
6 minute read
eçimiBasınçlı Kaplarda Boyut, Kalınlık, Malzeme S
by Eda
Çoklu kompresör kontrol sistemi (Master Kumanda) olmayan sistemlerde, Resim 4.’deki gibi geniş bir basınç bandı ile minimum basınç ihtiyacından oldukça yüksek basınçta hava üretimi gerçekleşir. 1 barlık basınç artışının; enerji sarfiyatını yaklaşık %7 oranında yükselttiği düşünüldüğünde, önemli bir oranda elektrik tüketimi artışı olması kaçınılmazdır (bkz. Resim 5.). Sistemde 5 adet 110 kW’lık kompresör örneğine bakıldığında; %7’lik artış toplamda yaklaşık 40 kW’lık bir sarfiyata sebep olurken, yıllık 7.200 saat çalışan bir işletme için 288.000 kWh/yıl fazladan tüketim anlamına gelecektir.
Resim 5. Kaskad (Cascade) Kontrol Modu Enerji Tüketimi
Advertisement
Kademeli olarak ayarlanan basınç set değerleri ile yükselen basınç bandını azaltmak amacıyla kullanılabilecek Master Kumanda sistemi ile ciddi oranda enerji tasarrufu sağlanabilir. (bkz. Resim 6.)
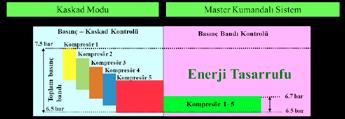
Resim 6. Master Kumanda ile Enerji Tasarrufu
Master Kumanda sistemleri temel olarak şu şekilde çalışır: Belli bir noktada bulunan bir basınç sensöründen (örneğin kompresör istasyonu çıkışı) hat basınç bilgisi alınır. Bu noktada basıncı olabildiğince sabit tutmak için sinyaller üzerinden haberleşerek kontrol ettiği kompresörleri, mümkün olan en verimli şekilde yönlendirerek istenen basınçlı havayı üretmek için geliştirilmiştir. Özel olarak geliştirilen akıllı ve adapte olabilen yazılım algoritması sayesinde; sistemdeki kompresörlerin performans verileri bilgisi ile mümkün olan en sabit, en düşük basınçtaki havayı, en verimli kombinasyonu seçerek (bkz. Resim 7.) üretilmesini sağlamaktadır. Resim 6.’daki örnekte; üst basınç limiti 7,5 bardan 6,7 bara indirerek, 0,8 barlık daha düşük bir basınç bandı sağlanmış olmaktadır. Basınç bandı düşürülerek yaklaşık %5-6 civarında enerji tasarrufu sağlanmış olur. Farklı sistemlerde bu rakam %20-25’lere çıkarılabilir.
Master kumanda ile kompresörler ve diğer ekipmanlar; RS485, Modbus, Profibus, Ethernet gibi ara yüzlerle haberleşebilirler. Ayrıca hat üzerinde; basınç, çiğlenme noktası, sıcaklık sensörü, debimetre gibi noktalardan da bilgi toplama ve kaydetme amacıyla analog bağlantı yapılabilir.
Kompresörler kontrol edilerek daha verimli çalışırken, aynı zamanda transfer edilen veriler kaydedilerek, gerçek zamanlı takip ve analiz olanağı da sağlamış olur. Geçmişe dönük uyarı, arıza ve çalışma performans parametreleri, hava tüketim trendleri, basınç eğrileri kaydedilerek, detaylı analize olanak sağlar.
Genel olarak Ethernet ile PC’ye kolayca bağlantı yapılarak, ek bir yazılım gereksinimi duyulmadan, web browser üzerinden anlık bilgilerin ve verilerin aktarımı ile incelenmesi sağlanabilir. Tüm sistemin izlenmesi ve analizinin yanı sıra bağlı ekipmanların bireysel olarak incelenmesi de mümkündür. (bkz. Resim 8.)
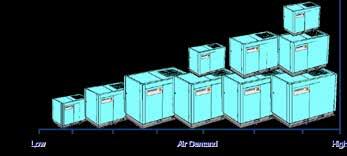

Resim 8. Master kumanda web server görüntüsü
Haberleşme sağlanarak; kontrol edilen ve bilgi transfer edilen veriler, işletmelerin kendi otomasyon sistemlerine entegre edilebilirler. (bkz. Resim 8.)
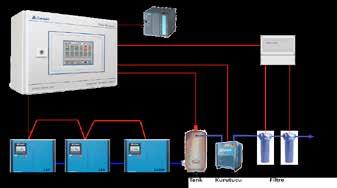
Resim 9. Master kumanda bağlantı ve haberleşme
Bağlı tüm ekipmanların çalışma performans verileri haricinde, arıza bilgileri de e-posta ve/veya SMS olarak kullanıcıya iletilerek hızlı bir şekilde bilgilendirme sağlanır.
Özet olarak; Master Kumanda kontrol sistemi kullanımı ile sağlanabilecek faydalar şu şekildedir:
+ Akıllı algoritma ile en verimli kompresör kombinasyonunun çalıştırılması + Enerji yönetim sistemi entegrasyon + Dar basınç bandı ile düşük elektrik tüketimi + Eş yaşlandırma ile optimum bakım maliyeti + Veri kaydı + Veri takibi, izleme ve analiz + Kestirimci bakım + Hızlı arıza müdahale
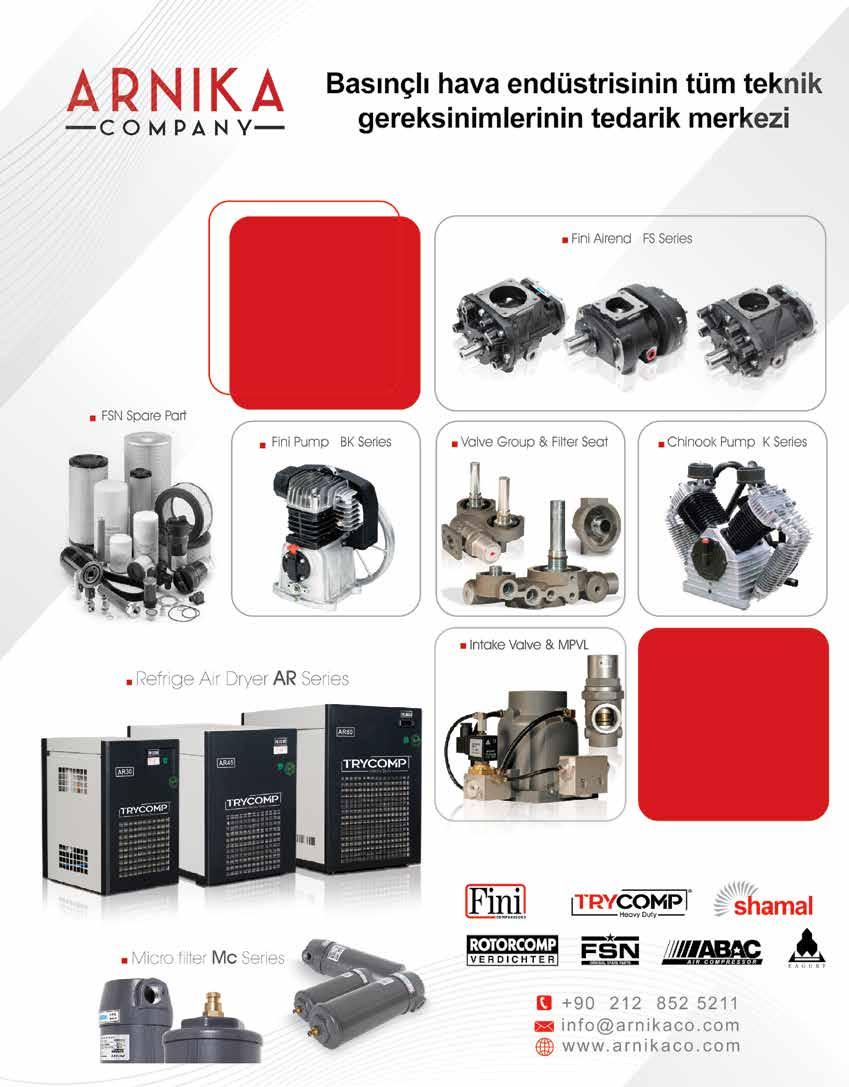
BASINÇLI KAPLARDA BOYUT, KALINLIK, MALZEME SEÇİMİ
UĞUR KARALI makine mühendisi & kaynak mühendisi urt müHendiSlik BaSınÇlı kaplar ceo Su

yüzbinleri aşan malzeme sayısı ve malzeme seçimi yapılacak alanların birbirleriyle ortak noktalarının azlığı, malzeme seçiminde belli bir alana odaklanmış seçim modellerinin geliştirilmesini gerekli kılmaktadır. Basınçlı kaplarda mevcut olan parçalar için en uygun malzemelerin seçimini yapacak bir yaklaşım geliştirilmelidir.
URT
MÜHENDİSLİK
BASINÇLI KAPLAR MAKİNA SANAYİ VE TİC. LTD. ŞTİ.
Basınçlı kaplar 0,5 atmosfer basınç ve üzerinde bir iç basınca sahip sıvı ve gazların üretiminde, taşınmasında ve depolanmasında kullanılan küre, silindirik veya koni şeklinde atmosfere kapalı ekipmanlar olarak tanımlanmış ve kullanım alanları ısıtma sistemleri, basınçlı hava-su sistemleri, kimyasal madde depolama ve sanayi gaz depolama tankları olarak verilmiştir. Basınçlı kapta ise depolanan veya taşınan akışkanın yüksek basınçlı ve uyguladığı basıncın değişken yapıda olduğundan dolayı mekanik özellikler oldukça önemlidir. Akışkanın neden olacağı korozyona ise tüm basınçlı kaplarda olduğu gibi bu kaplarda da önlem alınması gerekmektedir. Literatürde farklı tiplerde ve farklı amaçlarla kullanılacak basınçlı kaplar için malzeme seçimi yapan bir çalışma mevcut olmamasına rağmen, sadece belirli bir amaç için kullanılacak basınçlı kaplar için özel nitelikli malzeme seçimine yönelik çalışmalara rastlanmaktadır. Malzeme seçimine yönelik literatürde yıllık üretim miktarı, birim maliyet, sıcaklık, dayanım gibi malzemeden beklenen özelliklerde istenen değerleri sağlayan malzemeleri gösteren tabloları ve şekilleri kullanan klasik malzeme seçim yöntemleri ile beraber, son yıllarda literatürde yoğun olarak görülen çok kriterli karar verme (ÇKKV) yöntemlerini kullanan çalışmalar da bulunmaktadır. Malzeme seçerken; malzemenin sertlik, tokluk, Young modülü, kayma modülü, çalışma sıcaklığı, aşınma direnci, kimyasal direnç, boyut, şekil, yüzey sertliği, malzeme içi bağ dayanımı ve biyokirliliğe karşı direnç kriterlerini dikkate alınmalıdır.
Basınçlı kaplar için malzeme ve boyut özellikleri seçim yaparken ana hat belirleyici özellikler vardır.
Bunlar; • Çalışma basıncı • Çalışma sıcaklığı • Silindir kabın çapı • Basınçlı kap için kulanılan malzemenin akma mukavemeti • Basınçlı kabın dizayn standartına göre NDT grubu • Basınçlı kabın kulanılacak ortam şartları (rüzgar, deprem, korazif ortam vb durum yoğunluğu • Basınçlı kap içerik maddesi.
Bu özellikler dikkate alındığında basınçlı kap dizayn standartı hava tankları için • EN 13445 • EN 286-1 • AD 2000 Merkblatt • ASME SEC VIII DIV.1
Bu dizaynlar yukarıda belirtmiş olduğumuz değerler üzerinden basınçla hava tankların hem ölçüsel hem malzeme hem de içerik madde sıkalasına göre basınçlı hava tankı üretimi gerçekleşmektedir
Bilindiği üzere basınçlı hava tankı malzeme seçimi yapılırken sadece bu standart ve değerler dışında hammadde bulunulabilirliği ve standart malzeme üretim ölçüleri de burda dikkatimizi çekmekte ve tasarım yaparken maliyet sıkalamızı belirleyen en temel unsurlardan biri olmaktadır.
Biz basınçlı hava tankı üretimi ve projelendirmesi, dizaynı yaparken elimizden geldiğince, dizayn şartlarının el verdiği ve bulunabilirlik açısından değerlendirilmeliyiz. Basınçlı hava tanklarında ne kadar az kaynak uygularsak bizim için en sağlıklı basınçlı kabı üretmiş oluruz.
En az kaynaktan bahsettiğimiz konuda kaynak ısı girdisi buda bizim malzeme meterolojimizi bozmakta ve bize ITAB yani ısı tesiri altındaki bölge olarak geri dönmektedir. Yapılan incelemeler ve kontroller sonucunda ülkemizde ve dünyada basınçlı kap patlamalarının yüzde 90'ı neredeyse kaynak yüzeyinde değil, kaynak metalinin hemen yanındaki İTAB yani ısı tesiri altındaki bölgeden kaynaklandığını görmekteyiz. Bu şartlarda üretilen basınçlı hava tankları için iyi bir kaynak reçetesi uygulanmak zorundadır. Basınçlı kap üreticileri bunu akredite kuruluşlardan yararlanarak sistemlerine sağlamaktadırlar. Bunun başka bir boyutu da ısıl işlem yöntemidir ki ülkemiz için maliyetli bir yöntem olup, yüksek basınçlı tanklarda dizayna göre neredeyse zorunluluk derecesindedir.
Bu yöntemler ve kaynak hasasasiyeti olan bu ürünler için malzeme seçimi de bu derece önem arz etmektedir. Seçilen dizayna göre uygun malzeme temini kaynak prosedürüne göre önem arz etmektedir.
Piyasalarda ölçü karmaşası yaşanılan günlerde üretici istediği çap ve boy ölçüsünde tank üretmek için herhangi bir yasal ve standart zorunluluğu yoktur.
Buradaki amaç hammaddeye ulaşım ve malzeme çap ölçüleriyle oynayarak malzeme kalınlığının incelmesi veya artmasıyla maliyet olasılığı ve rekabetçi piyasa şartlarına göre mühendislik yöntemleriyle, müşterinin istediği hacimdeki bir tanka daha az ücret ödetmeye yöneliktir böyle bir bilimsel mühendislik çalışmasının önünde herhangi bir engel yoktur, sakıncası da yoktur.
Yöntem olarak belirtmeliyim ki ürünün kalınlığını düşürmek maliyeti düşereceğinden, basınç sabit bir basınçlı tank için • Tank çapı • Tank çalışma sıcaklığı • NDT kontrol presödürü
Basit olarak düşündüğümüzde bu üç değer tank kalınlığını yükseltip artıracak bir sonuç elde ettirir.
Örnek vermek gerekirse çap 1200 mm'den de 3000 lt basınçlı hava tankı, çap 1400 mm dende 3000 lt basınçlı hava tankı yapılır.
Ortalama piyasa kalınlığı baz alındığında çap 1200 mm için 6 mm çap 1400 mm için 8 mm kulanılması görüldüğü üzere çap arttığında sadece kalınlığı artırıp maliyeti artırmaktan başka bir şey ifade etmez, buradaki hesap ve yöntem mühendislik dizayn ve akredite kuruluşlarından alınan CE belgesi tip onayı ile ilgilidir.
Kısaca ben şu litreyi şu kalınlıktan yapıyorum söylemi yanlıştır, ya da ben şu litreyi şu çapta şu kalınlıktan yapıyorum değeri doğru bir değerdir.
Burada önemli olan kriter konu özet kısmı içerisinde basınçlı hava tanklarının ömür/yıl hesabı ve korozyon durumudur.
Bu ömür yıl hesabına göre tankların değişimi yıllık akredite kuruluşlar tarafından periyodik kontrolleri yapılmalıdır ve zorunludur.
Son dönemlerde çok duyduğumuz tankların test edilmeden yıllık muayene raporları verildiği yönündedir. Bu firmanız için alacağınız çok büyük bir sorumluluktur, hatta firmanıza bu ve bu gibi periyodik destek aldığınızda sizde mühendis arkadaşlara eşlik ediniz yada ettiriniz. İnsanımız milletimiz ve ülkemiz, bizim için değerlidir.
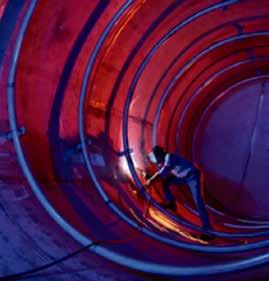