World’s most northerly paper mill makes sustainable choices with ABB
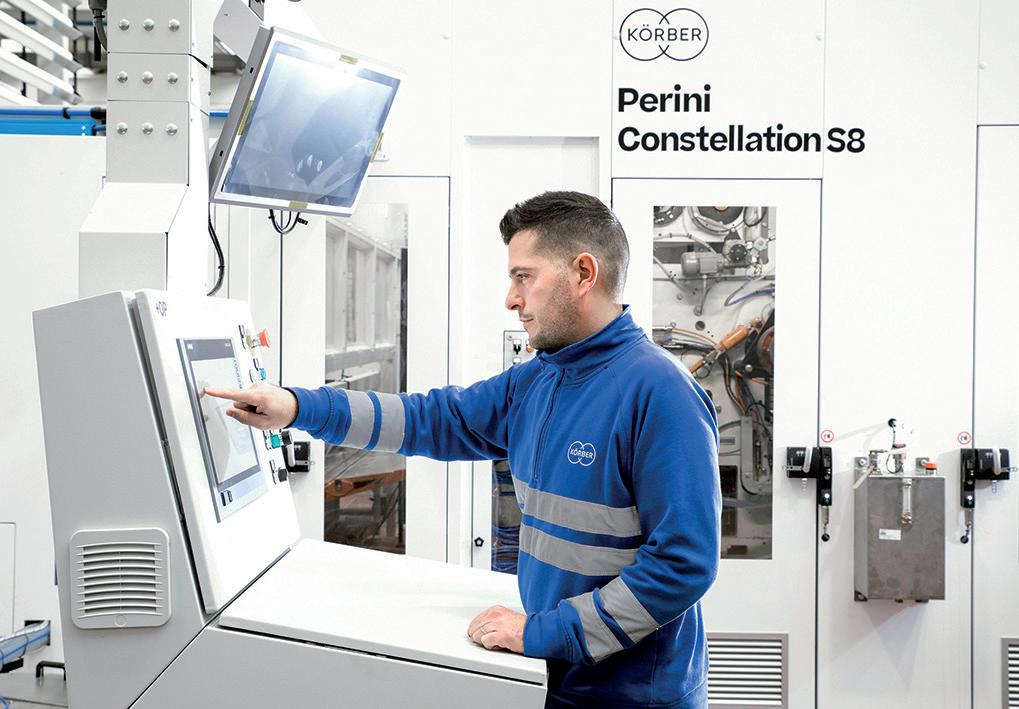
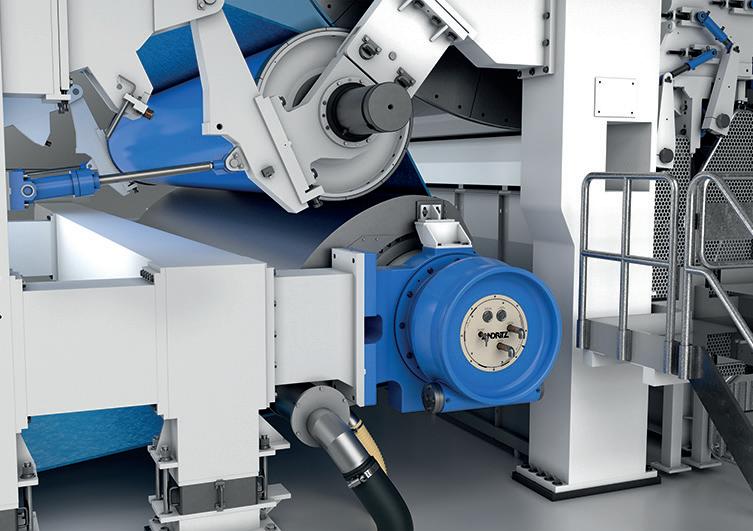
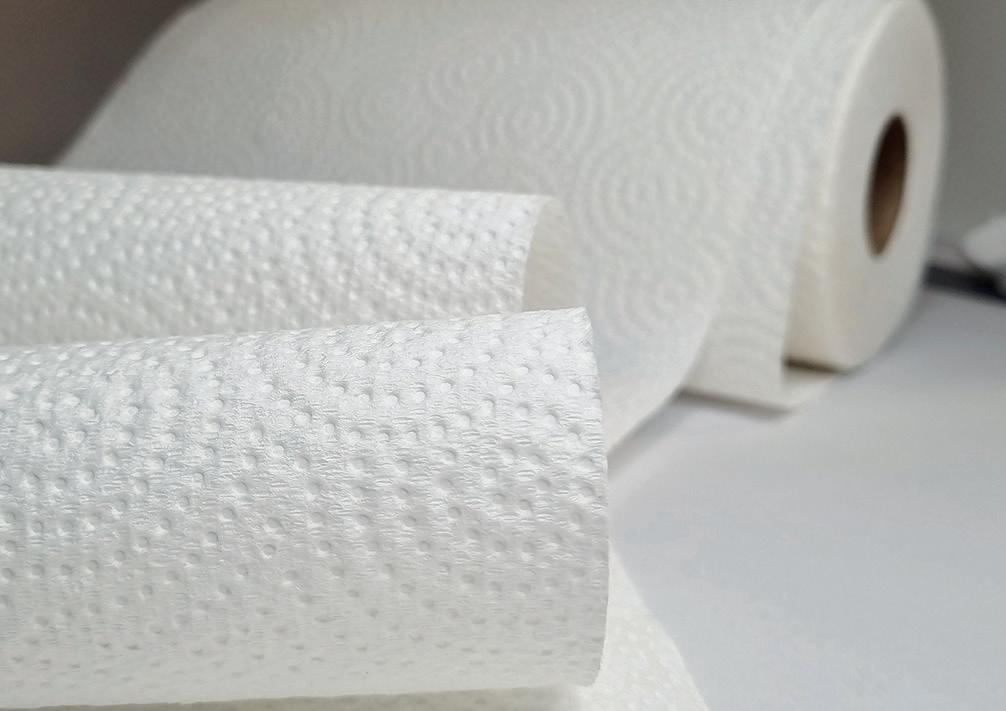
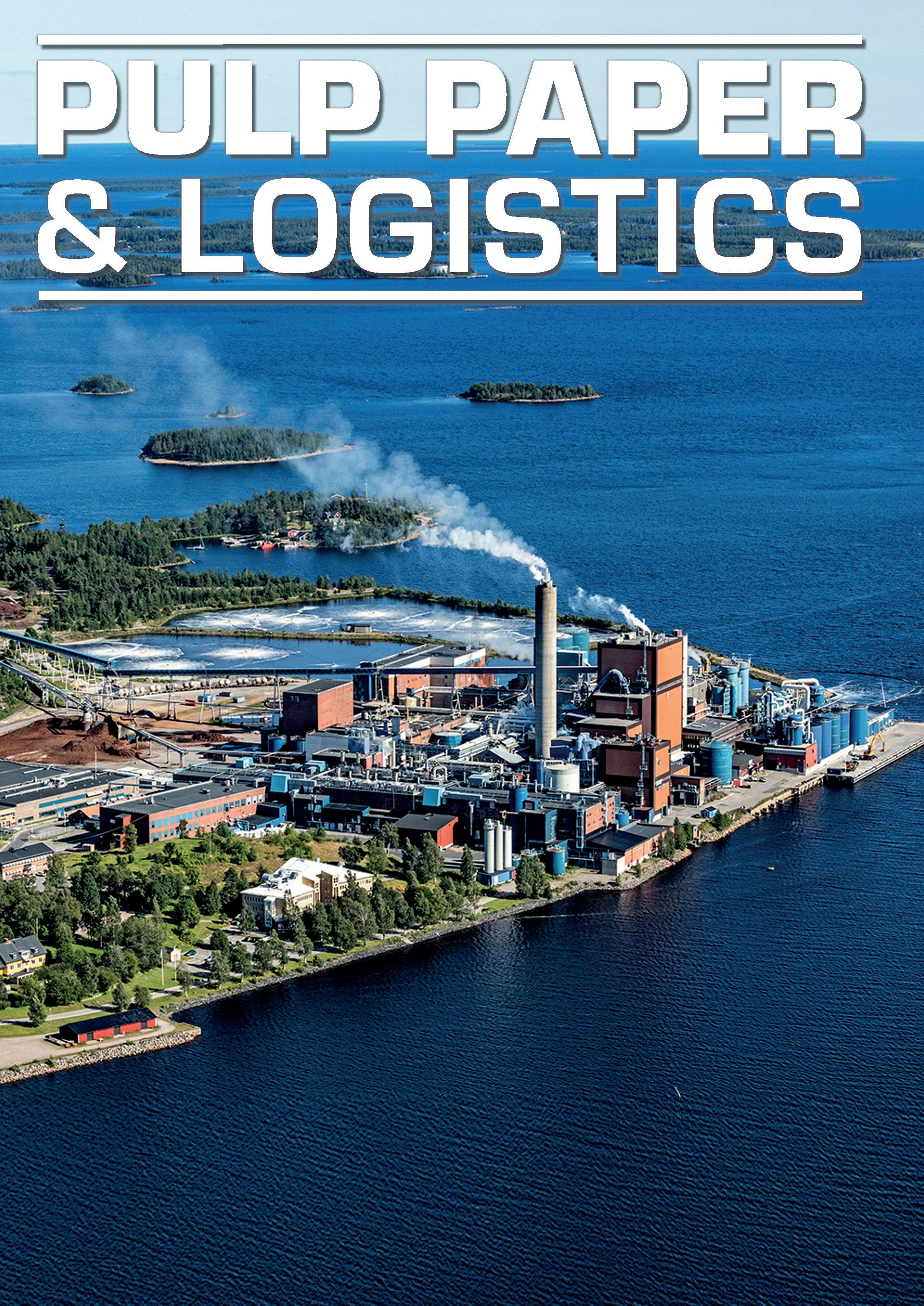
World’s most northerly paper mill makes sustainable choices with ABB
ANDRITZ has gone to great lengths not only to comply with tissue machine safety regulations, but also to go beyond them to ensure that every customer enjoys the highest level of safety in every machine the company supplies.
The tissue safety experts follow three main principles when it comes to tissue
machine safety: a safe machine ensures the safety of the operating personnel and the surrounding environment, a safe machine is the basis for a reliable process to create maximum output, and a safe machine is obligatory to fulfill legal requirements.
One important factor is the fact that in different regions there is a different
approach to safety in the tissue industry. Our tissue experts are always providing the very best safety solution for the respective market with additional features to choose from.
For further information, please contact us at tissue@andritz.com
Welcome to the May-June issue of Pulp Paper & Logistics. As consumers increasingly avoid the use of plastics in packaging products, so the major brands are providing a lead with moves to more sustainable alternatives.
The pulp and paper industry is responding to these demands and developing fibre-based alternatives, with recent development including kitchen and toilet roll wrapping thereby reducing the reliance on traditional flexible plastics.
The development of these alternatives by paper and corrugated manufacturers presents its own challenges. These may involve a change to the mill’s configuration and even the purchase of new converting machinery. There is also the need to ensure any new alternative will have comparable performance. Strength, durability and print ability are also key attributes that buyers and specifiers will be looking for if they are to replace traditionally-used but difficult-to-recycle options.
In general, and despite the costs, mill owners are continuing to invest for the future and develop sustainable and innovative products for the replacement of plastics within many sectors, including food and beverage and personal hygiene. At the same time, the mills are succeeding in cutting carbon emissions and providing a lead for other industries.
For the next issue of Pulp Paper & Logistics for July-August, we will be featuring machine clothing developments, mill re-configuration for packaging grades, plus pumps, valves and drives. Contributions for the issue should arrive no later than 13 July as a Word document and supporting print ready images.
Vol. 13 Issue No. 78, May/June 2023
ISSN 2045-8622 (PRINT)
PUBLISHER & EDITORIAL DIRECTOR
Vince Maynard
Tralee, Hillcrest Road, Edenbridge, Kent, TN8 6JS, UK
Tel: +44 (0) 1732 505724
Mobile: +44 (0) 7747 002286
Email: pulppaperlogistics@virginmedia.com
CONSULTANT EDITOR
David Young
Tel: +44 (0) 1737 551687
Mobile: +44 (0) 7785 796826
EDITOR
John Nutting
Email: johnnutting47@gmail.com
REGIONAL REPRESENTATIVE
Einar Johansson
Tel: +46 8 540 255 15
Mobile: 0046 70 234 80 85
Email: einar.lennart@gmail.com
PRODUCTION
Anthony Wiffen
ASTAC Business Publishing Ltd
Tel: +44 (0) 1460 261011
Mobile: +44 (0) 7557 280 769
Email: anton_print_1@mac.com
Tissue production – make it safe!
PRINTER
Brown Knight and Truscott
Tunbridge Wells, Kent, TN2 3BW
United Kingdom
Tel: +44 (0)1892 511678
UPM is cutting the use of fossil fuels with the use electric boilers in heat and steam production at its mills in Finland and Germany. A total of eight boilers will be installed, mainly to replace the use of natural gas. With the introduction of the electric boilers, the pulp and paper producer will take a step towards its 2030 target of reducing CO2 emissions from the fuels and purchased electricity by 65 per cent. In Finland, it says that new electric boilers will be able to reduce CO2 emissions from the use of fossil fuels by about 50,000 tonnes per year. In Germany,
electric boilers will improve security of supply for heat and steam generation and achieve even more emission reductions.
“In addition to improved security of supply and emission
reduction, electric boilers will significantly increase the mills’ ability to provide demandside flexibility to the electricity system and markets,” says Petri Hyyryläinen, energy director at
UPM Communication Papers.
UPM’s Tervasaari paper mill has already commissioned its first 50 MW electric boiler, which was transferred from UPM’s Kaipola mill. In the autumn, a new, moreefficient 60 MW electric boiler will be installed at the mill. The new boiler will not only produce steam and heat for the mill, but also heat for the surrounding Valkeakoski district heating network.
The remaining electric boilers will be installed at the Finnish and German mills by the end of 2023. Once operational, they will replace a significant amount of various fossil fuels, thereby reducing emissions at the mills and at UPM.
A system that is claimed to assess the recyclability of fibrebased products and materials in a consistent and credible way has been developed in the UK by Confederation of Paper Industries (CPI) with support from its member companies. Papercycle is described as certification service for fibrebased packaging products and materials for the UK and beyond.
With Extended Producer Responsibility (EPR) legislation on the horizon, this new service could not arrive at a better time, says the CPI.
The tool identifies whether fibre-based packaging materials can be recycled in the UK and which type of recycling mills are able to reprocess them.
Recyclability can be tested at any stage, for both finished and semifinished products.
Papercycle provides an instant diagnosis on recyclability following the online assessment, but for more complex products or materials, Papercycle can provide a technical review service on how a product behaves under lab conditions to give an insight into how the various components interact with each other, diagnose the most critical parts and signpost potential solutions for material modification. Papercycle can thus help prepare fibre-based packaging for certification and expansion in the UK and other markets, subject to local variations and requirements.
The CPI says that although all fibre-based packaging is recyclable in principle, innovations in material development means that some products more challenging to recycle.
The CPI suggests that with the EPR reforms under way, Papercycle’s certification service could enable a standardised labelling system where customers would receive a ‘recycle’ label as will be required by the UK’s mandatory recyclability labelling on packaging.
Packaging certified as ‘recyclable’ will also attract lower Producer Responsibility (modulated) Fees associated with complying with the reformed
Packaging Waste Regulations. Dimitra Rappou, CPI’s director of recycling, said: “As packaging materials have become increasingly complex, we have seen growing confusion over their recyclability, with an oversimplified assessment approach threatening the quality of recycling.
“Papercycle’s new service can remove the uncertainty faced by packaging designers, brands, retailers, and policy makers on the recyclability of fibre-based products. We see this playing a crucial role in promoting a circular economy for fibrebased packaging, helping to reduce waste and lower carbon emissions by keeping materials in use for longer.”
Plastic-free poppies that commemorate Remembrance Day in the UK every November have been developed by James Cropper in collaboration with the Royal British Legion (RBL).
Made entirely of paper, the poppies are part of the charity’s commitment to reducing singleuse plastic in all its activities
in a drive to be economical, sustainable, and less impactful to the environment.
Marking 45 years of partnership with the RBL, the paper provided for the new design is made from a blend of renewable fibres from responsible sources, 50 per cent of which has been recovered from paper coffee cup production at James Cropper’s CupCycling facility in Cumbria in the Lake District.
James Cropper, which is reorganising itself into four segments one of which is Technical Fibres, has collaborated with fellow luxury packaging specialist Rissman to create this Middle Eastern-inspired paper carrier bag using 100 per cent postconsumer waste recycled paper from James Cropper’s Rydal Packaging Collection
The new poppy design comes as James Cropper revealed a strategy to accelerate growth throughout the group, which is reorganising itself from three divisions (James Cropper Paper, Technical Fibre Products and Colourform) into four market-facing segments, all under the James Cropper name.
The four segments are Creative Papers, Luxury Packaging, Technical Fibres and Future Energy. These will be managed under two managing directors covering paper products and advanced materials respectively, reporting to Steve Adams, who was appointed chief executive in August 2022.
A key element of the new strategy will be significant changes
First installation of WestRock’s CanCollar Corsair, a machine that automatically applies paperboard-based multipack holders to 24-pack trays of cans, at a craft brewery is at Ska Brewing in Durango, Colorado. The machine enables Ska to offer all of its beers in packaging that
reduces plastics consumption by up to 95 per cent.
“The CanCollar, which promotes circularity, will immediately reduce the amount of plastic Ska contributes to the environment by approximately four tons per year,” says Ska’s operations chief Steve Breezley.
to the Paper division, including a proposal to reduce the number of operating paper machines from four to three, with two machines in production at any one time.
With the reorganisation and streamlining, this will lead to job losses, which will affect about a tenth of employees in the paper and group function. A 90-day consultation period has been started.
Adams commented: “We’re a purpose-driven business built on strong values and announcing potential job loses is not a decision taken lightly. We will work collaboratively with our employees, unions,
and representatives throughout this process. Change is difficult yet it is essential to ensure the sustainability and growth of James Cropper.
“Our strategic realignment will drive margin improvements by bringing greater focus on our customers and allow us to take better advantage of our size and remain agile and dynamic in our markets. Combined with our wealth of manufacturing knowledge, sustainability alternatives and pioneering abilities we will strengthen our position across multiple sectors as the preferred global partner of choice.”
The Zellcheming Expo 2023 trade show opens on 20 June for three days of pulp and paper exhibits and forums at the RheinMain CongressCenter (RMCC) in Wiesbaden, Germany.
“Both the content planning and the commitments for the Expo have developed very well. We expect to exceed last year’s already very good figures by a good 10 per cent,” explains Petra Hanke, managing director of the organisers.
Among the more than 100 exhibiting companies and organisations are many that traditionally support the trade fair. There is also a high level of interest from new exhibitors from Germany and Austria, along with the Netherlands, the United Kingdom, Italy, and Belgium.
On the first day of Expo 2023, the forum will be opened by Prof Helga Zollner-Croll, the future president of the Zellcheming association, who will moderate the lecture session “Innovative
energy concepts in the paper and fibre-based industry”.
“The topic has continued to gain significant momentum at all levels, political, operational and social, and I look forward to valuable contributions to the discussion that will shed light on the various perspectives.” Among others, the managing director of the Model Paper Factory, Peter Bekaert, will report on the latest developments of the pioneering joint project.
The Zellcheming Data Technical Committee will be hosting a session on ‘DigitalizationArtificial Intelligence’. Speakers include Rosario Othen from RWTH Aachen University and Christin Joachim from Papierund Karton-fabrik Varel, who will report on ‘Data Hackathons for and with Students – Added Value for All’ using the perspective of the younger generation.
Olav Dau from Bellmer, with Matthias Schmitt, representing
The PulPaper trade show has been rebranded as Pulp & Beyond 2024 to bring together the latest forest-based bio-economy innovations, products, services and technologies.
Being held from 10-11 April 2024 at the Helsinki Expo and Convention Centre in Finland, the event aims to provide the widest available showcase on the latest trends, and supports learning, employer branding
and competence development, along with a strong focus on sustainability, efficiency and functionality.
Voith Digital, will report on the use of ‘Augmented Reality in the paper industry’ and look at ideas from the supplier industry. The session is completed by Dr Michael Hunold from Steinbeis, who will present field reports together with Dr Philip Gerstner from Felix Schoeller and Dr Jörg Padberg from Koehler Paper.
The second day is aimed at women in the pulp and paper industry. The network now includes more than 300 female representatives of the industry. Mia Kainz, HR Strategy Manager at Mondi, will focus on the importance of diversity.
Zellcheming will be expanding is presence by organising Expo 2023 as a hybrid event with digital reach. Those unable attend in person will have the opportunity to join live. And for those who are at the show, the Expo app will offer extras to get more out of their visit.
More information from www. zellcheming.de/veranstaltungen/ zellcheming-expo
commented: “Now it is time to look forward and take one step ahead. You are welcome to join us on a journey into the future and beyond.
“Instead of the traditional PulPaper we are going to arrange a totally new event which will be inspiring, humanfocused and enabling. Now it was definitely time to start something new and open a new Nordic Arena for innovations.”
More than 100 representatives from the UK’s paperbased industries gathered in March on the House of Commons Terrace to celebrate their achievements.
The Paper Industry Gold Awards 2023 was hosted by Mark Pawsey MP, who chairs the APPG on Packaging, and attended by a number of Parliamentarians from across the chamber, including shadow cabinet members and constituency Members of Parliament.
The awards recognised success in five categories: Recycling,
Sustainable Innovation, Community Engagement, Health and Safety, and Skills. The six winners, with two winners in the Sustainable Innovation Category, were each recognised with a glass trophy.
Winners were: Recycling Award – VPK UK and Ireland; Sustainable Innovation Award – (winners) Swanline Group (EzeE-comm pack) and DS Smith; (highly commended) Fourstones Paper Mill; Community
Engagement Award – Smurfit Kappa Inspirepac, Chesterfield; Health and Safety Award – Saica Group; and Skills Award – Essity UK Ltd.
Andrew Large, director general of the Confederation of Paper Industries, said: “The awards showed that the industry has a lot to be proud of, and there are many remarkable individuals and businesses which do excellent work. I was extremely impressed by the number and quality of applications, and we were delighted to showcase this to senior politicians and stakeholders.”
The sale by Stora Enso of its newsprint mill at Hylte in Sweden to Sweden Timber, a sawmill and planing mill, was completed in April.
The €18 million deal had been announced at the end of January, and results in Stora Enso’s annual sales of €2.86 billion being reduced by €160m, or 5.5 per cent.
The transaction, part of the
Mondi is investing in its FunctionalBarrier Paper capacity to meet growing demand for sustainable paper-based packaging.
Mondi’s range is said to offer
earlier announced plan to divest four of Stora Enso’s five paper production sites, does not affect Stora Enso’s formed fibre and biocomposite operations located at the Hylte site.
Sweden Timber is operating the Hylte paper mill, which dates from 1907, as a separate entity. It was extensively modernised and automated in the 1990s.
In a statement on its website the company said: “Today we have
a paper machine in operation and have approximately 270 employees. This makes Hylte Bruk one of the largest private employers in Halland County. With its capacity of 245,000 tonnes, it remains one of the world’s largest newsprint mills and will continue to do so going forward!”
Stora Enso said the sale was in line with its strategic focus on long-term growth potential
tailored barrier properties that reduce the amount of plastic used in packaging, supporting the development of a circular economy.
The range is being backed with
an investment in a new extrusion coater and a slitting machine at Mondi Coating Štĕtí in the Czech Republic. Production is expected to start in 2024.
In addition, investment is currently under way at Mondi’s Jülich plant in Germany with the rebuild of an existing coater. Two new dispersion coating stations will improve barrier properties by ensuring good coverage on the base paper. The construction of a new coating kitchen is also part of the rebuild and will enable the pre-coating of base paper and expand the offering to include more paper grades, especially containing recycled content.
Mondi will also be investing in and optimising its Örebro production facility in Sweden, to further improve production of its FunctionalBarrier Paper range.
As a replacement for plastic films and laminates, the range offers fibre-based packaging alternatives that are particularly
for its renewable products in packaging, building solutions and biomaterials innovations.
In a separate announcement, Stora Enso said it was planning to to consolidate its book paper production and permanently close one of the two paper machines at Anjala in Finland following weak demand and “high input costs”, reducing the site’s annual capacity by 250,000 tonnes and sales by €100m.
suitable for fast-moving consumer goods which can be recycled in existing paper waste streams across Europe. With varying barrier levels, the range is tailor-made for industrial and eCommerce applications as well as personal care, frozen food and chocolate packaging.
Marko Schuster, operational chief for Functional Paper & Films at Mondi, comments:
“We are seeing a strong drive in the end markets to reduce the use of plastic and move towards more sustainable paperbased packaging solutions. Our FunctionalBarrier Paper range reflects Mondi’s commitment to this and promotes a circular economy, in line with our MAP2030 goals. We are excited to expand the portfolio and enable our customers to make a smooth transition to more sustainable packaging solutions to meet the growing needs of their consumers.”
Your paper machine certainly has a lot of potential, it‘s a question of getting it out: Start up faster, dewater more and run your clothing for longer - with our New-Tech fabrics you can increase performance and cost efficiency. Are you looking for process optimisation? Our experts can support you in reaching your goals with a combination of high-tech equipment and know-how. Learn more at:
www.heimbach.com
A€40 million investment by Smurfit Kappa has expanded its Pruszków corrugated plant into the largest of its kind in Poland, making it, says the company, one of the most high-tech and modern packaging plants in Europe.
Along with modern equipment, 50 more jobs will be created bringing the count to more than 250. The plant supplies leading brands in the FMCG food and beverage sectors both locally and internationally.
The investment, which doubles
output, includes the installation of a new high-tech corrugator and a range of ultra-modern
converting machinery. The plant is also equipped with a new finished goods warehouse, to
accommodate up to 12,000 pallets.
Commenting at the official opening event, Jacek Nieweglowski, chief executive of Smurfit Kappa North-East Europe, said: “We are delighted to officially unveil the new manufacturing plant here in Pruszków. This project took just over one year to complete and will enable us to continue to pursue our strategic goal of being the supplier of choice to our customers, particularly those looking for the most innovative and sustainable packaging solutions.”
Global paper-based packaging manufacturer Smurfit Kappa won two categories for its sustainability and safety at the Fastmarkets Forest Product PPI Awards, held at Prague in the Czech Republic, in April.
The awards are dedicated to recognising the achievements of companies, mills and individuals in the pulp and paper sector.
The Hyflexpower project, the world’s first integrated hydrogen gas turbine demonstrator, at Smurfit Kappa’s Saillat paper mill in France, was awarded the Green Energy and Biofuels award. The ‘100 Stories on Safety’, a project created by employees at the Smurfit Kappa Tijuana plant in Mexico which highlights the safety challenges
of working alongside machinery, won the Risk and Safety award.
Commenting on Smurfit Kappa’s success at the awards, Saverio Mayer, chief executive of Smurfit Kappa Europe, said:
“We are very proud of winning these two awards in the global PPI awards which has a very high standard of entries. It is great that the hydrogen pilot has been recognised, because at
Smurfit Kappa we are focused on reducing our emissions with the best available technology whilst at the same time trialling new technology to help us achieve our Better Planet 2050 goals.”
Juan Pablo Perez, chief executive of Smurfit Kappa North America, commented: “It is a great honour to see Tijuana’s 100 Stories on Safety project acknowledged at this year’s PPI Awards. Safety is a core value so we felt it was important to reinforce safe behaviour in a new and engaging way from the perspective of our employees working both in plants and offices. It has been a huge success so far and one we are keen to replicate across multiple sites.”
Anew generation of narrow-aisle lift trucks has been launched by material-handling specialist Crown.
The TSP Series is said to deliver an intuitive operator experience, improved ergonomics and more efficient picking capabilities.
“Our VNA trucks, which have proven themselves in practice many times over, are designed so they can be precisely adapted to specific applications,” explains Sven Vorreiter, senior manager for product marketing at Germanybased Crown.
“Whether they’re moving full pallets or picking high above the ground, operators always have the great feeling of being
in total control thanks to the lift truck’s exceptional ergonomics and comfortable working environment.”
The new trucks use an operating system that can be personalised for the operator so that all key functions such as operating hours, steering angle and battery state of charge are displayed in real time, ensuring that the information is easy to see, understand and use.
The system also has a Capacity Data Monitor, which provides at-a-glance details of load weights, lift heights and capacity limits. Colour-coded visuals – similar to a traffic-light system – indicate the truck’s current status to operators so they can stay within specified load limits.
Two optional, RFID-based semiautomation technologies for the TSP Series enable the truck driver to be alerted to hazards in its working environment. An ‘auto-fence’ restricts the lift truck’s travel speed or lift height
depending on where the truck is located – at intersections or in areas with lower ceilings. A system also automates travel and lift functions to deliver the most efficient route to the next storage location.
Finnlines operates numerous routes and vessels all the year round between the main ports in the Baltic Sea, the North Sea and Finland.
In-house transhipments of all types of commodities to and from the Mediterranean, West Africa, North and South America as well as Asia and Australia with Grimaldi and ACL.
New energy efficient vessels
Finnlines has invested EUR 0.5 billion to increase its environmentally friendly fleet. Three new hybrid ro-ro vessels transport cargo in a more sustainable manner.
The most efficient tonnage in the industry serves societies and customers responsibly.
Avoiding accidents and unplanned downtime by using the highest safety standards is one of the foundations of producing tissue at high speeds today. The industry’s safety measures and concepts already go hand-in-hand with the continuing increases of machine performance and capacities. Nevertheless, this part of the
tissue production process is subject to great dynamics, as not only technologies evolve, but also awareness of the importance of safety increases and the regulatory framework changes. In addition, the understanding and interpreting of the guidelines often varies by country and by supplier.
“Safety is quite a complex area for us as machine suppliers,”
says Thomas Nager, machine safety expert at Andritz. “On the one hand we want to supply the safest tissue machines on the market, however on the other hand we also want them to be the most productive machines when it comes to ease of operation. We try to live a culture that combines these two, often remarkably divergent, topics.”
Andritz has gone to great lengths both to comply with machine safety regulations, and to go beyond them to ensure that every customer enjoys the highest level of safety in every machine the company supplies. Andritz follows three main principles when it comes to tissue machine safety:
l A safe machine ensures the safety of the operating
The operational safety of a high-speed tissue machine depends not just on lists of rules and standards, but of inherently safe design. PPL talks to Thomas Nager, a specialist on the subject at Andritz
personnel and the surrounding environment
l A safe machine is the basis for a reliable process to create maximum output
l A safe machine is obligatory to fulfill legal requirements.
“The first and most fundamental of our principles when supplying tissue technology is that obviously we don’t want any operators to be hurt,” continues Nager.
“The second is reliability and machine performance, and third on the list is regulations and legal requirements.”
“Currently, European safety standards are the most detailed for tissue making and finishing machines. The basis for Andritz
machines is the risk assessment in combination with the standards. For the European market, additionally, the Machine Directive, as well as the Electromagnetic Compatibility Directive (EMC), Low Voltage Directive (LVD) and Pressure Equipment Directive (PED) and their harmonised standards must be fulfilled. Products in compliance with these directives are identified by the CE mark (Conformité Européenne) which signifies that the products sold have been assessed to meet the legal requirements for health and safety.”
Andritz already communicates with the customer in the sales phase about the implications of the risk assessment and the most advantageous route to take.
Nager explains: “There are always discussions early on about the CE mark for the European market, and whether, for instance, the whole plant must have a CE mark, or individual machines only. As an example, a tissue machine needs a CE mark of its own, as does a pressure vessel such as a Yankee. Andritz ’s advice is to have individual CE marks, as updating in the future tends to be easier and more flexible than with a mark covering the whole plant, even if it is not necessary according to the machine directive.”.
In addition to CE markings on
newly-supplied machines, Andritz provides audits on older machines to ensure that they comply with the current regulations. Furthermore, safety advice will be issued if it comes to major rebuild projects.
Other countries and regions also have their own conformity markings including the USA and Canada (e.g. UL for electrical components), China (e.g. CCC) and Russia and Eurasia (e.g. EAC).
“Of course all additional requirements in any given country or region will be respected and taken into account when delivering Andritz tissue machines,” adds Nager.
Under the European Machine Directive, which is the legal basis for machine safety in Europe, every machine that is placed on the market must have a risk assessment which is the core tool to ensure that safety has been seriously taken into account. This means identifying where any hazard areas may occur and taking defined steps to make those areas safe.
“This is not simply a case of ticking boxes,” says Nager. “This really is about reducing risks in the work environment, often in tight spaces. For example, it is quite common in the tissue industry for space to be a problem, and squeezing a machine into a tight area. If this happens, it
is particularly challenging that people are kept at a safe distance away from the hazardous areas.
“We are working closely with our customers to improve the safety of their tissue production process, for example: Which safety elements need to be eliminated or by-passed; which kind of smart solutions can we offer or develop conjointly to create a safe environment?”
The risk assessment ensures that nothing is left out or forgotten when it comes to all aspects of safety on tissue machines. Andritz realizes this with its high competence in various fields, fully understanding the mechanical demands and with all process know-how in house. This involves making a list of all important factors relating to risk on a tissue machine and defining measures how to mitigate these risks.
“These standards are split into A-, B-, and C-standards” explains Nager. “A-standards are general safety related standards, such as ISO 12100 which defines what a risk assessment must contain; B-standards are more precise, related to different types of risk and C-standards which break the safety topic down to individual components such as tissue making equipment.
“This is complex and difficult to do. However this long list ensures that every area is covered, and no part of the machine or process is left out or forgotten.”
But essentially making tissue machines safe is not all about lists and standards. Ultimately, the aim is to identify any risk area and make it as safe as possible while at the same time allowing full and maximum efficiency of production to take
place. This is where Andritz expertise comes into its own.
There are three areas Andritz concentrates on to ensure all parameters are covered when it comes to machine safety and maximum usability:
l An inherently safe design –‘safety by design’
l Guards and fences where interaction is not necessary during operation
l Functional safety where interaction is necessary during operation
Nager says: “The basic approach to making tissue machines safe is that, first of all, we try to avoid a hazard location altogether, for example by avoiding the interaction between human and machine. This is making the machine inherently safe.
“However, we all know that tissue production is a labourintensive activity and it’s not possible to avoid hazardous areas completely. This means that dangerous areas such as
roll nips must have nip guards, and other areas need a fence to avoid operators getting too close. We have also carried out a lot of work on the design of machines at Andritz where the operator is able to avoid a hazardous area altogether by being able to carry out a task without entering a hazardous zone, for example by being able to pull out a lubrication point on the machine.”
The third area is the important one of functional safety where interaction is necessary during operation, which is quite common when operators need to check the quality of the tissue being produced.
Nager says: “The reel section is where operators always like to go in and touch and feel the quality of the paper being produced. In this case, Andritz has designed certain movements and interlocks within the machine where it is possible to enter the reel section at given intervals and perform tasks safely. Another example to point out is our fully-cantilevered shoe press concept, which allows
for faster felt and shoe press belt changes while greatly increasing the safety of this process.”
“It must be noted that functional safety, although an important asset, is costly at the outset and has to be maintained on a regular basis.”
The subject of safety while carrying out cleaning and maintenance tasks is also an important factor, particularly in tissue making.
“Both cleaning and maintenance are very relevant areas when it comes to safety of operation,” says Nager. “Tissue production requires a high level of cleaning. We have focused our efforts in making sure that not only areas of the machine are more accessible for cleaning and maintenance, but we also have specially-designed CE-marked lifting equipment to avoid any accidents or injuries during maintenance such as roll changes.”
Safety and attitudes toward safety have come a long way in recent
decades. However, there is still work to be done when it comes to regional approaches to safety.
“Improvements in safety have increased over the last 25 years. ‘Common sense’ used to be an integral part of the safety concept,” says Nager. “Now safety relies much more on the machine to keep people safe, in a way to take out the human element, and safety engineers are working more and more to prevent operators from manipulating the safety measures put in place, for instance disabling guards to make the job easier.”
One important factor Andritz is working on as a global company is the fact that in different regions there is a different approach to safety. Nevertheless, Andritz is always providing the very best safety solution for the respective market with additional features to choose from.
More information by email at tissue@andritz.com
Improve your press section efficiency! SmartScan™ contactless sensor accurately measures paper web dryness after the press section 24 hours a day, 7 days a week. Using a proprietary microwave technology, it is developed to overcome the typical limits of the NIR (near-infrared) sensors. SmartScan™ is available both for fixed point positions or traversing web scan. To save hundred of thousands of Euros in energy costs, stop collecting samples, choose the safe accuracy of SmartScan™ technology.
With more than 200 improvements and three patents pending, the new generation of Valmet tissue reels is a better, safer and more reliable product – with fewer disturbances and higher productivity.
Since its development in 2005, Valmet’s family of reels has given tissue producers a competitive edge. The equipment is one of the most innovative winding systems on the market. To maintain it as the industry’s preferred choice, many continuous improvements to the product’s components have been made over the years.
Today, the product is mature, with a well-proven track record. It is compliant with all the standard safety requirements. Despite this, the team at Valmet believed that more improvements could be made, and so Advantage Softreel (P & L) evolved.
Product manager Mickey Lindevall explains: “Although we
had an excellent product, we wanted to aim for more. Over the last two decades, tissue production has certainly evolved. Today, safety awareness among our customers and in the overall
industry is higher. More mills are moving toward autonomous production, and the Internet of Things is playing a bigger role. Customers want to invest in products that are ready for the future.”
While many upgrades have already been made to the current family of reels, many more improvements have been collected separately during dialogue with customers and among Valmet’s product development teams.
Lindevall continues: “We came to a point when we had so many ideas we wanted to realise but felt that the current product had reached its maximum level of advancement. It was now time to
take all these improvement ideas and hand them over to the next generation of reels.”
Further development ideas were gathered in numerous interviews with people including sales, startup teams, customers, product owners and production teams. It was clear from the start that the core of the current reel should be kept – there is no reason to change a winning concept. However, the team were now equipped with the tools to make it even better.
Improved and upgraded
Johan Björn, sales director for the EMEA at Valmet, is looking forward to the introduction of this new generation of reels which will improve operations.
“I have great confidence in this product,” he said. “The new reel has modular possibilities,
and it’s prepared for more and new technology. All new full-line orders will include the new generation, but we are naturally happy to speak about potential replacements of current equipment as well.
“I’m proud to say that the
product is truly state-of-the art when it comes to safety. The dry end of the tissue machine is where the operators spend most of their time, so it’s also the place with the most safety risks. With new technology, we can limit the manual handling of the rolls, allowing a safer working
Advantage SoftReel also features a new and upgraded user interface, and it adds several automation features and Valmet Industrial Internet options, which makes it a significant improvement from the previous generation.
The development process has really been a joint effort. A broad team from the tissue organisation contributed to the project, including steering groups, product engineers, a reference team with specific competences and other functions such as supply, engineering, product safety and Valmet’s Industrial Internet team.
The new Advantage SoftReel is due to be ready to enter the market in mid-2023.
In a slow-growing forest in northern Sweden is a unique raw material: trees that produce extremely strong paper. Every day, 130 log trucks transport them to the nearby Billerud site in Karlsborg, the world’s most northerly paper mill, where they are transformed into mouldable paper branded as FibreForm, kraft paper, sack paper and bleached pulp in baled form ‒ a total of 350,000 tons every year.
Why buy new equipment when you can renovate and upgrade?
These are values that packaging giant Billerud lives by at its Karlsborg mill in northern Sweden. So a retrofit by ABB with new energy-efficient circuit breakers was a perfect match when its decades-old switchgear needed new life. PPL reports
This level of production is enabled in part by reliable technology, which is regularly tested and upgraded, and in part by a dedicated workforce of 440 employees.
“There is a lot of expertise in the area and many people who
work here have been doing it for a long time,” says Mikael Nordqvist, plant manager at Billerud Karlsborg. “You can work here all your life, but on different things. We know that many people who apply to us do so to work with sustainability
and contribute to a sustainable society.”
Located just outside the town of Kalix, the mill is the largest private employer in the municipality. In addition to its main production plant, it houses two application
laboratories with expertise in pulp optimisation and bag and sack packaging development. The manufacturing process is a circular system where chemicals are recycled, and the company is 75-78 per cent self-sufficient in electricity, perfectly positioning the operation to respond to the growing demand for more sustainable, plastics-free packaging products.
ABB and Billerud have been working together for many years to ensure production at Karlsborg
runs round the clock, as any unplanned stoppage may have a catastrophic effect on production and revenue, not to mention the safety of employees. That’s why Billerud tests its switchgear every three years and carries out scheduled maintenance and upgrades every seven weeks at various parts of the production process.
With many components provided by ABB, including lowand medium-voltage switchgear, UPS, motors, drives and 800xA control systems, ABB service teams are an important part of this process.
“ABB’s products work well for us and what we appreciate most of all is the local service we receive.
The fact that they are close to us when we need both products and their expertise is invaluable,”
says Henrik Jakobsson, electrical & automation technician at Billerud.
Every so often, however, a larger upgrade project is required to ensure the long-term reliability of the plant’s switchgear, which has been in service since the 1980s. In the second half of 2022 this involved two ABB service
engineers coming in on two occasions to replace incoming circuit breakers in seven selected items of low-voltage switchgear throughout the plant. Ten medium-voltage circuit breakers were also replaced.
“Billerud chose a site-built solution, which is the most extensive renovation you can do without replacing the entire switchgear. It is very cost-
effective and also a sustainable option that allows switchgear from the 1980s to have a new life and to live on,” says Patrik Granlund, sales manager at ABB Electrification.
Six breakers were replaced with new Emax2 breakers during a stop after the summer of 2022 and the seventh in November of the same year. Replacing the old ALG and ALH variants
in the switchgear improved the safety of the equipment and immediately increased the availability of spare parts.
Emax2 is also the only breaker of its kind that can both protect electrical circuits and reduce energy consumption based on user needs.
“Replacing a breaker in this comprehensive way takes about seven-to-eight hours,
but compared to replacing an entire switchgear, the loss of production and downtime is significantly less,” Granlund explains.
From a sustainability standpoint, only a few parts needed to be scrapped in an otherwise intact plant, with the new breakers now likely to last for several decades.
“The pay-off time for changing
the breakers can be anything from zero to 100 years but knowing that we have done what we could to secure the operation of the electricity and personal safety feels good,” concludes Billerud’s Jakobsson.
Continuous development and technological leadership are essential for economic, social and environmental sustainability. Investing in regular maintenance,
upgrades and occasional larger retrofits is just one example of how Billerud is living these values.
Billerud AB is a pulp and paper manufacturer with its headquarters at Solna in Sweden. In 2022 the company simplified its name from BillerudKorsnäs to Billerud with the acquisition of Verso, a US producer of coated paper.
Founded more than 150 years ago, Billerud believes that virgin fibres from slow growing
northern forests make for some of the best-performing packaging materials.
In addition to the Karlsborg mill, Billerud’s other production sites in Sweden are at Grums just outside Karlstad, Skärblacka close to Norrköping, in Gävle; in Finland at Frövi/Rockhammar south of Lindesberg, and in Jakobstad; its mills in the US are at Escanaba and Quinnesec in Michigan and at Wisconsin Rapids.
Its sales were a record in 2022, totalling SEK 42,590m (US$4.2 billion).
In today’s difficult market environment, reducing expenses and production time and effectively managing asset life cycles are essential factors for capitalintensive companies to remain competitive.
To this end, the Total Cost of Ownership (TCO) is a critical decision-making tool with which mill owners can proactively assess how the effectiveness of their plants and their associated components may develop, ensuring their continued functionality. A further benefit of the model is having a clear
view of costs and economic benefits deriving from correct maintenance.
In this systemic perspective, technology and automation provider Körber is committed to reducing the TCO by maximising the OEE of paper converters, thanks to its ecosystem, which integrates technologies and services designed to simplify the entire tissue manufacturing and packaging process, whether in the form of rolls or folded tissue.
Alessandro Borelli, customer service director of Körber’s tissue business, explains the scope of the company’s activities: “There
are more than 20,000 machines installed by Körber Business Area Tissue worldwide:
l 35 per cent in Western Europe
l 8 per cent in Eastern Europe
l 15 per cent in South America
l per cent in North America
l 8 per cent in Central America
l 8 per cent in APAC countries
l 6 per cent in China
l 5 per cent in Africa.
“As the leader in this technology, Körber has a structure dedicated to assistance, which, in addition to combining smart services with the capacity for developing the finished product, provides field-tested technical skills
capable of maintaining high plant performance in the long term. More and more customers rely on the experience and skills of OEMs and this is testified by the fact that sales of the entire service chain recorded a growth rate of 44.7 per cent from 2018 to 2022.
“For Körber, ensuring maximum continuity of customer operations, first of all, means constantly monitoring the current 3,000 production lines worldwide through its Tissue Performance Center, either with an ongoing diagnostic connection service or on demand. Secondly, Körber guarantees qualified and proactive
technical support remotely or on site to minimise downtime and support customers in identifying and solving problems, so that the installed base is always up-to-date and efficient.
“In 2022 alone, over 500 onfield activities were performed. A significant part of them were carried out within the framework of Technical Improvement Programs (TIP). Thanks to this service, technological adjustments are made to new- and oldgeneration systems to guarantee high standards of safety and efficiency.”
Greater sustainability, safety, efficiency, performance and productivity are the priorities for the customers to whom Körber Business Area Tissue caters with
more than 300 standard TIPs, already implemented today, to which those designed according to the specific needs of tissue companies should also be added.
There are six TIP macrocategories aimed at minimising the environmental impact of production and finished products and at guaranteeing operator safety in compliance with the most recent regulations. Activities may range from work on small machine parts to a complete overhaul of the entire line, giving it new life and sometimes a new registration and CE marking based on customer needs. This business model, that keeps the investment of Körber customers tenable in the long term, is also based on design criteria that presuppose the possibility of retrofitting machines with the most recent
process and product technologies developed for the new series, even over a large part of the installed base, to keep it always up-to-date.
With the replacement of the entire electrical cabinet for wrappers and bundlers, Körber’s offerings are designed to guarantee a stabilisation and an enhancement of the machine performance, in some cases even by 20 per cent.
The installation of the latest generation 4.0-ready components ensures the management of the motor logic, of the axis control, and of the on-board machine systems, simplifying the command interface and eliminating any obsolescence. For example, electronic limiters instead of physical systems acquire
itself what difference a technology leader can make in a mature market”
a higher efficiency in containing some critical forces for a significant reduction in the wear-and-tear of mechanical parts and of the cycle speed.
Furthermore, the installation of the Mguard system for the Expert Online connection simplifies
troubleshooting in favour of prompt remote work by Körber technicians.
Asset protection and fire detection: Thermo-cameras
TIP plus Fire fighting system
The main advantage of this improvement programme by Körber is the prompt detection of anomalous heat concentration on all converting and packaging lines by using thermo-cameras. This technology ensures a high level of detail in thermal images, which are sharper and make it possible to identify any components prone to malfunction more quickly and in real time and to take action promptly.
The intelligence applied to these systems is also able to determine whether, under the same production conditions, there are drifts in the expected temperature parameters, giving advance information so as to anticipate serious breakdowns and machine downtime.
In addition to thermo-cameras, an advanced fire detection system based on a simple but highly stable and functional technology can be installed on all lines. This excludes the use of optical sensors, which are typically unsuitable for the paper environment, and is free of dust, oil, water and dirt. Finally, extinguishing is achieved with a low-pressure water mist system. The latter can also be integrated into the machine’s logic functions in order to prepare all the necessary actions for the reduction of unexpected problems. These are solutions that safeguard operators and the capital invested in high-value equipment and play a crucial role in industrial production.
Simplifying tasks for operators and reducing downtime are Körber’s additional goals. Easy reel change and Auto web starter stand out
among the most requested TIPs from customers.
The first allows the replacement of finished reels on traditional unwinders and the restart of production in just 90 seconds with standardised and repeatable procedures. This option may be installed on Körber medium and high-level tissue unwinders without automatic reel change systems.
The phase in which the paper passes through the machine following an unexpected paper break, or a restart due to a production change, is by far the most critical moment in terms of safety, as well as a costly one in terms of machine downtime.
The new Auto web starter has revolutionised the process of the manual web thread-up through the machines.
This automates and facilitates the process by combining three systems in succession. In the first one, the insertion of the flap of paper into suitable plastic shuttles hooked to the belt
enables operators to govern the machine’s start-up from the HMI panel outside the perimeter casing, with doors closed. In the second system, provided that the line configuration is suitable, the shuttles carrying the paper are automatically swapped on distinct belt branches.
Ultimately, the line can be restarted with the doors closed and in a fully-automated manner without requiring any intervention from the operator. This standard technology for new plants is available to be customised on existing lines.
“The volatility of the cellulose market, the lack of skilled labour and the challenges generated by an increasingly global and sustainability-oriented sector are encouraging tissue companies to seek ever-more scalable solutions,” says Borelli.
“Every day Körber asks itself what difference a technology leader can make in a mature market. The answer lies in its ecosystem in terms of new plants and in terms of customer service experience. A unique supply of its kind which, in addition to making Körber a strategic partner, integrates innovative technologies, digital services and supply chain solutions fostering the customers’ competitiveness in terms of product differentiation and profitability over time.”
More information from Körber Tissue SpA, Via Giovanni Diodati, 50, 55100 Lucca, Italy.
Website: www.koerber-tissue.com
Körber is an international technology group with annual sales of about €2.5 billion, more than 12,500 employees and more than 100 locations worldwide that work in Digital, Pharma, Supply Chain, Tissue and Tobacco.
Launched by Valmet during customer open days in Copenhagen at the end of March, Mill-Wide Optimization (MWO) is said to enhance overall pulp and paper mill profitability. Using MWO, production teams are able to boost a mill’s performance by making better-informed decisions across various process areas towards shared goals.
MWO observes the entire mill balance in real-time and considers both the current and future states of the mill. As a result, individual processes that do not align with mill objectives can be avoided. MWO also provides the ability to balance environmental sustainability with production, quality, and cost, says Valmet.
Greg Fralic, product manager for Mill-Wide Optimization in the
automation systems business at Valmet, commented: “The pulp and paper industry is transitioning towards self-governing autonomous operations and towards a younger workforce with new roles and responsibilities.
“Valmet MWO helps to capitalise on these changes and unlock the
mill’s full potential.”
Mill-wide production planning helps mills to keep up with the daily changes in production bottlenecks. MWO reflects the mill’s current state and maximises production subject to existing and projected bottlenecks, while stabilising the process
and balancing pulp and liquor inventories.
Quality planning throughout the mill helps attain the desired final product quality while keeping the costs low. It adjusts the quality targets at each step from chip to finished product.
To move away from optimising individual processes, pulp and paper mills need to be evaluated as a whole. Valmet’s MWO Audit helps to reveal the true production potential and the corresponding return on investment.
Based on historical data, the audit helps to evaluate production increase potential, identify limitations, and highlight use cases of mill-wide optimization. It also helps to uncover development opportunities required for moving towards fully optimised operations.
Among a range of technologies and services for the wood industry featured by Andritz at the Ligna 2023 show held in May at Hanover in Germany, was
an autonomous logyard crane, claimed to the world’s first of its kind.
Under the heading ‘Building the Future Together’, the technology
giant was focusing on innovative technologies that enable customers to save energy, water, and raw materials in addition to reducing production costs and increasing product quality.
The autonomous logyard crane uses an artificial intelligence (AI) feature called Metris ANDI which is said to offer environmentallyfriendly, cost-effective log handling. The use of AI allows detailed tracking and classifying of the wood received in real time. Running on electricity, the crane emits no CO2 emissions and reduces noise pollution.
Also shown was a pellet mill. The high-performance PM30-6 mill
is designed for biomass pellets. Based on an optimised die speed and a patented feed system, it is aid to produce high-quality pellets at reduced maintenance cost and increased capacity.
An adjustable screw feeder shown uses state-of-the-art performance control enabling the use of dry and wet wood based on an adjustable design. With this design, compression can be adjusted to the moisture content of the fibres to optimise water removal in the plug screw feeder area and temperature requirements in the dryer thus reducing energy costs and CO2 emissions.
First deliveries of pulp from UPM’s newlybuilt mill at Paso de los Toros in Uruguay were expected in May after the final operating authorisation had been received from the local authorities a month earlier.
The mill’s annual capacity to produce 2.1 million tons of eucalyptus pulp doubles UPM’s output and makes it one of the largest suppliers in the world. In addition to the pulp mill, the overall investment of US$3.47 billion includes a deep sea-port terminal in Montevideo, a new
eucalyptus tree nursery and local investments in infrastructure and facilities.
UPM reported that the mill has gone through a comprehensive
The product portfolio of Mondi’s Neusiedler mill in Austria is being ‘refocused’ on the growth markets of Luxury Packaging, Professional Print, and Technical & Converting Papers.
Mondi says it will invest in the mill to get the best performance by changing the structure of its operations.
One paper machine will be closed, and the capacity of the finishing lines will be streamlined. Mondi admitted that the change in production capacity will inevitably have workforce
implications and as such, the paper maker has entered into consultations with its workforce at Neusiedler.
In addition, an investment of €20 million has been approved to increase energy efficiency at the mill and to ensure the necessary upgrades to machines, infrastructure and buildings. The investment is said to be also in line with Mondi’s MAP2030 sustainability commitments which includes reducing greenhouse gas emissions according to sciencebased targets.
and thorough permitting process. The Uruguayan environmental authority has monitored the construction of the mill on site throughout the project. The
operating authorisation process has included several inspections by the authorities, as well as third party audits by industry experts. UPM has an extensive environmental monitoring programme covering water and biota, air, soil, noise, and socio-economic aspects.
“We now have a balanced asset base and wood supply in two hemispheres. With two pulp mills in Uruguay and three pulp mills in Finland, we have a strong offering of sustainable hardwood and softwood pulp for our customers,” said Bernd Eikens, executive vice president of UPM Fibres.
Batı Kipaş Kağıt has ordered a complete machine clothing package from Valmet for a new PM3 board making line at its Söke mill in Turkey.
After the inauguration of the PM3 line, the facility will be one of the largest in Europe with a production capacity of 1,868 tonnes per day. The start-up of the PM3 is scheduled for the end of 2023.
“The machine will set new standards within the industry. We are happy to continue our strong collaboration with Batı Kipas Kagıt and will do our best to support the customer to successfully start up the newest member of their fleet,” says Huseyin-Feyzi Gunal, product sales manager for EMEA at Valmet.
Valmet’s paper machine clothing package for the start-up of the customer’s new container
board line includes forming fabrics, press felts, shoe press belts and dryer fabrics.
Kipaş Kağit Sanayi Isletmeleri AŞ started as a joint venture of Kipaş Holding in 2011 and produces high-quality containerboard paper from waste paper. Kipaş has two paper machines: PM1 in Kahramanmaraş with a capacity of 450,000 tons and PM2 in Söke with a capacity of 720,000 tons of coated grades.
Kipaş is currently installing another Valmet containerboard machine in Söke, also with a scheduled start-up at the end of 2023. The new 9,100mmwide (wire) board machine will produce recycled fluting, testliner and kraft top testliner grades with a basis weight range of 60–110 g/sqm. With a design speed of 1,800 m/min the machine will have an annual capacity of about 650,000 tons.
Turkey’s Lotus Teknik Tekstil has successfully started up a complete line to produce nonwoven roll goods for biodegradable, plastic-free wet wipes.
Delivered, installed and commissioned by Andritz, the neXline wetlace CP line combines the benefits of two technologies: wetlaid and spunlace. Natural fibres are processed gently to create a high-performance and sustainable wipe. Described as a next-generation wipe, Newipe combines the benefits of spunlace fabric, in particular remarkable strength in all directions, with the biodegradability and softness of a wetlace fabric. It is said to be produced with a lower carbon
Swedish pulp and paper maker
footprint, has a low lint rate, and does not generate dust during production.
Ceyhun Zincirkiran, co-owner and managing director of Lotus Teknik Tekstil, commented:
“We aim to be a part of the sustainable transformation. That’s why we have developed the Newipe next-generation viscose fabric. With the neXline wetlace CP line from Andritz we are setting new benchmarks on the market and securing our position as one of the industry leaders in wipes production.”
Lotus Teknik Tekstil is a leading nonwoven roll goods producer and a member of a group of four companies that operate end-to-end manufacturing including nonwovens, cardboard packaging, plastics, and finished wet wipe products.
Billerud AB has ordered a flue gas treatment system for its Gruvön mill from Andritz.
The system will enable the mill to increase the output of its soda recovery boiler while at the same time reducing emissions. The recovered soda is reused in the pulp manufacturing process.
Andritz will supply an electrostatic precipitator (ESP) including switched integrated rectifier technology (SIR).
The new precipitator will be installed in addition to the two existing ESPs, enabling the Gruvön mill to increase the capacity of its soda recovery boiler by more
than 30 per cent while keeping particulate matter emissions to well below 15 mg/cubic metre. The system will mean that the mill will be able to continue to operate profitably while complying with the strict local environmental regulations. Hand over is scheduled for the second quarter of 2024. Billerud operates ten mills, of which six are in Sweden.
Estonian Cell’s aspen pulp mill in Kunda, Estonia, has extended its service agreement with Valmet to an additional five years.
“We are happy to continue our partnership. With support from Valmet, we continue to develop our processes to increase the production availability and efficiency,” says Rain Pärn, chief technical officer of AS Estonian Cell. The service agreement covers
continuous collaboration on spare parts, process evaluations and condition assessment of the mechanical equipment, as well as yearly shutdowns of the fibre line and baling line.
Estonian Cell, owned by the Austrian Heinzel Group, produces 190,000 tons of aspen pulp a year, which is used in the production of printing paper, cardboard, tissue paper and special-use paper.
Anew recovery boiler and turbine has been inaugurated at Metsä Board’s mill at Husum in Sweden.
At the ceremony in May were, among others, project partners and representatives of Örnsköldsvik municipality. Started up at the end of 2022, the technology has increased the mill’s bio-based energy production that raises the mill’s electricity self-sufficiency to more than 80 per cent.
The new boiler and turbine are part of a €380 million project, the second phase of which will be the replacement of the two current fibre lines with one new line.
Chief executive of Metsä Board, Mika Joukio commented: “The renewal will strengthen the Husum mill integrate’s role as an efficient and sustainable platform for the long-term development of paperboard production and is an important step towards our target of entirely fossil-free mills.”
The renewal involved replacing
two old recovery boilers and three turbines. “As the new recovery boiler is of a completely new generation, we have trained our staff extensively,” said Olov Winblad von Walter, vice president of Husum Pulp & Board mill.
The project also includes a new control room and office,
which will gather the operation and maintenance staff on the same floor. “This will enable us to establish new integrated ways of working between technicians, engineers, maintenance and operators,” Winblad von Walter added.
An investment programme is also under way at the Husum mill
Gascogne Papier in south west France has ordered a PrimeLine machine glazed (MG) paper production line from Andritz for its mill at Mimizan with start-up planned for 2025.
The paper machine will have a web width of 6.8 metres and a design speed of 1,300 metres per minute producing basis weights from 25 to 120 gsm, using 100 per cent softwood unbleached
kraft pulp. The machine’s width will make it the world’s widest MG paper machine and with a capacity of 125,000 tons per year it will set a new industry benchmark for uncoated MG papers.
The core of the MG machine will be the world’s largest PrimeDry Steel Yankee. With a diameter of 26 feet (7.9m) the Yankee will, it is said, enable energy-efficient
drying while providing excellent surface properties such as gloss and dimensional stability.
The Yankee will be manufactured and transported in sections and assembled at the customer’s site.
The Andritz MG line will replace three of the mill’s four paper machines. The main target of the investment is to establish a multi-grade production line,
to increase the annual capacity of folding boxboard by around 200,000 tonnes. The investment is expected to be completed in the fourth quarter of 2023.
The Husum mill is an integrated board and pulp mill producing folding boxboard, uncoated white kraftliner and bleached chemical pulp.
capable of producing more than 80 different grades of ribbed and unribbed paper.
Dominique Coutière, chief executive of Gascogne Papier, explains: “Investments of that scale are a big milestone for companies in our business. The selection of the right partner is a decisive success criterion. The experience and references in the MG sector as well as the customer-orientated approach of Andritz convinced us. We are really looking forward to a great partnership.”
Mondi is upgrading its Dynäs pulp and paper mill in Sweden to improve energy and production efficiency.
The project will also raise the overall environmental performance of the mill, says Mondi, positioning it well to continue meeting customer demand for sustainable paper and paper-based packaging.
Part of Mondi’s flexible packaging business, the Dynäs mill produces high-quality sack and speciality kraft papers, used for a variety of paper-based packaging for industrial and consumer industries.
Also part of the work is a new cooking plant and along with upgrades will also further reduce air and water emissions, and result in better wood utilisation at
the mill.
Roman Senecky, operations chief at Mondi Kraft Paper, said: “The modernisation programme at Dynäs represents a significant investment in the future of this well-established mill. By producing
sustainable sack and speciality kraft paper, we continue to contribute to our MAP2030 goals and meet customer demand with innovative solutions such as Advantage StretchWrap, an alternative to plastic film pallet
wrapping, and Advantage MF EcoComp, used for high-strength packaging like paper bags for wet organic household waste. The mill supplies paper across Europe and plays an important role in the local community.”
Chinese paper maker Shandong Renfeng is to equip its new PM13 fluting paper line with a rewinder supplied by A.Celli Paper.
The E-Wind P100 will be delivered to the paper maker’s Huantai City mill, in Shandong province in the fourth quarter of this year.
The rewinder is designed to process Jumbo rolls of 60-120 gsm fluting paper with a diameter of 3,800mm and width of 6,700 mm at a design speed of 2,500 metres per minute.
Song Diafeng, owner of Shandong Renfeng Special
Materials Co, commented: “We are very pleased to have chosen A.Celli’s rewinder: theirs is
undoubtedly first-rate technology. We hope that this project is the beginning of a long-term
cooperation between us.”
Established in 2006, Shandong
Renfeng Special Materials is mainly engaged in the R&D, production and sales of packaging paper, special paper, paper base and paper-like special materials for domestic and foreign markets. It has capacity for 300,000 tons of packaging paper and 100,000 tons of special materials, with annual sales of 2.1 billion yuan.
A similar rewinder is also being installed at Henan Longyuan Paper in China for its testliner line at Zhoukou in Henan province. It will be used to process jumbo rolls.
Liansheng Pulp & Paper
Co in China has ordered two debarking and chipping lines from Andritz for its new pulp mill being built at Zhangzhou in Fujian province. Startup is expected in the third quarter of 2024. The order follows others made late last year for the mill.
The order for the woodyard includes two debarking lines with rubber tire supported drums along with horizontallyfed HHQ-Chippers. The line has a capacity to process 300 cubic metres of hardwood solid-overbark per hour. Also included is a bark handling system with three BioCrusher BSX machines and
bark storage with two ParaScrew travelling screw reclaimers.
Liansheng Pulp and Paper,
founded in 2020, is a new forest, pulp and paper integrated production base being built by
Tissue has had its digital control system modernised by A.Celli during planned downtime on the PM1 line at its Wetherill Park mill near Sydney.
The stopping to change the press and felt and the installation of a new Quality Control System (QCS) provided an opportunity to carry out other changes, including:
l The ‘virtualisation’ of the system, with the replacement of six physical PCs with a pair of redundant servers and virtual machines
l Replacement of two obsolete CPUs with a single latestgeneration CPU
l Integration of the new QCS system
l Preparation for communication between the PM1 and the upcoming PM2 which will also be supplied by A.Celli. The new system makes the plant ready for digitisation to Industry 4.0 standards, with the possibility of collecting data from the machines and sending them using Cloud technology for monitoring and optimisation purposes.
Commenting on the modernisation, Brandon Ly, director of ABC Paper Mills, said: “Since the beginning of our partnership in 2006 A.Celli has always provided strong support to us in our quest for continuous improvement. This is why we decided to rely on A.Celli both for the supply of the new PM2,
ITC Limited in India is having the PM1A board machine at its Bhadrachalam mill rebuilt by Valmet with start-up in the second quarter of 2024.
“ITC is the frontrunner in the Indian paper industry, applying the new technology to fulfill our customers’ needs,” said Vadiraj Kulkarni, divisional chief executive at ITC Limited. “The goal of the PM1A rebuild is to produce higher basis weight packaging grade for increasing the production to meet the future market demands. We selected Valmet as a supplier based on its proven technology and the previous projects executed successfully together
with them.”
The improvements will include an OptiFlo Fourdrinier headbox, modifications in the
Valmet is delivering a wash press to Holmen Paper AB’s Braviken mill in Sweden with start-up expected in April 2024.
The order includes TwinRoll washing press, electric motors, mechanical erection, basic engineering, commissioning, startup, process support and advisory services.
Holmen Paper’s production manager at Braviken, Fredrik Bragsjö, commented: “The TwinRoll wash press will improve the separation between the thermomechanical pulp (TMP) mill and the paper machine.
“With a better separation we believe the paper machine will get a cleaner system, resulting in
improved runnability and savings of chemicals, such as retention aid and similar chemicals. The good experience from the earlier installed TwinRoll wash press together with the possibility of common spare parts were also influencing our decision.”
forming section, an IQ Dryness Measurement, a press section rebuild, an IQ Steam Profiler and a coater section rebuild with an
OptiDry Coat and an IQ Induction Profiler.
After the rebuild, the PM1A will be capable of producing high quality solid bleached board (SBS), folding boxboard (FBB), art board grades (ART) and cup board (CUP) for consumer packaging with basis weights from 180 to 420 g/sqm. The wire width of the machine is 3,760 mm, and the machinery has been designed for a production speed at reel of up to 600 metres per minute.
When the PM1 was rebuilt in 2018, it was designed for 160,000 tons per year, and ITC Limited has been able to produce 200,000 tpy. After the rebuild, it will be able to produce 225,000 tpy.
Key technologies and automation systems for Henan Longyuan Paper’s new PM7 testliner line at its mill in Henan province in China have been ordered from Valmet. The order also includes a quality control system for the rebuild of the mill’s PM3 machine.
“The good cooperation with Valmet started with the headbox installation project for PM6,” said Yuzhou Wang, vice general manager of Henan Longyuan Paper.
“Valmet’s intelligent technology operating with low carbon emissions fits perfectly together with Henan
Longyan Paper’s efficient and environmentally-friendly concept, contributing to the local economy. We are looking forward to collaborating with Valmet again.”
The delivery includes a bottom dilution headbox and a Tri-nip press section and an automation package, including DNA machine controls (MCS), IQ Quality control system (QCS), dilution profiler for headbox, steam profiler, as well as Valmet services.
After the installation, PM7 will produce testliner products with a basis weight between 90-140 g/sqm and a design speed of 1,100 metres per minute.
Dongguan Jianhui
Paper in China has successfully started up a new mechanical pulping line supplied by Andritz including the world’s first TwinFlo Prime refiner.
The newly-developed TwinFlo Prime optimises the pulp flow to each refining zone by means of improved refining gap adjustment. This is said to reduce wear on the refiner plates and results in longer plate life and lower maintenance cost.
“We are very proud to be the first ones on the market with such innovative technology,” said Li Guihua, president of Dongguan Jianhui Paper. “With the TwinFlo Prime and the new mechanical pulping line from Andritz we have reached a very high level of flexibility both in
the use of raw materials and the fibre quality produced. This
will help us further expand our board business. The installation
perfectly meets our strategic targets.”
The pulping line, which has been installed at Dongguan Jianhui’s mill in Dongguan City, Guangdong Province, is based on Andritz ’s patented P-RC APMP process. At a design capacity of 600 tons per day, it processes eucalyptus wood chips for production of a range of top-quality board grades. The focus of the system is on chip impregnation and refining (HC and LC) with the highest production efficiency and welldeveloped fibres at low energy consumption.
Dongguan Jianhui Paper, founded in 2002, runs four paper making lines and specialises in the manufacturing of highquality white coated duplex board with gray back and test liner.
Following its entry to the tissue industry in 2021, MG TEC Industry in Romania has started up a second Andritz tissue line at its Dej mill.
Dorin Mocan, chief executive of MG TEC Industry, commented: “Energy-efficient production and perfect end-product quality: those were our key targets and together with Andritz we achieved them. I am proud to hold the first tissue in my hands now.”
The turnkey order included a PrimeLineCompact tissue
machine, a complete stock preparation system, pumps, automation, hall ventilation, and electrical systems.
The stock preparation system includes an approach flow system and broke handling. TwinFlo disc refiners lead to optimum development of fibre properties, and the ShortFlow concept enables fast grade changes and high flexibility. The 2.85m-wide tissue machine has a design speed of 1,900 metres per minute.
The start-up in November 2022 of the world’s largest kraftliner machine, SCA’s PM2 at the Obbola mill in Sweden was facilitated in part with commissioning training provided by Voith’s Papermaking Academy, and comprehensive documentation.
“A key factor to the successful start-up here in Obbola has been the training given to the employees,” says Lisa Lundström Hämälä, Process Engineer at SCA. “Voith prepared extensive
training materials, and Voith and SCA together made sure there were several occasions for each training so employees could attend while also running our old, now closed paper machine.”
With the Papermaking Academy, Voith offers target group-specific training programmes and courses that cover the entire life cycle of a paper machine and the plant’s components.
More information from: www. voith.com/papermakingacademy
Industry newcomer MG TEC starts up second tissue line
Start up of SCA’s new kraftliner machine speeded up by Voith trainingMing Xing, vice general manager at Dongguan Jianhui Paper Co (left) with Cui Ping, director of project and site management at Andritz (China) Ltd in front of the new TwinFlo Prime refiner
Norwegian manufacturer
Ranheim Paper & Board is having the dryer section of the PM5 at its paper mill near Trondheim in Norway rebuilt by Toscotec.
The PM5 line, which produces cardboard and solid board in the basis weight range from 220 to 540 gsm, will have its production capacity and efficiency improved when the project is completed in the third quarter of 2023.
The rebuild of PM5’s entire dryer section will have several phases. In the first phase Toscotec will supply new felt runs including stretcher and guide systems suitable for higher felt tensions, as well as some internal
felt loops to deliver improved cleanliness. The associated services include complete
erection with supervision, commissioning, and start-up assistance.
Winstone Pulp International is having a comprehensive twin wire press retrofit carried out by Andritz at its Karioi pulp mill in New Zealand.
The current Andritz twin wire press with a working width of 2m has been in operation since the mill opened in 1978. To improve the machine’s performance, reliability and safety, Andritz will replace the machine’s carbon steel frame with a stainless-steel version and modernise other machine components. The order was said to have been won on its ease of replacement.
The retrofit will leave the machine foundations and connections basically untouched. All installed rolls and bearings
will be reused, as well as the dewatering boards replaced by Andritz in 2019.
The press retrofit will include:
l a new cantilever system for easier and safer wire replacement
l a modernised headbox with modified outlet geometry for improved pulp sheet formation
l an upgraded drive section, and
l a new wire tensioning system Winstone Pulp International is
Øistein Vedahl, managing director of Ranheim Paper & Board, said: “This rebuild represents a strategic investment aimed to increase the production and efficiency of PM5. We selected Toscotec because we knew their ability to successfully manage rebuild projects, and we were impressed with their technical solution during the discussion of the project.”
With a history going back to 1884, the mill was renamed Ranheim Paper & Board after the restructuring in 2016 of Peterson Packaging group. With capacity for 120,000 tons per year of paper and 50 million square metres of solid board, it is owned now by Fundermax.
a privately-owned subsidiary of the Oregon Group and operates two sites: the Karioi Pulpmill and Tangiwai Sawmill. The Karioi pulp mill produces 220,000 admt of high-yield bleached chemical thermomechanical pulp.
Steve Murphy has rejoined Monadnock Paper Mills as director of supply chain and logistics.
Murphy has a long history with the US-based manufacturer of technical speciality and premium printing and packaging papers. He joined the company in January 1988 as an hourly employee and rose to the position of paper machine tender. In early 1997, he was promoted to the position of maintenance purchasing and stockroom manager.
Steve left Monadnock in 2007 to pursue his education and a career progression
As part of a new strategy to accelerate growth across the UK-based James Cropper Group and drive future growth through innovation, Patrick Willink has been appointed to the new position of chief innovation officer.
Willink will lead a Centre for Innovation at James Cropper, bringing a wealth of experience to this role, as former paper operations director, group chief technology officer, and most recently managing director of Colourform, James Cropper’s award-winning luxury packaging division.
with ENCON Evaporators in Hooksett, New Hampshire, during which he earned a bachelor of science degree. While attending college, he continued his career with ENCON, holding a range of positions from 2007 to 2023 including purchasing manager, operations and production manager, and supply chain manager.
“We are fortunate to welcome Steve to our leadership team,” said chief executive Richard Verney. “He consistently performed beyond expectations in positions of increasing responsibility during his tenure at ENCON. His skills in planning,
management and communications will serve Monadnock well in today’s challenging business climate.”
Micaela Thorström has been appointed as executive vice president, legal and general counsel and a member of the group leadership team at Stora Enso.
Thorström joined Stora Enso in 2015 as legal counsel and was appointed vice president of group legal in April 2022. Before joining Stora Enso, she held several senior-level positions at companies and law firms in Finland such as PricewaterhouseCoopers, Hannes Snellman, Lindholm Wallgren Attorneys and Roschier.
For more than 20 years, Thorström has gained extensive experience in the areas of corporate governance, finance-related legal advice, mergers and acquisitions and capital markets.
“I am delighted to appoint Micaela as our general counsel and welcome her to our group leadership team. Micaela’s experience and proven skills will make an important contribution in navigating the compliance and regulatory aspects of accelerating Stora Enso’s growth strategy. I want to express my gratitude to Christian Swartling for his excellent work as acting general counsel during the search for a new general counsel,” said Annica Bresky, chief executive at Stora Enso.
Commenting on her appointment, Thorström said: “Stora Enso’s legal
team is a core function in enabling Stora Enso’s transformation journey towards a regenerative future and work towards our sustainability strategy. The legal team also has a key role in ensuring the conducting of the business in a sound and responsible manner aligned with our values Do What’s Right and ethical standards. I am excited to take on the opportunity to work as Stora Enso’s general counsel and as part of the Group Leadership Team drive this work and our values further.”
Evolving market demands require agility and efficiency for mills to deliver products on spec and on time. Trust ABB and our MES specifically designed for pulp and paper to help you deliver the best operational results. Our comprehensive and modular solution covers all the core MES functionalities across the value chain, helping you achieve new levels of operational efficiency.
Learn more: abb.com/pulpandpaper