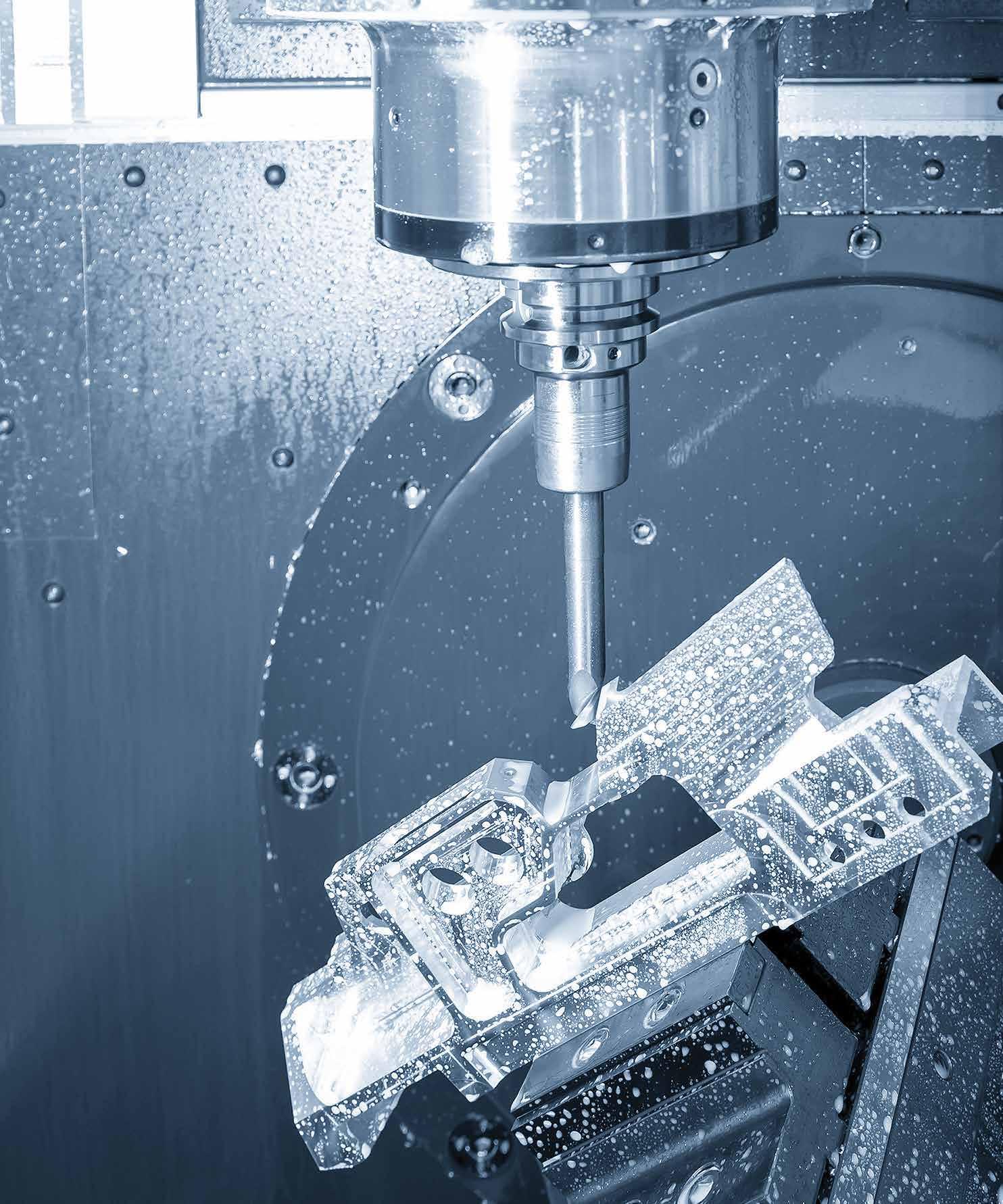
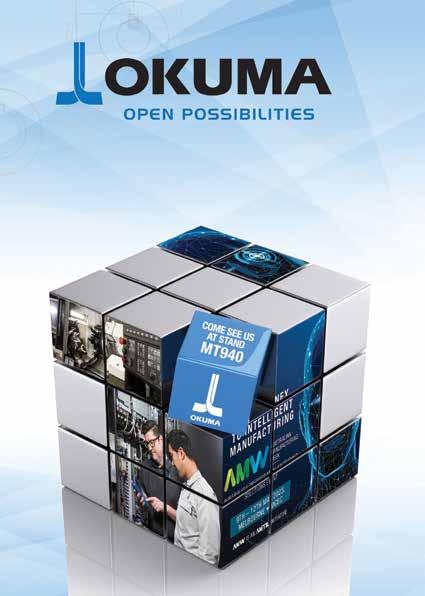


Okuma Australia’s stand at AMW 2023 will showcase the future of manufacturing, demonstrating the latest lathes, machining centres, multitasking machines and automation plus IOT Connectivity Solutions with the Okuma Connect Plan.
Okuma machines on Stand Number MT940 will be cutting metal with several Okuma specialists on hand to demonstrate the cutting power of the Okuma machines as well as Okuma Connect Plan, new Okuma OSP Suite and 5-axis Auto Tuning systems.
Highlighting the Okuma exhibit will be the all-new Okuma ARMROID with built-in robot packaged within the Okuma LB3000EXII. ARMROID functionality includes part loading and unloading, chatter suppression, chip removal, and in-machine cleaning, ensuring that your Okuma machine is consistently operating at its highest efficiency.
MELBOURNE: INTELLIGENT MANUFACTURING
AMW PREVIEW
Construction & Infrastructure
State Spotlight: South Australia
33 Brodie Street, Rydalmere NSW 2116
Ref. Mr. Heino Windhorst
T. +61 (02) 96389600
E. heino@mafosyd.com.au
The next best compact panel bender.
The flexible bending centre solution.
Made-to-measure modularity.
Custom solutions to widen versatility.
kit and batch-one production.
More autonomy and smaller batch sizes management.
Manage your factory, in real time.
Programming, quick and easy.
The METAMASTER Syncro series has been specifically developed to provide reliable & advanced bending features at an affordable price. With a range of machines from 40T to over 200T we have a machine to suit your needs.
5 CNC CONTROLLED AXIS (Y1, Y2, X, R, V) AS STANDARD
ALL MACHINES ARE FITTED WITH THE SWISS DESIGNED CYBELEC TOUCH 12
CNC CONTROLLER WITH INTUITIVE 2D GRAPHICAL TOUCH DRAW PART PROFILE PROGRAMMING AND STANDARD WITH AUTO BEND SEQUENCING
ITALIAN MADE LASERS & MONITORED SAFETY SYSTEM COMPLETE THE MACHINE WITH QUALITY COMPONENTS
Australia's most popular CNC plasma, With Swiftcut tables made in the UK & Hypertherm Plasma units made in the USA there is no compromise on quality.
Four Machine Sizes
UP TO 25MM CUTTING CAPACITY DEPENDING ON THE HYPERTHERM UNIT SELECTED DXF & JPEG PHOTO IMPORT FOR CREATION OF CUTTING FILES
SOFT SENSE DIGITAL TORCH-HEIGHT CONTROL (DTHC) QUICK RESPONSE FOR IMPROVED CUT QUALITY AND IMPROVED CONSUMABLE LIFE.
METALMASTER ClearAir mobile welding fume bench is a compact all in one downdraft table with 1120 x 825mm work area (with fume shroud closed)
HEPA H13 filtration ensures a safe & comfortable work environment
Our Euro Pressbrakes are fully featured with the latest premium technology from 5 axis to 9 axis machines we stock a huge range.
FEATURING THE LATEST DELEM DA66T (2D) OR DA69T (3D) CNC CONTROLS
GERMAN AKAS LASER GUARDING ENSURES ULTIMATE PRODUCTIVITY WITH UTMOST SAFETY
5 AXIS / 7 AXIS - 3 METER OR 4 METER WE STOCK A HUGE RANGE
Operator Control
METALMASTER ClearAir mobile welding fume extractors come in single arm & dual arm configurations. With HEPA H13 filtration Mig, Tig & Arc welding fumes are safely removed and filtered from the work area.
LYNX 2600SY - Doosan Fanuc I Series (0iPlus) CNC Controller
3 JAW HYDRAULIC POWER CHUCKS
The Metalmaster Deburr1380 manual deburring machine is the ultimate cost-saving solution for deburring, grinding, edge rounding and finishing of metal parts.
GREASE CARTRIDGE AUTO LUBRICATION SYSTEM SLAG REMOVAL PRE-GRINDING & DEBURRING
EPPINGER ROTARY TOOL HOLDERS WITH PRECIFLEX ADAPTER SET
A range of different types of pads and brushes for deburring, edge rounding, finishing, laser oxide removal and heavy slag removal are available.
1300 X 800MM TABLE WITH VACUUM AREA TO SECURE SMALL PARTS IN PLACE
GRINDING HEAD WITH MULTIPLE STATIONS AND ALLOWS FOR THE INTEGRATED EXECUTION OF DIFFERENT PROCESSES
VARIABLE SPEED ALLOWS FOR EASY SPEED ADJUSTMENT TO SUIT THE TOOL AND PROCESS
IF YOU CAN DRAW IT, DOWNLOAD IT, TRACE IT OR IMAGINE IT, YOU CAN CUT IT
Any table is a plasma table with ArcDroid™.
Portable powerful and easy to use. ArcDroid™ brings CNC plasma to your garage or workshop. ArcDroid™ combined with our custom operating system with Simple Trace™ can accurately reproduce your designs delivering fast, accurate and repeatable parts from your plasma cutter.
AUSTRALIAN MANUFACTURING WEEK 2023
- The Journey to Intelligent Manufacturing
Melbourne is ready for the return of the largest manufacturing showcase when AMW 2023 takes over the MCEC. Here's a preview of some exhibitors.
ONE ON ONE AMT speaks Natalie O'Brien, CEO of the MCEC, and Romilly Madew, the CEO of Engineers Australia.
PROFILE: SEVAAN
114
RED EARTH ENERGY STORAGE
flight to
Chris Winter is the brains behind RedEarth Energy Storage systems (BESS) and LFP Troppo batteries.
We offer the leading edge of ‘full service’ distribution and lifetime support for Okuma CNC machines. Solution focussed, our team work with our customers to provide machining realities, with exceptional results.
Our team gives you immediate access to decades of industry experience and a network of local and global machine tool experts. We partner with you from the very first meeting, guide you through project planning and support you through implementation, training and after sales care.
Technology
Reputation
AMTIL’s Australian Manufacturing Week is proof positive local manufacturers are up to the task of producing materials and products that are high-quality, ready-for-market, and fit for purpose.
Sheet metal manufacturing has never been busier. Businesses involved in CNC cutting, forming and fabrication, have not been busier in years. The feeling sensed in the crowd of manufacturers at the latest AMTIL industry event showed there was huge momentum in orders, and many had exceeded their capacity in forward orders due to the unavailability of raw materials. Juggling can be hard and full of risk if you don’t know where the balls are falling.
And the reason for that is that economically, the international picture is very cloudy. As KPMG’s Partner In Charge of Manufacturing and Life Sciences, Toni Jones, says in a recently released report on the world economy, divisions in the world economy were growing, well before war broke out in Ukraine or before COVID tightened its grip. Since then, these worldly tensions have caused companies to rethink their international strategies. Around 85% have discontinued working in Russia in particular, in response to the Kremlin’s moves on Ukraine, but globalisation is not necessarly retreating, it is more likely just changing shape.
Jones’ companion Stephane Souchet, the Global Head of Industrial Manufacturing at KPMG, cites an uncertain future for businesses, characterised by the disrupted patterns of global trade, geopolitical tensions and a growing investment drive into defence. The move into defence is a signal of changing shapes in our economy, not a retreat, as such. Jones adds that, “we have to not only focus on re-evaluating our sourcing locations, supply chain dependencies but also [to] foster nearshore and onshore capacity.”
Labour shortages here in Australia, increased costs for inputs, supply delays, wet weather and flooding were constraining factors in November. Interest rate rises have reduced demand from construction customers with builders delaying or cancelling orders. Import competition has increased. Despite all of this, surprisingly, new orders and stock deliveries were all positive in that month.
COVID-19 has also highlighted many risk and resiliency gaps. In another recent KPMG study citing global supply chain issues, 67% of CEOs indicated they would increase investment in disruption detection and innovation processes to reduce the impacts of disruption.
Government and industry leaders are also looking to build domestic capabilities to reduce their reliance on global supply chains. Of course, organisations must review their sectors’ supply chain flows and consider local inventory capabilities to reduce risk. Spreading the load of third parties to rely on for supply will ensure access to their stock. Relying on this ecosystem of vendors and having a wide-ranging strategic partnership within the domestic industry will keep parts coming in, and your knowledgebase up to date to future conditions. You should know everyone in your local network will want you to succeed as well. AMTIL knows the value of local networking during times like this, and it pays to stay connected.
The KPMG report confirmed the volatility of the Australian construction industry, with complexity becoming the new normal. As manufacturing is so much a part of the maze of construction and infrastructure ecosystems in Australia, learning to transform these projects into manageable business is paramount. Juggle as you stay on top of what you manufacture but keep all your balls in sight at all time.
Editor Paul Hellard phellard@amtil.com.au
Contributors
Drew Turney
Sales Manager Nicholas Raftopoulos nraftopoulos@amtil.com.au
Publications Co-ordinator
Caroline Robinson publications@amtil.com.au
Publisher Shane Infanti sinfanti@amtil.com.au
Designer Franco Schena fschena@amtil.com.au
Prepress & Print Printgraphics Australia
AMT Magazine is printed in Australia under ISO140001
Environmental Certification using FSC® Mix certified paper sourced using sustainable tree farming practices.
Contact Details
AMT Magazine
AMTIL Suite 10, 5 Corporate Boulevard Bayswater VIC 3153 AUSTRALIA
T 03 9800 3666
F 03 9800 3436
E info@amtil.com.au
W www.amtil.com.au
Copyright
© Australian Manufacturing Technology (AMT). All rights reserved. AMT Magazine may not be copied or reproduced in whole or part thereof without written permission from the publisher. Contained specifications and claims are those supplied by the manufacturer (contributor).
Disclaimer
The opinions expressed within AMT Magazine from editorial staff, contributors or advertisers are not necessarily those of AMTIL. The publisher reserves the right to amend the listed editorial features published in the AMT Magazine Media Kit for content or production purposes.
AMT Magazine is dedicated to Australia’s machining, tooling and sheet-metal working industries and is published bi-monthly. Subscription to AMT Magazine (and other benefits) is available through AMTIL Associate Membership at $190.00 (ex GST) per annum. Contact AMTIL on 03 9800 3666 for further information.
I have been banging on about Government procurement for a long time now. The need for a whole of government approach to their own procurement policies has supposedly been on the agenda for a number of years. However, we still have the situation where some industry sectors are left with significant roadblocks to overcome when dealing with state and territory governments on an individual basis. This is certainly the case with rail.
The Australasian Railway Association (ARA) has called for a national approach to rollingstock procurement in response to a new report that found governments missed out on $1.85bn in cost savings over the last decade due to inefficient local content policies in place across Australia. ARA Chair Danny Broad said state-based local content policies made operating in different states akin to operating in different countries. This led to the duplication of facilities and inconsistency between states, and made it too hard for some organisations to bid for key contracts.
“It is unfortunate to see cost savings on such a huge scale being left on the table at a time when demands on government budgets have never been higher,” Broad said. “State-based policies make it harder for industry to gain scale, drive innovation and adopt greater efficiency and productivity across their operations.
“This hampers their competitiveness over time and puts local jobs at risk in the long term.
“Australia has fantastic capability in rollingstock manufacturing, but its effectiveness is hampered by inefficient state-based local content policies that make it difficult for organisations to work across state lines to build economies of scale.
“These lost savings could have contributed to funding the huge infrastructure pipeline currently underway, or supported 1500 health and education jobs over the ten-year period.”
The report, authored by BIS Oxford Economics and the Hadron Group, identified foregone procurement cost savings from the last decade included:
• $717m of savings from increased scale
• $811m of savings from reduced complexity in planning and design
• $318m of savings from major componentry harmonisation
Assistant Minister for Manufacturing and Trade Tim Ayres welcomed the report’s findings.
“We know the different approaches by the states and territories to rail procurement and manufacturing leads to capabilities being
duplicated,” Assistant Minister Ayres said ahead of today’s launch. “This pushes up costs, exacerbates skills shortages, and constrains investment. “By working together to build and maintain modern passenger trains, Australia can reduce procurement costs while boosting manufacturing capability and creating high-skilled jobs in regional and outer suburban Australia.”
States and territories use different procurement policies for purchasing rail assets such as rollingstock, including state-based local content requirements. The report found that while this approach supported local jobs in the short term, it undermines the long-term sustainability of the rollingstock manufacturing industry. A national approach to rollingstock procurement would allow both governments and industry to achieve improved outcomes, realising the cost savings outlined in the report.
A national approach would also support the growth and competitiveness of the industry, supporting further jobs growth in this essential market. The rail manufacturing and supply sector generates $2.4bn in revenue per year and supports more than 4000 jobs, many of which are in regional areas.
Assistant Minister Ayres said the Albanese Government has committed to delivering the National Rail Manufacturing Plan, aimed squarely at coordinating a national approach to support and grow the Australian rail manufacturing sector. “The Australian Government wants Australia to be a smart nation that makes high-value products for the country, the region, and the world,” Assistant Minister Ayres said. The National Rail Manufacturing Plan's development is being led by the Office of National Rail Industry Coordination (ONRIC) in the Department of Industry, Science and Resources.
As part of the Plan, the government will shortly appoint a National Rail Advocate and Rail Industry Innovation Council to support and drive change in the rail manufacturing industry.
So it is now over to the Federal Government for action. Having recognised that this is indeed an issue which costs significant dollars, wastes resources and stymies investment, it will be interesting to see how they manage any change.
Australia is a wealthy, advanced nation. Where do you think we rank globally for 'economic complexity'? You might have guessed top 10 or 20. You would be wrong.
Australia languishes in 91st place, well down from countries with which we really like to compare ourselves. What about ‘manufacturing self-sufficiency’? Well, we rank dead last among OECD countries. And why does this matter? I will come to that later.
WA has always been a pioneer in manufacturing and innovation. From the Western Australian Boot Manufacturing Company, established in 1907, which produced over 100,000 pairs of boots a year, right through to the vast Kwinana Industrial Area which turbocharged WA's manufacturing sector and has supported tens of thousands of jobs since the 1950s.
And WA still leads the charge. Just two weeks ago I was in Perth seeing it first-hand. I visited ChemX and the Future Battery Industries Cooperative Research Centre who are both making headway to help Australia become a key player in battery industries.
I visited BGC’s concrete manufacturing operation which is looking at greener ways to produce building materials.
I also saw how Murdoch University is nurturing the next generation of innovators through its new robotics mentoring program for high school students. Sadly, for too long, Liberal governments have talked big on manufacturing but delivered little beyond glitzy advertising or election slush funds.
The idea of making things at home was an abhorrent idea for the Liberals. It’s resulted in jobs, skills and investment going offshore at an alarming rate. Those rankings I mentioned earlier. They point to a country that relies on others. One that doesn’t make enough anymore. That’s problematic for a range of reasons, but as we learned most recently at the peak of the COVID pandemic when we went looking for the things we needed, we didn’t have them.
In many cases – like in critical minerals – Australia exports resources, waits for the value to be added somewhere else and then imports them back at higher prices.
And as the Prime Minister recently said, "one of the lessons of the pandemic is that we need to be more self-reliant, we need to be
more resilient, we can’t just sit back and allow ourselves to be at the end of global supply chains." In short, we want Australia to be a country that makes things. And a country that makes things creates good, secure, fulltime work. WA has all the ingredients to be a manufacturing powerhouse.
Smart people using their know-how to build strong businesses, showing the rest of the country how to get things done. You have an abundance of raw materials, a strong R&D investment and longstanding trade relationships. And the state is thinking long term about its economy and jobs. Australia has a rich and diverse endowment of critical minerals that are crucial to the wires, batteries, magnets, and semiconductors that power clean energy technologies for the world.
That’s why I say if we mine it here, then we should make it here. It’s why we’re developing a National Battery Strategy. We’re building the National Reconstruction Fund. At $15bn, it’s one of the biggest investments in Australian manufacturing in living memory.
It will invest in businesses that want to grow and stay onshore. It will be managed by a board of people drawn from industry and investment circles. It will make decisions in the national interest instead of politicians’ interests.
There are several priority areas that have unique benefit to WA. We want to use this fund to boost medical manufacturing and enabling capabilities such as critical technologies and advanced manufacturing. The fund will also target projects which value-add in resources, agriculture, forestry, fisheries, food and fibre.
WA is at the forefront of production when it comes to many of these industries - which means WA and its businesses stands to benefit from the opportunities presented by the NRF.
It’s time to back Australian know how so we can grow our economy, create new jobs, and make sure that happens across the country including right here in WA.
And I know plenty in WA will be ready to step up and make that happen.
After two years of pandemic-induced interruptions, 2022 was a more stable and successful year for Australian business. While Australian business leaders are cautiously optimistic for 2023, they are readying plans to adjust to the challenges expected in the coming year.
Now in its tenth year, Ai Group’s annual Australian CEO Survey provides critical insights into business experiences over the past year, and how business leaders expect the coming year to evolve.
Our 2023 CEO Survey has revealed that businesses consolidated the post-pandemic recovery in 2022. Business conditions, turnover, employment and investment all improved as the dislocations of the COVID era gradually abated.
However, business leaders also contended with a new set of ‘supplyside’ challenges, as rampant inflation, chronic labour shortages and supply chain disruptions weighed heavily on performance. Business leaders have reported declining margins due to these supply-side pressures.
It is a testament to the resilience, flexibility and innovation of Australian business that we successfully navigated the challenges of post-COVID recovery in 2022.
There is, as always, a wide range of views about how 2023 will play out. But our Australian CEO Survey reveals several common themes that Australian business leaders largely agree on.
On balance, employers go into 2023 with cautious optimism. They expect business conditions and performance to improve again on the strong results of 2022. Despite the headwinds facing the Australian economy, business leaders are undertaking ambitious investment plans to adjust to the new market realities of the postpandemic era.
However, they also identify three challenges which will define their priorities in 2023:
1. Historically tight labour markets, which have exacerbated chronic staff shortages, particularly for skilled roles.
For the first time in the history of our CEO survey, staff training is the top investment priority. 90% of CEOs expect to be affected by staff shortages in 2023. They intend to invest in staff training and development to grow their in-house skills base.
In contrast, more conventional types of investment such as physical CAPEX — buildings and equipment — or research and development ranked very lowly for 2023.
This illustrates one of the hidden costs of the skills crisis in Australia today. As businesses are redirecting their investment plans to workforce, there's not much left over for growing industry or doing R&D. Given Australia ranks fairly poorly on international league tables for R&D, this could have significant implications for our future competitiveness in five to ten years’ time.
Perhaps unsurprisingly, given the national and global inflationary context, in 2022 business leaders reported the fastest rises in industry prices ever seen in the history of the Ai Group CEO survey. And businesses are expecting inflationary pressures of the past two years to continue, particularly for energy.
Investment in process improvements and technology are already underway to manage the effects of cost pressures on the balance
sheet: in terms of investment priorities, improving business processes was ranked second, while ICT investments were ranked third. While not strictly workforce, these investment priorities are in fact also very much related to skills shortages. Process improvement and ICT allow for a more effective deployment of a business’s current workforce and help adjust to conditions in which labour supply will remain constrained.
Business leaders have elevated supply chain resilience to be a top priority and nearly 90 per cent of CEOs plan to make a supply chain investment this year, looking to improve their logistics practices, cultivate new suppliers, and adjust their product offerings to manage this ongoing challenge.
Just under 20% of businesses say they plan to find new suppliers while a quarter of businesses say their only strategy is to increase their prices to recoup supply chain costs — effectively passing them on to customers.
A quarter of businesses might sound like a lot, but it is actually a worryingly low number. Given 79% of businesses say they're currently affected by supply chain problems, it tells us that most businesses don't expect they can recover those additional costs via pricing. The balance sheet is going to have to wear the difference. Our survey demonstrates that it will clearly be another challenging year for many businesses and the need for a relentless focus on productivity across the broader policy agenda has become even more important.
The strategies businesses deploy and their investment priorities are critical for Australia to achieve the economic resilience needed for prosperity in a time of global economic uncertainty.
The Federal Government in particular will also need to put productivity and flexibility at the forefront, especially when considering the further changes to workplace relations it plans to introduce later this year. We need to catch up on years of below-par productivity growth and we need to gear ourselves for at least a return to 1990s level growth. aigroup.com.au
Rather than planning for the future, too many politicians and governments have neglected the hard but necessary work of imagining what Australia’s built environment will need 50 years from now. Huge changes in industry, technology and housing have left enormous sections of our national infrastructure scrambling to keep up – or just falling further and further behind.
There are several reasons why this has happened. Privatisation and the rise of “consultancy culture” has hollowed out the public service and its institutional knowledge, and left governments captured by vested interests. For-profit companies are unlikely to consider any aspect of the projects they undertake other than profitability. And offshoring has sidelined the knowledge and experience of local workers who understand – and care about – the context and environment in which they work.
The results of this neglect are all around us. Investment in electric vehicle (EV) infrastructure like charging stations, especially outside the major cities, hasn’t kept pace with the rising demand for EVs. Cars banked up in regional towns along the Pacific Highway during the summer holidays as people waited to recharge. An important part of the energy transition is being held back by a simple lack of planning.
The same is true of our energy infrastructure. The number of largescale solar projects in the pipeline is bottoming out because our ageing grid is struggling to cope with the influx of renewables. Large amounts of energy generated by solar farms like Molong are going to waste – as is much of the electricity coming from millions of rooftop solar panel installations.
A lack of decent city planning is also letting people down. Property developers have been given free rein to build thousands of uninsulated, dark-roofed houses that rely entirely on air conditioning to keep cool. The suburbs these houses stand in are often built at the absolute limit of the urban fringe, with no access to decent public transport or basic amenities like parks, footpaths or shops. Many have only one access road in and out, creating enormous traffic snarls and presenting a risk in the case of natural disaster – which many of these suburbs are especially vulnerable to, being built in fire- or flood-prone areas. And areas that experience scorching temperatures have been completely cleared of trees, turning houses and tarmac into outdoor ovens and forcing people inside to their air con.
From the $50bn debacle that was the Turnbull government’s “mixedtechnology model” for the NBN to the ongoing failures on NSW’s public transport system, treating the complex and interlocking demands of our society as opportunities to make money has resulted in spectacular policy failures over and over again. The only people who benefit are a handful of investors and shareholders, who leave everyone else to deal with the consequences and clean up their mess. If we don’t urgently change this mindset, we could end up like the United States, with its crumbling roads, bridges and water infrastructure.
The Federal Government’s $15bn National Reconstruction Fund (NRF) is a welcome opportunity to start addressing this. After nearly a decade of inaction from the previous government, a big, ambitious plan to re-establish domestic manufacturing and build some badly needed national infrastructure is a refreshing change of pace. But throwing money at new projects won’t magically solve the underlying problems. If big businesses are given blank cheques without any conditions, they’ll do what they’ve always done –
spend taxpayer money on enormous white elephants that worsen the problems they’re supposed to fix.
That's why the NRF board needs the perspectives of workers when deciding where to spend its money. This can’t be through some box-ticking consultation process either. Workers must be in the room where these decisions are being made.
The idea that executives and public servants know more about manufacturing, infrastructure or construction than working people do isn’t just insulting – it's been disproven repeatedly by their own failures. Worker representation on boards is why industry superannuation funds consistently outperform commercial funds. Having worker representation on the board of the NRF would help ensure that $15bn doesn’t go to waste.
Because they’ll be trusted with public money, businesses that receive NRF funding should also demonstrate a willingness to consider the social, human and environmental effects of the projects they undertake. Requiring those businesses to have a collective bargaining agreement with their workers would help weed out those that see the NRF as an opportunity to put more money in executives’ pockets.
The NRF is a massive opportunity to fix our built environment – but if workers are empowered through its processes, it can become an opportunity to fix our policymaking as well.
amwu.org.au
VISIT US AS AMW 2023! - STAND MP350
Industry 4 0, digital processes & information all in one central location
Achieve unparalleled digitisation
Facilitates industrial operations across all sectors
Floor, wall & desk-mounted options
43” Touchscreen
Wirelessly connected
Ruggedised, powdercoated steel enclosure
Touchscreen or touchless
ip54 rated kiosk (for dust protection)
Email: integratransform@integrasystems.com.au
Website: www.integratransform.com.au
Phone: +61 3 9359 3133
Fully customisable
Australian-made
Dimensions: 700W x 2006H x 120T mm
Flip out keyboard & storage drawers
B0200 Ardcam camera & K5mic lav microphone
Intel Z8300 Quad Core 1 8GHz or equivalent
Operating systems - Windows 10/Linux/Ubuntu
Scan here to find out more
The
and environmental benefits generated by portfolio, with over $4.2bn in new revenue growth, 6,000+ jobs and $2bn investment in future R&D by 2030.
After seven years successfully supporting the transformation of Australian manufacturing, the Innovative Manufacturing Cooperative Research Centre (IMCRC) has concluded its operations.
Over its lifetime, IMCRC purposefully invested $40m of Commonwealth funding into industry-led R&D to grow Australia’s manufacturing capability and capacity and drive real-world commercial outcomes. IMCRC’s Achievements and Outcomes Report has just been published, summarising the substantial impact and legacy IMCRC leaves for Australian manufacturing.
From its initial pool of funding, IMCRC catalysed a $254m project portfolio comprising 71 collaborations between 78 industry partners, 13 universities and the CSIRO.
Backed by a transparent governance structure and clear framework for commercialisation, IMCRC facilitated collaborations that leveraged Industry 4.0 technologies to explore new ideas, business models, products, processes, services and platforms.
Many of these projects are already delivering substantial commercial outcomes that will shape the future of Australian manufacturing, including new revenues, business growth, high-value jobs and global exports. In 2022, these outcomes were quantified by leading advisory firm ACIL Allen in an independent impact evaluation report, “The Impact of IMCRC”. ACIL Allen found IMCRC’s business model had delivered ‘significant positive impacts for the Australian manufacturing industry’, including economic benefits of more than $4.2bn by 2030.
Further benefits include the creation of 6,000+ ongoing full-time jobs, 224 collaborations and new partnerships, planned investment of $2 billion in future R&D and a 3.3m tonne CO2 reduction in greenhouse gas emissions.
“What set IMCRC apart was its commitment to operating with strong commercial principals, and in a timeframe that met industry’s needs,” IMCRC’s Chair, the Hon Ian Macfarlane said. “This approach enabled IMCRC’s partners to realise significant return on investment, including through the ownership of intellectual property and commercialistaion of technology.
“I would like to thank the Board for their tireless dedication to the success of the IMCRC, and CEO and Managing Director, David Chuter, and his team for their incredible work supporting participants on their innovation journeys. Their efforts have made IMCRC arguably Australia’s most successful CRC.”
“IMCRC has been one of the best ever Cooperative Research Centres,” added IMCRC Director, Professor Mary O’Kane AC. “Thanks to the hard work and vision of the team and partners, IMCRC leaves behind a considerable legacy.” IMCRC has been an independent and for-impact cooperative research centre with a successful, proven and scalable model for catalysing research and business partnerships that drove transformative commercial outcomes for participating Australian manufacturers. Over its lifetime, IMCRC successfully co-invested in 71 R&D projects, catalysing $254m in transformative manufacturing research. imcrc.org
Supporting Australia’s battery manufacturing industry to charge ahead.
Minister for Industry and Science Ed Husic formally launched consultations for the country’s first National Battery Strategy at a visit to Energy Renaissance, an Australian lithium-ion battery technology and manufacturing company, at Tomago in the New South Wales Hunter Valley.
Developing the Strategy will be integral to help Australia transition to a decarbonised economy, hit our ambitious emissions targets, foster Australian innovation and support Australian industry.
Minister Husic said domestic battery industries will be buoyed by Australian know-how and domestic access to minerals to help power the move to clean energy here and around the world.
“Our general approach should be one where if we mine it here, we should make it here,” Minister Husic said.
“Large scale uptake and manufacture of batteries will be vital transitioning to net-zero. New battery capacity will help support grid scale capacity, power our homes, and electrify our transport sector.
“We know there is huge demand for energy storage to support the widespread uptake of solar generation by households, business and industry.
“Global demand for existing and next-generation batteries is forecast to increase nine to 10-fold over the next decade.
“That’s why it is important that we harness the opportunity to become a key player in battery manufacturing and export on the world stage.
“Australia has globally significant deposits of essential battery materials and strong local innovation and research capabilities. By drawing on these strengths, Australia can take its place in the profitable global battery supply chain.”
Globally, Bloomberg New Energy Finance estimates that 387 gigawatts of new energy storage will be added by 2030, providing an excellent opportunity for Australian battery industries.
Bolstering Australia’s battery manufacturing capability presents an opportunity to integrate and diversify global battery supply chains. A joined-up national approach to battery technology will also work to support Australia’s National Electric Vehicle Strategy.
“The National Battery Strategy will complement the development of Australia’s new Critical Minerals Strategy to articulate a clear pathway for integrated, end-to-end onshore battery minerals supply chains,” Minister Husic said. “A coherent, national approach to the development and uptake of emerging technologies won’t just deliver economic growth and jobs, but also help safeguard our national wellbeing,” Minister Husic said.
The Albanese Government will work closely with states and territories, and consult widely with industry, community and experts to shape the strategy and help grow globally competitive domestic battery industries.
Engagement on the Strategy will help inform other elements under the Australian Made Battery Plan including:
• creating a Battery Manufacturing Precinct, in partnership with the Queensland Government;
• establishing a Powering Australia Industry Growth Centre to support industry translation of research into local jobs and investment; and
• supporting 10,000 New Energy Apprenticeships.
The discussion paper can be found at: consult.industry.gov.au/national-battery-strategy-issues-paper
To mark International Women’s Day, Weld Australia is calling on the Federal Government to implement a proactive, targeted approach that: engages and recruits women into the trades; implements innovative trade training programs designed specifically for women; and sets measurable gender diversity targets on governmentfunded projects.
“Australia will have a shortfall of at least 70,000 welders by 2030,” said Weld Australia CEO, Geoff Crittenden. “Industry is already at capacity. Weld Australia’s members are currently operating at 50% to 70% capacity, and turning away work because they cannot find enough welders.” “Increasing diversity in the trades is one of the best ways to alleviate the looming skills shortage, and every effort needs to be made to encourage women to become welders,” said Crittenden.
“There are significant economic benefits for women in welding, from increased choice and availability of jobs, through to improved job security, higher than average pay and ample opportunities for progression and promotion. A career in welding is safe and secure—once you’re qualified, you can walk into a job tomorrow. Welding is in-demand because it is essential to the success of so many industries,” said Crittenden.
The five-year pipeline of major federally-funded infrastructure projects is valued at $237bn. On top of this, a veritable army of skilled welders will need to be assembled to build and install the wind and transmission towers, solar farms and other power generation assets needed to achieve the Federal Government’s 43% emissions reductions target by 2030 and net zero by 2050. Plus, there are countless projects in Defence, state government
funded projects, and other private developments. With all these government-funded projects in play, measurable gender diversity targets on government-funded projects would have a huge impact. In effect since 1 January 2022, the Victorian Government’s Building Equality Policy (BEP) is an Australian first and aims to disrupt gender stereotypes in the country’s most male-dominated industry. The BEP applies to new government projects, and mandates female representation in at least 3% of each trade role, 7% of each non-trade position and 35% of management, supervisor and specialist labour roles. It also mandates that 4% of labour hours for apprentices and trainees are performed by women.
“The Advanced Manufacturing Outreach Program is unique because it actually engages kids. It is hands-on, fun and educational. It is not just about studying more maths and physics textbooks. The Program uses Seaberry’s Soldamatic augmented reality welding simulators to gamify the learning experience. Anyone can try their hand at the welding simulators and be a star. A lot of these kids have never passed a test in their lives—the light in the kids’ eyes when the simulators gives them the all-clear is really something to see,” said Crittenden.
“Industry research demonstrates that investing in well-paid, secure jobs, expanding the Commonwealth Paid Parental Leave scheme, making early childhood education more affordable and accessible, and making workplaces safe from sexual harassment were key to getting women into work. All these measures must be implemented by both our governments and private industry,” said Crittenden. weldaustralia.com.au
Smart and robust modular units offer designers the opportunity to tailor projects to meet unique needs at low cost.
Lifgo
When fast, precise and synchronised linear motion is required, our Lifgo rack and pinion gear units have proven to be reliable in many industry sectors around the world.
A collaborative research centre of excellence will develop ultraprecise measuring devices that could enable high-speed internet, better medical screening technologies and carbon emissions monitoring.
RMIT University will lead a consortium of universities and industry partners in the new $72m ARC Centre of Excellence in Optical Microcombs for Breakthrough Science (COMBS), announced recently by the Australian Research Council.
They will focus on bringing optical frequency comb technology –which translates electronic signals into light waves for high precision measurement – out of the lab and into a wide range of real-world applications.
Centre Director, RMIT Distinguished Professor Arnan Mitchell, said it was a major milestone in the growing momentum of optical frequency comb technology.
“A photonic chip industry has finally emerged and the unique technology it produces will transform many fields of science,” Professor Mitchell said. “After so much hard work by so many people, the stars are finally aligning.”
The multi-disciplinary COMBS team includes world-leading experts from eight Australian universities (ANU, Monash, Swinburne, UTS, UniSA, Adelaide and Sydney) and 23 global partner organisations including The Garvan Institute, Advanced Navigation and the National Measurement Institute.
This investment in the Centre will develop a trained, versatile and diverse researcher workforce engaging collaboratively across fundamental science and technology, translation, enabling advances in multiple application areas.
Mitchell said the team spanning various career stages and disciplines had strength in diversity and a strong conviction to lead change in the Australian research community.
“We are passionate about improving equity, building Australian capability, educating the next generation and translating our research so that it really does achieve global impact,” he said.
RMIT Deputy Vice-Chancellor Research and Innovation and VicePresident, Professor Calum Drummond, said COMBS was perfectly aligned with RMIT’s mission to drive research with impact.
“The power of real-time information delivered by microcomb technologies is truly transformative. Microcombs will transform the way we measure everything around us, and in doing so change how we communicate, travel and live our lives,” Drummond said. “The high-impact applications we will see coming out of this new centre will catapult Australian research and industry into new domains."
Story: Michael Quin and Rachael Vorwerk rmit.edu.au scienceinpublic.com.au
Adelaide-based space industry-research centre SmartSat CRC and NASA team up to collaborate on astronaut emergency communications.
SmartSat Cooperative Research Centre, has announced a project agreement to further develop new Search and Rescue (SAR) beacon technologies with partner NASA.
Australia and the USA have a long history of cooperation in Search and Rescue. In 2020 NASA and SmartSat announced a collaboration to advance satellite-based emergency communications and Search and Rescue, combining communications and navigation technology. This new project deepens the strategic collaboration in this important field.
The project is studying a new search and rescue system for future human exploration on the surface of the moon, known as LunaSAR. Astronaut safety is paramount and the ability to reliably communicate an emergency incident must be maintained, even if other services are not available. Similar to distress beacons on Earth, this system will provide miniature low power radio beacons mounted on space suits and lunar rover vehicles. The technology will support SOS and two-way messaging over a lunar orbiting satellite constellation. It will also allow the beacon location to be accurately determined, in the absence of GPS. This information will be provided securely and quickly to both the mission control centre on Earth and the response team on the moon who are able to take immediate action.
Under the agreement, NASA’s Search and Rescue Laboratory (SARLab) at the agency’s Goddard Space Flight Center in Greenbelt, Maryland will bring experts to the project to help guide and review the technical direction. The research team will design a new specialised beacon for extra-terrestrial environments based on a new waveform. As well as direct Artemis applications, they will also investigate the
potential for enhanced services to extend beyond SAR to broader emergency management such as natural disaster warning systems.
Visiting Adelaide recently, the NASA Search and Rescue office Chief, Dr. Lisa Mazzuca gave this insight. “NASA is delighted to advance technology in this field, which will allow our astronauts exploring the Moon to do so knowing they have a system focused solely on their safety,” she said. “This is pioneering work that takes such a dedicated international partnership to get to fruition.”
Dr. Mazzuca’s SAR team also has the full support and sponsorship of the Space Communications and Navigation (SCaN) Program at NASA Headquarters in Washington, through Mr. James J. Miller, Deputy Director for Policy & Strategic Communications within SCaN.
“Australia is a unique location with many skilled and talented technologists who are fully capable as a full international partner of making major contributions to safeguard astronauts. We are proud to work with such like-minded experts to ensure the safety of our future astronaut corps.”
“This agreement is not just a fantastic development for Safety from Space’s low-power, high-efficiency safety technology, it signals that Australia’s space sector is developing globally important technologies,” SmartSat CEO Andy Koronios commented. “NASA has been instrumental in the development journey for this essential safety technology – and while it is early stages, we now have the further potential of this Australian-developed tech playing an important role in Lunar and Martian exploration missions under the Artemis program.” smartsatcrc.com
The managing partner of the Kübler Group was on site recently to open the brand new Kübler Australia distribution centre in Melbourne.
The Kübler Group is a leading global specialist producing position and motion sensors (including encoders), slip rings and transmission technology, counters and other process devices. The company is flagged as one of the 100 most innovative medium-sized companies in Germany for the fourth time running, in 2022. At the newly opened facility in Melbourne, Lothar Kübler noted the company’s year-onyear increase in revenue of just under 20% recently, and added that the most important element is their manpower. For the size of the company, with a good 500 employees worldwide, the strongly developed international sales and application network, as well as a high R&D share, are very important competitive advantages in the international business. In addition, at the end of 2021, Kübler set up an incubator team focused on digitalisation and Industry 4.0 solutions.
Kübler Group is a leading global specialist for position and motion sensors (including encoders), slip rings and transmission technology, as well as for counters and process devices. The company also supplies products and solutions for industries such as elevator technology, drive technology, wind power, mobile automation as well as intralogistics and mechanical engineering.
Kübler supplies products and solutions for industries such as elevator technology, drive technology, wind power, mobile automation as well as intralogistics and mechanical engineering. “We always want to understand exactly the application and future trends of our customers in their segments. This enables us to create the right product solutions,” says Lothar Kübler.
The new Australian team recognised that the pillar for Kübler’s success was the close customer dialogue, keeping them happy.
“Developing new ideas together and ‘continuously improving the existing’ is the motto,” said Australian Managing Director Jason Bouyer. “No less important is the manpower behind it. With the active R&D network at Kübler, a new portfolio of measuring wheel systems and bearingless encoders with IIOT functions are coming onto the market.”
kuebler.com/en/company/about-kuebler
Hetech teams up with EcoJoule to manufacture the PCB boards for the EcoVAR building products ready for distribution.
EcoJoule’s EcoVAR is improving and innovating electricity supply through smart grid technology.
The influx of solar on homes and businesses changes the way the local grid operates. EcoVAR technology helps improve voltages and increases the ability of solar to export clean energy.
The EcoVar is not only improving the quality of electricity in these areas, but it is also helping grid businesses like Ausgrid work towards a net-zero future.
With the rapid uptake of solar PV, the low voltage residential electricity network is being required to perform in ways it was never designed to perform. The main problem being experienced is worsening voltage regulation. The solar PV systems are generating at their maximum during the middle of the day when residential consumption is typically low, this then causes voltage rises on the low voltage networks causing solar inverters to trip, reducing the ability of solar panels to export clean energy. This sustained delivery of excess voltage levels is also diminishing reliability, reducing appliance lifetime and reducing appliance efficiency.
Hetech has teamed up with EcoJoule to manufacture the PCB boards for the EcoVar and they build the products ready for distribution. With many installations complete and delivering results in multiple states currently, the EcoVar is predicted to continue to roll out nationally over the coming months.
The EcoVAR technology helps improve voltages and increases the ability of solar to export clean energy to the grid. The benefits of this product are felt throughout the whole solar energy supply chain, with households benefiting from better energy utilisation, higher solar export volumes and lower bills.
Ausgrid has installed a three phase EcoVAR unit from EcoJoule Energy at Nords Wharf, which has successfully reduced the voltage fluctuation to consumers, also preventing the potential tripping of solar systems and delivering reliable outcomes in the delivery of power.
In the area where the EcoVAR unit has been installed there is a significant increase in the amount of solar energy that can be exported into the grid, virtually eliminating constraints on existing solar customers.
Not only is the EcoVar improving the quality of electricity in these areas, but it is also helping businesses like Ausgrid work towards a net-zero future.
“Ausgrid has a diverse and complex network and we are looking to use innovative technology to improve service quality for all of our communities,” Ausgrid’s Executive General Manager of Asset Management Junayd Hollis said. “That’s why we commenced these trials with the EcoVAR units, to improve customer voltage and quality of electricity supply. This is an integral part of our actions to increase hosting capacity for rooftop solar as well as other Distributed Energy Resources (DER), and reduce costs on our network. In turn this helps de-carbonise the grid and work towards a net-zero future.” hetech.com.au
Digital technologies for construction industry will improve safety and efficiency.
Victoria University researchers have developed state-of-the-art technology that will take outdated aspects of Australia’s construction industry into a modern digital age.
Professor Zora Vrcelj (Head of VU’s Built Environment) and Professor Yuan Miao (Head of VU’s Information Technology) and their teams have combined high-tech tools with engineering and architecture to improve safety training in the construction profession – which has one of the highest rates of preventable accidents and deaths of any sector in Australia.
With the help of a construction simulator (COSI) with virtual reality (VR) at VU’s Werribee Campus, the researchers want to reduce workplace injuries and deaths. COSI’s fully-immersive VR experience allows trainees to use high-tech goggles and equipment to enter and explore a detailed simulation of a construction site to learn about safety – a big change from learning it through an instruction booklet or computer modules.
The simulator lets users learn to climb ladders, move equipment, work in a confined space, or walk along narrow scaffolding, without any real risk. Already city councils, construction giants like Simonds Homes, and even the Victorian Building Authority – the state’s chief industry regulator –have expressed interest. Professor Vrcelj said the project would help modernise the construction industry, which is currently among the least digitised industries in Australia, leading to high rates of worksite injuries, a lack of quality control and inefficiencies.
Andrew Shea, CEO of the Builders Academy Australia, Simonds Group, said training workers via simulated experiences would make a real difference to a worker’s learning and have a, “genuinely positive impact.”
The VU researchers have developed a cloud-based platform where photographs and 360-degree scans of the building are uploaded, and can be accessed remotely in real time from a smartphone or iPad. VU.edu.au
New Touch Industries (NTI) is a progressive company with locations in Bayswater and Clayton South.
Our dynamic, rapidly expanding business provides high quality services in metal laser cutting, bending/ folding, welding and fabrication, delivering customers with precise streamlined project management with minimal margin for error.
This is achieved by our philosophy regarding the importance of teamwork and investing in staff. We pride ourselves on offering ‘pay for schooling’ and ‘promote from within’ policies, providing our staff with an environment to thrive. We are continuously striving to better serve our staff and become an employer of choice
Come and join a company where we believe happy staff are great staff!
Learn more at newtouchind.com.au, or contact us today.
How manufacturers can empower smart decisions that optimise operational efficiencies, increase productivity and minimise costs.
Manufacturers are now realising that digitalisation has the potential to fundamentally change their businesses. To ensure that Australia’s manufacturing capability is at the forefront of change and innovation in the Asia Pacific region, all manufacturing decision-makers should be moving towards Smart Manufacturing.
A Smart Manufacturing enabled organisation has all the information about the entire manufacturing process available in real-time, when and where it is needed and in the correct format to empower smart decisions.
Data analytics technologies and techniques provide a means of analysing data sets and drawing conclusions about them to empower smart decisions. Big data analytics applications integrated with an enterprise resource planning (ERP) system can enable manufacturers to analyse growing volumes of structured transaction information, plus other forms of data that are often left untapped by conventional business intelligence (BI) and analytics programs.
This encompasses a mix of semi-structured and unstructured data, for example, information from customer emails and survey responses, mobile phone records and machine analytics captured by sensors connected to the Internet of Things (IoT).
A smart ERP system provides embedded analytics that manage, analyse and process big data and provides manufacturers access to relevant and critical information from anywhere for better decisionmaking. However, to have full visibility of the whole business requires the business to be fully digitalised and interconnected.
Manufacturers must respond to demanding schedules while constantly seeking ways to lower costs, better manage inventory and streamline their processes. Add to that a constant need to innovate, as well as forecasting challenges and the ongoing pressures of supply and demand and this results in rising complexity in all areas of a manufacturing business.
For manufacturers that make-to-stock, make-to-order, engineerto-order, or employ project-centric, job shop, batch, or repetitive manufacturing approaches, they need a comprehensive ERP system to manage the entire manufacturing business that also provides them with a 360˚ view of their production.
Currently, many manufacturers are automating simple jobs and relying on people to manage the remaining processes, and this often places a heavy demand on their employees. As an alternative, a sophisticated system like Manufacturing Operations Management (MOM), implemented within an ERP solution, can help manufacturers to take control of their end-to-end manufacturing operations, without the risk of human error.
To provide more control of manufacturing operations, frontline managers need 360˚ visibility of the shop floor to prevent problems such as overruns, bottlenecks, downtime, poor employee or machine performance and excessive waste. MOM offers a unique level of delivery, cost and quality control of manufacturing operations for job shop, batch production, production line and mixed-mode environments.
With MOM, manufacturers have a single source of data and in turn, full visibility of production. Besides providing equipment status, employee performance and job status, data is digital and can be analysed to provide a predictive function to improve factory
performance. Once it is adopted, manufacturers will see how quickly their manufacturing operations gain efficiency and become more streamlined, with improved quality and increased profitability.
One of the simplest ways to improve operational efficiency is to leverage automation, one of the key components of Industry 4.0. Whilst employees still need to oversee and manage production, automation can eliminate the human errors that decrease efficiency; and Artificial Intelligence (AI) and machine learning can take a manufacturing business to the next level including basic, process, advanced, and “intelligent” automation.
The key to implementing automation effectively is ensuring the free flow of data and analytics. This will encourage manufacturers to finally give up on using spreadsheets and moving to systems that automatically allow the collection, organisation, analysis and distribution of data to all departments in a business. This level of data automation allows managers to make decisions based on current information without having to worry that the latest spreadsheet is updated and correct.
When configured and used to the best of its capabilities, automation can help businesses make better quality products, improve profitability, keep workers safe and increase overall operational efficiency to help meet and exceed business goals.
By pragmatically taking these steps and regularly iterating and improving operational efficiency does not need to be an allconsuming process. It's something that can be achieved gradually and is better-done step by step than when the business is forced to do it as a matter of urgency.
Getting buy-in from all levels of the organisation and making it everyone's job is one way to delegate responsibility during a technology transition. Keeping lines of communication open and rewarding transparency can reduce any potential problems. Once completed it will result in an improvement in product quality, increased productivity and reduced costs, which will all help businesses to retain their highly trained talent.
au.syspro.com
Sustainability is widely considered across industry. However, it is critical to purposefully understand what sustainability means for asset-intensive industries, including how to manage and comply with emerging sustainability standards. Opinion
Sustainability is defined in several ways including Oxford Languages (via Google) expressing it as the ability to be maintained at a certain rate or level; including avoidance of the depletion of natural resources in order to maintain an ecological balance. The Cambridge dictionary defines sustainability as the quality of being able to continue over a period of time; with the follow on, the quality of causing little or no damage to the environment and therefore able to continue for a long time. Finally, the American Heritage dictionary explains sustainability as being capable of being sustained; followed by capable of being continued with minimal long-term effect on the environment.
The initial statements in Google and Cambridge each represent maintaining a process, wherein American heritage is a little more ambiguous. Each follow on item in all definitions reflects minimal disturbances on the environment including depletion of natural resources. However, there are insufficient definitions to apply the appropriate context for industry sustainability.
In industry we dig a little deeper and expand the context of sustainability by defining at least three core pillars of sustainability, namely “economic, environmental, and social — also known informally as the: profits, planet, and people” – the three Ps. This brings in a third concept not mentioned in the foregoing dictionary definitions –the idea of not introducing social harm to people inside and outside of the company. Furthermore, some companies include a fourth sustainability pillar to track compliance with government regulations. In summary, we want to maintain the manufacturing process to make the profits, while not breaking the law, and supporting the continuing health of people and the environment. Consequently, we see manufacturing businesses implementing initiatives to actively reduce their environmental footprint, often described as green initiatives, while increasing their social responsibilities by eliminating practices that may disturb or harm people and to be sensitive to compliance issues.
Managing sustainability is hard. You can track relevant indicators such as energy consumption, waste, emissions in air and water releases, even labor standards, and safety records, build KPIs, place them in a dashboard to check how well you are performing.
As Peter Drucker, management consultant said, “If you can’t measure it, you can’t improve it.” A good first step, but you run the danger of all dashboards and few improvement activities. After all, the results are only lagging indicators and contain nothing proactive to control and manage sustainability. It’s a fallacy to believe that automated management and control of sustainability can come from computer applications. Sure, computer applications can watch and optimise energy usage but how about emissions, safety performance, and social behaviour?
Sustainability management and improvement is all about fashioning people’s behaviour to engage in activities and work processes likely to improve practices. And to do so people need to buy into the idea that sustainability has a major impact on corporate reputation, branding, and shareholder value in order to shape their behaviour in their day-to-day work processes. So, in the spirit of this article this begs a question.
We are not aware of tools that directly manage anything but the rate of production and perhaps energy consumption. You cannot use an application to reduce environmental impact or improve impact on people’s welfare. In one respect, sustainability effectiveness in APM applications is most often driven by recognition of and avoidance of the conditions and events that can cause disturbances in profits, the environment, and people safety.
The idea is that the application recognises an errant condition that can affect sustainability and issues alerts and potentially prescriptive advice for people to take action to avoid the issue. Alternatively, applications can simulate alternative operating scenarios to enable decisions to adjust conditions in design and operation for better performance. In all cases, it’s shaping the workers’ behaviour that is key.
For example, in recent years there has been a transformation in condition-based monitoring applications using new technologies of pattern recognition using machine learning. Such applications are capable of recognising patterns of behaviour that are abnormal and destructive well in advance of impending degradation and potentially disastrous situations; those conditions that can cause unexpected breakdowns, environmental emissions, and harm to people. Sudden emergency shutdowns often induce rushed and illconsidered decisions and actions that present unwanted danger and environmental releases. The APM application’s early alert capability provides the heads up to stimulate action to avoid the emergency unexpected shutdown. For example, in a chemical processing facility a 40-day warning of an imminent failure of a compressor allows the staff the time to plan and prepare to convert to a safe, orderly, managed shutdown that is unlikely to lift flare valves or safety valves, prevent release of toxins, and assure safe procedures avoiding harm to workers. All supporting sustainability improvements.
In summary, given the economic, environmental, compliance, and social pillars of sustainability in industry, APM applications provide insights into causes and guidance on what to do and what work processes to engage in order to support and improve sustainability. aspentech.com/en
Understanding Quality Management Systems (QMS) for commercial success in MedTech/Biotech.
The medical technology, biotechnology, pharmaceutical and digital health (MTP) sector is critical to Australia’s economy, the health outcomes of the population and the innovation ecosystem. In 2019 there were nearly 1,300 companies in the MTP sector that employed approximately 68,000 workers and contributed $5.2bn to the economy. The MTP sector added an additional 5,000 jobs across 2020 and 2021 and contributed around $5.5bn to the economy, respectively. The market capitalisation of MTP companies continued to grow strongly at 20% p.a. and MTP companies raised nearly $3.4bn in capital through 2020/21, as markets realised how resilient and vital the sector was to the broader economy.
MTPConnect is an independent, not-for-profit Growth Centre established to drive connectivity, innovation, productivity and competitiveness in Australia’s MTP sector.
In May 2020, MTPConnect was contracted by the Australian Federal Government to operate the Researcher Exchange and Development within Industry (REDI) program. This four-year initiative is backed by $32m in funding from the Medical Research Future Fund (MRFF) that aims to build an industry-ready workforce with the skills and capacity to keep pace with the demands of a rapidly changing sector – for now and the future – deploying an integrated three-pillar plan as per the figure below.
Within Pillar Two, REDI delivered a forward-looking 'root and branch' analysis of the MTP workforce to provide a deep understanding of current and future skills gaps. The November 2020 Interim Report identified skills gaps that need to be addressed across the sector in the near-term following assessment against four key metrics:
1. Alignment of the skills gaps with sector priorities
2. Alignment of the skills gaps with global megatrends
3. Breadth of impact across the MTP value chain
4. Depth of impact and estimated value from addressing the gap
The top three priority skills gaps were identified as those that can unlock significant value for the MTP sector if addressed, impact a broad cross-section of the MTP sector value chain, are not currently addressed by existing REDI programs and can be reasonably addressed within a short timeframe.
Priority Skills Gap One was identified as “Understanding of Quality Management Systems (QMS) and protocols” within the “Advanced manufacturing & supply chain” theme.
Overview
The MTP sector is highly regulated with manufacturers needing to be verified by government regulators (e.g. TGA in Australia and FDA in the USA) as meeting relevant quality standards before they are eligible to market products. Applicable international Quality Management System (QMS) Standards for manufacturers of MTP products include ISO 9001 (generic Quality Management), ISO 13485 (medical device Quality Management), ISO 17025 (competence of testing and calibration laboratories) and Good Laboratory Practice (GLP - quality control for non-clinical health, safety and environmental studies).
Stakeholder consultations highlighted that universities, start-ups and Subject Matter Experts within the MTP sector often lack the following skills related to quality management:
• Understanding of the importance of adopting and maintaining appropriate quality management systems among business leaders; and
• Lack of staff members with sufficient training in quality management systems to:
- Define best-practice quality management principles and protocols that are aligned to relevant industry standards;
- Design and implement a path for achieving greater alignment to industry accreditation; and
- Maintain quality procedures and quality systems to ensure high standard facilities
Although it is a core capability for commercial success in the MTP sector, adoption of QMS processes and maintaining informal alignment or formal certification to standards can be considered too time consuming and difficult.
Large and established companies tend have sufficient in-house capabilities due to their scale and deep knowledge of the regulatory requirements of the MTP sector. However, the QMS skills gap is particularly evident within start-ups and SMEs noting the emergence of more MedTech, Biotech and digital health businesses.
Broader adoption of Quality Management Systems and standards by start-ups and SMEs will drive greater commercialisation success, as companies will be better positioned for investor / partnering discussions, regulatory submissions and becoming preferred suppliers in a global market.
Developing greater quality management at the basic research level will also drive greater commercialisation outcomes long-term. Researchers will gain greater credibility among big MTP companies and increase the likelihood of obtaining licensing deals if the assets and data have been processed in compliance with international quality standards. There were instances highlighted in interviews where research was required to be repeated under GLP processes, slowing commercialisation.
Furthermore, the COVID-19 pandemic highlighted the value of appropriate quality certifications when responding to global supply chain disruptions. A number of potential domestic manufacturers of medical equipment and supplies were unable to effectively pivot their operations and contribute to the pandemic response because they didn’t have ISO 13485 certification.
SeerPharma, a consulting and training organisation servicing life science industries, was selected by MTPConnect as the REDI Partner to deliver a range of QMS training courses across Australia addressing ISO 9001, ISO 13485, ISO 17025 and GLP. To date, over 700 Australians have undertaken the free online and ondemand QMS Primer while over 300 people have undertaken a three or four-day deep-dive workshop learning the requirements of ISO 9001, ISO 13485 and GLP QMS Standards as well as how to meet them.
seerpharma.com/REDI
Talent retention and the rise of environmental, social and governance top issues for project management profession.
Australian Institute of Project Management (AIPM), identifies the pressure points among the profession, launching the 2022 ‘The State of Project Management in Australia’ report. With over 73% of respondents claiming projects experienced staff shortages, 52% reporting delays due to sourcing key skills and 62% expecting ESG requirements to influence their projects and programs in the future, AIPM representatives are calling for greater investment in attracting new talent, fostering career development and upskilling from leaders in the profession to improve business outcomes and stay relevant within today's market.
AIPM’s newly released annual report, based on a survey of the profession conducted with KPMG Australia, on the ‘State of Project Management in Australia’ aims to help identify and elevate the key issues within the project management workforce. The fifth instalment of the report brings to light the increasing pressure facing project management professionals including an ageing workforce, supply chain issues, digital transformation projects and the emerging influence of Environmental, Social and Governance (ESG).
“The broad effect of skills shortages and supply chain disruptions places immense pressure on the project management profession. These report findings raise the need for innovative and inclusive ways to bring more people into the profession and to retain and upskill the existing talent.”
“The C-suite critical leaders and decision-makers should consider attracting emerging talent, and mentoring and professional development are key focuses for their organisations. With 65% of respondents directly working on high-value projects in the past 12 months, it is crucial for the shortages not to hamper project success.”
The survey of project management professionals highlights trends and factors around the quality of project delivery. Topic areas also include:
Experienced project managers are approaching retirement with over 40% of respondents having 20+ years of experience. Organisations must focus on attracting and developing emerging talent to prepare for the looming skills exodus. Yet, 42% of respondents said their organisation wasn’t doing anything (or they didn’t know what they were doing) to attract and encourage emerging project professionals.
On-time project delivery has slipped in the past two years (32% compared to 42% in 2020), likely due to de-prioritisation, rise of complex projects, skills shortages, supply chain disruptions and other economic constraints. Delivery of most projects in line with business goals is steady (50% compared to 51% in 2020), demonstrating resilience and perseverance in challenging times. Concerningly, 48% of respondents claimed stakeholder satisfaction and only 36% of projects were delivered on-budget most of the time.
The report clearly calls for Australian organisations to deploy innovative and inclusive ways to attract people into the profession and to retain the experienced and qualified professionals already in place. 39% of respondents said team stress and burnout were increasing with a further 28% saying their own stress and burnout were increasing.
Several factors pointed to the under-valuing of project management as a profession. These factors included weakness in recruiting and appointing suitably skilled project managers and a need for greater investment in continuing professional development. Many respondents indicated that their organisations did not offer a professional development path and career opportunities and almost 30% indicated that their organisation committed none or less than one day of professional development per year.
Australian organisations have accepted the need for action on ESG issues, driving an increase in transformation projects. Organisations must recognise the need to put Project Management Offices at the helm to get the best ESG outcomes. Similarly, project professionals must upskill to lead these projects to success.
The report respondents clearly already understand the need for upskilling as organisations continue to incorporate ESG matters into business operations and strategy. The profession is already seeing the impact: ESG specific roles are already growing in demand, with hundreds of open positions in Australia alone.
Supply chain disruption
Supply chain constraints, resource scarcity and rising costs are some of the biggest disruptors facing the project profession. 44% of respondents had projects affected by supply chain disruption and 51% faced rising costs of materials and/or staff.
The report calls for supply chains to be reimagined to help organisations build resilience and avoid material shortages and spiralling costs to better navigate future volatility. Cultivating resilience through technology investment and strategic partnerships will help organisations better anticipate and respond to the unexpected.
Highlighting the need for evolution of project methods to keep pace with the complexity and agility of modern workplaces and projects, 57% of respondents believe that project complexity has increased with the use of artificial intelligence software increasing from 10% to 29% this year.
Artificial intelligence will help to absorb more transactional project tasks, addressing and improving support for project professionals and executives. 74% of organisations said its digital transformation projects are business-driven to improve customer experience, cost reduction and maintain competitive action.
AIPM is committed to continue to monitor new ways of working for impacts on its certifications, members and the profession as a whole. Its certifications are always aligned with best practices and ensure individuals can demonstrate their capabilities to drive project management excellence so they can meet strategic objectives for businesses in a dynamic environment.
aipm.com.au
Researchers from Basel and Tel Aviv discovered that friction varies with speed in specific graphene structures on platinum surfaces, defying Coulomb’s law which states that friction is speedindependent in the macro world.
Materials made of single atomic layers are highly valued for their lowfriction qualities, useful in reducing friction in hard disks or moving parts of satellites or space telescopes. Graphene, consisting of a single layer of carbon atoms arranged like a honeycomb, is a prime example and is under examination for its potential as a lubricating layer. Earlier studies showed that a graphene ribbon can glide almost friction-free across a gold surface.
If graphene is applied to a platinum surface, it has a significant impact on the measurable friction forces. Now, physicists from the University of Basel and Tel Aviv University have reported in the journal Nano Letters that, in this instance, the friction depends on the speed at which the tip of an atomic force microscope is moved across the surface. This finding is surprising because friction does not depend on speed according to Coulomb’s law, which applies in the macro world.
Swiss Nanoscience Institute, University of Basel
The international team was led by the University of Adelaide’s Professor Shizhang Qiao and Associate Professor Yao Zheng from the School of Chemical Engineering.
“We have split natural seawater into oxygen and hydrogen with nearly 100% efficiency, to produce green hydrogen by electrolysis, using a non-precious and cheap catalyst in a commercial electrolyser,” said Professor Qiao.
A typical non-precious catalyst is cobalt oxide with chromium oxide on its surface.
“We used seawater as a feedstock without the need for any pretreatment processes like reverse osmosis desolation, purification, or alkalisation,” said Associate Professor Zheng. The team published their research in the journal Nature Energy. “The performance of a commercial electrolyser with our catalysts running in seawater is close to the performance of platinum/iridium catalysts running in a feedstock of highly purified deionised water.
“Current electrolysers are operated with highly purified water electrolyte. Increased demand for hydrogen to partially or totally replace energy generated by fossil fuels will significantly increase scarcity of increasingly limited freshwater resources,” said Associate Professor Zheng.
Seawater is an almost infinite resource and is considered a natural feedstock electrolyte. This is more practical for regions with long coastlines and abundant sunlight. However, it isn’t practical for regions where seawater is scarce.
UniSA
The size of a Micro LED chip is not visible to the naked eye, with the length of one side being less than 50 μm (micrometers). For example, in order to manufacture one 4K display that has four times the resolution of a conventional high-definition screen, it is necessary to precisely array about 24.9 million chips. In order to improve the complexity and yield ratio of Micro LED chip manufacturing and the transfer process of each chip, Shin-Etsu Chemical has been working to take advantage of the latest materials technologies. They have lately solved the key manufacturing challenges of Micro LED display manufacturing.
The new process technologies introduce innovative technology that will transfer singulated anisotropic conductive film (ACF) of Φ80μm or less onto the targeted location by laser equipment. Employing this technology, it has become possible to transfer the singulated ACF only to the designated plate and mount the Micro LED chip. This makes the repair process in Micro LED display manufacturing easy to carry out, a matter which had been a large issue up until now.
As the world looks for ways to cut greenhouse gas emissions, researchers from Sandia National Laboratories have shown that a new 3D-printed superalloy could help power plants generate more electricity while producing less carbon.
Sandia scientists, collaborating with researchers at Ames National Laboratory, Iowa State University and Bruker Corp., have used a 3D printer to create a high-performance metal alloy, (superalloy), with an unusual composition that makes it stronger and lighter than state-of-the-art materials currently used in gas turbine machinery. The findings could have broad impacts across the energy sector as well as the aerospace and automotive industries, and hint at a new class of similar alloys waiting to be discovered.
“We're showing that this material can access previously unobtainable combinations of high strength, low weight and hightemperature resiliency,” Sandia scientist Andrew Kustas said. “We think part of the reason we achieved this is because of the additive manufacturing approach.”
Sandia National University
Using the powerful James Webb Space Telescope, the Swinburne University researcher, alongside an international team of scientists, has reportedly observed massive candidate galaxies at the beginning of time, up to 100 billion times the mass of the Sun. If confirmed, would contain more mass than was thought to exist in the whole Universe at that time. The research, published in Nature magazine, could upend our model of the Universe and force a drastic rethink of how the first galaxies formed after the Big Bang.
“We’ve never observed galaxies of this colossal size, this early on after the Big Bang,” says lead researcher Associate Professor Ivo Labbé from Swinburne University of Technology.
“The six galaxies we found are more than 12 billion years old, only 500 to 700 million years after the Big Bang, reaching sizes up to 100 billion times the mass of our sun. This is too big to even exist within current models,” adds Prof Labbé. Follow up measurements are being carried out to confirm the galaxies and rule out alternative explanations. “One alternative, equally fascinating, is that some of the objects belong to a new class of emerging supermassive black holes, never seen before,” Associate Professor Labbé says.
Swinburne University of Technology
Australia’s national science agency has signed a five-year agreement with US-based company SpaceX to support their future space missions. CSIRO’s iconic Murriyang telescope situated out in Parkes NSW, and other telescopes owned by the agency, will provide ground station downlink services to select SpaceX missions.
The Parkes telescope has a long history providing spacecraft tracking services for NASA and other international space agencies.
CSIRO also manages the Canberra Deep Space Communication Complex for NASA, and the New Norcia ground station for the European Space Agency.
Dr Douglas Bock, CSIRO’s Director of Space and Astronomy, said the agreement with SpaceX recognises CSIRO’s experience operating large, complex spacecraft tracking and radio astronomy infrastructure.
“Our Parkes radio telescope began supporting NASA space missions in 1962, when it tracked the first interplanetary space mission, Mariner 2, as it flew by the planet Venus,” Dr Bock said. The telescope, along with NASA’s Honeysuckle Creek tracking station, famously received the television signals from the Apollo 11 Moon landing watched by more than 600 million people around the world. Most recently, the telescope received data from Voyager 2 as it entered interstellar space in conjunction with the Canberra Deep Space Communication Complex.
“Providing ground station services for space missions complements the astronomy research conducted with our telescopes and helps to maintain their capabilities as world-class research instruments,” he said. While the telescope recently celebrated its 60th anniversary, its technical systems have been upgraded many times keeping it at the cutting edge of research into understanding our Universe.
CSIROA new RMIT-led international collaboration published in February has uncovered a distinct disorder-driven bosonic superconductorinsulator transition.
The discovery outlines a global picture of the giant anomalous Hall effect and reveals its correlation with the unconventional charge density wave in the kagome metal family, with potential applications in future ultra-low energy electronics. Superconductors, which can transmit electricity without energy dissipation, hold great promise for the development of future lowenergy electronics technologies, and are already applied in diverse fields such as hover trains and high-strength magnets (such as medical MRIs).
However, precisely how the superconductivity forms and works in many materials remains an unsolved issue and limits its applications. Recently, a new kagome superconductor family has attracted intensive interest for their novel properties. ‘Kagome’ materials feature an unusual lattice named for a Japanese basket-weave pattern with corner-sharing triangles.
The FLEET-led collaboration of researchers at RMIT University (Australia) and partner organisation the High Magnetic Field Laboratory (China) confirm for the first time the electric control of superconductivity and AHE in a van der Waals kagome metal CsV3Sb5. The team chose to test this theory on CsV3Sb5 which potentially has the largest spare atom space for proton intercalation. The devices were easily designed and fabricated based on the team’s rich experience in this field.
Further experimental and theoretical investigations indicate that this dramatic modulation of giant AHE originates from the Fermi level shift in the reconstructed band structures.
Nature Communications
Empower your team to create fully-functional, full-colour, engineering-grade parts today.
3D printing is still often associated with creating prototypes, but 3D Explorer shows it’s now possible to create durable, cost-effective, on-demand products that allow businesses to cater to their customer’s individual requirements.
With 3D Explorer’s cutting-edge technology, businesses large and small have access to the same production capabilities, whether it’s a one-off R&D item, rapid prototyping or a fullblown production. 3D Explorer gives businesses the ability to print one or one hundred products without sacrificing quality, affordability or time.
This flexibility is desired across many sectors but is especially essential in the healthcare sector, where customised solutions are often required. Such is the case for Korthotics, a leading orthotics service provider which offers off-the-shelf and customised orthotic products to its customers.
However, customised solutions can often become expensive, so when Korthotics needed a durable intricate cranial protective helmet made, they turned to 3D Explorer for help. Now, the helmet did not just need to be light, strong and durable; its surface also had to be smooth and skin-friendly to give the patient a comfortable experience. The team at 3D Explorer was happy to meet the challenge and made the entire process streamlined and easy. All that was required of Korthotics was to upload a 3D printable format file and specify the colour and finish.
And the finish is where 3D Explorer really delivered. As the only company in Australia with the AMT SP50 machine, which offers Vapour Smoothing to most 3D printed parts, they were able not only to manufacture the helmet to the highest standard but also provide the finish Korthotics required. The AMT PostPro Chemical Vapour Smoothing SF50 elevates the aesthetics and functionality of
3D prints. And the high-quality seal ensures the 3D product, model, or prototype is protected, smooth, and won’t lose its dimensional accuracy with time.
Of course, prosthetics and orthotics represent an important and thriving segment of 3D Explorer’s operations. However, there are several other sectors where 3D Explorer manufacturing proficiency is gaining in popularity.
For example, continuing in the health sector, 3D Explorer is now able to help surgeons turn organ MRIs into 3D printed models on which they can practice in preparation for complex surgeries – to find the most effective surgical path.
In the manufacturing sector, rapid, full-colour prototyping allows product designers and engineers to turn concepts into fully functional, engineering-grade parts that can be tested within tight timeframes. It also helps them to create electronic components, custom fixtures, jigs and guides, vital for precision and replicability in the manufacturing process. In the building and design sector, it allows architects, builders and property developers to create 3D architecture models, aiding their marketing efforts and helping their clients to visualise the proposed projects. In the adjacent art scene, artists are now capable of introducing 3D textures in their artwork and producing full-scale, coloured sculptures.
In addition, 3D Explorer has its own application and eyewear brand in consumer products, venEyes: 3D-printed customised eyewear. With each pair perfectly fitting the contours of the customer’s face. The ability to only print what is required helps consumer brands avoid overproduction and, in turn, lift their environmentally friendly status. This is particularly important within the health and fashion sector, which is often demonised for dumping last season’s inventory in the landfill. 3dexplorer.com.au
New cleanroom rated static eliminator is a lightweight handsfree solution.
EXAIR’s new Intellistat Ion Air Nozzle is the latest solution for static elimination in sensitive processes. Like the Intellistat Ion Air Gun, this new Nozzle provides a lightweight solution rated Class 5 for clean rooms and controlled environments per ISO 14644-1. The Ion Air Nozzle comes equipped with a mounting bracket to assist with remote mounting or benchtop assembly for hands-free use. It will reduce 1000 volts to less than 100 in 0.6 seconds and up to 610mm away. The Intellistat Ion Air Nozzle is a comprehensive solution for neutralizing static in sensitive processes like scientific and electronic testing, cleaning medical or pharmaceutical products and packaging, or removing debris from sensitive electronics. Including a compact stainless steel adjustable mounting bracket, the Intellistat nozzle can be mounted to benchtops and machine frames, for example, to provide hands-free operation when needing both hands to package, test or assemble parts and products. The nozzle is equipped with an LED indicator to assure proper functionality and employs an EXAIR-engineered air nozzle to maximise efficiency and meet OSHA requirements for sound level and dead-end pressure. Its durable static dissipative polycarbonate housing and non-marring nozzle assures the usefulness of the Intellistat in applications such as PCB or electronics manufacturing, and in sterile environments such as pharmaceutical and medical laboratories.
Leading international welding equipment manufacturer Kemppi has released its latest addition to its range of X5 FastMig welders – the new X5 FastMig Pulse.
The X5 FastMig Pulse multi-process welding system has been specifically designed for steel, aluminium and stainless steel welding in industrial environments. The machine delivers a range of features that help significantly enhance arc welding productivity.
Built using energy-efficient inverter technology, the X5 FastMig Pulse offers faster welding and quality welds thanks to Touch Sense Ignition, effortless operation, excellent welding ergonomics, flexible equipment setup and is industry 4.0 ready.
A high-performing machine, the X5 FastMig Pulse features the latest in ignition technology – Touch Sense Ignition – as standard. When combined with WiseSteel software, which is also included in the X5 FastMig Pulse, it delivers precise ignition capability and stable arc control.
The X5 Pulse tackles the challenges of globular arc by alternating between short arc and spray transfer. In short-circuit transfer, it improves the arc stability adaptively, providing better out-of-position steel welding capabilities. In spray transfer mode, micropulsing of the current and voltage increases travel speed significantly. In doing so, the X5 Pulse helps to minimise the spatter produced by a traditional globular arc, as well as the need for post weld cleaning, saving the welder both valuable time and cost, while helping to deliver better quality welds.
Created with the welder in mind, the ergonomically-designed toploading wire feeder improves occupational safety when changing the wire spool as it places less strain on the user’s back. The wire feeder can also be hung up and adjusted to multiple different angles for quick and easy access, even in a dual setup.
Power sources are available in 400 A and 500 A, and the modular nature of the X5 FastMig Pulse means that users can build the assembly that best suits their needs. Welders can choose from a range of excellent accessories including transport units, interconnection cables of various lengths, wired remote controls, and the SuperSnake GTX sub-feeding system for hard to reach welding environments.
The X5 FastMig Pulse is also industry 4.0 ready when combined with Kemppi’s optional WeldEye ArcVision. This digital, cloudbased solution collects welding parameters, arc-on time and filler material consumption. It lets users monitor welding activity in realtime to ensure that welding procedure specifications are accurately followed to help boost productivity.
Made in Finland, the X5 FastMig Pulse has been built to last. It features an injection-molded plastic casing that absorbs knocks, and together with the impact- resistant display panel, ensure the machine can withstand challenging environments.
kemppi.com
Ribcraft, British manufacturer of rigid inflatable boats, expands presence to Australia and Asia-Pacific.
Ribcraft, the world’s leading manufacturer of professional-grade rigid inflatable boats (RIBs), has opened a new sales and distribution office in Melbourne, Australia, due to growing demand in the wider Asia-Pacific region.
With manufacturing facilities in the UK, USA and Middle East, Ribcraft’s Australian operation will support the company’s expanding presence in Australia and the Asia-Pacific region, enabling further market penetration for its renowned commercial, military and leisure RIBs. “The growing demand for Ribcraft’s professional grade RIBs from a number of Australian and Asia-Pacific commercial and leisure customers has led Ribcraft to expand its footprint into the region. This is an extremely exciting time for Ribcraft, and we are proud to be making this global expansion,” states Toby Adams, Ribcraft CEO.
“Ribcraft’s move into the Australian and Asia-Pacific markets is testament to our reputation for producing the highest quality RIBs that are used across a range of industries, including by military and police forces around the world, as well as the growing tourism and leisure markets.”
Founded in the UK over 30 years ago, Ribcraft’s extensive range includes RIBs designed for a wide range of applications, with a broad client base from government organisations to commercial, sea-safari, search and rescue, coaching, safety and support, police and patrol, to leisure and military operations.
Built to the highest standards, featuring the acclaimed Ribcraft signature GRP deep V hull and heavy-duty Hypalon inflation tubes, reinforced hulls and pressure relief valves, Ribcraft RIBs range from 3.5m-12.5m and are custom designed to exact requirements for a client’s specific mission, such as load capacity, speed requirements,
agility manoeuvrability and stability, and layout options such as seating configuration and open, partially enclosed or fully enclosed cabins.
The move follows some of the company’s most recent innovations, including a new leisure range, sustainable composite construction and emissions-free propulsion. This is on top of Ribcraft being one of the only manufacturers in the world to design and construct RIBs in-house, ensuring Ribcraft’s RIBs are manufactured to the highest standard and quality.
Ribcraft has appointed Adelina Florescu as the new Managing Director for Ribcraft Australia. Ms Florescu brings extensive experience in managing commercial and leisure customer accounts, as well as government tenders in the Middle East and Europe.
“I am absolutely thrilled to be part of this expansion and look forward to bringing Ribcraft to the Australian and Asia-Pacific market and securing new partnership opportunities that continue to pave the way forward,” said Florescu. ribcraft.com.au
Dewalt is bringing two exciting new chemical adhesives to market to deliver a complete anchoring and installation system for the construction industry. Renowned for their consistent innovation, DEWALT Engineered By POWERS PURE500 and EA70-Pro build on previous solutions, offering improved performance and productivity for major infrastructure projects and commercial construction sites. Developing fit-for-purpose building products drives the Research and Development at DEWALT Engineered By POWERS. Both new products provide compliant anchoring solutions for concrete and masonry respectively while dispensing systems improve application effectiveness and efficiency. With comprehensive European Technical Assessment (ETA) pre-qualifications, both new products have been endorsed by the Australian Engineered Fasteners and Anchors Council (AEFAC) giving users the necessary confidence of meeting the stringent requirements of AS5216-2021 and in turn satisfy the relevant provisions of the National Construction Code (NCC 2019). For use in large commercial projects and major civil infrastructure projects for safety critical anchoring solutions, PURE500+ is a slow cure pure epoxy adhesive that is designed to be used in the most demanding of applications. PURE500+ builds on the previous PURE150-PRO and comes with new ETA approvals including a 100year design life, extensive seismic C1 & C2 approvals for threaded rod and rebar applications, and fire resistance approvals.
PURE500+’s two-component epoxy adhesive anchoring system includes injection adhesive in plastic cartridges, mixing nozzles, dispensing tools and hole cleaning equipment and can be stored for 24 months without leakage and dispensing problems often found with other epoxy systems.
“PURE500+ has several features including increased bond strength and easier dispensation which allow it to be used in a number of applications including in diamond cored holes and in wet and water filled holes,” said Justin Goode, Group Product Marketing Manager, Stanley Black & Decker. “It has been approved for use in several tunnelling and major road projects throughout Australia.”
The second of these new innovative products, EA70-Pro is an Epoxyacrylate adhesive injection system which supersedes PV45PRO. EA70-Pro is a medium duty, fast curing adhesive for threaded rod applications in concrete and masonry substrate. EA70-Pro comes with new ETA approvals for use in hollow and solid brick and substrates such as aerated concrete.
“The EA70-PRO is a two-component 10:1 ratio styrene-free epoxy acrylate adhesive anchoring system designed for use in the installation of threaded rod of variable length in solid concrete and masonry materials,” said Goode. “This medium duty, fast-curing formulation is recommended for use in concrete, solid brick and hollow brick materials. Benefits include the Epoxyacrylate formula, additional ETA Masonry approvals, and its anchoring capabilities in water filled holes.”
To support the launch, DEWALT Design Assist (DDA), a free structural design software that streamlines, automates, and optimises DEWALT anchoring products in accordance with Australian Standard AS5216:2021 has been updated to include PURE500+ & EA70-PRO chemicals into its design parameters. anchors.dewalt.com.au
Australian Manufacturing Week is back home to Melbourne, in a big way. Staged at the Melbourne Convention and Exhibiton Centre from 9–12 May 2023, AMW 2023 is Australia’s Premier Manufacturing Solutions Event.
Owned and organised by AMTIL, Australian Manufacturing Week is more than just an exhibition. AMW is a week-long celebration of manufacturing in Australia.
AMW had a massive show in Sydney last year, with 6,000 trade visitors and 170-plus exhibitors in 4,500 square metres of exhibition space spread over four days.
This Australian manufacturing show needs a week to run its course, and it is coming home to fill the biggest venue in Melbourne. We’re looking at 10,764 square metres, 330-plus exhibitors, spread across a week, just across the Yarra river from the great city of Melbourne.
Since the country opened up from lockdowns last year, we have seen a resurgence of market activity within Australia and manufacturers have answered the call to find new business. They are all enthusiastic to show off their best, newest and brightest skills, machinery and expertise.
There is such a variety of manufacturing happening in Australia, AMTIL has grouped the major sectors of manufacturing in their own areas, while still keeping everything under one roof, open to all. To demonstrate the advancements within each particular segment of the manufacturing industry, there are seven areas to explore. There is help at hand to find your way through the sea of stands as well. AMW’s organisers have teamed up with the event management software specialists Map Your Show to create a set of online tools and help during your visit, and in advance. There is also a completely rebuilt AMW App available so all you need is your phone to organise your days. It’s like having your own personal guide for AMW2023.
“When AMTIL started representing the Australian manufacturing industry some 23 years ago, I never suspected we would also be organising the annual industry show, now the biggest manufacturing exhibition in the southern hemisphere,” said AMTIL CEO Shane Infanti. “Welcome to AMW2023.”
AUSTECH – MACHINE TOOLS
Australia’s premier advanced manufacturing and machine tool exhibition, showcases machine tools and ancillary equipment
ADDITIVE MANUFACTURING
Spotlighting the latest advances in 3D printing
AUSTRALIAN MANUFACTURERS PAVILION
Showcasing the capabilities of Australia’s precision engineering and advanced manufacturing sector
MANUFACTURING SOLUTIONS
Offering optimised solutions to the most common challenges, from materials handling and safety to raw materials, software and integrated manufacturing solutions
ROBOTICS & AUTOMATION
Covering robotics, the internet of things, digitalisation, automation and controls, everything you need for increased productivity and optimisation of manufacturing operations
WELD & AIR SOLUTIONS
Highlighting advanced welding processes and air technology and reticulation
PLASTICS TECHNOLOGY
Covering all aspects of injection moulding, moulded plastics, raw materials and plastics processes
The AUSTECH Machine Tools Zone @ AMW 2023 will be epicentre of the entire exhibition. As the oldest zone within the exhibition, AUSTECH invites the top companies within the Machine Tools and Ancillary Equipment industries.
AUSTECH Machine Tools Zone is specifically targeted at the metalworking, machine tool and ancillary market in Australia and covers advanced manufacturing products and processes including: CNC Machinery, Lathes, Mills; Contract Manufacturing/Precision Machining; Cutting Tools, Tooling and Tool Holding; Forming and Fabricating Machines; Plasma, Laser, Waterjet and Ultrasonic Machines; Ancillary equipment suppliers.
Few of the well-known industry leaders exhibiting at AUSTECH are Okuma, John Hart, Headland Technology, Applied Machinery, Bystronic, Kraftech, Hare & Forbes, Sheetmetal Machinery Australia, Amada, Alfex CNC, Acra Machinery, SWI Engineering, IMTS Machinery, Stamac Engineering, Bystronic, Power Machinery, Iscar. Guhring, Multicam, Techni Automation, Modern Tools, Peddinghaus and FICAP.
With this wide range of technologies and industry leaders all on display at the one time and one place, the Australian Manufacturers pavilion should be on the must visit calendar for all the industry professionals and enthusiasts.
ISCAR Australia is a high-profile producer in the Australian metalworking sector.
As well as sponsoring the AUSTECH Machine Tools Zone, ISCAR is a producer of innovative cutting tools for metalworking, including turning, grooving, milling, hole making, boring and threading tools.
The Additive Manufacturing Zone will spotlight the latest advances in the technologies within this sector.
Techniques within Additive Manufacturing include Stereolithography, Selective Laser Sintering, Material Extrusion, Sheet lamination, Binder jetting, Cold Spray processing, Material jetting, directed energy deposition, powder bed fusion, VAT photo polymerisation and wire arc manufacturing (WAAM). Many of these will be represented within the Additive Manufacturing Zone.
With the likes of Bilby 3D, CSIRO Manufacturing, SLM Solutions, GoProTo (ANZ), Objective 3D, FormLab Inc., Titomic, Additive Australia, Thinglab, Metal Tech, and RMIT University, the range of exhibitors includes Additive Manufacturing users, suppliers, and supporters.
Additive Manufacturing is prominent in design and evaluation, modelling, rapid manufacturing, repair, tooling, fixturing and most importantly, production. With such an extensive array of technologies on display all on one floor, it would the ONE place to be for all Additive Manufacturing enthusiasts and professionals.
The Australian Manufacturers Pavilion will be showcasing the most advanced technologies within this sector. This home-grown Pavilion showcases the capabilities of Australia’s precision engineering and advanced manufacturing industry.
The Australian Manufacturers Pavilion is where AMW celebrates the very best in Australian manufacturing, providing a showcase for some of this country’s most accomplished component manufacturers, precision engineering firms, toolmakers, advanced manufacturers, and general engineering companies.
The various capabilities within Manufacturers Pavilion include Tooling, Cutting Technologies, w and prototyping, Aluminium Extrusion, Machining, Cutting and Milling Solutions, Sheet Metal fabrication, Powder Coating, Laser Cutting, Panel Folding and Digitisation. Many of these will be represented within the Australian Manufacturers Pavilion.
For quick manual deburring and edge rounding
– Fast, safe removal of dross and slag from plasma and flame cut parts
– Slag is chipped off using our HammerDisc Head
– Double spindle provides edge rounding capability in one setup
– Automatic Table Magnet holds the workpiece securely
– No skill set required, anyone can produce consistent results
– Easily 3–4 times faster than traditional methods
– European designed & made for best performance and lasting reliability
– Affordable with fast return on investment
https://www.loewer-online.com/metal/en/overview-machines/swinggrinder/
The Manufacturing Solutions Zone, sponsored by Adobe, offers optimised solutions to the most common challenges experienced by manufacturers.
From materials handling and warehousing to integrated manufacturing and safety solutions. The manufacturing industry would not be able to function effectively without a diverse array of ancillary technologies and support services.
With the likes of Adobe, Autodesk, All Manufacturing Personnel, Carbide Tools Ltd, Schmalz Australia, TXM Lean Solutions, Sterna Global Logistics, Simply Finance, Monash Smart Manufacturing Hub and MYOB, the Manufacturing Solutions Zone is where you can find answers.
The Manufacturing Solutions Zone incorporates everything from equipment for materials handling and logistics, and safety products, through to the latest software for streamlining manufacturing operations, and specialist service providers in areas such as law, finance, and skills, training, and recruitment.
The Robotics and Automation Zone will feature the latest state-of-the-art equipment and processes for the optimisation of manufacturing operations.
Robots are practical technologies, with artificially intelligent software brains, created and designed by engineers to refine, manufacture, and move Australian manufacturing ahead.
While countless works of science fiction have depicted robots as sources of wonder or menace, the reality today is much more common, with modern robots liberating human workers from an ever-growing array of repetitive and dangerous tasks.
And these innovative robotic technologies and the software that run them that will be featured at the Robotics and Automation Zone. Primary among the technologies and capabilities on display are Industrial Robotic Technology, Machine Tool Tending, Fibreglass and Gelcoat, Paint finishing. Materials handling, Shot blasting, process Control and measurement.
The Weld & Air Solutions Zone will highlight advanced welding processes and provide high-quality interactive experiences that demonstrate developments and applications in the welding sector.
The Weld & Air Solutions Zone, sponsored by Atlas Copco, will highlight advanced welding processes, and provide high-quality interactive experiences that demonstrate developments and applications in the welding sector. Welding is critical in metal fabrication and manufacturing today. In fact, it is used in creating more than half of the products manufactured in Australia. Welders, cutters, solderers, and brazers use hand-held or remotely controlled equipment to join or cut metal parts.
The various types of Welding Technologies at Weld & Air Solutions Zone would be Gas Metal Arc Welding (GMAW/MIG), Gas Tungsten Arc Welding (GTAW/TIG), Shielded Metal Arc Welding (SMAW) and Flux Cored Arc Welding (FCAW). An assortment of this tech will be represented within the Welding & Air Solutions Zone.
The Plastics Technology Zone is your hands on opportunity to inspect the latest in plastics machinery, mould-making technologies, raw materials, and plastics manufacturing processes.
This area will cover injection and blow moulding, extrusion, thermoforming, and compounding, mould making and tool making, raw materials and recycling, plastic technology processes. The Plastics Technology Zone will be showcasing the most advanced technologies including polymer manufacturing, compounding, distribution, processing, equipment & polymer tooling.
“PIMA was part of Australian Manufacturing Week (AMW) 2022 held at the Sydney ICC which we found was huge success,” said President of the Plastics Industry Manufacturers of Australia (PIMA), Grahame Aston. “PIMA will again be a part of AMW 2023 in Melbourne. Being there to discuss directly with exhibitors is so important as it gives everyone the opportunity to work out first-hand if they are the right fit for your product or if they are someone to do business with. I would certainly encourage anyone that has services to offer to get on board.”
RMIT University has outstanding research capability in Additive Manufacturing, advanced materials, industrial automation and sustainability.
Our multidisciplinary experience has been demonstrated in domains that include Defence, Transport, Medical and Energy. RMIT offers various learning and teaching opportunities in Advanced Manufacturing from online courses to short courses and industry events to Advanced Diplomas, Degree and Master’s programs. The new, expanded Advanced Manufacturing Precinct (AMP) based at RMIT's City Campus site is home to the Digital Manufacturing Facility (DMF), Micro-Nano Research Facility (MNRF) and Microscopy and Microanalysis Facility (RMMF). The newly launched precinct will provide manufacturing and characterisation from nanometre to metre length scales and digital automation technologies through collaboration with RMIT research centres and groups,
See the latest Plazmax CNC Controller technology.
When the team at Plazmax see there is a better way of doing things, they don’t just sit on their hands, they do something about it! In the same way they have revolutionised the plasma cutting industry with tables that are faster, more accurate and cheaper to run, they now are about to release the very latest in CNC controller technology after seeing other products in the market were falling well short of the mark.
After ten years of R&D and three years of in-house development, the Plazmax team are finally ready to release their new CNC controller software, MAX, at this year’s AMW show in Melbourne.
“The premise behind the need and development of this new controller was simple,” says Brad Johnston, Product Development Manager at Plazmax Technologies. “We were consistently seeing limitations in what our machines could deliver, not because of our hardware or design, but because of the software controlling them. By taking this monumental step forward in design and investment, we can now push our machines to limits no other product in the market comes close to.”
Aside from the optimisation of functionality in the vertical cutting position, the new controller also allows bevelling to move to a whole new level and allows the machine to cut bevels using any geometry whilst still producing a high-quality finish. Additionally, the user interface has been simplified by removing unnecessary steps in the job loading process. By doing this, the controller increases productivity and decreases the chance of user input errors.
Another massive benefit is the optimisation of their system in readiness for Industry 4.0 and means the controller is ready for integration with any other Industry 4.0 applications and machines. Plazmax’s software team are also working on extensive reporting capabilities which will allow indirect supervision over machine operators by monitoring KPI’s such as uptime, productivity per shift and profitability. These reports will allow customers to really keep their finger on the pulse of their operation, even when not on site. The story behind the success of Plazmax is not just limited to their new CNC controller. For years now, this New Zealand owned and operated business has challenged themselves to excel in every product they manufacture and innovation they implement. “Take traditionally designed plasma cutting tables”, says Managing Director, Darryl Aston, “The approach to how these machines are manufactured hasn’t changed in over 20 years and as result, plasma cutting systems are commonly known as slow, cumbersome and often produce poor quality cuts. We wanted to challenge this
while also pursuing further industry connections and projects. The Precinct brings together research, design and advanced manufacturing in one location, opening the doors to innovation and product development, focussing on additive manufacturing. It houses the largest concentration of additive manufacturing equipment in Australia covering both polymer and metal-based systems. A key focus of the AMP research, delivered through the Centre for Additive Manufacturing, is new products and processes based on additive manufacturing that can dramatically increase manufacturing flexibility and efficiency.
RMIT University
Stand AM460 rmit.edu.au
so designed our machines from the ground up with the goal of producing a machine surpassing anything else on the market. The result of this is a product that is faster, more accurate and has less down time. Because our machines run so much more efficiently, they are cheaper to run, and this results in a much better ROI to our customers”.
In more recent years, Plazmax has also moved into the field of synchronous robotic welding and has partnered with both ABB and Robotmaster to provide industry leading robotic welding solutions. With ongoing skilled labour shortages in the steel and fabrication industries, Plazmax sees automated solutions in both cutting and welding systems continuing to be a large part of their future growth. As well as the release of their new CNC controller, Plazmax will have a fully operational CutAce plasma cutting table on display providing live demonstrations. Their team will also be able to offer information around their latest robotic automation solutions.
Plazmax Technologies
Stand RA360 plazmax.co.nz
Since our arrival in Australia in 2015, ACCUD has become a known and trusted brand of reliable and accurate measuring equipment.
ACCUD manufactures a range of cost competitive gauges and instruments to rigorous standards and is proud to maintain ISO certification. We ensure the precision of many of our digital instruments through individual calibration with calibration certificates supplied where applicable. ACCUD products are backed by a full 12-month warranty. We’re pleased to be back at Melbourne’s 2023 Australian Manufacturing Week to show our range of modern engineering and high-tech measuring products. So come say hello to us at Stand MT280, and get a preview of some of ACCUD’s latest releases.
Quality: Our commitment to quality is clear in every facet of every ACCUD product. From the materials used in its construction, to the rigorous testing that each piece of equipment undergoes, ACCUD is dedicated to ensuring that customers receive goods that perform with precision. Our attention to detail and quality control has resulted in a loyal customer base that trusts ACCUD to provide them with high quality measuring equipment.
Test Certificates: Many of our digital measurement tools now come with individual calibration certificates, a feature unique to the field. Our customers can be confident that after multiple production tests, ACCUD certified products can be relied upon for accuracy.
Look out for our Calibration Certificate logo.
Range: Our products serve manufacturing, construction, automotive and engineering industries, and our range of measuring equipment continues to grow. From a 2-meter vernier to a test dial indicator and everything in between, ACCUD is sure to have the right tool for your needs.
Delivery: We strive to keep our website up to date so you can be confident that if our measuring equipment is listed, it’s in stock. And, we aim to ship ACCUD products to you the same day we receive your order.
ACCUD Stand MT280 accud.com.au
Okuma Australia’s stand at AMW 2023 will be demonstrating the latest lathes, machining centres, multitasking machines and automation plus IOT Connectivity Solutions with the Okuma Connect Plan.
Okuma Australia and Okuma New Zealand are 100% owned subsidiaries of Okuma Corporation, Japan offering full sales, service and support for Okuma Corporation as the leading global single source builder of highly productive Okuma CNC Machine Tools, Factory Automation & Support Services.
Okuma offers its customers a full suite of engineering capabilities and aims at delivering leading edge “full service” distribution and lifetime support for Okuma Machines and Computer Numerically Controlled (CNC) systems.
Long-standing, experienced engineers within Okuma Australia and New Zealand have the expertise and the passion to deliver customer’s requirements on time, every time. Okuma machines are amongst the longest serving machines available with installations in Australia and New Zealand since the mid -1970’s.
Okuma machines will be cutting metal with several Okuma specialists on hand to demonstrate the cutting power of the Okuma machines as well as Okuma Connect Plan, new Okuma OSP Suite and the Okuma 5-axis Auto Tuning systems.
Highlighting the Okuma exhibit will be the popular Multus U4000 1SW x 1500 Multitasking CNC Lathe. This machine has twin spindles, 0.0001 degree indexable B-axis with 12,000 RPM milling spindle, 1500mm Centre distance and 80 Tool Capto C6 Tool magazine. The all new OSP Suite on-board management system will set the standard for Machine Controller and adds to Okuma’s award winning Machining Navigation system, Hobbing, Skiving and Gear generation, variable spindle speed control, Collision Avoidance System, Thermo-Friendly Concept, API function and 0.0001mm control increments for axes.
Also attracting attention will be the all-new Okuma ARMROID with built-in robot packaged within the Okuma LB3000EXII. ARMROID functionality includes part loading and unloading, chatter suppression, chip removal, and in-machine cleaning, ensuring that your Okuma machine is consistently operating at its highest efficiency.
With one operation panel to control both the machine and the robot, operating the ARMROID is seamless and efficient, with easyto-use controls to best suit your needs. And with the option to switch between automated and manual operation, you have the flexibility to continually improve how you manage your operations.
Our new, next-generation, 5-axis vertical machining centre Okuma model Genos M460V- 5AX is specifically designed to manufacture high-precision parts and deliver impressive metal removal rates in a compact design. Its solid double-column structure, full 5-axis simultaneous control, and thermal stability performance give it the ability to easily cut a variety of materials.
Using a hypoid gear drive, the GENOS M460V-5AX features trunnion construction that offers exceptional accuracy, rigidity, and table rotation speed. The spindle produces less vibration and power loss at the tool tip for outstanding surface finishes and metal removal rates. This affordable, 5-axis machine provides high productivity and profitability in a small footprint.
Our MB-5000HII is a high-speed, thermally-stable horizontal machining centre offering quick acceleration, short tool changes, and high power to improve productivity. Compared to the previous model, this machine’s powerful cutting capabilities and high-speed automation increases productivity and reduces cycle time by up to 25%, while the 20% smaller footprint maximizes valuable shop floor space.
Don’t leave our stand before checking out how all these machines are connected via Okuma Connect Plan as all the machines on the Okuma stand at MT940 plus an additional Okuma machine on the SolidCam stand MS280 will be linked with the latest Okuma Connect Plan.
Okuma’s Connect Plan is a software-based system that collects machine tool data and provides detailed information that can be used to fine-tune processes and improve productivity.
Okuma Australia
Stand MT940 okumaaustralia.com.au
The Moreton Bay Region is a diversified high growth economy offering businesses
Already one of the strongest performing economies in Australia, Moreton Bay plans to turbocharge its economy over the next 20 years to reinforce the region's reputation as Queensland’s $40bn engine room. Moreton Bay’s history of powerful growth is underpinned by the evolution of key established industries, including advanced manufacturing. In fact, it is the largest export industry in Moreton Bay, valued at more than $1bn.
As a key initiative aligned with Australian Manufacturing Week 2023, Moreton Bay Regional Council have supported 10 manufacturers to attend the national showcase event through their inaugural Manufacturers of Excellence Program.
The program aims to enable businesses in the advanced manufacturing sector to showcase their latest innovations, technologies, and equipment. It will also help businesses drive growth across the manufacturing ecosystem and support investment into Moreton Bay. Support will be provided through a proud partnership with Gadens, a leading Australian law firm. In addition,
the partnership will provide business legal advice and support the ten selected businesses to accelerate their growth plans and strategies. The #TeamMoretonBay delegation attending this year's Australian Manufacturing Week will feature world-class businesses and innovative trendsetters in sustainability, robotics and automation systems, and contract manufacturing across various sectors. Moreton Bay's economy is predicted to more than double from $17.72bn to $40bn by 2041, equal to the entire state of Tasmania plus the Pacific Island countries of Fiji, Solomon Islands, Vanuatu and Samoa.
With an established industry, easy market access, and space to grow - Moreton Bay serves up more of the things you need to become a leader in your field.Want to invest in Moreton Bay? Contact invest@ moretonbay.qld.gov.au
Moreton Bay Stand MP370 moretonbay.qld.gov.au
Your defence against downtime.
Downtime is such a dirty word. It halts production, leaves your operators standing around scratching their heads, loses you money, and can mess with your reputation.
What would you say if we could help minimise and possibly prevent downtime? After over 30 years in the compressed air game, we’ve worked out that with one simple equation, “we can”. Top quality gear + meticulous servicing + a reliable and responsive hire arm = minimum downtime.
Subtract any one of those factors and, sooner or later, operations will grind to a screeching halt.
Just think of us as your defence against downtime. With downtime costing businesses an average of $1,200 per minute, helping to keep you running on air is our passion. Compressed air is the most critical aspect of your production process. And, just like everything else in your business, it’s exposed to wear and tear. So, when it comes to managing your compressed air system, you need a partner who knows what you need before you even know it yourself. And with our field service technicians available 24/7 to ensure that your equipment is always running at maximum efficiency - you can focus on what’s most important, growing your company.
Now, let’s go back and take a closer look at our equation. Top quality gear – We choose quality over price. We partner with the world’s leading brands to offer products that are designed and built to last.
Meticulous servicing – Whether it’s your gear, or ours, when it comes to downtime the best defence is a good offence. From routine maintenance and planned shutdowns to 24/7 emergency repair, our award-winning technicians will help you head off potential issues or quickly get you back up and running.
Reliable and responsive hire arm – With one of the largest Compressed Air hire fleets in Australia, Air Powered have a wide range of compressed air equipment ready to show up wherever and whenever you need. Oil free and oil flooded compressors, high pressure compressors, diesel, 3 phase and electric compressors, dryers, and everything else that’s designed to keep your production running on air can be found in our fleet.
From sales, to servicing, to equipment hire, with us on speed dial, downtime is something only other people worry about.
Air Powered Services
Stand WA140
airpoweredservices.com.au
Additive manufacturing, also known as 3D printing, is a rapidly growing technology that has revolutionized the way products are designed and manufactured. In recent years, Australian manufacturing factories have been embracing this technology and integrating it into their existing manufacturing processes to improve efficiency and reduce costs. Markforged, who recently launched its newest printer the FX20 in Australia, has already seen Australian manufacturers adopt its technology into their existing workflows on shop floors.
Six months after launching the FX20, Markforged has shipped and established a two-digit network of FX20s in Australia and New Zealand. The FX20 utilised Markforged’s Digital Forge, using the Eiger and Simulation software to develop parts quickly and easily.
One of the main advantages of additive manufacturing is its ability to produce highly customised parts and components. With traditional manufacturing methods, producing custom parts can be time-consuming and costly, requiring expensive tooling and specialised equipment. With 3D printing however, the process is much simpler and more efficient. Manufacturers can simply design the part using computer-aided design (CAD) software and then print it on a 3D printer. Many manufacturers around Australia have already recognised the contribution of Markforged 3D printers in the improvement of their production processes. An award-winning WA company Avicena prints over 100 components of the Sentinel Biosecurity Platform (molecular diagnostic instrument) in-house, speeding the time to market and enjoying freedom of design.
“In the early iterations of Sentinel, most small components were made of aluminium, and many were sourced as ready-made items. As we progressed, we redesigned many of the parts to improve functionality, and in many cases upgraded the materials we used to increase component strength,” said Avicena CEO, Tony Fitzgerald.
Over the last five years, the Formero has invested in additive technologies that print production grade materials for end use parts. For them, the FX20 allows them to build faster and more precisely with its large build platform and speed, along with its number of choices for materials to print in. As demand for local production capacity continues to grow due to supply chain issues, more customers are looking to Formero to develop high value, complex and lightweight parts. ANZ GM, James Sanders observes that, “many of our Australian customers have been rapidly transitioning to high value, complex and light weight products that we struggled to provide a solution for. The FX20 meets a market need with high strength, lightweight materials in a large format.”
In addition to producing customised parts and components, additive manufacturing is also being used to produce tooling and fixtures for existing manufacturing processes. Traditionally, producing tooling and fixtures can be a lengthy and costly process, requiring specialised skills and equipment. With 3D printing, however, manufacturers can produce these items quickly and easily using CAD software and a 3D printer. This has led to improved efficiency and reduced costs in many manufacturing processes.
SQP Engineering is another adopter of the FX20. David Miller, SQP’s owner, said “Printed parts from the FX20 look 10 times better than the ones we printed before. Customers are completely blown away when they see the surface finish.”
The FX20 will be the epicenter of SQP’s additive manufacturing workflow, accompanying the Metal X printer.
"If you're going to be competitive, you need to have a solution for all aspects of manufacturing. Not just what we've been doing yesterday. We need to evolve and embrace the manufacturing technologies of tomorrow as well,” David added. Another advantage of additive manufacturing is its ability to produce parts and components with complex geometries that would be difficult or impossible to produce using traditional manufacturing methods. This has led to the development of new products and technologies that would not have been possible otherwise.
Additive manufacturing is being implemented into existing manufacturing processes in Australian manufacturing factories with increasing frequency. As the technology continues to improve and costs come down, it is likely that 3D printing will become even more prevalent in the manufacturing industry in the coming years. Markforged, together with partners will be showcasing the FX20 at Australian Manufacturing Week. Partners include SFDesign (AM280), Emona Instruments (AM450), Konica Minolta (RA300) and Alfex (MT580).
To make the best of AMW2023, visitors are encouraged to book an exclusive meeting with the Markforged Expert by scanning the below QR code and choosing the suitable day and time for an exclusive tour. You’ll receive new insights into how you can optimise your manufacturing processes and reduce costs, to print parts at the point of need. But hurry, spots are limited. Markforged Stand AM280 markforged.com.au
Hi-Tech Metrology will have a comprehensive range of metrology solutions on display at this years’ AMW exhibition, including a wide array of smart portable equipment.
After more than 30 years Hi-Tech Metrology continues to deliver world-class metrology and reverse engineering solutions for Australian industry; solutions that are designed to deliver enhanced customer outcomes in productivity, quality and innovation.
Central to Hi-Tech Metrology’s display at AMW 2023 will be the very latest in automated measurement solutions from Hexagon Manufacturing Intelligence (MI) with the Shop-Floor ready, robotically loaded TIGO Coordinate Measuring Machine.
Also on display will be the very latest in dynamic laser scanning solutions from Creaform; portable measuring arm technology from Hexagon MI; vision metrology solutions from MicroVu; vertical measuring instruments from Trimos; and micron accurate digital instruments for your toolroom from Bowers and Sylvac. All hardware is complimented by world-leading software suites from Innovmetric (PolyWorks), Hexagon MI (PC-DMIS and QDAS), Creaform (VX suites), MicroVu (Inspec) and Sylvac (Sylcom). The extensive range of metrology and scanning equipment, combined with a complete array of after sales support services, enables Hi-Tech Metrology to tailor innovative solutions integrating hardware and software for virtually any measurement or reverse engineering task.
Hi-Tech Metrology Pty Ltd
Stand: MT490
hitechmetrology.com.au
Materialise incorporates 30 years of 3D printing experience into a range of software solutions and 3D printing services, which together form the backbone of the 3D printing industry.
Materialise’s open and flexible solutions enable players in a wide variety of industries, including healthcare, automotive, aerospace, art and design, and consumer goods, to build innovative 3D printing applications that aim to make the world a better and healthier place. Headquartered in Belgium, with branches worldwide, Materialise combines the largest group of software developers in the industry with one of the largest and most complete 3D printing facilities in the world. 3D printing represents one of the most promising print-ondemand technologies of the moment. Over the past three decades, it has expanded into virtually every market and industry. It allows for fast adoption and scaling, as well as combining technologies and software systems to get the best of all worlds in one production flow. For advanced adopters, the key challenges are no longer technological: they’re economical. Today, companies are in a race to boost productivity and efficiency in the 3D printing production, and it’s a race in which the decisive factor can be software.
In the upcoming AMW 2023, Materialise will be showcasing Materialise Magics 3D Print Suite, the platform of software tools that manage and control the 3D printing process more efficiently, allowing it’s users to meet the highest standards of the most demanding industries. The Materialise Magics 3D Print Suite includes design optimization, industry-leading data and build preparation software, quality inspection tools and production management systems, offering an end-to-end software Suite for AM production factories. It also includes software and control systems used by machine manufacturers to better bridge the gap between applications and 3D printers. Materialise AM solutions are open by nature, empowering co-creation and collaboration between different players in the 3D printing and manufacturing eco-system and providing the industry a solid foundation on which to expand and grow.
If you’re 3D printing parts for rapid prototyping, personalization, or volume production, you need a digitally connected experience from order entry to part delivery. The Materialise CO-AM Software Platform’s modular applications and ecosystem of partners provide you with the tools for fully streamlined and scalable workflows,
perfect for both qualified suppliers and internal 3D printing departments. At the heart of the CO-AM platform is a data-lake that connects to all production tools and keeps track of what is happening on the production floor. The ability to monitor and analyze production data will enable operators to define and store their own unique workflows in a knowledge database, empowering them to continuously improve the production process. This creates an AIpowered learning platform where every printed part has the potential to be better than the previous one.
The Materialise CO-AM platform presents an open software architecture that provides companies direct access to multiple hardware technologies and their preferred tools from Materialise and other software developers, supporting them along every step of their AM journey – from planning and printing to quality control.
Drawing on it’s decades of experience in building and scaling additive manufacturing (AM) businesses, Materialise also provides Design & Engineering services, Consultation and Co-creation opportunities to advance the AM adoption in businesses and industries. Representative from Materialise will be available during AMW to discuss opportunities with client who are seeking for guidance in harnessing the potential of additive manufacturing in their business - whether is to get started in AM, create an AM roadmap or create a custom application with 3D printing.
Materialise
Stand AM420 materialise.com
ANCA Motion: maximizing productivity with LinX® M-Series – Energy-efficient tubular linear motors made in Australia.
As technology advances, manufacturers seek ways to boost their operations' productivity while placing a growing emphasis on energy efficiency to reduce cost and environmental footprint. To meet these demands, ANCA Motion, a leading provider of motion control systems, has introduced the LinX® M-Series tubular linear motor. These technologically advanced motors are designed to replace pneumatics and ball screw actuators in various applications that require more complex, precise, and rapid motion profiles.
The LinX® M-series motor consists of a shaft containing strong magnets and a forcer containing wound copper coils. Due to its tubular design and strong circular magnetic flux, the motor can deliver superior efficiency with unprecedented speed and acceleration, producing a continuous force range between 80N and 287N and a peak force of up to 1,200N.
The LinX® M-Series motor features an integrated position sensor with 0.01 millimetres of resolution and 0.03 millimetres of repetitive accuracy, allowing precise transitioning between two or more linear motion strokes without needing external encoders.
LinX(R) M-Series is revolutionizing several industries with impressive performance capabilities. One such industry is packaging, where the motor's high acceleration and deceleration rates, combined with its precise control, enable packaging machines to operate at higher speeds with greater accuracy. With no cogging and no backlash, The LinX® M-Series is also gaining attention in the laser cutting and semiconductor industry. The motor's smooth and consistent motion further increases its appeal to manufacturers in this space. To maintain a competitive edge, businesses must be flexible and responsive to the market's ever-changing demands. In cases where modifications to an existing production line are necessary to meet new requirements, the LinX® system offers a simple solution. Adjusting parameters within the drive configuration allows operators to easily modify the system without costly and timeconsuming hardware changes. LinX® provides enhanced system flexibility and is particularly well-suited for applications that require precise control.
ANCA Motion Stand RA240 motion.anca.com
An impressively high cutting speed, an intelligent cutting process, and a new design: this is how the new ByCut Star presents itself. With 30 kilowatts and an optimised cutting process, it now cuts steel, aluminum, stainless steel, brass, and copper precisely and reliably – for even more quality.
The flagship of the Bystronic laser cutting machines is now available with a 30kW output. Companies in the sheet metal processing industry are thus further optimising their production – also thanks to the smart features of the new fiber laser.
Higher cutting quality and productivity thanks to newly even more laser power, but thanks also to smart features: In order to support sheet metal processors even better in the growing competition, Bystronic is now advancing into a new dimension of fiber laser cutting: the ByCut Star with impressive 30kWs of laser power.
The high-end fiber laser stands for high-precision Bystronic technology, a stable cutting process up to the highest laser powers, and for a wide range of applications. With it, sheet metal processors are taking a further major step in terms of productivity and efficiency.
To be successful on the market, sheet metal workers need not only a lot of laser power, but also intelligence, reliability, and sustainability. High performance certainly brings a lot, but it is the combination with intelligent processes and properties that makes the laser cutting process really satisfying and successful.
Thus, customer success is built on a concept of three pillars at Bystronic: Power, Intelligence, and Cutting Process Improvement. – e.g., with the MixGas technology. Smart features, such as the “Intelligent Cutting Process (ICP)”, the “Nozzle Control Tool (NCT) with KerfScan” or the “Parameter Wizard” optimise the entire cutting process and ensure that it stays on track, guaranteeing the customer optimum capacity utilisation and improving the production uptime without production downtime.
The technological leap from the previously available three to 20kW levels to the new 30-kilowatt level is considerable and opens new possibilities for Bystronic customers to optimise their production and thus remain at the forefront of the ever more fiercely contested competition.
The nature of the manufacturing industry means many businesses are equipment-heavy. For even the most profitable of businesses, this can require careful planning and at times hurdle-jumping to access the required finance to grow and serve customers.
This is where the right financial solution for the long-term comes into play, according to Paul Barker, Merchant Sales Director at Shift, a provider of credit and payments platforms to Australian businesses.
“What we’re seeing is that our business customers increasingly expect their payment platforms are easy to use, save time and help them create sales opportunities with their customers,” said Barker.
“This is where platforms that use online registration rather than manual applications make all the difference.
“With our Equipment Line, customers register online once, get a clear idea of their purchase limits and can then make ongoing purchases without repeat approvals.”
Cutting speeds on the ByCut Star increase twice as fast compared to 15kW and MixGas with sheet thicknesses between 6mm and 15mm, and more than twice as fast with thicknesses starting at 20mm. Piercing times are shorter for sheet thicknesses of 15mm and above. Sheet metal processors thus benefit from higher productivity at low unit costs, because with 30kWs the new ByCut Star cuts steel, aluminum, and stainless steel precisely and reliably. The 30kW laser power thus enables maximum flexibility for large series and spontaneous customer orders. Whether aluminum or steel: the powerful Bystronic cutting head impresses with maximum precision in thin and thick sheets. In addition, with the "Advanced Applications" option, high laser power (starting from 15kWs) now also enables expanded applications in steel and aluminum of up to 50mm. The new power level is exclusively available on the ByCut Star 4020.
Bystronic Australia Pty Ltd Stand MT945 bystronic.com
As a result, incorporating the right payment platform streamlines processes and reduces red tape for companies with regular equipment purchase needs.
Barker also explained the need for companies selling equipment and other goods to incorporate the right embedded financial solutions that create trade terms that help them grow sales by giving their customers payment flexibility.
“Shift Trade simplifies trade credit between buyers and suppliers, meaning suppliers get paid upfront while offering favourable trade terms to their customers.”
The Shift team will be at stand MS808 at Australian Manufacturing Week to show how Shift’s credit and payments platforms such as Shift Trade and Shift Online can make life easier for suppliers and their customers across the manufacturing sector.
Shift Stand MS808 shift.com.au
The ByCut Star optimizes your cutting process even better: With a laser power of up to 30 kilowatts and the intelligent ICP cutting process, you can cut steel (only with N2 and MixGas), aluminum, stainless steel, and sheet metal up to 50 millimeters in thickness with speed, high precision, and reliability.
The patented new TIG DynamicWire uses an innovative cold wire TIG welding system that enables the process to adapt to the welder. This means that welders can achieve perfect welds every time, even those without extensive training and experience.
With its automatic self-regulation feature, the TIG DynamicWire system actively adjusts the wire speed to the welding behaviour, torch position and current conditions—even automatically compensating for component tolerances of up to 30%. The automated self-regulation feature also distinguishes it from a traditional continuous wire feed. The welding system actively modifies the wire speed in accordance with the welding behaviour, torch location, and welding current settings.
When creating the cold-wire system Fronius considered all the details to deliver a product that welders could operate as efficiently as possible with the fewest number of steps and changes. This is a game changer as it supports all TIG operators from novice beginners to the more experienced and those more highly skilled in achieving excellent welding results quickly and easily.
Not to mention it’s safer. Self-regulating parameter settings and characteristics, a compensating active wirefeeder, and other features provide the required degree of safety and excellent quality. Even worn elements like the torch body, torch cap, and clamping sleeve experience less abrasion and last longer than equivalent solutions because the wire does not constantly travel back and forth during intelligent TIG cold-wire welding.“Thanks to TIG DynamicWire, welders can focus all their attention on the arc and the welding system regulates the optimal wire speed at all times.” – Manuel Rumpl, Head of Strategic Product Management Industrial Welding Solutions, Fronius International GmbH.
The new Fronius cold-wire components for iWave are lightweight and ergonomic, providing more flexibility for TIG welding which makes it easier for welders, even those with minimal training are able to operate the machine and produce seamless, high-quality TIG welds. Furthermore, there are no annoying vibrations at the torch handle, thanks to the innovative TIG DynamicWire cold-wire welding technology which completely eliminates the wire's mechanical forward and backward motion. Additionally, with its TIG SynergicMode, only one parameter needs to be set to start welding and the rest is applied automatically based on material-specific characteristics.
The Tungsten Fast Clamp system (TFC) is another innovation from welding specialist Fronius. The tungsten electrode is released and clamped in the spring-loaded clamping sleeve with a single press of the button. The electrode may be switched out in a matter of seconds, much like a mechanical pencil's lead. This system can now also be mounted to current torch bodies.
The iWave power source categories from 300i to 500i can be upgraded to the TIG cold-wire system. The TIG DynamicWire welding package is ready for use immediately through software activation and can also be retrofitted to existing iWave (300i to 500i systems) at any time.
With TIG DynamicWire, you can achieve seamless welds quickly and easily with less issues! Want to learn more about the Fronius TIG DynamicWire? Visit the SMENCO team at booth WA320 and learn more about our wide range of welding products and equipment!
SMENCO Pty Ltd
Stand WA320 smenco.com.au
Bosch empowering Australian manufacturers with quality automation and unique solutions. capable of meeting even the most stringent requirements. BAMS are experts in implementing unique solutions for food and beverage manufacturers. Often, these customers require novel solutions designed for the specific complexities of their manufacturing environment. Floor-space constraints, combined with everincreasing variability in the product mix and reduced batch sizes requires ingenious solutions specifically tailored to the customers operational requirements.
With a track record of streamlining production for companies across the country, Bosch Australia Manufacturing Solutions (BAMS) provides 135 years of Bosch quality and expertise to Australian manufacturers. By supplying bespoke robotics and automation solutions, manufacturing consulting and maintenance services, BAMS is committed to supporting Australian manufacturing.
Based in Clayton, Victoria, BAMS has over 100 engineers and support staff servicing local and international customers. BAMS has become one of the country’s leading factory automation companies, working with a diverse array of blue-chip, mid-tier and start-up manufacturers to automate their manufacturing.
As a leading supplier of smart manufacturing solutions to medical device manufacturers in Australia, BAMS supports Medtech manufacturers with the commercialisation of their medical devices. With deep experience in factory automation solutions, and a growing portfolio of Medtech clients, BAMS creates robust and resilient manufacturing processes. The ability to bring the BAMS automation expertise to support Australian Medtech manufacturing for a global market is a real positive for local manufacturing.
Businesses that deliver pharmaceuticals or medical technology and devices are bound to strict demands for precision and quality. With Bosch's reputation for high quality and precise equipment, they are
Local start-ups benefit greatly by partnering with BAMS. The Manufacturing Consulting team brings the global Bosch manufacturing competence and experience to the table. With the BAMS team by their side, start-up customers receive a level of support that only comes with decades of global manufacturing experience.
To register for a free tour of the BAMS Automation Centre in Clayton, Victoria, visit Bosch Australia Manufacturing Solutions (BAMS) on LinkedIn at https://www.linkedin.com/showcase/bosch-australiamanufacturing-solutions-bams/
Bosch Australia Manufacturing Solutions (BAMS)
Stand RA245 bosch.com.au
Camplex is a prominent reseller in Australia and New Zealand with a long history in the Australian CAM industry supporting high-end CAM software for toolmaking and advanced engineering.
There are a very large number of different CAM software available in the market today, from basic 2D milling to 3, 4 and 5-axis milling. Many CAM software packages also supports turning and more complex machines like Swiss lathes and mill/turn machines.
NCG CAM Solutions software originates from one of the early CAM software created in the 1990’s. It was also known as Toolmaker and Machining Strategist but since 2009 it is now developed and marketed by NCG CAM Solutions Ltd in the UK. NCG CAM is known for high quality toolpaths and fast calculation of complex toolpaths for 3D milling in 3, 4 and 5-axis simultateously.
NCG CAM Solutions Ltd provides CAM software solutions, offering all the tools needed to manufacture prototypes, models, moulds, dies, patterns and finished products. Their specialist area is 3D HSM CAM with NCG CAM.
METROM, a leading supplier of 5-axis CNC machines, presents the world's first mobile repair factory in cooperation with BTU Cottbus. A combination of 3D printing and mechanical machining in a mobile design can be quickly deployed on site at any time for power plants, mining facilities, chemical plants or shipbuilding.
The mobile machine (PM series) has already been available at METROM for 15 years, developed for exactly this special application: on-site machining. With the mobile 5-axis machines, METROM has
great know-how and many years of experience in the modification or repair of large components. The portfolio includes the machining of gas and steam turbines, containers for the food or pharmaceutical industry, press tool molds or areas of large machining plants.
The basic system has been designed so that it can be transported quickly and easily by truck or air freight. On site, the machine is individually positioned and fixed in relation to the component to be machined in just a few hours. The special feature here is that the frame in the form of an icosahedron, the temperature control to the environment and the calibration of the kinematics form a perfect unit. The additive manufacturing capabilities of the mobile repair factory will enable companies to manufacture parts immediately on site, reducing the need for inventory and extremely shortening lead and delivery times for spare parts. The developed repair processes with hybrid manufacturing will also allow companies to extend the life of components by repairing them directly on site and then continuing to use them. With the appropriate design and execution, repaired components can easily have a longer shelf life than original components in terms of their properties.
Camplex Pty Ltd
Stand MS112 camplex.com.au
Injectronics want you to know more about its dedication to providing electronic and mechatronic repair services to a variety of manufacturing markets.
Australian manufacturing has a long history and has grown efficiently with the use of electronic assisted production lines.
While we have some of the latest manufacturing technology, thanks to both local and international suppliers, we are also a country that maintains and continues to service existing equipment.
It is not uncommon for some of our production lines to be utilising ten or more year-old technology. For business owners and service agents, this creates a challenge when faults develop. Replacement parts are commonly no longer available, if they are in stock the parts are typically from European manufactures and take time to ship to Australia, often the price is prohibitive and this is all comes with the question – will the new part even fix the problem?
The service and repair sector of the automotive industry faced this exact challenge from the late 80s, as motor vehicles moved from a mechanically controlled system to electronic control modules. This issue had a solution - Injectronics. Part of the IM Group.
Injectronics is a leading supplier of quality new and remanufactured automotive electronic components, as well as the preferred repairer of electronic and mechatronic parts.
The business is a trusted repairer of electronics used for industrial applications, including but not limited to:
• Control Modules
• Industrial Control Panels
• Human Machine Interfaces (HMI)
• Programmable Logic Controls (PLC)
• Variable Frequency Drivers (VFD)
For production line managers, business owners and service and repair agents, Injectronics presents an attractive option when it comes to making a decision to repair, replace, or upgrade.
James Burt, general manager of Uneek4X4 Australia and Barden Fabrication, experienced this exact scenario when a control module on a plasma cutting line began to fault intermittently.
Service agents initially advised a wear and tear component required replacement; at $11,000 the part was installed only to find the same issue persisting. Production had already been offline for one week at this stage.
Round two on the diagnosis pointed to a control module needing replacement, presenting a three week wait and purchase price in excess of $15,000 with the advice this may not resolve the issue.
Down time is the enemy of any production line and facing a backlog in production, impacts on customer orders and company revenue, Burt was forced to make a decision.
Aware of the service Injectronics offer, Burt delivered the control module for inspection. The engineers quickly identified the faulty unit on the circuit board, while also identifying a potential root cause of the fault. A power output device was arcing against wiring on the PCB and causing external contactors to fail and throw fault codes. After some discussion and further testing with the service agents, the repaired control module and new contactors were installed returning the line to operation.
In hindsight, Burt believes the service Injectronics provided was the difference between a two week offline window and potentially over a month.
“For factory managers and business owners this service gives us options,” he said. “Service agents can’t keep parts on the shelf and can only offer a replacement service. It can feel like we are throwing parts at problems. Injectronics gave me the option to quickly gain additional data assisting in my decision. This is highly valuable.” Burt added that Injectronics can also recommend alternative parts that can be retrospectively installed. There are of course components that are specific to brand, but there are many key electrical items that could be replaced with better quality by Injectronics.
“It gives some peace of mind that I’m making a good business decision,” he said.
As a manufacturing line manager, business owner or service agent –Injectronics is a local alternative to costly replacement parts – offering a 24-48 hour inspection and advice turn around, with dedicated resources for industrial repair applications.
To stay informed with solutions on offer, visit industrial.injectronics. com.au or call the team on 1300 646 948.
Injectronics
Stand MS762 im-group.com.au
A guide to helping the manufacturing industry in Australia combat rising inflation costs and improve cash flow with asset finance.
The manufacturing industry is a critical part of the Australian economy, creating jobs and driving growth. Despite its significance, the industry faces various challenges, including inflation. This can significantly increase costs and negatively impact cash flow. Thankfully, asset finance brokers can help mitigate these costs and improve cash flow for manufacturing businesses.
Asset finance is a type of financing that enables businesses to purchase assets, such as machinery, equipment, or vehicles, which then generates income. This method provides an alternative to purchasing assets outright, allowing businesses to conserve their cash flow and working capital, especially for small businesses or startups that need to preserve their cash resources. Additionally, payments made under a finance lease or loan are considered taxdeductible expenses, providing businesses with the opportunity to claim tax deductions for interest paid on their finance.
Asset finance brokers are specialists in arranging finance for asset purchases. They work closely with businesses, understand their needs and goals, and provide customised finance solutions. Brokers have extensive knowledge of the various finance options, including loan and lease structures, and can negotiate with lenders to secure the best terms for their clients.
Inflation can significantly increase the costs of manufacturing businesses, particularly for assets like machinery and equipment.
By financing these assets through an asset finance broker, businesses can spread the cost over time, reducing the impact of inflation and conserving their cash flow. Furthermore, brokers can provide finance that is flexible, allowing businesses to adjust their repayments if their circumstances change, such as if they experience a decline in business activity due to inflation.
One of the primary benefits of asset finance is its ability to improve a business's cash flow. By financing assets, businesses can conserve their cash flow and working capital, allowing them to reinvest in their business. Additionally, by spreading the cost of assets over time, businesses can reduce the impact of large upfront expenses on their cash flow, improving their financial management, reducing debt, and increasing their bottom line.
In conclusion, asset finance brokers play a crucial role in the manufacturing industry in Australia. By providing tailored finance solutions and negotiating with lenders, brokers can help businesses combat inflation costs and improve cash flow. Whether it's a small startup or a well-established manufacturing firm, working with an asset finance broker can offer numerous benefits and help businesses secure the assets they need to grow and succeed.
Simply Finance Australia
Stand MS300
simplyfinance.com.au
“AMW is Australia’s premier advanced manufacturing and machine tool exhibition, and has always been a key date in our diary allowing John Hart to showcase Mazak’s latest generation of machine tools to a sector which provides the backbone to Australian manufacturing,” explained Mark Dobrich, John Hart’s General Manager – Machine Tools.
“John Hart is bringing the Mazak Integrex i-250HS, the QTE 300MY SG, Variaxis C-600, and the VCN-600 to the show as the ideal machines to exhibit Mazak’s innovations in machining productivity as well as Mazak’s Smooth Technology.”
The next generation of Mazak Integrex - the i-H Series is helping manufacturers respond quickly to ever-changing production demands whilst taking advantage of the new digital solutions offered by Mazak’s MAZATROL SmoothAi CNC.
The Mazak Integrex i-250H features Mazak’s MAZATROL SmoothAi CNC, the next generation of SMOOTH TECHNOLOGY. In addition to the conversational programming power of MAZATROL. The MAZATROL SmoothAi control leverages the power of artificial intelligence and machine learning algorithms to power innovative tools like SMOOTH Ai Spindle, SMOOTH CAM Ai, MAZATROL TWINS and more.
Mazak’s new QTE Series of high-speed, high-accuracy CNC turning centres are the first machines to be equipped with Mazak’s new SmoothEz CNC, the latest generation of touch screen MAZATROL CNC, which allows for easy setup, programming and operation.
The simple and compact Mazak QTE 300MY SG, which is manufactured in Mazak’s Singapore factory, is designed to fit into even the smallest machine shop, but with no compromise on power.
The Mazak QTE 300MY SG is equipped with a powerful 5,000rpm integral spindle motor that is capable of ultra-high-speed acceleration and deceleration delivering high-efficiency, high-accuracy machining.
The next generation simultaneous 5-axis vertical machining centre Mazak Variaxis C-600 uses rigid C-frame construction, a standard 30-tool changer, dual-supported tilting table and fast rapid traverse rates to reduce cycle times on demanding jobs.
The Mazak Variaxis C-600 is equipped with SmoothAi CNC, Mazak’s new artificial intelligence control, which has in-built learning capability to continually improve machine performance.
As well as offering excellent operator access and ergonomics, the Mazak Variaxis C-600 has been designed to integrate easily with a range of automation solutions, such as MPP and Palletech.
The new Mazak VCN-600 vertical machining centre is developed for high performance and designed to significantly improve productivity rates for manufacturers undertaking everything from heavy-duty cutting to high-speed dynamic milling. The compact Mazak VCN600 with BT No.40 features high rigidity construction to ensure high accuracy machining and is now available with extended Y-axis stroke. The Mazak VCN-600 is equipped with either the new MAZATROL SmoothEz or MAZATROL Smooth G advanced CNC both designed for ease of operation.
“We are also bringing the Agile Flex robotic loading system for CNC machine tools and the latest CAM software from OPEN MIND – hyperMILL 2023, to demonstrate technologies designed to get more from your CNC machine tool,” Mark Dobrich added.
The Agile Flex is a range of “out of the box” robotic loading systems, designed and built right here in Australia and marketed world-wide. Rapid to deploy, compact and easy to use, Agile Flex has been developed to add lights out machining at a very affordable price to any modern CNC machine tool. With up to eight drawers and an optional top mounted pallet, the Agile Flex can process up to 9 unique part numbers unattended. Combined with the ability to process castings and uneven parts, the Agile Flex brings real agility to CNC automation.
The Agile Flex state of the art user interface requires no robot programming knowledge and is specifically designed to be intuitive for the CNC machine tool user. It could not be simpler to configure complex robot motion and sequences in minutes on an Agile Flex CNC machine loading system. hyperMILL is the high-performance, complete CAM solution from OPEN MIND for 2.5D, 3D and 5-axis milling as well as mill turning and machining operations such as high-speed cutting (HSC) and high-performance cutting (HPC), with everything integrated in a single interface. Special applications for milling impellers, blisks, turbine blades, tubes and tire molds complete the range of functions available in hyperMILL.
Complete machining for milling and mill turning with just one CAM software and just one postprocessor results in integrated processes and minimized machining times, while also increasing reliability – for maximum process reliability, cost efficiency and quality. hyperMILL provides full compatibility with all current CAD solutions as well as for OPEN MIND's own ‘CAD-for-CAM’ solution - hyperCAD-S
John HartStand MT530
johnhart.com.au
Showcasing the latest in compressed air technology.
Kaishan Compressors Australia exhibits ‘World’s Best’ compressed air technologies.
Permanent Magnet Variable Speed, rotary screw compressors provide globally proven, energy saving performance for a wide range of demanding industrial applications.
These advanced 2-Stage air compressors offer savings of up to 50% over conventional single stage models through precise control of output to meet changing demands. No gears, belts or couplings mean long life operation and reduced maintenance costs.
OX Series, Scroll Orbital, Integrated systems provide the compact solution for all workshop and specialised applications. These advanced air compressors are the ideal replacement for old, piston type, reciprocating machines. They are more energy efficient, quieter and 100% continuous duty rated.
Kaishan Australia Stand MT403 kaishan.com.au
Where are you on the journey? Digital transformation in manufacturing is certainly not new but remains a hot topic.
Maybe you started the digitisation journey way back with the installation of a PLC or CNC machine (with CAD/CAM) but have not gone any further. Perhaps you installed an MRP or ERP, and it feels like you ended up with silos of data. Maybe you have integrated an IIoT solution but are disappointed in the results. Do you see value in data and analytics and machine learning (ML) but struggle to justify and deliver a satisfactory return on investment? The digital transformation process can seem complex and confusing, yet it is extremely beneficial when done well. To help you understand and navigate the process, we have outlined a high-level three-stage approach to digital transformation.
To have a ‘smart factory’, you need a ‘really good’ factory. As a baseline, you need to measure and understand your processes, business KPIs and the challenges you face, then analyse these to identify solutions that will maximise your ROI and business benefit.
If you rely heavily on manual resources, consider ways to ease this burden. Repetitive, mundane, and high-risk tasks can often be automated to reduce the need for additional labour or allow a reallocation of existing labour resources for better outcomes. Using visualisation (SCADA) will improve process management with fewer resources than if done manually.
Implement simple OEE/MES solutions to address the challenges experienced with productivity, performance, quality, production costs and compliance. If you haven’t done so, consider using Smart Andon for real-time feedback on production issues; Energy Management for monitoring and managing energy consumption; and Digital LEAN for digitalising your preferred LEAN methodology.
If you have most of this in place, you are certainly in a good position to capitalise further on digital transformation. At this point in the journey, it is worth considering more advanced uses of MES and vertical integration. If you have systems such as an ERP, MRP, PLM, or similar, there is a chance they operate as silos. Integrating these systems with MES creates the ‘backbone’ for transformation and provides high-quality data for analytics, leading to significant
business value. The key is to have as much interoperability as possible. When combined with machine learning (ML) and artificial intelligence (AI) solutions for process improvement, you have a powerhouse for effective change.
A business at this stage of the journey has done well in improving internal processes. It is now ready to look outside the four walls of its manufacturing operations to claim a competitive advantage using a connected supply chain. The aim is to differentiate yourself in a few significant areas including reducing the costs of raw materials through quality compliance, improving the efficiency of asset and material supply via automated inventory management, and achieving greater speed to market based on demand and customer trend feedback. The key to success will lie in the two-way exchange of information between you and your supply chain using a collaborative approach. Your ‘view’ of the supply chain should be both backwards and forwards, from suppliers to distribution centers to storefronts.
It is important to remember that digital transformation is not simply an engineering project; it is a journey. At Mescon, our goal is to help you be an excellent manufacturer and empower you to move from Good to Smart. If you are not sure where on the digital journey the business is, or you are keen to make a difference but are unsure how to get the best from your current environment, why not have a conversation with us?
Mescon Stand MA425 mescon.com.au
Bilby brings the latest Raise3D Pro 3 and FFF 3D with HyperSpeed Upgrade kit and a whole lot more.
Returning to Melbourne in 2023, Bilby3D will present the Raise3D Pro 3 PLUS large professional FFF 3D printer with impressive 300x300x600mm build volume, fitted with the new HyperSpeed Upgrade kit, allowing you to print at speeds 300-500% higher than before thanks to advanced acceleration and anti-harmonic technology. The smaller E2 and the E2-CF optimised for printing nylon+carbon fibre will also be on the stand.
The Photocentric LC Opus UV open material Resin 3D Printer uses an LCD screen to control light exposure, allowing whole layers to be exposed at a time without any distortion for high accuracy. It continues to impress with it's 310x174x220mm build chamber, though is dwarfed by it's bigger brother, the LC Magna with 510x280x350mm volume. The Opus features Photocentric's patented Vat-Lift technology to reduce peel force, as the vat back edge lifts synchronously with the platform.
Just released from Mayku, UK based manufacturer of Thermoformers, is their Multiplier. This is not just a vacuum former, but a desktop pressure former, allowing thicker materials, up to 5mm, and even higher detail. Forming at 60psi, it delivers an
equivalent to 5 tonnes of force to the 400mm diameter forming bed. The Multiplier is packed with sensors feeding the smart controller with information so it can intelligently guide you via with screen interface. It can receive updates and new material profiles via Wifi. Make fully transparent prototypes, detailed final parts and cast complex objects with flexible moulds. Create parts with a high level of detail and accuracy similar to injection moulding at a fraction of the cost.
3D Scanners are becoming more popular for reverse engineering and measurement in the field. The new Einscan HXred bundle includes SolidEdge (Shining3D Version) and Geomagic Essentials. The EinscanHX is a hybrid 3D scanner, featuring rapid LED scanning as well as laser scanning for reflective and dark surfaces. It's colour camera allows texture capture as well as adding tracking by texture to geometry and marker tracking.
Bilby 3D
Stand AM380 bilby3d.com.au
Pilz releases “Key-in-pocket” system for maintenance safeguarding at the Australian Manufacturing Week.
Pilz will feature solutions that address the industrial safety, security, and automation concerns that you may have. Apart from showcasing ground-breaking innovations such as our award-winning safety relay, myPNOZ, most-sought-after small configurable controllers, PNOZmulti 2, and the powerful automation system, PSS 4000, another highlight would be the newly released “key-in-pocket” solution for maintenance safeguarding and restart prevention.
Machine maintenance safety is an important part of any manufacturing process. Conventionally, manufacturers relied on “lock-out, tag-out” (LOTO) system to protect people from the hazards posed during maintenance work such as an unwanted restart of the machine. Pilz has re-evaluated the LOTO method and has released the “key-in-pocket” solution with the aim of increasing efficiency by using card readers over traditional processes.
Workers are protected from encountering hazardous machinery during regular operations by physical fences, light curtains, sensors, and doors, among other measures. But when the system is being worked on, the usual safety measures are frequently ineffective or unavailable. As a result, workers are exposed to the machinery should it start up while they are maintaining it.
Although LOTO (where employees lock the electrical box that powers the machinery one at a time) is a good method for ensuring employee safety, it can also be time-consuming and ineffective. This is particularly true if employees finish their shift at the plant and leave without removing their lock from the machinery.
Before the equipment may be activated again, specific protocols must be followed, and the lock on the electrical box must be manually taken off. This results in increased downtime and wasted labor.
With the new access permission system, PITreader, only authorised users are permitted entry into the area without the use of locks or keys. The system can effectively prevent accidental startup while workers are present.
This is how it works: using a transponder key, users authenticate themselves on the safety gate via the PITreader. A security ID is then stored in a safe list in the Pilz controller (PNOZmulti 2 or PSS 4000). The machine will then stop and can be accessed to carry out repair or maintenance work. The user retains the transponder (“Key-inpocket”) while doing the work. After leaving the plant, everyone must log off via the PITreader to put the plant back into operation. This results in the security IDs being removed from the safe list. When the list is finally empty, the machine is enabled and can be put back into operation.
Through the usage of their card reading system, Pilz's "key in pocket" solution offers clients the exclusive potential to reduce waiting times and increase the effectiveness of machine maintenance. Employees are free to enter and exit the work area while the reader observes the operation, making sure everyone has left before the machinery is restarted.
Pilz Australia
Stand RA110 pilz.com
PROLAQ is the latest innovation from Bio-Circle Surface Technology GmbH, a safe and environmentally-friendly way to clean spray paint equipment.
PROLAQ is not petroleum based and is suitable for water and solvent based paints. It is non-flammable, non-hazardous and does not require the use of PPE nor ventilation. Nonetheless, it cleans quickly and thoroughly. This makes it a suitable alternative to traditional solvent-based paint thinners.
Further, it can be used up to ten times – the paint residues form a sediment which can be removed and the remaining PROLAQ liquid re-used. This greatly reduces the volume of liquid to be disposed of, and the cost of cleaning your paint equipment.
PROLAQ liquids can be used manually in the PROLAQ Compact washer, or in the PROLAQ Auto spray gun washer. You can even convert your existing automatic washer to use PROLAQ, with a simple conversion kit. These systems allow the separation of the paint from the PROLAQ cleaner, making removal easy and recovery of the cleaner for re-use.
Bio-Circle Surface Technology
Stand MT352 bio-circle.com.au
Moss has been the supplier of choice for custom industrial component parts in a wide range of metal and plastic materials since 1948.
A dedicated team of engineers and professionals are implementing the latest technology, robotics and tooling solutions to create long lasting and effective component solutions in Australia.
One step at a time
Moss is all about the whole process. There are many steps required to generate a component which meets all customer needs. Moss proudly offers a full end-to-end process so that that the entire journey, from the customer's initial ideas through to component supply, is under control. This ensures the product which will ultimately be produced, is based on the needs communicated by the customer.
Moss has many years of experience developing and supplying components for industries such as consumer products, automotive, recreational vehicles, building, hardware, defence, instrumentation, sporting goods and high-tech agriculture.
Moss are experts in engineering plastics such as Nylon, Polycarbonate, ABS / ASA and Glass filled materials. They also have advanced expertise in high pressure Die Cast components, including part design and tooling.
The Moss process starts with direct collaboration between the customer and the design team. Moss designers use high-end 3D CAD facilities to apply the latest technologies to the customer's product. This reduces the cost of both tooling and the manufactured parts, while minimising time-to-market.
Moss has its own toolroom facilities, with fully trained and qualified staff, so it can ensure high quality and consistency, from design intent to end-product specifications. The integrating of high-end technologies with excellent customer collaboration makes these full journey solutions unbeatable in the marketplace.
Moss Industrial conducts all its design, development, testing and manufacturing right here in Australia. This enables a high level of quality control to be exercised at every step of the way. Design intent is quickly communicated to the tooling and manufacturing teams. Improvements and changes can be quickly implemented. Compare that with trying to source your parts from overseas. There is really no comparison!
When it all comes together, Moss is a leading manufacturer, breaking ground in their dedication to local manufacturing, applying engineering principles, and helping customers with their years of experience. Moss Industrial a great choice for customers needing some guidance and assistance to ensure they get the right components, in the right materials, for all their component parts.
Moss Products
Stand MP240 mossindustrial.com.au
INVENIO provides total industry solutions, from software sales to engineering services and even to talent and placement services. Established in 1986, Invenio aspires to build lasting, sustainable partnerships. Our team of experienced industry experts can provide quality, actionable consultations to help you pinpoint ways you can improve your workflow and productivity and to support your digital transformation journey.
Call us when you need:
Innofocus to launch Nano Manufacturing Plant at AMW 2023.
As the world continues to rapidly evolve and innovate, the manufacturing industry is no exception. As a leading high tech company in the areas of optics and photonics, Innofocus Photonics Technology continues to innovate in intelligent manufacturing, focusing on the development of new equipment, new processing and new materials, all of which is aimed towards one goal: to Reinvent Manufacturing at Nanoscale.
Last year, at AMW 2022 at Sydney ICC, Innofocus showcased its world-leading capability by introducing nanoLAB - the new product family including five different deep-tech models, as well as the selfcooling films and highly-encrypted anti-counterfeiting nano digitalID.
In 2023, Innofocus is still focused and determined than ever. At the upcoming AMW23, Innofocus will once again highlight the theme of “Reinvent Manufacturing at Nanoscale”, while presenting a much greater scale (doubles the booth space as compared to AMW22) and with more exciting game-changing achievements.
Innofocus is proud to showcase the sixth model of its nanoLAB product family, Roll-to-Roll FBG Fabrication System. It is the worldfirst commercialised equipment that can continuously fabricate FBG strings up to kilometres in length, enabled by built-in rollers specialised for fiber delivery and collection. Integrated with the patented intelligent fiber core recognition technology and PositionTime Synchronization Trigger function invented by Innofocus, it is capable of automating FBG fabrication process at high speed, high success rate, and high yield, thereby achieving ultrafast laser FBG manufacturing at industry level. Innofocus is thrilled to present both the nanoLAB r-FBG equipment and its wide range of FBG sensing devices this May at Melbourne Exhibition Centre to enable broader industry collaborations.
Innofocus is thrilled to announce that they will also be hosting an expert speak series at the event. A designated stage will be set up at the booth of Innofocus (#MS295) for a number of expert speak sessions, to provide a platform for attendees to engage in discovery of the intelligent laser nanofabrication and its capability to revolutionise the manufacturing industry. Technical experts from Innofocus will share their insights on this cutting-edge technology with their real case studies. By bringing together leading minds, Innofocus hopes to provoke thoughts, inspire innovations, and foster lager, deeper and even more valuable collaborations.
Through the exhibits, Innofocus aims to clearly demonstrate the exceptional value of its world-first Nano Manufacturing Plant, which was recently established in the north of Melbourne, in redefining the horison of advanced manufacturing sector, and creating new opportunities for Australia to build unique sovereign manufacturing capabilities.
Innofocus Photonics Technology Stand MS295 innofocus.com.au
Koenig Machinery and their manufacturing partner Gweike, bring you a range of quality and affordable fiber cutting machines, for metal sheet and tube cutting, metal fiber marking, non-metal CO2 laser cutting and UV printing machines.
The LF3015GAR fiber cutting machine is the king of the show. With a fully enclosed 3.0x1.5m cutting bed with rear exchange table, you can easily unload/reload stock while the machine continues to cut, saving on overall production time. Including a rotary chuck this model is the perfect all round metal cutting machine for your Engineering Department or Fabrication Shop. Talk to Koenig about their different power options and models from 0-30kW.
The next showstopper is the Fiber-CO2 combination machine in the new Koenig Enclosure. The combination machine with 280W CO2 power allows for acrylic cutting up to 30mm, wood cutting up to 25mm and metal cutting ranging up to 20mm in this combination model. This innovative machine is the key to kickstart or regenerate any small manufacturing business.
Check out the Koenig Cass 1 Enclosure, able to fit the range of economical open bed machines. This enclosure features a roller door spanning the front and top of the machine, automatically opening after the cut job is complete, allowing for easy loading by hand, forklift or overhead gantry crane. Finally, a fully enclosed single-table machine with a small footprint that improves rather than inhibit your production flow.
Around the corner you will find the classic range of Koenig’s servo driven CO2 laser machines, for all of your non-metal cutting needs, at extremely low prices. Whether you are looking to make switch
plates, labels, signage or packaging the Koenig Laser range will not disappoint. Take a look at the Fiber marking and UV printing machines you will be surprised by the various marking and printing applications you already have for these little gems.
Don’t forget to chat to the friendly Koenig Machinery Staff and Engineers, here to assist you with demonstrations and any questions you may have, not only today but for the life of your machine.
Koenig Machinery Pty Ltd
Stand MT965 koenigmachinery.com.au
It’s time we put an end to the poor financial performance and market reputation that comes with late deliveries. We need high-performing manufacturers that power the world economy and supply us with the products we know and love. These days customers don’t seem to want a generic off-the-shelf product, they want something that is made especially for them, and they want it now.
If you are like most companies, you have probably struggled to get your ERP’s scheduling module or APS system going, and it is only really useful in giving an overall indication of your load vs capacity. It is unable to answer simple questions like, “where is the job, how is it tracking?” or “What job do I work on next?”. Forget about answering the harder questions like, “When will our customer actually be able to get their order?”, or “Do we have enough people/machines to actually deliver most of our orders based on our 90-day backlog?”. This show LillyWorks and Chanel Partner The Execution Factor are showcasing Protected Flow Manufacturing™ (PFM™), a cloudbased software package that doesn’t require you to replace your ERP. Instead of trying to fix “scheduling”, PFM takes a new approach that is focused on implementing the right method and techniques to accelerate flow, to give you a competitive edge that will
• Improve your on-time delivery performance.
• Reduce Work-In-Progress and lead times.
• Speed cash flow and improve financial performance.
• Provide believable delivery date promises you can keep.
• Give you the confidence that the wheels will keep turning if you take some time off.
Look out for an editorial in a future edition of AMT magazine that will go into the details of the Dynamic Production Model that PFM uses.
If you can’t wait until then, we would be super-psyched if you visited us in the Manufacturing Solutions Zone at MS220. If you can’t make it to the show, or you are simply dying to know more now you can reach out to us at the link below.
We look forward to showing you how you can keep your ERP system and move into a flow based world and turn your manufacturing organization into a high-performing organization and make the world a better place.
Lilyworks Stand MS220 lillyworks.com/pfm
Outsource Institute (AUS) is proud to be showcasing its industry-leading expertise at the Australian Manufacturing Week. As a registered training organisation, we have been delivering vocational qualifications in Engineering, Welding, and specialised trade & technical skills for over 20 years.
Outsource Institute (AUS) are committed to providing our students with the skills and knowledge they need to excel in the Mining, Defence, Manufacturing, and Engineering sectors, both domestically and internationally.
One of the highlights of our display will be our partnership with SMC Pneumatics, an industry leader in the development of cobotic equipment. Cobots, or collaborative robots, are a new class of robots designed to work alongside human operators. They have become increasingly popular in the manufacturing industry due to their ability to perform repetitive and dangerous tasks while allowing human operators to focus on more complex work.
SMC Pneumatics has been instrumental in developing cobotic equipment by providing pneumatic components and control systems that enable cobots to operate safely and effectively in human-robot collaboration environments. At the Australian Manufacturing Week, we will be showcasing SMC Pneumatics' cobotic equipment and demonstrating how it can be used in various manufacturing applications.
In addition to showcasing our partnership with SMC Pneumatics, we will also be providing information about our Engineering apprenticeships and traineeships. These programs are designed to provide students with the practical skills and knowledge they need
to succeed in the industry. Our apprenticeships and traineeships are delivered in the workplace, which means that our students get hands-on experience working with real-world machinery and equipment.
We will also be showcasing our specialised engineering courses, which are designed to provide students with in-depth knowledge of specific areas of engineering. Our courses cover a range of topics, including welding, metal fabrication, machining, and hydraulics. They are delivered by industry experts with years of experience working in the field, which means that our students get practical, real-world knowledge that they can apply to their jobs. At Outsource Institute (AUS), we are committed to providing our students with the skills and knowledge they need to succeed in the manufacturing industry. Our partnership with SMC Pneumatics and other industry leaders, as well as our focus on practical, workplacebased training, ensures that our students are well-prepared to meet the demands of the industry. We are excited to be showcasing our expertise at the Australian Manufacturing Week and look forward to meeting with industry professionals to discuss the latest developments in manufacturing and engineering.
Outsource Institute (AUS)
Stand MS771
outsourceinstitute.edu.au
Leading international welding equipment manufacturer, Kemppi, will be showcasing a range of innovative welding solutions at the upcoming Australian Manufacturing Week show in Melbourne at Stand WA200.
Among the new Kemppi line up is the Master M range including the Master M 205 and 323, the much anticipated X5 FastMig Pulse, and the popular MasterTig and SuperSnake products. In the robotic category, Kemppi will be unveiling its new AX Robotic welding solution. The company will also be revealing its new Zeta welding and grinding helmet product range.
Visitors to the show will be able to inspect the entire Master M range including the newly released Master M 205 and 323. The Master M series delivers a range of features to help enhance industrial welding productivity and quality. Compact and powerful, the Master M comes with Weld Assist as standard, integrated welding programs, better arc performance for greater productivity, integrated and selfcharging LED work lights for worksite safety, automatic calibration, memory channels and optional digital connectivity.
The Kemppi X5 FastMig Pulse is a versatile arc welding powerhouse that uses energy-efficient inverter technology. Designed for steel, stainless steel and aluminium welding, the X5 FastMig Pulse delivers a range of features to help significantly enhance arc welding productivity including Touch Sense Ignition. It also offers effortless operation, excellent welding ergonomics and flexible equipment setup. The X5 FastMig Pulse can also be combined with WeldEye ArcVision to gather real-time welding data via the cloud.
Kemppi will also be showcasing its new lightweight Zeta helmet product range. Designed for multifunctional use where the face and eyes need protection, the Zeta helmets provide an excellent work experience for welding, grinding, inspection, and cutting processes.
Key characteristics of the range include advanced vision features, integrated work lights, conveniently designed battery pack, and a smooth inner surface for easy maintenance and improved hygiene. The new Beta e 90 welding mask for fast and easy hard hat attachment will also be on show.
Kemppi Australia is part of Kemppi Oy. Kemppi is the design leader of the arc welding industry. Kemppi supplies advanced products, digital solutions and services for professionals from industrial welding companies to single contractors. The usability and reliability of our products is our guiding principle. Kemppi employs almost 800 professionals in 17 countries and is headquartered in Lahti, Finland.
Kemppi Stand WA200 Kemppi.com
JMA will display technology to improve productivity, safety, and quality, the very factors that are required to not only compete with imported products, but to also keep costs as low as possible.
The centre of attraction will be the latest Table Spot Welding Machine from Japan, featuring “High Speed Welding Technology” allowing the capability of stronger welds without oxidization of the outer surfaces. Clean oxidization free welds in stainless steel are achievable with this patented technology. Equipped with the latest touch screen control, this machine makes its worldwide debut at AMW 23. Welds can be evaluated as we will display our simplified spot weld testing machine with reporting capability.
From Loewer Germany we will exhibit 2 machines from their extensive range of deburring, edge rounding, and surface finishing machines. The first will be the original SwingGrinder, developed by Loewer to bridge the gap between manual deburring and edge rounding of laser cut or punched metal workpieces and automatic through feed machines. The SwingGrinder can perform both tasks in a single setup. Both small and large workpieces can be processed, and the process is very safe for the operator, requiring minimal skill and effort. Processing parts using the SwingGrinder from Loewer is easily 3-4 times faster than the standard manual methods and safer. As well, we will debut the Loewer MiniSpin at AMW. The MiniSpin was developed using “disc” technology, to provide a very safe and effective way to remove laser lead in and micro joint tags. Excellent and consistent results are achieved by unskilled operators. Loewer are a leading manufacturer of fully automatic machines as well, including the patented “orbital finishing with disc” technology and we will have information available on our stand.
From Thomas Welding Systems we will display the Nomark 65+ aluminium capable CD stud welding machine, a proven performer from a leading European manufacturer. Great welding results that are consistent is a feature of the Nomark models. Thomas also produces arc stud welding machines for all applications.
From ERSM, also a machine not exhibited before is the latest model of “wheel up” CNC work follower for press brakes. Affordable with excellent specifications, our followers can be used with all types of press brakes including up stroke machines. The follower can be shared with multiple presses and is quick to setup. Providing safety, productivity and quality improvement, this machine also provides consistency by eliminating the mishandling of larger, awkward workpieces. From Australia, we present the iCON Press Brake Control and System upgrade, available for all brands of press brake. We strip the existing electricals, control, software, and guards and replace them with brand new technology, turning older machines into productive workhorses for a fraction of the cost of a new machine. With touch screen operation, and software features not found on older controls, improved productivity and safety provide a quick return on investment.
Also displaying our range of press brake die mark prevention products from Japan, as well as dies for preventing bend lines.
Jim’s Machines and Accessories Stand MT262 jimsmachines.com.auLeading business management platform MYOB is proud to showcase MYOB Advanced Manufacturing, an industryleading cloud-based ERP solution specifically designed for the manufacturing industry, at AMW2023.
MYOB Advanced Manufacturing brings together key business workflows, including accounting and tax, customer management, supply chain, project management, employees and finances, as well as specific manufacturing requirements such as quality management, production management and billing capabilities, into a single platform. It's the ideal solution for businesses looking to improve efficiency and productivity, while also reducing risk and costs.
As an industry, manufacturing is increasingly focusing on automation to remove manual and repetitive tasks, as well as a way to better manage workloads during significant and ongoing skills shortages. At the same time, the need to drive greater efficiency and productivity to remain internationally competitive has seen digitalisation become a major focus for the manufacturing sector. Australian manufacturers also report a growing demand for customisation, with 86% of manufacturers surveyed by MYOB in 2022 seeing an increase in demand for customised manufacturing. To support this, MYOB's new integration with CADTALK provides manufacturers with a real time, bi-directional link between CAD software and MYOB Advanced Manufacturing. This integration helps to reduce engineering-to-manufacturing handoff by 80%.
CADTALK uses artificial intelligence to turn engineering bills of materials from a CAD, PDM, or PLM application into manufacturing bills of materials and routings within MYOB Advanced Manufacturing.
This integration speeds up the data flow from sales to engineering and feeds accurate information to procurement and production. More importantly, it increases engineering productivity by removing manual data entry, decreasing errors, and saving hundreds of hours per year.
For manufacturers, integrating quality management across every facet of a business - from accounting and purchasing, to manufacturing and distribution - improves traceability, reduces compliance risks, improves customer satisfaction, and automates time-consuming manual tasks.
Supporting multiple types of manufacturing such as food and beverage, medical and life sciences, MYOB has added quality management capabilities to MYOB Advanced Manufacturing. With quality control being a critical part of the manufacturing process, MYOB Advanced Manufacturing unites your manufacturing teams, processes, and data in one place – making it easier to manage all audits, suppliers and quality-related events.
Wherever your manufacturing business is headed, MYOB adapts to meet your changing needs, providing the visibility and confidence you need to make better, more informed decisions.
MYOB
Stand MS265
myob.com/au
Sheetmetal Machinery Australia (SMMA) will be showcasing the latest in sheet metal machinery, tooling and software innovation and technology at AMW2023.
SMMA are excited to announce they will be launching and demonstrating the latest in Fibre Laser cutting machines during at AMW2023 at their stand: MT320.
Offering exceptional speed, accuracy and most importantly cut quality, the range of fiber lasers are perfectly suited to a wide variety of customer requirements. From standalone systems for flat sheet, to pipe and profile cutting to automated loading and unloading solutions for lights out production, there is a solution to suit your exact needs. For companies who cut both thick and thin material, a beam shaping option allows for the best possible cutting results for the complete range of thicknesses. Many other features and benefits include automatic nozzle changing and cleaning, piercing sensing, air cutting, linear drives and more.
More innovation on display and operating on the SMMA stand MT320 at AMW2023 will be the next generation in up/down long folding technology. Already the fastest long folder on the market today, this machine has seen 300% speed improvement since the last exhibition in Sydney. With uncompromised innovation, our folder is a result of decades of experience and years of research and development. In addition to its unparalleled speed, it is almost
maintenance free with low service requirements, fewer installed individual parts and being hydraulics free, there is no need to change oil. Energy consumption is five times less, providing 80% lower energy costs and no cooling is required due to low heat generation. This long folder offers unmatched 300-degree bending freedom (150-degree up and downwards), standing seam parts up to 180-degree without manual intervention, more flexibility through special functions and the highest safety standards with modern full light guarding, no swivelling out of the bending beam and quieter operation providing more comfort and less stress.
If you are looking for a unique hybrid bending solution with maximum efficiency, then go no further than the SMMA stand at AMW2023. Continuing the theme of energy efficiency and sustainability this hybrid press brake offers more than 30% higher productivity, up to 50% energy saving and considerably low oil tank volume (18-30 litres). Its superior combination of hydraulics and electronics allows for Y axis approach and return speeds of 230mm/sec!
Sheelmetal Machinery Australia
Stand MT320
sheetmetalmachinery.com.au
If you’re working with stainless steel, you should be working with a TIG brush.
Ensitech is an Australian-owned company based in Western Sydney, Australia. Established in 2006 by electrical engineer Clive White, Ensitech is the inventor and manufacturer of the renowned TIG Brush Stainless Steel Weld Cleaning System and has grown to be the global leader in stainless steel surface finishing.
Ensitech has a worldwide network of distributors and uses combined expertise in electrical engineering, chemistry, product design, innovation, and service to bring the world the best weld cleaning solution there is. Ensitech Inc. was established in Chicago, IL, USA in 2013 and from both locations, Ensitech continues to supply and export TIG Brush products across the globe.
The patented TIG Brush technology allows you to clean welds in a matter of seconds offering a radical improvement to outdated and dangerous weld cleaning processes. Electrochemical weld cleaning is used within the stainless steel fabrication industry to remove post weld impurities, including heat tint, surface rust and discolouration. It also instantaneously re-passivates the surface, thereby restoring the “TIG Brushed” surface to its original anti-corrosive state.
The process easy; all you need to do is dip the brush into one of the Ensitech NSF certified weld cleaning fluids, make contact with the weld removing the heat tint, rinse with water, spray the weld with the applicable neutralising fluid to remove any residual acid, and rinse again with water. It’s that simple. It’s no wonder fabricators around the world are moving away from other toxic and laborious cleaning methods such as pickling paste or abrasives and embracing the simplicity and effectiveness of the TIG Brush.
The TIG Brush is not only a weld cleaning device, when used together with the Branding Kit, the TIG Brush allows you to print and engrave onto stainless steel products. So, whether you want to add a logo, part numbers or barcodes onto your products, the Branding Kit has you covered. Once again, the process is simple;
the Branding Kit uses a special branding head, a felt pad and specific printing or engraving fluid to brand stainless steel with ease. Ensitech is excited we will be exhibiting and demonstrating the TIG Brush at the Australian Manufacturing Week (AMW) exhibition in Melbourne, 9-12 May 2023. Here we will showcase the TIG Brush Stainless Steel Weld Cleaning System, including the Ensitech NSF certified fluids, which cover everything from pre-weld cleaning, weld cleaning, neutralising, and finishing. Our demonstrations will show you the full range of safety, cost-saving benefits and technological advances the TIG Brush system can bring to improve your weld cleaning process and productivity.
If you have any questions about electrochemical weld cleaning, the TIG Brush, branding using the TIG Brush, or any of our products, visit our stand #WA220 and find out more about how the TIG Brush could change the way you clean welds.
Ensitech
Stand WA220
tigbrush.com
AMW MELBOURNE 2023
IT’S ALMOST HERE – DON’T MISS OUT! REGISTER NOW WE LOOK FORWARD TO SEEING YOU AT THE SHOW
Ms O’Brien joined MCEC in January 2023 and has brought a wealth of leadership experience in the tourism and events industry. She is a former CEO of Food and Wine Victoria, producers of Australia’s internationally acclaimed Melbourne Food & Wine Festival. Most recently she has managed her own strategy consultancy, while operating as a CEO for Wine Victoria, and previously interim CEO for Ballarat Regional Tourism, where she led the co-design of Visitor Economy Recovery Plans.
AMT: Your work history speaks of a deep knowledge and passion for public events. Tell me about the direction and drive that has kept with you in this sector.
Natalie O’Brien: It's only when you’re older, and reflect back on your career you ask yourself where did my passion come from? My passion is absolutely people and connecting with people. There’s so much energy for people to participate and collaborate in the community in Melbourne. I think my career in events, tourism and hospitality stems from being from four generations of hoteliers. My grandmother was an incredibly vivid role model in how to truly take care of people. From a young age, I worked in hospitality, then in tourism following an extended period at the Melbourne Food and Wine Festival, a time for me to learn about that industry in Australia which was growing at a rapid rate.
This was an incredible opportunity to ride the wave of growing food and wine events in Victoria. The events industry is full of very passionate people. I think that the diversity of events presently throws a spotlight on so many issues the public are thoroughly passionate about. This could be the environment, energy, business, or manufacturing. Music, or just fantastic food and wine. An event requires so many disciplines to work. Whether it’s logistics, HR, chef gardening talent or audio-visual expertise, it's extraordinary. I’m constantly amazed at the talent of people, particularly in Melbourne, who have the skills to not just to dream up events, but then implement and deliver them.
AMT: Give us an idea of what goes on behind the scenes, for the venue specifically, to stage such a big show like AMW2023?
NO: You can imagine an event to the scale of AMW2023, requires a lot of planning and coordination behind the scenes. One of the benefits of hosting an event at MCEC is that we have a dedicated event planner and technology planner assigned to look after clients from the beginning. Every client also has an event delivery manager who is their go-to person on event day.
We act as the conduit between them, their contractors and all our internal teams with the ultimate objective to understand our client’s vision and bring it to life. Planning an event can start more than a year in advance – in the case of AMW2023, we started planning seven to eight months prior to the event.
Every event is unique with expectations that can often range from simple to very technical. It’s our role to work with our clients to problem-solve and troubleshoot to ensure their event is safe, seamless, and all their guests have a wonderful experience at MCEC.
AMT: In January, you landed in the CEO position at MCEC, the major conference and exhibition venue in Melbourne. The venue has a full slate, for the next couple of years, because you are dealing with the re-emergence of businesses pushing to get out and exhibit their products and services.
NO: I am in the first couple of months, this is week nine for me. I am still learning from key stakeholders, customers and everyone in our team. There’s the opportunity to meet customers in the middle of their events on site, and our key stakeholders as well. I’ve tried to get to every corner of this building. Of course, the size and scope of the job together with the expanse of the venue was very overwhelming on my first day.
But there’s that opportunity to meet all of the employees, the pastry team, the uniform team, security, to our team in the event technology department. I try to physically walk the floor every morning to meet a whole raft of people who are working hard to deliver an exceptional experience for our customers. We are starting to prioritise many elements in this new operating environment. What does it look like for us going forward? We're looking at how new technology plays a role in supporting our back-of-house systems and overall business efficiencies during big events. We’re also looking into what some of the digital and AI opportunities are that can enhance the customer experience, and also support the hybrid event model, if required. Other things we’re focusing on are our skills and cultivating the diverse workforce we have. Making sure we are creating an environment, of continuous learning. In January, MCEC held a lot of master classes to lift technical expertise to rebuild the capability we lost to other sectors during the lockdowns.
It's a huge privilege to work in an industry and a sector that I absolutely love. I come into work every day and it's my team and then our visitors and customers we get to welcome every day.
I get huge motivation and inspiration from my team, whether it's Mark and Cheryl in uniforms or our hard working team in logistics. Face to face events are back and there’s that buzz of people talking about their sector or their industry. What an incredible role that I get to work with people on my team and then welcome people. All of this in an incredible location along the Yarra River in Melbourne. We’re also looking in terms of our future planning of events. What the long-term legacy events might leave for cities and regions. We had a conference here a couple of weeks ago where some customers are looking at what the event might deliver, in terms of long-term legacy to the local community. We know MCEC brings in visitors to Melbourne, and there’s a very good legacy of connecting people to the other experiences of the State, procuring local wines from Victoria and the very best food. The next extension is that conferences that may be dealing with important issues connect with the local community on such issues whether it's gender equality or sustainability, how do we make those connections with the community here as well?
We had a Pathology conference, a Pokemon event and a Toy Fair here the other week. The diversity of the topics and ideas and exchange is invigorating. In all of the nooks and crannies of this building, people are planning, connecting, generating ideas, solutions and trade. That energy is what we really want to continue to build on. And so I look forward to learning more about manufacturing when AMW2023 comes in 9th to 12th May.
I’m very much looking forward to welcoming the AMW 2023 event this year in Melbourne, back after four years.
AMT: Peter King was CEO before you for some eleven years. He left quite a legacy.
NO: Peter King had such an incredible tenure and brought together a really important community of partners. We have the Royal Children's Hospital Good Friday Appeal coming up which Peter was quite instrumental in supporting. Peter's contribution was also to the ongoing drive for industry sustainability and the environment and MCEC really pushed out front many years ago. And Peter is continuing that with incredible stakeholder relationships both here in Australia amongst the team, and then all of the global organisations that he was a part of during his tenure as well.
I am only the third CEO of the Melbourne Convention and Exhibition Centre. I look forward to welcoming you when you come. We've some exciting plans to explore technology and sustainability. And it feels like people have realized that connecting face-to-face is a hugely important part of our DNA. And the fact that we can do it again, I think is very exciting.
Engineers Australia is the peak body for the engineering profession in Australia. The organisation has over 115,000 individual members and acts as the voice of the profession. Prior to this position, Romilly was Chief Executive Officer of Infrastructure Australia, a Federal Government Agency which provides research and advice to government, industry and the community on infrastructure investments and reforms.
AMT: You’ve started as CEO at Engineers Australia with a strong direction. What do you see you’ve brought to the position in reflection on your prior appointments?
Romilly Madew: Way back before I started at Engineers Australia, I was at the Green Building Council of Australia (GBCA), which I started working at in 2005, and then took over as CEO in 2006. The GBCA created a rating tool for buildings and communities called Green Star. Each of the categories within the tool had a technical committee and the majority of those technical committee members were engineers. So my engagement with, and reliance on engineers really started back in those early days. Then I moved to Infrastructure Australia (IA) as CEO in 2019. IA is the Federal Government's independent infrastructure advisor. If you think of all our infrastructure projects, and there's so many in Australia, Infrastructure Australia considered both economic and social infrastructure, covering water, transport, energy, telecommunications, education, healthcare. Every single infrastructure project was reliant on an engineer for design, construction and operations in all its shapes and forms.
Secondly, I had come from an industry membership based background. I had previously worked at the Property Council of Australia then the Green Building Council of Australia, so I'd already come from a membership-based background. There were so many alignments with the work that I've done over the last 20 years to the work that I'm now doing at Engineers Australia.
AMT: So, are we going in the right direction?
RM: Across sustainainability, in pockets, we are, yes. In property and construction, we are very much moving in the right direction. There are a number of global benchmarks, which Australia has been leading for over 14 years. When you consider our office buildings, shopping centres, apartment buildings, and large residential communities, even our large-scale education facilities like universities. New South Wales healthcare and schools’ infrastructure, is world-leading. Of course, when you consider infrastructure, such as road, rail and ports, we see emerging levels of leadership.
AMT: Where do you see the focus of Engineers Australia in the rapidly changing economy, climate and workforce conditions shaking the world right now.
RM: With the incoming Federal Government and the introduction to changes to climate change requirements, there will be an increased focus in responding to climate change. And the difference really is the asset class. When you consider property and construction, many listed property trusts are involved. They have shareholders saying they're really not going to invest in properties that don't have a sustainability strategy. It's called a Green Dividend. However, when considering infrastructure, much of it is owned and built
by government. There is a disconnect there. All the states and territories have agreed to Net Zero by 2050, however, there’s been inconsistencies in how that’s been executed through state government procurement. It's all well and good that our leaders say, yes, sign up to Net Zero by 2050, however you need to see public servants acknowledging and implementing strategies to meet these targets. It needs to be embeded into the procurement of multi-million or multi-billion dollar infrastructure assets. With the change in Federal Government last year it's been embedded within Infrastructure Australia's legislation, for instance. All the states and territories are aligned with the Federal Government for a lot of their funding. And that’ll start filtering and cascading through. But infrastructure is very much following the path of property and construction.
Another priority for Engineers Australia is working with industry, government and educators to address the nation’s engineering skills shortage. Our economy and society are more reliant on the engineering profession than ever before. We need to ensure we have the engineers necessary to deliver on current government priorities and conceptualise the solutions needed to solve our society’s most complex problems.
Our research shows that for decades, this issue keeps cropping up: there is a systemic shortage of engineers in Australia.
AMT: Can you talk about the challenges behind sustainability in engineering?
RM: It all comes down to planning. In our policy and advocacy work we are very clear on what we see as issues holding Australia back and causing problems which have now come to the fore. In flood prone areas, we need to be very clear, with infrastructure, we have positions on project governance and planning. I mentioned project governance before in that we do believe government can improve, for instance, best practice procurement. It's not just sustainability and climate change. We need to have project teams engaged with the First Nations people about what they know about the area? Have they taken on board previous major events to make sure that they're planning for the right place.
Considering Lismore as an example. We need to be able to be bold in having the conversation with the community on what should be rebuilt and what should be rebuilt somewhere else. Within the area, but with an appropriate caveat. And there are so many case studies on this. This has happened elsewhere, both in Australia and overseas. So if you look at Christchurch, they have a colour code system on where you can, you can rebuild in Christchurch after the earthquake. Governments, councils and others shouldn't be afraid to have those conversations, because they can be backed up by science, and engineers on the ground.
AMT: What do you see as the largest part of your job as CEO of Engineering Australia?
RM: It's multifaceted and involves team leadership, governance, senior office bearer, member and skakeholder management, policy and public speaking.
We have over 115,000 members of Engineers Australia. And we need to harness the skills and expertise of our members. If we think about the infrastructure stimulus build and the energy transition, for
Romilly Madew has landed where her passion for enabling a community of professionals. The CEO of Engineers Australia spoke with AMT Editor, Paul Hellard.
instance. That means making sure that the engineers who gained their degree 10 years ago, can tap into the right courses and micro credentials and have opportunities in place so they can upskill.
There should be opportunities for them to pivot to those growing areas. Engineers are required for all these new areas. We still need chemical, civil and mechanical engineers, but making sure they're getting the skills they can be trained in robotics, green or blue engineering, AI, hydrogen energy. So the big thing for us is unlocking the untapped potential of our membership. And helping them to adapt and stay relevant.
Also, we need more engineers. We all know at Engineers Australia; we have an untapped potential in Australia. We have young girls at school who we want learning maths and physics. We want to make sure that engineering is an attractive career opportunity for them, and that they can see the potential across all the different facets of engineering.
But there are a number of challenges. One is that we are not getting the teachers in STEM subjects. The number of teachers with qualifications to lift students into the STEM is falling. Secondly, we know that for 90% of girls, engineering is not on their radar. So that means we need to make sure the parents, teachers and the career advisors understand and they see the role models and potential of engineering. And then thirdly, we need to ensure that the girls are studying maths and physics. They don't have to be brilliant at it. They just need to study it.
AMT: How crucial is it for engineers to continue learning. Adapting. To pivot. And to stay relevant?
RM: Engineers are natural problem solvers, often referred to as forever learners. And as a professional body as opposed to an industry body, Engineers Australia is there to ensure the integrity
of the engineering professional on their credentials, their training, their certification, the credentialing of the university courses, the migrant skills assessments, and the setting of benchmarks of our expectations of engineers and ensuring we do those assessments annually. This is to ensure people have respect and faith in our different levels of engineering including our chartered engineering, like a chartered accountant. Also with the professional body, it's an actual requirement in many cases that a project must be signed off by chartered engineering.
Our role in a rebuild after a disaster like the floods we’ve had along the NSW coast, and many, many other areas along the Murray and up in the Kimberley for instance, we should be able to support those engineers in the different colleges as well as our technical societies like the Infrastructure Public Works Engineering Association and specialist humanitarian response agency RedR Australia which we co-founded. We should be like the SES. We do have the ability to do this, but we need to be better. As soon as there’s an incident like the floods, you get all the Emergency Services backing each other in, but in many cases like that, you do actually need engineers. Is this structurally sound? Can we use it?
AMT: What is the best part of your job?
RM: Engaging, working and collaborating with five generations of engineers, from all facets of the engineering profession. Whether they're a professional or a technologist or an associate, they're passionate about their projects. You'll find that with engineers, it's an actual life passion for them. They want to make a difference and they want to have an impact. They want to help build a better life and surroundings for people. engineersaustralia.org.au new.gbca.org.au/about/what-green-building/
The home grown steel framed Tiny House company.
The Australian Häuslein Tiny House manufacturing company began after the business partners saw the boom happening in the US. Riding on the phenomenal momentum of the ‘recreational vehicle’ (RV) universe, where people were downsizing through either necessity, or searching for the freedom from a mortgage, they knew this was a wave worth catching. The small Australian team was so impressed, they got together and the company was born. At Häuslein, all the Tiny Houses and other forms of ‘hauler trailers’ are designed and manufactured entirely in Port Macquarie, NSW.
Sam Verlaan, Co-Founder and Director of Technical Services talks of the uptick in interest the group found from people wanting to take up the lifestyle. The practical problem for the team was to source the right steel framing, sheeting, wood panelling, as well as finding the best skilled fitters and joiners and construction people with the same passion to join them on the journey.
“There has definitely been an uptick in interest in tiny houses since we started nearly five years ago,” says Verlaan. The global lifestyle changes ignited in the pandemic sparked a huge leap in orders.
“We were inundated with build requests during 2020-2022 and with such demand many other tiny house builders have popped up.”
Using a mix of 2-5mm thick steel lengths procured in shared purchases through Southern Steel and Vulcan, the Häuslein crew cut the steel in packs on a bandsaw and assembled using timber templates and premarked tape measures. “It then gets tacked together, squared up and welded using MIG with argon. We use a combination of steel frame on the bottom as the chassis, and then a timber frame up top.”
“The recently released Häuslein Tiny Hauler was born out of our passion for dirt bike riding and mountain biking in the bush,” says Scott Rohdich, Häuslein Co-Founder and designer of the Hauler. “We wanted to create a really unique toy hauler trailer which was highly-functional and attractive. We wanted to design something which wasn't cluttered by ugly vents, flaps, panels, and gas bottles commonly found on conventional caravans in Australia.”
Scott Rohdich comes from deep within the building industry. With a background as a highly qualified carpenter and joiner, he built furniture, created stairs, guitars and components for houses during his early career.
A particular hurdle in fabricating these houses and trailers is staying in alignment to the customer’s state vehicle and building regulations. “Legally classed as a caravan, any guttering needs to be fitted once the house arrives on site,” explains Rohdich. “The guttering puts the tiny house over the road legal width restrictions. A local plumber may also assist in fitting the guttering as well as connecting your toilet or grey water and could do this at the same time.
“Strategically the new Häuslein Hauler model builds upon on the success of our core tiny house business and diversifies our product range into the caravan market with a bold new futuristic product," says David Boyd, Co-Founder and Director of Marketing at Häuslein Tiny House Co.
“At Häuslein we strive to build to the highest building standards possible, going beyond what is found in prefab granny flats and most conventional houses built today. We build everything from scratch right here in Australia and are creating homes that will last for generations, not houses that will look worn in a few years. Häuslein Tiny Houses are built by Australians to withstand transportation and Australia’s harshest conditions.”
Verlaan adds that there is a lot of competition out there right now. “This competition of course makes the work harder than ever before to get people across the line,” he says. “Our piece of the piece continues to get smaller.”
Of the range of Tiny Houses, Trailers and Haulers, the smallest trailer ‘Gunyah’ is a five-metre DIY weekender. Häuslein is now working to design a new single level house, but the Grand Sojourner remains, “the most popular design over the life of the business. Not only is this the efficent design for the team to put together but it is also easily the most popular Tiny House on the market.”
Häuslein Tiny House Co launched in 2018, on a mission to build high end tiny houses, trailers and products to help Australians live a simpler, less expensive, more sustainable way of life. hauslein.com.au
John Donovan goes through the technicalities of how different bracing systems work in the construction industry.
Without bracing, you don’t have a building. It’s a ubiquitous part of the construction industry, and yet many traditional bracing systems require difficult logistics and time-consuming installation. Tension-only rod bracing offers an alternative – ultimately saving time, effort, and costs across the board. You may know the basics of tension bracing – but how does it actually function? And is it really worth transitioning away from bracing methods that have been used for years?
In this article, we’ve taken an in-depth look at how different bracing systems work – both for the building and for the people creating it.
Traditional bracing systems for lightweight steel frame structures involve planning and calculations from structural engineers, complex logistics management, and precise installation on site. DonoBrace is the tension-only rod bracing system from Donovan Group that offers a different perspective.
Fundamentally, a bracing system uses compression and/or tension to hold a structure’s portal legs in place and support the weight of the building. For example, two of the most common systems are the equal-angle bracing and wire rope bracing, neither of which prioritise usability or efficiency. The equal angle steel brace, though antiquated, is one of the most recognisable bracing systems. Two rigid lengths of steel, which can be upwards of 16 to 18 metres in length, are bolted to the main structure in an ‘x’ shape between portal legs. The support depends on both compression and tension, with the weakest point of the system located at the bolts. An alternative to equal angle bracing is the wire rope tension bracing system, often associated with bridges. Two steel ropes, sized according to the structure’s capacity requirements, fitted with a dead-end and spliced wires that are wrapped back along the length of the steel rope. This system uses only tension to support the portal frame. Finally, there is tension-only rod bracing, with DonoBrace leading the system forward for Australasia. Using directaction tension, a rod is connected through the DonoBrace, and then tightened to pull the portal legs to a square position. Similar to wire rope bracing, DonoBrace supplies multiple sizes to suit varying capacity requirements. Unlike an equal angle bracing system, the DonoBrace system provides flexibility in design and installation.
In practice, tension bracing is a comparatively easy system to move around. Equal angle bracing usually requires shipping long, heavy steel lengths in one piece, and a crane to place it at the site. Wire rope and other tension bracing systems can be shipped in more manageable coils and pieces. This usually means less weight and easier handling – resulting in overall lower transfer costs. However, wire rope bracing systems often require greasing the cables before transit to protect the material. This means timeconsuming cleaning is necessary before installation. Thick wire ropes for larger capacity projects can also be difficult to manage. Tension-only rod bracing systems are designed with material efficiency in mind and therefore it is a complete system that doesn’t require greasing before transport or moving large rigid elements. DonoBrace is engineered to be handled easily on-site and in the transportation process, saving considerable time and effort while optimising shipping costs.
To produce great work, you need a well-rounded perspective. The best products are developed based on feedback from every corner of an industry – the engineers, the builders and the manufacturers.
In an equal angle bracing system, not only do you need to lift dozens of 18-metre-long steel beams, but you also need to get your portal legs perfectly plumb and in position to place the rigid elements. It’s a system that requires unrealistic precision and little regard for the real conditions of preparing a site for bracing installation.
While wire rope bracing requires less effort to physically position the system, it can be a time-consuming process. You need to use chains with hook & eyes to temporarily brace the structure. Then, installers must manually wrap the wire tendons, which becomes more difficult with thicker wires and dead-ends.
Installing a tension-only rod bracing system is a highly efficient process. Little heavy lifting is required, no chain is needed before setting the bracing system, and the portal frame placement is far less important because the tension can be manipulated after installation. Overall, DonoBrace makes installation faster, more straightforward, and limits the resources needed to get the system securely in place. It’s a process developed from real experience building steel frame structures. DonoBrace is simply unparalleled when it comes to on site usability and efficiency.
In traditional bracing systems, the structural engineer is responsible for completing the capacity calculations and identifying the bracing requirements. Tension bracing, however, shifts much of the labour and responsibility from the structural engineer to the bracing system provider. When it comes to planning, this means structural engineers don’t have to spend as much time on crunching numbers for the bracing system.
With our tension-only rod bracing system, DonoBrace provides the calculations, CAD drawings, detail drops, example calculations, and the specifications to guide the installation. In practice, this means structural engineers only spend a few minutes specifying the DonoBrace system. By taking the responsibility, we increase timeefficiency and eliminate risk for structural engineers.
So - Why tension bracing? Because it does the same job for less – less weight, less time, less installation effort, less planning for structural engineers.
Because we do what we say on the tin. We have experience from every perspective of the building and manufacturing process – from on-the-ground installation to dealing with suppliers – and we know what matters most: products that live up to their promise, and people who do what they say they’ll do. We have the brains and the customer service to make sure your bracing system satisfies every requirement with maximum efficiency.
donovangroup.com/donobrace-system
Trends in the construction industry: chemical anchor innovations.
Construction work in Australia is forecast to increase by 2.8% in 2023, generating over $256B of opportunities. Of this increase, engineering construction activity is set to surge amid a massive pipeline of projects across infrastructure, residential and mining sectors. With this upswing comes the sector-wide challenges of addressing material shortages, logistics and rising construction costs.
“2022 saw infrastructure projects stimulate the economy and employment, which in-turn, supported residential and commercial projects. In a 2023 COVID normal environment, we anticipate higher ‘work done’ volumes than previous recent years and see an effort to play catch-up to reign-in the delays in construction timelines from 2022,” says Jason Woods, National Training Manager, Anchors & Fastening, Stanley Black and Decker. “Hopefully next year we will see the industry getting back on its feet and the fast-tracking project starts that will serve the years ahead.”
Whilst material shortages, logistics, and rising costs are some of the issues facing the wider construction industry, the anchoring segment of the industry faces many of the same issues.
Some projects will continue experiencing sourcing delays. In the medium-term, supply chains will recover as approvals and project starts, as the government stimulates investment that supports the construction and renovation segment.
“From the outset of COVID, DEWALT ®Engineered By Powers has worked intensely with global supply chains to ensure we can achieve the best supply rates to support the industry with core products through these fluctuating times. Suppliers will continue to play a major role in building businesses and influencing success and profitability. It is critical to use trusted suppliers, ensuring that a mutually beneficial relationship is established,” says Woods.
Safety is always a concern, and meeting compliance and transparency standards is an obligatory requirement when it comes to working on major construction projects. In the post COVID-19 environment, health and safety is still the priority. “DEWALT is constantly pushing the boundaries to create innovative, highperformance tools for the construction professional, that provide on-site performance and user protection,” said Woods.
With this in mind, there’s been an identifiable progression in the market regarding anchoring compliance and ensuring that anchors used in certain applications are complying with the relevant standards, like the National Construction Code, as an example. “We have also seen research and development regarding anchors being fit for purpose when subjected to seismic activity. DEWALT will continue to meet the ever-growing demands of the construction industry to provide solutions that improve efficiencies, are code compliant and provide safer practice solutions with a focus on performance.”
The construction industry’s demand for tried, tested and trusted products constantly raises anchor benchmarks. This is especially so in Australia’s growing infrastructure segment of the industry
which is currently experiencing a record level of investment - known investment is set to peak at $52b in 2023. Infrastructure projects predominantly use chemical anchors due to the need for robust products which deliver as expected. With superior performance as the key marketdriver, chemical anchors often have the edge on mechanical anchors due to their advantages across a range of applications. When selecting an anchor’s suitability, load requirements, base material (type and strength), fixture material and thickness, and environmental conditions anchors will be subjected to, are key considerations. Mechanical anchors can be quick to install and convenient to use for a number of applications which are time-critical. Chemical anchors generally will give more load capacity as opposed to mechanical anchors and can be used when deep embedment is required or a thick base plate will not accommodate a mechanical anchor. Chemical anchors can be used close to slab edge as they are not as intrusive as mechanical anchors which can cause concrete blow out when used close to a slab edge.
DEWALT is continually innovating and continually keeping abreast of market and industry trends by engaging with end-users globally. Like other construction industry segments, compliance drives chemical anchor research and development. Anchors that continue to comply with building codes are the benchmark of the industry, while anchors that hold certifications such as a 100-year design life are also pushing the segment forward. Ideally, innovation delivers increased productivity, user-protection, and performance.
Along with compliance and European Technical Assessment (ETA) approved products, DEWALT Engineered By Powers consistently develops innovative solutions for the construction professional. An example of this is the new DEWALT Engineered By Powers PURE500+ and EA70-Pro.
PURE500+ comes with a 100-year design life, extensive seismic C1 & C2 approvals for threaded rod and rebar applications, and fire resistance approvals, while EA70-Pro comes with new European Technical Assessment (ETA) approvals for use in hollow and solid brick and substrates such as aerated concrete solutions. dewalt.com.au
An electrical industry leader who has witnessed first-hand for more than 25 years the changing tides of challenge and opportunity in the Low Voltage switchboard business says there is plenty to be optimistic about as Australia emerges from the current turbulent times – but some changes may be long-lasting or permanent.
Matthew Childs is Managing Director of AE Switchboards, a Division of Advanced Electric Solutions Pty Ltd, which serves major companies in sectors including food and beverage, packaging, retailing, agriculture, resources, mining and quarrying, recycling and waste and wastewater.
“One of our biggest industry challenges currently is supply of components and materials and their increasing costs. I believe this will continue for some time into the future – maybe not to the same extremes, but I have never seen prices come down,” says Childs, whose experience extends from shop floor manufacturing technologies through to high-level finance and negotiation, business planning, business development, and sales and marketing.
“Customer needs must be at the forefront of our thinking and planning to cope with these issues and the current skills shortage. This evolving situation gives rise to opportunities for switchboard manufacturers to review their current practices and to look to find solutions that are more cost-effective and/or engineered to overcome shortages – and ultimately to better meet the time and cost expectations of customers.
AE Switchboards serves some of Australia’s biggest and most sustainability-conscious companies who expect high quality product at globally competitive prices while adhering firmly to safety, compliance and verification requirements such as the relatively new AS/NZ 61349 Standard.
The proudly South Australian company operates nationally and has developed comprehensive in-house design and engineering facilities. These include full capability in electrical and control switchboards, network protections, and motor control, meaning the group can offer single-source supply for diverse energy control, distribution and generation needs.
“We believe also that we have a strong advantage in being a modular switchboard builder. We don’t custom-fabricate the cabinets and enclosures that we build into switchboards. Instead, we use various brands of enclosures in a variety of standard sizes and materials.”
AE Switchboards ensures its systems and processes are industryleading and its commitment to quality, safety, and the environment, is second to none.
“We are finding the bigger customer companies –are well aware of the safety, compliance and verification requirements of the AS/ NZ 61349 Standard but this is not always the case among smaller consultants and contractors.
“Over the last 12 months – five full years since the Standard was introduced – we are still finding customers who are not even aware of it. And you can’t blame them for questioning the cost of compliance when the goal posts have shifted seemingly without notice.”
“Non-compliance is a very risky route, because if anything does go wrong and your switchboard is found to be non-compliant, apart from the obvious safety concerns, there is also the potential for reputational and legal consequences.”
“Importantly, in this time of supply chain issues, local manufacture is a safeguard against future problems and an assurance that service will be there when you need it.”
“AS/NZS61439 Compliant local product – which we pride ourselves upon – offers better whole-of life value and our customers can rest safe in the knowledge it is designed and built for Australian conditions and fully verified at every step,” said Mr Childs, who’s company is a member of National Electrical Switchboards Manufacturers Association, NESMA, which he supports in its campaign to get all manufacturers committed to the new Standard.
Behind all the business planning, Standards awareness, technology and systems, an enduring component of business success comes back to having good people and strong skills training, says Matthew Childs.
“I feel strongly that people are the key to our success. We are fortunate to have an enormous amount of experience in our team and our people are passionate about what they do and without fail aim for the best outcome for our customers.”
“I believe that our customers’ expectations – over the broad spectrum of projects we undertake each year – are met if not surpassed, and that they see us as an honest, ethical and reliable partner to their business. Our reputation, built by our people, is at the core of our ongoing success.”
NESMA is campaigning for industry-wide adoption of AS/NZS 61439, which it says is an important and complex document that responds to wide-ranging change (including technical, environmental and safety issues) for both manufacturers and their customers as they adapt to major change in the country’s grid and local power supplies.
The new AS/Standard 61349 is now the critical standard governing low-voltage switchboard manufacture, after a five-year transition from the old Standard, which has elapsed. nesma.org.au
A NESMA leader at the forefront of custom-fabricated electrical switchboard technology says the new AS/NZS 61439 Standard Update is the biggest and most important change in the low voltage switchboard design and manufacturing industry for more than 20 years.
Compliance with the new Standards – and widespread support and education through NESMA about their importance – is critical at a time when managing energy is becoming more important than it has ever been before, says South Australia’s Anthony Spadavecchia, who is Managing Director of BE Switchcraft, which has been designing and manufacturing switchboards for over 50 years.
BE Switchcraft has, for more than 50 years, been a future-focused contributor to the advanced industrial fabric of South Australia, sharpening its technology capabilities as the State has progressively emerged as a world-leader in energy sustainability and green energy, with around 71% of the state’s energy now produced from renewable sources. SA is now using its expertise to help other nations kick green energy goals, drawing on the skills, resources and leadership of companies such as BE Switchcraft.
Maintaining its future commitment, in 2019, BE Switchcraft moved into purpose-built premises at Royal Park where the company produces advanced technologies including energy management systems and lighting and room control systems that are saving their client’s money and protecting the environment. Practising what it preaches about sustainability, the company has turned its own new rooftop into a solar power farm that cuts its own power consumption by more than two-thirds.
“Managing energy has never been more important than it is today, which is why, through our energy management systems, we deliver building owners valuable data that can help them to make decisions that can deliver substantially reduced costs with increased sustainability. Our lighting control and building automation proactively monitor and manage consumption,” says Mr Spadavecchia, who graduated in Software and Electrical Engineering at the university of South Australia before a career with global leaders in energy and automation digital solutions for efficiency and sustainability. He took over as Managing Director of BE Switchcraft in 2017.
“BE Switchcraft’s commitment to quality, compliance and innovation in switchboards has become part of the fabric of many of our most innovative buildings, from health to major industrial and commercial premises. We’ve also developed and retained a wealth of talented and experienced people, passionate about quality outcomes, which is why the introduction of AS/NZS 61439 is so important to all of us here and to our industry.”
“AS/NZS 61439 is a generational change, which really brings Australasia into line with world-best practice and IEC standards of safety, compliance, testing and sustainability. This is happening a time of momentous change in technology and needs when quality assurance and traceability has never been more important.”
“As the new Standard is increasingly written into contract specifications, starting from the time of its introduction last year, it is up to us as members of NESMA to demonstrate that we as low voltage switchgear manufacturers promote and adhere to the new Standards expected of us across the board.”
The new Standard applies to low-voltage switchgear and control gear assemblies, as well as to assemblies intended for use in connection with the generation, transmission, distribution and conversion of electric energy and for the control of electric energy consuming equipment.”
“We have had five years to prepare for this. Leading manufacturers have seen this change for what it is, a wonderful opportunity to demonstrate their leadership and equip ourselves for the future. Others may be willing, but a little unsure about what it all means and how to implement it. These are some of the companies NESMA needs to lead, because the changes are broad in scope and essential in their range of applications.
“This important new Standard isn’t an opt-in or opt-out choice –it is a defining commitment to quality, compliance and testing which companies ongoing must adhere to if they are to function responsibly, ethically and successfully. Our role in NESMA is to create a clear understanding of the benefits and to help all members achieve them, in the interests of our own industry’s quality and compliance standards and a visible commitment to our customers that we embrace quality principles and practice.”
nesma.org.au
Motion Control invests in new assembly machine, making it the first local distributor to offer certified assembly of Bonfiglioli solutions.
Adelaide-based power transmission specialist, Motion Control, has invested in a Bonfiglioli assembly machine, sourced from the company’s headquarters in Italy. This acquisition makes Motion Control the only local distributor (besides Bonfiglioli itself) certified and accredited to carry out complete assembly of Bonfiglioli solutions. “Our investment in the assembly machinery enables us to better service Bonfiglioli customers across South Australia,” explains Claude Masiero, General Manager, Motion Control.
Among the benefits now extended to Bonfiglioli customers in the region is faster turnaround on deliveries and support. “Previously we had to source products from Sydney and this meant clients waited for a week at least. Now we can offer the same day turnaround on delivery and don’t charge extra for it”. The company also offers 24/7 support service (including breakdowns) and the supply of spares and repair services, as well as local building of planetaries.
“With the geographical area of South Australia being as large as it is, servicing the market remotely from Victoria was very difficult. Having a distributor like Motion Control, with assembly capability that can react to market requirement very quickly, is invaluable,” says Danie De Vries, Bonfiglioli Regional Manager for South Australia.
“The South Australian market, including the Victoria and Tasmania regions, has always been an important part of our business, making up 20% of total sales. In spite of various challenges experienced in the last year, the opportunities for market growth are positive”.
Motion Control has been supplying complete power transmission
products to a wide range of industries (from food and beverage, to packaging, winery, automotive and mining) throughout South Australia, since 1993. The company provides solutions ranging from motor gearboxes to complete drive systems. Its large stockholding and extensive service offering has made it a valuable partner to Bonfiglioli. “We have found that the diversity of Bonfiglioli’s range of solutions makes it well-suited for use across industries, and in applications of all types. Customers could use one brand all the way through their plant and this simplifies maintenance,” says Claude.
The seamless and efficient collaboration between Motion Control and Bonfiglioli was demonstrated in a recent project completed for a steel plant located in South Australia. Motion Control was commissioned to upgrade a ball mill drive system and it recommended the installation of 2HD boxes, from Bonfiglioli’s range. “Bonfiglioli assembled these gearboxes in Sydney, where they were tested and laser aligned. Bonfiglioli also carried out the commissioning on site. The customer will be able to secure spare parts and service from Motion Control,” elaborates Claude.
“We have very good relationships with our partner OEMs. The good rapport we have established with these companies demonstrates the longevity of our relationships, and that we’ve seen each other through the good and bad times,” adds Claude. “Through our experience, we always work out the best solutions for customers.
Our investment in the new Bonfiglioli assembly machine now enables us to put together products and solutions in no time”.
bonfiglioli.com/australia/en
The source of corrosion in fabricated metal components is often obsure. Vyt Garnys from CETEC talks us through a case which brought up unexpected culprits.
A water authority responsible for public works submitted corroded pipe sections from their water treatment plant to CETEC Pty Ltd. They requested that CETEC investigate and identify the root cause of corrosion. CETEC was advised that soon after commissioning, the pipes developed pin holes.
Previous installations of several of these plants in the recent past, showed no evidence of corrosion. CETEC was advised that the welded pipes were made of high grade stainless steel and most pinholes were located near weld points.
The initial assumption was that ‘the fabricator had not followed the welding standard and had supplied a ‘defective product’.
It is critical when investigating problems to use an extensive methodology as possible to eliminate causes. At CETEC, the guidance used in assessing, solving and managing technical problems was one based upon appropriate and established risk management techniques and processes. This involves:
1. Context: To ensure that an understanding of the scope and parameters surrounding the problem.
2. Identification: A well-structured systematic process of identifying potential causes is critical.
3. Analysis: This next stage analyse potential causes.
4. Evaluation: Evaluate the probable causes from the analysis and align these with all the data.
Visual examination of the pipes showed that the defects were observed over the longitudinal weld sections. Corrosion was observed on the external surfaces of the pipes along with water leakage marks located near the Heat Affected Zone (HAZ). On the supplied samples, the accumulation of corrosion products was observed on the welds and weld toes. Away from the welds, there were no significant corrosion observed beside those related to the weld regions.
This supported the initial conclusion that the primary cause of failure was poor welding and fabrication.
However, on the inner surfaces of the supplied samples, where the welds and near weld regions experienced severe corrosion attack, domed morphologies (tubercles) were found. The presence of tubercles suggested the occurrence of microbiologically influenced corrosion (MIC). Material loss at the inner weld materials was also visible.
Chemical analysis using Inductively Coupled Plasma – Optical Emission spectroscopy (ICP-OES) and combustion techniques were performed on the base materials and weld to identify and confirm the grade of materials used.
The chemical analysis showed a close match and compliant to the relevant ASTM standards, but the material was at the lower end of the specifications.
Relevant specimens sampled from the supplied pipes were examined using Scanning Electron Microscopy (SEM) in conjunction with Energy Dispersive X-Ray (EDX). The analysis was performed to examine the corrosion products regarding their chemical compositions and morphology.
A fibrous morphology was also observed. In those zone, EDX analysis showed a high amount of manganese, whereas the ASTM standards indicate that there should not be a significant amount of Manganese. This elevated Manganese was an indication of presence of metal-reducing bacteria brought about during the plant operation.
Visual examination revealed that severe corrosion was mainly observed on the spiral welds for both samples. A heat tinted region was seen on some areas of the internal welds. Heat tint can cause welds to become more prone to corrosion attack because heat tint layer contains elevated chromium levels, leaving the region immediately below the heat tint layer relatively depleted in chromium, causing reduced corrosion resistance of the materials. However, the customer had not specified the grade for the weld fillers, nor provided details as to environment that the plant would be required to operate in.
SEM-EDX analysis was used to identify the elements present. The results suggested that two different bacterial types could be involved resulting in microbiologically influenced corrosion (MIC) on the piping system, which are the Sulphur reducing bacteria (SRB) and metal reducing bacteria (MRB).
Microstructure assessment for stainless steel was also performed on the samples. The structure consisted of homogeneous austenitic structure with minor amount of delta ferrite detected in the HAZ. No detrimental phases were detected. A study showed that the grain boundaries were preferred by the bacteria as their initial attachment site leading to the initiation of MIC.
Thus resolving the issues in this course of the investigation, it has been found that the corrosion failure of the submitted samples were due to the following reasons:
• Microbiologically influenced corrosion (MIC).
• The need to be aware of actual material specifications, not just compliance to standards.
• The need to be aware of the environment in which the plant operates
• The need to evaluate welding practices, including heat tint zone, weld defects and rough weld surfaces. Root cause failure analysis is a valuable tool for these complex situations. cetec.com.au
How DECO is setting a global benchmark for quality powder coating in Australia.
Quality control is crucial to any manufacturing process, and for the surface finishing industry this is no exception. A quality-controlled finishing process ensures the performance of the applied coatings or finishes to the surface material, ensuring aesthetic results are met, as well as achieving highest durability and longevity.
When it comes to powder coating – one of Australia’s most used surface finishes – QUALICOAT is the globally-recognised quality label for architectural powder coating; and we now have a QUALICOAT License applicator right here in Australia. After extensive audits of their powder coating process, DECO Australia has become the only accredited powder coater in Australia to hold the global QUALICOAT license.
“This is a very important part of our value proposition to our customers,” said DECO General Manager Richard Hamber. “It is not just saying we have the best quality, we now have proof and independent certification that we have an unrivalled position in the market when it comes to providing the best quality powder coating.”
To obtain a quality licence, powder coaters must undergo an audit of their processes from start to finish, as well as of the finished products, to make sure the highest level of quality is upheld at every stage, and the powder coating procedures all comply with international standards. Once the licence is received, QUALICOAT licensees must undergo continued regular audits to ensure their processes remain up to standard.
A quality-focussed surface finisher for nearly 20 years, DECO Australia entered the surface finishing world as a provider of sublimated, powder-coated timber-look finishes for architectural aluminium products. Today, they also provide a range of high-quality
finishes such as powder coating, anodising and other specialty finishes to industrial, defence and manufacturing industries, as well as having their own NATA-accredited laboratory where much of their in-house quality control processes are undertaken.
DECO strives to set an example for Australian industry, running extensive in-house testing on its own products and finishes to ensure optimal finish quality. Achieving the external quality accreditation from Qualicoat cements DECO’s position as one of the highest quality finishers not only in Australia, but across the world.
DECO Australia is an AMTIL and AIDN member and as well as holding a QUALICOAT licence, holds accreditation with Dulux and Interpon for powder coating. deco.net.au/protective-coatings
Efficient and sustainable parts cleaning for sophisticated high-tech components.
Whether it's a millimetre-small fastener, complex precision optics or metresized machinery parts, the cleanliness requirements for high-tech components are becoming stricter and more demanding in numerous branches of industry. Although the exact specifications vary depending on the part, sector and application, most conventional cleaning systems are unable to achieve the result required to ensure consistent product quality. Ecoclean has been supplying solutions for precision and high-purity cleaning applications for many years. With its wealth of experience, the company is constantly driving forward the development of cleaning systems, technologies and processes for this sector, including specially-designed feature packages.
Demands on the performance and reliability of components and parts have increased enormously and continue to rise, particularly in sectors such as the semiconductor supply industry, optical and optoelectronic industry, thin-film technology, vacuum, laser and analysis technologies, as well as the medical device industry. This has an impact on parts cleaning.
When it comes to components for semiconductor production equipment, due to new developments in wafer steppers and scanners for EUV lithography, for instance, mechanical components are not only becoming more and more complex in shape but also heavier and larger. Today, the diameters of these workpieces can be anything from one millimetre to over one metre in size, and this range is constantly increasing. At the same time, the diversity of materials used is also rising. Added to this, specifications regarding particulate, film-type -chemical, organic and inorganic cleanliness are becoming increasingly stringent. The situation is similar for vacuum components used in UHV, XHV and UCV applications, such as those for high-power laser systems or high-tech measuring and analysis equipment. In the case of precision optics like mirrors, lenses, prisms and micro-optical parts, more complex geometries and modified materials are also giving rise to new and challenging cleaning tasks. In coating technology, ever-more efficient processes call for exceptionally clean surfaces, regardless of whether parts such as machine tooling, automotive components and optical products are cleaned before or after coating.
For parts cleaning, this results in demanding tasks that span the entire manufacturing process. The cleanliness requirements vary depending on the product, area of application and company concerned. As a rule, particulate cleanliness specifications - which extend into the nanometre range for precision and high purity applicationsare defined by surface cleanliness classes (SCC). The specifications for the required film-type chemical, organic and inorganic surface cleanliness are usually based on individual specifications or factory standards, for example outgassing rates, which are evaluated by mass spectrometry. In order to solve these tasks in a needsbased, efficient and sustainable manner, not only is comprehensive technological know-how required but also knowledge of the applications and respective physical relationships. As an experienced fullservice provider of future-oriented solutions for precision and high-purity cleaning, Ecoclean has both. This ensures cleaning solutions designed and equipped to meet requirements, enabling defined cleanliness specifications up to the highest current requirements (for example Grade 1) to be consistently achieved.
Key criteria for selecting the most suitable cleaning process and plant technology are the required level of cleanliness, the type of contamination to be removed, and the material and geometry of the respective component. Based on this, it is possible to
determine which and how many process steps are necessary with which cleaning medium and which mechanics. Aspects such as the quality of the rinsing medium and the drying technology are included just as much in this consideration, as are cleanliness-compliant parts handling and the prevailing environmental conditions, for instance connection or integration into a cleanroom.
If the standard ‘oil-free and greasefree’ such as Grade 4 is defined as the specification, Ecoclean supplies compact and cost-efficient full-vacuum single-chamber systems, whose system technology, media routing, media preparation, and design have been specially adapted for high-end cleaning applications. These systems, which are operated with environmentally-compatible solvents or water-based cleaning agents, are capable
of achieving consistent results that meet such requirements, even if it concerns geometrically complex components. Process options that can be combined in almost any way, such as injection flood washing, spray, high-pressure, immersion, ultrasonic, megasonic and plasma cleaning, as well as Ultrasonic Plus or Pulsated Pressure Cleaning (PPC), contribute to this. Often, a modified alcohol (partially polar solvent) is used in these applications due to the plus points associated with the media, such as their ability to clean different materials. The limit of what can be achieved with these systems is, for example, Grade 2. Especially when it comes to large parts, chamber cleaning systems offer advantages due to the process mechanics concentrated in the working chamber, for example PPC, ultrasonics or megasonics and injection flood washing. In order to use these also to meet Grade 2 or corresponding cleanliness specifications, Ecoclean manufactures EcoCvela double-
chamber systems that use aqueous media for cleaning. In addition to the special highpurity features, completely separate circuits for cleaning and rinsing media ensure that the required cleaning result is achieved reliably and consistently. If, for example, due to a wide variety of materials, high throughput requirements or cleanliness specifications corresponding to Grade 1, the cleaning tasks cannot be solved with a chamber system, a multi-bath ultrasonic cleaning system is called for.
With its UCMSmartLine or UCMPerformanceLine series consisting of standardised modules, the SBS Ecoclean Group also offers efficient solutions in this area. Thanks to the electrical and control technology integrated into the modules for the process steps of cleaning, rinsing, drying, loading and unloading, as well as a flexible transport system, these can be easily adapted to the respective task and can also be extended if necessary. Individually-designed multibath ultrasonic cleaning systems such as
the UCM HighLine are typically used in high-end applications, for example in the semiconductor supply, laser and optical industries.
Which system concept is the right one in terms of cleanliness and cost-effectiveness is determined via cleaning trials with original components or test specimens. Ecoclean has appropriate High Purity Test Centers for this purpose. As a result, product-specific cleaning processes and process parameters can be developed and then stored as programs in the system controller. This ensures that each part is cleaned with the validated process parameters to achieve the required level of cleanliness in a consistent and reproducible manner. Furthermore, all relevant process parameters can be monitored, documented and transferred to higher-level systems.
ecoclean-group.net ucm-ag.com
After a generation of capital and resources flight to cheaper manufacturing centres around the world, one Aussie metal fabricator is doing better than ever. Drew Turney reports.
Plants and factories from automotive to apparel closed up in the globalisation age, and the narrative ever since has been of an industry that's long since fled to the third world in search of cheaper prices, never to return.
But some local players are bucking the trends, and just one is the Sevaan Group, a Sydney-based metal machining company that's going from strength to strength. Established in 1997 as Proline Technologies, owners and proprietors Jim and Artemis Tzakos built the business up strategically, surrounding themselves with a small team of manufacturing experts and acquiring a company in 2011, re-christening itself The Sevaan Group.
Supplying Original Equipment Manufacturers (OEMs), The Sevaan Group produces metal components for a range of industries including defence, mining, agriculture and gaming to aerospace, robotics, electronics and transit. Today the company has around 50 people and is in the throes of planning an advanced new facility to open late in 2023. But as CEO David Green explains, it’s still a family owned business in practice as well as spirit, and that might just be the secret to The Sevaan Group's success.
The localisation movement
Sevaan’s business actually grew during COVID and the company has a strategic business plan in place that takes into account the onshoring taking place, and the opportunities this will present. Delivery times have been extended and transport cost increases are reflecting the plug-ins and workarounds the pandemic economy has wrought. Green says the return of many manufacturing customers to Australian providers is ‘encouraging’.
But it’s not enough to just be there when customers turn their back towards home. Local manufacturers still can’t really compete on price (more below), but Green says the uncertainty has made his customers more comfortable sourcing products from down the street instead of across the water. So as things improve (current recession jitters notwithstanding), how do we stop jobs, tools,
expertise and cost-conscious users going back overseas when supply chains settle down?
“If you ask if we’re always going to be the cheapest provider likefor-like against overseas suppliers, the answer’s no,” Green says. “But when you look at the overall cost from a long term view, one that incorporates a life cycle and quality control, we become very competitive.”
Quality control has always been a USP of Sevaan. It’s not new. When the choice is between variable quality from a far-flung plant where delays might hold delivery up for weeks versus a partner across town you can visit to collaborate with on quality and which keeps delivery promises, the choice is obvious. Green thinks such quality control is assured over the long term because The Sevaan Group has a continual commitment to stay ahead of the curve. “We alway invest in the latest technology every 3-5 years to improve capacity and throughput. It’s about having a forward thinking philosophy in technology and training.”
The Sevann Group 4.0
A cornerstone of that effort is the adoption of Industry 4.0 practices and tools – in The Sevann Group’s case, investing in a lot of equipment that’s digitally controlled, programmed and operated. “The other side of that is big data,” Green says. “It lets us monitor production to ensure the best use of machinery and that productivity across the company improves, increasing capacity and capability.”
A recent move in that direction is the adoption of the ZOOMFAB platform, a system that monitors manufacturing and plant machinery, collects and synthesises the data from the performance of individual components in a workflow and presents analytics to let operators make the relevant changes and improvements proactively when and where they're needed.
So far, Green and his team are big fans. “From equipment set up through to when it’s in operation, ZOOMFAB lets us monitor power usage, productivity and returns.”
The company is planning to extend the ZOOMFAB deployment further across the operation, and Green adds that staff love the immediacy and mobility of viewing and actioning what comes out of it. “The guys operating the equipment have iPads that show the results from their operation and their interaction with the equipment, so they’re aware of exactly how things are going on a day-to-day basis.” Of course, there’s a trap awaiting any company trying to stay at the bleeding edge of process management, and it’s because technologies are coming along faster than the industry can absorb them – we simply can’t train engineers, managers and technologists fast enough.
As a statistic from Deloittle claims, talent shortages will result in two million unfilled manufacturing jobs globally by 2030. [https://www2. deloitte.com/us/en/insights/industry/manufacturing/manufacturingindustry-diversity.html]
How will The Sevaan Group overcome such a challenge, especially in Australia where it seems we’re constantly battling a brain drain?
“I’ve seen this across many companies,” Green agrees. “There's so much fluidity in people on the shop floor you can be left with technology you don’t understand or know how to deploy.”
The solution is a program called The Sevaan Academy. Originating with co-founder Artemis Tzakos’ background in organisational development and training, it’s a formalised process to understand, document and – when necessary – transpose skills and knowledge as things shift.
“Every position has established competency, experience and task requirements which are tested and adjusted when things change,” Green says. “It very effectively keeps people in front of the tasks they have to do.”
That means when a new technology is deployed in the company, having such a prescribed framework for skills and procedures lets operators upskill as much as necessary quickly to start using it. “Team leaders define the knowledge and skills required to be competent with new equipment or processes as well as the training needed to get staff there, and that's written in to the overall Sevaan Academy profile,” Green says.
But beyond the expertise needed today, it also informs on the company’s recruitment needs because managers are aware of exactly the skills they're looking for in candidates. And while you might think we’re just talking about job descriptions, The Sevaan Academy goes much deeper than that – right down to the nuts and bolts, in fact.
“Many organisations of course have their own training systems but sometimes they’re quite generic,” Green says. “What we're trying to do is get down to the nitty gritty of operating every piece of equipment or technology effectively and thoroughly.”
In fact, Green and his team are already looking at process certifications at the micro level – each component of each job given a micro-credential to establish every skill requirement transparently. But there’s been a deeper and very human impact that’s had a quite
different effect. “The focus on processes is allowing us to redesign or re-engineer what we do and consider how we can do it more effectively,” Green says. “There's more spontaneous discussion going on about improvements. It’s having a huge impact because it’s not something you do one day and then stop the next.”
And the effects so far have been tangible. In just one example, Green says The Sevaan Group’s structured approach to task and skills curation has made the company better at predicting market conditions. “If there are delays in our processes, we pick them up much quicker, which lets us keep the customer informed instead of taking them by surprise and more importantly, taking the necessary actions to accelerate a fix and get things back on track.”
The Sevaan Group can work with stainless steel, aluminium, bronze, brass, copper and more. Just some of its finishing services include cutting, folding, welding and powder coating.
All of which means that – just as unusual as being located in Australia and being in such rude health – every step of the process from initial design to final delivery is managed and performed under one roof. And because the company executes a project from end to end, its designers and engineers have deep and thorough experience in what customers want (and need), a business model Green describes as ‘integrated’. “If a customer goes somewhere else they may be looking at two or three separate suppliers to achieve what we can. Multiple processes contributing to a finished product is much more competitive under one roof.”
One of the primary reasons for that is because adhering to quality standards is much easier when applied only to your own operation rather than third parties whose company or regulatory standards might be vastly different from yours.
And, perhaps most crucially of all, Green says the people under that single roof care enough about quality to make the company a compelling choice. “It’s very much a family owned business,” Green says. “Quality control happens because of our processes but also very much because of our people. We have a very human-centred culture and the expertise in the organisation speaks for itself.”
We’re through the worst economic ravages of the COVID pandemic and global manufacturing has a strong incentive to get back to normal. But while some of the effects of the pandemic (like the international supply chain crisis we’re still in the grip of) have been good for companies like The Sevaan Group, how is it going to weather the storms to come, like if customers do flee back to China or the US in search of cheaper prices?
When AMT talks to Green, the company is putting the finishing touches on a five year plan. A large part of it will be further developing business with existing clients, but an important lynchpin will be increasing capacity.
“Thankfully, the business didn’t really slow down much during COVID,” Green says. “In fact we actually grew on paper, again because of supply chain issues and people buying locally. We’re hoping that habit sets and continues to grow, and our plan is to match that increase in demand in the next couple of years.”
The new premises is one part of that plan, offering more space and easier industry 4.0 integration. More acquisitions are also on the cards as a way of boosting staff numbers, technology and resources. “Several customers have told us they’re expecting demand increases of up to 5,000% in some cases based on them opening up new channels in overseas markets,” Green says. “We want to be alongside them when that happens, so we’re talking to them all the time about their needs so we can make sure we have the capacity to absorb that demand.”
sevaangroup.com.au
South Australian family business RCWilliams staying with OKUMA to stay competitive.
Third generation South Australian family owned precision engineering business, R.C. Williams Pty Ltd, is keeping abreast of the latest technology to remain internationally competitive and expand into new markets.
Founded in 1967 the company is run by brothers Sam and Nick Williams with a staff of ten highly skilled engineering personnel. As a family business, R.C. Williams prides itself on a long tradition of quality and service to customers, started by its founder Ron Williams more than 55 years ago. The company is a long-standing customer of Okuma having installed its first machine 34 years ago.
Now with a shop floor full of these impressive machines it’s not surprising the most recent investment was the latest Okuma Multus U3000 multitasking machine with a fully flexible and productive ASA robot system. “The new addition was carefully planned to complement our existing inventory, increase our capacity, flexibility and performance overall,” said Managing Director Sam Williams.
“Twin spindles, stacked magazines full of tools and in-process gauging means that we can do medium to large runs in quick time whilst never compromising on quality. ASA’s robots and expert programmers keep our operations efficient and we are not limited to bar feeding for high volume operations when the machine is unmanned.
“Okuma apps now give us full control and makes overnight machining of a wide range of components possible,” said Sam Williams. “The automation has dramatically extended our machining capability from 12 hours to 24 hours per day and increased component output by three times,” he said. Today the company services a broad range of industries across Australia with an emphasis on servicing the mining industry, load lifting equipment and defence industries with specialised services such as diamond cutting tools, sprocket, spline and gear cutting, general jobbing, turning and milling, reverse engineering and CNC 2D and 3D design capabilities to meet specifications. The company also produces components for agriculture, the fitness industry, R&D projects and special parts for University projects.
“The continual introduction of new advanced machines such as the new Okuma Multus U3000 multitasking machine creates an air of excitement within our plant, allowing our engineers to learn new skills on the latest technology and robotics. It is in this area that we take full advantage of the generous
training offered by Okuma Australia which is ongoing and at the end of a phone or face to face when we require it,” said Sam.
“This is important to all our engineers and particularly important to our apprentices under training. We currently have two apprentices and maintain two to three at any time to ensure that as an industry we have well trained skilled engineers in the future,” he said.
The new machine is now working 24/5 and has greatly reduced customer lead times and is opening up new market opportunities.
“It has been a great experience for me personally working with all three generations of the R.C. Williams family over the last
26 years. I strongly believe our long-term loyal customers are the cornerstone of our market here in South Australia and a very strong focus for Okuma Australia. Having long term customers such as R.C. Williams with so many generations of Okuma machine tools is a powerful statement to make within the engineering sector,” commented Rob Hall, Branch Manager-SA Okuma Australia.
With confidence in the Australian and South Australian economies this third generation family business is well placed to benefit from the potential of new markets opening up for precision engineering.
okumaaustralia.com.au
rcwilliams.com.au
Choosing the right machine tool tending automation system for your manufacturing needs.
In the world of robotics and automation for manufacturing, machine tool tending systems are a crucial process. These systems are available in various brands and styles, but there are two main categories: workpiece exchange and integrated fixture exchange. Each type of system comes with its advantages and disadvantages, which must be considered when selecting the appropriate system for specific machining applications.
Workpiece exchange systems involve the automated exchanging of raw material in and out of an automated clamping medium inside the machine tool, typically a pneumatic or hydraulic vice or chuck. In this setup, operators position the raw material outside the machine tool in a grid pattern, and the robotic end-effectors and clamping mediums are tailored to the material type, shape, and size. Workpiece exchange systems deliver an excellent return on investment in high volume - low mix applications. However, the robot must be retrained and the end effector and clamping medium modified or exchanged every time the grid changes. Therefore, these systems may not be ideal for manufacturing facilities with high part mix or small to medium-sized production runs.
Integrated fixture exchange systems, on the other hand, are suitable for manufacturers with a high mix of parts and/or low to mediumsized production runs. The most common type of integrated fixture exchange system is the integrated pallet exchange, which features a static end effector and clamping medium that only exchange a pallet. The tooling mounted on top of the pallet can be configured in several ways (vice, chuck, etc.) if it fits within the specified work envelope. However, these systems may not be cost-effective in high volume - low mix applications due to the expense of the pallets and additional top tooling required.
Recent developments in integrated fixture exchange automation utilize zero-point clamping studs to eliminate the need for a pallet. The affordable clamping studs ensure the reliability and repeatability of the entire system and process. These systems, such as the new RockLock pneumatic base from 5th Axis, utilize a static end
effector and zero-point clamping base, and the workpiece shape/ size has no bearing. Once installed, the robot does not require much interaction, making these systems popular for their simplicity. 5th Axis modular automation components employ a simple, modular cleat that is separate and external to the workholding. The design allows it to be attached to various fixture styles, shapes, and heights, making existing workholding compatible without requiring investment in a new brand or type.
In conclusion, selecting the appropriate machine tool tending automation system that best suits specific manufacturing needs is key. Understanding the pros and cons of each system type can help ensure that manufacturers invest with confidence and select a system that offers a good return and meets current and future manufacturing needs. livetools.com.au 5thaxis.com
French-founded automation giant, Schneider Electric partnered with Universal Robots to free up their staff’s time and enabled them to focus on value-adding tasks. Their plant in Bulgaria, predominantly focused on the production and assembly of mini circuit breakers, deployed two UR5 cobots to automate repetitive manual labour tasks, such as picking and placing power breakers and boxes.
Schneider Electric delivers solutions to homes, buildings, data centres, infrastructure, and industries, by combining energy technologies, real-time automation, software, and services. The plant employs more than 500 employees comprising of operators, administration, and support staff. “The cobots have been deployed to tackle non-ergonomic, repetitive, and boring daily tasks. This allows operators to be more focused on product quality and machine performance,” says Antoniy Petrov, automation engineer at Schneider Electric.
An innovative company, Schneider Electric is constantly seeking out modern and reliable solutions to enhance its operations. The UR5 cobots from Universal Robots precisely deliver this – more efficient and productive operations.
“Our cobots were programmed to pick power breakers from the manufacturing line and place them into boxes,” explains Masayuki Mase, Country Manager for Universal Robots Oceania. “Once this
task is completed, the cobot picks and places an empty box to be filled again, until the cart is filled with 10 boxes. Once the batch is finished, the cobot alerts the operator that it’s time for changeover.”
As one of the smallest cobots in the range, the UR5 is lightweight, flexible and tackles an array of tasks with ease. “It offers a reach of 850mm, a payload of 5kg, a footprint of 149mm and weighs in at just 20.6kg. This medium-duty robot integrates seamlessly and makes quick work of all tasks – as experienced at Schneider Electric.”
On this plant, the cobots follow processes like emergency stops. “The cobot can reject full conveyors to provide a safe working area for the operator to remove the units which are unfit for use. It can also alert the operator when changeover is needed, and handle manual requests from the operator to stop operation and move into a safe position,” Petrov explains.
The robot works fully autonomously, and the operator is only needed for the changeover. “The UR5’s return on investment in this particular setting is around 24 months.”
Speaking to the uptake of automation in the electronics and technology sector, Masa says, “We have seen strong demand across major sectors – including electronics and technology. COVID-19 highlighted the need for independent supply chains by local manufacturers.” universal-robots.com
AE Gibson & Sons new Robotic Training and Demonstration Technology Centre supports future manufacturing and upskilling of much needed engineers.
Australian engineering and family-owned business AE Gibson & Sons is in its fifth generation of operation, with historical roots that can be traced back to the late 1800s. They’re an awardwinning industry leader in designing, servicing, and supplying specialised machinery and optimised robotic automation systems, with a mission to help their clients implement more sustainable manufacturing operations in industries including timber, renewables, biomass, waste processing, infrastructure, agriculture, and other heavy industrial applications throughout Australia and the entire Asia Pacific region.
Located in Kendall NSW, AE Gibson’s has recently become the successful recipients of a share in $534,667 from round two of the NSW state government's Regional Job Creation Fund. The funding has helped to develop a newly established robot training and demonstration centre and facilitate AE Gibson’s mission to expedite training for their wave of apprentices that are brought into the business as well as junior engineer graduates, whilst upskilling existing employees.
The intent is to develop their skills in the areas of robotic automation as the business expands into emerging sectors in Australia and looks to support the reshoring of manufacturing to overcome supply chain backlogs in the industry.
“Our employees are very forward-thinking and have really embraced our vision to integrate robotics into our business model,” Curtis Gibson, AE Gibson General Manager says. “Customers who have come through the technology centre repeatedly mention their appreciation for being afforded the opportunity to see the advancements in engineering machinery face to face, but furthermore interact and program it themselves.”
This exposure has shown them not only why they need to adopt robotic automation in their businesses, but also how easy it is to do so.”
With his own expertise in adopting new technology and innovation such as 3D design modelling and Industry 4.0, Curtis acknowledges the welcome opportunity to train their employees and customers about the benefits of robotics and the future of automation.
The Centre currently holds an ABB IRB 1660 industrial robot, the market’s highest performing 10kg robot typically used for arc welding and machine tending. The robot selected for AE Gibson’s Technology Centre is ABB’s IRB 4600 industrial robot. It’s so compact and optimised that it can cut the cycle times of the industry benchmark in applications like palletising, dispensing, pick and placing, machining, measuring and assembly, by up to 25%.
The Centre is all about showing how versatile industrial robots really are. Software advancements have reduced programming complexity and design features are helping industrial manufacturers of all types and sizes to increase their operational performance and gain better access to a well-trained workforce.
"The role of automation in reshoring and improving productivity has the ability to bridge the current skills gap and labour shortages"
“The role of automation in reshoring and improving productivity has the ability to bridge the current skills gap and labour shortages we’re facing locally and internationally, but also propel Australia further onto the world stage,” Simon Parker, Global Business Development Manager said.
“Investment demonstrates growth. While working with a wide range of companies developing solutions I have found that generally by the time the first robot is installed the company is planning the next system after realising the benefits of automation to their business.”
Robotic demonstrations at the Centre feature standardised grippers and additional attachments that can be trialled in applications such as materials handling, palletising, timbers, and metals and plastics production. It’s significant because the manufacturing industry requires highly skilled, deeply trained professionals where the learning was previously done in-house.
Having a facility such as the Robotic Training and Demonstration Technology Centre means businesses can gain access to the latest technology with training provided intrinsically by AE Gibson - industry leaders in this space. With more sophisticated understanding, they can take employees who were previously doing the dirty, dangerous, and mundane jobs, and repurpose them into more appealing roles with opportunities for career advancement.
It also allows AE Gibson to showcase their capabilities to design, develop, commission, and provide after-sales support for tailored solutions to meet their customer’s distinctive requirements.
“We’re really proud to be a part of supporting AE Gibson & Sons in this project which is creating avenues for students and industry alike to learn about robotic automation and also give them a chance to develop integral skills in what’s becoming rapidly necessary in Australia,” Adrian Shore, Robotics in Manufacturing Sales Specialist for ABB Australia said. “With a longstanding history of supporting the local community, youth activities, and advocating for growing manufacturing in Australia, Curtis says, “this isn’t just about evolving our capabilities with modern technologies to keep up with the market, but just as importantly providing a launching pad for young people to learn and work and essentially keep jobs and manufacturing local.”
“The level of service and support we receive from ABB shows that they share in our immediate and long-term vision and that’s critical and why we chose them as a partner,” Parker added.
Thanks to another NSW Government funding approval, AE Gibson has become new recipients of an Innovation Grant. With this, they’ll start recruiting more engineers to join their business, with the hopes to develop a formal graduate engineering program and work with local universities to spur increased interest in STEM, influence research and development from an industry perspective, and also collaborate on uniquely innovative projects that will help to support Australia’s manufacturing future. abb.com aegibsonman.com.au
Brisbane-based company, Advanced Robotic Technology (ART), is offering a game-changing solution for Structural Steel Engineering companies looking to take control of their supply chains amid ongoing international shipping issues.
As supply chains are disrupted, and production delays continue, firms need to bring the cutting of all profiles in-house to stay competitive. ART's solution for backward integration allows companies to do just that. By partnering with ART, businesses can eliminate uncertainties and delays of outsourcing, ensuring a reliable supply chain while gaining a strategic advantage over competitors.
ART's solution is exemplified by the Metaltek XB1200 Plasma Beamline, a state-of-the-art structural steel processing system that's made, designed, and supported in Australia from a manufacturing facility in Brisbane.
This machine provides high-speed and quality coping, eliminating the disadvantages of manual fabrication. In partnership with industry-leading plasma manufacturer Hypertherm, ART has developed a solution that efficiently processes hot and cold-rolled structural steel profiles, reduces waste, and boosts productivity. The system can process all types of structural steel, from simple square cuts up to to complex mitres, copes and bevels in profiles up to 1200mm in width.
According to ART, the company's cutting-edge technology provides the perfect answer to problems facing Structural Steel Engineering companies. Bringing the cutting and chopping of all steel profiles in-house enables firms to secure a reliable supply chain and gain a significant competitive advantage. By leveraging the Metaltek XB1200 Plasma Beamline and other innovative solutions from
ART, companies can reduce waste, increase productivity, and stay ahead of the competition.
In today's fast-paced business environment, staying ahead of the competition is essential. For Structural Steel Engineering companies, partnering with Advanced Robotic Technology may be the key to success. With the supply of all profiles in-house and state-of-the-art technology driving their operations, these firms are well-positioned to thrive in today's challenging marketplace. artcnc.com
Güdel offers a wide range of linear tracks & multi-axis gantries to suit the most demanding applications for robots, logistics, handling & assembly processes.
TrackMotion modules TMF & TMO to accommodate every robot brand and a wide range of robot models. Available in travel lengths up to 100m with payloads up to 14,500kg (robots) & 20,000kg (static loads).
As the distributor for Güdel in Australia, New Zealand, Singapore, Malaysia, Thailand, Indonesia & Vietnam, CNC Design can support local technical & sales inquiries for all Güdel products.
CNC Design Pty Ltd, 137-145 Rooks Rd, Nunawading, VIC 3131, (03) 9417 2820
https://www.cncdesign.com.au/gudel-modules-components gudel@cncdesign.com
Emad Afghani, Vice President of Sales ANZ at TeamViewer, provides insights into how the industrial metaverse solutions can revolutionise the way the industry works to deliver more comprehensive user experiences.
The latest data indicates that Australians have some understanding of the metaverse, and with 26% of people now reporting they’ve actually engaged with it, it’s clear that interest is growing. At its core, the metaverse leverages augmented reality (AR) with digital representations of people and things to create integrated 3D virtual and social worlds.
However, while many people will see the metaverse as a place where they can use avatars in virtual social situations such as gatherings or shopping, the concept of the metaverse has been increasingly gaining traction in the industrial space, including in manufacturing and logistics. As a result, organisations are increasingly realising the value the metaverse can provide to their business, leading to more streamlined and efficient production, according to TeamViewer.
“Industrial workers constantly use their hands to repair, move, or maintain real-world objects. Even the most technically advanced processes in the industry require interaction with physical objects, no matter if they are machines, goods, or devices. There’s a misconception that using an AR headset could be counterproductive as it could cut workers off from the real world; however, that’s not necessarily the case.”
Data shows only 13% of Australians have engaged with a virtual reality (VR) or AR device and there’s a pervasive misunderstanding that connecting with virtual worlds means disconnecting from the physical world. However, the reality is that the metaverse can result in a continuing union of the physical world with the internet, powered by immersive technology. And, the industrial metaverse could leverage equipment to connect workers with digital and physical worlds at the same time for a more complete, augmented experience.
Deploying metaverse technology to enable industrial environments such as manufacturing, logistics, and automotive, requires a fresh approach. The industrial metaverse differs from more consumerfacing metaverses by digitising information and transferring it to workers, rather than digitising people to the virtual world. This information transfer empowers workers in a way that has never been seen before and has the potential to revolutionise the way the industry works, delivering more comprehensive user experiences. With augmented reality (AR) and the metaverse, workers are presented with relevant information or virtual objects in their field of view at the exact time they need them. Technological developments of AR and mixed reality (MR) have made devices like smart glasses or MR headsets possible. These devices not only display information, but also have the potential to provide entire step-by-step workflows or interactive 3D holograms that are blended into the real world
without obstructing the worker’s view. This lets workers engage in more streamlined processes, resulting in faster, more accurate results for the business.
“The potential for the industrial metaverse is almost unlimited, which makes it impossible to ignore,” Emad Afghani said. “Each and every task can be improved by having hands-free options and access to relevant information. The devices enable real world interactions while connecting to the digital one. However, the real power lies in the software itself. The software enables the industrial metaverse by displaying real-time data from backend systems, interactive and immersive training workflows, or step-by-step instructions to maintain machines, for example. This technology empowers employees to be more efficient, productive, and confident while promoting accuracy and helping to reduce error rates.”
Businesses are already exploring the industrial universe and technically advanced companies are using augmented or MR solutions to reduce error rates and improve training experiences in different areas.
The industrial metaverse lets companies digitalise individual processes as well as entire workflows by connecting the worker to the relevant data. Each step can also be accelerated with real-time data while training and management can be improved by evaluating accumulated data of processes working together. teamviewer.com
New research from Monash University presents the most effective approach to accurately predict vulnerabilities in software code and strengthen cybersecurity.
Software vulnerabilities are prevalent across all systems that are built using source codes, causing a variety of problems including deadlock, hacking or even system failures. Thus, early predictions of vulnerabilities are critical for security software systems.
To help combat this, Faculty of Information Technology experts developed the ‘LineVul’ approach, and found it increased accuracy in predicting software vulnerabilities by more than 300% while spending only half the usual amount of time and effort, when compared to current best-in-class prediction tools.
LineVul is also able to guard against the top 25 most dangerous and common weaknesses in source codes, and can be applied broadly to strengthen cybersecurity across any application built with source code. Research co-author Dr Chakkrit Tantithamthavorn, from the Faculty of Information Technology (IT), said standard software programs contain millions to billions of lines of code and it often takes a significant amount of time to identify and rectify vulnerabilities.
“Current state-of-the-art machine learning-based vulnerability prediction tools are still inaccurate and are only able to identify general areas of weakness in the source codes,” Dr Tantithamthavorn said.
“With the proposed LineVul approach we are not only able to predict the most critical areas of vulnerability but also are able to specifically identify the location of vulnerabilities down to the exact line of code.”
Future research building on the LineVul approach includes the development of new methods to automatically suggest corrections for vulnerabilities in software code. This research was supported by the Australian Research Council’s Discovery Early Career Researcher Award 2020-2022. monash.edu
OneCNC CAD CAM works directly with manufacturers and the leaders in machine tool innovation to drive the industry forward.
OneCNC has created user-friendly software platforms that are revolutionising the manufacturing industry. Supplying specifications in terms of tolerances and finishes upon designers or customers’ initiative. The manufacturing industry is evolving at a high demanding rate in which customers demand flexible production with a lean manufacturing focus.
The revolution industry 4.0 demands all machines to have a networking process in which the product is able to modify the process if needed in order to build a flexible production line.
OneCNC CAD CAM forward thinking approach to manufacturing allows for modification according to each specific product, this is an advantage for product personalisation.
This is a huge step forward in the manufacturing industry. Allowing optimisation of the resources of the company and supply chain suppliers while providing the customers with a complete quality product which can be easily adapted to the needs of current society. The high-performance of OneCNC and ease of use of the system offers powerful programming for any CNC machine tool.
OneCNC has solutions with functionality that includes programming for 2-5 axis milling, 2-5 axis turning, 2-4 axis wire EDM, 2 axis Profiler, multitasking mill-turn machining, and B-axis machine tools. Streamline your operations with the powerful and flexible CAD CAM, valued by CNC programmers for its extensive wizard driven machining cycles, tool control, and capacity to fully support the entire shop.
OneCNC has seamless CAD to CAM and directly imports part models from almost any source, fully intact, with no need for programmers to edit or rebuild geometry.
OneCNC directly machines from any combination of geometries of solids, surfaces, wireframe, or STL providing you with complete manufacturing flexibility.
Starting with 100% complete and accurate part geometry eliminates nearly all of the difficulty in programming complicated parts and dramatically reduces programming time.
onecnc.com.au
DevelopmentWA is the State Government’s land development agency, operating across Western Australia with a diverse portfolio of industrial, residential and redevelopment projects.
As a business unit of DevelopmentWA, the Industrial Lands Authority (ILA) continues to champion innovative and sustainable projects to ensure WA is ready to take advantage of the next generation of industrial growth and development.
With almost 60 industrial projects across WA, the ILA supports the full spectrum of industry operating in our State – from established sectors such as mining, logistics, and oil and gas, and emerging industries such as automation and robotics and renewable technology.
When it comes to renewable energy, our landscape is our advantage - it is vast, rich in critical minerals and natural resources. We have the opportunity to harness the abundant sunshine, consistent wind and tidal energy to power the future of renewable energy for our use and to supply the world.
And to help lay the foundations for our renewable future, DevelopmentWA’s ILA can help guide approvals for investment and get you the land your business needs.
Discover how we are helping fuel the transition to renewable energy at developmentwa.com.au/ons22
Subnanometre semiconductors had a scaling problem. UNSW has been on the case that could pave the way for emerging 2D electronic applications.
Researchers from UNSW Sydney have developed a tiny, transparent and flexible material to be used as a novel dielectric (insulator) component in transistors. The new material would enable what conventional silicon semiconductor electronics cannot do – get any smaller without compromising their function.
The research, recently published in Nature, indicates the potential for large-scale production of a 2D field-effect transistor – a device used to control current in electronics. The new material could help overcome the challenges of nanoscale silicon semiconductor production for dependable capacitance (electrical charge stored) and efficient switching behaviour.
According to the researchers, this is one of the crucial bottlenecks to solve for the development of a new generation of futuristic electronic devices, from augmented reality, flexible displays and new wearables, as well as many yet-discovered applications.
“Not only does it pave a critical pathway to overcome the fundamental limit of the current silicon semiconductor industry in miniaturisation, but it also fills a gap in semiconductor applications due to silicon’s opaque and rigid nature,” says Professor Sean Li, UNSW Materials and Manufacturing Futures Institute (MMFI) Director and principal investigator on the research. “Simultaneously, the elastic and slim nature could enable the accomplishment of flexible and transparent 2D electronics.” A transistor is a small semiconductive device used as a switch for electronic signals, and they are an essential component of integrated circuits. All electronics, from flashlights to hearing aids to laptops, are made possible by various arrangements and interactions of transistors with other components like resistors and capacitors.
However, there’s a scaling problem. Developing more powerful future electronics will require transistors with sub-nanometre thickness – a size conventional silicon semiconductors can’t reach.
“As microelectronic miniaturisation occurs, the materials currently being used are pushed to their limits because of energy loss and dissipation as signals pass from one transistor to the next,” says Prof. Li. The current smallest transistors made of silicon-based semiconductors are three nanometres.
To get an idea of just how small these devices need to be – imagine one centimetre on a ruler and then count the ten millimetres of that centimetre. Now, in one of those millimetres, count another one million tiny segments – each of those is one nanometre or nm.
“With such limits, there has been an enormous drive to radically innovate new materials and technologies to meet the insatiable demands of the global microelectronics market,” says Prof. Li.
For the research, MMFI engineers fabricated the transparent fieldeffect transistors using a freestanding single-crystal strontium titanate (STO) membrane as the gate dielectric. They discovered their new miniaturised devices matched the performance of current silicon-semiconductor field-effect transistors.
“The key innovation of this work is that we transformed conventional 3D bulk materials into a quasi-2D form without degrading its properties,” says Dr Jing-Kai Huang, the paper’s lead author. “This means it can be freely assembled, like LEGO blocks, with other materials to create high-performance transistors for a variety of emerging and undiscovered applications.”
The MMFI academics drew on their diverse expertise to complete the work.
“Fabricating devices involves people from different fields. Through MMFI, we have established connections with academics who are experts in the 2D electric device fields as well as the semiconductor industry,” says Dr Ji Zhang, a co-author of the paper.
“The first project was to fabricate the freestanding STO and to study its electrical properties. As the project progressed, it evolved into fabricating 2D transistors using freestanding STO. With the help from the platform established by MMFI, we were able to work together to finish the project.”
The team is now working towards wafer-scale production. In other words, they hope to see whether the material can be used to build all the circuits for an entire computer on one chip.
“Extensive data sets were collected to support the performance of these 2D electronics, indicating the technology’s promise for largesize wafer production and industrial adoption,” says Dr Junjie Shi, another co-author of the paper.
“Achieving this will enable us to fabricate more complex circuits with a density closer to commercial products. This is the crucial step to make our technology reach people,” says Dr Huang. The researchers also say their development is a promising step toward a new era of electronics and local manufacturing resilience.
“From shifting geopolitics and the pandemic, we have seen more disruption in the global semiconductor supply chain, and we believe this is also an opportunity for Australia to join and strengthen this supply chain with our unique technology in the near future,” Dr Huang says.
Currently, the technology is protected by two Australian provisional patent applications, with MMFI and UNSW looking to commercialise the intellectual property and bring it to market.
“We are currently fabricating logic circuits with the transistors,” says Prof. Li. “At the same time, we are approaching several leading industries in the Asia-Pacific region to attract investment and establish a semiconductor manufacturing capability in NSW via industrialisation of this technology.”
unsw.edu.au
IDW CAD/CAM and TopSolid celebrate a successful partnership with the Shell V-Power Racing Team.
The Repco Supercars Championship began its 2023 season with the Newcastle 500 in early March, after a three-year hiatus due to the COVID pandemic. Supercars is the premier touring car motorsport series in Australia and includes the famous Bathurst 1000 held in early October.
Dick Johnson Racing, racing under the Shell V-Power Racing Team name, was founded by Dick Johnson in 1980 and is Australia's oldest motor racing team competing in the Supercars Championship. Over the years, the team's drivers have won ten Australian Touring Car Championship titles and have taken four victories in the Bathurst 1000.
Behind the drivers and their success are not only the dedicated members within Dick Johnson Racing, but external partner businesses working closely with them. One such partner Is Ian Whitwood, from IDW CAD/CAM Solutions who, since 2009, has supported Dick Johnson Racing with TopSolid design and machining software. In that time, the team has won four drivers championships and three team championships. Ian and TopSolid have been an integral part of that winning/high-performance culture. Back in 2009, the team bucked the trend of implementing the more widely known software packages, instead opting for TopSolid CAD/CAM. Having tried other packages previously, they felt the combination of advanced 3D modelling and machining functionality in a single package was the best fit for their fast-moving environment. Along with the feature-packed software, it was Ian’s in-depth knowledge and experience that was a major factor in their decision.
In a highly competitive setting such as motorsport, every aspect of the car needs to perform at the highest possible level. The team at Dick Johnson Racing not only have the ability to seamlessly import third party designs into the software, a standard feature of most CAM products, but more importantly, they are able to design
complex parts in-house, using the same software. They can modify and improve the designs time after time with full traceability. The CAM side of the software features 3/4/5 axis milling and lathe capabilities. Being an all-in-one software package removes the need to use two to three different packages to get the job done, making it a cost-effective way to have all the features required to operate an engineering business, large or small. It’s these features that make TopSolid an invaluable tool for the Shell V-Power Racing Team.
As well as supplying the software, Ian Whitwood provides substantial training and support. Being an engineer himself, Ian understands the particular needs of a design and machining environment, and is able to provide solutions for his clients, no matter how large or small their business is.
TopSolid is an integrated digital manufacturing system developed in France and has been available in Australia for more than 20 years, yet it’s still relatively unknown here. The Shell V-Power Racing Team is one of a select group of companies who recognise the benefit of this style of software for design and manufacturing.
The Shell V-Power Racing Team has been working very hard getting ready for the start of the 2023 Repco Supercars Championship. There have been major changes to the cars for this season with the introduction of Gen3 Chevrolet Camaro and Ford Mustang vehicles. It’s claimed that Gen3 marks the biggest change to the Supercars since the introduction of V8-powered Commodores and Falcons in the ‘90s. The Gen3 cars are noticeably different from the previous Gen2 cars, as there is more of a similarity to their equivalent road vehicles.
The team at IDW CAD/CAM and TopSolid wish their partners, The Shell V-Power Racing Team, success in the forthcoming Repco Supercars Championship. idwcadcam.com.au
Adobe Commerce uses AI and advanced data sharing capabilities to create end-to-end personalised B2C and B2B commerce experiences from a single platform.
Unfortunately, it took a pandemic to lay bare a clear pattern in how the Fast Moving Consumer Goods (FMCG) industry is evolving. The resulting disruptions to supply channels have accelerated the key trends in marketing that will change how successful companies do business.
It’s the rise of marketplaces and the ability to converge, disseminate and activate data into monetary value. We’re talking about the untold riches that first-party data provides in guiding your future business decisions. It’s the power and control which comes from connecting directly with customers.
“It’s been coming a long time,” said Scott Rigby, chief technology advisor and principal product manager at Adobe. “And we’re now equipping businesses who not only see the massive opportunity it presents but the competitive necessity of maximising their use of e-commerce to create new revenue streams.”
Leading companies are developing brands using customer experience technology to continue to stay at the forefront of consumer expectations. The Adobe Digital Trends Index tracks the movement of customers and their behaviour from a technology perspective. It’s clear that companies who make investments in customer experience technology, commerce being one of them, are continuing to break away year on year.
“The gap between the leaders and the laggards in some cases is around 30 to 40%,” continued Rigby. “There’s also a significant and growing gap between the leaders and the mainstream. There is now an imperative for FMCG to adopt technology, get the foundations right and scale their capability. Because if they don’t – even if they consider themselves to be a fast follower – they will invariably be left behind.”
And now they want to take our cookies away too? With the deprecation of third-party cookies, the ability of FMCG players to build a first-party data strategy has never been more crucial. Without
the capability to build their own customer behaviour insights, FMCG companies will lose visibility on customer trends which allow them to manage their business and supply chain effectively. This is achievable through building their own database around the needs of their customers and creating niche marketplaces through D2C digital channels. By connecting directly with consumers (not as target segments, but real people), companies can generate their own lasting and engaged customers and advocates.
It may all seem a bit daunting to some, but here are a few practical steps that FMCG players can take to transition to a D2C model.
• First and foremost, invest in technology that gives you downstream customer data and the ability to transact.
• Build new brands exclusive to your digital channels. RXBar is the ultimate D2C e-commerce story, a new brand that got acquired for $600m, less than five years from inception.
• Explore working with partners who sell products that are complementary to yours. For example, Unilever worked with its competitors in the same marketplace in order to gain first-party enriched data. The company also launched its own D2C marketplace which resulted in a 40% increase in new customer acquisition.
• Leverage new delivery channels to distribute your products. For example, service stations, UberEats, Menulog, or Deliveroo.
“Obviously, D2C needs to be implemented in a way that is sensitive to existing legacy relationships. It offers more flexibility and innovation in creating new brands and products. The resulting data on customer behavioural trends going forward, is vital,” said Rigby. “New revenue streams, the ability to adapt to macro-economic situations as well as richer insights and understandings of your customers, which can drive the rest of your business. It’s a channel no one can afford not to activate.”
business.adobe.com
Decades of experience in developing specialised solutions, combined with our expertise in logistics and materials handling, makes Bonfiglioli your trusted partner.
https://www.bonfiglioli.com/australia/en
How to maximaise the profitability of your laser cutting job shop. There are nesting types, material price, scrap metal, quoting and other factors to consider says Felipe Lechuga, Director at Tempus Tools. charged for all the material that is used, given that the rectangular boundary around the part is always larger than the part itself. This means that a larger percentage of scrap is calculated in the part price. This generally results in a lower win rate of quotes, due to the material cost being higher than competitors that are using other methods.
The laser cutting industry is a complex one to master. The early years can be particularly difficult if you don’t set up your job shop operations and quoting systems in an optimal way.
As someone who’s been in the industry for decades, both at the practical, hands-on factory floor level, as well as management and ownership level, here’s my advice on how to maximise your profitability. There are great tips for startups and new players here, but the advice will ring true for laser cutting businesses of any age.
And you’ll need to change your quotes to match it. If you’re quoting a job based on an old part price, and your supplier varies the price of materials, you could end up losing money on the job or charging a price that’s too high for the market, you may end up losing customers, so it’s a fine line to tread. Using rules-based quoting software that ensures current material market pricing can help deliver accuracy and consistency every time. More on this later, but first, how are you quoting?
It’s a common issue amongst job shops. If your customer service staff are preparing the quote, they typically don’t have the experience to know how long different processes will take – from welding, to bending, to folding, to the cutting itself. So you find yourself in a situation where customer service staff are heading out to the shop floor to ask each specialist how long tasks will take. These specialists (usually some of the higher paid staff) then have to take time away from their work to answer questions or run simulations to determine accurate times. What you really need is a system that accurately and consistently quotes the job, including all secondary processes. This way, your customer will receive consistent part prices every time, because nothing annoys them more than receiving two different prices from two different sales staff within the same business! The customer then doubts the pricing, can lose confidence in the pricing, which can then lead the customer to verify pricing by seeking a quote from an alternate supplier.
Have you factored in scrap metal and material wastage?
A recent survey of 100 of our customers worldwide showed that over a two year period approximately 56% of revenue in laser job shops was derived from the sale of material. The problem of how much material is consumed in a month is always a very complicated calculation and depends on the value of material in work-in-progress, the value of the full sheets in your stores, and the value of the remnants of material you are holding.
It’s crucial that material wastage is considered in your part price calculations, or once again, you could lose money on jobs. Most cutting jobs produce a significant amount of scrap – and even with an optimal set-up, there will always be some material wastage. The key is to set up your material pricing correctly, so the customers are contributing. There are three common methods for calculating material consumption and therefore part price, and each creates a different result.
1. Area of a single part. Area based material consumption is where the area of the part (the part itself, not the bounds) is calculated and then divided into the sheet. It doesn't allow for any web and is quite inaccurate. In most cases, it gives a lower price per part than is actually consumed.
2. Rectangular bounds (with web allowance). Rectangular nesting is the safest in terms of making sure that you have
3. True shape single part nesting. This method uses the best of both worlds. Its main aim is to work out how many copies of a single part can be cut from a single sheet. The calculation for the material component of the part price allows you to apply rules that decide how you should price any remnant associated with the calculated sheet. This is vital as you may be willing to absorb a bit of scrap knowing there is a good chance of filling it when it comes to production. But in a situation where you are say cutting disks that are 65% of the sheet height, and you are cutting a lot of them, you can potentially be stuck with a huge amount of remnant. It is important to understand who is paying for that.
Let’s take a simple example of a triangular part with a 100mm base, 300mm apex, and 10mm thickness (we will use the material thickness as the web). We use a triangle here to represent a complex non-rectangular shape, although they are simple to nest and price. If we use three different costing methods (based on a sheet 3000x1500mm with a price of $500), we get three different results.
1. Area of a single art results in 300 parts per sheet, with a cost per part of $1.67.
2. Rectangular bounds (with web allowance) results in 131 parts per sheet with a cost of $3.82.
If you use the first method without a significant mark-up, you run a real risk of losing money on the material component of your quote as there is zero allowance for web and scrap.
In this case, if you use the second method, you will be unlikely to win any work. The third method is the closest to what you will achieve in production and is the safest, most competitive method. It does not make sense, at the quoting stage, to use multi-part nesting, because you do not know the final mix of parts to be cut, so you cannot be certain you are calculating the optimal price. Single-part nesting, on the other hand, is a highly effective way to calculate price. Drawing on Tempus Tools’ experience of more than one million parts quoted, our customers have found that true shape single part nesting delivers the best economic returns to their laser job shop.
The choice of nesting method also influences where you should set your material mark-up.
These variations may not be significant for low quantity jobs, but if you consider that an average laser cutting machine can generate in excess of $1m in material revenues in a year, you are looking at potential lost revenue opportunities from $50,000 - $150,000, depending on which material nesting you select for your quotations.
The preferred method of calculating material price for a part price is true shape nesting as it will rotate and interleave parts to make the best nest, with a close approximation to the CAM system that you’ll actually be cutting the parts with.
In addition to choosing the right nesting type, something that is often overlooked is the cutting times of different shapes. A CAM system will calculate cutting times based upon the geometry to be cut, but if you compare a square plate to a circle with the exact same cut length, the circle will be quicker for the machine to cut, because the laser mechanical system does not need to slow down when changing directions.
Ensure your quoting software has built-in algorithms that take care of acceleration / deceleration tolerances. Every second of laser cutting time lost is revenue lost.
You can see how easy it is for an inaccurate quote to mean that you can lose money, or lose customers. Getting the right quoting system in place is crucial to your job shop’s ongoing success and profitability.
ToolBox, by Tempus Tools, was developed as a rules-based SAAS solution with tools specifically designed for smaller job shops to simplify all facets of the quoting process.
Any staff can use ToolBox – no CAD or CAM training or software is required. With ToolBox, you’re not only delivering accurate and consistent quotes every time, but you’re doing it much more efficiently, which means you can respond faster to a Request For Quote, and you’re subsequently more likely to win the business.
Using our own data of more than one million cut parts, we found that an average quote incorporates 5.5 parts. The industry average to quote 5.5 parts is approximately 30 minutes, but with ToolBox, by Tempus Tools, 5.5 parts can be quoted in just two minutes. That’s 15 times faster than the industry average, and it’s totally repeatable, every time.
tempustools.com
Good tool inventory management leads to more profitable, more sustainable manufacturing.
The earliest example of a vending machine dates back to the first century, when Greek engineer Hero Alexandria created a machine that accepted a coin before dispensing holy water. While vending machines have since increased in sophistication, their principal remains the same — providing streamlined, instant access to the commodity the user requires. Here, Andreas Nyberg, CoroPlus Tool Supply specialist at Sandvik Coromant, explores how tool vending machine software and hardware can enhance a shop floor’s profitability, productivity and sustainability.
In many manufacturing operations, up to 60% of stock is never used, while around 15% of jobs fall behind schedule due to missing tools. What’s more, operators can spend as much as 20% of their time looking for lost tools. These findings, based on Sandvik Coromant's own research prove one thing: inadequate analysis of tool logistics drives up business costs.
A machine shop, no matter its size, should always be prepared to work quickly and cost-effectively. Machining parts for varying industries, from an ever-growing portfolio of materials, needs a wide range of tools at the ready. Another layer of complexity comes in the form of mass customization, as an increasing number of manufacturers produce unique products at larger scales. Having access to the right tools, at the right time, is essential.
Have too much or too little stock is largely a result of human error. If tools aren’t placed back in their correct cabinets and are left scattered across the shop floor, operators simply won’t know whether or not their tool stock is depleting. Sometimes, those working on the shop floor can create overstocks if they’re too frivolous with using new tools. If an upgraded version of their current tooling system becomes available, for example, manufacturers may automatically switch over to the new option and neglect their current stock of perfectly functioning, just slightly older, tools.
Sandvik Coromant’s CoroPlus® Tool Supply brings together tool storage hardware and software to automate many of the common headaches associated with tool management. The software keeps track of every registered tool in the inventory, shows its stock availability, high cost areas and what tools have been picked to what machine and by whom.
As well as enabling operators to pick and return their tools properly, the software can also manage restocking and maintenance of inventory, as usage of tools on the shop floor feeds data to the management and administration element of the software to support the tracking of cost, planning jobs and management of purchasing. On a practical level, tool logistics software also controls tool logistics hardware solutions, which are either open shelves, drawers with lids, or spiral–equipped vending machines depending on level of control required. The shelves and drawers can contain multiple quantities of tools for the user to pick from, whereas the spirals provide access to one tool at the time.
Automation software gives manufacturers an alternative to doing everything manually, and can avoid incurring downtime when there’s little time to spare. Because workers can track tool stocks via a tablet or other smart device, then rely on the software to automatically order and replenish that tool stock when needed, purchasing teams are no longer burdened with the unnecessary paper trail making multiple manual orders creates.
Because operators are never without the tool they need, neither do they have too much of the tools they do not need, the machines never have to stop running because they’ve run out of tools. And, besides creating a more profitable and productive working environment, good inventory management incurs a secondary benefit. It can help make the machine shop more sustainable. What’s more, automated tool supply can also account for the reconditioning and recycling of used tools. If, as an industry, we continue to consume the world’s limited resources in a nonsustainable way, we will run out of the materials we need to produce solid carbine tools. Estimated reserves of tungsten, for example, are around seven million tonnes, or 100 years of consumption. Having a workflow set up that automatically sends used tools for recycling can make taking steps towards more sustainable practice far smoother for the end user.
Like Hero’s invention, vending machines of today serve to streamline the inventory management process and get users the items they need in a more efficient manner. But today, they’re also capable of doing much more. Sandvik Coromant finds that users CoroPlus® Tool Supply software can increase their machine usage rate to 95%, compared to 50% if they aren’t using inventory management software. Having the correct hardware and software in place to manage tools isn’t just about keeping the shop floor neat and tidy. Implementing inventory management software makes the production environment leaner, greener and more cost-effective. sandvik.coromant.com
Do you want to increase the value of your business and achieve your desired exit outcomes?
We can work with you to ensure you achieve optimal value on the sale of your business and minimise the tax paid in proceeds.
For more information and to download our exit smart report which includes practical tips on how to plan an exit that will lead to favourable financial outcomes, scan our QR code or visit us at: williambuck.com/exitsmartsurvey
Visit us at Australian Manufacturing Week stand #MS535
Members of our friendly and knowledgeable team will be available to answer questions and give insights on how we can help you with succession planning, financial management, R&D grants and much more.
Fully understanding the hybrid press brake system gives clarity to its operation, but also makes it a more attractive solution to purchase. Lyndon Smith, National Sales and Marketing Manager at Complete Machine Tools, brings the details into focus.
With the steady growth in the industrial and manufacturing sectors, the expectations of the users and owners on their machinery and products have also grown exponentially. This is very true as far as sheet metal forging and manufacturing units and industries are concerned. That being said, CNC press brakes form a major constituent of the sheet metal sector. Here are the important features that you should know about your hybrid servo CNC press brake system, to help you correlate their benefits better.
Over the course of time, the simple CNC press brake system which started out as a torsion bar CNC set up has now evolved into the popular hydraulic CNC systems which are now in use in most renowned industries. The hybrid servo CNC press brake variant is the latest one in line, and we will discuss further press brakes in this article, taking this hybrid variety as the standard machine. The hybrid servo CNC press brake in simple terms is the consolidated trophy child of both electric and hydraulic press brake machines. The positive and beneficial factors pertaining to both of the mentioned counterparts are incorporated into a single system, thereby giving rise to the highly advantageous hybrid version of the conventional press brakes.
Generally speaking, hybrid brakes make use of less hydraulic fluid and unlike the conventional hydraulic press brakes, the fluid is not in a constant fluid motion. This is what makes your hybrid machine better than its hydraulic predecessor.
As it was hinted earlier, the hybrid press brake system compiles the best possible features of both hydraulic and electrical press brake machines. By doing so, all the discrepancies and concerns pertaining to each of the options were eliminated one by one.
This genius hybrid was achieved through the meticulous work of the researchers of the field, who were dead set on improving the already existing patterns of hydraulic machines and electrically operated systems as individual units. Somewhere along the line, they came up with an idea to unite both these research processes, thereby framing a highly powerful and advantageous mixture of all the desirable features and eliminating undesirable ones. From a fairly general point of view, the most noteworthy advantages which were
brought about by the introduction of the hybrid servo press brake system would be as follows.
1. It is highly environment friendly.
2. It helps save a significant amount of energy.
3. Functions with better efficiency.
4. It is fully automatic and does not require any manual assistance.
5. It provides great value for every dollar spent.
In the hybrid servo press brake systems, the servo pump itself acts as a functional replacement for the traditional servo proportional valve and control technology. With such developments made possible with the recent versions of the press brake machines, the hydraulic directional valves are also completely wiped off the screen entirely. By taking out this additional step in the process, users are allowed to save time that is otherwise wasted in monitoring and managing the valve shifts. With this effective replacement solution, there are additional savings made in the
dimensions of space, hydraulic oil usage, and energy consumption along with the process itself. The cut in the usage of oil is mostly due to the minimizing of throttling loss. By allowing its users to save from a third to one-fifth of general hydraulic oil usage, these hybrid systems help achieve real-time energy savings, especially when you look at the process in terms of a longterm scenario.
As we explained earlier in the environmental column and indirect control over the checking of energy expenditure, the direct contributions of the hybrid press brake system to the energy efficiency are also worth a mention. When compared with conventional press brake and bending systems, the energy efficiency shown by the hybrid system is at an unbeatable level. This is mainly because, in the case of a hybrid work system, the energy used by the system along most of the process is only the direct requirement of the press brake with no additional charges. Also, most pressure from the bottleneck is either
reduced, offset, or both, which allows the machine to reduce even up to 75% of the energy consumption in a few cases. The feature of energy efficiency can even apply to these genius hybrid servo press brake machines in their standby mode.
By the term performance, we include various aspects and dimensions like positioning accuracy, bending accuracy, return speed, working speed, effective maintenance of a suitable internal environment, as well as internal temperature. All of these minor additions, when observed from afar add to the overall exponential increase in the productivity and efficiency of work exhibited by the machine as a complete unit. An additional shout-out is given to the oil temperature maintenance system of the unit, because of its importance in preventing unnecessary overheating. By controlling the oil temperature in the device at a desirable level of 38 degrees celsius and not letting it rise beyond 50 degrees, the hybrid machine is indirectly protecting you from the risks of oil leakage, stability issues, and unnecessary service and maintenance checks.
With the new hybrid servo CNC press brakes, all the involved processes starting from the selection of tools to recognition and detection of results are completely handled by the machine itself. It can make all the necessary calls by itself, by means of thorough processing of available data and the input you provide. This provides better work efficiency and accuracy and allows minimal space for human error.
Apart from these key benefits, these hybrid systems also come with the perks of being very quiet. Though this might not seem like a game-changing factor, it can be quite important for industries that operate in relatively crowded areas, or shops that are looking to install a machine within or close to their store itself, in which case high levels of noise could be a major disturbance. The main feature controlling the noise production here would be the use of a twoway gear pump and a servo motor.
These hybrid press brake systems are the best of the press brake family, thanks to
their list of benefits. By providing its users with high levels of satisfaction and quality of work, the perception of such automatic alternatives to the traditional press brake systems is only seen to be growing. All the options provided by the machine manufacturers can also improve the output and efficiency of these machines. Make sure to go through them carefully and choose one that suits every single one of your requirements before making your purchase. With such effective press brake systems available, you are assured to observe visible changes in the overall accuracy and efficiency of the work that your industry puts out as a unit, ultimately improving your quality of work and bottom line.
completemachinetools.com.au
Critical, long-term labour shortages hit Australian manufacturing: how Australian businesses are using tech workarounds. in a factory,” said Headland CEO, George Yammouni. “Today, we have machines that can not only feed themselves material, they can fulfil multiple functions that might have been performed by several machines and operators,” adds Gason, “they can perform quality control, self-diagnosis and order parts or materials.”
The Australian Chamber of Commerce and Industry (ACCI) recently released a report outlining a significant conundrum facing the manufacturing sector.
On the one hand, Australian manufacturing is entering a strong period of growth, on the other that growth is being undermined by labour and supply chain constraints not seen in decades.
Chief Economist at ACCI, Dr Ross Lambie said in the report that, “Manufacturers [are] continuing to expand their workforce, and expectations for future employment remain positive. However, employers are having increasing difficulties finding experienced workers because of domestic and international border closures –these labour constraints are at levels not seen since September 2007.” Like other sectors, Australian manufacturing is finding it difficult to find staff to fill positions, which is not only impacting their ability to meet their own orders but is having knock-on effects in the broader economy as supply chain shortages create production bottlenecks elsewhere.
And for those thinking this is purely a COVID-related affair as national borders have closed and shipping almost ground to a halt, there are broader and longer-term issues at play.
With labour shortage a short, medium, and long-term problem, some businesses are using technology workarounds.
Re-tooling: the smart factory. Technology fixes to address the labour crisis Wayne Gason has a rural manufacturing business in Ararat that trims motors. Established in 1946, Gason has seen the rise, decline, and rise again of manufacturing. In the last decade, advanced technology – as well as a rise in relative wages and shipping costs – has changed the face of manufacturing and seen a return of manufacturing to Australian shores.
With demand booming, it has been a period of growth for Gason, but with a lack of available labour to fill the positions and meet demand, Gason has had to look to new technology to meet orders. Headland Technology recently installed a tool bending machine, the TruBend Cell at Gason, which automates the bending of simple and complex parts in any format precisely and cost-effectively.
“Historically, there has been roughly one worker to a machine, helping feed it materials, and someone else helping tool machines
Opie Manufacturing in Emu Plains is another manufacturing business that has found it hard to find welders to meet production quotas. Like Wayne Gason, Opie CEO Tristan Opie asked Headland Technology to provide them with a technology solution: a TruLaser Weld that can not only produce the output of at least three welders, it doesn’t require another worker to clean the welds and surface either.
Headland’s George Yammouni points out that long-term trends –from the closure of tech schools to a much more digitally aware and focused younger generations – are compounding with more immediate issues like COVID and supply chain issues to create a productivity crisis in Australia that only technology can fix quickly.
“Manufacturing jobs today are much more likely to be in software engineering and diagnostics, than toolmaking, welding, and boiler making,” noted Yammouni. “There is a growing and concerning gap between demand and the available labour pool which a technology fund is going to be critical to bridging,”
‘Those technology tweaks needn’t mean machines; it could be integrating existing machines and utilising software to get the existing technology to find efficiencies and overcome production road-blocks.’
Another piece of technology that is transforming manufacturing processes is the STOPA automated storage system. Connected to process equipment it controls work order, material flows, and facilitates production without supervision. Overnight, it will feed itself, and then process, raw material. The system dispatches semifinished and finished goods before the morning shift starts.
With fewer workers likely to be available year-on-year, and the cost of acquiring them going up, a technology solution which integrates the current workforce and high-productivity technology, and machinery is an important conversation to have.
headland.au
Hermes fulfilment centre is one of Europe’s largest and most advanced facilities. During a recent modernisation project, SEW-EURODRIVE’s MOVI-C® all-in-one solutions MOVIGEAR® performance significantly improved the conveyor lines’ energy efficiency.
Comparative energy improvements relating to one of the conveyor lines.
• 1710 kg/year fewer CO2 emissions
• 34% energy saving per conveyor line
57% average energy saving per drive
50% noise reduction thanks to fan-free drives www.sew-eurodrive.com.au
Raymax Applications has announced the supply and service of analytical instruments from Applied Spectra Inc.
As the leading supplier of analytical instruments, Applied Spectra stands at the forefront of laser ablation based elemental analysis techniques, simplifying the process of elemental chemical analysis, while delivering rapid, high-precision results that are environmentally friendly. Today, laser analysis offers a compelling value proposition over traditional chemical analysis methods.
A case of taking chemical analysis into space was the arrival on Mars, of NASA’s Curiosity Rover. Deploying a LIBS instrument, named ChemCam, it is analysing the chemical composition of the Martian terrain. Scientists from Applied Spectra worked in partnership with NASA to develop the instrument. An integrated module, ChemCam includes a laser, telescope, a stereo pair of navigation cameras and a three-channel optical spectrometer inside the rover itself (just to name some parts). The instrument permits Curiosity can take thousands of LIBS spectra a day and perform rapid elemental analysis of rocks and soils remotely making chemical analysis on the surface of Mars with unprecedented speed and communicating the results back to earth.
“Aside from this spectacular contribution to space exploration, Applied Spectra continue to develop their instruments making available elemental and isotopic detection capabilities that range from parts per million (ppm) down to the level of parts per billion (ppb), and across virtually all elements in the periodic table,” says John Grace, Managing Director of Raymax. “What this means, is the instrument can target and obtain ablated samples from material that is of the order of one or two microns is size,” Grace adds. “We are particularly excited to offer the J200 Series LIBS and LA-ICPMS platforms that are designed to allow the use of different laser parameters for sample analysis, extending the applicability over a wide range of sample matrices.”
So, what is LA? Laser ablation (LA) is a process where a laser beam is focused on a sample surface to remove material to enable chemical analysis. LA generates a bright ‘plasma’ on the sample’s surface. The light emitted from this plasma can be analysed to determine the presence and concentration levels of elements in the period table. This process is known as LIBS.
LA also creates a ‘flux’ of fine particulates that can be readily transported to a secondary source for ICP-MS analysis (LA-ICPMS). What is LIBS? Laser Induced Breakdown Spectroscopy (LIBS) is a rapid chemical analysis technology that uses a short laser pulse to create a micro-plasma on the sample surface. Currently used on Mars! And what is LA-ICP-MS? Laser Ablation Inductively Coupled
Plasma Mass Spectrometry is a powerful analytical technology that enables highly sensitive elemental and isotopic analysis to be performed directly on solid samples.
“The technology available in Applied Spectra instruments is already in use across Australia,” says Grace, “with installations of the RESOlution-SE. Incorporating the latest ATL laser technology with exceptional software, these instruments are being used for opportunities this laser technology now makes available.”
Alternative energy solar cells, next-generation batteries, manufacturing chemical analysis and metrology
Environmental detecting contaminants, hazardous analysis substances, and studying the carbon cycle
Forensic substance discrimination, counterfeit science analysis and nuclear material characterisation
Analytical development of LIBS and LA-ICP-MS research analytical protocols, and supporting the R&D community
Today there is a real need for cleaner power generation to meet the growing demand on power along with complying with strict environment regulatory requirements. Fast analytical techniques such as LIBS for assessing coal properties to optimize power generation, to ensure complete combustion, and to determine fly ash and volatile content, is becoming essential. In addition, rapid analytical technology is equally critical for monitoring structural integrity of the power plant steel pipes as they age, to ensure the safety of the plant operation.
Strength and durability of steel is largely determined by its carbon content. Carbon which is typically present from 2 – 4% in cast irons occurs in various forms that range from tiny graphite spheroids (nodular cast iron) to large flakes (grey iron). Measuring the amount of carbon is important because of how it affects the steel. A higher carbon content makes steel harder, but it is less malleable and more likely to break. A further consideration is that high carbon content decreases the melting point of steel. Hence the accuracy of measuring carbon and other alloy elements in cast iron is important to the end user. The J200 LIBS instrument from Applied Spectra uses short laser pulses to deliver high power density into the sample surface to directly excite tough materials like carbon flakes for accurate and rapid quantitative analysis. The J200 LIBS provides uses with a quality control tool able to classify metal and metal alloy samples based on fingerprint-like LIBS spectra on specific metal products.
Lithium-ion batteries are found in electronic devices from our smart phones, tablets and cameras to power tools and e-scooters. They are constantly evolving into smaller, light weight forms, yet power output and battery life have become increasingly demanding. Lithium-ion cells are made up of electrolyte and two electrodes (a cathode and an anode) on which LIBS technology can perform depth profiling analysis in the lab or on the factory floor. Impurities and variation of the active material chemistry may cause accelerated reduction in battery capacity with battery cycling and even result in thermal runaway with the battery catching fire or exploding. The recent spate of e-scooter fires across Australia could be the result of defective batteries. Fortunately, the performance specifications for the Lithium-ion battery are far more stringent for automotive applications with respect to power density,
energy density, cycle life, and reliability. Applied Spectra’s J200 LIBS instruments provide real-time analysis of raw Li-ion battery electrode materials making analysis of the composition of raw materials easy.
In a world where forensic analysis of artifacts from a crime scene is under intense scrutiny. The provision of forensic analysis tools that produce scientifically valid results and can reduce the potential for mistakes, is important to resolving criminal offences. Technology tested in the scientific world is helping investigators understand crime scenes and identify suspects by using LIBS to analyse trace evidence on sources of glass, paint chips, hair, soil particles, ink, narcotics, and even gun-shot residue. Criminal investigators in America are showing an increased use in two tools, namely the LA-ICP-MS and LIBS instruments from Applied Spectra. The J200 Tandem LA-LIBS instrument, offers both processes in one station and can provide information about the composite elements of a sample, offer high sensitivity, and discriminate among tiny samples with a limited mass in a few seconds. Accurate, fast sample analysis has the advantage of speeding up the preparation of forensic evidence.
Today the world is faced with the challenges of supplying adequate staple crops to sustain the growth in human consumption. This challenge requires analysis of the fertilizers used actually support quality crop yields, and do not contain contaminants hazardous to human health. Direct solid samples of fertilizer are possible using Laser Induced Breakdown Spectroscopy, or LIBS. Using a single laser pulse, it is possible to detect a ‘finger-print’ that represents atomic or molecular species in the fertilizer samples. Elemental analysis for quality control of fertilizers before applying them to
Guill announces a new 800 series hybrid extrusion tooling.
Guill announces the introduction of a new version of its popular 800 series, known as 800 Series Hybrid. In some extrusion applications that utilize crossheads and inlines, layers of the exact same material are applied multiple times, using a single die. This method is used to reduce the propensity for errors caused by gels breaking through a thin wall, weld lines, inconsistent wall thickness, plus material and process variations. Additional errors include difficult-to-process materials and demanding applications where there is zero fault tolerance.
Seeking to design the next generation multilayer die to overcome these challenges, the engineers at Guill looked for a way to incorporate this technology into an updated version of the 800 Series. This led to the creation of the 800 Series Hybrid. The inherent benefits of the 800 Series are retained, including compact design, low residence time and a common deflector bore that eliminates tolerance stack up. The challenge was to create a hybrid design that incorporates the benefits of layer overlapping, while reducing unnecessary complexity and making the technology more cost-affordable for customers. This was achieved by overlapping layers in each semideflector, using a single cone. The highly efficient design of the 800
the soil is crucial to verify the proper content of macro and micronutrients and the level of any toxic elements.
“Applied Spectra provides a range of systems to meet and even exceed elemental and isotopic analysis needs,” Grace says. “These are just some of the examples of applications, more are possible! With Applied Spectra we have expertise to offer your team to help guide and train you on the use of this reliable, innovative hardware with its unprecedented software and background of trustworthy support,” concludes Grace.
raymax.com.au
Series Hybrid reduces cost and size, as opposed to other methods of overlapping layers. Essential benefits of the 800 Series Hybrid include eliminating weld lines in materials through patented overlapping technology, producing a more consistent finished product; reduced sensitivity to changes in viscosity; reduced sensitivity to changes in line speed; myriad material and multi-layer application possibilities; works in all tubing and jacketing applications with a wide range of materials; low residence time; compact design and a low tolerance stack-up error factor, all resulting in improved concentricity.
The 800 Series Hybrid extrusion tool greatly reduces stagnation, because overlapping layers are more inherently balanced than single layers and also because each semi-deflector is ‘tuned to flush’. Conventional deflectors must simultaneously achieve a balance between flushing, balancing and eliminating the weld line. There is less difference between the slowest moving material and the fastest moving material in the deflector channels, thus making the viscosity more consistent in the deflector. guill.com
The birth of a new Australian industry, majority owned by Indigenous Australians. included investigation into the use of spinifex as a source of cellulose reinforcing agents. The knowledge and research generated also relied on the Traditional Indigenous Knowledge shared by the Indjalandji-Dhidhanu People through Bulugudu.
Uniseed and Bulugudu have agreed to invest $2.6m into Trioda Wilingi, a University of Queensland/UniQuest spin out company, to develop innovative medical gels from cellulose nanofibres extracted from spinifex harvested in north-west Queensland.
Trioda Wilingi has the exclusive global rights to develop novel injectable spinifex medical gels, which have many potential applications including osteoarthritis, drug delivery and cosmetic treatments. The concept was developed with the help of the Australian National Fabrication Facility (ANFF).
Early data shows that gels using the spinifex nanofibres will last longer, be easier to inject and may be safer than current medical gel products.
There’s a global multi-billion-dollar demand for cellulose nanofibres – very thin biodegradable fibres that have a vast number of applications. They can be used, for example, in medical gels, surgical gloves, nappies, transparent paper, and even flexible electronic components.
Companies around the world are currently using complex, energy intensive processes to make nanofibres from wood pulp, sugar beet, carrots, wheat straw and other materials. The University of Queensland, through the Australian Institute for Bioengineering and Nanotechnology (AIBN), discovered that spinifex has a unique chemistry that yields stronger, longer, thinner, and more flexible nanofibres. They developed a gentle, environmentally low-impact nanotechnology processing method.
“The spinifex fibres we produce are typically around three to four nanometres thick, about 20,000 times thinner than a human hair. They have an average length of about 1,600 nanometres, giving them an aspect ratio of about 500:1,” says AIBN Director, Professor Alan Rowan.
Spinifex is an extremely durable grass that can survive drought, controlled burning and bush fires. It grows widely across Outback Australia. This project uses Triodia pungens.
“Indjalandji-Dhidhanu people have long known of the uses and the strength of spinifex grass,” says Colin Saltmere AM, Director of Bulugudu Ltd. The company is owned by the Indjalandji-Dhidhanu people, the Traditional Owners of the upper Georgina River region. “Our traditional uses include building shelters and using resin from the grass as an adhesive to attach spearheads, and seal water vessels.”
The names of the companies are symbolic. “Bulugudu means ‘strong’ in our language. And trioda wilingi means ‘special grass’,” says Mr Saltmere. “I’m excited by today’s investment, which is the result of twelve years and $10m of research, development, and negotiation, supported by the Queensland and Australian governments,” he says.
“We’ve integrated traditional knowledge of the plant and how it grows, with the latest chemical nanotechnology advances, to create the beginnings of a new industry,” says Tim Case, interim CEO of Trioda Wilingi.
In 2008, the Dugalunji Aboriginal Corporation (now Bulugudu Ltd) and The University of Queensland were awarded an Australian Research Council Discovery Grant to explore the Aboriginal and Western scientific knowledge of spinifex grasses. This knowledge
They soon discovered that the strength of spinifex grass is due to microscopic cellulose fibres, and established Bulugudu to explore the potential of the fibres.
“The scientific challenge was to determine how to obtain the nanofibres without intensive processes, then we turned to ANFF, who helped us optimise and validate this extraction process,” says Professor Darren Martin, one of the inventors of the technology, from The University of Queensland’s School of Chemical Engineering. “ANFF have been vital partners on our journey.”
“This project is a clear example of the type of impact ANFF can have on the conversion of research into real-world products. We are so proud to have helped this work spin out into Trioda Wilingi, which will have positive influence in varied sectors,” says ANFF CEO Dr Jane Fitzpatrick.
The late Dr Ian Griffiths, the previous ANFF CEO, recognised the potential of the fibres in medical gels and started the commercialisation negotiations that led to the establishment of Trioda Wilingi and today’s agreement.
The investment opportunity was developed and led by ANFF-C, the new commercialisation arm of ANFF, which is part of Australia’s National Collaborative Research Infrastructure Strategy (NCRIS) funded by the Australian Government’s Department of Education. Most medical gels need a high water-content. The spinifex fibres help retain water by forming a three-dimensional network within the volume of water. Charged groups on the surface of the fibres hold the gel together, but also allow the gel to flow through a needle and then re-form.
“Spinifex grass is an ancient and sacred material to the IndjalandjiDhidhanu people. It is also a material we use all the time,” Mr Saltmere, Director of Bulugudu says.
“In Indjalandji-Dhidhanu culture, spinifex is a sacred thing. It belongs to Country, and to us, that’s what ‘sacred’ means.”
The use of this traditional material will now lead to jobs in a high-tech industry, and flow-on effects with more opportunities for Indigenous people to engage in STEM education.
Under the deal signed today, a portion of any future royalty stream will be allocated to an Indigenous education fund that aims to maximise training, education, and network opportunities for Indigenous Australians.
And the Traditional Owners will have an ongoing role in the harvesting and early-stage processing of the grass, creating jobs at Camooweal and other remote communities in northern Australia.
“Uniseed is pleased to be involved in bringing this Indigenous technology to the market and to help build a strong business opportunity,” says Paul Butler, Uniseed Investment Manager and an incoming Director of Trioda Wilingi.
“We are highly optimistic about the future of Trioda Wilingi, given our strong intellectual property position, a patented, secure and scalable supply chain, and a large, growing, global market,” says Mr Case, interim CEO of Trioda Wilingi. anff.org.au uq.edu.au
I have been associated with AMITL as a member since its inception and have known most of the AMTIL staff for considerable years therefore I feel that I can say the organisation is of the quality the members should be very proud of. AMTIL conducts its activities with the enthusiasm and direction needed to promote Australia’s manufacturing industry across all appropriate sectors of government and industry alike. Their methods are generally of a consultative nature as they seek out inputs from all concerned and then having done so their feedback is informative. Most certainly confidentiality of matters discussed is paramount for the competitive industry we are in and there is never a concern with regards to such matters where AMTIL is involved. Anyone who has ever attended or participated in a AUSTECH exhibition could only attest to the quality of the exhibition and this is as a direct result of AMTIL’s overall co-ordination of the event and their methods of working closely with all involved.
Since 1999, AMTIL has been connecting business, informing of opportunities and growing the manufacturing community.
To be become an AMTIL member contact our Corporate Services Manager, Greg Chalker on 03 9800 3666 or email gchalker@amtil.com.au
amtil.com.au
With electricity prices predicted to increase, storing your excess solar energy may be the investment you need to keep your ongoing costs down.
Chris Winter is the Co-Founder and the brains behind RedEarth Energy Storage’s battery energy storage systems (BESS) and LFP Troppo batteries.
Winter previously co-founded RedFlow, where he manufactured flow batteries alone. “But it’s a bit like biotech, where you have to put in a few years work before reaping the benefits,” he said.
“Building the flow battery took up a lot of my time, and one day I decided I should just produce a complete system, which is easy to install,” he said.
“RedEarth now manufactures complete energy storage systems, including our own battery, which are on-grid and off-grid, ready to power businesses, homes, SMEs, and retail outlets.”
One of RedEarth’s initial goals was to bring down the complexity of installation for the kits. Installers could also install the inverters, solar panels, and the battery power systems like a Meccano set. But more recently, Winter has moved into having the whole kit as an integrated storage system which includes inverters, batteries and monitoring that is ready to be plugged in to an energy source, like solar panels.
The simplicity of installation has been especially beneficial where electricity was urgently needed.
“I’ve seen a lot of RedEarth off-grid boxes being sent into bushfire areas, flooded areas, all parts of our injured country where the climate has hit us hard,” said Winter.
“But it’s also very useful in the wide expanse of remote areas of Australia, even in better times. These kits can be brought in and just switched on. They might have solar connected, or perhaps wind turbine systems. Battery energy storage solutions (BESS) for instance, are a game-changer for commercial and industrial operations. From reductions in ongoing operating expenses, to providing a safe and reliable backup power supply to ensure your operations continue to run smoothly in the event of a power outage, and achieving sustainability targets and compliance – the benefits and opportunities of energy storage go far beyond simple energy bill savings.”
RedEarth has a number of on- and off-grid energy storage solutions in a range of sizes suitable for sheds, homes, businesses and even commercial industrial application. Proudly Australian made – and with system names including the DropBear, HoneyBadger, BushPig, and Troppo, RedEarth sources its materials locally wherever possible, assembling its products at its factory in Brisbane, Darra. This has also kept RedEarth’s suppliers busy.
“We have our metal manufacturer and he’s just hit his limit of production. He can’t be busier.”
“Our enclosures are designed specifically for the applications that we've identified and targeting in our market,” said Winter. “As well as looking and being resilient to Australian conditions, we have certain characteristics in the enclosure to make it easier for the installer, and make it easier for the end customer to expand the system if their energy needs change.”
For manufacturing businesses needing to run machines, factories and processes in the 30-100kW power range, RedEarth’s PowerOasis works as a fully integrated, ready-to-run, modular Battery Energy Storage System (BESS). This all-in-one system includes batteries, inverters, a Battery Combiner Panel HVAC. There is an option of having an in-built solar PV Maximum Power Point Tracking (MPPT) or AC-coupled solar PV inverters. RedEarth
manufactures all the systems in Australia, all the way from the casing boxes, produced by Metal-Tech Industries in Wacol, QLD.
Parmjit Goraya is General Manager of Metal-Tech. The role of the company involves manufacturing of metal housing for RedEarth battery storage units to the required specifications, ensuring they were ready to populate.
Metal-Tech has been supplying sheet metal engineering components to RedEarth as well as their early storage company, RedFlow for a while now. Metal-Tech has supported RedEarth from developing prototypes to final production, using state of the art technology and equipment. “This has really taken off after RedEarth developed their line of energy storage products,” said Goraya. “In fact, we are investing in new technologies to keep up with requirements in this sector. The sourcing of skilled welders is a significant barrier for most of the industry currently, whereas sourcing raw material and fasteners is not a major issue. Metal-Tech have been supplying RedEarth with cases in assembly form, and other precision powder coated components as finished product. We assemble the cabinet
and other subsequent sheet metal parts, and obviously do not assemble electrical components. Our core competencies lie in precision sheet metal components. We are extremely good at producing client specific requirements including quantities and on time delivery. Our high-tech equipment combined with years of experience make us a reputable supplier of sheet metal components locally and overseas,” he added.
Stuart Dawson has a farm and the property has always been off-grid; when he had to replace the existing system (which was in place when he bought the property), he came to RedEarth so he could then upgrade instead of replace. He’s since started to move everything on his farm over to electric power. Dawson’s house is modern in design, with modern requirements; and after living through drought, fires and the heat, he just wanted to put in modern comforts like air conditioners, fridges, and coffee machines. “We really like the fact it was an Australian company and it was a system that was self-contained and ‘plugand-play’,” he says, in an interview in the Queensland Agricultural Leaders publication.
Dawson installed 30 solar panels (11kW) and had a RedEarth Honey Badger fully loaded with eight of RedEarth’s own 4.1kWh (total 32.8kWh) LFP Troppo batteries.
“We put up close to the maximum number of panels that we could fit because we wanted that fast refresh rate,” adds Dawson. “By 9:30am most days, our batteries are fully recharged. Anything after that is free electricity, and if you’re not using it, it’s getting wasted.”
So in the long run, Dawson knows the system is saving his money. “We’re conscious of energy use, but we were wanting more comforts like air conditioning, to make life liveable because when it gets up past 40-plus celcius, it’s unliveable. We wanted a system that was capable of catering to our immediate needs but we also saw the future.” redearth.energy
Future contracting for commercial and industrial electricity users - saving your business money through market timing.
Forward purchasing electricity contracts is not a widespread practice among businesses currently. However, securing electricity agreements early can be an excellent strategy for commercial and industrial users who want to reduce their costs and manage their consumption. Future or forward purchasing can be particularly beneficial for manufacturing businesses where power consumption is substantial.
Conventional behaviour for electricity consumers is to renew their contracts when their agreements are coming to an end. But given how infamously volatile the Australian energy market is, with wholesale prices often fluctuating up to 5c/kWh, in addition to the current global situation affecting supply and demand, future purchasing can be more advantageous to large energy consumers. Adopting this approach helps shield businesses from the unpredictability of Australian energy market prices.
Put simply, the idea is to secure the next contract in advance, when wholesale prices are low. This results in reduced retail rates and, subsequently, a lower total annual spend on energy. To do this successfully, market timing is essential.
Timing the market entails staying on top of developments in the National Energy Market and changes in wholesale prices. Businesses should ‘strike’ – that is, request electricity tenders for their next contract when prices are still relatively low.
But it’s not a cut-and-dried situation; there are many factors that can affect prices like diminished supply due to climate or environmental conditions (such as La Nina or bushfires), prolonged power station outages, and worldwide situations like the war in Ukraine, that can result in a drastic upswing in prices. The ideal scenario would be the opposite: steady power supply, low demand, a less severe climate, and putting a keen eye on movements in the National Energy Market is key.
Case in point, a Melbourne-based plastic moulding company had initially signed on to a contract set to end in December 2022. The agreement was made during a period marred by several longterm power station outages; thus, supply could not keep up with demand and prices were inflated. However, over the interim, power stations came back online and La Niña made for a milder climate; prices dropped to 5c/kWh after reaching 11c at its peak.
Whilst Dolphin Products was still in the middle of their contract in early 2021, Leading Edge Energy reached out to the plastics manufacturer advising them it would be ideal to go to market for their next contract seeing as wholesale electricity prices were exceptionally low.
Dolphin Products signed a forward contract for electricity that would start on January 1st, 2023. Because they were able to secure the
contract at the right time due to Leading Edge Energy’s advice, the secured rates for the new contract were significantly lower than the contract they were currently on.
And it was a good thing too as, towards the end of 2022, the world found itself gripped by an energy crisis and prices climbed to record highs. If the plastic manufacturer had chosen to renew their contract only when it was ending, their new contract would have been based on retail rates as high as 15 to 20c/kWh.
But since they went to market much earlier, capitalising on the low wholesale prices at the start of 2021, they were able to secure peak and off-peak rates between 2.5 to 5c/kWh. And aside from securing reduced rates, Dolphin Products found even more advantages to working with Leading Edge Energy.
Given how volatile Australia’s electricity market is, working with an energy broker, like Leading Edge Energy, that’s attuned to the shifts in electricity prices and familiar with the power requirements of commercial and industrial consumers is ideal. Energy brokers can take the reins in collating and analysing offers from energy retailers, give data-driven and experience-based advice, and assist with procurement, all in support of reducing energy costs. Additionally, Leading Edge Energy can also help companies reduce their carbon footprint and make significant energy efficiency improvements to their site, thus leaving clients to focus on activities that can grow their business.
Forward purchasing and timing the market just so can be rewarding but very time-consuming – having an expert handle these can make it more convenient and lead to better results, aka savings. leadingedgeenergy.com.au
Combining eco-friendliness with high productivity and high accuracy. The Smart Machine suited for a decarbonised society produced at Okuma's carbon neutral factories.
As a step towards turning the decarbonised society into reality, Okuma has defined the “Green-Smart Machine” as intelligent machine tools that contribute to resolving environmental issues by autonomously achieving both stable dimensional accuracy and reduced energy usage, and the company offers a full product lineup.
Okuma has been using automation and process integration as a part of its effort to reduce energy usage while still achieving highproductivity, high-accuracy machining for becoming carbon neutral at three Japan plants which are its main production bases. In addition to these measures, Okuma started using green energy from October 2022, and its three plants in Japan will become carbon neutral plants ahead of schedule (Scope 1 and 2).
In its wide lineup of products, which ranges from small 2-axis CNC lathes to multitasking machines, 5-axis machining centres, and large double-column machining centres, Okuma has incorporated Intelligent Technology to achieve high-accuracy and high-efficiency machining and enhanced the technology to contribute to highquality and stable-accuracy production. Okuma has issued a declaration that its "Green-Smart Machine" is an eco-friendly smart machine suited for a decarbonised society because of its autonomous reduction of energy usage and recording of CO2 emissions, which were made possible by Okuma's proprietary technology developed over the years.
Okuma will produce these products in its carbon-neutral factories and provide them to the world, and together with its customers, Okuma will contribute to offering solutions for the social issues faced by the manufacturing industry.
To reduce energy usage, technologies that shorten production time and that reduce energy usage during machine operation are essential.
In terms of the production processes, process integration by multitasking machines and 5-axis control machining centers would be effective in reducing energy usage. However, the complexity of the machine structure makes it difficult to achieve stable machining accuracy, and the warm-up operation and air conditioning control required to stabilise accuracy, as well as human intervention to check machining accuracy, use a large amount of energy and can inhibit customers' high productivity.
Okuma has solved this problem by developing machine tools that provide high-accuracy and high-efficiency machining. To achieve decarbonisation, Okuma has integrated its proprietary technologies, which are based on its machine tools developed up to now, for allowing machines to autonomously reduce their energy usage, and identifying as the "Green-Smart Machine."
[1] Clearly identifying the machine as a smart machine suited for a decarbonised society. A "Green-Smart Machine" emblem will be attached to machines in future orders for domestic Japan shipments from April 2023.
[2] Maturity model of machine tools for decarbonisation to identify the machine tools needed to achieve a decarbonised society. This will eliminate operator intervention requirements. The "Green-Smart Machine" required to maintain high accuracy and reduce energy usage, and achieves Level 4, "autonomous energy reduction with accuracy stability" where the machine autonomously controls the equipment.
[3] The "Green-Smart Machine" is manufactured in a carbonneutral factory
Plans are underway to expand the use of green energy through the installation of mega-solar facilities and the use of geothermal heat, for instance.
The Thermo-Friendly Concept, an Intelligent Technology that allows machines to autonomously maintain a stable high level of accuracy. This also reduces time and energy used on warm-up and dimensional correction processes for maintaining high accuracy. It also enables high accuracy to be maintained for a variety conditions, making equipment shutdown more feasible.
AI-based intelligent technology has been incorporated into more machines since its launch in 2001 and is standard on 125 models. This technology has a proven track record in production for customers around the world with a total of over 60,000 units produced in 20 years.
ECO suite plus
Autonomous energy-saving function “ECO suite plus” is incorporated as standard in Okuma's OSP series of NC units. This enables data analysis based on machine operating information and equipment-specific operating information and supports recording of CO2 emissions for traceability.
The ECO suite plus applies Thermo-Friendly Concept technology to maintain the required accuracy and proactively shut down equipment without operator intervention for achieving Level 4, "autonomous energy reduction with accuracy stability." More than 42,000 units have been delivered since its launch in 2014, reducing factory energy usage worldwide.
New operation control technology for spindle cooling systems that achieves Level 5, "autonomous balance of both accuracy stability and energy minimization under all operating conditions"
Demonstration tests of energy usage reduction, including during machining, were conducted on a sample workpiece simulating a stainless steel valve, and the effectiveness of the cooling system was confirmed by a 68% reduction in energy usage.
okuma.com.au
Super-thin chips made from lithium niobate are set to overtake silicon chips in light-based technologies, according to world-leading scientists in the field, with potential applications ranging from remote ripening-fruit detection on Earth to navigation on the Moon.
They say the artificial crystal offers the platform of choice for these technologies due to its superior performance and recent advances in manufacturing capabilities. RMIT University’s Distinguished Professor Arnan Mitchell and University of Adelaide’s Dr Andy Boes led this team of global experts to review lithium niobate’s capabilities and potential applications in the journal Science.
The international team, including scientists from Peking University in China and Harvard University in the United States, is working with industry to make navigation systems that are planned to help rovers drive on the Moon later this decade. As it is impossible to use GPS technology on the Moon, navigation systems in lunar rovers will need to use an alternative system, which is where the team’s innovation comes in.
By detecting tiny changes in laser light, the lithium-niobate chip can be used to measure movement without needing external signals, according to Mitchell.
“This is not science fiction – this artificial crystal is being used to develop a range of exciting applications. And competition to harness the potential of this versatile technology is heating up,” said Mitchell, Director of the Integrated Photonics and Applications Centre. He said while the lunar navigation device was in the early stages of development, the lithium niobate chip technology was, “mature enough to be used in space applications”.
“Our lithium niobate chip technology is also flexible enough to be rapidly adapted to almost any application that uses light,” Mitchell said. “We are focused on navigation now, but the same technology could also be used for linking internet on the Moon to the internet on Earth.”
Lithium niobate is an artificial crystal that was first discovered in 1949 but is “back in vogue”, according to Boes. “Lithium niobate has new uses in the field of photonics – the science and technology of light – because unlike other materials it can generate and manipulate electro-magnetic waves across the full spectrum of light, from microwave to UV frequencies,” he said.
“Silicon was the material of choice for electronic circuits, but its limitations have become increasingly apparent in photonics. Lithium niobate has come back into vogue because of its superior
capabilities, and advances in manufacturing mean that it is now readily available as thin films on semiconductor wafers. A layer of lithium niobate about 1,000 times thinner than a human hair is placed on a semiconductor wafer,” Boes said. “Photonic circuits are printed into the lithium niobate layer, which are tailored according to the chip’s intended use. A fingernail-sized chip may contain hundreds of different circuits,” he said.
“The team is working with the Australian company Advanced Navigation to create optical gyroscopes, where laser light is launched in both clockwise and anticlockwise directions in a coil of fibre,” Mitchell said. “As the coil is moved the fibre is slightly shorter in one direction than the other, according to Albert Einstein’s theory of relativity,” he said. “Our photonic chips are sensitive enough to measure this tiny difference and use it to determine how the coil is moving. If you can keep track of your movements, then you know where you are relative to where you started. This is called inertial navigation.”
This technology can also be used to remotely detect the ripeness of fruit. “Gas emitted by ripe fruit is absorbed by light in the mid-infrared part of the spectrum,” Mitchell said. “A drone hovering in an orchard would transmit light to another which would sense the degree to which the light is absorbed and when fruit is ready for harvesting.
“Our microchip technology is much smaller, cheaper and more accurate than current technology and can be used with very small drones that won’t damage fruit trees.”
Australia could become a global hub for manufacturing integrated photonic chips from lithium niobate that would have a major impact on applications in technology that use every part of the spectrum of light, Mitchell said. “We have the technology to manufacture these chips in Australia and we have the industries that will use them,” he said. “Photonic chips can now transform industries well beyond optical fibre communications.”
RMIT University and the University of Adelaide led this research in collaboration with Peking University, Stanford University, Harvard University, University of Southern California, Hyperlight, University of Rochester and University of California.
Co-authors are Andy Boes, Lin Chang, Carsten Langrock, Mengjie Yu, Mian Zhang, Qiang Lin, Marko Loncar, Martin Fejer, John Bowers and Arnan Mitchell. adelaide.edu.au
In an industry first, Ampol has partnered with Australian commercial electric vehicle manufacturer SEA Electric to support the transition of companies to zero-emissions commercial electric vehicle technology.
Through the partnership, SEA Electric and Ampol will be working together to develop flexible, sustainable and seamless charging options to support the uptake of lower emissions commercial vehicles in key parts of the transport sector.
The partnership will also focus on building an integrated charging solution for SEA Electric customers on the road at Ampol forecourts, at destinations and solutions at the workplace.
James Myatt, Ampol’s General Manager, Energy, said Ampol will work with SEA Electric and leverage its knowledge and strong relationships across industries to help support commercial vehicle owners' decarbonisation goals.
"Ampol is evolving to provide a range of fast and reliable charging solutions. We know our business customers are looking for lower emissions solutions and want to ensure their investment in commercial electric vehicles can be supported with efficient and reliable charging technologies," Myatt said. "Ampol is committed to developing an open access national charging network as well as home and business charging solutions to ensure vehicles can be on the road whenever needed."
For SEA Electric, the partnership provides flexible charging options for electric truck owners, with many Ampol customers moving into the EV space in cars and now with light trucks. The partnership will help reduce range anxiety for businesses looking to invest in electric trucks to reduce their emissions.
"SEA Electric is proud to partner with Ampol on this project, as both companies lead the country in the transition to sustainable transport," Bill Gillespie, SEA Electric President, Asia Pacific Region said.
"Through this collaboration, we are shining a light on the fact that electric powered truck fleets can be operationally flexible by accessing convenient charging infrastructure through the AmpCharge network.
"At SEA Electric, we are building an entire customer led ecosystem to simplify the transition to electrification, with a SEA Electric trained national dealer network for sales and service, full factory warranty, 24/7 support and roadside assistance, and a range of charging options at base or on the road.
"Ampol should be applauded for taking the lead with its future energy and mobility strategy, and we look forward to working together into the future on expanding the initiative." ampcharge.ampol.com.au sea-electric.com.au
William Buck’s Jeremy Raniti and Samantha Zebrowski break down the key components of achieving alignment across your business.
In today’s rapidly changing environment, it is critical that manufacturing businesses in Australia have a well-documented and cohesive vision, mission statement, set of values and strategy to remain competitive and achieve alignment across all divisions. These four pillars of an organisation are essential for capitalising on its strengths, positioning the business as a choice for customers, employees and stakeholders, and ensuring that it performs at its full potential.
Below, we break down the key components required to achieve alignment across your business.
Vision
Founders usually establish a manufacturing business for one of a few reasons:
• After identifying a gap in the market
• To capitalise on their passions, or
• To utilise efficiencies, expertise and developments in technology to advance society.
Your organisation’s vision should articulate what you aim to achieve and why. It is the foundation upon which your business is built and should be clearly communicated to all stakeholders. As your organisation grows and changes, it's important to revisit your vision to ensure it remains relevant. It’s also imperative that your vision is authentic and resonates with those who have a vested interest in driving change to achieve this goal.
Once your vision is documented, the next step is to formulate a mission statement. A mission statement defines how your organisation will achieve its vision. It should act as a blueprint for all within the organisation to follow and should include slightly more detail than the vision. Where the vision at times is more of an overarching philosophy, a well-thought-out mission statement should be clear, concise, and genuine. As advisors, we see well defined mission statements being the inspiration for:
• Critical decision-making
• Actions that protect the welfare of employees
• Assessing the profitability of a capital investment, and
• Discussions regarding an organisation’s ESG Policy. By publishing its mission statement, an organisation is also able to portray its vision and values to a wider audience, which can increase brand awareness and enable stakeholders including potential clients and customers to align with the business.
The values of an organisation are the principles that drive the business and the way in which it operates. These values should consider not just what the management of an organisation believes to be true, but also the perspective of both an organisation’s staff and customers. By determining your values this way, you work towards creating a culture which all stakeholders can align with. The process does not stop there. It's important to integrate these values into the administration, management and daily processes of your organisation to drive alignment across all departments. They must be visible in both a physical and behavioural sense to encourage staff to align themselves with the organisation's goals.
Only when you are clear on your vision, mission statement and values can you begin to develop a strategy to drive meaningful growth in your organisation. It will also ensure that the processes taken to drive this growth are considered and are aligned with your organisation's goals. This approach provides several benefits to management, including:
• Allowing divisions to act autonomously while still being aligned to an overarching strategy.
• Fosters an inclusive culture which celebrates innovation and diversity, and
• Increases profitability through improved efficiencies and best practices.
A well-documented and cohesive vision, mission statement, set of values and strategy are essential for achieving alignment across your organisation. Without these critical ingredients, your organisation can face a culture of misalignment, resulting in inefficiencies and decreased profitability. Therefore, it is essential for manufacturing businesses in Australia to invest their time and resources into achieving alignment across all divisions, with the hope of increased profitability, staff retention and a culture that fosters innovation and care.
Contact one of our manufacturing specialists for help developing your company statements or for a deeper look at your overall strategy.
Jeremy Raniti and Samantha Zebrowski are both Senior Managers in Business Advisory at William Buck. William Buck is a leading firm of accountants and advisors. Ph: 03 9624 8555 williambuck.com
With ever increasing penalties and powers, many employers fear a visit from WorkSafe. What you must do?
What you should do? Rob Jackson is a Partner at Rigby Cooke Lawyers and he spells out where WorkSafe steps in.
An Inspector visits if there has been a safety incident resulting in an injury or fatality. Or an Inspector may visit in the case of a ‘near miss’, where nobody has actually been injured.
The Inspector is at the centre of enforcing the Occupational Health and Safety Act 2005 (OHS Act), and also the Dangerous Goods Act 1985 and Equipment (Public Safety) Act 1994.
This article focuses on an Inspector’s powers under Part 9 of the OHS Act. This article therefore only applies only to Victoria. The offences, powers, rights and penalties that apply in the rest of Australian under the Work Health and Safety Act in each State and Territory are different to the OHS Act in Victoria.
An Inspector has power of entry to visit a workplace: ‘…. at any time during working hours’. If a business is closed, an Inspector cannot enter premises, unless an Inspector reasonably believes an immediate risk to a person’s health or safety exists.
An Inspector must take all reasonable steps to notify their arrival to the occupier, members of a designated work group and any health and safety representative (HSR).
An Inspector must produce their identity card, and warn a person a refusal to comply without reasonable excuse is an offence. The category of ‘persons’ who must co-operate include an:
• occupier or apparent occupier;
• employer with the management and control of a workplace; or
• employee at a workplace.
A person must provide their name and address, and answer an Inspector’s questions, unless an answer might incriminate the person giving answers.
An Inspector can demand any documents by issuing a notice under section 100 OHS Act. If the request includes any incriminating documents, for example, where a business has conducted its own internal investigation, revealing safety flaws, it must be provided!
In the workplace, the Inspector has six specific powers:
1. inspect, examine and make enquiries;
2. inspect and examine anything;
3. bring any equipment or materials to the workplace as required;
4. seize anything including a document as evidence;
5. seize anything for further examination or take a sample; and
6. take photographs, measurements, sketches or recordings.
An Inspector can still exercise any other OHS Act powers.
After their visit, an Inspector must provide an entry report to the occupier, members of a designated work group work, and any HSR. The entry report must detail time of entry and departure, purpose of entry, description of things done, summary of observations, and the Inspector’s contact details.
An Inspector may also issue a non-disturbance notice, an improvement notice or a prohibition notice. There is a limited timeframe to challenge any of these notices.
After the initial visit, the Inspector may visit again as needed, while WorkSafe consider whether to commence a prosecution against a
company, a director, or less commonly, an employee. For almost all offences, WorkSafe has a two year time limit to prosecute under the OHS Act. The exception is workplace manslaughter, where WorkSafe has no limitation period.
What should your business do?
How would your business react if WorkSafe visited your premises following a serious incident?
Can you answer the following questions?
1. Who calls an ambulance or doctor?
2. Who contacts the family of an injured worker?
3. Who arranges for professional counselling of fellow workers who have witnessed a traumatic incident?
4. Who ensures HSRs are involved?
5. Who notifies WorkSafe?
6. Who is nominated to speak to the media?
7. Who is the company contact person to assist a WorkSafe inspector?
You may have one person such as a safety manager, who performs all of these tasks. Or, these tasks might be allocated to different company employees, as part of an advance plan on managing a workplace incident.
The worst approach is to have no plan!
We have seen scenarios where the deceased’s family is never spoken to, or a casual employee is asked for, and gives, media comment, or WorkSafe is never informed of a serious incident. When shock and panic take control, it is too late to calmly each of these critical matters on the spot.
Legal advice can play an important part. For example,
• whether a workplace investigation can be conducted under legal professional privilege to obtain confidential legal advice about a possible OHS Act breach. The legal advice and any technical report is exempt from the obligation to provide documents under a section 100 notice;
• whether a director or employee is at risk of self-incrimination, if they answer all questions put by an Inspector. A director, or manager are usually at greater risk of a prosecution. If entitled to exercise a right to silence, then this right operates as a lawful reason not to answer an Inspector’s questions.
What’s your plan when WorkSafe calls?
Rob Jackson Partner, Rigby Cooke Lawyers rigbycooke.com.auAs the field of robotics continues to grow and develop, intellectual property (IP) protection will become increasingly important. Mark Metzeling, Principal Lawyer – Intellectual Property, Macpherson Kelley, talks about the challenges and opportunities.
Robotics involve a combination of hardware, software, and complex algorithms, all of which can be subject to various forms of IP protection. In the context of robotics, patents protect inventions and give their owners exclusive rights to make, use, and sell the invention for up to 20 years in Australia. Patents can be used to protect novel hardware designs, such as sensors, actuators, and manipulators, as well as novel software algorithms, such as path planning and machine learning algorithms.
Patenting robotics technology can be a complex and timeconsuming process, but it can also be very valuable. For example, a company that has developed a new type of robotic arm that is faster and more precise than existing arms could potentially patent the idea underlying the unique invention, preventing competitors from copying it. This can enable lucrative licensing opportunities for the patent owner for up to the next 20 years in all countries in which the patent is granted.
A trade secret is information that gives a company a competitive advantage, and which is kept secret by the company. In the context of robotics, trade secrets can include proprietary software algorithms, manufacturing processes, or unique designs for components.
Unlike patents, trade secrets do not need to be publicly disclosed, and there is no set period of time for how long they can be protected. However, valuable trade secrets can be difficult to protect, let alone kept secret, as there are usually several competitors attempting to uncover them. It is therefore unsurprising that companies that successfully maintain trade secrets (e.g. Coca Cola) have several practical protection measures in place to preserve these secrets, such as implementing access controls, non-disclosure agreements, confidentiality agreements, technology protection measures, encryption and many more.
Copyright
Copyright protects original creative works, such as books, music, and art. In the context of robotics, copyright is a powerful tool for protecting the source code of software programs that control robots. This means that others cannot copy the code for their own use (or for sale to a third party for its use), without permission from the copyright owner.
Another advantageous aspect of copyright protection is that it is instantaneous upon the work being published (i.e. put in the public domain), and is free to obtain. However, it should be noted that to be successful in a copyright infringement action, you need to be able to demonstrate that the source code is substantially identical and that it was copied from your source code, but a trusted advisor can typically provide an easy solution for this.
Trade marks are used to protect signs that indicate the source/ origin of a good or service. This can include brand names, logos, smells, colours, shapes, noises, and slogans. In the context of robotics, trade marks are used to protect the name and logo of a robot or robotic system, and potentially also the shape of the robot (if it is distinctive and unique).
For example, Boston Dynamics, a well-known robotics company, has a registered trade mark for the name and logo of their robot dog, Spot. This means that other companies cannot use the name or logo of Spot without permission from Boston Dynamics. A monopoly over the use of a trade mark can be protected indefinitely provided it is consistently used and properly renewed.
Designs in robotics are used to protect the appearance of a robot or the shape of a component part, where the appearance of the robot, or component part, is both, new and distinctive – and has commercial value. Designs can be extremely useful in robotics where the idea underlying the invention is unable to obtain patent protection eg. the shape of a robot’s hand may be changed to fulfil a certain purpose or to look a certain way that is artistically beautiful. Securing protection as a registered and certified design can provide a monopoly of up to 10 years for the exploitation of the design.
There are several reasons. First, robotics is a highly competitive field, and companies invest significant resources in developing new and innovative technology. IP protection can help ensure that these investments are not wasted and that companies can recoup their costs through the sale of products or licensing agreements.
Second, IP protection can help encourage innovation by giving inventors and companies the incentive to invest in research and development. Without the possibility of IP protection, companies may be less likely to invest in developing new technology because they would not have a way to protect it from competitors.
Third, IP protection can help protect consumers from unsafe or ineffective products. If a company can protect its IP, it can ensure that only high-quality products that meet its standards are sold under its name.
While there are several challenges associated with protecting IP in this field, one of the biggest is that robotics technology often involves a combination of hardware, software, and algorithms, which can make it difficult to determine which type of IP protection to use.
For the best course of action, connecting with an IP expert can ensure that your product is protected to the fullest extent.
Anneke Thompson, Chief Economist at CreditorWatch gives her view of rising costs and falling demand pressuring businesses.
This month we were able to get a guide on what listed Australian businesses are anticipating for the year ahead, as reporting season began. While most listed retailers reported strong earnings for the second half of 2022, many downgraded or emphasised caution in their outlook for sales in the year ahead.
Groups like Adairs, JB HiFi and Baby Bunting all highlighted that sales in the year ahead in many categories are likely to be lower. This year we will see the impact of many more consumers having less to spend each month, as up to 800,000 fixed rate loans on very low interest rates will convert to variable rate loans. We will also see the added impact of housing completions begin to trend down from about the middle of the year. This will affect sales in the furniture, white goods, and electrical goods categories.
Our Business Risk Index continues to highlight the higher risk of insolvency for sectors reliant on discretionary spending, with the food and beverage sector topping the list of riskiest sectors at a 7.3% probability of default. This is supported by a recent survey by Finder, which asked respondents if they were cutting back on their expenses, and if so in what categories. ‘Dining and drinking out’ was the top category where people were cutting back (51%), while more than a third (36%) had limited how often they go to events, like movies, sporting games and concerts. This emphasises the risk of this sector, as business owners will now not only be grappling with high costs, wages, interest payments and rents, but also lower demand.
Inflation continues to be the key metric that the whole world is watching. While many economists believe inflation peaked in Australia in the December 2022 quarter, when it came in at 7.8%, it is still well above the RBA’s target rate of 2-3% and may not get back to that level until 2025. Inflation in other economies also seems to have peaked but is still well above normal levels. This is partly because supply side factors, such as the Ukraine War and bad weather affecting crop harvests, are out of the control of central banks.
In February the ABS also reported an increased in the January 2023 unemployment rate, rising to 3.7% from 3.5% on a seasonally adjusted basis. While there are still almost 400,000 more employed people in Australia in Jan 2023 than there were in Jan 2022 (or a 3% difference) it is likely that the strong gains in employment that were recorded in 2022 won’t be repeated this year. The ABS has recorded a drop in the number of employed people for two straight months now, suggesting we reached a peak in employment in November 2021.
Businesses will be far more cautious in hiring, although the good news is that at this stage there doesn’t seem to be any increase in mass redundancy announcements. While increasing unemployment is not great news for jobseekers, it is better news for the economy overall, as it greatly decreases the threat of a wage price spiral.
Retail trade data for January 2023 revealed a 1.9% seasonally adjusted increased month-on-month. This was after a large fall in December of 4%. On a total dollar value, retail trade in January 2023 was roughly the same as it was in September 2022.
Most industry turnover is quite volatile over the summer period, so it is difficult to draw any major conclusions on trends, however, household goods retailing is one sector where trade is well below 2022 levels and is in fact trading at or about the level it was in October 2021. This is likely a result of households pulling back on large expenditure and a flow on impact of many people making large purchases for their houses during lockdown periods.
It is likely that as we see the peak of housing completions reached in around mid-2023, that household goods trading will continue to remain flat or even trend down.
Seek Job ads data for Jan 2023 also show that on a year-on-year basis, almost all sectors have recorded a drop in the number of advertised roles. The biggest year on year drop was recorded in the Information and Communication Technology sector, which was down 24.1%, followed by Hospitality and Tourism, down by 13.8%. The only industries to have a higher number of job ads in Jan 2023 versus Jan 2022 are Education and Training, Community Services and Development and Accounting.
Late payment rates for January were, on average, three times greater for small business relative to big business, reflecting differences in the ability of small businesses to enforce payment terms and collect on payment arrears, and the willingness of some businesses to treat smaller suppliers as an interest free bank.
Payment arrears have been slowly trending down across all industries but continue to be a problem in the construction industry due to inherent payment structures that incorporate delayed payments for projects. In January, 11.6% of small construction businesses had payments that were 60 days or more in arrears compared to just 2.3% of large businesses. creditorwatch.com.au
7 PRODUCT ZONES
As we build up excitement and momentum for Australian Manufacturing Week it is a great story that we tell that over 90% of exhibitors are local companies, making it a true celebration of Australian manufacturing.
The interesting breakdown of exhibitors by country is that of the 342 exhibitors in total so far, 310 are Australian based companies. Canada 1, China 3, Denmark 1, India 4, Ireland 1 Italy 3, Japan 1, Malaysia 1, New Zealand 6, Singapore 4, Spain 1, Taiwan 4 and USA 2 have companies coming from those countries to exhibit.
A good news story to tell for Australian Manufacturing being a strong eco system. From Original Equipment Manufacturers (OEM’s) right through the supply chain of local manufacturing and technology suppliers from around the country, AMW is the largest exhibition of manufacturing and technology ever held in Australia.
Australian Manufacturing Week will be held from 9th – 12th May at the Melbourne Convention and Exhibition Centre and promises to deliver on our mantra of “Where Technology Meets Innovation”. The ONE event that showcases the latest innovations, technologies and equipment in the advanced manufacturing sector. Explore new opportunities, meet and network with industry leaders and technology experts, all under ONE roof at ONE show.
Seven Product Zones covering Machine Tools, Additive Manufacturing, Manufacturing Solutions, Welding & Air Technology, Robotics & Automation, Plastics Technology and a special Pavilion for Australian Manufacturers, make for a worthwhile visit for any companies that are across any of these areas.
There are plenty of reasons to visit Australian Manufacturing week:
• Be a witness and a part of technological evolution.
• Be the first to experience innovative technologies, latest machinery.
• Meet and network with the innovators and trendsetting individuals who spearhead this technological revolution.
• Interact with peers and share ideas.
• Gain firsthand exposure to the companies who are at the forefront of technological excellence.
• See all the key industry brands all in one place at the same time.
We are truly excited to be delivering such a wonderful show and look forward to all our readers visiting at some point during the week.
Maton Guitars has celebrated 20 years as a member of AMTIL, as well as for being in business for 75 years.
Situated in Box Hill, Maton Guitars is where some of the finest quality guitars in the world come to life, each with a unique character and tone. Bill May pioneered the use of many Australian wood species in guitar construction and is regarded by many Australian luthiers as the founding father of their industry. The Blackwood series still sound as good as they did when they were released. Star guitarists like Neil Finn, Tommy Emanuel, Paul Kelly and Colin Hay count Maton Guitars as key to their great sounds.
“The main role AMTIL has played throughout the term of our membership has been one of great collaboration,” Managing Director David Steedman said. “In particular, Greg Chalker is a resource who knows this business and our industrial needs intimately. AMTIL contributes to this business in the identification of government programs or initiatives that are of interest to us whereby we can look to applying for federal or state government funding for various project works.”
“This role materialises in not only tangible wins and resultant long term collaborations such as Multicam CNC function, Sutton Tools (Carbitool) for tools, tool bits, cutters and grinders, as well as Go Proto for bridge alignment pins but also for the basis of compare/ contrast analysis for partnering with businesses on various other projects,” Steedman added.
Key to the above is the shared alignment of values within their businesses which always prefer working with the local partner where possible rather than the alternative.
Every Maton-made guitar embodies the passion and skill of the craftsmen who are part of their team, each of them drawing on the years of experience and dedication necessary to produce a truly remarkable instrument. Currently, Maton employs 70 people and remains 100% family owned and operated. maton.com.au
AMTIL would like to welcome the following companies who have signed up as new members of our association.
3D EXPLORER
19/591 Withers Road ROUSE HILL, NSW 2155 3dexplorer.com.au
AVWELD AUSTRALASIA
25 Raymond Road LAVERTON NORTH, VIC 3026 avweld.com
MOBILE AUTOMATION
Factory 30, 65-67 Canterbury Road MONTROSE, VIC 3765 mobileautomation.com.au
DELTA ELECTRONICS (AUSTRALIA)
Unit 18, 39 Herbert Street ST LEONARDS, NSW 2065 deltaww.com
MICROSCOPY AUSTRALIA
A14 Quadrangle University Of Sydney NSW, 2006 micro.org.au
HALDATEC PTY LTD
11/27 Thornton Cresent MITCHAM, VIC 3132 haldatec.com.au
ICONTROLS
5/12 Billabong Street STAFFORD, SA 4054 icontrols.com.au
OCEAN ELECTRIC AUSTRALIA Level 1, Suite 2, 424 St.Kilda Road MELBOURNE, VIC 3004 oceanelectric.com.au
ORBIMAX
501-503 Dowling Street WENDOUREE, VIC 3355 orbimax.com.au
3D META
Unit 25, 26 Burgess Road BAYSWATER NORTH, VIC 3153 3dmeta.com.au
CALLINGTON
30 Station Street RYDALMERE, NSW 2116 callington.com
JACK THOMPSON ENGINEERING P/L
1840 Frankston - Flinders Road HASTINGS, VIC 3915 jte.com.au
KANG INDUSTRIAL
3 Wayne Court DANDENONG, VIC 3175 kangindustrial.com.au
OUTSOURCE INSTITUTE (AUS) 1 Clunies Ross Court EIGHT MILE PLAINS, QLD 4113 outsourceinstitute.edu.au
PACIFICFACTORY
32 Container Street TINGALPA, QLD 4173 pacificfactory.au
AMTIL celebrates International Women’s Day with a fun morning of indoor lawn bowls and the opportunity to share their personal experiences.
On Wednesday 8th March, AMTIL staged the Women in Manufacturing Barefoot Bowls Competition at the Brighton Indoor Bowling Club with a great number appearing to have a valuable bond, on this International Women’s Day event.
Members spoke of the barriers broken down in the Australian manufacturing industry over the years. “There have been a lot of general improvements and we are all working on more barriers being lifted,” said one.
Back to the game of barefoot bowls, the William Buck team won first prize, the Integra team walked away with the chocolate spoon, and Danni from Sheetmetal Machinery won the door prize. After the game, the whole crew stayed for a BBQ spread for lunch.
In some countries, IWD is a public holiday, and in some countries it is, but only for the women. Other groups say it should remain as a day of activism, a “highly considerable and visible opportunity for impact.”
The global campaign theme for IWD 2023 is #EmbraceEquity.
Each of the four AMTIL lawn bowls teams wore colours depicting various values of the day. For instance, purple, green and white are the colours of International Women’s Day. Purple signifies justice and dignity and being loyal to the cause. Green symbolises hope. White represents purity, albeit a controversial concept. The colours originated from the Women’s Social and Political Union (WSPU) in the UK in 1908.
This annual Ambrose AMTIL Golf tournament was set among the gums at Riversdale Golf course in Mt Waverley.
The early morning tee off was accompanied by a glorious Melbourne summer morning, getting hotter as the day rolled on. In fact, the temperature reached 40C and rained at one point. Despite the challenging weather conditions, About 100 enthusiastic players showed up and demonstrated exceptional sportsmanship.
Following a day of strong competition on the course, all teams made their way to the clubhouse to enjoy a sumptuous barbecue lunch and drinks while networking with other attendees. The event concluded with an awards presentation, where well deserving participants were recognised for their performance.
Congratulations to the overall winning team: Paul Miller from Whistle Design, Garth O’Connor-Price from William Buck,
Kingsley Edgar (Hexagon) and [not in picture] Paul Brick (Marand). They won with a net Stableford score of 51.5 points. Trophies were presented by Sponsor Adam Mott from Metal Industries Insurance Brokers (MIIB) and Shane Infanti, CEO, AMTIL.
Congratulations also to the Runners up team from MIIB which included Nicholas Sear, Andy Fuller, Adam Carland and Brad Scalzo.
WooHoo!! Round 1 of the AFL Football Season 2023 was run and won at the time of going to print. What did we learn… Four new club coaches won their opening game – North, GWS, Essendon and the Saints all had good wins considering where they finished the previous season ; the Tiggies and Blues opened up proceedings with a boring 'snorefest' – albeit a draw ; the Cats and Pies put on an cracker of a game with plenty of goals, some spite and a highlight of seeing Ollie Henry dragged down in the goal square. The Bulldogs need a 'Plan B' quicktime as the Demons were a class above. The Swans got down to business and the surprise of the round was how Port Adelaide dismantled a genuine premiership contender in the Brisbane Lions. Yes, it is only Round 1 and we really can't read too much into these results, some supporters took hope and others shattered dreams into the next round – bring it on. Till next time… Sanchez
ROUND 01
Due to the ongoing Coronavirus pandemic, many industry events world-wide have been postponed, rescheduled or cancelled. Readers are advised to check with all event organisers for the latest information. For the latest international travel advice, please visit health. gov.au/health-topics/novel-coronavirus-2019-ncov – For more events, please visit amtil.com.au/events
INTERNATIONAL
INTERMOLD
JAPAN, Tokyo
12-15 April 2023
intermold.jp
HANNOVER MESSE GERMANY, Hannover
17-21 April 2023
hannovermesse.de
KOREA MAT
KOREA, Goyang
17-21 April 2023
koreamat.org
TAIWAN INTERNATIONAL
FASTENER SHOW
TAIWAN, Kaohsiung
3-5 May 2023
fastenertaiwan.com.tw
AISTECH 2023
USA, Michigan
8-11 May 2023
aist.org
PLAST-EX CANADA. Toronto
9-11 May 2023
admtoronto.com
CONTROL GERMANY, Stuttgart
9-12 May 2023
control-messe.de
STAINLESS CZECH Republic
10-11 May 2023
bvv.cz/de/stainless
INTERMACH & MTA ASIA
THAILAND, Bangkok
10-13 May 2023
intermachshow.com
STEEL BUILD
CHINA, Guangzhou
15-17 May 2023
steelbuildexpo.com
EASTEC
USA, Springfield
16-18 May 2023 easteconline.com
MACH-TECH HUNGARY, Budapest
16-19 May 2023
Parnapjai.hu
METALFORUM POZNAN POLAND, Poznan
30 May-2 June 2023
itm-europe/pl
WIN EURASIA
TURKEY, Istanbul
7-10 June 2023 win-eurasia.com/tr
DRONE & UNMANNED AVIATION 2023 CONFERENCE
SOUTH AFRICA, Johannesberg
1-2 June 2023
droneconference.co.za
METEC
GERMANY, Dusseldorf
12-16 June 2023
Metec.de
THERMPROCESS
GERMANY, Dusseldorf
12-16 June 2023
thermprocess.de
NEWCAST
GERMANY, Dusseldorf
12-16 June 2023
newcast.de
MESSE STUTTGART
GERMANY, Stuttgart
13-16 June 2023
messe-stuttgart.de
M-TECH
JAPAN, Tokyo
21-23 June 2023
manufacturing-world.jp
MANUFACTURING EXPO
THAILAND, Bangkok
21-24 June 2023
manufacturing-expo.com
MTA VIETNAM
VIETNAM, Ho Chi Minh
4-7 July 2023
mtavietnam.com
ALUMINIUM CHINA
CHINA, Shanghai
5-7 July 2023
aluminiumchina.com
VME
VIETNAM, Hanoi
9-11 August 2023
vme-expo.com
LASER TAIWAN
TAIWAN, Taipei City
23-26 August 2023
chanchao.com.tw/laserexpo
SCHWEISSEN & SCHNEIDEN ESSEN
GERMANY, Rhine-Westphalia
11-15 Sept 2023
schweissen-schneiden.com/joining-cuttingsurfacing/
EMO
GERMANY, Hannover
18-23 September 2023 emo-hannover.de
WORLD AVIATION FESTIVAL
LISBON, Portugal
27-28 September 2023
terrapinn.com/conference/aviation-festival/
CMTS
CANADA, Toronto
25-28 September 2023 cmts.ca
MEDICAL FAIR BRAZIL
BRAZIL, Sao Paulo
26-28 September 2023 medicalfairbrasil.com.br
METALEX
VIETNAM, Ho Chi Minh
4-6 October 2023 metalexvietnam.com
3D PRINT CONGRESS & EXHIBITION
FRANCE, Paris
11-12 October 2023
3dprint-exhibition-paris.com
CAMX USA, Atlanta
30 October-3 November 2023 thecamx.org
WESTEC
USA, California
7-9 November 2023 westeconline.com
MACTECH
EGYPT, Cairo
9-12 November 2023 mactech-eg.com/
PLAST IMAGEN
MEXICO CITY, Mexico
12-18 November 2023 plastimagen.com.mx/en
METAL MADRID
SPAIN, Madrid
15-16 November 2023 ifema.es/metalmadrid
METALEX
THAILAND, Bangkok
22-25 November 2023 metalex.co.th/
MANUFACTURING INDONESIA
INDONESIA, Jakarta
6-9 December 2023
manufacturingindonesia
DESIGNBUILD
9-11 MAY 2023
Bringing together Australia’s architecture, building, construction and design communities. Co-locating with Total Facilities and The Built Environment Summit. Includes the new Digital Building Zone. designbuildexpo.com.au
AUSTRALIAN MANUFACTURING WEEK MELBOURNE CONVENTION & EXHIBITION CENTRE
9-12 MAY 2023
The ONE event that showcases the latest innovations, technologies and equipment in the advanced manufacturing sector –all under ONE roof at ONE show. australianmanufacturingweek.com.au
WORKPLACE HEALTH & SAFETY SHOW SYDNEY SHOWGROUNDS
31ST MAY – 1ST JUNE 2023
The latest legal requirements and regulations, ensuring business follows best practice. Current workplace health and safety research, information, technology and innovative new products. whsshow.com.au
FOODPRO
23-26 JULY 2023
An important trade fair for the food and beverage industry in the Asia-Pacific region. The exhibitors present at the fair the latest products and ideas for the industry, including the latest trends in food production and the latest technologies to produce beverages. Visitors can find in depth and comprehensive information here about the latest developments, trends, products and services in various fields. foodproexh.com
MAINTAIN MOMENTUM AND EMERGE STRONGER IN 2023.
CEMAT
SYDNEY OLYMPIC PARK
25-27 JULY 2023
Experience, first-hand, the range of solutions and technology setting the standards and future direction of logistics and warehousing in the Asia Pacific. cemat.com.au
AUSTRALIAN WASTE & RECYCLING EXPO
ICC SYDNEY
25-27 JULY 2023
Discover an exciting showcase of full circle innovative products and sustainable solutions to collect, process and recycle waste more smartly. Future critical areas include Machinery & Equipment, Software & Services, Bins, Vehicles, Food & Organics and more awre.com.au
WA MINING
PERTH EXHIBITION CENTRE
11-12 OCTOBER 2023
As technology accelerates, it has never been more important for mining companies to connect with suppliers. WA Mining’s exhibition will showcase the latest technical and digital innovations across the entire mining value chain. Meet and do business with leading industry suppliers who are advancing the mining industry in Western Australia. waminingexpo.com.au
AUSBIOTECH
BRISBANE, QUEENSLAND
1-3 NOVEMBER 2023
Biotechnology Industry Forum in Australia. AusBiotech is dedicated to the development, growth and prosperity of the Australian Biotechnology Industry. ausbiotech.org/conference-information
YOUR INDUSTRY. YOUR MAGAZINE.
There has never been a more important time to ensure you are well marketed to industry and ready when opportunities open up. Reach out to 31,500 targeted readers and 63% decision-makers.
I would be delighted to have a non-obligatory chat on how we can help.
Nicholas Raftopoulos: 0431 753 381
The back story of developing the plans for Australia to begin making, an Australian car, in Australia.
The Secondary Industries Commission had been set up by the Curtin Labour Government to investigate methods of ensuring a smooth transition of war industries to a peace-time basis. It hadn't taken many sittings of the commission for its members to realize how important was the task they had tackled. And it did not surprise me that they had come very early to realise that car manufacture held the key to post-war economic stability.
Jensen was a close personal friend of Ben Chif!ey. He was a permanent civil servant, who had spent most of his life in Government munitions work. I had formed a great personal respect for him ever since I had accepted the appointment as Director of Ordnance Production. But I had given him no hint that I had anticipated the time would come when he, or another Government representative, would ask me about car manufacture.
I let him talk. He said there were many problems that had to be licked if Australia was to avoid industrial and economic troubles in the changeover from war to peacetime manufacture. I nodded agreement. Then Jensen said, “One of the first things I want to see is our own Australian car. Do you think General Motors would take it on?”
I said, “I think GM might do it, J.K.” But, I warned, they would have to be convinced that there was a reasonable profit in it before they would go ahead. Two weeks later, in Canberra, I had a conversation with Ben Chifley, then Minister for Postwar Reconstruction. He had called me in to get my views on the type of reparations Australia should demand from Germany and Japan when the war formally ended. “In my view, knowhow, technique and the use of patents-and some key personnel, “I said. “We could ask, instead, for millions of pounds, but right now I think brains are more important to us than bullion and, anyhow, reparations payments never seem to get paid.”
“I think you’re damn well right,” said Chifley, in his forthright way. Our little talk that afternoon led directly to the formation of an organisation known as ESTEA-Employment of Scientific and Technical Enemy Aliens. This was a committee, of which I was a member, to bring out German technical specialists to Australia. Our work won several highly skilled German and other European exenemies for Australia after the war.
Then ‘Chif’ got down to the second reason for his summons to me. “What about this car business?” he asked. “I know we must make cars ourselves, and I don't think these people out here in the car game will do it. They’re foreign: they’re not us; they represent overseas interests. Australia needs a car of her own. We must have it.”
He paused, then jabbed the end of his pipe in my direction and said, “I think you’re the bloke who can get it for us.”
“Maybe,” I said. “But I work for General Motors.”
“I'm aware of that,” said Chifley, “and I want to know what's the first step we should take.”
“We really should be taking it now,” I replied. “I’ve believed for years, as you know, that Australia should, and eventually will, produce its own car. But the first thing to do is to get rid of the Motor Vehicle Agreement Act.”
“The Motor Vehicle Agreement Act? What are you talking about?” Chifley asked. Apparently he didn't know, or had forgotten, the Act brought in by the Menzies Government in June 1940, which gave the sole rights on car manufacture to one firm: Australian Consolidated Industries. While the Act was in force, no one but W.J.Smith and his A.C.l. could legally make a car in Australia.
“Oh, surely you can’t be right?” Chifley said, almost stunned with surprise.
“I know I’m right, Mr. Chifley,” I replied. “Call for the Act and we can check it.” Chifley was already reaching for a buzzer. “That's just what I'm doing now,” he said. His private secretary went hurrying off to get a copy of the Act. When it came, Chifley sat down, grim-faced, and read it through. There it was, an Act of Federal Parliament giving the sole manufacturing rights for cars to A.C.l. “Well,” said Chifley. “We’ll have to wipe this. What’ll Gunboat Smith take to let us drop it, without a fuss? Fifty thousand? A hundred thousand? Anyhow, Hartnett, don't worry. We’ll get this legislation repealed.” We got back to talking car production. I told him, “General Motors pays me and it’s my duty to try my hardest to persuade them to make a car in Australia. I’m convinced that the car will be made here somehow.”
“I’ll be interested to hear what they say, Hartnett,” Chifley said, “but I have doubts that they’ll agree to it.”
Legislation to repeal the Act became law on 14 May, 1945. It removed the legal barrier to the making of an Australian car.
To be continued…