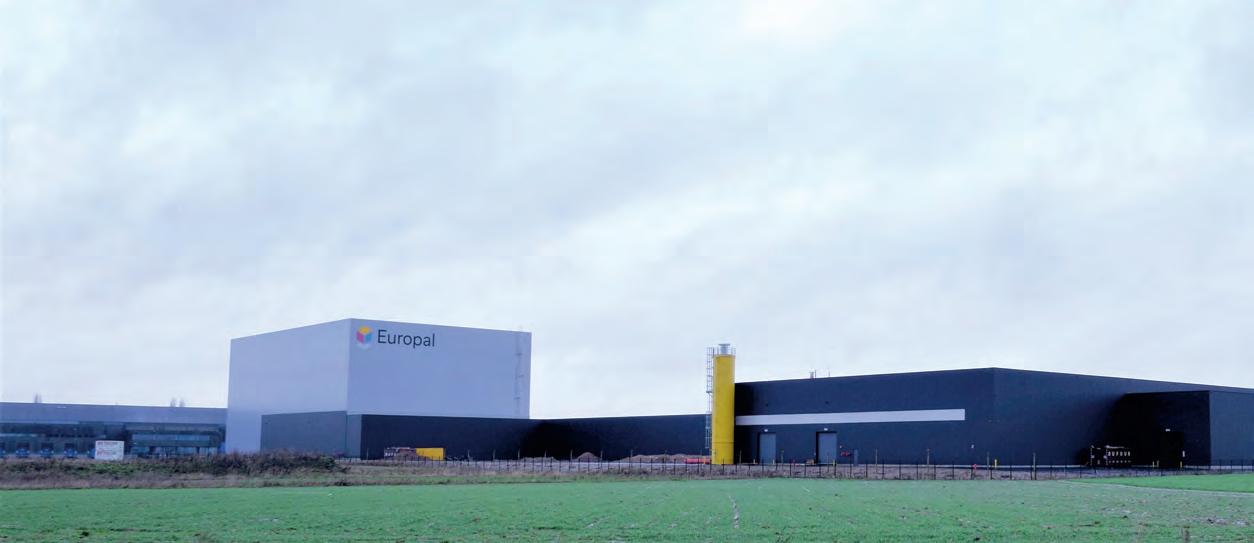
10 minute read
Case Study
EUROPAL PACKAGING BLANDAIN
De la page blanche à l’intégration verticale
Lorsque nous visitons le nouveau highbay d’Europal dans la zone industrielle de Blandain près de Tournai, il n'est en service que depuis quelques semaines. L'entreprise y a construit un entrepôt de 34 mètres de haut entièrement automatisé à côté de sa nouvelle usine qui, depuis septembre 2020, produit du carton ondulé utilisé dans les produits d'emballage d'Europal. Il s'agit de la dernière étape de l'intégration verticale complète du processus de production.
Arnaud Henckaerts
Le site Europal à Blandain s’inscrit dans le plan d'expansion stratégique de l'entreprise. L'activité logistique est en plein essor et la demande de matériel d'emballage est élevée. Jusqu'il y a peu, l'entreprise familiale achetait son carton ondulé à des fournisseurs pour servir de base à la fabrication de boîtes, de palettes en carton et d'autres types d'emballages. « Vous imaginez bien que ceci impliquait beaucoup de transports », déclare d’emblée Patrick Dejager, CEO d'Europal. « Des camions étaient remplis de carton ondulé découpé et façonné dans notre usine d’origine située à Mouscron, puis stocké dans divers entrepôts en attendant d'être livré au client. »
SE DÉVELOPPER ET PRODUIRE DE MANIÈRE PLUS FLEXIBLE
Europal a estimé que ce processus devait être amélioré. L'idée a donc germé de regrouper toute la production - y compris celle du carton ondulé lui-même - et la logistique sur un seul site. « À Mouscron, il n'y avait pas de place pour une opération de cette ampleur, mais la toute nouvelle zone industrielle de Blandain nous a offert cette possibilité, avec un excellent accès au réseau routier international. Nous disposons ici d’une superficie de 5 ha avec la possibilité de la doubler », explique Dejager. La production en interne de carton ondulé signifie qu’un grand nombre de camions qui transportaient des feuilles de carton épais ont pu être supprimés pour faire place à une flotte nettement réduite amenant des rouleaux de papier destinés à la fabrication de carton ondulé sur place. « Cela augmente notre flexibilité et notre capacité de production, ce qui doit soutenir notre croissance. Dans cette nouvelle usine, nous nous spécialisons, entre autres, dans le 'Limitless Packaging', du carton qui est utilisé, par exemple, par les acteurs du e-commerce pour réaliser un emballage sur mesure par envoi. Notre site d'origine à Mouscron sera utilisé comme usine spécialisée pour des produits spécifiques. » Chaque année, pas moins de 90.000 tonnes de matériaux d'emballage peuvent être produites à Blandain, ce qui nécessite une importante capacité de stockage. « Jusqu'à récemment, nous utilisions différents entrepôts pour stocker les produits finis. Cela impliquait également beaucoup de mouvements. Parallèlement à la nouvelle usine, nous avons d’emblée prévu un entrepôt satellite qui serait intégré au processus de production et permettrait d'économiser environ 25 trajets de poids lourds par jour. Entièrement automatisé, capable d’accueillir 20.000 emplacements de palettes et principalement utilisé comme zone de stockage intermédiaire et de pré-dispatch, en plus du stockage permanent, pour approvisionner efficacement nos 20 quais de chargement. A terme, 75 poids lourds partiront d’ici par jour », explique Patrick Dejager en décrivant l’ampleur de l'opération.
BÂTIMENT EN HAUTEUR
Pour accueillir les 20.000 emplacements de palettes sur une surface au sol relativement restreinte, Europal a opté pour un immeuble de 34 m de haut qui domine le paysage plat du Hainaut. « La structure elle-même est une construction Silo de Stow. Les rayonnages sont donc aussi la structure porteuse du bâti-
Europal, avec l'entrepôt en hauteur sur la gauche, est l'une des premières entreprises de la nouvelle zone industrielle de Blandain.


ment, avec les murs et le toit qui y sont fi xés. L'avantage, c’est une construction rapide sans la perte d'espace qui serait due à la structure supplémentaire du bâtiment. Sur une surface relativement limitée, nous disposons ainsi de 4 rayonnages qui peuvent accueillir 9 palettes en profondeur et 14 en hauteur. » Des grues entièrement automatisées effectuent leur travail dans les trois allées entre les quatre rayonnages. « Nous avons opté pour un système de Ceratec. Par mouvement, 3 palettes peuvent être placées sur une grue. La distribution des palettes à travers l'entrepôt se fait de manière totalement automatique. Un grand nombre de facteurs sont pris en compte, et grâce aux trois grues, nous avons une fl exibilité et un back-up en cas de problème. Si un problème survient avec l'une des grues, ou si un entretien est nécessaire, les deux grues restantes peuvent livrer les palettes avec les produits qui doivent partir. » L'entrepôt est connecté à un système de transport interne de Ducker. Celui-ci veille à ce que les produits fi nis se retrouvent sur des palettes de manière organisée et contrôlée. Ces palettes sont alors transmises au système Ceratec pour être stockées dans les rayonnages. Europal dispose également d'un système de qualité automatique qui vérifi e les Europalettes pour garantir un déroulement sans heurts. Lorsqu'il est temps de livrer les produits stockés aux clients, les grues saisissent les bonnes palettes et les transfèrent au système Ducker qui effectue un contrôle de qualité et de dimensions et amène le matériel au quai de chargement approprié. Au total, jusqu'à 15 chargements de camion peuvent être assemblés et empilés à l'avance de la manière dont ils seront transportés.
34 mètres de haut et entièrement automatisé ; une vue impressionnante.
FUTURE-PROOF
Patrick Dejager est manifestement fi er de la réalisation du nouveau site de production et de stockage. « C'est techniquement très novateur. Le processus de production du carton ondulé, le fait que l'on puisse, par exemple, imprimer le carton des deux côtés en un seul mouvement, l'automatisation totale et aussi l'entrepôt de stockage ... Si vous examinez le secteur d’Europal, je ne pense pas que quiconque en Belgique travaille avec un entrepôt satellite. En outre, l'ensemble du projet est également bien conçu dans une perspective de durabilité. Par exemple, il existe un système de récupération des eaux de pluie utilisé dans le processus de production, une isolation optimale, une récupération de chaleur et des panneaux solaires. Nous ne serons peut-être pas climatiquement neutres, mais l'empreinte écologique est limitée. De quoi garantir l'avenir d'Europal pour les prochaines générations », conclut le CEO.
Europal en chiffres
Création : 1947 Nombre d’implantations : 3 Nombre de collaborateurs : 90
RHENUS TERMINAL BRUSSELS
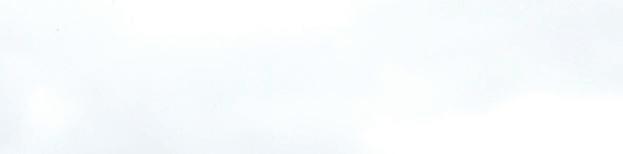
Les fl ux de recyclage sont l'un des piliers des activités du terminal.
Bart Van Rossen : « Un terminal acheté à l’intuition »
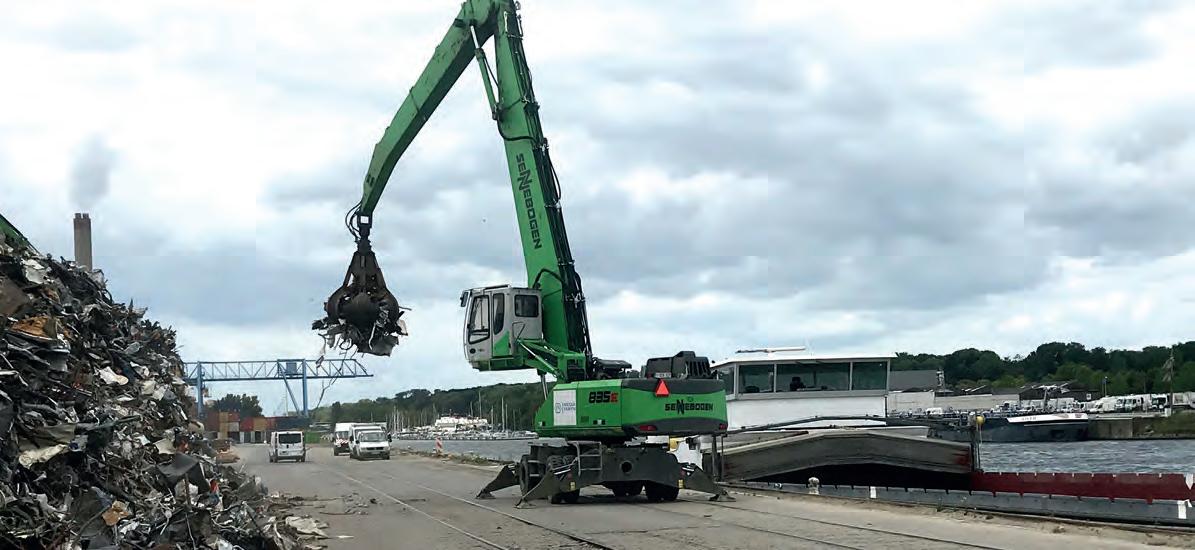
En 2019, le groupe logistique multimodal Rhenus reprend le terminal de Smet dans l’avant-port de Bruxelles. Selon le directeur général Bart Van Rossen, la reprise a été motivée d'une part par les bons contacts avec Duferco, un client de longue date, et d'autre part par l'intuition. L'objectif est de développer le terminal autour de trois piliers : les fl ux de recyclage, un hub de construction et une Container Freight Station (CFS).
Koen Heinen
L'ancien terminal de Smet est une valeur sûre dans l’avant-port de Bruxelles depuis 1927. « N'oubliez pas que le port de Bruxelles est un port maritime accessible aux caboteurs de 4.000 à 5.000 t. Avec le terminal, nous visons les clients industriels avec lesquels nous souhaitons développer des partenariats à long terme », déclare Bart Van Rossen.
DUFERCO
Rhenus est ‘asset light’ en Belgique et ne cherchait pas forcément un terminal dans le port de Bruxelles, mais la relation avec son client le groupe Duferco, qui coexploite notamment le Trimodal Terminal Brussels dans le port, a permis de concrétiser la reprise du terminal de Smet. « Ceci s'inscrit également dans notre développement stratégique avec, d'une part, des transports de conteneurs outre-mer pilotés via des plates-formes IT, et d'autre part des fl ux maillés où les contacts personnels sont importants. Nous voulons être un lien entre le transport maritime et le dernier kilomètre. Ce sont deux mondes que nous essayons de réunir via une plate-forme ouverte », explique Van Rossen.
TROIS PILIERS
Le but est de développer le terminal autour de trois piliers : le recyclage des fl ux de déchets, un hub de construction et une Container Freight Station (CFS) pour le dépotage et l'empotage de conteneurs. En ce qui concerne les fl ux de déchets, les cendres de l'incinérateur de déchets voisin sont notamment expédiées ainsi que les déchets de verre de la ville de Bruxelles. « La famille Rethmann qui a racheté Rhenus fi n 1998 possède une fi liale spécialisée dans le recyclage de déchets, Remondis. Par le biais de cette entre-
Bart Van Rossen, managing director de Rhenus Terminal Brussels.
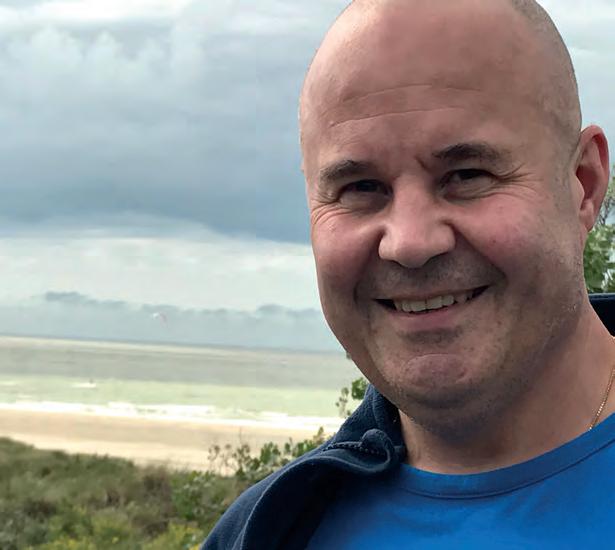
TL Hub Business Game
Rhenus Terminal Brussels a fourni une étude de cas pour la dernière édition du TL Hub Business Game, organisé par TL Hub, la fi liale de Transportmedia. Au total, 11 hautes écoles et une université y ont participé. La Haute Ecole Francisco Ferrer de Bruxelles est sortie vainqueur parmi cinq fi nalistes. « Nous avons acheté le terminal sans business plan en tête. Nous savons maintenant que nous voulons nous concentrer sur les trois piliers mentionnés. À titre d'exemple, les participants devaient dire s'ils étaient d'accord avec ces trois piliers ou avec lesquels ils ne l’étaient pas et pourquoi. Ils pouvaient également proposer quelque chose de complètement différent. Ils ont dû mettre leur choix en pratique. Les expéditeurs sont souvent coincés dans une routine et il est important qu'il y ait un pont entre le monde académique et la pratique », déclare Van Rossen.
« L'une des propositions de l'équipe gagnante était de combiner la logistique de construction aux fl ux de retour des déchets. Ils ont aussi proposé une extension avec un sous-hub au Biestebroekdok. Leur proposition se base également sur différents points de vue, tant fi nanciers que liés à la réduction du CO2. Outre l'élaboration d'un dossier, le TL Hub Business Game est important pour attirer de futurs collègues », conclut Van Rossen, qui souligne encore le lien local de l'école gagnante avec Bruxelles.
prise, nous procédons également au recyclage de déchets ménagers », explique Van Rossen. « En tant hub de construction, nous pouvons stocker des pièces plus volumineuses et, si nécessaire, les assembler, puis les livrer à la demande sur les principaux chantiers de Bruxelles. Nous répondons ainsi aux limites de l'espace public pour les grands projets de construction et opérons dans ce cas comme hub intermédiaire. Ce sont des avantages dont on peut rapidement profi ter », souligne-t-il.
CFS
Rhenus Terminal Brussels traite 1.700 TEU par an, surtout des fl ux d'importation. « Nous pouvons opérer comme centre de distribution pour toute l'Europe. Nous sommes ici sur l'axe Anvers-Bruxelles-Charleroi (ABC) et donc un partenariat avec le port d'Anvers est crucial. D'une part, nous pouvons contribuer à optimiser la capacité du port d'Anvers en y créant de l'espace et, d'autre part, nous pouvons rapprocher le chargement du consommateur fi nal. Les clients de la périphérie sud de Bruxelles gagnent ainsi deux heures », pointe Van Rossen en citant quelques avantages. « Le concept de distribution urbaine mûrit également. Dès qu'il y aura un contexte légal, cela pourra décoller. Nos connexions avec un réseau mondial nous permettent d’offrir une solution globale. Par exemple, l'opérateur de navigation intérieure Contargo Transbox fait partie du groupe Rhenus. Ces dernières années, nous avons vu les transports de conteneurs via le Trimodal Terminal Brussels augmenter fortement. »
COLLABORATION AVEC TTB
TTB n'est pas seulement un voisin du Rhenus Terminal Brussels. « Nous sommes voisins et chacun attire ses propres clients, mais nous collaborons également. Par exemple, TTB a quelques nouveaux trafi cs sortants qui sont déchargés chez nous et chargés dans des conteneurs : du chêne pour Unilin à destination de la Chine et de gros lots de sable en vrac. Il faut replacer cela dans le contexte d’un espace limité au TTB. C'est un défi logistique, mais à deux, on est plus fort que seul. Nous rêvons déjà de Schaerbeek-Formation », déclare le managing director. Le nouveau contrat de gestion récemment conclu par le port bruxellois avec le gouvernement régional prévoit une extension du domaine portuaire de 20 ha, soit la moitié du site de SchaerbeekFormation, qui a été racheté par la Région. Rhenus Terminal Brussels utilise également le service de barges de TTB.
« Nous voulons être un lien entre le transport de conteneurs outre-mer et le dernier kilomètre. »
27.000 M²
Le déménagement sur le site de SchaerbeekFormation n'est pas encore pour tout de suite, mais l'actuel terminal de Rhenus dispose déjà de 3.000 m² de stockage couvert pour les matériaux de construction et de 24.000 m² de terrain ouvert pour le stockage de l'acier, les fl ux de recyclage et les fl ux à valeur ajoutée. « Le port fonctionne avec un pool de dockers. Aux heures de pointe, nous travaillons ici avec 5 à 6 personnes pour 1 à 2 en heures creuses. Nous avons aussi 4 employés. Les matériaux de construction sont notre activité principale, suivis des fl ux de recyclage et troisièmement, la CFS », conclut-il.