DECARBONIZATION: A CHALLENGE FOR THE ENTIRE VALUE CHAIN
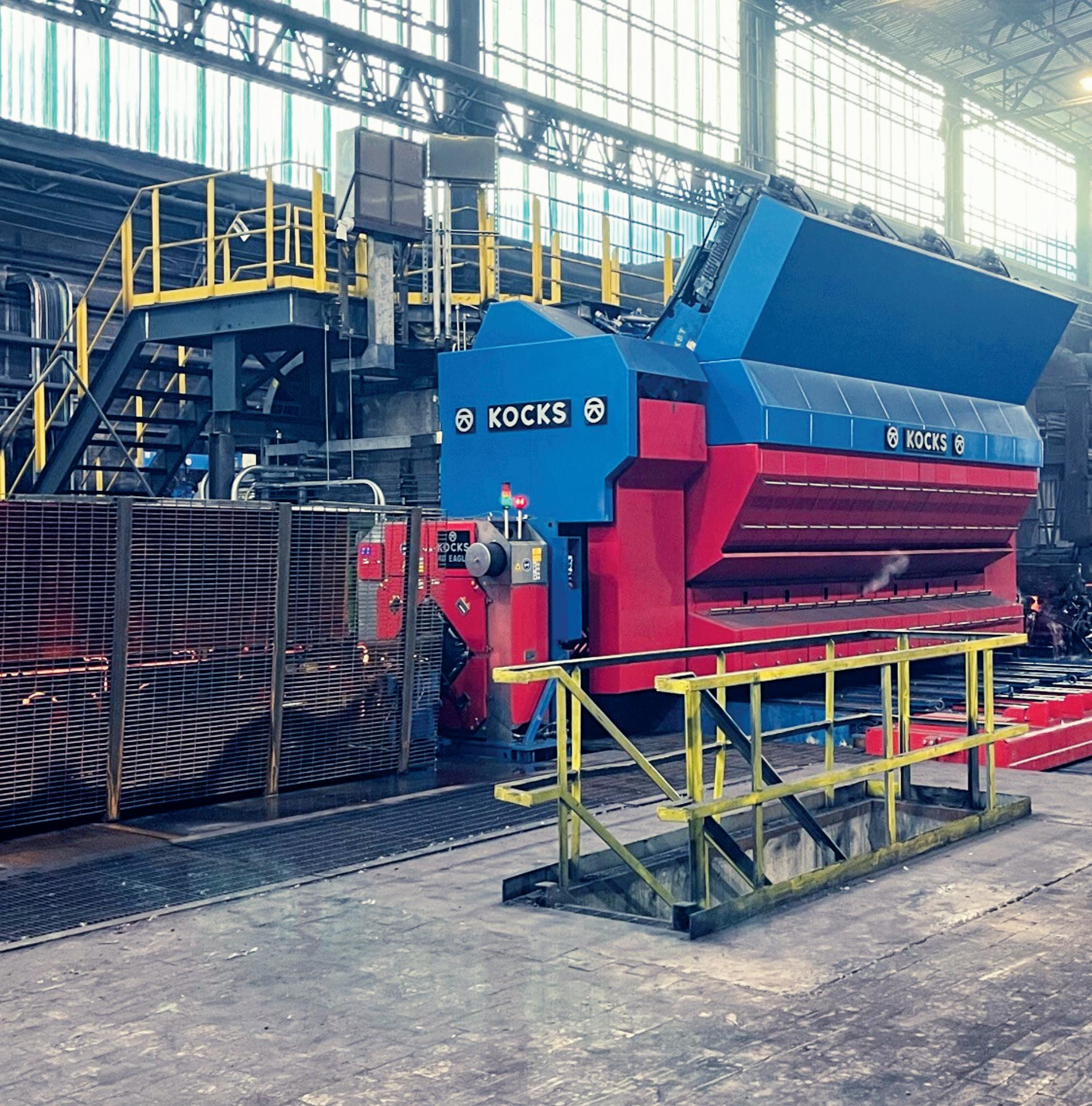
DECARBONIZATION: A CHALLENGE FOR THE ENTIRE VALUE CHAIN
Q-ONE reduces EAF overall OPEX with a shorter power-on time and very low network disturbances. It is a scalable system that can be implemented on new or existing AC EAFs, and it can be directly powered by renewable energy sources.
Front cover photo courtesy of Kocks
Successful integration of a KOCKS advanced 3-roll intermediate block in a rolling mill in the United States. With the iRSB®, steel producers benefit from a very compact reduction train with numerous advantages.
EDITORIAL
Editor
Matthew Moggridge
Tel: +44 (0) 1737 855151
matthewmoggridge@quartzltd.com
Editorial assistant
Catherine Hill
Tel:+44 (0) 1737855021
Consultant Editor
Dr. Tim Smith PhD, CEng, MIM
Production Editor
Annie Baker
Advertisement Production
Martin Lawrence
SALES
International Sales Manager
Paul Rossage paulrossage@quartzltd.com
Tel: +44 (0) 1737 855116
Sales Director
Ken Clark kenclark@quartzltd.com
Tel: +44 (0) 1737 855117
Managing Director
Tony Crinion tonycrinion@quartzltd.com
Tel: +44 (0) 1737 855164
Chief Executive Officer
Steve Diprose
SUBSCRIPTION
Jack Homewood subscriptions@quartzltd.com
Tel +44 (0) 1737 855028
Fax +44 (0) 1737 855034
Steel Times International is published 12 times a year (including four digital issues) and is available on subscription. Annual subscription: UK £215.00 Other countries: £284.00
ISSN0143-7798
Lately I’ve been thinking about the ‘Green Man’. You might have seen his head outside pubs, in churches, carved into ruins. He’s been around for centuries, the further afield and back you go – in 2nd century Iraqi architecture, in 4th century French chapels, in 12th century Welsh doorways – the Green Man is there. A symbol of nature reborn, of ‘green’ coming to bloom – his foliate head offers two interpretations; nature as manicured and tamed by man, or vegetation that spreads and suffocates, taking us prisoner through its radical, seasonal transformations.
We’ve long been fascinated, and perhaps even troubled by our relationship with the environment. Eco-poets struggle with the word ‘eco’; how do we write poetry that establishes nature without its blatant anthropomorphism? How do we reconcile ourselves in a world that often feels punished by our presence?
Catherine Hill Editorial assistant catherinehill@quartzltd.comIn recent news, a UN agency announced that in the next five years, temperatures are likely to rise by more than 1.5C above pre-industrial levels. How can the steel industry, historically, and currently one of the most significant polluters, possibly
enable decarbonization in this context? However, where there is smoke, there is potential – if steelmakers truly persist in their promises to cut emissions, the impacts will be immense.
Companies, like moon tech-provider Helios, are increasingly turning to often left-field, always hyper-advanced innovations to reach the lofty targets set by their governments. Blastr Green Steel is harnessing ‘Nordic advantages’ to build its first sustainable plant, the FerroSilva project is researching biogenic material as a reducing agent in DRI production. These technologies are attempting to grapple with centuries of history and tradition that albeit offering a remarkable narrative on human capacity to build and develop, have been hugely destructive to the world which they were designed to improve.
Whatever language is used –‘green’, ‘sustainable’,‘decarbonized’ – actions must seek to interrupt and impose. Long has the Green Man been held captive by our industry. Now, we face a point of divergence – to either be suffocated from the consequences, or attempt a complex, costly, yet crucial reconciliation.
The PROFILEMASTER® SPS is a light section measuring device for measuring contours and dimensions on profiles of all kinds in cold and hot steel applications.
Benefits:
Maximum measuring accuracy thanks to temperature-stabilized measuring systems
Shape fault detection (SFD) thanks to high sampling rate
High-precision measurements
Detects process problems at an early stage
Fast maintenance and easy cleaning
Baoshan Iron and Steel (Baosteel) has announced plans to build its first overseas ‘green steel’ plant in a joint venture with two state-backed companies in Saudi Arabia, as part of China’s Belt and Road Initiative. The company will invest $437.5 million for a 50% stake in the proposed joint venture, Baosteel said in a filing to the Shanghai stock exchange. Oil and gas company Saudi Aramco and Saudi sovereign wealth fund Public Investment Fund (PIF) will together invest the same amount and split the remaining 50% stake.
Source: South China Morning Post, 4 May 2023.
Canadian Pacific Kansas City Limited (CPKC) and Teck Resources Limited (Teck) have signed a long-term rail agreement for the transportation of steelmaking coal from Teck’s four operations in southeastern British Columbia. The agreement builds on existing services in place and will run until the end of 2026. CPKC and Teck will collaborate on the development of a unique pilot programme that integrates the use of CPKC’s hydrogen locomotives into Teck’s steelmaking coal supply chain, with the aim to reduce greenhouse gas emissions, with testing commencing in early 2024.
Source: Global Railway Review, 5 May 2023.
Energy service provider EWE and steelmaker Salzgitter AG have announced their collaboration on hydrogen supply and usage. EWE will produce and supply green hydrogen, which Salzgitter AG will use for near CO2free steel production.
‘‘In terms of climate protection, green hydrogen is particularly suitable for industrial applications such as steel production, which – conventionally operated –produces considerable CO2 every year. With our welldeveloped infrastructure, we offer the basis for reliably supplying a large-scale consumer like Salzgitter AG with green hydrogen on a large scale,'’ said EWE CEO Stefan Dohler.
Source: Market Screener, 5 May 2023.
Rishton Welding and Engineering Company Limited, a UK-based steel fabrication company, has drawn up a major redevelopment scheme to bring its factory ‘from the 1980s into the 21st century’. The business has asked the local council for planning permission for the demolition of its existing offices, extensions to the existing fabrication building and new windows to allow for the relocation of its offices.
Source: Lancs Live, 6 May 2023.
The National Union of Metalworkers of South Africa (Numsa) has signed a threeyear wage agreement with ArcelorMittal South Africa, following negotiations. The agreement consists of a 6.5% increase in year one and two. In year three, the raise will be in line with inflation but capped at 6.5%. ArcelorMittal
South Africa is the largest steel producer in sub-Saharan
Africa and the world’s second largest steel producer after China’s Baowu Group. Numsa general secretary Irvin Jim said: “We welcome the signing of this agreement particularly because we were on the verge of a strike.”
Source: Mail & Guardian, 8 May 2023.
Steel profile manufacturer
DS Stålprofil and steelmaker SSAB have announced a partnership for deliveries of fossil-free steel gradually starting in 2026. Denmarkbased DS Stålprofil plans to use the fossil-free steel in its roof cladding and facade products. Jan Meier, sales director for SSAB Europe, said: ‘‘The partnership will further strengthen DS Stålprofil’s position as a provider of sustainable, long service life, low-maintenance building solutions and brings SSAB closer to its aim to help create a fossil-free value chain.’’.
Source: Hydrogen Central, 9 May 2023.
Brazilian renewables group Casa dos Ventos has received antitrust approval for its 4.2 billion reais ($858 million) joint venture with the local subsidiary of Luxembourg headquartered ArcelorMittal to develop a wind energy project in the north-eastern state of Bahia. ArcelorMittal Brazil will hold a 55% stake in the project and Casa dos Ventos the remainder, with the venture due to generate 554MW of wind power.
Source: Latin Lawyer, 9 May 2023.
Liberty Galati, the largest steel producer in Romania, has completed the installation of a new automated pipe coating line following an investment of over €8.1 million. The new line will allow the company to become the only regional provider of 100% in-house coated pipes from its own plates and ‘highlights its commitment to providing end-to-end solutions for its customers across Romania, Central and Eastern Europe, the Middle East and the Americas’, the company has stated.
Source: Romania Insider, 10 May 2023.
UK business secretary Kemi Badenoch has met with senior executives from British Steel, and its owner Jingye, as the manufacturing giant and government continue negotiations over an aid package to allow the company to decarbonize its production. The visit came after 250 jobs were absorbed across British Steel’s Scunthorpe plant, with high energy prices and a volatile market continuing to plague the business. A British Steel spokesman said: “We discussed the significant challenges Britain’s steelmakers like ourselves face, and our pressing need for support from the UK Government on our journey to net zero.
Source: Business Live, 10 May 2023.
Renewable energy company
Iberdrola Deutschland has signed a 15-year power purchase agreement (PPA) that will power hydrogen production from its Baltic Eagle offshore wind farm, under construction in the German North Sea, which will then supply electricity to the Salzgitter low-CO2 steelmaking transformation programme. The 476MW Baltic Eagle project is due to go into operation at the end of 2024. Felipe Montero, Iberdrola Deutschland’s CEO, said initiatives of this kind were contributing to the transformation of Germany’s industry while also supporting the ramping up of green hydrogen in the market.
Source: Windpower Monthly, 11 May 2023.
In an attempt to secure long-term supply of liquified natural gas for its ferroalloys plant located in Odisha’s Jajpur, Tata Steel Mining Ltd (TSML) has signed a memorandum of understanding (MOU) with Bharat Petroleum Corporation Ltd (BPCL). As per the MOU, BPCL will supply the agreed quantity of natural gas through its pipeline to the ferroalloys plant at Jajpur, said TSML, an 100% subsidiary of Tata Steel. Source: DevDiscourse, 12 May 2023.
Tata Steel security department official B Dhananjay was injured after being shot at by three bike-borne criminals in Jamshedpur, India. Dhananjay was returning home from a friend’s house at about 11pm when he was shot at and injured. The victim sustained a bullet injury on his left wrist and was admitted to the Tata Main Hospital where he underwent treatment. From a preliminary
investigation undertaken by the local police, it seems that Dhananjay was shot at following a brawl between the victim and the criminals regarding his ‘riding style’.
Source: Lagatar News, 12 May 202.3
The Financial Services Compensation Scheme (FSCS) has announced that it is investigating Newport-based Prism Independent Financial Advisers. According to the FSCS, the firm is reportedly associated with claims regarding pension transfer advice given to members of the British Steel Pension Scheme and has not been regulated by the Financial Conduct Authority since 2020. A spokesperson for the FSCS said that the firm has been in liquidation for a period of time.
Source: UK Advisor, 17 May 2023.
BVS Cranes has delivered a new ingot crane to a leading steel manufacturer in western Turkey. Designed for an operating temperature of up to 65°C, the crane has two trolleys with a capacity of 75 tons and a lifting height of 11m, while the three beams span 20m – a design that BVS said is a compact structure, which brings ‘advantages in the hook approach distances of the trolleys and the movements they make together’. BVS added that the crane features ‘a special automation system’, as well as an automatic lubrication system and operator’s cab.
Source: Hoist, 18 May 2023.
US Steel has announced the closing of $240 million unsecured Arkansas Development Finance Authority environmental improvement revenue bonds, which carry a green bond designation. The company will use the proceeds from the bonds to partially fund work related to its new technologically advanced flat rolled steelmaking facility, Big River 2, currently under construction near Osceola, Arkansas. The facility will recycle, refine, and process scrap steel into finished steel products.
Source: Business Wire, 18 May 2023.
Metal engineering company Vesuvius has disclosed that a cyber incident it experienced earlier this year will incur a cost of $4.6 million. The exact nature of the incident remains unknown, as the company has not confirmed further details. However, in a statement to the Regulatory News Service, Vesuvius expressed that despite the episode, it has managed to surpass trading expectations. Vesuvius, which brought in over £1.6 billion in revenue for the 2021 calendar year, was the second British industrial ceramics manufacturer to announce a cyber incident in 2023.
Source: Steel Guru, 19 May 2023.
Global heavy machinery manufacturer SANY Heavy Industry has initiated a strategic partnership with steelmaker Guangxi Shenglong Metallurgical (Shenglong Metallurgical) to ‘drive a green transformation in the steel industry’, following the completion of a $12 million procurement deal which saw SANY deliver 35 EV550 electric tractors, 50 electric dump trucks, and a battery swapping station to Shenglong Metallurgical.
Source: Cision, 19 May 2023.
Swiss Steel says a CO2 emissions audit of its global operations will further enhance its sustainability rating, citing its use of scrap metal feedstock as a core part of its sustainability commitment. The audit, which reviewed operations in 2021, was conducted by Germany-based DNV Business Assurance Germany GmbH and examined Swiss Steel
melt shops and facilities in several nations. “Sustainable steelmaking is in the DNA of Swiss Steel Group,’’ Swiss Steel Group CEO Frank Koch said. “The audit statement will further enhance our sustainability rating, transparency and credibility as a leader in green steel.’’
Source: Recycling Today, 21 May 2023.
A museum in Sheffield, England is appealing to the public for help after thieves successfully broke in and stole 12 items relating to metalworking from the collection, according to Yorkshire Live. The offenders entered Kelham Island Museum, a history museum dedicated to Sheffield’s past as an industrial hub for metalwork and steelmaking, in the early hours of 14 May. “The historical significance of these items goes far beyond any financial value they hold,” said Kim Streets, chief executive of Sheffield Museums Trust. “They span one of the first objects hallmarked by Sheffield Assay Office to knives made by one of our last [local practitioners], the much-missed Stan Shaw, and are irreplaceable touchstones of Sheffield’s rich heritage.”
Source: Artnet, 19 May 2023.
The New Zealand government plans to spend up to $140 million aiding steelmaker NZ Steel, based in Glenbrook just outside Auckland, in its transition to lower carbon emissions. The company is owned by multinational company Bluescope, which alone makes up about 2% of the country’s entire greenhouse gas emissions. The investment aims to help the private company transition away from its current high use of coal. Source: NZ Herald, 21 May 2023.
A construction worker miraculously survived after falling and being impaled by a seven-foot-long steel bar that ran through his chest and exited before then entering his head. Shocking footage captured at the scene of the accident in Chongqing, southwestern China showed the injured man lying on a wooden plank placed atop two plastic stools keeping him immobilised. The cause of the accident remains under further investigation.
Source: The Mirror, 22 May 2023.
#itsmorethanjustamachine
3-ROLL TECHNOLOGY FOR SBQ SIZING.
A Reducing & Sizing Block for long products keeping its promises. Achieve your goals with KOCKS RSB®
up to 160mm
finishing size in round or hexagonal dimensions
up to 20% up to 10%
energy savings in the mill line
increase in production
Workers at Tata Steel in Shotton, UK, are preparing to welcome a new colony of bees housed in hives on one of the site’s spaces, as part of the company’s recent commitment to biodiversity. The site is already well known for hosting nesting sites for seabirds, which were present on the site’s former logo. Works manager, Bill Duckworth, said: “We have recognised that true sustainability requires a holistic approach. So our own commitment includes reducing our site’s carbon footprint, developing and producing products and services that support sustainable construction.’’
Source: The Leader, 22 May 2023.
JSW Steel has announced that it has reached an inprincipal agreement to establish a 50:50 joint venture (JV) with Japan’s JFE Steel to manufacture cold-rolled grain-oriented electrical steel (CRGO) in India. The agreement progresses an MOU signed between the two companies in May 2021. “The feasibility study has since been completed and both JSW Steel and JFE Steel have, in principle, reached an agreement to establish a 50:50 joint venture company. The JV will be able to manufacture the entire range of CRGO products at its proposed facilities at Vijayanagar, Karnataka, India,” JSW Steel said.
Source: Business Standard, 22 May 2023.
A Chinese salvage ship has been caught ‘looting the war graves of hundreds of British sailors’ for scrap metal off the coast of Malaysia. The World War II battleship HMS Prince of Wales was sunk by Japanese bombers in 1941 in the South China Sea. An older battlecruiser, the HMS Repulse, was also sunk just a few miles away, with the shipwrecks, located in Malaysian waters, having since been officially designated as war graves. However, a Chinese vessel has been spotted illegally within the area of the wreck, attempting to salvage the steel used in the manufacture of the warship's hulls.
Source: Daily Mail, 23 May 2023.
ArcelorMittal Dofasco has been fined $175,000 over a workplace incident that amputated a steelworker’s fingers. The fine was imposed after the Hamilton steelmaker pleaded guilty in virtual court to one charge under the provincial Occupational Health and Safety Act. A second workplace safety charge was withdrawn. The victim of the incident was a mill operator at the plant’s No.2 tube mill and lost four fingers from her left hand.
Source: The Hamilton Spectator, 24 May 2023.
Russian steelmaker NLMK Group has launched a rolled steel product with an antibacterial coating. First batches of the new product have been trialled successfully by NLMK partners: Grand Line and Albes Production Association. According to the company, the antibacterial coating protects the metal against harmful micro-organisms and makes it perfect for interior finishing of various facilities, particularly in the food industry and healthcare.
Source: Steel Orbis, 24 May 2023.
Electrical equipment manufacturer Plug Power has landed three containerized electrolyzer projects, including a partnership with APEX Group to demonstrate the feasibility of producing green steel through the decarbonization of ArcelorMittal’s local blast furnaces. Plug will deliver two 5MW electrolyzer modules with a capacity to produce 4.2 metric tons per day of green hydrogen to SWB, the city’s public utility company, by the end of this year. The long-term goal is full decarbonization of the steel industry in northern Germany and the rest of Europe.
Source: Green Car Congress, 24 May 2023.
German steelmaker Salzgitter has initiated a consortium comprising of companies including Tenova, Danieli, and DSD Steel Group to undertake the construction of a DRI plant at the site of Salzgitter Flachstahl in Lower Saxony, Germany. Salzgitter's goal is to achieve low CO2 steelmaking, with the plant planned to reach an annual production capacity of over 2Mt of DRI.
Source: Steel Guru, 25 May 2023.
Tata Steel has made a donation of around $120,000 to Tata Medical Centre (TMC) in Kolkata, India, as a token of ‘support and appreciation for their continued efforts to address the needs of cancer patients within and outside India’ The contribution was made possible through the auction of the first four coils (62Mt) of cold rolled steel produced at Tata Steel’s newly commissioned cold rolling mill complex unit in Kalinganagar, Odisha, according to a media statement.
Source: Goa Chronicle, 26 May 2023.
JSW Group is exploring possibilities to acquire coking coal mines in offshore markets, according to industry sources, which stated that the industrial conglomerate is exploring mineral assets in countries like Australia and Mozambique. Captive coking coal mines would assist JSW Steel in reducing its cost of production for manufacturing steel, the sources added, with the company currently meeting 60% of its coking coal requirement via imports.
Source: The New Indian Express, 28 May 2023.
Forza Steel, a Mexican industrial engineering company that manufactures structural tubing and helical pipe products, plans to build a new pipe plant in Brownsville, Texas. The company expects the new plant's imports will reach around 260kt/yr and produce 240kt/yr of pipe products. The new plant will supply steel pipes and tubes for the automotive, construction, and oil and gas industries. Forza Steel plans to begin rolling mill operations in July.
Source: Yieh Corp Steel News, 29 May 2023.
Pensioenfonds Hoogovens, the pension fund for workers of the Tata Steel plant in the Netherlands, is focusing its new climate policy on reducing the CO2 emissions of its current portfolio. In a move reminiscent of a recent announcement by Swedish pension fund AP7, Hoogovens said in its annual report that its policy will centre on realising ‘real world change’. The fund’s president, and PensionsEurope chair, Janwillem Bouma commented: “This means we will primarily focus on attaining reductions of emissions due to improvements in production processes and policies of the companies in our existing portfolio.”
Source: IPE, 2 June 2023
The Indian steel ministry has announced plans for a centre that will aid research and development projects to set up pilot plants for production and utilisation of green hydrogen in the iron and steel making processes. Investments for the centre have been organized under the National Green Hydrogen Mission to ‘support the domestic steel industry's endeavours to find scalable uses of hydrogen produced using environmentally sustainable practises’, the ministry said in a statement. Source: The Economic Times, 2 June 2023.
German steelmaker Thyssenkrupp's workers' union announced plans to hold protests in June over what they feared could be lower than anticipated government subsidies for a $2.2 billion German green steel plant. The demonstration, cited to take place at Thyssenkrupp's steel hub in Duisburg, followed on from weeks of uncertainty over whether Berlin would fulfil its commitment to co-fund the direct reduction iron (DRI) facility.
Source: Reuters, 2 June 2023.
Hydrogen Oman, a subsidiary of Energy Development Oman, has signed three agreements granting the first green hydrogen blocks in the Sultanate of Oman with a total investment value exceeding $20 billion. The three projects were signed with the consortia of Amnah, Green Energy Oman, and BP Oman. The consortium will develop around 200kt/yr of green hydrogen from 4.5 GW of installed renewable energy capacity for planned green steel plants located in the Port of Duqm, within the Special Economic Zone at Duqm. Source: Times of Oman, 3 June 2023.
• The UK generates 10Mt/yr of steel scrap of which 80% is exported to other countries for recycling.
Source: GHG Alliance.
• Already accounting for around 30% of global production, EAFs will increasingly replace primary plants that require reinvestment, meaning that the proportion of scrap in total worldwide steel production is likely to reach 40% in 2050.
Source: GHG Alliance.
• In the UK, the export of scrap metal should be approached with national strategic benefits and risks in mind.
Source: GHG Alliance.
• The UK produces large quantities of scrap, in excess of what UK steelmakers require for their own production. However, it is often in a poor condition.
Source: GHG Alliance.
• The Electric Arc Furnace (EAF) is currently the technology with the lowest carbon footprint. Typically, 500 to 800 kg of C02 are generated for each tonne of steel produced.
Source: CIX Inc.
• Projections of scrap availability between now and 2050 indicate that the quantity of scrap available for recycling will grow considerably.
Source: CIX Inc.
• The availability of sufficient quantities of DR grade pellets is questionable and in general, ore quality is declining globally.
Source: CIX Inc.
• Without ore-based-metals (OBMs) in the scrap mix, a significant portion of steel scrap will become impossible to recycle and will be destined for land fill.
Source: CIX Inc.
• Better design of products, such as automobiles and appliances, must be focused on easy dismantling at end-oflife so that free copper and other residuals can be more easily removed.
Source: CIX Inc.
• Improved technologies need to be developed to acquire detailed knowledge about the composition and quality of scrap to enhance its utilization.
Source: K1-MET/ Montanuniversitaet, Leoben
• Compared to steel production from primary raw materials, melting scrap requires less resources and decreases process-related C02 emissions by up to 75%.
Source: K1-MET/ Montanuniversitaet, Leoben
• In terms of sustainability and circular economy, it is important to keep the recycling rate of steel as high as possible.
Source: K1-MET/ Montanuniversitaet, Leoben
ABSOLUTE POSITION SENSORS WITH HIGH TEMPERATURE OPTIONS
Highest performance with Industry 4.0
and 85 ºC (185 ºF)
Higher temperatures up to +105 °C (+221 °F)
• Today, the steel industry needs around 2 billion cubic metres of natural gas per year in its processes; roughly as much as Berlin and Munich consume together.
Source: Hans Jurgen Kerkhoff
• The majority of European imports in the steel sector are from countries characterised by autocratic or non-marketeconomy structures.
Source: Hans Jurgen Kerkhoff
• The steel market for automotive and aerospace applications is expected to surpass $175 billion by 2027.
Source: Global Market Insights
• More than two-thirds of the world’s steel today is produced using the LD process.
Source: Roman Stiftner
• Global CO2 emissions amounted to about 40 Mt, and South Korea accounts for 2% of the total.
Source: POSCO
• The steel sector in South Korea, which is responsible for 14% of the country’s total CO2 emissions, is one of the main industries working to transform its traditional production process, that is, coal-based blast furnace ironmaking.
Source: POSCO
• The steel sector accounts for 2.6 Gt of carbon dioxide emissions annually, making up roughly 10% of the global total.
Oliver Wyman
• 70% of global blast furnaces are scheduled to be relined by 2030, the transition is rapid, and both risks and opportunities to steel producers are huge.
Source: Lanzatech.
• The average steelworks today emits two tons of CO2 per ton of steel. But as the industry transitions there is no single pathway but a range of solutions that will both compete and integrate to lower emissions.
Lanzatech
• Kobe Steel aims to reduce CO2 emissions in its production processes by 30 to 40% in 2030 (compared to fiscal 2013 levels) and to achieve carbon neutrality in 2050.
Kobe Steel
• While current production of silicon steel represents only 1% of global steel production, the market for electrical steel is expected to grow by 7.5% in the coming years.
Source: Primetals Technologies.
• The conventional combustion engine car contains approximately 25 to 30kg of silicon steel. By replacing the combustion engine with a highly efficient electric motor, car manufacturers achieve a lightweight design but effectively double the amount of silicon steel per car to anywhere from 60 to 70kg.
Source: Primetals Technologies.
Two major steelmakers have chosen Sarclad’s latest EDT roll texturing technology for their flagship plant expansions.
ArcelorMittal Nippon Steel (AM/NS), a joint venture between ArcelorMittal and Nippon Steel, has chosen the newly-launched Rolltex MSA 72 for its cold mill no.2 expansion in Hazira, India. Sarclad’s Rolltex MSA technology operates a Multi-Servo Array (MSA) to deliver high levels of texturing performance.
The 72-electrode MSA machine selected by AM/NS features two texture heads, each with 36 individually controlled electrodes. Steel Dynamics Inc. has also selected Sarclad’s Rolltex MSA for its mill investment in Sinton, Texas. The Rolltex MSA 36 features a single-sided texture head, which can be expanded to 72-electrode capacity by adding a second texture station in the future.
After over 40 years of consistent use, Tata Steel UK is upgrading and replacing the 6 x 1.8 MW Radyne Power converters installed at the end of the 1970s.
Reported at the time as being the largest induction heating installation in Europe, the induction generators are an integral part of the steel tube processing site which overall, produces approximately 250kt/yr of thin-walled tube from steel strip for the construction, engineering, and energy market sectors.
As a result of the upgrades, Inductotherm Heating and Welding is offering a turnkey solution of uninstalling their old Radyne converters then installing and commissioning the six new Inductotherm 1.8 MW converters with six off HV main transformers, 12 off induction heating coil assemblies, tubes drivers, water cooling systems and PLC controls. The new installation has a smaller footprint than the induction and gas furnaces it will replace, says Inductotherm, reflecting the development of the technology over time.
After supporting the old Radyne units for over 40 years the upgraded units are aimed to offer Tata Steel a more technically advanced and energy efficient equivalent replacement to ensure continued reliable production and aftermarket support.
For further information, log on to www.inductothermgroup.com
The texturing efficiency generated by MSA technology enables unrivalled accuracy, speed and consistency of surface texture on the roll and ultimately on the strip, says Sarclad, and is the ‘ideal choice’ for steel and aluminium flagship plants looking to increase volume and control of surface-critical strip into applications such as exposed automotive panels.
For further information, log on to www.sarclad.com
Fives, a leading engineering group with broad expertise in steel processing and technology, has designed and delivered thermal sections for a new annealing and pickling line (APL) and two new annealing and coating lines (ACL) for Baowu Steel Group’s Shanghai plant. The lines, designed to produce high quality non-grain oriented (NGO) grades for electric vehicle motors, delivered their first coil between December 2022 and February 2023.
The thermal section includes a horizontal furnace capable of reaching a strip temperature of 1100°C with the AdvanTek® combustion system, as well as technology for furnace atmosphere management, utilizing seal gates and high hydrogen-rich and dew point controlled sections to reach the required steel properties.
“This is a very important project for Fives Group with a privileged partner. The production of silicon steel grades presents a challenge to steelmakers, as it requires advanced technologies to produce high flux density materials with minimal core losses at high working frequencies. Fives has a broad experience in such technologies, as well as process expertise to accompany steelmakers on their road to new markets with new applications”, said Benjamin Michel, chief executive officer of Fives Stein, a subsidiary of Fives, specialising in thermal technologies.
“This global project from the operational point of view has been implemented during challenging times of lockdowns and travel restrictions. Resilience was a determining factor in succeeding to overcome difficulties and produce the first coil on all three lines, respecting the client’s targets and schedule”, added Guillaume Burstert, project manager of Fives Stein in China.
For further information, log on to www.fivesgroup.com
The Port of Trelleborg, located in Sweden, has received a Konecranes intermodal reach stacker for trailer and container handling at its intermodal terminal on the southern coast of Sweden. This new lift truck replaces an older unit that has reached the end of its service life.
Across the five Swedish core ports, Trelleborg is second in terms of throughput tonnage. In addition, it’s the largest railway port on the Baltic Sea, and the most sustainable port in the region. Trelleborg uses two intermodal reach stackers to provide fast, reliable and eco-efficient intermodal services between ship and rail.
“Intermodal traffic has been growing strongly in recent years, so it’s important for us to maintain our position as a leading intermodal hub,” said Thomas Ter-Borch, port operations manager, Port of Trelleborg. “We’ve been very satisfied with Konecranes equipment, so we’re confident that our new Konecranes reach stacker will help us to continue to provide our customers with the highest levels of sustainable productivity.”
“The fact that Port of Trelleborg chose a Konecranes reach stacker again highlights the quality of our products and the excellent service and business relationship provided by our long-term local distributor NC Nielsen,” commented Daniel Sjöstrand, sales support manager, lift trucks, Konecranes.
The new reach stacker is a Konecranes SMV 4538 CCX4, a lifting machine that can stack 45 tons in the first row up to four containers high. The truck runs on HVO100 renewable diesel and meets the emission requirements for an EU Stage V engine. TRUCONNECT® Remote Monitoring follows the truck’s performance through usage data stored at the yourKONECRANES.com customer portal.
For further information, log on to www.konecranes.com
Chinese producer of special bar quality products, Fujian Sangang Minguang Group Co., Ltd. (Sanming) has placed an order with Friedrich KOCKS GmbH & Co. KG for another Reducing & Sizing block. The RSB® 500++/4 in StarDrive design will be part of the company’s new rolling mill complex in Fujian province and will be used to produce steel products for various industries.
Sanming is familiar with the KOCKS 3-roll technology from a previous project and is confident in its high precision, efficiency, and reliability, says KOCKS. The integration of KOCKS’ 3-roll technology into the new rolling mill complex is expected to bring significant benefits to the production process.
The RSB® 500++/4 in StarDrive design is equipped with technology that allows the precise control of the rolling process. It comes with KOCKS proprietary software solutions and will be located as a finishing unit after a 2-high reversing roughing mill and 10 stands in H/V rolling mill arrangement to produce straight bars within a dimension of Ø 50 to 130 mm in an 800kt/yr mill line. The installation is expected to be completed in early 2024.
For further information, log on to www.kocks.de
Stainless steel producer Outokumpu and Swiss robotics company ANYbotics have partnered to deploy the ANYmal robotic inspection solution, as announced at the Green Steel World conference in Germany.
For what the companies are referring to as a first in the steel sector, legged inspection robots will be operationally deployed for improving and digitizing facility health monitoring and reducing unnecessary worker exposure to adverse environments. The solution is made available on a Robotics-as-a-Service (RaaS) basis, and Outokumpu is planning expansion after the initial deployments.
ANYmal is an autonomous, robotic end-to-end inspection solution that continuously monitors
plant health and equipment. As a ‘ready-to-go’ solution, ANYmal enables customers to automate inspections via frequent visual, acoustic, and thermal inspections, which allows ANYmal to monitor assets and equipment and detect anomalies at an early stage. This, says the company, assists Outokumpu in pursuing three goals: increasing safety by reducing employee exposure to hazardous substances and environments, optimizing production through preventive maintenance, and decreasing environmental impact.
For further information, log on to www.anybotics.com
As part of Combilift’s celebrations for its 25th anniversary, the Irish materials handling specialist has announced that it is donating its 75,000th truck – an Aisle Master articulated forklift – to Convoy of Hope, a non-profit humanitarian and disaster relief organization.
Convoy of Hope works alongside communities and its wide network of volunteers aim to alleviate poverty and hunger and to bring help and hope wherever they are most needed in the world.
Combilift supplied its first Aisle Master to be used at Convoy of Hope’s distribution centre four years ago, and a further three units were delivered last year. Convoy of Hope’s senior director of distribution, Jeff Smethers, commented: “A lot of our exponential growth has been down to the Aisle Masters as they enable us to get more loads
in and out faster. And thanks to Combilift’s free warehouse layout service and the Aisle Master’s narrow aisle capability we have achieved the best possible storage density and very efficient operation.”
Combilift’s CEO and co-founder Martin McVicar said: “The work that Convoy of Hope does is invaluable to relieve suffering around the world and we wanted to make our own contribution by donating our 75,000th truck to this very worthwhile charity.”
For further information, log on to www.combilift.com
Measuring instrument supplier IMS Messsysteme, and German steelmaker thyssenkrupp have reached another milestone in their business relationship, with IMS’ combined 2D/3D surface inspection system having been installed for the first time in the pickling line at thyssenkrupp’s Rasselstein site in Andernach, the world’s largest production site for packaging steel. The system was successfully put into operation in November 2021.
At thyssenkrupp Rasselstein, pickling is the first processing stage of the hot-rolled strip on its way to fine sheets with thicknesses from 0.100 to 0.499 mm. Surface defects are required to be detected at an early stage in order to be able to guarantee the high product quality of the rolled products, creating the need for inspection systems to check surface quality accurately, and without delay.
With the newly implemented 2D/3D surface inspection system in the pickling line, thyssenkrupp Rasselstein is hoping to set new standards in the industry. The 3D height measurement is based on the laser triangulation method. A laser line is projected on to the material surface, which is reliably detected by a camera positioned at an angle.
Each pixel position in the image recorded by the camera correlates with a calibrated height position – a measuring principle that IMS has been using successfully in various systems for more than 20 years. Lasers that are developed and produced in-house by IMS make it possible to display the height profile determined in this application as a coherent, high-resolution image.
‘‘Together with IMS, the idea arose to use the proven 3D technology in the pickling process as well in order to reduce the effects on the subsequent rolling process through automatic
detection and depth measurement of the defects and thus to minimise disruptions caused by broken strip or roll damage.
These considerations were confirmed by a test installation, so that a productive system was installed in a short time. Since it was commissioned, the system has completely fulfilled expectations and contributed to a sustained increase in the quality of the rolling process,’’commented Yves Unnützer, online measuring systems engineer at thyssenkrupp Rasselstein. IMS is a leading manufacturer of non-contact optical, x-ray and isotope measuring systems that gauge height, width, depth, profile, flatness, length, thickness, coating, and weight.
For further information, log on to www.ims-gmbh.de
WITH a growing propensity to producing what is called green steel, America’s steel industry seems to be today less reluctant to act in producing steel that is low in carbon emissions, which is the chief determinant in the evaluation of environmentally-friendly steel production process.
Most steel executives of steel-producing companies have been saying, whenever there is a debate, that the US steel industry is one of the world’s cleanest steelproducers, particularly when the debate turns to supplies from China, India and other ‘environmental sinners’.
Industry pundits noticed a shift in the steel industry with a growing lean towards low carbon steel production. Various studies point to this shift among steel producers, the latest being one issued by the Ohio River Valley Institute, a think tank, which concentrated on US Steel’s Mon Valley Works, using it as a potential model to show the shift from traditional carbonintensive steelmaking to green steel that relies on green hydrogen which is produced using renewable energy, and a renewablypowered electric arc furnace.
According to the ORVI report, nonfossil fuel steel production could radically
transform a declining regional steel industry stuck with the old 20th century technology, uplift the quality of air and also quality of life, besides considerably reducing the region’s carbon footprint.
These factors, coupled with the region’s skilled workforce and a century old existing steel-producing infrastructure, abundant water resources, availability of iron ore and untapped potential for wind energy in the neighbouring Appalachian Mountains, offer a strong basis for a new generation of steelmaking in the United States.
The world’s iron and steelmaking sector is said to contribute some 7% of greenhouse gas emissions and a quarter of industrial carbon emissions. The International Energy Agency has set the bar for reducing emissions from the steel industry by 50% by the year 2050 in order to meet global climate goals. With the worsening of the climate crisis, there is also public, political and market pressure on steel producers to intensify their decarbonization efforts.
Indeed, these pressures are having a strong impact on steel producers who are now looking at ways and means to considerably reduce emissions. In its report entitled ‘Roadmap to 2050’, US Steel,
*US correspondent, Steel Times International
for instance, has been emphasizing its commitment to reduce carbon emissions even though it has yet to indicate its commitment to new investments needed for the purpose.
But Jessica Graziano, the company’s chief financial officer, stated recently at an event in Pittsburgh that ‘being green means that you make green’ and that ‘we’ll be part of the solution’.
The conventional process of steel production resorts to the use of carbonrich coke for melting iron ore in large blast furnaces before making it, finally, into steel. US Steel uses this process at its Edgar Thomson Works in Braddock. On the other hand, a non-fossil fuel direct reduced iron (DRI) process, fueled by hydrogen made from renewable solar and wind energy, using electric arc furnaces powered by renewable electricity, is the ‘most viable option near-term for achieving zero-emission primary steel production’, according to the report.
A New York based metals analyst dismissed talk in some quarters that ‘green steel is a fad’. “Green steel is not a fad … it is becoming a necessity and will help us save resources such as iron ore, and use
As calls for decarbonized steel grow, America’s steel industry is rapidly becoming more open about going green. By Manik Mehta*
When it comes to building equipment to process ferrous and non-ferrous metals, nobody does it better than Butech Bliss.
For 135 years, steel producers and steel service centers have counted on Butech Bliss to deliver the design, engineering and technological advantages necessary to help them succeed. From entry to exit end we build it all. Our product lines include roller and stretch leveling technology, a full line of shears, material handling equipment and complete coil processing lines. We are more than a scrap chopper manufacturer.
Learn more about our world-renowned coil processing technology call +1 (330) 337-0000, visit ButechBliss.com or email sales@butech.com.
If our name is on the machine, it’s built better.
Combilift is the perfect fit for the steel industry. Our multidirectional forklifts, straddle carriers and mobile gantry cranes are perfect for handling long product, allowing you to maximise your storage, efficiency and safety.
• Safer product handling
• Optimised production space
• Improved storage capacity
• Increased productivity & output
• Enhanced profits
combilift.com
environmentally less harmful processes, thus contributing to decarbonization,” he said.
US Steel recently announced that it has pioneered a version of electrical steel that is wider and thinner than other steel varieties; but it is also, according to the company, lighter, stronger and better for electrical environments, besides being corrosion resistant. This steel is said to be ideal for electric motors and its announcement is also timely because the nation is trying to increase automotive production at home.
At the recent Ceres Global conference in New York City, US Steel senior vice president and chief strategy and sustainability officer Richard L. Fruehauf unveiled the company’s InduX electrical steel product during the Corporate Climate Leadership panel – Ceres Global brings together institutional investors, corporate executives, policymakers, and other capital market influencers to accelerate action on the world’s most urgent sustainability threats – and emphasizes that ‘we are doing our part by collaborating to find new business approaches and to develop new technologies’. ‘Moreover, steel’s adaptability and near-infinite recyclability make it the ideal material to build safe, modern, and sustainable societies,’ Fruehauf said.
InduX electrical steel will be manufactured at Big River Steel in Osceola, Arkansas. The line construction is currently in progress and will be capable of producing up to 200kt of InduX electrical steel per year once it becomes fully operational.
Meanwhile, the prices of iron could fall by as much as 28% by the end of 2023 triggered by a decline in Chinese steel
demand and production, according to Morgan Stanley analysts who say that iron ore prices will decline amid the production slowdown in China, the world’s biggest steel-producing nation which is now turning to using steel scrap. Despite the country’s post-Covid re-opening, China’s steel production or demand is not likely to reach its pre-pandemic levels – at least not in the short term.
Global steel demand is forecast to rebound by 2.3% from the previous projection of 1% to reach 1.82 billion tonnes in 2023, and will see a further growth of 1.7% to 1.85 billion tonnes in 2024, according to the latest short-range outlook for 2023 and 2024 released by the World Steel Association on 18 April.
The World Steel Association (worldsteel) said that steel production in the 63 countries reporting to it was up by 1.7 % in March 2023, compared to March 2022.
The 165.1Mt produced this March represent a dramatic 15.9 % increase from the prior month, when just 142.4Mt of steel was made globally.
While extra work days likely contributed to increased output in the United States, healthy demand also could have played a role in US steel output growing by 11.7 % in March compared with the prior month.
Whereas US producers made 6Mt of steel this February, they were able to churn out 6.7Mt in March.
The strong post-pandemic rebound of the US economy has run its course with the Federal Reserve’s steep interest rate hikes to contain inflation. Growth in 2023-2024 is expected to be subdued by recessionary pressure. Furthermore, as of writing this update, experts are still monitoring the full impact of the recent Silicon Valley Bank bankruptcy on the economy and the steel industry.
Rising interest rates as well as land and material costs are putting negative pressure on construction, particularly for the residential sector, while recovery in the nonresidential sector is expected to continue.
Recent legislation such as the 2021 infrastructure law and the Inflation Reduction Act (IRA) will provide a much-needed shot in the arm for US infrastructure. Steel demand in the energy sector is also expected to benefit from expanding energy production.
US manufacturing sector activity has slowed from the strong post-lockdown rebound. Rising car prices, high gasoline prices, and interest rates have put downward pressure on US auto sales, with sales of light vehicles declining by a further 8% in 2022. They are expected to recover by 8% in 2023 and an additional 7% in 2024 with a potential decline in interest rates. However, sales will only reach 94% of 2019 levels.
After a fall of 2.6% in 2022, US steel demand is expected to grow by 1.3% in 2023 and then by 2.5% in 2024. �
THE global relevance of wind energy is growing quickly. According to the International Energy Agency (IEA), wind electricity generation amplified by a record 273TWh (up 17%) in 2021. This was a 55% higher growth than that achieved in 2020 and was the most significant compared to other renewable power technologies. Such rapid development was possible due to an unprecedented rise in wind capacity additions, which reached 113GW in 2020, compared with 59GW in 2019. Furthermore, wind remains the leading nonhydro renewable technology, generating 1,870TWh in 2021, almost as much as all the others combined.
Graph 1 shows that global wind energy installations in total skyrocketed from 24GW in 2001 to 906GW in 2022. The compound annual growth rate was extremely high. In the years 2001-2010, it reached 26%, which can be attributed to a low basis. Afterwards, it was equivalent to 17% in the period 2010-2015 and 11% in
2015-2022. The same graph demonstrates that the share of offshore wind has also enlarged from ~1% during the period 2001-2009 to 7% in 2021-2022.
The Global Wind Report 2023, published by the Global Wind Energy Council presented installed capacity by the largest players. In terms of Latin America, Brazil leads the pack, having widened its capacity from 15.5GW in 2009 to 25.6GW in 2022 (Table 1). As a consequence, it amplified its regional participation from 55.3% to 57.4%, respectively. Mexico, due a relatively mild expansion from 6.2GW to 7.3GW during the 2019-2022 period, lost share from 22.2% to 16.4%. Chile improved its relative importance in the region by 1.9%, while a similar trend was observed by Argentina, with an additional 1.7% points.
Latin America’s onshore wind energy installed capacity was equivalent to 4.5% of the world in 2019 and to 5.3% in 2022. No data was provided about offshore wind energy capacity in the region as of 2022.
It can be argued that steel and wind energy have a symbiotic relationship in the context of decarbonization. On the one hand, wind energy, in particular offshore, is a steel intense activity. It is estimated that more than 80% of the parts of towers of wind turbine generators are made of steel. On the other hand, steel companies can utilise wind energy to clean their respective energy matrix.
With this in mind, at least four investments in wind energy were announced by Latin American steel firms recently. In September 2022, ArcelorMittal Acindar agreed to join forces with Argentina’s PCR to increase its investment in the San Luis province’s wind farm project by $70m. Eight more wind turbines with a joint capacity of 36MW will be added to the 17 existing wind turbines (with a total capacity of 76.5MW) installed as part of the first phase of the project. It is also
With a rising impetus for companies to tackle climate change, the use of wind energy is becoming increasingly relevant in steel production as a crucial route to avoid costly emissions.
planned to build a solar power plant with a 18MW capacity in the same territory. The total investments of PCR and ArcelorMittal Acindar in new energy capacities will amount to $210m. Thanks to the projects, the steel producer will be able to cover more than 30% of its electricity needs from renewable sources in the second half of 2023.
In February 2023, Tenaris unveiled plans to invest $190m in the construction of a wind farm in Buenos Aires, Argentina. The wind park would supply close to 50% of Tenaris’ electricity requirements for its Siderca mill, reducing CO2 emissions by 152kt/yr. It would include 24 turbines with a combined power of 100.8MW, generating a total 509GWh of annual electricity production. It is planned to become operational in the second half of 2023. Its capacity factor (or the average output concerning the peak power capacity) is expected to be 57%, one of the highest outputs in Argentina in terms of wind farms.
In March 2023, Ternium Argentina announced that it will invest approximately $160m to build a new wind farm in Buenos Aires from which it will source electricity in Argentina. It is programmed to be operational during the second half of 2024 and will have a nominal power capacity of 72MW. The company plans that it will replace approximately 65% of the electricity that its Argentinian subsidiary currently purchases from third party providers. The company also anticipates that the wind farm will help Siderca reduce its CO2 emissions by 92.5kt/yr.
are subsidiaries of Techint group.
In April 2023, ArcelorMittal unveiled the establishment of a joint venture with Casa dos Ventos to construct a 554MW wind power project (with 123 wind turbines) in Brazil. ArcelorMittal Brasil will hold a 55% stake in the venture, with Casa dos Ventos holding the remaining 45%. The total investment will be equivalent to $800m, while ArcelorMittal’s total equity investment will be $150m. It is estimated it will provide 38% of ArcelorMittal Brasil’s total electricity needs in 2030. The company’s current electricity consumption is 500MW, half of which is generated by its own hydroelectric plant and by recovered blast furnace gases from the Tubarão steel mill. In 2026, due
to the expansion of industrial facilities, its consumption will jump to 750MW.
The so-called ‘Babilônia project’ will be located in the central region of Bahia, north-eastern Brazil. The site location has been selected due to several competitive advantages, including high-capacity forecast load factors (in excess of 50%) and a short distance (23 km) to connect to the national electricity grid. There is also the potential to expand the capacity of the project by adding a further 100MW of solar power. The project is currently at an environmental and regulatory permitting stage, with construction work anticipated to start later this year, and is expected to be operational by January 2026. ArcelorMittal Brasil will enter a 20-year power purchase agreement with the joint venture for the supply of electricity. Babilônia’s output will avoid the emission of 208kt/yr of CO2
It is interesting to realise that regarding these four projects, two belong to Techint group’s subsidiaries and two to ArcelorMittal’s ones.
Considering only wind energy, the combined installed capacity amounts to 939.3MW, of which 66% will be produced in Brazil and, conversely, 34% in Argentina. It should be highlighted that two of the projects are planning to produce solar energy as well.
It is expected that in the coming years additional wind energy projects will be announced by Latin American steelmakers aiming to adhere to decarbonization strategies. �
Amid infrastructure headwinds, India is tackling its greatest challenge head on – as the country attempts to decarbonize production while ramping up production.
STEEL consumption determines the economic growth and prosperity of a nation, which is directly linked to its infrastructure development. With the Reserve Bank of India estimating 6.5% of India’s gross domestic product (GDP) growth, the country’s steel consumption is expected to grow at 7-8% in FY2023–24 (April – March). However, India’s steel consumption is estimated to have grown by a staggering 12.7% to a record 119.17Mt/ yr in FY2022-23, at a 6.4% growth of the GDP. At 120Mt/yr of crude steel production in FY2021-22, India surpassed Japan as the second-largest crude steel producer after China.
This being said, economic growth and prosperity bring in a lot of carbon emissions. The steel sector in India has a high carbon footprint and contributes almost a third of direct industrial CO2 emissions, contributing 10-11% of the total release of this obnoxious gas in the country. This remains a concern considering that the Indian steel industry will grow at high rates, increasing production by 40Mt in the next five years. Therefore, if adequate measures
By Dilip Kumar Jha*Particulars
Total crude steel production in the financial year FY 2022-23
Total finished steel consumption in the financial year FY 2022-23
Present crude steel production capacity
Target to achieve by 2030
Per tonne energy consumption in an integrated mill
average per tonne energy consumption
Average carbon emissions by steel mills (2005)
Target achieved by Indian steel mills (2020)
Commitment to reduce carbon emissions in steel mills by 30-35% by 2030
India’s cumulative target
up 4.2% from the previous year
up 12.7% from the previous year
giga calorie
in 2015
in 2020
To achieve carbon neutrality by 2070
Source: Ministry of Steel, Government of India; Mt/yr = Million tonnes per year; T/tcs = Tonnes/ tonne of crude steel; Financial year runs in India from April 1 to March 31
are not taken to reduce its carbon footprint at the earliest, it will be responsible for huge carbon emissions in the coming years.
As per a 2020 report by the International Energy Agency (IEA), Indian crude steel production will increase to 180Mt/ yr in 2030 and 350Mt/yr by 2050. The government of India, in its National Steel Policy, targets India’s crude steel production at 300Mt/yr by 2030. To achieve this target, the government of India is working on the Production Linked Incentive (PLI) scheme to
*India correspondent, Steel Times International
boost investment in the steel sector. With a massive production plan in place, the carbon emission volume in India is estimated to rise by 2.5 times by 2030, contributing to more than 5% of the country’s greenhouse gas (GSG) emissions. According to an estimate, steel mills across India consume an average of 6-6.5 gigacalories of energy compared to the world’s average of 4.5-5.0 gigacalories. With such a high energy consumption, average carbon emissions by integrated
steel mills in India were measured at 3.1 tonnes per tonne of crude steel (T/tcs) in 2005, which was brought down to 2.65T/tcs in 2015 and further to 2.5T/tcs in 2020 through several efforts made by the government. Carbon emissions by the average integrated mill are again targeted to reduce by at least 30-35% from its 2005 level to 2.4T/tcs by 2030.
Therefore, India’s steel industry needs to set an impactful pathway to evolve into a low-carbon yet growing manufacturing sector. The entire value chain in the steel industry, i.e. producers, distributors, exporters, importers, suppliers, and consumers, needs to go green. Owing to India’s heavy reliance on coal throughout various steelmaking processes, the task is not easy. The Indian steel mills are heterogeneous and plagued by using a wide range of equipment, with some dated and insufficient technologies. There are numerous players from small-to-medium steel mills that are often less efficient and more polluting.
To make the policy prudent, the government of India recently introduced the Green Hydrogen Mission to promote the utilisation of green hydrogen instead of fossil fuels like coal and reduce carbon emissions in the steel industry. However, this mission continues to face headwinds such as poor infrastructure for producing green hydrogen, storage, and transportation from the production centre to the fuelling spots. Despite the government working overtime to encourage investment in the entire hydrogen channel, the plan remains on paper. As one of the largest polluters, the steel industry needs to adopt green hydrogen technology and reduce carbon emissions for the sector’s sustainable growth. Green hydrogen is projected to mitigate an overall 50Mt of carbon emissions and save India’s fuel imports INR 1 trillion by 2030.
Meanwhile, the Steel Association of India (SAI) has prepared a list of policy enablers that can push green steel investment in India. These include preferential public procurement of green steel, the introduction of standards, and incentives across the value chain sectors, i.e. from production and transportation to consumption sectors.
Steel mills in India have already started taking voluntary measures to reduce carbon
emissions. For example, Tata Steel, which has a production capacity of 34Mt/yr, has a mission to bring down carbon emissions to 1.8T/tcs by 2030. The company now aims to become water-neutral by 2030 for all its sites and a zero-effluent organisation by 2025. In addition, it plans to produce a major portion of its steel from scrap-based production processes in the coming decade. The scrap-based steel production process is less carbon-intensive than the traditional blast furnace or oxygen furnace route.
Leading from the front, Tata Steel has set up a 0.5Mt/yr scrap processing plant in Rohtak, Haryana. For the existing process, Tata Steel looks forward to enabling hydrogen-based sustainable steel production as a step towards achieving the company’s vision of net-zero emissions. It also undertook a trial for the continuous
of India (SAIL) has a total production capacity of 21Mt/yr. The Ministry of Steel has already submitted the Intended Nationally Determined Contributions (INDC) for reducing GHG emissions in the iron and steel sector, while projecting CO2 emissions of 2.2 - 2.4T/tcs in the blast furnace route and 2.6-2.7T/tcs in the direct reduced iron (DRI) – electric arc furnace (EAF) route by FY2030, from 3.1T/tcs during 2005. SAIL has set a target of reducing carbon emissions by 2.30T/tcs by FY2030.
Jindal Steel and Power Ltd (JSPL), which has a production capacity of 8.6Mt/yr in India and 2.4Mt/yr in Oman, aims to significantly reduce its carbon footprint by almost half as part of its ESG objectives. At its site in Angul, Odisha, JSPL adopted the DRI-BF-EAF route for manufacturing steel. To overcome the challenge of the nonavailability of natural gas and coal, the steel mill set up a gas plant on its site and used locally available high-ash coal to convert it into synthetic gas (Syngas).
injection of coal bed methane in the blast furnace of its largest plant at Jamshedpur, Jharkhand, to reduce carbon emissions.
With its annual production capacity of 18Mt/yr, JSW Steel focuses on a circular economy by optimizing water, waste, carbon, and energy footprint. The company has set a target of achieving CO2 emissions of 1.95T/tcs by 2030. JSW Steel secured a power purchase agreement for 2.5GW renewable projects and commenced operations at a 225 MW solar power plant in Vijaynagar, Karnataka, in April 2022. The firm also secured tie-ups with various states for 5-gigawatt hydro-pumped storage projects. Furthermore, the company has 1.26 GW of wind projects in the pipeline to start operation by FY2023. In an optimistic scenario, the company’s renewables-led growth may reach 10 GW capacity by FY2025 and 20 GW by FY2030.
The government-owned Steel Authority
Rashtriya Ispat Nigam Ltd (RINL), also known as Vizag Steel, has a production capacity of 7.3Mt/yr. Now, the company is striving to reduce CO2 emissions in all stages of steelmaking by installing state-of-the-art cleaner technologies, improving processes, recycling waste, and afforestation. The company claims a reduction of 1.3Mt/yr of CO2 emissions is possible as a result of using state-of-the-art cleaner technologies during the design stage, as well as a reduction of about 3Mt/yr of carbon dioxide by installing energy-efficient technologies, modifying processes, enhancing the capacity of sinter plants, and rebuilding blast furnaces.
In India, the government has drafted a ‘master plan’ and outlined an investment of $1.3 trillion in infrastructure development. According to Ernst & Young, this along with future investments would help India become a $5 trillion economy by FY2025 and $26 trillion by FY2047 when India will be celebrating its centenary year of independence. Amid the government’s continued focus on the construction of roads, railways, ports, and airports, Moody’s Investors Service estimates India’s steel consumption growth to rise by 10% until FY2026. Therefore, India is now considering implementing a law to curb carbon emissions, that will require steel mills to dedicate a portion of their annual production through green routes. �
The Sustainable Steel Strategies Summit 2023, brought to you by the makers of the Future Steel Forum and Steel Times International, is shaping up to be an exciting two-day event aimed exclusively at the global steelmaking industry.
As the steel industry strives for a more sustainable future, the Sustainable Steel Strategies Summit will hear what the steelmakers themselves have to say about climate change and how they intend to make greener steel in the near future.
If you would like to present a paper at the Sustainable Steel Strategies Summit then please contact programme director: MATTHEW MOGGRIDGE | matthewmoggridge@quartzltd.com
GENERATE NEW LEADS
POSITION YOUR BRAND
DEMONSTRATE YOUR PRODUCTS & SERVICES
If you would like to exhibit or discuss sponsorship opportunities, please contact the international sales manager: PAUL ROSSAGE | paulrossage@quartzltd.com
THERE is little doubt that the push to generate electricity from renewable power sources is accelerating in the United States, driven by governmental policies such as the recently passed Inflation Reduction Act (IRA). This is good news for the producers of plate and other steel products that are used to generate, store and transmit energy and/or use such clean power to produce greener steels.
Over the last few decades there has been fairly steady growth in the amount of US electricity generation capacity coming from renewable energy sources, particularly from solar, wind and hydropower sources. In fact, according to Mark Morey, senior electricity advisor to the US Energy Information Administration (EIA), it has already grown to the point that renewable energy currently accounts for about 21.5% of all utility-scale electricity generation in the US.
He noted that while there are also certain other technologies emerging, such as those related to geothermal, hydrogen, carbon capture and wood pellets, those
technologies have been dwarfed by the growth in wind, solar and hydroelectric power generation with the EIA reporting that currently about 12% of US utilityscale electricity generation is coming from wind power (about 5-6% from solar and about 6% from hydro). In fact, John Anton, director of the steel pricing and purchasing service of S&P Global Market Intelligence, said that wind power generation is currently surpassing that for coal in the US.
While it has taken some time for them to achieve this, Paolo Frediani, a senior analyst for Fastmarkets, said that it has gotten to the stage where there is a proper economic case for renewable energy to go mainstream, with its use continuing to grow going forward.
In fact, largely spurred on by such government initiatives, particularly the IRA, Willis Thomas, head of CRU+ Consulting, said that it is expected that by 2050, as much of 70% of US energy needs could be met by wind and solar, although over that timeframe the growth rate for other means of renewable power generation will be much less remarkable, as they aren’t as directly impacted by the IRA. In fact, he said
that about $30 billion of tax credits in the IRA will be going toward wind and solar projects.
Evidenced by the incentives in the IRA, and also to a lesser extent the IIJA bipartisan infrastructure bill, Teresa Wagler, Steel Dynamics’ executive vice president and chief financial officer, said that it seems as if the US government is finally starting to participate more on the capital side of the equation, catching up with some other governments around the world.
In mid-May, the Biden administration proposed a new Environmental Protection Agency (EPA) rule that would require power plants burning such fossil fuels as coal and natural gas to cut their GHG emissions by as much as 90% or shut down by 2040.
There are, however, other factors driving the energy transition. Demand for renewables in the US is being driven by corporate initiatives and corporate branding moves, especially with the transition being more of an ongoing process with no real end game, said John Villali, research director for IDC Energy Insights.
He noted that demand for renewables also varies regionally with the initial boom
Recent US legislation has driven headwinds in the renewable market, with steelmakers increasingly adding production capacity to keep up with demand. By Myra Pinkham*
for wind being in the Midwest and West Texas, where there is plenty of land and plenty of wind, while you see a lot of solar capacity either in very sunny states or where there are high expectations for environmental compliance, like California or the Northeast.
When it comes to the IRA, Brett Smith, senior director of government relations for the American Iron and Steel Institute (AISI), said it provides clarity and more certainty to renewable electricity producers, knowing that renewable electricity tax credits – both investment tax credits and production tax credits – will remain in place through 2029.
“While there have been inroads, the renewables market also faces certain challenges,” Miriam Falk, a senior analyst for Fastmarkets, pointed out. For example, even though the cost of renewable power capacity has been declining, it is still more expensive than that for fossil fuels, making it difficult for such projects to be competitive, especially given that there is an ample supply of oil and natural gas in the US. However, Falk noted that the push by the Biden administration to have the US reach certain climate goals has helped.
Sophie Karp, a senior analyst and director of electric utilities, power and renewable
energy for KeyBanc Capital Markets, stated that the IRA is more likely to encourage more solar projects versus wind power and other renewable energy projects due to the way that the tax credits are structured and the fact that solar has a greater need for such incentives. That is partly because solar power generation has been more expensive and less efficient than wind power generation, although Karp said its cost has been coming down.
Currently, she said that the rate of growth for solar projects is outpacing that for wind
power, partly because of how many wind farms – particularly onshore wind farms –have already been built in key regions in the wind corridor, but also because solar is picking up steam.
Also, while there is growing interest, the US offshore wind market has been slower getting off the ground, although governmental incentives are expected to eventually help that market as well.
John Begala, vice president of state and financial policy for the Business Network for Offshore Wind, noted that currently there are only two operational offshore wind projects in the US – off the coast of Virginia and Rhode Island, although there are two more projects beginning construction this year – one off the coast of Long Island and the other off the coast of Massachusetts.
While offshore wind is less intermittent than most other renewable power generation sources, Begala said that one of its challenges is that it involves large, complex projects with long timelines, which can increase material and transportation costs, making it challenging for those projects to go forward.
Another challenge is getting the steel they need given that they need 90-150 mm thick heavy plate, Begala said, noting that
only seven mills worldwide can produce 120-150 mm thick plate with none of those mills being in the US. He said that even Nucor’s new Brandenburg, KY, plate mill will only be producing heavy plate up to 100 mm thick. However, AISI’s Smith said that new investments by domestic steelmakers could fill that gap, maintaining that the greenfield mill that Nucor plans to build in West Virginia is largely being put in place to serve the offshore wind market.
Hydrogen has also recently come onto the scene as another viable renewable energy source, Alan Hollis, Evraz North America’s vice president of business development for emerging energy markets, said, noting that a multitude of companies are exploring a range of opportunities. In fact, in April, Evraz became the first North American line pipe producer to have a product qualified for high-pressure, 100% hydrogen pipeline transportation.
While being on the table for a while, Philip Gibbs, a senior metals equity analyst for KeyBanc Capital Markets, said that without the incentives in the IRA many ‘green’ hydrogen projects that are now seen as being viable would not have been considered for another decade given its cost. That, Villali explained, is because while hydrogen itself is clean, traditionally its production process is dirty, involving the use of such fossil fuels as natural gas, oil and coal and there is a lot of cost involved in switching to the use of renewables instead, including building solar or wind farms to make that ‘green’ hydrogen.
Due to the intermittent nature of renewable power sources – for example, when the sun doesn’t shine and when the wind doesn’t blow – there continues to be a need for such baseload power, as natural gas, coal or nuclear power, AISI’s Smith pointed out. Begala, however, maintains that isn’t necessarily the case for offshore wind, which he calls ‘renewable baseload power’ with the wind blowing more offshore.
For the same reason, SDI’s Wagler said that the energy storage of renewable energy, including the development of new battery storage technologies, is also very critical to guarantee the reliability of the
electric grid for steelmakers and other significant power consumers.
“The amount of steel that will be used for these renewable power generation facilities remains to be determined,” Evraz’ Hollis declared, pointing out that it is still anyone’s guess as to how much planned new capacity will actually come to fruition and when.
Hollis pointed out that different types of renewable projects have somewhat different impacts upon not just steel demand in general but upon different steel products.
Steel demand
CRU’s Thomas pointed out that it will not only have an impact upon carbon steel, but upon stainless steel as well. And even for carbon steel, S&P Global’s Anton maintained that the overall net steel demand won’t increase dramatically, given that there is also less of a need for pipelines with many forms of renewables.
But certain specific types of steels, most notably carbon steel plate, will see a big boost. “Already the growth of generation capacity for such renewable energy sources as wind power has had an impact upon US demand for steel plate,” Frediani said, predicting that in the near- to mediumterm the building of wind towers could account for as much as 10% of US plate demand. “While that is a lot, it won’t be transformational,” Frediani said, given the impact that construction and some other major end-use markets will have upon plate consumption. In anticipation of this, he said that US plate production capacity has already ramped up about 10%, including the start-up of Nucor’s Brandenburg mill.
This push is also exponentially increasing demand for both grain oriented and nongrain oriented electric steel – products that are already in deficit, Anton observed, stating that if there isn’t more electrical steel production capacity built – preferably at a rate of four new mills per year – that will be one of the single biggest choke points for renewables. While US Steel’s Big River Steel facility will soon be making electric steel and Baosteel and ArcelorMittal are both adding production capacity,
Anton said that won’t be enough to meet demand. Frediani agreed, calling it just ‘baby steps.’
Several other steel products are also expected to benefit from the push for new renewable energy generating capacity, including hot-rolled and galvanized sheet, rebar, structural steel, tubular products and specialty steels. US steel mills are generally doing what they can to support this increased demand. For example, Hollis said that Evraz’ research and development centre in Saskatchewan, Canada, is very focused upon developing renewable energy related technologies and products.
Smith said that there are several examples of US steel producers working with companies producing renewable electricity to use electricity to make clean energy products.
For example, Wagler noted that SDI (as well as some other steelmakers) supports some renewable energy developers and the electricity grid through virtual purchase power agreements (VPPAs) that guarantee the power companies that the steelmaker will be pulling a certain amount of power from the grid where they will be introducing renewable energy. “It doesn’t necessarily mean that we will be using that renewable energy directly,” she noted, “But we will be supporting the grid, offsetting some of the cost of the renewables while also getting renewable energy credits that we can use to reduce our Scope 2 emissions.”
Meanwhile, some steelmakers have made investments to help them have more access to renewable energy. For example, Evraz has a commitment with Xcel Energy to build a solar farm on the grounds of its Rocky Mountain Steel mill in Pueblo, Colorado.
“Many steelmakers are doing things to play the game and to look better to their customers,” Gibbs said. While he thinks it’s a positive development for US steelmakers, it won’t ever usurp such other large end-use markets as construction and automotive. “But’’, Gibbs said, ‘’it will be a source of growth for companies that have been targeting the energy market for some time.” �
By embracing new ideas and processes, steel manufacturers can future-proof their businesses ready for the hydrogen transition – while at the same time reducing their carbon footprint and optimizing production to meet demand. By Frederik
STEELMAKING is undergoing a radical transformation, primarily driven by the urgent need to reduce carbon emissions by replacing coal with renewable alternatives such as hydrogen, while at the same time optimizing production to meet increased
Esterhuizen, Mukesh Jain, and Tarun Mathur*.demand using digital and automation technologies.
To address the former issue first, producing ‘green’ steel using hydrogen and deploying carbon capture solutions is the future of the industry, but high costs,
*All authors work for ABB.
limited resources and the absence of a unified policy framework all mean this is still some way off becoming a reality on an industrial scale.
In the interim, the focus for steelmakers and technology providers like ABB must be
Like mining, steelmaking is traditionally a conservative, risk-averse sector that relies on systems and processes that have been established over many decades. However, while perennial challenges such as optimizing production and reducing raw material costs remain, the landscape has changed; steel operators face a host of new requirements around environmental certification, energy costs, plant and furnace design, and the implementation of advanced process control (APC) and digital technologies.
Steel melt shops, for instance, are under increasing pressure to produce the same tonnage while reducing operating expenditure (OPEX). This can be achieved by fingerprinting the operation to identify ‘dead time’ when processes are not being optimized, and then deploying digital solutions that eliminate equipment and process bottlenecks, improve throughput, and reduce energy usage and carbon footprint.
Such environments are typically characterized by high temperatures and batch processing, which means installing sensors throughout the factory to gather performance data can be a challenge.
on developing technology solutions that reduce energy consumption, costs and waste, while also formulating a strategic digitalization and decarbonization road map ahead of the impending hydrogen transition.
In this article, we discuss why collaborating with a partner with an indepth understanding of metals processes is key to making this happen, why technology must be supported by the transformation of processes and people, and take a closer look at solutions provided by specialist technology providers like ABB around energy recovery, reduction, substitution, management, and optimization.
ABB AbilityTM Smart Melt Shop integrates more pragmatic, customized data solutions on top of generic internet of things (IoT) sensors and optimization apps, thus enabling the move towards a fully connected, autonomous and optimized steel melt shop. It does this by connecting operations with both ladle tracking and crane scheduling based on data including thermal modelling1. The industry-first smart factory solution has been deployed at JSW Steel’s Dolvi Works plant in India, boosting profits by an estimated $2m through 4% higher casting speeds and additional output of 24kt a year2
Meanwhile, considerable savings can be made regarding machines and raw material. Sandvik, SSAB, Ovako, University of Gävle and ABB are co-developing methods for predictive maintenance in an example of digital and analytics solutions maturing for plant reliability and efficiency.
Another of our steel customers is working with ABB and Microsoft on energy optimization, and to improve reliability by 5%, through the use of digital technologies, so there is real evidence that the industry is engaging with the digital/automation
and hydrogen transition, as well as an awareness from manufacturers that they must start laying the groundwork now to future-proof their operations.
ABB is committed to improving efficiency and reducing the carbon footprint of its industrial products at every stage of the production chain. This holistic view
digitalization and automation, technology solutions must be supported by the transformation of processes and people. What do we mean by this? Well, when
As we mentioned at the outset, partnering with a technology provider with deep domain expertise in metals can help prepare steel manufacturers for the hydrogen transition, while simultaneously ensuring they optimize production and maintain a critical competitive edge in the here and now.
Consteerrer® was developed as part of a collaborative project between ABB and Tenova. Based on ABB’s ArcSave® technology, this electromagnetic stirring (EMS) solution for continuously charging electric arc furnace systems is already paying dividends at Italian steelmaker Acciaieria Arvedi’s record-breaking melting unit (furnace tapping size 300Mt). EMS has boosted productivity by 5%, reduced electrical energy consumption by 3.6%, and significantly improved metallic charge yield3
Solutions such as these and furnace optimization control systems that improve reheat furnace control to reduce heat losses and optimize the energy consumption, as well as an advanced process control that communicates with installed level one distributed control system (DCS) controllers, are designed to help steelmakers meet the dual challenges of maximizing yields and hitting sustainability KPIs. Combining them with ABB’s Energy Management System4 offers operators even more value by enabling them to manage energy demand, supply and price volatility, as well as reduce costs by as much as 15%.
extends to circularity; for example, recycling copper, aluminium and steel offers energy savings of 75–95% compared with virgin production. To this end, ABB is using Boliden’s certified recycled and lowcarbon copper in its electric motors and electromagnetic stirring technologies. The ultimate goal? To improve performance and product quality in electric arc furnaces, reduce greenhouse gas emissions and drive the transition to a more circular economy.
That road is a long and winding one, however. Let’s take something as fundamental as the blast furnace as an example. Many manufacturers, particularly those located outside of Europe, are still building and installing blast furnaces powered by coal as opposed to newer electric arc furnaces.
These blast furnaces will likely be in use until around 2080. Stringent environmental regulations in the EU are welcome, but if steelmakers in Europe import steel from other countries with less strict rules while being penalised for their emissions at home, any benefits in terms of circularity are lost. So, for the circularity concept to really work, governments must also work to level the playing field when it comes to legislation, import and export rules, and knowledgesharing between countries.
Earlier we mentioned that steelmaking is a conservative industry, and that for customers to really reap the benefits of
we talk about the digital transformation, rather than just frame that conversation around futuristic technology, we should also talk about how it is a commitment to continuous improvement and perpetual change.
The hydrogen revolution will inevitably require new skillsets to allow personnel to make sense of as well as augment technological innovations such as IoT, advanced process control and artificial intelligence (AI). Successful change management is, therefore, key to upskilling and preparing the workforce for new models and processes, not to mention attracting and retaining a new generation of digitally literate talent for whom sustainability is a priority.
Encouragingly, we have detected an identifiable shift in the industry from a digital and sustainability perspective in the past few years, with manufacturers really recognizing the benefits of innovations in process control solutions and products like high efficiency motors. Many companies now have dedicated and independent digital teams with a mandate and budget to invest and develop digital technologies. Maybe a decade ago, these issues were only being engaged with at leadership level; now, we see them trickling down to the lower levels of businesses as well.
It is not just multinationals such as ArcelorMittal and Tata Steel that are partnering with start-ups and established vendors such as ABB; the smaller players in
steel, of which there are countless numbers, of course, are also becoming much less resistant to change. Instead of settling for just small energy efficiency changes, for example, they are beginning to understand the power of new technologies to not only improve their production, but also emissions and regulatory compliance.
At ABB, we realise that our environmental responsibilities extend beyond developing technology solutions that help our customers. With our 2030 sustainability strategy, we are actively enabling a lowcarbon society as well as working with our customers and suppliers to implement sustainable practices across our value chain and the lifecycle of our products and solutions. As a company, we also place great importance on the power of industrywide knowledge-sharing and collaboration5 Three ongoing projects illustrate this best in the context of green steel production and the hydrogen revolution. In Sweden, our electrification and automation solutions are part of HYBRIT (Hydrogen Breakthrough Ironmaking Technology), the world’s first large-scale, fossil-free steelmaking plant. In the realm of carbon capture, ABB
has equipped a team at Imperial College London with the latest control technology and control room equipment to provide students with the skills they need to run tomorrow’s industrial processes, including steelmaking. In France, the company is supplying a control solution for automation of Lhyfe’s first ever green hydrogen clean energy production facility. Lhyfe designs, installs and operates hydrogen production units.
Conclusion
With energy costs and global demand for steel increasing in tandem, manufacturers are faced with the challenge of maintaining steel production while simultaneously preparing for the impending industry transition from using fossil fuels (coal) for both fuels and feedstock to using hydrogen.
Digital, automation and electrification technologies are key to achieving these goals, offering unprecedented visualization, control, and optimization of steelmaking processes across the entire value chain. However, they should not be viewed as a silver bullet.
Collaboration, and a willingness to invest meaningfully in new innovative working models and practices, as well as in human capital to ensure that as the current
generation retires, new, forward-thinking employees take their place.
By addressing company culture, replacing entrenched ideas with innovative thinking, and deploying the latest emissions-saving technologies, the steel industry can continue to provide the materials that are so vital to modern life – and contribute to a cleaner, safer world for future generations.�
Sources:
1. ‘The steel melt shop is getting smarter’ – Tarun Mathur, Steel Times International, 2021
2. https://new.abb.com/news/detail/79684/ abb-completes-melt-shop-digitalizationproject-with-indias-leading-steel-companyboosting-productivity-and-profitability
3. https://new.abb.com/news/ detail/90023/abb-and-tenova-receivefinal-acceptance-for-innovative-chargingmelting-and-electromagnetic-stirringsolution-on-a-large-electric-arc-furnaceeaf#:~:text=Leading%20metals%20 industry%20suppliers%20ABB,the%20 world’s%20highest%2Dyielding%20EAF.
4. https://new.abb.com/industrial-software/ sustainability/energy-management-systemenms
5. https://global.abb/group/en/sustainability/ sustainability-strategy-2030
2023
The Future Steel Forum, now in its SEVENTH successful year, is heading for Vienna this September to examine the important relationship between digital manufacturing and the decarbonization of the steelmaking process. Come and listen to experts from the two most important areas of global steelmaking at present. This is a must-attend conference for anybody with an interest in the fast-developing world of Industry 4.0 technologies and those responsible for sustainable steel manufacturing.
CONFIRMED SPEAKERS FOR FUTURE STEEL FORUM IN VIENNA INCLUDE:
Alexander Fleischanderl* has always been passionate about ‘cleaning things up’ and following on from a year since his appointment as head of green steel at Primetals, the drive to make the world a greener place has never held a more urgent significance. By
TO the wider public, the terms ‘sustainable’ and ‘steel’ aren’t likely neighbours, with the steel industry being one of the largest culprits of CO2 emissions, water pollution, and energy consumption – with all climbing, until recently, alongside its rampant rise in production. In terms of environmental impact, blast furnaces are top of the hit list-churning out 90% of the industry’s total emissions, and causing catastrophic damage to the surrounding wildlife and landscape. Despite this, steel can – and must – be part of a sustainable future. Enter Alexander Fleischanderl, head of green steel at Primetals, and driver of a task force that cracks the code of making one of the world’s most renowned ‘dirty’
industries, clean, green, and fit for the next generation.
Since his appointment as head of green steel just over a year ago, Alexander Fleischanderl has been reflecting on the ‘passion for innovation’ he sees in his team; with all 20 members ‘continuing the work [he] did 15 years back’ in the sustainability sector. ‘‘I’ve been working in this space many years more,’’ Fleischanderl told me, ‘‘going back to during my PhD, I studied municipal waste incineration plants, so a completely different thing to green steel, but there I developed a new system for municipal waste, so the sustainability area of heavy industry is not new to me, it’s always been my passion.’’
And it’s not just about decarbonizing the industry; for Fleischanderl, the changes taking place in global steelmaking must and will account for a ‘broader context in terms of sustainability’, dealing with all aspects of the chain, and forcing change from the inside out.
But what changes have taken place in the last decade? According to Fleischanderl, it’s all ‘in the private sector – starting from 2019 with the announcement of the European Green Deal in 2019’. ‘‘Before,’’ said Fleischanderl, ‘‘there was always a ‘laugh in the backyard’ when I was promoting topics of bi-product treatment, heat recovery, and emissions reduction… the view was that ‘it’s not paying off, and
it might be possible, but nobody’s interested’’. This led to a ‘triggering point’, he continued, saying that when the deal formed, the industry came to represent the sustainability focus that we see in so many sectors today.
Maintaining traction towards a sustainable industry is a separate matter, however, with Fleischanderl citing two main systems in place to incentivize the market; penalties, and premiums.
‘‘People are more prepared now to pay a
premium, and that is a good thing, because a system that relies on penalties and taxes is not the best,’’ he said, adding that the ‘driving force’ for change has to be the premium, given that green steel is more expensive, and likely will remain so for the next few decades. Motivation for companies to purchase green steel hasn’t always maintained the market though, with Fleischanderl referring to the driving force of ‘ESG topics’ creating a demand for netzero that companies are bound to adhere to. ‘‘[Companies] need ‘green stories’ for their shareholders, so all of them have made their strategies. It’s wise doing this, otherwise they will miss the train’’.
The ’train’ of sustainable action is not so smooth-running, however, due to complex conditions in the raw materials market. ‘’Unfortunately, there are not so many established mechanisms to manage
raw materials like scrap’’, Fleischanderl said, adding that the ‘whole of Europe is exporting large amounts of scrap’, with scrap dealers having not established technologies to clean the scrap. In spite of this, Fleischanderl concedes that progress is being made in terms of producing ‘advanced high strength steel’, but this only furthers the importance of controlling scrap - ‘‘copper is the real enemy of advanced high strength steel – this is one of the focused topics for Primetals… we are developing intelligent sensors and an online analysis system to identify and remove certain pieces from scrap to get crafted, clean scrap’’. According to Fleischanderl, the same goes for iron ore – with the market due to see ‘quite a challenge in the future’. ‘‘On the one hand, it’s good that more scrap requires less iron ore, but it’s a matter of fact that we will see less blast furnaces and coking plants in the next three decades – that will leave a lot of lower grade iron ore in the market’’. The solution, said Fleischanderl, is to utilize lower grade iron ore with DRI technology, and he believes that this will become a ‘major trend’ as a result of its necessity. An example of this utilization of DRI technology exists in Primetal’s HyRex process; a steelmaking method that manufactures molten metal using iron ore fines and hydrogen, based on Korean steelmaker POSCO’s FINEX fluidized reduction technology. Through this process, two
sustainable goals can be achieved in one swoop; the utilization of lower grade iron ore, and the replacement of fossil fuels with hydrogen, meaning that water is generated as a bi-product rather than CO2
The use of hydrogen is another example of a ‘major trend’, in Fleischanderl’s eyes, but the logistical side remains a tricky knot to untangle; with issues of liquifying, shipment, and cost being significant concerns for an urgent transition. ‘‘Unfortunately, as we look to the ‘hydrogen generation’, it’s always promoted that we look to regions where renewable energy is cheap, but the cost is still there – and the logistical cost is significant. The truth is even that if we’re optimistic, we end up with no less than $6 per kg of hydrogen if you deliver it over the fence for the next few years. If we compare that to natural gas, which is tricky because prices are unstable, with the pre-Ukrainian war price, it requires around $1 per kg of hydrogen delivered to the steel mill to stay at the same cost level’’. In short, the major concern, says Fleischanderl, is on the ‘pace of establishing a hydrogen eco-system at a reasonable price level’. Solutions to the issue of pricing are not going to be smallfry either – with Fleischanderl gesturing to the possibility of ‘the relocation of the industry’. ‘‘There are simply more favourable producers in the world in terms of green iron, like the Middle East, Australia, Chile, USA and Canada, Norway, and Spain. If we look at the Middle East and Australia where a lot of iron ore is, you avoid the transport of hydrogen – you could look into iron hubs at a large scale that ship
Walk away informed and inspired about your company’s sustainability journey. SIM Europe in Maastricht offers attendees a deep-dive into the latest solutions for sustainable manufacturing, break-through technology, and the future direction of industrial processes.
INCLUDING SPEAKERS FROM:
China Hongqiao Group
Henkel Global Supply Chain
General Electric
British Glass
Linde PLC
Titan Cement Interational
Holcim
SABIC
Heidelberg Materials Group
Schneider Electric
AGC Glass Europe
ABB Process Industries
Thyssenkrupp Steel Europe
Plus a whole host of NEW tech disrupters including Net0, CemVision, BioBTX, Magsort, Carbon Clean and many more…
100+ SPEAKERS
Follow our LinkedIn group for updates
ROUNDTABLE DEBATES
NETWORKING EVENTS
Europe’s only event dedicated to the met coke, coal and steel industries
With over 300 attendees and 28 expert speakers at the 2022 event, can you afford to miss out?
Eurocoke is a fantastic platform for people in the met coke industry from all over the world to exchange ideas and information - ACRE
www.eurocokesummit.com
SAVE 10% WITH CODE ECOKE23STI
HBI or green pig iron from Australia or the Middle East into countries where steel is produced but energy is expensive.’’ This, said Fleischanderl, ‘will have impacts on the value chain and employment rates, and it’s likely it’s going to happen in the mid-term’.
Despite the ongoing efforts to convert to green steelmaking, all the clichés of smokestacks pumping out fumes exist for a reason, and a huge discrepancy continues to plague the industry – of blast furnaces still being built, while other regions are converting to cleaner production processes. ‘‘It’s no secret that the lifetime of a blast furnace is 50 years plus’’, said Fleischanderl, and so in his view, the only way out for regions such as Southeast Asia and China continuing to invest in emissions heavy production is carbon capture and utilization; ‘it’s one of the passways to solve the issue and come closer to netzero’. Other than that, it’s a waiting game for legislation to catch up with the remaining blast furnace stronghold, with the ‘introduction of mechanisms’ such as CBAMs and emissions trading schemes, as well as market incentives to switch to greener production methods.
While this fight continues, Fleischanderl turns to the 20 strong task force he works within, which after a year since its commencement, has ‘never been better
integrated’, nor more passionate about the drive to decarbonize the industry. The ‘one disadvantage’ of working within the task force, said Fleischanderl, is ‘not doing the deep dive work’ that has given him over 100 patents to his name, but that research is ‘now with the next generation’– one that he feels is inspired to propel deep and meaningful change through the steel industry. Looking back to his beginnings, Fleischanderl refers to a childhood that was spent ‘playing around with chemical tools, changing colours, and making reactions’–always with the underlying thought of ‘cleaning things up’. One of his proudest moments to date is the development of MEROS; a maximised emissions reduction system for sintering and pelleting plants. Designed as a modular system, it removes almost all harmful substances found in the off-gas of sinter plants and other steel production units. This includes elements such as sulfur oxides, nitrogen oxides, dust with particle sizes as tiny as 2.5 nanometers, dioxins, furans, polyaromatic hydrocarbons, heavy metals like lead or mercury, acidic gases, and various other harmful organic compounds. It’s a gamechanging innovation, with a surprising backstory. Fleischanderl recalls holidays in Italy with his family, where they stayed near a steel mill that had a ‘brown plume
always hovering over’, a sight he said which ‘threatened’ and disturbed him as it continued to billow out into the nearby town, causing illness, dense clouds of pollution, and damage to the wildlife.
‘‘99% of all dioxin emissions from Italy were from that one stack’’, he said, which led him to stage a return to his holiday haunt in 2005 – where he and his team built a MEROS pilot plant and waited with bated breath to see the community’s reaction once it commenced operations in 2007. As it turned out, it was worth the wait.‘‘If you look now at that stack, all the people in the city love to see it – you don’t see [fumes], it’s zero emissions. This is why I love to work in sustainability, because it’s contributing to society and the well-being of people...it was a city with some of the highest cancer rates, and hopefully this is gone now.’’
It’s not just about steel then, for Fleischanderl, it’s the knock-on effects of an industry that, for a long time, has existed in contradiction – both contributing to the development of society, and causing detrimental effects to the world in which it functions. Yet, with the advancements of systems that work to offset the costs, the unlikely neighbours of ‘sustainable’ and ‘steel’ might finally be able to exist in an unexpected, and indeed crucial alliance. �
The Centre for Advanced Steels Research (CASR) discusses its current projects, which aim to enable a hydrogen economy and streamline the transition to decarbonized and digitalized steel production. By Pentti
IN the Glasgow Climate Pact 2021, 197 countries agreed to limit the global temperature increase to 1.5°C by reducing greenhouse gas emissions. This calls for a climate-neutral Europe by 2050 and Finland has an ambitious aim to become carbon-neutral already by 2035 and carbon-negative soon thereafter. The steel industry is responsible for ≈7% of annual CO2 emissions globally. Therefore, the steelmaking and mechanical engineering industries have an important role to play in addressing the challenges arising from the long-term strategy on climate goals. Replacing carbon partially or even completely with hydrogen and non-fossil renewable electricity generation are the key
factors, by means of which the universal targets of CO2 emissions and climate change could be achieved. The EU Green Deal identifies clean hydrogen as a priority in the green transition and electrolytic water splitting using sustainable electricity is at present considered as the primary preference for green H2 production, but it fails in covering the huge demand. Furthermore, hydrogen, as causing hydrogen embrittlement, is detrimental to the properties of high-strength steels, needed as a critical construction material to reduce the CO2 emissions.
Advanced steel research at CASR
In Finland, the Centre for Advanced
Steels Research (CASR) was founded in the University of Oulu in 2006 in order to co-ordinate steel-related research (https://www.oulu.fi/casr/). Currently CASR consists of 10 members, seven research
units from the University of Oulu, and a unit from LUT University, Turku University and Åbo Akademi, with a total of about 140 researchers. CASR is currently headed by Professor Jukka Kömi. Well before the age of the CASR, in the early 1990s, research related to thermomechanical
processing of high strength steels was initiated, particularly focused on physical simulation and direct quenching technology in processing high-strength plate steels. It is estimated that the use of advanced ultra high-strength steels can decrease total CO2 emissions worldwide by up to 15%. The direct quenching technology was adopted by Rautaruukki (now known as SSAB Europe Oy) in Finland in the early
1990s. For potential future technology, based on the physical and laboratory rolling simulations of quenching and partitioning (Q&P) processing, a novel direct quenching and partitioning (DQ&P) process has been proposed by CASR.
Currently, in the line of numerous research groups globally, CASR focuses very closely on the challenges of targeting carbon-neutral/carbon-free green steel processing and the manufacturing of ultra high-strength steels for weight reduction. In this research field, some projects have already been completed but numerous ones are currently going on and are planned.
As a starting point for the current efforts, a five-year-long academic project entitled Genome of Steel – Physics for strong, tough, and sustainable steel, funded by the Academy of Finland, was conducted over the years 2017–2021. In the Genome of Steel (GoS), the co-operation of material physicists and steel researchers formed a successful integration of experimental and theoretical physics with process and physical metallurgies. The multidisciplinary approach pushed the traditional engineering research towards novel physics-based atomic-level understanding of metallurgical routes and microstructure evolution under the influence of processing parameters for realizing sustainable ultra high-strength steels; and boosted
steel research utilized to-day in projects concerning the hydrogen transition of steelmaking. The multi-disciplinary research has been and will be further utilized in several hydrogen-related projects (see Fig 1). The short descriptions of the projects can be found on the webpage of CASR: https://www.oulu.fi/en/research/researchinfrastructures/centre-advanced-steelsresearch/research-projects-casr)
Most of the projects are concerned with carbon neutral steelmaking using hydrogen reduction.
Digital TWINs for a green hydrogen transition in the steel industry (TWINGHY) is an RFSC-funded project aimed at demonstrating new ways to use, monitor and control hybrid NG–H2 burners for reheating furnaces, progressively decarbonizing the reheating process through an increase of H2 in combination with O2 and monitoring and controlling it through a digital twin. TWINGHY will contribute to the synergetic green and digital transitions of the steel industry.
Hydrogen technologies for the decarbonization of industrial heating processes (HyInHeat) is a Horizon EUIA funded gigantic project, with the participation of 31 beneficiaries, aiming to demonstrate how 100% H2 can be used in industrial high-temperature heating processes. HyInHeat contributes to the objectives of decreasing CO2 emissions of the processes while increasing energy efficiency in a cost competitive way, keeping NOX emission levels and resource efficiency at least unchanged.
Two big national projects, Advanced Steels for a Green Planet (AS4G) and Hydrogen Future as a Climate Change Solution (H2Future), funded by two Finnish foundations (with a budget of €2m for four years) and the Academy of Finland for six years together with the University of Oulu (with a budget of €8m) will be initiated shortly. Researchers are working on these two projects with the common objectives of the transformation to a hydrogen economy and the conceptualization of a zero waste plant. These objectives are anticipated to be achieved through effective clean
hydrogen production solutions; carbon-free steel manufacturing, advanced steels and the utilization of industrial side streams. Accordingly, the AS4G is organized in five themes as follows: (Fig 2)
(led by Professor Marko Huttula)
At present and in the near future, the supply of renewable green electricity is not realistically sizeable enough to support electrolytically driven processes required for generating green hydrogen. The photocatalyst, sun light-assisted hydrogen electrolysis, can be anticipated to serve as the core technology for a truly sustainable hydrogen economy in the future, powered by direct sunlight.
Based on some previous investigations, novel high-efficiency photocatalysts for hydrogen evolution will be developed and applied to iron ore reduction processes. The timeline of the development of high efficiency catalysts is between three-to-five years, piloting in five-to-seven years, and having industrially-scaled readiness in seven to 10 years.
Carbon-free steelmaking by hydrogen use
(led by Professor Timo Fabritius)
The study focuses on the replacement of fossil carbon with hydrogen as the reducing agent. Iron ore reduction will be accomplished by using varying mixtures of CO-H2 atmospheres, followed by a continual increase in H2 content until reaching a pure H2 atmosphere. Globally, CO2 emissions from iron ore-based steelmaking (~1,200Mt of steel per year) could be decreased to nearly zero using this
step-by-step approach.
Industrial collaboration is based on very close connections with companies in their own business areas: SSAB (hydrogen reduction of iron ore in a shaft furnace), Hybrit (fundamentals of hydrogen reduction), Outokumpu (hydrogen plasma reduction), Ovako (hydrogen in electric arc furnace steelmaking), Metso Outotec (electric arc furnace process development) and Fortum (hydrogen reduction of multi element systems).
Metallurgy of advanced steels for sustainable applications
(Led by Professor Jukka Kömi)
The objective of this study is to develop the 3rd and 4th generation hot- and coldrolled ultra-high-strength steels without the excessive use of expensive alloying elements. The yield strength is targeted in the range of 900Mpa to beyond 2000 MPa, with elongation exceeding 20% and having good low-temperature toughness and high sustainability.
Two kinds of steel will be investigated: nanostructured medium-carbon martensitic and bainitic steels and medium-Mn steels, both having ultra-high-strength for weight reduction as well as good resistance against hydrogen embrittlement for service in a hydrogen society.
Optimizing ultra-high-strength steel solutions (a) develops testing technique(s) for detection and analysing the detrimental influence of atomic H in iron lattice, (b) develops novel microstructure(s) for enhanced local H-trapping and crack propagation resistance, and (c) improves the understanding and modelling of H-steel interaction from atomic to macro scale and vice versa
(Led by Professor Jari Larkiola)
The Virtual Steelmaking platform (VSP) makes it possible to consider new and changed process steps before the actual production begins. The impact of hydrogenbased steelmaking on process efficiency, potential bottlenecks, the formation of desired side streams, final mechanical properties of the steel, and carbon footprint can be solved virtually.
(Led by Professor Mirja Illikainen)
A transition to hydrogen-based ironmaking will hugely change the amount and composition of the slags, which in turn will pose a challenge for their future use. Moreover, full capture and utilization of steel production dusts and sludges are inevitably needed to achieve the concept of ‘zero waste plant’.
Slags will be treated by CO2, resulting in carbon capture and utilization. After that, the carbonated slags will be benefited as supplementary cementitious material. This will not only support and advocate the idea of a zero waste concept but would also offer the possibility of globally alleviating the carbon footprint emerging from cement production.
An example of a result of recent research is a special testing method developed by Dr Renata Latypova in her doctoral studies to assess the risk of hydrogen embrittlement; a novel tuning-fork test (TFT). TFT utilizes an integrated loadcell system used during hydrogen charging that allows tracking of the applied force throughout the tests, enabling the detection of initiation and propagation of cracking and time-tofracture. A trustworthy threshold stress level
can be determined with a longer testing period. (Renata Latypova: Development and Application of a Tuning-Fork Test in Studying Hydrogen-Induced Fracture in As-Quenched Martensitic Steels, Acta Univ. Oul. C 856, 2022. https://cc.oulu. fi/~kamahei/z/tkt/vk_RenataLatypova.pdf – see Fig 3)
In addition to an existing Linseis furnace for reduction experiments with H2 and a small-scale EAF furnace for melting of DRI, two special devices for novel state-of-theart sample environments are aimed to be developed in the ongoing projects:
In situ SR dilatometer
A synchrotron radiation dilatometer will be designed together with CASR and MAX IV laboratory for employing the hard X-ray beamlines at MAX IV for following up phase transformations as a function of temperature and time, while monitoring the changes in macroscopic properties of the material.
Ambient pressure x-ray photoelectron spectroscopy (APXPS) unit for photocatalysis and high temperatures This is the combination of advanced characterization of a photocatalyst with real time measurements of its activity and selectivity under real working conditions. The new sample environment will be specifically suited for the characterization of photocatalytic processes such as hydrogen production, hydrogen-based reduction processes, as well as high temperature steel studies in reactive atmospheres.
In addition to research projects, there are numerous activities regarding hydrogen economy with steels, in which CASR’s members have also been involved. One is the Hydrogen Research Forum Finland, co-ordinating hydrogen-related academic research in Finland. An international hydrogen conference in 2024 is also planned. The activities of CASR are also firmly embedded in the Oulu Innovation Alliance, a regional strategic coalition aiming to promote innovations and sustainable growth both locally and globally, including a robust steel and mechanical engineering industry value chain.
The targets towards the transition to green steel are parallel to planned changes in steel production taking place in the near future, where CASR will have its role.
In 2021, SSAB announced an extensive research project to replace fossil fuels with renewable hydrogen in steelmaking, and publicized plans for a new steel production concept based on carbon-free technology in Sweden and Finland.
This would lead to a reduction of around 7% in the total CO2 emissions of Finland.
Further points include Nordic collaborations on steelmaking and a hydrogen economy, including Hybrit, a joint venture company aiming to have a completely fossil-free process for steel making by 2035, and BotH2nia, an international initiative for around the Gulf of Bothnia and the Baltic Sea.
in Nickel-Based Plasmonic Core@Shell Hybrid Nanostructure for Photocatalytic Water Splitting, Applied Energy 322, 2022, 119461
Shi, X., Zhang, M., Wang, X., (...), Cao, W., Huttula, M., Nickel Nanoparticle-Activated MoS2 for Efficient Visible Light Photocatalytic Hydrogen
building a large-scale hydrogen economy
Evolution, Nanoscale 14(24), 2022, 8601-8610
Heidari, A., Niknahad, N., Iljana, M., Fabritius, T., A Review on the Kinetics of Iron Ore Reduction by Hydrogen, Materials 14(24), 2021, 7540; https://doi.org/10.3390/ma14247540
References:
Singh, H., Alatarvas, T., Kistanov, A., Aravindh, S., (…), de Groot, F., Huttula, M., Cao, W., Fabritius, T., Unveiling Interactions of Non-Metallic
Inclusions within Advanced Ultra-High Strength Steel: A Spectro-Microscopic Determination and First-Principles Elucidation, Scripta Materialia 197, 2021, 113791. https://doi.org/10.1016/j. scriptamat.2021.113791
Wang, S., Kistanov, A., King, G., Ghosh, S., Singh, H., Pallaspuro, S., Rahemtulla, A., Somani, M., Kömi J, Cao, W., Huttula, M., In-situ Quantification and Density Functional Theory
Elucidation of Phase Transformation in Carbon Steel during Quenching and Partitioning, Acta Materialia 221, 2021, 117361. http://doi. org/10.1016/j.actamat.2021.117361
Talebi, P., Kistanov, A.A., Rani, E., (...), Huttula, M., Cao, W., Unveiling the Role of Carbonate
Latypova, R., Seppälä, O., Tun Nyo, T., (...), Kömi, J., Pallaspuro, S., Influence of Prior Austenite Grain Structure on Hydrogen-induced Fracture in As-quenched Martensitic Steels, Engineering Fracture Mechanics 281, 2023, 109090
Latypova, R., Seppälä, O., Nyo, T.T., Kauppi, T., Pallaspuro, S., Mehtonen, S., Hänninen, H., Kömi, J., Hydrogen-Induced Cracking of 500 HBW Steels Studied Using a Novel TuningFork Test with Integrated Loadcell System, Corrosion 76(10), 2020, 917-966. https://doi. org/10.5006/3592
Abdelrahim A., Nguyen H., Omran M., Kinnunen P., Iljana M., Illikainen M., Fabritius T., Development of Cold-Bonded Briquettes using By-Product-Based Ettringite Bindere from Ladle Slag, Journal of Sustainable Metallurgy 8(1), 2022, 468-487, DOI: 10.1007/s40831-02200511-1
With an expanding economy, demand for steel is increasing – making the optimal use of resources a priority. FerroSilva, a project involving multiple steelmakers, suppliers, and academics, offers the novel use of biogenic material as a reducing agent in DRI production – with plans to build its first plant and commence operations by 2026. By Rutger Gyllenram*, Peter Samuelsson** and Göran Nyström***
IT is not difficult to produce iron from iron ore; we have done that for a couple of thousand years. Fossil free iron production was the dominant way until the coking process was invented at the end of the eighteenth century, and charcoal blast furnaces are still used in some countries. However, high-volume, low-cost production
demanded the unmatched energy efficiency of the blast furnace process and the smooth logistics of fossil coal – so the blast furnace/ basic oxygen furnace is the dominant process route for steel from iron ore. This position is now challenged by the need to decrease global emissions of carbon dioxide in order to avoid a climate catastrophe.
*Founder and CEO, Kobolde AB
It is human to hope for a new metallurgical process that will solve all our problems immediately. However, abating emissions of climate gases is an issue not only for the steel industry but for all people, and replacing coal will make almost all other
**MSc in metallurgy and materials science, PhD in metallurgy, KTH Royal Institute of Technology
***MSc in materials physics, Uppsala University
resources scarce for the decades to come, and process development will to a large extent depend on optimal use of limited resources. The transition to fossil-free steel will affect every aspect of steelmaking. Blast furnaces that are modified and combined with CCUS, will probably keep their position in order to make use of high gangue ores. Direct reduction from reformed natural gas combined with CCUS and followed by melting in electric arc furnaces using renewable electricity is one alternative and finally, making the reduction with hydrogen made from fossil-free electricity is another. They will all have their place in due time when technology reaches a high readiness level and new trade patterns are stabilised.
From both an economical and an ecological perspective, the optimal route would be to benefit from resources that are not used to their full potential today. Such resources include sawmill waste and forest residue, i.e., tops and branches. The latter is often not harvested but left to rot. Other biogenic resources can be found in the vast and diversified agricultural sector. The drawback of biogenic material is that it is voluminous, it often must be collected from large areas, and the available volumes are limited. There is however more biogenic raw material available than is normally recognised and logistic systems are being developed that can manage the material. The price is normally determined by the value of generated district heating and electricity which limits acceptable costs for transport
and building up logistic systems. If, on the other hand, the product is a reducing gas that can replace natural gas or hydrogen, the value is higher and can cover more extensive harvesting and transport, which increases availability. The final advantage is that biomass generates biogenic carbon dioxide that does not require allowances and when stored, or used in products, creates a carbon sink.
When the number of electric arc furnaces increases and the number of blast furnaces decreases there is a risk of a shortage of high-grade scrap with low amounts of tramp elements. This was the major concern that made three Swedish steel companies,
Ovako, Alleima and Uddeholm, team up with two providers of wood chips and saw dust pellets, Sveaskog and Lantmännen. Together with KTH Royal Institute of Technology and Chalmers University of Technology, M3Advice and Kobolde & Partners, and with additional financing from the Swedish Energy Agency, the consortium performed a feasibility study finalised in September 2022. This has now resulted in plans to build a first FerroSilva plant of 50kt of DRI at the Ovako Hofors plant with the intention to start production in 2026.
The process is based on three technology building blocks, all of them in operation at full scale, but can be found across three separate industrial segments.
Gasification in a fluidised bed is nothing new and can be found at some companies in the pulp and paper industries. Often the aim is to produce heat or electricity. In this case the product is a biogenic syngas with a composition close to what is achieved when reforming natural gas. Today, there are the following designs available with a high technical readiness level; TRL, Dual Fluidised Bed (DFB), and Circulating Fluidised Bed (CFB), all with slightly different performances. The biomass is dried before it is entered into the gasifier where a raw syngas is produced as is shown in Fig 1 The tar is then removed and after that, carbon dioxide and acid gases. The carbon dioxide removal process is commonly used in refineries and petrochemical plants. The resulting gas is then either heated and injected as reduction gas into a DR-shaft
of the same type as is used for reformed natural gas, or injected cold in the bottom as cooling carburising gas. Carbon dioxide and water is removed from the top gas and hydrogen and carbon monoxide is recycled as reduction gas. The high-grade iron ore pellets that are charged at the top of the furnace leave the shaft as DRI. The shaft furnace is like the ones already applied today in the natural gas processes. Finally, the captured biogenic carbon dioxide is compressed, liquified and transported to a partner for further processing. (Fig 1)
The key to efficiency is to use energy streams in the process. Approximately 1.4 tons or 3.7 m3 biomass is used, equal to 3500kWh. Electricity use is 300kWh and biogenic carbon dioxide generation is approximately 1 ton per ton of DRI.
Life cycle assessment for steel using FerroSilva DRI
The three major environmental impacts that must be observed in the FerroSilva process form the Global Warming Potential (GWP) which in large part is about uptake and emissions of carbon dioxide and other climate gases, the soil carbon, and the biodiversity. For a company like FerroSilva, all these three are of great importance and demand close co-operation in the supply chain.
Working with certified forestry companies and following up on research and compliance with standards is part of the core business.
For carbon dioxide, the follow-up must include how the captured liquid gas is transported and processed to new materials or fuel.
Fig 2 shows the GWP, i.e., the carbon dioxide equivalents balance, for one ton of crude steel made in an electric arc furnace from FerroSilva DRI. As can be seen, the steelmaking and carbon dioxide liquefaction emits 360kg direct and indirect emissions (scope 1-3). This leaves a carbon sink of 845kg if this carbon dioxide is brought out of the circuit or used to replace fossil carbon in any way.
It is always tricky to compare production costs from processes that do not yet exist. Reduction with natural gas and 100% CCS of the generated CO2, full-scale reduction with hydrogen or using biogenic syngas and CCU are here compared using published consumption figures and investment costs based on a reference case and estimated differences between the different technologies. As can be seen in Fig 3 the price of the reduction agent has a huge impact on the production cost. The price in euros for natural gas and biomass per MWh is shown on the x-axis, and production costs in EUR/ton DRI on the y-axis. The thickness of the lines shows the difference in cost between in a price range for electricity between 32 and 65 EUR/MWh.
The calculations are made with varying energy prices, iron ore costs, and transportation. This means that distance to the mine or the market may change the differences in production cost between technologies. For FerroSilva, the calculation indicates that it is competitive at a medium natural gas price.
The first FerroSilva plant is planned to be located within the production site of Ovako in Hofors. There are excellent rail and road connections and much of the needed utilities infrastructure are available in proximity to the FerroSilva plant, including the residential district heating, where residual energies from the
DRI production can be put to good use. Furthermore, the process for securing environmental permits will be substantially simplified, being within Ovako’s industrial area rather than at a greenfield site.
The melt shop where the produced DRI will be used in steelmaking operations is located some 200 metres away from the FerroSilva plant. Liquid carbon dioxide will be shipped via rail to other users, such as the production of bio-methanol, that can be used for the production of aviation fuel, but also for further synthesis into products that today are reliant on fossil raw material;
such as plastics, pharmaceuticals etc.
The way forward
With an expanding global economy, demand for steel is increasing and using our resources in an optimal way is necessary. A sustainable use of biogenic material with the FerroSilva process will no doubt play an important role in countries with a well-managed sustainable forest industry. The same is also valid for countries with a significant agricultural industry, where substantial quantities of residues are available. Contrary to the popular view,
suitable bio resources, and thus residues, are available in many parts of the world and are not limited to the boreal and northern temperate forest ecosystems. After setting up the initial plant, the plan is to construct and commission an even larger scale plant and to further expand the geographical footprint of the FerroSilva technology.
For further information, log on to www.ferrosilva.com, or email info@ferrosilva.com
SEVERAL steel-producing companies are active in the Nordic region, which is known for its green technology, innovation, and fossil-free energy. Blastr Green Steel is one of them. Established in 2021, it aims to become an integrated producer of ultra-low CO2 steel, leveraging Nordic advantages, and is estimated to grow into one of the largest industry start-ups in the Nordic region.
Blastr Green Steel´s vision is to decarbonize the entire steel value chain. Its concept is based on locating its activities adjacent to attractive European markets, accessing raw materials locally, and utilizing
ice-free ports with efficient and green logistics. With this integrated approach, the company aims to produce steel with ~90% lower CO2 emissions across scopes one to three than average steel producers today. Emissions will be reduced throughout the entire value chain and in areas such as logistics, heat recovery, and circular economy in addition to the use of hydrogen and fossil-free energy in the production processes. By developing local, sustainable, and scalable value chains for ultra-low CO2 steel production, the company is setting out to challenge the status quo of the steel industry.
Inkoo – an ideal location for ultra-low CO2 steel production
Finland offers an ideal environment for energy-intensive green steel production, with abundant renewable energy resources, a robust infrastructure, and a commitment to sustainability. Blastr evaluated several sites for its steel plant in Northern Norway and Finland, and ended up selecting Inkoo, located approximately 50 kilometres southwest of Helsinki, the capital of Finland. The country offers several benefits for developing green industries: it has abundant fossil-free energy, supportive and predictable operating conditions, and
Blastr Green Steel, a Norwegian steelmaker of the future, discusses plans to establish a pellet plant in Gildeskål, Norway and a steel plant with an integrated hydrogen production facility in Inkoo, Finland.
a highly qualified workforce. Furthermore, Finland´s ambitious political energy transition agenda facilitates stable and competitive prices for its fossil-free energy, providing a cost advantage for steel and hydrogen production.
The Inkoo site is well-suited for a steel plant. The southwest region of Finland has a long industrial history, also in steel production. Closeness to the capital with its highly skilled labour force and strong transport connections enables attracting the needed 1,200 employees for the steel plant. Blastr´s €4 billion investment will bring not only direct but also significant indirect opportunities for employees and businesses, and economic effects for the municipality and the region.
The brownfield area planned for the steel plant previously hosted a now dismantled coal-fired power plant. The site has strong access to Finland’s main energy grid with direct connection to several 400 kV and 110 kV power lines and a pre-existing high-
voltage substation at the site´s boundary. The deep ice-free port enables efficient, low-carbon logistics all-year round, as well as smooth international, as well as regional access to raw materials, such as recycled scrap metal and direct reduction pellets to be used in the process. The growing European market for Blastr’s finished ultra-low-CO2 steel products is also wellaccessible.
The Inkoo site is currently owned by Nordic energy company Fortum, with which Blastr is developing a strategic partnership for site development and energy sourcing. In addition, Blastr’s ambition is to secure a significant share of its own power needs from directly or indirectly owned wind parks, advancing clean energy production in Finland.
Steel production based on fossil-free hydrogen Blastr will employ the so-called mini-mill concept with state-of-the-art technologies
across all key areas. The steel production process will use fossil-free hydrogen instead of coal. An integrated hydrogen facility to be linked to the steel plant will ensure a constant supply of hydrogen. Large-scale electrolyzers will produce hydrogen at scale with a capacity exceeding 500 MW.
The hydrogen-based direct reduction iron (DRI) plant will have a capacity matching the largest reference projects to secure economies of scale. Hot DRI will be transported to the electric arc furnace (EAF) melt shop, ensuring the lowest possible electricity consumption. The process route includes a ladle furnace and degassing station before feeding the alloyed steel to a direct casting and hot rolling mill, fully avoiding the use of fossil energy for slab reheating to minimize CO2 emissions and energy consumption. This line can produce hot-rolled coils thinner than conventional mills, which eliminates the need for cold rolling for part of the product portfolio.
Part of the hot rolled coils will be further
processed in the downstream processing lines providing additional thickness reduction, surface treatment, and protective coating to meet the most demanding end-product requirements. Automation and digitization will be leveraged across all processes to ensure an end-to-end optimization of the plant.
The steel plant will produce 2.5Mt of hot-and cold-rolled coils, and hot-dipped galvanized coils made from self-produced high-quality direct reduction pellets and recycled scrap steel from Northern Europe. The product offering will be targeted to European customers, for example, in the automotive and construction sectors seeking sustainable products to support their ambitious CO2 reduction goals.
The steel plant project is progressing at full speed on many fronts. The land use planning of the Inkoo site is currently
ongoing, as well as the Environmental Impact Assessment. These are prerequisites for acquiring the necessary permits for plant construction and operations. Also, the pre-feasibility study is ongoing to deepen the engineering and support the permitting process with necessary technical input.
Blastr is in the process of building up its organizational capabilities and has already secured strong steel industry expertise on the company and its Board. The start-up is currently owned and funded by Vanir Green Industries, a Nordic investment company that invests in, develops, and scales green businesses that are needed to accelerate the energy transition. Blastr has recently initiated its Series A financing with the aim of attracting strategic and financial investors. The target is to close the first financing round in late 2023 to secure funding to complete the engineering and feasibility studies for the plants, as well as the organizational build-up. In 2024, the project will move into a
feasibility study and permitting phase. The Series B financing is aimed to be closed towards the end of 2024. The final investment decision is planned to be taken in 2025, around the time of receiving the permit decisions. The production is planned to start commissioning in 2027, with the ramp-up of the integrated value chain to full capacity taking pkace between 20282030.
A key aspect in ensuring a high quality of the raw material will be the self-owned direct reduction pellet plant, currently planned to be located in Gildeskål municipality in Northern Norway. Blastr is developing a partnership with Cargill for sourcing iron ore feedstock for the pellet plant.
The coastal location of Gildeskål provides an ice-free harbour with access to the seaborne iron ore market. In the pellet plant, Blastr will convert the iron ore pellet feed into high-quality direct reduction pellets, producing 6Mt of raw material annually. Part of this volume will be feedstock for Blastr’s ultra-low CO2 steel production at Inkoo, and the rest will be sold on the growing world market for direct reduction pellets.
The pellet plant will utilize hydropower from the Norwegian grid. The plant will require a more than €1 billion investment and will offer approximately 120 direct jobs when operational. Blastr is expecting to make a final investment decision on the pellet plant in 2025, subject to relevant permits and agreements being in place by then. The plant is planned to start production in 2027-2028.
Blastr’s long-term plan is to set up additional steel plants, utilizing the feedstock capacity of its own pellet plant. The company believes that its vision will be reached by working closely with different industry players and customers to find solutions to decarbonize steel production. This will be accomplished through developing strong, long-term strategic partnerships along the value chain. All in all, it´s all about taking a quicker leap together to a more sustainable future. �
What links conspiracy theories, cheese, James Stewart, and things that howl in the night?
The moon is as much a fixture in our cultural life as it is suspended in space. It is also, for a growing company in Israel, a unique opportunity to decarbonize steelmaking – a readyto-go base for mining materials that have been exhausted on Earth. ‘’No-one has done this before’’, Jonathan Geifman* tells Catherine Hill**. His company, Helios, is the beginning of a lunar revolution, that despite its critics, sees life in Ferris Bullerian terms; it moves pretty fast – what was once implausible, will soon be trivial.
‘MAN is by nature a social animal’, said Aristotle. Another interpretation: we’re hardly more adapted to our environments rather than short-circuited by what appears to be important. Living is, for an overwhelming part of the global population, an earthly concern; birth, death, relationships, and work all taking place under the clingy weight of gravity. However, for a select few, office smalltalk isn’t about diets, weather and missed weekends – for Jonathan Geifman, founder and CEO of Helios, water cooler chat has been about NASA’s Space Launch System (SLS), an American super heavy-lift expendable launch vehicle, which at the time of interview, had yet to make its first attempt to enter space.
When I ask him if he thinks the launch suggests that we are living in a second space race, he quickly interjects as I struggle to remember the date the launch was scheduled to take place. ‘‘Two and a half weeks.’’ Later, I ask him if his work ever feels as extraordinary to him, as it appears to outsiders – with a business focus on researching human life and industry on Mars and the moon. ‘‘When you’re in this’’, he tells me, ‘‘and especially when you work with the space industry….it’s trivial. I mean, you just talked about SLS. Most [people] don’t know about SLS. In the space sector, it’s all that we’re talking about. We know the companies who are building it, designing it. We know the contract for sending the astronauts to the moon, et cetera. When you’re invested in this, when you’re part of this community, it all seems very trivial’’.
This ‘trivial’ work culminated in the form of Helios, an Israel-headquartered company focused on developing a reactor that can process lunar soil and Martian soil in to oxygen and metals. Through engineering the required technology, however, the company stumbled upon a ‘novel method to produce iron from iron ore, requiring only thermal energy, and emitting only oxygen.’ The aforementioned technology is contained in a special module which is directly integrated into DRI (Direct Reduced Iron) furnaces, which, it is claimed, reduce cost and facilitate faster adoption. In short, Helios claims it has developed a way to use space technology to decarbonize the steel industry.
The steel industry was not the first area of focus for the company, however, as its initial aim was to establish infrastructure in space; processing oxides on the planetary surfaces into oxygen and metals in order to create a liveable, breathable environment. The metals would be used to build storage and accommodation, resource transportation, and surface tiles and roads, allowing ‘future colonization’ of the moon and Mars, with the development and application of Helios’ planet-proof processes.
Developing Helios’ processes started, says Geifman, by returning to the first principles; ‘literally opening the periodic table and trying to figure out what we can do differently that will meet the harsh requirements of the lunar environment.’
It was ‘out of necessity’, he continues, that Helios came up with a method to extract resources from the surface soil of Mars and the moon, which includes four processes of extraction, separation of oxides, processing of the material, and storage, throughout which metal biproducts – including iron, aluminium and titanium – are reaped from the soil. Through researching these processes, the company realized that ‘one of the methods might be a great fit for the steel industry’ as when iron was extracted via their modules, there were ‘no direct emissions, as carbon isn’t used, and indirect emissions are also reduced as 50% less energy is used compared with how steel is produced today.’ With the modules’ use of thermal energy rather than traditional high-emitting fuels, Helios claims it has created a cleaner way to make steel. ‘‘If you run the numbers’’ Geifman says, ‘‘you see that it will reduce the production cost of iron in the process by up to 20%.’’ Helios’ green steel technology is based on sodium as the reducing agent, a two-step process in which sodium is used to reduce first row transition metals (like iron), and in the second step, the by-product sodium oxides are dissociated to reclaim the sodium in metal form and keep it in a closed loop within the system.
Geifman feels the topic of so-called ‘green premiums’– the high costs associated with converting to sustainable production methods – is often ignored, particularly in the context of reaching the goal of net-zero by 2050. ‘‘All the green
Furnaces International is an English language journal dedicated to the production of furnaces. Circulated each quarter in March, June, September and December to our database of over 20,000 readers across the Aluminium, Glass, Furnaces and Steel industries, Furnaces International contains a digest of global news, events, and statistics as well as more detailed technical articles, company and country profiles, and regular regional economic briefings.
Aluminium International
Today (AIT) is the leading bi-monthly English language journal dedicated to all sectors and regions of the international aluminium manufacturing and processing industry.
Subscribe to the free weekly newsletter at aluminiumtoday.com
Glass International o ers readers the latest news from across the hollow, container, flat, and speciality glassmaking industry and is the o icial media partner for Glassman events. In addition to 10 English language issues per year, it is also published in French and Spanish.
Subscribe to the free weekly newsletter at glass-international.com
PUBLISHED BY OFFICIAL PUBLICATION FOR
www.furnaces-international.com
Steel Times International is an English language magazine containing a digest of global news, events and statistics, as well as detailed technical articles, company and country profiles, conference reports and regular regional economic briefings.
Subscribe to the free weekly newsletter at steeltimesint.com
solutions for iron making that we are aware of that are going to be running around the world, mostly in Sweden, but around the world, are going to increase the cost of production. This is a major issue because we all know the numbers. We all know that politicians are targeting 2050 to become carbon neutral. We all know that in order to make this happen way before 2050, the only viable way to do it is by providing an alternative that not only reduces emissions, but also gives a better competitive edge for those who will use it commercially, regardless of carbon emissions. So, when we approached this project and we did the economic analysis, we disregarded carbon emissions. We said, what if we were living in a world where no one cared about CO2 We wanted to make sure that even in that world, our technology will win. And, if that is your case, then I think you have a viable path to actually change the industry.’’
And what about the goal of 2050? Is that problematic in itself?
‘‘When someone says 2050’’, Geifman continues, ‘‘I hear it’s not my problem. It’s my kid’s problem’’.
We move onto the Helios process. According to Geifman, it’s a ‘direct reduction process, but opposed to using hydrogen, we are using a reducing agent that is fully reclaimed in a closed loop system. The only two things that we need to feed the system with is iron ore and energy, and the output is iron and oxygen. The reducing agent that we use is taking the oxygen from the ore, and then we have a process where we know how to break the oxygen from that producing agent. And we keep it in a closed loop; we emit the oxygen out of the system. The temperatures at which we do this reaction are much lower; the reaction happens below 400 degrees Celsius.’ Additionally, the Helios process does not require steelmakers to alter their energy infrastructure, as the
technology can be integrated into their existing infrastructure, which reduces cost and facilitates faster adoption, says the company, emitting only oxygen as a by-product (if a renewable energy source is used) making the whole process 100% carbon emissions-free.
There’s no denying the potential of the project. But the complexity of its delivery lies beyond sheer feats of engineering. One of the murkier areas of inter-planetary technology is the legislation, which is struggling to contend with the legally unfamiliar territory of mining and extracting the moon for resources. According to Geifman, it is currently ‘the wild west’ in terms of regulations. Humans have been mining the earth for thousands of years. Even with hundreds, if not thousands, of laws and limitations in place, it continues to be a hugely complex socio-political process – that has affected indigenous habitats, cultural sites, biodiversity, and led to human rights abuses, and conflict over resources. The moon, as an untapped source of materials, has all the potential to help us reach crucial decarbonization targets, but may also mirror the same issues we face on Earth – which can be reduced to who can lay claim to what, with what rights, and at what cost. ‘‘No-one has done this before,’’ Geifman says, in terms of extracting resources from the moon, ‘‘hopefully it will settle very quickly. There are some question marks, and uncertainty, but we’re all moving in the same direction’’.
And what about criticism?
‘‘I can understand it…., why should we spend so much money on establishing infrastructure on the moon and exploiting resources? I mean, did we not do enough here on earth? Why should we do this on other planetary bodies? But first of all, we don’t really spend that much on space exploration. The technologies that humanity is benefiting from the space industry and
from projects like going to the moon are insane. We would never ever think of how to do this process if we didn’t have that extreme frame of reference to try and do this on the moon. I’m pretty bullish on the idea that a lot of the technologies that will be required in order to solve our climate issues and sustainability issues will come from solutions that will be provided to establish infrastructure beyond earth because of that different frame of reference, that extreme environment, that requires it. And to have them on the moon, the moon is a desert. The only biospheres we should care about are biospheres where you have life; that’s my personal opinion. People are saying that we’re ruining nature. We are nature. We’re a part of nature thinking that we are apart from nature. I think that’s the flaw. If we want to keep life and to make it sustainable, let’s do the dirty work where there is no life – and the moon is the perfect place for this.’’
Geifman has a Star Wars book propped on the bookshelf behind him, as well as a foot tall toy space rocket. I ask him how, if the average human experience has little to no contact or interest in life outside of Earth, Helios can be understood – and even accepted as a company with a necessary incentive.
‘‘Think about it like this: babies who are born today will be just toddlers when humans will set foot on the moon again. And we’ll start establishing permanent infrastructure on the moon. They will grow up as teenagers when there are already bases on the moon. We have short lives, but for the next generation, most of what we’re talking about now will be trivial. And they will probably see it differently.’’
The biggest question, for Geifman, isn’t what limits us, but what we are able to do ‘for future generations; for our grandchildren’. Shoot for the moon, aim for the moon. �
“Think about it like this: babies who are born today will be just toddlers when humans will set foot on the moon again. And we’ll start establishing permanent infrastructure on the moon. They will grow up as teenagers when there are already bases on the moon. We have short lives, but for the next generation, most of what we’re talking about now will be trivial. And they will probably see it differently.”
Too many companies got caught up in the ‘early hype’ of digital transformation, says Joe Maczuzak*, leading to conservative views on its potential, but the results speak for themselves – as the uptake of industry 4.0 offers energy efficiency, increased sustainability, and even improved safety.
1. How are things going at ROVISYS? Is the steel industry keeping you busy?
The steel industry got hot in February 2021 and has been rolling ever since. Modernization investments in automation and projects in the information space have made up the bulk of our work since coming out of the COVID-19 slowdown.
2. What is your view on the current state of the global steel industry?
From our view we see the US steel industry busily updating its facilities. Energy efficiency and environmental improvement projects currently have priority. Somehow the industry continues to roll through the ongoing global geopolitical and economic uncertainties.
3. In which sector of the steel industry does ROVISYS mostly conduct its business?
Cokemaking, ironmaking, and steelmaking on the primary side are key for RoviSys. Our headquarters in the US Great Lakes Region is located near many integrated steel mills.
4. Where in the world are you busiest at present?
We are busiest in the US, but we provide solutions globally from our offices in Asia and Europe also.
5. Can you discuss any major steel contracts you are currently working on?
Without specifics, our current major steel projects include large-scale drives/PLC/ DCS/SCADA modernization projects in the cokemaking and ironmaking segments.
6. Where does ROVISYS stand on the aluminium versus steel argument?
Producers of both of these metals continuously innovate and improve their
products which is healthy competition that benefits us all. RoviSys works with customers in both metals industries, so we’re open-minded.
8. Hydrogen steelmaking appears to be the next big thing. What’s your view?
There is a long road ahead in steelmaking’s decarbonization transition, to fully realize the potential of hydrogen steelmaking and to build the required infrastructure. It is encouraging to see the journey has begun with significant investments in these processes and others.
9. In your dealings with steel producers, are you finding that they are looking to companies like ROVISYS to offer them solutions in terms of energy efficiency and sustainability? If so, what can you offer them?
Energy efficiency and sustainability projects are certainly top-of-mind for our customers. These types of projects often include analytics, IoT devices, historians, and/or machine learning.
7. What are your views on Industry 4.0 and steelmaking and how, if at all, is ROVISYS using it?
RoviSys assists customers with all aspects of industry 4.0, from road mapping, to design, to implementation, to organizational change management and deployment. We have a systematic approach to industry 4.0 that tackles each aspect of digitalization and building one project onto another to reach a true digital transformation.
We look at networking modernization, data infrastructure, data consolidation and warehousing, OEE/KPIs, visualization, MES, analytics, and AI to create a holistic strategy that’s tailored for each of our customers, ensuring the right priorities are put in place which keeps things running smoothly.
RoviSys offers all of these services, and we work closely with our vendor partners who provide the hardware and software tools for successful projects.
10. How quickly has the steel industry responded to ‘green politics’ and are they succeeding or fighting a losing battle?
Many readers will know that steel accounts for 8% of global GHG emissions, emitting at a rate of 1.8 tons CO2 per ton of steel. Innovative minds in the industry have solutions in development today that can reduce emissions; however, each technical solution requires supporting solutions to be viable.
These latter challenges may be more daunting than the technical. We all have a stake in this fight and its outcome.
11. Where does ROVISYS lead the field in terms of steel production technology?
RoviSys has a unique approach to industrial AI called Autonomous AI. It incorporates the best of existing machine learning with the most advanced techniques, including deep reinforcement learning. It typically leverages both historical data and simulation to provide significant improvements to existing processes –especially processes that currently have heavy operator involvement.
12. How do you view ROVISYS’s development over the short-tomedium term in relation to the global steel industry?
RoviSys’ investments in artificial intelligence, cyber security, and digital transformation consulting knowhow are complementing our core control and information systems expertise.
These investments benefit our customers as they modernize and take their operations to the next level.
13. Where do you see most innovation in terms of production technologies – primary, secondary or more downstream?
Right now, there are low-cost IoT devices which offer many new capabilities to downstream producers, for example, by
improving the ability to track and trace material through production in discrete processes in real time. At the other end, complex primary steelmaking processes will benefit from DRL artificial intelligence solutions by augmenting the knowledge the industry already possesses.
14. How optimistic are you for the global steel industry going forward and what challenges face global producers in the short-to-medium term?
We’re optimistic that in the short term, the steel industry will remain healthy and opportunities for investment will continue. However, our customers are approaching the short-to-medium term with caution.
15. What exhibitions and conferences will ROVISYS be attending in over the next six months?
RoviSys just presented at the AIST Digital Transformation Forum in Pittsburgh. We also regularly attend vendor conferences hosted by partners such as Schneider Electric, Rockwell, AVEVA, and SAS.
16. ROVISYS is headquartered in the US but what’s happening steel-wise in the country?
We see many projects related to improving OT connectivity and cyber security. Making process data available for use, securely, is
the first step in any successful digitization effort.
17. Apart from strong coffee, what keeps you awake at night?
Missed opportunities for digital transformation. Too many companies got caught up in the early hype with digital transformation, were sold a story by highpaid consultants, then had little to show for their investment.
This has made many companies too conservative, and stalled real grassroots digital transformation projects that could have a large positive impact on productivity and revenue.
18. If you possessed a superpower, how would you use it to improve the global steel industry?
No question, the answer would be to improve safety. By its nature, steel production is a dangerous process. We take the benefits of steel for granted, but visiting one of these plants shows you how violent the process is for human beings to shape raw materials into steel.
As much as possible, if we can reduce the danger to humans by improving automation, leveraging robotics, or using AI to minimize unsafe conditions, that would be a win for the industry. �
WOOD charcoal was, from the Iron Age to the 18th century, the only successful combined fuel and reductant for the extraction of iron from its ores. Although coal was recognised as early as Roman times as an alternative fuel to wood, or the hotter burning charcoal, attempts to employ it for the reduction of iron ore had little success. In Britain, patents(1) were granted to smelt with coal as early as 1611 to Sturtevant, and in 1613 to Rovenson, but with no evidence of success. Later, in 1622, Dudley took out a patent for the use of coal in the blast furnace. This followed the application of coal in copper and lead smelting and glass making. Dudley has the more credible claim for success having made changes to his furnace, and was fortunate in using low sulphur coal, and limestone as flux, from his residence in Staffordshire. Examination of residues of one of his furnaces at Himley, Staffordshire, showed that the slag contained coked coal, but whether this was from coking in the furnace, or it being charged to the furnace,
cannot be determined. The sulphur content of the slag was 1.2% suggesting the iron would be unsuitable for refining to bar iron in the charcoal hearths in use at this time, the major market for blast furnace iron. According to Dudley, his trials were terminated by rioters and lawsuits and his patent was not renewed in 1660. Nearly 50 years later, in 1709, Abraham Derby Ist was the first to make a commercial success of smelting with coal which he initially converted to coke. Having experience in using low sulphur coal from an earlier role as a malt maker, he recognised the value of the low sulphur Shropshire coals (0.500.55% S) taken from the upper strata. Also, his need was for an iron for casting to make thin-walled pots, previously made in expensive brass, and his high phosphorus iron produced a fluid metal ideal for such thin-walled casting which solidified to the more ductile grey iron.
A modest blast furnace producing 100 tonnes a year required about 36 hectares of woodland to supply sufficient charcoal.
The demand from refining forges was also high; while the finery hearth had to use charcoal, it was possible to use coal in the chafery hearth where the refined ‘loup’ of iron was reheated for consolidation under the hammer. In the chafery, the lower surface area of the metal reduced the risk of sulphur pick-up. Later, the Lancashire Hearth, popular in Sweden and for the tinplate industry in South Wales, provided an enclosed ‘oven’ for refining pig iron, making more efficient use of the charcoal required. It was not until the principle of the reverberatory furnace arrived with John Wood in 1761, that coal could be used as the fuel for refining since the fuel was kept separate from the iron, heat being transferred by ‘bouncing’ off the roof of the furnace. This was later developed into the puddling furnace by Cort in 1816.
Charcoal iron was still in demand for the forges and it would take many years for charcoal blast furnaces to be replaced by coke furnaces. Indeed, on the Weald of Sussex, coke was never used and the
*Consulting editor, Steel Times International and a member of the Historical Metallurgy Society
Charcoal holds an important place in steelmaking both today and in the past. It was used in the earliest versions of furnaces, and today offers a carbon neutral alternative as a substitute for coal injection in the blast furnace. By Dr T Smith*A traditional charcoal clamp The charcoal store (front left) dwarfs the Fourneau Saint-Michel at Saint Hubert, Belgium
last furnace did not close until 1813. In Cumbria, the Duddon furnace operated until 1871 using charcoal. The Backbarrow ironworks in Lancashire did not convert to coke until 1921. Elsewhere, in Sweden, where charcoal was readily available, some furnaces still used charcoal until the 1960s. Indeed, even today, charcoal blast furnaces operate in Brazil producing some 3Mt/yr using wood taken from Eucalyptus plantations – although evidence shows that some virgin wood from the Amazonian forests has found its way into charcoal production. Here, massive kilns that enable a lorry to back into them to discharge its load are used.
As late as 1864, John Percy, in his threevolume treatise ‘Metallurgy’(2) devotes 58 pages to the properties and manufacture of wood charcoal, with further pages on torrefied wood (‘white’ or ‘brown’ charcoal produced at a lower temperature) and on peat charcoal.
Percy summarises production using earth clamps, the general method of the day. In this case, mid-age wood (a coppicing cycle of 15-19 years was common) is used as the source, cut in winter when free of sap. This should be de-barked and air-dried and left for some months before charring. The best results are obtained before the wood is completely dry to slow down the
rate of charring which improves the yield and quality. Steam must be free to escape. Rotten or worm-eaten wood should not be used as the result is too friable for the blast furnace. Water-logged wood, such as from wood stacks not protected from rain, or timber floated down rivers for more than 10 days, should be avoided. The ground on which the clamp is built must be level and impervious to air to avoid too much air ingress which will consume part of the charcoal product. A layer of charcoal dust can make the base air-tight. A clay ground is unsuitable as fissures may form by shrinkage from the heat of the burn enabling ingress of air. On moist ground, a foundation of wood covered by soil should be made. The pile must be covered in fine soil and protected from wind by either a sheltered location or by erecting hurdles to prevent uneven burning. The wood consumed on lighting the clamp should be replaced with more wood or charcoal browns to fill in the gaps.
Charcoal, he states, should not be used in blast furnaces or forges immediately after burning, as it has been found to improve by keeping for at least several months. With the same charge of ore and flux in a blast furnace, the same quantity of freshly burnt charcoal was found to be less effective than charcoal which had been kept during two years well under cover. The workmen, as well as the masters, of the Catalan forges in the French Pyrenees, were of the opinion that it was desirable to leave charcoal ‘at rest’ for a while, even if in a slightly damp place, from the belief that after such treatment it supports the blast better and is less quickly consumed. Coppiced charcoal from younger wood transports better, producing less waste than charcoal made from split thick woods, but this is the reverse of the needs of the storehouse.
In the charcoal barn, charcoal in contact with walls or the ground may absorb saline matter and deteriorate. The waste of charcoal in the store-house from this and other causes is very variable, and has been estimated at 8 – 11%. Percy states he is at a loss as to why the quality of charcoal should improve on keeping.
Not addressed by Percy, however, is the risk of spontaneous combustion. Evidence of this is seen in some charcoal stores where fire has damaged the walls. To reduce the risk of fire, charcoal was stored in piles often in separate bunkers. This necessitated the charcoal store being the
largest building on the site.
The reason for debarking the wood prior to charring is partly because of a higher phosphorus content in the bark in certain woods such as fir. Also, oak bark was held in value for the leather tanning industry.
Charcoal is carbon neutral when burnt as it releases the carbon which the tree had absorbed from the atmosphere during growth. Because of this, the use of charcoal in certain modern steelmaking practices have been considered. In September 2021, worldsteel prepared a ‘Fact Sheet’ on the topic ‘Biomass in Steelmaking’. Tests have been made in Australia to substitute pulverised coal injection in the blast furnace with suitably charred wood waste. At Arcelor Mittal Ghent, the use of torrefied wood waste – produced at a lower temperature than traditional charcoal – has been undertaken. Two reactors have been built to produce 40kt/yr of ‘bio-coal’.
However, a major concern is the sustainable supply of wood waste in particular following an increasing demand for wood pellets as an alternative fuel for space heating and power generation. Worldsteel quote the conversion of four of the six generating units from coal to wood pellets at UK’s Drax power station. This now supplies 5% of the UK’s electricity and accounts for 10% of its renewable energy supply – attracting a Government subsidy so far amounting to £6bn(3). But, although waste wood is part of the supply, imported from Canada with associated transport emissions, the demand of 500 tons per day cannot be met without felling Canadian virgin forests as revealed in a BBC documentary(4). Hence, before reverting to charcoal as a modern bio-fuel, take a look at the biomass supply chain(5) to check if a supply is sustainable or is ‘greenwashing’.�
1 A History of Metallurgy by R F Tylecote p105
2 J Percy ‘Metallurgy The Art of Extracting Metals from Their Ores’ Vol 1 Introduction, Refractory Materials and Fuel’ pp 354-411 available as a Google scan at https://books. google.dk/books?id=nhZKAAAAMAAJ
3 https://grid.iamkate.com/
4 https://www.bbc.co.uk/news/scienceenvironment-63089348
5 www.worldbioenergy.org
Packed with information on the steel industry and continually updated with news for steel professionals, steeltimesint.com also features special articles and interviews with leading industry figures.