

Full Colour 3D Print
It’s All Over
Your search for a 3D printer capable of producing complex & creative models in up to 10,00 0,00 0 colours is over . T he new Mimaki 3DUJ-22 07 delivers extraordina r y detail in full colour.
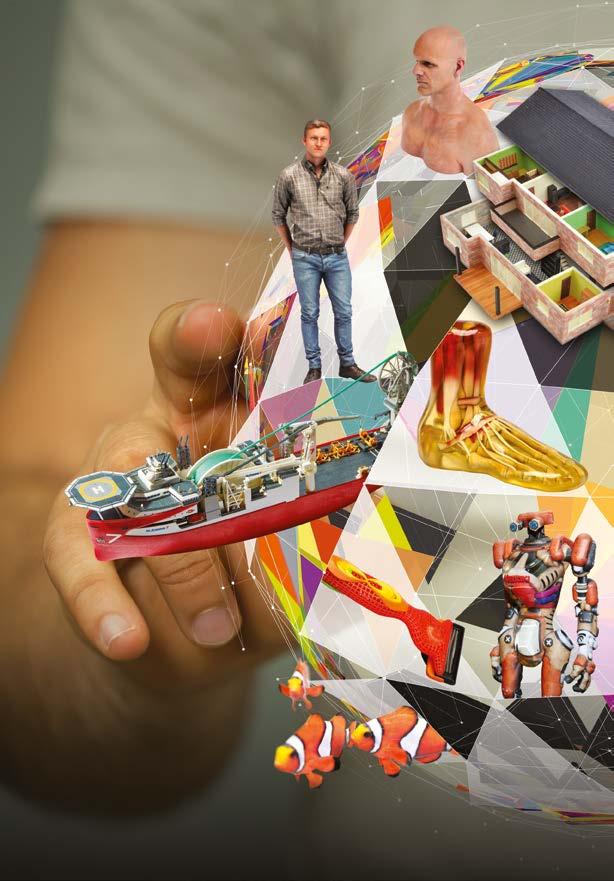
E xplore a wor ld of colour for just
£ 3 4,995
Take control of your design and production process with Formlabs’ fastest, most powerful SLS 3D printer yet.
Formlabs Fuse 1+ 30W SLS Printer
With four Nylon powders to choose from, 3D print productionready, end-use parts on the Fuse Series.
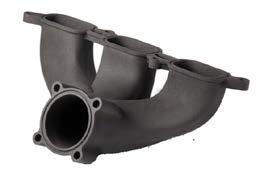
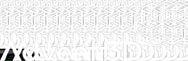
The Fuse 1+ 30W printer's inert gas environment ensures that you'll get industrial quality parts, every time, while the user-friendly workflow enables anyone to take ownership over production.
With a more powerful laser and enhanced scanning speed, the Fuse 1+ 30W delivers parts at up to twice the speed as previous generations, allowing designers, engineers, and manufacturers to go from design to finished part overnight.
Find out how the Fuse 1+ 30W can improve your production performance, call 01295 672600.
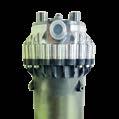
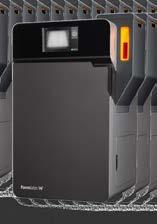
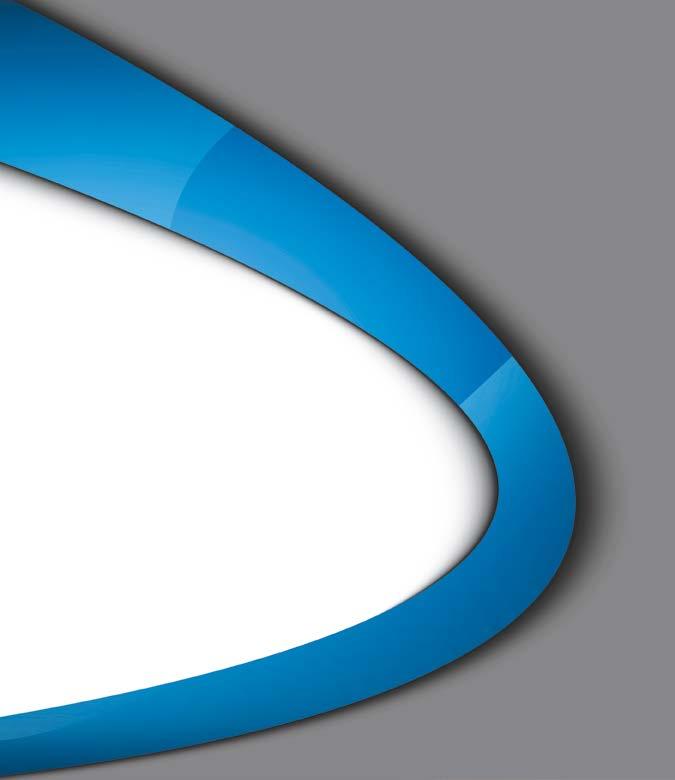
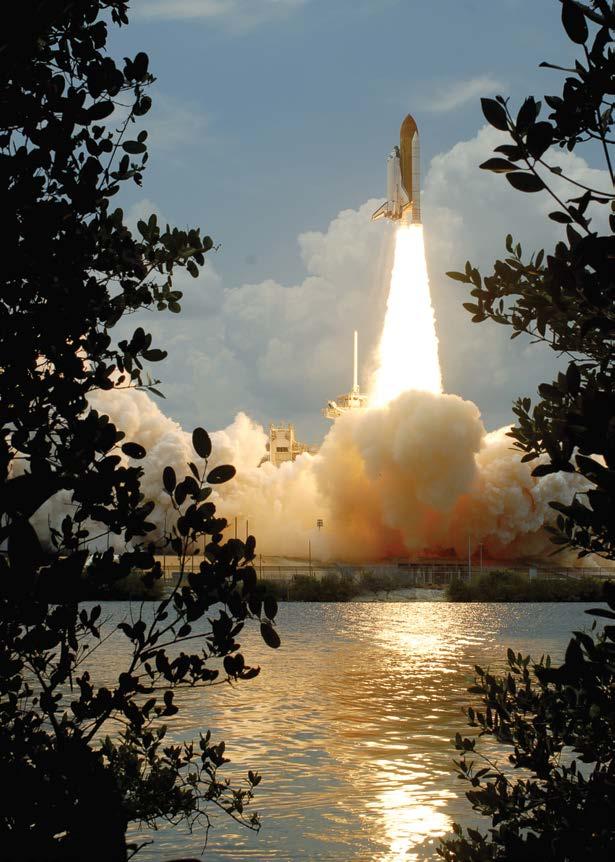
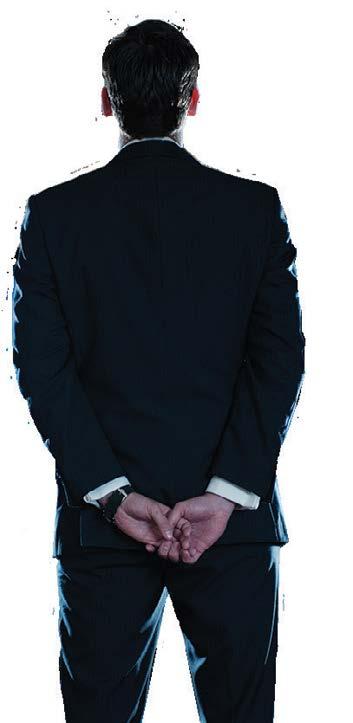
FROM THE EDITOR SAM DAVIES
Additive Inspiration
The Wednesday evening social at this year’s AMUG Conference was the same as any other, until it wasn’t.
We were nearing the end of a week full of conferencing, networking, and learning. Two out of three keynotes had been delivered, ten DINO Awards handed out, and its famous offsite event successfully kept secret. Most attendees were leaning into the steampunk aesthetic, gambling for raffle tickets, and raising the roof with some karaoke classics.
Except for the 50 or so people huddled around a flat screen TV. These people had room for more. They waited patiently. First for a passing boat to get out of the way, and then for some high winds to die down. They searched for the best vantage point, they reached for their phones, and they counted down from ten, nine, eight, seven.
At one, there was a pause. A burst of flame obscured the view momentarily. And then the place erupted. Some hugged, some cheered, some profaned. Relativity Space had done what some in attendance thought wouldn’t be done, maybe even couldn’t.
The first rocket made up nearly entirely of 3D printed parts passed Max-Q – the point in the launch sequence where a rocket experiences maximum dynamic pressure – and the 100km Kármán line. Though it didn’t quite reach orbit, it certainly had lift off, and the engineers, designers and
operators watching on were jubilant. 3D printing was proven to be viable for what might be the most inspiring application of the technology to date.
In our aerospace-focused issue, we unfortunately don’t have more from Relativity – they’ve been kinda busy – but we do explore 3D printing in outer space through the additive manufacture of a satellite set to launch on the SpaceX Transporter-9 later this year (P11), the use of the technology for satellite sensors (P15), and, as you'll have seen on the cover, in the 3D printing of a liquid rocket engine (P8). At 30,000 feet, meanwhile, we dig deep into GE Aerospace's AM journey, application by application (P12), and Cranfield University present findings from a feasability study centred on aircraft landing gear (P17).
Bringing us back down to earth are five industry experts who give their perspectives on one of AM’s most burning issues: cost per part (P21). But there are also reasons to be cheerful. We have insights from AM business leads at Renishaw (P30) and Evove (P38), and we hear from a selection of metal AM newcomers who are poised to deliver 3D printing at scale with their proprietary technologies and parts as a service business models (P27).
And somewhere in between, we take a look at what’s to come at this year’s TCT 3Sixty event in Birmingham (P32), which has a jampacked conference agenda and is set to have an equally busy show floor. We’ve gathered the highlights, and we look forward to seeing you there for more additive inspiration.
Shape the future
We are shaping the future of manufacturing and product development
Transforming Manufacturing: The Power of the UltiMaker 3D Printing Ecosystem with Briggs Automotive Company.
Briggs Automotive Company (BAC) is a British sports car manufacturer best known for the Mono model, a single-seater road-legal supercar.
BAC has successfully integrated 3D printing into the production of the Mono R Supercar by harnessing the full potential of the Ultimaker Ecosystem to produce high-quality parts.
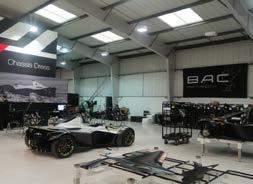
The UltiMaker 3D Printing Ecosystem has benefited BAC in some of the following ways:
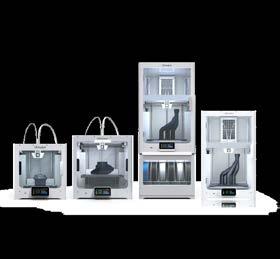
• Enabled fast and inexpensive production of highly customisable parts
• Optimised supply chain management through the UltiMaker Digital Factory
• Enhanced design flexibility and geometric complexity
• Accelerated design iteration cycles and reduced time-to-market
Vist UltiMaker at TCT3Sixty
Unlimited application potential
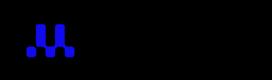
The power of the S Series lies in its versatility. Explore new 3D printing applications using the widest choice of materials on the market. These printers enable rapid iterations and customisations making them the perfect desktop 3D printers for manufacturing and product development.
Andrea Gasperini will be taking the stage to show how the UltiMaker 3D Printing Ecosystem can benefit manufacturers. You will also find out more about how BAC harnessed the UltiMaker 3D printing platform to its full potential.
Location: TCT Introducing Stage
Date: Wednesday 7th June at 1 pm - 1:30 pm
08. THE CUTTING EDGE SLM Solutions details the additive manufacture, postprocessing and inspection of a liquid rocket engine capable of reaching the Kármán line.
11. NIGHT & DAY
Sidus Space tell Sam Davies about its use of 3D printing in the design of a lightweight satellite set to launch off SpaceX’s Transporter-9.

12. A FLYING START
We look at GE Aerospace’s success with AM, application by application.
15. SPACE BOUND
Oli Johnson speaks to MIT about its application of 3D printing for satellite sensors.
17. ENABLING WAAM IN MANUFACTURING AIRCRAFT LANDING GEAR
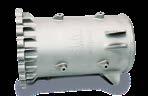
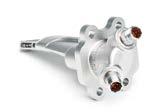
Cranfield University shares its findings after carrying out a feasibility and reliability study on 3D printed aircraft landing gear.
21. THE COST PER-PART CHALLENGE
AM experts give their perspective on how users can overcome their cost-per-part headaches.
25. STEP BY STEP
Production 21 11
Evolve Additive Solutions explains the benefits of its recently launched Production Assessment Program.
METals
27. PARTS THE PLAY
Sam explores the technologies and business models of several metal AM firms coming to market with proprietary processes.
30. RENISHAW IS READY
As the company celebrated 50 years of engineering, Laura Griffiths sat down with Director of AM Louise Callanan to discuss collaboration, productivity and ‘applying innovation.’
32
32. 23 REASONS TO ATTEND
We round up all the things to look forward to at this year’s TCT 3Sixty, including exhibitor highlights, conference sessions, and networking opportunities.
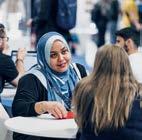

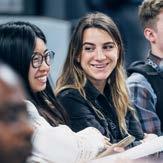
EXEC Q&A 38
38. LEAPS AND BOUNDS
We speak to UK-based Evove, a company using binder jet additive manufacturing to advance filtration membrane technologies.
THE CUTTING
In southern California, a group of engineering students look skywards.
They enrolled at San Diego State University (SDSU) to understand the science of how engines and structures are manufactured, from design through quality assurance. And now, they not only need to put those learnings into practice, but in doing so they have been tasked with reaching the edge of space.
The Kármán line, a commonly recognised boundary for space at 100km, is the target for their liquid rocket engine, designed to be built in Inconel 718 with the support of SLM Solutions and its dual-laser SLM 280 2.0 metal additive manufacturing system. SLM Solutions is guiding the development process, helping to reduce the engine from over a hundred parts to just five. It is to be manufactured at the SLM North American applications centre in Wixom, Michigan, before Hot Isostatic Pressing (HIP) at the Quintus Technologies Application Center in Ohio and quality testing with CT scanning by Avonix Imaging are performed.
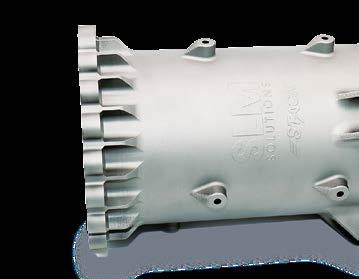
But it has been roughly a year in the making, with myriad design reviews, prototypes and test procedures required to achieve the optimum engine system consisting of a twopart outer shroud, a two-part inner liner, and an injector. The parts are printed in Inconel 718 powder with 30-micron layer thicknesses in an argon atmosphere, before being de-powdered and stress-relieved at 1066°C for 1.5 hours in an argon environment. Wire EDM cutting technology is then used to separate the parts from the build plate.
Throughout the project, additive manufacturing is affording the team to rapidly prototype design ideas, generate complex geometric shapes and hollow out structures. It all adds up to an engine that can meet the performance specs at a lighter weight.
Leveraging AM has not been without its challenges, however.
Having embarked on a design optimised for a metal powder bed fusion printing process, the team has identified the grains in the additive manufactured material are not equiaxed, rather they are columnar in the build direction.
The size of the crystalline grains is of great importance to the mechanical properties of metal materials, since the Hall-Petch equation dictates that the yield stress at room
temperature is inversely proportional to the square root of the average diameter of the grains. Therefore, the smaller the grains, the stronger the material. This is resulting in anisotropic mechanical properties, and so the team is having to take measures to reduce the imperfections in the metal and increase fatigue resistance.
When a metal is exposed to temperatures above the recrystallisation temperature, its grains will increase in size. The higher the temperature and the longer the exposure time, the more the grains grow. Traditionally, temperatures of 1,163-1,200°C and an exposure time of four hours have been used for HIP treatment of Inconel 718. But several studies suggest these settings cause substantial grain growth and can have a detrimental effect on fatigue strength.
The solution to this problem is to reduce the temperature and/or the exposure time. Quintus Technologies has performed a study together with University West in Sweden which shows that all the positive effects in terms of defects elimination can
be achieved at lower temperatures than traditionally used, while minimising grain coarsening. Since the ASTM standard for HIP treatment of Inconel 718 states the temperature should be between 1,120°C and 1,185°C, Quintus tested samples of Inconel 718 that had been HIP treated at the extremes of that range with a consistent pressure of 100 MPa and fourhour duration. The results show that the elimination of pores was just as effective at 1,120°C and 1,185°C, while porosity was reduced from 0.15 vol.% to 0.01-0.02 vol.% at the lower temperature. There was also clear grain growth in the powder bed fusion samples at 1,185°C, while the grains HIPed at 1,120°C were significantly finer. Further tests have shown that combining HIP treatment at 1,120°C with solution treatment and a shortened two-step ageing process can even reduce the grain size compared to the as-built material.
Taking the knowledge gained on HIP of additively manufactured Inconel 718, Quintus Technologies is applying an optimised HIP cycle to homogenise the microstructure and minimise grain growth while targeting a fully dense structure. The
SLM Solutions on the additive manufacture of a liquid rocket engine capable of reaching the Kármán line.SHOWN: LIQUID ROCKET ENGINE COMPONENT
EDGE
smaller printed assemblies of the rocket motor are HIPed in the Quintus Application Center, applying a soak with a temperature of 1,120°C, pressure at 100MPa, while being held for four hours. The cycle is also leveraging the URC functionality to rapidly cool the HIP unit to minimise process time for improved productivity.
The 3D printed liquid rocket engine is then passed onto Avonix Imaging to undergo computed tomography scanning. This project requires both 3D cone beam scanning and 2D linear array scanning, with the former being leveraged to capture several thousand radiographic images to produce a large three-dimensional volumetric datasheet in a single scan, and the latter being used to overcome any image degradation from the cone beam CT scan which might prevent defect detection.
Deploying the cone beam scanning approach, Avonix scans the rocket motor with a 450KV microfocus source, 61.5-micorn voxel size and 4mm copper filtration to capture 3,000 projection images in a 45-minute process. No indication of porosity in the printed parts has been found, with Avonix then deploying its linear approach to validate the findings. For this second scan procedure a 450KV microfocus source is used at a 100-micron voxel size with 2mm copper filtration. More than 1,600 Z-slices are captured in a process time of 45-seconds per slice, amounting to 19 hours in total.
By the end of the process, SLM Solutions, Quintus and Avonix are returning a rocket engine to the students that has a reduced part count, heightened complexity, increased fatigue strength and less variability in its mechanical properties. The partners have also highlighted a problem with current HIP standards for 3D printed Inconel 718, which have been developed for castings and transferred over to additive manufacturing, despite AM materials having different microstructures. And with the help of quality assurance tests, they have reinforced that metal additive manufacturing, in conjunction with HIP, can be used to make high-grade applications for space and aviation without sacrificing quality.
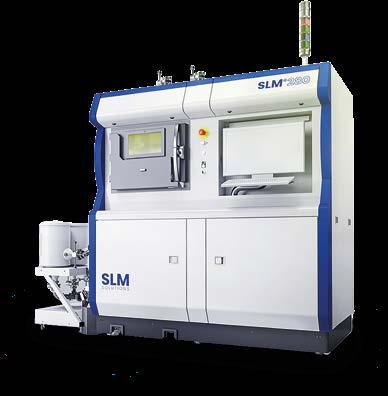
It is now over to the SDSU students to get its 3D printed liquid rocket engine over the line.
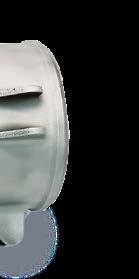
“SLM Solutions has reinforced that metal AM can be used to make highgrade applications for space without sacrificing quality.”
Second to none.
Designed by engineers, for engineers. The reliable and proven Neo series of 3D p r i n t e r s b u i l d h i g h - q u a l i t y p a r t s w i t h superior surface quality, accuracy and detail.
Open resin system
An open material system means users are not restricted by the usual parameter constraints, this offers the ability to utilize any 355 nm hybrid resin chemistry
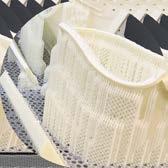
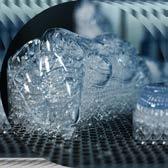
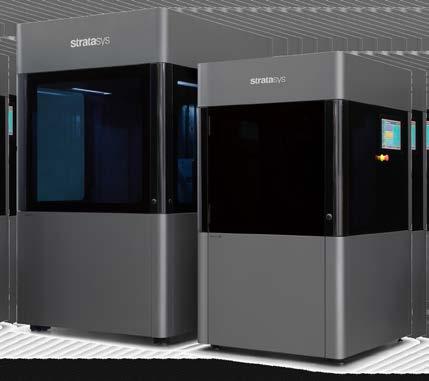
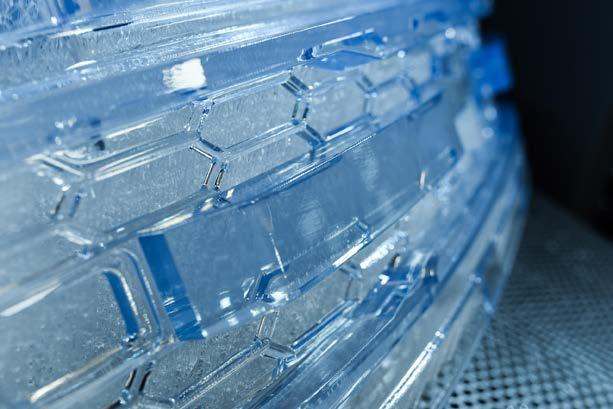
Proven reliability and quality assurance
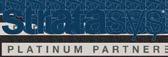
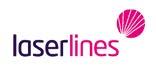
D e s i g n e d b y e n g i n e e r s f o r e n g i n e e r s , t h e N e o i s c a r e f u l l y engineered throughout using state-of-the-art technology, proven components and aesthetic finishes.
Reduce finishing time by up to 50%
The Neo produces highly accurate parts with unparalleled industry quality Optimising the machine design and utilising the latest cuttingedge technology available for laser and scanners, our beam delivery system produces exceptional layer-to-layer alignment repeatability
The printed parts are dimensionally accurate, with exceptional sidewalls and crisp feature resolution.
Find out more, visit Stand No. D51 at TCT 3SIXTY 2023

As he extols the virtues of the technology facilitating a satellite weighing less than 100kg, Tony Boschi shows the depth of his experience with the repeated use of two words: rapid prototyping.
Boschi has been working with 3D printing technology for so long, that he not only refers to the processes using that phrase, but he also has the war stories. When he first used the technology, for example, he and his colleagues took to squirting hairspray on stereolithography (SLA) parts to prevent the sticky texture they were left with when coming out of the printer, and in turn allowing any paint applied to the components to dry faster.
“It was one of the greatest things in the world,” he recalls thinking. But such glee is relative. These days, as Lead Design Checker at Sidus Space, he has printed sample holder parts in Markforged’s Onyx carbon fiber-filled nylon material that formed part of a flight test platform installed on the outside of the International Space Station (ISS) for a year. That the parts survived on the ISS with next to no degradation emboldened Sidus Space to push forward with the idea of producing the structure of its LizzieSat satellites with 3D printing.
Sidus Space was founded by Carol Craig, a former US Navy officer who became the first woman eligible to fly combat aircraft in the US Navy, to carry customer sensors and collect data for a multitude of different customers at the same time.
The partially printed LizzieSat constellation will launch for the first time later this year on the SpaceX Transporter-9, if it weighs less 100kg.
This has represented a significant challenge for Boschi and the Sidus team, especially since integral
& DAY
componentry like batteries and computers take up a significant portion of the satellite's overall weight. But it is one they backed themselves to overcome with the combination of their engineering prowess and 3D printing technology.
In the design of the LizzieSat, they have applied Markforged’s composite 3D printing technology to the entire structure of the 31 x 31 x 18 inch satellite, harnessing the company’s Onyx FR and Onyx FR-A materials on eight vertical and eight horizontal components that hold in place a honeycomb structure. With this use of carbon-fibre filled nylon, Sidus says it is able to leverage similar strength qualities to aluminium, while reducing the weight and iterating on designs much more quickly.
During design iteration, Boschi incorporated fastening functionality into the structural components so that parts fit into a slot and lock into place. This has not only helped to shave off weight by removing screws and bolts but has also made the satellite sturdier.
“When we started doing the preliminary analysis, you could see that when the parts were bolted together, they were all separate,” Boschi says. “But when we
made the locking feature, then the entire ring became one piece, so that we’re only pulling on one structure, as opposed to 16 pieces –because there are eight columns and eight pieces in between to hold them together. Now we put everything together, they all get bolted to the honeycomb or the aluminium pan on the other side, it’s more of a stronger, stout structure.”
At the time of writing, Sidus is in ‘full print’ mode ahead of the prospective SpaceX launch later this year. The design has been locked in, the honeycomb and base plate are due for arrival in April, and then the satellite will go through an extensive testing process to prove out its durability. The LizzieSat satellite has been built for a five-year life, while Sidus has had to keep in mind that as it is launched into outer space, it will have to take 5G loads, withstand solar radiation, and deal with vast temperature swings of around 200°C as it goes from the exposure of direct sunlight to
For Boschi, he’s never been more sure that 3D printed parts can manage it. “When I first did parts years ago with SLA machines, we would break them taking them out of the machine. If you didn’t put it down right, it would break. And it’s advanced from that point forward. Now we’re in nylon. Better materials, it’s changing everything. From that point when I was first [using 3D printing], it’s night and

Sam Davies speaks to Sidus Space about its use of 3D printing in the design of a lightweight satellite set to be launched on the SpaceX Transporter-9.
“From when I was first using 3D printing, it's night and day.”
GE Aerospace’s additive manufacturing journey, application by application.
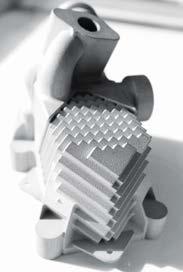
It is August 2016, and the US Army has granted GE and the Advanced Turbine Engine Company – a joint venture between Honeywell and Pratt & Whitney – 24-month contracts to take their proposed engines for the Boeing AH-64 Apache and Sikorsky UH-60 Black Hawk military helicopters through preliminary design review. By April 2018, it is time for demonstrations.
One of the key requirements of the contract, in addition to power increases of, say, 50%, and fuel consumption reductions of, say, 25% was that the new engines fit inside the existing airframes. To successfully validate its engine design fit correctly in the helicopters, GE leveraged its polymer 3D printing lab at its Additive Technology Center (ATC) in Cincinnati to develop a printed prototype of its T901 engine true to size.

GE’s T901 engine includes numerous technological advancements that were successfully demonstrated in this rig and engine testing phase, which led the US Army to award GE with a 517 million USD contract that will allow it to flex its metal additive manufacturing (AM) muscle once again. Engineering and manufacturing of several additive metallic T901 engine components is progressing well. The first development engine ran in 2022 and the first flight test engines are now scheduled to be delivered by the fall of 2023.
In March, on a tour of GE Aerospace’s ATC in Cincinnati, TCT was given some context behind the T901 AM applications for the Apache and Black Hawk platforms. Here is GE Aerospace’s AM journey, application by application.
THE FIRST FAA APPROVED PART
“It all started with this one part,” is the line GE likes to use to refer to its 3D printed LEAP fuel nozzle tip. And while this tip – with its 25% weight reduction and 30% cost efficiency increase – did kickstart the company’s additive manufacturing voyage, it was the quick turnaround of the GE90 T25 sensor housing that brought the first FAA-approved 3D printed part eight years ago. The part needed to undergo a redesign, so the ATC was enlisted to use additive
manufacturing to quickly develop and industrialise a new solution. Ten parts were consolidated into one, and 12 units were printed in a single build. Approximately 400 of these components were manufactured and installed on the GE90-94B engines.
“We needed to do it quickly and be able to iterate fast, which is why we used 3D printing,” ATC Site Leader Chris Philp says.
HEAT EXCHANGERS
After enhancing the T25 sensor housings, similar design concepts were quickly applied to heat exchangers, with significant reductions applied to part assembly, size, weight, and cost. On the GE9X engine, for example, GE has incorporated an aluminium F357 heat exchanger manufactured on the Concept Laser M2 that is 40% lighter. It also boasts a part consolidation of 163 traditionally manufactured components into a single printed piece.
“A [conventional] heat exchanger has a lot of tubes welded together and we've 3D printed it as a solid body,” Philp explains. “So, it's a lot more durable and has less source of failures.”
A NEW APPLICATION
Having proved to the FAA it could additively manufacture reliable aircraft parts, GE was buoyed. As it stepped into its GE9X engine platform, it saw the opportunity to leverage 3D printing in its new engine.
The team decided to apply additive manufacturing to a flowpath component, that could otherwise not be produced conventionally within the constraints of the engine.
OVER 180,000 3D PRINTED LEAP FUEL NOZZLE TIPS HAVE NOW BEEN SHIPPED, WITH 1,000 UNITS MANUFACTURED EVERY WEEK AT GE’S AUBURN MANUFACTURING FACILITY.SHOWN: ADDITIVELY MANUFACTURED ADVANCED TURBOPROP FUEL HEATER FOR THE CATALYST TURBOPROP ENGINE INSTALLED ON THE CESSNA DENALI WORDS: SAM DAVIES
In doing so, GE designed a cyclonic inducer component which uses centrifugal forces to ‘divert particles of dust to the outside of the flowpath, before being ingested into the main stream, improving durability,’ per Philp.
GE was so confident in the additive design of this component that it had developed its engines with the part in mind before FAA certification was granted. This component is manufactured on the Concept Laser M2 system in a cobalt-chrome alloy and has been consolidated from 13 parts into one. It is also said to be twice as durable as before. Eight 3D printed cyclonic inducers are fitted to every GE9X engine.
THERE ARE PLANS TO RE ENGINE AROUND
1,300 SIKORSKY UH-60 BLACK HAWK HELICOPTERS AND
600 BOEING AH-64 APACHE HELICOPTERS. EACH HELICOPTER HAS TWO ENGINES.
LOW PRESSURE TURBINE BLADES
As previously detailed in TCT Magazine, GE is also having success with the Arcam Electron Beam Melting (EBM) technology. A total of 228 low pressure turbine blades are being additively manufactured on the Arcam EBM A2X in titanium aluminide for each GE9X engine. These components are contributing to an improved fuel efficiency of 10% and are 50% lighter than their traditionally manufactured counterparts. Because of the EBM process raising the temperature inside of the machine to 1,200°C, there are smaller thermal gradients generated and the components experience less residual stress during the build.
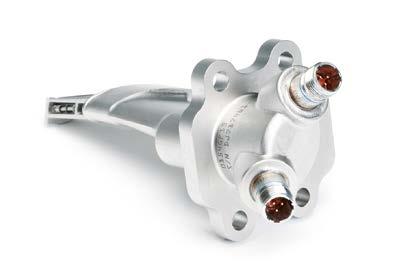
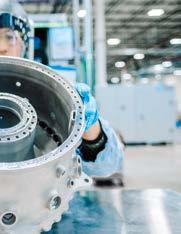
ONE ENGINE – ZERO TOLERANCE TO FAILURE
GE has also thrown 3D printing at its Catalyst
this engine. This is the next step up,” Philp says. In the additive manufacture of the turboprop engine components, GE has incorporated integrated airfoils into the interiors of engine components to facilitate better performance. The engine is also said to burn up to 20% less fuel and achieve 10% more power than other engines in the same class. Among the parts printed for the Catalyst engine are an advanced turboprop fuel heater, exhaust case and C Sump component.
T700/CT7 MIDFRAME
“This is one of the hardest parts still to make, and we’ve been making it for 35 years,” Philp notes of the T700/CT7 midframe.
GE prototyped an additive version of the CT7 midframe, again, focusing on part consolidation. One of the weight-saving opportunities it had recognised was to consolidate parts so that it could remove flanges, nuts, and fasteners in a bid to help save weight, and so it could remove the ‘very complicated’ welding, brazing and assembly of parts. In the development of this prototype, which was subsequently validated on a development engine, GE incorporated 3D printing as much as it could, with the performance ‘exceeding expectations’ of previous iterations of the engine.
Philp suggests the work carried out to additively manufacture larger, more complex components like the CT7 midframe has helped the company to land the T901 contract, within which GE has currently printed and tested additively manufacture components to be used in engine qualification and flight testing.
“We use those lessons learned, that knowledge [from previous projects], to say 'maybe we took it a bit too far, let’s pull it back a little bit.' What you see here are all components for new engines, and that’s really where we see the most bang for our buck in 3D printing,” Philp says.
“It’s not just saying I can replace this one part in an engine – that sensor housing was a separate story –when you start to design the engine as a system, with all the benefits of 3D printing, that’s when you gain the performance, weight and fuel savings.”
“This is the next step up.”

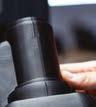
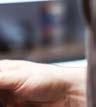
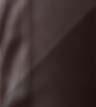
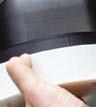
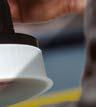

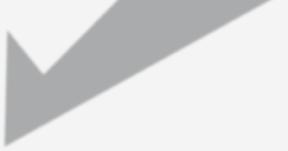
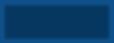

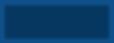
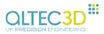
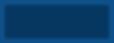
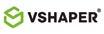
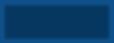
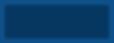
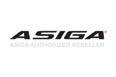
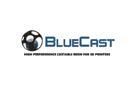
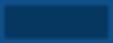
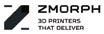
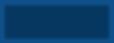
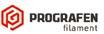
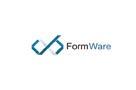
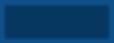
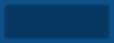
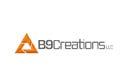
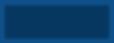
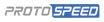
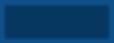

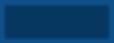
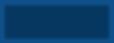
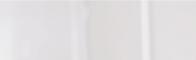
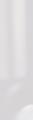

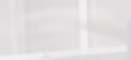








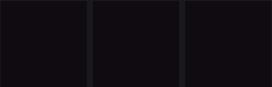












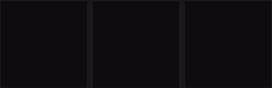

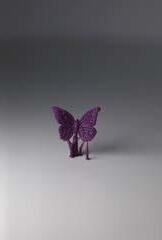

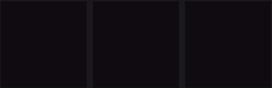


SPACE B O UND
but it has been mainly used to make polymeric parts. There are new advances in the technology and that’s how we can make the parts out of this ceramic. This is very important because the traditional way to make ceramics with additive manufacturing is using powders and a laser, and at the end you get this part that is coarse and there is porosity, so it’s not something that’s really meant to be used in space.”
In August 2022, Massachusetts Institute of Technology (MIT) published research from a team that created completely digitally manufactured plasma sensors for satellites such as CubeSats, known as retarding potential analyzers (RPAs). The research team said that the 3D printed and laser-cut hardware performed just as well as stateof-the-art semiconductor plasma sensors that are manufactured in a cleanroom. CubeSats are a type of research spacecraft that typically weigh less than 1.33 kg (3lbs).
So what exactly is an RPA? An RPA is a type of sensor used in satellites to detect energy in ions in the ionosphere, and have been used in space missions since 1959. The ionosphere is made of plasma, which is a state of matter that occurs when gas is heated, and stretches roughly 50 to 400 miles above Earth’s surface, right at the edge of space. Along with the neutral upper atmosphere, the ionosphere forms the boundary between Earth’s lower atmosphere, and the vacuum of space. A lot of the issues surrounding global warming are influenced by what happens in this region.
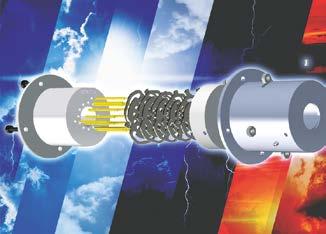
Dr. Luis Fernando Velásquez-Garcia, Principal Research Scientist at MIT’s Microsystems Technology Laboratories (MTL) and senior author of the study, told TCT: “The truth is, we don’t know enough
about the ionosphere. So we really need better instruments and better data to be able to develop better models and to be able to face the global warming phenomenon. The second issue that an RPA can help you with is a mass spectrometer. Mass spectrometers are the gold standard for chemical analysis. If you want to know the composition of a sample, then you use mass spectrometry. They are based on using electromagnetic fields to sort out the ionized sample.”
Dr. Velásquez-Garcia said that having more information and better information on the ionosphere will allow for better predictions on weather conditions, and give a better understanding of things like the water cycle and how water is lost and replenished, which he says will be very useful.
RPA’s include a dielectric, also known as an insulator. The team led by Dr. Velásquez-Garcia manufactured this part using VAT photopolymerisation for this project, and printed it in a glass ceramic material.
Dr. Velásquez-Garcia added: “The process is fairly safe and fairly robust,
The team that worked on this project are also working on other kinds of hardware for CubeSats, such as propulsion systems, mass spectrometers and Langmuir probes. Speaking about this, and how AM is being used in this area, Dr. Velásquez-Garcia said: “We are taking this vision of how to make better hardware via multi-material 3D printing. In some cases, the technology is not quite there, so what you need to do is create new printing capabilities, and that’s some of the work that we have done. For example, we have harnessed micro plasmas, which are plasmas that you can strike atmospheric pressure and with that you can create high-quality materials.”
Speaking further about the potential for multi-material 3D printing in aerospace, Dr. Velásquez-Garcia added: “In my view, multi-material additive manufacturing has a tremendous role for space, and in particular CubeSats. I feel that CubeSats are like an unfulfilled promise, by that I mean we can make them better and more capable, and in many cases, take over the traditional satellite. Traditional satellites are made with something that is called a death spiral. This is an issue because failure is very expensive, there is a redundancy in the systems and you end up having very big, very expensive pieces of hardware. I think the idea to make these compact satellites is an amazing idea, but it hasn’t been fulfilled because we really need to apply all our ingenuity to make the very best hardware we can, and at a very low cost. With that, I think we can break this cycle and be able to make the technology accessible to many people. Space does not need to be something that is only accessible to a few countries, I think the big issue is the barrier in the cost.”
Oli Johnson speaks to Dr. Luis Fernando Velásquez-Garcia,
a Principal Research Scientist at MIT about a project involving 3D printed sensors for satellites.SHOWN: MIT CUBESAT SENSOR
Compact Enough for the Office. Robust Enough for the Factory Floor.
Formlabs Form SLA 3D Printer
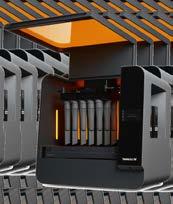
Scale up your in-house print production with the Form 3L, an easy-to-use large format 3D printer for reliable production of prototypes at an unprecedented value.
No specialized technicians required. The Form 3L offers automatic resin dispensing, simple print preparation software, and an interface anyone at your company can use.
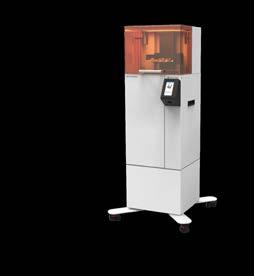
Get started now Formlabs 3D printers are ready to plug and print right out of the box, no specialized training required.
The Form 3L has a build volume of 33.5 × 20 × 30 cm, it can typically print up to 20 nozzles in a single build. Find out how the Form 3L can improve your production performance, call 01295 672600.
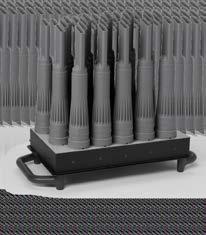
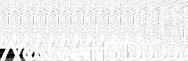
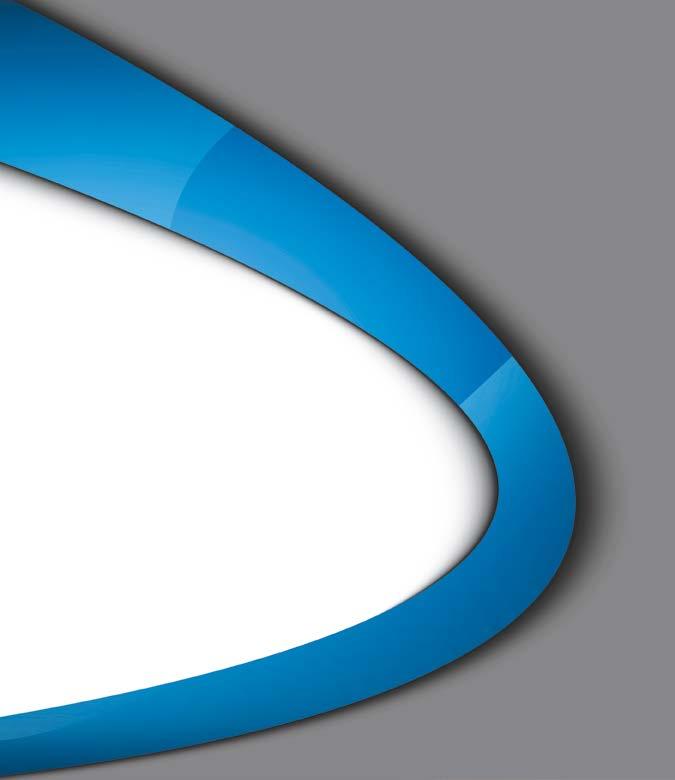
Find out more, visit Stand No.
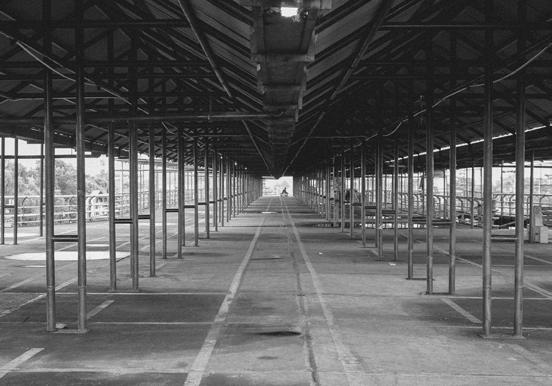
ENABLING WAAM IN MANUFACTURING AIRCRAFT LANDING GEAR
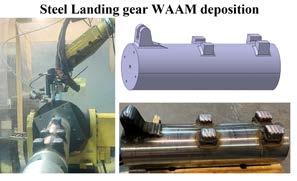
Landing gear systems are one of the most critical components of an aircraft, providing principal support for the aeroplane when parked, taxiing, taking off or landing. To meet the stringent demands of bearing large loads in long-term service, 300M ultra-high strength steel (UHSS) is regarded as one of the most ideal materials for manufacturing aircraft landing gear, benefiting from its high strength, sound toughness and excellent fatigue performance. However, severe notch sensitivity and local stress concentration make 300M UHSS challenging to be processed into complex structures using conventional forging techniques. Moreover, a massive post-machining workload is required in the manufacturing process after forging, significantly increasing the Buy-To-Fly (BTF) ratio and prolonging the lead time. Currently, industry-wide, manufacturers across the world are seeking manufacturing processes, designs and methods with the purpose of reducing the cost of manufacture, lead times and supporting the race to net zero. Wire Arc Additive Manufacturing (WAAM) offers an alternative approach with great promise for 300M UHSS landing gear due to high cost-effectiveness, short lead time and design flexibility.
The Welding and Additive Manufacturing Centre at Cranfield University recently teamed up with Airbus to demonstrate the feasibility and reliability of using WAAM technology in depositing steel landing gear components. The project was funded by the Aerospace Technology Institute (ATI), the ‘Hybrid Direct Energy Deposition Sprint’ project, with partners including National Manufacturing Institute Scotland (NMIS), Cranfield University and the Northern Ireland Technology Centre (NITC) at Queen’s University Belfast, along with an industry steering group of more than ten companies.
To ensure that WAAM can produce aircraft landing gear that is free from
defects and performs to the required standard, Cranfield conducted a comprehensive investigation of WAAM 300M UHSS. This involved feature deposition studies, interface studies, and post-heat treatment studies. In the feature deposition work, both gas metal arc (GMA) and plasma transferred arc (PTA)-based WAAM processes were applied to deposit various features under different shielding conditions. It was found that both GMA and PTA-based WAAM are feasible for the manufacture of defectfree 300M features. However, all the as deposited 300M features had lower strength but higher ductility compared with forged ones. To overcome this, a postheat treatment investigation was done by austenisation using oil quenching, followed by lowtemperature tempering with water cooling. These treatments refined primary austenite grains through recrystallisation, dissolved the carbide precipitates, and eliminated residual stress, thereby obtaining good comprehensive performances. The results show that this heat treatment scheme could normalise
the microstructure and mechanical performance evolution along the building direction and make the strength and fracture toughness of the WAAM 300M deposits meet the qualification. These fundamental studies provide sufficient confidence to apply WAAM to produce aircraft landing gear.
Subsequently, a 300M UHSS Landing gear demonstrator was deposited using the PTA-based WAAM method with optimised process parameters. The demonstrator with dimensions of Ф200mm × 700mm was designed to replicate the main features of a landing gear system, with WAAM deposited features extruding away from a forged rod to connect braces and actuators. The deposition work was conducted in a global shielded inert environment with argon, 7kg of material was deposited at a deposition rate of 1.3kg/hr and took 16 hours to finish, including setup. The BTF ratio was decreased from 5.9 to 2.0 for the demonstrator when compared with conventional subtractive manufacturing,
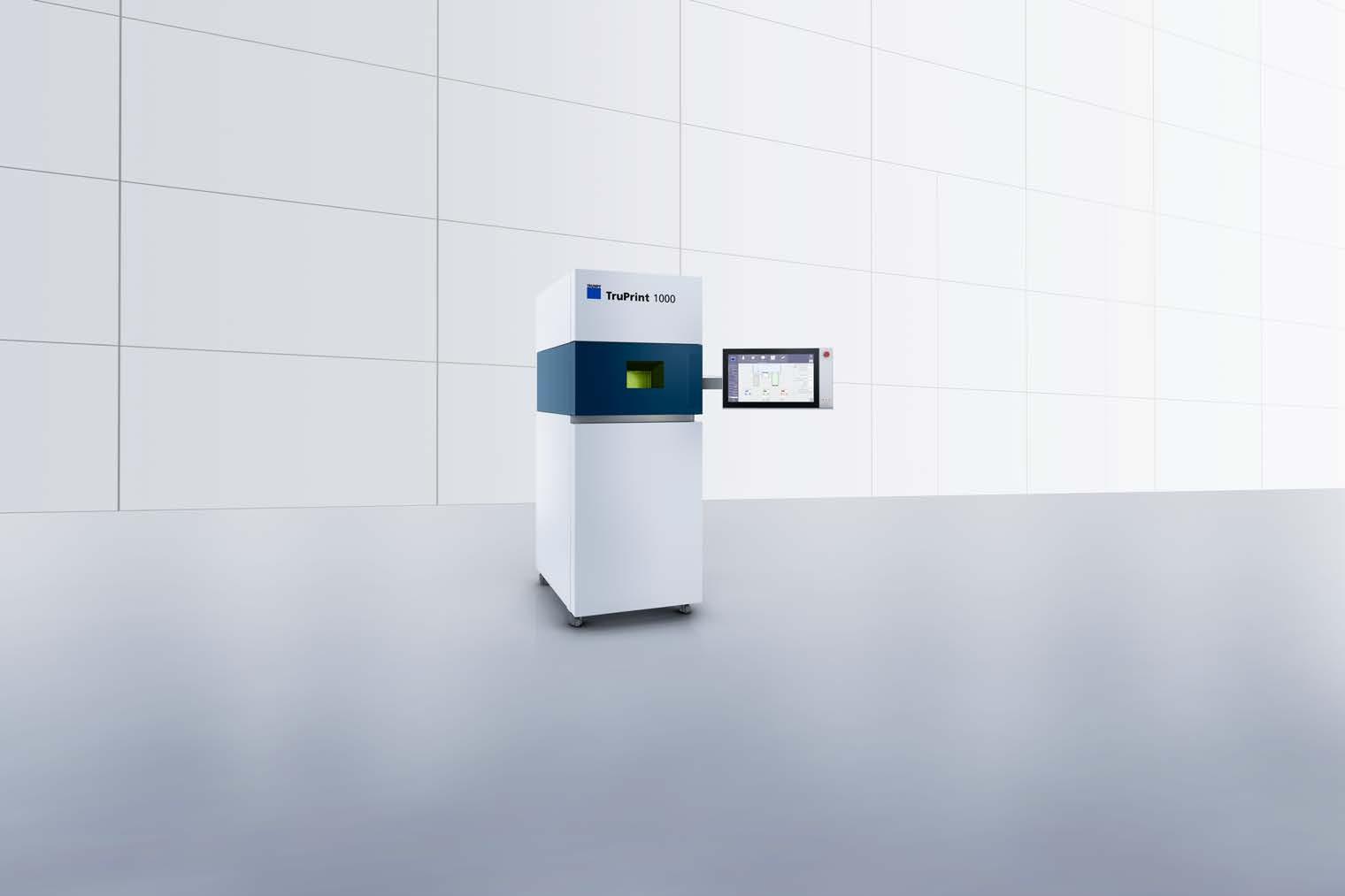
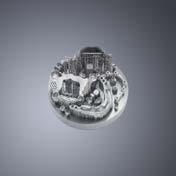
reducing the material used by 65%. This demonstrated that WAAM can not only produce geometrically accurate features without any defects on radial forged substrates but also greatly increase cost-effectiveness and reduce lead times.
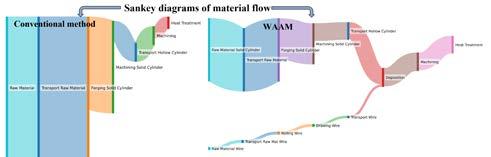
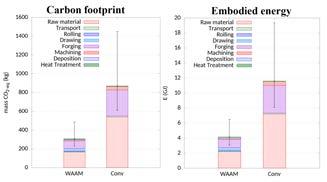
An environmental impact assessment study based on a “cradle-to-gate” life-cycle approach (including the cumulative effect from raw materials extraction until the shipment of the component to the customer) has shown very promising results. Dr Emanuele Pagone, researcher in the Sustainable Manufacturing Systems Centre at Cranfield University, observed: “Our study shows that producing the landing gear component with WAAM rather than traditional, subtractive approaches reduces significantly the required amount of raw materials to be extracted and refined. This also has a knock-on effect on all manufacturing processes with less material to be heat treated, machined, and transported. We have estimated that the carbon footprint of the component can be roughly halved when substituting traditional machining with WAAM. Embodied energy consumption estimates show similar results and suggest that, approximatively, other environmental impact indicators (including emissions
to air, water and land) are roughly halved as well. Furthermore, WAAM creates the opportunity to repair a damaged part re-depositing only what is necessary, an option not available by traditional means. Our studies in this area have shown that repair with WAAM can reduce the environmental impact by orders of magnitude, even including the additional transportation required to repair.”
Therefore, WAAM appears as one critical technology to significantly reduce the environmental impact in manufacturing and to support the industry in the ambitious, yet absolutely important race to Net Zero.
Overall, this investigation will promote many opportunities and benefits for the whole aerospace industry as we incorporate additive manufacturing into a hybrid solution that can realise significant savings and achieve a pathway for critical component manufacturing to access more sustainable modern technologies.
For the next step, Prof. Stewart Williams, the Director of the Welding and Additive Manufacturing Centre, added: “We are currently applying our newly developed CW-GMA process to the manufacture of aircraft landing gears. This process can achieve high deposition rates of up to 15 kg/h whilst providing precise thermal control with a wide heat input range.”
Beyond that, a further exciting new development in WAAM technology is the RoboWAAM coherent hardware-software ecosystem developed by WAAM3D. It generates programmes seamlessly with any CAD model and oversees the whole deposition process, providing process monitoring and governance over the many health and safety capabilities, as well as a fully auditable process trail.
“The carbon footprint can be roughly halved with WAAM.”
Demand for increasingly complex and customized parts is rising. Product cycles are becoming shorter. Established supply chains are being called into question. Sustainability is playing an ever greater role. Industrial production is becoming more demanding.
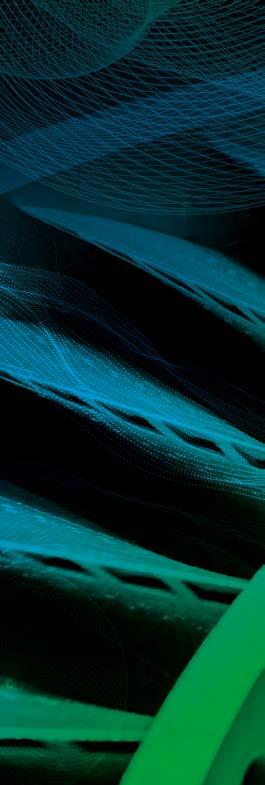
Help the industry meet these challenges with your solutions for Additive Manufacturing or technologies along the process chain.
Become part of Formnext and innovative production.


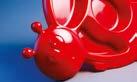
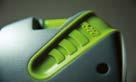

Where ideas take shape
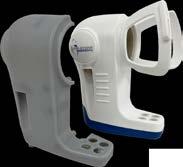
THE C ST PER PART CHALLENGE
KIERON SALTER, CEO, Digital Manufacturing Centre
At a recent panel event, a longtime additive manufacturing (AM) professional remarked: ‘if you can manufacture something in any other way, you probably should.’ I’m paraphrasing, but the challenges around building an AM business case for production are well documented and multi-fold. Cost is just one, and according to some, the biggest. Here, we asked five experts for their take on AM’s cost per part challenge and what we can do to overcome it.
“Currently additive can still be an expensive option when looking at piece price, largely driven by machine cost and speed of build. These two factors mean that machine cost and amortisation make up a large percentage of the component piece price - often well over 50% of the cost is machine cost. Lots is being done to increase productivity. In metals, we have quad laser machines, but as well as productivity we need machine builders to continue the drive towards lowering machine cost and increasing utilisation rates. Polymer technologies like SAF, SLS and DLP are doing a good job in driving price down.
I say to all prospective users of AM: you have to choose AM for a real benefit otherwise you will not win. AM offers lightweighting, reduction of tooling costs and the ability to create complex geometries or consolidate parts. If you are achieving any of these then AM will likely work for you. If you’re reducing mass, it’s probably for a good performance reason and therefore likely to be prepared for higher piece price. If you are eliminating tooling then the business case stacks up at a certain volume breakpoint. Similarly, if you are increasing complexity or integrating systems into one component, the business case often makes sense when you look at cost savings as a whole. It’s only when you look at the piece price in isolation that it doesn’t compare – you have to look at AM differently to understand the costs. That said, as machines get more cost effective and materials become more competitive, AM will continue to grow into a bigger manufacturing solution for large-scale digital production.”
BART VAN DER SCHUEREN, Chief Technology Officer, Materialise
“3D printing enables design optimisations that often create cost advantages that impact the overall end-to-end manufacturing cost. In fact, a recent survey commissioned by Materialise shows that “the ability to reduce the overall manufacturing cost” is cited as the most important benefit of 3D printing. But that doesn’t necessarily mean that the 3D printing process itself is cost-efficient. Several factors determine the cost of 3D printing parts, including the materials required, production time per part, the type of printer but also energy cost.
There are two important ways to reduce this. The first is by working more efficiently to increase production capacity. Software plays a major role in this, by making it possible to optimise the build and to tune the printing process to make it more efficient and repeatable. The second, less obvious one, is using tools that improve quality. Because quality comes at a cost. If we consider certified manufacturing in the medical or aeronautics industry, for example, we see that up to 70% of the production cost is in quality control. A good example is the Process Control software for metal 3D printing we just released. The software uses artificial intelligence to automate quality control, helping manufacturers to take control of the 3D printing process and ultimately save time and money.”
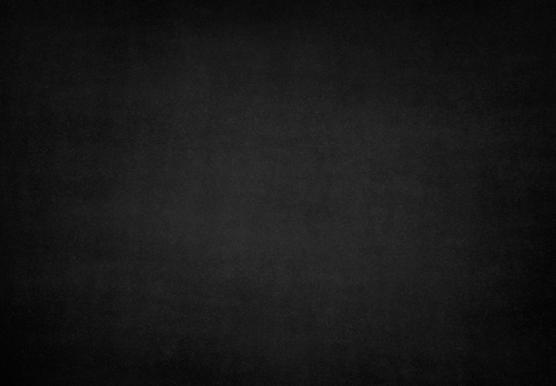
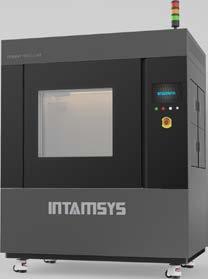



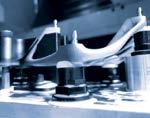
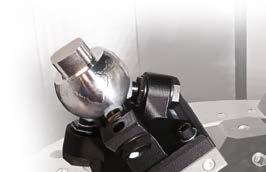
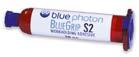
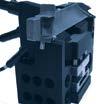
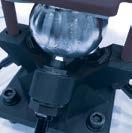
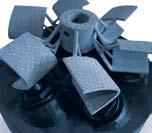
MELISSA ORME, Vice President of Additive Manufacturing, Boeing
“From the perspective of the aerospace and defence industry, additive manufacturing finds value in complex parts that are difficult to machine, such as part consolidations, assemblies, parts with added functionality such as internal cooling, and parts in which welds or brazes have been eliminated with the use of AM. Generally, such parts have a positive business case and provide cost savings, in addition to performance and quality improvements. Hence, the Boeing Company focuses on the aforementioned complex parts in our AM portfolio.
On the other end of the spectrum, simple parts such as brackets, clips, or direct replacements of castings that are not optimised will be more expensive to produce with additive manufacturing and also require more energy to produce than traditional manufacturing and thus will have negative business and sustainability trades. The Boeing Company does not consider such parts good candidates for additive manufacturing unless the intent is to mitigate a critical supply chain shortage of the traditionally fabricated components.
Additionally, nonrecurring testing is a heavy cost in AM’s nascent stage, which will slowly diminish over time as the technology matures. For the correctly selected part portfolio, even with the inclusion of nonrecurring testing, the cost is still favourable for AM.”
HODA AMEL, Technology Manager, Additive Manufacturing, The Manufacturing Technology Centre
“There is no doubt that AM can still be too expensive for producing large quantities of simple geometries, but there are still ways we can address this challenge. Reducing build failures and waste parts, increasing the life of feedstock by better understanding the effect of recycling and potential routes to rejuvenate, automating pre- and post-processing steps are a few steps we can take to tackle the cost per part problem without challenging the material and machine costs.
We also need to become smarter with our use of AM and use it where it offers the most benefit.”
TERRY WOHLERS, Industry consultant & President, Wohlers Associates
“People often asked about the most significant challenges the AM industry faces. At or near the top of the list is the cost of machines and materials. The price-to-performance ratio of AM products continues to improve, but it is far from where it needs to be.
One possible solution to the price of machines is to improve build speed. If speed improves by 2x, you can build twice as many parts in a given period of time. This spreads the machine depreciation cost over these parts, which reduces the cost per part. Imagine this cost reduction if a machine is 3-5x faster.
The price of materials needs to decline dramatically before adoption becomes mainstream among manufacturing companies. Some materials are priced orders of magnitude higher than similar materials for conventional manufacturing processes. This is mostly acceptable for prototyping and tooling quantities but becomes a “showstopper” when scaling to production volumes.
AM must create value. If it does not, companies cannot justify its use. Consolidating two or more parts into one, reducing material and weight, and improving a product’s performance are design methods that can help create value. This, along with a reduction in the price of machines and materials and improvement in build speed, will lead to a greater adoption of AM for production applications.”
● Stereolithography (SLA)
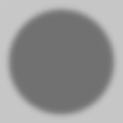
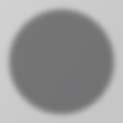
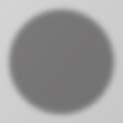
● Metal Additive Manufacturing (DMLS)


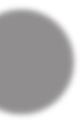
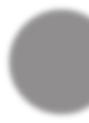
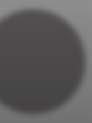
● Selective Laser Sintering (SLS)

● Fused Deposit Modelling (FDM)

● Multi-Material Printing
40


YEARS
OF ADDITIVE MANUFACTURING & PRECISION ENGINEERING




Market leading in-house technology combined with a skilled, experienced team ensures that CA Models Precision Prototyping services continually surpass customer expectations across the UK and Internationally.
01786 464434

sales@camodels.co.uk
www.camodels.co.uk
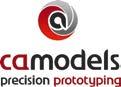
● Vacuum Casting
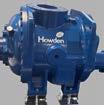
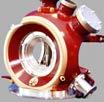
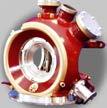
● CNC Precision Machining


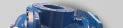



● CMM Inspection & 3D Scanning
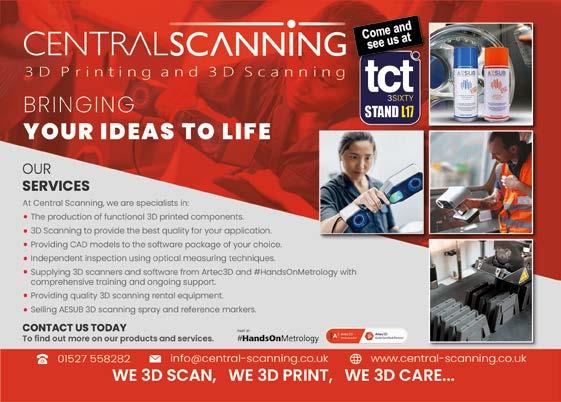
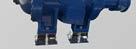
● Traditional Modelmaking
● Specialist Painting and Finishing


STEP BY
Oli Johnson speaks to Jeff Hanson, VP of Sales and Marketing at Evolve Additive Solutions, about the company’s recently launched Production Assessment Program.
Evolve Additive Solutions launched the Production Assessment Program in March 2023. The program analyses and validates business cases for additive manufacturing applications for Evolve’s clients. Users work with a team of engineering experts on Evolve’s Scaled Volume Production (SVP) platform, which is powered by Selective Thermoplastic Electrographic Process (STEP) technology.
The STEP technology was in development for over a decade, initially under the umbrella of Stratasys before Evolve was spun out into its own company in 2018.
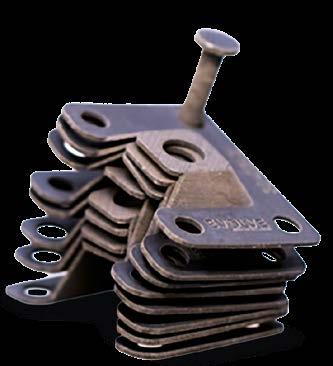
Jeff Hanson, VP of Sales and Marketing at Evolve, told TCT that the programme was created to handle the large number of queries coming in about the SVP platform as the company took the technology to market. Hanson said: “The volumes of queries coming in created a priorities issue, so the Production Assessment Program allowed us to have real conversations with the OEMs that are looking at real production and manufacturing efficiencies. The Production Assessment Program is where we take their applications, which are talked through with the application engineers, and then the geometries are packed for production efficiencies and total cost of ownership.”
Clients of Evolve that go through the Production Assessment Program receive information about the cost of the system, cost of materials, cost of service packs, maintenance agreements, the licensing of the software, and access to the system which has build envelopes of 280 x 590 x 50mm or 200 x 300 x 75mm.
Prior to the programme, clients would ask Evolve for sample parts in certain geometries, and according to Hanson, 'it was out of control.' Since the introduction of the programme, the process to identify and qualify opportunities for OEMs to use the technology has become more efficient.
Hanson says that what Evolve has identified as good applications for the STEP technology are those that are low profile, with a high surface area, and that these show a strong return on investment for clients when stacked against traditional manufacturing processes. But why were companies so keen to use the SVP platform and the STEP technology? Hanson says that the parts coming off the SVP platform are 'best in class.'
Cheryl Hillman, Senior Marketing Manager at Evolve, told TCT: “What’s really exciting when you think about STEP technology, because it is so different, it’s really hard to classify ourselves into any category today that’s out there. We had AMPOWER visit Evolve about a year ago and we spoke with them, and they wanted to put us into an additive manufacturing process category. They produce the polymer report every single year, and we wanted to make sure they understood STEP technology. So they put us in a category that we own 100%. Nobody else sits there. It’s really helpful for us to have that third party validation that says, 'Evolve STEP technology is
something that is completely new in the industry.'”
With the launch of the Production Assessment Program, Evolve also expanded its facility in Minnetonka, Minnesota, doubling the square footage and creating a new “Production Acceleration Center”, which contains an SVP platform, wash solution capabilities, and metrology capabilities to give the production assessment mechanical property and dimensional accuracy reports.
Speaking about what the future holds for Evolve, Hanson added: “We’re coming to market with ABS today because the system is working flawlessly. The part quality is best in class. Coming soon is PA11 nylon and beyond that is where we will be turning on more features of the SVP platform that will facilitate multi-material 3D printing.”
Hanson spoke about the technology being used for a badging application for automotive, and said that the manufacturers of the parts have looked at the technology, compared it to existing processes and decided that STEP is a “really unique” solution for the application.
Hanson added: “The messaging you’ll be hearing about Evolve is about shop floor agility, the flexibility that this technology allows on the production floor. The ability to modify your production plans on a moment's notice.”
ARE YOUR LBPF JOBS ON TRACK?
Firefly 3D is the next generation 3-axis scan head designed specifically for Laser Powder Based Fusion (LPBF) machines. Boost LPBF machine performance with real time process monitoring and powerful AdM trajectory control to enable real time scanning operation changes. The fully enclosed design includes a hermetically sealed optical chamber to maximize reliability and multi-headed machine capability for larger area processing.
Mass Finishing
Efficient systems engineering and innovative technologies – powerful and economical
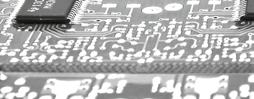
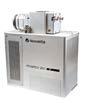
Individual systems engineering and intelligent process solutions – reliable and energy efficient
Metal 3D Printing
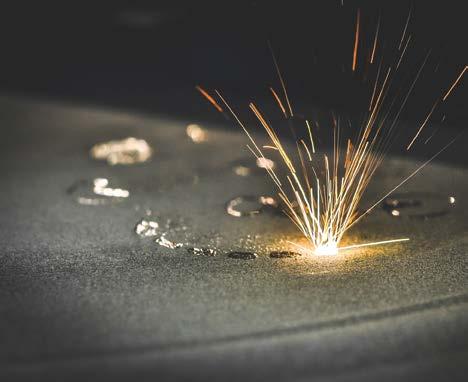
PBF Part Removal Just Became Fast and Simple
Designed for PBF (powder bed fusion) metal print plate
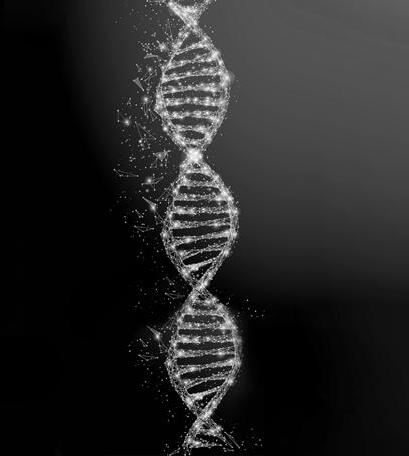

No EDM wire or other cutting saw is needed to remove the printed parts from the build plate Separation is achieved by heating on a hot plate, plate size is 3.5" –

PARTS THE PLAY
Meet the metal AM firms bringing proprietary technologies to market through parts as a service offerings.
Things are looking exciting,” is the conclusion reached after a near ten-minute monologue tackles the question: “What’s been going on since we last spoke… six months ago?”
At Seurat Technologies, there has been a lot to catch up on. But co-founder and CEO James DeMuth duly obliges, detailing the work being put in to define material parameters, build out production plants and fulfil orders for its customers. All this before we come to the reason TCT has grabbed 30 minutes of his time on a busy Thursday morning.
Why is Seurat bringing its proprietary metal 3D printing technology to market by selling parts rather than machines? And why are the likes of Fabric8Labs, VulcanForms and Freeform doing similar?
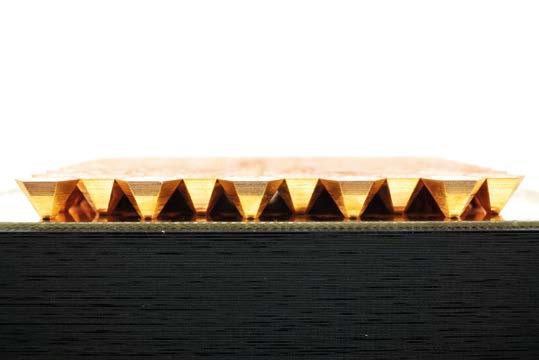
The four companies have all come to the attention of the ever-curious additive manufacturing community off the back of steep investment rounds and, to varying degrees, limited detail on how their technologies work. But they have all identified the same opportunities. Namely, localised production at scale, with its customers achieving quicker time to market.
“This business model provides customers with greater speed to market because we derive the process parameters in advance, eliminating iterative development, and ensuring rapid qualification and scale-up,” explains VulcanForms co-founder, President, and CEO Martin C. Feldmann.
VulcanForms is the company leveraging the largest amount of capital, having procured 355 million in venture funding during its latest financing round. Valued at over 1 billion USD, the company is vying to realise metal additive manufacturing at scale by integrating its process into a digital manufacturing system that is said to represent ‘the next generation of advanced manufacturing infrastructure.’
Emerging from an MIT lab headed by Professor John Hart, who also helped to establish Desktop Metal, VulcanForms has been working to improve the throughput and quality of metal laser powder bed fusion technology since 2015. What they are now offering to customers is a technology that delivers up to 100kW of laser power to the powder bed. Importantly, however, this technology is being supplemented with precision machining, industrial automation, a proprietary digital thread, and its in-house engineering expertise. Its facilities therefore encompass know-how across AM, heat
treatment, cleaning, surface engineering, precision machining, coatings, and inspection.
“In the bigger picture, one of the greatest opportunities America has is to build a manufacturing ecosystem that leverages advanced technology and automation,” cofounder Hart says. “There is a fundamental shift in the ways manufacturers need to adapt to global supply chain challenges and the increasing demands for product design flexibility. The offshored manufacturing is not coming back in its analog form.”
The onshoring of manufacturing was also noted by Fabric8Labs as a trend it can take advantage of. That said, the Californian outfit sees its reach going far beyond the United States.
Having recently closed a 50 million USD financing round, supplementing a 19.3 million Series A round in July 2021, Fabric8Labs is bringing to market a technology that utilises electroplating and electrochemistry to form 3D structures. Combining electroplating with proprietary printhead and micro electrode array technology, Fabric8Labs is able to print fully dense 3D metal components, featuring complex geometries and resolutions of 50 microns, from a room temperature water-based feedstock.
“This model provides greater speed to market.”SHOWN: WAVEGUIDE PRINTED WITH FABRIC8LABS TECHNOLOGY WORDS: SAM DAVIES
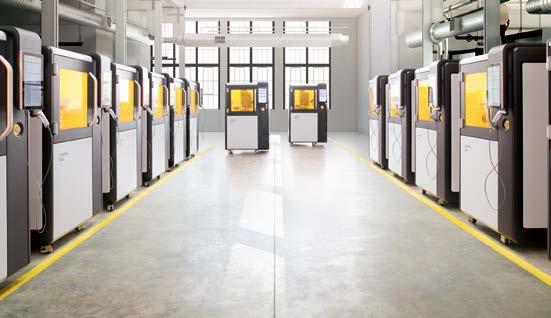




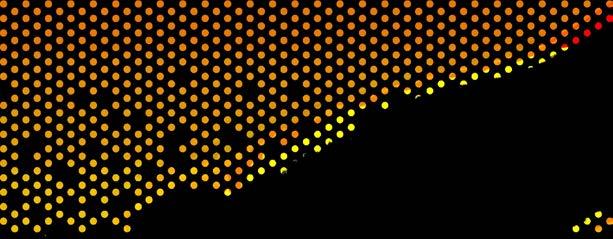


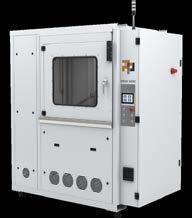
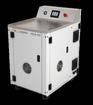
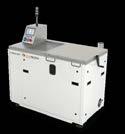
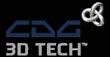

The company also claims its Electrochhemical Additive Manufacturing (EAM) process often doesn’t require thermal post-processing steps, with parts ready to ship after rinsing, and that its technology is able to achieve significant greenhouse gas emission reductions compared with other additive processes.
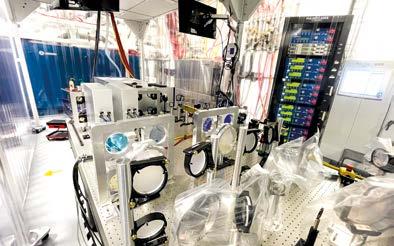
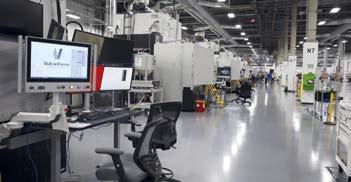
“It’s a totally different process than anything that’s out there,” says Ian Winfield, VP of Product and Applications at Fabric8Labs. “Our goal is to scale it up as quickly as possible to preserve a broad set of customers. As we’re looking at that in a way that the process can be efficiently run, in a factory setting, we reached the conclusion that the best way to scale the technology would be for us to stand that up and operate it ourselves. That reduces the option of a customer potentially getting an R&D machine, playing around with it for a couple of years, and then trying to convince their internal stakeholders that they want to scale it up.”
Fabric8Labs has primarily targeted OEMs in its customer acquisition, and in its early stages was encouraged to become a tier one or tier two supplier itself, rather than sell manufacturing equipment into their supply chain. Currently, the company is building on a pilot facility in San Diego, which will service its benchmark customers and demonstrate economies at scale, before opening up a larger US facility in 2024/25.
Seurat too is in the process of building out its manufacturing footprint, with an R&D facility and pilot plant facilitated by a total funding of 79 million USD. In the next month or two, the company expects its first-generation Alpha machine based on its Area Printing technology to come online, with parameter development of Inconel 718 and M300 tool steel ongoing. Stainless steel 316L is already 'dialled in.' Area Printing utilises a pulsed infrared laser source and blue light projection to melt material, with optics technology helping to control the cooling rate on a per pixel basis. While this allows Seurat to focus on part quality, it also has a roadmap that will see its machines grow in size, speed, and resolution. While currently capable of 10 features/mm and 3.0kg/hr in a 450 x 450 x 450 mm build volume, by 2025 the aim is to be at 14 features/ mm and 30kg/hr in a 1.2 x 1.2 x 1.2m build volume.
Because of these aspirations – and there’s a target of 20 features/mm, 1,700kg/hr and 9.6 x 9.6 x 9.6m build volume by 2030 – Seurat has also decided to proceed with a business model akin to a contract manufacturer. Should it get to 2030 with machines meeting those specs, DeMuth
estimates being able to deliver parts at 25 USD per kilo. And his calculations suggest a machine based on Area Printing would be setting customers back half a billion dollars to buy just one platform.
“There’s not a whole lot of customers who are going to buy a machine that big, but there’s a lot who buy parts at 25 dollars a kilo,” he says. “There’s an opportunity for all those parts in that price range to turn it more like a software company: make it quick, make it agile, make it accessible. Forget about the benefits of additive [for a second]. On a per price basis, that’s an explosion right there. But now you apply additive to it, you can get your new capabilities, your new functionality that was never possible before.”
In February, another metal 3D printing company, Freeform, announced a fund raising of 45 million USD to support its parts as a service offering. Details beyond taglines such as ‘metal 3D printing simplified’ and ‘softwaredefined autonomous factories’ are so far not forthcoming. But that a fourth company carrying such a business model, and attracting such venture capital investment, has come to market suggests there is more than just a sense of the opportunity for the contract manufacturing of metal printed parts, especially in this economic climate.
“Additive is intrinsically a flexible manufacturing technology, but we understood the need to build integrated production systems ourselves to deliver the necessary quality at scale, and provide engineered solutions to customers,” Feldmann concludes. “VulcanForms reduces friction and accelerates the adoption of AM by eliminating risk for the end user – no capital investment, no operating expense, and no need to pay for components that do not meet all specifications.”
“The decision was driven by our customers,” Fabric8Labs Founder and CEO Jeff Herman offers. “When we talked to them and they saw the potential, we asked them how they would want to use this technology. Do they want to buy a printer and embed it into their factories? In most cases, they said, 'no, what we want is parts.' The quickest path was for us to stand up the manufacturing capability.”
“What’s the rule of thumb? You need three years to become an expert in anything. They need to become experts in the machine, so they feel comfortable moving it to production,” DeMuth adds. “Our [view] is that since we fundamentally have control over what’s in the machine, we have to be the best at operating the machines. We’re teed up to say, ‘just give us more volume, and we’ll print you those parts.’ It lowers the barrier to entry because the customer doesn’t have to buy capital equipment. We take that on for them, and we just give them parts.”
RENISHAW
On a particularly snowy day in a quiet Welsh village, a company is celebrating a milestone.
It’s been 50 years since Renishaw, now a global engineering firm, was formed off the back of an invention that would solve a tricky measurement problem for Rolls Royce.
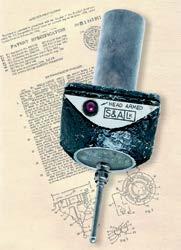
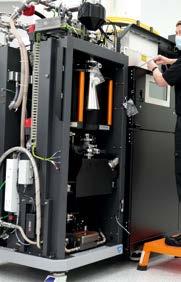
Sir David McMurtry, now Executive Chairman of Renishaw, had designed and built a prototype touch-trigger probe for co-ordinate measuring machines (CMMs) used to measure the instrumentation pipes on the Olympus engines that propelled the Concorde supersonic aircraft. The invention was a success, and McMurtry, together with colleague, John Deer, now Renishaw’s Non-executive Deputy Chairman, believed this technology breakthrough could hold much greater commercial promise. After Rolls Royce agreed to licence the patent, but only to a limited liability company, the duo went and purchased an ‘off-the-shelf’ company and on April 4th 1973, Renishaw Electrical Ltd. was registered.
Cut to March 2023, we’re sat in a small meeting room in Miskin, opposite the space where Renishaw’s additive manufacturing (AM) systems are manufactured, waiting to hear from a panel of senior executives. There are whispers that McMurtry, who stepped down as Chief Executive in 2018 but is never too far away from the action, might make an appearance. Sure enough, he does, and his presence and bullish opinions on everything from sustainable business practices to nurturing engineering talent, captivate the room.
The conversation is far reaching and while today’s story focuses on the origins of a company that has its roots in industrial metrology and precision measurement, one thing is palpably clear: McMurtry is invested in the next generation of metal AM.
What this next generation will look like or unlock is not for today’s conversation but Louise Callanan, Director of Additive Manufacturing, has been tasked with
leading and is careful not to give a micron of that progress away.
“In terms of the future, I suppose the most important thing really is to say that we're continuing to invest in AM in many areas - in our people, and in the technology,” Callanan told TCT.
When we meet, Callanan has been in the role for just over a year and still counts herself as a newbie to the AM industry. Yet she has built a long career at Renishaw after joining as a Graduate Design Engineer 26 years ago, and has always been aware of the technology’s benefits whether supporting development functions internally or facilitating very low volume production runs.
“It was just the excitement, from a development point of view of being able to quickly visualise your concepts, to be able to iterate those really quickly, and ultimately, to be able to accelerate the development process,” Callanan said.
Callanan’s tenure is a prime example – and there are several on the panel with similar stories – of how Renishaw seeks and maintains its talent, something she believes will be integral to this next phase of AM growth.
“I think that commitment to the future of AM means we can really start to attract and retain the right talent, the highest quality talent, which is massively important to the success of the future.”
Renishaw first ventured into additive in 2011 with the acquisition of MTT Technologies, a UK-based manufacturer of laser melting systems, which McMurtry noted at the time for its potential in aerospace and medical markets. Today, Renishaw’s technology is used in everything from custom implants and neurological drug delivery systems to complex heat exchangers and aircraft assembly parts. Recently, the company announced the extension of one already successful partnership with British Cycling ahead of the 2024 Paris Olympics. The pair previously worked together to develop a track bike featuring metal powder bed fusion parts for the Tokyo Olympics and
Laura Griffiths takes a tour of Renishaw’s Miskin facility as the company celebrates five decades of UK engineering.
RENISHAW IS READY
tour. I’m waiting for the inevitable ‘no photos, please’ but instead, Renishaw has laid bare its production bay featuring rows of RenAM 500 systems in various stages of completion.
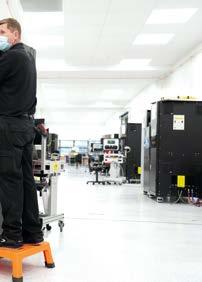
The RenAM 500 is Renishaw’s flagship machine. It can be equipped with one or four 500W lasers across its 250mm x 250mm x 350mm build platform, but all configurations adopt the same gas flow system, safety and precision digital optics, and smart connectivity capabilities. While eight, even 12-laser systems are now not uncommon in additive (Callanan doesn’t reveal if this next generation will follow a similar trajectory), Renishaw was one of the first companies to introduce a multilaser system of this size back in 2017 and has quietly iterated on features like automatic and flexible powder and waste handling options, and intelligent software solutions ever since.
“We know that we don't want to rest on our laurels and we do need to make sure that we remain competitive,” Callanan said. “And that means that we need to continue to ensure that we're also delivering quality parts in a cost-effective way. So we're continuing to work on projects to improve the usability, and to improve the productivity of the current 500 platform.”
untold, the ‘where’ is not so closely guarded. Last Summer, Renishaw announced an investment of around 65 million GBP to almost double the footprint of its Miskin site and help meet its weighty Net Zero emissions targets. Its ambitions include the development of 400,000 sq ft of lowcarbon buildings that will house a new production hall for its AM machines. We’re invited to get a peek from the top floor of its current site that’s currently tightly packed with an orchestra of machining, electronics, precision and large equipment assembly operations downstairs.
“Our strap line is ‘apply innovation’ and I think it's definitely more than just a strap line,” Callanan said. “It's something that's completely embedded within the company and it gives us that ability to challenge the status quo, to always be pushing technology innovations forward and really looking at the future in terms of the long term.”
What that means for additive in particular, we’ll have to wait and see, but Callanan says its success in AM won't be just about the machines.
2022 Commonwealth Games, securing seven Olympic medals in the process, and now plan to increase the bike’s speed with an enhanced design.
“I think the common thing with all of those [partnerships] is that companies may operate in different industries but they're partners to us who share that same passion for technology and quality, that passion for innovation,” Callanan said. “I think that's really what makes those partnerships work very well together. There's a lot of mutual respect for each other's area of expertise.”
Taking a walk through Renishaw’s facility feels like getting a covert behind the scenes
The RenAM 500 Flex has been designed to allow for easy switching between material types and was first put to work at the UK’s Digital Manufacturing Centre to verify its capabilities in a commercial production environment. In November, the Royal Air Force announced it would be using the system to produce custom-built structural aircraft components for rapid repairs and advanced component manufacturing, a first for the organisation.
“One common vision for everybody in AM is the adoption of additive manufacturing as a viable high volume production technology,” Callanan said. “And we're no different there, certainly from a next generation perspective. That's where we're really focused and really looking to make a step change in that productivity benefit and cost per part and looking to open up that additive technology to more applications.”
While the ‘what’ and ‘when’ around Renishaw’s next move in additive remains
“We're a part of the Renishaw family, we can offer that end-to-end process and I think that really is where we bring something different than anyone else. So whilst AM seems relatively new, for Renishaw, we're in our 12th year at this stage, so we're not really the newbies anymore, and our long-standing history shows that we have got that track record of sticking with new technologies that we believe in. We're just a member of the Renishaw team. That's how we see it, we see it being an area that will continue to grow, and we will definitely establish ourselves at the table alongside our more traditional manufacturing technology product lines, industrial metrology and position measurement. But I think the key thing for us is the overall success and growth of Renishaw, which we're very confident about.”
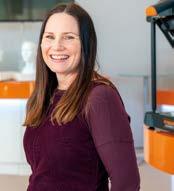
1. The UK’s largest AM event
With nearly 200 exhibitors confirmed for the show floor, TCT 3Sixty is the UK’s definitive and most influential additive manufacturing event. In addition to expanded portfolios from technology providers like Laser Lines, which will be bringing along Stratasys' Selective Absorption Fusion, Stereolithography and P3 polymerisation machines, you can expect to hear from newcomers like Makertech3D and Defiant3D who will both introduce new hardware.
2. “More than just machines”
As Robert Pitts, sales manager at Tri-Tech 3D, explains, “Establishing a successful AM process is about more than just machines.” Technical support is important to help guide the process of choosing and implementing the right AM technology, and while all important machines from the likes of Formlabs, XJet and Markforged will be present on booths from 3DGBIRE, Additive-X, and more, the floor will have plenty of expertise on offer from experienced teams ready answer your questions.
3. World’s best FREE AM conference
The TCT 3Sixty conference is an absolute must wherever you are on the additive adoption curve. Filled with application stories from real end-users like Collins Aerospace and LEGO Group, the latest research from University of Birmingham and Anglia Ruskin University, and market
23 REASONS TO ATTEND TCT 3SIXTY

TCT 3Sixty 2023 takes place on June 7-8th at the NEC Birmingham, UK. Need a reason to take a day out of the office to attend the UK’s biggest AM showcase? How about 23?
analysis and trends from Phil Reeves and CONTEXT, you simply cannot get this level of AM content for free anywhere else on the planet.
4. Oscar-winning insights to Jurassic prints
Seriously, where else can you hear how one animation studio used 3D printing to create the intricate puppetry for this year’s Oscar-winning film Pinocchio, or how the technology is providing opportunities for conservation, exhibition, and engagement at the Natural History Museum?
5. Introducing Stage And if three conference stages weren’t enough, the ever-popular TCT Introducing Stage returns as the best place to soak up the latest AM product information in short, easy to digest, 20-minute segments. Hear from experts at Nexa3D, Wayland Additive, EOS, Wazp, Massivit and more.
6. Inspired Minds CREATE Education Project will collaborate with TCT once again to inspire the next generation of engineers. TCT Inspired Minds works to provide high school students access to a variety of technologies and training in a classroom style workshop right on
the show floor. Paul Croft, Founder of The CREATE Education Project says, “We want to make innovation and digital creativity accessible to all students, equipping them with the skills and knowledge to enter high-quality STEAM careers of the future.”
7. In the know
The TCT Knowledge Bar, powered by Additive Manufacturing UK (AMUK), is your opportunity to speak 1-on-1 with a selection of experts from the UK's AM community. At the Knowledge Bar you will be able to learn more about the UK’s new AM trade association, and put your questions to some of the leading lights in the industry; if they don’t know the answer, they likely know someone who does.
8. Knowledge partners
Speaking of knowledge, this year we have a host of additional Knowledge Partners on board including PrintCity, Women in 3D Printing and Design for AM Network. Expect lively panels with a range of experts sharing real AM adoption journeys. Gold sponsor HP will also be bringing along real endusers users to share how they are implementing its Multi Jet Fusion 3D printing into their workflows. Be sure to bring your questions.
9. UK opportunity
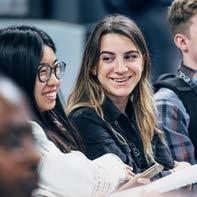
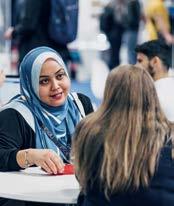
The UK has one of the largest installed bases of machines in the world, and in 2021, the Ultimaker 3D Printing sentiment survey ranked the UK second with significant growth potential. At the show, you'll find plenty of UK innovation whether it's Matsuura's state of the art Additive Manufacturing Centre with HP MJF expertise, which has placed over 75 MJF machines with UK manufacturers, or NEWAM, a £10M research programme developing next generation large-scale wire-DED AM.
10. TCT Connect Lounge

Use the TCT Connect Lounge, hosted by Silverstone Technology Cluster, to meet with existing connections or set meetings up with new ones made through the Event Hub. If you register in advance you'll receive contact recommendations, so you can expand your network and maximise your time at the event. You'll also have the opportunity to meet some of the members of the STC in the lounge.
11. First TCT UK User Group TCT 3Sixty week will kick off with the inaugural TCT UK User Group meeting on June 6th June. This invite-only event promises a deep dive into the roadblocks hampering AM adoption by providing a range of opportunities for debate and knowledge exchange. Highly regarded commentator and presenter, and long-time TCT Advisor, Todd Grimm will facilitate the day with his pace, enthusiasm for the subject and energy giving the day cadence and ensuring the session discussions are challenging, engaging and informative.
12. And the winner is… Bridging two days of AM knowledge exchange and business is the annual TCT Awards, an evening of celebration that highlights the best AM applications, technologies,
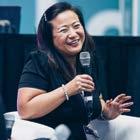
and collaborations. This year’s TCT Awards, sponsored by HP, received 140 submissions applications across eleven categories including global names such as Microsoft, European Space Agency, Marvel Studios, Swarovski and many more. Thank you to our category sponsors Nano Dimension, Revopoint, Metrom, 3D Micro Print, Jeol, and Polygonica. Get your tickets at tctawards.com.
13. Hall of Fame
We’ll also welcome this year’s inductees into the highly coveted TCT Hall of Fame, which shines the spotlight on individuals who have made a significant and long-term impact on the industry. Diana Kalisz, Joe Beaman, Andy Christensen, Jean-Pierre Kruth, Melissa Orme, and Nora Toure are this year’s nominees. We’ll also be presenting our third TCT Women in 3D Printing Innovator Award, and the first Sanjay Mortimer Foundation Rising Star Award
14. Your host for this evening …
The TCT Awards host this year is F1 sporting legend Johnny Herbert. Throughout his incredible career in F1, Johnny was at the forefront of the sport, testing himself against some true greats like Ayrton Senna, Michael Schumacher, Damon Hill and Nigel Mansell. Involved in all types of motor racing Johnny has enjoyed particular success at LeMans 24 Hours, winning the title in 1991. Now retired from Grand Prix racing, Johnny continues to promote the sport. He was a regular contributor on Sky Sports F1 for eleven years, where he regularly offered post-race analysis for the channel and also appeared on the dedicated F1 show.
15. Matchmaking
The TCT Event Hub allows you to tap into all TCT 3Sixty has to offer and maximise your time at the show before the doors to the NEC's Hall 1 even open. Register now to start building your profile, make connections with the people and products relevant to you, create your conference schedule, and receive suggestions based on your unique needs.
16. See what’s new Wiith over 400+ products across the show floor, TCT 3Sixty promises the UK's largest showcase of new AM products. IPFL will be running a live demonstration of Boston Micro Fabrication's microArch S240 micro 3D printer, which produces components to an accuracy of 10 microns (μm), while Scott Bader will exhibit four new Crestaform material additions including Crestaform 8K, engineered for nextgeneration 8K LCD and DLP 3D printers.
17. Are you an E, A or O?
Evaluation, Adoption and Optimisation are the three pillars of TCT 3Sixty's renowned content programme. Whether you're new to the industry or looking to take your AM investment to the next level, you'll find content geared towards wherever you are on the adoption curve, from market analysis to give you an overview of the state of the market, to in-depth looks at topics like sustainability and supply chain.
18. Application inspiration
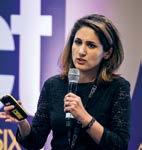
Europac 3D will be exhibiting Uniontech's Large Volume SLA RSPro Series of 3D printers, with a particular focus placed on its RSPro 2100. Europac has already sold one unit of this machine to an entertainment company based in the UK, with print jobs scheduled through to the end of the year, and has also supported a US defence company in developing a prototype dashboard for a military vehicle. This dashboard, which spans almost the entirety of the 2100mm the printer is capable of printing, was printed in one piece with three lasers working to build the part layer by layer inside 75 hours, and will be exhibited as it comes off the build plate, support structures and all.
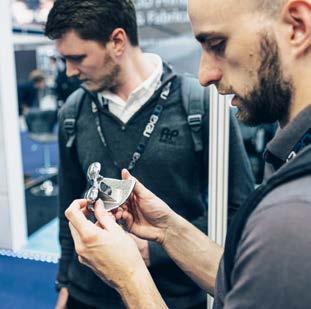
19. Additive ecosystem
From MES and workflow software by AMFG to post-processing solutions by Rosler, materials by Oerlikon, or automation from KUKA, the full end-toend AM ecosystem will be there to ensure you leave well-equipped with all of the information you need to fully adopt AM into your business. Whether that means installing your own hardware from leading brands like 3D Systems, DMG MORI or TRUMPF, or enlisting services from 3DPRINTUK and 3D Print Bureau, you are guaranteed to find the right AM pathway for your specific application needs.
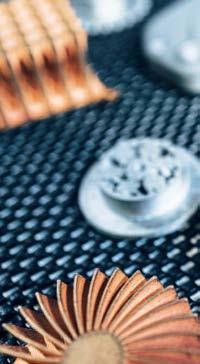
20. Quality assured
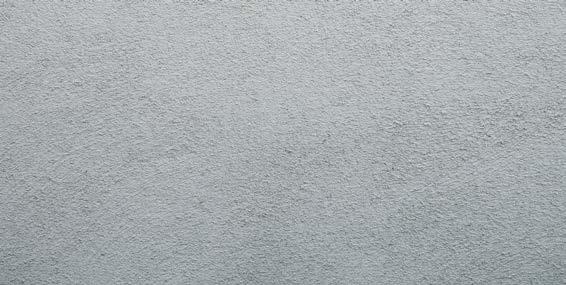
If you can’t measure it, you can’t make it, and TCT 3Sixty will feature a range of technologies that ensure parts are up to spec. ZEISS Additive Manufacturing Solutions will be showcasing a range of the industrial quality solutions including the latest T-SCAN hawk 2 and the Smartzoom
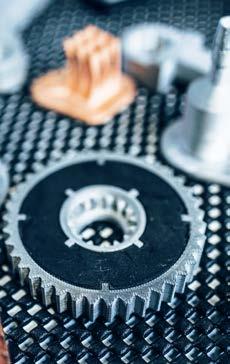
5 Microscope, while Manchester Metrology will be demonstrating laser trackers, reverse engineering services, CMM arms, 3D scanners.

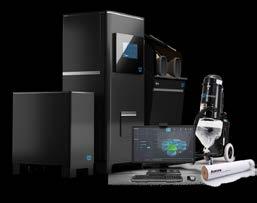
3D Measurement Company will also present its range of portable 3D measurement solutions, including E.V.A, a bespoke automated metrology station that offers a level of accuracy in-line, previously only possible in the inspection lab.

21. Research
The UK is thriving with AM research, with some of the most exciting developments happening at our world-leading universities. During the conference, you’ll be able to hear about some of the latest findings coming out of some of these institutions, while on the show floor, you can meet the teams like WAAM3D that took that research and turned it into an industrial solution.
22. Do business
In addition to AM learning opportunities, above all, TCT 3Sixty is where business happens. With brands like Ford Motor Company, Unilever, Rolls Royce and Dyson already signed up to attend, you're sure to make the connections you need.
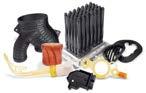


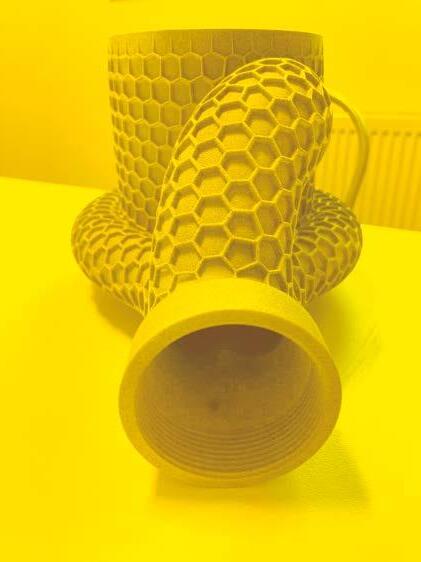
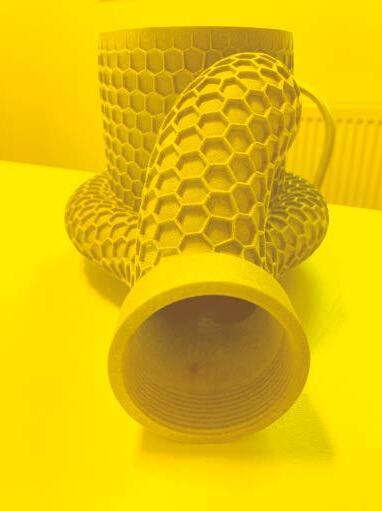
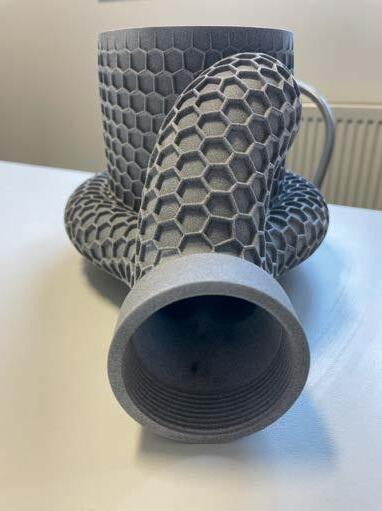
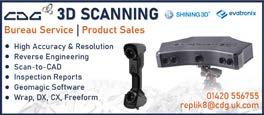
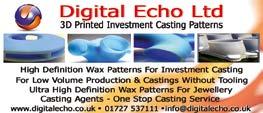
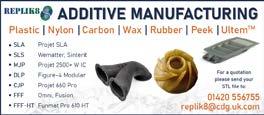
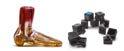
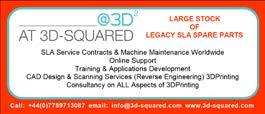
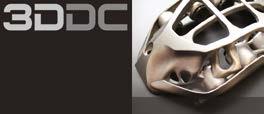

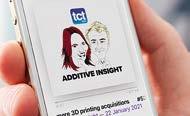
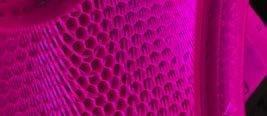


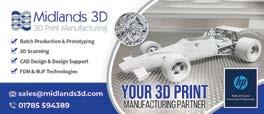

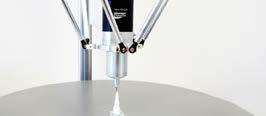
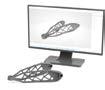




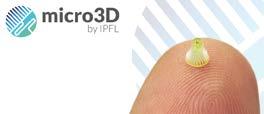
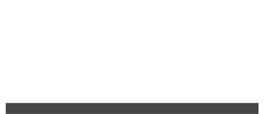
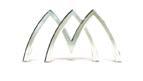
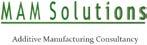
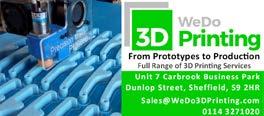

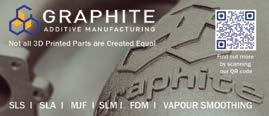
LEAPS AND BOUNDS
On a recent Additive Insight podcast, we were welcomed to the headquarters of Evove, a UK-based company leveraging 3D printing technology to enable precise filtration membranes.
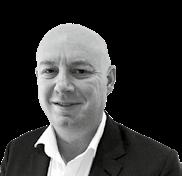
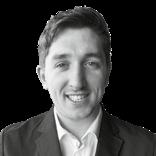
Evove is developing its own binder jet 3D printing platform, which it intends to scale up to develop enhanced membrane technologies at volume for the desalination, water, green hydrogen, and food & beverage markets.
Below, Evove CEO Chris Wyres [CW] and Senior AM Engineer Richard Finch [RF] explain why 3D printing and computational fluid dynamics are integral to its membrane products.
What would we need to know about your technology to understand what the aims of Evove are?
CW: We have two technology platforms. Our Enhance range of products improves the performance of existing membranes. That includes the graphene oxide coatings that the business was originally founded on. Spacers, which we 3D print, are inserted in between membrane layers to manage the fluid flow and inserts, which are spiral shaped 3D printed products, are inserted into tubular membranes to manage the fluid dynamics. All retrofittable to existing membranes and in terms of performance gains we see everything from a doubling in selectivity to a 5X increase in throughput to an 80% reduction in energy consumption for processing a given volume of fluids. Pretty transformational performance gains.
The second range of products we call Separonics, and that's wholly 3D printed membranes where we're precisely engineering the architectures for a specific purpose. Separonics was really where it all started. We recruited the team specifically to help drive that programme forward.
RF: Separonics is a reactive binder jet process. So, instead of a conventional method of printing a polymer binder, we're printing a reactive binder. We're
printing ceramic onto ceramic. The binder then contains particles which fill the interstices within the powder bed. So, not only do we end up with a denser green part, we also reduce the thermal budget required for sintering, which also improves the commercial viability of the process. And it reduces the postprocessing time, which makes it very commercially applicable.
A couple of the application examples you have here are spiral inserts and spacers. Could you outline the impact 3D printing is having on those parts?
RF: With the spacers in particular, we’re able to change the features down to tens of microns, [from] which you will see a dramatic performance gain. And we're shifting it over to a high throughput process, which we've managed to do with additive manufacturing. So, not only have we been able to increase the performance, we’ve also been able to then change it to make it customer specific to their own applications and compared to a conventional spacer or mesh structure. We're leaps and bounds ahead.
CW: And if we look at one of our big applications for this in desalination, we’re able to reduce the energy consumption in the desalination process by up to
30%, and given that there’s an increasing requirement globally for desalination, this could have a really big impact.
Talk me through the significance of computational fluid dynamics and what that enables you to do.
RF: So if we go to conventional spaces, they are basically a filament that is extruded and there is no other feature for that than just to provide a flow channel between two membrane sheets. We've got a very talented CFD engineer who's looked into how we can model these existing spacers and he's identified areas where we can improve. So, we're printing hydrofoils onto the spacers that improve the flow [and] reduce the pressure drop across the membrane.
And we're talking about struts, these hydrofoils are about 200 microns tall, with a curve profile that can actually guide the flow through it. We’ve then spent several months correlating what we get with the CFD performance, the printing performance, and then our CFD model can then influence what we're printing.
CW: And that whole generative design process has really accelerated our time to final product. We're busy investing now and scaling that technology.
THE AM REVOLUTION CONTINUES
APRIL 23-25, 2024
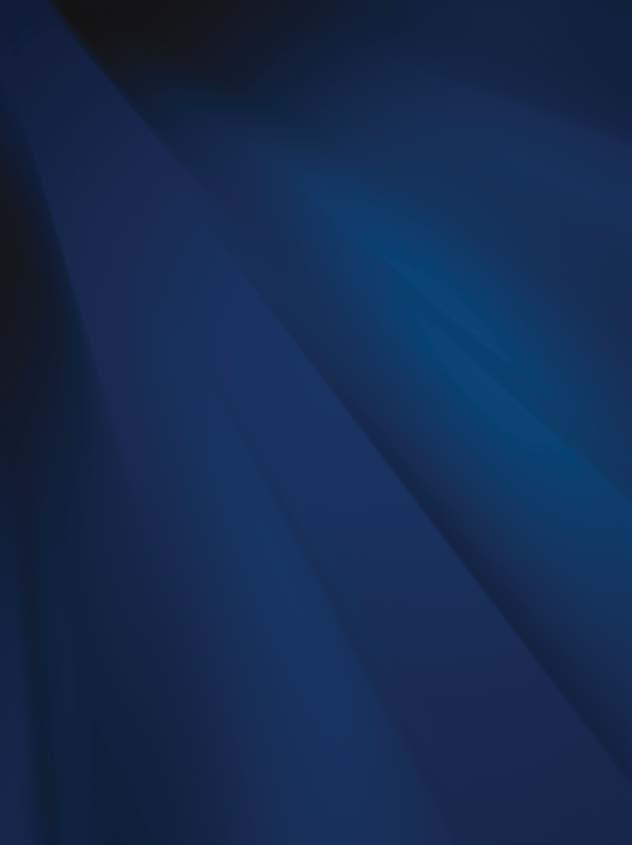
ANAHEIM CONVENTION CENTER
ANAHEIM, CALIFORNIA
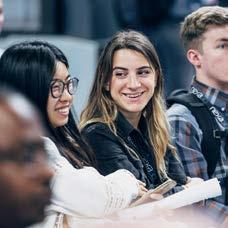
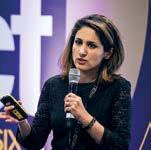
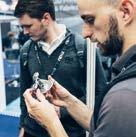

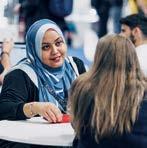



