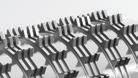



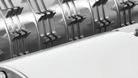

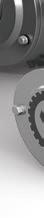
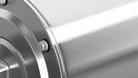
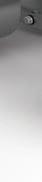
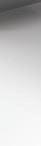
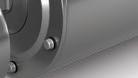
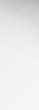

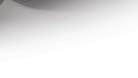



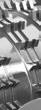
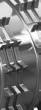

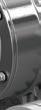
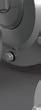
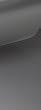
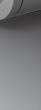
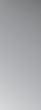

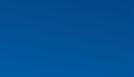
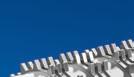


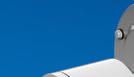
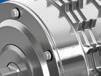

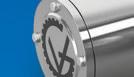






The new patented SSV-XP Drum Motor features an exchangeable profiled sleeve on the drum to drive various modular conveyor belts using the same drum motor.
The profiled sleeve is quick and easy to remove and replace with another profiled sleeve to match the belt required on the conveyor. The profiled sleeve is available for all belt manufacturers.
PACK EXPO International Innovations Report
How to Build a Food Safety Program
Vertical Startup Will Deliver Results
Fill one bulk bag per week or 20 per hour with REAR-POST, TWIN-CENTERPOST™ and SWING-DOWN® Bulk Bag Fillers
Flexicon’s extra-broad model range, patented innovations and performance enhancements let you exact-match a ller to your speci c cost and capacity requirements. Patented TWINCENTERPOST™ models maximize strength, accessibility to bag loops and economy. Cantilevered REAR-POST models allow passthrough roller conveyors. SWING-DOWN® models pivot the ll-head to the operator at oor level for quick, easy and safe spout connections. Optional mechanical and pneumatic conveyors.
Loosen material solidi ed in bulk bags during storage and shipment with BLOCK-BUSTER® Bulk Bag Conditioners
Opposing hydraulic rams drive contoured conditioning plates to crush and loosen solidi ed bulk material safely and easily. Bulk bags can be raised, lowered and rotated to allow complete conditioning of the entire bag through the use of automated turntables and scissor lifts, or electric hoist and trolley assemblies. Offered as stand-alone units for loading with forklift or electric hoist and trolley, or integrated with bulk bag dischargers for reduced cost, footprint and loading time.
Save time, money and space with BULK-OUT® Multi-Function Bulk Bag Dischargers and Weigh Batching Stations
Condition, de-lump, screen, feed, weigh batch, combine with liquids, and convey as you discharge, with a custom-integrated, performance-guaranteed, dust-free discharger system. Offered as stand-alone units for loading with forklift or electric hoist and trolley, split frames for low headroom areas, economical half frames and mobile frames. All available with mechanical and pneumatic conveyors, ow promotion devices, bag dump access, automated weigh batching packages, and much more.
Stand-alone units to complete, automated systems integrated with mechanical and pneumatic conveyors
Our GEA MaxiFormer can produce 250,000 chicken nuggets per hour. Its patented step filling system and unique drum design provides maximum shape retention, weight accuracy and knock-out control, using only air to release the product. Available in 600 and 1000 mm widths, the drum former is designed for high volume production of virtually any kind of 2D and 3D shaped product. What’s more, the fully automated sensor-based cleaning system, works to provide 100% drum cleanability and maximizes production time.
2QO\0XOWL X[®*06PL[HUVIURP*HULFNHLQFOXGHDSURSULHWDU\ GRXEOHURWRUGHVLJQWKDWGLUHFWV\RXULQJUHGLHQWVLQWRD XLGL]HG VDIHW\]RQHIRUthorough - yet gentle - mixing and blending in as little as 30 seconds:KHQLWȇVWLPHIRUFOHDQLQJWKHHQWLUH IURQWGRRURSHQVDQGWKHRSWLRQDOFDQWLOHYHUHGPL[LQJPHFKDQLVP VOLGHVRXWRQUDLOVIRUGHJUHHRSHQDFFHVV)RUKLJKTXDOLW\ UHVXOWVHYHU\WLPHWKLVLVWKHZD\
*HULFNH86$ΖQF:RUOGV)DLU'ULYH6XLWH&6RPHUVHW1-ȏ[ȏVDOHVXV#JHULFNHJURXSFRP
Gericke is the way to a uniform, homogeneous mix, and fast, easy, complete cleaning.
Remote Troubleshooting: Telemedicine for Your Equipment
Just as it did for consumers’ willingness to visit their doctors over a video call, the pandemic signaled a shift in how food and beverage producers view remote troubleshooting from their OEMs.
16 OpX Intel: Vertical Startup Will Deliver Unimaginable Results Reach full production faster—while engaging employees, reducing waste, and producing more finished product—with full commitment of cross-functional leaders and stakeholders.
Check out the latest industry innovations that were unveiled during PACK EXPO International 2022.
120 Tech Today: Advantages of Adding Inspection Further Up the Line Product recalls and new demands from retailers in 2023 are impacting inspection placement in food manufacturing facilities.
ProFood World’s Leaders in Processing section recognizes many innovative suppliers to the food and beverage manufacturing industry.
EDITORIAL
EDITOR-IN-CHIEF AARON HAND 312/488-3392 ahand@pmmimediagroup.com
SENIOR EDITOR MICHAEL COSTA mcosta@pmmimediagroup.com
NEW PRODUCTS EDITOR MORGAN SMITH msmith@pmmimediagroup.com
CONTRIBUTING EDITORS
JEANNE SCHWEDER, STEPHEN PERRY, STEPHEN SCHLEGEL, JEFFREY BARACH
ART
ART DIRECTOR KATHY TRAVIS
CREATIVE DIRECTOR DAVID BACHO
PMMI MEDIA GROUP
VICE PRESIDENT, SALES WENDY SAWTELL VICE PRESIDENT, DIGITAL ELIZABETH KACHORIS
SENIOR DIRECTOR, CLIENT SUCCESS AND MEDIA OPERATIONS KELLY GREEBY DIRECTOR, DIGITAL MEDIA JEN KREPELKA
SENIOR DIRECTOR, CONTENT & BRAND GROWTH MIKE PROKOPEAK
SENIOR DIRECTOR, EVENTS TREY SMITH DIRECTOR, MARKETING SHARON TAYLOR
SENIOR MARKETING MANAGER AMBER MILLER
CONNECT WITH US
@ProFoodWorld
@ProFoodWorld
www.linkedin.com/ showcase/profoodworld
PRESIDENT, PMMI MEDIA GROUP DAVID NEWCORN
FOUNDING PARTNER AND EXECUTIVE VICE PRESIDENT, INDUSTRY OUTREACH, PMMI JOSEPH ANGEL
FOUNDING PARTNER LLOYD FERGUSON
ADVERTISING
PUBLISHER PATRICK YOUNG pyoung@pmmimediagroup.com
• 610/251-2579
ACCOUNT EXECUTIVE BRIAN J. GRONOWSKI bgronowski@pmmimediagroup.com • 440/564-5920
BRAND OPERATIONS MANAGER CLAUDIA SMITH csmith@pmmimediagroup.com • 312/222-1345
PRODUCTION MANAGER GEORGE SHURTLEFF gshurtle @pmmimediagroup.com
FINANCIAL SERVICES MANAGER JANET FABIANO jfabiano@pmmimediagroup.com
Questions about your subscription or wish to renew? Contact circulation@pmmimediagroup.com.
ProFood World • PMMI Media Group 401 N. Michigan Ave., Suite 1700, Chicago, IL 60611 Phone: 312/222-1010 • Fax: 312/222-1310
Email: info@pmmimediagroup.com • Web: www.profoodworld.com
PMMI, The Association for Packaging and Processing Technologies 12930 Worldgate Drive, Suite 200, Herndon, VA 20170 Phone: 571/612-3200 • Fax: 703/243-8556 • Web: www.pmmi.org
Sta at PMMI Media Group can be contacted at info@pmmimediagroup.com.
Artificial intelligence and automation won’t replace us just yet. For now, let them take the grunt work o our shoulders.
For as long as there have been robots, there have been conversations about them taking our jobs. Not just robots—any technology that o ers to make our jobs easier also threatens to make our jobs so easy, they become obsolete.
Automation and digitalization have become increasingly popular topics among food and beverage producers. It’s been an ongoing journey for years. But suddenly, exacerbated by the pandemic, manufacturers are finding it next to impossible to find the workers they need to get the job done.
It’s di cult not to sco these days at continued concerns about robots stealing jobs. In most cases, manufacturers simply cannot find the workers to complete the jobs. But then news came through about this hot new artificial intelligence (AI) capability from OpenAI called ChatGPT, and suddenly the shoe was on the other foot. Editors around here—some who had espoused the ideas of automation for a better workplace—were suddenly fearing for their jobs. Give it a prompt (“Write a 2,500-word article on remote troubleshooting in food manufacturing”), and soon out pops a reasonably constructed bit of prose.
How soon would we all be out of a job?!!
But really, the idea that a chatbot could soon take over live reporting and reasoning is no more an argument than automation pushing skilled humans out of the manufacturing space. Instead, we go back to an idea comparable to using robots for the dull, dirty, and dangerous tasks. Use ChatGPT to write the social media blurbs or newsletter subject lines, say, while we focus instead on producing richer content.
In this issue, I like the example from Evolution Fresh (page 141), the cold-pressed juice maker that worked with Hiperbaric to automate tasks that were no fun for any of those workers. The robots are now doing the heavy repetitive lifting while the people focus on the things robots aren’t so good at.
EDITORIAL ADVISORY BOARD
CHRISTINE BENSE
CHIEF SUPPLY CHAIN OFFICER
Turkey Hill
GREG FLICKINGER
CHIEF OPERATING OFFICER
Nobell Foods
JOHN HILKER
FORMER DIRECTOR OF MANUFACTURING
Blommer Chocolate Company
VINCE NASTI
VP, OPERATIONS
Nation Pizza & Foods
JIM PRUNESTI
VP, ENGINEERING
Conagra Brands
LISA RATHBURN
VP, ENGINEERING
T. Marzetti
MARK SHAYE
VP, ENGINEERING
Ken’s Foods
TONY VANDENOEVER
FORMER DIRECTOR, SUPPLY
CHAIN ENGINEERING
PepsiCo
DIANE WOLF
FORMER VP OF ENGINEERING AND OPERATIONS
Kraft Foods
BROOKE WYNN
SENIOR DIRECTOR OF SUSTAINABILITY
Smithfield Foods
JOE ZEMBAS
DIRECTOR, ENGINEERING AND TECHNICAL SERVICES
The J.M. Smucker Company ahand@pmmimediagroup.com
MUNSON® Ribbon, Paddle and Plow Blenders force agitators through stationary materials, imparting shear needed to reduce agglomerates and blend pastes and slurries. Choose from basic, low cost industrial units to state-ofthe-art designs of 304/316 stainless with heating/ cooling jackets, liquid spray additions, high-speed choppers/intensi ers, and nishes to USDA Dairy and other standards. Extreme vessel rigidity allows tight agitator-to-vessel wall tolerances, resulting in a minimum “heel” of residual following discharge. Heavy- and extra-heavy-duty batch and continuous models in capacities from 1 to 1,150 cu ft (.03 to 32 m3).
MUNSON® Vee-Cone
Blenders feature smooth internal surfaces free of baf es, shafts and bearings, allowing unobstructed material ow, plus complete discharge through a gate valve for rapid cleaning or sanitizing of the easy-access interior. Uniform blends are typically achieved in 5 to 15 minutes with equal ef ciency at ll volumes from 100% to 25% of capacity. Ideal for dry and granular materials, these blenders provide a tumbling action that is gentler than machines that force agitators through stationary material. Options include spray bars for liquid additions, Clean-In-Place (CIP) systems, abrasion-resistant steel construction, ASME-coded jackets and weigh batching accessories.
100% Uniform blending and/or liquid additions to 1 ppm in 2-1/2 minutes
Total discharge with no segregation
Ultra-gentle tumbling action (versus blades forced through batch)
Ultra-low energy usage
Equal ef ciency from 100% to 15% of capacity
Unlike other rotary mixers:
– No internal shaft or seals contacting material
– Every internal surface accessible
– Signi cantly faster washdown
– Seal changes 10x to 20x faster
Unlike Ribbon and Paddle Blenders with a single agitator shaft, MUNSON® Fluidized Bed Mixers feature two shafts with paddles that counter-rotate at higher speeds to uidize material, achieving homogeneous blends in 10 seconds to 2 minutes. Low shear forces minimize friction with little or no degradation and insigni cant heat generation of <0.6°F (1°C). Drop-bottom gates provide rapid discharge with no segregation and minimal residual. Ideal for short cycles and gentle handling of low- to medium-density powders and fragile akes 50 lbs/ft3 ( 800 kg/m3) with or without liquid additions. Capacities from 0.21 to 283 cu ft (6 L to 8 m3).
Remove lumps and agglomerates from bulk foods, nutraceuticals and pharmaceuticals, or break down friable materials. Dual rotors with threepoint, single-piece breaking heads rotate with minimum clearance inside a curved, perforated bedscreen. On-size material exits through bedscreen apertures. The low pro le design ts tight spaces between upstream and downstream process equipment, while side-removal bedscreens allow fast, in-place sanitizing. Square or rectangular inlets range from 15 to 48 in. (38 to 122 cm) in width—classifying screen apertures from 1/32 to 2-1/2 in. (0.8 to 63.5 mm) in diameter.
Also known as Centrifugal Impact Mills, these MUNSON® machines deliver coarse to ne grinding of friable powders, akes and granules into controlled particle sizes at high rates per HP/kW. High-speed rotation of the inner disc creates centrifugal force that accelerates bulk material entering the central inlet of the opposing stationary disc. As material travels from the center to the periphery of the discs at high speed, it passes through a path of ve intermeshing rows of rotating and stationary pins, with the desired tight particle size distribution obtained by controlling the rotor speed.
No other bulk solids mixer delivers this unique combination of bene ts:
The new M VersaPro® Dicer (MVP) excels at shreds and strips.
Patented fl uted crosscut provides gentler cutting action.
Deeper knife penetration improves cut quality. Interchangeable 5 or 6" (127 or 152 mm) circular knives and spacers to match your product.
Powerful 5 HP (3.7 kW) VFD-equipped crosscut plus your choice of a 5 or 10 HP (3.7 or 7.5 kW) motor. Explore the new MVP to improve your line.
#1 Best selling provider of industrial cutting machinery throughout the world.
ONE OF THE FASTEST-GROWING SEGMENTS of high-pressure processing (HPP) today is raw pet food. As HPP technology evolves to remove foodborne pathogens in fresh and uncooked ingredients, so do the options for pet owners to feed their cats and dogs raw meals.
Processing raw pet food through HPP requires the same meticulous testing as human foods like guacamole, fresh juices, dips, and deli salads before reaching store shelves. One pet food company committed to HPP as a food safety and nutrient preservation tool is St. Louis-based Instinct Pet Food. Positioning itself as a premium brand of raw pet food, the company has carved a niche in this growing segment through diligence in applying HPP every step of the way.
Instinct’s COO, Bobby Harris, addressed attendees at the Cold Pressure Council’s annual conference in Chicago, and explained his company’s strategy for using HPP to ensure safe production of its raw pet food. Here are some of the highlights from Harris’ session, which are applicable to any company looking to manufacture raw pet food.
Harris cited a University of Helsinki study of more than 4,000 dogs that determined raw foods have a higher nutritional value and can reduce incidences of allergies and illness in canines. The study concluded that if just 20% of a dog’s diet is raw food, the animal will start to realize those health benefits. Conversely, if a dog’s diet is less than 20% raw foods—replaced by heat-treated, commercially produced dry kibble, for example—the risk of allergies and illness increases.
Mondelēz is selling its developed-market gum business in the U.S., Canada, and Europe, excluding France, to Perfetti Van Melle Group for $1.35 billion.
The guidance explains the requirements to analyze the hazards in food, evaluate a potential foreign supplier’s performance and the risk posed by a food, and determine and conduct appropriate foreign supplier verification activities.
Maple Leaf Foods has announced current president and COO Curtis Frank will become president and CEO by spring of this year.
The new Bowling Green facility will produce specialty and metabolic powder nutritional products, some of which serve as the sole source of nutrition for people with extreme allergies.
Nestlé plans to spend about $2 billion in Saudi Arabia over the next 10 years, beginning with a $100 million manufacturing plant, which is expected to open in 2025.
Part of Instinct’s food safety strategy is to source high-quality ingredients from approved suppliers that meet the company’s food safety standards, making it more likely the finished product will pass pathogen tests.
“We’re really riding on the backs of this study, showing some pretty definitive outcomes that feeding raw has advantageous nutritional benefits, as well as some disease mitigation,” said Harris. “So, we’ve been committed to this journey since the inception of the company.”
While the study shows the benefits of raw pet food, many in the veterinarian community, according to Harris, are skeptical of raw pet food, primarily because of the increased risk of pathogens such as salmonella, listeria monocytogenes, E. coli, campylobacter, yersinia, and others in raw meats.
This is where HPP enters the process. HPP extends the shelf life of fresh and perishable foods by applying carefully calibrated pressure to a product, which destroys bacteria and pathogens that can cause foodborne illness. HPP can add 90 to 120 extra days of shelf life without altering the texture, flavor, or color. For Instinct, some varieties of its raw pet food go through HPP before being further processed to freeze-dried.
“We believe that HPP allows us to create safe raw pet food as part of a multifaceted component without breaking that protein bond. It also retains a lot of the heat-sensitive bioactive compounds that are so important for palatability,” said Harris.
Harris detailed how he wanted Instinct to serve as an example for the rest of the industry regarding raw pet food and food safety with a “multi-
hurdle” HPP testing approach, so the company partnered with the University of Nebraska and the Illinois Institute of Technology to carry out those tests. The ultimate goal in the future, said Harris, is for Instinct’s raw pet food to be recognized by the USDA, APHIS, and the FDA. It is already certified SQF for food safety and quality by the Safe Quality Food Institute.
“We know we have competitors out there that choose not to HPP certain proteins, and we think that’s a mistake,” noted Harris. “We think given enough time with enough product in the marketplace, [those companies] are putting themselves at risk. And, quite frankly, they’re putting the category at risk.”
Part of Instinct’s strategy includes avoiding a one-size-fits-all HPP test for pathogens, instead measuring how each type of meat used—rabbit, beef, salmon, venison, lamb, and others—reacts individually to HPP from a time, pressure, and temperature standpoint.
“You need to understand what the individual components are for your particular [raw pet food] formulas,” explained Harris. “This lets you determine an HPP SOP [standard operating procedure] for your products. If you try to cut and paste somebody else’s formulas, you may be creating a disadvantage for your customers, and perhaps your company. Not all meats respond the same to HPP pressure. There’s a max pressure that most HPP manufacturers would recommend, but within that pressure, find what’s right for your company.”
Harris used beef as one example of Instinct’s multi-hurdle approach to HPP testing, noting they used two di erent lots with six di erent strains of salmonella. “We had a very encouraging outcome, and with the combined time, pressure, and temperature we used, we were able to achieve a greater than five-log reduction,” he said, adding that the tests showed HPP is also very good at reducing or completely mitigating viruses, yeasts, and molds.
“Our studies that we’ve done in combination with the universities indicated no destruction with key nutrients, and meet the criteria of being a fullmeal component via ethical standards and palatability,” said Harris. “We found through work with the University of Nebraska that grind size matters, the fat content within your formula matters, and the bone particles matter—they all play a role in developing a unique formulation for your brand.”
Consistency and accuracy are mandatory in any dry material processing system, and Vibra Screw’s volumetric and gravimetric feeders deliver both. They employ controlled vibration to control material density variations and ensure smooth movement
throughout the feed process.
The result is the highest accuracy feeders on the market today. Our experts work to understand the VSHFL¿FQHHGVRI\RXUDSSOLFDWLRQGLPHQVLRQDO constraints, unusual temperature, heavy loads, moisture content, long distances, high wear, or other unique factors. Then we recommend a solution optimized for your application. Vibra Screw feeders are designed to handle a wide
range of the most problematic materials.
The most trusted name in dry solids processing
973-256-7410 www.vibrascrew.com
SHIFTING CONSUMER TRENDS through the COVID-19 pandemic have continued to prompt adaptation from snack brands, says David Walsh, SNAC International vice president of communications.
Walsh detailed the state of snacking at the PACK EXPO International Industry Speaks stage in Chicago, noting trends ranging from an increase in e-commerce to a focus on functional snacks.
Snacking was the second highest contributing category to retail dollar growth during the pandemic. It trailed only personal care products including toilet paper and similar items that consumers rushed to buy. “And even as the economy may take a few years to fully recover, we’re expecting the snacks market to really kind of hold strong, and continue to grow,” Walsh says.
Stemming from the lifestyle shift forced by the pandemic, one prominent trend in today’s snacking landscape is the move toward snacking from home.
“Pre-pandemic, it was all about on the go, portability, convenience,” Walsh says. “Now, with more [people] working from home or even schooling from home, snacking from home has become really important.”
E-commerce snack shopping has also grown in popularity, with a 27% increase since the onset of the pandemic and an 83% increase in 2020 alone.
“There’s still a real major opportunity to capture some of that online growth,” Walsh says. “Many consumers still, believe it or not, don’t think to buy snacks via e-commerce yet.”
Snacking frequency has increased in recent years. The average consumer snacks 2.7 times per day, and the number of consumers who snack five or more times per day is on the rise.
Walsh says Millennial and Gen Z consumers (ages 18 to 34) are setting the stage for this increase, and their buying power is increasing as they get older. “They’re the ones that are snacking all throughout the day, many meals, grazing throughout the day,” he explains. “They’re most likely to replace meals with snacks, so there’s that meal replacement trend that has become so important. 92% actually replace at least one meal per week with just a snack.”
A broadened definition of snacking has also contributed to the trend toward higher snacking frequency. As consumers snack from home more, snack choices have started to include items like cereal, packaged fruits and veggies, and even leftover meals.
Another growing trend is functional snacking, as more consumers adjust to health-focused lifestyles. “Things like high fiber, protein, calcium, fortified vitamins, minerals, antioxidants, just to name a few, are really kind of finding a home for innovation in the snack category,” Walsh says.
He cited trending ingredients like cassava for healthy digestion and ashwagandha for immunity and brain health as further examples.
“Snack producers are really turning up the heat to extreme levels,” Walsh says, as consumers increasingly demand spicy options across categories.
Nuance behind the heat is important, though, as consumers are searching for di erent types of peppers, hints of lime, cheese pairings, and other adventurous variations.
Sweet snacks, including fruit flavors, chocolate, maple, and nut butters, are also gaining popularity and even competing with treats in the candy aisle, Walsh says.
International flavors including those from Latin America, Asia, and the Middle East had “been very popular pre-COVID, and it kind of has come back now that we’re heading away from the pandemic,” Walsh says.
Adedicated design-builder will expend as much energy into constructing a successful food facility design as in delivering a project on time and on budget. According to the Design-Build Institute of America (DBIA), design-build strategies can deliver projects up to 102% faster, with 3.8% less cost increase than traditional design-bid-build models. Such savings of time – and money – are achievable thanks to these streamlined strategies deployed by savvy design-builders.
1. Work with subcontractors to lock in pricing. A design-build delivery maintains open communication with subcontractors to better understand the current cost escalation that they are facing with suppliers. “Communication is key when getting input from subcontractors as to if and when suppliers will issue price increases, when pricing can be locked in, and when a project site can receive materials,” says Mark Livesay, vice president Automated Warehousing, ESI Group USA. “We will explore locking in pricing on stocked material and issue letters of intent to hold the material until it is required to be on the jobsite. Steel material pricing cannot be locked in until the time of
QUICK FACTS
rolling. If we can lock in orders, we have a better chance of holding the pricing to avoid potential price hikes down the line.”
2. Preorder essential materials. Choosing a general contractor and getting the design to a point where critical materials can be preordered before the final IFC (issued for construction) drawings allows for a shorter duration from design to completion. “With today’s environment unless you can buy, take delivery, and store materials onsite, no one can guarantee a material esca-
of companies see improved budget/schedule performance with BIM Construction materials used in nonresidential projects are up nearly 30%
of construction costs stem from reworks of faulty or incorrect builds
50% 17%
lation will not occur.,” says Livesay. “Some of our suppliers can hold the pricing if we take earlier delivery of the material and store the material on site.”
3. Negotiate various contract options. The biggest cost risk to any project is material escalation. Livesay says that Open Book pricing, also referred to as a cost-plus contract, gives the customer the right to receive additional bids if a certain division of work experiences a significant escalation. This opportunity ensures there is no price gouging, and the customer is a part of the contractor selection process. Alternatively, if a customer opts to contract for a guaranteed maximum price (GMP), the general contractor assumes the risk and will have to account for contingencies, which usually yields a higher project cost.
4. Use building information modeling (BIM) to identify obstacles early. 3D modeling can reveal conflicts or interference with all aspects of the design-build. “It also allows for equipment placement, identifies where there could be issues with equipment layout, and identifies problems before construction starts, thus eliminating costly changes and time delays,” says Livesay.
He adds that customers must understand there will be unforeseen supply chain challenges, fuel supply, and price issues. “Sometimes we have to have difficult discussions with customers when pricing is simply out of everyone’s control. But, as a design-build firm, we will do our best to keep those costs as low as we can for the customer.”
Value engineering can be used to explore alternate designs and alternate materials, and choose materials that are readily available and do not have long lead times. “We can also utilize scheduling tools that allow us to optimize construction times and enable subcontractors to continue working without waiting on other trades,” explains Mark Livesay, vice president, Automated Warehousing, ESI Group USA.
Livesay recalls one project that required a long cabling run of 460V 3-phase power. “As an alternative, we used medium voltage gear and cabling that saved more than $1.5 million. In another case, a customer had specified a certain brand of dock equipment that was not as robust as another brand, which was an acceptable substitute. We presented the differences in the equipment and the cost savings, and the customer ultimately saved more than $100,000 on
six dock positions.” “When we get the subcontractors involved early on a project, they are more encouraged to seek alternate ideas not initially considered.”
ROCKWELL AUTOMATION’S 31st annual Automation Fair drew more than 18,000 attendees over two days in Chicago, giving industry professionals an inside look at how Rockwell is addressing current challenges and trends through industrial automation and digital transformation.
One session during the event featured food and beverage executives discussing how technology and automation can be applied to ongoing labor issues, plus other processing challenges. Here are some of the key takeaways from that session.
The panelists agreed that before any technology options are implemented into a food processing facility to help with labor—such as adding robots, for example—the company culture from the top executive down to every new hire needs to be infused with a sense of purpose.
“Really think about the culture of your organization,” said Michael Chaney, retired senior vice president of product supply at Procter & Gamble. “If you’re dependent on [retaining sta through higher wages], it’s not enough.”
Brian Marsh, senior director, digital manufacturing at Nestlé, added, “There’s not a large enough labor pool out there to fill our needs. There’s lots of options for people to do other things now, so it’s really important for us to create a new environment for people to come into manufacturing. We’re constantly looking at new ways of working in our factories to try and make it more fun and easier by eliminating jobs nobody wants to do.”
Marsh mentioned one new initiative he created that combines technology and team communication is an OEE workgroup made up of line operators at Nestlé that meet regularly and parse data to identify trends on their equipment and give them a chance to solve challenges together.
Andrea Zaman, COO, Pearson Packaging Systems, posed a rhetorical question to the audience that cut to the core of today’s training issues for new hires. “What if your entire production floor is all brand new at the same time with no experience? Now there’s your workforce challenge.”
New workers are needed to contribute faster than ever due to ongoing (and widening) gaps in the food manufacturing workforce, so technology such as digital twins is becoming an essential training tool today.
“Nobody wants to go sit in a classroom and read 3-inch binders full of standard operating procedures. So how do you get them on the floor and engaged quickly? Give them the information they need at their fingertips so they can start doing something vital,” Marsh said. “Being able to build these virtual environments, you can get people trained on things before they ever even touch [a machine]."
Passing down tribal knowledge from experienced workers was another topic of discussion, and how social media and smartphone/tablet video recording can make it easier for retiring workers to transfer crucial information to today’s digital native workforce.
Marsh said at one of Nestlé's pizza plants, they have a machine operator “who loves TikTok so much that he started creating videos on how to do di erent things on the line. My team can build a training video, but what he was doing was much better. We had people laughing on the floor and everybody wanted to see that video. We’re now trying to create a new job for him because of his passion around making those videos. So, if you see what I call the ‘bright lights’ in your organization, try to embrace them, even if it means creating a new job for that individual within your organization. They love what they’re doing and they’re
‘What if your entire production floor is all brand new at the same time with no experience?
Now there’s your workforce challenge,’ said Andrea Zaman (standing) from Pearson Packaging Systems. Also pictured L-R: Michael Chaney, P&G (retired); Joe Francel, Microsoft; Brian Marsh, Nestlé.
EGISTRATION IS NOW OPEN for EXPO PACK Guadalajara 2023 (June 13-15; Expo Guadalajara), the largest and most comprehensive packaging and processing trade show in Latin America this year, according to show producer PMMI, The Association for Packaging and Processing Technologies.
After four years without an in-person event in Guadalajara, EXPO PACK Guadalajara 2023 will return, even larger than the previous show. Attendees will experience a wide variety of machines, materials and other goods and services from 700 leading international suppliers along with unmatched networking and education opportunities.
After a strong debut at EXPO PACK Guadalajara 2019, and an even stronger showing at EXPO PACK México 2022, daily EXPO PACK Keynotes will be presented in collaboration with Mundo PMMI. Keynotes will feature speakers from leading companies such as Grupo Herdez, PepsiCo, Danone, Pfizer, and others, covering topics on sustainability and the state of the industry.
And for the first time during EXPO PACK Guadalajara, the Packaging and Processing Women’s Leadership Network (PPWLN) will host a keynote session highlighting successful women in the industry.
In addition to these daily sessions, the return of the Innovation Stage will feature presentations on breakthrough technologies and techniques directly on the show floor.
(continued from page 13)
going to be more passionate than anybody you’ll find outside your organization.”
Outside of workforce issues, the panel discussed using technology and the associated data it generates to solve specific challenges in a food manufacturing environment. “Prioritize what your business is trying to solve,” said Joe Francel, director, business programs, manufacturing service line, Microsoft. “Don’t collect data just because you can. Determine the value of that data and use it to make decisions in your process.”
Francel also emphasized that when real-time data is applied, it can help solve problems before
EXPO PACK Guadalajara 2023 features
seven International Pavilions featuring global manufacturers from Argentina, Brazil, Canada, China, France, Italy, Spain, Turkey, and the U.S.
The Boost PyME program will spotlight exhibitors who o er financing, discounts, and additional support for small to medium-sized companies.
The EXPO PACK Verde program will highlight exhibiting companies who o er sustainable solutions, either in new materials or technology (such as biodegradable materials, or technology to reduce carbon footprint). Exhibitors will be denoted with an EXPO PACK Verde icon in their booths as well as the online exhibitor directory.
The Mexican Packaging Association (AMEE) will celebrate its Annual National Congress on Tuesday, June 13, and will host the awards ceremony for its renowned Envase Estelar program.
To learn more, search exhibitors, and register, please visit expopackguadalajara.com.mx Attendees can register for EXPO PACK Guadalajara 2023 for $100 MXN until May 5. After May 5, the registration fee will increase to $200 MXN.
they happen, while the opposite is true when that data is ignored. To highlight this, he told a story about working with a co ee manufacturer that relied on a historical shift report for past sales rather than real-time data to gauge the volume of Christmas blend co ee to produce that holiday season.
“The co ee was extremely popular that year,” Francel said. “We had the [sales] information, we knew people were buying it, but we weren’t using [the real-time data]. So, we ran out of Christmas blend co ee before Christmas occurred. We had the information from the stores, we knew demand was at a higher rate than originally expected, but nobody looked at [the data].”
Contributors:
Paul Schaum, Partner, Manufacturing Coach, FSO Institute | Mark Cacciatore, Manufacturing Coach, FSO InstituteReach full production faster—while engaging employees, reducing waste, and producing more finished product—with full commitment of cross-functional leaders and stakeholders.
THE TWILIGHT ZONE captured the imagination of huge TV audiences with chilling tales of science fiction. As host Rod Serling opined some 60 years ago, “It isn’t enough for a sole voice of reason to exist.”
Those words could not be truer today, particularly in the case of achieving vertical startup of your company’s capital projects. Vertical startup—in which new operations reach full production quickly—will accrue benefits to all aspects of the business, so it stands to reason to enlist several voices of reason, engaging all functional areas as “investors” in the project’s success from Day 1.
Vertical startup requires a full commitment of cross-functional leaders and stakeholders to the success of the project—investment of key resources early on and a regular review and oversight process to quickly provide direction, eliminate barriers, and react to the unexpected challenges.
This new commitment to vertical startup of the project begins by creating BOA (buy-in, ownership, and advocacy) among all stakeholders. It has been proven to be a force multiplier to deliver the company’s key initiative. Some formerly “unimaginable results” include:
• 85% reduction in startup waste
• Additional 450,000 lb of finished product
• Full production reached 12 weeks faster, and sustained
• Well trained and engaged employees at all levels Contributing to the vertical startup discussion for this article are two industry leaders and FSO Institute coaches: Paul Schaum, former COO and CTO of Pretzels Inc., and Mark Cacciatore, former senior vice president of operations of Conagra, and Campbell Soup.
FSO INSTITUTE: Paul, these results noted above were from your recent project. When you were the chief technical of cer for a mid-size snack food manufacturer, can you describe how you successfully engaged others in the senior leadership team to fully support vertical startup?
PAUL SCHAUM: Our company’s business driver was meeting the customers’ demands for capacity and quality. Beginning with the end in mind, I shared the data of past projects done the traditional way— engineering owned the project and turned it over to production when construction was complete. In that approach, expectations, timelines, and budgets were rarely met. Most importantly, full production at the required quality levels took many months to achieve and sustain. That loss of time and product was a significant limitation to our ability to meet customers’ needs.
Recognizing the limited resources available as a smaller company, we had to develop a plan that created BOA in all key departments. This was crucial as all individuals involved realized this e ort was a vital—and additional—part of their job, while all normal functional responsibilities remain.
The all-hands-on-deck commitment was certainly di cult at times, particularly in the early stages. For example, purchasing questioned why they should be engaged so early before the project was completed (“we never had to do that before”). Vertical startup requires sustained operational reliability and, as a result, purchasing had to be aligned with demand forecasts for each period going forward. We could not a ord to run out of materials and ingredients with the accelerated production.
The plan was also to hire the operators,
supervisors, management—basically begin sta ng the plant six months before the project concluded, not wait to hire until the last two weeks. This major investment is directly correlated to the ROI from reduced waste (85% less than normal), expanded capacity, and the quality of product that exceeded customer requirements. The time spent training, onboarding, getting comfortable with the equipment, maintenance helping with installation all contributed to hitting and maintaining full production. What’s more, the teams on all shifts were so engaged that the retention rate of the factory floor personnel exceeded all historical records.
For our company, the biggest result was the continued high performance of the team and manufacturing lines after one year of operations. The real value is in achieving sustained operational excellence, and we did that.
FSO INSTITUTE: Mark, your career has been with large multinationals with considerable capital expense budgets. Can you describe the value vertical startup made in your experience?
MARK CACCIATORE: As leader of a large food manufacturing/canning facility, I had the opportunity to put these tenets to practice as the site was awarded
significant capital to start up the first aseptic packaging line in the company. Of note, a large capital investment just two years before had a very poor startup, resulting in significant negative business impacts. Given this past performance, management viewed investing in a new line of business at the facility as risky. As such, success of the project was critically important for the future of the plant.
The site leadership committed to a di erent approach, incorporating vertical startup best practices to not only win approval for the project but, in the end, deliver the best new-line startup in company history. The project started up three weeks early, below budget capital and expense, and delivered 87% overall equipment e ectiveness (OEE) in month one with continued improvement to 90+% in succeeding months. This operation quickly became the benchmark performer for the entire division and the learning and training ground for operational excellence across the company.
In my experience some key takeaways include:
• Gain commitment from all cross-functional leaders and stakeholders. It is crucial to the success of the project to get personal engagement of leaders, with joint ownership for project deliverables, including startup and ongoing performance metrics.
• Organize the project with a strong cross-functional project delivery team, including a dedicated delivery leader (ideally the operations leader responsible for the ongoing operations). Additionally, identify a cross-functional leadership project steering team that provides a decision-making forum to help eliminate barriers, resolve conflicts, or provide resource needs.
FSO INSTITUTE: Paul and Mark, given your career experiences of operational responsibilities and large capex projects, you have both expressed a powerful view of manufacturing readiness. Can you share a nal thought?
CACCIATORE: For manufacturing readiness, a commitment to sta the project at the very early stages with high-quality talent is critical. Key roles include a dedicated startup leader, maintenance leader, line leader, and safety and training resources.
SCHAUM: Lessons learned from vertical startup contributes to the daily requirements of manufacturing readiness—worker safety, product quality, personnel engagement, and performance e ciencies.
+ Dual use TVP and HMMA extruder allows fast changeover and high flexibility
+ Plant based ingredient material handling equipment from source to packaging
+ Proven industry leader with installed TVP and meat analogue systems globally
+ Strict adherence to cGMP guidelines and standards, FDA approved materials
+ High accuracy loss-in-weight feeding of powders and liquids
+ Worldwide service network
Achieving “first hour full power” following changeovers is a direct beneficiary of vertical startup.
Vertical startup is a proven winner in capex projects and can be equally transformative to the organization. How’s that for unimaginable results?
PMMI’s OpX Leadership Network has produced more than 20 manufacturing process-improvement documents for CPGs and OEMs. The FSO Institute has facilitated the adoption and implementation of these documents, especially for food and beverage manufacturers. This series of articles shows how CPGs are using OpX and FSO documents to improve their overall manufacturing health and collaboration with OEMs and other suppliers. Learn more at www.opxleadershipnetwork.org and www.fsoinstitute.com.
It’s important that your machine can stand the test of time and adapt to your packaging needs as your goals and VWUDWHJLHVFKDQJH:LWK+DUSDN8/0$\RXFDQH[SHULHQFHWKHPDQ\IDFHVRIÀH[LELOLW\LQSDFNDJLQJ
• 'LVFRYHUKRZÀH[LELOLW\FDQKHOS\RXDGDSWWRFKDQJHDQGVFDOH\RXUSURGXFWLRQ 6HHKRZÀH[LELOLW\DOORZVXVWRSURYLGHSURGXFWLYHFRVWHI¿FLHQWODVWLQJSDFNDJLQJVROXWLRQV
Rest easy knowing you’ve got ongoing world-class customer service and support
• 5HOLDEOHVXSSRUWIURPLQKRXVHVSHFLDOL]HG technicians and 24/7 customer service
• ([WHQVLYHQHWZRUNRI¿HOGWHFKQLFLDQV for exceptional after-sales service
PepsiCo commits to growing its percentage of refillable/reusable packaging options, including expanding its SodaStream in-home and in-o ce sparkling water systems.
ONE PRIME EXAMPLE of a refill-at-home system is SodaStream, founded in 1903 in the UK, with the invention of the aerating machine. While the brand stagnated for many decades after its introduction, it was revived in the 2000s, and in 2018, PepsiCo purchased Israel-based SodaStream International for more than $3.2 billion.
The SodaStream Sparkling Water Maker is a home carbonation system that includes a machine, a carbon dioxide cylinder, and a plastic bottle designed to be reused for up to three years. PepsiCo also o ers a range of bottle options for purchase separately, including glass carafes and dishwasher-safe, on-thego containers. There are about 60 concentrate syrups to choose from, including soft drinks, flavored waters (PepsiCo’s bubly sparkling water brand), and kombucha.
To create a carbonated beverage, consumers insert the CO2 cartridge into the back of the machine, place a bottle filled with water into the front, and push down on a carbonating block to create the carbonation. Consumers then add the desired concentrate flavor to the sparkling water. They can also mix concentrates for a customized beverage. According to PepsiCo, by using the system, a consumer can save about 63 plastic bottles in a month, or 772 in a year.
To further minimize packaging waste, PepsiCo also o ers a system whereby consumers can exchange their spent CO2 cylinders for new ones. With each online order, cylinders are shipped in a corrugated box that also contains a preprinted UPS label. Consumers are encouraged to keep the box for use in returning the empty cylinders. Cylinders can also be exchanged in-store. SodaStream then sterilizes, inspects, and refills the cylinders with fresh, dietary-grade CO2
In early December 2022, PepsiCo announced that it will be pursuing four approaches to reusable packaging to double the percentage of all beverage
servings it sells that are delivered through reusable models—from 10% to 20%—by 2030. PepsiCo is an Ellen MacArthur Foundation New Plastics Economy Global Commitment signatory, and its four approaches align with the four models outlined by EMF in its “Reuse – Rethinking Packaging” framework. Says PepsiCo, reuse is one of several critical levers it is using to meet its goals to reduce virgin plastic per serving by 50% by 2030, eliminating the need for more than 200 billion plastic bottles by 2030, and to become Net Zero by 2040.
The company’s refill-at-home strategy involves the expansion of its SodaStream business, both at home and in the workplace through SodaStream Professional. PepsiCo adds that many of its brands, including Gatorade, Propel, Muscle Milk, and Evolve, are o ered as concentrated powders or tablets that allow consumers to customize the drink to their preferences in their own containers—another option for refill at home. As part of its goal to increase its reusable packaging options, the company says it plans to accelerate growth in its powder and concentrate business as well.
The SodaStream Sparkling Water Maker is a home carbonation system that includes a machine, a carbon dioxide cylinder, and a plastic bottle designed to be reused for up to three years.
At 48 g, BEG Destilaria’s 500-mL aluminum refill bottle is nine times lighter than a glass bottle, greatly reducing GHGs from transport vs. the distillery’s custom-molded heavy glass bottle.
BEG DESTILARIA is the first spirits company to develop an aluminum refill bottle in Brazil for its artisanal gin, in partnership with Trivium Packaging. Founded in 2015 in Brazil, BEG produces all of its products by hand whereby once the botanicals have been distilled, the resulting spirit is diluted with water rather than neutral alcohol in order to reach the alcohol by volume required for bottling.
When BEG switched from a standard glass bottle for its gin to a unique mold and branded bottle, the company realized that in an e ort to appear more premium, it had added more weight and consequently a bigger carbon footprint to its product.
“For the on-trade market [bars and restaurants], that factor [custom packaging] counts little, unless for bottle service, and even more glass was ending up in the trash,” says Arthur Flosi, BEG Boutique Distillery’s founding partner and master distiller. “Day after day, we received various feedback on social media regarding how beautiful our bottle is and how pitiful it was to throw that beauty away. That’s how the idea of launching a sustainable alternative was born.”
While BEG considered a range of alternatives for the refill bottle, including aseptic cartons, lighter glass bottles, and even aluminum cans, Flosi says that none were up to the quality of the distillery’s gin or felt as premium as the brand’s unique glass bottle. Instead, it chose a 500-mL stock aluminum bottle, which is produced using an advanced alloy, allowing for a lightweight, 48-g container with a low carbon footprint when compared with the original glass bottle, notes Marcelo Nery, coordinator of R&D for Trivium Packaging-Brazil. According to BEG, the refill bottle is nine times lighter than glass, “meaning less fossil fuel per volume transported.”
“The aluminum bottle from Trivium is perfect,” says Flosi. “It looks great, it feels great, it’s more versatile—aluminum goes where glass can’t—it costs less for our customers, and it’s way more sustainable. In Brazil, 98.4% of all the aluminum packaging is recycled.”
One of the considerations in developing the refill bottle was the selection of a coating for the inside of the container. Nery shares that Trivium is using a special food-grade liner that resists the high content of alcohol to protect the properties of the product and extend its shelf life. Notes Flosi, “We are already at 12 months of real shelf-life testing without any change in flavor and/or chemical structure.”
The stock bottle is custom printed using two processes: dry o set printing and heat transfer to allow for di erent graphics for small orders.
The refill system was launched at retail in Brazil in late 2021. BEG o ers five di erent aluminum bottles that correspond to each of the glass bottles it sells in Grupo Pão de Açucar, the biggest retailer in Brazil. The cost of the refill is 33% less than that of the glass bottle. “Each aluminum bottle has 500 mL vs. 750 mL from glass,” explains Flosi. “The price of the aluminum is 50% cheaper, so the customer would be able to buy 1 L of BEG gin for the same price as 750 mL in glass.”
Just as it did for consumers’ willingness to visit their doctors over a video call, the pandemic signaled a shift in how food and beverage producers view remote troubleshooting from their OEMs. Sometimes it’s just what the doctor ordered.
THE COVID-19 PANDEMIC made a big di erence in how consumers see the need to visit their doctors in person. By avoiding in-person visits, patients could protect themselves and/or others in the waiting room. And in many cases, in-person visits simply weren’t available.
Remote troubleshooting in food manufacturing shares many similarities with telemedicine. In much the same way, we’re trying to get our systems up and running again as quickly as possible. Both rely on remote communication technologies to diagnose and solve problems, and both require skilled professionals to navigate complex systems.
The technology to make connections between OEMs and their equipment residing on customers’ plant floors has been around for years. Willingness to use that technology, on the other hand, has been scant. However, many food and beverage producers found, during the pandemic, that there really was no other way to get the problems diagnosed. And since lockdowns have eased, remote troubleshooting continues to be essential for maintaining continuity in the face of disrupted supply chains, reduced sta ng, and other challenges.
Even before COVID, some food manufacturers had already seen the benefit of saving time and money when something went wrong with the equipment. A major multinational CPG, which asked not to be identifi ed because of the sensitivity of some of the information, has been using remote troubleshooting on its equipment for more than a decade.
“We needed a mechanism to have remote support because having the OEM come to the facility—to travel to every single issue—is very expensive,” says an automation engineer with the CPG. “And it’s not only expensive, sometimes it’s not timely. The OEM may not be available for, say, 48 hours. Whereas if they had a mechanism just to log in, we’ve seen many times that it can be resolved remotely.”
Tetra Pak is one large equipment maker driving more toward gaining connections to its systems at customer sites. With such a wide range of equipment, it helps to be able to access the right expertise wherever it resides in the world. “This possibility of having someone that is based in a di erent location supporting a customer with the right knowledge necessary for that demand, for example, is incredible because we are saving costs internally as well,” says Livia Marra, solution design manager, PSE Automation & Solutions, for Tetra Pak. “The customer is paying less for the service, but also the downtime is reduced, and it results in less waste.”
Tetra Pak also provides connectivity for sending analytical data to the cloud for predictive maintenance solutions, Marra adds.
One key piece of advice is to make sure that your IT and OT departments know how to play nicely together. That was an important reason the CPG was able to get remote support set up earlier than many companies in this industry.
“We are very integrated with our friends in IT,” the engineer says. “In most organizations, there are two di erent worlds—IT lives in their own world, and OT, which is the operational technology world, lives somewhere else. In our case, we are very converged.”
The shop floor has tended to avoid IT as much as possible, comments Dan Barrera, product manager for ctrlX Automation at Bosch Rexroth. “But COVID accelerated things; it created that demand to really incorporate the IT and the OT world together.”
It’s important to maintain transparency between IT and OT, and between brand owners and their OEMs. “If you are not clear, if you say, ‘We are just going to have a device,’ the IT organization will never allow you in,” the CPG engineer says.
The cybersecurity part of this discussion could fill its own article (see “Put Your Cyber Defenses Up Before They Take You Down,” pfwgo.to/7504), but it’s a vital consideration as any CPG works toward a troubleshooting solution. According to a 2020 sur-
vey of CPGs done by PMMI, cybersecurity concern was the top barrier to setting up remote access.
“Users are very suspicious of hooking anything up behind their firewall. And there’s a raging battle right now between the IT department and the OT department about who even should get to control the what and who hooks up the equipment on the factory floor behind the firewall,” says Spencer Cramer, founder, chairman, and CEO of ei3 , and a pioneer in remote connectivity. “So if you’re a machine builder, and you don’t have a fully featured sta of experts who are putting together your IoT solution, you’re going to find that the end customer is going to be very suspicious of putting your system online.”
troubleshooting can enable technicians to get support from experts, even if they’re not physically in the same room with them.
There is plenty of reason to be concerned about the security of connections within your manufacturing facility. “Many in the food and beverage industry will be concerned about losing intellectual properties if they connect equipment and put the wrong data in the wrong hands,” Cramer says.
The benefits are too real to be ignored, however. So rather than deny the connections, Cramer recommends partnering with companies that can help address vulnerabilities.
A key element of remote access is that everyone has a unique capability and also their own way of doing it, notes Mark Fondl, vice president of product management for remote access at ei3. He also leads the Digital Transformation Workgroup at The Organization for Machine Automation and Control (OMAC), working on best practices for remote connectivity. “All these di erent variations can be very di cult,” he says. “There needs to be a collaborative acceptance between the IT organization and the OT organization for how to handle safe and secure access and then limit that to a specific type of technology—so that you can control it and manage it.”
Key to this success is coming up with a connectivity solution that not only satisfies the demands of IT but also enables OT to be flexible when there’s a problem. Otherwise, OT will go right back to ignoring IT and putting in a solution that bypasses the IT organization, Fondl says.
The vast majority of OEMs will adapt to a food or beverage producer’s needs, according to the CPG. “But there are some who are new to this. They may have developed one solution and they just o er that solution,” the engineer says. “That is where we will get into trouble, if they are not nimble.”
Though a less experienced end user might welcome accepting whatever the OEM is prepared to provide, a larger company with a higher level of maturity will likely have di erent demands, he notes. “That company will say, ‘We are not going to allow a foreign device that can get unrestricted access to our network. You have to come through our system so we can manage who comes into our system, and we can monitor what is being done.’”
That’s exactly the sort of thing this large multinational company is able to do. To standardize on how OEMs from all over the world can access their respective equipment, the CPG developed engineering stations at each of its 16 plants and asks that the OEMs log in through those stations. The CPG uses Rockwell Automation’s FactoryTalk AssetCentre as a repository and disaster recovery for all its software. It’s through this that OEMs get access—after logging onto the server through the VPN—to the software and documentation they need to get the job done.
At the end of the day, there is likely not only one way to make the right connection to machines to enable remote troubleshooting. But there’s usually a way to get it done safely.
Remote connections have somewhat of a renegade history, with people throwing a cellular connection on a machine to get access. “Through lack of anything else, that’s the way people were doing it, and it’s really very insecure,” Fondl says. “And so the industry tended to be very much against remote capabilities in manufacturing.”
There’s also a general skepticism in the industry about whether the OEM will be able to correctly diagnose a machine remotely, according to Bryan Gri en, senior director of industry services for PMMI. “When I was with Nestlé, there were times that we would bring OEMs in to fix the machine, and the guy on site would really struggle trying to fix his own machine,” he says. “So there’s some lack of confidence that the remote connectivity is actually going to solve the problem.”
Prior to COVID, remote connectivity tended to be a taboo subject, with customers refusing to connect their machines, says Justin Garski, Americas OEM segment manager for Rockwell Automation. “And then the world shut down, and all of a sudden
FPS provides a remote monitoring system that enables its technicians to monitor customer freezer units.
people were like, ‘Man, our factory’s not going to run unless somebody fixes this thing.’”
It was in this atmosphere, in late 2021, that Rockwell launched a remote access solution to help OEMs more easily realize the benefits of using remote access. It combines cloud-based software with a remote access router. “The OEM connects to the cloud, the machine connects to the cloud, they get married there, and then you’ve got this tunnel back and forth,” Garski describes.
Though the food industry might’ve been a little late to connect, the pandemic opened some doors to technology that had previously been blocked, Gri en notes. “All of a sudden, sometimes my only option was: I’ve got to open a channel here and let somebody into my equipment.”
But that kind of hurried response to connectivity introduced exposed operations to possible attack. “We were in an emergency mode. We were just going and doing what needed to be done,” Gri en says. “Now let’s clean this up. Let’s make sure that it’s a good option going forward.”
Because of the growing importance of remote access in manufacturing, OMAC put together a workgroup in September 2020 to address the need for best practices. The group created a Practical Guide for Remote Access to Plant Equipment, which details many of the considerations that manufacturers will need to think about.
There are several options for connecting to equipment, including direct VPN, converged network, cell modem access, and others. A large
majority of respondents to OMAC’s study use VPN along with other methods.
“One of the challenges is that the OEMs, if not given some level of guidance, will choose a way that they will do it on their own. And so it creates a little bit of challenge in that particular regard,” Fondl says, noting that this was a key goal for OMAC creating the remote access best practices. “Some end users, they may say what is the best, most secure solution that is agreeable to both the IT organization and the OT organization, and then try to do some level of standardization.”
Bosch Rexroth released a new control platform, ctrlX Automation, around the end of 2021. Along with that is CtrlX World, an ecosystem that allows third-party vendors to create apps for their technologies. One of those apps is a VPN, but there is a range of apps specialized in various aspects of connectivity, says David Boeldt, product manager, ctrlX Automation. “This could be for doing MQTT and other types of communication protocols, but it also opened the door for vendors that are specialized in security,” he says.
This makes it much easier, for example, for an OEM to incorporate VPN capabilities into its machine. “The OEM doesn’t have to create anything; they just have to select the apps that are required for them,” Boeldt says.
“The OEM can create a VPN connection to the customer and be able to translate themself into the machine without physically having to be there,” Barrera adds. “That allows us to really see the code, look at the alarms, and then we’re able to do that in our computers. We can even ask, remotely, the maintenance guy to run the machine in a certain way so we can actually review what the code is doing or what the drives are doing.”
The expertise might not always be coming from OEMs, but from subject matter experts within the CPG itself. Through its Movicon industrial software platform, Emerson has a customer implementing a pilot project with an expansion to 50 plants.
“They’re using augmented reality to share subject matter experts between plants for maintenance,” says Daniel Millar, business development manager of factory automation at Emerson.
Such visibility could enable an expert at another location to get a better view of what the technician on site is seeing. Though augmented reality is certainly not yet universal, Millar estimates that three of the 10 projects he’s working on now include augmented reality. “For two of them, it was helping maintenance maintain the equipment
Hygiene
CIP with Pasteurization
Flexibility
Horizontal Airflow
with subject matter experts around the plants that was key to why they’re using Movicon,” he says.
Through its partnership with PTC, Rockwell Automation provides Vuforia Chalk, which combines AR collaboration tools with real-time video communications for remote troubleshooting. It also incorporates the ability for the expert on one end to draw on the screen to help the technician on the other end, Garski explains.
It’s a fallacy to think that remote troubleshooting means you don’t need anyone local on the scene, Fondl comments. But with remote expertise, the person on site does not have to have such a high level of knowledge. This is a big part of where augmented reality can come in handy—to use the technician on the plant floor to give eyes to the expert at another location.
To take this discussion in another direction, not all remote connections are about troubleshooting failing systems. The flip side is ongoing analysis, in many cases to keep the system from going down in the first place.
With its OEM customers, Emerson has been focusing increasingly on helping them understand how to create new revenue models with the connection capabilities available. “Using Movicon and/or IoT, they now can monitor and provide data to themselves at their home o ce that will help maintain that equipment and predict failure for the customer,” Millar explains. “I think that you’re going to start seeing that more and more, where end users will be demanding that from their OEMs.”
In some cases, it’s hardly even possible to get physical access to the machine to check on any potential issues. This was the situation for House of Raeford’s plant in Hemingway, S.C., which makes mini corndogs. Every product in the facility goes through its spiral freezer at some point. To say a spiral freezer is di cult to maintain is a bit of an understatement.
“For someone who has never had exposure to the spiral freezer, they have no idea that walking on the inside is like walking in a hurricane,” says Dean Page, plant manager for House of Raeford. “We operate from about -36°F to -40°F, so it’s extremely cold. The wind that is generated by the large-velocity fans is tremendous, so it doesn’t present a good opportunity for a technician to diagnose issues or work on problems once they’re found.”
The spiral freezer House of Raeford has from Ashworth, however, is equipped with a SmartSpiral system—designed to help users run and maintain the equipment correctly. The system analyzes data for alarms, which are sent to the customer.
Unplanned downtime used to cost House of Raeford about $6,000/hr, according to Page, with no way of seeing into the spiral to anticipate bearing failures and belt crashes. Now, with SmartSpiral, the food company has reduced downtime by 200%.
It can be di cult to get customers to understand the importance of the trending data and what it can discover, explains Chris Trinch, senior product engineer for Ashworth, recalling a time when they spotted a deviation with a customer in Minnesota.
“We saw a pattern of a certain temperature range— it was -33 to -32°F. Well, one day we started seeing about a degree and a half fluctuation in that temperature range,” he says. “But when we notified the customer, the customer elected not to do anything about it. The week after that, they crashed—the entire plant refrigeration, not once, but twice.”
FPS Food Process Solutions has had its Remote Monitoring System (RMS) out in the industry for about a year to help its customers monitor their freezing systems. It’s been a vital development in the industry, according to Brock Price, manager of global reliability and maintenance programs for FPS.
“Production’s huge right now in food and beverage,” he says. “Downtime and their equipment not creating the quality they need is not an option. So
The nature of a spiral freezer—like walking inside a hurricane—makes it di cult for technicians to diagnose issues or work on problems once they’re found. The SmartSpiral system makes it easier to know where to focus maintenance e orts.
they’re moving toward this more predictive style of remote monitoring tools.”
A key driver for remote monitoring is the trouble that companies are having hiring the skilled workforce they need, Price says. “This is a way to get ahead of that resource issue that a lot of companies are having today,” he says. Remote monitoring also helps bridge the gap between experienced and inexperienced workers. “Now they have a place to call to get some help.”
For its remote monitoring, FPS relies on Ignition technology from Inductive Automation. “It’s a oneway communication, so we can’t go back past the MQTT module and back into the PLC and do anything with their equipment,” Price explains.
This kind of established security is key to bringing the data out safely. “For most companies that we’re working with, that works well for them,” Price says. “Secure information is a huge concern for all of our
customers, as well as us.”
There is plenty to be said about the value of remote connections that allow the OEM to continually analyze the data coming from the machine. But it also brings up an increasingly hot topic of data governance—which data should be available for which parties. “Just because the data has some value to one and no value to the other doesn’t mean that all data should be denied to leave the facility, but rather sophisticated data governance policies should be put in place so that the data can be carved out in ways that make sense,” Cramer says.
Tetra Pak has seen more concerns even just within the past year from its customers about what is happening with the data that the equipment maker gathers, Marra notes.
“There are a lot of customers that their main valuable asset nowadays is data,” she says.
that their main valuable asset
“Everyone knows how to do a lot of things, and equipment is the same, basically. What is going to change is how they are operating, how they are improving the way that they operate, the parameters that they are using, especially when we are talking about new kinds of products.”
cially when we are talking about
OEMs are finding that the data gathered for ongoing analytics can be helpful within the day-to-day troubleshooting as well. Remote troubleshooting is no easy task. “Being by the machine and being able to see and smell and feel and hear all those things that are going on really aids in your troubleshooting ability. So if you’re being called up to do a remote connection to the machine, a lot of the things that would have been available to you when you were there aren’t available,” Cramer notes. “So what do you replace it with? You replace it with the data.”
gathered for ongoing analytics can
That data can often be considerably more fruitful than trying to get the information from the people on the other end of the line, as Garski describes.
“When the service phone rings, the first question the guy asks is, ‘What did you do to it? What changed?’ And the operator or the maintenance guy always responds, ‘Nothing. I didn’t do anything.’”
From there, the detective game starts.
“Historically, that fault history would have been stored on the machine itself. So now you’re rely-
OUR PASSION FOR YOUR PROJECT’S SUCCESS RUNS AS DEEP AS YOUR OWN
ing on a human being to connect with a computer or a USB stick or something else to try to get you this log file to be able to walk backwards in time,” Garski explains. “If I don’t need to rely on somebody to do that, it’s faster.”
Just like doctors cannot diagnose every illness without running extensive tests, not every mechanical issue will be able to be resolved through a remote diagnosis.
“There are situations that are a combination of programming, mechanical, electrical—it could be a hotspot of five di erent things, almost impossible. But there are other things that are really easy to solve,” the CPG’s engineer says. “It goes both ways—not every problem can be solved remotely; that is the trick. But some can be.”
If nothing else, the remote diagnosis can often provide an indication of which technician it would be best to send out for on-site servicing, Garski notes.
“I don’t think there’s ever a fix for not having a great maintenance person in your plant,” says Jonathan Darling, CPG industrial automation market segment leader at Schneider Electric. “But what remote connectivity allows you to do is to be a Band-
Aid of sorts, or a fix to where, even if your maintenance team hasn’t been there for 25 years and they can hear that tick as they’re walking by that piece of equipment and know something’s wrong, they can connect with the OEM who made the piece of equipment, can sit there on their iPad or whatever, and be able to, with that tech, who is an expert on that equipment, look at what’s going on, look at the data that’s being produced, have visibility into the equipment and the diagnostics, and be able to help make decisions on how to fix that piece of equipment.”
The general consensus is that remote troubleshooting is a necessity. “It should always be the first thing before we call out a technician,” Gri en says. “There’s absolutely value there, but let’s not fool ourselves into thinking that means we won’t ever need to have a technician on site again.”
Ashworth www.ashworth.com
Bosch Rexroth www.boschrexroth.com
ei3 www.ei3.com
FPS Food Process Solutions www.fpscorp.com
OMAC www.omac.org
Rockwell Automation www.rockwellautomation.com
Schneider Electric www.se.com
Tetra Pak www.tetrapak.com
Engineered from the ground up to provide unsurpassed performance in food processing plants. These high performance, 100% synthetic lubricants provide extended lube intervals, multiple application capability, lubricant inventory consolidation and improved performance. All while maintaining strict H1 safety requirements. Available products include...
SFGO ULTRA SERIES MULTI - PURPOSE FLUIDS
s 5LTRA HIGH PERFORMANCE SYNTHETIC 0!/ BASED mUID LUBRICANTS
s !VAILABLE IN )3/ VISCOSITY GRADES FOR A WIDE VARIETY OF APPLICATIONS
s %XTREMELY 6ERSATILE 2ECOMMENDED FOR AIR COMPRESSORS HYDRAULIC systems, bearings, gearboxes, chains and more.
SYNXTREME FG SERIES GREASES
s SYNTHETIC CALCIUM SULFONATE COMPLEX TYPE GREASES
s 3UPER MULTI PURPOSE IDEAL FOR A VARIETY OF APPLICATIONS
s 4HEY PROVIDE EXCELLENT ANTI WEAR AND EXTREME PRESSURE PROTECTION
s (IGH TEMPERATURE STABILITY EFFECTIVE TO & #
PGO-FGL SERIES GEAR LUBRICANTS
s 5LTRA HIGH PERFORMANCE POLYALKYLENE GLYCOL 0!' BASED GEAR OILS
s 4HE ULTIMATE GEAR LUBRICANTS FOR DEMANDING APPLICATIONS
3CAN 12 #ODE FOR -ORE )NFORMATION
!BOUT ,UBRIPLATES 0RODUCTS AND 3ERVICES
BACK AFTER FOUR YEARS, PACK EXPO International convened more than 44,000 attendees during its Oct. 23-26 run at Chicago’s McCormick Place, thus surpassing the 2018 event. With 2,200 exhibitors showcasing groundbreaking packaging and processing innovations over 1.2 million net sq ft, PACK EXPO International was the one and only time the entire industry came together last year.
“The success of PACK EXPO is a testament to our industry’s continued growth as well as PMMI’s commitment to bringing the industry together to share cutting-edge innovations,” says Jim Pittas, president and CEO, PMMI. “The event showcased countless end-to-end solutions, o ering attendees everything they need to compete in a changing marketplace.”
Industry growth translated into buyers coming in significant numbers, ready to see the latest packaging materials as well as technology in action. Improving operations, reaching sustainability goals, and checking out new innovations are just a few of the drivers that brought consumer packaged goods (CPG) and life sciences companies to PACK EXPO International. The buzz on the show floor confirmed that exhibitors and attendees from companies of all sizes found a rewarding, and some claim unparalleled, experience at the four-day event.
Answering the need to come together, network and see advances, PACK EXPO International 2022 o ered more show features than ever before, bringing value to all market segments.
A record-breaking Packaging and Processing Women’s Leadership Network (PPWLN) breakfast brought together nearly 1,000 professionals to hear Dawn Hudson, former
Next up in the PACK EXPO portfolio is EXPO PACK Guadalajara (June 13-15, 2023), followed by PACK EXPO Las Vegas (Sept. 11-13, 2023; Las Vegas Convention Center). Information for the upcoming show can be found at packexpolasvegas.com.
chief marketing o cer at the National Football League and former president and CEO of Pepsi-Cola North America, talk about her experiences in the workforce. The PPWLN event, aimed at advancing the future of women in the packaging and processing industry, was sponsored by Emerson, ID Technology, Morrison Container Handling Solutions, Plexpack, Septimatech Group, and SMC Corporation of America.
Developing the future packaging and processing workforce was a top priority at PACK EXPO International, with the largest number of students in attendance in the history of the event. More than 1,500 students attended the show and participated in many opportunities to get them excited about careers in this industry. In addition to the prestigious Future Innovators Robotics Showcase, educational Amazing Packaging Race sponsored by Emerson, and Students PACK the Expo programs, this year six teams faced o in a brand-new machine building PACK Challenge, sponsored by PepsiCo.
With robust education o erings, the focus on developing our industry went beyond students. PACK EXPO International held over 120 education sessions, beginning with the one-day Emerging Brands Summit ,
making its debut at the show. The education continued throughout the show on various on-floor stages, o ering educational sessions such as the Innovation Stage, Processing Innovation Stage, PACK to the Future Stage, The Forum, and Reusable Packaging Learning Center.
Additionally, the PACK EXPO Association Partner Program connected attendees to leading associations from all segments of packaging and processing. This year’s program was the largest in PACK EXPO history, with 50 partners.
“We would like to thank PMMI’s board of directors, our membership, exhibitors, and all attendees who supported PACK EXPO International and made this show a tremendous success,” says Laura Thompson, vice president of trade shows, PMMI.
Once again, the editors of PMMI Media Group were on the job covering the innovations shown by the exhibitors. Our report begins on the next page, and it’s divided into four main categories: Food Processing & Packaging, Sustainable Packaging, Robotics, and Controls. This report is brought to you by:
Matt Reynolds, Chief Editor, Packaging World Pat Reynolds, Contributing Editor, Packaging World
The winners of the 2022 Technology Excellence Awards at PACK EXPO International 2022 are:
• Proxima Tethered Closure (Berry Global)
• IMA Ilapak Vegatronic 6400 (IMA North America)
• CueSee Mix/Dual Chambered Device for storage of liquids/powered/lyophilized components (Eurotrol)
• ClipCombo (Graphic Packaging International) Visit pfwgo.to/7867 to learn more about them.
Anne Marie Mohan, Senior Editor, Packaging World David Greenfield, Director of Content/Editor-in-Chief, Automation World
Stephanie Neil, Editor in Chief, OEM Magazine
Keren Sookne, Director of Editorial Content, Healthcare Packaging
Aaron Hand, Editor-in-Chief, ProFood World
Melissa Gri en, Editor, Contract Manufacturing & Packaging
Casey Flanagan, Editorial Assistant, PMMI Media Group
Joe Derr, Contributing Editor, PMMI Media Group
Michael Costa, Senior Editor, ProFood World
Lilián Robayo, Editor, Mundo PMMI
Notable at PACK EXPO International was a new application (1) of Claranor’s pulsed-light decontamination, a technique used to decontaminate surfaces by killing microorganisms using short pulses of light in an intense broad spectrum that’s rich in UV-C light. This Claranor technology, in use since about 2005, brings Extended Shelf Life (ESL) to food, beverage, pharma, and cosmetics packaging.
The application debuting at PACK EXPO falls into the dairy category. Think polypropylene cups of yogurt, for example. These are usually sealed by way of a pick-and-place approach in which pre-cut lids are pulled from magazine feeds and heat-sealed to filled containers. Recently, however, a Danish firm called PrimoReels came up with a machine that replaces pre-cut lids in favor of roll-fed lids fed from perforated reels. Because as many as 40,000 lids come on a single roll, this approach greatly reduces the need for operators to refill magazines with fresh lids. PrimoReels also says the cost of the lidding can be reduced by 30%. That’s because the cut-and-stacked lids need to be in the 50- µm range to be su ciently machinable in the pick-and-place equipment, while the roll-fed lids can typically be in the 36- µm range and some metallized polyester lids can be as thin as 23 µm. PrimoReels, it’s worth noting, is also the converter and supplier of the perforated roll-fed lidding.
Until PACK EXPO, the PrimoReels machine relied on UV light for decontamination. But the system demonstrated at PACK EXPO was the first to use Claranor’s pulsed light instead, which yields a more thorough decontamination. “This is especially true on microorganisms like molds, which are a constant quality challenge where yogurt products are concerned,” says Christophe Riedel, Claranor CEO.
On the system demonstrated at PACK EXPO, cups were being lidded eight across. The Claranor pulsed-light unit was positioned at floor level on the side near the roll-fed lid unwind cabinet. This arrangement occupies minimal space. In fact, just one Claranor pulsed light unit performs the decontamination task. The system brings eight lids into the unwind cabinet, the lids pause briefly so that the pulsed light can do its thing on the cup-contact side of the lids, and then those eight lids proceed into the part of the machine where two things happen:
First, specialized tooling— not a blade but more like a hammer—strikes the perforated reel in just the right way to cleanly separate each lid from the roll.
Second, vacuum cups pick all eight lids and rotate down 180 degrees to place them on the cups waiting below; a spot seal tacks the lids to the cup so the lids stay properly positioned until the cups reach the heat sealing station. Important to note here is the role played by a patented mechanism similar to a feed screw that causes the placement devices to separate left and right just the right distance so that each lid lands squarely on its designated cup.
Operating speeds are in the range of 45 cycles/ min when cups are being sealed 10 across. Riedel says that no commercial applications of the Claranor/PrimoReels solution are in place yet. But he believes it’s only a matter of time. “We saw a good fit between PrimoReels and our pulsed-light decontamination,” says Riedel. “For one thing, pulsed light does not involve heat the way some alternative decontamination methods like hydrogen peroxide do. That’s another reason why it’s possible to use a very thin plastic material for your lidding.”
Polypropylene, polyester, or metallized polyester can all be supplied by PrimoReels.
PrimoReels is now licensing suppliers in the U.S. to make it easier for brand owners to purchase rollfed lidding materials from multiple local sources. Also worth noting is that the new decontamination system can be retrofit onto existing fill/seal lines. a video of the Claranor/PrimoReel solution at pfwgo.to/7809.
The Versatech from Synerlink, a BW Packaging company, is a modular, ultra-flexible machine (2) that can fill cups from 40 to 150 mm at 12,000 cups/hr, with changeover from one format to another, including different shapes, materials, diameters, and heights, taking just 20 min from last to first container.
One key to the fl exibility of the system is its modular design, which allows functions to be added, switched, or removed easily and quickly— from half a day to two days, according to Fabien Jégo, design leader and product marketing leader at Synerlink. Each module is plug-and-play via a centralized cabling network. Through this network, each module automatically integrates with the rest of the system, both pneumatic and electric. The indexed position of the modules allows for simple placement and calibration, with a positioning accuracy of 0.1 mm.
Another feature that facilitates this flexibility is the machine’s ability to automatically load and unload slats, which Jégo says allows the customer to perform a slats change “in record time.” It also allows for fast and easy cleaning of the slats, with no tools required. Another advantage of the system’s fast return system is that fewer slats are required.
According to Jégo, the Versatech was engineered to address the top six issues currently facing users of cup filling machines. One is late-
stage customization by brand owners. With the Versatech, “a project manager can place an order without having full specifications,” he explains. “The modular design allows fi nal packaging design integration and functions modifications until the last minute.”
The second is a need for packaging versatility, as it allows a brand to respond to rapidly changing markets without having to wait for long lead-time machine redesigns. Jégo says the potential—in terms of the range of cup sizes, shapes, and materials that the Versatech can handle—is infi nite. “We can process any cup within the mechanical range of the machine [40 to 150 mm diameter and 160 mm high], from standard stackable to non-stackable cups in plastic, cardboard, and glass,” he says. “Moreover, if a new generation of cup arrives on the market, the modularity of the Versatech will allow us to develop new functions and to implement them on the machines already in production.”
The cup filler has also been designed to adapt to a customer’s changing requirements, negating the need for packagers to purchase additional equipment as their business grows. Says Jégo, “We can imagine that a yogurt producer who starts his business might equip himself with a basic machine, and later on, when his market has evolved, he might add capacities to his machine, such as decontamination of the cups with pulsed light, a second dosing device for a fruit coulis at the bottom of the cup, or a snap-on lid.”
And, on the subject of fl exibility, the fourth issue the Versatech addresses is the ability to handle mixed batches, especially for customers such as co-packers who are running smaller-volume jobs. “It has never been so easy to fulfill mixed orders for a production manager,” says Jégo, who cites the machine’s 20-minute changeover capability.
The cup filler also tackles issues around labor, such as ease of use and ergonomics. “It is very important for a site manager to limit the turnover of his operators and to keep the experienced people,” says Jégo. “Our machine is designed to be extremely convenient to operate. The loading of consumables, such as cups, lids, and toppers, is done at chest height.” In addition, loading can be done while the machine is running. High visibility throughout the entire production process ensures the correct functioning of the machine and adjustments to the slats’ changeovers, transparency, weight, and size, reducing the risk of operator error.
Synerlink particularly recommends the Versatech for applications that include dairy products, desserts, baby food, and fruits and vegetables.
An innovative semi-automatic stretch/seal application for food trays (3) made its debut at PACK EXPO International at the Point Five Packaging booth. “The idea is to address the problem of moisture buildup that you commonly see in film-wrapped trays of poultry or meat,” says Greg Levy, president of Point Five. “Too often this moisture leaks out of the pack and onto the consumer’s refrigerator shelf or kitchen counter, creating a most unwelcome mess. We’re using the same basic stretch film material, but we seal it to the tray flange rather than wrapping it fully around the tray and heat sealing it on the bottom.”
Fuji. “Another advantage would be related to shipping of the product. It currently takes three trucks to ship product packaged with foam trays for every one trailer truck of ground meat product without the tray.”
Removing the tray also eliminates the need for packagers to purchase, ship, store, and handle the trays. “Customers aren’t getting three or four truckloads a day of trays, so they’re able to reduce the footprint in their warehouse because they need less storage space,” Brenton remarks. “They can also reduce the amount of labor they have, which is a huge challenge for everyone right now. Just having someone move trays around the plant all day is kind of a waste when you don’t have to do it. You can then use those people somewhere else in the plant.”
Another benefit of the new process is that it eliminates a number of machines currently used in the tray-packing process. “End users can take out three machines from their current line because they no longer need a tray denester, a tray wrapper, and then an overwrapper to wrap three or four finished packs in a master pack,” Benton explains.
He adds that with the current tray-wrapped packs, the shelf life for the ground meat product is typically around 24 days, if the package stays within the master pack. Once it’s removed from the master pack for display at retail, the shelf life is just four to five days. Packages produced using the Formost Fuji system o er a 24-day shelf life with 18 to 20 in. of mercury on the seal test, Benton shares.
With this approach, the moisture has no opportunity to leak out. Plus, it yields a film cost savings because the film extends only to the tray perimeter rather than wrapping around the sides and down to the tray bottom.
a PACK EXPO video of this technology in action at pfwgo.to/7810
Another PACK EXPO International exhibitor that was focused on meat packaging was Formost Fuji But in this case, it was ground meat being flowwrapped without the foam tray so commonly found in U.S. supermarkets. The FW3710B Box-motion, wet-duty stainless steel wrapper (4) can handle ground meat portions up to 40 lb in an 8-in-wide format at speeds up to 120/min plus.
The most notable advantage of the new packaging system is the elimination of the non-recyclable polystyrene foam tray traditionally used for this type of product. “That’s the obvious benefit,” says Lee Benton, South Central sales manager for Formost
The system uses a polyethylene film with an anti-fog coating that can be preprinted with branding information. Benton says that Formost Fuji is currently working with a major ground meat producer in Nebraska to test-market the packs in a regional grocery retailer.
Demonstrated at the Orics booth in the South Hall was the D-Series delta-style robotic pick-and-place tray loading system (5) for pieces of protein products like chicken or steak.
Randomly spaced items to be picked are conveyed beside an automated tray denester that relies on servo motors to adjust width and length when a new tray size needs to be introduced. A Cognex vision system captures the location and orientation of each item on the conveyor belt and shares that
CANDY EQUIPMENT
COOLING EQUIPMENT
CUTTER SLICERS & DICERS
HOMOGENIZERS
INDUSTRIAL KETTLES
INDUSTRIAL MIXERS
INDUSTRIAL PUMPS
INDUSTRIAL TANKS
MEAT PROCESSING EQUIPMENT
MATERIAL HANDLING
INDUSTRIAL SIFTERS & SEPARATORS
VISIT OUR WEBSITE OR GIVE US A CALL US TO GET YOUR PROJECT STARTED TODAY!
data with the system’s controller. The controller then communicates with the robot so that it can go precisely where it needs to in order to make a clean pick from the conveyor belt and place the item in a tray.
The delta-style robot, designed and built by Orics, is all stainless steel and thus suitable for washdown. The product grippers are made of foodgrade silicon by Soft Robot Tech . “It’s a gripper that works with a special control system from STXI Motion that regulates vacuum and pressure,” says Orics president Ori Cohen. “When you pressurize those gripper fingers, they close like the fingers of a hand. When you release the pressure, they open.”
The softMC compact size controller, developed by Servotronix with an EtherNet/IP interface developed by STXI Motion, features a powerful algorithm that can control numerous axes simultaneously and achieve the desired kinematic motion of the robot. Compared to other manufacturers’ controllers that support three to eight axes, the softMC controller can control up to 32 axes.
The Orics D-series robot is equipped with STXI Motion motors, drives, and harmonic drive reducers with zero backlash. Engineered to allow full control of acceleration, deceleration, and velocity with
high-speed performance, the Orics D-series robot is suitable for pick-and-place applications where high-accuracy product placement is crucial. The system also has a self-teach programmable mode. This unique system will memorize positions of pick and place and will repeat them with minimal motor motions. The system can also receive a signal from a video camera and position its actuators, vacuum suctions, or grippers for random pick and place. And an orientation position system enables the robot to orient the transferred objects as they are randomly placed in the production or assembly line.
Cohen describes one application where the robot is just what the doctor ordered. “We put in a short goods pasta line within the last few months for ready meals. If the protein component is small—like diced chicken—it can be weighed and deposited mixed in with the pasta by the combination scale that is part of the system. But for chicken cutlets, for example, which are fairly large and randomly shaped, right now the customer places them by hand. This is where our robot system will come into play.”
a video of the Orics system at pfwgo.to/7812 .
The news at Serac’s PACK EXPO International booth was that BluStream (6), an electron-beam decontamination technology that has been in development for some 15 years, now has a commercial installation. The user of the technology is Sources Alma, a producer of bottled water as well as juice and tea drinks that is located in Saint-Yorre in Central France. The firm is using BluStream to decontaminate caps in the place of paracetic acid used previously on an aseptic filling line for beverages in PET bottles.
“With Drinktec last September and now PACK EXPO, we are formally introducing BluStream to the marketplace,” says Nicolas Ricard, managing director at Serac. “We had a lot of interest in it at PACK EXPO, so we expect to have a U.S. customer soon.”
Serac describes its electron-beam technology this way: “BluStream is a low-energy e-beam treatment that can be administered at room temperature. It’s capable of ensuring a 6-log bacteriological reduction in 1 second without any chemicals. This module is intended for use on bottling lines of non-refrigerated and ESL 90-day beverages. E-beam is a physical dry treatment. To sterilize the surface, e-beam dispenses a beam of electrons over the surface of the product. The electrons quickly destroy the microorganisms by breaking their DNA chains.”
Electron-beam decontamination is not new. It’s common enough in the printing industry. In the packaging space, Tetra Pak is among those using it to decontaminate its carton board packaging. The innovation here is that to decontaminate a cap— and soon, says Serac, the inside of a blown bottle— you have to have a highly specialized emitter to get the electron beams inside the cap or bottle.
Messer leverages our decades of hands-on experience with protein industry challenges to deliver safe cryogenic solutions that help increase throughput, improve efficiency, save labor and support more resilient supply chains.
Differentiated technologies that improve temperature control at any step of your process:
•Celebrating 100 nitrogen bottom injection installations that increase production, quality, and security of cryogen supply in processes traditionally offered only in carbon dioxide.
•The new Messer Digital Freezer monitoring system offers processors more accurate process control to achieve a step change in quality, traceability, and productivity.
•The latest tunnel freezing technologies designed to boost production hot products or crust-freezing.
•Messer’s family of spiral freezers, the industry’s proven workhorse, increase throughput in a small linear footprint to meet production goals.
As an alternative to paracetic acid or hydrogen peroxide, both used widely today in aseptic and ESL packaging, electron-beam technology is attractive to beverage bottlers because it lets them get away from chemicals. It also eliminates the need for considerable amounts of water to rinse the chemicals. The other benefit to the customer is the simplicity of use. You push a button and begin decontaminating
caps immediately for aseptic applications. On the Sources Alma line where BluStream operates, paracetic acid is still used to decontaminate the PET bottles. Finding an alternative to chemical decontamination for caps was a key driver behind the firm’s interest in BluStream. “Serac was the only solution we could find,” says Romain Leclercq, carbonated and soft drinks division manager at Sources Alma. “It’s a real innovation in the beverage market. On the chemical preparation side, there used to be a lot of e ort involved checking the concentration of paracetic acid, and of checking the temperature, too. Now for cap decontamination we just switch on the BluStream machine and it’s ready immediately. For operators, it’s greater comfort at the work station and fewer tasks to perform.”
According to Serac, electron-beam treatment depends on only three critical parameters: voltage, current intensity, and exposure time. By comparison, hydrogen peroxide sterilization depends on at least
The new GVC -18000 (7 ) from Goodway Technologies is designed for most manual deep cleaning and sanitizing applications in food production plants. According to the company, the low 5% moisture content lends itself to cleaning around sensitive electrical components and in dry, clean areas.
At 290°F, the dry steam melts away fats and sugars, and kills bacteria and other microorganisms on contact. The system’s multiple cleaning tools are suitable for flat surfaces as well as the cracks and crevices that are often ideal for the growth of bacteria and mold.
The CVC-18000 has a heating power of 18 kW and steam production of 50 lb/hr.
six: output, ambient temperature, temperature and time for hot air, and concentration and time for hydrogen peroxide.
“We also save on space,” says Leclercq. “And we now use a conventional cap hopper as opposed to several wet hoppers. Plus, the BluStream module is positioned above the capping machine. So it didn’t occupy additional floor space. We’ve been very satisfied in terms of performance and decontamination e ciency.”
Leclercq notes that where caps are concerned, the current goal is to substitute BluStream decontamination for paracetic acid throughout the company’s operations. When asked about cost, he says that with the cost of electricity fluctuating so wildly at present, it’s di cult to make an accurate comparison. “Maybe we can do so once we’ve recovered standard prices for energy,” he adds.
Nicolas Ricard, managing director of Serac-USA, says that Serac now plans to install a BluStream module for decontamination of bottles at a customer facility in Europe. As with the system for caps, it will once again be a rotary system. And it will be suitable for either PET or HDPE bottles.
a video of the technology at pfwgo.to/7813 .
In Lakeside Center, Unifiller Systems demonstrated its new +Series Depositors (8), digitally controlled pneumatic depositors designed to deposit batters and other products with more ease and precision. The system brings into reach technology that often only large-scale customers have access to.
Launched in September, the +Series Depositors combine pneumatic machines with smart control. Using a smartphone or tablet connected via Bluetooth, users can control speed, volume, splash reduction, pre-charge, and deposit pressure profiling
for the most accurate deposits.
The new depositors connect to Unifiller’s cloud-based Total Care App, which provides real-time data analytics. Hundreds of recipes can be stored in the Total Care App’s cloud. Any machine settings and recipe adjustments can be digitally controlled through the app.
“This is the first time we are o ering a smart-controlled depositor with built-in Bluetooth features,” comments Sonia Bal, director of
•Potato and vegetable preparation
•Frying and oil management
•Drying and roasting
• 7IEWSRMRKERHƽEZSVMRK
•Conveying and product handling
•Weighing, bagmaking, and casepacking
•Foreign object and defect inspection
•Controls and information systems
We are successful when you are successful. That’s why we apply creativity, engineering excellence, and determined perseverance to every project to help our customers get the performance their business demands— [LIXLIVQIEWYVIHF]ƽEZSVIƾGMIRGMIW sustainability, improvement, or innovation.
info@heatandcontrol.com | heatandcontrol.com
global marketing for Unifiller. “It’s a very low-cost program. Usually, this kind of technology is reserved for more complex systems owned by large-scale customers. However, we’ve been able to develop it for our standard machines, as small as the Compact depositor, which means that even operators at a retail level can a ord this innovation.”
Compared to previous depositors, the +Series can han-
dle more complex applications, in part because of its connection to the Total Care App. “The +Series combined with the Total Care App allows for recipe storage, so complex recipes (deposit speeds and volumes) can be fine-tuned one time and stored for easy recipe recall in the future,” Bal explains.
The +Series Depositors are built for ease of use and cleaning. No special training is required to operate the machines, and detailed explanations and video instructions are provided for advanced functions. All electrical components are enclosed in a washdown case that will withstand tough, industrial washdown conditions, meeting IP69 standards.
This kind of connected technology is already in demand for large-volume producers, Bal notes. “We wanted to extend the same innovation to even our simplest machines. Customers have responded very well and are keen to try it out. We have already completed successful field testing,” she says. “What’s great about the Total Care App is that not only does it work with the +Series Depositors, but with a simple addon, it can actually turn previously owned manually adjusted pneumatic depositors into smart-controlled depositors.”
Another kind of food depositing technology was on display at the PACK EXPO booth of Hoosier Feeder. The company unveiled a unique product placing system (9) for various food products like chicken breasts or hamburger patties. It
relies on a centrifugal feeder that orients products into a single fi le. At that point, the product drops into a collator that drops individual products into a tray or, as was demonstrated at PACK EXPO, onto a hamburger bun. a video of this product placing system at pfwgo.to/7814 .
Inspection tech on display
Debuting at PACK EXPO International from TDI Packsys was the XR-6080SH X-Ray Inspection System (10). The detection technology built into the XR-6080SH can find 3-mm thickness of bone, which is especially useful for poultry, since those bones can be hollow and di cult to detect.
A lot of our customers can’t talk about their secret to safe, smooth, gentle conveying but everyone knows the secret is Volkmann. Our patented pneumatic vacuum conveyors automatically transfer powders and other bulk materials from one point to another in fully enclosed, dust-tight, explosion-proof systems.
▪ Automated, hygienic and quiet
▪ Easy to use, easy to clean
▪ No tools disassembly
▪ Stainless steel as standard
▪ Fast lead times, easy to install
“Our customers were asking for something that could get a little more micron, especially for packaged meat,” says Israel Mateos, director of quality and integration at TDI Packsys. “We can also find 0.3-mm metals, like stainless steel, ferrous, and non-ferrous, which is unheard of across the industry. We can do that with great accuracy.”
Mateos adds that while the detection technology in the XR Series is ideal for chicken and other poultry, it also works for other meats too. “If this system does well on di cult-to-detect, hollow chicken bones, it can do great on beef and pork bones that are denser and bigger.”
Technology driven by artificial intelligence continues to establish itself as a fixture in our world of increasingly smart factories, and Contact 4.0 from Fortress Technology is a great example. On display at PACK EXPO International, this smart data-capture solution is aimed at food manufacturers operating multiple metal detectors and weighing machines across multiple facilities.
Using web-based architecture, Contact 4.0 captures valuable production data across an entire suite of networked Fortress inspection machines. It can remotely monitor the performance of equipment, track events, and document all potential product safety risks. In other words, it turns massive data streams into tightly monitored and thus highly useful operational insight.
palletizing, pick and placement or carton loading with safe, IXOOZDVKGRZQURERWLFV
MIX
LFLQJVƮOOLQJVDQGPRUHWR perfect consistency with /LNZLƮHUKLJKVKHDUEOHQGHUV
SHAPE
up to 48,000 portions per hour and still achieve that perfect homestyle bite.
MOVE your ingredients with hygienically designed conveyors, dumpers, loaders, hopper chunkers and other engineered solutions.
What’s more, for the fi rst time, it lets food processors connect multiple front-end inspection machines to back-end reporting software in real time. It’s live, it’s streamlined, and it’s centralized. So rather than reacting to various production scenarios, customers can export dashboards and reports in the format that is most closely aligned with their common reporting standards. This enhances traceability and gives operational sta the info needed to address time-critical events. And for those already operating Fortress machines, you’ll be happy to know that Contact 4.0 can be installed on all Fortress digital Stealth, Interceptor, and Interceptor DF metal detectors, as well as on the Raptor Checkweigher, Raptor XL Caseweigher, and the Raptor combination checkweigher/metal detector.
Speaking of Raptor checkweighing, it made its o cial debut for Fortress at PACK EXPO, as previously the firm did not have a checkweigher in its product portfolio. On display at the Fortress booth was a combination metal detector and checkweigher ( 11). Individual reject mechanisms, one for packs that are detected to have metal and one for packs that are detected to be the incorrect weight, are part of the combo system. The operator can control the entire combo system from a single human-machine interface (HMI).
a video of the combo system at pfwgo.to/7815 .
Featured at the PACK EXPO booth of Schenck Process, the Global Hygienic Airlock (GHA), a USDA Dairy accepted dismountable airlock, is suited to applications where dry raw or finished products are being handled in the process and where inspection or system clean-out is required ( 12). At PACK EXPO International, Schenck Process was displaying not only the GHA itself, but new features it
has since made available on the airlock.
The Rotor Assist Device (RAD), for example, was recently made available to help disassemble the valve housing for cleaning. “These 12-, 14-, 16-, 18-inch valves can get quite heavy,” comments Jon Goecker, industry manager for Schenck Process, who demonstrated the unit at the company’s booth in Lakeside Center.
With the RAD, the valve rotor slides out easily on rails, enabling the rotor to be cleaned without workers having to lift the heavy equipment. Then it slides into the housing again easily.
Goecker also showed o the Valve Interference Detection (VID), which keeps the airlock from being damaged and protects product from contamination caused by friction between the valve rotor and the housing. “Without this, there could be metal shavings in the process,” Goecker explains. “That’s why we have metal detectors and sifters in the process,” but of course better to keep the shavings out in the first place.
The VID system electrically isolates the moving rotor from the valve housing and drive system so that a closed circuit would indicate resistance between the rotor and housing. Any interference that’s detected would show up on the HMI.
Following the ongoing trend toward automated material handling solutions, Syntegon Packaging Technology debuted at PACK EXPO International its new, Intelligent Direct Handling (IDH) pick-and-place system (13) designed for the flat (pile) or on-edge (slug) handling of cookies, crackers, biscuits, and similar products. The advanced pick-and-place concept uses linear motor technology—Beckho ’s XTS system, to be more specific—and the smooth movements of the linear motors ensure gentle handling of the fragile products.
“Product is fed into the IDH system from an oven or cooling towers, either random or in rows, with a tray denester positioned in parallel with the infeed,” says Daniel Bossel, product manager at Syntegon. “But the heart of the IDH is in the pick-and-place movers.”
Manufacturing food and beverages require robust, reliable, and durable equipment solutions. In addition, ingredients must be handled gently, added precisely, and mixed e ciently. We have extensive knowledge of food and beverage production, and our application experts can develop and deliver a solution to handle your most demanding applications.
www.scottmixers.com
Based on the XTS linear servo platform, these movers are instructed by a vision system as to the location of each layer of products. They then adjust themselves, in parallel with the product flow, to the placement of random biscuits as they are fed into the system. At the show, a row of 26 movers, arranged at an intersection with the infeed product flow, used vacuum end-of-arm tooling to gently pick up the biscuits, rearrange themselves from random to directly in-line, and carry them at a transverse 90-degree angle into waiting trays that had just been denested in parallel to the product infeed.
“The linear motor means that we have low acceleration and low vacuum,” Bossel says. “This makes for very gentle handling of the biscuits. Also, the machine’s footprint is very small, and we can do a lot of di erent pack styles.”
The machine moves at about 30 cycles/min, and with 26 independent movers, that means close to 800 biscuits/min. These speeds
with extra gentle, low-acceleration movement are meant to complement more traditional delta robot pick-and-place o erings that may be faster, but given di ering acceleration and deceleration ranges, may also be less gentle.
At the booth, the IDH was also integrated with a Syntegon Pack 202 horizontal flow wrapper, with low back-pressure infeed, to form a turn-key system for packaging biscuits or cookies into trays that were then overwrapped with printed film. The company adds that this full system could use more readily recycled monomaterial films for the overwrap, or paperboard trays instead of plastic trays, to add to a brand’s desired sustainability profile. video of this system at pfwgo. to/7816 .
Making its PACK EXPO International debut was the Yamato Gravimetric Flex Weigher (GFW), which the company says was designed with flexibility in mind (14). This bulk weigher features four weigh-heads to support target weights that range between 5 and 20 kg. According to the company, the Yamato GFW-1104CC scale o ers high speed with supreme
accuracy. At 5 kg, for example, this scale can operate at up to 60 weighments per minute, at an accuracy of ±5 g. Use this system to weigh a variety of bulk dry, free-flowing grains, granules, and powders into bags, boxes, gaylords, and totes of all sizes. Automation like the GFW handles higher target weights, and complements Yamato’s high-speed, high-accuracy combination scales, that tend to be more suited to lower
1,000 Kg of mayonnaise in 10 minutes!
Yes, it is possible with the Standard Production Plant from IKA®. This complete, all in one batching system in mayo execution provides the means to significantly decrease production time while delivering constant product results and quality.
Read our whitepaper here: www.ikausa.com/mayo
weights with greater precision.
video of the Yamato technology at pfwgo.to/7817.
In a dramatically di erent application, weight-wise at least, weighing and filling leafy greens can be a challenge to automate, and labor is getting harder to find. To address this, Yamato demonstrated how to remove manual labor from packaging lines and fill and tamp salad with its Yamato Automatic Diving Funnel (ADF). Featuring a rugged, low-maintenance design, this in-line tray filler ( 15) seamlessly places and tamps leafy greens into trays, bowls, and other rigid containers. The hygienic design keeps product safe from contamination, and ratio filling minimizes product damage. Increase production capacity while drastically reducing labor costs with the Yamato ADF.
video of the weigher in action at pfwgo.to/7818 .
The new patented hygienic SSVXP Drum Motor ( 16) from VDG (Van der Graaf), making its debut at PACK EXPO International, is designed with an exchangeable profiled sleeve that enables di erent belt profiles to be used without changing the drum motor. The profiled sleeve slides o the drum motor and is easily removed and replaced with another profiled sleeve to match the modular belt required on the conveyor. With the SSVXP design, if the belt on the conveyor is
required to be changed to a di erent belt profile, then only the sleeve needs to be changed over and not the entire drum motor.
“From a design perspective, the main point is sanitation,” says Alex Kanaris, president of VDG. “The traditional way of driving conveyor belts [sprockets on a square drive shaft] is not sanitary. A traditional belt drive has many crevices and spaces that trap food byproducts and harbor bacteria, and it takes twice as long to clean using a significant amount of water. The drum motor with the continuous profile sleeve eliminates these harborage areas and is faster and easier to clean, saving time and water.”
The hygienic SSV-XP Drum Motor is available in a range of diameter sizes, belt speeds, horsepower, and profiled sleeves for a variety of conveyor belt manufacturers to suit various belt conveyor applications.
The SSV-XP also has a slide-on/slide-o continuous profiled sleeve over the drum motor that attaches simply with six screws, provides the fl exibility to adapt to various types of conveyor belts without removing the drum motor, and exceeds sanitary standards.
Mepaco showcased its ThermaBlend batch cookers (17), which provide up to 50% more heat transfer area than hemispherical kettles and other conventional jacket cookers. ThermaBlend cookers deliver quick, homogenous blending while minimizing shear with e ective agitator designs, and also minimize burn-on while optimizing heat transfer with a durable, bi-directional scraper system.
•Reduce labor costs
•Improve food safety
•Minimize service and maintenance
Learn how Key can optimize your business at key.net.
“For a stew product or a chili, companies want every one of those vegetables, beans, or pieces of meat to be intact so that it looks just like you might make in your home kitchen, but on a much larger scale. We have a steam jacket, much like you do in your kitchen where you have a pot sitting on top of a heating element, and you’re heating that pot indirectly,” says Tom Ho man, director of sales at Mepaco.
Ho man adds that the ThermaBlend batch
cookers come with direct steam injection as well as a steam jacket for the full range of steam and cooking options. ThermaBlend also has CIP capability, and the option to batch chill as well.
“You can bring a product up to 180 degrees, cook it, and hold it through an intervention step if necessary,” he says. “Then, you can actually bring it down to whatever temperature you want all the way down to 40 degrees in a relatively quick period of time.”
The new Urschel M VersaPro Dicer (MVP) rolled out at PACK EXPO International with a slate of cutting-edge features for creating dices, strips, and shreds from meats and vegetables (18). The MVP is the fourth generation in Urschel’s M-series, with 33% increased feeding capacity compared to Urschel’s M6 due to wider, 12-in. infeed and takeaway belts, and increased horsepower.
The MVP features stainless-steel construction throughout, with an IP69K certifi ed electrical enclosure and double-sealed door for extra protection during washdowns, while the cutting spindles have a sanitary design and are cantilevered for quick changes. Speaking of cutting, the width
Process
is determined by a gang of circular knives followed by a series of cross-cutting knives that determine the length. The machine has the option of 5-in. diameter knives for 1-in. thick product, or 6-in. diameter knives for product thickness of 1.5 in.
“In addition, on the machine we have an optional HMI that gives you the ability to set cut sizes along with reci-
pes for the di erent products you have,” says Tim O’Brien, sales director at Urschel Laboratories. The optional Allen-Bradley HMI touchscreen also contains the entire user manual for ease of operation and maintenance.
a video of the machine in action at pfwgo.to/7819.
Pneumatic conveyor pioneer Vac-UMax put its expertise on display at PACK EXPO International, showcasing several of the company’s bulk material handling systems for dry foods and other dry products.
Vac-U-Max’s pneumatic conveyors ( 19) feature all stainless-steel and sanitary design, with easy disassembly for cleaning, including the filter, which is washable. Because some of the machines are positioned high in a processing facility, VacU-Max developed a solution to lower the machine rather than risk injury to a worker climbing a ladder to clean it.
“We’ve come up with what we call a column lift. You put the machine on a pedestal, you raise it up by hand, and you can crank it over to get it over the process,” says Vince Macaluso, regional sales manager for Vac-U-Max. “Now you can clean it. You just pivot the machine over and lower it down to the ground, where it’s at fl oor height and you’re ready to clean it out.”
Macaluso demonstrate VacU-Max’s pneumatic conveyors at pfwgo. to/7820.
A single Columbia palletizer can handle all of these products and more with ease.
Ryson Spiral Conveyors need less floor space than conventional conveyors and are faster and more reliable than any elevator or lift.
Unit Load Spirals convey cases, totes and packaged goods smoothly on our slat style belts and come in 9 standard slat widths ranging from 6” to 30”. Available in powder coated carbon steel, stainless steel, wet environment and freezer versions.
Mass Flow Spirals handle full and empty bottles, cans and jars in mass up to 2000 units per minute. Available in 4 different slat widths ranging from 6” to 20”.
Narrow Trak Spirals are super compact and designed to handle your smaller loads. Our 6” and 9” wide nesting slats can end-transfer small cartons and packages or side-transfer small bottles and containers in a single file or in mass at speeds in excess of 200 FPM.
Ryson’s Bucket Elevators combine vertical and horizontal transportation of bulk materials in one integral unit.
Ryson Bucket Elevators are designed for gentle handling and well-suited to transport a broad range of bulk products. Our signature feature is that they are completely enclosed with overlapping pivoting buckets, that prevent spillage and helps mitigate foreign debris.
Their modular design enables us to customize with ease. They can be configured with multiple inlets or outlets that can be controlled individually. The design makes them easy to install and modify. Available in three standard bucket sizes, yielding capacities up to 300, 700 or 1,800 cubic feet per hour. They can also be delivered in powder-coated carbon-steel, stainless-steel or wet environment versions.
All Ryson equipment is modular and built to order. No matter the application, the Ryson team is up to the challenge of finding solutions for your conveying needs. For application assistance or more information, give us a call or visit www.ryson.com
Fristam Pumps USA debuted its next-generation colloid mixer (20) at PACK EXPO International, featuring real-time gap adjustments and hands-o clean-in-place (CIP). This new colloid mill features on-the-fly gap changes with an external gap adjustment lever, which can widen or shorten the gap to produce more or less shear without moving the inlet or outlet ports, or pausing the operation.
Redzone introduced its Frontline Learning Module (21), an addition to the company’s workforce solutions software platform. Richard Tester, Redzone’s co-founder and CEO, says the new module aims to take tribal knowledge about operating manufacturing equipment out of the heads of machine operators and onto Redzone’s platform as video, where it can be watched as a best practice by other employees.
“If you’ve run a filling machine, for example, for 25 years, you know the best way to use it, or do the startup or changeover on it,” Tester says. “With our new module and an iPad or iPhone, you can record a quick two- or three-minute video, which can become a best practice for that machine at your company. It’s like a YouTube application for the plant floor. Like anything in life today, if we want to learn how to change a tire on a car, for example, we can go to YouTube and watch a five-minute video, right? So we’re introducing that technology onto the plant floor, and it looks at the
The new mixer’s variable gap allows the user to dial in the particle size needed for shelf-stable emulsions, resulting in more consistent particle sizes with a tight distribution. Some applications for this mixer include mayonnaise, dressings, dips, oil and fat emulsions, condiments, dairy solids, and more.
“We have a blender, but blenders only go so far,” says Jim McCoy, sales manager, Americas, Fristam Pumps. “We were getting a lot of requests saying, ‘Hey, I need you to move down the particle size range.’ So this is the result of that, and we can meet their exact, precise requirements for particle size. Plus, this mixer fits in with our whole portfolio of products.”
The Fristam FCM also features CIP without disassembly, designed for hands-o use that allows you to adjust the gap to the maximum setting and CIP through the mill without removing any parts. The mixer has a max shear rate of 143,000 1/s, can handle sub-micron particle size, has a max inlet pressure of 250 psi, a max product fl ow rate of 50 GPM, a max CIP fl ow rate of 100 GPM, is bi-directional, and has a 50 HP motor size.
whole frontline employee experience, which we think is something that’s been massively overlooked in manufacturing for the last couple of decades.”
The Frontline Learning Module comes on the heels of Redzone’s other recent addition, the Reliability Module, which puts basic machine maintenance knowledge into the hands of operators and tracks machine OEE and maintenance schedules, so maintenance crews can focus on crucial repairs, especially helpful for manufacturers with a labor shortage.
“The technology really drives all of the daily operating behavior for the frontline teams,” Tester explains.
“Whether it’s running the line and tracking performance, whether it’s quality, whether it’s maintenance— this gives operators the ability to do basic preventive maintenance. So we shift maintenance resources away from performing day-to-day tasks and move basic care for the equipment into the role of the operator.”
Axiflow Technologies debuted its bulk drum unloader (22) at PACK EXPO International. This new tool for removing fluids and soft solids up to 3 ⁄4 in. from plastic, metal, and fiber drums of 16, 20, 30, 55, and 75 gal features a speedy 50+ gal/min (GPM) unloading, with discharge pressures up to 375 psi. This CIP-ready bulk drum unloader can handle product viscosities over 500,000 centipoise, and it can be fitted with custom plates for di erent sized drums, as well as mix kettles and pots. The plates are also removable for pumping out totes and tanks.
Graco unveiled its updated electric pump (23) for food processing, boasting energy savings up to 80% more than traditional pneumatic air diaphragm pumps. According to Je rey Sha er, senior product manager and North American sales manager hygienic equipment at Graco, the company has been making electric pumps for about six years, but Graco recently developed patented technology that eliminates the need for a gearbox inside a pump, reducing the footprint and significantly increasing its energy savings.
“We have the motor and drive package right in the middle of the pump, but there’s no gearbox now, which reverses package size and cost to the user,” explains Sha er. “A big benefit with electric is it reduces your energy costs as far as e ciencies by up to 80%. So while a pneumatic pump might cost you $2,000 a year to operate, this might cost you $200 a year. So big savings, and it also qualifies for energy incentives from our company.”
Sha er adds that the new version of Graco’s electric pumps works seamlessly with facility control systems that can monitor the pump’s usage around the clock, which facilitates predictive maintenance, saving time and labor.
PROTECTION FOR PERSONNEL, PRODUCTS & EQUIPMENT.
AUTOMATION TO LEVERAGE FULLSTREAM PERFORMANCE.
Dust collection and containment systems leave you with clean up, disposal, and material waste on your hands. The National Bulk Equipment enclosed dust recovery system keeps your valuable material in the product stream and your throughput at its peak.
Enclosed Dust Recovery Stream
Proper routing and filtering of displaced air during discharge enables dusted product to be reintroduced to the material stream.
E3TM Dust-tight Bag Spout Interface Bag spout is fully enclosed during discharge; 3/4-inch thick clamp plate prevents deflection and dust release.
Fullstream Material Management
Integrated automation of upstream and downstream equipment ensures optimal process-wide performance.
Air Flow Volume Controller
Automated modulation of air flow volume during bag spouting, material flow, and filter cleaning prevents dusting and material waste.
From raw material discharging to finished-product packaging, NBE bulk material handling equipment spans the fullstream of processing and packaging applications. Leverage the full portfolio of NBE equipment to bring optimal process performance to your production operation.
Move beyond the constraints of build-to-order and engineered-to-order equipment builders. Avoid settling for application input that falls short and project and production resources too limited to keep pace. Ensure optimal project performance from pre-RFQ feasibility testing through installation and turnover, with NBE engineered-to-application project delivery.
See for yourself. View product feature demos, watch a test of your material from your computer or mobile device, or request a rep visit. To get started, visit: nbe-inc.com or, call: 616.344.5520
Lubriplate debuted several new products at PACK EXPO International, including refillable bulk loading grease guns and grease transfer pumps for 35-lb grease pails and 120-lb kegs (24). Lubriplate’s hand pump provides grease gun loading direct from the bulk containers, and the kegs have an option to use an automatic pump for tasks that require more volume.
Also new from Lubriplate at the show was their Lubriplate Synthetic Food Grade Drilling & Tapping Fluid, which is a full synthetic fluid designed specifically for drilling and tapping. This product is NSF H1 registered, making it ideal for food processors, food package manufacturers, and the pharmaceutical industry.
One more debut from Lubriplate is its SYN-FG SDO food-grade synthetic sugar dissolving oil, ideal for beverage manufacturers or those working with
sugars and syrups. SYN-FG SDO is NSF H1 registered and is specifically designed to remove sugar deposits and to lubricate machine components exposed to sugar contamination, thus reducing and preventing future sugar buildup. All of Lubriplate’s spray cans now feature the company’s patented Secure Straw dual-spray nozzle with a permanently attached straw.
Unibloc rolled out its multi-size line of QuickStrip FoodFirst pumps (25), which now range from the QS FF 300 to the QS FF 677, featuring 1.0- to 6.0in. outlet sizes and flow rates from 28 to 500 gal/ min, depending on the model size. All QS FF pumps
feature Unibloc’s patented CIP features with toolfree disassembly.
“The largest version of our FoodFirst pumps was originally made for meat and poultry. But over time, we realized there’s more than just those markets that can use this technology, so we expanded across the product line with di erent sizes, and our customers love it,” says Mark Boyd, vice president of sales at Unibloc.
Also new at PACK EXPO International from Unibloc was the company’s Flotronic Air Operated Double Diaphragm One-Nut Pump. The stainless steel pump’s unique design allows for disassembly and cleaning in a fraction of the time it takes to do the same with a standard pump—from an hour or more down to just minutes—significantly reducing downtime.
“It’s the only air-operated double diaphragm pump in the world where you can use CIP rig,” explains Leighton
Jones, director of sales at Unibloc. “We added a reinforced backing plate, and that supports the diaphragm when you put in the CIP pressure. It’s so unique that most engineers don’t even know it can be done. So one of the big things is to educate engineers so they can spec this double diaphragm pump on a CIP application.”
Elsewhere in the world of pump manufacturing, Alfa Laval has been making several advances over the past year or so that work, in particular, to ease maintenance concerns from a number of vantage points. Last year, Alfa Laval introduced its DuraCirc positive displacement pump (26), a departure from the typical circumferential piston pump (CPP), delivering on durability, reliability, e ciency, and hygienic performance. Rather than compromise on tradeo s, manufacturers across the dairy, food, beverage, confectionery, and personal care industries can get it all.
Mitigating food safety risks starts with thoroughly understanding the hazards and developing safeguards.
(PSOR\HHVZKRDUHWUDLQHGDQGFHUWLƮHGLQWKHODWHVW best practices of preventive controls are crucial to successful implementation of a food safety plan.
:HRƬHUFRQYHQLHQW)63&$WUDLQLQJERWKRQOLQH and in-person for individuals or groups.
'D\3UHYHQWLYH&RQWUROV IRU+XPDQ)RRGV
'D\3UHYHQWLYH&RQWUROV IRU+XPDQ)RRGV3DUW
'D\,QWHQWLRQDO$GXOWHUDWLRQ &RQGXFWLQJ9XOQHUDELOLW\ $VVHVVPHQWV,$9$
7RVLJQXSIRUDQXSFRPLQJFRXUVHYLVLW dennisgroup.com/services/food-safety. )RUJURXSLQTXLULHVFRQWDFW.DUD6FKHUHU at scherer@dennisgroup.com.
dennisgroup.com info@dennisgroup.com
+1.888.514.7270
United States Г Canada Г Brazil
“We spent years figuring out how to get into the U.S. market. We were looking at all our customers’ sore points,” says Russell Jones, commercial manager for pumps at Alfa Laval. “This tackles about five common problems.”
One improvement is the elimination of contact between the pump’s rotor and casing. Traditional CPPs have constant contact between the rotor and plate, Jones notes. Alfa Laval guarantees no contact until at least 360 psi, he adds, helping to increase durability and pump life while also reducing the chance of media contamination.
The pump is certified to meet 3-A Sanitary Standards, but goes beyond those standards to ensure cleanliness. The fully CIPable design is standard. “After the CIP cycle, it’s not only clean, but there’s no residue,” Jones says. That’s true even with viscous products, which can have challenging particulates, he adds. Also meeting EHEDG guidelines, the DuraCirc pump assures process integrity and product quality. For a crevice-free design with no dead zones, all product-wetted elastomers are made of FDA-conforming materials and profiled and defined compression as standard; this reduces contamination risks and cuts both cleaning time and costs. The all-stainless steel construction is also suitable for hygienic washdown.
Maintenance is also reduced through an FDAconforming oil lubricant that has an extended service interval—about 3,000 hours vs. 750 hours for a typical competitor. Front-loading self-setting mechanical seals are easy to get to, making them quick and easy to change without the need to remove the pump from the system.
More recently, Alfa Laval introduced a subscription-based digital monitoring system for pumps and other rotating equipment such as agitators and mixers in hygienic processing industries. CM Connect enables operators to access data from a remote location. It provides operators the information they need to make informed maintenance decisions—such as actual runtime, trend analysis, and time to the next service. Advanced vibration analysis enables early detection of any deviation from pre-set equipment threshold values.
Equipment for depalletizing also made a splash at PACK EXPO International, especially at Ska Fabricating. Though the U.S. has standardized on mainly one pallet size, this is not the case in Europe, where manufacturers are dealing with a much broader range of pallets. With this in mind, Ska introduced an international configuration of its Microbus depalletizer (27 )—now able to handle six of the world’s common pallet sizes.
Like the original Microbus launched earlier in 2022 in the U.S. and Canada, the International Microbus, which made its debut at PACK EXPO International, is a semi-automatic empty-can depalletizer that features a manual hand crank to raise the pallet carriage and an automatic belt sweep that advances cans onto a rotary table prior to rinsing and filling. Capable of speeds to 30 CPM, the portable depalletizer is optimized for lower-speed applications in the smallest of spaces.
“This is a good fit for really small companies because it folds up and can be tucked away,” says Jake Kolakowski, chief customer o cer for Ska Fab. Both the rotary infeed table and the automated sweep can be folded and locked down for storage after canning runs. This reduces the footprint of the already small machine to about half its full size, which is much needed in many small craft brew facilities, Kolakowski notes. “These places are so packed in, they don’t have a lot of space to work with,” he says.
Ska Fab also showcased the fruits of its acquisition early this year of GR-X Manufacturing , which specializes in depalletizing and palletizing equipment systems for consumer products and food and beverage industries. Though both companies play firmly in the palletizing/depalletizing space, there is very little overlap in their market segments.
Wipotec used PACK EXPO International to showcase its new Traceable Quality System with Modular Design (TQS-MD). The system (28) uses a “building block” concept yielding compatibility with a broad array of products.
“This system is designed for trays, for food products, medical device, and more,” says Daniel Brandao, regional sales manager at Wipotec. “We have the system set up with infeed metal detection integrated into our weigh cell, then we have our labeling device for top and bottom labeling. The bottom labeler includes a printer for variable data. The system applies those labels and scans for posi-
Best-in-class industrial grade magnetic metal separators.
Designed for your process application and built to last.
» Captured Metal
» Product Purity
» Equipment Protection
» Employee Safety
» Plant Uptime
» Maintenance Costs
» Headaches
HACCP International Certified and USDA AMS Accepted Equipment. Our Sanitary Grade Rare Earth Magnetic Tubes are certified by HACCP International for direct contact with food product as well as USDA AMS accepted Dairy, Meat and Poultry magnetic separator processing equipment.
tion and accuracy of the print, and finally there’s a reject station for all three of the upstream devices: the metal detector, weigh cell, and labeler.”
All TQS-MD models employing a weighing station feature the company’s high-tech ElectroMagnetic Force Restoration (EMFR) weigh cells, a di erentiating engineering design that guarantees precise weighing results, the company says.
Another TQS-MD setup, geared toward food applications, can weigh, label, and inspect for metallic foreign bodies in a single process step. And by adapting product handling modules to a larger dimension, TQS-MD models also can be arranged to handle big boxes like shipping cartons. Since such cases generally entail unit-level information for serialization, aggregation, or shipping, a track and trace module is also usually engaged in these instances.
Wipotec’s TQS-MD series can comprise a wide array of configurations. Typically applied to print “best before” dates, batch codes, or lot numbers on boxes, the popular basic setup marks, it verifies and weighs products on a footprint of just 1 m in length, and it can be upgraded to execute full serialization where required.
A cornerstone of Wipotec’s new series is central control. Regardless of the number of functionalities a TQS-MD models entails—a lengthy list that includes weighing, marking and verifying, labeling, metal detection, and serialization/aggregation integration, among others—the unit o ers one user interface. This makes product changes, article setup, and layout modifications less error-prone and more user-friendly.
the quality control system in action at pfwgo.to/7798 .
Pressco Technology also highlighted its filling line and high-speed vision inspection solutions (29) at PACK EXPO International. Pressco’s Intellispec platform provides a comprehensive set of modular
solutions for high-performance filling lines. Pressco systems are designed to be integrated into various blow-molders, fillers, cap feeders, and labelers.
“This is an entire manufacturing process right here,” says Michael Coy, director of marketing at Pressco Technology. “Most companies that do vision systems only focus on one part of that process. We’re up and down the line, we’re everywhere. We have a modular approach, so even with all those operations in your factory, you can have one inspection system, and you only need to learn one software and train your sta once. It’s a single control point for all those inspections, so it’s a much more e cient way to operate.”
Coy adds that Pressco’s systems not only collect inspection information on each part inspected, but correlate that data back to the specific machine component causing the defect. This minimizes troubleshooting time, improves machine uptime, and reduces scrap.
“Our machine uses multiple cameras, so we can look all the way around a bottle closure and make sure that the closure is on correctly,” Coy says.
Atlas Copco Compressors has a strong history in compressed air, and innovation in that area will always be a strong focus, says Paul Humphreys, vice president of communications and branding. But at PACK EXPO International, the supplier was debuting some capabilities beyond compressors, demonstrating innovations in process filtration and chillers (30). “We’re getting away from the compressor room and going more downstream,” he says.
The process filtration range—focused on liquid, steam, and air—extends Atlas Copco’s filter product portfolio into multiple industries, including food and beverage, microelectronics, pharmaceutical, cosmetics, and chemical. The filter range, which exceeds ISO 8573-1 Class 0 requirements, is
designed to prevent microbial contamination and protect the quality of the final product. All components meet the EU and U.S. requirements for food contact use in accordance with FDA CFR Title 21 and with EU Regulation No. 1935/2004 and its subsequent amendments.
The range includes bags, filters, and cartridges. The complete cartridge range comprises unit construction from
Realize your vision with Festo’s approach to smart automation for food processing and packaging. Partner with Festo today.
melt blown fiber and pleated fiber for particle removal, and pleated membrane for bioburden reduction. The cartridge range includes powder sintered filters for steam and gases as well as pleated filters for high-temperature and corrosive liquid applications. Carbon powder sintered filters and carbon rolled felt filters are also available for chlorine, odor, and color removal processes. The product range is completed with polypropylene, polyester, and nylon bag filters.
Many of Atlas Copco’s latest innovations come from recent acquisitions, and its TCX 4-90A Process Cooling Chiller range is one such example. Atlas Copco entered the industrial cooling market with its acquisition of Italian supplier Eurochiller.
The TCX range features a compact, all-in-one water chiller with an air-cooled condenser and integrated hydro module, with units available in a variety of sizes. The chillers are specifically designed to cool water (or a mixture of water and glycol) for a wide range of industrial segments. The TCX range’s state-of-the-art microchannel condensers require 30% less refrigerant, making the units more environmentally friendly while lowering potential maintenance charges.
The process chillers feature a touchscreen controller, the Elektronikon Mk5 Touch controller. Smartlink 24/7 monitoring is also available as part of the chiller’s total package. This enables Atlas Copco not only to log in to help maintain and troubleshoot the equipment, but also to trend performance over time.
CIP 2.0 is designed for food, dairy, and beverage plants. Our systems are designed to be scalable to meet your needs today and in the future.
CIP 2.0 incorporates smart machine technology to enhance performance, flexibility, and reporting.
Based on the Rockwell Automation ® control platform, CIP 2.0 controls cycles using process parameters.
• Built-in predictive and preventative maintenance program with valve cycle count and pump runtime analysis.
• One to four tank configurations with single or dual supply.
• Process parameters deliver a more accurate and repeatable process than a time-based approach, and enables users to manage chemical, water, and other resource consumption.
• Allows authorized in-house users to make and track all changes.
• Automated record-keeping verification occurs after each cycle, designed to comply with regulatory standards CFR21 and S88.
Many times at a PACK EXPO booth it’s the display case that best reflects recent innovations an exhibitor has successfully brought to the marketplace. This was certainly the case at Berry Global. Two we’ve already reported on, a lightweight Mars candy container using PCR (pfwgo.to/7822), and a 100% rPET food color bottle by McCormick (pfwgo.to/7823).
But three other notable items not familiar to our editorial team were also on display:
• Tchibo co ee capsules—A partnership among Berry Global, its customer Tchibo, and its feedstock supplier Neste has resulted in a potentially game-changing development in the co ee capsule market with the introduction of a thermoformed PP capsule made partly from renewable sources ( 1). Rather than virgin PP that is made from non-renewable fossil fuel sources, the polymers used for the Tchibo capsules are sourced from renewable raw materials such as residue cooking oils and fats. A lifecycle assessment by the Technical University of Berlin, carried out in compliance with ISO 14040/44, has shown that the conversion of the Qbo capsule material results in about 35% fewer CO2 emissions compared to materials more commonly used today.
“We are pleased to o er Qbo capsules made of PP, now produced from 70% renewable raw materials,” says Marius-Konstantin Wiche, development manager, capsule and innovation at Hamburg, Germany-based Tchibo. “This makes the entire Qbo range—containing sustainably grown Qbo co ee brewed in Qbo machines—one of the most sustainable capsule systems on the market.”
The renewable materials are supplied via an approach certified by the International Sustainability & Carbon (ISCC PLUS) system. This certification makes it possible to articulate on the
packaging the proportion of renewable raw materials used to make the package. So the certification provides full traceability throughout the supply chain, from raw materials to finished co ee capsule, as well as sustainability validation of the raw materials. Just as important, the new capsules provide an identical performance and consumer experience. Plus the renewable feedstock can be easily introduced into existing production lines with no changes required.
“We needed to ensure that the high quality and great taste of the Qbo co ee would not be a ected,” says Wiche. “That’s why we focused on replacing the raw materials for the capsules, not the PP itself. The renewable materials go into producing PP polymers with the same quality as virgin PP; you won’t see or taste any di erence.”
Berry says it combined its sustainability leadership in the selection of the right qualified raw materials with its technical skills for the e cient manufacture of the capsules to accelerate the conversion to this more sustainable, circular solution. The company’s expertise in design for circularity allows for multiple potential solutions to be developed for the future manufacture of co ee capsules, thanks to its ISCC PLUS certified site in Bremervörde, Germany. The ISCC PLUS certification not only ensured that food contact approval was granted for the new materials, it also allows for the quick transition to additional applications over time.
“We chose Berry for this project as they have experience with our product and hold the required ISCC PLUS certification to produce the capsules from renewable materials,” says Wiche. “The company’s knowledge of extrusion and thermoforming for our capsules is excellent, and we also appreciate their in-house engineering and machining of related parts for our products.”
FLEX-TURN® CONVEYORS
Theh The hygienic way to convey around corners
LADDER-FLEX® CONVEYORS
Theh The hygienic way to spread, converge, diverge
STRAIGHT CONVEYORS
Desig Designed for your application
• 8NRUQNᠴJI\FXMYMWTZLMHTSXYWZHYNTS
• 4UJSXJHYNTSQJLKWFRJX
• (QJFSNSUQFHJ
• *FX^YTXFSNYN_JHQJFSFSIRFNSYFNS
• -NLMIJSXNY^GQZJUQFXYNHHTRUTSJSYX
• 3TUQFHJKTWGFHYJWNFFSIFQQJWLJSXYTMNIJ
For Berry, the introduction of the new capsules supports its recently announced commitment to achieve 30% circular plastics use across its fast-moving consumer goods packaging by 2030 as the company envisions decoupling from virgin plastic and fossil fuels in the long term.
“Supporting our customers’ growing sustainability commitments is a key priority as we plan for the future needs of a net-zero, circular economy,” says Jean-Marc Galvez, president of Berry’s Consumer Packaging International Division. “Delivering the infrastructure and manufacturing capabilities to design products for circularity is one of our core competencies. I am incredibly proud of this partnership and its commitment to demonstrate the potential of renewable raw materials to lower the environmental impact of capsules.”
“Together,” says Wiche, “our Tchibo/Neste/Berry team has created a fantastic result. The Qbo co ee still maintains its premium quality, but now in a capsule produced with less CO2 emissions.”
• Tesco/Heinz/Berry project—Berry Global is collaborating in a first-of-its kind project launched by Heinz and Tesco in the UK to permit the chemical recycling of flexible film packaging dropped o by customers at Tesco’s in-store collection points. Also on the team are recycling technology experts Plastic Energy and SABIC , and together the team has launched a pioneering trial with the development of new Heinz Beanz Snap Pots (2) that incorporate 39% ISCC PLUS-certified recycled flexible film.
According to Berry, the flexible films collected in Tesco’s stores are taken to Plastic Energy and physically segregated for conversion by pyrolysis— the thermal decomposition of materials at elevated temperatures in the absence of oxygen—into an
optimal oil feedstock. This feedstock, which Plastic Energy calls Tacoil, is combined with virgin material by SABIC to produce an alternative feedstock for making food-contact-approved plastic pellets. These pellets are sent to an ISCC-certified Berry Global site and combined in a coextrusion of PP/ EVOH/White Masterbatch/PP-based adhesive. Then comes thermoforming, also by Berry. After Heinz fills and lids the pots, they undergo thermal treatment at 121°C for about 30 minutes to render them shelf stable at ambient temperatures.
“This is a prime example of an innovative advancement in circular packaging design made possible by collaboration across the entire value chain,” says Berry’s Galvez. “This approach helps capture and reuse plastics that currently go unrecycled, to keep materials in use and out of our oceans and landfills.”
The 50/50 joint venture between London-based Plastic Energy and Saudi-based SABIC is fascinating, to say the least. It’s called SPEAR (SABIC Plastic Energy Advanced Recycling), and it’s being executed with a Top Sector Energy Subsidy from the Ministry of Economic A airs in the Netherlands. That country, specifically the town of Geleen, is also the site of the new production facility. SABIC and Plastic Energy have worked together with leading customers and converters to produce and commercialize certified circular polymers since early 2019. But with the Geleen facility in commercial operation, SABIC can significantly upscale the production of certified circular polymers to provide customers with greater access to sustainable materials that have been recycled, repurposed, and produced in a way that can provide a drop-in solution that helps protect the planet’s natural resources.
“Advancements in this pioneering project take us one step closer to driving the change needed to become a circular global industry,” says Fahad Al Swailem, vice president, PE and sales at SABIC.
“We have overcome significant external, global challenges to reach this important milestone and remain fully committed to closing the loop on used plastic. We are continuing to collaborate on an unprecedented level with our partners upstream and downstream to achieve this.”
“It has been an exciting journey in making our vision of building advanced recycling plants come to life,” says Carlos Monreal, founder and CEO of Plastic Energy. “We have worked jointly with SABIC towards our common goal of making plastics more sustainable and moving towards a more circular economy for plastics.”
The 39% recycled plastic that the new snap pots contain was validated using an approach endorsed by ISCC. This makes it possible to track the amount
and sustainability characteristics of materials used in the manufacturing process. The recycled material meets the requirements of food-contact safety regulations and provides a replacement for virgin PP in the thin-wall pack with no compromise on processability or mechanical performance.
“We want our Snap Pots to be more sustainable while retaining the features that make them so popular with consumers: their convenience, handy snappable format, microwavability, and ensuring the product remains fresh,” says Héloïse Carlier, senior packaging development technologist at Heinz. “With this project and our introduction of the new Heinz Beanz Snap Pots, 22 tons of [flexible film] will be recycled.”
To date, flexible film packaging has been notoriously di cult to recycle. Until 2020, just 6% of the material was being recycled in the UK. It is hoped this venture will inspire the wider industry to take action in tackling this issue, both in the UK and other countries across Europe.
“We’re proud to have teamed up with leading experts to bring this important innovation to our customers,” says Jojo de Noronha, Heinz’s president Northern Europe. “Our hope is that this prompts an industry-wide look at what more can be done to address the lack of [flexible film] being recycled in the UK, and we can, as a collective, get better when it comes to developing new packaging solutions that are good for both our consumers and for our planet.”
• Technology Award Winner—Also newsworthy is that Berry Global’s Proxima tethered closure (3) with tamper-evident band was named a winner of a PACK EXPO Technology Excellence Award in Sustainability from PMMI.
The Proxima tethered closure enhances opportunities for reducing litter and increasing recyclability of the closure, while still o ering consumers a convenient and comfortable drinking experience
Zeppelin Systems is the Market leader in design, and supply of automated ingredients handling systems around the globe. We are well known for our innovations such as pre-hydration with DymoMix and continuous mixing with Codos for bakeries and other food plants. We provide engineered and turn-key solutions customized to the speci c needs of our clients, with an emphasis on the integration of these systems into the rest of the client’s enterprise as a Rockwell GOLD LEVEL System Integration Partner with decades of full integration experience. Additionally, we provide a highly skilled technical service network, a variety of after-sales services, and comprehensive spare parts support.
PLANTS WE SERVE: Fresh Baked Goods | Extended Shelf Life Baked Goods | Biscuits | Cereals Starch |
To learn more about us and our engineering solutions, please visit us at www.zeppelin-systems.us
Zeppelin Systems USA, Inc.
(Food Processing Plants Division)
13330 Byrd Drive
Odessa, FL 33556
Phone:813-920-7434
info@zeppelin-systems.us
for cold fill and aseptic applications, including still water and functional drinks. The design of the injection-molded PP closure features a special tamper-evident band that, once broken, does not a ect the closure’s ability to remain attached. When opened for drinking or pouring, the closure is positioned at a wide angle, adjacent to the neck of the bottle, thus ensuring the bottle can be easily reclosed for consumer convenience.
This solution provides two important sustainability benefits. Because the closure is designed to remain intact with the bottle, it is less likely to be thrown away or littered. This can greatly reduce the possibility of the closure leaking into the environment. Equally important, keeping the closure on the bottle decreases the danger of littering and unnecessary plastic waste when closures are carelessly or thoughtlessly discarded.
Proxima is available in 29- and 38-mm diameters to fit various neck finishes. In addition to its user-friendly features, the closure can be specified in a variety of colors to help individualize product branding and maximize on-shelf appeal. Proxima meets current legislation on single-use plastics including the EU Directive 2019/204, which requires plastic beverage bottles up to 3 L in size to have closures that remain attached to the container throughout its intended use from 2024 onwards.
ClipCombo was big news at the PACK EXPO International booth of Graphic Packaging International An innovation that combines multiple packaging solutions over a modular machinery system, it was selected as one of four PACK EXPO International Technology Excellence Awards by PMMI.
This new machinery approach to beverage packaging comes in two flavors, one for cans and one for PET bottles. ClipCombo for cans runs EnviroClip, which is essentially a flat piece of paperboard that e ciently holds cans together. But the same machine can also run KeelClip (4), which is positioned as more of a premium option because it folds over the top and has more room for graphics—not to mention the fact that cans can be oriented to maximize branding opportunities. A third option that can also be run on this machine is GripClip, which is similar to KeelClip except that it doesn’t include the center keel, which means it brings savings in paperboard cost.
ClipCombo for PET bottles runs EnviroClip or Cap-It (5). Designed for PET bottles with neck rings, Cap-It provides an on-the-shelf di erentiation from other multipacks by combining both a beautifully printable paperboard billboard while still allowing a portion of the bottles to be visible. Like other options in GPI’s clip portfolio, Cap-It is designed to maintain its pack integrity through the supply chain while also providing a comfortable consumer experience.
Boasting high speeds of up to 400 packs per minute (depending on application) and rapid changeovers as part of an impressive list of benefits, ClipCombo enables customers to di erentiate between brands and position premium or standard options—all on one machine. Worth noting is that GPI also supplies the paperboard material for its various paperboard carrier o erings.
“We know many of our customers take their sustainability goals seriously, as do we,” says Doug Hicks, vice president of the packaging machinery division at Graphic Packaging. “We also know that markets change and there is a need to future-proof machine system choices. That’s why we’re delighted to reveal the ClipCombo concept, a game-changing machinery philosophy that enables customers to select from a wide range of existing and new packaging options as well as container and configuration choices. Packers can combine products over a single
3D smart sensors provide an automated, non-destructive, and cost-e ective way to meet strict production, quality, and safety standards in the food industry. This inspection approach leverages 2D and 3D image analysis and data processing across a wide variety of applications to achieve 100% quality control and material optimization.
Quick system setup, intuitive web browser user interface, multi-sensor networking capability, and built-in measurement tools make inspection easy and e cient.
machinery system, and be confident they have the options needed as the market evolves.”
GPI is by no means the only company on the supply side of the packaging arena working diligently on paper-based substitutes for plastic ring carriers, and PACK EXPO International was a great place to catch up on at least three others:
• Krones o ers equipment for the standard LitePac Top, a flat piece of paperboard that holds cans together. But it also has equipment for LitePac Top Promo Skirt (6) should customers want more room for graphics and branding. Also part of the portfolio is equipment for LitePac Top for bottles where a paperboard strap or “banderole” provides additional holding properties ( 7 ). Krones in its approach to these novel packaging concepts stays focused on mechanical machine engineering and partners with a number of paperboard packaging material suppliers.
• KHS o ers a variety of paperboard can “toppers” that can be applied by its Innopack Kisters CNP (Carton Nature Packer) systems, including both a GreenClip option, which is a standard flat piece of paperboard that holds cans together,
as well as the more premium-level TopClip (8) for more graphics and branding opportunities. Even more recently, KHS has introduced a paper wrapping concept that replaces plastic shrink film with paper (9). Like Krones, KHS focuses on the machinery side of the equation and partners with packaging machinery suppliers.
• Westrock ’s CanCollar family of sustainable beverage packaging solutions ( 10) comprises six options. Like GPI, Westrock takes the “razor and the razor blade” approach in going to market, as users of CanCollar technology purchase the paperboard from Westrock. In the center is CanCollar Classic. Left to right are CanCollar Shield, CanCollar Shield Plus, CanCollar EcoPlus, PremCollar, and CanCollar X. Most impressively, the CanCollar Fortuna machine featured at Westrock’s PACK EXPO booth is capable of producing five of the six members of the CanCollar family. This capability is due in large part to the machine’s use of the ACOPOStrak linear drive system from B&R
a video of Westrock’s CanCollar Fortuna at pfwgo.to/7824 .
For over 50 years, we've pioneered the design and production of industrial refrigeration products, systems and controls. Now, we're leading the way with natural refrigerant-based packaged systems that are safe, sustainable, and energy efficient in all climates.
Packaged Systems
• Low charge ammonia packaged chillers from 40–400 tons at 5ºF to 50ºF outlet fluid
• Low charge ammonia condensing units from 30–160 tons at -20ºF to 45ºF SST
• Packaged cascade ammonia/CO2 Systems from 40–200 tons at -20ºF to -60ºF pumped CO
Packaged Systems
• Transcritical CO2 industrial chillers from 50–500 tons at -40ºF to 40ºF outlet fluid
• Transcritical CO2 condensing units from 10–85 tons at -40ºF to 40ºF SST
• Transcritical CO2 industrial racks from 50–400 tons at 40ºF to -50ºF SST or 50ºF to -40ºF fluid temperature
Recycle-ready with no compromise on performance was a prominent theme at the Amcor booth, as Amcor Flexibles introduced a range of AmPrima PE Plus applications (11). A portfolio of more sustainable choices, AmPrima employs a variety of technologies that deliver the sti ness, clarity, graphics, and machineability that match the performance of current nonrecyclable alternatives. Especially impressive were these:
• Beverage, puree, and sauce pouches—These pouches require moisture and oxygen barriers to preserve the contents inside, as well as highly durable hermetic seals along pack edges and around opening spout fitments. Previously, only mixed-material film structures have delivered such performance characteristics, structures that are di cult to recycle. But now Amcor o ers an innovative and recycle-ready high-barrier flexible film providing superior heat-resistance, a custom-engineered sealed layer for improved hermeticity and leak prevention, and puncture and scu -resistance for durability throughout distribution. Amcor describes it as the first high-barrier, high-speed, heat-resistant, recycle-ready solution for beverage, puree, and sauce spouted pouches.
• Shredded cheese pouches—Capable of running at high speed and o ering all the heat-resistant properties needed, AmPrima PE Plus film for shredded cheese o ers high barrier and is compatible with recycle-ready zipper solutions. Its environmental benefits have been calculated by ASSET, Amcor’s unique Carbon Trust-certified Life Cycle Assessment service, and the results are impressive. Compared to a current market o ering such as 48-ga OPET/
•Robotic Palletizers
•Integrated Bagging Lines
•Collaborative Robots
Let’s talk about your project today!
For over 60 years LPS® has earned a reputation for both quality and performance in critical industrial applications. LPS® DETEX® combines that expertise with food safety programs to produce a full line of maintenance solutions specifically formulated for food processing facilities.
LPS® DETEX® lubricants, penetrants, electronic cleaners, and greases save time and money by extending equipment life, reducing repair time, and lowering frequency of preventative maintenance.
Plastic components used to package LPS® DETEX® products are both metal & X-ray detectable, helping to reduce the risk of foreign object contamination within your facility.
DETECTABLE EET C
PE/EVOH-PE/mLLDPE, AmPrima Plus film, when recycled, delivers a 75% reduction in non-renewable energy use, a 58% reduction in carbon footprint, and a 54% reduction in water consumption.
Also on the innovation front, Amcor Rigid Packaging introduced its DairySeal line of packaging ( 12) that features ClearCor, an advancement in oxygen barrier technology for PET bottles. The new
barrier technology, says the company, has “higher levels of concentration encapsulation in the center of the preform, allowing less barrier to be used while being more e ective.” This allows for more PCR in use, longer empty bottle shelf life, and improved design options for the fluid dairy segment. The technology has a positive impact on the overall performance of the barrier and maintains recyclablilty.
“PET is the most recycled plastic in the world, with more than 1.8 billion lb of used PET bottles and containers recovered in the U.S. each year alone,” notes Greg Rosati, Amcor Rigid Packaging vice president of marketing and strategy for specialty containers.
“With the development of our DairySeal line, we are able to o er PET packaging that helps improve sustainability for brands in the dairy alternatives, nutritional drinks, and ready-to-drink co ee space.”
Rolling out at PACK EXPO International this year was TC Transcontinental’s vieVERTe recycle-ready PCR flexible packaging material, which comes in two variations: one with 38% PCR, and the other with 50% PCR. Rebecca Casey, senior vice president of marketing and strategy at TC Transcon-
Xtreme® MetalDetectorconveyorsystems Metal Detector conveyor systems withfullyautomatedrejectdevicesenabl with fully automated reject devices enable continuousproductionwithnobeltstoppage. continuous production with no belt stoppage.
•AirBlastorPushArmrejectdevices
• Air Blast or Push Arm reject devices
•Easy-to-usetouchscreeninterface
• Easy-to-use touchscreen interface
•6”,12”and18”beltsizes
• 6”, 12” and 18” belt sizes
• Numerous options available
•Numerousoptionsavailable
•Customsystems
• Custom systems with fast shipping available withfastshippingavailable
We understand how you strive for constant product quality and optimized costs.
You are poised to meet your safety and quality requirements while optimizing resources and securing process repeatability.
•Highly accurate fluid density measurement and concentration determination for use as a final product quality indicator
•Exceptional density measurement performance under real-world process conditions
•Ideal for fluids with entrained gas thanks to the patented Multi Frequency Technology (MFT)
•Widest usable flow range on the market thanks to lowest pressure drop
tinental, says vieVERTe is aimed at the home and personal care market, but is also ideal for the evolving pet food market (13).
“Pretty much the whole premium pet food side of the business revolves around having recyclable packaging,” says Casey. “That’s driven by consumers. And when we look at back at 2018, when China decided they didn’t want to take our plastic waste anymore, it became more evident to consumers that, as a country, we weren’t really recycling our materials. And I think they’ve become more educated. When we talk about only 9% of plastic is recycled in the U.S., consumers know they put more than 9% of plastic in their recycle bins. So they’re putting a bit more pressure on the consumer product companies, and a lot of consumer product companies are saying we need to do the right thing for our planet.”
Debuting at PACK EXPO was a first-of-its kind flexible pouch from Printpack, the Preserve PE Advanced Recycled Content Polyethylene Pouch (14) that is not only recyclable after use, but also contains 30% post-consumer recycled material obtained through advanced recycling technologies. The pouch is the result of a partnership between Printpack, Pregis, and ExxonMobil, where Print-
Vibratory infeed conveyor
Powder & liquid application
Loss-in-weight feedback system
Removable plastic tumbling drum
Onboard controls w/ touchscreen HMI
&HQWUDOL]H\RXUYDFXXPVXSSO\ ZLWKWKHOHDGHULQYDFXXP
SDFNDJLQJ
8372
(1(5*<
Ȏ0D[LPL]H\RXURXWSXWZLWKOHVVLQSXW
• Easier and faster maintenance
Ȏ,PSURYHGZRUNLQJHQYLURQPHQW
/RRNLQJWRVDYHHQHUJ\DQGPRQH\"2XUH[SHUWVFDQKHOS\RXXQORFNXSWR VDYLQJVZLWKDFHQWUDOYDFXXPV\VWHPFrom there, we’ll work together to identify DGGLWLRQDOEHQHↅWVWDLORUHGVSHFLↅFDOO\IRU\RXUQHHGV/HWXVVKRZ\RXKRZ
6FDQ45&RGHIRUPRUHLQIRUPDWLRQ
pack’s machine direction-oriented PE print film is used in combination with Pregis Performance Flexibles Renew Series sealant film made with ExxonMobil Exxtend advanced recycling resin technology.
Preserve PE Advanced Recycled Content is the latest addition to Printpack ’s Preserve sustainable packaging platform. “This encompasses a portfolio of eco-friendly structures that use renewable and post-consumer recycled content, as well as maximizing design opportunities for greenhouse gas and source reduction and an optimal end-of-life condition,” explains Bill Barlow, sustainable innovations manager for Printpack. “The Preserve Recyclable PE packaging solutions o er many of the benefits of current flexible packaging, including ease of transport, product-to-package weight ratio, and reduction of carbon footprint, as well as several barrier options.”
The Preserve Recyclable PE line meets brand owners’ growing desire for mono-material flexible packaging that can be recycled via store drop-o . As Barlow shares, this past year, Printpack was part of the largest store drop-o recyclable PE launch for the snack bar market in collaboration with General Mills and the Nature Valley brand.
While there are quite a few options available today for flexible films that can be recycled through store drop-o , more of a challenge has been to
Looking for information on how to get started with sustainable packaging? This Packaging
World primer provides an overview on what sustainable packaging is, what’s driving the push for more sustainable packaging, and how to reduce the environmental impact of packaging. It also includes links to resources. Download this free PDF today at pfwgo.to/7345 .
the es. Download today
provide brands with film that contains recycled content—especially for food applications—given the limitations of mechanical recycling and FDA guidelines for food contact.
“We actually have been successful with mechanically recycled PCR content within a finished package up to about 30% recycled content. However, there are limitations due to the grades available in the market—with FDA no objection letters—and also due to performance issues with the addition of high levels of mechanically recycled content,” says Barlow. “Additionally, there are still some aesthetic issues with mechanical PCR such as gels, degraded material, fibers, and other contaminants; these are di cult to mask in a flexible package.”
Using resins made from an advanced recycling process completely eliminates these issues, as the resins from the process are identical to those made with virgin plastics. In addition, Barlow notes that with advanced recycling technology, the potential to create a flexible film pack with greater than 90% PCR has become a reality.
ExxonMobil’s Exxtend advanced recycling technology breaks down plastic waste to its molecular building blocks while removing contaminants. These are the molecular building blocks that form the raw materials for making its products, which are identical to those made from virgin fossil feedstocks.
According to Barlow, ExxonMobil approached Printpack in August 2022 regarding the project, which the company welcomed without hesitation.
“We view both Pregis and ExxonMobil as strategic partners of polyethylene resin and film in the flexible packaging market, and we were looking for an opportunity to collaborate with companies like this that share a similar sustainability vision to ours.”
Exxtend circular polymers are certified according to the ISCC PLUS program. The resin can be o ered in an array of PE grades, which Barlow says is attractive for Printpack and Pregis, as it allows them to develop flexible packaging films to meet the same performance requirements as conventional packaging structures.
Pregis’ sealant film contains 45% advanced recycled content. When laminated to Printpack’s PE film, the overall pouch structure contains 30% recycled content. The resulting structure also is prequalified for the How2Recycle store drop-o label and meets the Association of Plastic Recyclers (APR) Design Guidelines for Flexible Packaging.
Product is limited as these companies work to scale up production. Barlow says Printpack hopes to have a major brand on board soon to commercialize the new film and help build volume.
Leading-edge technology trusted worldwide for superior product inspection and contaminant detection.
Your brand is on the line, so you need equipment that’s better than good. Anritsu systems deliver performance, reliability and low total cost of ownership.Plus, we back our long-lasting equipment with unparalleled service and support.
Discover what you’ve been missing. Learn how to advance your product quality and operational efficiency at anritsu.com/infivis.
M6 METAL DETECTOR XR75 X-RAY SSV CHECKWEIGHERAn exampleof increased packaging automation muscle in the fulfillment center and e-commerce space came from ABB, which debuted its new Robotic Item Picker (1) at the show. The Item Picker helps customers automate order picking and sorter induction operations, and it fulfills ABB’s vision of a fully automated warehouse by combining automated storage with automated order picking, the company says.
“This is a fantastic new application that we’re unveiling here at PACK EXPO,” says Ali Raja, global marketing and sales director for ABB. “It’s powered by ABB’s own AI software, some of the latest techniques in machine vision and, of course, our famous robot planning. All of that in combination allows us to be the fastest item picker on the market. We’re achieving peak throughput of 1,500 picks per hour.”
Target customers include system integrators serving e-commerce, logistics, healthcare, and CPG. It also takes aim at end-user customers in 3PL, e-commerce, and fulfillment centers, all to serve common applications such as order picking, replenishment, receipt picking, and fashion sorting.
Raja says the Robotic Item Picker provides high picking quality of 99%+, meaning no double picks and no dropped items. He says it also o ers ease of use and it’s easy to integrate. Plus, it has easy-to-operate application control configuration and parametrization for integrators and sophisticated, yet intuitive controls for end users. He also claims best-in-class price/performance ratio. a related video at pfwgo.to/7831 .
The result of a decade of R&D, the Bastian Solutions SmartPick fuses a warehouse execution system with a six-axis robot, machine vision, and advanced artificial intelligence (AI) to create an autonomous product picking system (2).
This advancement in robotic order fulfillment o ers customers faster, more accurate orders while answering the need for a more reliable solution that can grow alongside operations—turning a goodsto-person (GTP) system into an e cient goods-torobot (GTR) system.
Bastian Solutions presented its first vision-driven bin-picking robot back in 2010. It relied on a pretrained vision platform, transporting products from one stationary bin to another. The company has improved on those capabilities considerably since then, and can now pick a complex assortment of products from the back end of a GTP system with 99% accuracy.
“The key to the SmartPick is the autonomy—the ability to route orders through our warehouse execution system down to the robot autonomously with pickable products for the robot to handle,” says Steven Hogg, applications engineering manager for Bastian Solutions. “We also have an AI-based vision system that has deep machine learning to where we can learn on the fly—we don’t have to pre-program any of the images in, and the vision system continuously improves as it picks.” At the heart of the system is a robotic piece-picking sys-
tem with custom-designed end-of-arm tools that can adapt to a wide variety of product shapes, sizes, and surfaces, he adds.
The system integrates seamlessly with Bastian’s ML2 autonomous mobile robot (AMR). “It is designed to be autonomously routed throughout the warehouse facility or throughout the manufacturing facility to deliver products to various manufacturing lines or also order fulfillment,” Hogg says. “It can have a static stand on top of the AMR or a conveyor to route totes between the various production lines.”
The AI and physical systems integrate with Exacta, the company’s proprietary intralogistics software, to enable the cells to run with higher autonomy. “This is what is driving the orders being brought down to the autoserve port,” Hogg says. “This right here is showing the bin that’s being delivered to the workstation. The robot is working in the background to start and stop the cell. We go to the individual bin and are picking pieces out and are placing to the AMR ML2.”
SmartPick is a turnkey GTR fulfillment system that increases picking throughput, adjusts to labor availability, reduces picking errors, allows for 24/7 automated operations, and improves customer satisfaction.
a video of the system in action at pfwgo.to/7832
In a trend toward food processors designating less space for their palletizing operations, EnSight Solutions has developed a fenceless robotic palletizer (3) that gets the job done in a footprint of just 12 x 5 ft. The system combines Sick safety sensors with a Stäubli collaborative robot (cobot) to eliminate the need for fencing.
“With our area scanners, as the robot moves, you have a warning area where the light will turn yellow. It’ll move the robot very slowly,” explains Heath Clifton, director of automation and controls for EnSight Solutions. “As you walk in closer, you’ll get a red area, which is a safety stop for the robot.
As you move back out of the area, it’ll slowly start speeding up. And then once you get into the green area, it’ll move back to its full speed.”
Unlike standard robots, the payloads that cobots can handle tend to be smaller. The Staübli cobot, however, enables larger payloads. “The thing that di erentiates our cobot palletizer from others is it can lift up to 75 lb,” Clifton says. “If we’re doing a single pick, we can pick up to 18 boxes a minute. But with a 75-lb weight limit, we can pick up multiple boxes at a time to hit a higher rate.”
Stäubli also has cobot options with hygiene standards suitable for food processing areas. “One of the great options about our palletizer is that it’s a full stainless-steel design,” Clifton says. “We’re using a Stäubli robot, so it’s a full washdown robot as well. It’s a great application for the food industry. You can put it in a full washdown room if you’re palletizing in there, or a secondary pack application that’s wipe-down.”
a video of the system in action at pfwgo.to/7833 .
Artificial intelligence (AI) applications have been growing rapidly in a variety of industrial technologies, ranging from data analytics and quality inspections to autonomous mobile robots. Now the technology is being applied to robotic grasping applications to enable accurate picking and placing of random objects in unstructured and changing environments.
Siemens says it is working to democratize AI-enabled robotics by encapsulating systems for complex problems in easy-to-use software. To this end, the company is developing an as-yet-to-benamed software technology designed for use by system integrators and OEMs to create cost-effective, advanced AI-driven piece-picking systems that can “reliably pick and place objects that are unknown to the system at runtime.”
Traditional automated pick-and-place systems follow fixed, pre-programmed routines in a structured environment. Applying AI enables robotics to perform generic tasks in unstructured and dynamically changing environments.
Explaining how the technology Siemens is developing di ers from the use of 3D vision to enable robots to pick and place random objects, Eugen Solowjow, head of the Robotics & AI Research Group at Siemens, says, “Picking and placing unknown objects is still relatively new. It has existed for, at most, two years in the market and, up until now, has not been very commonly distributed. These existing systems rely on AI—more precisely,
Eliminate lumps, clumps and fish eyes; wasted ingredients; and clogged filters. Fristam’s FS Series Shear Blender for inline mixing is the perfect solution when existing in-tank mixers are not able to produce the quality mix you need.
Rather than replacing your in-tank system, simply supplement it affordably with an FS Shear Blender. The FS Shear Blender, placed after a mix tank, disperses particles into liquid in just one pass and produces consistent product time after time.
Watch short video at www.fristam.com/fs
•
Deep Neural Network technology—to randomly pick oriented objects that are known to the system during setup and/or engineering.
Thus, the key di erentiator with the developing Siemens technology is its ability to pick unknown objects.
According to Siemens, this new software will enable users to move from using robotic systems with static pick points to AI-driven piece-picking robots in less than an hour. Setup for the system is accomplished in four steps: Set the robot arm and related end-of-arm tooling to move safely to static pick-and-place points; mount the 3D camera; install the Siemens software for piece picking on the target runtime hardware of choice; and follow the guided setup via the user interface for calibration.
With these steps implemented, calculated pick points are then continuously provided to the robot motion program, enabling the robot to grasp any object. “The setup takes only 30 minutes through an easy and straightforward calibration process,” Solowjow says. “The user interface is very simple and clear.”
Target applications for this technology include order fulfillment operations with a high number of
SKUs requiring 500 to 1,200 picks per hour, such as goods-to-person tote picking, conveyor induction and sortation in e-commerce, e-grocery warehouse automation, and food and beverage packaging.
Inputs to the Siemens pre-trained, AI-powered vision software in the PLC come from the 3D camera’s point cloud, with the output being the grasp pose for any object at runtime. A Siemens HMI is used to interface with the PLC and software; and Siemens TIA Portal can be used to program the entire system—Siemens PLC and HMI as well as the robots, vision system, and gripper.
The Siemens AI-driven piece-picking system also provides for collision avoidance for all actions in the robot workspace, enables robots to master challenges such as handling tightly packed boxes using low-cost 3D cameras, and reduces errors through features such as automatic bin detection.
“We pretrain the AI skill for grasping using simulation,” says Solowjow. “Similar to a human, the AI learns how to grasp in general—as opposed to specific objects—so that grasping of unknown or previously unseen objects is possible.”
The Siemens AI picking software is robot and end-of-arm tooling agnostic. In its exhibit at PACK
In 2023, Atlas Copco celebrates our 150th anniversary. From the compressed air and gas team, we want to say a heartfelt ‘thank you’ to all our employees, customers, and suppliers who have been part of our journey. We could not have achieved it without you! As we pass this milestone, our unwavering commitment is to continue to provide innovation which empowers our customers to grow and drive society forward.
EXPO International (4), Siemens used a KUKA Agilus KR3 robot and a Robotiq EPick vacuum gripper to demonstrate the technology.
In a move meant to remove the barriers of automation for small and mid-size manufacturers, robot startup Formic, founded in 2020, is building a robotics-as-a-service business model that democratizes automation to make it more a ordable and accessible.
Buying a robot can be a pricy proposition requiring much more than just the initial hardware investment. After buying, say, a $40,000 robot, the additional cost of integration with other machinery can escalate the total investment to upwards of $200,000. That is cost-prohibitive for many manufacturers.
Having worked in the robot industry for years, Formic co-founder Misa Ilkhechi also recognized that
Sophisticated variety-pack capabilities (5) were on display at the Aagard booth. That’s where a Comau robot powered by Rockwell Automation controls—said to be the first such combination in the packaging space— was picking three di erent items from the movers of a Rockwell iTrack linear servo motor system and placing them in a carrier in the order specified by an operator at the HMI. That HMI, says applications engineering manager Jonas Capistrant, was the Rockwell ASEM 6300 HMI.
A new automation arrow in the Aagard quiver, it permits Aagard to o er more features, including better analytics and the ability to play training videos, while o ering an improved HMI experience all around.
related videos at pfwgo.to/7845 and at pfwgo.to/7847.
manufacturers are struggling to find labor. Formic was created to solve these problems. The company takes over the design and deployment of turnkey robotic systems and charges customers an hourly rate vs. an upfront investment. That means manufacturers pay only for operational output with performance guarantees and unlimited 24/7 service.
“We are a fi nancing meets service meets robotics company,” Ilkhechi says. “Our business has to have all three working well because at the end of the day the customer is not buying a machine or components, they are buying productivity.”
Charging an hourly rate for a robot is just like hiring a person, but with the built-in guarantee that the machine will run. Each machine Formic supplies includes an edge device that sends machine data back to the Formic service team, who proactively solve problems before downtime occurs. This is important for the customer and important for Formic. “In order for us to make money, our machine has to work,” Ilkhechi says.
The company partners with robot suppliers and machine builders to build custom turnkey systems. The plan is to have a large portfolio of robots, with the first being the SL20 Palletizer (6) launched at PACK EXPO.
The SL20 Palletizer, designed for end-of-line
Paxton’s high HɝFLHQF\EORZHUV
DQGDLUGHOLYHU\GHYLFHV LPSURYHGU\LQJRIFDQV
DQGERWWOHVIRUKLJK TXDOLW\ODEHOLQJDQG
FRGLQJZKLOHXVLQJ ȂOHVVHQHUJ\
W\SLFDOO\JLYLQJD RQH\HDU52Ζ
packaging processes, palletizes up to 20 cases/min in a small footprint (10 by 12 ft). Built by Sourcelink Solutions, based around the Yaskawa HC Series collaborative robot, it lifts up to 20 kg/cycle.
NO WATER OR COMPRESSED AIR NEEDED
3D[WRQȇV1HZΖRQL]HG
$LU6\VWHPUHSODFHV
ERWKZDWHUULQVLQJDQG
FRPSUHVVHGDLUULQVLQJ
XVLQJOHVVHQHUJ\ DQGQRZDVWHG UHVRXUFHV
DUST AND DEBRIS
BOTTLE AND CAN
More manufacturers are turning to palletizing operations with collaborative robots (cobots), and ONExia is a system integrator that has made it easier for its clients to use cobots as a drop-in replacement for end-of-line workers. With the drag-anddrop software that comes with the PalletizHD collaborative palletizing system (7), anybody can program the cobot easily to achieve the desired palletizing operations.
Tim Pelesky, marketing manager for ONExia, was at PACK EXPO to demonstrate how easy it is to set up the system. Users have complete control of the entire system through the embedded touchscreen on the PalletizHD lifter base. To create a program, a user can touch the screen to select a new pallet configuration, and then add box dimensions (weight, length, width, and height) and pallet dimensions (length and width). “We also o er a box edge gap in the event that you’re worried that your boxes might not be completely uniform or your pallet configuration requires it,” Pelesky says, noting the ability also to create a reference edge. “We also o er the ability to do a dual pick in the event that you want to pick two boxes at one time using the 38-lb payload.”
Paxton’s SRZHUIXODLUGHOLYHU\ UHPRYHVSDUWLFXODWHV
GXVWDQGGHEULV
HɝFLHQWO\DQGH HFWLYHO\
$QGLIVWDWLFFOLQJLVDQ
LVVXH3D[WRQȇVΖRQL]HG
$LU6\VWHPVGLVVLSDWH
WKHVWDWLFWKHQEODVW
WKHGHEULVDZD\
All Paxton Air Systems are custom-engineered to maximize performance and minimize energy usage.
All Paxton Blowers carry a full three year warranty.
Vmeca , a PACK EXPO
International exhibitor based in South Korea that specializes in compressed air driven vacuum pumps, suction cups, and other accessories, introduced its Magic Gripper head (8) at the show. Suitable for attachment to either an industrial robot or a cobot, it has a decentralized vacuum that lets it use as many or as few grippers as an application needs. Suitable for cartons, cases, or flexible packages, it also features a silencing technology that deadens some of the noise traditionally generated in compressed air applications.
a related video at pfwgo.to/7846
Flexible, e cient and safe facilities to deliver the latest food + beverage innovations to your customers.
Once the box and pallet parameters are entered, it’s time to create your pallet configuration. “To get started to create your fi rst layer, press the plus, hit Edit Layer, and your boxes are on the screen ready to go. All you’ve got to do is drag and drop them into place. There’s no programming; nothing like that,” Pelesky says. “Once you’ve completed your entire layer, you’re able to center it left and
20,000+ QFR Pallet Positions Installed and the qfr zone® is still the most efficient blast freezing solution ever! • pallet fit™ door fits any pallet height
reduces labor
works with full, partial, or single layer pallets • no more need for plug pallets, zone can run with one or multiple empty pallet positions • increased airflow
right and up and down to make sure the robot’s going to place a good and tight pallet configuration.”
After the fi rst layer is created, it’s easy to copy and paste it as the next layer or customize each layer di erently.
“The last step in building this pallet is we have to teach certain points because we’re not using any integrated vision,” Pelesky explains. Just two points need to be taught—the nesting position, where the box comes from the infeed conveyor; and the fi rst-place position on one of the pallets.
“You would then come over, hit that button where the position’s taught, and then you’re able to mirror it on the other side,” Pelesky says. “The last step would be to press Save, go back Home, and all of your pallet configurations are there, ready to go, on the fly, and can be adjusted as production changes within the line.”
Users can easily save and recall di erent pallet configurations based on production demands.
a video of the system at pfwgo.to/7842
The PMMI Robots and Cobots Report presents emerging technologies and compiles predicted growth in the years ahead. It examines the predictions made four years ago in the 2019 Robotics Report— which predictions have been fulfilled, and which have yet to materialize. It also explores the key trends underpinning the robotics industry and how those trends are likely to impact deployments and manufacturing strategies into the future. Visit pfwgo.to/7657 to download an executive summary of the report for free.
and we never stop asking ourselves how to do it better.
KAESER compressed air solutions meet and exceed the highest expectations for durability and performance. We continuously improve products based on customer demands for maximum energy efficiency and uptime.
Rely on us to deliver the air you need year after year.
The eXtended Transport System (XTS) was a highlight of the Beckho booth at PACK EXPO International. The unique technology features movers that can move independently or be synchronized in groups for material handling in a variety of applications, such as consumer packaged goods (CPG) packaging applications. The XTS features built-in collision avoidance, and tooling on the XTS movers can be used to open and close bags, cap bottles, or move parts down the line.
“XTS is not just a substitute for lower-cost solutions like chain-driven systems with lugs and buckets, it’s a fundamentally di erent way to approach material handling transport processes,” says Je Johnson, mechatronics product manager at Beckho Automation.
The news at PACK EXPO was that Beckho has updated its XTS ( 1) with its No-Cable Technology (NCT) for contactless, continuous power supply and synchronous real-time data transmission to the XTS movers. To enable this, the XTS modular system has been expanded to include a special motor module and electronics mounted on the mover. With this addition, no further connections or supply lines are required, meaning that processing steps and quality control can be accomplished directly on the mover while a process is running.
“Traditionally, if you wanted to grip something on linear transport systems, you’d have to have two movers mechanically linked to do the gripping,” says Johnson. “Now that we’ve integrated power and data on the movers, you can mount things like vacuum generators on the movers to do vacuum pickup of materials. You can even use mechanical actuators—really any end-of-arm robot tooling can be mounted on the movers to pick and place product.”
A few XTS with NCT application examples include the ability to divide and reunite product flows using mechatronic transfers between two movers; sort products using an integrated pusher on the mover; pick and place products for product sorting using vacuum suction units; and pick up individual products from unsorted and irregular product flows and be able to sort them into good and bad parts or place them correctly for final packaging.
Explaining how XTS with NCT can increase production output, Johnson says with energy being wirelessly transferred to the mover with NCT, this energy is available to realize di erent motion sequences directly on the mover with the help of motors. The system’s CNC-based motion synchronizes positioning of the movers in real time, and the central software approach in TwinCAT allows synchronization with external processing stations. These features enable the movers to become an active part of the manufacturing process as a mobile processing station. For example, the mover can be used to manipulate a product to position a carton or screw on a cap.
With this level of synchronization, process times for feeding and removal at alternative processing stations are eliminated and the product flow no longer need be interrupted. As a result, the e ciency of the machine increases, as does the production output.
Throughput can be increased by adding movers. Each mover can perform multi-axis movements, allowing for product alignment along the X, Y, and Z axes. Additional degrees of freedom can be achieved by rotary movements using TwinCAT to control the interaction of the axes via CNC functions.
High-margin CPG industries like spirits, confectionery, and cosmetics are early adopters of a trend toward heightened personalization, both in what’s placed in packaging by automation and on the packaging itself. In these highly personalized environments, often referred to as “batch size one,” we see packaging applications emerging on the bleeding edge.
One such technology that plays in this space, demonstrated by B&R at PACK EXPO International, is called Acopos 6D (six degrees of freedom) (2).
WIPOTDBlaa`opekӣjlqelkmol_r^qt`ecdekcqd[q_`hes`op mo`^epelk[k_[^^ro[^vekol]rpq[mmhe^[qelkpҼXӣo[vp^[kk`op[k_ sepelkpvpq`jpql`kpro`m[^g[c`ekq`coeqvҿtdeh`j[uejexekcall_ p[a`qv]v`hejek[qekcalo`eck]l_v^lkq[jek[qelkҼS`oe[hex[qelkጃ @ cco`c[qelkplhrqelkqlcr[o_[c[ekpq^lrkq`oa`eqmol_r^qp `kq`oekcqd`chl][hprmmhv^d[ekҼ
`^g `ecd`o HB @
wipotec Ҽ com ጃrp
S`oe[hex[qelkጃ@cco`c[qelk TQSӣBP
In it, magnetic levitating shuttles move individual products freely through the machine environment, potentially carrying products to be packaged. Acopos 6D is ideal for small-batch production with frequent changeover between products of di erent designs and dimensions.
Corey Morton of B&R demonstrated the technology at the show. “What we’re creating here is mixed packages [of di erent dice colors and types, in the demo] that are built to order, so it’s actually batch
three sizes of the EcoStruxure MDC (3), which feature the Stratus ftServer (Fault Tolerant), to highlight their use in CPG and pharma/life sciences applications:
• Small: Stratus ftServer powered by a 1.5 kVA
Smart-UPS in a 6U enclosure
• Medium: Stratus ftServer powered by a 2.2 kVA
Smart-UPS in a single 12U enclosure
• Large: Stratus ftServer powered by a 3 kVA
Smart-UPS in a 42U, NEMA-12 rated enclosure
The di erent size options were presented to highlight the MDCs’ application flexibility in a range of CPG operations. Size can scale up from 6U to 42U depending on how many devices and how much networking equipment need to be embedded in the panel with the ftServer and uninterruptible power supply (UPS).
Key features of the edge ftServer include embedded cybersecurity, no unscheduled downtime with failure prediction capabilities, single button restoration, and remote monitoring ability.
size one production,” he says. “This type of technology gives you no wear, since there’s no rails that it’s riding on. The other thing is it gives you six degrees of freedom of movement.”
Even when only using the X and Y planes in the demonstration at the show, the demo format would allow packagers to collate product, bu er product, and pull product for a specific order from any position within the bu er. The levitating shuttles can also move on other planes, like vertical Z access, tipping on edge, and rotating. That’s why, in a small footprint, this technology could provide packagers a high degree of order customization.
a video of this system in action at pfwgo.to/7862 .
Data centers—which are typically housed in their own separate section of a facility for consolidation of routers, switches, firewalls, storage systems, servers, and application controllers—are a key aspect of enterprise IT. Micro data centers (MDCs) are small, modular versions of data centers used to manage the computing workloads of specific operations. With their ability to be installed nearly anywhere in a facility, MDCs are quickly being recognized for their key role in industry’s IT/operations technology (OT) convergence.
At PACK EXPO International, Stratus Technologies and Schneider Electric showcased
While MDCs are typically designed for IT workloads, Stratus and Schneider Electric note the EcoStruxure Micro Data Center is suitable for OT applications like on-premise automation and control systems in the CPG and pharmaceutical/life sciences industries.
“In e ect, what we are providing customers and partners is a complete o ering—originally meant for IT applications—that can be used for HMI/ SCADA, historians, batch processing, manufacturing execution systems, asset performance management, and cybersecurity solutions,” says Jay David, senior manager for solutions marketing at Stratus.
Integration with existing equipment in a production facility is handled in the same manner as any brownfield project, he adds. “The Micro Data Center can replace any or all of the components
The Krones Process Group North America provides sanitary process system expertise backed by the global depth and experience of KRONES. We understand each
SURGXFWKDVLWVRZQXQLTXHQHHGVDQGZHRↂHUWDLlored solutions from a single source — no matter your location.
FlexLink’s high-performance production flow delivers results. Our solutions for the food and dairy industries are safe and modular with a one-week shorter ramp-up compared to the competition and reduced cleaning time by over 25%. The FlexLink offer, including conveying solutions, handling functions and line control, lowers your total cost of deployment, increasing your overall equipment effectiveness by one percent or more.
For more information call FlexLink on +1 610-973-
associated with the server control panel, such as automation and control software, computers where the software is installed, UPS and power supplies, and networking equipment.”
Because the MDC comes with everything pre-installed and tested, it is easier for non-IT customers to deploy the automation and control systems, says David.
“OEMs can use the MDCs to develop repeatable automation and control systems; system integrators can create solutions that contain standardized code and applications, which they can then drop into a virtual image
The SaniTrend Cloud Lite online process data recording system from sanitary process cleaning systems provider Sani-Matic is a software-as-a-service (SaaS) product (4) that provides automated, secure data acquisition of critical process or cleaning data for any cleaning system, including clean in place (CIP) and clean out of place (COP), in a customer’s facility. SaniTrend Cloud Lite captures continuous process data, while SaniTrend Cloud Lite+ uses running signals from equipment to consolidate the process data into individual reports.
Among the capabilities of SaniTrend Cloud Lite, it provides cloud access to all accessible data, via phone, tablet, or mobile; it allows for unlimited users; it has store and forward capabilities; it provides cloud documentation storage, live dashboard views, and email and SMS notifications; and it delivers analog and digital data trending information, with comments. SaniTrend Cloud Lite+ o ers all of these features, as well as cycle-based reporting, downloadable cycle reports, and cycle-based comments and approvals. Both Lite and Lite+ can handle up to eight analog input signals and up to 12 digital input signals.
Sani-Matic has partnered with Rockwell Automation and PTC to provide its SaniTrend Cloud line, which also includes SaniTrend Cloud and SaniTrend Cloud Pro, through PTC’s Cloud platform, using PTC’s ThingWorx product.
flexlink.com
All of PTC Cloud’s data and user security has been integrated into the SaniTrend Cloud o ering.
a related video at pfwgo.to/7864
FlexLink is part of Coesia, a group of innovation-based industrial solutions companies operating globally headquartered in Bologna, Italy. www.coesia.com
of the ftServer; and end users can use the MDCs to consolidate disparate applications in a single platform,” says Elliott Jepson, strategy and innovation manager for the Secure Power Division at Schneider Electric. “And thin clients can be used with the MDCs to enable monitoring and control outside of the control room via mobile phones, tablets, and laptops.”
Jepson adds that the EcoStruxure MDC with Stratus ftServer comes completely validated, pre-wired, and with the automation and control software pre-loaded. “This way, customers, integrators, and OEMs can focus on their key expertise,” he says. “Because everything is tested and prebuilt, the MDC can be commissioned by controls engineers or technicians who don’t have any IT experience.”
Though it’s been discussed for years, and its capabilities are increasingly being incorporated into automation hardware and software of all types, artificial intelligence (AI) remains a bit of a mystery to many end users. The mystery is not necessarily created by a lack of understanding about AI—it’s the application of the technology that raises many questions, since it can be used for everything from machine control to cloud-based data analytics.
To demonstrate how AI can be used in consumer packaged goods (CPG) production operations, Festo introduced its Festo Automation Experience (AX) at PACK EXPO International (5). By using advanced analytics, Festo AX maps data to learn a component, machine, product, or system’s healthy state and provide information for the correction of anomalies when data begins trending out of the normal range. Festo AX can be operated directly on equipment at the edge of the network, on data center servers for general on-premises applications, or in the cloud.
Festo AX begins with condition monitoring and preventive maintenance calculations for components, machines, and complete systems. Data collected from the factory floor is used to make uptime-based maintenance suggestions, enabling maintenance to be more e cient. From this starting point, the capabilities of
Festo AX can be extended with AI. The AI technology used in Festo AX analyzes live data in real time, meaning that users are made aware as soon as an anomaly occurs.
According to Festo, Festo AX can lower waste by more than 50%, reduce product rejection costs by more than 45%, increase machine availability by more than 25%, and reduce unplanned downtime by more than 20%.
Aerzen offers three blower technologies with reliable process control while requiring low maintenance for yeast and enzyme production.Aerzen Blowers feature:
•Side-by-side Installation to reduce footprint
•Quiet operation for operator safety
•Energy e cient providing cost savings
LET’S TALK about the best blower technology for your yeast and enzyme production process.
www.aerzen.com/en-us
While Festo AX, of course, works with any Festo components, its use of common industry communications and networking technologies such as OPC UA and MQTT means that it can also be integrated with third-party components and machines. For example, linking Festo AX to Festo Smartenance or a third-party maintenance management program can extend Festo AX’s e ectiveness by providing the maintenance department with a tool to help them keep automated equipment performing at optimum energy consumption.
“One of the key strengths of Festo AX is its ability to work with small data sets, meaning that it’s not necessary to have prepared Big Data available,” says Frank Latino, product manager at Festo. “To detect data anomalies, for example, Festo AX relies on unsupervised learning algorithms to fit a use case, such as field maintenance, quality, or energy use applications.”
Festo AX continuously learns about the state of your assets in a process that continuously improves the algorithms.
But these algorithms don’t work in a vacuum. Festo AX keeps the human in the loop by incorporating their feedback into the process to classify anomalies and connect them with recommended courses of action. As a result, the next time the anomaly occurs, the individual receiving the notification will know exactly which system is a ected, what happened, and what to do next.
Festo o ers AX turnkey systems for food and beverage packaging, pneumatic components, welding systems, and machine tools.
The complex operation of packaging lines now finds an essential analysis and data sharing tool to elevate its productivity levels in digitalization. Through solutions like Share2Act, the IIoT cloud-based platform by Krones, it is possible to supervise from any place and in real time the state of a packaging line and its machines, as well as visualizing key performance indicators (KPIs).
“These tools provide a general view in real time of the current states of your machines and allow you to visualize the production process’s most important KPIs,” explains Martin Braun, digitalization sales director at Krones North America.
“Therefore, they can pinpoint exactly those areas with untapped potential so you can continue growing your packaging line’s productivity.”
Considered as a social network for manufacturing plants in the food and beverage industry due to their intuitive and collaborative use, the tools presented during PACK EXPO International guarantee total transparency of production processes and gather critical information needed to timely implement any needed maintenance actions or to correct issues during the operation of a production line.
The traceability o ered by Krones through their new digitalization tools— which are part of the Krones Digital Factory concept—along with the availability of data for operators, managers, and maintenance personnel, extend from beginning to end of a process. “With these new digitalization tools, we can connect every system with each other and provide a complete tracking report. So if, for example, there is a problem with a bottle, its full trajectory can be traced, from the inflow of raw materials to the delivery of finished products at a warehouse,” Braun says.
With Share2Act, you can also generate what Krones calls plant guides, essentially systems dedicated to providing data to operators in real time that provide them with guidance whenever they need to take special actions. Through a cellphone or an app, operators receive precise information about what they need to do, regardless of where they are.
Real-time visualization of a production line’s performance—with diagrams summarizing the information on the state of the machine, its speed, and the number of units being produced, among other indicators—optimizes running times and increases e ciency. It’s a way of guaranteeing the transparency of processes for the operator and generating information that is essential for the decision-making process regarding line transformations or expansions.
The presence of dedicated sensors along the lines with an approach called Action-Based Monitoring gives these new digitalization services by Krones the ability to guarantee a high availability of equipment and machinery in a line. It also
facilitates the assigning of production or maintenance actions to the appropriate area. “Not only are operators using these solutions, we at Krones also use them to o er specific services and recommendations to our clients on how to maintain their equipment e ciency at very high levels,” Braun explains.
video of this digitalization solution at pfwgo.to/7863
Product recalls and new demands from retailers in 2023 are impacting inspection placement in food manufacturing facilities.
ACOMMON SIGHT at the end of most food and beverage processing lines is an inspection system. Depending on the product being produced, these machines can either be X-ray or metal detection, and in some instances, a combination of both. An X-ray system detects materials such as glass, bone, rubber, stone, plastic, and some metals, depending on density, while a metal detection system is calibrated to identify all
types of metal based on their magnetic and conductive properties.
The strategy behind placing a detection system at the end of a processing line is that once an item is packaged, no new contaminants can be introduced, so inspecting after packaging is a final safeguard before distribution to customers.
However, the number of food and beverage product recalls has increased in recent years,
which can be partially attributed to an unreliable supply chain for ingredients—resulting in unfamiliar, alternate suppliers being used when materials are scarce—and an influx of inexperienced workers on the lines due to the ongoing labor crisis. As a result, major retailers like Costco are pushing processors in 2023 to expand their overall detection capabilities further up the line to catch contaminants before the packaging stage.
Adding inspection upstream can provide additional food safety protection to consumers. But the cost of adding machinery, coupled with a possible lack of space to install that equipment, are the main reasons this idea hasn’t previously taken root throughout the industry. Now, with retailers feeling pressure from consumers over recalls, that urgency is being transferred to the processors.
“Many [retail] brands are demanding specific inspection steps be performed prior to product being sent to them by suppliers,” says Marco Azzaretti, director of marketing for Key Technology. “This trend has been growing in conjunction with consumers’ increased attention to the quality and safety of food products, which in turn has made food safety incidents and recalls more common and more costly for brands to absorb, both in terms of operational costs to correct and the impact on the brand’s reputation.”
For manufacturers who worry about the upfront cost of adding inspection to their existing lines, Geri Foley, product manager, X-ray, for Mettler Toledo, o ers this perspective: “The average cost of a product inspection product is somewhere between $25,000 to $135,000, depending on the technology. One product recall can be in the millions.”
While the food safety benefits of adding inspection equipment further up the line are numerous, there are also hidden savings over time to a facility that
processors might not see immediately.
“The cost of a reject [further upstream] is much lower vs. rejecting finished product or anything further along in the process,” says Eric Garr, regional sales manager for Fortress Technology. “Also, consider that rejecting one larger contaminant upstream may mitigate a much higher quantity of rejects downstream if that contaminant is broken down into smaller fragments. Further, there would likely be some fragments too small to detect with end-of-line inspection.”
Catching contaminants in the early stages can also save wear and tear on equipment as items are processed down the line. “Larger contaminants, like bigger pieces of metal or stone, if removed at the front end, can protect equipment such as grinders, mixers, and fillers that are located further downstream,” says Lanel Menezes, sales director, USA at Mettler Toledo Product Inspection. “Ultimately, non-conforming product is rejected prior to value being added through packaging.”
Sustainability goals are another benefit of adding inspection upstream. Overall food and packaging waste will be reduced if a contaminant is detected early, rather than at the end when packaged goods would be thrown out. In addition, today’s inspection systems are built with energy savings in mind, so adding this equipment to a line won’t use as much power as in years past. “This is accomplished in a multitude of ways such as deploying energy-e cient
Many food manufacturers are being asked by major retailers like Costco to expand their inspection programs this year as an added layer of food safety protection.
In addition to metal detection and X-ray options, digital sorters can also be used when processing raw ingredients at the front of a line.
X-ray generators, using magnetically driven motors, using LED lights instead of incandescent bulbs, reducing heat dissipation from the machines, and more,” Menezes says.
An inspection system can go almost anywhere along a processing line, but there are certain areas where processors can maximize the detection capabilities of their equipment, depending on the product being produced.
“At every stage throughout the process, inspections can be conducted, starting with raw material receiving,” says Robert Rogers, senior advisor for food safety and regulations at Mettler Toledo. “Liquid products can pass through a metal detector or X-ray
pipeline system, and dry goods can pass through metal detection systems. In the batching area, large container product can pass through inspections as they are dismantled into smaller batch materials, like a 50-lb bag of flour, through a throat metal detector as it is being weighed into a batch-level item.”
Raw material receiving is a logical place to add an inspection system, since that’s where many contaminants can be introduced from the outside. “Inspecting raw product at receiving allows the input to the line to be profiled, which helps optimize downstream processes,” Azzaretti explains. “Along the production line, placing inspection systems and sensors before and after critical transformative steps such as frying, baking, and blanching allows processors to collect valuable data that can be used to control those processes and maximize line performance.” Inspection right before packaging can be another useful area of placement, he adds.
In addition to metal detection and X-ray options, digital sorters can also be used when processing raw ingredients at the front of a line. “Today’s optical sorters are more capable in di erentiating with consistent accuracy what is good in-spec product, what are product defects that need to be managed, and what are foreign material contaminants that must be removed from the product stream,” Azzaretti says. “At the same time, these modern inspection systems are designed to be much easier to use and maintain.”
Simplified operation on today’s inspection equipment can include touchscreens and icon-based use, which can help companies with high turnover and the need for a short learning curve.
A shorter learning curve to use today’s inspection equipment is a crucial advancement given the ever-dwindling labor pool and the need for new hires to learn as quickly as possible. “Introducing a new piece of equipment into operations will have an impact on your employees and it is important to ensure that the necessary support is given for them to adopt the technology and trust it,” says Menezes. “This means providing the necessary training, ensuring smooth integration, collecting feedback for improvements, and ensuring ease-of-use and serviceability.”
Simplified operation on today’s inspection equipment can include touchscreens and icon-based use, which helps companies “with high turnover, or in some cases not enough individuals in the workforce,” Foley says.
Today’s processors must adapt to a quickly changing market: Deville takes care of helping you achieve the perfect cut
while designing hygienic, simple, ;uv-ঞѴ;-m7;-v |o1Ѵ;-m1 মm] voѴ ঞomv|_-|;m-0Ѵ;ruo1;vvouvѴ-u]; and small, to keep up with demand. Because we don’t just see food, we see the whole picture.
Combination systems can combine more than one inspection function into a smaller footprint than two standalone machines, helping processors with limited floorspace in their operations.
Though it’s possible for a manufacturer to adjust its budget to purchase additional inspection systems, it might be more di cult to find room within a facility to place those systems. Many processors have limited footprints in their plants, so custom-engineered equipment can be one path to overcoming those challenges.
“It is important for food processors to engage closely with inspection system suppliers and express their specific requirements, because every line in every plant is unique, even when processing the same product type, and the inspection system should be tailored to each instance to maximize value,” observes Azzaretti.
Combination systems are becoming more popular because they reduce the footprint over multiple standalone systems, Garr notes. “Also, specific to metal detection, something to consider is that the aperture size and resulting metal-free area will dictate the minimum overall length for a system,” he says. “So, ensure that metal detection apertures are as small as possible, fitted for the product that is being inspected.”
Not all product inspection equipment will require additional space, according to Foley. “In many applications, the equipment can be inserted into the existing line space whether using the customer’s existing material handling solution or replacing a section of their existing line with product inspection equipment,” she says.
Calibration and testing of new inspection
systems upstream is also a vital step before finalizing installation, especially since inspection will be new to those parts of the line. “Prior to making a purchase decision, it is essential to validate and measure the performance of the system through application tests that replicate the actual product and production conditions in which the equipment will operate,” says Azzaretti.
Today’s inspection systems feature a variety of innovations, and while not designed specifically for upstream placement, they are helpful for processors to maximize their investment. “First and foremost is the ability to detect varied, ever-tinier contaminants, as well as the capability of defining when contaminants are introduced into the production process,” says Kelvin Binns, food and CPG director for Wipotec-OCS.
“Inspection systems for contaminant detection have become more powerful in terms of what they can detect,” Garr says. “To put it simply, the technology is being doubled up to cover holes and improve performance. Metal detectors operating multiple simultaneous operating frequencies and electromagnetic field orientations are innovations that help improve performance. Similar is true with X-ray inspection where dual-energy detection is allowing detection of less dense contaminants than was possible in the past.”
Connectivity and data collection are also features that can help processors make sense of target inspection areas further up their lines. “The ability to pull live data into plant monitoring software and ERP [enterprise resource planning] systems is becoming more of a prerequisite than ever before,” Garr explains. “This makes sense as having live data to make on-the-fly operational decisions can be invaluable.”
Menezes adds, “We live in a connected world that demands transparency. Traceability [of ingredients] and connectivity are becoming vital requirements in the marketplace.”
Ultimately, processors will have to weigh their financial and facility footprint options before adding one or more inspection systems upstream to comply with recent retailer demands. Assessing the big picture might help make that decision a bit easier. “Product inspection should play a central role in any manufacturer’s production line upgrades,” Binns says. “Leaving it out of an upgrade budget may leave a food producer out of a retailer’s supplier network.”
Gorman-Rupp manufactures a complete line of self-priming, standard centrifugal, submersible and positive displacement pumps for the food processing industry.
Whether your application requires handling abrasive and corrosive chemicals or liquids containing large solids, Gorman-Rupp has the right pump for the job. Our pumps continue to perform reliably month after month, year after year, in the most demanding environments.
And, they are all backed by the best distributor network and parts inventory in the industry. Contact your local Gorman-Rupp distributor today for more information on how our pumps will meet all your food process pumping needs.
Since buying its first Air Products freezer 20 years ago, Totally Cool continues to improve throughput with new cryogenic tunnel freezers to help its upward trajectory.
SHOPPERS BUYING STORE-BRANDED ice cream cakes and frozen novelties might think those desserts were made onsite by retail sta , but depending on the location, there’s a chance they were manufactured o site by Totally Cool. For more than 25 years, the Baltimore-area company has created ice cream cakes, pints, and cups for private-label and wholesale clients across the U.S.
Totally Cool was founded by CEO and President Mike Uhlfelder in 1992. Inspired by his work at a Carvel ice cream manufacturing and retail store when he was 15, he funneled that passion into his own company seven years later. Uhlfelder’s business model as a co-manufacturer and private label partner took o quickly, and by 2003, demand for his ice cream cakes—Totally Cool’s core product—was exceeding his ability to produce them.
“We could not get enough throughput,” says Uhlfelder. “At the time [our ice cream cakes] went into specific molds for di erent sizes. Then those cakes went into a blast freezer, which is static freezing, so our turnaround time to further process that product was 24 hours. The next day we would take the cake out of the molds, and decorate, package, and finish them.
So, we had a huge lag time, and the only way we could get ahead was to freeze items instantaneously, like 20 to 30 minutes as opposed to 24 hours. That’s why we bought our first tunnel freezer.”
Uhlfelder purchased an Air Products Freshline CryoQuick nitrogen-chilled tunnel freezer, which “was the major stepping stone for me to grow this business and expand,” he says. “Before the
Air Products freezer, we were using about 2,000 molds [for ice cream cakes]. And when we bought this tunnel freezer, we reduced it to around 200 molds because the product comes out completely frozen, so we can release it from the mold instantly and wash and fill that mold again without any overnight lag time.
Overall, this tunnel helped us reduce labor costs, material costs, and we significantly increased throughput.”
The tunnel freezer also reduced wear and tear on Totally Cool’s conventional walk-in blast freezer by not having to use it for overnight freezing anymore.
“We ran it at around -50°F all the time, so the tunnel helped us reduce energy costs with the walk-in,” notes Uhlfelder.
Air Products’ tunnel freezers have helped Totally Cool meet increased demand for its ice cream products—like these cakes— while alleviating production bottlenecks due to faster freezing with nitrogen.
In the ensuing 20 years from that first Air Products tunnel freezer purchase, Uhlfelder bought a non-Air Products tunnel freezer in 2011, but returned to Air Products in 2018 to buy a second Freshline CQ. Then in 2022, he bought a 30 ft Freshline IQ tunnel freezer, and a second 30 ft Freshline will be installed this quarter. All four of those Air Products freezers will be used for production in 2023, and Uhlfelder says each purchase has marked a timeline in his company’s upward trajectory.
The fourth Air Products tunnel freezer at Totally Cool will be installed in Q1 this year, and all of them will be used for production in 2023—including the first one purchased 20 years ago.
“You grow to a certain point where your throughput starts to bottleneck, so if your tunnel is at full capacity, it makes it di cult to meet demand,” explains Uhlfelder. “When we bought our second tunnel, it took a lot of pressure o the first tunnel. We were able to run two tunnels but at a slower speed to get a longer dwell time, which is a more e cient use of the nitrogen, and produces a more stable product.”
With four Air Products tunnel freezers populating Totally Cool’s 42,000-sq-ft plant, the company can produce up to 1.5 million ice cream cakes, pints, and cups per month, according to Uhlfelder.
The controls on each Air Products tunnel freezer have evolved for ease of use over the years, which is essential for employees working on the lines, Uhlfelder adds. “All the tunnels are fairly easy to operate,” he explains, “and the new ones have touchscreens and Allen-Bradley controls. They also link to Air Products’ [Smart Technology], which helps with troubleshooting and optimizing in real time, in case there’s an issue. These machines run at -320°F, so that option really helps with operator safety, too.”
Air Products www.airproducts.com/equipment
•Bagging solutions for valve bags, open-mouth bags, FFS bags, and big bags.
•Semi to fully automatic bagging systems
•Complete plants from product feed to final transport
•Robotic and conventional bag palletizing integrations
The Linde plate belt freezer uses a solid surface conveyor belt in lieu of a chain link belt to reduce belt marks and virtually eliminate sticking and dripping. The Cryoline PB plate freezer belt is chilled in the freezer to cryogenic temperatures, quickly crust freezing the product surface to lock in moisture, brine, marinade, and sauces.
Linde | linde.com
The Linde cryogen system rapidly lowers temperatures during batch mixing or blending. The valve-nozzle assembly of the Accu-Chill LXC cryogen bottom-injection system features a valve-nozzle assembly, including an all-stainless-steel, in-line valve for cryogenic service and a nozzle component that automatically closes once the cryogenic liquid has been injected. A selfclosing mechanism minimizes the risk of food particles getting trapped in the nozzle opening, reducing nozzle blockage and cross-contamination between batches.
Linde | linde.com
Capable of operating in temperatures as low as -400°F, Graphite Metallizing bearings are suitable for industrial freezers, frozen pizza conveyors, general frozen food conveyors, flash-freeze seafood applications, and cryogenic applications. The Graphalloy bearings maintain lubrication at extremely low temperatures due to the self-lubricating feature of the material of construction, a graphite/metal alloy formed from molten metal, graphite, and carbon. The uniform, solid, self-lubricating bushing and bearing material also is available as plain bushings, flange block units, pillow block units, and cam followers, and in FDA-acceptable grades.
Graphite Metallizing graphalloy.com
Optimize your process, boost yield, and improve product quality with the latest Linde innovations in food freezing.
CRYOCONNECT® RM – remote online monitoring system facilitates optimization of cryogenic freezing performance across operations.
ACCU-CHILL® LXC – the most advanced cryogen bottom-injection system provides rapid, precise temperature reduction during batch mixing or blending.
CRYOLINE® PB – plate belt tunnel freezer uses a solid stainless-steel VHJPHQWHGFRQYH\RUEHOWWRTXLFNO\FUXVWIUHH]HGLIÀFXOWWR handle products.
O ering milling flexibility and powder processing e ciency, The Fitzpatrick Company and Quadro Engineering SDx Series platform o ers three distinct powder processing solutions on a single, common drive. The smart drive exchangeable milling/screening platform allows operators to interchange three heads for specific processing requirements. The platform uses an equipment feature that automatically recognizes the head being installed and adjusts rpm to the appropriate level. Users can opt for a single platform and select the most appropriate powder processing technology to suit each application.
IDEX MPT | idex-mpt.com
Automating control over dense phase pneumatic conveying systems, the Gericke control system features 14 languages, delivering operation instructions, selections, and other information to operators in their native tongue. The STP 61 pneumatic control system provides language selection on the opening screen of the full-color, touchscreen display before advancing to selections for desired throughput rate, bulk density of the conveying material, and other properties. The system is delivered preconfigured and ready to operate.
Gericke USA | gerickegroup.com
Hiperbaric HPP systems include loading tilting stations that allow an automatic flow of products into the HPP baskets prior to highpressure processing. Pre-feeders automatically load the baskets into the HPP vessel, where RFID tags and data matrix codes are placed on them. After HPP, an unloading robotic station takes products out of the baskets, and shaker conveyors remove excess water on the packaging. Robotic arms then pick items to pack single or multiple cases per cycle. Custom carriers, carrier carts, elevators, turntables, and tote dumpers are available.
Hiperbaric | hiperbaric.com
The Krohne capacitance level switch o ers point-level detection of liquids and solids, with IO-Link communication, for overfill and dry-level protection. The Optiswitch 6700 can monitor CIP and SIP cleaning processes, media separation, clogged or blocked pipes, and moisture levels. Its double output can be individually programmed to monitor di erent processes or media. Suitable for adhesives and di cult products, the switch’s performance is not a ected by product buildup, foam, or condensation.
Krohne | us.krohne.com
FOOD SAFETY, EXTENDED SHELF LIFE AND CLEAN LABELS WITHOUT HEAT OR PRESERVATIVES
Guacamole and Salsa
Thanks to Avure HPP, avocado has a shelf life of up to 45 days.
Ready-To-Eat Meals
HPP offers the great taste and fast preparation times that consumers demand.
Vegetables
Fresh-picked taste and long shelf life. No chemicals or preservatives.
Seafood
Our seafood machine boosts yield and reduces costs.
Baby Food
Convenient, all natural with no additives or preservatives for little ones.
High Pressure Processing is a natural method of food pasteurization that uses pure cold water, and up to 87,000 psi (6,000 bar) to inactivate pathogens, and dramatically extend shelf life. No chemicals . No heat.No additives . Learn more about how high-pressure processing works.
Beverages & Juices
Avure HPP machines process most of the world’s HPP treated juice!
Wet Salads & Dips
Boost shelf life. Ditch additives. And dip into new markets with HPP.
Meat
Safe and great shelf life.
Pet Food HPP offers health benefits for pets.
Dairy
Extend shelf life for cheese, sauce, dips, and milk and other beverages.
WHY AVURE:
•Most Experienced
•Highest Productivity
•Robust Engineering
•Application Expertise
•24/7 Support
WHY HPP:
•GREATER PROFITABILITY: Than Conventional Processing
•FRESH TASTE: Not Altered by Heat, Chemical or Irradiation
•CLEAN LABEL: Aligns with Consumer Trends
•LONGER SHELF LIFE: Drastically Reduces Spoilage
•FOOD SAFETY: Extreme Pressure Inactivates Pathogens
Using an indexing motor coupled with an ultrahygienic, ultrasonic blade, the Deville Technologies portion cutter facilitates the reduction of a variety of products that come in a rectangular loaf format, from those that are extremely soft and/or sticky in texture to firmer products, which are subsequently fed to a downstream dicer or centrifugal shredder. The blade is constructed of 304 stainless steel, while the welds are polished to Ra32 (34 finish). The portion cutter is equipped with a human-machine interface (HMI) screen to facilitate recipe settings.
Deville Technologies | devilletechnologies.com
Typically installed at receiving, the Key Technology air cleaner separates and removes extraneous vegetable matter and debris early on the production line. The #16 air cleaner uses positive airflow, which moves through the product as it falls above a diagonal screen, to push light debris up and into a collection hood. It o ers airflow up to 538 m3/min (19,000 cfm), depending on the application. Suitable for wet or dry products, each air cleaner is integrated with either a dewatering shaker or transfer shaker.
Key Technology key.net
Scalable from 4,000 to 7,000 lb, the Quintus high-pressure processing system features an 18.5-in. diameter vessel. The modular QIF 400L system has a 700-sq-ft footprint for streamlined installation and an algorithm-based condition monitoring system that reduces the risk of unplanned stops. It incorporates features such as frequency-controlled motor drives, cloud-based press management software, and a wire-wound pressure vessel design. Quintus Technologies | quintustechnologies.com
Rated up to IP69, the Atkore hygienic conduit provides a visual indication of sanitary conditions and prevents contamination from oils, dirt, dust, and liquids. The FDA-approved Calbrite white, liquid-tight, stainless-steel flex conduit has a compression strength up to 225 psi, tensile strength to 285 lb, and an operating temperature range of 0 to 275°F, making it suitable for washdown and other harsh environments. ROHS- and REACH-compliant, the conduit also meets NSF and ANSI 169 requirements. Atkore | atkore.com
The Beckho transport system includes no-cable technology that enables individual movers to serve as mobile handling and processing stations, essentially creating a flexible multi-robot system. The hardware required for the transmission technology is fully integrated into a motor module that mounts on the eXtended transport system mover. Control of the hardware is fully implemented in standard TwinCAT software. With the no-cable technology, the quality of products on the mover can be checked while the process is running. The data communication is real-time capable and can synchronize system-wide events.
Beckho Automation | beckho .com
Featuring a self-priming, seal-less design, the Graco double-diaphragm pump o ers a range of materials of construction to support multiple hygienic applications. The electric Quantm pump is built to be a reliable dropin replacement for current pneumatic pumps or greenfield construction. With built-in controls and no gearbox, the pump fits seamlessly into most fluid transfer applications.
Graco | graco.com
Designed to transfer a variety of powders, granules, pellets, and other dry, bulk materials, the AFC screw conveyor allows full access to the bottom of the hopper and tube inlet for the emptying of residual material. The Spiralfeeder Push Unit solid screw conveyor sets the drive mechanism, hopper, and screw conveyor o the floor on a rolling, open, steel frame. To empty the system, an operator shuts o the power, removes a tri-clover fitting, places a collection bin or bag underneath the conveying tube, and turns the screw conveyor on in reverse. Material entrained inside is automatically collected for return to storage or for reuse.
Automated Flexible Conveyor | afcspiralfeeder.com
Simco-Ion systems provide in-line ionization for neutralizing static charges on materials passing through pneumatic conveying systems. The IQ Power BPS-C upgrade allows advanced monitoring and control of static eliminators located within Simco-Ion Conveyostat systems. When connected to an IQ power control station, the upgrade allows the static elimination system to communicate directly with a PLC via one of six supported protocols, enabling information to be reported and recorded at it.
Simco-Ion | simco-ion.com
Suitable for plant-based meat products, Readco Kurimoto continuous processors integrate mixing, heating, flavoring, seasoning, forming, and texturizing steps into a single, automated step. The units feature a co-rotating, twin-screw configuration with a variable paddle arrangement inside a sealed, ASME-rated barrel that combines multiple liquid and dry ingredients simultaneously. High-shear zones disperse proteins and other sticky ingredients in the required proportions. Emulsions are formed quickly and remain in suspension throughout the process.
Readco Kurimoto | readco.com
FDA-approved, the Ross dual-shaft mixer batches dispersions, suspensions, and emulsions with viscosities up to several hundred thousand centipoise. The FDA-3500 mixer has a maximum working capacity of 3,500 gal, a two-zone stainless-steel dimpled jacket for heating/cooling, 4-in. pneumatic discharge valve, and explosion-proof load cell system rated for up to 20,000 lb. The multiagitator system is equipped with independently controlled drives. Powered by a 300 hp TEFC inverter duty motor, the disperser runs at tip speeds up to 5,000 ft/min, while the 60 hp three-wing helical agitator feeds product toward the disperser blade. Teflon scrapers on the anchor wipe materials from the vessel wall.
Used to process meat, poultry, and alternative proteins, the Urschel dicer delivers 2D dices, strips, or shreds from product of a predetermined thickness. The belt-fed M VersaPro dicer has 12-in. infeed and takeaway belts that work together to provide even transitioning of product and prevent product buildup. An IP69K-certified electrical enclosure features a double-sealed door. A fluted crosscut option is driven by a 5 hp (3.7 kW) motor equipped with a variablefrequency drive to allow the adjustment of cut sizes.
Urschel Laboratories | urschel.com
Bete tank cleaning nozzles remove di cult soils from small vessels or compact areas inside equipment. FDA-compliant, HydroWhirl Mini rotational nozzles come in PVDF and 316L stainless-steel versions that clean up to a 3.5- or 6-ft diameter, respectively. Both versions o er 360-degree spray coverage.
Bete Fog Nozzle | bete.com
The Multi-Conveyor wire-belt conveyor has a pivoting discharge end that comes down to convey o a bad batch or group of bad product into a tote or bin. After the batch or group has been rejected, the discharge end pivots back up. A pneumatic air-operated box enclosure houses controls for the air-actuated reject to pivot in the up or down position. A manual override selector switch allows an operator to pivot the discharge on demand. The sanitary, food-grade, stainlesssteel wire-belt conveyor features hygienic, articulating, adjustable pad-style feet and bearing caps that keep grease from gathering inside, while cleanout holes and an open mesh top enable spraying water all the way through the conveyor. Multi-Conveyor | multi-conveyor.com
Providing control of process media fluid dynamics and the path of least resistance, the Stock batch retort process produces shelf-stable in-container food and beverage products. The ImmersaFlow process uses a closed-loop column of process water, channeled through a plenum and closed wall baskets. Outside the basket, the retort shell is primarily empty. The process can achieve 4- to 6-min come-up times, with as little as a 2°F spread between the geometric center and perimeter of the load.
Stock | stockamerica.com
Built to convey a range of bulk products, Ryson bucket elevators combine vertical and horizontal transportation. Overlapping pivoting buckets prevent spillage and help mitigate foreign debris. Available powder coated or in stainless steel with multiple inlets and outlets that operate independently, the bucket elevators have a modular design that allows them to be built to order and enables customization.
Ryson International | ryson.com
Fabricated of 304 stainless steel, the Munson Machinery paddle blender features a stationary U-shaped vessel with a flat cover, bottom discharge valve, and horizontal flange-mounted agitator. The Model HD-2.55-SSI sanitary blender has a 10 hp (7.45 kW) washdown-duty motor that drives the agitator shaft assembly configured with 16 radial arms and short-length paddles. Additional shear is provided by four independently powered intensifiers, each driven by a 5 hp (3.73 kW) washdown-duty motor. The paddle blender de-agglomerates dry bulk solids, pastes, slurries, and/or emulsions of low- to medium-density materials in batches up to 25 ft3
Munson Machinery | munsonmachinery.com
• Withstands temperatures up to 1,000° F
• Self-Lubricating
• FDA Acceptable
• Perfect for use in ovens, fryers, roasters, steamers, etc.
• Withstands harsh, corrosive washdowns
• Reduces maintenance and downtime
Our 3D v is ision, soft
JUDVSLQJ D JUDVSLQJDQGDUWL FLDO
LQWHOOLJHQFH LQWHOOLJHQFHVROXWLRQVDUH
VROYLQJWKH VROYLQJWKHPRVWSUHVVLQJ
FKDOOHQJHV FKDOOHQJHVLQWKHIRRG
SURFHVVLQJ SURFHVVLQJLQGXVWU\ȃ
RQHSLFNDW RQHSLFNDWDWLPH
Contact us to see where we can help.
ZZZVRIWURER ZZZVRIWURERWLFVLQFFRP
ΖQIR#6RIW5RER ERWLFVΖQFFRP R R
High-pressure processing is essential for improving the taste and shelf life of cold-pressed juices. Partnering with Hiperbaric, Evolution Fresh made it a less labor-intensive operation.
EVOLUTION FRESH, a subsidiary of Starbucks, has long used high-pressure processing (HPP) to create a fresh tasting juice with a considerably extended shelf life. HPP is a non-thermal process that not only helps keep the cold-pressed juice safe by inactivating foodborne pathogens, but the non-thermal process also helps to protect both nutrients and flavor.
However, HPP tends to be a highly manual, labor-intensive process. So after five years of using machines from Hiperbaric—Evolution Fresh now owns five Hiperbaric 420 machines, which can process 1,000 gallons of juice per hour—the juice maker undertook a project to add automation to the HPP process. It partnered with Hiperbaric to create a state-of-the-art automated HPP operation line.
At PACK EXPO International’s Processing Innovation Stage, Evolution Fresh and Hiperbaric talked about their journey. “What we’ve been working on is how do we make this HPP process more sustainable from a labor perspective and from an e ciency perspective,” says Michael Durbin, plant director for Evolution Fresh in Rancho Cucamonga, Calif. “This has been a project we’ve been working on over the last several years.”
It’s more important than ever for manufacturers to explore what processes they can automate. Roberto Peregrina, Hiperbaric USA director, points to data showing how many manufacturing jobs were lost to the pandemic. More than 40% of those jobs have yet to be recovered. “One of the main challenges that companies are facing right now is getting entry-level employees in the door,” he says, commenting on a study showing that U.S. manufacturing executives are finding it 36% harder to find the right talent than it was in 2018.
This was a key impetus behind Evolution Fresh’s move to an automated process, but it certainly wasn’t the only one. Besides addressing labor shortages, automating HPP processes reduces labor costs, improves productivity and consistency, prevents operator injuries, and minimizes waste.
One of the main challenges that HPP faces is that it’s still a batch process, Peregrina comments. “It’s a post-packaging technology, so the product needs to be put into a chamber and then extracted and then put into cardboard in the final cases,” he says.
An operator puts the bottled juices into canisters. The canisters are then loaded into a chamber. After plugging each end, the vessel is flooded with water and the pressure is increased up to 87,000 psi. After maintaining the pressure for a predetermined amount of time, the vessel is depressurized, and then the product can be unloaded.
“It’s still a very manual operation,” Peregrina says. “We have worked extensively over the years
After HPP processing, a robot unloads the juice bottles onto a drying shaker table.
Pick-and-place robots line bottles up to ready them for packaging.
with Evolution Fresh, and they have been a champion on allowing us to help automate their operation.”
Evolution Fresh started this project in 2015 by looking at ergonomic concerns. “We had a lot of injuries, repetitive motion, lifting, a lot of triple handling, which we wanted to eliminate. So we created some tilting stations that we were able to fill our products into, and then use a forklift to load the product,” Durbin says. “When we did this, we also added barcodes to the carrier, so it was easier to track the product and our processing parameters that were needed.”
In 2015 and 2016, Evolution Fresh focused on the pre-HPP material handling equipment, including automated filling stations and pre-feeders. In 2021 and into 2022, the juice company also moved into robotic unloading and pick and place to get the bottles back onto the line. Post-HPP automation equipment was installed, with automated dumping of carriers and standup of bottles.
“There are many reasons to do this. One is we want to increase our OEE [operational equipment e ectiveness], which we increased by about 15% since we started this journey,” Durbin says. “But injury is a big story. We reduced injuries more than 90%.”
Before implementing more automated measures, an HPP operator would lift about 16,000 lb/day of crates of juice before dropping them into carriers. That kind of repetitive motion was not only hard on the operator’s body, but it didn’t particularly inspire them to come into work the next day when they woke up sore from the previous day. So a major goal of the change was to eliminate the risk of injury to employees, Durbin notes.
“We also eliminated more than half of the transportation waste,” Durbin says, pointing to the inefficiency of putting bottles in crates, dumping them out into the HPP carriers, and then unloading the carriers. “There’s just a lot of handling there. By streamlining the process, we fill the carriers, load them into the HPP, and empty them all in one motion.”
Evolution Fresh has not only been able to save time with the streamlined process, but also reduced labor by more than 50%. “It’s getting harder and harder to find people that want to do hard jobs that are manual and in a cold room. And COVID just added to this,” Durbin says. “I couldn’t always count on people being there due to illnesses or di erent issues surrounding that.”
Since automating the process, the only lifting that workers are doing is placing the empty carrier onto the tilting station, Durbin explains. “The forklift is lifting the full carrier so that the strain is taken o of operators,” he adds.
In addition to automating the labor, the process is making use of barcodes to store information. “It’s really great for traceability, so we can track everything that’s been processed,” Durbin says.
Automating the HPP operation is not for every company, Peregrina notes. “One of the main challenges is the return on investment for a company,” he says. “Obviously, the more you use the machines or the closer you get to 24-hour operations, the easier it is to get a return on your investment.”
In terms of functionality, automation might not be as flexible if it is needed for a series of unrelated tasks. Hiperbaric
Though shaving an hour and a half o cleaning tanks every day is great, this craft brewer has been particularly happy with how CSI’s cleaning system reduces employee exposure to chemicals.
SINCE BREWING ITS FIRST Mr. Beer brew kit over a kitchen stove and fermenting it in a bathroom tub in 2004, Four Corners Brewing has outgrown its production environment time and time again. O cially launched as a company in 2012, the craft brewer moved from a home garage to a bigger automotive garage. In 2017, it moved to its current home—an even bigger garage—in the Cedars neighborhood just south of downtown Dallas.
With each move came a system upgrade as well. Any craft brewer trying to compete in the burgeoning market over the past decade has had to increase system e ciencies, continually striving for process improvements. Four Corners’ newest operations included adding multiple process vessels in its cellar, including fermenters and brite tanks.
The latest move was also the first time Four Corners owned its own space rather than leasing. “We expanded into this facility and increased our production capability,” says Caton Orrell, facilities and maintenance manager. “Once we were actually in the facility, we began to soup everything up and begin to lay the process out in more of a permanent way.”
By last year, the brewery had realized that it was going to have to reevaluate not only the e ciencies of its production systems, but also the e ciencies of its cleaning equipment. Without the ability to clean tanks and piping quickly and e ectively, breweries open themselves up to product integrity issues, increased downtimes, and increased labor costs—all significant threats to a company trying to grow in a highly competitive market.
The equipment expansion that Four Corners had gone through meant its existing clean-in-place (CIP) equipment was not large enough to e ectively complete cleaning. The system was not designed to clean the new tanks properly and could clean
only one piece of equipment at a time—leading to increased downtime, longer tank turnover periods, and ine ective cleaning of vessels.
The existing CIP system had its share of limitations, according to Orrell. They were only able to run one CIP circuit at a time, creating scheduling conflicts, along with other issues.
“We were doing a lot of what you would call one-and-done type CIP processes,” he explains. “We would make up a reservoir inside of a tank and recirculate it. Then, once the allotted time was up, whether the tank was clean or not, you just open the drain and put that into your sanitary sewer. Then you do your inspection and your rinse, and your tank is going to be clean—or it’s not. There’s a possibility that you’re going to have to redo that and then put more chemical down the drain.”
This setup brought all kinds of problems with it, particularly related to chemical handling and inefficiencies. “First, our guys were having to handle a lot of non-diluted bulk chemicals, which can get
Dallas-based Four Corners Brewing crafts several di erent beers under the slogan “Celebrando la Vida” (celebrating life).
A key benefit of the CIP 2.0 system is the handling of the cleaning chemicals. The new system doses itself, reducing chemical handling by operators by 95%.
you sideways with OSHA real quick,” Orrell notes. “Then, it was very labor-intensive to set the whole thing up—mix the chemicals up in the tank, recirculate it, have them walk around and not really be terribly engaged in anything else while the CIP was running.” Then, he adds, the tank would have to be opened without having any confirmation about how e ective the clean cycle was.
Orrell contacted Central States Industrial (CSI) to engineer, design, and build a CIP system that could not only handle the expansion in process equipment that Four Corners had taken on, but that could also provide a safer, more sustainable cleaning process.
The completed system from CSI consisted of two skids: A three-tank CIP with dual supply headers and a standalone hot water set. The CIP has a hot and cold customization that allows operators to bypass the tank—which provides the option to perform a hot or cold rinse for anything in their process. The hot water set was engineered by CSI to meet the requirements of Four Corners’ steam availability system in the plant. Providing hot water to the CIP system and other areas of the facility, the hot water set is more e cient and replaces an existing—and leaking—hot liquor tank. The new system also allows the brewery to clean two pieces of equipment at once, translating to significant increases in uptime and faster tank turnover.
The new system will save considerable cost and time, Orrell notes. With two CIP supplies and two unique returns, operators no longer have to wait for 30 minutes at the end of their shift to run a CIP cycle. Running three cleaning cycles a day, Four Corners’ operators are saving 90 minutes of downtime every day, adding up to 7.5 hours a week.
But even more important to Orrell than the time savings is the e ciency in chemical usage and the improved safety to the operators. “We’re recovering more chemicals, and we’re using less energy to heat this stu because we’re not doing a one and done. It’s recirculated and put back into an insulated tank,” he says. “But the biggest benefit to me was that we minimize our employees’ exposure to handling bulk undiluted chemicals.”
Previously, Orrell explains, employees were having to work with a lot of hoses in multiple locations. Four Corners has been able to incorporate more hard piping into the system, which helps from a sanitary and safety standpoint, he says.
“The new system doses the chemicals itself, so operators don’t have to touch anything,” Orrell says. “By eliminating operator exposure when dosing chemicals, we’ve essentially reduced their chemical handling by 95%.”
Four Corners has also reduced overall chemical usage for CIP by 40% during standard production cycles. CSI provided custom programming for the system to meet the brewery’s sanitization process needs. Operators are able to handle the cleaning from one central location, selecting a pre-programmed recipe that better streamlines and homogenizes the process. Rather than operators guessing how long they might need to run the system for a full clean, the new system automatically programs the correct titration, temperature, runtime, etc.
The brewery has realized significant improvements in repeatability and traceability for its cleaning processes, allowing for refinement and standardization. With better control of what is sent to the wastewater system, thanks to the controlled titration of chemicals, Four Corners is also seeing a reduction in its wastewater bills with the city.
This new equipment allows Four Corners to e ectively and reliably clean its separator. In addition, the increased capacity of the three-tank system enables Four Corners to reuse some of the cleaning solution by storing it in the third tank, reducing chemical consumption. This will save the brewery thousands of dollars each year and help the environment, health, and safety (EHS) protocols of the plant.
ProFood World added a new category to its annual Sustainability Excellence in Manufacturing Awards. The Processor/Supplier Partnership Category recognizes the growth and importance of collaboration between processors and industry suppliers in protecting the planet.
Learn how past winners in this new category—
Li ey Meats and Graphic Packaging International—worked in tandem to create a new PaperSeal tray for Lidl.
Welcome to the 2023 Leaders in Processing (LIP) section of ProFood World.
Leaders in Processing (LIP) is ProFood World ’s signature supplier branding program.
Participants in the LIP section have both print and online branding and receive prominent, year-round exposure on ProFoodWorld.com.
Business
•
•
•
•
3711 Iowa Street, Alexandria, MN 56308
Phone: (320)763-6043
www.aagard.com
Email: sales@aagard.com
By engineering your EXACT SOLUTION, we make every square inch count for Case Packing, Cartoning, Palletizing, Variety Case Packing, Retail Ready, Robotics, Sleeving, and Combination machines. Our custom approach is a mix of inventive problem-solving and a willingness to take on challenges.
Aagard is a leading engineering innovator of secondary packaging automation. Check out a few of our innovative solutions:
• apid Launch- ew product set-ups in minutes, no programming, no change parts, no retrofits
• alk-Through Caser acker set up for lights-out manufacturing
• Fully Automated ariety Case acking, ncluding etail eady ackaging
• One Case acker for Cartons and ags, ith Auto Changeover
• Telescoping Conveyor, Accessibility ithout Steps Or Draw ridges
• Expanded Capability with ntegrated Options
TOTAL PROJECT SUCCESS happens with partnership and an iterative design process. We work together to understand the complete picture, creating the optimal solution that mitigates space, speed, and flexibility challenges to drive results.
Since 1997 we have specialized in engineering and building customized integrated combination packaging systems that fit our customers’ specific needs and spaces. Our unique packaging machines can combine many solutions into a single turn-key system with one integrated control package using our proven innovative technologies.
Whether the need is for a design solution with a small footprint or an agile system that can produce 1000s of product combinations, we will deliver
T E AAGA D E E E CE EL G OUT CUSTOME S
Admix is recognized as a leader of high shear, high flow, and high-speed sanitary mixing equipment with a special focus on powder induction & dispersion and particle size reduction. Serving industries such as food & beverage, meat & poultry, dairy, pharmaceutical and chemical, our experience has led us to develop a diverse product line to meet nearly any mixing challenge. For 30+ years we have manufactured in-tank batch mixers, inline mixing and milling equipment, powder induction & dispersion systems and static blenders. We manufacture both high shear and low shear mixers, many of which are offered in sizes ranging from lab scale to full production configurations.
With extensive applications and equipment knowledge, we’ve helped the world’s most well-known food & beverage manufacturers mix ingredients perfectly. Admix customers have drastically improved overall mixing time, improved end-product quality, reduced ingredient waste due to unmixed ingredients getting left behind, achieved energy savings, and improved ergonomic safety for workers!
When it comes to high shear batch mixers, the Admix Rotosolver is the market leader. The Rotosolver offers the highest flow on the market, superior wetting out of powders, and an easy-to-clean, 3-A compliant design.
In addition to high shear and low shear batch mixers, we offer high shear inline emulsifiers and wet milling machines for particle size reduction and producing shelf-stable emulsions. Powder induction and dispersion systems round out the portfolio, inducting powders at speeds up to 500 lbs. per minute.
Whether you need high shear in-tank mixing, inline mixing and milling, or powder induction and dispersion, we can help. We encourage you to schedule a mix test with your ingredients in our fully equipped lab. On-site equipment trial programs are also available so you can use Admix equipment at your own facility with your own operators before you buy! Your Ingredients, Perfectly Mixed. Contact us to see how!
Aerzen is a worldwide manufacturer of positive displacement, hybrid, and turbo blowers. Aerzen is an innovator since it was founded in Germany in 1864. Aerzen manufactures positive displacement blowers, turbo blowers, screw compressors, and vacuum pumps that supply oil-free air to processes in food and water treatment. Since 1983, Aerzen USA has been supplying and supporting Aerzen equipment in the USA, and with sister companies in Mexico and Canada expanded throughout North America. Aerzen’s positive displacement machines are known for high reliability and efficiency and are chosen for harsh environments, difficult applications and where high turndown capability is required.
Aerzen provides various types of dry, single-stage, air-cooled positive displacement blowers and compressors for pressures to 50 psig and vacuum to 25.5” Hg. Blowers are used for processes such as pneumatic conveying in both vacuum and pressure modes to handle the transfer of dry bulk materials.
The Delta Hybrid Blower was developed with the focus on increasing energy efficiency and achieving a significant reduction of energy costs and greenhouse gas emissions. The wire-to-process energy usage reduction can exceed 30% over typical positive displacement blowers depending on operating conditions and turndown range.
Aerzen Turbo Blowers are single-stage high-speed radial turbo blowers designed to meet the varying flow and pressure requirements in many different processes. This modern frequency-controlled, gearless driven machine, along with lubricant-free aero bearings, guarantees an economical, reliable and maintenance-free compressor operation.
Aerzen Rental provides temporary oil-free blower and compressor solutions under 50 psig. Rental units are available for immediate deployment in the event of a production failure or shortfall, as well as longer-term operational leasing and rent to own programs. AERZEN offers you 100% oil-free process air for various applications in food technology. For 100% product purity and safety solutions visit: www.aerzen.com/en-us
1940 Air Products Blvd., Allentown, PA 18106-5500 USA
Phone: 800/654.4567
airproducts.com/food
Email: info@airproducts.com
Air Products’ Freshline® solutions offer food processors high-purity food-grade gases (N2 & CO2) and equipment to chill or freeze a wide variety of foods. Select equipment highlights includes:
• Freshline® F ts highly efficient design allows processors to produce consistent, high-quality individually quick-frozen products in larger throughputs than standard spray freezing cryogenic F freezers, without re uiring the high li uid nitrogen consumption of immersion freezers.
• Freshline® Spiral Freezer roviding efficient, continuous freezing chilling to a broad range of meat poultry products in a small footprint at high production rates.
• Freshline® njection Cooling System A tailor-made temperature control system that uses li uid nitrogen or carbon dioxide to deliver rapid, precise temperature control to a blender or mixer grinder, enabling food manufacturers to optimize processing speed and product quality.
The benefits of these cryogenic systems include faster freeze times, increased throughput, improved product uality and more. e also offer gaseous solutions including controlled atmosphere stunning, wastewater treatment, modified atmosphere packaging (MAP) and inerting.
e can test a customer’s product on commercial-scale e uipment in our state-of-the-art food laboratory, or bring our mobile food lab to you to determine the feasibility of using cryogenic freezing or chilling for their specific process.
For more information about Air roducts’ complete portfolio of Freshline® solutions for food processing, call - - outside of the U.S. - - or visit www. airproducts.com food hone . Email info airproducts.com Air roducts lvd., Allentown, A - USA.
2045 W Mill Road, Glendale, WI 53209 USA
Established in 1948 Ampco Pumps Company manufactures the most complete line of sanitary pumps, mixers and blenders in the food processing industry.
POSITIVE DISPLACEMENT PUMPS: The PATENTED ZP1+ and ZP3 circumferential piston pumps offer upgraded materials and improvements including a maintenance saving frontloading seal design that surpasses inefficient styles of the past. No longer is there need to disconnect from the piping for daily cleaning and O-ring replacement.
The AL Series rotary lobe pumps are affordable options for many applications, offered in a variety of seal, rotor and jacket options.
Ampco offers the SLH twin screw pumps from ITT Borenmann, the leader in twin screw technology. The dual-duty SLH Series are capable of handling both process and CIP applications and are backed by Ampco’s superior customer service and support.
CENTRIFUGAL PUMPS: Ampco sanitary centrifugal pumps are second to none and include standard, heavy-duty, high pressure, self-priming and front-loading seal designs. The AC+ offers an improved shaft design. The L Series offered in several options includes the LF front-loading seal option for ease-of-maintenance. The self-priming SP is ideal for products with entrained air and CIP return applications.
MIXERS & BLENDERS: Ampco Applied Products offer a vast selection of inline and in-tank mixing and blending products. Blend wet and dry ingredients, stabilize emulsions and enhance textures while improving process efficiencies. The SBI, SBH and SHEAR-max inline mixers have options to fit any process. The JET-shear in-tank mixer comes in multiple sizes, and configurations.
Ampco Pumps manufactures quality products with enhanced features, competitively priced and with the best delivery times in the industry. Ampco is ISO 9001:2015, 3A and EHEDG Certified.
12885 Wayne Road, Livonia, Michigan, 48150
AmTrade offers leading-edge food processing systems. From Livonia MI, with team and distributors in several states, we offer custom solutions, technical recommendations, system design, sales, installation, commissioning, training and aftersales spare parts and service support.
SCHRÖTER – Leading Quality: The latest technology in smoke generators, smokehouses, fermentation and steam cooking ovens, drying, defrosting and intensive chilling chambers, and exhaust cleaning systems tailored to each customer’s exact needs.
REX Technologie – Innovative and high-quality vacuum stuffers, portioners, forming systems, link cutters, and other attachments and accessories. AmTrade offers REX equipment through distributors in California, Colorado and Ohio, and through our Livonia office.
GLASS GmbH & Co. – Made in Germany: Food mixers and meat or plant-based processing machines, temperature-controlled mixing & cooking systems and fine choppers tailored to the customer’s needs.
HOJA Food TEC – Industrial frying - Home-cooked Taste: if you are making potato pancakes, pancakes, crêpes, blini, meat balls, rissoles, hamburger, steak, chicken, vegetables, naan bread, pita breads and many more other delicious products prepared to the highest quality standards.
LASKA – With more than 140 years of experience and expertise, Laska machines are some of the most robust and technically advanced bowl cutters, grinders, mixers and emulsifiers in the world. Our machines bring utmost satisfaction to thousands of customers – all around the world.
NOCK Maschinenbau GmbH : Know-how in Food Processing – Manufacturer of derinding machines, membrane skinners, combined systems with derinding and skinning machine capabilities, circular blade vertical slicers for strips and jerky meat, specialty poultry skinning machines for whole birds or individual pieces, fish skinner, frozen drum skinners and scale ice machines.
710 Innovation Drive, Suite A, Elk Grove Village, IL 60007
www.anritsu.com/infivis
Manufacturers worldwide rely on Anritsu’s contaminant detection and quality inspection equipment. We deliver a level of precision, reliability and support that truly advances the quality of your products and the efficiency of your operations.
How much of your products do consumers inspect?
100% Reduce consumer complaints and product recalls with the world’s most installed food X-ray. Anritsu X-ray systems give producers the best combination of performance, reliability and low cost of ownership.
The Anritsu X-ray Advantage
Anritsu X-rays come standard with HD imaging that outperforms competitors in finding metal, bone, glass and stone contaminants. The fully-featured XR75 series offers longcomponent life plus easy operation & maintenance.
• food x-ray supplier worldwide with over , installations
• ndustry-leading performance for both metal and low-density contaminants
• Low TCO Up to longer tube and detector life
• eliability Lowest warranty rate in the industry
• U.S. assembly of popular models
Discover hat ou’ve een Missing. DETECT O E FECT O ™
156 PROFOOD WORLD | February 2023 | www.profoodworld.com
#206 – 9775 188 St., Surrey, B.C, Canada V4N 3N2
Phone: 778-298-8292
www.apexmotion.com Email: info@apexmotion.com
Apex Motion Control is a passionate group of highly skilled, creative thinkers dedicated to developing innovative and automated equipment solutions that helps automate highly repetitive tasks within the food and baking industry.
Our equipment experts and engineers have a deep understanding of the industry and provide installation and support of our systems across the world, which includes Canada, USA, Korea, Australia and Europe.
We design and manufacture turn-key automation systems specializing in robotics, machine automation and vision for the baking and food industry.
We develop, innovate and introduce equipment process automation that helps our customers increase production capacity, lower manufacturing costs, reduce downtime and reduce workplace injury.
MAKE LIFE SIMPLE. HIRE A ROBOT
Visit our website — www.apexmotion.com
Follow us LinkedIn: https://www.linkedin.com/company/apexmotion/ Facebook: https://www.facebook.com/ApexMotionControl/
Need anything else? Email us at info@apexmotion.com
Since 1983, Assured Automation has been Making Valve Automation Easy for our customers. Assured Automation is a leading supplier of automated valves; compact on/ off valves, 2-way ball valves, 3-way ball valves, butterfly valves, plug valves, lead-free valves, PVC valves, stainless steel valves, fire-safe valves; as well as quarter-turn electric and pneumatic valve actuators, digital flow meters, mechanical flow meters and valve accessories.
Our customers appreciate the quality products, excellent service, and ability to help solve unique challenges. By focusing completely on valve automation, we have developed unmatched expertise in the field, making us an invaluable resource.
In addition to our standard offering of stocked products, we provide special order and custom assemblies for unique applications. Easy selection of quality products is what our customers have come to expect and what we strive to provide every time.
Build, view, price, and order valve packages easily and quickly with our unique online Valve configurator. Simply click the configurator icon and start choosing your options. Photo, part number, description, and price all update instantly.
Our new 3D Configurator provides on-demand 3D CAD models and dynamically generated PDF datasheets. This new tool significantly reduces design time for anyone specifying valves for a project.
Assured Automation has been ISO 9001:2008 certified since 2010 and achieved the upgraded 9001:2015 standard in 2017. We became an ITAR Compliant Valve Manufacturer in 2018. These standardizations help us achieve our goal of consistently meeting customer needs to enhance satisfaction through thoughtfully defined objectives.
www.atlascopco.com/air-usa
In 2023, the Atlas Copco Group celebrates its 150th anniversary. As we pass this milestone, our unwavering commitment is to continue to provide innovation which empowers our customers to grow and drive society forward.
Headquartered in Rock Hill, South Carolina, Atlas Copco Compressors provides innovative solutions, including world-class air and gas compressors, gas generation and carbon capture systems, renewable gas fleet fueling solutions, air blowers, industrial chillers, process filtration, quality air products, and 24/7 service, including remote monitoring and auditing capabilities. Atlas Copco Compressors is your local, national, and global partner for all your compressed and gas air needs.
Atlas Copco Compressors’ promise is your goals are our goals. We fully understand that manufacturers cannot achieve their sustainability goals, and maximize today’s efficiency, without an efficient compressed air and gas system. To underpin this commitment, Atlas Copco were the first air compressor company to sign up to Science Based Targets (SBTi). It’s all about doing more and taking customers on the connected efficiency journey. Meaning going further and deeper in every aspect of our offering – a promise that extends way beyond products.
Axiflow Technologies is a U.S. based corporation that specializes in Sanitary Twin Screw Pumps. Twin Screw Pumping Technology is the use of two intermeshing feed screws, timed for non-contacting and rotating in opposite directions to create product flow.
Axiflow has 3 locations including an R&D Pilot Plant and Engineering facility in Charlotte NC and Fabrication Facility in Tampa FL. Twin Screw is all we do!
One significant benefit of Twin Screw Pumping Technology is the capability of the pump to operate at a given speed for the process conditions and then operate at a higher speed to perform the required Clean In Place (CIP) condition. This 2 in 1 capability simplifies the system to one pump and eliminates the need for the separate CIP By-Pass. There are several other process benefits which include low product shear, virtually pulse free, gentle pumping of soft solids, low NPSHr, high vacuum capability and others.
Why should a customer consider Axiflow first and foremost for their Positive Displacement pump applications?
Axiflow personnel has over 100 combined years of process and pumping experience in Food, Beverage, Dairy, Plant Based Foods and Pharma Industries, with the largest Sanitary Twin Screw Pump installed base and inventory in North America. The many applications handled over the years enable Axiflow to use their experience to help avoid pitfalls and assist our customers in determining the best processing solutions. Our Maintenance Technicians provide on-site start up and maintenance training support when needed.
Axiflow Technologies has a vast array of pump sizes and configurations available for either On-Site Testing or Rental. The typical free trial is 3 weeks from the date of shipment with only shipping cost incurred.
Our R & D Center and Pilot Plant in Charlotte NC offers Viscosity/Shear Rate Analysis and Product Process Testing. The tests are comparable to the actual processing conditions. Send us your samples and we will provide data to give a better understanding of your products behavior in the proposed process.
Phone: 770/760-1130
www.haverusa.com
Email:
Behn + Bates is a leading global manufacturer of fillers, baggers, and palletizing machinery. We supply equipment using various degrees of automation and requirements for dry bulk materials and liquid products. We focus on consistent quality, weight accuracy, high output rates, simple operation, and user-friendly maintenance.
For the food industry, we specialize in food-grade machinery for liquid filling, baggers, and Palletizing.
Our aim is to provide the marketplace with high-quality machinery to get the job done right. Our machinery ranges from semi-automatic to fully automated equipment. Our product portfolio is below:
Our Machinery
• Valve Bag Packers
• Open-Mouth Baggers
• Form-Fill-Seal Baggers
• Big Bag Fillers
• Drum and Tote Fillers
• Pail and Canister Fillers
• Conventional and Robotic Palletizers
Let us help you provide the best packaged goods for your customers.
Bepex is the secret behind the industry’s most challenging solids processes. For over 100+ years, we have delivered continuous solids processing equipment and systems that do what others cannot. Whether it’s a difficult material transformation, dramatically improving product quality characteristics, or delivering a more sustainable method of processing, Bepex leads the way.
Our greatest strength is our Process Development Center in Minneapolis, MN. This is where new ideas, products, and technologies are brought to life in a pilot-scale setting. We can design, develop, and test new continuous processing systems, making tweaks to put together the best solution for your material.
We are the experts in solids drying and thermal processing. Our customers make us their first call when evaluating a new drying project because we can make quick and accurate assessments of their material, requirements, and advise on the most applicable technology for developmental testing.
With solutions for both dry (pressure) and wet agglomeration, we can dial in your density, particle size, solubility, and other key material characteristics.
We offer a line of grinding equipment that can produce particles ranging from ½” down to a D(50) of 3µm. Our technologies range from large block grinders that decrease downstream cook time, to an air classifying mill capable of drying and micronizing solids simultaneously.
Email:
www.big-d.com
We have an appetite to build and a zeal for success. Since our first project for Western General Dairies in 1967, our annual revenue has grown to more than $2 billion, with Food & Beverage | Cold Storage | Warehouse & Distribution facilities making up a significant portion of this revenue. And we are hungry for more.
A Language All its Own
Food and Beverage facilities are built on a language of their own – where critical control means systematically identifying, assessing, and controlling health hazards – from construction to production. We speak it. Without a hint of an accent.
In fact, we are fluent in Food Processing Plant language, not just Construction language. Besides the value of understanding your product requirements, we have purchasing power with national vendors/subcontractors in dairy brick, specialty flooring, insulated metal panels, refrigeration systems, sanitary drains, low temp doors, dock equipment, and numerous other specialty construction products/trades.
Menu of Capabilities
Our company understands the needs and demands of your facility and the requirements to comply with regulatory requirements and plant specifics such as FSMA, GMP, HACCP, PSM/RMP, and other programs. The ingredients for success for our customers
renovation/addition
an existing facility,
never
cold storage
facility,
Bunting is an industry leader in the design, manufacture, and sales of innovative magnetic technology, metal detection, and conveyor systems for many industries, including food packaging.
Bunting’s HF Series Drawer Magnets provide powerful magnetic separation suitable for mechanical and gravity flow applications in all industries. HF Series Drawer Magnets are equipped with high-power magnetic cartridges, configured with arrangements of two or more cartridge trays that are staggered to increase contact with the product stream. HF Series Drawer Magnets come standard with our NUHI™ Neo Ultra High Intensity Cartridge Magnet.
Bunting’s metal detectors sense and reject extremely small particles of ferrous and nonferrous metal while maintaining efficient product flow. The quickTRON™ 07RH is a reliable solution for powders and fine granular materials. It has a fully automatic metal detection and rejection mechanism to minimize processing interruption.
Bunting’s pneumatic metal detection and separation equipment detects and rejects all ferrous metals, non-ferrous metals, and stainless steel metal contamination within enclosed pipe systems. They are ideal for implementation in pressure, suction, or vacuum conveyor lines.
Bunting’s custom design capabilities ensure that no matter what industry you are working in, you will receive a custom designed piece of equipment that meets the exact needs of your specific application.
516 Viking Drive, Virginia Beach, VA 23452 USA
Phone: 800-USA-PUMP
www.buschusa.com
Email: info@buschusa.com
Busch Vacuum Solutions combines the precision of German engineering with Americanmade know-how to offer an extensive range of vacuum pumps, blowers, and systems tailored for your unique application.
Busch is proud to offer high quality, reliable solutions crafted in the US. Our key products for processors are proudly constructed with a combination of US-made components and international materials - giving customers both reliability and value.
At Busch, quality and innovation come first. Our expert engineering team is committed to creating vacuum systems that meet the unique requirements of our customers. With such dedication to excellence, it’s no wonder we are a leader in system building!
Keeping your production running smoothly is our top priority. Our nationwide network of service centers or on-site Field Service Specialists provides expert maintenance and repair solutions, including 24/7 support for unexpected breakdowns. Invest in peace of mind knowing that with Busch you can maximize uptime, optimize safety, and improve efficiency.
OUR PRODUCTS:
• acuum umps
• lowers Compressors
• acuum Systems
• Spare arts Accessories
• Measurement E uipment
OU SE CES
• ationwide Field Service
• ationwide Service Centers
• acuum ump Exchange
• epair Overhaul
Phone: 417/831-1411 Springfield, MO | Grand Prairie, TX | Durham, NC | Modesto, CA
Central States Industrial Equipment (CSI) is an engineering, design, and fabrication partner for hygienic liquid processors. CSI also supplies value-added process components for the food, dairy, beverage, pharmaceutical, biotechnology, and personal care industries.
The CSI team includes experienced process engineers, project managers, and designers. We listen, analyze, and problem-solve every project regardless of size to ensure a successful outcome. CSI uses 3D scanning of your environment so you can visualize how your system will before we begin fabrication. We employ AR and VR technology allowing customers to review and critique the process of systems development. Our experienced and certified craftsmen, combined with ASNT Level II inspectors, ensure components and equipment meet regulatory industry standards.
We offer a variety of custom equipment such as Clean-in-Place, process skids, utility stations, transfer panels, holding tubes, valve manifolds, jacketed tubing, pump carts and more! Our Clean-in-place (CIP) systems are scalable to meet your needs today and in the future. Smart machine technology is used to enhance performance, flexibility, and reporting. Our process systems are designed to solve existing hygienic process issues and optimize new processes. Systems are skid-mounted and built on time, pre-tested, and ready for utility hook-up to avoid costly delays.
CSI has four warehouses located across the United States for the distribution of sanitary processing equipment along with installation materials including fittings, pumps, valves, tubing, and instrumentation. We also stock complete lines of corrosion-resistant Super Alloys™ AL-6XN® and Hastelloy® C-22®.
Processors, OEM’s, mechanical and electrical contractors, engineering firms, and resellers in the processing industry turn to Central States Industrial Equipment for its breadth of experience, depth of expertise, and innovation. More information can be found at www.csidesigns.com.
3249 East 80th Street. Cleveland, OH 44104 USA
Phone: 800/641-9000
www.clevelandgear.com
Email:
The Cleveland Gear Company has been manufacturing gears for over 100 years.
An early member of AGMA, Cleveland is a pioneer and world leader in worm gear technology. Today, Cleveland Gear manufactures all types of open gearing including: helical, double helical, spur & worm gear.
We also provide a wide variety of enclosed gear drives: Helical shaft-mount & Screw Conveyor, Standard worm-gear reducers (1.3” to 36” C.D.), Standard parallel shaft and Custom enclosed drives. New products include Stainless Steel Worm Gear Reducers.
Cleveland further repairs reducers of all types and will reverse engineer drop-in replacements for larger obsolete gear boxes. We have provided “drop-in mounting” replacements for: Philadelphia Gear, Linkbelt, Foote-Jones, Falk, Nuttall Gear etc...
Cleveland recently launched its Stainless Steel Worm Gear Speed Reducer offering for the Food & Beverage markets. PRODUCT FEATURES INCLUDE:
• 316 Cast SS Housing, Covers & Motor Flanges.
• 303 SS Solid & Hollow Output Shafts.
• O-ring sealed Bearing Covers & Motor Flanges.
• Double lip, Spring loaded Encapsulated Viton seals.
• All fasteners are SS solid cap screws & all housing plugs are SS male type.
• Every unit includes a Mounting Accessory Kit – SS motor mounting bolts, SS breather vent & O-ring to provide a positive seal between the motor & gearbox flange.
• STAINLESS REDUCERS ARE ASSEMBLED TO ORDER IN THE USA & SHIP IN 3 TO 4 DAYS.
Phone: 360/694-1501
www.palletizing.com
Email: pallsales@colmac.com
Columbia’s conventional palletizers are the most flexible palletizing solutions available and handle virtually every package type, including shrink bundles with and without a pad, plastic totes, high CG, unwrapped trays, and more.
Part of the flexibility comes from Columbia’s ability to provide zero time changeover from one SKU or package type to the next.
Industry Leading Standard Safety Features
Columbia’s standard safety package contains Category 3 electrical safety components, including dual circuit safety interlocks & full height light curtains. This safety package provides a fully guarded, Performance Level D palletizer to keep your employees safe while enhancing OEE and production demands.
Complete System Integration
Columbia Machine manufactures conventional high speed, high level, floor level and robotic palletizers, load transfer stations and provides complete system design and integration. With the most flexible and modern palletizing solutions available, Columbia is the leading palletizer solutions provider in North America.
High Performance AND Sustainability
Columbia has a palletizing solution for virtually any application, each equipped with standard features designed to safely maximize OEE, throughput and uptime.
301
Phone: 877.204.7444
Email: collcsales@colmac.com
https://columbiaokura.com/products/
Columbia/Okura LLC is a leading robotic palletizing integrator. Our team applies expert knowledge, gained through over 25 years of business, with the right tools to solve customers’ “End of Line” production challenges for a diverse range of businesses, products, and applications. The historical success of our company can be attributed to an exclusive focus on end of line palletizing systems and applications.
We provide design, integration, and commission of end of line robotic palletizing system. Integrating most equipment, including:
• industrial robots
• cobots
• automated bagging machines
• integrated e uipment
• alve packers
• allet and sheet dispensers
• Conveyors
By providing custom engineered solutions, we develop robotic palletizing systems to meet demanding customer requirements.
Our team are well versed in providing solutions for most major manufacturing industries including:
• Animal utrition
• eans, Lentils, ulses
• uilding Materials
• Chemical roducts
• Food everage
• Milled roducts
• Medical harmaceutical
ith nearly robotic palletizers installed throughout orth, Central, and South America, and beyond, Columbia Okura is unparalleled in the industry.
Phone: 785/825-1611
www.coperion.com
Email: info@coperion.com
For decades, global food manufacturers of all sizes have relied on the extensive application experience and design expertise offered by Coperion and Coperion K-Tron. Our components for feeding and material handling offer the highest technology options, while our systems designs can help to optimize and automate your process.
A variety of equipment designs are available, depending on the specific needs and sanitary requirements of the application. Whether adhering to EHEDG, FDA, FSMA and/ or GFSI initiatives, standards and regulations, the systems and equipment provided by Coperion and Coperion K-Tron ensure optimal product and process safety.
With more than 30 locations, 2,500 employees and numerous representatives worldwide, Coperion and Coperion K-Tron can respond quickly and offer local support. In addition to the highest accuracy standalone ingredient feeders, or rotary and diverter valves specifically designed for the highest hygienic standards, we also offer a wide variety of pneumatic receivers, product pick up components, and unique quick release bin vents for silos and large bins. In addition, our high efficiency twin screw extruder systems provide versatile configurations ideal for a wide variety of food extrusion applications.
Whether transferring the raw ingredients from the truck, railcar, bulk bag or silo, and/ or batch weighing, feeding and scaling of macro and minor ingredients, all the way to the mixing and twin screw extrusion process steps, Coperion and Coperion K-Tron have experienced technical engineers available to discuss your application in detail.
At Coperion and Coperion K-Tron, we offer not only the best components, but even better systems…the recipe for perfect food!
1251 NW Briarcliff Parkway, Suite 500, Kansas City, MO 64116 USA
Phone: 877/4-CRBUSA
www.crbgroup.com
Email: info@crbgroup.com
Safe, high-quality, value-driven food + beverage facilities fuel your growth and success.
Scale up a small process or expand and improve a large-scale operation. No matter your size or goals, you need an adaptable facility that quickly responds to consumers’ constantly changing tastes and meets increasingly strict regulatory standards. Get engineering, architecture, construction and consulting solutions to help you:
> Increase production rates
> Optimize energy efficiency
> Improve speed to market
> Achieve food safety compliance
Have confidence in your project knowing that we understand the intricacies of your operating environment and the complexity of your industry. From planning to production, you’ll get a safe facility that meets your budget and requirements, minimizes long-term operating costs and maximizes your return on investment.
Quality food + beverage products rely on excellent processing plant design and construction. Deliver the best products to your community and the world with our help.
4300 Round Lake Road W
Phone: 800-328-5558
delkorsystems.com
Email: info@delkorsystems.com
We are a leading manufacturer of advanced case packing and cartoning machinery. Our talented 350+ employees have proven to be one of the most inventive teams in the packaging industry. Delkor has changed the landscape of retail ready packaging and is now widely recognized for creating a new generation of cutting-edge machinery and fresh package concepts.
Form
Form both corrugated and paperboard material, the Trayfecta® line of Formers can handle cases, cartons, and trays at various speeds and sizes.
Pack
Quick changeover, compact footprint, and smart machine technologies set these world class case and carton packers apart from the rest.
Close
Closing solutions for tri-seal and flange seal cases, cartons, trays, and retail ready packages. Small footprint, and smart machine technology come standard.
Palletize
Finish your line with a robotic palletizer. Available in multiple in/out options, for a variety of package formats at once.
For more information on Delkor’s highly adaptive and intelligent packaging equipment using smart package designs, visit delkorsystems.com
Since 2015, ENR has annually ranked us the #1 Food and Beverage Design Firm. We’ve built a specialized team who understands the unique challenges faced by food manufacturers and how to solve them. From small-scale studies to large greenfields and everything in between, we have the internal resources to support you.
Our more than 650 employees spend every day working on food and beverage projects, and our project managers average more than two decades of experience in the food industry. We specialize in:
• Food Safety
• Project Definition
• Facility & Process Audits
• Site Search
• Sustainability
• Civil, Structural, Architecture
• Mechanical
• Electrical
• Plumbing
• Wastewater
• Process Design
• Modeling & Simulation
• Automation
• Packaging Integration
• Project Management
• Permitting
• Procurement
• Construction Management
• CQV
Deville Technologies is a solutions oriented manufacturing technology company that provides high capacity shredders dicers and slicers for cheese, meat, fruits and vegetables. We work with companies ranging from Fortune 500 members to small entrepreneurs requiring sanitary, durable, practical, and efficient food cutting equipment.
Cutting edge technology coupled with traditional craftsmanship, quality materials and intelligent, hygienic principles, allow us to deliver a complete line of solutions that provide high performance with low maintenance.
With over 40 years experience in the sanitary food equipment industry and our exclusive North American partnership with FAM (one of Europe’s most respected brands in the industry), we provide the ultimate food cutting solutions.
Deville has two state-of-the-art Client Centers so that clients may run trials with our equipment without incurring the cost of halted operations. Our detailed trial reports provide the necessary data to review cut quality, options and gain an understanding of the impact our sanitary cutting equipment will have on their business; all of which assist informed investment decisions.
Our technical experts are always available to meet our client’s needs; whether it be to provide telephone-based support, a customized engineering solution to solve a specific challenge, or to schedule an on-site visit to assist with expansion planning.
We have a vast inventory of genuine parts for all our equipment readily available; because we understand the cost of recurring labor for replacing parts can quickly consume a maintenance budget.
4500 110th Ave N. Clearwater, FL 33762
Phone: 727/461-3477
www.dougmac.com
Email: info@dougmac.com
A leading container washing and sanitizing systems provider specializing in designing and manufacturing innovative solutions industry-built to address your unique needs.
Quickly and efficiently clean containers of various sizes and shapes including pans, trays, molds, screens, pallets, lugs, totes, racks, bins, vats, baskets, buckets, waste containers, scale parts, drums, and shipping/distribution containers.
Discover how to proactively implement food safety compliance, lessen risk, changeover time, save time and energy, streamline manpower and throughput, grow revenue by reducing costs and increasing productivity.
We can design and build a customized washing and sanitizing system for you.
Our standard and custom racks help clean your containers, tools, and equipment, as well as racks specifically created to hold scale parts chutes, buckets, feeder pans, and weigh hoppers. Designed and manufactured in the USA using only the highest quality materials. With over 80 Standard models we have an effective, efficient solution to meet your processing/manufacturing requirements and budget.
Eirich Machines, member of worldwide Eirich Group, is a leading designer and manufacturer of top-quality mixers, blenders, dryers, grinders, and ancillary equipment. Eirich Machines has two product lines, American Process Systems® (APS) and EIRICH, and offers the most comprehensive range of material processing equipment for manufacturers in various industries across the globe. With over 150 years of experience, we take pride in our continuous drive for research and innovation to deliver the most efficient and reliable material preparation solutions.
The American Process Systems® product line includes sanitary equipment for blending, mixing, drying, and reacting:
• Fluidizing Paddle Blenders
• Ribbon Blenders
• Paddle Blenders
• Plow Blenders
• Ancillary equipment (bag dump workstations, filters, delumping units, and more)
Our fluidizing paddle blender OptimaBlend® is efficient yet gentle, it ensures very homogeneous mixes in short times. The capacity of the OptimaBlend® ranges from 1.5 ft³ to 400 ft³, lab model FPB-1P5 is perfect for small batches and R&D.
The newest addition to our APS product portfolio is the OptimaDry® Microwave Mixing & Drying System. It’s suitable for applications with sensitive ingredients, where characteristics like aroma, consistency, color, and nutrition must be contained. Application examples include herbs, spices, and hemp.
We have a fully equipped, in-house test lab in Gurnee, IL, and welcome you to personally test your product in our equipment. If you want to avoid traveling, you can sign up for a virtual lab test where you will be able to follow the test via livestream video and interact with our test lab manager. You can also rent our machines and do testing at your own facility.
Contact us today with questions or to book a lab test. We look forward to hearing from you!
2350 Endress Place, Greenwood, IN, 46143 USA
Phone: 888-ENDRESS
us.endress.com
Email:
Endress+Hauser is a global leader in measurement instrumentation, services and solutions for industrial process engineering. They provide process solutions for flow, level, pressure, liquid analysis, gas analysis, temperature, recording and digital communications, optimizing processes in terms of economic efficiency, safety and environmental impact. The company serves a variety of industries, including chemical, oil & gas, food & beverage, water & wastewater, life sciences, power & energy, and primaries & metals.
Endress+Hauser, a Switzerland-based company, was founded in 1953, and expanded operations to the U.S. in 1970. More than 80% of all Endress+Hauser instruments ordered and shipped within the U.S. are manufactured in the U.S. This means customers can rely on Endress+Hauser to deliver the products they need quickly. This strong manufacturing base is complimented by a complete network of sales partners and service locations to support its customers – wherever their instruments are installed.
Premium services, customized solutions, project management and IIoT applications round out Endress+Hauser’s offering, helping customers gain efficiency, increase quality and maximize plant availability.
Phone: 417/736-2195
ensightsolutions.us
Email: sales@ensightsolutions.us
EnSight Solutions is dedicated to serving our customers with creative solutions to help them improve quality, increase efficiency and protect team members. Our team brings decades of food processing experience to help every customer overcome their challenges and meet their goals.
The EnSight lineup includes Likwifier, A-One and Bridge–all storied brands with reputations for durability, quality and reliability. Whether you need to move, shape, mix or blend product or automate processes, we have the machine you need to get the job done right.
The EnSight solutions design team all have hygienic equipment training and experience, ensuring every machine solution we build will meet your washdown and sanitation needs, while also reliably performing for years to come. In addition, EnSight works closely with Stäubli, the premiere hygienic environment robot manufacturer. We have been honored as the Stäubli Food Processing Strategic Partner of the Year in 2021 and 2022.
Our experience and industry partners help us design, tailor and build top-quality, hygienic equipment you and your organization can rely on for years to come.
We’d love to help you share your special product with the world!
Your Best Defense Against Metal Contamination Whether it’s protecting equipment from damage, or ensuring your consumer products are free of metal contaminants, Eriez offers equipment and systems to protect product purity and increase the efficiency of your process--from the moment ingredients enter your plant to the time the end product ships from your dock. Eriez’ wide range of Metal Detectors, Magnetic Separators and Vibratory Feeders, Screeners and Conveyors are designed for the unique needs of the food manufacturing industry.
Xtreme® Metal Detector—Eriez’ Xtreme® Metal Detector sets the standard for “bestinclass” performance and offers the greatest dollar-for-dollar value of any detector on the market. This feature-rich, multi-frequency unit is designed to achieve the highest levels of sensitivity to detect small ferrous and non-ferrous metal contaminants.
Magnetic Separators — Eriez, the world leader in magnetic separation technology, offers the widest selection of permanent and electromagnetic equipment to remove ferrous contaminants from any process application. From purifying powder with a Dry Vibratory Magnetic Filter to removing steel fragments in a grain chute with a low-cost ProGrade grate magnet, Eriez has a solution for every process. Our line of Magnetic Separators effectively draw out fine tramp metal along critical points of your production line. These separators— including Plates, Grates and Traps—come in different styles and magnetic strengths, so you can choose the right product for your particular needs.
Feeders... For Every Application — Looking to feed, convey, meter or screen a food product? Start with Eriez’ line of Electromagnetic and Mechanical Feeders, designed for everything from bulk granular ingredients, fine fluffy powders and sticky or even leafy food products. Our line of compact electromagnetic feeders are used for everything from simple metering to moving difficult leafy products, powder/talc or gummies, as well as high- speed packaging and high material load applications.
ESI Group is a nationally recognized design-build engineering and construction management firm dedicated to supporting companies that safely feed the world. We are experts in the design and construction of cold storage facilities. Our team of experts focus on food and beverage storage solutions to improve efficiencies, mitigate costs, and ensure compliance.
ESI Group wants to improve the way you work today and meet the demands of tomorrow. In our 30+ years the team at ESI Group has completed more than 475 quality food automation, distribution, and specialty food manufacturing and processing facilities including those earning LEED Certification. This includes companies who work with meat, dairy and cheese, bakery, poultry, fruit, vegetable, organic, and beverage, as well as grocery, foodservice, and cold storage.
Our highly experienced team of specialists is accredited and consists of ESI Design Services and ESI Constructors. Together, they provide services including site search and evaluation, process layout, simulation and visualization, facility layout and design, material handling analysis, and construction management.
Our Single Source, Three Phase Approach provides better communication, faster completion of projects, and lowers overall costs. By managing each project from concept to completion, ESI Group ensures a Guaranteed Maximum Price and each facility will meet or exceed industry standards. These factors, combined with our first-rate safety record, are key to obtaining an 85 percent rate of repeat work.
At ESI Group, we take pride in our history, our work and our long-term client relationships. Our success is driven by serving our clients’ needs and by providing value to help build, manage, and grow their businesses. We put our customers first, so you can put your customers first!
To learn more about our cold storage solutions, and our company, please visit ESIGroupUSA.com.
1377 Motor Pkwy. Ste 310 Islandia, NY, 11749 USA
Phone: 800/99-FESTO
www.festo.com Email:
Festo US has become known as an innovative and preferred supplier of pneumatics and electromechanical automation solutions through its 50 years of working with U.S. partners.
A leading organization helping to improve customer productivity, Festo US has made significant investments in its U.S. infrastructure, from people to resources. In 2016, the company opened the Festo Regional Service Center in Mason, Ohio. The service center lowers customer inventory requirements by stocking components and ensuring prompt shipment. The facility houses the Festo Customer Solutions Center for custom solutions.
With a range of 30,000 products, including Fabco-Air inch-based pneumatic cylinders, Festo supports the most complex automation and production requirements across multiple industries, including medical testing and diagnostics, providing smart automation solutions from a single source. Within this line are Festo’s “core range” of affordable pneumatic and electromechanical products that meet 80% of all application needs. The core range simplifies ordering, lowers the cost and time of product acquisition, and improves the uptime of systems through global availability of core parts.
Digitalization is a core competency of Festo. The online catalog, engineering productivity tools, component-based digitalization capabilities, and artificial intelligence (AI) initiatives are all integral to the company’s digital transformation capabilities on behalf of customers.
Festo Didactic Learning Systems, the world-leading provider of equipment and solutions for technical education, creates hands-on technical training systems and digital and blended learning solutions to help train the next generation of workers. Didactic Learning Systems training can be on location or time-and-location independent.
Flexicon Corporation is a leading worldwide manufacturer of bulk handling equipment and systems that can handle virtually any bulk food material, from large pellets to submicron powders including friable materials, free- and non-free-flowing products, and materials that pack, cake, plug, smear, fluidize or separate.
The Flexicon line of stand-alone equipment includes: Flexible Screw Conveyors, Tubular Cable Conveyors, Pneumatic Conveying Systems, Bulk Bag Unloaders, Bulk Bag Conditioners, Bulk Bag Fillers, Bag Dump Stations, Drum/Box/Container Dumpers and Weigh Batching and Blending Systems. Numerous model configurations are offered within each equipment category, as basic, low-cost units up to engineered, automated, highcapacity machines.
Customers can alleviate the burden and risk of designing large-scale bulk handling systems, coordinating multiple suppliers, integrating components and trouble-shooting start-up, by relying on Flexicon’s Project Engineering Division for it all. Regardless of whether customers purchase one piece of equipment or an automated plant-wide system, the Flexicon Lifetime Performance Guarantee assures a successful result. Flexicon equipment is available in carbon steel, carbon steel with stainless steel material contact surfaces, and In all-stainless construction finished to food, dairy, pharmaceutical or industrial standards worldwide.
Flexicon’s worldwide testing facilities simulate full-size customer equipment and systems, verify performance prior to fabrication, demonstrate newly constructed equipment for visiting customers, and study the performance of new designs. Flexicon manufactures equipment in the USA, United Kingdom, Australia and South Africa; maintains dedicated factory representation in Spain, France, Germany, Singapore, Indonesia and Malaysia; and also markets equipment and systems through an extensive network of Applications Engineers worldwide.
6580 Snowdrift Road, Allentown, PA 18106
Phone: 610/973-8200
www.flexlink.com
Email:
FlexLink, a Coesia company, is a leading manufacturer of food handling conveyors and automated food processing equipment. With a dedicated team of industry specialists, we support the food industry worldwide. We provides systems that are easy to design, assemble, integrate into machines and eventually modify and redesign, significantly facilitating new product introductions.
With over 40 years of experience delivering turn-key solutions to the food industry, we are the perfect partner when facing your production challenges. Working closely with customers, we provide innovative, automated solutions to produce goods smarter, safer and at lower operating costs. With a dedicated team, we support the industry directly in over 31 countries and are represented in more than 60.
FlexLink focuses on providing our global customers with the highest quality service and products. We focus on improving your overall equipment effectiveness (OEE) by balancing production flow, offering compact solutions, and lowering your maintenance cost and requirements. We offer high quality products that are easy to wash down and reduce the amount of bacteria build-up – reducing your chances of a recall. Our toolbox of products and services include line design, conveyor equipment, product manipulations and line balancing and controls.
FlexLink offers a variety of options for the food industry such as: Stainless Steel/Hygienic Conveyors, Chain Conveyors, Modular Belt Conveyors, Spiral Conveyors, Elevators, Line Balancers, Line Control, Cleaning Devices and Robotic Palletizers.
As part of your collaboration with FlexLink you can also utilize our line simulation tools. We truly offer a complete solution for all your production needs.
You can find out more about our solutions and global team by visiting our website www. flexlink.com.
FOCKE & CO is an international leading engineering company for packaging machines within the tobacco, food, savoury snacks, and hygiene industry. With more than 60+ years in business, we are proud to offer high-level machinery with top technology. FOCKE & CO is well recognized for providing engineering solutions for primary packaging, end–of–line packaging, and palletizing.
FOCKE & CO’s case packers offer careful handling alongside the flexibility to accommodate american case, tray, and tray-with-lid packaging. In fact, our machinessuch as the HFP Base (Highly Flexible Packer) - provide multiple pack configurations that normally cannot be achieved with a typical case packer.
And, like all our machines, it stands true to our corporate philosophy to provide packaging machines that:
- Conform to the highest quality standards and
- Stand out for their efficient production, reliability, and longevity.
With a clean machine concept and a compact footprint, our HFP Base is designed to fit perfectly into typical snack food production lines.
With sales and service centers worldwide, FOCKE & CO has the capabilities to deliver local technical support, training, and spare parts. FOCKE & CO has repeatedly set new benchmarks in terms of output and product quality. Our ground-breaking technologies in the field of motion control combined with components featuring extreme dimensional accuracy are highly acclaimed in the industry. This is why we are the leader in Packaging Solutions.
Your number one priority is cleanliness, which is why we build drainage systems that are sanitary and safe for all types of food production applications. Drains matter — they’re the most used tools on your production floor. They see constant traffic, experience non-stop use, and require constant cleaning, no matter how busy things get.
Thankfully, we can help with drainage systems that stand up to the roughest wear, keep both your floor and products bacteria-free, and are easy to clean. Whatever your application, we have the custom drainage solutions to fit your unique needs.
- FoodSafe Slot Drain - People, equipment, and your products are constantly moving, and your floor needs to stay safe. That means you need drainage that is bacteria-resistant, durable, and easy to clean to sanitation standards — you need a Slot Drain system. Our Slot Drain systems are built to integrate into your existing workflow and equipment placement and feature no-niche designs that are easy to clean, with options to suit all applications.
- FoodSafe Trench Drain - When solid materials accumulate and plug a drain, it can create backups, which can cause accidents and delays in your workflow. With several design options to choose from, you can safely, quickly, and easily dispose of solids.
- FoodSafe Area Drain - Standing water can cause a multitude of issues in your facility, from bacterial accumulation to accidents, terrible odors, and worse. Our area drains can help make your facility more hygienic, safer, and can help reduce nasty odors. FoodSafe area drains also feature tamper-proof strainers, allowing you to protect your facility by ensuring that only designated employees can access them.
Contact us today to talk about any upcoming projects - our drainage experts are ready to assist!
Suite #110 – 13911 Wireless Way, Richmond, BC V6V 3B9 Canada
Phone: 604/232-4145
www.fpscorp.ca
Email: sales@fpscorp.ca
FPS Food Process Solutions is a global leader in turn-key food freezing and cooling equipment. We provide innovative systems to ensure the highest efficiencies and to meet the most stringent sanitary demands. These factors transform into superior food quality, lowered total cost of ownership and maximized profits.
Established in 2010, FPS has a combined 600,000+ sq. ft (55,742 sq. meters) of space in 14 locations including its Canadian headquarters, manufacturing and warehouse facilities as well as international sales offices across five continents.
We offer a range of innovative technologies for maximizing performance and ensuring the highest hygienic standards, all integral aspects to lowering total cost of ownership. They include Spiral Freezers, IQF Tunnels, Impingement Freezers, CF/VRM MultiPass™ Freezers and the Spiral Immersion System (SIS)™.
Industry Sectors
• Meat oultry
• Fruits egetables
• eady-to-Eat, eady-Made Meals
• Alternative roteins lant- ased
• et Foods
• Seafood
• akery aked Goods
CUSTOM AT O T OUG COLLA O AT O
We believe in building long term partnerships with our customers. We listen to each of your unique needs and concerns and incorporate these in your freezer and cooler design. From basic packaged products to sensitive, ready-to-eat foods, our custom designs ensure your equipment is optimized for each application.
245 E North Avenue, Carol Stream IL, 60188
Phone: 630-629-9900
www.frain.com
Email: sales@frain.com
From kettles, bins and totes to extruders, granulators, hoppers and boilers, Frain has a wide range of processing equipment ready to ship to your facility in days – not weeks or months. Each machine that ships out from our facility arrives to yours completely dialed into your product so when the machine arrives at your facilty, you’re ready to begin your manufacturing process.
Equipment Rentals:
Invest only in what you need when you need it with processing equipment rentals from Frain. We only carry industry-leading brands that ship dialed into your product so you can begin production faster and more efficiently. Ideal for seasonal items, special edition products and new product development, Frain’s processing machinery rental program allows firms to conserve capital and maximize profit. No long-term commitment necessary.
Pay As You Go:
With Frain’s Pay As You Go flexible capital program, you’ll only pay for processing equipment as you use it. There’s no leasing and no large capital investment. Instead, you’ll have the financial flexibility to invest in more projects, take more chances and get products to market faster – and all on your schedule.
Consulting & Technical Support: Professional setup, inspection, repair and training is all part of the Frain difference. All Frain rentals and purchases come with up to 8 hours of technical training from Frain engineers to get you started – and we’re standing by to help with other maintenance and service to keep operations humming.
Contact Frain:
For more information on Frain and to inquire about the next piece of equipment for your processing line, contact us today at 630-629-9900 or visit www.frain.com. Need new packaging equipment? Frain can help with that too.
2410 Parview Road, Middleton, WI 53562 USA
Fristam is the leading manufacturer of high-performance stainless-steel pumps, blenders, and mixers. Our equipment is designed for precision and durability to outlast and outperform all others. Our products are made in the USA and we employ an expert staff of engineers to help you determine the best solution for your application.
Blenders and Mixers: Our Shear Blenders remove agglomerates and prevent lumps/ masses in product while reducing raw material usage and processing times. They easily and affordably improve existing mixing set-ups too, when placed after a mix tank they disperse any unblended particles. While Fristam’s Powder Mixer tabletop system provides quick and thorough, repeatable blending of wet and dry ingredients into a fluid stream.
Twin Screw Pumps: The versatile Fristam FDS Series is designed to be the easiest to operate and maintain, most reliable, robust and long-lasting twin screw pump available. It pumps the widest range of products gently and reliably and easily lifts product from totes and drums due to its high suction capability. Additionally the FDS pump handles both product transfer and CIP duties, eliminating the need for extra CIP pumps and piping.
Positive Displacement Pumps: Fristam offers the widest selection of PD pumps from heavy-duty, high-pressure to gentle, standard-duty to low-pulsation, and high-suction. Our FKL Series is built to last with heavy-duty construction that ensures hassle-free operation. The standard FKL is CIP’able with all parts in, a COP version is also available.
Centrifugal Pumps: Fristam centrifugal pumps serve as the industry benchmark for quiet, efficient, low-maintenance operations. They include standard-duty, heavy-duty, highpressure, front-loading seal and self-priming centrifugal pumps.
At Fristam, we know one size doesn’t fit all. That’s why we offer a wide selection of pumps, blenders and mixers.
From raw bulk materials discharge, to filling and packaging finished product in the container of your choice — and every process in between — GEA can engineer, manufacture and install the most appropriate equipment to suit your product handling requirements. GEA has long specialized in the field of filling and packaging applications, offering design, manufacture, installation and start-up services throughout the world.
Recent innovations include the GEA SmartPacker CX400 D-Zip and GEA LeakCheck and OxyCheck.
The GEA SmartPacker D-Zip is a continuous motion vertical packaging machine that creates re-closeable stand-up pouches for retail and food service. It combines fast, highquality operation with maximum flexibility and uptime. In addition to producing premium quality D-ZIP bags, this easy-to-use machine can produce more than 10 different bag styles for a wide variety of applications.
GEA LeakCheck and OxyCheck are inline quality-control systems that can be integrated into our thermoformers to verify the oxygen (O2) content of all MAP packages and identify leakages after the form-fill-seal process. We also offer filling solutions for sensitive and non-sensitive beverages. Our GEA Visitron Filler ALL-IN-ONE is an ideal choice for small- and medium-sized beverage manufacturers wishing to carry out all necessary functions, on just one machine. Customers packaging sensitive beverages can rely on the variety of top-class sterilization technologies that are offered. As an example, the GEA ABF 2.0 combines an aseptic blow molding module with aseptic filler and capper modules and features dry hydrogen peroxide-based sterilization technology for preforms and caps.
Powder packaging is another GEA specialty. Our range of multi-wall bag/sack fillers is designed to pack powdered products at rates from less than 1 ton/h up to more than 12 ton/h with an accuracy better than 10 g (0.35 oz).
14 Worlds Fair Drive, Suite C, Somerset, NJ 08873-1364 USA
Gericke is a fourth-generation, family-owned company offering a complete range of state-of-the-art equipment and expert engineering services for the automated handling of dry, bulk raw materials from the railcar, silo or bulk bag through to the processing and filling lines. The company custom-designs, manufactures, installs and services pneumatic conveying systems, sifters, feeders, mixers, valves, bag handling stations and other products and accessories. Founded by Walter H. Gericke in 1894 in Zurich, Switzerland, the company operates nine facilities in Europe, Asia, South America and North America, including the Gericke USA headquarters in Somerset, New Jersey, encompassing, design engineering, manufacturing, assembly, testing, sales and technical services. Only Gericke offers the scale, capabilities and experience of a worldwide organization with the handson, personal attention, care and concern for each customer of a family company.
Gericke offers food-grade bulk processing equipment and systems to promote the safe, sanitary, dust-free transport and secure storage of ingredients for food, beverage, nutraceutical and other products. Its GMS Multiflux® batch mixer has earned acclaim for achieving maximum homogeneity quickly with a gentle mixing action that protects fragile ingredients. Similarly, the Pulse-Flow™ PTA dense phase pneumatic conveying system has become standard equipment for gently transporting fragile ingredients up to hundreds of yards, whether powdered, granular, coarse or agglomerated. The Gericke Nibbler for deagglomeration and other size reduction needs features an optional proprietary advance that helps safeguard against combustible dust issues.
Gericke offers free material testing services in its test laboratory at the company’s Somerset, New Jersey headquarters. For a test with your material, facility tour or quote, call 855/888.0088 x 805 or see GerickeGroup.com.
P.O. Box 1217, Mansfield, OH 44901, USA
Phone: 419/755-1011
GRPUMPS.COM Email:
When you specify Gorman-Rupp, you benefit from worldwide service centers, knowledgeable engineers and a selection of nearly 3,000 pumps. Gorman-Rupp has been manufacturing pumps and pumping systems since 1933. Many of the innovations introduced by Gorman-Rupp have become industry standards.
Gorman-Rupp has manufactured high performance, high quality pumps and pumping systems required for lasting service in the industrial, water, wastewater, sewage, municipal, construction, petroleum, and OEM markets. Our extensive line of products includes, self-priming centrifugal, submersible, trash, priming-assisted and rotary gear pumps. In addition, Gorman-Rupp manufactures a complete line of state-of-the-art packaged lift stations and booster stations that include pumps, motors, controls, piping, accessories and enclosures.
Gorman-Rupp’s 825,000 square foot manufacturing facility and corporate headquarters located in Mansfield, Ohio, accommodates the most advanced technology available. State-of-the-art, fully automated machining centers provide high-speed, high-quality machining of pump castings.
We have an experienced staff of engineers dedicated to the design of the most efficient and serviceable pumps in the industry. Our representatives are trained to help you select the proper pumps and related equipment for your specific application. They are also available to offer suggestions on maintaining your equipment for maximum performance.
Should a problem occur, Gorman-Rupp is available to provide service and fast parts supply for your pump. Cast Iron, Bronze, 316 Stainless Steel, CD4MCu and G-R Hard Iron are available to handle your corrosive and abrasive fluids. Gorman-Rupp pumps are at home anywhere dependability and ease of service are essential.
That’s what makes Gorman-Rupp THE RIGHT PUMP FOR THE JOB. Markets: Industrial, Mining, Construction, Municipal Sewage, Petroleum, Agriculture, OEM
1050 Nepperhan Avenue, Yonkers, NY 10703
Phone: 914/968-8400
www.graphalloy.com
Email: 914/968-8400
FDA Acceptable GRAPHALLOY® Bushings eliminate maintenance and frequent replacements in food applications. Graphalloy is self-lubricating and requires no grease or oil, performs in temperatures from –400°F (-240°C) to +1000°F (535°C), works submerged in low viscosity and corrosive liquids, and there is no lubricant loss in steam or pressure wash.
A bakery oven OEM was using rolling element bearings on the conveyor circuit of a tunnel oven with a temperature range from 450°F to 650°F. To reach these bearings, mechanics would have to crawl over the oven belt when the machine was shut down, thus causing damage and presenting a safety risk. Another issue was caustic washdowns that rusted the ball bearings. In some applications, bearing life was as little as 2 weeks. They were researching solutions when they discovered GRAPHALLOY. Graphalloy self-lubricating bushing materials thrive in high temperature environments, handle caustic washdowns, and are maintenance-free. These Graphalloy bushings in stainless steel pillow block housings have been running in this application for several years with no issues.
A seafood processing plant in the Southeast was running a conveyor in their freezer area to “flash-freeze” fresh seafood. The environment is a difficult one: The temperature is cold (28°F/-2°C) and wet and the system requires frequent washdown. The conveyor bearings were being replaced every month. The plant maintenance superintendent contacted GRAPHALLOY about the problem. It was determined that the current bearings could not hold lubrication under these conditions and, as a result, breakdowns were occurring frequently. Graphalloy 4-bolt flange block assemblies were installed and have been running successfully for more than five years!
See all the Leaders in Processing at www.profoodworld.com/leaders
Hapman is a worldwide manufacturer of bulk solids handling equipment including conveyors, feeders, bag handling equipment, lump breakers, liquid/solid conveying systems, and more.
Hapman understands your needs to maintain product quality and safety. We offer sealed conveyors, dust containment, cleanability options, foodgrade components, automation through controls, minor ingredient addition, and custom-engineered, complete systems. Our application experts have extensive experience with bakery products, dairy product, grain products, snack products, sugar and confectionary products beverages, and more.
Rely on us for the expertise to design and deliver equipment and systems that rise to meet your unique challenges. Our engineers have experience with over 2,700 distinct materials, 12,000+ applications and customer relationships in 26 countries.
Trust Hapman equipment to stand up to your application. We draw on decades of proven engineering, fabrication, and materials of construction to ensure long life and reliable performance. We can point to a 98.9% success rate, with only 1.1% warranty claims since 2014. Some Hapman equipment is still operating in the field after 40 years.
Hapman equipment speeds cleaning and batch turnarounds. It’s designed for fast, easy disassembly and reassembly to maximize food processing uptime. Since 2012, we have made 22 design improvements to maximize serviceability, including 12 made specifically for tool-less access.
Hapman maintains live support 24 hours a day, seven days a week, 365 days per year to provide customers the parts or service needed to maintain uptime. You can rely on Hapman to keep your process moving.
Looking for the lowest total cost of ownership and highest quality packaging automation solutions available? We can help you navigate today’s complex, rapidly changing packaging landscape. We help balance costs and functionality with innovative and emerging processes, materials, and advanced technologies; enhance your profitability and improve the performance of your primary and secondary packaging operations. Our full-service solutions address installation, training, spare parts, service and customer support.
Our capabilities span robotics and automation, thermoforming, tray sealing, filling, flowwrapping, stretch, blister, skin pack, and vacuum. Every smart, connected G. Mondini and ULMA packaging platform utilizes Rockwell Automation’s Integrated Architecture to reduce solution complexity and maintenance costs, while realizing better quality, capacity, and throughput. We also partner with PTC to incorporate Augmented Reality tools. It all lets us leverage data to enhance your operation and realize greater productivity and efficiency.
We are focused on the environment, aiming to help you meet demand while meeting your sustainability initiatives. Our sustainable packaging options include less plastic use, thinner gauge films, optimized package sizes, reduced film scrap, and alternative packaging materials.
Our customers rely on us to help them optimize their overall packaging investment, from start to finish. We offer package design and prototyping services, and can help solve production concerns with comprehensive flexible and efficient systems. We help strategize how to tackle today’s most complex packaging challenges, such as sustainability, eCommerce, robotics and digital transformation.
We focus on lowering your TCO and offering the most reliable systems available. With consistent, professional and timely customer and technical service, our partnership extends well beyond your purchase.
21121 Cabot Blvd. Hayward, CA 94545 USA
Heat and Control®, a world-leading equipment manufacturer, offers the latest technology and the highest quality equipment for processing, coating and seasoning, conveying, weighing, packaging, inspection, and control/information systems and develops innovative solutions for production challenges. Established in 1950, they are a privatelyowned company and have 12 manufacturing, warehouse, and associated facilities, 10 test centers and more than 30 offices globally.
Heat and Control builds food processing and product handling equipment for the food industry, and it can also integrate complete lines and systems, including equipment for unloading, washing, storing, seasoning, coating, cooking, frying, roasting, conveying, weighing, inspecting, and packaging. Heat and Control has partnered with other global manufacturing leaders, including Ishida (weighing packaging and inspection) and CEIA® (metal detection), and their brands include FastBack® (horizontal motion conveyors and on machine seasoning), Mastermatic (fryers), and Spray Dynamics® (coating and seasoning application systems). They can assist manufacturers with equipment for all types of food as well as provide pre- and post-sale technical support, including applications assistance, engineering, installation, parts, service, and training to maintain peak efficiency.
They have built an extensive knowledge bank and developed a wealth of experience and expertise with access to production and technical support from a network of engineers, food technicians, field service technicians, skilled tradespeople, and support teams to provide food and non-food manufacturers with the ability to achieve their production goals.
2250 NW 84th Ave. Unit #101, Doral, FL 33122 USA
Phone: 305/639-9770
www.hiperbaric.com
Email: marketing@hiperbaric.com
High Pressure Processing – Food Safety. Extended Shelf Life. Clean Label.
Hiperbaric is the world’s leading supplier of High Pressure Processing (HPP) equipment for the food and beverage industry
HPP technology is a non-thermal processing technique by which products are subjected to a high level of isostatic pressure to inactivate foodborne pathogens such as Salmonella, E. coli and Listeria, extending the shelf life considerably, without the need for preservatives.
HPP also preserves the quality of fresh food, opens opportunities to new markets for clean label products due to the extension of shelf life and protects brands against recalls.
HPP is a highly versatile technology that can be applied to a wide range of foods: juices and beverages, meat, fish and shellfish, fruits and vegetables, wet salads, dips, and sauces, pet food products andReady-To-Eat products.
Hiperbaric industrial High Pressure Processing (HPP) units are designed to be the most reliable systems in the market, with the widest throughput range of industrial HPP machines meeting the requirements of start-ups, small-medium enterprises and large corporations.
Its horizontal layout and ergonomic design simplify installation and operations. Each machine can reach up to 6,000 bar / 600 MPa / 87,000 psi. In addition to the HPP In-Pack equipment (post-packaging process), Hiperbaric offers HPP Bulk equipment for the processing of largevolumes of HPP liquids beforepackaging.
Hiperbaric also offers fully automated turnkey solutions for HPP equipment.
Hiperbaric is headquartered in Spain, with offices in Miami, Mexico, Singapore and Australia.
659 Van Meter Street, Cincinnati, OH 45202
Phone: 513/241-1230
Email:
www.hixson-inc.com/PFW23
Since 1948, Hixson has provided comprehensive, innovative design services for food, beverage, and ingredient companies of all types and sizes, including some of the most well-known companies in the world. Our design services include building architecture and engineering, process engineering, and project management – including Capital Project Management.
The members of Hixson’s 20 technical disciplines – all co-located – collaborate seamlessly on our projects. This results in lean, high-quality design solutions delivered cost-effectively and with unparalleled speed.
Hixson’s in-house capabilities include:
E
Hixson designs complex projects across all industry segments, including meat, dairy, flavors and ingredients, beverages, plant-based proteins, prepared foods, bakery, and fruits and vegetables.
We invite you to learn more about how Hixson can help your company solve its toughest challenges. Contact us today!
400 Pilot Court Waukesha Wisconsin 53188
Phone: 800-952-0121
www.hydro-thermal.com
Email: info@hydro-thermal.com
Introducing the Hydron Sanitary Hydroheater® - the latest innovation from Hydro-Thermal. This 3A-certified direct steam injection cooker is designed to provide ultimate process flexibility and stability while maintaining product quality.
This 3A-certified direct steam injection cooker is designed for fast and precise temperature control without any degradation in quality. Its fully CIP-able capabilities allow easy maintenance and cooking of thick mashes and sauces with ultra-precise temperature control without any burn-on.
The Hydron’s unique internal geometry controls the steam injection process, and its variable-area nozzle/stem plug regulates steam flow for 100% heat transfer efficiency and precise temperature control. This eliminates the hammering and vibration often experienced with less sophisticated heaters.
This sanitary solution is perfect for food and beverage applications where a consistent product is necessary. It can heat many end products, from baby food to tomato paste, while maintaining particulate integrity. The result is a great-tasting product, consistent batches, and a bacteria-free environment.
The Hydron’s versatility puts Hydro-Thermal heaters above other heating systems like heat exchangers. Our Direct Steam Injection solutions can cook thoroughly in-line or cook to a stage of completeness like parboiling, emersion cooking, or tank heating, depending on the process or product’s recipe. Many customers see a return on investment in less than three months.
Don’t settle for less. Contact Hydro-Thermal at info@hydro-thermal.com or call 1-800952-0121 to learn if a direct steam injection heater is the right choice for your application. Upgrade to the Hydron Sanitary Hydroheater for ultimate process flexibility, stability, and product quality.
Phone: 910/452-7059
ikaprocess.com
Food manufacturers are always seeking innovative mixing technologies. At IKA they will find what they are looking for, regardless of the individual technical demands.
With IKA mixing technologies, products retain exclusive organoleptic characteristics and a particularly appetizing look. IKA possesses an extensive know-how when it comes to the food industry’s multifaceted mixing processes: emulsifying and homogenizing, wet grinding, dispersing and powder input, drying and mixing of free-flowing solids.
For example, IKA offers two powerful machines for the production of high-quality emulsions such as mayonnaise and ketchup: The Master Plant and the Standard Production Plant with a patented dispersing module. Both work under pressure or vacuum. During the everyday production process, they ensure maximum flexibility: they can mix, disperse, suck in and moisten solid substances, temper the mixture and eventually discharge it.
IKA colloid mills and inline dispersing machines clear the way for particularly smooth spreads, horseradish and mustard matter. CMX machine developed by IKA enables the instant preparation of starch and sugar solutions in any desired amount.
Additionally, IKA is revolutionizing bread baking. IKA machines make it possible for dough masses to be produced as part of a continuous process. A particular version of the inline machine ULTRA-TURRAX UTL does not only achieve a previously unmatched productivity, but also gives the dough its own special baking characteristics.
All of IKA machines and equipment meant for the food industry are made exclusively from high-quality materials. They meet the highest hygienic requirements and are scalable. 3A certified machine version are also available.
Indfumco.com Email:
877/477-4432
13420 W 99th St, Lenexa, KS 66215 USA 200 PROFOOD WORLD | February 2023 | www.profoodworld.com
Since 1937, IFC has provided a full range of products and services exclusively to the food industry, from harvest to distribution. This expertise gives us a distinct advantage and understanding of every type of food handling environment. Our mission is to provide superior service and value to our clients while maintaining our role as the industry leader with innovative and effective pest management and sanitation solutions.
Pest populations explode quickly if they find a good habitat. In facilities like yours, pest pressures can be inevitable due to the surroundings, ingredients, processes, and potentially, structural conditions. We take a different approach with our Integrated Pest Management Program. Our highly trained team uses a variety of services, products, and tactics to ensure your facility and products are pest free and exceed audit requirements!
Communication, prevention and safety are key elements for success in our Integrated Pest Management (IPM) strategy. Following a thorough initial inspection, we will provide an Initial Facility Assessment. This report will include detailed observations and recommendations for a progressive, customized pest management program for each facility.
Our services include integrated pest management programs centered on prevention, audit support, fogging and fumigation, bird control, chlorine dioxide decontamination and other related services specifically for the food industry.
For over 85 years, we have made it our mission to stop pests from ruining reputations and destroying bottom lines.
Providing industry leading magnetic metal separation solutions since 1961.
Industrial Magnetics, Inc. (IMI) is an industry leader in providing both permanent magnets and electromagnets for magnetic separation for over 60 years.
Our specialty is custom fabricating. We design, engineer and manufacture magnetic assemblies and magnetic separation devices for our customers’ specific requirements, and take pride in the quality and performance of our products.
We are always striving to make things better. Many of our magnetic separation products are HACCP International Certified and USDA AMS Accepted Equipment. Our Sanitary Grade Rare Earth Magnetic Grate Tubes are certified by HAACP International and fully conform to HACCP International’s Food Safety Standard (0909MAGSEP 1-2010) for direct contact with food product as well as USDA AMS accepted Dairy, Meat and Poultry magnetic separator processing equipment.
With worldwide distribution through a combination of a direct sales force and channel partners, we strive to provide personalized service and innovative solutions to meet the exact needs of our customer’s application.
IMI is proud to be a United States- based manufacturer of magnetic assemblies and our USA M.A.D.E™ logo is how we like to show it. You will find our USA M.A.D.E™ logo on any of our products that are Manufactured • Assembled • Designed • Engineered here in the USA at our facilities.
IMI employs over 130 personnel, with departments including: Sales, Marketing, Engineering, Manufacturing and more.
Phone: 800/782-8850
www.jax.com
Email: info@jax.com
JAX has been developing innovative industrial and food-grade lubricants for over 65 years.
We offer a wide range of synthetic, semi-synthetic and mineral based lubricants for use in both food and industrial applications. These include hydraulic, gear, compressor, conveyor, chain, and eco-friendly lubricants, as well as grease and aerosol products. They are proudly made in the United States.
Are you in need of food grade lubricants for your plant? JAX services a diverse customer base from bakeries to meat packers to beverage bottlers. We pioneered food-grade lubrication in 1962 and currently have over 200 NSF certified lubricants, along with ISO 9001 and ISO 21460 certifications.
Our team of technical service representatives, scientists and chemists provide customers with continuous assistance for optimal machinery performance. Field service representatives are ready to support your business and provide training as needed.
All research and development activities are conducted in-house to identify products and formulas to meet your desired specifications. We also have our RPM lab, which conducts all of our in-house used oil analyses to monitor performance and troubleshoot any potential concerns.
Innovation is the core of our business. If you have a unique challenge, let us know. Our team is ready to help you develop a solution.
1830 Airport Exchange Road, Suite 160, Erlanger, KY 41018 USA
Phone: 513-433-2500
Email: hello@jbtc.com
https://www.jbtc.com/avure
HIGH PRESSURE PASTEURIZATION (HPP) is cold pasteurization in pure water; it uses ultra-high pressure purified water to keep packaged food pathogen-free to stay fresh longer. At very high pressures bacteria such as Listeria, E. coli, and Salmonella are inactivated. Foods using HPP include ready-to-eat and ready-to-cook meats, readymeals, fruits and vegetables, juices and smoothies, soups and sauces, wet salads and dips, dairy products, seafood and shellfish. HPP helps producers increase food safety and extend shelf-life while providing consumers with nutritious, natural, flavorful food.
Avure Technologies created the first commercial high pressure processing system more than 60 years ago. Today, Avure features multiple HPP systems, including the AV-X, with upgradeable, energy-efficient and space-saving designs, worldwide tolling centers and partnerships with more major food brands than every other HPP manufacturer.
Avure’s expandable machines enable a producer to buy the machine that best suits current needs, and as the company grows and volume expands, the machine can be upgraded to keep up with increased demand. With Avure HPP, producers are manufacturing in record volumes, reducing shrinkage and growing their distribution overnight.
Avure also manufactures a vertical machine, the AV-S, developed specifically to allow seafood producers to more efficiently process shellfish, removing 100% of the meat from the shell, increasing yields by up to 30%.
Avure operates an in-house research and development facility to help partners perfect their HPP-friendly recipes plus maintains service centers around the globe to answer questions, provide on-site maintenance and spare parts fulfillment.
511
Phone: 866/516-6888
us.kaeser.com
Email: info.us@kaeser.com
OVER 100 YEARS OF ENGINEERING... and we never stop asking ourselves how to do it better.
KAESER Compressors is a world leading manufacturer of industrial compressed air and vacuum equipment. Everyone talks about reliability but no one else in the industry has KAESER’s rigorous “built for a lifetime” philosophy -- exceeding the highest expectations for durability, energy-efficiency and performance.
KAESER is not intimidated by demanding applications. It’s our commitment to designing the best engineered solutions that results in compressed air systems that remain reliable even in the toughest of applications and harshest environments.
While the need for stable pressure, good air quality, system reliability, and energy efficiency is nearly universal, we understand that each application is unique. Our wide product range lets us tailor each air system to meet your specific challenges.
An unparalleled service network provides expert design, installation, maintenance, remote monitoring and system audits that all contribute to the value our customers have come to expect from the KAESER name.
Let us help you improve yield and uptime while saving you thousands in energy costs every year.
150 Avery Street. Walla Walla, WA 99362 USA
Phone: 509/529-2161
www.key.net
Email: product.info@key.net
Key Technology offers food processors the single most complete source of high performance digital sorting, conveying and process automation systems.
The VERYX® family of belt-fed and chute-fed digital sorters achieve new levels of foreign material (FM) and product detection and removal. With all-sided surface inspection, multisensor Pixel Fusion™ and the highest resolution cameras and laser sensors available on a digital sorter, VERYX improves product quality and maximizes yields while easing use.
Key’s industry leading product line of camera/laser sorting systems improves product quality, optimizes yield, reduces labor, and improves process control plant efficiencies. These sorters are complemented by Key’s other processing systems – Iso-Flo® vibratory conveyors; Zephyr™ horizontal motion conveyors; Impulse® electromagnetic conveyors; equipment for sizing, grading and separating; systems for blanching, air cooling, air cleaning, washing and feeding.
Additional services include application testing, line integration, installation, start-up and training as well as customizable service packages from our global SupportPro service organization for maintenance, repairs and more.
Phone: 941/493-5502
www.kingplastic.com
Email: sales@kingplastic.com
King Plastic Corporation is a leading manufacturer of quality polymer sheets, slabs and massive shapes - including several products pioneered by the company. Its polymers are made in the USA and sold worldwide through a network of top plastics distributors to customers who fabricate products for the marine industry (King StarBoard® brand), signage, food service, healthcare, architectural, industrial and other markets. King continues to raise the bar with new products, new production techniques and new standards of excellence.
High-Performance Polymers:
• King StarBoard®
• King StarBoard® ST
• King ColorBoard®
• King ColorCore®
• King Hy-Pact®
Phone:
www.kpfilms.com
In the kp Food Packaging division, the sustainable protection of everyday needs is very important to us. Our aim is to ensure you get the most sustainable total food packaging solutions that not only protect your food products while extending shelf-life and reducing food waste, but that can also be recycled. We operate across a vast range of fresh food categories, supplying thermoformed trays, rigid films for form, fill and seal applications as well as flexible barrier and stretch films to protect your products.
With 20 manufacturing and distribution facilities across 14 countries worldwide, we maximise the value we deliver to our customers while understanding and meeting local needs.
Supplying solutions for the food packaging starts by understanding market and consumer trends and anticipating their needs. kp works with top brands and retailers to understand and develop unique solutions to make them innovators in their markets.
Our inhouse PET flake cleaning process allows us to use up to 100% post-consumer recycled PET to further support your sustainability goals and optimize the carbon footprint throughout the entire value chain.
www.profoodworld.com | February 2023 | PROFOOD WORLD 207
850 Main Street, Wilmington, MA 01887 USA
Phone: (978) 694-7000
www.kochseparation.com
Email: getinfo@kochsep.com
Koch Separation Solutions (KSS) provides innovative separation technology for the food, beverage, and dairy industries. Our applications expertise spans across product concentration, clarification, and purification as well as caustic recovery and water & wastewater treatment. We provide customers around the world with industry-leading membrane filtration and RELCO® thermal separation technologies, powder handling & packaging equipment, and cheesemaking technology.
KSS is committed to driving innovation in the food industry by offering comprehensive, start-to-finish solutions. Our membrane filtration products integrate seamlessly with RELCO® evaporation and drying technology to purify and concentrate a variety of animal and plant-based proteins, gelatin and hydrolyzed collagen, sugars and starches, nutraceuticals, fermentation products, and more. Our portfolio of membrane products and systems for process water treatment and wastewater treatment offers customers a wide variety of configurations and options to streamline the usage of this very valuable resource in food manufacturing processes. We help customers achieve their sustainability goals while minimizing waste effluent by treating wastewater to meet discharge requirements or for reuse in the process.
Our technologies are constructed with sanitary materials to meet the most stringent hygienic requirements in the food industry. We help customers achieve a high-quality and profitable food product while minimizing operating costs and improving process efficiencies.
Phone: (800) 282-8808
Email: sales@kronesusa.com
www.kronesprocessgroupna.com
Serving the beverage, food, dairy, HPC and pharmaceutical industries, Krones Process Group North America provides sanitary process system expertise backed by the global depth and experience of KRONES. Leveraging over 165 years of combined experience, Krones North American subsidiaries Javlyn Process Systems, W.M. Sprinkman Corp. and Trans-Market have aligned, combining resources and knowledge to afford customers the highest level of quality.
By offering one seamless line solution Krones Process Group North America has the horsepower to support the entire process: from engineering, to automation, to fabrication, installation, and full regional after-market Lifecycle Services support. Whether its brewhouses for beer or processing lines for beverage or consumer packaged goods, we understand each project has its own unique needs and deliver tailored solutions from a single source – no matter your location.
Krones Process Group North America offers the highest quality products and services available in the industry. We are part of the KRONES global network covering every region of the world.
• More than 5,300 employees in the global service team
• Prompt spare-parts supply
• Lifecycle Service for an entire line
• Digitalized support solutions and connectivity
• 24/7 support
Phone: 504/733-6009
https://www.lapeyrestair.com Email:
The stair experts at Lapeyre Stair have been crafting sanitary access solutions since 1981. Our pre-engineered stainless steel stairs and platforms are designed to easily integrate into complete, custom systems for food processing and packing facilities and equipment.
“The Original” Lapeyre Alternating Tread Stair
Patented in 1979, our alternating tread stair delivers on its promise of “maximum safety, minimum space.” They are the safer option over ladders or ship stairs when space restrictions prohibit the use of standard stairs. Alternating tread stairs are available in stainless steel, carbon steel with a powder coat finish, carbon steel with a galvanized finish, and aluminum with your choice of angle and handrail options.
Safely overcome virtually any obstacle with stainless steel code-compliant crossover stair and platform systems. Crossover systems are available with a choice of alternating tread stairs or bolted access stairs plus your choice of handrail, and platform decking options. Choose from one of our standard systems or have our in-house engineers design a custom system to your exact specifications.
Provide workers with sanitary code-compliant, custom-built safe access for daily operations, routine maintenance, or any other application. Our fixed work platforms are pre-engineered in stainless steel to easily integrate with our bolted access stairs and alternating tread stairs. They are available in a variety of configurations and a choice of options.
Our pre-engineered stairs are quick and easy to assemble without the need for welding or special equipment. Bolted access stairs are available with a choice of handrail, tread, and finish options. Each order is designed to meet your specifications and applicable code requirements.
Rapid heat removal with cryogenic liquid nitrogen or liquid carbon dioxide offers processors a variety of options that meet their processing needs. Customers working with Linde’s industrial gas and equipment systems can boost productivity and maintain high product quality targets in freezing, chilling and cooling operations. Tunnel, spiral, flighted, snowing and in-line cooling systems provide cost saving benefits to our customers.
For Linde and the food processing market areas we serve, there are three unique competencies to address the needs of our customers. The focus on 1) product temperature through precise heat removing properties of cryogenic gases, 2) the scientific application knowledge of the gases and gas atmospheres acquired by servicing thousands of customers, and 3) the system support coupled with engineering experience that allow our customers to rely on Linde to help improve productivity.
Linde is a leading global industrial gases and engineering company. We live our mission of making our world more productive every day by providing high-quality gases, application technologies and services which are making our customers more successful and helping to sustain and protect our planet.
The company serves a variety of end markets including chemicals & refining, food & beverage, electronics, healthcare, manufacturing and primary metals. Linde’s industrial gases are used in countless applications, from life-saving oxygen for hospitals to highpurity & specialty gases for electronics manufacturing, hydrogen for clean fuels and much more.
For more information about the company and its products and services for the food processing market, please visit www.lindefood.com.
Phone: 1-604-636-1011
Email: contact@lmi3d.com
https://lmi3d.com/smart-3d-inspection-for-food-processing
LMI Technologies brings 40+ years of leadership experience in developing smart 3D scanning and inspection solutions for the food processing industry. There are three primary applications LMI Gocator 3D Smart Sensors are used for: Process Control, Machine Control, and Packaging & Logistics.
With Gocator’s built-in 3D inspection tools, real time volume information of material flow can be provided to downstream equipment, for example the volume of flour on a conveyor belt.
A common example of machine control is container fill level, which is critical to product quality and customer satisfaction and safety. Another example is portioning of product based on volume. Since the density of the product is known, the volume measurement alone will provide the information necessary to portion the product to the exact weight needed, no scales required. Grading of meat proteins requires a system to be able to provide more than just a simple PASS/FAIL no-go result. LMI’s FactorySmart AI solutions are being used by some of the world’s largest meat producers to effectively grade meat products. Aspects such as fat content or ratio as well as bone location and size can be used in our AI solutions to perform complex grading decisions.
Finally food packaging requires strict adherence to regulation and trace-ability. Gocator sensors provide seal presence or absence and integrity information. After a product is placed in a box, sensors are used to calculate the amount of packaging materials needed to fill the empty space.
LMI now offers a Gocator 2490 NTEP Legal for Trade-certified solution for the accurate data capture of multi-dimensional measurements (LxWxH) used in the calculation of dimensional weight for packages in the food processing industry.
LPS® DETEX®
241-8334
www.itwprobrands.com
For over 60 years LPS® has earned a reputation for both quality and performance in critical industrial and aerospace applications. LPS® DETEX® combines that expertise with food safety programs to produce a full line of maintenance solutions specifically formulated for food processing facilities. Including lubricants, penetrants, electronic cleaners, greases, and specialty products, LPS DETEX covers a wide variety of maintenance tasks. These premium-performance chemicals save time and money by extending equipment life, reducing repair time, and lowering frequency of preventative maintenance all while food is in production.
LPS DETEX packaging is also designed with food safety in mind. Utilizing a unique patented formula, the plastic packaging components are both metal & X-ray detectable. Additionally, the slip-resistant can features NSF® ratings clearly marked on top, and highly visible bright blue lithographed labels that won’t tear or smudge.
Newark, NJ 07105 / Toledo, OH 43605
Phone: 800-733-4755
www.lubriplate.com
Email: LubeXpert@lubriplate.com
Lubriplate Lubricants Company
Advancing Lubrication For 153 Years.
Back in 1870, Lubriplate’s founders set out to make the highest quality, best performing lubricants available. In doing so, they helped pioneer the use of anti-wear additives that significantly increased lubricant performance through the years. Today, that innovative tradition continues with their complete line of ultra high-performance, 100% Synthetic, NSF H1 Registered, Food Grade Lubricants. Manufactured under strict NSF/ ISO 21469 Certified and ISO 9001 Registered quality control standards, these lubricants are formulated to deliver a number of significant, cost effective advantages, including; extended lube and fluid change intervals, multiple application capability, lubricant inventory consolidation and improved performance. Clean, safe and non-toxic, their use can eliminate lubrication as a critical control point in HACCP programs.
All Lubriplate Lubricants come with Lubriplate’s ESP Extra Services Package at no additional charge. Services include; a complimentary plant lubrication survey by a factory direct representative, color coded lubrication charts and machinery tags, a toll free technical support hotline and email, and follow-up lubricant analysis.
M&M Carnot, founded in 1960, is a pioneer and manufacturer of natural refrigerant-based products [ammonia and carbon dioxide], packages, systems, and controls. Our commercial and industrial refrigeration applications include refrigerated warehouses, food processing, wineries, dairies, arenas, pharma, data centers, and supermarkets. M & M Carnot headquarters is in Annapolis, MD; manufacturing locations are in Maryland, Florida, and Quebec.
AQUILON INDUSTRIAL Transcritical CO2 Packaged System
A plug and-play transcritical CO2 industrial rack with Parallel compression and robust highpressure design. Microprocessor-based controls. Capacities 50 to 400 tons.
AQUILON CHILL Transcritical CO2 Industrial Chiller
Our high-pressure design eliminates the need for a backup generator and synthetic condensing unit during off-cycle. VFD on lead compressors. Cooling capacities 50 to 500 tons
AQUILON DS Transcritical CO2 Condensing Unit
A plug-and-play transcritical CO2 condensing unit. Featuring a power block connection for evaporators. Heat recovery options. Capacities 10 to 85 Tons.
PURE CHILL Low Charge Ammonia Packaged Chiller
A plug-and-play low-charge ammonia packaged chiller. Features Industrial VFD-driven Sabroe compressor. PLC-based controls. Capacities 40 to 400 Tons.
PURE COLD Low-Charge, Ammonia Condensing Unit
A Plug-and-play low-charge ammonia condensing unit. Features dual screw compressors; VFD on lead. Water, air-cooled, or adiabatic heat rejection. PLC-based controls. Capacities 30 to 100 Tons.
PURE FREEZE Packaged CO2 and Ammonia Cascade System
A plug and play cascade ammonia/CO2 system with industrial VFD driven Sabroe compressors. Water, air-cooled, or adiabatic heat rejection. PLC-based controls. Capacities 40 to 200 Tons.
1214
Phone: (269) 673-2125
Email: sales@materialtransfer.com
www.materialtransfer.com
At Material Transfer (MTS), we believe there’s always a better way. That’s why, for more than 30 years, we’ve been singularly focused on delivering the highest performing bulk handling equipment and systems to transform customers’ operations into more than they can imagine. Our Inspiring a Better Way brand drives us to ensure that everything we do for customers – from their first interaction, to the design and build process, to equipment lifecycle services that enhance productivity and ROI – is designed to find the better way.
Power-Fill® Bulk Bag Fillers – Our Bulk Bag Filling Systems offer a complete range of filling solutions, from a simple, durable unit for low-volume filling to a highly sophisticated, automated system for high-volume production.
Material Master™ Bulk Bag Conditioner – Our newly enhanced Bulk Bag Conditioner leverages our patented design and unique feature set to bring customers the most advanced conditioning technologies in the market.
Material Master™ Bulk Bag Dischargers – Our Bulk Bag Dischargers are designed to withstand the rigorous demands associated with bulk material processes – offering advanced technologies fit to serve the needs of customers in a variety of industries.
Container & Drum Dischargers – Designed by our customization experts, the Container and Drum Dischargers, release contents of bins, drums, boxes, gaylords, carts, or other containers, into existing receiving equipment.
Our equipment and systems are supported by the highest standards of excellence in service. Our service doesn’t end when our products ship. From operator training to equipment evaluations, service contracts, remote equipment monitoring and more, our teams are focused on doing what’s right for every customer: keeping equipment up and running efficiently and safely.
200 Somerset Corporate Blvd., Suite 7000 Bridgewater, NJ, 08807 USA
Phone: 800/755-9277
Email: sales@messer-us.com
www.messer-us.com/food-beverage
Building on decades of hands-on food industry experience, Messer delivers cryogenic solutions that help increase throughput, use labor more efficiently and support resilient supply chains. Proven at hundreds of customer sites, Messer’s differentiated technologies improve process temperature control for small-scale start-ups through large-scale operations.
Over 100 Installations of Nitrogen Bottom Injection Chilling:
Messer’s nitrogen bottom injection chilling system improves production, quality, and security of cryogen supply in processes traditionally offered only in carbon dioxide.
Messer Delivers an Unmatched Portfolio of Freezing Technologies:
Messer’s latest tunnel freezing technologies can boost production on new and existing lines for individually quick frozen (IQF) products, hot products or crust-freezing. The new Digital Freezer monitoring system offers processors more accurate process control to achieve a step change in quality, traceability, and productivity. Plus, its family of spiral freezers -- the industry’s proven workhorse -- increases throughput in a small linear footprint to meet production goals.
Whether helping processors improve production in a smaller footprint, convert from carbon dioxide to nitrogen or conduct product testing onsite or at the state-of-the-art Messer Technical Center in Cleveland, Ohio, the company grows with you to help expand your brands. Messer is your partner for next generation freezing and chilling solutions.
The Messer difference (right) in nitrogen bottom injection chilling vs inadequate chilling. Crust-chilled chicken which locks in moisture.Phone: 813/889-9500
www.mt.com/pi
Email:
METTLER TOLEDO is the world’s largest manufacturer of metal detectors, checkweighers, X-ray and vision inspection equipment, delivering a wide range of solutions for foreign body protection, regulatory compliance, and improved profits. Systems range from economical to state-of-the-art with customized material handling solutions.
Safeline metal detectors automatically reject all types of metal contaminants, including the most difficult to detect stainless steel. Systems are offered for dry, bulk, packaged, liquid or frozen products for gravity feed, conveyorized, pumped and throat applications. Safeline x-ray inspection systems use high-performance image processing to detect and reject all types of dense physical contaminants, as well as measure mass, check for missing or broken product, and confirm fill levels to guarantee product and package integrity.
CI-Vision machine vision systems verify label content and integrity to prevent recalls. The use of these systems in your food safety program can help you prove due diligence, pass regulatory audits, and protect your brand.
Hi-Speed checkweighers deliver productivity and profits. A wide range of sizes and configurations are available to handle nearly any container type or package design even at high production rates to ensure accurate product delivery, reduced giveaway, and optimized production processes. Patented weighing technology and over 50 years of package handling expertise ensures repeatable performance from the first to the last package weighed maintaining tight production tolerances.
As a member of OMAC, METTLER TOLEDO is committed to connectivity and data storage and retrieval to help meet regulatory requirements. Inspection systems can be connected using a variety of methods, including our own ProdX data collection and management software. METTLER TOLEDO inspection systems are backed by the most comprehensive engineering solutions, product testing, and training in the industry with nationwide customer service and 24 hour telephone support.
Phone: 888-309-5574
Email:
https://miuraboiler.com/products/miura-connect
The future belongs to Food Processing companies that respond quicker and more effectively to events as they happen.
With real-time, anytime, 24/7 remote monitoring, Miura Connect allows customers or their representatives to set preferences and receive real-time boiler room notifications and alerts (from all connected equipment) directly on their smartphone or other digital devices quickly, accessing critical information including supporting documents such as water logs and maintenance procedures, while accessing manuals and technical documentation in seconds.
Another innovation from the world leader in industrial steam boilers, Miura Connect is a game-changer, providing a next-generation mobile, cloud-based, real-time remote monitoring and customer accessible platform, which features a smart new web-based portal. By viewing connected equipment in real-time, boiler operators, company management, representatives, and technicians can quickly and easily access boiler room data from anywhere the internet is available.
Engineered to continually optimize and add new features and value, this remote monitoring application and the IoT Technology that enables it will allow Miura to add features and value along the way, ensuring that Miura Connect will be a living application, with upgrades and benefits automatically available without the need for on-site visits or additional hardware in most cases.
Consider a traditional situation where a steam boiler operator would receive a caution or alarm from the boiler and call their rep to request service. Now, the rep or facility operator can look into historical and real-time data to be better informed and get a head start rather than figuring it out on-site.
Munson Machinery Company is a leading manufacturer of mixing, blending, size reduction and separation equipment serving the food, dairy, coffee/tea, nutraceutical and hemp industries.
Munson offers the industry’s widest selection of equipment for mixing and blending of bulk food products (with or without liquid additions) including: Rotary Batch Mixers, Ribbon/Paddle/Plow Blenders, Cylindrical Plow Blenders, Vee-Cone Blenders, Fluidized Bed Mixers, Rotary Continuous Mixers, and Variable Intensity Blenders.
For size reduction of spices, herbs, nuts, dates, roots, grains, beans and other bulk food products, Munson manufactures Lump Breakers, Pin Mills, Attrition Mills, Screen Classifying Cutters, Knife Cutters, Shredders, and Hammer Mills.
For solids separation, Munson’s Centrifugal Sifter can sift and scalp bulk food materials at high rates with virtually no product degradation.
Munson equipment is available constructed of #304 or #316 stainless steel and finished to food, USDA dairy or pharmaceutical standards, with optional CIP systems.
The exceptionally broad selection of full size equipment in Munson’s test laboratory allows side-by-side testing of your actual material, and documents precisely how effective — or ineffective — any given machine would be at meeting your specific performance requirements. This assists customers in specifying a machine at no cost or obligation— and takes the risk out of purchasing bulk food processing machinery.
Since 1823, Munson has offered unparalleled experience in solving challenging problems encountered by customers through two centuries, continuously improving equipment performance to a level unmatched by any comparable manufacturer worldwide.
12838 Stainless Drive, Holland, MI 49424, USA
National Bulk Equipment (NBE) designs, engineers, manufactures, installs, and commissions equipment, systems, and fullstream projects for processing and packaging of dry and liquid bulk materials. NBE bulk material handling applications include: discharging, filling, conveying, mixing, storage, packaged-product reclamation, and material infeed. The extensive portfolio of NBE equipment, resources, and project delivery capabilities is applied across the full scope of processing and packaging operations.
The NBE fullstream advantage provides upstream raw material discharge and storage systems, midstream raw material conveying and processing systems, and downstream finished-product packaging and reclamation systems. CPG project owners, contract packagers, contract manufacturers, AECs, and OEMs leverage the NBE engineer-toapplication (ETA) project delivery experience to move their bulk material processing and packaging projects beyond the constraints of build-to-order or engineered-to-order machine manufacturing. ETA project delivery brings mutually defined expectations, tangible performance benefits, and long-term project confidence to bulk material processing and packaging projects delivered by NBE.
See how NBE will advance your project delivery experience and improve your total process performance. View product feature demos, schedule a livestream test of your material, or request a rep visit at: nbe-inc.com or, call 616.344.5520
National Bulk Equipment is a portfolio company of NBE Holdings Company, based in Holland, Michigan.
USA Manufactured Canning Line Equipment for Beer and Beverage Companies. Since 2015, we have installed over 125 lines globally. Our systems range 40-400 Cans Per Minute. Standard-Sleek-Slim Formats with easy changeover designs. We provide complete solutions including de-palletizers, ionized rinse systems, filler/seamers, in-line carbonation/blending, blower systems, tunnel warmers and pasteurizers, integrated labeling, date Code Conveyors, and modular conveyance. We provide complete solutions
Independently owned and operated with manufacturing in Lafayette, IN USA. We provide the following canning line production systems, based on filling carbonated 12oz. cans.
• 60 CPM 12/1 Gen 4 Rotary Counter Pressure with gravity fill including single head mechanical seamer
• 120 CPM 12/4 Gen 4 Rotary Counter Pressure with gravity fill including 4- head mechanical seamer
• 240 CPM 24/4 Gen 4 Rotary Counter Pressure with gravity fill including 4- head mechanical seamer
• 360 CPM 36/6 Gen 4 Rotary Counter Pressure with gravity fill including 6- head mechanical seamer
• 40 CPM 6/1 Gen2 In-Line Counter Pressure with gravity fill including single head mechanical seamer
— Our CPM rating is based on minimum for Carbonated Product, not Still Product as it will run faster. Lower Carbonated (<2.5 v/v) and cold beer/beverage (<34F) will run faster.
— Production Grade & Hygienic Design for 24/7 type Operation that outperforms anything in its class
— TPOs Under 100 PPB. Many customers achieve less than 50 PPB TPO added
— Low Seam Defects and Zero Leakers with the latest seam profiles and tooling
— 100% Stainless Steel Design Filler, Seamer, De-Pal, & conveyors – Including Frames/Bases
— Allen Bradley Logix PLC/HMI Touch Screens on fillers & De-Palletizers
— Digitally Controlled Product Bowl with IFM German instruments
See all the Leaders in Processing at www.profoodworld.com/leaders
Paratherm - Heat Transfer Fluids has been in business for over 30 years. We are a dedicated team of service-oriented people with a variety of training, skills and experience. Our sales engineers can help you select the appropriate heat transfer fluid for your application. We also offer technical services to assist with troubleshooting along with a superior fluid analysis program. Paratherm products are always in stock and available globally. In a pinch, Paratherm can provide shipments same-day, and sales engineers are on-call 24 hours a day to get you what you need when you need it.
Paratherm’ s fluid analysis laboratory analyzes thousands of samples a year. Our state-of the-art laboratory provides streamlined results that you can be confident in. Results and recommendations are provided in a clear, concise report, and follow-up consultation is included with every analysis.
Paratherm has been a leader in food grade heat transfer fluids since it’s inception. Hundreds of systems in the food processing industry count on Paratherm’s industry leading fluid technology for their critical operations, including several of the largest food processors in the world. Paratherm offers several food grade heat transfer fluids registered with NSF and compliant to FDA 21 CFR 178.3570 suitable for a wide operating range to meet all food processing application requirements. Paratherm is well equipped to provide several food grade heat transfer fluids over a wide operating range. We your preferred heat transfer fluid supplier for over 30 years.
10125
Phone: 513/891-7474
Email:
https://www.paxtonproducts.com/
Paxton Products manufactures high efficiency centrifugal blowers and customengineered air delivery devices used for drying, air rinsing, and blow off, to improve product quality through better cleaning, rinsing, labeling, marking, and coding processes. Air Delivery Devices are custom-engineered to maximize and improve the quality of drying, blow off, and cleaning of products and surfaces. Our team configures the air delivery device specifically for your unique application - sizing air knives, nozzles, and manifolds for peak efficiency.
Available in both aluminum and 304 stainless steel, Paxton’s Air Knives and Knife Systems are designed to give maximum efficiency for high velocity drying and blow off applications. These systems feature a continuous, uninterrupted air slot design that gives uniform air coverage over the targeted area. Because of this, you’re able to significantly reduce the amount of product quality rejects for your business.
Coupled with Paxton’s high efficiency centrifugal blowers and air delivery devices, Paxton’s Ionizing Rinsing Systems remove particulates, dust, and contaminants using powerful ionization. The Ionizing Rinsing System provides static control and static elimination so that dirt and dust don’t adhere to surfaces, and then blasts contaminants away using a Paxton PX-series centrifugal blower.
For drying, Paxton’s patented PowerDry Drying System sets the standard for a complete, power drying and blow off air system that can used for a wide variety of cans, bottles, jars, and pouches. By incorporating Paxton’s PX-series centrifugal blower, the PowerDry System lowers energy costs by as much as 80% through reduced compressed air usage in bottling, canning, and other packaging operations.
Phone: 800-848-8483
www.perfex.com
Email: perfex@perfex.com
Leading manufacturer of hygienic cleaning tools for food manufacturing environments. Perfex is the pioneer of heat-fused brushes for food processing facilities and TruCLEAN® disinfection systems for pharmaceutical cleanrooms. Perfex® Lite-N-Tite Brooms and Brushes are built to tackle a wide range of cleaning tasks. Patented heat-fused fiber design eliminates premature fiber fall-out and areas for contaminants to collect. Impactresistant polypropylene material handling tools such as scoops, scrapers, and shovels. One-piece assembly eliminates weak points and areas for contaminants to collect. We also supply laboratory & scientific brushes for removing toxic residue from glassware and testing equipment.
Perfex cleaning tools can be found in diverse industries across the globe such as food processing, packaging, pharma manufacturing, plant facilities, and industrial sanitation. We are committed to supplying high quality products with first-class customer service. Our customer support team is trained to find the ideal product to meet and exceed your sanitation goals. Same-Day Shipping - No Minimum!
500 E.Illinois St. Newberg, OR 97132
Phone: 503/537-5319
Email: nisch@ppmtech.com
neil.anderson@ppmtech.com
With more than 120 years of manufacturing food processing equipment, we like to think we know a thing or two. That experience helps us provide the most innovative and creative solutions to our customers’ challenges.
Our focus on conveying, frying, seasoning & coating allows us to support our global customer base with well-engineered and manufactured solutions for producing snack foods, cereals, nuts and seeds, fruits and vegetables, meats and plant based-meat alternatives, seafood and poultry, confectionary products and much more.
We produce a standardized range of products, but also have the ability to customize a solution to meet the needs of an ever-evolving market of unique product applications.
Our extensive range of vibratory conveyors, belt and bucket elevators, provides many options for material handling of pre-processed and post-processed food products. Our ingredients and coatings product lines can provide a wide range of oils, tacs and gums and slurries as well as dry powders, seasonings and particulates. Complete systems include heated mix and use kettles with fully automated PLC controls.
Our brands include Allen Machinery, Aseeco, Wright Machinery and PPM Technologies Holdings LLC, for which we provide all OEM parts and service, from our USA and UK locations.
9524 Gulfstream Rd., Frankfort, IL 60423, U.S.A.
Phone: 815/464-1540
www.q-t-s.com
Email: info@q-t-s.com
Quantum manufactures high speed, automated portion and apply systems utilized in the wholesale frozen pizza, prepared meals, and bakery industries. Our systems are used to apply sauces, cheeses, IQF ingredients, meats, dry ingredients, and a variety of other ingredients.
We offer standard production systems as well as custom designed equipment for various production requirements. Our in-house engineering team works closely with customers to create the best solution for their application. The sanitary, easy-to-use, streamlined design of our equipment sets the standard in the industry.
Incorporated into every Quantum machine is high speed, non-contact application, and highly durable stainless steel construction. In addition, our machines are wash down capable, and have an easily accessible open design requiring no tools for sanitation.
•• TARGET and WATERFALL PORTION AND APPLY SYSTEMS ••
Quantum Target Applicators and Waterfall Applicators are available with automated feed systems to ensure consistent deposit portions.
•• TARGET SAUCE PORTION AND APPLY SYSTEMS ••
Quantum Target Sauce Applicators apply a consistent deposit with a sauce-free border. High quality and accurate weight control are features of all Quantum sauce applicators.
•• PEPPERONI SLICER PORTION AND APPLY SYSTEMS ••
Quantum pepperoni slicer / applicators are servo driven to provide precise deposit patterns and are available in many configurations to meet volume requirements.
Quantum has supplied production equipment from small wholesalers to large manufacturers since 1991.
For application assistance or to learn more, please contact us at www.q-t-s.com, or 815464-1540.
710 Old Willets Path. Hauppauge, NY 11788 USA
Phone: 800/243-ROSS
www.mixers.com
Email: mail@mixers.com
Serving all the process industries in virtually every industrialized country, ROSS offers experience and production capacity that no other manufacturer of specialty mixing and blending equipment can match. In the US, ROSS operates five plants dedicated to engineering, R&D, manufacturing, and process testing. Overseas, ROSS equipment is manufactured in four state-of-the-art plants in China and India.
The ROSS Test & Development Center in Hauppauge, NY, is the industry’s best-equipped laboratory for process testing. Hundreds of ROSS customers visit the test center each year to confirm their equipment selections and optimize processes.
Ribbon Blenders – High quality and available in customizable configurations. Laboratory sizes to 1000 cu. ft. Many models in stock.
Batch and In-Line Rotor/Stator High Shear Mixers – Single-stage and multi-stage models for fine emulsions and dispersions.
SLIM Solid/Liquid Injection Technology – Eliminates the persistent clogging of conventional eductor-based systems.
Multi-Shaft Mixers – Multiple independently-driven agitators work in tandem to ensure fine solids dispersion, efficient turnover and uniform heating/cooling.
In-Plant Trial/Rental – The industry’s largest fleet of rental mixers and blenders. Meet short-term demand or test equipment in your process prior to purchase.
Control Systems – From single-axis to multi-axis designs, ROSS control systems offer unprecedented accuracy and flexibility in the mixing and blending process.
Tanks & Vessels – Custom-fabricated storage tanks and pressure vessels built to exacting standards at competitive prices. Capacities from 1 to 80,000 gallons.
See all the Leaders in Processing at www.profoodworld.com/leaders
The Ryson Bucket Elevator is a robust conveyor that combines vertical and horizontal transportation of bulk materials in one integral unit. They are a unique and highly effective solution for bulk material conveying.
Our Bucket Elevators are designed for gentle handling and well-suited to transport a broad range of bulk products in the food, agriculture, pharmaceutical, cosmetic, chemical, ceramic, glass, recycling, building, metallurgical and other industries.
The Ryson Bucket Elevators’ signature feature is that they are completely enclosed and have overlapping pivoting buckets, that prevent spillage and keeps out foreign debris.
Additionally, our Bucket Elevators stand out compared with our competitors because they can have any number of inlets and outlets that can be individually activated. They are custom build to each application and are fully modular, and easy to modify later - for future growth or repurposing.
Ryson Bucket Elevators have earned a reputation for being the most durable vertical bucket elevators in the marketplace. Their robust and forward-thinking design combines a number of features—from gentle handling and rugged construction to minimal maintenance and modular design—businesses have come to benefit from and deeply value.
Ryson also manufactures a full line of Spiral Conveyors that need less floor space than conventional incline conveyors and are faster and more reliable than any elevator or lift. They are especially well suited for Consumer Packaged Goods companies and any warehousing operations.
For additional information about Ryson Bucket Elevators, or any of our vertical conveying solutions, visit www.ryson.com
2855 Innovation Way, Sun Prairie, WI 53590
www.sanimatic.com
Let Sani-Matic solve your problems with process integrity or capacity through automation of sanitation and cleaning processes including CIP, COP, Tunnel Washers, and more.
• SaniCab® pan, tray, bucket, hose, and more automated CO washer
• SaniTrend® Cloud and local automated data recording and OEE optimization
• C uilt to purpose Clean- n- lace Systems
• CO Clean-Out-of- lace systems for every need
• Tunnel ashers Conveyorized, high capacity washing
• Centralized ashdown systems oosted pressure systems and rinse-foam-sanitize stations
• Sanitary Components - process strainers, static spray balls, rotary sprays, jet sprays, supply tubes, tank components spray deflectors, sight glasses, sanitary sight glass lights, vents, sample valves, level control, and more , washdown e uipment, tanker spray washers, CO parts baskets, chemical delivery solutions, and more.
Services - Sani-Matic’s team of field service engineers provides onsite cleaning system audits and optimization, preventive maintenance, system start-up, and aftermarket services. Our customer success team stays in touch and makes sure processes are running smoothly with periodic visits after field service has occurred.
Sani-Matic has been improving food and beverage processors’ production uptime and sanitary results for 80 years. It’s been that way since the Sani-Matic story began in . That’s when we developed a Clean-Out-of- lace CO arts asher for the dairy industry and began a precedent of high-quality equipment innovation at the forefront of automating sanitary cleaning processes.
Schenck Process engineer’s cutting-edge technologies and solutions across the bulk material handling spectrum, delivering unmatched precision and accuracy for dry powder pneumatic conveying, mixing, depositing, extruding, forming, milling, sifting, weighing and feeding. For plant safety a wide range of dust collection systems are also part of the product portfolio. Through the integration of a wide range of entities over the last 15 years Schenck Process boasts a streamlined business model that enables it to deliver a unified process solution for customers in every corner of the world.
Technology Growth – With the integration of Baker Perkins into the Schenck Process Group we further serve the food industry by offering the following technologies:
• Mixing Dough Feed Systems
• Sheet Forming Cutting
• aking andling
• Food Extrusion
• Depositing
• Cooking
Competencies in these technologies provide an even wider solution package from Schenck Process to bakery, confectionery, cookie, cracker, breakfast cereal and pet food end-markets.
roject Management At Schenck rocess, everything we do is centered on customer satisfaction. We strive to make your equipment and systems robust and efficient. Our project management teams become an extension of your business with a direct line of communication to the many resources within the Schenck Process global network. Your Schenck Process Team will take command of the design/build process from project kickoff to process commissioning. From start to finish, our teams are dedicated to meeting your business goals.
scottmixers.com
For nearly four decades, Scott Mixers has designed and manufactured high-performance, high-shear mixers and turnkey mixing systems in the food, beverage, pharmaceutical, cosmetic, personal care, and chemical process industries. Whether your challenge is formulation development, process scale-up, or full-scale manufacturing, we offer a full range of mixing technologies and solutions to meet these challenges. Across North America, Scott Mixers is the premier choice for manufacturing a wide variety of consumer products, including salad dressings and sauces, creams and lotions. Our high-shear mixers and mixing systems excel for your powder-wetting, dispersing, de-agglomerating, and emulsifying needs.
The Scott Mixers’ head uniquely draws product from the top and bottom of the batch simultaneously, rapidly dispersing the product throughout the tank. This rotor technology provides excellent horizontal and vertical batch flow, ensuring that the product will be evenly sheared and dispersed, saving you time and resources. The unique design of the mix head develops high pumping rates not achieved with traditional batch style high shear mixers. No matter the application, a successful mixer installation relies upon more than just selecting the right mixer. Choosing a suitable vessel geometry (height to diameter, bottom shape) is a critical step toward a successful installation as well as understanding how the mixer or mixers should be operated (mixer rpm) at any stage of the process. A mixer specified and provided by Scott Mixers, along with the integrated vessel, accessories and controls will ensure high performance and reliable operation. We offer a wide range of high and low-shear mixers for batch mixing. Scott Mixers has developed a number of application-specific mixing systems in the food processing industry that address the most challenging material handling and mixing applications you will come across. Contact us to improve your process and reduce costs.
SEW-EURODRIVE is a leading manufacturer of gear units, motors, and automation control systems. SEW- EURODRIVE solutions set the global standard for high performance and rugged reliability in the toughest operating conditions. With its global headquarters in Germany, the privately held company’s U.S. operations include a state-of-the-art manufacturing center, 5 regional assembly plants, more than 70 technical sales offices, and hundreds of distributors and support specialists. This extensive representation enables SEW- EURODRIVE to provide local service, support, and manufacturing from coast-to-coast and around the world.
The extreme conditions found in food processing facilities can cause serious motor damage, resulting in an abnormally short life span. SEW’s Food Industry Option Package (IOP) consists of specialized features and components designed to overcome the demands of chemical washdown environments. These components save you downtime and money by extending the life of both the gear unit and the motor. Our IOP washdown protection package includes an industry-leading 2-year warranty covering any motor failure that results from moisture damage.
TorqLOC® Hollow Shaft Mounting System SEW-EURODRIVE’s patented TorqLOC® mounting system is the premier choice for a hollow shaft connection. Its corrosion resistance and non-fretting design make it the perfect solution for wet environments. The keyless, taper bushing design allows easy installation and removal, even after years of operation in a chemical or wash-down environment. Unlike a shrink disc that requires a ground shaft with very high tolerance, TorqLOC can use standard stock material without additional machining. TorqLOC offers advantages to both the OEM and the end user by reducing costs for machining, inventory, and installation. No wonder it is SEWEURODRIVE’s best-selling shaft design!
Phone: 501/492-3893
sleeveseal.com
Email: sales@sleeveseal.com
The RFL Series range of roll fed labelers was born from the same need as our shrink sleeve labelers - a need for faster, more efficient, more robustly built machines with Allen Bradley controls. In a market where efficiencies and cost of ownership are everything, Sleeve Seal has a proven history of fast, precise label application with minimal maintenance costs. Our engineers have an unparalleled depth of knowledge that has been applied to a new style of label application for today’s market. Sleeve Seal is proud to present our new range of RFL Series of roll fed labelers.
Sleeve Seal is focused on a new era of repeatable labeling performance. Built-to-last American manufacturing expertise and modern engineering are combined to produce speeds from 25 to 1600 CPM on robust machines equipped with intelligent Allen Bradley controls. Heavy weight construction and the fastest, most durable drive train in the industry provide high efficiency runs for countless hours. Sleeve Seal machines are engineered to provide quality labeling performance with simple, tool-less changeovers between container formats. Other patented innovations, such as a multi blade cutter assembly with quick-change blades have been developed for ease of maintenance.
The line of Sleeve Seal shrink tunnels features a new style of tunable controls that make shrinking labels on containers both precise and repeatable. Our shrink tunnels are available in a broad range of sizes that compliment all our labelers for shrinking labels at high speeds. In addition to newly designed controls, Sleeve Seal tunnels feature 316 stainless steel interior lining and components for maximum corrosion resistance. Every shrink tunnel model features external controls that allow the adjustment of individual arrays without exposing the operator to heat.
32 Crosby Drive, Suite 101, Bedford, MA 01730 USA
www.softroboticsinc.com
Soft Robotics is an industry-leading and award-winning technology company that designs and builds automated picking solutions using proprietary soft robotic grippers, 3D machine perception, and mGripAI™ artificial intelligence. The company’s transformational robotic automation solutions enable machine builders to solve the hardest piece picking problems in the food and beverage industry. We are dedicated to constant innovation and collaboration and are proud to be the face of the rapidly growing food automation industry.
Soft Robotics offers revolutionary food-grade robotic automation solutions that solve the many challenges in the food processing industry. Our mGrip and mGripAI solutions are easy-to-integrate enabling the deployment of robots in food processing, previously reliant on human labor.
The mGrip modular gripping system is a suite of configurable soft grippers and controller products that enables reliable, high-speed picking of traditionally hard-tograsp items in the food processing industry. mGrip’s proven soft gripper technology allows robots to safely and efficiently pick and pack products while also increasing throughput and efficiency.
3808 N Sullivan Rd, Bldg 4H, Spokane Valley, WA 99216 USA
Spokane Stainless Technologies is a leading manufacturer of custom engineered stainless steel tanks designed to meet the specific needs of the Processing and Packaging industries. Our tanks are made in the USA of high-quality stainless steel, providing superior durability and resistance to corrosion.
With a wide range of features, including mixer/agitators, ASME steam jackets, ports, a variety of manways, tank finishes, and sizes, we are able to create tanks that meet the specific requirements of our clients. Whether you are looking for a tank for storing liquids, mixing chemicals, or other applications, we have the expertise and experience to design and manufacture a tank that will meet your needs.
Our engineering team is the foundation of our commitment to customers. Using stateof-the-art solid modeling tools, we embrace customer challenges, envisioning innovative solutions that are on the leading edge. We provide ASME Pressure/Vacuum Vessel & UL Code certified design. If product support is required, our team will assist you and get the issue resolved quickly! We are committed to your complete satisfaction.
At Spokane Stainless Technologies, we take great pride in our commitment to quality, accuracy, and customer satisfaction. Our team of experienced engineers and fabricators is dedicated to providing high-quality tanks that are designed to last, ensuring that our clients receive the best value for their investment.
If you are in need of a custom engineered stainless steel tank, look no further than Spokane Stainless Technologies. Contact us today to learn more about our products and services. We look forward to starting or continuing a lasting business relationship with you!
Spokane Stainless Technologies is headquartered in Spokane Valley, Washington, USA.
1840 St. Regis Blvd. Dorval QC H9P 1H6 Canada
Phone: 888/278-5555
www.starview.net
Email: sales@starview.net
Starview Packaging Machinery, Inc. is a primary manufacturer of tray sealers for food tray packaging with over 25 years of supplying standard and custom packaging systems to our customers and distributors.
Providing the Processed Food Industry with Innovative Packaging Machines for:
• Fresh Foods
• Frozen Foods
• Ready to Eat Meals
• Customized Packaging Equipment
• Systems with Automation and Integration
We design, engineer, and manufacture a comprehensive line of manual, semi-automatic, and automatic tray sealing machines. Available in shuttle, rotary, and inline conveyor configurations, a variety of standard and custom sealing areas are available to meet the specific requirements of customers and maximize productivity. Machines are configured to suit specific applications with a focus on efficient, easy to operate, safe to use, and cost effective to run.
Starview’s distinct competitive advantage is in providing a range of both standard and customized quality packaging systems backed by solid machine designs, robust machine construction, and superior service.
Starview offers many value-added features for our machines such as auto tray loading, fillers, product sensing, printing and/or verification, automatic packaging materials loading, automatic lid placement, finished package unloading with reject feature for noncompliant packages.
Sterling Systems & Controls, Inc. has over 50 years of experience and a unique industrial application knowledge base. Our reputation is earned. We are a premier provider of efficient solutions for automated batching systems, weighing, bulk bag filling, bulk bag unloading, process controls, and plant automation. We create custom designed, engineered and manufactured systems based on the exact goals and needs of each customer. Today, our custom state-of-the-art designs utilize the latest technology specializing in weighing and batching systems, data management, as well as raw material and production data tracking.
Sterling Systems & Controls software, electrical and mechanical engineers design complete processing systems for various automation requirements within a wide array of industries. These systems include automated weighing/batching systems, complete plant automation, modular weighing systems, and upstream/downstream equipment including raw material handling systems, bulk bag filling stations, bulk bag unloading systems, conveyors, and post batch material handling systems. In addition to process equipment, we provide process controls, motor control centers, control panel fabrication and general automation utilizing many standard hardware and software platforms.
Our forte is custom batching systems, material weighing systems, as well as process and plantwide automation systems. Sterling Systems provides the best single-source solutions due to our eye for details and a well-rounded history in working with the Food, Baking, Feed, PetFood, Agriculture, Chemical, Rubber, Plastics, and other industries. We also can integrate our automated process and plant control systems with your general business system. And if you need remote monitoring of your control system data, we can provide this capability with our WebCentral™ software application. WebCentral is a browser based application that allows you to access the database of the automated control system. Because it is browser based, it is very simple and intuitive to use. Similarly we offer our preventative maintenance planning software application, PMPlanR™, as a browser based solution as well.
stollemachinery.com/prc
Stolle PRC WeightControl Fillers can fill a wide variety of food products, including meat, poultry, seafood, vegetables and pet foods. They are widely regarded as the most accurate container filling machines available, with accuracies equal to ±½ to 1%, even on difficult to fill products. This unparalleled filling accuracy reduces wasted product due to overfilling and eliminates rejects due to underfilling. The machine uses a unique method of portioning and filling which provides an exceptionally gentle fill that maintains the integrity of delicate and easily damaged products. There are no valves, sharp corners, restrictions or other product-damaging components. With a long history of reliable operation, Stolle PRC Fillers have a simple rotary design and few moving parts for low maintenance and nearly zero downtime. In fact, many of the earliest machines built are still in operation.
Features of the WeightControl Filler include a durable main gearbox, automatic lubrication system, and central shaft bearing protection. Other features include a tungsten-carbide coated cavity plate and filling stations and motorized portion control with a no can / no fill system, and motorized safety cam. The machines are ruggedly constructed of heavyduty stainless steel and other non-corrosive materials to withstand daily cleansing, and the open design makes all parts easily accessible for cleaning and maintenance. As the world’s leading supplier of machinery for the 2-piece canmaking industry, Stolle has unparalleled global reach and support resources, including supplying OEM parts for existing PRC food equipment – just send us your machines’ serial numbers and we will supply the correct parts to keep you in production.
Founded in 1983, ThermOmegaTech® is an innovator in the design and manufacture of self-actuated thermostatic technology. We are a privately held organization located near Philadelphia, Pennsylvania.
Our company provides solutions for a wide range of applications including washdown, freeze & scald protection, tepid water delivery, mixing & diverting, thermal relief, and other temperature control needs. Over 95% of ThermOmegaTech®’s products are manufactured, calibrated, and tested in-house. R&D, prototype development, integrated solutions, and engineering support are also on site. ThermOmegaTech® is ISO 9001:2015 & AS9100 certified.
STVM Washdown Station - ThermOmegaTech’s STVM® Washdown Station delivers a high temperature wash at a user-defined temperature using a proprietary mixing valve to combine steam & water. Our Silent Venturi Mixing Valve (STVM®) design is self-scouring which minimizes mineral buildup and reduces maintenance frequency.
Maintaining competitor washdown units is time consuming due to complex disassembly, special tooling requirements, and non-reusable components. Our washdown station utilizes a simple cartridge design which can be removed with a wrench & cleaned in a descaling solution before reassembly. The station is in-line serviceable, so the operator simply switches out the cartridge with a spare and the unit is back up and running in minutes, significantly reducing downtime. The station operates at around 20 decibels less than competitor mixing units, reducing operator stress and improving workplace conditions.
Safety is our priority which is why the unit includes interlocking shut-off ball valves that instantly shut-off of both inlets & prevents accidental steam only operation. Our thermally actuated over-temperature shut off design will also reduce flow if the output temperature exceeds the factory set point (150°F/185°F) & will completely shut down 15°F above that to protect personnel.
9009
Phone: 260/490-3000
Email: tippsales@tippmanngroup.com
www.tippmanngroup.com
Tippmann Group is a unique combination of two companies, Tippmann Construction and Interstate Warehousing, which are dedicated to safe and efficient design, construction and operation of multi-temperature processing and distribution facilities for the food industry.
In business since 1968, our refrigeration expertise and owner/operator experience make Tippmann Group your single-source provider for all of your temperature-controlled facility needs.
Tippmann Group’s QFR Zone® utilizes improved airflow to provide an energy and labor efficient blast freezing solution, freezing products faster and more cost efficiently than traditional blast systems. The QTR Zone® utilizes the same technology for thawing frozen product quickly.
Tippmann Construction
Design/build construction of multi-temperature warehouse and production facilities; New builds, expansions and renovations; Master site planning; Members of U.S. Green Building Council; Owner/operator experience & knowledge
Interstate Warehousing
4th largest PRW in United States; 115,000,000 cubic feet of cold storage space; SQF certified facilities; Customized distribution solutions; Retail and Foodservice consolidation programs; Comprehensive management development & training program
www.tnasolutions.com
tna is a leading global supplier of integrated food processing and packaging solutions with 40 years of industry experience and 14,000 systems installed across more than 120 countries. The company provides a comprehensive range of products for snacks and confectionery including material handling, processing, seasoning, coating, starch molding, distribution, metal detection, verification, packaging, weighing, inserting and labelling. tna also offers a variety of production line controls integration & SCADA reporting options, product testing, training and after-sales-support. tna’s unique combination of innovative technologies, extensive project management experience and 24/7 global support ensures customers achieve faster, more reliable and flexible food production at the lowest cost of ownership.
A customer-centric approach dominates tna’s business philosophy. To help food producers address labor shortages and boost production efficiency, tna is offering end-to-end production lines from a single source. The latest iteration of its flagship vertical form fill and seal packaging system (tna robag® 3e) sets high performance and quality standards, capable of producing a wide variety of products at speeds of up to 250 bags per minute. The system’s superior design results in product waste levels as low as 0.1%, offering a more efficient, sustainable packaging operation. tna aftermarket services provide real-time remote assistance for collaborative maintenance, repairs and inspections.
It is tna’s belief that a company’s performance must be measured by its contribution to building economic, social and environmental capital, enhancing societal sustainability. It is through this belief that the Nadia and Alf Taylor Foundation has evolved into a humanitarian organization that works towards providing education to kids in marginalized communities across the globe.
242 PROFOOD WORLD | February 2023 | www.profoodworld.com
Phone: 219/464-4811
www.urschel.com
Email: info@urschel.com
New from Urschel, meet the M VersaPro™ (MVP) next-generation protein powerhouse. The 2-D dicer excels in the processing of meat, poultry, and alternative proteins. The machine provides the best in sanitary design and the ultimate in the versatile cutting of all types of protein.
The MVP offers a 33% increased feeding capacity versus the standard M6 due to wider belts, optimized cutting, and increased horsepower. The belt-fed MVP delivers 2-dimensional dices, strips, or shreds from product of a predetermined thickness. A new patented, fluted crosscut option provides gentler cutting action. A deeper circular knife to feed drum penetration produces an improved cutting method. Available intuitive touchscreen HMI option easily gathers data, monitors machine components including sensors and amperage; adjusts operating speeds, and saves recipes. Touchscreen swivels for full visibility.
Explore the new laser cut Model CC Slicer frame. This bold, improved design offers increased sanitation and flexibility. Open internal corners and angled support sides reduce bacterial collection areas offering faster, more effective washdowns. The optional top cover is easily removable. Space for hand knobs after removal ensures they are not lost or placed on the floor. Hoops, electrical boxes, and motors are all field replaceable for maintenance or future upgrades.
The DiversaCut 2110A® 3-D Dicers produce precision dices, strips, and slices at high production capacities to maximize yield. The close proximity of each cutting station establishes a compact zone to increase the exactness of each cut. The discharge conveyor-equipped model facilitates batch processing into totes or onto conveying systems or platforms. This design also eases routine servicing by maintaining the machine at floor level.
Successful processors partner with Urschel to achieve their production line goals. Contact Urschel to learn more about Urschel cutting advantages.
VAC-U-MAX is a worldwide leader in the design and manufacture of bulk material handling systems that convey, weigh, and batch over 10,000 various powders and bulk materials to food processing and packaging lines. With strong application expertise in the food industry and being a subject expert on conveying powders and granular bulk solids, VAC-U-MAX food ingredient handling systems incorporate pneumatic, aero-mechanical, and flexible screw conveying technologies designed to handle many types of materials including powders, flakes, granules, pellets, fibers, tablets, seeds, coatings, sugar, and other granular bulk materials.
Since 1954, VAC-U-MAX has been a pioneer in pneumatic conveying, developing the first air-powered venturi unit, advancing technologies for direct-charge loading of vacuum tolerant process equipment, and the first to design vertical-wall “tube hopper” material receivers for difficult to convey materials. A vacuum receiver represents the heart of a food ingredient handling system, conveying materials from drums, bins, totes, bulk bags, super sacks, and bag dump stations for dust-free material handling.
VAC-U-MAX product range includes vacuum receivers, bulk bag loading and unloading systems, aero-mechanical and flexible screw conveying systems, bag dump stations with integrated dust collection and empty-bag compaction, diverter valves, feed bins, and vacuum pump packages. VAC-U-MAX is a UL-listed manufacturer and supplier of control packages that are easily integrated into existing plant PLC’s. Product range also includes a full line of portable, continuous-duty, and central vacuum cleaning systems for plantwide clean-up of many types of materials including combustible dusts.
VAC-U-MAX systems focus on waste reduction as in topping and coating applications that require placement of seeds, flavorings, sugar, salt, and coatings onto finished food product. Excess or non-placed toppings are reclaimed, recycled and reused, greatly reducing waste. For more information visit www.vac-u-max.com and fill out RFQ.
13771
VDG is the leader in the design and manufacturing of drum motors for belt conveyors, with a strong focus on safety, reliability, and longevity. Manufacturing in-house in USA and Canada for 37 years using cutting-edge production technology and automation, along with continuous improvements through R&D, VDG ensures product quality, fast delivery, and after sales support.
All drive components of the VDG Drum Motor, including the electric motor, gear reducer, and bearings, are enclosed inside the drum, increasing energy efficiency, operator safety and optimizing space. VDG Drum Motors are designed for 80,000 hours of continuous operation before maintenance, minimizing downtime and reducing maintenance and operational costs.
VDG’s stainless steel SSV Series Drum Motor features an IP69K rated sealing system, withstands up to 3,000 psi washdown pressure, and drives modular, wire mesh, and monolithic conveyor belts without using sprockets. The SSV Drum Motor eliminates crevices that trap food by-products and bacterial harborage, reducing washdown time and water usage by 50% and providing the most efficient and hygienic drive solution for food processing and handling belt conveyors.
SSV Drum Motors are available either with the belt profile machined directly on the stainless steel drum or on the new removable profiled sleeve (XP). The VDG patented SSV-XP Drum Motor with the removable profiled sleeve enables different belt profiles to be used with the same drum motor by simply removing the sleeve and exchanging it to match the desired belt profile.
The IntelliDrive™ Drum Motor features new synchronous permanent magnet motor technology, delivering 40% increased electrical efficiency, a wider range of belt speeds without loss of torque and an increase in electric motor lifespan compared to a traditional conveyor drive. It enables onsite diagnostics, full motor indexing speed control, and communications with other automated plant equipment.
VDG Drum Motors are available in a range of diameter sizes, belt speeds, horsepower, and belt profiles for all belt manufacturers to suit various belt conveyor applications.
For more than 60 years, VEGA Americas, Inc. has provided industry-leading products for the measurement of level and pressure. VEGA’s full product line of level and pressure measurement instrumentation allows us to provide one of the most complete ranges of measurement solutions in the industry.
VEGA’s continued innovation in radar, pressure, differential pressure, and point level switches ensures food and beverage operations of all sizes can continue to improve their processes and keep up with ever-shifting market demands. VEGA believes the future of instrumentation lies in the ability to produce high-quality, innovative products that keep pace with technology, and provide service and value to our customers in today’s competitive environment. Our measurement solutions have helped make more batches, maintain inventory of raw ingredients, and save energy.
Always in pursuit of technology that improves operational efficiency for our food and beverage partners, VEGA created the VEGABAR 39 universal pressure transmitter for measuring gases, vapors, and liquids at up to 130 °C. Designed to aid in such processes as pasteurization and separation, the VEGABAR 39 employs inventive solutions like a 360° colored light ring for enhanced status readability from across a facility. Because integration can be just as important as operation, the VEGABAR 39 is also equipped with IO-Link communication for simple integration into control systems.
Located in Cincinnati, Ohio, VEGA Americas combines manufacturing, distribution, and service for products that represent the most sophisticated process measurement technologies anywhere in the world. VEGA Americas is a wholly-owned subsidiary of VEGA Grieshaber KG in Schiltach, Baden-Württemberg, Germany.
VEGA understands the benefit of investing in community and employees, because it’s people who make the difference in achieving success. This success fuels future innovation and transfers to the solutions we provide to customers.
Phone: 1.844.VERITIV
www.veritivcorp.com/food
As a North American leader in packaging solutions, Veritiv® helps you keep up with the latest food packaging innovations—from primary packaging to tertiary packaging.
• Direct food contact our experts bring the science to packaging to prolong the life of your product and increase consumer sales
• ackaging automation increase throughput and reduce labor costs
• Sustainability recyclable options with the right amount of materials
• Cold chain packaging solutions to keep your product at its ideal temperature
From concept to delivery - hether you need a more sustainable packaging option, a new, innovative design to catch the eye of consumers, greater speed-to-market capabilities, or a fresh approach to your existing process, look to eritiv and our team of experts to help you meet and exceed your food packaging objectives.
Differentiate through design - Competition is fierce, especially in food. To stand out, your packaging must deliver in form, function and flexibility. From primary to tertiary packaging, Veritiv’s custom packaging designs help your product keep its freshness, stand out on the shelf and provide ease for consumers to use and dispose.
readth and depth of product - As a material-neutral supplier with distribution centers all over North America, we provide a full spectrum of supplies for your whole facility. From boxes and bags to films and trays, eritiv knows packaging. e can also protect your people with our full line of facility solutions products including cleaning supplies, hand hygiene, E and more.
roof is in our people - From identifying inefficiencies in your operations to providing custom solutions to fix them, our team of food specialists, material specialists, structural designers, e uipment technicians, and supply chain experts develop new ideas and custom processes that boost efficiencies and cut costs, while protecting your product and elevating your brand.
755 Union Blvd., Totowa, NJ 07512 USA
Phone: 973-256-7410
www.vibrascrew.com
Email: info@vibrascrew.com
Vibra Screw Incorporated was founded in 1955 by Eugene A. Wahl, whose experience in solving problems in the process industries led to revolutionary ways to discharge and meter dry solids.
Today, with a staff of experienced and talented engineers and technicians, Vibra Screw is the leader in dry solids processing, with high quality equipment to store, discharge, meter, convey, size and blend.
Vibra Screw serves its markets through a world wide network of sales representatives, licensees and subsidiaries.
Vibra Screw is staffed with experienced, professional engineers who solve problems. From initial study, through testing & design, our goal is to satisfy our Customer’s unique requirements efficiently & cost effectively. Our modern facility in Totowa, NJ handles every aspect of equipment manufacture from sandblasting, fabrication & assembly to full electronic control production.
The most trusted name in dry solids processing. Vibra Screw Inc. prides itself in being able to bring ground-breaking solutions to your solids processing challenges. Vibra Screw currently manufactures: bulk bag unloaders, volumetric feeders, bin activators, vibrating feeders/vibrating conveyors, flexible screw conveyors, loss-in-weight feeders, storage pile activators, live bottom bins, screeners, continuous blenders, and process controls.
No other Industry source stands behind its products with the confidence & assurance of Vibra Screw, because no other Company engineers & manufactures to our uncompromising standards:
VIBRA SCREW EQUIPMENT IS UNCONDITIONALLY GUARANTEED TO PERFORM IN THE SERVICE FOR WHICH IT WAS SOLD OR WE WILL REFUND YOUR MONEY –PERIOD!
See all the Leaders in Processing at www.profoodworld.com/leaders
1900 Frost Road, Suite 200. Bristol, PA 19007 USA
Volkmann USA designs and manufactures hygienic, explosion-proof pneumatic vacuum conveying systems to safely transfer powders, pellets, granules, and other bulk materials from one point in a process to another point while safeguarding particle integrity and mixture homogeneity. Proven worldwide in transferring ingredients for foods, pet foods, beverages, nutritional supplements, and more, as well as finished products ready for packaging, these automated, sanitary conveyors feature patented vacuum technology that eliminates the potential for ignition even when transferring ignitable, fine particles and combustible dusts. By operating entirely pneumatically without electricity, without rotating parts, without generating heat, and with proper electrostatic grounding, our conveying systems earned the ATEX certification as suitable for safe installation in all dust explosion areas.
Our conveying systems can be quickly disassembled without tools for easy access to the interior, complete cleaning and inspection. Our experienced engineering team customdesigns the powder transfer conveyors for sanitary, cleanroom, hazardous, and any type of process.
Volkmann also designs and manufactures the companion bulk material handling equipment typically specified when conveying dry materials and ingredients. Bulk bag unloading stations, bag dump stations, lump breakers, and accessories are all available, custom-engineered to suit the installation.
Serving North America from our Bristol, PA headquarters near I-95, we offer material testing on fully operating pneumatic conveying systems and accessories in a dedicated test laboratory. The family-owned, global organization based in Germany operates subsidiaries in Great Britain, USA, France and the Netherlands with more than 100 employees worldwide.
us.weberweb.com
Weber is the leading supplier for fully integrated slicing and packaging lines in the food processing industry. From automatic infeeding, slicing, handling, product loading and packaging, Weber delivers application driven solutions designed around your business needs. With an impressive breadth of product portfolio, Weber has a unique philosophy on complete line solutions bridging the gap between the “tech” and “food” industry. Solutions from one source, seamlessly integrated and intelligently networked, boundaries between individual components disappear as the complete slicing line evolves into one system. This makes Weber’s solutions highly adaptable to specific customer requirements and can bring unprecedented optimization and high-performance to the production process.
With innovative technology at each step of the process, including Weber’s own OEM designed and manufactured software, vision, and robotics, Weber challenges consensus when it comes to integration and line control – with the solution truly integrated, mechanically, electrically, and digitally. Further complimented by a complete suite of digital products, starting with the Weber One Control and rounded out by its Factory Cockpit real time production monitoring tool – Weber’s approach to true integration and application specific solutions are why many customers choose Weber as a trusted partner they can grow with.
WestRock is a global leader in sustainable paper and packaging solutions. We are materials scientists, packaging designers, mechanical engineers and manufacturing experts with a shared purpose: Innovate Boldly. Package Sustainably. Guided by our values of integrity, respect, accountability and excellence, we use leading science and technology to move fiber-based packaging forward.
WestRock’s best-in-class innovation engine leverages the largest set of fiber-based substrates, a vast network of converting and distribution capabilities and an unmatched packaging machinery platform to power the next generation of renewable, recyclable packaging. Our broad portfolio is operated in four segments – Corrugated Packaging, Consumer Packaging, Global Paper and Mill Operations. A uniquely integrated Commercial, Innovation and Marketing function offers unrivaled end-to-end solutions and support to solve our customers’ greatest challenges.
Our global operations include:
– More than 50,000 employees in the Americas, Europe and Asia-Pacific
– More than 30 containerboard and paperboard mills
– More than 320 operating and business locations
– Products in a wide range of markets, including beauty and personal care, beverage, e-commerce, healthcare, home and garden, media and electronics, packaged food, pizza and retail
Sustainability and innovation are fundamental to WestRock’s vision to become the world’s best paper and packaging company. By innovating for our customers and their customers, bettering the planet and supporting people and communities, we’re imagining and delivering on the promise of a sustainable future.
825
Phone: 678/344-8300
www.wipotec.com/us
Email: Info.usa@wipotec.com
Processing applications have their own unique challenges when it comes to product inspection. Our bulk flow X-Ray scanners ensure that pre-packaged foods such as meat, poultry, and grains are free of foreign body contamination as the product enters the processing line. After packaging other types of scanners and vision systems ensure package integrity, and product labeling accuracy. For dairy processors, our line of IP69K checkweighers deliver precise, accurate, and repeatable product and package weighing results in wash down environments. In drug processing applications Wipotec’s serialization and aggregation machines guard against counterfeit products entering the global supply chain. Wipotec manufacturing takes place in Kaiserslautern, Germany. The Atlanta metro area is home to the company’s North American operations.
Checkweighers prevent under filling and overfilling of product, resulting in brand protection and cost reduction due to less product giveaway. Wipotec checkweighers use EMFR weigh cells to deliver the fastest and most accurate product weights possible at throughputs up to 650 ppm. The modular design of these machines enables support for a wide variety of machine options including metal detectors.
Our X-Ray scanners and vision systems prevent expensive product recalls. These machines maximize product safety and packaging integrity. X-Ray scanners are ideal for foreign body contaminant detection, package completeness, and fill-level checks. Vision systems do a great job verifying product label contents and correct placement on your packages.
These modular machines ensure end-to-end tracking of packaged goods in order to keep counterfeit products out of the supply chain.
17 Colby Court, Bedford, NH 03110 USA
Phone: (603) 644-2500
www.wirebelt.com
Email: sales@wirebelt.com
Wire Belt Company is the leading manufacturer of open-mesh stainless steel conveyor belts and a full line of conveyor solutions. With over 85 years of industry knowledge, we keep our customer’s conveyor lines up and running. Our conveyor belts are used extensively in applications such as: breading, battering, baking, coating, frying, cooking, and cooling. Our world-class Customer Service and Technical teams have the knowledge to help you find the right belt or conveyor to fit your applications needs.
• Flat-Flex® stainless steel conveyor belts - USDA Accepted, open-mesh clean-in-place design. Available in different pitches and wire diameters to meet your application needs.
• Eye-Flex® heavy-duty metal modular conveyor belts - Designed to take on your toughest applications.
• Compact-Grid™ conveyor belts - Engineered to offer superior support for small products. Compact-Grid’s belt design offers long belt life. Compact-Grid™ is easy to join on your conveyor, which will get you up and running quickly.
• Ladder-Track™ conveyor belts - Designed for baking applications. Easy to join and to install on your conveyor.
• Flat-Turn® Conveyors - Maximize your space with tight transfers and maintaining product orientation around corners.
• Straight Conveyors - Open design with maximum cleanability and custom designed for your application.
• Ladder-Flex™ Conveyors - Spreading, converging and diverging conveyors with a positive drive and ability to run narrow conveyors to save space.
Call us to talk about a specific application or for further information at (603) 644-2500.
https://www.yaskawa.com
At Yaskawa, we help you explore what’s possible, and open new doors to opportunity. Rather than accepting the status quo, we invite you to wonder, “What if?” And then we make it possible. That dedication to innovation is what makes us different.
Experience is often the difference between solving a problem the right way and settling for “good enough”. Our global expertise is unmatched and unquestioned, with 100+ Years of manufacturing excellence, 30 countries with sales, service, and manufacturing locations, and $4.5 billion in global sales per year.
We provide both standard products and tailor-made solutions, all backed by proven quality and reliability. We continuously work to save you money, time, and energy, because we believe your machine can always run faster, smoother and more productively. It’s about making the correct diagnoses, creating the right automation machinery, and implementing it in the best way possible.
Yaskawa AC Servo Systems come to a precise position with a speed and consistency that is unmatched in the industry. Connect our rotary, linear, and direct drive servo motors to an advanced Yaskawa machine controller to achieve SINGULAR CONTROL, the ability to manage robots, servos and drives with a single controller and familiar IEC 61131-3 programming.
Yaskawa low and medium voltage AC Variable Frequency Drives cover every automation application need in the industrial plant, with power ranges from fractional HP to 16,000 HP and a legendary reputation for reliability and advanced technology. Our latest variable frequency drives provide simple motor setup with highly flexible network communications, embedded functional safety, no-power programming, and easy-to-use tools featuring mobile device connectivity with our DriveWizard® mobile app.
254 PROFOOD WORLD | February 2023 | www.profoodworld.com
Zeppelin Systems is the market leader in the design, manufacture, and supply of automated material handling systems for powder and liquid ingredients and innovation in dough technology for food processing plants. Recognized in the industry for our highquality equipment and process reputation in automated ingredient handling systems and known for our extensive innovations in food process technology in more than 2,000 projects successfully completed in North and South America.
We design each system according to the customer’s needs and supply complete process automation. Additionally, we rank with the world’s largest technical network for bulk material handling systems, provided by highly skilled and capable field service support with flexible and quick response 24/7, and backed up with exceptional spare parts and after-sales service.
Food Processing Plants we serve: Fresh baked goods, extended shelf-life baked goods, pasta products, confectionery, dairy products, cereals, finished mixes/baking additives, spices, instant beverages, baby food and pet food, among others.
Our areas of expertise include: Receiving, storage, conditioning, bulk silos for dry and liquid ingredients, pneumatic conveying (dilute and dense phase: vacuum and pressure); mechanical conveying (screws, trays, bucket elevators, belts), preparation-sifting, sugar handling, grinding systems, liquid ingredients handling (continuous and batch fermentation), minor and micro ingredients handling, pre-blending, pre-hydration with DymoMix® and continuous mixing systems (CODOS®). As a Gold Level in the Rockwell System Integrator Partner Program, we provide world-class process automation and controls, and we offer our proprietary system software PRISMA®, a recipe and production management system.
Zeppelin Systems can be a turnkey supplier with overall solutions from one source: Equipment and components, Process technology, Automation and controls, Project Management and Service and Support.
KAESER
King Plastic
ProFood World® (ISSN 2476-06760, USPS 22310) is a registered trademark of PMMI, The Association for Packaging and Processing Technologies. ProFood World® is published 7x a year (February, April, June, August, September, October, December) by PMMI Media Group, 401 North Michigan Avenue Suite 1700, Chicago, IL 60611; 312.222.1010; Fax: 312.222.1310. Periodical postage paid at Chicago, IL, and additional mailing offices. Copyright 2023 by PMMI. All rights reserved. Materials in this publication must not be reproduced in any form without written permission of the publisher. Applications for a free subscription may be made online at www.profoodworld.com. Paid subscription rates per year are $55 in the U.S., $80 Canada and Mexico by surface mail; $130 Europe and South America. $200 in all other areas. To subscribe or manage your subscription to ProFood World, visit ProFoodWorld.com/subscribe. Free digital edition available to qualified individuals. POSTMASTER: Send address corrections to: ProFood World, 401 North Michigan Avenue, Suite 1700, Chicago, IL 60611. PRINTED IN USA by Quad Graphics. The opinions expressed in articles are those of the authors and not necessarily those of PMMI. Comments, questions and letters to the editor are welcome and can be sent to: ahand@pmmimediagroup.com. We make a portion of our mailing list available to reputable firms. If you would prefer that we don’t include your name, please write us at the Chicago, IL address. Volume 7, Number 1.
by
Each year, ProFood World recognizes outstanding food and beverage processing and packaging innovation projects via the Sustainability Excellence in Manufacturing Awards competition.
Multiple awards will be named for projects such as:
Reduction in water and energy
Waste conservation
Pollution prevention
Packaging reductions
ENTER THE RECENTLY ADDED PROCESSOR/ SUPPLIER PARTNERSHIP CATEGORY!
View a past winner’s video at pfwgo.to/meat
Join past winners such as Campbell Soup, Land O’Lakes, McCormick, Smithfield, Conagra Brands, Hormel, Hiland Dairy, Big Heart Pet Brands, Bob’s Red Mill Natural Products, Li ey Meats, and Graphic Packaging International. View past winning entries and learn more at pfwgo.to/sema
Entries are due March 17, 2023.
Produced Awards to be presented atA winning food safety strategy incorporates HACCP and FSMA guidelines, strong leadership, and end-to-end oversight of a processing operation.
WHEN IT COMES TO DEVELOPING a worldclass food safety program, the most likely factors that guarantee success are being knowledgeable and organized, and having a continual flow of both data and verbal communications. It should be obvious that without using all these skills, the program will probably be incomplete and, at worst, ine ective.
So the challenge is to define what constitutes a food safety program and then use those skills to develop the plans to create one. As an instructor of Hazard Analysis Critical Control Points (HACCP) and Food Safety Modernization Act (FSMA), my students often question the di erence between a food safety program and a food safety system. A correct understanding of these terms lays a pathway forward to success. In food safety terms, a “program” can be the overall strategy to produce safe and wholesome food, whereas a “system” consists of the components, tactics, and tools to make the program work.
A good place to start is to develop a program that incorporates the current regulatory requirements. For most products regulated by the U.S. Food and Drug Administration (FDA), these regulations are outlined in the FSMA rules. For products regulated under the U.S. Department of Agriculture (USDA), HACCP rules apply. These food safety requirements must be developed satisfying the minimal rules. In practice, many consumer packaged goods (CPG) companies go well beyond these minimal requirements in their programs. Unfortunately, some CPGs might mistakenly believe their food safety program starts at the loading dock and ends at the shipping bay.
The FDA generally looks at food safety from “farm to fork” and, therefore, it seems appropriate to develop a total program using that same lens. In light of this broad scope, CPGs should consider
where all their ingredients and packaging materials come from (even including local water as an ingredient), who their consumer is, and every step of production within the supply chain.
The heart of any food safety program is the FDA or USDA required Food Safety Plan. This written plan is based on food safety principles and incorporates a system of hazard analysis, identification of preventive controls, and action steps to ensure consistent production of safe and wholesome food. It should be noted that each facility might have di erent types of issues based on the ingredient and packaging suppliers, process flow layout, equipment use and location, and even the food safety culture of the facility.
The major components are the development and incorporation of current Good Manufacturing Practices (cGMP), HACCP and/or FSMA into working food safety plans and the supporting prerequisite foundational activities. A facility might also have a food defense plan that covers the security of the plant, visitors, and the employees. There are many tools available to help build a food safety plan such as that provided by the FDA called the “FDA Food Safety Plan Builder.” Also, the FDA has provided a “Food Defense Plan Builder v2.0” to assist CPGs in food security needs. These software programs can be obtained as downloads from FDA’s website. Additionally, many certification and software companies and consulting firms have their version of plan builders, which can be helpful if that skill does not exist in-house.
The plan is necessary and required, yet today’s program should expand to become a more comprehensive program approach and should also
include the aspects of leadership and data management. Remember that a food safety plan is a living document and must be re-evaluated periodically, and when changes in ingredients or production occur that could alter the risk analysis conclusions.
For CPGs, packaging typically has a di erent meaning than the topic of this article. To be clear, this discussion is about making certain a food safety program is constructed (packaged) to contain the food safety systems that are legally required and e ective, and that accomplish food safety goals. The system components to consider for the program are shown in the sidebar below.
In the past, many food safety activities were related to the planning and preventive controls part of the package. Packaging these four components (Leadership, Planning, Preventive Controls, and Data Management) into the program will accomplish three goals.
First, it gives the program more depth by expanding the input and influence of personnel other than just those directly handling the manufacturing of the product. Next, it brings in the concepts being promoted by the FDA through its New Era of Smarter Food Safety Initiative, announced in July 2020, that outlines operational goals to enhance traceability, improve predictive analytics, respond more rapidly to outbreaks, reduce contamination of food, and foster the development of stronger food safety cultures. Finally, it emphasizes the importance of collecting data and managing it for the company as well as for the agency.
Today’s FDA is taking a new approach to food safety, leveraging technology and other tools to create a safer and more digital, traceable food system. These concepts are outlined in more detail in the FDA’s New Era Blueprint and include the ones that are most relevant to this discussion of a food safety program package. Specifically, the new concepts in Blueprint Core Element #1 (Digital Data Control and Management for Traceability) and Core Element #4 (Food Safety Culture) should be included in the program. These New Era activities are now added to the basic principles and plans to expand and modernize the scope of a food safety program.
In this world of global food sources and supplies, the expanding, reconstructing, and repackaging of a food safety program is both timely and essential to remain competitive in global markets. A properly packaged program will satisfy the needs of all involved in the production chain, while a well-developed and organized program will add to corporate goals of safety and profitability as well as meet current regulatory requirements.
n Sanitation of facility and equipment with attention to line-worker habits and health
n Hazard analysis of ingredients, processes, packaging, labeling, storage, and shipping
n Food Safety Plan incorporating preventive controls to mitigate biological, chemical, physical hazards and curb possible intentional adulteration
n Written procedures to be followed for:
• Monitoring the activities and preventive controls
• Corrective actions when a deviation occurs and root cause determined
• Verification of activities and validation of processes
• Record keeping practices and data validity confirmed
n Procedures to track and manage U.S. and international ingredients (foreign supply chains)
n Recall plan, aided by digital data, to expedite communication and product recovery
n Periodic audits to ensure systems are performing as intended
The stainless steel gear units from SEW-EURODRIVE keep things moving wherever machines and systems are subject to particularly intensive cleaning. Regardless of whether the gearmotors are used for material handling, intralogistics or sanitary
applications, their hygienic properties, long operating life, and maintenance friendliness make them optimally suited in the food and beverage and pharmaceutical industries, and in permanently wet environments.