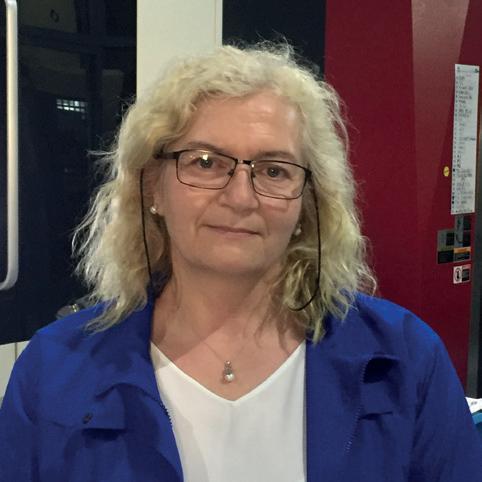
9 minute read
LEAN MANUFACTURING
by CEFAMOL
MERCEDES DOMINGUES Centimfe – Centro Tecnológico da Indústria de Moldes, Ferramentas Especiais e Plásticos

LEAN MANUFACTURING NA INDÚSTRIA DE TOOLING
O objetivo deste artigo de opinião é apresentar os conceitos e os princípios da filosofia Lean Manufacturing (Lean) e a sua aplicabilidade na melhoria da eficiência dos processos e sistemas de produção da indústria de Tooling. Como complemento são apresentadas algumas ferramentas e metodologias para a sua implementação e indicadas as suas principais vantagens.
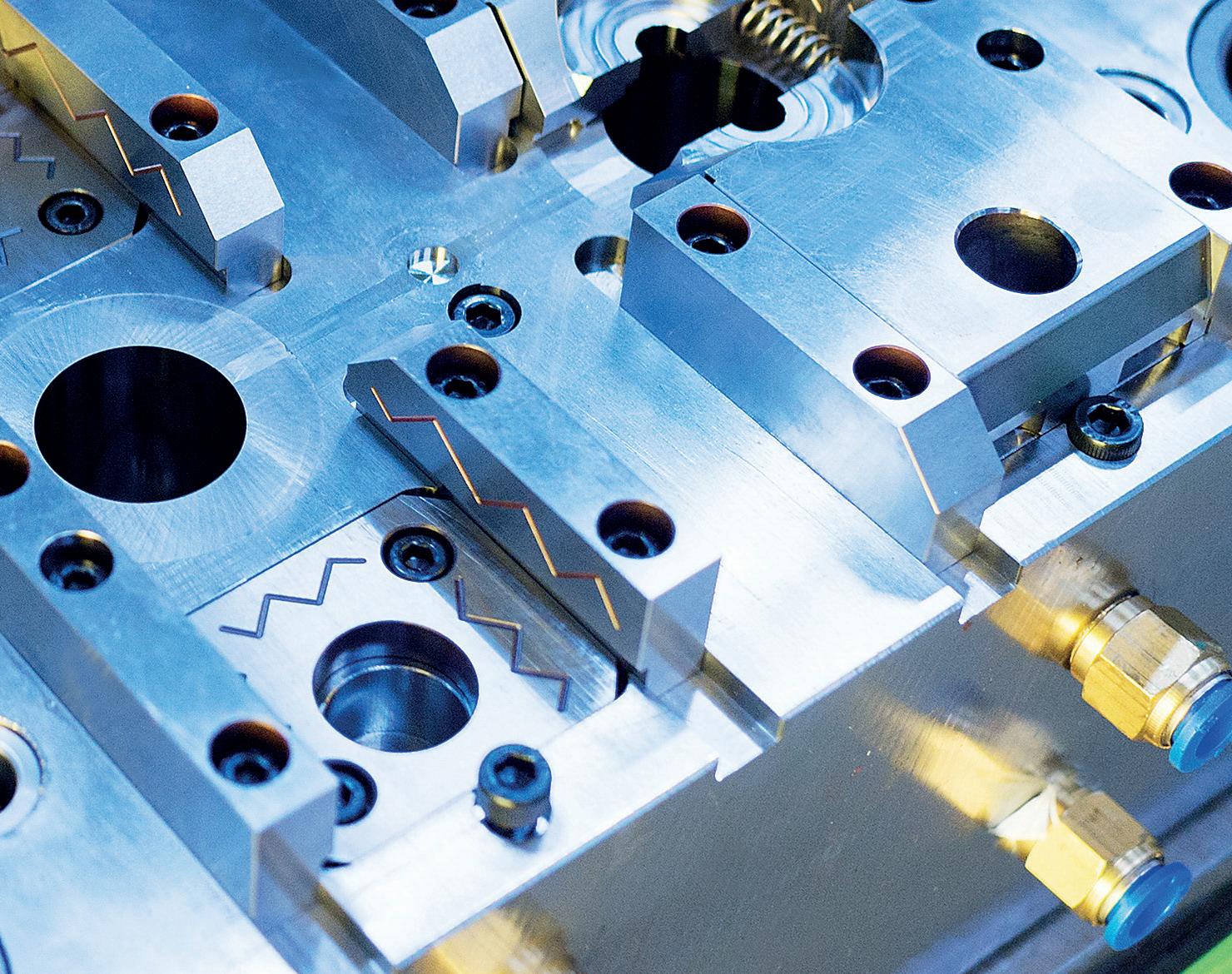
A INDÚSTRIA DE TOOLING
A indústria de Tooling é dinamizada, essencialmente, por pequenas e médias empresas que dispõem de recursos humanos altamente qualificados e de sistemas produtivos dinâmicos e complexos. As características de produção unitária e a grande quantidade de componentes que se encontram em curso de fabrico e em diferentes etapas do processo dificultam o planeamento e a dinâmica de produção. Isto favorece a geração de ineficiências e desperdícios de espera e de não qualidade que, por sua vez, originam custos e prazos acrescidos e degradam a eficiência do sistema produtivo. Os esforços para melhorar os sistemas de produção e os seus processos focam-se na redução do tempo de execução (Lead Time) recorrendo, normalmente, à introdução de novas tecnologias e equipamentos. Esta abordagem centrada neste importante fator, não anula a necessidade de uma visão mais integrada e organizada da gestão produtiva que seja capaz de criar rapidez e qualidade e o uso eficiente dos recursos disponíveis. O lean manufacturing tem sido adaptado e implementado na indústria de Tooling com bons resultados na eficiência e no aumento da produtividade.
Tabela 1. Tipos de desperdício Lean
Tipo de desperdício
Defeito
Transporte
Excesso de stock
Movimentação
Excesso de processamento
Espera
Excesso de produção O desperdício ocorre
Ocorre quando o produto está não conforme com as especificações e tem de ser retrabalhado ou corrigido ou é considerado sucata. A sucata e os retrabalhos acrescentam custo e tempo de produção.
Ocorre quando se transportam, movimentam ou transferem, de um local para outro, materiais ou informação desnecessariamente. O que se traduz em perda de tempo e escusada utilização de recursos.
Ocorre quando qualquer material ou produto existe em quantidade superior à necessária, o que aumenta os custos com o armazenamento.
Ocorre quando se realizam movimentos desnecessários de pessoas. Estas movimentações reduzem a disponibilidade das pessoas para realizar operações de valor acrescentado.
Ocorre quando são empreendidos demasiados esforços ou alocados recursos desnecessários para a realização de atividades que não acrescentam valor ao produto.
Ocorre quando os materiais não estão a ser trabalhados ou quando os recursos produtivos e as pessoas estão parados à espera.
Ocorre quando se produz mais do que o necessário ou antes de ser necessário.
Figura 1. Princípios do Lean Thinking

LEAN MANUFACTURING
A filosofia de produção Lean surgiu no Japão, após a segunda guerra mundial, como um sistema de produção capaz de recuperar a indústria local. É uma abordagem simples, assente num conjunto de princípios e suportada por metodologias e ferramentas operacionais que podem ser usadas na identificação e eliminação sistemática de desperdícios. Neste contexto, são considerados desperdícios todas as atividades que consomem tempo e/ou induzem custos e que não acrescentam valor ao produto. Os tipos de desperdício considerados nesta abordagem são os indicados na tabela 1.

O Lean é a metodologia mais indicada para criar valor e eliminar desperdícios. Contudo, a identificação do desperdício nem sempre é uma tarefa fácil. Em algumas situações a convivência com os desperdícios transforma-os em características típicas dos processos que geram custo e degradam a eficiência interna. Do trabalho de campo, realizado pela equipa Lean do Centimfe, pode constatar-se que o desperdício que mais ocorre e degrada a eficiência produtiva são os defeitos. A correção dos defeitos obriga a ciclos de retrabalho com consequente aumento dos custos e prazos. A gestão Lean dispõe de metodologias e técnicas capazes de promover a prevenção dos defeitos e assegurar a sua atempada identificação de modo a minimizar a sua propagação no processo produtivo. LEAN THINKING
São cinco os princípios que estruturam o pensamento Lean. Estes princípios orientam para a eliminação de desperdícios, para a estruturação de processos mais eficientes e orientados para o cliente. Além disso, ajudam a identificar o que cria valor para o cliente, a compreender e estabelecer as atividades e a sequência da cadeia de valor, a assegurar um fluxo contínuo puxado e fluido nos processos de modo a obter melhores resultados. Resumindo, produzir mais em menos tempo, usando eficientemente os recursos, para entregar ao cliente no tempo acordado o que ele valoriza. A figura 1 apresenta os cinco princípios base do pensamento Lean.
O valor pode ser definido como o conjunto das características do produto/serviço que têm influência na decisão de compra do cliente. A cadeia de valor é definida pelo conjunto das realizadas numa dada sequência para transformar um pedido num produto a fornecer ao cliente. A análise da cadeia de valor permite identificar as atividades que agregam e as que não agregam valor (que são desperdício), podendo ser eliminadas. A perfeição decorre da melhoria contínua que advém da aplicação sistemática, transversal e a todos os níveis, dos princípios anteriores. Neste pensamento os conceitos de valor e desperdício estão intrinsecamente ligados.
FERRAMENTAS E METODOLOGIAS LEAN
Existem diversas metodologias, técnicas e ferramentas para a aplicação dos princípios e conceitos Lean para identificar e eliminar desperdícios, implementando a mudança. É importante que estas sejam usadas com o propósito adequado e de forma sistemática. Contudo, para que a mudança seja real é necessário que ocorra primeiramente uma mudança na forma de pensar a organização, para que se crie a vontade de querer mudar e o comprometimento das pessoas com os procedimentos da mudança. Na indústria de Tooling as metodologias e ferramentas Lean mais usadas nestes processos são: Value Stream mapping (VSM), Single Minute Exchenge of Die (SMED), Metodologia 5S e Indicadores Lean.
Value Stream Mapping (VSM)
O VSM é uma ferramenta Lean de diagnóstico utilizada para mapear a cadeia de valor de produtos e/ou serviços. Permite representar qualitativa e quantitativamente todas as atividades do processo desde a adjudicação até à entrega ao cliente. É uma ferramenta de apresentação gráfica, o que facilita a compreensão da cadeia de valor. Ao tornar visíveis e quantificáveis as ineficiências, cria as condições para a análise e a discussão do processo atual e para a definição de uma

proposta do processo do estado futuro (processo desejado).
Figura 2. Etapas VSM
A utilização desta ferramenta requer a realização das etapas indicadas na figura 2 em ciclos sucessivos de melhoria até que se alcance o processo desejado.
O processo do estado futuro (processo desejado), deve ser desenhado com a contribuição de todos e aprovado pela gestão de topo, devendo ainda privilegiar um fluxo contínuo e, sempre que possível, a eliminação das atividades que não acrescentam valor.
Tabela 2. Indicadores Lean
Indicador
LTt - Lead Time Total LTf - Lead Time do fabrico
TP - Tempo total de produção
Toc - Tempo total de ocupação dos recursos
Tva - Tempo total de valor acrescentado
Tsetup - Tempo total de setup
Tcont - Tempo total de controlo
Trework - Tempo total de retrabalho
OEE - Eficiência global do equipamento Métrica
LTt = (Data de aprovação interna do molde) - (Data de adjudicação do molde) LTt = (Data de aprovação interna do molde) - (Data de chegada do aço) TP = (Soma dos tempos de produção considerando todas as operações do processo) Toc = (Soma dos tempos de ocupação dos recursos considerando todas as operações do processo) Tva = (Soma dos tempos de valor acrescentado considerando todas as operações do processo) Tsetup = (Soma dos tempos de setup considerando todas as operações do processo) Tcont = (Soma dos tempos de controlo considerando todas as operações do processo) Trework = (Soma dos tempos de retrabalho considerando todas as operações do processo) OEE = disponibilidade x desempenho x qualidade
Os constrangimentos que ocorrem na aplicação desta ferramenta na indústria de Tooling prendem-se com o facto da cadeia de valor do molde se subdividir no fabrico nas múltiplas cadeias de valor dos seus componentes. Neste caso, o que se recomenda é o mapeamento da cadeia de valor de um conjunto de componentes que representem a cadeia de valor do molde.
Single Minute Exchenge of Die (SMED)
O SMED é uma metodologia da filosofia Lean usada para reduzir o tempo de setup. O tempo de setup é o tempo gasto na mudança de produtos e ferramentas e em ajustes e reajustes realizados no decorrer do processo de produção. Durante o setup, o processo não produz valor, pelo que este tempo é considerado um desperdício e, como tal, deve ser minimizado.
A implementação eficaz da metodologia SMED minimiza os tempos de paragem das máquinas, o que se traduz em mais disponibilidade dos recursos e maior flexibilidade do processo e, como consequência, em custos de produção mais baixos. A aplicação desta metodologia pressupõe a realização das etapas indicadas na figura 3, em ciclos repetidos, até que sejam atingidas as metas definidas.
Na indústria de Tooling, o impacto da redução do tempo de setup traduz-se no aumento, considerável, de disponibilidade de máquina o que contribui para o aumento da capacidade produtiva. Quando esta capacidade é usada eficazmente melhora a eficiência do processo produtivo.

Metodologia 5S’s
Esta metodologia de base da filosofia Lean, tem como objectivo a eliminação de desperdícios pela implementação de práticas de organização e limpeza do posto de trabalho. A sigla 5S refere-se às iniciais de cinco palavras Japonesas que começam com a letra S: Seiri, Seiton, Seiso, Seiketsu e Shitsuke. O objetivo implícito à implementação de cada um dos cinco sensos está apresentado na figura 4.
A implementação desta metodologia na indústria de Tooling gera melhorias importantes no desempenho dos processos, promove um ambiente de trabalho mais agradável, seguro, competitivo e produtivo. Para a implementação eficaz desta metodologia é determinante o comprometimento das pessoas.
Indicadores Lean
Os Indicadores Lean permitem expor, quantificar e visualizar os desperdícios e ajudar a influenciar e a promover o espírito competitivo e o pensamento Lean. Estes indicadores são também importantes para a tomada de decisão e para perceber e melhorar o desempenho organizacional em termos de eliminação de desperdícios e de eficiência global. Na tabela 2 apresentam-se alguns dos indicadores que poderão ser usados.
Figura 3. Etapas metodologia SMED
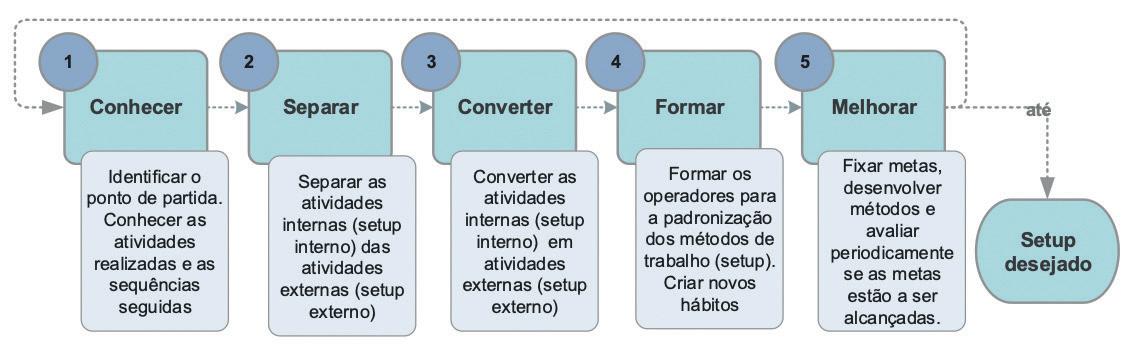
Figura 4. Etapas metodologia 5S


Na indústria de Tooling, a utilização de indicadores que gerem informação sobre a eficiência do processo produtivo reveste-se da maior importância. Do trabalho de campo realizado pela equipa Lean do Centimfe pode constatar-se que existe uma janela de melhoria que importa explorar e admitem-se ganhos de eficiência significativos.
CONCLUSÃO
Na indústria de Tooling a implementação da filosofia de gestão Lean gera melhorias de eficiência por ser possível reduzir significativamente alguns desperdícios e inoperâncias. Contudo, para que os ganhos sejam majorados é importante que a abordagem à eliminação dos desperdícios seja sistemática e para isso é necessário que seja acomodada na cultura da empresa.
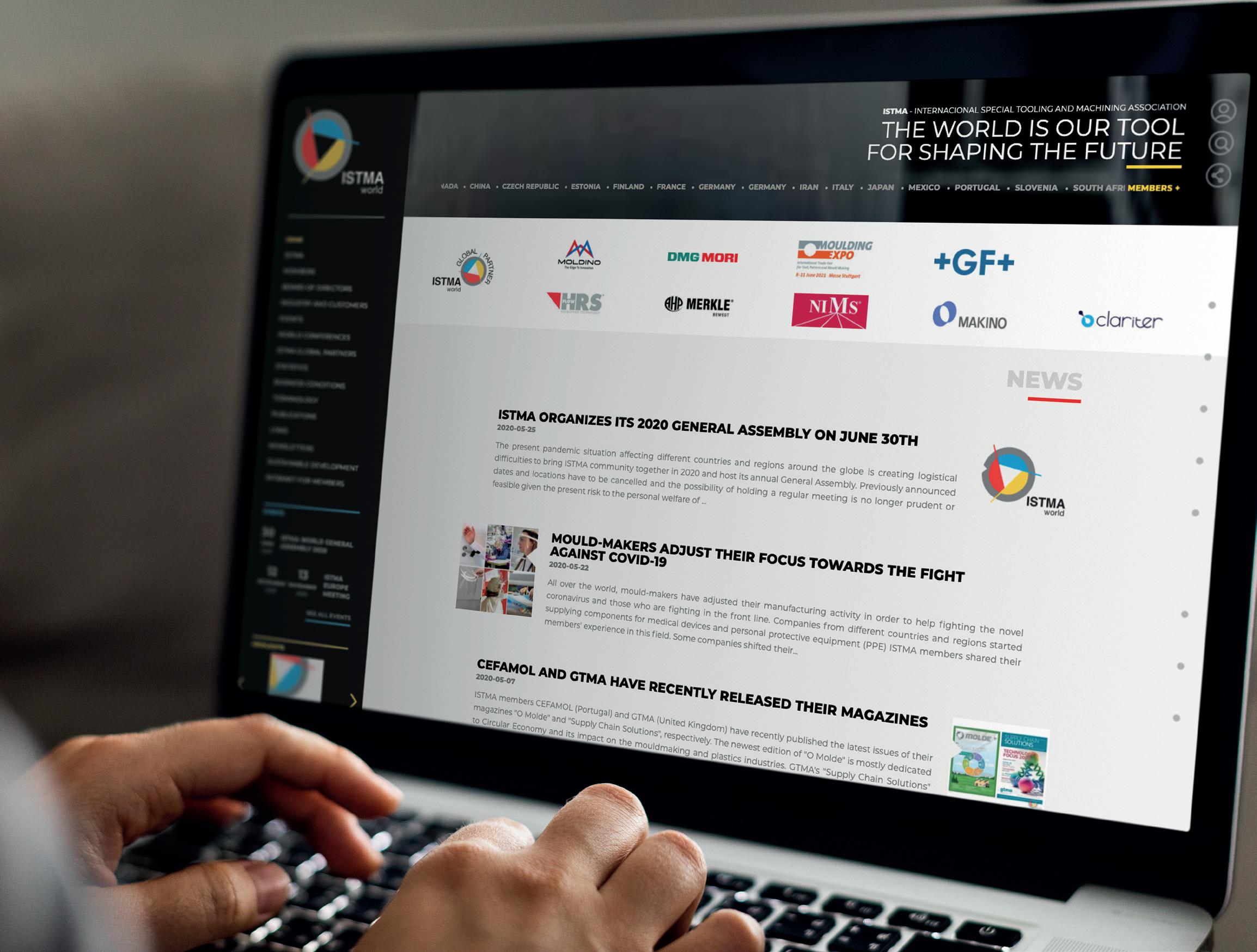
www.istma.org
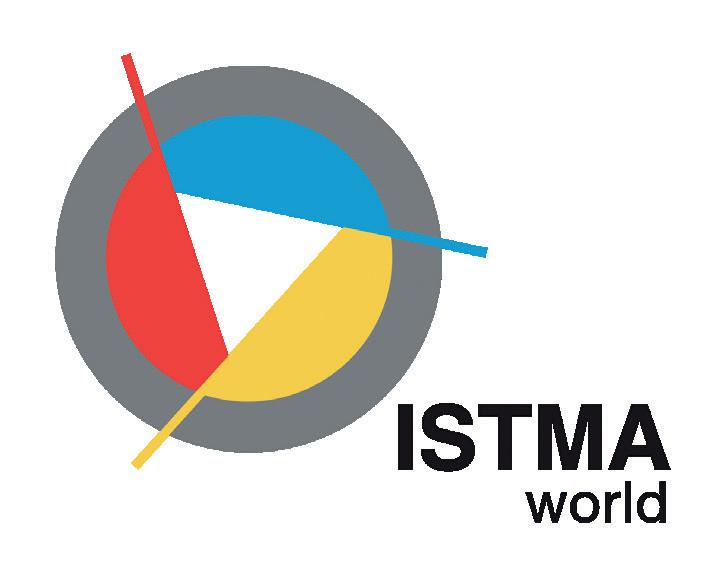