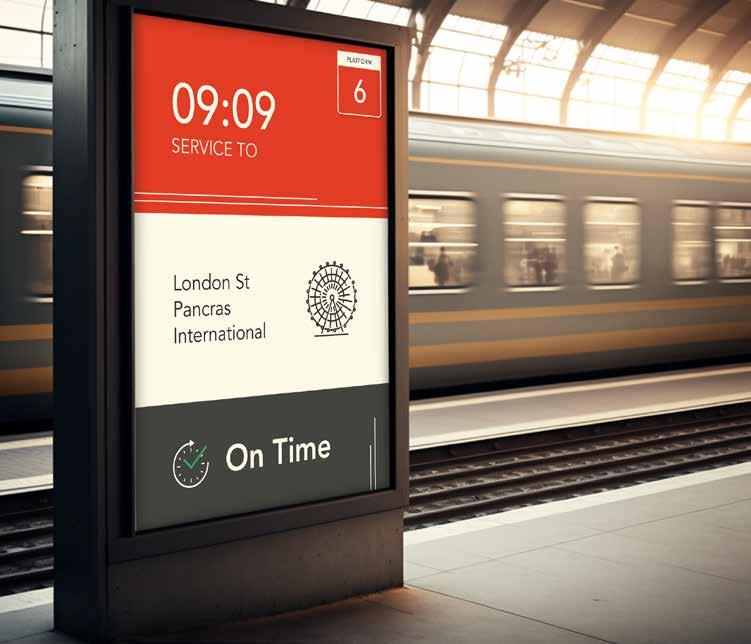
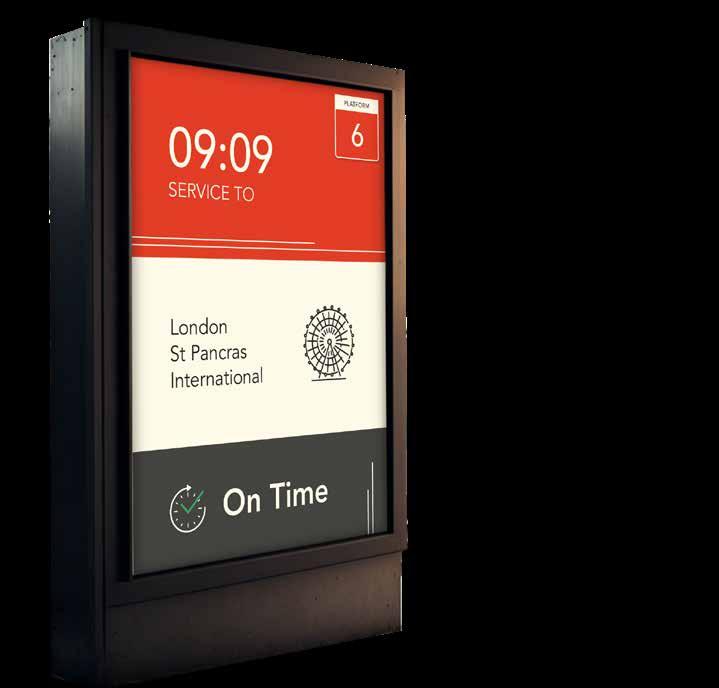
Simply working & sustainable
Since 1985 we have installed more than 1,850 km of track 1.7 billion load tonnes | equivalent of 50 years use
Application: Ballast, Slab Track, Steel Construction and Direct Fastening
Can carry Axle loads of up to 65 tons
Use on High Speed Rail up to 300 km/h
Maintains long term track geometry
Contact with ballast similar to timber sleepers
Workable properties like timber sleepers
26|
32|
34
RAIB’s annual report shows no room for complacency 2022 saw 16 railway accidents on the main line network. RAIB’s report addresses its most significant areas of concern.
New fleet introduction and fleet cascades
With 8,000 new vehicles ordered in the 2010s, their introduction and the cascade of older vehicles was far from smooth.
Train depots for today and tomorrow
Rail Partners brought operators, suppliers, and other stakeholders together to discuss depot safety and productivity.
Designing a safe and efficient depot
The Train Depots for Today and Tomorrow event examined the concept for HS2’s forthcoming Washwood Heath depot.
34|
How can robots make depots more effective?
Our final report from the Rail Partners depot event gave us a glimpse of the future.
66
36|
44|
48|
54|
60|
And then there was AI Malcolm Dobell reports from the Rolling Stock Maintenance and Depot Innovation conference held in June.
The connected asset –when a cab radio is not (just) a radio
The GSM-R cab mobile asset could be used to reduce costs, increase operational efficiency, and improve customer benefits. Customer information developments
Accurate information is essential for customers, as Paul Darlington discussed with Network Rail and the Rail Delivery Group.
HS2’s future stations
We take a look at the progress made at HS2’s new stations in London and the West Midlands.
Rail Live 2023
The UK’s largest outdoor rail show returned in June to Porterbrook’s Long Marston Rail Innovation Centre.
64|
66|
Energy harvesting & ‘fit and forget’ wireless sensors
Intelligent infrastructure and remote condition monitoring systems are essential for the maintenance and management of today’s railway assets.
HS2: an eco-plant test bed
HS2 is collaborating with the industry and its supply chain to accelerate innovation in low carbon plant and equipment.
68| Best challenge yet
76|
The quality of entries at this year’s Railway Challenge was the highest the judges have ever seen.
Unlocking innovation at the robotarium
RIA’s latest event brought a wide range of delegates together at Edinburgh’s Heriot-Watt University.
2018 saw the last Long Term Passenger Rolling Stock Strategy (LTPRSS). Yet with the UK’s rolling stock fleet comprising of 14,000 vehicles and costing £3 billion per annum, there is clearly a need for the overview that LTPRSS used to provide.
In 2021, the Government’s Transport Decarbonisation Plan committed to an ambitious electrification programme and the deployment of battery and hydrogen trains. Yet there is no visibility of any such plans. That year also saw the Williams Shapps report which bemoaned the absence of strategic planning which the McNulty Review highlighted in 2011. It noted that work had started on a 30-year Whole Industry Strategy Plan (WISP) to be produced in 2022.
Infrastructure schemes are part of the Rail Network Enhancement Pipeline which was published in 2018 and has not been updated since 2019 despite the promise of annual updates.
The Great British Railways Transition Team (GBRTT) is expected to publish a WISP, of which rolling stock is a subset, by the end of the year. Yet, with no sign of a rolling electrification programme, and no orders for conventional rolling stock for almost four years, decisions are needed now. Doing nothing is an expensive option. Against this background, the Railway Industry Association (RIA) has done the industry a great service by publishing its report ‘The UK Rolling Stock Industry – making 2023 the year of opportunity not crisis’. It shows how the ‘boom and bust’ procurement that characterises
UK rolling stock orders has resulted in factory closures and downsized the UK’s train upgrade capability. The current lack of orders will increase costs in the longrun as the lack of continuous production reduces productivity and reduces the skilled workforce. In addition, increasingly elderly trains will become significantly more expensive to operate and maintain.
In 2011, the UK had one new build factory. Following a glut of 7,300 vehicles ordered between 2012 and 2017, there are now five. These factories, and thousands of jobs, are now at risk. One has already run out of work and two will do so next year. The RIA report shows that UK rolling stock is a high productivity industry with the average employee generating gross value added of almost £105,000. This compares to an average of £65,000 in the manufacturing industry.
FIG 1case for new trains can be disputed, ‘no brainer’ would be a better description.
Introducing the 8,000 new vehicles ordered in the 2010s presented many notso-obvious challenges both for their new operators and those receiving cascaded older vehicles. In a comprehensive feature, Malcolm Dobell explains how train fleet introduction is a major business change programme for which detailed planning and building effective collaborative relationships is essential.
By 2030, around 2,600 vehicles will be over 35 years old. New trains are needed, not only to reduce costs, but to improve passenger services and meet decarbonisation commitments. ETCS also has to be considered given the cost of retrofitting old trains. Another issue is the lack of electrification plans which makes it difficult to specify the type of trains, though such uncertainties can be partly addressed by procuring battery EMUs and bi-mode trains.
RIA’s report also points out that, unlike infrastructure investment, new trains don’t need a large upfront public investment as the use of private finance to procure rolling stock is common practice. It explains why ordering new trains is a ‘no regrets’ decision. As it is difficult to see how RIA’s
A recent seminar considered how these large new fleets presented many challenges for depot operators. This included a GBRTT presentation on the emerging strategy for train maintenance, depots, and stabling to address the rapidly developing mix of all traction types. It focuses on location, aligned objectives for all concerned, best use of data, and best possible maintenance delivery.
On a much smaller scale, producing, modifying, maintaining, and operating miniature locomotives for the Railway Challenge has provided hundreds of young engineers with an excellent development opportunity. As we report, this event has been run by volunteers from the IMechE’s Railway Division since 2012 and was the best challenge yet.
Continuing the depot theme, we describe how HS2 is designing its Washwood Heath depot to be as safe and efficient as possible and how Artificial Intelligence (AI) and robots can make depots more effective. The National Robotarium was the location of a wide-
FIGURE 1 - Class 385 unit being built at Hitachi’s Newton Aycliffe factory which opened in 2015.ranging RIA Unlocking Innovation Event which showed how the widespread use of robots may not be many years away.
Fitting 12,000 upgraded GSM-R cab radios also presented significant challenges for which improved quality of communications is just one benefit. Others include Connected Driver Advisory Systems, and train-borne condition monitoring. Perhaps most importantly, they are future proofed as they can be upgraded to use the Future Railway Mobile Communication System.
The cross-industry Smarter Information, Smarter Journeys programme aims to communicate better and simpler customer information. As Paul Darlington reports, effective collaboration has delivered a range of initiatives. He also considers the latest in customer information displays at stations.
Our article on HS2’s stations includes the sad saga of HS2’s London Euston terminus where high costs have forced a pause and a third design rethink. The resultant abortive design work was cost hundreds of millions of pounds.
The Controlling the Elizabeth line feature included in the printed edition of Rail Engineer 202 (May/June 2023) unfortunately contained an incorrect statement that the Rigid Overhead Conductor (ROC) system used instead of a catenary was installed because it was perceived to require less maintenance and that in practice this was not the case.
In the public discussion about Euston, hardly anything is said about how terminating at Old Oak Common or reducing Euston’s platforms reduces HS2’s capacity. Tens of billions are being spent on the HS2 phase one line which will provide benefits of an equivalent value and free up a large amount of capacity on the existing railway.
As this is intended to be the trunk of Britain’s high-speed rail network, it is designed to carry 18 trains per hour. The latest leak suggest that Euston may only have seven platforms. If this is true, it would significantly reduce HS2 phase one’s capacity and so throw away benefits worth billions. This would also irrevocably reduce the capacity of any future high-speed network.
Safety on our railways is a good news story, though as the Railway Accident Investigation Branch’s (RAIB) annual report shows there is no room for complacency. Our feature highlights the key issues in this report which we hope will encourage readers to study the incident reports and summaries of learning published by RAIB that relate to their work.
The reality is that the ROC system was chosen primarily for the management of limited clearances and has given such good performance that it has been possible to double the period between maintenance inspections as a result of operational experience.
Although the online version of the article and the online PDF of the magazine contains the correct statement, Rail Engineer would like to assure readers of the printed edition of the magazine that the ROC system offers significant clearance and maintenance benefits.
Rail Engineer apologies for this error.
Editor
David Shirres
david.shirres@railengineer.co.uk
Production Editor
Matt Atkins matt@rail-media.com
Production and design
Lauren Palin
lauren@rail-media.com
Adam O’Connor adam@rail-media.com
Engineering writers
bob.hazell@railengineer.co.uk bob.wright@railengineer.co.uk clive.kessell@railengineer.co.uk david.fenner@railengineer.co.uk graeme.bickerdike@railengineer.co.uk malcolm.dobell@railengineer.co.uk mark.phillips@railengineer.co.uk paul.darlington@railengineer.co.uk peter.stanton@railengineer.co.uk
Advertising
Asif Ahmed asif@rail-media.com Craig Smith craig@rail-media.com
Rail Engineer
Rail Media House, Samson Road, Coalville Leicestershire, LE67 3FP, UK. Switchboard: 01530 816 444 Website: www.railengineer.co.uk
Rail Engineer Videos http://rail.media/REYouTube
Editorial copy to Email: news@rail-media.com
Free controlled circulation
Email: subscribe@rail-media.com
The small print
Rail Engineer is published by RailStaff Publications Limited and printed by PCP Ltd.
© All rights reserved. No part of this magazine may be reproduced in any form without the prior written permission of the copyright owners.
Part of: ® www.rail-media.com
On 27 July, a court sentenced Transport for London (TfL) and Tram Operations Ltd (TOL) to fines of respectively £10 million and £4 million for safety offences in respect of the fatal Croydon tram accident on 9 November 2016. This occurred after a tram overturned due to its overspeeding on a sharp curve. This followed a hearing in June 2022 when TfL and TOL both pleaded guilty to breaches of section 3 of the Health and Safety at Work etc Act 1974. This requires them not to expose persons not in their employment to risks to their health or safety. In June this year, the tram driver was found not guilty of failing to take reasonable care of his passengers after a trial at the Old Bailey.
The Rail Accident Investigation Board (RAIB) report published its report on the Croydon tram crash in December 2017. This concluded that the driver probably lost awareness and that the tunnels approaching the curve did not have sufficient identifying features to alert drivers
as they approached the curve. The report also found that the driver “had no record of driving at excessive speed, had no known relevant medical conditions and was regarded by TOL as reliable and compliant with the rules.”
RAIB considered that an underlying factor was that TfL and TOL “did not recognise the actual level of risk associated with overspeeding on a curve”. One reason for this was that there was a reluctance of some drivers to admit their own mistakes. A further issue was that the risk from excessive speed around curves was “neither fully understood by the safety regulator nor adequately addressed by UK tramway designers, owners and operators.”
Prior to its opening in 2000, the Croydon tramway was approved by Her Majesty’s Railway Inspectorate (HMRI) which became part of the Office of Rail Regulation (ORR) in 2006. This approval was on the basis of relevant standards including guidance published by HMRI which was based on line-of-sight driving. Other than speed signs, this document did not require mitigation at curves.
The RAIB report specifically considered the role of the ORR and found “no evidence that HMRI/ORR had fully recognised the potential for multiple fatality accidents involving trams.”
Recommendations in the RAIB report included the need for the UK tram industry to:
» Develop a body for effective UK-wide cooperation on safety, good practice, and standards.
» Systematically review operational risks.
» Install suitable measures to automatically reduce tram speeds at high risk locations.
» Consider systems to detect and automatically respond to low level of driver alertness.
In response, the Light Rail Safety and Standards Board (LRSSB) was formed in 2019. Much other work has been done to implement these recommendations. This includes the development of an overspeed protection system, as reported in issue 173 (April 2019) and the trial of wrist worn devices to monitor driver alertness.
Prosecuting the companies responsible for the Croydon tram crash cost £1 million (the costs they had to pay) and took nearly seven years.
In his sentencing remarks, the Judge explains that he considered both parties to be highly culpable as there was no effective risk assessment for overspeeding on curves. Moreover, tunnel lighting needed to assess braking points had been defective for some time, recommendations for extra signage and a near-overturning incident at this location had not been considered.
FIGURE 1 - Tunnel gaps on approach to the curve were used as braking points. In the dark, these gaps were not visible to the driver due to defective lighting CREDIT: RAIB
His remarks explain how, as well as high culpability, sentencing guidelines also require consideration of the severity of the event and the size of the organisation. Taking all factors into account he fined TfL £10 million and TOL £4 million. The judge felt that the deterrence value of this fine would benefit the travelling public in the long run.
The preface of every RAIB report states that the purpose of its investigation “is to improve railway safety by preventing future railway accidents or by mitigating their consequences.” RAIB’s report into the fatal Croydon accident took just over 12 months. Thereafter, the industry implemented its recommendations. This included the formation of LRSSB which has improved the tram sector’s understanding of risk and set recognised industry standards. In addition, new safety measures are now being implemented to prevent trams speeding around tight curves and manage driver attentiveness.
In contrast to this ‘no blame’ approach, it took seven years and cost £1 million for the judicial process to fine the companies concerned a total of £14 million. In his sentencing remarks the judge noted that “neither TfL not TOL were charged with causing
deaths.” Their failure was not to control a risk, the actual level of which was not appreciated. However, as the RAIB report showed, the lack of understanding of the potential for multi-fatality accidents was common throughout the industry, including the ORR which launched the prosecution against both TfL/ LOR and the driver.
Readers are invited to draw their own conclusions on which approach better prevents accidents.
A multi-fatality accident such as the Croydon tram crash clearly has a devasting impact on all concerned including the driver whose mistake cost the lives of seven people. In this respect, the judge in the TfL/TOL case demonstrated his understanding of the driver’s position by noting that he “had an exemplary driving record and was a careful driver who took pride in his job. He was one of the network’s best and safest drivers. The derailment that morning could have happened to any of the drivers on the network; it just happened to be him.”
Whilst making these comments the judge quoted from HSE publication HSG48 ‘Human failure and accidents’ which challenges the belief that incidents are simply the result of ‘human error’ as “organisations must recognise that they need to consider human factors as a distinct element which must be recognised, assessed and managed effectively in order to control risks.”
Whilst it is questionable whether multi-million-pound fines prevent accidents, it is good to see the judiciary recognising that human failure does not necessarily make someone a criminal. It is not that long ago when a rail worker was jailed for such a mistake.
This year’s Railway Accident Investigation Branch (RAIB) annual report shows that, in 2022, there were 16 railway accidents on the main line network requiring RAIB investigations. During the year the Branch published 14 full reports and 8 safety digests as shown in table 1.
The report describes how RAIB had published nine ‘Summaries of Learning’ (SoL). These address the most significant areas for which RAIB has concerns about the control of risk due to
recurrent issues since its first investigations in 2005. Table 2 shows the relationship between these themes and those of RAIB’s annual report which form the basis of this feature which primarily concerns incidents on the GB main line railway network. However, RAIB’s remit also covers Metros, Heritage Rail, the Channel Tunnel, and Northern Ireland. In 2022 it considered five Metro accidents as shown in table 3.
Graph 1 shows the significant reduction in fatal train accidents over the past 50 years and how the Train Protection Warning System (TPWS) has reduced such accidents. Whilst fatal train accidents are rare, other types of fatal accidents regularly occur on the national rail network, for example workforce, platform, and user worked crossing accidents. Table 4 shows a 37% reduction in such rail fatalities over the past ten years. Yet, sadly, annual suicides have increased from 216 to 261 over this period. Whilst this safety improvement is good news, RAIB’s annual report shows that much more needs to be done, especially as, in slightly different circumstances, some accidents could have been multi-fatality events.
DAVID SHIRRES Derailed tank wagons at Llangennoch CREDIT: RAIBTable 2 shows how operations accounted for the highest number of accidents considered by RAIB in 2022. These included two buffer stop collisions and two signals passed at danger. Maintaining full concentration whilst driving trains is a demanding task. Hence RAIB recommends research into the detection and mitigation of driver’s loss of attention, and support for drivers in respect of fatigue and lifestyle management.
TPWS was implemented over 20 years ago as a stop-gap measure until the implementation of automatic train protection provided by ETCS. Although it is not a failsafe system, it has significantly reduced operational risk. Yet, with widespread ETCS deployment remaining many years away, RAIB questions whether TPWS provides sufficient risk mitigation.
An overspeeding incident at Peterborough in April 2022 showed how neither TPWS nor current signalling standards provided sufficient risk mitigation for a train routed from the Up Fast to the Up Slow line. As the train approached the junction control signal was displaying in red aspect until the train was 790 metres away travelling at 25mph. It then changed to a green aspect with its junction indicator (a string of five white lights) showing that the train was routed on to the Up Slow. The driver did not react to this indicator and then applied power which accelerated the train to pass the signal at 64mph, after which it passed over a set of points restricted to 30mph at 76mph.
FIGURE 1 - Driver did not react to this signal’s junction indicator when its red aspect changed to green CREDIT: RAIB
Thirteen months later, there was another overspeeding incident at this signal. Since then, the approach control at this junction control signal has been changed to display a yellow aspect when a route
requiring the junction indicator to be illuminated is set.
Since 2005, RAIB has investigated 58 incidents involving track workers and moving trains. Of these, 10 resulted in deaths and 12 in injuries. The SoL showed that
the safe system of work in place during these incidents included 24 instances of unassisted lookouts, 12 possessions, and 12 line blockages. It identified the following concerns:
» Planning work.
» Quality of site leadership.
» Supervision and monitoring of track workers.
» The way information is presented to track workers.
» Standards of lookout working.
» Staff installing possession protection equipment.
» Management of contingent labour.
» Staff willingness to challenge unsafe practices.
The fatal accident at Surbiton in February 2021 was followed by five track worker near misses, investigated in 2022. The Surbiton report showed that the individual killed was working outside the protected area and recommended action to keep track workers within safe limits. It also recommended that Network Rail review working practices to understand reasons for non-compliances. This, and previous reports, highlighted the need to reduce the amount red zone working.
FIGURE 2 - Cab video shows track worker near miss at Paddington CREDIT: RAIB
RAIB’s annual report notes that improved technology and planning reduce the occasions that workers are on track when trains are running. However, as RAIB’s chief inspector Andy Hall notes: “whether working in planned red zones or not, lower-level risk controls relating to safety behaviours and site safety leadership remain important, if we are to avoid the type of near miss we continue to see, that one day may turn out to be another tragedy.”
RailStaff has been championing the rail industry’s workforce since 1997.
As well as getting to the heart of ‘what you need to know’ each month, its team of writers focus on the latest developments in:
• Health
• Safety
• Wellbeing
• Careers and training
We also cover stories that celebrate the great achievements of staff.
Such is the freely-distributed magazine’s success that the only industry-wide people recognition scheme, the RailStaff Awards, was launched in 2007, and has been held ever since.
Request a free subscription at www.railsubs.com
Call 01530 816 444 or visit www.railstaff.co.uk for more information
Weather related incidents considered by RAIB in 2022 were a train hitting a fallen tree at Balderton in November 2021 and a train running over a washed-out line at Haddiscoe in January 2022. Prior to the Balderton incident, RAIB found that Network Rail had not considered all relevant meteorological data. Though these incidents only resulted in minor damage, the tragic Carmont accident, on which RAIB published its report in March 2022, highlighted the dangers of bad weather.
structures, trains hitting objects, unsupported track, and brakes affected by ice and snow.
The annual report notes that modern weather forecasting can predict exceptional events, allowing operators to implement focused precautionary measures to reduce the need for blanket speed restrictions over areas that are not at risk.
The importance of clear communications when imposing such emergency speed restrictions was emphasised in a safety digest issued in November 2022 following various overspeeding incidents. This highlighted the need for appropriate methods, including available technology, to ensure that weather-related speed restrictions reached the staff who need to act upon them.
passenger fell off a platform which did not have tactile edge markings.
With several million people getting on and off trains every day, ensuring that everyone is clear before departure is a challenge, especially for trains with repetitive stops at busy stations. Hence RAIB reports have recommended measures to support drivers to maintain attention and awareness.
RAIB’s weatherrelated events SoL refers to 19 reports concerning management of earthworks and structures; response to adverse weather; snow and ice; and heat. These show the varying consequences of bad weather events including track buckling, scour undermining
RAIB’s SoL of platform-train interface incidents refers to 15 such reports at train and tube stations and tram stops. Of these, 11 were trap and drag incidents and, in three cases, a passenger fell between train and platform. In a further incident, a visually impaired
Reports have shown that the detection of trapped objects by door control systems needs to be improved. Investigations have shown that drivers and train dispatch staff were unaware of this problem and so relied on the door interlock indications to confirm that nothing was trapped. In one accident a driver did not realise that a trapped passenger’s hand could not be detected by the door interlock.
Another misconception is that, as shown by RSSB research, 58% of passengers mistakenly believe that, like lift doors, train doors will reopen if they are obstructed. In one case a passenger became trapped when she placed her hand between the closing doors in an attempt to re-open them as she attempted to board the train.
FIGURE 3 - Carmont accident in August 2020 CREDIT: RAIBRAIB’s User Work Crossing (UWC) SoL shows that it has published 24 UWC reports which highlight the following concerns about Network Rail’s 2100 user worked crossings:
» Briefing by authorised users.
» Signage.
» Signaller’s judgement.
» Signaller’s understanding of type of vehicle.
» Power operated gates.
RAIB issued four reports concerning UWCs and footpath crossings in 2022. The incidents at Coltishall Lane and Kisby both showed that users did not know how to use a UWC. As well as reviewing signage, RAIB recommended that Network Rail, with ORR and DfT support, should review current arrangements that required authorised users to brief potential crossing users given the increase in delivered goods and services. As Andy Hall noted: “we still have a nineteenth-century concept in a twentyfirst century environment.”
Both reports on the fatal accident at Lady Howard footpath level crossing and near miss at Farnborough North level crossing showed that insufficient action had been taken to mitigate the known high risk at these crossings.
Though steel wheels on steel rails make for a highly energy efficient railway, moisture and other contaminants can significantly reduce the friction between wheel and rail. Two quite different consequences arose from the two low adhesion incidents that RAIB considered in 2022. At Pencoed and Llanharan in March 2021, severe wheel flats on a freight wagon caused track damage as wheels locked after a normal brake application due to low adhesion.
A serious incident occurred on at Sailsbury Tunnel junction in October 2021 when a passenger train was unable to stop and collided with another train at about 54mph. This was the first collision between passenger trains at speed that RAIB has investigated since its formation
in 2005. It resulted in a driver being seriously injured and 13 passengers taken to hospital. Had the train collided with one travelling in the opposite direction, the consequences would have been far more severe.
RAIB’s interim report, issued in February 2022, confirmed that, for two miles before the collision, the railhead was contaminated with crushed leaf material. It considered that this reduced the coefficient of friction close to an exceptionally low value of 0.02. Rail Engineer has featured various reports on the work of Adhesion Research Group. RAIB’s investigation into the Sailsbury Tunnel Junction accident will no doubt provide added impetus to this group’s essential work.
With the passage of time, most in the industry today did not experience the shock of learning how a loose wire caused the catastrophic Clapham Junction accident in 1988. This wrong side failure (WSF) was particularly disturbing for signal engineers who responded by producing new signalling staff handbooks on works testing, maintenance testing, installation, and design. These incorporated all the lessons from the Clapham accident and were supported by enhanced training. At the time all concerned knew why these handbooks were so important.
In 2022, RAIB considered two WSF incidents. In September 2022, it published its report into a derailment at Dalwhinnie caused by a wiring error when a points machine was replaced nine months earlier. In October 2022, a train running under green signals at Wingfield was unable to stop when it unexpectedly encountered a red signal. This occurred
after the signal had been disconnected for planned maintenance work. Fortunately, there were no significant consequences from either of these incidents.
RAIB’s annual report suggests that the lessons of Clapham are being forgotten. To highlight these, RAIB recently introduced a SoL on WSFs. This considers the Dalwhinnie and Wingfield incidents as well as a 2016 irregularity at Cardiff East Junction, a 2017 collision at Waterloo, and loss of signalling data on the Cambrian Coast line in 2017. It identifies the following areas of concern: commissioning signalling projects, maintenance renewals and assurance of software products.
Poor freight wagon maintenance has been a matter of concern in several RAIB investigations. The freight train derailments SoL references 22 RAIB reports on freight train derailments and two on track damage caused by freight trains.
Poor wagon maintenance was further highlighted when, in January 2022, RAIB published its report into the Llangennech freight train derailment as reported in issue 194 (Jan-Feb 2022). This recommended a comprehensive review of freight wagon maintenance management. During this investigation RAIB issued an Urgent Safety Advice on the need to manage the risk of malfunctioning wagon braking systems.
Since the Llangennech derailment, there have been freight train derailments at London Gateway in December 2021 and Pettril Bridge Junction in October 2022, for which reports have yet to be published.
The SoL refers to five cases of freight train derailments being caused by track condition and, in particular, the failure of rail fastenings on tight radius curves. It also showed that three freight train derailments had been caused by uneven loading.
The SoL on the safety of on-track plant (OTP) and trolleys considers: Road-Rail Vehicle (RRV) braking; operator competence; vehicle conversions; and trolley/ trailer braking systems.
RAIB has published nine reports on RRV runaways which almost all concern ineffective braking during on and off tracking of ‘high-ride’ RRVs. These have rail wheels with a hub that is driven/braked by the machine’s rubber-tyred road wheels. If such RRVs are not properly on-tracked, contact between road and rail wheels may be lost which can result in a runaway.
FIGURE 6 - Positions of road and rail wheels on OTP after runaway at Bradford in June 2018 CREDIT: RAIB
Following a spate of such incidents, all such RRVs were fitted with a Direct Rail Wheel Braking (DRWB) system. However, this did not entirely prevent such incidents as shown by the RRV runaway at Belle Isle in May 2021 which was due to an ineffective DRWB system due to a valve left open following maintenance.
The RAIB reports into RRV collisions at Cholmondeston in September 2018, Rochford in January 2020, and Ramsden Bellhouse in May 2021 concluded that current rules lacked clarity about who was in charge of the safe movement of track plant. These reports recommended that Network Rail should review and clarify the roles of those responsible for plant operations in possessions and work sites, to avoid duplication of responsibilities and minimise confusion between roles. This recommendation is still being progressed.
The Cholmondeston report also found that there was very limited visibility ahead, when the RRV was driven in reverse. It noted that RRVs spend an equal amount of time travelling in both directions and recommended that the relevant controls need to consider practicalities of such limited visibility.
Runaway hand trolleys and a trailer were considered by reports into incidents at Haslemere in September 2011, Raven Crossing in November 2014, Hope in May 2017 and at Ramsbottom in March 2018. The issues raised by these reports included poor brake maintenance, standards not considering whether the brake is a parking or service brake and that planning had not adequately considered the gradients on which this equipment was to be used.
The SoL on braking system integrity considers trains that cannot stop, stopped rail vehicles running away, and derailments due to wagon braking faults. This last topic essentially overlaps the freight train derailments SoL. For two of the incidents of trains not being able to stop, the locomotive provided the only brake on the train. A freight train passed a signal at danger at Crofton West Junction in May 2020
because its wagons had no brakes as, after a brake test had been undertaken the night before, the locomotive had been used for instruction and the instructor had left the brake pipe and reservoir pipes isolated.
In August 2019, the driver of a sleeper train was unable to control its speed through Haymarket East Junction and was unable to stop at Edinburgh Waverley. This was an incident with potentially catastrophic consequences. RAIB investigation concluded that that the Brake Pipe Isolating Cock (BPIC) had almost certainly been inadvertently closed whilst the electrical supply plug was being connected when the train was split at Carstairs. It made recommendations concerning brake continuity testing and preventing unintended operation of the BPIC.
The locomotive, ‘Vale of Ffestiniog’, on the heritage narrow gauge West Highland Railway entered a single line section without authority in April 2019 when it was unable to stop as it descended a 1 in 40 gradient through Beddgelert. This was found to be due to a brake system modification made 18 years previously.
FIGURE 7 - 600mm gauge ‘Vale of Ffestiniog’ locomotive CREDIT: RAIBThe importance of ensuring parking brakes are applied was shown by the runaways of a rake of 22 wagons running away at Toton sidings in January 2021 and an unattended engineering train at London Liverpool Street station in October 2022.
Another SoL considers incidents during abnormal events. These concern passengers detraining, usually of their own volition, and safety incidents from poor communications. Although RAIB did not have to consider any such events in 2022, this SoL is still highly relevant.
Drivers only very rarely encounter incidents in which their trains fail and become stranded. When this happened in May 2011 at Kentish Town, in March 2018 at Lewisham, and in July 2019 at North Pole Junction, passengers decided to detrain themselves onto the live railway. When a train was stranded 30 metres from Peckham Rye station in November 2017, a decision was taken to detrain passengers who were then close to the live conductor rail.
RAIB found that in such cases drivers were sometimes poorly supported by the control room and made poor decisions as they were overwhelmed by events. It also concluded that operational interfaces between different train operating companies, signallers and control offices were poorly managed. It recommended enhanced training and exercises to enable operating staff to effectively manage train stranding incidents and recognise that such incidents on a busy urban railway can rapidly create an unsafe situation.
Reports on unsafe situations during abnormal
events were a near miss between a train and a driver who was on the track examining his train at Stafford in March 2018, and a driver moving a train past a red signal without the signaller’s permission at Bethnal Green in April 2018. Both incidents were due to poor communications.
RAIB’s annual report is a good and essential read. As well as its many specific safety lessons, it highlights some key general points. Historically, railways have improved safety by learning from accidents, yet some recent accidents suggest that lessons from the past are being forgotten. Another issue is that, in a complex environment with competing pressures, it can also take too long to mitigate known high risks.
It is also important that those responsible understand what is actually happening rather than what they think should be happening. This needs a culture which encourages a flow of information from the sharp end. Understanding what does and can happen is essential if risk is to be effectively managed, as compliance with standards, in itself does not guarentee safety.
RAIB’s SoLs are also an essential read for those concerned with their specific themes. Its reports on each incident are also a good read, though of necessity these are comprehensive lengthy reports. Rail Engineer understands the pressures on everyone’s time but hopes that this feature encourages its readers to read the RAIB publications applicable to their work given the importance of understanding and implementing the lessons in RAIB’s publications.
Protect your staff from pit falls
Easily retrofitted to any pit with a light recess
No civils work required
Minimal working space lost
Air operated
Quick & easy operation
The Premier Hinged Cover (patent No. E2 886-747-B1) is an air operated fall restraint made up of 2.5m steel mesh panels. The panels are operated by pneumatic cylinders connected to a central control box for an easy one person operation. The stairs of the pit are covered by individual sections which are manually lifted, and have the additional benefit of acting as a hand rail for ingress and egress.
The Premier Hinged Cover enables clients to protect their staff with minimal disruption whilst keeping the maximum working space, and can be installed on existing steel, concrete or block pits.
In May 2023, a month after the ‘Train depots for today and tomorrow’ conference (see page 26), Rail Partners and Rail Delivery Group hosted a fleet introduction and cascades lessons learned event. Around 8,000 new vehicles, not all yet in service, were ordered by many operators in the 2010s. This resulted in the cascade of older vehicles to other operators. With such a big programme, some problems were inevitable.
Mark Molyneux, national fleet performance manager, Rail Delivery Group (RDG), set the scene, discussing the well-publicised problems of the May 2018 timetable. This debacle put the rail industry’s problems into sharp focus and the delay to fleet introduction kept rail in the headlines. He reported that the biggest cause of delay to the industry Public Performance Measure were ‘fleet related’ issues. Fearing that the influx of new trains would cause further harm, RDG commissioned the report ‘Risks to Network Performance from New Train Introduction’.
This report sought to address the questions: Is there a risk to system performance from unreliability of new rolling stock? Is there a risk to timetable delivery from late introduction of new and refurbished rolling stock? The report identified factors increasing these risks and proposed actions and mitigations to ease the short-term situation and make major improvements for later projects. Mark reported that the output from an RDG-convened New Trains Colloquium in October 2018 and the above report led to
the development during 2019 of the RDG Guidance Note ‘New Trains – A Good Practice Guide’ that was first published in March 2020.
Mark reported that, despite this worry, the average Miles per Technical Incident (MTIN) has remained remarkably consistent since 2018. He had also examined the growth in MTIN performance over the first year in service for each new fleet introduced since 2018. Some fleets have achieved MTIN significantly better than the national average, whilst others have delivered slower reliability growth. See FIGURE 1.
The difference between suppliers is significant. One supplier’s fleet exceeded the national average MTIN in 15 months from entry into service, whilst another took over 54 months for just one of its fleets to pass the average MTIN figure. See FIGURE 2.
Of course, the context of each fleet varies and there are differences between new designs, duty cycles, and follow-on orders for established designs.
Steve Clarke, senior project manager at Angel Trains, described a collaborative project with Hitachi in which 19x5-car trains were supplied to TransPennine Express (TPE) and 5x5-car trains were supplied to Hull Trains, both financed by Angel Trains. They were ordered in October 2016 and delivered in 2019-20. Although similar to the class 802 units supplied to GWR, these have a larger fuel tank, higher output engine, bigger rheostatic brake, and a revised catering area. The bodyshells were to be built and painted in Japan, and assembled in the UK, but, in fact, seven units were fully built in Japan, the remainder assembled/ finished at Hitachi’s plant in Pistoia, Italy, and all were commissioned at the UK plant in Newton Aycliffe.
Steve said that the collaboration was grounded on these key behaviours: a shared sense of success, a shared fear of failure, relying on each other, and holding each other accountable.
“If everyone performs well, we will all succeed...but if one fails, we all fail,” said Steve. He added that trust in each other was essential. Steve told the audience that part of the success was to give the contract a voice and understand what it was trying to accomplish.
People tend to focus on the parts of contracts that emphasise procedures if things go wrong, but Steve stressed the importance of maintaining a preventative mindset, as well as collaborative behaviours when corrective action was needed.
A joint risk register of project risks (which focused on things that might throw the project off course rather than financial or safety risks) was in place, with mitigation activities managed by the organisation best placed to do so. For example, TPE and Hull Trains managed gauging.
A similar approach was taken for other interfaces, with one organisation in the lead but the others having actions. Collaborative project management works, as Steve concluded. It requires hard work and care, but all must want to work together. As one delegate put it: “you can’t collaborate at someone”.
Martin Beable, engineering director at Greater Anglia (GA), talked about the pitfalls of introducing their new trains. GA’s 2016 franchise agreement provided for the then current fleet to be replaced by Alstom
Class 720 and Stadler Classes 745 and 755 units. The original plan showed that all these would be in service by the end of 2020 but there were delays, mostly caused by Covid. Martin showed the actual timeline and reported that the last of the legacy fleet had now been withdrawn. Another change was to make the suppliers responsible for maintenance, with many staff transferred to them under TUPE, and depots had to be extensively rebuilt as discussed in the Depots article elsewhere in this magazine. The split of responsibility between GA and the suppliers was slightly unusual, as shown below.
Martin stressed the importance of constant reassurance for staff who knew they were to be transferred up to five years before the event happened. Martin described a lesson learned from Norwich Crown Point depot. Although both GA and Stadler personnel were on site and strategy and responsibilities had been set out clearly in contracts, physical and cultural walls made meaningful collaboration difficult, and silos emerged. Martin commented that in practice, the contract did not cover all situations and was too commercially led. GA and Stadler implemented joint initiatives, which should have been in place from the start, with a one team approach under a ‘putting the passenger first’ banner.
Possibly the biggest challenge of all was capacity, particularly during the Stadler FLIRT fleet introduction. Martin said that Stadler was delivering as fast as it could, but, while the depot was managing commissioning and cascades, capacity was reduced while the site was rebuilt and there was nowhere to put the new trains. In addition, there was only three months of overlap between receiving new trains and handing back the old ones, leading to last minute deals with ROSCOs and the train operators who were supposed to be receiving the cascaded fleets. This led to the most important and frequently revised working document, the fleet cascade plan, and the weekly cascade meeting.
Martin gave his own mental scoresheet for the transition in exam style, resulting in an overall ‘pass’ mark for their new fleet introduction.
Neil Bamford, fleet director at East Midlands Railway (EMR), turned to the subject of fleet cascade. This was not unlike GA, where eight different fleet types become three but, for EMR, only one fleet is new. The incoming fleets were the Class 360 from GA and 2- and 3-car Class 170s from Govia Thameslink Railway, West Midlands Railway, ScotRail, and Transport for Wales. In addition, as stopgaps before the Hitachi Class 810 units arrive, EMR’s HSTs were replaced by redundant (but more compliant with the NTSN for People of Reduced Mobility) HSTs from LNER and ex-Hull Trains Class 180s. Outgoing Class 15x units were cascaded to Northern or are going off lease.
To add to the mix, EMR was working with four ROSCOs (Angel, Eversholt, Porterbrook, and Rock) and a huge amount of legal documentation was involved, including 15 leases, six subleases, and literally hundreds of extensions, amendments, side letters and associated documents, handover/hand back documents, conditions, and liabilities. This task alone was time consuming and expensive, with each ROSCO having a different approach.
While all this was going on, performance had to be maintained. For the cascaded units, timely technical and traincrew training needed to be undertaken, tools and equipment put in place, technical documentation needed to be accurate and understood, and a float of material obtained. In addition, said Neil, depot capacity and throughput was a challenge and delayed refurbishments, such as Class 360, didn’t help. One might think, mistakenly, that all the Class 170 units transferred in to EMR would fit easily with the existing fleet. Besides obvious things such as livery and pre-recorded announcements, there were all sorts of differences - see table below – some of which could be corrected quickly and others which took longer. In the meantime, trains still had to be brought into use.
To mitigate risks, train and fleet staff visited Selhurst, Tysley, and Cardiff Canton to see and understand the configuration of the various units. Despite that, differences between inherited fleets have caused operational incidents. Extensive briefs were provided to mitigate further risks and safety validation panels have been held.
Neil reported that introducing the Class 360s was relatively straightforward, partly because they were to operate a new service. A sub lease was put in place with sister company GA and Siemens remained as maintainer (under a new TSA contract). Initially, only 14 from 21 units were required and reliability has steadily grown. Two big issues are the outstanding refurbishment and provision of maintenance facilities. There has only been limited upgrade work at Bedford Cauldwell depot and units still need to be loco hauled to Northampton, Kings Heath once or twice per week. But further upgrades at Cauldwell are due to be complete by August 2023 (overhead crane, lifting jacks etc.) to reduce the reliance on Kings Heath.
In summary: the ever-changing plan had knock-on effects to internal resource and the supply chain. Neil said that there must be clarity and trust about handover and hand back. He also wondered whether contractual process and methodology need to be so complex?
Returning to new trains, Liam Hockings, new fleet introduction manager at Avanti West Coast, covered the multitude of issues to be dealt with when a new fleet is being introduced. He identified 69 separate activities, with assurance, training, and compatibility representing a minority of the activities.
Moreover, as non-tilting units, they will currently be limited to 110mph on the fast lines. Avanti and Network Rail are working on the Multiple Unit (MU) Line Speed Enhancement project, to maintain route capacity with non-tilting trains. Liam said that there will be no physical track works, just new signs showing, for example, ‘MU 125’, and detailed planning is ongoing to integrate the driver training required for the new trains, the new speed profile, and the introduction timetable whilst maintaining the train service. The work also includes a detailed risk assessment to understand and mitigate the risks associated with operating a mixed fleet with potentially different means of managing the safe speed of the train.
Liam outlined the validation work to show that 42 stations with over 200 platforms, many shared with other fleets/ operators, were ready for the new trains but this was complicated by three different train lengths being introduced, and the positions of multiple wheelchair, cycle, and catering doors needed to be considered for all train formations. Liam said that 30 miles of walking with a measuring wheel was required to complete these assessments.
Station stop signs are an issue, with some locations needing many. At Milton Keynes Central, for example, the two operators will be operating trains from three cars to 12 cars with lengths between 72 and 265 metres. Another consideration was signalling, e.g., making sure trains don’t stop with a wheelset over an axle counter. Liam reported that validating the catering vehicle layout is more complicated
The Classes 805 bi-mode and 807 electric Hitachi Inter City Express trains are nearly standard units, but they are new to Avanti and all staff using them will require training including maintenance staff from Alstom.
than one might think. Issues include: does it meet the expectations, has the catering offer changed since the train was specified, do the coffee pots fit and are the chillers big enough for a reasonable stock of sandwiches?
Renowned as the global market leading depot protection system, the SMART DPPS™ delivers physical protection from vehicle movements to rail depot staff whilst providing visual and audible warnings.
The Smart DPPS™:
• Protects staff and equipment
• Ensures safe and controlled movement of rail vehicles into and out of the depot
• Allows train maintenance operations to be conducted without endangering the safety of staff or damaging infrastructure
It is:
• Fully configurable, flexible and functional
• Proven in use and installed globally
• Capable of interfacing with third party equipment including signalling systems.
• Adaptable to the safe requirements of the depot
New trains affect Network Rail infrastructure, of course, and might have an impact on other operators’ activities. Organisations introducing new trains into service or moving existing trains to a new route have several legal duties to undertake including demonstrating compatibility with the lines on which they will run.
David Galloway, network technical head for System Compatibility and Traction & Rolling Stock, Network Rail (NR), outlined some of the issues. Duty Holders (i.e., Train Operator for trains, NR for, e.g., new stations) must demonstrate their changes are safe, comply with relevant international, national and railway specific standards and are compatible with the rest of the system, though, in general, fleet cascades generally need only consider compatibility.
Considering new trains, train operators sometimes delegate responsibility for some of the work to the train supplier. Network Rail also must satisfy itself that trains are compatible with its infrastructure, so it is important that organisations collaborate, a process, David said, best started early with open dialogue between affected parties. Railway and general health and safety law imposes the duty of cooperation between Duty Holders, but to make the railway work, there must also be cooperation with ROSCOs, manufacturers, neighbours and others who are not specifically identified in the law.
Whilst there is plenty of guidance on what factors to consider, there cannot be a definitive list. David cited 24 relevant Group and Railway Industry Standards that usually need to be considered. Key topics include power, signalling and train protection, gauging, acceleration/braking curves, track wear, selective door operation and electromagnetic compatibility.
As well as demonstrating compatibility, duty holders have to demonstrate safe integration; making sure that a change (e.g., a new vehicle type, network project, subsystem,
component, software, procedure, organisation) fits into, and does not create an unacceptable risk for, the resulting system.
Rich Fisher and Maria Cliff, from the Great British Railways Transition Team looked at future rolling stock, depot,
kilometres of electrification. He said that it would be wise not to assume that this plan is the only solution. He said that a balance of rolling stock and infrastructure solutions will be necessary, and he anticipated that rail will need to use offsetting and bio-fuels to demonstrate net zero carbon beyond 2050. That said, electrification scenarios have been
Rich presented a graph showing what type of traction might replace the diesel fleet over the next nine control periods (45 years). This programme would see the virtual elimination of diesel only passenger trains but would retain a significant number of bi-mode diesels (or other fuelled internal combustion engine). He said that hydrogen has limited role, due to cost and energy density, but this could be revised if technology develops. He added that electric passenger trains outperform diesel which brings carbon gains through modal shift and benefits all customers whilst delivering lower operating and maintenance costs.
Rich’s views on trains for the future focussed on improving from the short termism of specifying new trains to win a franchise. He added that the supply chain has been getting inconsistent messages from the industry, hindering investment in innovation, and increasing costs. He wants the emerging strategy to consider trade-offs and choices (e.g., seats vs luggage vs bikes) and to quantify them where possible. There will be a vision to help the supply chain deliver for both funders while meeting the needs of passengers, but the strategy will not be about designing new trains, more it will be about linking the long-term strategy to existing good practice.
Maria considered some near-term decisions required, specifically the ‘legacy’ DMU fleet (Classes 150, 155/6, 158/9, 165/6) which are nearing life expiry. Although some operators have begun to engage with the market for replacement trains, she said “a network-wide vision will help support individual operators and ensure best value decisions”. That said
the default position is that most replacements will be diesel powered or, in a small number of cases, batteries. Options being evaluated include bringing younger off lease diesel trains back into service, selective life extension to defer replacement, and/or accelerate deployment of battery trains (new or upcycled) to low-risk routes.
Maria and Rich expect that with better planning and more homogeneity, trains might be introduced more efficiently.
For your writer, key messages from the event included: introducing a train fleet isn’t just an engineering challenge, it’s a major business change programme for the operator and others in the industry. As Liam Hockings said, new trains don’t put themselves in service, people do, and the importance cannot be overemphasised of detailed planning and investing the time to build open and honest, collaborative relationships between operators, manufacturers, rolling stock owners and infrastructure managers so challenges can be shared and solved. Finally, there are still over 1,000 vehicles from the pre-2020 orders to place into service and this means that there is still plenty of opportunity to apply lessons learned here and from the RDG Guidance Note: New Trains – A Good Practice Guide.
Thanks to Mark Molyneux of RDG and Neil Ovenden of Rail Partners for the opportunity to attend and report this industry event. Photos and other illustrations provided by presenters unless otherwise stated.
Rail Partners, the trade body for train operators, organised the ‘Train depots for today and tomorrow’ event to bring train operators, suppliers, and other industry stakeholders together to discuss how to improve depot safety and productivity. It covered the importance of depots and the constraints within which they work, something not fully appreciated but critical to the performance of the railway. Late starts from depots, for example, affect network reliability.
Depots are safety critical environments and, although new build depots offer opportunity to get things right and improve safety, provide a better working environment, and complement the local landscape, the process of upgrading a depot can introduce safety challenges. The event also provided opportunities for sharing good practice and, looking to the future, considered plans for HS2 and how robotics can improve productivity and reduce workforce exposure to dangerous, dirty, unpleasant, or repetitive tasks, something covered in separate mini articles.
Neil Bamford, fleet director at East Midlands Railway and formerly, West Midlands Trains (WMT), opened the event stating several challenges. Clearly, depots are there to achieve top class safety (both in terms of the depot production environment and the rolling stock itself), train performance, and train presentation. On some projects, he observed that civil engineers have, perhaps, “held sway” when building or upgrading depots and the engineer/ operator voice has not been heard loud enough. He also said that Network Rail route studies did not always consider the criticality and importance of train depots and outstations with the desired output of consistently delivering excellent operational performance.
Neil worried that engineers always find a way to deliver the service in the end, but asked: “Do we compromise too much, relying on a make do and mend approach, leading to 363 days (excluding
Christmas Day and Boxing Day) a year of work arounds and the consequential inefficiency and increased cost?”
He emphasised the importance of planning and management, making sure that required downtime for maintenance, servicing, and train presentation is delivered and that delays leaving depot (code MP701A, known as 701A) are correctly attributed so that the correct root causes are identified, understood, and acted upon. He added that we must move to depots that operate more efficiently and Train Servicing Agreements that are properly managed.
His final words were: “if you plan to run at 100% capacity then you’ll plan to fail; you must build in some contingency and headroom.”
Several speakers rightly highlighted safety; the prerequisite of all other activity. Neil Bamford drew attention to the fatal accident at Tyseley depot on 14 December 2019 where a driver was killed when passing between two units, just 350mm apart. The RAIB recommended improvements to hazard identification, risk assessment, and WMT’s safety assurance processes.
Dave Baston, in charge of Norwich Crown Point depot, described the safety challenges of an influx of construction workers unused to working in depots, together with another group of nonEnglish speakers involved in the commissioning and support of their new trains and completely unaware of UK safety law and practice. As a result, he had to put in place additional management resource just to help to manage these activities safely.
Seamus Scallon, operations and safety director for First Rail, cited the Tyseley accident as part of the catalyst that led to setting up a Depot Working Group. This and three other depot fatalities in very different circumstances reinforced the need to improve depot safety. There had also been expensive damage to trains in depot derailments and, in January 2020, the Network Performance Board challenged depots
to improve wrong formation and 701A performance. At that time, the depot delay incident count across the network had increased by 86% since the start of Control Period 5 (CP5).
Seamus summarised the challenges. There had been limited industry focus on depots (including yards and sidings) and there was no clear industry-wide picture of risk, safety, and performance. They were often treated as a black box i.e., what went on inside was less clear. He added that a factory type environment with moving trains was an added risk and there was limited good practice guidance. The rail industry’s health and safety strategy, Leading Health and Safety on Britain’s Railway (LHSBR), recognises that there is no clear industry-wide picture of risk and safety performance in depots and calls for improved industry-wide understanding of depot risk.
In response, train operators created the Depot Working Group, a task and finish group reporting to the Passenger Operators’ Safety Forum. Initially, it included joint working between RSSB and The Rail Delivery Group but transferred to Rail Partners although retaining the RDG and RSSB links. With the challenges of Covid and lockdown the group rarely met face to face, but a great deal of useful work has been done. RSSB carried out a deep dive on depot safety – mostly slips trip, falls and
issues such as a peak in accidents after the morning peak. The Depot Working Group has enabled improved collaboration between depots and has developed a Depot Good Practice Guidance Note (on the RDG website). There is also a Train Depot Good Practice Guidance note 07 available on request from Rail Partners.
RSSB is currently working on understanding practical depot capacities, ensuring the timetable works for depots and depot performance benchmarking.
Seamus added that RSSB has delivered many activities such as economic modelling and bow tie safety/ hazard modelling.
Seamus said that the task and finish group has completed its work. There is much work still to do and will now link more closely with LHSBR and there is an opportunity to widen the work to HS2 and freight. He concluded that collaboration between train depots is still needed, and Rail Partners will link depot managers together via events, workshops, and webinars.
Peter Williams, fleet and performance data manager at Avanti West Coast, took up the theme of Learning Lessons from the Past. Peter also chairs the subgroup aiming to reduce 701A delays of trains leaving depots. His theme was that depots were the ‘Cinderellas’ of the railway (according to the Collins Dictionary: “a poor, neglected or unsuccessful person or thing”).
This view came about because depots are not considered to be part of the ‘main line network’ with an inference of not being important. They tend to be treated like a black box with top management only interested in ‘what’ and not in ‘how’, and they are expected to work miracles. As Peter said: “Management thinks depots have supernatural powers to magically reset the clock at midnight, because irrespective of the carnage on the network the day before, the following day all the trains needed are expected to be offered for service on time, fully repaired, reliable, and clean”.
Peter said that depots are not adequately considered in timetable development and that not all Empty Coaching Stock (ECS) moves are even timetabled. “How can the depot plan for when trains are going to arrive?”, he asked. He added that some new trains have been ordered without any clear depot maintenance agreement and there have been examples where the trains are too long to be accommodated satisfactorily in the nominated depot(s). These two issues came as a shock to your writer with his 40+ years’ experience in London Underground, where trains are always timetabled for all moves, and where depot alterations are always part of new train procurement projects. In the general discussion, the need for closer working between depots, TOC operations, Network Rail Operations and Network Rail timetable planners was echoed by most present, including representatives from Scotrail where the TOC/ Network Rail relationship is closer than anywhere else in Great Britain.
FIGURE 1 - Peter showed a 2019 graph illustrating the 86% increase in 701A incidents since the start of CP5.
Although 701A incidents are low compared with other causes, he said, they often trigger knock on delays. The delays fell to a very low value during the Covid lockdowns and have gradually risen since, but not to the same level as in 2019. Peter’s subgroup’s tasks were to review the national data and work towards providing the necessary insight in relation to filling the gaps in the depot performance data; consider and propose how the 701A data could be used to ‘fairly’ compare depot performance; consider and propose how depot performance can be improved; reduce the number of 701A incidents; and develop good practice proposals.
One team in his group is developing a methodology to determine depot capacity.
For example, a simple fan siding set might be capable of operating successfully if all sidings are occupied, but a depot might need to leave some roads vacant to allow trains to be moved around for servicing, fuelling, maintenance etc., and if those roads are filled, the depot will not be able to operate.
Some depots have defined Depot Rules (not unlike rules of the route/plan) that outline what each depot can: accommodate (frequency of incoming trains); store (capacity); maintain (maintenance activities/ requirements); and deliver (times/ frequency of departing trains). These rules will be used to confirm that new or changed timetables are compatible with these requirements.
Peter asked attendees to help raise the priority of depot needs in relation to decision making, develop and enforce Depot Rules, review delay attribution processes, and make sure that incidents allocated to a depot are really within its gift to resolve.
Dave Baston talked about Safety during Change drawing on his experience managing Norwich Crown Point depot which formerly looked after the London-Norwich loco hauled Mk3 carriage push pull sets and a motley collection of diesel multiple units.
Earth).
When the current Greater Anglia contract started, it was announced that all of these (and the Stansted Express) were to be replaced by 20, 12-car Stadler EMUs, 24 4-car and 14 3-car diesel electric bi-mode regional units, all from Stadler. They represented a significant change in technology and, for passengers, probably the single biggest innovations were train floors which were more or less level with the platforms and automatic sliding steps to bridge the gap between train and platform. Dave explained the pain involved with such a massive change, the more so because Crown Point was not originally planned to be the depot for these trains as the proposed site in Manningree proved to be unsuitable.
He summarised the depot team’s journey in three stages:
» Pre-October 2016 – Evolution.
» One team, stable facilities, availability matched to service, high performance, stable franchise environment.
» 2016-2022 – Revolution.
» Split teams (some existing staff transfer to Stadler under TUPE), major depot change, major fleet change, low performance.
» Present – Evolution.
» Common goals, stable fleet, stable facilities, marginal gains, one team.
FIGURE 2 - Norwich Crown Point Depot from above (GoogleDave highlighted several issues with interfacing the new trains with the depot, not least was the sheer length of the 12-car trains at nearly 237 metres, needing very careful set out of all the depot touch points – toilet and sand servicing points, for example – as well as the compatibility of wash plant brushes with a new train where the bodysides are lower than on the trains they replace. In addition, the first new depot facilities needed to be available before the new trains first ran and grew as the operational fleet grew.
Dave said that they were often “struggling to keep up” and “a high level of maths and planning was required”. But, in the end, there was a big gap between theory and practice. They found that servicing a 12-car train was a lot harder, and they sought and used alternative sites (Derby Etches Park, Ilford, and Bounds Green) to reduce the maintenance load for the legacy fleets when 70% of the maintenance sheds were lost to construction.
Dave described several of the bigger changes. On the older trains most of the maintenance was carried out from underneath, and vehicles were lifted on jacks for bogie changes. On the new trains, roof access was required for equipment displaced from underfloor locations because of the lower floors, side access to exchange diesel generators, and a bogie drop to facilitate bogie exchange on articulated vehicles that are not easy to split. Also, and inevitably, the shore supplies were different.
Managing all this safely proved to be a major task as the construction work fell under the CDM regulations and physical, interface, and management responsibilities between site management and the construction contractor, had to be defined.
There were many visitors to site including the new maintainer and commissioning teams (TSA and MSA), the transferred staff now working to the new maintainer’s rules, many construction contractor workers (in excess of 150 not familiar with depots and the OHLE environment). As Dave put it, “Piccadilly Circus moved to Crown Point”, but he noted that his responsibility as depot facility operator remained and there was a high risk to safety and operations. His advice for managing visitors included:
» Put in dedicated contractor controllers.
» Have a dedicated and separate safety team to take ownership of and investigate any accidents, incidents and near misses.
» Robustly audit and demand feedback.
» Check and approve work package plans, safety packs and lift plans.
» Make time to be out on the shop floor; don’t rely on the mountain of paper.
» Communication/briefing and toolbox talks to staff are vital.
» Have a robust induction programme (many visitors from outside the industry mean you need to act swiftly before any accidents occur).
» Have the confidence to remove/ban from site people who don’t behave safely.
Dave’s conclusion was that anyone managing a large fleet cascade will have to cope with big plans constantly changing; solutions that seem to have unacceptable compromises (e.g., bean counters say ‘no’); trying to run business as usual in the middle of a huge building site; all whilst introducing new stock and retiring and/ or cascading legacy stock. There will be a backdrop of conflicting requirements hour by hour, and uncertainty for many people such as TUPE, role changes, and possibly voluntary severance. And safety is only maintained by sticking to core principles.
Finally in this section, Mark Knowles, leading on train maintenance/depot/stabling strategy for the Great British Railways Transition Team, outlined the emerging strategy for the sector. The current proposal assumes ‘targeted’ electrification roll out and decarbonisation objectives. The strategy is aimed at meeting the maintenance needs of a very rapidly developing mix and deployment of fleet traction types: electric, battery, diesel, bi mode, and hydrogen.
» ‘Principal depots’ will be a centre of excellence for rolling stock traction type.
» Existing commercial agreements would be re cast to align objectives/interests.
» There will be a template commercial model for new and cascaded stock to align interests.
» Stabling locations will be selectively developed to improve capability.
» The operator’s role as ‘maintenance controller’ will be enhanced with improved data, analysis, and knowledge.
» Operational excellence model will be developed and deployed throughout.
Mark said that deployment of this strategy will create better control for the operator, improve standards, create required flexibility, provide for growth, reduce operational costs, and equip maintenance operations for the future. He identified four ‘pillars’ that would be used to enable change:
Pillar 1 is intended to help locate depots in the right place. Mark highlighted a depot and stabling facilities case study and said that once the train plan/ timetable is determined, the purpose of Pillar 1 is to define the future roles for depots and align capacity and capability for forecast needs (including growth) driven by electrification and decarbonisation objectives and traction solutions. This strategy also proposes an enhanced role for stabling locations reducing demand for further depot development, improving service delivery, and reducing ECS costs.
The purpose of Pillar 2 is to create more permissive agreements between asset owners, maintainers, and train operators which align objectives and create the environment for flexibility, innovation, and change which will be required in the future railway.
The purpose of Pillar 3 is to make full use of available data regarding train performance and faults to inform intelligent planning, deliver timely interventions, and avoid over maintaining rolling stock fleets in order to optimise reliability at lower cost.
Finally, the purpose of Pillar 4 is to make rolling stock maintenance and service delivery a fully planned, resourced, and expertly delivered activity using best practice.
Mark concluded with expected benefits including efficient, cost-effective maintenance delivery; stable, highly trained and capable maintenance teams; lower industry costs per vehicle mile; fewer empty stock movements; greater flexibility/agility to deal with changes resulting
from decarbonisation and electrification; and reduced need for depot development/ extension in response to increased demand. His final remark was that there would be opportunities for private the sector.
This seminar and a subsequent new and cascaded fleet event were intended to provide lessons learned for others’ benefit and to publicise good practice guidance now available. A takeaway was that the message had certainly landed with the Great British Railways Transition Team which is working hard to deliver a strategy that will avoid the challenges caused to depots by the recent major programme of new and cascaded vehicles.
- Depot Protection Systems (DPS)
- Depot Control Systems (DCS)
- Combined DPS/DCS
- Locally Operated Points Systems (LOPS)
- SIL 2 Rated Systems as Standard
+44 (0)1621 743 743
info@ rstclass-safety-control.co.uk www.FirstClass-Safety-Control.co.uk
At the Rail Partners ‘Train Depots for Today and Tomorrow’ event, Matt Spence, who was speaking on behalf of Dr Stuart Smith, Ergonomics & Human Factors Lead at HS2, talked about the concept for the forthcoming HS2 depot partly on the site of the former Metro-Cammell factory at Washwood Heath in Birmingham. It will be the operational base and maintenance hub for the HS2 fleet and will also be the location of the HS2 Network Integrated Control Centre (NICC).
A huge site, it will be a 24/7/365 depot with most activity at night. At the Birmingham end there will be 16 stabling roads each capable of accommodating 400-metre-long trains (one unit or two, 200-metre units coupled). It is planned that trains will be driven between the main line and the sidings in ATO mode. At this end of the depot, train cleaning and servicing activities will take place and there will be a building with train simulators and other facilities for the circa 200 drivers, and cleaning and servicing staff.
MALCOLM DOBELL OUTLINE LAYOUT OF DEPOT (LABELS OVER © HS2 LTD PLAN)At the east end of the stabling sidings are fans into two tracks leading toward the maintenance depot that will have six roads plus a wheel lathe building and two external sidings each capable of accommodating one 200-metrelong unit. The NICC will be between the sidings and the maintenance building and will house typically 100 staff, and the maintenance building will accommodate approximately 250 staff.
Matt discussed the core principles for the depot: a design for everyone to benefit and enjoy, a design for a sense of place, and a design to stand the test of time. The concept design has been carried out with human factors involved at all stages so that the depot can deliver its operations effectively whilst ensuring safety, equality, inclusivity, health, and security. Matt said that RSSB research had indicated that 20% of total harm to the UK rail workforce takes place in depots and sidings and there is a death in a depot approximately every 2.5 years. The aim is to design out risks rather than try and mitigate them.
Matt outlined how human factors have been involved all through the delivery, along with assurance of concept design with an inclusive design approach. People were at the heart of the design approach, which acknowledges diversity and differences, particularly recognising and challenging previous limitations to roles based on mobility and ability.
HS2 is also designed for how people will actually use the depot: ‘work as done’, not ‘work as it’s imagined it’s done’. Much use was made of Day in the Life Of studies, taking account of movements of people, equipment, waste, and vehicles.
A particular issue is access to the stabling sidings where ATO will be in use. Train servicing crew and train managers will need to travel from the ‘Cleaners and Drivers’ (C&D) building to the stabling platforms to get to the trains. In conventional depots, access would be by board crossings to get to a train, with cleaning kit, etc. At Washwood Heath, there will be an underpass from the basement of the C&D building, running underneath the stabling roads, with access to each platform via stairs or lift. Trolleys will be available to move cleaning kit which will be stored in the basement.
Cleaners will collect waste from the train in their trolleys and then drop the waste into chutes on each platform into larger waste collection trolleys in the underpass. Tugs will move the filled waste trolleys from the underpass. Thus, there will be no crossing roads, no risk of being struck by a train, and reduced manual handling of waste.
There will also be protection and isolation systems on each stabling road platform for train presentation crew. These will minimise
the hazard of a train moving with cleaners either on board or trying to get on or off to undertake cab end cleaning activities. The platforms will, of course, be designed with appropriate lighting, surfaces, drainage, and edge protection to minimise risk.
One of the gaps in the concept stage was lack of information about the train design. For example, location of sand, water, and effluent points and visibility from the cab to see ground signals beyond the ATO area (see Visibility of Ground Signals below). These and other details of the train design will be critical for the detail design of the depot. There will also be challenges in managing a site operated by multiple organisations, e.g: HS2, the Train Maintenance supplier, and other contract organisations, each of which might have different organisational cultures and safety behaviours.
Finally, Matt said that there are, and will continue to be, cost pressures for both CAPEX and OPEX.
On a recent IMechE visit to Scandinavia, delegates travelled on a section of railway north of the Arctic Circle. In these areas, snow can be ‘quite deep’ and the Infrastructure Manager has installed their ground signals some 1 – 1.5 metres above ground level. Mounting ‘ground’ signals at an appropriate height to minimise visibility issues would seem to be a simple solution to the issue raised by Matt in his presentation.
The Rail Partners Depots for Today and Tomorrow event offered a glimpse of a possible future.
Professor Gareth Tucker and Dr Hamidreza Faham from the University of Huddersfield, and Dr Mingfeng (Ming) Wang from Brunel University London, described and demonstrated how robotics might automate certain maintenance, inspection and servicing tasks. Initial priorities will be to automate tasks which are repetitive, unpleasant, or relatively unsafe.
Gareth highlighted how robots have transformed manufacturing of mass-produced automobiles and are being used for nondestructive testing of air frames, automated bricklaying, and even concrete printing. Drones and other remote-controlled vehicles are also
increasingly being used for inspection on railways. Other devices including visual and other sensing systems to assess the condition of trains are already in use in some depots.
Gareth presented a long list of potential applications, and benefits could include increased accuracy and repeatability of maintenance tasks leading to increased productivity and train reliability. Robotics could also reduce workforce exposure to previously mentioned dangerous, dirty, unpleasant, or repetitive tasks therefore improving safety and reducing the risk of long term muscular-skeletal injuries for train maintenance staff.
For some tasks, maintenance could be carried out more quickly, all this leading to improved availability. The systems would automatically record what they’ve seen and done and, with direct connection to maintenance management and Remote Condition Monitoring (RCM) tools, they would help achieve maximum component life and minimum resource usage.
Gareth presented slides and videos of the robotics workshop that has been built in the University of Huddersfield, an element of the ‘Smart Rolling Stock Maintenance Research Facility’, part funded by the European Regional Development Fund. In addition to research into robotics for train maintenance, the facility also focuses on the use of AI for optimised depot operations such as planning and processing of remote condition monitoring data to work towards prognostic maintenance.
The robotics lab includes a short section of a standard gauge pit road with an industrial robot on each side and another, smaller, collaborative robot in the pit. This is supported by a digital twin to help programmers test their ideas without using workshop time.
Gareth illustrated a variety of applications including a laser scanning head on the robot to assess the condition of pantograph carbons. Another early demonstration was the automated removal of brake discs from wheels already removed from the axle, for application in a bogie overhaul facility.
Ming presented Brunel’s work to develop automated methods to deal with train fluids service (e.g., CET). CyberFluids, a prototype autonomous robot for servicing the fluids on trains, is funded by Innovate UK and RSSB. In early work, Ming’s team had identified that misalignments between the train fluid port and attachment head
of the automated operation device (e.g., CyberFluids’ robot) always exist. The train might not stop accurately for maintenance at the depot, and the height of the attachment points might vary. They had assumed that trains would stop inaccurately and that the attachment heads would be mounted on tracks that would allow reasonably accurate longitudinal alignment. The heads would then be designed to accommodate small longitudinal and vertical misalignments without damage or excessive insertion or removal force.
Ming’s team proposed and developed a proof-of-concept, novel compliant endeffector (a device the robot uses to perform its proposed task) for robotic train fluid servicing, which can accommodate large misalignments with significantly reduced insert force. So far, full scale prototypes and field testing are in progress, but commercialisation is some way off. Gareth outlined many of the challenges to be overcome.
As Ming had highlighted, trains do not stop in the same place every time they arrive in a depot road, sidings, or fuel point. Components may be dirty, worn, damaged, or missing and, up to now, trains have not been designed to accept robotic maintenance. Gareth suggested that due to the limited volumes of work for each specific task (compared to an automated manufacturing line in a car factory) each robot arm will likely need to do multiple jobs to create the required cost benefit and might have to work on multiple fleet types and vehicle types within a fleet at a given depot. For some more complex jobs, it might be necessary for multiple robot arms to interact. And for cleaning or working outside, robot systems will require a suitable IP rating.
Currently there is a lack of demonstrators to clearly show feasibility and realistic benefits, so it is hard to demonstrate a business case, although Ming’s team is working on field trials of novel compliant end-effectors for train fluid servicing with Chiltern Railways. This compounded by shorter contracts which can make it difficult to justify investments where the benefits are only delivered in the longer term. There is no clear leadership, drive, or critical mass in this area and Gareth highlighted that it can be difficult to implement significant changes to working practice in the rail industry.
Gareth isn’t daunted though, and outlined next steps with the labs at the University. There will be further familiarisation with the existing equipment and further lab-based demonstrations, further research into inspections using vision systems and into robot programming to accommodate worn and dirty components and allow for adjustments to accommodate train stopping position and worn state of components (e.g., wheels).
A digital twin/simulator will be used for larger scale off site concept development. Gareth wants to build a larger robotic demonstrator in a more realistic depot/ overhaul factory environment, conduct research into the application of AI to plan robotic tasks and modify robot code, integrate robot control with a condition monitoring/asset management tool, and integrate robotics with a ‘virtual depot’ scheduling tool.
Finally, there’s the all-important task of developing a cost benefit analysis for the application of robotics to rolling stock maintenance and overhaul.
Rail Engineer will watch developments with interest.
FIGURE 1 & 2 - Full scale robotic cyberfluid rig (R) and close up of connector (L) (Brunel University London). FIG 1In June 2023, London Business Conferences held a multi-day conference and Elizabeth Line Old Oak Common depot visit: ‘Rolling Stock Maintenance and Depot Innovation’. Now in its eleventh year, Rail Engineer previously covered this event in 2015, 2016, 2018 and 2019 (Issues 136, 148, 171, and 181). After more than 10,000 words, what’s left to say? Quite a lot, actually.
Issue 136 described many operators using Remote Condition Monitoring (RCM) and a few pioneers making baby steps in Condition-Based Maintenance (CBM). Roll forward to 2023, and there was a consensus that RCM has come of age and CBM has, perhaps, progressed to toddler status. Many presenters, referring to data lakes, implied being overwhelmed by with data and struggling to gain useful insights.
Some were taking baby steps with machine learning and Artificial Intelligence (AI). This article covers the highlights.
Railways are still struggling to recover their pre-Covid revenue and often cannot reduce services whilst under pressure to cut cost. This was emphasised by Ian Rawlings, TfL’s head of vehicles engineering. Ian explained that, in
London, there’s now far less travel for work purposes whilst leisure travel is exceeding pre-Covid levels especially at weekends. He said that the Elizabeth line is performing ahead of expectations and has drawn traffic from, especially, the Central and Jubilee lines. Ian cited different thinking represented by the recent trial of a midweek engineering closure on the UK East Coast Main Line, leading him to wonder whether TfL could, perhaps, close the central area of the Central line for upgrade to allow track, signalling, and rolling stock to be more efficiently upgraded.
Passengers could use the Elizabeth line instead. Would a five-month closure be better than five years of weekend closures, he mused? Ian also described the range of techniques his team have employed to double, gradually, the interval between overhauls on the 192-train S stock fleet from 762,000km to 1,524,000km using condition assessments at the higher mileage, failure data, and materials usage.
MALCOLM DOBELL FIGURE 1 - An unusual method of collecting leaves from the line found during condition assessment of a LU S stock bogie frame.Each train supplier generally provides data using its own format. Paul Staples from TransPennine Express (TPE) explained that this applies to his four fleets. The Class 802 bi-mode uses Hitachi’s monitoring tool and the class 397 EMU and mark 5a coaches use CAF’s LeadMind. The oldest, the class 185 DMU, has an early Siemens data system able to transmit 110-character text messages; more flexible than one might expect, Paul said. For the class 185 system, TPE is upgrading upgrading with Siemens Railigent to provide extra features.
The four fleet’s systems all do similar jobs but require TPE engineers to interrogate different systems. In discussion, it was clear that Paul’s ambition is to have a common system for his team. In that context, Johannes Emmelheinz, CEO of Siemens Mobility Customer Services said that Railigent could accept and manage data from different suppliers’ trains using Application Programming Interfaces (APIs) to translate different formats.
Keith Mack, LNER’s quality standards manager reported on monitoring wheelsets. Failed wheels, axles, and bearings can and do cause derailments, and he highlighted methods to prevent such failures and also give early warning of impending failure so that vehicles can be scheduled for maintenance rather than being summarily stopped and recovered at low speed. LNER, jointly with GWR has been supporting its train service supplier, Hitachi, in fitting condition-based monitoring equipment to their Intercity Express Trains. This equipment will monitor the condition of wheels and all the bearings –wheel, gearbox and motor. In brief, vibration sensors monitor the wheels and bearings and
transmit data wirelessly to a receiver on each vehicle. This data can be accessed on board and remotely. Very occasionally an on-board alert might recommend immediate action but usually the remote monitoring gives plenty of warning to help depots plan interventions. This equipment is supplied by Perpetuum, now owned by Hitachi and was described in previous articles.
In issue 202, Clive Kessell described the integrated control room for the Elizabeth Line. CPC Systems’ Phil Dubery outlined many of the challenges involved in managing reliability growth during trial running. Phil’s team have been based in the control room since May 2019, monitoring performance and identifying root causes of delays quickly so that the key suppliers, principally Alstom (trains),
Siemens
The diagram below shows how severe delays usually occurred in clusters and helped to identify obscure cross system issues that were being masked in train-bytrain analysis. More feedback came from
drivers on, for example, train performance, platform alignment, to help identify other operational and technical issues. Operator feedback assisted understanding and provided more detail for the investigations, leading to modifications to assets and process improvements.
This diagram covering typically 7 trains in service would not be easy to read when there are 50-plus trains in service and Phil described a CPC Systems development (page 39) that that shows a day’s performance on a page.
Phil’s colleague, Alex Barber described a different innovation. Alex, part of the control room team, would observe controllers struggling to locate all the drivers and when they needed to be relieved when there was disruption using several separate data sources. Alex developed a specification for software taking data from six sources and which presents: which driver is on which train, when each driver needs relief, and when the drivers’ duties end. The controllers liked it and suggested further improvements.
Train washing status was added (from wash road routing data). Alstom colleagues at Old Oak Common depot asked to be able to add maintenance requests – low, medium or high priority. Depot managers assign trains to duties and, if a train is due for maintenance that night, they will put it on a duty which returns to the depot in time for the night shift. But if there’s disruption, the train might be sent to stable elsewhere, and if the controller knows that the train is urgently needed for maintenance, different decisions might be made.
Phil concluded that modern rolling stock cannot be considered in isolation as there are too many interfaces to other systems. Stress testing the railway is essential to improve system robustness and reliability. Data is often available and can be made into better
information by combining multiple data sources. Probably most importantly, good leadership, communication and teamwork is essential.
With many speakers reflecting on the vast amount of data they’re storing, it was time for Henri Felsenstein and Felix Bert from Deutsche Bahn’s AI Factory to present some of the ‘baby steps’ they are taking to help them address DB’s challenges. To respond to rising passenger and cargo traffic, their AI factory has been set up to use their vast amount of data to automate processes and gain insights using AI solutions. The ‘factory’ name was applied because they decided straight away to apply structured processes from feasibility through to product. Their case study was a capacity and analysis tool. With many network upgrades being carried out, there was a need to provide alternative routes for services on what is already a busy network. They explained that often no one was aware of conflicts between construction sites affecting capacity, and data was viewed in isolation and regionally. This led to uncertainties in the early phases of timetable creation and lots of manual planning. The AI solution examined construction programmes, proposed closures, and
timetable impacts, took account of capacity bottlenecks and recommended alternative routing for trains for humans to consider, and/or action to adjust construction programmes/possessions. In these early steps with AI, there were useful results, and much was learned:
» Intelligent use of data can tackle DB’s key challenges, helping to coordinate construction activities leading to better use of limited capacity.
» Data availability/quality is key; data collection/cleansing are basic requirements for further AI developments.
» Domain experts are the real data experts; data scientists must work with domain experts if a project is to succeed.
» AI’s use should always be business driven, not because it’s AI.
» Eighty percent success rate is not enough; to be accepted, you have to solve the last 20%.
Adam Bevan from the University of Huddersfield Institute of Rail Research reported on work to use machine learning to analyse very large amounts of data. The project used a year’s event data collected from a fleet of DMUs. There were over 1,200 individual files containing nearly 14.5 million records with 379 attributes. The task was to predict engine stop events (ESBT)
aiming to alert control to a problem before engine stop events occur. Filtering was required, such as ignoring all messages except those referring to engine, gearbox, or vehicle, and only using events that occur during service operation.
Put simply, for each ESBT, data analysis looked back over the preceding three-hour time window to identify events that might be precursors. This technique was applied using Decision Tree and Random Forest machine learning techniques. The best model delivered accuracy in the range 83% to 88%. Large volumes of real-world data taken from a fleet of DMUs was processed to demonstrate how highly predictive machine learning models can be trained. Whilst the most frequently observed precursors might be obvious to diesel engine experts (low/overtemperature coolant, low level or pressure oil) a methodology capable of processing sparse event data was demonstrated. Imagine the potential when the technique is applied in real time.
All modern electronic/software train systems suffer obsolescence. This might happen because of lack of supplier supports, there’s no one left who understands, parts are unobtainable, or technology has moved on.
Joao Duarte from Fertagus, Portugal’s first private operator to manage and operate a railway, explained how they had overcome obsolescence issues on their 20-year-old fleet of 18, 4-car double deck EMUs.
Fertagus needed to resolve component failure due to voltage/current spikes on inputs/outputs, extended repair times from the OEM, and lack of compatible components to make the repairs. It adopted the reverse engineering approach for its electronic/software systems working with local engineering companies eliminating all the weak points described above and providing additional features. It was obvious that Joao’s experience was shared by many delegates.
The trains were fitted with a proprietary system to manage passenger information, and train monitoring etc. Their operation from Lisbon to the more southerly town of Setúbal, 57 minutes from Lisbon by train.
David Shirres’ article about the IMechE’s visit to Scandinavia (issue 202), showed Helsinki as a city that is expanding its public transport. Antti Vigelius, Helsinki City Transport’s head of rolling stock maintenance outlined the city’s plans to grow its tram depot facilities to support the larger fleet being provided to serve a new light rail line and several extensions. The biggest will be a new depot on a triangular site at Koskela, in the northeast of the city. This will provide more space and allow older depots unsuitable for modern trams to be closed. With a total cost
of nearly €275 million, it will have 41,500 square metres of useable space in Phase 1 with another 8,200 square metres in Phase 2. The contract was placed in Spring 2023 and the depot is due for completion in 2028. Antti described the layout of what is a slightly challenging triangular site - but that’s all they had.
There will also be expansion at the Roihupelto depot adjacent to metro and bus depots in the east of the city. This depot is used to repair and overhaul repairable components such as bogies, wheelsets, gearboxes, door gear, brake callipers, compressors, pantographs, and electronic modules. The extension will be primarily used for bogies and Antti showed how 3D walkthroughs had been used to help optimise the design of the workflow. He also explained the importance to Finns of a feature not usually found in UK depots – saunas.
In all its designs, Helsinki City Transport has tried to use modular designs that might support future changes over the next 20-100 years. It also hopes there will be ‘adaptive infrastructure on technical and social areas’ supporting city development. It will, of course, have solar panels, water recycling, energy saving solutions such as automated ventilation, lights etc., so that the depots become more self-sufficient.
In two presentations, Professor Dr Fiona Zhang and Felix Guo from DTEC GmbH introduced their robotic vision and wayside vision gate solutions that can automate what are otherwise labour-intensive inspection jobs. They explained how cameras fitted around a gantry over the trains can scan the vehicles. Felix cited 20 such installations on high-speed lines, 40 in metros, and 50 for locomotives. They are also developing a slim, mobile,
camera unit which fits in the ballast track bed and can travel under a rake of coaches or wagons to examine their undersides in parking yard sidings. FIGURE 7 - DTEC Visiongate: Metro. FIGURE 8 - DTEC Visiongate: High speed Train. FIG 8Felix showed examples of information presented to operators; photos of actual or suspected defects such as bolts missing, or damage for maintenance, which managers can confirm or deny. They have a generic machine learning algorithm which covers about 70% of the features typically encountered on a train and various degrees of customisation, helping the system recognise a component type it has never seen before, and can take the accuracy to 100%. This helps the development task when the system is deployed on a new fleet.
Pip Stone, training strategy and development manager at Eurostar, described Eurostar’s approach to helping maintenance engineers diagnose and rectify faults efficiently and effectively. This requires expertise in technical systems and data driven production processes, with the objective of improving availability and reliability, whilst reducing cost. He said that traditional training priorities such as compliance with standards might come before focussing on what is actually required, and, having been trained, the trainee emerges with the required (not desired or best) competence. Pip outlined Eurostar’s new approach, giving staff the knowledge to determine root cause and then plan the action necessary. When using data, the train usually tells you what’s wrong, and staff should be able to pinpoint defects leading to ‘fix first time every time’. For this to work, training needs to be carried out in quite a different way, with a great deal of emphasis on self-learning. But just dumping a huge amount of data on a technician is a hindrance. Rules (software/ human) need to be used to turn data into useful information and can then be used to
establish location and cause of the fault (train or track). It is also possible that a system might be malfunctioning because of a fault on another system.
Pip’s colleague Pat McNamara turned to skill shortage and motivation. Unlike the UK’s national railways, Eurostar received no government support during the Covid lockdowns and service was reduced to just two return trips a day. Eurostar worked closely with trades unions making agreements allowing them to respond rapidly to the situation and implement radical solutions including: fair application of furlough, reduction of hours and pay, staff working one week in eight, reforming teams to ensure availability of skills with limited staff, and agreeing no permanent erosion of terms and conditions.
Pat confirmed that pre-Covid team structures and terms and conditions have been restored, whilst there has been a pay deal and additional annual leave for long service. Improving morale and performance was, Pat said, vital to the Eurostar family (merged Eurostar and Thalys) as the business grows. For the maintenance organisation, growth means improving availability from 70% to 80% by reducing the number of sets stopped for maintenance during the day at Temple Mills depot, from seven to five. A culture of continuous improvement is being fostered by a mixture of technology, such as depot Wi-Fi, tablets to access documentation and provide reports, and better tools.
Govia Thameslink’s Neil O’ Connor discussed the challenges that had to be managed because of the significant changes in demand following the Covid pandemic. Business and commuter travel has significantly reduced, and leisure travel has increased. Whilst overall passenger numbers are approximately back to pre-Covid levels, revenue is only 70% of the former sum.
Fleet mileage has been falling and DfT has been seeking cost reduction. GTR has eliminated the classes 313, 365, and 455 –a reduction in fleet size from circa 2,800 to 2,500 vehicles. With all these changes, the mileage per vehicle has actually increased.
Neil described the impact of eliminating the older trains on some of the maintenance staff who have never worked on anything else. He explained that workload is increasing, (more overhauls, corrosion repairs, further reliability improvement). This means that jobs are secure. Indeed, there are vacancies, and staff can be retrained to work on the more modern Electrostar trains.
The final presentation summed up the vital ingredient in all train maintenance activities – people. Jared Hoag, a native of California, is the manager of Aberdeen Clayhills, London NorthEastern Railway’s only depot. With 49 staff, it carries out servicing work on LNER/Hitachi class 800s, ScotRail HSTs and classes 158 and 170, and for Caledonian Sleeper. Jared emphasised the importance of working safely with a learning, just culture that helps keep everyone safe whilst delivering trains required for service.
Whilst Jared emphasised safety, it was clear that his attitude to safety applied to his management style which was one of mutual respect and engagement whilst using data to improve continually. As he put it “no changes are permanent, but change is”. Believe it or not he had used the experience of the Van Halen rock group and their requirement for a bowl of M&Ms in their dressing room, with a clear instruction that there should be no brown ones. This was the group’s simple test of whether a concert promoter, responsible for setting up vast quantities of lighting, sound, and other potentially hazardous kit, was exercising competent attention to detail – something just as relevant in rolling stock maintenance.
Reflecting on the conference, your writer found it was different from previous events, mainly because there were fewer in-person attendees, complemented by a large on-line audience. In some ways this helped the networking between the sessions, but it’s clear that shared experiences lead to improved rolling stock maintenance.
Thanks to Jane Thomas and Meghna Mohanka from London Business Conferences Group. Anyone interested in the Van Halen anecdote can see more here:
The railway of today faces many challenges and these include the need to reduce costs, improve operational efficiency, and improve passenger / freight customer benefits. The industry needs to make the best use of the assets already invested, and providing reliable data connectivity for trains can deliver huge benefits for operators and customers. This article discusses how the GSM-R cab mobile asset, already fitted to main line train fleets in Britain, could be used to meet these objectives.
Railways consist of a huge number of assets which must all work seamlessly together to deliver a good, consistent service to passenger and freight customers. Every asset will show signs of wear and tear over time. These signs will appear differently depending on the type of asset, how it’s used, and what components fail first. Maintainers and asset managers won’t always notice changes in conditions or be able to associate these with particular hazards or failures. However, connected remote condition monitoring can provide information on how asset condition measurements on both trains and ground systems are changing over time, and allow interventions to take place before failure occurs. To achieve this requires a good train data connection.
Fitting new communication and control technology equipment to existing rolling stock is a challenge. First-in-class train fitments can be costly and not run to programme. Any new device will need space on the train, connection to an existing reliable power supply, an interface to on-board systems, an external antenna causing no interference or compromising the vehicle integrity, and a means of sharing information with train staff. No two types of rolling stock design are the same and each will have its own peculiarities and limitations. Any fitment programme will take valuable trains out of service and require a competent resource to plan and undertake the work. All of this takes time and money the rail industry cannot afford.
Siemens Mobility SVR-411 V4 cab radios, however, have already been fitted to all of the British main line fleets by the GSM-R project,
providing reliable, secure track-to-train voice comms’ across the network. This required many years of engineering to provide a spaceefficient, robust, and flexible cab radio rack in the space available, together with a compact control panel unit for the use of train drivers. A little-known fact to many in the industry is that the Siemens cab radio hardware / software is designed and made in Britain, so all the knowledge and capability to support and enhance the product is readily available. To date, over 12,000 cab units have been fitted to trains in Britain and the technology has also been successfully deployed in other countries including Denmark, Australia, Ireland, and Norway.
The design of a unit to allow the scale of deployment achieved by the GSM-R project required a special ‘gland box’ system to allow easy installation and replacement, and the development of an optional uninterrupted power supply unit to provide up to four hours backup power in the event of failure of train power. Two versions of the unit were originally created, one to provide voice communications only, the other to enable ETCS L2 data connectivity with the ground system. The very high availability requirements were met by a design which provided good thermal efficiency and shock resistance. The mean time between failures currently runs at around 250,000 hours, and the mean time to replace a unit is around 30 minutes. In Britain, a textual display is used to provide the human machine interface, but a full graphical unit is also available if required.
So, we have a successful product sitting on practically every train in the country, but what else could it do?
Rail Engineer first reported on using the GSM-R cab mobile to support Driver Advisory Systems (DAS) and other applications in 2016, along with how the cab mobile would need to be enhanced to provide additional connectivity and functionality. GSM-R was originally based on 2G ‘voice only’ connectivity, and the limited bespoke data connection was only for the setting up of calls and very limited text information for the driver. GSM-R radio coverage has been provided along all Network Rail routes with the provision of over 2,400 base-station sites with heights between 15-29 metres (50-100ft), and 350 repeater sites, covering tunnels, cuttings, and other areas such as stations. Public 4G Long-Term Evolution (LTE) radio will not cover the rail network in the same way, however it is surprisingly good on some rail routes and in some parts of the country, but only if a good, efficient train roof top antenna is used.
Obvious signal blockers for public 4G are deep cuttings and tunnels. Trains also run through rural areas with few villages, towns, or roads and therefore little public mobile coverage. With busy trains carrying the equivalent of a small village-worth of people, all attempting to connect to their nearest mobile operator’s base station from inside a ‘Faraday cage’, public mobile coverage on trains can be poor. A Faraday cage, to which modern trains can be likened to, shields its contents from electromagnetic fields, such as radio signals. So, when a radio signal hits the cage, the electromatic charge remains on the outside rather than travelling inside.
In 2020, Transport Focus found that train passengers only receive a good 4G connection some 58% of the time. However, using a good, efficient train roof top antenna can dramatically improve coverage, compared to inside a train, and Siemens has developed a new multiband antenna called SMBA (Siemens Multi-Beam Antenna) to provide reliable GSM-R/ 4G / GNSS / Wi-Fi connectivity, all within the footprint of the original GSM-R train antenna.
The cab mobile has also been enhanced to provide GSM-R, 4G LTE, GNSS/GNNS, Wi-Fi, and with SD & SSD memory cards for other applications. A Secure Digital (SD) card is a compact and removable storage device with extensive capacity, and a Solid State Drive (SSD) is a faster alternative to the old storage hard drive. Accelerometer functionality has also been
integrated into the processor module along with optional 4G modules. All this functionality seamlessly connects to the external antenna, and the processor card supports all the main features for an extensive application platform with reliable connectivity. The cab mobile is no longer 2G ‘voice only’.
The British roll-out of the GSM-R cab mobile system started in 2009 and all the units have since been upgraded with the additional functionality. The creation and installation of the mobile cab radios led the Siemens team to realise that having overcome the major challenges of on-board installation –space, power, interfaces – there was an opportunity to provide a range of new functionality inexpensively, and with minimal impact on train fleet availability.
In a similar manner to other items of modern electronic equipment such as smartphones, by developing ‘apps’ to run on the additional SVR-411 processor, affordable new functionality and improved operational efficiency can be provided in a number of ways.
The first ‘app’ to be developed by Siemens used the in-built GNSS capability and three-axis accelerometers within the radio to continuously monitor the train’s ride. This is known as Train Borne Condition Monitoring (TBCM).
Trials in the South West of England have demonstrated the system can reliably pinpoint areas where there are voids under switches/crossings and on
plain track, which can be used by the maintainer and asset steward to prioritise further investigation and plan the appropriate intervention. TBCM can also identify areas of ‘rough riding’, especially if reported by several trains passing through the same part of the network. ‘Dip track’ locations, which can ultimately result in derailment if not detected and mitigated, can also be identified.
By adding this functionality, every train can continuously monitor the state of the track, and communicate the status back to the maintainer / asset steward to instigate an intervention in real time, without the need for anything other than a new plugin card and a software update.
Connected Driver Advisory System (C-DAS) allows calculated information to be continuously sent to train drivers. The important difference to Standalone Driver Advisory System (S-DAS) is the connectivity aspect and having a real time data link between train and trackside, so schedule updates on disruption are automatically sent to the C-DAS for use on-board. With S-DAS, the system stops operating when the train is running significantly off-timetable due to disruption. Another example would be platform changes, the signalling system may have to route a train into a different platform than planned due to another train running late. C-DAS can keep up to date with the new route as well as any changes in line speed and speed profile due to the different route.
Some may think C-DAS takes responsibility away from a driver, but this is not the case and (as the name suggests) C-DAS only ‘advises’ a driver. A competent driver is still required to control the safety critical aspects of the train. Several
successful C-DAS applications have been created and used on several railways across the world. Generally, for new C-DAS, it is necessary to add new on-board processing and communication equipment, as well as driver machine interfaces to convey information to the drivers. However, with the cab-mobile version of C-DAS, the mobile radio’s connectivity is used to exchange data with the ground system using 4G.
The minimum requirement is to upgrade the existing GSM-R antenna with the SMBA that supports 4G LTE and GNSS/GPS as well as GSM-R. This would use the existing fourline GSM-R display, but a graphical display to provide additional information in addition to just train speed is available. This is easy to install as it reuses the existing location of the standalone S-DAS display via an adapter bracket. Trials of the system have demonstrated fuel savings of typically up to 15%, which is a very strong business case for activation of the app.
The main benefit of C-DAS over standalone or networked DAS is the connectivity to the C-DAS trackside server to ensure the driving advice is automatically based on the latest operational plan. One challenge is that there is no common railway location referencing scheme in Britain used by all the sources of data C-DAS requires, so the trackside software must map between them, for example:
» Temporary Speed Restrictions (TSRs) and quarter mile post locations (to display the current location to the driver), which use Line of Route (LoR) and Engineers Line Reference (ELR).
» Schedules and schedule updates, which use Timing Point Locations (TIPLOCs) that are areas such as junctions and stations, as well as line in and path out codes.
» Data on static speed, gradient and signal locations (for train describer berths) from scheme plans, which use meters from a datum.
» Track centrelines, which are GNSS Latitude and Longitude polylines to allow the C-DAS on-board to map it’s GNSS location of the train to the schedules, TSRs, and the static speed profile and gradient profile of the track ahead.
The national passenger information system, Darwin, provides schedule updates that C-DAS can use in areas without a suitable deployment of Traffic Management (TM). Darwin adjusts the schedule timings for late running detected by the train describer stepping feed, and shares any platform changes from the baseline timetable entered by operators. TM plan/ re-plan systems aim to optimise the overall current plan of train movements to an agreed Key Performance Indicator (KPI), allowing plan
changes to be tested first in a sandbox environment and the evaluation of knock-on impacts between trains, before commitment.
Where TM is deployed, it is important that C-DAS makes use of the TM published schedule updates, via the Network Rail Layered Information Exchange (LINX) system. In some scenarios, this would provide earlier awareness of any plan changes, which C-DAS could use to advise a reduction in speed further in advance than with a later Darwin update, potentially saving even more energy. This also ensures the C-DAS driving advice is based on a current plan, consistent with what is being fed to the Automatic Route Setting (ARS) systems controlling the signalling route setting.
Another system functionality app that has proved useful is the Cab Radio Remote Management Terminal (CRMT), which allows the management of cab radios remotely via an IP connection. Using the radio’s in-built connectivity, a whole fleet’s set of cab radios can be monitored, with everything from versions and serial numbers through to error logs being accessible remotely. Software can also be updated remotely, along with phone book entries and message templates. The implementation of CRMT removes the need for a technical visit to the train, improving efficiency and reducing the cost and risk that every train visit entails.
With the cab radio now effectively becoming a mobile communications gateway, many other apps can be provided for other systems on the train using the SMBA 4G LTE capability and Ethernet network interface.
Currently under development are solutions that allow remote public address announcements to be made to trains or groups of trains for enhanced passenger information. Timely accurate passenger information can help to keep passengers who face delays informed so they can plan ahead. Having a journey disrupted annoys passengers, but knowing why their journey has been disrupted, what is being done to resolve things, and what their options are, can all help to maintain their confidence in rail.
The cab secure radio system which preceded GSM-R also had a train public address link, but it only allowed the signaller’s radio dispatcher to make train public address announcements. The problem was that signallers are not trained, or do not have the time, to make public address announcements, and it was only used in emergency situations.
With the GSM-R cab radio app, a secure IP connection can easily be provided to any train operator’s GSM-R dispatcher or automatic public address system.
Whilst the original 2G GSM-R has performed well for many years, the need for a new communication technology is driven by the obsolescence of GSM-R, and the move to 5G-based communications is essential to provide the voice and data communications which
the railway will need from 2030 onwards. The replacement of GSM-R with Future Railway Mobile Communication System (FRMCS) is still some years away and will take some time to implement, so each of the app ideas are important for deployment now.
From 2030, however, the implementation of enhanced radio solutions with FRMCS will offer the potential for an even greater step change in train and trackside service integration. Siemens says its GSM-R cab radio platform is capable of being upgraded to use FRMCS, so any investment in the cab radio should not be wasted and FRMCS will see faster, more secure, and more reliable communications which can be exploited in future applications.
The train-borne apps of today will be superseded by solutions that can benefit from more bandwidth, for example video systems to monitor passenger spaces, and allow higher grades of automation. Far more data from the complex ‘system of systems’ that will make up new rolling stock will need to be transmitted back to control centres, so that data can be integrated with information from a multitude of trackside systems to provide a system-wide integrated view of the railway. The railway of the future will see connectivity and data as critical to a smooth, efficient, and reliable network, which is the obvious choice for travellers. This can only happen if rail can be made affordable and make the best use of the assets it already has.
Futureproofing technology is critical if the industry is to keep up with the rapid change of system technologies, especially in areas like communications; but it is possible to mitigate the impact of both obsolescence and technology change. A lot of time, effort, and money has been involved with fitting GSM-R equipment to trains. The experience of providing additional functionality to the on-board cab radio has demonstrated that it is possible to build on this investment, to add additional capability in an inexpensive and nonintrusive way, and be a step to FMRCS.
In times of rail disruption, having poor information can annoy and frustrate customers. But if people are informed of the extent of their journey disruption and what their options are, this can help to maintain their confidence in rail. Timely accurate customer information is essential so that people can plan ahead. With customer information being so important, Rail Engineer recently met up with Network Rail and the Rail Delivery Group to learn more of the developments in customer information systems.
At the end of 2022, independent watchdog Transport Focus consulted more than 15,000 people to help the railway invest on the improvements that matter most to customers. The top three issues for rail customers were the cost of train tickets and value for money, reliability and punctuality, and sufficiently frequent trains. At number four of the top 10 issues was receiving accurate and timely information about train times. At number seven was being kept informed about train delays and the options customers have in times of disruption.
Four years ago, the Office of Rail and Road (ORR) commissioned research on the provision of information to customers. This showed that whilst there had been some improvements in providing information to customers, it is a challenge, particularly during disruption. The research found there was no clear industry strategy for delivering better customer information, poor understanding of what good information looks like, and a lack of accommodating the needs of all customer groups.
In response to the ORR’s report, the Smarter Information, Smarter Journeys (SISJ) programme was launched in early 2020. It is a cross-industry programme with a remit to deliver better and simpler customer information. It is a fantastic example of cross-industry collaboration and what can be achieved for the good of the customer and the industry when industry minds from Network Rail, the Rail Delivery Group, and train operating companies come together.
The programme focuses purely on the customer and the desire to enhance customer satisfaction with customer information. It is a very welcome development in improving customer information based on the core principles of customer insight, transparency, and industry collaboration. The goal is to provide customers with all the information they want, when and how they want it. It aims to ensure that customers always have a consistent and simpler customer information experience, irrespective of which train operator they travel with.
Recent results show an impressive increase in customer satisfaction with 67%* of customers being satisfied with information during disruption in May 2023, this is a 10%* increase since SISJ launched.
*Source: InfoTracker Survey Q1 Results (AprilJune 23)
The SISJ programme has delivered a range of initiatives. Examples include:
» Work undertaken with train operators, retailers, and suppliers to build a tool which notifies customers who have bought a ticket via website/app when their train journey is impacted (known as personalised journey notifications) by timetable changes or other delays. This initiative has been implemented by almost all rail retailers/train operators and to date there have been over 1.9 million passenger notifications.
» Developing a blueprint for train operators to adopt and follow which clearly sets out the type, quantity, and occurrence of onboard announcements, to make sure there is consistency across the network. This was in response to the need to improve on-board announcements and reduce their frequency and repetitiveness as outlined in the Williams plan for rail as shown here.
» Implemented a ‘Data Visualisation’ tool for Operational Information Screens (OIS). This tool looks at how to improve the awareness of asset locations and their condition across the network. The aim is to better prioritise resources and target more accurately faulty devices. For engineers across the network who repair OIS assets, having an updateto-date ‘Data Visualisation’ tool is a more efficient and effective way of working. Engineers can now quickly locate the assets, understand their condition, and rectify any problems in a timely manner.
» Created a Best Practice Guide that is used during severe disruption. During the worst disruption, this guide helps improve the speed and consistency of publicised information and provides train operators with guidance on message creation and customer friendly language. The guide was developed between Network Rail, Rail Delivery Group, the Office of Rail and Road, and Transport Focus.
» Reviewed the functionality of the customer information screens via a specifically set up industry group to agree on a baseline set of functionalities that should be available on all customer information screens across Great Britain’s rail network, regardless of system provider, Network Rail managed station, or train operator. Software upgrades were made where needed and this included, improvements to disruption mode capabilities,
providing information about future delays affecting a train’s onward journey before customer boards and providing details of alternative services to certain key calling points in public address cancellation announcements.
To measure the impact each SISJ initiative is having in driving customer satisfaction and monitor if value is being delivered, SISJ uses a customer information survey tool called InfoTracker. Customers were recently surveyed and findings showed the pattern remains – customers want accurate, timely, and frequent information about their journey as and when they need it, especially during disruption.
It was identified that 95% of customers are satisfied with the information they receive when their service runs normally (non-disrupted) compared to only 71% of customers being satisfied with the information they receive during disruption. During disruption, customers desire information improvements in the reliability, frequency, and amount of information they receive.
Even though customer satisfaction with information is improving, the industry recognises there is still work to do to enhance customer information. This is why the SISJ team launched SISJ V2 in April this year. This is a continuation of SISJ V1 and is a clear customer information vision that will take the industry forward to 2030. SISJ V2 includes a range of people, processes, and technology changes.
It is important that the SISJ programme aligns with the wider strategic plan for rail which is being led on behalf of the industry by the Great British Railways Transition Team (GBRTT). SISJ V2 is therefore interdependent on GBRTT’s Customer Strategy, Fares Ticketing and Retail (FTR) and National Rail Accessibility Strategy (NRAS).
The SISJ programme must be congratulated on the improvements it has made to customer information and its approach to working in real collaboration. It is a true reflection of how powerful it can be, not only for the industry but also for the customer, when all are aligned to the same goal – to create a simpler, better railway for everyone in Britain.
To hear more about SISJ V2 and its initiatives, you can listen to the SISJ team’s podcast on Spotify using the below QR code, visit www.raildeliverygroup. com/sisj, or, if you would like to speak to a SISJ team member, email SISJ@ raildeliverygroup.com.
Customer information systems have always been subject to continuous development. The evolution of data communications, information technology, and displays has rapidly improved over the years. Typically, a customer information system will be replaced around every 10 years. This is not necessarily because the asset is ‘worn out’ and no longer reliable, but because the performance and facilities improve so much that the asset effectively becomes obsolete quite quickly. It’s similar to domestic televisions. These are also now more reliable than ever and the TV repair ‘person’ is a thing of the past, but TV facilities and display technology is continually improving and TVs are very often replaced before they fail. It’s the same with customer information systems.
The Equality Act 2010 requires that reasonable steps are taken to ensure disabled people are not discriminated against. Train and station operators are also required by their operating licences to establish and comply with an Accessible Travel Policy (ATP) approved by the Office of Rail and Road (ORR).
European and UK standards covering Persons with Reduced Mobility (PRM) have been simplified over the years and made less prescriptive. However, good practise for persons with limited reading capability is that customer information displays should have good contrast and use upperand lower-case font with clear descenders and ascenders.
A descender is the part of the letter below the midline of a typeface letters, such as the tail of the letters g, p, q, and y. An ascender is the portion of a lowercase letter that extends above the midline of a typeface, such as the top of A, h or f. Ascenders, together with descenders, increase the recognisability of words and this is why customer information systems and signs for situations requiring high legibility, such as road signs, use upperand lower-case letters.
When the first railway customer information systems were introduced, some systems used all upper case with poor descenders and ascenders. Things have greatly improved over the years and today’s LED and TFT information displays have developed to provide excellent readability with good contrast upper- and lower-case font, with clear descenders and ascenders.
Displays should also be sized to show individual station names or words of messages, and each station name, or words of messages, should be displayed for a minimum of two seconds. If a scrolling display is used (either horizontal or vertical), then each complete word needs to be displayed for a minimum of two seconds and the horizontal scrolling speed should not exceed six characters per second. Scrolling of several pages of information should be avoided as even waiting a few seconds for information can seem a long time when people want to find their train.
For mainboard solutions at larger stations, the latest customer information display development is the use of fullmatrix LED colour RGB displays. These displays are based on advertisement sign technology but have been adapted for customer information to provide wider viewing angles, improved contrast ratios, and the ability to show enhanced graphical notices in a flexible and dynamic format.
The control software has been developed to manage the flexibility, and graphical widgets and preformed templates are used to allow station operators to easily change the format of the displays at the touch of a button. This helps to manage the information presented to customers dependent on the operational needs of the station. For example, in times of severe disruption the display format can be changed, if required, to show an alphabetical list of next train destinations, rather than
displaying columns of cancelled trains, which doesn’t help customers. Other templates are also provided and it’s all about providing the right information at the right time to help people with their train journey. This could not be done with the previous fixed column format of next train information displays.
Colour on customer information displays must be used carefully, with good content presentation. Certain combinations of colour can hinder readability and much care and attention goes into the detailed design of such displays. For example, simple amber or white on black provides one of the best contrast ratios. It’s important that customer information designers work closely with disabled people and their representative organisations such as the Royal National Institute of Blind People (RNIB), Guide Dogs, or the Royal National Institute for Deaf People (RNID). The good news is that modern display technology is more flexible and designs are not embedded. So changes based on user feedback are now far easier to implement.
Full-matrix LED colour RGB displays made up of modular tiles were initially trialled at two small areas at London Victoria and London Waterloo stations in 2020 and were very well received. One good use of the colour capability has been to introduce ‘wayfinding arrows’ to indicate to customers which way to go to find their train. Fullmatrix LED colour RGB displays have now also been rolled out to other London major stations.
Some of the large London stations are no longer provided with the traditional ‘main board’ column display – London Euston, for example. Instead several smaller displays have been provided and located around the station to help customer flow. Display brightness has also been improved with the latest LED display technology development, allowing displays to be located outdoors with no shading from bright sunlight. This would have been impossible with the previous generations of display technology. The opportunity has also been taken with the new, more flexible, LED colour RGB displays to connect and show real time information from other third-party train operators on the main station displays, such as Transport for London.
Much has been done to consolidate and connect information platforms together, to provide consistent ‘one version of the truth’, but it is an area where things will continue to improve. For example, there are ‘standalone’ information systems on the network which have to be operated separately from one another and do not always provide consistent messaging content to customers. Better integration of all information systems with the customer information system ‘back office’ platforms would help to provide better consistent information to customers.
Audio public address systems have long been provided for railway customer information, and they are also used for emergency purposes when linked to fire detection systems. A badly designed sound system will quickly annoy customers and may result in negative comments and poor publicity.
Systems should be loud enough to please those intending to hear the message, but not too loud to annoy neighbours and residents close to a railway station, or train passengers who may not need to hear the announcement. Intelligibility is a very important requirements of a PA system and can be where some systems fall short if not designed correctly.
A typical railway station will need careful design of its speaker system to make the best of what can be a very
challenging acoustic environment. Simply specifying a sound pressure level and intelligibility may provide a system acceptable for rail users, but one which annoys nearby residents.
There have been cases where PA systems have been renewed with an overall lower volume, but with better intelligibility resulting in more complaints from neighbours. An extreme case resulted in a noise prohibition notice and for the station PA to be switched off until the problem was resolved.
A fairly recent development for railway station PA systems has been the introduction of intelligent speakers. This allows the speaker to be programmed to ‘steer’ the beam of audio so that it can be projected to the location requiring the announcement, with minimal ‘over spill’. The audio can be set so that the level drops significantly within a few metres. This can also help to reduce reverberation and provides far more control than previous generations of PA systems.
Another recent development in public address is Audio-over-IP (Internet Protocol). This should not be confused with internet streaming. Streaming services send low bandwidth, compressed audio to devices with no attempt at synchronisation or low latency, because this doesn’t matter when each
receiver is separate from one another. Audio-over-IP however is a technology used to distribute real-time, tightly synchronized uncompressed audio to speakers. To hear train announcements the sound must not be delayed or compromised.
Audio-over-IP allows many simultaneous channels of excellent digital audio to be transmitted over a data network with certainty. Audio-over-IP has transformed professional audio, enabling systems to be more flexible and expandable, but it can’t currently be used for Public Address Voice Alarm (PAVA) systems. PAVA requires special fire-safe wiring, auxiliary power sources, equipment redundancy, and self-checking alarms. However Audio-over-IP for PAVA may be the next development for customer information systems.
Customer information systems and processes will continue to develop and change, and there will always be a need for better information and communications. The industry must also consider those who are less technology confident and not just rely on digital technology. Some passengers, which can include older or disabled people, may be less confident using digital apps and websites, and even those who are technologically savvy will often want to speak to someone to reassure them of their travel arrangements. Which is why staff on stations and trains will always remain important.
HS2 phase one will eventually have four new stations in London and Birmingham. These stations are designed to be modern, spacious, and sustainable, accommodating the expected increase in passenger demand. As this highspeed project gathers pace, we take a look at the recent progress at three of these new stations and consider why it is likely that Euston will not see high-speed trains until 2040.
HS2’s landmark station, Old Oak Common, celebrated a key milestone in June as it marked two years of permanent construction. The ‘super-hub’ station is planned to be one of the busiest in the country with high-speed rail services to the Midlands, Scotland, and
the North, and access to central London and Heathrow via the Elizabeth line. It will boast 14 platforms, six of which will serve high speed trains and will be situated below ground. These will sit within an 850-metre-long station box, large enough to house 6,300 Routemaster buses. There will be an integrated connection to the adjoining conventional station at ground level via a stylish shared overbridge, and a light and airy concourse will link both halves of the station.
In June 2021, Grant Shapps MP, then the Secretary of State for Transport, gave the thumbs up for permanent work to begin. Since then, work has gathered pace and significant progress has been made. A total workforce of 1,900 people now supports the delivery of the station, with the site itself welcoming around 1,000 workers each day.
In March, HS2’s Station Construction Partner, Balfour Beatty VINCI SYSTRA Joint Venture (BBVS JV) completed the installation of the 1.2-mile diaphragm wall for the underground box which will contain the six new high-speed platforms. The team installed 275 diaphragm wall panels and 161 bearing piles, the largest of these being 2.2 metres in diameter and 57 metres in length. The first base slab concrete pour in the western end of the station box took place in May, as reported in Rail Engineer 202 (May/June).
The excavation of the station box is also well underway with over 465,000m3 of London clay already removed out of a total of 930,000m3 from across the site. The excavated clay from the site is now being taken away via part of a 1.7-mile conveyor network, removing thousands of lorry movements from local roads.
Over 900 of the 1,600 concrete piles have been installed into the ground where the HS2 station superstructure and overground platforms for the conventional train network will be constructed. Piling work also began earlier this year on the second half of the station – the eight platforms that will be served by Great Western Mainline and Heathrow Express services. Platform construction will start later this year.
In addition to all of this, the demolition of the Wycombe Line Bridge, over Old Oak Common Lane, was completed at the end of May. The disused rail bridge was removed following a weekend road closure and makes way for the construction of the new Network Rail bridges which allow the Great Western Mainline track alignment to be widened as it approaches the new station.
“Here at Old Oak Common, we are well underway in our work to construct London’s newest super-hub station,” said HS2’s Project Client Director, Huw Edwards. “Our work is supporting nearly 2,000 jobs and we
are already seeing that the new station is becoming a catalyst for regeneration in the Old Oak and Park Royal area.
“Upon completion, it will harness the close linkage with the newly opened Elizabeth Line, dramatically improving connectivity and creating a new destination to live and work in London.”
Later this year, the eastern end of the 10-hectare site will be handed over to HS2’s London Tunnels Contractor, Skanska Costain STRABAG joint venture (SCS JV), for the breakthrough of the Tunnelling Boring Machine, named Lydia, which will have completed the construction of an 850-metre-long logistics tunnel from the nearby Atlas Road site.
The SCS JV team will then receive two further TBMs delivered to Old Oak Common, in 2024, which will be assembled in the station box, ready to bore the five-mile Euston Tunnel.
A project update for Old Oak Common can be found here:
On 17 July, Transport Secretary Mark Harper visited Birmingham with his Australian counterpart, Minister for Infrastructure, Transport and Regional Development, Catherine King. The pair were there to see the construction of HS2’s iconic new Curzon Street Station taking shape.
Built on the site of Birmingham’s 19th Century station at Curzon Street, the new station will be the first brand new intercity terminus station built in Britain since the 1800s. Curzon Street Station will welcome high-speed services into the heart of Birmingham city centre, connecting cities and towns across the West Midlands and beyond. Eventually, there will be nine trains per hour direct in each direction from the station.
Harper and King took an exclusive first walk on top of the grand, 300-metre-long HS2 viaduct to see first-hand the view passengers will witness when travelling into the city on HS2 trains. The walk marked a key construction milestone, celebrating the half-way point of the viaduct’s completion, which now has 15 of its 30 V-shaped piers in place.
Each pier takes up to four weeks to be fully installed on site, with the tallest pier reaching up to six metres above the ground. After the piers are in place, teams will begin to form the deck spans connecting the piers using system falsework and formwork with the longest span between each pier stretching over 28 metres across the site.
Curzon No.3 Viaduct is 65 metres at the widest point, and as it approaches the station, the deck widens from a single deck at the eastern end to four separate decks at the western end, creating opportunities for a usable, flexible public space with maximised daylight under the viaduct.
Once built, HS2’s Curzon Street Station will be one of the most environmentally friendly stations in the world, eventually welcoming nine highspeed services per hour into the city centre. With seven terminal platforms, it will form part of HS2’s opening phase, with the first services expected to run from West London into the station by 2033, serving around 25,000 passengers a day.
On his visit, Transport Secretary Mark Harper said: “The fantastic city of Birmingham is a hive of construction, with HS2 supporting thousands of high-skilled jobs and apprenticeships, as we gear up to bring its services into the city centre over the next decade.
“As Europe’s largest infrastructure project, HS2 is being recognised globally and, alongside the Australian Transport Minister today, I take great pride in seeing this once-in-a-generation opportunity come to life, which will better connect our regions and grow the economy for years to come.”
The construction project is already delivering huge benefits, and is expected to create over 1,000 jobs, including 100 new apprenticeships and a ‘Restart’ scheme to support unemployed people. Even more jobs will be supported and created as work ramps up across the region in the years to come, with the HS2 Interchange Station set to be built in Solihull.
A brief history of Curzon Street Station from Rail Engineer 194 (Jan-Feb 2022) can be found here:
Interchange Station will serve Solihull, Birmingham Airport, and the NEC. The station will form part of a new public transport interchange serving Solihull and the West Midlands, with links to local roads and the UK motorway network.
Once completed, there will be up to five trains per hour passing through Interchange Station in both directions, with an estimated total of 175,000 seats per day, making this one of the best-connected transport interchanges in the country.
The station has been designed to maximise views over the surrounding Arden landscape, providing a pleasant passenger experience. Focussing on sustainability, HS2 has designed the roof to maximise natural daylight and capture rainwater for recycling, which will reduce the demand for electricity and water.
Its design has seen Interchange become the first railway station globally to achieve the BREEAM ‘Outstanding’ certification – a measure of sustainability for new and refurbished buildings –putting it in the top 1% of buildings in the UK for eco-friendly credentials.
The construction site for the station covers an area of 150 hectares within a triangle of land formed by the M42, A45 and A452. Significant progress has already been made on the site, including construction of modular bridges over the M42 and A446 as part of a remodelled road network in the area to facilitate access to the new station.
HS2’s Main Works Contractor Balfour Beatty VINCI is currently preparing the site where the new station will be built. Laing O’Rourke Delivery Limited will build the station.
Passengers and visitors will be moved between Interchange Station, the NEC, Birmingham International rail station, and Birmingham Airport by a new Automated People Mover (AMP) system which will carry up to 2,100 passengers per hour in each direction on a six-minute journey.
The APM will run on an elevated 2.2km long viaduct, and range in height from six metres to 14 metres, crossing the NEC, West Coast Main Line and M42 Motorway.
In July, HS2 announced it has started the search for a contractor to design and supply the APM, as well as a 25year transport operation and asset maintenance contract.
HS2’s Procurement and Supply Chain Director, Andrew Cubitt, said: “We’re pleased to be starting the procurement process for the APM Systems Contract, which is worth up to £270 million. The APM is a vital piece of infrastructure in the HS2 project, connecting high speed rail passengers to the classic rail network, and supporting the shift from car use to public, mass transit transport, which is so important in achieving the UK’s target of net zero carbon.”
Shortlisted companies will be invited to tender early next year, with the contract due to be awarded towards the end of 2024. The search for the APM Infrastructure contract will start later this year, with invitations to tender in 2025 and contract award in 2026. A virtual tour of the future Interchange Station can be found here:
The construction contract for HS2’s London Euston was let in 2019. Since then, over £350 million has been spent on preliminary utility and demolition work. However, in contrast to the other phase one HS2 stations, work at London Euston has now been halted. This follows a Government announcement in March that that HS2 programme will “address affordability pressures to ensure the overall spending profile is manageable” and that “we will take the time to ensure we have an affordable and deliverable station design, delivering Euston alongside high-speed infrastructure to Manchester.”
Nonetheless, a National Audit Office (NAO) report, published shorty after this statement, concluded that the impact of HS2’s deferring spending will be additional costs which could lead to an overall increase in spend in the long term due to the costs of contractors stopping and restarting work, contractual changes, and managing sites and the project for longer. At Euston there will be costs associated with maintaining its large, demolished site for which HS2 is attempting to find alternative temporary uses.
As a result of this announcement, the timescale for HS2 phase one has been extended by two years. When it opens in the early 2030s, its London terminus will be Old Oak Common station. London Euston is not now expected to open until the HS2 line to Manchester is operational in the early 2040s.
The latest review is the third iteration of the design of HS2’s London Euston. As a result, it is likely that much of the £200 million design work to date will be abortive. In 2015, an HS2 press release announced that London Euston will have eleven new platforms built at the station in two stages as part of a phased approach with less
disruption for passengers. Six platforms to the west of the station were to be built for HS2 Phase One which was then estimated to be opening in 2026. Once HS2 phase one services replaced conventional services from Euston, this would free up space in the existing station to construct a further five HS2 platforms for phase two services.
In February 2020, the Oakervee review of the HS2 project concluded that “the management of the whole Euston project is muddled” and that there was limited joined-up thinking between the three connected projects at Euston which are: HS2 station; Network Rail’s station redevelopment; and the over site development. It also found that the HS2 Euston station design was not satisfactory and added unnecessary cost. In April 2020, HS2 had a £2.6 billion budget for the HS2 Euston station, but by June 2020, it had estimated that its cost might be as much as £4.4 billion.
As a result, in November 2020, DfT instructed HS2 Ltd to proceed with 10-platform station built in a single stage construction although little structural design work could be done until the extent of over site development had been specified. It took almost another year (September 2021) for the DfT to confirm this.
Currently it would seem that when the first HS2 services start early in the 2030s with Old Oak Common as the London terminus, it could be a further 10 years before high-speed services run from London Euston. This is controversial as many consider that the inconvenience of Old Oak Common will discourage passengers. Indeed HS2’s modelling concluded that once HS2 was operational to Euston, only one-third of passengers would choose to travel via Old Oak Common.
Yet a more significant issue is lost HS2 capacity which significantly reduces benefits valued at billions of pounds whilst HS2’s terminus is at Old Oak Common. This is a little reported issue which was not considered by the NAO report. HS2’s phase one original business case for a 10 trains per hour (tph) service shows a present value of benefits and revenues totalling £48 billion. An Old Oak Common terminus is likely to at least half these benefits.
Old Oak Common will have six platforms. Yet, unlike Euston, its track layout is specified only for an emergency turnback. This is all that can now be accommodated within the allowable land take specified in the HS2 Act. As a result, it is estimated that, at best, 6 tph could be run from Old Oak Common. This could be three for Birmingham Curzon Street and one each for Manchester, Liverpool, and Glasgow. An hourly service pattern for these three cities is sub-optimal as their other, slower, conventional services would still be running to Euston.
The HS2 line from London to the West Midlands is a very expensive investment which is designed to have a capacity of 18 tph. However, it can well be only operating at a third of its capacity for its first 10 years. Hence HS2 would not be able to offer, to any meaningful extent, its key benefit of released capacity to allow a significant increase in local, interurban, and freight services.
Moreover, even when Euston becomes HS2’s London terminus it is unlikely that its 10-platform design will enable the HS2 network to operate at its full capacity. While the DfT’s view that 10 platforms are sufficient, this is disputed by this expert advice which considers that a 10-platform station can only reliably support 16 tph.
Eventually HS2 will provide a more connected and sustainable future for transportation in the UK with hubs offering smoother and more efficient travel experiences. In the long term, they are set to drive growth and regeneration, attracting investment, stimulating job creation, and promoting the development of new businesses and industries.
The environmental advantages of these stations should also not be overlooked. By encouraging more people to opt for sustainable and efficient high-speed rail travel over other modes of transportation, the project has the potential to reduce carbon emissions, alleviate congestion on roads, and minimise the overall environmental impact of transportation. The incorporation of eco-friendly designs and practices in station construction can set a precedent for future infrastructure projects.
Unfortunately, it will be almost 20 years before HS2 realises its full potential. There are many reasons why costs have risen, and why the project is years late. It is clear that one reason is the focus on annual project spend with little consideration of lost benefits or overall cost increase. At Euston, muddled management and design changes have resulted in HS2 not being able to deliver its full potential until the 2040s.
It is to be hoped that some lessons will be learnt from this.
Two hot and sunny days in June saw the return of the UK’s largest outdoor rail show at Porterbrook’s Long Marston Rail Innovation Centre (LMRIC) in Warwickshire, which was billed as being an even bigger and better Rail Live than ever. It is believed that there were around 6,230 visits over the two days - an impressive increase of 11% on last year.
Formerly known as the Quinton Rail Technology Centre, the 135-acre site includes a two-mile-long circular test track and almost 12 miles of sidings for secure train storage. It is linked to the national network via a two-mile branch line to Honeybourne, and rolling stock owning company Porterbrook took over the management of LMRIC in June 2021.
The site was purchased by the Ministry of Defence in 1940 as a centre for military operations. The branch line to Honeybourne is the surviving stub of a through route to Stratford-upon-Avon (itself part of the Great Western Railway’s main line between Birmingham and Cheltenham) which was closed following a derailment in 1976. It is currently the subject of a reopening campaign that has received development funding from the Government’s Restoring your Railway scheme. Since taking over the site, Porterbrook has invested more than £10 million to upgrade LMRIC, including hard surfacing the roads, refurbishing buildings, and providing improved signage. On a part of the site closed to Rail Live visitors, more than £3 million has been invested in a three-road, fully-pitted shed that can accommodate a six-car set, with 460 metres of new rail. In the future, the intention is to also upgrade the test track to higher speed running with electrification and ETCS Level 2.
Visitors were greeted to Rail Live by an extensive array of yellow ‘plant’ worth tens of millions of pounds, lining the main avenue.
Rail Live was originally established by Network Rail as a ‘plant show’ at its Westwood training centre. Over the years it has grown significantly to cover all aspects of rail infrastructure.
The LMRIC site is huge, with ample room for all shapes and sizes of rail plant and trains, and an impressive programme of seminars and keynote speakers took place in the Rail Live Theatre. There was also a wide range of rail equipment on display along with live demonstrations. This included a variety of exhibitions such as Network Rail’s Air Operations Team and the firearms and dog units of the British Transport Police. Over 270 exhibitors were present, representing all parts of the supply chain.
The Rail Live site is remote, with no station nearby, but a regular passenger train shuttle service consisting of Porterbrook’s Class 769 tri-mode trains ran from Honeybourne station to the site’s own private platform. The ‘769s’ are converted from a Class 319 dual-voltage electric multiple unit, with the additional capability to run on diesel power. At Honeybourne, a temporary platform was provided. The platform was constructed using Glass Reinforced Plastic (made from recycled material) and featured an advanced tri-tone surface for optimised anti-slip endurance. The lightweight, portable, and fully sustainable platform is planned to be reused at other temporary high-demand locations. A shuttle bus service was also in place from, and to, Strafford Upon Avon and Warwick Parkway stations.
PAUL DARLINGTONThere were many other highlights at Rail Live 2023, including Rail Minister Huw Merriman who attended on Thursday 22 June when he launched the second day’s seminars. He headed a highprofile attendance list that included Network Rail chair Lord Peter Hendy of Richmond Hill and HS2’s CEO Mark Thurston.
A Transport for Wales Class 756 Stadler FLIRT unit was among the main rolling stock attractions. Twenty-four of the tri-mode units will be introduced on South Wales Metro services, powered by discontinous electrification on lines north of Cardiff and diesel
A Track Demo Viewing Platform and giant video screen formed one of the centrepieces in the Network Rail Village, providing visitors with a clear view of the track demonstrations by the Wales and Western
HS2 was a first time Rail Live exhibitor, showcasing a model of its Tunnel Boring Machine (TBM) named ‘Dorothy’. The full size, 125-metre-long, 2,000-tonne machine started its journey at Long Itchington Wood Tunnel’s North Portal site in Warwickshire in December 2021, and broke through the wall of the reception box at the South Portal site in July 2022. Dorothy and its huge cutter head, weighing 160 tonnes with a 10-metre diameter, was then relaunched in November last year, taking four months to complete its one-mile second bore. Work is now underway to dismantle the TBM, ready for transportation to Birmingham, where it will begin a 3.5-mile tunnel bore between Water Orton and Washwood Heath in early 2024.
The industry body Rail Forum hosted a series of mini-networking sessions to give its members across the supply chain the opportunity for networking with major buying organisations, Tier 1 contractors, and other stakeholders. The five sessions covered SME engagement, on-track plant, level crossings, seasonal delivery, and overhead line equipment.
to the south, to provide crosscity connectivity. Seamless travel will be promoted through the use of overhead lines at 25kV, and through on-board battery power on non-electrified lines. To keep emissions to a minimum, diesel power will be limited to specific areas. Low flooring ensures level boarding, making it simpler for passengers to get on and off, and reduces dwell time. Air-conditioning, new passenger information systems, Wi-Fi, and areas for wheelchairs, bikes and pushchairs also feature.
Other highlights at the show were Great Western Railway’s Fast Charge Battery Train. The Class 230 unit 230001 features a Fast Charge system which unlocks the use of battery trains across the network. This train and its charging system were developed at Long Marston by the now defunct Vivarail company. The Fast Charge engineering team was on hand to discuss the technology and the future potential of the systemincluding the planned trial on the West Ealing-Greenford line.
Region. The demonstrations and associated displays had been developed with three Rail Systems Alliances. Rail vehicles on display included a Mobile Maintenance Train, a track tamper, Rail-Road vehicles (RRVs), and a universal material handling vehicle that is able to receive materials and distribute material via a series of conveyors.
As part of Project FRoOG (Freight Resilience of Operational Geometry), Network Rail was displaying a new vehicle that has been developed with geometry measurement equipment, to dynamically measure infrastructure. It can measure all areas of track under load and, in places where its current fleets don’t run, and measure high-risk derailment sites.
Examples of Network Rail’s Road Vehicle Fleet included a range of electric vehicles from large transit vans to much smaller vehicles. Members of Network Rail’s Commercial and Procurement, Intelligent Infrastructure, and Research and Development teams were also on hand, as were experts in Project SPEED (Swift, Pragmatic and Efficient Enhancement Delivery), which has been designed to challenge how projects are currently delivered.
Network Rail’s team of station hawks were also on display. Provided by Rentokil, these specially trained birds of prey are flown to deter gulls and other pest birds without causing them harm. Rentokil’s bird handlers use their experience and expertise to identify the most appropriate vantage points from which to fly the raptors. Also in the air, the Network Rail’s Air Ops team had its drones unit and two helicopters on display, with the opportunity to meet those who fly them.
Network Rail had a presence in Rail Live’s Signalling Zone, including a stand for the East Coast Digital Programme, and the Network Rail village was full
of exciting innovation including Robodog (Spot) created by Boston Dynamics. Unlike a regular dog, Spot can detect radiation, complete thermal inspections, and gather data in his shiny yellow coat. Within the Network Rail Village, the Sentinel team was available to meet customers and users, and to answer questions on how the core safety system allows users to check authority to work before going trackside and experience Sentinel’s recent digital makeover, the biggest enhancement to the system for a while. Intelligent Infrastructure is a digital transformation programme to improve asset management and to provide the basis for a ‘predict and prevent’ maintenance strategy. Network Rail’s experts were on hand to explain the apps and tools which take raw data and transform it into intelligence to support effective decision making. By the end of April 2024, they will have delivered 20 new apps and tools, helping to make the right decisions at the right time to provide improved services for passengers and freight customers.
Cost-effective electrification relies on more than just technology, and this was one of the themes for Siemens Mobility at Rail Live. Siemens Mobility’s electrification experts were exhibiting and explaining its technology and demonstrating its approach to delivering cost-effective electrification for a lowcarbon UK rail system. This covered in-house design, UK manufacturing, delivery, and installation.
Siemens Mobility’s product portfolio was on display to show how it can optimise the use of energy across the network, including AC and DC traction power supply equipment, as well as contact line and network systems. Visitors were able to see demonstrations of the latest overhead line innovations including the SICAT SX and surge arrestors which have been developed to affordably electrify over 1,800km of Denmark’s railways. Air insulated switchgear was also on display, which is currently used in the UK, with a model of a compact version in development.
The Rail Live Theatre featured many very interesting and topical subjects and speakers. On the opening day of Wednesday June 21, John Larkinson, CEO, Office of Rail and Road covered the ‘Next steps in rail regulation: PR23 and beyond’. Andrew Haines, Network Rail chief executive and Great British Railways Lead discussed ‘Where next? The future of Britain’s railways’. Ed Akers, principal programme sponsor, East Coast Digital Programme explained ‘Digital signalling: The next generation railway.’ Mark Thurston, CEO, HS2 Ltd gave ‘An update on HS2: Overview and insights’. Emma Porter, managing director, Story Contracting discussed ‘Why diversity and inclusion matters’.
On Thursday June 22, Milda Manomaityte, innovation director, Railway Industry Association covered ‘Innovation - the supply chain perspective’. Huw Merriman, Rail Minister presented ‘Giving back control: Letting TOC MDs manage and direct.’ Lord Hendy of Richmond Hill, chair, Network Rail explained ‘Rail reform as a catalyst for the future’. After lunch, Ian Prosser CBE, HM chief inspector of Railways covered ‘Health and safety challenges in CP7’. Rikke Carmichael, head of Air Operations, Network Rail; Bradley Sparkes, national drone manager; Sean Leahy, national aerial survey specialist collectively covered ‘Aerial derived data – reaching new heights’.
The equipment on show did not only include large, yellow plant and trains. For example, Encortec was typical of many of the smaller suppliers and was demonstrating its vibration and electromagnetic energy harvesting technology. Developed from research by the University of Exeter, Encortec is removing the need to charge and replace batteries, and the need to use power cables connected to the mains for infrastructure monitoring. The concept is for a ‘fit and forget’ remote monitoring device, powered by electromagnetic energy harvesting from AC traction systems.
Helped by the warm weather, Rail Live was an outstanding event and this report only covers a small part of the excellent stands, discussions, and exhibitions on display. There was a vibrant buzz around the site and there was much enthusiasm evident for the future of rail.
LMRIC is a fabulous site for Rail Live, it’s just a shame it’s difficult to get to by rail. The rail link shuttle to the south was great, but how about one with the north? The success of Rail Live and the increase in numbers attending did cause some issues, notably traffic volume in and around Long Marston, long queues at registration, visitors parking on the road, delays in entering and exiting the parking, and some visitors not having badges.
It would appear that many enthusiastic visitors and exhibitors arrived at the same time and Rail Live was a victim of its own success. Many journeys to the exhibition were also delayed to due to a motorway accident, which resulted in traffic suddenly arriving at the site in the same short time. On day one, there was an incredibly long queue forming around the site. So due to health and safety concerns, with the heat and lack of shade, the decision was made to allow a number of visitors into the show without badges (approx. 350), but steps are in place to put clients and visitors in contact, in compliance with GDPR. Like all good projects, an action plan to review the arrangements is under way and to ensure lessons are learnt and the delays do not happen again. We are sure this will be the case and we wish the organisers every success for the future of Rail Live.
With Trimble® GEDO systems, modern technologies are individually combined according to the respective applications. The Trimble GEDO CE 2.0 track measurement trolley can be equipped with total station, GNSS, laser scanner and inertial measurement technology. With evolving requirements and new development requests, the exible and modular design allows Trimble GEDO systems to be adapted.
Intelligent infrastructure and remote condition monitoring systems are now essential tools for the efficient and cost-effective maintenance and asset management of all types of railway infrastructure.
No matter what an asset is or how well it is made, the asset will show signs of degradation over time. Depending on the type of asset, how it is used, and what elements fail first, the signs of degradation will appear differently. The changes may be so subtle that it is difficult to initiate an intervention until it is too late, so the asset fails or gives rise to a hazard.
However, intelligent connected infrastructure and remote condition monitoring can provide information on how an asset is changing over time, and allow an intervention to take place before a failure or hazard occurs. To achieve this requires a reliable sensing device and a data connection, and the sensing device and associated data transmitter will need a power supply. Given that the main line railway in Great Britain is 15,935km (9902 miles) long, providing a power supply to support a remote sensing device can be tricky.
Many existing remote sensors are battery powered. However, battery life is affected by many factors including the energy capacity stored, current drawn, operational time, the battery’s discharge characteristics, and environmental conditions, but can be typically two or three years or less for frequent monitoring. With potentially thousands of sensors needed for comprehensive railway monitoring this is not a sustainable solution. Battery replacement will be required at some point, which can come around quickly, and many batteries may need changing at the same time.
From an environmental perspective, replacing and recycling batteries should be avoided. They contain hazardous substances and, if not correctly disposed of, can cause health issues. Even when correctly disposed, environmental risks
can persist for some battery types as their recycling processes are not ideal. Handling batteries also requires care. For example, lithium batteries can explode or catch fire if punctured or are short-circuited. Battery replacements can be costly and resource hungry, and every visit to a railway asset is a safety risk which should be avoided if at all possible.
A solution to this problem is being developed by Encortec Ltd, in collaboration with Network Rail and Unipart Rail, for its electromagnetic energy harvesting technology to deliver sufficient usable power for its intelligent wireless sensors. The development is part funded by an Innovate UK Smart Grant.
Innovate UK, part of UK Research and Innovation says the funding is to: “support SMEs and their partners to develop the disruptive innovation with potential for rapid economic return to the UK.” It offers funding that is “business focused, with deliverable, realistic, adequately resourced plans to achieve return on investment, growth and market share following project completion.”
Encortec’s vision is to remove the barriers to providing electrical power and to provide ‘fit and forget’ energy harvesting powered technology for asset condition monitoring and effective maintenance. This will remove the requirement to charge and replace batteries, and the need to use power cables connected to the mains for sensors.
The energy harvesting technology was instigated from research undertaken by the University of Exeter and one of the outputs of the research identified using electromagnetic flux energy of a 25kV AC electrified railway for energy harvesting to provide power for ‘fit and forget’ sensors.
Electrified rail track energy harvesting uses the principle of the coupling of magnetic field lines created by the return electric current of an AC electrified railway in the rail by passing trains, to power the Encortec energy harvesting rail sensors. The electrical energy harvested is in the order of 0.25W - 4.0W, which is sufficient to transmit >2048 data bits per second using Industrial Internet of Things (IIoT) LowPower, Wide-Area (LPWA) communications to monitor asset changes.
Communications for the sensor is currently being developed to use Vodafone’s Narrowband Internet of Things (NB-IoT) LPWA network using licensed and secured spectrum. This is a reserved channel on the Vodafone LTE network designed to connect assets such as vehicles, cameras, traffic lights and environment sensors. The service, offering enhanced capability such as enhanced coverage penetration for connectivity in remote or underground location, has been optimised to handle small data messages, with low power consumption and for largescale deployments, such as the Encortec energy harvesting rail sensors. Encortec is also looking at other communication options for its sensor, such as low orbit satellite communications.
Two of the biggest risks to railway operational reliability are flooding and excessive rail temperatures, and with climate change these two risks are only going to increase. This is why Encortec has initially focused its wireless ‘fit and forget’ sensor to monitor rail temperature, vibration, and flooding. The sensor device can be easily fitted underneath a rail in minutes, anywhere on an AC electrified railway, with no special training required.
The sensor will improve safety by reducing the requirement for human trackside activities and provides accurate real-time condition data for predictive and preventative maintenance, together with asset condition data to determine a robust asset renewal strategy. The inexpensive monitoring is aimed at increasing track availability and reliability,
and improving productivity and efficiency. The device will be sustainable with a near zero carbon emission footprint. Encortec is already looking at other use cases for its ‘fit and forget’ wireless sensor. For example, as the power is from the AC traction return current, it could potentially be used to monitor the return current in real time and provide intelligence on bonding condition. The device has also been found to be very good at detecting wheel flats and counting train axles using the vibration sensing. So, with appropriate safety validation could it be used for train detection and integrity proving on AC powered lines - and all with no power supply?
When real time monitoring is taken to the next level and all kinds of ‘fit and forget’ sensors are embedded in the assets, a digital twin of the complete rail network and assets could be created. This will enable far better prediction and planning of maintenance and asset management as, in this digital twin, the complete environment and change can be monitored. Providing extensive, remote, power-free sensors,
and creating a digital twin opens up many possibilities in the rail industry to monitor assets. Multiple sensors providing a large amount of data could be combined with statistical methodology using AI to provide far better use of the railway’s resources.
The mature prototype sensor has already been extensively tested with very encouraging results and is at the stage of being far more than just a concept. It is currently being developed to a manufacturable design with appropriate ‘design for reliability’ and product approval certification in place.
Network Rail’s plans for spending £44.8 billion for Britain’s rail network from April 2024 to March 2029 – the period known as Control Period 7 (CP7) – has been reviewed by the ORR in its draft determination. Its assessment said that while Network Rail’s plans largely deliver the government priorities, a greater focus is needed on train performance and renewing core assets. Assets like track, structures, and earthworks need to be resilient - especially with the challenges presented by climate change.
So, could ‘fit and forget’ wireless sensors be part of the greater focus?
Aiming to achieve net zero carbon from 2035, and with a target of achieving diesel-free construction sites by 2029, HS2 is collaborating with the industry and its supply chain to accelerate innovation in low carbon technologies, such as fully electric machinery, alternative fuels, and renewable energy solutions. Rail Engineer has kept a close eye on the green technologies in use on the HS2 project and here we give you an update on developments in the past six months.
In Issue 197 (July/August 2022) the article ‘HS2 Going Green’ touched upon the trial of two GeoPura 250kVA hydrogen power units (HPUs) as a replacement for diesel generators at HS2’s Victoria Road Crossover Box in Ealing. The power units were being used to provide 100% renewable and emission free power derived from a hydrogen fuel cell, with power capabilities ranging from 20kW through to 2MW. They used 100% green hydrogen produced from renewable energy provided by a hydrogen tube trailer and hydrogen cannisters. Data from the trial showed that running the units for 400 hours eliminated around 51 tonnes
of carbon compared to using standard diesel generators. They were also quieter than standard diesel generators.
In March this year, GeoPura announced it had raised £36 million in funding to accelerate the manufacturing and deployment of its HPUs across the country. Investors included GM Ventures, Barclays Sustainable Impact Capital, SWEN CP, through its fund SWEN Impact Fund for Transition 2, and Siemens Energy Ventures.
Working closely with Siemens Energy, GeoPura will now expand the production of its HPUs to replace traditional diesel-powered generators in a wide range of ‘off-grid’ applications.
Geopura estimates that over the operating life of a single HPU, up to 1,800 tons of carbon emissions can be avoided compared to electricity generated from a diesel generator. The company intends to deploy more
than 3,600 HPUs by 2033, displacing more than 6 million tons of carbon emissions over their combined operating life.
Andrew Cunningham, CEO of GeoPura, said: “This investment allows us to build on our installed base of HPUs and hydrogen production infrastructure to stimulate the green hydrogen economy, and then expand the use of clean fuels into other hardto-decarbonise areas of our energy system.
“We have secured the right mix of investors, forming strategic partnerships that not only provide the funds to enable us to scale rapidly, but also the skills and resources to accelerate the transition to zero emission fuels. With the support of our investors, we can help turn the market on its head and build a green hydrogen economy this decade, not next.”
Back in April, HS2 took a further step forward in decarbonising its construction projects by installing four 30-metre deep piles on a London site using a hydrogen dual-fuel piling rig.
The trial took place as part of work done in partnership by ULEMCo and Cementation
Skanska, working with the Business Research Establishment (BRE), funded through the BEIS Phase 1 Red Diesel Replacement competition.
ULEMCo and Cementation Skanska successfully modified a medium sized CFA piling rig, converting it so that the machine component operated using energy from on-board hydrogen tanks. Using the dual-fuel system, both diesel and biofuels (HVO) can be mixed with hydrogen, displacing the fuel with hydrogen, resulting in a reduction in fuel use and lower CO2 emissions.
Following successful yard trials simulating the technology, the rig was brought onto a HS2 site in London where it successfully completed piling works for HS2, demonstrating that the dual-fuel adaptation can be applied more widely across the construction sector supporting the decarbonisation of plant and machinery.
“HS2 is continuing to drive a positive change in the construction sector and is providing an important environment to develop the real-world use of hydrogen energy technology,” said Andrea Davidson, Head of Environmental Sciences for HS2 Ltd.
“The development of dual-fuel systems that can be used to adapt existing equipment so it can run off cleaner, low carbon energy sources, could be a game changer across the construction sector.”
Now that it has been shown that the technology can work in a real-world scenario, ULEMCo and Cementation Skanksa are looking at how this technology can be used more widely, reducing embodied carbon in construction and reducing impacts on local communities near construction sites.
“Using this rig in a real-world environment to install piles on a commercial site is an exciting milestone, said Terry Muckian, managing director at Cementation Skanska. “It follows the success of the simulated trials last year and is the next step towards rolling the technology out more widely.
“This project goes beyond piling and ground engineering, it provides proof of concept for converting other types of heavy construction equipment, paving the way to construction site decarbonisation.”
In the past few months, Cementation Skanska has also trialled an electric drilling rig on one of HS2’s London sites. The trial took place at one of the London Euston sites, before work on the station was paused. The BAUER eBG 33 is powered by an electric drive, which thanks to an on-site substation, was able to draw directly from the grid.
The 100 tonne drilling rig is the world’s first allelectric, high-capacity drilling rig, and, says Bauer, offers an overall reduction of 1,292kg of CO2 per day compared to a traditionally powered rig, while reducing noise by 50%.
The rig was previously trialled on an HS2 site in Birmingham, where it ran on generators to test the viability of handling the cable in a live environment. By connecting to the local power grid in London, Bauer and Cementation were able to put the eBG 33 through its paces and gather valuable data on power consumption throughout the piling operation. This data will be used in the further development of the eBG 33H – a batterypowered version recently introduced by Bauer. Warren Arnold, general manager of Bauer Equipment UK Ltd, said: “We are all incredibly proud of this unique rig which is setting standards. All the data recorded during operation will help Bauer in the further development of our environmentally friendly rigs and in our ambition to be the leading supplier of sustainable equipment for specialist foundation engineering. This really is a great opportunity to showcase what the eBG 33 can deliver in real terms and the benefits to the local community and environment.”
In November 2022, HS2, launched its Diesel free plan, which sets out how all HS2 construction sites will eliminate diesel use by 2029. To date, 19 construction sites on the project are now operating completely diesel-free and HS2 continues to work with the construction industry to pioneer cleaner and greener ways of working, and increase the use of reliable, proven dieselfree alternatives.
Though the project has attracted considerable scrutiny and criticism in recent months, it continues to provide an ideal test bed for eco-friendly equipment that will help the entire industry minimise its construction emissions.
At this year’s Railway Challenge award ceremony, its chief judge, Bill Reeve announced that, without doubt, this was the best challenge yet as the quality of entries and locomotive performance was the highest that the judges had seen. He advised that the judges considered it a privilege to work with the teams and learn of their clever ideas.
This report shows that it is hard to disagree with these comments. It also demonstrates how organising and running this complex challenge is a significant achievement that greatly benefits the industry by developing future engineers. The circa 20-strong team of judges and other volunteers from the Institution of Mechanical Engineers (IMechE) Railway Division deserve much credit for making the challenge happen.
The Railway Challenge takes place on the 3km, 10 ¼ inch gauge Stapleford Miniature Railway on the Gretton Family estate near Melton Mowbray, operated by the Friends of the Stapleford Miniature Railway (FSMR). A Railway Division steering group directs the production of the competition’s rules and technical specification. Items covered by the rules include:
» Maximum team size is 15, with no more than 40% previously entering the challenge.
» Members must be over 18 and either a student, graduate of no more than two years, or an apprentice.
» Safety requirements including the need for method statements for defined hazardous activities.
» The method of scoring and application of penalties.
The technical specification gives the teams the flexibility to meet specified performance requirements. It requires them to produce a locomotive weighing no more than 2,000kg with an axle load not exceeding 500kg and have a maximum speed of 15km/hr. It must be able to operate for three hours without refuelling at a continuous 5km/hr up a 2% gradient with a 400kg trailing load.
Other requirements include:
» Fit within the Stapleford railway’s loading gauge.
» Ninety-five percent of locomotive, by mass, must be recyclable.
» Refuelling to 100% capacity within 120 seconds, this may include the replacement of energy storage assets.
» Operation under all forms of precipitation, at temperatures between -10 and +40 degrees centigrade and between 0 and 90% humidity levels.
» Operate on track with 20 metre radius minimum horizontal curvature, maximum twist gradient of 6 mm over 0.25 metres and maximum gradient of 1 in 84.
» A maximum braking rate of 1.3 m/s/s
» Warning lights and horn, remote control operation, functional status indications to be seen by both driver and judge.
For the autostop challenge, an automatic braking mode must stop the train exactly 25 metres after passing a lineside marker. For the energy storage challenge, there needs to be a clear indication that the locomotive is being powered only by energy recovered from bringing the locomotive to a stand.
The specification also requires a comprehensive set of documents including: outline project plan; bill of materials; a top down and a bottom up safety analysis; business case presentation; a driver’s manual; innovation paper; method statements; detailed drawings including a control schematic; maintenance manuals; video of the locomotive under test; and a design report.
Prior to the event, the teams must submit their design report, innovation paper, method statements and video of their locomotive testing, as well as delivering a virtual business case presentation. This requires teams to act as representatives of a company selling their locomotive to a large corporation and requires teams to show that their design meets the customer’s demands and can be profitably manufactured.
The Railway Challenge takes place over four days. On Thursday 22 June the teams were individually briefed and then unloaded their locomotives in accordance with their method statements. The teams also set up their campsites on the ground
This design report must outline the locomotive’s design philosophy and contain a matrix demonstrating compliance with each of the specification’s clauses. Calculations demonstrating adequacy of the locomotive’s structure and safety of the vehicle’s suspension are also required. These need to consider curving wheel flange forces and show that maximum wheel unloading will not exceed 60% of normal load. For the poster challenge, teams have also to supply an A0 poster summarising the locomotive’s system architecture and its functional principles.
adjacent to the station. The IMechE staff, led by Fiona Wong, set up the marquee which was the administrative base and was used for briefings, the Friday night social evening, and the award ceremony.
On Friday, the first task was scrutineering led by the Railway Division’s Tim Poole whose team had a 33-point check list to confirm that locomotives were safe to run and built to the specification. To pass scrutineering, locomotives had to collect seven coloured stickers awarded for each scrutineering aspect. These were static tests of a physical inspection; documentation and calculations; indications; markings; user guide; and evidence of reliability. After static testing, locomotives were allowed to run on the railway for dynamic scrutineering.
FIGURE 1 - A judge is ready to measure distance travelled by Sheffield’s locomotive during its energy storage challenge FIG 1Friday also saw some refuelling and maintainability challenges. The latter required a powered wheelset to be removed and replaced in the fastest possible time. This was another potentially hazardous task requiring a method statement. To minimise the risk, this was also done in stages monitored by the judges. For example, prior to lowering the locomotive, the judges confirmed it was safe to do so.
Maintainability and refuelling challenges continued during the Saturday. One at a time, each team was also given the opportunity to give their locomotive a test run to try each of the dynamic challenges. The test often highlighted issues so some teams spent much of Saturday working on their locomotives.
gradient to a 1.2km balloon loop. During the weekend, each locomotive was planned to run around this loop three times (dynamic scrutineering, test run, and dynamic tests). On the Sunday, FSMR also provided spectator trains.
FSMR’s contribution is crucial to the success of the event. Led by Richard Coleby, it controls all train movements, provides a rescue locomotive, and a guard on each train. An important principle is all train movements are controlled by an FSMR controller who only accepts requests for movements from the Railway Challenge’s operational controller, Bridget Eickhoff. Her role includes changing the operational plan as required, for example in the event of a locomotive failing or not being ready in time.
On the Sunday, this plan enabled up to four trains an hour to be run. These were: the spectator train, the FSMR’s rescue locomotive, and up to two competitor’s test trains consisting of a team’s locomotive hauling two FSMR carriages for the driver, riding judge, and FSMR guard.
The first steam hauled spectator train left the station at 09:00, thereafter the plan was as follows:
Sunday was the day for the ontrack dynamic challenges. It was also the day for spectators, for whom FSMR provided a steam hauled train. As described below, with up to four trains an hour, this had its operational challenges.
Stapleford station has various sidings and a turnaround triangle. From the station, an 800-metre single line runs down a 1 in 80
2. Test train 1 leaves the station to do the autostop challenge (A to B). It is followed by the rescue locomotive as it does its challenges.
3. Test train 1 then does the ride comfort challenge. To do so it is fitted with an accelerometer (D) then goes around the loop to point E where the accelerometer is removed.
FIGURE 3 - The Network Rail / Colas team take the locomotive for a test run on the Saturday FIGURE 4 - Birmingham’s locomotive was only able to run on the Saturday for dynamic scrutineering CREDIT: Tom Moore FIGURE 5 - FSMR’s ‘Warship’ rescue locomotive FIGURE 6 -FSMR’s 4-4-2 Atlantic locomotive with rotary valve gear named ‘John H Gretton’ hauls the spectator train 1. Spectator train stops briefly at the Haven, then goes around the balloon loop and halts at the signal before the points at the Haven. FIG 6 FIG 3 FIG 47. Once test train 2 has passed point D, test train 1 moves to point G for its traction challenge and noise challenges (H to I), after which it returns to the station.
8. Test train 2 does the traction and noise tests (H to I) and returns to the station.
Rail Engineer has reported on the Railway Challenge since the first event in 2012 when four locomotives faced five challenges: traction; energy storage; ride comfort; business case; and design. This year the teams faced 12 challenges. Those additional to the 2012 event are: noise (2014); maintainability (2015); reliability (2016); innovation (2016); poster (2018); autostop (2019); and refuelling (2022).
There was also an energy efficiency challenge in 2015. However, precisely measuring energy consumption for the variety of traction at the event was not practicable and remains elusive.
4. Once the test train passes point D, the spectator train returns to the station.
5. Test train 1 does the energy storage challenge (F).
6. After the spectator train returns to the station, test train 2 does the autostop (A to B), ride comfort (D to E), and energy storage (F) challenges.
This enables a maximum of 12 test trains to be run over a six-hour period during the challenge day and easily accommodated the seven operational test trains on the main challenge day. Yet a significant increase in entries would present a real-world problem of rail capacity management.
The traction mix has changed significantly over the years. In 2012, three locomotives were powered by petrol generators, whilst the University of Birmingham fielded the UK’s first hydrogen locomotive. The 2017 challenge saw the first battery powered locomotive and nine locomotives were powered by generator sets. In 2022, only one locomotive was petrol powered and six were battery powered. This year, for the first time, there were no generator sets. The increasing use of battery traction was encouraged by a rule change allowing refuelling by changing batteries.
The maximum number of entries has been 11 locomotives on site, although the maximum number able to undertake the dynamic tests has been seven. The organising committee aims to attract many more entrants. However, although the Stapleford miniature railway is ideal for the Railway Challenge, its layout needs to be enhanced to realise this vision.
One such enhancement is a line from the station headshunt to a new turntable with 12 track spurs, and passive provision for another four. These will have hardstanding with each able to accommodate two locomotives and so will provide additional space for teams to work on their locomotives with the flexibility of despatching them in the required order. At the challenge weekend, work on this facility was seen to be well advanced. It is expected to be operational for next year’s Railway Challenge.
As well as travelling the furthest, the German FH Aachen & Reuschling and Polish Poznan University teams were, this year, entering their second railway challenge. Hence both had thoroughly tested locomotives. Together with a team from Nuremburg, they entered the European Railway challenge between 2-4 June at Bad Schussenried, Germany, which used the UK Railway Challenge rules and technical specification. This event was won by the Poznan team.
Noteworthy aspects of Aachen’s locomotive are a digital twin to simulate its operation and a radially steerable bogie. The Poznan locomotive has two roofmounted 100-watt photovoltaic panels to minimise power consumption. The team was also proud of the plastic bogie swing arms.
Professor Simon Iwnicki, who proposed the Railway Challenge in 2010 and has chaired the organising group ever since, explained that this work has been generously supported by Network Rail which surveyed the site and designed the turntable, as well as donating ballast. FSMR has also actively supported this project for which various volunteer weekends have been organised which have included Railway Challenge teams and Railway Division young members.
Also under consideration is a new chord by the Haven signalbox to enable trains to make multiple loop circuits without returning to the station.
The shortest journey to Stapleford was that of the combined Alstom and University of Derby team. This year their locomotive had been fitted with a glass fibre composite roof as well as chain tensioners to improve reliability. A Raspberry Pi used for traction control had improved coding for the autostop challenge and to enable an XBox controller to be used to drive the locomotive. Its extendable battery trays enabled rapid ‘refuelling’. Megan Cavanagh advised that testing on the Chesterfield miniature railway had been useful in resolving brake and control problems. She noted that component procurement had been a challenge.
The University of Sheffield’s team was formed of Mechanical Systems, Structures, and Electronics sub-teams who collaborated to produce their locomotive. Its members were from the Railway Challenge at Sheffield, an extracurricular student led club which has around 30 students in all year groups. Jacob Kunz advised that, except for wheels and motors, this year’s Sheffield locomotive was new. Its design started in September and its build, which used some 3D printed parts, started at the end of April. It was also tested at Chesterfield.
The combined Network Rail graduates and Colas apprentices team had built their locomotive at Colas’s depot in Rugby. Dan Manchee advised that although Network Rail’s graduates were encouraged to participate in the Railway Challenge, it was not part of the programme. Hence, this was an extracurricular activity taking around three
days a month throughout the year. For this year’s challenge, their locomotive included an autostop for the first time.
Transport for London’s (TfL) team was made up of graduates plus two apprentices and had mechanical, electrical, and project management sub teams. Eddiz Selay advised that the TfL locomotive had been enhanced to improve its reliability. Its testing at the Watford Miniature Railway helped refine its autostop capability. It was also commemorating the 100th anniversary of the introduction of the 1923 stock which were amongst the last tube trains with manually operated doors.
The smallest team present was a team of seven mechanical engineering students from Newcastle University. It was also the only one from an organisation new to the challenge. John Moorhouse advised that their locomotive had been delayed by Covid so was
designed over a three-year period. The team’s dual gauge locomotive was first tested on the 9 ½ Lakeshore South Shields Railway. Spacers and friction locks enabled it to be converted to the 10 ¼ Stapleford gauge in a few hours.
The locomotive is intended to be run on the railway at Newcastle’s Exhibition Park and so was larger than needed for the challenge. On the Saturday, it was doubtful that the locomotive would be operational for the dynamic trials due to a control software problem and ‘fried’ brake control module.
The University of Birmingham’s entry was not as originally planned. Peter Amor advised that the manufacturer of key components for their new locomotive had gone into administration. As a result, just six weeks prior to the challenge, it was decided to use the Hydrogen Hero locomotive that was used in the 2018 challenge and had been on static display in the University. Resurrecting this locomotive required the repair of poor electrical connections and hydrogen leaks.
Unfortunately, whilst running on the Saturday, the locomotive failed due to a problem with its DC/DC converter.
On the Sunday, seven of the eight locomotives did their dynamic test runs. Unfortunately, Birmingham had not been able to repair their locomotive despite phoning the original designer in America. Newcastle found a workaround for their software control fault and hastily modified
the brake control, though this provided only on or off braking. TfL’s locomotive failed on its way from the station for testing and was hauled back to the station by FSMR’s rescue locomotive. A control circuit had tripped when the new energy recovery status display was switched on. After this was repaired, TfL’s locomotive left the station 45 minutes late for its dynamic tests.
Although the results of the on-track tests were on a notice board, those for the non-track challenges were not. Due to this, and the judge’s assessment of any penalties incurred, the overall results announced at the prize giving ceremony were a genuine surprise. The results for the presentation, reliability, and on track challenges were as shown in the table. The top three places were very closely fought with the winner being Poznan (1648), closely followed by Derby/Alstom (1631), and FH Aachen / Reuschling (1629).
The University of Newcastle’s locomotive was the only operational locomotive on the Sunday that did not win a prize. However, producing a new locomotive that was able to enter at least some dynamic challenges was an impressive achievement worthy of note, particularly for such a small team.
Indeed, Bill Reeve noted at the award ceremony that past participants who are increasingly filling quite senior roles within the railway industry say that the Railway Challenge experience is the highlight of their training.
The Railway Division has plans for this competition to accommodate more teams, though these will only bear fruit if there are more entrants. Whilst the organising committee is considering how best to attract more teams, there perhaps needs to be greater awareness within the industry of the benefits of this event.
When reporting on the Railway Challenge, it is always a pleasure to experience the buzz at Stapleford and see the effort and enthusiasm displayed by the teams. It is also impressive to see how the FSMR, Railway Division volunteers, and IMechE staff ensure the success of this event and its smooth running.
The real prize for all who take part is experiencing the realities of delivering engineering projects to strict deadlines in a risk-free environment. Since 2012, a total of 77 teams have come to Stapleford for this experience which is roughly around 750 developing engineers. In this respect the IMechE’s Railway Division is providing a huge service to the industry.
Mention must also be made of the event sponsors whose financial contribution is essential. These were: Atkins; Angel Trains; LNER & Hitachi; Porterbrook; Railway Industry Association; RSSB; and Network Rail.
The National Robotarium at Edinburgh’s Heriot-Watt University was a particularly appropriate venue for the Railway Industry Association (RIA)’s latest Unlocking Innovation event for which the theme was Track and Train. This was introduced by Milda Manomaityte who explained how RIA’s Unlocking Innovation programme aims to promote innovations within the UK rail industry and bring businesses together to create new opportunities to innovate. Bringing 100 people from different organisations to hear 16 presentations and tour the University’s Robotarium and Heavy Structures laboratory was certainly a good way of promoting these aims.
The University’s associate principal for impact, Professor Marc Desmulliez advised that HeriotWatt University was founded in 1821 and now specialises in engineering, business, and science. Its graduate apprenticeship scheme offers work-based academic learning in partnership with 250 businesses. The University has also worked with InnovateUK to create Knowledge Transfer Partnerships supporting 84 businesses. Its collaborative R&D work includes that with Celestia Technologies to develop antenna technologies for high-speed data acquisition. Heriot-Watt has been offering online degrees since 2003 and now has 11,000 students from over 160 countries. It has campuses in Dubai and Malaysia and its new GRID (global research, innovation and discovery) provides a globally networked space for global collaborative working between academic disciples and industry partners. This is supporting global
research on robotics and AI, earth and marine sciences, health & care engineering, and net zero energy transition.
It is also part of the UK Rail Research and Innovation Network (UKRRIN)’s centre of excellence in infrastructure.
The National Robotarium’s CEO Stewart Miller, advised that this 4,000 sq. metre facility opened in September after construction started in March 2021. Its £22 million cost was largely funded by the Edinburgh and South East Scotland City Deal with the aim of establishing the region as Europe’s data capital.
It is the home to world-leading Artificial Intelligence (AI) and robotic experts from Heriot-Watt University and the University of Edinburgh whose focus is the development and testing of robotics and associated AI solutions across three distinct areas; robotics and autonomous systems, human and robot interaction, and high precision manufacturing. Stewart advised that the aim of this research is to keep people safe and healthy and make them more productive as well as developing talent and shaping the future.
He advised that the Robotarium aims to help companies reduce time, cost, and risk of introducing robotics by demonstrating proof of concept. It can also provide SMEs from across the UK with a gateway to the UK Robotics sector. He noted that the use of robots for manufacturing was now well established and felt that robotics offered particular benefits for the healthcare, hospitality, agriculture, and construction sectors. The afternoon tour of the Robotarium
demonstrated some of its robots in its laboratories and outdoor test area. This included the Boston Dynamics robot ‘dog’ which had an uncanny lifelike movement.
When Transport for Wales (TfW) was established in 2018, the aim was to significantly enhance the customer experience to encourage modal shift from car to public transport. As well as a large programme of investment in infrastructure, stations, and new trains, it was recognised that TfW needs to utilise the best emerging technologies.
In his presentation, TfW’s innovation manager, Michael Davies explained how the TfW Lab works with early-tomid-stage start-ups. Since 2019, the Lab has completed four cohorts of a total of 30 companies selected from 300 applicants. These companies were asked to provide solutions for challenge statements. To do so they are supported by a 12-week accelerator programme which includes access to TfW personnel, workshops, and mentoring before pitching to an expert panel at a demo day from which a cohort winner is selected. The winners of the four cohorts were:
1. Joint winners were Briteyellow which digitises indoor spaces to accurately locate, track, and guide customers and staff, and PassageWay which provides smart digital signs with real-time passenger information.
2. Spatial Cortex which has developed wearable technology to reduce the risks from manual handling tasks.
3. RoboK which offers a battery/solar powered system to monitor use and behaviours at footpath level crossings.
4. Cufflink, a security and regulatory compliance company which manages the distribution of sensitive data footpath.
From the four cohorts, there are now 12 ongoing projects for which contracts to the value of £500,000 have been awarded. The TfW Labs have helped these companies raise a total of £1.6 million funding and investment. An invitation to participate in a fifth cohort closed at the end of June.
In response to the need for an affordable light rail system, Coventry City Council has been promoting the development of a Very Light Rail (VLR) network as reported in issue 197 (July –August 2022). One reason for this is that the city has significant exceedances of air pollution limits and that, unlike buses, light rail does not have the non-tailpipe emissions from brake pads and tyres.
Angus Brummitt-Brown, Coventry’s senior VLR project manager for Coventry City Council explained the background to this project for which, in January, the West Midlands Combined Authority agreed the first instalment of an expected £72 million investment. As a result, the Coventry VLR system will be showcased between the railway station and city centre in a few years’ time.
He explained why the VLR is expected to cost around £10 million/km. This compares with £56 million/km for the recently opened Edinburgh tram extension to Newhaven. This low cost is largely due to a novel track form which significantly reduces the number of infrastructure diversions required and simpler battery powered vehicles that don’t require overhead catenary.
Angus noted that pioneering this novel form of transport was not without its challenges. Funding is difficult as the VLR project has significant uncertainties, though these will be alleviated by thorough testing the Very Light Rail National Innovation Centre (VLRNIC) in nearby Dudley. Approving something
that “does not fit into a box” is a challenge for which the VLRNIC will also be helpful.
Compliance with the public contracts regulations for the procurement of a unique product and its associated R&D activity is also problematic.
The presentation given by Martin Bignell, Scottish and Northern Representative, Rail Freight Group (RFG) concerned the way rail freight works in Scotland. In respect of innovation, this is more about a different way of doing things in Scotland rather than introducing new technology.
In Scotland there are six competing freight operators who run about 300 services a week. Of this, 14% is internal Scottish traffic, 35% is traffic to Scotland, and 52% is from Scotland. Of the AngloScottish trains, about 80% run on the West Coast Main Line. Eighty percent of Scottish rail freight is intermodal and construction traffic.
As the RFG representative for Scotland and Northern England, Martin felt that the ‘Scotland’s Railway’ approach had been particularly successful and more collaborative. He considered that the reasons for this included:
» The Scottish High Level Output Statement (HLOS) brings clarity (e.g., it includes specifics such as gauging, power supplies, electrification, and a specific 8.7% CP7 freight target that are not mentioned in the HLOS for England and Wales published by the DfT).
» Holistic planning of infrastructure and operational interventions.
» Enhanced reporting of freight metrics.
» A quarterly Scottish freight joint board that provides collaborative governance which puts the industry at the centre of planning and investment decisions to bring transparency, shares best practice, and highlights specific requirements e.g., review of section running times and digitalisation of freight train load book.
He felt that, with a clear commitment from the Scottish Government, this approach showed that a ‘guiding mind’ for track and train doesn’t have to mean vertical integration of infrastructure and operator. Instead, the objective should be about behaviours and enabling a mixed-use railway to work in accordance with its customers’ requirements.
in December 2022.
CREDIT: Network Rail
Martin felt that it was essential that rail freight has the flexibility to respond to changing demand such as that from new hubs. Yet rail infrastructure has very, very long-term planning horizons. Hence, freight operators need confidence that there is sufficient capacity for them to grow in the medium and short term. He concluded by noting that, if there is to be modal shift, there must be space for it to grow into.
FIGURE 3 - First freight train from the new Highland Spring terminal in Perthshire. This was part-funded by the Scottish Government and openedThe development of a robotic Railway Inspection and Repair System (RIRS) was the subject of a presentation by Miftahur Rahman, a PhD student of Cranfield University. His project is the development of an autonomous vehicle to undertake track inspection and repairs. He noted that this had the potential to automate hazardous on-track tasks.
travelled, and recognising known trackside objects. He explained how the limitations of a forwardfacing camera are overcome by having the manipulator arm take multiple images from different positions to provide a data rich 3D model of an object which can be compared with 3D models of other similar objects to detect any anomalies. When working off-track, the vehicle can optimise its route to avoid obstacles and it has object detectors to avoid collisions when working on track. The prototype has been tested on track when it detected simulated rail damage and sent accurate information about its location. Yet various challenges remain. Miftahur advised these include track access, communications, refining location awareness, power, task verification, and cybersecurity. When these have been addressed, the RIRS vehicle is likely to be the first autonomous prototype robotic rail maintenance demonstrator. It will be interesting to see when such robots first see practical use.
developed in collaboration with the Royal National Institute of Blind People and is now being piloted at London Euston.
RIRS uses a Warthog ground vehicle robot with an adaptive trolley that enables it to travel on and off-track. It has a robotic manipulator arm and multiple onboard sensors including LIDAR, real time kinematic (RTK) GPS camera, multiple types of cameras, wheel odometry and an inertial measurement unit (IMU) which measures the three degrees of linear acceleration as well as the three rotational rate components. The vehicle is controlled by Kinetic Kame robotics operating software which uses Gazebo development libraries to provide advanced 3D graphics and simulate dynamic loading.
Miftahur explained that the vehicle can determine its position from RTK GPS, distance
A feature of the RIA Unlocking Innovation events is their elevator pitches when presenters are given a few minutes to convince those present of the benefits of their innovation. Of the nine pitches, only one featured innovative hardware whilst most of the others used AI to improve asset management or provide meaningful customer information. Helping visually impaired people navigate the UK public transport network was the focus of a presentation by GoMedia’s Sven Koster. Its app does this by reading NaviLens codes which, unlike QR codes, can be read from up to 20 metres without the user knowing where they are placed. This has been
Rob Franklin described how his company, Jnction, had worked with rail companies to provide tools customised for their needs using AI. Its ‘Aubin’ wayfinding app is designed to assist the autistic community by providing a journey planner that avoids aspects that cause stress. It is soon to be trialled at Bristol Temple Meads station. The founder of WorkfromHub, Neal Byers, believes there is a need for private working spaces in easy-to-access locations. To satisfy this demand, his company is setting up a network of working hubs which can be booked using an app.
The benefits of AI for asset management were illustrated by Tim Flowers who explained how his company, KONUX offers predictive maintenance, network usage, and traffic monitoring and planning solutions for railway infrastructure management. In particular, KONUX Switch can increase the life of a rail switch and monitor the traffic over it.
AI also offers improved station safety as Duncan Kennon of Createc illustrated by describing how ‘Situate’ offers real-time crowd monitoring using long range LIDAR sensors. As this doesn’t use cameras, there are no privacy issues. Crosstech’s
FIGURE 4 - RIRS on track.Hubble application does use a camera, specifically forward-facing video which is analysed by AI to identify and prioritise asset faults as Haydon Bartlett-Tasker described.
Milo Lloyd of ‘The Formal Route’ described how the SafeCap toolset has been developed to provide a fully automated verification signalling
interlocking data. It has Network Rail approval and, over the past three years, has been successfully used to verify 60 interlockings developed by different suppliers and identified some safety issues.
In contrast to the other pitches, Stuart Jackman of Jackweld pitched innovative hardware that had been
developed to address Network Rail rail welding process challenge statement. This shows that there are around 40,000 aluminothermic welds a year with a 2% rejection rate. Jackweld’s solution is a vibrationless orbital friction welding system which moves a thin steel disc clamped between the rail faces. This provides a solid-state welding process with no melting of the parent metal, and so retains the parent metal’s structure and does not result in fatigue failure initiators. It also has a much-reduced heat affected zone and uses less than 25% of the energy of thermic welding. For these reasons, orbital friction is more reliable and cost effective than thermal welding as well as being ideal for advanced metal alloys. Stuart advised that the system is currently awaiting a Network Rail trial.
Prior to visiting the University’s heavy structures laboratory, Professor Omar Laghrouche explained how its work has supported the rail industry. This included the 2015 report ‘Geodynamics of train-track-soil under high-speed train loading’ which was undertaken to address concerns raised during the HS2 Bill process. At the time, it suggested that high-speed trains may be derailed due to ground instability due to their travelling close to the wave propagation velocity of the supporting track-ground system.
In collaboration with Balfour Beatty, the University has also developed XiTRACK polyurethane ballast reinforcement which has been used in heavily trafficked locations such as Clapham Junction. Another example is accelerated full-scale testing of railway slab and ballasted tracks on the GRAFT rig which can simulate a year’s loading in a day. The Geo-pavement and Railways Accelerated Fatigue Testing facility (GRAFT) is one of only two academic facilities of its kind in the UK. It has a hydraulic capacity of 200 tonnes (150 tonnes cyclically) which enables accelerated testing of existing and new railway products in realistic railway conditions.
Whilst visiting the heavy structures lab, those present saw the GRAFT rig about to be used to test novel composite sleepers. Also on display was 3D printing of free form structural members and synthetic bricks recycled from construction waste.
As always, RIA’s innovation events are thought provoking. This one highlighted the opportunities and challenges of AI and robotics for which there are currently few general use applications. This is perhaps not surprising as, for example, the Boston Dynamics robot dog went on sale to the public in 2021 for $75,000. Whilst few can now afford such robots, production at scale could soon see their widespread business and domestic use in the same way that initially expensive mobile phones are now ubiquitous. Yet the event also showed that railway engineering is fundamentally about heavy engineering to control the large forces generated as, for example, a 450-tonne train is supported and guided by rails at 200 km/hr. This is only possible as a result of the research done at universities such as Heriot-Watt.