

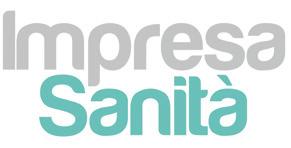
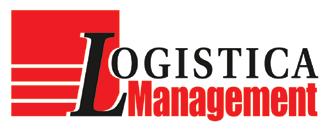
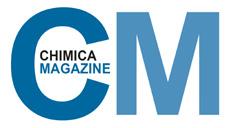

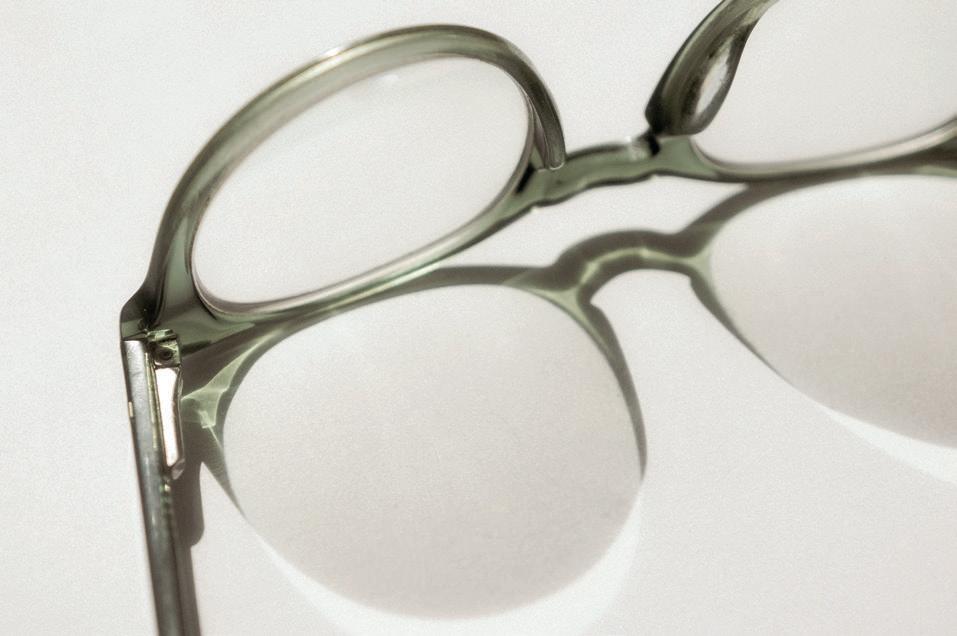
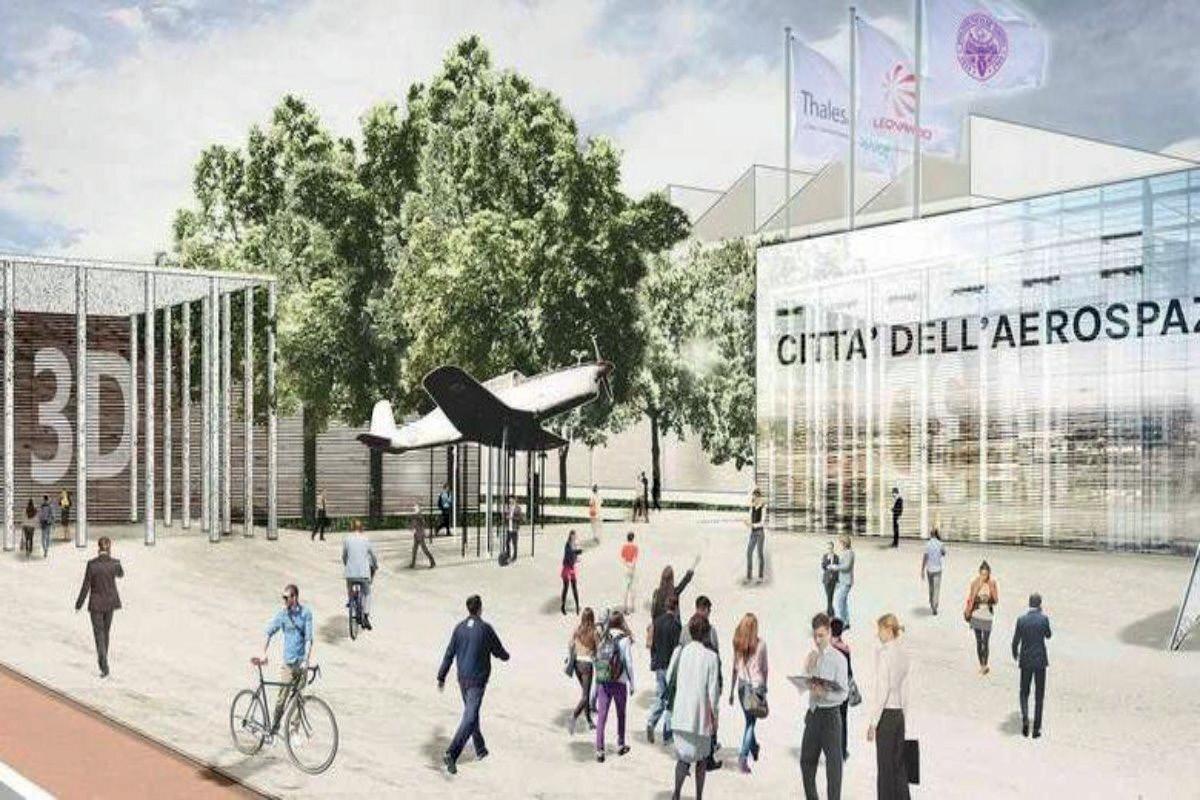
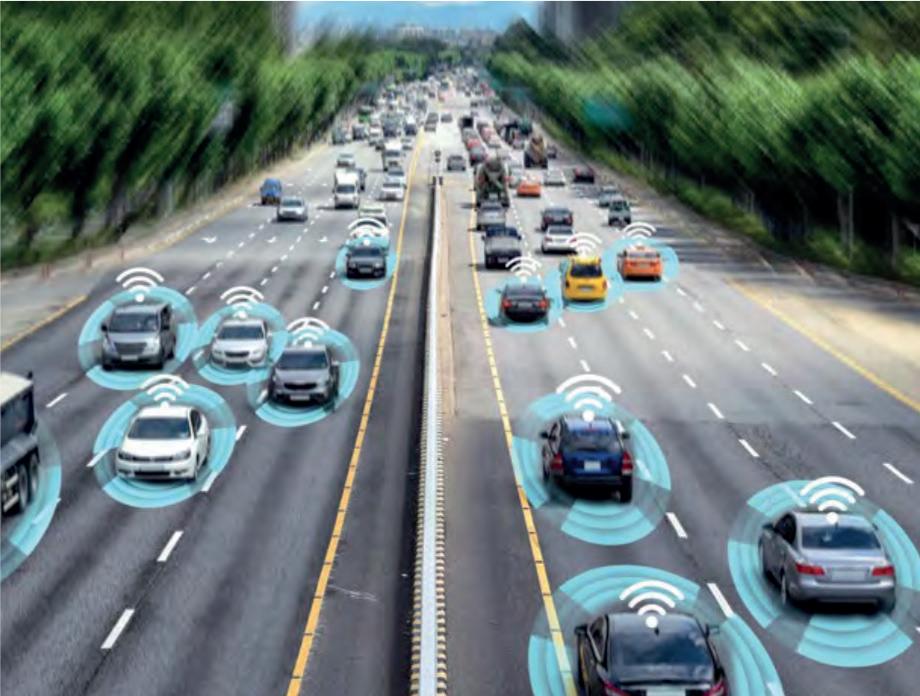
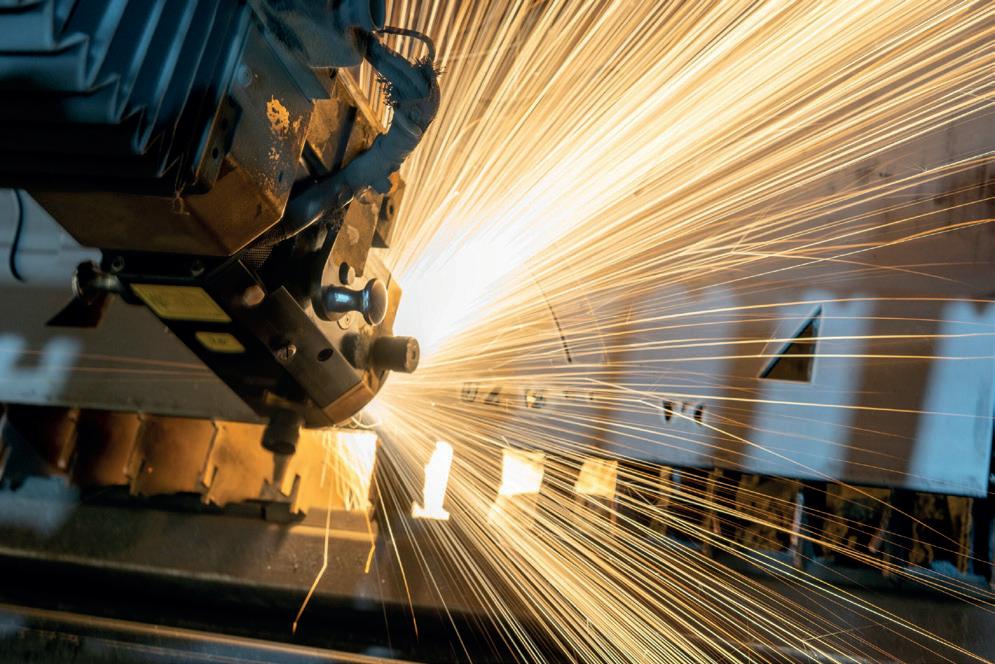
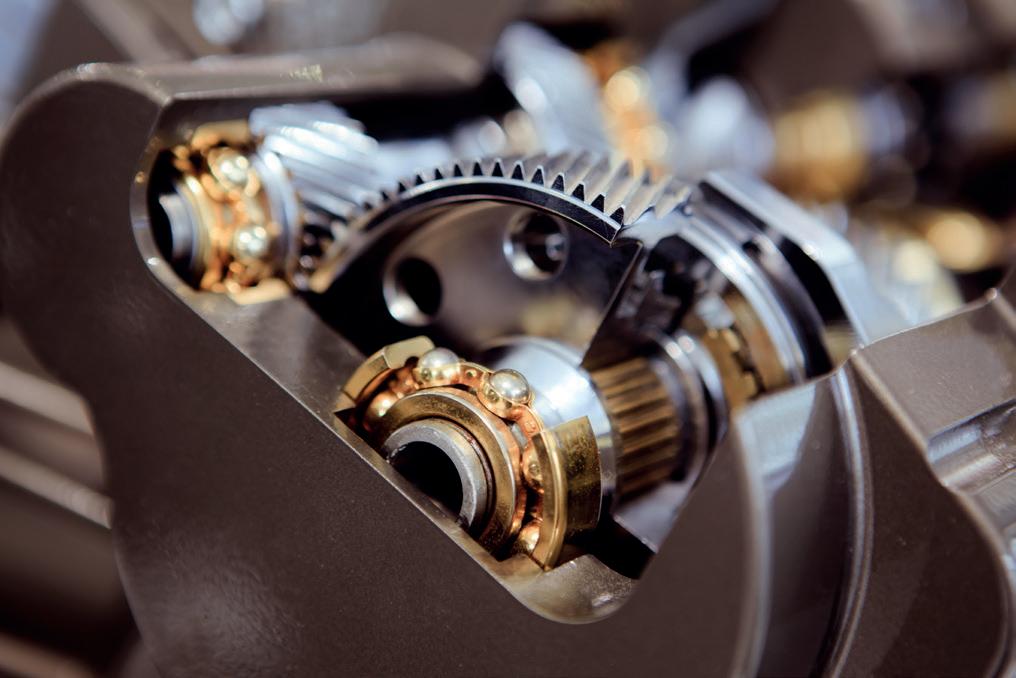
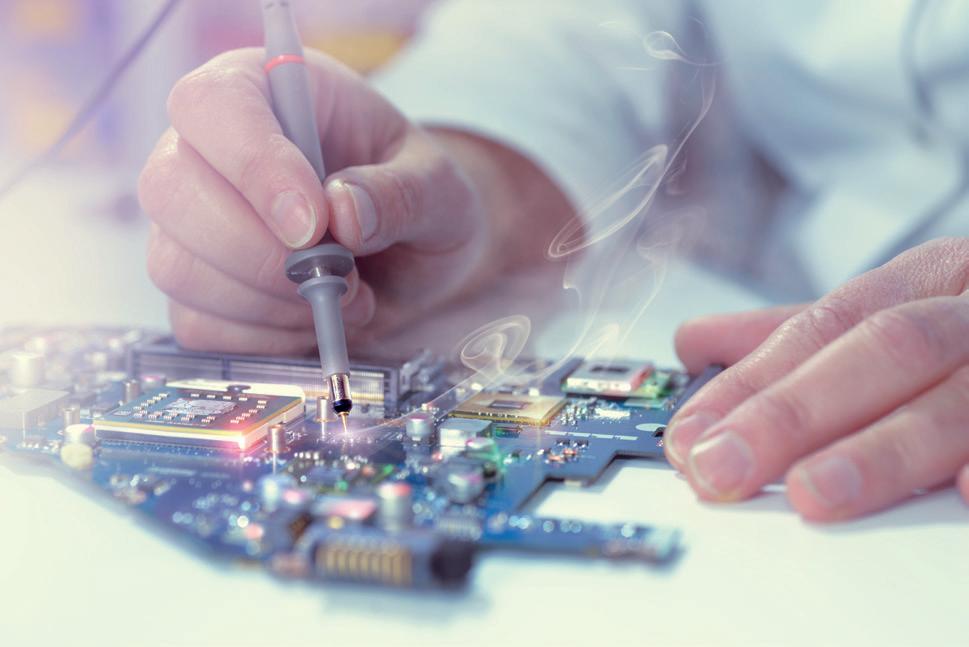
Ci avviciniamo al Natale e ai giorni di vacanza che questa festa porta con sé, che possono essere occasione per sottrarsi almeno temporaneamente dal turbine dell’attualità per dedicarsi a qualche ora di riflessione e approfondimento. Un classico di questo periodo è la scelta delle letture, per la quale voglio darvi qualche indicazione fra i libri che ci sono stati proposti negli ultimi mesi da autori o editori.
Cominciamo con l’industria farmaceutica, che viene approfondita dal volume “Impresa farmaceutica e organizzazioni”, di Leonardo Frezza, Managing partner di Frezza & Partners e Jefferson Wells Advisor, edito da Edizioni Edra. Il libro descrive nel dettaglio l’organizzazione e i processi su cui si fonda un’impresa farmaceutica: dal contesto alle strutture, dal capitale intellettuale a quello professionale, fotografando l’interno di un’impresa che opera nel mercato farmaceutico e life science.
Alla chimica, ma con un forte taglio divulgativo, è invece dedicato “La chimica nel monolocale”, di Stefano Cinti, professore associato in chimica analitica presso il Dipartimento di Farmacia dell’Università di Napoli Federico II, edito da tab edizioni. L’autore si propone di far capire anche a chi è digiuno di studi specifici che sotto ai nostri occhi avvengono continuamente reazioni chimiche e anzi che queste sono la base di tutti i processi, non solo di quelli sfruttati per la produzione o trasformazione industriale, ma anche di quelli domestici che a torto chiamiamo banali. La chimica riempie il nostro mondo e vale la pena di ricordarlo a tutti coloro che utilizzano la parola “chimico” per dire “cattivo” contrapposta a “naturale” per dire “buono”.
È dunque una questione di punti di vista e di approccio alla materia, che ci avvicina anche al titolo successivo:
“Conversazioni sul change management - Assochange, 18 anni di passione evolutiva”, scritto da Moira Masper, Presidente di Assochange, e da Giorgio Vizioli, giornalista e comunicatore, responsabile dell’ufficio stampa di Assochange fin dalla sua fondazione oltre che autore e collaboratore anche per le pagine di Chimica Magazine. Assochange si propone come luogo di confronto, approfondimento e buone pratiche sul Change Management; il libro ne intende scattare una fotografia completa, attraverso le persone e i progetti che ne hanno tracciato la storia.
Ultimo suggerimento per le letture invernali, è “Procurement rievolution. Perché il Chief Procurement Officer è oggi una delle funzioni più strategiche per l’azienda”, di Lorenzo Zacchetti, giornalista, e Fabio Zonta, Group Chief Procurement Officer di Engineering Ingegneria Informatica Spa, edito da Franco Angeli. Secondo l’autore, la crisi degli approvvigionamenti non deriva solo da un’effettiva carenza di componenti o materie prime, o si può interamente ascrivere ai gravi fenomeni geopolitici in corso, bensì si deve affrontare e risolvere attraverso una profonda revisione dell’organizzazione manageriale, capace di dare spazio a funzioni come quella del procurement, del risk manager, del supply chain manager o dell’AI manager.
Sono solo alcuni spunti che vi proponiamo come occasioni di riflessione, per ripartire a gennaio 2023 pronti per affrontare le sfide che il futuro vorrà riservarci, e possibilmente, con le armi che ci consentiranno di trasformarle in nuove opportunità di crescita. Il mio augurio sincero è che queste, come tutte quelle si spendono normalmente nei giorni di Natale, non siano solo parole.
Cecilia BiondiNasce un nuovo centro di competenza per l’implementazione delle tecnologie e servizi additivi: Weaream Srl, che avrà sede in un’apposita struttura di nuova costruzione di circa 400 mq all’interno del campus AQM, e fornirà alle aziende nazionali ed europee e alle istituzioni pubbliche e private, le competenze specialistiche, i servizi ad alto valore aggiunto e le soluzioni concrete per operare al più alto livello qualitativo e concorrenziale sul mercato internazionale della manifattura 4.0, sfruttando al meglio la sinergia offerta dalle tecnologie additive (metal additive manufacturing, in primis), dai nuovi materiali e dalla reingegnerizzazione funzionale di prodotti, processi e filiere produttive. I cinque soci fondatori di Weaream Srl rappresentano l’intera filiera della manifattura additiva, con forte integrazione verticale tra nuovi materiali (F3nice, Seamthesis), simulazione di processo-prodotto e generative design (Seamthesis), tecnologia produttiva per l’industria 4.0 e innovative stampanti 3D a filo (Buffoli Industries), applicazioni avanzate di prodotto AM in ambito oil&gas ed energia (Valland), all’interno della più ampia e strutturata competenza tecnico-scientifica di Seamthesis in ambito manifattura additiva e metallurgia delle polveri, coniugata all’esperienza di AQM nell’ambito della caratterizzazione avanzata e validazione di materiali, prodotti metallici e processi di fabbricazione in ambito metallurgico. I soci nella foto, da sinistra: Matteo Vanazzi di F3Nice (cofondatore e CTO di Weaream), Francesco Buffoli di Buffoli Industries (Azionista e CEO di Weaream), Paolo Folgarait (Presidente e CEO di Weaream), Gabriele Ceselin, CEO e GM di AQM, Giacomo Mondora di Valland (Azionista di Weaream).
Eventi fieristici sempre più sostenibili per Italian Exhibition Group (IEG) che, tra le prime società del settore a livello europeo, è riuscita ad aggiungere la certificazione ISO 20121 ai suoi numerosi primati in campo ambientale, sicurezza, tutela della salute e sostenibilità. IEG infatti ha certificato i quartieri fieristici di Rimini, Vicenza e l’organizzazione di Ecomondo, da 25 anni salone europeo per l’economia circolare, e a inizio 2023 l’iter riguarderà anche il Palacongressi di Rimini. Percorso di sostenibilità ambientale che parte da lontano, dal giorno di inaugurazione del nuovo quartiere fieristico, nel 2001. A partire dal prestigioso riconoscimento internazionale Elca, Edilizia Verde di Norimberga, IEG ha poi ottenuto la certificazione ISO 14001 Ambiente, la ISO 450001 salute e sicurezza sul lavoro, il GBAC Star Global Biorisk Advisory Council. Per il complesso iter di certificazione, IEG ha scelto di avvalersi della consulenza e delle competenze del Gruppo Hera, che ha fornito il proprio supporto sui vari aspetti documentali, gestionali, organizzativi e operativi, per completare sotto i profili di sostenibilità ambientale, economica e sociale, il quadro necessario ad ottenere la ISO 20121.
Ottimizzare la produzione energetica degli impianti fotovoltaici per accrescere le rese e ridurre le perdite grazie all’intelligenza artificiale. È quanto realizzeranno ENEA e TeaTek nel progetto MARTA (MARTA Monitoraggio e gestione Avanzata in Rete di impianTi FotovoltAici), che conta su un finanziamento di 4,6 milioni di euro del Ministero delle Imprese e del Made in Italy nell’ambito degli accordi per l’innovazione. Il progetto, unico nel suo genere a livello nazionale, prevede la realizzazione di una piattaforma informatica di monitoraggio e gestione di impianti fotovoltaici flessibile e scalabile da parte di ENEA e di TeaTek spa, gruppo internazionale specializzato in impianti fotovoltaici. Verranno inoltre realizzati specifici dispositivi IoT da applicare ai pannelli, le cui informazioni consentiranno lo sviluppo di algoritmi innovativi di intelligenza artificiale finalizzati ad assicurare la massima produzione energetica e a evitare le perdite che possono arrivare a superare anche il 40%.
I destinatari di questa piattaforma saranno principalmente i gestori di grandi impianti, ma sarà accessibile anche da comunità energetiche rinnovabili (CER) e, attraverso una semplice app gratuita, da singoli cittadini titolari di piccoli impianti.
COD.9003T
COD.5100
COD.5500
5500. Texlon® piattine soffici autoadesive. Guarnizione automodellante a nastro in 100% PTFE non sinterizzato espanso soffice e flessibile. La piattina Texlon® resiste a prodotti chimici ad eccezione di sostanze alcaline ed è abitualmente fornita con una pellicola biadesiva che ne facilita l’applicazione. Texlon® è inoltre approvato “TA Luft “ in base al metodo TÜV e VDI 2440 e soddisfa i requisiti TÜV-Testing Standard MUC-KSP-A 0066. 5100. Semi-lavorati in PTFE. Nella categoria semilavorati rientrano tondi, barre, tubi, nastri, rondelle e manicotti in PTFE. Gli stessi possono essere caricati (nel processo di lavorazione con la polvere di PTFE viene inserita una percentuale di specifici componenti) vetro, grafite, rame, bronzo, molibdeno, carbone. 9003T. Taglierina per guarnizioni. È un dispositivo per la realizzazione di guarnizioni con diametri compresi tra 80 mm e 1250 mm. Si possono realizzare guarnizioni circolari su misura. Si può tagliare qualsiasi materiale per guarnizioni: quelli esenti amianto, grafite, gomma, PTFE, pvc, cartone e cuoio.
Texpack® srl - unipersonale
Via Galileo Galilei, 24 25030 Adro (BS) Italia
Tel. +39 030 7480168 - Fax +39 030 7480201 info@texpack.it - www.texpack.it
IMPIANTI RichiedeteDal miglioramento della gestione dei processi all’efficientamento energetico, dalle nuove opzioni di manutenzione alla possibilità di raccogliere dati a più livelli e per più obiettivi, anche all’interno di nuovi software di intelligenza artificiale e machine learning. Il senso dell’innovazione nell’industria manifatturiera e nell’industria di processo coincide con un obiettivo di progresso e innovazione che queste industrie interpretano da sempre, e apre ai loro fornitori scenari sempre nuovi di business e opportunità applicative, con il ricorso a soluzioni quali automazione e robotica, IoT, additive manufacturing, IA, tecnologie predittive e così via. Questo tema sarà sviluppato nello speciale di questo mese, con alcuni esempi pratici o soluzioni implementate che danno la misura dell’evoluzione in atto nel mondo industriale.
Per approfondire questi temi, la redazione di Chimica Magazine ha anche in programma la partecipazione alla Fiera A&T – Automation & Testing (www.aetevent.com), un appuntamento specificatamente dedicato a innovazione, tecnologie, affidabilità e competenze 4.0.
Due gli incontri previsti nel 2023: il primo all’inizio del prossimo anno, dal 22 al 24 febbraio, presso l’Oval Lingotto di Torino, mentre il secondo è l’edizione Nord Est, ideata per dare risposta alle aziende della zona e in programma a Vicenza dal 25 al 27 ottobre 2023. In entrambi i casi l’appuntamento si compone di una parte espositiva, che mette in mostra le tecnologie di ultima generazione legate all’Industria 4.0, e parte una convegnistica di elevata qualità, con sei focus contenutistici in particolare: smart manufacturing, testing e metrologia, logistica, additive manufacturing, controllo produzione e controllo di processo. Da sottolineare infine il Premio Innovazione 4.0, che punta a far emergere i casi applicativi più rilevanti nel percorso di innovazione condotto dalle aziende del settore, ai quali la rivista Chimica Magazine intende dare visibilità nelle varie uscite previste nel corso del 2023. Un denso programma di diffusione e condivisione delle informazioni, del quale lo speciale del mese intende darvi solo un primo assaggio. Buona lettura.
Parlando di industria, una corretta gestione delle operazioni, oltre che del business in generale, richiede che si agisca specificatamente sulla sicurezza, sull’affidabilità e sull’efficienza, e inoltre sulla flessibilità necessaria per potersi adat-
tare velocemente alle innovazioni richieste dal mercato. La tecnologia in questo caso offre una risposta tempestiva a queste esigenze: soprattutto se viene inquadrata in un approccio che ha la completa autonomia dei processi come obiettivo complessivo.
A proposito di industria smart, è interessante il criterio utilizzato da Honeywell per definire un viaggio attraverso cinque livelli di applicazione tecnologica, descritti in un white paper sul tema che l’azienda ha condiviso con noi.
Tali livelli, per i quali naturalmente Honeywell mette a disposizione la relativa tecnologia, traguardano una gestione dei processi sostanzialmente autonoma. Li vediamo riassunti nel modo seguente.
Livello 1: Operazioni controllate e ottimizzate. Viste come metodologie valide per l’intero ciclo di vita produttivo, tenute continuamente aggiornate incorporando i benefici delle più nuove tecnologie e servizi, ad esempio utilizzando connettività remota per il controllo del processo.
Livello 2: Operazioni intelligenti. Il termine digital twin (gemello digitale) è un concetto ben noto, ma la sua applicazione è ancora piuttosto parziale, in quanto limitata all’uso offline, nella progettazione o nel training dell’operatore. Il digital twin fa la vera differenza quando usato durante le operazioni, dove può essere applicato in vari modi, dalla replica del processo vero al suo modello euristico.
Livello 3: Operazioni remote. Dove la metodologia di esecuzione del progetto riesce ad abbracciarne l’esecuzione remota. Invece di avere dozzine di persone nelle località reali, il processo può essere eseguito in cloud. La tecnologia che Honeywell propone a tale scopo si chiama LEAP, acronimo di Lean Execution of Automation Projects.
Livello 4: Operazioni resilienti. Essere resilienti significa che il sistema continua ad operare in emergenza anche in presenza di guasti, cessati i quali torna alla normalità. Molto spesso, questo si verifica tramite contolli ridondanti, che si attivano durante il guasto e fino alla sua fine. In Honeywell questo si realizza nella più recente release di Experion HIVE (Highly Integrated Virtual Enviroment).
Livello 5: Operazioni autonome. L’autonomia industriale può oggi sembrare inverosimile per un impianto petrolchimico o una raffineria, ma vediamo di considerare alcuni esempi. Innanzitutto la maggior parte delle operazioni upstream lo sono: le pipeline ne sono l’esempio. Anche le celle solari o le pale eoliche. Ad un livello superiore lo sono anche le piattaforme offshore. Sono certo possibili, ed esistono oggi piattaforme senza presenza umana, ma, ove essa è ancora necessaria, i casi vanno continuamente limitati. A questo obiettivo è funzionale l’apparato tecnologico descritto.
L’autonomia industriale, e qui risiede l’aspetto più rilevante di questo nuovo approccio proposto da Honeywell, consente di conseguire un notevole incremento della sicurezza, dell’affidabilità e dell’efficienza richiesta dai processi. All’introduzione di questa metodologia sono poi connesse altre innovazioni nei processi aziendali, altrettanto funzionali al pieno successo del percorso. Per esempio, non è corretto pensare che la gestione di queste tecnologie rimanga in mano ad un gruppo ristretto di esperti. Per la sua trasversalità infatti questo percorso interessa tutta la struttura e dunque ciascuno dei suoi operatori, che avrà la possibilità di acquisire competenze specifiche su queste soluzioni. Proprio perché supportata da tecnologie di controllo, sensoristica e relative conoscenze, potrà produrre un cambio di direzione che si rifletterà su tutte le operazioni dell’impianto. Tendere all’obiettivo dell’autonomia operativa ha la sua validità nel percorso stesso, e ognuno degli step conseguiti comporterà i suoi benefici. L’industria autonoma è insomma un diverso modo per dire “digital transformation”, ma finalizzata all’utilizzo di tutte le tecnologie digitali oggi disponibili e alla loro implementazione diffusa, in modo che tutta l’azienda ne sia coinvolta e tutta l’azienda ne ricavi dei benefici. Non parliamo però di tecnologie avveniristiche o di fantascienza, bensì solo di qualcosa che si basa e porta avanti un discorso di innovazione che l’industria conosce da sempre. Si tratta solo di inquadrarlo in un approccio metodico, in grado di esprimerne tutto il valore.
L’industria autonoma è insomma un diverso modo per dire “digital transformation”, ma finalizzata all’utilizzo di tutte le tecnologie digitali oggi disponibili e alla loro implementazione diffusa
Le industrie sono i principali motori dell’economia e della prosperità nazionale, migliorare le loro prestazioni e l’efficienza contribuisce alla crescita economica. I produttori competono in termini di innovazione, tempi di risposta rapidi ai cambiamenti del mercato, prodotti affidabili e a basso costo per soddisfare le richieste dei consumatori finali, infine questa competizione ha portato alla produzione intelligente, alla digitalizzazione dei processi e al controllo cyber-fisico negli impianti di produzione per gli sbocchi commerciali. La maggior parte dei Paesi ha già introdotto da qualche anno le proprie politiche per incentivare lo sviluppo di sistemi cyber-fisici e di fabbricazione digitale per il futuro della produzione. La Germania ha da tempo presentato la quarta rivoluzione industriale chiamata “Industria 4.0” che utilizza fondamentalmente sistemi di lavorazione interconnessi che interagiscono tra loro per la pianificazione della produzione, la programmazione degli impianti, la personalizzazione dei prodotti, la produzione flessibile, l’identificazione e il ripristino dei guasti.
Il concetto può essere visto come la forma integrata di Internet delle cose (IoT), sistemi cyber-fisici (CPS), produzione digitale, tecnologie di produzione intelligenti, produzione additiva, comunicazioni mobili 5G, tecnologie robotiche, elaborazione dei big data, analisi dei dati, integrazione dei sistemi, simulazione e sistemi di produzione flessibili.
Con Smart Manufacturing System (SMS) si intende la digitalizzazione di ogni parte del sistema produttivo
La Cina ha annunciato il piano denominato “Made in China 2025” e il programma Internet plus, per portare le industrie manifatturiere a un livello superiore di efficienza e produttività.
Programmi simili sono stati implementati anche in Giappone con “Society 5.0” e negli Stati Uniti con “Industrial Internet Consortium”. L’evoluzione dei sistemi di produzione distribuiti, che sostituiscono le classiche modalità di controllo gerarchico, è essenziale per realizzare una produzione intelligente che sia in grado di affrontare la crescente personalizzazione, le improvvise fluttuazioni della catena di fornitura e sia adatto a lotti di produzione più piccoli. Le industrie manifatturiere di recente sviluppo, che impiegano tecnologie intelligenti nativamente, hanno una produttività maggiore del 17-20%, grazie a un migliore utilizzo delle macchine e all’ottimizzazione dell’uso dell’energia da parte dei sistemi di produzione intelligenti.
L’interesse dell’automazione dei processi nasce dalla necessità di ridurre al minimo l’interferenza umana nei sistemi per evitare rischi per la salute dei lavoratori e aumentare la produttività. I vantaggi di questa scelta sono ravvisabili nell’aumento della produttività e della qualità, una maggiore accuratezza, il risparmio dei costi dei materiali e dell’energia. Nel manifatturiero l’automazione si è evoluta dall’uso di sistemi idraulici e pneumatici di base ai moderni robot, mentre il sistema di automazione basato su reti wireless viene adottato in diversi tipi di sistemi e l’uso dell’IoT in essi è volto a facilitarne il funzionamento. L’uso di Internet nei sistemi di controllo è stato inizialmente introdotto per i vantaggi che esso offriva nel telerilevamento, nel controllo a distanza, nei sistemi di acquisizione dati più semplici e nella flessibilità del sistema di automazione sviluppato nelle industrie e nei sistemi energetici e di potenza. Il concetto di Internet of Things offre un ampio campo di applicazione e tecnologie emergenti, può essere implementato in vari sistemi per semplificarne il funzionamento e ridurre l’intervento umano nel controllo automatizzato con un’infrastruttura di rete globale. Il concetto di produzione intelligente, così come le micro-reti, le reti intelligenti, i sistemi di misurazione avanzati, i sistemi centralizzati di dispacciamento e controllo del carico, l’automazione del sistema di distribuzione ecc. utilizzano le caratteristiche dell’IoT.
Con Smart Manufacturing System (SMS) si intende la digitalizzazione di ogni parte del sistema produttivo con interoperabilità, controllo e monitoraggio in tempo reale, produzione flessibile, risposta rapida ai cambiamenti del mercato, sensori avanzati e big data analytics con una maggiore produttività. L’SMS opera in due modalità: semi-autonoma e completamente autonoma. Nel sistema semi-autonomo, l’ingegnere di produzione definisce gli obiettivi e imposta i parametri del sistema. In un sistema completamente automatico, l’SMS stesso definisce i parametri operativi ottimali e viene implementato automaticamente a tutte le unità di produzione interconnesse. Per il produttore, operando in un mercato competitivo le sfide principali sono quelle di avere una gestione efficiente dei costi, una produzione ottimale che riesca a garantire la
Examples of relevant products from chemistry and advanced materials industry
Drones Photovoltaic (PV)
Wind energy Smartphones and tablets
Flexible displays (e.g. wearable devices. VR TVs)
High-speed internet
More efficient and smaller integrated circuits
Annual sales of electric vehicles 2020: 4.9 million
Market size for drones* 2015: $10.1 billion 2020: $14.9 billion
Installed PV capacity worldwide 2015: c. 245 GW 2020: > 500 GW
Installed wind power 2015: 413 GW 2020: 712 GW
Mobile devices in use 2015: 8.6 billion 2020: 12.1 billion
Market for AMOLED** displays 2016: $2 billion 2020: $18 billion
Fixed broadband speed 2015: 24.7 Mbps 2020: 47.7 Mbos
Processor logic gate length 2015: 14mm 2019: 7mm
qualità e la flessibilità nella personalizzazione del prodotto, con tempi di consegna certi. Pertanto, la capacità di qualsiasi sistema di produzione di mantenere e migliorare continuamente le prestazioni, utilizzando come fattori di cambiamento le informazioni e l’ambiente è un fattore competitivo da non sottovalutare. Esiste un gran numero di tecnologie sviluppate per creare un sistema intelligente, la scelta potrebbe essere uno dei problemi principali per convertire un sistema esistente in smart manufacturing system. Esistono alcune strategie per effettuare la scelta; il Supply Chain Readiness Level, la Manufacturing Enterprise Solutions Association (MESA) e Manufacturing Transformation Strategy (basata sui metodi ISA-95) sono strategie comuni. Non utilizzano le informazioni e le comunicazioni come base primaria, ma si concentrano sulla singola tecnologia o sul sistema di esecuzione della produzione, inoltre le tecnologie informatiche devono essere utilizzate per valutare e passare a un sistema intelligente.
I diversi servizi dell’industria possono essere convertiti in servizi intelligenti, che collegano i processi aziendali con una gestione efficiente dei dati e dei processi del sistema.
Plastics, composites and battery technologies
Plastics, composites and battery technologies
Perovskites, crystalline silicon and thinfilm technology
Wind turbine coatings, foams and silicones
Substrate, backplane, transparent conductor, barrier films and photoresists
Substrate, backplane, transparent conductor. barrier films and photoresists
Ultrapure glassis chlorosilane
Dielectrics, colloidal silica, photo resists, yield enhancers, and edae-bead removers
Il concetto di industria 4.0, inteso come rivoluzione tecnologica nei sistemi di automazione industriale, è stato introdotto per identificare una nuova generazione di sistemi di automazione industriale robotizzati, definiti anche come sistemi cyber-fisici o IoT, la cui architettura è fondamentalmente suddivisa in quattro livelli. Il primo livello comprende sensori e attuatori che sono integrati nell’hardware per raccogliere le informazioni. Successivamente, si ha il livello di rete, per la trasmissione dei dati raccolti dai sensori alle unità di controllo e da queste ultime agli attuatori. Per accedere ai servizi basati sulle esigenze dell’utente e per interagire con le unità di controllo, vengono definiti il livello di servizio e il livello interfaccia. Le informazioni provenienti dal sistema fisico vengono raccolte attraverso l’uso di sensori e di diversi strumenti di apprendimento automatico. Queste informazioni sono poi gestite sistematicamente ed elaborate dai dispositivi intelligenti. Le informazioni elaborate vengono inviate al livello applicativo attraverso la rete, per l’implementazione nei rispettivi campi. La tecnologia di produzione intelligente è il risultato collaborativo dell’informatica, delle tecnologie relative alla produzione industriale e della creatività umana, che
ha portato a una rapida rivoluzione del sistema di produzione. Il Current Standards landscape for Smart Manufacturing Systems pubblicato dal National Institute of Standards and Technology (NIST) nel febbraio 2016, il German Standardization Roadmap Industry 4.0 pubblicato dalla Commissione tedesca per le tecnologie elettriche, elettroniche e dell’informazione di DIN e VDE nel 2015, il National Smart Manufacturing Standards Architecture Construction Guidance pubblicato dal Ministero dell’Industria e dell’Information technology cinese (MIIT) e dalla Standardization Administration of China (SAC) nel 2015 sono le principali norme pubblicate per l’implementazione di un sistema di smart manufacturing in varie parti del mondo. Oltre a queste, anche l’International Electrotechnical Commission (IEC), l’International Society of Automation (ISA), l’International Standards Organization (ISO) e l’American National Standards Institute (ANSI) hanno pubblicato norme su diversi aspetti del sistema di produzione intelligente.
I sistemi di produzione intelligente sono in grado di far fronte a diverse sfide e complessità affrontate dalle industrie esistenti, ma esistono ancora alcune problematiche che sorgono durante la loro implementazione. Si ritiene che i sistemi di smart manufacturing debbano affrontare problemi di sicurezza, mancanza di integrazione, mancanza di ritorno degli investimenti nella nuova tecnologia e problemi finanziari durante la realizzazione di nuovi sistemi intelligenti o durante l’aggiornamento delle industrie esistenti con la tecnologia smart manufacturing. Per sistema di produzione intelligente si intende l’uso di un sistema di rete integrato in un sistema di produzione per la condivisione di informazioni tra le unità di produzione o di lavorazione e i clienti finali. La condivisione di informazioni attraverso Internet richiede la sicurezza dei dati e delle informazioni in vari punti del sistema, con un’identificazione univoca globale e una crittografia dei dati end-to-end. Pertanto, ogni nodo della rete deve essere protetto da attacchi esterni e dall’uso improprio dei dati quindi, uno degli aspetti più importanti da considerare durante la progettazione di sistemi in rete, è quello di garantire la sicurezza del sistema stesso e del processo nel suo complesso.
Un’altra sfida dell’implementazione di un sistema smart manufacturing è l’integrazione delle nuove apparecchiature tecnologiche con quelle esistenti. La compatibilità dei dispositivi esistenti, con quelli più avanzati tecnologicamente, può causare diversi problemi nell’installazione dei dispositivi per aggiornare il sistema produttivo. I vecchi macchinari controllati da alcuni protocolli di comunicazione potrebbero essere obsoleti e i nuovi dispositivi potrebbero avere un protocollo differente. Inoltre, la comunicazione da macchina a macchina e l’interconnessione del sistema richiedono un sistema di comunicazione di ultima generazione, per supportare tutti i dispositivi connessi allo stesso tempo (il tasso di adozione del protocollo IPv6, secondo Google, a novembre 2022 è del 72,5% in Francia, 65,7% in Germania, 34.7% in Portogallo, del 7,5% in Italia, 3,1% in Spagna). L’interoperabilità è la capacità di diversi sistemi di comprendere e accedere alle rispettive funzioni in modo indipendente, questa caratteristica supporta lo scambio di dati e informazioni tra di essi, indipendentemente dal produttore del loro hardware o software.
La condivisione di informazioni attraverso Internet richiede la sicurezza dei dati e delle informazioni in vari punti del sistema
Senza un’adeguata corrispondenza dei protocolli e degli standard di comunicazione, la caratteristica dell’interoperabilità non può essere raggiunta in modo efficiente. Le differenze tra larghezza di banda di comunicazione, frequenza operativa, modalità di comunicazione, capacità hardware determinano i limiti dell’interoperabilità del sistema. Durante l’implementazione del sistema cyberfisico o dei sistemi robotici industriali si deve prestare la massima attenzione a ridurre al minimo qualsiasi tipo di rischio meccanico, elettrico, termico, di rumore, di vibrazioni, di radiazioni, di rilascio di sostanze nell’ambiente di lavoro. Ad esempio sono le problematiche poste dal cobot, o collaborative robot, un particolare tipo di robot che può interagire in modo sicuro e fisico con gli esseri umani nello spazio di lavoro e può collaborare introducendo nuovi paradigmi di interazione uomo-macchina. La Federazione internazionale di robotica definisce la collaborazione uomo-robot come la capacità del robot di coordinarsi con i lavoratori nell’ambiente industriale per eseguire compiti specializzati. Le considerazioni principali devono riguardare la salute e la sicurezza sul lavoro del personale che lavora nel sito, evitando qualsiasi ambiente pericoloso e mantenendo la necessaria salute e sicurezza. I sistemi di
smart manufacturing devono gestire operazioni multilingue, essi devono essere in grado di interpretare qualsiasi istruzione data in linguaggio umano nel linguaggio macchina, per istruire la macchina per l’operazione desiderata. Per rendere realistico il termine smart manufacturing, per implementare l’intelligenza artificiale e le tecnologie avanzate, nei sistemi di produzione, questi dovrebbero essere in grado di ricevere le istruzioni direttamente dall’operatore, sia in formato vocale che testuale.
Infine, quando si passa a una tecnologia più avanzata rispetto a un sistema di produzione esistente, l’analisi finanziaria e il ritorno dell’investimento devono essere analizzati molto attentamente. L’investimento aggiuntivo, che dovrebbe essere effettuato per adottare una tecnologia più recente viene confrontato con le perdite di produzione durante l’aggiornamento, così il tempo necessario per recuperare il ritorno dell’investimento con il reddito del sistema esistente influenza l’adattamento di una tecnologia più recente.
Le potenzialità di quella che possiamo chiamare rivoluzione digitale nell’industria chimica sono molto interessanti. Essa avrà un impatto significativo, con il potenziale di cambiare le catene del valore, portare a una maggiore produttività e innovazione e creare nuovi canali di accesso al mercato. I modelli operativi delle aziende chimiche si stanno rimodellando influenzati da tre tendenze; i massicci progressi della tecnologia e dell’innovazione, la rapida evoluzione delle esigenze dei clienti e la crescente pressione sui costi e sulla produttività. Tali tendenze sconvolgono i vecchi modelli portando un cambiamento delle strategie e delle tattiche, inclusa la trasformazione digitale completa.
La maggior parte degli impianti chimici genera continuamente un’enorme quantità di dati, ma ne scarta la maggior parte. Le aziende dovrebbero invece raccogliere i dati e interpretarli
I processi aziendali delle aziende chimiche, tra cui la produzione, il marketing e le vendite e R&S, presentano opportunità di miglioramento delle prestazioni basate sull’acquisizione e l’interpretazione dei dati. L’eccellenza funzionale ha generato significativi miglioramenti della produttività negli ultimi due decenni, la transizione al digitale fornirà i mezzi per sbloccare un nuovo livello di aumento della produttività. La produzione rappresenta una delle aree con maggiore opportunità, questo riguarda tutti i segmenti dell’industria, dal petrolchimico ai pesticidi. La maggior parte degli impianti chimici genera continuamente un’enorme quantità di dati, ma ne scarta la maggior parte. Le aziende dovrebbero invece raccogliere i dati e interpretarli per scoprire come ottenere rendimenti e produttività più elevati, consumi energetici inferiori e una manutenzione più efficace. Per molte di esse, si tratta di risultati potenzialmente facili da ottenere utilizzando i sistemi informatici e di controllo dei processi esistenti, mentre quelle che ampliano i tipi di dati raccolti possono essere in grado di ottenere ulteriori vantaggi. Il contributo ai profitti può essere sostanziale, si potrebbe riuscire ad aumentare la produzione di un impianto di alcuni punti percentuali senza effettuare alcun investimento di capitale, o a generare un risparmio sui costi. Per molti sottosettori dell’industria chimica, questa opportunità si estende oltre la produzione all’intera catena di fornitura.
Le analisi avanzate renderanno possibili previsioni più accurate, con conseguenti miglioramenti nell’intero processo di pianificazione delle vendite e delle operazioni. Ciò consentirà anche una migliore programmazione della produzione in lotti, tempi di consegna più brevi e scorte di sicurezza più basse, con un livello di flessibilità più elevato.
Sono almeno tre le modalità con cui il digitale influenzerà l’industria chimica. La prima è l’utilizzo di approcci abilitati dal digitale per migliorare i processi aziendali. La seconda è il potenziale del digitale di influenzare i modelli di domanda nei mercati finali, con implicazioni per le catene del valore dell’industria. Il terzo è quello in cui gli sviluppi digitali portano a cambiamenti nei modelli di business, attraverso i quali le aziende chimiche catturano e creano valore per i clienti.
La digitalizzazione offre anche significative opportunità nella ricerca e sviluppo, per creare prodotti a più alto valore aggiunto e con margini più elevati a un ritmo più veloce, in particolare nei prodotti chimici speciali e nei prodotti per la protezione delle colture. Le aziende saranno in grado di utilizzare l’ottimizzazione high-throughput per sviluppare e regolare le molecole che offrono più valore, saranno inoltre in grado di impiegare analisi avanzate e apprendimento automatico per simulare esperimenti, utilizzare il potere predittivo del digitale per ottimizzare
OECD eChemPortal
Pharma Innovation Platform Singapore
eChemPortal is a free depository of properties of compounds, including ecotoxicity and human toxicity data.
PIPS is a public-private consortium involving MSD, Syngenta, Pfizer, GSK as core members; it has initiated a number of projects towards achieving full digitalisation of process development and manufacturing
iDMT is a business support initiative by AstraZeneca, Shionogi and the University of Cambridge to support small and medium size enterprises (SMEs) in digitalisation of chemistry R&D
Public consortia towards open
Several public consortia aimed at creating open chemistry data tools to enable ML/Al-based research in chemistry
https://echemportal.org
https://a-star.edu.sg/pips
Source: Transition to sustainable chemistry through digitalization. Chem Vol. 7, Issue
sistematicamente le formulazioni in termini di prestazioni e costi, sfruttare le informazioni disponibili da esperimenti passati riusciti e falliti. Molte di queste pratiche sono già consolidate nell’industria farmaceutica, ma erano in gran parte inaccessibili per le aziende chimiche. Con l’emergere di una potenza di calcolo poco costosa, su scala massiccia, questa situazione è destinata a cambiare. I cambiamenti causati dal digitale hanno il potenziale per modificare alcune, se non la maggior parte, delle catene del valore e dei mercati finali serviti dai produttori di sostanze chimiche, e questo a sua volta potrebbe portare a cambiamenti nei modelli di domanda. Ad esempio, il digitale è alla base dei progressi nello sviluppo delle auto a guida autonoma, ma le conseguenze per i produttori chimici potrebbero non essere immediatamente evidenti. Un effetto inaspettato sulla domanda di prodotti chimici deriva dalla maggiore sicurezza stradale promessa dalla guida autonoma, con una riduzione degli incidenti è probabile che la domanda di rivestimenti per carrozzeria diminuisca drasticamente, con conseguenze importanti per i produttori di questa componente e per le aziende chimiche che producono ingredienti per i rivestimenti.
La migrazione del commercio verso le piattaforme online potrebbe influire sulla domanda di prodotti. Ad esempio,
https://idmt.online
https://nfdi4chem.de, https://docs.openreaction-database.org
i generi alimentari vengono acquistati sempre più spesso tramite piattaforme online e i consumatori prendono la decisione di acquisto senza vedere il prodotto fisico, con possibili effetti per gli imballaggi, che sono uno dei principali mercati di sbocco dell’industria petrolchimica e delle materie plastiche. Poiché l’aspetto e la sensazione del packaging diventerebbero meno importanti nel determinare una decisione di acquisto, ciò potrebbe provocare cambiamenti nel settore. Mentre l’importanza degli imballaggi decorativi diminuirebbe, gli aspetti più funzionali del design potrebbero guadagnare importanza, come ad esempio quelli studiati appositamente per essere funzionali a essere stoccati in un furgone per le consegne o che includono un meccanismo di raffreddamento per prevenire il deterioramento durante la consegna. Anche in questo caso, tali tendenze potrebbero interessare un numero significativo di aziende che vendono nella catena del valore dell’imballaggio, con una possibile perdita di attività per alcune e nuove opportunità per altre.
Infine, un’altra area abilitata dal digitale che sta aprendo opportunità per la domanda di prodotti chimici è la stampa 3D, detta anche produzione additiva. Il mercato dei polimeri e dei prodotti chimici utilizzati nella produzione additiva è in forte crescita. Lo sviluppo di polimeri econo-
mici e ad alte prestazioni per la stampa 3D sta guidando la crescita del mercato dei polimeri per la fabbricazione additiva. L’Acrilonitrile Butadiene Stirene (ABS) è una plastica forte e resistente. L’acido polilattico (PLA), invece, è un polimero biodegradabile che possiede una maggiore resistenza e, pertanto, la sua forma di filamento viene utilizzata principalmente per i processi DLP (Digital Light Processing) e SL (Stereolitografia). Poiché la domanda industriale di stampa 3D sta aumentando rapidamente, diversi attori che operano nel mercato della produzione additiva hanno iniziato a sviluppare polimeri avanzati.
Probabilmente, nel corso del prossimo decennio, la transizione al digitale cambierà le modalità di vendita e distribuzione dei prodotti chimici e, di conseguenza, il flusso di valore. Si assisterà a un passaggio dalla vendita di prodotti alla vendita di servizi e soluzioni e potranno emergere soggetti che disintermedieranno i produttori dai loro clienti, come è accaduto con le piattaforme B2C in altri settori. I diversi segmenti dell’industria avranno risposte diverse a queste domande: in linea generale, mentre i prodotti chimici per la protezione delle colture e alcuni segmenti chimici speciali sono a rischio di interruzione del modello di business e alcuni distributori chimici si considerano potenziali attori di possibili disintermediazioni, i prodotti petrolchimici saranno probabilmente meno colpiti. I modelli di business che rimangono collegati al prodotto in uso potrebbero fornire un’opportunità sostanziale in alcuni settori, ad esempio attraverso sistemi che monitorano le ap-
Le aziende che hanno adottano per prime le nuove tecnologie, concentrandosi sulle innovazioni digitali e ottimizzando i processi aziendali a emergendo e sono vincenti. Ripensando la propria strategia e le proprie operazioni, le aziende hanno sfruttato le nuove tecnologie digitali per trasformare e ottenere ottimi risultati, come accelerare l’innovazione portando un nuovo livello di analisi e collaborazione con ricerca e sviluppo, hanno ridefinito la loro proposta di valore ai clienti (quale valore le aziende chimiche forniscono e vendono ai clienti) grazie all’IoT e al digitale in tempo reale, che rilevano e integrano i modelli di consumo.
plicazioni chimiche nei processi industriali. Suscita molto interesse il modello performance pay, invece di vendere semplicemente il prodotto permette al produttore di ottimizzare il processo produttivo dei suoi clienti con un servizio a pagamento, e offre l’opportunità di costruire una base di conoscenze ampia e preziosa che può essere utilizzata per migliorarne l’uso, un esempio è il mercato dei catalizzatori negli Stati Uniti. Diversi modelli di questo tipo sono in fase di sviluppo da oltre un decennio in alcuni settori dell’industria e vi è il potenziale per un’accelerazione della loro adozione legata al digitale. Tali approcci non saranno applicabili a tutta la chimica, l’attenzione è rivolta soprattutto ai casi in cui una specialità chimica svolge un compito particolare, come un catalizzatore o una sostanza chimica per il trattamento delle acque.
In secondo luogo, sembrano emergere opportunità per modelli di business basati sulla proprietà intellettuale, che generano diritti di licenza o di consulenza. Secondo questo modello, un’azienda potrebbe richiedere un compenso per fornire indicazioni su come utilizzare al meglio il proprio prodotto, oppure potrebbe concedere la produzione di una molecola proprietaria a un altro produttore. In terzo luogo, stanno emergendo modelli di servizio basati su dati e analisi in segmenti mirati. In agricoltura, un’azienda potrebbe combinare dati geologici, meteorologici e geospaziali con la sua conoscenza di sementi, fertilizzanti e composti per la protezione delle colture e, invece di vendere questi input, potrebbe chiedere un pagamento basato sulla resa o sul profitto ottenuto dal coltivatore. Altri segmenti dell’industria chimica che hanno una forte componente B2C nel loro sistema commerciale potrebbero trovarsi di fronte a uno sviluppo simile.
D’altra parte, una serie di modelli che stanno ricevendo un’attenzione sostanziale in altri settori è molto meno probabile che abbiano un impatto sulla maggior parte dell’industria chimica. La creazione di piattaforme come canali, che collegano terze parti, è ben consolidata in molti altri settori. Ma potrebbe essere difficile da realizzare nell’ambiente chimico, dove il numero di fornitori è limitato, i loro nomi sono noti ai potenziali clienti e molti produttori chimici dispongono di un know-how proprietario che non sono disposti a condividere. Tuttavia, ci sono maggiori possibilità che tali modelli si affermino in segmenti più frammentati, con molti produttori che gestiscono i loro impianti con tassi di utilizzo insufficienti e che hanno urgente bisogno di movimentare i prodotti per incrementare i ricavi delle vendite,
quindi molto interessati a nuovi canali. Il numero e il volume limitato di prodotti venduti ai clienti più piccoli solitamente non sono sufficienti a giustificare il tempo che gli esperti di applicazioni chimiche dedicano a soddisfare le esigenze dei clienti. Oggi, tuttavia, le soluzioni possono essere digitalizzate e migliorate continuamente grazie all’apprendimento automatico, a patto che i fornitori abbiano accesso ai dati degli utenti. Da lì, le piattaforme digitali possono aggregare i dati delle applicazioni.
Le aziende chimiche devono decidere attentamente quando e con quali prodotti entrare in una piattaforma, se mai lo faranno. In generale, i prodotti standard sono più adatti a piattaforme aperte di fornitori multipli, in grado di soddisfare in modo rapido ed efficiente le esigenze dei clienti che hanno familiarità con tali prodotti. Esempi di questi prodotti sono le materie plastiche standard e i prodotti industriali standard, come acidi, pigmenti e solventi, inoltre, i prezzi di questi prodotti sono spesso più trasparenti, poiché i clienti li conoscono già. Per costruire una piattaforma digitale di successo, le aziende devono innanzitutto capire quali sono le esigenze dei clienti esistenti e identificare i problemi che la piattaforma risolverà. Gli operatori del settore chimico devono comprendere gli investimenti necessari e le metriche di successo per costruire una piattaforma digitale. Questa impresa può essere costosa e richiede un impegno totale da parte di tutta l’organizzazione. Sono fondamentali anche le ca-
pacità analitiche avanzate, l’integrazione di algoritmi di next product to buy che offrono prodotti adatti ai singoli clienti sarà un passo fondamentale, così come la possibilità per i clienti di ricercare i risultati che si vogliono ottenere piuttosto che l’input, o i requisiti specifici delle proprietà tecniche. Il digitale nell’industria chimica rappresenta un’opportunità molto importante, ma le aziende hanno bisogno di una strategia per avere successo in questo nuovo scenario che si sta delineando. I cambiamenti stanno iniziando a verificarsi a un ritmo senza precedenti, ma l’impatto è disomogeneo e l’incertezza è notevole.
La strategia è l’arte di fare scelte difficilmente reversibili in anticipo di fronte all’incertezza, per creare know how e profitto, pertanto per le aziende è necessario sviluppare chiare strategie digitali basate sulla comprensione di dove e come si verificheranno gli impatti nel loro settore. È necessario riconoscere che le aziende sono su una linea sottile e che devono mantenere il giusto equilibrio; si tratta di un territorio nuovo e rischioso, con un’alta possibilità di commettere errori, ma agire rapidamente e correggere la rotta se necessario rappresenta un rischio molto più basso che essere troppo esigenti e rimanere indietro. Al momento è ancora difficile affermare che un’azienda chimica si sia ritagliata un vantaggio competitivo significativo grazie al digitale, ma è probabile che le cose cambino e che ciò avvenga nel corso dei prossimi anni.
Con il termine Smart Factory si identifica il nuovo modello per la predisposizione degli impianti produttivi che utilizza l’intelligenza digitale su tutti i processi industriali. L’obiettivo è quello di ottimizzare i layout produttivi, la comunicazione (e interoperabilità) fra macchine, impianti, flussi logistici e intralogistici e rendere i processi molto più flessibili ed efficienti. Pertanto, attraverso sistemi gestionali ERP, MES e WMS vengono monitorati e scambiati dati e informazioni tra macchine e sistemi. Sono proprio i dati che rappresentano la vera sfida, ossia quella di riuscire a raccoglierli e analizzarli in modo da poterli sfruttare per efficientare la produzione.
Il processo di digitalizzazione va ad integrare e armonizzare tutti i componenti dell’impianto con lo scopo di orchestrare le tecnologie di campo verso i sistemi gestionali. All’interno di un impianto industriale, possono essere presenti sistemi RFID, beacon BLE, barcode, Electronic Shelf Label (ESL), mobile e wearable device, ma anche robot mobili AMR, dispositivi di picking elettronico e altri dispositivi IoT. La presenza di questi dispositivi produce (e richiede) una notevole quantità di dati, il cui flusso deve essere ordinato in modo preciso, puntuale e bidirezionale
verso i sistemi gestionali. Oramai siamo nell’era della omnicanalità e sempre più spesso le aziende che digitalizzano i processi fanno uso di piattaforme cloud in alternativa a sistemi proprietari. Pensiamo, ad esempio, alla diffusione delle web app: la non implicazione attiva degli ambienti cloud limiterebbe i risultati, avrebbe maggiori costi di sistema e andrebbe a penalizzare potenzialità e performance oltre che impedirne lo sviluppo.
Nonostante dalla digitalizzazione dei processi si ottengano molteplici benefici, c’è tuttavia una parte più complessa che comporta alcune problematiche, tra le quali l’indirizzo dei dati, una volta acquisiti, verso i sistemi gestionali, rendendoli fruibili. Nella maggior parte dei casi, le aziende scelgono di utilizzare un sistema gestionale compreso fra i tre o quattro più quotati. Questi sistemi possono avere difficoltà nel ricevere dati dai dispositivi in campo oppure, al contrario, non essere in grado di ritrasmetterli pur avendoli ricevuti. A questo punto occorre mettere in collegamento le tecnologie sul campo (sensori, ecc.) direttamente con il sistema gestionale per creare una comunicazione bidirezionale che trasferisca informazioni e segnali.
Per raggiungere questo obiettivo è necessaria una piattaforma, conosciuta anche come Orchestrator che consente l’orchestrazione tra i sistemi informatici che vengono utilizzati, come ad esempio ERP, WMS, MES, e tutta la serie di tecnologie e sistemi installati sul campo. La piattaforma di orchestrazione è il “cuore” di tutto il sistema perché deve gestire in modo coerente ogni informazione proveniente dalla produzione come anche dalla logistica: dai dati relativi alla progettazione, i contenuti del sistema gestionale, fino ad arrivare a quelli raccolti in tempo reale direttamente dalle linee di produzione oppure da robot mobili AMR. Il software di orchestrazione monitora e gestisce tutte queste informazioni con l’obiettivo di migliorare tutti i processi attraverso il controllo di ogni singola fase operativa in relazione ai dati raccolti.
Per fare un esempio pratico, in un flusso produttivo ipotetico vi è tutta una serie di dispositivi che raccolgono e inviano informazioni: - tag RFID per l’identificazione dei materiali;
- mobile device come palmari per la ricezione e/o invio di informazioni;
- etichette elettroniche (ESL); - dispositivi per il picking (ad esempio pick to light); - altri dispositivi IoT; - robot mobili; - PLC; - sistemi di yard management.
Immaginiamo quindi una rete a stella i cui rami sono formati dai sistemi gestionali, i dispositivi sopracitati, un eventuale cloud e altri sistemi per l’analisi dei dati acquisiti o anche la blockchain per l’autenticazione dei processi o dei prodotti. Al centro della rete c’è la piattaforma di orchestrazione, la quale riceve, gestisce, invia le informazioni da e per i rami della rete. Va inoltre considerato che i connettori per lo scambio dati verso i sistemi informatici si basano (o si possono basare) su tecnologie Web service, DBMS, file systems, tabelle di frontiera, OPC UA, MQTT, GPRC (Google Remote Procedure Code), Bus di campo. Con questo tipo di impostazione la rete può essere implementata con altri rami, a seconda delle specifiche esigenze, ottenendo così il completo controllo di qua -
lunque scenario all’interno della fabbrica. Ad esempio, grazie alla comunicazione in tempo reale dei dispositivi di picking, è possibile ottimizzare la gestione delle scorte e predisporre con precisione il riassortimento (o il mantenimento) del materiale e ciò può essere fatto in relazione ad un certo tipo di prodotto che dovrà essere realizzato. Per fare un altro esempio, si può implementare un sistema di manutenzione predittiva attraverso i digital twin, come anche gestire una flotta di robot mobili massimizzandone il rendimento.
Bisogna infine tenere conto che sistemi come quello descritto richiedono un elevato livello di protezione dei dati, pertanto l’ambito della cyber sicurezza è un tema estremamente importante per la digitalizzazione. Le piattaforme di orchestrazione devono essere in grado di essere certificate per garantire la protezione dei dati sensibili. Ogni dispositivo potrebbe rappresentare una zona scoperta e vulnerabile diventando la backdoor per pericolose intrusioni.
Un interessante esempio applicativo dell’interazione fra sistemi di identificazione e software di orchestrazione è quello di un impianto per la gestione e rigenerazione delle bombole di gas tecnico, destinate agli impianti industriali e alle strutture ospedaliere. L’impianto prevede l’intero flusso di carico e scarico delle bombole, dall’arrivo dei vuoti alla riconsegna al cliente finale, passando per le fasi di rigenerazione. L’applicazione, sviluppata da FasThink, si avvale di sistemi di identificazione vocale, label RFID, PLC e la piattaforma Connect Orchestrator che interagisce con il sistema gestionale in uso presso l’azienda.
Tutte le bombole di gas sono dotate di un codice numerico. Una volta che le bombole vuote arrivano presso l’impianto di rigenerazione, un operatore attraverso un sistema vocale legge il codice numerico impresso sulla bombola. Il sistema riconosce il codice che viene automaticamente inserito nel sistema gestionale e in contemporanea su una label RFID on metal applicata sulla bombola stessa. Da questo momento la bombola segue tutto il processo di rigenerazione che prevede sabbiatura, verniciatura, riempimento, immagazzinaggio e riconsegna al cliente. Tutte le bombole sono tracciate con precisione in qualunque momento, in modo da ottenere la situazione in tempo reale dell’intero processo. La particolarità di questo impianto è che sono state utilizzate diverse tecnologie quali RFID, sistema vocale e la connessione di PLC provenienti da differenti operatori di automazione industriale. Attraverso un’unica piattaforma Connect Orchestrator è stato possibile comunicare con il sistema gestionale, sebbene installato in una sede al di fuori dell’impianto. Inoltre, la digitalizzazione del sistema ha consentito di ottimizzare via via i processi, grazie alla gestione dei dati attraverso soluzioni di data analytics e intelligenza artificiale.
Come noto, per la produzione della Fiat 500 elettrica, il nuovo veicolo con una veste evoluta e contenuti ancora più tecnologici, che segue lo storico modello strettamente concatenato alla motorizzazione del Paese dal lontano 1957, FCA (Fiat Chrysler Automobiles) ha scelto di attrezzare lo storico stabilimento Mirafiori. Un progetto importante di automazione e smart factory al quale ha collaborato CPM SpA, parte del gruppo Dürr, che in particolare si è occupata di ridefinire il nuovo layout dell’impianto di carrozzatura per l’assemblaggio del veicolo.
La sfida prevedeva non solo il recupero dello stabilimento Mirafiori, in quanto impianto considerato “culla” della storia automobilistica italiana, luogo che, nonostante i cambiamenti progressivi e l’adozione di tecnologie innovative per lo sviluppo di modelli sempre più all’avanguardia, preserva quella tradizione e quella storicità uniche e caratterizzanti nel contesto internazionale; ma anche di realizzare un nuovo layout flessibile e scalabile, che fosse in grado di consentire il passaggio dalla produzione di un modello ICE, ossia a combustione tradizionale (es: Alfa Romeo MITO) a uno full electric (appunto Fiat 500 BEV).
Il progetto di carrozzatura è stato gestito da CPM in modalità turnkey e ha previsto la fornitura di:
- un’ampia area dedicata alle preparazioni meccaniche, dove vengono allestiti i cosiddetti “pallet” (grandi supporti piani su cui vengono posizionati quei gruppi, come il motore elettrico, le sospensioni, la batteria, ecc., che andranno poi montati sulla vettura);
- Light Deck, ossia un impianto di carrozzatura (detto anche “mariage”, il cuore di qualunque fabbrica di automobili), in questo caso specifico progettato per le medie produzioni (circa 30 vetture all’ora), che è dove la scocca, finalmente abbinata alle sue parti meccaniche, diventa Fiat Nuova 500 elettrica;
- un loop di ProFleet, ovvero una flotta di AGV (Automated Guided Vehicle) di nuova concezione.
Si tratta praticamente di veicoli a guida autonoma che, spostandosi tra l’area delle preparazioni meccaniche e il Light Deck, si occupano di caricare le parti meccaniche della vettura, di scaricarle sulle linee di preparazione, di permetterne le operazioni di assemblaggio ed infine di trasferirle alla linea di carrozzatura. Queste tecnologie in combinazione tra loro costituiscono un concetto di produzione altamente innovativo, estremamente flessibile e destinato a rivoluzionare il tradizionale concetto di linea di montaggio per l’Automotive. Ed è proprio ProFleet che ha visto la collaborazione proattiva tra CPM e SEW-Eurodrive.
Questo veicolo a guida autonoma è volto a trasformare un impianto di General Assembly in un impianto mol-
flessibile, quindi è più veloce da rimodulare, ampliare o anche spostare, all’occorrenza, per un maggiore vantaggio competitivo nel mercato. Diventa più facile aumentare o diminuire le unità/ora da produrre, così come utilizzare lo stesso impianto anche per segmenti di vetture diversi. In caso di malfunzionamento, inoltre, un AGV può essere escluso dalla produzione, mentre un altro prende il suo posto durante la sua riparazione. In questo modo i tempi dei fermi produttivi vengono ridotti al minimo. Le navette richiedono inoltre pochi e semplici interventi di manutenzione.
CPM e SEW-Eurodrive hanno lavorato insieme alla progettazione e allo sviluppo degli AGV a induzione ProFleet e realizzato una tecnologia estremamente innovativa. In particolare questi AGV sono equipaggiati con: un PLC con piattaforma software AGV Basic, un pacchetto software che permette la configurazione e la programmazione del veicolo; azionamenti e motorizzazioni CMP per la gestione del moto del veicolo tramite differenziale elettronico e gestione degli altri asservimenti motorizzati; PLC di sicurezza per garantire la movimentazione in totale sicurezza del veicolo; HMI interfaccia uomo-macchina per la visualizzazione dello stato del veicolo; Movitrans, con due pick-up da 1,5 kW ciascuno.
Queste tecnologie costituiscono un concetto di produzione innovativo, flessibile e destinato a rivoluzionare il tradizionale concetto di linea di montaggio per l’Automotive
to più innovativo e flessibile rispetto ad un impianto tradizionale. La flotta di ProFleet sostituisce infatti il concetto di line feeding classico, molto più rigido e vincolante dal punto di vista strutturale e delle opere civili, e al contempo garantisce un altissimo livello di sicurezza.
Gli AGV ProFleet si integrano infatti nel modello Industria 4.0, che utilizza tecnologie sempre più intelligenti per rendere più efficiente la produzione, ma anche per alleggerire i carichi di lavoro e demandare alle macchine le operazioni più ripetitive.
La raccolta e l’elaborazione dei dati generati dagli impianti durante la produzione permettono di intervenire tempestivamente in caso di necessità, evitare fermi produttivi, razionalizzare i consumi e scandire correttamente le attività di manutenzione, evitando sprechi e spese inutili a vantaggio della produttività. Lo stabilimento è così
La parte stazionaria invece è composta da quattro sistemi Movitrans completi, tre da 16 Kw e uno da 4 Kw per la baia di ispezione; e per la gestione delle linee da PLC DHE21B per ogni cabina Movitrans. Il tracciato induttivo in totale è lungo 220 m e consente il caricamento delle batterie senza prevedere il fermo del veicolo.
In totale i ProFleet installati a Mirafiori sono dodici e sono AGV a induzione (inductive guidance). Ogni ProFleet, lungo 3,370 mm e largo 970 mm, nella parte superiore è dotato di un sistema che permette il trasferimento del pallet dalle linee di preparazioni meccaniche al Light Deck; un sistema pneumatico di bloccaggio pallet ne permette un’operatività in sicurezza. Ogni ProFleet ha un’accelerazione / decelerazione di 0,3 m/s2, una velocità massima di 30 m/1’ (500 mm/sec). ProFleet rispetta le esigenze più restrittive in materia di ergonomia e sicurezza.
Marchesini Group progetta e produce una vasta gamma di macchine e linee di confezionamento per rispondere a qualsiasi tipo di richiesta, standard o straordinaria, dell’industria farmaceutica e della cosmetica. Così ciascuno di essi è diverso da ogni altro per layout operativo, dimensione dei prodotti da
manipolare, fasi di lavorazione, ecc. Ogni impianto è quindi un unicum progettato e costruito ad hoc che va montato, provato e collaudato in fabbrica qui in Italia prima di essere smontato, imballato e spedito al cliente, che spesso è all’estero. Perciò è necessario che il tecnico della filiale Marchesini di riferimento venga nella sede italiana per assistere e partecipare alle operazioni di assemblaggio e funzionamento, in modo da poterle replica-
re nello stabilimento del cliente. È quindi fondamentale che i tecnici responsabili del montaggio e dell’assistenza alle linee abbiano una elevata competenza non solo su tutte le tipologie di impianto e sulle più comuni problematiche, ma anche sugli specifici impianti che si troveranno poi a gestire. Perciò durante il loro percorso professionale ricevono più volte un’adeguata formazione, sia presso la sede locale sia in Italia. Un’altra soluzione è far lavorare stabilmente i tecnici italiani nelle filiali estere in modo che possano formare “da vicino” i dipendenti locali e trasferire loro il know-how e le competenze necessarie.
Nonostante tutto questo, però, accade che ci siano situazioni che il personale locale non riesca a risolvere ed è quindi indispensabile richiedere l’intervento di un tecnico senior che risiede in Italia. «Fino a qualche tempo fa» racconta Mirko Ballo, Customer Care Director di Marchesini Group «questo significava lunghe telefonate, scambio di immagini e video, spiegazioni rese difficoltose dalla differenza di lingua e dalla specificità della terminologia e delle operazioni da svolgere (controlli, regolazioni) che in molti casi non portavano alla soluzione del problema, con conseguente necessità di mandare un tecnico senior direttamente sul campo per trovare la causa e rimettere in funzione l’impianto». Con conseguenze
facili da immaginare: costi e tempi elevati, oltre alla difficoltà di avere un sufficiente numero di tecnici senior da inviare laddove è necessario, in paesi sparsi ovunque nel mondo.
La ricerca di una soluzione a questa problematica ha portato l’azienda a prendere in considerazione gli strumenti che utilizzano la realtà aumentata, come smartphone e tablet, che però hanno il limite di non permetterne un utilizzo a mani libere, indispensabile per il lavoro di assistenza di apparecchiature come quelle prodotte da Marchesini Group.
Tramite Icona, il partner che ha fornito il software Acty per l’utilizzo degli smartglass, l’azienda si è orientata verso i Moverio di Epson: «Li abbiamo scelti» spiega Mirko Ballo «perché sono una soluzione affidabile che ci ha permesso di mettere a punto un servizio di assistenza remota assicurando una perfetta e completa operatività a mani libere». L’utilizzo della realtà aumentata ha consentito di lavorare costantemente, garantendo fermi macchina limitatissimi e risolti in tempi davvero brevi. Una scelta che si è rivelata fondamentale e ancor più vincente durante il lungo periodo di lockdown dovuto alla pandemia da Co-
Gli smartglass hanno permesso ai tecnici di andare ben oltre il tradizionale servizio di troubleshooting, consentendo anche attività di montaggio
ronavirus. «In questo periodo di piena emergenza sanitaria – conferma Mirko Ballo – dove non era possibile uscire per fornire assistenza sul posto, gli smartglass sono stati di fondamentale aiuto perché ci hanno permesso di continuare a dare supporto dal vivo a chi lavora da lontano, nostri tecnici o clienti, rivelandosi un servizio ancora più necessario e a valore aggiunto».
I vantaggi dei Moverio sono oggi ben conosciuti in Marchesini Group: dalla netta riduzione del tempo impiegato per risolvere un problema rispetto a quello richiesto per essere fisicamente sul posto, al conseguente minor fermo macchina e maggiore produttività. Non solo: con il lockdown, gli smartglass hanno permesso ai tecnici di andare ben oltre il tradizionale servizio di troubleshooting, consentendo anche attività di montaggio. «Durante questi mesi» continua Mirko Ballo «abbiamo effettuato più di sessanta interventi da remoto, garantendo alle aziende clienti una produttività ininterrotta. Tutto questo non sarebbe stato possibile in tempi di normale operatività perché è ancora molto radicata la mentalità di preferire il tecnico sul posto piuttosto che la tele assistenza. Il Coronavirus
dunque ha obbligato in toto l’uso di questa soluzione, che si è rivelata un servizio ancora più utile e performante perché ha permesso di gestire la situazione in modo trasparente, ma anche perché ha dimostrato a colleghi e clienti la validità della realtà aumentata e l’economicità del suo utilizzo».
Tanto è vero che oggi questo “pacchetto Acty-Moverio” è offerto a contratto a tutti i clienti e garantisce la teleassistenza attraverso due modalità: da una parte con la risoluzione di eventuali malfunzionamenti, dall’altra con l’intervento sul software da parte del tecnico in sede. Gli smartglass Espon usati da Marchesini sono i Moverio BT-350, un modello che fin da subito si è rivelato ergonomico e facile da usare. L’innovativa tecnologia di proiezione dei Moverio permette infatti la perfetta sovrapposizione dei contenuti in realtà aumentata alle immagini del mondo reale, consentendo una visione stereoscopica. Il risultato è un campo visivo dettagliato a schermo pieno. Inoltre, a livello di comfort questo modello può essere portato senza problemi anche sopra gli occhiali da vista, mentre i naselli assicurano una vestibilità perfetta e le aste regolabili garantiscono la massima comodità.
Un’accurata analisi del mercato è alla base del successo di idee innovative.
Ma quali sono le informazioni necessarie per lanciare un prodotto/servizio che apportino benefici concreti ai consumatori? CiaoTech PNO, società leader in Europa nella gestione dell’innovazione e nell’ottenimento di finanziamenti pubblici, ha sviluppato un approccio strutturato per condurre un’analisi strategica di settori innovativi:
- analisi degli stakeholder; - analisi di mercato.
Nell’ambito del progetto BIOBESTicide - BIO-Based pESTicides production for sustainable agriculture (GA 886776), CiaoTech - responsabile delle attività Exploitation & Dissemination, ha condotto una Technology Intelligence per favorire l’introduzione sul mercato di un nuovo biopesticida, efficiente in termini di costi, al fine di contrastare l’impatto delle malattie che colpiscono i vigneti con severe conseguenze per l’industria del vino. Il lavoro di CiaoTech ha permesso di identificare le principali tendenze e op -
portunità nel mercato europeo e globale per la protezione di piante e colture, individuando 254 stakeholder, di cui 111 end-users, attivi oggi nel settore dei biopesticidi: un risultato che faciliterà la commercializzazione del prodotto finale di BIOBESTicide.
Assicurati che la tua innovazione trovi i suoi clienti: affidati all’esperienza di CiaoTech per lo sviluppo di una strategia tarata sulle esigenze della tua azienda scrivendo a: infociaotech@ciaotech.com.
CiaoTech PNO
Via Napoleone Colajanni, 4 00191 Roma
www.biobesticide.eu - www.pnoconsultants.com infociaotech@ciaotech.com
Fondato nel 1922, Socomec è un gruppo industriale specializzato nella progettazione, produzione e assistenza di sistemi di continuità (UPS) e nelle soluzioni di energy storage destinate al settore delle energie rinnovabili. L’indipendenza del gruppo Socomec garantisce il controllo di tutto il processo decisionale, nel rispetto dei valori promossi dalla famiglia dei propri azionisti e condivisi anche dai dipendenti. Con circa trenta filiali distribuite in tutti e cinque i continenti, il Gruppo persegue lo sviluppo internazionale concentrandosi sulle applicazioni per i settori industriale e dei servizi, nei quali la qualità della sua esperienza fa la differenza.
Avendo progettato e adottato un sistema smart di manutenzione preventiva da remoto, l’azienda è stata una delle protagoniste degli incontri “Servitization Stories” organizzati da ASAP Service Management Forum dell’Università di Brescia, durante il quale ha illustrato il progetto di smart servitization dedicato agli UPS.
Socomec investe quasi il 10% del suo fatturato in Ricerca e Sviluppo. Questo consente al Gruppo di soddisfare la sua ambizione di essere sempre all’avanguardia dal punto di vista tecnologico e di migliorare costantemente i suoi settori di competenza in modo da offrire ai clienti soluzioni idonee e sempre più personalizzate.
Supportato da due centri di eccellenza europei (Francia e Italia), il Gruppo dispone anche di siti di produzione competitivi, ad esempio in Tunisia, e sedi dislocate nei principali mercati emergenti (India e Cina). Tutti questi siti sono stati oggetto di una politica di costante miglioramento, basata sui principi della Lean Management e sono quindi nelle condizioni ideali per fornire alti livelli qualitativi e rispettare le tempistiche e le richieste a livello di costo da parte dei clienti. «La nostra esperienza di costruttore - Mauro Frizziero - Creation Marketing Manager Socomec - si estende a una gamma completa di servizi progettati per agevolare la ricerca, l’implementazione e l’uso delle nostre soluzioni. I nostri team di assistenza si sono costruiti la loro reputazione garantendo consulenza, competenze flessibili e reattività».
La crescente domanda di energia di alta qualità, per l’alimentazione di Data Center e altre infrastrutture critiche, rende l’UPS uno degli elementi più importanti dell’architettura elettrica. Sebbene l’affidabilità sia integrata a livello progettuale, le apparecchiature UPS non sono immuni da eventi imprevisti in grado di influire negativamente sulle prestazioni e, in ultima analisi, sulla continuità aziendale, ma monitorando l’UPS 24/7 e prevenendo i problemi prima che si verifichino, è possibile effettuare interventi di riparazione rapidi e mantenere la continuità operativa. «L’obiettivo principale di ogni organizzazione –racconta Frizziero – è la protezione continua di persone e risorse, con la certezza della continuità operativa e aziendale. Mantenere i sistemi perfettamente in funzione significa individuare i problemi prima che si presentino ma, se comunque si verifica un problema imprevisto, la capacità di reagire rapidamente e ridurre il tempo medio di riparazione (MTTR) può fare una notevole differenza». Socomec ha sfruttato la potenza delle più recenti tecnologie digitali smart per migliorare i servizi di assistenza, studiando una tecnologia basata sull’Internet of Things per mettere in connessione tra loro UPS, utenti finali ed esperti Socomec con una velocità e una trasparenza senza precedenti. Integrando tecnologia smart all’interno di un’infrastruttura elettrica, i nostri servizi innovativi consentono il monitoraggio continuo dei parametri dell’UPS. I guasti possono essere evitati prima che si presentino e, se si verifica un’anomalia, è possibile avviare azioni proattive senza attendere la chiamata da parte dell’utente finale. Tutto questo ha dato vita al servizio di manutenzione smart SoLink, «Grazie al quale siamo in grado di identificare ed eseguire interventi tecnici a distanza, senza la necessità di trovarci fisicamente di fronte all’apparecchiatura. - aggiunge Frizziero, che prosegue -
Gestione servizi in loco
110,000 Interventi / anno 98 ,5% Livello di servizio 94 ,9% First time fix rate 99 ,995% Safety rate
Linea diretta di assistenza tecnica Competenza certificata
25+
Lingue parlate 3 Centri di supporto di alta expertise 94, 9%120,000+ Richieste di supporto gestite / anno
8,000 Ore di training tecnico effettuate / anno 480+ Tecnici formati in presenza e da remoto / anno
ed eventi. Per ciascuna macchina viene visualizzato lo stato di funzionamento e gli eventuali allarmi, in questo modo, poiché vengono visualizzati anche informazioni relative alle specifiche installazioni UPS, la dashboard live permette l’analisi in tempo reale da remoto e la notifica istantanea delle anomalie.
Grazie agli aggiornamenti in tempo reale sullo stato di ogni UPS – inclusivi dei parametri di potenza, tasso di carico globale, capacità e autonomia della batteria oltre alla temperatura dell’UPS - l’app garantisce che tutti gli UPS lavorino in condizioni normali e permette agli utenti di reagire tempestivamente agli eventi imprevisti con un netto impatto sul MTTR (Mean Time To Repair).
La raccolta dei dati di installazione ed esercizio consente inoltre di individuare in maniera predittiva potenziali problemi e quindi attivare eventuali gruppi di backup o rimettere in funzione apparecchiature difettose.
Se, tuttavia, si rende necessario un intervento sul posto, un tecnico Socomec può essere inviato immediatamente con un briefing prediagnostico e tutti i ricambi eventualmente necessari. Grazie a questo approccio, siamo in grado di ridurre significativamente il rischio di downtime (periodi di inattività), con risparmio di tempo e risorse umane e finanziarie, in ogni fase del percorso».
L’interazione tra i tecnici Socomec e l’utente finale è possibile tramite SoLive, una feature del servizio di telemonitoraggio da remoto, attraverso il quale tutte le installazioni del cliente vengono monitorate 24h, non-stop, direttamente dal Centro di Assistenza Tecnica Socomec più prossimo.
SoLive raccoglie i dati da tutti i sistemi UPS installati nell’impianto elettrico e presenta, su una dashboard collegata in modalità “live”, le informazioni relative a soglie
L’analisi delle performance legate al funzionamento degli UPS consente agli specialisti Socomec di acquisire una migliore comprensione dell’ambiente operativo caratteristico di ciascuna delle applicazioni reali e, quindi, di proporre interventi di manutenzione predittiva in maniera più informata. Inoltre, in caso di anomalie, SoLive crea un collegamento diretto con i centri di assistenza locali rendendo il supporto della rete globale dei tecnici specializzati Socomec sempre a portata di mano. In questo caso, i tecnici specialisti Socomec si attiveranno proattivamente nell’analisi e nella risolu zione di eventuali anomalie notificate direttamente dal Link-UPS e, se necessario, nel contattare il cliente per proporre l’azione corret tiva più rapida secondo gli accordi definiti nei contratti di manutenzione Socomec.
CLICK
L’azienda non si è fermata alla sola digitalizzazione del servizio di manutenzione, ma si è spinta oltre, mettendo al servizio la stessa tecnologica per rendere smart anche l’installazione degli UPS, una fase fondamentale per garantire affidabilità, funzionalità e prestazioni ottimizzate: sono necessari controlli per garantire il corretto posizionamento, la connettività elettrica, il corretto dimensionamento e la protezione delle batterie. «Per garantire una corretta installazione e la sicurezza degli utenti, abbiamo introdotto l’app eWire che, utilizzando tecnologie a realtà aumentata, riconosce l’UPS da installare quando il dispositivo è inquadrato con la fotocamera dello smartphone dell’installatore. Tutte le informazioni sull’UPS sono acquisite automaticamente dall’app per gestire correttamente l’installazione. eWire fornisce istruzioni passo-passo per posizionare correttamente l’UPS, verificare la protezione elettrica e guidare il cablaggio sia dell’UPS che della batteria» spiega Frizziero.
Nulla è lasciato al caso: al completamento dell’installazione, eWIRE guida l’installatore nell’esecuzione di una
serie di verifiche, comprese le misure elettriche, per confermare che l’installazione sia stata effettivamente eseguita correttamente. Una volta completata l’installazione, eWIRE invia un rapporto dettagliato al Centro assistenza Socomec per la convalida del report di installazione e l’autorizzazione della messa in servizio da parte del team di assistenza Socomec.
Infine, Socomec ha brevettato una tecnologia per effettuare da remoto qualsiasi operazione direttamente nei gruppi di continuità dei clienti. Si tratta della soluzione Remote Xpert che, attraverso un collegamento virtuale, consente al tecnico esperto di Socomec di eseguire a distanza sull’UPS test, diagnosi, reset di allarmi, riconfigurazione parametri messa in servizio e altre operazioni di manutenzione, con la stessa precisione ed affidabilità di un intervento in presenza. Grazie alla tecnologia brevettata Remote Xpert, è possibile fare qualsiasi diagnosi da remoto sull’UPS: si può consultare lo storico, ricercare l’eventuale guasto e, in taluni casi, perfino risolvere il problema a distanza senza dover inviare un tecnico sul posto.
Fonte: https://www.socomec.com/files/live/sites/systemsite/files/UPS/linkups/doc- 0002702en- SoLink.pdf
Chimica Magazine: Che cosa significa per voi il concetto di “innovazione” e come lo avete declinato nella vostra realtà?
Sergio Valletti: Il primo significato di innovazione per noi riguarda il prodotto, con numerosi piani di rinnovamento avviati già da diverso tempo, anche se, a dire il vero, l’innovazione di prodotto che avevamo in mente non è stata pienamente raggiunta, per quello che è successo negli ultimi due anni. Terranova Instruments produce strumentazione elettromeccanica: il nostro prodotto è composto sia da parti meccaniche che da parti elettroniche, quindi si può dire che siamo stati colpiti in tutte le direzioni. I microprocessori su cui si basano le nostre schede elettroniche sono gli stessi utilizzati nel settore automotive, facendo ricadere anche su di noi gli effetti della scarsità di componenti e materia prima, quali semiconduttori, resine e così via.
Queste condizioni non hanno facilitato il raggiungimento degli obiettivi di innovazione su alcuni prodotti che noi avevamo impostato da circa tre anni a questa parte ed è ancora difficile, in questo momento, capire quando potremo riprendere questo percorso. Ad esempio, erano previste nuove release di prodotto a partire da fine 2021, ma in questo
momento il lead time per i microprocessori di cui abbiamo bisogno è a 52 settimane. Per le aziende del nostro settore, parliamo di uno scenario davvero pesante. Detto questo però, di fronte a questa grande crisi che riguarda gli approvvigionamenti, abbiamo cercato di migliorare il più possibile quello che possiamo chiamare “l’esistente”, andando oltre un’ottica di breve periodo e rapportandoci con quelle che saranno le principali evoluzioni tecnologiche del nostro settore, che riguardano in particolare i protocolli di comunicazione. Cerchiamo insomma di sfruttare questo tempo per orientare i nostri prodotti attuali in vista di questo passo ulteriore, riprogettandoli in modo che possano incorporare sia le modifiche che abbiamo già messo in programma dal punto di vista tecnico, sia quelle che sono in via di definizione e sviluppo da parte dell’industria. E
piamente consolidati sul mercato praticamente da decenni.
CM: Di quali evoluzioni tecnologiche si parla?
SV: Principalmente dell’introduzione dello standard di comunicazione Ethernet APL, che apre per noi delle prospettive molto interessanti, in rapporto al mondo dell’IoT e con il resto del mercato. I nostri competitor, che sono le grandi multinazionali tedesche, americane o giapponesi, stanno gradualmente orientando il nostro settore verso un nuovo protocollo di comunicazione, in sostituzione dei tipici bus di campo che sono sempre stati utilizzati nella nostra industria, come possono essere ad esempio Hart, Fieldbus, insomma la tipica uscita che consente al dispositivo di comunicare in un sistema di automazione. Rispetto a questi protocolli molto specifici per il mondo industriale, avremo invece lo standard Ethernet APL, che consente l’utilizzo di un normale cavo LAN per la connessione di qualsiasi dispositivo, come già avviene negli ambienti più consumer dell’informatica o della domotica. Ecco, le aziende stanno operando per far sì che questo protocollo possa essere implementato anche nell’industria: un percorso abbastanza rivoluzionario perché in questo contesto bisogna tenere conto di regole molto più stringenti rispetto a quelle domestiche o civili, in termini
di sicurezza o di vincoli ambientali. Parliamo ad esempio di certificazioni di sicurezza intrinseca, di standard relativi ad emissioni, irradiazioni o disturbi elettromagnetici, e allo stesso tempo della necessità di garantire la stabilità del segnale, un aspetto fondamentale per garantire la qualità dei processi, cosa indispensabile in qualsiasi tipo di industria. Tutto l’installato dovrà essere aggiornato alla luce di questa evoluzione, per impattare il meno possibile sull’economia degli impianti esistenti. E tutto questo comporta uno studio accurato sulle caratteristiche del prodotto, che noi abbiamo incorporato nel nostro sviluppo e che stiamo portando avanti adesso in modo da arrivare pronti, quando sarà il momento, con una gamma prodotti totalmente in linea con la nostra concorrenza.
CM: Che impatto avrà questa evoluzione sul mondo dell’automazione?
SV: Renderà l’accesso agli impianti più facile e fruibile, anche nel rispetto di tutti i protocolli di sicurezza che saranno emessi dalle varie legislazioni nazionali o europee. È lo stesso percorso virtuoso della standardizzazione, che abbiamo visto in tanti altri ambiti dell’elettronica. Normalizzare linguaggi diversi, che storicamente hanno senso in quanto nati in mo-
menti o in luoghi diversi, puntando invece all’integrazione, ad una comunicazione uniforme, dà sempre un risultato positivo: forse non arriveremo all’esperanto, che rimane una chimera, ma potremo almeno intenderci in inglese, che è già un risultato adeguato. In questo nuovo scenario, il linguaggio dei sistemi di automazione potrebbe essere veicolato anche tramite device standard quali PC, tablet o smartphone. Diciamo che questo filone si inserisce in pieno nel solco dell’Industria 4.0, in quanto contribuisce a realizzare il concetto di Internet of Things. Posso prendere un device da campo e metterlo in comunicazione – ad esempio – con il forno di casa, perché serve solo un’interfaccia tra i due sistemi ma il linguaggio di comunicazione è già lo stesso: devo semplicemente farli incontrare.
CM: Torniamo, invece, al tema della supply chain e alle difficoltà di approvvigionamento. Come le avete affrontate?
SV: Per quanto riguarda la parte elettronica, la parola chiave è senz’altro scouting, almeno dove è stato possibile. In pratica abbiamo dovuto dividere in modo netto quello che poteva essere ricercato da quello che non poteva essere ricercato. I componenti elettronici o microprocessori sono sostanzialmente prodotti da ST Microelectronics oppure da aziende cinesi per ST. Di conseguenza, abbiamo cercato questi componenti ovunque, trovandoli dove possibile, ovviamente a prezzi lievitati perché la domanda è diventata molto superiore all’offerta. Altra possibile soluzione sarebbe stata quella di trovare prodotti alternativi, ma questo per noi significherebbe rifare tutto il progetto relativo al nostro dispositivo, perché ogni nostro strumento si basa sulla logica del suo microcontrollore. E anche risolvendo questo aspetto, non sempre questi potenziali fornitori erano in grado di darci garanzie di approvvigionamento per i due, tre, cinque anni successivi, tali da poter avviare una nostra produzione. Su questi fronti ci siamo dovuti fermare, mentre abbiamo proseguito le ricerche presso stockisti, broker, trader di vario tipo per limitare i danni ed evitare di rimanere senza componenti critici, piuttosto pagandoli un po’ di più. La scarsità dei materiali si è fatta sentire anche per quanto riguarda la parte meccanica, più precisamente gli acciai speciali, quelli realizzati con leghe specifiche: anche in questo caso abbiamo dovuto fronteggiare difficoltà di approvvigionamenti e prezzi lievitati anche di tre o quattro volte negli ultimi mesi. D’altra parte, invece, tutto questo ci ha anche portati ad aprire nuove porte, magari con fornitori che prima non venivano considerati semplicemente per rapporti di fidelizzazione già in essere o piani di consegna concordati.
CM: Lo shortage è sicuramente una delle tendenze di cui si è parlato di più ultimamente, ma ve ne sono anche altre, come ad esempio la sostenibilità ambientale. Questo obiettivo rientra nel vostro percorso di innovazione e se sì come?
SV: Sì, innanzitutto dal punto di vista del contenimento dei consumi. E questo punto di vista viene introdotto in tutte le fasi progettuali che riguardano non solo il prodotto in sé, quindi il suo funzionamento, ma anche tutto quanto comporta la sua lavorazione e più a monte la sua supply chain, a partire dagli approvvigionamenti. Questo orienta anche la scelta dei fornitori e non necessariamente a parità di costo: in pratica cerchiamo di scegliere il fornitore più idoneo fra quelli più vicini a noi, anche se risultano un po’ più costosi. Oggi insomma non possiamo più ignorare la variabile “distanza” nella scelta dei fornitori. Le aziende ci sono ed è compito nostro trovarle, che siano sia vicine che capaci di lavorare bene come serve a noi.
Su un altro fronte, quello della produzione di energia, stiamo cominciando a perseguire nuovi e interessantissimi settori di mercato. Ad esempio, abbiamo cominciato a produrre una nuova linea di trasmettitori di livello a immersione, dispositivi che misurano il livello di pozzi, falde, o altro tipo di bacino, specificatamente progettati per gli impianti di gestione delle biomasse. Si tratta in pratica di cisterne che raccolgono il percolato che si genera dai rifiuti: i nostri trasmettitori sono in grado di rimanere immersi in questo tipo di liquido, che è particolarmente aggressivo, per misurarne il livello e quindi per migliorare l’efficienza della gestione di queste vasche, utilizzate nella produzione di energia da fonti di recupero. Dal nostro punto di vista è un settore di mercato totalmente nuovo: fino al 2020 per noi neanche esisteva, quest’anno invece è stato messo a budget perché comincia a rappresentare una parte rilevante anche nella nostra produzione. C’è poi tutto il fronte dell’idrogeno, che abbiamo ben presente e sul quale ci stiamo documentando continuamente, anche presenziando alle fiere internazionali nel settore energia e oil&gas. In questo caso però il nostro ruolo è di supporto: facciamo praticamente quello che siamo in grado di fare da sempre, fornire tecnologia adeguata per resistere ai parametri di questo processo in termini di pressione, temperatura, resistenza agli ambienti e alla corrosione, che in un sistema di produzione o utilizzo di idrogeno possono essere anche molto gravosi. In un certo senso non stiamo vivendo questa evoluzione da protagonisti, d’altro canto però siamo già totalmente in grado di supportarla con una gamma di strumentazione adeguata ai suoi vincoli di processo.
CM: Ci sono altre soluzioni che fungono da abilitatori per le vostre innovazioni? Anche finanziarie, ad esempio con l’accesso a contributi per lo sviluppo tecnologico, magari legati ai fondi del PNRR?
SV: Dal punto di vista finanziario, abbiamo alcuni progetti in corso: la nostra amministrazione sta infatti valutando dei contributi legati all’adozione di nuove tecnologie per migliorare il processo interno. Fra le tecnologie che stiamo valutando vi sono ad esempio dei marcatori ottici, in pratica delle telecamere intelligenti che si possono collegare direttamente con il sistema di gestione della produzione. Questo progetto dovrebbe rientrare in un’area di finanziamento che potrebbe sbloccarsi nel giro dei prossimi mesi. E come questo abbiamo altri progetti in corso per il rinnovamento dei nostri processi produttivi. ìDal punto di vista delle nuove tecnologie, guardiamo con attenzione all’area del 3D non tanto per la prototipazione,
cioè per la produzione di prototipi in modalità additiva, quanto piuttosto dal punto di vista del software, quindi con soluzioni di tipo vettoriale che noi utilizziamo specificatamente per la progettazione. In questi anni abbiamo investito tantissimo su soluzioni quali Inventor o Autocad per portare tutto ciò che era disegno su tavola, quindi bidimensionale, in un ambiente software tridimensionale. In questo modo oggi sviluppiamo non solo i pezzi meccanici ma anche l’insieme dei pezzi meccanici con quelli elettronici, verificando le tolleranze e il funzionamento sul campo, in un ambiente tridimensionale completo. Che tra l’altro è sempre più richiesto anche dal nostro cliente, che per primo vuole vedere il nostro device all’interno del suo impianto o del suo skid, simulando totalmente la sua performance reale. La stampa 3D, tuttavia, potrebbe risultare utile per valutare i prototipi di custodie o housing, ma va anche detto che proprio grazie alla progettazione in 3D e alla prototipazione che questa consente, la fase di produzione stessa risulta enormemente più precisa, in quanto le tolleranze di errore sono ridotte al minimo. Fra gli abilitatori di tipo tecnologico e i progetti di innovazione sulla gamma dei prodotti devo poi aggiungere un’operazione importante, effettuata alla fine dell’anno scorso: l’acquisizione di TM Tecnomatic, azienda con sede a Cremona che dagli anni Sessanta produce una gamma di strumenti di misura di elevata qualità e del tutto complementari alla nostra. Questa operazione ci consente di innovare rapidamente dal punto di vista del portafoglio prodotti e delle sinergie che si possono avviare a livello di produzione. Non siamo nuovi a questo tipo di operazioni, dato che già oggi la gamma di Terranova Instruments include altri tre brand, frutto di analoghe acquisizioni condotte nel corso degli anni, quali Valcom, Spriano e Mec-Rela. Da quest’ultima acquisizione ci aspettiamo di migliorare ulteriormente la nostra posizione sul mercato, con soluzioni più integrate che in quanto tali sono molto più apprezzate dal punto di vista dei clienti. L’accordo con TM Tecnomatic dimostra infine che, nonostante le complessità che stiamo vivendo negli ultimi tempi, e anche di fronte alle interruzioni che abbiamo dovuto subire da alcuni punti di vista, non ci siamo lasciati fermare e abbiamo anzi espresso le nostre capacità, anche finanziarie, su altri aspetti, come quello delle strategie e degli obiettivi futuri. L’operazione inoltre rafforza la nostra compagine aziendale, con altre venti persone di alto profilo che si aggiungono alle nostre quaranta, e consolida ulteriormente uno dei nostri maggiori punti d’orgoglio: la produzione interamente made in Italy, un aspetto strutturale della nostra storia sul quale puntiamo fortemente anche per il nostro sviluppo futuro.
(*) L’esperienza di Stefano Giunteri nel mondo dell’automazione industriale ha inizio nel 1990 come Sales Engineer Instrumentation alla Foxboro, in seguito divenuta parte di Schneider. In quel periodo, ha maturato un forte interesse per il mondo del Process Automation, imparando le basi della Strumentazione Industriale dai maggiori esperti del settore. Ha maturato inoltre una considerevole competenza nel mercato della Factory Automation e relative applicazioni, grazie all’esperienza svolta per IFM Electronic in Italia. È poi entrato a far parte della “famiglia” Pepperl+Fuchs, dove attualmente ricopre l’incarico di Direttore Commerciale della divisione Process Automation, per il Middle East ed east Mediterranean, una delle regioni più strategiche per l’azienda per il ruolo in essa ricoperto dall’industria Oil & Gas. Grazie al suo completo backround tecnico e alla conoscenza dettagliata dei prodotti per l’automazione di processo e le loro applicazioni, Stefano Giunteri supporta la clientela con attenzione specifica ai problemi relativi alla sicurezza ed efficienza, con una proposta tecnica e commerciale coerente con il ruolo di leadership mondiale svolto da Pepperl+Fuchs nel mercato dell’automazione di processo.
In qualità di primario operatore mondiale nell’interfacciamento di aree pericolose e pioniere nei numerosi aspetti della protezione dalle esplosioni, la sicurezza è sempre la prima parola a cui pensiamo in Pepperl+Fuchs. I valori che sono alla base dell’azienda non sono mai cambiati, mentre si è continuamente rafforzato lo spirito imprenditoriale finalizzato a sviluppare le tecnologie più innovative in grado di soddisfare le richieste dei nostri clienti. Che si tratti di sviluppare sistemi di interfaccia a sicurezza intrinseca e protezione contro le sovratensioni per applicazioni convenzionali o di innovare con con nuove tecnologie come Fieldbus o dispositivi intelligenti, il nostro impegno per il miglioramento continuo non diminuisce mai. Questo è evidente ora più che mai, essendo noi in prima linea nell’assistere e sviluppare la trasformazione digitale di Industry 4.0, con la nostra ultima innovazione su rete Ethernet per l’automazione dei processi: APL (Advanced Physical Layer), che consente alle aziende di sfruttare la tecnologia e le competenze per migliorare i processi e creare applicazioni capaci di realizzare l’IIOT.
Dal punto di vista tecnologico, diverse aree mostrano una domanda crescente; fra queste vi sono ad esempio il mobile computing, la tecnologia di misurazione a due e tre fili e la migrazione dei dati. Smartphone e tablet sono già entrati nelle fabbriche e negli stabilimenti e la connettività Ethernet che consentirà di facilitare la raccolta dei dati è ora una realtà. I dati sono essenziali per creare processi di produzione trasparenti per gli operatori degli impianti attraverso nuove applicazioni web based e soluzioni cloud,
offrendo il potenziale per un continuo incremento di efficienza.
Ridurre il numero dei lavoratori che devono operare in ambienti pericolosi, fornendo loro la possibilità di far funzionare l’impianto da un ambiente sicuro, aiuterà a ridurre notevolmente il rischio. Allo stesso tempo questa è una chiara risposta a un’altra sfida, la carenza o comunque la disponibilità limitata di risorse in grado di svolgere attività in questi impianti complessi. Dotare i tecnici di uno strumento di base come uno smartphone semplificherà lo svolgimento delle loro attività, migliorando la comunicazione e l’interfaccia con il mondo digitale, fornendo anche vantaggi aggiuntivi come la protezione del lavoratore attraverso la funzione di attivazione automatica dell’allarme.
Quando si progetta un impianto completamente nuovo o si aggiorna una struttura esistente, il riferimento non è semplicemente lo stato dell’arte di ciò che è stato fatto prima: dobbiamo invece adottare la tecnologia che ci consentirà di progettare un impianto per il futuro. Un’infrastruttura sicura, semplice, digitale e flessibile: questa è la visione che guida Pepperl+Fuchs fin dal 2015, condivisa con molti esperti di automazione dei processi, che riconoscono all’azienda un ruolo trainante nel dare una risposta “hardware” a questa esigenza del mercato.
Il risultato è Ethernet APL (Ethernet Advanced Physical Layer), una versione rinforzata di Ethernet adatta agli ambienti ostili che si riscontrano nel campo, all’interno degli impianti di processo. Per la prima volta, gli utenti di processo possono applicare Ethernet dagli uffici amministrativi, oltre che dalla di sala di controllo e dal campo: cosa che fornisce un accesso continuo, trasparente e in tempo reale alla strumentazione. Questo rende possibili applicazioni completamente nuove e analogamente rinnova il modo in cui gli utenti lavorano con la strumentazione e e con tutto ciò che è installato in campo negli impianti di processo.
Ethernet-APL definisce nuove specifiche per il funzionamento in campo all’interno degli impianti di processo. La tecnologia di installazione e collegamento si basa su un cavo schermato a due fili con terminali a vite. Ethernet APL può utilizzare il cavo Fieldbus di tipo ‘A’ esistente. È simile all’attuale infrastruttura tecnologica di bus di campo: alimentazione e comunicazione su un lungo
cavo a due fili e sicurezza intrinseca dello strumento. I cavi possono rimanere installati favorendo il processo di migrazione e gli aggiornamenti a Ethernet APL per le installazioni brownfield. Vediamone gli aspetti principali.
Gli switch possono gestire due diversi livelli fisici: Ethernet APL e Manchester Bus-Powered (MBP) per Profibus PA. L’interruttore rileva e si adatta automaticamente alla comunicazione del dispositivo in campo. Questa tecnologia, brevettata da Pepperl+Fuchs, è un vero elemento di differenziazione. Se il dispositivo fornisce dati tramite il protocollo Profibus PA, lo switch li converte in Profinet secondo la tecnologia Proxy standardizzata. Ciò consente architetture miste tramite un’unica infrastruttura, dove il funzionamento in parallelo delle tecnologie Ethernet e Fieldbus consente di risparmiare i costi di investimento mantenendo la base installata di apparecchiature.
Gli switch di campo FieldConnex APL monitorano la qualità del livello fisico. Lo switch rileva immediatamente la deviazione di alcuni parametri critici o un guasto, fornendo allarmi sul sistema di controllo mentre il dettaglio del guasto o anomalia è disponibile sul web server integrato nello switch e tramite un server web. Ciò consente agli utenti di intervenire in modo mirato, spesso prima che si verifichino guasti critici. Ciò garantisce la massima sicurezza per le persone e l’ambiente, garantendo al contempo un’elevata disponibilità dell’impianto e ottimizzando gli sforzi.
L’infrastruttura di rete consente l’accesso alla diagnostica e alla configurazione in parallelo e indipendentemente dal sistema di controllo. Ciò prepara il terreno per processi di lavoro automatizzati e guidati digitalmente, economici e sicuri. Questo protegge le persone ed evita errori da azioni non intenzionali.
Ethernet APL fornisce i dati che consentono agli utenti di ridurre i rischi, semplificare la progettazione, accelerare l’implementazione, aumentare l’ottimizzazione delle risorse e quindi ridurre il costo totale dell’impianto. Con gli switch Ethernet APL FieldConnex®, gli uten-
ti possono guidare la trasformazione digitale con i dati provenienti dal campo del loro impianto di processo. Il funzionamento dell’impianto grazie a questa serie di dati consente agli operatori di ottimizzare in modo continuo e permanente il potenziale dell’impianto stesso. Gli switch da campo Ethernet APL Rail di FieldConnex® sono i primi del loro genere sul mercato. Robusti e dotati di elettronica altamente efficiente per contenere la dissipazione di potenza o dissipazione termica, ingrediente chiave per una lunga durata, hanno un alto numero di porte per dispositivi da campo, nonché architettura di switch ad alte prestazioni.
Ethernet-APL trasporta qualsiasi tipo di protocollo. Nelle industrie di processo, i più diffusi sono Ethernet-IP, HartIP, OPC/UA o Profinet. Il protocollo definisce i contenuti e la struttura dei dati e delle informazioni. Per esempio, i protocolli industriali definiscono segnali come un ingresso analogico, un messaggio di avviso, una comunicazione di sicurezza, ecc. Altri protocolli come il protocollo HTML (livello 7) descrivono l’aspetto di una pagina web e come raccogliere l’input dell’utente tramite moduli. Gli switch FieldConnex forniscono un facile accesso allo stato, alla configurazione e alla diagnostica tramite un web browser. I dispositivi fanno lo stesso. I protocolli facilitano altri compiti. Esistono protocolli specializzati per la gestione della rete, l’identificazione delle porte e altro ancora. Un sistema basato su Ethernet consente a qualsiasi dispositivo o sistema di accedere a un altro dispositivo o sistema contemporaneamente e senza gateway.
Il livello fisico è l’infrastruttura che trasporta il segnale e fornisce energia. Ethernet APL è la versione rinforzata per il campo. Anche Ethernet standard, Fast Ethernet o Gigabit sono livelli fisici per Ethernet, così come l’intera gamma di Ethernet a coppia singola (SPE). I livelli 1 e 2 del modello ISO OSI definiscono il livello fisico.
Ethernet APL consente completa libertà di progettare e implementare qualsiasi topologia, tra cui le più diffuse come la rete ad anello, a stella, trunk... Gli switch FieldConnex collegano le reti Ethernet APL a reti di livello superiore. Le soluzioni per l’installazione e le Intelligent Field Junction Boxes sono simili a quelle Fieldbus.
I sistemi bus di campo come Foundation Fieldbus H1 e Profibus PA sono definizioni complete che descrivono sia il livello fisico che il protocollo. Incorporano sia una definizione di protocollo che una definizione di livello fisico.
Manchester Bus Powered (MBP) è il nome del livello fisico secondo IEC 61158-2.
Ethernet-APL è progettato per utilizzare il cavo di tipo “A” risparmiando sui costi di installazione. Con la tecnologia brevettata Pepperl+Fuchs e gli switch, gli utenti possono naturalmente utilizzare dispositivi Ethernet-APL e Fieldbus sulla stessa infrastruttura.
Molti vantaggi di MBP sono anche incorporati nella progettazione di Ethernet-APL. Sono:
• Alimentazione e comunicazione su un cavo a due fili, tipo ‘A’.
• Topologia Trunk-and-Spur ad alta potenza.
• Stessa facile validazione della sicurezza intrinseca, denominata 2-WISE.
Ciò consente una facile migrazione dei sistemi di automazione con Profibus PA a e switch FieldConnex. Non esiste ancora una sostituzione facile per Foundation Fieldbus H1 perché non esiste ancora una standardizzazione per la trasmissione di dati ad altri protocolli. Ethernet-APL in generale risolve molti problemi di limiti: più lunghezza del cavo, più potenza, più velocità.
La sicurezza e la protezione sono entrambe implementate dai protocolli nel livello 7. Ethernet-APL è solo un livello fisico (livello 1). Poiché il livello 7 è completamente separato dal livello 1, Ethernet-APL consentirà la gestione dei concetti di sicurezza e protezione, come qualsiasi protocollo, oggi e in futuro. La sicurezza è sempre un concetto chiave di sistema. Ci sono specialisti per questo compito che forniscono servizi di consulenza per l’implementazione. Gli standard IEEE e IEC sono disponibili e pubblicati. Qualsiasi fornitore può essere parte di questa tecnologia attraverso una delle quattro organizzazioni di utenti. Ci aspettiamo inoltre che più organizzazioni di utenti incorporino Ethernet APL nei loro standard di comunicazione.
uella delle guarnizioni è una nicchia di mercato. Una nicchia sottovalutata, però. La guarnizione è l’ultima cosa a cui pensa un impiantista ma è anche la cosa che può fare più danni. Con la guarnizione sbagliata, l’impianto non funziona» afferma Lorenzo De Lorenzi, direttore commerciale di Caast, descrivendo il core business dell’azienda che da sempre è rappresentato dalle sealing solutions: guarnizioni, sistemi di tenuta in generale e tutti i dispositivi a corredo. Si tratta di componenti critici che sono realizzati in accordo con le sempre più esigenti specifiche richieste dai mercati di oggi.
Caast produce internamente tutte le tipologie di guarnizioni da lavorazione meccanica, con riferimento a due grandi famiglie di materiali componenti, plastici o termoplastici ed elastomerici, passando per tutte le possibili varianti, quali ad esempio polimeri fluororati (Viton), HNBR (NBR idrogenati), fino ad arrivare ai materiali PTFE per applicazioni più particolari. Nella gamma Caast vi è anche la divisione dedicata agli o-ring, quasi esclusivamente realizzati in mescole speciali. Altra linea di prodotto è quella delle guarnizioni energizzate (spring energized), specifiche e spesso customizzate per il settore oil & gas; un prodotto che ha richiesto forti investimenti nella ricerca e sviluppo, per gestire correttamente il calcolo strutturale delle spinte date dalle molle interne in relazione alle prestazioni e alla tenuta della guarnizione. A completamento della gamma prodotti, a copertura delle applicazioni critiche ci sono le guarnizioni metalliche che l’azienda fornisce in modalità rivendita: è questa la fascia di prodotto più critica in assoluto, dato che il metallo subentra laddove tutti i materiali plastici visti fin qui non sono più sufficienti, per questioni di temperatura, di pressione, di compatibilità o di dimensioni dell’applicazione. Anche in questo caso però l’azienda garantisce una competenza specifica, supportata da partnership di lunga data con i propri fornitori specializzati.
La linea di prodotto nella quale l’azienda si distingue maggiormente è però quella delle grandi dimensioni: Caast infatti è in grado di produrre guarnizioni con diametro anche di oltre tre metri. Si tratta di una competenza importante soprattutto in vista dei nuovi mercati aperti dalla transizione energetica: tali misure infatti sono tipicamente richieste
dai sistemi di produzione di energia che sfruttano fonti naturali quali gas, acqua oppure vento. Nel settore idroelettrico, ad esempio, le valvole che regolano l’entrata dell’acqua nelle turbine possono raggiungere i quattro o cinque metri di diametro. Si tratta in particolare, in questo caso, di un settore anche piuttosto datato, nel quale può succedere di dover sostituire vecchi prodotti magari a base di gomma telata, con nuove soluzioni realizzate con materiali termoplastici oppure elastomerici. Un esempio di sviluppo particolarmente innovativo, legato anch’esso alle grandi dimensioni, riguarda i prodotti forniti per una turbomacchina che convoglia il gas nei gasdotti –un mondo che oggi è sotto i riflettori per le questioni legate alla Russia, ma che indubbiamente rappresenta una parte ancora molto importante del nostro futuro energetico. L’azienda cliente utilizzava sistemi di tenuta di tenuta ad anello chiuso di circa tre metri di diametro, caratterizzata da notevole complessità nelle fasi di montaggio e adattamento. In questo caso, Caast ha sviluppato una guarnizione di grandi dimensioni e divisibile in due parti, che semplifica tali fasi riducendo il tempo di installazione da oltre tre ore a trenta minuti.
L’area produttiva di Caast presenta innanzitutto un magazzino semilavorati, che contiene le billette dei materie termoplastiche, plastiche oppure elastomeriche (parte delle quali conservate in una apposita area climatizzata). La produzione per Caast avviene prevalentemente per tornitura e asportazione di truciolo, mediante macchinari e soluzioni specificatamente dedicate a questo tipo di prodotti, quindi
con utensili e sistemi di rotazione fatti apposta per lavorare la plastica e la gomma. Di fatto, la guarnizione che esce da queste macchine presentano finiture superficiali paragonabili ai prodotti ottenuti per stampaggio, nel rispetto delle tolleranze richieste per questo tipo di materiali. Questo per quanto riguarda i prodotti soggetti a tornitura; nel caso di prodotti realizzati mediante stampaggio (proposti da Caast anche in collaborazione con fornitori specializzati) si parte invece dal granulato e dalla formulazione della mescola di base, che vengono formati in appositi stampi. Altre tecnologie utilizzate sono estrusione e vulcanizzazione.
Un asset importante della produzione Caast è rappresentato dalla sala metrologica, allestita con svariate soluzioni per tutte le attività di misurazione o collaudo finale dei prodotti e per la prova delle caratteristiche meccaniche dei materiali. La sala, a temperatura controllata, è dotata di svariate strumentazioni, da quelle più tradizionali quali durometri, micrometri, calibri digitali e così via, una stazione per le prove meccaniche, di trazione e allungamento, densità, durezze, fino ad arrivare a macchine a visione ottica di nuova concezione. L’ultima arrivata in particolare, fiore all’occhiello della gamma Keyence, è in grado di effettuare gran parte delle misurazioni necessarie in modalità sostanzialmente automatica, semplicemente richiamando il disegno del prodotto, controllandone parametri e tolleranze in tempi rapidissimi. Altra soluzione metrologica Keyence è un profilometro, un proiettore laser in grado di misurare il profilo dei prodotti senza doverli sezionare materialmente, utile soprattutto in caso di cavità interne.
«Ci troviamo in una fase di mercato molto particolare, nella quale ci chiedono anche soluzioni per applicazioni che oggi
non sono ancora veramente partite: è il caso ad esempio dell’idrogeno. Le aziende ancora non sanno che cosa dovranno gestire, e nemmeno come, ma già devono disporre di soluzioni di tenuta e solo dopo, con i prodotti che forniamo loro, possono effettuare i test di compatibilità» prosegue Lorenzo De Lorenzi. «Questo è uno degli estremi a cui ci porta il mercato di oggi, complice anche la situazione geopolitica: prodotti sempre all’avanguardia, in tempi zero. Ma è qui che possiamo far emergere tutto il nostro valore, che si basa sull’elevata qualità del prodotto, sulla profonda competenza di settore, sul servizio tecnico capillare».
Fra le certificazioni di qualità conseguite dall’azienda, che è ISO 9001 fin dal 2006, vi è anche il sistema AS9100 per il settore aerospazio e difesa, un traguardo raggiunto sempre con l’obiettivo di entrare in nuovi settori applicativi interessanti e coinvolgenti. «Un percorso complicato, non solo per la severità della norma, ma anche per il modo in cui essa è formulata» conclude Lorenzo De Lorenzi. «La certificazione 9100 infatti richiede che l’azienda riceva un ordine entro i primi due anni, pena la perdita della qualifica; ma i clienti di questo settore – compresa l’azienda per la quale abbiamo cominciato la procedura – possono acquistare solo prodotti già certificati. L’azienda in questione aveva avuto una rottura di stock per un o-ring destinato ai propulsori degli aerei, un elastomero che doveva arrivare a 320 °C di temperatura. Nel giro di un mese e mezzo abbiamo preso un nostro prodotto ancora non omologato ed effettuato i test necessari per soddisfare tutti i parametri richiesti. Un errore in questa fase non era ammissibile perché ci avrebbe estromessi per sempre dal settore. I test sono riusciti perfettamente e ora ci muoviamo in modo sempre più solido anche in quest’area, con diversi clienti internazionali».
Ing. Giacobbe Braccio, dipendente Enea dal 1987, esperto di fonti rinnovabili, in particolare biomasse ed energia solare. Attualmente responsabile della divisione bioenergie, bioraffinerie e chimica verde, costituita da circa settanta ricercatori strutturati con attività di ricerca finalizzate alla valorizzazione delle biomasse e degli scarti agricoli per la produzione di energia elettrica/termica, biogas/biometano, biocarburanti avanzati e intermedi chimici, a supporto anche del sistema agroenergetico e agroindustriale per aumentarne la produttività e redditività economica. Il tutto attraverso il frazionamento delle biomasse e l’utilizzo di processi chimici e biotecnologici proiettandone lo sviluppo nella direzione delle bioraffinerie.
La chimica verde è una particolare concezione che rappresenta le fondamenta su cui si basano gli studi della chimica e dell’ingegneria chimica focalizzata sulla progettazione di prodotti e processi che riducono al minimo o eliminano l’uso e la generazione di sostanze pericolose. Per approfondire l’argomento ne abbiamo parlato con l’ing. Giacobbe Braccio, che all’interno di ENEA ha la responsabilità della divisione bioenergie, bioraffinerie e chimica verde. Costituita da circa settanta ricercatori strutturati con attività di ricerca finalizzate alla valorizzazione delle biomasse e degli scarti agricoli per la produzione di energia elettrica/termica, biogas/biometano, biocarburanti avanzati e intermedi chimici, la divisione supporta anche il sistema agroenergetico e agroindustriale per aumentarne la produttività e redditività economica. Il tutto attraverso il frazionamento delle biomasse e l’utilizzo di processi chimici e biotecnologici proiettandone lo sviluppo nella direzione delle bioraffinerie.
Chimica Magazine: Prima di addentrarci nel discorso chimica verde, possiamo definire che cosa si intende per bioeconomia, da quando se ne è iniziato a parlare e con quali obiettivi?
Giacobbe Braccio: Per bioeconomia si intende l’utilizzo sostenibile di risorse rinnovabili di origine biologica per la produzione di materia e/o energia. L’uomo da sempre ha fatto uso della bioeconomia per soddisfare i propri bisogni, in maniera più o meno sostenibile, fino all’inizio dell’era antropocene, quando l’uomo ha iniziato a usare quasi esclusivamente le fonti fossili.
CM: Uno dei principali strumenti per attuare gli obiettivi della bioeconomia è operare per una chimica verde. Può dirci cosa si intende per chimica verde?
GB: La chimica verde si distingue dalla chimica grigia per l’approccio utilizzato nella progettazione e produzione di prodotti chimici e punta a ridurre o eliminare la produzione di sostanze nocive per il pianeta terra, gli ecosistemi e le emissioni climalteranti. Essa si caratterizza per l’approccio
utilizzato nella progettazione e produzione di prodotti chimici che include:
- Impiego di fonti rinnovabili, non fossili, preferibilmente di tipo residuale.
- Impianti di piccola taglia distribuiti. Questo consente la valorizzazione di risorse/rifiuti locali eventualmente disponili riducendo l’impatto dovuto al trasporto e allo stoccaggio.
- Processi a basso consumo altamente integrati e ad alta efficienza.
- Processi in cui viene massimizzato il riciclo di alcune correnti (es. l’acqua) riducendo al massimo l’impiego di nuove risorse.
- Processi caratterizzati da un minore livello di emissioni (anche attraverso maggiore controllo on line e abbattimento).
- Impiego di catalizzatori al posto dei reagenti con la prospettiva di recuperarli e riutilizzarli a fine processo.
- Riduzione dei solventi e sostituzione dei solventi, possibile sviluppando processi di sintesi che impieghino l’acqua o utilizzando “solventi” alternativi come i fluidi supercritici, liquidi ionici e i solventi eutettici profondi (DES).
- Prodotti finali caratterizzati da una minore tossicità. In questo settore confluiscono quindi diverse tecnologie, comprese sia le biotecnologie che le tecnologie chimiche e chimico-catalitiche caratterizzate da un miglioramento in termini di sostenibilità complessiva.
CM: Qual è la situazione attuale in Italia?
GB: La situazione italiana è positiva. Nel 2020 le attività connesse alla bioeconomia hanno generato quasi 320 miliardi di euro, occupando circa 2 milioni di persone. In particolare, circa 70 miliardi sono stati generati da settori quali tessile bio-based (25 miliardi), chimica bio-based (5 miliardi), gomma e plastica bio-based (2 miliardi), bioenergia (3.5 miliardi) e valorizzazione rifiuti biodegradabili (7.4 miliardi) (dati Rapporto Federchimica).
CM: La chimica verde rappresenta un rischio o un’opportunità? Può rappresentare a suo avviso un motore per l’economia circolare?
GB: La vera sfida è sostenere la ripresa e diminuire il consumo delle risorse. La chimica verde può rappresentare una vera opportunità se accoppiata a politiche in grado di innescare una rivoluzione culturale, che va oltre anche il concetto di economia circolare. Gli scienziati si occupano di mettere a punto nuove tecnologie sempre più sostenibili, ma sta alla politica definire una strategia di medio-lungo periodo in grado di disaccoppiare la crescita economica del Paese dal consumo delle risorse. Chimica verde ed economia circolare rappresentano quindi due pezzi dello stesso puzzle: utilizzo virtuoso delle risorse nel rispetto dell’ambiente e degli ecosistemi. Più specificatamente, l’obiettivo chiave della transizione ecologica è la decarbonizzazione dei settori produttivi. Se la decarbonizzazione del settore energetico punta all’introduzione di tecnologie “distributive” basate sull’impiego dell’idrogeno già nel prossimo decennio, la decarbonizzazione del settore della chimica verde passa attraverso l’incremento del carbonio rinnovabile nelle produzioni chimiche.
In generale un’efficace transizione ecologica in tutti i settori richiederà una trasformazione incrementale che passerà, anche nel settore dell’energia, attraverso l’impiego di biocarburanti di seconda generazione o prodotti di tipo drop-in.
Numerose sono le sfide a carico della ricerca scientifica chiamata anche a sviluppare percorsi congiunti con il settore produttivo e i decisori politici. Gli equilibri geopolitici degli ultimi mesi, in seguito alla guerra, hanno enfatizzato non solo le criticità energetiche del nostro paese, ma anche quella di beni di prima necessità come il grano per il quale arriva dall’Unione Europea il via libera all’incremento delle semine. Tutto questo sarà associato verosimilmente a un incremento anche di sottoprodotti delle lavorazioni al quale sarà necessario dare una vita utile. Queste materie prime residuali insieme a quelle derivanti dalla gestione dei rifiuti solidi urbani potranno offrire l’opportunità per sviluppare filiere locali e possono dare un contributo alla diversificazione degli approvvigionamenti e la creazione di percorsi virtuosi in cui i cascami di processo diventano carbonio organico da restituire ai suoli sotto forma di ammendanti o biostimolanti. Tutto questo però richiede un adeguamento anche del sistema normativo che deve sia stabilizzare il mercato lato domanda sia fornire riferimenti normativi nuovi rispetto ai nuovi bioprodotti che possono essere immessi.
CM: Quali sono le proiezioni per il futuro?
GB: La guerra in Ucraina ha innescato una crisi economica ed energetica alla quale bisogna rispondere, a livello europeo, con una strategia industriale in grado di diversificare l’utilizzo delle risorse e valorizzare le peculiarità del territorio europeo. Alcune missioni e strategie erano state definite a valle dell’emergenza pandemica. La guerra in Ucraina ci obbliga a rivederle e proporre una nuova visione per l’Europa, soprattutto in termini di energia e consumo di materie prime.
CM: Adesso spostiamoci sul quadro normativo. Qual è la situazione attuale?
Chimica verde ed econo mia circolare rappresentano due pezzi dello stesso puzzle: utilizzo virtuoso delle risorse nel rispetto dell’am biente e degli ecosistemi
GB: L’utilizzo di residui per dar vita a materiali di uso comune è un aspetto fondamentale nella revisione della direttiva UE sui rifiuti, che prevede la riduzione della quantità di rifiuti da smaltire in discarica al di sotto del 25%, entro il 2025, con precisi target di gestione su rifiuti riciclabili e biodegradabili (tal quali) e un tendenziale azzeramento dello smaltimento in discarica entro il 2030. Inoltre con il decreto legislativo numero 199 del 8 novembre 2021, viene recepita in Italia la direttiva 2018/2001 UE sulle energie rinnovabili nota anche come RED2. Con tale atto inizia ufficialmente in Italia il percorso che deve portare all’adozione di un nuovo quadro legislativo. Le nuove norme devono supportare il conseguimento degli obiettivi del piano nazionale di ripresa e resilienza (PNRR) e supportare soprattutto l’obbligo del raggiungimento dei target del piano nazionale energia clima (PNIEC), attualmente in fase di riformulazione in seguito alla presentazione e attuazione del piano “Fit to 55” e “RepowerEU”. Nel campo energetico la bioenergia, ossia l’energia ottenuta dallo sfruttamento delle biomasse, svolgerà un ruolo fondamentale per il raggiungimento degli obiettivi che l’UE si è prefissata.
CM: In conclusione, che cosa si aspetta dal legislatore nel prossimo futuro?
GB: Un quadro normativo chiaro e stabile e di medio periodo, a supporto di una strategia industriale condivisa a livello europeo, fondata su azioni complementari e tra di loro dipendenti.
Il nostro dibattito nazionale si arrocca di tanto in tanto sul progetto del termovalorizzatore di Roma, città che personalmente amo e in cui peraltro proprio in questi giorni abbiamo ufficialmente inaugurato una sede della Scuola di Management del mio Ateneo. Traggo quindi ispirazione dalla controversa (sarebbe meglio dire mancata) gestione dei rifiuti romani degli ultimi venti anni per dedicarmi in questo editoriale al tema della circolarità del rifiuto urbano.
Al di là delle polemiche di parte, è necessario sottolineare che la soluzione della termovalorizzazione del rifiuto è regolata dal piano d’azione dell’Unione Europea per l’economia circolare, cui si sottolinea, sin dal 2015, che la transizione verso un’economia circolare richiede “un’azione lungo l’intero ciclo di vita di un prodotto, dalla produzione alla creazione di mercati per le materie prime secondarie”. Oltre all’esigenza quindi di classificare i rifiuti in base alla priorità data alla rigenerazione, al riuso e al riciclo, è necessario impegnarsi anche per ridurre la quantità di rifiuti smaltiti in discarica. Il recupero di energia dai rifiuti ha quindi un ruolo fondamentale, che diventa oltremodo prioritario in questa fase di impennata dei costi energetici e delle relative materie prime.
Uno degli argomenti contro la realizzazione degli impianti di termovalorizzazione pare essere la confusione tra gli obiettivi di circolarità dell’economia e la possibilità di riutilizzare in misura integrale il rifiuto prodotto. Tuttavia, per ragioni tecnologiche, di logistica del rifiuto, di sicurezza e anche di sostenibilità finanziaria dei processi di rigenerazione, riuso e riciclo, anche le città più virtuose generano comunque circa il 30% di rifiuti residui. Il versamento di questi in discarica è una non soluzione al problema della circolarità e risulta contraria a qualunque scelta di buon senso, poiché la discarica ha comunque dei costi e un impatto ambientale non irrilevante per cicli di vita molto lunghi. Va inoltre sottolineato che l’Unione Europea ha adottato l’obiettivo di ridurre il conferimento dei rifiuti in discarica al 10% entro il 2035. I dati di Eurostat indicano che in Germania, Olanda, Svezia e Austria questo obiettivo è già stato raggiunto e solo una piccola percentuale di rifiuti finisce ancora in discarica, mentre approssimativamente
il 60% dei rifiuti viene riciclato o riutilizzato e la restante parte è trattata in impianti di termovalorizzazione. Questa soluzione tecnologica è, dal punto di vista tecnico, peraltro irrinunciabile, specie nel caso di città complesse come Roma. Infatti attualmente poco più del 40% dei rifiuti romani viene riciclato, mentre il resto per la maggior parte viene spedito fuori dal territorio comunale. Quand’anche si allineasse il tasso di riciclaggio dei rifiuti della capitale agli standard europei raggiunti da altre città italiane, rimarrebbe comunque quel 30% degli 1,7 milioni di tonnellate di rifiuti generati annualmente nel Comune che dovranno essere trattati. Per evitare di smaltire questo restante 30% integralmente in discarica e per rispettare il requisito europeo di limitare il conferimento in discarica al 10% entro il 2035, sarà inevitabile perseguire una strada di natura tecnologica come appunto l’impianto di incenerimento a energia. Per inciso, non stiamo parlando di tecnologie dell’impero del male, ma di impianti che in Italia sono in funzione da decenni in città italiane come Milano, Torino e Brescia.
L’aumento dei prezzi dell’energia dovrebbe dare ulteriore impulso alla costruzione dei termovalorizzatori. L’utilizzo dei rifiuti per la produzione di elettricità o calore consentirebbe di diminuire le importazioni di combustibili fossili e di ridurre lo smaltimento in discarica. Ad esempio, il risparmio annuo dell’impianto di Torino è stimato in 70.000 tonnellate equivalenti di petrolio che, al prezzo del greggio al giorno in cui rilascio questo editoriale, equivalgono a quasi 50 milioni di euro risparmiati in un anno dalla città.
Oltretutto, la termovalorizzazione del rifiuto consente un beneficio ambientale immediato grazie alla riduzione delle emissioni fuggitive di gas importato. Ad esempio, il gas importato dalla Russia viaggiava per migliaia di chilometri dalla Siberia fino al nostro confine, generando perdite stimate fino al 10% del totale trasportato. È da notare che le emissioni di metano, in particolare, hanno un’impronta di carbonio spaventosa poiché una tonnellata di metano ha lo stesso potenziale di riscaldamento globale di 20 tonnellate di CO2.
È evidente quindi che ancora una volta il tema su cui si dibatte non è tecnico, poiché questa soluzione e la com-
L’aumento dei prezzi dell’energia dovrebbe dare ulteriore impulso alla costruzione dei termovalorizzatori
binazione di tecnologie sono tecnicamente note e note sono le soluzioni ai problemi che possono generale. Inoltre sono ambientalmente sostenibili e finanziariamente convenienti. Il punto su cui si dibatte è quindi ideologico e parte dal presupposto che la progettazione di un sistema industriale e sociale basato sulla circolarità possa e debba raggiungere l’obiettivo del 100% della re-immissione nel ciclo produttivo e dei consumi delle materie utilizzate nel ciclo precedente.
Poiché si tratta di una prospettiva ideologica, altrettanto ideologicamente non possiamo che essere d’accordo sull’esigenza di puntare verso questo obiettivo ambizioso. Rimane tuttavia il fatto che le grandi trasformazioni sociali e culturali, in contesti sempre più complessi e iperconnessi, non possono avvenire in tempi brevi e, per essere ancora più precisi, mi pare difficile che avvengano in una legislatura.
Sarebbe molto più intelligente, anche ideologicamente, proporre dei percorsi che rapidamente avvicinino verso l’obiettivo più ambizioso, sapendo anche che quanto più ci si avvicina, tanto più, per la legge dei rendimenti mar-
ginali decrescenti, inevitabilmente serviranno tempi più lunghi e investimenti maggiori. Nel breve, tuttavia, per fare un esempio, la termovalorizzazione potrebbe essere combinata con altre tecnologie, come la produzione di biogas dai rifiuti biodegradabili contenuti nella porzione solida urbana. L’investimento in questi impianti consentirebbe di soddisfare gli obiettivi del Piano nazionale italiano per il clima e l’energia, che prevede l’obiettivo di produrre 7 miliardi di metri cubi di biometano entro il 2030, pari a quasi un quarto delle importazioni italiane di gas naturale dalla Russia nel 2021. Sempre a beneficio degli ambientalisti (ma a casa degli altri) la deviazione di una tonnellata di rifiuti biodegradabili dalla discarica alla digestione anaerobica per la produzione di biogas può impedire fino a 2 tonnellate di emissioni di CO2 equivalente, che non è certo un valore trascurabile.
I n definitiva, la circolarità del rifiuto è perseguibile se si è consapevoli dei tempi della sua realizzazione. L’assenza di questa consapevolezza finisce per indurre nella spirale del rifiuto per cui, a esser contrari a prescindere, si rinuncia a tutto comunque.
La circolarità del rifiuto è perseguibile se si è consapevoli dei tempi della sua realizzazione
La coltivazione di un terreno finalizzata alla produzione di biocombustibile anziché di prodotti alimentari non è vantaggiosa, né dal punto di vista economico, né da quello ambientale. Quando invece si tratta di convertire in biocarburanti gli scarti e i residui di colture già esistenti, il discorso cambia. Tuttavia, ottimizzare una catena di approvvigionamento per questi rifiuti, in modo che funzioni in termini ambientali, economici e sociali, non è semplice, come io stesso ho scoperto, in questo studio realizzato in collaborazione con i colleghi colombiani Marcela María Morales Chavez (Universidad Libre Seccional Pereira) e William Sarache (Universidad Nacional de Colombia).
I flussi che abbiamo modellizzato provengono dalle piantagioni di caffè, ma le problematiche che abbiamo analizzato sono adattabili a molti flussi originati da rifiuti reali e potenziali.
I rifiuti agricoli in questione sono generati, di solito, al momento del raccolto, anche se con alcune colture possono essercene altri, ad esempio come nel caso ci siano cicli di potatura o di diradamento. Il momento della raccolta è incerto: dipende dalle variazioni climatiche durante la stagione di crescita e, in alcuni casi, dalle condizioni del terreno;
la resa (del raccolto e degli scarti) può variare in base alle condizioni di crescita della stagione. Ma per una produzione di biocarburanti efficace dal punto di vista dei costi, i convertitori, le raffinerie e la distribuzione al dettaglio a valle richiedono un flusso equilibrato e costante di materie prime durante la “campagna”. (Una raffineria può, ovviamente, lavorare altri scarti di altre colture in periodi diversi dell’anno).
Dobbiamo quindi pianificare un flusso costante di materiale verso la raffineria per garantire che quest’ultima lavori al massimo dell’efficienza il più a lungo possibile. Ma non possiamo limitarci ad accumulare il materiale: questo ha i suoi costi e gli scarti possono deteriorarsi.
Non si tratta solo di un singolo flusso. In genere, si cerca di raccogliere e pre-trattare i rifiuti, ad esempio essiccandoli e compattandoli per rendere più efficiente il trasporto. L’ideale sarebbe trovarsi vicino all’azienda agricola o alla piantagione, ma “vicino” è un termine flessibile e può comportare il trasporto di rifiuti non trattati per molti chilometri, magari attraverso terreni difficili. Le modalità di trasporto e i veicoli che trasportano dall’azienda agricola al pre-trattamento e da quest’ultimo alla raffineria possono variare: potrebbe non essere possibile, ad esempio, utilizzare camion di grandi dimensioni in zone montuose (la qualità del caffè si degrada se le temperature sono troppo calde, quindi le migliori piantagioni, almeno in Sud America, si trovano in genere ad alcune migliaia di metri sul livello del mare).
Ci siamo quindi posti la sfida di creare un modello per le filiere dei biocarburanti basati sui rifiuti agricoli. Questo modello avrebbe tre obiettivi interconnessi: ottimizzare l’ubicazione (e il numero) dei centri di raccolta/prelavorazione e delle bioraffinerie; garantire un flusso adeguato di materiale per soddisfare la domanda in ogni fase e affrontare la pianificazione del percorso per una flotta di veicoli inevitabilmente eterogenea. Questo problema di localizzazione-inventario-indirizzamento (LIRP) è ben noto e diffuso.
Ci è parsa emergere un’ulteriore complicazione. Tutti i modelli devono fare delle ipotesi semplificative e la maggior parte della modellazione convenzionale del LIRP presuppone che le varie strutture di elaborazione siano fisse, per quanto riguarda la loro capacità fisica, la loro ubicazione e i tempi in cui sono operative. Nessuna di queste ipotesi è necessariamente vera o ottimale: un determinato flusso di rifiuti di solito aumenta, raggiunge picchi e diminuisce nell’arco di settimane o mesi, quindi non c’è alcuna ragione per cui un particolare impianto all’interno di una rete debba essere operativo all’inizio della campagna, o debba continuare fino alla fine, o non debba ridurre o aumentare la propria capacità durante la stagione. (Anche se non abbiamo considerato specificamente questo caso, è possibile che le strutture di pre-elaborazione, in particolare, possano essere mobili, spostandosi da un’azienda agricola all’altra man mano che il raccolto si sviluppa a diverse altitudini o climi. Potremmo esaminare questo aspetto in un lavoro futuro).
Ci sono quindi molte variabili, molte delle quali sono “stocastiche”, nel senso matematico: ovvero pur non essendo strettamente casuali, possono essere modellate come se lo fossero. L’approccio classico è quindi quello della programmazione non lineare a integrazione mista.
Ma c’è un problema: un approccio di questo tipo, per un problema di questa portata, richiede un’enorme quantità di potenza di calcolo e, cosa forse più importante, di tempo: non c’è alcun vantaggio nel ricavare una soluzione matematicamente ottimale per il raccolto dell’anno scorso - abbiamo bisogno di un’approssimazione vicina per la situazione di quest’anno. Abbiamo quindi sviluppato una strategia per convertire il nostro modello originale in una formulazione di programmazione lineare, con la capacità di essere efficiente in termini di tempo di esecuzione e di essere altamente competitiva, in termini di qualità della soluzione, con gli approcci di “metodo esatto”.
Il modello è necessariamente complesso, ma crediamo di aver colto l’essenziale nel modo seguente: abbiamo le quattro fasi di produzione (aziende agricole, centri di raccolta, bioraffinerie, impianti di miscelazione), molteplici tipi di rifiuti agricoli (da colture alternative, o perché i rifiuti possono essere generati sia al momento del raccolto, sia separatamente se la coltura ha una fase di potatura o diradamento), infine molteplici periodi di tempo. I fornitori (aziende agricole) non sono legati a una specifica stazione di raccolta, né a una specifica raffineria. Le decisioni che riguardano lo stoccaggio riflettono i requisiti delle raffinerie per le materie prime, ovviamente, ma anche la deperibilità o degradazione dei rifiuti in attesa di lavorazione e la capacità di stoccaggio dei centri di raccolta. Il modello riconosce anche il valore temporale del denaro e il fatto che l’aumento della capacità delle stazioni di raccolta o delle bioraffinerie può non produrre economie di scala, anzi, i costi fissi e variabili della lavorazione possono aumentare. Questo è uno dei motivi principali per cui questo problema essenzialmente non lineare deve essere “linearizzato”.
la rete basata sull’apertura, la variazione della capacità e la chiusura di impianti di raccolta/prelavorazione e bioraffinerie. Poi abbiamo ottimizzato le variabili relative al flusso dei materiali, della biomassa come input e del biocarburante come output. Ciò include la gestione dei livelli di inventario nelle stazioni di raccolta/prelavorazione e l’ottimizzazione del percorso dei veicoli per la raccolta dei rifiuti dalle fattorie/piantagioni, tra le stazioni di raccolta e le bioraffinerie e da queste alle stazioni di miscelazione (perché i biocarburanti sono raramente utilizzati “puliti”).
Possiamo quindi confrontare i nostri risultati con le soluzioni “esatte” per gli scenari specifici per vedere quanto ci avviciniamo al “vero” optimum, tenendo presente che la vita reale e la stagione del raccolto sono troppo brevi per calcolare soluzioni esatte per ogni possibile combinazione di valori delle variabili, soprattutto perché stiamo cercando di ottimizzare fattori ambientali e sociali, oltre che puramente economici - emissioni di carbonio, occupazione rurale e così via.
Abbiamo ottimizzato le variabili relative al flusso dei materiali, della biomassa come input e del biocarbu rante come output
La nostra modellazione si è rivelata molto competitiva sia in termini di tempo di calcolo che di approssimazione ai risultati calcolati “esatti”.
Forse la scoperta più importante è che una strategia dinamica degli impianti, in base alla quale i centri di raccolta e le bioraffinerie possono aprire, espandersi, contrarsi o chiudere a seconda dei casi all’interno della campagna, se può essere adeguatamente modellata e gestita, facilita davvero una maggiore produzione di biocarburanti, una supply chain più redditizia, la creazione di un maggior numero di posti di lavoro e un migliore utilizzo del territorio, in modo che la produzione di biocarburanti occupi quanto meno terreno agricolo possibile, lasciandone spazio di conseguenza alla produzione alimentare.
Per i matematici, il nostro modello di ottimizzazione è definito “NP-hard” (o NP-difficile), quindi abbiamo utilizzato un approccio euristico in due fasi. Abbiamo progettato una serie di 15 problemi o scenari su piccola, media e grande scala. Nella prima fase abbiamo definito la struttura del-
Allo stesso tempo, abbiamo anche cominciato a familiarizzare con l’impatto dell’incertezza – quella derivante dalla disponibilità di scarti agricoli – sulle performance economiche delle supply chain basate sul biocarburante che deriva dai rifiuti. Questo suggerisce alcune linee di ricerca per il futuro, in particolare per coprire le aree di input che oggi sono particolarmente carenti di dati, come ad esempio la domanda di mercato verso i biocarburanti o i tassi di conversione dei carburanti in generale.
Terza e ultima parte:
Analisi della norma ISO 9001.2015 – requisiti 8-10
Prima parte: pubblicata su Chimica Magazine di aprile 2022
Seconda parte: pubblicata su Chimica Magazine di ottobre 2022
Nei numeri scorsi, abbiamo cominciato ad esaminare singolarmente i requisiti della norma ISO 9001.2015 suddivisi secondo il ciclo di Deming PDCA PlanDo-Check-Act. Nella seconda parte dell’articolo sono stati analizzati i requisiti da 4 a 7, corrispondenti a tutte le attività di pianificazione, mentre i requisiti da 8 a 10 (Do, Check, Act) sono approfonditi nelle pagine che seguono
La struttura della norma ISO 9001.2015 si può sovrapporre al ciclo di Deming PDCA, quindi Plan-Do-Check-Act, come si vede nell’immagine accanto (Figura 8): questa sintetizza il ciclo completo con i sette titoli dei capitoli in cui la norma è suddivisa, da 4 a 10, e come questi sono inseriti nel ciclo. Questo è il quadro generale che consente ai requisiti dei clienti di trasformarsi in soddisfazione. Nelle pagine che seguono, riprendiamo il discorso dal punto 8, quello relativo al Fare; i requisiti da 4 a 7, corrispondenti a tutte le attività di pianificazione, sono stati pubblicati sul numero di ottobre di Chimica Magazine.
La norma prescrive cosa e come si deve realizzare ciò che si è pianificato nei requisiti da 4 a 7. Il paragrafo 8.1: controllo operativo della pianificazione. Per realizzare ciò, la norma prescrive che “L’organizzazione deve pianificare, attuare e controllare i processi (controllati) necessari a soddisfare i requisiti di fornitura di prodotti e servizi e ad attuare le azioni determinate al punto 6”, determinando i requisiti per i prodotti e servizi; stabilendo i criteri per i processi; mettendo a disposizione le risorse necessarie per garantirne la conformità. Per realizzare ciò in pratica i processi chiave, quelli ausiliari e quelli di misura e controllo pianificati, possono esse tenuti sotto controllo utilizzando schemi operativi per la produzione, stabilendo cicli di lavoro (anche per i cantieri esterni), individuando
responsabili e dotando i processi di chiari indicatori di efficienza ed efficacia. Anche per questo requisito è obbligatorio mantenere informazioni documentate (R).
Il paragrafo 8.2 tratta dei requisiti per prodotti e servizi. Riveste grande importanza la comunicazione con il cliente sui prodotti/servizi, il che comporta una chiara produzione di informazioni tecniche e commerciali (dépliant, cataloghi, modalità di impiego, listini prezzi ecc.) e una profonda preparazione e conoscenza per tutti i componenti del front line; la comunicazione prevede anche un feedback da parte dei clienti che possono essere una preziosa fonte di informazioni, utili per comprendere le loro opinioni e percezioni, per reagire tempestivamente ai reclami e alle eventuali azioni di emergenza.
È inoltre consigliabile operare un riesame dei requisiti relativi ai prodotti e servizi, ad opera dei collaboratori
tecnico commerciali. La norma non impone una metodo se non quello di documentare come l’organizzazione prepara le offerte, elabora gli ordini/ contratti, comunica le conferme d’ordine. Di tutto ciò è necessari dare evidenza con informazioni documentate (R). Se avvenissero dei cambiamenti ai requisiti di prodotto e servizio, “l’organizzazione deve assicurare che le pertinenti informazioni documentate siano modificate e che il personale interessato sia informato dei requisiti modificati”.
Il paragrafo 8.3: progettazione e sviluppo di prodotti e servizi, recita “L’organizzazione deve stabilire, attuare e mantenere un processo di progettazione e sviluppo appropriato ad assicurare la successiva fornitura di prodotti ed erogazione di servizi”, considerando la natura della progettazione e delle attività di sviluppo; il processo controllato di progettazione
Se un processo, o parte di un proces so, è fornito da un fornitore esterno, anche in questo caso l’organizzazione se
(process owner, risorse a disposizione, descrizione attività, controlli, coinvolgimento di partner e collaboratori esterni, eventuali modifiche ecc). L’organizzazione è tenuta a dotarsi di informazioni documentate (R) necessarie per confermare che e come i requisiti dello sviluppo e di progettazione siano stati soddisfatti.
Il paragrafo 8.4: outsourcing, afferma che “l’organizzazione deve assicurare che i processi affidati all’esterno, e i relativi prodotti e servizi siano conformi ai requisiti specificati”, qualora i prodotti e i servizi forniti da fornitori esterni siano incorporati nei propri prodotti e servizi dell’organizzazione o forniti direttamente al cliente. Inoltre se un processo, o parte di un processo, è fornito da un fornitore esterno, anche in questo caso l’organizzazione se ne deve assumere la responsabilità.
Il paragrafo 8.5: produzione ed erogazione dei servizi. “L’organizzazione deve attuare produzione e erogazione di servizi in condizioni controllate”. È pertanto necessario fornire informazioni documentate sulle caratteristiche dei prodotti e dei servizi, le attività da svolgere e i risultati da raggiungere; è fatto obbligo di documentare le attività di monitoraggio e di misurazione nelle fasi appropriate per verificare che i criteri di controllo dei processi e gli output di processo. Bisogna in-
fine specificare la struttura del processo di fornitura, la validazione, e rivalidazione periodica, della capacità di conseguire i risultati pianificati dei processi di produzione e di erogazione di servizi, l’attuazione di azioni atte a prevenire l’errore umano, l’implementazione della distribuzione/rilascio di prodotti e servizi, consegna e le attività post-consegna. Questo requisito richiede la disponibilità di informazioni documentate (R) che definiscano le attività da svolgere e i risultati da raggiungere.
La norma prevede anche la necessità di identificazione e rintracciabilità. “L’organizzazione deve utilizzare mezzi idonei per identificare gli output, quando ciò è necessario per assicurare la conformità dei prodotti e dei servizi”. “Si tratta di identificare, verificare, proteggere e salvaguardare la proprietà del cliente o del fornitore esterno, per l’uso o incorporazione in prodotti e servizi. Le proprietà che appartengono a clienti o fornitori possono essere assai differenti in funzione dei diversi contesti applicativi delle organizzazioni”.
Il paragrafo 8.6: il rilascio di prodotti e servizi al cliente non deve avvenire fino a quando le modalità previste per la verifica della conformità siano state completate in modo soddisfacente. Le informazioni documentate (R) devono fornire l’evidenza della conformità ai criteri di accettazione e la tracciabilità della/e personale che autorizza il rilascio di prodotti e servizi per la consegna al cliente.
Il paragrafo 8.7: si riferisce al controllo degli ouput non conformi, l’organizzazione deve deve pertanto assicurare che l’output di processo, prodotti e servizi che non sono conformi ai requisiti siano stati identifi-
cati e controllati per impedirne l’uso non intenzionale o la consegna. Tali non conformità devono essere gestite attraverso opportune azioni basate sulla natura della non conformità stessa e dei suoi potenziali effetti. Le non conformità devono essere gestite correttamente, ciò significa che devono essere esplicitati tutti gli scostamenti riscontrati nel controllo degli output, devono essere tenute le registrazioni delle non conformità, parti non conformi devono essere segregate. Questo vale anche per i prodotti e i servizi non conformi rilevati dopo la consegna dei prodotti o durante la fornitura del servizio non conforme.
Passiamo alla prossima fase del ciclo di Deming: check.
Il paragrafo 9.1: monitoraggio, misurazione, analisi e valutazione prescrive che l’organizzazione determini che cosa, come, quando il monitoraggio e le misurazioni devono essere effettuate e come analizzare i risultati di tale valutazione; deve inoltre tenere evidenza per mezzo di informazioni documentate (R) i risultati rilevati e i miglioramenti eventualmente operati.
Particolare importanza è la misurazione della soddisfazione del cliente riguardo a come le sue esigenze e aspettative sono state percepite e realizzate. Le informazioni raccolte in modo diretto e/o indiretto devono essere opportunamente analizzate e formeranno la base su cui lavorare per realizzare l’obiettivo del miglioramento continuo. I punti di misura suggeriti dalla norma riguardano la conformità dei prodotti e dei servizi, le prestazioni e l’efficacia
ne deve assumere la responsabilità
del SGQ, la completezza della pianificazione, il modo di affrontare rischi per trasformarli in opportunità, le prestazioni dei fornitori esterni, le aree di miglioramento individuate e i punti di forza. E infine i metodi statistici eventualmente utilizzati.
Il paragrafo 9.2: audit interno. La norma recita: “L’organizzazione deve condurre audit interni ad intervalli pianificati per fornire informazioni se il SGQ è conforme ai requisiti definiti dall’organizzazione e se è efficacemente attuato e mantenuto”. Come realizzare l’obiettivo è analizzato nella ISO 1901.
Un efficace audit deve essere condotto in modo imparziale e i risultati devono essere condivisi da chi partecipa all’audit, vale a dire l’auditor (in generale il responsabile della qualità o un suo collaboratore) e il responsabile dell’ufficio sottoposto all’indagine. L’incontro deve essere pianificato, comunicato e deve essere rispettato il programma di audit che includa la frequenza, i metodi, le responsabilità, i requisiti di pianificazione e reporting, e che prenda in considerazione l’importanza dei processi interessati, i cambiamenti che impattano sull’organizzazione e i risultati degli audit precedenti. È necessario che siano definiti e comunicati i criteri e lo scopo. Le azioni di miglioramento individuate devono essere concordate e attuate senza ingiustificato ritardo. Devono infine essere protocollate informazioni documentate (R) come evidenza dell’attuazione del programma di audit e dei suoi risultati.
Paragrafo 9.3 il riesame della direzione è in momento fondamentale per operare un check veramente utile ed efficace. Viene effettuato ad intervalli programmati, in genere all’inizio
TECNOLOGIA
Nuova
Vicina a quella esistente
SEMIRADICALE RADICALE
INCREMENTALE SEMIRADICALE
Vicino a quella esistente Nuovo MODELLO DI BUSINESS
dell’anno sociale e deve (input) “essere pianificato e condotto prendendo in considerazione lo stato delle azioni definite nei precedenti riesami della direzione, i cambiamenti nelle questioni interne ed esterne che sono rilevanti per il SGQ, compresa la sua direzione strategica e le informazioni sulla qualità delle prestazioni; gli output del riesame della direzione devono comprendere le decisioni concrete e le azioni relative alle opportunità di miglioramento continuo. Può comprendere eventuali modifiche al SGQ, deve indicare e mettere a disposizione le risorse, economiche, tecniche e stabilire chi fa che cosa. L’organizzazione deve conservare informazioni documentate (R) come evidenza dei risultati del riesame. Ultimo argomento per chiudere il ciclo di Deming è la fase Act.
Il paragrafo 10.1 recita “l’organizzazione deve individuare e selezionare le opportunità di miglioramento e attuare le azioni necessarie per soddisfare i requisiti del cliente e accrescerne la soddisfazione”. Il miglioramento può essere effettuato in modo reattivo (ad esempio, azione correttiva), in modo incrementale (ad esempio il miglioramento continuo), dal cambiamento radicale (ad esempio breakthrough), innovazione o riorganiz-
zazione. La grande novità che appare è il concetto di innovazione che non è solo un semplice cambiamento, ma è un concetto che, come mostrato in figura 13, matrice dell’innovazione, coinvolge sia la tecnologia che il modello di business.
Oggi una qualsiasi organizzazione, se vuole “sopravvivere”, non deve solo migliorare ma deve innovare.
Abbiamo voluto mostrare che cosa bisogna fare per ottenere la certificazione di qualità, seguendo la norma ISO; è chiaramente un percorso impegnativo ma, se ben eseguito, può abbattere i costi della “non qualità”. Ci domandiamo ora: se seguiamo la norma, siamo sicuri di essere una organizzazione eccellente? La risposta è complessa: una organizzazione eccellente deve essere in grado di misurare il suo livello di qualità.
La certificazione assicurerà gli stakeholder sull’applicazione della normativa, ma solo il confronto con un modello di eccellenza potrà dire con buona approssimazione a quale livello di eccellenza è stato raggiunto e quali sono i tuoi punti di forza e le aree da migliorare. Ciò comporta una autovalutazione che l’organizzazione sarà in grado di effettuare applicando il modello. Quello oggi maggiormente usato è il modello EFQM (European Foundation for Quality Management).
A conclusione di questa rubrica dedicata all’impatto dei brevetti sull’industria chimica, proponiamo un esempio pratico, quello della produzione dell’ammoniaca, uno dei maggiori composti chimici realizzati a livello globale, utilizzato prevalentemente nel settore dei fertilizzanti ma anche come efficace vettore energetico. La ricerca dei brevetti su questo tema fornisce utili informazioni sullo stato dell’arte di questo materiale e della sua filiera
ammoniaca è uno dei prodotti di sintesi più importanti, attestandosi come il secondo maggiore composto chimico realizzato a livello globale, con 150/160 milioni di tonnellate annue prodotte. Circa l’80% dell’ammoniaca generata è utilizzata nell’industria dei fertilizzanti e per sintetizzare compositi azotati, come l’urea. L’ammoniaca è ossidata ad acido nitrico che, fatto reagire con ammoniaca, produce il nitrato d’ammonio. [1]
Avendo un contenuto d’idrogeno pari al 17,6% in peso e non contenendo carbonio, l’ammoniaca è anche considerata un promettente vettore energetico.
L’ammoniaca è comunemente prodotta tramite il processo Haber-Bosch, che si basa sulla reazione tra idrogeno e azoto in fase gassosa (miscelati in un rapporto 3:1) su catalizzatori a base di ferro, a temperature (400 –530 °C) e pressioni elevate (100-250 bar).
La reazione da considerare è la seguente: 3 H2 + N2 2 NH3
L’idrogeno è prodotto in impianti di steam reforming del metano, mentre l’azoto deriva da impianti di reforming secondario. Sebbene si tratti di una reazione esotermica (ΔH° = -91,8 kJ/mol), il triplo legame dell’azoto richiede un’elevata energia di dissociazione (941 kJ/ mol). Da un punto di vista termodinamico, questa reazione richiede una bassa temperatura e un’elevata pressione per poter fornire rese accettabili, ma da un punto di vista cinetico sono necessarie temperature elevate. Per la produzione di ammoniaca su scala industriale si utilizzano catalizzatori a base di ferro [in particolare di magnetite (Fe3O4)] e alluminio, potassio, calcio e ossidi metallici (Al2O3, K2O) come promotori (aumentano la stabilità termica del ferro verso la sinterizzazione), wustite, rutenio supportato su grafite (Ru/C), MgO, γ-Al2O3, γ-Al2O3 -KOH (con bario e cesio come promotori), o di cobalto o nichel, con una percentuale di conversione del 10-15%.
L’elevato costo del rutenio e la sua bassa stabilità[1] rende ancora preferibile l’uso di catalizzatori a base di ferro, almeno da un punto di vista industriale. [2] Recentemente sono stati testati, come supporti del rutenio, i cosiddetti elettruri (C12A7:e-,
L’AUTORE:
Massimo BarbieriLaureato in chimica nel 1993, lavora al Politecnico di Milano (Technology Transfer Office) come tecnico (D3 – Senior Specialist) nell’ambito della tutela della proprietà industriale: valutazione delle invenzioni (principalmente nel settore della chimica e dell’ingegneria chimica), ricerche brevettuali e contratti di licenza.
Nel 2019 ha conseguito la certificazione QPIP (Qualified Patent Information Professional https://www.qpip.org/qpips/190).
E-mail: massimo.barbieri@polimi.it
cl = "C01C1/02/low" AND ftxt = "Ca2N:e-"
cl = "C01C1/02/low" AND ftxt = "C12A7:e-"
cl = "C01C1/02/low" AND ftxt = "Y5Si3" 3
cl = "C01C1/02/low" AND ftxt = "LaScSi" 3
cl = "C01C1/02/low" AND ftxt = "LaRuSi" 1
Ca2N:e-1, Y5Si3, LaScSi, LaRuSi, CeRuSi), ossia composti ionici O2- in cui gli elettroni agiscono come anioni; purtroppo, la loro limitata area superficiale non li rende utili da un punto di vista pratico. [3]
Le ricerche brevettuali sono state eseguite con Espacenet (https://worldwide.espacenet.com) e Orbit Intelligence (database FamPat, https:// www.orbit.com), utilizzando sia parole chiave sia codici di classificazione. L’elenco dei simboli di classificazione e delle stringhe di ricerca è riportato nel dataset [4], nel file di testo README. I principali codici di classificazione sono i seguenti: C01C 1/02 (Preparazione di ammoniaca), C01C 1/04 (Preparazione di ammoniaca mediante sintesi in fase gassosa), C01C 1/405 (Preparazione di ammoniaca mediante sintesi in fase gassosa da azoto e idrogeno in presenza di un catalizzatore) e C25B 1/27 (Produzione elettrolitica di ammoniaca).
Dall’analisi dei brevetti risulta che i metodi termocatalitici, in particolare il processo Haber-Bosch, sono ancora i più rivendicati; a seguire i metodi elettrocatalitici, mentre quelli fotocatalitici e sul looping chimico dimostrano una tendenza in decrescita (v. Figura 1).
Per quanto concerne i brevetti sui sistemi catalitici, quelli a base di ferro (Fe3O4, Fe1-xO, Fe2O3) con promotori quali K2O, BaO e Al2O3 sono i più numerosi, seguiti da rutenio, cobalto, nichel e nitruri metallici (v. Figura 4, dove i dati sono stati elaborati utilizzando la seguente stringa di ricerca: cl = “C01C1/02/low” AND claims =
“Metal” e filtrando i risultati per data di pubblicazione a partire dal 2015). Risultati pressoché analoghi si sono ottenuti con la banca dati Orbit (v. Figura 5): in questo caso, al posto delle parole chiave, sono stati utilizzati solo i codici di classificazione. Da notare che la magnetite è l’ossido di
ferro che ricorre maggiormente. Per quanto riguarda l’uso degli elettruri, la ricerca brevettuale su Espacenet ha fornito pochi risultati, che sono riassunti nella Tabella 1 e dove il codice di classificazione (IPC/CPC) C01C 1/02 si riferisce ai metodi di produzione dell’ammoniaca.
La sintesi dell’ammoniaca a bassa temperatura rimane una delle sfide che la catalisi dovrà affrontare, a causa della natura inerte dell’azoto. I sistemi catalitici a base di ferro, oggi i più comunemente utilizzati industrialmente, non sono in grado di lavorare alle temperature di reazione del rutenio, che però è molto costoso. Temperature inferiori ai 300° C possono essere raggiunte utilizzando sistemi a base di nichel supportati su LaN o BaH2 oppure a base di cobalto. [5]
Supporti in grado di aumentare l’attività catalitica sono ossidi di terre rare, quali CeO2, La2O3 e Pr2O3, sotto forma di nanoparticelle. [6]
L’analisi brevettuale ha dimostrato questa tendenza allo sviluppo di sistemi catalitici alternativi a quelli a base di ferro e rutenio.
Tra i metodi di produzione dell’ammoniaca, oltre ai processi termocatalitici, si segnala un incremento nel numero di brevetti relativi ai processi elettrocatalitici.
[1] A. E. Yüzbasıoglu et al., Curr. Res in Green and Sus. Chem., 5, 100307 (2022)
[2] P. Puspitasari, N. Yahya, 2011 National Postgraduate Conference (2011) doi: 10.1109/NatPC.2011.6136449
[3] J.A. Faria, Curr. Opin. Green Sustain. Chem., 29, 100466 (2021)
[4] M. Barbieri, “Data for: Industrial synthesis of ammonia”, Mendeley Data, V1, doi: 10.17632/r2gyg24frj.1 (2022)
https://data.mendeley.com/datasets/ r2gyg24frj
[5] J. Humphrey et al., Adv. Energy Sustainability Res., 2, 2000043 (2021)
[6] J. Feng et al., Catal. Sci. Technol., 11, 6330-6343 (2021)
Hörmann propone i nuovi portoni scorrevoli tagliafuoco OD, ideali per tutte le aree - commerciali, industriali, agricole, hospitality o pubbliche - in cui si voglia proteggere persone, spazi e oggetti non solo dal fuoco ma anche dalla diffusione di gas potenzialmente letali, in caso di incendio. Realizzati in acciaio e in acciaio inox, questi modelli sono presentati a uno e due battenti, nonché in esecuzione telescopica. Proposti in versione antincendio ignifuga (El 2 30) come anche incombustibile (El 2 60, El 2 90 e El 2 120), i nuovi portoni dispongono del marchio CE e
Wolters Kluwer Tax & Accounting Italia amplia la dotazione del suo ERP Arca Evolution con un nuovo modulo che consente il dialogo automatizzato a due vie tra il gestionale e le macchine o gli impianti di produzione e logistici. L’azienda ha sviluppato il nuovo modulo del suo principale gestionale Arca Evolution, partendo dalla necessità per le PMI italiane di poter contare su strumenti digitali dall’acclarata semplicità d’uso e universalità di adozione proprio per poter contare su uno strumento ideale anche nell’alveo di Industry 4.0.
soddisfano pienamente le normative EN 16034 ed EN 13241, valide a livello europeo. Idonee per rispondere ad ogni necessità, le chiusure OD sono disponibili, a richiesta, nell’esecuzione tagliafumo (S 200) o a chiusura ermetica (S a) e possono essere dotate di portina pedonale inserita, con o senza soglia (solitamente equipaggiata con chiudiporta aereo su guide di scorrimento), per facilitare il passaggio pedonale e il transito con carrelli di trasporto.
industria farmaceutica deve oggi affrontare diverse sfide per riuscire a soddisfare i rigorosi requisiti che vengono imposti alle aziende. Le imprese che producono e commercializzano farmaci devono infatti garantire la loro conformità agli standard GMP (Good Manufacturing Practice). A questo proposito, Klüber Lubrication ha sviluppato una vasta gamma di prodotti volti a rispondere alle esigenze tecniche del settore, quali ad esempio un’ottima resistenza alle temperature elevate e alle possibili contaminazioni dovute a sostanze chimiche.
Oltre ad essere registrati dalla NSF (National Sanitary Foundation), i prodotti sono omologati NSF H1 e conformi agli standard GMP e NSF ISO 21469. Queste soluzioni offrono diversi vantaggi tra cui: una maggiore produttività dovuta al prolungamento della vita utile delle applicazioni, una durata superiore dei componenti grazie ad un’elevata protezione antiusura e un funzionamento più affidabile dell’impianto industriale. Un esempio di particolare rilevanza che mostra l’efficacia dei prodotti di Klüber Lubrication riguarda lo sviluppo del Klüberpharma UH1 4-220, un olio lubrificante nato appositamente per rispondere alle esigenze di un’azienda farmaceutica che non riusciva a trovare sul mercato una soluzione adeguata al raggiungimento dei propri obiettivi: conformità alle norme FDA, garanzia di non contaminazione del farmaco in compressa, proprietà anticorrosive e la riduzione dei tempi di inattività del macchinario causati da danneggiamento o da impurità sui pistoni. Il macchinario su cui era necessario intervenire era una comprimitrice che produce fino a 400.000 capsule all’ora e che richiede una corretta lubrificazione dei punzoni. Il Klüberpharma UH1 4-220 è un olio lubrificante sintetico studiato appositamente per la lubrificazione dei punzoni in acciaio nelle presse per compresse farmaceutiche. Questo lubrificante offre un’ottima resistenza al bronzo e una buona protezione antiusura, prolungando al contempo la vita utile dei componenti. In seguito al suo utilizzo, nel caso in oggetto, è stato dunque possibile evitare contaminazioni del farmaco e ridurre i fermi macchina dovuti all’usura meccanica del pistone. In questo modo, l’azienda è stata in grado di ridurre i costi operativi, nonché di estendere gli intervalli di manutenzione e di cambio dell’olio.
Sick propone un innovativo interblocco di sicurezza che, attraverso la RFID e un raggio di attuazione continuo di 180º, offre un’elevata flessibilità nell’installazione sicura di porte, sportelli e cancelli, anche con apertura ridotta. Il sistema di montaggio del dispositivo è stato progettato ricercando semplicità e facilità di integrazione nelle macchine, anche in caso porte scorrevoli. Il sensore flexLock offre un elevato grado di sicurezza grazie al perfomance level e per il monitoraggio di porte e serrature, con una scelta di grado di codifica basso o alto. L’elevata forza di tenuta fino a 3.150 N assicura che la porta rimanga bloccata in modo sicuro e affidabile fino a quando non vi è alcun pericolo per le persone o il processo di produzione. Conformemente alla norma EN ISO 14119, flexLock offre un’elevata protezione contro le manomissioni grazie al suo elevato livello di crittografia. Il sensore ha un grado di protezione IP67 e IP69K.
Emerson annuncia l’evoluzione dell’ecosistema digitale Plantweb che integrerà la gamma di soluzioni software per l’ottimizzazione degli asset basate sull’intelligenza artificiale di livello industriale di AspenTech, per creare il portafoglio di trasformazione digitale più completo del settore. L’ecosistema digitale Plantweb di Emerson, ottimizzato da AspenTech, consente ai produttori industriali di tutti i settori di “vedere, decidere, agire e ottimizzare” le proprie operazioni. Grazie a una robusta suite di sensori, software e tecnologie di controllo, Plantweb ora consente alle imprese di ottimizzare le prestazioni, in termini di produttività e sostenibilità, dei propri impianti o dell’intera azienda mediante sofisticati software per l’ottimizzazione degli asset e delle operazioni.
SI PARLA DI
Achema 10-13
A&T Automation & Testing 8 AQM 4
Caast 41-43 CPM 21-23 Dürr 21-23 Ecomondo 4
Emerson 63 ENEA 5, 44-46 Epson 24-26 Fiat 21-23 Hera 4 Honeywell 8, 9, 36-40 Hörmann 62 IEG 4
Klüber Lubrication 62
Marchesini 24-25 Sew Eurodrive 21-23 Sick 63 Socomec 28-31 TeaTek 5 Terranova 32-35 Weaream 4 Wolters Kluwer 62
A&T Automation & Testing 2
CiaoTech PNO 27 Plannet IV C. Texpack 5 TSC 63
https://www.aetevent.com/fiera-torino 22-02-2023 24-02-2023 Italia Torino COSMOPACK www.cosmoprof.com 16-03-2023 18-03-2023 Italia Bologna K.EY (KEY ENERGY) www.keyenergy.it 22-03-2023 24-03-2023 Italia Rimini ENERGY MED NAPOLI www.energymed.it 30-03-2023 01-04-2023 Italia Napoli
A&T Automation & Testing
WASTE MANAGEMENT EUROPE wme-expo.com 18-04-2023 20-04-2023 Italia Bergamo LOGIPHARMA LIONE https://logipharmaeu.wbresearch.com/ 25-04-2023 27-04-2023 Francia Lione
OMC 2023 www.omc.it 23-05-2023 25-05-2023 Italia Ravenna POWTECH 2023 www.powtech.de 26-09-2023 28-09-2023 Germania Norimberga
BFWE Accadueo, ConferenzaGNL, Hydrogen Energy Summit&Expo, CH4, Fuels Mobility, Dronitaly www.bfwe.it 11-10-2022 13-10-2022 Italia Bologna
A&T NORD EST 2023 https://vicenza.aetevent.com/ 25-10-2023 27-10-2023 Italia Vicenza
REFRIGERA https://refrigera.show/ 07-11-2023 09-11-2023 Italia Bologna
L’efficienza della gestione dei processi sanitari www.logfarma.it 09-11-2023 09-11-2023 Italia Sesto S.G. (MI)
IVS INDUSTRIAL VALVES SUMMIT 2024 https://industrialvalvesummit.com 15-05-2024 16-05-2024 Italia Bergamo
ACHEMA 2024 www.achema.de 10-06-2024 14-06-2024 Germania Francoforte
VALVE WORLD EXPO www.valveworldexpo.com 29-11-2022 01-12-2022 Germania Düsseldorf
Pubblicazione registrata presso il Tribunale di Milano n° 302 del 5 dicembre 2016
DIRETTORE RESPONSABILE
Ernesto Salvioli
DIRETTORE EDITORIALE
Cecilia Biondi
REDAZIONE
Michela Del Pizzo press@editricetemi.com
HANNO COLLABORATO A QUESTO NUMERO
Giovanni Abramo, Massimo Barbieri, Marco Colombini, Maurizio Carpigiani
DIREZIONE MARKETING
Anna Dall’Osso anna.dallosso@editricetemi.com
PUBBLICITÀ advertising@editricetemi.com
Paola Cuzzolin
STAMPA
Aziende Grafiche Printing Srl
Via Milano 3/5 - 20068 Peschiera Borromeo (MI)
Chimica Magazine
è una rivista bimestrale e viene distribuita in abbonamento. Testi e disegni: riproduzione vietata. Pubblicità: inferiore al 50%.
Italia quota annua 25,00 euro
Versamento in conto corrente postale intestato a: Editrice TeMi Srl n. 37982204
Versamento in conto corrente bancario intestato a: Editrice TeMi Srl, c/o Deutsche Bank – IBAN IT04 P031 0420 4000 0000 0820 652
EDITRICE TEMI SRL
Sede legale: Via Vittorio Emanuele II, 36 – 20900 Monza (MB) Direzione, redazione, amministrazione, pubblicità: Corso Milano 19 – 20900 Monza (MB) Tel. 039 2302398 – Fax 039 2302383 press@editricetemi.com
Presidente Ernesto Salvioli Amministratore delegato Pietro Salvioli
Editrice TeMi Srl con sede legale in Monza (MB) e sede operativa in Monza (MB) Corso Milano, 19, CF e Partita IVA 11489470150 (in seguito “Titolare”), in qualità di Titolare del trattamento, ai sensi dell’art. 13 D.Lgs 30/06/2003 n.196 (in seguito “Codice Privacy”) e dell’art. 13 Regolamento UE n. 6016/679 (in seguito“GDPR”) garantisce la massima riservatezza dei dati da lei forniti. Con il conferimento dei suoi dati, esprime il suo specifico consenso al loro trattamento per gli scopi legati al servizio richiesto (Servizio) che Editrice TeMi Srl fornisce. Responsabile del trattamento è il legale rappresentante di Editrice TeMi Srl, Corso Milano, 19 20900 Monza (MB). I dati personali forniti per l’erogazione del servizio sono trattati con modalità elettroniche e cartacee, esclusivamente per l’attivazione e la gestione del servizio e per le operazioni contabili e di fatturazione. Per tale finalità, il conferimento dei dati è obbligatorio: in loro assenza non è possibile fornire il servizio. Al suddetto responsabile è possibile rivolgersi per esercitare diritti che la normativa sulla privacy in vigore riconosce (accesso, rettifica, integrazione, cancellazione dei dati, opposizione al trattamento, ecc.) nonché per conoscere l’elenco aggiornato degli ulteriori responsabili del trattamento e le categorie di soggetti ai quali i dati personali possono essere comunicati o che possono venirne a conoscenza. Con il conferimento dei dati, Editrice TeMi Srl potrà utilizzare i dati forniti anche per finalità promozionali proprie e di terzi mediante sistemi cartacei e/o automatizzati (quali per esempio fax, email, sms, ecc.). Le segnaliamo che se siete già nostri clienti e/o lettori e/o avete partecipato a nostri eventi, potremo inviarle comunicazioni commerciali relative a servizi e prodotti del Titolare analoghi a quelli di cui ha già usufruito, salvo Suo dissenso (art. 130 c. 4 Codice Privacy). Attraverso il conferimento dei suoi dati personali conferma anche di aver letto l’informativa GDPR sul trattamento dei dati, pubblicata su www.chimicamagazine.com. Potrà chiedere ogni informazione scrivendo a amministrazione@editricetemi.com
COMPASS 10 is the innovative digital platform for supply chain advanced planning, finite capacity scheduling and production real-time control. Developed according to a modular approach, guarantees maximum scalability and flexibility to meet the specific requirements of every company context.
Simple solutions for complex scenarios. Total control and monitoring in real-time.
FINITE
More efficiency, better service. Monitor, analyze and optimize energy consumption.