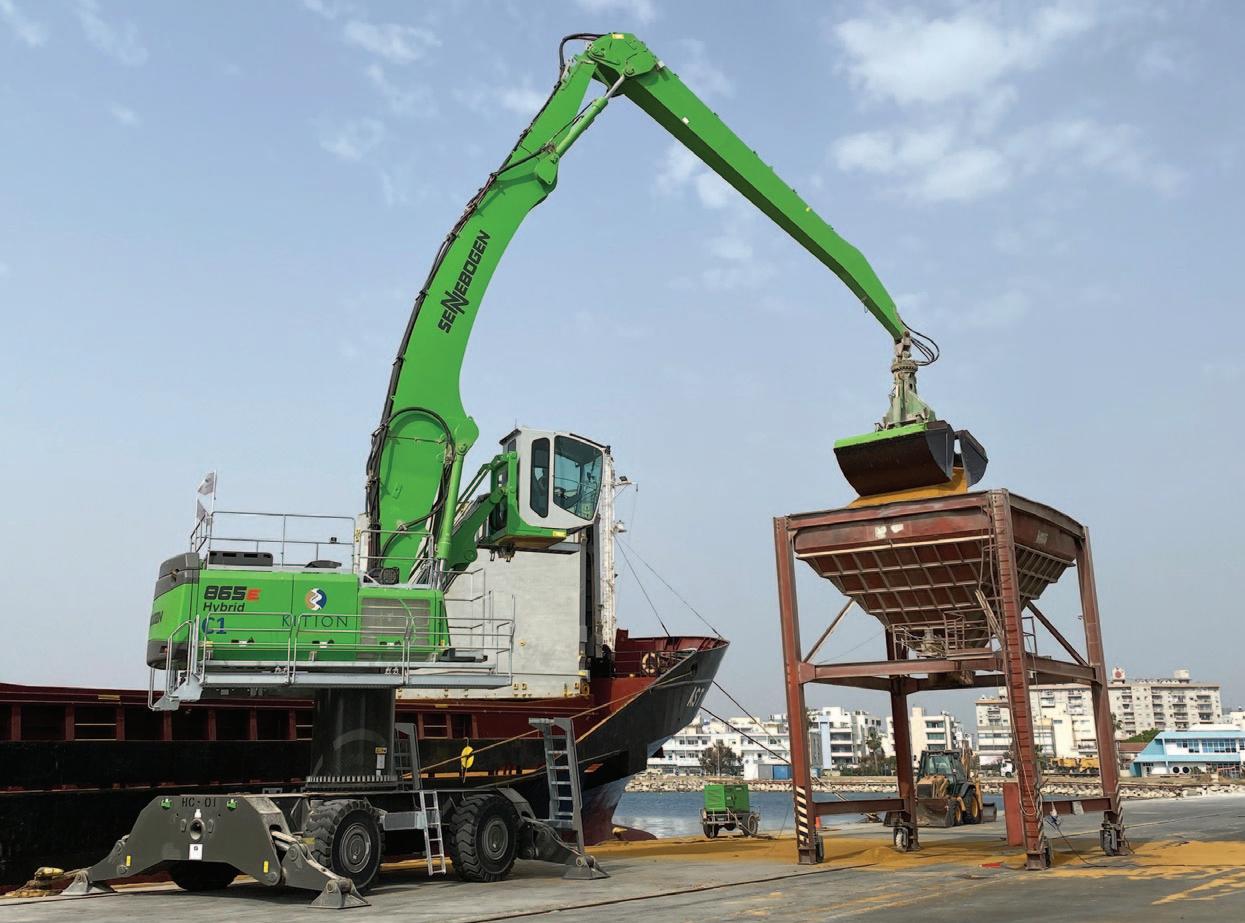
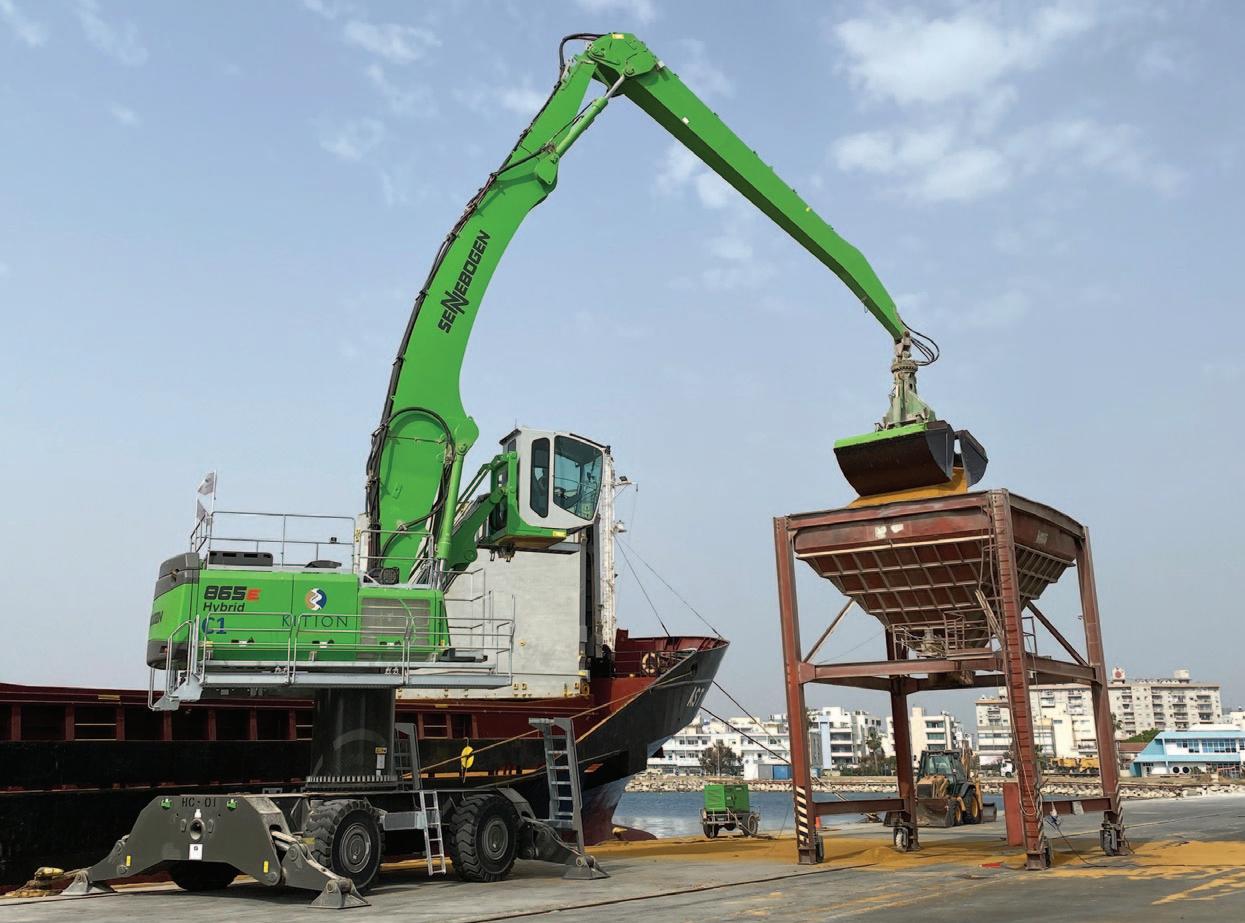
Some of the most valuable things in life are invisible.
Port and transshipment solutions
EDITORIAL
featuring...
TRADE & COMMODITIES

Restraints on dry bulk trade growth
Russian coal ban kicks in
SALES
ADMINISTRATIVE OFFICE
Business
MARKETS
SHIPPING & TRANSPORT
Water lubricated propeller shaft bearings found to reduce fuel consumption
Reederei Gerdes orders second Damen Combi Freighter 3850
BOAT
PORTS, TERMINALS & LOGISTICS
Port of Ipswich number one for agri-products exports for 17 years in a row
Resumption of grain shipments from Ukraine to Euro-Silo at North Sea Port
Gdynia and Riga Freeport sign memorandum on coal
ENGINEERING & EQUIPMENT
New CRS Maxebeam transforms reach stackers into dedicated Rotainer handlers
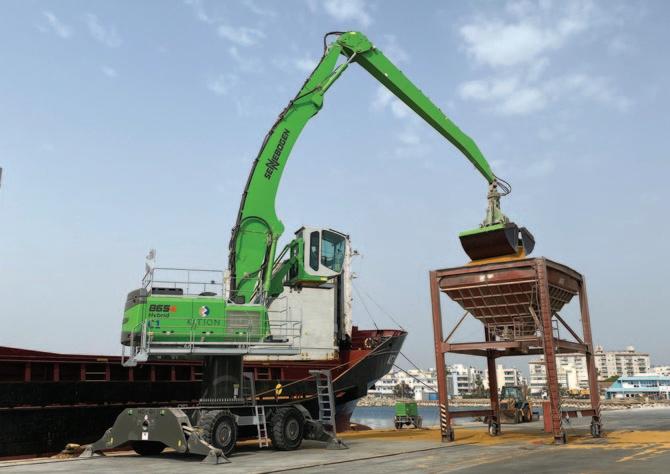
BULK HANDLING
YEARS OF AUMUND:
CARGO:
WITH
HEAD OFFICE
Trade
GRAIN:
COVER
HELP FROM TENOVA’S HIGH TECH SYSTEMS
INTERNATIONAL TECHNOLOGY
AND WHY IT IS SO IMPORTANT
CONVEYORS,
HANDLING
BREAKBULK & BAGGING
& TECHNOLOGIES
EASIER WITH THE
Restraints on dry bulk trade growth
During recent months signs of restraints on commodity trade imports into numerous countries have multiplied. As a result, earlier expectations of significant albeit modest growth in global seaborne dry bulk trade in 2022, compared with last year, have diminished and a flat outcome now looks more likely.
Adverse effects arising from severe inflationary pressures around the world, China’s slowdown and the war in Ukraine are inhibiting the world economy’s performance. The IMF’s latest assessment emphasized that risks are “biased to the downside”, hinting that further downgrading of economic growth forecasts beyond those already made could materialize. Unfavourable consequences for dry bulk trade are implied.
GRAIN & SOYA
Global grain trade, comprising wheat plus corn and other coarse grains, is expected to reflect lower import demand and restricted export supplies within the 2022/23 crop year ending June 2023.
According to the International Grains Council’s mid-August estimates, world total trade could fall by 15mt (million tonnes) or 4% from the previous year’s 424mt volume, to 409mt
The biggest change envisaged among major buyers is a decline of 8mt in China’s grain imports, from exceptionally high volumes in the past two crop years (61mt in 2020/21 and 54mt in 2021/22), to 45.5mt in the
current period. Elsewhere imports into the Middle East region and a range of other smaller importing countries seem likely to be lower. However there is more evidence of a reduced grain harvest in Europe this summer, possibly resulting in additional foreign purchases.
COAL
Increased coal imports into the European Union, India, Japan and a few other countries this year are envisaged by some analysts. But there is uncertainty about whether these rises will be sufficient to fully or more than offset weakness in China and elsewhere, enabling the world seaborne coal trade total to remain flat or even rise slightly.
Amid tight energy supplies in Europe, especially natural gas, an emphasis on fuel sources immediately available which can be used to offset shortfalls has intensified, especially in the approach to the winter season. Coal is seen as a contributor. One example of changes envisaged is a recent estimate by Germany’s coal importers association, suggesting that the country’s steam coal imports could increase by almost a fifth in 2022 from last year’s 27mt volume, reaching 32mt.
IRON ORE
Weaker import demand in China looks set to prevent any growth in world seaborne iron ore trade during 2022, even though some positive changes may occur among other buyers. The unfolding deterioration in many nations’
MAJOR GRAIN EXPORTING AREAS (MILLION TONNES)
economic activity, with direct effects on steel consumption and production in iron ore importing countries, is becoming more apparent.
Although there is still uncertainty about events in the remainder of the year, China’s annual iron ore imports are expected to decrease. Downwards pressure on economic activity and steel production has been prominent and prospects for a pickup in the months ahead are unclear. In the first seven months of 2022, China’s crude steel output was 6% lower, while iron ore imports declined by over 3% to 627mt.
MINOR BULKS
Among the many and varied elements of the minor bulk commodity trade segment, growth prospects this year seem limited. A large proportion (steel and forest products for example) is associated with manufacturing output and construction work, much of which is becoming more restricted by economic activity headwinds.
BULK CARRIER FLEET
Slower expansion of the world bulk carrier fleet is evolving, as shown in table 2. In 2022 another large fall in newbuilding deliveries is likely to be a feature, but earlier expectations of substantially higher scrapping now seem unlikely to be fulfilled. Fleet deadweight tonnes capacity growth could decelerate to well below 3%, from 3 4% annually in the past few years.
TABLE 2: WORLD BULK CARRIER FLEET (MILLION DEADWEIGHT TONNES)
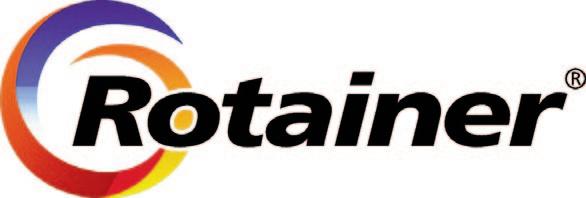
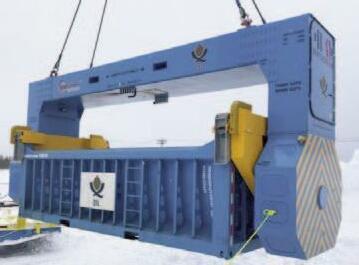
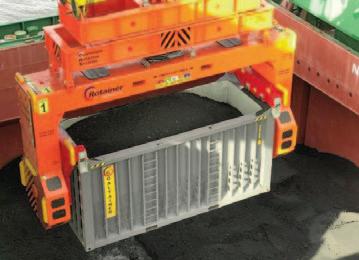

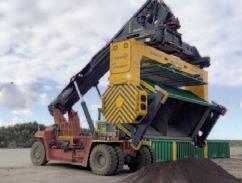

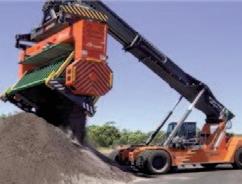


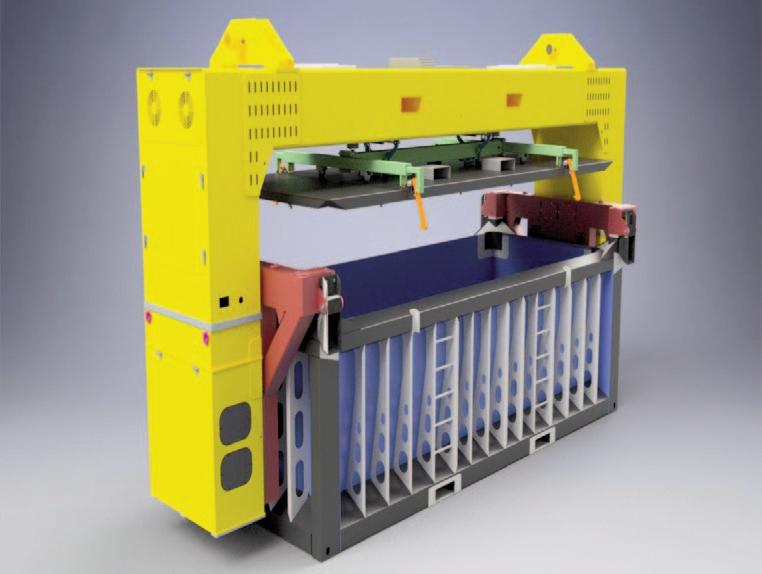
EU Russian coal ban kicks in
As of 10 August, the European Union placed a total embargo on all coal imports from Russia. This formed part of an earlier sanctions package first announced in April. The delay is explained by a buffer period, in which European countries could either negotiate with new coal source providers or increase their own domestic production. Alternatively, they could also use the time to bring forward plans to use alternative energy generators, such as renewables.
The EU had relied heavily on Russian thermal coal, which accounted for 70% of thermal coal imports for electricity production. Poland and Germany were significantly locked into this source of
supply. With Europe also switching away from Russian gas to generate electricity, EU countries were also expected to import more thermal coal to replace this.
Australia, Colombia and the United States are all now exporting more coal to Europe than previously.
In June, for example, countries in Europe imported 7.9mt (million tonnes) of thermal coal, which was at least double the same amount in June 2021. Despite this, overall reliance on coal is diminishing since this figure was 2mt less than in both April and May.
Colombia is particularly benefiting, exporting 1.2mt to Europe in June, which compares with around 287,000 tonnes in
the same month in the previous year. However, Australian thermal coal imports of 1.1mt in June are its most ever, despite the long distance involved. The United States also reports that its coal exports to Europe were up 28% in June.
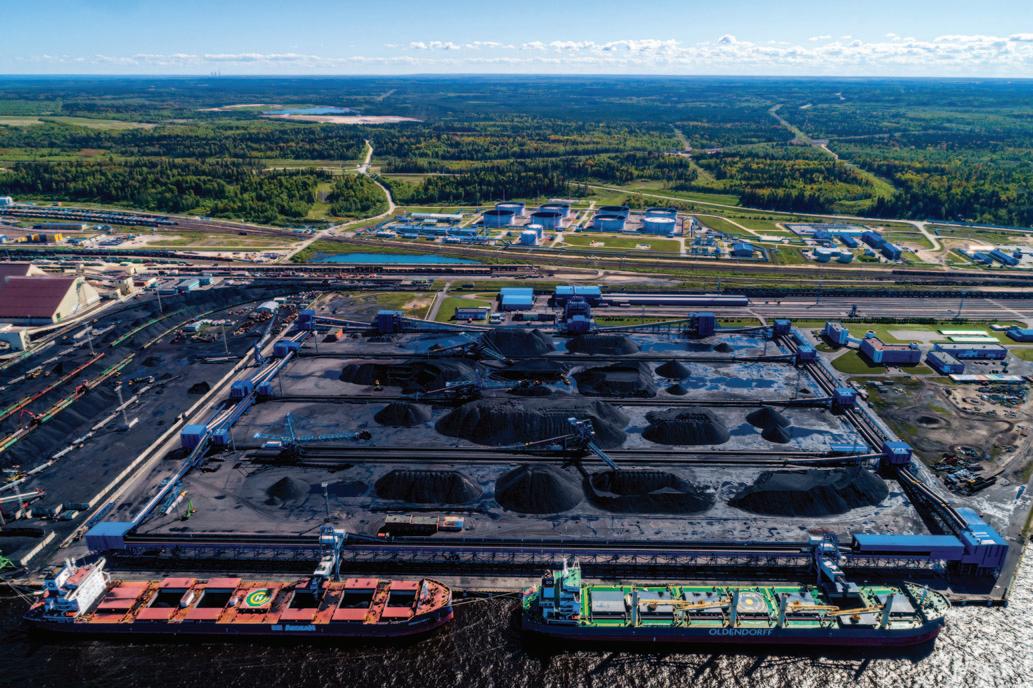
This trend is expected to continue as EU countries continue to retain sanctions against Russia because of its invasion of Ukraine. Indeed, with Russian oil imports due to be phased out in the longer term, more coal will be needed to replace them. Maritime oil imports from Russia will cease in their entirety in December and petroleum products in February 2023. In the meantime, pipeline imports remain unchanged. Barry Cross
Strike action from Ukrainian coal miners
Workers at a state-owned coal mine in Ukraine have decided to strike, despite martial law and a ban on all protests.
Striking workers at Mine No. 9 in Novovolynsk, who include miners as well as management, voted to strike over what they say is an attempt to seize control of the mine.
Long-standing corruption is cited as
the reason for the strike, with the miners recently prevening a new director from taking over because of his links to embezzlement at another mine.
Workers believe that the director was appointed by the local ‘smotriashchiy’ — corrupt unofficial overseers of Ukrainian coal mining. The miners have gone on strike to protect
their jobs and working conditions.
Early in Volodymyr Zelensky's admin istration, the Ukrainian president vowed to stamp out corruption in the coal sector. Workers at Mine No. 9 link recent appointments to the possible return of corrupt practices. The strike is not the only protest in the western Ukrainian coal fields since Russia’s invasion.
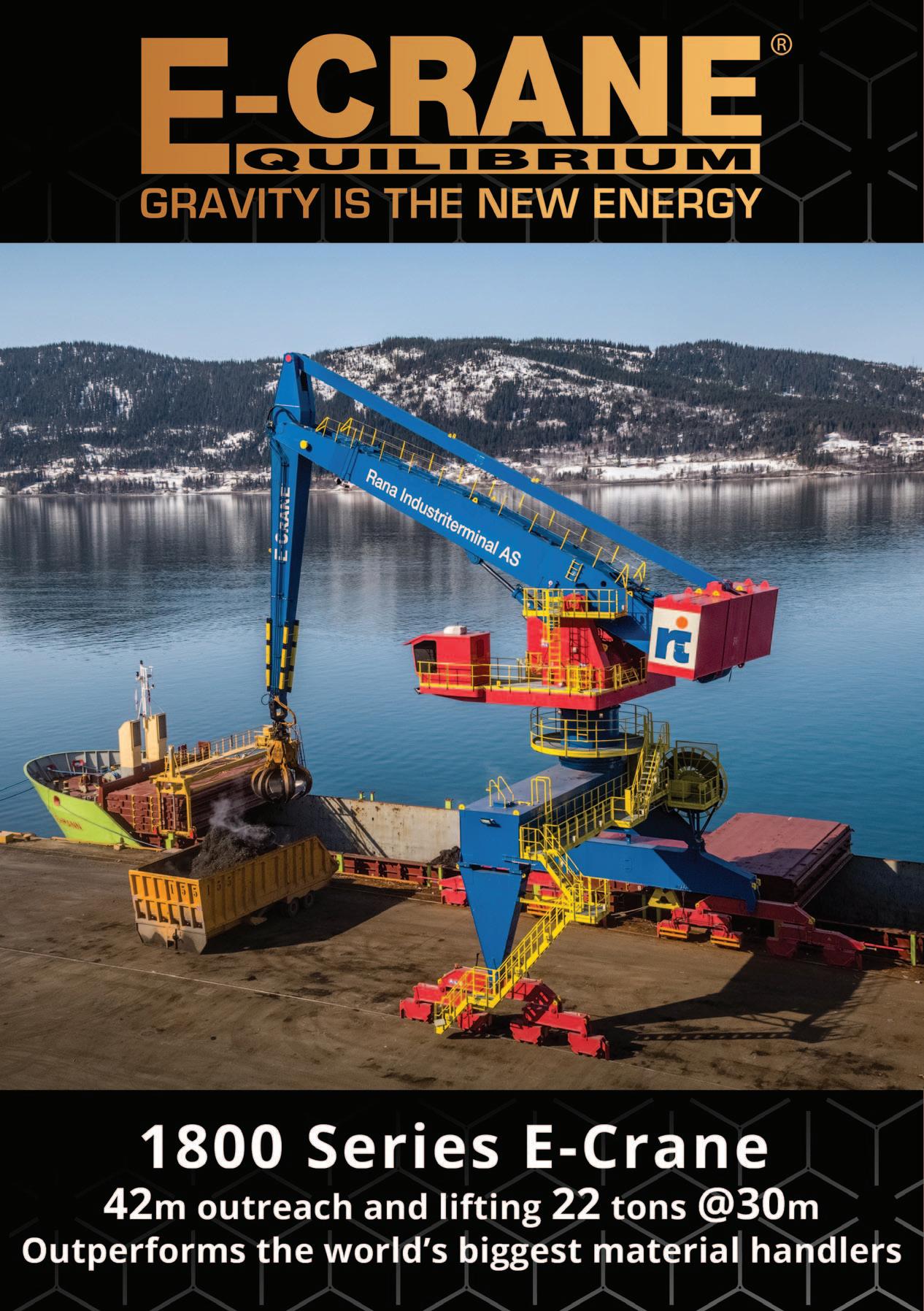
SGS Secured Document – protecting the commodity industry against document fraud
Fraudulent documents are a major concern across the commodity industry due to the large quantities of commodities being moved, strict regulations that must be adhered to, and the multimillion-dollar contracts involved, writes Frederico Stewart, Head of Business Solutions and Market Intelligence at SGS
This situation is made even more challenging by complex supply chains that often span several nations, as well as the endless number of parties and contractors involved in every transaction.
Sophisticated malware software has made validating the authenticity of documents increasingly challenging. As personal signatures can no longer be relied upon to safeguard against falsification, how can we guarantee the authenticity of reports and certificates that testify to the integrity and quality of commodities?
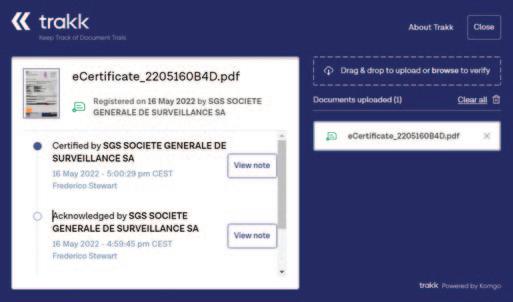
As a solution, SGS has launched SGS Secured Document — a blockchain-based registration system that gives users secure access to a document’s history, enabling the verification and authentication of its origin.
SGS Secured Document is powered by Trakk, a tool developed by Komgo that
provides a secure network to register, trace and authenticate digital documents. Tried and tested in the global banking and trading ecosystem, Trakk makes it easier to identify fraud by building a unique and immutable audit trial behind every document.
BLOCKCHAIN — HOW SGS SECURED DOCUMENT GUARANTEES AUTHENTICITY
The SGS Secured Document process utilizes blockchain technology to generate an accurate audit trail for a document. Blockchain technology is most well known for recording digital transactions; however, the secure nature of the technology also makes it ideal for validating and authenticating the origin of e-documents. In short, a blockchain acts as a digital ledger of transactions that is duplicated and distributed across the entire network of computer systems on the blockchain.
Using blockchain to track a document creates a unique, time-stamped and encrypted transaction record that enables users to see a document’s origin and its subsequent pathway. Once an SGS expert signs a document, their activities are registered in real time on the SGS Secured Document platform.
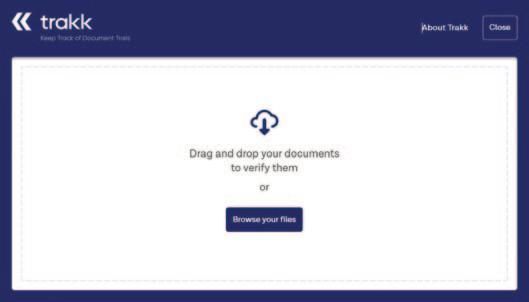
While the underlying technology of our solution may sound complex, its everyday use couldn’t be easier. Documents can be verified simply by dragging and dropping the PDF file into a widget on the SGS website, or directly in your email inbox via the Trakk plug-in feature.
REDUCED OPERATIONAL RISK
All stages of the supply chain are at risk of document fraud, including commodity inspection and testing certificates. Using a blockchain-based system like SGS Secured Document enables companies to reduce operational risk by protecting against fraud, increasing the efficiency of the audit process and building trust amongst customers. SGS guarantees that documents can be trusted, as the blockchain ensures documents cannot be duplicated, altered or falsified.
Additionally, the Trakk software provides an all-in-one tool that raises alerts and detects potential fraud sooner in the process. Crucially for the end customer, secure documentation builds trust as the supply chain can be validated. As technology and cyber threats become more advanced, it’s more important than ever to protect documentation against falsification, shielding our customers throughout the supply chain.
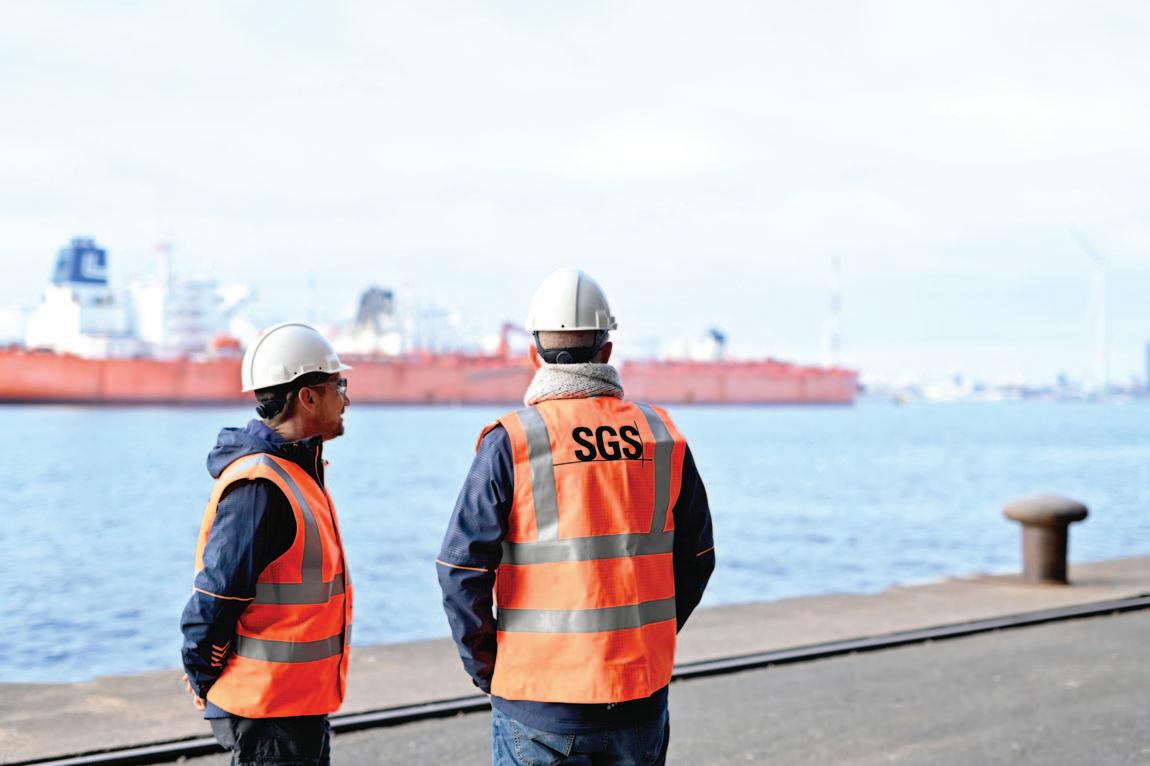
global outlook
Feed markets on edge, volatility high
grains & oilseeds trades

deteriorated
throughout 2022 amid high inflation, aggressive monetary tightening, the uncertainty caused by the war in Ukraine and the lingering Covid-19 pandemic. *Soaring food and energy prices
eroding real incomes, triggering a global
crisis,
vulnerable groups. Growth in the
exacerbating fiscal and balance of
in many developing
three largest
EU
with
US, China
spill-over to other countries. At
same time, rising government
large capital
The United Nations (UN)
substantial downward revision
the global economy, projected to grow between
and 2.8% in 2022.
markets
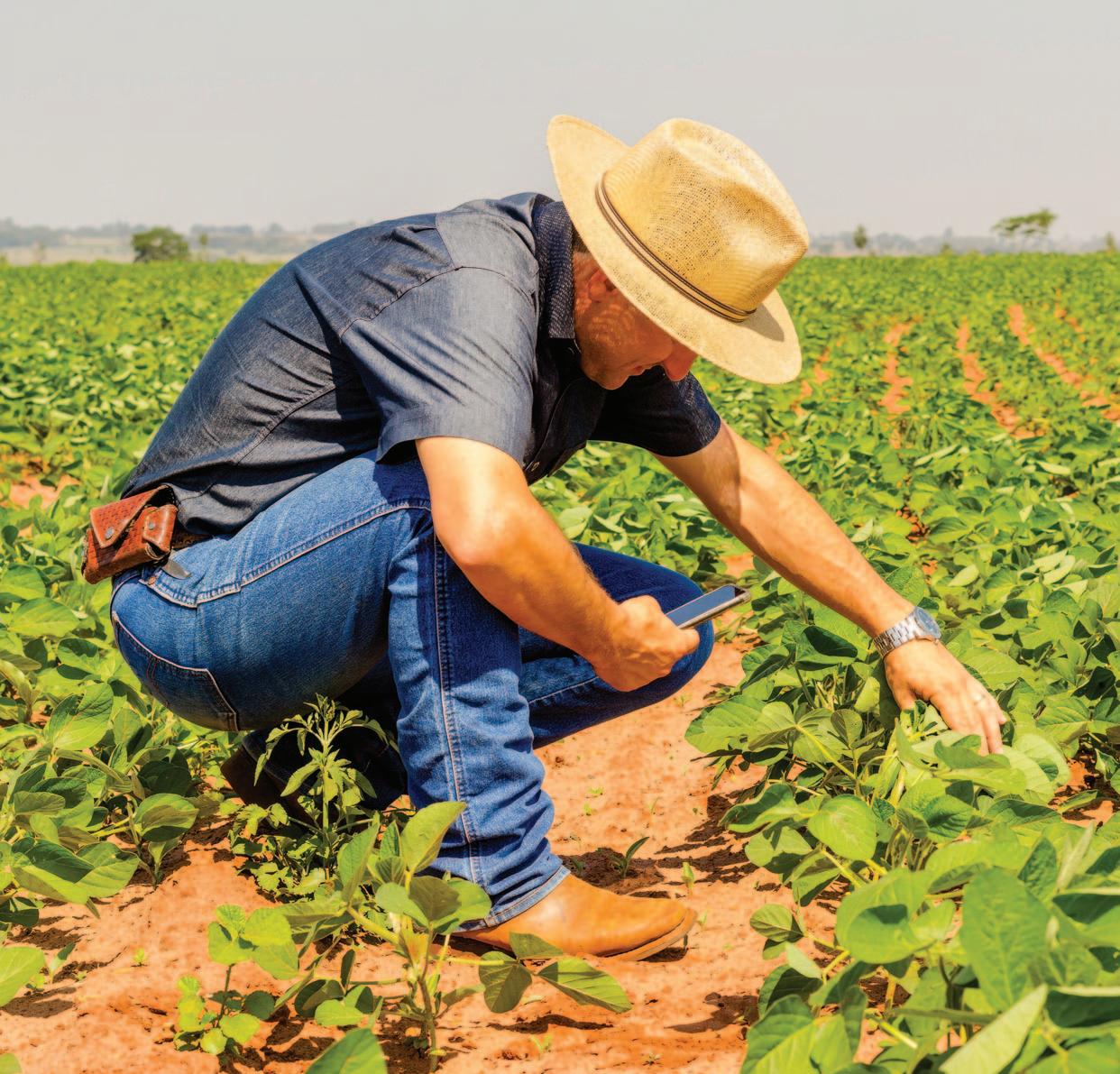
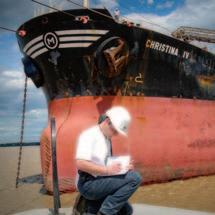

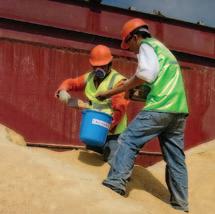
susceptible to bouts of extreme volatility. The unprovoked Russian war in Ukraine continues to exacerbate the global food security crisis, with high and volatile energy, food, feed and fertilizer prices, restrictive trade policies and supply chain disruptions. The partial re-opening of Ukraine's Black Sea ports backed by the UN relieved pressure from global food markets by providing a corridor for grain exports from Ukraine. Rising tensions could sharply escalate the war and disrupt Black Sea shipments again. Persistent drought in some northern hemisphere countriesincluding the US, EU and China, adversely affected yields for wheat and coarse grains, expected to tighten global corn supplies. Looking ahead, geopolitics, weather and southern hemisphere crops, critical to bolster global food and feed supplies. The Food and Agricultural Organization (FAO) preliminary forecast for wheat and coarse grains pegged global output at 2.25bn/t in 2022/23.
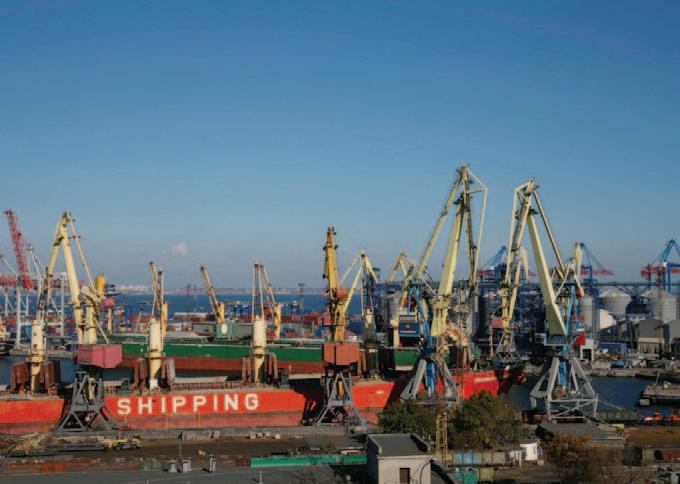
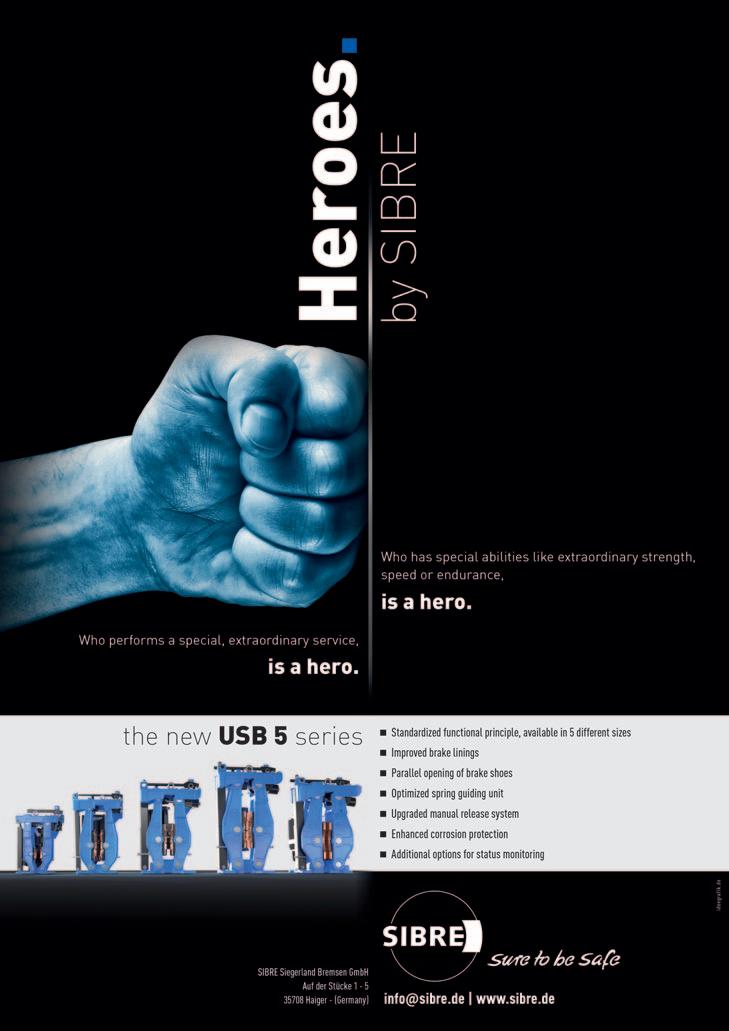
WAR AND DROUGHT CUT FEED SUPPLIES IN 2022/23
Global wheat output at 784mt (million tonnes) is marginally increased due to better wheat crops for Russia recovery in Canada, the US and in some other countries, partially offset by a drought-reduced EU wheat crop. Following Russia’s invasion of Ukraine, wheat and coarse grain output has been significantly reduced. Global coarse grains are forecast lower at 1.46bn/t, due to exceptional dry conditions that mostly affected corn output in the US and in the EU. High soybean prices supported by demand for food, feed and renewable biofuels and soaring fertilizer prices encouraged many farmers to favour less-fertilizer-intensive crops, such as soybeans in 2022/23. Soybean acreage in the US and South America increased, with the global oilseed crop pegged at a record 645mt.
FEED USE OF OIL MEALS EXPECTED TO RISE IN 2022/23
Overall global consumption of wheat and coarse grains is forecast to fall by 21mt to 2.26bn/t. Wheat for feed use is forecast lower at 155mt, more feed wheat use in Russia, Ukraine, offset by less feed wheat in the EU and a sharp fall in
China by 5mt to 30mt, Covid-19 restrictions/lockdowns impacted demand, while higher wheat prices encouraged a switch to other feed ingredients. For coarse grains feed use is expected to fall by 6mt to 906mt with more corn and barley fed and less sorghum this year. With increased oilseed supplies anticipated, feed use of oil meals is expected to rise to a record 351mt in 2022/23.
TRADE IN OILSEEDS EXPECTED TO INCREASE IN 2022/23
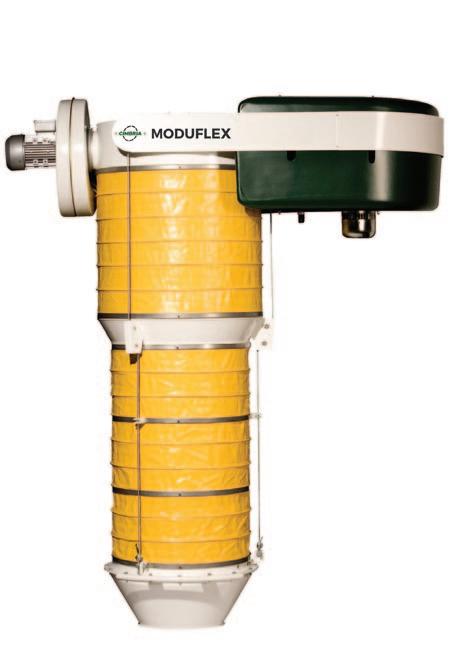
Global trade in wheat and coarse grains is projected to fall by 8mt to 435mt in 2022/23 due to slow demand and higher prices. A small increase in trade for wheat 208mt offset by an 11mt cut in coarse grains to 227mt, with combined global stocks of wheat and coarse grains expected to fall to 599mt. Tight stocks, especially for corn are anticipated to support prices for the remainder of the season. Trade in oilseeds is anticipated to rise by 19mt to 197mt with global stocks increased to 119mt.
GLOBAL WHEAT HARVEST FORECAST AT 784MT
Global wheat harvest in 2022/23 is
EU
Other Europe
CIS Baltic’s
GLOBAL WHEAT
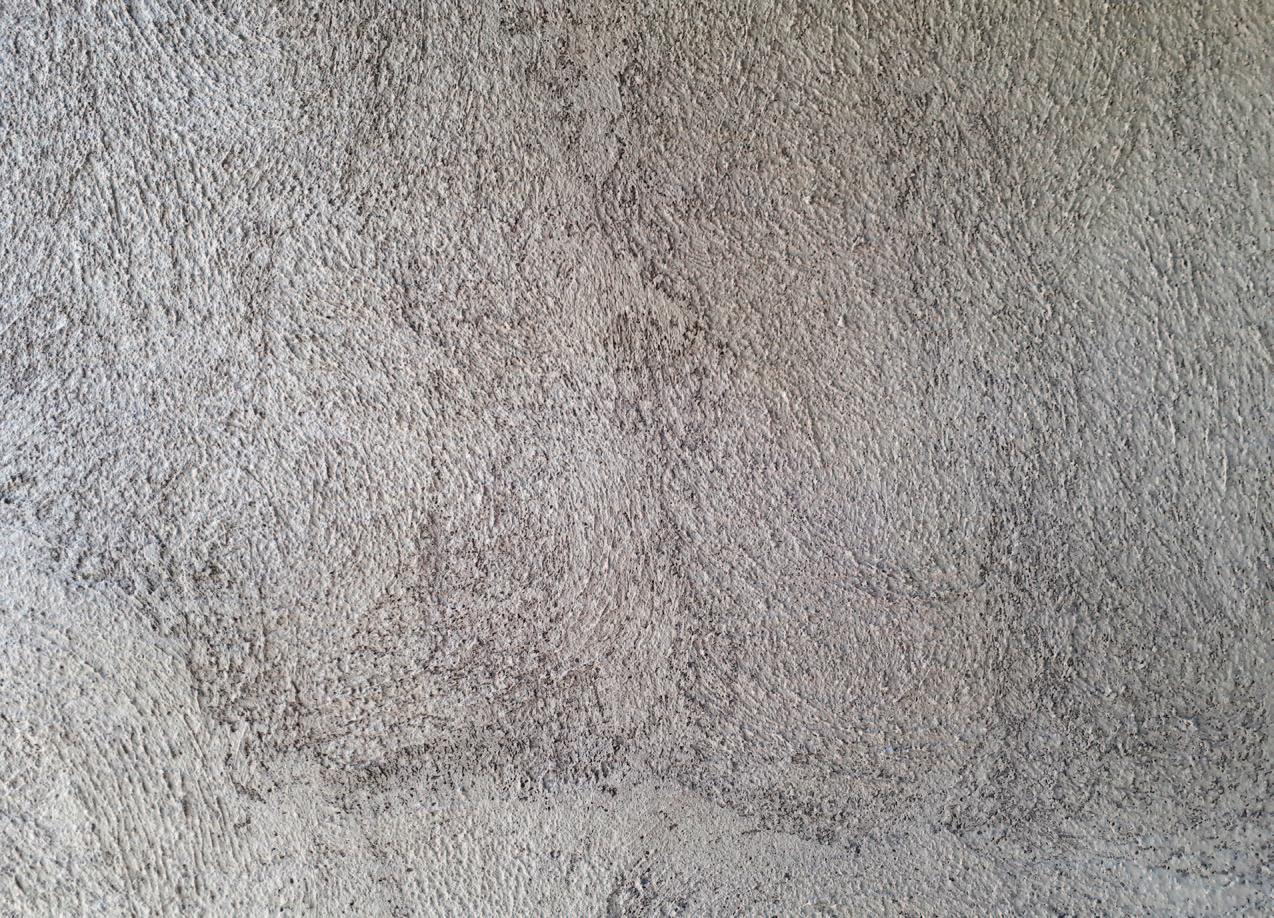
2018/19 2019/20 2020/21 2021/22 2022/23
139 127 138 132
16 10 15 15
4 4 4
129 139 134 139
N & C America
S America
N East Asia
F East Asia
Oceanic
Total
Source:
Sources:
89 88 70 87
29 28 34 32
43 43 35 37
272 277 283 277
26 25 30 27
15 33 37 34
780
GLOBAL WHEAT SUPPLY & DEMAND 2018-2022/2 (MT)
2018/19
provisionally forecast at 784mt, though likely to be revised higher. Recovery in wheat output mainly in Canada 35mt, Russia 91mt (revised c.95 99mt) and the US 49mt bolstered output, while searing drought affected several countries in the EU that led to a smaller wheat crop of 132mt — France is expected to increase acreage in the new season by relaxing rules on crop rotation and mandatory fallow. By contrast floods cut India’s crop by 7mt to 103mt. The Russian invasion reduced Ukraine’s wheat crop from 33mt to 21mt as farmers could only harvest 4.6m/ha compared to 6.7m/ha in the previous year. Ukraine’s Agrarian Council (UAC) believes farmers may shrink the winter grain area from 6m/ha to 3.8m/ha due to a rising costs of seeds and fuel combined with low selling prices. Longer term, the pace of recovery of Ukraine’s agriculture influenced by, the increase in hostilities, extent of the destruction to infrastructure, labour disruption and the ability to harvest, store and export grain.
DRY CONDITIONS LIKELY TO AFFECT ARGENTINE WHEAT
Argentina’s main grain producing areas are facing the driest conditions not seen for thirty years. Lack of rain and continued dry conditions impacted wheat plantings and its early development. The Rosario Grains Exchange, estimates the planted area for
wheat at 6.1m/ha and confirmed some planted areas have been abandoned — reports indicate that 42% of the crop is in a poor condition. Wheat output has been revised lower to c.16.5 17.5mt with harvest expected to begin in late October/November.
UPBEAT FORECAST FOR AUSTRALIA’S WHEAT
The wheat crops have excellent yield potential heading into spring following a strong start in most cropping regions and above-average winter rainfall, particularly in eastern states. Abares forecast wheat production at 32.2mt in 2022/23, the second-highest wheat harvest on record. Heavy rainfall in Queensland and large parts of New South Wales caused waterlogging issues in some regions experiencing ongoing wet conditions, delaying the planting of winter crops. The possibility of a wet spring could interrupt harvest and negatively impact grain quality in some regions.
REDUCED ACCESS SUPPORTS HIGHER GLOBAL WHEAT PRICES
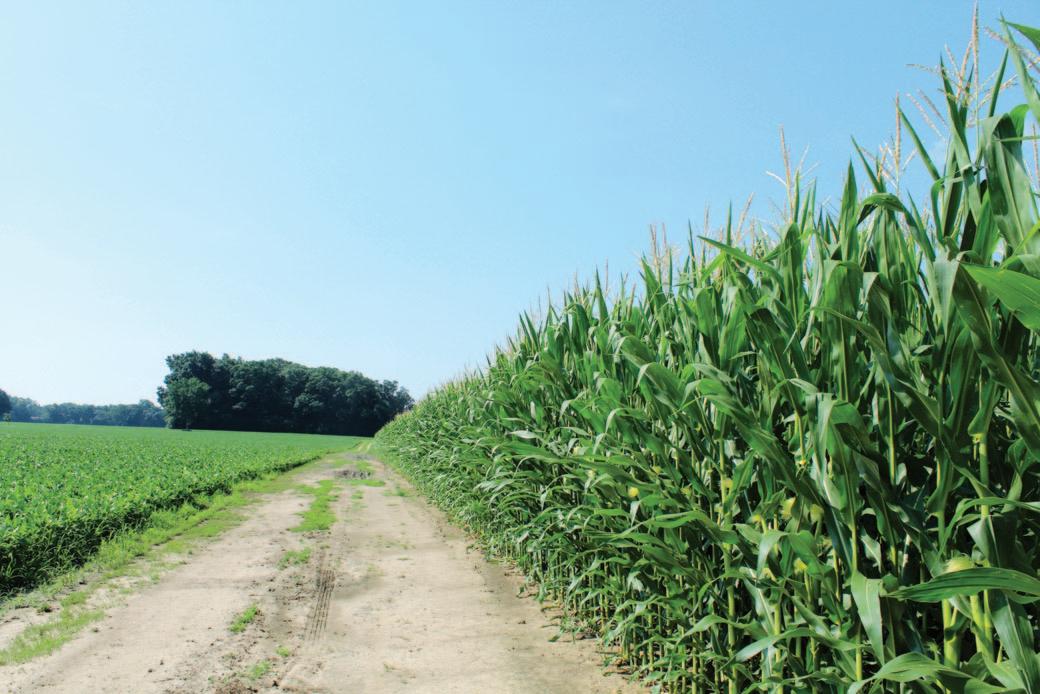
Since July, the agreement referred to as the ‘Black Sea Initiative’ brokered by the UN, made it possible to ship Ukraine’s exports of cereals, coarse grains, oilseeds-meals and oils, via a designated corridor to Black Sea ports. According to the UN this is working
with close to 5mt being shipped having either arrived at their destinations or enroute. The agreement is in place until November, but rising tensions suggest there may be limited scope for it to be renewed. Ukraine’s continued logistical challenges (access to farmland, grain storage capacity, freight insurance and the availability of farm inputs and labour) is expected to limit the availability of their wheat on the world market, leading to higher wheat prices. The uncertainties regarding production and exports from Ukraine, may continue to be a source of volatility in the short-term.
MOROCCO, TURKEY AND INDONESIA INCREASE WHEAT IMPORTS
Increased imports into Morocco 7.5mt due to prolonged and widespread drought, Indonesia 11.2mt for food and feed, the EU 5.5mt due to drought and in some other countries, increased global trade to 208mt. With demand for wheat outpacing supply, wheat stocks are drawn lower to 269mt (world 125mt, China 144mt), stocks in key major exporting countries to fall to 57mt.
RUSSIAN WHEAT TRADES BELOW COMPETITORS
Wheat prices expected to remain strong given the uncertain outlook for the agreement to keep open the three Ukraine ports for exports. Demand for wheat in
price-sensitive markets in Africa, the Middle East and South-East Asia has been strong. Despite finance restrictions and higher freight costs Russian wheat has been trading below key competitors' since harvest-with exports pegged at 42mt. Exports from Canada have recovered to 26mt, US 23mt, EU 33.5mt and Ukraine11mt in 2022/23. Chicago wheat futures fell on strong supply soft demand and a surging US dollar CBOT Wheat SRW Contract Dec ‘22 closed-$8.60/bu ($315.96/t-16 Sept ’22). EU FOB Rouen ($340/t -16 Sept ’22); UK Feed Wheat Futures Contract Nov ’22 closed ($297.66/t-8 Sept ’22).
ARGENTINE CORN REVISED LOWER
Buenos Aires grain exchange cut its forecast for Argentina’s corn crop to 50mt (previously 55mt), with provisional estimates for exports at 41mt.
The revised output for corn is due to the third consecutive year of the La Niña weather pattern that limits precipitation and reduces yields. The World Meteorological Office (WMO) predicts the current La Niña event — capable of exacerbating drought and flooding in different parts of the world — is drawing to the end of a three-year-cycle in February ’23; until then, there is a 70% per cent chance of occurring between SeptemberNovember ‘22, gradually decreasing to 55% percent between December February
2022/23.
Conab forecasts Brazilian farmers will produce a record 126mt corn crop due to a larger planted area. Producer margins for corn are said to remain positive, despite the rise in input costs. Brazil’s exports are forecast at 46.5mt in 2022/23, given large available supplies, favourable exchange rates and robust demand.
DROUGHT CURBS COARSE GRAINS PROSPECTS
Global coarse grain output is forecast to fall by 43mt to 1.46bn/t in 2022/23. Mostly due to reduced output in the US Midwest, where hot, dry weather curbed yield prospects for corn. Severe drought also affected EU countries, reducing coarse grain output to 139mt. While in Ukraine, the war severely cut coarse grain output by 15mt to 39mt.
COARSE GRAIN DEMAND TO FALL IN 2022/23
For the first time in ten years, global feed, food/industry use of coarse grains, is set to fall by almost 17mt to 1.47bn/t in 2022/23. This includes a 11mt cut mainly in food/industry use to 577mt with feed use reduced by 6mt to 906mt.
GLOBAL DEMAND FOR FEED LOWER IN 2022/23
Global corn output on a reduced corn area of 204m/ha is forecast to fall by 47mt to
1.17bn/t, and reflects a switch to planting oilseeds soybean and sunflower due to higher prices and lower fertilizer requirements. Hot, dry weather conditions in the US and EU contributed to drought stress for corn crops, decreasing yields, with output lower in the US 354mt, EU 59mt and in Ukraine 31.5mt, partially offset by a better crop in China of 274mt. Global demand is cut by 4mt to 743mt. Feed use expected to increase in China 214mt, Brazil 66.5mt, Mexico 26.3mt and Ukraine 11.5mt.
TIGHT CORN STOCKS DRIVE CORN PRICES
HIGHER
Global corn stocks have fallen to 305mt in 2022/23 (China 207mt World 98mt), with major exporters stocks 52mt. Since August major exporters’ quotes increased — Argentina Feed (Up River) $299/t (Sept 8 ’22); Brazil Feed (Paranagua) $290/t (Sept 8 ’22); US 3YC (Gulf) $324/t (Sept 8 ’22).
MODEST EXPANSION FOR MEAT TRADE IN 2022/23
Despite the challenging environmentwidespread animal diseases, conflicts and rising input costs. Only a modest expansion in world trade in meat and meat products is anticipated in 2022/23, reflecting limited export availabilities from exporters and a likely decline in China’s pig meat imports.
Higher beef prices-incentivized major
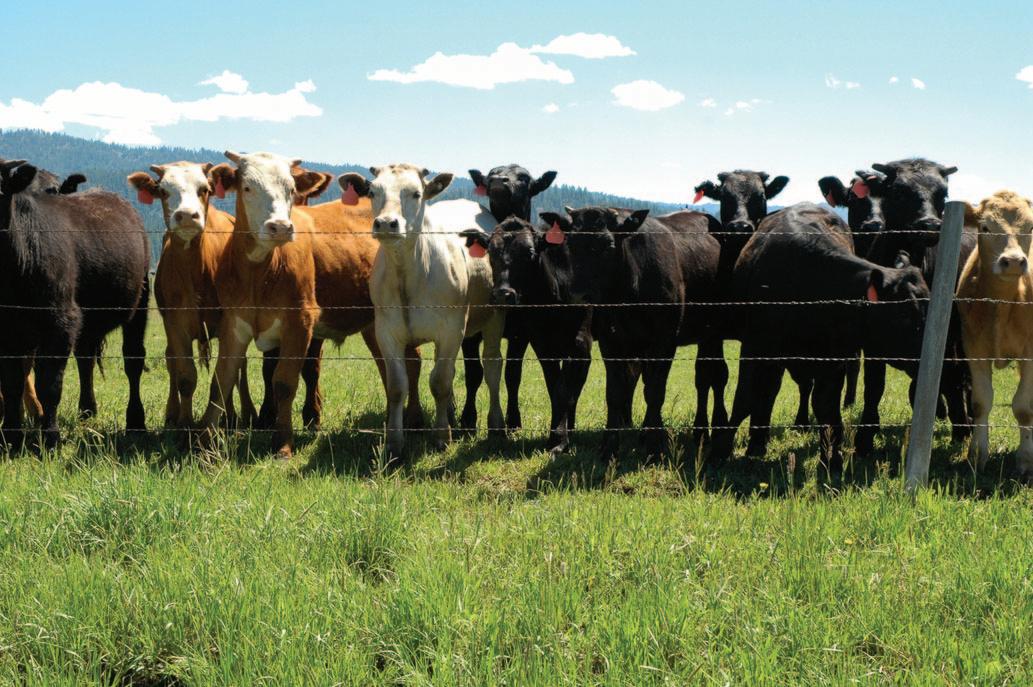
producers in the US to cull animals, resulting in a high level of exports at competitive prices; improved rainfall led Australian producers to retain more heifers for breeding. Production growth in Brazil, Canada and Mexico offset a reduction in Australia. China’s beef production to rise to 7.4mt with imports lower at 2.5mt; low domestic prices, weaker economy, to impact imports of high value beef. Despite inflationary pressures and logistical issues global beef demand is expected to remain strong, helped by some countries lifting Covid-19 restrictions.
With a decline in pork production in the EU and Brazil-global pork production is forecast at 110.7mt in 2022/23 — upward revision for China 52mt (below pre-African Swine Fever (ASF) levels) offset by lower output in the EU 22.6mt, Brazil 4.3mt slow exports weigh on prices. Pork exports revised lower to 10.6mt 2022/23, due to a cut in China’s exports to 1.85mt, despite increases for South Korea, Mexico, Japan and the Philippines.
Rise in Ukraine’s chicken meat outputincreased global production to 101mt, largely offsetting weak domestic demand in Brazil. While, the EU continues to grapple with elevated feed prices and the highly pathogenic avian influenza. Chicken meat exports are slightly higher to countries, other than China and expected to fall as domestic pork production rebounds and eases demand for other animal proteins.
IMPROVED PROSPECTS FOR BARLEY
Despite a smaller global area, production of barley is forecast at 148mt in 2022/23.
GLOBAL COARSE GRAIN SUPPLY & DEMAND 2018-2022/23 (MT)
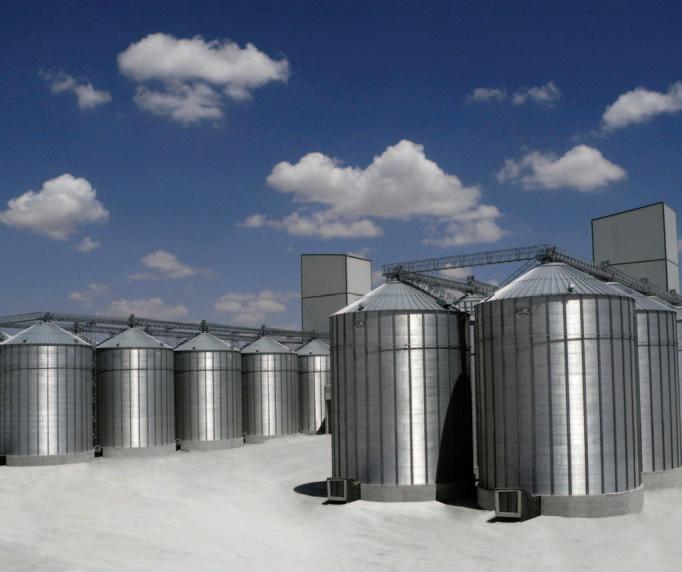
2018/19
2020/21 2021/22 2022/23
Production 1,403 1,420 1,441 1,506 1,463
Consumption 1,424 1,434 1,456 1,490 1,473
Trade
Stocks
which China:
Key Exporters*
235 238 227
323 339 330
207 211 208
Source: IGC/USDA * US, Argentina, Brazil, Russia, Ukraine, EU, Australia, Canada
GLOBAL CORN SUPPLY & DEMAND 2017-2022/23 (MT)
2018/19
Production
Stocks
which China:
Exporters*
Source: IGC/USDA * Argentina, Brazil, Ukraine, US
Good yields improved output in Russia 21mt, Canada 10mt and Turkey 7.4mt partially offset by smaller crops in the EU 50mt, Ukraine 6.4mt and Australia 12.2mt. Feed use is forecast at 101.2mt with increases for Canada and Russia. Barley exports increased to China 9.5mt, Thailand 0.5mt, Vietnam 0.7mt, Saudi Arabia 4.7mt, Iran 2.5mt and in some other countries-a small increase in global trade to almost 30mt. International prices for barley remain firm — Jordan bought 120,000/t of feed barley $328/mt CFR for delivery Jan Feb 2023. Feed Barley FOB Rouen $299/t (8 Sept’22) and FOB Argentine (up-
river) $320/t (8 Sept’22).
SORGHUM OUTPUT IN 2022/23
Global sorghum output has increased in several countries, but a much reduced US crop of 6.4mt cut global output to 60mt in 2022/23. Sorghum exports are forecast at 9.7mt. China is the largest market importing 8mt to support feed demand mainly for pig and poultry and the production of Baijiu (a national spirit beverage) made by fermenting cooked sorghum or other grains. Major sorghum exporters include the US, Argentina and Australia. Sorghum values, like other coarse grains have increased FOB Texas $361.59/t (8 Sept ’22).
SIGNIFICANT RISE IN SOUTH AMERICAN SOYBEAN ACREAGE IN 2022/23
In the southern hemisphere Brazil is primed to plant a much larger soybean area, rising by 4m/acres to nearly 106m/acres — with a crop estimated at 149mt. The Argentine crop is pegged at 48mt (USDA 51mt) and Paraguay 10mt. This crop year meteorologists predict that Brazil and Argentina may experience the re-emergence of La Niña-type precipitation to be limited in the South of the country but adequate in the North. This type of weather pattern last year was responsible for cutting Brazilian soybean production by over 20mt.
RECORD GLOBAL OILSEED OUTPUT DRIVEN BY SOYBEANS IN 2022/23
USDA’s latest forecast for global oilseed crops predicts a rise of some 43mt to
645mt in 2022/23, driven by a record output anticipated for soybeans of 390mt — this includes a downgrade to the US crop by 4mt to 119mt with yields of 50.5bu/acre, due to hot and dry weather in western growing areas.
There were also gains for rapeseed 82mt following a recovery in Canada, cottonseed 43mt, palm kernel 21mt, with groundnuts 50mt and copra 6mt unchanged. Lower output for sunflower seed 52mt, mainly due to the war that reduced Ukraine’s sunflower seed crop from 17.5mt to 9.5mt.
GLOBAL DEMAND FOR OILSEED MEALS FORECAST AT 357MT
Global demand for oilseeds is expected to increase in 2022/23 though oilseed prices are expected to ease as potential rising supply offsets rising demand for its three major uses — meal fed to animals, oil used for cooking (food) and for fuel. Trade in oilseeds is forecast to rise by 19mt to 197mt in 2022/23, with increased imports into China, EU, Mexico, Argentina, Egypt, Turkey, Thailand, Pakistan and in many other countries.
SLOWDOWN IN CHINA REDUCES DEMAND FOR SOYBEANS IN 2022/23
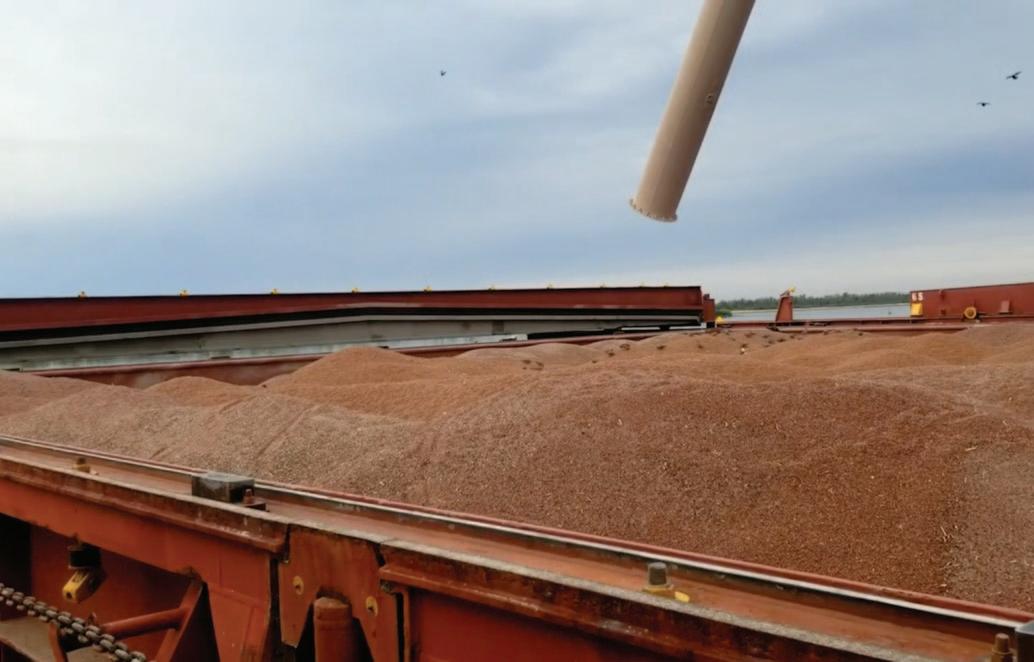
China's slowing economy and zero tolerance-Covid-related restrictions and widespread lockdowns weakened demand for oil meals for swine and poultry rations and vegetable oil for food use. USDA
Sorghum cargoes.
2018/19 2019/20 2020/21 2021/22 2022/23
Production 601 581 607 602 645 of which (soybeans) 362 340 368 353 390 Crush 489 508 508 512 532
Consumption* 328 340 344 345 357
Trade Meals* 95 96 97 96 98
Trade Seeds 172 191 192 178 197
Stocks 134 112 116 109 119 of which (soybeans) 91 65 65 60 67 key exporters**
Source: USDA/*Meals cons/trade-excl. fishmeal. **Argentina, Brazil, US
forecast China will import 96.5mt of soybeans this season, 1.5mt lower than previously forecast.
HOG PRICES BEGIN TO IMPROVE
Following months of lacklustre soybean imports and negative crush margins, soybean meal prices on the Dalian exchange picked-up at the end of August, on firm demand from hog farmers-who fatten their herd during this period to meet seasonally higher demand for pork products in winter. With hog prices beginning to recover, improved profits for pig producers while increasing the demand for soybean meal, helping to drive-up soybean meal prices.
SHORT TERM SHORTAGE OF SOYBEAN MEAL
While China is expected to meet increased soybean demand by producing and
importing more soybeans — a short-term soybean meal shortage developed, with prices soaring in some provinces in September ahead of the Chinese National Day holidays. Spot prices of soybean meal rose in some of the main processing hubs of Guangdong and Shandong according to data from Shanghai JC Intelligence Co. and reflected in rising soybean meal prices on the Dalian Exchange for November delivery-4,525yuan/t ($635.89/t-15 Sept ‘22). Soymeal stocks fell to 493,000/t in mid-September well below the five-year average of 845,000/t. Chinese importers have stepped-up soybean purchases in recent weeks, notably from Argentina and with the US harvest under way likely to ease supply tightness in the coming monthsthe Mysteel Group predict China to import 6.8mt of soybeans in September, 5mt in October and 8.8mt in November.
Water lubricated propeller shaft bearings found to reduce fuel consumption
Peer-reviewed research by Thordon Bearings into the hydrodynamic lubrication efficiency of a ship’s propeller shaft bearing has found that the use of seawaterlubricated elastomeric polymer bearings reduces fuel consumption.
The environmental and financial benefits of adopting a seawater-lubricated propeller shaft system are well documented, but this is the first indication that the arrangement reduces hydrodynamic resistance enough to improve fuel consumption, compared to a conventional oil-lubricated bearing arrangement.
The groundbreaking research is based on new methodology for calculating the performance of seawater-lubricated bearings, which, until now, has been based on decades-old theory developed for oillubricated propeller shaft bearings.
“Classic rigid surface bearing theory is valid and commonly used for oil-lubricated metal bearings. However, two major factors of seawater-lubricated bearings, namely low lubricant viscosity and deformability [of the polymer bearing surface], make the application of rigid surface bearing calculations
susceptible,” Thordon Bearings’ Chief Research Engineer, Dr. Gary Ren, says in his peer-reviewed paper published in the July edition of the Elsevier journal Tribology International
“We believe Dr Ren’s method is more accurate, because it takes into account the characteristics of seawater as a lubricant, the polymer materials used, bearing pressures, viscosity, friction and so on,” said Elena Corin, Senior Manager, Special Marine Projects, Thordon Bearings. “This is the first time anyone has investigated whether there are differences in friction coefficient between the two types of bearings. And there are!”
Corin furthered that the new methodology provides “strong evidence” to quantitatively support the benefits of a Thordon COMPAC system. “By applying the results, we were able to determine the minimum required shaft speed for hydrodynamic lubrication efficiency, the coefficient of friction as well as the water film thickness at any given load and shaft speed,” she said.
“Test results confirmed that fuel losses due to the friction coefficient
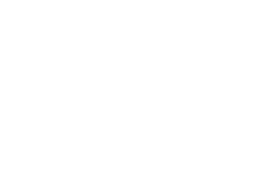
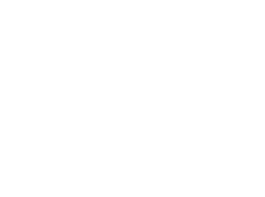
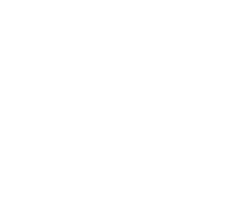
[hydrodynamic resistance] of an oillubricated propeller shaft bearing system can be reduced by as much as 85% by using seawater-lubricated polymer bearings.”
Thordon Bearings used the methodology to compare the fuel consumption of a Panamax containership and an Aframax tanker operating a 640mm (25.2in) diameter oil-lubricated propeller shaft bearing versus the same ships operating an open COMPAC seawaterlubricated bearing system.
Each vessel was assumed to run on VLSFO (very low sulphur fuel oil) at a global average price of US$890/mt, operating for 70% of the time.
“The results confirmed that fuel losses due to the friction coefficient (hydrodynamic resistance) of an oillubricated propeller shaft bearing system can be reduced by as much as 85%.
“Fuel costs will depend on the operational profile of the vessel, but we conservatively estimate annual savings of at least US$10,000 per vessel,” said Corin. “This is in addition to the other life cycle cost savings associated with a Thordon seawater-lubricated bearing system.”

Reederei Gerdes orders second Damen Combi Freighter 3850
EFFICIENT SHORT SEA GENERAL CARGO VESSEL
German short sea shipping specialist ship owner company Reederei Gerdes signed the order for Damen Cargo Vessels to build a second Combi Freighter 3850, following delivery of the Benabell G in September last year. The new vessel of the same type will be named the Kalli G. This addition to the fleet will increase overall efficiency.
Impressive performance of the Damen CF 3850 that was taken into service end of 2021, convinced Reederei Gerdes to order the next vessel of this type. Now that European short sea shipping is experiencing a period of growing demand, fleet renewal is key to be prepared for future operations. Tightening environmental regulations require fleet upgrades. The CF 3850 performs well within the requirements from IMO and port states, making it a future-proof vessel. Additional benefit for the ship operator is of course the low fuel consumption at high deadweight.
“It is important for us to utilize the resources available in a responsible manner,” states Nicole Gerdes, managing partner at the ship owner company. “We focus on longevity and sustainability to retain our competitive advantage in coming years.”
Kalli G can sail at over ten knots carrying full cargo load, with less installed propulsion power. Optimized design of the hull reduces water resistance and enables substantial fuel savings. The 89.70-metre length over all, 12.50-metre beam vessel has a 1,104kW main engine. The relatively small power source is enough to maintain her 11.8 knot design speed even in
rough conditions. The vessel carries 3,830 tonnes of load. Cargo hold tanktop strength is reinforced to carry 15 tonnes per square metre. The CF 3850 takes 172 containers: 108 in the hold and 64 on deck.
Gerdes, with its associated chartering company over-C GmbH & Co. intends to employ the ship in the European coastal trade. Dennis Clavier, Director at over-C states: “The size, in combination with its ‘NAABSA notation’ make the CF3850 a good vessel for calling smaller tidal ports for example in the UK. The movable bulkheads which can be used as partial tween-decks offer flexibility to carry grain, animal feed, fertilizer, steel but also project cargoes from time-totime.”
Damen Cargo Vessels, located in Drachten, the Netherlands, serves ship owners in the short sea trading with standardized designs for combi freighters, tankers and container feeders, building in stock and where needed to client specification.
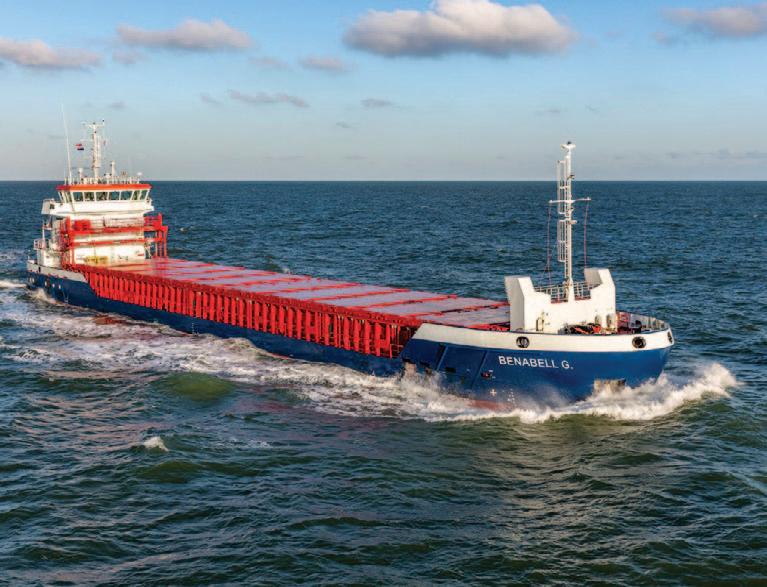
By 2021, four vessels of the CF 3850 design were available ready built, all of them have been taken into service in the
last year and 13 more contracts have been signed for vessels of the same design.
DAMEN SHIPYARDS GROUP —OCEANS OF POSSIBILITIES
Damen Shipyards Group has been in operation for over 90 years and offers maritime solutions worldwide, through design, construction, conversion and repair of ships and ship components. By integrating systems, Damen creates innovative, high quality platforms, which provide its customers with maximum added value.
The company’s core values are fellowship, craftsmanship, entrepreneurship and stewardship. Its goal is to become the world’s most sustainable shipbuilder, via digitalization, standardization and serial construction of its vessels.
Damen operates 35 shipyards and 20 other companies in 20 countries, supported by a worldwide sales and service network.
Damen Shipyards Group offers direct employment to more than 12,000 people.
MCTC celebrates 10 years of supporting vessels and their crews improve seafarers’ health with nutritious meals
Leading maritime catering management provider MCTC is celebrating its first decade of improving catering standards onboard ships by focussing on healthy and nutritious meals.
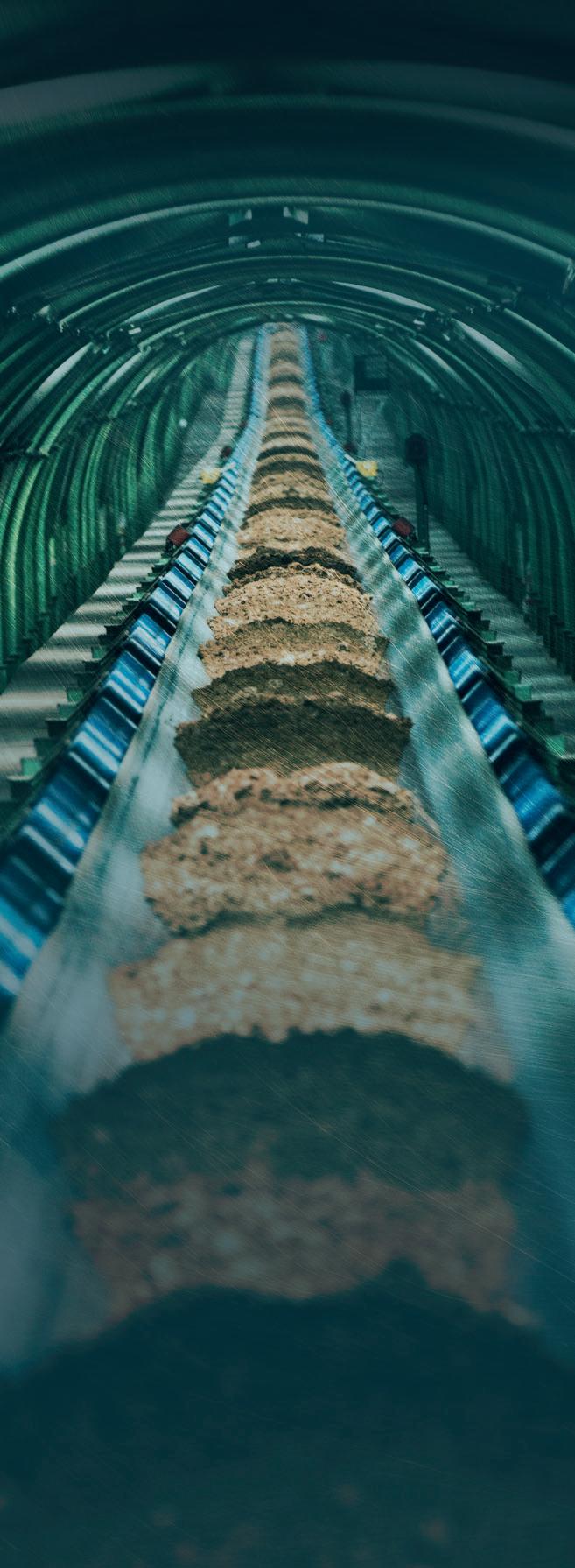
MCTC has been celebrating its milestone year with a special anniversary party and events throughout the year.
The company launched in 2012 with the aim of improving catering standards in the galley, serving healthy and nutritious meals and improving crews’ overall health, while reducing dietrelated illnesses in crew members that are caused through consumption of fatty and high-calories foods.
MCTC started with offering training courses in catering and health and nutrition, with its flagship programme being the Catering Competency Development Programme. This offered the full training programme, as well as access to an experienced team of consultants, regular vessel visits, trade tests and weekly practical evaluations.
Over the years, the company evolved to offer full catering management services along with its training packages, taking care of the full spectrum of a vessels’ needs from budget planning, creating recipes and ordering supplies. MCTC is now on target to soon have 1,000 vessels under its service.
CEO of MCTC, Christian Ioannou said: “We are delighted to have reached our tenth anniversary and have enjoyed celebrating with numerous events throughout this year. The business has evolved significantly over the last decade and we are immensely proud to have gone from offering training to now offering a full scope of catering management services, along with our training programmes. “MCTC started with the aim and vision to improve standards in the galley and there has certainly been a big shift in vessel managers and owners’ mindsets when it comes to health and nutrition over the last few years, particularly following the Covid pandemic. The new generation of seafarers are heavily invested in their physical and mental health and it is important that as an industry we are ensuring we are meeting this new set of needs.”
Alongside its training and catering management packages, MCTC has a team of experts who are on hand 24/7 with advice and support. All galley staff under its management has access to a fully interactive digital platform where they can receive nutrition advice, recipe ideas, communicate with the team, or access any of their training modules. It also places focus on keeping fit and promoting a positive mindset to ensure seafarers are looking after both their physical and mental health.
ABOUT MCTC
MCTC offers a full Catering Management Programme covering the vessel’s entire catering management needs such as ordering supplies, recipe planning, menu management, and health and nutrition. It also provides a Catering Competency Development Programme designed to increase standards in the galley through a safe food handling and nutrition course; onshore upgrading culinary course; trade tests, briefings, on board visits and also crew conferences.
THINK THAT RAW MATERIALS TRANSPORT REQUIRES TRUCKING. WE THINK DIFFERENT.
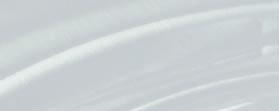
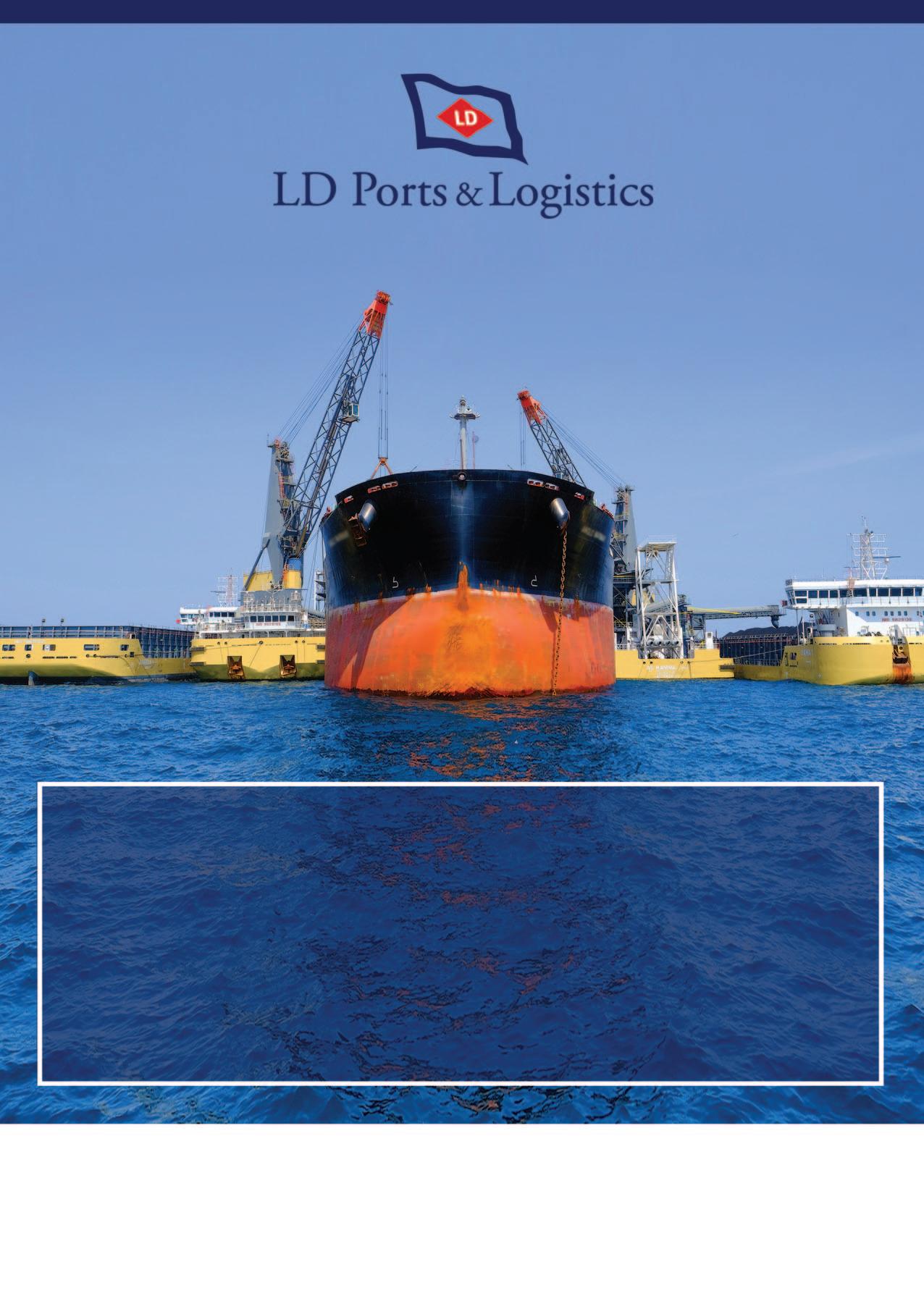

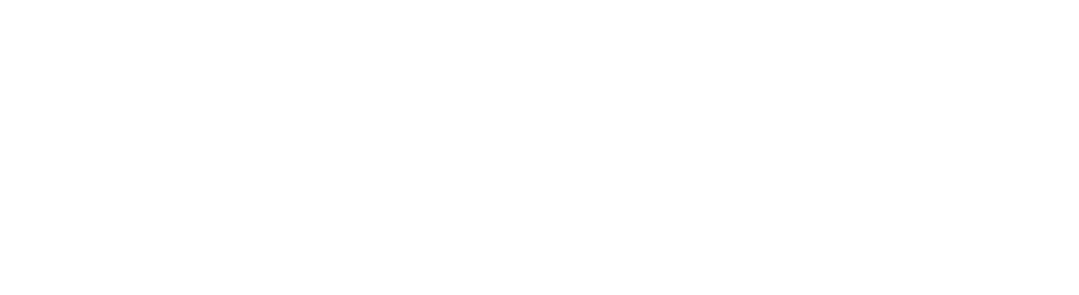
Keeping the boat afloat bulker services, safety & maintenance
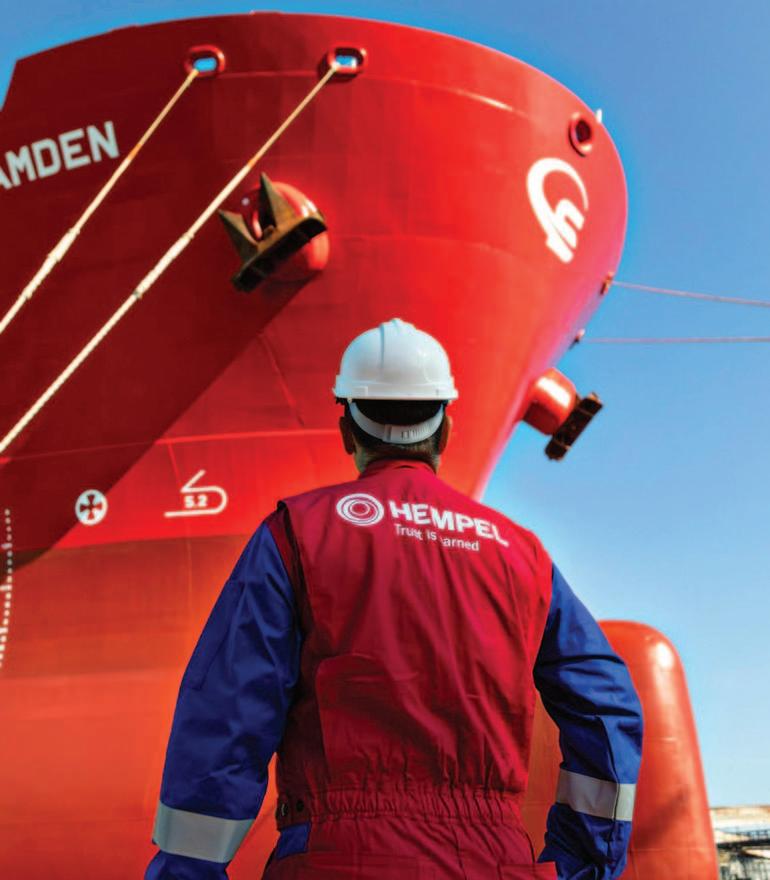
Hempel coats 3000 ships with flagship hull coating, Hempaguard
Coatings company, Hempel A/S, has passed a landmark number of ships coated with Hempaguard. Alexander Enström, Executive Vice President of Marine at Hempel, explains why passing this milestone is so impactful. “Our customers are looking for technologies that can support them on their sustainability journey. Three thousand applications of Hempaguard is equal to removing 27 million tonnes of CO2, corresponding with 8.6 million tonnes of fuel saved by having a smoother hull.”
“The adoption of Hempaguard is growing exponentially. This year alone, we have seen sales of Hempaguard systems grow by 82%,” continues Enström. “The antifriction properties of Hempaguard help shipowners and charterers save on fuel usage and thereby emissions, so it’s the obvious choice for our customers.”
With stricter regulations related to decarbonization coming into force in 2023, Hempel is seeing a widening range of clients seeking its advice, including an increasing number of bulker, tanker, containership and cruise operators and owners all keen to keep their vessels in
operation come next year.
The new regulations being introduced by the International Maritime Organization are the Carbon Intensity Indicator (CII) and Energy Efficiency Existing Ship Index (EEXI). Hempel’s data suggests that about 80 per cent of the world fleet will be required to take action to secure a good CII rating while reaching the required EEXI. Vessels will be forced out of the market if their owners and operators do not identify and adopt a comprehensive emissions’ reduction pathway.
CALCULATION METHOD
The savings related to the 3,000 vessel applications have been calculated by estimating the fuel savings of each Hempaguard application against a market average coating, based on market average numbers from the Fourth IMO GHG Study.
For Hempaguard applications, the consumption, activity, duration until next dry dock and relative savings from the IMO GHG Study are estimated and the impact from the full DD cycle is summarized in the year of Hempaguard application, where
the coating choice and thus fuel savings decision is taken.
ABOUT HEMPEL
As a supplier of trusted coating solutions, Hempel is a global company with strong values, working with customers in the decorative, marine, infrastructure and energy industries. Hempel factories, R&D centres and stock points are established in every region.
Across the globe, Hempel’s paints and coatings can be found in almost every country of the world. They protect and beautify buildings, infrastructure and other assets, and play an essential role in our customers’ businesses. They help minimize maintenance costs, improve aesthetics and increase energy efficiency.
At Hempel, the company’s purpose is to shape a brighter future with sustainable coating solutions. It firmly believes that it will succeed as a business only if it places sustainability at its heart. Not only is this the right thing to do, it will also strengthen the company’s competitive position, make it more resilient and reduce its risk.
Polish Register of Shipping classification services on the way to assure bulk carriers safety in sea trade
Bulk carriers play a major role in the global economy. Dry bulk cargoes cover a wide range of products, writes Marek Narewski, Rules Development Department, Polish Register of Shipping (PRS).
The most commonly shipped dry bulk materials are for example: coal, cement, grain, sulphur, fertilizers, iron ore and sugar. These products are generally transported in large quantities in bulk in the typical holds arranged in the construction of the specialized ship — bulk carrier. The portfolio of safety-related services for bulk carriers involved in international trade is provided by class societies associated in IACS, and one of its members is the Polish Register of Shipping (PRS).
Currently designed and constructed bulk carriers and implemented survey procedures present high engineering quality necessary to ensure cost-effective, safe and reliable operation. Based on experience gained from the past, the safety of the current world fleet of bulk carriers is much better, as can be seen in EMSA (European Maritime Safety Agency) or IMO statistics. The progress in safety assurance is the result of parallel class societies efforts and flag states activities related to verification of compliance with international and national regulations. This is particularly important in the case of aged ships that require compliance with business standards requested by shipowners and ship operators to keep required level of competitiveness.
IACS class societies play a vital role in and are committed to the safety of existing and future bulk carrier fleet. According to EQUASIS 2019 the fleet of ships over 500 GT is dominated by ships classed by IACS members (56% by number and 78% by tonnage). In the case of bulk carriers, IACS societies are classing over 83% of the total world bulk carrier fleet. We can expect that the number of IACS classed ships will be on a steady increase both in numbers and in GT. The high rate of IACS classed bulk carries means that the majority of the world bulk carrier fleet has a major impact on the safety of commodities trade.
Some studies conducted recently touched subjects of prediction of commercial fleet future structure and certain ship types development as well as the rate of new-buildings and scrapping old ships. One of the studies is forecasting that the number of bulk carriers will remain almost constant within the coming three
decades. Considering the maritime safety aspect, EMSA reports contain some statistical data on ship accidents and incidents rates, and these statistics show that the figures for new ships are much better than in the case of old ships.
The ship classification is a special type of business activity where specific and wide expert knowledge and safety consider ations are of utmost importance. The basis for classification societies activities are their rules dedicated mainly to shipping industry as well as to specific parts of the oil & gas industry, energy generation, rail & road transport or aviation. PRS as a classification society offers portfolio of services focused mainly on safety assurance. The set of PRS Rules has been developed based upon the society’s own experience and is continuously amended by inclusion of own R&D work results, e.g. IMO and IACS requirements as well as other applicable international technical and safety standards.
At present, PRS has over 500 seagoing ships classed and bulk carriers constitute about 16% of all classed ships. The substantial number of classed bulk carriers is of the medium age. PRS experience gained when dealing with older ships enabled the society to elaborate effective and high quality survey services. The last two years PRS was on the list of high performance classification societies of the Paris Memorandum of Understanding on Port State Control. Only classification societies that have a low ratio of detentions by PSC can get on the list of recognized organizations with the high performance result, what underlines the quality of their work and at the same time is one of the determinants allowing a vessel to be the Low Risk Ship. Being high on the performance list of Paris MoU shows PRS’ commitment to keeping a high level of services.
Over the years class societies took several steps to enhance the safety of bulk carriers. These have included the introduction of the corrosion protection requirements for ballast spaces, minimum thickness requirements for side shell web frames in cargo areas, tough regime of Enhanced Surveys and most notably the introduction of Common Structural Rules for Bulk Carriers (CSR) in 2005 followed by Common Structural Rules for Bulk Carriers and Oil Tankers (CSR BC & OT) in 2015. PRS implemented CSR Rules into its own
activity and developed a set of related PRSCSR software for verification of the bulk carrier strength. The software has been assessed and positively verified according to IACS procedures.
Another important aspect of bulk carriers safety assurance is related to winter navigation in ice-infested waters. Like other class societies, PRS has implemented rules dedicated for seagoing ships that must have a sufficient strength of hull and machinery during navigation where increased risk of damage by brash ice blocks to the propulsion system exists. PRS’ practical experience in that area covers also special surveys and repair of damages caused by ice during ship operation.
An example is a serious ice damage that happened a few months ago when a fully loaded bulk carrier suffered failure to propeller blades. Due to circumstances, the only solution to the problem was to conduct repairs underwater at the nearest harbour. The repair was done after detailed underwater inspection, carried out under supervision of a classifier. Damaged blades were cut and straightened by the professional diving and underwater service provider company. Underwater repairs completed fully underwater has been surveyed by PRS and allowed to release the ship to sail fully loaded across the Atlantic.
PRS provides a specially tailored expert service dedicated to ships involved in commodities trade called Condition Assessment Program (CAP). CAP service is already well established within the tanker industry, but is also implemented as vetting practice in case of bulk carriers as a proved method leading to improvement bulk carriers risk assessment. It is an important voluntary service that provides independent evaluation of the technical condition of a bulk carrier. Based upon CAP process results, third parties can assess the suitability of the ship to be chartered and its current condition in relation to its age.
CAP assessment provides a charterer with a technical evaluation of the condition and maintenance of a vessel above standard requirements for a class. It is applicable to bulk carriers of 15 years of age and above. The CAP programme scope covers a detailed survey of the hull structure including verification of gauging as well as extensive testing of ship
machinery, equipment and cargo systems. Gathered information, combined with a strength and fatigue engineering analysis, is transferred into a numeric rating to be assigned to the verified ship — from 1 (Very Good) to 4 (Unsatisfactory).
A specific class activity is related to evaluation of novel technical solutions for implementation in ship technology. Newly developed designs and equipment prototypes are being verified by class societies to be implemented on board of ships using marine engineering practice. Completion of certification process allows for legal introduction of new solutions on ships and is a proof of the compliance with existing sound marine engineering and new
safety and environmental standards as required by law.
Class societies are here to assure that ship technology developments are compliant with the mandatory requirements for technical and operational safety of bulk carriers as well as other ships involved in international trade.
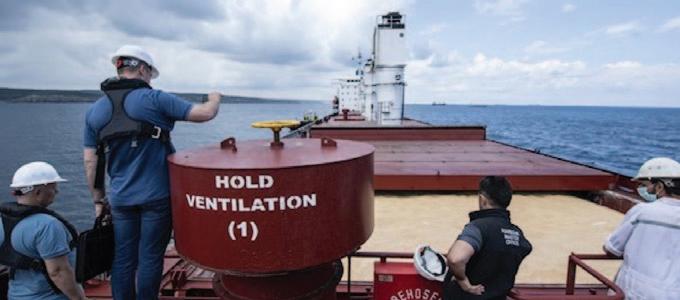
ABOUT PRS
Polish Register of Shipping (PRS) is an independent expert institution acting on the international market, whose business is conducted for the benefit of the community. Through the formulation of the requirements, survey and issue of the appropriate documents, PRS assists State
Progress report: Black Sea Grain Initiative
The Joint Coordination Centre (JCC) was inaugurated in Istanbul on 27 July following the Black Sea Grain Initiative launched by Russian Federation, Türkiye, Ukraine and the United Nations.
From 1 to 15 August, the JCC has authorized a total of 36 movements of vessels (21 outbound and 15 inbound) through the maritime humanitarian corridor in the Black Sea to facilitate the safe exports of grain, foodstuffs and fertilizer, including ammonia, from Ukrainian ports.
During this period, 21 vessels have been authorized to move from the Ukrainian ports of Odesa (11), Chornomorsk (6) and Yuzhny/Pivdennyi (4) under the Initiative. Those vessels are carrying a total of 563,317 metric tonnes of grain and other foodstuffs.
BREAKDOWN:
451,481 tonnes of corn 50,300 tonnes of sunflower meal 41,622 tonnes of wheat 11,000 tonnes of soya beans 6,000 tonnes of sunflower oil 2,914 tonnes of sunflower seed
According to information provided to the JCC, the preliminary destinations of Ukrainian food exports so far include:
Turkey: 26%v
Iran: 22%v
Republic of Korea: 22%v
China: 8%v
Ireland: 6%v
Italy: 5%v
Djibouti: 4%v
Romania: 2%v
To be determined: 5%v
Routes of commercial vessels and cargo
ownership are determined through commercial activity and they may change en route. The food en route to Djibouti is 23,000 tonnes of wheat purchased by the World Food Programme (WFP) to contribute to the drought response in Ethiopia as part of the WFP’s humanitarian operations.
From 1 15 August, the JCC has conducted a total of 27 inspections through its joint inspection teams on inbound and outbound vessels. All ships inspected so far were cleared.
As part of its responsibilities, the JCC has been closely monitoring the inbound and outbound movement of vessels through the maritime humanitarian corridor in the Black Sea. It has so far observed on two occasions vessels deviating from the corridor and it has responded appropriately by contacting captains and advising them to follow the co ordinates.
The JCC is also providing pre-transit briefs to inbound masters during the inspection process in Istanbul. The JCC continues to assess and review the procedures put in place to ensure the safe passage of vessels through the maritime humanitarian corridor.
Administrations, Underwriters and the Society’s clients in ensuring the safety of people, floating objects, land undertakings, the safety of carried cargo and that of the natural environment. PRS is IACS member and acts also as RO upon over 40 authorizations of Flag States.
ABOUT THE AUTHOR
Marek Narewski is a specialist and expert in PRS R&D Division with wide experience resulting from involvement in number of various marine and offshore R&D projects, novel technologies implementation in ship design and construction including marine application of composites and alternative fuels.
The Black Sea Grain Initiative aims to respond to high food price inflation and to global food insecurity which is at record levels with tens of millions of people at risk of famine. According to the UN’s Food and Agriculture Organization, Ukraine contributes about 10.3% and 12.6% of global exports of wheat and maize respectively. Its share for sunflower products (seeds and oil) is 48.2%. Restarting exports will free up storage space in Ukraine and avoid wastage. It will also ensure a supply chain of food for this and subsequent harvests.
The deal aims to improve global food supply and calm markets. Prices across different food commodities are volatile and can be subject to a range of economic and climatic influences that go beyond Ukrainian exports.
Terminology:
Outbound: merchant vessels departing the ports of Odesa, Chornomorsk and Yuzhny (Pivdennyi) heading to Istanbul
Inbound: merchant vessels departing from Istanbul heading to the ports of Odesa, Chornomorsk and Yuzhny (Pivdennyi)
A perfect storm for the dry cargo sector
INTERVIEW: KOSTAS GKONIS, SECRETARY GENERAL INTERCARGO
The time frame required to change the direction of a bulker is frequently quoted in management speak, and many of the issues faced by the dry bulk shipping sector could be said to follow the same pattern. The dry cargo industry is used to making decisions for the long term and dealing with complex issues that have a lengthy lifespan and wide implications.
Today however, dry bulk operators are facing a perfect storm of circumstances to deal with.
Kostas Gkonis, Secretary General of INTERCARGO explains: “Following the turbulent pandemic years, the industry now finds itself dealing with the situation in Ukraine, the legacy of Covid and of course the incorporation of IMO’s greenhouse gas (GHG) reduction targets into everyday operations. Yet these issues are coupled with the safety, security environmental and regulatory challenges that the dry bulk industry has always faced.”
Gkonis explains that progress is being seen in some areas, but other issues are not so transparent.
“Our Association welcomed the Black Sea Grain initiative to resume grain shipments from Ukraine,” he says. “But amid the very public discussions regarding insurance and chartering, it must be stressed that the safety and security of the vessels, and their crews, must be at the heart of the debate.
“Practically, this means that there must be continued assurances at berths and anchorages in Ukrainian ports as to the safety of vessels and their crews, the security of cargoes, and that shipping in the area is free from attack. The creation of a mine-free sea corridor protected by naval escort is essential.”
The issue of Covid is now rarely in the news, but INTERCARGO members have advised of continuing difficulties. “The shipping industry is facing its own version of ‘long Covid’,” says Gkonis. “Seafarers worldwide continue to face major issues with crew change, port entry and changing vaccination requirements. New waves of infection persist at ports, and once again we are seeing local authorities creating
their own interpretation of the rules.” He also explains that in a number of ports globally seafarers are finding access to shore leave restricted, and in some cases are finding it difficult to access nonemergency medical assistance.
Liquefaction too remains on the agenda, and industry partners could still do more to ensure the safety of crews, says Gkonis. INTERCARGO recently submitted its latest Bulk Carrier Casualty Report to IMO where it warned that not only were IMSBC Code requirements not being followed, especially in relation to testing and certification of cargo condition, but that there was also lack of adequate assessment and monitoring of the condition of cargoes being loaded in the cargo holds by representatives of all interests.
“Despite high levels of awareness from shipowners themselves of the dangers of improperly loaded cargo, the Report identified that liquefaction continues to be the greatest contributor to loss of life in the bulk sector,” says Gkonis.
“Between the years 2012 to 2021, 27 bulk carriers over 10,000dwt have been identified as total losses and 92 seafarers lost their lives. Liquefaction accounted for about 19% of the total vessel casualties in the past ten years yet was the cause of 76% of the total loss of life, as a result of five related bulk carrier casualties, four carrying nickel ore and one carrying bauxite.”
Ship operators are well aware of the risks to their crews and their vessels caused by carrying cargoes prone to liquefaction and make every effort they can to mitigate those risks, he says. “It is the lack of consolidated effort and commitment from many stakeholders to resolve the problem that is evident. These can include shippers, receivers and port state authorities at loading and discharging ports. We need action from those our industry relies upon for its safety — the IMO, legislators, and suppliers to ensure that the minimum obligations under the IMSBC Code are properly fulfilled. The industry is simply talking to itself if we cannot force action from our other stakeholder groups.”
Of course, all this is taking place against the backdrop of an industry striving to
Kostas Gkonis, Secretary General, INTERCARGO.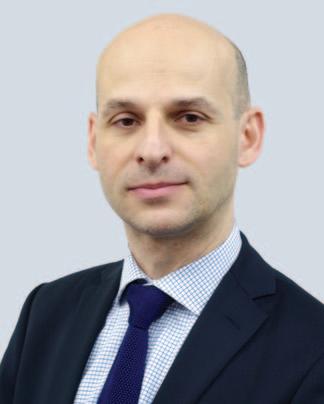
achieve IMO’s target of zero emission shipping by 2050, and facing a confusing array of MARPOL amendments, circulars, resolutions and guidelines, as they work to achieve this ambition. “You cannot place responsibility for meeting IMO’s zero emission shipping targets fully on the shoulders of shipowners,” warns Gkonis.
“It must be remembered that the commercial development of these solutions is within the control of a spectrum of stakeholders. Such a target requires a drastic and urgently needed acceleration in the commercial development of the required technologies, fuels, propulsion systems and related infrastructure.
“The net-zero target will only be plausible if governments take the necessary action to achieve this at IMO.”
Returning to the Bulk Carrier Casualty Report, INTERCARGO is pleased to also report good news, with statistics of ship losses and consequential seafarer fatalities suggesting that the safety performance of the bulk carrier industry is showing a clear trend of improvement.
“We note positively that these figures continue to head in the right direction,” says Gkonis. “However, there is no room for complacency and we at INTERCARGO will continue to seek further improvement by re-evaluating and implementing enhanced measures to address cargo safety and safe navigation.”
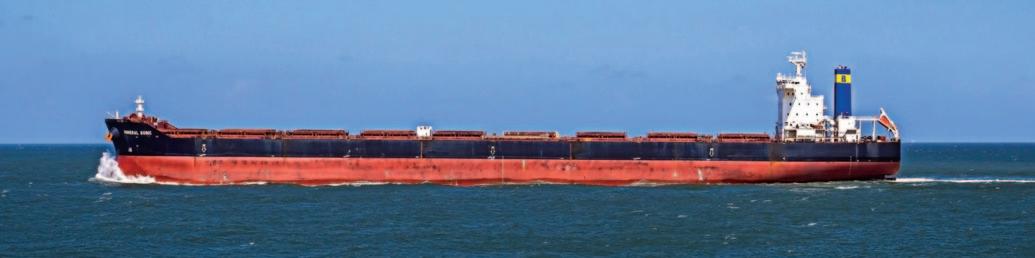
Oldendorff inks a contract with Blue Water for voyage optimization and fleet decarbonization by implementing BOSS after a year-long trial
The largest German bulk carrier company, Oldendorff Carriers, and Indiaheadquartered maritime technology company, Blue Water, announced the official signing of their contract to implement Blue Water’s “BOSS Voyage Optimisation Suite” for Oldendorff’s Cape & Baby Cape fleet of owned and time chartered vessels.
The BOSS Suite will propel Oldendorff’s continuous efforts towards a greener maritime trade by reducing emissions through intelligent voyage optimization, weather routing, vessel performance analysis and efficient fleet management.
Capt. Dexter Jeremiah, Managing Director Operations at Oldendorff, said: “After one year of successful trials, we chose the BOSS Suite for our Cape & Baby Cape Fleet since it met our needs for optimizing voyage operations, whilst enabling us to see real-time CII analytics for the vessels in one platform. The level of customization and development of advance voyage monitoring tools in the BOSS ecosystem with a quick turnaround has been second to none.”
Adding to the announcement, Capt. Kumaresh Gupta, Managing Director at BlueWater, said: “We are elated to have Oldendorff’s Cape & Baby Cape fleet in
BOSS. Throughout the trials, we were presented with challenges to develop certain customized solutions for operational excellence and performance analysis, and the BOSS team turned them into opportunities to further showcase the platform’s customizability, scalability, and an eagerness to make significant changes to suit Oldendorff’s needs.”
About Oldendorff Carriers: since its establishment in 1921, Oldendorff Carriers has grown into one of the world’s leading
dry bulk owners and operators, operating about 700 vessels around the world.
About Blue Water: the company provides a host of Software as Service for voyage optimization including its pioneer cargo heating management for tankers. Blue Water employs 100+ personnel in its Dehradun office and currently optimizes over 700 vessels of various type for maritime industry leaders, and provides quantifiable savings through a verifiable benchmarking system.
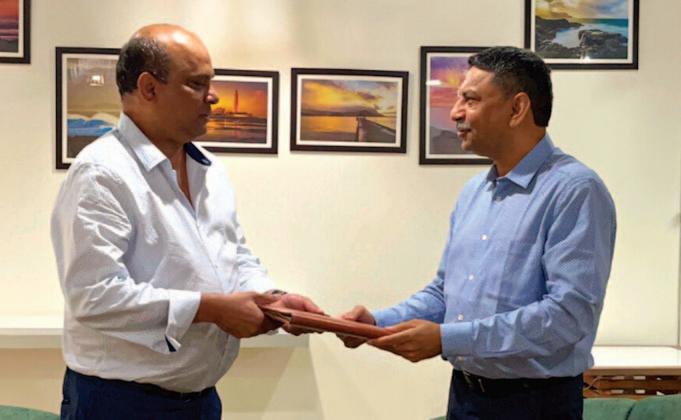
Barnacle-laden bulkers: bad for business, bad for CII ratings
For as long as people, products and raw materials have been traversing the oceans, ship hulls have acted as attractive structures for marine life. Biofouling, whether by shell-forming creatures or soft organisms such as slimes and algae, significantly increase the amount of frictional resistance across a ship’s hull when it moves through the water.
Increased frictional resistance requires a ship to burn more fuel to maintain a set speed, or if operating on fixed shaft power or fuel consumption, then speed losses will occur. A 2007-published study by Michael. P. Schultz proclaimed that a vessel with 10% barnacle coverage would need a 36% shaft power increase to maintain the same speed. Put simply, the greater the barnacle fouling coverage, the greater the fuel demand. These are creatures that you do not want on your ship when profit margins are tight.
In June 2020, the results of a study commissioned by I-Tech AB and carried
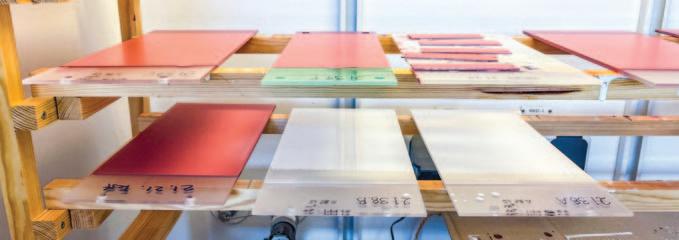
out by global marine consultants, Safinah revealed the true scale of highly impactful hard biofouling present across the global shipping fleet. A 249-ship sample was surveyed at drydock with their underwater hull condition inspected. The sample spanned all major ship types coated with biocidal and foul release coatings of different grades and generations, covering a wide range of activity and trading routes.
Following the analysis of the hull condition inspection data, it was found that
every vessel surveyed had some level of hard fouling. Troublingly, 44% of vessels surveyed had more than 10% of underwater hard fouling coverage. When looking at the breakdown of fouling by vessel type, it was found that across vessels with relatively lower activity, the frequency of barnacle fouling was greater. On lower activity vessels it was found that 45% of vessels had barnacle fouling coverage greater than 10% compared to just 27% observed across higher activity vessels.
When factoring in data from another Schultz study, published in 2011 that investigated the performance penalty of biofouling, we can assume that levels of barnacle fouling across >10% of the hull surface is present on just under half the global shipping fleet. This means that the global shipping fleet is producing an excess of least 110 million tonnes of carbon emissions per year due to barnacle fouling alone. Furthermore, barnacle fouling on the hulls of ships is estimated to account for an additional US$6 billion spent on fuel per year for the global commercial fleet. The true figure is likely to be even higher, as this is a conservative calculation based fuel prices in 2020 and only assumes a 10% coverage of hard fouling on the fleet.

Since the underwater hull plays a huge role in ship performance, coatings play an equally huge role for a vessel to achieve good Carbon Intensity Indicator (CII) rating. Biofouled hulls, particulary those with any hard fouling, will negate important gains made by installing fuel efficiency enhancing technologies or using cleaner fuels.
The bad news is that the issue of biofouling will only worsen. As we sail further into the future, a greater number of ships will face a higher risk of biofouling creatures and barnacle infestations on the hull and bulk carriers are not immune to this. Any bulk carriers sitting at anchor for a period of a few days, or more are at a great risk of biofouling accumulation. The majority of antifouling coatings rely on a vessel moving through water to function
effectively. So, what happens when a vessel stops? Usually that means that barnacles can attach and accumulate at a rate of knots.
The greatest concentration of biofouling creatures are found in the warmer waters of the tropics and subtropics. Since the 1990s, a shift in global trade has resulted in ships visiting ports in tropical and sub-tropical waters. Furthermore, vessels are spending significant periods of idle time in these ports either loading or unloading or queuing in increasingly congested waiting zones. During this time, they face a high risk of picking up hard fouling organisms.
Therefore, an insurance policy against hard fouling is needed. Since idle periods can hinder the efficacy of biocidal and foul release coatings, most coatings can only offer 14 21 idle days performance guarantees. The development of antifouling coatings that better protect vessels which may sit idle or longer than standard idling


guarantee offered by coatings manufacturers during a three or five year service period is essential, if not vital.
Yesterday’s solution will not work for tomorrow’s problems. This has catalyzed great innovation in the marine coating sector. An increasing number of ship owners are demanding 30-day plus guarantees and for antifouling coating manufacturers, one way that this can be achieved is through the inclusion of the active agent, Selektope®
Selektope® is an organic, non-metal active paint ingredient that is relatively unique compared to traditional biocides currently found in many marine paints. Through natural receptor stimulation, Selektope® activates hyper-mobile behaviour in barnacle larvae, which prevents them from attaching themselves to the hull and niche areas. The effect is temporary while they are in close proximity to the coated surface and ultimately leaves them unharmed. When used in antifouling paints, all ship types can remain idle or at low speeds for extended periods of time, even in extreme barnacle fouling conditions.
Out of the top six marine coatings manufacturers, three of them have commercialized products containing Selektope® in the past five years: Chugoku Marine Paints, Hempel and Jotun. The technology is also being used in many outfitting coating products following demand from shipyards located in South Korea who were facing the issue of barnacle fouling during long fitting out periods.
The use of Selektope® also presents a significant advantage over a reliance on hull-cleaning technologies for hard fouling removal and reduces the risk of coating damage after cleaning. Also, as opposed to the need to constantly monitor hull condition, antifouling coatings with Selektope® confer relative peace of mind to bulker operators that their ship hulls will remain barnacle-free.
Making vessel operations future ready: Blue Water rolls out BOSS CII Estimator
Blue Water being cognizant of the recent CII developments, has introduced a smart and practical CII Estimator, that allows vessel owners and operators to assess future operational impact on their fleets, and gives them estimates to improve efficiency, optimize CII ratings and help with their decarbonization targets.
Serving as an intrinsic feature of Blue Water’s BOSS Voyage Optimization Suite, the BOSS CII Estimator readily calculates the yearly CII based on multiple parameters using BOSS’ extensive AI & ML assisted vessel digital twins.
HOW BOSS CII ESTIMATOR WORKS
The BOSS CII Estimator simulates hundreds of trading patterns at a flick of button to estimate how the operational parameters will impact the vessels’ CII rating. Further, it answers the following most commonly sought questions by vessel owners and operators:
What is the vessel’s current CIIv rating?
What will be the impact of CO2v emissions on the current CII rating due to the future trade pattern? How to identify the most suitablev trading pattern for better CII ratings? How to determine the optimumv speed instructions for a vessel for a certain trade route?
BOSS CII ESTIMATOR FEATURES
2,000 Simulations at an Instant:v Considering 100 Cape Vessels in a fleet, simulating all Baltic route combinations for eco and full speed at both laden and ballast conditions would have taken 2000 simulations. BOSS CII Estimator dramatically cuts this down to one click & one second.
Supports Vessel Specific Balticv Routes: Computes vessel class specific Baltic Routes at a click of button, and generates the estimated CO2 emissions and corresponding CII rating.
Estimations basis Vessel’sv Performance: Uses vessel’s past data or sensor data to generate a digital twin and provide realistic estimations. Estimations basis Vessel’s SnC datav Draft and Load Condition Specificv Simulations
Dynamic Sea Margin: The estimatorv does not only consider a standard sea margin for simulation, but also provides an option to use historical weather data to calculate sea margin.
Vessel Specific Retardation Factors:v Apart from Sea Margin, the BOSS CII estimator also takes in vessel class specific weather and sea retardation factors to compute speed and emissions details, giving a much
transparent and practical estimates.
Determine Optimum Speed &v Trading Pattern: On simulating the different trading routes, BOSS CII estimator suggests optimum speed and trading pattern to optimize CII rating of vessels.
Fuel Specific Calculations:v Calculates CO2 emissions based on fuel type usage.
Interactive UI: Removes the need forv both tedious excel sheets and evaluating results on multiple routes. Instead, an interactive interface provides a much simpler way to conduct route and speed comparisons.
Share Simulation Reports: BOSS CIIv estimator lets the user easily export and share simulation details with anyone.
ABOUT BLUE WATER
The company provides a host of Software as Service for voyage optimization including its pioneer cargo heating management for tankers. Blue Water employs 100+ personnel in its Dehradun office and currently optimizes over 700 vessels of various type for maritime industry leaders, and provides quantifiable savings through a verifiable benchmarking system.
ABB and shipping company Wallenius Marine have introduced OVERSEA — the maritime industry’s first digital offering and fleet support center available as a service. The two companies have developed OVERSEA to help ship owners, operators and managers enhance the efficiency and sustainability of vessel operations.
OVERSEA leverages ABB’s extensive expertise in ship technologies and the ABB Ability™ Genix Industrial Analytics and AI suite, combined with fleet management knowledge from Wallenius Marine, to enable measurable performance improvements for vessels, leading to decreased fuel consumption and reduced emissions.
OVERSEA helps address such aspects of vessel performance as hull and machinery, speed and route planning, as well as emissions and carbon intensity reporting. With deeper insights into vessel’s
operational data, backed by advanced analytics, OVERSEA centre experts will be able to recommend concrete actions to shipping companies to help them improve energy efficiency, safety and reliability of operations.
OVERSEA is scalable to meet the various and ever-changing needs of shipping companies. With OVERSEA digital solution, shipping companies with in-house fleet support centres can collaborate on the same data with vessels and onshore office to get insights, provide recommendations and manage improve ment actions. In addition, shipping companies in need of further support can rely on the assistance of OVERSEA center experts for daily advice, periodic performance reviews and reporting, and on-demand performance consulting.
“We talk a lot about innovations that will make us more sustainable in the future,
and OVERSEA makes a real difference already today. From our experience, we know that the operation of a vessel has a deep impact on released emissions and fuel consumption,” said Johan Mattsson, CEO, Wallenius Marine. “With clear recom mendations to the crew, based on datadriven analysis, vessel owners and operators are able to significantly reduce both their environmental footprint and fuel cost.
“ABB is committed to driving shipping decarbonization, and OVERSEA has been developed to further support this target,” said Jyri Jusslin, Head of Service, ABB Marine & Ports. “OVERSEA allows turning insights into actions that can significantly improve the efficiency and sustainability of vessel operations. We are confident that this pioneering innovation will serve as a new standard in fleet and vessel performance optimization.”
ABB and Wallenius Marine introduce pioneering digital offering driving efficiency gains for ships
Rivertrace launches SMART VISCO sensor for Main Engines
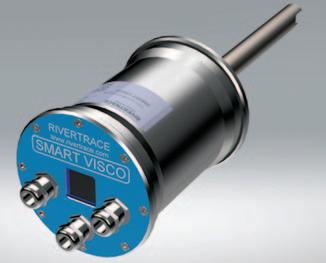
Rivertrace, an ISO9001 Quality-Assured Company and market leader with over 30 years of experience developing environmental monitoring solutions for the marine market, launched its innovative SMART VISCO sensor at the SMM Maritime Fair, which was held in early September in Hamburg, Germany.
The SMART VISCO sensor is designed to measure the viscosity and temperature of fuel oil before injection into the main engines of large ships. The monitor then reports this data via both analogue and digital outputs, with volt-free relay contacts.
The SMART VISCO sensor measures all grades of HFO using ultrasonic guided wave technology. Due to the high frequency and speed of ultrasound, ambient vibration and flow speed have no impact on the measurements. The monitor incorporates an LCD display that visually indicates all parameters. The viscosity and temperature data can also be easily retrieved using RS485 or a USB stick.
The fuel oil’s viscosity provides a direct indication of its impact on engine performance and efficiency. The availability of this information aid in the prevention of engine damage, reduces maintenance costs, and helps to minimize greenhouse gas emissions.
This SMART VISCO, with its digital capabilities can be integrated with the RIVERTRACE CONNECTED service to collect and share the data with ship management to monitor and analyse trends in fuel performance at both a vessel and fleet level.
The RIVERTRACE CONNECTED service initiative provides calibration compliance and equipment performance data. It can either be viewed on a cloud platform or shared through an API to the vessel/fleet management systems. The digital service is designed to support customers seeking simplified, continuous monitoring and efficient operations.
Martin Saunders, Managing Director of Rivertrace, says: “Monitoring environ
Stellium and Voyager Portal announce partnership
DIGITAL TRANSFORMATION, PARTNERSHIPS, SUPPLY CHAIN, VOYAGER
Stellium and Voyager Portal have announced a first of its kind partnership to bring a fully integrated SAP TM and Bulk shipping operations platform to global markets.
Until now, Transportation Management solutions have struggled to handle the nuances and complexities of global bulk commodity shipping. Instead, TM solutions have been focused on helping businesses manage rail, truck and container freight operations.
“Bulk commodity shipping is a highly complex and fragmented mode of marine transport. Over 90% of ships crossing the ocean will transport bulk commodities such as crude oil, gas, petrochemicals, agricultural products, heavy equipment, and minerals. Given the complexity and variability of each shipment, the operations teams often work exclusively with email and XLS for tracking, planning and execution activities,” says Matthew Costello, CEO of Voyager Portal.
Voyager Portal helps bulk shipping teams digitally manage their operations with their external parties in a shared collaborative environment. Their low-code workflow technology provides customers with the flexibility to design and execute
their unique processes, then surface the data for Exceptions Based Management and reporting. The platform allows teams to manage hundreds of common operational workflows such as vessel nominations, survey appointments, terminal clearances, ETA tracking, demurrage and cargo claims.
Working closely with its global customer base of manufacturers, Stellium identified a need in the market for a digitally integrated solution. One that would help customers capture their entire transportation value chain from bulk inbound raw materials, through to outbound finished goods, within a single solution, regardless of mode.
“Our team has extensive first hand experience implementing SAP TM for our customers. Through our many business consulting and system integration engagements we have become acutely aware of both the importance of bulk shipping to our customers, and also the inherent risks that exist with this unique mode. With Voyager and SAP TM, our customers’ planning, production and sales teams can have a true end-to-end picture of their transportation operations in one place,” notes Randeep Nambiar, CEO of Stellium.
“What attracted us to Stellium as a
mental discharge has been at the core of Rivertrace’s ethos for over three decades. However, in recent years we have also embraced digital transformation and provided solutions to automate and analyse the data by making our services smarter, and by connecting into the marine digital ecosystem. The SMART VISCO probe extends our offering to encompass onboard monitoring and expands our environmental solutions to include minimizing greenhouse gas emissions, as well as our oily water pollution prevention system.”
partner was not just their deep domain expertise around SAP, but their extensive reach and global reputation. The Middle East & APAC/India regions are one of the largest importers and exporters of bulk commodities in the world, so we look forward to accelerating growth off the back of the partnership,” says Costello,.
ABOUT VOYAGER
Voyager Portal is an operations management platform for bulk commodity shipping. The SaaS application allows Voyager customers to collaboratively manage their operations with internal and external stakeholders in a unified environment. By streamlining operations and data flows across organizations Voyager is able to help teams manage through exception, automate manual processes and deliver real-time insights.
ABOUT STELLIUM INC
Stellium is a specialized management consulting firm committed to designing and delivering solutions that improve businesses worldwide. Stellium Inc. is headquartered in Houston, USA and its regional head office resides in Bangalore, India and Toronto, Canada. Stellium has a geographic presence in North America, Asia Pacific and the Middle East region.
Freight Market exports Black Sea & Mediterranean after war
By Levent Karacelik, Marvel Consultancy & Shipping Inc.Black Sea was one of the major areas where cargoes, especially for coaster size vessels, were generating and loaded for many years, even close to 100 years.
In normal conditions every year there is around 12 to 16mt (million tonnes) of grain cargo shipped from Black Sea countries and almost 80% of this volume is loaded from Russian and Ukrainian ports in the black sea. Grain cargo ex Kazakhstan/ Kyrgyzstan/Turkmenistan/Azerbaijan are also loaded from Russian Black Sea ports.
Also, those two countries, Ukraine and Russia, are the main coal exporters and coal exports of other countries in the area, such as from Kazakhstan/Kyrgyzstan/ Turkmenistan Belorussia are also loaded from Ukrainian and Russian ports, thus making total coal cargo loaded from the ports of those two countries around 15 to 20mt (million tonnes) minimum per yer.
Fertilizer exports from the Black Sea ports of those two countries is also between 2 4mt per year. When you add steel products, scrap to those cargoes you are talking about yearly around 35 to 45mt of cargo which were loaded from the Black Seaports of Ukraine and Russia.
Once the war started for almost three months there was no cargo movement except the cargoes which were already loaded on the ships just before the war, but even the majority of these ships were blocked at Ukrainian ports, including all Azov Sea ports and navigation in Black Sea was very much limited due to mines left by both sides into open sea.
The biggest negative effect of this situation was on the coasters between 3,000/15,000dwt and sea river type vessels between 3,000/7,000dwt, which were almost 90% depending on the cargoes coming out from Russian Azov Sea ports and Mariupol/Berdyanks and Odessa/ Nikolayev, which were all closed for quite some time.
The number of vessels calling Ukrainian and Russian ports in Black Sea in January 2022 were around 500 and in February 304 and in March that number went down to 99 vessels. There were no alternative cargoes for the vessels to replace the cargoes lost due to the war.
Sometime later the shipments of coal and some grain cargoes started from Russian Azov Sea ports but that did not help the rates to go up as much as they fall. However, some cargoes were moved from Ukraine to ports like Reni/Izmail/Sulina
COAL EXPORTS TO MIDDLE EAST INCLUDING TURKEY
MONTH 2021 2022 %
February 1.345 879 -65%
March 1.961 1.367 -70%
April 1.218 1.089 -10%
May 1.442 1.105 -23%
June 1.570 2.115 40%
* Numbers are in million tonnes.
Source: Metalexpert
canal where due to congestion, vessels were waiting almost 40/50 days to berth and load cargo and freight rates went up almost 300%. Such as a 5,000mt cargo from Reni to Turkish Marmara: Sea freight went up to US$110/120 from US$30/35 levels.
EXPECTATION IN THE FUTURE AND THE EXISTING SITUATION IS THAT
The EU’s sanctions do not have any direct implications for Turkish buyers as Turkey is not an EU member. This means Turkish buyers can source Russian coal at steep discounts against API 2 index. Prices for non-Russian coal offered to Europeans buyers — including from Australia, Colombia, South Africa and the US — have risen to record highs. Turkey’s power sector, is expected to continue sourcing most of its needs from Colombia for the remainder of this year, as buyers have term deals in place.
Also China & India who do not follow sanctions are serious buyers of Russian coal. Chinese buyers are now paying in Yuan for coal from several large Russian producers.
Indian companies are also paying for Russian coal cargoes in rupees, although such transactions are made predominantly for trades of thermal coal.
The bulk carriers (Handy/Supramax/ Panamax size), which were coming to eastern-Mediterranean ports and with cargoes were either taking cement or clinker or some minerals from Turkey or Egypt and some from Greece, but majority was ballasting to Ukraine/Russia to load grain/urea/fertilizer/slag/clay/coal/iron ore. The volume of such cargoes decreased almost 70%. Only four major Russian grain traders were shipping almost around 12mt together but since the beginning of the war their export ex black sea ports is not even 30% of this quantity. Turkish coal import from Russia was almost 7mt but that went down to 100,000/150,000 metric tonnes in a period of total 4 months.
QUANTITY CARRIED LESS DUE TO WAR BETWEEN FEBRUARY – MAY 2022
466 tonnes 594 tonnes
129 tonnes 337 tonnes
Total: 1,526,000 tonnes
Equals to 305 voyages basis 5,000 tonnes lots.
Source: Metalexpert
Grain carried before war between January 2021 January 2022 from Ukraine and Russia only to Turkey was around 7mt in total.
From February 2022 until July 2022 it is around 1mt. So 6mt cargo as grain disappeared which is equal to 1,200 voyages of 5,000 metric tonnes each.
Voyage shipments of grain started to increase after Russia, Ukraine & Turkey signed in beginning of August and since then only in August only 2mt grain shipped out of Ukraine and Russia to various destinations.
Thanks to Turkey, who did not follow the sanctions declared by USA/EU countries to Russia, there were still some grain and coal cargos moving, which would otherwise have seen a lot of owners bankrupting.
Besides the decrease in the volume of the cargoes ex Black Sea, there also was sanctions applied to the vessels which were calling Russian ports and that was applied not only to the vessels calling Russian Black Sea port, but all Russian ports. That had affected the export and import of other ex-CIS countries who were only using Russian ports because they do not have any shore on the sea.
Now, as of July 2022, it seems that shipment of grain cargoes and all other agri products and coal is going to be free and there will be no sanction to the ships calling Russian ports.
This will help the freight market to recover and start going firmer.
However, due to the decreasing grain and coal FOB and CFR prices, especially buyers in Turkey are very reluctant to conclude purchase deals and Egypt who’s the biggest grain importer in this area have great difficulties in making the payments. As a result of this now the coaster freight market is very low and depressing as well as the time charter rates of bulk cargoes out from Med to Far East and also to US Gulf destinations are low.
How BSM is supporting to meet new IMO regulations “A win-win situation for owners and charterers”
In BSM’s central Fleet Monitoring
and
performance
in real time, including energy efficiency.
Bernhard Schulte Shipmanagement (BSM) has long been a key player in the dry cargo segment, presently having more than 170 bulkers ranging from handysize to very large ore carriers (VLOC) under management, writes Firoze Mirza, Managing Director BSM Hong Kong.
As part of its technology leadership, BSM has established a Fleet Performance Centre (FPC) and Fleet Monitoring Centre (FMC) to optimize the operations and efficiencies of the managed vessels.
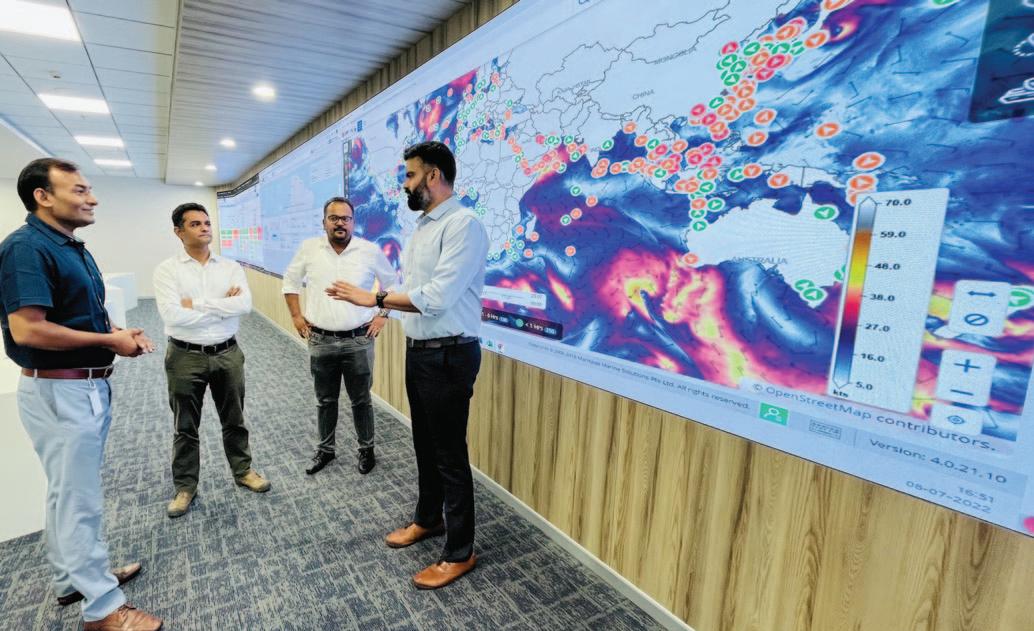
The issue of vessels’ voyage performance, especially in relation to their carbon footprint, has been given greater urgency by the new IMO regulations, with the Energy Efficiency Existing Ship Index (EEXI) and Carbon Intensity Indicator (CII) taking effect in 2023. However, BSM has long recognized the role that enhanced fleet performance plays as part of its service to shipowners, keeping in mind that reducing fuel consumption and thereby emissions automatically saves fuel costs, and thus is a win-win situation for all vessel operators, their customers, and the environment.
Through a holistic process of vessel performance monitoring, decarbonization management, data collection and data analytics managed out of our own Fleet Performance Centre, BSM is helping
owners navigate the complexities of the new IMO requirements.
BSM developed an in-house EEXI calculator to compute the required and attained EEXI values of the managed fleet and generate the corresponding EEXI technical files. The data-backed recommendations target technical and operational improvement methods for the ships. Similarly, BSM developed a CII calculator addressing the CII ratings of its entire fleet. This year, BSM’s Fleet Performance Centre will release additional tools for CII performance monitoring services, including predictive algorithms, to assist owners with vessel CII improvement investigations.
The aim of all these initiatives is not merely to ensure compliance with the IMO’s EEXI and CII requirements, but rather utilize these as tools for continuous and ongoing benchmarking and improvement, to reduce carbon emissions and minimize fuel costs.
As part of the FPC, the Fleet Monitoring Centre offers a 24/7 vessel operations and compliance monitoring service. This state-of-the-art facility is supported by nautical and technical experts and fleet performance analysts.
The FMC offers decision support to crew, technical staff on shore and continuous
improvement of vessel operations. A dedicated fleet performance team models ships and builds a unique digital twin that enables comparison of ships’ actual performance to its ideal performance.
The FMC acts as a central support team for BSM fleets to improve the navigational and commercial aspects of vessels through three key areas:
Increasing energy efficiency andv ensuring CII compliance by monitoring major consumption contributors, such as the main engine, auxiliary engines, and boilers as well as compressors.
Operational risk mitigation, assistingv fleet teams to prevent any emergencies through weather warnings and routings, emissions area monitoring, canal transits and piracy area monitoring.
Voyage optimization: the FMC canv enhance the commercial performance of managed vessels through voyage planning and tracking and post-voyage analysis.
The FPC has developed a benchmark, dubbed vessel performance rating (VPR), which is an aggregate of voyage performance, reporting quality and machinery performance, each of which are themselves a collection of individual
VESSEL PERFORMANCE RATING (VPR)
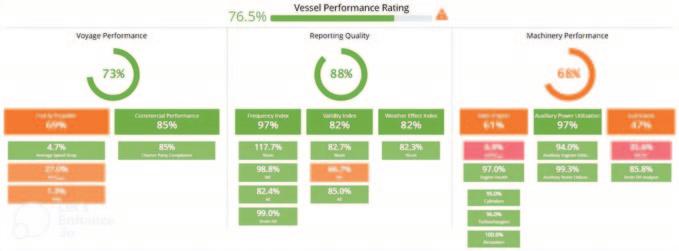
Since measurement of the VPR began, considerable improvement has been noted across the entire BSM Fleet, with the average VPR increasing from 55% in September 2021 to 65% in June 2022.
One challenge we have observed when discussing our performance optimizing services with clients across all shipping sectors, including the bulker industry, is that most benefits (voyage efficiency and fuel savings) achieved through investment are mainly realized by the charterer, as opposed to the shipowner and manager who bear the costs of investing in the improvements.
Due to the archaic charterparty contracts still utilized, there is no mechanism for the owner to share the
benefits. This results in a less than optimum situation, where owners are unable or unwilling to invest in latest technologies (such as telemetry) which would enhance performance, and charterers lose out on potential fuel savings, and the opportunity of zero cost (or even negative cost) carbon reduction is wasted.
As the industry moves into 2023 and beyond, IMO’s initiatives will result in greater acceptance by ship owners of investment in carbon reduction (and fuel saving) opportunities. At the same time, the end-user charterers will agree to pay a premium for the same, resulting in a winwin situation for all.
Accelleron and Hoppe Marine to partner on data collection for improved vessel performance analytics
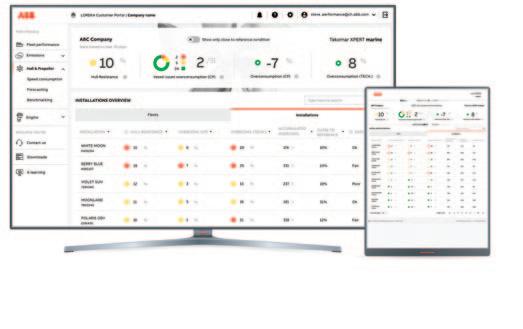
On June the 8th, 2022, Accelleron, the new face of ABB Turbocharging, and Hoppe Marine, the German provider of maritime measurement solutions, have signed a partnership agreement which will facilitate rapid onboard data collection for Accelleron’s digital solutions used in dedicated engine analysis.
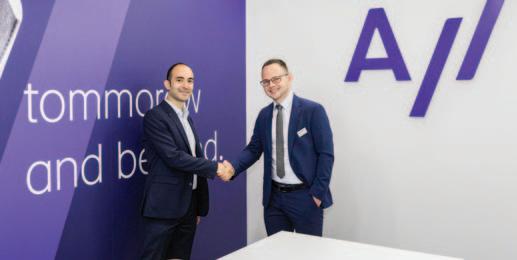
In particular, Tekomar XPERT marine, Accelleron’s comprehensive digital suite that delivers customers with powerful insights into vessel’s hull and propeller performance, as well as emissions tracking and forecasting, will be further enhanced with continuous data connectivity.
Hoppe Marine has extensive experience with data generating systems on board, including automation systems and sensors from different suppliers. This data is delivered in a highly structured and standardized way, and will enable Accelleron to pre-populate the input to Tekomar XPERT marine, thereby increasing
efficiency and effectiveness.
“Having fast and accurate information is an essential basis for optimizing vessel performance. This agreement will allow us to leverage Hoppe’s established onboard data collection services to serve our customers even better with value-adding analytic support. The data can be transferred swiftly and accurately, eliminating the need for manual data collection by the crew, and is essentially a ready-to-go system,” said Mauro De Micheli, Head of Sales, Marketing and Partnerships for Digital solutions, Accelleron.
Hoppe Marine’s system infrastructure is designed to enable the collection of data from a wide range of onboard systems. This eliminates the need for shipowners to install additional IoT solutions on board to provide data.
This means that high quality data analytics can be carried out continuously,
rather than being based on ad-hoc engine readings.
“We are pleased to enter into this important cooperation agreement with Accelleron. Both companies are committed to supporting the maritime sector in its efforts to become carbon neutral. By working together to enable owners and operators to achieve fuel savings, emission reductions, and optimized engine performance, we are delivering concrete evidence of this commitment,” said Hauke Hendricks, Head of Sales at Hoppe Marine.
Customers retain full control over their vessels’ data, and operational signals can be shared via ship-to-shore connectivity. Furthermore, by having enhanced and continuous readings to provide engine and vessel insights, trends become quickly apparent enabling any required actions to be promptly taken. No cabling or wiring onboard ship is required to connect the two systems.
What is the vessel’s current CIIv rating?
What will be the impact of CO2v emissions on the current CII rating due to the future trade pattern? How to identify the most suitablev trading pattern for better CII ratings? How to determine the optimumv speed instructions for a vessel for a certain trade route?
BOSS CII ESTIMATOR FEATURES

2,000 Simulations at an Instant:v Considering 100 Cape Vessels in a fleet, simulating all Baltic route combinations for eco and full speed at both laden and ballast conditions would have taken 2000 simulations.
BOSS CII Estimator dramatically cuts this down to one click & one second. Supports Vessel Specific Balticv Routes: Computes vessel class specific Baltic Routes at a click of button, and generates the estimated CO2 emissions and corresponding CII rating.
Estimations basis Vessel’sv Performance: Uses vessel’s past data or sensor data to generate a digital twin and provide realistic estimations. Estimations basis Vessel’s SnC datav Draught and Load Condition Specificv Simulations
Dynamic Sea Margin: The estimatorv does not only consider a standard sea
margin for simulation, but also provides an option to use historical weather data to calculate sea margin.
Vessel Specific Retardation Factors:v
Apart from Sea Margin, the BOSS CII estimator also takes in vessel class specific weather and sea retardation factors to compute speed and emissions details, giving a much transparent and practical estimates. Determine Optimum Speed &v Trading Pattern: On simulating the different trading routes, BOSS CII estimator suggests optimum speed and trading pattern to optimize CII rating of vessels.
Fuel Specific Calculations:v Calculates CO2 emissions based on fuel type usage.
Interactive UI: Removes the need forv both tedious excel sheets and
evaluating results on multiple routes. Instead, an interactive interface provides a much simpler way to conduct route and speed comparisons.
Share Simulation Reports: BOSS CIIv estimator lets the user easily export and share simulation details with anyone.
ABOUT BLUE WATER
The company provides a host of Software as Service for voyage optimization including its pioneer cargo heating management for tankers. Blue Water employs 100+ personnel in its Dehradun office and currently optimizes over 700 vessels of various type for maritime industry leaders, and provides quantifiable savings through a verifiable benchmarking system.
Lloyd’s List Intelligence launches Predictive Fleet Analytics
- CUT DELAYS AND COSTS WITH TRANSFORMATIVE MARITIME ANALYTICS
- PREDICT DESTINATIONS WITH UP TO 70% ACCURACY
- PREDICT TIME OF ARRIVAL TO PORT WITHIN +/- 10 HOURS AND TIME TO BERTH WITHIN 1-2 HOURS
Twenty seven per cent of vessels fail to arrive within 24 hours of their published Estimated Time of Arrival. This lack of accurate AIS-based data puts pressure on ports, hampers logistics and pushes up costs. This could soon change, however, thanks to transformative new analytics from Lloyd’s List Intelligence, the maritime data experts, trusted by more than 60,000 professionals across the globe to power their decisions in operations, compliance, and risk management.
Introduced from 8 August 2022, Lloyd’s List Intelligence ‘Seasearcher Predictive Fleet Analytics’ is the first ever ‘air traffic control’ for the world’s commercial shipping fleet. It combines near-real-time
data collected from 3,000 sources, resulting in over 327 million AIS vessel positions monthly across the global fleet. Specially designed advanced analytics, AI, and machine learning transform this unique data into accurate estimated times of arrival into port (ETA), arrival times at berth (ETB), and times of departure (ETD) for key active commercial vessels, along with current and future estimates of port congestion.
Lloyd’s List Intelligence are the first to bring ETBs and ETDs to market, and no other provider brings together a broader range of predicted, actionable insight.
INDUSTRY-WIDE PROBLEMS
Currently, over a third (36%) of Automatic Identification System (AIS) messages are missing ETA data, while another 27% of vessels fail to arrive within a day of their published ETA. Even destination data is unreliable, with 63% of vessels publishing one port destination but ending up at
another (source: Lloyd’s List Intelligence 2020 AIS message analysis).
A POWERFUL SOLUTION, REQUESTED BY CUSTOMERS
Destination and ETA data gaps represent one of the most severe business challenges to the supply chain – impacting the ability of businesses to work efficiently, effectively and profitably:
Financial losses: like demurragev charges, additional waiting and handling fees and invalid pricing Damaged customer relationships:v from delivery misjudgements, schedule changes and reassignments
Loss of sales: from a lack of visibility,v reactive service delivery which have a negative impact on customer experience
Informed by over 100 customer and stakeholder interviews across companies and government organizations, Predictive Fleet Analytics has been built in response
to these widespread industry challenges.
Delivered as API data and integrated into the Seasearcher platform, Predictive Fleet Analytics helps customers gain greater certainty around estimated destination, arrival, berthing, and departure times, along with port congestion status and waiting times. This greater level of insight is key to more efficient voyages and port operations and the optimal use of vessels, fuel, port facilities and services, and the teams that operate them all, resulting in time and cost savings.
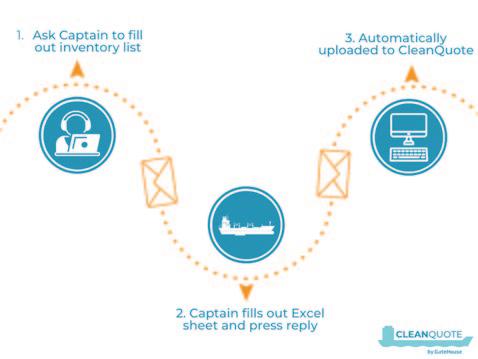
With analytics powerhouse partner
SAS, a leader in artificial intelligence (AI), data mining, modelling and forecasting, Lloyd’s List Intelligence have developed this pioneering new method of calculating, predicting, and learning from vessel movements and behaviours in ways that were not possible before.
The AI and machine learning models predict destinations with an accuracy of 70%, ETA to port within ±10 hours, and ETB to within 1 2 hours, catering for key vessel types in the commercial fleet operating to both fixed and non-fixed schedules.
“Predictive Fleet Analytics allows our
customers to let decisions on scheduling and routes be driven by the best quality data, so that shipping companies can save on resources and costs,” says Parvin Conners, Vice President of Product and Data for Lloyd’s List Intelligence.
“This new level of prediction around destinations and arrivals helps ports to optimize their services and facilities and for maritime servicing businesses to run more smoothly. All of this is possible thanks to the strength of our data and analytics and how we use AI and machine learning.”
Start-up company CleanQuote launches major software update to eliminate hidden vessel cleaning costs
When operation managers tend to their fleet of vessels, their main focus is typically on fuel, food, and crew. But in many cases, the vessels also need extensive cleaning — for instance when a dry bulk vessel changes cargo from coal to grain. Recent findings show that cleaning expenses are taking an increasingly large toll on operation budgets. Often, cleaning supplies are not ordered in time, or cleaning crews are not booked until the very last minute, which leads to longer port time and higher costs.T o avoid this, CleanQuote has digitalized the entire vessel cleaning process and is now introducing a new tool kit enabling operators to gain valuable insights never seen before.
It has been a busy summer for Danish start-up company CleanQuote. While tending to more than 500 existing users of the CleanQuote digital platform, developers have also laid the final touches on a new tool kit that will make a real impact when dealing with vessel cleaning.
“Originally, we set out to make a digital platform that would help maritime operators get their work done faster and easier.” says co-founder Lasse Ekdahl. “Therefore, we built the CleanQuote platform and made it free of charge for our users to send requests for cleaning supplies or cleaning crews. But with the new tool kit, we are really taking things up a notch.”
The new tool kit is called CQ Operator, and it focuses on inventory lists – or ‘ROBs’ as they are called in the industry, which is short for ‘Remaining on Board’.
Via CQ Operator, operators can with a press of a button have captains generate and send ROBs. Furthermore, they can also define stock minimums — for instance if they always wish to carry at least 1,000 litres of a certain cleaning chemical.
The system can automatically setup alerts and notifications when items are removed or missing from the stock, making it a lot easier for the operators to ensure that the necessary cleaning products are available on site as soon as the vessel in question is ready for cleaning.
“The biggest advantage of the new tool
kit is that it gathers all communication between operators and their vessels in one user-friendly and manageable solution.” explains Ekdahl. “Until now, many of our customers have had to handle their ROBs as spreadsheets, which are often lost or misplaced making the communication a real struggle. Especially when handing over a vessel from one operator to another. They simply haven’t had a suitable tool to generate the perfect overview of when and how a specific vessel was last cleaned. Now, they can register everything in CQ Operator — including cleaning history and data on chemical consumption.”
Remaining on Board flowchart.
cleanquote.com and is available to both existing and new customers. Basic use of the CleanQuote platform is free of charge, while use of CQ Operator requires a monthly fee.
ABOUT CLEANQUOTE
Precise inventory of consumed chemicals per vessel cleaning is also valuable information for ship owners and operators committed to reducing their environmental impact. Currently, several global ship owners are seeking to optimize their cleaning processes by cutting down on the use of bleach and other substances. In support of this, CQ Operator can also provide useful insights.
The new module can be accessed via
CleanQuote helps simplifying the purchasing process with an easy-to-use platform with a clear focus on cost and time optimization. The continued development of CleanQuote is based on input from numerous operators, ship managers and suppliers involved in hold and tank cleaning all over the world. The company is dedicated to adding value to the carrier cleaning challenge and give its customers the right tools to make optimal decisions.
Anemoi Rotor Sails continue to gain momentum
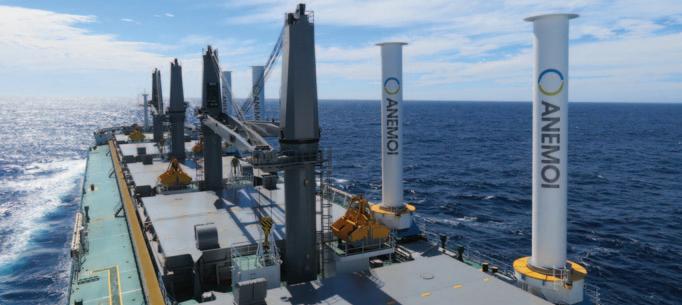
It has been a busy 2022 for Anemoi, a global player in wind-assisted propulsion for commercial vessels, with the company expanding in London and China to meet growing demand for its emission reduction solution.
In July, Singapore-based dry bulk owner Berge Bulk announced that it had signed agreements with Anemoi –– to supply and fit two vessels in its dry bulk fleet with Anemoi Rotor Sails. Berge Bulk is a leading independent shipowner which has put sustainability at the heart of its operations.
The first vessel, Berge Neblina , a 388kdwt Valemax ore carrier built in 2012, was made ‘wind-ready’ earlier this year. This means the structural integration required prior to installing the technology was carried out during a scheduled dry dock.
Four of Anemoi’s large folding (sometimes referred to as tilting) deployment Rotor Sails are set to be installed to improve vessel performance. Folding Rotor Sails can be lowered from the vertical to mitigate the impact on air draught and cargo handling operations.
This flexible ‘wind-ready’ approach has been taken to align with vessel availability and Anemoi’s production slots.
The same approach has been taken with a second vessel, Berge Mulhacen — a 2017built 210,00dwt Newcastlemax bulk carrier — which will also receive four folding Rotor Sails. Plan approval has been obtained for both ships from DNV.
“The agreement with Berge Bulk is a further confirmation that forward-thinking shipowners are turning to wind-assisted propulsion to help them achieve their environmental objectives. It proves, once again, that Rotor Sails are a realistic and workable solution that result in significant carbon savings,” said Kim Diederichsen, CEO of Anemoi.
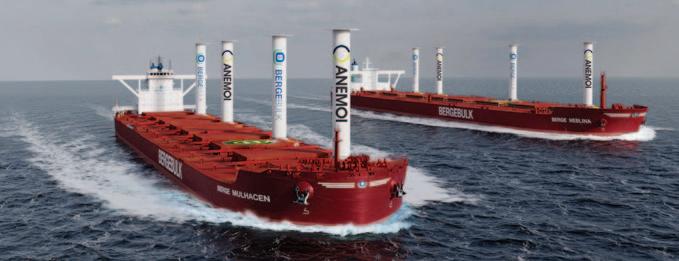
APPROVAL IN PRINCIPLE
In June, classification society Lloyd’s Register granted Approval in Principle (AIP) for an SDARI (Shanghai Merchant Ship Design and Research Institute) designed 210,000dwt Newcastlemax bulk carrier installed with Anemoi Rotor Sails to significantly improve efficiency and reduce environmental impact.
The Newcastlemax AIP is part of a pioneering joint development project (JDP), signed in 2020, with Anemoi, Lloyd’s Register and SDARI.
It brings together the OEM, classification society, ship designer, and ship
owner to develop a series of energyefficient vessel designs equipped with Rotor Sails. Oldendorff Carriers is the shipowner partner for this Newcastlemax design.
The AIP covered the structural integration for a ship design with six 5x30m Rotor Sails and Anemoi’s Rail Deployment System, which sees the Rotor Sails move transversely across the deck to avoid inference with cargo handling; and the structural integration for a ship design with four of Anemoi’s folding (tilting) 5x35m Rotor Sails.
Lloyd’s Register assessed the calculation used to estimate the impact the Rotor Sails will have on the Energy Efficiency Design Index (EEDI) and validated that the newbuild would have its EEDI score reduced from 1.92 to 1.37 (29% reduction) by installing six 5x30m Rail Rotor Sails and 1.47 (23% reduction) by installing four 5x35m Folding Rotor Sails.
“We were very pleased with the outcome for the first vessel included in the JDP. EEDI is a significant driver for the installation of Rotor Sail technology and, as we grow closer to the implementation of EEXI and CII, they too become important incentives for Rotor Sails, along with the overarching reductions in fuel consumption and associated emissions,” said Nick Contopoulos, the Chief Operating Officer at Anemoi.
“To have the impact pre-validated by LR has been a key step in continuing to prove the importance of our technology in the
context of the decarbonization of shipping. Both design configurations (folding and rail) of Rotor Sails for a Newcastlemax vessel are available to order now.”
Other vessels included in the JDP and to follow are an 85,000dwt bulk carrier, a very large ore carrier (VLOC), a 114,000dwt Aframax tanker, a 50,000dwt MR tanker and a very large crude carrier (VLCC).
TECHNOLOGY REIMAGINED Wind propulsion, which was used to power ships for thousands of years before fossil fuels became readily available, is back in the agenda for shipowners. As a completely renewable resource, wind is an appealing and beneficial option in the race towards decarbonization.
Rotor Sails make use of the aerodynamic phenomenon known as the ‘Magnus Effect’. As the cylinder rotates within an airflow, a forward thrust force perpendicular to the apparent wind direction is created, which delivers additional thrust to the vessel. The thrust generated can either provide additional vessel speed or maintain vessel speed by reducing power from the main engine. The tall cylindrical sails can be installed on the main deck, bow or elsewhere with sufficient space.
Rotor Sails, also known as Flettner Rotors, were first installed on a vessel over 100 years ago. But through research and innovation, Anemoi engineers have reimagined the technology for modern use.
ioCurrents & ScanReach partnership benefits merchant fleet and offshore
Data analytics specialist ioCurrents and ScanReach, a groundbreaking maritime wireless IoT solutions provider, have formed a strategic partnership to help ship operators and the offshore sector become more efficient and sustainable.
ScanReach has spent years researching and testing its systems so that it can confidently offer the industry a robust wireless technology that will collect vessel data from onboard sensors without the need for costly and disruptive equipment installations.
This data will then be analysed by ioCurrents to provide invaluable insights that will improve the safety and performance levels on vessels and offshore installations.
ioCurrents specializes in data analysis
using AI and machine learning to output real-time fact based insights. This helps improve decision making with the ultimate goal of achieving operational efficiencies and reduced OpEx which will also help contribute to a more sustainable business model and improve crew safety.
“Linking up with ioCurrents was an easy decision to make. I have worked with the team before and know how using the insights from their proprietary platform MarineInsight™ can have a dramatic positive effect on a company’s operations,” said Sven Brooks, ScanReach’s Chief Commercial Officer.
ScanReach’s technology can even be used for onboard personnel tracking and location during emergency situations to aid precision rescue team involvement and
automatic mustering count.
Jon Best, Director of Business Development for ioCurrents, said, “Forming a partnership with ScanReach is really exciting as their wireless solution makes data collection so much easier than having to install miles of cabling on a vessel or offshore platform.
“Their tried and tested technology works on even the most complex steel environments and their ‘plug and play’ solution means that clients can do the whole installation themselves with minimal operational disruption. When adding sensors, such as ConnectFuel, ioCurrents can seamlessly ingest the ScanReach data and perform actionable insight to strengthen output with MarineInsight’s analytics.”
MoorMaster automated mooring completes one million moorings
Cavotec’s MoorMaster™ automated mooring systems have completed more than one million moorings at bulk, ferry, Ro/Ro, container handling and lock applications all over the world, making ports safer, more efficient and more sustainable.

MoorMaster replaces hazardous conventional mooring lines with remotely operated automated vacuum pads that moor and release vessels in seconds at the push of a button.
The technology dramatically improves safety and operational efficiency, optimizes the ship-toshore interface, and in many cases enables ports to make infrastructure savings.
Passing one million moorings is a major milestone that highlights MoorMaster’s key role in transforming the maritime industry by improving safety, maximizing productivity, and minimizing environmental impact. MoorMaster remains the only widely used automated mooring technology on the market today.
As more and more operators discover the stepchange MoorMaster offers, Cavotec expects to reach two million moorings even faster than it reached one million.
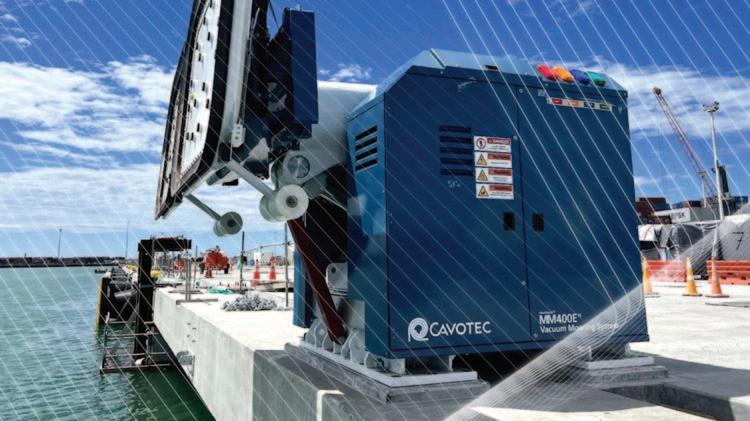
Unikie enables even smarter ports
How many times have you heard people asking “When” in a port? Ports are complicated ecosystems where everyone’s actions have an impact on others, writes Anders Berg, Senior Manager Maritime Solutions, Unikie Sweden.
Ports have been the heart of international logistics for centuries. Ports, just like all the other segments of modern society, have been digitized heavily in past decades. Still, in today’s ports, the most frequently asked question is: ‘when?’.
Despite heavy investments to port digitalization, a significant part of daily operations at ports are still managed manually. When something changes, very often the primary communication channel is phone calls. A lot of service and business orders are sent by email and processed manually. Even complex operations are planned and scheduled by using Excel. All these manual processes and one-to-one messages are causing significant inefficiency to ports simply because of the lack of information, data, and communication.
Unikie has during the last three years developed together with ports and authorities a digital solution — based on the open ecosystem platform — that now is in use in 20 different ports in the Nordic countries. Unikie’s Port Activity App (POLO) brings all port call process stakeholders together and enables increased situational awareness and optimized efficiency. The open platform principle emphasizes co operation and an organically grown ecosystem by taking full advantage of existing systems, better visibility, and utilization of existing data.
All development, both current and future, is created in close cooperation and synchronization directly with ports. POLO provides a new toolset for ports to improve the overall efficiency of port flow,
Fig 1. Service providers get notifications and also have the possibility to receive automated calls in POLO.
covering the end-to-end chain of actions and operations related to vessel visit. It is a user interface for port digitalization and communication based on open ecosystem and open interfaces, strengthening collaboration both inside the port community and between ports. It creates an ecosystem for awareness, automation and autonomous operations using four
layers:
Knowledge: a centralized place ofv information and common situational awareness; Communication: a digital toolchainv replacing traditional phone calls and emails; Workflow: enabling a sharedv workflow for efficient port operations and extended planning horizon; Intelligence: optimizing businessv operations with real-time data analytics and AI.
Some recent examples of development are the service order feature and predictive berth planning tool feature. The service order feature enables agents to

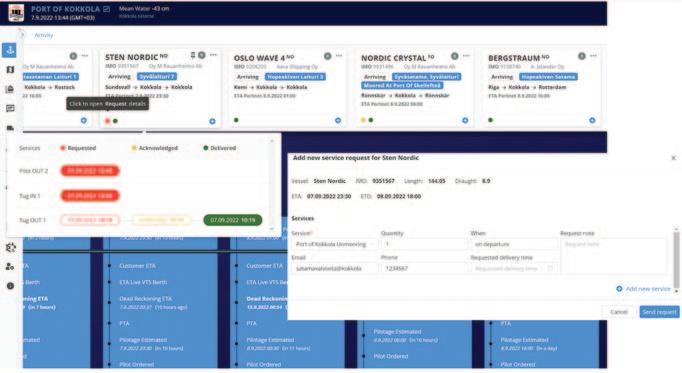
order any service or permission that a vessel needs in port. The service providers get notifications and also have the possibility to receive automated calls. These processes are clearly visualized in POLO (Fig 1).
And on top of this, it is possible to integrate service orders to external systems via REST API.
Predictive berth planning tool is another new feature that calculates the vessel discharging and loading times based on the cargo commodity and known discharging or loading efficiency. With this information it's possible to get a much better estimated time of departure (ETD) than using any AI or history based data. Improved predictability for ETD leads to higher possibility to achieve Just-In-Time Port Calls.
THIS IS DONE BY:
Reserving needed cranes & forkliftsv per vessel to have full picture of resource usage
Adding cargo details (commodity,v amount, loading & discharging) and operations efficiency to estimate absolute operation duration
Defining work time modes (normal,v non-stop, overtime) which is used to calculate actual operation times
Adding & modifying commodities andv operational efficiencies
Adding & modifying local holidays andv worktimes
Predictive berth planning tool is another new feature that calculates the vessel discharging and loading times.
These are the new developments that ports in the Nordic countries are starting to implement. There are also numerous features and their implementations that are the outcome of utilizing the open ecosystem in close cooperation directly with ports. One exciting ongoing
development is the Just-in-Time principle where ports are challenging the “first come, first served” principle with assistance of POLO.
POLO is however merely step one on port digitalization journeys ahead. True value of digitalization is achieved when those using new solutions understand them and, more importantly, use them. POLO offers all information port call stakeholders need at their fingertips in an easy-to-understand way, but to find the benefits and optimize port calls the human element is essential. It’s also good to keep in mind that this is just the beginning. Once data collecting and sharing processes
and tools are in place, we are ready to start optimizing port business and gaining a real competitive advantage for ports, shipping and the maritime world.
ABOUT UNIKIE
Unikie is a Finnish software technology company that develops technologies for protected real-time processes. Its services concentrate on the crossroads of three global macrotrends — IoE, 5G, and AI — where our technology solutions enable a constant awareness of the surroundings, as well as decision-making and control based on this awareness. Clients include pioneers of real-time data utilization in the
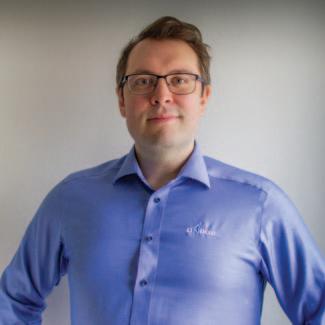
automotive industry as well as other industries and telecommunication companies worldwide.
Cygnus launches a brand new Ex Certified thickness gauge
Visitors to the Cygnus stand at The Materials Testing Exhibition earlier in September 2022, were first to see the much anticipated, new Cygnus Ex-certified product in the flesh. Now, it’s time to reveal what the new Cygnus 1 Ex Ultrasonic Thickness Gauge is all about.
This rugged, IP67-rated, intrinsically-safe instrument is specially designed to take reliable thickness measurements in Zone 0 Explosive Atmospheres, including: oil and gas;v mines;v chemical plants;v fuel depots;v road tankers;v oil and gas tankers;v explosive atmospheres; andv hazardous storage tanks.v
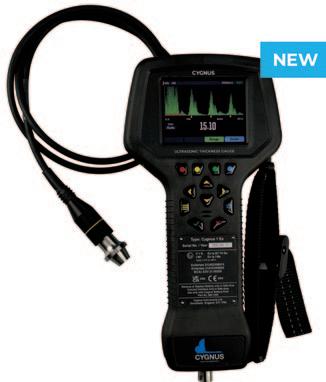
WHAT IS SPECIAL ABOUT THIS LAUNCH?
Like its predecessor, the Cygnus 1 Ex is the only one of it’s kind in the world certified to ATEX, IECEx, UKEX for Zone 0 and NRTL for Class 1, Division 1. But the Ex takes a giant leap forward, offering impressive new selectable features including live A-Scan, comprehensive datalogging and manual measurement mode, which brings Cygnus’ Intrinsically Safe offering up to speed with Cygnus’ most advanced gauges.
First of all, the 3 measuring modes that one may be familiar with amongst Cygnus’ surface range, designed for varying levels of corrosion, multiple materials and throughcoat measurement capability, are now built into this new gauge and available to hazardous and explosive environments.
Measurement verification and recording are also far more advanced. The addition of Live A-Scan and B-Scan allows precise measurement verification with on-screen
visuals via the large 3.5” outdoor-readable display, and the comprehensive data-logging feature ensures seamless data analysis and report generation.
The entire gauge, from how it sits in one’s hand, to collecting and storing measurements, is entirely geared towards the best user experience, making inspection quick and easy, despite the challenging environment. Four new function keys are purposely integrated to maximize ease and speed of control, four dynamic screen views aimed to suit user requirements, and a user access feature to prevent access to protected features.
WHY ARE INTRINSIC SAFETY AND EX CERTIFICATION SIGNIFICANT?
Carrying out inspections with testing equipment certified to a suitable protection level is vital to ensuring the testing operation does not jeopardize the safety of hazardous environments. It is important to understand which is the correct equipment, and where to use it.
For equipment that contains electronic components including batteries, the intrinsically safe protection concept ensures that under both normal uses and with applied fault conditions, no arc or spark can be generated, and no component can heat up enough to cause an explosion.
SOME INTRINSICALLY SAFE DESIGN CRITERIA :
The output energy at the terminals isv limited so a spark cannot ignite an explosive atmosphere.
The equipment must be anti-staticv and not be able to hold a static electricity charge.
Voltages must be electrically ‘clamped’v to safe levels.
The use of redundant safetyv components.
If a battery or component fails, itv should not produce high temperatures that could be incendiary.
In both IECEx, ATEX and North American NRTL systems, intrinsically safe equipment can be used in any Zone or Division with the correct equipment protection level.
Under the IECEx and ATEX systems, explosion-proof/flame-proof equipment cannot be used in Zone 0 areas, regardless of equipment protection level.
Most importantly, only equipment that has an Ex Certificate (ATEX/IECEx/ UKEX/NRTL) can be considered for use in Zone 0/1/2 areas.
In the USA equipment that only has a MIL-STD-810G, Method 511.5, Procedure I test pass CANNOT be used in Zone 0/1/2 areas.
The Cygnus 1 Ex, like all Cygnus products, is manufactured in the UK and is the only Zone 0 (Ga, Ma) Certified UTG available today (for ATEX/IECEx/ UKEX/NRTL).
Alfa Maritima International — chartering bulk carriers since 1990
Since 1990 Alfa Maritima International AMI, Reliability & Security, has been chartering bulk carriers for dry bulk maritime transportation for grains, minerals, bauxite, iron ore, cement, clinker, and fertilizer, among other dry bulk commodities.
AMI specializes in developing ideas and strategies which lead to achieving the objectives of its commercial allies and suppliers, generating solutions, efficiency, and added value for the grains, minerals & other dry bulk commodities. Its supply chains provide reliable transportation on bulk carrier vessels for North American and Latin American industrial corporate customers such as EMPRESAS POLAR, CEMEX, FERRO ALUMINIO, among others.
In 2020, Luis Urdaneta Eraso established AMI in Cleveland, Ohio, USA.
The company is focused on industrial manufacturers, steel, alum, cement, chemicals, grain, food and beverages, all corporations that require to move, their dry bulk raw materials and recycled commodities located in the United States of America, Canada, and Mexico. Taking into account Mr Urdaneta’s background and his experience of more than 30 years with proven results, AMI is ready to develop synergies with these industrial corporations, offering the following:
Development strategies that lead tov
generating solutions, efficiency, and added value.
Supply of expertise in chartering bulkv carriers for the transportation of dry bulk commodities.
The economy of scale solutions.v
The Alfa Maritima Internationalv strategic vision becomes an added value to its allies.
Research & development of reliablev business alliances between industrial commodities manufacturers and firstclass ship owners for efficient supply chains.
Define the scope and timeline of itsv service & operations.
Charter Parties Administration forv charterers to a time charter smooth operation during the hire of the bulk carriers vessels and for the COA executions.
Co ordinate operations of thev different supply chain actors, performing between the shipowners and our charterers and other commercial allies to assure the implementation and execution of smooth operations across the supply chain.
Develop regular evaluations to assurev quality, reliability, and security in its services operations.
Keep frequent communications tov
explore new opportunities and develop projects.
Develop expertise in maritimev transportation for dry bulk commodities within its charterer's customers.
AMI will present solutions tov transportation problems to assure efficiency along the different links of the supply chain.
Reliability and security for maritimev transportation.
Currently, AMI is working on mineral projects to ship it from South America to the European Union and other destinations. AMI is attending to different charterers to deliver grains from North America to Latin American countries and transport chemicals between the United States to Latin American customers.
AMI is able to supply added value to its clients’ operations for or from LATAM. AMI is able to assist clients in developing their plans together, by leveraging its direct relationships with the most reliable and best shipowners worldwide.
Despite having 30 years of performance experience in chartering dry bulk commodities, Luis Urdaneta Eraso got the Shipbroking and Chartered Vessel Operations certification from the ASBA New York Shipbrokers Association on 5 October 2020.
How dry bulk can benefit from data standardization
The much-discussed Energy Efficiency Existing Ship Index (EEXI) and Carbon Intensity Indicator (CII) regulations are now just a few short months away from taking effect, writes Tor-Arne Berger, Veson Nautical’s Spokesperson and Q88 Product Manager.
This will have a huge impact on dry bulk carriers. Estimation and analysis from Simpson, Spence and Young suggests more than 75% of the existing tanker and bulker fleet will not attain EEXI baselines and will need to take action to achieve compliance.
Data is a powerful tool for companies in the dry bulk sector that can drive more openness, transparency, and accountability. However, knowing that data can be harnessed to meet ESG regulations, ensure compliance and improve operational efficiency is only part of the puzzle.
In recent years, the amount of data that each vessel generates has increased exponentially. This spans from the information a vessel produces technically
(from automation systems etc.), as well as commercial data on where the vessel is, and where it will be, based on the rapid development and sophistication of prediction algorithms. There is so much data noise for companies to sift through –from different sources, stored in disparate locations — that it can be near impossible to make sense of the information, let alone drive actionable insights.
Bulker owners and operators could be using data not only to inform them on vessel compliance, but to manage documentation, handle vessel question naires and enhance commercial communications with charterers, brokers and agents. Keeping data to yourself is no longer viable in today’s shipping market. Strategically sharing information can drive more collaboration, more visibility and means organizations are not making decisions based solely on their single view of the world.
However, being able to share data
strategically within the dry bulk sector requires organizations to speak the same data ‘language’. At present, there is no standard way to exchange, interpret information, or effectively speak in a common language across the maritime industry. A lack of common data standards makes it very difficult to exchange information, as data from different sources do not match up or use different formats to describe the same thing.
To maximize data usage and analytics, a normalized language needs to be developed and collaboration across the industry is central to achieving this. Veson’s recent acquisition of Q88 feeds into this vision of working together to define and enable the adoption of a standard that is set to facilitate and drive communication and optimize efficiencies.
The original Questionnaire 88 was built to create standardization around vessel suitability and risk and has long been an established industry standard for
information on tankers for vetting purposes. For the dry bulk industry, the Baltic99 questionnaire is the most common, but it’s not as central as the Q88 is for tankers — yet. As ESG and green initiatives become increasingly more central to doing business, we expect that a standardized questionnaire will become a key method to share vessel data and win business. The questionnaire is a great starting point, but there are many different types of documents and different data points involved. Q88 has evolved to help make fleet certificate management simple
for bulk owners and operators, with its Q88Dry solution. Additionally, Q88 Dry enables charterers to programmatically include vessel details into their workflows for greater ease and standardization in maintaining a vessel database.
Having a single source of vessel data can improve efficiency, compliance, and collaboration within the dry bulk sector. Owners and operators could gain full accountability from an audit trail and use that data to maximize fleet utilization, ensure compliance with changing regulation, and respond rapidly to vessel
information requests.
The future potential for what can be achieved with data within the maritime industry is exciting. Direct sharing of information between different counter parties will become commonplace within the dry bulk sector, helping to drive more open transactions, better transparency, and compliance.
Willing participation and collaboration are the key to creating the industry-wise protocols and standards that will drive this pace of change, facilitate communication, and optimize efficiencies.
NEOGUARD hold protection reduces routine maintenance for ‘Starnes’
The Nippon Paint Marine NEOGUARD anti-corrosive coating applied to the cargo holds of the 40,000dwt bulker Starnes has been a key factor in ship manager HJH Shipmanagement GmbH being able to extend cargo hold maintenance.
Starnes, delivered from the Chengxi Shipyard in 2020, arrived with a full range of Nippon Paint Marine protective coating and antifouling systems.
“We have not had the chance to physically inspect the tanks ourselves,” says Olaf Riecken, Business Development Manager, Nippon Paint Marine (Germany), “but HJH is very satisfied that the vessel is not expected to require any remedial coating work to the holds until drydock in mid-2025.”
“The bulker carries crushed stones and other aggregates, so the holds needed special attention to mechanical impact, abrasion and corrosion. The owner’s exacting requirements were met with our NEOGUARD range, which was applied to all cargo holds and unloading tunnels,” furthers Riecken.
The 190m-long vessel can self-discharge at a rate of 5,500tph (tonnes per hour). The self-unloading system, which features one of the largest booms ever installed on a self-unloader, can handle lump sizes up to 300mm and free flowing materials with a bulk density in the range of 1.2-3.5t/m3
Paying special attention to the cargo holds, Nippon Paint Marine applied its HI Epoxy 1494 coating, a zinc-rich epoxy primer, to bulkheads and tanktops, prior to two 200μm coats of NEOGUARD 100 GF. For unloading tunnels, two 125μm coats of NEOGUARD TOUGHNESS were applied before a single 50μm finish coating of E MARINE Finish M.
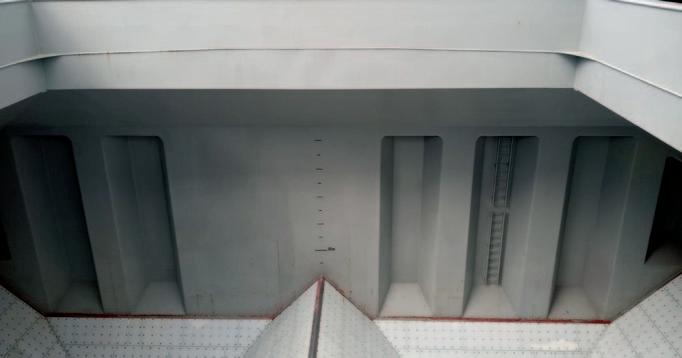
While Nippon Paint Marine has applied its coatings to existing tonnage operated by the HJH, Starnes was the first newbuilding project with this owner.
Other vessels applied with the same coating include the self-unloading bulkers Bulknes and Sandnes, with the operator noting that extend coating repairs could not be achieved without a NEOGUARD application.
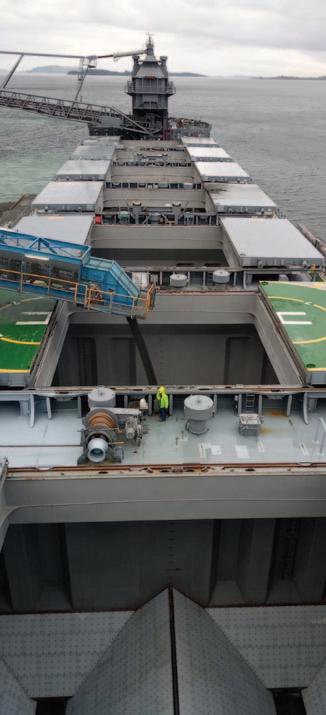
Commenting on the success of the coating, HJH Shipmanagement’s Newbuilding Manager Michael Jäger says: “It is vitally important to choose the right anticorrosive paint for a newbuilding early on in the project. Based on our previous experience of Nippon Paint Marine systems during repair and maintenance projects we wanted the ultimate cargo hold protection for Starnes. We found that with NEOGUARD, which has exceeded our expectations and helped reduce coating maintenance costs.”
NEOGUARD 100 GF is flexible, surface tolerant multipurpose glass-flake epoxy developed to provide unparalleled corrosion and abrasion protection from seawater, chemicals and mechanical impact. And NEOGUARD TOUGHNESS is a heavy-duty epoxy anticorrosive paint newly developed to exhibit resistance against abrasion and impact to provide long-term protection for cargo spaces.
The Nippon Paint Marine NEOGUARD anti-corrosive coating applied to the cargo holds of the 40,000dwt bulker Starnes
StormGeo Announces Carbon Footprint Dashboard to streamline decarbonization reporting

StormGeo, a major provider of weather intelligence and decision-support solutions for the shipping industry and part of Alfa Laval, will release a new Carbon Footprint Dashboard to help its customers reduce carbon emissions more effectively. The new dashboard will be the third decarbonization solution released by StormGeo in 2022.
SINGLE SOURCE OF TRUTH
Specifically designed for energy efficiency and decarbonization managers but available to all s-Insight users, StormGeo’s Carbon Footprint Dashboard compiles all relevant data in one place to monitor decarbonization metrics, set carbon intensity targets, and streamline regulatory reporting processes.
“The Carbon Footprint Dashboard provides a single source of all CO2 emissions data. It gives access to the analytics necessary to review the impact of implemented measures, identify corrective actions, and report on carbon intensity alignment with industry trajectories to internal and external stakeholders,” says Madeleine Engelhardt, Product Manager, Fleet Compliance and Technical Perfor mance at StormGeo. “The dashboard helps shipping companies focus on the
decarbonization metrics that matter.”
With several pre-configured widgets, the dashboard provides numerous graphs and diagrams to visualize the carbon footprint of all shipping activities. The system calculates and displays various CO2 emission indicators for fleets, vessel subgroups, and individual vessels for each leg of the voyage. These insights will be available to all dashboard users, helping to ensure transparency and improve collaboration on decarbonization initiatives across organizational departments.
CARBON FOOTPRINT DASHBOARD TO BE ADOPTED BY STORMGEO CUSTOMERS
Many of StormGeo’s customers have already expressed interest in the new Carbon Footprint Dashboard. For example, the German shipping company F.A. VINNEN & CO. will leverage the dashboard to better understand the real operational impact of their actions on carbon emissions.
“StormGeo’s Carbon Footprint Dashboard will help us keep detailed track of how much CO2 our shipping activities emit into the atmosphere and quickly gives us the necessary overview to see whether parts of our fleet aren’t performing as they should,” says Bernd Hein, Managing
Director at F.A. VINNEN & CO. “It will enable us to drill down into the data and see how something as small as a single leg of an individual vessel impacts our overall emissions and get the decision-support necessary to correct any issues.”
AVAILABLE SOON StormGeo’s Carbon Footprint Dashboard will be released in October 2022 as part of s-Insight, a world-leading fleet performance management solution that ensures vessel compliance and provides simple, trustworthy data reporting systems. The Carbon Footprint Dashboard will be available for all route advisory and fleet performance management customers.
ABOUT STORMGEO
StormGeo is a global provider of weather intelligence and decision-support services, with leading solutions for shipping, oil and gas, renewable energy, onshore industries, and aviation. Offering solutions toward decarbonization, more than 12,000 ships rely on StormGeo software or services for navigational planning, route optimization, weather routing, and fleet performance. The company has 24 offices in 16 countries, including eight 24/7/365 global operations centres.
HAROPA PORT continues its growth in 2022, despite small drop in bulk
After a record year, HAROPA PORT remains on a growth trend in 2022. The half-yearly traffic report shows a 5% increase in maritime traffic and a 31% increase in river container traffic in Gennevilliers. The announcement of major investments such as MSC-TiL in Le Havre heralds prospects for sustainable growth.
IMPROVED RESULTS IN 2022 COMPARED TO 2021
Several traffic figures for the first half of 2022 show a clear increase compared to the same period last year. This is particularly the case for: maritime:
42.08mt [million tonnes] (+ 2mt); liquid bulk: +14.5% (+2.62mt) in connection with the restart of the Gonfreville refinery.; containers: stable with 1,485 MEVP (+2% on the inland); ferry freight vehicles: + 26%; passengers: + 24%; dry bulk: 4.2%, despite a positive dynamic in the cereals segment (+2%) with a 2022/2023 campaign estimated to be as good as 2021/2022; aggregates for the construction market are down: 22% or 260kt at the end of June, but up (+8 %) on average and remain on historical highs driven by the dynamics of work; Roro: 19.4%, but gained ten variation points in June.
HAROPA PORT STANDS UP WELL TO NATIONAL AND INTERNATIONAL CRISES
The war in Ukraine has had a considerable impact on the trade of agricultural products worldwide. In particular, the export of wheat, corn and oilseeds, which are mainly exported by sea, has been blocked in the Black Sea ports and will also hamper the next harvest.
This situation, however, highlights the essential place that France occupies in the supply of wheat and barley to structurally importing countries and thus opens up new market opportunities.
Port of Ipswich number one for agricultural products exports for 17 years in a row
ABP’s Port of Ipswich has retained its place as the number one export port for agricultural products for the 17th year in a row, beating London, Bristol and Belfast to claim the title. This was confirmed by the Department for Transport’s UK port freight statistics, reporting that the Port of Ipswich shipped 409,000 tonnes of agricultural products in 2021, exporting 22% of UK major ports’ outwards agricultural products tonnage last year.
The Port of Ipswich’s performance
reflects its key location at the heart of the Suffolk and North Essex agricultural community, and the role of East Anglia as the ‘bread basket’ of the UK.
In addition to holding the accolade of being the biggest exporter of agricultural products, ABP’s Port of Ipswich is also the seventh busiest port in the UK overall for both imports and exports of agricultural products and plays a key role in supporting supply chains in East Anglia, including aggregates and cement for the UK
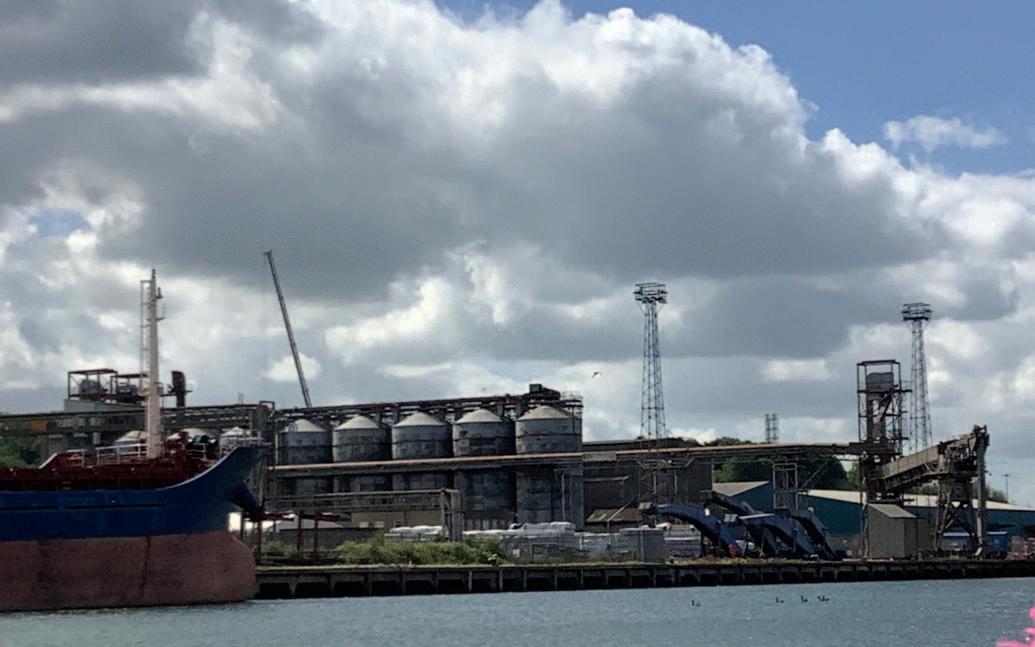
construction industry.
Paul Ager, Divisional Port Manager for ABP, said: “It is fantastic that we have seen continuously high agricultural export volumes, which have helped our port retain its top position as the UK’s number one export port for agricultural products.
“Our business plays an important role in supporting supply chains in East Anglia and we are grateful to all our customers for continuing to choose ABP’s Port of Ipswich to handle their imports and exports.”
Port Tampa Bay to expand bulk berths
Port Tampa Bay will receive $12.6 million in grant funding from the U.S. Department of Transportation to expand and diversify a berth at fast-growing Port Redwing. The port’s funding allocation is part of $1.5 billion in grant funding made available through the Rebuilding American Infrastructure with Sustainability and Equity (RAISE) discretionary grant programme.
Port Tampa Bay will use RAISE funding to create Berth 301 at its satellite facility, Port Redwing. The new berth will provide room for a third large ship to be worked efficiently.
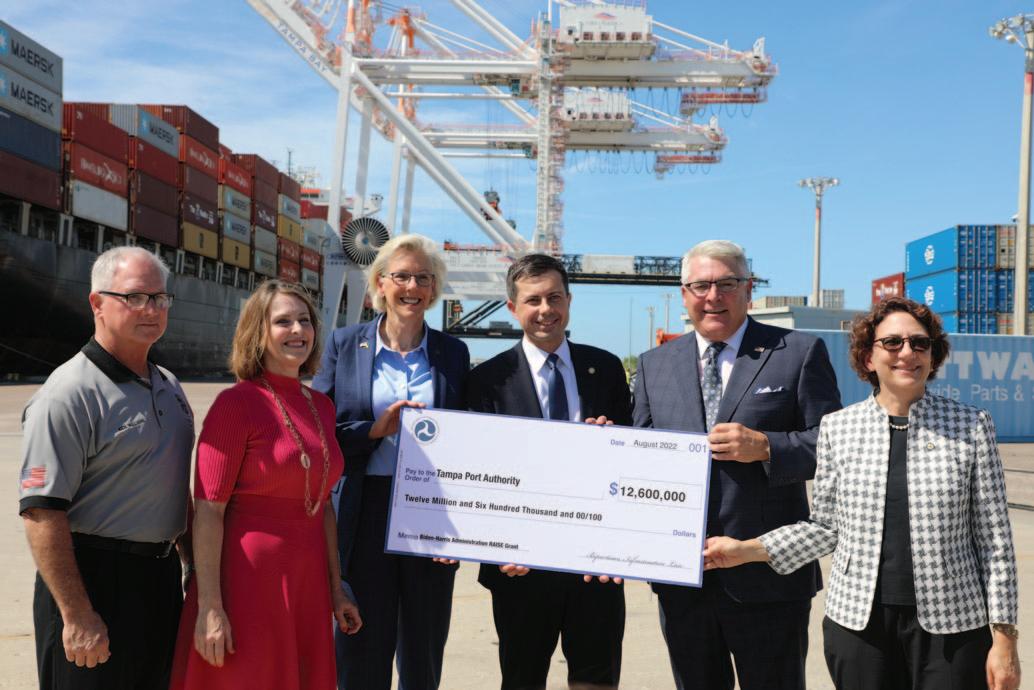
“The berth 301 project will have a generational impact on our community in terms of economic development and wellpaying jobs. Port Redwing has seen tremendous growth since the deepening and expansion of the Big Bend Channel. As our community continues to see record population growth, it is important to
provide an efficient way to move construction and other bulk cargoes. This project optimizes supply chain economics and helps keep wear and tear on roads to a minimum,” explains Paul Anderson, Port Tampa Bay CEO & President.
In the past 12 months, the port handled over one million tonnes at Port Redwing. Port tenants and customers — including The Mosaic Company, Logistec, SESCO, Ardent Mills, and Precision Build
Solutions/Tampa Tank/Florida Structural Steel — will directly benefit from this project, as they are able to diversify their operations and make long-term plans and commitments to serving the region.
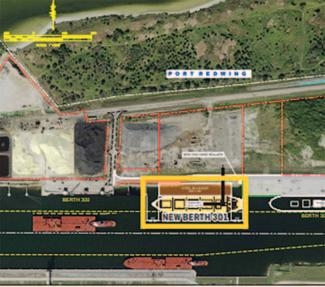
The project makes an important and immediate economic difference for West and Central Florida’s non-containerized industries — including cement, prilled sulphur, aggregates, steel, food and agriculture, wallboard and construction, and project cargo, among others.
Nearly ten million people reside within 75 miles of the port, and roughly 200,000 new residents have made their homes in Hillsborough County in the last decade. In addition to the numerous economic benefits, this project will also eliminate nearly three million truck miles annually and reduce wear and tear in nearby communities, which will cut emissions, enhance roadway safety, and improve truck operations.
– Henry Ford
“A man who stops advertising to save money is like a man who stops a clock to save time”
Resumption of grain and seed shipments from Ukraine to Euro-Silo at North Sea Port
After months of blockades, on Friday 9 September a grain ship from Ukraine arrived at North Sea Port. The vessel moored at Euro-Silo at Sifferdok in Ghent.
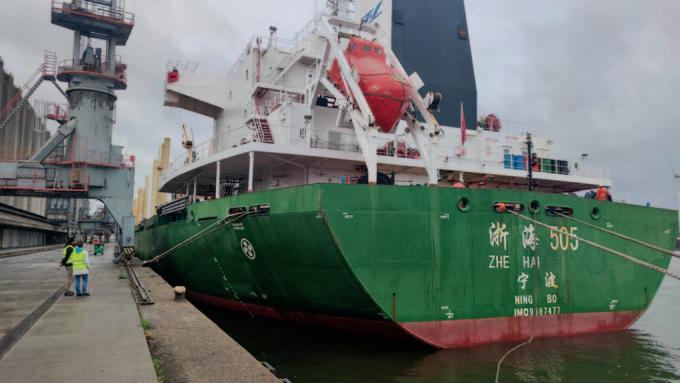
The ship, Zhe Hai 505 left the port of Odessa with 30,000 tonnes of rapeseed on board. More ships are scheduled for mid and late September, which will help restart the transshipment of grain from Ukraine. During the first eight months of this year, the amount of grain shipped from Ukraine to North Sea Port fell by 60% compared to the same period in 2021.
In a normal year, some 1.5mt [million tonnes] (2021) are imported, rising to as much as 2.1mt (2019).
Euro-Silo receives 4.5mt of grain, seeds and derivatives annually, of which 25 30% comes from Ukraine, depending on
the harvests.
Under the auspices of the United Nations, a corridor for grain ships has been created in the Black Sea to allow the export of grain from Ukraine. Euro-Silo and North Sea Port are helping to establish this grain corridor.
From the very start of the conflict between Ukraine and Russia, North Sea Port has been supporting companies and organizations that are seeking to mitigate these terrible events.
ABOUT NORTH SEA PORT
North Sea Port is a West European port that extends for more than 60 kilometres, 9,100 hectares, and across two countries: Belgium and the Netherlands. Because of its location at the North Sea, the port is
directly accessible by sea-going vessels, benefiting global trade.
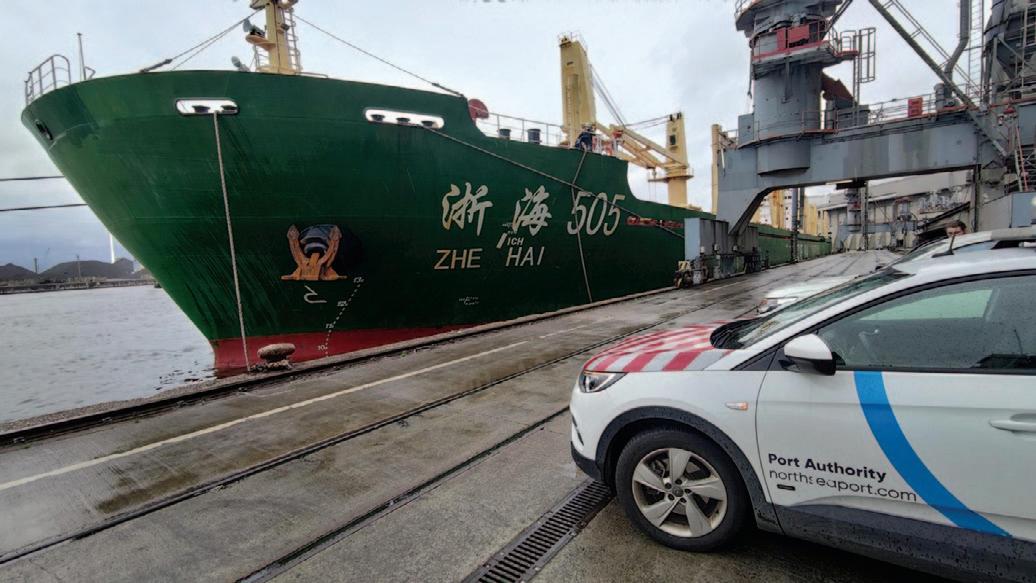
Its central location in Europe makes North Sea Port a logistics hub through which goods flow smoothly to all corners of Europe and even China. North Sea Port is also part of the Rhine-Alps, North SeaMediterranean, and North Sea-Baltic transport corridors, which ensure that goods can be delivered quickly and efficiently by rail, road, and/or inland shipping to their final destination.
Its location, multimodality, and diversification in goods make North Sea Port an important European port: the third most important in terms of added value and ninth in terms of freight traffic.
ABOUT EURO -SILO
Euro-Silo Sifferdok was founded in 1968 and started with two pneumatic unloaders and a silo storage capacity of 18,000 tonnes. This capacity was gradually increased to 240,000 tonnes.
Euro-Silo Rodenhuize was founded in 1978 as ‘Ghent Grain Terminal’. From 1978 until 1994 the storage capacity of this terminal was raised up to 410,000 tonnes. In January 1992 Euro-Silo Sifferdok took over Ghent Grain Terminal and renamed this installation Euro-Silo Rodenhuizedok.
Today Euro-Silo has a total storage capacity of 650,000 tonnes at two sites in the port of Ghent: Euro-Silo Sifferdok and Euro-Silo Rodenhuizedok.
ABP signs new contract with ADM Fertiliser
Associated British Ports (ABP) welcomes long-term customer ADM’s fertilizer division to the Humber in a new contract.
ADM Agriculture, one of the largest fertilizer suppliers in the UK, has signed a three-year extension agreement with ABP for the import, handling, bagging, and processing of fertilizer at ABP’s Bulk Park at the Port of Immingham. It will see extensive fertilizer volumes come through the UK’s largest port by volume of tonnage.
Simon Bird, Regional Director of the Humber ports said: “We’re delighted to welcome ADM’s fertilizer division to the ABP family at the port of Immingham. ADM are a long-term customer of ours, a premier global human and animal nutrition company and one of the world’s largest agricultural processors.
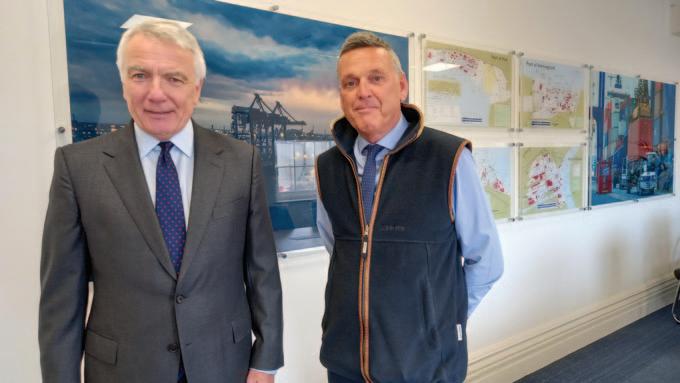
“This new partnership highlights the port’s key location in global trading and that we remain the port of choice for many.”
Calum Findlay, Head of Fertiliser for ADM, said: “The Port of Immingham is key to the on-going development of our UK fertilizer business, and we are delighted to be in partnership with ABP.”
ADM Agriculture supplies an extensive range of fertilizer products.
ABP’s Immingham Bulk Park offers more than 1.3 million square metres of undercover storage. In 2018 it won ‘Best Dry Bulk Port’ at the International Bulk Journal awards.
ABOUT ABP HUMBER
ABP Humber Ports complex form the UK’s busiest trading gateway. The four ports of Immingham, Grimsby, Goole, and Hull
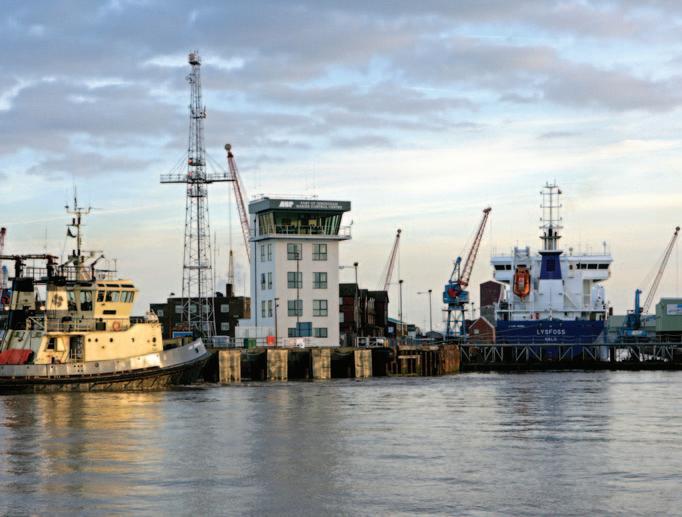
handle more than 58mt (million tonnes) of cargo between them each year worth approximately £75 billion. Across the Humber, the ports support 34,900 jobs and contribute £2.5 billion to the UK economy.
ABP Humber’s major investment programme ensures the ports offer state-of the-art cargo handling infrastructure and equipment, alongside a highly skilled team who can handle a vast array of cargo safely, efficiently and sustainably.
ABP Humber works collaboratively to build long-term partnerships and deliver the right supply chain solutions for customers, including value-added services and new facilities tailored to suit their business needs.
Its Port Operations are complemented by the Pilotage Service and Vessel Traffic Service which ensure vessels are safely navigated through the Humber Estuary.
ABP Humber offers 364 hectares of development land across its port locations
capable of attracting investment and delivering transformational benefits for the economy both locally and nationally.
The ports are all part of the new Humber Freeport, which offers three tax sites with an exceptionally business-friendly tax and regulatory environment for potential manufacturing investors.
ABP Humber supports its local communities. The ABP Humber Coastal Half Marathon and 5k is now in its sixth year and complements ABP’s race sponsorship across the country.
ABOUT ABP
ABP, the UK’s leading ports group is Keeping Britain Trading with 21 ports and other transport-related businesses, creating a unique national network capable of handling a vast array of cargo.
ABP is driving growth, contributing £7.5 billion to the UK economy every year and supporting over 119,000 jobs. Its current investment programme promises to further increase its contribution to regional economies around the UK.
ABP is also an essential partner for the Offshore Wind industry, providing Operations and Maintenance (O&M) for over 50% of the sector’s activity, as well as investing in infrastructure to realize future renewable energy generation.
ABP in numbers:
~ 90mt of cargo handled each year;v 5,000 hectares of port estate ownedv 1,000 hectares of open storage;v 1.4 million square metres of coveredv storage; 87km of quay;v
> 1.5 million vehicles every year;v a quarter of the UK’s rail freightv generated; and
> £55 million investment made in lowv emission and renewable energy generation technologies.
Port of Rotterdam Authority encourages noise measurement of moored ships
Under the name ESI Noise, the Port of Rotterdam Authority will be giving vessels a financial discount if — on the basis of an internationally accepted standard — the amount of noise produced by the vessel when moored has been made transparent.
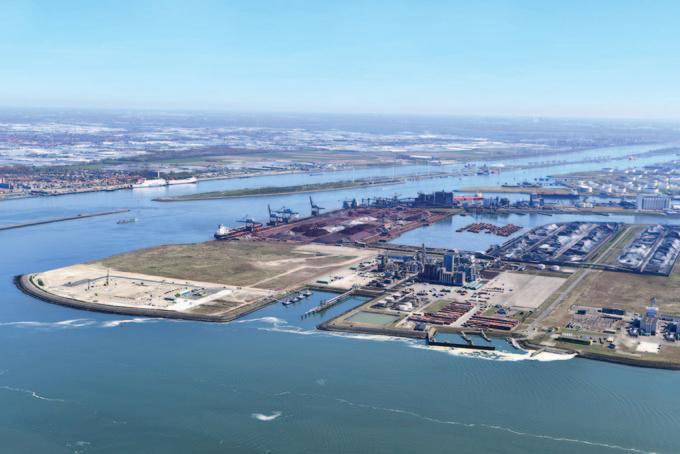
The incentive is in line with the Port of Rotterdam Authority’s policy to develop the port sustainably in harmony with the environment. Seagoing vessels are currently only subject to noise requirements in terms of working conditions on board, but not in terms of noise production impacting the residential area and the environment. With the incentive based on ESI noise, the Port of Rotterdam Authority is drawing attention to the noise produced by vessels with regard to the surroundings.
NEPTUNES
The noise report must be drawn up according to the international Neptunes protocol. The resulting score is adopted by the Environmental Ship Index (ESI). In Rotterdam, vessels can now receive a discount of €312.50 per visit up to a maximum of €1,250 per year for having an ESI noise report. This discount scheme will be valid in any event until the end of 2023.
REGIONAL MEASUREMENT PROGRAMME
In addition to the incentive scheme for individual ships based on ESI noise, the Port Authority, in collaboration with the Municipality of Rotterdam, the Province of Zuid-Holland and DCMR Rijnmond Environmental Service, will soon be starting a regional measurement programme regarding the noise of moored vessels in general. ESI noise and the regional measurement programme are both contributing to increasing knowledge about the noise of moored vessels and to increasing national and international attention for this problem.
ENVIRONMENTAL SHIP INDEX
This is an internationally accepted measure that, until now, has focused only on the air quality and climate-related emissions of seagoing vessels. The new ESI noise index also reflects the performance of vessels in terms of noise.
The ESI is a global index. By mid2022, nearly 7,000 seagoing vessels had an ESI score that allows them to receive a discount in nearly 60 ports. Rotterdam is the second port after Hamburg to draw attention in this way to quieter vessels.
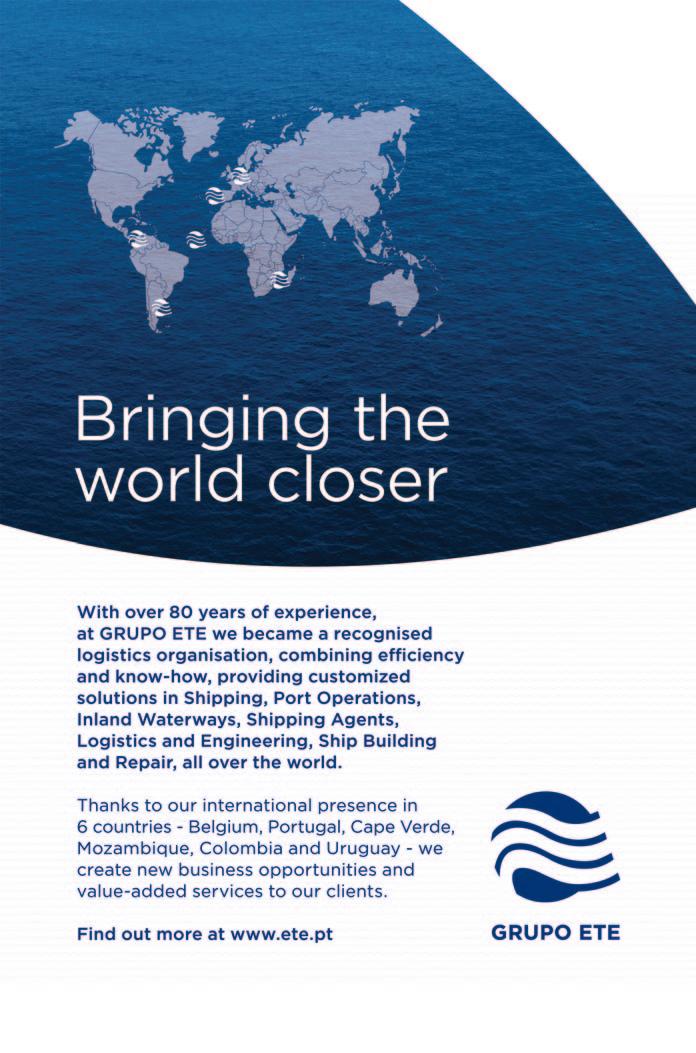
New grain terminal for the Port of Vysotsk
The Russian Port of Vysotsk is to build a new grain terminal, which will have an annual capacity of four million tonnes.
As per its planned design, it will be able to handle rakes of six rail wagons at a time and have storage on site for up to 240,000 tonnes. It will serve grain producers in the Leningrad Region, which are increasing production all the time, and the new terminal will help them focus more on export markets. Total investment will be around $91 million.
A further two grain terminals are already under construction in both Vyborg and Kingisepp districts of the Leningrad Region.
Barry CrossDry bulk imports up in Cartagena

Spain’s Mediterranean Port of Cartagena reported total traffic of 18.25mt (million tonnes) in the half year to 30 June. This is its best result since 2005 and represents yearon-year growth in the region of 18%.
Dry bulk performed well in these first two quarters, with imports up 16.85% based on traffic of 3.4mt and around 1.5mt being inbound grain. These originally came from Ukraine, but new sources have since been found, given the difficulty in getting grain out of Ukrainian ports because of the war with Russia.
According to the port, “Cereals continues to generate very good figures thanks, first of all, to the fact that our farmers (…) were very far-sighted and concentrated imports in the first months of the year, but also because we have (…) established commercial relations with other booming markets such as the United States, Germany, Brazil or France.”
Clinker and cement also did well, with 100,000 tonnes more imported in 2022 than in 2021, equivalent to a 60% uptick. Customers in Spain and Italy remained in place, and new alliances established with Algeria and Turkey.
The port points out that the new rail connection at Escombreras with central Spain has also boosted traffic, especially cement traffic generated by Cementos El Tajo. This new line means that clinker now flows from the port to different parts of Spain.
Barry CrossGdynia and Riga Freeport sign memorandum on coal
Gdynia Port Authority and Riga Freeport have signed an Memorandum of Intent that will pave the way to enable greater co-operation between them. One of the results should see the Port of Riga handling at least five million tonnes of coal by the end of the year.
The two ports hope to take advantage of the unstable situation in the global energy market and disruptions in freight supply chains by leveraging spare capacity to be found at the Latvian and Polish ports.
In particular, Riga wants to better use the state-of-the-art multi-purpose Krievu Island terminal, which became operational at the end of 2018. This facility has equipment to handle and crush coal, as well as transport and store it. It has the most up-to-date infrastructure in the Baltic region as well as being very environmentally friendly.
Coal handling, for example, is effectively a sealed activity, with an automated wagon dumper system. Furthermore, a closed conveyor belt network transports coal to and from docked vessels. In order to reduce dust escaping into the air from open coal storage areas, the coal is regularly misted; in winter, snow cannons are also used for the same purpose. There is also a 23-metre-high dust fence to prevent the spread of coal dust into the immediate environment.
The port authority has also placed an air quality monitoring station on Krievu Island.
Liebherr Transform: unleash the full potential
Liebherr Transform is the new upgrade, modification and overhaul service that has a tailor-made solution for customer needs. It is available for ship to shore container cranes, rubber tyre gantry cranes, rail-mounted gantry cranes, mobile harbour cranes, offshore and ship cranes.
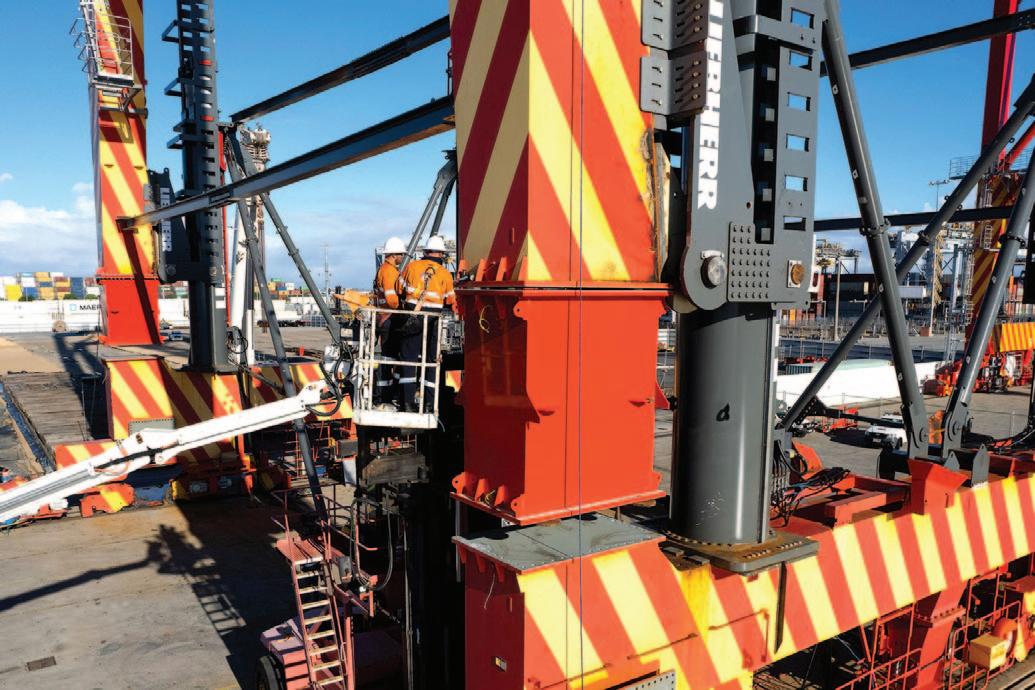
The new Liebherr Transform provides tailored solutions that respond to the continuously growing demands on today’s businesses. A range of ingenious upgrades, clever retrofits, machine overhauls and service modifications breathe new life into customers’ existing machines. Using the latest technology and years of experience,
Liebherr brings a combination of sustainability, smart technologies, maximum productivity and cost-effectiveness in one complete solution. This allows existing equipment to reach its full potential.
New service solution includes overhauls, upgrades, retrofits and much more It is inevitable that equipment becomes outdated over time but that does not mean it has to be replaced.
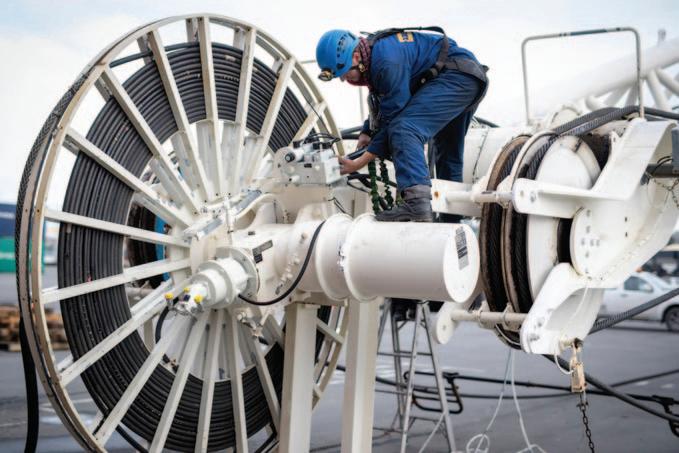
As the name suggests, existing machines are transformed using affordable complete or partial machine overhauls, retrofits and upgrades. This not only saves the increased capital expenditure of investing in new
machines, but also reduces the carbon footprint by avoiding the need for new equipment through the extension of the service life. A number of retrofits and upgrades are available which increase versatility and performance, or ensure compliance with more stringent regulations, and so open up a wider spectrum of opportunities. At the same time, operators do not have to get used to new machines and can continue to benefit from their vast experience with existing equipment. The Liebherr team of expert engineers takes care of the entire planning and implementation of Transform projects — from consultation, through to installation and technical support and service.
STRONGER , FASTER , SMARTER , GREENER
Companies are under pressure to increase volume and performance, widen scopes, or reduce emissions and costs, the list is endless. Liebherr Transform helps to lighten the load through a comprehensive range of structural, electrical, mechanical, ergonomic or digital modifications. Through the application of new technologies and expertise, Liebherr machines are transformed for the workplace of the future. They are stronger, faster, smarter, greener, and ultimately...better.
Solid partners join forces and consolidate expertise and know-how
Muller Beltex BV, V.A.V. Aandrijvingen BV and Germany based Bechtel GmbH have announced their strategic alliance. By a transfer of shares, the owners Lars Muller and Emiel Schoutsen have established this co operation.
The know-how and expertise in components for bulk handling equipment is not limited to the Netherlands and Germany, where the three companies are located. They operate worldwide and the close co operation between the three companies will therefore provide major benefits for their entire, geographically widespread, customer base.
Both owners emphasize that this alliance is not a merger and that the companies will retain their own identities. Company locations and contact points will remain unchanged.
The advantages arising from the collaboration are, in particular, the bundling of their expertise and the use of each other’s network, especially abroad. In certain markets or geographic regions, the one partner is better represented than the other. “This collaboration will enable all three of our companies to better position themselves in the market and to provide our customers with materials, knowledge and service in an even better and more efficient way,” Muller and Schoutsen state.
V.A.V. Aandrijvingen is globally known for its chain applications in the feed and grain handling industry. It is able to deliver immediately from stock, or within days, all components for chains as well as elevator components and parts for various screw conveyors.
Muller Beltex providing solutions for
the bulk handling and process industry and specializes in bucket elevator trouble shooting. Further to this its components, Polysur® elevator belts, Kryptane abrasion resistant polyurethane liners, and the Atex approved monitoring systems are known worldwide.
Bechtel GmbH is a strong service related supplier of components for bucket elevators and chain conveyors. Its knowledge of chain conveyors and problem solving capacity enables it to build, for the entire German industry, all types of chain conveyors even for the most complex applications.
The alliance of the three companies wishes to further improve their already very high service level to the bulk handling industry, and thus securing quality and continuity of their efficient supply chain.
Bobcat unveils its most powerful compact loaders
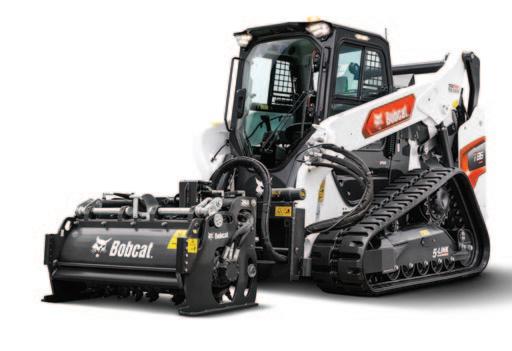
Bobcat has expanded the company’s next generation RSeries range of products with the launch of the new S86 and T86 compact loaders. The new S86 R-Series SkidSteer Loader and T86 R Series Compact Track Loader replace the previous 700 and 800 M-Series loaders and complete the current R Series loader line-up.
Commenting on these new product introductions, Mike Vought, Vice President Product Management at Doosan Bobcat EMEA, said: “The S86 and T86 are exceptional machines — the most powerful compact loaders we have ever built, providing even more versatility as both tool carriers and workhorses.”
TOP OF THE-RANGE : THE S86 AND T86 COMPACT LOADERS
Delivering a higher engine and hydraulic output, the Bobcat S86 and T86 are the most powerful compact loaders the company has ever built. Both machines use a well-proven Stage V compliant 3.4 l Bobcat engine – producing 78kW (105 HP) at 2,600RPM. Just like all R-Series loaders, the engine is mounted in-line with direct drive, which improves the cooling capacity of the engine and hydraulic components. This change
increases reliability in high-intensity applications such as road construction and forestry work.
John Chattaway, Loaders Product Manager at Bobcat, commented: “The S86/T86 follow on from the very successful introduction of the smaller S66/T66 and S76/T76 loaders. The S86/T86 top-of-the-range models continue the same trend by setting new industry standards in every area, from incab comfort and safety to available power and attachment versatility. The S86/T86 take what is possible with compact loaders to a whole new level.”
The new S86 and T86 workgroup design increases the ability to lift more, carry more and reach further. This is achieved by a new workgroup geometry that improves lifting capability
throughout the lift arm’s range of motion. When combined with the high hydraulic performance and the lighter and stronger cast-steel lift arm sections, the loaders offer higher capacity throughout the lift cycle — even at full height.
Along with the S66/T66 and S76/T76 models launched over the last two years, the S86/T86 set new industry standards for incab comfort. This includes the low noise and vibration levels inside the one-piece sealed and pressurized cab, together with the intuitive SJC controls as standard, and the informative displays. The cab also has an HVAC system as standard and increased operator visibility, which can be further enhanced with the innovative Clear Side cab option.
With the latter, 75% of the side windows are mesh-free, ensuring an unobstructed view from the cab. Bobcat has also added a rear-view camera as standard equipment to the list. In addition to the standard five-inch in-cab display, Bobcat offers as an option, an advanced seven-inch display that provides even more detailed machine information and unprecedented device connectivity.
New CRS Maxebeam® transforms Reachstackers into dedicated Rotainers
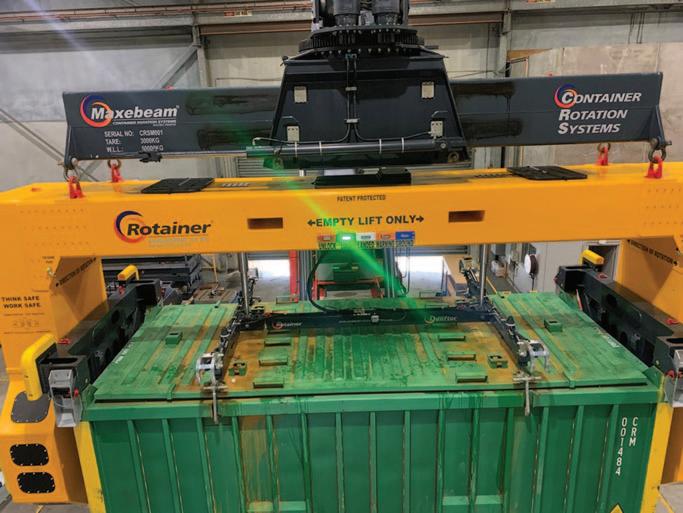
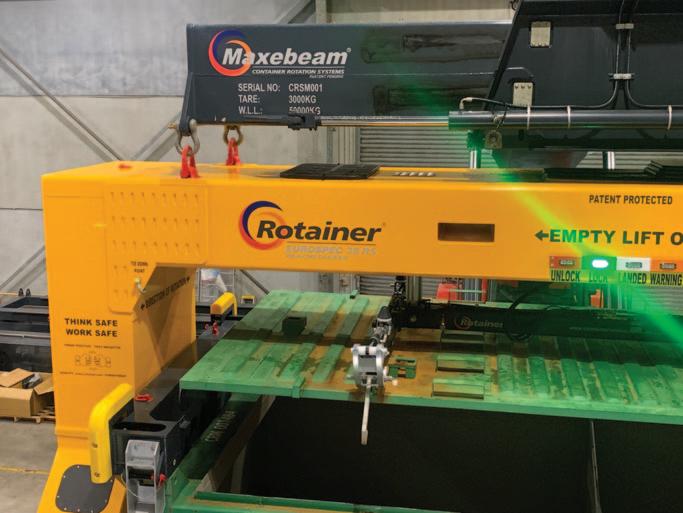
The engineering team at CRS has come up with another innovative addition to its specialized products portfolio.
The company’s astute customers are continuously looking to maximize container payloads, 35 to 40 tonnes are the new norm for open top container weights in the Australian region.
Unfortunately, add a container rotating device and most reachstackers are pushing the designed boundaries when it comes to rotating containers; this is especially true if an automated lid lifting apparatus is required.
Most commercially available reach stackers have 45-tonne first row lifting capacity as standard.
Heavy duty open top containers such as the CRS Rotorcon® have gross capacities of 38 tonnes, other non-CRS containers can have 35 tonnes as gross weight.
One of CRS’s clients has 1,400 containers that are over ten years old which generally operate with around 32 tonnes gross weight.
Rather than replace their container fleet, the client approached CRS to come up with a way to increase gross weights to 35 tonnes and still be handled with their current fleet of 45 tonne reachstackers; this would leave only seven tonnes for a container rotating device.
Considering a lightweight Rotainer® Eurospec 38 set up with reachstacker attachments comes in at around 12 tonnes, add the 35 tonnes and we need to lift approximately 47 48 tonnes.
CRS’s solution: the CRS Maxebeam® This apparatus is (patent pending) a fixed spreader beam replacement system to allow reachstackers to become dedicated Rotainer handlers.

By removing the standard 20/40 spreader and fitting a fixed beam it would increase the lifting capacity of the reachstacker.
After reviewing the application, it was decided that the beam needed to be a quick release (easy to change) whilst meeting the operational envelope of the standard 20/40 container spreader, while still having full side shift, left and right, and keeping the versatility of the normal rotating head frame.
To achieve these results a unique internal steel frame structure was developed to absorb the spot loads during side shift without adversely affecting the main beam on the reachstacker.
Fully tested and certified this beam can be adapted to any brand of reachstacker
Efficient bulk handling with help from Tenova’s high-tech systems
Tenova is a renowned worldwide partner for sustainable, innovative and reliable solutions in the metals and the mining industries.
From DRI to EAF, reheating furnaces to heat treatment furnaces, cold mills to processing lines and roll grinders, Tenova’s technologies minimize the environmental impact of its customers’ activities, operations and final products.
Tenova is active in a wide range of technologies, including: iron & steel technologies;v aluminum technologies;v hydrometallurgy;v pyrometallurgy;v grinding & texturing;v port facilities;v green solutions;v digital & process control; andv industrial gas analysers.v
Materials handled by Tenova technologies and systems include: iron & steel;v aluminium;v
boron;v copper;v ferro-alloys;v lithium;v manganese;v nickel & cobalt;v phosphate — PPA;v platinum group metals;v rare earths;v rockwool;v silicon metal;v titanium; andv uranium.v
This article focuses on the company’s expertise in the port facilities segment, specifically shiploading and unloading. Follows a brief run-down of the shiploading and unloading technologies available from Tenova.
QUADRANT SHIPLOADERS — RADIAL , LINEAR AND DUAL LINEAR
The Tenova quadrant shiploader is a very flexible solution to reach the best

compromise between quayside civil works cost and the loading system.
Tenova quadrant shiploaders are suitable for operation on a wide range of vessel sizes, and can handle from very-freeflowing bulk material to complex very abrasive or sticky products.
The shiploaders are specifically designed to the exact requirements of the client, and incorporate various solutions according to their specific application and existing site conditions. There is always a strong focus on minimizing environmental impact.
Tenova quadrant shiploaders can be supplied in three different configurations, depending on the client’s specific needs: radial type (front radial rail and rear pivot), linear type (from linear rail and rear revers bogies) or dual linear (from linear rail and rear perpendicular and linear rail). All of them can perform multiple movements: front travelling (radial or linear) with luffing and shuttling booms. In addition, they can be equipped with a variety of different loading chutes such as cascade type,
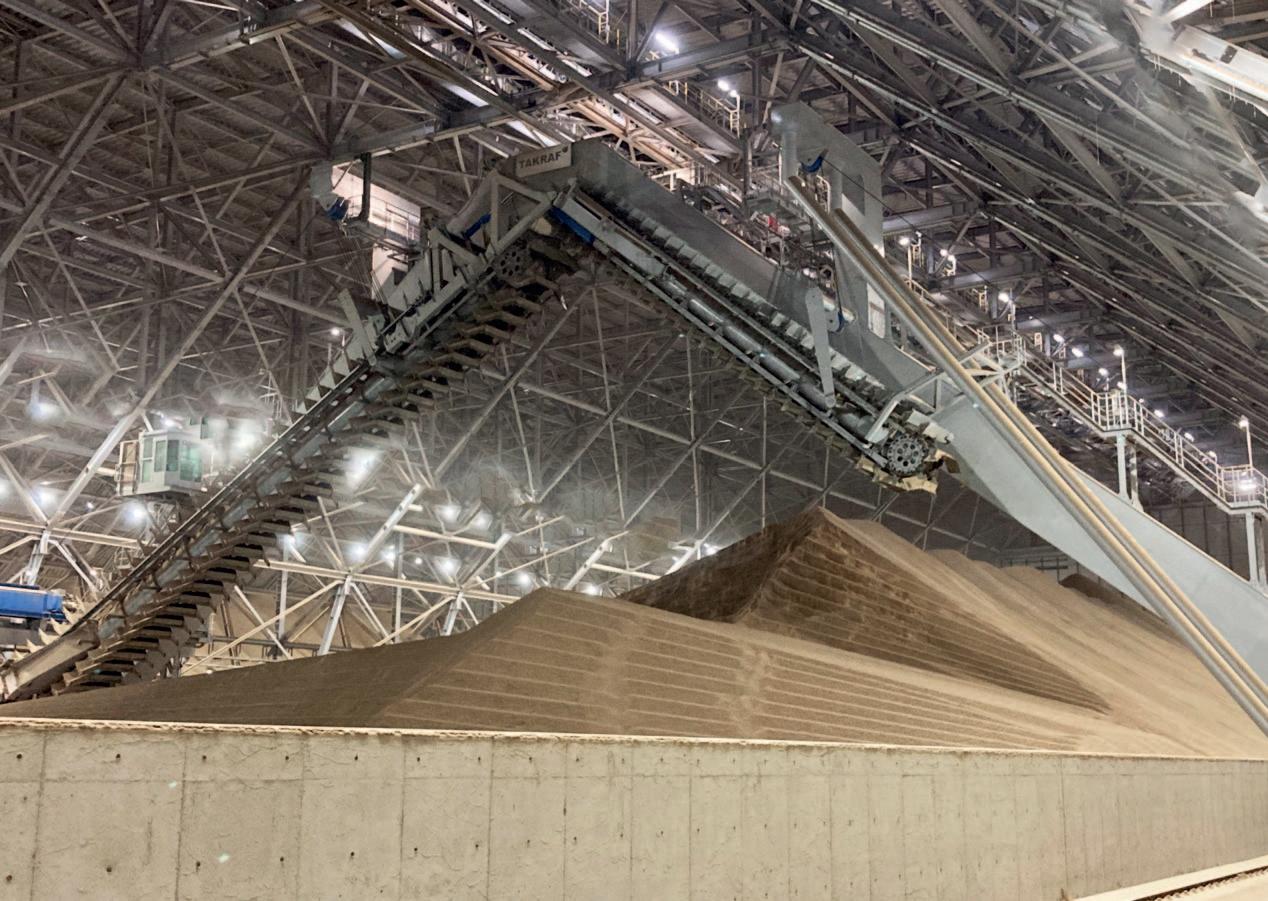
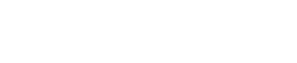
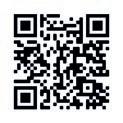
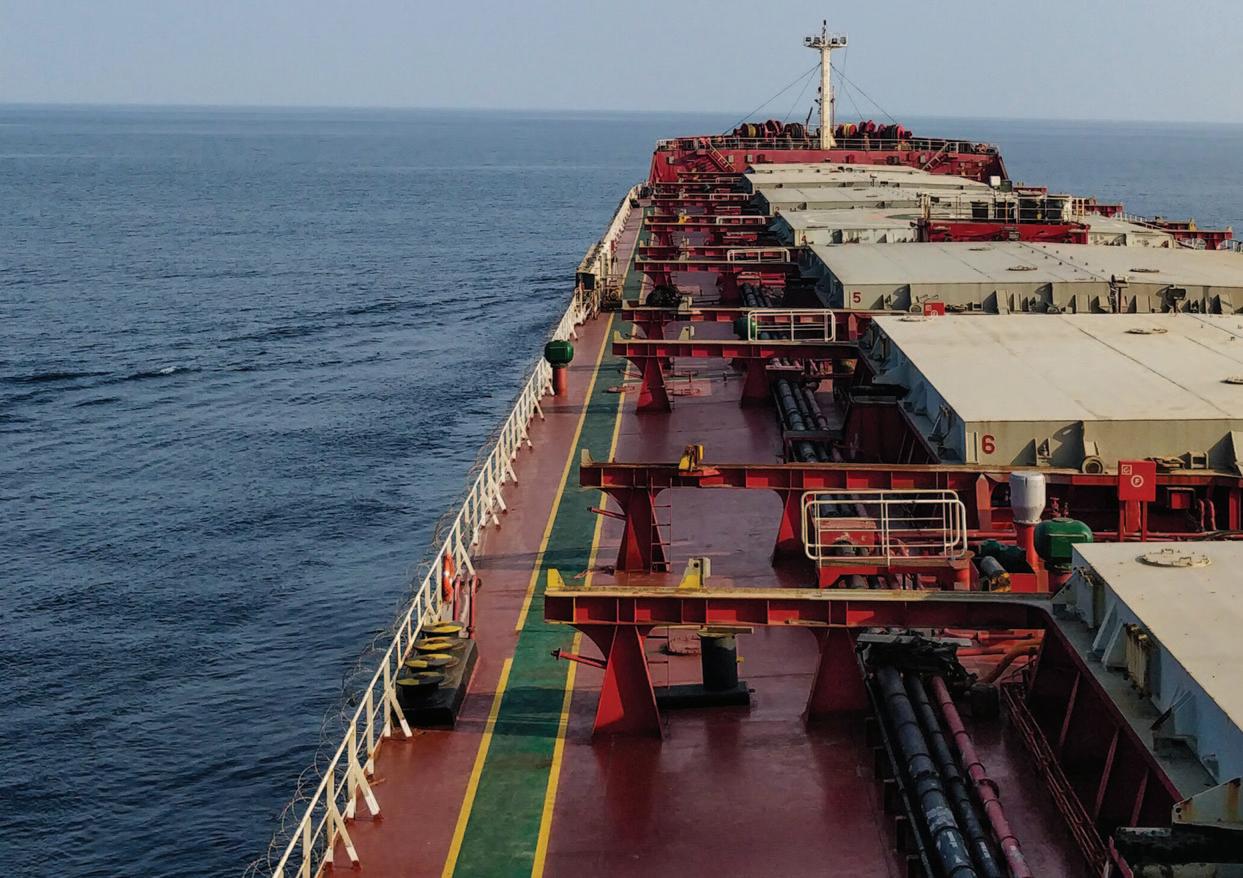
telescopic type or curved type, depending on specific applications, customer special needs and required environmental conditions.
Tenova specializes in fabricating and fully assembling off site and in shipping the shiploader to the final destination in a single unit by heavy lift ship (Lo-Lo) or by flat deck ship or barge (Ro-Ro).
Tenova’s quadrant shiploaders are very versatile machines with: unloading capacities from 500tphv (tonnes per hour) up to 20,000tph; the ability to unload vessels ranging inv size from 30,000dwt up to 400,000dwt;. an overall efficiency (throughv complete shiploading process) of ~95% depending of characteristics of unloaded material; reliability: ~98%;v availability: ~96%;v rail radius and wheel loads based onv customer needs: standard value between 60 80m and 35 60 tonne wheel respectively; and transformer size from 500kVA tov 2,000kVA.
BUCKET CHAIN TYPE CSU
Bucket chain continuous unloaders (CSUs) are the most advanced technology for highly efficient and environmentally friendly unloading. Tenova’s CSU are suitable to operate on a wide range of vessel sizes, and
can handle products ranging from very free flow bulk material to complex very abrasive or sticky products.
Tenova’s CSUs cover a wide-range of capacities and vessel sizes; CSUs are highly efficient, environmentally friendly and capable of unloading large volumes of different material types within a shorter time period compared with traditional systems operated by grabs.
The boom is equipped with a Tenova patented tailor-made bucket-chain to efficiently collect the material from the ship’s hold and transfer it to the jetty/port conveying system. Since unloading operation is continuous, these machines are characterized by very high performances and very low environmental footprint. The fully enclosed and sealed material path means that Tenova’s CSUs significantly reduce the environmental impact, specifically in terms of spillage, dust and noise emissions — they are therefore suitable to operate in particularly sensitive areas.
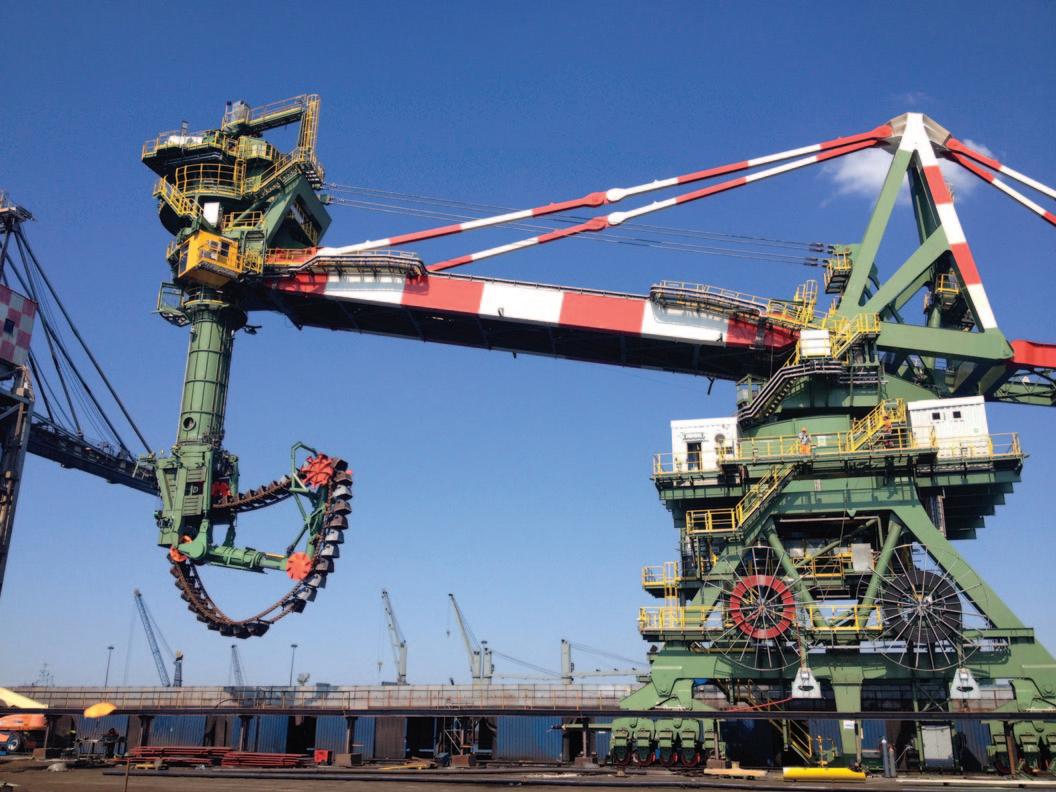
Tenova specializes in fabricating and fully assembling off site and in shipping to final destination CSUs in a single unit by heavy lift ship (Lo-Lo) or by flat deck ship or barge (Ro-Ro).
Tenova’s CSU are very flexible machines. They offer: an unloading capacity ranging fromv 500tph (tonnes per hour) up to 7,200tph;
ability to service vessels ranging in sizev from small barges up to 400,000dwt ships; overall efficiency (throughout thev entire ship-unloading process): ~70 75% depending on the characteristics of the material being unloaded; reliability: ~98%;v availability: ~96%;v rail spans and wheel loads based onv the needs of the customer: standard value between 10 15 m and 25 50 tonne wheel respectively; and transformer size from 630kVA tov 2,500kVA.
CSU – SCREW TYPE
With the knowledge that it has gained from decades of experience with CSU technology, Tenova is now bringing out a screw-type version. Tenova has developed its own versatile design, which is suitable for handling a good range of products, and which also offers an optimum ratio between machine weight and performance.
GRAB SHIP-UNLOADERS
Tenova’s grab ship-unloaders (GSUs) are in many different capacities, and can service a wide range of vessel sizes. They are particularly convenient for ports that unload different types of cargoes, as the grab system can work across various materials.
This consolidated technology has demonstrated good operability and reliability over decades of activities.
Among the available models, Tenova can offer double trolley (with shuttle trolley), single trolley and self-powered trolley.
Tenova specializes in fabricating and fully assembling off site and in shipping the GSU to the final destination in a single unit by heavy lift ship (Lo-Lo) or by flat deck ship or barge (Ro-Ro).
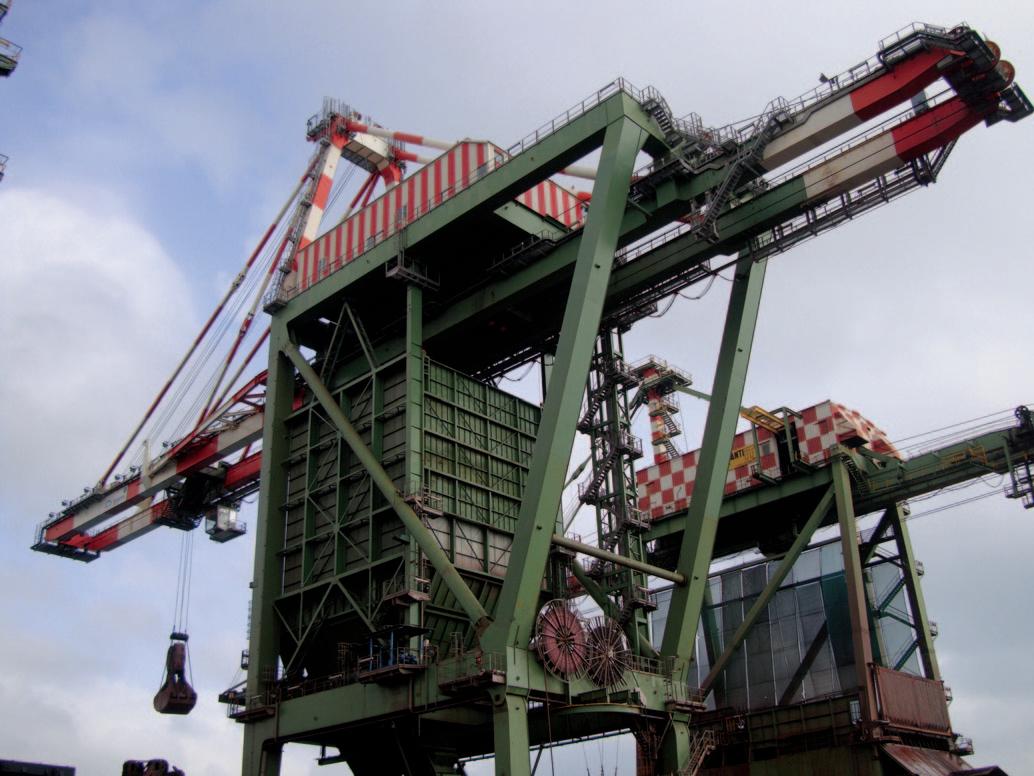
Tenova’s GSUs are very reliable machines and offer:
hoisting capacity from 12.5 tonnes upv to 85 tonnes; unloading capacity: from 350tph tov 3,100tph; the ability to serve vessels ranging inv size from barges up to 400,000dwt; overall efficiency (through completev ship-unloading process): ~55 60% depending of the characteristics of the material being unloaded; reliability: ~98%;v availability: ~96%;v rail spans and wheel loads based onv the needs of the customer: standard value between 15 25 m and 25 50 tonne wheel respectively; and transformer size: from 630kVA tov 3,150kVA.
Grab ship-unloader.
INNOVATION IS KEY
Technological innovation is the foundation of Tenova’s competitiveness with its shiploaders, CSUs and GSUs.
Tenova’s engineering process is the driver of R&D. The company has developed a flexible, individual and effective design concept. In the case of the shiploaders, the shuttling system and the loading chute are the key to finding the ideal solutions for each customer. In the case of the CSU, the digging device and the chain, along with the bucket connections, are key. Tenova’s GSUs are notable for the main control centre of the motors, and the transfer of the material from the main hopper to the wharf conveyor.
By embracing innovation, Tenova is able to offer its customer cutting-edge solutions for both CSUs and GSUs.
SAFETY
In all its work, the health and safety of all employees — in addition to environmental protection — are a top priority in the design of Tenova shiploaders, CSUs and GSUs. Its shiploaders and CSUs can be operated also from portable remote control systems, or from a remote on the ground control room.
With the principle of Zero Harm as an
integral part of its own business, Tenova is committed to designing shiploaders, CSUs and GSUs for a safe working environment.
AUTOMATION
Tenova’s shiploaders, CSUs and GSUs are highly automated machines which implement automatic operation for most of the unloading process.
Tenova is continuing to develop innovations in this field, and it will soon be able to achieve unmanned and remotely supervised operation.
DIGITALIZATION
Digitalization is essential to ensure highly automated, safe and reliable machines. Tenova uses the most up-to-date digital technology so that it can offer products that are highly connected and efficiently maintainable.
Soon, on customer request, Tenova will combine its products with: virtual reality simulator for thev training of personnel; predictive maintenance based on linev monitoring of vibrations and temperatures; and smart anti-collision systems tov support remote and unmanned operation. DCi
100 years of AUMUND
On 3 August 1922, Heinrich Aumund founded the company for AUMUNDPatente MB.H. in Berlin, an invention and engineering office, which laid the cornerstone for the globally operating AUMUND Group of companies, today employing around 500 people of more than 30 nationalities. With approximately 24,000 references in around 150 countries, the AUMUND Group is one of the global players and technology leaders in high-performance conveying and storage of bulk materials. At first, AUMUND established itself as a global brand in the cement industry, and followed on into the most varied of other key bulk materials industries internationally. Today AUMUND Group machines, systems and process technologies are in operation in cement, metallurgy, mining and minerals, lime and gypsum, chemicals — in particular
fertilizer, foundries, power plants, agribulk, ports and terminals, as well as in the area of alternative fuels with its current significance in environmental politics and environmental technology. The 100-year history and development of AUMUND spans three generations and is inextricably linked with the business leaders Prof. Dr.-Ing. h.c. Heinrich Aumund, Günter-Claus Aumund and Franz-W. Aumund, who is currently Chairman of the Board.
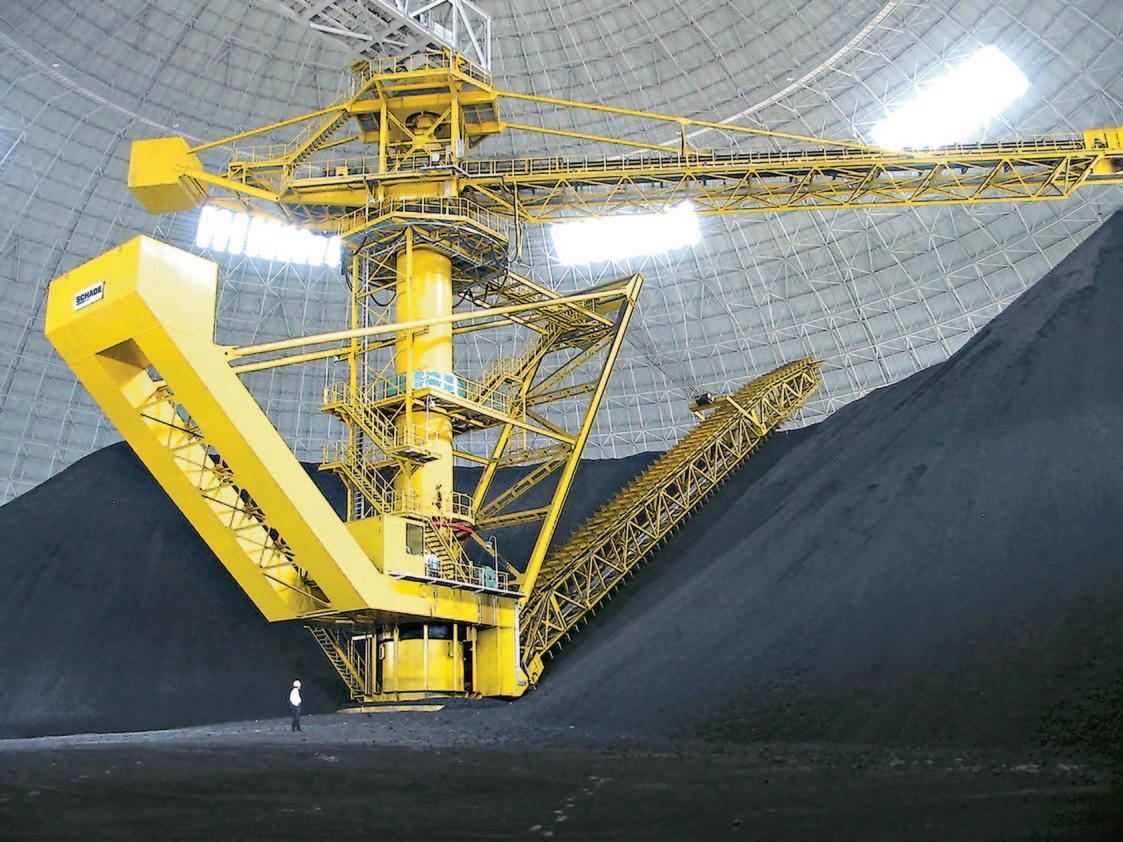
Franz-W. Aumund embodies the third generation and has been active in the company since 1966. In 1982 he was appointed Managing Director and became Managing Proprietor after the death of his father GünterClaus Aumund on 30th July 1984. Since 2022 Franz-W. Aumund has been Chairman of the Board.
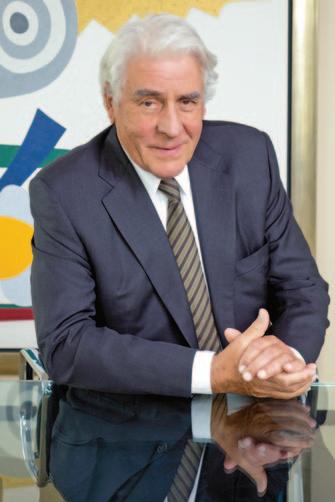
How an inventor and engineer’s office became an international conveying and storage technology brand
‘Human and machine’ – an impressive size comparison: a SCHADE stacker reclaimer in circular storage.
The AUMUND Group today comprises the following companies:
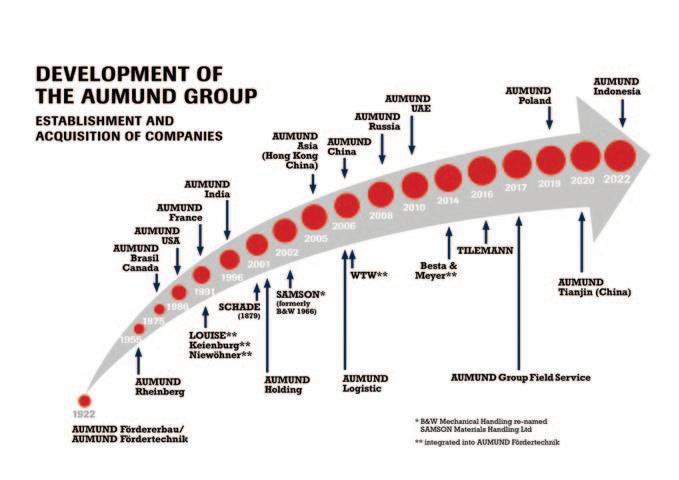
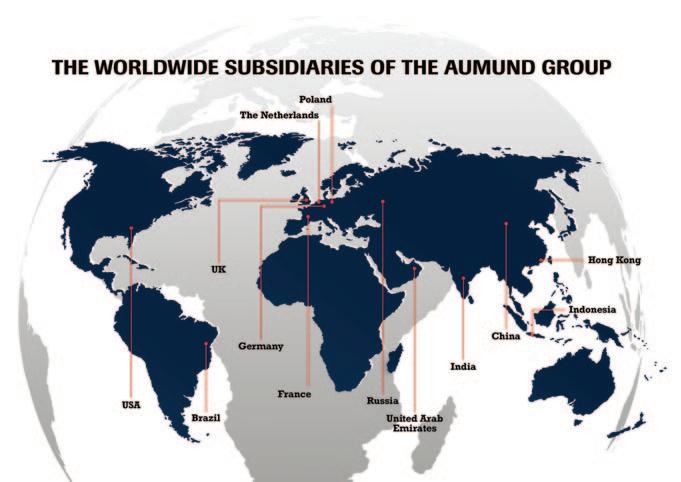
AUMUND Fördertechnik GmbH,v Rheinberg, Germany;
SCHADE Lagertechnik GmbH,v Gelsenkirchen, Germany;
SAMSON Materials Handling Ltd, Ely,v UK;
TILEMANN GmbH Chains &v Components, Essen, Germany;
AUMUND Group Field Servicev GmbH and AUMUND Logistic GmbH, both located in Rheinberg, Germany.
The global conveying and storage business is currently driven internationally by 20 locations in Europe, North and South America and Asia, supported by five Service Centres in Germany, Hong Kong, USA, Brazil and Saudi Arabia, and reinforced by approximately 80 representations and a network of around 100 supervisors and inspectors who advise on and accompany installation, commissioning and on-site inspections with the PREMAS® Preventive Maintenance Service for AUMUND, SCHADE and SAMSON machines as well as for those of other manufacturers.
Effective mid-2022, after 100 years of family management Franz-W. Aumund, who had been Managing Proprietor of the AUMUND Group for 38 years, has handed over his operational activities to the Management of AUMUND Fördertechnik, in the persons of Dr Pietro de Michieli, Reiner Furthmann and Uwe Altena.
Dr Pietro de Michieli has been Managing Director Sales for four years and has now been appointed additionally as CEO of AUMUND Fördertechnik GmbH and AUMUND Holding B.V. Reiner Furthmann has been responsible for technology, design and production at AUMUND Fördertechnik GmbH for around 20 years, and was appointed Managing Director Technology in March 2018. Uwe Altena has held the function of Commercial Managing Director since mid-2021.
Franz-W. Aumund: “From the early stages my objective was to market AUMUND machines all over the world, which is today the guarantee for the continuity of the AUMUND Group. In 1975 the AUMUND subsidiaries in Brazil and Canada were created, followed by USA in 1980, France in 1991, India in 1996 and Hong Kong in 2005. The AUMUND rep. office for technology, purchasing and production was opened in Beijing, China, in 1994 and this was followed by the incorporation of the AUMUND subsidiary in Beijing in 2006. AUMUND has had its own representations in Russia since 2008 and Dubai since 2010. In 2022 an office was established in Indonesia.’
Dr Pietro de Michieli: “For more than four decades over 85% of AUMUND Group production has been exported. Focusing on the customer has been part of the company’s DNA for a long time. Our global sales headcount is more than 100, and is reinforced by our network of representatives. This gives keeps us close to our customers, enabling us to meet them and speak with them at any time.”
Reiner Furthmann: “With a product depth of more than 70 application-based machine types of the highest quality and reliability, for both horizontal and vertical conveying, and storing and discharge of the most varied of bulk materials, the AUMUND Group has the widest global spread in the conveying and storage technology market. Our motto ‘WE CONVEY QUALITY’ does not only refer to the quality of our products, on which we place the highest demands, but also includes the aspiration to always find the very best technical solution for our customers. The success stories of products from AUMUND started with the development and manufacture of curved steel pan conveyors
for underground coal mining from the end of the 1940s, and the further development of pan conveyors and bucket elevators for the cement industry from the early 1960s. Today
AUMUND Fördertechnik offers a multitude of high-performance conveyors for continuous vertical and horizontal conveying, which provide the links between the processes of our customers. The portfolio covers not only pan conveyors and bucket elevators but also chain conveyors, stationary material feeders and discharge systems. The technological know-how is reflected in more than 200 national and international patents. The technological and production know-how for the key components of the AUMUND products lies with AUMUND Fördertechnik in Rheinberg, where technology, research, development and design work hand in hand.”
PRODUCT RANGE AND DIVERSIFICATION
Products and solutions from the AUMUND Group product companies AUMUND Fördertechnik GmbH, SCHADE Lager
Expansion and strengthening of the product range of the AUMUND Group
technik GmbH and SAMSON Materials
Handling Ltd can be found around the world in all key industries for the conveying and storage of bulk materials.
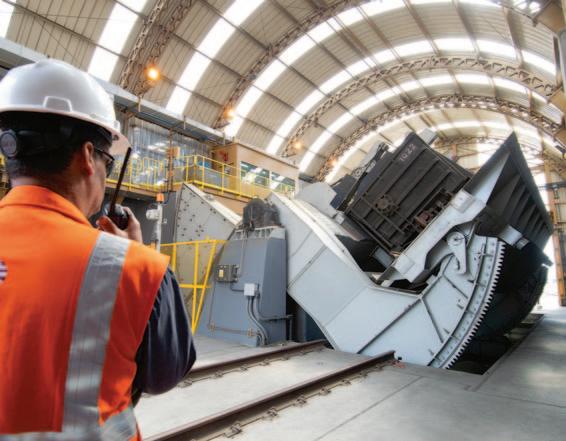
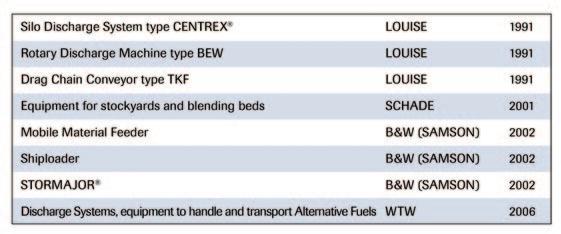
MERGERS AND ACQUISITIONS

PURPOSEFULLY IMPLEMENTED
Acquisitions are an important source of richness of ideas and strength of innovation
for the AUMUND Group, whilst adhering to the proven AUMUND parameters for takeovers, which Franz-W. Aumund describes as follows: “We are machinery manufacturers and will remain so in future. We analyse owner-operated companies as well as business areas of corporate groups. The products and services must complement our portfolio and it must be
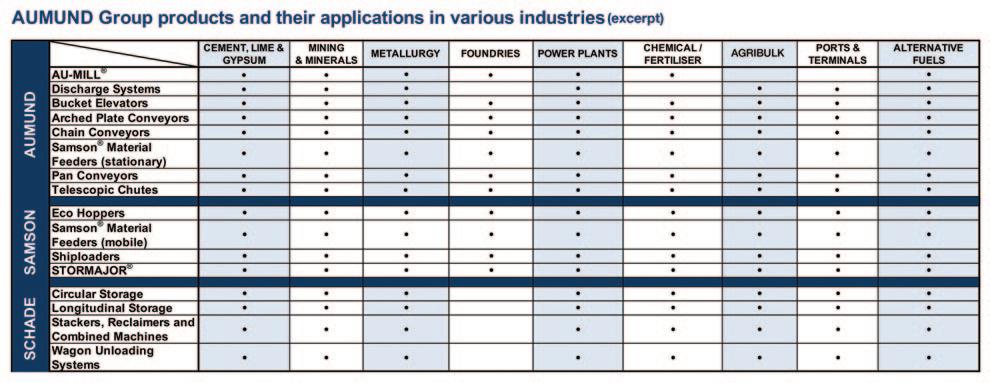
possible to leverage sales synergies. There are no geographic boundaries and that will certainly never change. On the contrary, international vision in company acquisitions has become even more significant over the recent decades of AUMUND globalization and will remain relevant in future.”
With the acquisitions of Maschinenfabrik LOUISE GmbH in 1991
and WTW Engineering Maschinen- und Förderanlagen GmbH in 2006, AUMUND expanded its product range and its product know-how in rotary discharge machined and drag chain conveyors. The purchase of the spare parts business for Silo Discharge Systems of Besta & Meyer GmbH in 2014 fitted with this portfolio, and the acquisition of the spare parts business of KoWey GmbH in 2021 was appropriate in connection with bucket elevators.
Diversification was the strategy behind the acquisition of Gustav Schade Maschinenfabrik GmbH in Dortmund, today SCHADE Lagertechnik GmbH, and of British company B&W Mechanical Handling Ltd, today SAMSON Materials Handling Ltd, in 2001 and 2002 respectively. Both companies serve market segments adjacent to those of AUMUND. B&W/SAMSON manufactures mobile material feeders, shiploaders and ecological (Eco) Hoppers, which are predominantly used in ports and terminals but also in industrial applications. SCHADE designs and supplies machines such as stackers and reclaimers for bulk materials stockyards and blending beds, which are particularly in demand for handling bulk materials in the most varied of key industries. The rail wagon tipplers which were originally sold by AUMUND were integrated in to the SCHADE portfolio at the beginning of the 2010s. This was not only because SCHADE had a customer base in coal handling operations, but also because Wagon Tippler specialists are employed by SCHADE in the design office in Bristol, UK.
With the acquisition of Th. Tilemann GmbH Gelenkketten- und Räderfabrik, Essen, Germany, in 2016, the AUMUND Group gained an experienced manufacturer of high-quality chains and associated components. In the integration process the company was re-named TILEMANN GmbH, and equipped with the latest production and assembly technology for the fabrication of AUMUND bucket elevator chains, and also conveying chains to supply to manufacturers of stockyard and blending bed equipment and scraper conveyors, including SCHADE.
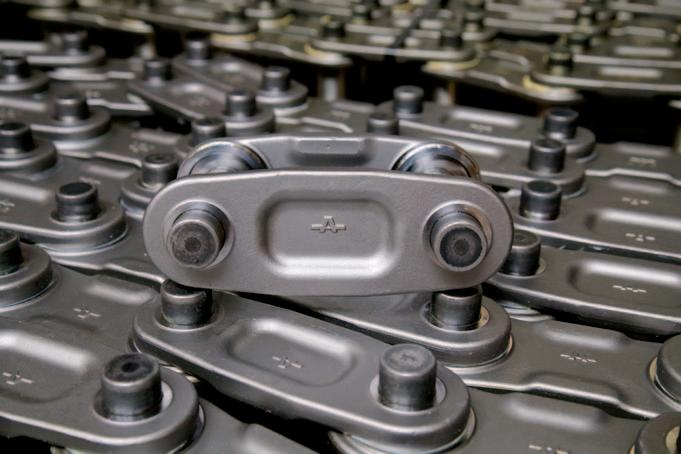
DIGITALIZATION IS ON THE ADVANCE AT AUMUND
The topic of digitalization is gaining in significance for the future in the AUMUND Group. One example of this is the PREMAS® 4.0 Predictive Maintenance Solution . The system for predictive maintenance was developed together with PREMAS AG, Switzerland, and it monitors safe, energy-efficient machinery operation
and analyses the condition of the machine with the aid of algorithms. The AUMUND Group is currently offering PREMAS® 4.0 predominantly for belt bucket elevators, various types of chain bucket elevators, pan conveyors, and for the CENTREX® silo discharge system. PREMAS® 4.0 can also be installed on equipment made by other manufacturers, for example as part of a conversion.
KEY INDUSTRIES FOR BULK MATERIALS —
THE ‘HOME’ OF AUMUND GROUP PRODUCTS
Way over half of the 24,000+ pieces of equipment operate in the cement industry all over world. The logistics of the various raw materials, combustibles and additives play a significant role in the cement production process. Limestone and other raw materials must be kept available in sufficient quantities to keep the production process running continuously, with an
The Ste. Genevieve cement plant in Missouri, USA, which is considered to be one of the largest of its kind in the world, is equipped with a wide range of AUMUND products.
additional buffer in case there is an interruption in supply. The careful planning and design of clinker storage and clinker conveying makes a major contribution to the economic viability of the complete plant. This is a discipline in which AUMUND Fördertechnik has more than 60 years of technological expertise. From a broadly positioned range of products, optimized solutions are offered, for example for raw material processing, kiln feed, raw meal conveying to the heat exchanger, reception, storage and conveying of combustibles (both coal and alternative fuels) and hopper discharge. Solutions for clinker loading, clinker dispatch and clinker storage are also part of the portfolio. In metallurgy, the handling of hot bulk materials such as sinter, pellets, DRI, HBI, fines, coal and coke takes on a special role, and here AUMUND products are operated in conveying, charging, and discharge, if necessary with cooling or conveying under

inert gas. A partner to the iron and steel industry since the 1960s, AUMUND offers solutions as integrated process elements which support customers’ production flows. This is shown as an example in connection with the development of CO2 reduced production processes. Since the beginning of the 2000s direct reduction has proved its worth as a largely available alternative to the classic blast furnace process, where sinter and coke are used as charge. Direct reduction using natural gas produces pig iron from iron ore pellets. Depending on the technology, the sponge iron products are either DRI or HBI. For the handling of these products, i.e. the cooling and charging in the manufacturing process, the operators of direct reduction plants can take advantage of very innovative solutions.
In the direct reduction sector
AUMUND co operates with MIDREX, USA, and with the plant construction company for steelworks technology, PRIMETALS, Austria.
A hot material conveyor feeds the material continuously from the direct reduction plant straight into an EAF (electric arc furnace). AUMUND hot DRI charging transports hot DRI on an AUMUND bucket apron conveyor under heat-insulated and inert, non-oxidizing conditions from the MIDREX direct reduction shaft furnace straight into the EAF in the steel plant. The main advantages of hot charging of DRI into the EAF are reduced energy consumption and shortened smelting cycle times.
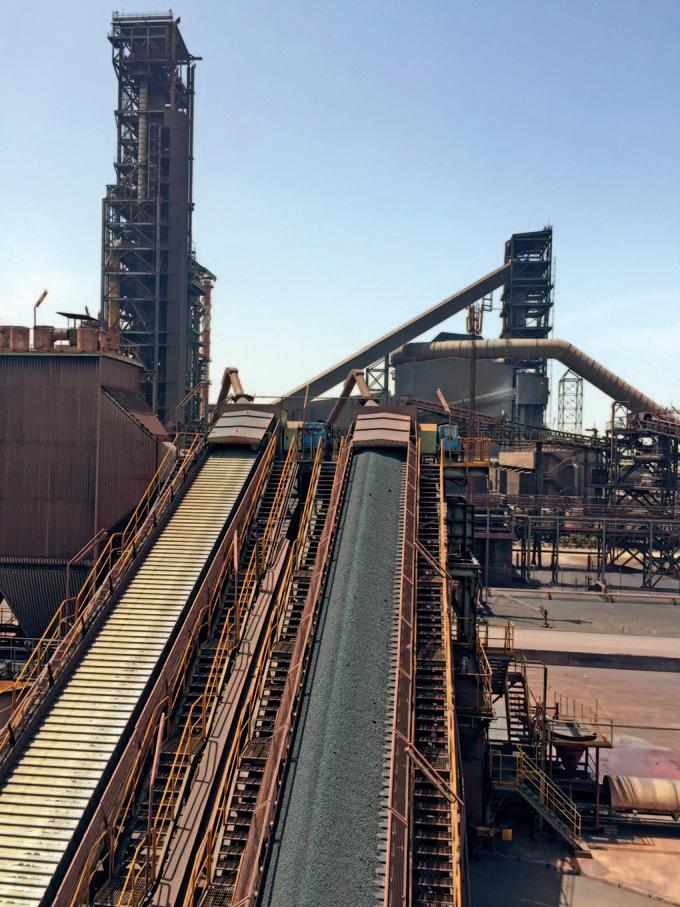
For the conveying and cooling of HBI, hot briquetted sponge iron, the patented AUMUND mist cooling process comes into its own. The HBI is sprayed with water mist on an AUMUND flat plate conveyor and gently cooled down, for example from 800°C to 100°C, in a patented process which does not damage the product (HBI
slow cooling).
Careful conveying of castings is often crucial for the quality of the parts. Therefore, it is particularly important to select the correct conveyor for the purpose. AUMUND offers conveying technology for the complete process chain in foundries which manufacture on the
basis of wet moulding. These include conveyors for degating, sorting and cleaning of castings, cooling conveyors for transporting and cooling of hot castings, bucket elevators for vertical conveying and conveyors for feeding furnaces with scrap metal.
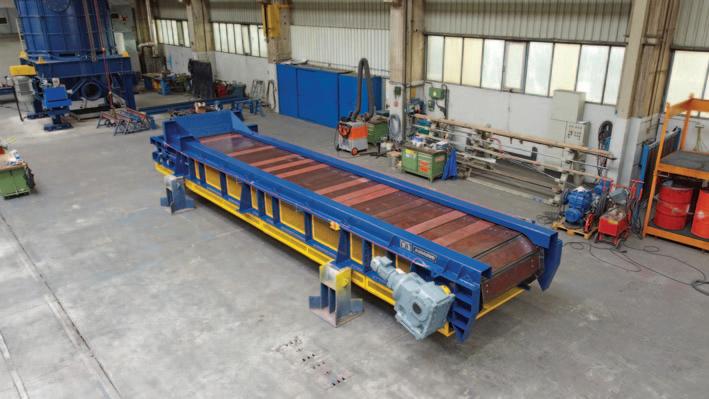
AUMUND products also have a long tradition in the mining and minerals sector, with optimized solutions for every process stage for conveying, storage and loading of often abrasive and sticky bulk materials. AUMUND has experience with the handling of the most varied of materials such as basalt, bauxite, dolomite, ores, fly ash, urea, potash, limestone, clay, petcoke, phosphate, pozzolan, salt, sand, sulphur, and zinc oxide. The application and the characteristics of the materials determine the conveyor. Precise planning is of the utmost importance because this is the basis for the economic success of the plant.
For many years AUMUND has been supplying equipment for conveying and storage of raw materials with the most
varied of characteristics for operation in the chemicals industry. Machines are matched precisely to the particular stage of the production process and to the site where they will operate. If required for the application for example, AUMUND can supply bucket elevators in a stainless steel version. AUMUND is particularly in demand in the widely varying processes and production technologies of the fertilizer industry, where products are in operation in the areas of material extraction and processing, raw material and additive conveying, loading and handling.
AUMUND equipment is also part of the machinery in power plants for example for reception of coal, calorific domestic waste (RDF), biomass or limestone in various types of firing plant whether it be grate firing, pulverized coal firing or fluidized bed
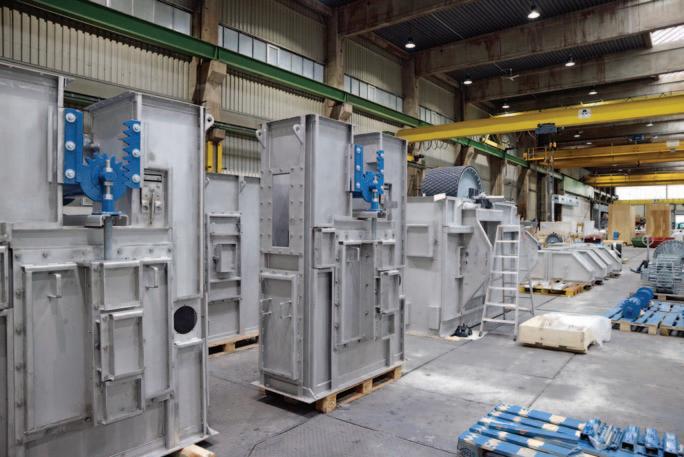
AUMUND arched plate
conveyors, also in heavy-duty design, are used to transport all kinds of minerals.
AUMUND can react to the requirements of the fertilizer industry by supplying bucket elevators in stainless steel.
from the recently created Alternative Fuels division of AUMUND Fördertechnik.
The AUMUND Fuel Mill, AU-MILL® for short, prepares calorific plastic waste, known as RDF (refuse derived fuel) to pass on for use as an alternative fuel in place of coal, oil or gas, for example in the rotary kiln in a cement plant.
The AUMUND range of products for conveying alternative fuels includes solutions such as the trailer docking station, the walking floor, the screw discharger, and a specially modified drag chain conveyor. The alternative fuels handled are categorized into two groups. The first of these is CO2-neutral biomass such as wood chips, wood pellets,
combustion, as well as for export of materials such as gypsum, ash, sludge and dust.
For more than 60 years AUMUND has been supplying bucket elevators for the agribulk industry. These were specially developed to convey cereals and similar agricultural bulk materials. More recently, renowned sugar producers have been placing their trust in AUMUND conveying technology, such as specially designed screw dischargers for residue-free emptying of white sugar silos. Any machinery parts which come into contact with the sugar, such as the screw and the discharge chute are supplied in stainless steel.
Energy-intensive sectors such as the cement and steel industries, and power plants, are being called upon to adopt climate-friendly processes, and they are seeking cost-effective solutions in order to achieve this. Such solutions are available
A specially designed discharge system was supplied for the Al Khaleej Sugar Group plant in Dubai for complete emptying of a white sugar silo with a diameter of almost 60m. The photo shows the 27m-long screw discharger which was supplied in three parts ready to assemble in Dubai.
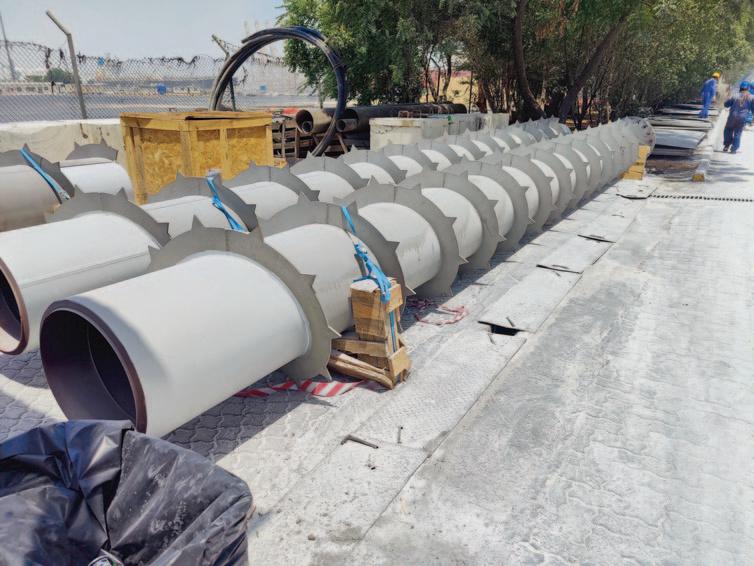
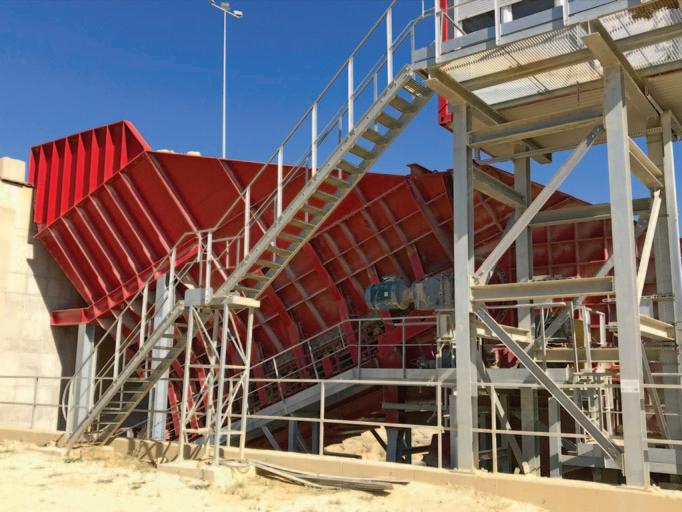
sunflower seeds, coconut shells, soiled straw and hay as well as sewage sludge. The second large group comprises materials such as plastic, used tyres, refuse from the medical sector and textile manufacture, shredded paper and animal meal.
WHEREVER MOBILITY AND SPEEDINESS ARE REQUIRED
For import and export of material the AUMUND Group offers a very wide spectrum of machines and equipment in conveying and storage technology. For ports and terminals the mobile (i.e. driven) shiploading and unloading systems such as shiploaders, Eco Hoppers, and the Samson® material feeder are particularly attractive.
SAMSON Materials Handling has developed a range of shiploading and
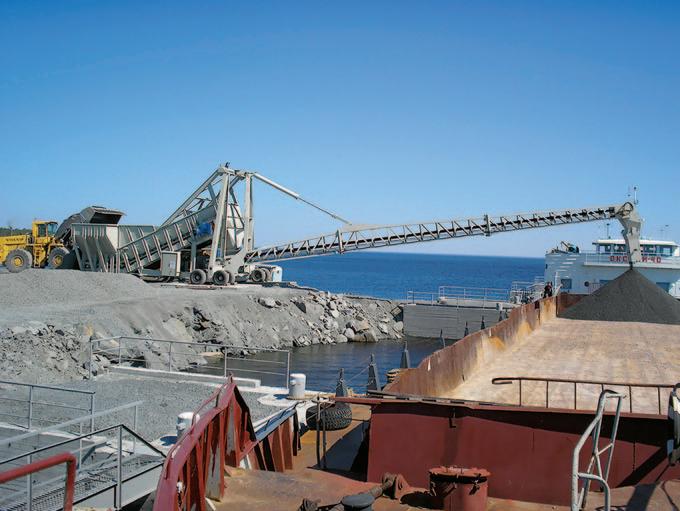
With the SAMSON STORMAJOR®
mobile shiploading is possible even under the tightest of conditions.
Japan: AUMUND drag chain conveyor type LOUISE for conveying alternative fuels at the Ofunato power plant of Taiheiyo Cement in Iwate Prefecture.

PREMAS® 4.0), repairs and spare parts, to the training of customers’ maintenance personnel. AUMUND Group Field Service GmbH, which was incorporated in 2017, ensures a globally standardized commitment to quality in installation and commissioning of AUMUND, SCHADE and SAMSON machines, and also of equipment manufactured outside the Group, with its international network of around 100 supervisors and inspectors.
Provision of high-performance service was also the basis for the incorporation in 2007 of AUMUND Logistic GmbH as an autonomous company. The focus of its activities is worldwide dispatch of machines and machinery parts by sea freight, air freight and land transportation for AUMUND, SCHADE, SAMSON and TILEMANN as well as for the overseas
unloading equipment, adapted to the handling of dry bulk materials, which offers flexibility both for operators of existing berths and for high-performance loading. Mobile shiploaders, material feeders and also the STORMAJOR® can be operated on any quay independently of each other or parked out of the way until they are required for the next job. The mobile technology is configured by SAMSON to create a system which matches precisely the requirements of the individual port or terminal.
SERVICE IS THE KEY TO CUSTOMER PROXIMITY AND CUSTOMER SATISFACTION
The AUMUND Group offers extensive after-sales and customer support services all over the world, ranging from consulting to upkeep, preventative and predictive maintenance (PREMAS® and
One-stop shops: The international logistics for original spare and wear parts is decentralized; five AUMUND Service Centres enable rapid supply to customers.
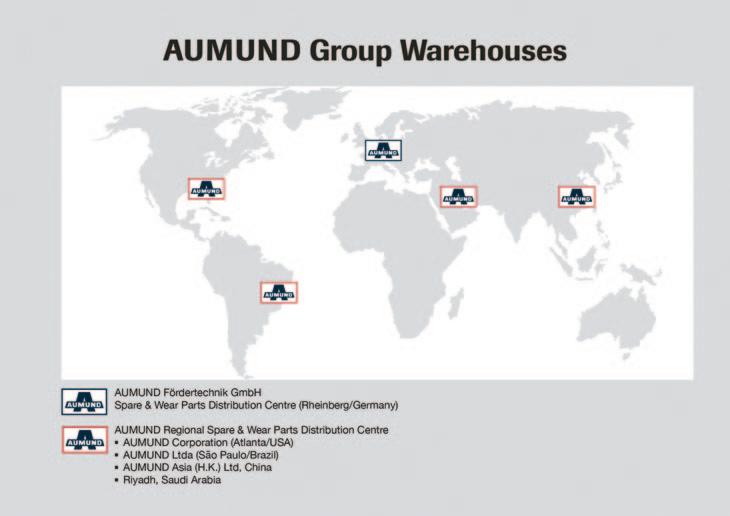
AUMUND companies. Not only spare parts packages and products manufactured by AUMUND are forwarded, but collections are also organized of machines and parts from other locations which need to be transported to a customer or installation site elsewhere.
‘WE CONVEY A GREENER FUTURE’
“The linking of ecological aspects and business considerations, for the benefit both of our customers and of the AUMUND Group itself, has defined our thinking and actions for decades, in fact even before concepts such as conservation, sustainability and reduction of CO2 emissions became important for so many companies all over the world. In this the AUMUND Group is one of the pioneers in the bulk materials conveying and storing sector,” says Franz-W. Aumund.
“WE CONVEY A GREENER FUTURE” applies to the two fields of activity where the AUMUND Group unites ecology and business:
1. The product companies AUMUND, SCHADE and SAMSON support customers on their journeys to environmentally conscious production processes, and activities which comply with environmental legislation.
2. The AUMUND Group takes its responsibility for conservation of resources and protection of the environment seriously on its own sites as well. As an example, no fossil fuels are utilized in machinery manufacture, and additional measures are consistently being undertaken to save energy.
The cement industry, the steel industry, and power plants predominantly use fossil fuels for their processes currently, which release climate-damaging CO2. At the same time these industries must fulfil more and more national and international legal require ments to reduce their CO2 emissions. Alternative fuels, which can be prepared and transported with AUMUND solutions play a significant role in achieving these targets.
As a technology leader in hot material conveying, and in the cooling of the direct reduction products, DRI and HBI, AUMUND conveyors contribute to the benefit of customers to the reduction of CO2 emissions in the iron and steel industry. This AUMUND know-how from the metallurgical process also works to the advantage of the cement industry, which is working on the development of LC3 cement. The blending in of calcinated clay to this new cement type means LC3
produces emissions of up to 40% less carbon dioxide. With cooling conveyors from AUMUND the burnt, calcinated clay can be cooled down from 800°C to 100°C, at which point it can be mixed with the clinker and milled to become LC3 cement. Cooling takes place in an inert atmosphere which can be created with nitrogen from an air separation unit.
For reduction of dust emissions, and for other reasons of environmental safety, SCHADE offers covered storage systems for bulk materials volumes of 800,000 tonnes or 1,000,000m3 even on a small surface area. Stockpiling is carried out by mobile tripper cars installed beneath the roof of the storage building, and the pile is reclaimed by full-portal or semi-portal reclaimers. Depending on customer requirements or official regulations, the equipment can be adapted to the height of the storage building using a design incorporating two booms on the Reclaimer. In an indoor circular storage facility, storage capacities of 360,000 tonnes are achievable.
The SAMSON Eco Hopper fulfils strict standards for the reduction of dust emissions. The Eco Hopper is used for importing bulk materials in ports and terminals, and has a comprehensive range of dust protection features, including a system which reduces the impact of sidewinds, the Flex-Flap dust sealing system and a mechanically driven sliding roof.
At its headquarters in Rheinberg AUMUND has been acting with environmental responsibility for many years. The office and production facilities are fitted out with energy-optimized features, such as thermal insulation, energysaving LED lighting, and ventilators which prevent heat rising to areas where it would be wasted, such as up to the factory roof.
The production facilities do not generate CO2, because AUMUND does not use gas. Back in 2010 AUMUND invested several million Euros in a sustainable environmental protection measure, installing solar panels on the roofs of nine of its production halls, which makes AUMUND a generator of on average around 700,000kWh annually, far more electricity than is required for its own purposes.
At TILEMANN in Essen, environmental awareness also prevails. By installing ceiling ventilators in the works halls gas consumption was reduced by 33%. Also the lighting was converted to LED. Cooling fluids previously utilized in fabrication were replaced with more up-to-date and ecological alternatives. The abrasives used are also environmentally friendly and do not pose a health hazard for the employees, and only re-useable packaging is used by TILEMANN.
FIT FOR THE FUTURE
Franz-W. Aumund: “I am convinced that we are well-positioned now and for the future and that we will always have the right ideas to enable us to recognize and fulfil the requirements of our customers. In this connection innovation and investment are of the utmost importance to me. They secure the future of the individual companies, and with them the future of our Group. We have an investment agenda which takes into consideration markets, manufacturing locations, ideas, innovations, employees and much more. This is why we do not only concentrate on activities in our familiar key industries, but we also open up new futureorientated areas such as alternative fuels. ‘Fit for the future’ also means for the AUMUND Group that it should continue to develop in a healthy way. This means with a combination of
Green electricity: 3,358 solar panels produce energy at AUMUND. Of the total roof surface area of approximately 18,000m², around 5,550m² is used for solar panels.
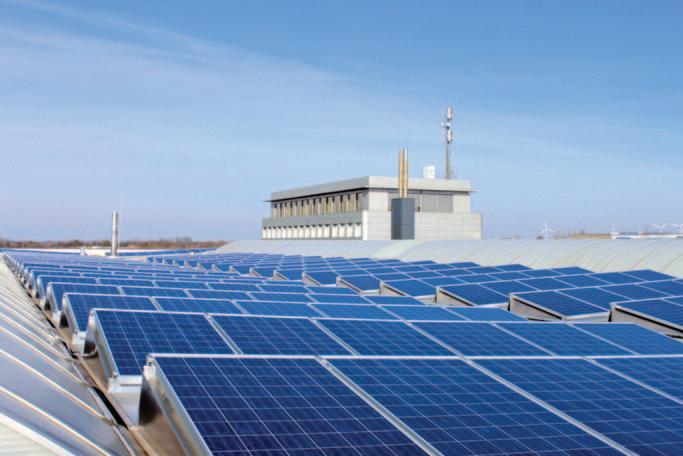
organic, self-generated growth and inorganic growth, for example generated by acquisitions.”
YESTERDAY. TODAY. TOMORROW: THREE GENERATIONS, THREE EMPHASES
What is special about this corporate development is the high degree of continuity with which AUMUND, through Heinrich Aumund (1873–1959), GünterClaus Aumund (1912–1984) and Franz-W. Aumund (b. 1944) has written company history and continues to do so.
The cornerstone for success was laid by Prof. Heinrich Aumund in 1922 when he founded the company for AUMUNDPatente MB.H, which dealt with the exploitation, monitoring and marketing of existing and future national and international AUMUND patents. One of these was the patent registered to Heinrich Aumund in 1929 for the rail wagon tippler for unloading coal. Back in 1920, Heinrich Aumund had designed a short plate conveyor for underground mining, the first conveyor fabricated from steel and which could be guided around bends.
In 1937 AUMUND-Patente MB.H., Berlin, was re-named AUMUND Fördererbau GmbH, and from 1945 was located near Bremen. The new name signified a decisive new business direction. The emphasis from now on was on development, design and construction of conveying equipment. The focus was on continuous conveyors, and the company developed large metallic conveyors which become an AUMUND trademark. After the end of the Second World War in 1945, AUMUND innovations such as the pan conveyor and the pivoting pan conveyor made a ground-breaking impact on the market.
The curved and inclining AUMUND pan conveyor, which was patented in 1948, revolutionized underground conveying in coal mining. In the following years Heinrich Aumund worked, supported by his son Günter-Claus Aumund, from the new premises in Duisburg-Homberg in close proximity to the coalmining and steel industries in the Ruhr area, primarily on improvements and new inventions of conveying equipment for mining. Every year new patents were registered domestically and abroad.
Günter-Claus Aumund not only successfully continued the business in his period of guidance of over 30 years, but also developed it further, not only in new equipment, but AUMUND increasingly worked on spare parts and maintenance and repair of conveyors, developing its own customer service department alongside
“I will always succeed, as long as I believe in my own ability. But if I have doubts, success will be a distant dream.” This was the favourite saying of company founder, inventor and university professor, Heinrich Aumund (1873–1959).
development and design. Production was carried out only about 20km away from Duisburg-Homberg, in Rheinberg. In November 1955 Günter-Claus Aumund bought the first parcels of land amounting to 4,800m² at auction. From these beginnings today’s AUMUND Industrial Park was born, and now comprises 73,000m² of infrastructure including administration and production buildings and storage yards.
For the assembly of the rail wagon tipplers, Günter-Claus Aumund had his engineers develop a mobile portal crane in 1957. The portal crane prototypes were followed by more than 6,000 AUMUND cranes with large spans and impressive load capacities, supplied all over the world. Business with portal cranes, bridge cranes and container cranes was booming for a long time, resulting in AUMUND becoming a crane specialist. However, the reunification of Germany and the opening up of Eastern Europe led to ruinous price pressure in the crane sector in the early 1990s. At the end of 1994 AUMUND withdrew from the crane business.
Businessman and leader Günter-Claus Aumund led AUMUND Fördererbau GmbH, later AUMUND Fördertechnik GmbH, and the beginnings of the AUMUND Group, as Managing Proprietor from 1952 to 1984.


After AUMUND products had originally been manufactured almost exclusively for the German market, Franz-W. Aumund worked on successively increasing the percentage of equipment exported. The foresightedness of positioning the AUMUND Group internationally and not being dependent on one market or one industry has been shown in particular in times of economic difficulty. “The international locations guarantee the greatest possible proximity to customers and enable the establishment of a longstanding mutual trust which cannot be shaken even by a crisis, such as most recently the coronavirus pandemic, which we approached with the required caution and necessary measures,” says the globalizer, world traveller and visionary, Franz-W. Aumund.
Franz-W. Aumund – globalizer, world traveller and visionary.
SOCIAL ISSUES AND EDUCATIONAL SUPPORT: A SUBJECT CLOSE TO THE HEART OVER THREE GENERATIONS OF AUMUND Social commitment begins in 1930 with the support of needy students by Heinrich Aumund, and continues from the 1970s when the centre for vocational training and retraining is initiated by Günter-Claus Aumund in Rheinberg. It is expanded intensively in the era of Franz-W. Aumund, among other things by the privately founded Franz-W. Aumund-Stiftung in 2006, and with the philanthropic activities of the AUMUND companies from 2007, without losing sight of the origins. For
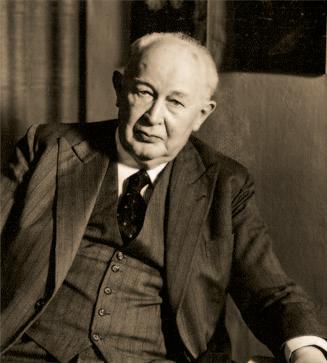
example, since 2009 more than 50 mechanical engineering and business engineering students have been supported by the scholarship programme initiated between Franz-W. Aumund and Prof. Detlev Borstell from Koblenz University of Applied Sciences. The close connection to partner universities in Germany which has existed since 2011, annual scholarship students and alumni meetings in Rheinberg, and the offer of gaining experience in the overseas AUMUND subsidiaries, make the scholarship award from AUMUND a very desirable sponsorship programme.
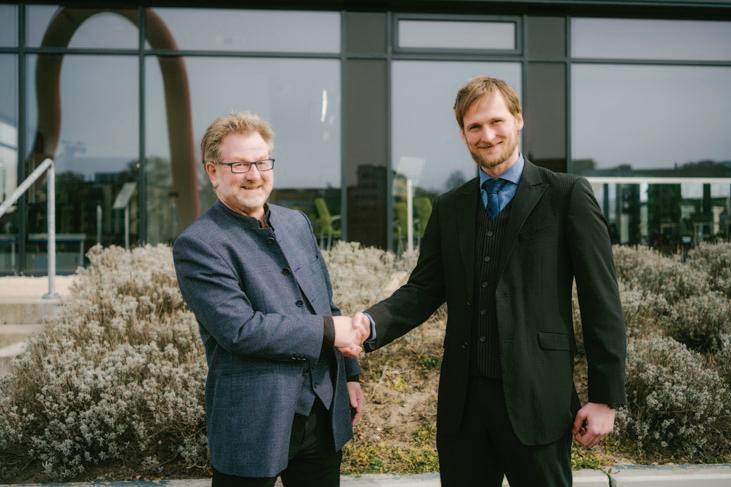
In 2013, Franz-W. Aumund was appointed Honorary Senator of Koblenz University of Applied Sciences, as his grandfather Heinrich Aumund had in his time been appointed Honorary Senator of the Gdansk University of Technology and of the Technical University of Berlin.
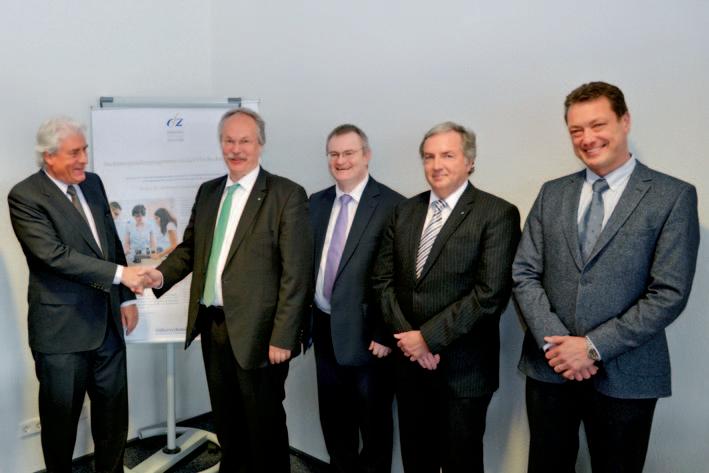
The year 2019 was marked by the establishment of the second private foundation by Franz-W. Aumund, the Aumund Foundation, which is a strategic expansion and deals in particular with supporting humanitarian and medical projects overseas.
One hundred years after the founding of the company, a circle was closed in April 2022 with the establishment of the Prof. Heinrich Aumund Endowed Chair at HTW Berlin (Berlin University of Applied Sciences) with which Franz-W. Aumund has erected an ideological monument to his grandfather.
ABOUT THE AUMUND GROUP
Franz-W. Aumund in animated conversation with two students at The Sagar School in India. The school belongs to the international ‘Round Square’ Network. The Aumund Foundation awards scholarships to children from underprivileged families in order to enable young people to visit a ‘Round Square’ School.
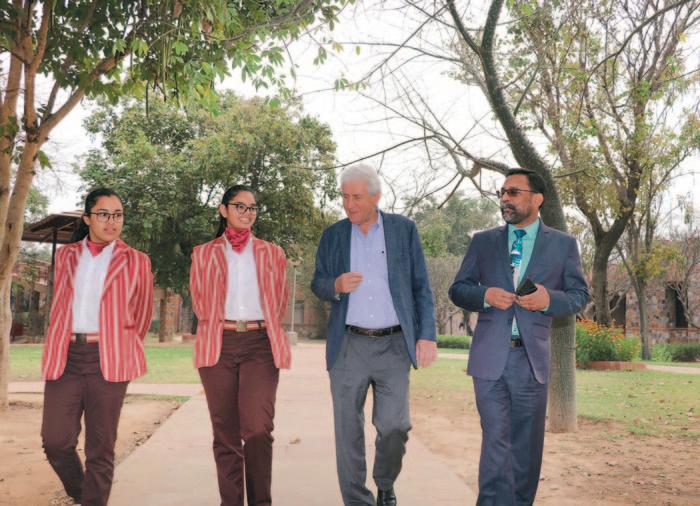
The AUMUND Group is active worldwide. The conveying and storage specialist has special expertise at its disposal when dealing with bulk materials. With their high degree of individuality, both its technically sophisticated as well as innovative products have contributed to the AUMUND Group today being a market leader in many areas of conveying and storage technology. The manufacturing companies AUMUND Fördertechnik GmbH (Rheinberg, Germany), SCHADE Lagertechnik GmbH (Gelsenkirchen, Germany), SAMSON Materials Handling Ltd (Ely, Great Britain), TILEMANN GmbH Chains & Components (Essen, Germany) as well as AUMUND Group Field Service GmbH and AUMUND Logistic GmbH (Rheinberg, Germany) are consolidated under the umbrella of the AUMUND Group. The global conveying and storage technology business is spearheaded through a total of 20 locations in Asia, Europe, North and South America and a total of five warehouses in Germany, USA, Brazil, Hong Kong and Saudi Arabia.
“I feel very honoured to be able to carry on the scientific and educational work of Prof. Dr.-Ing. h.c. Heinrich Aumund here in Berlin and I would like to thank the Franz-W. Aumund-Stiftung and HTW Berlin for your confidence,” says Prof. Dr. Rico Meier (right), with HTW President Prof. Dr.-Ing. Carsten Busch.
Moving with the times — and the market
mobile equipment, and why it is so important
Mobile shiploading – environmentally friendly and efficient
THE PORTALOAD MOBILE SHIPLOADER FROM BÜHLER
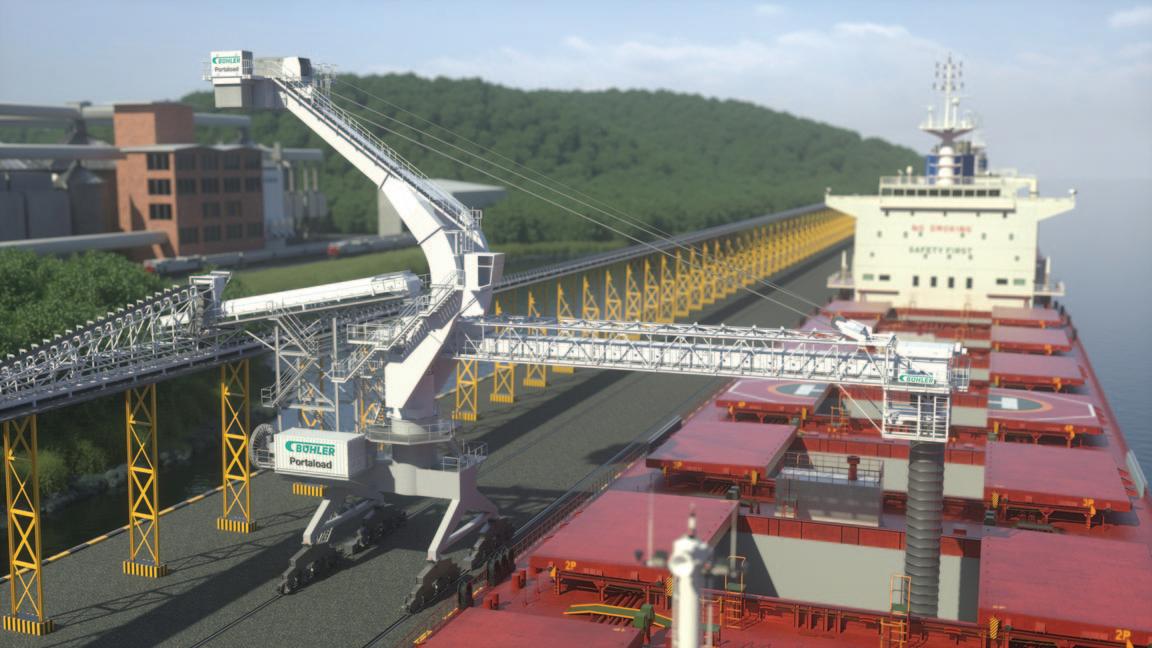
Swiss engineering and technology company
Bühler has introduced the new mobile shiploader with a capacity of up to 2,800tph (tonnes per hour). The loader features a wealth of functions designed for maximum efficiency, availability and safety.
The new design has also been carefully thought through to reduce harmful dust emissions — an increasingly important topic for the health of people and the environment.
The benefits of mobile shiploaders, as opposed to stationary loaders, lie in their flexibility. “Mobile shiploaders provide operators with a cost-efficient solution for a wide range of applications,” says Stefan
Anshelm, Product Manager at Bühler Group. “They are ideal for businesses that have an existing berth and possibly share it with neighbouring companies.” Usually mounted on rails, they are connected to a high-capacity pier conveyor and tripper car. High performance and minimal handling help to reduce operating, personnel and mooring costs.
WHAT’S NEW?
Bühler’s mobile Portaload has been developed following thorough analysis of existing systems. The complete redesign achieves optimal load distribution, reducing quay requirements. Additionally, wind resistance is decreased, and the robust design offers better protection against
storms and earthquakes.
One look at Bühler’s mobile shiploader shows the difference. The vertical pylon is elegantly curved, meaning there is no interference with the fixed feeding conveyor. The construction of the counterweight has been optimized to greatly reduce torque forces. To make maintenance tasks as easy as possible, the open design ensures access to all critical parts. Great care went into optimizing all the movements required for loading, so that berthing times are kept as short as possible.
NO HYDRAULICS — NO LEAKAGE RISK
In addition, many features of the mobile Portaload are designed to address

environmental issues.
Most loaders are operated with hydraulic operated kick-systems placed at the tip of the loading beam to extend the range. The Portaload functions without a hydraulic driven kick-in/kick-out system. Instead, it is operated with a winch system that enables the loader to reach into the corners of the cargo hold.

This greatly differentiates the loader from other solutions as it eliminates the risk of spillage of hydraulic fluid into the product or the water. “Leakages do not occur frequently. But if they happen, the consequences are severe. Contamination of the product results in huge wastage. Leakages over water require comprehensive cleaning efforts and must be avoided under all circumstances,” says Andreas Herzer, Head of Market Segment Ship Loader/Unloader at Bühler Group.
The new feature is in line with Bühler’s strategy to reduce the environmental impact of the industries in which it is a player. “The idea to design out the hydraulics sprang initially from a conversation with a customer,” says Herzer. “The customer wanted to address the problem of potential product contamination. The new design was developed following that dialogue.” Removing the hydraulics has other benefits too, as it also reduces maintenance time.
INNOVATIONS TO TACKLE DUST
Environmental protection is a key requirement in every industry today. For shiploading and unloading, one area that is attracting increasing attention is dust emissions. The dust created through loading and unloading dry goods can impact on the environment. It can also harm the health of people living close to port facilities and personnel working on the piers. For this reason, regulations regarding dust emissions caused by port facilities are being tightened in many regions. Complying with ever-stricter environmental governance is becoming a key topic for many stakeholders in the industry.
Bühler’s mobile Portaload tackles dust emissions with a bundle of optional features. The key measure for reducing dust emissions is to control the product flow. By managing product speed and air content within the transported product, dust emissions can be significantly reduced.
Two alternative options efficiently manage the product flow. The Portaspoon installed at the muzzle of the loading spout bundles the product so that loose particles are integrated in the main product stream. Bühler’s innovative dust suppression system delivers even better results. It controls the product flow and can be adjusted according to the requirements of each product. Managing product
transportation speed also ensures that sensitive products such as oil seeds, soybean meal or grains are handled safely. The low-speed discharge reliably prevents product degradation.
In addition, the mobile Portaload comes with a completely enclosed belt conveyer, which both prevents dust from escaping and protects the product. The enclosed product transfer points are fitted with spot filters for direct aspiration.
A further serious issue relates to safety. Dust can develop into an explosive atmosphere with catastrophic consequences. By keeping dust emissions to an absolute minimum, the Portaload ensures a safe and healthy environment. This also benefits the product because removing dust from grain results in a cleaner product that can be stored more efficiently and sustainably.
STAYING AHEAD OF THE GAME
“It is just a question of time before efficient dust reduction becomes a universal requirement around the globe. Businesses need to future-proof their operations today,” says Herzer. “This is why we took up the challenge and developed a shiploader that ensures that emissions are kept below legal limits, and that efficiently protects the product, the environment and personnel.”
The worldwide grain trade is increasing year by year and demanding an advanced supply chain for these valuable commodities.
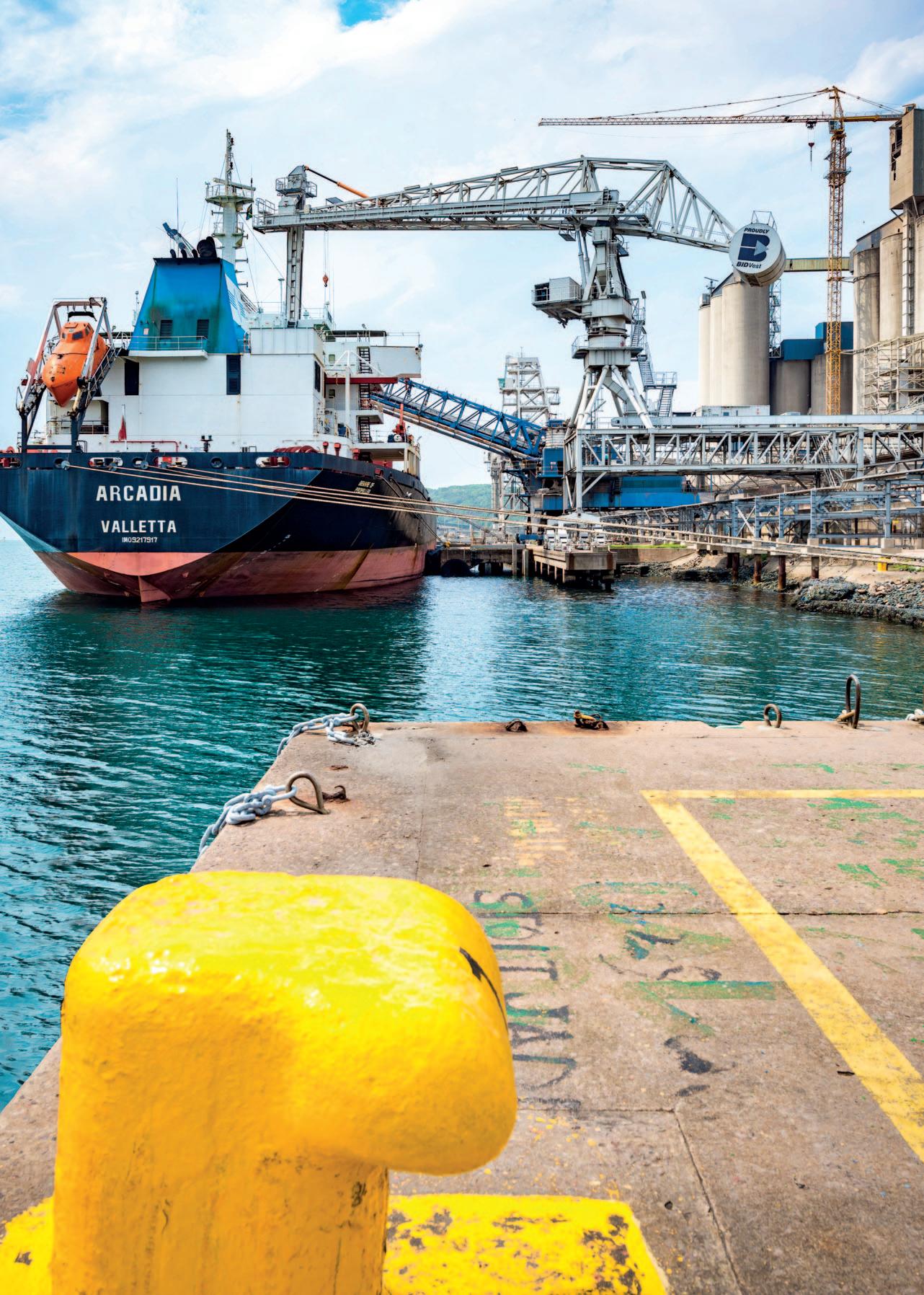
Bühler Grain Quality and Supply is the leading manufacturer of highly e cient loading and unloading equipment combined with low operating costs. Uptime, reliability and e ciency are only three keywords de昀ning the values on which the solutions of Bühler are developed on. Learn more: buhlergroup.com/gqul
Reliable and e cient.
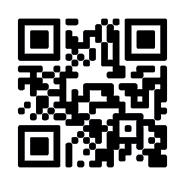
SANY Europe: competitive presence in the mobile market — and elsewhere
SANY Europe, part of SANY Heavy Industry in China, offers a wide range of high-performance machines. Its product line includes: a broad spectrum of mobile equipment for use in ports; reachstackers; empty container handlers; heavy-duty forklift trucks and cranes; material handlers; hydraulic excavators and other earthmoving machines.
SANY’s equipment is suitable for all types of commodity, and the company prides itself on its ability to transport any cargo from A to B without any difficulties. For breakbulk cargoes, SANY offers a range of heavy-duty forklift trucks, with capacities ranging from 16t to 32t.
For container handling, SANY offers diverse cranes as STS (ship-to-shore), RTG (rubber-tyred gantry cranes) and RMG (rail mounted gantry cranes).
Furthermore, SANY offers mobile container handling machines: several sizes of reachstackers for loaded containers, and ECH (Empty Container Handlers) with a choice of lifting heights and single-box and double-box capabilities for empty containers.


Most of SANY’s sales are carried out through its international dealer network. In addition, there are also direct sales to port operators. The dealer network is stable and SANY has a steadily growing customer base. Personal contact is very important. Winning over a new dealer usually requires discussions over several years. SANY keeps growing the dealer network, making it possible to reach and service a broader base of customer.
SANY operates in a very competitive market, with competing companies that include: Kalmar, Hyster and Konecranes in the segment of mobile port equipment. Kalmar, Konecranes, Liebherr, Kuenz and XCMG are crane competitors. In terms of material handlers, companies such as Sennebogen, Fuchs and Liebherr are major
competitors. In order to remain competitive in such a tight market, SANY has a broad product range that always satisfies customer needs and which will be further expanded in 2022. In addition to the know-how from head office in China, SANY Europe has its own R&D department and sources the steel components from its own production. It also works together with many European brand manufacturers.
In essence, SANY benefits from inhouse production of all structural steel components on the one hand, and the use of European-based components such as engines, axles, transmissions, hydraulic pumps on the other. Therefore, the products have excellent durability, and this is supported by a warranty of up to five years.
Electrification is SANY’s greatest ambition for the next years. The company already has 100 empty container handlers and 40 electric reachstackers out in the Chinese and Southeast Asian markets, all running on high hours of autonomy. The experience SANY has already gained in
practical use in China and other Asian countries has been permanently incorporated into the further development of the machines. With the adaptations to both European standards and operator habits, as well as the successful certifications, the starting signal in Europe for the electric port machines has now been given. Delivery of the machines is scheduled for the first half of 2023.
ABOUT SANY EUROPE
SANY Europe is a company of SANY Heavy Industry based in Changsha in China, which is one of the three largest manufacturers of construction and port machinery worldwide, with a turnover of around US$27 billion in 2021. The company, founded in 1989, offers a wide range of products, with more than 26 product families and over 300 machine models. These are developed, produced and sold by just under 40,000 employees around the world.
SANY’s European site has been in Bedburg, near Cologne, since 2011. The site employs around 90 staff in sales, service and in adapting products for the European market. In 2021, SANY Europe sold over 2,000 excavators in its European sales area. With the help of more than 100 dealers, the turnover across the whole of Europe was over €100 million in 2021.
SANY Europe’s portfolio predominantly focuses on construction machinery such as excavators and wheel loaders, as well as port machinery. The SANY site, measuring approximately 140 hectares, provides space for a production hall and warehouse. Proprietary painting facilities, as well as an administration building and the SANY Hotel are also located on the premises.
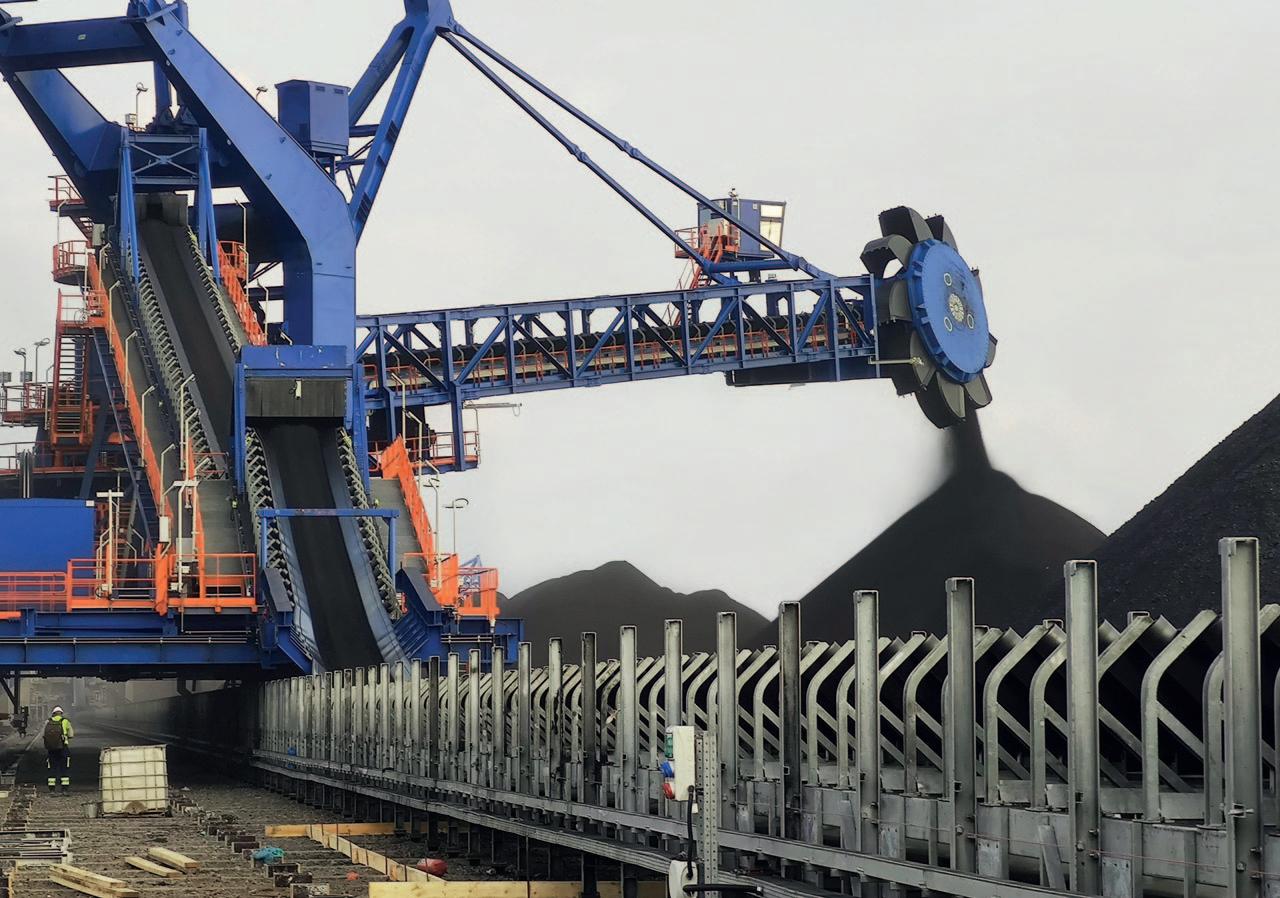

Liebherr sending three additional LHMs to Noatum terminals in Spain
The port of Rostock serves as one of Liebherr’s central maritime production locations, effectively connected to global water shipping lanes.

Two LHM 420 and one LHM 550 arev being shipped to Noatum Terminals in the West Mediterranean.
The three LHM models are joining anv LHM 420 that was deployed earlier in the year and is operating at Noatum Terminal Sagunto. With the flexibility to handle bulk,v containers, project cargo, and more, Liebherr’s LHM mobile harbour cranes are among the most popular in the portfolio due to their adaptability in handling the most common cargo types at port terminals.
The first crane arrived on January 5, 2022. Three new Liebherr mobile harbour cranes are joining the fleet at Noatum port terminals in Castellon, Sagunto and
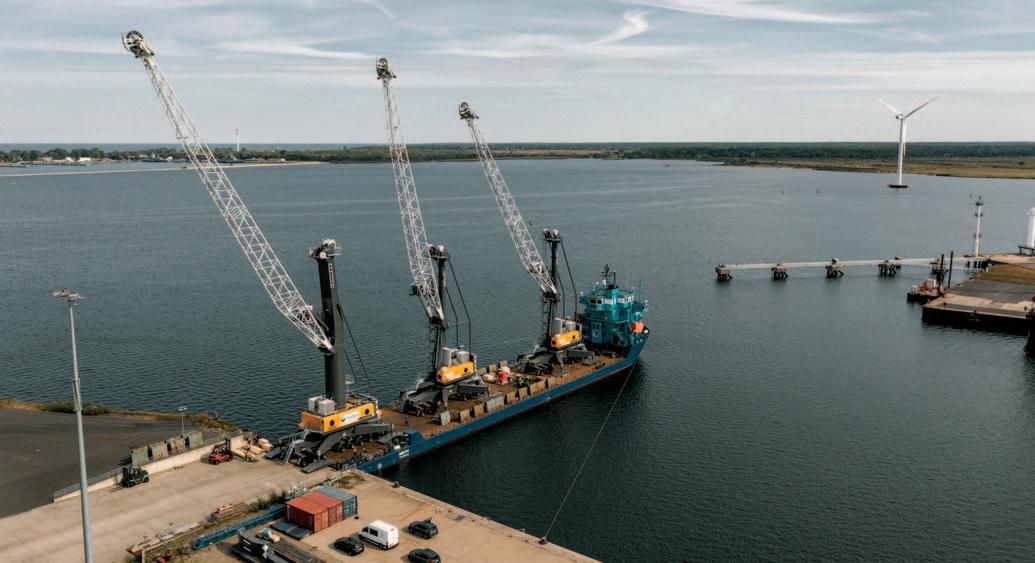
Tarragona. The cranes will enable the terminals to improve their handling efficiency for various cargo types.
Boarding the Heavy Load Carrier MERI in the morning hours of 5 September, three Liebherr mobile harbour cranes were prepared for their journey to Spain. Three terminals operated by the Spanish company will benefit from the performance of the LHM 420 and LHM 550 models.
OPERATIONS FOR A VARIETY OF CARGO, SUPPORTED BY LIEBHERR CRANES
Port terminals operated by Noatum support a variety of commodities around their global supply chain.
Agricultural goods, minerals in bulk, steel, project cargo, and, containers, and
more are all part of Noatum’s logistic network. With their carrying capacity of 124 and 144 tonnes, respectively, the LHM 420 and LHM 550 can lift and handle a variety of cargo.
IMPROVED PRODUCTIVITY AND REDUCED ENERGY CONSUMPTION PART OF HALLMARK OUTCOMES
Liebherr mobile harbour cranes offer effective solutions for reduced energy consumption while improving cargo handling productivity. This is in part achieved by Liebherr’s proprietary hydrostatic drive, in which closed hydraulic loops are used for all main functions such as lifting, turning and luffing. The hydrostatic drive allows the operator extremely
Two Liebherr LHM 420 and one LHM 550 being loaded onto the heavy load carrier MERI for transport to Spain.


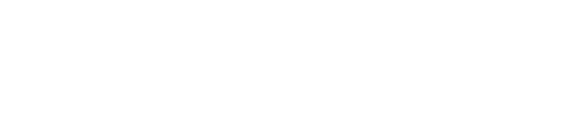
Arriving at the port in Castellon, the three Liebherr mobile harbour cranes get ready to be unloaded in Spain.
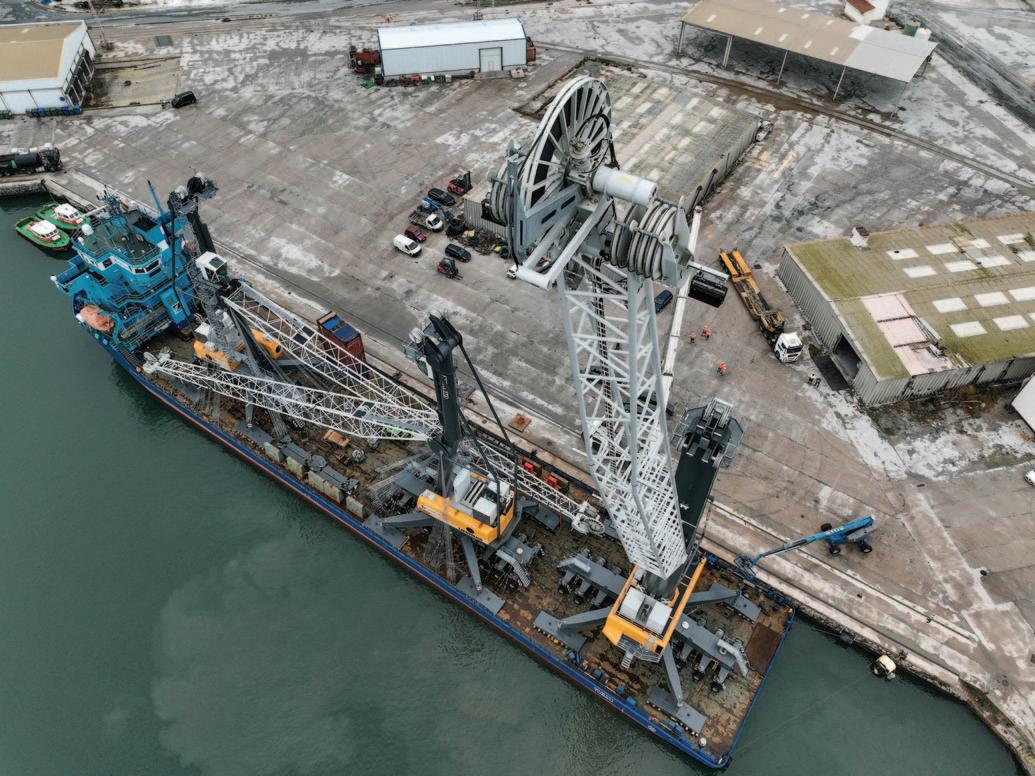
precise control. Additionally, service personnel benefit from a minimum number of components, and the operating company benefits from reduced fuel consumption.
Juan Carlos Jiménez, Divisional Manager Maritime Cranes in Liebherr Ibérica, remarks: “Liebherr is pleased to contribute to our customers’ strategic value to provide continuous improvements. For our Spanish client Noatum, this includes supporting them in their aim to reduce their overall environmental footprint while still meeting the demands of increased global cargo traffic both in terms of volume and mass. The LHM 420 and LHM 550 meet their specific tonnage and diverse cargo needs at their Castellon, Sagunto and Tarragona terminals. With the LHM 420 model alone, they anticipate an improvement in productivity of up to 38 containers per hour.”
ABOUT LIEBHERR-MCCTEC ROSTOCK GMBH
Liebherr-MCCtec Rostock GmbH is one of the foremost European manufacturers of maritime handling solutions. The product range includes ship, mobile harbour and offshore cranes.
Reachstackers and components for container cranes are also included in the product portfolio.
ABOUT THE LIEBHERR GROUP
The Liebherr Group is a family-run technology company with a broadly
The two LHM 420 and one LHM 550 join a fleet that will be operating at three different Noatum terminals in Spain (f.l.t.r. Marco Gonzalez, Liebherr Sales Manager for Maritime Cranes at LIB; Juan Carlos Jiménez, Liebherr Divisional Manager for Maritime Cranes at LIB; Oscar Magdalena, Noatum Terminal Manager in Castellon Port; David Jiménez, Noatum Maintenance Manager in Castellon Port).
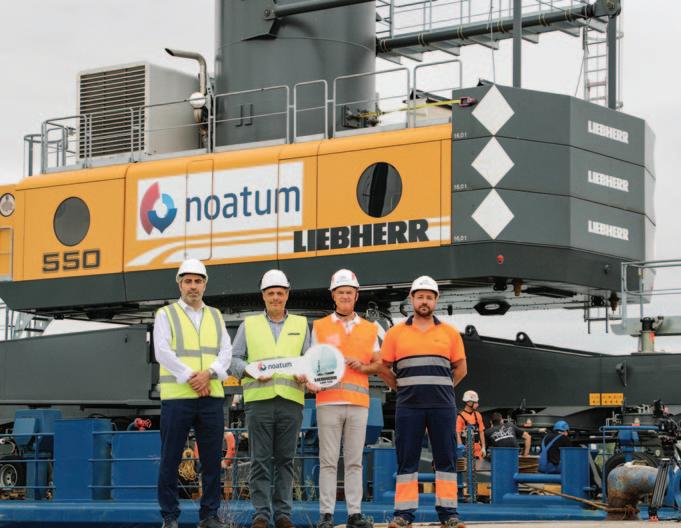
diversified product range. The company is one of the largest construction machinery manufacturers in the world. However, it also offers high-quality, user-oriented products and services in many other areas.
Today, the group comprises more than 140 companies on all continents. In 2021, it employed more than 49,000 people and
generated a total consolidated turnover of over €11.6 billion. Liebherr was founded in 1949 in Kirchdorf an der Iller in southern Germany.
Since then, the employees have pursued the goal of convincing their customers with sophisticated solutions and contributing to technological progress.
Rugged Energy & Data Transmission Systems
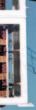
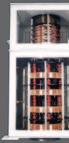



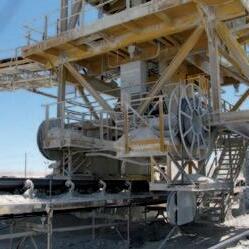
has one critical mission:


keep your bulk material handling operations











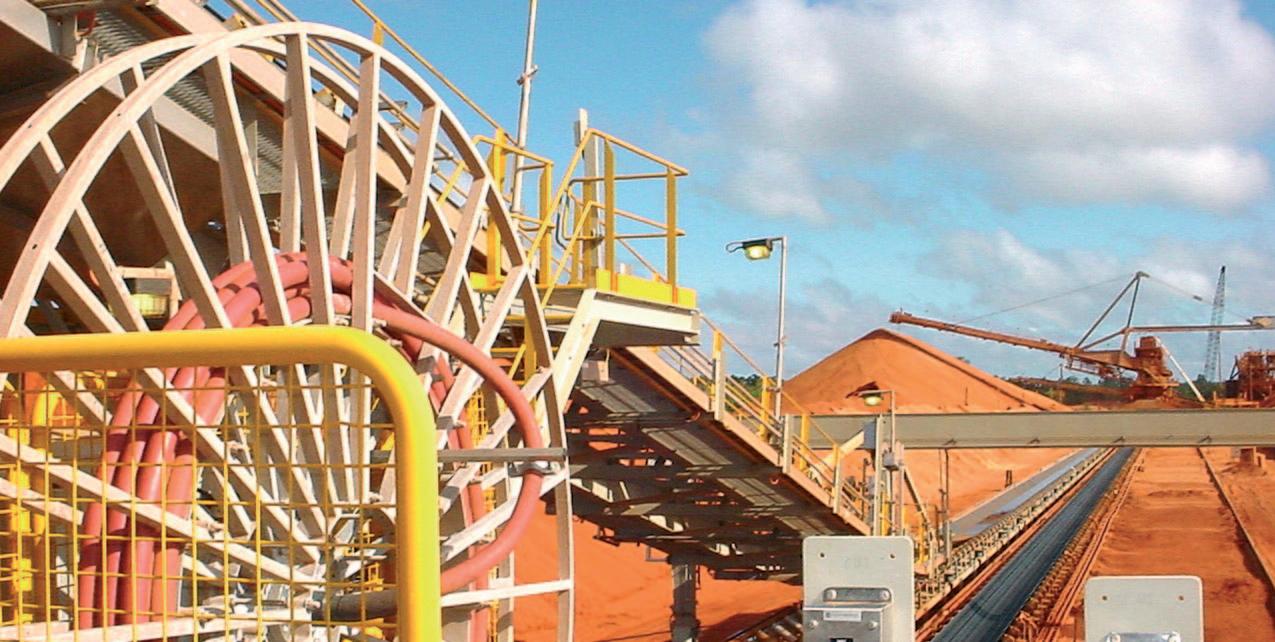

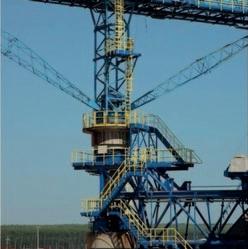
24 / 7 / 365. You need proven, worryfree energy solutions - and Conductix-Wampfler has them. Our systems provide reliable electric power and water to stacker/reclaimers, barge and ship loaders/unloaders, bulk conveyors, tripper
and gantry cranes.
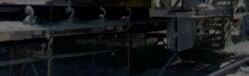
rugged, low maintenance, and timetested
tough,
Hitachi ZW180-7 wheel loader puts customers in the driving seat
Hitachi has unveiled the ZW180-7, a smaller next-generation model from its Stage V-compliant wheel loader range, which has been carefully designed to appeal to both owners and operators. With
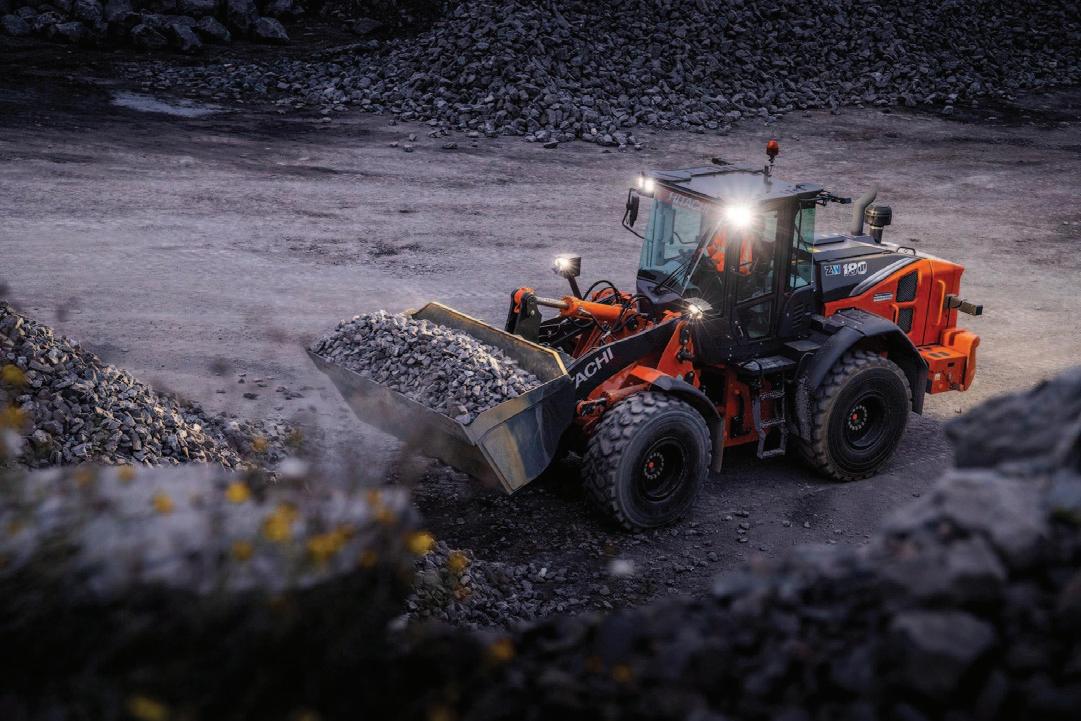
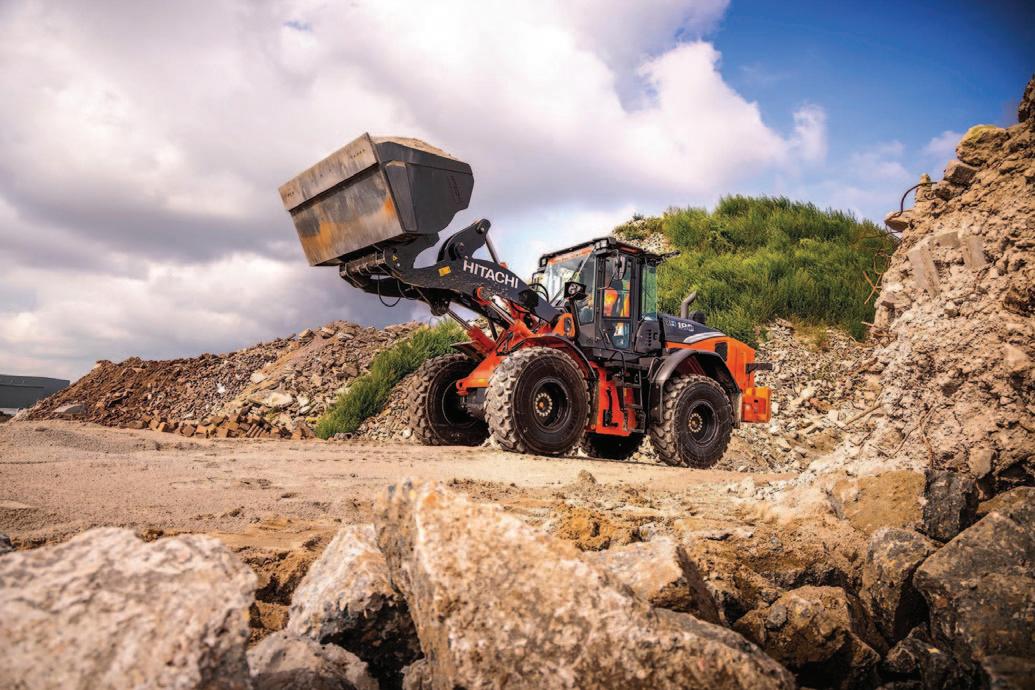
unrivalled comfort in the cab, operators feel in complete control of their workspace. Owners benefit from the new model’s exceptional efficiency and maximum uptime, as this gives them greater
fleet, thanks to remote monitoring tools and services provided by Hitachi.
FEEL THE DIFFERENCE
After spending the day in the spacious, fully
refreshed rather than fatigued, and satisfied at their ability to work more productively. The ZW180-7 epitomizes the ultimate in comfort, with some of the lowest noise and vibration levels in the market. Much consideration has been given to easy operation with the improved seat with mounted electric pilot control levers, ergonomic multifunction lever, anti-slip steering wheel, 40% larger and fully adjustable armrest with integrated controller and convenient side switch panel. The hi-res screen is also easier to view.
Operators will also feel secure in the cab of the new ZW180-7 — one of the safest machines on the market — thanks to superb all-round visibility and intelligent systems. With the Aerial Angle camera system, they have an exceptional 270° bird’s-eye view of the job site and can work confidently in challenging conditions with the full LED work lights package. If anything is close to the rear of the machine, they are alerted immediately by the rear obstacle detection and warning system.
IMPROVE PROFIT AND MAXIMIZE UPTIME
Owners will be able to increase their profits due to the impressive fuel economy, efficiency, and versatility of the ZW180-7.
This model can be used on a wide range of applications, with three types of lift arms available: standard, high and parallel.
Faster and more efficient short loading operations due to the Approach Speed Control feature, which reduces fuel consumption by 16%, further satisfy owners’ requirements. Productivity is boosted by reduced cycle times gained by the auto power up function. This automatically increases the RPM to maintain travel speed on inclines.
The performance and traction force of the ZW180-7 have also been enhanced by significant improvements to the engine torque. This results in easier bucket filling, faster cycle times, and higher productivity with reduced fuel consumption.
The new ZW-7 model loads trucks more accurately, saving time and money, using the payload monitoring system. In addition, operators can monitor the fuel consumption thanks to the new ECO gauge and performance can be improved with several adjustable functions.
An ultra-reliable performance to significantly boost uptime is possible because the ZW180-7 is built with durable components, intelligent prevention systems and easy maintenance features such as the improved cooling package. The use of high-
quality Hitachi buckets, customized to suit the application, and robust ground engaging tools that are easy to install and replace, further maximizes uptime.
TOTAL CONTROL AND SUPPORT
To support owners and operators throughout the life cycle of the new ZW-7 wheel loaders, Hitachi provides a wide range of after-sales services, and access to vital data and tools so they can manage their machine effectively. These include remote monitoring systems, Owner’s Site and ConSite (part of Global e-Service), and the ConSite Pocket app, which help to monitor performance, track location and plan maintenance.
“With Hitachi ZW-7 wheel loaders, we put our customers firmly in control of their workspace, their business and their fleet,” says Bill Drougkas, Manager Product Management of Hitachi Construction Machinery (Europe) NV.
“The new ZW180-7 offers a superior experience in the cab and exceeds expectations in terms of efficiency and performance. By working in partnership with our customers — providing industryleading equipment, innovative technology and wide-ranging after-sales support — we can help them to create their vision.”
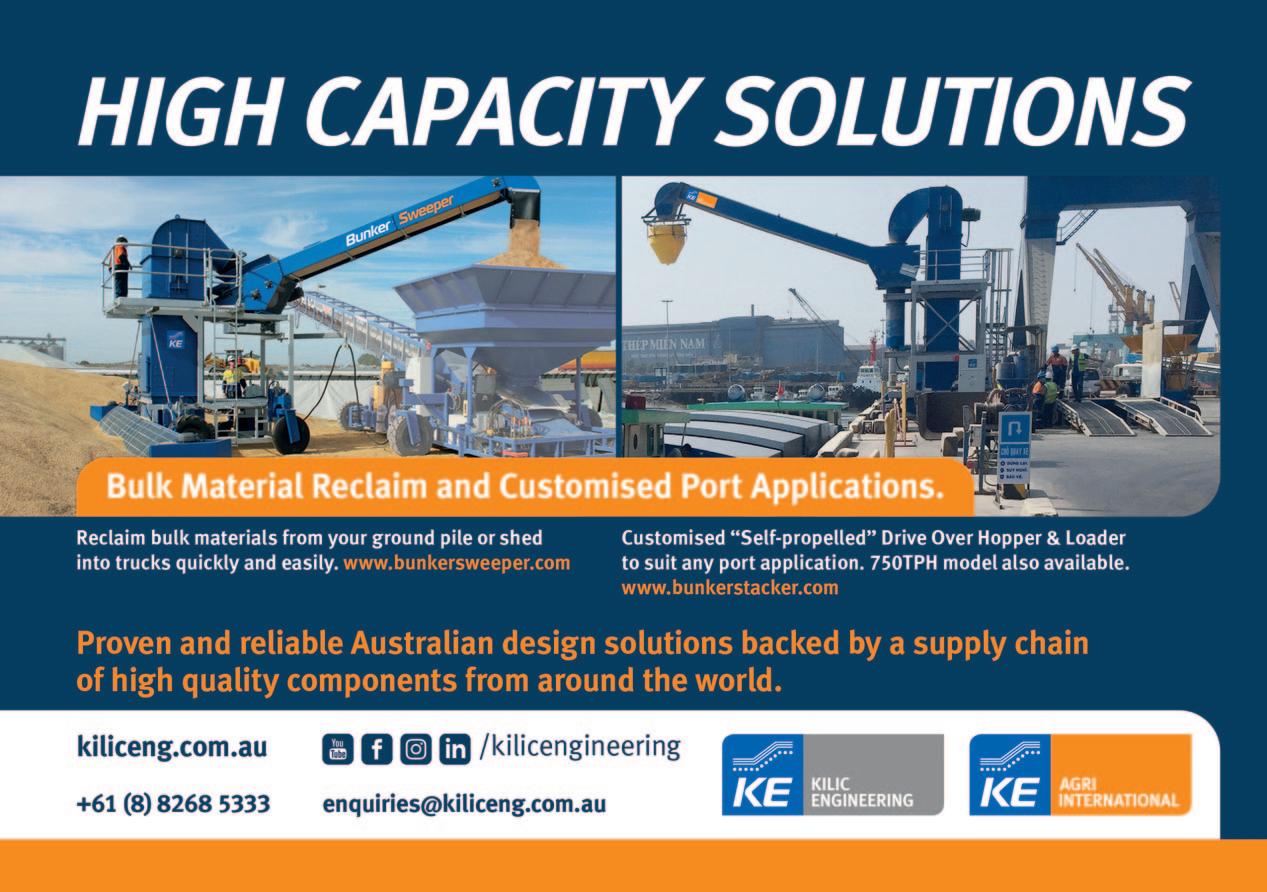
Ship unloading at Belgian cargo handling service provider
GWS Kraanbedrijf in the Belgian region of Flanders can look back on many years of experience in the provision of bulk and general cargo handling services: constant companions are the now eight
SENNEBOGEN material handlers, about which young managing director Stan Goeyvaerts draws an excellent conclusion in the interview.
Walter Goeyvaerts once demonstrated
entrepreneurial flair when he restructured and modernized his father’s cargo handling company, founded in the 1960s, shortly after the turn of the century: the result today is GWS, a thriving cargo handling
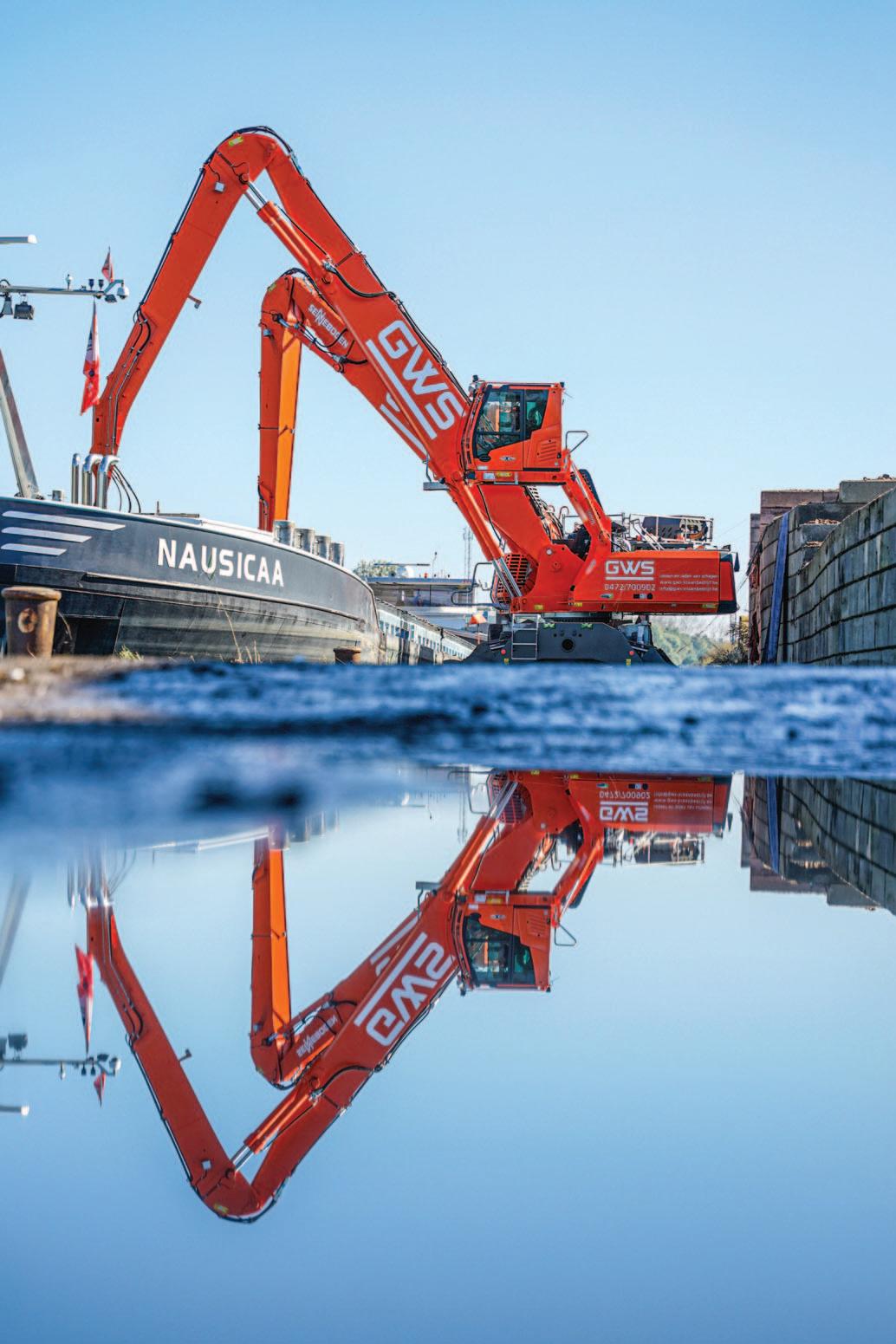
Minimise Capital Investment
Radial and telescopic features allows operator to easily and safely work within the constraints of the jetty
Trimming of the hold achieved from one fixed feed in point
Mobile solution perfect for multi- cargo berth (Multiple Use)

Customised shiploading system designed specifically for the application
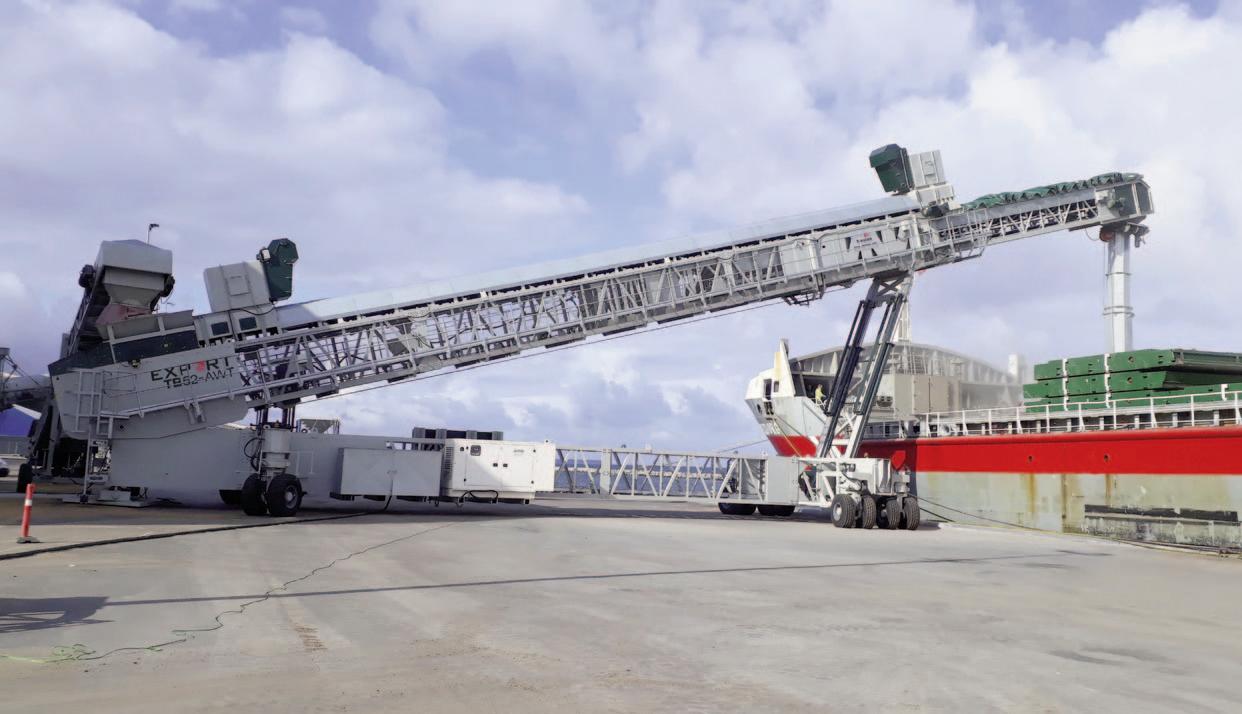

service provider specializing in loading and unloading ships.
His son Stan, the third generation, has now taken the wheel. For him, growth means constantly investing in new handling equipment to respond flexibly to increased market demands. The latest acquisition is a SENNEBOGEN 835 E in the mobile version, which was delivered by the sales and service partner SMT in Belgium. “In terms of size and tonnage, this is the most flexible machine you could ask for,” says Stan Goeyvaerts.
The reestablishment of the cargo handling company GWS took place in 2012 and builds on the experience of the traditional company, whose material handling activities go back two generations.
“Initially, we were mainly active in the Antwerp region, but we are now active throughout Flanders,” Stan Goeyvaerts continues. A success story that can be attributed especially to the personal contact with the customer, to which father and son attach great importance. “I still climb into the cabs of our material handlers myself. That also impresses our customers! In addition, we always try to stay on the ball
technically by having an extensive machine park at our disposal.”
EXCELLENT RATING IN TERMS OF HANDLING CAPACITY AND OPERATIONS
Ship unloading in a double pack: cargo handling service provider GWS Kraanbedrijf in Antwerp has relied on SENNEBOGEN material handlers since the very beginning.

Today, the GWS machine park has grown to 12 material handlers, including eight SENNEBOGEN machines. “We started with three machines at that time. Two of them were used, the third was already a machine from SENNEBOGEN. We really appreciate the mobility of these material handlers, and that was crucial for our first customers, because they were located in close proximity to each other over a distance of 2km. With SENNEBOGEN, we could easily from one customer to the next, without having to leave the cab. But apart from that, these are machines that stand out for their capacity and their handling . They are very easy to operate and at the same time keep productivity high. My employees enjoy
ENVIRONMENTALLY FRIENDLY AND RELIABLE STAGE V TECHNOLOGY FOR MORE PERFORMANCE ON THE QUAY
“In terms of size and tonnage, this is the most flexible machine you could ask for,” explains Goeyvaerts, referring to the new, orange 835 E-Series material handler. In addition, this one operates with a reducedemission, fuel-efficient Stage V engine. “As environmental legislation becomes more stringent, we always include this aspect in our investment decisions.”
Service was also essential for him: “With SMT, we couldn’t have asked for a better partner. They are available to us day and night, if there are ever any problems. As a cargo handling company, we can’t afford any downtime, because a ship has to be able to leave the port as quickly as possible. Thanks to SMT and the intelligent design of the machines with a focus on mechanical components, we can often easily solve minor problems ourselves. In this way, we can always concentrate fully on our customers.”
Take control with the Hitachi ZW310-7 wheel loader
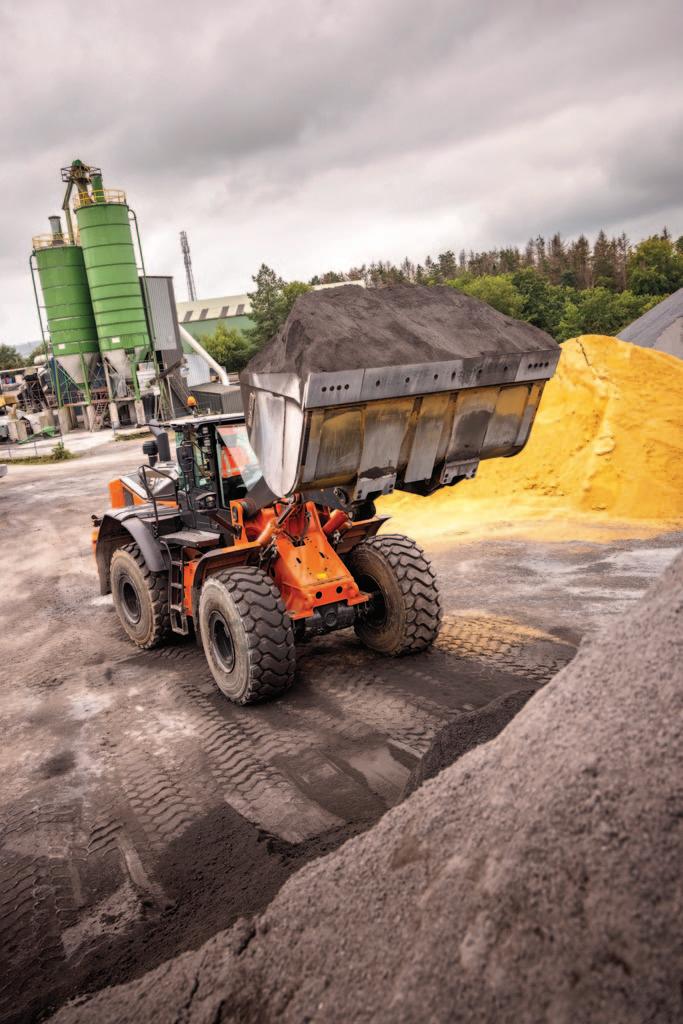
Hitachi is introducing a larger nextgeneration model from its Stage Vcompliant wheel loader range. The ZW310-7 has been designed to put operators in complete control of their workspace — and master even the toughest job site conditions — with top quality safety features and supreme comfort in the cab. Owners will feel in total control of their profit — thanks to its powerful performance, low total cost of ownership and exceptional efficiency — as well as their fleet and workload, due to remote monitoring tools and services provided by Hitachi.
SAFETY AT THE FOREFRONT
The ability to work safely is vital, not only for the operator’s wellbeing, but also for the successful completion of any project. The new ZW310-7 is ideal in this respect, as it’s one of the safest machines on the market, thanks to superb all-round visibility and intelligent systems.
To protect the operator and machine from potential hazards, it allows a superior view from all angles — especially with the excellent visibility to the rear and either side of the narrow engine hood. With the Aerial Angle camera system, operators also have an exceptional 270° bird’s-eye view of the job site, while the rear obstacle detection and warning system alerts them immediately if anything is close to the rear of the machine.
After working a full shift in the spacious, fully redesigned cab, operators will feel less tired and more satisfied at their ability to work more productively. The ZW310-7 epitomizes the ultimate in comfort, with some of the lowest noise and vibration levels in the market. It is especially easy to use thanks to features such as the improved seat with mounted electric pilot control leavers, new monitor controller and convenient side switch panel.
LOW TOTAL COST OF OWNERSHIP
Owners will be able to increase their profits due to the powerful performance, low total cost of ownership and exceptional efficiency of the ZW310-7. High levels of productivity are ensured by fast cycle times, a high breakout force and loading capacity, and improved acceleration on inclines thanks to sensors installed on several machine components. The RPM are automatically increased thanks to the auto power up function, which maintains the machine’s travel speed when moving uphill. As a result, the reduced cycle times
enhance productivity and reduce fuel consumption.
Faster and more efficient short loading operations due to the Approach Speed Control feature further satisfy owners’ requirements. The new ZW-7 model also loads trucks more accurately, saving time and money, using the payload monitoring system.
In addition, operators can monitor the fuel consumption thanks to the new ECO gauge and performance can be improved with several adjustable functions.
An ultra-reliable performance to significantly boost uptime is possible because the ZW310-7 is built with durable components such as the axles and frame, intelligent prevention systems and easy maintenance features. This can be further maximized by the use of high-quality Hitachi buckets, customized to suit the application, and robust ground engaging tools that are easy to install and replace.
AFTER-SALES SERVICE
To support owners and operators throughout the life cycle of the new ZW-7 wheel loaders, Hitachi provides a wide range of after-sales services, and access to vital data and tools so they can manage their machine effectively. These include remote monitoring systems, Owner’s Site and ConSite (part of Global e-Service), and the ConSite Pocket app, which help to monitor performance, track location and plan maintenance.
“The new ZW310-7 wheel loader has been designed to give a powerful performance, low total cost of ownership and exceptional efficiency to European customers,” says Bill Drougkas, Manager Product Management of Hitachi Construction Machinery (Europe) NV. “Built to the highest quality standards, it will significantly boost productivity on busy quarries and large recycling plants, and have a positive impact on profits.”
Grab
Mobile Harbor Cranes ensure highly efficient handling of bulk materials of all kinds.

Generation 6 four-rope grab cranes will impress
with their robustness. With their 74 t grab curves and high classifications for a long service life, they handle up to
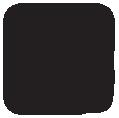
tph. The result: strong performance over
long term – even in continuous operation.

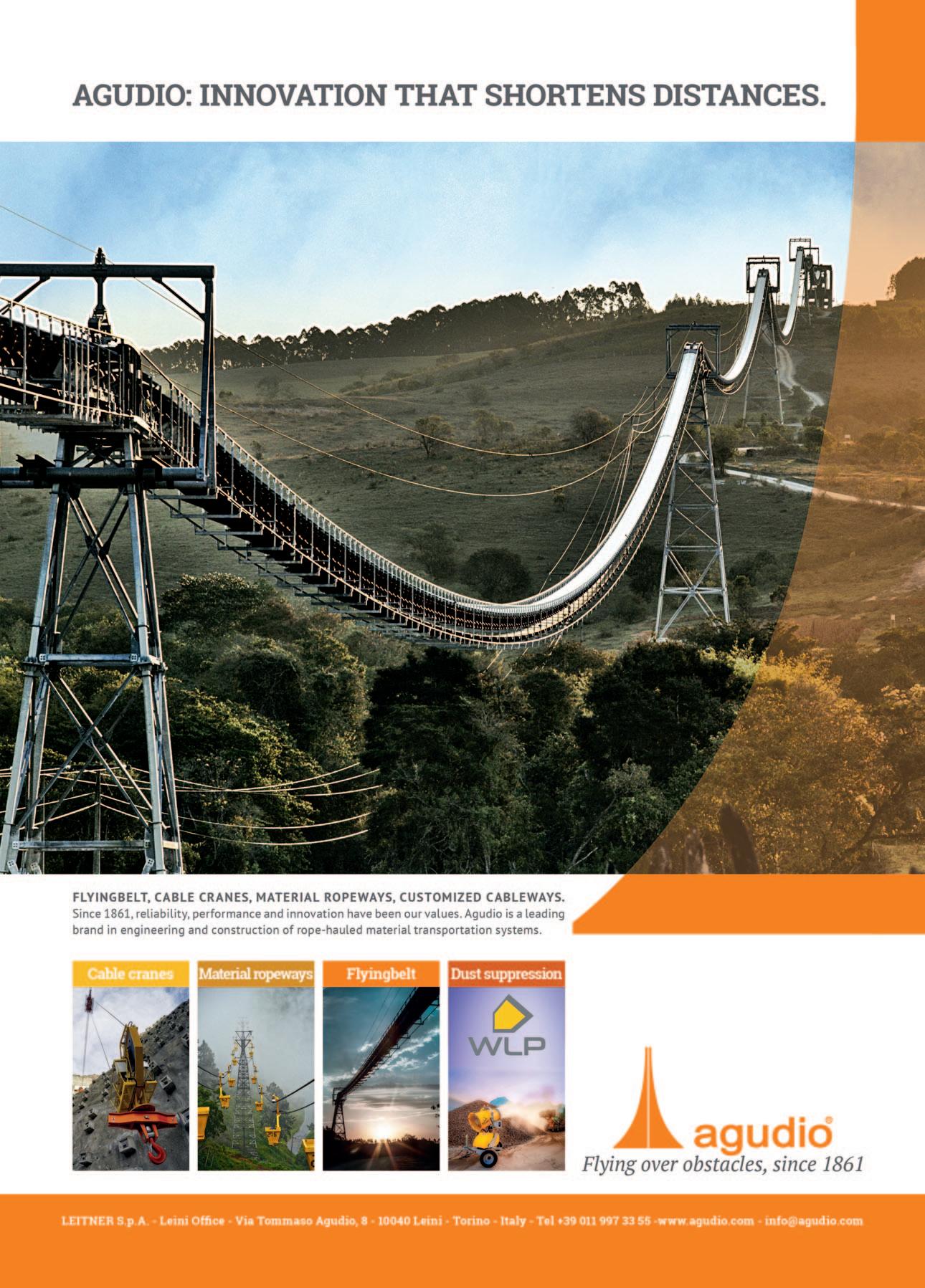
Bulk cargo: travelling in style
conveyors, components & technologies
Metso Outotec awarded a major conveyor package order in the Americas
Metso Outotec has been awarded an order for a large belt conveyor package for delivery to a mining customer in the Americas. The value of the order is approximately €60 million, of which a third was booked in Minerals’ second-quarter orders received and the rest in the third quarter.
Metso Outotec’s scope of delivery includes 3.5km overland and in-plant conveyors as well as shuttle head conveyors with a nominal equipment capacity of up to 21 kilotonnes per hour).
Metso Outotec has the capability to design and deliver even the largest conveyor systems with high project quality. Metso Outotec overland solutions provide flexible and reliable material transportation with increased energy savings for the lowest total cost of ownership.
ABOUT METSO OUTOTEC
Metso Outotec is a frontrunner in sustainable technologies, end-to-end solutions and services for the aggregates, minerals processing and metals refining
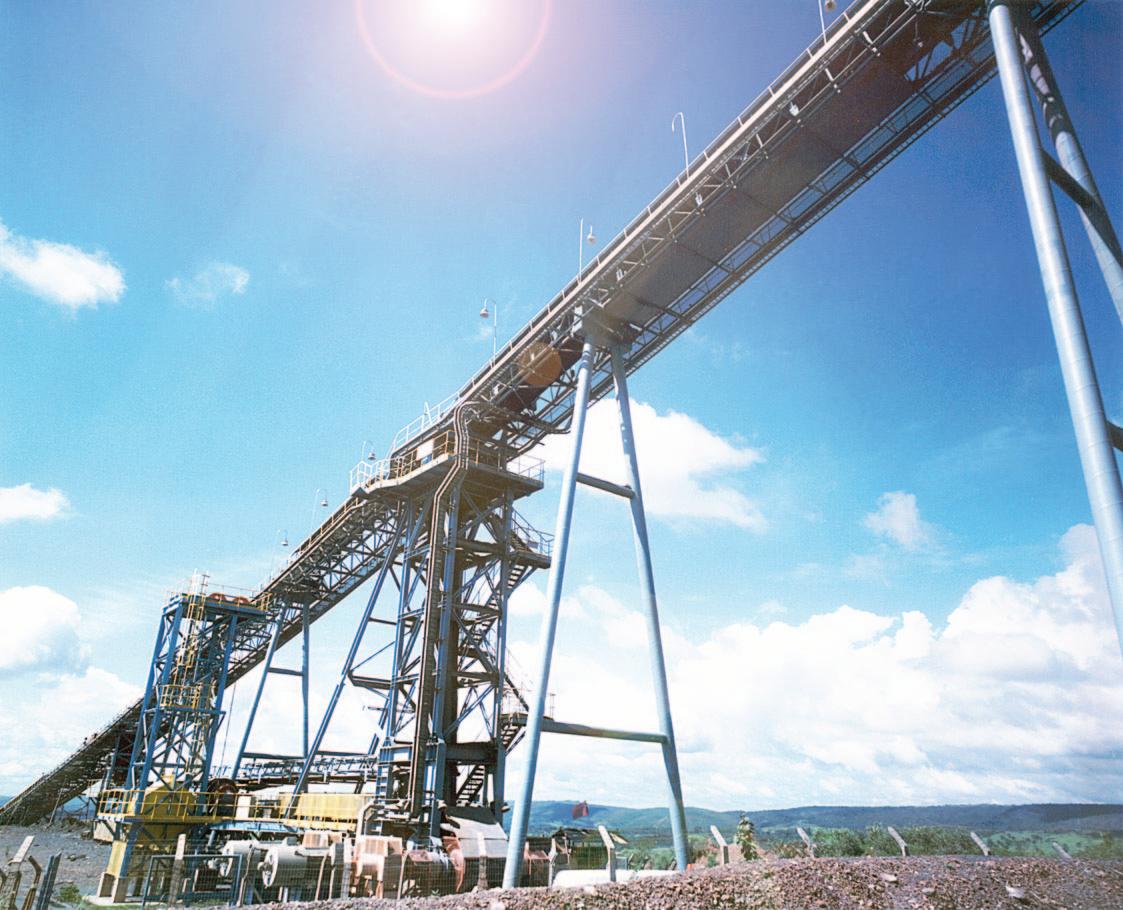
industries globally. By improving its customers’ energy and water efficiency, increasing their productivity, and reducing environmental risks with our product and process expertise, it is a great partner for positive change. Metso Outotec is committed to limiting global warming to 1.5°C with Science Based Targets.
Headquartered in Helsinki, Finland, Metso Outotec employs over 15,000 people in more than 50 countries and its sales for 2021 were about €4.2 billion. The company is listed on the Nasdaq Helsinki.
Belt tracking with help from Kinder Australia’s K-Commander®
Misaligned conveyor belts are the principle cause of a variety of issues associated within in the transportation of bulk products. This includes material spillage and reduced life to conveyor belting and the conveyor structure. Ideally, a pivoting, self-centralizing belt training system — which rotates freely when the belt experiences mistracking behaviour — should be installed. Other options include fixed tracking solutions without rotating structure. The team at Kinder Australia can assist with belt tracking with the installation of a solution from the K Commander® Series.
K-Commander® Prime Tracker Alldirection belt tracking featuring flexible 360° rotational capability, with its separate axial and rotational function allowing for the double axis pivot bush. The K Commander® Prime Tracker has been designed with two key stages. The first stage focuses on the inner shell which contains the shaft and an engineered pivoting bush allowing the axial movement of the tracker. The inner shell is protected by a flexible EPDM rubber boot. The second stage focuses on the roller bearings, which allows the rotational movement of the tracker. The roller bearings connect the inner shell and the outer shell and are protected by a labyrinth seal.
K-COMMANDER® CONTROL SERIES
The installation of the K-Commander® Control Series is only for the return side, being the most critical surface of the belt in order to maintain belt alignment. The unique engineered action of the central ball and socket link is encased in a rubber covered steel tube. This protects the internal mechanics and ensures that the belt runs true.
K-COMMANDER® DIRECT SERIES
The installation of K-Commander® Direct Series can also assist with correct conveyor belt tracking. These are a pivoting base style, available in both trough and return applications automatically providing belt centring.

The outboard servo rollers cause the idler frame to pivot as they contact the belt edge and this swivel action causes the belt to realign automatically. To aid belt tracking further, Kinder Australia offers rubber lagged rollers (trough and return) as an option for your belt tracker. The results are: better tracking performance in heavyv duty applications; increased roller durability against thev constant scuffing nature roller shells in trackers experience; and increased belt training response.v
K-COMMANDER® TRACKING DISCS
The K-Commander® Tracking Discs fit both flat and vee return rollers as well as selected troughing rollers. Ideally, they are located in pairs prior to the tail pulley to help align the conveyor belt, and so eliminating spillage from mis-tracked belts. They can also be installed after the feed area on troughing sets to help keep the belt aligned. The key benefits are: easy installation — split on one side tov slip over the roller; no need to remove rollers;v high wear-resistant grade ofv polyurethane used; and No damage to belt edges.v
K-COMMANDER® GUIDE SERIES INV
This in an all-purpose conveyor belt alignment idler ideally suited to short centred or reversing conveyor applications. The two inverted vee rollers put pressure down onto the belt, promoting centralized belt training. The universal frame adjusts to all types of mounting structures and is installed just after the head pulley, or prior to the tail pulley. The key benefits include: limiting belt damage;v controlling spillage;v suitable for reversing belts;v easy to install; andv available for all belt widths, ex-stock.v
Quarry Mining LLC: solutions for all its customers’ challenges
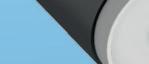



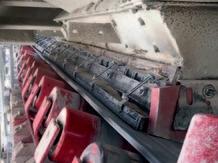
Quarry Mining LLC has been trading since 1999. The company specializes in the design, manufacture and installation of industrial mineral processing plants, bulk handling systems and environmentally sustainable material handling technologies.
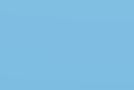
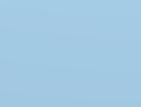
Quarry Mining (QM) provides international best practice solutions and value for money to its clients and is a reliable partner for some of the world’s leading technology suppliers. Supporting industries in the MENA (Middle East/North Africa) region, QM has developed many successful bulk handling systems during its long history. These include turnkey designed and built mineral processing plants meeting the very latest environ mental standards through the introduction of dedusting filter systems for a wide variety of industrial applications. QM is certified to ISO Certificate 9001:2015 Quality Management and ISO Certificate 14001:2015 Environmental Management System by the German Technical Inspection Association TÜV Rhineland/Germany.
Working in the field of bulk handling and mineral processing plants for more than 20 years, QM has accumulated vast experience in this field and provides the very latest

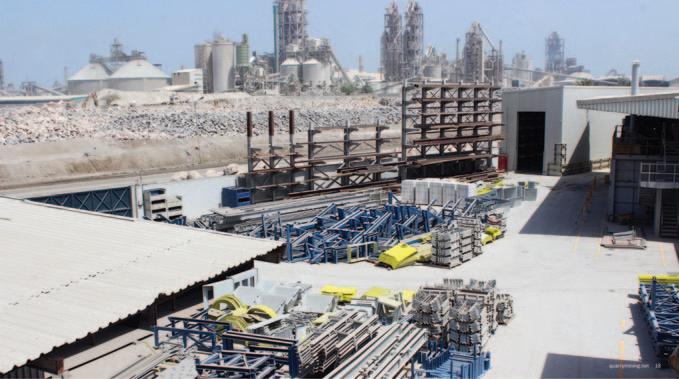
state-of-the-art solutions to its clients. One of its most recent projects is a 3,000tph (tonnes per hour) in-pit crushing and conveying system with total length of 1.5km, the fourth such installation at the same mine site. In order to meet the client’s requirements of 3,000tph throughput, QM supplied the largest Kleemann jaw crusher ever made — the SStR2100x1600 — with feed opening of 2,100mm x 1,600mm as well as designing a series of eight interconnecting downhill conveyors which feed the secondary processing plants with the
primary crushed material.
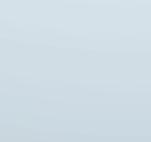
The specialty of QM’s downhill conveyor systems is its contribution to sustainability and reduced environmental impact through electrical power generation. This allows the end-user to transport the material from the pit down to the processing plants at zero energy costs and zero emissions, while also generating enough electricity to supply the primary crushing plant and its accessories.
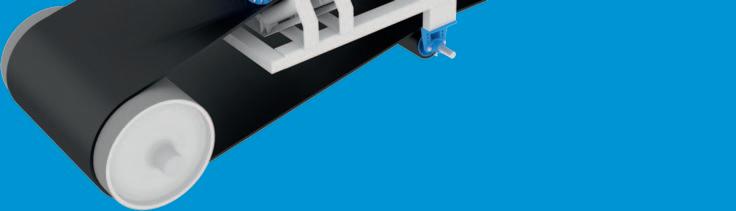

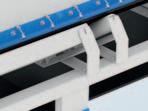
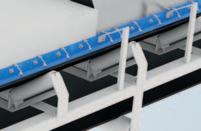

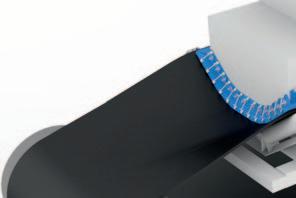
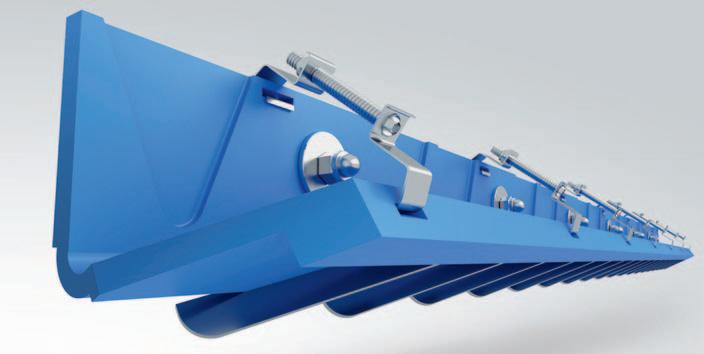
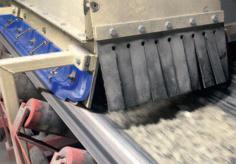
Christian Drewes, Technical Manager of QM, says: “In 2009 we successfully delivered
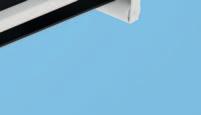
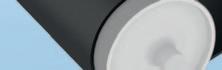
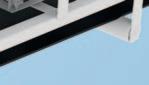

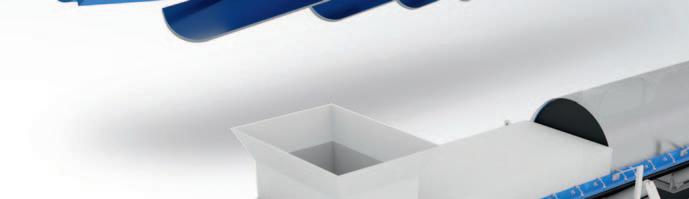
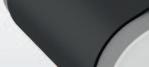
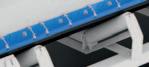

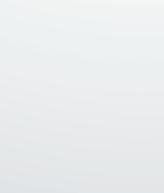
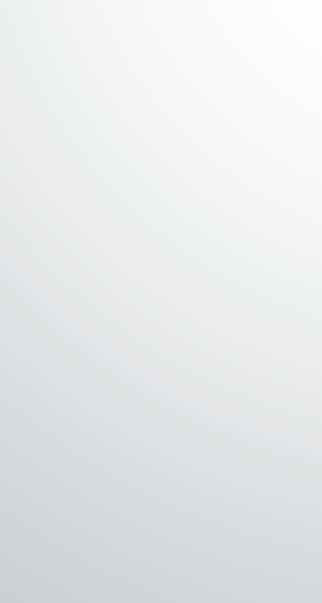
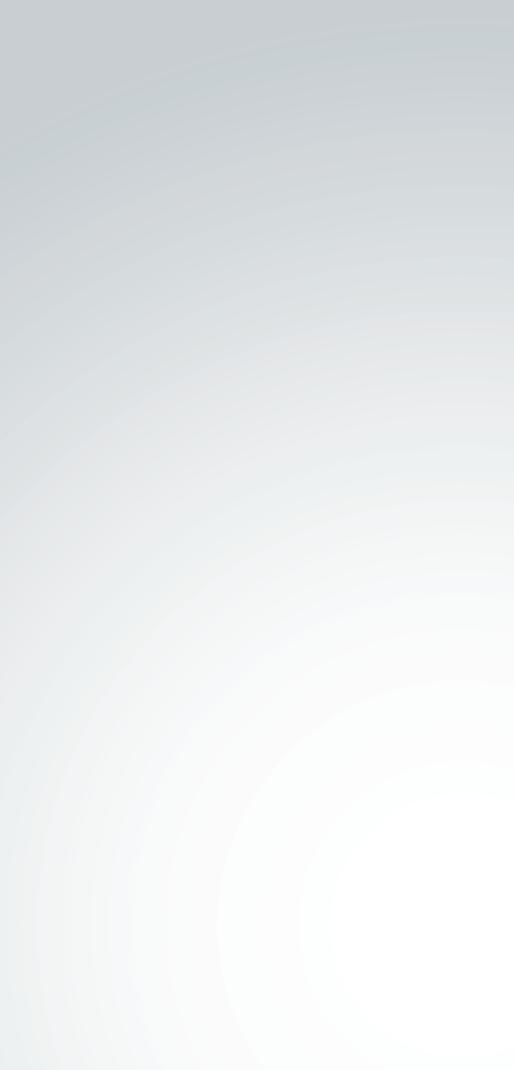
the first pioneering project in this field. Due to this success in 2015, a larger 4,000tph 3.5km system was designed and installed at the largest limestone quarry in the world, located in Ras al Khaimah. It was the first downhill conveying system in the region and, with this system, our client has significantly reduced the transportation costs per tonne, dramatically reduced harmful CO2 emissions and improved site sustainability.”
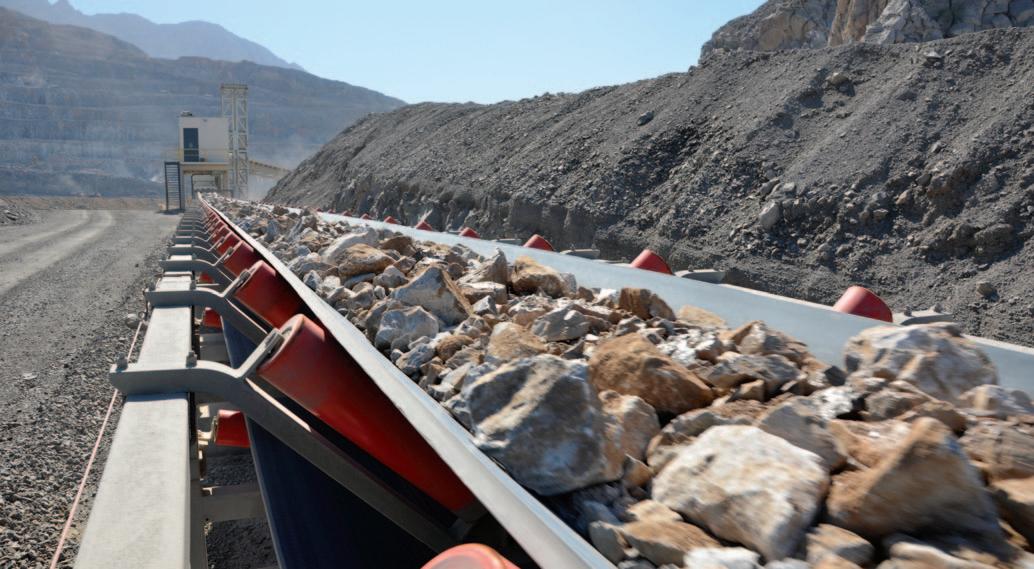
In 2020 and 2021, during high Covid 19 season, QM successfully partnered with Haver & Boecker and IBAU Hamburg, two of Germany’s biggest names in processing machinery and special bulk handling equipment. QM supplied a total of 31 conveyors for potash handling and material loading; the conveyor systems ranged between 80–2,000tph, and also included a fully automatic container loading system for standard sea container with dry bulk.
QM is also busy with a design, fabricate and install turnkey shiploader project
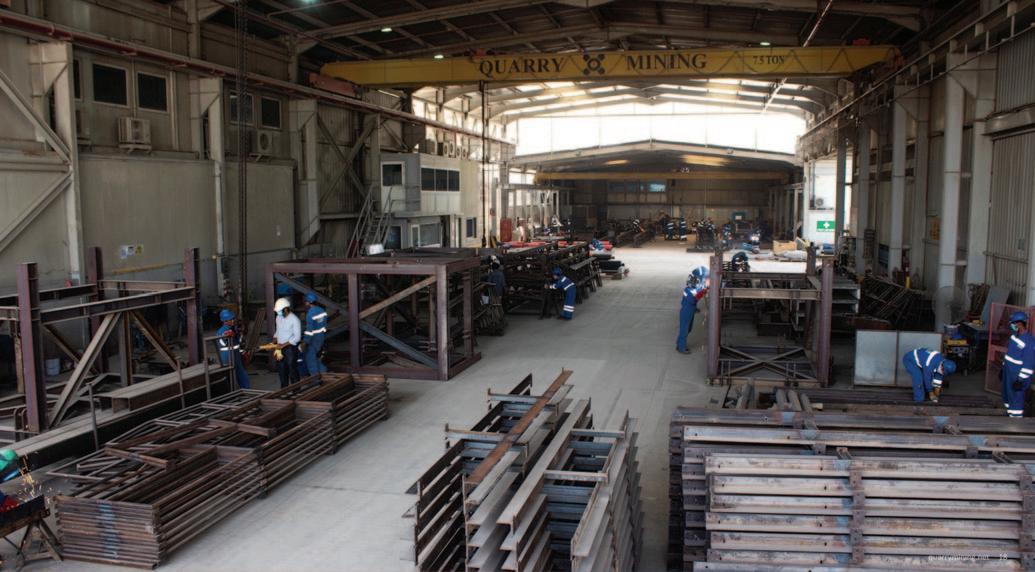
capable of handling dry bulk cargo at 3,000tph. Featuring an advanced slewing and luffing system, it is capable of accepting a large variety of bulk cargo vessels and is also equipped with the very latest in cascade chute technology to maintain end product quality. The system was fabricated entirely in the UAE and, such is the extent of QMs capabilities in this area, that the company is also handling the assembly, installation and programming of the unit in house.
As well as providing complete material handling systems, QM is also a one-stop solution for individual component supply for all bulk handling spare and wear parts requirements. It carries a large portfolio of drums, belts and rollers together with an on site Stiebel gearmotor facility enabling it to provide the highest German-quality components with minimal lead time and best value pricing.
continuously invests in new equipment, tooling, machinery, CAD software, ERP systems and most important of all, its employees. All plants are designed using 3D, RFEM and performance-tested special software simulations to guarantee the equipment’s performance and durability to the highest international standards. In addition, QM is certified with EN1090, allowing European clients to source fabrication in the UAE which is guaranteed to the same standards they would expect with European suppliers, but at a very competitive price.
Staying competitive in the market is one of the most essential elements of any successful, long-term business.
QM
With such a diverse portfolio of capabilities including design, manufacturing, installation and component supply all underwritten by its commitment to the highest possible quality standards in combination with its ability to offer solutions right across the Middle East and Africa, Quarry Mining is an ideal long-term partner for all bulk handling and processing requirements.
Steering clear of trouble: quick reference guide to conveyor belt alignment
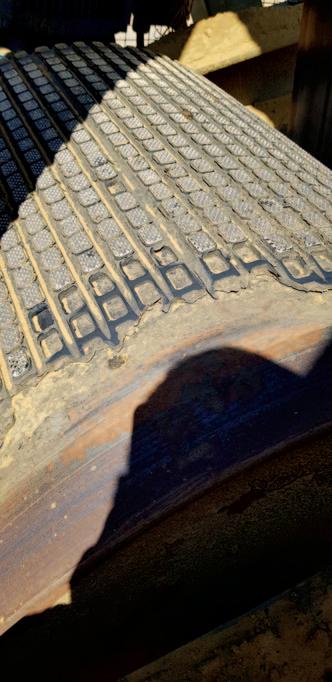
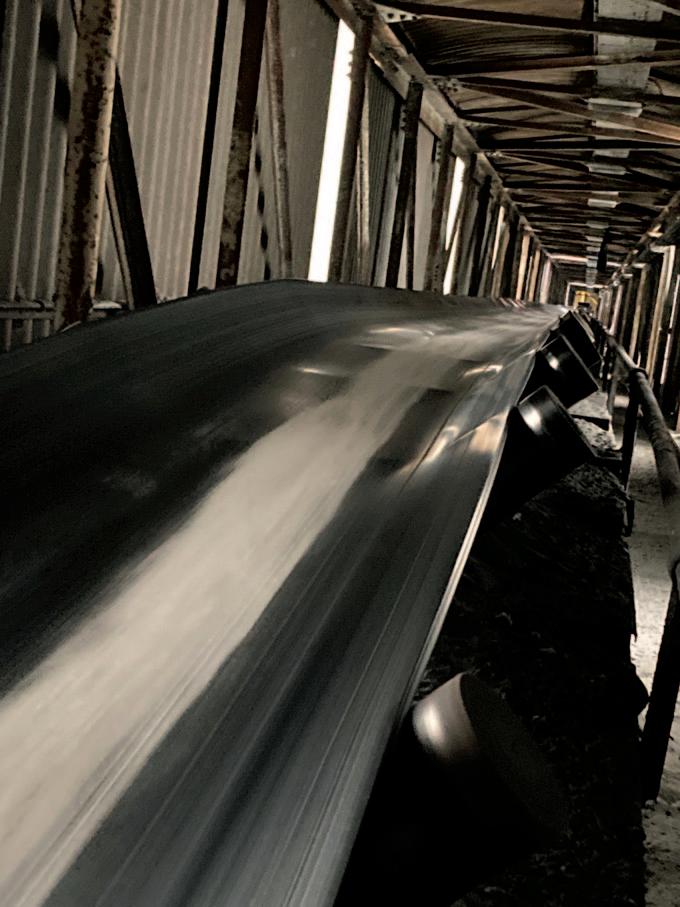
To be truly efficient and reliable, conveyor belts need to run straight and true. When they do not, then the cost in terms of lost output, belt damage and spillage can be very serious. Despite steering and handling problems being a fairly frequent occurrence, little is ever written on the subject. Here, Jeroen Kattouw, one of Netherlands-based Dunlop Conveyor Belting’s most experienced and highly regarded application engineers, provides helpful guidance on the most common causes of belt alignment problems and how best to avoid and resolve them.
IDENTIFYING THE SOURCE OF THE PROBLEM
When conveyor belts are misaligned, the first step is to identify the source of the problem. Although there are two distinct sources — the conveyor itself or the actual conveyor belt — it should be noted that there can sometimes be a combination of causes. The recommended approach is therefore a process of elimination.
CAUSES OF MISALIGNMENT DUE TO CONVEYOR PROBLEMS
Pulleys may not be mounted level andv square to the centre line of conveyor causing the belt to run off on the slack side.
Idlers may not be properly aligned.v The belt may not be loaded centrally.v
Worn drums or lagging can cause tracking problems.
If the material loaded on the belt is offcentre, then this will make the belt run off to the empty side. The only remedy is to re-design/re-align the loading chute.
The belt may be exposed to windv turbulence, especially cross winds. The belt may be dragging againstv protruding stationary parts of the conveyor framework.
The tripper may be askew because ofv clearance between rails and wheel flange.
Misalignment and/or wear of thev drums.
Pressure of belt scrapers not uniform.v Dirty/unclean environment.v Incorrect pre-tensionv
CAUSES OF MISALIGNMENT DUE TO BELT PROBLEMS
The belt may not be troughingv sufficiently to give proper contact with
the horizontal centre idler of trough idlers.
The belt itself may not be straight.v The belt may not have been joinedv (spliced) square and true.
TIME AND PATIENCE REQUIRED
A methodical approach and patience is absolutely essential when aligning an industrial conveyor belt. Gradual correction should take place over a period of several days or perhaps longer. Overadjustment will almost certainly occur if hasty corrections are made.
The training or alignment of a belt involves causing it to move towards the centre, from either the left or right hand side. A useful trick is to imagine that a packing case is being moved on rollers. If the case needs to travel towards the right hand then the left end of the roller should be advanced or the right end shifted back. The opposite is true if the belt is running to
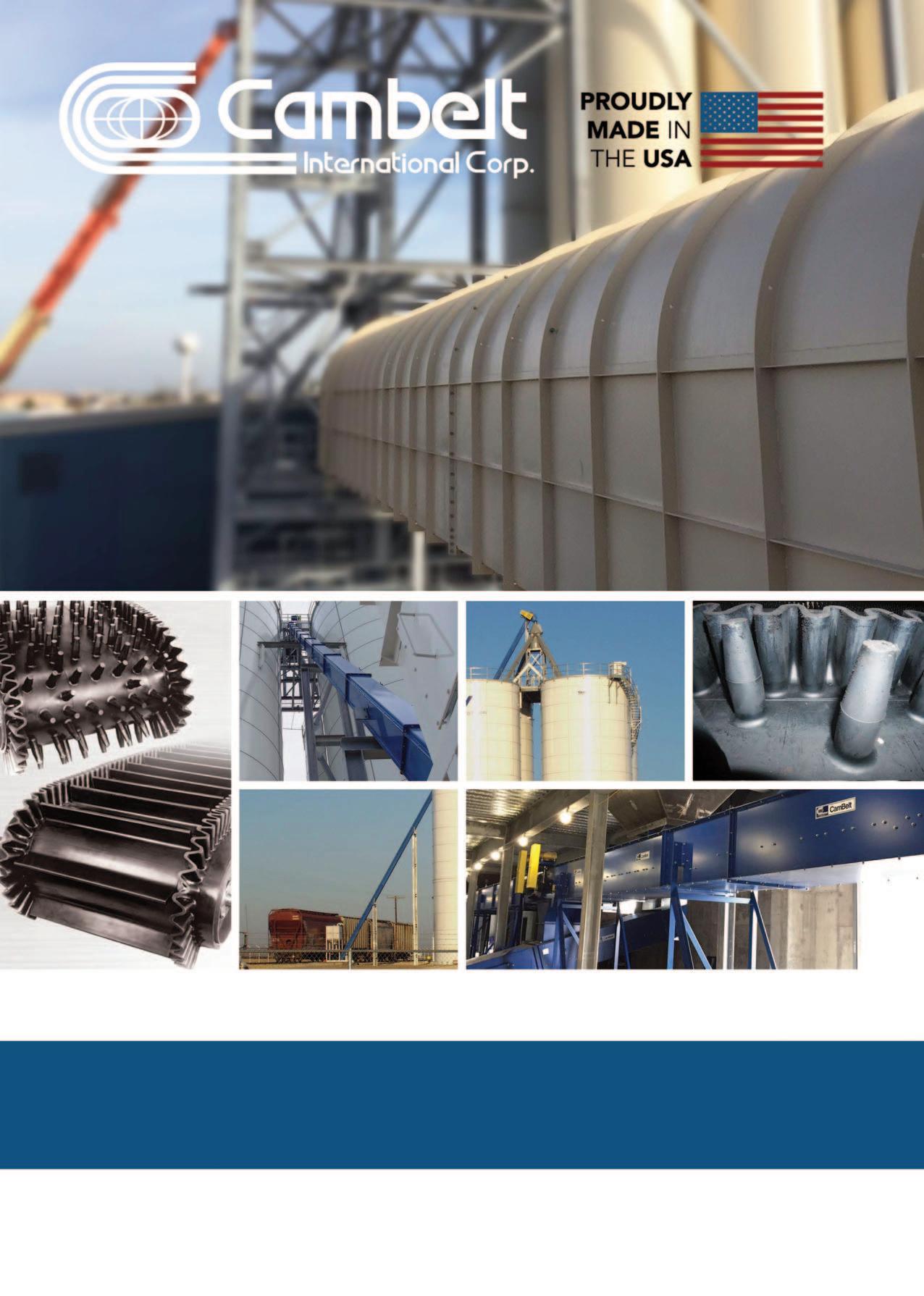


Diagram 1A: centreing adjustment

the left of the centreline (looking in the direction of travel). If it needs to move towards the right hand then the idlers in question need to be slewed out of centre so that the left side is moved forward and the right side brought back.
The easiest way to find out where correction needs to be made is simply to look along the edge of the travelling belt in the direction of travel. This should make it easy to watch curving along the belt edge due to the belt travelling off centre. Having established where such curve exists, the adjustments can be made as follows.
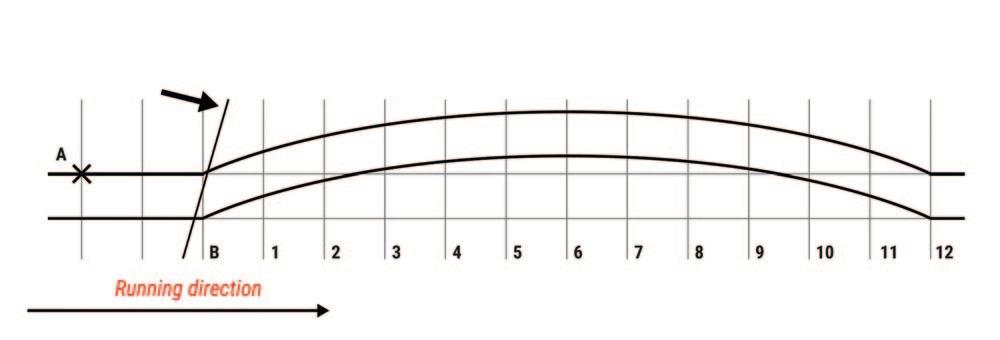
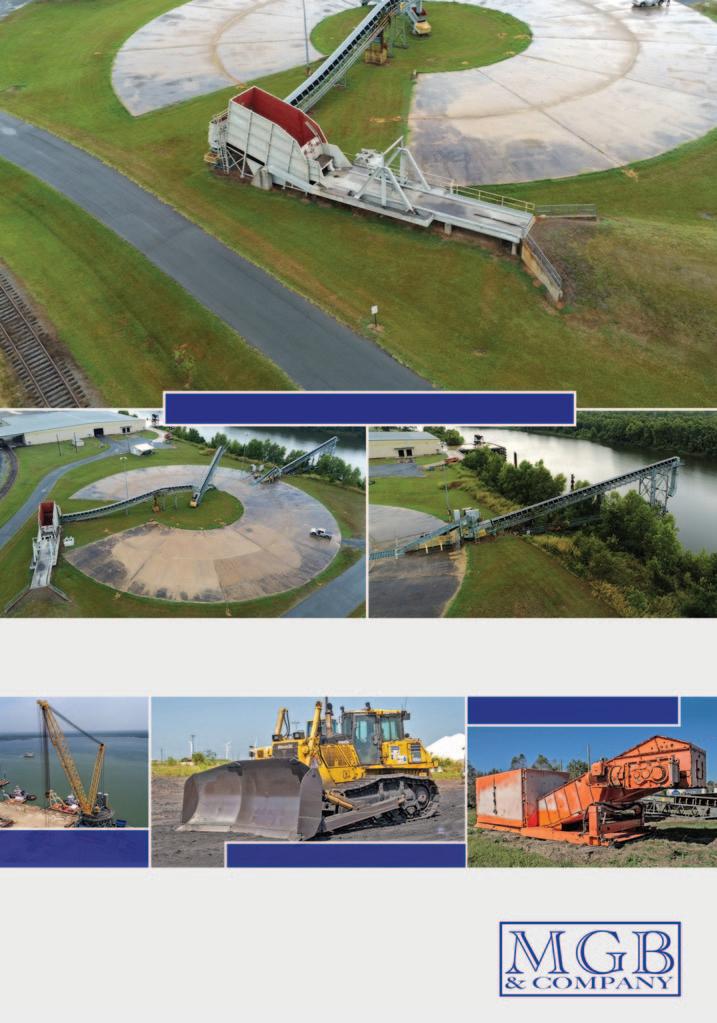
Referring to the diagram 1A, the observer at point A will watch in the direction of belt travel along the belt edge and observe a definite curving out between idlers marked 2 and 11. Such a curve may extend only over three or four idler spaces or over a much greater distance. It is a good idea to mark idlers 2 and 11 with chalk in order to definitely fix the extent of the curve. It will also be necessary to mark several idlers between 2 and 11 and the belt edge in order to have a reference mark to judge the effect of the adjustments after they have been made. It is important to note that if the belt starts running off at idler 2, it means that the correction of the idler setting will need to be made one or two idlers forward of this point. In this case, idler 1 or even the idler at point B will require slewing.
WATCH AND WAIT
After each adjustment has been made it is important to observe the effect for a sufficiently long period by allowing the belt to travel at least once right round the conveyor before the next adjustment is made.
This is necessary because few belts are perfectly straight. As a result, there is always a certain amount of ‘weaving’ to
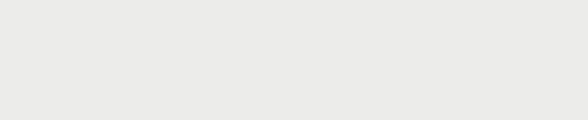

be expected at each idler so the position of the belt at any one idler position should be judged as the average position of the weaving motion.
MISALIGNMENT CAUSED BY POOR JOINTING
It is usually very easy to identify when a poor connection joint is causing a belt not
to run straight. Looking down the line of the conveyor, the belt will pass by running centrally for a time but then start to veer off centre for a period just before the joint arrives before eventually re-centreing itself after the splice has passed. This repeats itself on the next circulation of that section of belt. If the wandering is sufficiently serious, such as sections of the belt touching the conveyor frame for example, then the only solution is to have the joint re-made.
TRAINING A NEW BELT
Training a belt should always begin on the return run beginning at the head or driving pulley, following the direction of the belt travel. Having centred the return belt, the top belt (carrying run) should then be trained, starting at the tail pulley and proceeding in the direction of belt travel towards the head or driving pulley. If the top belt runs so much out of centre that it cannot be run for any length of time, it will be necessary to roughly train it before training the return belt. In this situation, the top belt should only be trained sufficiently so that it can be run without risk of damage to belt edges. The return belt is then centred, followed by training the top belt as previously described.
Having trained the belt when it is empty should mean that the belt will also run true when it is loaded. If not then the cause is almost certain to be that the material is not being fed centrally onto the belt. This can be corrected by modifying the feed chute by either changing the shape of the chute or by introducing deflecting plates or bars so that the material is loaded centrally. If it is not possible to re-position the chute
then it may be necessary to train the belt in such a way that the belt runs slightly off centre while empty. This should then correct itself when the belt is loaded.
In virtually all cases, a belt should only be trained by realigning idlers and snub pulleys. Head or driving pulleys and tail pulleys should never be set out of square. It is sometimes convenient to use the tail pulley for temporary adjustment if the belt is running off so much when first starting up that running is not really possible but this should only ever be as a temporary measure. As soon as the return belt has been sufficiently centred, the tail pulley should be set up square again before final training is completed. If a belt is running off centre because of wind turbulence, then the only thing to do is to provide suitable wind screening. If the belt is being dragged out of center by protruding stationary parts of the structure then obviously those parts need to be removed immediately.
BELT TROUGHING
In the case of new belts, especially those with a thick, heavy construction in relation
to their width are unlikely to trough very well to begin with. When empty, thick new belts will usually rest almost entirely on the inclined rollers with very little surface of the belt in contact with the central horizontal rollers. It is important to remember that it is the horizontal rollers that do the training or centreing whereas the inclined rollers have a tendency to pull the belt out of centre. This is why, when a new belt is first started when empty, difficulties can often be experienced. It is therefore advisable to train the belt as much as possible so that it will at least run without being damaged.
The belt should then be run under load for several days and, during this time, the belt should be gradually trained until it runs true. This will usually remove the initial elasticity (stretch) and allow the belt to trough more easily and have better contact with the centre rollers, helping to keep the belt centred. If the problem persists, then it may well be worth having the belt specification recalculated because it may be over-dimensioned.
COMMON PROBLEMS ASSOCIATED WITH POOR QUALITY BELTS
The carcass provides the innate strength of any conveyor belt. Very significantly, the strength under load needs to be consistent throughout the belt both longitudinally and transversely in order for the belt to steer and handle correctly. Although they may be the same basic specification, there can be very big differences in the quality of the fabric plies between one belt and another.
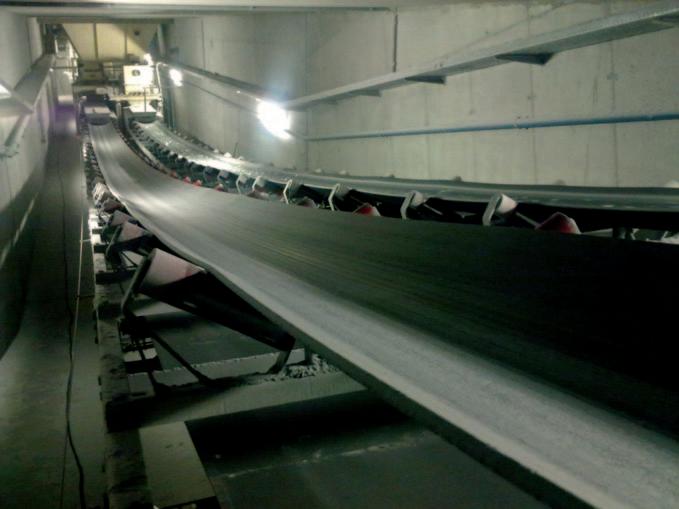

Training a belt when it is empty should mean it will also run true when loaded.
In cheaper, lower quality fabrics, although the amount of material used in the longitudinal (polyester) strands of the fabric may be adequate, the amount of transversal weft material (nylon) is kept to a minimum in order to reduce cost. Although the required tensile strength may be achieved, the longitudinal elasticity may be too low. This can cause problems with transition distances and a general inability to accommodate the contours of the
Observe the effect for a sufficiently long period after each adjustment has been made.
The N2Position Indicator remotely monitors the position of the belt cleaner blade, allowing estimation of blade life, notification of when re-tensioning or replacement is required, and warnings in the event of abnormal conditions such as temperature changes, or low battery life.
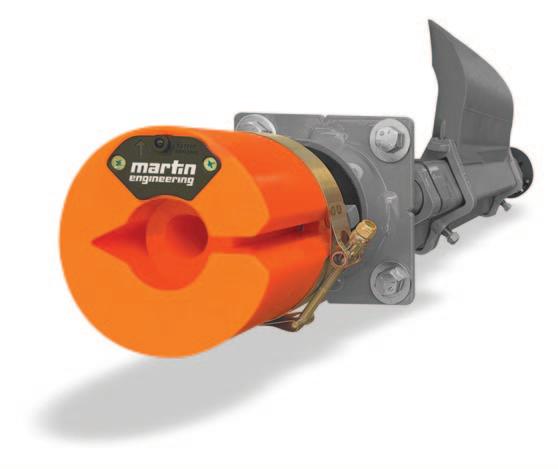
Remote monitoring enables condition-based, predictive maintenance and support. Which means you
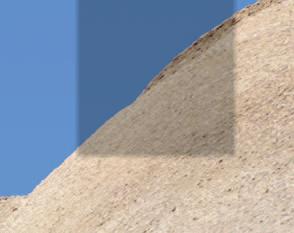

Knows when blade change is required
physically inspect a piece of equipment or plan scheduled downtime when the data tells you that a service is needed or the end of life is approaching.
Up to 200 N2 Position Indicators can wirelessly transmit information to a single N2 Gateway, which then sends the data to cloud storage. Retrieval of the details for remote monitoring is accessible via our proprietary Smart Device Manager application.
Without shutting down the belt, remote monitoring lets you assess real-time conditions ensuring safety, efficiency and cost effectiveness making best use of time and resources and ultimately maximizing uptime and profitability.
material limits
Nothing should stand in the way of your productivity – least of all the materials you move. With our compact Hägglunds direct drive systems, you can adapt easily to the job at hand, taking advantage of full torque at an in昀nite range of speeds. And should an overload try to stop you, the drives’ low moment of inertia and quick response will keep your machines protected. We’ll support you too, with an agile global network and smart connectivity to bring you peace of mind. Driven to the core.
a brand
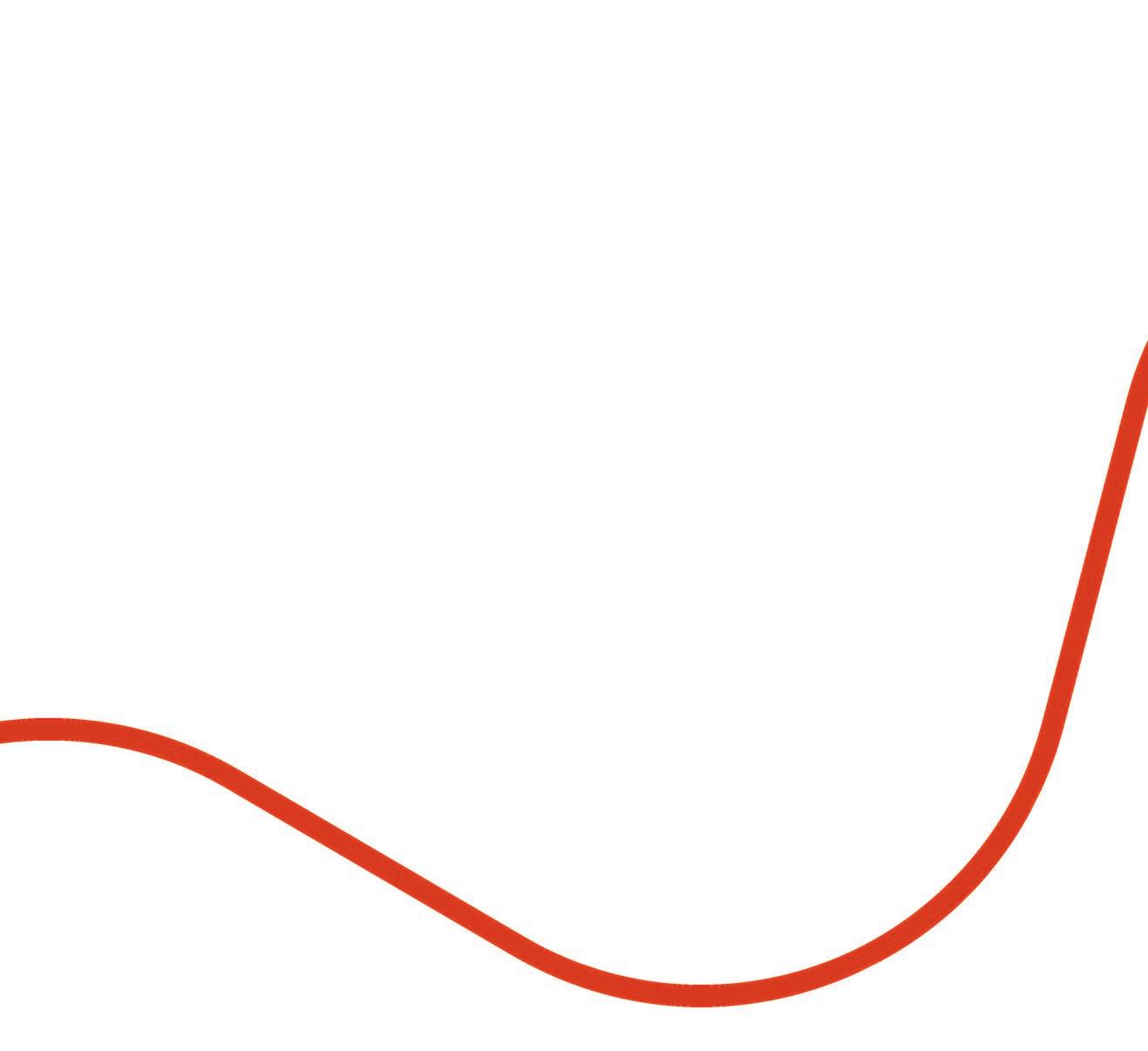
The carcass provides the innate strength of any conveyor belt.
conveyor and its drums and pulleys and ultimately lead to the premature failure of the belt.
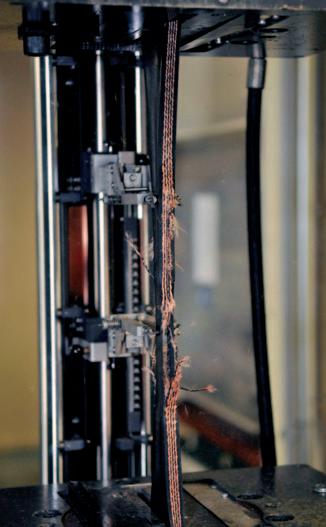
An increasingly common problem involving low grade ‘economy’ conveyor belting is the use of totally polyester (EE) fabric plies in a carcass that has been sold as being an EP carcass (polyester/nylon mix) construction. The whole basis of using

An unclean environment is a common cause of misalignment.
a mix of polyester and nylon fabric (EP) is that it has the best balance of mechanical properties including allowing a conveyor belt to run straight and true, to trough, to flex round pulleys and drums, stretch, provide sufficient transversal rigidity, longitudinal strength and much more besides. The use of totally polyester (EE) fabric compromises a whole range of essential mechanical properties*. The biggest danger is that a polyester weft can
(*Author’s note: The use of fabrics made entirely of polyester (EE) has its place in certain belt types and constructions. However, in those cases the declared specification of the belt should clearly be EE and not EP).
cause low transverse elasticity, which reduces the troughability of the belt as well as causing tracking issues.
PREVENTION IS BETTER THAN A CURE
Once a belt is correctly aligned and running straight and true, the next objective is to keep it that way with the minimum of intervention. A simple programme of routine checking and preventative maintenance not only helps to prevent unnecessary stoppages for adjustment, it also helps to increase the operational lifetime of the belt. Regular checks should therefore be made on the state of all drums, pulleys and idlers. Failure to replace
these components when they begin to show signs of wear is almost always a false economy.
Finally yet importantly, it is important to keep the working environment as clean as possible, particularly when the conveyed materials that are damp or sticky and have a tendency to build up on pulleys or return idlers because this will cause the belt to run out of line.
STAY CLEAR , STAY SAFE
Industrial conveyors can be extremely dangerous pieces of equipment. To those of us who regularly work with them, it is all too easy to become complacent and forget even the basic safety disciplines. When carrying out procedures such as aligning a belt or checking drums or idlers, always stay well clear of any moving parts when the belt is actually running. Finally, do not work alone — always make sure that there is a colleague close by who can quickly stop the conveyor in an emergency.
ABOUT THE AUTHOR
Jeroen Kattouw has worked in the conveyor belt industry for over 30 years. During that time, he has become one of the most experienced and highly respected application engineers in the industry.
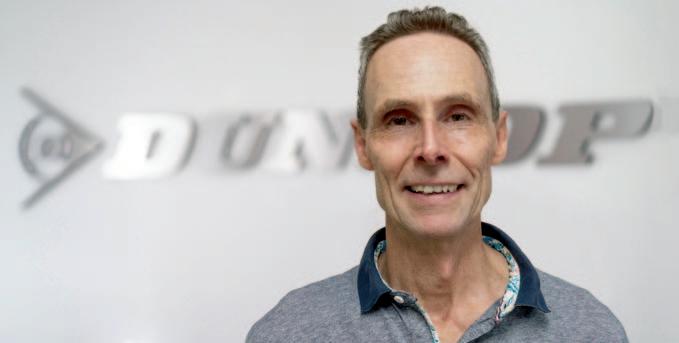
Martin Engineering’s ‘Go Pink!’ breast cancer campaign expands to conveyor products
A renowned pioneer in industrial vibration and bulk material handling technologies is announcing this year’s annual programme to support breast cancer education, screening, treatment and research around the world. Continuing its commitment during National Breast Cancer Awareness Month in the US, Martin Engineering invites customers to ‘Go Pink!”‘ For the month of October, along with replacing the traditional Martin orange paint scheme on truck vibrators, the company will add the option of conveyor guarding, Twist Tensioners and inspection doors to Go Pink as well. This is to honour all those affected by the deadly disease which has touched so many Martin employees and their families. By merely saying, “Make mine pink” when purchasing the company’s popular Cougar DC Truck Vibrator or Cougar THD Hydraulic Vibrator, Martin Engineering will donate a portion of its sales revenue to support the Susan G. Komen® Foundation.
“Since 2017, this popular campaign has allowed Martin Engineering to donate almost $50,000 to the Susan G Komen organization,” said Vibration Business Development Manager, Susie Orlandi. “Every contribution supports those in need
Freshly painted industrial vibrators dry in preparation for the Go Pink! campaign.
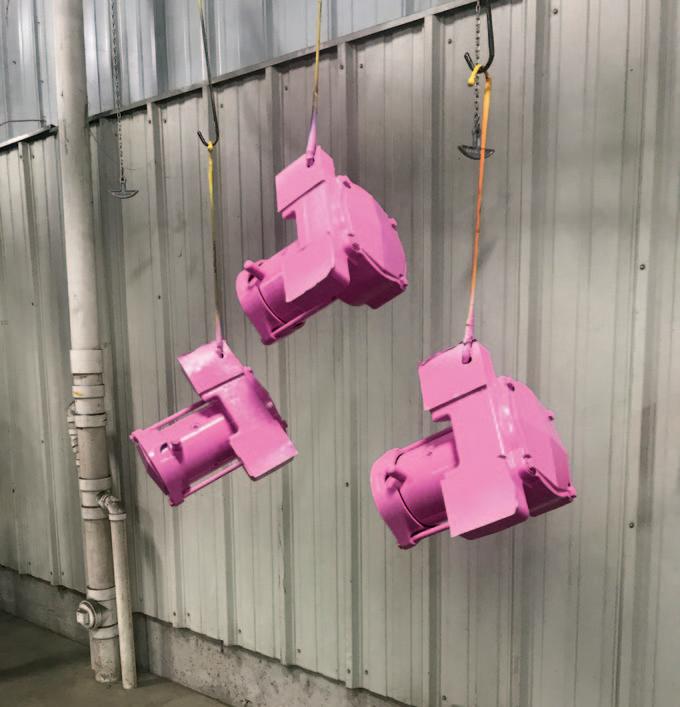
today, while the researchers continue their work for a cure.
“With over 900 employees worldwide, we’re a family-owned company that is all too familiar with the impact breast cancer has on individuals, families, friends, colleagues and communities,” she
The Cougar truck vibrator is the go-to replacement unit because of its long equipment life.
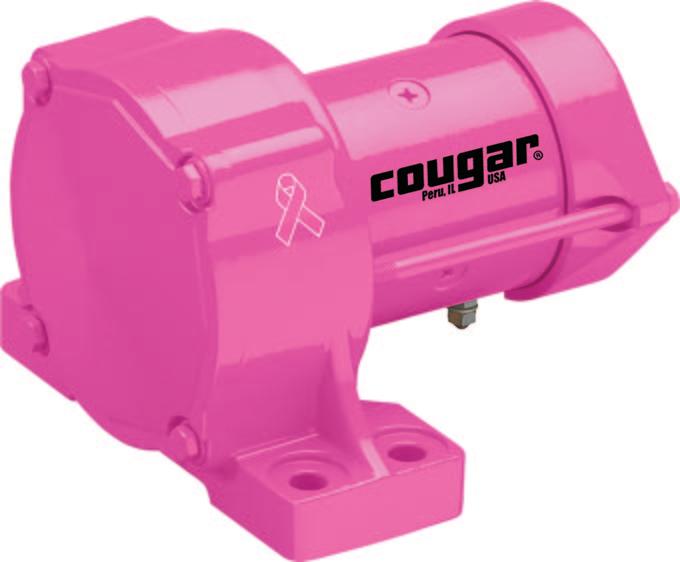
continued. “It affects such a large number of people that just about all of us have been touched by it in some way.”
That’s why this programme also garners huge support from the staff. In addition to its donations, Martin Engineering hosts a team in Komen Peoria’s More Than Pink Walk® to raise awareness and encourage individual contributions to this worthy cause. “Every step is one step closer to a cure,” Orlandi said. “Whether it’s with the helpline, financial support or assisting patients in navigating their care journey, we trust the Komen Foundation to support patients and families. Funds go directly to support breakthrough research and provide help for the women and men facing breast cancer.”
Since its formation in 1982, the Susan G. Komen foundation has raised over $3 billion in more than 60 countries. With a mission of supporting those with the fewest resources, it has helped to reduce breast cancer-related deaths by an estimated 40%. The organization has played a critical role in virtually every major advance to combat breast cancer — transforming how the world talks about and treats the disease and helping millions of breast cancer patients become cancer survivors.
According to the National Breast Cancer Foundation®, about one in every eight women will be diagnosed with breast cancer in her lifetime, along with thousands of men. The organization has contributed
to several breakthroughs including the identification of genetic links, less-invasive surgical techniques and advanced drug therapies, as well as advocating for more federal funding of additional research and early detection programmes.
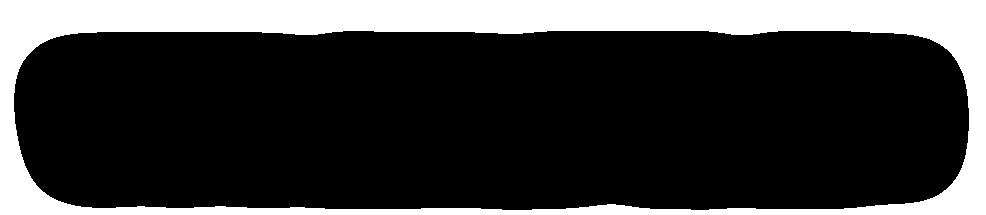

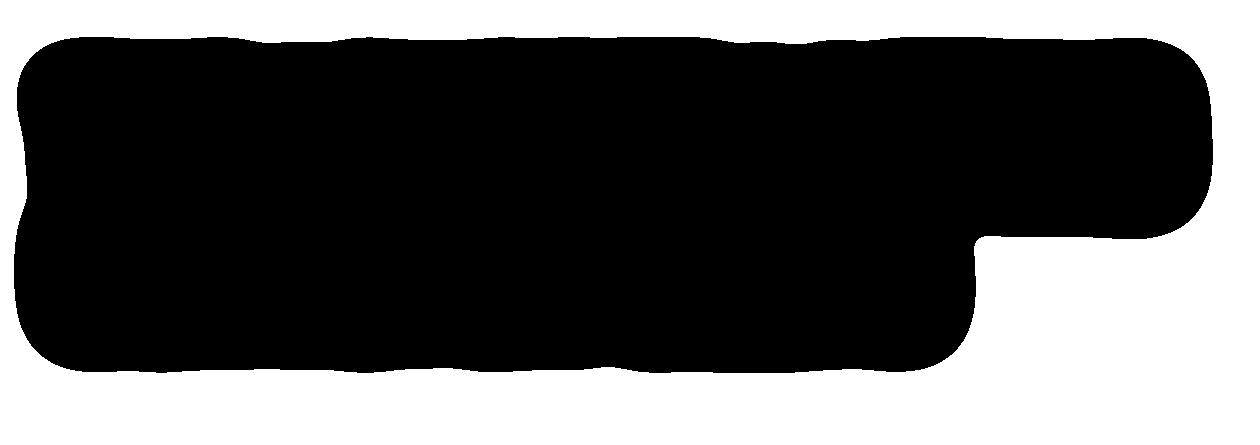
“Every year, our customers generously join us in this fight, placing orders to contribute to its success,” Orlandi added. “Programmes like this allow the pink colour scheme to represent the cause yearround, generating awareness and getting people talking.”
Along with the colour change, the equipment retains the same high-quality standards. Discharging heavy and often compacted material from dump trucks, hopper rail cars, and other vehicles can require a lot of vibration power in a punishing environment putting high demands on equipment. Operators choose Cougar® DC Truck Vibrators and Cougar® THD Hydraulic Vibrators to replace OEM vibrators that tend to have a limited service life. Reliable and durable truck vibrators like the DC and THD reduce manual labour and downtime while ensuring the safe evacuation of cargo.
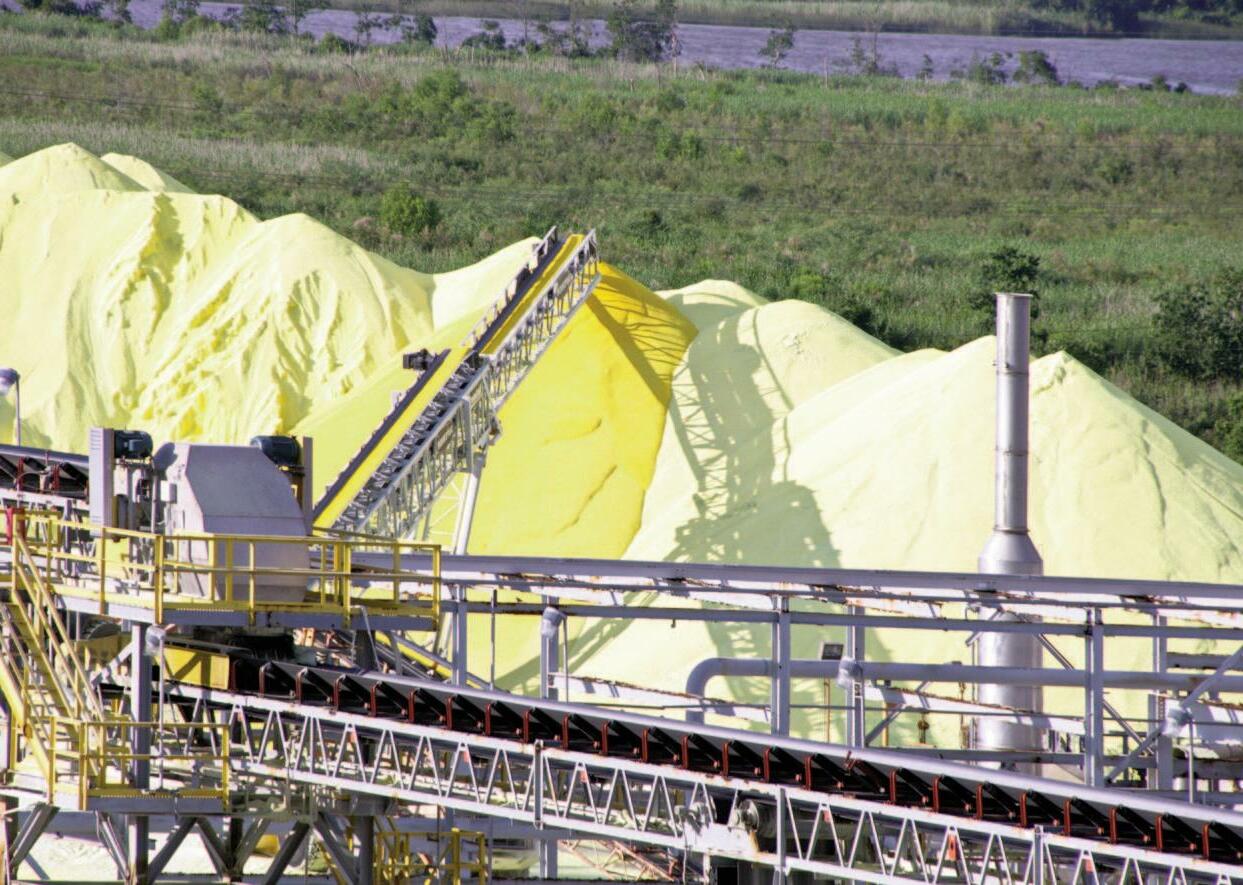
Faster unloading increases the number of trips by operators, improves efficiency
Pink guarding protects workers and is a prevalent reminder of Breast Cancer Awareness.
and reduces the cost of operation.
To further boost awareness, all the Cougar DC Truck Vibrators or Cougar THD Hydraulic Vibrators ordered in October will be painted pink unless orange is requested. In addition, conveyor guarding, twist tensioners and inspection doors will also be included as items
customers can choose to order in the pink colour scheme. The conveyor guards protect workers from the hazards of a working conveyor. Twist Tensioners ensure that conveyor cleaner blades stay in proper contact with the belt to adequately discharge and clean adhered material from the surface. Inspection doors are attached
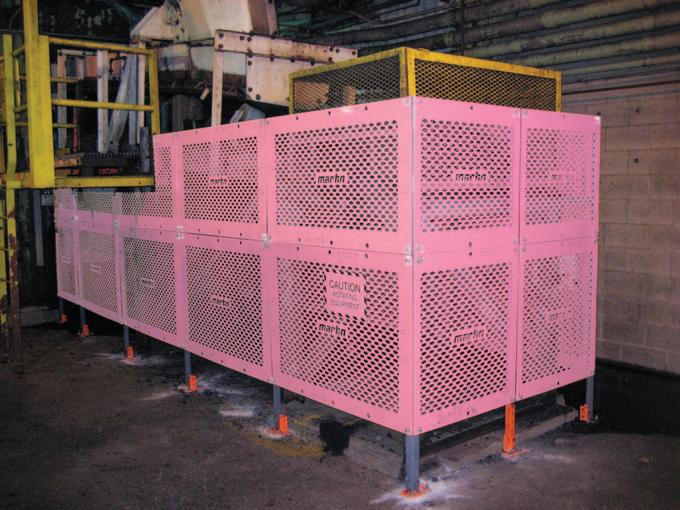
to sealed chutes and enclosures that contain dust and spillage, allowing workers to safely view bulk handling operations. These items are prominent exterior components that, when made pink, commemorate lost loved ones and remind people of the ongoing battle against breast cancer.
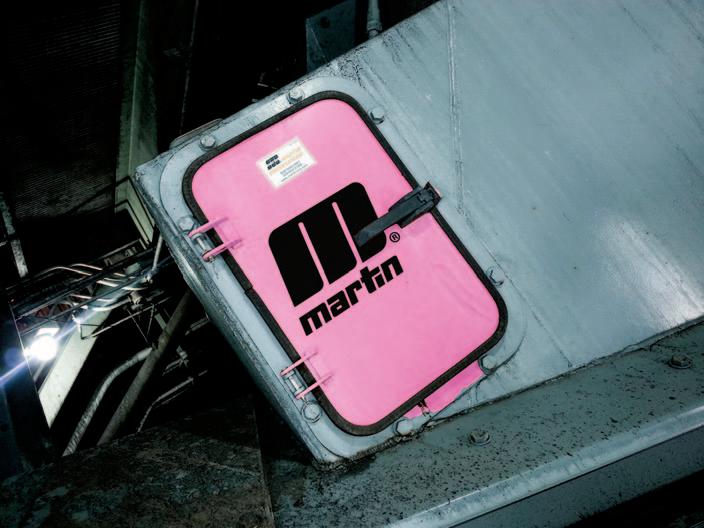
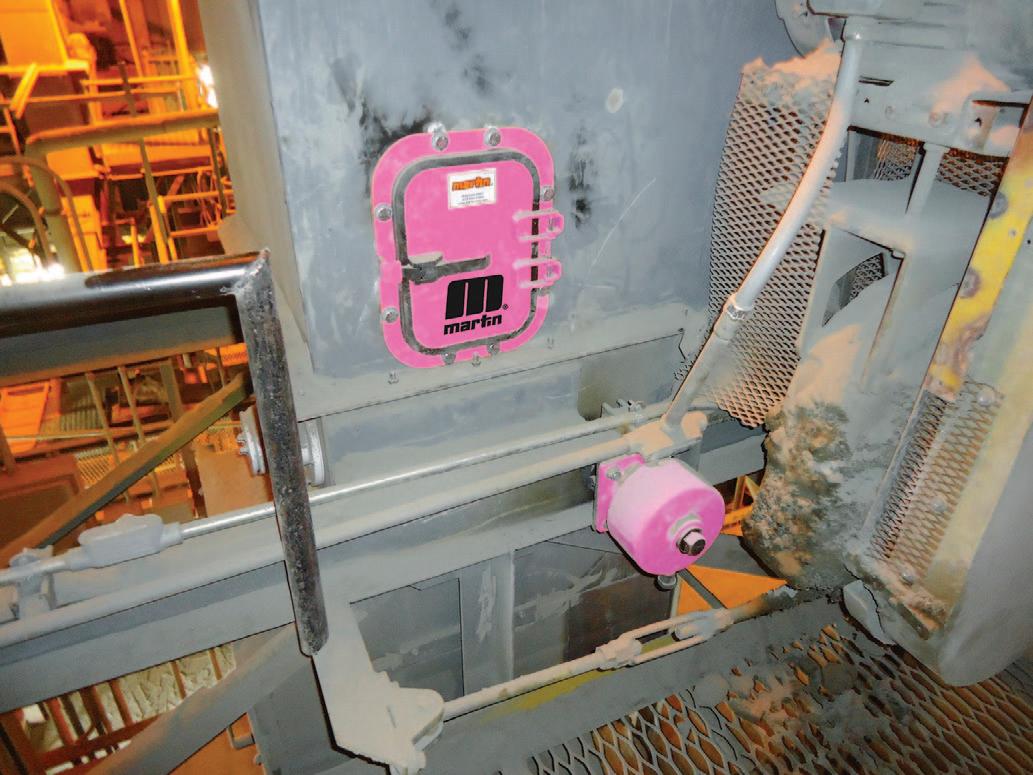
“Like us, the Komen family has roots in the Peoria, Illinois area,” added Martin Engineering Chairman Ed Peterson. “It’s a tight-knit community that supports each other, so we’ve always felt a special connection to the cause. I’d like to think that the midwestern spirit of generosity and community contributed to the success of the cause.”
Inspection doors allow safe viewing of critical systems during operations.
Pink inspection doors and twist tensioners bring colour to an otherwise grey aesthetic.
A twist tensioner mounted on a bracket at the discharge zone, helping ensure a clean belt.
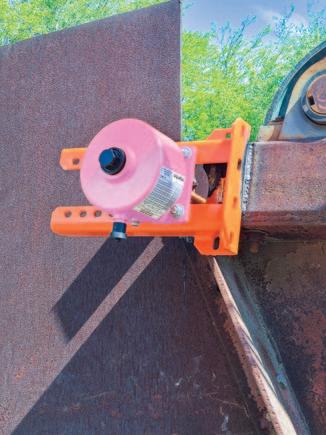
ABOUT MARTIN ENGINEERING
Martin Engineering has been a global innovator in the bulk material handling industry for more than 75 years, developing new solutions to common problems and participating in industry organizations to improve safety and productivity. The company’s series of Foundations books is an internationally recognized resource for safety, maintenance and operations training — with more than 22,000 print copies in circulation around the world. The 500+ page reference books are available in
several languages and have been downloaded thousands of times as free PDFs from the Martin website. Martin Engineering products, sales, service and training are available from 17 factoryowned facilities worldwide, with whollyowned business units in Australia, Brazil, China, Colombia, France, Germany, India, Indonesia, Italy, Mexico, Peru, Spain, South Africa, Turkey, the USA and UK. The firm employs more than 1,000 people, approximately 400 of whom hold advanced degrees.
FLSmidth to supply overland conveyor system for a major copper-gold mine in Southeast Asia
FLSmidth has been chosen to supply an overland conveyor (OLC) for a large, established copper-gold mine in Southeast Asia, which follows a large equipment order from the same customer and site earlier in 2022. The pit-to-plant conveying system, which is over 5km in length, has gearless drive technology. The order, including design and supply, was booked in Q3 2022 and is valued at approximately DKK330 million.
The conveyor order follows the Q1 2022 announcement that FLSmidth had been chosen to supply two gearless SAG mills, two gearless ball mills and thickener technology to the same site. This new FLSmidth overland conveyor will deliver the ore from the pit to the new FLSmidth SAG and ball mills at the process plant.
The conveying system, part of the newly acquired tk Mining portfolio, is
expected to deliver a significant reduction of OPEX due to its gearless drive technology, which uses less energy, and results in less maintenance and higher availability during operations.
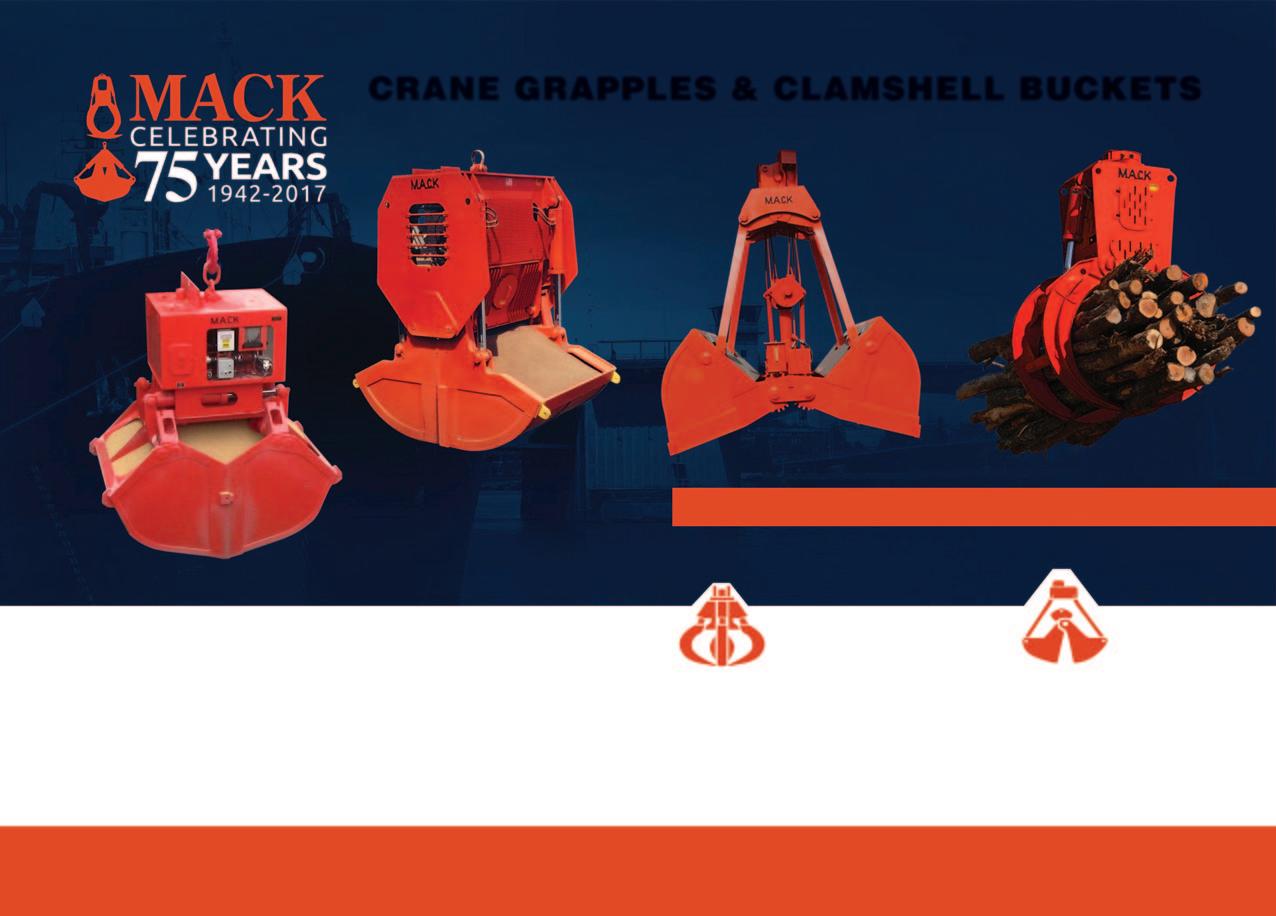
“This overland conveyor system order not only continues our robust relationship with this customer, but it also demonstrates the strength of our portfolio following the acquisition of the tk Mining business. This is evidence that FLSmidth is a global leader in overland conveyors and gearless drive technology. The customer will benefit from our full flowsheet coverage, and we are proud to have provided the majority of the equipment to this mine site expansion,” comments Mikko Keto, Group CEO at FLSmidth.
The order supports FLSmidth’s MissionZero ambition to enable customers to mine in a more sustainable
manner. Overland conveyors significantly reduce the need for dieselpowered truck fleets on mine site and makes material transportation more cost-effective and resource efficient.
ABOUT FLSMIDTH
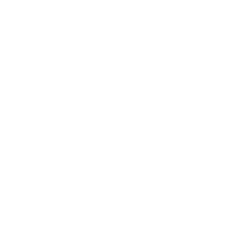
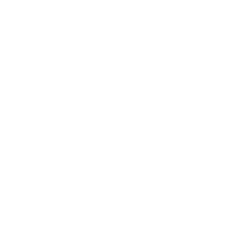
FLSmidth provides sustainable productivity to the global mining and cement industries. The company delivers high-tech products and service solutions that enable its customers to improve performance, drive down costs and reduce environmental impact.
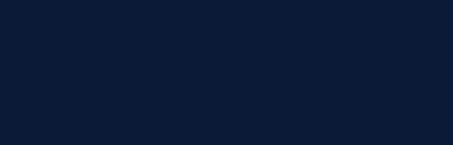
FLSmidth has ‘MissionZero’ as its sustainability ambition towards zero emissions in mining and cement by 2030. FLSmidth works within fully validated Science-Based Targets, and is committed to keeping global warming below 1.5°C and to becoming carbon neutral in its own operations by 2030.

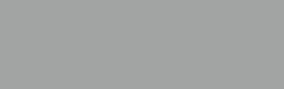
Happy birthday RULMECA: 60 years strong, and still at the top of its game
Great celebrations were held in Italy on Friday 9 September at the headquarters of the RULMECA Group, a globally renowned supplier of rollers, stations, pulleys, motorized pulleys, drum motors and drives for belt conveyors in bulk handling applications and for intralogistics.


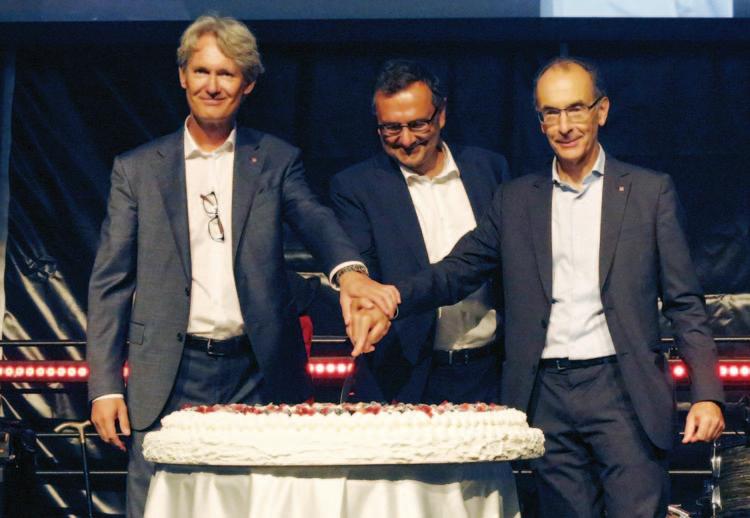
The company is celebrating its first 60 years, and what better opportunity to bring together more than 700 people among collaborators, partners and their families?
Speeches by President Marco Ghisalberti, Honorary President Emilio Moreschi, CEO Fabio Ghisalberti and Carsten Spanggaard were joined by the greetings of local authorities and those of the two non-profit environmental associations sponsored by the RULMECA Group. Big Blue Ocean Cleanup and Race For Oceans are engaged in a constant fight against pollution caused by plastic in the oceans.
The occasion provided an important moment of reflection to remember and thank the 1,200 employees of the 17 production and sales companies located around the world. Through their daily commitment and professionalism, they make it possible to achieve important goals, such as those achieved during these long 60 years. This is a clear sign of a company solidity built over time thanks to the skills of an expert but above all closeknit group.
There was also lots of entertainment. For children, there was a dedicated area with food, games and shows. For adults a rich aperitif and buffet dinner was accompanied by DJ sets, and at the end of the evening, the engaging music of the rockabilly band ‘Slick Steve and the Gangsters’.
The celebrations, which will continue until the end of the year with the events in Canada, Germany, Poland and the United States, do not want to be a point of arrival
but a push towards further strategic growth of the Group, through: further investment in customerv service; the increase in production space andv
capacity; brand strengthening through globalv communication; increased investment in R&D; andv digitization of production facilities.v
Marco Ghisalberti, Executive President and Carsten Spanggaard, Vice President.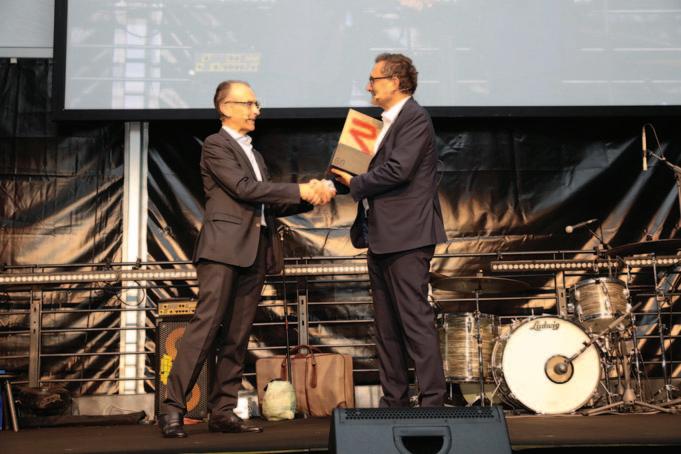
RopeCon ® Ef昀cient Solutions for Bulk Material Handling
Wherever

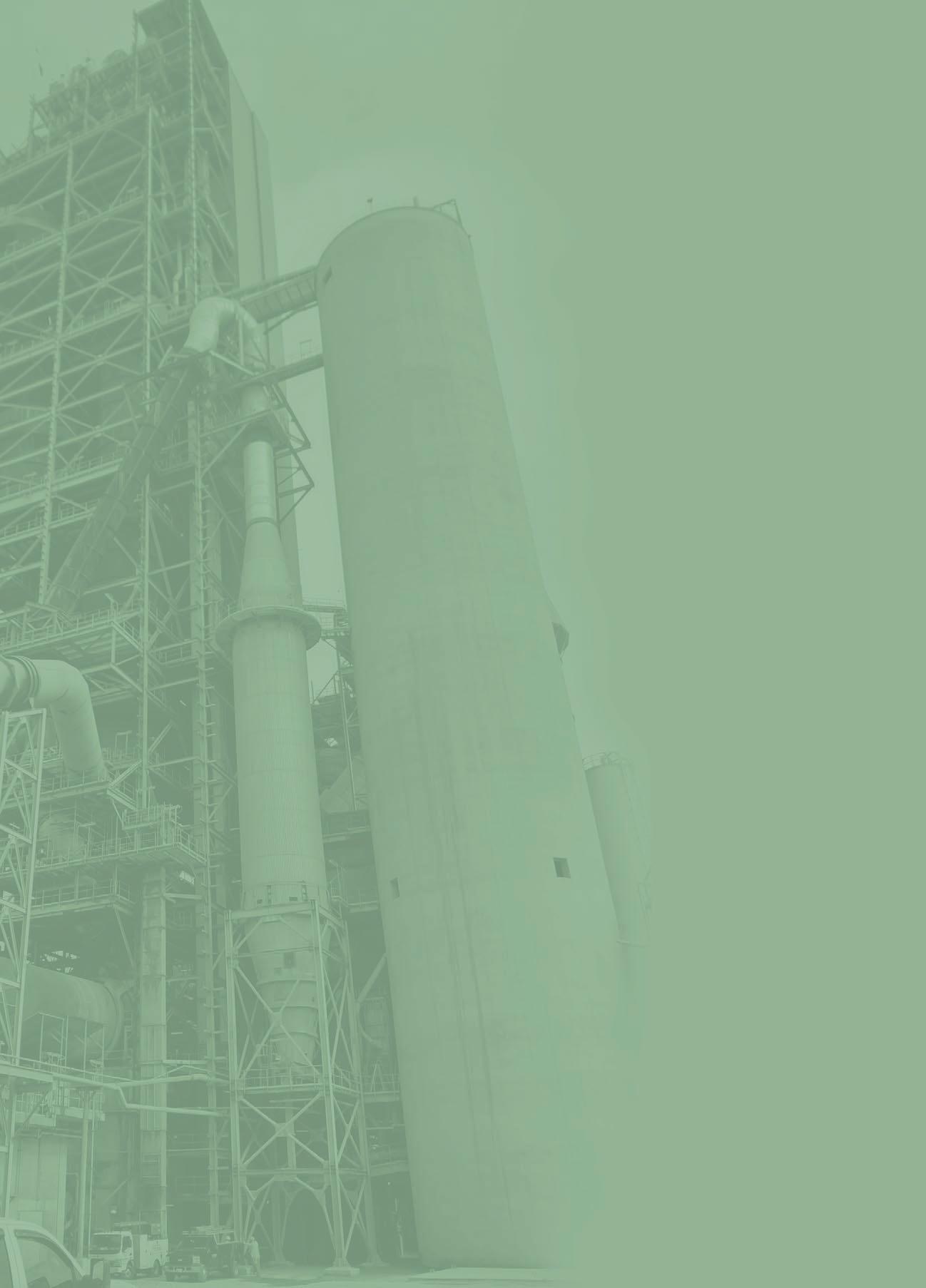
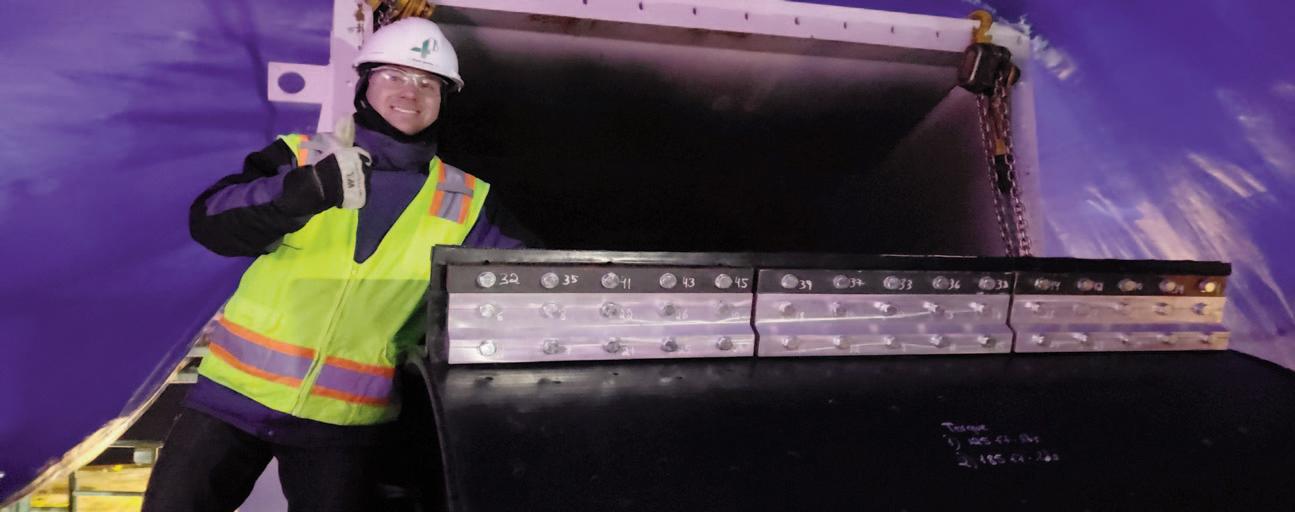

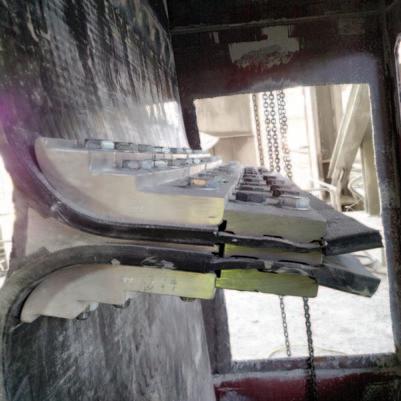
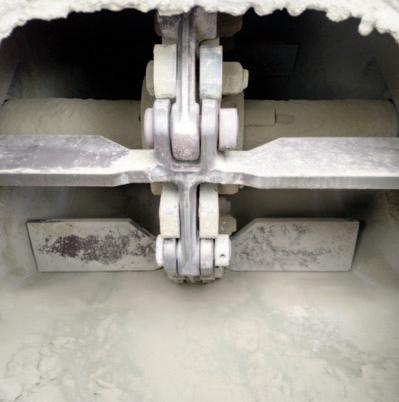
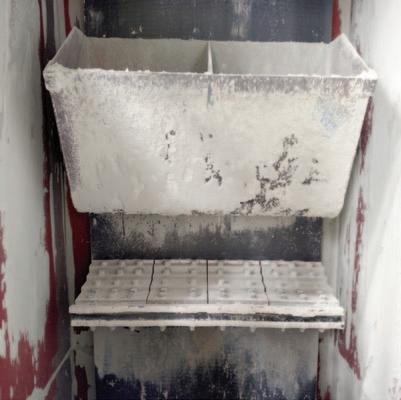
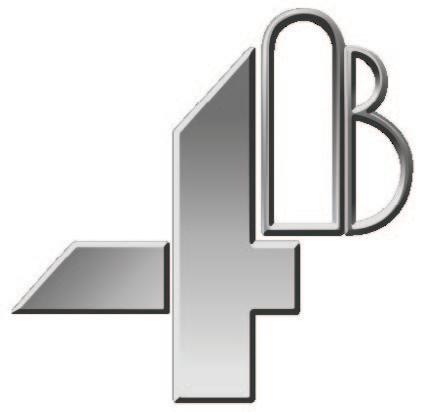
Installation is one thing, upkeep is another
Belt conveyors are some of the most widely used and relied upon material transfer systems in the world, writes Lindsay Gilliland, Executive Admin. & Marketing Coordinator at Bruks Siwertell. They made their debut in ports in around 1795 and, in one guise or another, remain ubiquitous today.
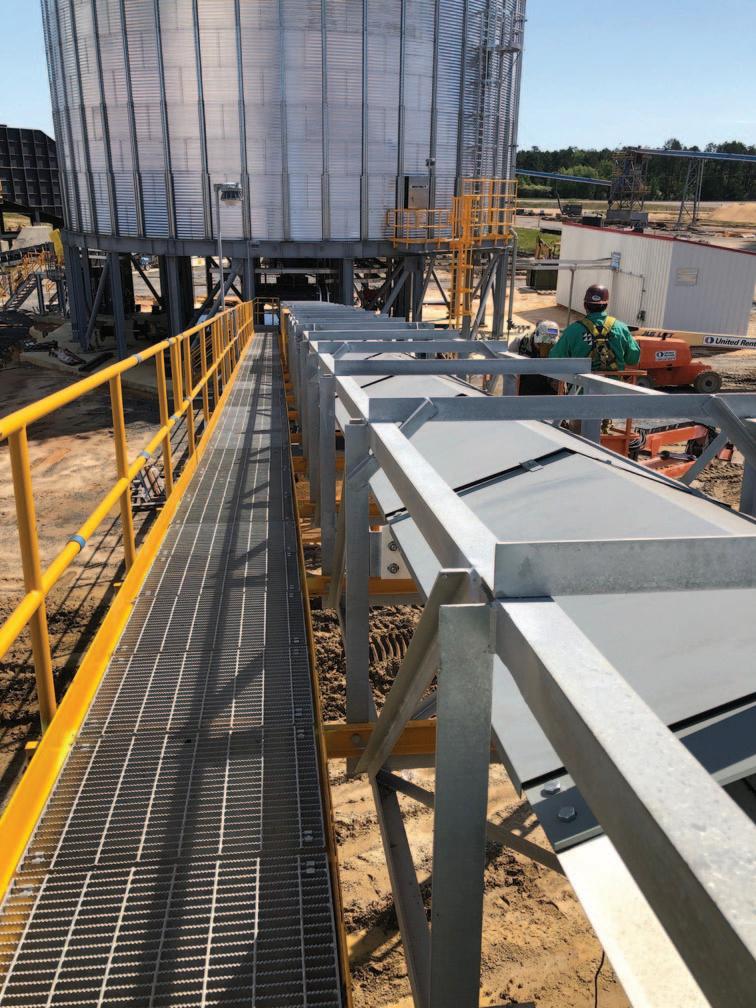
Different developments have seen them adapted to various industries, from the first roller conveyor patent, filed for in 1908 by Hymle Goddard, to Henry Ford incorporating them into automobile assembly lines in 1913. Today’s conveyor belts are an industrial mainstay. So, why look again at their design?
For all their amazing qualities, such as high-capacity conveying, robustness and relatively inexpensive installations, they are incredibly maintenance heavy. They rely on
a flat, rubberized belt stretched over unpowered rollers, or idlers, positioned at intervals of about 1.2m. When these are
scaled up, spanning huge facilities, there may be thousands of rollers, each requiring oiling and maintenance to ensure that it does not seize up, cause friction, and therefore potentially lead to a fire.

Aside from equipment wear, there are also other elements that often need addressing with traditional idler belt conveyors, including material degradation, spillage, and dust emissions.
ADVANTAGES WORTH CONSIDERING
Bruks Siwertell has one of the most comprehensive range of conveyor systems available to the market, and each is specified depending on their application, from very high-capacity traditional belt conveyors, to totally enclosed robust screw conveyors and those that employ the use of pressurized air. Its air-supported conveying systems are gaining industry interest because they are offering some unique advantages to operators.
In a nutshell, low-friction, aircushion conveyors eliminate rollers, and therefore deliver huge benefits in terms of operational and maintenance costs. On top of this, they offer high-capacity conveying with no material degradation and minimal equipment wear.
Bruks Siwertell’s air-supported conveyor range comprises the Tubulator™ and The Belt Conveyor™. In addition to the significant reduction in maintenance and operational
costs, by eliminating rollers, the ‘bumpy ride’ caused by the belt passing over the idlers and idler sag — the dip in the belt between rollers — is also removed, along with material degradation.
Idler sag can also lead to material roll back at greater inclines. Both systems, but especially Tubulators, can reach angles that would not be possible using traditional idler conveyors.
Tubulators were introduced to the market several years ago, and now have over 620 installations worldwide. They are extremely effective at handling lower density materials, such as cement, shredded waste, grain, and sugar, and especially those liable to degrade easily and therefore generate more dust.
The Tubulator and The Belt Conveyor are closed systems ensuring no spillage or dust emissions. They both use pressurized air beneath the belt, but this is delivered in different ways for each conveyor type.
For the Tubulator, sectioned into 12mlong steel tubes, enabling them to fit into a 40ft standard shipping container, a rubber belt runs at high speed on top of an air cushion created by a series of in-line fans.
Because of their structural integrity and significantly reduced weight, they require fewer supports and are easier to install over existing equipment when compared with traditional conveyor frames, so can, in fact, be installed at considerable heights. Tubulator conveyors are self-supporting up to 25m, and have a free-span of up to 80m when using cable towers, or up to 30m between standard supports.
The Tubulator is an ideal enclosed conveyor system for very specific applications that need some or all of its unique capabilities of low-friction, idler-free conveying in addition to high, long, and potentially steeply inclined installations.
EXPANDED CONVEYING CAPABILITIES
The Belt Conveyor, does deliver something commercially different. Customers were asking for an air-supported conveyor that could carry a wider variety of materials and incorporate features of both the Tubulator and conventional conveyor design. These were the reasons that Bruks Siwertell embarked on its development programme.
Instead of using a pipe enclosure, The Belt Conveyor uses a central air manifold to provide the air pressure to suspend the belt. Each three-metre section of the belt has access to a common header of pressurized air, and under the carry-side pan is a three-metre pressurized air enclosure system, otherwise known as a plenum. Air pressure sensors and flow
meters along the length of the belt ensure the optimum amount of air is delivered for the weight of the given cargo, reducing running costs.
The Belt Conveyor offers flexibility, and can handle higher-density materials using standard belts and standard parts, which reduces costs. It has a simple modular design with a cradle that supports a formed carrying trough and covers. This is the same shape as a 35° idler conveyor, so that it still meets industry-standard calculations for the USA’s Conveyors Equipment Manufacturers Association (CEMA).
Basic components include the head and tail unit and three metre-long intermediate sections. The only moving parts are the head and tail pulleys. Third-party components, like weigh-scales, metal detectors, magnets and material sensor areas, can all be incorporated as well.
A COMMERCIAL REALITY
In 2020, one of the largest manufacturers of containerboard and corrugated packaging in the United States took The Belt Conveyor into use at its highest-volume mill in Tennessee. The conveyors were added as part of a new log-line to increase the capacity of the plant.
At this mill, the same system is being used for three different types of material, bark, unhogged bark and wood chips. The requirements of these three materials are similar, but still distinct. Hogged bark, for example, contains high levels of dust.
The new fully-enclosed conveying system comprises a 1,400mm (54in) beltwidth x 122m (400ft) long conveyor, which handles wood chips at 550tph (tonnes per hour); and two further conveyor units, one 1,000mm (36in) x 39.6m (130ft) and one 1,000mm (36in) x 91.4m (300ft), for handling hogged and unhogged bark at a

rate of 60tph. The belt conveyor systems were manufactured at Aztek Technologies in Monterrey, Mexico.
Also in 2020, Barrette-Chapais’ new 210,000 metric tonnes/year wood pellet production plant, Granule 777, in Quebec, Canada, commenced operations using a combination of both Tubulator and The Belt Conveyor technologies.
With a rated capacity of 800tph for carrying wood pellets, its air-supported conveying system comprises a 100m-long The Belt Conveyor and a 250m-long Tubulator. The Belt Conveyor carries material from the facility’s two pellet storage domes, before transferring it to the Tubulator system, which feeds it to the dock where the pellets are loaded onto bulk carriers, bound for Europe. The combination offers the plant extraordinary levels of efficiency, environmental protection, and through-life operational and maintenance savings.
INTERESTED?
Bruks Siwertell has a test facility in Whitesburg, Georgia, USA, specially built to showcase the performance capabilities of The Belt Conveyor against other commercially available designs. It is open to the public upon request.
Located near Atlanta Hartsfield International Airport, about one and a half hours from Bruks Siwertell’s Alpharetta, Georgia, office, operators are able to bring their own materials to run at the facility. Through live demonstrations, Bruks Siwertell is able to answer questions and it is a very practical way for customers to test The Belt Conveyor’s capabilities using materials they handle on a daily basis.
The facility is also used for continuing research and testing products in various applications with different materials.
By its wording, this category of software informs, in a very explicit way, the function it performs in its field of application, for any type of machine or equipment, writes conveyor expert Marc des Rieux, from C3 Expert SAS. Here, it is dealing with an industrial production tool.
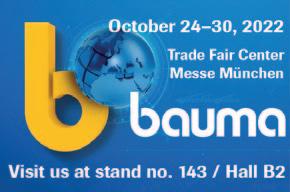
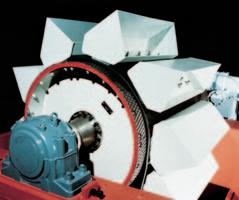
We can summarize the purpose of the application of these ‘predictive maintenance’ software systems by saying that, from the moment a machine or piece of equipment (or a series of machines contributing to the same operation) has at least one part in motion in relation to a fixed part, there will inevitably be wear and tear. This is because, by definition, the two are linked by some means.
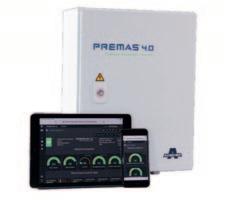
In fact, predictive maintenance is economically justified, since it predicts the best time for preventative maintenance, before the machine breaks down. This implies an ‘on time’ supply of the spare parts and a ‘planning’ of the maintenance at the best time, in accordance with the production, so that this maintenance operation does not negatively impact the production process. Logically, this ‘predictive’ approach is more economical than systematic preventative maintenance; this is all the more true when industrial equipment is complex and requires a large number of different skills.
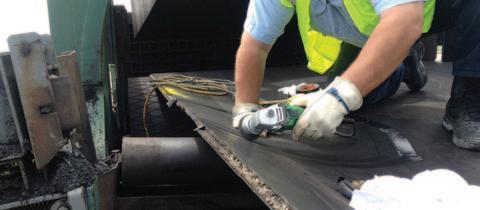

In principle, the idea is marvellous, because it is the assurance, the guarantee, of a better world, without untimely breakdowns and with a known maintenance budget, which is easy to integrate into the cost price of production, with little uncertainty.
Nevertheless, it is necessary to look in detail at the ‘who, how, what’.
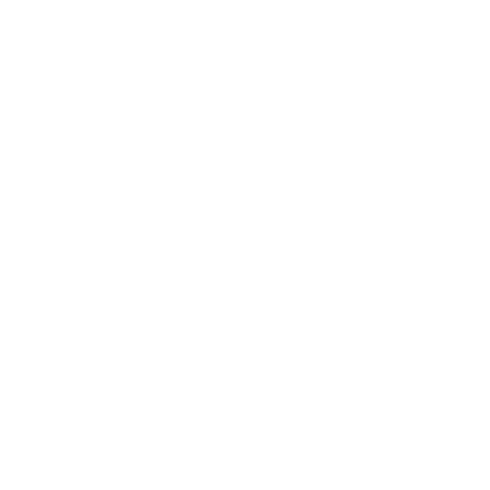
For example, considering a simple machine with only two parts, one of which is in motion relative to the other, the first question to ask is whether this ‘moving’ assembly has benefited from the best design and whether the interface between the two parts benefits from the best technology to reduce wear on one or both parts. The design of this assembly, depending on the context, can be very rustic to very sophisticated. In a very simple example, it should be defined as a full, multiple, one-way rotation, which has nothing to do with an alternative partial rotation. The designer must take into account the mass in motion, the torque generated, the speed of rotation, the shape and material of each part, and the characteristics of the environment applied to the machine. With his knowledge of the rules of the art, his calculations, his standards, his habits and customs and his budget, he will be able to define the design of the interface between these two parts, one of which is in motion. This interface is without lubricant or with a lubricant and which one; it includes or not a ring, a bearing, one or several bearings, it is a magnetic or air bearing, etc.
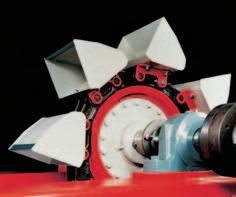
High
The synthesis of the previous paragraph is: “Shouldn’t we make sure that the machine complies with the rules of the art, prior to managing the maintenance with predictive maintenance software?” The corollary to this suspicion of an ill-ordered strategy is to know if the publisher of the predictive maintenance software is, on the one hand, ‘judge and jury’ and, on the other hand, how and on what basis the maintenance predictions have been built and calculated. This is the second real question.
Some examples to support the reflection:
In the 1990s, I gave a training on thev components adjustment of conveyor in an underground mine. After six months, when the performance of the training was evaluated, a net saving of €30,000 (after deducting the expenses incurred) was found on one production line.
o Based on this encouraging start, the mine asked me to provide theoretical training. On this occasion, a maintenance engineer presented me with his ‘predictive’ maintenance table on conveyor rollers. The analysis of the various causes of wear and destruction showed that the predictions were wrong, if the causes of the damage were solved, which was done. Since then, the service life of the rollers has been increased by a factor of five to ten.
A maintenance engineer had forgottenv to budget for the replacement of 3km of 27-year-old belt, which put him in a difficult position. My intervention removed all the causes of the damage inflicted on the belt, for a budget of ≈€50,000, by correcting design and adjustment errors. When the belt reached its 33 years, six years later, the maintenance replaced only 1.2km of the total 3km length.
A large belt with sidewalls andv buckets, installed on a large two-bend lift conveyor, after four years of service, showed significant damage to its edges. At the same time as repairing the edges, we eliminated the design errors most damaging to the belt and adjusted the components of conveyor. The customer changed his belt 14 years later... to be on the safe side.
On a 25km-long belt, the operatorv regularly changes sections, following scanner inspections of the steel carcass. The total number of section replacements is equivalent to replacing
the entire belt every 13 years for the past 40 years, when a state-of-the-art conveyor would allow a belt life of at least 50 years... This would not be good news for the belt manufacturer and the ‘scanner’ service provider.
o However, more than ten years ago, I informed maintenance of the causes of the damage. As for the ‘scanner’ service provider, he only indicates the weakened belt sections and nobody tries to find out ‘why’... for 40 years!
o A predictive maintenance software, backed up by an A.I. (artificial intelligence), would indicate the number of sections to be replaced according to their age and duration of operation on the conveyor, with no better performance than the scanner solution, probably at a lower cost.
Following two training courses, led byv myself, on conveyor technology and their adjustments, a simple technician, rich in common sense and method, undertook, against all odds, to eliminate, step by step, the main and secondary causes of damage to the belts. In eight years, the annual belt consumption has been reduced from more than 15,000m to less than 5,000m. In addition, there are many savings on pulleys, rollers and energy consumption, etc. Well done to the ‘maintenance professional’.
I have many examples, each more relevant than the last, to demonstrate that, in addition to the convenience of budgetary and operational planning by predictive maintenance software, it is imperative that the software be able to recalculate its predictions on the basis of updated data... to realize, in the end, that a simple spreadsheet is enough to establish a safe, effective and very economical maintenance plan, at least for belt conveyors. Which is to say: “don’t put the cart before the horse.”
If it seems logical that the designer and manufacturer of the equipment is also the publisher of the predictive maintenance
software, since he can feed the databases of his software with his resources, the said logic is not so obvious if the conditions of the ‘good application of the software’ impose on the operator of the equipment to get spare parts from the manufacturer and owner of the software. Going further, one can also imagine that the manufacturer makes no effort to question his machine designs to bring them up to the best level of the state of the art, since his interests are linked to the sale of spare parts. This flaw is all the more true when the manufacturer benefits from the strong reputation; it will be difficult for him to contradict himself by acknowledging his design errors (ask for my anonymous examples).
To avoid this pitfall at least, it is necessary to ensure that the operator of the equipment is not ‘bound hand and foot’ to the manufacturer who produces the software, by requiring him to provide a list of spare parts available from third parties approved by him.
CONCLUSION
Yes, there is a real industrial and economic interest in the use of predictive maintenance software for complex equipment, which, in my opinion, does not include belt conveyors, taken in a ‘maintenance’ approach. With the same budget, would it not be more relevant, logical and economical in the long term to require conveyors that comply with standards and rules of the art, with an optimized design and whose ‘maintenance’ management would be done on a simple spreadsheet. In addition, it would be appropriate for the belt of strategic conveyors to be monitored by video, coupled with an image recognition system associated with an automatic comparison with its database of typical defect images, because a break suddenly does not occur.
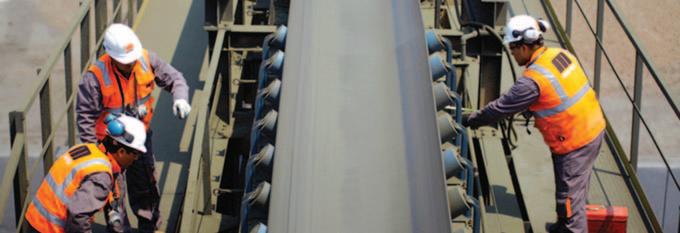
Remember, the longevity of a large belt is more than 30 years and in that time the initial predictive maintenance software will have changed many times.
In conclusion of the conclusion: the engineers and technicians of conveyor field take back control of their machines.
Dry argument: the ScrapeTec dust protection system
The AirScrape belt skirting — innovative, highly efficient and maintenance-free.
DUST PROTECTION AT CONVEYOR TRANSFER POINTS
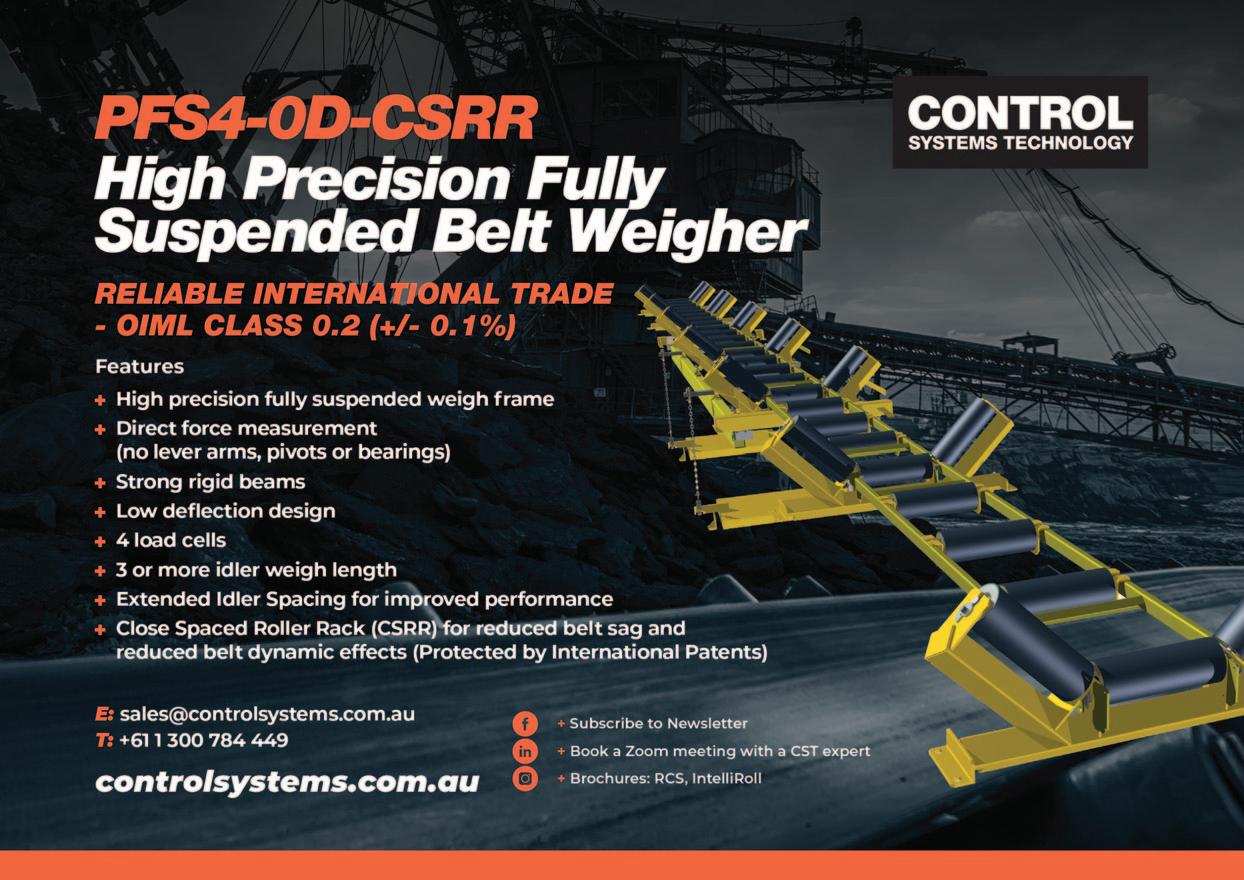
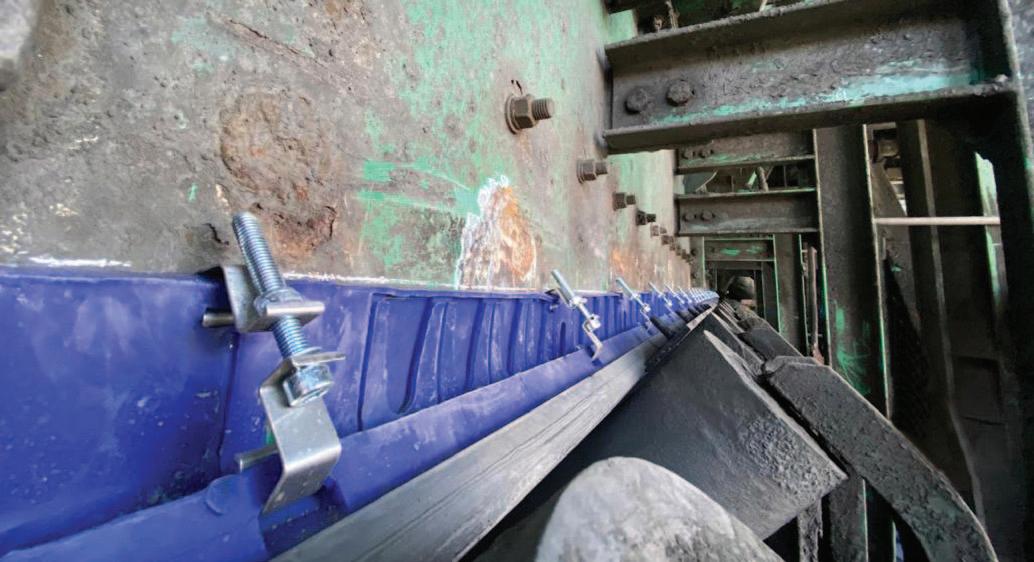
Unavoidable. This is the argument of many operators of conveyor systems for dry bulk materials when it comes to the immense dust problems. At ScrapeTec Trading
GmbH from Kamp-Lintfort in Germany, things are different. With a system of products around the transfer points, you can achieve results that offer almost 100% no dust. With effective and sustainable added value.
The founding of ScrapeTec was based on the idea of improving the stressful circumstances at transfer points for people, material and the environment. Owner and company founder Wilfried Duennwald had already improved the working conditions
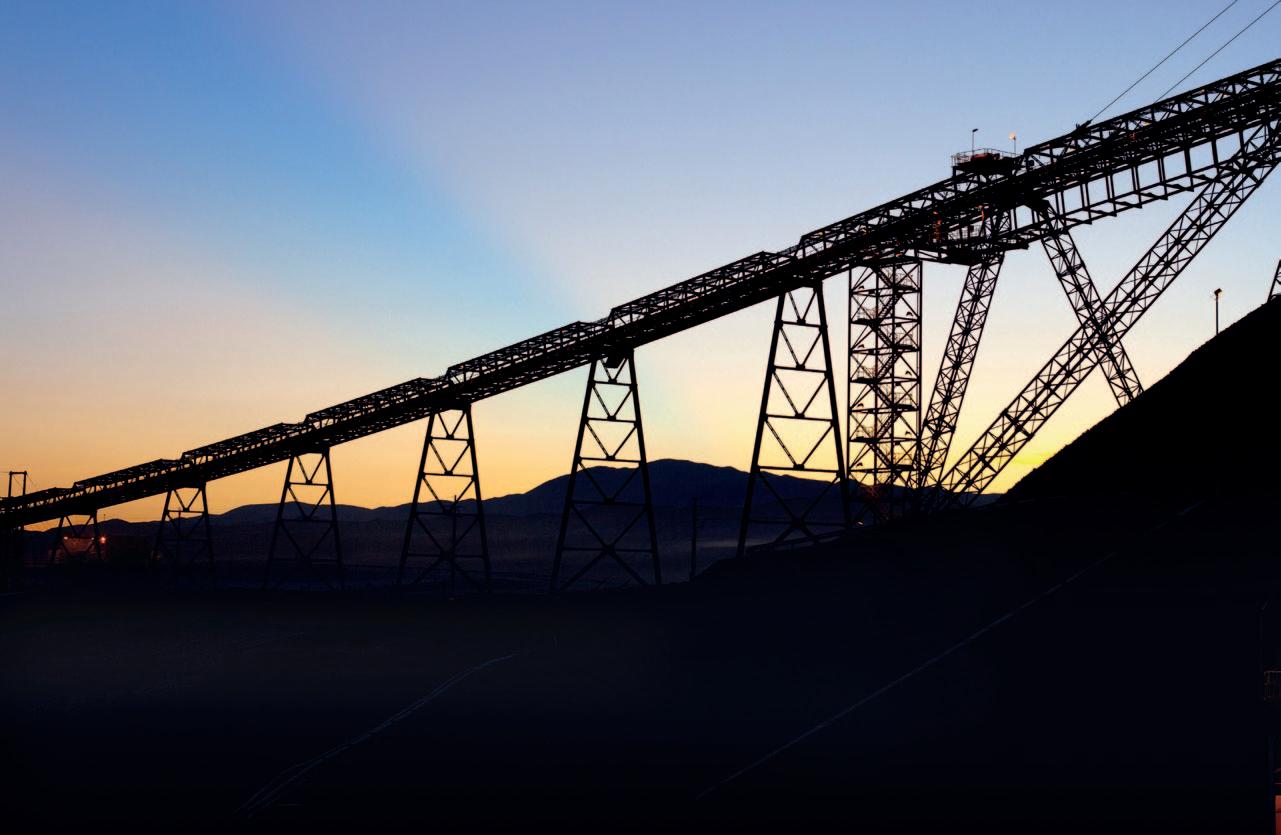
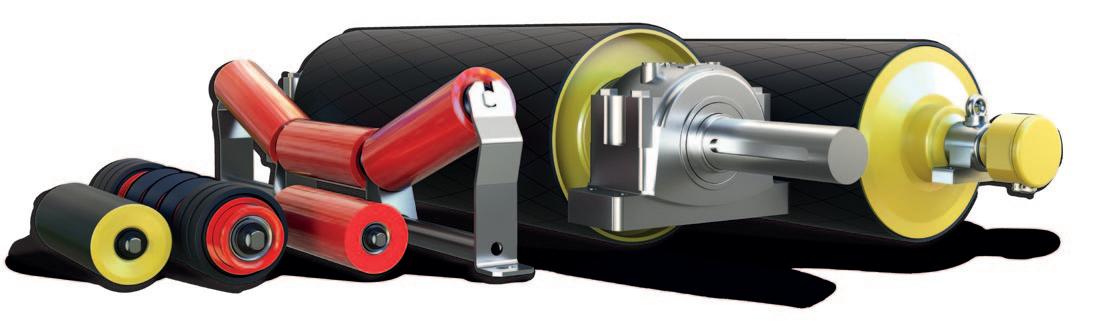
The ScrapeTec dust protection system achieve results that offer 100% no dust and spillage.
underground through targeted develop ments when he was a mining engineer. With his company, he now offers a portfolio of products that are perfectly tailored to use at the transfer point and the surrounding belt area and continue this idea.
SCRAPETEC DUST PROTECTION SYSTEM
The product that is now one of the best known worldwide is the AirScrape — an innovative conveyor belt skirting that, unlike conventional solutions, works without contact to the conveyor belt. The specially arranged blades of the seal suck in air from the outside thanks to the negative pressure effect caused by the belt speed. As a result, no dust can penetrate to the outside in the sealing area. They also keep the bulk material in the middle of the belt, which prevents the usual material losses. In the rear area of the chute, the TailScrape from ScrapeTec works according to the same principle — contact-free and with a suction effect. It can be perfectly adapted to the trough of the belt. Dust that can escape upwards with the air flow of the conveyed bulk material in the front area of the transfer is filtered out by the DustScrape in conjunction with the suction effect of the AirScrape and thus eliminated. The special, hard-wearing filter cloth has been specially developed for the extraction of dust particles and is available in different versions — including anti-static. “And how do you ensure that the non-contact seal
works if the conveyor belt gets off track?”
This question is justified and is often asked at trade fairs. The answer also comes from the ScrapeTec product portfolio. Better: the answers. On the one hand, the PrimeTracker conveyor belt tracking assistant ensures that the belt is automatically corrected when the belt starts to misalign. The cylindrical roller is mounted in the lower run of the belt conveyor, is mounted on an axle and independently corrects changes in track when the belt is running. That is answer 1. Answer 2: On the other hand, ScrapeTec offers another solution to ensure the distance to the belt and thus the effectiveness of the AirScrape. Behind the term SureSupport are slide rails that prevent belt deformation in the feed area — so to speak, as a compaction of the distance between the rollers. Anyone who has read this far has surely recognized the systematic use of these products around transfer points. That is why ScrapeTec is also referred to as a dust protection system.

SYSTEMATIC ADDED VALUE
The interaction of all products ensures results such as 98% dust reduction and 0% material losses in the feed area. Ergo: cleaning costs are also reduced. The maintenance effort is reduced and costintensive investments for new belts are also reduced due to the lower material wear. Not to forget the improvement in working
conditions for the people who work on the systems. International customers use ScrapeTec solutions specifically for dust protection in order to improve employee health and satisfaction — with great success. ScrapeTec is aggressively entering the market with its dust protection system solution and sustainable, effective arguments, and is encountering increasing interest. For example, at this year’s trade fair appearances in Germany, Sweden or Chile, the number of visitors was high and the interest enormous.
As a result, inquiries and orders increased sharply. Based on the experiences of the discussions and individual customer requirements relating to dust reduction, ScrapeTec soon wants to create a white paper that will help those responsible for conveyor systems with their internal arguments in order to promote solutions.
IN DEMAND INTERNATIONALLY
Meanwhile, ScrapeTec sells its products alone or in co operation with many partners in the target countries in Europe, Chile, Peru, Brazil, Australia and most recently also in Israel. From there, a spontaneous order came from the local technology service provider S.F.I., which ordered several PrimeTrackers for its customer ICL Group and used them directly. Other notable customer names include Codelco, Cosentino, Currenta, LaFarge, Holcim, K+S, Knauff or RAG.
FLEXCO Europe to present ‘Conveyor belt technology 4.0’ at bauma
The bauma trade fair for construction vehicles and construction & mining machinery will take place in Munich from October 24 to 30. In its booth, FLEXCO Europe will show how conveyor belt problems such as carryback, spillage and belt mistracking can be remedied, and how preventative maintenance can reduce and even completely avoid belt downtimes in the future — and data plays a decisive role here. FLEXCO Europe has now developed the Elevate online platform — an intelligent Industry 4.0 solution that enables operators to continuously monitor their conveyor belt systems.
If conveyor belts fail unexpectedly in mines or cement plants, a downtime can prove expensive for the operators. Thanks to its holistic monitoring system, FLEXCO’s Elevate is the ideal solution to reduce and even avoid these downtimes.
The Elevate devices attached to the conveyor belt cleaners collect data that can be retrieved in real time via app or dashboard, regardless of location. Installation, commissioning, and monitoring procedures are fast and easy to handle.
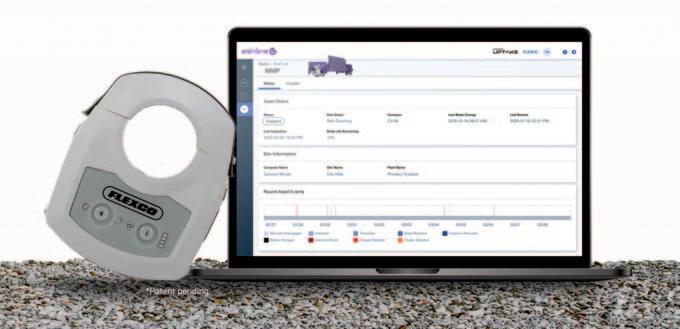
Thanks to all this data, operators can make well-founded decisions in good time and determine any measures that may be necessary. For example, in the event of a malfunction signal that involves a preventive belt inspection on site, operators can remedy such problems early and not simply react when a serious failure has already occurred.
The Elevate system can also be used to optimize maintenance tasks, so they can be planned in a more targeted manner and carried out more efficiently.
The trade fair highlight ‘FLEXCO Elevate’ will be showcased together with fresh insights into the large FLEXCO product family, which has again grown this year. There are two new conveyor belt maintenance tools, a new powered belt skiver and a combination device of belt
The Elevate devices connect to the cloud via Wi-Fi or cellular at the touch of a button, eliminating the need for cables.
The new powered belt skiver makes conveyor belt repairs easier and safer than ever before.
cutter and skiver. A new fastener system that makes conveyor belt repairs easier and safer than ever before will also impress visitors.
Conventional belt cutters and skivers are not very user-friendly in manual operation, but the FLEXCO innovations offer fast, simple and, above all, safe handling. Both new products benefit from rechargeable battery power, which also enables significantly faster processing.
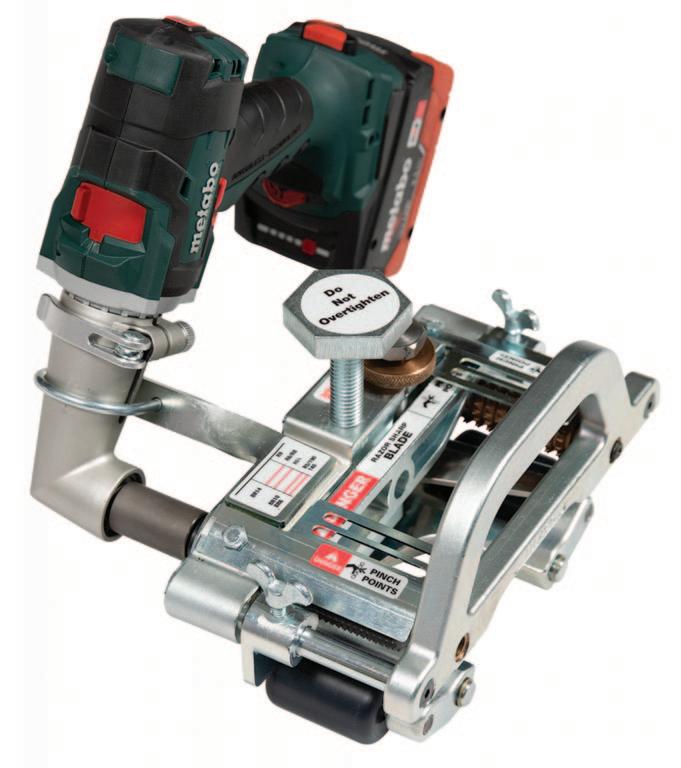
When it comes to mechanical fasteners for conveyor belts, FLEXCO is the acknowledged specialist, and the company will also showcase its innovative solution
for steel cable conveyor belts. These belts are often used in systems where long distances or steep gradients necessitate high levels of safety. With its innovative fastener concept for steel cable conveyor belts, FLEXCO now offers a solution that allows fastener to be made in only half the time compared to existing mechanical fastener systems on the market and up to one-third of the time compared to vulcanization procedures.
ABOUT FLEXCO
Flexible Steel Lacing Company (FLEXCO), headquartered in Downers Grove, Illinois in the USA, is a major international specialist for mechanical conveyor belt fastener systems, belt cleaners, belt positioners, impact beds, pulley lagging, segmented transfer plates and accessories for light- and heavy-duty applications. With the company’s innovative solutions, endusers can substantially reduce downtime and increase productivity.
FLEXCO Europe GmbH is the German subsidiary of FLEXCO, and is headquartered in Rosenfeld, where the company currently has about 90 employees.

































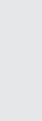

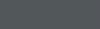


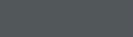
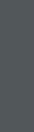

Henry
“A man who stops advertising to save money is like a man who stops a clock to save time”
Continental further strengthens industrial business with acquisition of the Vulk & Montage Group in Sweden
Continental has acquired the conveyor and maintenance company Vulk & Montage, based in Karlstad, Sweden. This acquisition complements the portfolio of Continental and establishes the technology company in the heart of Sweden’s industrial area. “With the Vulk & Montage Group, we are able to offer an entire service & solution package in addition to the current Continental product portfolio to our industrial customers in Central Sweden. The acquisition underscores again our goal of further expanding our service business directly with our customers and aligning our focus accordingly,” explained Song Qi, who is responsible for the global business with conveyor belt system
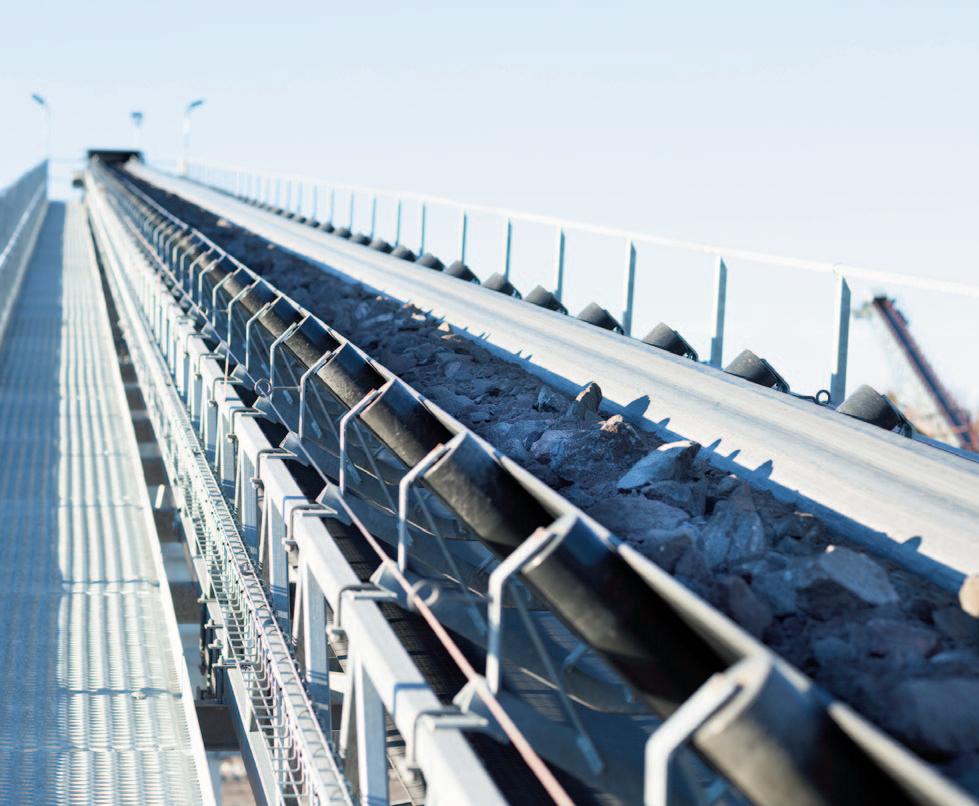
solutions at Continental. Completion of the acquisition is subject to approval by the competent antitrust authorities. The two parties have agreed not to disclose the purchase price.
Vulk & Montage has four locations in Karlstad (Headquarters), Örebro, Mora and Stockholm, Sweden. The company is a highly respected service provider for the conveyor industry in central Sweden, operating out of its four branches and one rubber workshop. Vulk & Montage provides add-on products such as belts, belt scrapers, industrial hoses, screens, wear rubber, lightweight conveyor belts, technical plastics and additional services like lining (cold and hot), spraying polyurethane,
sandblasting, and paintwork.
Continental’s Conveying Solutions is one of the world’s foremost specialists in conveying and off-highway solutions, with customers in key industries such as mining, agriculture, automotive and plant engineering. Beyond its comprehensive product portfolio, Conveying Solutions’ goal is to respond to specific customer needs and to provide holistic and efficient solutions for every conveying task in the most environmentally friendly way possible — from plant design, production and installation to preventive maintenance and repair. Conveying Solutions has more than 5,800 employees at 54 locations in 16 countries.
At Jehander’s quarry, Continental conveyor belts are being used for the smooth transportation of rubble from the Stockholm mega-tunnel so that it can be reused for the road construction requirements involved in the infrastructure project.
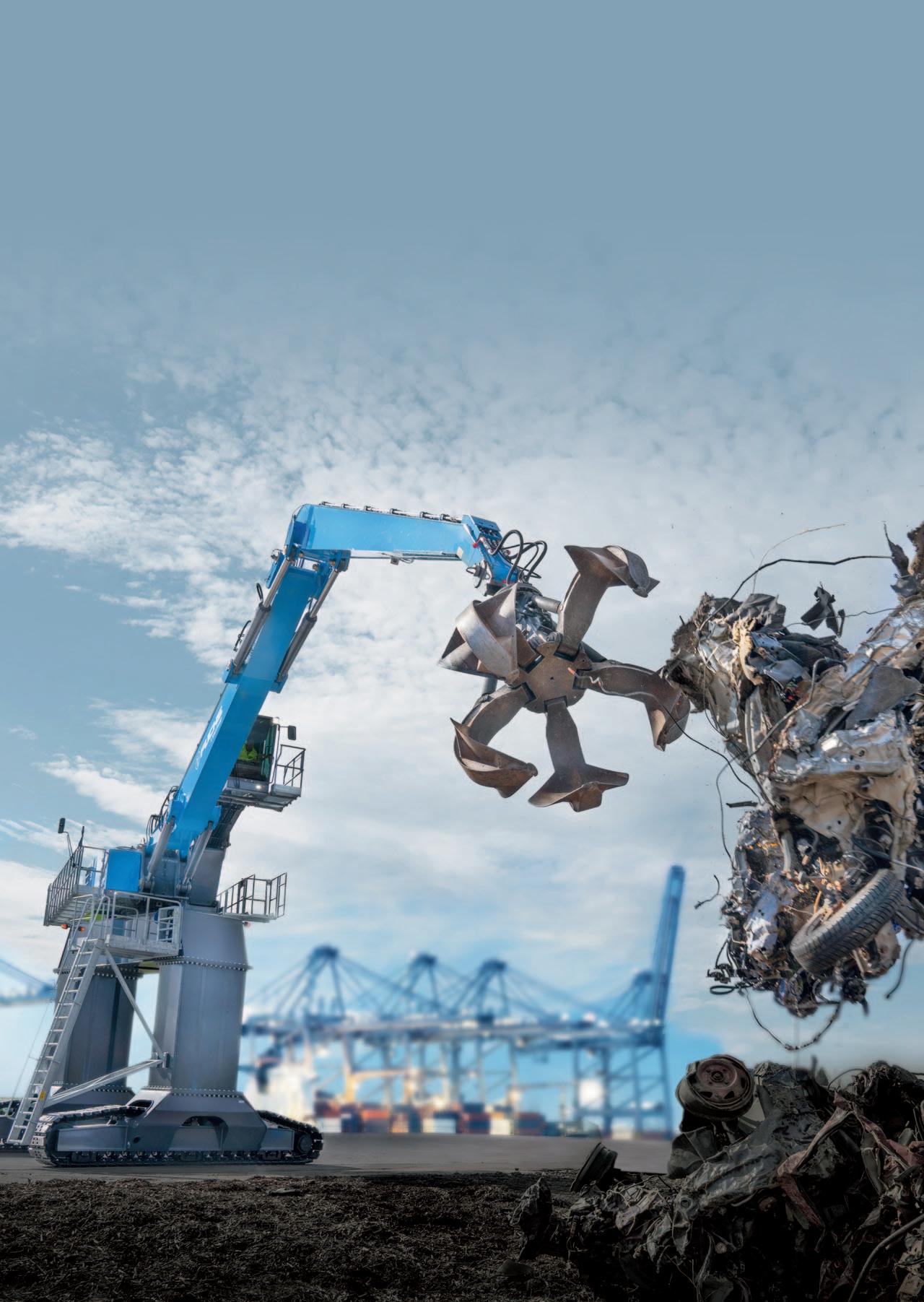
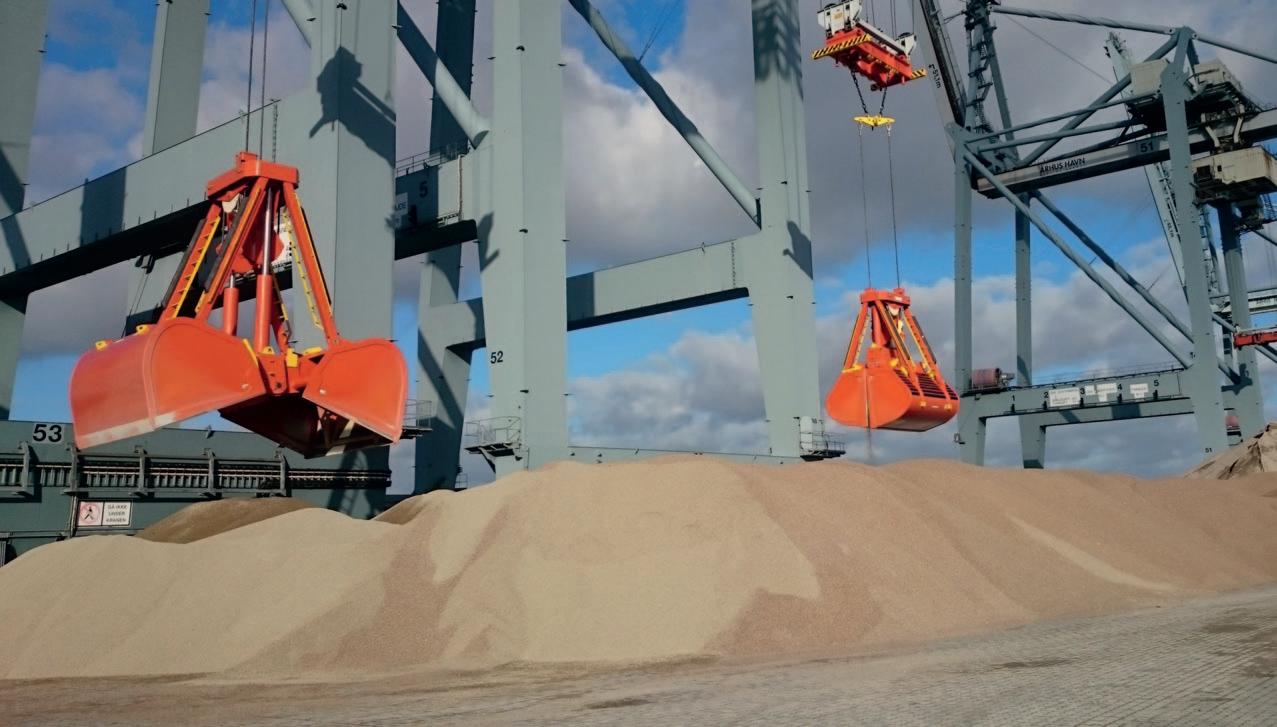
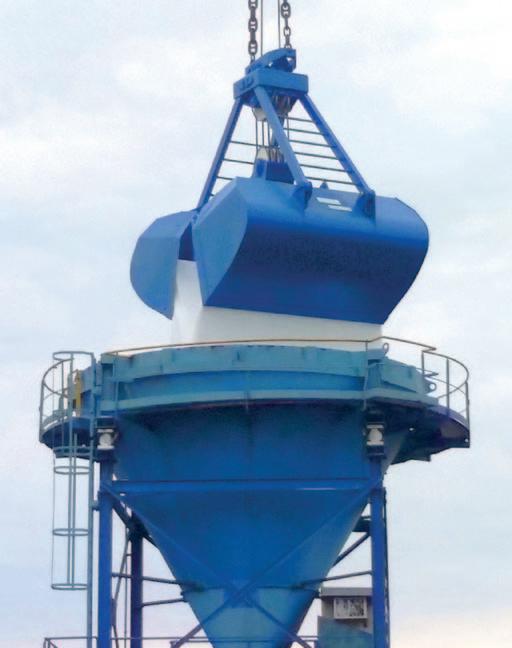
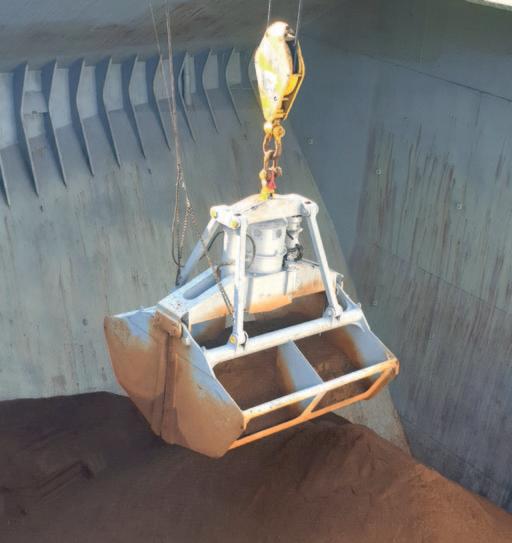
Going with the grain
Cimbria is increasing its massive presence in Egypt with a recent order of a huge silo complex at Port Said, the Egyptian city at the entry point of the Suez Canal. The silo
complex consists of eight silo bins with a capacity of 12,500 tonnes each and will be used for the secure storage of wheat.
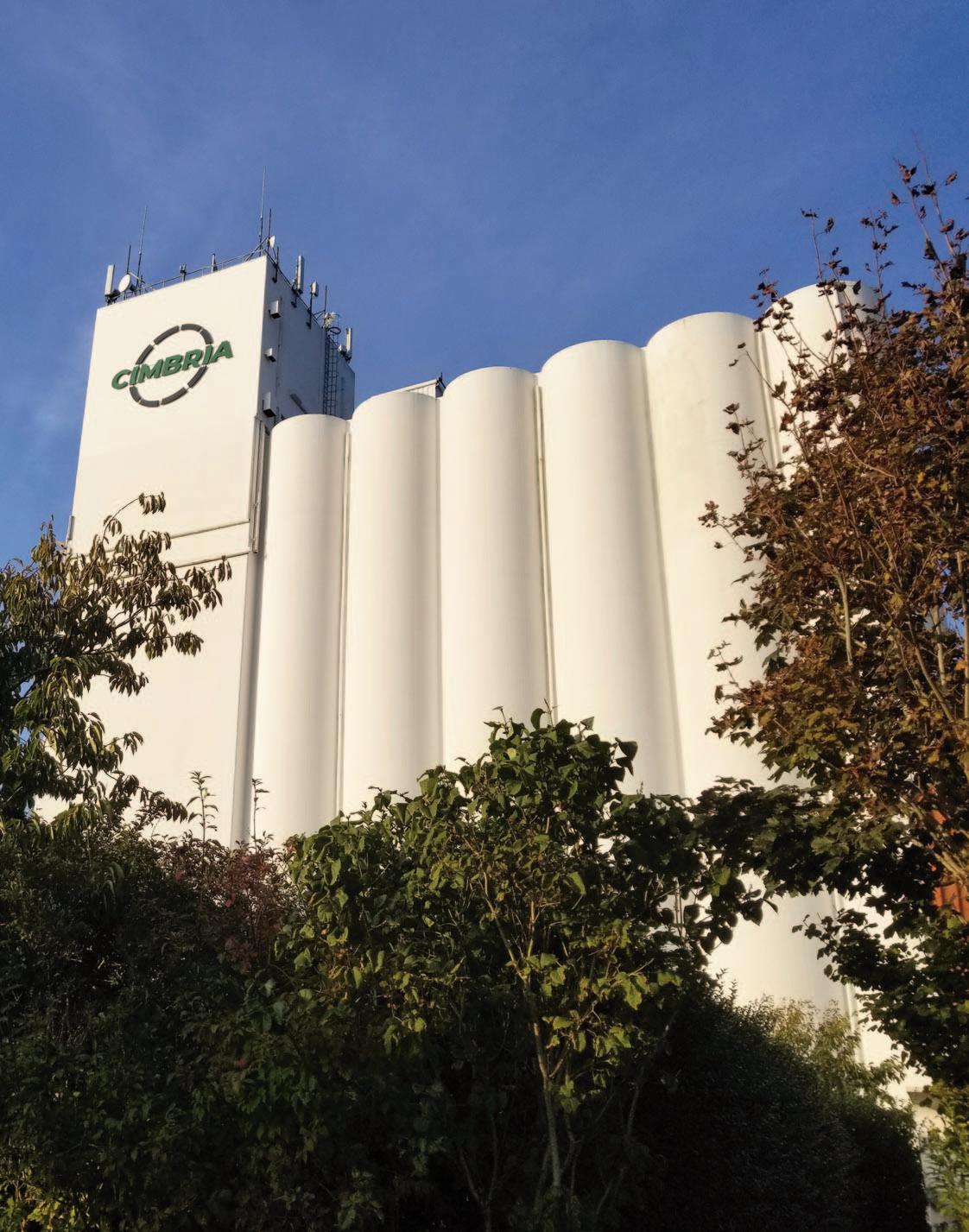
The city of Port Said in Egypt is now
Louise Dodds-Ely
getting its first silo complex for secure storage of imported wheat. Cimbria has been present in Egypt for more than 30 years and knows the Egyptian market very
Supporting secure food storage: Cimbria builds its first port silo complex in Egypt
storing and handling made easier with the right equipment
well. In fact, 95% of all silo complexes in Egypt — with a total storage capacity of 2.5mt (million tonnes) — has been delivered by Cimbria. However, the silo complex at Port Said is the first Egyptian port silo complex from Cimbria. With the population increasing by 2.5% every year, there is a great need for safe storage complexes in the country:
“The 100,000-tonne silo complex for Port Said will be an important contributor to secure food storage in Egypt. Therefore, we are very proud to support the Egyptian government’s efforts in securing safe and sufficient food for the growing population of Egypt with this order,” explains Sami Salah El Din, Regional Director of Cimbria in Egypt.
Every year, the Government of Egypt imports around 9mt million tonnes of wheat from countries like Russia, Ukraine, France, America, and Australia. A significant share of the imported wheat is used to produce 300 million pieces of the traditional Egyptian flatbread balady daily. Balady is an important part of the everyday diet for the population of 100 million people in Egypt. Additionally the private sectors are importing around three million tonnes of wheat for white flour.
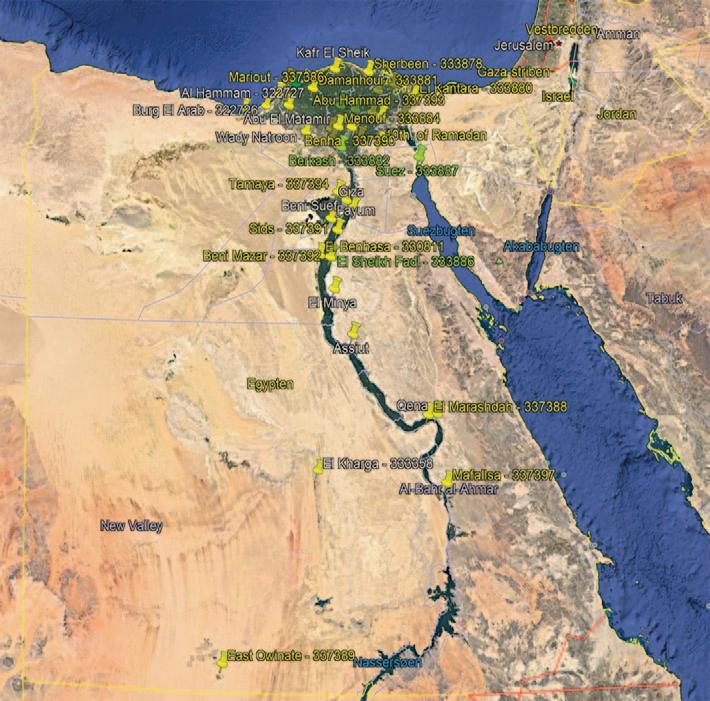
Port Said’s new silo complex includes
grain bins, conveyor systems, fully electronic control system, and loading equipment for railways and trucks. It is designed with state-of-the-art technology and the operation of the complex will require onsite training for the operators.
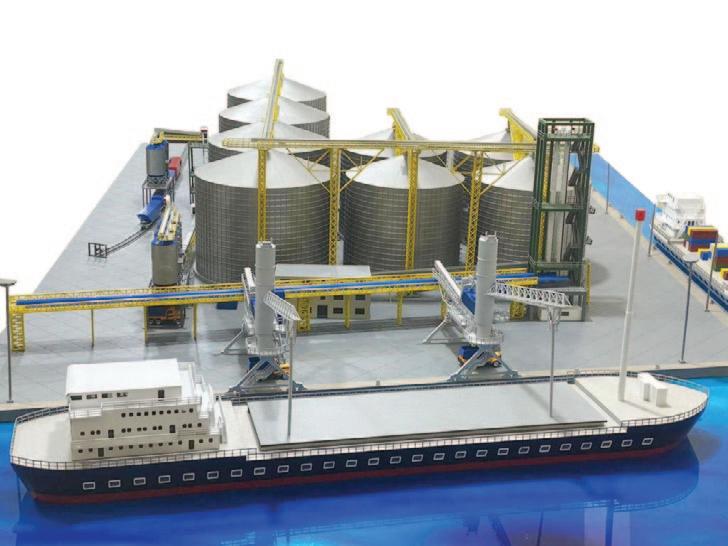
“The complex is a strategically important part of the Egyptian government’s aim of building safe stockpiles of grain and wheat reserves as a withstand to fluctuations in market prices due to
future market developments,” says Sami Salah El Din.
The construction of the new silo complex in Port Said is done with local labour and will be managed with onsite supervision from Cimbria. The work started in February this year and is expected to be finished within two years. The funding of the complex is cofounded by the GOE & OPEC Fund for The General Company for Silos and Storage (GCSS).
ABOUT A/S CIMBRIA
Cimbria is a world leader in industrial processing, handling, and storage of cereals and seeds, as well as animal feed, food, and other bulk products. Cimbria works closely with its customers to design, manufacture, install, and service customized solutions, individual machines, and complete turnkey systems. Cimbria is a global brand owned by AGCO Group.
ABOUT AGCO
AGCO is a global expert in the design, manufacture and distribution of agricultural machinery and precision ag technology. AGCO delivers customer value through its differentiated brand portfolio including core brands like Challenger®, Fendt®, GSI®, Massey Ferguson®, Precision Planting® and Valtra®. Powered by Fuse® smart farming solutions, AGCO’s full line of equipment and services help farmers sustainably feed our world. Founded in 1990 and headquartered in Duluth, Georgia, USA, AGCO had net sales of approximately $11.1 billion in 2021.
NUMBER
Are you looking for a new grab?
Please contact us. At Verstegen we are fully specialised in rope-operated mechanical grabs. Our goal is to provide the optimal grab for your specific operation. A new Verstegen grab leads to higher production rates and lower maintenance costs through extreme reliability and long lifetimes. Tell us how you want to improve your operation and together we will find the best solution.
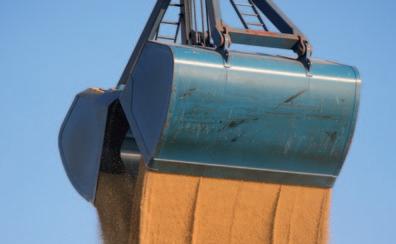
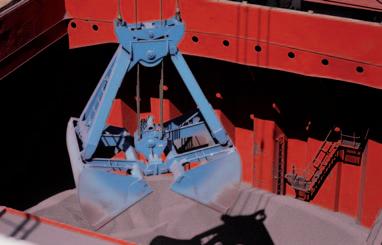


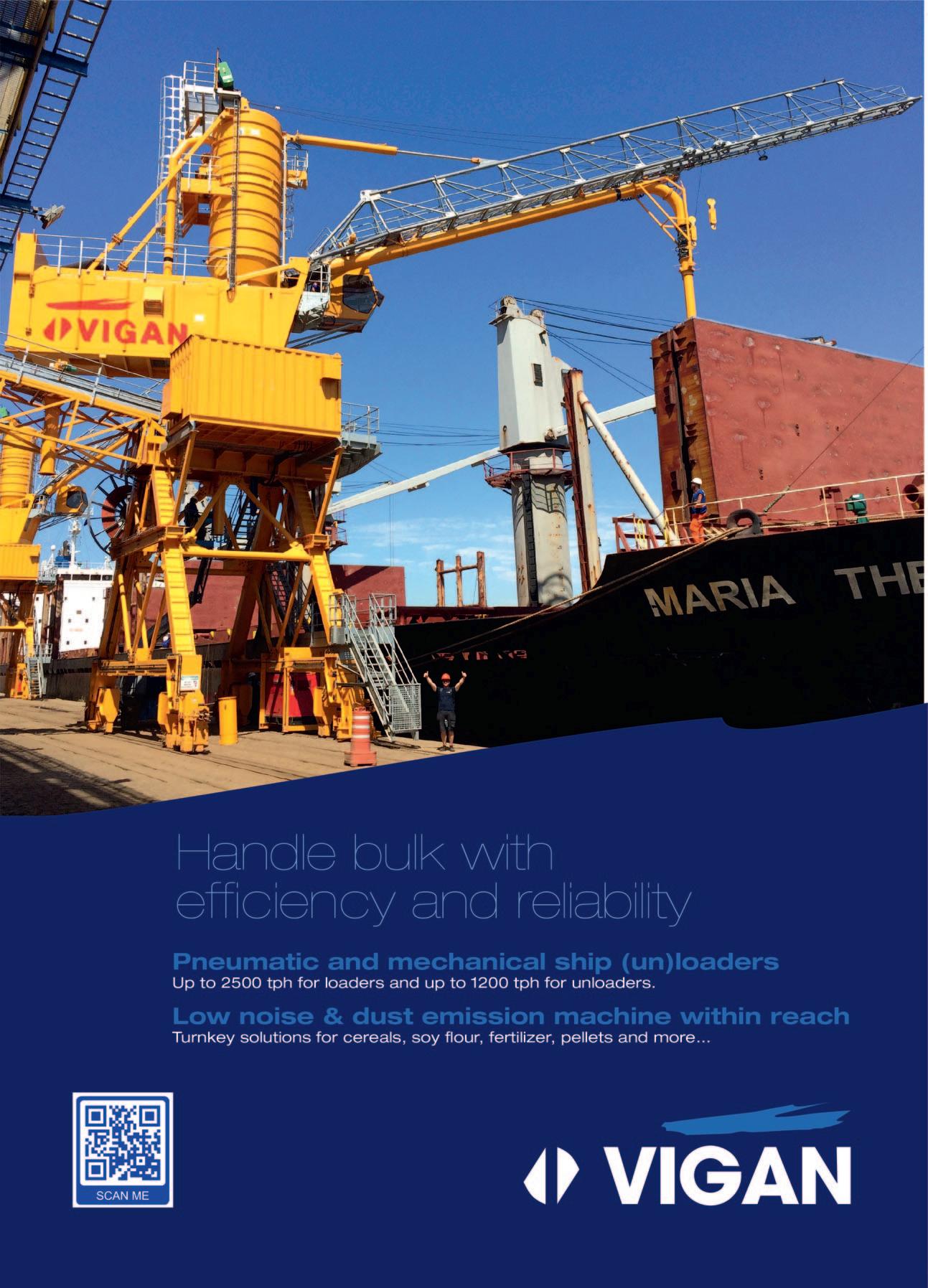
Ten metal silos and new flat store begin operating at the Port of Tilbury’s Grain Terminal
NEW SILOS AND FLAT STORE HAVE COMBINED CAPACITY OF 36,000 TONNES
The Port of Tilbury’s Grain Terminal in the UK has completed major construction works with the commissioning of ten, 30-metre-tall, steel silos and a flat store with a combined storage capacity of 36,000 tonnes.
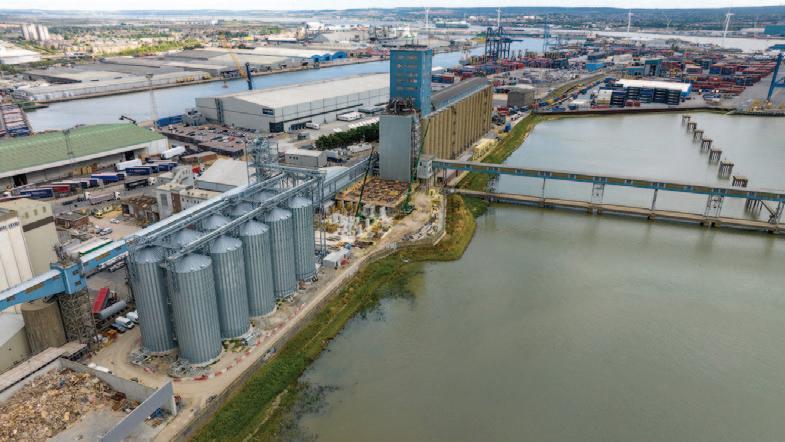
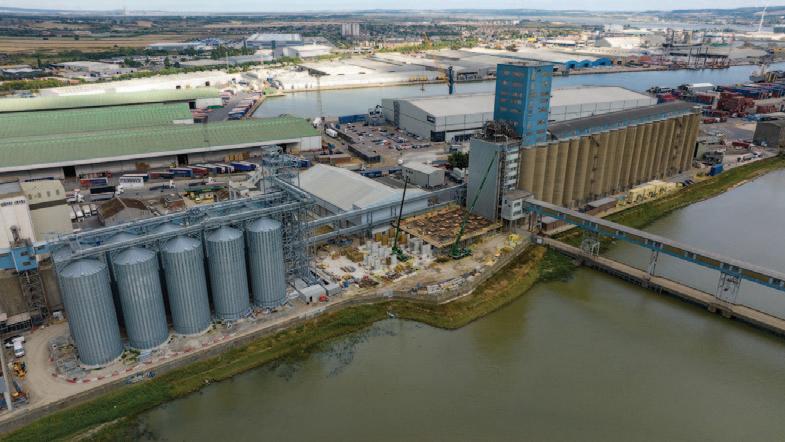
The metal silos will be filled and emptied using a new 650 tonne per hour transfer conveyor system. The conveyor also serves as an automated filling system for the 16,000-tonne flat store which has a direct delivery system to two customer flour mill sites. Once fully operational — scheduled to happen this month (September), the combined silo and flat store facility returns the terminal’s total on site storage to 100,000 tonnes.
Works are also under way to replace the concrete silo and this is due for completion in December 2023. The new concrete silo will add a further 34,000 tonnes of automated storage, underpinning the grain terminal as the UK’s largest import/export grain handling facility.
Peter Ward, Commercial Director at The Port of Tilbury said: “We are extremely pleased to start the commissioning of our new metal silos and high-speed conveyor system. Coupled with the construction of the concrete silo, the Grain Terminal will be back to full capacity on one site this year.
“Our terminal is a key facility in the South-East of England and an essential part
of the UK agricultural supply chain for imports and exports and benefits from the full multimodal services at the Port of Tilbury including river barge transportation into central London.”
The Tilbury Grain terminal has been in operation for over 50 years and is a key strategic facility in the South-East of the UK for the grain import and export markets handling over two million tonnes of product from around the world. Grain is a key commodity in the UK food supply chain for a number of uses, most notably within the flour milling and bakery industries. The terminal also operates a monthly coastal shipping service from Tilbury to its sister port in Kirkcaldy, Scotland for Carr’s Milling.
ABOUT FORTH PORTS/PORT OF TILBURY
Forth Ports Limited owns and operates Tilbury, alongside seven other commercial
Aerial view of the terminal, showing the ten steel silos, conveyor system, flat store and the ground construction works for the concrete silo.
ports on the Firth of Forth and the Firth of Tay: Grangemouth, Dundee, Leith, Rosyth, Methil, Burntisland and Kirkcaldy.
The Port of Tilbury is the number one UK port for forestry products, construction materials, paper, grain, recyclables and warehousing space. The port has a strong market presence in bulk commodities, ro-ro, cars and cruise vessels. The port’s London Container Terminal handles a mix of short and deep-sea services, is the UK’s number four port for containers and has the greatest reefer (refrigerated container) point connectivity in Europe. Tilbury’s strategic location makes it a natural point for distribution, with nearly 20 million people living within 75 miles. Serving the UK’s market, the port offers customers excellent transport links to and from the UK’s capital and across the South East where over 50% of the population live and work. The port is a diverse multi-modal hub, covering around 1,100 acres (850 acres and the London Distribution Park, in addition to the Tilbury2 site) and is well positioned to access the M25 orbital motorway and the rest of the UK’s national motorway network. In addition, there are direct rail connections within the port and dedicated barge facilities.
*The fire at the grain terminal was in July 2020 and damaged the silo tower and some other equipment. No one was injured.
AGI equipment for handling grain and other commodities
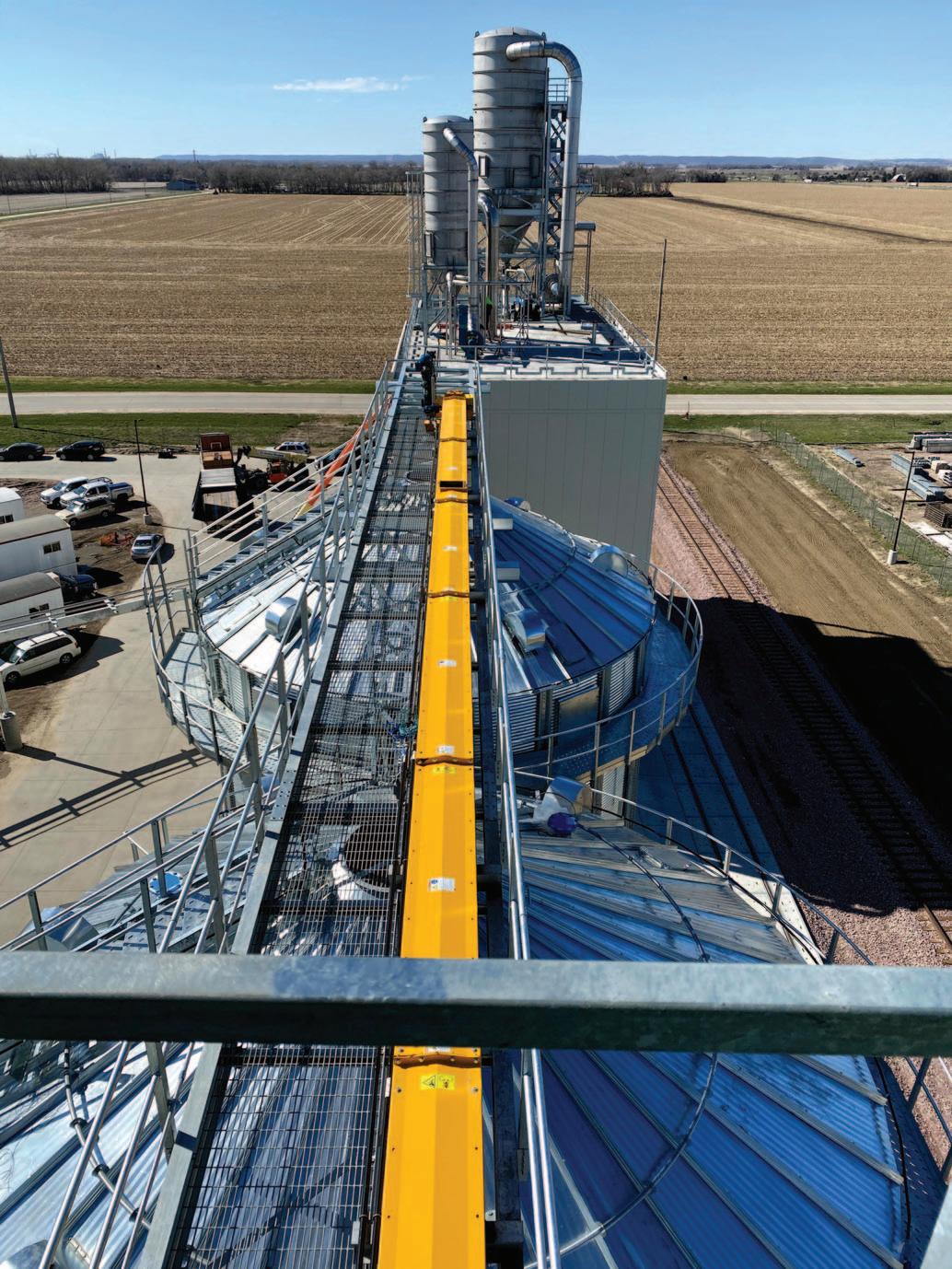
For over 50 years, AGI Tramco has held a reputation for designing and producing reliable, heavy-duty equipment that can withstand severe processing applications.
The complete line of industrial conveyors
are designed to handle a variety of materials at competitive industry prices.
With increasing demands for safe operation, rugged construction standards, and design flexibility, firms continue to look
to AGI Tramco for their bulk-material handling solutions.
Top of the line versatility and durability have gained AGI Tramco widespread acclaim across multiple industries.
AGI Tramco’s

engineered-to-order conveyors are highly customizable and can accommodate unique plant layouts and material handling requirements. Every conveyor is individually designed to meet the customer’s requirements for performance. This level of customization ensures success regardless of the application. From simple grain or bulk material handling operations to more complex oilseed processing facilities, AGI Tramco is guaranteed to have a conveying solution to meet the customer’s unique requirements.
A proven combination of engineering, component selection and manufacturing excellence make AGI Tramco conveyors an ideal choice in bulk handling applications. The Model RB™, Bulk-Flo™ or Model G™ all possess versatility that is unmatched across various applications and industries. After considering material properties, required capacity and specific operating conditions, AGI Tramco experts can recommend the most efficient and costeffective bulk-handling solution. Each conveyor can work as part of a complete material handling solution, or individually as the customer requires.
The AGI Tramco Model RB™ conveyor is specifically designed for the handling of soft stock or materials that are easily
crumbled or broken, such as seed, feed, pellets and other fragile materials. All components are jig welded to ensure their interchangeability and are checked for precise fit by the strict AGI Tramco 100% inspection policy. The Model RB™ is built standard with 10-gauge construction. The U-shaped trough is available in widths of 9”, 12”, 14” and 16”. Its ‘total quality process’ means that customers can rely on years of quiet, trouble-free performance from the AGI Tramco Model RB™ conveyor.
The AGI Tramco Bulk-Flo™ is a heavyduty chain conveyor that can easily handle the most challenging materials such as wet and sticky products, changing material sizes and densities, and abrasive or corrosive materials. Offering a wide variety of possible configurations, the Bulk-Flo™ can tackle inclines up to 90°, support multiple inlets and outlets and curved conveying applications.
The AGI Tramco Bulk-Flo™ can be designed in L-Path, S-Path, Loop or Closed-Circuit configurations. Even when space is limited and product elevation is required, the Bulk-Flo™ chain conveyor is the most reliable and ideal choice for transporting bulk products.
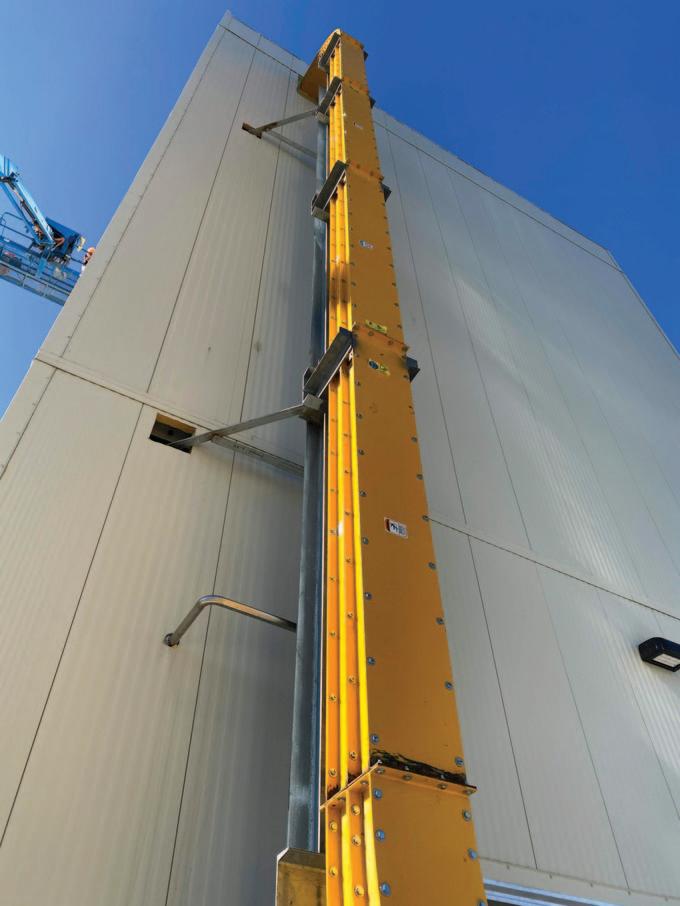
The Model G™ En-Masse Conveyor is designed to handle the most extreme applications ensuring uncomplicated

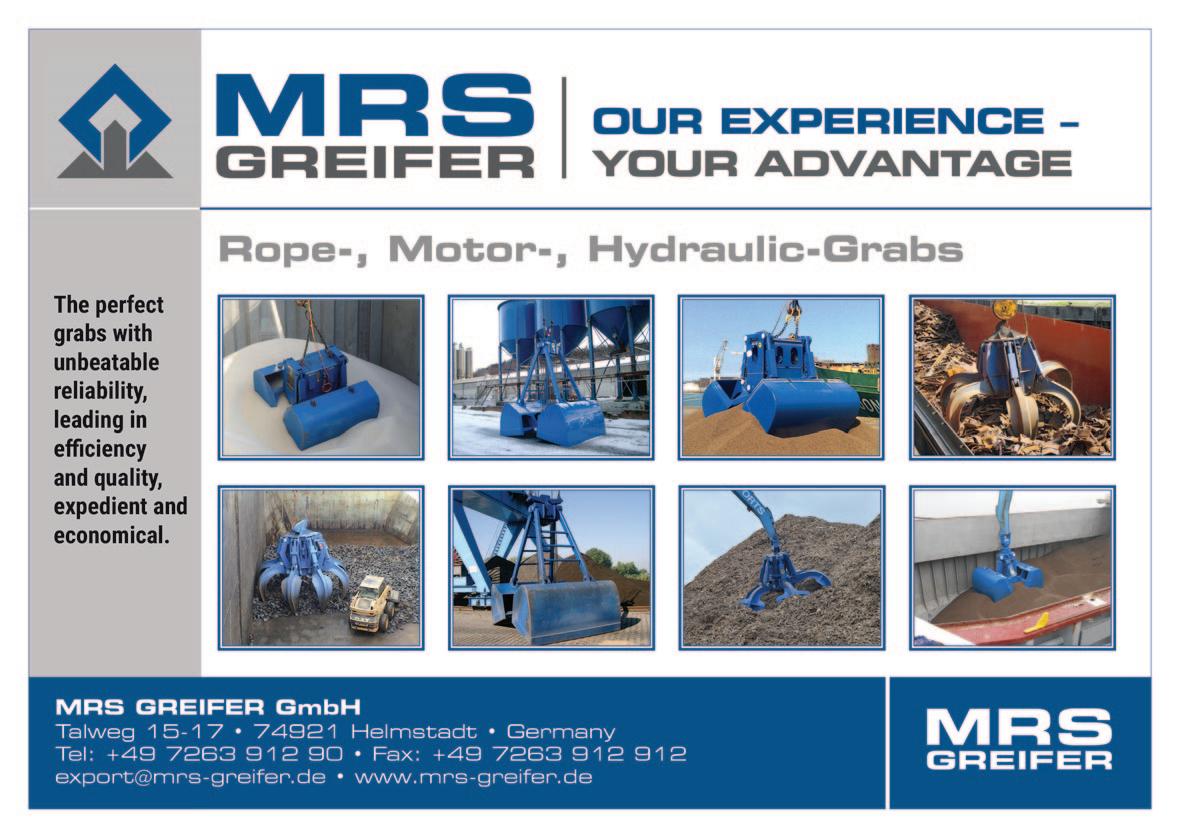
solutions for years. All conveyor sections are pre-assembled on a level 215ft fixture, match-marked and dowel-pinned for field assembly. With proper rigging practices, intermediate sections can be assembled and shipped in multiples of up to 40ft. lengths to save on field time.
AGI recently supplied the material handling equipment for a pea protein
processing plant in the United States. AGI Tramco supplied a Bulk-Flo™ L-Path conveyor with multiple inlets for rail receiving, a long Bulk-Flo L-Path conveyor with a discharge height of eight metres and a short Model G™ conveyor to transfer peas from rail receiving. A Model G™ conveyor with multiple discharges is used to fill several hopper-bottom storage tanks.
A Bulk-Flo™ S-Path conveyor with a discharge height of 16.7 metres is used to reclaim the pea storage hopper tanks and to transfer them to the processing plant. All conveyors were specified as food-grade. The unsurpassed quality and rugged construction of AGI Tramco conveyors series assures years of dependable service even in the most severe conditions.



The great cover-up
protecting commodities with enclosed storage solutions
Jay VenterGeometrica earns Bechtel’s 2022 Supply Chain Excellence Award
Geometrica has announced that it has been selected as a recipient of Bechtel’s 2022 Supply Chain Excellence Award.
Companies are evaluated on multiple factors including overall performance, ability to deliver quality services/supplies on time, ability to work collaboratively to meet milestones, and meeting or exceeding project expectations in aspects of safety, performance, technical expertise, and environmental compliance.
Geometrica recently collaborated with Bechtel on Teck Resources Ltd. Quebrada Blanca II project in Chile. The project team informed Geometrica of their need for a coarse ore storage dome. However, they didn’t need just any dome, they needed a solution that would fulfill strict goals: Safety: Bechtel is relentless in keepingv people safe from harm. Safety was the absolute first priority in the project. The dome had to be built with thev stacking conveyor gallery already in place, and
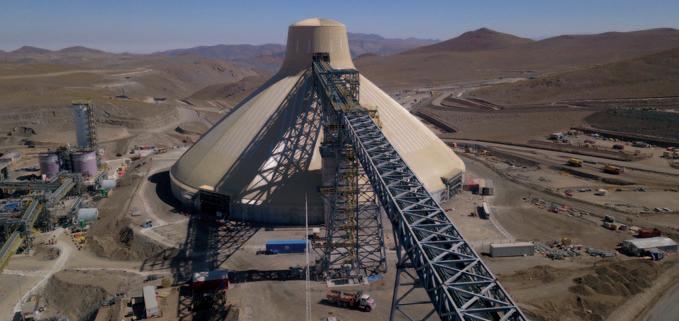
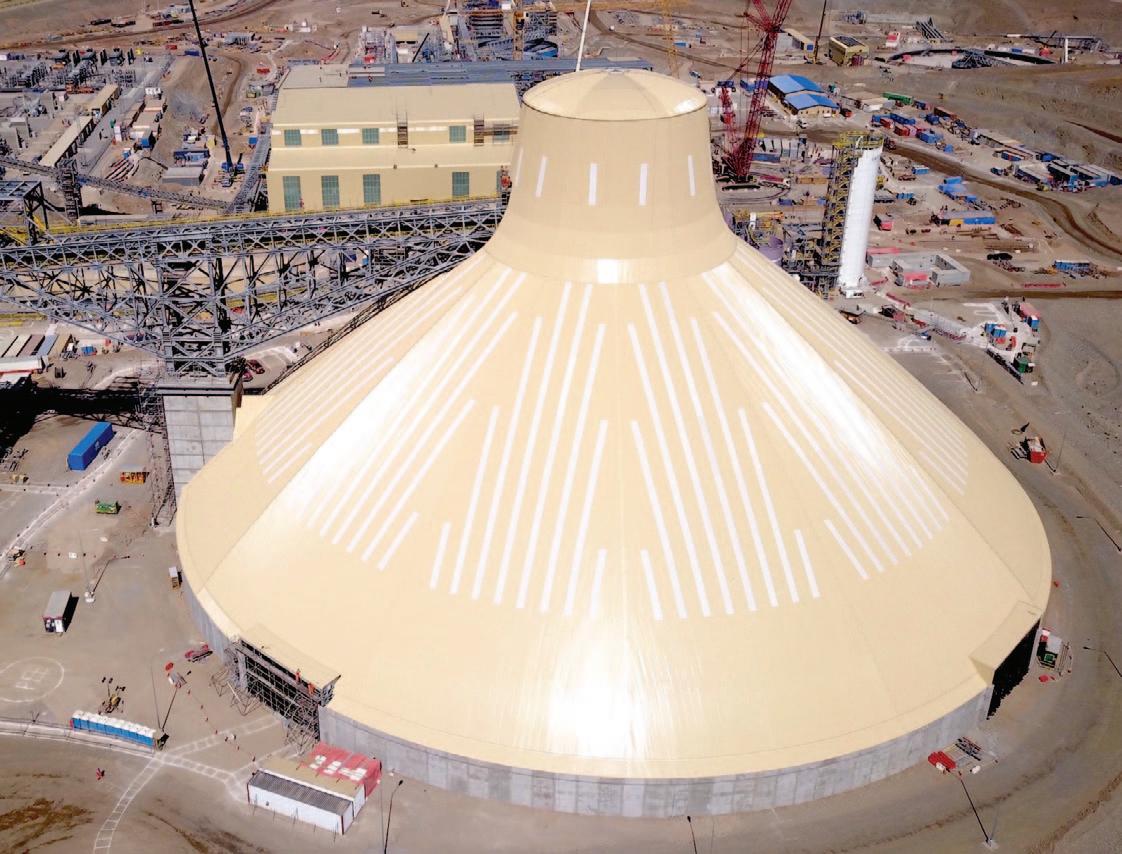
The structure had to enclose thev stacking conveyor’s header structure.
Geometrica met the challenge: a ‘hyperbolic’ dome geometry to be built
using a lifting tower. The geometry provided for coverage of the existing conveyor header, and Geometrica’s hydraulic tower lifted the whole dome as it was being built. Nearly all dome assembly work took place at ground level, eliminating such hazards inherent to assembly at heights. Throughout the project the Bechtel and Geometrica teams worked in close co ordination with the client, with the erection contractor and with each other to deliver a successful installation.
According to Geometrica, it was a great honor for everyone at the company to
have earned Bechtel’s prestigious recognition.
ABOUT GEOMETRICA
Geometrica has designed, manufactured and installed domes and space frames since 1992. The company has developed unique technology to build amazing, long span structures for architectural and industrial buildings. With offices in Houston, Texas and Monterrey, Mexico, and a global network of representatives, Geometrica has delivered domes and space frames in more than 40 countries in North and South America, Europe, Asia and Africa.
successfully delivered
With three 100,000m3 coal silos for the EMBA Hunutlu power plant in Turkey, ESI received its largest order ever in 2019.

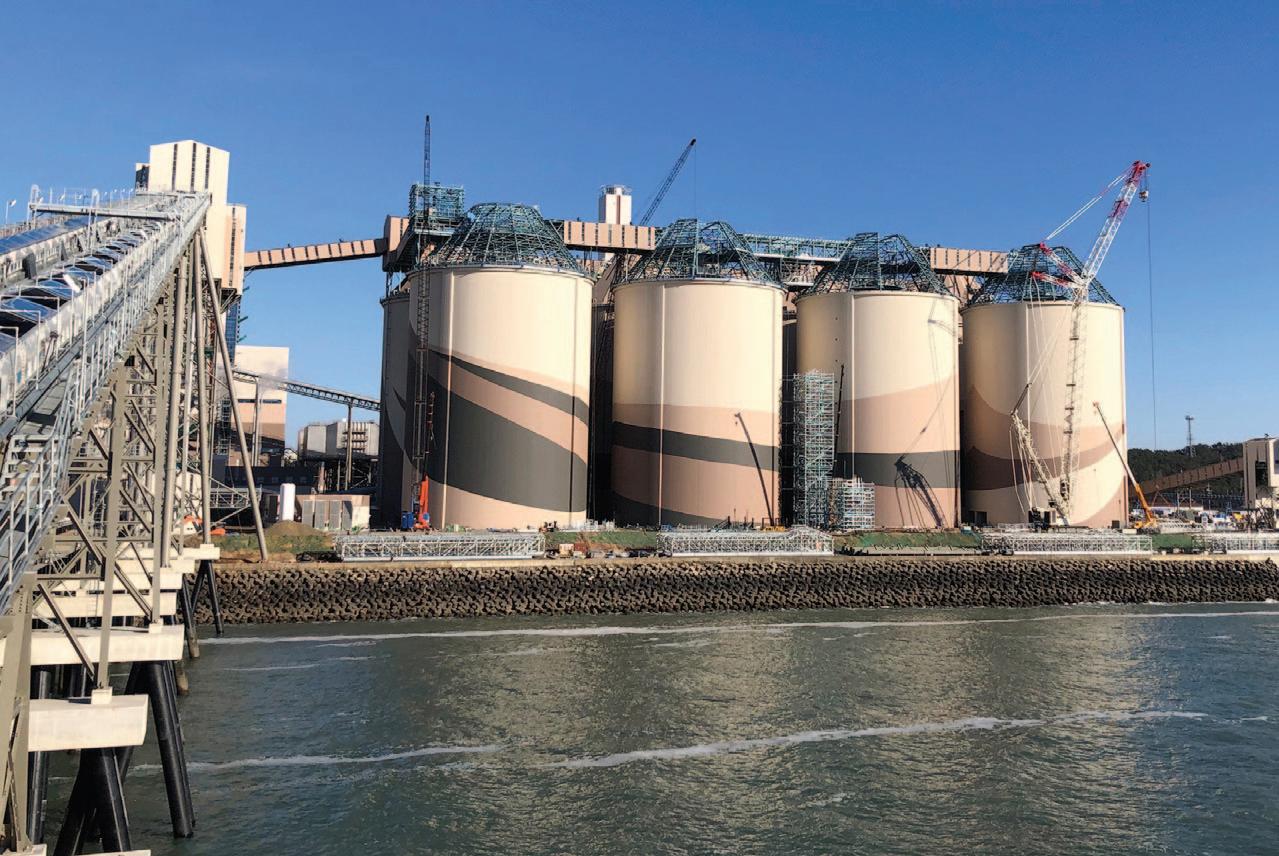
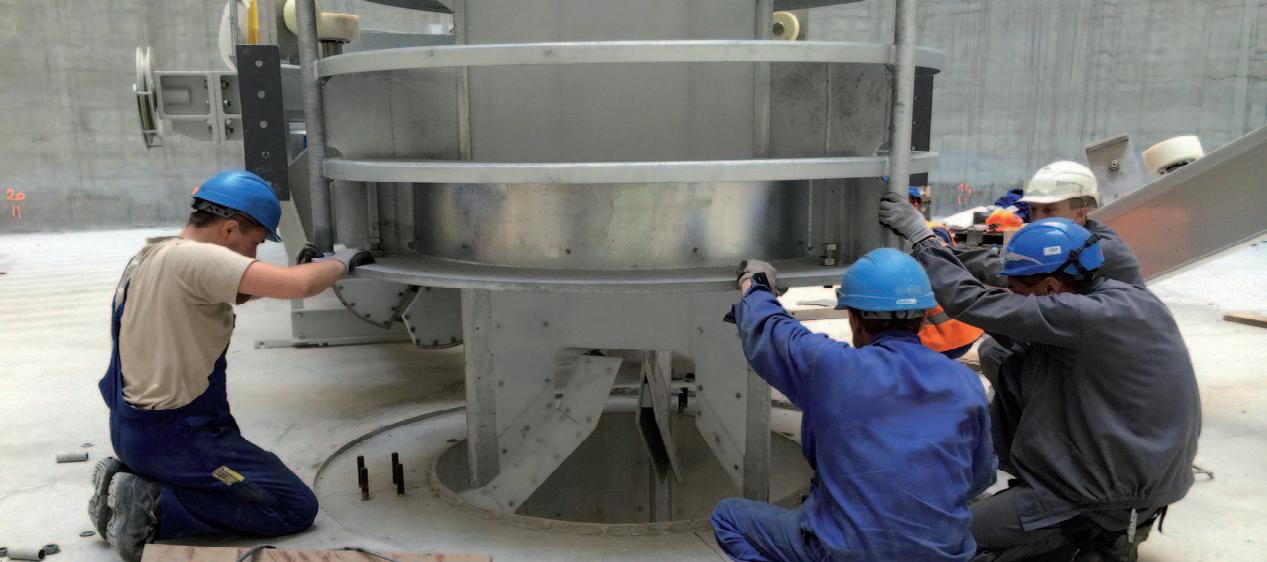
What started as a huge undertaking has come to an end in July 2022, with the successful commissioning of the three Eurosilos along the shoreline of the Mediterranean Sea. Jan-Willem Hanskamp, Manager Project Department ESI, made a final visit to the site to finalize the handover to the local team.
UNPRECEDENTED CHALLENGES

Jan-Willem: “The three Eurosilos are already in operation and feed the first of the two 660MW boilers at the thermal power plant. When the second comes
online, both boilers will be fuelled by the fully enclosed Eurosilos. The scale of this project has posed unprecedented challenges, both in technical terms and in terms of capacity and logistics. On top of that, the pandemic hit the world in 2020, which required a huge number of workarounds to keep the project going.”
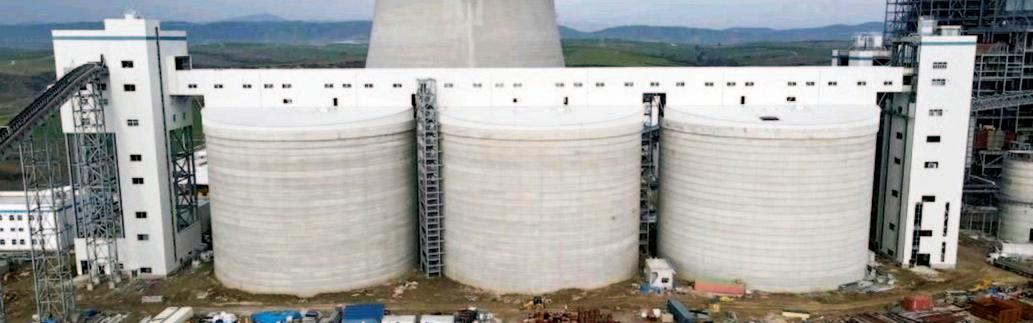
“So, it was really great to hear during the visit that all the efforts payed off well. According to Mr. Li Ying, our point of contact and project leader at the site, the silos operate more stable than other systems, which I take as great compliment. He also noted that ESI has thought about literally everything in the storage system. From safety for workers and the
environment to automation and reliable throughput.”



MOST ENVIRONMENTALLY FRIENDLY COALFIRED POWER PLANT
EMBA Electricity Production Co. Inc. is a joint venture of the Shanghai Electric Power Co., two Turkish investors and the AVIC-INTL Project Engineering Company. EMBA has developed this coal fired thermal power plant in Turkey with a capacity of 2 x 660 MW at an investment of US$1.7 billion. The project is aimed at delivering one of the most environmentally friendly, clean coal-fired power plants ever, with high capacity, high reliability and high efficiency.

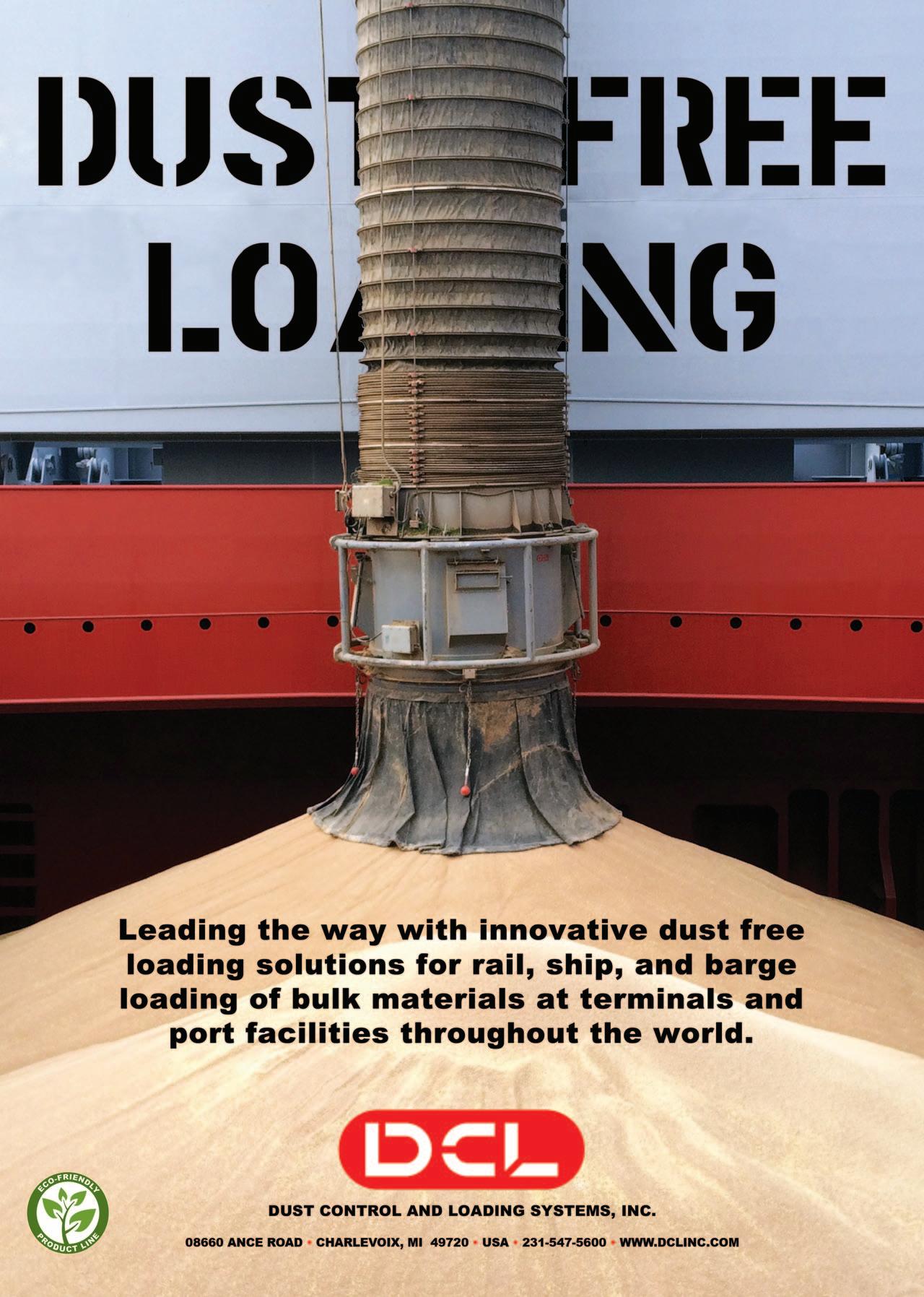
Particles on the run controlling fugitive dust
LIFTUBE® on the conveyor at Geocycle Belgium.
Jay VenterLIFTUBE® enables plants to meet safety and environmental standards
Today, industrial sites are subject to increasingly strict standards for the transfer of bulk materials and are looking for solutions to minimize their impact on the environment and increase the safety of their employees. In terms of conveyor belt conveying, the answer to these challenges is the LIFTUBE®. Indeed, this equipment developed by STANDARD INDUSTRIE INTERNATIONAL, perfectly integrates belt conveyors in order to optimize their tightness. This system guarantees the safety of the operators, confines the material by avoiding dust emissions and product losses and drastically reduces maintenance costs.
The LIFTUBE® replaces stations
equipped with three rollers on conventional conveyors. In concrete terms, standard onemeter modules can be perfectly integrated into all or part of a new or existing conveyor, keeping the belt, frame and, in most cases, the original motorization. This system is often installed at the right of the chutes and on all or part of the belt length.

Available in widths ranging from 500 to 1,600mm, in high temperature, food grade or self-extinguishing versions for ATEX constraints, it avoids any contamination of the transported product with the outside. This watertight system also allows for safe and minimal maintenance by tilting the edges and the central roller.
CUSTOMER CASE : LIFTUBE, USED ON WASTE RECOVERY UNIT CONVEYORS
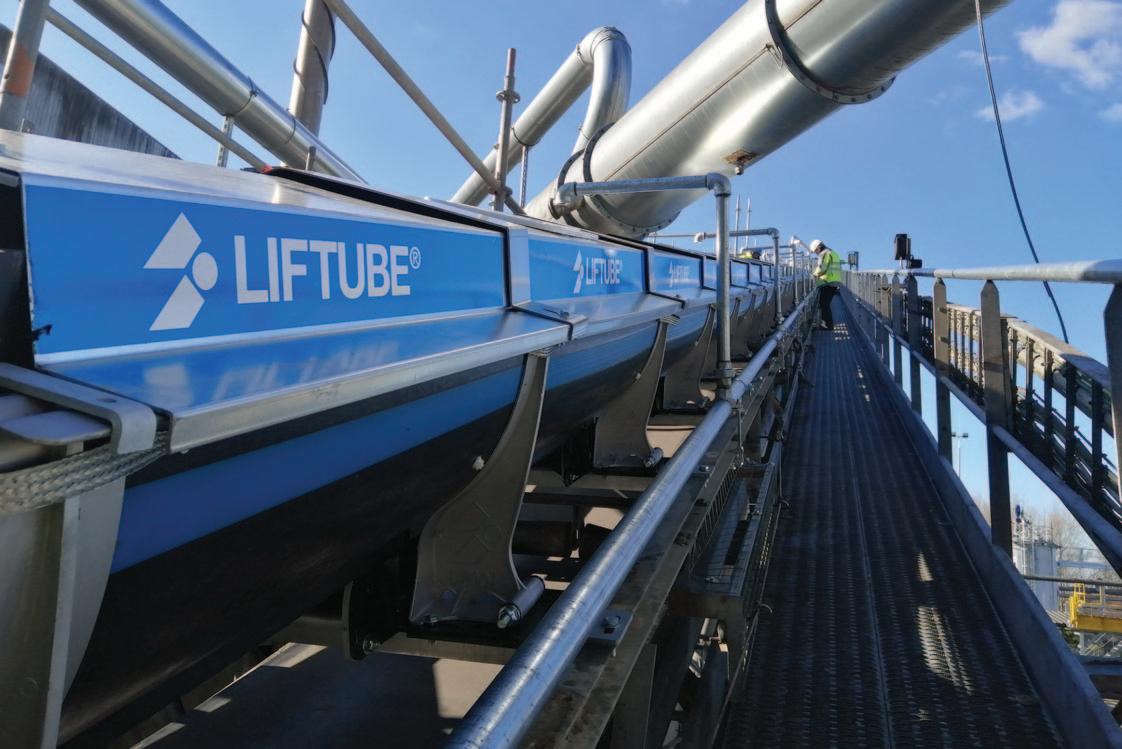
GEOCYCLE, SEVESO site, which is at the forefront of the management and treatment of recyclable waste, recovers used oil cans for its Seneffe plant in Belgium. The product of this recycling (impregnated sawdust) falls on the conveyor belt and is transported over several hundred metres to be used as an alternative fuel in the preheating towers of the HOLCIM group’s cement plants.
Originally surrounded by grids or simply covered, these conveyors regularly spilled over at the level of the chutes and generated significant environmental nuisances (dust and solvent odour) not only for the plant operators but also to the detriment of the nearby urban environment. The customer therefore agreed to equip its three conveyors with the LIFTUBE® 800 special self-extinguishing version.
With LIFTUBE®, the transported material is completely contained. As a result, odour emissions are drastically reduced and there is no material spillage. The LIFTUBE® allows a constant flow of material on the belt and protects the incoming points. Finally, the plant saves considerably on the maintenance of its LIFTUBE-equipped conveyors, since the first conveyor equipped in 2018 has still not required any intervention.
Cleveland Cascades completes refurbishment for Phillips 66 – Immingham
Cleveland Cascades Ltd. commissioning engineers have recently returned from Immingham in the UK where they were assisting one of its long standing customers, Phillips 66. Acting alongside the planned maintenance shutdown team of Phillips 66, the scope of work was to supervise and oversee the installation of a spare parts package that was supplied earlier in the year.
All components were successfully fitted to the Cascade system which has the capacity to load petroleum coke at rates of
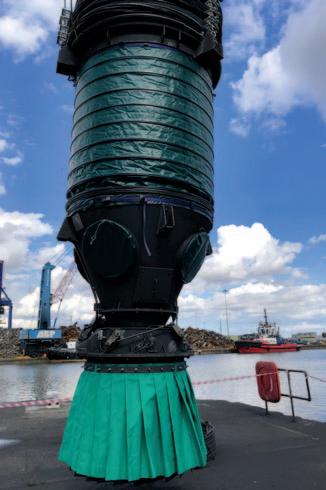

up to 620 tonnes per hour.
Following the spare parts installation, cold commissioning checks and function testing of the electrical components was to be performed. Unfortunately, due to unforeseen issues with the shiploader boom ropes, this work couldn’t be completed.
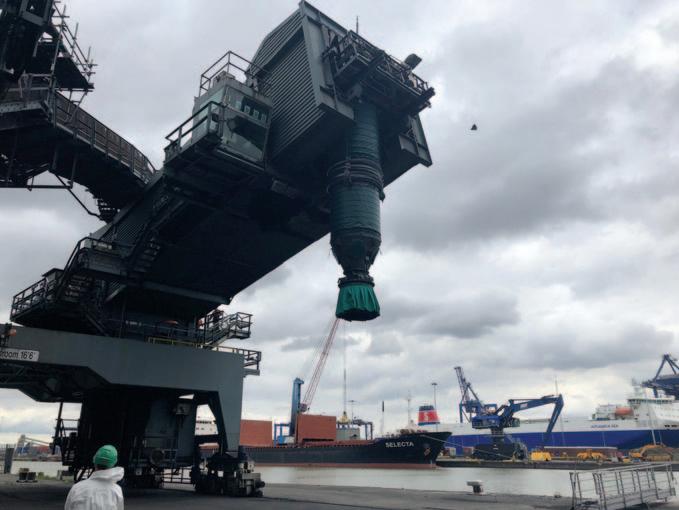
Once rectified, Cleveland Cascades hopes to return for another visit in order to verify the system setup and witness the loading procedure adopted by Phillips 66 operatives, advising on any potential
methods to be employed in order to achieve optimal system performance.
Allowing Cleveland Cascades trained personnel to complete the commissioning procedure is invaluable and the results speak for themselves. Doing so ensures that the systems potential is fully realized and that dust emissions from loading operations are drastically reduced, a further benefit is that material degradation is minimal due to the mass flow generated by the cones resulting in a quality product for shipping.
With the newly installed parts, the system is looking almost brand new.
Raring Corp’s dust emissions measurements
When we talk about dust emissions, what comes first to our minds are industrial sources of emissions, even though dust emissions are part of our day to day lives, writes Gonzalo Campos Canessa, CEO, TRC.
They normally occur because of two reasons: lack of moisture and dirt moving. When dirt is dry, it is easier for its fine particles to become airborne if wind blows or if dirt is being moved somehow.
Mining and other industrial facilities are material handling intensive, which means that the amount of dirt (ore, coal, chemical products, grains, wood by-products and others) being moved around these facilities
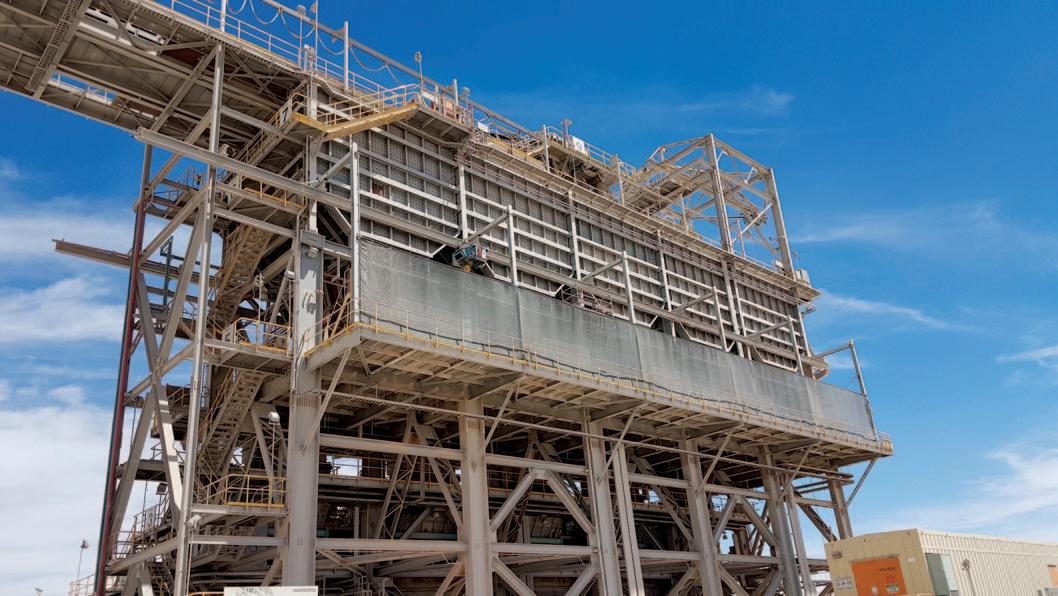
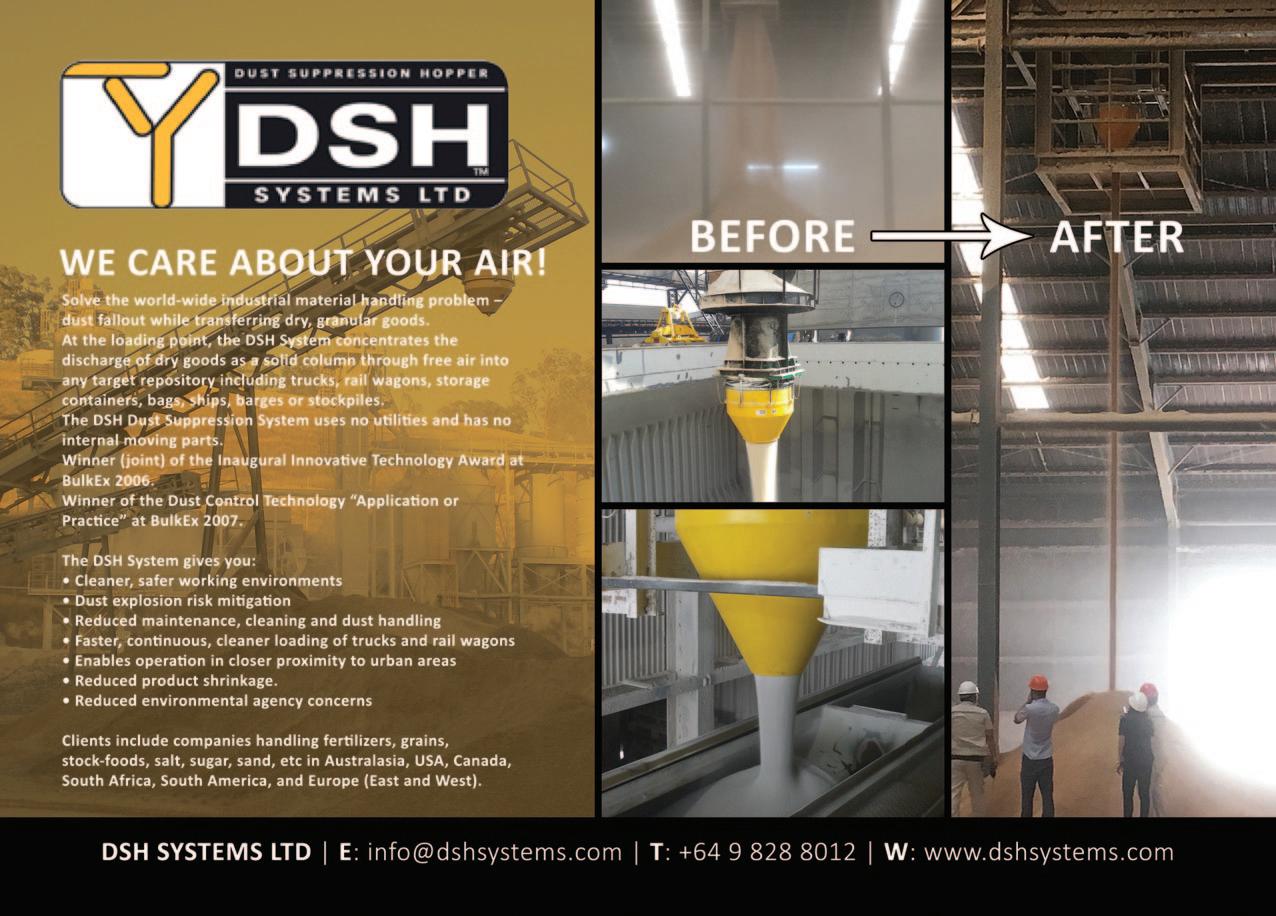
is significant and there is a potential for producing dust emissions and affect neighbouring communities and the environment if they don’t invest on dust control strategies and technologies. Let’s think about the material handling on a hard rock mining plant:
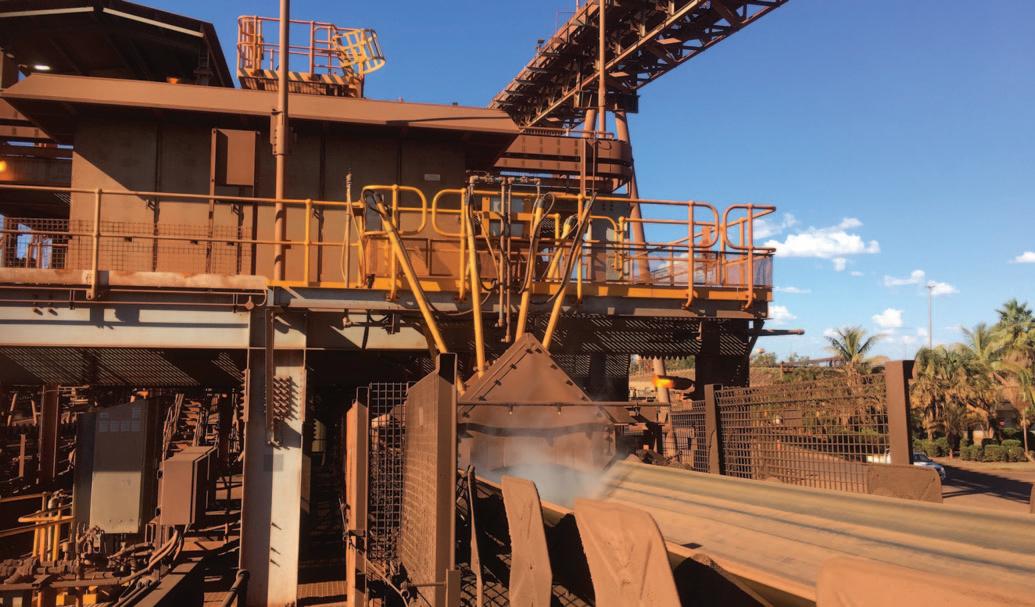
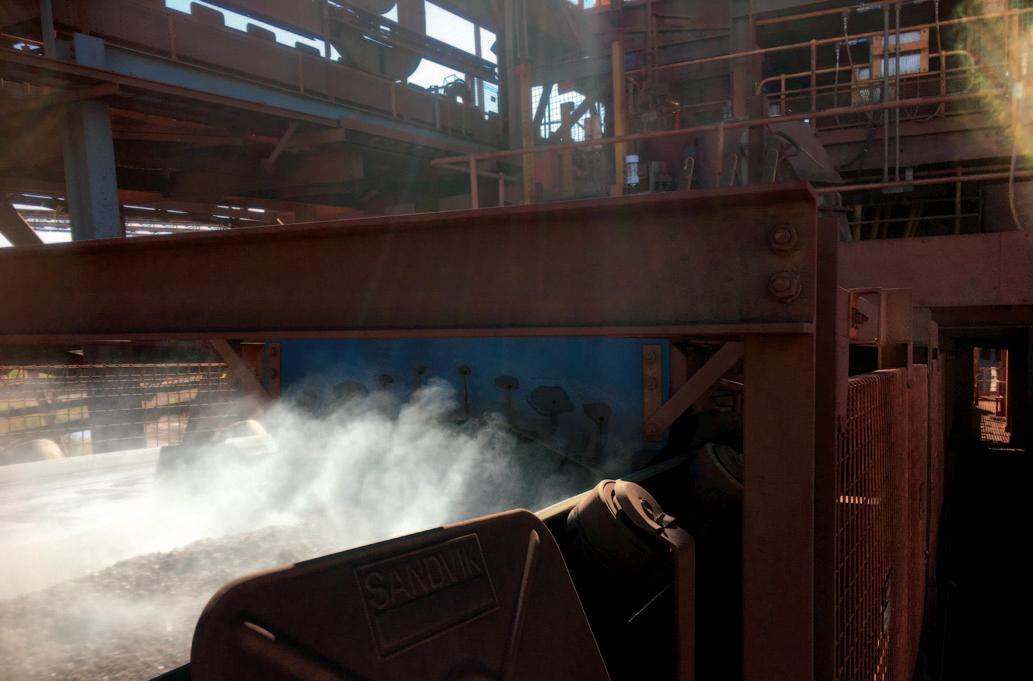
1.The first source of dust emissions comes with the blast needed to break the ground into rocks. This process which creates airborne dust which is difficult to control because of the massive scale and the lack of containment especially in open pits.
2. Machinery is needed to load these rocks into haul trucks. Dust is generated because of material falling down into
the truck’s beds and the impact inside it.
3. These trucks then transport the rocks to the crushing plant, which results in a big number of trucks driving around the plant through dirt roads. The dirt sitting on the ground is moved by the truck’s wheels and generate emissions.
4. The trucks them dump the material on a hopper/crusher. This operation produces emissions when the material falls into the hopper and also because of the turbulence produced inside of it.
5. The ore travels within the crushing plant (multiple crushers, screens and transfer points) before getting to the stock yards. Dust is generated due to the multiple transfers of material.
6. At the end of the process, the ore sitting in the stockpiles is exposed to wind gusts and becomes another source of dust emissions.
In this whole process, miners use different strategies and approaches to keep dust emissions low and controlled. At The Raring Corp, the company offers its clients dust control solutions focused on the crushing plant, from the truck dump to the stockpile, using Agglomerative Dust Suppression Systems (ADSTM Fog) and Water Spray Systems (WSS). Also, we always stress the importance of Passive Dust Control as it was mentioned in our May 2022 Dry Cargo International article:
“Passive dust control system, we can say
that it is as important as the Active one, and they cannot work apart because of the high interrelationship of passive and active systems. The Passive dust control system is the key element that creates a controlled volume to isolate the point where dust is generated allowing the Active one to do its job.” Wind fences from our partner
WeatherSolve Structures are a good example of Passive Technologies that can successfully be integrated with TRC’s Dry Fog in multiple applications, and to offer our clients integral dust control solutions for their facilities.
Over the years, requests for measuring dust control efficiency have become more common even though it is normally challenging to implement them correctly.
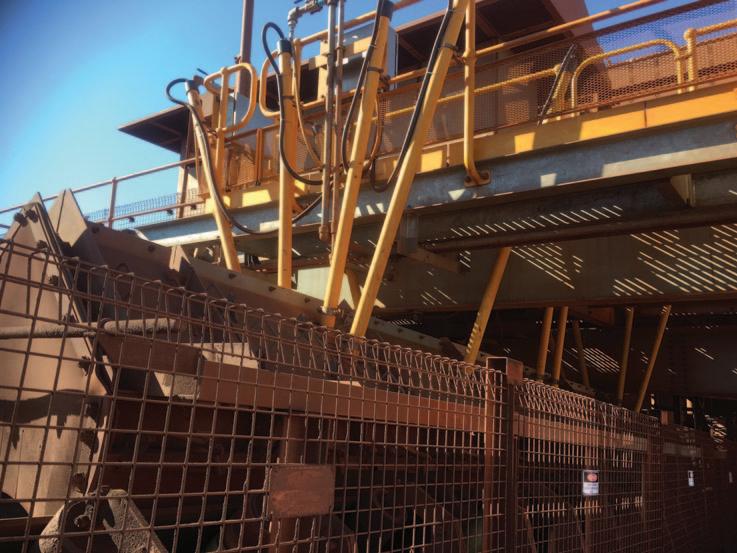

Over all these years, we have developed the following procedure for measuring dust control efficiency in transfer points, which can be scaled for other applications.
For determining the efficiency of a Fog based Dust Suppression System the total amount of dust generated needs to be measured using high volume samplers.
a) The amount of Base Dust is obtained by measuring the amount of ambient dust in the vicinity of the selected transfer point. This test must be done without any other equipment loaded and running in the neighbourhood of the transfer point being measured. Also, the Dust Suppression System will remain in the OFF mode until data is gathered.
b) The amount of total Ambient Dust is obtained by measuring the ambient dust in the same point measured on a). In this case all surrounding process equipment should be loaded and running. Dust Suppression System will remain in the OFF mode.
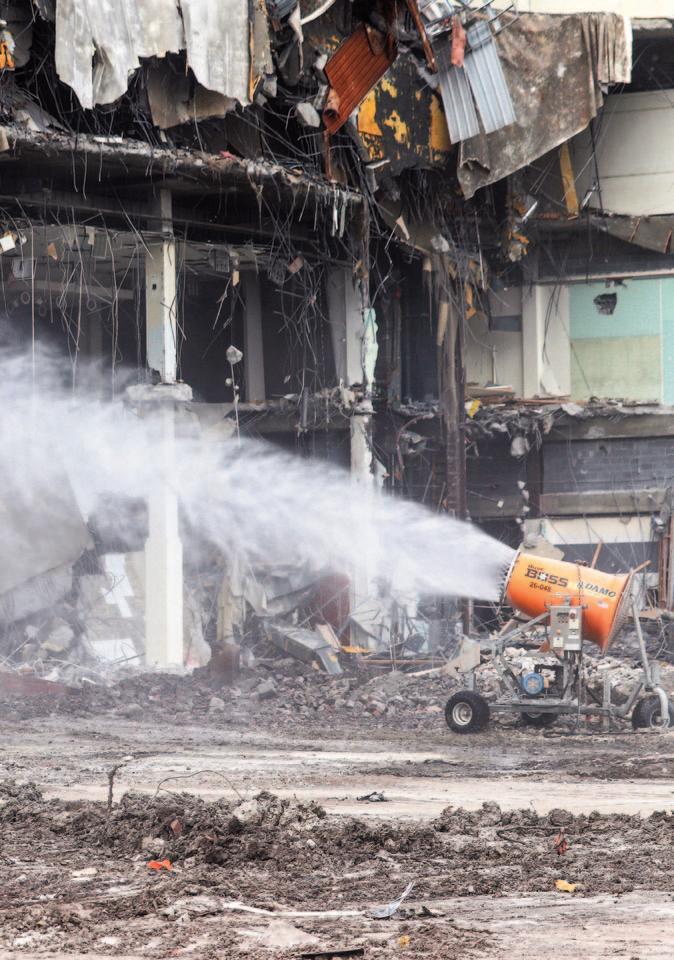
c) The Remaining Ambient Dust is measured with all surrounding equipment loaded and running and this case with the Dust Suppression Systems running
The formula to estimate the dust suppression system Efficiency is the following:
Eff = 100 *((b)
Using the methodology described in this document, we have averaged 99.22 % efficiency for TRC’s Dust Suppression Systems in transfer points.
Emissions sources can be anywhere, so in most of the cases the combination of multiple sources is the result of fugitive emissions. This fact makes emissions’ measurements challenging and representative for one specific spot.
Dust suppression technologies and its impact on ports

THE PROTECTIVE GROWTH
The contemporary bulk material handling landscape continues to impose new practical and low-impact environmental demands on many businesses in regard to ship loading/unloading system, writes Petar Karaivanov, Marketing and Communications Manager, Samson Materials handling Ltd.
Because infrastructure facilities are necessary to allow varied activities, researchers, designers, and managers have focused more on flexibility, adaptability, and eco-friendly solutions.
Many existing industry projects have design lives of many decades and must meet current and future demands by increasing the likelihood of returns on investments while also contributing to sustainability via effective use of resources and equipment.
AVOIDING THE DUST BARRAGE
Many dry bulk commodities are prone to spillage and can produce dust pollution, posing issues for ports that will become more and more widespread due to ever tightening of pollution guidelines, regulations and laws. This is especially concerning for low volume operators that work occasionally or seasonally and will not be able to invest in hefty infrastructure projects as easily as operators and ports with regular flow.
Port operators rely largely on cuttingedge low-impact technology in their infrastructure investments to maximize the use and durability of current and future assets. Many of the ageing machinery now used in ports and terminals will lose flexibility and adaptability as a result of ongoing global pollution reduction programmes.
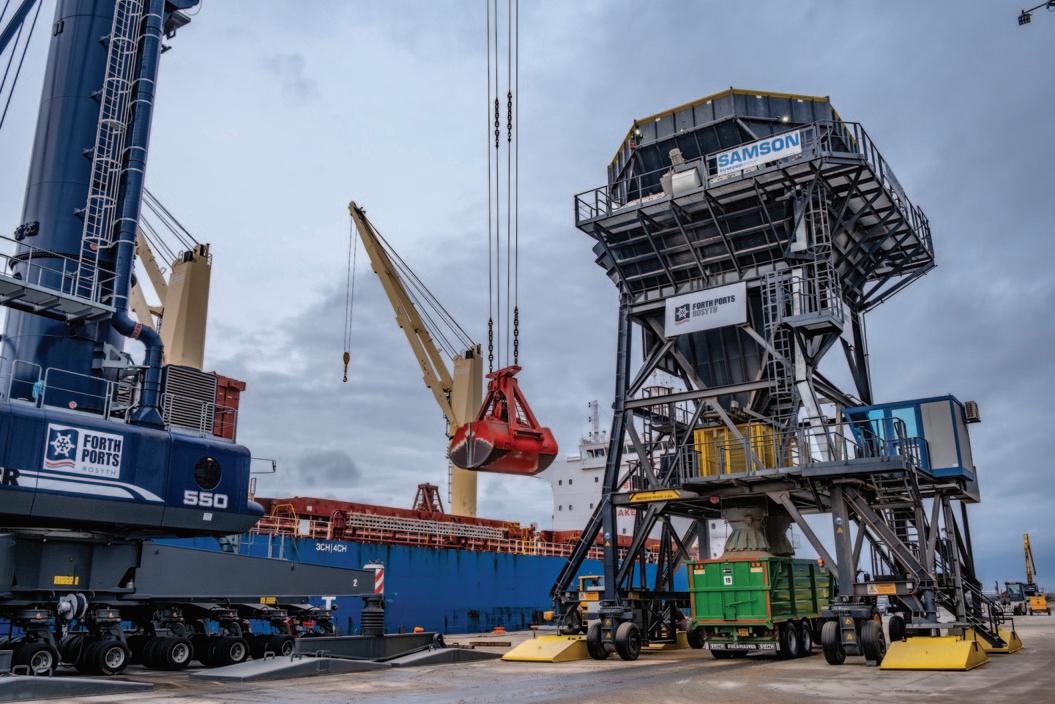
Cereals, animal feed, mineral ores, coal and coke, cement clinker, biomass, phosphate, and other fertilizers are common bulk cargoes in ports. Handling these commodities produces a lot of dust. Environmental effect may be reduced while processing these cargoes by installing new and better dust control filter systems on future equipment, or by converting existing ones.
Ports that handle dry bulk must examine the huge variations between managing containers and dealing with dry bulk items. When handling bulk materials, six major parameters influence dust generation and therefore the equipment used in the process. These are falling distance, loading rate, environmental considerations (rain, wind, and other conditions), mode of transport, material properties (moisture content and particle geometry), and loading/unloading practise. Flexibility and environmentally friendly solutions will raise demand for new
Image 1: Example of large quantity of dust generation during bulk cargo unloading while using a regular hopper.
infrastructure investments or conversion projects for existing ones.
CASE IN POINT
An excellent solution example for bulk materials unloading is an ECO HOPPER (as featured in image 2 below). It is an ecologically sensitive solution fulfilling all
Image 2: Port of Rosyth, SAMSON Eco Hopper with extensive dust control features and filters.
needs for the efficient import of dry bulk cargoes. The hoppers are designed to suit the characteristics and flow properties of effectively any dry bulk material.
Fitted with state of the art dust suppression filters for the lowest possible environmental impact benefitting both port operators and the surrounding environment around the port location.
Eco Hoppers can be suitably designed to receive bulk materials, which will be unloaded at the Quay area via a Crane Grab.
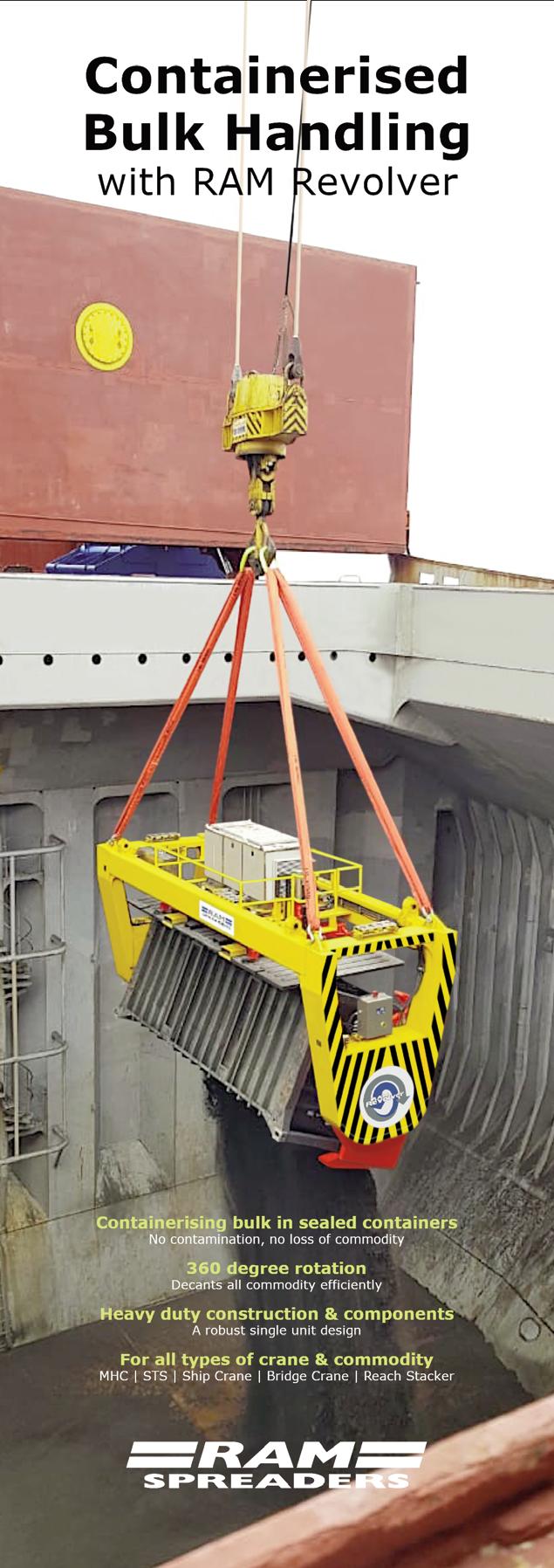
The above featured hoppers, have integrated:
Tapered Inlet Shroud designed to allow for a grab to bev lowered within the reception area before opening. This will minimize dust generation created by cross winds and disturbance of airborne dust during the unloading operation.
Inner Hopper Isolation Shield – An inner hopper shieldv designed to isolate the dust filter elements from the main material flow optimizing the filter media operation.
Flex-Flap Dust Seal System – Special sealing systemv incorporating braided flexible strips to maintain a negative air pressure within the hopper to contain dust.
The Port of Rosyth unloads and stores agri-bulk with a SAMSON Ecological Hopper and their story is one of success. Importing large quantity of bulk materials that need to be handled on site when they arrive, in safe, effective and dust free manner. Considering this, the port invested in a new Liebherr mobile harbour crane for bulk handling capability and to manage dust emissions, a SAMSON ecological hopper is also in place. The eco hopper is the first of its kind in the UK and forms a key component of the new agri-bulk hub facility. As of May 4th 2022 the port has reached its 1million tonnes milestone.
CONCLUSION
Future ship loading and unloading systems must offer flexible and environmentally friendly import and export solutions for all bulk materials if they seek to increase the maximum potential returns of investments and increase the lifespan of equipment.
Distinctively tailored designs to match various types of vessels (e.g. from barges to Panamax size) and customer demands will provide an adaptive approach and enhancement in quality of operations at a low price in the long run.
The examples of equipment provided by SAMSON Material handling are equipped with state of the art dust filtration systems which brings the environmental impact close to zero ranking them among the top current experts in the fields of adaptability and low ecological impact of operations in loading and unloading systems.
ABOUT THE AUMUND GROUP
The AUMUND Group is active worldwide. The conveying and storage specialists have special expertise at their disposal when dealing with bulk materials. With their high degree of individuality, both its technically sophisticated as well as innovative products have contributed to the AUMUND Group today being a market leader in many areas of conveying and storage technology. The manufacturing companies AUMUND Fördertechnik GmbH (Rheinberg, Germany), SCHADE Lagertechnik GmbH (Gelsen kirchen, Germany), SAMSON Materials Handling Ltd (Ely, England), TILEMANN GmbH Chains & Components (Essen, Germany) as well as AUMUND Group Field Service GmbH and AUMUND Logistic GmbH (Rheinberg, Germany) are consolidated under the umbrella of the AUMUND Group.The global conveying and storage technology business is spearheaded through a total of 19 locations in Asia, Europe, North and South America and a total of five warehouses in Germany, USA, Brazil, Hong Kong and Saudi Arabia.
Banishing dust with Golden West Industries
Golden West Industries (GWI) is a USbased dust mitigation company specializing in providing custom chemical solutions to mining, shipping and material handling industries globally. GWI works closely with ocean going vessels as well as landbased loading/unloading companies to ensure proper dust abatement, satisfying clients in the US, South America, the Pacific Rim/Asia and anywhere shipping occurs.
GWI’s speciality products are used with self-unloaders as well as non-self-unloaders across the world with extremely satisfying results.
The products are manufactured in the US and distributed via multiple containers including bulk, ISO containers and totes. This allows the vessels to load the product, or be used at ports/ports of loading. The equipment is also in house and is provided to the end user or fleets with an additional cost(s).
Professional technical services directors are part of the equation and are available for installations and 24/7 questions and port of call — maintenance or servicing in all regions of the world.
Golden West Industries provides custom solutions for three main types of dust control problems: dust control for crushing plants andv ore transport systems; dust control for unpaved roads;v dust control sealant for open areas,v stockpiles, hillsides and contaminated areas.
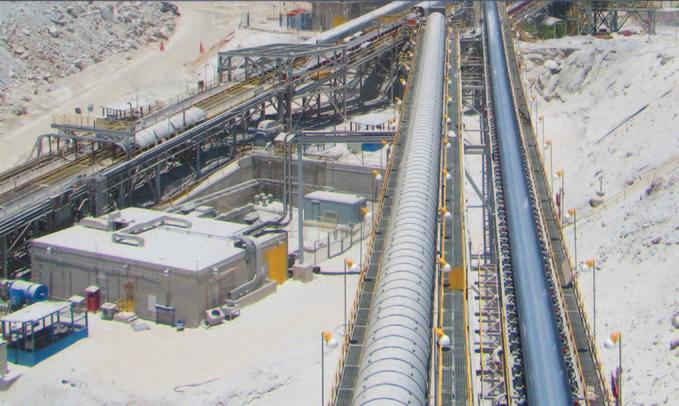
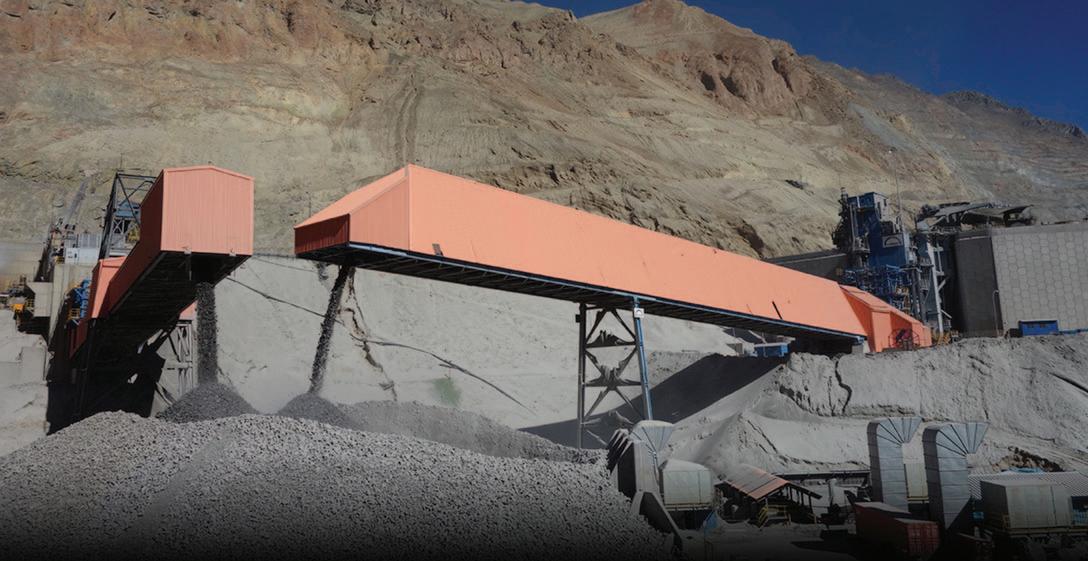
GWI’s dust reductions with coal, gypsum, iron ore, copper (even food grade products), are guaranteed to reduce
fugitive dust to 80% reduction levels — however, its standard operating levels are at 90–95% reduction level on average.
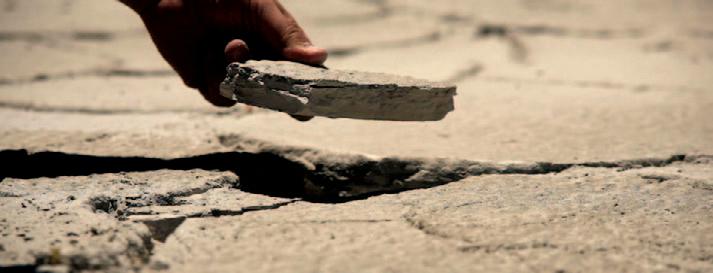
Regardless of the size of shipment/cargo intentions/vessel dynamics, Golden West Industries is prepared to handle any and all situations. Its highly trained members of staff are available for any situation and dedicated to the company’s clients.
Generally speaking, GWI’s products are liquid in nature and reduce water consumption by up to 80% with highly favourable results. The equipment is small and easy to operate, install and function for years to come — even in salt water conditions.
GWI has been treating material on ocean going vessels since 1999, and on land facilities since 1991.
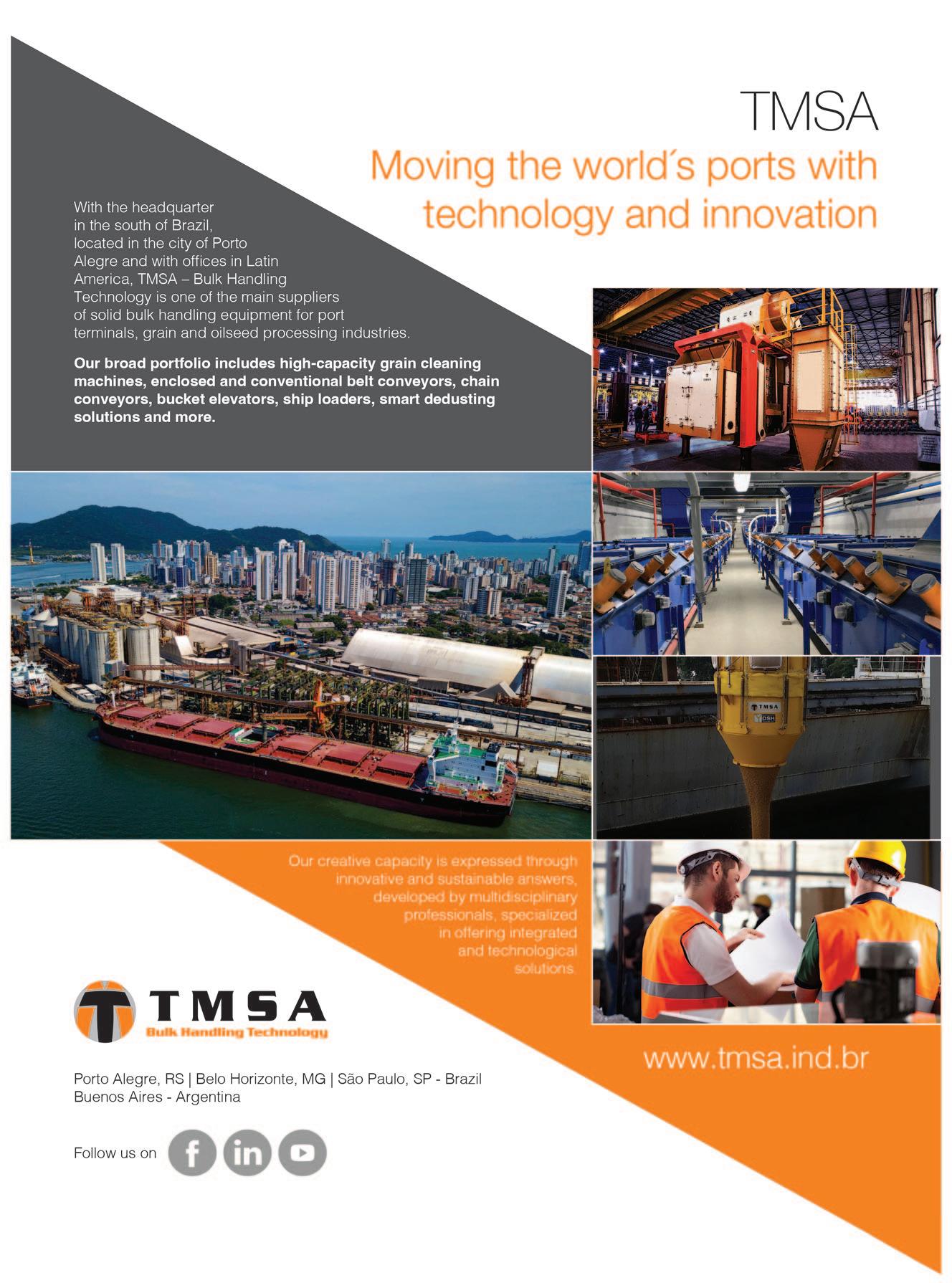
Dust control in fertilizer production with Martin Engineering
In response to global shortages, fertilizer producers are stepping up production, contributing to higher conveyor speeds and greater volumes of cargo, causing more dust within manufacturing facilities, writes R. Todd Swinderman, P.E., CEO Emeritus, Martin Engineering. For the most part, these facilities are enclosed to prevent odour and dust from affecting surrounding communities, but most workplace safety regulators closely monitor workplace conditions relating indoor air quality.
Some components of fertilizers can produce microscopic dust particles that are invisible to the naked eye which, over longterm exposure, can lead to chronic medical conditions, and thus are highly regulated. Dust can also clog bearings and other mechanical components, requiring more cleaning, maintenance and replacement parts. With this in mind, many fertilizer producers have improved workplace air quality by retrofitting conveyors to better seal the systems and thoroughly clean the belts.
MANY CONVEYORS, MANY RECIPES
The manufacturing process for organic fertilizer differs from plant to plant, but most high-volume producers employ a multi-stage system with a throughput driven by conveyors. Many operators generate various mixes of fertilizers by adding precise measurements of different ingredients at specific intervals in the production cycle. Conveying and processing any dry bulk material runs the risk of dust emissions, but many of the hazardous ingredients found in fertilizer need to be ground to a fine powder before incorporation. This lighter, smaller particle size makes the additives more prone to becoming airborne.
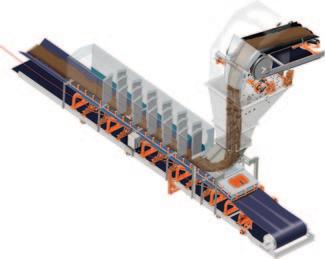
Dusty particulate material (PM) can be as small as 2.5 microns (μ) and easily becomes airborne with agitation. At this size, the particles are invisible and small enough to bypass the body’s natural defences, penetrating deep into the lungs. Workplace regulators often test for PM10 and PM2.5 using personal testing devices carried by workers throughout their shifts.
Discharge chute with dust curtain and sealed openings.
Equation
(all images ©Martin Engineering 2022.)
Fertilizer dust can lead to violations because it contains regulated substances. There’s no disputing that fine powder phosphorus dust is toxic to humans and animals, causing serious long-term health issues.[1] Potash is less hazardous, but low dust levels of crystalline silica still appear during testing, which can violate OSHA air quality regulations.
Once a violation is identified, regulators have a number of options. They can set a deadline to solve the problem, issue fines, recommend a medical assessment of the entire staff, or even order a shutdown until the issue is resolved.
SEALING A FERTILIZER CONVEYOR SYSTEM
Enclosing the system to contain fugitive dust depends on controlling air flow and ensuring there are as few openings as possible. Two areas to focus on are the discharge and receiving chutes.
SEALING THE DISCHARGE ZONE
A sealing system that is maintained with no gaps between the belt and skirting is critical to controlling airflow, dust and spillage. Because the process is continuous, the discharging material acts like a fan pulling air into the enclosure. As air is induced into the transfer chute, particles separate, leaving the head pulley and flowing onto the receiving chute.
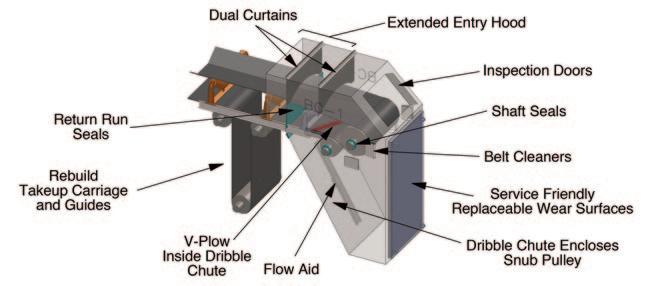
Installing curtains or barriers where the belt enters the discharge chute and sealing gaps in the chute reduce the open areas where air is drawn in. This air must discharge through the exit of the skirtboard enclosure. The skirtboard
Dust
enclosure should be designed tall and long enough with intermediate curtains that cause dust to recirculate and agglomerate or collect on the curtains.
Induced air flow is proportional to the throughput, particle size and drop distance, so minimizing the free fall of material in the discharge chute — while still allowing adequate space for belt cleaning — is important. Where air flow is greater than what can be controlled passively, provisions for active dust collection should be included in the design.
SEALING THE LOADING ZONE
Regardless of how many belts arev discharging onto a single ‘main belt’, the receiving system should be enclosed with sealed chutes. After the last feed belt, the enclosure should be long enough to give dust and fines time to settle, called the ‘settling zone.’ Although fertilizer isn’t a particularlyv heavy material, the belt support system should be able to absorb the impact of the heaviest cargo to protect the belt. Closely spaced idlers or cradles withv support bars help avoid sags in the belt that allow gaps where fines can escape, while easing material disruption. Externally adjustable or self-adjustingv skirting traps fine particles in the enclosure and adapts to fluctuations in the belt plane.
Easily serviced wear liners can bev changed from outside the chute
Sealed loading zones might include elements like dust curtains, enclosed discharge zones, and belt support.
Cleveland

Cleveland Cascades are Specialists in the design



and manufacture of bespoke dry bulk loading chutes.

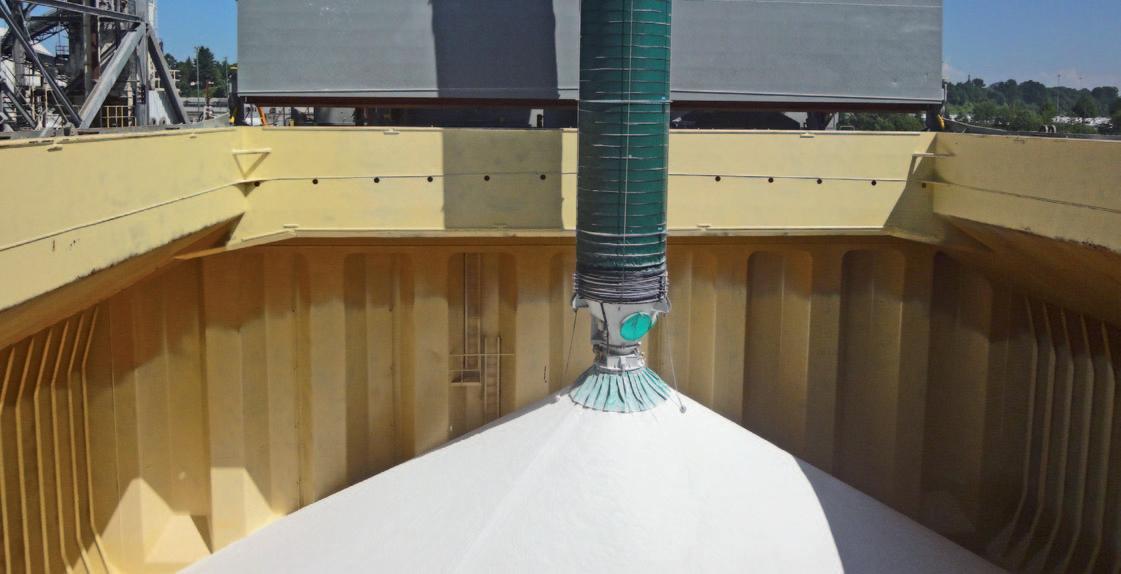
Our bespoke solutions are designed to meet each customer’s specific requirements from a tool kit of proven components, utilising the expertise of a team of specialist in house design engineers.


We lead the loading chute industry & set the standard for dust emissions and environmental pollution control in dry bulk handling.
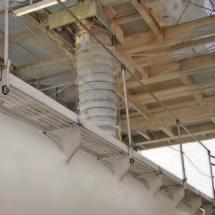
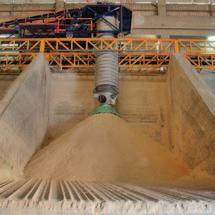
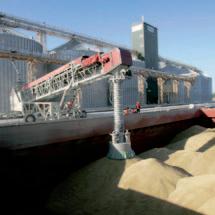
Our worldwide reputation is built on high quality, well-engineered, robust, high performance chutes, backed up by excellent customer service and global lifetime product support.
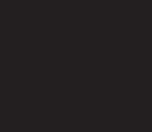

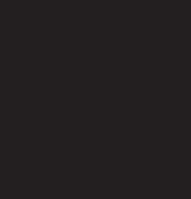
without confined space entry.
Dust curtains strategically placedv throughout the enclosure control airflow and help settle dust.
Dust bags or mounted air cleanersv collect tiny, highly active particles when induced air flow is too great to be controlled in the enclosure.
Inclined belts are common in fertilizerv production. A sealed tail box protects the tail pulley from the backflow of fines, dust and spillage.
An exit curtain set back slightly from thev end of the chute is required to help prevent fugitive dust from escaping at the settling zone and prevent ‘popcorn’ spillage caused by the exit curtain.
CONVEYOR BELTS FOUND IN FERTILIZER PRODUCTION
As the belt passes over the head pulley, material generally does not discharge completely due to static, flaws in the belt’s surface, ambient humidity and adherent qualities of the cargo. Whatever is not discharged or removed with a belt cleaner is carried back along the belt’s return and is one of the main causes of fugitive dust. This carryback not only throws off the proportions of carefully weighed additives, but also results in lost product as material drops from the belt along the entire length of the system.
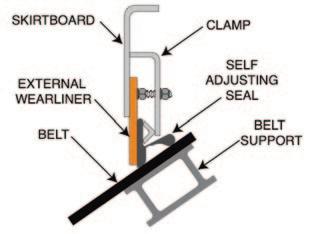
Due to the type of belting commonly found in fertilizer production, dust emissions from carryback are especially
problematic. Since the cargo is relatively light, producers rarely use expensive heavyduty belting, instead choosing more costeffective polyvinyl chloride (PVC). Antistatic rubber belts are available with flat top surfaces, but PVC belts are often seen as a lower priced option without considering the cleaning, maintenance and safety costs of dust. This cheaper PVC belt tends to have tiny depressions caused by shrinkage of the PVC into the top layer of the solid woven belt carcass. The belt face resembles a hammered metal surface, with fines getting trapped in the dimples and not falling off during the return by gravity. A primary belt cleaner installed on the discharge pulley will remove heavy build-up, but this does not address the particles captured in a dimpled or damaged belt surface which is a main source of dust on the return run.
The fertilizer production process can also have several inclined conveyors fitted with ribbed, flighted, grooved or chevron belts. These ridges can resemble wheel
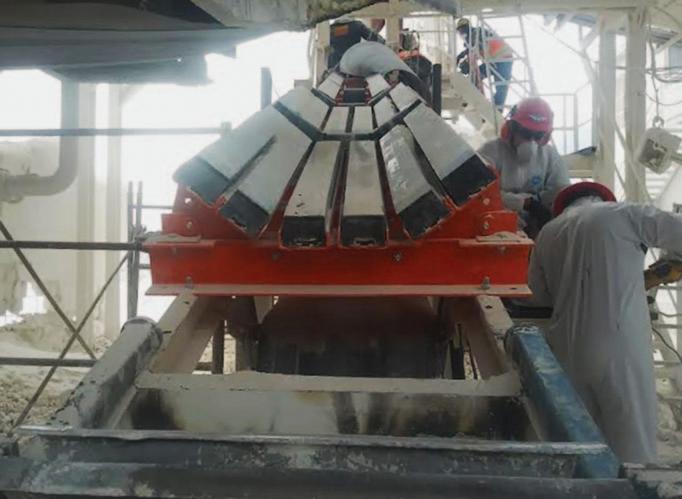

tracks or tyre treads which the cargo attaches to as it is pulled upward. Textured belting is impossible to clean effectively using a standard belt cleaning system designed for flat belts, so maintenance tends to leave the belt uncleaned. As carryback piles underneath the system, workers typically shovel it back into the material flow, which adds more labor to the cost of operation and exposes the workers to potential injuries.
BELT CLEANING IN FERTILIZER PRODUCTION
Because of the tendency of the fertilizer to accumulate static charges, all components in the system — including belt cleaners and chutes — must be grounded to reduce
The tensioner puts enough pressure on the blade to clean the belt but easily pass over splices.
The belt passes through a pressure spray cycle, then the water is removed by blades.
dislodged dust from re-attaching to the belt surface. Primary cleaners are most effective on a flat (non-crowned) head pulley, and if crowned pulleys are used, segmented precleaner blades are recommended. High quality polyurethane blades can be shaped in a curved ‘constant angle and pressure’ (CARP) design to ensure that a consistent wear surface and pressure are applied to the belt throughout the life of the blade.
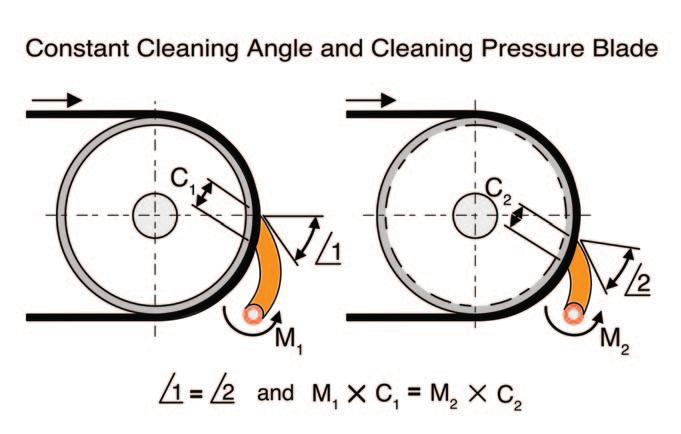
The tiny depressions in PVC belting can also sequester material beneath the belt’s surface plane, allowing it to bypass primary cleaner blades. To mitigate this, a specialized mechanically grounded and static dissipating rotating brush cleaner has bristles that can remove trapped dust and fines. The brush is also well suited for the removal of fines and residue from ribbed,
flighted, grooved or chevron conveyor belts. The fine polypropylene bristles are rotated using a one or two-horsepower motor (depending on belt width) to dislodge trapped material. Enclosed discharge zones should be designed to fully encase brush cleaners, since the rotating brushes can release dust from dry cargo. The brush cleaner will create generated air and its use may require a mechanical dust collection system. Air cleaners inserted above the discharge enclosure are preferred.

An alternative to brush cleaners is the ‘wash box’. The typical configuration is one or two high pressure spray bars for applying water, followed by two or three secondary belt cleaners, all contained within the wash box housing. The final blade is generally designed for removing
water so that the belt leaves the box relatively dry, and most of the water is drained at the base of the unit. In the case of ridged belting, an internal rotating brush cleaner can be used in place of secondary blades.
DUST COLLECTION SYSTEMS
When evaluating strategies to control dust in fertilizer manufacturing, some plants may assume that a central collection system is the best or only option, largely because the equipment is widely available. But the cost of these systems is high, and they require significant ongoing maintenance, leading managers to assume that the cost of dust control is going to be prohibitive. In comparison, the mechanical solutions outlined above typically require minimal investment, and there are also highlyeffective options that don’t require massive central collection systems with a cost to match.
Two common pieces of filtration equipment are dust bags and integrated air cleaners. Installed above the conveyor loading zone, dust bags collect particles without energy consumption. In a wellsealed chute with properly controlled airflow, the air is directed through the upper openings, where dust agglomerates in the fine mesh bag.
Once full, a short stoppage in the system allows the bag to relax and the collected dust falls safely onto the belt. Some fertilizer ingredients can emit combustible dust so static-dissipating bags and proper grounding are recommended.
Air cleaners are individual mechanical collectors that use a reverse air pulse in the collection chamber to return dust to the main cargo stream. With low power consumption and easy maintenance , some operators have found air cleaners offer a
Several dust bags
be utilized,
CONCLUSION
The current fertilizer shortage has exposed the fragility of the global supply chain, but workplace safety does not need to take a back seat to production. Managers of production facilities are generally aware of air quality issues, but with only a moderate increase in production, operators are often surprised by the dramatic increase in dust emissions these modest changes can produce.
Retrofitting equipment that improves both production and working conditions results in avoidance of dust-related violations, less unscheduled downtime and a lower cost of labour for clean-up. This reduces the total cost of operation
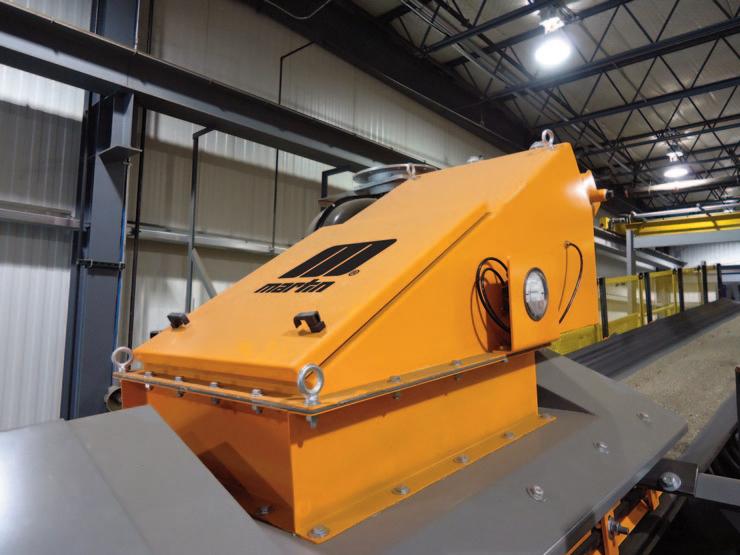

the
of loading
dust
belt.
presenting at conferences and customer facilities around the world and holding more than 140 active patents. He has served as President of the Conveyor Equipment Manufacturers’ Association and is a member of the ASME B20 committee on conveyor safety. Swinderman retired from Martin Engineering to establish his own engineering firm, currently serving the company as an independent consultant.
ABOUT MARTIN ENGINEERING
Mechanical air cleaners are low maintenance and improve \ the air quality around the system.
greater long-term
and most importantly,
in a safer
Protection Agency
ABOUT THE AUTHOR
R. Todd Swinderman, P.E. /CEO Emeritus/ Martin Engineering, earned his B.S. from the University of Illinois, joining Martin Engineering’s Conveyor Products division in 1979 and subsequently serving as V.P. and General Manager, President, CEO and Chief Technology Officer. Swinderman has authored dozens of articles and papers,
Martin Engineering has been a global innovator in the bulk material handling industry for more than 75 years, developing new solutions to common problems and participating in industry organizations to improve safety and productivity. The company’s series of Foundations books is an internationally recognized resource for safety, maintenance and operations training — with more than 22,000 print copies in circulation around the world. The 500+ page reference books are available in several languages and have been downloaded thousands of times as free PDFs from the Martin website. Martin Engineering products, sales, service and training are available from 17 factoryowned facilities worldwide, with whollyowned business units in Australia, Brazil, China, Colombia, France, Germany, India, Indonesia, Italy, Mexico, Peru, Spain, South Africa, Turkey, the USA and UK. The firm employs more than 1,000 people, approximately 400 of whom hold advanced degrees.
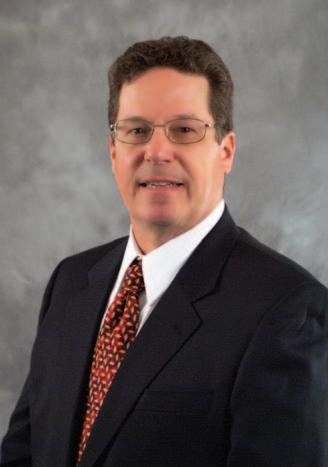
Ensuring a healthy work environment with systems from Spraystream
We all like to reside in a healthy, dust-free environment. However, the spread of dust cannot be avoided in some sectors and is harmful to the environment and to health. Health and environmental regulations continue to become increasingly stringent in this respect. In other words: dust control is essential. Spraystream offers cutting-edge atomizer technologies that reduce the spread of dust by about 90%. This allows users to create a dust-free and safe work environment, not only for all employees, but also for the entire neighbourhood.
Spraystream only uses the most reliable technologies of the highest quality in its dust-suppression systems. This means that the company only delivers the most efficient solutions with excellent service. Its ecological dust prevention systems also contribute to a more sustainable world thanks to their limited water and energy consumption. The use of water atomizing allows for the atomizing of the largest possible surface area.
In addition, Spraystream’s innovative technologies help suppress unpleasant odours and allow for the cooling and decontamination of the space. These are always tailored to the extent of the client’s issue and in compliance with the latest industrial standards.
Operations like, for example, grain handling, can generate large amounts of dust (above). This is where the Spraystream system comes into its own.
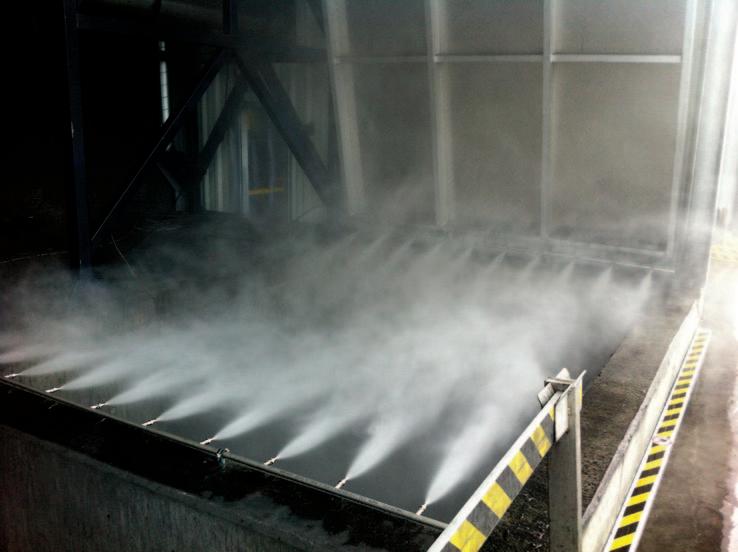
LOADING, UNLOADING, AND TRANSSHIPMENT: THESE PROCESSES
RELEASE A LOT OF DUST — SPRAYSTREAM SOLVES THIS ISSUE
Port companies load and unload large quantities of (bulk) goods on and from ships every day. They also take care of the safe transshipment of commercial goods.
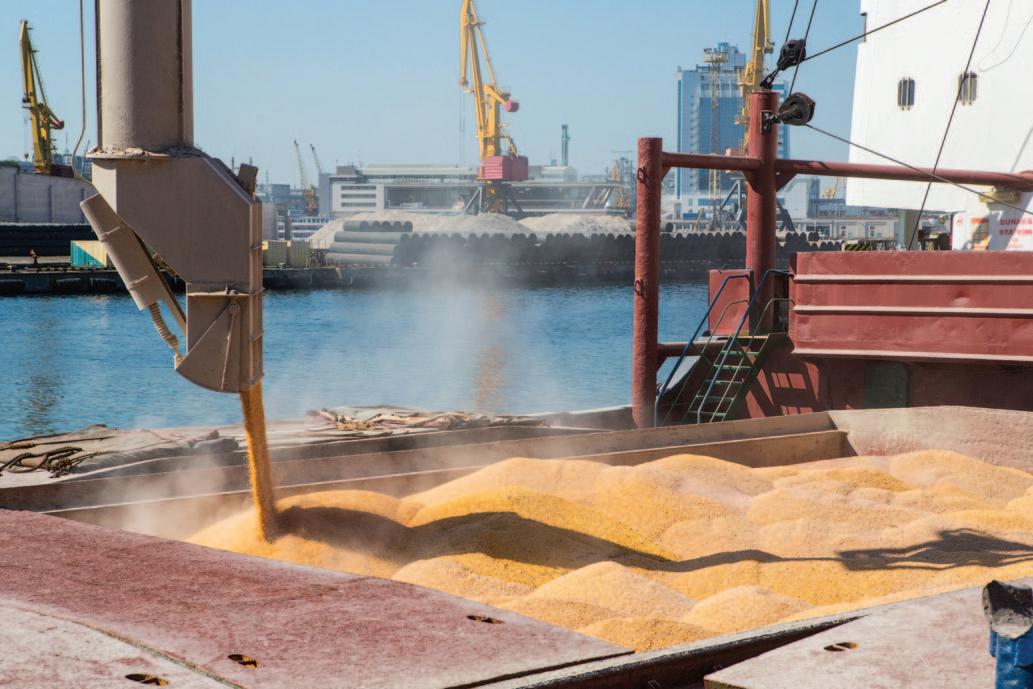
However, these processes release a lot of dust. This leads to unsafe working conditions, the loss of various raw materials, and wear of equipment.
Spraystream has developed various
solutions to load, unload, and transship goods in a safe and controlled manner and to control the emission of dust. The company has an extensive range of fog cannons and fixed nozzle systems that absorb the hazardous substances and remove them from the air using the atomizing of small micro-droplets.
Anyone requiring a specific solution should get in contact with the company, which will be able to provide an ideal system, tailored to meet the exact needs of the project.
ABOUT SPRAYSTREAM AND THE SAVIC GROUP
Spraystream is a subsidiary of the WestFlemish machine builder Savic Group. Mirko Savic, founder and owner of Savic Group, incorporated his company in 2004 with a single mission: designing sustainable, innovative, and high-quality atomizer technologies to handle all odour and dust issues.
As a pioneer in its field, the Savic Group has a its own dedicated internal R&D department and production unit. A team of driven engineers ensures the careful handling of all projects, from quotation to after-sales service. There is also the option to hire one of the company’s cutting-edge machine.
“Our job is to create a healthy and safe environment,” says Mirko Savic.
INNOVATIVE SOLUTIONS OF THE HIGHEST QUALITY FOR ALL CUSTOMERS
Cutting-edge solutions of superior quality make Spraystream a global leader in the field of atomizer technologies. Quality has always been, and remains, absolutely paramount to Spraystream as a company, which strives to innovative its technologies every day to sell the best possible systems. Sustainability is key in this respect: Spraystream’s systems are ecological and designed with wear-resistant materials for extensive use. Spraystream always observes the needs of its customers, striving to establish a long-term relationship thanks to its excellent service.
TECHNOLOGY
Spraystream uses innovative methods to prevent and control dust, based on the principle of atomizing. Because large surface areas are nebulized at the same time, Spraystream focuses on efficient and sustainable dust control.
MIST INSTEAD OF WATER
When micro-droplets (mist) come into contact with dust, both matters merge. They subsequently fall on the floor together, eliminating the dust from the air. This is not the case when using large water droplets; where the dust particles move around the droplets. By controlling the size and quantity of the micro-droplets,
Spraystream can create the best solution for customers’ issues.
SPRAYSTREAM FOG CANNONS: A HIGH QUALITY SOLUTION
Spraystream offers an extensive range of fog cannons with various options. These machines create a micro-droplet mist curtain with a range of up to 150 metres, in part thanks to the use of high-quality materials:
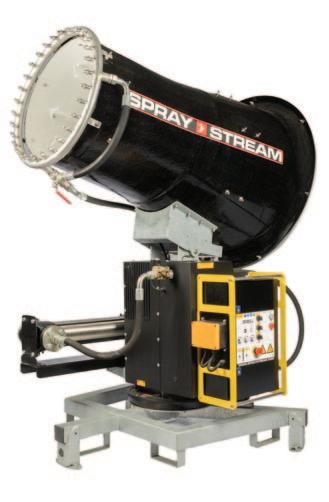
The patented cone shape isv aerodynamic and made from a composite. This high-quality material creates lighter machines, has an attenuating effect, and has a lower risk of corrosion. The cone shape leads to a maximum range with a minimum capacity and water.
Spraystream also uses GRUNDFOSv maintenance-free pumps of the highest quality.

Spraystream’s intuitive machines arev also very easy to use and can be controlled remotely.
The Spraystream machines have av default electrical oscillation and the fans can withstand high performances.
The wind guides make sure that av turbulent air flow is converted into a laminar air flow. This leads to minimum water flow losses and thus to more targeted and more efficient atomizing.
The atomizers can be replaced easilyv because rapid-lock systems are used.
Port Saint John is positioning itself for the future
Port Saint John is the fourth-largest port in Canada by tonnage and is located on the East Coast of Canada. Handling a variety of different cargoes, including containers, dry bulk, liquid bulk, and breakbulk, it sees an average annual volume of 27mt (million metric tonnes). This is in part due to a deep-water, year-round ice-free harbour, that remains fluid and uncongested.
However, it also speaks to the partnership with three Class I railways: CN, CP and CSX, regional truckers, three stevedores, and a growing labour force. Together these assets ensure the port is positioned for performance in all sectors, including bulk. The port is also closer by nautical mileage to South America than many of the US East Coast ports giving Canadian exporters, and importers a Canadian East Coast hub for their product to move through.
Specific to dry bulk, Port Saint John currently handles two major commodities: potash and recycled metal, but has room to grow with new materials and products. In 2021, over 1.6mt of potash were exported through the port, a 167% increase from 2020. This bulk operation is made possible through a partnership between Canpotex, Nutrien and CN Rail. These numbers are expected to remain high in 2022. American Iron and Metal saw over 254,000 metric tonnes of recycled metal flow through their terminal in 2021. Outside of these commodities, their Lower Cove Terminal’s 16.8 acres remains open for business as a common user terminal for dry bulk commodities. In the past five years the terminal has seen up to 180,000 tonnes handled at the facility including but not limited to: gypsum, rock, limestone, and salt.

Beyond its common user terminal, Port Saint John also hosts DP World. Its multi-
use terminal is currently undergoing a quarter billion-dollar upgrade. New features will include:
Widening and deepening of thev overall harbour;
An additional new berth (2,000 lbsv per square foot lift capacity, and 17.1m depth);
21 new acres of terminal space;v 2 additional quay side cranes (super-v post-Panamax);
Increased rail capacities;v Technology upgrades.v
These upgrades coupled with over 55 acres of existing space, four large on dock warehouses (each over 100,000ft2 in size), and access to CP, CN, and CSX rail enables
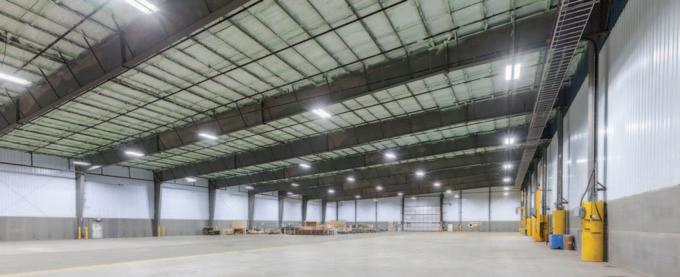
DP World to offer innovative solutions for moving bulk products around the world including forestry products.
Forestry products are currently primarily moved by container through the Port of Saint John, with the on-site warehouses serving a vital role in ensuring these supply chains remain fluid.
Finally, while many bulk products continue to move in bulk vessels it should be noted Port Saint John is serviced weekly by CMA, MSC, and two Lloyd container services. The most recent addition of a Northern Europe seasonal service by Hapag Lloyd enables Port Saint John to now directly connect to Antwerp and Hamburg.
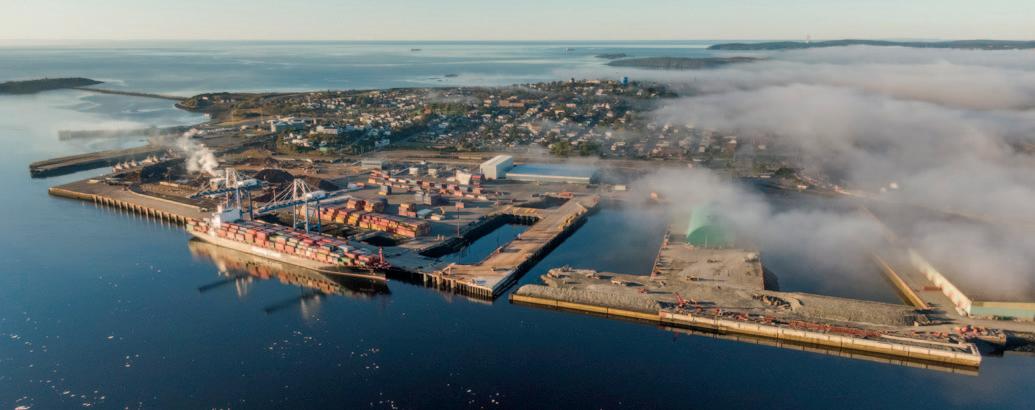
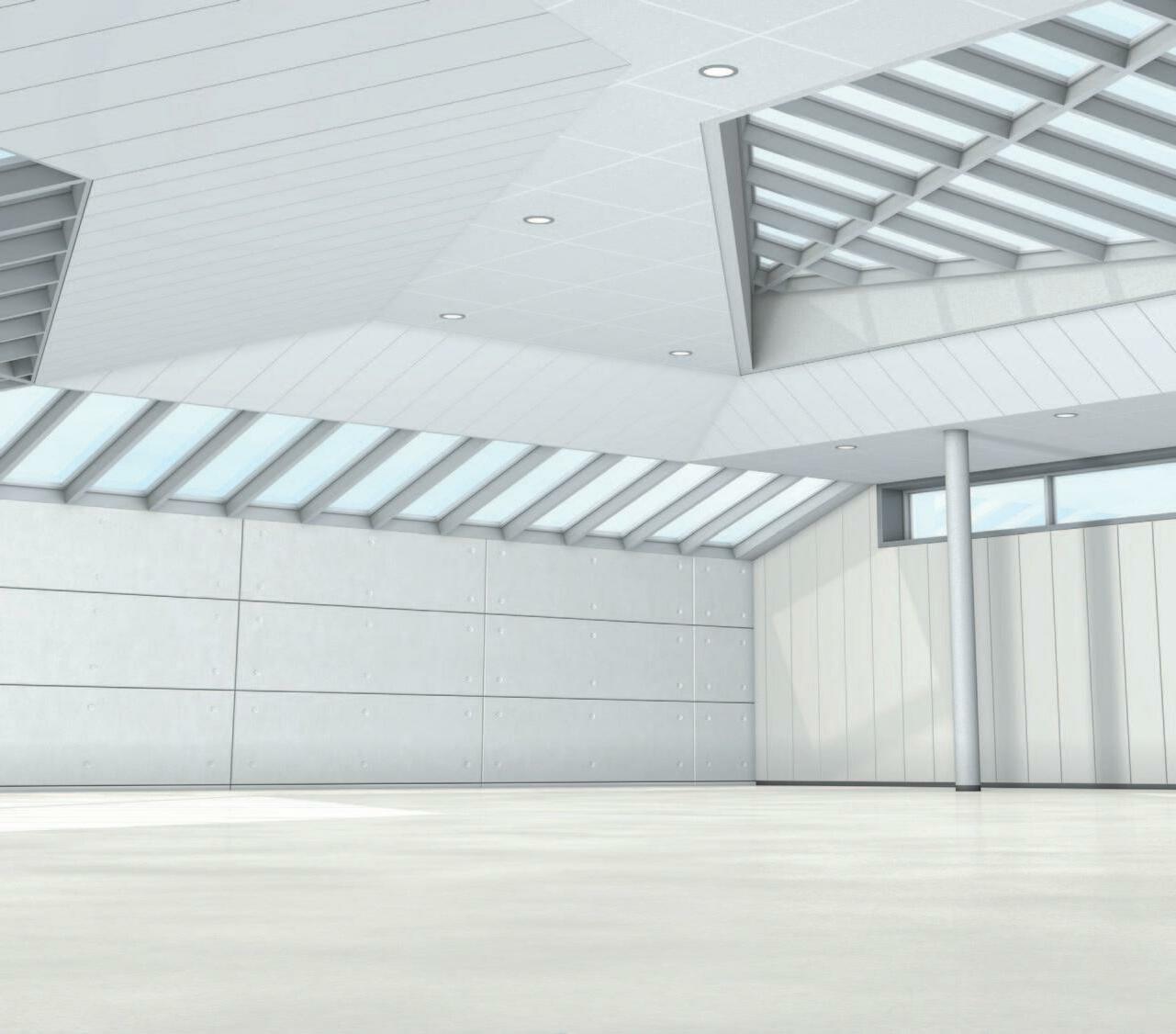

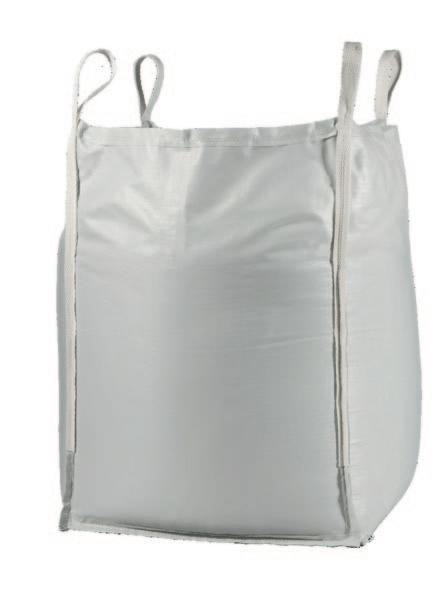
K
2022: Starlinger unveils the cement bag of the future
Block bottom valve bags made of woven plastic are not only a tear- and moisture-resistant packaging for dry bulk goods — they are also becoming an increasingly sustainable packaging alternative in this sector.
Starling is taking a stand at this year’s K Show trade show for plastics and rubber, which will take place in Düsseldorf, Germany, in mid-October.
Starlinger will be demonstrating the production of AD*STAR® block bottom valve bags with 22% recycled content on the new ad*starKON SXneo bag conversion line at its K 2022 trade fair stand. AD*STAR® bags are used all over the world for the packaging of dry bulk materials, in particular cement (photo: ©Starlinger).
“With our packaging technology, we want to promote the growing focus on sustainability in the industrial sector and offer packaging manufacturers innovative and viable solutions,” explains Hermann Adrigan, Sales Manager at Starlinger. “This year, we will be producing our AD*STAR* block bottom valve sacks with 22% recycled content on our new sack conversion line ad*starKON SXneo at the Starlinger stand. In this way, we want to show that it is possible to use recycled material in woven plastic packaging, which is manufactured in a complex process, without having to accept a loss of quality. Starlinger customers are even producing highperformance packaging such as big bags with recycled polypropylene on our lines.”
In addition, Starlinger’s new, patented gripTEC technology, which will also be on show at the trade fair stand, can increase the coefficient of friction on the bag surface to significantly reduce slipping of stacked bags. This lowers the risk of personal injury from bags slipping down, and saves tonnes of bulk material and packaging. What’s more, the CO2 generated during replacement production is eliminated — another contribution to sustainability.
CLOSING PACKAGING CYCLES
Starlinger lines can produce and process woven fabric not only with recycled polypropylene (rPP), but also with recycled PET. “As a member of the Austrian platform ‘Verpackung mit Zukunft’ (Packaging with a Future), creating closed cycles for plastic packaging is of particular importance to us,” says Adrigan. “Our circular packaging concept paves the way for a closed packaging cycle in the industrial sector. Industrial packaging such as big bags made of woven polypropylene are equipped with a material passport that makes it
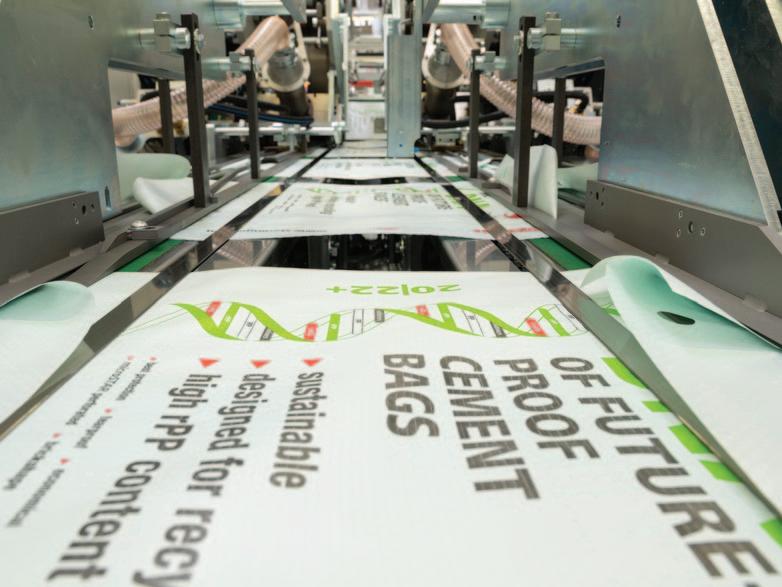
possible to trace their life cycle from production and use to return and recycling. This means that new big bags can be made from used big bags without quality loss, and the packaging cycle can be closed.” Big bags with rPP content produced by Starlinger customers will be on display at the Starlinger stand. The initiative ‘Verpackung mit Zukunft’ will also be represented at the Starlinger stand, providing information to interested parties on the topic of circular economy.
WOVEN BAGS AND BIG BAGS MADE OF PET: PERFECTLY RECYCLABLE Mono-material packaging made of PET is virtually made for recycling: in the recycling process, this material can be processed in such a way that it has the properties of virgin material — including food grade quality — and can be recycled repeatedly. With the technology for producing tape fabric from PET and rPET, Starlinger has harnessed this major benefit for woven packaging and is the only supplier to offer this process. PET tape fabric is highstrength, food grade, has excellent creep resistance and can be made from 100% recycled material. As with bottle-to-bottle recycling, this enables ‘bag-to-bag’ recycling and closes the packaging cycle. This not only lowers raw material requirements, but also CO2 emissions and energy consumption. Both PET and rPET tape fabrics have already been used successfully in the production of big bags. Due to their
excellent dimensional stability, PET big bags are ideal for long-term storage of bulk goods and provide a cost-effective alternative to octabins and cardboard cylinders. As a monomaterial solution, they can be recycled easily after use and can be reprocessed as often as desired.
ABOUT STARLINGER & CO. GES.M .B.H.:
Starlinger is an Austrian machine manufacturing company based in Vienna with production sites in Weissenbach and St. Martin, as well as in Schwerin, Germany and Taicang, China. As a global specialist in the supply of machines and complete systems for the production of woven plastic bags, as well as systems for plastics recycling, PET extrusion and finishing, the Starlinger brand is synonymous with quality and technological leadership in more than 130 countries.
Founded in 1835, the family-owned company has been exporting its products around the world for more than 50 years and achieves an export quota of over 99.5%. The company has its own sales and service centres in Brazil, China, India, Indonesia, Mexico, Nigeria, Russia, South Africa, Thailand, the United States and Uzbekistan, each of them guaranteeing swift and professional technical service.
Starlinger is a participant of the United Nations Global Compact, the world’s largest corporate sustainability initiative, and adheres to the principles for responsible business set out therein.
be
Green Efficiency Drive electric travel drive at
Hybrid technologies are not only on trend, they can also significantly save energy if used correctly. With the
Green Efficiency Drive (GED), SENNEBOGEN has developed a drive technology that represents a hybrid system with a mix of diesel and electric drive. The GED is an electric
Efficient timber handling
Material handler with electric travel drive for Pick & Carry
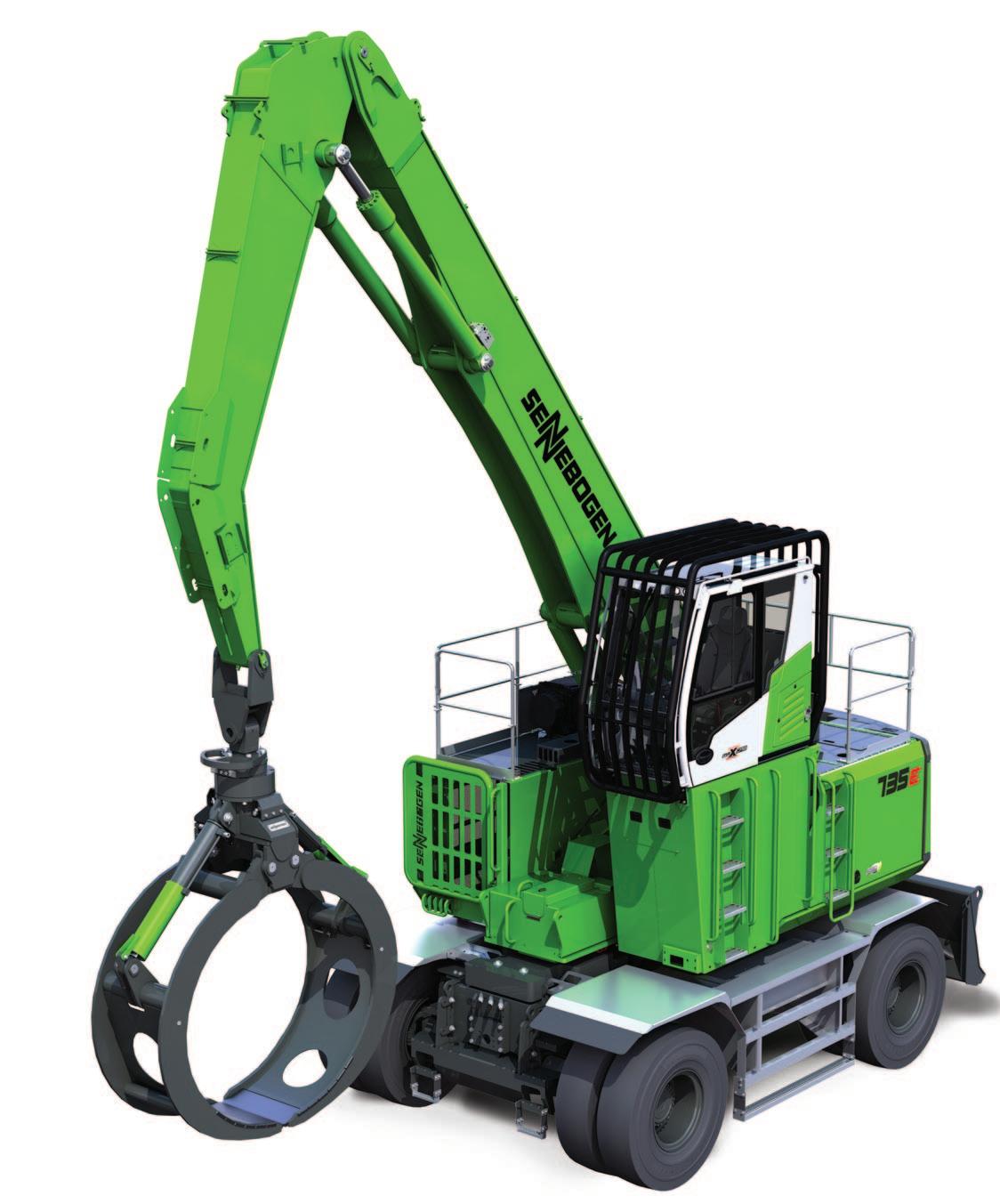
travel drive for material handlers, which is particularly useful when the machines are designed for continuous operation, for example in sawmills, timber handling or log yards. The 735 GED saves up to 30% in energy with the same performance. This not only significantly reduces operating costs, but
the machine is also more dynamic and quieter.
The Green Efficiency Drive is used where the largest share of energy demand is generated — when driving. Material handlers in particular do quite a lot of driving, which is why there is the greatest potential for savings here.
Equipped with the GED electric travel drive, the 735E saves up to 30% energy and therefore significantly reduces operating and service costs.
ENERGY RECOVERY VIA ELECTRIC TRAVEL DRIVE
The system solution, based on Bosch Rexroth components, was jointly developed into a marketable product, and was launched by SENNEBOGEN under the name ‘Green Efficiency Drive’. The Pick & Carry material handler 735 E is the first machine to contain the series production technology for electric travel.
While the machine is moving around the log yard, the diesel engine drives a generator, which generates the necessary electricity for the electric engines. During deceleration, the electric drive engines act as generators. This means that they supply
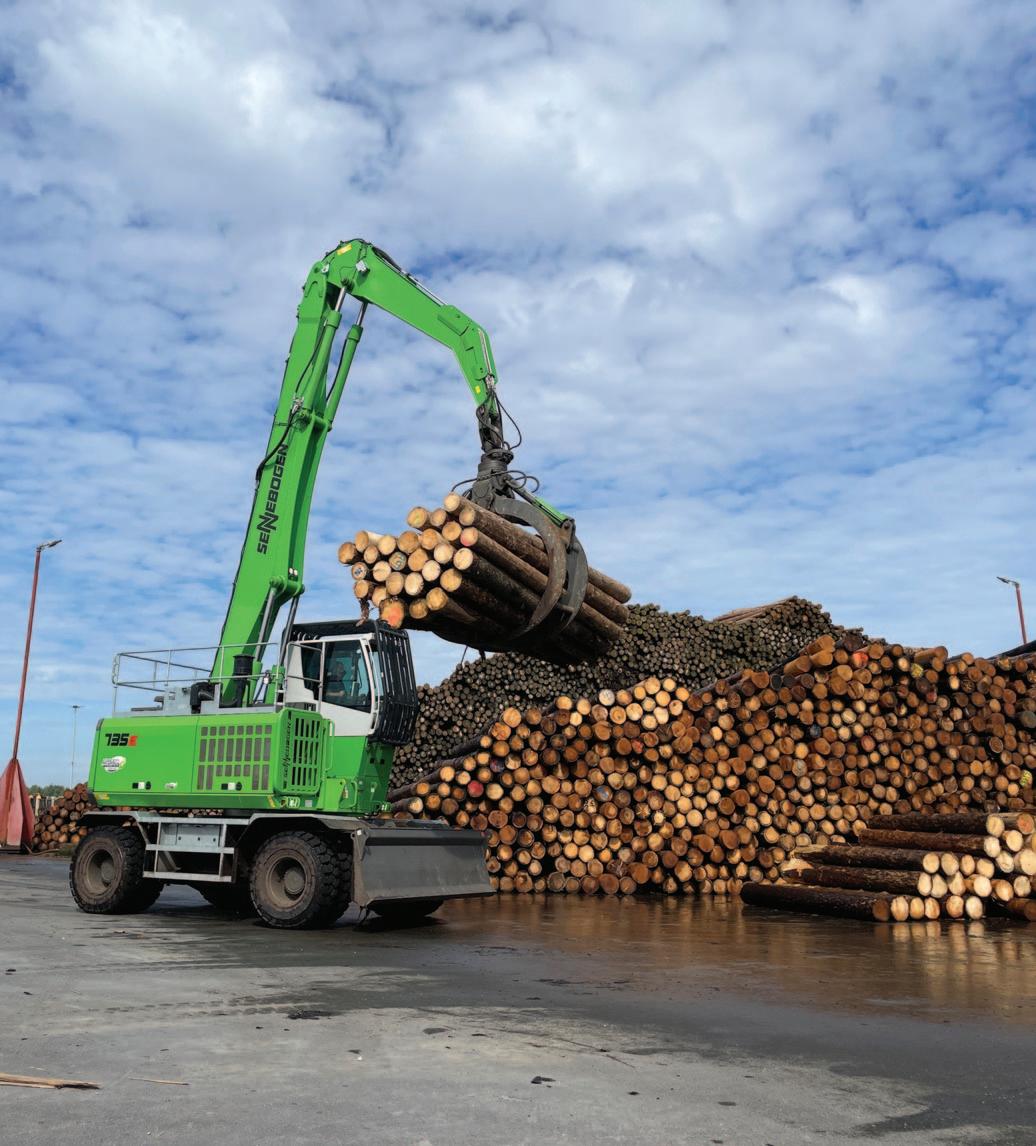
the auxiliary equipment with the energy required and relieve the diesel engine. The recuperated energy can even be stored for a short time, increasing the drive power.
Another advantage is that the use of modern components in the electrical system reduces heat loss. This can also save engine power for system cooling and achieve higher working dynamics.
GOOD FOR NATURE AND WALLETS — UP TO 30% ENERGY SAVINGS AND LOWER EMISSIONS
Over the entire product life cycle, the 735 GED saves up to 30% energy with the same performance level and therefore
saves operating and service costs on a large scale. Rightsizing the engine makes it possible to save on the machine’s consumption and thus also on emissions. Vibrations and noise are also significantly reduced — for pleasant and quiet operation, which relieves strain on people and the environment in the long term.
IMPRESSIVE HANDLING
Thanks to the electric drive motors, the 735 GED also has outstanding responsiveness when moving off and positioning. This results in a vehicle that can be moved dynamically and precisely, but that is also a pleasure to drive.
Supporting the transition to greener steel
sustainable steel production is essential...
... if the industry is to meet its target of halving emissions by 2050
With green steel being touted as a potential solution for the steel industry’s decarbonization goals, the industry is looking to capable partners to support their efforts.
Steel remains one of the most sought-after commodities in the global economy due to its role in most engineering and construction projects, as well as in the growing development of renewable technologies such as wind turbines and solar panels.
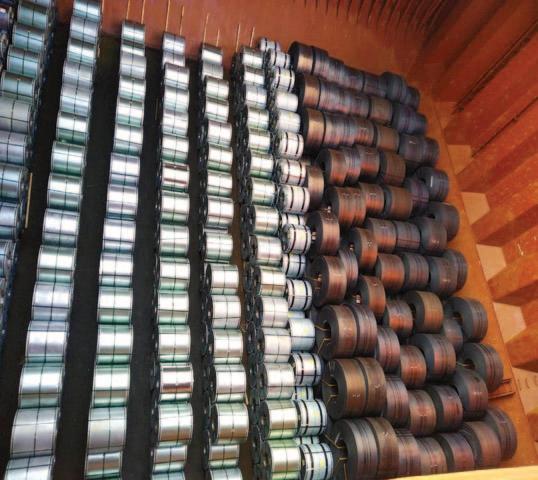
According to the World Steel Association, more than 330mt (million metric tonnes) of steel and steelmanufactured goods were traded in 2021: a sharp increase compared to 270mt transported the year before.
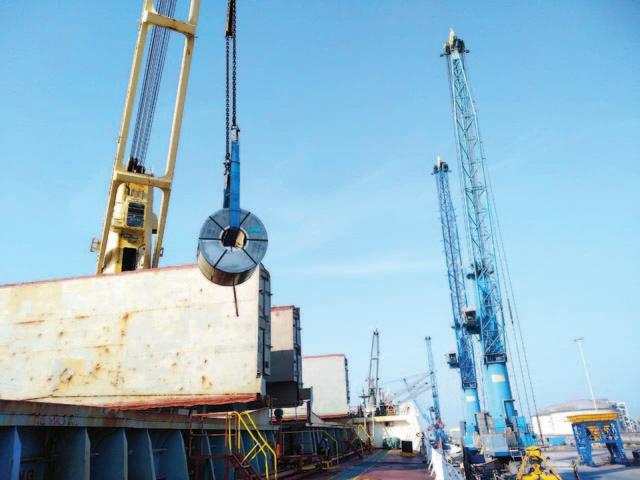
The materials needed to produce steel using traditional blast furnace processes —
specifically iron ore and coking coal — have also seen noticeable upticks in global trade over the past two years.
As a result, the steel industry now accounts for approximately 8% of total global carbon emissions, with every tonne of steel produced emitting about 1.85 tonnes of carbon dioxide. It is no surprise that the industry is now under pressure to become more sustainable.
According to the International Energy Agency (IEA), the steel industry is predicted to grow 33% by 2050 and has to at least halve its carbon emissions to meet global climate goals by the same year.
However, doing so economically, while keeping up with growing demand, is a challenge.
GREEN STEEL
‘Green steel’ is being touted as one
solution that could push the industry towards a long-term sustainable future.
To make green steel, coking coal is replaced in the production process with more environmentally friendly products, such as hydrogen, while electric furnaces take the place of traditional blast furnaces.
Hydrogen has proven to be an effective replacement for traditional coking coal in the steelmaking process. In April 2020, Swedish steel maker Ovako’s trial at its steel mill demonstrated that hydrogen is a viable source of energy with no negative impact to the steel quality produced.
A 2020 report from the European Parliament noted that replacing coal with hydrogen could decarbonize the steel industry. However, in doing so, it would drive up global steel prices by about onethird, although further refinement would reduce that gap in the following years.
EFFORTS SUPPORTING GREEN STEEL
Projects involving green steel have popped up around the world. Europe, in particular, has seen a vast number of steel production companies producing or transitioning to green steel, including SSAB in Sweden, Tata Steel in the Netherlands, and ArcelorMittal in Germany, as the continent looks to become a technological powerhouse for the industry.
In Asia, South Korea is set to be a major player in the development of green steel, with leading steelmaker POSCO creating a new entity to develop more sustainably produced steel.
India has also started on projects to reduce its dependence on coking coal. National steel producers Reliance and Adani have begun hydrogen-based production, while the Steel Authority of India and Rashtriya Ispat Nigam Ltd are striving to reduce carbon emissions from their production process.
Several other producers have taken similar steps. British Steel is looking into the use of green hydrogen to develop netzero steel, Australia’s BlueScope Steel is upgrading its traditional blast furnaces, and Germany’s Salzgitter just approved a significant funding proposal to produce low-carbon steel by 2033.
CHANGING COURSE
The development of green steel is likely to impact the global dry bulk cargo trade, including iron ore and coking coal, particularly when it comes to total commodities and its freight routes.
Currently, the majority of the world’s iron ore (54%) is shipped from Australia to China, which produces about 53% of global steel for smelting, with similar levels of coking coal finding their way to East Asia. However, with Europe leading the charge for green steel production, these commodities could soon find themselves changing course.
“Dry bulk cargoes are often not subject to major geographical shifts,” says Lars Hardeland, GAC Group Operations Director Shipping. “Australia and the Far
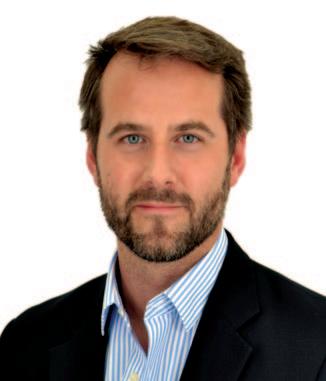
East remain the engine of the steelmaking industry but as new technology comes online and processes are refined, we could well see these patterns change.”
Despite dry bulk freight rates sliding from a recent high of 5,650 in October 2021 to 1,002 in September 2022 based on the Baltic Dry Index, demand for dry bulk remains high and is expected to grow for the steel industry.
EXPERIENCE IN DRY BULK
As one of the world’s foremost providers of shipping, logistics and marine services, the GAC Group has six decades of experience handling dry bulk vessels, with a very high level of expertise and a global network that can adapt to changing industry trends without impacting supply chains. As a major dry bulk agent, it is active in a diverse range of dry bulk markets and is ideally placed to handle increasing demand, particularly for the steel industry.
As green steel becomes more viable and commonplace, the need to ensure that hydrogen supplies are in the right locations will become even more paramount: a challenge that GAC is ready to take on.
“Having been providing tanker agency services since the 1970s, our tanker pedigree is also unmatched. Just as with the dry bulk industry, we are a global specialist agent for all tanker types. As customers explore the adoption of alternative fuels, we recognize the need to adapt to changing supplies, both in terms of the amount of cargo and where it is being shipped to,” says Hardeland.
PROVING THEIR METAL
GAC is already demonstrating its value around the world as a dry bulk partner as the sector embarks on it decarbonization journey.
“We are seeing increasing amounts of cargo arriving at Sohar to meet global steel demand,” says Ashan Silva, GAC Oman’s Business Manager at the port of Sohar.
“Turning a vessel around quickly is vital for port operations due to the high demand for berths. Our role is to monitor operations and readjust operational plans where needed to mitigate problems and optimize efficiency for our customers,” says Theodale Johns, the company’s Business Development Manager.
Meanwhile in India, the world’s secondlargest steel producer, steel production capacity is set to treble by 2030, which will have significant energy, environmental and economic ramifications.
Sankar Narayanan, Senior Manager –Shipping at GAC India, says GAC’s local experience and capabilities in handling dry bulk cargo vessels means that they are prepared for changes.
“Our well-planned loading and discharging operational expertise enable us to adapt to the changing demands of the dry bulk industry. Our market research tools, including commodity-based line-ups, delay analyses, tonnage updates and industry trends, help customers stay abreast and plan for operations intelligently,” he adds.
On the challenge of fast turnaround times, Narayanan adds: “Our research desk runs 24/7 and is committed to providing customers with information analyses to facilitate smooth planning and minimize waiting times.”
SUSTAINABILITY
GAC supports the steel industry’s bid to decarbonize with its own corporate sustainability efforts, which set the goal of becoming net carbon zero by 2050. A Sustainability Roadmap is in place to guide its operations towards an environmentally friendly future.
As the green steel transformation gathers pace, GAC aims to become knowledgeable and experienced in the development of this new-found technology, as well as standing ready to support industry partners in the transition and when green steel becomes mainstream.
Group Operations Director“As ship agents, we are committed to supporting bulker operators and managers to enhance their efficiency by ensuring a fast turnaround time through cost-effective solutions. We are here to remove any bottlenecks from a vessel’s operation while at port. Our team works closely with terminals round-the-clock to support cargo operations, sharing information with key stakeholders and keeping the global bulker fleet moving.”
In South Africa, GAC has noted a steady incline of dry bulk cargo arrivals as the economy reopens following the pandemic.
The transition will not be cheap but the industry is gradually realizing the long-term benefits. And by working with reliable ship agents who embrace sustainability, the transition will undoubtedly be smoother, easier and trouble-free.
As a renowned and respected ship agent, GAC looks to be ideally placed to support the steel industry, as well as the wider dry bulk community, with its decarbonization efforts through costeffective and modern solutions that keep global trade moving and turn around vessels at port in record times.
New all-electric heavy lift ship crane
Liebherr expands heavy-lift ship crane portfolio with new 800-tonnes crane.
Liebherr’s heavy lift crane series is being expanded with an 800-tonnes crane.
The aim with the new crane is to establish itself in the growth market of ever larger wind industry components. The crane is fully electrically powered and thus enables a reduction of CO2 emissions on the ship side in scenarios typical for heavy lift vessels.
The growth of wind turbines is leading to increasingly heavy individual component weights. In addition, the handling of large components requires a longer outreach of the cranes used than is often the case in the market. The supply of heavy lift vessels with cranes offering a maximum lifting capacity of 800 tonnes is lower than the expected future demand. Liebherr therefore sees a growth market in this crane segment and in the matching new shipbuilding. The Liebherr ship crane enters a new segment and expands the product portfolio of heavy lift ship cranes. “The new cranes follow on from a long tradition and decades of experience in building ship cranes. The first ship crane was delivered by Liebherr in 1958. The push into the 800 tonnes size segment does not represent new territory —
Liebherr unveils 800-tonnes crane
Liebherr has already supplied onshore and offshore cranes in the 3,000 5,000 tonnes category,” comments Gregor Levold, Sales Director for Liebherr Offshore, Ship and Port Cranes.
ALL-ELECTRIC AND CO2 EMISSION-FREE
In addition to the much larger dimensions of the crane, the LS 800 E is particularly impressive due to its all-electric drive concept. All sections of the crane are electrically driven. As a result, the machine achieves higher energy efficiency and thus significantly reduces the ship’s CO2 emissions. Liebherr is already meeting future environmental requirements in the maritime industry. “We have many years of experience with all-electric drives from the port equipment sector, among others.
As usual, the development of the crane is done completely in-house. We can also cover the procurement of individual components largely in-house at Liebherr. These are invaluable advantages for our customers, especially nowadays,” adds Levold. In addition, all drive components are installed inside the crane. This facilitates the integration of the crane into the ship’s design and enables better
utilization of the areas below deck.
TRADITION MEETS FUTURE
The new ‘Master V’ control unit offers the highest computing power. The accompanying faster data processing enables the integration of future assistance systems and semi-automated process applications. All heavy-lift cranes are characterized by the Litronic control system developed in-house. It combines speed and precision and thus ensures a safe and at the same time efficient loading process. Continuous further development means that the latest features and applications will continue to be available to Liebherr ship cranes in the future.
NEW CRANE DESIGNATION AND DESIGN
During the design of the LS 800 E, the designation of the Liebherr ship cranes was also adjusted. Instead of the previous CBB crane designation, the cranes will in future be called LS. The new terms and the capital letters used allow a direct assignment as Liebherr (L) ship crane (S). The number, as part of the designation, provides information about the maximum load capacity, which is 800 tonnes for the
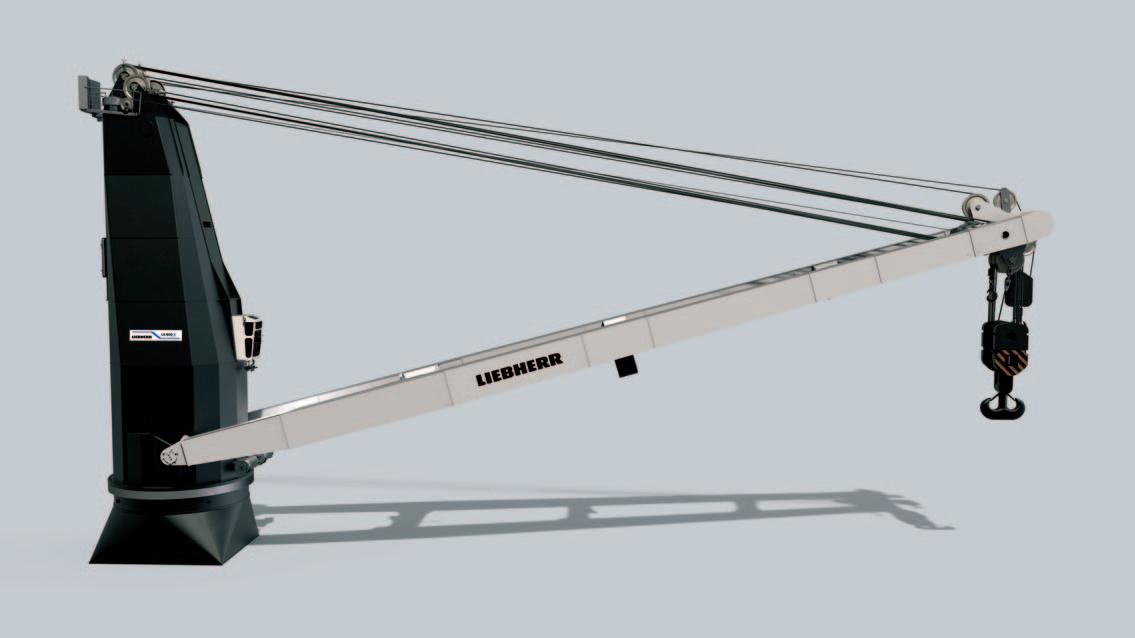
LS 800 E. The E stands for the electric drive and is supplemented by the suffix ‘Allelectric’ in the case of fully electric cranes such as the LS 800 E.

The exterior design of the crane has been renewed. The crane is factory coloured in white and grey and the designation of the crane is on the tower. The blue accent and the blue E symbol next to the crane type designation visually clarify the electric drive of the machine. This allows all future customers to directly communicate advanced and environ mentally friendly crane technology to their stakeholders.
ABOUT LIEBHERR-MCCTEC ROSTOCK GMBH
Liebherr-MCCtec Rostock GmbH is a major European manufacturer of maritime handling solutions. The product range includes ship, mobile harbour and offshore cranes. Reachstackers and components for container cranes are also included in the product portfolio.
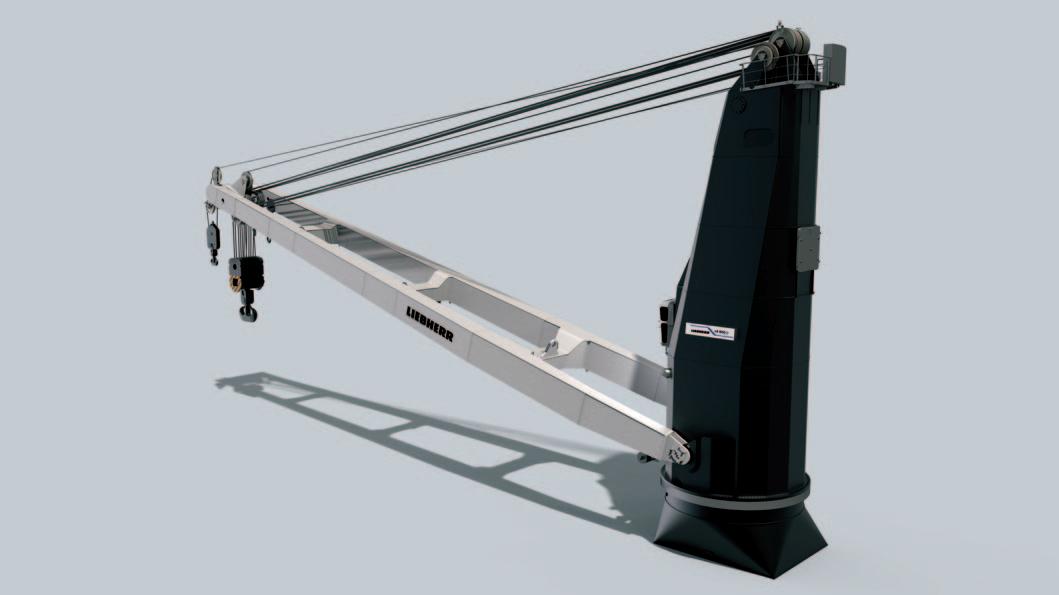
ABOUT THE LIEBHERR GROUP
The Liebherr Group is a family-run technology company with a broadly diversified product range. The company is one of the largest construction machinery
The new terms and the capital letters used allow a direct assignment as Liebherr (L) ship crane (S). The number, as part of the designation, provides information about the maximum load capacity, which is 800 tonnes for the LS 800 E.
The LS 800 E has all-electric drives and offers a working radius of up to 39 metres.
manufacturers in the world.
However, it also offers high-quality, useroriented products and services in many other areas. Today, the group comprises more than 140 companies on all continents. In 2021, it employed more than 49,000 people and generated a total consolidated turnover of over €11.6 billion. Liebherr was founded in 1949 in Kirchdorf an der Iller in southern Germany. Since then, the employees have pursued the goal of convincing their customers with sophisticated solutions and contributing to technological progress.
Company Page Company Page
4B BRAIME Components Ltd 98
A/S Cimbria 10
Agudio / Leitner S.p.A 80
Alex Stewart International Corporation Ltd 8
AUMUND Foerdertechnik GmbH (AUMUND Group) 101
Bedeschi SpA
BEUMER Group GmbH & Co KG 17
BossTek 129
Bühler AG, Grain Quality and Supply 65
Cambelt International LLC 69, 86 Cleveland Cascades Ltd 135
CLIIN Robotics 15 Conductix-Wampfler
Control Systems Technology Pty Ltd 103
CRS — Container Rotation Systems Pty Ltd 3
DCL, Incorporated 124
Doppelmayr Transport Technology GmbH 97
DSH Systems Ltd. 127
Dunlop Conveyor Belting 93 E-Crane Worldwide 5
ESI Eurosilo BV 123
Hägglunds AB 90
Italgru S.r.l. 76
J & B Grijpers b.v. 121 Kilic Engineering 73 Konecranes Port Solutions - Konecranes GmbH 79
LD Ports & Logistics 18
Liebherr-MCCtec Rostock GmbH Inside Front Cover Mack Manufacturing Inc 95 Martin Engineering 89
MGB & Company 87
MRS Greifer GmbH 119
N.M. Heilig B.V. 63 Negrini Srl 117
Neuero Industrietechnik GmbH Back Cover ORTS GmbH Maschinenfabrik Inside Back Cover
PEINER SMAG Lifting Technologies GmbH 110
RAM SMAG Lifting Technologies (UK) Ltd 131
RULMECA HOLDING S.P.A. 104 ScrapeTec Trading GmbH 83
SENNEBOGEN Maschinenfabrik GmbH Front Cover
SIBRE - Siegerland Bremsen GmbH 9 Starlinger & Co. Gesellschaft m.b.H. 142
TAKRAF GmbH 49
Telestack Limited 75
Terex Deutschland GmbH 109 TMPB (Terminal de Multiusos do Poço do Bispo) 43 TMSA Tecnologia em Movimentação S/A 133 Van Beek 107
Verstegen Grijpers BV 113 Vigan 114
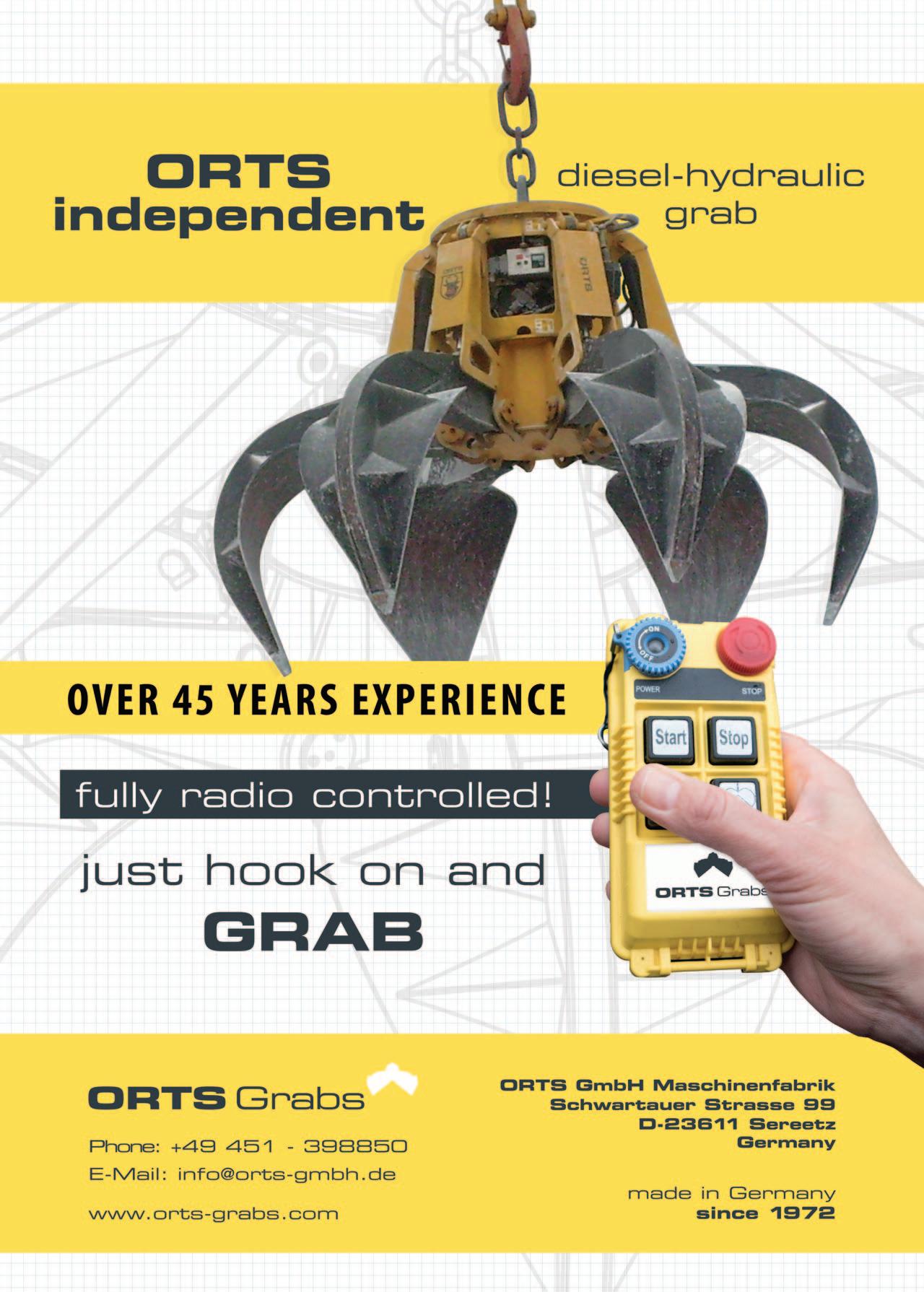
SHIP LOADER SPECIALIST
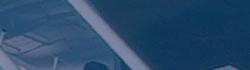

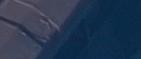

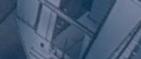

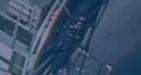
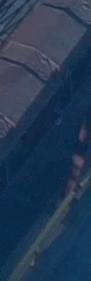
NEUERO produces the most reliable and high-quality bulk ship loaders worldwide. Environmentally friendly with less dust, less noise and more efficiency | neuero.de/en
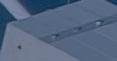
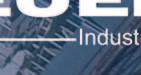
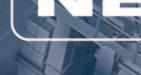

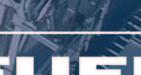
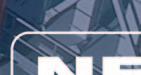
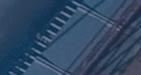
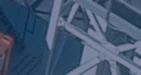


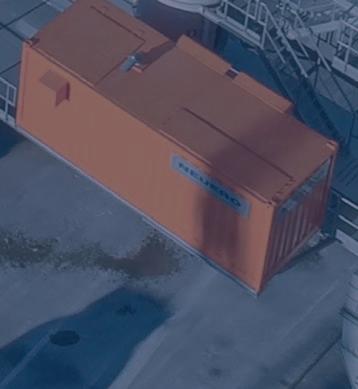
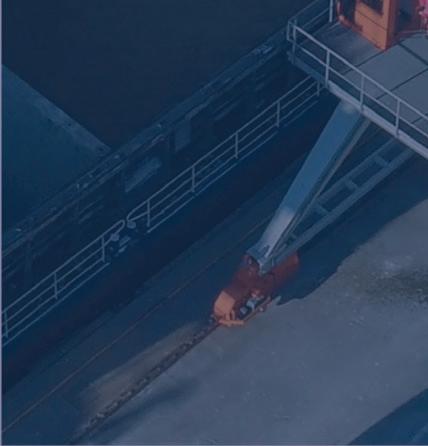
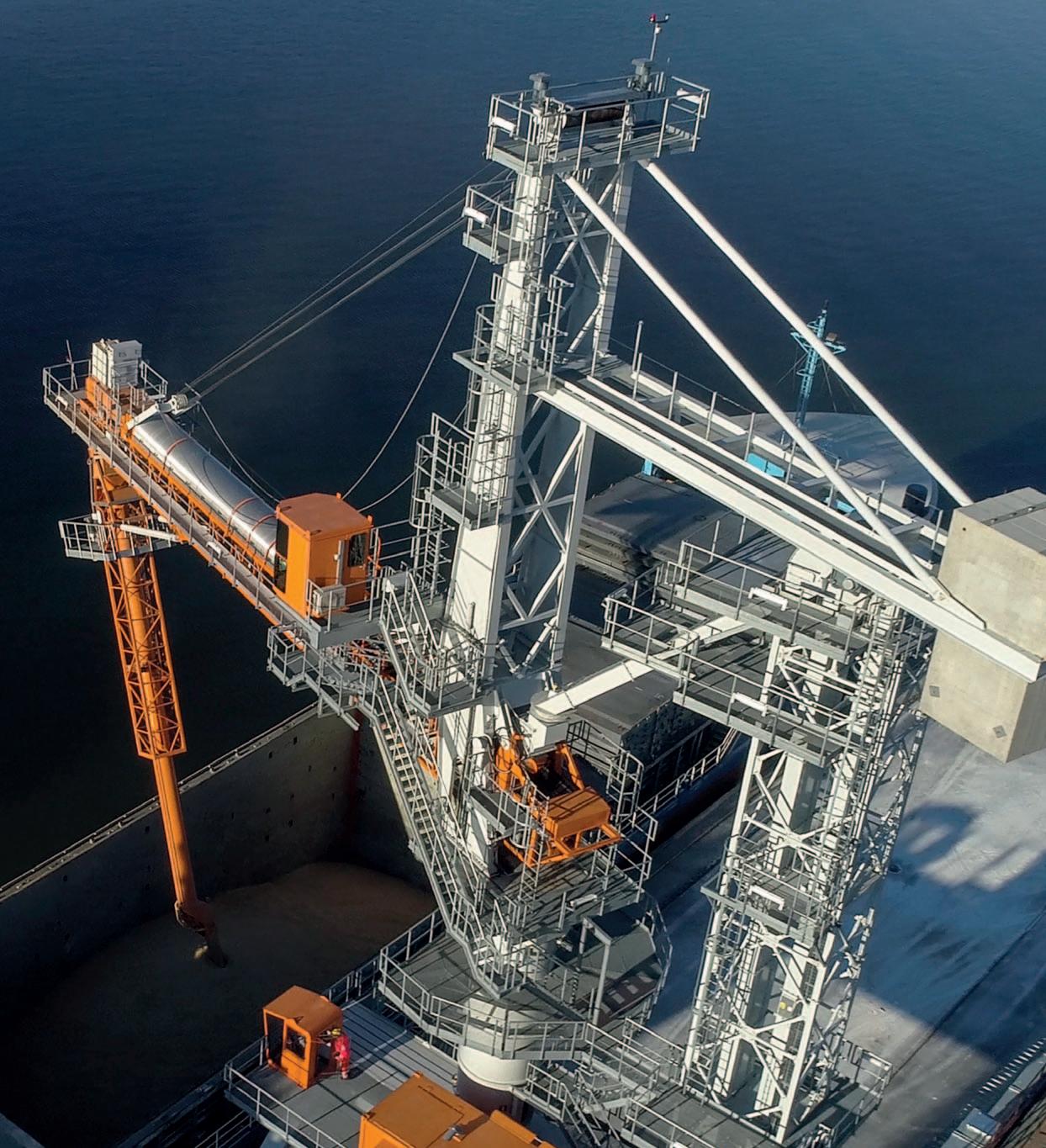