RAMTIN HAGHNAZAR (KOUCHAKSARAEI)
Selected Projects 2011-2022
Blacksburg, VA, ramtin@vt.edu
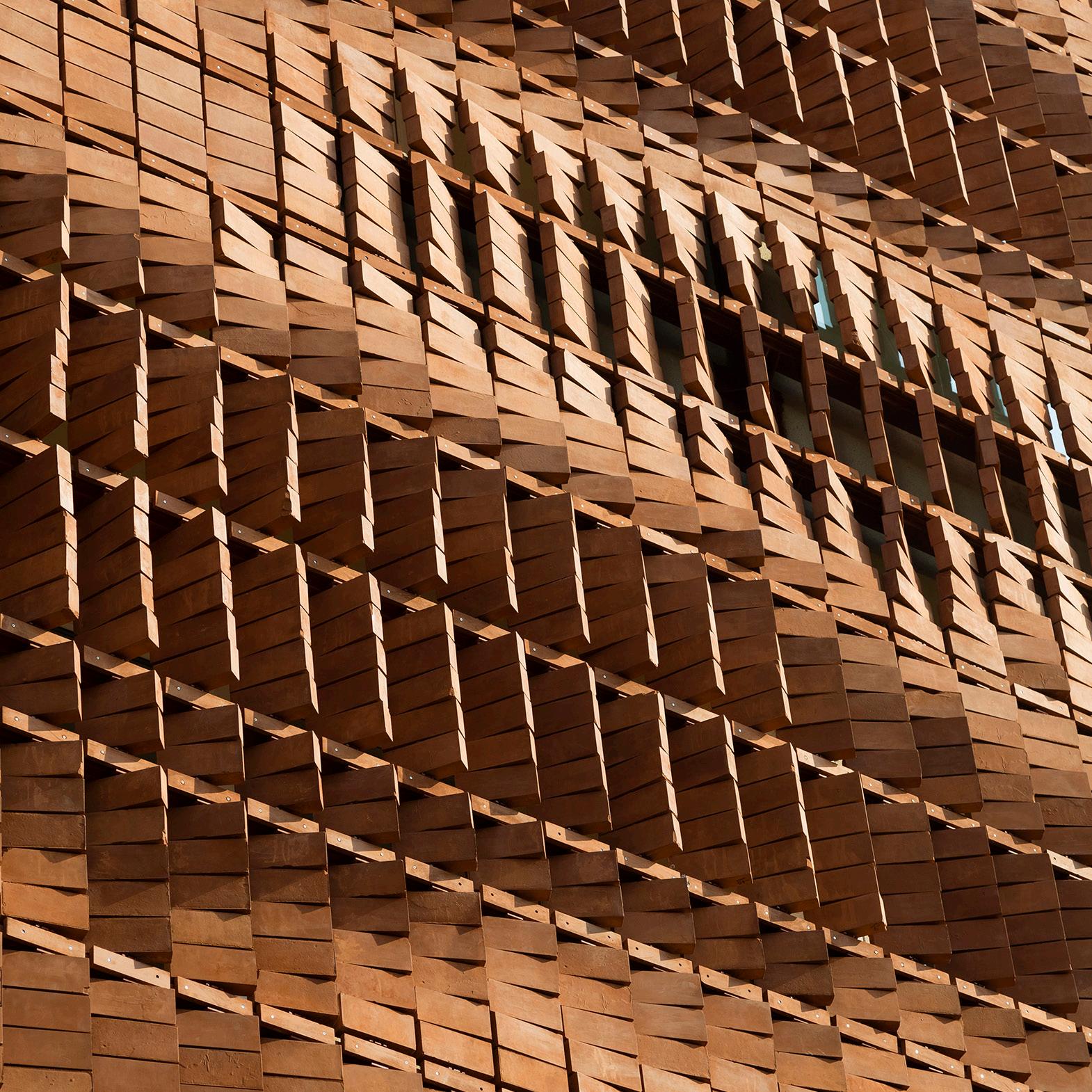
Table of Content
Click on the title to go to the project
RAMTIN HAGHNAZAR (KOUCHAKSARAEI)
Selected Projects 2011-2022
Blacksburg, VA, ramtin@vt.edu
Click on the title to go to the project
Tensile Formwork for GFRP
Yazd, Iran, 2020 page 2
Tensile Formwork for GFRP
Yazd, Iran, 2020 page 6
Wooden Bended Elements
Tehran, Iran, 2019 page 10
2 Sided CNC Milled Elements
Karaj, Iran, 2019 page 14
Robotism
Robotic Assembly
Tehran, Iran, 2019 page 18
CADF98
Suspended Plates
Tehran, Iran, 2020 page 22
CADF96
3D Printed Space Structure
Tehran, Iran, 2018 page 24
Ply-House
Digital Fabricated Tiny House
Tehran, Iran, 2017 page 26
To see the full version of the portfolio containing CV please click here.
Floating Circle Design And Fabrication
Tehran, Iran, 2020 page 28
OTHER PROJECTS
Associate Designer and Fabricator
83, Virginia
Associate Designer and Fabricator
Toronto, Canada, 2021 page 42
Freeform
BIM Modeling & Digital Fabrication
Tehran, Iran, 2017 page 32
Cloaked in Brick Integrated Design And Fabrication
Tehran, Iran, 2014 page 36
Digital Wood Crafts Artwork
2019-2021 page 46
Role: Manager and Tutor
Credits: Photos and diagrams were created by the workshop students and instructors. https://issuu.com/ramtinhaghnazar/docs/bamboobam_-_a4_001113
Freeform Space Structure Workshops are held for research and practice of the two areas of “free form structures” and computer integrated “construction and design” methods. Each of these training programs deals with a specific way of constructing free form structures. This workshop was held with the participation of 42 students in 6 groups. 13 instructors helped them through the research and development process within four months.
During its process, the workshop tried to cover five major research areas: material studies, sustainability, computational design, form-finding, structural design, and digital fabrication. These disparate fields demand a diversified set of skills, abilities, and experiences. We had instructors and partners from various institutions and backgrounds who willingly offered to share their talents and expertise to ensure that we could cover the topics to the extent required for a workshop.
In the first chapter of this summer school, a team was tasked with researching bamboo as a natural, non-standard material, its qualities, applications, and construction possibilities. Following that, we conducted a market survey to determine the sorts of bamboo available. We identified four varieties and conducted a preliminary investigation, evaluating their quality, geometric and mechanical features, and workability, among other characteristics.
In the second chapter, in a series of brainstorming sessions, various systems were proposed until a handful of them were shortlisted. The shortlisted systems were then prototyped, with the fabrication method for each being investigated. We undertook an evaluation procedure based on several criteria to determine the benefits and drawbacks of each system. We chose the final of these four options and proceeded with it.
Evaluation Criteria:
- Visual elegance
- workability
- Structural Performance
- Durability
- Cost
Images:
Left - Studying the accessible bamboo material (local species) and gathering its properties like thickness, dimensions, and strength. Additionally, researchers test the effect and functionality of digital fabrication tools such as laser cutters and CNC milling machines.
Right Top - Prototypes of the joint systems.
Right Bottom - Final joint.
we developed a “digital design workflow” in a parametric modeling platform known as “grasshopper”. This digital workflow fully automates the modeling process and delivers the required outputs in a timely manner. The workflow starts with getting two general inputs from the user: first, the wire mesh generated during the form design phase, and second, some
numerical inputs about bamboo, CNC machine, Bolts and nuts, and node design preferences.
After collecting and interpreting these data, it generates a completely comprehensive 3D model with labels for each element. As a result, it can be utilized as a coordination model during the assembly process.
For the bamboo poles, we understood they would need four bolts at each end and not alighned to one another to connect to their respective joints. Three-axis CNC milling machines already existed that could drill vertically through the bamboo poles. Our poles couldn’t be rolled due to the fact that the drilling was only going one way. A rotary axis that was not affordable and might not fit our CNC bed had to be purchased or we had to design a custom one. We decided to go for the latter solution.
The rotary consisted of three main parts. A gripper to grab the pole firmly in place while drilling and meanwhile align its center to the rotary axis. A rail and an adjustable wagon for different pole lengths. And a rotator to orient the pole at the right angle.
We decided to buy a low-cost 3-jaw concentric gripper for one end and 3D print a cone-shaped piece for the other end that would attach to a plywood wagon. It was built to go easily along the Y-axis on a rail, making it flexible to the length of the bamboo pole.
Images:
For the rotator, we built a harmonic drive, also known as a strain wave gear, using 3d printed and laser cut parts, ball bearings and a stepper motor along with An Arduino board.
With the rotary axis in place, We only needed the precise toolpath to drill the poles with our CNC milling machine and the correct angle to rotate the poles after drilling the first two holes after the rotary axis was in place. The rotation angles of each pole are collected from the grasshopper BIM model and used to construct the Arduino program for each rotation.
Images: Fabrication and assembly process.
Role: Manager and Tutor
Credits: Photos and diagrams were created by the workshop students and instructors. https://issuu.com/ramtinhaghnazar/docs/fss3-portfolio-honar-pages
Freeform Space Structure Workshops are held for research and practice of the two areas of “free form structures” and computer integrated “construction and design” methods. Each of these training programs deals with a specific way of constructing free form structures. This workshop tried to design and construct a composite structure by examining free-form fabric structures. At first, students have created ways to develop the form by studying the materials and understanding their behavior. Then, they have developed their designs using digital fabrication tools and produced them on a real scale. After digital designing, the final fabric structure is formed by cable and then reinforced with polyester resin and fiberglass. This workshop held in Yazd in three weeks. In the end, students built a 25sqm pavilion.
The first phase of the workshop consisted of two parts: training and experience. In the training section, students were introduced to the Grasshopper software as a digital design tool to realize their potential in design. Students were then asked in the experience section to try to create a free-form structure or part of it using fabric and plastered with white shell plaster. In this section, the students succeeded in designing several different prototypes. In the next step, Students were introduced to the materials used in the main structure and produced the final prototypes. In the last step, one work was selected by students’ vote and was made on a real scale.
In the pre-workshop , different methods of fabrication of these types of structures and different types of fabrics were tested for their elastic behavior. As a result of this process, the raven fabric was selected as the desired prototyping material and tensile fabric for use in the final work. In the initial tests, the plaster was replaced by polyester resin as a fabric hardener.
In the design phase, three different concepts were presented by the students. Digital simulation added to the physical form finding to accurate the final model and estimation.
Images:
Three finalist ideas. The left one selected for final construction because of its unity and complexity. Moreover, the fabrication method can have only one smooth and finished side, thus the second concept was not suitable for it.
The first product of this workshop is the pavilion that placed in the Nurse Park of Yazd city. The pavilion consists of a free-form fabric structure held by a cable. At the end, the structure is stabilized using polyester resin and fiberglass, then cables removed. At first, this form was made in smaller dimensions, then, depending on the location of the pavilion and the construction restrictions, the final design was achieved. To make this pavilion we used two pieces of fabric with almost the same elasticity in both directions. Dimensions of each piece are 2*2m for the base and 3*4m to cover the top. At the junction of the columns, holes were made based on the digital model of the pavilion, and the upper and lower parts of the structure were sewn together using punched metal plates.
Images:
The top row show the fabrication process of the final structure. Installing the tensile structure. Add resin and fiber glass to create GFRP. Finishing process.
Bottom row shows the final product.
Role: Manager and Tutor
Credits: Photos and diagrams were created by the workshop students and instructors. https://issuu.com/ramtinhaghnazar/docs/sas-portfolio-pages-200
Like the previous FSS program, students studied a novel way of freeform making. FSS#2 focused on bent elements. Students studied material and digital fabrication abilities and tried to make two proximately 25sqm pavilion.
This workshop simultaneously held in the Art University and the University of Tehran in three weeks. In the end, students built two different pavilions in the universities.
The main idea of this workshop was based on Negar Kalantar’s research named “Surface Active”. Thus, students tried to make a freeform surface by Bending Active Structure approach.
The second concept is the result of the weaving of two bent elements. In this Idea, two elements bent by force. Then, they stabilized by joining to each other. This action formed the elements and made them much stronger.
Left: Design process
Right: Form generation diagram
Bottom: Strips to arch form elements
This prototype was assembled at Art University, Tehran. Assembling takes two days. The structure stood alone, and there was no foundation. All three legs bounded to each other by a triangle made by 1mm thick cable.
Tehran, Iran | Winter 2019
Role: Manager and Tutor
Credits: Photos and diagrams were created by the workshop students and instructors. https://issuu.com/ramtinhaghnazar/docs/fss1-nexorade-portfolio2
FSS program, Freeform Space Structure, is a part of long term research which leads by me in Digital Craft House. This research tries to study different ways to build a freeform space structure.
In each step, the various researcher focuses on a topic and try to develop it. The result of this development appears in an academic workshop. FSS#1 was an academic workshop that worked on the Nexorade structure based on Olivier Baverel’s research. FSS#1 was a 10 days workshop.
In the second phase, students experienced integrated computational design and fabrication. They tried to design a Nexorade which was able to build using 3mm thick plywood and laser cutting system. They consider a simple joint detail and developed a Grasshopper code to generate model and shop drawing.
In the beginning, students tried to understand the logic of the Nexorade. Thus, they tried to build a simple structure by overlaying simple wooden sticks.
Below: Students’ samples for the first phase.
In the final phase, one of the students’ models accepted for the final real scale model. This proposal contained a partition which separated two parts of the DCHouse. Here, students try to find the best detail for the joints considering restrictions; material was restricted to 12mm thick plywood, and technique was limited to CNC milling machine.
Preliminary wire mesh
Extending the elements Rotating the elements
Generating the surface
Three things added the final model:
Footprint of the element
Pattern drawing
A line considered design and carved the CNC to show nailing position
Rotating the elements
Making the elements’ base
Generating the final shape of the elements
Extending the elements
To ease in assembling, footprint of each element engraved on the
After creating the model as illustrated, the team has tried to make a G-Code for the CNC milling machine to cut the elements in the designed angle. Then, the structure footprint considered as the base plate. Next, students
tried to place elements one by one to the end. During this process, a person navigates the others and tells them how to place each element. Installation takes around 15 hours.
in the carved bay show the position
assembling, element other.
added to model: Numbering Nailing line the other element model Fabrication
Tehran, Iran | Fall 2019
Role: Instructor
Credits: Photos and diagrams were created by the workshop students and instructors. https://issuu.com/ramtinhaghnazar/docs/booklet_robotism____fall2029
ROBOTISM was a ten-day workshop held in December 2019 at the University of Tehran, focused specifically on the computational design and robotic fabrication. The workshop included 45 undergraduate and graduate architecture students who were divided into groups of 5 to 6 and practiced working with the robot. KUKA KR6 with a KRC2 controller was used in this workshop.
After teaching the KRL Syntax at the beginning of the workshop and elaborating on how to generate G- odes, the students did two series of basic exercises in their groups to learn the concept of paths in robot simulation in the first part of the workshop. For the first exercise, they were asked to draw continuous curves with specific patterns in grasshopper 3d and define the motion path of the robot and after generating the G-codes they started to light painting by using a simple LED as a tool that was placed on the robot’s head. Groups produced corresponding G-codes to make the robot follow the specified paths and print the pattern with the light. In the next exercise, each group was asked to design a structure by placing wooden pieces with specific sizes and numbers, making sure that it could maintain its stability throughout the assembly without the need for screwing or gluing.
Top: Light Printing. Bottom: Brick laying practice.After performing introductory tasks by the teams and getting acquainted with practical challenges like properly defining planes to prevent collision of the robot arm with its surroundings, and installation of the pneumatic gripper and air pump, students embarked on designing a pavilion on a scale of one to one. The major restriction to be considered in designs was the amount of available material, 40 square meters of 18-mm plywood. All of the proposals were assessed by the jury, and eventually, one of them opted for the final project. Modifications were also made to finalize the design.
The final design had to be prepared for the assembly process. Given the limitation of the robot’s reach to 1.6m and the conditions of the site, we decided to halve the arch and also split each half to 4 and 5 sections respectively, making a total of 9 sections. Two methods were proposed for connection of wooden pieces; utilizing a glued roller to which each wooden piece would be rubbed by the robot and placed at its position, or using a collaborative human-robotic fabrication technique in which someone would use a pneumatic nail gun to fasten objects together after being placed by the robot. Considering some practical issues and time constraints, the latter was preferred. the fabricated sections in the workshop space were transported to the campus and assembled over two hours.
Form finding and discretization DIagrams:
- Main surface.
- Discretization.
- Dividing the installation to 9 parts considering robot size and stability of each part.
Assembly Diagrams:
The arm picks each element from the designed stand and places it in a specific position. In the grasshopper code, we checked some critical points. Firstly, each part has to be stable by itself during and at the end of the placing process. Thus, the code checks its stability in every step. Next, some of the elements, shown in red, do not have suitable support, and their pivots are out of the below elements. Therefore, we placed extra blocks without connecting them to the main ones to make the red blocks stable.
Role: Lecturer at the University of Tehran Credits: Photos and diagrams were created by the workshop students and instructors. https://issuu.com/ramtinhaghnazar/docs/cadf98a-portfolio-pages
CADF98 is a 2-credit course for undergraduate students at the University of Tehran in 2020. The purpose of this course was to provide students with an integrated digital design experience and familiarity with digital fabrication tools and facilities. Our ultimate goals were to produce an installation by students in the court of the Faculty of Fine Arts. This installation was constructed with plywood sheets and using a technique of suspended structures. Manufacturing of all parts of this installation were all digitally produced. This course was attended by 36 students and 3 instructors. Students experienced integrated computational design and fabrication. They tried to design an installation and developed a grasshopper code to generate a model and shop drawing. In the final phase, one of the students’ models accepted for the final real scale model. Students try to find the best detail for the joints considering restrictions; the material was restricted to 9mm thick plywood, and the technique was limited to the CNC milling machine.
After creating the model as illustrated, the team has tried to make a G-code for the CNC milling machine to cut the elements. The structure is made of a cubic frame which is 2.4×2.4×2.4 m³ and several suspended panels with cables. All the parts cut from 9mm thick plywood sheets by CNC milling machine and assembled by students in the court of the Faculty of Fine Arts.
Role: Lecturer at the University of Tehran Credits: Photos were created by the workshop students and instructors.
Like the previous CADF program, in this course, students tried to experience another type of fabrication. This year, students wanted to work on a spacial lattice structure using 3D printed joints.
Dahi Design Studio and Kade 3D printing lab were the commercial sponsors of the projects, providing 3D printers freely. The final installation was a 4-meter height column.
At first, students studied the basics of computational design, and after that, students started to make proposals for an installation. In the second phase of the class, five groups prepared a proposal for the final product. Proposals contained various techniques and generated a digitally fabricated model. All of them, which are presented in the pictures, demonstrate the technique of the fabrication. Finally, students voted, and the first technique was selected for the final project.
In the final sector, students finalized the design and selected PLA as the final material; then, they developed the code which was able to generate all the details and shop drawings. All the joints were 3D printed and assembled by students.
All of the linear elements are 1cm diameter steel pipes. The thickness of the pips is 0.1cm, and the joints are the rigid type made by PLA. Therefore the weight of the structure is less than 50kg, although it can carry loads much more than its weight because of the space frame feature.
Wires ended to a joint | Sphere as the basic geometry to calculate intersection | Basic mesh, containing convex hall of the points from intersection plus sleeve of the elements | Relaxed mesh | Final Model
Design | Test printing | Final joints, rings around sleeves show the orientation of the joint | Cutting elements based on the model data | Printed joints | AssemblyTehran, Iran | Summer 2017
Role: Manager and instructor
Credits: Photos were created by the workshop students and instructors.
In this fabrication workshop, the problem was the design and manufacture of a tiny house for an emergency. Thus, we need a little home which can build quickly with ordinary people. Students were limited to work only with plywood and CNC milling machine because they are available everywhere and every time.
In the first phase, several students team had designed different tiny houses, and at the end of this phase, instructors select a project to build on a real scale.
Then, Students tried to make a BIM model of the house and built it in 3 days.
This course took three months to design and three days to built with 20 students at the University of Tehran, Center of Excellence in Architectural Technology.
Tehran, Iran | 2020
Role: Designer and Fabricator, member of the team. Credits: Photos and diagrams were created by Dahi Studio team.
The “floating Circles” is a false ceiling which is designed and constructed for the Mofid Securities Co. branch. The main project was designed by ..., and the very high ceiling that was not suitable for its function was the critical problem of the space.
Based on the occupation, the hall was divided into several spaces for a counter, lobby, sitting area, and VIP meeting room. Thus, these spaces need different heights. In order to tackle the objective, the design team tried to create a free form false ceiling which can perform various height in relation to the needs.
On the other hand, there was not an ability to add a secondary structure for the free form ceiling. Therefore, the only way was to suspend light plates from the ceiling. Moreover, it was a lot better to distribute the loads through the ceiling panels.
Colors change from the dark green, which was the company brand color, to white which was more suitable for the hall.
The
The
The research group tested several methods of suspension which was capable of suspending the plates in a specific position and specific tilt and rotation considering that we cannot have anchor where ever we want. The final method connects three points of the roof to three points of the plates with six cables which create six triangles and hold the plates in a specific position.
Top Row: Initial Prototyping. Specific ruler design for the project which helped us to create fixed length cable considering the hook.
Labels for each cable. Final installed plate. Bottom Row: The hall area. Beyond the surface.
Tehran, Iran | 2017
In cooperation with EMRE ISTIKAM Co. Role: Writing the generative code which converts the wire mesh model to full detailed BIM model. Credits: Diagrams by Danial Keramat. Link to the paper.
In this project, we tried to find a way to make shop drawings for freeform spacial frames automatically. In this type of structure, which is shown in the picture, every element, joint, and glass are unique. Therefore, it is hard to make a shop drawing one by one by an operator, because it takes a lot of time and may cause some human errors. Thus, in this project, we create a code in grasshopper software which converts a simple wire mesh to a full detail model (BIM).
Terminology
Node Axis
Fabrication Method
By this program, there is no need for an operator to make a model, generate shop drawings, check the errors, etc. and it is easy to design this kind of structures and buildings. So, the designer can make a simple wire mesh and see a real-time full detail model. The designer also can edit the model and see the result immediately.
Up to 2020, two different free-form surfaces were designed and built in Tehran by this code.
After generating the shop drawing of the nodes and beams, the code has to generate shop drawings of the glasses. In this part, based on the data was generated in the previous part, the code generates drawings for the inner layer, outer layer, and how they attached to each other. >>>
Tehran, Iran | Spring 2014
Role: Associative Designer, Facade designer, and fabricator, in cooperation with Admun Design Studio
(2016) Gold Medal, in “Architizer A+ Award” in the USA, in the “Brick” category with Visitors.
(2016) Gold Medal, in “Architizer A+ Award” in the USA, in the “Brick” category with Jury.
(2015) Shortlisted, 9 projects were shortlisted, in 39th “ The Annual Brick Awards” in the UK, in the “Best international and worldwide project” category.
(2015) Honorable Mention, in “Memar Awards”, in “Residential Apartment” category, Tehran, Iran.
Credits: Photos by Parham Taghiof and Mostafa Karbasi, and diagrams by Mostafa Karbasi.
http://www.archdaily.com/775030/cloaked-in-bricksadmun-design-and-construction-studio
This project is a façade which covers a residential/ official building, and it was done in co-operation with Admun Studio. The façade was designed base on Iranian vernacular and traditional architecture, which has some key features such as Privacy and special material, “Brick”. The façade was desired to be built mainly of yellow brick, while it should be novel and deconstructive as the client want. To reach this goal, the project was designed by placing bricks on the other, in a different way, and the opening created by rotating the brick around their axis in a parametric form. The inner layer of the façade was a transparent one which contains wide and large windows. To manufacture and build the façade, the regular steel structure was designed, and long screws prepared to keep the bricks. We considered two holes in each brick, and the position of these holes define the location and rotation of bricks. To have bricks from various angles, we used a milling machine and read data from the Grasshopper.
The property of the behind room defines the rotation of bricks. For example, to prepare proper lighting in the living room, as it is shown in view I, the bricks rotate, but they do not show the bars and columns. The details designed in a way that just bricks and an 80x80mm steel bar are visible from the inside.
Toronto, Canada | 2021
Role: Associate Designer and Fabricator (only the wooden second skin), Meanders Co.
Credits: Photos by Meanders and diagrams by Hanie Omid.
Top: The second skin form generation.
Bottom: Open and closed form.
The mold and fabrication process of each element. Each element needed a unique mold, and the molds were built two-sided to save material consumption. It takes a day for the glue activation process, and we could only fabricate two elements per day.
This project is a second skin for a residential facade in Toronto that covers the windows to control daylight. The elements are fabricated from 5 layers of 9mm thick plywood glued together in a mold’s curved shape. Due to the parametric form of the facade, each element had its unique mold made by MDF using a CNC milling machine.
Each element had a specific shape, and each layer of the elements was different from the others and unrolled with Grasshopper 3D and made by a CNC machine. Two parts of the facade had retractable elements that could open the view of the user according to user needs.
All elements were fabricated in Iran and shipped to Canada by a container. The mechanical components of the retractable parts are assembled on stainless steel in Iran, while the windows’ sizes are larger than the container’s width. Thus, the customized container was built with angled racks to handle and grab the oversized frames.
build these elements, we used standard exterior plywood and coated them with natural oil wood stain.
FABRICATED
Tehran, Iran | 2021
Role: Designer and Fabricator in colaboration with Yasaman Ashjazadeh.
Credits: Photos by Yasaman Ashjazadeh and Shakiba Shekarkhand. https://www.instagram.com/dahicraft/?hl=en
Dahi studio, as a research group in the field of computational design and digital fabrication, supports start-ups and ideas. In 2019, Yasaman Ashjazadeh started Dahi Craft in collaboration with Dahi studio, and I designed and fabricated several objects, a chair, and two tables in this startup.
Left: Sufi.
To create this object, we use hardwood called Beech; the wood’s high density allows us to have a very smooth surface after sanding. After creating the 3D model, we used a 12mm ball nose tool and a CNC milling machine.
Right: Lavak.
Lavak is a computational design plate that lets the user design a customized version of the plate. After finalizing the design and dimensions, the object will be fabricated by a CNC milling machine. Up to now, we have designed and manufactured over 30 versions of this object.
We are supposed to have a web-based design tool in which customers eseally select the number of points and define some parameters like the position and radius. Then the app generates the form, and you can have the price estimation and final volume. The customer orders the object and can have it soon. Although we did not make an online app, we generated several models costomized based on our client’s needs.
THANK YOU FOR YOUR ATTENTION
To see other projects please visit: ISSUU