ASSET MANAGEMENT AT ITS BEST
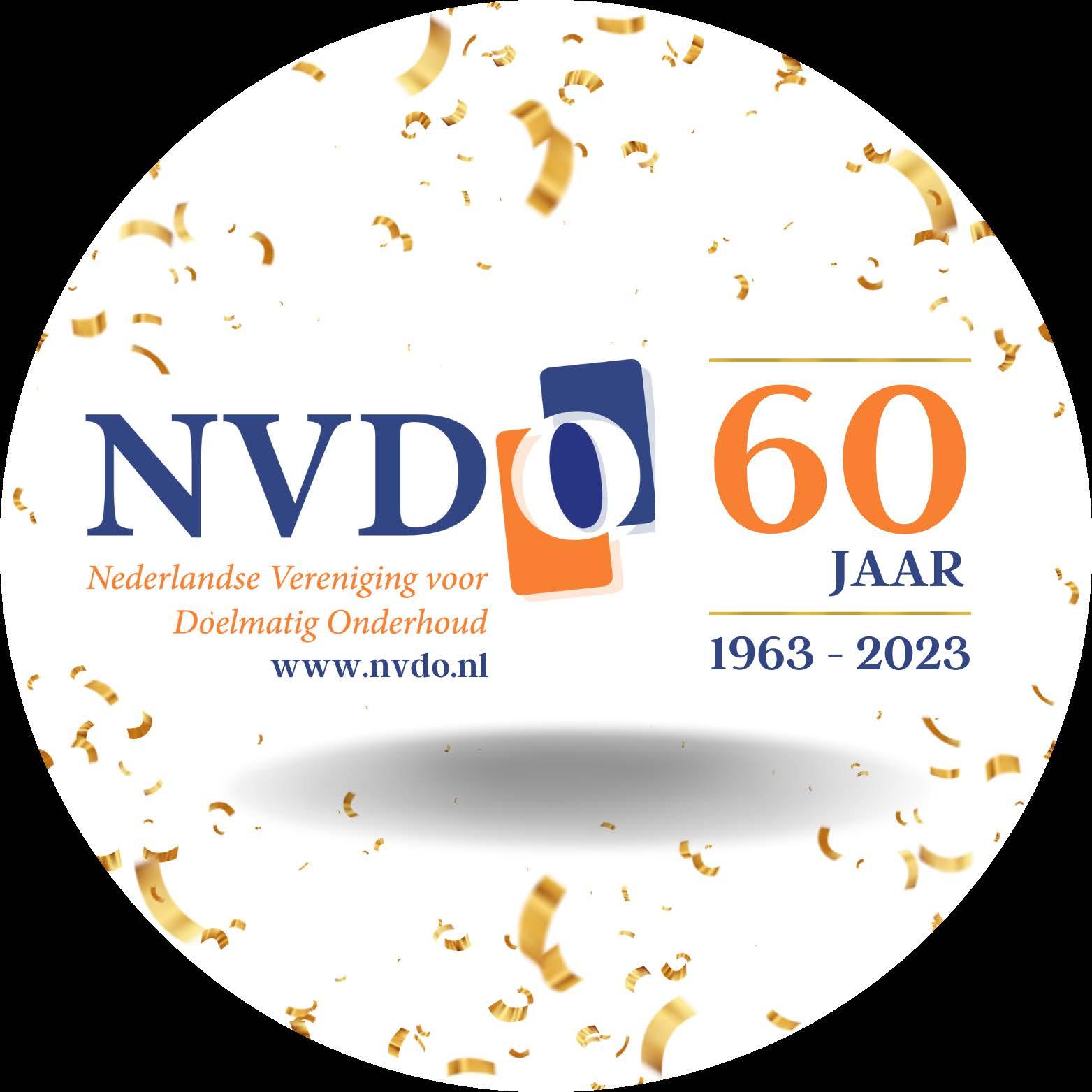
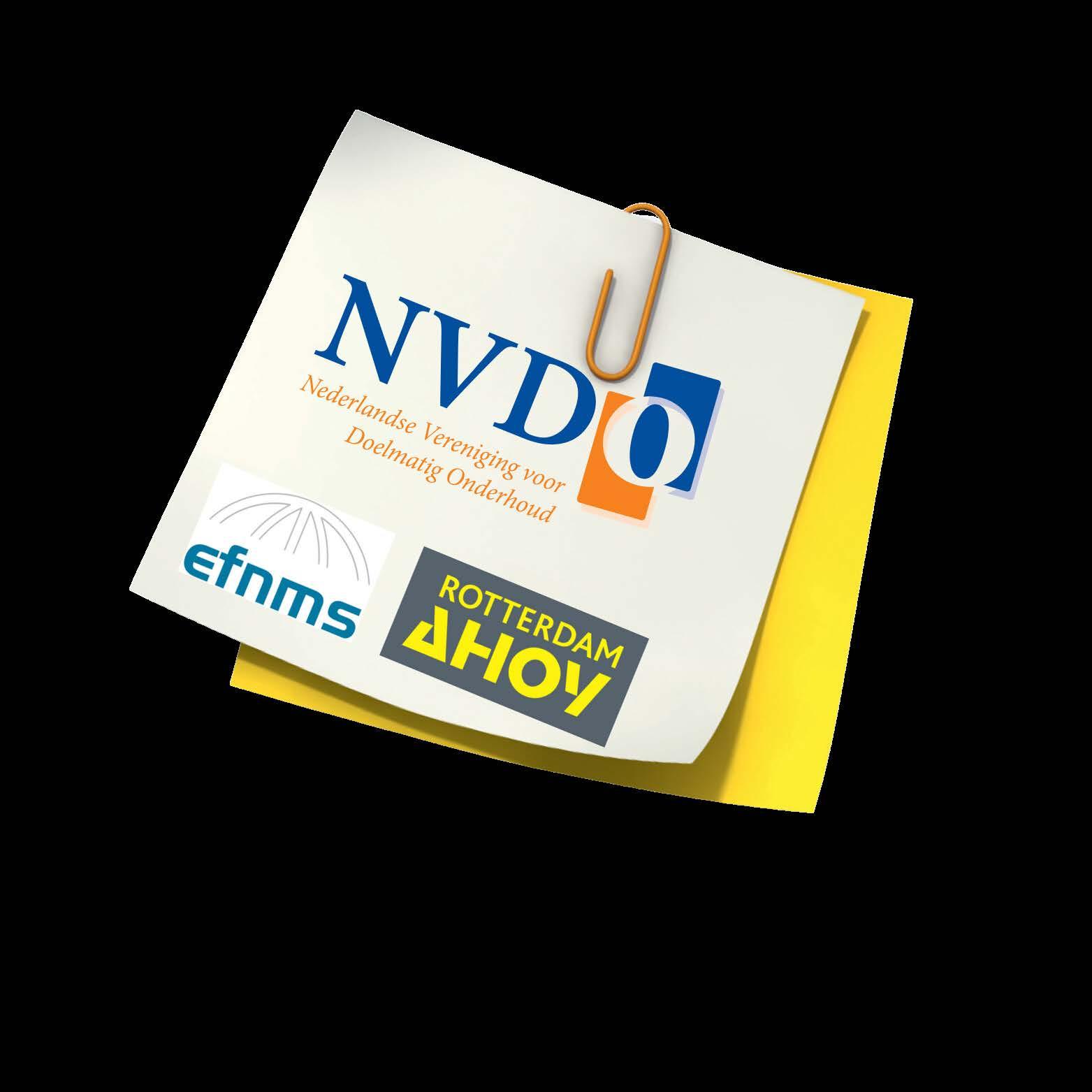
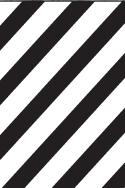
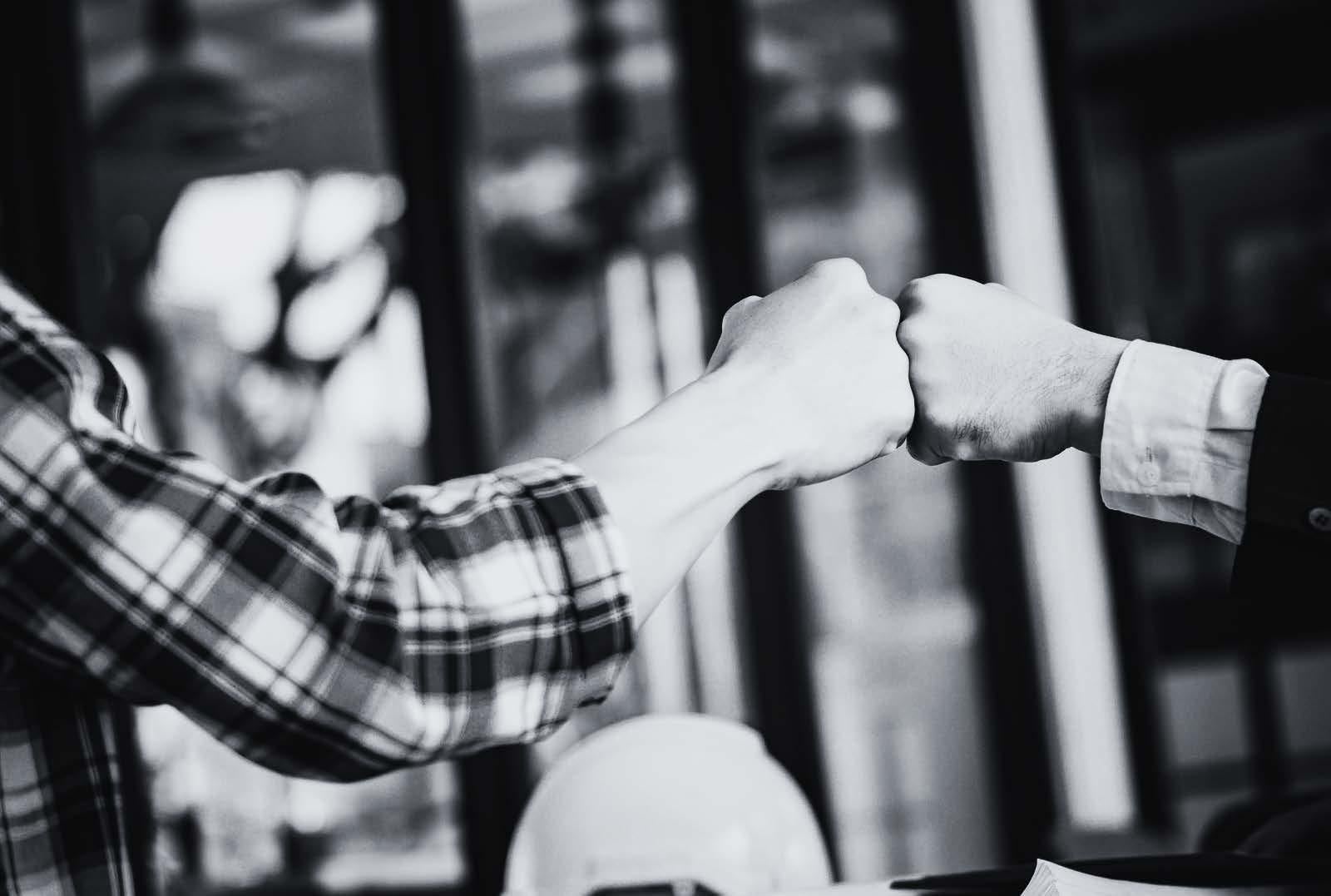
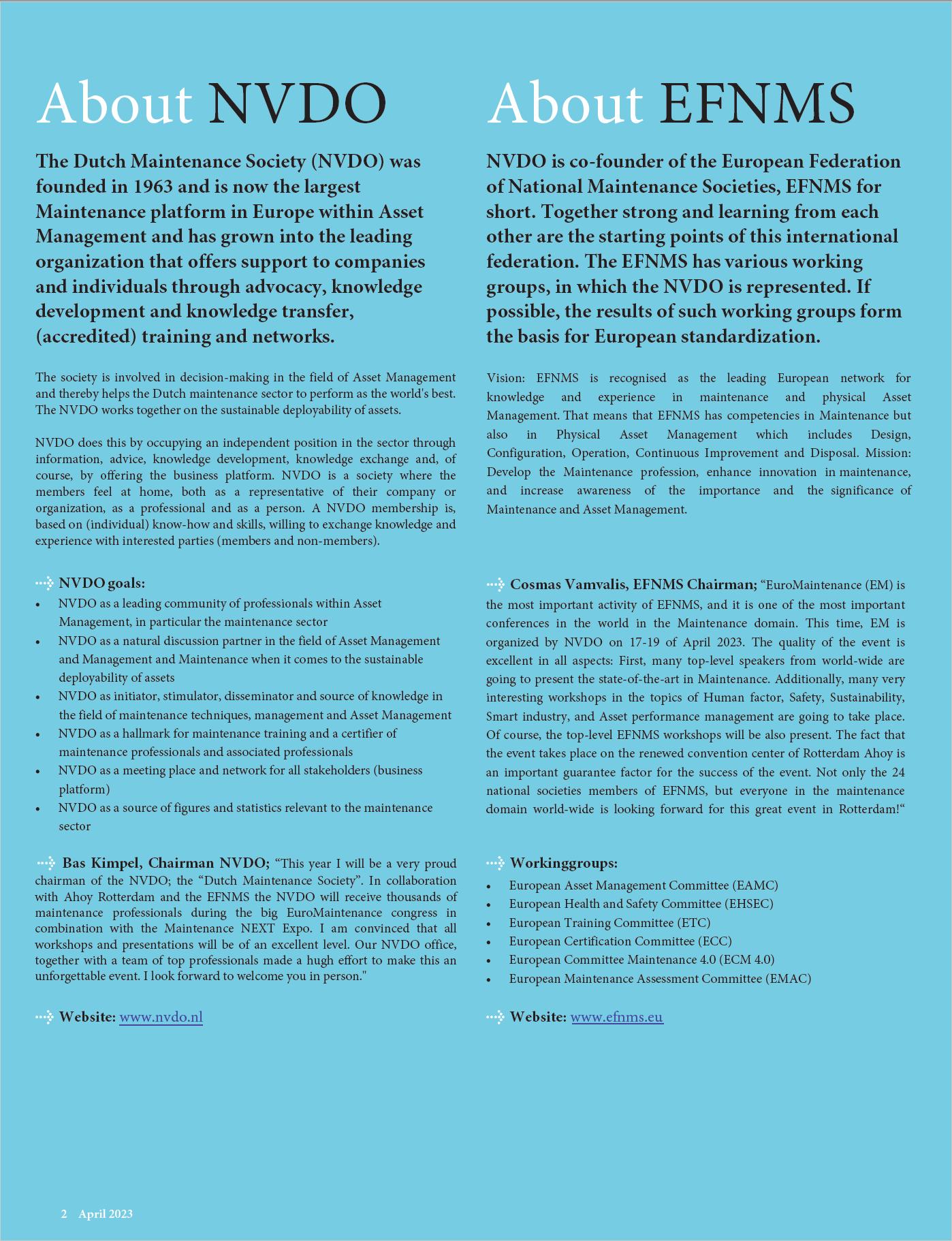
ASSET MANAGEMENT AT ITS BEST
The Maintenance workforce has grown again this year. However, there are challenges facing the sector. For example, the increasing ageing of the population is causing a high average age (46 years), an increase in the number of vacancies (15 vacancies per maintenance organisation) and an increase in the outflow (8,9%). Of the outflow, a large group (43,5%) leaves the organisation because of retirement.
In the coming years, efforts should be made to increase the inflow of new personnel. One way to achieve this is by attracting more women (current share 8,4%) and more people with a migrant background into Maintenance. Furthermore, efforts should be made to retain these groups within the maintenance organisation.
“These and many more questions cry out for an answer”, says Ellen den Broeder, General Manager NVDO and leader of the EuroMaintenance projectteam. “A solution that we may be able to find with many hundreds of professionals during EuroMaintenance in Rotterdam, the Netherlands. But we also like to share the rosy picture: the sector is that there is increasing confidence in recruiting enough staff. 60% of companies say they are confident about attracting enough technical staff and 71% say they are confident about attracting enough technological staff”. The outflow due to dissatisfaction has decreased (35,5%), which means that Management and Maintenance is an attractive sector to work in. These and many more figures are the outcome of the yearly Maintenance Benchmark in the Netherlands.
The NVDO Maintenance Compass is an annual publication and provides insight in the status of and trend in the Asset Management industry. Based on key figures, trends and vision documents the NVDO aims to help the Asset Management industry deal with developments, challenges and opportunities in the Asset Management field. Den Broeder; “Our maintenance market amounts to rougly 36 billion Euros, equivalent to roughly 4,5% of the gross domestic product (GDP). The maintenance market as a whole employs roughly 300.000 professionals, this means that 3,0 to 3,5% of the Dutch working population is employed in the maintenance sector”. These and those deverse an high level conferention!
Den Broeder; “Since there are a couple of changes in the total employee base that catch the eye, we decided to give the Huma Factor prominent place at EuroMaintenance. Not just the keynotes will cover the theme, some of the workshops will give an answer to the problems we all deal with”. Besides the workshops and the keynotes, there is an Inspiring Table at the end of second conference day to inspire the audience. EuroMaintenance welcomes 36 workshops, 11 keynotes and 3 Inspiring Tables. All of them are of the highest quality and of of international stature.
EllendenBroeder-Ooijevaar,General Manager NVDOAs a venue Rotterdam Ahoy is well known among the ‘biggest on earth’ since 1971. A worldclass venue offering infinite possibilities with over 50 years of experience in hosting concerts, sports-, business events and much more. Therefore it is the perfect location for a high quality congress such as EuroMaintenance and Maintenance NEXT, the leading maintenance and technology exhibition in the Benelux. But, Rotterdam Ahoy is more than just a venue.
> Rotterdam Ahoy Convention Centre. Last year was the opening of the new state-of-the-art Rotterdam Ahoy Convention Centre (RACC). This expansion gives Rotterdam Ahoy thirty-five additional spaces in which to host (international) conventions and gatherings. The RACC boasts thirty-five spaces with capacities ranging from 50 to 1,000 people. RTM Stage is the building’s largest space. It can be used as a music hall for 7,800 visitors (a so-called mid-size arena) and as a theatre/auditorium. With a capacity of 2,750 seats (or 4,000 seats in the XL variant), RTM Stage is the largest theatre hall in the Netherlands.
Another one of the building’s remarkable spaces is the expo foyer ‘De Rotterdam’, located on the third floor. It grants visitors a stunning view of the skyline of Rotterdam’s inner city. Bar Restaurant Seventy One, named after the year of Ahoy’s opening, will welcome visitors
on the Ahoy square. The new development has a direct connection to the rest of the event accommodation, making it possible to create various combinations with the building’s many other spaces.
> Het Hart van Zuid (The Heart of South). The completion of the building is not only a milestone for Rotterdam Ahoy, but also for the area development of Hart van Zuid. The large-scale quality improvement of Hart van Zuid continues at a rapid pace. The Swimming Centre Rotterdam and Zuidplein Theatre with a location of Rotterdam Library are already in use. An expansion of Shopping Mall Zuidplein, a new bus terminal and movie theatre, residences and food service establishments are all still in development. This gives leisure a full place within the area development and further improves Hart van Zuid’s status as a city centre.
> Sustainable future. Investing in sustainability initiatives is one of Ahoy’s top priorities. Therefore the Municipality of Rotterdam, Rotterdam Ahoy and Hago Nederland (cleaning company) are joining forces to start on the realisation of an urban water buffer (UWB), a system in which rainwater is collected, retained, filtered, stored and reused. The water collected in the underground storage facility will be purified with plants and stored deep in the subsoil until it can be reused.
The water from the water buffer will be used for window cleaning and floor cleaning. The water will also be used to flush the toilets at the new cinema. With the UWB Ahoy expects to be able to reuse 20,000 cubic metres of the collected water annually.
As you can see Rotterdam Ahoy is more than just a venue. The possibilities, location, ambition and the social role it plays, make it the perfect stage for the combination of EuroMaintenance and Maintenance NEXT. Hopefully you will witness it in the third week of April 2023.
‘Rotterdam Ahoy is more than just a venue’
Gered Gereedschap is a Dutch NGO which has been making a consistent effort for craftsmen and women in developing countries for the last 40 years. Projects supported by Gered Gereedschap strengthen technical vocational education and entrepreneurship in Africa.
Not only tools but often also sufficient skilled people, knowledge and funds are lacking in the areas Gered Gereedschap is actively working. Therefore, they support craftsmanship in broadest sense of the word. In practice, it means that Gered Gereedschap is focusing even more on quality vocational education, available to everyone. They support students after completing their training and encourage entrepreneurship.
> Origin of the tools. The required tools and machines are collected in the Netherlands by Gered Gereedschap through 400 collection points. These are then refurbished and prepared for a second life by some 500 volunteers in 26 independent workshops of Gered Gereedschap. Every year about 100,000 tools and 1,000 sewing machines find their way to projects in Africa, to support vocational education and entrepreneurship like setting up the tool rental shops.
EuroMaintenance supports this fantastic charity to give people in the poorest areas of the world the opportunity to train themselves in Technology and Maintenance. EuroMaintenance will take care of the refurbishment of old tools, the purchase of new tools and technical education.
Their support is practical, tangible and comprehensive. From tool sets and machines for schools, fully equipped sewing workshops to the education of technical vocational teachers. All their support is directed towards one purpose: promoting technical craftsmanship as a basis for self-reliance.
> Training the next generation. “Gered Gereedschap has already achieved a lot in her history. They supported 1,650 organizations with tools and created 132,000 fully equipped vocational training places for craftsmen. They will continue to further develop on this success. Besides collecting, refurbishing and sending tools from their 26 workshops in the Netherlands, they do more.
The reason for this is very simple. The organization knows from experience that a flourishing craft sector in developing countries offers great opportunity to a better life for large groups of people.
> More information. Want to know more about Gered Gereedschap and the programmes they carry out in Africa under the name of EQUIP? EuroMaintenance will inform you during the upcoming months! <
‘
’
‘Give your old tools a second life in developing countries and give people a future’Malawi Technical drawing Foto: Gered Gereedschap
Much has changed in the world of Maintenance and Asset Performance Management in MaxGrip’s 25 years as a consultancy firm. However, having done projects across the globe and in a variety of industries during those years we can say that one thing is indisputable: people are a key success factor.
In Asset Management improvement projects, middle managers are usually the owner of the project. They have to get employees on the shop floor to go along with the changes. Senior managers act as a sponsor in the background. Maintenance, Operations, Engineering and other departments ideally work together, understanding and respecting each other’s intents and perspectives while striving for a common, overarching goal.
> Variety. Obviously, this is too simplistic as we all know from experience that reality is not that straightforward. There are many interests and factors at play that can vary from company to company. To name a few: the financial possibilities, running processes, systems and tools, KPIs, laws and regulations, people’s ability to change, the company culture and national culture. Factors like these make every project seem unique. Yet, in the consultancy projects we carry out at MaxGrip we also see many similarities in challenges, themes and ambitions between companies, irrespective of their location or the industry they operate in.
> Human Factor is key. One such recurring theme is the ‘human factor’ and internal adoption of changes; how to act so that people embrace a transformation making business improvements stick. Despite all the attention given to digital transformation, Industry 4.0 and technological advancements, people are pivotal for successful asset management. It is therefore not surprising that the human factor is one of the themes of EuroMaintenance 2023. The conference is an excellent opportunity for our consultants to share their knowledge and experience with industry peers. To partner with our customers and share best practices in workshops. To engage in conversation with participants and conference guests, to inspire and be inspired.
MaxGrip is a proud partner of EuroMaintenance 2023. We look forward to coming together next year with all those Maintenance and Asset Management professionals with whom we share common interests. Now that really is ‘Asset Management at its Best.’
Lisa Kamphuis Global Marketing Manager MaxGrip <‘ ’
‘MaxGrip is a proud partner of EuroMaintenance 2023’Lisa Kamphuis
‘’To help create a network for young maintenance professionals and to assist them in the start and early development of their carreers’’. That’s the mission of the Salvetti Foundation. The foundation aims to award excellence in maintenance management and to contribute to bringing young maintenance professionals together in order to retain this group in the professional field and motivate them in their careers in cooperation with EFNMS and relevant European Union-organisations.
The Salvetti Foundation awards different categories of maintenance every two years. The European Maintenance Manager Award and the Scientific awards.
> Scientific awards. The Salvetti Foudation supports the work done on maintenance in the academic world. The objective of the academic awards is to promote, encourage and motivate the theoretical and applied R&D related to maintenance knowledge and practice amongst the students at the European Universities and Research Institutes. A network of 24 professors support the review process. Each theses report has been reviewed by 2 independent professors. At EuroMaintenance the winning students will also be congratulated.
> EFNMS European Maintenance Manager Award. EuroMaintenance welcomes the Salvetti Foundation in April 2023. It is with great pleasure then that, for the sixteenth time, EFNMS and the Salvetti Foundation will be able to award the winner of the EFNMS European Maintenance Manager Award (EMMA). The first time was in 1988 and ever since they presented the award to a worthy winner. This 16th contest, took a rather long period due to Corona issues. President Stefano Salvetti; “We discussed extensively how to organise a formal award ceremony after postponing EuroMaintenance 2020 and 2021 due to the pandamic”.
“This time the EMMA Jury consisted of four members; myself, founder of the Salvetti foundation, two representatives of EFNMS and the Salvetti Foundation Secretary. All nominees met the stringent qualification criteria of the national maintenance societies who selected their candidates. After this national qualification the real challenge of the EMMA Jury started. All nominees actually earned at least a runner–up qualification”.
> Congratulations to the winner. The winner, Mr. Alexis Agustín Lárez Alcázarez was nominated by the Spanish maintenance society ‘AEM’. The laureate is technical director at Enova Levante, a company specialized in technical services. Salvetti; “Alexis is an experienced leader associated with Asset Management and technical reliability in Spain and countries in Latin America. He has more than 22 years international experience in various types of industry. He is Lead Auditor in Asset Management and quality systems based on ISO 55001 and ISO 9001. Additionally, he is University Lecturer in master and postgraduate programmes”. As shown in his cv, he possesses many certificates and skills. Eq, criticality and analysing tools as, RCM, FMECA, RCA, and a strong knowledge of industry processes on strategic, tactical and operational level. He is author of the book Tools of Reliability. “Alexis is respected for his very broad experience and therefore a very welcome and appreciated speaker at international conferences”, according to the jury. A number of published and registered papers from him can be found in international magazines. Salvetti mentiones as well that Alexis has a PhD Degree in computer technology and environmental engineering. Skills which he practised as leader in the cement industry when he was involved in the implementation of the environmental standard ISO14001. These environment related skills become more and more important as maintaining assets should support new sustainability goals”. For these highlights in Alexis carrier the jury unanimous concluded that he should be the winner of the European Maintenance Manager Award 2021.
> Runners-up. Next to the winner there are two excellent runners up which should be mentioned. On behalf of the Finnish maintenance society, mister Ilkka Palsola was nominated. Ilkka retired in 2015 after a long and very successful carrier in a variety of positions for the global chemical company Kemira. Over the last years of his employment he acted as global expert and engineering team leader in the pulp and paper fabrication. In his last position he acted as global engineering director supporting all production sites. IIkka is still a very respected and valuable board member of Promaint and member of the EFNMS certification committee.
From the Swedish maintenance society, mister Fredrik Blomkvist was nominated. Fredrik is maintenance manager for the AstraZeneca pharmaceutical packaging factory in Södertälje. His journey to improve a number of maintenance processes started in 2017. Among a number of excellent achievements, it should be especially noted that in 2020 his team reduced downtime with 37% and maintenances cost per dose with 15%. Maintenance staff closed more than 250 competence gaps and safety goals were met: Zero incidents.
Both organisations, EFNMS and the Salvetti Foundation congratulate Alexis, Ilkka and Fredrik and wish him success in their profession. During the next EuroMaintenance event in Rotterdam the formal handover of the award will take place. Salvetti; “I am looking forward to EuroMaintenance at Rotterdam where the NVDO, Ahoy Rotterdam and EFNMS will take care of an excellent conference and Rotterdam will be the Maintenance Capital of Europe. I will be there!” >
’
‘The award is in recognition of extraordinary accomplishment in the field of maintenance’Alexis Agustín Lárez Alcázarez Foto: private collection
The world around us continues to shift. Sustainability, digitalisation, electrification and regionalisation are megatrends forming the future. And that’s not to mention recent challenges in raw material availability and resulting lead times and ever increasing energy costs.
The landscape is more competitive than ever before. Suppliers offering digitalisation, connectivity and analysis are competing with low-cost companies for customer loyalty. However, production company goals will remain unchanged; increase machine availability, reliability and performance, reduce costs and enable a safe working place for our employees in a sustainable environment.
SKF is a leading global supplier of solutions for rotating equipment. We combine hands-on industry experience with a vast product portfolio and knowledge around bearings, seals, lubrication management, condition monitoring and maintenance services. One of our strengths is the ability to keep developing new technologies that offer competitive advantages to customers, and at the same time, contribute to a sustainable society. Ingredients that enable us to be a reliable partner for our customers and bring value to their business.
> To another approach. But what do we mean when we say we want to deliver real customer value? We want to better understand the business drivers for our customers and how SKF’s products and services can deliver the most value. We want to know what the actual needs, challenges, pain points and opportunities for our customers are, both from a personal and business perspective. That’s why we have moved from a solution-oriented mind-set to a needs-based approach. SKF is a customer-centric organization, which means we look at our customers from an outside-in perspective. SKF doesn’t decide excellence, the customer defines ‘what’s best’ and makes us listen, understand and learn so we can help our customer make better choices. More and more companies expect their main suppliers to be an advising partner rather than a sales contact point.
> Intelligent and Clean. SKF has something that very few industrial companies have: a deep understanding of almost all industrial applications. Everywhere there is rotation, there is a good chance that SKF products, capabilities and skilled colleagues are providing value in the form of improved operational performance and reduced emissions, based on two concepts: intelligent and clean. Intelligent means providing connected and tailored offerings for our customers, as well as using technology to make operations more efficient. Clean reflects our ability to enable a more sustainable industry. New technology and partnerships provide us with scale and easy access to our data analysis and machine performance competence.
You can find SKF’s products all over the world and in a large variety of rotating applications, ranging from renewable energy, such as wind and ocean power, to heavy industries like mining, metal, and pulp and paper.
> Looking forward to EuroMaintenance. SKF is excited to be one of the main sponsors of Euromaintenance 2023. Meeting professionals in all fields of expertise, on all organisational levels and sharing thoughts and experiences to be best-in-class. See you in Rotterdam where ‘we will reduce friction to help the world move forward’.
Ringo van Voorst Marketing Manager Europe South-West <‘ ’
‘SKF is excited to be one of the main sponsors of EuroMaintenance 2023’‘Ringo van Voorst’
Within half a year, EuroMaintenance will take place in the vibrant city of Rotterdam. A city full of activity in the field of manufacturing, transport, logistics, infrastructure as well as culture. A working-class city where a hands-on mentality and the latest technologies come together. A region where so many impressive achievements have been realized and where the people know that together, more can be achieved.
rated very good or good, in most answers the reason was clear and regular communication and information-sharing between the teams. For the managers who rated the cooperation as average, needing improvement, or bad, the poor performance seemed to stem from a lack of interaction, which often seemed to be heightened by understaffing. Many respondents also said departments are too siloed and lack joint interest, affecting how efficiently they can work together.
I believe that the outcome of visiting EuroMaintenance should be that people have a better understanding of the latest trends and technologies in Asset Management. But above all, I hope that it will inspire to improve collaboration within and between organizations and that new relationships are established. Teamwork is the only way through which we can further improve productivity as well as sustainability.
I am looking forward to the conference where asset and maintenance professionals from all over Europe can meet and inspire each other on how to deal with all their current challenges and how to improve their businesses. With the disruption brought on by the pandemic, widespread supply chain challenges and material shortages, the impending skills gap, and the skyrocketing energy costs, asset owners have a lot on their plate. Challenging times ask for strong leadership, also in the field of asset and maintenance management. To keep the long run in mind, to demonstrate empathy and transparency and to keep team members unified. And last but not least, stimulate crossteam collaboration and create synergies with other departments and organizations. Because Together, more can be achieved.
> International survey. In a recent major international survey among Maintenance and Asset Management professionals we conducted, we see a strong focus on people. Over 40% of the respondents want to prioritize investing in the workforce and focus on improving communication and collaboration. This suggests that even with the best assets, the operation is not secure unless it’s managed by skilled people who are able to share knowledge effortlessly. There seems to be a recurring theme in the answers. When asked to rate cooperation between the maintenance team and other departments, the responses revealed a simple categorization. When the collaboration was
Ewout Noordermeer CMO, IFS Ultimo‘
’
‘People will have a better understanding of the latest trends and technologies in Asset Management’Ewout Noordermeer
Techsharks participates in Maintenance NEXT as an exhibitor and has committed itself as a Gold Partner to EuroMaintenance. As a specialist in the field of technical vacancies, they will mainly focus on the human factor.
Techsharks has had experience in the manufacturing and process industry since 2002. As a result, they have built up a pool of 250 qualified technical specialists (sharks). The specialized organisation knows what moves this special breed. Whatever assignment any organization has, they will advice and help to solve challenges. Their sharks are:
• driven to make the production process extremely effective
• always hungry for more to keep learning and developing
• highly adaptive as they are, they adapt to any work environment - and situation
• determined to achieve goals
• naturally equipped with a healthy dose of pride and self-confidence
• a breath of fresh air, because they have often carried out an as signment for several partners
Currently there is a lot of stress within the Industry to attrack and to preserve good technicians. This is a topic which is already a boardroom item at Techsharks for many, many years. Because of that
they already managed to set up an excellent strategy to become an attractive employer. Mainly by offering challenging projects, stimulating education and personal development and offcourse a more then decent income. Besides these important conditions Techsharks has a unique culture which is defined in specific core values. Joining Techsharks is not just becoming their next employee. It’s being part of the current in the blue ocean of technical talent.
“To mention ‘the war on (tech)talent’ is a lousy excuse from companies who don’t have a good strategy to attract and preserve their most valuable asset: people!” says Jeroen Tijink, CEO Techsharks. Christian van Vessem, Commercial Director; “It is in our DNA to seek the constant connection with other parties. Think of regular educa-tion, government and industry. Alone you go far, together you go further!” Van Vessem is convinced that many ideas will be exchanged during EuroMaintenance when it comes to the technical labor mar-ket. In addition to a Key Note, Techsharks also provides a workshop and organizes a live Inspiring Table.
Asset Management is at its best when it is able to contribute to Operations and their business drivers such as Overall Equipment Effectiveness (OEE) and Total Cost of Ownership (TCO). Together with MaxGrip and the senior manager of an industrial company, Bob Francis of LNS Research will take the stage at Euromaintenance 2023 to share his vision.
proven way to drive a unified purpose-driven culture, adoption and collaboration across Operations, Maintenance, Reliability, IT, EHS, etc. is to publish the organizations OpEx metrics and show how the Asset Management program metrics roll up and positively impact the plant and enterprise OpEx metrics. Everyone is a stakeholder according to Francis.
> What are the trends in the market in APM?. LNS Research studies and weekly briefings from both end users and software suppliers, indicate that adding OT/Time Series data to APM predictive / prescriptive analytics models is trending up significantly. Specifically, these software tools automate the extraction of industrial data from historians, IoT sensors, and operational technology (OT) systems to provide “real-time” condition, anomaly detection, and alarm data, greatly enhancing the accuracy of the models.
Bob Francis is a Research Analyst with LNS Research. He is focused on coverage areas including. asset performance (APM 4.0), digital transformation, organizational readiness and operational excellence. LNS Research’ vision is a world where industrial companies are agile, autonomous, and sustainable.
> Why is Asset Management important to improve Ope-
rational Excellence? It is very difficult, if not impossible, to positively impact the Operational Excellence performance metrics in an industrial operation without an effective asset management program. Organizations will be hard pressed to achieve greater Overall Equipment Effectiveness (OEE), extend the life of their assets, maximize throughput, increase operating margins, or lower the Total Cost of Ownership (TCO) without a modern (digital), comprehensive and integrated asset management approach.
Francis; “One of my mentors, Ron Moore, taught us that a reliable plant is a safe plant, is a cost-effective plant, is an environmentally friendly plant. A new generation of Asset Management platforms for APM, EAM/CMMS are now utilizing advanced technologies like artificial intelligence, machine learning, and natural language processing (NLP) in what is known as APM 4.0 and greatly enhance the capabilities of Asset Management systems with direct benefits to Operational Excellence performance”. While the Asset Management technology enables OpEx gains, it also brings organizations together around common metrics shared across historically siloed groups. A
> Why are you presenting together with MaxGrip and an asset owner? Francis; “The three of us combined represent over 150 years of expert knowledge and front-line experience on the topic of Asset Management and how these programs are a direct contributor to operational excellence. I will keep the name of the asset owner a surprise, but I do want to say that he is a leader in his field. MaxGrip adds valuable insights with them being a global consultancy firm known for their domain expertise and experience in APM. I am very excited about speaking at EuroMaintenance together with these leaders”.
‘
’
‘Essential role of Asset Management for Operational Excellence’
Dr. Eduardo Calixto, Germany is one of the International Workshopleaders during EuroMaintenance in Rotterdam. His professional career is within ECC of which he is the Founder and CEO. As a RAMS Expert he is also member of the Safety Committee of EFNMS.
Calixto; “One of the most fastastic Maintenance conference in the world, the EuroMaintenance will take place again on 17th to 19 April 2023. Now is time to join to this fantastic event with the most hot topic at moment in Europe such as Artificial Intelligence for Maintenance 4.0, Safety, Asset Performance Management, Sustainability, Human Factor and Smart Industry. I am very happy to give a contribuiton by two workshops such as Reliabiltiy 4.0 and Asset Integrity Management on the Asset Performance Management and Safety workshop sections respectively. On the first case, the reliability 4.0 workshop will demonstrate the intelligent and easiest way to perform reliabiltiy prediction and measure the asset reliabiltiy performance as part of Asset Management process. On the second case, the Asset Integrity Management workshop will demonstrate how the asset integrity management process is integrated to the Asset Management routine and manage the safety crittical asset on daily basis”.
“EFNMS Committee EHSEC’s (European Health, Safety and Environment Committee) vision is to continuously strengthen the cultural pillar of Safety and Environmental Protection in all maintenance activities. In this framework, EHSEC has developed an extroverted way-forward including its participation to actions that promote a sustainable maintenance. EuroMaintenance provides one such opportunity which EHSEC strongly supports. At first, EHSEC has already served as a liaison to assure the active participation of EU-OSHA during the event which will ascertain the mutual cooperation. EHSEC serves as a source of other renounced speakers from the European HSE Network like ENETOSH and ENSHPO. Additionally, EHSEC will submit papers and deliver presentations on key sustainability-related areas and will also present their publications to all visitors. Finally, EHSEC members will support the whole event by organizing and facilitating at least two workshops. We are proud to be involved”, says George Scroubelos, Chairman EHSEC
Asset Management at its best will be the theme for this edition of EuroMaintenance. Business leaders will share their vision on developments and the future of the industry and best practices will be showcased. More than 40 workshops will focus on the main themes in Asset Management:
In addition to the workshops, international Key Notes take the stage to share their knowledge and inspire. Part of the Euro-
Maintenance program are the ‘Inspiring Tables’. Laura van der Linde, Marketing Communications Coordinator at Mainnovation will host this unique inspring part of EuroMaintenance. Three tables, Five themes. Her job will be to ensure that the conversation is not only inspiring, but also informative, educational and entertaining as well.
We live in one of the most inspiring timeframes for our future Asset and Maintenance Managers, -Technicians and -Engineers. This timeframe is full of choices to make and create a sustainable future in domains of Smart Industries, Sustainability, Asset performance Management, Safety and Human Factor. Now at the end of Industry 4.0, it is time to reconsider the role of the human factor, resilience and the sustainability in an increasing smart technological environment.
> From one point to another. Rather than taking emergent technology as a starting point and examining its potential for increasing efficiency, a human-centric approach in industry puts core human needs and interests at the heart of the productionprocess. Rather than asking what we can do with new technology, we ask what the technology can do for us. Rather than asking the industrial worker to adapt his or her skills to the needs of rapidly evolving technology, we want to use technology to adapt the productionprocess to the needs of that professional, e.g. to guide and train him/her.
Industry 4.0, announced by the former Chancellor of Germany Angel Merkel at the Hannover Messe mid-2011, has become a globally adopted term in the past decade. Industry 4.0 -better known as Smart Industries Industry 4.0- was about nine topics as for example The Internet Of Things, Digital Twins, Vertical and Horizontal Aggregation of Information and more.
> From 4 to 5. At the ten-year mark of the introduction of Industry 4.0, the European Commission announced Industry 5.0 in 2021. Industry 4.0 is considered to be technology-driven, whereas Industry 5.0 is value-driven. Industry 5.0 recognises the power of industry to achieve societal goals beyond jobs and growth to become a resilient provider of prosperity, by making production respect the boundaries of our planet and placing the wellbeing of the industrial worker at the centre of the productionprocess.
The analysis of the Industry 5.0 -as far as we know now-, shows a lot of uncertainty about what it will bring and how it will disrupt business in detail, as well as about its potential to break down barriers between the real world and the virtual one. Industry 5.0 will be defined by a re-found and widened purposefulness, going beyond producing goods and services for profit. This wider purpose constitutes three core elements: Human-Centricity, Sustainability and Resilience.
Although the other two topics of Industry 5.0, Sustainability and Resilience, the human factor as one of the five topics of the EuroMaintenance conference in Rotterdam 2023, inspire me the most. It encourages me to overthink and discuss how to educate, train and motivate our NextGen’s and prepare them. These are the questions that confront me and fellow European Maintenance and educational organisations. I am looking forward to meet, share thoughts and insights at the event.
Jan Stoker, Chairman of the European Training Committee EFNMS and Sr. Lecturer in Asset & Maintenance Management
‘Let’s discuss the human factor and it’s themes at EuroMaintenance’Jan Stoker Photo: Private Collection
Human ears can’t hear the frequency of ultrasound and ultrasonic vibrations. Ultrasound provides early detection of bearing damage and lubrication problems. It is understood to mean frequencies that are generally above the human hearing limit of about 18 kHz. Wear on rotating and reciprocal machine parts is often accompanied by ultrasonic detection, so this technique can be used to overcome this wear. Ultrasound technology can overcome insufficient lubrication or the breaking of a lubricating film layer.
Ultrasound is considered the first line of defense when detecting defects that could shut down the equipment. The first signals that change the operating conditions of a part are usually identified in the ultrasonic frequencies. Only when the part is already in a worse state of deterioration do other condition monitoring technologies come into play. For planners, a maximum time frame to order parts, plan downtime and allocate work resources is a huge advantage.
> Ultrasound is one of the three types of sound. In addition to infrasound and audible sound, Ultrasound refers to any sound pressure wave with a repetition rate greater than 20 kHz. The characteristics of ultrasound, especially around 40 kHz, are of particular interest to inspectors listening for symptoms of component failure.
> Case-by-Case solution. At EuroMaintenance we will learn from Haris Trobradovi�, SDT International. The material (Gearbox – Electrical motor – Lubrication – Low-speed bearing – Leaks) is a collection of five different cases where Ultrasound was successfully used in detecting and resolving problems, as well as preventing a problem in the first place and/or mitigating its consequences. Trobradovi�; “All five cases are coming from different companies and different industries, with details describing the implementation and evolution of the Ultrasound CM program, up to the successful case and its benefits evaluation.
> Gearbox – Aluminium facility, main conveyor gearbox. During the EuroMaintenance workshop, Trobradovi� takes you in Electrical motor, Steel Mill, broken rotor bar, Lubrication, Chemical plant, extraction fans. But he will also catch you up with Low-speed bearings – Barit mine, mill and Leaks (glass bottle manufacturing, forming machine). Trobradovi�; “The cases shown are highlighting Ultrasound capabilities as a sole CM technology used, as well as part of the multitechnology approach in mature CM systems. Additionally, the user profile will clearly be specified, as an important part of CM optimization”.
‘Ultrasound: first line of defense in condition monitoring’Foto: NVDO
Developments due to robotization ensure that employees can reach more difficult places more easily by carrying out digital inspections in advance. Virtual Reality/ Augment Reality makes it easier for employees to watch from a distance, which improves work safety. In addition, there is also increasing social pressure, which means that legislation and regulations are being tightened up.
will ensure that the tasks of employees in Management and Maintenance will change and that different knowledge will be needed to perform this task.
> Increasing automation level. David Lopez, Siteplant (Spain) is one of the EuroMaintenance workshopleaders; “Companies are drastically increasing their automation level, both in routinary tasks and in non routinary tasks. In this scenario, robotics seeks for new fields of application, not necessarily related with productive tasks. Moreover, reliability will be the key transversal function to be empowered within these ‘automated’ organizations and Artificial Intelligence will provide (in fact, it is providing…) robots with new analytics and decision-making capabilities that boost their autonomy”.
> The Workshop. Robotics has been widely used in the manufacturing processes, but in other activities such as maintenance their use is barely limited to simple inspections, according to Lopez. “New fields of robotics applications can be developed to increase the operational reliability of assets. In our workshop, we will expose the several potential applications of robotics to maintenance activities and, in general, to increase assets reliability, along the whole reliability value chain (design, construction, start-up, operations, maintenance and dismantling). Also, the current state of the art of autonomous robots will be discussed under a pragmatic point of view, and specific use cases will be explained, such as inspections rounds performed by robots or their polyvalence and flexibility to alternate supervisión, safety and inspection tasks within a manufacturing enviroment”.
This includes preventing the release of harmful substances and other safety protocols. Preventing disruptive effects caused by, for example, legislation and regulations, can ensure that companies give an even more central position to a safe working environment.
> Everything automatically controlled by data. In addition to the fact that assets are becoming increasingly complex, more and more information is being released in the form of data. The amount of available data is increasing almost exponentially, giving companies more and more insights into important maintenance processes that could not be obtained before. The rise of Artificial Intelligence and the Internet of Things will ensure that the role of data continues to grow and will even make it possible to make predictions about the future without a person intervening. Moreover, the combination of the use of robots and artificial intelligence ensures that more and more tasks in Management and Maintenance will be automated. This
‘
’
‘Not a threat, but an opportunity’
Simply put, stage one (1) is during the Capital Project design of the life cycle, and stage two (2) is during the lengthy period of Operations and Maintenance. The former requires that maintenance issues are covered fully by the experienced site maintenance related personnel within so-called ‘Early Asset Management’. The latter takes place following the receipt of data and information on operation of the asset systems within their working environment; or when cost reductions or other significant change demands that it takes place. The implementation of the investment project management strategy at each of the stages 1) and 2) includes the two types of strategy involved in Maintenance. One is the Asset Strategy, which is the set of job activities to be implemented; the other is the Maintenance Management Strategy. They both are influenced by, and have an impact on, Asset Management throughout the lives of the asset systems. The importance of creating interaction and strength within the triangle of the top-down and bottom-up actions of Project, Operations and Maintenance supporting Asset Management will be represented widely with the presentations throughout the forthcoming EuroMaintenance Conference at Rotteredam.
> The value of LCC. Janez Tomazin is Chairman of the EFNMS Asset Management Committee and supports the fact that the greatest opportunity for influencing projected Life Cycle Cost occurs during the initial design stages of the life cycle. “Once the investment has been put into service, there is relatively little flexibility in influencing the overall committed cost. Preparation during the design, build, commissioning and handover stages includes the preparation of the policies for Asset Management and maintenance within it, but also the inclusion of O&M personnel in the project management team and the evaluation of previous operating performance and failure information of similar assets”. Besides these Tomazin mentions also the aimed at assets reliability and maintainability objectives, and associated configurations, checks on the anticipated life-cycle costs at each stage of the life cycle design and build and the definition of the operability, safety, ESG, and wider organisational objectives of the project.
The required support to the operations and maintenance stage should be in place on the first day of the commissioning function, and its verification should be part of that activity. It matters little that the asset is brand new, it can fail, and if the right spare is not available or the people are not trained, then the expectation for the budget and commissioning time may be compromised
> Support. The application of standards, those existing and those being considered, is supported strongly by EFNMS personnel through their national societies. The standards applied may include the most recent issues of those shown in the diagram, which illustrates a
structure having EN 16646 Maintenance within Asset Management as key support to the Asset Management ISO 55.000 series. Tomazin; “I will strongly recommend everyones attendance to EuroMaintenance. Maybe we can inform you about these kind of standards”.
The EFNMS Asset Management Committee recognises that there are at least two stages of an asset’s life when the Maintenance Strategy is prepared, or reviewed, to be in line with the objectives of an organisation’s Asset Management.Janez Tomazin Photo: Private Collection
‘
’
‘The EFNMS Asset Management Committee actively supports certifiable Asset Management’
We all recognize the daily intensive consultation regarding the scheduling of maintenance of our assets? These consultations between production department, safety & health department and maintenance department are often ad hoc decisions in which is mostly supported by the use of excel and mail.
reason prior to a shutdown or stop for planned maintenance the coordination of safety and health procedures such as Work Permits, LOTO (Lockout Tagout) are extremely important.
Grisel; “Today, one can use a highly integrated system where the production department, safety & health department and maintenance department can use the same data to identify key risks and is successfully able to mitigate those risks in an efficient way. Work Permit and LOTO integration in Maintenance Planning is required to reduce these risks during the maintenance process. The SAP ERP system in combination with the Ready4 Asset Management solution enables us to integrate Work Permits and LOTO and makes it visible prior to and during the planning of work orders & tasks and thus ensures that work can only be done on released and secured Assets”. Creating a safer working environment whilst gaining efficiency as an organization.
Nowadays securing health and safety in the workspace are even more important than in the past. We value safety of our customers and employees highly and are emotionally and by law obliged to do everything possible to make sure that this will be achieved.
> No risks are wanted. The consequences of not achieving this are incalculable in personal health and also financially the organizations are held accountable. In order to document the maintenance processes, organizations have implemented maintenance software as a supporting system where in many cases there is no integration with existing health & safety systems. “The production department needs to ensure that machines are secured so that the maintenance department can safely start to carry out maintenance. By having to search and consult various systems to perform these crucial and difficult tasks, the process is prone to mistakes with all consequences of this”, says Charles Grisel, Sr Account Manager at SOA People. “However, organizations try to avoid risks and reduce mistakes during the execution of the process”.
> Lockout Tagout more important than ever. Maintenance is a high-risk activity with specific hazards and risks for customers and engineers. For maintenance engineers, this includes working alongside a running process where they are in close contact with machinery. If mistakes are made, customers can also be effected. For that
> Looking forward to EuroMaintenance. Grisel; “SOA People is part of EuroMaintenance because we do feel that it’s important for organizations to adapt their business processes in order to be able to use an integrated system and optimize their maintenance. With the combination of tooling and business consulting services SOA People is the organization which can help you achieve efficiency goals and optimize the availability of your assets. Therefore we are here to improve your bottom line results”. <
The first few weeks of the new year are usually all about looking ahead. Experts who predict trends for the year, people making their new year’s resolutions (and trying to stick to them), companies finetuning their plans and strategies. For me, as a Maintenance Professional, if I look at 2023 there’s one big event that stands out: EuroMaintenance 2023 | www.euromaintenance.net
> Empowered to perform MaxGrip will also be heavily involved in the conference. At our consultancy firm, we have worked hard to bring together various perspectives on asset management for EuroMaintenance this year. We are skilled at bringing together people and perspectives within companies across the globe in many different industries and with various technology partners. After 25 years in business I can safely say that we know how to empower companies to perform and get the results they require.
> Our clients’ perspectives I am especially proud of the two key note presentations and five workshops that MaxGrippers will host during the conference. These are presentations given by clients such as Waternet, the Public Water Authority of Amsterdam, TenneT, the Dutch transmission system operator, ONE-Dyas (oil & gas exploration and production company) and Victrex (chemical company) as well as presentations with partners like IFS Ultimo and LNS Research.
This year, the Dutch Maintenance Society (NVDO), in close corporation with the EFNMS (European Maintenance Federation), is organizing the biannual conference, which is held in Rotterdam (Ahoy) from April 17th until 19th. As a board member of the NVDO, I am very proud of our maintenance society (the largest of Europe) and country to host such a great event. With a theme of ‘Asset Management at its best’ and a strong program in place including an exhibition, I expect the event to be a great success. Together we will make Rotterdam the maintenance capital of Europe!
A personal new year’s resolution I made is meeting more clients and relations face to face. EuroMaintenance will be an excellent opportunity for me to engage with other Maintenance Societies, participants, conference guests, clients, partners, and others. Let’s share our perspectives on asset management and inspire each other to make 2023 the best year yet for all of us.
Marcel Morsing Senior BD consultant/Board Member NVDOThe Maintenance workforce has grown again. However, there are challenges facing the sector. For example, the increasing ageing of the population is causing a high average age (46 years), an increase in the number of vacancies (15 vacancies per maintenance organisation) and an increase in the outflow (8,9%). Of the outflow, a large group (43,5%) leaves the organisation because of retirement.
In the coming years, efforts should be made to increase the inflow of new personnel. One way to achieve this is by attracting more women (current share 8,4%) and more people with a migrant background into Maintenance. Furthermore, efforts should be made to retain these groups within the maintenance organisation.
The rosy picture of the sector is that there is increasing confidence in recruiting enough staff. 60% of companies say they are confident
about attracting enough technical staff and 71% say they are confident about attracting enough technological staff. The outflow due to dissatisfaction has decreased (35,5%), which means that Management and Maintenance is an attractive sector to work in.
Let’s discuss the changes at the EuroMaintenance Inspiring Table ‘Human Factor; Opportunities instead of problems’
Incidents and accidents are almost always due to a complex of factors. Human failure in the broadest sense (such as shortcomings in safety awareness, competencies, instructions, communication) is in the majority of the incidents one of the most important basic causes. At the same time lifetime extension and replacement of assets by assets with the same or one additional functionality are the most important measures to an aging asset base to keep in operation. Asset owners are more likely to plan to implement a functional improvement when replacing assets. Reasons for investing in such targeted
improvements include the need to meet higher production targets. Other reasons are the stricter climate and energy targets and the use of the possibilities offered by smart assets.
What do the aging asset base and security have to do with each other?
Let’s discuss the challenges at the EuroMaintenance Inspiring Table ‘Asset performance management versus Safety’
Maintenance organizations are aware of the ever-increasing sustainability within Management and Maintenance and are aware (87%) of the sustainability objectives that their organization sets. Even though sustainability already has a high priority, we see that one of the main difficulties that organizations face when implementing sustainable initiatives in the field of Management and Maintenance is to release a budget (45%) and making sustainable investments profitable (48%). However, the Management and Maintenance sector is well on its way, with 91% of those surveyed already investing their organization in
energy saving and efficiency. The transition to a circular economy is also well underway and the importance of it is recognized. Sustainability offers several benefits that can be achieved with the right amount of attention. For example, it brings cost savings, makes a positive contribution to reputation management, ensures satisfaction both internally and externally, and offers certainty for the future.
The workshops, the conference and the inspiring tables provides tools to contribute with maintenance to the sustainable goals of your organization!
By mid-2022, an oleochemical plant in the Netherlands, was facing a seven-fold increase in energy costs. A leader in hydrogenating vegetable oils into solids for use in food, cosmetics and countless other everyday products, the hydrogenation process depends on steam, steam that is made using natural gas.
Unable to pass on the increased price pressures, they asked Royal HaskoningDHV if it could identify cost-cutting opportunities. The company was doubtful – its hydrogenation process was already felt to be pretty efficient – but it doesn’t hurt to ask the question amid a global energy crisis. Bart Vander Velpen, Director Net Zero Industry at Royal HaskoningDHV; “They were astonished that, despite their already high efficiency, we were able to identify a number of issues that they had not been able to see. All by using data”.
> Strategic versus tactical Asset Management Royal HaskoningDHV, a long-established engineering consultancy, is fast evolving into an engineering and Asset Management specialist. Where once its role ended when an engineering project concluded, its Asset Management team can show you how to make further improvements on an ongoing strategic basis. The driver? Data. “We support the creation of professional Asset Management organisations that can
use data to set strategic goals for their assets and improve their work processes, structures, responsibilities and accountability year after year,” explains Michelle Ham-Oudkerk, Associate Director Asset Management Consultants at Royal HaskoningDHV.
In essence, where an engineering team will focus on a single issue, Royal HaskoningDHV’s Asset Management specialists employ data to consider the complete picture over a longer timeframe. By securing, analysing and using data to make the best short, medium and longterm decisions, they can help the client to future-proof its assets – its physical resources – and make both strategic and everyday decisions that weigh performance, costs, risks and so on both immediately and down the line. “Having access to data enables you to keep these in balance and to make the right decisions at the right moments,” says Ham-Oudkerk.
Foto: Royal HaskoningDHV> Deep insight into how the organisation really works Asset Management’s integrated approach reflects the fact that today, through data, we can get a far better insight into all the ways in which processes, work structures, responsibilities, sign-offs, lifecycles, life expectancy, maintenance schedules and so on overlap with and impact on each other. And then there are strategic issues like CO2 reduction, managing energy costs, circularity, adapting to a shrinking labour pool and more. The implication here is that in managing your assets, you shouldn’t just think about CO2 reduction, say, but also consider things like circularity, extending a maintenance period, automation or robotisation and when to replace an ageing asset.
This is the difference between traditional maintenance management and the data-driven Asset Management that Royal HaskoningDHV advocates. Ham-Oudkerk; “An Asset Management policy should apply to every aspect of the work floor, and everything you do should align with the organisation’s strategy and top management goals”.
She gives the example of a company that wants to end its reliance on gas by 2030. This will involve switching to renewables. In the meantime, at local level, a unit has plans to move from oil to gas, because gas is cleaner than oil. The problem with this from a strategic Asset Management perspective, is that such a move now could prove to be a waste if shortly after the unit has to re-engineer its operations to run on renewables. Multiply this one example across dozens or even hundreds of projects and maintenance cycles and you get an idea of the complexity.
And this is where data comes in. Through dashboards at tactical and strategic level, Royal HaskoningDHV helps organisations to align individual decisions with the wider strategic Asset Management goal. Basically, it helps individual teams avoid making choices that, unintentionally, undermine or complicate the wider strategic ambition.
So what of the oleochemical plant? Back to Bart Vander Velpen; “We began as we always do by collecting data, in this case to understand their steam use –when, how much, continuously or intermittently – and the first thing we saw was that they were generating more steam than they were using”. And not just a little more, either. Initially, Royal HaskoningDHV expected they could reduce their energy needs by 9% a year. In reality, the team found a potential 14% reduction. “This was just the
easy wins,” notes Vander Velpen. “We also saw that, with some investment, they could reduce their energy consumption by up to 30%. Among the opportunities the data revealed were fixing leaks and the realisation that the plant’s operators were, in effect, demanding that steam should be continuously on tap while their operation was in effect a batch process”.
Throughout, Vander Velpen and his team of strategists, data specialists, programme managers, and engineers followed their usual approach to strategic Asset Management: collecting data, analysing it, validating assumptions with the client, verifying these conclusions and then moving to implementation.
This is the same methodology that Royal HaskoningDHV uses throughout its Asset Management service, and the same approach the firm advocates for the much bigger challenge facing industry: moving to net zero. “Vander Velpen; “You cannot get to net zero if you are wasting a lot of energy. It will cost too much. So, first, you have to optimise the performance of your current installation. Make savings. And making savings also helps you to understand your process better and who is responsible for what. Next, you need the required insights from data, which means you need to install sensors, to develop specific dashboards that can present the data in a practical way. Then you need to train your facility people or maintenance people in strategic, data-driven Asset Management. Once you have this in place, you can start to build a roadmap towards net zero”. <
CALL TO ACTION: Royal HaskoningDHV is a sponsor of EuroMaintenance 2023, where it will be holding two Asset Management workshops, one on Smart Industry and the other on Sustainability.
To find out more about Royal HaskoningDHV Asset Management services go to royalhaskoningdhv.com
‘Bart Vander Velpen’ Foto: Royal HaskoningDHVEverybody who matters in the industrial maintenanceworld can be found in Rotterdam Ahoy on 18, 19 and 20 April 2023. Several thousands of maintenance professionals and technical service providers will then be attending the leading technology and maintenance exhibition in the Benelux: MaintenanceNEXT.
They are coming to the exhibition to acquire new knowledge and expertise and to be immersed in the latest new technologies, innovations, technical solutions and high-tech products that the many exhibitors will be showing. MaintenanceNEXT offers three days of the latest and the best of the industrial maintenance sector.
> More than 11.000 visitors “When we got the opportunity to combine our Maintenance NEXT exhibition with EuroMaintenance, we did not hesitate a moment” says Pieter Bas Dujardin, exhibition manager of Maintenance NEXT. During the exhibition, more than 250 national and international exhibitors will present the most important innovations in the field of (industrial) maintenance on the exhibition floor, which is visited by more than 11,000 visitors every two years. Dujardin explains; “To add such a well-known conference with international top speakers to the exhibition is a great opportunity and makes Rotterdam the maintenance capital of 2023”.
Saskia Vernooij, General Manager Exhibitions & Events bij Rotterdam Ahoy; “At Rotterdam Ahoy we love nothing more than organizing wonderful events. We are therefore eager to get back to work with
everything on the agenda. A high quality congress such as EuroMaintenance, with international allure and top speakers, is really adding value to that agenda. Because of the corona pandemic, not only we, but the whole of Europe has had to wait too long for this essential congress for the sector. The fact that it is taking place at the same time as our own exhibition, Maintenance NEXT, strengthens both initiatives. We are continuing our earlier plans from 2021 to establish the largest maintenance platform in Europe. In the third week of April 2023, we will bring together the entire chain of maintenance professionals and treat them to inspiring presentations, workshops and demonstrations. That is why I am eagerly looking forward to the renewed collaboration to make Rotterdam ‘The maintenance capital of 2023”.
Production
Pack & Parcel is a marketing agency that supports you in the promotion of your company.
Your customer is our concern. The service ranges from concept to realisation. Passionate designers, beautiful printing, storage and distribution. Whether it’s a one-off campaign or an ongoing process, you’ve come to the right place.
Many companies use their Enterprise Asset Management (EAM) system mainly as an electronic card index or a digital work order system, unaware of the possibilities it has for Asset Management. EAM Systems like Maximo, IFS Ultimo, HxGN EAM and SAP EAM have evolved tremendously. They now offer functionalities for Asset Investment Planning, Project Portfolio Management, Asset Performance Management, Business Intelligence and Predictive Maintenance. Major steps have also been taken in the field of Mobile, GIS and BIM integration.
Are you ready for Next Generation EAM?
Our VDMXL experts can assist you with further professionalisation and automation of your Maintenance & Asset Management organisation.
www.mainnovation.com