CELEBRATING A DECADE OF SUCCESSFUL COLLABORATION
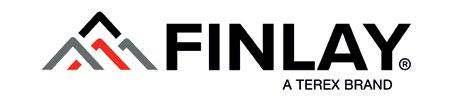
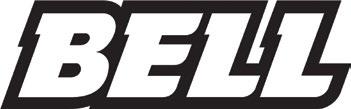
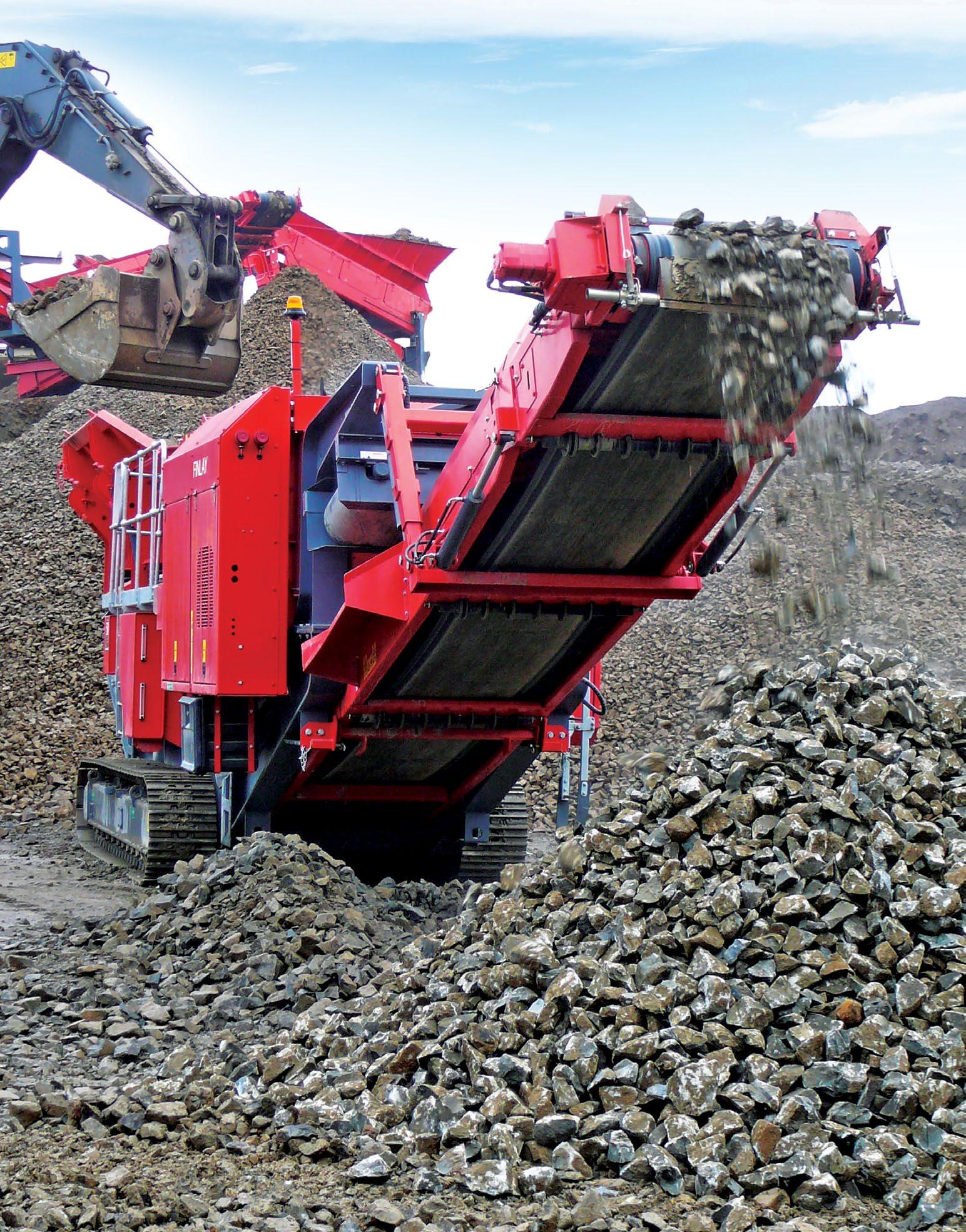
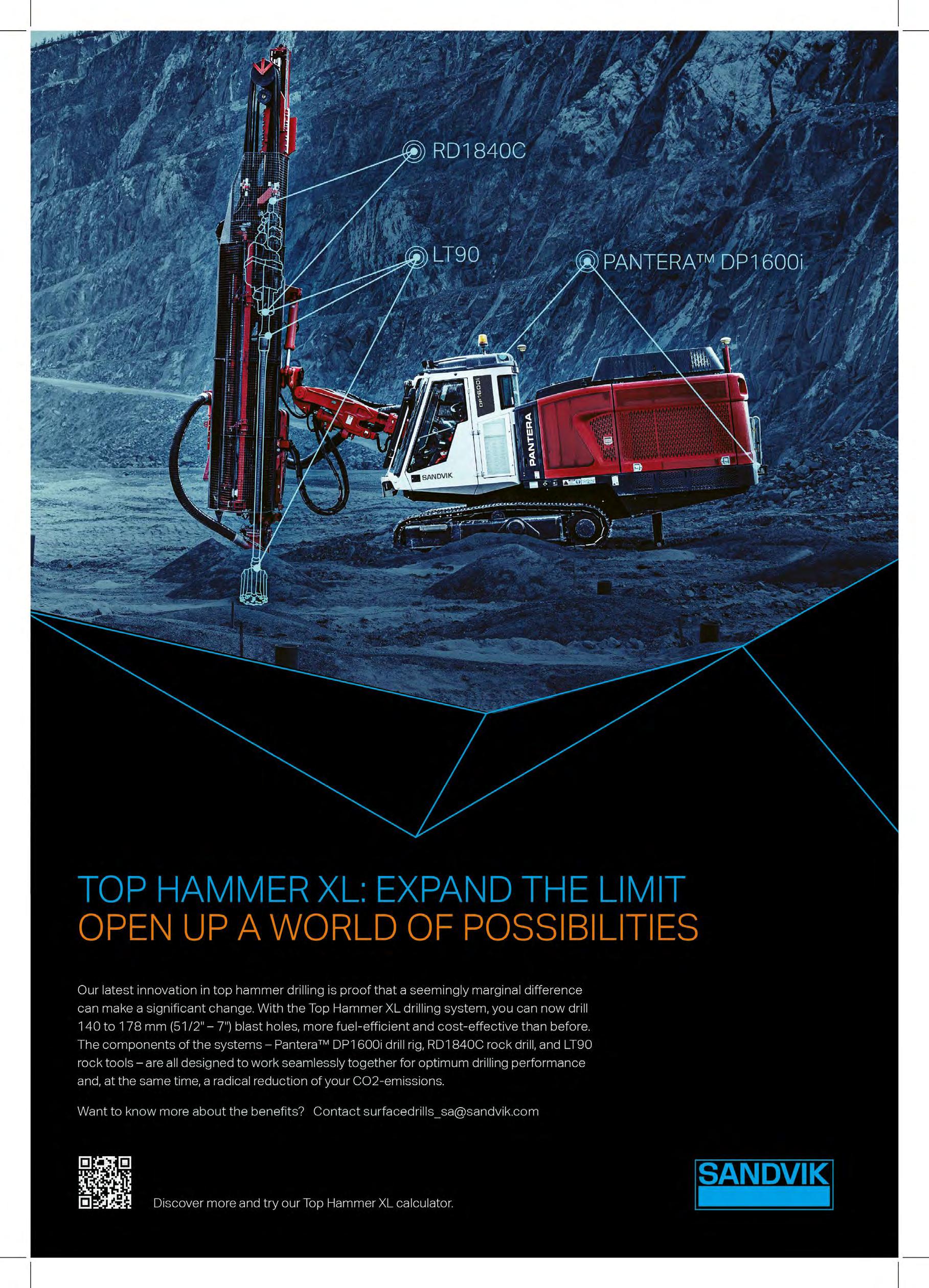
The environmental impact of quarrying activities and opencast mining operations at large cannot be underestimated. While quarrying is a vital industry which is critical to the economy of every country, it can be damaging to the environment. Traditionally, the industry has sometimes been blamed for paying lip service to environmental compliance.
However, the focus on the environment and Environmental, Social and Governance (ESG) issues in general, has grown in recent years and it is now a priority for quarrying companies as they become even more conscious of the impact on the long-term sustainability of their businesses.
In my recent conversation with ASPASA director Letisha van den Berg, she noted that under her leadership, the association will further cast the spotlight on environmental compliance, which in her view will grow in importance to even surpass safety in the near future. If findings and observations from ASPASA’s 2022 Environmental audit are anything to go by, the industry is truly putting the environment at the core of its activities.
As you will see in this edition of Quarrying Africa, a total of 66 audits were conducted last year, with some 23 Showplace scores (95% and above), a true indicator that the level of compliance presented by local operations is exceptional.
One of the key talking points from the 2022 audit was the need for improving waste management at quarries. It is estimated that 175-million tonnes (t) of quarrying waste are produced each year, and although a portion of this waste may be utilised on site, such as for excavation pit refill or berm construction, it is often difficult to find meaningful use for all waste stone and fines produce. Coupling this with the industry’s other waste streams, such as wastewater sludge and general site trash, it is essential that all operations in the natural stone
industry develop and abide by a waste management plan.
Through implementation of a proactive waste management strategy, unnecessary fines, occupational exposures and environmental degradation may be avoided. Additionally, an opportunity exists for companies to distinguish themselves as socially responsible and environmentally considerate operations.
Decreasing the amount of material lost during the quarrying and crushing processes increases efficiency and the quantity of profitable product. In effect, the company sees a greater return for every tonne of product sold. In addition, comprehensive, proactive waste management practices will result in a reputation for social responsibility and greater community acceptance of the quarrying operation.
Waste from quarry operations can be unsafe and environmentally detrimental. Scrap stone can create dangerous working conditions as well as an undesirable visual impact if piles are stacked carelessly or not well organised. Runoff from the scrap mounds can cause erosion problems, and fines introduced into natural waterways can suffocate local ecosystems.
We cannot deny the growing focus on ESG in the extractive industry. It is, however, still a concept that fits into the global environmental plan, however, not everything has yet been legislated, but one can see that it’s coming.
As regulators and communities continue to demand that extractive industries place more emphasis on environmental issues, this might be the perfect time for quarries to start taking active steps on their environmental protection agenda.
The lack of environmental compliance can have dire consequences for operations. Remember, it is one of the key aspects that can lead to the revoking of a mining licence. In my view, it is as important as safety management, but at present it is not a concept well understood by all. a
Publishing Editor: Munesu Shoko
Sub Editor: Glynnis Koch
Business Development Manager: Elmarie Stonell
Admin: Linda T. Chisi
Design: Kudzo Mzire Maputire
Web Manager: Thina Bhebhe
Quarrying Africa is the information hub for the sub-Saharan African quarrying sector. It is a valued reference tool positioned as a must-read for the broader spectrum of the aggregates value chain, from quarry operators and aggregate retailers, to concrete and cement producers, mining contractors, aggregate haulage companies and the supply chain at large.
Quarrying Africa, published by DueNorth Media Africa, makes constant effort to ensure that content is accurate before publication. The views expressed in the articles reflect the source(s) opinions and are not necessarily the views of the publisher and editor.
The opinions, beliefs and viewpoints expressed by the various thought leaders and contributors do not necessarily reflect the opinions, beliefs and viewpoints of the Quarrying Africa team.
Quarrying Africa prides itself on the educational content published via www.quarryingafrica.com and in Quarrying Africa magazine in print. We believe knowledge is power, which is why we strive to cover topics that affect the quarrying value chain at large.
Printed by:
Contact Information
Email: munesu@quarryingafrica.com
Cell: +27 (0)73 052 4335
Afrimat has announced that its sector classification on the JSE will be reclassified from the Basic Materials, Construction sector to the General Mining sector. FTSE Russell announced that the quarterly classification change was made after the market close on Friday, 17 March 2023 and will be effective on Monday, 20 March 2023.
Andries van Heerden, the CEO of Afrimat, states that the move is sensible given where most of the group’s earnings are now generated, and that the new classification will also better the position of Afrimat amongst its peers in the marketplace.
“After we listed in 2006, Afrimat was focused on aggregates and quarries, with our Construction Materials segment being the only contributor to profitability. We then embarked on a conscious diversification strategy to broaden our product offering through a multicommodity portfolio to ensure the longterm success and sustainability of the business,” says van Heerden.
“This involved expanding into Industrial Minerals and later into Bulk Commodities, which now includes the mining, processing and sale of iron ore and anthracite. We are adding phosphate, rare earth elements and vermiculite to our product offering through the development of Glenover mine. The newly formed Future Materials and Metals segment will house the Glenover operation.”
Van Heerden explains that as a result of the diversification strategy, the group’s Construction Materials segment now contributes less than 20% towards
operating profit. “The Bulk Commodities segment generates the majority of our revenue and operating profit and therefore, a sector change was required.”
An extract of The Industry Classification Benchmark Ground Rules defines General Mining as, “Companies engaged in the exploration, extraction or refining of minerals not defined elsewhere within the Mining sector. It also includes companies engaged in diversified metals and mining, marketing of mining commodities, and providers of contracted drilling services.”
Van Heerden indicates that Afrimat will continue with its diversification strategy to consistently deliver exceptional results.
“This strategy, coupled with the innovation of traditional products and inputs, has effectively protected Afrimat against lower economic growth rates in South Africa. Deeper diversification into bulk and other commodities will help position the group as a Rand-hedge, able to earn foreign currency.” a
SRK Consulting (South Africa) has appointed Vis Reddy as its new chairman, following an eight-year term as managing director.
Reddy has also assumed the role of regional coordinator for Africa, on behalf of SRK Global – as part of the company’s strategic expansion into African markets. He explains that his focus will build on the work of previous chairmen in promoting innovation, technology, excellence and collaboration which also align with the
company’s strategic focus areas.
“The international SRK network has grown considerably, and it remains important to work as one team to leverage our one-stop-shop capabilities,” he says. “We have always strived to be a leader in our field, and to serve clients in a diverse range of skills and offerings as markets evolve.”
SRK will celebrate five decades in business next year, and has grown to about 1 600 employees in over 40 offices worldwide. a
In 2023, continuing the trend from last year, the industry focus is on CO2 reduction measures and technologies (alternative fuels, alternative raw materials), a main priority in operation plans of all the cement players.
But these short-term actions will not be enough to reach the CarbonZero target, which is why all the companies are working (with different intensities) to develop carbon capture utilisation and storage projects (CCUS) technologies integrated in the cement production.
Antonio Clausi, global director, Heidelberg Materials Competence Centre Cement is speaking about this sector revolution at CarbonZero Alternative Fuels and Raw Materials Global Conference and Exhibition 2023 on 26-27 October, InterContinental Hotel Dieu, Lyon, France.
With his background as a chemical engineering graduate from the University of Trieste, Italy, Clausi’s expertise and passion are embedded in his role of heading the organizational efforts into Decarbonisation through the development of new technologies such as carbon capture amine-based, oxyfuel, calcium looping and LEILAC.
Additionally, he is leading the Industry 4.0 innovative direction with activities related to advanced automation, expert system, artificial intelligence, predictive maintenance, and the digitalisation of production processes. a
As the construction sector holds on for the more effective implementation of government’s infrastructure expenditure programme, the recent national budget speech held both promise and uncertainty. Speaking at AfriSam’s regular Budget Breakdown event in Johannesburg this month, Dr Azar Jammine said if government puts its spending plans into action, it would be a game changer for the economy.
Dr. Jammine said he was encouraged by the growth from R812-billion to R903-billion in the estimates for public sector infrastructure expenditure from the 2023/24 to 2025/26 financial years.
“These numbers are so big that if we were to see their full implementation, it would be a game changer not only for the construction sector, but for the entire economy,” he said. “Where the real hope lies in government getting its act together and starting to implement its capital projects.”
He noted the importance of how Finance Minister Enoch Godongwana dealt with plans to restructure Eskom’s capital debt, as any worsening of the energy crisis could undermine the economic predictions in the budget speech. If loadshedding was exacerbated, he felt that the country may not even reach its meagre 0,9% growth target for the year. In such a scenario, government’s own spending plans would be further dampened by lower tax revenues.
The question he posed was whether there was the political will within the governing party to allow Eskom’s debt restructuring to take place. Such a move was inevitable, however, as he foresaw a complete realignment of politics in the general elections of 2024.
Focusing on the construction industry, Dr Jammine once again painted a sobering picture – but highlighted the sector’s potential to deliver economic benefits. He reminded his audience that construction provides 7,8% of the country’s employment, even though it makes up just 2,6% of GDP.
“Implementing government’s infrastructure projects would spark massive job creation, and the economy would grow by 5-6% a year,” he said. As it was, business confidence among building contractors continued to deteriorate, although last year this deterioration had slowed.
Commenting on Dr Jammine’s presentation, Richard Tomes, Sales and Marketing Executive at AfriSam said: “Although the operating environment remains challenging, one of the positive elements AfriSam has noted is the increase in the infrastructure spend budget allocation, and we remain hopeful that the implementation of the infrastructure projects will gain momentum and start delivering true value for the construction industry.”
Considerable overcapacity was still evident in the non-residential building sector, especially
commercial office and retail space. The value of non-residential building plans passed averaged just about R1-billion in value compared to R3billion in 2016. The brief recovery in the residential building sector – as homeowners renovated for home offices – had tailed off. Cement demand suffered negative growth in 2022, and was expected to improve only marginally over the next few years, he said.
About this annual event itself, Tomes remarked that AfriSam’s purpose is to make valuable information available to the various stakeholders that
interact with its business. “With many of us operating in the same industry, material matters such as the external environment we operate within not only relates to AfriSam but also to our stakeholders’ businesses.” a
Bell Equipment and its crushing and screening principal, Finlay, are this year celebrating 10 years of a successful dealer partnership in southern Africa. Based on the gains of the past decade, the two companies have reached a new distributorship agreement, effective 2023, encompassing a shared vision for new product introductions and services to the market. By Munesu Shoko.
Behind every successful equipment brand in any market is a good dealer, which is ultimately the differentiator between success and failure. Having been appointed the Finlay dealer in 2013, Bell Equipment has been the force behind Finlay’s firm growth in southern
Africa over the past decade.
Bell’s jurisdiction covers South Africa, Namibia, Swaziland, Lesotho, Zimbabwe, Mozambique, Botswana, the Democratic Republic of Congo (DRC) and Zambia. While Bell supports the brand through its own operations in South Africa, Zimbabwe and Zambia, it works through a number of
TheFinlay 683 screen is
said to be very much at the forefront of the market, due to its ease of operation, maintenance and all-around durability and robustness.
Having been appointed the Finlay dealer in 2013, Bell Equipment has been the force behind Finlay’s firm growth in southern Africa over the past decade
Bell’s jurisdiction covers South Africa, Namibia, Swaziland, Lesotho, Zimbabwe, Mozambique, Botswana, the DRC and Zambia
Despite the recent unprecedented Covid-19 setbacks, along with multiple industry challenges, Bell remains one of Finlay’s top 10 global dealers worldwide
Later this year, there will be further additions to the cone and impactor offerings across southern Africa, with a series of next generation crushers set to arrive
sub-dealers in other territories.
Key to the success of the decade-long partnership are the shared values between the two companies. Neil McIlwaine, Global Business Development & Marketing director at Finlay, says by striving for the best sales experience, complemented by a legacy of dependable aftersales support, both companies are driven by the same principles.
“With over 25 sales and service hubs across sub-Sahara Africa, Bell has provided our customers with the best possible levels of support over the past 10 years,” says McIlwaine.
Stephen McNeill, Product Marketing Manager at Bell Equipment, agrees that the shared core values between Bell and Finlay have been the key to the success of the partnership. “Bell and Finlay have a similar approach to doing business,” he says. “Finlay is a company that puts value on the quality of its products, but more importantly on supporting its customers. Similarly, Bell is a company that built its reputation on quality products supported by a strong aftermarket regime.”
McNeill says the past decade has been a journey of learning from each other to provide the best products, solutions and support to customers in the region. The partnership, he says, has been a win-win collaboration between the two companies, as they both leverage each other’s strengths. Finlay’s range of crushing and screening gear complements Bell’s existing product offering and is in line with Bell’s strategy to provide a one-stop shop for first class equipment solutions to its customers
throughout southern Africa.
On the other hand, Finlay has benefited from Bell’s reputation in the market, as well as from its extended support infrastructure. This has offered the leading crushing and screening manufacturer a great platform to further develop new equipment sales and support the large existing population of machines across the region.
Over the past 10 years, Bell has recorded some major successes with the Finlay brand. On average, says McNeill, the company has sold about 30 machines per year over the past decade. “Overall, we have been very successful, particularly on the screening side of the business,” he says.
Despite the recent unprecedented Covid-19 setbacks, along with multiple industry challenges, McIlwaine tells Quarrying Africa that Bell remains one of Finlay’s top 10 global dealers worldwide. The superior customer service and support, he says, has grown Finlay’s market share in the region through stock availability, coupled with multiple service sites strategically located across southern Africa.
A major highlight in Bell’s 10-year dealership was the Outstanding Achievement in Parts Business Support award at the Finlay dealer conference held in Jacksonville, Florida, United States in November 2018. The award was recognition for bolstering parts holding by 20% to better support customers and offer classleading aftermarket support.
Parts support, says McNeill, is a critical arm of the company’s business and for this reason Bell is strategically focusing on ways to improve parts availability for its customers.
“We are continuously re-evaluating our parts strategy in line with our customer needs. In today’s operating conditions, downtime due to parts unavailability is out of the question for equipment owners. We have since increased our parts stockholding to ensure maximum uptime for our customers,” says McNeill.
Bell currently holds about R30-million worth of Finlay parts at its Global Logistics Centre. Leveraging a network of 23 branches in South Africa, these can be delivered in 24 hours anywhere in the country, even direct to customers.
“We continue to increase our machine inventory. We have had stock challenges in the past two years as a result of the global supply chain challenges, but this year we are aiming to increase our machine stockholding to well over R110-million worth of machines in South Africa alone,” says McNeill.
Bell offers a wide range of Finlay mobile crushers, screens and conveyors to its customers in the region. These, says McNeill, comprise eight crushers, 10 screens and two conveyors. The 883+ scalping screen and the 893 heavy duty screen in particular have been the most successful models.
McIlwaine agrees, saying that over the past 10 years, the market-leading 893 heavy duty scalping screen and Spaleck screen models, have been the top sellers.
“Given that Finlay has one of the largest product ranges in the industry, a number of models have proven popular within the southern African market. Most notably, the J-1175 has an established reputation in the crushing market, especially for its capabilities within hard rock mining applications,” says McIlwaine. “To provide context, a number of units operating in the field have clocked in excess of 30 000 hours without any major overhauls needed.”
Finlay’s C-1540 mid-sized cone crusher has also proven popular. With open circuit and recirculation options available, this unit provides the much-needed flexibility for small to mid-tier producers. It boasts the proven Terex 1000 cone chamber with direct variable hydrostatic drive,
With over 25 sales and service hubs across sub-Sahara Africa, Bell has provided our customers with the best possible levels of support over the past 10 years.
McIlwaine, Global Business Development & Marketing director at
automatic tramp relief and hydraulic closed side setting (CSS) adjustment.
“From a screening perspective, our heavyduty scalpers continue to lead the way in the marketplace. Most notable is the top selling 883+, complemented by its big brother, the 893. All current heavy-duty screens are fitted with apron feeders as standard to face up to hard, abrasive materials while reducing customer downtime through belt repairs,” says McIlwaine.
New technologies such as the Spaleck screen box have also proven popular for niche applications, while Finlay’s standard incline screen offering continues to develop and meet the needs of customers in a range of applications and environments.
“Our 694+ and 683 screens are very much at the forefront of the market, again due to the ease of operation, maintenance and all-around durability and robustness. Additionally, the introduction of a comprehensive conveyor and feeder range has given further solutions to customers for specific contracts, and is growing in popularity,” he adds.
Looking ahead, McNeill is excited about the new dealer agreement, which further extends the partnership between the two companies.
He is particularly thrilled about the shared vision for new product introductions and services to the market to be announced this year. “The planned new product line up is quite exciting for our market,” says McNeill.
“Later this year, there will be further additions to the cone and impactor offerings across southern Africa, with a series of next generation crushers set to arrive,” confirms McIlwaine.
Commenting on some of the trends in the marketplace, McIlwaine says the adoption of telemetry solutions through the Bell organisation has allowed for greater efficiency on all levels of customer support.
The same view is shared by McNeill, who noted a marked increase in the uptake of telemetry solutions. “Customers are increasingly wanting to take advantage of available technology to improve productivity and efficiency within their operations,” he says. “Telemetry solutions help fleet managers to optimise the use of their assets and reduce operating costs.”
In 2003 Bell Equipment launched Fleetm@tic to become the first heavy original equipment manufacturer to offer its customers a fully global remote fleet management system with pole-to-pole coverage. Finlay, on the other hand, offers its T-Link system, which enables customers to remotely connect with and keep track of their equipment, monitor work progress, manage logistics, access critical machine information, analyse and optimise machine performance and perform remote operator support.
“A major advantage is that the two systems – Bell’s Fleetm@tic and Finlay’s T-Link – can be integrated. For example, where we have both Bell trucks and Finlay machines running on a quarry, we can pull the Finlay system into the Bell fleet management system to allow the customer to have a centralised portal where critical information about all their mission-critical assets on site can be accessed,” explains McNeill.
Apart from the uptake of telemetry solutions, McIlwaine has seen the need for larger units for increased, consistent production on long-term job sites. Similarly, within some segments there is a downsizing of equipment due to short contracts and lower tonnage requirements.
“Of late we have seen customer diversification across various segments/applications/contracts in response to an ever-changing market. Testament to this is the recent high uptake of machines in the mining sector, notably in coal and other high-value minerals,” says McIlwaine.
The introduction of hybrid technology to the local market, says McIlwaine, has been slower than in European and North American markets, for example. However, he expects the uptake of this technology to gain momentum in the coming years, pending, of course, local requirements on carbon reduction and potential increased fuel costs.
“More generally, while customers first and foremost seek to purchase equipment ideal for their industries and applications, the importance of service and aftersales support continues to be a key trait. As the next step, we see evidence of how our digital offering on machines has now improved customer efficiencies, through reduced downtime and improved operation techniques together with an overall improvement in fleet management,” concludes McIlwaine. a
We have had stock challenges in the past two years as a result of the global supply chain challenges, but this year we are aiming to increase our machine stockholding to well over R110-million worth of machines in South Africa alone.Stephen McNeill, Product Marketing Manager at Bell Equipment
At a time when many conflicting and ambiguous messages are shared easily on various platforms, coupled with the proliferation of substandard products and services, we saw the need for authoritative engagement with all stakeholders. This led to the unification of the previous three industry bodies into one unified voice for all stakeholders.
CCSA is mandated to promote and support the industry, drive growth and deliver shared value through a unified platform for cement and concrete.
Having previously been represented by three fragmented bodies, the cement and concrete industry in 2021 decided to consolidate the three organisations to create a single voice of the industry, Cement & Concrete SA
CCSA is mandated to promote and support the industry, drive growth and deliver shared value through a unified platform for cement and concrete
For the past two years, the association has already delivered on this promise through collaboration, skills development, innovation and the highest standards in sustainable cement and concrete materials and products
The association has been structured into three divisions – Industry, Technical and Business Development
Having previously been represented by three fragmented bodies – The Concrete Institute (TCI), Concrete Society of Southern Africa (CSSA) and the Association of Cementitious Materials Producers (ACMP) – the cement and concrete industry decided in 2021 to consolidate the three organisations thereby creating a single voice for the industry.
CCSA is mandated to promote and support the industry, drive growth and deliver shared value through a unified platform for cement and concrete. For the past two years, the association has already delivered on this promise through collaboration, skills development, innovation and the highest standards in sustainable
7%
Given
2050
To comply with climate change commitments in line with Nationally Determined Contribution and Paris agreement, CCSA member companies aspire to net zero emissions by 2050
About 1,5-million m³ of concrete will be used on the N2 and N3 projects in the next couple of years
South Africa has an installed cement production capacity of 22-million tonnes per year
cement and concrete materials and products.
“At a time when many conflicting and ambiguous messages are shared easily on various platforms, coupled with the proliferation of substandard products and services, we saw the need for authoritative engagement with all stakeholders. This led to the unification of the previous three industry bodies into one unified voice for all stakeholders,” says Perrie.
The association has been structured into three divisions – Industry, Technical and Business Development. Led by Dr Dhiraj Rama, the Industry leg deals with environmental issues, particularly in cement production.
Given that the cement industry accounts for about 7% of total global CO2 emissions, CCSA is leading from the front when it comes to driving sustainability in the industry. To comply with climate change commitments in line with South Africa’s Nationally Determined Contribution (NDC) and the Paris agreement, CCSA member
Following the amalgamation of three different organisations in March 2021 to form Cement & Concrete SA (CCSA), the association has, over the past two years, successfully taken the lead on all matters cement and concrete in South Africa, particularly championing the sustainable development of cement. In a one-on-one with Quarrying Africa, CEO Bryan Perrie unpacks some of the initiatives, successes and issues affecting the industry. By Munesu Shoko.
companies aspire to net zero emissions by 2050, with milestones informed by decarbonisation along the 1,5-degree trajectory. The key interim milestone will be set at 2030.
The net zero target boundary is based on the Greenhouse Gas (GHG) inventory target as per South Africa’s GHG Technical Reporting Guidelines for the cement sector, in line with the Intergovernmental Panel on Climate Change (IPCC) reporting framework.
“The Industry leg of CCSA deals with our climate response action, underpinned by the ‘just transition’ framework. It also engages government on several issues of importance to our industry, such as Carbon Tax, the Mining Charter and cement imports, amongst others. CCSA is also part of the South African Bureau of Standards (SABS) Committee to ensure that proper standards are in place,” explains Perrie.
Dr Rama provides sound support, direction and leadership to members and also monitors progress at sector level. One of the key areas of focus is the net zero target monitoring, which covers both Scope 1 and Scope 2 emissions of cement companies. With supported technology interventions, as well as improved overall nationally-developed Scope 3 emission monitoring programmes implemented by stakeholders, the GHG inventory will be expanded accordingly.
The Technical division, led by Perrie himself, takes care of training, the information centre (library and publications), consulting and advisory services.
“Over the past two years, we have demonstrated our passion to grow industry expertise and build capacity by developing and offering courses, seminars and training materials. The provision of information, research, advisory and on-site technical
consulting services is another service offering that is available to our members,” says Perrie.
The third leg of CCSA, Business Development, looks after the membership of the association and all the events it runs, including the famed Fulton Awards, The Young Concrete Researchers, Engineers and Technologist Symposium (YCRETS) and ConPaveStruc, a national conference on Concrete Roads and Allied Structures, which CCSA will run later this year together with the South African Road Federation, the Council for Scientific and Industrial Research (CSIR) and The South African National Roads Agency (Sanral).
The influx of imported cement in South Africa has over the years been ‘a thorn in the side’ of local cement producers. Imported cement gained a footprint for the first time in the country’s history when local producers operated at close to 100% capacity in the build-up to the 2010 FIFA World Cup.
To provide context, South Africa has an installed capacity of 22-million tonnes per year (tpy). Due to the lack of meaningful infrastructure investment, the industry currently produces in the region of 12-million tpy. Yet, there is about a million tonnes of imports coming into the market annually, mainly in the
coastal areas of the country. With the industry already battling with about 10-million tpy of extra capacity, Perrie says there is definitely no need for cement imports in South Africa.
“In 2014, we managed to prove that cement imported from Pakistan was being ‘dumped’ in South Africa; in other words, it was being sold at a cheaper price than in its country of origin,” explains Perrie. “We successfully applied for anti-dumping tariffs on Pakistani cement, which were valid for five years. In 2020, we successfully reapplied, and the tariffs were once again granted for another five years.”
The problem with anti-dumping tariffs is that they are country-specific, and are dealt with on a case by case (country by country) basis. While the imposition of tariffs reduced imports from Pakistan, Vietnam has become the new source in recent years. Apart from international imports, there has of late also been an influx of cement from Mozambique.
“To protect the local cement industry from unfair competition, we are therefore engaging the government on the possibility of implementing a general import tariff. However, this is a difficult measure due to the World Trade Organisation guidelines,” says Perrie.
Apart from tariffs, CCSA has in recent years advocated for cement designation on government projects. After lobbying for several years to protect the local cement industry and local jobs from the threat of ‘cheap’ imports, government finally took what was hailed as decisive action on November 4, 2021, following National Treasury’s announcement that cement had been designated, meaning that the use of imported cement on all government-funded projects was prohibited.
At the time, National Treasury issued a circular to all relevant state departments of the new ruling in terms of the Preferential Procurement Regulations. The designation of cement would apply to all projects entered into by state entities, including national, provincial and local authorities, as well as state-owned enterprises (SOEs).
The designation prescribed that all organs of state must, from November 4, 2021, stipulate in tender invitations that only SA-produced cement, produced with locally-sourced raw materials, would be allowed for use on all public sector construction projects. National Treasury stipulated a 100% threshold for both common and masonry cements.
However, the designation was a shortlived relief for the industry following the Constitutional Court’s declaration in February 2022 that the Preferential Procurement Act was unconstitutional. The basis of the ruling was that it was unconstitutional for national
government to dictate to all other spheres of government. Effectively, cement designation became null and void. Fortunately, says Perrie, Sanral, which is effectively the biggest source of infrastructure investment in the country, has designated cement on its projects, which gives some much-needed relief to the industry.
“The biggest problem with cement importers is that they don’t compete on an equal footing with local producers. Although imported cements reaching South Africa may conform to regulatory standards, South African cement producers have many other compliance issues to deal with, including the Mining Charter, transformation targets as well as social and labour plans, none of which importers have to comply with. Compliance, by its very nature, costs money and consequently puts local producers in an unfair position. In addition, local producers are subject to carbon tax, which the importers are also exempt from,” he says.
That the industry is reeling from the current economic slump, which has been exacerbated by the lack of meaningful infrastructure projects, is no overstatement. However, Perrie is encouraged by government’s R903billion promised public sector infrastructure expenditure in the next three years.
“Government realises that public infrastructure, including water treatment works, roads, and bridges, needs urgent upgrades. If all the planned projects were to be implemented, this would be a shot in the arm for the whole industry and the economy at large,” he says. “I am, however, concerned about government’s track record when it comes to execution.”
On the other hand, Perrie is encouraged by Sanral’s current roll out of meaningful infrastructure projects across the country. The roads authority has issued about R15-billion worth of projects during the last year or so.
Projects of note include the N2 and N3 road upgrades in KwaZulu Natal. Part of the 62 SIPs gazetted as part of the Infrastructure Investment Plan approved by Cabinet in 2020, the N3 national road upgrade alone – which focuses on an 80-km section from Durban to Pietermaritzburg – comprises 14 packages estimated to be in excess of R20-billion.
More encouraging, says Perrie, is the growing appetite for concrete pavements on Sanral projects. “As we work closely with the roads authority, we have seen renewed interest in concrete roads, particularly on the ongoing N2 and N3 road projects in KwaZulu Natal. To provide context, about 1,5-million m³ of concrete will be used on these two projects in the next couple of years,” concludes Perrie. a
A key takeaway from ASPASA’s 2022 Environmental Audit is that the majority of participating companies grasp the significance of environmental compliance. Speaking at the 52nd IQSA conference, environmental auditor Anthony Bowen noted that site teams have generally shown commitment to achieving compliance in order to prevent unnecessary conflict and legal exposure.
In 2021, surface mining association, ASPASA, announced its all-new environmental audit system for its members. The new system was aimed at simplifying the previous About Face Audit and improving member companies’ ability to undertake effective environmental management.
The new audit, which kicked off in 2022, has been described as more inclusive than the previous one, with criteria that are easy to understand and implement. The new system also calls for a comprehensive attitude towards environmental compliance, rather than the traditional ‘tick box’ approach.
“Our aim is to achieve environmental compliance for all ASPASA member operations with a user-friendly, practical compliance audit. We also aspire to equip site managers with the correct information and knowledge to be able to deal with regulatory authorities and other
By Munesu Shoko.interested and affected stakeholders,” says Bowen.
Having successfully implemented the new audit in 2022, Bowen has expressed his satisfaction with the industry’s drive to achieve high levels of environmental compliance. The risk of non-conformance, he says, is high and companies are eager to equip managers and staff with sufficient environmental knowledge to ensure compliance.
A total of 66 audits were conducted –20 online and 46 physical audits. The online audit achieved five Showplace scores, with 18 more Showplaces for the physical audit. With a whopping 96,39%, Afrimat Hluhluwe took home the Top Performer Award for the online version of the audit. “The level of compliance presented by the operation was exceptional,” says Bowen.
Solid waste management is a fundamental component of the quarrying value chain.
diligence by all levels of management and staff,” comments Bowen.
In addition, Lafarge Empangeni was awarded the Most Innovative Project Award for a paper recycling project initiated by quarry manager, Patrick Ndlwana. The recycled paper was donated to a home for disabled children and was also used to generate funds to build a bakery at the same home. The initiative was highly successful; not only is the bakery providing bread for the home, but it is also able to sell excess produce to generate additional funds.
The 2022 ASPASA Environmental Audit has highlighted that the majority of participating companies grasp the significance of environmental compliance
The risk of non-conformance is high and companies are eager to equip managers and staff with sufficient environmental knowledge to ensure compliance
On a positive note, operations demonstrated good oil storage practices, pollution control measures, biological control of alien vegetation and repurposing of old tyres and conveyors
Waste management, says Bowen, should be a key area of focus for the industry going forward, especially in a country that generated 122-million tonnes of waste in 2022
With a 96,19% score, Midmar Quarry clinched the Top Performer Award in the Independent Quarry category of the online audit. Bowen commends the high level of compliance at the KwaZulu-Natal-based operation.
The Top Performer Award in the physical audit segment was awarded to Raumix Alpha Sand, with a 97,78% score. “The level of compliance on a site that is surrounded by natural wetlands and sensitive areas is outstanding,” says Bowen.
With a 97,61% score, Blurock Quarry was named the Top Performer in the Independent Qaurry category of the physical audit. “Blurock had a well-presented audit and the site was an example of dedication and
Several individuals were awarded for their outstanding contributions to the industry’s environmental compliance cause. Ashleigh Cockart from Afrimat KZN took home the Exceptional Performance Award for her dedication, exceptionally high standards of documentation and the guidance given to the site managers and staff during preparation for the audits. “Her involvement in the actual audit process demonstrated the commitment and passion she has to ensure that the various Afrimat sites achieve a high level of environmental compliance,” says Bowen.
Ronelle Affinand and Paul Charmen from Noshcon were also awarded the Exceptional Performance Award for their dedication and consistently high standard of documentation examined during the various environmental audits that they presented.
Afrimat KZN’s Anton Marnewick took home the Exceptional Performance Award for achieving three Showplace (above 95%) scores for the three sites that he manages.
On a lighter note, Loriaan van Tonder from Raumix was presented with the Response of The Year Award for the exceptional response she displayed when she heard of her operation’s high score in the environmental audit. “It was an example of exceptional dedication and commitment to the success of the audit,” says Bowen.
Commenting on key findings of the audit, Bowen notes good and bad practices in equal measure. On a positive note,
operations demonstrated good oil storage practices, pollution control measures, biological control of alien vegetation and repurposing of old tyres and conveyors. While investment in renewable energy seems out of reach for small operations, Bowen also commended a few that have gone the solar power route.
However, Bowen says there are several issues to be addressed for the industry to maintain high levels of environmental compliance. Reporting of non-conformances, in particular, is not up to standard, he says. Some operations are doing it right and some are not.
Waste management, says Bowen, should be a key area of focus for the industry going forward, especially in a country that generated 122-million tonnes of waste in 2022. While non-functional local government waste facilities make it difficult
for all stakeholders, Bowen says operations should find other cost-effective ways to manage their waste on site.
“Solid waste management is a fundamental component of the quarrying value chain. For both economic and environmental benefits, it is recommended that each operation establishes a waste management plan that includes continuous minimisation and proper management, particularly reuse, recycling and lawful disposal, of all site waste streams,” says Bowen.
Other focus areas include non-conformance of satellite industries, such as readymix plants on site, water management (on and off site), soil contamination, settlement dams, understanding of air quality tests, understanding of water quality tests and corrective actions, as well as CO2 footprint monitoring and recording. a
Judging from interactions with the quarrying community at the recently ended IQSA conference, Loadtech believes that there is a better understanding of the innovation imperative in the local quarrying industry, which has been key to the growing uptake of payload management systems.
Akey takeaway for Loadtech from the 52nd Institute of Quarrying Southern Africa (IQSA) annual conference, which took place on 14-15 April 2023 in Durban, is that there is a growing appetite for digital systems in the local quarrying fraternity, particularly for payload management systems. This, says Loadtech sales director Glen Webster, is driven by the industry’s drive to eliminate guesswork out of quarry loadout
processes, thus increasing efficiency, productivity and ultimately the bottom line.
“Consistent with what we have seen in recent years, there was a lot of interest in our load weighing systems at the IQSA conference,” says Webster. “In recent years we have observed increased uptake of these systems in Africa, as local mines and quarries increasingly see value in digital systems.”
Loadtech’s growth in the past two to three years, he says, is a clear indication that the market is maturing. The authorised
15%
Loadtech has recorded a substantial 15% business growth in the past three years
360°
There is a growing appetite for digital systems in the local quarrying fraternity, particularly for payload management systems
Loadrite dealer in sub-Sahara Africa for the past 24 years, Loadtech has recorded a substantial 15% business growth in the past three years.
“We believe it is largely to do with the maturity of the local market, which is now ready for digitalisation of processes. Some, however, still operate in the ‘stone age,’ but the majority of customers now understand what they have to do to survive and succeed in such a cut-throat business environment,” explains Webster.
This is driven by the industry’s drive to eliminate guesswork out of quarry loadout processes, thus increasing efficiency, productivity and ultimately the bottom line
The company used the IQSA conference to showcase its full line-up of Loadrite solutions available for the local industry. These included the L-Series SmartScale for loaders, the X-Series excavator payload management systems, the C-Series conveyor belt scales and the InsightHQ for actionable insights, dashboards and notifications.
Loadtech’s growth in the past two to three years is a clear indication that the market is maturing
The major drawcard at the show was the Loadrite L3180 Smart Scale, which is said to usher in a new era in load weighing systems. A major talking point, says Webster, is the use of angle sensors instead of the traditional rotary triggers. This allows the system to offer accurate weighing in tough conditions.
The major drawcard at the show was the Loadrite L3180 Smart Scale, which is said to usher in a new era in load weighing systems
Webster notes that the next generation L3180 loader scale is the company’s best yet, changing the game in the industry by being able to adjust for rough terrain, with technique and movement so new that skilled operators can load with greater
accuracy, precision and speed.
“Intelligence in the weighing software and new hardware gives operators of all skill levels the ability to load more speedily and more productively than ever before.”
The Loadrite L3180 SmartScale uses weighing intelligence and solid-state sensors for more accurate, precise and faster loading. It also connects machines and devices for the collection and syncing of data via the built-in WiFi to the InsightHQ reporting portal. When using the cloud-based InsightHQ quarry reporting portal, personnel can gain access to site production and operator performance KPIs on desktop or mobile devices.
Another key exhibit was the Loadrite 360 – a new loadout automation and reporting system for quarry loadout activities. It comprises a wheel loader onboard scale, an automated communications connection and a performance reporting tool. Jobs are entered in the office and selected in the loader, reducing data entry, eliminating mistakes and improving customer satisfaction.
The technology is designed to transform the way in which quarries have always conducted their loadout processes. Traditionally, operations have relied on weighbridges alone. These are known to be prone to product errors and weight challenges.
With the Loadrite 360, aggregate producers can turn their workflows around – literally. Instead of having a weighbridge at the exit, it could be moved to the entrance area, where information about the truck – including the registration, tonnage and product required – is captured and relayed to the loader. As soon as the truck drives in, the loader operator already knows the quantity and type of material to be loaded. This reduces loading-, waiting- and idle-times.
“The Loadrite 360 can holistically improve
loadout operation through performance metric tracking, job data automation and real-time 360° job visibility. It connects the loader and the weighbridge so as to provide data sharing of loadout jobs, resulting in greater efficiency, improved visibility and higher product sales,” says Webster.
The two-way automated communication shows jobs requested at the weighbridge as a job list on the scale inside the loader cab and completed loadout data is fed directly into the weighbridge ticketing system. This reduces double entry work and data entry errors for both the operator and the weighbridge attendant. Accurate on-screen job data reduces error-prone verbal communications and allows more time for loading.
The Loadrite 360 in-cab indicator clearly presents a list of loadout jobs in order of priority by truck registration. By providing simple, relevant and prioritised job data to the operators, they are empowered to complete jobs more quickly across the site with no loss in loading accuracy. The list of loadout jobs also provides richer loadout job queue data and thus reduces verbal communication errors and truck waiting time.
The system uses shared visibility of payload data, job data automation and performance metric tracking to highlight opportunities for improvement. The performance reports track loader metrics including tonnes per hour (tph) across multiple or individual loaders, actual time spent on truck loading activities and loader operator efficiency which highlights staff training needs.
With the InsightHQ reporting option, managers can monitor site production and performance anywhere, at any time, on any mobile device or web browser. InsightHQ also allows centralisation of data from excavator and belt scales.
“Although the Loadrite 360 is primarily a tool to improve the accuracy and speed of loadout operations, it can also reveal hidden improvement
opportunities,” says Webster. “The system enables users to drill into production data to see individual trucks, loaders or even bucket-by-bucket data and identify opportunities to improve.”
“With the Loadrite 360, quarry operators can reduce fuel and maintenance costs by avoiding unnecessary idling of loaders and trucks in loadout. It also provides quarries with increased truck visibility to ensure that trucks are loaded to capacity in the shortest possible time,” adds Webster.
Loadtech also used the conference to showcase some of its old generation technology such as the Loadrite L2180, which comes with superior weighing technology having accurate and consistent weighing within +/-1% of payload with optional ground slope compensation.
The rotary position sensor continuously monitors boom position over the entire lift, allowing multiple measurement points. Multi-point weighing allows variations in weights calculated to be averaged out or even discarded if they are outside tolerance levels. These variances can be caused by inexperienced operators or weighing on rough ground.
Another key exhibit was the C-Series conveyor belt scales. The Loadrite C2850 is an advanced conveyor belt weighing system designed in particular for rugged industries such as aggregates, construction, scrap metal recycling and mining. It is the ideal tool for monitoring inventory, production output and product loadout, while, at the same time, providing essential data management tools to drive productivity and machine performance decisions.
The C2850 scale consists of four main components: the load cells, scale frame, speed sensor and an integrator which processes the signal from the conveyor belt scale. The load
cells react to vertical forces, giving an accurate weight, while the belt speed is monitored by the speed sensor. The weight and speed signals are electronically converted to a digital weight, which appears on the display in pounds, kilograms or tonnes per hour.
“The key message at this year’s show was to remind quarry operators how Loadtech can help them improve productivity and efficiency at their operations. In a world where data has become the ‘new currency’, payload management technology is a must-have on quarry sites. The systems help operators accurately and effectively load haul trucks to capacity, within production, path-to-zero-harm and loading unit parameters,” concludes Webster. a
With its ability to drill holes from 102 to 178 mm in diameter, the Pantera DP1600i – the newest addition to Sandvik Mining and Rock Solutions’ Pantera DPi series family – changes the game in top hammer drilling, writes Munesu Shoko.
178 mm
Being capable of drilling holes up to 178 mm in diameter, the Pantera DP1600i expands the hole size range of previous top hammer drills and challenges traditional DTH drilling on large quarries and surface mines
The very first Pantera™️ DP1600i drill rig from Sandvik Mining and Rock Solutions has arrived in southern Africa, ushering in a new era in top hammer drilling. A major talking point is the drill’s ability to drill hole sizes from 102 to 178 mm in diameter, making it the largest top hammer drill on the market.
According to Vanessa Hardy, BLM for Surface Mining at Sandvik Mining and Rock Solutions, top hammer drills have always been limited in terms of hole sizes. To provide context, the previous Pantera DP1500i could only drill holes up to 152 mm in diameter and anything beyond that would traditionally call for a switch to down-the-hole (DTH) drilling.
50% Results from field tests showed a 50% reduction in fuel consumption compared with the DTH drilling method under specific conditions
“We are excited to bring the first Pantera DP1600i drill into southern Africa. Being capable of drilling holes up to 178 mm in diameter, the new machine expands the hole size range of previous top hammer drills and challenges traditional DTH drilling on large quarries and surface mines,” says Hardy. Designed for large hole size drilling, the Pantera DP1600i
We are excited to bring the first Pantera DP1600i drill into southern Africa. Being capable of drilling holes up to 178 mm in diameter, the new machine expands the hole size range of previous top hammer drills and challenges traditional DTH drilling on large quarries and surface mines.
is ideally suited for a variety of applications, including pre-split and production drilling in large quarries and surface mines. In extensive field tests conducted by Sandvik Mining and Rock solutions, the machine has proven to be a faster, fuel-efficient and cost-effective alternative to DTH drilling in hard, competent rock formations. Here, DTH drills typically use substantial amounts of energy to fracture the rock, while the top hammer system uses less energy to get the job done.
Developed as a combined project between Sandvik Surface Drills, Rock Drill and Rock Tools, the three key components of the system – the Pantera DP1600i drill rig, the RD1840C
The very first Pantera DP1600i drill rig from Sandvik Mining and Rock Solutions has arrived in southern Africa, ushering in a new era in top hammer drilling
A major talking point is the drill’s ability to drill hole sizes from 102 to 178 mm in diameter, making it the largest top hammer drill on the market
In designing the Pantera DP1600i, Sandvik saw the need to provide a cost-effective option to down-the-hole drilling that could fit certain drilling applications with greatly improved performance
Controls are easy and similar to the previous models, so the transition for the operator from a DP1500i, for example, to a DP1600i, is effortless
rock drill and the new LT90 rock tools – are all optimised to work seamlessly for optimal drilling results.
“One of the key talking points are the three main components of the drilling system – the drill rig, the rockdrill and the tools – which have all been reviewed, redesigned and mutually optimised,” says Hardy.
With its 49 kW of drilling power, the new RD1840C rock drill is also built for large hole drilling, boasting a robust design and wellbalanced long piston percussion package for demanding conditions. Its new layout of pressure accumulators maximises efficiency and minimises hose vibrations.
Developed to match the other components in the system, the LT90 rock tools consist of a shank
adapter, MF tube rods and drill bits, offering the best possible drilling dynamics and rock breaking efficiency. The tools increase productivity, improve hole straightness and provide great coupling characteristics and a long service life.
In designing the Pantera DP1600i, Sandvik saw the need to provide a costeffective option to DTH drilling that could fit certain drilling applications with greatly improved performance. This new offering is therefore highly fuelefficient, offering mining and quarrying customers a considerable reduction in their carbon (CO2) footprint in the process.
Results from field tests showed a 50% reduction in fuel consumption, 25% reduction in total drilling costs and a 15% increase in productivity, compared with the DTH drilling method under specific conditions.
25%
The Pantera DP1600i also has a special design focus on safety. A case in point is the machine’s support for high-level automation solutions, which speaks directly to improved operational safety.
The Pantera DP1600i has proven itself in many locations around the world, including Europe, the United States, Canada, Australia, South America and West Africa, where it has been deployed in a variety of open pit conditions with great operational outcomes.
“As always, Sandvik’s priority is the safety of the people operating and maintaining our products,” says Hardy. “All Sandvik surface drills built in Finland are designed and manufactured to strict CE (Conformité Européenne) requirements, which means that the manufacturer takes responsibility for the compliance of a product with all applicable European health, safety, performance and environmental requirements.” With ease of operation in mind, Sandvik chose to base the machine on its already proven DPi series platform. Consequently, operating the
machine is just as easy and efficient as the existing DP1100i and DP1500i models.
With the Sandvik Intelligent Control System Architecture (SICA) common control system, a key component of the iSeries family, and the integrated GUI touch screen, all the controls and adjustments are monitored and adjusted using Sandvik’s i-Torque control system, thus eliminating the need for operators to constantly adjust parameters.
“In addition, all service points are easily accessible, therefore reducing downtime related to routine service and maintenance. While this has a massive effect on machine uptime, it also has a knock-on effect on safety,” says Hardy.
“Controls are easy and similar to the previous models, so the transition for the operator from a DP1500i, for example, to a DP1600i, is effortless. There is about 80-90% similarity between the new machine and the previous DPi offerings,” says Hardy.
Because the DP1600i is based on the existing DPi platform, servicing and maintenance are similar to the previous models. Thus, service technicians who are well versed with the previous DPi models can easily work on the DP1600i with minimal to no training required.
Like all other Sandvik products, the DP1600i benefits from the company’s proven aftermarket regime. Sandvik offers a full suite of aftermarket services that are tailored to each customer’s operational requirements.
“From a servicing point of view, there are several options available. For example, we offer full maintenance contracts, where we have a Sandvik crew on site to service and maintain the machines on behalf of the customer. However, depending on customer needs, we can have an expert on site who does not do the nuts and bolts, but is only there to guide and coach the customer’s service personnel,” concludes Hardy. a
Blasting practices in mines and quarries have undergone many changes in recent times and continue to evolve to meet the changing demands of the industry. Speaking to Quarrying Africa, Ralf Hennecke, MD of BME, discusses some of the emerging trends in the blasting industry.
By Munesu Shoko.25-million
In South Africa alone, BME consumes almost 25-million litres of used oil annually and plans to increase its collection and processing capacity steadily over the next few years 11
The oil collection network’s extensive logistical arrangements include taking used oil from its mining customers, but also from its group of 11 approved suppliers – or bulking points.
Over the years, the development, advancement and utilisation of innovative technologies has been one of the key talking points in the blasting industry and the mining sector at large. In order to improve efficiencies, the blasting industry is rapidly adopting technology in all its forms.
In modern mines and quarries, developments in the areas of planning and design of blasts, drill monitoring, drillhole deviation, drill machine navigation systems and laser profiling systems, to mention just some, have taken root in the last few years.
Apart from technological advances, Hennecke believes that one of the interesting trends that has
emerged in the aftermath of the Covid-19 pandemic is a re-focus on the security of supply for key mining inputs such as explosives.
The industry’s supply chains, he says, had been honed for many years to become as cost-efficient as possible, often driven by the ‘just-in-time’ philosophy. The economic lockdowns, closure of borders and logistical disruptions worldwide have led to a reevaluation of this approach.
“Customers now tend to be more concerned about security of supply, and often adopt more of a ‘just-in-case’ attitude. It was interesting to note that, throughout the Covid-19 disruption, BME was able to continue supplying its customers within and across borders without a single stock-out,” he says.
One of the interesting trends that has emerged in the aftermath of the Covid-19 pandemic is a re-focus on the security of supply for key mining inputs such as explosives
Another important trend is the move towards decarbonisation of mining and quarrying operations, with blasting service providers being expected to contribute to customers’ efforts to lower their carbon footprint
BME has pioneered the inclusion of used oil in its emulsion explosives and is said to be the largest consumer of used oil in the explosives sector. The initiative contributes to a circular economy by safely disposing of used oil in a responsible manner
The blasting industry has been proactively leveraging the power of electronic and digital technology to improve the way mines and quarries can plan, execute, monitor and improve their blasts. An important trend in this process is the integration of blast-related data and results in customers’ own enterprise management systems
“
Customers now tend to be more concerned about security of supply, and often adopt more of a ‘just-in-case’ attitude. It was interesting to note that, throughout the Covid-19 disruption, BME was able to continue supplying its customers within and across borders without a single stock-out.
Ralf Hennecke, MD of BME
Hennecke says the generally buoyant commodity market is allowing most customers to prioritise production, even if the cautious approach is not as cost-efficient. At the same time, there is significant cost-inflation creeping into the industry, and thus the pressure on companies to control costs is escalating.
Another important trend is the move towards the decarbonisation of mining and quarrying operations, with blasting service providers being expected to contribute to customers’ efforts to lower their carbon footprint.
“The global drive to adopt more sustainable business practices gathers momentum constantly. As part of the Omnia Group, BME is committed to innovation to enhance life, together creating a greener future,” he says.
Commenting on how BME is responding to these trends, Hennecke says the company
is committed to sustainable principles in the way it approaches its business. BME constantly innovates its explosive solutions and technology to provide customers with more efficient and productive operations – thus helping to reduce their energy consumption as well as the carbon emissions generated.
The company has also pioneered the inclusion of used oil in its emulsion explosives and is said to be the largest consumer of used oil in the explosives sector. This initiative contributes to a circular economy by safely disposing of used oil in a responsible manner, while preventing any of this oil from contaminating water or land.
It is estimated that it takes only a litre of oil to contaminate a million litres of water, making the safe disposal of oil a strategic global imperative – especially for waterscarce countries. BME’s used oil initiative is aligned with the United Nation’s Sustainable Development Goals (SDGs) – which focus
on goals such as access to clean water, food security and eradication of pollution.
In South Africa alone, the company consumes almost 25-million litres of used oil annually and plans to increase its collection and processing capacity steadily over the next few years.
The company’s oil collection network has evolved over time – aligning each phase with its ISO 9000 quality certification. It is also registered as an approved collector and processor with the Recycling Oil Saves the Environment (ROSE) Foundation.
environment – winning the CAIA Responsible Care initiative of the year award, in the company projects: Category A segment.
The oil collection network’s extensive logistical arrangements include taking used oil from its mining customers, but also from its group of 11 approved suppliers – or bulking points. The oil is processed and tested at the company’s dedicated facility in Delmas, from where it can be channelled into its emulsion production.
In 2021, the company was recognised by the Chemical and Allied Industries’ Association (CAIA) for its contribution to a cleaner
Looking to the future, Hennecke says the blasting industry has been proactively leveraging the power of electronic and digital technology to improve the way mines and quarries can plan, execute, monitor and improve their blasts. An important trend in this process is the integration of blast-related data and results in customers’ own enterprise management systems.
“This is enabling the continual streamlining and fine-tuning of on-site operations, giving management more transparency and control for continuous improvement. The blasting industry is therefore an integral player in supporting the mines and quarries of the future and ensuring that this industry can grow sustainably,” concludes Hennecke. a
A key emerging trend is that the mining industry tends to be more concerned about security of supply.The company’s oil collection network has evolved over time –aligning each phase with its ISO 9000 quality certification. It is also registered as an approved collector and processor with the Recycling Oil Saves the Environment (ROSE) Foundation
Like any other segment of the capital equipment sector, the mobile crushing market is undergoing immense changes.
Speaking to Quarrying Africa, Neil Robinson, Powerscreen product and applications manager, unpacks some of the new dynamics in this market. By Munesu Shoko.
In 2022, Powerscreen launched its Chieftain 2100XE, which has a small engine for tracking but is powered by an external power source
Government legislation and net zero strategies are playing a substantial role in the shift from traditional diesel hydraulic machines to electric and hybrid machines
That the mobile crushing market is evolving is no overstatement. Leading original equipment manufacturer
Powerscreen has seen a growing shift particularly from traditional diesel hydraulic machines to electric and hybrid machines.
“We have also seen an increase in newer applications for our crushing and screening solutions, for example, in biomass and recycling,” says Robinson. As more and more demolition waste, for example, is being diverted from landfills and into a circular economy, recycling is becoming a large market for mobile crushing solutions.
Commenting on the drivers behind these trends, Robinson says that the increasing focus on both environmental impact and
reduction of carbon footprint have played a part. “Government legislation and net zero strategies are also playing a substantial role. All our customers and users want maximum efficiency and productivity on site and for those with easy access to electric supplies, electric and hybrid machines are the answer,” he says.
In line with these trends, Powerscreen is placing a major focus on electrifying its machines, both its current range and new designs. A case in point is the 2022 launch of the Chieftain 2100XE, which has a small engine for tracking but is powered by an external power source. This sits perfectly alongside the hybrid Warrior 1400XE, Premiertrak 420E
Powerscreen has seen a growing shift particularly from traditional diesel hydraulic machines to electric and hybrid machines
Powerscreen has seen an increase in newer applications for its crushing and screening solutions, for example, in biomass and recycling
In line with these trends, Powerscreen is placing a major focus on electrifying its machines, both its current range and new designs
Looking to the future, the market will place a huge focus on digital solutions to aid users in getting the most out of their machines
The Titan range, which includes three models – the Titan 600, Titan 1300 and Titan 2300 – is a simplification of Powerscreen’s high-performing Warrior range.
3The Titan range, which includes three models – the Titan 600, Titan 1300 and Titan 2300 – is a simplification of Powerscreen’s high-performing Warrior range, using key features that customers love about the Warrior machines and tailoring them to a different section of the market at an attractive price point
and 1000E.
“In 2020, we launched our Gladiator range of wheel plant for the North American market. Due to the success we have seen in North America, we have been developing our range of wheel plant, our Gladiator World Series, which is being launched this year –stay tuned for these exciting plants!”
In 2021, Powerscreen launched its Titan range, a new range of secondary scalping screens that provide a cost-effective solution in high volume, smaller sized, or recycling applications.
“The Titan range, which includes three models – the Titan 600, Titan 1300 and Titan 2300 – is a simplification of Powerscreen’s highperforming Warrior range, using key features that customers love about the Warrior machines and tailoring them to a different section of the market at an attractive price point,” he says.
Looking to the future, Robinson believes the market will place a huge focus on digital
solutions to aid users in getting the most out of their machines. Powerscreen is continually investing and developing its Powerscreen Pulse telemetry system, which gives users a complete view of their machine in real time, such as hours worked, fuel usage and locations. The company is working on improving and developing these solutions to maximise efficiency for its dealers and customers.
“No matter where you are in the world, Pulse lets you stay on top of production by giving you accurate up to date information direct to your PC, tablet or smartphone. We have taken a lot of time to get the system to perform exactly as customers want, so that this robust platform will generate massive cost and time savings for equipment owners and operators alike,” concludes Robinson.
Powerscreen crushers are available exclusively from ELB Equipment in Southern Africa with a network of branches and dealerships that span the width and breadth of the region. a
Amid evolving customer requirements and the subsequent continued product innovation, Francois Marais, sales & marketing director at Pilot Crushtec International, discusses some of the emerging trends shaping the mobile crushing equipment market.
Trends in capital equipment generally come from two separate places – market demands (customer needs) and innovation (continuous improvement by the OEM) – which is the case in the mobile crushing market, reasons Marais.
In line with customer demands, he says, trends such as the move towards bigger mobile crushing equipment and hybrid
solutions have in recent years come to the fore in southern Africa. As part of the innovation imperative, telemetry solutions, such as Metso Outotec Metrics, continue to evolve, allowing customers to keep a finger on the pulse of their crushing operations.
According to Marais, the move towards bigger crushing gear has taken root in southern Africa in the past three to
3-5
The move towards bigger crushing gear has taken root in southern Africa in the past three to four years
30%
Another key trend being driven by market demand is the growing popularity of dualpowered (hybrid) mobile crushing solutions
The amount of data available to the customer from the field is much larger than it has ever been before. Telematics are therefore playing an increasingly significant role in crushing operations over the past several years, as OEMs such as Metso Outotec continue to advance their existing systems.
As part of the innovation imperative, telematics technology is developing at a rapid pace
four years. “One of the major drivers of this trend is the changing face of the contracting fraternity. Traditionally, contracts were long term, allowing contractors to mobilise their equipment for three to five years on a single site. The situation, however, has changed in the past few years, with contracts becoming much smaller and shorter,” he says.
Another trend that has not really taken root yet but is being spoken about in factory corridors is the idea of modular mobile solutions
To operate profitably in such an uncertain business environment, contractors are therefore turning to bigger mobile crushing equipment such as the Lokotrack LT120 jaw crusher and the
Lokotrack LT300HP cone crusher to allow them to execute the fewer jobs more speedily. This allows them to increase the volume of work that they can complete within a certain timeframe.
“Given the nomadic nature of such operations, opting for larger crushing equipment means that contractors are able to minimise the number of machines that they have to mobilise from one site to the other. Less kit is easy and cost-effective to move between sites,” he says.
Another key trend being driven by market demand is the growing popularity of dualpowered (hybrid) mobile crushing solutions. The trend, says Marais, is largely being driven by contractors operating in the commodity sector, where infrastructure is readily available.
Meaningful operational gains are realised when customers can connect hybrid machines to the grid. By and large, the price of electricity is lower than that of diesel, so there is a chance to reduce operating costs significantly.
“Being able to plug directly into the grid is a big cost-saving on diesel,” says Marais. “Having a direct power supply means that crushing plants can cut operational costs and ultimately improve the cost per tonne of end products. Contractors running these units have seen massive fuel economy benefits and are insistent on procuring more hybrid units.”
A case in point is a major contractor already running a total of five Lokotrack E-models, namely two LT120e jaw crushers, an LT330D mobile cone crusher and three ST2.8E mobile scalping screens. Having realised a 30% saving on its hybrid jaws compared with the conventional diesel counterparts, the contractor
is converting its entire fleet to hybrid units.
“The customer is operating on a mine where there is mains electricity infrastructure to support economic operation of the hybrid units. As a result of the massive cost benefits, the company is due to expand its hybrid crusher fleet with two more units – a Lokotrack LT120e and LT106e,” explains Marais.
As part of the innovation imperative, telematics technology is developing at a rapid pace. The use of telematics provides OEMs with a platform to communicate and collaborate with their distributors and customers alike, using machine data to improve productivity, drive efficiencies and reduce downtime, thus maximising financial gains and return on investment for the customer.
In a low-growth environment, quarry operators are therefore increasingly looking for ways to increase efficiencies while reducing costs. With data being the new currency for crushing and screening businesses, telematics and the real-time usage of data is quickly moving from being optional to being a requirement and is becoming an invaluable tool to gain a competitive edge and remain one step ahead in tough economic times.
“The amount of data available to the customer from the field is much larger than it has ever been before,” says Marais. “Telematics are therefore playing an increasingly significant role in crushing operations over the past several years, as OEMs such as Metso Outotec continue to advance their existing systems.”
As part of its continuous improvement process, Metso Outotec has recently launched
an upgraded version of its Metrics, an innovative cloud-based tool for real-time monitoring for Lokotrack mobile crushers and screens.
“The new system moves from the traditional satellite feed to a GSM signal infrastructure. The new remote monitoring solution brings significantly better connectivity and optimisation benefits to customers’ crushing processes. Other features include CO2 tracking for sustainability benefits, 24/7 access to realtime data, a maintenance module, and critical dashboards for utilisation and geolocation,” says Marais.
Furthermore, the new Metrics allows remote troubleshooting and the user interface can be tailored to address different customer needs. New features and functions can also be updated remotely.
“In recent years, we have seen increased interest in telematics technology, particularly from larger, sophisticated contractors who are looking to refine their operations. It’s those type of customers who want to know every detail of their operations, including plant availability, performance, reliability and profitability, who find value in this technology,” says Marais.
Another trend that has not really taken root yet but is being spoken about in factory corridors is the idea of modular mobile solutions. This is something Marais expects to see in the near future.
“It’s not available yet, but in the next few years we expect to see a single chassis platform being used for three or even four different mobile crushers, with interchangeable components. This will offer customers greater versatility,
allowing them to chop and change components such as crushers, feeders and discharge belts, as they wish, to create different types of machines on a single chassis platform,” he says.
Commenting on the state of the market, Marais tells Quarrying Africa that while the South African construction sector is still very much under pressure, he is encouraged by several SANRAL road projects that have come to market. A case in point is the recent awarding of four major construction tenders in KwaZuluNatal and the Eastern Cape worth a total of R7-billion.
“This is a welcome boost for an industry that has been in dire straits for almost a decade. However, these contracts have not necessarily translated into meaningful business for us from a capital sales perspective. In fact, the South African market remains under pressure from a supply chain point of view,” he says.
However, Pilot Crushtec has seen massive growth in the rest of southern Africa in the past year. Countries such as Zimbabwe, Zambia and the DRC, among others, have shown the desire to invest in infrastructure projects, says Marais.
“We have shipped a few mobiles to some of our existing customers in these countries. Unlike in South Africa where we have not sold a single fixed plant in the past three years, we have supplied four greenfield modular plants in southern Africa in the past six months. It is encouraging to see that the majority of our sales growth in these countries is coming from greenfield quarry and aggregate crushing projects,” concludes Marais. a
The Lokotrack LT106 jaw crushing unit is especially designed for crushing hard rock types such as granite, basalt and gneiss.That electromobility is a notable trend in the mobile crushing industry is no overstatement. Speaking to Quarrying Africa, Marcel Kerkhofs, marketing manager at Keestrack, says all forms of crushers – jaw, cone and impact – big or small, are now available with full electric plug-in. By Munesu Shoko.
As the industry seeks to simultaneously drive efficiencies and reduce its carbon footprint, the move towards electric crushers is in full force. One of the manufacturers at the forefront of the electric revolution is Keestrack, which has already brought to market an extensive range of commercial units.
“The main driver behind the electrification trend is sustainability – the need to reduce carbon (CO 2 ) emissions. We all want to contribute to the creation of a better and healthier world without having to compromise on quality and efficiency,” says Kerkhofs.
Leading from the front Keestrack first ventured into the electric game in 2012 with the introduction of its e-drive – an electric plug-in with an onboard gen-set for operating environments which has no mains power available on site.
“The e-drive machines invigorated the mobile crushing sector with a drop-off gen-set which could power several crushers, screens and stackers, in the case of no electric connection being available. This way the total production train is driven by only one engine, resulting in reduced fuel, maintenance and operational costs,” he says.
In recent years, Keestrack has introduced its ZERO-drive machines, a 100% electric
100%
In recent years, Keestrack has introduced its ZERO-drive machines, a 100% electric offering
40%
Compared
offering. In this range, electric motors drive most of the equipment and power some necessary hydraulics systems.
A wide range of Keestrack equipment –namely the H6e and H7e cone crushers, all impact crushers, all scalper screens (except the K8), C6e classifier, all stackers, all jaw crushers (except the B3) and the A6 tracked apron feeder – are available in ZERO-drive.
“At this point electric drive systems are the greenest and most cost-effective options on the market, as they are more efficient than conventional hydraulic systems. They enable the end-user to be less dependent on a specific engine supplier. If there is no electric plug-in available, end-users can choose their own gen set or select one of the Keestrack (tracked) engine/gen-set units,” says Kerkhofs. Compared to conventional diesel-hydraulic
KEY TAKEAWAYS
As the industry seeks to simultaneously drive efficiencies and reduce its carbon footprint, the electrification of mobile crushers is gathering pace
The main driver behind the electrification trend is sustainability – the need to reduce carbon emissions
Keestrack first ventured into the electric game in 2012 with the introduction of its e-drive
In recent years, Keestrack has introduced its ZERO-drive machines, a 100% electric offering
“The main driver behind the electrification trend is sustainability – the need to reduce carbon (CO2) emissions. We all want to contribute to the creation of a better and healthier world without having to compromise on quality and efficiency.”Marcel Kerkhofs, marketing manager at Keestrack Watch: Keestrack’s Join the Evolution video. The M5 tracked engine unit, with an integrated genset, can power several electric driven machines in case there is no plug-in connection from the grid available.
The drop-off engine unit, with integrated gen-set, can be placed on the tracked platform, on the chassis of the machine, or just next to the equipment, and can power several electric driven machines in case there is no plug-in connection from the grid available.
units, diesel-electric-driven plants directly save up to 40% of fuel. While working in production trains, the attributable fuel consumption may even decrease by 70% when the hybrid screens and stackers are powered directly via the plugout supply of an upstream or downstream electric crusher.
When plugged into the grid, savings are even bigger (depending on the local electricity price), as operational and maintenance costs will decrease drastically.
A completely new mobile concept from Keestrack is the tracked horizontal reversible impact crusher (RIC), the Keestrack I4e. Due to the innovative RIC technology, the machine can be used in secondary and tertiary crushing of rock, oversized gravel and recycled materials such as asphalt.
The specific design of the reversible horizontal impact crusher with a large variable crushing chamber, powerful rotor (Ø1 100 mm; 4 blow bars) and electronically monitored hydraulic gap adjustment (+80 to -220 mm with new tools) allows feed sizes up to 250 mm and ensures consistently high-quality end products of up to 0/2 mm in closed circuit.
“Secondary and tertiary crushing can be combined in one highly mobile solution, which makes the Keestrack I4e a real alternative to mobile cone crushers or vertical impact crushers, especially with regards to its outstanding production capacities from 100 to 250 t/h,” says Kerkhofs.
According to Keestrack, the system also offers lower wear, better quality of end products (grain
shape) and significant energy savings in typical applications (for example, sand production 0/4 mm: approximately -30% compared to cone crushers; -30 to -40% compared to VSI impact crushers). This is largely due to the advanced electric ZERO drive concept, backed up by the dropoff engine/gen-set consisting of a 447-kW diesel engine and 300-kVa generator.
Electric drives for the crusher (160 kW), feeders and conveyor belts as well as the system hydraulics enable particularly cost-efficient and emission-free plug-in network operation. Three specific patents illustrate the innovative potential of the new Keestrack I4e concept.
The compact system, with transport dimensions of 15,27 m x 3 m x 3,31m, weighs in at 42 t and comes with a single deck afterscreen with a return conveyor of oversized material. The closed circuit ensures production of 100% final material with high-quality global standards.
Looking ahead, Kerkhofs expects the industry to continue searching for the most costeffective and sustainable drive systems. Several options are already being evaluated, including hydrogen, fuel cells or battery packs.
“Furthermore, I expect the mobile crushing product range to grow in both ways –smaller equipment for city centre-based applications, and bigger mobile crushers for quarrying, mining and recycling,” concludes Kerkhofs. a
The extractive sector is at a pivotal moment in its history, especially given the incessant changes in technology that could transform the industry. Thus, the importance of adopting a digital transformation strategy cannot be stressed enough, especially in businesses such as quarrying and mining that involve repetitive jobs and moving substantial amounts of materials.
By Munesu Shoko.Digital transformation has the potential to help quarrying and mining companies reduce their costs and improve profits by streamlining their work processes and providing greater data insights with which to drive strategic decisions.
In a one-on-one with Quarrying Africa, Andrey
Komov, Head of Productivity – Sales Region International, Volvo Construction Equipment, warns that failing to adopt a digital transformation strategy can have devastating consequences.
Even small efficiency gains per tonne moved, he says, can add up to significant savings over time, making the business more competitive and improving the bottom line. In complicated quarry environments, traditional methods may struggle to detect these efficiency gain opportunities, highlighting the need for digital technologies.
Digitalisation, Komov stresses, is not a cureall solution, but rather a tool that can help increase efficiency. The key is to use it in the right way and for the right purposes.
“At Volvo Site Solutions, we have developed Site Efficiency Programmes that combine various digital services, training and consultancy to help customers achieve their
1-million t
If an operation moves 1-million tonnes per year, one can always find efficiency gains of at least US$0,1 per tonne with Volvo’s Site Solutions
Digital transformation has the potential to help quarrying and mining companies reduce their costs and improve profits by streamlining their work processes and providing greater data insights with which to drive strategic decisions
Even small efficiency gains per tonne moved can add up to significant savings over time, making the business more competitive and improving the bottom line
Volvo CE’s approach to digitalisation entails four steps: Insight, Analyse, Improve and Sustain
By automating processes and reducing waste, digitalisation eliminates extra administration, paperwork and routine, allowing workers to focus on more important tasks
goals, such as reducing costs, lowering CO 2 emissions, or increasing production,” he says. Volvo CE’s approach to digitalisation entails four steps: Insight, Analyse, Improve and Sustain. In the Insight phase, the company uses digital tools to establish a baseline of current performance and identify areas for improvement. “Once you can measure it, you can improve it,” says Komov.
“In the Analyse phase, we help quarry owners define key problem areas and simulate the outcome of changes to the site layout and fleet using a digital twin of the site. Here, we can also assist in setting new performance targets,” he adds.
The Improve phase involves implementing the proposed changes. For example, the company offers digital tools to help operators perform better and provide site managers with a better understanding of daily performance.
“In the final step, Sustain, we check whether our targets were met. For example, we check if we achieved the reduction in fuel consumption
208
One
manager
that we thought was possible. We also monitor progress over time, looking for opportunities to improve and ensuring that the circular approach to improvement never stops,” explains Komov.
By following these four steps, Volvo CE customers can achieve sustainable results and improve their operations in the long term.
“At Volvo Site Solutions, we understand that every customer has unique challenges and objectives. That is why our programmes are tailored to fit the specific results our
Starting small is a better approach to digitalisation. It is better to start and make adjustments ‘on the go’ rather than trying to make the perfect plan for digitalisation and never taking action. By implementing small, simple changes with immediate gains to the bottom line, a company can achieve quick wins.
Andrey Komov, Head of Productivity – Sales Region International, Volvo Construction Equipment
customers are looking for and may differ from one customer to another. In cases where a customer faces a challenge for which we do not have a ready-made solution, we see it as an opportunity to brainstorm and develop a custom solution,” he adds.
Volvo CE is always eager to learn more about the problems its customers are facing, as this helps the company to develop tools that meet customer-specific needs. “We believe that the key to success is listening to our customers and working together in partnership to find solutions. So, we encourage our customers not to face these challenges alone. Instead, we work together in partnership, as we believe that partnership is the new leadership,” he says.
Digitalisation, adds Komov, is a journey that drives change and new ways of working in a company. Therefore, the entire team should be on board and fully committed. Success in digital transformation cannot be delegated to just one person or group. It requires the involvement and dedication of the whole team.
Connectivity on site is crucial for successful digitalisation. To measure parameters in realtime, it is essential to have strong connectivity using machine telematics or tablet solutions. Unfortunately, stresses Komov, there are no shortcuts to achieving this. Volvo CE machines can be equipped with satellite telematics in areas without mobile network coverage, but this option is more expensive due to the cost of satellite connectivity.
Starting small is a better approach to digitalisation, he adds. It is better to start and make adjustments ‘on the go’ rather than trying to make the perfect plan for digitalisation and never taking action. By implementing small, simple changes with immediate gains to the bottom line, a company can achieve quick wins.
“At Volvo, we offer solutions that are brandagnostic and affordable, which means customers can use them regardless of whether they have a Volvo machine in their fleet. We have also developed tablet versions of our digital tools that allow customers to ‘plug and play’ with any machine, providing wider functionality when integrated into a Volvo machine via Co-Pilot. We are continuously learning together with our customers, and our list of solutions will continue to grow over time,” says Komov.
Digitalisation is often perceived as expensive. However, Komov believes this is a misconception. “At Site Solutions and Productivity Services, we challenge and change this paradigm. Our solutions are subscriptionbased, allowing quarries to start with any budget without the need for huge upfront investments. Our customer success managers ensure that customers receive a premium support level and an excellent experience with our solutions,” he says.
For instance, he adds, if an operation moves 1-million tonnes per year, one can always find efficiency gains of at least US$0,1 per tonne with Volvo’s Site Solutions. This translates to a saving of US$100 000 per year, giving the operation more budget to invest in improving efficiency.
Volvo CE offers a range of digital tools and solutions that can help quarries optimise their site management, increase safety and improve efficiency.
Performance Indicator is a tool that provides live information about production volumes from each machine (measured using the onboard weighing system on Volvo CE machines), payload utilisation (underloading, overloading, carry-back), fuel efficiency (tonnes per litre), and more. Customers can set target volume and see deviations in real-time, allowing them to take
immediate corrective measures. Data can be sent straight into the management system in digital format, eliminating paperwork. This tool works best together with Connected Map.
Connected Map gives both machine operators and site managers visibility of the site. Operators can see each other’s position on the Co-Pilot screen inside their Volvo CE machine or on a tablet screen in non-Volvo machines. This increases safety, especially on sites with curved or narrow roads. Operators can also see each loading unit and choose to reduce speed or go to an alternative loading unit with fewer or no queues.
Site management has a full picture of the site on their PC or tablet and can manually despatch machines if there is a need due to congestion or deviations from target production volumes in certain areas. The tool is brand-agnostic and can work on any machine.
“In the 21 st century, air traffic is primarily controlled by humans using digital tools from airport control towers. Similarly, Connected Map serves as a digital tool that provides quarry managers with real-time visibility and control of their operation. While some mining operations have implemented costly automated despatching solutions, these solutions are not always effective without human input,” says Komov.
Connected Map, on the other hand, offers an affordable and reliable solution that allows for human intervention to ensure maximum efficiency. Additionally, Site Management features, such as restricted areas and speed limits, can be set up to improve site safety and overall productivity. Just like the radar screen in an air traffic control tower, Connected Map provides a critical tool for managers to optimise their quarry operations.
Task Manager is a Volvo CE tool that is mostly used in infrastructure projects and connects
At Volvo Site Solutions, they understand that every customer has unique challenges and objectives. That is why their programmes are tailored to fit the specific results customers are looking for and may differ from one customer to another.
people, machines and projects, giving real-time status updates. It can also serve the needs in quarrying if there are no Volvo CE machines on site with integrated on-board weighing systems. The tool allows for manual tracking of production volumes and can generate loading receipts for operators. Site managers can get the full picture on their PC or laptop.
Connected Load Out is a solution that simplifies the load-out process by digitising orders and load tickets and connecting loader operators, site offices and incoming trucks. The real-time overview leads to more efficient choices and control of the process, saving both time and money.
Site Simulation is used for site optimisation by creating accurate scenarios of different site layouts, fleet set-ups, ground conditions and more. Customers can immediately see potential improvement gains on a cost-per-tonne level.
EcoOperator is a training programme that uses Volvo simulators, which allow for significant speedup of operator competency development without burning diesel or damaging machines.
“Recently, we made it possible to deliver this training to anywhere in the world by putting simulators into mobile containers with climate control. We have found that operator experience can influence productivity by around 20%, so this programme is a crucial part of increasing efficiency,” says Komov.
Poor operating behaviour, he adds, can also lead to machine downtime, which is why operators are such an important part of the equation and why improvements through digitalisation can be significantly lower if operators are left out of scope. Volvo CE has therefore built in operator coaching functions into Volvo Co-Pilot Operator Coaching, which provides feedback to operators on their behaviour and areas for improvement.
ActiveCare is a machine monitoring service
Volvo CE has built in operator coaching functions into Volvo CoPilot Operator Coaching, which provides feedback to operators on their behaviour and areas for improvement.
that uses telematics to check the health of Volvo CE machines, analyse error codes and diagnose issues using artificial intelligence. This helps prevent breakdowns and increase uptime. The service is free for five years for Volvo heavy machines working in quarry and mining segments.
Digital transformation brings numerous benefits to quarries, including guaranteed efficiency gains that lead to savings and increased profitability, says Komov. By automating processes and reducing waste, digitalisation eliminates extra administration, paperwork and routine, allowing workers to focus on more important tasks. Moreover, digitalisation helps reduce the quarry’s carbon footprint and make the business more sustainable.
“One of the most significant benefits of digital transformation is the live picture it provides of the production process and volumes. This realtime monitoring allows quarry managers to see deviations immediately and act accordingly, optimising production and reducing downtime,” says Komov.
In addition to extra efficiency gains, digitalisation makes the quarry a better place to work and helps attract top talent on the competitive labour market.
“Another important benefit of digital transformation is increased site safety. With tools such as Connected Map and Task Manager, quarry managers can monitor the site in real-time, track machine and operator behaviour and create no-go zones to prevent accidents. By using data to identify safety risks, quarries can proactively implement safety measures and avoid accidents before they happen,” he adds.
Over the years, Volvo CE has successfully partnered with numerous quarrying businesses to help them transform their operations through the implementation of its digital technologies. The joint efforts with customers have yielded positive feedback, which has been a major source of motivation for the company in its digital journey.
“One of our customers who adopted our Performance Indicator and Connected Map technologies reported saving four hours per week on reduced administration time. This translates into 208 hours per year, or 26 working days for a top manager,” he says.
Several customers who have implemented Volvo’s Connected Map technology have reported increased operator awareness of vehicle traffic flow. Operators can now slow down when they see a line forming to be loaded by an excavator, instead of rushing to the spot and waiting. This, combined with speed zone implementation has led to a positive effect on fuel consumption.
By conducting site optimisation work, Volvo CE can analyse cycle data from a customers’ operation and help them identify improvement potential. In one instance, Volvo noted a long waiting time for truck loading and dumping. Further investigations revealed that the wheel loader operator was not working efficiently, causing loading to take an excessive amount of time.
“By creating a digital twin of the site, Volvo CE was able to analyse the impact of process changes and concluded that they could reduce cost per tonne by 18% with minor changes in their cycle time. Operator training from Volvo CE was recommended as one of the next steps,” concludes Komov. a
Ctrack has a long history of managing movable assets and its locally built hardware, along with a variety of bespoke software solutions, has proven to be ideal for harsh mining conditions.
As the mining industry has progressed, become more sophisticated, and more reliant on machinery, the need for precise control of movable assets has increased drastically.
Ctrack has a long history of managing movable assets and its locally built hardware, along with a variety of bespoke software solutions, has proven to be ideal for harsh mining conditions.
“The mining industry is a major contributor to the country’s GDP and a massive job creator. Ctrack understands the importance of this industry and we pride ourselves on being able
to deliver tailor made solutions that help this industry remain profitable, compliant and efficient,” says Hein Jordt, CEO of Ctrack Africa.
Mining operations rely on a wide variety of vehicles and the operation of these vehicles is strictly regulated with specific licences required for each type of vehicle, as well as for vehicles with various load-carrying capabilities.
Drivers are required to complete specific training on each class of vehicle before being
24/7
Ctrack’s Bureau service gives these clients access to highly trained fleet managers, who monitor all data 24/7
licensed. Each licence needs to be renewed on a yearly basis, and the renewal process includes a training refresher session. In addition, if operators do not operate that class of machinery for a period of 180 days, the licence expires and they need to attend a training session to ensure that they are current, before that licence can be reinstated.
These complex licensing requirements mean that driver management with a large team of operators and across a wide variety of machinery, is an extremely complex task.
Ctrack has developed a system where drivers are able to use the same ID card that they do for functions such as access control in order to manage vehicle operation. The ID card contains information on all the vehicles that an operator is licensed to operate and needs to be swiped before a vehicle can be started. When the driver is trained and licensed for any additional classes of vehicles, it is automatically added to their profile, by means of the same access card.
This system ensures that fleet managers know exactly who is driving which vehicle and when; it also compiles a digital record of all operations. Most importantly, it ensures that only licensed
Ctrack has a long history of managing movable assets and its locally built hardware, along with a variety of bespoke software solutions, has proven to be ideal for harsh mining conditions
Ctrack has developed a system where drivers are able to use the same ID card that they do for functions such as access control in order to manage vehicle operation
Ctrack’s SMILE technology, which is a proprietary scripting language, allows for the development of very specific software solutions with an endless number of options
Ctrack’s fleet management system is also able to seamlessly integrate with a variety of vehicles through the vehicles CAN bus or other inputs
180
If operators do not operate that class of machinery for a period of 180 days, the licence expires and they need to attend a training session to ensure that they are current, before that licence can be reinstated
drivers are operating the class of vehicles for which they are licensed. The system also eliminates one driver being allocated to more than one vehicle at a time.
Ctrack has made provision for extensive licensing categories and only drivers who are correctly licensed and with a valid licence will be able to start and operate that particular machinery.
Daily reports will alert the fleet manager of licenses that are nearing their expiry date, which
The use of Ctrack’s fleet management system has been proven to ensure control of costs relating to fuel and productivity, as well as improving the way in which vehicles are used, which thereby ensures compliance, increases productivity and reduces accidents, all of which are critical in running a successful mining operation.
Hein Jordt, CEO of Ctrack Africa
Ctrack offers a variety of hardware that allows for effective tracking of any movable assets, from large dump trucks to non-powered equipment such as trailers, for example.
assists with booking of necessary training and licence renewals and minimises driver downtime.
Ctrack’s SMILE technology, which is a proprietary scripting language, allows for the development of very specific software solutions with an endless number of options. In the mining industry it allows for the creation of completely bespoke solutions.
Dust management is an important factor in a successful and compliant mining operation. Specially designed bowsers are utilised to spray a water and glue combination on a variety of surfaces. However, each of these surfaces requires a different mixture ratio and spray pattern and therefore centimetre-precise control is needed as the bowser moves from one surface to the next.
Using SMILE technology and precise GPS mapping, Ctrack has been able to completely automate this process, which allows the driver to simply follow the prescribed route with the software-controlled spraying equipment adjusting automatically according to predetermined parameters.
Another example of these specialised operations is where large bulldozers have to move and manoeuvre coal towards ‘coal valves’, through which this raw material gets placed on a conveyor belt. Due to the limited visibility from within these vehicles and the fact that they are moving around heaps of coal, steering safely and efficiently can be rather complicated. By implementing and utilising precise geo zones, drivers are assisted via a series of warning lights as they get closer to the depositing location, which assists them in carefully completing the operation without incident.
Furthermore, geo zones allow for easy management of speed and stop street violations as well as the monitoring of vehicles being stopped in unauthorised locations. The information gained is
passed on to drivers as part of their regular training regime.
Ctrack’s fleet management system is also able to seamlessly integrate with a variety of vehicles through the vehicles CAN bus or other inputs, allowing operators and fleet managers to get a clear picture of exactly how the vehicle is used, with all the relevant information displayed on one easy-to-use platform.
This includes monitoring of engine performance, fuel consumption, and hours used, as well as any hardware installed, for example, breathalysers or cameras. Functionality examples include on board weighing, production and cycle counts, which are invaluable in managing factors such as overloading and half loads and in that manner ensuring that assets are used as efficiently as possible.
Mining operations often occur on large sites in remote areas, making the ability to have eyes on a large fleet of vehicles vital to an efficient operation. Ctrack offers a variety of hardware that allows for effective tracking of any movable assets, from large dump trucks to non-powered equipment such as trailers, for example.
Managing a large fleet in a dynamic environment such as a mine requires specialised fleet management expertise. Ctrack’s Bureau service gives these clients access to highly trained fleet managers, who monitor all data 24/7, thus allowing them to proactively assist in managing these sophisticated operations and to tailor solutions to each specific operation as and when the need arises.
“The use of Ctrack’s fleet management system has been proven to ensure control of costs relating to fuel and productivity, as well as improving the way in which vehicles are used, which thereby ensures compliance, increases productivity and reduces accidents, all of which are critical in running a successful mining operation,” concludes Jordt.a
Well known for its Trio jaw and cone crushers, Trio feeders, Enduron high pressure grinding rolls (HPGRs) and Enduron vibrating screens, Weir Minerals Africa is also able to put all these together for customers in a complete plant. This speeds up the design and construction phases, so they can be quickly put to work, says product manager for comminution
Theo Hendricks.
This has proved very valuable to customers wanting to rapidly ramp up their production in light of rising commodity prices in recent years, according to Weir Minerals Africa product manager for Comminution
Theo Hendricks. With much of each plant’s equipment available ex-stock, and some even locally manufactured, the lead times for these plants can be considerably reduced.
“These tend to be process plants on the smaller side of the size spectrum, up to about 500 tonnes per hour capacity,” says Hendricks. “Designed in a modular format, these are fitted with any combination of our wellknown Trio jaw and cone crushers, Trio feeders and Enduron vibrating screens.”
The turnkey approach includes providing all the structures for the equipment, and the conveyors to move material between different sections of the plant. Weir Minerals Africa Advanced Applications Engineer Karabo Moalamedi emphasises that best practice is applied in all aspects of the engineering and design. This ensures safety, performance and easy access for regular maintenance.
At the front end of the plant is the primary station – which usually includes a ROM hopper, a Trio vibrating grizzly feeder, a Trio jaw crusher and Enduron screen. Where the material has a high clay or moisture content, a Trio apron feeder is recommended. At the secondary crushing stage, a combination of Trio cone crushers and Enduron screens are usually installed, while Enduron HPGRs are also included in the tertiary phase where finer material is required.
To accurately plan the design and
Metso Outotec’s Annual General Meeting (AGM) yesterday approved the Board of Directors’ proposal to change the company name to Metso Corporation.
“After the successful integration of Metso and Outotec, we will focus on growing a strong unified Metso company and brand,” says President and CEO of Metso, Pekka Vauramo.
“We have combined two valuable companies into one strong Metso. Our focus is clear: we continue enabling sustainable modern life and transforming the industry with a clear strategy and strong culture, supported by a name that is short yet established and well recognized among all our stakeholders. Services are an extremely important part of our business, requiring a strong name,” he continues.
Outotec continues as a product brand and carries significant value as the name of some key technologies and products.
The change of the parent company name Metso Corporation is effective starting May 4, 2023, but globally the change will be implemented in a phased manner. The visual identity of the company remains unchanged, but the new name is reflected in the company logo.
Metso Outotec’s Executive Team has been renamed Metso Leadership Team (MLT). a
location in existing facilities, 3D scanning is used to plot where infrastructure is already in place, says Moalamedi. The plant design itself can also be rendered in 3D, showing the customer and design team a detailed visualisation to guide final decision-making.
The plant is trial-erected at Weir Minerals Africa’s facility before being shipped to site, and its specialist technicians will supervise the on-site installation and commissioning. Ongoing technical support is then available from Weir Minerals Africa’s extensive branch network around the continent. a
Today’s digital technologies create vast quantities of data, which is where opportunities for improvement lie. However, much of it goes unused.
In fact, the average plant uses only 20% of the data it generates. The successful companies of the future will be those that can capitalise on this data quickly, efficiently, cost-effectively and across the enterprise through an effective data analytics strategy that encompasses site, edge and the cloud.
Data, technology and digital capability need to be brought together to build rapidly deployable analytics and AI/ML applications to increase productivity while decreasing costs and, in turn, improving sustainability and safety compliance.
Clients are afforded the opportunity to unlock the value of contextualised data through IIoT and Industrial AI. Here a prebuilt industry standards based cognitive data model can provide actionable insights to achieve operational performance, asset integrity, energy efficiency, sustainability and safety. However, bringing together multiple data sources to assist customers to make better informed business decisions is easier said than done. The challenge lies in finding a way to manage and analyse huge volumes of data stored within disparate networks that could be either on the premises or in the cloud. If successful this will result in improved productivity and optimum utilisation of plants and assets, process improvements and cost-savings.
“As a global leader in integrated industrial automation with deep domain expertise, ABB has advanced analytics to help customers accelerate their operational and business performance,” says Charles Blackbeard, business development manager, ABB Ability Digital Solutions.
ABB Ability Genix Industrial Analytics and AI Suite is a scalable suite consisting of an advanced analytics platform and prebuilt easy-to-use applications which is coupled with ABB’s implementation expertise. The suite connects, collects, and contextualises data from operational, IT and engineering systems. It empowers clients to unlock value from their data, driving better business results
Its modular nature means it can be structured to meet client needs, protecting existing investments while supporting seamless integration. It can be deployed from edge to fleet, plant, on premise, hybrid, cloud and multi-cloud based on the clients’ roadmap. ABB also offers an impressive range of business value applications, including system anomaly detection, opportunity loss manager and machine performance analytics.
ABB provides advanced consulting, predictive maintenance, performance optimisation and remote assistance for a range of industries, including oil and gas, chemicals, power generation, water utilities, mining, cement, pulp and paper and marine and ports. a
Achieving the best results in the process circuit starts with matching the crushers and screens, argues Kenny MayhewRidgers, regional business director at Sandvik Rock Processing Solutions South Africa. With the Kwatani product now being part of the global Sandvik group, this alignment becomes easier as customers get the benefit of one supply partner who is focused on both the screening and crushing parameters when designing a solution.
“The Kwatani product can now give their vibrating screen customers added benefits in this regard, being part of the global Sandvik group – which is well known for its crushing solutions,” says Mayhew-Ridgers. “The advantage is that the Kwatani screens can be specified and optimised with Sandvik’s range of crushers – ensuring that the key elements of the circuit are perfectly matched.”
Earlier this year, Kwatani and the mining related business of Schenck Process Group (SP Mining) were incorporated into the Sandvik group within Sandvik Rock Processing Solutions South Africa. Mayhew-Ridgers explains that the screens and crushers in any mineral processing plant are two critical lines of equipment –and they need to be well integrated to optimise the performance of both.
“There is a risk that operators and service technicians may focus on the one item without taking into account the impact of the other,” he says. “The settings and parameters on both the screens and crushers must suit the mined material and must be perfectly aligned for best results.”
If the crusher is not delivering the required size distribution of material, for instance, the screen will not perform to expectation. The Kwatani product is now able to specify a vibrating screen along with the optimal Sandvik crusher specification, he explains.
“With Sandvik as the OEM for both equipment lines, we bring our in-depth product insight into how the different equipment will best serve the customer’s specific requirements,” he says.
An integrated solution is based on a careful assessment of the nature and size distribution of the material which will be fed into the crushing and screening circuit, says Gavin McLaggan, Lifecycle Services Manager for Africa at Sandvik Rock Processing Solutions South Africa. This opens the door to increased efficiency and bottom-line profitability.
“Among the improvements that can be achieved are reduced energy consumption and less wear on the crusher liners – while gaining more throughput,” says McLaggan. “Where there are changes to the orebody and resulting material, there may be an opportunity to change the particle size distribution (PSD) and raise the throughput further.” a