LINEAR MOTION: Linear actuators power mobile machinery
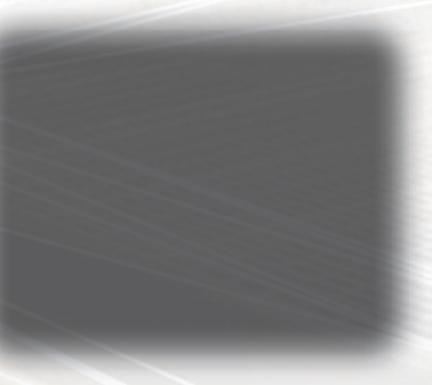
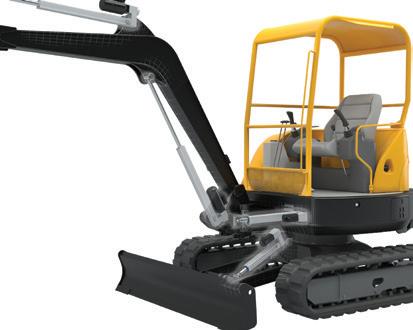
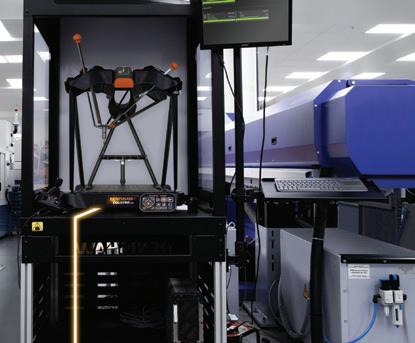
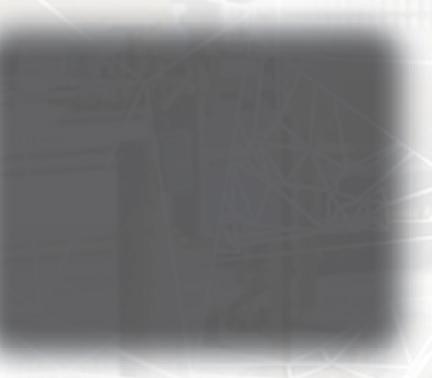
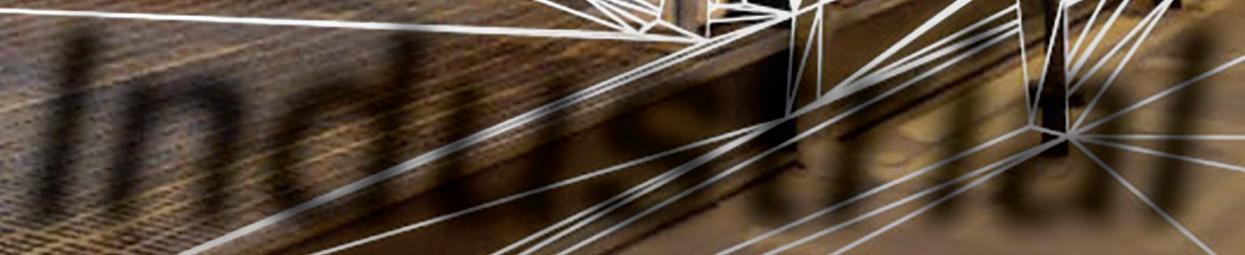
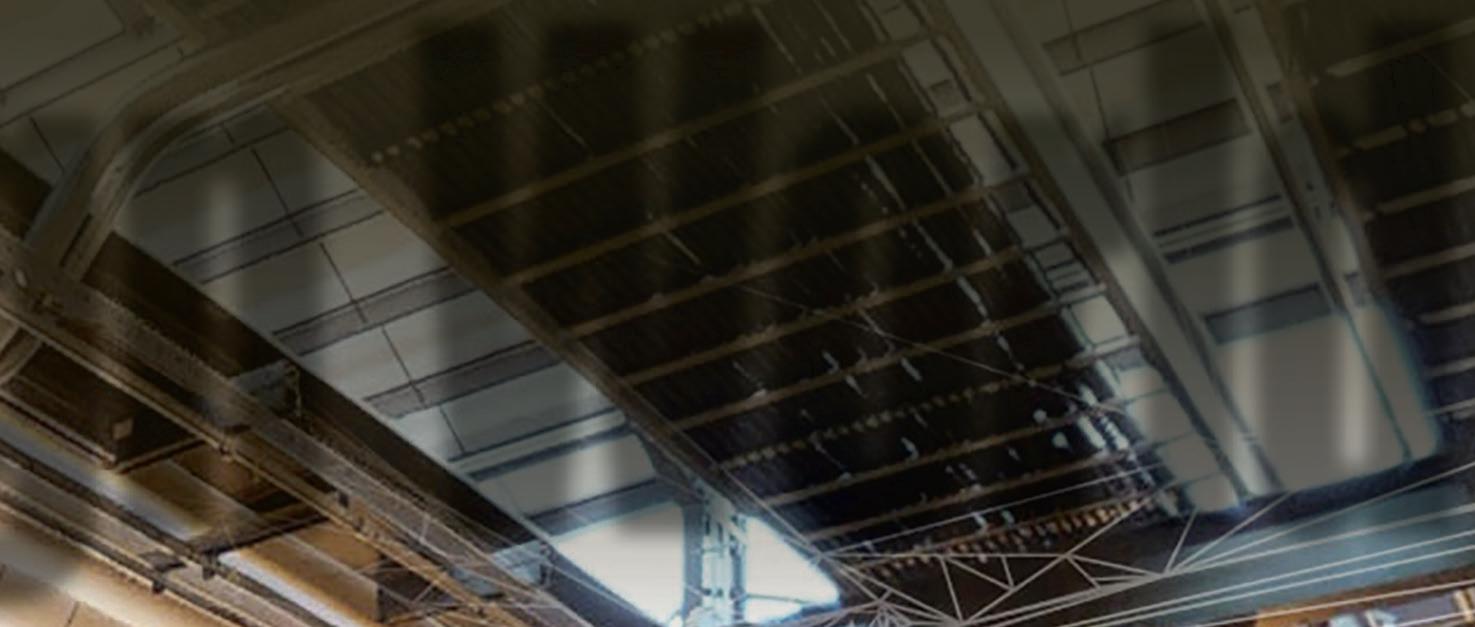
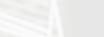


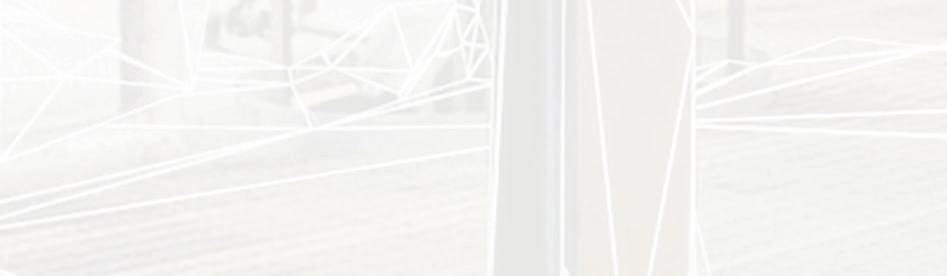
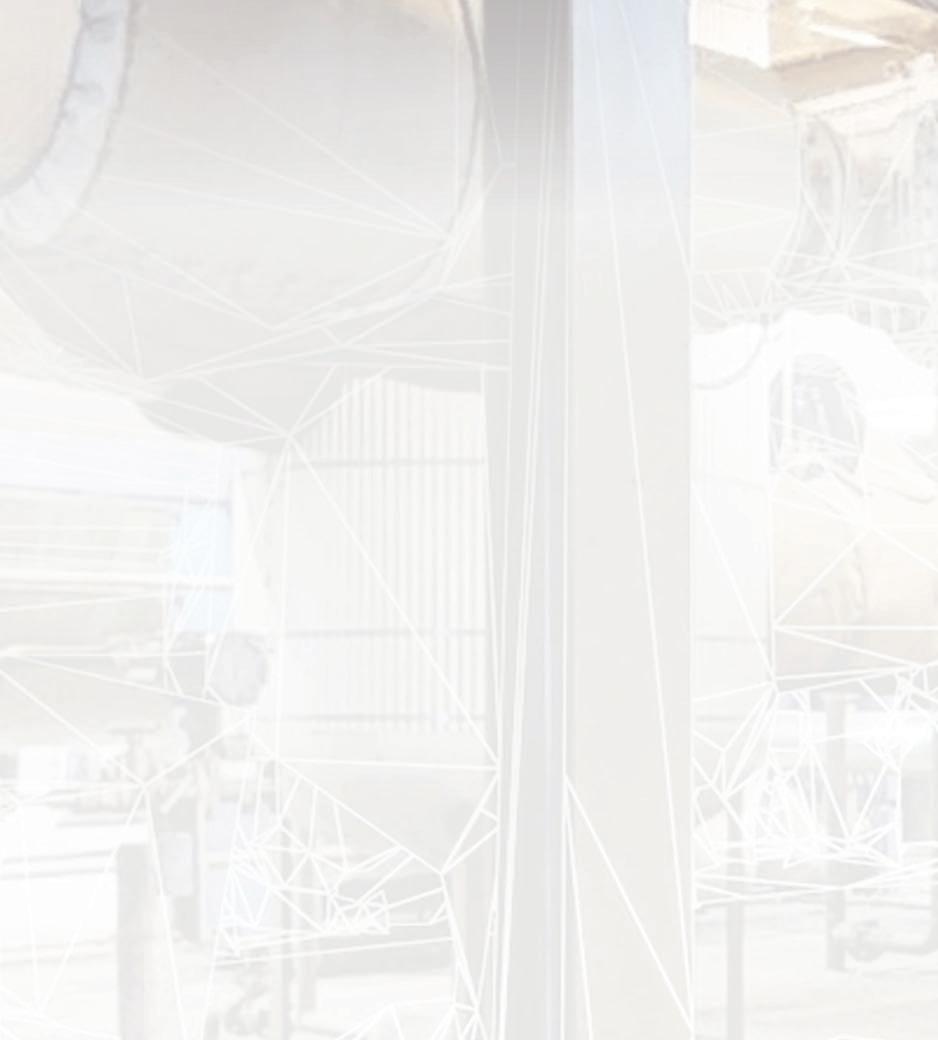
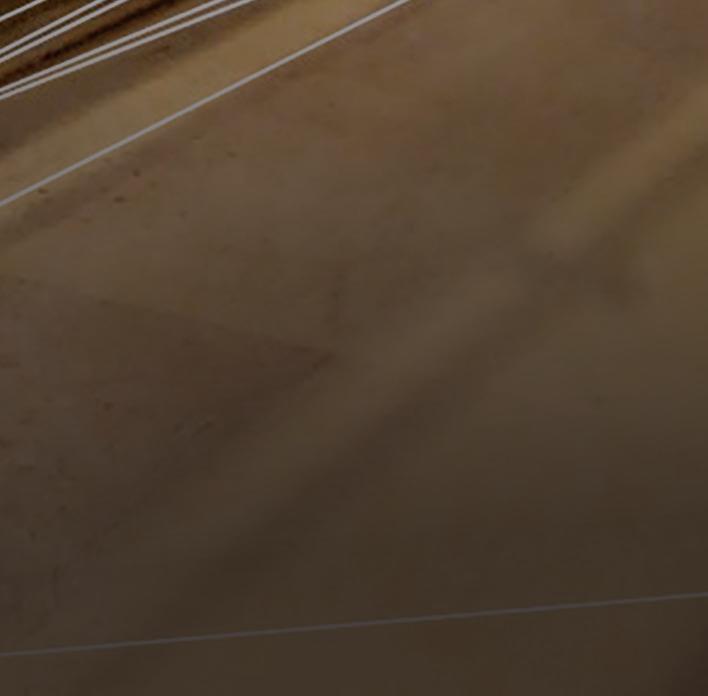
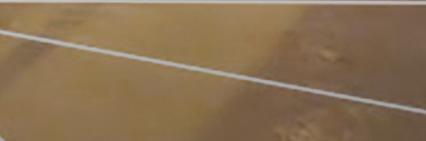
p. 46

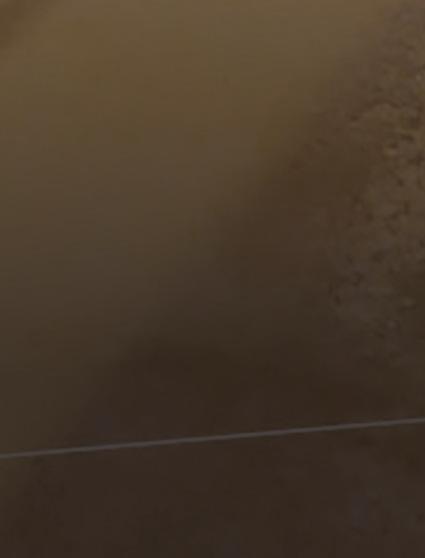
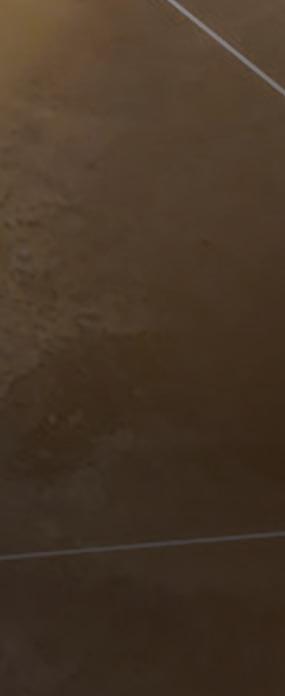
DIGITAL
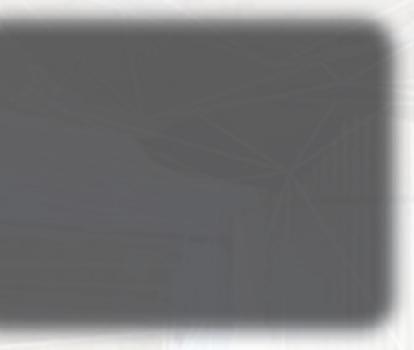
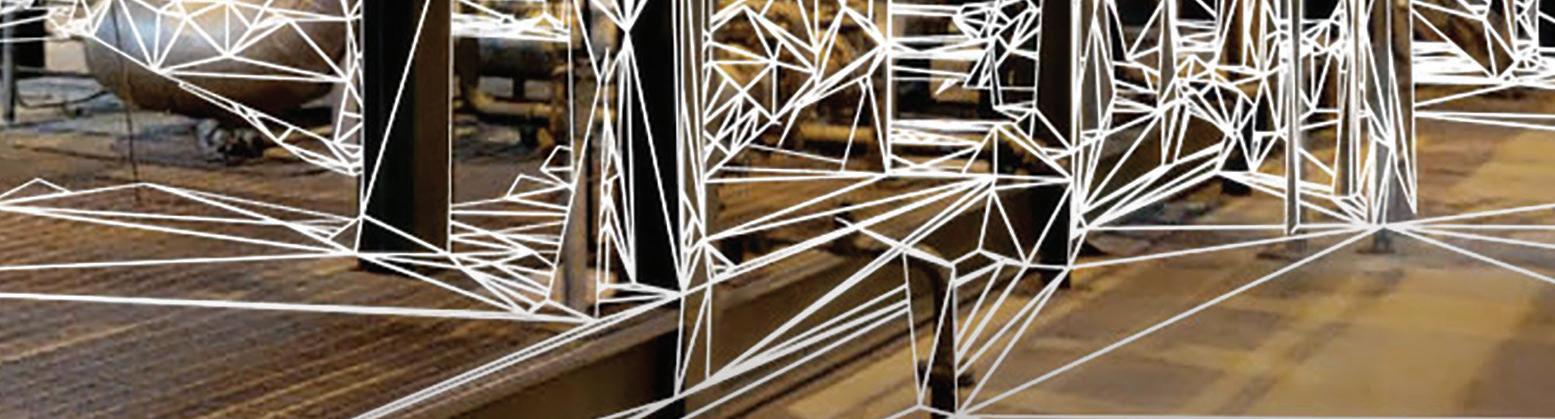
Move






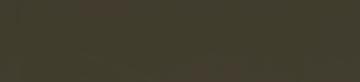
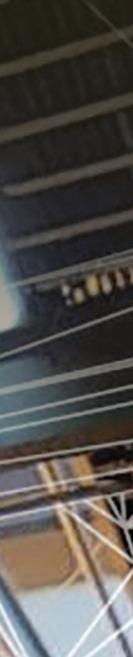


MEDICAL TIPS SUPPLEMENT: Illuminated device takes a big step for safety
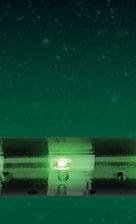
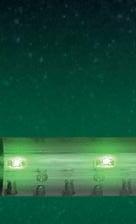
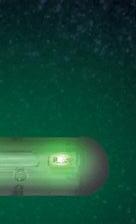


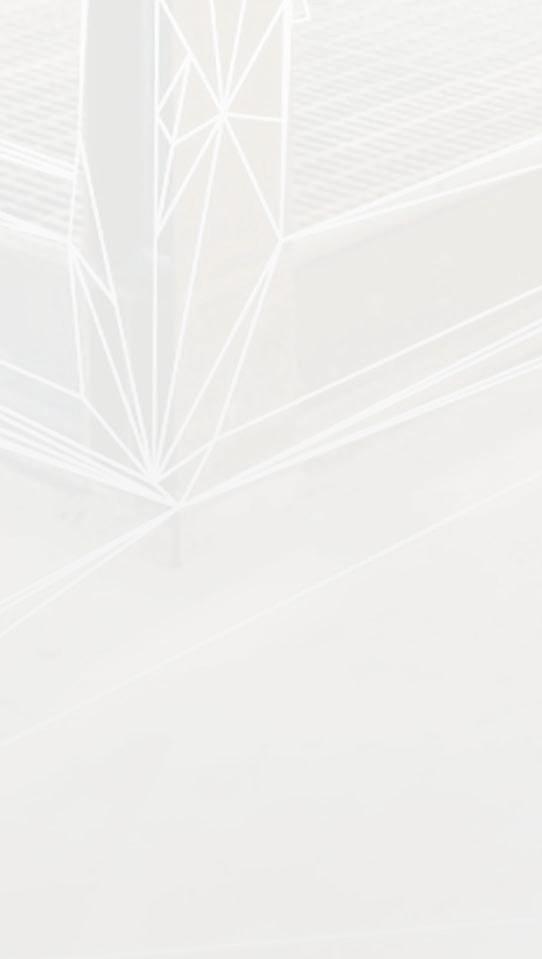

p. 58
LINEAR MOTION: Linear actuators power mobile machinery
p. 46
DIGITAL
Move
MEDICAL TIPS SUPPLEMENT: Illuminated device takes a big step for safety
p. 58
PRICED AT $995.00 (10.01.49.00090)
End-of-arm tooling starter kits include all the components needed to create a single-beam or dual-beam end-of-arm tool for a vacuum pick-and-place application. Kits are simple, save time and money, but still allow a degree of customization.
First, cut the structural rail to the desired length, determine the location of the suction cups, and then assemble the unit. Once assembled, add the robot interface flange for your brand of robot or drill your own using the included blank robot flange. That’s all it takes and your tooling is ready to go!
Features
• Starter kits are easily assembled
• Includes structural rail, connectors, cup mounts, vacuum tubing, vacuum cups, fittings, basic ejector, flange for Universal robot, and a blank robot flange
• Can be built to use internal or external vacuum
• Additional robot flanges are available to connect to Fanuc, Rethink, Universal, and Yaskawa robot arms
• Single profile kit with minimum active 20 pound-force load (90 N), maximum active 78 pound-force load (350 N)
• Double profile kit with minimum active 56 pound-force load (250 N), maximum 140 active pound-force load (625 N)
Also Available
• Vacuum suction cups in flat and bellowed styles made from Elastodur, silicone, or Nitrile in sizes up to 78mm
• Vacuum ejectors with a high suction rate of up to 860 I/min
• Spring plungers for vacuum cup mounting
• Couplers in G1/8 and G1/4
According to AAPEX, adoption of battery electric vehicles (BEVs) in the U.S. has increased substantially in recent years — they accounted for 6% of new vehicle registrations in 2022 and are forecast to reach 56% of vehicles sold in 2035 and 81% in 2045. This would translate to 19% of the U.S. fleet being BEVs or hybrids in 2035.
Personally, I’ve long been intrigued by the idea of electric cars. I know they’re not the green panacea that some proclaim them to be. Making (and disposing of) those batteries doesn’t come without an environmental cost, and the electricity used can come from many sources, some distinctly not green. However, I do think they’re a step in the right direction toward better sustainability. But what would it take to get more people to make the leap?
As the proud new owner of a 2020 Tesla Model 3, I can only tell you what made me finally take the leap last month. And that was knowing people who already had done so — early adopters, I suppose. Riding in my friends’ EVs, getting behind the wheel myself, and seeing how simple the recharging aspect was (and how prevalent the stations are today) made the decision seem much easier.
Lifestyle changes helped, too. I now work from home full time, so gone are the days of a 50-mile daily roundtrip commute into the city. Most of my days consist of not driving at all or perhaps driving a dozen miles — getting groceries or driving my son to and from lacrosse practice. (Plus, my husband still drives a gasoline car, so we have that at our disposal for longer trips.)
Even the home charging is easier than I would have guessed. The included mobile charger plugs into the 110V outlet in my garage, so I’m putting o the decision to have an electrician come install a 240V outlet. The 110V is slower; it gets me about 5 miles of charge every hour, so roughly 120 miles every day. But as I rarely drive that much, the slow charge is fine for my needs.
One argument I always heard was the slowness of the on-the-go charging. I’ve found it to be convenient and fast. Charging to full with a Supercharger took about 20 minutes for me, and I was surprised how many were in and around my mid-sized city. They’re placed unassumingly in the corners of supermarket parking or gas stations; I’d never noticed them before. And should we take a road trip, the on-board computer knows where the chargers are along our route, when to stop at one, and how many charging slots are open. The car even starts warming up the battery as we’re closing in on one, to optimize charging times. Brilliant.
Maybe that’s my favorite thing about it. I feel like I’m driving a well-designed computer that’s constantly being upgraded with the latest software. The engineer in me appreciates that, and maybe I’ll pay it forward by showing more of my friends that they, too, can take the leap. DW
Clinics, hospitals, pharmacists and care services require adaptable, highperformance devices that provide you with the best possible support in medical settings. Whether the system has to cool, air condition, lift, pump or drive, ebm-papst’s ventilation and drive solutions make diagnosis and treatment more simple, efficient and cost-effective.
Please contact sales@us.ebmpapst.com for more information.
Engineering, it seems, has been in the public eye much more these days. Just look at the number of news items about climate change — or more recently the AI revolution and what it portends for society. Engineering wasn’t always this newsworthy unless there was some catastrophic event like the Space Shuttle Challenger explosion or a bridge failure that would suddenly thrust engineers into the spotlight.
The idea, of course, is for engineers to have done their due diligence and designed products and systems that reduce the risk of such catastrophic failures as best as possible. This is even more pressing when new technologies are in question.
To that end, I recently I had the chance to attend the fPET Conference (Forum on Philosophy, Engineering and Technology) held at the Technical University of Delft in the Netherlands. fPET brought together philosophers and engineers to examine the various ways that technology impacts human society and how best to address these issues.
Among the topics covered by presenters over the three-day conference were current issues such as climate change and the rapid development and deployment of AI. But the major theme was value change in engineering and design. Specifically, how values change with technological
development and how these changes might impact design.
So, what exactly do we mean by values and value change? Here values are understood as beliefs about what is good or desirable, like human autonomy, safety, sustainability, or privacy. The further idea is that design is hardly ever value neutral, as many would claim or like to believe, but that every design embeds values within the designed artifact whether their designers are conscious of it or not. For example, sustainability was not always a relevant design value in energy technologies, but has emerged as one with the climate crisis and the realization that there are negative consequences to burning fossil fuels. Another example involves the development of wind turbines as sustainable alternative energy sources. While there are benefits from using wind to generate energy, an emerging body of evidence shows that they come with downsides for people living nearby such as noise that contributes to mental health issues, not to mention the damage to migrating bird populations that are well documented. And so, while wind turbines may satisfy one value (sustainability) they call for weighing
one value against others (human health, ecological impacts).
What’s more, the values that become a part of design decisions early on have repercussions for political attitudes and judgements that may impact society more broadly and in unforeseen ways. At the same time, value changes can lead to a shift in preference for policies that focus on security or conformity or social stability.
This is why designers and engineers should take into consideration both existing values as well as emerging or changing values that technological innovation brings about and integrate them into the design process as necessary. There are a variety of existing approaches that aim to proactively address issues during a new technology’s early development and design phases. For example, the IEEE 7000 standard addresses ethical concerns during the system design phase by integrating human and social values into traditional systems engineering and design.
By paying attention to social and moral values throughout the entire design process, engineers can ensure that the technology they design truly serves the public interest. DW
mbudimir@wtwhmedia.com
WITH an eye toward achieving its global decarbonization goals, Danfoss North America recently signed a power purchase agreement with CIG Capital, a U.S.-based project financing firm, to purchase about 75 MW of solar power from a solar farm in Texas, starting in 2025. The initial agreement term is 12 years, allowing Danfoss to fully replace its annual electricity usage in North America with green energy through at least 2037.
The new agreement will provide Danfoss with green certificates, signifying that they are supplying the North American electrical grid with the full amount of green electricity needed to power all 24 factories and 36 locations in North America. This will reduce Danfoss’ carbon footprint in the region by 75%.
“As part of our ESG goals, Danfoss has committed to achieving carbon neutrality across our global operations by 2030,” said Soren Revsbech Dam, Head of ESG and Decarbonization, Global Services Real Estate, Danfoss. “This agreement to secure green energy for our North America operations will reduce our global emissions by 21%. This is not only a significant step in our journey to becoming carbon neutral, but it also demonstrates that we are serious about putting sustainability at the heart of our business.”
CIG Capital is building the six square mile farm in the Texas panhandle, with groundbreaking in November 2023. The farm will be fully operational by Spring 2025. The solar farm capacity is projected to be 509 MW of solar power, of which Danfoss will use 15%.
The next focus for Danfoss in its decarbonization journey will be on reducing and reusing energy across its North America locations, employing various Danfoss technologies, such as oil-free, variable-speed compressors and other heating and cooling solutions that support heat recovery and energy e ciency.
“Danfoss is committed to playing a leading role in the energy transition. Meeting our ESG goals and living up to our commitment to combat climate change means developing innovative solutions,” said Rick Sporrer, President of Danfoss North America.
As part of the Science Based Targets initiative (SBTi), the company is committed to become carbon neutral in its global operations (scope 1 & 2) by 2030 and said it will reduce its value chain emissions (scope 3) with 15% by
2030. This commitment is included in the targets of its three step-change initiatives on Decarbonization; Circularity; and Diversity, Equity & Inclusion.
The company already has seen progress in decoupling environmental impact from business growth by delivering 7% decrease in scope 1 and 2 emissions while growing 15% organically in 2022. The company’s 250,000 sq-m headquarters campus site in Denmark became carbon neutral in 2022. This was achieved through energy saving projects, use of excess heat from processes and data centers, sourcing of green energy, and o setting residual emissions. DW
Danfoss North America
www.danfoss.com
“This agreement to secure green energy for our North America operations will reduce our global emissions by 21%.”
In the first part of this series, we heard from industry experts about discrete automation’s latest edge devices and the rise of fog computing. Here we detail the holistic approaches needed for an operation to realize a digital transformation.
To meet the growing demand for electrification, manufacturers are designing more powerful electric actuators for mobile equipment.
Move over AI: shops pave digital journeys with actionable data
Capturing the right information to find machine data that improves process control.
Follow the whole team on twitter @DesignWorld
EDITORIAL
VP, Editorial Director
Paul J. Heney pheney@wtwhmedia.com @wtwh_paulheney
Managing Editor
Mike Santora msantora@wtwhmedia.com @dw_mikesantora
Executive Editor
Lisa Eitel leitel@wtwhmedia.com @dw_lisaeitel
Senior Editor
Miles Budimir mbudimir@wtwhmedia.com @dw_motion
Senior Editor Mary Gannon mgannon@wtwhmedia.com @dw_marygannon
Senior Editor
Rachael Pasini rpasini@wtwhmedia.com @WTWH_Rachael
Associate Editor Heather Hall hhall@wtwhmedia.com @wtwh_heathhall
CREATIVE SERVICES
VP, Creative Services Mark Rook mrook@wtwhmedia.com @wtwh_graphics
Senior Art Director
Matthew Claney mclaney@wtwhmedia.com @wtwh_designer
Art Director Allison Washko awashko@wtwhmedia.com @wtwh_allison
Senior Graphic Designer
Mariel Evans mevans@wtwhmedia.com @wtwh_mariel
Graphic Designer
Shannon Pipik spipik@wtwhmedia.com @wtwh_shannon
Director,
Bruce Sprague bsprague@wtwhmedia.com
WEB DEV / DIGITAL OPERATIONS
Web Development Manager
B. David Miyares dmiyares@wtwhmedia.com @wtwh_webdave
Senior Digital Media Manager Patrick Curran pcurran@wtwhmedia.com @wtwhseopatrick
Front End Developer Melissa Annand mannand@wtwhmedia.com
Software Engineer David Bozentka dbozentka@wtwhmedia.com
DIGITAL MARKETING
VP, Digital Marketing Virginia Goulding vgoulding@wtwhmedia.com @wtwh_virginia
Digital Marketing Manager
Taylor Meade tmeade@wtwhmedia.com @WTWH_Taylor
Digital Marketing Coordinator Meagan Konvalin mkonvalin@wtwhmedia.com
Digital Marketing Coordinator Francesca Barrett fbarrett@wtwhmedia.com
Webinar Coordinator Emira Wininger ewininger@wtwhmedia.com
Webinar Coordinator Dan Santarelli dsantarelli@wtwhmedia.com
Controller Brian Korsberg bkorsberg@wtwhmedia.com
Accounts Receivable Specialist
Jamila Milton jmilton@wtwhmedia.com
EVENTS
Events Manager
Jen Osborne josborne@wtwhmedia.com @wtwh_jen
Events Manager Brittany Belko bbelko@wtwhmedia.com
Event Marketing Specialist Olivia Zemanek ozemanek@wtwhmedia.com
VIDEO SERVICES
Videographer Garrett McCafferty gmccafferty@wtwhmedia.com
Videographer
Kara Singleton ksingleton@wtwhmedia.com
PRODUCTION SERVICES
Customer Service Manager
Stephanie Hulett shulett@wtwhmedia.com
Customer Service Representative Tracy Powers tpowers@wtwhmedia.com
Customer Service Representative
JoAnn Martin jmartin@wtwhmedia.com
Customer Service Representative Renee Massey-Linston renee@wtwhmedia.com
Customer Service Representative
Trinidy Longgood tlonggood@wtwhmedia.com
Digital Production Manager
Reggie Hall rhall@wtwhmedia.com
Digital Production Specialist Nicole Johnson njohnson@wtwhmedia.com
Digital Design Manager
Samantha King sking@wtwhmedia.com
Marketing Graphic Designer Hannah Bragg hbragg@wtwhmedia.com
Digital Production Specialist Elise Ondak eondak@wtwhmedia.com
A traditional coordinate measuring machine (CMM) calibrates a toolmaker’s inspection equipment and supplies it with conventional metrology tools, such as verniers and micrometers. It can measure tolerances about ten times smaller than a 3D articulated arm, as positional feedback is from linear scales rather than absolute angle encoders within rotary joints. However, articulated arms a ord more freedom of movement around a part, making them ideal for nonrepetitive applications and custom components.
Founded in 2011, toolmaking and subcontract machining company GT Tooling spent one year using conventional manual metrology equipment to measure components before investing in a 3D articulating arm — a six-axis model with a 1.2-m reach. Three years later, the company moved to a bigger factory and invested in a machining center, which meant larger prismatic parts had to be inspected in two operations. Although satisfactory, the procedure was time-consuming and risked introducing errors during arm relocation.
“We considered manually operated and CNC CMMs. However, the repeatability of measurement on the former was not good enough, while the
latter did not o er su cient flexibility. Neither type had the reporting capability that was up to our standards or those of our customers. We also felt that programmable CMMs were better suited to series production because we machine mainly one-o s and small batches,” said Greg Simmonds, owner and director of GT Tooling.
In May 2022, the company purchased a seven-axis Freedom Classic Scan portable arm with a 2-m reach from LK Metrology. The arm provides accurate results when measuring dimensions with ±0.1 mm tolerances. If there is a need to check tighter features, inspectors can
use conventional metrology involving bore and pin gauges, for example. The company chose the seven-axis over the six-axis arm to enable laser scanning as an adjunct to touch-probing discrete points. It also sought more comprehensive data collection on free-form surfaces in less time, more comprehensive reporting, and less risk of missing machining errors.
Ryan Leaves, sales engineer and inspector at GT Tooling, confirmed that the entire quality control process — including alignment, inspection, and reporting — is now faster and more flexible with the new arm. Speed is important, as some urgent jobs require a 24-hour turnaround. An internal report typically takes 15 to 20 minutes to prepare, while a full FAIR (first article inspection report) requires about one hour. Inspecting large parts previously required two-arm setups, as Leaves was essentially doing the job twice, but now inspection time is halved.
The resulting documentation is now exactly what the user wants without unnecessary content or interpretation. GD&T (geometric dimensioning and tolerancing) reporting was previously a laborious exercise but is now more user-friendly with InnovMetric’s PolyWorks software.
“The PolyWorks Inspector reporting software is easy to use. By pulling out the required dimensions and pressing a button, reports can be manipulated freely into di erent, easily digestible formats to suit each customer’s preference,” said Simmonds. “Until now, we have produced inspection reports on about 40% of our machined components, as not every end user requires one. Now that the process is quicker and easier, we are looking to more than double the number.”
The arm is used almost exclusively on a dedicated inspection table for checking components, but occasionally it is mounted on a machining center table to verify the part accuracy before being removed from its fixture or before further machining.
Other benefits of the laser scanning arm include inspecting delicate and deformable components and reverse engineering legacy components for which no data or drawings exist. The company can use this capability on parts machined in-house to win new customers and to sell an inspection service to other manufacturers on a subcontract basis if there is spare capacity.
Crafting works of art from metal isn’t anything new. Many of us would instantly think of the Statue of Liberty or the Ei el Tower, while those versed in contemporary art may think of the Chicago Picasso or Sir Antony Gormley’s Angel of the North. But how would one combine several famous works of art using stainless steel and artificial intelligence (AI) to create a new modern masterpiece?
In partnership with Sandvik Group, Sandvik Coromant developed a statue that will go down in art history. Made using AI modeling and cutting-edge manufacturing solutions, the sculpture combines the styles and influences of Michelangelo, Auguste Rodin, Käthe Kollwitz, Kotaro Takamura, and Augusta Savage — uniting some of history’s most famous artists from a period spanning 500 years. Weighing 500 kg and standing 150 cm tall, the Impossible Statue was o cially inaugurated at
Tekniska Museet, Sweden’s National Museum of Science and Technology, in April 2023.
“We needed a phenomenally precise digital simulation to help us machine the statue,” said Henrik Loikkanen, technology area manager at Sandvik Coromant. “Digital manufacturing means we can prove that whole complex machining process beforehand. The only time we spend on machines, therefore, is actual production time. It also meant we didn’t produce a single scrap component during the entire project.”
The team started with a 2D design and translated the model into a complete 3D image. They used depth estimators to build the 3D model, human pose estimators to refine the body, video game algorithms to generate realistic fabric, and specialized AI to reintroduce fine details lost in previous steps. Mastercam software
Digital manufacturing tools made the Impossible Statue possible and reduced scrap components.
converted a design for a statue with over six million surfaces and complex details.
“We treated producing the statue as we’d treat machining highly specialized, complex parts like those found in the aerospace industry,” said Loikkanen. “An additional challenge came from the statue’s chosen material — stainless steel from Alleima — as ISO M materials are notoriously di cult to machine. The material group is characterized by its high work hardening rates and poor chip-breaking properties during machining. Careful attention, therefore, must be paid to the tools selected for machining the material.”
Sandvik Coromant chose several tools to help sculpt each intricate part of the statue. The Coromant Capto tooling interface was used to connect the arm and head to the torso of the statue; solid round tools from the CoroMill Plura and Dura families were responsible
Loikkanen (le ) and Pettersson (right) converted a 2D design to a 3D model and used a digital twin for testing.
| courtesy of Sandvik
for finishing all the statue’s surfaces and features; and CoroMill MH20, a high-feed milling cutter launched in 2021, was used to machine the bulk of the stainless steel removed from the workpiece.
Naturally, machining the impossible isn’t without challenges, and the team made several adaptations to its machining strategy.
“The initial 3D model was not the type of model CAD/CAM systems can work with,” said Loikkanen. “It had to be converted from a 3D-mesh model, which is essentially a shell of surface polygons commonly used in 3D animation studios, to a solid 3D model with density, and that was a pretty challenging process. Once completed, the model was sectioned into 17 pieces, and all interfaces between them had to be modeled with a tight fit to make the intersections invisible when the parts were put together. It took time to get everything perfect.”
“We also had some challenges during rough machining due to the size of the component in relation to the machines,” said Jakob Pettersson, CAM and machining specialist at Sandvik Coromant. “This was solved by simulating NC-code and finding all the areas where we would reach the machine work envelope limit and by altering the CAM sequence.”
In the end, a statue that seamlessly blends the works of five artists was made possible. But developing a never-seen-before statue wasn’t the only accomplishment.
“Along the way, we implemented several techniques that can be applied to future digital machining projects,” said Loikkanen. “Because of the pure amount of programming work, building the statue would have been impossible without a digital twin. All the testing was done digitally to save time that would otherwise be spent on trial-and-error testing. This is certainly something we can apply in future projects to save time and reduce the number of scrap components.”
Now on display for art and technophiles alike to admire, the statue serves as a reminder of the creativity both digital and physical manufacturing tools can accomplish. DW
Sandvik Coromat www.sandvik.coromant.comUnnoticed tool breakage increases scrap and wastes precious production time and costs. To quickly sense tool breakage during use within a machine tool, Heidenhain introduced the TD 110 tool breakage detector for contactfree inspection of drill bits and end mills. The detector can determine whether a tool is broken o by more than 2 mm as it passes within a machine tool, yielding significant time and money savings.
The TD 110 can be placed in the work envelope so that it is fast and easy to reach during the tool change. Its inductive sensor detects tools as they pass by while spinning at operational speed. With rapid scanning technology, it even detects small tools made of HSS steel and carbide.
The breakage sensor can then generate either a floating or an HTL switching signal, and the machine control can evaluate it via standard instruction sets. These signals/outputs can connect to a Heidenhain TNC control, PLC, or any other IOs of nearly every CNC control manufacturer. In addition, an LED signals whether a tool has been flagged.
Overall benefits of the new TD 110 tool breakage detector include a maintenance-free sensor for reducing nonproductive time for breakage inspection; cooling lubricant and tolerance for lightly contaminated tools; and universally retrofittable with standard interfaces for tool touch probes. DW
Heidenhain
Laser processing machines can achieve highly accurate positioning with sub-micron-level precision and repeatability. This level of precision is crucial in many industries, such as aerospace, automotive, and medical device manufacturing, where the accuracy of laser processing can have a significant impact on the quality and safety of the final product. They enable manufacturers to produce high-quality, intricate parts with speed and precision. Today, laser processing machines can cut complicated shapes but they are typically limited to working in two dimensions. This means that when more complex geometries or cuts are needed, it is necessary to cut in one dimension, turn the part, and cut again. This often makes the process prohibitively time-consuming and expensive. Therefore, motion control systems for laser processing can benefit from 6D repeatability performance validated by the 6D Point Precision performance specification.
“Laser processing is often faster and more cost-e ective than traditional machining methods, and with increasing demand for miniaturization, customization, and automation, laser processing technologies are poised to play an even more significant role in the future, driving innovation and improving productivity in various industries,” said Bill Hennessey, president of Alio Industries.
As a manufacturer of high-precision motion control systems, Alio uses 6D Point Precision to validate the 6D repeatability performance of its single
and multi-axis motion control systems used in laser processing applications. The 6D Point Precision methodology involves measuring six different points in space, including X, Y, and Z position, pitch, yaw, and roll. By taking measurements at these six points, the company ensures its motion control systems can achieve high-precision positioning and repeatability across all six degrees of freedom.
NIST has now produced the ASME B5.64 standard “Methods for the Performance Evaluation of Single Axis Linear Positioning Systems,” which advocates a new method for defining the precision of advanced motion control solutions, similar to suggestions made by Alio moving away from conventional planar methodologies.
By validating its motion control systems using 6D Point Precision, Alio can provide its users with a high level of confidence in the performance and reliability of its products.
The company also offers a range of linear motion control stages, including air-bearing and mechanical-bearing stages, that can provide high-precision linear motion control for laser processing. These stages offer a variety of features, including sub-micron level precision and repeatability, long travel
ranges, and high load capacity, and are designed to provide a high level of accuracy and reliability, even in harsh industrial environments. They can be customized to meet the specific needs of each laser processing application. Its Hybrid Hexapod, for example, is a multi-axis motion control system that combines the precision and accuracy of a hexapod with the long travel range of a linear stage.
“We have also developed True Nano precision rotary motion stages with a sub-arc-second resolution, making them ideal for a variety of laser processing applications where nanoscale precision is required, such as laser cutting, welding, and marking, and can also be integrated into larger motion control systems to provide multi-axis control, further expanding their applications,” said Hennessey. DW
Alio Industries
www.alioindustries.com
• Adjustable handles and knobs replace standard hardware and can be used to torque components without tools.
• Levers can be used with Ruland shaft collars for quick installation and adjustment.
• Slit couplings are available in short and long styles giving designers a variety of body sizes to choose from to t application envelope and performance requirements.
• Control ex is a highly exible encoder coupling designed for applications with high speed, low torque, and wide differences in shaft sizes (up to a 4:1 small to large ratio).
• Slit couplings are available in bore sizes from 1.5mm to 12mm (1/8” to 1/2”) and control ex couplings are available in sizes from 6mm to 40mm (1/4” to 1-1/2”).
Ruland Manufacturing is proud to support the FIRST Robotics Competition as a Gold Supplier of precision shaft collars & couplings.
• Available with OD ats and holes for direct mounting of the collar to other components.
• Proprietary manufacturing processes ensure superior t, nish, and holding power.
• Manufactured in a variety of sizes, styles, and materials.
• Widest selection in the industry: over 3000 standard single and double universal joints to start your next design with.
• Available from Ruland in 2 weeks or less for the shortest lead times in the industry.
• Yokes, pins, and blocks are precision machined, ground, and selectively heat treated for smooth operation at high operating angles.
• Assortment of components that allow users to build small assemblies for mounting sensors, conveyor rails, machine guards, and more.
• Optional pre-designed kits make it easier to select the right system for your application.
• Hand operated: no tools required to install, remove, & adjust.
• Best suited for systems that require frequent adjustments.application.
All products available directly on RULAND.COM www.ruland.com |
Medical device manufacturers continuously seek ways to decrease component footprints without compromising power. maxon recently introduced the first size of its new ECX Prime motor family, the ECX Prime 6, a small but powerful brushless motor with 4-pole rotors and slotless windings. It has a diameter of only 6 mm and is designed for demanding applications with limited space or where special performance or controller dynamics are required, such as hand prosthetics, surgical tools, or implants.
The ECX Prime 6 o ers speeds of up to 50,000 rpm and continuous torques of up to 0.57 mN-m. The 4-pole technology, already known from larger motors, has been further developed for customized designs and optimized for industrial production in such a small diameter. The motor is made of the best possible materials, including four rotor magnets and the magnetic return of the stator, reducing losses to a minimum and giving the motor a very low speed/torque gradient. This enables stable and dynamic closed-loop control, even when the load increases or fluctuates.
The new motor is available in a High Power (HP) version with Hall or commutation signals. It can be combined with the ENX 6 MAG encoder type and the GPX 6 A gearhead of the standard modular system. For customized versions, the GP 6 S screw drive can be attached via the Flex channel. DW
WHITTET-HIGGINS manufactures quality oriented, stocks abundantly and delivers quickly the best quality and largest array of adjustable, heavy thrust bearing, and torque load carrying retaining devices for bearing, power transmission and other industrial assemblies; and specialized tools for their careful assembly.
Visit our website–whittet-higgins.com–to peruse the many possibilities to improve your assemblies. Much technical detail delineated as well as 2D and 3D CAD models for engineering assistance. Call your local or a good distributor.
Whether responding to shifting budget priorities or the urgent need to assist an ally, the U.S. military must be flexible and adaptive. Chief among these requirements is battlefield superiority in potential future global conflict. How the defense sector responds to such challenges is therefore critical, and the U.S. must use every tool at its disposal to encourage military innovation, particularly in the field of hypersonics.
Advanced metal additive manufacturing (AM) is one of these tools. With it, manufacturers can produce components with thin-walled parts, intricate internal channels, and complex lattice structures — qualities that can be particularly transformational for hypersonic systems.
Hypersonic propulsion and vehicle developers have taken notice and turned to metal AM for the design, rapid iteration, and production of mission-critical components. While much of the defense-focused development remains out of the public eye, one example with good visibility is Hermeus, an Atlanta-based company developing reusable hypersonic aircraft for defense and commercial applications. Hermeus recently began using advanced metal AM to dramatically reduce lead times on components for its dual-mode ramjet Chimera engine.
According to CTO Glenn Case, this has allowed Hermeus to “increase performance, consolidate components, reduce weight, and minimize external dependencies” in the Chimera-equipped Quarterhorse, a remotely piloted aircraft with a goal of briefly hitting Mach 4+ speeds and demonstrating reusability. Its concept proven, Hermeus will then expand its hypersonic e orts to Darkhorse, a UAS (uncrewed aerial system) designed for defense and intelligence missions with the ultimate goal of delivering a human-crewed commercial hypersonic aircraft — dubbed Halcyon — by 2029.
In addition to cutting-edge technologies such as hypersonic propulsion, there is a parallel push towards shrinking, simplifying, and reducing the cost of gas-turbine engines. As these engines become smaller, it is important to optimize features to drive higher e ciencies, potentially at lower costs. The units feature dozens of highly complex individual components that have long been fabricated using a combination of casting, five-axis machining, brazing, and welding to produce a completed assembly. This process, however, presents numerous logistical hurdles, including long lead times and costly, often di cult manufacturing steps that require significant technical skill.
Advanced metal 3D printing, with its ability to consolidate assemblies of multiple components into a single, monolithic structure, greatly simplifies this process. California-based Sierra
The cross-section (le ) of Sierra Turbines’ microturbine shows fine inner details of the unicore design (right) made possible with metal AM.
| courtesy of Sierra Turbines
3D-printed valves with identical quality and performance characteristics were additively manufactured in six different locations to demonstrate how AM can quickly deliver complex parts on a global scale.
| courtesy of Velo3D and IMI Critical
Turbines discovered these benefits firsthand when it engaged with metal AM experts early in the design process, allowing the team to consolidate 61 discrete parts into a single unicore design. Doing so cut the overall part count almost in half without sacrificing quality or performance. It also increased power density by a factor of 10, the time between overhauls (TBO) by 20, and overall e ciency by 40-fold.
Success stories such as these extend beyond aerospace and defense. Consider IMI Critical, a world leader in flow-control solutions that was tapped by a major oil and gas operator recently to validate metal AM’s potential to reduce lead times on critical
components. One of these was a choke valve cage, which the company aimed to produce in a scalable, predictable manner using a global supply chain.
Partnering with metal AM solution provider Velo3D, IMI Critical redesigned the choke valve cage and locked it into a set of unique printing instructions that could be delivered to any certified, in-network printer anywhere in the world. Parts of identical quality and performance were printed at six di erent locations, several of them overseas.
Each of these examples used metals that most machinists would recognize. Inconel 718 and 625, Haynes 282, and titanium Ti-6Al-4V are just a few of the
Aerospace/Military
high-performance alloys common to the aerospace, defense, and energy industries. Yet advanced metal AM is helping to develop new, even stronger alloys that will push the boundaries of what’s possible.
Staying ahead of competing nearpeer world powers with new programs is a primary driver for the U.S. defense sector, but this e ort doesn’t address one of the more immediate concerns of servicing legacy assets. The pandemic taught us many painful lessons, not the least of which is the imperative of a diversified supply chain. Relying on fragile overseas supply chains for critical components is a troubling concern for any industry, but it is often not even possible for those supplying defense parts.
With its ability to reduce iteration durations and lead times while also improving performance, metal 3D printing is becoming a transformative force in several aerospace and defense applications, including hypersonics, propulsion systems, and legacy vehicle maintenance. DW
Velo3D www.velo3d.com
German motion plastics company igus has held the biennial manus awards since 2003. This competition recognizes creative, economical, innovative, and sustainable applications that incorporate plastic lead screws, linear actuators, plain bearings, linear bearings, and slides into industrial designs. This is the third iteration where Design World’s own VP, Editorial Director, Paul J. Heney, served on the international jury that selected the winners.
The awards ceremony was held on April 20th at igus’ large booth at the Hannover Fair, considered as the largest industrial trade show in the world. This year’s golden manus award was given to J&M Manufacturing, an Ohio manufacturer of grain handling equipment. The winning design is for its Para-Linkage coulter, which is used on J&M NitroGro nitrogen applicators.
These applicators are used by farmers to apply liquid nitrogen fertilizer to crops such as corn, potatoes, and wheat. Applying the nitrogen is an extremely time sensitive matter; sometimes farmers only have a couple of days in which to receive the maximum e ect of putting the nitrogen fertilizer on the crops. What’s more, it’s easy for the nitrogen to be wasted with the older version of these devices. The older designs often will spill some of the nitrogen on top of the ground, where it can be lost.
The Para-Linkage coulter is a springloaded, parallel arm style device that keeps the knife and blade at the same level and parallel to the ground. This keeps more nitrogen in the ground, where it can be retained. The ParaLinkage coulters feature the igus GSI poly sleeve bearings in all pivot locations.
There are five pivot locations in all, each using 6-in. igus bearings, with an additional bearing on the optional row closer. The number of coulters used on
one of J&M Manufacturing Company’s NitroGro Nitrogen applicators ranges from 11 on a 30-foot toolbar to 37 on a 60-foot toolbar. This means the end customer is saving a great deal on grease, as well.
This type of application would be challenging to any bearing. The conditions are dusty and dirty, with a variability in temperatures. The machinery is used very sporadically, due to the seasonality of crops. And liquid nitrogen itself is highly corrosive to any
steel, which rules out many types of products — and pushes the di culty in solving this application to the next level.
Judges reviewed 480 entries from 36 countries for the award. The first prize in the contest is €5,000. igus also awards a Silver (€2,500), Bronze (€1,000), and a Green prize (€1,000), which honors products for their sustainability.
The silver manus award went to a French exoskeleton with a slim design. This exoskeleton is used for high-pressure cleaning and provides a reliable, robust, and e cient solution that protects user health.
Aufratech, based in Cabris, France, uses linear slide bearings and corrosion-free polymer plain bearings from the iglide J3 series in its EXO N exoskeleton. At the core of the design is a control system that enables the user to guide the attached lances while keeping the back straight. Engineers succeeded in implementing a slim design that grouped as many functions as possible around an aluminum shaft. The hollow structure of the shaft allows integration of the hydraulic control hoses and the steel water spray lane so that the valve body can be moved to the rear of the lance and the system is balanced around the user’s center of gravity.
The bronze manus award went to a telescopic high-pressure cleaner from Germany. Fiedler Maschinenbau und Technikvertrieb GmbH built a highpressure cleaner for municipal vehicles in which the unit’s working area can be changed at the touch of a button.
Based in Schmolin-Putzkau, the core of the company’s cleaner is the FSB 1500/2600 double spray boom mounted in front of the vehicle, equipped with side nozzles, a middle section, and electronically switchable high-pressure underfloor nozzles for cleaning services with high water pressure.
The double spray boom can be telescoped up to 500mm on each side. The adaptability enables the driver to clean large areas faster or to drive between park benches and rubbish bins with complicated steering maneuvers. Engineers selected profile guides and pillow blocks from the igus drylin W series for the telescopic function. Lastly, the green manus award went to a dry-running coupling from Germany. Rockinger Agriculture GmbH in Waltershausen, Germany, developed farm equipment that no longer requires lubrication to win this sustainability award. The company designed KS80 ball couplings and wear inserts to be used on balers, loader wagons, manure spreaders, tippers, and field sprayers. The couplings are made with highperformance plastic from the iglide series and were developed by igus, especially for Rockinger.
Inserts in the coupling survived two million load changes with a support load of 4.5 tons. If 33% of tractors in Germany were equipped with KS80 and the wear insert, approximately 8,300 couplings would not require lubrication and this would save eight tons of grease per year.
Find out more about the winners and all 480 entries at: www.igus.com/manus.
Manufacturing companies and machine builder OEMs have been digitalizing their automation designs for decades. But in recent years, the iterative process of identifying and solving problems using data and technology to support the work of people has been termed digital transformation, which encompasses many aspects, from the plant floor up to the cloud. One trend within industrial digital transformation is that the number of field sensors and devices, and their capability and intelligence, have been increasing dramatically.
Along the digital transformation journey, users have certainly experienced success transitioning away from traditional hardwiring methods and toward more modern digital solutions for connecting with the growing number of field devices. However, as industry faces workforce challenges, there has been a renewed focus on choosing technologies that are easily deployed and supported by available operations and maintenance personnel.
At the on-machine and plant-floor level of operations, the IOLink protocol, media, and compatible field devices often provide a superior solution for OEMs and end users alike. Considering the widespread and growing availability of products supporting IO-Link, designers must consider including this technology in their projects.
signals remain important, many newer field devices like this Emerson Aventics AF2 Series flow sensor can provide significant bidirectional operating, configuration, and diagnostic information using IO-Link.
There are already many standard industrial digital fieldbuses for communicating with intelligent and data-rich field devices like input/ output (I/O) systems, instruments/analyzers, and more. Examples include PROFINET, Modbus TCP and RTU, EtherCAT, EtherNet/IP, DeviceNet, and others. Some of these fieldbuses use specific wiring methods, while more modern versions are typically Ethernet-based. So, what is the attraction of IO-Link?
Digital transformation and industrial Internet of Things (IIoT) initiatives are built on data, much of which is sourced from the field. And although high and low complexity field devices are relatively sophisticated data sources requiring equally complex communications, there are many basic discrete and analog devices, such as presence and pressure sensors, valve controls, and more which are gaining capabilities where digital signaling would be useful. Throughout their service lives, the configuration and diagnostic data trapped inside these devices needs to be readily available to best manage the system and minimize customer downtime.
Historically, much of the I/O on machines and in automated manufacturing has been used for one-way signals — whether input or output — between the field device and the supervisory controller I/O system. Examples include:
• Discrete input signal from a photoswitch
• Discrete output command to a solenoid manifold valve
• Analog input signal from a basic pressure transmitter
• Analog output command to a pressure controller
Hardwiring requires significant fieldinstalled conduit and wire, and the result provides just one signal. One global standard for augmenting analog signals is the HART protocol, which superimposes digital communications over analog hardwiring so users with the right host system can access extended configuration, diagnostic, and status information.
Therefore, many users lack a convenient way to implement important digital communications for much of their automation needs unless they commit to implementing complex designs and using costly products, which are impractical for many applications.
To address these and other concerns, IO-Link was developed to provide bi-directional digital communications between a field device and a master device in a form factor well suited for industrial installations. Specified by IEC 61131-9, IO-Link uses common unshielded three-conductor cables to supply the 24VDC power needed for typical industrial devices, and it o ers connection distances of up to 20 meters. There are two port classes, A and B, with the latter capable of supplying more power. For additional cable reduction, IO-Link Wireless is a newer standard providing even more installation options.
A wired IO-Link architecture employs “masters,” which are connected using industrial Ethernet network “in” and “out” ports, and the modules are powered by 24VDC “in” and “out” ports, so the devices are easily daisy-chained to minimize cabling length and costs. Each master module can connect with several IO-Link field devices, typically 4 to 8 per IO-Link master (Figure 2).
An important capability with many models of an IO-Link master is support for simultaneous links to di erent hosts. For instance, an IO-Link master network could be connected to a host PLC via PROFINET for monitoring and control and to other hosts, such as a historian and an asset management system via OPC UA, MQTT, or Modbus TCP for supplying data (Figure 3). PROFINET is particularly attractive for missioncritical industrial systems, and it can be configured as a redundant ring supporting media redundancy protocol (MRP).
Field device wiring to master modules is simple and consistent. Users can select field devices and panel-mount masters, each using traditional wiring methods. However, for many applications, users are finding that surface-mount IP67-rated masters and connections made using standardized A-code M12 connectors
networking connections are daisy-chained.
provide the greatest advantages. These devices are simple to install and service compared with conduit and wire, while traditional IP20 and IP67 form factors are complementary and can be mixed and matched as needed.
IO-Link provides a superior balance of performance and e ciency for many applications, and it has many enhancements, which make it easier to deploy and maintain than most traditional protocols. IO-Link devices can transmit up to 32 bytes of essential data cyclically and other supplementary data asynchronously. More than one process value — whether discrete or analog, input or output — is available at all times, and users can perform device configuration and access diagnostics remotely via their host system.
Whereas HART devices require commissioning to be repeated for each device, IO-Link master devices support the concept of capturing device configuration “recipes,” so all customization settings can be saved and replicated for subsequent similar devices. More importantly, replacement devices will auto-configure to match the setup of the previously installed device, so even inexperienced technicians can replace field components and get back up and running quickly. DW
Emerson | emerson.com
CGI Motion standard products are designed with customization in mind. Our team of experts will work with you on selecting the optimal base product and craft a unique solution to help di erentiate your product or application. So when you think customization, think standard CGI assemblies.
Connect with us today to explore what CGI Motion can do for you.
The Space Enterprise Berkeley (SEB) team launched their first-ever liquidfueled rocket, Eureka-1, which reached 11,024-ft in December last year. The collegiate team partnered with Protolabs to create parts for Eureka-1’s plenum and complex parachute system using selective laser sintering (SLS).
“3D printing made sense for creating a part that could combine functionalities. It had to mount a parachute swivel, secure the avionics bay, and integrate a camera. That would’ve been a complex part with traditional manufacturing,” said Asa Garner, structures lead for SEB.
Garner used CAD to create the assembly design. He made a block diagram to show where the parts should be, and sub-teams with di erent requirements
agreed on a general layout. Then, each team designed its individual parts in CAD to develop the general geometries. Garner knew that 3D printing would be the best solution for many parachutes and outer plenum components.
“As soon as we realized we wanted to 3D-print these parts, I looked up all the datasheets for the various Protolabs materials. Then, I simulated options in nTopology and eventually settled on PA12 40% glass-filled nylon,” said Garner. “With PA12 glass-filled, we didn’t have to compromise on strength. We added a little bit more material than we would with metal, but it ended up being about the same weight and way easier.”
Aerospace commonly uses SLS and glass-filled nylon to make lightweight components, especially for rocketry and uncrewed drones. SLS provides material strength and consistency and is helpful for custom and complex parts. By building parts additively, engineers can skeletonize the designs and remove any mass that doesn’t contribute to the part’s functionality.
“As a practical measure, you can reduce the number of parts and decrease assembly times,” said Eric Utley, application engineer at
The lattice design made the part lighter, stronger, and able to withstand anticipated stress during flight.
Protolabs. “Initially, I thought people used 3D printing to save on CAD work and assembly. But once it scales up to a production setting, it also saves administrative time. For example, if an aerospace customer has a 13-piece component, they have 13 di erent purchase orders and must keep track of the 13 di erent vendors and their quality certifications. Extrapolate that to a larger product like a rocket. If you can go from 100,000 pieces down to 5,000 pieces, it’s tremendously less supply chain management.”
With 3D printing, design engineers can also accelerate product development by quickly creating parts, collecting feedback, and iterating on the design.
“Software developers started the mindset where you can roll out a product and it doesn’t have to be perfect. You get it out there in people’s hands, then iterate and improve it. That mindset is trickling into hardware,” said Utley.
The SEB team used nTopology to simulate forces on the 3D-printed part and how the part would respond when the parachute opened. They assessed how it would handle stress and located stress concentrations or peaks. Using a lattice design, they could smooth out such peaks, dissipating stress across the part and leveraging the material e ciently.
Garner used nTopology to simulate how the 3D-printed parts would respond to stress during flight.
“By changing the lattice thickness, you can make a part sti er or softer,” said Utley. “If you design in CAD, it’s a rapid change, and you’re not constrained by manufacturing.”
In addition to SLS, the SEB team uses multi-jet fusion (MJF) for its LAD rocket program.
“At the peak of that program, we were cranking out a LAD rocket almost every week, which is astounding. That would’ve been impossible without 3D printing,” said Garner.
Garner projects that SEB will use a combination of various 3D printing methods and CNC machining to create durable, lightweight, multi-function parts for future projects. And they’re busily working on their second installation, Eureka-2, scheduled to launch in the fall of this year. DW Space
In the first part of this series, we heard from industry experts about discrete automation’s latest edge devices and the rise of fog computing. Here we detail the holistic approaches needed for an operation to realize a digital transformation.
Sandro Quintero | Business development for electric automation • Festo
Will Morris | Category manager • RS Americas Inc.
Paul Thompson | V.P. solutions engineering • Matterport
Chris Gottlieb | Director — Drives and controls • Kollmorgen
Bill Paczkowski | Senior product manager for PACEdge • Emerson
Craig Scott | CEO and president • MFGx
Boaz Eidelberg | CTO • SAAR Inc.
Pramit Nandy | Product marketing manager — 16-bit microcontroller division • Microchip Technology
JP Wollersheim | Senior director of product management • Matterport
transformation
is the application of software, programmable hardware, and operational technologies (OTs) to fundamentally transfigure a company’s operations and end products for the better. DX programs can be undertaken by industrial organizations, machine builders, or a vast array of other businesses; the involved OTs typically include machine-monitoring systems, connectivity, and online web and cloud access — especially via tools with internet of things, IIoT, or Industrie 4.0 functionalities.
What new capabilities do your designs incorporate to support functions related to fog computing?
Paczkowski: Fog computing includes data handling, storing, and processing on a local network at a site. Although edge devices such as sensors and PLCs are becoming more capable (and enterprise or cloudbased resources have enormous capabilities) onsite fog computing lets users e ciently operate with large amounts of data in a stable, low-latency, and secure manner.
Nandy: Complex products require connected and secure devices. Microchip’s solutions support M2M security with secured boots, secured firmware upgrades, secured communications, and mutual authentication. Our solutions let users increase network availability and securely perform remote deployments. Industrial-system robustness, reliability, and safety are also becoming more important than ever. In several applications, safety requirements are formalized
Both discrete automation (for the machining, assembling, otherwise working, and transporting separate discrete workpieces) as well as process automation (for the distillation or other use of liquids, systems of fluids, and other batches subject to continuous chemical reactions, temperature controls, and metering) have benefitted from the burgeoning benefits of DX. Here we primarily focus on discrete automation examples.
Use
| Dreamstime • Ekkasit919and mandatory, while in others this is implemented to di erentiate the product by making it safer and more reliable. Microchip’s functional-safety hardware, software, and documentation help engineers design highly robust and safety-compliant systems.
Paczkowski: Edge-enabled IPCs can serve as fog environments through which developers can rapidly deploy analytics and other advanced computing. Another option is a hybrid platform using an edge controller having deterministic PLC-type realtime control and generalpurpose PC-type computing resources. In fact, fog computing is a great steppingstone for locally developing solutions before scaling them to the cloud. In addition, there are many data-intensive digital transformation applications for which data transport costs can be significant. Here, a fogcomputing solution is preferred for aggregating and preprocessing data prior to moving it in bulk to other enterprise assets.
of digital twins is a core approach in the digital transformation of industrial automation.
The use of so-called digital twins (or virtual or digital replicas) is core to the digital transformation (DX) of industrial automation.
Beginning a digital transformation
The most successful digital transformations engage every employee at the organization from management to seasonal plant personnel and continually evolve in response to quantified results and personnel feedback.
But whether instituted by a team internal to an organization or hired consultants, digital-transformation initiatives can face pushback at established companies — especially from naturally skeptical engineers. Exacerbating this issue is the way in which products supporting DXs are inherently reliant on the adoption of complementary elements to work. That means a given smart sensor (to give on example) can require adoption and integration of dozens of other disparate components and elements to support a grander initiative. In some cases, the suppliers of such components and tools eschew marketing that touts IoT functions for communications that instead address the specific business concerns of an industry.
Suppliers best equipped to support digital transformations of business models are those with long histories in engineering and manufacturing and extensive product lines with smart
products and services leveraging data analytics.
Though all organizations have mission-critical issues that (if solved) could mean business-model quantum leaps, those issues shouldn’t be tackled in nascent DX trials. Starting small on more manageable processes needing improvements is the wisest approach to an inaugural deployment.
The first step in a successful DX is to define lingering problems internal to a company or a ecting the industry at hand as a whole. Despite the industries’ di erences, common challenges are found in industrial automation, energy management, building automation, data centers, and public utilities.
Those most familiar with the issues needing solutions are information technology (IT) personnel and those directly supporting operations and lineof-business services. They’re also the most likely to have connectivity wish lists — whether for:
• Automation functions (via device, control, machine, and cloud integration) or
• Data access and use so important to IIoT functionalities.
For the former, leading trends include the rise of edge computing (including
the use of industrial gateways) as well as services that support cloud connectivity, Ethernet-based networks, wireless communications for industrial components, various forms of standardized protocols, open-source programming code, and unifying software environments to facilitate interoperability.
For the latter, automated company data sharing along with advanced analytics and artificial intelligence (AI) are the IoT capabilities leading DX e orts. The connectivity-heavy nature of such DX implementations means that many organizations fund and support them through IT departments who must in return stay current with the IoT networking, data storage, and improvement programs the organization develops, deploys, or employs.
Where organizations involve line-ofbusiness teams in DX initiatives, they can often help solve challenges faced R&D, engineering, operations, maintenance, and corporate teams. Solving such operational issues ultimately benefits endusers and other external entities that interface with the organization.
What new o erings of yours leverage artificial intelligence (AI)?
Wollersheim: We recently introduced Property Intelligence — proprietary AI that can analyze any property or portfolio at
scale. These insights help managers answer business-critical questions and dramatically reduce the time it takes to get hands-on analytics … and in many cases, generate previously unattainable insights. In fact, Airbnb recently leveraged Property Intelligence to analyze and verify a collection of Adapted-branded homes to ensure they meet accessibility standards for guests with mobility needs.
Eidelberg: We plan to soon o er two artificial intelligence (AI/ML) product lines — the RoboChair and the Exollent to give people assistive mobility. Both may run o three di erent controllers. A bang-bang on-o controller may su ce for elderly users needing help standing. Or a PID controller running a specific motion profile might help a patient in rehabilitation. Or a reinforcement-learning (RL) motion controller with hundreds of optimized neural-network parameters might drive autonomous functions to assist highly disabled patients. The latter will learn via simulation to optimize performance using a reward function — including the balancing of conflicting safety, speed, power, and comfort parameters. The system will track the environment via
Mitsubishi Electric Automation, Inc. has released its MELSOFT Gemini 3D Simulator Software to allow users to expedite the design and construction of manufacturing projects as they introduce new automation components to their facility. By connecting to various software and factory devices, Gemini provides visualization, simulation, and the streamlining of work processes. Gemini operates using a PC-based 3D digital space and connects directly to factory devices without having to go through an OPC server. This enables 3D data to be updated in digital spaces approximately 12 times faster than OPC environments. As engineers use the software for their verification purposes, they can test and debug the automation logic for machines and systems, as well as check the operation of the planned production facility prior to construction.
gyrometer, position, and force sensors and drive autonomous actuators. Once RL simulations achieve their maximum reward, the neural-network control parameters will be deployed in a real system and run as a model-free controller.
The use of so-called digital twins (or virtual or digital replicas) is core to the digital transformation (DX) of industrial automation. These digital twins — essentially software-based copies of real-world machines, processes, systems, operating environments, and products — are exceptionally accurate. That’s because digital twins are based on massive amounts of data collected from previous designs’ performance; feedback from sensors on installed equipment; and advanced replication coding. The result are models that let organizations explore, control, and optimize designs in e cient and cost-e ective ways. In addition, digital twins support communications between interconnected IIoT systems. That’s because these digital models tend to standardize the programmatical
Suppliers best equipped to support digital transformations of business models are those with extensive product lines with smart products and services leveraging data analytics.
descriptions of component parameters and interrelated definitions. Ultimately, that in turn lets operations output product with just-in-time approaches in smaller batch sizes. Digital definitions of interconnected machine modules and controls also make quick changeovers and reconfigurations (say, to temporarily output a specialty product) more feasible.
What systems as a service (SaaS) and digital-transformation (DX) solutions do you o er?
Gottlieb: Kollmorgen recently signed a go-to-market agreement with MTEK to sell the MBrain solution — a no-code paperless smart-manufacturing platform. MBrain handles enterprise complexity at scale, including work instructions for
line setups. The latter can be useful to machine builders using motion control or analyzing data captured during manufacturing across any facet. MBrain users realize vast improvements … even to 70% value-stream throughput increases in addition to hard savings on paper as well as training and onboarding. The MBrain solution naturally fuses into Microsoft Azure cloud-based configurations, on-premises configurations, or hybrid configurations. In short, MBrain has been instrumental in helping design engineers boost product quality, run rates, and human-resources deployment.
Thompson: We’re leading the digital transformation of facilities management. With our scanning and software, operations can capture buildings in
photorealistic 3D for ROI and reduced facility design, management, and maintenance costs. A Matterport digital twin gives immersive access to the physical context of a facility, machine, or area. Recently, John Deere employed our Digital Twin Platform and 3D capture technology for remote management of more than 60 facilities across the globe.
Scott: Fuuz by MFGx delivers platform as a service (xPaaS) capabilities for companies with complex processes. More specifically, Fuuz xPaaS provides prebuilt industrial apps and pro-code to no-code app-development tools that consolidate technologies into cohesive user experiences that are fast and easy to learn. With rapid deployment of standalone apps and connections to existing software, businesses can capture data. Plus they can unite processes, people, and machines in one ecosystem. In fact, the software integrates and augments all open data sources to let companies
LEMO’s rugged T Series self-latching connectors support 1000Base-T1 single-pair Ethernet.
Some industrial automation-targeted AI can analyze plants an machines to help managers answer business-critical questions and minimize how long it takes to procure useful analytics.| AdobeStock
leverage current solutions, industrial equipment, and operating systems … with integration capabilities that let design engineers connect to devices within their enterprise as well as other databases and sites.
• One health-snack producer needed a new point-of-sale system, as their current system (among other things) couldn’t integrate data into their ERP. Fuuz helped the company scale inventory management, transportation, and shipping — plus capture activity data across multiple e-commerce environments and dropship programs. Now, data is automatically processed to invoice into their ERP — and the company’s inventory management, accounts payable automations, and 3PL shipping partner integrations feature upgraded functionalities.
• One injection-molding and formedfiber designer and manufacturer needed to compile metrics and KPIs in an accurate format. Here, Fuuz enabled machine integration with the company’s cloud ERP provider; automated print jobs; and simplified data capture. Now, machine-data capture happens in realtime so associates can focus on product quality and production targets.
• One semiconductor maker with multiple stamping and heat-treating operations integrated Fuuz into its cloud ERP to simplify the work of its IT experts on productivity-boosting custom applications.
The most e ective DX implementations are those that are operable across business systems (especially as the IIoT continually evolves) while prioritizing cybersecurity protections. Component suppliers and solution vendors most capable of supporting machine builders and plants with DX e orts are those connected to comprehensive partner networks that standardize on certain protocols, software tools, and design ecosystems. These in turn allow assembly of various vendors’ technology elements to build
customized end-to-end IoT solutions … in some cases, complete with continued support from licensed integrators or digital services designed for a given industry.
Benefits to OEMs and facilities that adopt DX approaches include the ability to satisfy 21st-centuty demand for customized end products (from foods to electronics to homes) as connected companies are the nimblest and most capable of flexible production routines.
In some cases, DX enables new business models that turn data (processed by analytics or AI) into salable products. This can take the form of subscription-based or valueadd machine-monitoring products. The benefit to end user is the ability to remotely fix problems without having to wait for a technician to fly or drive to the facility.
Digital transformation solutions are nearly always scalable, allowing OEMs and endusers to experiment with a new system in one location and then leverage what’s designed and learned in more places later — often with significant savings from the economy of scale.
DX also frees automated facilities from classical single-file production lines that are limited by inherent ine ciencies and (especially in manufacturing) workforce shortages. AI especially complements personnel functions and enables more nuanced factory flows — freeing humans from data analysis and assessing situational contexts to serve as the so-called missing middle and inform (or sometimes even trigger) realworld actions.
In some cases, long-term partnerships with industrial suppliers can help vendors and endusers keep current in their DX e orts. Such arrangements deemphasize product-centric businesses and emphasize support services and operating platforms. What’s more, step-by-step design approaches (like production approaches) must yield to more flexible design and prototyping approaches. Here, the typical trial-error
iterative process involving mostly siloed in-house design teams is replaced by open and holistic design work.
Supporting such approaches are socalled design ecosystems and platforms from industrial suppliers. To complete such o erings, suppliers often partner with professional services companies specializing in digital services that are applicable to industrial automation. The result is an array of throughput analysis, predictive maintenance, asset tracking, customer service, and energy optimization tools targeted to specific automation operations. The largest machine builders with long-term relationships with suppliers can expect help in analyzing business problems and tailor-made DX solutions.
Whether led or informed by the organization’s IT department, DX e orts always include integration of shopfloor operational technologies (OT) into business IT systems. Smart connection of plant OT to the enterpriselevel IT helps organizations enjoy all the benefits of digitalization. Edgecomputing technologies help link such OT and IT systems. This so-called OTIT convergence addresses how these separate breeds of data-handling systems traditionally have very di erent processing structures — with the former increasingly expected to process and transmit data in realtime (or nearly so) and IT systems sampling and processing much more slowly.
Cross-capitalization of both systems’ data (in some cases, massive volumes of unfiltered data) requires translation and interpretation to glean information relevant to the operations at hand. Cloudbased computing can help aggregate, manage, filter, and analyze such data. Otherwise, local platforms are needed to inform production adjustments in realtime.
Read the rest of our experts’ insights in Part 1 of this series by visiting designworldonline.com and searching on Gottlieb. DW
Mobile equipment such as fork lifts and other o -highway equipment is changing. With more emphasis on rethinking the drive systems for this type of equipment, there is a slow but steady turn toward other drive technologies, one of these being electric actuation.
Electric actuators for mobile machinery have seen a steady uptick for a number of reasons. For one, electrification is a broad trend across all mobile machinery. This is due to a number of reasons including legislation to reduce CO 2 emissions, limits on noise emissions in urban centers, and growing sustainability targets pushing for improved energy e ciency.
The fact is, that over the years, electric actuators have gotten more powerful, with power densities comparable to old standbys such as hydraulic systems. Another is the simplicity of electric actuators themselves; they are a lot simpler to install and maintain than other systems. Electromechanical actuators have steadily replaced hydraulic cylinders in a few places, including auxiliary control and steering functions.
To meet the growing demand for electrification, manufacturers are designing more powerful electric actuators for mobile equipment.
New electric linear actuators in Ewellix’s CASM series are hydraulic replacement actuators for mobile machinery with 3-ton, 6-ton and 15-ton lifting capacities.
As a result, manufacturers are designing systems and actuators to accommodate these changes. A case in point is the linear motion and actuation company Ewellix.
Take the new e-MOVEKIT from Ewellix. It’s aimed at helping designers and manufacturers of mobile machinery simplify the specification, assembly, and testing of electric linear actuation systems.
The e-MOVEKIT was developed in response to the growing trend towards electrification of motion systems in mobile and o -highway equipment. In particular, the demand to replace traditional hydraulic devices with a new generation of electric actuators that o er high levels of power-density, greater maximum force capacity, energy e ciency, safety, and reliability.
The new e-MOVEKIT is a complete system with all the components that are needed to drive and control linear motion in mobile machinery fi tted with a 24-V power source, with either analog or CAN-bus standard controls.
At the heart of each e-MOVEKIT is an advanced modular electric actuator. These are designed to be used with a wide range of high-performance motors, gearboxes and end attachments, all of which are supplied as part of each kit. Each kit includes all the connectors, cables and mounting attachments needed to simplify installation. The electric actuators o er a range of benefi ts to be easily built into each machine. For example, regenerative braking can be initiated when each actuator is being driven under load, while safety features such as a descent speed limiter, back-up nut, and electromechanical motor braking can easily be incorporated.
The concept behind the e-MOVEKIT is to make it easy for engineers who are already experienced in linear motion, and those who may not have previously worked with electric actuators, to be able to quickly and easily specify, customize and configure a linear actuation system for mobile equipment. With the simplicity and speed of specification that the e-MOVEKIT o ers, it makes it suitable for both prototype development projects as well as fullscale equipment build.
The kit looks to transform the way electric linear actuators are specified and used by OEM designers, providing a plug-and-play option for replacing
The fact is, that over the years, electric actuators have gotten more powerful, with power densities comparable to old standbys such as hydraulic systems.
It’s an old debate that continues today — hydraulic actuation or electric?
For many years, hydraulic actuation has been the go-to choice for applications requiring high force. Hydraulics are generally understood to be rugged and relatively easy to deploy. What’s more, the cost per unit of force is lower than for other actuation methods. That’s in part why hydraulic actuation has been the standard choice in applications requiring large force including in mobile equipment as well as in other industrial uses.
For example, because of their high operating pressures (typically ranging from 1,500 to upwards of 5,000 psi) hydraulic cylinders can produce high forces of well over 100,000 kN. Also, because hydraulic cylinder force is a product of pressure and area, high forces can be achieved by relatively smaller cylinder sizes with high pressures.
One of the most common alternatives to hydraulic cylinders are electric rod-style actuators. These electric actuators o er more flexibility and precision than hydraulics in addition to being more reliable, with less maintenance involved than what is needed for hydraulic systems.
However, it’s still the case that hydraulic systems o er more force than electric actuators, although electric actuators have been catching up. In fact, newer product o erings are capable of output forces that comparable to some higher-end hydraulic cylinders, making them a viable option for replacing hydraulic systems in many instances, including mobile equipment and o -highway applications.
traditional hydraulic cylinders, while helping to reduce design complexity and commissioning times.
A new generation of electric actuators
Ewellix has specifically designed electric linear actuators for use in mobile applications. From agricultural and construction machinery to lift platforms, these new actuators combine greater power-density with high levels of energy e ciency, position and motion control and repeatability. The first products to be released later this year will include actuators with 3-ton and 15-ton lift capacities, with future versions to include intermediate capacities as well as an electromechanical steer-by-wire option.
The new actuators were developed to help OEMs transition from traditional hydraulic power to electrically controlled motion systems. In particular, these will o er a reliable and e cient alternative that is clean, simple to install and use, with a lower total cost-of-ownership. It can o er even more with regenerative braking when the actuator is being driven under load. To achieve all functions as a hydraulic cylinder, the CASM actuator can be equipped with safety features such as a descent speed limiter, back-up nut, and electromechanical motor braking.
This new generation of products has been developed from Ewellix’s CASM series of electric actuators and shares the same robust, modular construction. The new actuators add
Electric actuators can provide smooth movement, improved energy efficiency, and lower total cost of ownership for mobile equipment such as excavators.
Elements of the e-MOVEKIT from Ewellix include the actuator and motor with front and rear attachments, centrifugal brake, a number of motor control options, plus the necessary controller, sensor, and power cables.
a more compact design, a wider range of end-attachments, and an even higher efficiency motor package, with IP ratings that meet the needs of tough offroad environments.
The new 3T actuator delivers 3.6 kW peak power output, at the cross section of 80 x 80 mm. The 5T actuator (CASM100) delivers 10 kW peak power output at the narrow cross section of 105 x 105 mm of the linear unit. And the 15T actuator supplies 17 kW of peak power output at 130 x 130 mm.
The modular construction of the new actuators will also give design engineers and OEMs added flexibility. For example, it will be possible to choose ball-screw or roller-screw drive mechanisms, different highperformance motors, and either parallel or in-line gearbox options. Plus, designers can configure the base actuator components, including attachments like the T-bar, the pivot and the rear attachment that connect each cylinder to the moving parts on mobile or off-road machinery.
The new generation of actuators
are being engineered to provide a long and reliable operating life, with minimal maintenance requirements. Depending on the configuration, it will be possible to achieve maximum linear speeds (unloaded) up to 300 mm/sec, at accelerations of up to 6 m/sec, and stroke lengths of up to 2 m. DW
Ewellix | www.ewellix.com
With the simplicity and speed of specification that the e-MOVEKIT offers, it makes it suitable for both prototype development projects as well as full-scale equipment builds.
As manufacturers seek more unified operations with greater visibility, many jump at the chance to gather data only to find themselves buried in meaningless and costly information. Renishaw Central aims to capture the right information and reveal hidden machine data that improves process control and quality.
The cloud is often revered as a sacred watering hole where all data may happily gather and intermingle under the magical governance of AI, which can transform any hopeless datum into a meaningful contrail of predictive knowledge.
But storing mass information doesn’t equate to storing the right information. And sorting through the noise can be costly and unproductive.
Plus, many manufacturers prefer to hold onto now-called legacy systems that still serve their purpose while adding new technology incrementally. Collecting and pooling data from many machines of di erent eras can be a massive undertaking with no guarantee that the information will be helpful.
“They are very much dreaming of the cloud, but when it comes to a 20-year-old controller, the dream can evaporate and become a nightmare,” said James Hartley, applications and marketing manager of Renishaw’s Machine Tool Products Division.
Deciding where to capture information and how to use it to improve processes can be burdensome. Why would anyone waste time collecting data and creating reports if the same manufacturing problems persist? If data isn’t doing anything useful to improve production times, scrap rates, or quality metrics, then it just wastes more time and money, adding to ine ciencies.
All too common, data flows are visible until they get to the machine shop. Machine shop personnel hold valuable knowledge about what makes each machine work. They know which machines perform the best for specific jobs or need more frequent servicing. This knowledge remains at the shop level, and people learn to adapt to the machines.
But reliance on personnel know-how creates a data vacuum and counters more unified facility control systems. To plant engineers, there seems to be an invisibility cloak over the shop until quality data pops up later. And without visibility, they can’t make real-time data-driven recommendations on the process.
“Many people have the hardware, skills, and technology, but they just don’t have a grip on what’s really going on behind the scenes,” said Guy Brown, development manager of Renishaw Central.
Renishaw’s Equator gauging system captures near-line quality information and sends it to Renishaw Central, which sends updates to the machine to improve part consistency and quality.
But what if there was a way to extract hidden information from the machines? What if real-time data exchange could provide a holistic view of the machine shop so it’s no longer a data vacuum?
Renishaw Central, an on-premises connectivity and data platform that connects machines and extracts actionable data, aims to do just that — and more.
time and not at the end of the line. With patented Intelligent Process Control (IPC) software, it can also capture nearline quality information from an Equator gauging system, for instance, and send information such as tool-offset updates back to the machine to improve consistency and control.
“If someone manually changes a tool offset or if a tool offset is wrong, the process is inaccurate, and the quality can go haywire. So, we’ve paid just as much attention to the collection of toolsetting data as we have for workpiece setup or inspection,” said Hartley.
The engineering company Renishaw is known for its metrology, measurement, motion control, and manufacturing technologies. The supplier also develops advanced analytical instruments and machines for healthcare. As a manufacturer of its own products, company engineers deeply understand the end-to-end challenges that OEMs face and how data visibility can improve process control.
In fact, such control is the core of Renishaw Central. The platform connects a range of new and legacy equipment to help operators understand what’s happening at the machine level.
The intention is to limit variability and monitor quality in real
While collecting data is one task, acting on it is quite another. In the 1980s, Renishaw printed most measurement results for backup with dot matrix printers. But the information typically sat dormant unless they found a quality problem and referenced it in a post-mortem investigation. Though Renishaw pioneered on-machine process control, even they weren’t actively using the data.
Then, in the 1990s and early 2000s, a shop floor data collection system worked over the DNC system that could push up programs to the machines, take down measurement results, and store
the data centrally. The data was still not mined or analyzed for any purpose other than figuring out quality control issues after they occurred.
“We collected a lot of data and never went back to look at it. It was just kept for historical purposes — for traceability reasons — but filed away and not really addressed,” said Brown. “A very small portion was functional and worked with the kitting stations, but 90% of the data just sat there.”
In the 2010s, they implemented an external Industry 4 platform to connect more equipment, but it didn’t collect metrology or measurement data and required user input in many cases. So, the system depended on the quality of manually inputted information.
Now, in the 2020s, they have Renishaw Central to build upon previous efforts and add a real-time data analysis piece — but not just for data analysis’ sake. Renishaw Central extracts and reveals actionable data that would otherwise remain hidden and unshared.
“We started asking, ‘Why do machines stop? Why are things not quite what we expect them to be? What have we missed? What are the unknown unknowns?’” said Brown. “And we wondered how we could use the data day by day to transition from a reactive to a proactive position.”
To test its own product, the company deployed the platform in the U.K. at its
low-volume, high-variety manufacturing facilities in Miskin and Stonehouse. The platform connected 67 machines across both facilities, revealing that two error types were responsible for 82% of automation stoppages. After remedial action, automation stoppages decreased by 69%. Additionally, using the IPC set-up feature, set-up times on sliding-head lathes decreased by more than 85%.
A global selection of pilot customers also confirmed that Renishaw Central provided the right data and insights to improve their processes and performance.
The Renishaw Central platform is machine-agnostic and uses APIs to connect different machines to a unified, on-premises network.
“No one company is going to own Industry 4,” said Hartley. “Therefore, Renishaw is a neutral party, providing all the big controller manufacturers and OEMs with software. We are a licensee for almost all their APIs, which means we can make native connections to those controllers.”
In some cases, data flows one way from machines to Renishaw Central, which collects measurement results, quality metrics, cycle time, status, utilization, warnings, alerts, yield rates, offsets, and other process control information.
Need a power cord supply chain with 1-week lead-times? Let Interpower® worry about manufacturing your cords and cord sets while offering its industry-unique 1-week lead-times.
Our cord sets and accessory power systems ship straight from the factory. Want the cords hanked, coiled, tied, bagged and boxed? Need 1-D or QR barcodes for easier warehousing? Customize cord lengths and colors for countryspecific cords configured and ready to use right out of the box!
• World-class customer service 7 a.m. to 6 p.m. CST
• In-stock cords ship the same day
• No minimum orders
• Value-added options such as colors, lengths, labeling and packaging
®
®
What differentiates the platform is its two-way communication capability. For processes the platform can control, there’s a two-way data exchange in which the system analyzes the data received, makes real-time decisions, and then sends updates back to the machines.
“Data is not enough,” said Brown. “The data itself is just values, and those values by themselves can often mean nothing. It’s only when you start to put thresholds around data and add context that it becomes informative and actionable. If you can’t perform an action at the end of it, what’s the point?”
During Renishaw’s pilot program, Brown noticed that the data showed
Interpower North American and international cords and cord sets provide the correct country-specific amperages and voltages, ensuring the end user has the correct connections to the local mains power. Interpower manufactures reliable state-of-the-art electrical cord sets for global markets, cords manufactured in Lamoni and Oskaloosa, Iowa.
lots of little stoppages, yet when he walked over to the machines, they all seemed to be working fine. He learned that operators adapted to the machines’ behavior and pressed a button to resume the process whenever it stopped. The practice became routine and unnoticed until Renishaw Central revealed each occurrence.
“These somewhat hidden stoppages were accepted, and the solution was to quickly check something and press cycle start,” said Brown. “This is a problem when you’re running lights out.
If you step out of the factory at 10:00 pm on a Friday and a machine stops five minutes later, you’ve lost the whole weekend.”
Interpower cords and components are manufactured in accordance with Interpower’s product quality plan: hipot testing, continuity testing, ground testing, and inspections after each process. Interpower also offers value-added options such as custom lengths, colors, packaging and labeling with no minimum order requirements, and expert customer service from 7 a.m. to 6 p.m. CST.
®
®
Toll-Free Phone: (800) 662-2290
E-mail: info@interpower.com
Business Hours: 7 a.m.–6 p.m. CST
Order Online! www.interpower.com
Instead of having engineers lead remediation by evaluating the data and making changes, Renishaw brought in all the people closest to the process as a continuous e ort, not a one-o exercise. They started with a workshop-type approach, where engineers, operators, and maintenance personnel looked at the data and initiated interesting conversations. Each team chimed in with their viewpoints to validate and challenge each other’s perspectives. As it turned out, Renishaw’s digital journey sparked a cultural change that now lines its pathway toward even smarter manufacturing.
“It wasn’t one resolution, it was three resolutions, and it needed all three teams to make it work,” said Brown. “They all had to do something di erent to help resolve this one particular problem.”
To be clear, the data isn’t meant to target people — it’s all about the machines. It’s about the measurement data, tool setting data, in-cycle gauging data, and o set update data combined with alerts generated from the machine to notify when things are out of control or about to be out of control.
Additionally, Renishaw Central isn’t designed as a catch-all for any factory data. However, it does use a Web API that can connect to various data sources and software. For instance, during the resolution workshops, Renishaw realized they needed to aggregate multiple data sources to build dashboards. So, they started using Power BI to create custom reports and review past data.
“The CNC machine provides limited information,” said Hartley. “Let’s say it knows its tool number 10. But to make an intelligent decision further down
the line, we want more details — that tool number 10 is a slot drill and comes from manufacturer A, for example. Such analysis can reveal tooling from manufacturer A is better than tooling from manufacturer B. Unconnected machine tools will never give you that kind of information. But software such as Power BI can with data from multiple sources, including Renishaw Central.”
Renishaw Central is best suited for manufacturers already on a mature data journey with in-house IT departments and a networked factory. It provides machine-shop connectivity, consistency, control, and confidence with actionable end-to-end data. The ability to predict, identify, and correct process errors before they happen is the crux of automation for long-term productivity, capability, and e ciency. DW
Renishaw | renishaw.com
ndolumik's story started a few years ago as the FDA sounded the alarm over the risks of internal surgical staplers.
In 2019, the federal agency warned healthcare providers that it had received more than 41,000 medical device reports (MDRs) related to surgical staplers and staples for internal use from 2011 to 2018. Those MDRs tallied more than 32,000 malfunctions, at least 9,000 serious injuries and 366 deaths.
Two years later, the FDA increased the risk level associated with the staplers, reclassifying the devices from Class I to Class II and subjecting them to premarket review and special controls.
Bariatric surgeon Dr. Nova Szoka had already been working on a device that could prevent some of those injuries. She envisioned an illuminated gastric calibration tube that would shine near-infrared light
through stomach tissue and fat. This camera-visible fluorescence would make it easier to see the tube inside a patient, lessening the risk of a surgeon perforating the stomach or stapling the tube to the stomach during bariatric procedures.
In 2020, Szoka founded Endolumik with Mara McFadden, now CEO of the Morgantown, West Virginia-based device developer. In 2022, they submitted their device to the FDA under the new Safer Technologies Program (STeP) and this year won the agency's fi rst STeP authorization.
"Safety was always the most important thing," Szoka told Medical Design & Outsourcing.
FDA's STeP initiative
As Szoka and McFadden got started at Endolumik in 2020, the FDA prepared to launch the STeP initiative. The FDA based STeP on the Breakthrough Devices Program, which offers streamlined reviews for devices designed to treat life-threatening or irreversibly debilitating diseases or conditions.
STeP also offers accelerated review times, but for devices that treat or diagnose less serious diseases or conditions than the breakthrough program. The FDA's goal for both programs is to get safer, better devices to patients faster than the agency's traditional pathways alone.
"Advancements in medical devices that are ineligible for the Breakthrough Devices Program but offer a signifi cant safety advantage in treating and/or diagnosing less serious diseases or conditions >>
can also provide an important public health benefit," the FDA said when launching STeP in 2021. "... Efforts to improve safety are directly related to improving overall clinical benefits and may also help patients experience fewer serious adverse events."
Medical device developers can ask to join the voluntary program through a Q-Submission. Then, they'll work with the FDA to chart the best path to marketing authorization, whether that be premarket approval, de novo or 510(k).
The FDA accepted 14 STeP requests out of 30 applications last year, according
to the Center for Devices and Radiological Health's annual report.
Taking the big STeP Endolumik's founders were sure they should take the 510(k) pathway, and in a Q-Submission meeting with the FDA in 2022, both sides decided the device was a good fit for STeP.
"We found them to be really responsive in terms of timely, interactive review," McFadden said in an interview. "Sometimes you hear horror stories of submissions just sitting for the full 90 days before you hear much of anything, which was not our experience. They got back to us pretty quickly, and we had the opportunity to interactively go back and forth."
Medical device developers should clearly understand STeP's eligibility requirements and be prepared to discuss in depth how their device improves safety, McFadden said.
"It's non-trivial to demonstrate that you are safer," she said. "You have to show at least one of four different factors. You can either reduce the Endolumik co-founders
Dr. Nova Szokaoccurrence of a known adverse event, reduce the occurrence of a known failure mode, reduce the occurrence of a known user hazard or user error, or improve the safety of another device. You really have to do your homework and be ready to speak in depth in terms of how you're going to have an impact on safety."
"McFadden recommended getting help from a regulatory consultant for the STeP request and 510(k) submission. Endolumik used Nilo Medical Consulting Group, led by former FDA reviewer Michael Nilo.
"The process for novel Class II medical devices is not always as straightforward as it may seem with the 510(k) program," Nilo said. "FDA does a great job of setting up programs for innovative, safer devices that can help developers get better access to the review teams and encourage collaboration. I'd advise developers to look into all the programs and give it a shot. They are free to apply to, and the worst outcome is an introduction to the review team that you'll be working with."
Creating a tube with 'Goldilocksperfect' balance
Endolumik's contract manufacturer, Virtec Medical, was indispensable, McFadden said. The biggest challenge in designing the device was balancing fl exibility and rigidity.
Too stiff, and the device couldn't safely navigate through the throat and might punch a hole through the esophagus or stomach. Too soft, and the device would "buckle like a spaghetti noodle" before reaching the stomach, McFadden said.
The trial-and-error process started with the first 3D printed prototypes in pig and cadaver testing.
"Holding the balance of the functional dimensions we needed in
terms of the outer diameter and the size of the electrical lumen and getting the cross-section correct to get the mechanical properties we wanted — buckling and kink resistance and that sort of thing — took more iteration than I would've guessed from the fi rst go," McFadden said. "That was one of our biggest unanticipated challenges."
The tube is made of a PVC-like material, with one lumen for the near-infrared LEDs and another to provide suction so surgeons can remove stomach juices as needed. To determine the right material and dimensions, the team went beyond durometer testing of existing gastric tubes to fi nd a "Goldilocks-perfect" balance.
"Our engineering team really broke down different characteristics of this device: kink pressure, buckle pressure, twisting pressure — basically quantifying all those things and then dialing it in," she said.
At the final cadaver lab, the team invited some surgical residents to give it a try.
"Once I was able to see some trainees — who had never used a device before — safely introduce it, that's the point where I felt we were ready to jump to a human-grade device in a clinical trial."
Endolumik's clinical trial has treated 22 patients so far without any adverse results, Szoka said.
What's next for Endolumik
Endolumik's florescent gastric tube is a single-use device. One goal for future improvements is to design for sustainability, including improved recyclability.
And while McFadden declined to go into detail about other possibilities for the company, she referenced the growing number of nearinfrared cameras in operating rooms that could give surgeons better visibility with Endolumik devices of the future.
"It's really prompted us to start thinking long and hard about where else in the world of minimally invasive surgery are there hazards created by not having a great line of sight to a tool," McFadden said. "We defi nitely have one other product in the R&D pipeline that we're really excited about, that we think is solving an equal, if not greater, pain point in the anatomy."
"We think it's the beginning of a digital surgical tool revolution that we're being able to exploit the tools that are in the OR today, the towers that are in the OR today, to give surgeons advanced visuals," she continued. "And we're really excited to be part of what's next as even more digital surgical tools come on the market, and to see what the next generation of cameras can do."
It’s good to know where you come from. At Nitto Kohki, we come from a line of engineers and businessmen dedicated to exceptional manufacturing execution. In our line of vacuum and pressure pumps, this is seen in the unique linear-piston design, where one moving part resolves to exceptional reliability, low vibration and noise, high energy efficiency, and long, consistent performance life (>10,000 hrs.) for a host of critical medical applications. It’s why the medical device industry has specied Nitto pumps for over sixty years— the quality in our DNA. Find out how you can use it to your advantage.
“We think it’s the beginning of a digital surgical tool revolution...and we’re really excited to be part of what’s next.”
SALES
Ryan Ashdown rashdown@wtwhmedia.com 216.316.6691
Jami Brownlee jbrownlee@wtwhmedia.com
224.760.1055
Mary Ann Cooke mcooke@wtwhmedia.com
781.710.4659
Jim Dempsey jdempsey@wtwhmedia.com
216.387.1916
Mike Francesconi mfrancesconi@wtwhmedia.com
630.488.9029
Jim Powers jpowers@wtwhmedia.com
312.925.7793
@jpowers_media
Courtney Nagle cseel@wtwhmedia.com
440.523.1685
@wtwh_CSeel
Publisher Mike Emich memich@wtwhmedia.com
508.446.1823
@wtwh_memich
CEO
Scott McCafferty smccafferty@wtwhmedia.com
310.279.3844
@SMMcCafferty
EVP
Marshall Matheson mmatheson@wtwhmedia.com
805.895.3609
@mmatheson
DESIGN WORLD does not pass judgment on subjects of controversy nor enter into dispute with or between any individuals or organizations. DESIGN WORLD is also an independent forum for the expression of opinions relevant to industry issues. Letters to the editor and by-lined articles express the views of the author and not necessarily of the publisher or the publication. Every effort is made to provide accurate information; however, publisher assumes no responsibility for accuracy of submitted advertising and editorial information. Non-commissioned articles and news releases cannot be acknowledged. Unsolicited materials cannot be returned nor will this organization assume responsibility for their care.
DESIGN WORLD does not endorse any products, programs or services of advertisers or editorial contributors. Copyright© 2023 by WTWH Media, LLC. No part of this publication may be reproduced in any form or by any means, electronic or mechanical, or by recording, or by any information storage or retrieval system, without written permission from the publisher.
Subscription Rates: Free and controlled circulation to qualified subscribers. Nonqualified persons may subscribe at the following rates: U.S. and possessions: 1 year: $125; 2 years: $200; 3 years: $275; Canadian and foreign, 1 year: $195; only US funds are accepted. Single copies $15 each. Subscriptions are prepaid, and check or money orders only.
Subscriber Services: To order a subscription or change your address, please email: designworld@omeda.com or visit our web site at www.designworldonline.com
DESIGN WORLD (ISSN 1941-7217) is published monthly by: WTWH Media, LLC; 1111 Superior Ave., Suite 2600, Cleveland, OH 44114. Periodicals postage paid at Cleveland, OH & additional mailing offices.
POSTMASTER: Send address changes to: Design World, 1111 Superior Ave., Suite 2600, Cleveland, OH 44114
SDP/SI creates precision gears, superior mechanical components, and customized motion control solutions for medical device OEMs. With over 70 years of experience and proven performance SDP/SI provides the reliability that the medical industry requires. Partnering with companies that include Abbott Laboratories, Intuitive Surgical, Siemens Healthcare, Medtronic, and many more, we provide support from the early design stage through delivery.
• Precision CNC Manufacturing
• Engineering Development – with years of experience we know how to make systems smaller, lighter, and faster.
• ISO 7 Class 1000 Cleanroom for Assembly
• Gear Cutting / Bevel Gear Cutting
• Custom Drive Systems / Gearboxes
Send an RFQ online, discuss your project with our engineers, visit our facility. We look forward to working with you!
Nitto Kohki’s DC motor-driven air compressors and vacuum pumps are ideal for applications requiring exceptionally reliable air flow, pressure or vacuum performance. Featuring oil-free operation, a single moving part, low noise, and low vibration, this line of linear air compressors comes in 12V and 24V models. Other benefits include:
• Very low power consumption
• Self-cooling design
• Exceptional service life (rated at 10,000 hours)
• Easy maintenance
Ideal for demanding applications in the medical device and laboratory equipment industry, including dialysis machines, blood separators, blood analyzers, incubators, heart assist devices and more.
Bubbles. Bubbles are a brilliant idea. I wish I had thought of it.
The sheer brilliance of some inventions fills me with envy. Many innovations create awe. The iPhone. I could immediately see how important it was. It was a collection of inventions put together to create a cool product. There was no one invention that stood out. I never invested energy in figuring out what would make a better phone. I hadn’t really spent a single clock cycle investigating needs, gaps, and potential solutions in phones. The iPhone created awe, but not envy.
We’ve all heard of Thomas Edison. Reading about him inspired awe, not envy. He made R&D a process. He identified problems and created an organization to attack those problems. He cranked out inventions, but most were optimizations, built on the work of others and made by a team he employed. Alessandro Volta, Warren de la Rue, and Joseph Swan all could claim to have invented the lightbulb. Edison figured out how to make it practical, but he didn’t originate the idea that light could come from electricity. Optimization is certainly important, but it doesn’t invoke envy. I reserve envy for those inventions demonstrating a flash of creativity, those inventions that appear obvious once you see them, those inventions that make me wish I had thought of it.
Before bubbles, the work of Russell Morris Selevan set my standard for an envy-invoking invention. Selevan elegantly assembled three simple components. Here, I was overcome with envy, slapping my forehead because I hadn’t thought of it when I first saw Selevan’s invention.
I used self-inflating mattresses for backpacking. I am well aware of check valves from exposure to hydraulic, pneumatic, and laboratory systems. I was aware of the whoopee cushion.
Russell Morris Selevan was granted a patent for coupling a foam core, a check valve, and a whoopee cushion — inventing the self-inflating whoopee cushion. Whoopee cushions are hard to blow up. He took components I knew well and solved the problem. The inventive moment Selevan experienced eluded me. I am still envious.
Bubbles simply made me envious. I’ve thought long and hard about the problem of plastic in the environment. I know much of the plastic pollution reaching the ocean comes out of rivers. I stood on the banks of the Mississippi, counting a piece of plastic trash about every 8 seconds, watching all the boat tra c on the river. I felt it was impossible to capture the plastic while allowing the boats to pass. I just couldn’t imagine a way.
Others were more imaginative than me. The Great Bubble Barrier collects plastic while allowing boat tra c with bubbles. A curtain of bubbles at an angle relative to the flow of the river lifts and diverts plastic toward the bank for collection. I wish I had thought of it. I’m envious. Others are trying to dissuade my envy by pointing out that pneumatic barriers are commonly used. The envy is still there. It is such a simple and elegant solution to a problem I pondered — without imagining a solution. DW
PBC Linear supplies American-made cut-to-length steel, stainless steel, and aluminum shafting with various available machined end options. Their modernized manufacturing facility is set up to keep shafting products in-stock and their Midwestern location offers quicker and cheaper shipping while avoiding the uncertainty of border customs.
Matching your bearings and shafting is critical to maximizing system performance. PBC Linear certified shafting works in sync with Simplicity bearing product lines for optimal plain bearing performance.
Designing efficient systems involves much more than simply understanding a few basic principles. There is a true art to balancing the specific requirements of an application in order to achieve the desired goals in the best possible way. Help us understand the unique needs of your application and together, we’ll develop something that surpasses what any of us could have done alone.
Contact