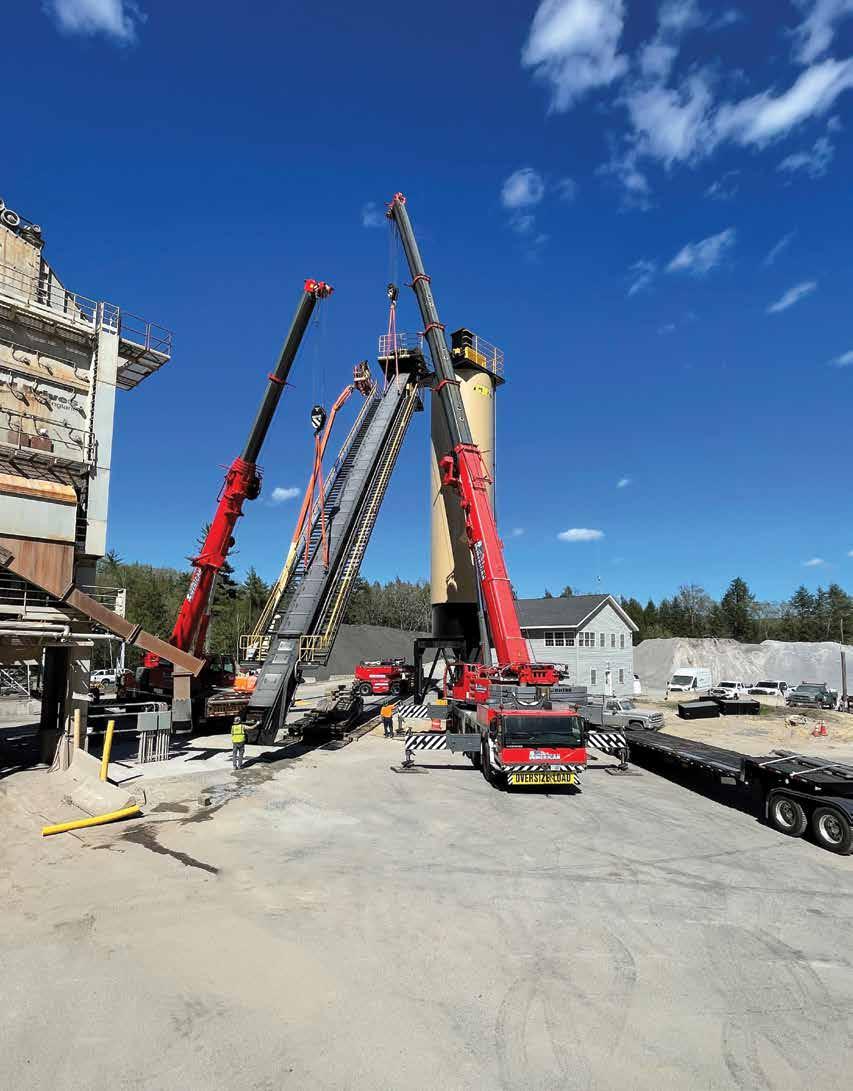
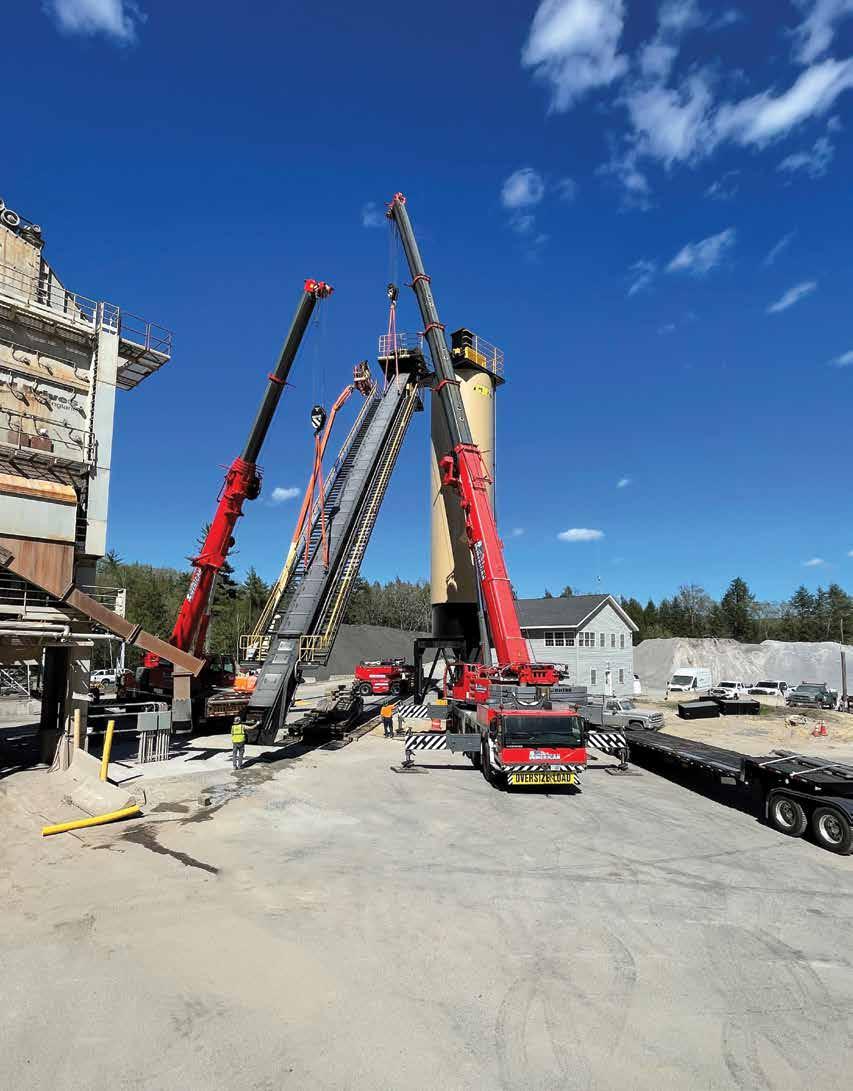
BUILT TO CONNECT
Single-Source Supplier Advantage
Astec provides a significant advantage as a single-source supplier for the diverse products and services involved in building and maintaining an asphalt mixing plant. Astec liquid AC storage tanks, tank farms, and heating system controls feature high quality construction and unmatched efficiency. We offer a variety of sizes and configurations that can be fully customized. Optimize your asphalt storage tanks and hot oil heaters with the addition of the Recon® mobile monitoring system to receive status updates on a smart phone, tablet or PC.
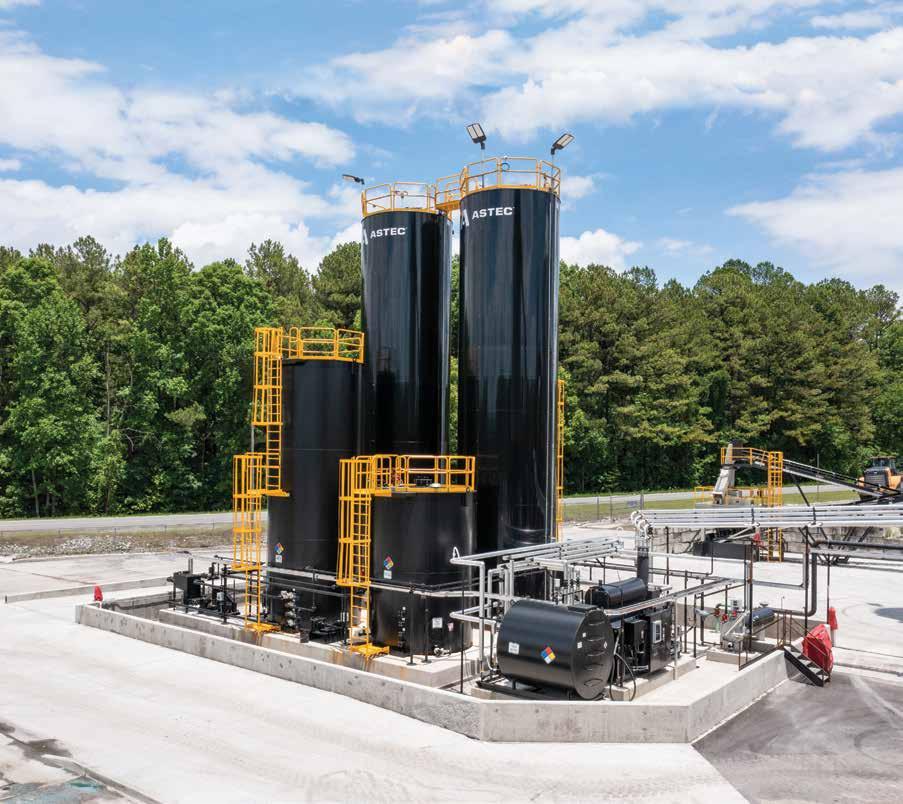
COME VISIT BOOTH C30235
MARCH 14-18, 2023 • LAS VEGAS, NV
Scan QR code to see Astec’s full line of Tank Farm Components.

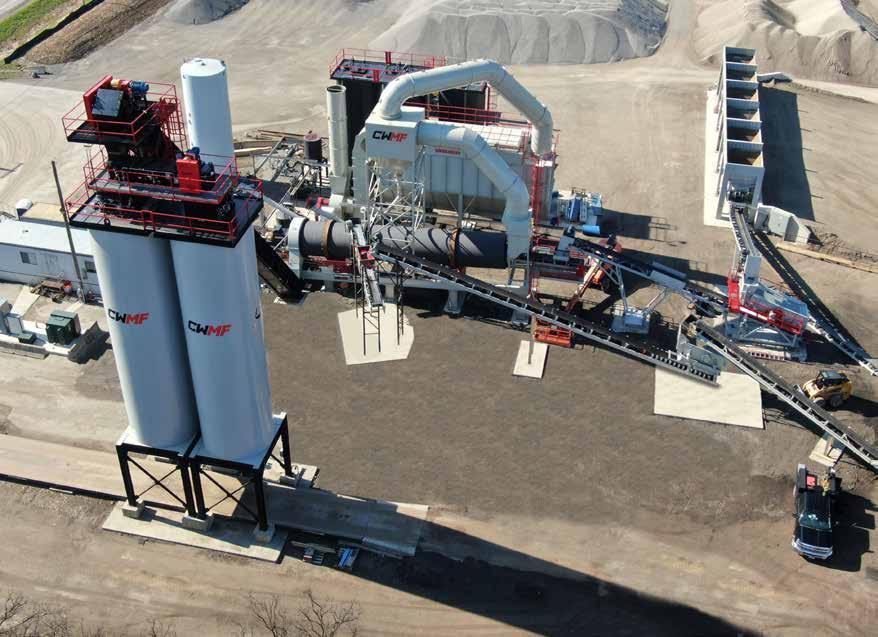
The Blaw-Knox University, now in its 58th season, is dedicated to training paver operators and foreman on proper Paver Operation and Maintenance and applied Best Paving Practices through classroom-style and hands-on application courses.
For over a half a decade Blaw-Knox has earned its reputation as the go to source of training and instruction on hot mix paving.
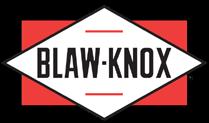
Blaw-Knox provides improved technical and problemsolving skills on a variety of paver operations and maintenance topics. Course instructors share decades of field and teaching experience with attendees, including training on the latest DOT requirements.
Blaw-Knox offers multiple dates to satisfy the demand for its popular courses.

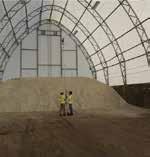
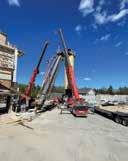
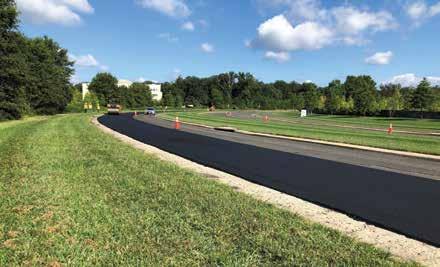
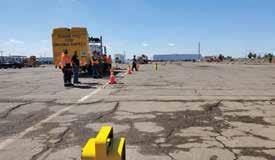
Tax Deductions in the Ash Clouds
At press time, I couldn’t find reliable stats on the amount of methane be ing released from the alleged sabo tage of Nord Stream 1 and Nord Stream 2. Suffice it to say, the bubbling gas devastat ing marine life in the Baltic Sea was proba bly more than your properly operated, Tier IV Final wheel loader at the asphalt plant. I can’t say if the pipelines’ greenhouse gas (GHG) or particulate matter emissions ri val the collective emissions from Strom boli, Erta Ale, Nyiragongo, Piton de la Fournaise, Dukono, Ibu, Krakatau, Mera pi, Semeru, Lewotolo, Popocatepetl, San tiaguito, Fuego, Masaya, Nevado del Ruiz, Reventador, Sangay, Sabancaya, Nevados de Chillán, Mount Erebus, Kilauea, Ya sur, Shiveluch, Ebeko, Sakurajima and Su wanose-jima, considering those volcanoes currently erupt at different rates of spew.
Until our global elite focus on the big emitters of GHGs (whether naturally oc curring or based in China), it is criminal that our industry continues to be target ed, maligned and forced to comply with ever-narrowing regulations. When a state agency dictates private business owners can no longer purchase robust pieces of machinery for infrastructure construction and/or maintenance, it irks me. When an unelected agency dictates to the asphalt in dustry, which has been ratcheting down its emissions numbers and carbon footprint on its own, that we have a new, magic num ber to attain instead, it makes me wonder about the reading comprehension skills of the person at the top.
Any CEO worth his or her salt will tell you to lean on your employees’ strengths. Bring them to the table to explore attain able solutions together. Instead, the elitists have come up with random numbers, sta pled money to the clouds around the ash plumes of the above-listed volcanoes, and demanded of us, “Meet this target next.”
Before this note becomes too negative, let me say the construction industry over all has an opportunity to grab some of our country’s recently printed dollars waving above the ash plumes.
Take the tax credit bribes for purchas ing equipment with batteries comprised of Rare Earth Minerals as an example. Your electric vehicle (EV)—depending on its gross vehicle weight rating to battery ca pacity ratio—could be tax deductible.
On page 34, I’ve included another in stallment of the series on upcoming grant monies through the dubiously named In flation Reduction Act (IRA). With the Advanced Industrial Facilities Deploy ment Program, the Department of Energy (DOE) is making available $5.8 billion in rebates for facilities that can prove a 20% reduction in their GHGs with installa tion of advanced technologies. The Inter nal Revenue Service (IRS) is expanding its credits for purchases of “clean” equipment. In fact, if you look at Section 45 of the IRA, not only will you develop a migraine, but you will also get a sense that the IRS will reward you with tax incentives for pur chasing EVs and advanced technologies.
I’m not a tax advisor. Please take that whole section to your tax professional.
But examine the concept behind Sec tion 45W, where it is implied the electric off highway vehicle doesn’t have to be sourced from North America. Again, let a tax pro fessional read it more thoroughly and advise you on the specifics.
Let me finish by saying, installing ad vanced technology to lower emissions at any facility is a responsible move. If it’s possible to cut extra emissions from an operation, that’s a laudable goal. If the DOE is willing to hand you a 50% rebate for achieving the goal, that’s even better. If the IRS is willing to extend an extra tax credit to you for the business expenditure, why not take advan tage of that while it’s available?
So far, the asphalt industry has been making these strides out of a desire to be good stewards of the land and a willingness to placate homeowners who built right up to our property lines. It’s nice to think fu ture strides come with a side of rebate from Uncle Sam. What has me a little on edge is the idea that government entities and agen cies are demanding lower numbers from an industry that’s already lowered its num bers. We can’t single-handedly make up for the 26 volcanoes currently erupting around the globe. Honestly, I don’t think it’s fair to ask us to.
Have a Safe and Lovely Holiday Season, Sandy Lender
asphaltPRO
602 W. Morrison, Box 6a Fayette, MO 65248 (573) 823-6297 • www.theasphaltpro.com
GROUP PUBLISHER Chris Harrison chris@ theasphaltpro.com
PUBLISHER Sally Shoemaker sally@theasphaltpro.com (573) 823-6297
EDITOR Sandy Lender sandy@theasphaltpro.com (239) 272-8613

DIGITAL EDITOR Sarah Redohl sarah@theasphaltpro.com (573) 355-9775
MEDIA SALES
Cara Owings cara@theasphaltpro.com (660) 537-0778

ART DIRECTOR Kristin Branscom
BUSINESS MANAGER Susan Campbell (660) 728-5007

AsphaltPro is published 11 times per year. Writers expressing views in AsphaltPro Magazine or on the AsphaltPro website are professionals with sound, professional advice. Views expressed herein are not necessarily the same as the views of AsphaltPro, thus producers/contractors are still encouraged to use best practices when implementing new advice.
SUBSCRIPTION POLICY: Individual subscriptions are available without charge in the United Sates, Canada and Mexico to qualified individuals.
One year subscription to non-qualifying Individuals: United States $90, Canada and Mexico $125.00. For the international digital edition, visit theasphaltpro.com/subscribe/
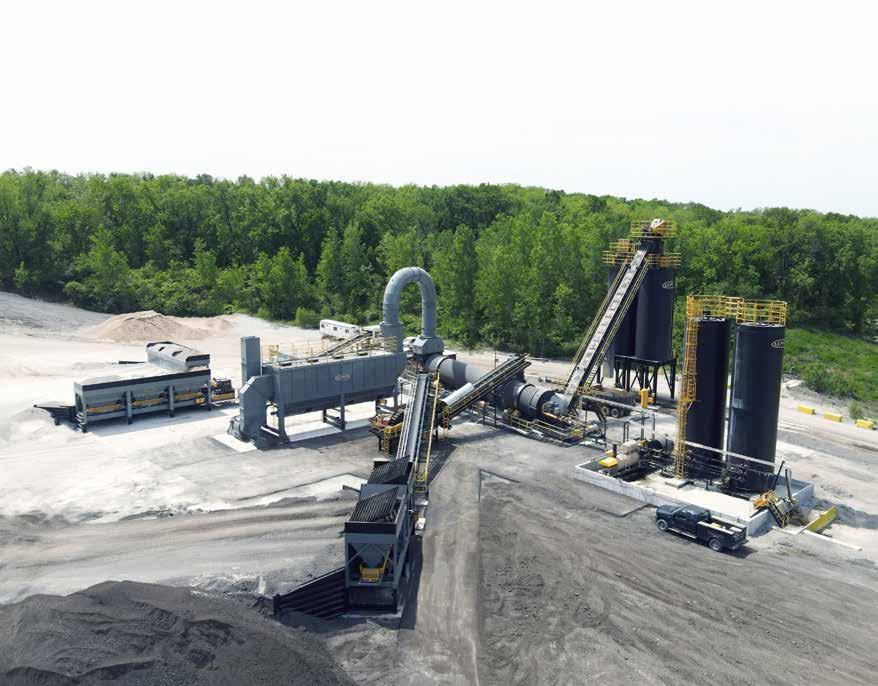
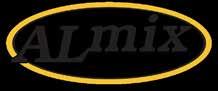

Caltrans Investigates Work Zone Intrusion Alarms
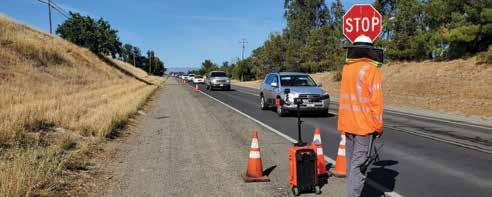
Between 2016 and 2020, work zone fa talities increased from 782 to 857, ac cording to the American Road and Transportation Builders Association (ART BA) National Work Zone Safety Information Clearinghouse. One safety trend that aims to reduce work zone fatalities is the imple mentation of Work Zone Intrusion Alarm (WZIA) systems.
WZIAs alert workers and drivers of poten tial intrusions into the work zones through the use of alarms or alerts connected to radar-, camera-, infrared-based or other hardware and software.
The California Department of Transporta tion (Caltrans) has partnered with a research team led by Associate Professor Ghazan Khan of California State University Sacramento's Department of Civil Engineering to investi gate some of the WZIA options.
“With the availability of new systems and safety solutions on the market, there was a need to review and analyze WZIAs to see how we can supplement the best practices already in use to further improve safety,” Khan said.
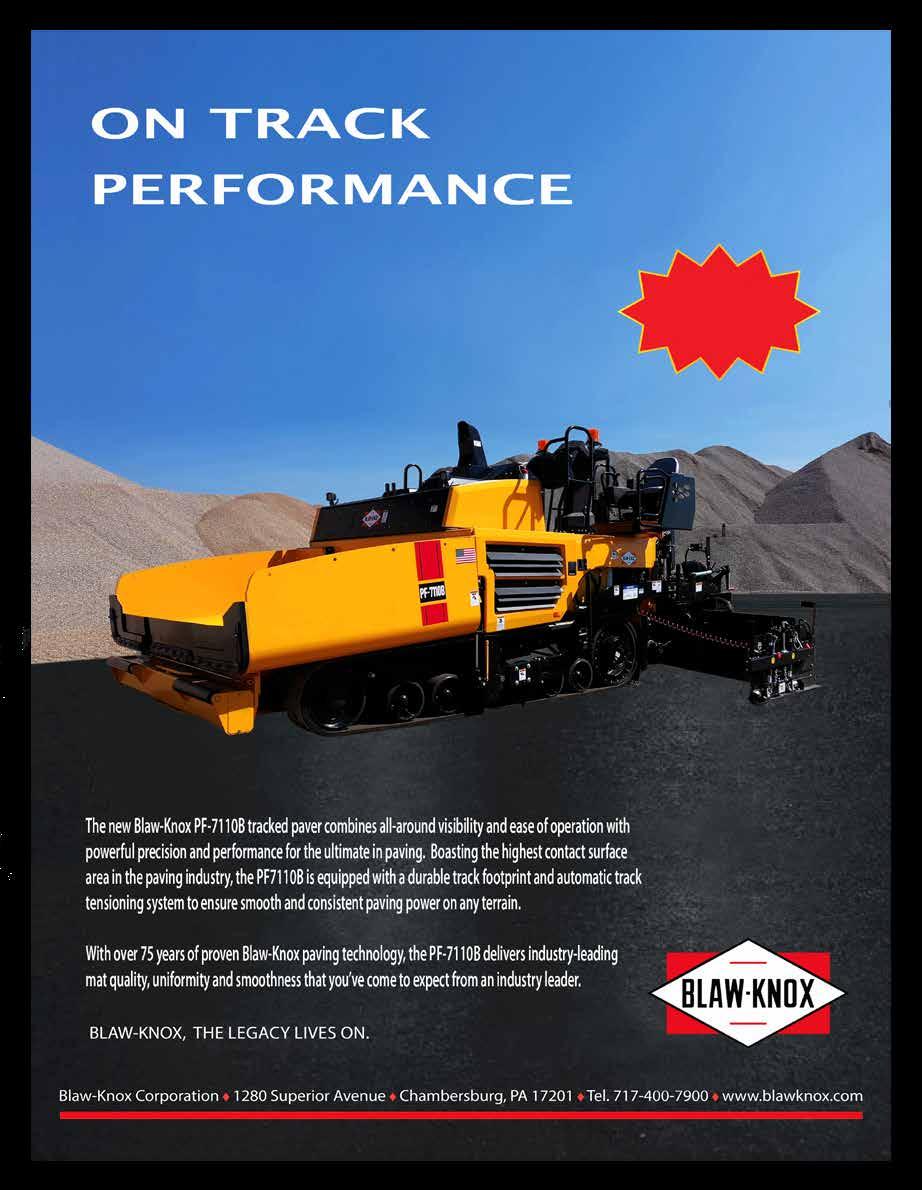
What sets the research conducted by Khan’s team apart from existing research is the em phasis placed on the workers’ perspective. “How are crews going to perceive these sys tems, what issues will they identify and how will they utilize these devices—that was our goal,” Khan said.
His team identified five different WZIA systems to test in close-to-traffic conditions and trained Caltrans maintenance crews on their use prior to deployment in an ac tive work zone. The five systems selected by Khan’s team were the Traffic Guard Work er Alert System, SonoBlaster, Intellicone In cursion Prevention and Warning, Intellicone Single Sentry Beam and AWARE Sentry. Let’s take a closer look at each system.
1. Traffic Guard Worker Alert System
The Traffic Guard Worker Alert System (WAS) includes a 12-foot lightweight, portable trip hose and sensor assembly that when driven over sends a wireless signal to an alarm and flashing light. Multiple hoses can be connect
ed wirelessly to offer a larger area of coverage, Khan said. However, the team found that for long work zones, it may be difficult to main tain alarm ranges and hoses may have to be re deployed as the work zone moves forward.
His team recommended hoses be placed within 225 feet of an alarm device, compared to the manufacturer’s range of 1,000 feet. The team also recommended using three or four alarm units to enhance the warning sound in the work area, as the volume of a single alarm (60 to 70 dBA for five or six seconds) may not be sufficient.
They also discovered that the alarm units don’t perform well if placed on the ground, but that the magnet on each unit makes it easy to attach them to any metallic structure or vehicle at a height of 4 feet or higher.
Khan and his team did not measure time-delays for each device, but Khan noted that “the time involved when a device is activated and when the alarm goes off was almost imperceptible, hence we decided it was sufficient for the needs and in the context of work zone application.”
“One unique feature of WAS is the personal safety device (PSD) workers can carry in pock et or on their body to provide audible and vi
bration warnings that an incursion has oc curred and they should take evasive action,” Khan said.
Khan's team tested the WAS device in an ac tive work zone on westbound U.S. Highway 50 (65 mph speed limit). The project entailed a closure of the four-lane freeway’s shoulder so crews could repair some fencing. The crew de ployed three sensor hoses parallel to the move ment of traffic right where the closure was at the start of the work zone. “We had recom mended they place them diagonally in the clo sure, but the workers actually deployed it this way because they thought it would be more ef fective given the nature and speed of traffic at that location,” Khan said.
Setup of the four alarm units at various lo cations (two on one truck, one each on two other trucks) took only five minutes. The crew reported that deployment, operation and re trieval were easy. “A lot of them also liked the flexibility of the device and the ability to place it wherever they’d like,” Khan said.
During the operation of WAS, there were five false alarms, four of which were the result of one worker accidentally pressing a button on his PSD and one from a worker accidental ly stepping on the hose.
2. SonoBlaster
According to Khan, SonoBlaster is essentially a pressure horn activated by a CO2 cartridge that can be mounted on traffic cones, drums, delineators, a-frames and other barricades. “When the cartridge is punctured, such as
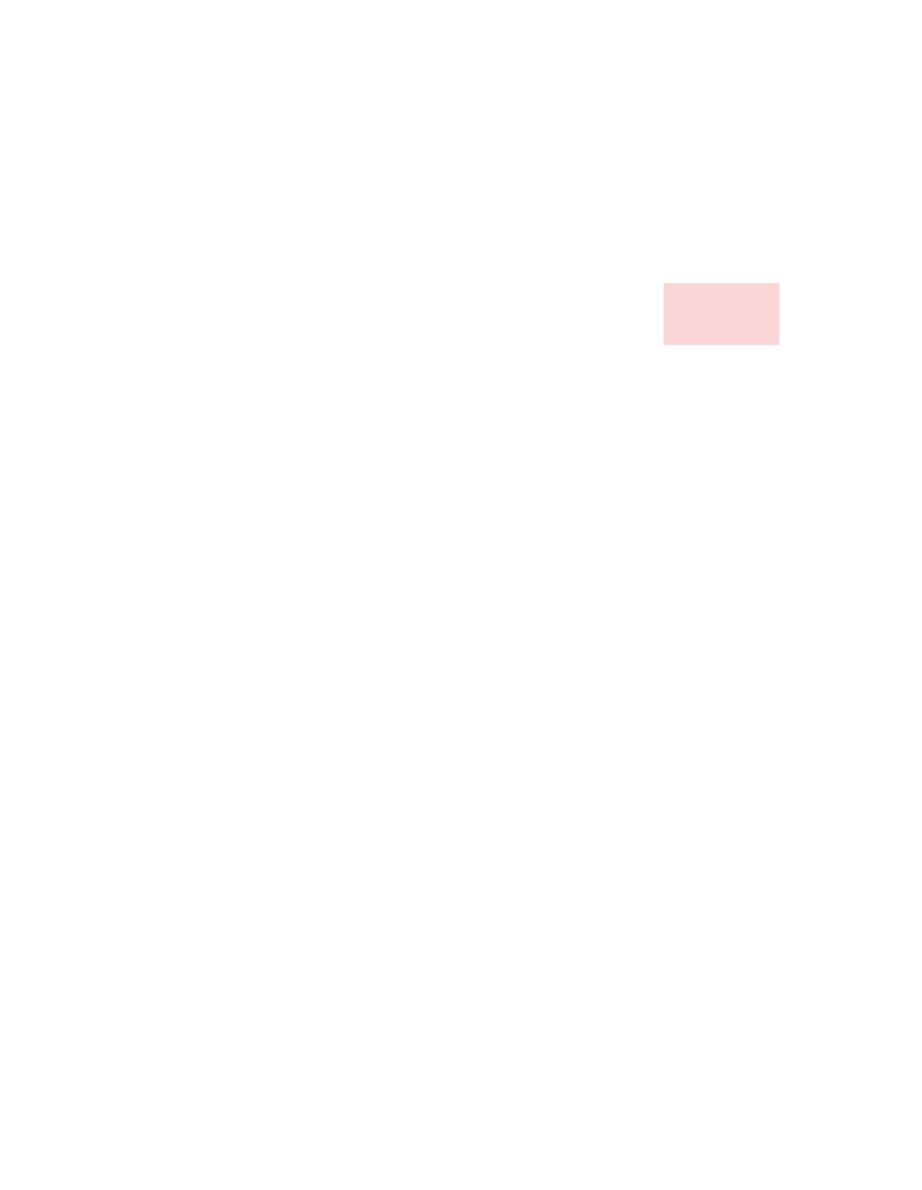
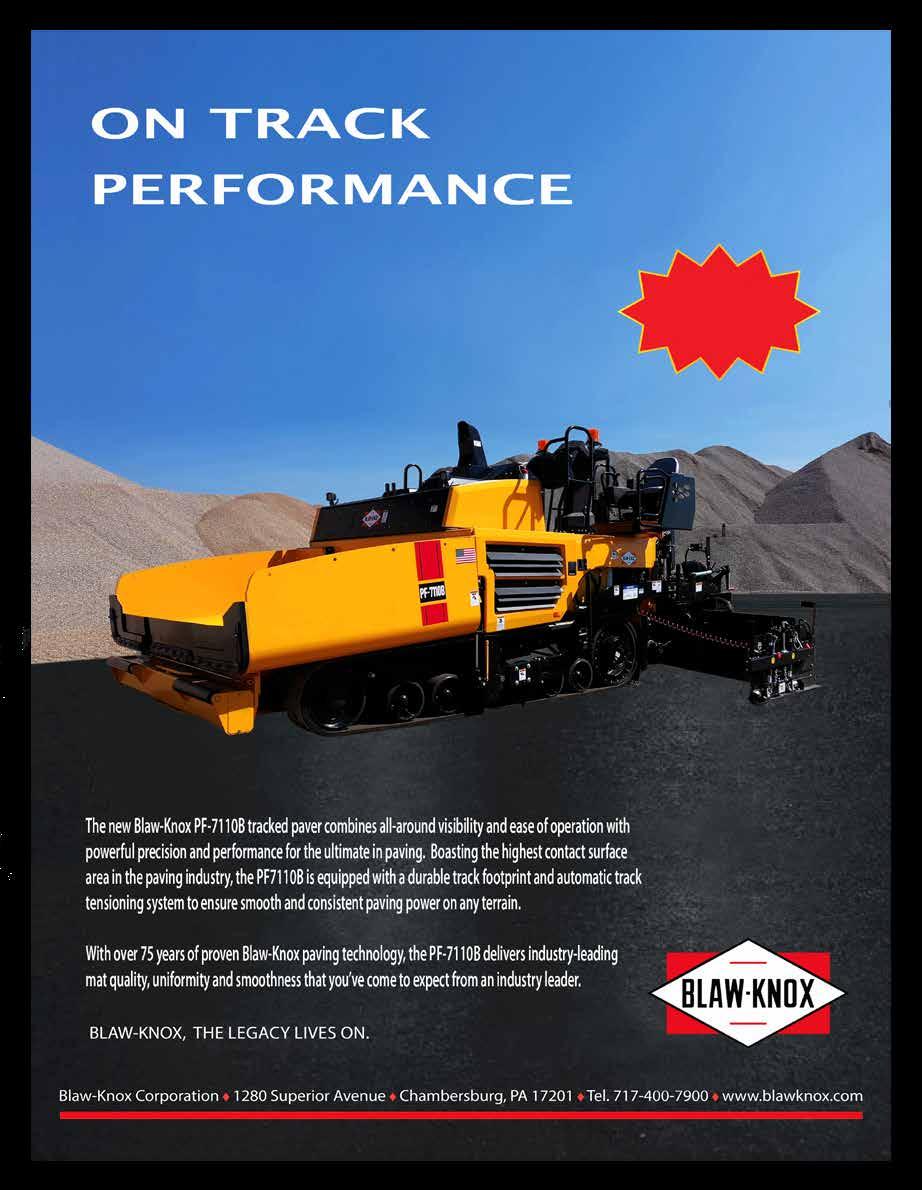
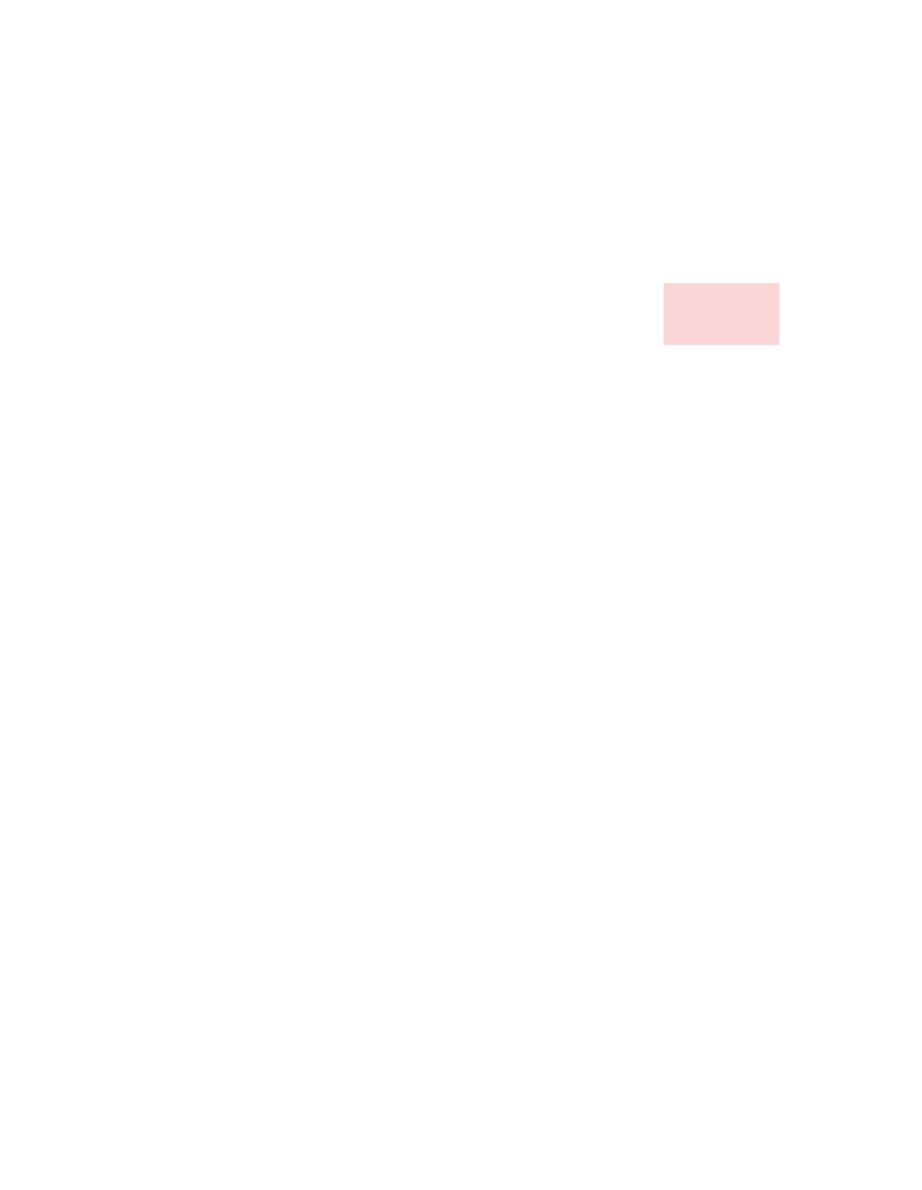
when a vehicle hits a cone that SonoBlast er is installed on, it releases a pressurized gas, which blows the horn to warn work ers,” he said. The audio alarm sounds at 125 dBA, by far the loudest of the devices Khan’s team tested, for anywhere between 15 and 90 seconds depending on how the cartridge is punctured.
“There’s no need for batteries or charging, but the coverage is limited to cones on which SonoBlasters are installed,” Khan said, add ing that installation takes some time. Once the Caltrans maintenance crew Khan’s team taught to install the devices had gotten fa miliar with the process, each device installa tion averaged 10 to 12 minutes. When Khan’s team conducted trials with the device, 16 were successful and four failed as a result of improper seating of the CO2 cartridge. Furthermore, it’s also possible to trigger the alarm when deploying or clearing cones. “There’s a switch that has to be turned on to arm the unit and once turned on, if the cone tilts, this can trigger the alarm unit.”
The researchers also discovered that cones equipped with SonoBlasters could not be transported in two rows at the back of a cone body truck, though the cones can still stack on top of one another for deployment from the front of a truck.
SonoBlaster was deployed on a live work zone along eastbound U.S. Highway 50. It was intended to be deployed in the ramp closure area of the project, but when the project supervisor decided the ramp didn’t need to close down on the day of testing, the crew deployed SonoBlasters along the lane closure portion of the project but stopped after only arming three units.
“Very quickly the workers decided it was not a good idea because of exposure to traf fic,” Khan said. Ultimately, Khan’s team found that SonoBlasters may only be suit able for specific types of work zones, such as ramp closures.
3. Intellicone Incursion Prevention and Warning
The Intellicone Incursion Prevention and Warning (Intellicone) system consists of a Portable Site Alarm (PSA) and lamps in stalled on the tops of traffic cones. “When a cone is hit and the cone lamp is dislodged, it triggers the alarm, which can warn the workers,” Khan said. This results in a visu al alarm (rotating lights on the cone lamp) as well as a three-tone audio alarm of 70 to 90 dBA for 30 seconds. “We found that to
be sufficiently loud, especially if you utilize multiple alarm units,” Khan said.
The cone lamps connect wirelessly with each other and the alarm units at a range of up to 100 feet, “so you can provide as much cover age as you would like as long as you ensure the maximum distance between two units is not more than 100 feet,” Khan said. He also not ed the ability for two alarm units to connect to each other via the cellular network at an un limited range, “but obviously that depends on the availability of cell phone coverage.”
The Intellicone system also offers broader work zone management features such as an online management dashboard and mobile alerts.
Ten Intellicone lamps were deployed in a work zone on westbound U.S. Highway 50. “Some workers shared concerns about expo sure while deploying the cone lamps,” Khan said, adding that the team is discussing best practices for safe deployment. However, they considered deployment and utilization of the system easy, and the PSA setup and con nection took about two minutes.
4. Intellicone Single Sentry Beam
The Intellicone Single Sentry Beam porta ble laser (Intellicone Laser) is a device that shoots a laser beam at various distances (set by the user) between 35 and 110 feet. Any disruption of the laser beam triggers the same PSA unit used in the Intellicone In cursion Prevention and Warning system.
Although the Intellicone Laser provides more continuous coverage than the other Intellicone system, Khan said, the range of 35 to 110 feet is limiting, especially if laser deployment is desired parallel to the mov ing traffic, and considering that multiple lasers cannot be connected to extend cov erage. However, the limited range makes sense; “That’s to prevent any accidental ac tivations if you want to deploy it on a sin gle lane or limited space,” Khan said.
The Intellicone Laser has a battery life of 120 hours.
The research team observed that the la ser should be within 175 feet of the PSA,
SAFETY SPOTLIGHT
which is less than the manufacturer’s range of 250 feet. Khan said a single laser/alarm pair might not be sufficient for high speed or longer work zones and that multiple pairs might be required to provide ade quate coverage and warning.
Despite the crew’s concerns that the system might not provide ample warn ing, they did find the system easy to de ploy, operate and retrieve. During the live work zone test on eastbound Highway 50, the crew placed the laser perpendicular to oncoming traffic after initial setup/range configuration and the PSA on a truck in the work area.
5. AWARE Sentry
The AWARE (Advanced Warning and Risk Evasion) Sentry is a radar-based system with a 15-hour battery life that monitors nearby traffic speed within a range of 600 feet to predict potential incursions. “If it assumes a high probability of an incursion, it triggers an alarm that warns workers and drivers,” he said. The alarm includes an audio alarm that sounds somewhat like a police siren and a visual alarm of flashing white and amber lights.
If a vehicle is traveling slightly above the speed threshold (set manually by the oper ator), AWARE will alert the driver to slow down. If a vehicle is traveling significant ly faster than the speed threshold, AWARE will alert both the driver and workers.
“This cuts down on any false alarms which might make the workers immune to these alerts,” Khan said. “Not only does [the sys tem] warn workers and drivers, but it’s also the only system that doesn’t have to wait for an incursion to occur.”
LEARN MORE
These devices are sold at a variety of traffic control suppliers. Contact your local or regional safety device distributor and ask for the system by name. Let them know you saw the product detailed in AsphaltPro Magazine. This article will appear on theasphaltpro.com under the Safety Spotlight department for easy reference.
BUILT TO CONNECT
Efficiency and Productivity
Designed with safety and operator comfort in mind, the SB-3000 Shuttle Buggy ® material transfer vehicle features adaptive cruise control, bright LED lighting, four-wheel steering for easy transport and ground-level maintenance access for added convenience. Operators can rely on clear sightlines and the ground operator is safely protected inside the structure of the machine. The Roadtec SB-3000 is the perfect blend of traditional craftsmanship and modern technology.
Scan to learn more about the SB-3000.

AWARE Sentry also comes with a personal safety device workers can carry to provide an audio and vibration alarm if an intrusion occurs. Furthermore, the system can record a short video anytime the alarm is triggered for later review.
The speed threshold is set by the user via a mobile app. Khan said the crews would have preferred the option of configuring the Sentry directly from the device. Setting the right speed threshold is particularly im portant to the system’s effectiveness to min imize false alerts.
When AWARE Sentry was deployed in an active work zone, a flagging operation on the two-lane Highway 16 (55 mph speed limit), the initial speed threshold of 35 mph was too low. “We were having a lot of triggers because so many cars were traveling faster than that,” Khan said. “Anytime this system is deployed, it’s critical to make sure the system is set up
properly for the traffic flow and speed.” Prior speed information would be useful in appro priately setting the thresholds.
THE BOTTOM LINE
According to a survey Khan’s team conduct ed after the crew training but before the ac tive work zone deployment, the crew rat ed the WAS, Intellicone and Intellicone La ser as the most effective in mitigating work zone crashes. However, the crews generally reported that they thought all devices would increase work zone safety. “This was reflect ed in discussions with them also, that any device or system that can provide a warn ing to workers or drivers would be beneficial given the safety issues they face every day in these work zones,” Khan said.
Ultimately, Khan’s team uncovered several key takeaways. For example, the importance of designating a supervisor or lead worker to take responsibility to make sure the system is deployed and used correctly.
Another key takeaway was that certain systems are best suited for certain locations.
For example, they found the AWARE Sen try is ideal for flagging operations and slow moving traffic. “Detailed information about the active work zones where the systems are to be deployed is critical to ensure the right devices are utilized at the right location,” Khan said.
Khan’s team tested these five WZIA sys tems in active work zones with high-speed traffic, but in the future plans to test them in work zones with lower traffic speeds to eval uate their performance in various types of traffic and work zone conditions. Khan said some concerns with deployment and ex posure in the initial active work zone tests might not be an issue at sites with relatively lower speed limits, “as such the results may vary in the future with further tests.”
Next, Khan and his team plan to perform additional testing in active work zones, con duct further surveys with Caltrans crews who have used the systems, coordinate with manufacturers on the team’s recommenda tions, and investigate new devices such as Guardian Cone.
ON THE ROAD TO NET ZERO EMISSIONS, WE CAN HELP YOU FIND YOUR WAY.
Are you exploring NAPA’s climate challenge, but unsure of your navigation? We can help you take at least one step forward — by replacing your tank heaters, hot oil heaters, fuel oil preheaters, and distributor truck heaters with our zero-emission, 100% efficient, Lo-Density® drywell-style electric heat.
Check out our new operating cost calculator at processheating.com!
www.processheating.com
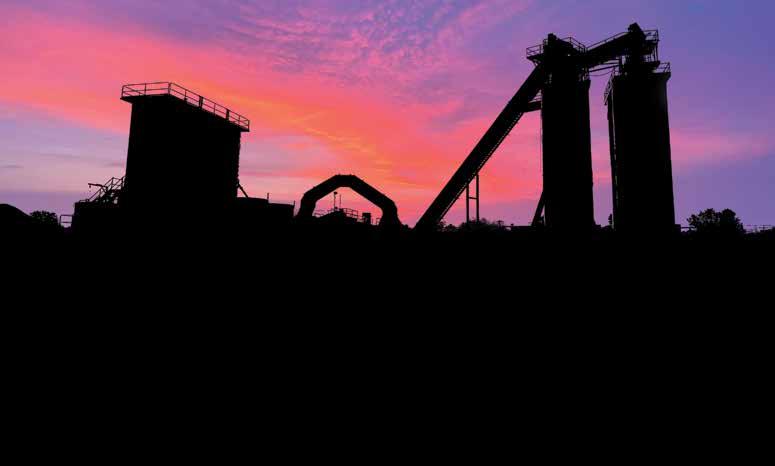
PaveScan® RDM 2.0
PaveScan RDM 2.0 is ideal for uncovering inconsistencies that occur during the paving process, helping to avoid premature failures such as road raveling, cracking and deterioration along joints.

IMPROVE QUALITY Quickly assess the quality of pavement during the paving process. Finally, you can fix low density issues related to cold mix, paver stops and breakdowns.
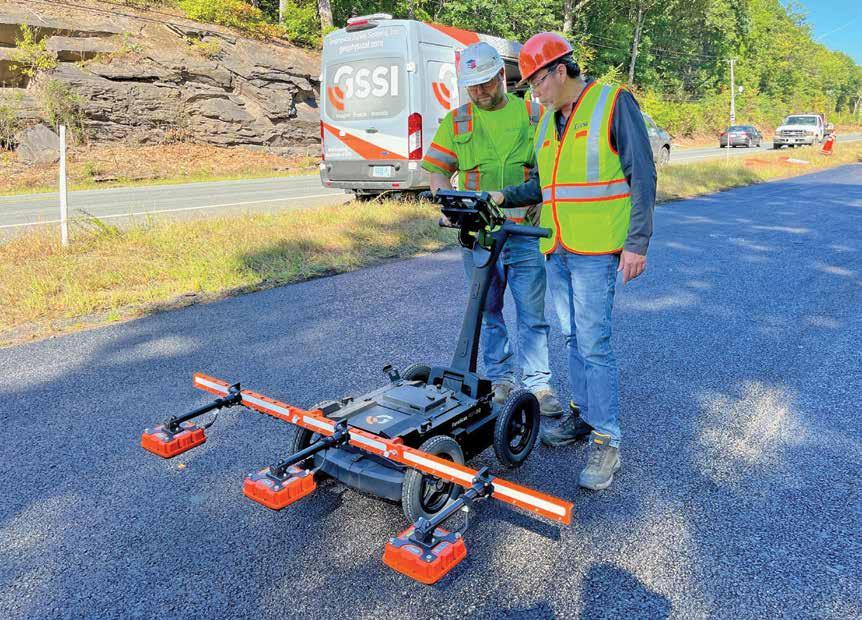
IMPROVE LIFE SPAN Detect problems to help avoid such premature failures as road raveling, cracking and deterioration along longitudinal joints.
IMPROVE SAFETY Reduce the need to core and expose fewer workers to the dangers of work zones.
THE POWER

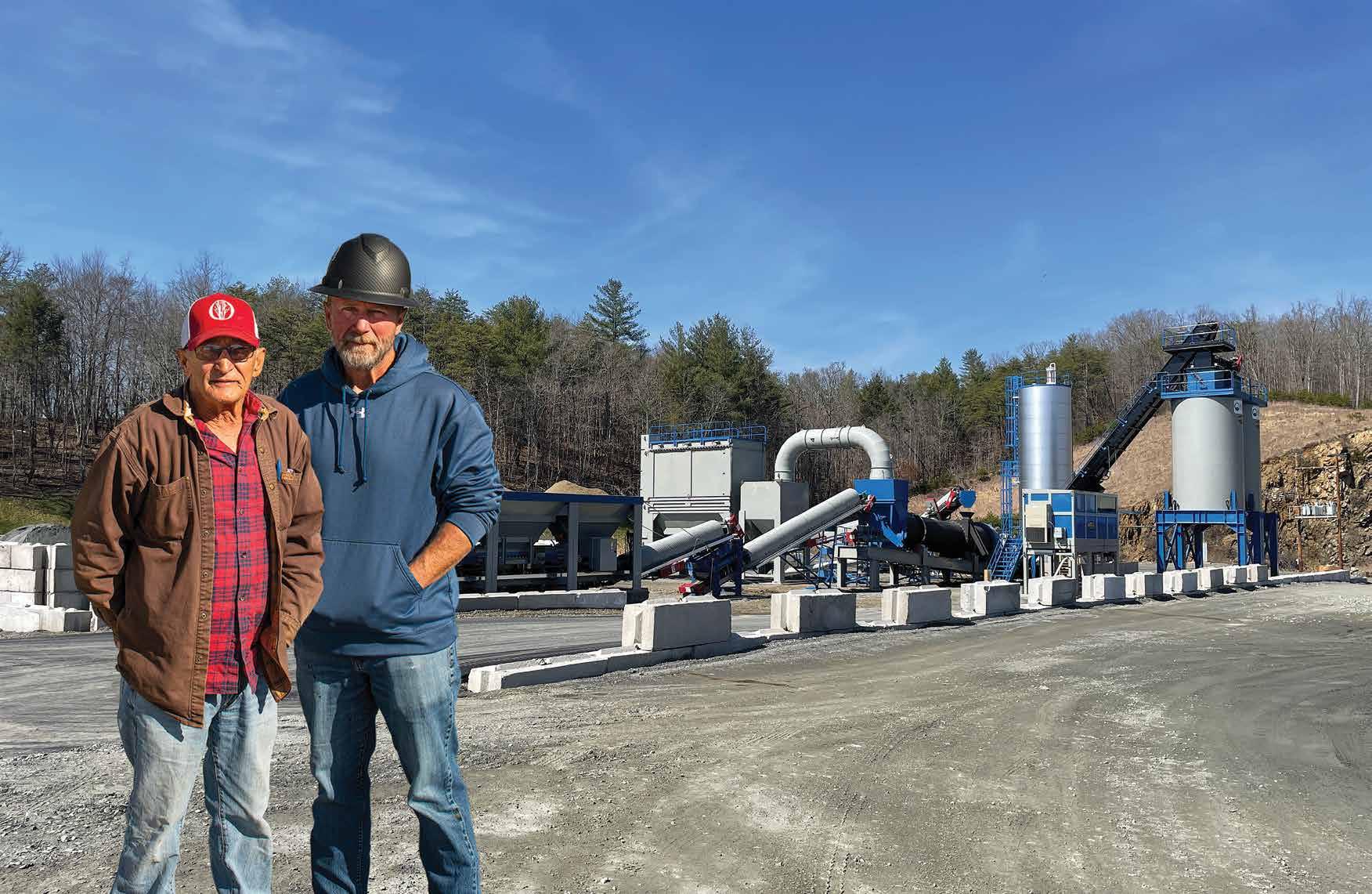
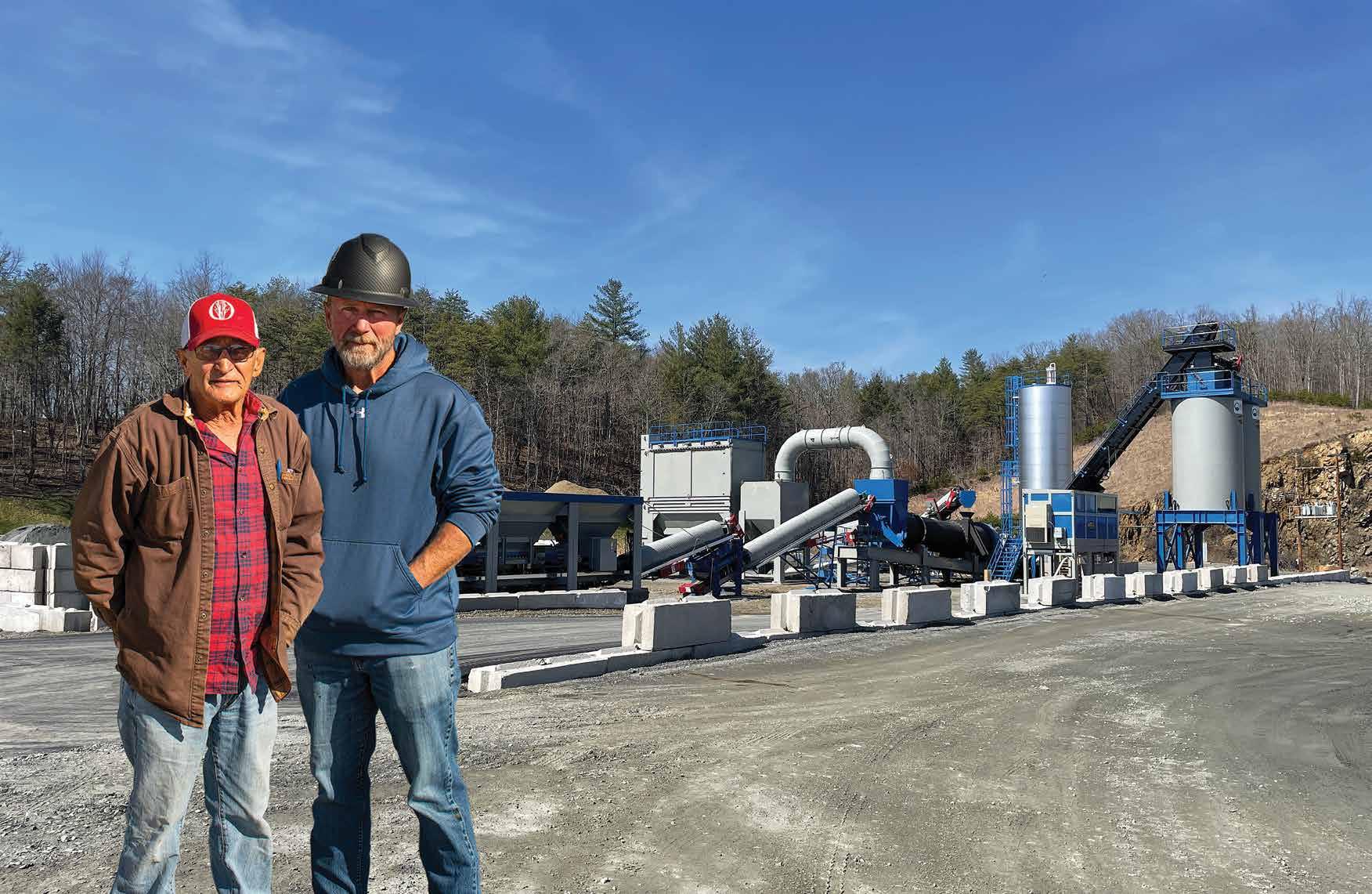
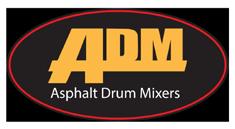
Zero-Speed System Fits Reference Device Category
Surface Systems and Instruments Inc. (SSI), Larkspur, California, col lected profile data under multiple conditions to replicate acceleration, decel eration and stopping during a data collec tion rodeo for the National Cooperative Highway Research Program (NCHRP). The scenarios selected tested the accuracy and repeatability of the Zero-Speed Iner tial Profiler under various conditions.
The SSI Zero-Speed inertial profiler uses multiple sensors to collect data over a range of 0-100 miles per hour (mph). This eliminates the collection speed floor and speed dropouts, which can introduce Interntional Roughness Index (IRI) error for project and network level roads. The Zero-Speed Inertial Profiler is designed to eliminate the noise of accelerometer drift over time while collecting an accu rate profile at any speed, even through stoppages.
NCHRP 10-106 testing was created to learn more about the AASHTO r56 equip ment certification. SSI took this opportu
nity to collect three stop-and-go scenar ios plus additional constant speed runs with traditional inertial profilers. All runs were analyzed for repeatability and accu racy against well-known walking-speed inertial profile reference data. The three scenarios—plus constant-speed collec tions—were:
Six low speed runs at 10 mph for ana lyzing the Zero-Speed system as a refer ence device;
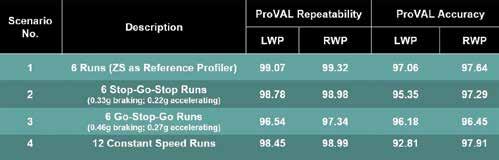
Six Stop-Go-Stop runs (with no run up or run out, accelerate to 30 mph during collection);
Six Go-Stop-Go runs (start collection at 50 mph, stop in middle of track, accelerate to 30 mph to end); and
Twelve constant speed traditional iner tial profiler collections (six at 50 mph, six at 30 mph).
The requirements for an inertial profiler to be compliant with American Associa tion of State Highway Transporation Offi cials (AASHTO) r56 are 92% repeatabili ty and 90% accuracy. The Zero-Speed de vice achieved a passing certification score under AASHTO r56 for each of the above scenarios (see Table 1 for data).
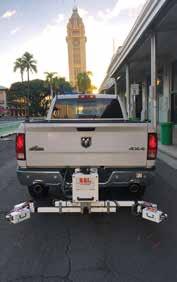
Table 1. MS NCHRP 10-106 Repeatability and Accuracy Data
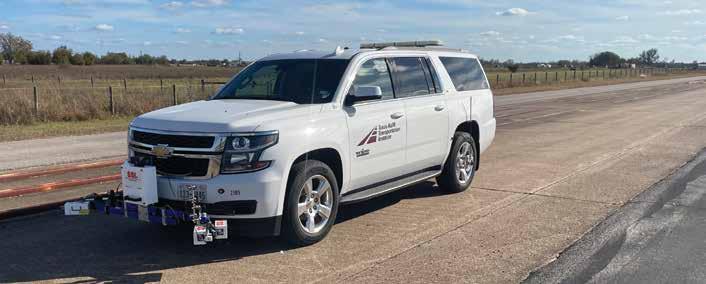

The fourth, constant-speed scenario was collected in the left wheel path (LWP) on the second day of testing; the walking pro filer reference data was collected on the first day. The inertial profilers and the Ze ro-Speed had IRI values of around 90 inch es per mile where the walking profiler had a reference IRI of 94 inches per mile. The sur face may have changed, which may explain the discrepancy between the LWP accura cy and the first-day, right wheel path (RWP)

Runs
accuracy of almost 98%. This may highlight the importance of collecting reference data at the same time or as close to the time of the certification as possible.
REFERENCE DEVICE LABEL
For a device to be considered a “refer ence device,” the system must have three runs that are at least 98% repeatable against itself. Most department of trans portation (DOT) certification tracks will
make multiple runs in each wheel path with their walking reference device and compare them for repeatability to con firm the runs are similar to each other. Repeatability in the Profile Viewing and Analysis (ProVAL) app is a function of profile amplitude and trends. It consid ers more than the ride value number so that the elevation profile is the driving comparison metric.
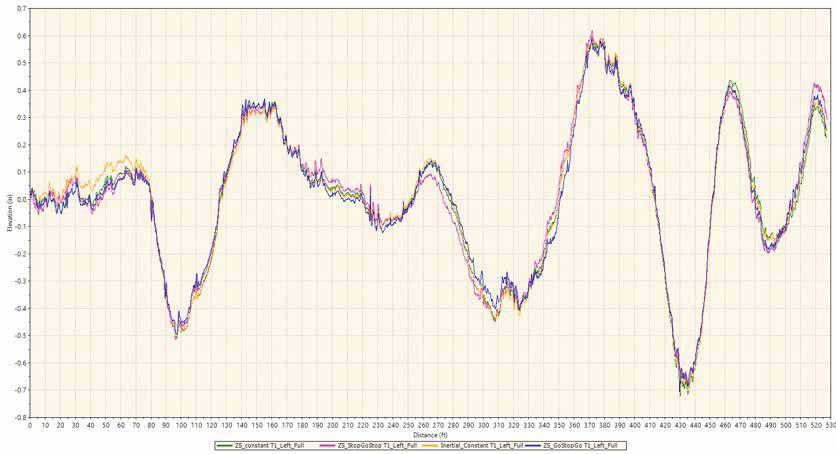
A 4 - day training and technical conference
Join us for Hotmix University in Louisville, Kentucky. During the intense exchange sessions, participants enjoy a combination of lectures, and hands on workshops on actual equipment.
PLANT MANAGERS are interested in making their plants run better while maitaining maximium profitably. Other topics include:

Industry changes and trends which require Plant Response/Modifications.
Tuning Plant Asphalt Automation to achieve 100% End Results and Project Bonus Pay.
Importance of Combustion and Air Systems to Achieve Production Rates.
Benchmarking and Measuring Plant Performance.
PLANT OPERATORS will invest half of their course time at our manufacturing facilities. The other half of the course time will be invested in learning via classroom-style presentations. Topics include:

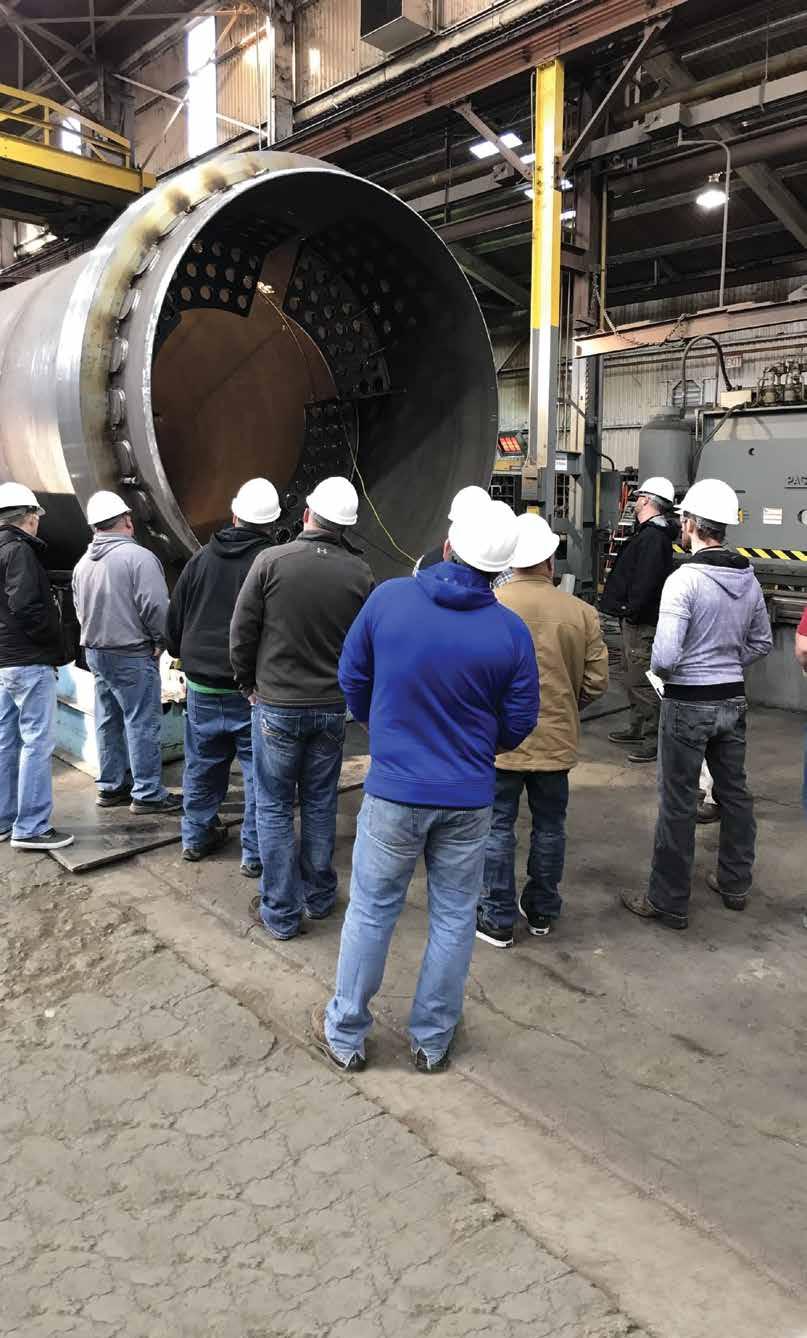
Specifies where the Hot Mix Asphalt Plant fits into the entire business operation including the management of aggregates, liquid A.C., paving, and quality control.
Dr ying Systems: Alignments, lighting, and troubleshooting.
Slat s & Silo System monitoring and wear-reduction.
Plant Automation and Multiple Liquid Blending.
Scenario 1. Plot vs Speed: Zero-Speed Reference Profiler Collection


Scenario 2. Plot vs Speed: Stop-Go-Stop Collection (No Run Up or Run Out)

Scenario 3. Plot vs Speed: Go-Stop-Go Collection
Scenario 4. Plot vs Speed: Constant Speed Zero-Speed System Collection

Table 2. Reference Device Repeatability Data
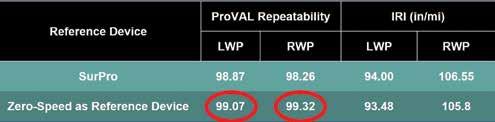
The Profile Viewing and Analysis (ProVAL) engineering software application is a product sponsored by the U.S. Department of Transportation’s Federal Highway Administration (FHWA) and Long-Term Pavement Performance Program (LTPP). It’s designed to let users view and perform analyses including, but not limited to: ride statistics, profilograph simulation, profiler certification, smoothness assurance modeling (SAM), and so on.
The SSI Zero-Speed device achieved ref erence level repeatability and introduced a concept of using the Zero-Speed device as a faster way to collect baseline reference pro files for certification tracks. More data is re
quired to progress this methodology, but the data for the Zero-Speed as a reference device was proven on the Mississippi track with the NCHRP 10-106 project.
The benefit of using the Zero-Speed system as a reference is the speed of collection; it may reduce reference collection time by an order of 15. The Zero-Speed data was collected at 10 mph (15 feet per second) compared to a walking profiler, which usually collects under 2 feet per second. The SSI Zero-Speed system also cancels vehicle motion and dynamics,
lessening the susceptibility of the system to operator-induced error.
This testing shows the SSI Zero-Speed In ertial Profiler is a compliant method of collec tion data throughout the speed range of 0-100 mph and through stoppages. The Zero-Speed system can also be used to collect data with out run up or run out distance; a highlight for tightly constrained projects such as airfield paving.
For more information, visit https://www. smoothroad.com.
Let’s grow the future of asphalt.
At Colorbiotics, our soybean-based science is changing the asphalt industry just as much as it changes the molecules inside recycled asphalt. But having the best science in the business only makes a difference if we have the best people, too.
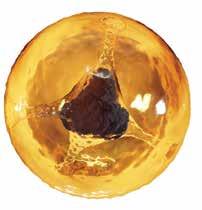
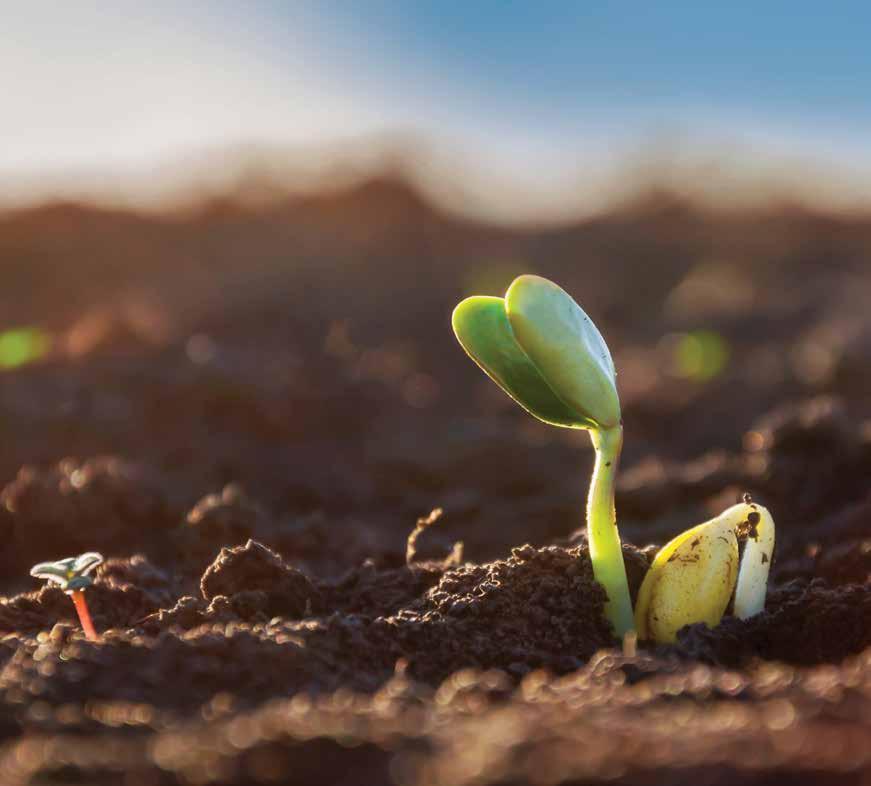
We are looking for sales people to join our team — so let’s talk about your future and get to growing together.
Give us a call: 888-663-6980 | Apply today: invigorateasphalt.com
Colorbiotics is a registered trademark of MBCC Group. © 2022 MBCC Group. All Rights Reserved.
Scenic Mountain Road Gains Smoothness with CIR
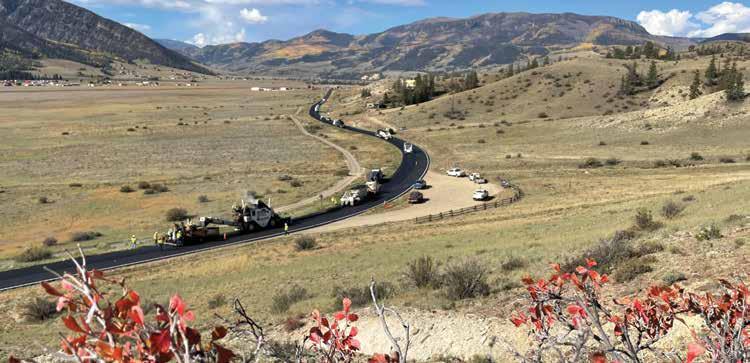
Prior to 2022, the 43-mile section of Colorado’s State Highway 149 between Creede and Lake City had not seen any pavement surface treatments in more than 20 years, and up to 40 years in some sections.
After passing through the historic mining town of Creede, CO-149 winds through the San Juan Mountains before passing through Spring Creek Pass (elevation 10,901 feet), Gunnison National Forest and Slumgullion Pass (elevation 11,361 feet) and descending into the town of Lake City.
However, the existing pavement of the scenic highway had reached the end of its useful life. According to Colorado Department of Trans portation (CDOT) Region 5 Materials Engineer Tim Webb, the pave ment consistently contained at least ¼-inch wide and 4- to 5-inch deep cracks (primarily transverse) throughout the 43-mile span between Lake City and Creede.
“The driveability life of this stretch of highway was zero to one year,” Webb said, based on a condition-based index system within CDOT’s statewide pavement asset management approach of quantifying sever al surface distress criteria. “The resulting existing ride was not smooth and there was no useful life remaining in the existing surface.”
When CDOT received special senate bill funding for rural roads, Webb’s Region 5 teamed up with neighboring Region 3 to pool funds to repair a large section of CO-149 across the border of the two regions.
“We don’t always have such funds for a rural road like this, but that enabled us to cover a significant number of miles on this one project,” Webb said. With a fairly short paving season and the harsh winter con ditions in Colorado, Webb said CDOT prefers to complete projects in one construction season, “especially in mountain passes like where this project is.”
With such a large project and limited time, CDOT opted to perform cold in-place recycling (CIR) on this job. “A faster construction method like CIR helped us achieve that goal because it allowed us to resurface 40 plus miles in a single construction season,” Webb said.
CIR is a process that cold mills and recycles the top 2 to 5 inches of asphalt using a continuous train operation. According to the Pavement Preservation & Recycling Alliance (PPRA), CIR reduces construction times by anywhere between 20 and 40% compared to conventional re construction methods.
Furthermore, the conditions of the existing pavement were a perfect fit for CIR as a treatment. “When you have older pavement that has cracks that are primarily top-down but are pretty severe, that’s a perfect candi date for CIR,” Webb said. The CIR on CO-149 recycled the top 4 inch es of the existing pavement, “basically eliminating all of those cracks,” Webb said.
The sustainability aspect of CIR was another selling point to CDOT, as the process reuses 100% of existing materials and can reduce greenhouse gas emissions by up to 90%, according to PPRA.
Discover the strength of the most versatile, durable, and reliable crushing equipment on the market today. Take on even the toughest applications with confidence. Experience unparalleled parts and service support, 24/7. Let Eagle Crusher keep you up and crushing, year in and year out.


TRUST THE STRENGTH OF EAGLE CRUSHER
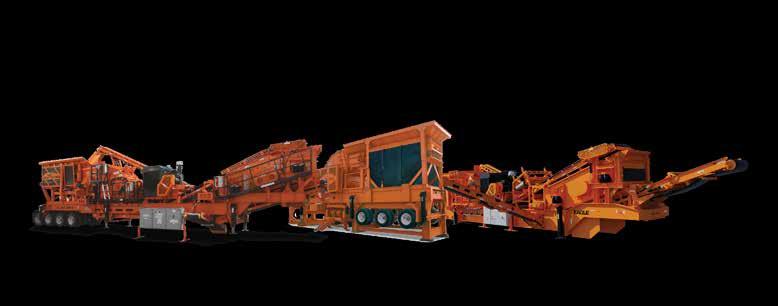
“We strive to use recycling methods when it fits the existing road way conditions,” Webb said. Webb shared that using the existing ma terials in place negated the environmental impact of a project that would transport new materials to the site from a remote location.
ABOUT THE PROJECT
The two sections of the project included 22 miles between the town of Lake City and the north side of Slumgullion Pass and 19 miles south of the pass to the town of Creede, for a total of 82 lane miles. The project was divided in two sections because the section of the road passing through Slumgullion Pass had received a more recent resurfacing treatment.
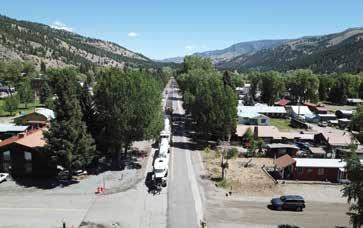
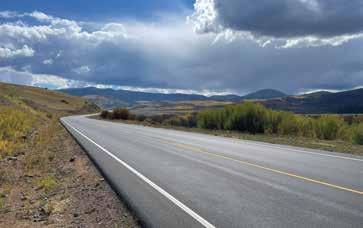
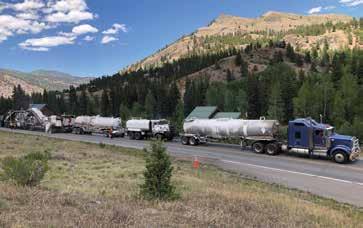
United Companies, Grand Junction, Colorado, a subsidiary of CRH North America and the midwestern extension of Staker Parson in Utah, was the prime contractor on the project.
“The majority of CIR bids on the western slope are installed by my crew,” said United Paving Foreman Ramon Chavez. When United won a bid on its first CIR project eight years ago, Chavez’s crew was the one tasked with the new challenge. “At that time, we thought we drew the short straw, but it turned out to be the long straw.”
To date, his crew has performed six CIR projects in the last eight years. “My crew is probably the most experienced crew in western Colorado with this process.”
United subcontracted the recycling portion of the project to Cough lin Company Inc., St. George, Utah. The 101-year-old company has been milling asphalt since 1992 and expanded into asphalt recycling in 2006. Today, Coughlin has 23 roto-mills and three recycling trains that trav el throughout the western United States, including Arizona, California, Colorado, Idaho, Nebraska, New Mexico, Nevada, Oregon, Washington, Wyoming and Utah.
Coughlin frequently works with United, said Coughlin Safety Manag er Stephen Steed. “They’re a great outfit to work with,” he said. “We can’t compliment them enough.”
Recycling on the project began in May and the new asphalt overlay was completed in October. Coughlin milled to a depth of 4 inches at a full-lane width of 12 feet, 6 inches wide with a production rate of 23 to 25 feet per minute with its Astec (Roadtec) RX 900e. “We have quite a few of those,” Steed said. “They’re very powerful, dependable machines.”
In total, Coughlin recycled approximately 86,000 tons of material.
Coughlin injected a lime slurry into the cutting drum of its roto mill at 1.5% based on weight of dry recycle. “We put lime slurry in there as well to help with the conditioning of that asphalt to be like new again when it’s laid that back down,” Webb said.
Next came Coughlin’s recycle unit, an Astec (Roadtec) RT-500. The impact crusher within the 100% enclosed unit crushed the recycle to size, 1 inch minus, before running it up through the machine’s weighbridge. The material is then dropped into the pugmill where the rejuvenating agent (AC emulsion) is introduced and mixed before it’s dropped out of the pugmill into a windrow where it can be picked up by the paver on the other end of the recycling train.
The RT-500’s onboard computer helps determine the amount of emul sion based on specifications. For the CO-149 job, Coughlin operated in the 3.2 to 3.4% emulsion content range.
“To be successful with the recycling portion of the project requires you to go in and calibrate all the different components to make sure you’re putting the specified amount of emulsion, lime or other addi tives on the job,” Steed said. “You can’t meet the specification if you don’t get the calibration done right.”
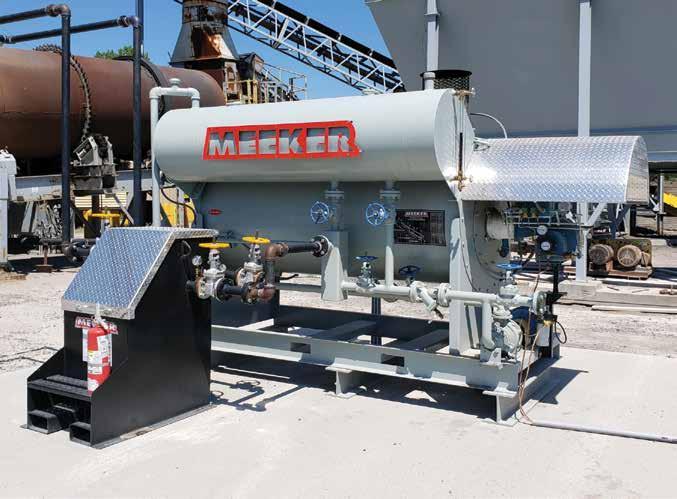
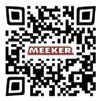
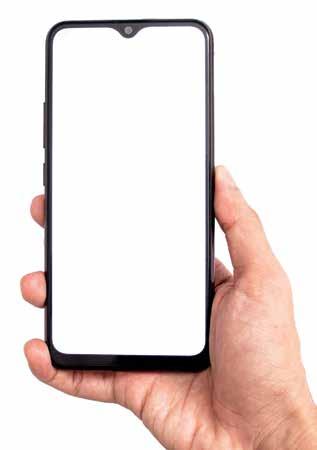
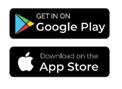



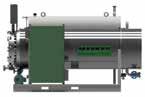
Steed said the most unique aspect of the job to him is its location. “It’s beautiful country out there,” he said, adding that the crew even saw a moose on the side of the road. “The scenery is just unbelievable. You just can’t ask for a better place to work.”
LOCATION-RELATED CHALLENGES
According to Webb, CDOT doesn’t perform many CIR projects, but the lion’s share of CIR jobs in Colorado take place on the state’s western slope due to its remoteness.

“The project took a lot of coordination and logistics to get the material out there,” Steed said, adding that teamwork is key to the company’s success on the project. Although using CIR reduced the number of trucks needed to get the required materials to the job site, Steed said “it can still be a challenge when you have to move even the amount of material we did need (emulsion, lime, etc.) at that distance.”
Coughlin located unused gravel pits midway through both ends of the project to use as its staging areas. It set up a couple tanks of emulsion at those sites that could be brought to the recycling train with transfer trailers. Lime slurry was mixed at the staging area and transported to the recycle train by supply tankers.
The remote job also spanned a number of challenging road condi tions, including portions that are narrow, winding and steep. Steed said the south end of the project was fairly easy because it was rel
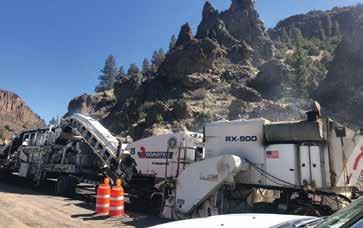
atively straight and flat without a lot of sharp turns. However, the northern side had many narrow areas where Coughlin had to stop traffic entirely to give the train enough room to maneuver.
“There wasn’t much room for traffic on those mountain roads alongside that CIR train,” said United QC Manager David Fife. “The traffic going through some of the canyons was a challenge.”
At one point, the road became so narrow, the recycle train result ed in a one-hour delay to the traveling public. Although it was un fortunate for the traveling public in the short term, Coughlin was assured of the importance of the project to local residents when the recycle train pulled into Lake City.
“You don’t see a recycling train going through the main street of a town very often,” Steed said. “We had shop owners coming out tell ing us how excited they were to see the road getting fixed and how much it means to them.”
COMPACTING COLD IN-PLACE
Because the material changes throughout the project as it’s milled up, the rolling pattern must also change, Chavez said. “With a tradi tional HMA job, you can fine tune everything on the test strip,” he added. “With CIR, it’s like the mix design is changing throughout the entire project.”
Results from the modified Proctor tests performed on material from the project ranged from 110 to 130 pounds per cubic foot. “It’s easy to get density on 130 pounds, but it’s harder to get density on 110 pounds,” Chavez said. “It seems counter-intuitive, but if you’re not able to get heavy densities with the hammer, it tells you that ma terial doesn’t compact well.”
The modified Proctor test is a CIR mix design method (in accordance with AASHTO T 180, Method D) where loose material is put in a cylinder and struck a preset number of times with a 10-pound weight to determine optimum moisture content (OMC) at peak dry density of the material.
To compact the rejuvenated asphalt behind the recycle train the crew started with a breakdown roller (Volvo DD140) running two full passes on the edges and one in the middle, followed by two rubber tire pneu matic rollers (Bomag BW27RHs) until the breakdown roller finished the next section. “That might result in 15 or 16 passes,” Chavez said. Then, United’s Volvo DD120 finish roller passed through to achieve final den sity, which must be 100% of lab compacted density in accordance with Colorado Procedure 53 (CP-53).
“There was a bit of a learning curve early on, but once we got going the process went pretty well,” Fife said. “With CIR, you shoot for different densities based on where you are on the project, so we were monitoring densities behind the rollers with a nuclear gauge to make sure we were compacting to the appropriate percentages.”
This is where the unexpected weather the crews faced became particu larly challenging. Although the weather was often good for the first twothirds of the day, it would get overcast, humid and cool most afternoons and frequently rain, shutting down that day’s production, Chavez said.
“Achieving compaction in such a constantly changing climate was the biggest challenge we faced,” he said, adding that CIR is dependent on

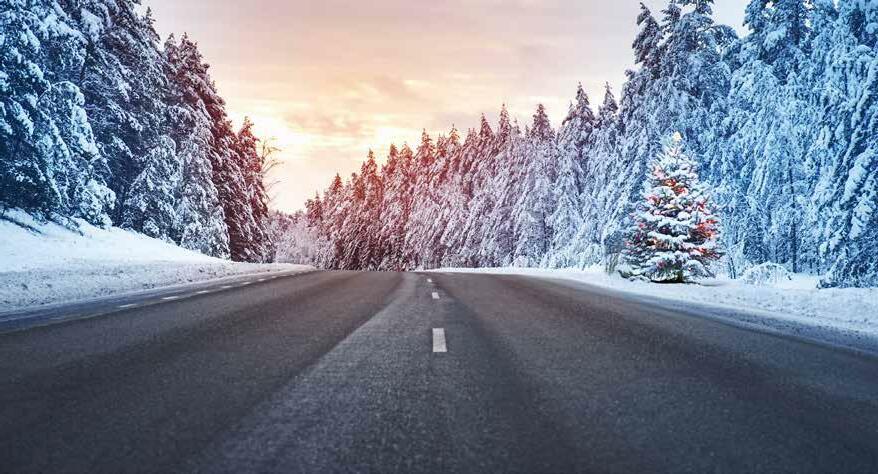
temperature. “It’s difficult to get good densities in the types of weath er we were working in.” Chavez said his crew’s expertise was critical to overcome these weather-related challenges.
“When it comes to traditional HMA jobs, you have this trigger telling you have a certain window to achieve density,” he said. “But with CIR, there’s no set amount of time. So much depends on the weather. You have to understand how the material works to know how and when to roll it. Most of my guys know based on the color of the mat and the feel of it from the rollers if it’s the right time. And that’s what my guys did, and they were able to get compaction throughout the project.”
“We thought the weather might give us problems with raveling, but in actuality, we had very little raveling despite the rain,” Steed said. He attributes a large portion of this to the performance of the AC emulsion used on the project.
“The emulsion we used was an awesome emulsion,” Steed said. “At the end of the day, we could put traffic on that road and it looked like a regu lar hot mix paved asphalt road even though it was recycled.”
EMULSION MASTERS
To determine the chemistry of the emulsion, cores were taken from the road to develop a mix design for the project. Arkema-Road Science, Tul sa, Oklahoma, provided the surfactant, ArrTekk 800 series High Perfor mance chemistry, to make the engineered emulsion used on this project.
During the design phase, several high performance specialty tests outlined in the specification were conducted to establish predictability of the mix for long term performance. The tests included Lottman test CPL 5109 on freeze/thaw, Marshall stabilities, indirect tensile strength for crack resistance and raveling tests to indicate cure time of the emul sion itself. “Ultimately, these tests determine what emulsion content and chemistry is appropriate for the climate conditions of the project,” said Arkema-Road Science Account Manager Jeff Weitzel.
“The raveling test is very important,” Weitzel said. “The raveling test (ASTM D 71 96) is a short-term strength test that must result in less than 2% raveling. This indicates if the material will cure fast enough to allow traffic rolling on it without raveling. You don’t want to build a road out in the middle of nowhere that you can’t put traffic on for a week. You want to put traffic on it that same day the CIR was done.”
Weitzel said Arkema-Road Science recommended that CSS spe cial asphalt emulsion be used on CO-149 based on the emulsion’s early strength build and cure. “This chemistry enables maximum emulsion dispersion throughout the mix itself and provides heavy film thickness, while lowering void content, delivering better rut resistance and better thermal and fatigue cracking resistance,” Weitzel said. “Even with all the thunderstorms and varying temperatures in this mountain region, we still had no raveling or rutting issues.”
The cure time following the CIR portion of the project was a min imum of 10 days, however, poor weather struck again. “We generally like to be paving on it within a couple weeks, but a ton of bad weather up here held us up,” Fife said. However, he added, the CIR still held up really well. “Instead of paving on top of a crumbly old road, CIR gave us a really nice product to pave on top of that I think will be a really nice road for years to come.”
Even without the wearing course, Fife said the CIR alone dras tically improved the smoothness of the road. The Coughlin crew agreed. “The level of smoothness we were able to achieve with the CIR left a much easier job for the paving crew to come back through and pave,” Steed said.
As soon as the weather allowed, United’s paving crew returned to the jobsite to place the asphalt overlay with its Cat 1055F paver. The overlay consisted of a 1-inch leveling course on the Creede side, an ST mix with PG58-28 and a ⅜-inch nominal maximum aggregate. On both sides, the crew placed a 1.5-inch wearing course, an SX mix with PG58-34 and a ½-inch nominal maximum aggregate. The Lake City side contained 30% RAP coming out of United’s pit in Gunnison, Colorado. “On the Creede side, we didn’t have RAP available to us, so that’s a virgin mix,” Fife said.
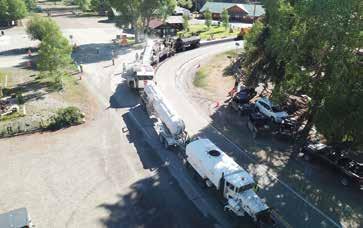
In total, the project required 64,000 tons of the SX HMA.
SMOOTH & SCENIC
Ultimately, both companies and CDOT are pleased with the results of the project. “We were able to remove the severe cracking in the roadway, place a recycled pavement surface without cracks, top it with two lifts of fresh HMA, and give the traveling public a very smooth ride,” Webb said.
By eliminating those cracks, the CIR will not only improve ride ability but also the longevity of the roadway by preventing water from infiltrating the pavement, Webb added. PPRA estimates CIR adds 15 to 20 years of life to that pavement. “They’ve gained quite a few years by putting down CIR under the asphalt overlay,” Fife said. “The CIR and overlay combined should result in a nice road that should last a long time.”
“The job turned out really well,” Steed said. “It’s definitely a big improvement on ride quality.” The average IRI for the north seg ment of the project was 185 before construction began, and now has an average IRI of 65.
In addition to the success of the project, this may be the one of the largest, if not the largest, CIR project in the western United States. “I’ve been doing this for 30 years, and it’s definitely the largest I’ve ever seen in this region,” Weitzel said.
“I’ve always taken pride in my crew’s expertise with CIR,” Chavez said. “To know we’ve been involved in such a history-making proj ect fills me with gratitude.” Steed agreed: “It’s an honor to be able to have been involved in a project of this size, and it’s a very successful project to boot.”
From innovative designs to Caterpillar dealer service and support, Weiler is paving the way to success for contractors across North America. Weiler’s material transfer vehicles, commercial pavers, road wideners, windrow elevators, static compactors, soil stabilizers, rock drills, tack distributors and front mount screeds are engineered with innovative features to increase productivity while reducing operating costs.
Weiler equipment is sold and serviced exclusively at Caterpillar dealers throughout North America.
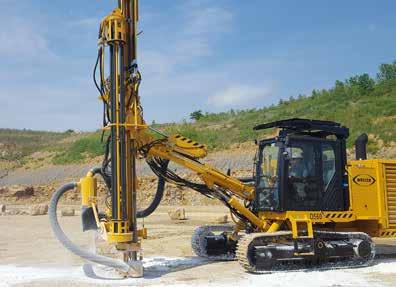
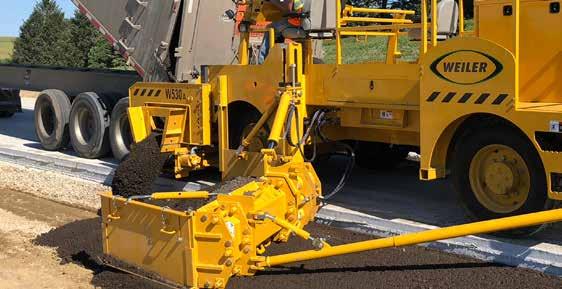

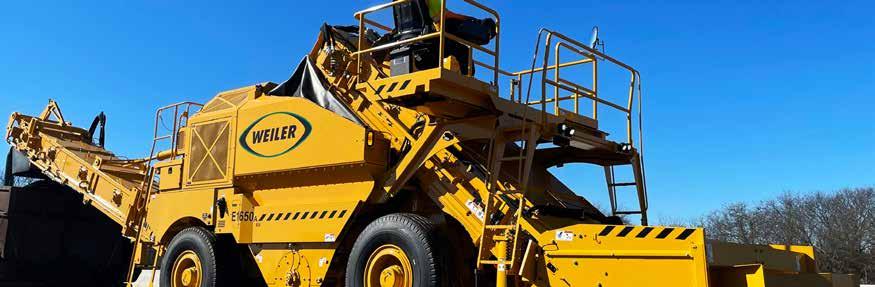
GMI Maximizes Trucks, Fuel, Labor
GMI Asphalt has invested in a new drag, silo and flop chute from ALmix to improve haul truck cycle times and reduce fuel and labor costs.
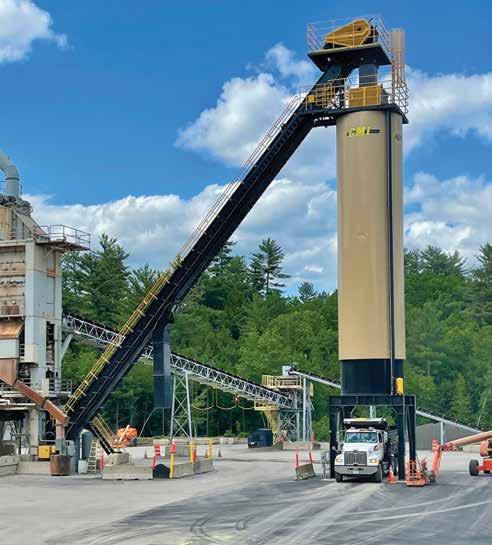
Every five or so years, GMI Asphalt, Belmont, New Hampshire, has made at least one major investment in the growth of the company. From buying oth er construction companies and acquiring its quarry and sand pit in Boscawen, to pur chasing its 6-ton Barber Greene batch plant in Franklin, the company only seems to know one way to go: forward.
“We bought the plant to be more compet itive in our market and to take the next step in GMI’s growth,” said Neil Arruda, gener al manager of GMI Asphalt’s materials divi sion. “With our quarry, sand pit and asphalt plant, we now control the whole process and are able to price ourselves accordingly.”
Through each investment, GMI Asphalt has kept the end goal in mind regardless of the challenges they may face—and they have faced their share of challenges.
“When GMI bought the plant, it had only made 40,000 tons of mix total,” Arruda said. “I can’t even begin to describe the problems we faced in order to get the plant up to state spec and capable of producing 200,000 tons of consistent mix a year.”
For example, GMI invested in a fugitive dust fan to manage high dust content in the mix, as well as a blower and airlock to fur ther control dust content, and a reclaimed asphalt pavement (RAP) system. “It’s been a continuous process of improvements,” Ar ruda said.
Having its own plant has enabled GMI to compete for state work, which was particularly important during the height of the COVID-19 pandemic when the municipal and private work that makes up the majority of GMI’s work was delayed or canceled.
Arruda estimated that 15% of GMI’s book of work in 2022 has been for the New Hampshire DOT.
Then, in October 2021, GMI made perhaps the most significant investment in its plant: a
GMI Asphalt's new drag, silo and flop chute from ALmix enable the company to distribute mix from two points, at the batch plant tower drive-through and the silo. And, for the first time, the plant can store mix as needed.
300-ton silo, 500 TPH drag conveyor and cus tom flop chute from ALmix, Fort Wayne, Indi ana. “We made those investments so we could produce more mix at the plant and also in crease our production and trucking efficien cies,” Arruda said.
BIG SILO, BIG BENEFITS
Having the silo allows GMI to distribute mix from two points, at the batch plant tower drive-through and the silo. And, for the first time, the plant can store mix as needed.
“The silo allows the plant to run contin uously and enables us to fill the silo in the morning or the night before,” Arruda said. He’s also noticed a number of cost savings re lated to GMI’s latest investments. First and foremost, in terms of trucking.
“We went from an average time for a truck in the yard of 35 minutes to less than 10 min utes,” Arruda said. “Just loading the truck used to take 7 minutes from the batch plant. With the silo, we’re at 1 minute, 5 seconds to fully load a truck. That has been particularly
beneficial during the current truck shortage because it enables us to run with fewer trucks. A line at the plant to get loaded is just wast ed money.”
Arruda has also noticed savings related to labor costs as having the silo has enabled the operators to make what they need for the day, store it in the silo, and start shutting down the plant a bit earlier than before.
He also estimates that GMI has saved 5% on its total fuel and electric bills by reduc ing startups and shutdowns. “Being able to continue to produce mix even if there’s not a truck in the yard also allows us to produce a more consistent mix.”
Around the same time that GMI installed the new drag, slat and chute, the company also installed a Libra Self Service Kiosk from Command Alkon so truck drivers don’t have to get out of their cabs to grab their tickets. “That was planned in conjunction with the silo because we needed to get the final location of the silo to see how traffic was going to flow before we could build the building and stand in which the printer sits,” he said. “That’s also reduced our truck times by a few minutes.”
A TALL ORDER
Although the investments have brought big benefits, GMI’s plant location and its tim
ing goals brought on additional challenges. This included difficulties with the layout of the plant, limited space between the batch plant’s legs for the flop chute, and a short timeline to complete the installation.
In fact, Arruda said GMI had signed a contract with another OEM who ended up backing out of the project when it couldn’t figure out how to make the flop chute work. “Then we talked to ALmix, and they were willing to find a way to make it work while offering a competitive price and delivering within our time constraints,” he added.
“We wanted a 300-ton silo because it’s the only one we were installing,” Arruda said, adding that the silo itself is 85 feet. But GMI also wanted a weigh batcher on the bottom of the silo because the layout of the plant made it impractical to install a truck scale.
“That left us with two ways to approach the problem,” said Ryder Harman, ALmix’s sales and marketing manager. “Either we could put the whole silo on load cells or we could build a weigh batcher into the silo.”
Ultimately, GMI opted for the weigh batch silo, and ALmix designed an 8-ton, fully lined weigh pod built on top of three load cells beneath the silo. As the silo dis charges mix into the weigh pod, the pod weighs it and then discharges it into the truck below while safeguarding against mix segregation. It was the more economical option, but it added an additional 8 feet of height to the silo.
The total height of the silo (91 feet, 6 inch es) called for a 36-inch by 116-foot drag con veyor. “We’re no stranger to drags this large,” Harman said, adding that although the con
veyor wasn’t the largest the company has ever made, it is among the largest in recent years. The drag conveyor is powered by a 150-horsepower drive system, allowing it to feed the 300-ton silo at top production rates.
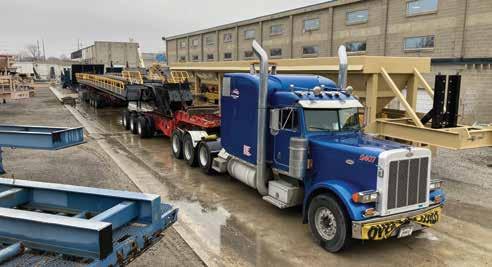
Instead of being supported by stiff legs lo cated midway up the conveyor, this drag con veyor is constructed using cambered bridge beams. “The drag expands and contracts due to the changes in temperature depending on if the plant is running or not, and when you have those legs attached, they don’t allow the drag the range of motion it needs,” Harman said. That’s why ALmix opts for cambered bridge beams on drags of this size. “They're a more expensive approach to constructing drag conveyors, but the strength and cam bering of the beams allows for the conveyor to be quite long and not sag over time with out the need for stiff legs.”
The strength of the silo is derived from structural steel legs, and the 1/4-inch, 100% double welded silo tube is housed within the frame supports. The silo walls are insulat ed and covered with pre-painted aluminum sheeting to keep heat loss at a minimum. Silo top decks are insulated with 10 inches of high-density insulation and covered with diamond decking, toe kicks and OSHA ap proved handrails. A caged ladder is provid ed to access the bird’s nest on the main drag. ALmix also built the silo with 6-foot railings at the top, which is standard for the compa ny’s silos.
GMI's plan to install additional silos in the future meant that even more height was added to the new silo setup. To account for the future addition, ALmix included a chute where a future transverse conveyor can be installed, allowing mix to be diverted to the new outboard silo, making the future instal lation an easier process for GMI.
“When it comes to adding silos and drags to batch plants not originally designed for them, we have a lot of experience with these projects,” Harman said. “We also manufac ture a complete line of batch mix plants, so we are quite familiar with engineering
“WE WENT FROM AN AVERAGE TIME FOR A TRUCK IN THE YARD OF 35 MINUTES TO LESS THAN 10 MINUTES.”—NEIL ARRUDA
LEFT: In early spring, GMI took advantage of rainy days and scheduled any work installing the new equipment that
have otherwise shut down the plant for those days, and as the season progressed, on nights and weekends. MIDDLE: Throughout
process,
plant, average time for a truck in the yard went from 35 minutes to less than 10 minutes, with loadout dropping from 7 minutes to 1 minute, 5 seconds.
plant only had to be shut down for one day, the day the flop chute was installed. RIGHT: With the latest additions
around them. We’ve faced enough challeng es in the past that we knew our tenured staff of engineers would be able to solve these problems, with enough information from Neil and enough elbow grease.”
Around 90% of the mix GMI produces is for its own projects.
A FOLDABLE FLOP CHUTE
GMI wanted to continue to use its batch plant after adding the silo so it would have dual loadout ability. This was particularly chal lenging to achieve, given the drag conveyor’s width of 36 inches and the 40-inch clearance between the batch plant’s legs. GMI was also looking to limit any modifications to the orig inal plant, including the tower legs where the drag would need to be positioned.
“We could see right away why other com panies might have been scared off by the flop chute in particular,” Harman said. However, ALmix’s engineers were up to the task, land ing on a flop chute design with two folding functions.
First, the flop chute folds out from be tween the batch plant’s legs. Then, the chute extends using pneumatic cylinders allowing the chute’s opening to expand up to the dis charge gates of the batch tower to catch the
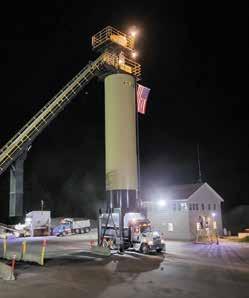
mix. The flop chute can fold up and into the side of the drive-thru area, allowing trucks to load out from the batch tower when the chute is not in use.
“Being a larger batch plant, the discharge opening is quite a bit larger and you have to of course cover that whole opening,” Arruda said. “They also had to make sure the chute could take the larger drops that come out of a 6-ton batch plant and funnel it down into a 30-inch opening.”
With the photos and measurements Ar ruda provided, “everything ended up fitting perfectly without any modifications to the ex isting plant,” Arruda said.

“[Arruda] was a champ,” Harman said. “He got us every single measurement we needed and helped us every step of the way to ensure that our designs would meet GMI's needs and that everything would fit perfectly.”
Arruda has worked at GMI for 15 years. “I started as a truck driver and have grown my way through the company since then.”
A TIGHT TIMELINE
In early spring, GMI took advantage of rainy days and scheduled any work installing the new equipment that might have otherwise
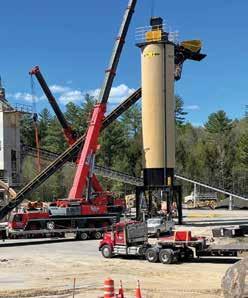
shut down the plant for those days, and as the season progressed, on nights and weekends.
It was also a struggle to find subcontractors to perform some of the work related to the installation of the silo. “In the end, we end ed up self-performing a lot more than we had originally intended,” Arruda said. This in cluded the concrete work, dirt work, plumb ing, and erecting the silo and drag. “We had a tight timeline and didn’t want to wait for la bor to become available once we got our per mits in place. Doing that work ourselves gave us more control.”
Once all was said and done, the batch plant had only been shut down for one day, the day the flop chute was installed. “Other than that, the plant was running the whole time the silo and drag were being erected,” Arruda said.
“This was a fun project for us to be a part of,” Harman said. “We like to be involved in the decision making process, see the chal lenges they’re facing, and build custom solu tions. Being able to design and build bespoke asphalt equipment and facilities is what we’ve become known for.”
As GMI continues to grow, Arruda and the rest of the leadership team is equipped to tackle whatever challenges that may present. “Our owners, Warren Colby and Mark Bour geois, are very driven and focused on year over year growth. I don’t see that changing anytime soon. Our hope for the future is that we continue to grow.”
It takes a road to get there.



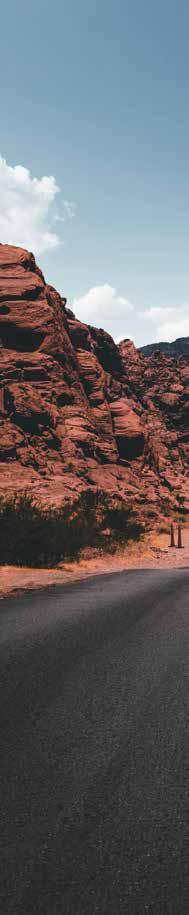
And a world of experience to build that road. As the global leader in road construction and minerals processing technology, we‘ve seen just about everything there is to see. In every climate, every condition, every twist, turn and terrain. And we put that world of experience in your hands, so you can experience exceptional performance and results at every phase of the road construction cycle.


OOwners of hot-mix asphalt (HMA) sites and quarries have the oppor tunity to not only upgrade existing facilities for best environmental per formance, but also to receive government funding for a portion of the cost, according to information from a recent National Asphalt Pavement Association (NAPA) update. During a Sept. 8, 2022, member briefing, Jay Hansen, executive vice president—advocacy for NAPA, shared infor mation about the $5.8 billion available through the Advanced Industrial Facilities Deployment Program, through which facilities owners can re ceive rebates of up to 50% of the cost to design and install advanced tech nology at their plants.
This is merely one piece of the overall $369 billion pie that is supposed to drive down greenhouse gas (GHG) emissions to achieve a 40% re duction below 2005 levels by the year 2030. The program is run through
the Department of Energy (DOE), and that is the entity to which an as phalt company owner will apply to receive a grant to upgrade or replace the plant.
Identifying and installing appropriate technology while applying for a government-embroiled grant to receive half the cost back may sound like a lot of effort to the average reader. The payoff is a more efficient op eration that could more reliably hit your sustainability goals than current equipment, with money back. And, as Hansen stated during the Sept. 8 briefing, “If you’re not doing this, you can bet your competitors are.”
What is “this” that leaders among the asphalt industry should be look ing into? We shared some grant-writing resources with the introductory article “Learn How to Write a Grant” for the plant product gallery de partment of the November 2022 edition of AsphaltPro. Next month, the January 2023 edition will look specifically at upgrading and updating the HMA plant with various advanced technologies. Right now, let’s dig a lit

tle deeper into the concept for which the DOE had yet to provide specifics at press time, and for which the Internal Revenue Service (IRS) seemed to be seeking clarity during the month of October.
Oct. 7, the Department of the Treasury (Treasury Department) issued a “Request for Comments on Energy Security Tax Credits for Manufacturing Under Sections 48C and 45X.” Notice 2022-47's purpose, as explained in Section 1 of the official document, was to receive general and specific comments of questions the Treasury Department had prior to developing guidance for implementing and administering the two codes, which are part of the Inflation Reduction Act (IRA).
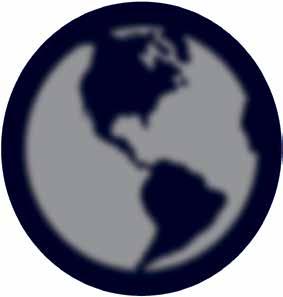

Keep in mind, the IRS request is looking at how to provide tax credits on qualifying technologies; the DOE will award grants based on its own set of qualifying technologies. The two will not necessarily be identical, although industry would be short-sight ed to think they will not overlap. When speaking with NAPA’s Hansen, it became clear our industry has an opportunity to guide the categories of what is logically considered an advanced energy property designed to reduce GHGs, but our focus should be on partnering and avoiding a prescriptive list in any paradigm.
Hansen shared that the comments NAPA submits, on behalf of the asphalt industry, ahead of the Treasury Department’s Nov. 4 deadline, will reflect that the association supports the tax credit goal of re-equipping plants to achieve a 20% reduction in GHG emissions. “We don’t think listing out specific technologies is the way to go,” Hansen explained. “Rather, set the goal and let the manufacturers of asphalt mix deploy current technologies and de velop future innovations to achieve the reduction. No one technol ogy will get you there. It will require multiple combined technolo gies and some that have not yet been developed.”
Innovation is a hallmark of the asphalt industry, after all. Whether providing tax-reference guidance, grants or otherwise, the industry has a chance to work hand in hand with agencies that have yet to release any specifics.
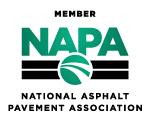
“This is an opportunity for a new partnership,” Hansen said. “We don’t know what’s eligible for grant money yet. Will man ufacturers of asphalt mix be able to apply for grants to reim burse installation of electric or solar charging stations? We don’t know yet.”
The Energy Security Tax Credits for Manufacturers was ex tended and expanded under the IRA. Specifically, Section 48C of the Internal Revenue Code, known as the “qualifying advanced energy project, provides a 30% investment tax credit on qualify ing projects,” Hansen explained. “IRA was expanded to include a project that re-equips an industrial facility such as an asphalt plant with equipment that is designed to reduce GHG emissions by at least 20%. The IRS is seeking comments from the asphalt industry on how the credit should be applied.”
The request for comments offered an intriguing sense of lat itude for asphalt plant owners who will write their future grant applications. The request referenced the IRA’s Section 48C(c)(1) (A)(ii), stating it adds to the list of eligible projects any project which installs low- or zero-carbon process heat systems, carbon capture, energy efficiency and any other technology designed to reduce GHG emissions.
The IRS sought guidance to define terms in that paragraph, of course, but also for how a qualifying advanced energy project would substantiate its eligibility for tax credits. In other words, how will the equipment, technology or advanced energy project prove its worth? That’s where cooperation among industry pro fessionals must come in.
WINTER MAINTENANCE
WE’RE ALL IN THIS TOGETHER
“The federal government is the largest purchaser of construction materi als,” Hansen said. “We’re on the cusp of innovation and we have to part ner with the federal government, state transportation agencies and oth ers to make it happen.”
We also must partner with one another. The top-of-mind example of industry working together is in the verified environmental prod uct declaration (EPD) tool industry professionals and stakeholders as sembled over years of data-mining, in conformance with ISO 14025 and EN 15804. NAPA’s website states these standards systems “estab lish principles and procedures for developing a Type III environmental declaration program and describing the potential environmental im pacts of a product.”
EPDs for Idiots from 2019 = https://theasphaltpro.com/ label-asphalt-sustainable/ Eco-Emerald Label information with video = https:// www.asphaltpavement.org/programs/napa-programs/ emerald-eco-label
Another obvious example incorporates OEMs, their customers, and the vital collection and exchange of data—telematics.
Consider the use of training directors, heavy equipment distributors, and fleet operations managers who teach wheel loader operators best loading, stockpile management, cold feed delivery, and other practices. As Cat.com points out, fuel represents 50% of the cost to operate a ma chine; thus, you obviously want operators learning best practices to keep fuel use optimized.
The learned wheel loader operator lowers the environmental cost of operating the machine with best practices, with optimum routes through the yard, with perfected bucket loading for least trips to and from stock piles and cold feeds, with adequate lift to fill the right bins between bum pers, and so on. The fuel economy is the amount of work he accomplish es per unit of fuel burned. To get good fuel economy is to save money, yes, but it’s also a way to lessen fuel expenditures and emissions.
The company owner isn’t just saving money by training wheel loader operators on best practices, but he’s also introducing good environmen tal practices to the operation in the yard. Is that training something he can put a dollar figure on? Is it something he can write into a grant or En ergy Star Program application?
Where synergy and cooperation come into the fuel economy dis cussion starts with telematics. Copious fleet management software companies flood the AsphaltPro email inbox with article pitches to tell readers of their latest iteration to track equipment movement, fuel use, idle time, and so on. If your fleet is large enough, you might be saving enough on fuel use—through good tracking and best operator practices, thus tailpipe emissions—to warrant putting that on a grant application. You won’t know until you track it; the telematics provid er is there to help.
Now let’s talk about the obvious GHG reduction zone of “heat,” and what cooperative effort is available to producers there. Even members of the Treasury Department can recognize the burner at the asphalt plant is an area where industry has made strides in reducing emissions in re cent years. From implementing warm-mix asphalts (WMAs) that lower production temperatures—which should be worth grant money—to in stalling Lo-NOx and Ultra Lo-NOx burner technologies to manipulate combustion gases and burner flame, asphalt producers have already been finding ways to turn down the heat at the drum.
OEMs are willing to partner with customers to show how to reduce heat and emissions all around the tank farm and yard. Ron Herman,
business development manager of Enerquip Thermal Solutions, Med ford, Wisconsin, spoke of helping a customer find ways to reduce ener gy use for its U.S. Environmental Protection Agency’s (EPA) ENERGY STAR® industrial program goals.
“I’ll do the math for them,” Herman said. While his company doesn’t sell or install insulation packages for existing liquid asphalt tanks, he was willing to work on the equation to show a company how the 100,000 BTU/hour heating load increased by 25 times without insulation, mak ing the “expense” of insulating a tank well worth its investment. “The sav ings on the utility bill alone pays for that in a season,” he said.
The researchers at Heatec Inc. (now Astec Industries) prepared Tech nical Paper T-140 “Heating and Storing Asphalt at HMA Plants,” which not only looked at the cost-per-unit of energy to heat liquid asphalt (and emulsions) but also discussed a heater’s thermal efficiency. The bottom line is a heater’s efficiency can change over its lifetime and that change in efficiency can influence how much energy is required to maintain tem peratures.
The team at Process Heating Company (PHCo), Seattle, has more than 70 years of experience in manufacturing its Lo-Density® low-watt-den sity, drywell-style electric heating systems designed to spread heat over large surface areas. The researchers at PHCo state: “An electric-powered asphalt tank heater or hot oil heater...operates at 100% efficiency; there is no heat or emissions exhausted into the air. And over the lifetime of the heater, that efficiency never drops.” To help customers prove this, PHCo performed a fuel cost comparison of maintaining 30,000 gallons of liq
LEARN MORE
States Get Started with Initiative Funds
The White House released a fact sheet Oct. 20 regarding a convening at the White House for “Buy Clean” commitments. The federal Buy Clean Initiative “leverages the Federal Government’s power as the largest purchaser in the world to advance low-carbon construction materials across its procurement and funded infrastructure projects,” according to the sheet.
Through the Initiative, the Department of Transportation announced that 25 states are receiving the first Federal Highway Administration (FHWA) Climate Challenge grants—to the tune of $7.1 million— to support sustainable pavements. The Department of Energy will coordinate Inflation Reduction Act funds for an Advanced Industrial Facilities Deployment Program. This will help industrial facilities retrofit, upgrade, or install industrial technologies and produce lowcarbon materials. More information can be read at the WhiteHouse.gov briefing room documents.
Those first 25 entities are Alabama DOT, Arizona DOT, Caltrans (three projects), Colorado DOT, State of Delaware DOT, State of Hawaii DOT, Illinois DOT, Indiana DOT, Iowa DOT, Louisiana DOT & Development, Maryland DOT and MD Port Administration, Minnesota DOT, Mississippi DOT, New Jersey DOT (two projects), New York State DOT, North Dakota DOT, Oklahoma DOT, State of Oregon DOT, Puerto Rico Highway and Transportation Authority, Rhode Island DOT, Texas DOT, Virginia DOT, West Virginia DOT Division of Highways, Washington DOT. Four local agency projects in the City of Seattle and in the Port of Authority of New York and New Jersey will receive technical assistance only.
uid AC at 300°F for 24 hours with natural gas, LP propane, No. 2 oil, No. 6 oil and electric at a heater’s “year 1” and at its pro jected year 8.
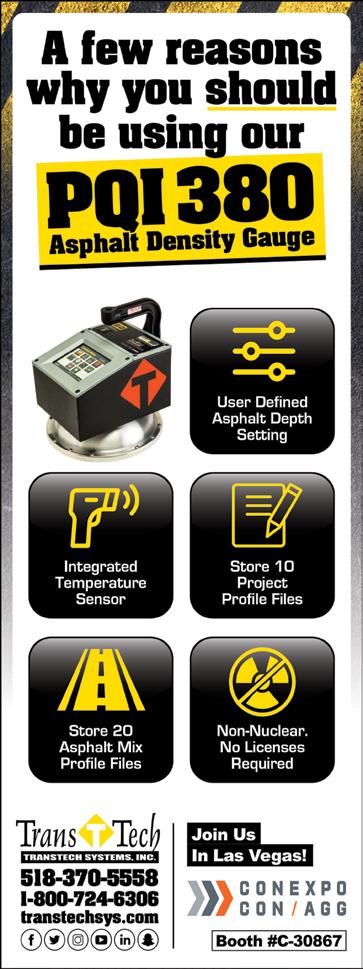
Check out PHCo’s “By the Numbers—Electric is Better” comparison chart at the company’s home page at processheating.com. There are dynamic fields where you can input your utility costs to calculate results.
Armed with actual figures, a company can plug everything from simple to complex technology into any number of green energy rating system program proposals such as an ENERGY STAR program or Institute for Sustainable Infrastructure (ISI) Envision® application. And the CFO can plug those numbers into a DOE Advanced Industrial Facilities Deployment Program grant proposal as well.
Enerquip’s Ron Herman had a host of ideas we’ll be sharing in the January equipment and technology installment of this article series, but here are basic “hot spots” he recommended customers look at for energy and money savings.
• Replacing tank fire tubes with bottommounted tank coils, which removes an emissions source at each tank on the site
• Addressing tank insulation, whether that’s repairing or installing
• Repairing or replacing old hot oil heaters with new technology
• Replacing boilers with hot oil heaters and steam generators
• Going Lo-NOx or Ultra Lo-NOx on burners
Maybe the OEM you approach can share its scope 3 emissions to improve the upstream numbers you’re compiling. For example, the team at Honeywell, headquartered in Houston, has unveiled its ECOMAX® LE burner. The team developed it for furnace OEMs that need to meet tightening global nitrogen oxide emissions re quirements and end users who want to increase fuel gas savings. The ECOMAX LE offers both flame and flameless operation, switching into flameless when a set temperature is reached, to de liver an average of 30% fuel gas savings compared to a typical cold air burner, according to the manufacturer.
With IRS seeking guidance and industry stakeholders willing to strategize alongside asphalt producers, it seems the asphalt in dustry is poised to take advantage of its innovative charge on The Road Forward. As Hansen pointed out, the DOE guidance on grants will be different from the guidance that ultimately comes from the Treasury Department, but our industry can hope that both offer guidance that sets a goal and is not prescriptive.
“The one difference may be that while the IRS tax credit is for re-equipping plants, the DOE grants might make plant replace ment eligible,” Hansen said. When you consider the number of older facilities that have been replacing components or updating one aspect of the plant at a time, the idea of having $5.8 billion in grant money available to replace an entire plant with something exceedingly more efficient is mind-boggling. “This could be a big deal for the asphalt industry,” Hansen said.
Crestview Bypass Project Innovates Through Supply Chain Issues
BY SARAH REDOHLTThe town of Crestview, Florida, is located along Florida State Road 85, U.S. Route 90 and just north of Interstate 10. It’s a major route for tourists making their way south to Florida’s many beaches and Eglin Air Force Base 20 miles south of town.
“A large population travels from Crestview down to Eglin or the Gulf Coast to support the military and tourism industry,” said Jason Autrey, director of Okaloosa County Public Works. Pair that with the city’s population increasing by 30% between 2010 and 2020, ac cording to the U.S. Census Bureau, and Okaloosa County faced “a classic case of a community growing and the need to find a better way for the people of Crestview to get around town.”
That’s why Okaloosa County began work on the Southwest Crest view Bypass more than 15 years ago, the first four phases of which included the widening of P.J. Adams Parkway connecting I-10 and SR-85 from a two-lane roadway to a four-lane roadway. In Septem
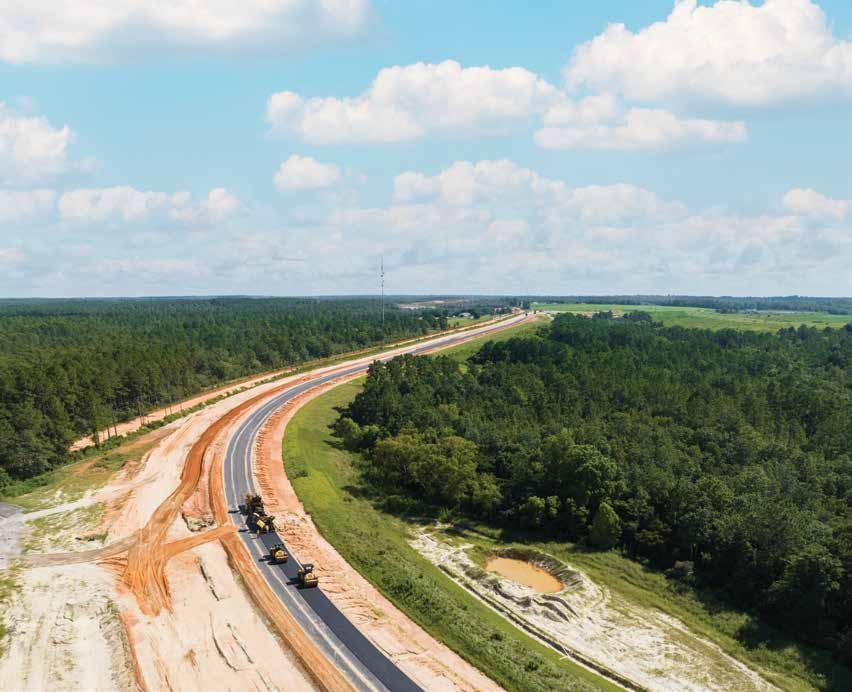
ber 2021, Anderson Columbia Co. Inc., Marianna, Florida, began the largest phase of the Southwest Crestview Bypass.
Anderson Columbia is performing both the Phase Five Corridor, which includes 3.1 miles of a four-lane roadway, as well as the EastWest Connector, 2.2 miles of two-lane roadway. “Phase Five is the missing link to complete the Bypass,” said Kevin Buchanan, project manager and estimator for Anderson Columbia.
“We’re confident the work on Phase Five will have a huge impact on our local area,” Autrey said. “The community really needs this new route. Once Phase Five opens up, it’s sure to be heavily utilized and appreciated.”
Anderson Columbia is also performing the work on a related Florida Department of Transportation (FDOT) project, a new in terchange on I-10 near P.J. Adams Parkway in Crestview. “We won that job about 8 months after we won the bid on Phase Five and the East-West Connector,” Buchanan said, adding that construction be gan in the summer of 2022.
The interchange will be known as Exit 53 and is the first new FDOT interchange in 30 years, Autrey said. “That will also have a dynamic impact on the way traffic moves through Okaloosa County.”
“Our big goal, which is still many years out, is to create a loop road around Crestview,” Autrey said, adding that the county is actively working on a Project Development and En vironment Studies (PD&E) timeline for the northwest quad rant of the eventual loop road. “We’re constantly thinking about how to improve traffic flow in the future.”
ONTO PHASE 5
When Anderson Columbia won the bid for Phase Five and the East-West Connector, it seemed like an ideal project for the company. “This type of project is right in our wheelhouse,” Bu chanan said. “Plus we had an asphalt plant just 5 miles from the project and local crews available, so the timing was perfect.”
Anderson Columbia was started by Joe Anderson Jr. in 1958 as Anderson Contracting. When the company later bought out an asphalt company called Columbia Paving, Anderson Columbia was born.
Now, the company has around 1,250 employees and per forms heavy highway and bridge construction, mostly for state departments of transportation, in Florida, Texas, North Carolina, South Carolina, Georgia and Alabama.
“We may have started out in earthwork, but it was asphalt paving that has allowed us to become what we are today,” Bu chanan said. “Although we are an asphalt paving company, we also perform grading, base, drainage, concrete and build bridges. We’re a one-stop shop.”
The $44 million project requires 1.7 million yards of earth work, construction of a 1,700-foot bridge over the Florida Gulf and Atlantic railroads and roughly 17 lane miles of as phalt paving.
With a contract time of 1,100 days, Anderson Columbia be gan work in August 2021. The project is currently 40% com plete and is expected to be finished in 2025.
Already, asphalt has been placed on the very southern end of the project in the northbound lanes. “The bridge is the con trolling factor,” Buchanan said. “Right now, we’re working on the foundation and are facing some challenges with driving the piles.”
Ultimately, the pavement design on the four-lane portion of the project will have 12 inches of stabilization, which Buchan an said is typically stabilized with clay because the existing material in the region is primarily sandy. That will be followed by 8 inches of limerock base and three lifts of asphalt: 3.5 inch es of structural course followed by a 2-inch lift, a 1 ½ inch lift, and ¾ inches of open graded friction course. The two-lane part will also be stabilized to a depth of 12 inches, followed by 8 inches of base, 2 ½ inches of structural asphalt and 1 inch of friction course.
In total, the project will require 33,000 tons of asphalt, all of which comes from Anderson Columbia’s Astec drum plant in Holt, Florida, one of Anderson Columbia’s three asphalt plants in the Florida panhandle and 11 asphalt plants in the state.
NOT ALL EASY
Although the project’s location, scope and schedule seemed ide al, extenuating circumstances have made what was otherwise a
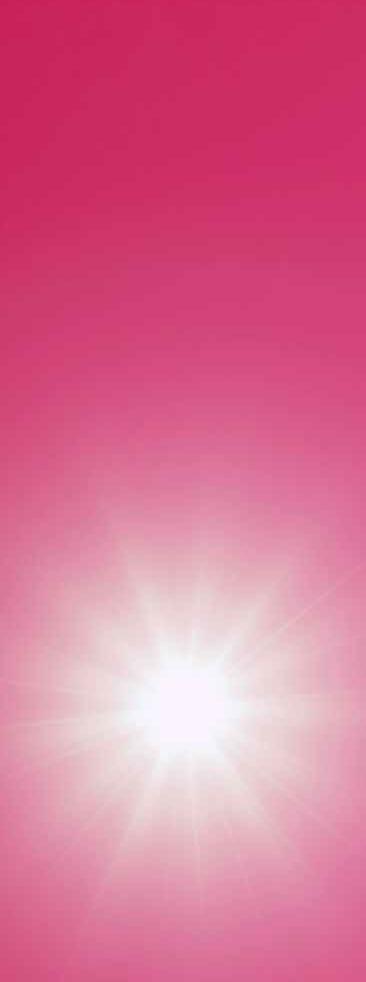
Join Women of Asphalt’s 2O23 SessionS:
Women in the Workforce: Recruit, Retain, and Promote
Taking place at BOTH:
NATIONAL PAVEMENT EXPO
January 26 | 8:30 - 10:00 AM Charlotte, NC
CONEXPO-CON/AGG
March 17 | 1:00 - 2:00 PM Las Vegas, NV
Diversity and inclusion are key to our future sustainability as an industry. This session will discuss management efforts to recruit, retain, and promote women into the asphalt industry. A panel of industry leaders will address the importance of attracting qualified women and addressing the needs of women to keep them in the industry, while developing a culture of inclusivity.
womenofasphalt.org
straightforward project more challenging. These include material short ages, cost increases and trucking shortages.
“In our particular part of the Panhandle, we’re experiencing such an economic boom that material shortages have been particularly bad,” Bu chanan said. This includes aggregate for asphalt and concrete as well as roadway base material.
“It isn’t unusual to call up a concrete company for a night job for the DOT when they won’t allow daytime lane closures and struggle to find a company willing to keep the plant open at night,” he said. In some cases, Anderson Columbia is left to use a volumetric concrete mixing truck to self-supply concrete.
“The aggregate shortages related to asphalt are mostly driven by the railroads not being able to deliver material we need consistently,” Bu chanan said. The company has a rock quarry operating under the name of Junction City Mining that supplies its aggregates for its asphalt opera tions in Florida out of Talbotton, Georgia. “All our plants in the panhan dle of Florida are serviced by rail from that mine.”
Buchanan said this leaves the company dependent on the rail com panies, which are frequently unable to supply the volume of aggregate needed. “If we normally get 60 cars every two weeks, we might get 30 cars every four weeks.”
Anderson Columbia is also facing challenges finding labor, for this job and beyond. “It’s hard getting people to work for us because of the type of work we do,” Buchanan said. “If they can go make $15 an hour at Mc Donalds, they may not choose to work in the heat or at night in order to make a little more money.”
He said they are hiring new people every day, but are only keeping an average of one out of every five new hires. “Many people who apply nev er get back to us, while others don’t make it through the drug test, don’t show up for their first day, or work half a day and decide it’s not for them,” Buchanan said.
BREAK AC’S WAY
Despite these challenges that are pervasive across many regions and in dustries, there are several aspects of the Crestview Bypass project that are
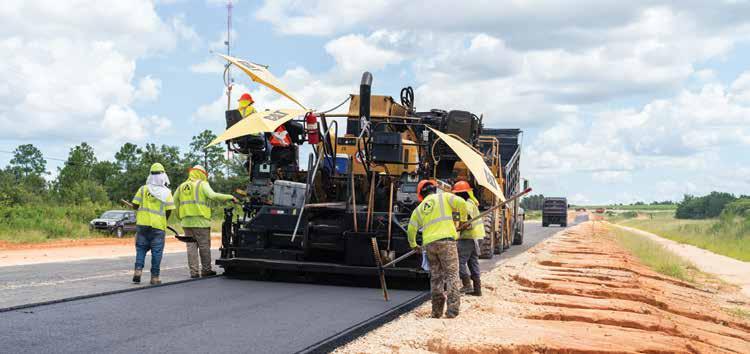
helping overcome some of the supply chain and labor issues Anderson Columbia is facing.
“The work hours on these jobs are also nice,” Buchanan said. “There are almost no nights on this job. It’s like working bankers’ hours, at least until we get to the very end.”
As new construction, the project has fewer concerns with traffic con trol. “We don’t have to worry about the traveling public,” Buchanan said. “We’re almost in complete control, and that makes these types of proj ects really nice.”
Autrey also noticed the benefits of this being new construction, and also the relative rarity of local governments building new roadways. “Most municipal and even state work these days is to augment existing facilities,” Autrey said. “But the notion of putting in a new roadway that opens up new corridors and alternative routes, while bringing new op portunities for commercial development and activity? You don’t see that very often these days.”
The construction costs of Phase Five and the East-West Connector are funded in large part through a grant from Triumph Gulf Coast Inc., a nonprofit that oversees the expenditure of funds recovered by the Flori da attorney general for economic damages to the state that resulted from the 2010 Deepwater Horizon oil spill.
“The fact that there are no federal or state funds involved in this proj ect, the county has more control,” Buchanan said. “That makes it more appealing because there is less paperwork, and federal wage rates and mandatory training programs don’t apply.”
Although Triumph funding is a major component of the construc tion costs of Phase Five and the East-West Connector, Triumph is just one of four major funding sources contributing to costs related to the bypass, including other phases as well as design, land acquisition and PD&E studies.
“The reality is we couldn’t have received the $64 million grant from Triumph without the $35 million from the county and the DOT’s com mitment to construct the new interchange at a cost of $100 million,” Au trey said. The money from the county is coming from a half-cent surtax for infrastructure enacted in 2019. The city of Crestview also contribut ed some of its funds from the half-cent surtax. “I think [the four major
funding sources of the bypass] have done a fantastic job leveraging the dollars available for this project.”
“This is a community/regional partnership,” Autrey said. “Ultimately, Okaloosa County is the contracting entity on this project outside of the new interchange, but it couldn’t have happened without Triumph funds.”
This project is also earthwork-heavy, with most of the dirt coming from the site itself. “That way, we don’t have to rely on on-road haul trucks to bring material to the job site,” Buchanan said, adding that they have off-road trucks available to move the material around the project site. What on-road trucks the project does require, Anderson Columbia strives to make as efficient as possible, “We’ll load them up with some thing that needs to go that way anyway so no truck ever runs empty.”
The agency, Okaloosa County, is also offering fuel and bituminous cost adjustments. “The fuel adjustment and bituminous adjustment re ally help with fuel and asphalt liquid prices continuing to increase,” Bu chanan said.
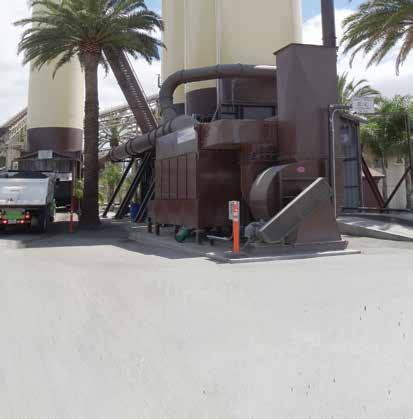
“Every cubic yard, square yard or ton of material is loaded into a spreadsheet factoring in fuel usage to calculate the cost to move that ma terial compared to the cost of fuel when we bid the job. We‘ll eat the first 5% up or down, but anything beyond that and we get an adjustment where the county gets money back if fuel prices drop or we get extra money if fuel prices go up,” Buchanan added.
Although that’s quite common on DOT jobs, Buchanan said it’s less common on county projects like this one. “Given the current climate, we’re very grateful they’re doing it that way.”
Autrey said fuel and bitumen cost adjustments are common for long-duration projects in Okaloosa County. “We may not offer [adjust ments] on a 6-month contract, but when you’re talking about a project of this size, volume and duration, that’s the only way to be fair for both the contractors and the county,” Autrey said. “We recognize what’s happen ing in the global oil market right now.”
Along with others, Anderson Columbia is trying to encourage more local municipalities to adopt FDOT specs and standards, and this is one of those instances where the county has done so, Buchanan said. He added that doing so streamlines the bidding process because con tractors are more familiar with what is expected. “When that happens, we don’t have to spend as much time or resources educating our crews on what is expected. It removes one extra hurdle and makes the pro cess more uniform.”
Buchanan said Okaloosa County in particular has come a long way in adopting DOT specs, along every phase of the bypass. “We’ve done a


lot of work with them in the last three or four years,” he said. “We have a great relationship with the county.”
According to Autrey, the vast majority of Okaloosa County’s design standards are consistent with FDOT’s standards. “We don’t need to rec reate the wheel,” he said. Not only are FDOT’s standards proven meth ods of roadway construction, but Autrey said utilizing state specs also creates consistency among roads within the county, adding that the by pass will function a lot like many of the state roads passing through Oka loosa County.
Autrey said Okaloosa County strives to streamline the construction process on all its projects. “The most difficult aspect of any project is get ting decisions made,” he said. That’s why Okaloosa County aims to make decisions quickly and identify and mitigate problems as early as possible. “We never want analysis paralysis to slow our projects down.”
“Our mission statement when we make a contract is that we’ll pay good money for good work,” Autrey said. “As long as the contractor is doing a good job, we want to let them do their thing and say thank you at the end. And Anderson Columbia is doing a great job.”
Other than the supply chain and labor issues, the project is quite straightforward, and Buchanan is grateful for that. “There’s nothing very complex about this project, which is good given the difficulties of the world we’re currently living in,” he said. “We’re trying to do all we can with the trucks, material and people we have while remaining profitable. How can we do more with less? That’s the big question we’re asking our selves a thousand times a day.”
Although we may not know when these challenges will subside, An derson Columbia’s project on the Crestview Bypass is an example of just some of the ways creative problem solving can help contractors over come these issues.


Meet a Woman of Asphalt: Atlanta Paving’s Mandy Neese
didn’t believe we would be operating like the Jetsons in my lifetime. I watched my mom who was in the telecommunications industry deal with major changes and buyouts, and I want ed to find a long-term career. Twenty years lat er we are still not operating like the Jetsons. Although Elon Musk and EV technology are beginning to make an impact on the future of road construction, we still have potholes to re pair and roads to resurface.
AsphaltPro: What does your job as the vice president at Atlanta Paving require of you?
every day to facilitate involvement from my team to be as accurate as possible. I have to send my crews in to a project to succeed and working with those people prior to a bid and getting their insight builds a great team, but creates buy-in from the crews.
AsphaltPro: What do you find most re warding (or what do you look forward to most each day) about your role as vice pres ident for Atlanta Paving?
BY SANDY LENDERAfter graduating from Georgia Tech in 2002 with a degree in Civil Engineer ing, Mandy Neese joined the asphalt industry as an estimator for APAC. When the rumors of a buyout started a few years lat er, she elected to go from the APAC corporate office to a position in Major Projects at APAC Inc. Neese joined Atlanta Paving in 2009 and now serves as the company’s vice president, where a big part of her job is securing work for the crews and leading her team of estimators and project managers. Even with a degree and plenty of experience under her belt, she’s work ing to complete an MBA at the University of Georgia. She took time from a busy 2022 con struction season to share her story as a wom an of asphalt.
AsphaltPro: What enticed you about a de gree in Civil Engineering?
Mandy Neese: I grew up watching my old er brother who was a grader and my grandfa ther who had a small concrete plant operation. I always loved being outside and loved play ing with LEGO bricks. I guess when you hit high school you try to figure out what direc tion you want to follow, but I made my deci sion based simply on stability and long-term career opportunities,” Neese shared. “I grad uated in 1998 from high school and certainly
Mandy Neese: The largest part of my job is securing work for our crews by leading my team of estimators and project managers.
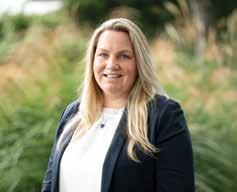
AsphaltPro: What part of your education relates best to the role you’re in now?
Mandy Neese: I joke and tell my daugh ter in high school that most of what I do each day involves 9th grade geometry taught by Mrs. Dukes. Education is incredibly import ant, but I certainly don’t disregard people’s life experience in this industry. My ability to work with field employees to facilitate the best plan is something that isn’t taught in school, and I think it makes me a little different.
AsphaltPro: What part of your educa tion would you recommend or “highlight” to women wishing to become estimators in our industry?
Mandy Neese: If you have ever done a group project and had that gut feeling that it was going to be a disaster—learn from that project. Being able to work with people, peo ple you like, people you don’t like, is an ev eryday function, but as an estimator you have to facilitate pulling information from field crews, accountants and customers to have the best understanding of your projects and how to bid projects. I would argue that just look ing at reports at the end of a job or labor re ports and so on is great insight, but I work
Mandy Neese: The men and women I work with are my family. We have been through ups and downs, but each day I know they have my back. My goal is to see each person who works with us reach new po tential. I have watched some of our employ ees grow up, get married, have children, and those moments are just as important as see ing them pave a new taxiway at Hartsfield Airport or a Chick-fil-A around the cor ner. My crews are some of the most versatile and that agility and ability to tackle projects makes me so proud. I know what they are capable of and I know they take pride in the work we do no matter how large or small.
AsphaltPro: Why did you choose to join Atlanta Paving 13 years ago?
Mandy Neese: I was at APAC in the cor porate office in Atlanta at the end of my ten ure with APAC. I wanted more flexibility in my life and took some time off to determine what that would look like. Unfortunately, that frustration is something that destroys careers for many women. I wanted to be in volved in something where I could be more involved from start to finish but not con tinue to reside in a corporate environment where I was just another badge number.
AsphaltPro: What do you think is the most important skill you’ve brought to your position in upper management in the asphalt industry? (And how would you encourage other women entering the industry to hone a similar skill?)

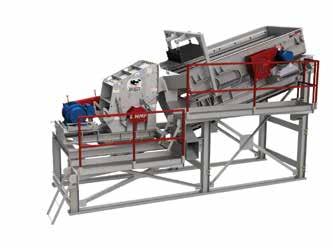
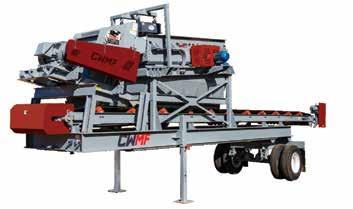
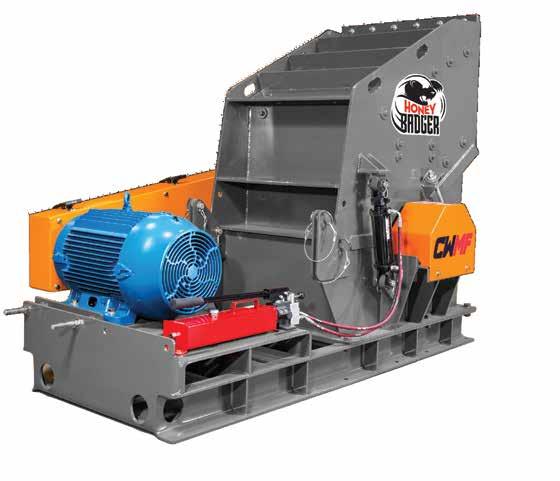
Mandy Neese: I am passionate about what we do and seeing the company and its employ ees succeed. The pressure I put on myself to do my job well so that those who depend on me is something that is genuine. I go to sleep at night thinking about how to keep 175 employees working and what can be done to make their jobs rewarding to them.
AsphaltPro: What would you say was the most challenging “obstacle” you, as a female in the asphalt industry, had to overcome in the past 20 years, and how DID you overcome that obstacle? How do you think other women in the industry can incorporate that skill or habit into their workdays?
Mandy Neese: To be able to confidently speak in a room of 20-30 men knowing ev eryone is listening to your words—especial ly as a woman—can be terrifying, but I have been able to overcome that by building rela tionships with the people in the room. I have a network of men and women that support me. I have continued meeting my customers in per son, having lunch, dropping off breakfast so that we have more than an email relationship. Knowing that I have focused on building rela tionships that are long term has been critical to growth in this industry as a woman.
AsphaltPro: Let’s talk about the workforce. Could you share with the readers what you told me about finding a flexible work environ ment for balancing workdays with family com mitments there at Atlanta Paving?
Mandy Neese: Scheduling in construction is a challenge. It is the heartburn we face daily. I don’t know that we have anything perfected, but we are learning. When I came to work for Ernie, I had a daughter with a serious medi cal condition. He made it known from day 1 that my children and my role as a mother was the most important part of my life. We have employees cross-trained and have superinten dents who fill in when someone has an obli gation. It’s not easy because these projects are unforgiving, but having employees who have flexibility in their skills to be able to accommo date other employees’ needs is crucial to filling in voids and keeping projects going. We currently have numerous women work ing for us in the field. Our newest plant em ployee is a young mother who started working in the field, but she needed a more predictable schedule because of her children. We moved her to the plant, and she has made a huge im pact on that operation. Being able to have an organization that allows employees to balance
their personal lives with work is the end goal. This industry is not conducive to it, but we are working on it. Covid has shown how much is possible when we are flexible.
AsphaltPro: Would you be willing to share the story of why you invited your son into the asphalt industry/Atlanta Paving?
Mandy Neese: Joseph is the perfect illus tration of a smart kid who did not want to at tend college. He wants to work with his hands, wants to work outside, likes to get dirty and is mechanically inclined. When he graduated, I encouraged him to go work for another con tractor we do business with that would expose him to general site construction exposure and how another company does things.
After a year at RDJE we had a few open ings in our milling operations and I wanted to fill those positions with young employees that we could grow; so, what better way to tap into a young man you know? We have plenty of nepotism at Atlanta Paving and know the benefits of having family working within the organization. I laugh when I see him on jobsites because he is usually filthy and has this huge smile. He loves it and I expect to watch him grow beyond being an operator and make that progression into be ing a foreman and so on. Tapping the high school graduates that can get lost once they cross that stage in the Spring is going to be imperative for the construction industry to fill workforce gaps.
AsphaltPro: Let’s talk about perceptions. What do you think is an incorrect perception that we, as an industry, can re-educate young people about to encourage more women to consider a career in the asphalt business? What is something you would tell a young lady to encourage her in this industry?
Mandy Neese: The most obvious is that women don’t belong in science or math-driv en fields because they are “masculine.” We know that there are social belief systems that encourage or discourage girls to follow cer tain paths, especially after middle school. I would love for more companies or state agencies to become involved in STEM pro grams and technical school programs in their localities. The most impressive effort is being made in Georgia by GHCA and our governor to facilitate technical training and open doors for youth.
While these efforts are huge, I think it’s im portant for organizations to make sure they are mindful of being inclusive in advertis
ing these programs to young girls. My dad al ways told us we could do anything; honestly, he encouraged us to avoid stereotypical career choices because he wanted us to think beyond normal careers. We can’t influence families at home, but the opportunity for outreach in high schools is imperative for girls to feel they are welcome and included in STEM programs. I am an avid hunter and outdoorswomen and I constantly see companies snub female hunt ers. I don’t know that it’s intentional to leave women out, but those companies that do em brace women will reap the benefits and I think the asphalt industry is no different. Having a trade show and not having women present in the photographs or having recruiters that don’t engage young women is a loss.
AsphaltPro: What is the most challenging aspect for you of being in the asphalt business overall?
Mandy Neese: Certainly, the demands of the schedule; we have crews that work all the time. My phone rings early in the morn ing and late at night. There are days when it is chaos and the idea of taking a vacation seems like a pipe dream, but those days are not the norm, but unfortunately those are the ones that so many people see.
AsphaltPro: What is the most rewarding aspect for you of being in the asphalt business overall?
Mandy Neese: Seeing the final product is the icing on the cake for me. Annoying my younger kids and saying, “We built that,” or getting on a plane and seeing our pavement at the airport is always exciting. It seems to never get old.
AsphaltPro: Will you tell us about a person who served as a mentor for you? What advice would you share from this person?
Mandy Neese: Buddy Jump at CW Mat thews Contracting.
Buddy has built everything at Hartsfield Airport; he is a living history book of the con struction of the airport. From the first time we worked together he was willing to always tell me stories, techniques, and encourage me to keep pushing forward. He wanted to see me do well and that encouragement is some thing that has facilitated my confidence in my skills and place in the industry. “Engage with your co-workers and others in order to build your network. Get involved with indus try groups and don’t be bashful to learn.”
CYCLEAMI
In 2019, a 1969 Dundee High School graduate donated $1 million to the Dundee Community School Board to be used toward a new athletic complex. After 85 years of playing prep football in the same location, Dundee officially closed the doors on its stadium with plans to move into a brand-new athletic complex.
Scan The QR Code To Learn More About

This Project
A core strength of Asphalt Materials, Inc. (AMI) is the formulation, manufacturing, and research & development of asphalt binders and emulsions. Our Asphalt companies supply high quality products and services around the United States, allowing AMI to excel in pavement preservation techniques and construction services.

This award-winning project will be officially recognized at the breakfast banquet of the 2023 AEMA-ARRA-ISSA 47th Annual Conference. (Litchfield Park, Arizona February 27 – March 3, 2023.) To

In the spring of 2018, a Dundee School Board member and project consultant contacted Asphalt Materials, Inc. to discuss possible cost-saving options for reconstructing the campus parking lots. Meetings were held where the AMI team presented alternative options. Scott Assenmacher, P.E. spearhead this project and utilized tools within roadresource.org to explain the different ways recycling methods were a more environmentally friendly and cost-effective solution.
Using real data, Scott was able to utilize Sustainability and Structural Calculator tools to show projected cost savings, structural benefit, and environmental benefits of choosing an optimized recycling solution.
In Fall of 2019, Heritage Research Group performed sampling of the parking lots for the high school. The existing parking lot consisted of an average of 4.7 inches of Hot Mix Asphalt (HMA), over 3-6 inches of crushed aggregate base. Common failures throughout the site included full depth cracking and stripping within the pavement.
The overall recommendation was to perform a recycling method called Full Depth Reclamation (FDR), a 6-inch recycling treatment utilizing engineered emulsion. Isolated areas showed potential for full depth patching of the underlying sub grade and base, using structural fill.
Since 1980, our in-house R&D laboratory, the Heritage Research Group, has helped our industry, customers and partners address and tackle our industry’s biggest challenges. Today, our labs provide innovative products, processes, and training to create longer lasting, safer roads.
www.asphalt-materials.com
VDOT DEMO REJUVENATES HIGH-RAP
BY DEEPAK MADANRRecently, the Virginia Department of Transportation (VDOT), North ern Virginia (NOVA) District, organized a demonstration project to pave roadways in Ashburn, using a high reclaimed asphalt pavement (RAP) mix dosed with the recycling agent ReLIXER® from Sripath Tech nologies® LLC, Mahwah, New Jersey.
ReLIXER is a bio-based asphalt rejuvenator. It is designed to soften and restore the functional properties of the aged binder, aid workability and compactability of the asphalt mix, deliver the required roadway per formance and durability, and reduce the need for virgin binder. “ReLIX ER has been vetted, tested, approved/listed, and is trusted by experts, authorities and paving contractors around the world since 2015,” said Krishna Srinivasan, president of Sripath Technologies.
The ReLIXER demonstration project was a joint effort between the VDOT NOVA District and Virginia Transportation Research Council (VTRC); Associated Asphalt Partners LLC–the binder supplier; Supe rior Paving Corporation—the asphalt mix producer; Commonwealth Paving Inc.—the paving contractor; and Sripath Technologies LLC—the ReLIXER rejuvenator supplier.
FROM PLAN TO EXECUTION
Prior to the on-site demonstration, an exhaustive round of labora tory testing of the binder and high-RAP mix was organized by the
VTRC research team. Pre-testing was conducted by the laboratories at VTRC, Associated Asphalt and Superior Paving with input from Sripath Technologies.
Sripath Technologies supplied its recycling agent to Associated As phalt ahead of the trial. Associated Asphalt blended ReLIXER with a PG64S-22 binder at their terminal in Martinsburg, West Virginia, and shipped approximately 70 tons of the ReLIXER-dosed binder to Superi or ahead of the planned job.
“ReLIXER was easy to incorporate into our binder plant operation,” said Mike Tyree, technical services, Associated Asphalt. “We were able to readily blend the ReLIXER into our binder to create a ReLIXER-dosed binder, which was easy and safe to transport.”
Over a two-day period, the Superior operations team did a fantastic job in manufacturing and shipping approximately 2,000 tons of a highRAP mix, produced using 40% RAP, virgin aggregates, and the ReLIX ER-dosed binder supplied by Associated Asphalt.
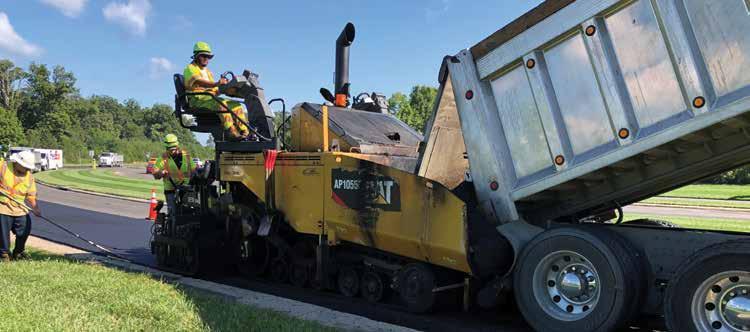
The high-RAP mix was shipped to the paving site on Riverside Park way / Woodridge Parkway in Ashburn, Virginia, about 5 miles from the plant. All four lanes on stretches of the parkways were paved by Com monwealth Paving. Sufficient high-RAP mix was produced to pave a 1.5inch wearing course on approximately 5 lane-miles of the parkways. Lo cal VDOT Inspectors were present on-site to monitor the job.
Observers noted the high-RAP mix was easy to produce, easy to ship and transfer, and easy to pave and compact on the prepared road surface. The ReLIXER-dosed high-RAP mix was easy to work, even in handwork sections, according to Commonwealth Paving. The paved surface was smooth and exhibited no flaws. The parkways were opened to traffic within a few hours of paving.
MULTIPLE TEAMS WORK TOWARD SUSTAINABILITY
VDOT, with overall responsibility for managing, funding, and oversee ing all state-maintained roadway projects in the Commonwealth of Vir ginia, was a key stakeholder in this project. “The VDOT NOVA Dis trict and VTRC teams did an excellent job in coordinating the ReLIX ER demonstration job, effectively engaging all parties involved with the
TOP: VTRC took multiple samples of the high-RAP mix rejuvenated with ReLIXER at the Superior Paving Corporation hot-mix plant for testing at its lab. BOTTOM: This section of Riverside Parkway required hand work of the high-RAP mix rejuvenated with ReLIXER. The team reported the mix was easy to work, easy to pave and easy to compact.
project. They managed and executed the project flawlessly. It was a plea sure to work with them,” Srinivasan said.
The VTRC team arranged for the collection of a number of binder and mix samples and field cores over the course of the two days of production and laydown. They plan to conduct a comprehensive evaluation of the mix and monitor the performance of the paved roadway.
Senior Research Scientist Jhony Habbouche, who was overseeing this project for VTRC, stated, “Over the last several decades, VDOT has eval uated the use and performance of several technologies that can help re duce environmental burdens from pavements, including the use of rela tively higher RAP contents. The ReLIXER field trial will help the agency characterize and assess the effectiveness of using recycling agents in as phalt mixtures. This will enhance and facilitate the incorporation of in novative materials as part of the agency’s balanced mix design initiative.”
VTRC Associate Principal Research Scientist Stacey Diefenderfer said, “Improving mixture and pavement performance is a priority for VDOT. Evaluating different tools for achieving this goal in a sustainable manner, such as the incorporation of higher RAP contents and recycling agents into mixes, is an important part of this effort.”
Associated Asphalt is a large, independent asphalt terminal, storage, and distribution company on the east coast of the United States. Backed by over seven decades of industry experience and a 6-million-barrel ca pacity, they serve customers with a focus on quality, safety and environ mental responsibility.

Mike Worden, technical service manager at Associated Asphalt, stated, “It was easy to blend the ReLIXER into the binder. We can easily and reliably produce a ReLIXER-dosed binder at our terminal. On our 70-ton production run, we achieved almost exactly the same test values as we did on our initial lab samples.”

Superior Paving is one of the largest asphalt producers and pav ing contractors in Northern Virginia. Superior Paving is dedicated
to providing quality paving for the safety of the traveling public and have been recognized for the quality of their work and the strength of their leadership, employees and customer responsiveness.

Superior Paving was the host for the ReLIXER demonstration project. Danny Poole, director of quality assurance at Superior Pav ing, said, “We appreciate the opportunity for us to partner with VDOT and VTRC, Associated Asphalt, and Sripath Technologies to explore these rejuvenation technologies and continue to build sus tainable pavements. This research, which will take time to draw to conclusion, could possibly aid in our balanced mix design efforts. We achieved good results on IDEAL-CT and Cantabro tests for both the mix design and during production.”
Sripath Technologies develops, manufactures and markets a wide range of innovative additives, such as rejuvenators, oils, and poly mers to enhance the performance of bitumen and asphalt for paving and roofing applications, worldwide. One of Sripath’s key products is its RAP recycling agent ReLIXER.
“ReLIXER is a specially engineered blend of bio-based oils, de signed to rapidly penetrate RAP particles and restore the functional ity of the aged binder in RAP,” Srinivasan said.
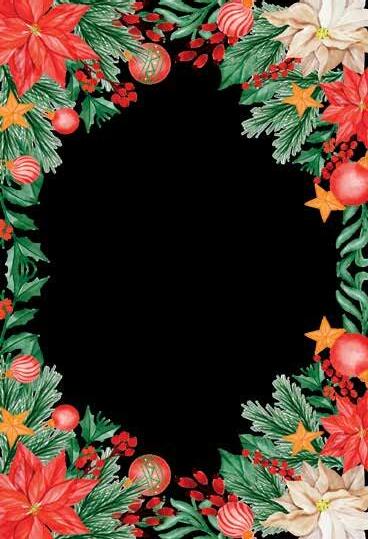
As spokesperson for the company shared its application to sus tainability: “ReLIXER helps reduce the carbon footprint and green house gas emissions. It reduces the need for virgin bitumen and low ers the overall cost of the mix....We are glad to see that ReLIXER is an integral part of VDOT’s green initiative.”
Deepak Madan is the chief marketing and business development officer at Sripath Technologies. For more information, visit sripath.com/.
Thank You for Supporting the Asphalt Industry
Thank You for Supporting the Asphalt Industry
BY SANDY LENDERWWelcome to the first holiday and workforce special section of AsphaltPro Magazine, wherein we set aside pages in the final issue of the calendar year to thank readers and vendors alike for another successful season of sharing knowledge to advance the industry. It’s natural and appropriate to reflect on what we’re grateful for around the holiday season, and I want to start by acknowledging the advertisers who stepped out on a limb with us to support this inaugural effort. In alphabetical order, CWMF, Kenco Engineering and Reliable Asphalt Products join us in expressing grati tude to their employees, customers, vendors and agency partners who make day-to-day operations possible.
Thank you also to John Ball of Top Quality Paving & Training for his willingness to share expertise with you all in this special section. It’s no secret the construction industry in general has seen skilled workers reaching retirement age and leaving our workforce in droves at a time when recruiting fresh workers to our industry has been less than easy. I have good news for those of you working with state associations, voca tional schools, departments of transportation and labor union appren ticeship programs, and the like to bring the younger generation of work ers into your companies.
As Tim Taylor, the director of research for the National Center for Construction Education and Research (NCCER) shared with us, “con struction workers report higher levels of job satisfaction than all other industries combined—not just today, but through four distinct econom ic cycles since 1974...As little as 86% and up to 89% of people working in the construction trades like their jobs.” He’s quoting data from the Na tional Opinion Research Center at the University of Chicago and offer ing the combination of excellent pay and career-path flexibility as rea sons behind satisfied workers.
“While just over 9% of craft professionals are trained in more than one skill area, the availability of a multiskilled craft workforce has steadily increased since 2005, and the trend is expected to continue into 2030,” Taylor explained. He shared that the increase in “multiskilling” has been driven by the employees themselves.
I find that notable as we work toward appealing to a new workforce and keeping workers around.
Christa Fairchild, product marketing manager for CM Labs, also spoke about the incoming generation of workers to be trained in our industry. “Younger workers seem to be naturally attracted to simula tion-based training,” Fairchild shared. “They are familiar with the im mersive experience and have fewer issues with perspective on screen due to their familiarity with video gaming and entertainment. Both Millen nial and Gen Z workers are accustomed to using technology in their ev eryday lives and are comfortable learning new technology.
“Both Millennial and Gen Z workers look for clear and consistent feedback from their employers,” she continued. “CM Labs simulators al low organizations to standardize operator training practices by tracking, measuring and benchmarking performance. In addition, instructors can interact directly with trainees, set scoring targets, adjust weather, trigger random mechanical faults, and monitor the actions and progress of each
operator. Objectively tracking and recording a student’s progress helps eliminate scoring errors, bias, or guesswork. These built-in performance metrics provide succinct, objective and instant feedback about the train ee’s performance.”
Where I think employers will find their best success is in making train ing and feedback available across an entire company. As Fairchild point ed out, instructors can use simulators to assess operator competence quickly when hiring, of course, but can also use simulators to objective ly put existing operators to the test or refresh skills. “Simulators are also great for cross training, which is important for retention,” Fairchild said.
While specific data points you’ll want to assess will depend on your equipment and your company growth needs, having a way to nurture skills and measure them objectively is vital to showing workers you wish to invest in them. You wish to invest in their careers as well as your com pany and the industry.
Fairchild is approaching the concept from the view of training with simulators: “The most critical factor is that using simulators to train op erators in different scenarios makes them more versatile. It allows oper ators to gain familiarity and confidence in a safe, low-stress environment before taking control in the field.
“This familiarity breeds success. Experience gained through simula tion-based training not only improves safety and performance, but also provides the confidence to learn and perform under high-pressure sit uations. In her 2017 paper, “Learning from Errors,” psychologist Janet Metcalfe draws a close correlation between mistakes and learning. Based on her research, Metcalf argues that students benefit significantly more from making and correcting mistakes than from avoiding them. Train ing simulators allow operators in training to experience limits without consequences. In the field, mistakes often prove catastrophic—on the simulator they are valuable lessons learned.”
However you approach the concept of nurturing and measuring mul tiple skills in your workforce, AsphaltPro Magazine is thankful for your continued participation. At this time of year when many companies are “slimming down” for equipment maintenance during the off season, we wish you a safe and stress-free holiday filled with good planning sessions for the 2023 construction season. We wish you a peaceful and prosper ous upcoming construction season with skilled workers who fit perfect ly in the category of liking their jobs and growing their skill level for top quality pavements. We join our goodwill advertisers who wish you—and their workers—well.
WEB EXTRA
Check out this article online at www.TheAsphaltPro.com under the Training department to see graphs and additional information.
FROM YOUR FRIENDS AT

Happy Holidays
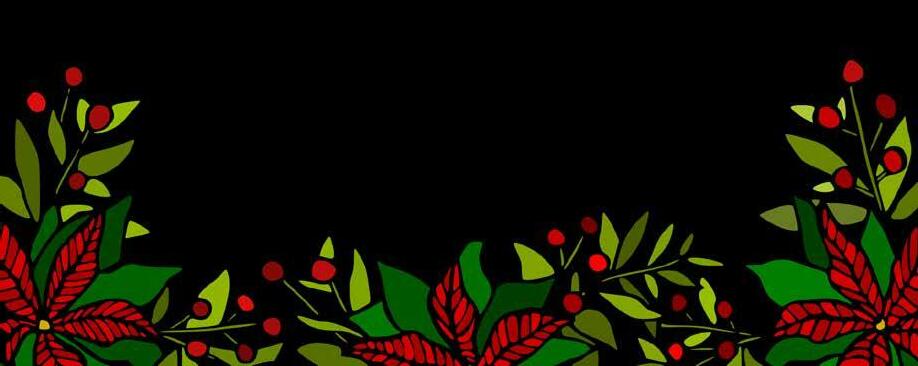
We’d like to take the opportunity to thank our readers, advertisers and team for making 2022 a great year!
How Your Workers Grow a Successful Paving Operation
How Your Workers Grow a Successful Paving Operation
BY JOHN BALLYYou can read any number of articles about the financial side of start ing and running a paving business. The Off the Mat department in this magazine is set up to help with that. But if you don’t have the right people with the right attitude committed to running the right equipment the right way, all that business work will stop there on paper.
I’ve had the pleasure to work with many great companies over the years. I’ve seen some good laborers and good equipment operators grow into great workers—great workers who advance their careers while helping to advance the whole crew and company with an atti tude of committing to excellence.
Let’s talk about how to nurture those employees at your company and grow your paving operation through training.
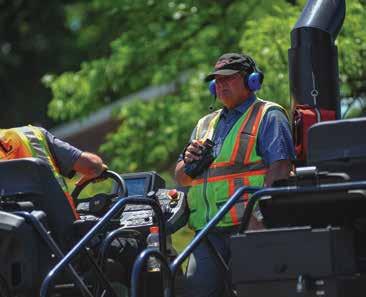
We’ll start with an assumption. Let’s assume you’ve worked with local agencies, your state asphalt pavement association (SAPA) and/ or trade schools to hire people who are interested in construction. The researchers at the National Opinion Research Center at the Uni versity of Chicago have data showing us that construction work ers have reported higher levels of job satisfaction than all other in dustries combined over the past four distinct economic cycles since 1974. You can see a detailed page of stats from the National Center for Construction Education and Research (NCCER) regarding “Job Satisfaction in the Construction Trades.”
If you can pull the right folks into your company, you’ve won half the battle. But if you’ve hired someone who doesn’t really want to work in the construction industry or who doesn’t understand we have long hours during the height of paving season, you’re setting yourself up to lose that person. As soon as the weather turns hot enough, the worker who was never committed to the industry will walk away. So, let’s assume you’ve done your homework to make sure you hired the right people for this industry.
BRING LEADERSHIP ON BOARD
You know that building a safety culture in your company starts at the top, with the leadership. The same is true for building a quality mindset in your employees. You want to bring leadership on board with the idea of getting quality out of every project, which starts with every worker buying into quality. You want every employee from the laborers to the CEO to understand the importance of equipment maintenance, the paving process, best practices and safe operations.
Bringing everyone into the same headspace may look different for your company, but when I go to a client’s home office, I sit down with management and go over what we’re going to do to improve their entire operation—not just the project (or projects) we’re working on that week. I include leadership in the pre-plan and in the report at
the end of the week, so everyone is on board and buying into the mission to grow the whole operation.
It’s important to make sure everyone is on board with training for pav ing excellence—from the top down.
PLAN AHEAD
One of the factors in getting excellent quality is to plan ahead. Whether that’s in our pre-planning meeting at headquarters or whether that’s the gameplan the paving superintendent puts together before the first day of a paving project, you need to know where you’re going before you take your first step. (Check out the article titled “Train Paving Laborers to be the Best Superintendent Ever” on theasphaltpro.com for tips on how to help your superintendent pre-plan the job.)
The same is true for your training program. If you know ahead of time that you’re training Laborer A to grow into a foreman someday and La borer B to grow into an estimator, they may both start with the same ba sic skills and information, but their paths will diverge. When and how they diverge is up to your training director.
Maybe you have two laborers with unknown skill sets and the deci sion to set them on different paths hasn’t been made yet. You know what your company needs to have in place next season, the season after and five seasons down the road. By planning ahead and watching the atti tudes and aptitudes of the new workers today, you can guide them into the training programs for tomorrow.
FROM THE TEAM AT
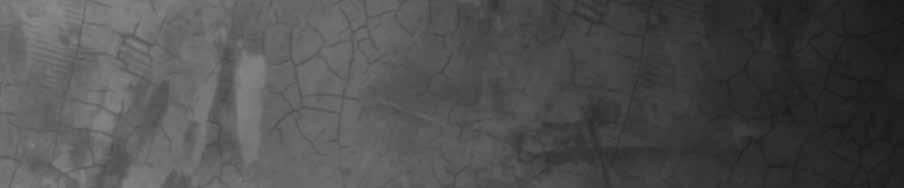


SELECT THE RIGHT EQUIPMENT
Picking out the right equipment for each project is just as important as choosing the right employees for your company. Think about your potential for success if you show up to a highway paving project with a paver, equipped with a hopper insert, and all the haul trucks arriving (whether they’re on time or not) are belly-dumps. You better scramble to get a pickup machine to the site in a hurry. (And look into what fell apart during pre-planning.)
Having the right pieces of equipment on the job gives workers their best chance at doing the job right. In the example above, the paver op erator might be one of the best in the industry and might be fantastic at communicating with haul truck drivers and screed operators alike. But if you handicap him with a mess in front of the paver or trucks that can’t get material to the hopper, he can’t do his job. Imagine his frustration level as he sits there waiting atop a machine where he’s already input settings to get a full day’s work for a bonus-worthy mat.
Another element of getting the right equipment is having the correct compaction equipment on hand for projects. Wider is not always better if you’re watching your fuel economy. (Check out the article titled “How to Roll for Bonus: Part 2” on theasphaltpro.com for tips on selecting the right size and type of roller for the right job.)
At this time in history, contractors are being asked to retire machines that may or may not be at their end-of-life in an effort to remove older diesel-run engines (whether Tier IV Final or not) from the national fleet in favor of electric off highway construction vehicles (EOHVs). If you have the money to spend on the machine, its charging infrastructure, its best maintenance schedule and its replacement battery, this may be the time to prepare for upcoming bidding opportunities that will be reserved for contractors who have a set percentage of EOHVs in their fleets.
Beyond the heavy equipment, don’t forget the smaller technology that makes life easier for workers and could entice them to stay with your company and crews.
We all know our paving operations are hot and noisy. No matter how many battery-powered engines you put out there, the backup alarms, raising and lowering haul truck beds, passing traffic, vibratory rollers, plate compactors, and the like, will make noise for workers to shout over to be heard. If this shouting makes for a tense environment, do you think the new employee who has never experienced a real-world paving oper ation before is going to be excited to come back tomorrow?
Investing in a system of headsets that cancel some ambient noise while giving foremen and supervisors a clear line of communication with op erators and laborers is an option. You can check out a number of arti cles about their positive use at theasphaltpro.com, including “Use Head sets to Communicate with Your Crew.” The team at Eartec Co., head quartered in Narragansett, Rhode Island, has released the self-contained EVADE headsets, which feature a compact, full duplex transceiver built inside the ear cups. The complete system, like many others on the mar ket, relays digital signals to and from a “main” unit and “remotes.” For the Evade system, the team at Eartec says theirs link automatically without a hub or base station; the Evade connects up to nine users within a 400yard range. The point is to enhance coordination, productivity and safety.
Have you looked into the ergonomics of the operator cabs of your equipment? Your workers spend an 8-hour or longer shift in the ma chine’s cab. You want that environment to be one that’s comfortable
enough for the worker to accomplish his or her tasks efficiently and with top quality while avoiding lumbar or other injuries due to repetitive mo tions. You want a healthy and happy worker to come back tomorrow.
I’m not suggesting the construction industry is coddling workers; just consider how excited you would be to return to a machine’s cab if it was made in the 1950s with a board bench for a seat. By offering your work ers the best in class—or at least the best that you can reasonably afford— you're offering a work environment they’ll be more willing to return to day after day and a work environment that is more conducive to safe and quality performance.
ROUND OUT THE ATTITUDE
This takes us back to the initial hiring decision. When you bring a new worker to the crew, you’ll be able to tell how he or she is adapting to the job. You don’t want to assume that a person who hangs back and watch es how things are done is going to be a lazy worker; this person might be learning by example. But if you see a trend of this person letting every one else do all the work, maybe you’ve brought on someone who would be better off in a different position. You don’t want to assume that a per son who shouts a lot on the job is going to be an argumentative or bully ing team member; this person might be hard-of-hearing or might be try ing to be heard above engine noise. But if you see a trend of this person shouting on and off the job site (or using improper language in front of customers), maybe you’ve brought on someone who would be better off working alone or in a different company.
By using mentors and supervisors to track new workers’ behavior and progress, you not only train the new workers more quickly, but you also have the chance to catch attitude patterns before they be come problems. You have the opportunity to notice and nurture the workers who will grow their careers alongside your quality projects and your quality crew.
John Ball is the proprietor of Top Quality Paving & Training, Manchester, New Hampshire. He provides personal, on-site paving consulting services around the United States and into Canada. For more information, contact him at (603) 493-1458 or tqpaving@yahoo.com.
LEARN MORE
Who Did You Hire?
The person you hire today will move up the ranks to be tomorrow’s equipment manager, supervisor, estimator or other important leader in the company. The way to build a quality mindset throughout the entire company is to start with the workers who will carry a quality mindset through all those positions. You want to look for some common, positive traits in the workers you bring on board:
• A positive attitude
• Timeliness
• A proactive nature
• Willingness for teamwork
• Willingness to learn
• Personal responsibility
• Safe, respectable clothing.
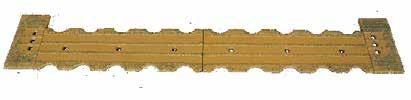
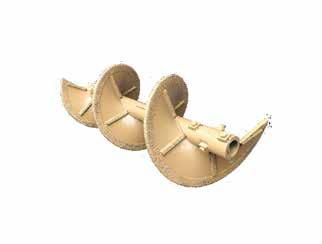

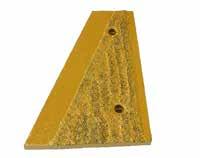
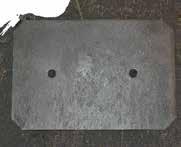
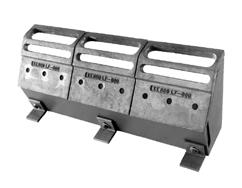
Military Airfield Testing Introduces December Lab Equipment Gallery
FROM DYNATESTDynatest A/S, headquartered in Copenhagen, Denmark, deliv ered a heavy vehicle simulator to the U.S. Army in Septem ber. The Danish-American company also has a department in Gainesville, Florida, and develops, manufactures, and services equip ment and software for testing and evaluating pavement on roads and runways.
“When the giant C17 military aircraft lands, enormous forces hit the ground,” Dynatest CEO Jesper Rantala said. “This requires a runway built for that purpose. When it comes to U.S. defense equipment, noth ing is left to chance. Everything is thoroughly tested. This also applies to the pavement on the runways that the defense has at its disposal.”
Jesper Rantala became CEO of Dynatest in 2019 when the company became part of the Danish technology group Eltronic Group.
The heavy vehicle simulator has been nicknamed Titan, which em phasizes that it is the largest of its kind. The machine is 150 feet long and weighs 125 tons, and Dynatest engineers spent two years develop ing, producing and delivering it. Now, it is up and running at the mili tary base in Vicksburg, Mississippi, where the U.S. Army Development Department, U.S. Army Engineer Research and Development Center (ERDC) will be using it in their research.
Jeb Tingle is senior scientific technical manager at the U.S. Army ERDC’s Geotechnical and Structural Laboratory. Tingle said, “The heavy vehicle simulator, Titan, built in partnership with Dynatest, is a critical research tool to evaluate new materials, design methods and construc tion techniques to optimize transportation infrastructure facilities. It has been a long process to get us where we are today, and with this new ca pability added to the ERDC toolkit, we will be able to discover, develop and deliver solutions to the Warfighter and nation much more quickly.
“We are also proud to claim that the Titan has the ability to apply a dynamic impact load to simulate impact loadings from aircraft touch down and vertical takeoff and landing aircraft,” he continued. “No oth er heavy vehicle simulator is capable of performing these critical tests. The Titan also has some first-of-their-kind features to help ERDC sup port military transportation needs.”
THE PENDULUM WHEEL
With a wheel that goes back and forth, the task of the heavy vehicle simulator is to imitate the forces of a military aircraft and thereby test the strength of the runway.
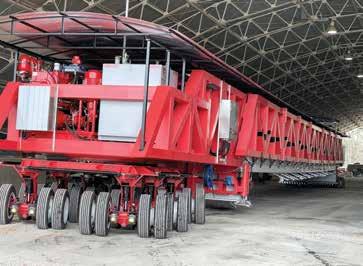
“It is not possible to determine whether a runway is worn out just by looking at the surface,” Rantala explained. “The pavement consists of several layers, all of which must be in good condition to ensure that
Titan weighs 125 tons, and is 150 feet long, 16 feet wide, and 17.5 feet high. All photos courtesy of Dynatest
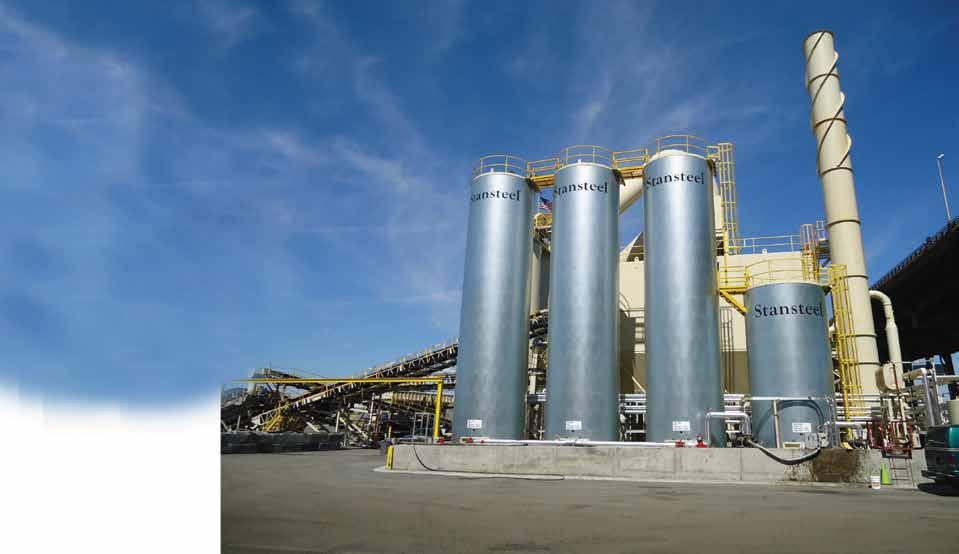
For more than 46 years, Dynatest has manufactured equipment and software to evaluate runways and roads. Over the years, the company has supplied equipment to more than 70 countries.
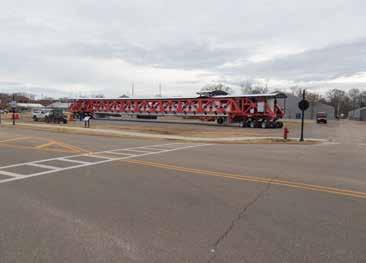
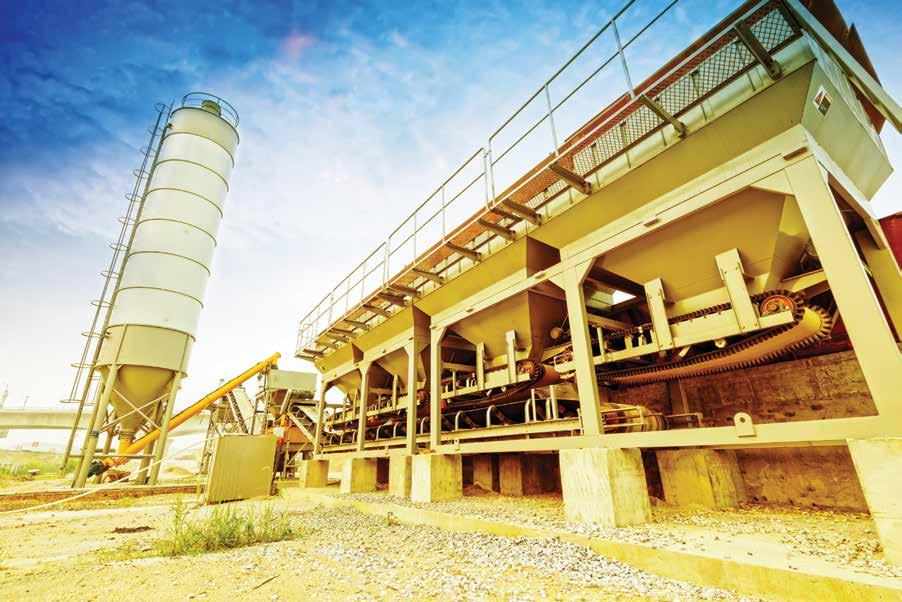
“THERE IS NO DOUBT THAT WE ARE ‘NERDS’ IN OUR FIELD. WE HAVE A STRONG FOCUS ON IMPROVING DETAILS AND FURTHER DEVELOPING OUR EQUIPMENT.”—JASPER RANTALA
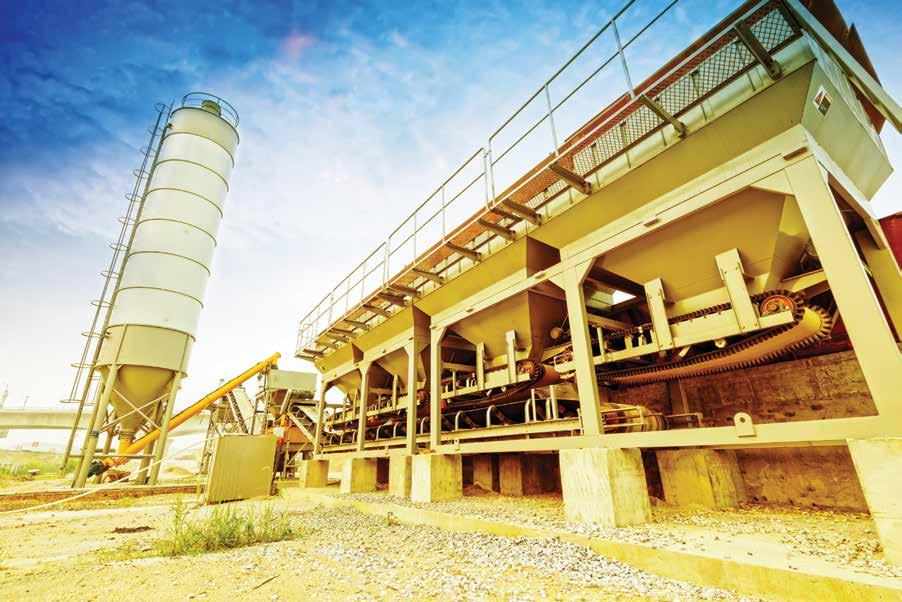
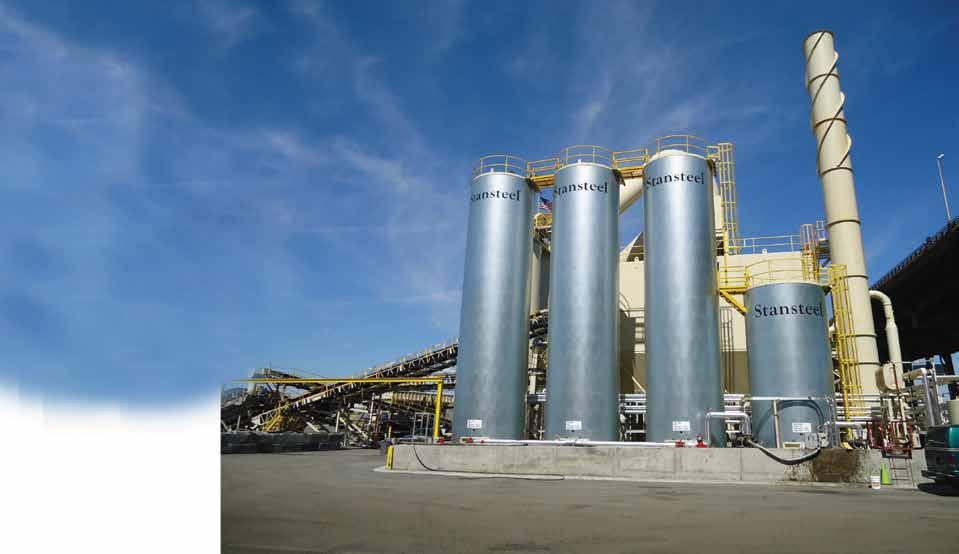
the load-bearing capacity is strong enough. With the heavy vehicle simulator, you can test how 20 years of use affects the pavement in just three months. It provides an accurate and realistic picture of the con dition of the runway, and in this way, you get the opportunity to de velop better runways.”
CONTROLS
CONTROLS S.p.A., headquartered in Milano, Italy, presented, among other products, its new range of electromechanical compact universal testers at Bauma Oct. 24-30 in Munich. The company shared: “We’ll be unveiling our new range of multipurpose premium testers—all using the electromechanical technology and fully automatic, with an integrat ed advanced controller.” The manufacturer was unable to provide fur ther information prior to press time.
For more information, visit the IPC Global website.
GSSI
GSSI has released the PaveScan® RDM 2.0, which is an asphalt density assessment tool designed to provide real-time measurements to ensure pavement life and quality. The company unveiled PaveScan RDM 2.0 for the United States and Canada at the Transportation Research Board 2020 Conference in January.
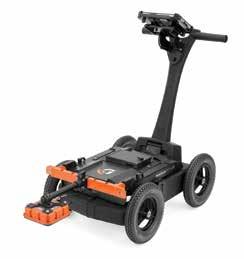
PaveScan 2.0 incorporates a new sensor design built specifically for the extremes of the asphalt paving environment, foldable deployment arms with high-visibility for work site safety and has a warm-up time of under one minute when ambient temperature is over 70° F. The manu facturer states it PaveScan RDM is ideal for uncovering problems that occur during the paving process, including poor uniformity and signif icant variations in density. By avoiding these problems, PaveScan RDM helps avoid such premature failures as road raveling, cracking and dete rioration along joints.
This system automatically measures the dielectric value to identify anomalies in real-time. In addition, the dielectric values can be used as a means to correlate percent voids and density in new pavement. The technology enables users to obtain critical density data for quality con trol/quality assurance (QC/QA) of new pavements.
Integrating with GPS systems, PaveScan features a flexible, modu lar design that facilitates easy and efficient operation and data collec tion, according to the manufacturer. It is offered as a single sensor or a three-sensor cart-based configuration.
As of April 2019, this pavement density measurement technology is an accepted American Association of State and Highway Transpor tation Officials (AASHTO) specification, PP 98-19.
For more information, visit www.geophysical.com.
IDOT
A new 1-mile test track in Clinton County will help the Illinois De partment of Transportation (IDOT) Bureau of Research calibrate equipment used to assess pavement condition. Under construction at press time, the track will be one of only four of its kind in the nation when it is completed in 2022.
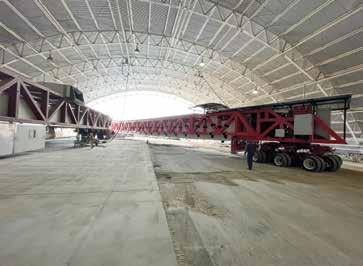
“What makes our track unique is that it will have all pavement types—continuously reinforced concrete pavement, full-depth hotmix asphalt pavement and jointed plain concrete pavement—for cer tifying equipment,” said John Senger, engineer of pavement technol ogy in the Bureau of Research. “Additionally, this track will offer var ious textures to challenge the capabilities of the equipment to ensure it is working properly.”
Located along the south side of U.S. 50 between Breese and Tren ton, the track covers multiple disciplines in pavement testing, includ ing ride, friction and structural assessment. It also will offer at least six different textured surfaces for skid testing correlation, as well as copper plates for ground-penetrating radar testing.
“The goal was to make the facility as multifunctional as possible to maximize the return on our investment,” Senger said. “We anticipate other states and private companies paying to use the track as well.”
IDOT regularly tests state highways for ride quality, friction avail ability and structural integrity. Data collection vans are used to col lect various metrics every year. To ensure accuracy, each test vehicle must be certified annually. Certification—and any necessary calibra tion—will be completed on the test track, which will not be part of the regular roadway or be open to traffic.
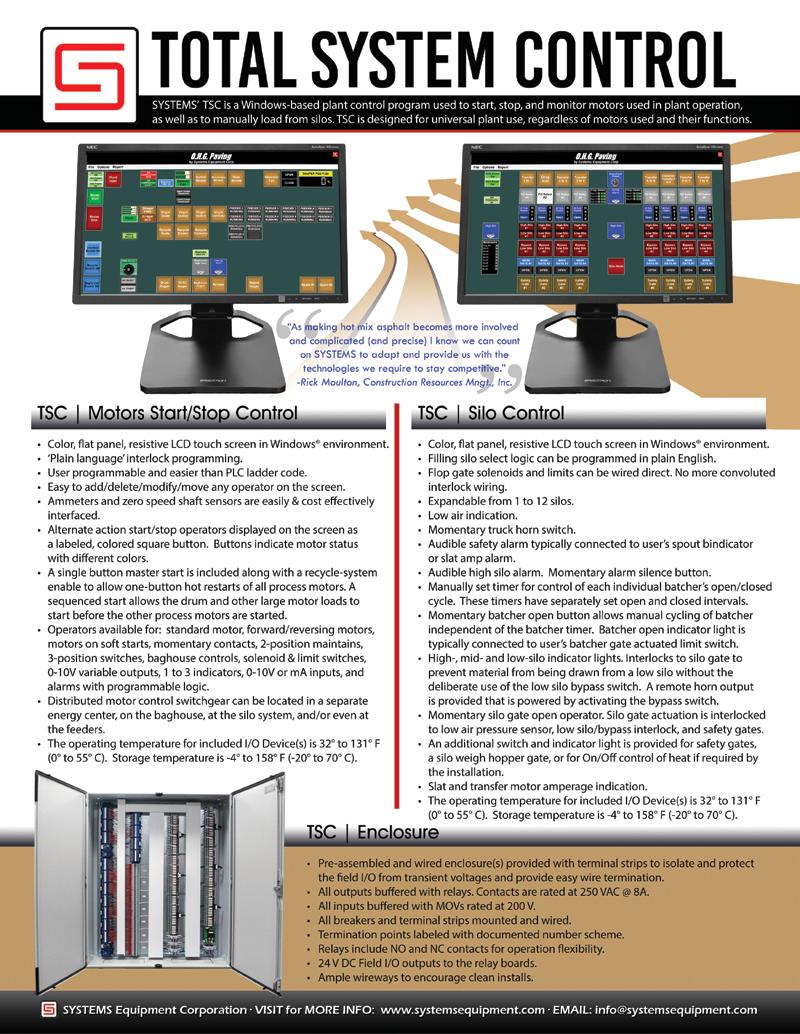
SRIPATH
Sripath Technologies, Mahwah, New Jersey, recently established an agreement with VA Asphalt Pavement Technologies, for Vince Au rilio to act as a technical advisor for Sripath Technologies in Cana da. Sripath® develops, manufactures and markets a range of innova tive additives used to enhance performance of bitumen and asphalt mixes. Sripath is a global company with offices, affiliates, agents and advisors in the United States, Canada, India, Australia, United King dom, Brazil, and South Africa.
Aurilio, owner and president of VA Asphalt Pavement Technolo gies, has 40 years of experience in pavement design and materials engineering for roadways and airports in both the private and public transportation sectors in Canada. His area of expertise includes: hotmix asphalt technologies, testing and design; warm-mix additives, high-RAP mixes, stone matrix asphalt mixes, mix plant production, paving quality control and assurance, in-place pavement recycling, and full depth reclamation. He is an active leader within the asphalt paving and roofing industries in Canada.
“Vince brings decades of technical and business development ex pertise to our team and provides us with a valuable leverage to pur sue and develop new opportunities within Canada. We are thrilled to have him on our team,” said Deepak Madan, chief marketing & busi ness development officer of Sripath.
For more information visit sripath.com.
STANSTEEL
To ensure the accuracy of your plant’s liquid asphalt metering sys tem, hot mix producers should periodically run a calibration check. Liquid asphalt cement (AC) can be calibrated and weighed by a sep arate holding vessel, which is supported on multiple load cells and calibrated with a known weight. The team at Stansteel Hotmix Parts & Service®, Louisville, Kentucky, offers the Stansteel Automatic A.C. Calibration System.
With the Stansteel Automatic A.C. Calibration System, AC can be diverted from the run line on the plant directly to the calibration tank (using the proper piping and valving). The tank is loaded with a spe
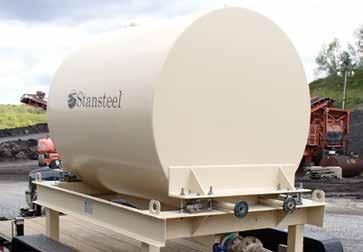
cific amount of material and then stopped with a weight registered on the electronic digitizer located in the control house. After the mate rial is weighed, the process can be reversed and pumped back to the AC storage tank so that no waste occurs.
According to the manufacturer, this offers the benefits of:
• Reduced man hours;
• Accurate calibration;
• Quick and easy installation to the current system;
• Vertical, horizontal and portable options; and
• Prompt delivery of units in stock and ready to ship.
For more information, visit: https://stansteel.com/asphalt-plantcomponents/asphalt-calibration-system/
TRANSTECH
TransTech Systems invented an innovative use of capacitance tech nology and has continuously developed and improved it over the course of 25 years for the use of non-nuclear technology for quali ty control in determining in-process asphalt density. A quarter of a century ago, TransTech Systems invented and patented the use of a well-established electrical technology for a new purpose: character izing asphalt during construction and determining its density in a matter of seconds.
The first prototype for this technology, developed for determining the density of longitudinal joints, became the Pavement Quality Indi cator, or PQI 100. Since this first commercial unit was introduced to the marketplace, TransTech has continuously made advancements to its flagship product in order to improve its accuracy, reliability, rug gedness and user-friendliness for a wide variety of mixes and condi tions, according to the manufacturer.
The latest fourth generation Model 380 features items such as a GPS status display, the ability to download files to/from the PQI via USB drive, a touch screen GUI, and an advanced data management system.
The PQI is now used worldwide, and the company has distributors in over 87 countries. When combined with the Soil Density Gauge, TransTech has over 5,000 units in use every day.
For more information, visit http://transtechsys.com/products.
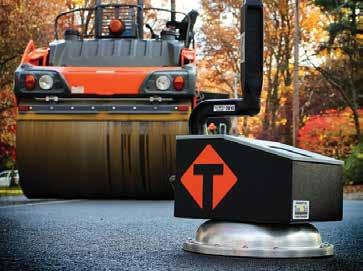
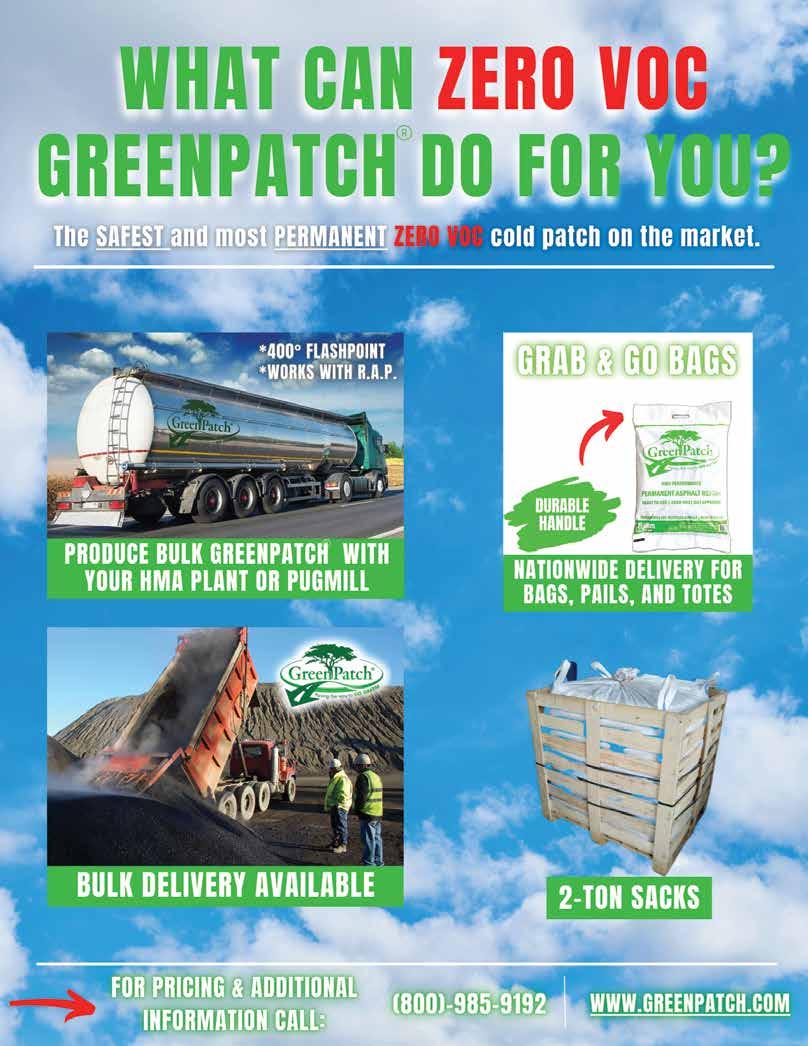
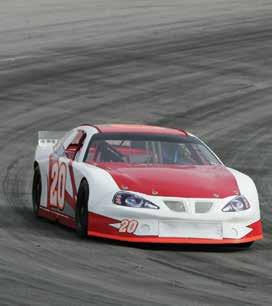
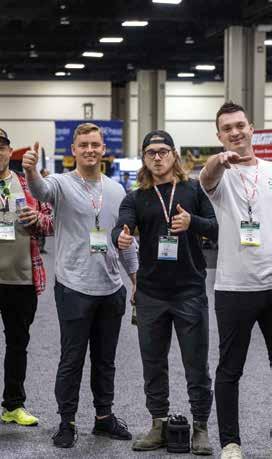
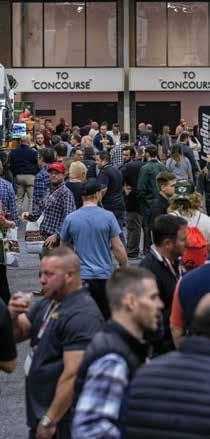
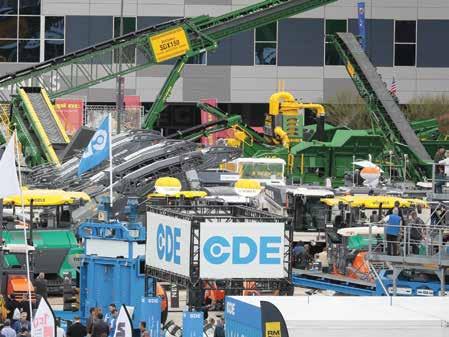
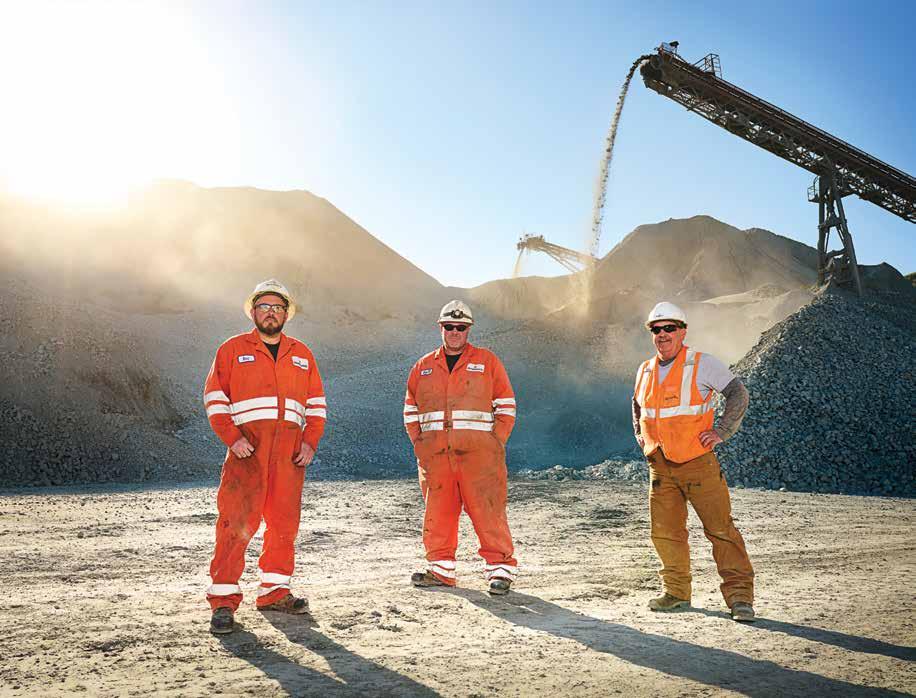
A decidedly human touch to plant automation.
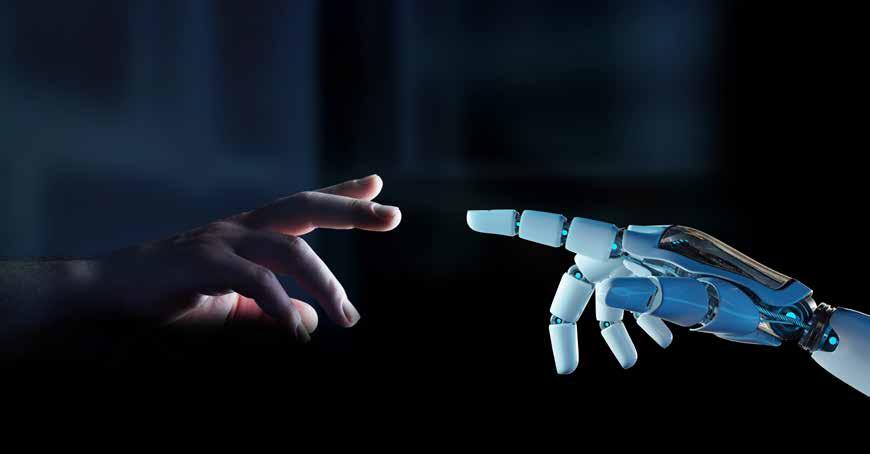
Designed around real people.
“The plant control system that MINDS designed for us has worked very well. The graphics depict the plant almost identically as built and are very easy to follow from the control room. Each value is shown with its position indicated by colours that make identifying issues, such as a stuck valve, extremely easy. The materials that we have produced with the system have been very consistent from the first production run.”

Allen
Hendricks, Vise President, Asphalt Divisions Manager Blythe Construction, Inc.For the past 25 years, MINDS has built a reputation for user-friendly, advanced, customizable plant automation control systems. As of April 2022, we became part of the Astec family to add to their Rock to Road solution for asphalt road building. MINDS provides award-winning desktop software, mobile apps, and hardware for many applications:
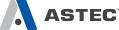
Drums, Batches, Combo/hybrid hot mix plants, Emulsion plants, Liquid Terminals.
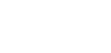
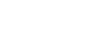
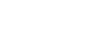
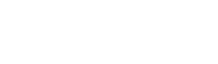
Silo load-out, Ticketing, and Cloud-based data management for the Rock to Road industry.
Better data. Increased control. Higher profits.
How to Construct an ESOP
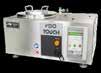
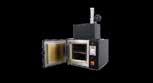

You’ve set up your management team. You’ve built a strong business that generates good income. You’ve gone through the due diligence and now you’re ready to set up an employ ee stock ownership plan (ESOP). What’s next?
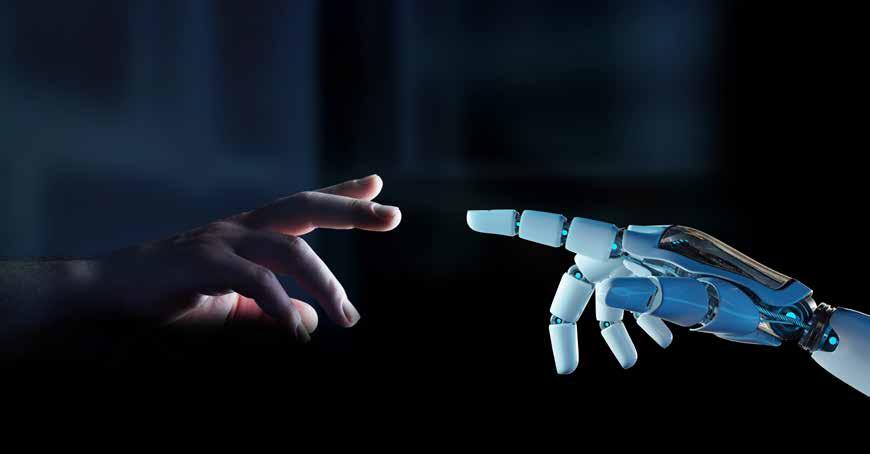
As a refresher, an ESOP is a structure used to sell a business to employees. Often this allows a business owner in the construction industry to maximize the value obtained from the sale of the busi ness. We’re going to walk you through an abridged version of set ting up an ESOP.
First, we need to assess if all the owners are on board. Don’t take this step for granted. In terms of paving, this is the grading and sub base. If you screw this up, it doesn’t matter how well you perform the next steps. Make sure that all owners are, at a minimum, open to discussion.
Second, create a feasibility study. This is your proof roll. We’re confirming that everything is well laid out and finances are going to support the structure to come. You may want to try and do this inhouse, but we would recommend finding an advisory firm that spe cializes in buyout and merger and acquisition (M&A) strategies. A good firm will be able to compare different types of plans and find a slightly better fit through informed adjustments. Analysis should
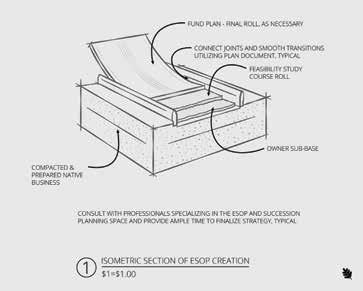



confirm sufficient cash flow devoted to the ESOP and fulfilling the stated purposes of the ESOP.
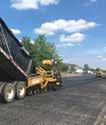
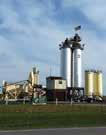
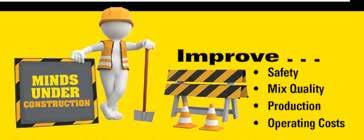
Additionally, you’ll need to confirm the company’s payroll is ad equate to make ESOP contributions deductible for participants. Fi nally, the repurchase obligations of the company will need to be es timated.
Third, you’ll need to value the company’s stock. The asphalt con nects the substructure (ownership) to the business end of the pave ment (the employees). That connection is the value of the company. Everyone needs to agree to a price.
It is critical that you value the company before implementing a plan. You may want to start with a preliminary valuation to see if this route is a non-starter. However, if you go this path, you’ll want a separate appraiser for the detailed valuation. You do not want a regulator raising concerns about objectivity. The reasoning is that a preliminary valuation is done for the current owner of the company and the detailed valuation is done on behalf of the potential ESOP. To that end, the ESOP trustee should select and hire the appraiser for the transaction. A valuation professional will look at cash flow, profits, assets, goodwill, market conditions, values of comparative companies, etc.


Fourth, you can move on to drafting a plan. You’ve laid out every thing and now you need to connect all the dots, butt those joints, and smooth out transitions. If you’ve hired a company to help with the process, they should be able to refer you to an attorney. If you’ve done everything in-house, you’ll need to hire an ESOP attorney. You’ll want
an attorney for this part. Attorney’s have E&O insurance. If they screw up the document, they are on the hook for damages. This is cheap in surance for a bad document.
Fifth, you’ll need to fund your plan. This is your finish rolling. This can be done through a traditional bank, private parties, or the seller of the business. Additionally, the company could make ongoing contri butions or company benefit plans. Most ESOP experts find that tem porarily investing outside of company securities is advisable to build up funds to buy out ownership. Employees can also contribute to the plan through wage and/or benefit concessions. Regardless, the fund ing should match the long-term goals of ownership.
Sixth, you must maintain the plan. Just like pavement needs main tenance, an ESOP needs maintenance. And if you do a good job, it won’t need replacement. An ESOP requires oversight, compliance and reporting to maintain its preferential tax treatment. Also, a plan to communicate with employees that are becoming owners is invalu able. This will represent a new chapter for many employees. As we all know, an ounce of prevention is better than a pound of cure. Educa tion and communication is the best way to provide that protection.
Disclosure: Standing Oak Advisors and Centaurus Financial Inc. do not offer tax or legal advice. Scott Eichler is a registered investment advisor and founder of Standing Oak Financial, as well as author of best-selling book “Don’t Play Chicken with Your Nest Egg.”
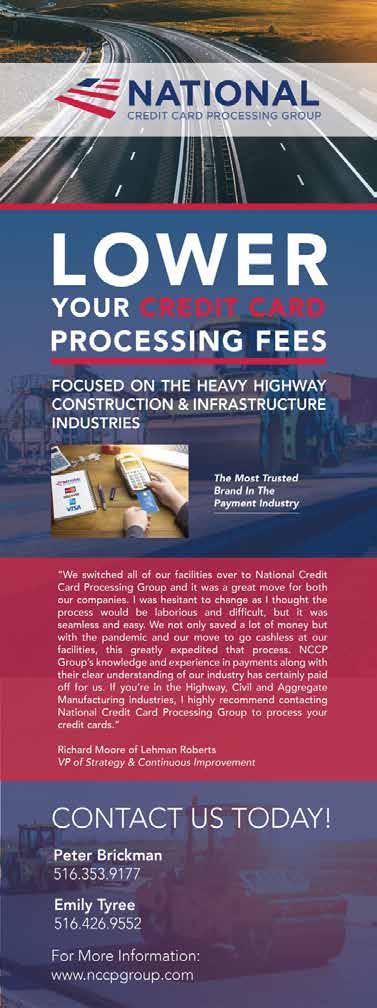
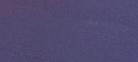
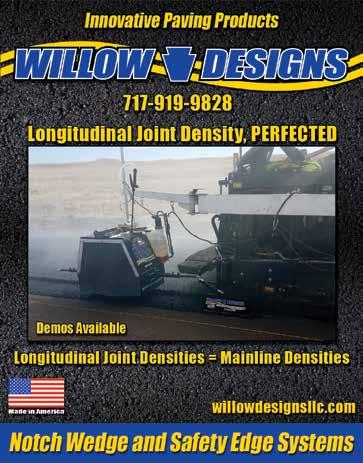

AD INDEX
ALmix 7
Applied Test Systems 65
Asphalt Drum Mixers, Inc 14, 15
Asphalt Materials Inc 47
Astec Industries Inside Front Cover, Inside Back Cover, 11
B&S Light 42,43
Blaw-Knox 4, 9 Blue Smoke Control 41
BROCK 69
Cargill 27
Clarence Richards Company 66 Colorbiotics 21
CONEXPO-CON/AGG 63
CWMF 3, 45, 53
D&H Equipment 68 Eagle Crusher 23 Fast Measure 67 Greenpatch 61
GSSI 13 KENCO 55 Meeker 25 Minds, Inc 64 National Credit Card Processing 67 NPE 62
Process Heating 12 Reliable Asphalt Products Back Cover, 49 Stansteel 19, 57 Systems Equipment 17, 59 Tarmac international 35 Top Quality Paving 68 TransTech Systems, Inc 37 Weiler 29 Willow 67 Wirtgen 33 Women of Asphalt 39

AsphaltPro’s advertiser index is designed for you to have quick access to the manufacturers that can get you the information you need to run your business efficiently. Please support the advertisers that support this magazine and tell them you saw them in AsphaltPro magazine.
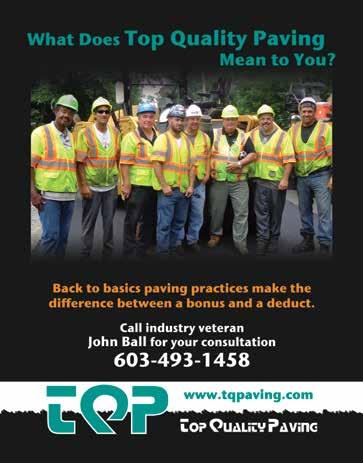

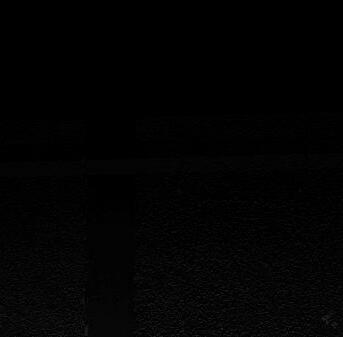
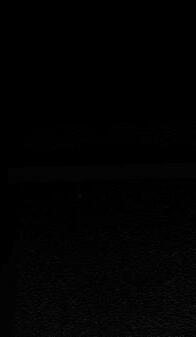
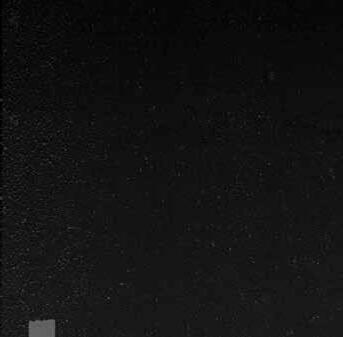
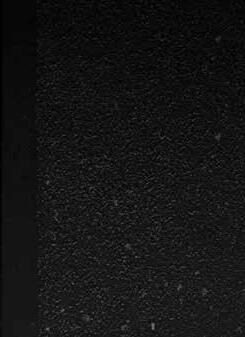
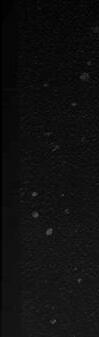
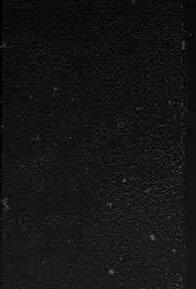
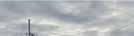

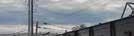



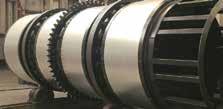
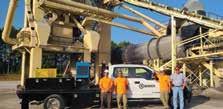

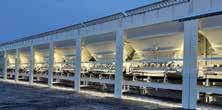
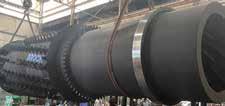
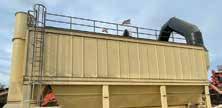
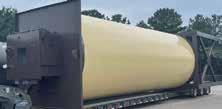
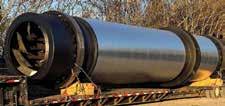
INDOT, Purdue Partner Up to Measure Stockpiles
BY SARAH REDOHLManaging stockpiles of aggregates is a constant concern. That’s why the Indiana Department of Transporta tion (INDOT) funded research at Purdue Uni versity, West Lafayette, Indiana, into a fully au tomated, portable system to estimate the vol ume of stockpiles of bulk supplies known as SMART (stockpile monitoring and reporting technology).
Jeremy McGuffey, statewide winter op erations manager for INDOT, said the cat alyst behind INDOT’s investment into this research was to monitor the department’s nearly 120 salt storage buildings around the state, most of which visually estimate volume. However, he added, SMART can also be used to measure the state’s cold-mix asphalt and aggregate inventory.
“We’re guesstimating our inventory of those materials just as we do with salt,” McGuffey said. “If I pointed to a pile of stone on the ground, could another person accurately tell me the volume of that stone based on sight alone? SMART removes that guesswork.”
McGuffey said traditional methods to mea sure stockpiles use field survey procedures that last several hours and expose surveying crews to dangerous conditions. Although a few lo cations are equipped with survey equipment to take measurements based on the exterior size—the height and width—of the stockpile, those systems don’t account for depth.
“Many state DOTs have recognized the is sues related to measuring stockpiles and have been looking for a more accurate way to mea sure the millions of dollars' worth of materials they have stockpiled,” McGuffey said. SMART is INDOT’s attempt at a solution.
SMART was developed by Ayman Habib and Darcy Bullock, both from Purdue's Lyles School of Civil Engineering. Habib and Bull ock claim SMART is more precise, more cost-effective and safer than traditional com mercial technologies to estimate the volume of stockpiles of bulk materials.
For example, although drones can be used for measuring volumes of outdoor stockpiles, they cannot be used for indoor stockpiles.
The catalyst behind INDOT’s investment into this research was to monitor the department’s nearly 120 salt storage buildings around the state. However, the system can be used for stockpiles of any material.
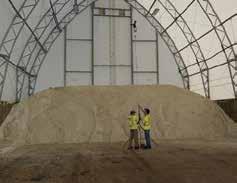
“Particularly in buildings that block GPS sig nals used for navigation,” Habib said. Given that some producers opt to cover their stock piles to minimize excessive moisture, a system like SMART could be an alternative solution for indoor stockpiles.
“SMART can be used for any type of stock pile,” Bullock said. “If you can put a pole up into the air and spin it around, SMART can build a 3D model of that stockpile and estimate the volume within a couple percentage points.”
The data collection process, Habib said, takes less than five minutes and relies on off-the-shelf technology to capture the data. SMART’s measurement tools include two low-cost light detection and ranging (LiDAR) units, a GoPro camera, a small computer known as a Raspberry pie and a 19-foot tripod.
The LiDAR system bounces light off the pile millions of times to collect the information needed to determine the volume, McGuffey said. After the measurement, it takes a few hours for SMART to process the data and cal culate the stockpile’s volume.
“The technology estimates volume with less than 1% error in actual volume,” Habib said, adding that the nature of the stockpile material (including moisture content) does not impact the error percentage.
SMART can also create colorized point clouds that can be used as a visual record of the stockpile over time.
A paper about the SMART platform was published in the peer-reviewed journal Remote Sensing.
GET RESULTS
McGuffey said SMART has already brought positive results to INDOT. “The biggest benefit has been the system’s accuracy,” he said. “One benefit I hadn’t realized before was the speed of the measurement process.” Another benefit, he added, is that the system is mostly automated.
McGuffey said INDOT first plans to utilize SMART at its salt storage facilities as they fin ish the research project with Purdue. “In terms of its use case in the aggregate space at INDOT, I think the mobility of the solution could make this an attractive way to measure outdoor stockpiles,” he said.
Although the mobility of the platform makes it a more flexible solution, Bullock and Habib said the next step is to package the system to be permanently mounted in stor age facilities to allow for automated data col lection. “The higher up the unit is, the better the measurements will be,” Habib said. “That’s why we’re planning for the system to be per manently installed at stockpile facilities.”
“Although it’s more cost effective to move one unit around, we believe this solution will be affordable enough to mount one unit per facility,” Bullock added.
“In the next few years, as the technology becomes more affordable, I could see these devices becoming even more cost effective,” McGuffey said.
The commercialization of the SMART plat form remains a challenge for the private sector. “We’ve developed the technology,” Bullock said. “Now is where the private sector comes in. There are several groups now evaluating alter native business models to help us scale quickly.”
The Purdue Research Foundation Office of Technology Commercialization has applied for a patent for SMART from the U.S. Patent and Trademark Office. For information about licensing opportunities, contact Dhananjay Sewak of OTC at dsewak@prf.org about 2021HABI-69512.
Power and Portability
Our portable plant configurations feature a variety of components including jaw crushers, cone crushers, impact crushers and a variety of screening plants. Without sacrificing power or productivity, portable options deliver efficient and reliable performance with extra portability and adaptability.
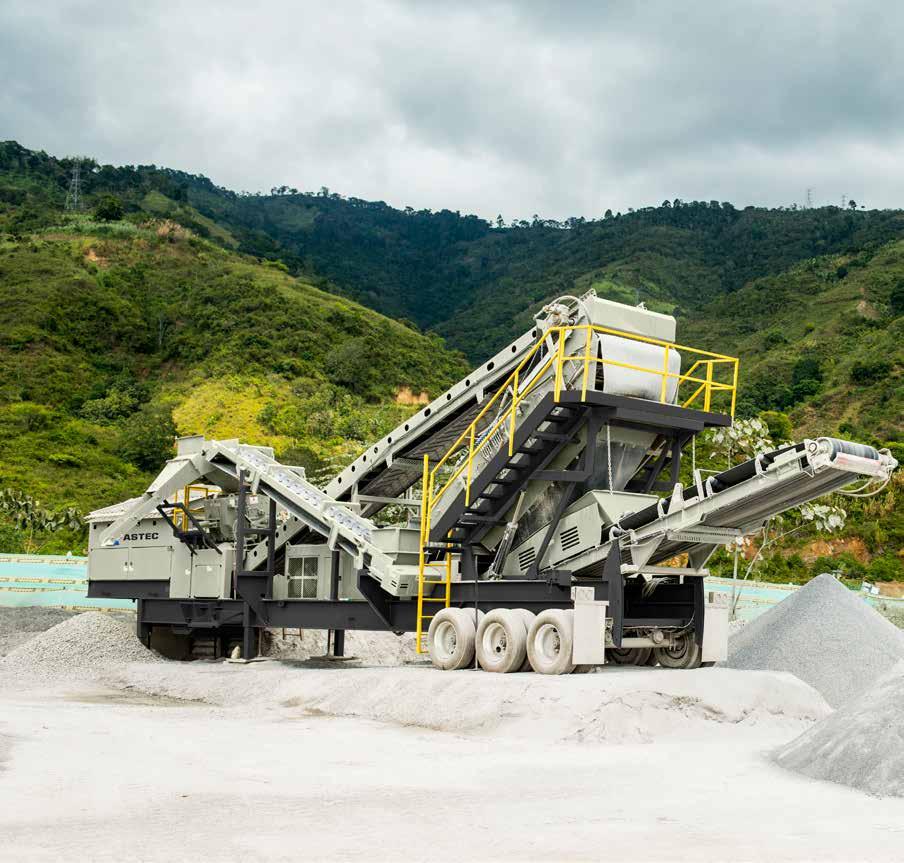
BUILT TO CONNECT
Scan to see the full line of portable products.
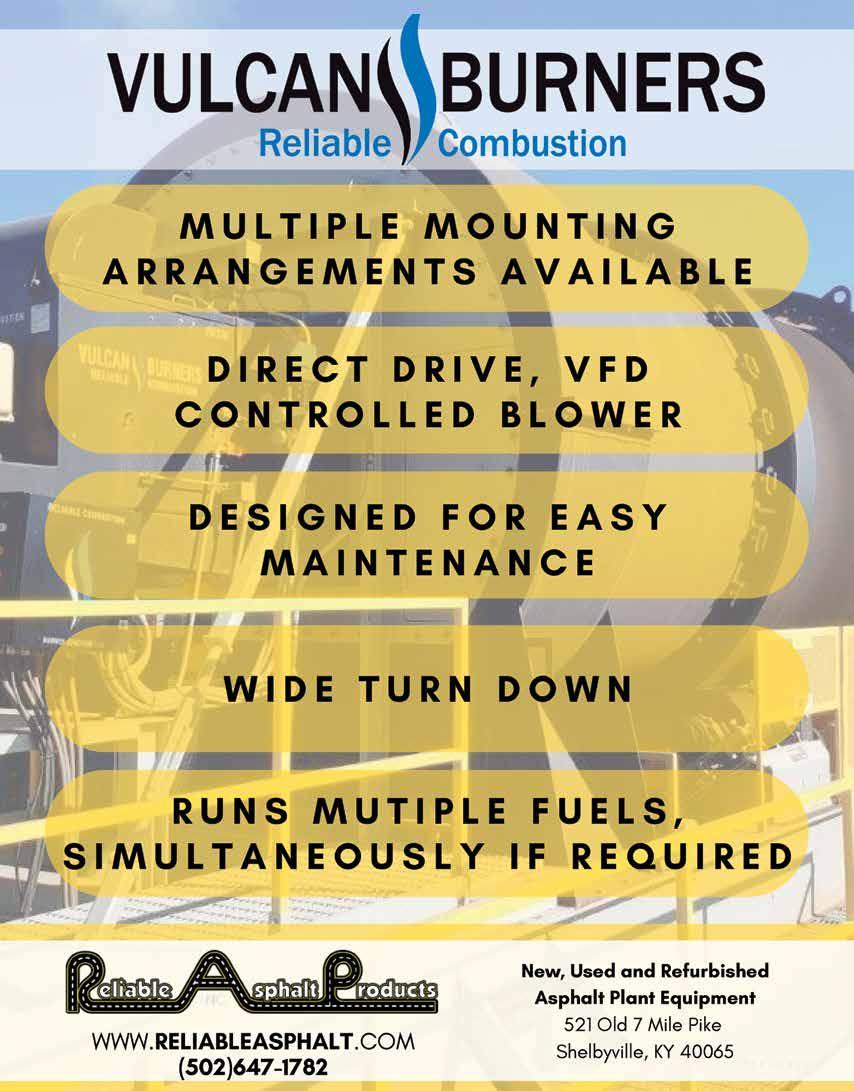