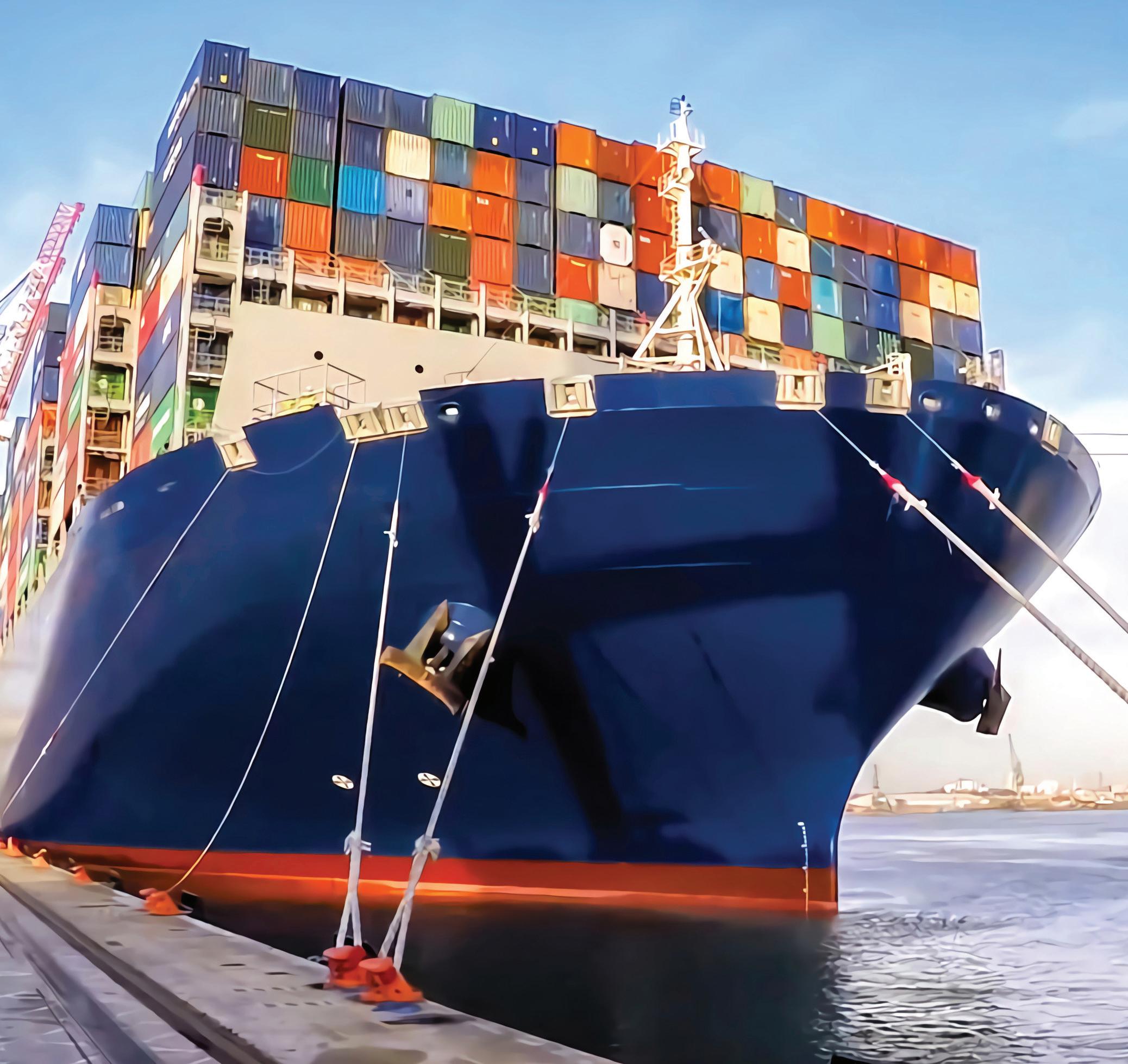
5 minute read
Control de corrosión inteligente y sostenible para el acero
por ZONA DE PINTURAS
Una nueva generación de inhibidores está impulsando actualmente la innovación en el mercado de recubrimientos industriales.
Advertisement
El 3,2% de las emisiones mundiales de CO2 provienen del acero recién fabricado para reemplazar el acero corroído, lo que le cuesta a la economía mundial billones de dólares al año. En 2016, la NACE International (anteriormente conocida como Asociación Nacional de Ingenieros de Corrosión) estimó este costo en US$2,2 billones.
Por su parte, el 40 % de todo el acero nuevo se usa para reemplazar el acero dañado o destruido por la corrosión, lo que equivale a un estimado del 3,2 % de las emisiones mundiales de CO2 solo en mantenimiento, de acuerdo al doctor Hoffman (2020).
“A medida que el mundo está despertando a una nueva era verde, una de las mayores ineficiencias del mundo no se aborda”, es una de las citas que junto a los datos anteriores presenta la compañía Hexigone Inhibitors, fundada en 2015, y con una tecnología producto de décadas de trabajo en la búsqueda de alternativas a los cromatos en el Grupo de Corrosión de la Universidad de Swansea (Reino Unido).
Hablamos con su fundador, el Dr. Patrick Dodds, quien es licenciado en Química y cuenta con una Maestría en Tecnología de Acero, además de un doctorado en Ingeniería de Materiales.
El Dr. Dodds, quien además es miembro honorario de Investigación en la misma Universidad de Swansea, descubrió un mecanismo de protección altamente efectivo ante los desafíos expuestos.

Cuenta que durante 30 años la academia ha buscado un reemplazo para el cromato hexavalente. “Esa es la razón por la que se llevó a cabo la investigación, porque buscábamos tecnología y lo hicimos un poco diferente; así que no solo tomamos lo que había en el mercado, creamos nuevos inhibidores”, comenta.
Desafíos estructurales
En un artículo de 2020, la asociada técnica de Halliburton, Kausalya Tamalmani, sostuvo que la corrosión es una de las principales razones de las fallas de la infraestructura dentro de la industria del petróleo y el gas.
A su vez, según la misma NACE, el costo anual de la corrosión para la industria del petróleo y el gas solo en los Estados Unidos es de aproximadamente US$27.000 millones. Esto ha llevado a algunos expertos, como el presidente de CorrMagnet Consulting, Sankara Papavinasam, a estimar que el costo anual global para la industria del petróleo y el gas supera los US$60.000 millones.
“Evidentemente, todos los metales son susceptibles a la corrosión, pero la naturaleza del propio petróleo crudo promueve aún más la corrosión debido a sus impurezas nocivas como el ácido nafténico y el azufre”, señala Hexigone Inhibitors.
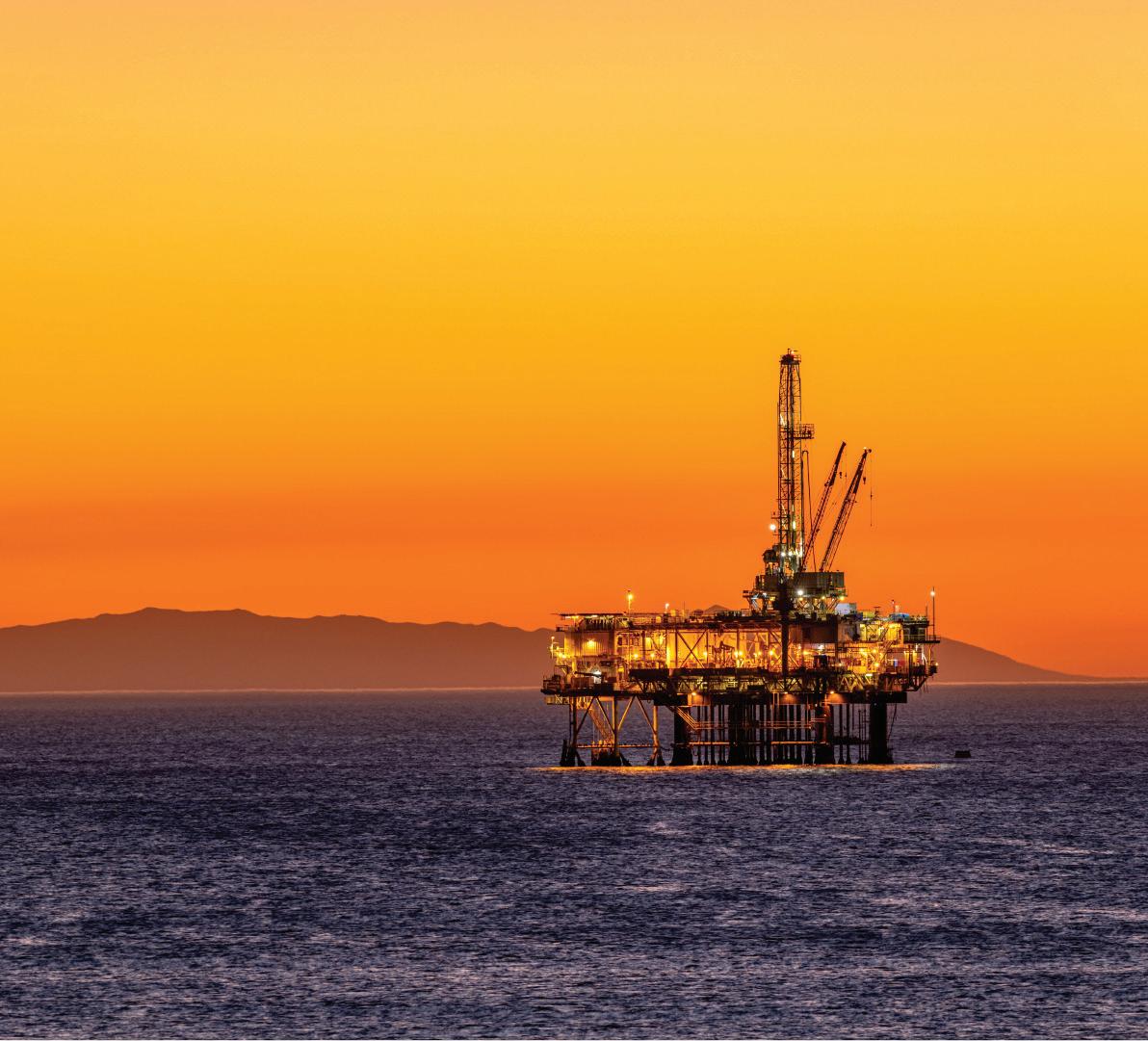
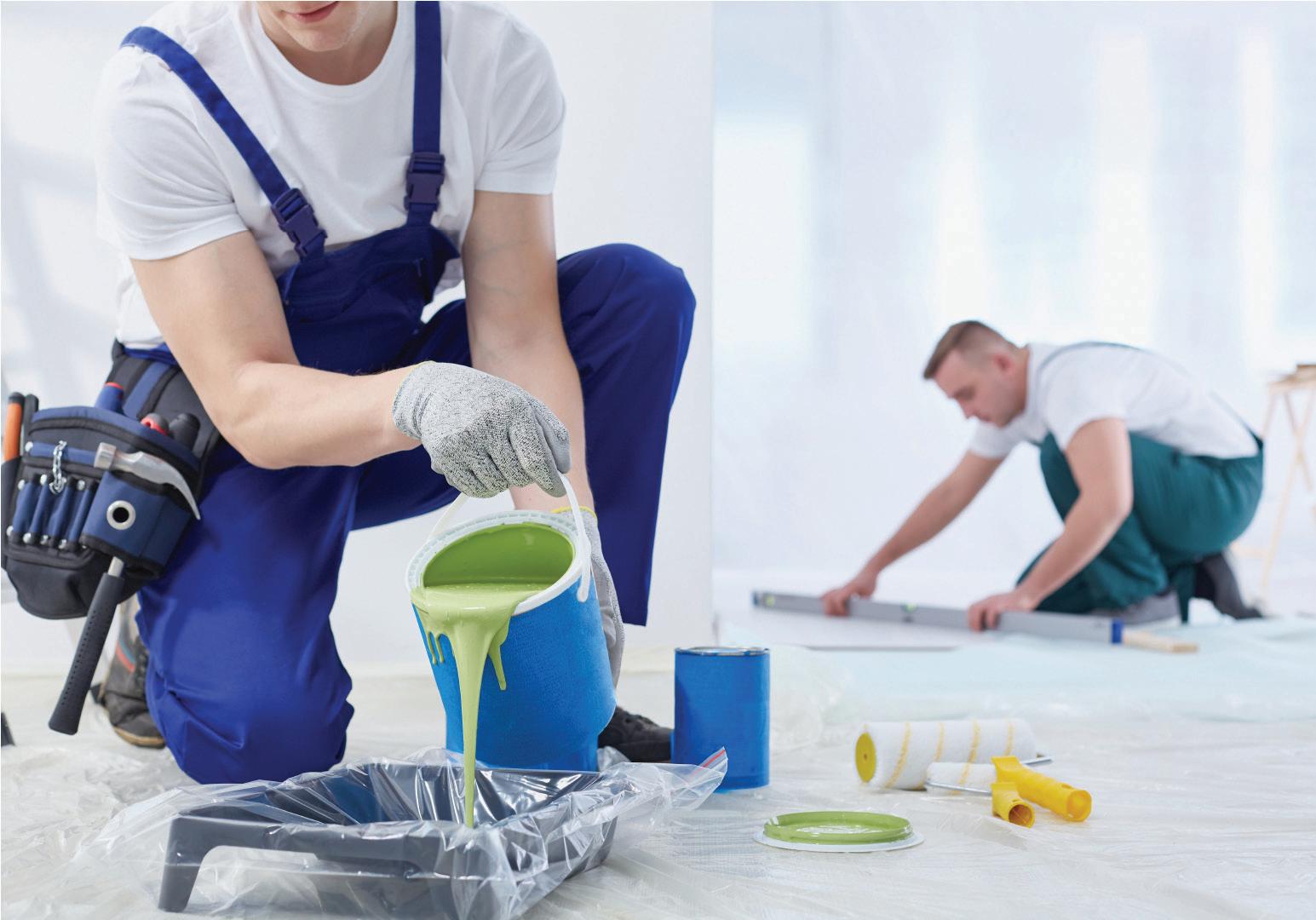
Acorde a la compañía, el problema se agrava aún más dentro de la industria, pues el 90 % de los materiales utilizados en la red de petróleo y gas son metales.
Por lo tanto, según Hexigone, la gestión eficaz de este fenómeno natural no solo ahorrará dinero a las empresas, sino que también salvará el medio ambiente, mediante el ahorro de recursos y menos reparaciones y reemplazos.
Alternativa de protección
Durante décadas, numerosas industrias clave, como la marina, la automotriz y la del petróleo y el gas, han confiado en el cromo hexavalente [Cr(VI)] para la protección contra la corrosión.
Este químico es claramente altamente efectivo en su objetivo de proteger los activos metálicos. Sin embargo, tal como lo documentó el Departamento de Trabajo de los Estados Unidos en 2020, este genera cáncer en humanos y animales.
Desde que se eliminó gradualmente, una alternativa popular en la industria del petróleo y el gas ha sido el fosfato de zinc. Aunque algo eficaz, este inhibidor no iguala el rendimiento de los complejos de cromato. A pesar de una extensa investigación desde la década de 1980, el cromo hexavalente sigue siendo el compuesto preventivo de corrosión de referencia en la mayoría de las industrias (O Gharbi, 2018).
Solución inteligente
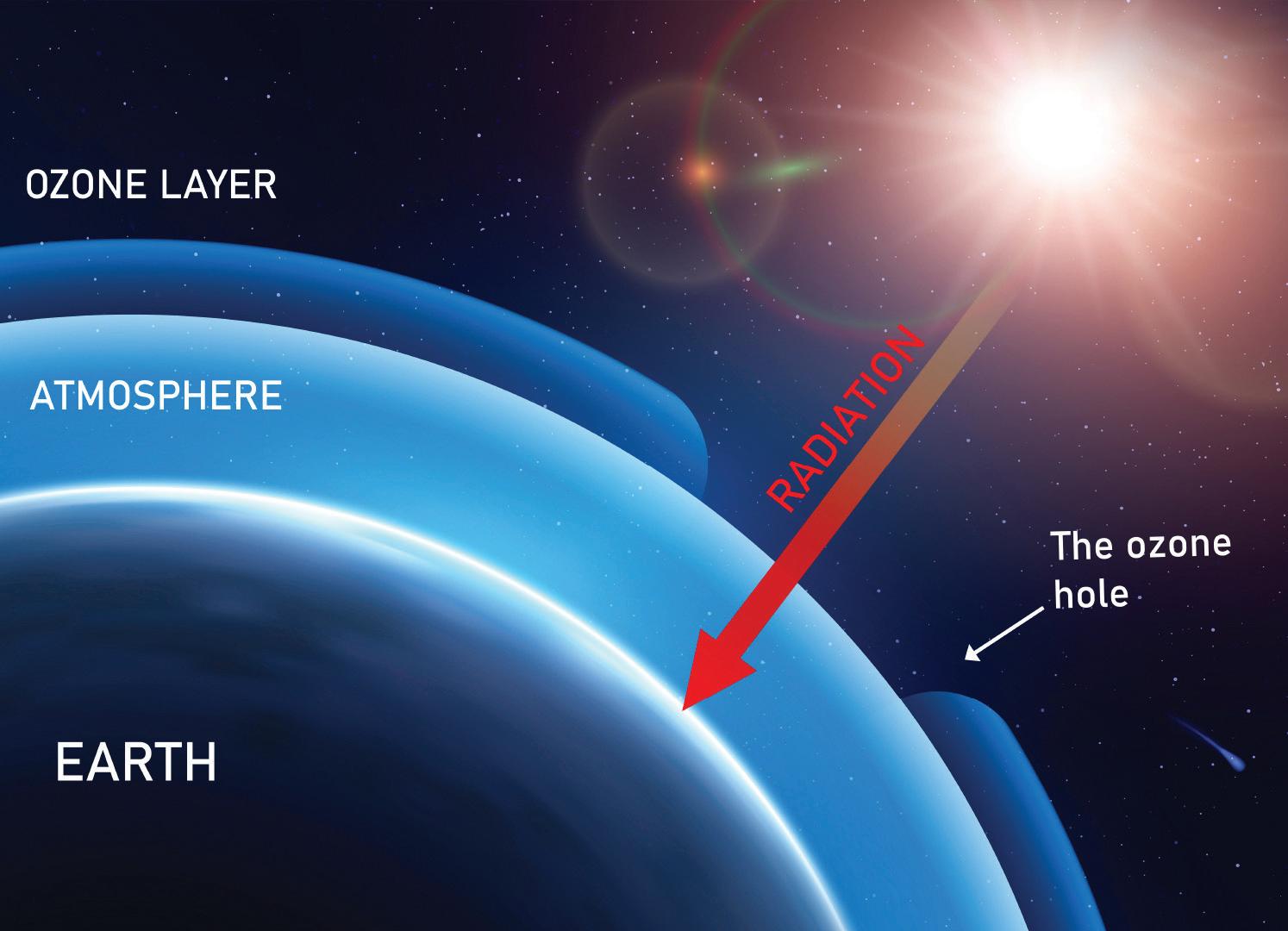
Así pues, debido a su tecnología de microdepósito, una nueva generación de inhibidores impulsa en la actualidad la innovación en el mercado de recubrimientos protectores. “Hexigone Inhibitors fabrica una tecnología anticorrosión patentada y galardonada que está diseñada para reemplazar por completo los inhibidores de metales pesados y cromatos o combinarse con inhibidores de fosfatos”, indica el Dr. Patrick Dodds.
Hexagon está utilizando flujos de desechos y reciclándolos en los productos Intelli-Ion. Esto evitará, según la empresa, que miles de toneladas de material vayan a parar a los vertederos o a la incineración.
El ‘Intelli-ion’ de Hexigone Inhibitors incorpora un ingrediente activo que nunca se ha utilizado de manera efectiva en los recubrimientos, lo que según la compañía lo convierte en una innovación completamente única.
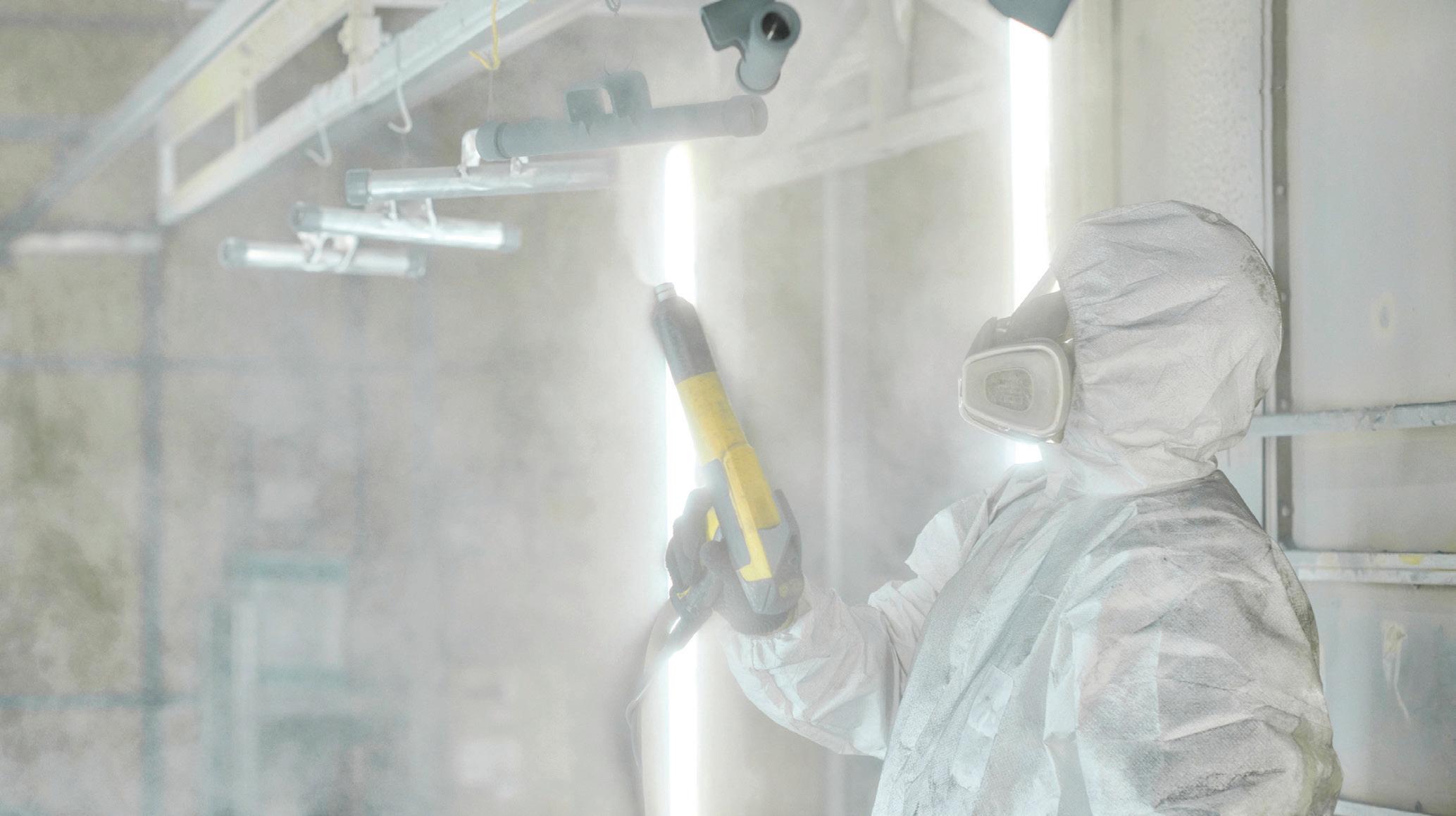
La tecnología protege de forma “inteligente” a través de tres modos de protección electroquímica. El ingrediente activo permanece inactivo en un microdepósito y se activa “bajo demanda” cuando se detecta corrosión en la superficie del recubrimiento, a través de iones o cambios de pH.
Los iones que pasan a través del recubrimiento son secuestrados, lo que los vuelve neutrales y también desencadena la liberación del inhibidor para que migre a la superficie del metal a proteger.
Un defecto en el recubrimiento o incluso un corte en el mismo, una vez bajo ataque corrosivo, tendría la misma respuesta del sistema de reservas.
El inhibidor forma una nanocapa protectora sobre la superficie de metal, en el ánodo y en el cátodo, y forma sales insolubles con cualquier ion de metal disuelto, lo que evita el transporte masivo de iones corrosivos y modera el pH debajo de la interfase película-metal.
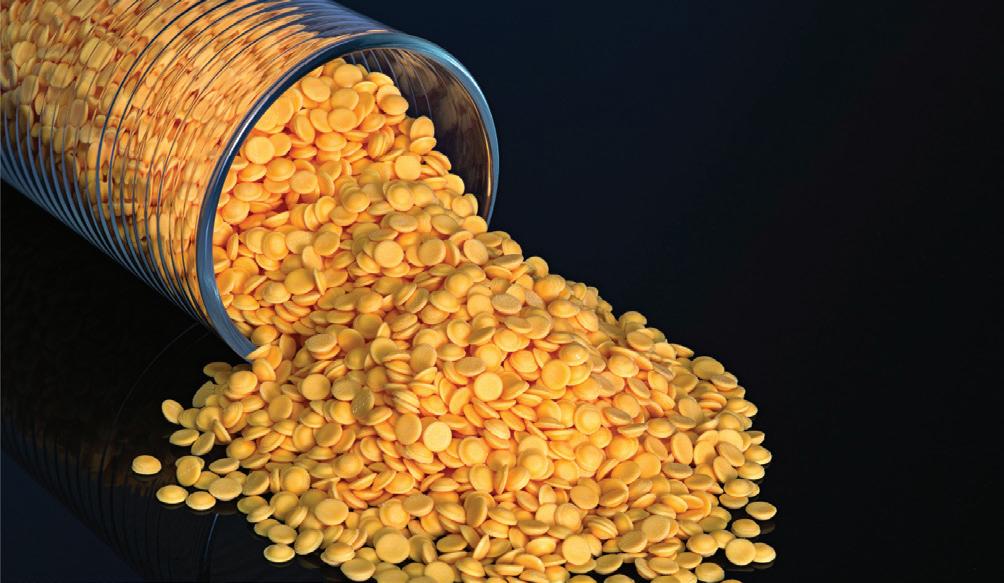
Acorde a Oliver Peña, técnico de First Quality Chemicals, aliado de Hexigone, Intelli-ion permite reducir la cantidad de inhibidor utilizado, así como la cantidad de CO2 producido por litro de pintura.
Peña brinda un ejemplo: reducir las cantidades de antico- rrosivo empleado en formulación de un 9 % de fosfato de zinc a 1 % Intelli-ion 3 % ZnP, con una producción de 30.000 litros por año, lo cual permite ahorrar 30,240 KG de CO2 a lo largo de tres años.
A su vez, el representante de First Quality Chemicals sostiene que, a través de esta tecnología, los recubrimientos serán colocados en la categoría 4 de riesgo ecológico. “Esto significa que se podrá remover las etiquetas de riesgo ecológico del empaque de tus recubrimientos”, señala.
Finalmente, destaca que una menor gravedad específica y un rendimiento superior (v ZnP) puede causar ahorros atribuidos de hasta el 30 % por litro de pintura.
Desarrollo de recubrimiento de matriz metálica resistente al calor y corrosión
Los investigadores de SUSU analizan nuevas composiciones y métodos para obtener recubrimientos con compuestos no metálicos e intermetálicos de alta entropía.
Este desarrollo hace parte del nuevo proyecto de Materiales
No Convencionales del programa Prioridad 2030. El estudio recibió el apoyo de la Russian Science Foundation (RSF).
El uso de tecnologías de fabricación aditiva hace posible crear recubrimientos con una composición única, que otorgan propiedades materiales tales como resistencia al calor, resistencia a la corrosión, resistencia a la radiación ionizante y la capacidad de absorber o reflejar la radiación electromagnética.
En las últimas décadas, se ha desarrollado activamente una nueva tecnología para producir piezas utilizando capas aditivas de material.
Este método de sintetizar productos se denomina fabrica- ción aditiva y se utiliza para fabricar productos a partir de diversos materiales, plástico, metal, hormigón, etc.
Actualmente, esta tecnología se utiliza ampliamente para crear prototipos metálicos y no metálicos y productos funcionales.
Con el apoyo de una subvención de la Russian Science Foundation fue posible aplicar tecnologías de fabricación aditiva (revestimiento láser y pulverización por detonación) para obtener revestimientos compuestos de matriz metálica con una composición fundamentalmente nueva.
Los recubrimientos consisten en partículas de compuestos altamente entrópicos no metálicos e intermetálicos.
Este proyecto es único en el sentido de que se utilizan tecnologías aditivas para crear recubrimientos con fases de alta entropía a partir de polvos que consisten en una mezcla de componentes puros o de polvos de aleaciones de baja entropía.