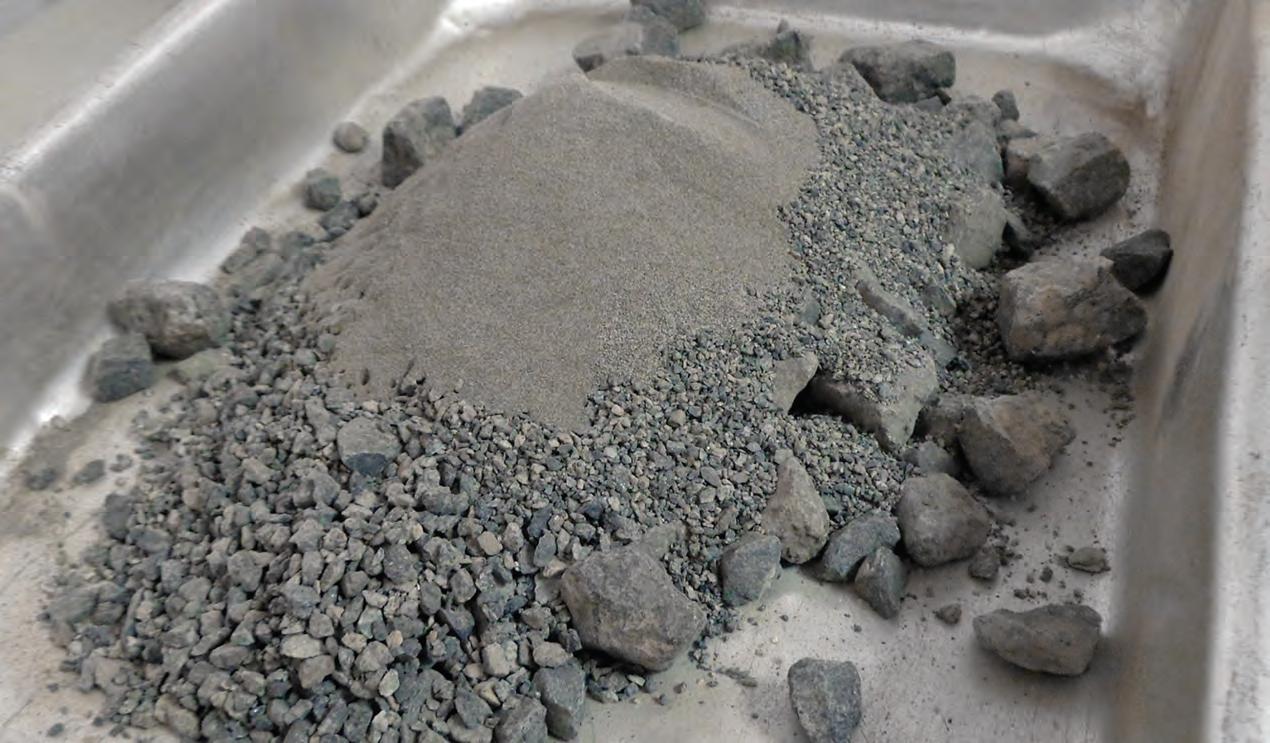
12 minute read
Mix-design delle miscele bituminose
asfalti&bitumi
MIX-DESIGN
Advertisement
DELLE MISCELE BITUMINOSE
ANALISI DELLE CURVE GRANULOMETRICHE E PROPORZIONAMENTO DEGLI AGGREGATI SECONDO IL METODO DI BAILEY PER LA CORRETTA IMPOSTAZIONE DELLA COMPOSIZIONE VOLUMETRICA DELLE MISCELE
L’aggregato in un campione di miscela bitumosa a seguito della prova di estrazione
La progettazione delle miscele bituminose, confermata l’idoneità dei materiali costituenti disponibili, prevede, come noto, una fase iniziale di selezione e impostazione dei diversi parametri secondo valori target compresi entro intervalli (valori minimi/massimi) 1 generalmente specificati a livello di Norme tecniche contrattuali e documenti guida di riferimento (per esempio, MS-2 Asphalt Mix Design Methods/7th edition). In questa fase, è altrettanto noto che il proporzionamento degli aggregati disponibili, con le correzioni necessarie per l’ottenimento del volume desiderato di vuoti nella miscela rappresenta uno dei passaggi più importanti e complicati del processo di progettazione delle miscele. Sebbene la scelta della curva granulometrica compresa entro il fuso di riferimento richiesto sia di solito considerata un’arte essenzialmente basata sull’esperienza e il giudizio personale, nel presente articolo si vuole illustrare una procedura oggettiva volta alla definizione, in tempi rapidi, di una curva granulometrica affidabile che, oltre a rispettare le tolleranze previste, è tale da garantire il costante soddisfacimento dei requisiti di composizione volumetrica e durabilità attesi. Tale procedura (metodo di Bailey per il proporzionamento degli aggregati 2 di cui al sito www.asphaltinstitute.org) rappresenta quindi un utile strumento a supporto delle specifiche contrattuali, in grado di semplificare l’attività di laboratorio, riducendo infine al minimo quel dispendioso processo basato su tentativi ed errori che - soprattutto nei cantieri di nuova installazione e/o dove il personale dell’impresa non ha, di fatto, un’esperienza tale da apporre efficacemente le correzioni necessarie - è spesso causa di ritardi inaccettabili.
Al fine di garantire una adeguata lavorabilità degli impasti durante la costruzione 3 e una adeguata durabilità del materiale in opera, è necessario disporre di miscele bituminose (Figura 1) con valori di vuoti intergranulari (e di conseguenza bitume) superiori rispetto a quelli ottenibili mediante le curve granulometriche di massima densità 4 . Pertanto, per ottenere un contenuto di vuoti intergranulari sufficiente, la granulo-
1 Per evitare valori non conformi, e al fine quindi di rendere possibili le correzioni richieste a seguito dei risultati ottenuti dalle miscele di prova e/o durante la costruzione, è chiaro che tali parametri iniziali dovrebbero essere scelti in modo tale da ricadere al centro degli intervalli specificati. 2 Questo metodo può essere utilizzato con qualsiasi procedura di mix design (Superpave, Marshall, Hveem). 3 Movimentazione, posa in opera e compattazione. 4 Definito il diametro massimo delle miscele e le dimensioni dei setacci, le curve di massima densità presentano un assortimento granulometrico ottimale, in grado quindi di determinare il raggiungimento della condizione di massimo addensamento e, pertanto, del minore contenuto di spazi tra le particelle (vuoti intergranulari / VMA: Voids in Mineral Aggregate).
1. Nelle miscele bituminose, gli spazi esistenti tra le particelle di aggregato (vuoti intergranulari/porosità del solo aggregato) sono in parte occupati dal bitume (e la parte restante, generalmente intorno a valori di mix design pari a circa il 4%, è il volume occupato dai vuoti d’aria della miscela compattata)
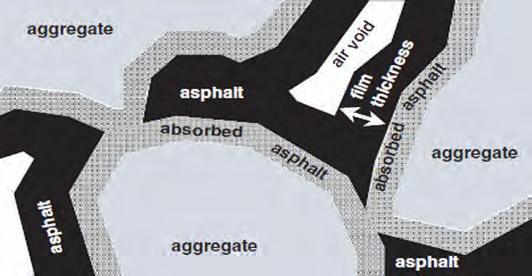
MISCELE BITUMINOSE
metria delle miscele di prova non deve seguire precisamente la curva di massima densità (mediante la quale si otterrebbe, infatti, un volume di vuoti troppo basso) ma deve discostarsi significativamente da essa (Figura 2). Per avere una rappresentazione grafica più chiara dell’andamento della curva granulometrica preliminare ottenibile con gli aggregati disponibili, di come questa si discosta dalla curva di massima densità e di come intervenire per apportare le modifiche necessarie, durante il proporzionamento degli aggregati (definizione delle percentuali iniziali secondo cui dosare le diverse classi granulometriche) si può fare utile riferimento a grafici del tipo riportato in Figura 3 (maggiore è la deviazione dalla linea di zero sul grafico CMD, maggiore sarà il contenuto di vuoti nella miscela risultante).
METODO DI BAILEY PER IL PROPORZIONAMENTO DEGLI AGGREGATI E COMPOSIZIONE VOLUMETRICA DELLE MISCELE
Il contenuto di vuoti intergranulari dipende da: •metodo di compattazione (per esempio Marshall) ed energia impiegata (per esempio numero di colpi); •caratteristiche dei granuli (forma, tessitura superficiale, resistenza meccanica); •distribuzione granulometrica (grado di assortimento dimensionale degli elementi granulari). Per un dato tipo ed energia di compattazione, la combinazione delle diverse classi granulometriche disponibili determina quindi il grado 2. Il confronto tra curve granulometriche (massima densità, fuso granulometrico previsto dalle specifiche contrattuali e miscela di prova) di addensamento della miscela (da cui densità e contenuto di vuoti intergranulari). Pertanto, la corretta identificazione degli aggregati utilizzati per quanto riguarda impianto di produzione, origine del materiale e caratteristiche individuali (rapporti di prova) riveste una parte fondamentale della procedura di mix design 5 . Secondo il metodo di Bailey, il setaccio che separa l’aggregato grosso da quello fine è noto come PCS (Primary Control Sieve) ed è definito come il setaccio più vicino al risultato della formula: PCS = NMPS × 0,22 dove: NMPS (Nominal Maximum Particle Size) rappresenta la dimensione del setaccio più grande del primo setaccio con trattenuto superiore al 10%. La porzione grossolana della miscela, pertanto, è la porzione compresa tra NMPS e PCS. Nel combinare tra loro le diverse classi granulometriche è importante prima conoscere la quantità e la dimensione dei vuoti creati dagli aggregati grossi in modo da riempire successivamente questi vuoti con la quantità appropriata di aggregato fine. A differenza di quanto avviene normalmente nelle procedure di mix-design, ne consegue quindi che nella fase iniziale di proporzionamento, gli aggregati devono essere combinati in base al volume e non in base al peso. Nelle miscele definite “a granulometria grossa” il volume dell’aggregato fine non eccede il volume dei vuoti interstiziali presenti all’interno della struttura (scheletro) creata dall’aggregato grosso e, pertanto, è la frazione grossolana della miscela di aggregati a 3. Il confronto tra curve granulometriche (massima densità e miscele di prova)
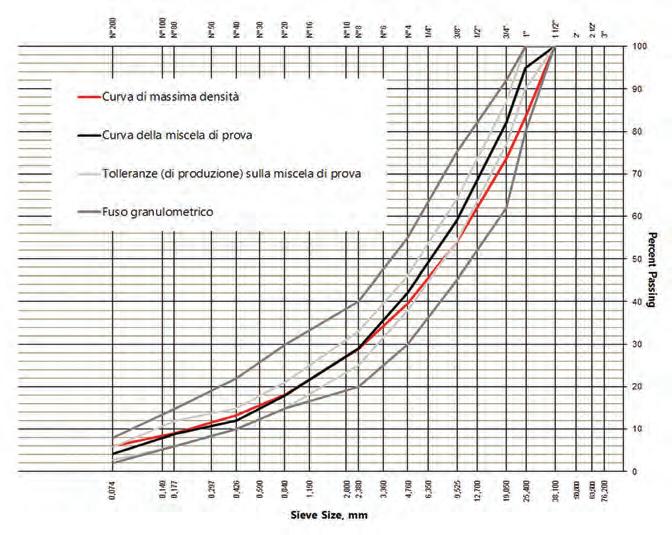
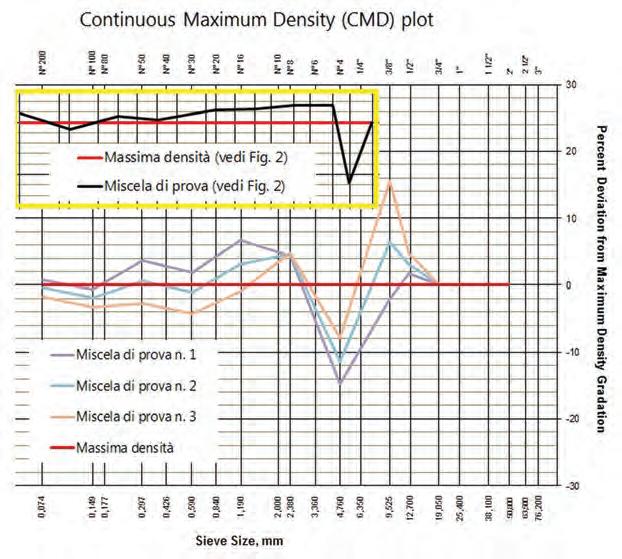
5 È bene comunque ricordare che nelle miscele bituminose il contenuto di vuoti intergranulari dei provini compattati cambia in funzione della quantità di bitume presente, per cui, valutata preliminarmente la composizione granulometrica, occorre fare le verifiche su impasti di prova secondo la procedura di mix design adottata (per esempio procedura Marshall: impasti con incrementi di bitume del 0,5%). Successivamente i risultati ottenuti potranno essere gestiti, come descritto nel prosieguo del presente articolo, in modo da correggere il tiro con gli impasti seguenti.
asfalti &bitumi
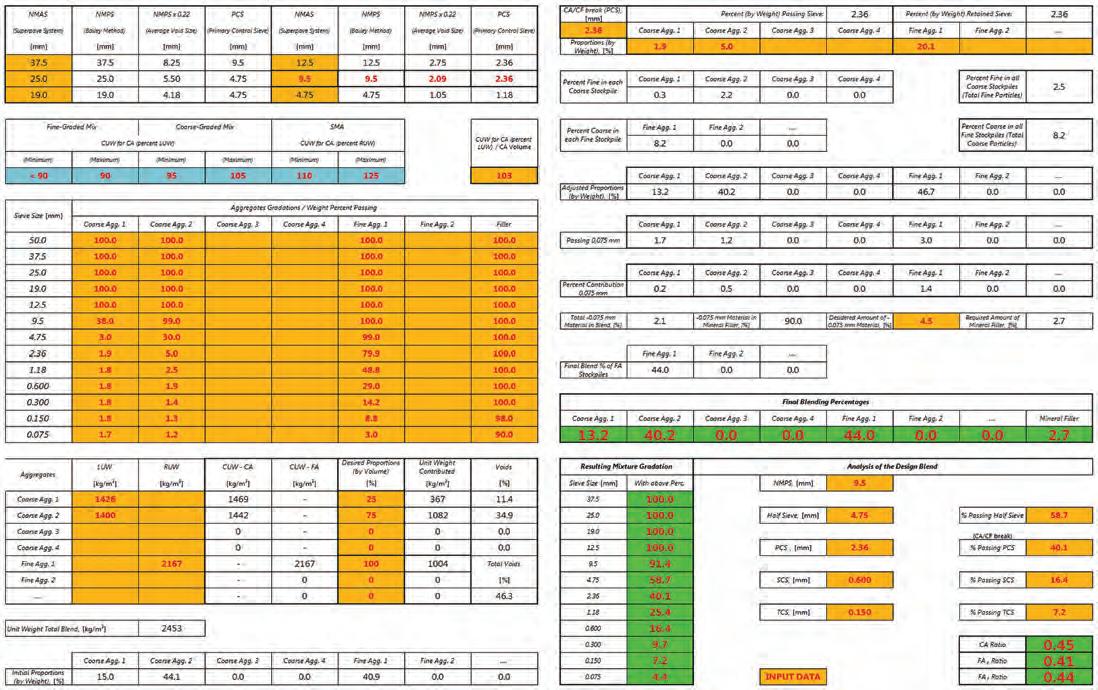
4. Esempio di foglio di calcolo sviluppato per la determinazione delle percentuali in peso corrette e dei parametri necessari all’analisi (ed eventuale modifica) della miscela ottenuta a partire dalla combinazione volumetrica degli aggregati a disposizione
sopportare la maggior parte del carico, a determinare la struttura dei vuoti interstiziali e a svolgere, infine, il ruolo predominante in termini di resistenza alla deformazione permanente. Nelle miscele “a granulometria fine”, invece, il volume dell’aggregato fine eccede il volume dei vuoti interstiziali presenti all’interno dello struttura 6 creata dall’aggregato grosso e, pertanto, è la frazione fine della miscela di aggregati a sopportare la maggior parte del carico. Il presente articolo tratta unicamente del primo caso (miscele a granulometria grossa). Ciò premesso, prima di iniziare la combinazione volumetrica, occorre conoscere (mediante alcune semplici prove di laboratorio) la massa volumica in mucchio degli aggregati disponibili. In particolare, in aggiunta alle solite prove di laboratorio richieste durante il mix-design, il metodo di Bailey prevede l’esecuzione delle due seguenti semplici prove 7: • AASHTO T-19 / ASTM C 29 Paragrafo 12 (bulk density “unit weight” in loose condition LUW - shoveling procedure/massa volumica in mucchio senza compattazione): metodo di prova richiesto per gli aggregati grossi 8; • AASHTO T-19 / ASTM C 29 Paragrafo 10 (bulk density “unit weight” in compacted condition RUW - rodding procedure / massa volumica in mucchio con compattazione): metodo di prova richiesto per gli aggregati fini 9 . Eseguite tali prove, per procedere alla determinazione del volume di aggregato fine compattato da utilizzare nella miscela, occorre selezionare il valore di massa volumica in mucchio (senza compattazione) degli aggregati grossi (CUW). Per miscele a granulometria grossa il valore scelto è generalmente compreso tra il 95% 10 e il 105% del valore ottenuto a seguito delle prove di cui al punto 1 11 (sono questi valori a stabilire il volume totale di aggregato grosso nella miscela e, di conseguenza, il grado di addensamento e il volume a disposizione degli aggregati fini). In Figura 4 è presentato un foglio di calcolo sviluppato per eseguire i calcoli richiesti, dalla combinazione volumetrica degli aggregati alla determinazione delle percentuali in peso corrette e calcolo dei parametri necessari all’ulteriore analisi della miscela ottenuta.
6 In questo caso, le particelle degli aggregati grossi non si toccano (non formano quindi lo scheletro) e, di conseguenza, la struttura dei vuoti è determinata principalmente dall’aggregato fine. 7 Ad ogni modo, si evidenzia che queste verifiche hanno senso solo se eseguite su aggregati conformi alle specifiche del progetto e rappresentativi del materiale prodotto e disponibile in cantiere. 8 Esclusi i Stone Matrix Asphalt (SMA) per i quali è richiesta la prova con compattazione. 9 Esclusi i Stone Matrix Asphalt (SMA) per i quali è richiesta la prova senza compattazione. 10 Il valore sembra basso: tuttavia a seguito della miscelazione si ha sempre un consolidamento aggiuntivo (per effetto del bitume, della presenza di aggregato fine negli aggregati grossi, ecc.) in grado di generare la struttura tipica delle miscele a granulometria grossa (nell’ambito di queste miscele le particelle degli aggregati grossi si presentano uniformemente a contatto tra di loro). 11 Valori minori del 90%, pertanto, nel caso di miscele a granulometria fine.
MISCELE BITUMINOSE
Ottenute le percentuali in peso delle diverse classi granulometriche (aggregati grossi, aggregati fini, filler) corrette secondo i calcoli riproposti nel foglio di calcolo, per analizzare la struttura dei vuoti presenti nelle varie porzioni 12 della miscela risultante, si procede alla determinazione dei seguenti parametri (Fig. 4): • rapporto CA: determina le modalità con cui le particelle dell’aggregato grosso della miscela si uniscono tra loro e, di conseguenza, il grado di impacchettamento e struttura dei vuoti a disposizione dell’aggregato fine; • rapporto FAc: determina le modalità con cui le particelle della porzione grossolana della parte fine della miscela si uniscono tra loro e, di conseguenza, il grado di impacchettamento e struttura dei vuoti a disposizione della parte fine dell’aggregato fine; • rapporto FAf: determina le modalità con cui le particelle della porzione fine della parte fine della miscela si uniscono tra loro e, di conseguenza, grado di impacchettamento e struttura dei vuoti che rimarranno nella porzione complessiva di aggregato fine della miscela. In sostanza, si tratta di rapporti tra i passanti percentuali ad alcuni setacci (individuati dal metodo) utilizzati per rappresentare la granulometria della miscela nell’ambito della frazione grossolana (CA), della frazione grossolana della parte fine (FAc) e della frazione fine della parte fine (FAf). Modificando questi tre parametri (foglio di calcolo) è quindi possibile modificare il contenuto di vuoti intergranulari della miscela. L’intervallo consigliato per i tre rapporti nel caso di miscele bituminose a granulometria grossa è mostrato in Figura 5. Valutati (mediante analisi della composizione volumetrica dei provini bituminosi compattati) i risultati di una curva granulometrica iniziale (ottenuta, ad esempio, con le percentuali in peso di cui sopra) occorre, nel caso in cui il contenuto di vuoti intergranulari ottenuto non corrisponda a quello desiderato e/o la miscela bituminosa presenti problemi di scarsa lavorabilità, ridefinire la curva granulometrica secondo nuove percentuali in peso, intervendendo sui seguenti quattro parametri: 1. CUW (massa volumica in mucchio scelta di ciascun aggregato grosso): • all’aumentare del volume di aggregati grossi (ossia all’aumentare della massa volumica in mucchio scelta) si ha un aumento del volume di vuoti (se le caratteristiche della frazione fine rimangono le stesse); • all’aumentare del volume di aggregati grossi (ossia all’aumentare della massa volumica in mucchio scelta) la compattabilità del materiale diminuisce. 2. rapporto CA: • all’aumentare del rapporto CA si ha un aumento del volume di vuoti; • se il rapporto CA è troppo basso, la miscela potrebbe presentare problemi a causa di eccessiva segregazione; • se il rapporto CA è troppo alto, la miscela potrebbe presentare problemi a causa di scarsa compattabilità. 3. rapporto FAc: • all’aumentare del rapporto FAc si ha una diminuzione del volume di vuoti. 4. rapporto FAf: • all’aumentare del rapporto FAf si ha una diminuzione del volume di vuoti. È bene evidenziare che le raccomandazioni di cui alla Figura 5 forniscono un valido un punto di partenza quando per un dato gruppo di aggregati non siano disponibili i risultati provenienti da precedenti prove di laboratorio. Se invece esiste un’esperienza precedente, i dati disponibili provenienti da miscele bituminose già in uso possono essere utilizzati in modo da creare intervalli più ristretti (più accurati) verso cui indirizzare i futuri mix-design per specifici gruppi di aggregati. Nel caso di miscele in uso con evidenze di scarsa lavorabilità del materiale durante la posa in opera e la compattazione o altre carenze, le formule dovrebbero essere riesaminate con il metodo di Bailey al fine di apportare le modifiche necessarie (e verificarne l’efficacia).
CONCLUSIONI
Le tolleranze granulometriche, generalmente richieste a livello di Norme tecniche contrattuali, sono ben note; tuttavia, in fase di qualifica di nuove miscele bituminose, è altrettanto noto che l’impiego di curve granulometriche semplicemente rispondenti alle tolleranze richieste non basta ad assicurare l’ottenimento, in tempi ragionevoli e senza l’esecuzione di un eccessivo numero di tentativi (impasti di prova), di miscele bituminose conformi ai requisiti volumetrici richiesti. È per tale motivo che in questa fase l’esperienza e la capacità di giudizio dei Tecnici coinvolti sono quasi sempre da ritenere elementi indispensabili ai fini del successo del processo di mix design. Tuttavia, al fine di snellire il volume di prove e per sopperire alla mancanza di informazioni nel caso di nuove produzioni di aggregati, è sicuramente consigliabile ricorrere a strumenti guida in grado di indirizzare correttamente, su base oggettiva e ripetibile, il processo di mix design e predisporre quanto necessario al conseguimento dei requisiti finali richiesti. In questo senso, il metodo di Bailey rappresenta uno strumento eccellente che, in considerazione delle modalità di incastro e del grado di impacchettamento degli aggregati, consente di prevedere il cambiamento del contenuto di vuoti intergranulari in risposta alle sole variazioni granulometriche. Intervenendo sui parametri definiti dal metodo, infatti, è possibile modificare il contenuto di vuoti intergranulari, la lavorabilità del materiale durante la posa in opera e la compattazione, la resistenza alle deformazioni permanenti e, infine, le prestazioni a lungo termine della pavimentazione. n
5. Le raccomandazioni per la scelta dei parametri CA, FAc e FAf
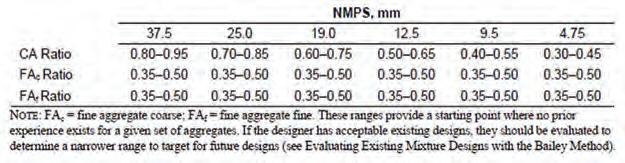
12 Porzione grossolana della miscela (porzione compresa tra NMPS e PCS), porzione grossolana della parte fine della miscela e porzione fine della parte fine della miscela. (1) Geologo, Consulente ed Esperto internazionale (QC/QA e ingegneria dei materiali)
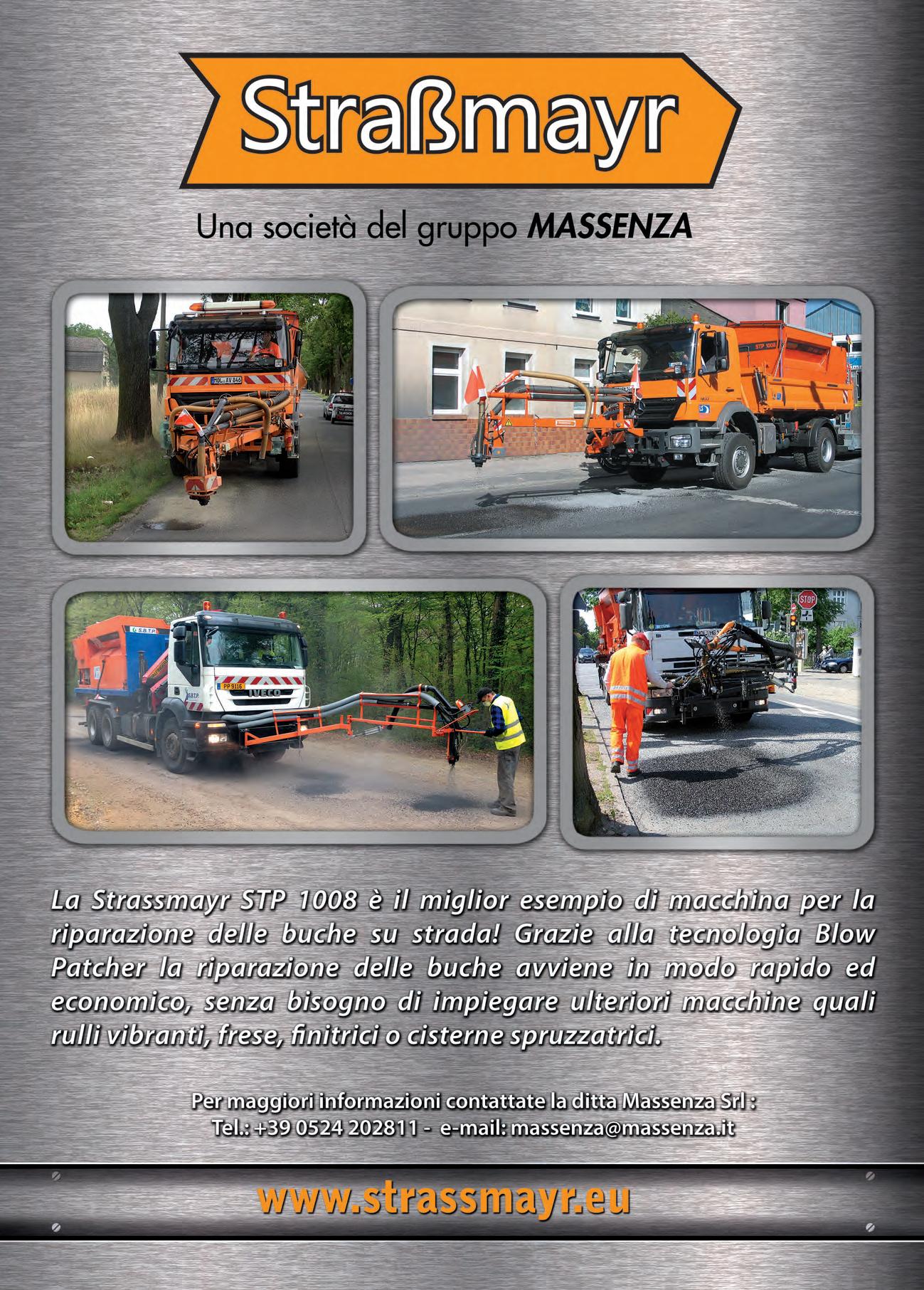