
8 minute read
ıMetal Endüstrisinde Azot Gaz
by Eda
UYgULAMAYA gÖRE İSTEnEn SAFLIKTA, YERİndE AZOT ÜRETİMİ
tuğba memİLİ
Advertisement
ar-ge takım lideri mehmet Yanardağ
ar-ge uzman yardımcısı
Soluduğumuz havanın yüzde 78,1’ni oluşturan ve çoğunlukla saf halde bulunan azot gıda endüstrisinde, elektronik, kimya, metal sanayi vb. gibi sektörlerde geniş kullanım alanına sahiptir. azot, inert özellikleri, atmosferdeki bolluğu ve üretim kolaylığı nedeniyle endüstriyel, bilimsel ve laboratuvar uygulamaları için ideal bir gazdır.
Bilinen metotlarla azot Sağlamak yerine, kendi azotunuzu üretmek, uygulamaya göre yüzde 50 ile yüzde 90 araSında taSarruf Sağlar.
Azot gazlarının genel olarak özellikleri renksiz, kokusuz, tatsız ve kuru olmasıdır. Azot gazı başlıca şunlar için kullanılır; • Malzemelerin oksidasyona karşı korunması • Bakteriyolojik büyümelerin engellenmesi • Yanma riskinin azaltılması • Kuru ve oksijensiz ortam sağlanması
Ticari olarak kullanılan azot gazının büyük çoğunluğu, az sayıda üretici tarafından damıtma metoduyla üretilmektedir.
Atmosferi oluşturan her bir gaz çok düşük sıcaklıklarda kaynama noktasına sahiptir. (CO2 için bu değer donma noktasıdır) n Oksijen -184 °C (eksi 184 santigrat derece) n Argon -186°C (eksi 186 santigrat derece) n Azot -196°C (eksi 196 santigrat derece) n Karbondioksit -79°C (eksi 79 santigrat derece)
Ayrımsal Damıtma yöntemi için büyük miktarlarda basınçlı hava kullanır, filtreleme yolu ile temizlenir ve aşamalı olarak soğutulur. Bu yöntemde azot gazı sıvı hale getirilir ve sıvı halde depolanır, sevk edilir. Genel olarak damıtma yöntemi pahalı bir işlemdir. Azot fiyatlandırmasına ek olarak, gizli maliyetler arasında tank kiralama ücretleri, teslimat ücretleri, çevre ücretleri, tank muayeneleri yer almaktadır. Bu maliyetler göz önüne alındığında azot yıllık maliyetine on binlerce lira eklenebilmektedir.
Sıvılaştırma yöntemi ile azot üreten firmalar, kriyojenik sıvı, sıvı ve gaz azot tüpleri ile azotu kullanıcılara sağlarlar. Havadan sıvılaştırma ile azot gazı üretimi enerji, işletme sahiplerine önemli ölçüde maliyet oluşturur.
Gelenekselleşmiş yöntemlerin dışında kullanıcıların kendi tesisleri içinde azot ihtiyacını karşılaması günümüz teknolojisiyle artık hem daha ekonomik ve avantajlı hem de daha kolay olmaktadır. Üretim kapasitesine uygun, sürekli, güvenli ve daha düşük maliyetlerde azot jeneratörleri ile azot ihtiyacı karşılanabilmektedir.
Bilinen sıvılaştırma yöntemi ile azot jeneratörü teknolojisi kıyaslandığında, azot jeneratörü teknolojisi ile, uygulamaya ve kullanım miktarına göre %50 ile %90 arasında tasarruf sağlanabilmektedir. Azotu toplu olarak satın almakla karşılaştırıldığında, azot jeneratörlerinin kararlı, güvenilir ve en önemlisi, uygun maliyetli olduğu görülmektedir. Azot jeneratörleri yatırımının kendini amorti süresi ortalama 1 ile 3 yıl arasındadır.
Azot jeneratörlerinin kullanılabilirliği
Üretim tesislerinde düzenli olarak azot ihtiyacı duyuluyorsa, mevcut yöntemlerle, tank kiralanarak ya da satın alınarak bu ihtiyaç sağlanabilmektedir. Bu tanklar hem çok pahalı hem de üretim tesislerinde çok büyük alanları işgal ederler. Yüksek basınç altında doldurulan tankların güvenlik riskleri de göz önünde bulundurması gereken önemli bir konudur. Gelişen teknoloji ile bu sorunları ortadan kaldırma odaklı çalışmalarda en önemli gelişme, kullanıcıların kendi azot ihtiyacını yerinde üretebilmesi olmaktadır. Yerinde azot üretimi sağlayan iki yöntem bulunmaktadır. Bunlar; PSA (Pressure Swing Adsorption – Basınç Salınımlı Adsorpsiyon) Azot Jeneratörleri ve Membran azot jeneratörleridir. Membran, oksijen ve azotun ince bir hollow fiber membran yüzeyinden geçirgenliğini kullanarak azot üreten yöntemdir. Buradan oksijenin membrana nüfuz etme hızı azota göre daha hızlıdır. Bu fark sayesinde oksijen ve azot yüzeyde ayrışır ve azot oranı zenginleştirilir. Ancak bu yöntemle maksimum 99,9% saflığa kadar azot üretilebilmektedir. Diğer yöntem PSA, azot ve oksijenin ayrıştırması için adsorplayıcı olarak karbon moleküler sieve (CMS) kullanılmaktadır. CMS’in özelliği, basınç altında havadaki azotun geçmesine izin verirken oksijen gazını tutuyor olmasıdır. Basınç düştüğünde CMS oksijeni serbest bırakır ve rejenerasyon gerçekleşir. Basınçlandırma ya da basınçsızlaştırma döngüsünde, azot jeneratörü ile kullanılan buffer (depolama) tanklar sayesinde sabit azot saflığı ve debisi sağlanır. Yerinde azot üretim yöntemlerinin temel avantajları saflık kontrolü, güvenli üretim, maliyet tasarrufu ve verimliliktir.

Mikropor PSA tip Azot Jeneratörü
Saflık Kontrol
Gaz şirketleri azot tanklarını bütün müşterilerine standart olarak %99,99 saflıkta azot ile doldururlar. Çünkü %99,99 saflıktaki azot sektördeki uygulamaların büyük çoğunluğunu karşılamaktadır. Ancak yüksek saflıkta azot tankı alan bu işletmeler için düşük saflıkta azot (%95, %97, %98 veya %99) yeterli olabilir. Lazer kesim, elektronik lehimleme, plastik ekstrüzyon gibi başlıca uygulamalarda %99,99 saflıktan daha düşük saflıkta azot yeterli olabilmektedir. Azot jeneratörleri ile, tüketiciler ihtiyaç duyulan azotu, istenen saflık seviyesine göre ayarlayıp üretebilirler, bu da yüksek saflıkta depolanmış azotun maliyetiyle karşılaştırıldığında genellikle önemli bir maliyet tasarrufu sağlar. %95 saflık seviyesinde azot üretmek, %99,99 saflıkta azot üretmeye göre çok daha ucuz bir yöntemdir ve gerekli basınçlı hava ve dolayısıyla kompresör seçimi üç kat daha düşüktür. Azot jeneratörleri ile yerinde azot üretimi saflık ihtiyacına bağlı olarak, 12 ile 24 ay arasında kendini amorti edebilmektedir.
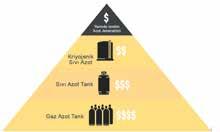
Güvenli Üretim
Yüksek basınçta doldurulmuş azot tüpü ağırlığı yaklaşık 45 kg’dır. Bu tüpler taşınırken çarpması, düşmesi ya da devrilmesi durumunda büyük tehlike yaratmaktadır. Diğer bir yandan, sıvı halde taşınan azotun, temas halinde soğuk yanık riski bulunmaktadır. Azot jeneratörü ile üretim sırasında bu riskler minimize edilir.
Maliyet Tasarrufu
Azot jeneratörü teknolojilerinin maliyet tasarrufu sağlamasının en cazip nedeni yatırımının kısa vadede amorti edilebilmesidir. Ayrıca, işletme sahiplerinin tank kiralamak için ödedikleri ücretler, azot jeneratörü kurulumundan sonra ortadan kalkacaktır. Sahada yalnızca sahip olunan azot jeneratörü bulunacak ve istendiğinde ihtiyaç duyulan miktar kadar azot üretilebilecektir. Ve buna ek olarak, kiralanan tüplerin iade edildiğinde içinde ücreti ödenen ancak kullanılmadan kalan azot dolayısıyla oluşan zararlar da ortadan kalkacaktır.
Verimli ve Çevre Dostu Olması
Azot jeneratörü sayesinde sıvılaştırma işlemi olmayacağından dolayı, azot gazını sıvı hale getirmek için kullanılan enerjiden tasarruf edilmektedir. Azot jeneratörleri için ilk kurulum sonrası herhangi bir taşıma işlemi yoktur, bu sayede, azot tüpü dağıtım araçlarının ürettiği karbondioksit emisyonlarını azaltır ve teslim edilen her bir tüp için ihtiyaç duyulan üretim ve teslimat aşamalarını ortadan kaldırarak verimlilik ve çevresel faydalar yaratır. Ayrıca kısmen de olsa dolu tüplerin geri dönüşümde boşaltılması/havalandırılması sırasında azot kullanılır. Azot jeneratörleri ile bu atık azot kullanımı da olmamaktadır. Azot jeneratörleri ilk yatırımını çok hızlı bir şekilde karşılayabilen bir takım avantaj ve kolaylıklar sağlar. Bunlar; • Daha az
bakım/arıza
gerekliliği: Azot jeneratörüne sahip işletmelerde sürekli azot üretimi olacağından tanklarını kapatmak zorunda olmayacaklardır, bu durum da bakım/arıza sürelerini azaltacaktır. • Daha az iş gücü: Tankları düzenli olarak açıp/ kapatma ihtiyacı olmayacağından bununla ilgili işçilik maliyeti düşecektir. • Daha az risk: Tankların taşınma durumu ortadan kalkacağı için taşıma sırasında ortaya çıkacak yanma, patlama vb. durumlar büyük ölçüde azalacaktır. • Daha az depolama alanı ihtiyacı: Azot jeneratörüyle sürekle doldurulan tek bir tank ile üretim tesislerinin fazladan tank depolama ihtiyacını ortadan kaldıracaktır. Böylelikle tesisler içinde farklı amaçlar için kullanılmak üzere değerli bir alan sağlanacaktır. • Daha az atık: Azot jeneratörleri belirlenen basınç, debi ve saflıkta azot üretebildiğinden, gerekli saflık seviyesine ulaştırmak için hiçbir gaz boşa harcanmaz. Kiralanan tüpler, içinde bir miktar azot ile iade edilir. Özellikle yüksek miktarlarda azot kullanan işletmelerde bu durum büyük israfa neden olabilir. Ayrıca uzun süre kullanılmayan tüplerin, tahliye vanasından bir süre azot gazının boşaltılması gerekmektedir. Bu işlemler maliyeti ödenmiş bir kaynağı israf eder.
Saflık ve Azot debisine göre en uygun Azot tedarik yöntemi grafiği
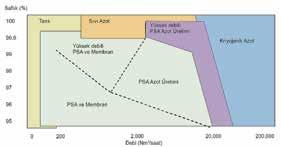
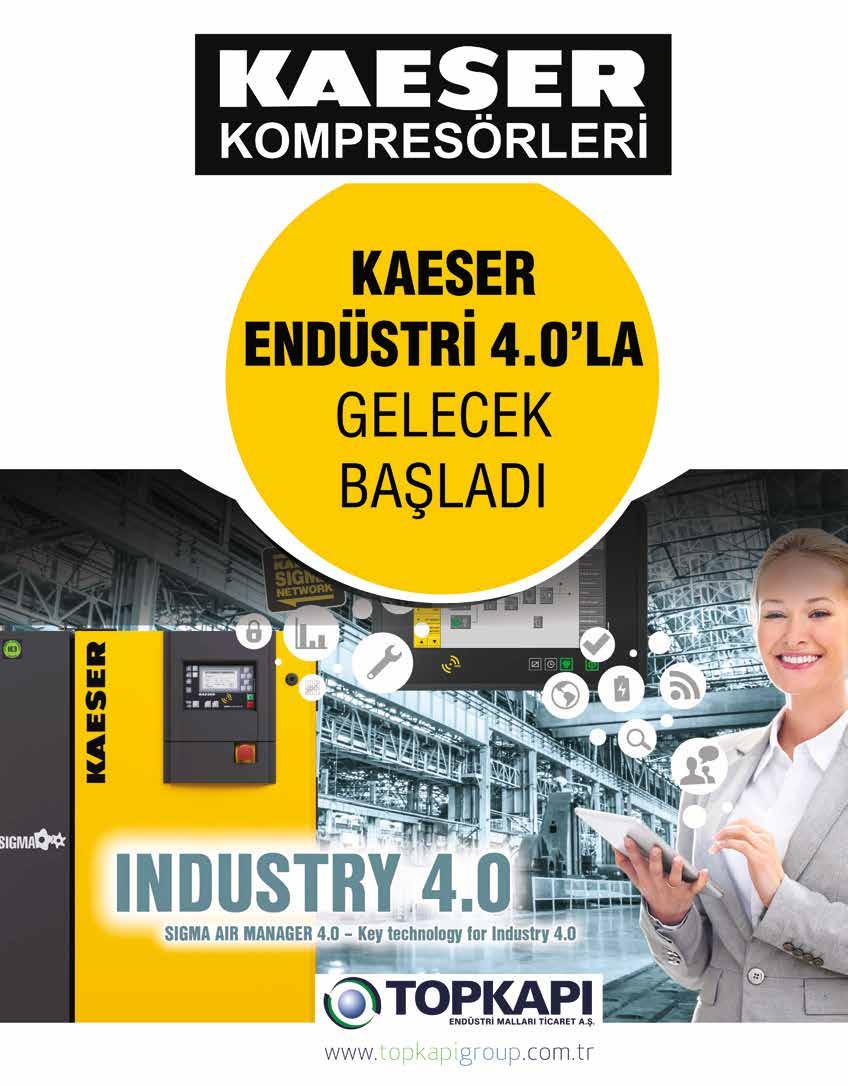
METAL EndÜSTRİSİndE AZOT gAZI
CEngİZ ATEŞ kimya yüksek mühendisi penta gaz Sistemleri
azot gazı işlem görecek malzeme yüzeyinde oksijenin etkisini ortadan kaldırmak için uzun yıllardır endüstride pek çok alanda yaygın olarak kullanılmaktadır.
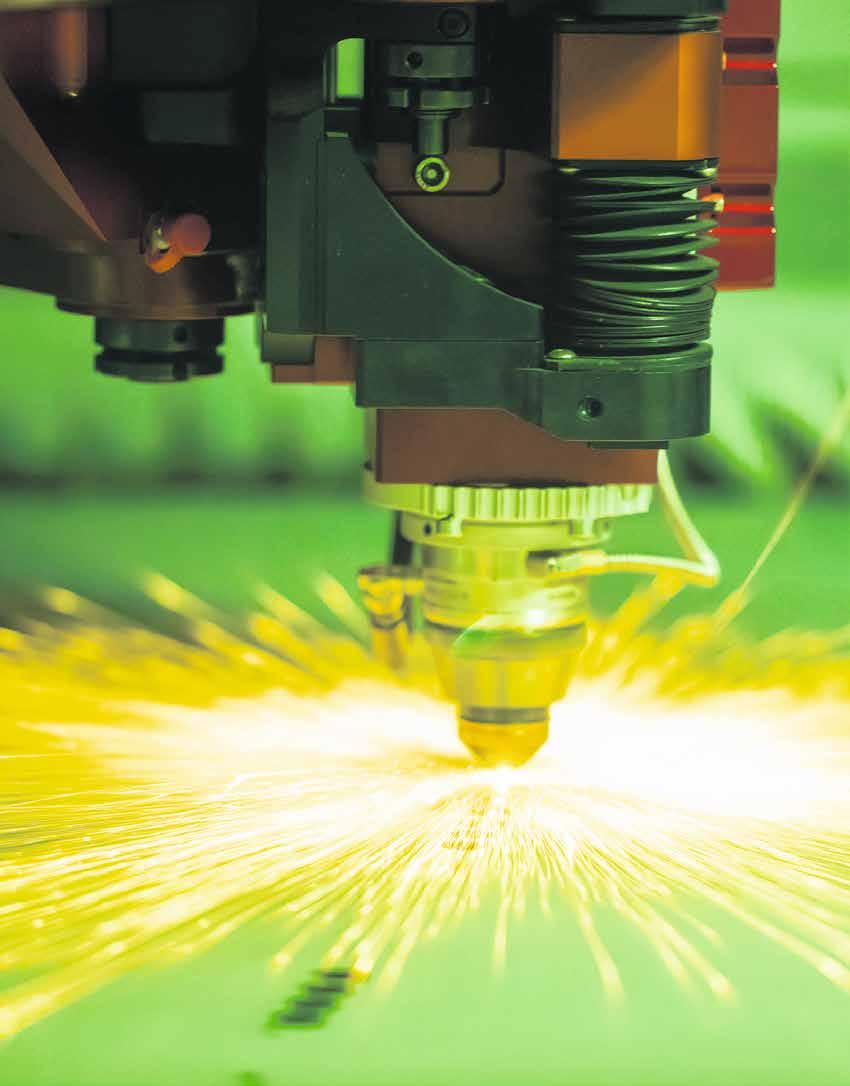
işletmelerin temel iHtiyacı optimum maliyetle makSimum verim ve kÂrlılıktır. Bu nedenle proSeS gerekSinimleri doğru analiz edilmeli; Buna uygun SiStem ve Çözümler üretilmelidir.
Yerinde azot üretim sistemleri yaygınlaşmadan önce dış kaynaklardan tedarik edilen azot gazı AZOT Jeneratörleriyle birlikte ihtiyaç duyulan miktarda ve kalitede kullanıcının kendi gazını üretmesine imkan sağlamıştır. Örneğin %95 saflıkta azot gazının ihtiyaca cevap verebildiği durumda çok daha yüksek saflıklarda, dolayısı ile daha yüksek maliyetlerle gaz üreticisinden satın alma bir zorunluluk iken bu durum tamamen değişmiştir.
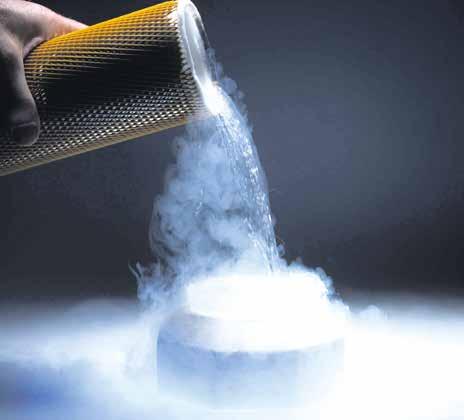
LAZER KESİM
Lazer kesim metal sektöründe üretim kabiliyetleri, hızı ve şartları değiştiren bir teknoloji haline geldi. Özellikle son dönemlerde yük güce sahip lazer kesim makinelerinin erişilebilir fiyatlarla piyasaya arzı kullanıcı imkanlarını ve sınırlarını da ciddi ölçüde değiştirmiştir. Lazer kesim makinelerinde azot gereksinimi CO2 ve FIBER makineler için paslanmaz çelik kesiminde aynıdır. Paslanmaz kesimde temiz bir kesim yüzeyi için 99,999 % saflıkta azot kullanımı önerilen referans kalite değeridir.
Daha önce oksijenle kesimin zorunlu olduğu malzeme kalınlıkları yüksek güçlü makinelerin kullanımıyla birlikte azot ile daha yüksek hızlarda kesilebilir hale gelmiştir. Kesim kalitesi ve hızını artırmak için sektörde yeniliklere öncülük eden firmalarda azot ve oksijenin belli oranlarda karıştırılarak kullanıldığı bir süreçteyiz. Esas olan veriye dayalı çözümler üretmektir. Bu maksatla sektörler arası iş birliği ve proje geliştirilmesi öncelenmelidir.
6 kW FIBER LAZER
Kalınlık 4 mm 4 mm Kesme gazı Kesim hızı mm/dak Oksijen 4.000 Azot 10.000
15 kW FIBER LAZER
Kalınlık 4 mm 4 mm Kesme gazı Kesim hızı mm/dak Oksijen 3.600 Azot 26.000
Tablolardan görüleceği üzere, ortalama bir güçte lazer makinasında bile kesme gazı değişikliği kesim hızında 2,5 kat bir artışa neden olmakta; bu değer aynı kalınlıkta malzeme için 15 kW bir makinede 10 kata çıkmaktadır. Sonucun en basit değerlendirmesi ortalama güçte bir makinede bile kesme gazının değişimi ile bir makine ile üç makine üretimi gerçekleştirilebilir. Bu durum üretim alanının yatırım kaynağının verimli kullanılması konusunda dikkate alınmalıdır.
İlaveten yüksek güç lazer kesim makineleri ile kalın çelik plakaların 6-7 kat hızlı kesimi söz konusudur.
15 kW FIBER LAZER
Kalınlık 10 mm 10 mm Kesme gazı Kesim hızı mm/dak Oksijen 1.200 Azot 8.000
ISIL İŞLEM
Isıl işlem metallerin mekanik ve kimyasal özelliklerinin yüksek sıcaklıklarda kontrollü olarak değiştirilebildiği bir prosestir. Bu işlem sırasında ortamda oksijen varlığı sadece istenmeyen oksit yüzey değil parçanın mekanik özelliklerini de etkileyen olumsuz sonuçlara neden olur. Isıl işlem prosesinde ihtiyaç duyulan azot saflığı 99,999 % (10 ppm O2) mertebesinde olmalıdır. Yukarıda genel değerlendirmesi yapıldığı üzere ihtiyaç duyulan kriterlerin iyi analiz edilmesi yatırım ve işletme maliyetlerinin optimizasyonu açısından son derece önemlidir. Azot Üretiminde küçük ve orta ölçekteki sistemlerde PSA teknolojisi 99,99 % azot üretimi için makul işletme maliyetleri sunarken, daha yüksek saflıklarda (99,999 % ve üzeri) hem yatırım hem de işletme maliyetleri ciddi ölçüde artmaktadır. Bu nedenle özellikle yükse saflık ihtiyacı olan yerlerde PSA ileri saflaştırma sistemi (DeOXO) ile entegre edilmelidir. Böylelikle daha düşük işletme maliyeti ile sürdürülebilir yüksek saflıkta azot gazı üretmek mümkün olur.
99,999 PSA PSA+ DeOXO
Hava Azot Oranı 12:1 4:1
Kurulu Güç 3 Birim 1 Birim
Seçimler yapılırken bütüncül yaklaşım; işletme ihtiyaçlarının tanımı ve hedeflerine hizmet edecek sistemin seçimi açısından çok önemlidir. Teknik gereklilikler, seçim öncesi tercih edilecek teknolojilerin avantaj/dezavantajları iyi analiz edilmeli; işletmenin hedefleri göz önünde bulundurularak çalışma şekillendirilmelidir. Unutmayalım ki;makinelerin suçu olmaz, önerenin yada seçenin suçu olur.