. 01 C7 (2001), 50 x 44 x 5 cm. F. Zonta, courtesy of The De Santillana Foundation
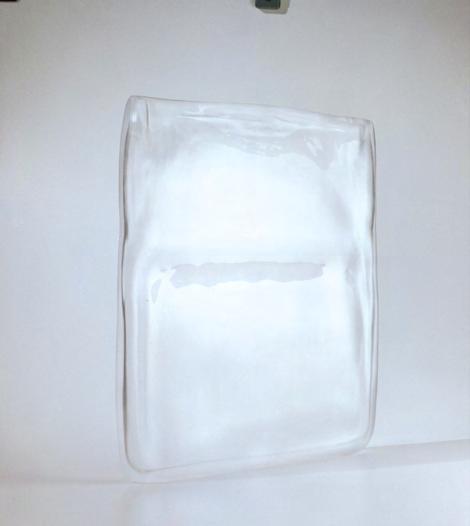
Fig. 02 Series C1-C7 (2001). F. Zonta, courtesy of The De Santillana Foundation
Fig. 03 Tokyo-Ga (2017), 30.5 x 22 x 4.5 cm. F. Zonta, courtesy of The De Santillana Foundation
in the procedure than the end result. In her work she becomes the designer of a process that hands to the maker a set of instructions as a “framework for composition and improvisation” (De Santillana, 2001). In her working notes “Ragas”1 she explains that it is through seeing the work materialize that she understands how to proceed and why she should take a particular direction next. In an interview De Santillana (2014) says: “It’s the idea of a field, an enclosed, fixed, regulated, environment, inside which you can move about freely, like my own flat rectangular forms, within whose framework everything is possible, where things can follow any kind of organic development, staying always inside precise spatial boundaries. In an ongoing dialogue and through a process of constant evolution, she and the maker learn to master the process she designs until it is refined more and more specifically. The artwork becomes part of a greater whole, a sequence, whereby each iteration explains the next (De Santillana, 2001). Her work was most often produced as part of a series making each individual piece part of an ongoig project of research. In the case of the Tokyo-Gas (1999-2019) (Figure 03) or the Flags (1999-2016), for example, the subject of this exploration was the pairing of colors, which changed as she progressed through the series. In this continuous dialogue with the making process, she broke with traditional ways of making and transported the material of glass to places it had not yet been.
From 2013 onwards, parallel to her work in Murano and to her production the United States, which took place on and off from 1986, Laura de Santillana started to produce work in the Czech Republic. There, she opened a new chapter of creative intervention through a completely new process “slumping” glass. Shapes were first blown into a mold, and then collapse inside an enormous kiln that was programmed by an engineer. Again, she became a designer of a process of making, handing over a set of instructions to a third
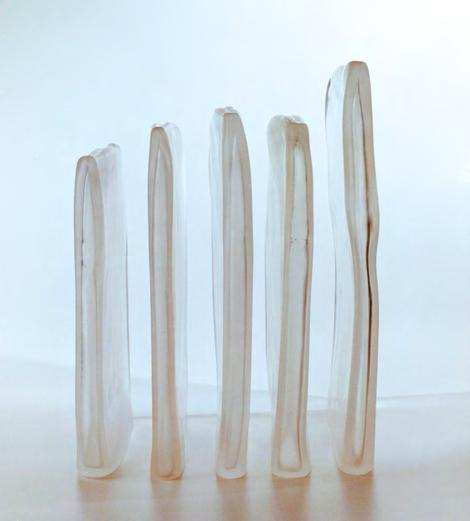
1 Raga is a melodic framework for improvisation in Indian music.
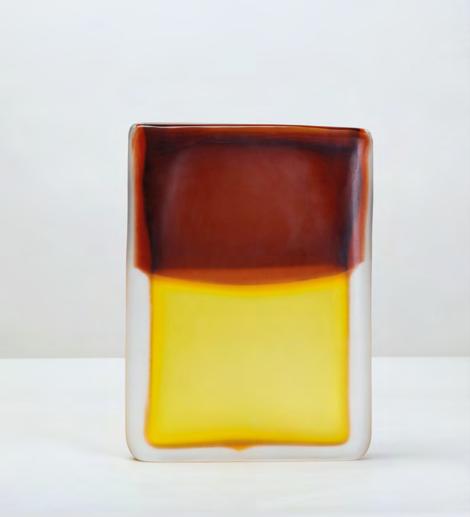
party. Only this time, she found herself in dialogue with a machine that was programmed by an engineer. This shift from the “hand” to the “machine” is concurrent with the shift between her two main sites of production: the hand in Murano and the “machine” in the Czech Republic. Through this lens, the making the work of Laura de Santillana becomes an interesting case study to observe the evolution in her making process of two very different ways of working the material of glass, that of being in a dialogue with a master glassmaker in Murano versus the Czech process in which the role of the master glassmaker was replaced by an engineer.
This touches upon an interesting definitional question: Does the role of the designer/artist changed by this change of mediator? How is the artwork itself affected by this? With these questions in mind, we should return to LdS’ work itself. The objects produced in each place can further an investigation of what the consequences were of these shifts of location and practice, beginning with her work in Murano, and then turning to the “machine-made” work in the Czech Republic.
Laura de Santillana’s work in Murano
Creating works in Murano through the free hand of a craftsman might have been the most natural way for Laura de Santillana to work. Having trained as a designer in a glass factory, she internalized the principle that while the designer might not touch the glass, their role was to steer the glassmaker’s hand as if an extension of the designer’s own. In the film La foglia d’oro (Calderone, 2019) she explained that she considered making something with her own hands, even a drawing, private. Her public, artistic work needed to be mediated by something else. Working in Murano, this intermediary was the master glassmaker. She says,: “Il maestro soffiatore, con la sua secolare esperienza e maestria, al quale si sottoponeva un disegno e che veniva seguito ed indirizzato durante il percorso della realizzazione dell’opera…” Her role was to accompany and instruct the master glassmaker. In doing so, she became an “active observer” who indirectly, through the hands of somebody else, intervened in the material. The master glassmaker, with their training and experience, was an essential part of her artistic practice. In an interview with M. Bethenod, De Santillana explains that delegation and the idea of distance were important aspects in her practice (De Santillana and Bethenod, 2014). Such distance crucially allowed for events that were outside her control. Rather than dividing the realization of the work between a pre-meditated design and a craftsman’s execution, Santillana saw glassmaking as malleable, open to modifications to the design throughout the entire process. This became an important aspect of Laura’s work: as she partially moved away from designing a finalized object, she became instead the designer of a process within which chance could intervene.
Laura’s collaboration with Simone Cenedese, the master glassmaker she eventually would work with exclusively in Murano, started in the 90’s and lasted until the end of her artistic career. Instead of a finalized drawing, Laura would hand over to Simone a set of instructions, which usually included the amount of glass, the dimension of length and the width, and the sequence of colors to be used. This set of instructions are documented meticulously inside a socalled furnace book LdeS would bring with her during every work session. The book helped her to remember the process of making every individual piece, as she included information such as the date, dimensions, sequencer of colors, and any other observations that arose during the making process. These notes came to serve as a kind of formula that LdeS used to standardize the process of each series of works. By varying the determined parameters of her formula she obtained variety in her results. She thus approached her work with the mindset of a scientist, more preoccupied with the scope of her overall procedures, sets of controls and variables, than the outcome of each individual work. It was not the unique piece but the process in which it was embedded that was important to her. Simone executed these sets of instructions given by LdeS under her close observation and guidance. After years of experience in working together almost no words were necessary, since the slightest gesture by Laura was understood by Simone. One might think that this endless repetition of the same sequence would have become boring to a skilled craftsman, but the opposite seems to have happened, as Simone explains in a film by Gianluigi Calderone that documented the relationship between de Santillana and her master glassmaker. Even though the work steps repeated themselves there was always something new in the process. The work was a continuous and long evolution, he says in the film, mutating bit by bit. Development occurred through dialogue with the maestro. He describes a sense of complicity in the experimentation between the designer/artist and the maker. Working with LdS was technically challenging (Calderone, 2019). Her ideas guided his making in a given direction but his execution might bring forward a result LdeS was not able to foresee. What first might have seemed like an accident could easily turn into a discovery that changed the course of the project. This moment of confrontation and dialogue between the designer/artist and the maker during this process was crucial for the evolution of the work. De Santillana’s work remains beautiful evidence of this slow and steady evolution that investigated endless possibilities.
Her work in Murano demonstrates how Santillana applied industrial notions to the unique object, that is, the work of art. The seemingly repeated object carried vestiges of the manual process of creation. The standardization of each process carved out a “window of chance” that made every piece unique. In fact, it is the repetition that visually underlines the uniqueness of every individual piece. In her work, Santillana is able to correlate opposing ideas, such as “standard and unique”, “order and chaos”, “intent and chance” creating a set of hybrid processes.
Laura de Santillana’s work in the Czech Republic
In 2013 Laura de Santillana visited the Czech Republic to explore producing some work there. Originally attracted by uranium glass2, which was no longer available in Murano, and an initial interest in casting, she visited various factories with the help of her friend and technical advisor Charles Parriott. What started as a simple experiment in slumping a small piece in uranium glass (Figure 04) turned into an on-going research that de Santillana pursued until her death in 2019.
After years of experience with glassblowing she found herself working with an engineer who programmed a machine. It was no longer the glassblower’s hand but the engineer’s algorithm that shaped the material and became Laura de Santillana’s mediator in her working process. In this new situation Laura de Santillana described her intention: “Provo a dare una forma razionale ad un complesso di azioni e reazioni diverse che compongono, sinora, il complesso percorso iniziato in questo nuovo progetto che chiamo “boemo” e che si sviluppa intorno ad una nuova tecnica, mai affrontata precedentemente da me, (ne’ forse da altri)”. This new making process described above was divided into two phases. In the first step, cylinders were made by blowing glass into a mold. According to LdS, this first phase was a fairly simple procedure. As she explained: “è stato in questo caso ridotto ad un semplice maestro soffiatore, che poteva indifferentemente essere sostituito da una macchina”. In a second step, these blown cylinders were placed inside an enormous kiln where they slowly collapsed on top of a mold under the guidance of an programmed heating and cooling cycle (Figure 05). It was at this particular moment the object took its final shape. Every cycle was accompanied by a series of checks at the various temperature stages. This allowed the artist to have an understanding of what was going on inside the kiln and to instruct the engineer accordingly as to whether the temperature should be increased or if he should start the cooling process. In this way, the artist participated in the process.
Again, LdeS, as the designer of a process, handed over a set of instructions to the maker that shaped the material. Here, these instructions were comprised of the dimension and colour sequence of the cylinder to be collapsed, the type of mold and its exact position (inclination), and the maximum temperature of every cycle. She learned to control and modify the environment within the “machine” in such a way that she could shape the material without touching it. In an attempt to gain more and more control over the process and to identify areas that she could manipulate she brought manual work into the industrial process and confronted the machine like a craftsman. LdS describes her relationship to this change and how it affected her act of creation in the next part of her earlier quote about her relationship to the master glassworker, describing how the creative moment shifts: “...il
momento creativo che risiedeva nelle sue mani si è trasferito in un ingegnere che deve programmare un ciclo di riscaldamento e successive raffreddamento del vetro dal quale vien fuori l’opera”.
The creative moment thus became an event happening behind closed doors. Only through punctual checks was de Santillana able to see what was occurring inside the kiln to give instructions to the engineer. Like in Murano she was present and gave instructions as to how to proceed during the making. She decided when the maximum temperature had been achieved, when the cycle should come to an end and the cooling process should start. As natural as the work appears, in its irregular, melted forms,the process she designed was very complex. In fact, she explained: “Questo nuovo “maestro”, in realtà, non è ancora nato perché il processo attraverso cui si possa formare l’esperienza necessaria a sapere quali sono gli interventi necessari durante questo ciclo è molto costosa, e l’intenzionalità e la formazione artistica di questi ingegneri è pressappoco vicina allo zero”. De Santillana studied every cycle after it was done to understand the parameters she could adjust to gain more and more control over the process. Even though LdS greatly enjoyed the scientific dimension of the making, as she said “We’re discussing only viscosity, temperature, gravity, as if it were a scientific experiment: We’re going to try this thickness, that temperature, we’re going up to 750º over 20 minutes instead of 10” (De Santillana and Bethenod, 2014, p. 124) she also mentioned the lack of a common language on aesthetical terms. She approached the engineer in Bohemia like a craftsman, demanding a level of detail and precision the workshop wasn’t used to, and at times was not able to provide. Her records show that on multiple occasions she tried to obtain better control over colour in terms of intensity and overlays, even trying to create her own new colours. Similar attempts can be found related to the shapes of her cylinder works in terms of thickness and preparatory work prior to the slumping process. She persisted in identifying procedures and formulating standards and protocols that would allow her to exert the high degree of control over the process that she desired.
Fig. 04 One of the first slumped pieces in uranium glass (2013). Courtesy of The De Santillana Foundation
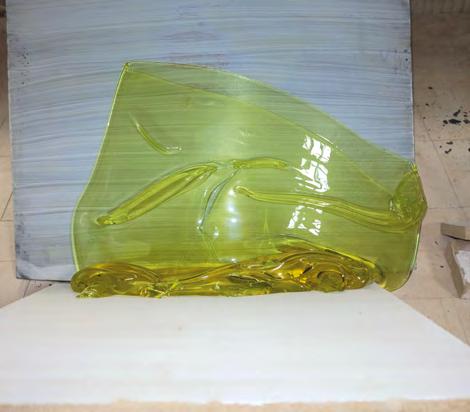
Fig. 05 Experiments after slumping process inside the kiln (2019). Courtesy of The De Santillana Foundation
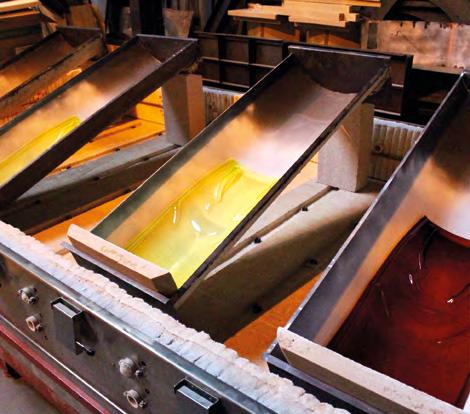
Fig. 06 Various typologies of slumped glass arranged by LdS (2015). Courtesy of The De Santillana Foundation
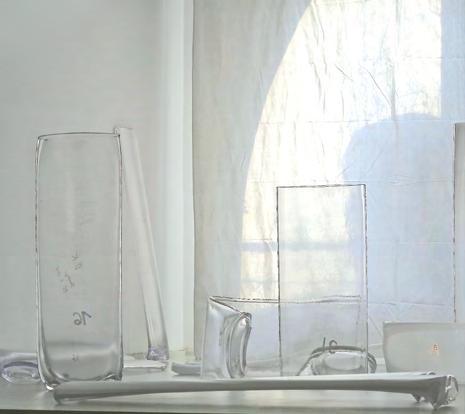
This evolution can be seen in her work, which demonstrates how steadily, not only more precision and control was obtained, but also heightened complexity. In the Czech context, her work remained of a sequence of experiments, in which each object set the terms for the next. She moved from collapsing one element to two elements in 2016 in the I Fedeli/Twin series (Figure 7) and added yet another variable when she included three cylinders in the 2019 series Triplet (Figure 8). Despite this new way of making, mediating a kiln based on trial and error, the works produced by de Santillana have the visual feel of a natural evolution. They become pure matter, as if de Santillana hands over more space to the material itself and through her process invites it to perform. Almost effortlessly, the material melts into a freestanding position, recalling a glass screen. Just like her work in Murano, these works carry the traces of making and attest the moment of creation orchestrated by de Santillana. In her sets of directions, de Santillana listened without dominating the material by carefully studying its behavior after every experiment. Years of experience in navigating somebody else’s hand made LdS an excellent observer during the process of making. She understood what she could interfere to steer the process in the desired direction. With the care and diligence of a craftsman de Santillana puts in meticulous work to modify the environment inside the machine in such a scientific and specific manner that she shapes the material without touching it.
Conclusion
The work of Laura de Santillana throws into question the binary divisions of machine-made and handmade, industrial and craft. The two centers of de Santillana’s production become the two sites of this opposition. And yet de Santillana’s working practices moved fluidly between the two in an unorthodox manner. In fact, by transferring the elements of one form of making into another, for example the individuation of handmade glass into the iterated forms of her “slumped”pieces, her work becomes a hybrid. This fusion challenges the notion of such a separation, as they become intrinsically interrelated. In her work, the specific material exigencies of glasswork serve to undermine the idea of such absolute categories in ways that extend beyond the field of glass itself. For years, De Santillana conduit to the material process had been a master glassmaker. Her work produced in the Czech Republic demonstrates how this experience might have translated when she found herself intervening in an industrial process. Thanks to her particular training as a designer inside the context of a glass furnace, she was able to work with both the handmade and the industrial equally.
According to Moravánszky, “Concept and material are engaged in a constant process of transformation in which material, craftsman, worker, technician, machine, image and meaning determine and influence each other” (Moravánszky, 2018, p. 12). The work created in both centers of productions is evidence of a slow and continuous dialogue between de Santillana and
APPARENT DIVIDE. AN OBSERVATION OF THE HANDMADE AND THE MACHINE-MADE THROUGH THE WORK OF LAURA DE
Fig. 07 Untitled (2017) from the I Fedeli/Twin series, 122 x 41 x 14 cm. F. Allegretto, courtesy of The De Santillana Foundation
Fig. 08 Untitled (2019) from the Triplet series, 118 x 48.5 x 28 cm. F. Allegretto, courtesy of The De Santillana Foundation
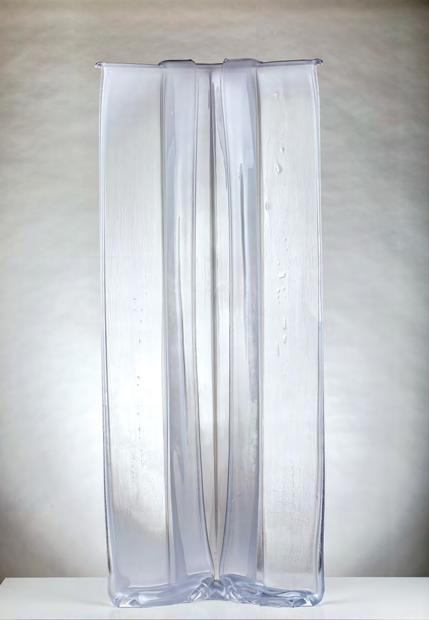
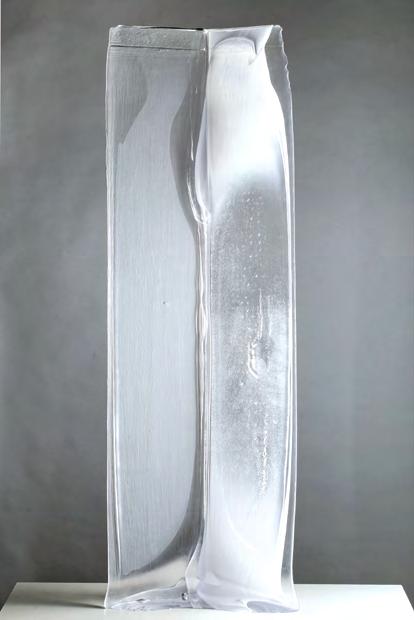
the maker that stipulates an evolution in the way of making. This on-going exchange between a technical understanding and knowhow from the maker, and an innovative vision of the material from the designer/artist is the motor that can lead towards development of new techniques. Laura’s work shows how blending notions from handiwork and industrial manufacturing processes can have fascinating results, wedding traditional skills to the possibilities offered by digital technologies to develop hybrid forms. De Santillana revealed the possibilities inherent in the traditional way of doing things and built upon the Murano tradition, incorporating new technical investigations of practice and design. Her working model offers a way of keeping tradition alive, by reimagining it and embedding it in the spirit of the contemporary. She bridges an apparent divide, where the separation line of an opposition becomes blurry and transgressive, resembling the encounter of two colours in her Tokyo-Ga.
As a model for how such hybrid forms might produce new results, de Santillana’s work remains open. Since the artist’s death, her estate, in collaboration with the Pentagram Siftung, has been in the process of cataloguing the artist’s archive in order to make it available for further study. As her materials become available in the near future, scholars and artists will be able to draw on LdS’s rich body of work, perhaps continuing her explorations of process under new parameters. I would like to express my gratitude towards Laura de Santillana and the estate that represents the artist today to enable this reflection in the form of a case study.
References
Calderone, G. (Director). (2019). La foglia d’oro. Film at Le stanze del Vetro. Calderone, G., De Santillana, L. (2009). 3 Visions in Glass (Exhibition Catalogue). Stuttgart: Arnoldsche. De Santillana, L. (2001). Works (Exhibition Catalogue). Cinisello Balsamo: Silvana Editoriale. De Santillana, L., Bethenod, M. (2014). I Santillana: works by Laura de Santillana and Alessandro Diaz de Santillana. Milano: Skira. Moravánszky, Á. (2018). Metamorphism. Material Change in architecture. Basel: Birkhäuser.
Digital manufacturing for Murano glass
OMRI REVESZAThe project Isole aims to explore new application possibilities of Murrine, through the integration of digital technologies along its production process.
Traditionally Murrine are being used for creating small decorative objects such as plates and jewels. The dimensions of those objects are limited due to a long and complex manual process, causing a narrow range of product applications and artistic expression. These technical limitations are reducing the commercial possibilities of the industry and appear unattractive to the younger generation of entrepreneurs and designers. Through an experimental process of using Murrine glass canes on their long side, Isole suggests an innovative production technique that allows to significantly increase the dimensions of murrine products and the velocity of their manufacturing, while revealing surprising artistic expressions of traditional craft, digital craft, colours and transparency.
A sustainable future for Murano glass means a shift from a segregated introverted mindset to an extroverted one. Digital and manual don’t necessarily have to be contradictions, but rather complementary.
A Department of Design, Università Iuav di Venezia and Omri Revesz Design Studio, Venice, Italy.
KEYWORDS: MURANO GLASS, DIGITAL TECHNOLOGIES, INNOVATION
Introduction
Murrine glass has very ancient origins, the first works date back to 3,0002,000 BC by Syrian, Egyptian and Roman glassmakers. During the Middle Ages, the murrine glass technique was lost but was taken up again later towards the end of the XIX century by Vincenzo Moretti.
The process of crafting a murrina object is long and complex. It requires manually slicing murrine canes into small pieces of about 5 millimetres, to be then arranged in a compact pattern on a ceramic plate and then heated in a furnace until they fuse into a single and further formed over a mould to the desired shape (History of Murrine, Murano Design Venezia). The decorative character of the artefact is determined by the colours and sectional drawing of the canes, and by the order in which the slices are placed one next to the other.
Given the complexity of the process, the dimensions of the artefacts are limited to small-scale objects, which in turn reduces the product application possibilities. Nonetheless, the colourful detailed patterns of murrine objects, the expressive language, and thus the emotional value of the artefacts are limited to those patterns of the given canes. These technical limitations are reducing the commercial possibilities of the murrine industry on one hand, and on the other appear unattractive to the young generation of entrepreneurs and designers to join in the industry and evolve it into contemporary forms of markets (Figure 01).
“Since the beginning of the economic crisis in 2008 until 2015, almost 94,400 craft workshops have closed, which amounts to a 7.26 % rate of decrease. In order to face these challenges, craft entrepreneurs must be innovative and review the ways in which they provide value to customers” (Bonfanti et al., 2018, p. 17). In recent times, industries of artisan craft are facing a similar problem, that can usually be analysed through three channels: manual work that doesn’t fit the spirit of the time, long production times that cause high costs, higher costs of the end product resulting in narrow target markets. Often the stakeholders of those industries are torn between the emotional attachment to the tradition of the practical well-established practices and the desire to innovate and bring their industry to the front of contemporary use.
Part of the frame Glass-Matters, the project Isole is an initiative of the FabLab of Ca’ Foscari University of Venice, and involved a collaborative exploration process between the FabLab institute, the company Ercole Moretti, pioneers and leaders of murrine production, Lunardelli Venezia experts of wood crafting and design studio Omri Revesz. Aiming for an economical and socially sustainable future for the glass industry of Murano, the project was centred around the question of how might digital manufacturing technologies can be integrated along the production process, to create innovative product applications, without losing its well-appreciated historical DNA?
Murano glass DNA can be often defined as a dialogue between materiality
and craftsmanship, represented through colours and transparency. The project Isole uses Murrine glass canes in their long side allowing to significantly increase the dimensions of glass surfaces and the velocity of its creation.
Murrine are not seen anymore as an extrusion of materials but as layers. A further carving into the glass surface reveals a surprising symphony of traditional craft, digital craft, colours and transparency.
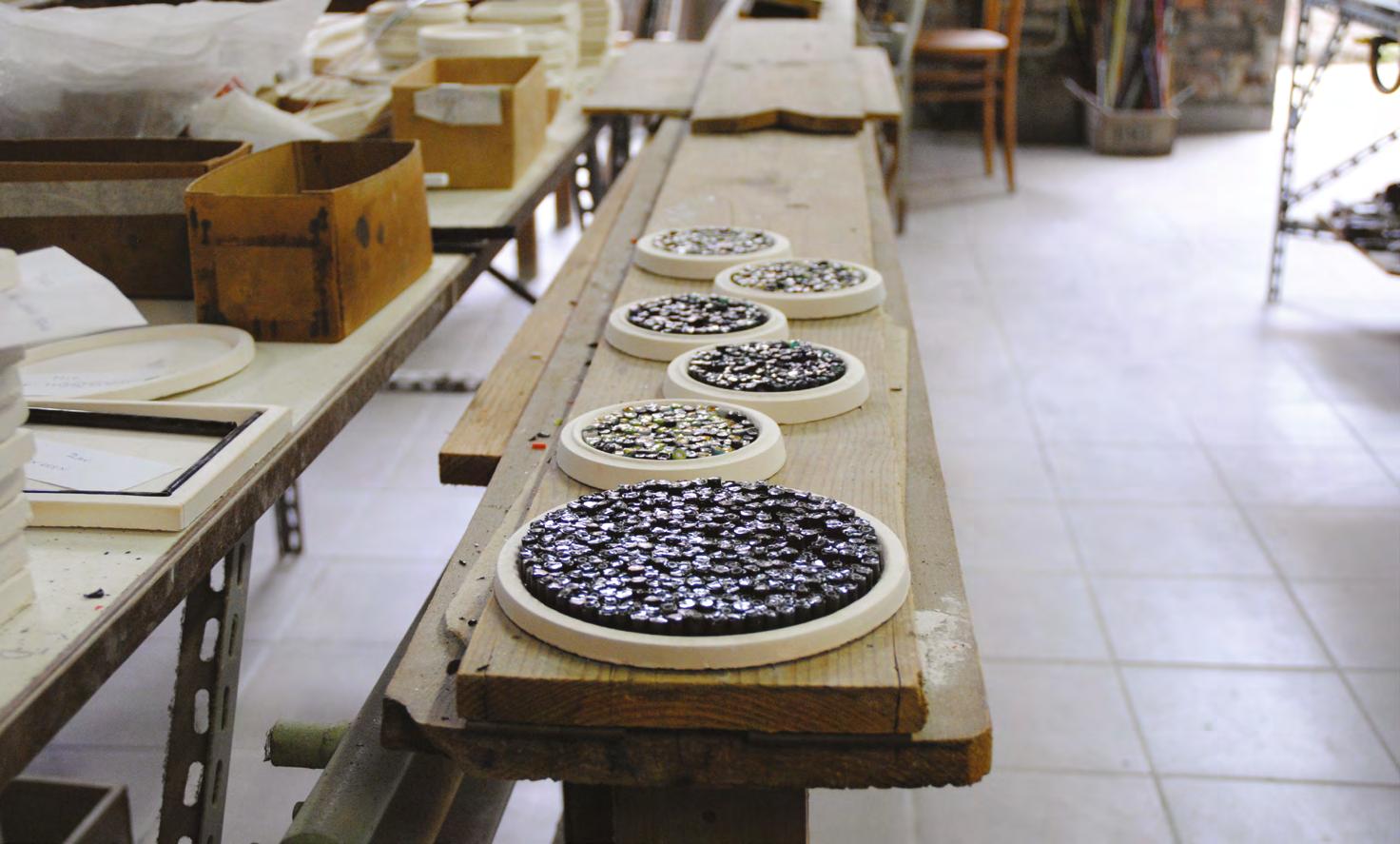
Objectives
Two spheres are setting the goals for the project: Inspirational, providing a ground for a new line of thought for Ercole Moretti and the Murano glass industry, and practical, developing openings for innovative processes and product applications. Whilst the inspirational sphere is harder to measure, the measures of success of the practical sphere were set around the following factors:
• structural characteristics of larger scale surfaces;
• cost efficiency of the process;
• expressive design language.
The dimensions of the glass surfaces were defined as a key factor to reach new product typologies, the efficiency of the process is referring to reducing the times of manufacturing and the amount of manual repetitive work, and the expressive design language refers to the freedom applied by considering the layered glass surface as a blank terrain from which to extract hidden content rather than a predefined pattern to assemble.
Methods
With goals centred around structural characteristics, material DNA and design languages, and through a constant dialogue between design, glass experts and digital manufacturing experts, a series of empirical experiments were set to isolate each of the factors that could affect the accomplishment of the goals.
Structural factors: Murrine canes in their source form are provided in different diameters, and once fused together are creating thicker or thinner glass surfaces. Further, the size of the mould affects the thickness as the melted glass spreads wider and thinner in the relatively larger mould. The experiments held in order to test the structural resistance of each murrine diameter were set through predefined 10x10 centimetres ceramic moulds, fusing in them 4, 5, 6, 7, 8 millimetres diameter of canes (Figure 02). The experiment showed that during their fusing process and spread along a surface, rather than along a circular section, the canes would lose up to 30 per cent of their sectional dimension. 6, 7 millimetres of murrine resulted as the minimum viable dimensions for the formation of a one square metre surface. An 8-millimetre diameter of canes allowed a bigger surface of two square metres. The dimensions for the Isole project were limited solely according to the dimension of Ercole Moretti’s Fornace, measuring 180x120 centimetres.
Static factors related to the volumetric geometry of the end product were tested through the boundaries of curvature of the glass surface. The experiment included a series of moulds with different angles and inclination, and glass surfaces fused on them in a furnace of 800 degrees for 8 hours, to test if the surfaces can remain in the shape of the mould, or if it accumulates by gravity at the bottom of it. Results showed the possibility to incline the surfaces 15 degrees between plans and still obtain full control of the outcome surfaces.
Material DNA: Colours and transparency are the most crucial characteristics of murrine to study and control within the process of Murano glass innovation. In a sectional view of the murrine canes, concentric circles of different colours and opacity are arranged to create the drawing stamp of a specific murrine. At the same time, according to the concept of working on the long side of the canes, those circles can be seen as layers of colour and transparency. Once fused to a surface, the canes deform from their original circular section to a quasi-square section, with layers arranged from the centre toward up, down and sides. The external layer of glass defines the first visible colour of the surface, while when carving on the surface further layers of colour and transparency are revealed out of the surface.
The control of this characteristic, which will later define the expressive language of the surface, was measured across factors of:
• depth, in order to reveal inner layers of coloured glass, external layers can be removed by carving in the glass surface. The deeper the carve goes the more layers are being revealed;
• direction, the carving can be made along the direction of the canes revealing a continuous line of colours, or perpendicularly to the direction of the canes revealing a dashed line of colours, diagonal and circular carves reveal diverse patterns of continuous and dashed lines;
• opacity, light effects can be controlled by using canes made of inner transparent layers, or outer ones. Inner ones create a three-dimensional depth effect, while outer layers will be almost entirely transparent as the outer layer once fused remains continuous throughout the entire thickness of the glass surface (Figure 03).

Expressive language: The artistic expression or design language is measured by the amount of graphics freedom associated with any Isole glass surface. To test the limits of graphic freedom, the experiments consisted of the study of different techniques of material removal. The first experiments included the configuration of specific 10x10 centimetres moulds, made by laser cutters, 3D printers and CNC milling of refractory materials. The moulds were flat at the bottom, but with nukes of different shapes and depths in them. Canes were placed in the moulds, and once fused in the furnace took the shape of the bottom and nukes. Subsequently, the moulded nuke shape was removed by using a circular sanding disc, to flatten back the surface and expose the inner layers of colours. This technique provided complete freedom of graphic expression, but at the same time demanded a complex post-process with the circular disc, when working on a larger scale of a glass surface. The second technique and most successful was tested through

a process of laser cutting a mask of the desired graphics from a polymer sheet, placing it on the glass surface and sandblasting the exposed parts of the mask. The longer the sandblaster stayed on one spot, the more material was removed and therefore, deeper layers of materials were revealed.
By defining the structural and dimensional limitations of the glass surface, achieving control of the material DNA in terms of colour and light, and developing a semi-digital process that allows complete freedom in terms of expressive language, the ground was set for the developing a new range of product applications.
Results
Within the practical sphere, the experiments resulted in a 20 fold larger surface than previously obtained by Ercole Moretti, made in a significantly reduced time. Through this structural advantage, new diverse product applications are possible. The sandblasting decoration technique allows a complete freedom and aesthetic control over the design language applied to each surface. On the inspirational level, a new range of products designed by Omri Revesz Design Studio got internationally acclaimed at Milan Design Week, part of the exhibition Reflected/Reflections at Teatro Franco Parenti and at Venice Glass Week.
The design concept for the product range Isole follows the very essence of the production process that was developed during the experimental phase: reveal. Isole is a collection of tables made of a solid Mahogany base and a murrine table top, inspired by the relation between the islands of the Venetian lagoon and the natural phenomena of a constant water tide that covers and reveals them every day.
Venice’s lagoon is studded with 123 islands, whether hidden or tentatively exposed beyond the water’s unassuming surface. Every island tells the story of an ancient treasure buried beneath the sands of time, or of contemporary productive reality. Within the design process, the islands of the lagoon were mapped according to their natural environments, agriculture, architecture and human activity. A schematic graphical representation of the islands was created and simplified to abstract direct geometries (Figure 04 and 05).
Graphics were laser cut out of a polymeric sheet to be applied as a mask on the glass surface. Murrine canes were studied according to their layers of colours and transparency to be associated with each island representation. The collection in its first batch included 4 island tables in different scales, and a standing lamp called Moon, as a metaphor for the natural forces that control the tides. All surfaces include an intact part of outer glass layers and a decorative part of diverse colours and transparency. The island Poveglia becomes a side table, represented through its water canal that divides the island into a natural environment and a man-made architectural one. Mazzorbo,
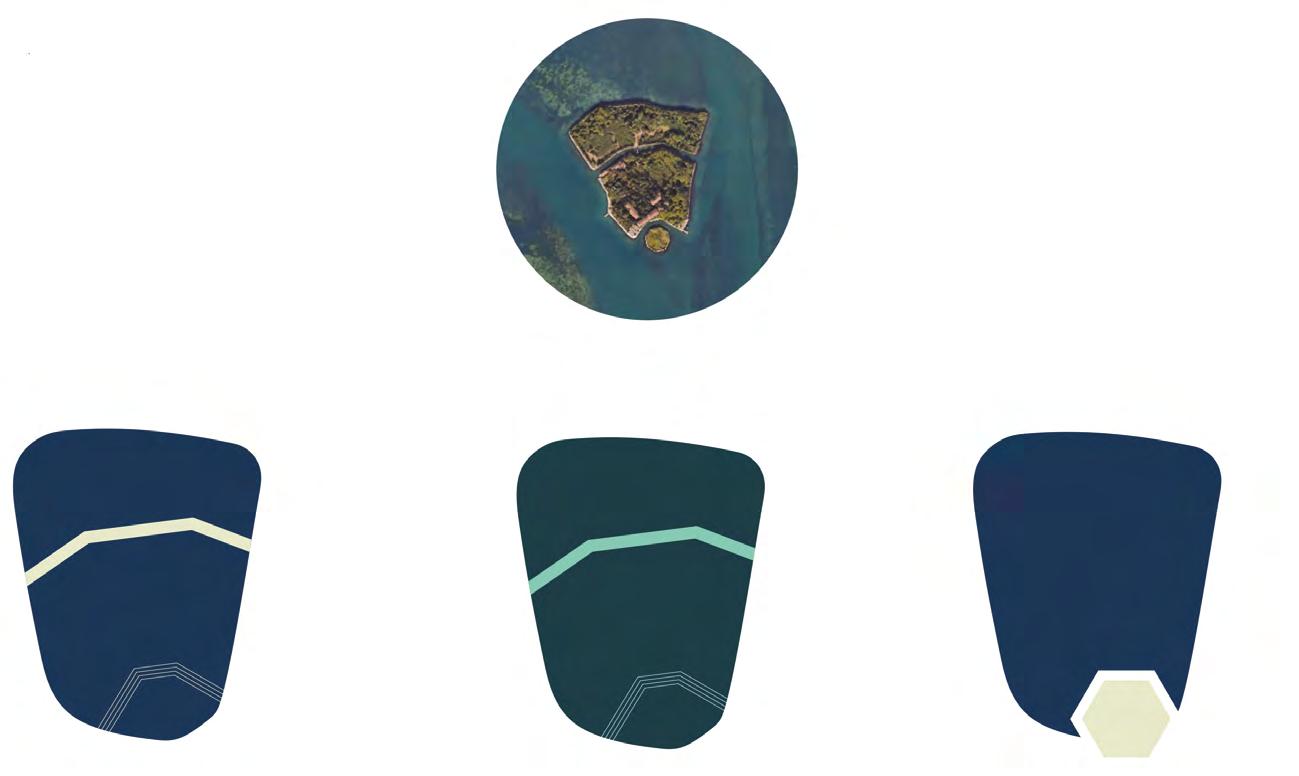
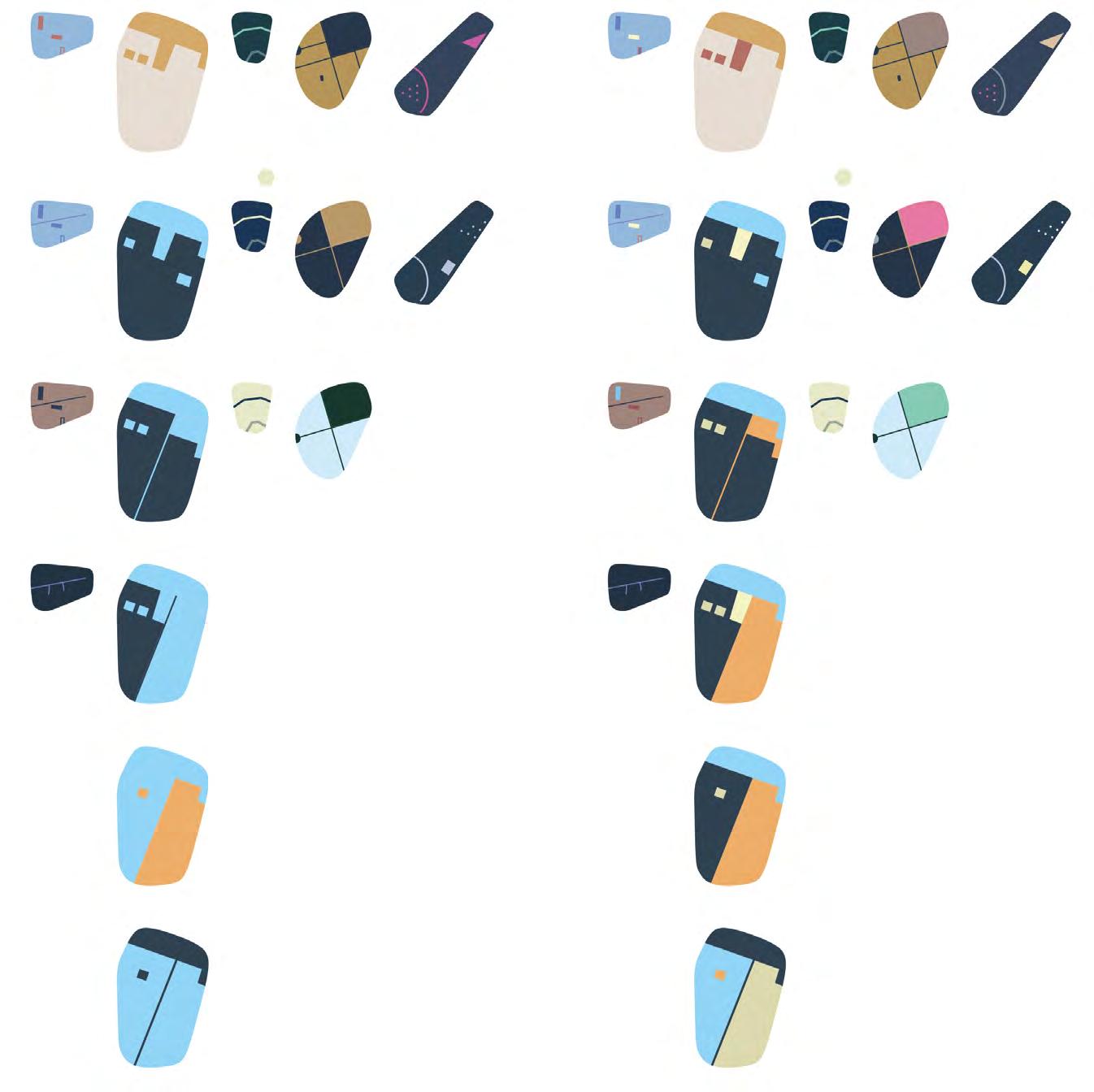
narrow and long in its form, becomes a higher console decorated with dots and lines, a symbol of its local Castraure artichoke fields (Figure 06, 07 and 08).
Lunardelli Venezia, a local PMI with a long heritage of manual and digital woodcraft, beyond the formation of the moulds of the experimental phase, had worked on the manufacturing of the wooden base for the tables and lamps, using a combined process of CNC milling of the legs and manual craft finishes. Further, to add value to the products and tell the story of the context and process, Lunardelli integrated a digital chip into the solid wood, inviting people to use digital devices and link back to an online media page. The wooden base structure was inspired by the bricole pillars in Venice lagoon that rise out of the water level to mark the paths of navigation canals.
Conclusions1
A sustainable future lies within the intersection of cultural heritage, human aspirations and technological advantages. Through this project, a solid collaboration between four cross-disciplinary realities was created to explore the synergic opportunities of shared know-how of the private sector and universities on a strictly local scale. The project raised interest both from local and international communities as an inspirational reference both for its cultural aspirations and technical solutions. The project was exhibited first during the Venice Glass Week and further at Milan Design Week Fuorisalone, part of the exhibition Reflected/Reflections at Teatro Franco Parenti, including the complete collection and the entire sample batch of the process. Further, the collection formed a social space at Venice Pavilion during Venice Art Biennial.
A sustainable future for Murano glass means a shift from a puritan to contaminated thinking and manufacturing. Even Though the craft of Murano is historically considered a highly reserved practice, where methods and know-how are kept secret from other industries, the collaboration, in this case, showed clear advantages in terms of innovative thinking and results. Digital and manual are not contradictions but complementary. Often, when facing the conflict between digital and manual craft, these two are perceived as concurrent. The combination of these two dimensions in the project Isole results in an equilibrated outcome, where both techniques are represented and needed.
Technical development requires a commercial orientation. A multidisciplinary project such as Isole must also include a commercial marketing partner, to create strategies and direct the implementation to the market from the very early stages of work. Technical, artistic and commercial know-how are crucially equal parts of the whole.
1 Isole project is a shared effort of Omri Revesz, Giada Consegnani and Marco Kotov from Omri Revesz Design studio, Damiano Frison from FabLab Ca’ Foscari University, Marcello and Paolo Moretti from Ercole Moretti and Agnese and Sebastiano Lunardelli from Lunardelli Venezia.
Social sustainability and continuity: Reducing costs and therefore reducing labour carry a risk of damaging the social structure of an industry. Nevertheless, while looking at the bigger picture, without evolving those processes into an up-to-date cultural heritage, the risk is a complete extinction of that industry for a lack of interest from the young generations. A constant exploration and evolution is a key to maintaining those industries alive, rather than their preservation. As stated by Mark Wigley in the book Preservation is overtaking us (Koolhaas and Otero-Pailos, 2014, p. 11) “Preservation is always suspended between life and death - calling on us to get smarter, faster, deeper, longer, sharper, and I would say more tender”.
Tradition and the human factor: desires, interest, satisfaction. By intervening in the traditional process and introducing digital technologies, new methods and product applications are possible. Thus, the industry becomes more attractive to younger entrepreneurs and designer generations. If cultural heritage testifies to the spirit of an epoche, it is only reasonable to investigate how the technologies that are associated with our times can impact, contribute and help evolve the art of Murano glass.
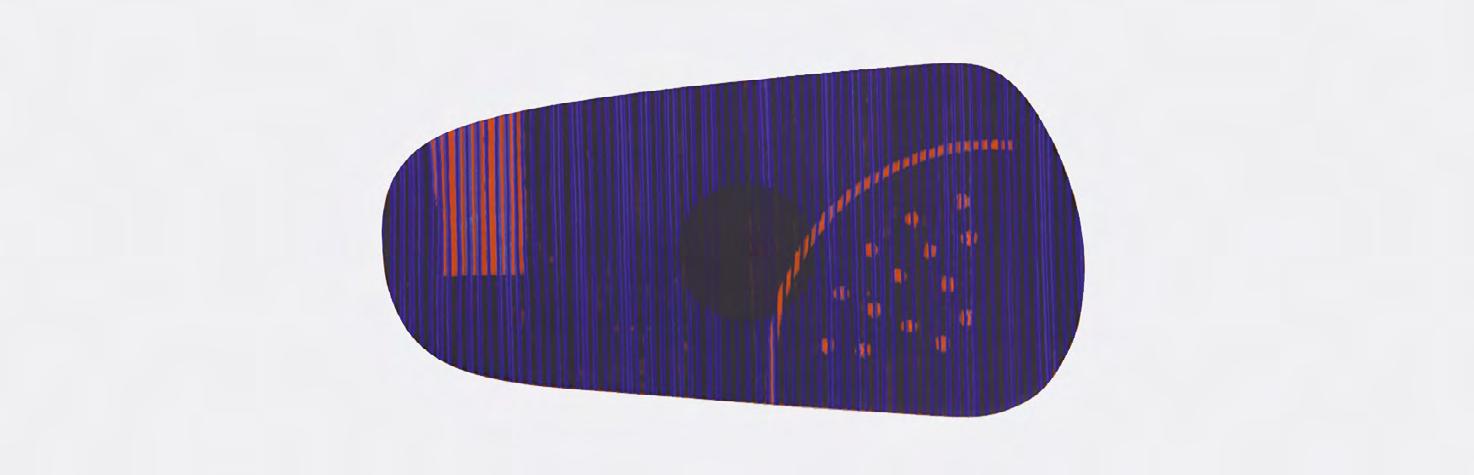


References
Bonfanti, A., Del Giudice, M., Papa, A. (2018). Italian craft firms between digital manufacturing, open innovation, and servitiza tion. Journal of the Knowledge Economy, vol. 9, n. 1, pp. 136-149.
Johnson, O. T. C. (2015). Glass, Pattern, and Translation: A Practical Exploration of Decorative Idiom and Material Mistranslation using Glass Murrine. PhD thesis. London: Royal College of Art.
Koolhaas, R., Otero-Pailos, J. (2014). Preservation is overtaking us. New York: GSAPP Books.
muraNEWABLE: from the needs of glass comes a new energetic opportunity
GIULIA CAZZADORA, GIANMARCO GNOATOA, DANIELE VENDRAMEB, SOFIA ZANANDREABIn a rapidly changing world, in which getting access to energy supplies is a great challenge both from an economic and ethical point of view, it is imminently necessary to adopt a renewable energy system.
The island of Murano, a global excellence which has been historically considered the “homeland” of decorated glass, represents an emblematic case in need to be preserved and appreciated. While aiming towards a more sustainable structure, it is necessary to consider that it’s not always possible to maintain the traditions and culture of a millenary art together with a new energetic system. For this reason, a shift in perspective becomes necessary: there are many different renewable energy sources that can cover not only the energetic needs of Murano, but also of the entire Venice lagoon. Furthermore, a solution that fully embraces the concept of circular economy would be to replace the natural gas used in the furnaces with biogas from algae, produced in new generation bioreactors, with the help of glass waste itself as a fertilizer. This would then allow us to see Murano not as a self-sustaining entity, but as a piece of a more complex scheme, positively impacting on the whole city of Venice.
A Università Ca’ Foscari di Venezia.
B Università Iuav di Venezia.
KEYWORDS: ENERGY, MURANO, CIRCULAR ECONOMY

Fig. 01 Infographic relating to the energy consumption of a Murano glass factory compared to the entire municipality of Venice.
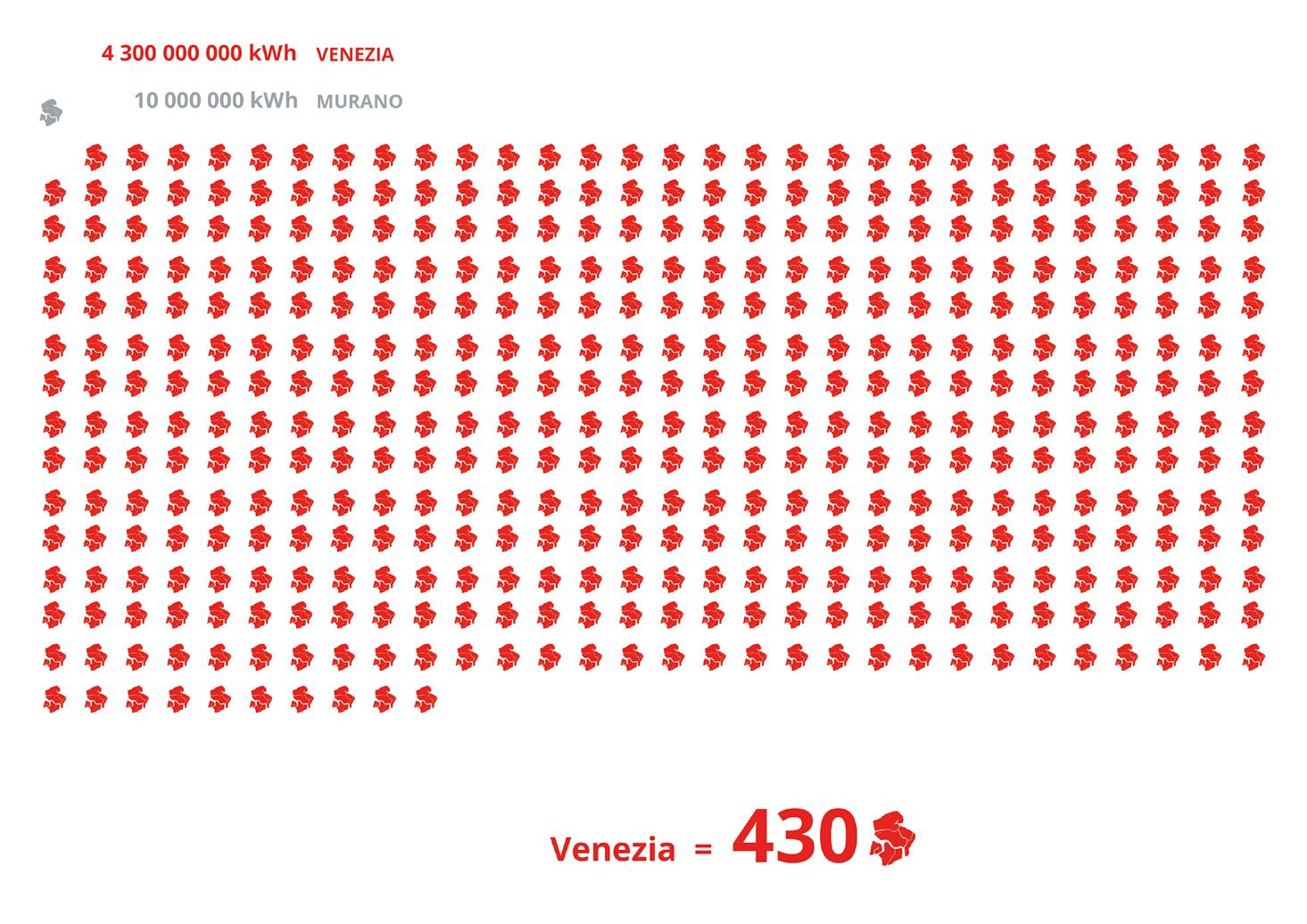
Fig. 02 Visualization of the island of Murano in an energetic synergistic scenario.
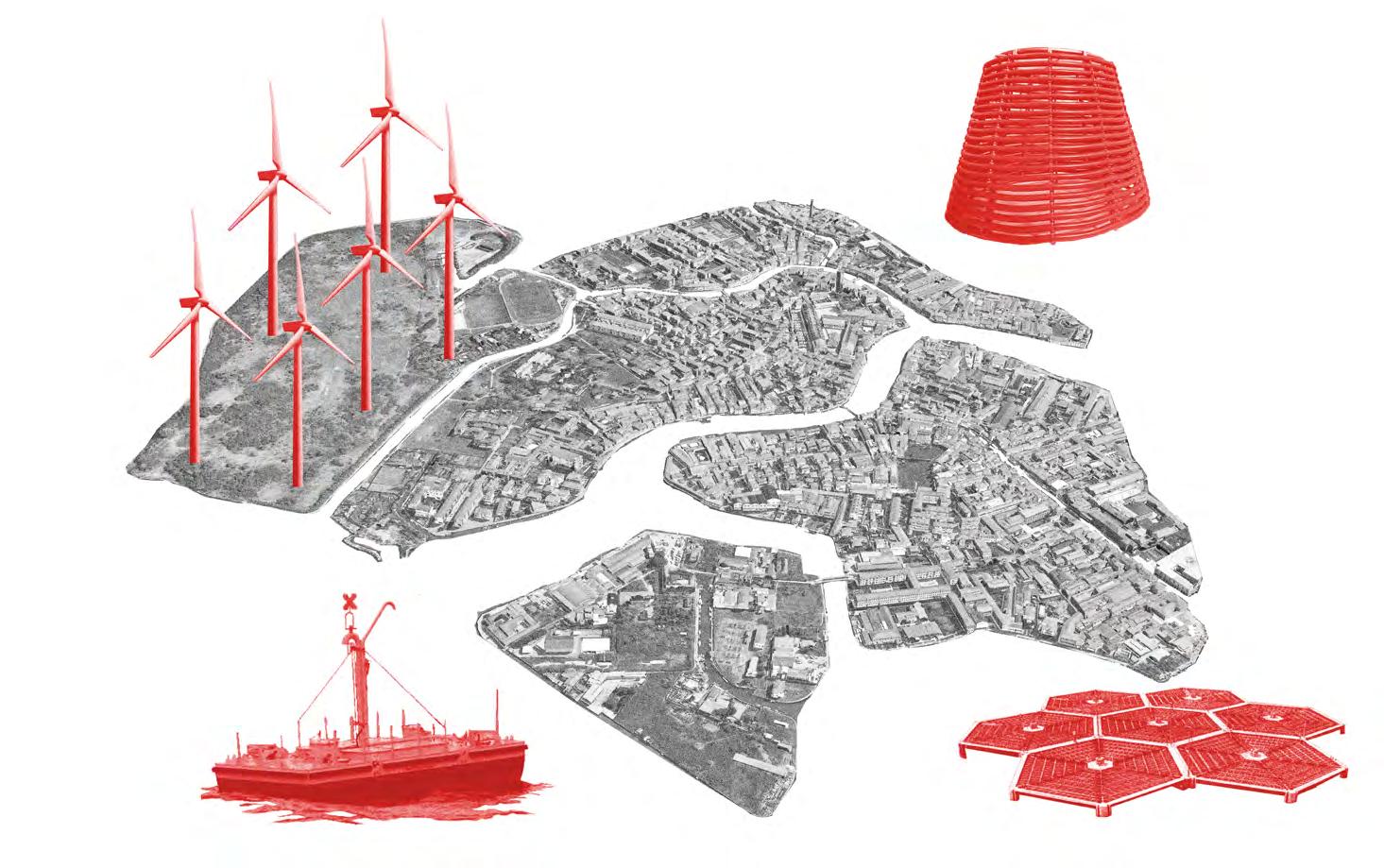
poroVE: the fluid value of the waste
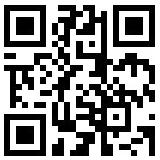
Giving added value to the waste material is a current challenge and the glass industry is fully involved. What we offer with poroVE is the production of a filter which arises from the recycling of glass waste from construction field and favors the water softening process. Through a chemical-physical reaction which increases the porosity of the expected glass matrix, the filter would shrink metals heavy from drinking and not drinking water. An eventual functionalization of this filter would pave the way for the abatement of biological contaminants. This technology is applied here to a bottle whose filter is integrated to the cap in a way to be easily replaced and regenerated. This will be the test case for extend it to larger volume purification systems drinking water deficient areas.
A Università Ca’ Foscari di Venezia. B Università Iuav di Venezia.
KEYWORDS: WATER, FILTER, SINTERING
Fig. 01 The bottle with poroVE: sketches.
Fig. 02 Bottles with poroVE: render.
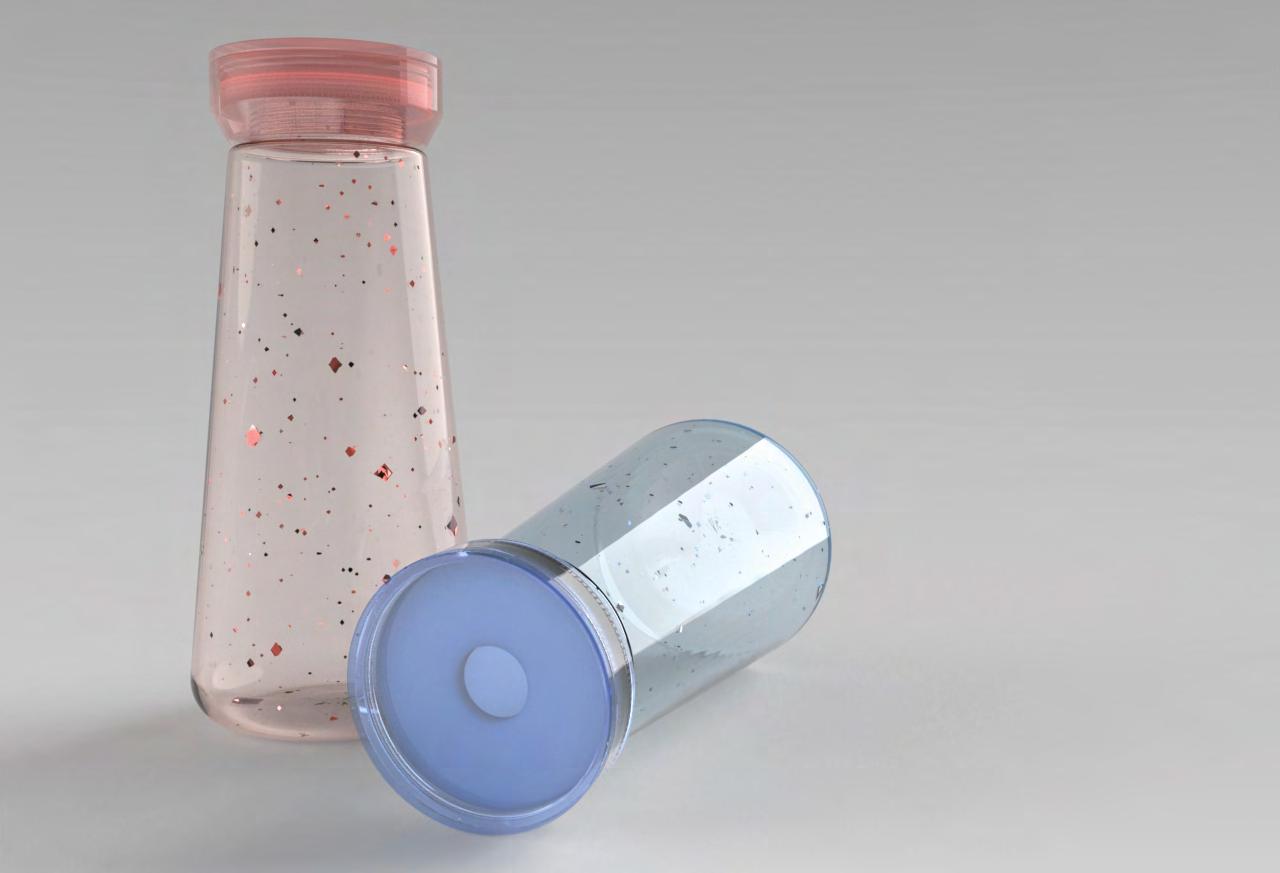
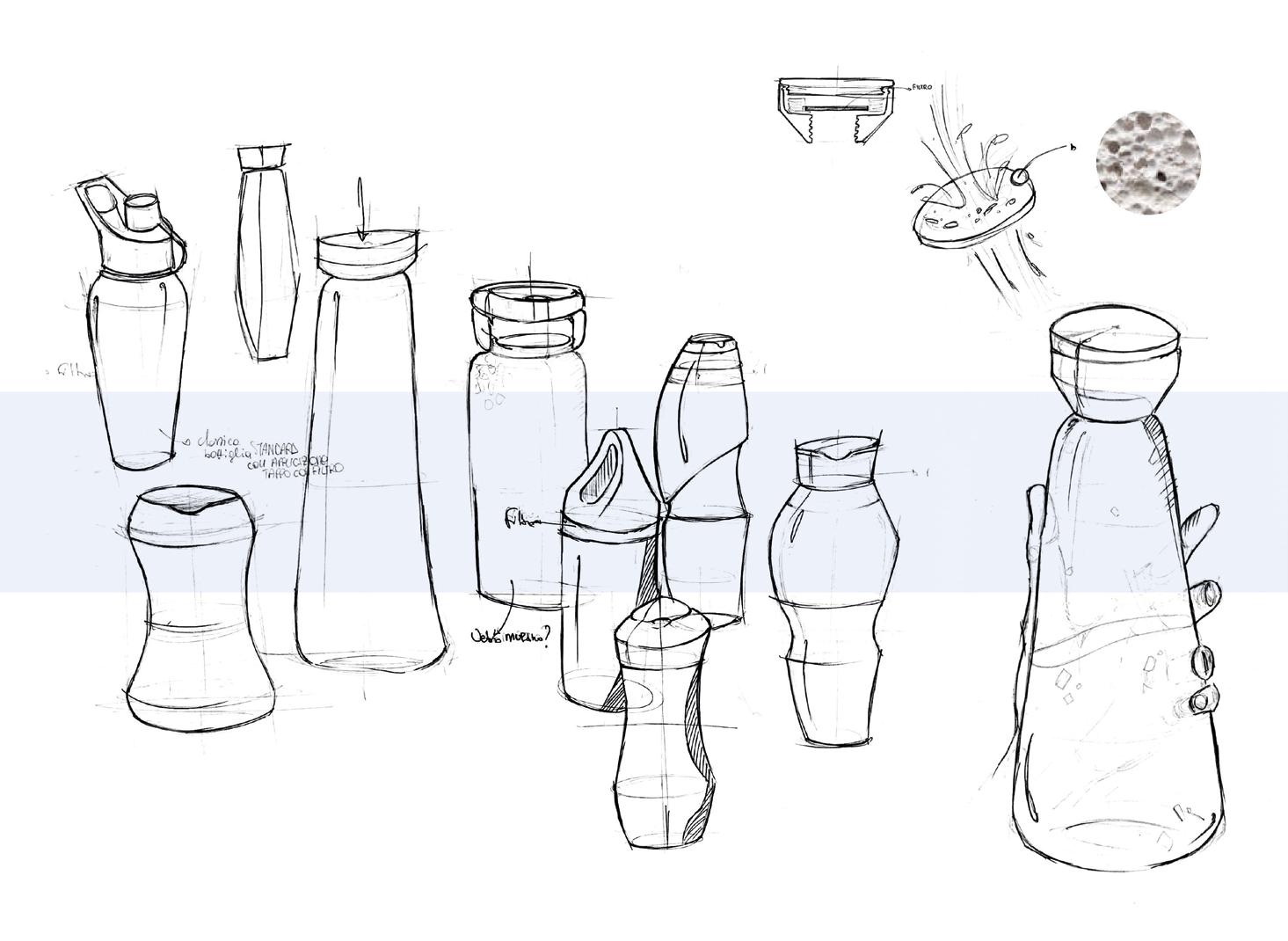
wearGLASS: from waste to resource for wearable
GIULIA DA PIANA, SERENA DE CONTIB, NICOLA MASSIMIA, MICHELE MESCOLINBGlass is a ubiquitous material, omnipresent in our daily lives with a multiplicity of applications that make it irreplaceable to our living needs. Since it is also a “permanent material,” that is, a material whose inherent properties do not change during use or as a result of being recycled repeatedly countless times to make new products, the glass industry is investing in the research and development of processes that are increasingly aimed at sustainability. A direct consequence of the extensive use of the material is the production of mostly unused waste. Among the most abundant at the industrial level are those from the construction sector to which are added those from the art glass sector; for example, just in the reality of Murano are produced 800t of scrap to be reiterated. One possible solution is to exploit the composition of these scraps for the production of high-performance materials such as aerogels. Such compounds are widely used in multiple sectors due to functional qualities such as light weight, waterproofing, thermal insulation and fireproofing.
The most innovative application may be in the textile sector in the context of fiber or padding, leading to the replacement of currently used harmful chemicals (PFAS). This is how glass, born for artistic creations and industrial purposes, continues its life cycle and gives rise to innovative and sustainable solutions.
A Università Ca’ Foscari di Venezia. B Università Iuav di Venezia.
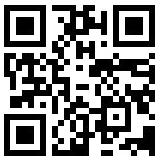
KEYWORDS: WASTE, CLOTHING, AEROGEL
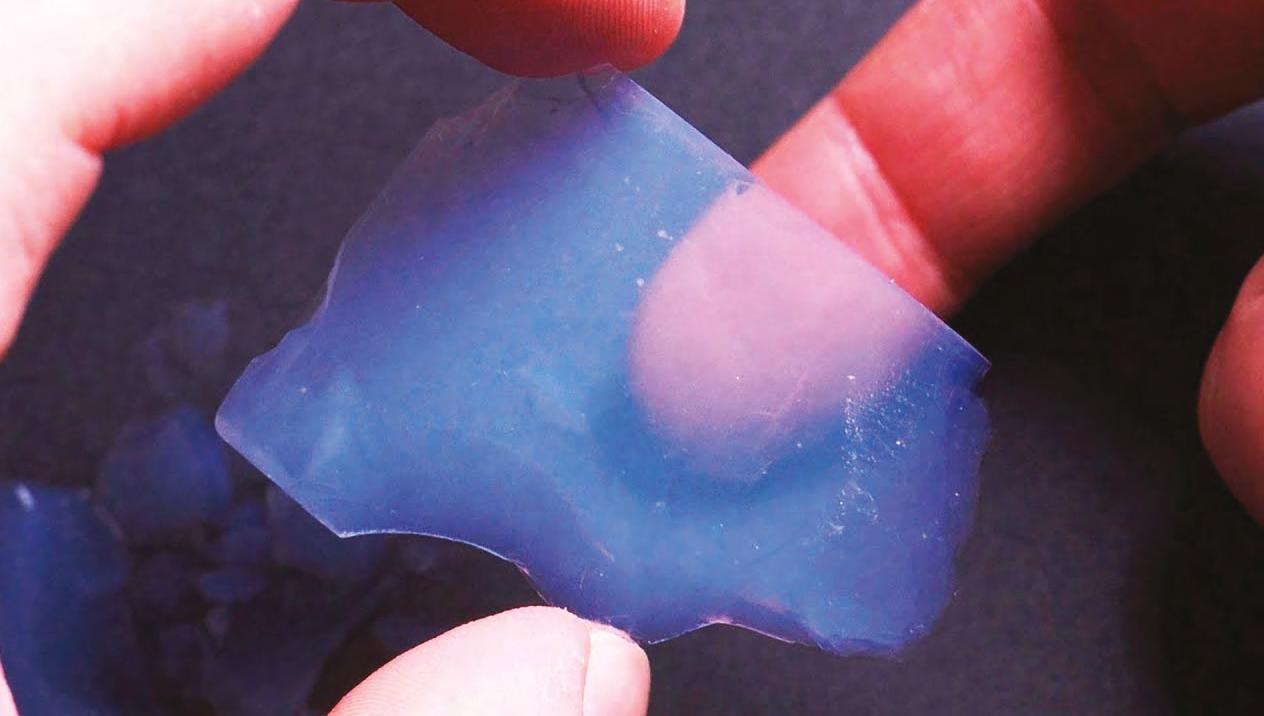
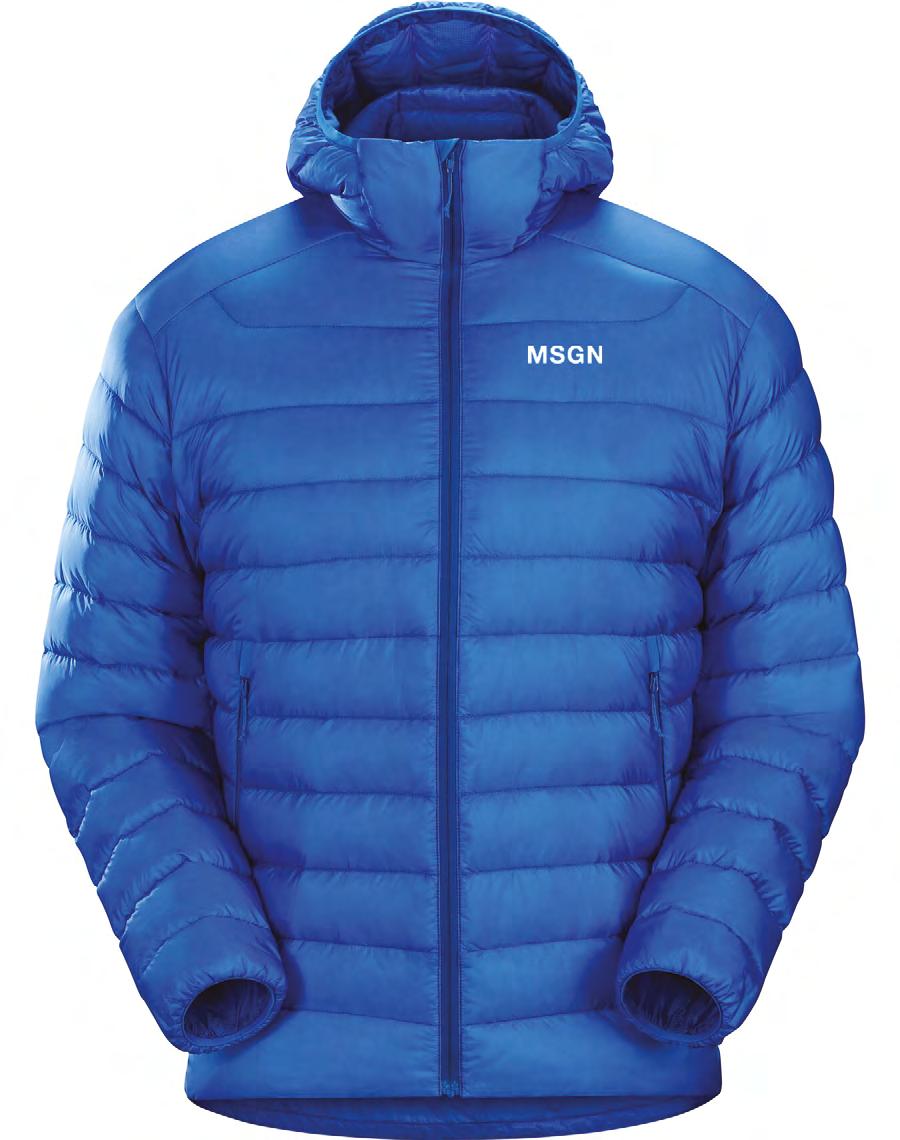
is ANTIFRAGILE
throughout history, it faces challenges, crises, and innovations. Glass, its design and its technologies are in a constant state of transformation by fulfilling different functions, affirming some of its characteristics and modifying others, adapting to changing contexts and demonstrating a capacity for innovation. In the International Year of Glass, this book presents the work of researchers and scholars who highlight the differences and at the same time the commonalities between three different fields of study: Science, Design and Architecture. The aim of this book is to share descriptions of the glass and its innate aptitude for innovation.