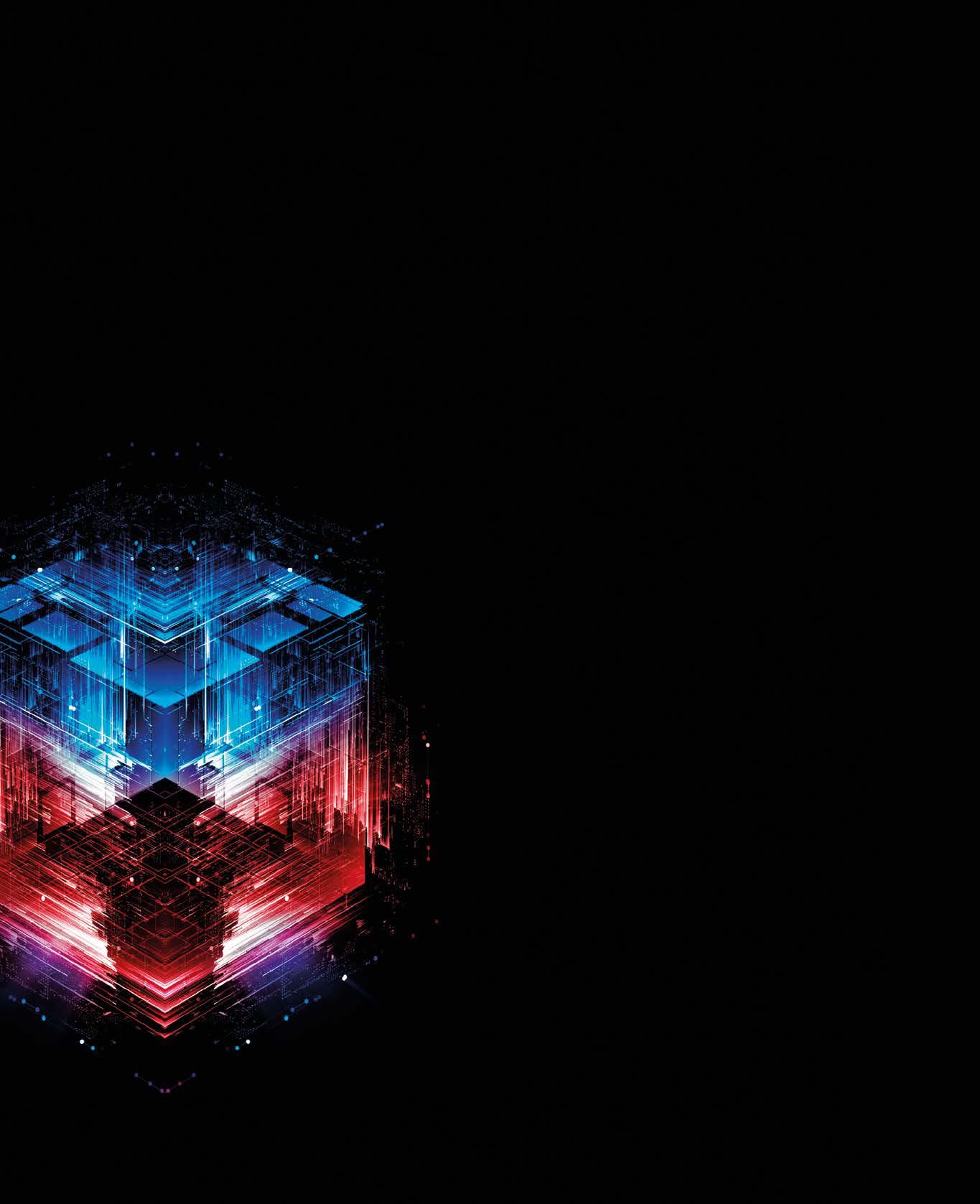

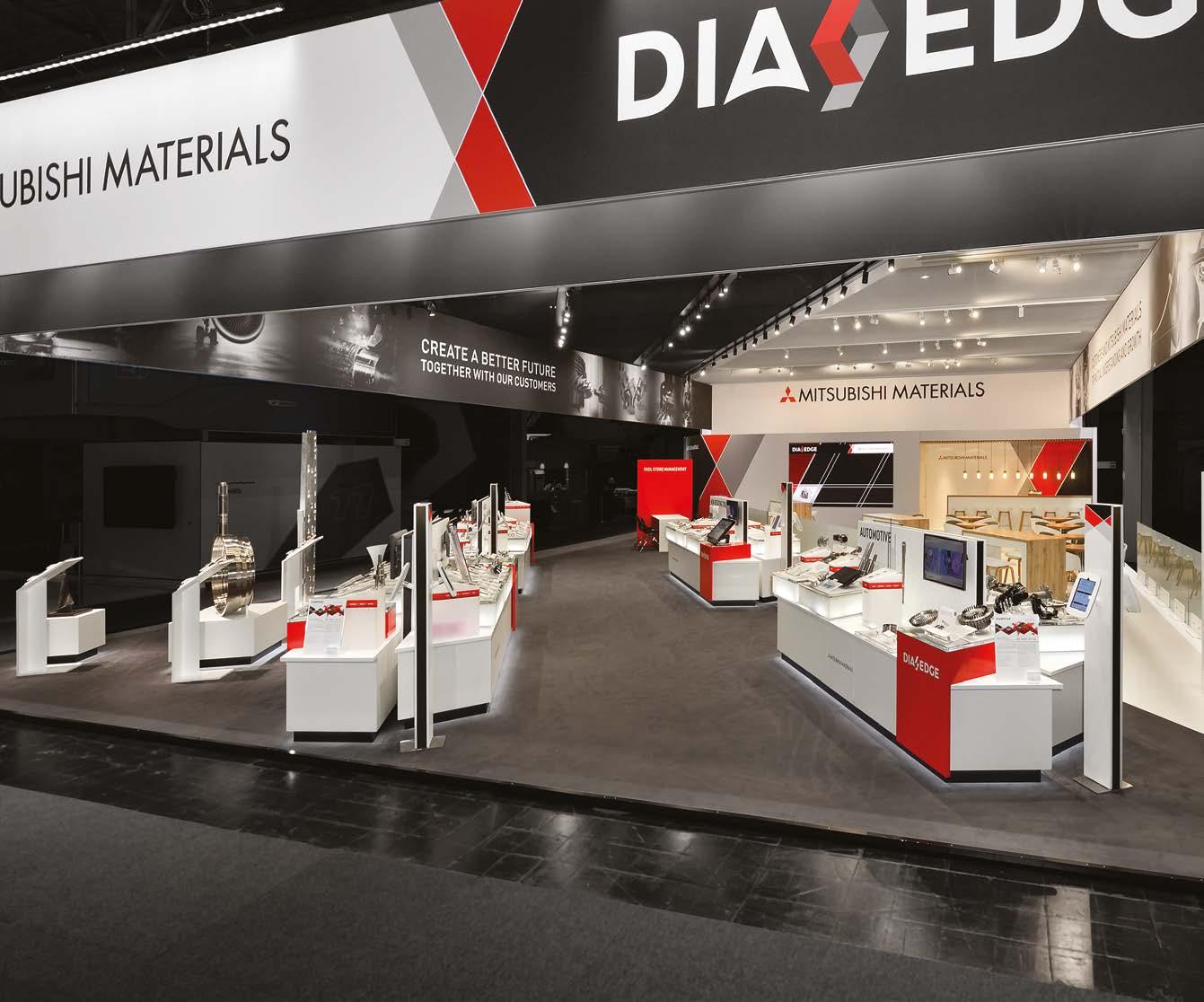
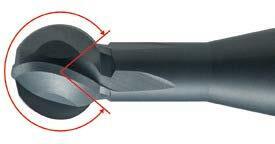
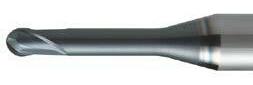
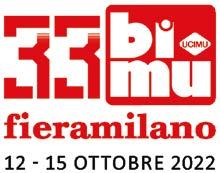
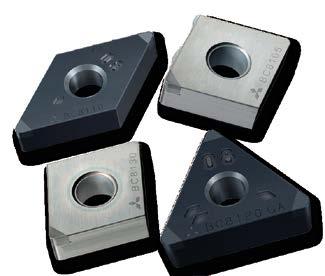
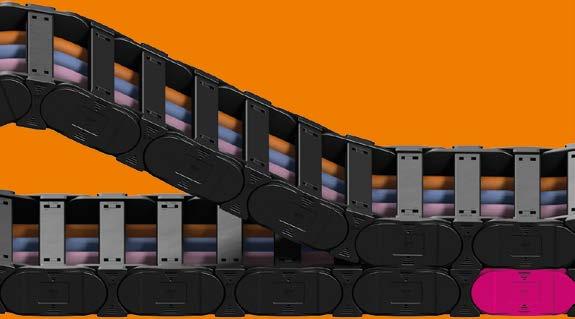
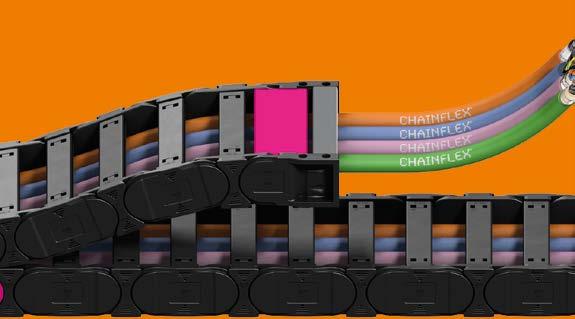
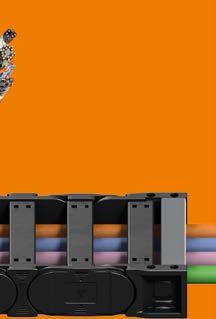
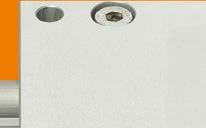


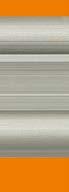
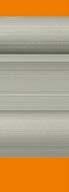

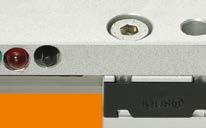






























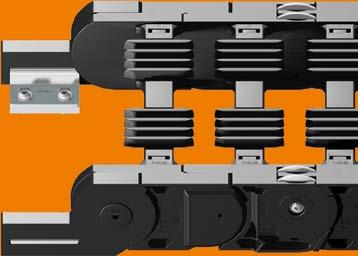
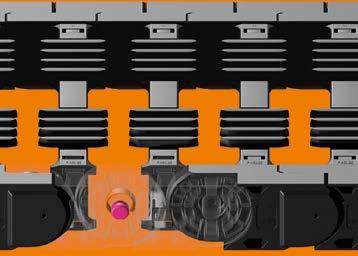
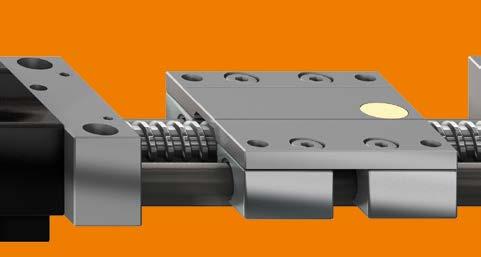
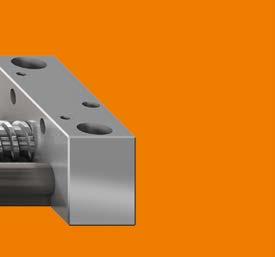








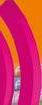

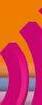
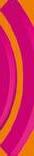
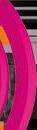

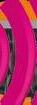

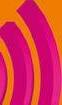


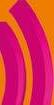

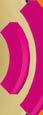
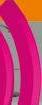

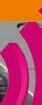

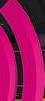





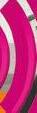

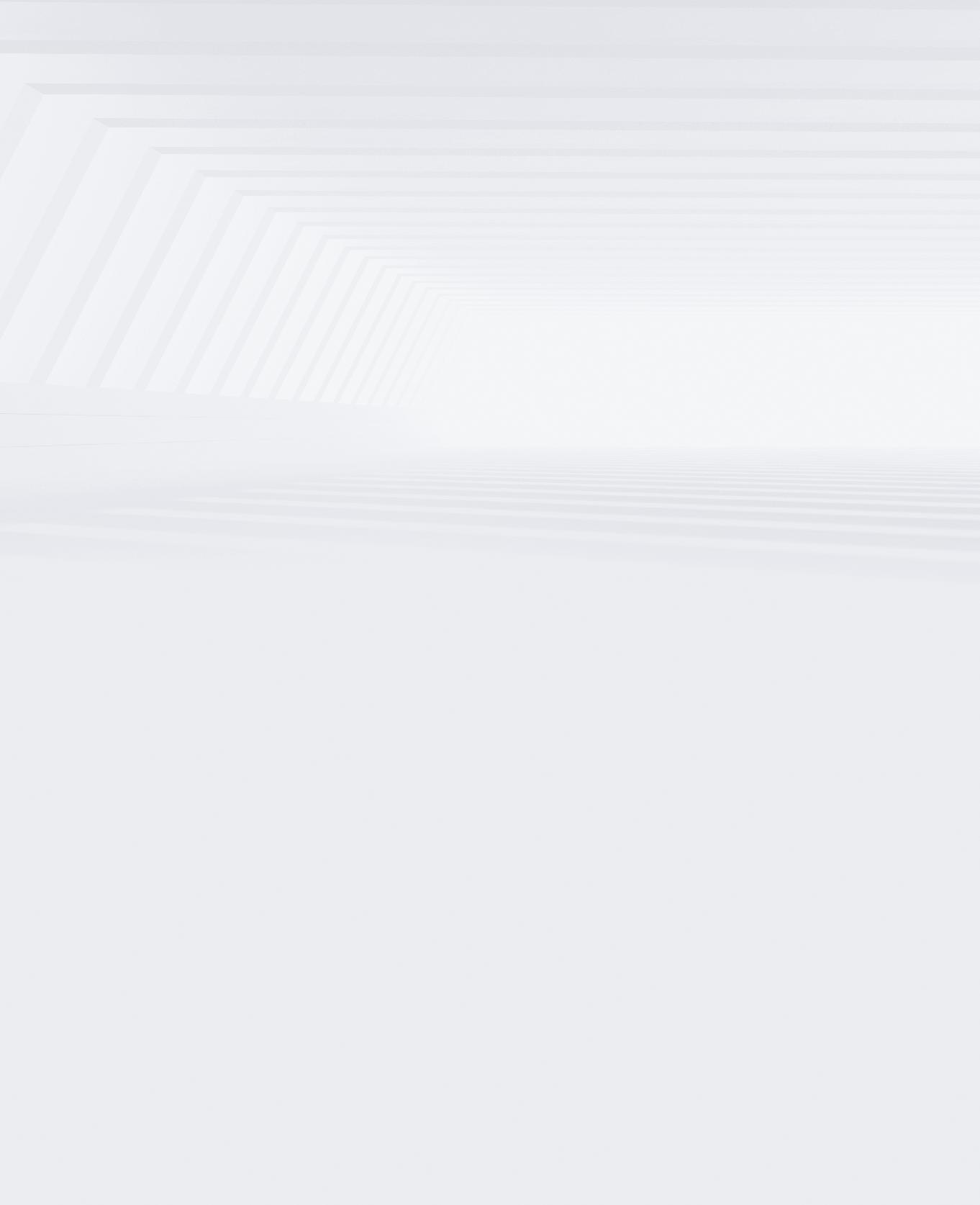

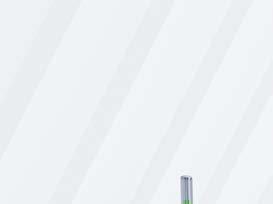
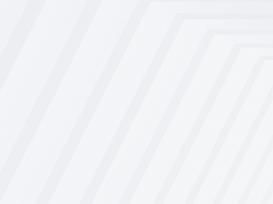




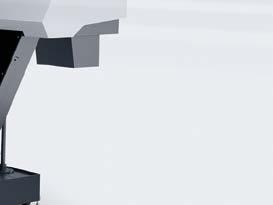



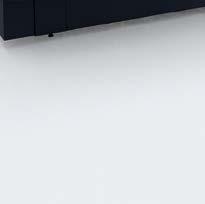
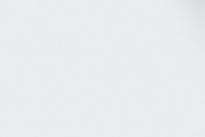

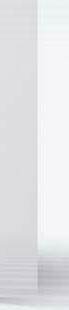
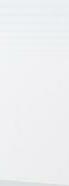



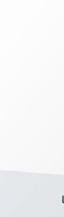
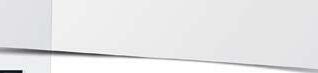
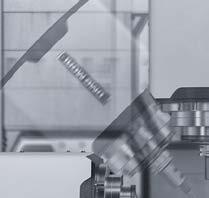
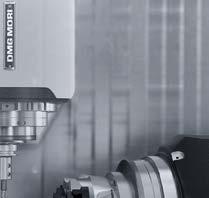





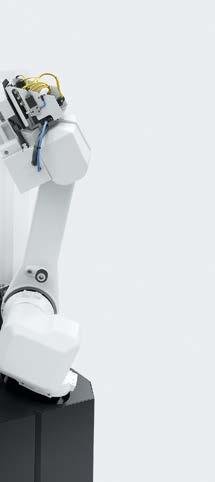
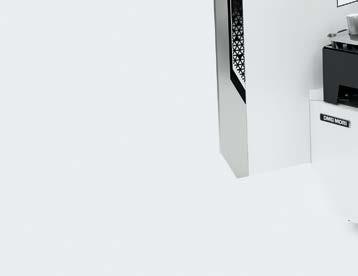

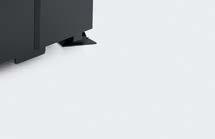



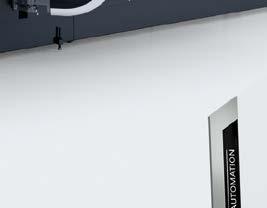




PParlerò anch’io di energia? Si! ma non quella che ci si aspetta. Lascio a voci più autorevoli e competenti affrontare le problematiche di cui siamo quotidianamente attori, spettatori o semplici lettori e che stanno nuovamente mettendo a dura prova l’equilibrio mondiale.
Parto dalla definizione fornita dall’enciclopedia Treccani: energia: capacità che un corpo o un sistema di corpi ha di compiere lavoro. So che rappresenta forse un piccolo volo pindarico ma, questa facoltà, mi ha fatto venire in mente l’energia espressa dalla robotica. Ho pensato a come robot industriali pesanti, robot collaborativi, manipolatori mobili, esoscheletri, macchine autonome o interagenti con l’operatore, riescano a portare energia all’interno di un processo produttivo, nei luoghi di lavoro, nelle case, negli ospedali, nella vita di tutti giorni.
Suggestioni e spunti personali a parte, grazie alla ricerca e sviluppo e alle applicazioni offerte dal mercato, da diversi decenni, i robot sono una tecnologia capace di aggiungersi all’individuo o sostituirsi ad esso in lavori usuranti o non accessibili (es.la movimentazione di parti pesanti ed incandescenti). Oltre ad offrire un ventaglio di abilità operative (es. manipolare, fresare, saldare, puntare, pallettizzare, lucidare), oggi la robotica, è in grado di dare energia a chi non ne ha abbastanza o non ne ha più, e anche, grazie all’ integrazione con telecamere e sensori, vedere e percepire dove, quando e quanta ne serve.
Parallelamente lo sviluppo della cultura e dell’utilizzo di nuove tecnologie robotiche a supporto dell’uomo da un punto di vista
cognitivo e fisico, hanno ridato dignità e valore alle persone sia come risorse produttive che come individui. Il concetto di “cognitive automation” si sta facendo strada portando a nuovi asset aziendali. Ambienti pensati per combinare la versatilità e le doti del ragionamento umano (attività ad alto valore aggiunto) a cobot progettati per essere “user friendly” e garantire la massima sicurezza o integrati alla ripetibilità delle azioni dei robot comandati dai più evoluti algoritmi.
Un presente in cui investire certamente, ma senza dimenticarci che, come scritto in un recente report dell’Agenzia europea per la sicurezza e la salute sul lavoro (EU-OSHA), “per favorire una interazione più naturale tra robot e persone è fondamentale” definire nuovamente ruoli e compiti dell’operatore; utilizzare una chiara e diretta comunicazione delle novità tecnologiche per avere il sostegno della forza lavoro; formare e aggiornare il personale e gli utenti per evitare dequalificazione o perdita delle competenze acquisite. C’è ancora tanto da costruire applicare e migliorare; occorrono visione, risorse e concretezza e…tanta tanta energia umana. chiara.tagliaferri@cnr.it
dell’industria aerospaziale
Macchine altamente produttive e flessibili
AXISET check-up, il sistema Renishaw per le macchine mutitask
I software per l’ottimizzazione di scorte e profitti
Soraluce, soluzioni multitasking “all in one”
S36, tecnologia di rettifica all’avanguardia per un ottimo rapporto qualità/prezzo
Index G320: il centro di tornitura e fresatura per pezzi di medie dimensioni
Multiswiss qualità di lavorazione e produttività senza pari
utensili prodotti ogni mese: ciascuno sottoposto a 3 controlli qualità, ciascuno perfetto. Una leadership costruita con passione, maschio dopo maschio, dal 1923.
Il Consiglio Generale di AsstelAssotelecomunicazioni, associazione di rappresentanza industriale della filiera delle Telecomunicazioni in Italia, ha nominato, su proposta del Presidente Massimo Sarmi, Andrea Missori, AD Ericsson Telecomunicazioni, Vice Presidente dell’Associazione.
Completano la composizione della squadra presidenza di Asstel i Vice Presidenti: Andrea Antonelli Presidente Almaviva Contact, Aldo Bisio AD Vodafone Italia, Alberto Calcagno AD Fastweb, Gianluca Corti AD Wind Tre, Luigi De Vecchis Presidente Huawei Italia, Pietro Labriola AD e Direttore Generale TIM, Mario Rossetti AD Open Fiber, Salvatore Turrisi Presidente e AD Sielte.
Il 2022 riserva grandi novità per LOVATO Electric. Il raggiungimento dell’importante traguardo dei 100 anni non è il solo evento di grande importanza. Il lancio del nuovo sito internet è sicuramente tra i principali appuntamenti. Totalmente nuovo e con un look moderno, il nuovo sito nasce dall’esigenza di rendere l’esperienza di navigazione ancora più positiva. Visto il numero elevato di prodotti offerti, il nuovo sito permette di identificare in modo facile ed intuitivo il prodotto desiderato. È possibile cercare i prodotti per codice, descrizione, caratteristiche tecniche, oppure tramite dei filtri che, con la logica di un configuratore, consentono di ottenere un unico risultato.
Identificato il prodotto ecco che si accede alla nuova scheda prodotto: una pagina semplice e chiara, ma ricchissima di contenuti. All’interno, infatti, è presente tutto quello che riguarda il prodotto: immagini (comprese panoramiche a 360 gradi), documentazione tecnica, disegni CAD 2D e 3D, certificazioni, etc. Ci sono anche collegamenti a video tutorial, alle FAQ e ai prodotti correlati.
Anche la parte istituzionale è stata completamente ripensata e resa più completa e facilmente fruibile: la sezione Hub Documentazione, ad esempio, è un archivio completo di tutta la documentazione tecnica disponibile. Dalla homepage è possibile prendere visione dei prodotti in evidenza e delle notizie corporate più recenti, comprese le iniziative dell’azienda.
Utile è anche il collegamento diretto dalla homepage ai siti dedicati alla formazione, all’energy management.
La richiesta di assistenza tecnica e commerciale è stata migliorata e semplificata grazie a moduli ben strutturati. Responsive e mobile friendly, il sito LOVATO Electric è disponibile alla consultazione da qualsiasi dispositivo digitale sia desktop che mobile (smartphone o tablet).
Il nuovo sito è stato un progetto imponente che ha coinvolto tutte le 15 filiali del gruppo; è stato tradotto in 12 lingue ed è stato personalizzato per ciascun mercato.
La nuova sede è stata progettata per favorire la collaborazione e rispondere alle esigenze di un mondo del lavoro in evoluzione.
La filiale italiana di Mitsubishi Electric ha inaugurato i nuovi uffici pensati per supportare al meglio le attività lavorative delle diverse business unit e le nuove modalità di collaborazione.
Il nuovo building, dal nome MIRAI, che in giapponese significa futuro, è un edificio moderno e all’avanguardia all’interno dell’Energy Park di Vimercate, già sede di altre aziende innovative e situato in una posizione strategica rispetto alle grandi arterie di comunicazione del Nord. Il building ha la certificazione di efficienza energetica e impronta ecologica “LEED Core and Shell”.
“L’apertura della nuova sede di Mitsubishi Electric rientra in un’ampia strategia di sviluppo della nostra azienda in Europa e coinvolge l’Italia quale importante hub dell’innovazione”, afferma Shunji Kurita,
Presidente e CEO di Mitsubishi Electric Europe, che è intervenuto per l’occasione.
Il piano terra del nuovo edificio è quasi interamente dedicato allo Showroom. Si accede a quest’area passando attraverso un
area è inoltre dedicata a laboratori e training room, in grado di ospitare oltre 80 persone.
suggestivo portale dove gli ospiti vengono accolti nel “mondo Mitsubishi Electric” grazie alla proiezione di contenuti istituzionali e storici per poi entrare nell’area espositiva altamente moderna e tecnologica in cui poter visionare i prodotti delle diverse aree di competenza: Climatizzazione, Factory Automation, Automotive e Semiconduttori. Un’ampia
Gli interni dell’edificio sono stati progettati da DEGW, con la collaborazione di FUD, brand del Gruppo Lombardini22 specializzato in grafica e comunicazione visiva. Fulcro della progettazione è stata la distribuzione flessibile e funzionale degli spazi, disegnati sulla base delle attività lavorative. Gli open space, concepiti per incoraggiare la collaborazione e l’interazione tra colleghi e collaboratori, sono affiancati da un ricco menu di supporti, che favoriscono privacy e concentrazione. Insieme compongono un ambiente attrattivo, pratico e confortevole, innovativo e rilassato, grazie anche all’alternarsi in modo fluido di tematiche istituzionali ed evocative e suggestioni italiane e giapponesi. Grande attenzione è stata posta ai temi della sostenibilità, del comfort luminoso, acustico, climatico e, in prospettiva futura, della facile manutenzione.
OML, alla BIMU di Milano (PAD. 9 – STAND C32), avrà il piacere di presentare a tutti i visitatori il nuovo catalogo generale A5 già disponibile sul sito www.omlspa.it
In questo catalogo di 640 pagine, sono raccolti tutti i prodotti con l’obbiettivo di dare alla clientela uno strumento di consultazione efficace e unico nel suo genere. 640 pagine di prodotti innovativi adatti a qualsiasi macchina utensile di fresatura (3 assi, 5assi, orizzontali) ma anche compatibili con l’industria 4.0 e conseguentemente all’automazione. Siete tutti invitati a ritirare la vostra copia alla BIMU!
Terranova Instruments conferma la partecipazione a ADIPEC che si terrà ad Abu Dhabi dal 31 ottobre al 3 novembre prossimo. Ospitato dall’Abu Dhabi National Oil Company (ADNOC), ADIPEC è l’incontro più influente al mondo per i professionisti del settore energetico.
ADIPEC 2022 accelererà la transizione energetica, sbloccherà il valore reale in un futuro decarbonizzato, presenterà tecnologie rivoluzionarie ed esplorerà strategie e soluzioni attuabili alle sfide e alle opportunità create dalle complesse dinamiche del mercato energetico globale.
Terranova Instruments, leader nel settore della strumentazione di processo con gli storici marchi Valcom®, Spriano® e Mec-Rela® partecipa alla manifestazione insieme all’acquisita Tecnomatic® presentando i seguenti prodotti:
- trasmettitori di pressione, livello e temperatura per applicazioni onshore e offshore
- interruttori di livello digitali con sistema di autocalibrazione
- soluzioni per la misura di portata multifase
- misuratori di portata (Venturi, Orifizi, Annubar, Dischi calibrati)
- misuratori di nebbia d’olio in atmosfera
Terranova e Tecnomatic Flow Elements ad ADIPEC: stand CN48
Cella pronta all'uso per la misura e l'analisi automatizzate di componenti piccoli e complessi
Compatta e portatile. Veloce e precisa. Posizionamento del sensore controllato dal robot nel modulo VMR Soluzione innovativa per il controllo automatizzato di qualtà e processi
Il 30 agosto Nidec Corporation ha firmato a Kyoto (Giappone) un accordo di joint-venture con FREYR Battery Norway AS, società norvegese che produce batterie semi-solide agli ioni di litio con una tecnologia innovativa in termini di qualità e processo produttivo, utilizzando esclusivamente energia idroelettrica rinnovabile pulita disponibile in loco.
Gli azionisti della joint-venture saranno Nidec per il 66,7% e FREYR per il 33,3%. La sede centrale sarà ubicata a Oslo (Norvegia).
Le soluzioni di accumulo di energia a batteria (“BESS”, Battery Energy Storage Solution) di Nidec forniscono alla rete servizi che consentono di accelerare l’adozione della generazione di energia rinnovabile, contribuendo alla realizzazione di una società carbon neutral. FREYR produrrà batterie semi-solide agli ioni di litio ecocompatibili utilizzando il 100% di energia rinnovabile, grazie a un contratto ad hoc per l’acquisto di energia con Statkraft (leader europeo per la produzione di energia rinnovabile) basato sull’uso esclusivo di energia idroelettrica. La partnership con FREYR assicurerà un approvvigionamento stabile di batterie semi-solide agli ioni di litio, pulite e competitive per le soluzioni BESS di Nidec. Ciò contribuirà a una riduzione significativa delle emissioni di CO2 nel corso dell’intero processo, dalla produzione delle batterie all’utilizzo delle soluzioni BESS da parte dei clienti.
A fronte della joint-venture, Nidec svilupperà, produrrà e venderà moduli e soluzioni per blocchi di batterie a basse emissioni di CO2 altamente competitivi per applicazioni di sistemi di accumulo di energia per il settore industriale e l’ambito utility.
Nel quadro dell’accordo, tra il 2025 e il 2030 FREYR fornirà alla joint-venture celle per 38 GWh, con l’opzione di aumentare il volume a 50 GWh nel corso dello stesso periodo e la possibilità di ulteriori incrementi dopo il 2030.
L’obiettivo della partnership sancita dalla joint-venture è quello di diventare un fornitore leader a livello globale di prodotti di accumulo di energia a batteria su scala utility, sfruttando l’innovativa tecnologia delle batterie a bassa emissione di carbonio di FREYR e la posizione leader di Nidec nei sistemi di accumulo di energia su scala utility.
“Attraverso questa alleanza strategica, forniremo al mondo tecnologie innovative per la gestione delle batterie di accumulo e dell’energia, contribuendo alla promozione dell’energia rinnovabile e alla realizzazione di una società decarbonizzata. Inoltre, con la conclusione dell’accordo di joint-venture, Nidec intende rafforzare la partnership strategica con FREYR e punta a una futura, ulteriore espansione del business delle soluzioni BESS”, ha dichiarato Laurent Demortier, Presidente della divisione Energy & Infrastructure di Nidec. Nidec ha fissato l’obiettivo strategico nel medio termine, “Visione 2025”, e mira a raggiungere la neutralità carbonica entro il 2040. In particolare, Nidec contribuirà alla decarbonizzazione utilizzando i propri prodotti e ridurrà le emissioni di CO2 da attività aziendali.
L’accordo di joint-venture sarà favorevole per entrambi. Nidec continuerà a favorire la realizzazione di una società carbon neutral attraverso investimenti proattivi in misure ambientali.
Gefran partecipa al più importante evento del settore globale delle materie plastiche, in scena a Düsseldorf dal 19 al 26 ottobre. Fil rouge dello stand (Pad. 10, Stand F09) l’elevato know how di processo che contraddistingue e posiziona l’Azienda in qualità di Partner di riferimento per OEM, system integrator ed End User. Un’offerta che si declina in prodotti innovativi e, grazie a Gefran Soluzioni, nella progettazione e realizzazione di sistemi di automazione, quadri elettrici e software dedicati al mondo della plastica.
“Gefran partecipa all’edizione 2022 del K con grande entusiasmo, in virtù di quanto il Gruppo ha saputo realizzare, in controtendenza rispetto ad uno scenario di mercato estremamente complesso” afferma Marcello Perini, Amministratore delegato di Gefran, che prosegue “La fiera sarà l’occasione per rinnovare a Clienti e Partner il nostro impegno nell’essere protagonisti dell’evoluzione tecnologica grazie alla profonda conoscenza delle principali applicazioni nel campo della plastica, maturata in oltre 50 anni di esperienza nel settore. Eccellenza di prodotto, innovazione continua e utilizzo di standard di comunicazione aperti sono alla base della nostra offerta e rappresentano la chiave per cogliere le tante opportunità derivanti dalla trasformazione digitale.” conclude Perini. Sensori intelligenti, prodotti e soluzioni di automazione saranno al centro delle novità in presentazione.
informazione. È un progetto di trasformazione digitale che ci aiuta a trasferire valore eliminando le distanze e i confini geografici.”
Èsempre più digitale l’esperienza che SMC Italia offre ai propri clienti. Il nuovo progetto digital è il Virtual Tour dello Showroom e dell’Application Center, che permette a utenti da tutto il mondo di accedere virtualmente a uno spazio espositivo che occupa una superficie di 1200 m2 presso la sede di Brugherio.
“Abbiamo voluto sperimentare soluzioni alternative per permettere ai clienti di vedere le tecnologie e le soluzioni a marchio SMC per i diversi settori applicativi, in cui l’azienda opera, anche senza doversi spostare dal proprio ufficio o dal proprio Paese - spiega Andrea Trifone, marketing manager di SMC Italia. - Questo progetto ci consente di creare un percorso efficace anche a distanza, per rimanere vicini ai nostri clienti con un semplice tablet, smartphone o computer e accedere così a ogni tipo di
L’obiettivo di questo progetto è dotare l’azienda di uno strumento in grado di innovare la customer experience e rendere ogni prodotto, ogni novità, ogni ambiente interattivo e fruibile da tutti i device, e al quale è possibile accedere in totale autonomia sulla base dei propri bisogni e necessità.
Il virtual tour si presenta come uno spazio innovativo sempre aperto e pronto ad accogliere i visitatori, ideale per stabilire nuove modalità di interazione tra cliente e azienda.
È possibile muoversi all’interno della sede o utilizzare i pratici menu per spostarsi velocemente da un ambiente all’altro e per scegliere i contenuti da visionare che più interessano.
L’esperienza di navigazione consente di percorrere i diversi spazi dello Showroom e dell’Application Center e accedere ai numerosi touch-point (punti di interesse) per approfondire la conoscenza dei vari prodotti e delle soluzioni offerte.
Cliccando su ciascun punto di interesse è possibile visionare i video tutorial, in cui gli esperti di SMC Italia illustrano dettagli tecnici e funzionalità delle varie soluzioni applicate, consultare la documentazione
tecnica, le informazioni commerciali, approfondire attraverso link interattivi. Nello Showroom sono presenti soluzioni e tecnologie per diversi settori applicativi: dal trattamento aria alla strumentazione, dalle valvole agli attuatori per l’industria Automobilistica, Elettronica, Alimentare e Life Science.
Nell’Application Center è possibile navigare tra tre aree tematichePneumatic Solutions, Fluid Control e Mechatronic&Network - e apprezzare l’ampia gamma di automazione pneumatica e le tecnologie complementari quali thermo-products, valves automation, mechatronic e industrial network. Un’area dove incontrare Tecnici qualificati in grado di identificare la migliore soluzione per ogni necessità applicativa.
Reale e virtuale si fondono così in un ambiente unico, intuitivo e in continua evoluzione grazie a nuovi contenuti tecnici, ai video e alle soluzioni presentate.
L’ingresso nel Virtual Tour è semplice e immediato: basta semplicemente iscriversi a questo link https://www.smc.eu/it-it/smcitalia/virtual-tour-smc-italia per accedere alla piattaforma.
Da settembre 2022 FasThink entra nel partenariato del Competence Center.
“MADE Competence center è un partenariato di aziende, università ed enti pubblici, che collaborano con un unico obiettivo: trasferire competenze e conoscenze alle industrie manufatturiere italiane, specialmente al tessuto delle PMI. Da settembre diamo il benvenuto tra i nostri partner a FasThink, una realtà che negli ultimi anni ha saputo affermarsi sul mercato grazie alla qualità dei propri prodotti e servizi” – commenta il Prof. Taisch presidente di MADE - Competence Center “Le soluzioni di FasThink sono già presenti nel competence center, nei dimostratori di Lean Manufacturing e Logistica 4.0, ma soprattutto l’azienda ha collaborato a interconnettere diversi sistemi industriali tra loro creando un sistema fabbrica intelligente.
Ora, con la partecipazione diretta di FasThink nel Compentence Center, queste tecnologie potranno
Industria 4.0
MADE Competence Center Industria 4.0 è un ecosistema che propone un modello di fabbrica digitale a supporto delle imprese manifatturiere che vogliono intraprendere progetti di innovazione in ottica di Industria 4.0. MADE mette a disposizione delle aziende, in particolare delle piccole e medie imprese, un ampio panorama di conoscenze, metodologie e strumenti con focus sulle tecnologie digitali, che spaziano dalla progettazione all’ingegnerizzazione, dal controllo della produzione, fino alla gestione del termine del ciclo di vita del prodotto.
Le aziende che si rivolgono a MADE hanno la possibilità di confrontarsi direttamente con l’innovazione e di comprendere, anche “toccando con mano”, come le soluzioni attualmente disponibili sul mercato possano essere impiegate per migliorare la loro competitività.
Maggiori informazioni su: www. made-cc.eu
essere ulteriormente potenziate in collaborazione con gli altri partner che contribuiscono al dimostratore, aumentando così le competenze a disposizione del centro per la realizzazione dei progetti di trasferimento tecnologico”.
Da oltre dieci anni FasThink progetta, realizza componenti e sistemi dedicati all’identificazione automatica, alla tracciabilità e all’automazione aziendale aiutando le aziende nella trasformazione digitale dei processi.
Opera nei mercati dell’industria manifatturiera: automotive, alimentare e farmaceutica, nei settori della produzione, della logistica e dei servizi.
“Per FasThink partecipare al MADE Competence Center è una ottima opportunità, perché ci consente di dimostrare alle aziende ciò che è possibile fare a livello di integrazione di Industria 4.0” esordisce Marco Marella, General Manager FasThink.
“Non solo parole o presentazioni, ma risultati misurabili, progetti tramite i quali siamo in grado di dimostrare come
un processo possa essere migliorato grazie alle tecnologie dell’Industria 4.0 e grazie all’integrazione con i sistemi gestionali in essere.
Oggi le aziende hanno la grande opportunità di sfruttare la trasformazione digitale per migliorare i propri processi. Aziende come FasThink mettono a disposizione il proprio know-how per le realtà italiane dando loro la possibilità di migliorare i propri processi, introducendo automazione e integrazione di tecnologie. Crediamo che, all’interno del sistema del Competence Center, questo processo possa accelerare”.
Da sinistra, Augusto De Castro, Direttore Generale MADE Competence Center Industria 4.0 e Marco Marella, General Manager FasThink Marco Taisch Presidente di MADE Competence Center Industria 4.0Lo studio rivela inoltre che spesso vengono presi più panni del necessario per evitare troppe interruzioni. Per aiutare le aziende a combattere gli sprechi, Tork ha creato il calcolatore gratuito degli sprechi Tork Motion, che consente alle aziende di misurare l’impatto di un posizionamento inefficace dei panni per la pulizia.
La riduzione degli sprechi per aumentare la produttività è un principio fondamentale della Lean Manufacturing: quell’insieme di metodi e strumenti per portare l’azienda verso un’organizzazione efficiente che consenta di produrre ottimizzando le risorse. Per comprendere meglio come migliorare l’efficienza Tork, un marchio Essity, ha condotto una ricerca* nei reparti di produzione. I risultati mostrano che il posizionamento dei panni, se non ottimizzato, può generare sprechi di tempo e di prodotto, oltre a causare stress tra i lavoratori.
La ricerca mostra che:
- Il 44% dei lavoratori interrompe il lavoro almeno 20 volte durante la giornata per procurarsi o smaltire i panni.
- Il 74% degli addetti prende più panni di quelli necessari, per evitare di dover andare a prenderne altri.
- Il 69% dei lavoratori dichiara di essere
stressato se viene interrotto nel suo lavoro quando ha molto da fare.
- Il 90% dei lavoratori concorda che avere Dispenser di panni industriali robusti e professionali a portata di mano, supporterebbe la pulizia, l’efficienza e la loro soddisfazione.
La soluzione consiste nel posizionare i panni sulla postazione di lavoro, in modo che gli operatori delle macchine non debbano percorrere alcuna distanza per prenderli. Ma poiché gli ambienti di produzione sono vari, può essere difficile trovare una soluzione adatta a ogni azienda.
Ecco perché i dispenser Tork Performance® sono stati progettati con una serie di opzioni di montaggio uniche e flessibili, che consentono di posizionarli dove sono più necessari, a portata di mano dell’operatore.
Questa caratteristica progettuale elimina efficacemente la causa principale degli spostamenti inutili e degli sprechi di materiale evidenziati dallo studio.
“Grazie alla nostra conoscenza dell’ambiente produttivo, siamo in grado non solo di aiutare le aziende a identificare nuove fonti di spreco, ma anche di fornire una soluzione al problema. I nostri prodotti
possono aiutare le aziende a migliorare continuamente riducendo gli sprechi di tempo e di prodotto”, ci spiega Riccardo Trionfera, Direttore Commerciale di Essity Professional Hygiene.
Un nuovo strumento di facile utilizzo: il calcolatore dello spreco di tempo per gli spostamenti Nell’intento di sostenere i clienti nella loro ricerca di riduzione degli sprechi, Tork ha sviluppato un nuovo strumento gratuito di facile utilizzo: il Calcolatore degli sprechi. Questo strumento basato sul web consentirà alle aziende di comprendere rapidamente quanto il posizionamento dei dispenser incida realmente sul lavoro quotidiano degli operatori.
Per provare Tork Calcolatore di movimentazione improduttiva click qui https://www.tork.it/la-tua-attivita/ soluzioni/panoramica/produzione/ riduzione-deirifiuti/Calcolatoremovimentazione-improduttiva#calcolatore
Per saperne di più su come ridurre gli sprechi di tempo e di prodotto e per esplorare il sistema di erogazione Tork Performance, visitate il sito www.tork.it/ riduzionedeirifiuti
*Fonte: Ricerca Tork sugli operatori di macchine (Luglio 2019)
Gli armadi componibili della Linea RamBlock, offrono una vasta gamma di soluzioni applicabili in ambito di automazione industriale e della distribuzione di energia in bassa tensione. Efficienza, versatilità e modularità sono elementi distintivi dell’intera gamma che è stata progettata per facilitare le operazioni di installazione e manutenzione.
L’elevato grado di protezione IP55 e di resistenza meccanica garantiscono sicurezza e affidabilità per soddisfare ogni esigenza di applicazione.
Il nuovo Corporate Design è stato sviluppato dallo studio Martin et Karczinski di Monaco di Baviera, l’agenzia che si occupa di strategia, design e trasformazione del brand ed è specializzata nel tradurre concretamente l’identità di un’azienda attraverso le variabili del contenuto, della forma e del comportamento. Il Gruppo Mewa, terzo fornitore di servizi tessili in Europa, negli ultimi anni si è molto rafforzato a livello internazionale grazie alla crescita del mercato e della clientela. Come pioniere dell’economia circolare e del riutilizzo dei prodotti tessili, l’azienda utilizza il termine “Textilsharing” per ottenere una maggiore visibilità del marchio. In collaborazione con la società Martin et Karczinski di
Monaco di Baviera, specializzata nella gestione olistica del marchio, nel corporate design e nella trasformazione, l’identità aziendale è stata elaborata partendo dall’immagine dell’azienda come impresa familiare orientata ai valori e innovativa, pur rimanendo legata alla tradizione. Tutti gli elementi visibili del marchio, come il logo, il font aziendale, il colore e le immagini, sono stati completamente rivisitati e allineati all’identità legata ai valori, alla vision e alla mission. “Il mondo in cui operiamo è cambiato in modo radicale. E, con esso, siamo cambiati anche noi. È arrivato quindi il momento in cui ci è risultato chiaro che, parallelamente alla nostra strategia di brand awareness, si dovesse evolvere anche la nostra immagine, per garantire
la nostra capacità di orientarci al futuro”, commenta Michael Kümpfel, responsabile marketing e vendite di Mewa. Il gruppo Mewa è un’azienda familiare che vanta oltre cento anni di storia. La nuova strategia del marchio prevede anche di abbandonare la posizione di “campione nascosto” e di dare al marchio Mewa una visibilità autoconsapevole tra il pubblico. Michael Kümpfel: “Naturalmente siamo orgogliosi delle nostre radici, ma se abbiamo avuto successo negli ultimi cento anni è proprio perché non smettiamo mai di porci domande e di pensare oltre: cosa c’è di nuovo, dov’è il potenziale, di cosa hanno bisogno i mercati e i clienti, come sarà il mondo del lavoro di domani? Questo è ciò che vogliamo raccontare nella nostra
Il logo Mewa è stato graficamente ridotto all’essenzialebrand story. Peter Martin, fondatore e CEO di Martin et Karczinski, commenta così la nuova immagine Mewa: “ La forma esprime in modo ottimale il valore di un marchio. In questo caso siamo riusciti a collegare la storia di Mewa con il futuro e a rendere visibile la sua identità nel design”.
L’agenzia Martin et Karczinski ha ricevuto dalla direzione aziendale un incarico molto preciso per la nuova immagine: l’obiettivo della rivisitazione era disegnare un marchio in grado di conservare gli elementi essenziali, di essere sinonimo di crescita e allo stesso tempo di esprimere l’approccio ecologico dell’offerta di servizi di Mewa.
“Non abbiamo voluto reinterpretare radicalmente il marchio Mewa, ma elaborarlo ulteriormente permettendo di mantenere tangibili la sua tradizione e la
sua storia di successo. Allo stesso tempo per noi era importante esprimere anche nel design il marcato orientamento al futuro e la vocazione alla sostenibilità della Mewa”, dichiara Simon Maier-Rahmer, Direttore Creativo di Martin et Karczinski, che ha sviluppato la nuova immagine insieme al suo team. Il logo rappresenta un fiore, sinonimo di purezza e igiene, ambiente e sostenibilità e allude a un’idea di sviluppo, crescita, evoluzione e innovazione. Per esprimere questo mix di concetti, il segno figurativo è stato rivisitato e formalmente ridotto all’essenziale. Il nuovo fiore appare nobile e potente e diventa simbolo di crescita consapevole. Il nuovo lettering Mewa ricorda i fili incrociati, poiché le lettere “M” e “W” seguono una trama immaginaria nel loro allineamento, creando così una associazione ideale con i prodotti tessili, fonte del successo dell’azienda e caratterizzanti la stessa fino ai giorni nostri.
Mewa fornisce un servizio completo di gestione dei tessili aziendali dal 1908 ed è quindi considerata pioniera del Textilsharing. Oggi con 46 sedi è in grado di raggiungere tutta Europa: abbigliamento da lavoro e protettivo, panni per la pulizia, tappeti assorbiolio e zerbini e ne cura la gestione, la manutenzione, lo stoccaggio e la logistica. Inoltre, è possibile ordinare articoli sulla sicurezza sul lavoro. Mewa ha ricevuto numerosi riconoscimenti per il suo impegno verso la sostenibilità, per il suo agire responsabile e per la gestione del marchio. Nel 2021 l’azienda ha ottenuto da Confindustria in Italia il riconoscimento di “Best Performer dell’economia circolare” nella categoria Grandi Imprese di Servizi.
Mewa ha anche abbandonato i caratteri maiuscoli del nome, optando per il carattere maiuscolo solo per la lettera iniziale. “Le lettere maiuscole rappresentano l’acronimo del nome che il nostro fondatore Hermann Gebauer diede all’azienda nel 1908: Mechanische Weberei Altstadt”, spiega Michael Kümpfel: “Oggi, con 46 sedi internazionali, possiamo usare con orgoglio ‘Mewa’ come marchio e non più solo come acronimo”. Il nuovo font aziendale è stato sviluppato esclusivamente per Mewa in collaborazione con typemates. Anche in questo caso, l’azienda è rimasta fedele a sé stessa nel coniugare innovazione e tradizione: il font è infatti moderno, chiaro e preciso e il nome lo ricollega alle radici dell’azienda. Il nuovo carattere Mewa si chiama infatti come la famiglia fondatrice: “Gebauer”. Attualmente Mewa opera in 21 Paesi europei, ha un organico di 5.700 collaboratori e serve oltre 190.000 aziende clienti. Il fornitore di servizi in ambito B2B è sinonimo di soluzioni tessili sostenibili per le aziende ed è uno dei leader del settore nella gestione dei prodotti tessili. Più di un milione di dipendenti in Europa indossano indumenti professionali, protettivi o business forniti da Mewa e quasi tre milioni di persone utilizzano ogni giorno un prodotto Mewa per tenere pulite le macchine nei capannoni di produzione e nelle officine. Chi utilizza il servizio Mewa può contare su affidabilità, sicurezza e trasparenza.
Il carattere “Gebauer” è stato creato in esclusiva per MewaTRA TECNOLOGIE DIGITALI, FLESSIBILI E SOSTENIBILI PER LA PRODUZIONE DI DOMANIDAL 12 AL 15 OTTOBRE SCHUNK SARÀ IN SCENA 33.BI-MU di C.G.
L’evento, ospitato a Rho Fiera Milano, è stato scelto da SCHUNK Italia come vetrina privilegiata per mostrare gli ultimi sviluppi tecnologici: componenti digitali per l’asportazione truciolo e nuovi dispositivi di bloccaggio sostenibili ed efficienti. L’azienda si presenterà all’insegna del nuovo motto “Hand in hand for tomorrow”, fortemente orientato al futuro con la promessa di accompagnare mano nella mano clienti e partner nella produzione di domani.
L’industria meccanica sta attraversando una fase di grande transizione. La carenza latente di lavoratori qualificati, unitamente alle difficoltà legate alla supply chain, agli aspetti ambientali e ai conseguenti cambiamenti delle modalità di vendita, fanno emergere nuove esigenze. Qualche anno fa l’attenzione si concentrava
esclusivamente sulla precisione e sul risparmio di tempo, ora sono necessari approcci flessibili per poter processare piccoli lotti, o riattrezzare le macchine e configurare i dispositivi in modo più sostenibile e conveniente, con attenzione alle risorse. Alla BIMU SCHUNK, infatti, mostrerà le tecnologie per rendere i processi di asportazione più digitali, efficienti, flessibili e sostenibili.
Come fornitore di soluzioni applicative complete, SCHUNK intende offrire ora ancora più opzioni nel campo dell’asservimento macchina automatizzato. La serie di morse automatiche TANDEM3, dotate di sensori per monitoraggio integrati di serie, ha ora un modello aggiuntivo per il bloccaggio flessibile del pezzo: KRP3. Con questa nuova morsa potente e compatta,
anche i pezzi circolari possono ora essere bloccati automaticamente sia dall’esterno che dall’interno, in spazi relativamente ridotti. Come tutti i dispositivi di serraggio stazionario SCHUNK, può essere montata in modo rapido e semplice sui moduli del sistema di serraggio a punto zero VERO-S utilizzando le apposite piastre. La morsa
automatica è disponibile anche nelle versioni idraulica (KRH), a molla (KRF) ed elettrica (KRE).
Varietà nel serraggio del pezzo SCHUNK è impaziente di poter finalmente presentare dal vivo la versatilità senza precedenti e le caratteristiche di manutenzione ridotta del suo autocentrante a serraggio manuale ROTA-M flex 2+2. Il mandrino dispone di 4 griffe con compensazione 2+2, a corsa lunga. Che sia circolare, cubico o di forma irregolare, ROTA – M flex 2+2 consente di bloccare pezzi di geometrie differenti su centri di fresatura/tornitura con un solo dispositivo di serraggio. Le guide a tenuta garantiscono una forza di serraggio affidabile e lunghi intervalli di manutenzione.
Un altro dispositivo muli-tasking per la lavorazione di pezzi grezzi e finiti è stato ulteriormente sviluppato e ottimizzato: la nuova morsa manuale KONTEC KSC3 è protetta dalla corrosione grazie al corpo base in nichel. Il design ancora più piatto e ottimizzato, unitamente ad un’ampia varietà di ganasce offrono miriadi di
combinazioni. Il mandrino incapsulato e una posizione di pulizia preimpostata della ganascia contribuiscono a ridurre sensibilmente i costi di manutenzione.
Eccellenza e sostenibilità premiate Nello sviluppo dei suoi prodotti, SCHUNK si concentra su approcci che consentono di risparmiare risorse ed energia. L’autocentrante a cambio rapido ROTA THW3, premiato con il riconoscimento “iF Design Award”, consente set up brevi e intervalli di manutenzione estremamente lunghi. Gli sviluppatori del mandrino autocentrante hanno optato per una riduzione del peso, plus che riduce il fabbisogno energetico e consente accelerazioni e frenate della macchina molto più rapide.
Grazie alla tenuta stagna, risulta un prodotto sostenibile in quando riduce il consumo di lubrificante fino a 10 volte rispetto a mandrini autocentranti simili.
Anche il portautensile intelligente iTENDO² non passerà inosservato sullo stand SCHUNK. Questo strumento elabora dati in tempo reale e rileva l’usura dell’utensile.
Oltre a un’affidabilità di processo elevata nella lavorazione, il portautensile intelligente garantisce una maggiore durata dell’utensile e un minor numero di scarti. SCHUNK offre ora il portautensile, che è stato premiato con il “German Innovation Award 2022”, in una nuova variante iTENDO² easy connect con una semplice interfaccia dati che può essere utilizzata per il monitoraggio di macchine e processi. SCHUNK vi aspetta al Pad. 13, Stand C14
Idea, forma e funzione: questi erano solo alcuni dei criteri utilizzati dagli esperti di design per determinare i vincitori di quest’anno dell’iF Design Award. L’autocentrante a cambio rapido morsetti ROTA THW3 ha convinto la giuria internazionale su tutti i punti. Esteticamente, il mandrino ha ottenuto ottimi voti grazie alla sua geometria esterna ottimizzata e al minor numero di spigoli. Ma si distingueva soprattutto per le caratteristiche tecniche, e per la sua funzionalità evidente sotto vari aspetti. Gli sviluppatori hanno ridotto il peso in modo coerente nella progettazione del prodotto. Ciò aiuta a ridurre l’energia necessaria e consente al tornio di accelerare e decelerare in maniera più rapida, pur mantenendo un corpo base estremamente rigido che garantisce un bloccaggio affidabile del processo anche se sottoposto alle massime forze. Dotato di un sistema di cambio rapido morsetti, ROTA THW3 può essere convertito rapidamente per una nuova lavorazione e ha un’eccellente precisione di ripetibilità delle griffe fino a <0,02 mm. Ciò significa che il mandrino può essere adattato rapidamente e con alta precisione a mutevoli attività di bloccaggio ed è particolarmente interessante per gli utilizzatori che producono lotti di piccole e medie dimensioni. Oltre alla sua funzionalità, la giuria è rimasta colpita anche dall’attenzione alla sostenibilità che SCHUNK assicura a questo dispositivo di bloccaggio innovativo. La tenuta brevettata ha consentito di prolungare gli intervalli di pulizia e manutenzione fino a 20 volte rispetto a prodotti comparabili. Ciò riduce l’uso di lubrificanti, detergenti e acqua e aiuta a salvaguardare l’ambiente. Utilizzando le risorse con moderazione, contribuisce con successo alla produzione sostenibile garantendo al contempo una funzionalità ottimale.
Giunto alla terza edizione a testimonianza dell’importanza strategica del settore, l’appuntamento è un’imperdibile occasione per produttori e distributori nazionali ed internazionali per mettere in mostra i propri prodotti e servizi, oltre a presentare le ultime innovazioni e ritrovati tecnologici. Sono 160 le aziende che hanno confermato la loro partecipazione all’evento ospitato presso gli spazi di Fiera Milano City (padiglione 3) provenienti da 15 Paesi, con una forte rappresentanza di imprese provenienti da Italia, Germania e Turchia. Tra gli espositori Ambrovit S.p.A., Bontempi VIBO S.p.A., Bralo Italia, Carlo Salvi S.p.A., CHAVESBAO (CHAVES BILBAO S.A.), Di Costa Guiseppe Srl, Dimac Srl, Fastbolt Schraubengroßhandels GmbH, Lederer GmbH, MEVI ITALIA Srl, Piloni Srl, SOM FASTENERS,
Teknoform Bağlantı Elemanları San. ve Tic.A.Ş., VIPA S.p.A., VISION Srl, VITAL S.p.A. e molti altri ancora. “Siamo entusiasti di vedere il ritorno degli eventi in presenza e non vediamo l’ora di dare il benvenuto all’industria a Fastener Fiera Italy 2022 - commenta Liljana Goszdziewski, Portfolio Director per le fiere europee Fastener Fair. - La forte partecipazione degli espositori alla fiera è un segnale positivo che indica la necessità del settore di tornare agli eventi di persona per facilitare il networking e le attività commerciali tra imprese. I visitatori che
partecipano a Fastener Fair Italy potranno scoprire soluzioni moderne per il settore di viteria, bulloneria e sistemi di fissaggio e ottenere approfondimenti reali sulle ultime tecnologie presentate dai principali fornitori del settore”. Dopo il successo della precedente edizione, a cui hanno preso parte un totale di 2.700 visitatori tra manager, ingegneri e buyer, Fastener Fair Italy 2022 includerà seminari gratuiti su innovazioni, argomenti e tendenze rilevanti per l’intera catena di fornitura industriale. Condotti da esperti del settore, questi appuntamenti consisteranno in aggiornamenti su questioni tecniche, normative e di mercato. Ideati da Event Partners in collaborazione con Mack-Brooks Exhibitions, organizzatore della fiera, i seminari saranno aperti sia agli espositori che ai visitatori. È inoltre possibile registrarsi gratuitamente come visitatori all’appuntamento sul sito https://www.fastenerfairitaly.com
La più importante fiera al mondo nel settore della lavorazione della lamiera è di ritorno, pronta ad accogliere dal 25 al 28 ottobre 2022 nell’area fieristica di Hannover in Germania. 1.300 espositori da 39 Paesi sono già pronti a presentare le loro più recenti soluzioni di produzione innovative, su un’area espositiva di 88.000 m2. Dopo un periodo di fermo
obbligato, la comunità della lavorazione della lamiera è ansiosa di incontrarsi di nuovo di persona, su scala internazionale. EuroBLECH 2022, la più importante fiera al mondo nel settore, offre l’opportunità di conoscere finalmente le innovazioni sviluppate negli ultimi anni nonché di incontrare contatti commerciali nuovi ed esistenti. “Vedere macchine e sistemi in azione, favorire i rapporti commerciali e scoprire il futuro della
lavorazione della lamiera. Tutto dal vivo, in presenza. Ecco cos’è EuroBLECH!”, afferma Evelyn Warwick, Event Director di EuroBLECH, per conto dell’organizzatore Mack-Brooks Exhibitions.
“Coprendo l’intera catena tecnologica legata alla lavorazione della lamiera, gli espositori presenteranno la loro offerta per l’innovazione e la digitalizzazione del processo di produzione. Stiamo parlando
EVOLUZIONE VERSO L’AUTOMAZIONE E LA DIGITALIZZAZIONE DELLA CATENA PRODUTTIVA, CON L’OBIETTIVO DI AUMENTARE PRODUTTIVITÀ ED EFFICIENZA
cura della redazione
di aziende del calibro di ADIGE SPA, Amada GmbH, ArcelorMittal Commercial Germany GmbH, BAYKAL MAKINA SAN. VE TIC. A.S., BLM Spa, Bystronic Laser AG, DURMAZLAR Makina San. ve. Tic. A.S., ERMAKSAN MAK. SAN. VE TIC. A.S., KUKA Deutschland GmbH, LVD COMPANY NV, Mazak EU Laser HQ, Mitsubishi Electric Europe B.V, MOTOFIL Group, Otto Bihler Maschinenfabrik GmbH & Co. KG, PRIMA POWER GmbH, SafanDarley B.V., SALVAGNINI, Salzgitter AG, Schuler Pressen GmbH, ThyssenKrupp Steel Europe AG e TRUMPF Werkzeugmaschinen SE + Co. KG, solo per citarne alcune”, conclude Evelyn Warwick. I principali Paesi espositori sono Germania, Italia, Turchia, Cina, Svizzera, Paesi Bassi, Spagna, Belgio, Polonia, Austria, Portogallo e Stati Uniti.
Oltre alle innovazioni e alle numerose dimostrazioni dal vivo presso gli stand espositivi, i partecipanti potranno usufruire dell’Area presentazioni di EuroBLECH 2022. Situata nel padiglione 26 (stand L60), nella nuova area si terranno circa 20
sessioni nel corso dei quattro giorni della fiera in cui si parlerà di aziende e progetti innovativi, con preziose opportunità di networking. La partecipazione è gratuita per tutti i visitatori e gli espositori registrati, e verranno fornite ulteriori informazione in prossimità della data di inizio dell’evento.
Elenco degli espositori e anteprima della fiera disponibili Lo strumento elenco degli espositori di EuroBLECH e l’anteprima della fiera online con informazioni dettagliate sui diversi espositori e prodotti vengono aggiornati regolarmente e sono disponibili su www.euroblech.com. Lo strumento elenco degli espositori permette agli utenti di preparare in modo efficace la visita grazie all’utile funzionalità che permette di cercare le aziende e i prodotti di interesse. L’Anteprima della fiera online offre una panoramica dell’ampia varietà di innovazioni, tecnologie e sistemi in mostra all’evento.
Grazie alla trasformazione digitale e al relativo impatto sui profili professionali, le giovani generazioni stanno acquisendo
sempre più importanza nel settore della lavorazione della lamiera. Inoltre, negli ultimi anni è stato difficile entrare nel settore a causa del numero insufficiente di eventi in presenza e della scarsezza di opportunità di networking. Di conseguenza, EuroBLECH offre agli studenti l’occasione di visitare gratuitamente EuroBLECH. Venerdì 28 ottobre 2022, gli studenti potranno entrare gratuitamente alla fiera presentando all’ingresso un tesserino universitario valido. Negli altri giorni della fiera, potranno effettuare la visita pagando il biglietto giornaliero con riduzione studenti (18 €).
La nuova app EuroBLECH per Android e iPhone potrà essere scaricata dall’App Store a partire da metà settembre. Comprende una mappa interattiva dello spazio espositivo e una funzione di ricerca degli espositori e di pianificazione della visita, nonché altre funzionalità che torneranno molto utili ai visitatori di EuroBLECH.
EuroBLECH 2022 si svolgerà nei padiglioni 11, 12, 13, 14, 15, 16, 17, 26 e 27 dell’area fieristica di Hannover in Germania. Gli orari di apertura sono i seguenti: da martedì 25 ottobre 2022 a venerdì 28 ottobre 2022, dalle 9.00 alle 18.00. I biglietti d’ingresso per EuroBLECH 2022 sono disponibili a un prezzo scontato tramite la biglietteria online. Inoltre i biglietti si possono acquistare in loco per tutta la durata dell’esposizione. Grazie ai numerosi collegamenti internazionali e all’eccellente infrastruttura locale, l’area fieristica di Hannover è facilmente raggiungibile per chi arriva in aereo, in auto e con i mezzi pubblici. I visitatori che necessitano di un visto per viaggiare sono invitati a organizzarsi con largo anticipo. Maggiori informazioni sono disponibili sulla sezione dedicata ai viaggi del sito Web. Ulteriori informazioni sulla fiera, nonché su viaggio e alloggio, sono disponibili sul sito Web della fiera all’indirizzo www.euroblech.com.
In tutti i settori industriali, i produttori e i loro fornitori di servizi di magazzino cercano costantemente l’ottimizzazione dei processi per affrontare sfide come la carenza di manodopera, l’aumento della concorrenza e la necessità di una produzione agile come anche riuscire ad effettuare consegne rapide. Gli AMR (Autonomous Mobile Robots) sono diventati in pochi anni un mezzo efficiente per automatizzare le attività di trasporto interno per le aziende in tutto il mondo. Man mano che gli AMR si sono affermati come tecnologia innovativa, i produttori, i magazzini e le strutture di distribuzione hanno esigenze sempre più sofisticate con l’aumento di richiesta di supporti automatizzati specificatamente progettati per la movimentazione: dagli AMR generici ai carrelli elevatori e ai carrelli ad alta portata, fino ai veicoli a guida automatica (AGV) per ricevere, immagazzinare, spostare e spedire gli articoli in modo più rapido e preciso. Molto spesso i sistemi logistici provengano da fornitori diversi, con standard operativi differenti e sistemi di controllo separati e questa complessità non è ideale per l’utente finale che cerca facilità d’uso e un unico meccanismo di controllo e supporto per l’intera flotta di AMR e veicoli automatizzati.
L’interoperabilità è quindi un argomento molto importante e interessante da approfondire. Ecco le cinque domande che i
clienti pongono più spesso- a MiR.
Che cos’è l’interoperabilità per gli AMR? La prassi attuale vede ogni fornitore di AMR utilizzare il proprio software di gestione della flotta, il che rende difficile per gli utenti finali gestire in modo efficiente una flotta di AMR e AGV di marche diverse. In parole povere, l’interoperabilità è la capacità di un sistema di gestione centrale di comunicare e coordinarsi con l’hardware della flotta di diversi fornitori in un’unica fonte di controllo e in un’unica interfaccia, riducendo così gli ostacoli che rappresentano un freno all’ulteriore adozione degli AMR.
Quali sono le principali sfide dell’interoperabilità AMR?
L’interoperabilità ha molto senso dal punto di vista iniziale del cliente: perché essere legati a un singolo fornitore se il mercato può essere mercificato? Tuttavia, anche se la base per gli standard di interoperabilità è stata stabilita oggi (come MassRobotics e VDA 5050), c’è ancora molta strada da fare per sfruttare appieno i vantaggi che essa offre.
L’interoperabilità implica alcune sfide commerciali. La proprietà delle prestazioni del sistema è una zona grigia: è il fornitore della gestione flotte di terze parti a essere responsabile dei malfunzionamenti del sistema o sono i produttori di robot, anche se non hanno progettato il sw di flotte, ma forniscono comunque i dati? Oppure è l’interfaccia che si collega al sistema ERP/WMS del cliente finale ad essere il problema? Questo aspetto è ancora da definire.
Da un punto di vista tecnico, ogni fornitore ha tipicamente due tipi di software: il software del robot che controlla la pianificazione basata sul robot stesso e il software che gestisce la pianificazione della flotta e non è chiaro come gestire mappe e configurazioni diverse da fornitori differenti in un sistema di terze parti. Inoltre, la qualità dei dati dei sistemi di gestione delle flotte non è standardizzata e quindi può essere difficile individuare quali dati possono essere scambiati tra due sistemi AMR.
Che cosa sono il VDA 5050 e la MassRobotics?
VDA 5050 è un’interfaccia standardizzata progettata per comunicare tra diversi AGV, potenzialmente di fornitori diversi, e un sistema di controllo ed è lo standard europeo per l’interoperabilità di AGV e AMR. Questo standard descrive le interfacce e i protocolli tra il livello di controllo e gli AGV. Gli AMR possono rientrare in questo
di Cristina Gualdoni
standard a patto di rinunciare a una parte della loro autonomia.
Come intuibile, l’obiettivo di questo standard è quello di consentire ad AGV e robot mobili conformi di lavorare insieme utilizzando in comune un software di gestione della flotta. Il VDA 5050 descrive la comunicazione tra due entità: l’AGV e il sw della flotta, e pertanto il VDA 5050 dovrà essere implementata a entrambi i margini del canale di comunicazione per poter funzionare correttamente. L’intenzione del VDA 5050 è quella di controllare il processo a basso livello, in contrasto con la possibilità di avere diversi fornitori di soluzioni per flotte che potrebbero coesistere e interoperare in fabbrica.
Il VDA 5050 è stato sviluppato da una collaborazione tra l’Associazione Tedesca dell’Industria automobilistica (VDA) e l’Associazione per la Movimentazione dei Materiali e l’Intralogistica VDMA. Anche se al momento è promosso dalle associazioni industriali tedesche, sarà presto utilizzato in tutta Europa e probabilmente anche in altre regioni.
MassRobotics è il più grande centro indipendente di innovazione robotica senza scopo di lucro che rappresenta il concetto americano dello standard di interoperabilità.
La missione del gruppo è quella di sviluppare standard che consentano di predisporre AMR e altre apparecchiature di automazione provenienti da diversi fornitori e di farli lavorare insieme nello stesso ambiente. Questo standard consentirà a robot di diverso tipo la condivisione di informazioni sullo stato e schemi operativi in modo da poter coesistere in modo efficiente.
Sia il VDA 5050 che MassRobotics sono nella fase iniziale poiché le versioni attuali si
limitano alle funzionalità di base, come ad esempio la comunicazione dei comandi agli AMR/AGV e l’invio di compiti. Non sono ancora coperti gli altri numerosi fattori che devono essere gestiti per garantire il successo di un’installazione multi-robot.
I sistemi di gestione della flotta di terze parti rendono ridondanti i software e i sistemi di gestione della flotta specifici per il fornitore?
L’interoperabilità porta molti vantaggi e, a un certo punto, vedremo sistemi di gestione della flotta di terze parti che potranno occuparsi della pianificazione del traffico e di alcuni scambi di dati. Tuttavia, il percorso verso questo traguardo non è agevole e siamo ancora in una fase iniziale. Gli standard sono ancora in fase di sperimentazione e nessun sistema di gestione flotte di terze parti è in grado di fornire le stesse opzioni di gestione della flotta e gli stessi dati di quello del fornitore: il MiR Fleet, ad esempio. Come già accennato, dovremo affrontare molte sfide sia commerciali che tecniche quindi, il software del robot e il software di gestione della flotta specifici del fornitore sono ancora indispensabili per garantire le prestazioni degli AMR, e lo saranno per gli anni a venire.
In un futuro prossimo, sarà più realistico vedere una coesistenza tra i sistemi, con i
produttori di AMR che renderanno nativa l’interoperabilità nei loro sistemi. In questo modo i robot potranno essere integrati in un sistema di gestione della flotta di terze parti o funzionare come sistemi di gestione di terze parti che gestiscono il controllo generale del traffico da diversi AMR e altri veicoli automatizzati. Per le funzioni avanzate, la raccolta dei dati, la manutenzione predittiva, gli sviluppi, ecc. il software all’avanguardia del produttore di AMR è ancora la chiave per un’integrazione di successo.
Qual è l’opinione di MiR sull’interoperabilità?
In quanto organizzazione orientata al cliente, riconosciamo pienamente la necessità di interoperabilità tra diversi AMR e AGV per una gestione efficiente del traffico tra i vari brand. Per questo motivo, in MiR abbiamo un team dedicato all’interoperabilità, siamo coinvolti nella VDA 5050 e facciamo parte del MassRobotics AMR Interoperability Working Group.
Inoltre, offriamo un’interfaccia aperta, che per sua natura può integrarsi con sistemi di gestione della flotta di terze parti. MiR fa parte del progetto: 5G-Robot - 5G Enabled Autonomous Mobile Robotic Systems, dove svolge un ruolo attivo nel progetto 5G-Robot, che è una collaborazione tra l’Università di Aalborg, MiR, Universal Robots, Intelligent Systems, Technicon, Telenor, Nokia e gli utenti finali industriali Novo Nordisk, Grundfos, Danfoss e LEGO. Il progetto è sostenuto dal Fondo Danese per l’Innovazione e mira ad abbassare le barriere per l’automazione dei processi con i robot. MiR fa parte di questo progetto per contribuire a ridurre la complessità delle implementazioni robotiche, consentendo ai propri robot mobili di lavorare in sistemi di gestione della flotta di terze parti.
Siamo sicuri che l’interoperabilità diventerà una componente sempre più importante dell’intralogistica, perché i clienti vogliono poter creare la loro soluzione di automazione ottimale e gestirla da un punto centrale: questi requisiti stanno ridisegnando lo scenario della robotica autonoma e porteranno a nuovi standard di automazione.
IL GAS NATURALE LIQUEFATTO (O GNL) È UNA FONTE ENERGETICA IN USO GIÀ DA ANNI E CHE STA VIVENDO UN AUTENTICO BOOM, POICHÉ IL CONFLITTO TRA RUSSIA E UCRAINA HA SPINTO L’OCCIDENTE INDUSTRIALIZZATO A UNA MAGGIORE DIVERSIFICAZIONE DELLE PROPRIE FONTI ENERGETICHE E QUESTO IMPLICA UN AUMENTO NELLA PRODUZIOEN DI VALVOLE SPECIFICHE. APPUNTAMENTO FONDAMENTALE PER AFFRONTARE QUESTO TEMA VALVE WORLD EXPO DAL 29 NOVEMBRE ALL’1 DICEMBRE 2022 A DÜSSELDORF di Eleonora Segafredo
Secondo la piattaforma specializzata LNG Edge di ICIS, le importazioni mensili europee di gas naturale liquefatto avevano raggiunto già nel gennaio 2022 un livello record, superiore agli 8,1 milioni di tonnellate. In Europa, sono in funzione 37 siti di rigassificazione, dei quali 26 si trovano nell’UE. La capacità di rigassificazione continentale è pari a circa 243,6 miliardi m3 annui. Dopo l’inizio della guerra in
Ucraina, sono stati avviati altri 20 progetti riguardanti il GNL, una materia prima per cui si prevedono, quindi, nuovi record di importazioni. In Germania, per esempio, è in programma la costruzione di due nuovi rigassificatori. Secondo il Ministero tedesco per gli Affari economici e la difesa del clima, tali impianti potrebbero coprire fino al 20% del consumo annuo di gas del Paese. I rigassificatori e le corrispondenti infrastrutture di produzione contribuiranno alla sicurezza degli
approvvigionamenti, ma richiedono forti investimenti, che coinvolgono anche componenti fondamentali come raccordi e meccanismi di azionamento. Herose, per esempio, si è concentrata da tempo sull’emergente settore del GNL e, secondo i dati in proprio possesso, il settore sta acquistando ulteriore importanza. Tuttavia, per consentire alle aziende di raggiungere i propri obiettivi, i raccordi per il gas naturale liquefatto devono soddisfare standard
molto severi. “I veicoli per il trasporto del gas naturale liquefatto criogenico sono soggetti a notevoli sollecitazioni, dovute alla frequenza di riempimento, trasporto e scarico a destinazione”, spiega Herose. Per lo stoccaggio del GNL, sono, inoltre, fondamentali aspetti quali durata di servizio, prestazioni operative, sicurezza e affidabilità. Anche l’utilizzo del GNL per il rifornimento di veicoli richiede raccordi potenti.
Al mercato del GNL è interessata pure Emerson. L’azienda fornisce soluzioni di automazione e controllo destinate ad ambiti quali produzione, liquefazione e trasporto del gas, rigassificatori e gasdotti; inoltre, si è posta l’obiettivo di “contribuire a migliorare l’efficienza energetica, ridurre le emissioni e aumentare la produzione e l’uso di energie rinnovabili e combustibili più puliti”, sottolinea Emerson Automation Solutions. L’azienda sviluppa valvole automatiche per uso criogenico.
Dal punto di vista tecnico, le operazioni di produzione e trasporto richiedono un preciso controllo di pressione e temperatura, massima affidabilità degli impianti e sistemi in grado di minimizzare le perdite e la variabilità dei processi.
“Emerson sta aiutando i produttori di GNL a raggiungere una maggiore efficienza operativa grazie alla digitalizzazione, ad avanzate strategie di controllo dei processi e a soluzioni di ottimizzazione delle prestazioni degli stabilimenti”, spiega l’azienda. I raccordi prodotti da müller co-ax ag sono destinati a settori quali propulsione navale e riliquefazione a bordo delle navi metaniere. Le condizioni di movimentazione del GNL sono molto complesse. Il gas naturale, infatti, diventa liquido a una temperatura di circa - 162 °C. Anche per quanto riguarda la sicurezza, gli standard di utilizzo sono molto stringenti, perché, quando evapora,
il GNL produce un gas esplosivo. “Le nostre valvole rispettano le linee guida vigenti in materia di protezioni antiesplosione e vantano la certificazione ATEX”, spiega l’azienda. Il GNL potrebbe costituire anche un carburante alternativo prontamente disponibile per imbarcazioni, mezzi pesanti e treni. Tale applicazione rappresenta “una tecnologia di transizione, ma anche un ponte verso soluzioni quali il GNL sintetico”, afferma Herose. Un rigassificatore, infatti, può essere utilizzato anche come punto di trasferimento o stoccaggio per il gas naturale sintetico, come negli impianti Power-to-Gas. “Infrastrutture già esistenti potrebbero consentire, grazie al tramite del gas naturale, di stoccare e distribuire notevoli quantità di energia eolica. Una fonte fossile diventa in questo modo climaticamente neutra”, spiega l’azienda. Il carbonio destinato a finire nel metano verrebbe, infatti, estratto dall’atmosfera durante la sintesi dell’idrogeno. “Dai serbatoi di combustile fossile non viene,
quindi, rilasciata in atmosfera nuova CO2. Condutture e serbatoi di stoccaggio per il gas naturale sono già presenti e non sono necessarie nuove linee per l’alta tensione.” Un elemento fondamentale degli impianti a GNL è costituito dalle valvole di sicurezza, come quelle prodotte da LESER. L’importanza di queste valvole è davvero cruciale, dato che, per essere liquefatto, il gas naturale viene refrigerato a -162 °C. In caso di surriscaldamento, tuttavia, possono generarsi sovrapressioni da monitorare con attenzione. “Per quanto riguarda il controllo della sovrappressione, la catena di approvvigionamento è caratterizzata da standard variabili e il cui rispetto deve essere garantito da apposite valvole di sicurezza, per esempio valvole filettate compatte oppure valvole di sicurezza a controllo pilotato tecnologicamente complesse”, spiega LESER. È necessario riuscire a soddisfare le esigenze e le specifiche di ogni singola fase di gestione del GNL ed eventualmente procedere a un ulteriore sviluppo dei prodotti. L’improvvisa crescita del settore del GNL implica l’aumento della domanda di valvole di sicurezza, controllo e arresto. In Europa, i produttori di valvole sono numerosi; pertanto, il mercato non ha problemi di dipendenza dall’estero. Inoltre, grazie ai loro prodotti di qualità, queste aziende sono pronte ad assecondare i massicci investimenti destinati al settore energetico e, in particolare, agli impianti a GNL. Una tendenza, quindi, ricca di rosee promesse per le aziende del settore valvole. Dal 29 novembre all’1 dicembre 2022, le aziende leader nel settore delle valvole industriali presentano i propri prodotti a Düsseldorf in occasione di VALVE WORLD EXPO e della sua conferenza di accompagnamento. Esperti provenienti da tutti i continenti trasformeranno Düsseldorf nella capitale del mondo dei raccordi, presenteranno le proprie innovazioni e si confronteranno sugli studi più recenti e sui più avanzati processi di produzione. Dopo un’interruzione di quattro
anni, si respira un’atmosfera di ottimismo e le aziende che producono valvole industriali sono impazienti di tornare a incontrarsi di persona all’interno degli stand della fiera, scambiarsi informazioni faccia a faccia e toccare con mano le ultime innovazioni tecnologiche.
Gli espositori presenti a VALVE WORLD EXPO 2022, in programma dal 29 novembre e all’1 dicembre nei padiglioni 1 e 3 della fiera di Düsseldorf, metteranno in mostra l’inesauribile capacità di innovazione del settore. La partecipazione delle aziende si annuncia entusiastica. Leader di settore come MRC Global, KITZ, Emerson, Samson, AUMA, Omal/Actuatech, Zwick Armaturen, Pekos Valves, Böhmer, Ari Armaturen, Effebi, Hoerbiger, Galperti, Neles/metso, Neway e Crane saranno grandi protagoniste della fiera. Tuttavia, a Düsseldorf saranno presenti anche numerose aziende di medie dimensioni. Un’anteprima sull’andamento delle iscrizioni era disponibile sul sito www.valveworldexpo.com già alla fine di febbraio. Le aziende interessate a
partecipare hanno comunque potuto iscriversi anche successivamente. Preziosi eventi di accompagnamento, come la Valve World Conference (padiglione 1) e il Valve World Expo Forum (padiglione 3), favoriranno la trasmissione dei know-how e il passaggio dalla teoria alla pratica. La primissima edizione della Valve World Conference si terrà nel nuovo padiglione 1, struttura congressuale all’avanguardia sia dal punto di vista architettonico che tecnologico. Durante i primi due giorni della fiera (29/11 e 30/11) Vulkan-Verlag organizzerà Expo Forum, evento gratuito in lingua tedesca che si svolgerà nel padiglione 3. Nel terzo giorno di fiera, la palla passerà a KCI, che organizzerà una serie di interventi in lingua inglese. VALVE WORLD EXPO 2022 ospiterà anche la campagna ecoMetals, iniziativa che punta a evidenziare la crescente importanza di sostenibilità, efficienza energetica e conservazione delle risorse, in particolare nei settori più energivori. Il programma della fiera sarà, infatti, arricchito da visite guidate (le cosiddette
Per la prima volta, durante la fiera sar à assegnato il Valve Stars Award , evento organizzato da Vulkan-Verlag. Per essere selezionati come candidati al Valve Star Award, prima della fiera gli espositori potranno inviare una presentazione dei propri prodotti. Il voto si svolger à online. I vincitori delle quattro categorie (“Valvole”, “Azionatori”, “Tecnologie di sigillatura” e “Industria 4.0/Automazione”) saranno premiati a Düsseldorf nel corso della fiera. In questo modo, VALVE WORLD EXPO porta ulteriormente in primo piano i prodotti delle aziende pi ù innovative.
“ecoMetals-trails”) che toccheranno gli stand degli espositori impegnati a produrre in maniera consapevolmente sostenibile. La partenza avverrà da un punto di ritrovo appositamente segnalato nella zona del nuovo Ingresso Sud. Ulteriori informazioni su VALVE WORLD EXPO, sulla Conferenza, sul Forum e sulla campagna ecoMetals sono disponibili nel portale Internet www.valveworldexpo.com.
Il primo volo dei fratelli Wright nel 1903 è durato solo dodici secondi ma, per oltre un secolo, ha segnato il decollo delle attività di ricerca e sviluppo nel settore aerospaziale. Dal volo del primo aereo a motore, la produzione aerospaziale ha dovuto superare molte altre sfide.
I nuovi materiali svolgono un ruolo importante nell’affrontare le sfide che si presentano in questo settore. Ma l’introduzione di nuovi materiali nelle attività di ricerca e sviluppo comporta una serie di difficoltà. Di conseguenza, i costruttori di componenti aerospaziali devono collaborare con fornitori di utensili esperti e competenti, in grado di aiutarli a rispondere alle nuove esigenze. Sandvik Coromant, a questo proposito, rappresenta il punto di unione tra le conoscenze di lavorazione e le soluzioni di attrezzamento fin dal 1942.
All’inizio del 20° secolo, la sfida principale per l’industria aerospaziale era
semplicemente far volare gli aerei. Ora, invece, ai costruttori si chiede molto di più. La necessità di ridurre l’impronta di carbonio dei viaggi aerei ha richiesto la costruzione di aerei più leggeri, in modo da risparmiare carburante.
La riduzione del peso aiuterà a ridurre l’elevato consumo di carburante degli aerei. Per fare un esempio, quando ha cambiato la carta della sua rivista di bordo rendendola più leggera, la United Airlines ha risparmiato oltre 170.000 galloni di carburante all’anno. Ogni grammo conta, che si tratti di componenti di grandi dimensioni come lo scatolato alare o dei complessi motori nei sedili reclinabili dei passeggeri. Anche il passaggio a velivoli più efficienti in termini di consumo del carburante sarà importante, con l’obiettivo finale di realizzare aerei completamente elettrici.
In altri casi, i servizi di manutenzione, riparazione e revisione (MRO) dell’industria aerospaziale sono stati tra gli aspetti più complessi da gestire.
Molti costruttori, di conseguenza, hanno cercato modi per ridurre i costi di manutenzione. Per farlo, ci si è avvalsi di dati simulati che permettono alle compagnie aeree di pianificare in anticipo le loro attività di manutenzione e riparazione.
I progressi fatti a livello di materiali hanno creato diverse nuove opportunità per le aziende aerospaziali. È aumentato l’uso dei compositi e del grafene, oltre che di materiali leggeri come il titanio. Altre innovazioni nella tecnologia dei materiali includono l’uso di polveri metalliche e processi di produzione additiva per costruire parti metalliche leggere e più sostenibili.
Il titanio è del 30% più robusto dell’acciaio ma più leggero di quasi il 50% e ciò lo rende un materiale chiave per affrontare le sfide poste dalla ricerca di efficienza e sostenibilità. Tuttavia, la lavorazione di materiali come il titanio presenta una serie di problematiche. Le leghe di titanio possono avere una durezza doppia rispetto alle leghe
d’acciaio e, se si considera anche la loro bassa conducibilità termica, risulta evidente che i carichi termici e meccanici a cui sono sottoposti gli utensili sono elevati.
Un partner di fiducia Collaborando nel tempo con l’industria aerospaziale, Sandvik Coromant ne ha seguito l’evoluzione, ne conosce le sfide e continuerà a sostenere il settore nel suo percorso verso nuovi scenari. Con oltre 1800 brevetti nel
suo portfolio, Sandvik Coromant è in grado di fornire utensili, soluzioni e un incomparabile know-how applicativo. Grazie alle sue attività di ricerca e sviluppo e alla stretta collaborazione sia con i clienti che con i costruttori di macchine, Sandvik Coromant può vantare di avere un’offerta davvero competitiva per l’industria aerospaziale. Per fare un esempio, Sandvik Coromant investe molto nello sviluppo di utensili specifici per materiali difficili da lavorare. La fresatura laterale ad
quegli strumenti digitali che possono ottimizzare le operazioni e migliorare la produttività. Per molte aziende, disporre degli utensili giusti al momento giusto può essere difficile. La pianificazione della disponibilità all’interno dell’officina meccanica richiede trasparenza in tutte le operazioni. La raccolta manuale di dati e documentazione può diventare lunga e noiosa mentre le nuove opzioni di connettività permettono di ottimizzare la trasparenza e le attività di pianificazione e produzione.
consente di aumentare velocità di taglio, grazie alla diminuzione del calore, dello spessore del truciolo e delle gamma CoroMill® di utensili è solo un esempio dell›offerta che Sandvik Coromant superleghe resistenti al Oltre che gli utensili più
Coromant aerospaziale anche
CoroPlus® Machining Insights di Sandvik Coromant rende prontamente disponibili tutti i dati necessari, aiutando a migliorare l’efficienza dell’officina e l’efficacia globale delle macchine. Grazie all’accesso immediato a informazioni quali consumo degli utensili, dati macchina e prestazioni del processo, una parte vitale delle attività MRO può diventare significativamente più snella. L’industria aerospaziale ha alle spalle oltre un secolo di innovazione che ha fatto diventare realtà ciò che prima era impossibile. Ma l’evoluzione non si ferma ed è necessario adattarsi alle esigenze in continuo cambiamento della nostra società. Per rimanere competitivi e volare alto non basta una profonda conoscenza delle tendenze del settoreoccorre anche conoscere i materiali e le tecnologie che rappresentano il futuro dell’industria aerospaziale.
LLe macchine di nuova generazione, in particolare le multitask, sono macchine estremamente complesse che offrono notevoli vantaggi in termini di prestazioni. Queste macchine, al giorno d’oggi, hanno riformulato il concetto di multitasking, tradizionalmente associato all’integrazione in un’unica macchina di processi di tornitura e fresatura, e, grazie allo sviluppo di tecnologie avanzate, hanno integrato in un unico set-up anche le operazioni di rettifica, insieme alla fresatura e tornitura. Questo permette di effettuare differenti operazioni di lavorazione con un’unica macchina e di ridurre i tempi ciclo ed i costi, aumentando, nel contempo, il livello di efficienza dei processi di lavorazione. I vantaggi offerti sono notevoli: riduzione dei tempi di carico, scarico e allineamento dei pezzi, riduzione dei tempi di attrezzaggio macchina, esecuzione delle differenti lavorazioni in un’unica macchina, miglioramento della precisione e della qualità di lavorazione dei differenti pezzi e tanto altro ancora. Proprio per la loro complessità, le multitask di nuova generazione hanno bisogno di sistemi di messa a punto efficaci. Questi consentono, ad esempio, di eseguire l’analisi delle prestazioni degli assi rotativi per identificare i problemi causati da impostazioni non corrette, collisioni o usura. Per effettuare lavorazioni corrette, infatti, è necessaria la conoscenza della posizione del centro di rotazione degli assi rispetto agli assi lineari. Se non si conoscono con precisione questi punti, il controllo della macchina non può guidare gli assi in maniera affidabile e i risultati di lavorazione saranno incoerenti. Nel dossier viene presentato uno strumento in grado di determinare i centri di rotazione in modo semplice, veloce ed accurato, in modo che, direttamente in macchina ed in maniera automatizzata, si possano effettuare le verifiche per poter garantire la precisione della macchina nel tempo. Altri strumenti efficaci, in termini di efficienza operativa, ottimizzazione delle risorse e aumento del fatturato, sono i software e le soluzioni che consentono una mappatura virtuale e in tempo reale della produzione mediante il completo collegamento in rete di macchine, sistemi di automazione e processi, in ottica di digitalizzazione e integrazione nelle catene del valore della creazione di prodotti globali. Tra questi, anche l’utilizzo
di software di attrezzamento specializzati che contribuiscono ad automatizzare la gestione delle scorte, aiutano a risolvere i problemi associati alla gestione inadeguata delle scorte e a superare la riluttanza a passare al digitale, aumentando di conseguenza il fatturato. Accanto alle macchine multi-task “all-in-one”, il dossier presenta anche le ultime novità in fatto di centri di tornitura e fresatura, che garantiscono efficienza nella produzione e lavorazione ad alte prestazioni di pezzi di medie dimensioni, molto complessi e diversi tra loro, spesso richiesti nell’ambito dell’industria meccanica, automobilistica e aerospaziale, e di macchine rettificatrici. La domanda di tecnologie di rettifica all’avanguardia è cresciuta negli ultimi anni, insieme ad altri fattori, anche a causa del rapido sviluppo della mobilità elettrica e di altre propulsioni alternative. La forte spinta, esercitata a livello mondiale, per la riduzione delle emissioni di CO2 e dell’inquinamento atmosferico ha determinato una rapida trasformazione dell’industria automobilistica, portando cambiamenti e nuove tendenze del mercato che tutti i costruttori di macchine e di componentistica stanno monitorando con grande attenzione. Cambiamenti che comportano una maggiore produzione di propulsori elettrici, che hanno un cambio in cui vengono utilizzati anche alberi a pignone conico, e di autocarri elettrici a celle a combustibile, che richiedono alberi e manicotti di alta precisione per i compressori ad alta pressione, per i quali servono macchine rettificatrici adatte. Oltre alla costruzione di veicoli, le nuove rettificatrici trovano impiego anche in una vasta gamma di comparti industriali, quali i settori dell‘aerospaziale, dell‘idraulica, della produzione di pompe e della fabbricazione di stampi e utensili. Le rettificatrici di nuova generazione sono dotate di sistemi e funzionalità automatiche che consentono di aumentare qualità e produttività, come il mercato richiede. È bene infatti ricordare come anche nel processo di rettifica l’automazione sia imprescindibile per una qualità riproducibile. Nel dossier che segue, vengono presentate e approfondite le soluzioni di alcune delle aziende del settore. La prima parte del dossier è stata pubblicata sul numero di settembre.
AAxiSet Check-Up fornisce un processo semplice e affidabile per l’analisi delle prestazioni degli assi rotativi e per identificare i problemi causati da errori di impostazione, collisioni o usura. In pochi minuti gli utilizzatori di centri di lavoro multiasse e di macchine multitasking possono identificare eventuali errori sull’allineamento, la geometria e i punti di pivot che porterebbero a pezzi non conformi e perdite di tempo nella preparazione dei processi. Se possibile, AxiSet Check-Up corregge automaticamente i parametri dei punti di pivot in macchina. Le macchine di nuova generazione, in particolare le multitask, sono macchine estremamente complesse che offrono notevoli vantaggi in termini di prestazioni e per le quali sono necessari sistemi di messa a punto efficaci: processi semplici e al contempo affidabili per eseguire l’analisi delle prestazioni degli assi rotativi, che identifichino i problemi causati da impostazioni non corrette, collisioni o usura. Un punto chiave per effettuare lavorazioni corrette è la conoscenza della posizione del centro di rotazione degli assi rispetto agli assi lineari. Se non si conoscono con precisione questi punti, il controllo della macchina non può guidare gli assi in maniera affidabile e i risultati di lavorazione saranno incoerenti. È necessario dunque uno strumento che sia in grado di determinare i centri di rotazione in modo semplice, veloce ed accurato, in modo che, direttamente in macchina ed in maniera automatizzata, si possano effettuare le verifiche per poter garantire la precisione della macchina nel tempo. AxiSet™ Check-Up, il sistema di Renishaw costituito dal tastatore Rengage™ e dal software AxiSet™, rappresenta la soluzione più conveniente per controllare le prestazioni di allineamento e posizionamento degli assi
rotativi e aiutare gli utenti a preservare la stabilità dell’ambiente di lavoro.
Il sistema costituito dal tastatore Renishaw Rengage™ e dal software AxiSet™ effettua semplici tastature su una sfera in varie posizioni degli assi rotativi in modo che il software possa determinare i valori dei centri di rotazione da immettere nei parametri del controllo numerico. Il nome della famiglia di sonde utilizzate, Rengage™, sta per Renishaw – strain gauge, a ricordare la tecnologia di base del sensore di tipo estensimetrico. Questa consente una precisione più elevata rispetto ai tastatori tradizionali, con un metodo 100% elettronico, in cui il segnale del tastatore, inviato al controllo numerico, misura la forza del tastatore a contatto con il pezzo. Questo garantisce eccellenti prestazioni di misura tridimensionale (3D) e ripetibilità al sub-micron.
Questo sistema può essere utilizzato sia dal costruttore nelle fasi di costruzione e montaggio della macchina ma anche e soprattutto dall’utilizzatore, che disponendo del sistema a bordo macchina, può utilizzarlo con cadenze regolari per monitorare lo status della macchina e applicare delle correzioni, laddove queste si rendano necessarie. Infatti, se utilizzato correttamente, il sistema consente di compensare le piccole variazioni che si determinano in officina ed avere dei centri di rotazione sempre accurati in qualsiasi condizioni di lavoro.
AxiSet Check-Up Renishaw fornisce un metodo di prova accurato
degli errori, e poi eseguire la rettifica, in quanto questa lavorazione richiede maggiore precisione e accuratezza.
Le sonde Rengage™, impiegate nel sistema AxiSet Check-Up, incorporano una tecnologia estensimetrica di provata affidabilità, con elettronica ultracompatta e un design meccanico di precisione per prestazioni e capacità che non temono rivali. Sono adatte per un’ampia gamma di applicazioni su macchine utensili e superano le limitazioni legate alle prestazioni 3D che affiggono molte altre sonde. I più recenti prodotti Renishaw che includono questo tipo di tecnologia sono MP250, OMP400 e RMP600.
Nelle sonde Rengage™, i componenti estensimetrici sono disposti in modo da rilevare le tensioni su tutti gli assi e i loro output vengono combinati elettronicamente tramite alcuni algoritmi brevettati. Quando si raggiunge il livello di soglia in una direzione qualsiasi, viene generato un segnale di trigger con forze decisamente inferiori rispetto a quelle necessarie per le sonde convenzionali, che comporta notevoli vantaggi in relazione a un’ampia gamma di problemi applicativi. Le sonde Rengage sfruttano il meccanismo cinematico Renishaw per riportare lo stilo in posizione. Il sistema vanta 30 anni di continui perfezionamenti e garantisce un ritorno ripetibile, elemento fondamentale per una metrologia accurata. Dato che la rilevazione è completamente indipendente dal meccanismo della sonda, i dispositivi Rengage sono caratterizzati da bassa forza di trigger, elevata ripetibilità ed una caratteristica di comportamento costante, tutti fattori che non sono ottenibili con sonde dal design convenzionale.
e ripetibile usando routine di ispezione automatiche su un pezzo di riferimento e include una analisi semplice e completa. Per i test si utilizzano sonde a contatto collocate nel mandrino, complemento standard già a bordo della maggior parte delle macchine multiasse, in combinazione con routine di ispezione generate usando macro software specifiche per il modello di macchina e fornite con AxiSet Check-Up.
Il piazzamento è rapido e semplice. Per eseguire la prova si colloca all’interno dell’area di lavoro della macchina una sfera calibrata, utilizzando una semplice base magnetica, mentre la sonda misura automaticamente diversi punti sulla sfera, guidata dalle macro generate dal software. L’utente ha sempre il pieno controllo del processo e può definire specifici angoli di prova per assicurarsi di provare la macchina nelle orientazioni critiche.
Questo sistema può essere applicato su ogni tipo di macchina multitask ed è anche possibile retrofittare una macchina di ultima generazione che preveda una compatibilità con il sistema.
In particolare, nel caso di macchine che effettuino anche lavorazioni di rettifica, prima di questa lavorazione, sarebbe opportuno lanciare il sistema, eseguire il controllo e la verifica della cinematica della macchina, eventuale fare l’aggiornamento e la compensazione
Il confronto tra le sonde dotate di tecnologia Rengage™ con prodotti convenzionali di altre marche, effettuato con esempi basati su test reali e una tipica macchina da produzione, mette in risalto le eccellenti prestazioni della tecnologia Rengage. L’errore medio a 40 µm è 10 volte superiore rispetto a quello della sonda Rengage. Quindi, l’accuratezza 3D delle sonde Rengage è 10 volte migliore. L’utilizzo della tecnologia Rengage in combinazione con macchine ad elevata accuratezza, grazie alla sua ripetibilità unidirezionale di soli 0,25 µm 2σ, garantisce un’accuratezza senza paragoni su tutti i piani. Inoltre, consente di eliminare fino al 90% gli errori di lobing, che altro non sono che l’errore metrologico del tastatore quando effettua misure interpolate. Nelle applicazioni a due assi, tale riduzione rende superflue le operazioni di calibrazione, mentre nelle applicazioni a tre assi o con geometrie complesse garantisce prestazioni assolutamente impareggiabili. Di questa famiglia fanno parte tastatori sia a trasmissione radio che infrarossi.
La miniaturizzazione dei componenti e la tecnologia a stato solido vengono combinate per dare vita a una serie di sonde Rengage compatte e ultracompatte, in grado di fornire soluzioni innovative per soddisfare le esigenze odierne di accuratezza e di installazione in macchine di piccole dimensioni.
Dal 1974 Losma progetta e costruisce sistemi di depurazione dell’aria e dei liquidi lubrorefrigeranti. Un know-how maturato in quasi 50 anni di attività che l’azienda mette a disposizione dei propri clienti per rendere più sano e pulito l’ambiente lavorativo di fabbrica.
In Losma, abbiamo a cuore la salute dei lavoratori e, giorno dopo giorno, ci impegniamo nella ricerca di nuove soluzioni che aiutino anche le altre aziende a preservare l’ambiente che le circonda e le persone che lo vivono.
LLa gestione inadeguata delle scorte è una delle principali cause di perdite di tempo. Per i costruttori, avere a disposizione l’utensile giusto al momento giusto è fondamentale. Da una ricerca svolta da Sandvik Coromant tra i propri clienti, è emerso che tipicamente, in un’officina, gli operatori possono arrivare a dedicare il 20% del tempo alla ricerca degli utensili, mentre il 15% delle operazioni viene riprogrammato o rimandato a causa dell’impossibilità di trovare gli utensili giusti. Questi risultati dimostrano quanto tempo possa far perdere un’inadeguata gestione delle scorte, che può condurre a livelli di inventario eccessivi, obsolescenza di grandi volumi di stock o esaurimenti delle giacenze, il che implica l’impossibilità di poter reperire un determinato utensile proprio quando serve di più. Inoltre, in questo modo, misurare le prestazioni degli utensili diventa difficile e i costi di gestione delle scorte ed elaborazione degli ordini aumentano. Come ben noto,
nel settore manifatturiero, il tempo è un fattore determinante e certamente non dovrebbe essere impiegato nella ricerca utensili e parti di ricambio. Il problema è dato dal fatto che i sistemi di gestione e distribuzione degli utensili restano spesso separati e le aziende, spesso, si affidano a operatori umani per ispezionare e rifornire gli armadietti di utensili. In quest’ottica, la digitalizzazione e quindi l’integrazione dell’Industria 4.0 con processi aziendali consolidati - come i sistemi di pianificazione delle risorse (ERP), i sistemi di controllo di supervisione e acquisizione dati (SCADA) e i sistemi di esecuzione della produzione (MES) – porterebbe senz’altro dei benefici in termini di risorse, efficienza operativa e fatturato. Sandvik Coromant mira a cambiare tutto ciò nel corso dei prossimi cinque anni aiutando i clienti ad automatizzare la gestione delle scorte attraverso l’utilizzo di software di attrezzamento specializzati. Così facendo, sarà possibile
GRAZIE AI SOFTWARE DI ATTREZZAMENTO SPECIALIZZATI DI SANDVIK È POSSIBILE AUTOMATIZZARE E DIGITALIZZARE LA GESTIONE DELLE SCORTE E MIGLIORARE PRODUTTIVITÀ E FATTURATOSANDVIK
risolvere i problemi associati alla gestione inadeguata delle scorte e superare la riluttanza a passare al digitale, aumentando di conseguenza il fatturato.
I dispositivi dell’Industria 4.0, tra cui sensori sulle linee di produzione e assemblaggio, consentono di acquisire dati in tempo reale e migliorare così le capacità di analisi e assunzione di decisioni. Come per la gestione della catena di approvvigionamento, il principio dell’acquisizione di dati ottimizzata si applica anche alla gestione delle scorte.
Il che rappresenta una sfida, perché la gestione delle scorte è composta da numerosi elementi, che includono il monitoraggio dei livelli di inventario e sapere quando ordinare nuovi utensili, in modo che la produzione non debba mai fermarsi. Ad esempio, la gestione delle scorte digitalizzata, attraverso un sistema di monitoraggio della durata utile automatizzato per ottimizzare i livelli di inventario ed evitare l’esaurimento delle scorte, non solo fa risparmiare tempo all’azienda, ma favorisce anche tempi di produzione più rapidi. Tutto ciò non è riservato soltanto alle grandi multinazionali, che in alcuni casi già implementano queste soluzioni, perché con l’aiuto di uno strumento software, anche i costruttori medio-piccoli possono automatizzare i propri complessi processi di gestione delle scorte.
Ci sono molti metodi logistici di distribuzione la cui implementazione è gratuita, che però non aggiungono alcun valore ai processi. Al contrario, CoroPlus® Tool Supply di Sandvik Coromant è progettato proprio per aggiungere valore attraverso il rafforzamento dell’automazione, con una maggiore efficienza e sostenibilità rese
possibili da dati e informazioni.
CoroPlus® Tool Supply riunisce componenti hardwarenello specifico, magazzini utensile - e software. Al cliente viene fornito un armadietto di distribuzione progettato appositamente, dotato di un sistema di cassetti, in combinazione con una potente piattaforma software accessibile tramite un PC o tablet. Il software di automazione fornisce ai costruttori un’alternativa alle operazioni manuali e consente di evitare sprechi di tempo, quando questo scarseggia. CoroPlus® Tool Supply è progettato anche per gestire i molti elementi che compongono la gestione delle scorte, come il monitoraggio dei livelli d’inventario, e integra una funzione per l’automatizzazione dell’acquisto degli utensili.
Tale funzione rappresenta un enorme valore aggiunto del software CoroPlus® Tool Supply. Con essa, un collaboratore incaricato di tracciare manualmente i contenuti di un armadietto di utensili può affidarsi a CoroPlus® Tool Supply per ordinare e rifornire automaticamente lo stock. Il software consente di prelevare e restituire gli utensili e supporta la gestione del riapprovvigionamento e la manutenzione dell’inventario — tutto in tempo reale.
In altre parole, esseri umani e programmi software possono lavorare insieme senza problemi.
Un altro vantaggio di CoroPlus® Tool Supply sono le interfacce utente basate sui ruoli (RBUI). Le RBUI sono l’ultima tendenza nel campo dei software ERP e consentono ai collaboratori che devono svolgere mansioni ripetitive di accedere alle applicazioni più usate in maniera estremamente semplice, il che può essere fondamentale per conquistare il loro consenso in officina. Attraverso l’offerta CoroPlus, la piattaforma CoroPlus® Tool Supply permette di accedere ai dati degli utensili. Il sistema si connette ai database di diversi fornitori e permette di importare informazioni sugli utensili, compresi parametri ISO, distinte di materiali e parti di ricambio. Oltre al software CoroPlus Tool Supply, Sandvik Coromant può fornire anche gli armadietti che contengono gli utensili.
Per gli specialisti, l’automazione è parte integrante dell’ottimizzazione dell’efficienza e della sostenibilità dei clienti. Dopotutto, un aspetto fondamentale della sostenibilità, soprattutto in termini di efficienza energetica, è la possibilità di analizzare e prevedere l’utilizzo delle risorse, comprese le scorte di utensili. Mentre l’Industria 4.0 aumenta la sostenibilità sulla linea di produzione con sensori e altre soluzioni, CoroPlus® Tool Supply può fare lo stesso con le scorte, assicurando che vengano utilizzate con la massima efficienza in termini di tempo, costi ed energia.
Il software può quindi aiutare a decidere quale utensile utilizzare nella pianificazione della lavorazione di un nuovo componente, oppure può essere più direttamente collegato a macchine e operazioni specifiche. In questo modo, ad esempio, nella progettazione di una lavorazione di 50 o 100 componenti, grazie al software, si possono monitorare il numero di utensili necessari, l’usura e la possibilità di completare il lavoro con le scorte attuali. Non c’è dubbio che questo tipo di automazione si svilupperà nel corso dei prossimi anni. Ma già da oggi i costruttori possono utilizzare gli strumenti software per assicurare che la produttività rimanga sempre al primo posto.
Con CoroPlus® Tool Supply l’inventario è semplice e immediatoGGrazie ad oltre 20 anni di esperienza nella fornitura di soluzioni multitasking, le macchine Soraluce consentono operazioni di fresatura, tornitura e rettifica in un unico set-up, permettendo così di effettuare differenti operazioni di lavorazione con un’unica macchina e di ridurre i tempi ciclo ed i costi, aumentando, nel contempo, il livello di efficienza dei processi di lavorazione. A fronte di una produzione di soluzioni multitasking che raggiunge il 30% delle macchine Soraluce, il concetto di multitasking sviluppato dall’azienda, può essere integrato in tutta la gamma di macchine sviluppate dalla stessa. Numerosi i vantaggi offerti: riduzione dei tempi di carico, scarico e allineamento dei pezzi, riduzione dei tempi di attrezzaggio macchina, esecuzione delle differenti lavorazioni in un’unica macchina, miglioramento della precisione e della qualità di lavorazione dei differenti pezzi e tanto altro ancora. “Soraluce ha riformulato il concetto di multitasking, tradizionalmente associato all’integrazione in un’unica macchina di processi di tornitura e fresatura, grazie allo sviluppo di tecnologie avanzate che permettono di incorporare anche i processi di rettifica in una soluzione “all in one”. Questa operazione costituisce la fase che richiede maggior precisione e permette di concludere lavorazioni di pezzi industriali ad alto valore aggiunto”, ha sottolineato Silvia Alducci, Vice Presidente di Soraluce Italia. La scelta di un sistema multitasking permette di ridurre l’investimento nel numero di attrezzature, riduce lo spazio necessario per l’impianto e il numero di operatori richiesti. Allo stesso tempo, i sistemi multitasking sono versatili, compatti, presentano una grande flessibilità, migliorano l’efficienza del processo e rendono possibile la produzione di piccoli lotti in modo efficiente. Riducendo la quantità di fermi macchina
e il tempo richiesto per la preparazione dei pezzi e minimizzando i tempi ciclo e il rischio di errori, queste soluzioni rispondono appieno ai requisiti di versatilità, produttività ed efficienza propri del concetto “multitasking”.
I centri multitasking SORALUCE vanno dai centri di lavoro SORALUCE modello TA-M e TR-M, ai montanti mobili della serie F, fino alle macchine a portale gantry o con tavola mobile della serie P, dotate di traversa fissa o mobile. Nei diversi settori merceologici, al fine di aumentare la produttività, è stata evidenziata la necessità di realizzare componenti in un unico piazzamento del pezzo. Per rispondere a questa esigenza SORALUCE ha sviluppato numerose macchine utensili atte alla fresatura/tornitura/rettifica pensate per clienti attivi in differenti settori: beni strumentali, meccanica generale, energia, stampi, ferroviario, aeronautico. Più che mai oggi i clienti hanno la necessità di lavorare rapidamente, riducendo i costi di manutenzione e di attrezzaggio e incrementando le tipologie di operazioni effettuabili in un’unica macchina.
Le soluzioni multitasking possono essere applicate all’intera gamma di macchine Soraluce. Le macchine Soraluce incorporano il mandrino multitasking ad alta coppia con una potenza fino a 43 kW e una coppia di 1220 Nm, con indexaggio ogni 2,5º o 0,001º. La testa multitasking integra un innovativo sistema di bloccaggio rotazionale, che include un blocco del mandrino per qualsiasi angolazione durante le operazioni di tornitura. Questo sistema di bloccaggio previene il danneggiamento dei cuscinetti. Con questo design unico, è possibile
macchine. DAS+® include il monitoraggio del livello di vibrazione, il rilevamento delle vibrazioni in tempo reale e due diverse strategie extra per sopprimere le vibrazioni: le funzioni di sincronizzazione della velocità del mandrino e della variazione della velocità del mandrino. DAS+®rende la macchina più intelligente e aumenta la produttività e la robustezza del processo eliminando le vibrazioni e così facendo riducendo i tempi di ciclo, aumentando la durata dell’utensile, migliorando significativamente la qualità della superficie e riducendo l´usura della macchina. Comprende tutte le conoscenze e l’esperienza di SORALUCE nel campo delle dinamiche di lavorazione, a beneficio dei clienti.
definire l’orientamento della testa e del mandrino con qualsiasi angolazione, evitando così le interferenze con il pezzo e ottimizzando la capacità di lavorazione.
Utensili e mole vengono caricati direttamente nel mandrino utilizzando il sistema di cambio utensili automatico senza la necessità di elementi intermedi. Oltre alla vasta gamma di teste di fresatura, Soraluce dispone anche di teste di tornitura specifiche con elevata capacità di taglio. Inoltre tutte le teste possono essere cambiate in automatico, come gli stessi utensili sia di fresatura che di tornitura (orizzontale/verticale) con attacco C6, C8 e C10. Sono previsti supporti per barre di alesatura lunghe da Ø 100 a Ø 250 mm, con lunghezza fino a 2500 mm, inclusa la soluzione per il cambio testa automatico. Tornitura esterna/interna sono possibili con una sola testa.
Tutte le teste di fresatura, multitasking e tornitura possono essere cambiate in automatico consentendo così un cambio accurato delle teste tramite flange di accoppiamento. L’azienda dispone di un’ampia gamma di tavole girevoli e rototraslanti sia di fresatura che di tornitura. Tavole girevoli con portata da 2 a 200 ton, con diametri fino a 8 m. Viene utilizzata la tecnologia TBS (Table Balance System) per bilanciare le tavole, per correggere la distribuzione dei carichi asimmetrici e garantire un’elevata precisione. La soluzione multitasking incorpora cicli specifici sviluppati da Soraluce presso la Soraluce Software Factory per facilitare le funzionalità di tornitura e rettifica: come la possibilità di gestire contemporaneamente sia i cicli di fresatura che di tornitura, il passaggio dalla modalità fresatura alla modalità tornitura o rettifica automaticamente o la facile programmazione della tornitura e cicli di molatura.
SORALUCE offre ai propri clienti tutta la tecnologia sviluppata dall’azienda per aumentare precisione e produttività, come i dispositivi: Chip Breaker, Adaptive Control, Accura Heads e il suo rivoluzionario sistema DAS+® (Dynamics Active Stabilizer), che include più funzioni per aumentare la capacità di lavorazione delle
Le macchine sono realizzate con una struttura interamente in ghisa e adottano guide lineari a ricircolo di rulli combinate con pattini smorzatori, elementi che garantiscono rigidità dinamica ed elevata precisione volumetrica. La scelta fatta da SORALUCE relativa all’impiego di una struttura totalmente in ghisa è legata al fatto che quest’ultima soluzione non risente di tensioni interne di saldatura che si generano invece nelle strutture elettrosaldate, un fattore che su macchine di medio-grandi dimensioni può alterare considerevolmente la geometria dell’impianto, provocando errori geometrici sul componente da lavorare. Inoltre, la ghisa presenta un elevato coefficiente di assorbimento delle vibrazioni e consente quindi all’utensile di lavorare nelle migliori condizioni, con un conseguente aumento della vita dell’utensile e della qualità della finitura del pezzo. Il sistema delle guide lineari a ricircolo di rulli combinate con pattini smorzatori è importante e garantisce elevata dinamica, rigidità e precisione nelle lavorazioni, ottenendo così un’eccellente produttività, riducendo i costi di manutenzione al minimo. Quindi, estrema rapidità nelle lavorazioni senza rinunciare alla precisione e alla produttività. Flessibilità, dunque è la parola d’ordine per le macchine multitasking SORALUCE le quali permettono di effettuare diverse lavorazioni, tra cui operazioni di fresatura, tornitura, alesatura, foratura, maschiatura e rettifica in un’unica macchina ed in un unico piazzamento. Ciò è oggi possibile con efficienza e precisione per pezzi di differenti dimensioni e forme.
LA NUOVA RETTIFICATRICE CILINDRICA DI PRODUZIONE PER PEZZI DI MEDIE DIMENSIONI È NATA PER SODDISFARE LE ESIGENZE DI UN COMPARTO PRODUTTIVO CHE STA VIVENDO UNA PROFONDA
LLa rapida trasformazione dell’industria automobilistica e la notevole pressione politica esercitata a livello globale per ridurre le emissioni di CO2 e l’inquinamento atmosferico sono foriere di cambiamenti e nuove tendenze del mercato che tutti i costruttori di macchine e di componentistica stanno monitorando con grande attenzione. Tali cambiamenti significano anche grandi opportunità: tutti i propulsori elettrici hanno un cambio in cui vengono utilizzati anche alberi a pignone conico, mentre gli autocarri elettrici a celle a combustibile richiedono alberi e manicotti di alta precisione per i compressori ad alta pressione.
Il rapido sviluppo della mobilità elettrica e di altre propulsioni alternative quindi è una delle cause, insieme ad altri fattori, che ha determinato l’aumento della domanda di rettificatrici adatte per una nuova varietà di componenti nella costruzione dei veicoli. Particolarmente attenta a quelle che sono le nuove tendenze del mercato, in risposta alle nuove esigenze, STUDER - azienda del gruppo United Grinding - ha sviluppato la nuova rettificatrice cilindrica S36, presentata in anteprima mondiale, insieme al nuovo sistema di carico uniLoad, alla prima edizione
di GrindingHub 2022, la fiera internazionale delle tecnologie di affilatura tenutasi lo scorso maggio a Stoccarda.
La S36 si colloca tra la compatta S11 per pezzi piccoli e l’S22 per pezzi di medie dimensioni. Molte caratteristiche della nuova S36 sono simili al suo predecessore, che ha venduto più di mille unità, con l’aggiunta di nuove funzionalità destinate a soddisfare le esigenze di un comparto produttivo che sta vivendo una profonda trasformazione. “La richiesta di soluzioni di rettifica economiche per serie mediograndi rimane costantemente alta, anche con la mobilità elettrica”, ha dichiarato il responsabile del progetto Martin Habegger. Oltre alla costruzione di veicoli, la nuova macchina troverà applicazione anche in una vasta gamma di comparti industriali servendo i settori dell’aerospaziale, dell’idraulica, della produzione di pompe e della fabbricazione di stampi e utensili.
La macchina è progettata per la rettifica esterna produttiva di pezzi a mandrino e di alberi. Una caratteristica eccezionale della nuova macchina è la sua grande mola, che ha un diametro di 610 mm e una
Rettificatrice cilindrica di produzione STUDER S36 Testa portamola della nuova rettificatrice cilindrica di produzione STUDER S36larghezza massima di 125 mm per il momento. La S36 si colloca pertanto al di sopra dello standard nella propria categoria.
La S36 ha una testa portamola fissa, con l’angolo della mola selezionabile a 0, 15 o 30°. La distanza tra le punte è di 650 mm e il peso massimo del pezzo è di 150 kg. Per la sua realizzazione si è fatto ricorso a componenti collaudati, compresi un basamento della macchina in Granitan® e una testa portapezzo con cuscinetti volventi di alta precisione. Inoltre, la macchina è dotata di C.O.R.E. OS, il sistema operativo intelligente e multimarca dello UNITED GRINDING Group - comprensivo di touch panel e comando intuitivo. Grazie all’architettura software uniforme di C.O.R.E., lo scambio dati tra le macchine è possibile senza problemi. Scambio possibile anche con sistemi di terze parti grazie all’interfaccia Umati integrata. Permette anche l’accesso ai prodotti UNITED GRINDING Digital Solutions™ direttamente dalla macchina e senza la necessità di installare hardware aggiuntivo. C.O.R.E. non crea solo la base tecnica per queste e altre applicazioni IoT e dati, ma anche per un comando unitario, semplice e rivoluzionario.
Gli ugelli SmartJet® di nuova concezione per l’alimentazione efficiente e automatica del lubrorefrigerante sono montati di serie. Consentono, d’ora in poi, la gestione del raffreddamento da parte del sistema di controllo della macchina. Come componenti centrali vengono utilizzati una pompa controllata in frequenza e un’unità di misurazione della pressione dinamica mediante le quali diviene possibile regolare la portata in volume con precisione e in linea con il processo - per la sgrossatura, la finitura o la finitura fine. Il fluido
refrigerante raggiunge la mola attraverso un elemento di distribuzione e ugelli a flusso ottimizzato e aggiornabili. “Il concetto garantisce un raffreddamento preciso, efficiente e riproducibile”, sottolinea Martin Habegger, che aggiunge: “proponiamo la S36 con tutta questa moderna tecnologia di rettifica ai clienti con un ottimo rapporto qualità-prezzo”.
In tema di nuovi prodotti, con il sistema di carico uniLoad, STUDER punta sull’universalità e sulla velocità. Grazie a questo nuovo sistema, gli utenti delle rettificatrici cilindriche esterne S31 e S33 hanno quindi l’opportunità di aumentare la qualità e la produttività con l’ausilio del sistema di caricamento automatico. La destrezza dell’operatore nella lavorazione di precisione è un pregio insuperabile. Per una qualità riproducibile, tuttavia, non si può fare a meno dell’automazione nel processo di rettifica.
Grazie al sistema di controllo moderno e intuitivo, uniLoad è così facile da usare che non è necessario alcun addestramento speciale alla programmazione. È stato sviluppato da Wenger Automation e continua la filosofia operativa di STUDER. La conoscenza della programmazione non è richiesta. L’utente deve solo conoscere le dimensioni e il peso del pezzo da lavorare per utilizzare il sistema di carico. Poi la procedura guidata di setup lo accompagna comodamente attraverso i passaggi necessari fino a quando il programma di rettifica non può essere avviato. uniLoad viene proposto con una cella a portale lineare con due pinze parallele ed è adatto per pezzi di alberi fino a una lunghezza del pezzo di 350 mm e un diametro del pezzo di max 100 mm. Quindi, copre una gran parte dello spettro dei pezzi prodotti su queste macchine. Il trasferimento dei pezzi avviene mediante un nastro prismatico regolabile. L’involucro del modulo base adattato al design della macchina e dotato di portello di carico di serie, consente il funzionamento sicuro e pulito dell’impianto. Attualmente, uniLoad è adatto per distanze fra le punte di 650 e 1000 mm. Il sistema di carico viene accoppiato alla macchina da sinistra e raggiunge una lavorazione automatizzata con piena capacità dei piani di carico in un’ora circa. Per i pezzi con un diametro esterno di 34 mm e un diametro delle pinze di 22 mm, 50 pezzi possono essere caricati automaticamente. L’aspetto del sistema di carico si riflette nel design estetico della macchina che, da prodotto standard, consente tempi di risposta e di consegna rapidi. Inoltre, sono possibili anche soluzioni personalizzate. uniLoad è altresì espandibile in modo da poter coprire anche le esigenze future.
STUDER S31 con il nuovo sistema di carico uniLoad Vista dettagliata della testa della pinza dal caricatore uniLoad Catena cadenzatrice regolabile con appoggi prismatici per un massimo di 50 pezziLLa tendenza del futuro ad eseguire lavorazioni complete del pezzo mediante centri di tornitura e fresatura, in grado di gestire alla perfezione entrambe le tecnologie, ha portato già nel 2018 il reparto di sviluppo di INDEX a presentare sul mercato il nuovo G420, un centro di tornitura e fresatura con caratteristiche speciali. Il successo del centro di tornitura multitasking ha determinato l’ampliamento della serie con la variante più grande e potente, INDEX G520, per poi proseguire con il modello leggermente più piccolo INDEX G320, distribuite in esclusiva per l’Italia da Synergon, azienda nata nel 1985 quale rappresentante esclusivo di prestigiose case costruttrici di macchine utensili per la tornitura e lo stampaggio, che oggi è presente sul mercato nazionale con una struttura d’avanguardia,
in grado di assicurare servizi tecnico-commerciali puntuali ed efficienti sia prima sia dopo la vendita delle macchine.
Il G320 è un centro di tornitura e fresatura innovativo che appartiene a una classe a sé stante, soprattutto quando si tratta di efficienza nella produzione e lavorazione ad alte prestazioni di pezzi di medie dimensioni, molto complessi e diversi tra loro. Il centro INDEX G320 offre le migliori prestazioni per l’industria meccanica, automobilistica e aerospaziale, con elevata disponibilità e affidabilità di processo.
La concezione di successo della macchina non è cambiata nel tempo. Grazie a un basamento rigido e ammortizzante
I NUOVI CENTRI DI TORNITURA E FRESATURA INDEX G300 E INDEX G320 INTEGRANO LA GAMMA DI PRODOTTI INDEX. CON UNA LUNGHEZZA DI TORNITURA DI 1400 MM COMPLETANO L’OFFERTA PER UNA EFFICIENTE TORNITURA E FRESATURA DI PEZZI DI MEDIE DIMENSIONIcon struttura a blocchi in ghisa minerale e a guide lineari di grandi dimensioni negli assi X e Z, anche il nuovo G320 offre straordinarie proprietà di stabilità e ammortizzazione nonché valori dinamici per risultati di lavorazione di altissimo livello con un elevata produttività.
Come per i modelli INDEX G420 e G520, il mandrino portafresa motorizzato posizionato sopra l’asse di rotazione con l’asse Y/B con cuscinetti idrodinamici è un elemento essenziale. I suoi potenti azionamenti consentono le più disparate lavorazioni di fori e fresature fino alla lavorazione a cinque assi. In alternativa è possibile scegliere fra 16,6 kW, 72 Nm, 12.000 min-1 (100% ED) o 16 kW, 45 Nm, 18.000 giri/min (100% ED). In parallelo al tempo principale, il mandrino portafresa motorizzato attinge da un magazzino utensili che può contenere fino a 115 utensili (HSK-T63 o Capto C6). INDEX G320 garantisce una truciolatura efficiente anche grazie alle due torrette portautensili montate in basso. Le dodici stazioni possono essere attrezzate costantemente con utensili motorizzati. La torretta può essere traslata non solo in direzione X e Z, ma anche in direzione Y.
La massima lunghezza di tornitura di INDEX G320 è di 1.400 mm. I due mandrini di lavoro identici (mandrino principale e contromandrino) sono raffreddati a liquido e offrono un passaggio del mandrino di 102 mm a 4.000 giri/min. Sono idrodinamici e potenti (44 kW; coppia 525 Nm con 100% ED).
L’ampio spazio di lavoro e la distanza fra mandrino principale e contromandrino consentono di procedere alla truciolatura contemporaneamente sul mandrino principale e
sul contromandrino con il mandrino portafresa motorizzato e le torrette portautensili senza rischio di collisione. La capacità di abbassamento delle torrette portautensili consente inoltre di evitare situazioni con rischio di collisione.
È prevista anche l’automazione del centro di tornitura e fresatura con un’unità di manipolazione a 2 assi integrata e/o la cella robotizzata iXcenter con la quale i pezzi grezzi e quelli finiti possono essere caricati e scaricati in modo rapido, sicuro e flessibile. Come unità di controllo è stata adattata una S 840D SL di Siemens che come sempre può essere utilizzata facilmente con la soluzione cockpit iXpanel di INDEX.
Tutte le fonti di calore ad alta dispersione del G320 vengono raffreddate direttamente con diversi mezzi di raffreddamento tramite circuiti di fluidi. Oltre al mandrino principale, al contromandrino, all’elettromandrino di fresatura e al motore torque dell’asse B, anche il sistema idraulico e l’armadio di controllo hanno un loro circuito di raffreddamento. Il calore residuo viene assorbito direttamente nel refrigerante, spostato dal centro della macchina e convogliato per un altro utilizzo, se necessario: ad esempio, per la produzione di riscaldamento per l’ambiente di lavoro, per l’acqua di servizio o per altre fasi della produzione. Il recupero del calore residuo della macchina consente una riduzione sostenibile dei costi energetici dell’azienda. Se il calore residuo della macchina immagazzinato nel mezzo di raffreddamento non può essere utilizzato in altro modo, l’interfaccia “acqua fredda” consente di dissipare il calore senza ripercussioni sul clima.
LLe macchine da tornitura hanno la capacità di poter produrre pezzi lunghi, che superano il limite di 2,5 volte il diametro. Questa possibilità che costituisce la principale caratteristica delle macchine da tornitura è realizzata dalla boccola di guida, elemento centrale, insieme al mandrino mobile della macchina, che consente di trascinare la barra. In base al funzionamento tipico della tornitura, l’utensile è fisso e la barra si muove a Z, diversamente dai torni a fantina mobile nei quali gli utensili sono mobili. Questo principio vale anche per i torni plurimandrino, dove la barra rimane fissa dopo la sua alimentazione. Dal 2011, con la MultiSwiss 6x14, Tornos ha inaugurato un concetto innovativo, il mandrino mobile che consente in particolare di separare le guide e quindi irrigidire gli elementi. Autentica rivoluzione, MultiSwiss rappresenta una nuova linea di prodotti che costituisce l’anello di congiunzione tra torni multimandrino e torni monomandrino. Dispone di 6 o 8 mandrini mobili che utilizzano la tecnologia della motocoppia per l’indicizzazione del bariletto. Estremamente rapida, consente di avvicinare i tempi di ciclo dei multimandrini a camme.
Tutte le macchine MultiSwiss sono dotate di mandrini a
motorizzazioni sincrone di grande potenza, che permettono elevati livelli di dinamicità della macchina con tempi di accelerazione molto brevi (0-8.000 giri/min in meno di un secondo su una MultiSwiss 6x16), e dispongono di coppie importanti. Ciascun mandrino è indipendente in termini di velocità e posizionamento angolare. È possibile assicurarsi un posizionamento angolare tra i mandrini nonché con il contromandrino. Oltre al proprio asse C, ogni mandrino ha un proprio asse Z guidato da cuscinetti idrostatici. La tecnologia idrostatica è una delle chiavi del successo delle macchine MultiSwiss. Ciascun mandrino è infatti dotato di cuscinetti idrostatici in ceramica per garantire stabilità termica, precisione e durata anche in caso di carico elevato. Questa tecnologia permette di aumentare lo smorzamento durante la lavorazione. La durata della vita utile degli utensili può essere prolungata, in alcuni casi, di oltre il 30%. Lo smorzamento supplementare prolungato permette anche di ottenere degli eccellenti stati di superficie di lavorazione e, contemporaneamente, di lavorare serenamente i materiali più duri.
Il bariletto costituisce il cuore della macchina e alla
UNA NUOVA LINEA DI PRODOTTI CHE COSTITUISCE L’ANELLO DI CONGIUNZIONE TRA TORNI MULTIMANDRINO E TORNI MONOMANDRINOsua realizzazione viene accordata particolare attenzione. Compatto, quest’ultimo può essere equipaggiato con 6 oppure 8 elettromandrini a motorizzazioni sincrone. La produttività dei torni multimandrino è oggi più che mai essenziale: ogni centesimo di secondo conta. Il bariletto delle macchine MultiSwiss garantisce la massima precisione in tutte le posizioni. Grazie alla tecnologia di indicizzazione tramite motocoppia, MultiSwiss permette di ottenere tempi di indicizzazione record, inferiori a 0,4 s e nel modo più silenzioso. L’assenza di dentatura Hirt consente di risparmiare secondi preziosi, generalmente dedicati al bloccaggio e sbloccaggio del bariletto.
La precisione di una macchina è strettamente correlata al suo comportamento termico. La temperatura della macchina è interamente controllata dall’olio di taglio che, a sua volta, è controllato da uno scambiatore di calore a piastre. Il cuore della macchina viene mantenuto a temperatura costante (+/- 0,5 gradi) anche durante un eventuale arresto dovuto a un intervento nel corso della produzione. La macchina dispone di una doppia vasca caldo/freddo che consente di ottimizzare permanentemente la temperatura del cuore. MultiSwiss utilizza l’olio da taglio per la gestione della tecnologia idrostatica in grado di eliminare i rischi di contaminazione.
Il motore coppia che aziona il bariletto e i motomandrini garantiscono anche alle macchine MultiSwiss una particolare silenziosità, che rende il loro utilizzo ancora più sicuro e confortevole per l’operatore.
Mentre le macchine monomandrino utilizzano la tecnica della boccola di guida per sostenere il pezzo, questo non avviene per la macchina MultiSwiss, sulla quale è stata privilegiata la soluzione di supporto. Tornos ha riflettuto a lungo sull’utilizzo di
una boccola che potesse essere montata sul bariletto, ma questa soluzione poneva diversi problemi legati all’evacuazione trucioli e, soprattutto, alle regolazioni e all’avviamento della macchina. Oggi le macchine MultiSwiss godono di un’ottima accessibilità e sono rapide da avviare, l’evacuazione trucioli è eccellente e la tecnologia idrostatica integrata nel mandrino della macchina offre risultati ottimali e consente di ridurre l’usura degli utensili anche con i materiali più particolari.
L’aggiunta di una boccola di guida avrebbe compromesso le caratteristiche principali della macchina ed è stata quindi adottata una soluzione più classica, con supporti montabili nell’area di lavorazione. Questa soluzione consente di garantire un’eccellente ripetibilità e assicura un avviamento rapido senza compromettere l’evacuazione trucioli.
MultiSwiss è stato pensato per l’operatore: quest’ultimo può entrare nella macchina e sostituire i portautensili senza doversi chinare all’interno della macchina. L’accesso frontale è semplice, ergonomico, sicuro, innovativo e unico sul mercato: nessuna macchina raggiunge tali livelli di libertà. L’evacuazione dei trucioli è esemplare, grazie alle slitte verticali che cadono direttamente sul convogliatore.
Il sistema 8x26, presentato alla fiera EMO del 2021, grazie alle sue otto postazioni, permette di effettuare operazioni complesse. Ogni postazione può ricevere 4 utensili ciascuna. Nel caso di pezzi più semplici, il numero di postazioni incrementate permette di eseguire operazioni di sgrossatura in grado di aumentare lo stato di efficienza. Il contro-mandrino, montato su due assi, consente di lavorare in totale autonomia con 4 utensili di cui 2 girevoli. La macchina è disponibile in 3 configurazioni: base senza asse y, intermedia con 3 assi Y e completa con 6 assi Y per i pezzi più complessi.
Cresce l’automazione nel mondo e aumentano sempre di più i robot impiegati nella produzione industriale. La digitalizzazione del mondo industriale, oltre all’implementazione dei processi produttivi, ha reso i robot protagonisti di tutto ciò che è legato alla “movimentazione” dell’Industria 4.0, identificandoli con gli elementi che meglio rappresentano la trasformazione e l’automazione di nuova generazione delle aziende. Il tutto reso possibile da una robotica sempre più agile e flessibile, capace di soddisfare non solo le esigenze del settore automotive e del mondo della lavorazione dei metalli, comparti storici di applicazione dell’automazione industriale, ma anche di settori industriali diversi, che oggi richiedono appunto soluzioni di automatizzazione più flessibili, come quelli del packaging, food&beverage, farmaceutico, cosmetico, ecc. L’integrazione tra macchinari, sistemi e robot è la chiave per lo sviluppo dell’automazione di nuova generazione. La convergenza tra automazione e intelligenza artificiale rappresenta nuove opportunità per i processi aziendali, destinate, nei prossimi anni, a crescere a livello globale e a diventare terreno fertile per definire le proprie strategie di automazione.
Il mercato della robotica Dal 2019 ad oggi, il mercato dei robot a livello globale ha subito una notevole accelerazione, dovuta anche alla pandemia. L’industria della robotica ha un tasso di penetrazione altissimo, in particolare modo per quanto riguarda il comparto della logistica, dove quella di magazzino registra dati incredibili. Per il 2021 l’IFR ha stimato una crescita delle vendite del 13% a quota 435.000 unità, superando così il livello record raggiunto nel 2018. Rispetto al 2015 il mercato è raddoppiato con una previsione di valore al 2025 da 73 miliardi di dollari. Questa crescita, che oggi viene in parte vista come una tendenza dettata dal processo di digitalizzazione delle imprese, tra un paio di decenni potrebbe trasformarsi in una necessità, a fronte
dell’invecchiamento della popolazione europea che, entro il 2050, potrebbe portare ad una carenza di manodopera giovanile, già oggi difficile da reperire, soprattutto se qualificata. Secondo uno studio delle Nazioni Unite da qui al 2050, le persone in età lavorativa – ossia tra i 20 ed i 64 anni – saranno ben 95 milioni in meno rispetto al 2015. La Germania, che appartiene ai cinque principali mercati di robot nel mondo (Cina, Giappone, USA, Corea, Germania) detiene il 33% del totale delle installazioni in Europa. Segue l’Italia con il 13% e la Francia con l’8%. Nel 2024 si dovrebbe raggiungere il notevole traguardo di 500.000 unità installate all’anno in tutto il mondo (fonte: World Robotics 2021 report). L’aumento del mercato dei robot è dovuto principalmente a quelli collaborativi o cobot, più flessibili e, spesso, più sostenibili in termini di investimento e di ritorno già nel breve-medio termine. Il settore di robot, cobot e tecnologie connesse ha un potenziale enorme. Le stime indicano una crescita per i prossimi cinque anni fino ad un valore complessivo del comparto pari a 190 miliardi di dollari (fonte: Allied Market Research).
La situazione italiana Nel 2021, la produzione italiana di robot è cresciuta del 6,6%, rispetto al 2020, attestandosi a 2.220 unità. Il risultato positivo è stato determinato, esclusivamente, dall’incremento delle consegne sul mercato interno cresciute del 22,6% a 1.215 unità. Le vendite sui mercati esteri si sono invece contratte a 1.005 nuove unità, in calo del 7,9% rispetto all’anno precedente. È quanto emerge dai dati Siri (Associazione italiana di robotica e automazione) e Ucimu (Associazione dei costruttori italiani di macchine utensili, robot, automazione), presentati alla scorsa edizione di Lamiera. Per quanto riguarda il consumo, particolarmente dinamica è risultata la domanda interna di robot che, dopo due anni consecutivi di calo (biennio 2019-2020), è tornata a crescere. In Italia, la diffusione della
ROBOT E AUTOMAZIONE LE SFIDE PER L’INTEGRAZIONErobotica nelle aziende italiane ha toccato un nuovo record nel 2021. Rispetto al 2008, le vendite sono aumentate del 156%, passando da 4.556 unità a 11.672 robot installati con una crescita del 50% sul 2020, superiore anche rispetto alle consegne del 2019 (+28,7%) e con un tasso medio annuo di incremento delle vendite del 7,5%. I dati sono positivi sia per la produzione che per l’export, l’import e consegne. La vivacità del mercato domestico ha premiato gli acquisti dall’estero come dimostra il dato di import, risultato pari a 10.457 nuove unità installate (+54% rispetto al 2020). L’incremento del numero dei nuovi robot installati nel 2021 in Italia è risultato di quasi il 30% superiore al numero delle unità acquistate nel 2019, prima della pandemia. Più nel dettaglio, tra le vendite nel 2021, l’area di applicazione predominante, con 8.377 unità, è quella dei robot per manipolazione (72% del totale), seguono la saldatura (1.239 robot per una quota del 10,6%) e l’assiemaggio (1.149 unità che rappresentano il 9,8% del totale). I più venduti sono gli Articolati (9.268 unità), seguiti dagli Scara (1.362 unità) e dai robot Cartesiani (670 unità). Tutte le tipologie hanno fatto registrare crescite a doppia cifra sia sul 2020 sia sul 2019. Entrando ancora più nel merito delle suddivisioni per categoria, nella manipolazione il 44,1% delle applicazioni attiene ai materiali, il 22,1% riguarda il carico e scarico e il 18,4% la pallettizzazione. Rispetto alla saldatura invece, le vendite di robot per saldatura quella ad arco risultano in crescita molto più di quelle per la saldatura a punti, che restano ancora dietro ai numeri del 2019. Da ultimo, nell’assiemaggio la componente inserimento e montaggio cresce più dell’assiemaggio meccanico (fonte: Siri, l’Associazione Italiana di Robotica e Automazione, e Centro Studi Ucimu –Sistemi per Produrre). Crescono quindi le vendite e l’impiego dei robot industriali in tutto il mondo, in tutti i settori, nell’elettronica e nell’automotive in particolare, e l’Italia è il sesto Paese al mondo e il secondo nel Vecchio Continente, per vendite e implementazioni di robot industriali e uno dei protagonisti assoluti nella ricerca che vede nell’intelligenza artificiale uno dei principali driver.
Ai robot vengono principalmente affidate operazioni di asservimento di macchine e utensili (31%), assemblaggio (31%), pick-up dei prodotti e di handling di piccoli prodotti o manufatti anche complessi che devono essere montati nelle linee, ed infine pallettizzazione. Il mondo della robotica non contempla solamente robot, cobot e bracci robotici, ma anche tool e tutto ciò che attiene alla parte di controllo e a sistemi di calcolo sempre più potenti in grado di supportare soluzioni sempre più prestazionali. CPU che permettono notevoli aumenti di potenza e definiscono nuovi standard nella velocità di elaborazione, consentono all’utilizzatore non solo la realizzazione di sistemi più complessi, ma costituiscono anche la base per una significativa riduzione dei costi per l’hardware. Nel segno dell’integrazione, in questi ultimi anni, un numero sempre maggiori di aziende hanno offerto ambienti di sviluppo integrati dedicati dapprima a soluzioni di controllo logico, safety e motion, ed oggi estesi anche a sistemi di visione e robotica applicata in fabbrica. Tutto ciò proprio grazie alle velocità di calcolo delle CPU sempre maggiori, in grado di coordinare tutte le funzioni della macchina.
Si tratta di piattaforme completamente integrate che offrono una
connessione biunivoca tra i dati del sistema centrale PLC con i movimenti e le operazioni dei robot in azienda. Un incrocio di dati che permette di individuare anche eventuali malfunzionamenti e anomalie, in ottica di manutenzione preventiva e predittiva.
I tool sono la parte essenziale della robotica collaborativa. Non basta infatti avere robot collaborativi se non sono dotati di utensili collaborativi, in grado di migliorare l’integrazione del robot con la linea di produzione e più in generale con le attività legate alla produzione. Le più moderne soluzioni di robotica e di automazione sono sempre più dotate di tecnologie e applicazioni legate all’intelligenza artificiale (AI). Anzi possiamo senza dubbio affermare che l’intelligenza artificiale sia ormai un elemento centrale della robotica, caratterizzando sempre di più il robot come elemento intelligente in grado di connettere la percezione all’azione. L’AI è uno dei principali driver dell’industria 4.0 e della smart industry. I suoi progressi sono caratterizzati da un tasso di crescita sempre più elevato e coinvolgono tecnologie, piattaforme e partnership su diversi livelli. Con la possibilità di disporre di una rete sempre più prestazionale, potenze di calcolo elevate e sensori molto più sofisticati, l’intelligenza artificiale è diventata parte imprescindibile delle strategie di automazione industriale, che hanno nei dati e nelle informazioni da essi ricavate ed elaborate l’elemento fondante. È proprio grazie a tool sempre più spinti, che si aggiungono al classico controllo, che è possibile interagire con i gemelli digitali e migliorare i processi produttivi con strumenti preventivi e predittivi. Sono sempre di più le aziende che dichiarano di impiegare una robotica integrata con l’intelligenza artificiale. Questo ormai inevitabile progredire di tecnologie che si basano sull’uso dell’intelligenza artificiale tuttavia richiede competenze di automazione, motion, visione, sviluppo software e interfacce, e-learning, protezione dati e contenuti, integrazione dei dati, identità digitali, ecc.
L’enorme progredire della robotica è frutto anche di sensori intelligenti (smart sensor) in grado di raccogliere più dati e in modo più mirato e alla migliore capacità di intervenire sull’ambiente lavorativo grazie all’intelligenza artificiale. Grazie all’AI è possibile gestire anche ambienti fisici di lavoro non perfettamente strutturati, che presentano degli elementi di complessità. Un tipico esempio è costituito delle operazioni di picking, tipiche della logistica, relative all’operazione di carico o prelievo di oggetti e prodotti da un contenitore in cui sono presenti pezzi alla rinfusa per il successivo posizionamento su scaffali o imballaggio. Queste operazioni richiedono l’uso di intelligenza artificiale per la risoluzione di problemi fisici in scenari complessi; cosa ben diversa dalla risoluzione di problematiche di “pura informazione”. Il plus offerto dall’intelligenza artificiale, e più propriamente dal machine learning e dal deep learning alle macchine, è la capacità di imparare a svolgere compiti specifici elaborando grandi quantità di dati e riconoscendo i modelli. Nella robotica industriale questo corrisponde alla possibilità di contare su moltissime operazioni svolte in ambiente reale che, diversamente, non sarebbe sempre possibile portare a termine.
artificiale è la computer vision. Tutte le operazioni svolte dal robot sono conseguenza delle immagini ricevute. Dalle immagini e dalla visione si passa all’azione. Con il termine “machine vision” o visione artificiale si intendono “le attività di estrazione e di elaborazione di informazioni tramite video o immagini digitali ottenute da telecamere”. Lo scopo di queste attività industriali è riconoscere, misurare ed esaminare oggetti o ambienti per migliorare la qualità generale dei processi produttivi. La visione artificiale è il risultato dell’integrazione di componenti ottici in grado di acquisire immagini, di soluzioni embedded (hardware) in grado di elaborare informazioni e di piattaforme software per interpretare il flusso di dati. La continua evoluzione dei sistemi di visione industriale nei processi di controllo fa sì che questi sistemi trovino una sempre maggiore applicazione in vari ambiti e settori, tra i quali il riconoscimento e il tracking di oggetti, l’ispezione visiva di prodotti o catene di produzione, l’autoapprendimento tramite machine learning, l’analisi predittiva e molti altri. Questo, in virtù dei molti benefici che sono in grado di apportare le soluzioni di machine vision ad un progetto di intelligenza artificiale applicata all’automazione industriale. Tra i principali vantaggi possiamo elencare:
• il controllo qualità: un migliore controllo del processo produttivo favorisce un prodotto finale costantemente verificato con affidabilità e precisione;
• la riduzione dei costi: la possibilità di operare in modo ripetitivo 24/7 consente l’ottimizzazione delle risorse interne;
• migliori performance: i processi di ispezione industriale e monitoraggio predittivo rendono l’intero processo produttivo più efficiente.
Un’altra direttrice su cui si sta muovendo la robotica è la facilità di programmazione, resa possibile da software dedicati che fanno uso di diagrammi a blocchi e si basano su una logica drag and drop. Grazie ad interfacce utente semplificate che abilitano una semplice programmazione o la regolazione e la guida manuale dei robot, implementare un robot non è più un compito complesso. Molto spesso, le aziende produttrici così come i fornitori terzi offrono dei pacchetti hardware e software che rendono sempre più semplice questa operazione. Sono quelle che vengono definite offerte “ecosistemiche”, in grado di ridurre lo sforzo e il tempo di funzionamento. La disponibilità e l’ampia offerta di robotica a basso costo comporta una maggiore facilità di configurazione e installazione, con applicazioni specifiche e, in alcuni casi, preconfigurate. I fornitori offrono programmi standard combinati con pinze, sensori e controller, mentre gli app store forniscono routine di programmazione per varie applicazioni e supportano l’impiego di robot a basso costo. Un altro aspetto riguarda la maggiore capacità di
interazione o collaborazione con l’operatore. Oggi sono disponibili applicazioni collaborative che sono in grado di sostituire l’operatore nello svolgimento di mansioni pesanti, faticose, ripetitive. In base al grado di interazione con l’uomo, si possano utilizzare diverse tipologie di robot. Nel mercato della robotica collaborativa, ogni giorno vengono presentate nuove applicazioni, la cui scelta è funzionale ad un’analisi preliminare sulla produttività della macchina ed è legata alla frequenza dell’interazione tra uomo e robot (assente, occasionale o continuativa). Dove è assente l’interazione può ancora essere impiegata la robotica industriale; per le applicazioni che vedono uomo e robot fianco a fianco, è meglio ricorrere ai robot collaborativi, che sono in grado di condividere lo spazio di lavoro con gli operatori in modo più semplice, più versatile e più produttivo. I robot quindi possono essere robot industriali equipaggiati con nuovi dispositivi per renderli collaborativi, oppure robot “nativamente collaborativi”, con un design specifico e una forma del cobot smussata in ogni possibile punto di contatto con l’esterno per assicurare all’operatore un senso di maggiore sicurezza e armonia.
A questo proposito, è bene ricordare che un altro aspetto importante è quello della sicurezza dell’interazione fra l’uomo e la macchina.
Altra sfida per i produttori di robot è il potenziamento dei meccanismi di interazione uomo-macchina che non riguardano soltanto la robotica collaborativa ma anche la capacità dell’operatore di addestrare i robot e istruirli affinché una volta istallato possa eseguire operazioni in base ai comandi. Si tratta di un processo ancora complesso che quindi è importante semplificare, soprattutto per chi finora è stato abituato ad utilizzare un’automazione meno complessa. La robotizzazione dell’asservimento macchina, prima con l’introduzione dei robot tradizionali e poi con l’aggiunta dei collaborativi, può rappresentare uno step difficile da superare. Occorre perciò lavorare per integrare due mondi che molto spesso “parlano” lingue completamente diverse. In tal senso, le celle robotizzate su postazioni mobili possono essere d’aiuto, potendo essere programmate per determinate funzioni e poi spostate in diversi punti del processo produttivo per risolvere commesse da evadere su diversi tipi di macchinari senza costruire tanti impianti ad hoc. Con un unico cobot e la stessa cella di programmazione ci si può spostare, ad esempio, in una prima fase, per gestire il carico e scarico di materiali, e in un secondo momento per aiutare l’operatore mediante il passaggio di pezzi e componenti. Sono soluzioni anche a misura di PMI che spesso permettono la lavorazione di lotti di dimensione ridotta e consentono di gestire continui cambi di produzione. In conclusione, facilità di programmazione, flessibilità operativa e limitazione degli ingombri sono alcuni dei vantaggi offerti da robot e cobot di ultima generazione e le leve che spingono le aziende a integrarli nelle linee produttive.
Le telecamere intelligenti AX di Baumer combinano l’acquisizione di immagini di alta qualità e una potente elaborazione delle immagini in un alloggiamento di livello industriale, rendendole la piattaforma di elaborazione delle immagini perfetta per l’Industria 4.0 e le applicazioni di Intelligenza Artificiale (AI).
Il mercato dell’elaborazione industriale delle immagini si è sviluppato rapidamente negli ultimi anni e oggi è difficile immaginare molti settori senza di essa. Sempre più applicazioni sono coperte da tecniche di imaging, ad esempio per rendere i processi produttivi il più possibile flessibili ed efficienti. In passato, le soluzioni di elaborazione delle immagini erano solitamente sviluppate da integratori di sistemi altamente specializzati, ma oggi gli utenti finali e gli OEM lo fanno sempre più spesso in modo indipendente.
L’intelligenza artificiale e il Deep Learning completano l’elaborazione industriale delle immagini
Il mercato dell’IA nell’elaborazione delle immagini continuerà a crescere. Questo non dovrebbe sorprendere: l’elaborazione delle immagini, con i suoi dati complessi, si presta particolarmente bene all’uso di algoritmi basati sull’IA. Tuttavia, i classici processori (CPU, Central Processing Unit) non sono molto adatti a lavorare con le reti neurali. Per
questo motivo, spesso vengono utilizzati processori grafici ad alte prestazioni (GPU, Graphics Processing Unit) o circuiti integrati appositamente ottimizzati e specifici per le applicazioni (ASIC, Application-Specific Integrated Circuit), che sono più adatti per i calcoli di rete necessari grazie alla loro architettura altamente parallela. Le smart camera AX integrano direttamente questi due aspetti e sono dotate della piattaforma leader di mercato NVIDIA Jetson, che oltre a una GPU ad alte prestazioni offre anche ASIC appositamente progettati per l’IA sotto forma di core DLA (Deep Learning Accelerator cores
Industria 4.0 e lavorazione at-the-edge L’Industria 4.0 offre significativi guadagni di efficienza e riduzioni dei costi grazie alla completa digitalizzazione, dalla progettazione del prodotto alla produzione e alla distribuzione. Ad esempio, le informazioni necessarie sull’oggetto da produrre possono essere ottenute direttamente dal cloud per
Le Smart Camera AX, liberamente programmabili, combinano una robusta tecnologia di telecamere di livello industriale, moduli NVIDIA Jetson AI leader di mercato e sensori CMOS di Sony ad alte prestazioni per creare una piattaforma di elaborazione delle immagini liberamente programmabile. (Foto: Baumer)verificare le caratteristiche specifiche del cliente. Il risultato può essere comunicato al PLC. Se l’elaborazione dei dati avviene direttamente nella telecamera, come nel caso delle telecamere intelligenti AX, si parla di vision-at-the-edge.
Telecamere intelligenti: piattaforme di elaborazione delle immagini di oggi e di domani Spinto dalle tendenze dell’IA e del Deep Learning, nonché dall’Industria 4.0 e dall’edge processing, il mercato dell’elaborazione delle immagini continuerà a subire grandi cambiamenti nei prossimi anni. Molte attività che attualmente vengono gestite con sistemi PC convenzionali saranno ancora più facili da implementare in futuro con l’aiuto di piattaforme di elaborazione delle immagini liberamente programmabili come le smart camera AX. La potenza di calcolo dei moduli NVIDIA, l’apertura del sistema e il supporto di standard consolidati svolgeranno un ruolo decisivo nel loro successo. Le smart camera AX rappresentano la piattaforma di elaborazione delle immagini perfetta per oggi e per domani.
Le aziende cercano di fare più efficienza, puntano a ridurre i costi e aumentare la capacità produttiva. Allo stesso tempo, la produzione ‘just in time’ e personalizzata con i magazzini pieni di scorte non è più sostenibile: se non c’è il materiale necessario a disposizione, la produzione si blocca subito.
Ecco perché per centrare tutti questi obiettivi un’intralogistica moderna ed efficiente è ormai fondamentale. L’azienda moderna e al passo con i tempi, la Smart Factory, è un ambiente e un sistema dove tutto deve girare alla massima efficienza e velocità. Ogni attività è sincronizzata, ciò che serve deve essere dove serve, al momento giusto. Non ci devono essere intoppi, niente perdite di tempo o blocchi delle operazioni. E a fare funzionare bene l’azienda sono l’intralogistica e le sue tecnologie, che gestiscono ogni cosa che si muove all’interno degli impianti –materie prime, materiali, pezzi e componenti, scorte, semilavorati, prodotti finiti –, da quando arriva dai fornitori a quando esce per i clienti. L’efficienza della produzione dipende anche, e innanzitutto, dall’efficienza dell’intralogistica. Perché se non funziona, la macchina produttiva rallenta, si inceppa, si blocca. Migliorare l’intralogistica significa quindi migliorare le linee produttive e tutta l’azienda in generale e i suoi risultati.
Produzione e intralogistica devono essere più flessibili La produzione deve essere sempre più flessibile, e quindi allo stesso modo anche l’intralogistica aziendale: il robot collaborativo diventa il migliore alleato della squadra che segue l’assemblaggio, mentre la tracciabilità delle operazioni è essenziale per far funzionare al meglio l’intera macchina aziendale. Per montare centinaia di varianti sulla stessa linea servono pezzi e componenti corretti nel momento giusto. Ecco perché l’intralogistica a monte e a valle della produzione deve essere altrettanto efficiente, flessibile e totalmente integrata nell’ambiente produttivo. Deve seguirne il flusso, condividendo in modo smart le informazioni del pezzo che andrà assemblato. Un sistema intralogistico efficiente ed evoluto permette di ottimizzare i tempi, ridurre sprechi, consumi anche energetici, e quindi tagliare i costi. Le tecnologie e le soluzioni Bosch Rexroth per l’intralogistica aziendale danno risposte concrete ed efficaci in tutti questi ambiti.
Tecnologie per l’intralogistica smart e più efficiente Ottimizzare il processo di produzione, automatizzare e rendere più efficiente una linea complessa, velocizzando i tempi e riducendo gli spazi necessari. Nello stabilimento Bosch a Homburg in Germania,
questi erano gli obiettivi da centrare e da raggiungere, e sono stati realizzati con l’utilizzo dei cobot APAS di Bosch Rexroth, in grado di garantire flessibilità operativa e produttiva e che hanno portato all’automazione completa del processo. Nello stabilimento tedesco, Bosch doveva in pratica aumentare la capacità di produzione per tenere il passo con la rapida crescita della domanda di mercato, ad esempio per quanto riguarda i sistemi di iniezione per veicoli commerciali. Con l’assistente APAS il gruppo ha a disposizione una tecnologia robotica altamente flessibile, ha automatizzato i processi di produzione, alcuni dei quali prima venivano eseguiti manualmente. Alleggerendo il carico di lavoro dei dipendenti e aumentando la produttività in condizioni in cui lo spazio è un fattore critico.
Ottenere meno errori, meno sprechi e meno fermi macchina
È anche il caso, ad esempio, dello stabilimento Bosch a Feuerbach, sempre in Germania. In questo impianto l›assistente di produzione APAS assicura la massima qualità del prodotto finale: l›ispezione di fine linea viene infatti eseguita da un ispettore mobile APAS. I pezzi da testare sono consegnati in blister su carrelli, vengono prelevati da due robot e nell’ultima stazione un cobot equipaggiato da un complesso sistema di telecamere controlla da tutti i lati e cattura varie immagini a scatto singolo. Un altro esempio è quello dei robot mobili, intelligenti e interattivi ActiveShuttle, in grado di muoversi e orientarsi in modo autonomo all’interno della fabbrica. ActiveShuttle comunica perfettamente con i sistemi di assemblaggio e gestisce in modo avanzato ogni singola attività della flotta. Con queste soluzioni tecnologiche, Bosch Rexroth soddisfa le esigenze dell’intralogistica moderna che oggi richiede flussi di materiali sempre più complessi con un’ampia varietà di componenti ed elevati numeri di produzione. Grazie al trasporto autonomo, i processi intralogistici sono resi più flessibili senza dover modificare l’infrastruttura dello stabilimento. Il futuro delle fabbriche, della produzione e del lavoro è costituito da un ponderato mix tra nuove tecnologie, intelligenza artificiale, machine learning e competenze adeguate. La visione e le soluzioni di Bosch Rexroth si sviluppano in questa precisa direzione con l’obbiettivo di ottenere meno sprechi, meno errori e meno fermi macchina.
Una soluzione che abbina il meglio del machine learning e della visione tradizionale basata su regole in un sistema di visione completamente integrato. A tutto vantaggio della semplificazione della factory automation. La risoluzione di problematiche di automazione di fabbrica complesse, senza bisogno di conoscenze di deep learning o di visione artificiale oggi è possibile.
L’innovativa soluzione In-Sight 2800 di Cognex consente ad aziende di ogni dimensione di semplificare l’integrazione, di soddisfare gli specifici requisiti applicativi e di ottenere una più elevata qualità dei prodotti grazie ad una facilità d’uso elevata, alla funzionalità multiclasse e di aree multiple di interesse. Veloce implementazione davvero alla portata di tutti La visione artificiale e il deep learning sono note per la loro alta capacità e, di rimando, per la complessità di una efficace implementazione. Ma passi avanti nella factory automation, hanno portato alla creazione di una serie di strumenti di semplicissima usabilità.
Sistema di visione Cognex In-Sight 2800.
In-Sight 2800 è stata progettata per essere semplice da configurare, senza bisogno di una programmazione avanzata e con un addestramento del tutto simile a quello di un nuovo addetto alla linea. L’Edge learning incorporato nella soluzione è in grado di eseguire le necessarie distinzioni apprese molto rapidamente.
L’Edge learning è un sottoinsieme del deep learning in cui l’elaborazione avviene direttamente sul dispositivo utilizzando un insieme di algoritmi pre-addestrati. La tecnologia è semplice da impostare, richiede per l’addestramento meno tempo e meno immagini rispetto alle soluzioni più tradizionali basate sul deep learning. In queste ultime, l’automazione di diverse applicazioni di classificazione può richiedere vari giorni o settimane, oltre che centinaia di immagini e ore di analisi da parte di esperti nella visione
e nel deep learning. Per contro, l’implementazione degli strumenti di Edge learning di In-Sight 2800 richiede pochi minuti, una manciata di immagini di addestramento e l’attenzione di un tecnico che sa del problema da risolvere, ma che non deve necessariamente avere conoscenze specifiche di visione o di deep learning.
Machine learning facile da usare con una flessibilità senza precedenti Sviluppati grazie ad anni di esperienza nella factory automantion, gli strumenti di visione Cognex sono specificamente focalizzati sui fabbisogni delle operazioni di linea. Il vantaggio di questa ben collaudata tecnologia diventa sempre più evidente man mano che gli errori diventano più impercettibili e difficili da rilevare. Ad esempio, un capsulatore rotante può sbagliare la filettatura, danneggiare o lasciare uno spazio vuoto durante la tappatura di una bottiglia. Molti sistemi sono in grado di rilevare facilmente grandi errori visibili. La differenza emerge quando il gap è quasi impercettibile. Altri sistemi possono non rilevare un errore di questo tipo, causando potenziali perdite o contaminazioni. Grazie alla combinazione dell’innovativo Edge learning e strumenti di visione artificiale mirati, In-Sight 2800 classificherà i difetti quasi impercettibili come inaccettabili. Facile da usare, addestrabile con poche immagini, capace di operazioni multiclasse e multi-ROI (region of interest – aree di interesse), il sistema di visione In-Sight 2800 di Cognex sta trasformando la factory automation.
macchina, al fine di ottimizzarne le impostazioni ed evitare sovratemperature che potrebbero introdurre false o mancate letture del cursore. Completa il set di funzioni la rilevazione di out of range, ovvero dello spostamento del cursore fuori dall’area di lavoro, dovuto a perdite del segnale, anche di pochi mSec, non rilevabili dal PLC.
Tra gli smart sensor di Gefran –multinazionale italiana specializzata nella progettazione e produzione di sensori, strumentazione per il controllo di processi industriali, azionamenti elettrici e sistemi per l’automazione –spicca la serie di trasduttori di posizione magnetostrittivi WPL (HyperWave Profile IO-Link), dotata di interfaccia IO-Link 1.1, che assicura un’integrazione e una comunicazione ottimizzata con le nuove architetture 4.0 tipicamente utilizzate negli impianti di medie-grandi dimensioni, destinati ad un’ampia varietà di applicazioni, tra cui plastica, alluminio, metallo, legno, ceramica, vetro e automotive.
I sensori WPL, certificati cULus, sono gli unici sul mercato in grado di fornire, contemporaneamente, dati ciclici relativi a posizione e velocità di spostamento del cursore, disponibili anche in versione
con 2 uscite SSC (Switching Signal Channel), utili per l’impostazione di soglie di controllo o di allarme. Degne di nota anche le informazioni acicliche acquisite dai sensori, dati validi sia ai costruttori di macchine per valutarne lo stato di utilizzo e i potenziali guasti, così da migliorare la progettazione delle serie successive, sia agli utilizzatori finali, per mantenere l’impianto in perfette condizioni e per discriminare le cause di errore, in caso di riparazione. Nello specifico, il sensore memorizza il numero di Km realizzati e il time in movement, a favore di una manutenzione periodica programmabile (ad es. ingrassaggio, cambio delle guarnizioni, pulizia). Consente, inoltre, di registrare velocità e accelerazione massime, con l’obiettivo di ricostruire le potenziali cause della produzione di lotti anomali, nonché la temperatura più alta raggiunta dalla
La sostituzione del trasduttore risulta altresì particolarmente veloce, in quanto il master IO-Link riconfigura i parametri, rendendoli idonei al nuovo sensore. In aggiunta, i cavi di connessione IO-Link, standardizzati, facilmente reperibili in commercio e ready-to-use, sono garanzia di un’installazione semplificata. Inoltre, Gefran ha introdotto i sensori di posizione WPA-F e WRA-F: i primi con tecnologia magnetostrittiva HYPERWAVE e connettività PROFINET®, disponibili con protocollo di trasmissione RT (Real-Time Ethernet) o IRT (Isochronous Real Time) Synchronized.
I nuovi trasduttori si distinguono per la capacità di rilevare contemporaneamente posizione e velocità fino a 16 cursori indipendenti su una corsa di 4.000 mm, con una frequenza di aggiornamento di lettura della posizione pari a 4kHz, ovvero oltre 4.000 volte al secondo, per una lettura puntuale con il massimo grado di ripetibilità. Tra le novità dei modelli WPA-F e WRA-F, entrambi certificati cULus, spiccano le funzioni di diagnostica volte a segnalare, ad esempio, anomalie nel sistema di alimentazione, il raggiungimento di temperature fuori range, la non corretta parametrizzazione all’avviamento, l’eventuale mancanza di comunicazione tra elettronica ed elemento sensibile o, ancora, l’assenza di un cursore magnetico all’interno della zona di lavoro. Infine, è possibile monitorare il tempo di funzionamento effettivo del trasduttore, oltre che la temperatura reale e massima raggiunta.
Il nuovo sensore i.Sense EC.W permette - con costi contenuti - di monitorare in tempo reale le condizioni di sistemi per catene portacavi in scorrimento. Internet of Things, Big Data e robot autonomi: la transizione verso l’Industria 4.0 è più attuale che mai. Il processo interessa i componenti utilizzati nelle macchine, divenuti da tempo smart per fornire, per esempio, dati sul proprio stato. Spesso però, le aziende hanno difficoltà a integrare queste tecnologie avanzate e devono ricorrere a interventi di installazione esterni. “Abbiamo anche notato che, mentre i servizi online sono molto diffusi nella vita privata, nell’ambiente aziendale persiste una forte diffidenza verso le connessioni di dati esterni. Molto spesso, infatti, la connessione IoT della macchina non viene richiesta. Allo stesso tempo, il cliente non vuole rinunciare alle funzionalità smart e all’integrazione nei sistemi di controllo esistenti”, spiega Richard Habering, Responsabile della divisione smart plastics presso igus. Ed è proprio qui che entra in gioco igus, con il nuovo sensore di durata i.Sense EC.W per sistemi per catene portacavi in scorrimento. A partire da soli 248 euro, questo sensore low cost consente di rilevare l’usura in tempo reale e, grazie ai contatti a potenziale zero integrati, può essere collegato direttamente al sistema PLC di controllo della macchina anche senza una connessione internet.
Sensore, cavo ed elettronica di analisi sono inclusi nel pacchetto. Gli utenti possono inoltre collegare il sensore a una varietà di reti e sistemi IoT tramite il modulo i.Cee, integrandolo in un programma di manutenzione predittiva. Il sensore di durata è disponibile per le catene portacavi igus E4.32, E4.42, E4.56 e E4.80 – sono in programma altre misure per le serie E4Q, E2.1 e E2/000.
Determinare la durata d’esercizio in modo semplice e rapido –anche da remoto
Il principio alla base del nuovo sistema di sensori low cost è molto semplice: gli elementi conduttivi sono incorporati nei polimeri ad alte prestazioni di quasi tutti i prodotti igus nelle aree sollecitate dal punto di vista dell’usura. Il posizionamento strategico di questi elementi all’interno del componente permette, in caso di interruzioni elettriche o di modifiche alla resistenza, di formulare previsioni chiare sulla durata
residua del prodotto. Queste informazioni possono essere semplicemente trasmesse all’operatore tramite il monitor del sistema e - al raggiungimento di una soglia del 25%, per esempio - possono essere associati ai dati sulla sostituzione della catena. Il sensore i.Sense EC.W offre un notevole valore aggiunto, specialmente per gli ambienti difficili e sporchi o per quelle applicazioni difficili da raggiungere o con un’elevata frequenza ciclo. Montato sull’ultimo traversino sul lato del punto fisso, registra lo stato attuale delle maglie della catena. Il sensore misura la distanza tra i traversini, che si restringe in proporzione all’usura delle maglie della catena. Il sensore può essere utilizzato per monitorare da remoto ogni componente soggetto a usura nella macchina – in futuro, un vantaggio anche per molte altre motion plastics.
Riduzione dei costi dell’80% grazie alla manutenzione programmabile
I messaggi di allarme basati sulle condizioni prevengono fermi imprevisti e sostituzioni superflue o premature della catena – con un notevole vantaggio in termini di sostenibilità. In questo modo le catene portacavi non vengono più sostituite in base agli intervalli di manutenzione, ma solo quando è davvero necessario – con una riduzione significativa dei costi di manutenzione. Il collegamento diretto del sensore per la durata d’esercizio al sistema di controllo dell’impianto può ridurre i costi fino all’80%.
Per garantire la massima qualità del prodotto, igus esegue numerosi test all’interno del suo laboratorio di prova. Ogni anno vengono infatti eseguiti e analizzati oltre tre miliardi di cicli di prova solo per le catene portacavi. I test sono importanti per l’ottimizzazione e il perfezionamento costanti dei prodotti igus. Per esempio, i progettisti hanno diminuito sensibilmente l’ingombro del sensore che ora misura 2,5mm x 4mm, così da poter effettuare misurazioni anche in altri punti e generare dati chiari per quasi ogni applicazione in scorrimento. In combinazione con i tool di calcolo della durata d’esercizio messi a disposizione da igus, il potenziale risulta illimitato.
Dispositivi di gestione delle catene portacavi a partire da 248 euro: il sensore EC.W è conveniente e permette di monitorare le condizioni e di pianificare la manutenzione – per tutta la durata utile della catena. (Fonte: igus GmbH)La digitalizzazione dei processi produttivi, la raccolta e l’analisi dei dati sono diventate esigenze ormai imprescindibili per un contesto produttivo che ambisce a diventare una vera e propria Smart Factory dotata di una avanzata digitalizzazione dei processi di produzione.
R+W ha così introdotto sul mercato degli organi di trasmissione la Tecnologia AIC: una soluzione innovativa che arricchisce il giunto di una funzione di rilevazione delle grandezze fisiche coinvolte, coppia, velocità di rotazione, vibrazioni e forze assiali di trazione e compressione, oltre alla sua funzione di trasmissione.
La funzione principale della Tecnologia AIC applicata a una catena cinematica è di determinare quanti più dati possibili, nelle condizioni di esercizio, misurandoli direttamente all’interno della trasmissione.
Il principale vantaggio è quello di ottenere una stima quanto più precisa dello stato effettivo della macchina, al fine di procedere all’esecuzione degli
opportuni programmi di manutenzione.
Un obiettivo che si raggiunge senza andare a gravare sui pesi e gli spazi coinvolti.
La soluzione proposta da R+W si rivela risolutiva grazie alla particolare struttura modulare realizzata che rende facilmente integrabile i componenti finalizzati alla raccolta dati all’interno degli spaziatori.
Per questo motivo AIC trova la sua applicazione con tutti i Giunti dotati di spaziatore intermedio: giunti lamellari delle serie LP2, LP3, LPA; giunti con allunga delle serie ZA, ZAE ed EZ2.
Il giunto intelligente è composto da un amplificatore di segnale per trasmettere i dati ad un qualsiasi device che abbia come sistema operativo Android. L’AIC è dotato di un microprocessore di calcolo integrato: i dati raccolti possono essere visualizzati, analizzati e salvati all’interno dell’app R+W o esportati su file CSV.
Se si prevede la comunicazione dati via gateway è possibile assegnare tramite app le misurazioni di ogni rilevazione ad una specifica uscita analogica del gateway stesso.
Utilizzando la porta seriale possiamo trasferire lo stream di dati ad un computer, il gateway viene identificato come una porta seriale COM e può essere riconosciuto da diversi programmi come Serial Plotter, MATLAB, LabView etc.
I dati rilevati dal giunto AIC vengono trasferiti secondo protocollo UART, un dispositivo hardware, di uso generale o dedicato, che converte flussi di bit di dati da un formato parallelo a un formato seriale asincrono o viceversa.
I prodotti con sensoristica integrata possono essere dotati di batteria ricaricabile da 2000 mA oppure possono essere alimentati ad induzione, tramite apposito sistema di ricarica, in modo da garantire un’operatività continua.
Attraverso questa configurazione la Tecnologia AIC si rivolge direttamente ai principi dell’IoT: andando ad incidere direttamente sulle capacità di condivisione e acquisizione di dati all’interno delle fasi produttive.
Con l’obiettivo di creare le condizioni per sfruttare pienamente il potenziale della digitalizzazione industriale Schneider Electric propone al mercato EcoStruxure Automation Expert: il primo sistema di automazione industriale centrato sul software. L’evoluzione delle tecnologie di machine learning, realtà aumentata, analitycs in tempo reale, IIoT promette enormi opportunità per il settore, la cui realizzazione è limitata dall’uso di piattaforme di automazione chiuse e proprietarie, che ostacolano l’integrazione e hanno elevati costi di aggiornamento e manutenzione. Con EcoStruxure Automation Expert, Schneider Electric fa appello a tutto l’ecosistema di utenti, vendor, OEM, system integrator e contractor perché scelgano il nuovo modello dell’automazione universale, abilitato da componenti software di automazione “plug & produce” basati sull’adozione dello standard aperto IEC 61499. EcoStruxure Automation Expert è una nuova categoria di sistema di automazione industriale che integra lo standard IEC61499, offrendo numerosi vantaggi.
Esso consente di costruire applicazioni di automazione usando componenti software asset-centrici, portabili, di uso collaudato, a prescindere dall’infrastruttura hardware sottostante; permette all’utente di distribuire applicazioni su qualsiasi architettura di sistema hardware scelga – altamente distribuita, centralizzata o con entrambe le caratteristiche – con attività di programmazione aggiuntiva minima o nulla; supporta l’utilizzo di consolidate best practice software, per semplificare la creazione di applicazioni di automazione interoperabili con i sistemi IT.
Le prime release di EcoStruxure Automation Expert supportano piattaforme di automazioni tradizionali quali i PLC
Modicon e i variatori di velocità e PC Altivar di Schneider: per la prima volta si possono programmare e distribuire sul controllore del drive complessi algoritmi di controllo multidrive senza dover utilizzare un PLC centrale. A completare la proposta, è disponibile un controller software virtualizzato che opera in container Linux Docker®-powered, che supporta sistemi di controllo e informazione distribuiti anche nelle architetture di edge computing. Sono inoltre state distribuite nel corso dell’ultimo anno e mezzo nuove release focalizzate sulle esigenze del settore CPG e Water & Waste Water. Sfruttando la natura orientate agli oggetti dello standard IEC61499, in EcoStruxure Automation Expert si usano dei componenti software definiti Composite Automation Types (CATs) per modellare gli asset combinando funzioni di controllo in tempo reale con altre fonti, come ad esempio l’interfaccia uomo-macchina. Questo approccio centrato sugli asset porta vantaggi in termini di costi e performance senza precedenti, e dà al personale la libertà di innovare, automatizzando i compiti a basso valore e eliminando la duplicazione di task sui vari strumenti in uso. Un’ analisi che ha messo a confronto EcoStruxure Automation Expert con i sistemi di automazione in uso oggi ha evidenziato una riduzione da 2 a 7 volte del tempo necessario a realizzare le tradizionali attività di automazione. Inoltre, EcoStruxure Automation Expert supporta le più diffuse best practice in ambito IT, consentendo un vero cambiamento di passo nell’efficienza degli asset e del personale, grazie a tecnologie evolute quali manutenzione predittiva, digital twin e altre ancora. Il sistema riduce anche il TCO incorporando I sistemi legacy con un approccio “incapsula e riusa” (wrapand-reuse).
EPF nasce nel 1961 operando nell’ambito dell’automazione industriale per i sistemi elettromeccanici, fino a diventare una moderna azienda le cui attività spaziano fino alla robotica e sviluppo software. Con sede a Carrù, nel cuore delle Langhe, EPF è profondamente radicata nel territorio ma le sue attività hanno respiro internazionale. Oggi comprende tre settori: automazione, energia e stampaggio plastico. EPF integra da tempo tecnologie Siemens. “La nostra mission aziendale - spiega Franco Filippi, CEO di EPF - è integrare l’Intelligenza Artificiale all’interno del nostro ecosistema. Siamo andati a cercare nuove soluzioni sul mercato perché volevamo approfondire le potenzialità nel settore della Machine Vision (visione artificiale). EPF ha una cultura specifica su queste tecnologie grazie al team di sviluppatori software, ma avevamo bisogno di un hardware industriale in grado di risolvere problematiche legate in particolare al controllo qualità sulla linea. Per controllo di qualità, mi riferisco ai controlli visivi che con tecniche tradizionali non è possibile eseguire. Pensiamo al riconoscimento di difetti, o all’ orientamento di componenti o ai sistemi di packaging di prodotti tutti diversi come può essere la frutta. La flessibilità è il vantaggio più importante che porta una soluzione tecnologica di AI”.
L’esigenza era quella di realizzare una macchina in grado di riconoscere in modo automatico componenti di prodotti o rilevare anomalie.
La macchina di EPF esegue dei controlli di qualità a valle di una linea di assemblaggio e confezionamento per i componenti per il settore automotive, alla fine del processo produttivo.
Durante il trasferimento dei componenti dalla cella di assemblaggio a quella di confezionamento (o packaging), esegue delle ispezioni visive automatiche degli stessi, assicurando il soddisfacimento delle specifiche prescritte dal produttore. Tra queste vi è la necessità di verificare la qualità del materiale di attrito. Gli algoritmi di visione integranti l’intelligenza artificiale rappresentano dunque tecnologia abilitante, vista l’estrema difficoltà di realizzare tali controlli con gli algoritmi di machine vision tradizionali. “L’utilizzo delle innovative soluzioni software di EPF e del modulo SIMATIC S7-1500 TM NPU
di edge computing di Siemens hanno permesso di soddisfare la necessità del nostro cliente, portando a bordo linea le più avanzate tecnologie e permettendo di ottenere prodotti di qualità ed affidabilità crescenti.”
Il nuovo modulo S7-1500 TM NPU
è dotato del processore Myriad™X
Vision di Intel Movidius™ che consente l’elaborazione efficiente delle reti neurali. L’intelligenza artificiale garantisce al robot di riconoscere oggetti e relative classi di appartenenza non noti a priori grazie a un preventivo addestramento della rete neurale, che raccoglie e sfrutta tutta la relativa esperienza.
“Il vantaggio per i nostri clienti è la disponibilità di macchine più robuste e adattabili, che rispondono ad esigenze di controllo di qualità. L’AI può rilevare difetti mai catalogati. Anche in termini di addestramento del modello, posso affermare che questa soluzione implica tempi di sviluppo inferiori rispetto alle soluzioni sviluppate con algoritmi tradizionali.
L’addestramento è stato fatto con risorse interne formate allo scopo” conclude Filippi di EPF.
“Il progetto di computer vision realizzato con E.P.F. è strategico, abbiamo infatti avuto la possibilità di collaborare con un’azienda che oltre ad avere forti competenze di automazione è anche focalizzata sulle tecnologie emergenti tipiche del mondo IT come machine learning ed edge computing” spiega Davide Maffei Technical Sales Support Professional Edge & AI di Siemens.
Scoprite la nuova generazione di relè di sicurezza Pilz. Sperimentate le illimitate possibilità di combinazione, le funzionalità di prodotto intelligenti e l’innovativo myPNOZ Creator.
Create your safety – individual, tailor-made, easy.
Per saperne di più:
NELLA MODERNA SMART FACTORY, UN SISTEMA DI VISIONE ASSISTE L’OPERATORE IN MODO DISCRETO, RISPETTANDO LA SUA PRIVACY: SONO LE NUOVE FRONTIERE DELLA FABBRICA COLLABORATIVA a cura di Smart Robots – Andrea Mazzoleni AFIL
SSi chiama Smart Robots ed è un sistema di visione tridimensionale che sfrutta l’In telligenza Artificiale per garantire l’azzera mento dell’errore umano nelle postazioni di lavoro manuale. Il risultato? Processi certificati, una riduzione dei costi legati alla non-qualità, un incremento dell’efficienza.
L’evoluzione delle Human-Machine Interface (HMI) prosegue verso lo sviluppo di sistemi sempre più avanzati, che oggi sono in grado di generare un’interazione immediata, reciproca e naturale tra la per sona e l’oggetto automatizzato.
Se inserito nell’ambito della Smart Factory, la “Fabbrica Intelligente”, questo scenario si contraddistingue per l’integra zione di tecnologie diverse, le cosiddette advanced manufacturing solutions, solu zioni rapidamente programmabili che favo riscono la collaborazione tra l’operatore e la macchina. Parola d’ordine: interconnes sione. Va da sé che le HMI giochino un ruolo decisivo nel garantire uno svolgi mento dei processi fluido e senza soluzione di continuità, in una parola: seamless.
Lo sa bene Roberto Rossi, co-Founder e General Manager di Smart Robots, società milanese del Gruppo industriale e-Novia, che ha realizzato una soluzione sistemica e scalabile in grado di assistere l’operatore all’interno della Smart Factory, riducendo gli scarti e migliorando la qualità dei pro cessi: un sistema silenzioso, che segue in modo discreto l’operatore e i suoi movi menti, oggettivandone le attività attraverso l’Intelligenza Artificiale.
L’obiettivo? Azzerare il rischio di errore che, per definizione, è umano. Spesso det tato dalla routine, dalle distrazioni, dallo stress o, perché no, dalla complessità di alcune operazioni, l’errore in ambito mani fatturiero ha un tasso di incidenza che si aggira tra lo 0,5 e il 3%, con costi assolu tamente non da poco per le aziende, che devono far fronte agli eventuali reclami del cliente, alla gestione dei resi e alla perdita di nuove commesse. Eliminando l’errore manuale, Smart Robots permette di azze rare i costi legati alla “non-qualità” nei pro cessi industriali.
Il prodotto di Smart Robots si inserisce in un trend in atto nell’ambito della Fab brica Intelligente: la riscoperta del valore inestimabile dell’operatore nei processi produttivi. L’unico in grado di eseguire
compiti complessi, impossibili da automa tizzare, garantendo flessibilità, adattabilità, saper fare.
«Grazie alla nostra soluzione, anche gli operatori poco formati possono garantire la stessa efficienza di quelli più esperti, grazie a un assistente virtuale che li guida e li avvisa in caso di errore», afferma Roberto Rossi. «Non solo: anche qualora non si verifichi un errore, Smart Robots oggettiva il processo, certificando quindi l’assenza di errori. In questo modo, le aziende che installano il nostro prodotto ne traggono beneficio non solo in termini di ottimiz zazione dei processi, ma anche di risposta a eventuali reclami da parte dei loro clienti, con un conseguente vantaggio competitivo rispetto ai loro competitor».
La soluzione di Smart Robots si basa su un sistema avanzato di Human-Machine Interface. Questo riconosce istantanea mente i movimenti dell’operatore, com prende dove vanno le sue mani, cosa fanno, dove vengono posizionati gli attrezzi che utilizza e intervenendo sull’errore non appena questo si verifica. In che modo? Il sistema di visione tridimensionale distin gue i passaggi della sequenza svolta in quel momento dall’operatore e li confronta con una sequenza di passaggi predefiniti, il tutto mentre l’operatore sta lavorando. Nel frattempo, le istruzioni sul display si aggiornano automaticamente, senza la necessità di ulteriori movimenti o comandi aggiuntivi.
E in caso di errore? Il sistema interviene segnalandolo, oppure bloccando momen taneamente l’automazione della stazione.
Addio alle classiche guide cartacee o alle istruzioni digitali che richiedono la conferma attiva dell’operatore: qui l’inte razione è implicita e la persona non deve interrompere il suo lavoro per essere com presa dalla soluzione.
«Anche le altre macchine della sta zione di lavoro possono essere abilitate da Smart Robots al momento giusto e senza la necessità di un comando esplicito dell’ope ratore», prosegue Roberto Rossi. «Inoltre, il sistema permette nuove modalità di inte razione. Per esempio, l’atto di posizionare la mano in un determinato punto equivale a premere un tasto virtuale, con il quale l’operatore può impartire dei comandi alla stazione stessa».
Il sistema di Smart Robots interagisce con il gestionale dell’azienda in tempo reale, fornendo al manager anche una reportistica anonimizzata e una visione globale del processo, consentendogli di programmare le attività in modo agevole ed efficiente.
La soluzione è, quindi, scalabile poiché facile da installare, configurare e modifi care, il tutto in piena autonomia del cliente.
Ma quanto ha inciso l’Intelligenza Artificiale nello sviluppo del prodotto? «Moltissimo», risponde Roberto Rossi, «Il nostro sistema basa il suo funzionamento proprio sull’Intelligenza Artificiale, ser vendosi di complessi algoritmi per il rico noscimento del movimento umano e delle azioni dell’operatore. Sono algoritmi che non dipendono dalla singola persona e che pertanto si possono adattare al cliente senza effettuare di volta in volta un trai ning specifico. La nostra soluzione è difatti plug-and-play. È per noi fondamentale che il cliente finale possa essere indipendente nella configurazione e nell’installazione del sistema, per adattarlo alle proprie esigenze di produzione».
I clienti che hanno installato il prodotto di Smart Robots operano in diverse macroaree, in Italia e all’estero. Ci sono i produt tori di componentistica per auto e moto, così come i fornitori di elettrodomestici. Si tratta tanto di PMI quanto di multina zionali, in cui il comune denominatore è sempre lo stesso, la presenza dell’operatore,
che esercita attività manuali codificabili: asservimento macchine, assemblaggio, montaggio sequenziale, packaging o anche realizzazione di kit per il passaggio da una stazione all’altra.
Senza contare le attività di preparazione delle macchine. La tecnologia di Smart Robots trova largo uso nello stampaggio o nella pressa, dove è necessario attrezzare lo stampo con i componenti necessari, da disporre correttamente; nella saldatura, anche qui per l’allestimento preparatorio; e anche nel controllo qualità, nel collaudo e nel testing. In questi ultimi tre campi di applicazione il prodotto di Smart Robots gioca un ruolo decisivo, poiché si inserisce in sequenze che devono essere realizzate tutte, senza errori o negligenze.
«Un aspetto fondamentale della tecno logia di Smart Robots è che questa agisce
nel pieno rispetto della privacy dell’opera tore», aggiunge Roberto Rossi. «Le imma gini e i video realizzati dal sistema non possono in alcun modo essere registrati o archiviati dal datore di lavoro. L’operatore della stazione può solo visionarli in tempo reale sul proprio monitor. Una volta ela borate, dopo pochi millisecondi vengono immediatamente cancellate».
Ecco quindi che, in ambito manifattu riero, entra in azione il concetto di “Fab brica Collaborativa”. Che cosa significa? Significa che la persona al centro è la vera discriminante che, superando gli ormai ripetuti slogan, segna una svolta nel rap porto tra la fabbrica e la risorsa umana.
Per rendere la manifattura efficiente e competitiva davanti alle sfide che la attendono, è necessaria la massima col laborazione non solo tra le macchine, le attrezzature, gli strumenti e le interfacce, ma anche tra questi e le persone che lavo rano nella fabbrica.
Nessuna contrapposizione, nessuna competizione. «Studi autorevoli confer mano che nel 2030, a livello mondiale, soltanto il 5% delle attività manuali attualmente svolte nelle fabbriche sarà completamente automatizzato, mentre il 95% continuerà a richiedere l’intervento umano, con la conseguente necessità di moderni strumenti di assistenza e ausi lio nella postazione di lavoro», aggiunge Roberto Rossi.
La Fabbrica Collaborativa si inseri sce perfettamente in alcuni trend in cui è coinvolta la fabbrica manifatturiera in senso ampio: la personalizzazione di massa (alla quale si contrappone la riduzione delle dimensioni del lotto minimo); il reshoring
Smart Robotsdella produzione all’interno dei confini europei, che oggi consente alle aziende di competere sui mercati internazionali grazie a un maggior valore aggiunto; e ancora la necessità di tenere alta la qualità della produzione, punto di forza dell’arti gianalità delle PMI europee e in partico lare di quelle italiane. Che cos’hanno in comune questi macro-trend? La centralità dell’operatore.
E infine, la Fabbrica collaborativa si coniuga perfettamente con i temi dettati dalla Commissione Europea nell’Industria
5.0, il cui rapporto pubblicato a gennaio 2021 riporta come sottotitolo: Verso un’in dustria europea sostenibile, umano-centrica e resiliente. Definita dalla Commissione Europea un “completamento dell’’industria
4.0”, la Fabbrica Collaborativa è una vera e propria rivoluzione culturale, che ricol loca l’industria nella contemporaneità in cui agisce. Una industria che si basa sulla collaborazione.
AFIL – Associazione Fabbrica Intelligente Lombardia – è il cluster tecnologico per il manifatturiero avanzato ufficialmente riconosciuto da Regione Lombardia. Attraverso le Strategic Communities, ovvero gruppi di lavoro formati da grandi imprese, PMI, start-up, associazioni, università e centri di ricerca che lavorano su tematiche strategiche per il manifatturiero lombardo, AFIL accompagna i suoi associati in un percorso collaborativo di crescita attraverso incontri tematici, workshop, webinar, matchmaking, missioni internazionali, favorendo lo sviluppo di progettualità di filiera e promuovendo la R&I anche a livello interregionale. Le Strategic Communities di AFIL ad oggi sono 5: De- and Remanufacturing for Circular Economy, Digital Transformation, Advanced Polymers, Additive Manufacturing e Secure and Sustainable Food Manufacturing. In particolare, la Strategic Community “Digital Transformation” ha lo scopo di concepire, sviluppare e favorire l’adozione tra le imprese lombarde di soluzioni legate alla digitalizzazione e all’intelligenza artificiale assicurando la centralità dell’uomo. Coloro che volessero ricevere maggiori informazioni sulle attività di AFIL sono pregati di scrivere ad andrea. mazzoleni@afil.it. Per associarsi ad AFIL visitare www. afil.it
L’industria automotive sta cambiando radicalmente: le aziende di questi settori e tutti coloro che desiderano partecipare alla mobilità del futuro devono ora proporre strategie più complete e fare affidamento su soluzioni innovative. Inoltre, servono competenze digitali. Secondo Gartner, un approccio di collaborazione open data e open source, ecosistemi olistici e part nership tecnologiche stanno diventando sempre più importanti. I concetti di Smart
Factory che combinano automazione inno vativa, digitalizzazione e approcci intelli genti all’intralogistica sono necessari per affrontare la carenza di lavoratori qualifi cati, soddisfare i requisiti di mercato e dei clienti, aumentare l’efficienza e la produt tività e rafforzare la sostenibilità. Questi approcci sono diversi: mentre alcuni pre feriscono l’Industry 4.0, altri parlano di “Fabbrica del futuro”, altri ancora di Indu strial Internet of Things (IIoT). Tuttavia,
indipendentemente dal termine utilizzato, la cosa più importante è iniziare subito e cercare partner solidi per garantire la con nessione internazionale.
Gli ACES richiedono approcci multilivello
Le tendenze principali sono riunite nell’ambito di ACES o CASE: veicoli autonomi, connessi, elettrici e condivisi. L’obiettivo generale è quello di consen
QUATTRO I PILASTRI DELLA SMART FACTORY - DIGITALIZZAZIONE, INTRALOGISTICA, INTEGRAZIONE IT-OT E GLI ECOSISTEMI INDUSTRIALE - CHE DETERMINERANNO LA PRODUZIONE AUTOMOTIVE DEL FUTURO. CHE COSA BISOGNA ASPETTARSI ORA IN TERMINI DI MOBILITÀ AMBIENTALE
di Henry Claussnitzer, Business Engagement Manager Automotive per l’area EMEA di OMRON
tire nuovi paradigmi di mobilità e modelli aziendali e fatturato che abbiano il poten ziale di cambiare il modo in cui i consu matori interagiscono con i veicoli. Per quanto riguarda la Smart Factory, l’atten zione è sempre più concentrata non solo sul miglioramento dei singoli processi, ma anche sulla creazione di sinergie e, ad esempio, sull’avvio e sulla trasformazione dei processi di produzione nel settore automotive. L’attenzione si concentra su sostenibilità, flessibilità ed efficienza. I siti di produzione sono progressivamente controllati e ottimizzati dai Big Data, la collaborazione uomo-macchina viene for zata e devono essere affrontate questioni di sicurezza, protezione dei dati ed etiche. Anche il raggiungimento di un sistema di gestione decentralizzato viene portato avanti nel corso dello sviluppo ACES. A ciò si aggiunge il collegamento tra la cono scenza dei prodotti, i dati degli stakeholder e il processo decisionale.
Le strutture produttive orientate al futuro vogliono migliorare l’agilità e la cen tralità del cliente, la resilienza delle catene di distribuzione, la rapidità delle operazioni e la produttività, nonché la sostenibilità. La produzione e le catene distributive E2E (end-to-end) facilitano l’identificazione più rapida delle preferenze dei clienti. Ciò, a sua volta, consente un adattamento più rapido delle operazioni di produzione nelle linee produttive modulari per raggiungere livelli più elevati di personalizzazione. Le catene di distribuzione stabili rappresen
tano un vantaggio competitivo e richiedono ecosistemi di fornitura in rete riconfigura bili, oltre alla regionalizzazione. Velocità e produttività si ottengono grazie a un livello superiore di automazione e a un aumento delle dimensioni della forza lavoro in com binazione con misure di qualificazione e conservazione. Infine, ma non meno importante, l’ecoefficienza diventa una priorità per ottenere un vantaggio compe titivo e garantire la conformità in un pano rama normativo sempre più complesso. Gli approcci Smart Factory dovrebbero contri buire a implementare tutti questi obiettivi nel modo più efficiente possibile in termini di costi e risorse. Il prerequisito di base è rappresentato dalle tecnologie digitali, in quanto sono responsabili di trasformare gli impianti di produzione in aziende real mente “intelligenti”.
Questi sono i quattro pilastri degli approcci Smart Factory nel settore auto motive:
Digitalizzazione e intralogisticaproduzione di carburante
La digitalizzazione (inclusa la tecnolo gia AI) è la chiave per avere accesso a tutte le informazioni, i processi e i componenti di un impianto, per esempio per unire e ottimizzare la pianificazione operativa o di produzione, gli acquisti, l’esecuzione spe cifica per il cliente e molto altro ancora. L’intralogistica è un secondo pilastro che trasforma e semplifica le operazioni. Ciò include soluzioni robotiche innovative, come i robot mobili. Per esempio, la società
automobilistica BMW si affida ai robot LD mobili di OMRON per il trasporto dei materiali. Questi robot mobili auto nomi (AMR) sono dotati di un accessorio trasportatore attivo e regolabile in altezza (dispositivo di movimentazione del carico) sviluppato dall’integratore di sistemi cts. L’intralogistica descrive tutti i processi in cui vengono movimentati materiali, pro dotti e prodotti dei fornitori. Di conse guenza, anche la logistica delle consegne, i movimenti nello stabilimento, i nastri tra sportatori, i carrelli elevatori, i magazzini a scaffali alti, i robot SCARA, i cobot e altro ancora fanno parte dei processi intralogi stici. Un esempio può essere la produzione di batterie: una batteria nell’ambiente di e-mobility viene spostata e trasportata molto frequentemente fino al suo comple tamento. Ciò richiede numerose tecnologie e soluzioni a supporto dell’intralogistica, che siano strettamente interconnesse.
La crescente importanza degli ecosistemi industriali per promuovere l’innovazione
Collegamenti come questi attraversano le aree più diverse della Smart Factory perché il futuro dell’industria automo tive non è immaginabile e non può essere realizzato da solo. Anche i valori signifi cativi dei clienti possono essere realizzati solo congiuntamente. Sempre più spesso, si tratta di collaborare con i partner per sviluppare e promuovere soluzioni che coprano le esigenze individuali e i requisiti del mercato nel modo più rapido ed effi cace possibile. Un recente studio IDC evi denzia l’importanza di tali ecosistemi: gli esperti presumono che, fin dal 2026, quasi un terzo dei ricavi delle maggiori aziende
a livello mondiale provenga da dati con divisi, applicazioni e iniziative operative all’interno degli ecosistemi del settore. Le aziende hanno valutato gli obiettivi cen trali della partecipazione agli ecosistemi del settore come segue: innovazioni più rapide (31%), nuovo potenziale di reddito (29%) e promozione della sicurezza e della qualità dei propri prodotti (26%).
Integrazione di IT e OT, promozione della digitalizzazione e dell’intralogistica Secondo IDC, anche un’integrazione IT-OT più fluida, ovvero la connessione dell’IT e di altre tecnologie in produzione, è essenziale per il successo dei progetti IIoT. La tecnologia operativa nell’am biente automotive include soluzioni di automazione, sensori e motion control. Per collegare questi due livelli, OMRON, un esperto di OT, collabora con i partner che ottengono punti con il know-how IT. Un esempio è Dassault Systemès, un’azienda multinazionale di scienza e tecnologia che crea ambienti virtuali collaborativi come “esperienze gemelle virtuali” del mondo reale. Insieme a VAF e Dassault Systèmes e utilizzando la piattaforma 3DEXPE RIENCE di Dassault Systèmes, OMRON ha sviluppato una cella impilatrice robotica per l’assemblaggio di celle a combustibile. Con l’aiuto del gemello digitale, i processi di produzione possono essere simulati in ambiente virtuale, per pianificare meglio e migliorare lo sviluppo. IT e OT vengono quindi uniti in soluzioni di produzione fles sibili e scalabili. Un altro partner OMRON è Synaos. Sebbene Dassault Systèmes agisca come digitalizzatore, Synaos è un fornitore di intralogistica che si occupa del trasporto nelle aziende tramite software e
collega i diversi flussi di lavoro nel processo. Alcuni esempi sono la catena di distribu zione, ERP, ECM, l’acquisto di materie prime, produzione o consegna. OMRON, insieme a partner come Dassault Systèmes, VAF o Synaos nell’ecosistema, accompagna le aziende verso la Smart Factory.
I Big Data supportano processi di produzione innovativi
La Smart Manufacturing (Produzione intelligente) si affermerà come una strate gia olistica che abbraccia l’intero processo, dalla progettazione all’ottimizzazione, alla produzione e alla consegna fino all’intero ciclo di vita del prodotto. I vantaggi deri vanti dalle maggiori possibilità di comunica zione e dalla generazione e gestione dei dati saranno utilizzati per migliorare, stabilire e rinnovare i processi. Allo stesso tempo, i processi nei moderni impianti di produzione possono essere ottimizzati in modo costante e indipendente grazie all’intelligenza arti ficiale (AI). La Smart Manufacturing supporta metodi sofisticati di produzione e assemblaggio per migliorare la qualità, aumentare l’efficienza globale delle appa recchiature (OEE) e la flessibilità, miglio rando al contempo sostenibilità, prestazioni e costi. Usando i dati generati dai sensori e/o dai controller, le macchine intelligenti possono adattarsi dinamicamente ai pro cessi e alle condizioni operative in continua evoluzione. Allo stesso tempo, i dipendenti beneficiano di flussi di lavoro più semplici. Questo sta diventando un fattore sempre più importante, dal momento che la crescente carenza di lavoratori qualificati è oggi al suo massimo. Nella Smart Factory, un mondo basato su ecosistemi del settore, interazione tra IT e OT, digitalizzazione, intralogistica, intelligenza artificiale e innovative soluzioni di automazione, le prestazioni di macchine e processi diventano prevedibili grazie alle tecnologie di simulazione digitale. Le tec nologie digitali con manutenzione predittiva e prestazioni adattive prolungano la durata delle macchine. La Smart Manifacturing ridurrà i tempi di introduzione sul mercato e i costi di sviluppo. Allo stesso tempo, le fabbriche digitalizzate rappresentano la base per la flessibilità, l’uso efficiente delle risorse con qualità prevedibile e l’offerta di nuovi modelli aziendali. Dopo tanta teoria è il momento di mettere in pratica!
I“Il mondo è in continua evoluzione: le imprese stanno modificando le strutture esistenti e adottando nuove tecnologie per affrontare le sfide e le incertezze del futuro, con l’automazione robotica che svolge un ruolo fondamentale”, ha dichia rato Sami Atiya, Presidente della divisione Robotica e automazione discreta di ABB. “Abbiamo bisogno di investimenti signi ficativi nella formazione continua per preparare la nostra forza lavoro attuale e
futura a prosperare in un’epoca di robotica e automazione; è quindi importante non solo per prepararsi ai cambiamenti dif fusi a cui stiamo assistendo, ma anche per creare società prospere in futuro.”
Nonostante queste parole un’indagine globale di ABB ha rivelato come una cre scente tendenza delle imprese statunitensi ed europee a delocalizzare le attività per costruire una capacità di resistenza di fronte alle sfide globali, coincida con il
crearsi di un significativo gap formativo nelle competenze necessarie per il suc cesso di queste strategie.
L’indagine condotta da ABB nel 2022 tra i leader delle aziende statunitensi ed europee ha rivelato che il 74% delle aziende europee e il 70% di quelle statu nitensi stanno pianificando operazioni di riallocazione o di nearshore per aumentare la resilienza della propria supply chain in risposta alla carenza di manodopera,
UN’INDAGINE ABB RIVELA CHE LA REINDUSTRIALIZZAZIONE ÈA RISCHIO A CAUSA DEL “GAP EDUCATIVO” GLOBALE NELL’AUTOMAZIONE di Cristina Gualdoni
alla necessità di un’impronta globale più sostenibile e all’incertezza globale.
La maggior parte di queste aziende considera l’automazione come il fattore abilitante di questi cambiamenti, con il 75% delle aziende europee e il 62% di quelle statunitensi intervistate che pre vedono di investire in robotica e automa zione nei prossimi tre anni per facilitare questo spostamento delle operazioni.
Nonostante questa necessità di auto mazione, l’indagine ha rilevato un divario significativo nell’istruzione e nella for mazione necessarie a garantire le com petenze per lavorare nei luoghi di lavoro del futuro, sempre più connessi e auto matizzati. L’80% dei professionisti della formazione intervistati a livello globale ritiene che la robotica e l’automazione influenzeranno il futuro dell’occupazione nei prossimi dieci anni, mentre solo un istituto di formazione su quattro utilizza attualmente i robot come parte dei propri programmi di insegnamento.
Per contribuire a colmare il divario di competenze, ABB ha rafforzato il suo programma globale di formazione sulla robotica e l’automazione con nuovi centri di formazione, tra cui il campus globale di innovazione e formazione in Austria, del valore di 100 milioni di euro. Il nuovo sito, insieme ad altri nuovi centri di for mazione regionali nel Regno Unito, a Berlino e in Brasile, espande le strutture di formazione di ABB a oltre 40 siti a livello globale, formando ogni anno più di 30.000 studenti di scuole, college e uni
versità, nonché apprendisti e lavoratori.
I siti si aggiungono all’offerta formativa esistente di ABB, che consiste in pacchetti software, tra cui Wizard Easy program ming, RobotStudio® e RobotStudio® AR Viewer App, nonché hardware sotto forma di celle robotiche collaborative e pacchetti applicativi. Grazie a più di 100 partner ship globali con scuole e università, ABB genera materiale didattico in collabora zione con i fornitori di servizi educativi per aiutare a formare le future generazioni e prepararle ai lavori di domani.
“Il cambiamento deve avvenire ora”, ha aggiunto Atiya. “Mentre le aziende si rivolgono all’automazione robotizzata per compensare la carenza di manodo pera, migliorare l’efficienza e aumentare la resilienza, i lavoratori hanno bisogno di competenze per utilizzare l’automazione
L’80% dei professionisti della formazione afferma che i robot e l’automazione guideranno il futuro dell’occupazione nei prossimi dieci anni. Tuttavia, solo un istituto di formazione su quattro utilizza i robot nei programmi di insegnamento, nonostante il 70% delle aziende statunitensi ed europee preveda di investire nella robotica e nell’automazione nei prossimi tre anni a causa dei cambiamenti nella catena di fornitura*. Il programma globale di formazione di ABB, con oltre 100 università che formano più di 30.000 studenti all’anno, si espande con l’apertura di nuove strutture di formazione in robotica e automazione. Per ulteriori informazioni sull’offerta per l’istruzione, esempi di progetti educativi che coinvolgono ABB e i suoi robot e software, e un white paper che spiega come l’insegnamento dell’automazione può aiutare a formare la forza lavoro di domani, visitare la pagina del portale ABB dedicata all’istruzione.
*Sondaggio ABB sulla catena di fornitura, 2022. Questa pubblicazione combina i risultati dell’indagine ABB sulla Supply Chain e sulla formazione, entrambe condotte nel 2022.
per svolgere il proprio lavoro e migliorare il proprio ruolo. Le aziende devono unire le forze, collaborando con gli istituti di istruzione e i governi per garantire che la società sia preparata ai lavori del futuro. Solo così potremo utilizzare appieno l’au tomazione flessibile e sbloccare il valore della reindustrializzazione in corso”. Questa indagine ha infatti evidenziato la necessità critica di promuovere l’insegna mento della robotica e delle competenze in materia di automazione.
{!}$ = [4]%! {x}
territorio nazionale. Approderà nelle scuole. Andremo a spiegare agli studenti l’importanza di sostituire la plastica con il vetro non solo dal punto di vista ambientale, ma anche per quanto riguarda il gusto e la conservazione dell’acqua”.
Con [X]M matrice modale ottenuta raccogliendo gli n autovettori, ovvero i modi di vibrare corrispondenti alle pulsazioni ωni trovate.
Si possono disaccoppiare le varie matrici che, diventando diagonali, rendono i calcoli molto più agevoli, trasformando il sistema sotto riportato in una serie di equazioni risolvibili singolarmente.
[5]$ {!}$ + [& ]$ {!}$ + [*]$ {! }$ = [4]% ' {, }
In generale, le vibrazioni vengono distinte in deterministiche, descrivibili mediante opportune relazioni matematiche, e casuali, il cui andamento non è prevedibile, motivo per cui vengono considerate come disturbi o rumore.
Il nuovo impianto di imbottigliamento che rispetta l’ambiente di Acqua Minerale di Calizzano è entrato ufficialmente in funzione per l’imbottigliamento in vetro di ultima generazione. Con l’inizio del periodo estivo, e completata la fase di test, la nota azienda dell’Alta Val Bormida ha finalmente completato la messa in funzione della sua nuova linea produttiva: un investimento complessivo di 6 milioni di euro, per un iter realizzativo durato poco meno di un anno, che ha visto un efficientamento anche grazie al supporto di SEW-Eurodrive. Il risultato? Maggiore efficienza e affidabilità, in ottica di sostenibilità!
Perché vogliamo migliorare proprio le vi brazioni?
Bisogno del cliente: Al pari di SEW-Eurodrive che nel corso degli ultimi anni ha intrapreso un cammino verso la sostenibilità con un approccio sistemico e trasparente, in grado di sviluppare un forte orientamento anche all’innovazione e alla tecnologia, anche la politica e l’etica di Acqua Minerale di Calizzano sono ancora più attente alla sostenibilità del proprio prodotto e alla protezione ambientale.
Questo fenomeno, insieme agli urti, concorre al catti vo funzi onamento ed al precoce deterioramento delle macchine e delle strutture, nonché all’inquinamento acustico dell’ambiente circostante. Anche la salute dell’uomo ne è influenzata negativamente, con conseguenze sempre più oggetto di attenzione da parte dei responsabili preposti alla sicurezza.
Come già spiegato nell’articolo Lo smorzamento delle vibrazioni nelle macchine utensili | Blog RW Italia le vibrazioni nelle macchine utensili sono dovute principalmente a tre fattori :
squi l i bri degl i al beri rotanti, come quello di trasmissione che collega il motore al mandrino, passando dai giunti e dalle ruote di trasmissione; difetti dimensioonali di alcuni componenti che costituiscono gli azionamenti; un ingaggio intermittente fra l’utensile ed il pezzo da lavorare.
OEM e END USER: Nel nord Italia, dove le montagne abbracciano una bellissima costa, si trova la piccola comunità di Calizzano (Savona). Il produttore locale di bevande Acqua Minerale di Calizzano Srl, dal 1961 produce bevande di alta qualità con l’acqua che sgorga dalle sorgenti delle Fonti Bauda che scaturiscono dalle Alpi Marittime a circa 1.080 metri sul livello del mare. Tutti i prodotti, oltre ad essere venduti in tutta Italia, vengono anche esportati in oltre 13 Paesi in tutto il mondo quali Inghilterra, Stati Uniti, Canada, Messico, Australia, Francia.
Tutti questi eventi generano delle forze periodiche che vengono convertite in vibrazioni forzate , che raramente causano problemi, e vibrazioni autoindotte , note anche come chatter, che sono uno dei limiti più importanti alla produttività dei processi di lavorazione. Già nel 1907 Taylor definì il chatter come “il problema più oscuro e delicato che si affronta nella lavorazione meccanica”. Esse si manifestano con l ’ aumento del l a vel oci tà di lavorazione, parametro molto importante per incrementare il rendimento delle macchine o durante il processo di finitura dei componenti; la diretta conseguenza è la generazione di asperità molto evidenti di geometria particolare sulla superficie del componente, causandone spesso lo scarto. I modelli matematici di Arnold o di tipo B (ampiamente analizzati nell’articolo https://blog.rw italia.it/smorzamento vibrazioni macchine utensili) constatano che questo fenomeno dipenda dalla lunghezza e dalla profondità del taglio, dallo smorzamento dell’utensile e da un fattore relativo alla forza.
Nel corso dei decenni, l’azienda è cresciuta gradualmente sino ad arrivare alla terza generazione di imprenditori. I dati attuali parlano di una produzione che si aggira sui 40 milioni di bottiglie all’anno. Il portfolio comprende però anche differenti bibite: l’acqua delle Fonti Bauda viene infatti altresì impiegata nelle produzioni di bibite analcoliche gassate, prodotte seguendo la tradizionale ricetta che prevede l’utilizzo di solo zucchero, in una varietà di otto gusti sia in confezioni di PET che di vetro.
“L’obiettivo è puntare sul vetro ed eliminare almeno il 60% delle bottiglie di plastica nel breve periodo – afferma Angelo Nan, CEO presso Acqua Minerale di Calizzano Srl. Abbiamo varato un progetto di sostenibilità ambientale che mira a ridurre drasticamente il consumo di plastica sia per quanto riguarda le bottiglie da litro sia per quelle da mezzo. Si tratta di un’iniziativa che parte dalla Liguria, ma che è già attiva in Emilia Romagna e nel Veneto e che presto si svilupperà su tutto il
Per questo motivo l’azienda dell’Alta Val Bormida ha deciso di investire oltre 6 milioni di euro sulle referenze in vetro, puntando in particolar modo sul “riutilizzo” dell’imballo piuttosto che sulla sua “riciclabilità”. “Riutilizzare – continua Angelo Nansignifica impiegare risorse ed energia solo per la realizzazione iniziale dell’oggetto, utilizzabile, se ben conservato, infinite volte; riciclare invece comporta un continuo dispendio di energie per trasformare la stessa materia prima per un numero limitato di volte. La bottiglia di vetro non la si può utilizzare più solo se si rompe e in tal caso al massimo torna sabbia o silice. Tanto più riutilizziamo una bottiglia di vetro, tante meno bottiglie in plastica occorre produrre, tanto più l’ambiente e l’ecosistema ci diranno grazie”. La famiglia Nan nel corso del mese di giugno 2022 ha inaugurato un nuovo impianto di imbottigliamento delle bottiglie in vetro, che occupa una superficie pari a circa 1.400 metri quadrati: ciò include la macchina per il lavaggio delle bottiglie, la riempitrice, l’etichettatrice, l’incassettatrice, il pallettizzatore nonché i sistemi di trasporto.
L’impianto ha visto il supporto sia dell’OEM Krones AG, quale fornitore dell’intero impianto, sia di SEW-Eurodrive che ha supportato l’utilizzatore finale mediante la fornitura delle tecnologia di azionamento MOVIGEAR® classic e MOVITRAC® advanced.
Due sono state le principali esigenze da dover soddisfare: maggiore efficientamento e affidabilità.
Il pieno potenziale di efficienza delle
moderne macchine sincrone ad eccitazione permanente può essere sfruttato solo con un sistema meccatronico perfettamente coordinato. Per questo Acqua Minerale di Calizzano Srl, per il proprio nuovo impianto, ha scelto di affidarsi alla combinazione tra MOVIGEAR® classic e MOVITRAC® advanced grazie alla quale è possibile ottenere notevoli vantaggi in termini di sviluppo di potenza e campo di regolazione della velocità: Hans-Jürgen Menzl, R&D tecnologie di azionamento presso Krones AG, spiega “con MOVITRAC ® advanced, SEWEurodrive offre un convertitore di frequenza che completa perfettamente MOVIGEAR® Classic. Grazie al loro utilizzo congiunto è possibile ottenere una trasmissione perfettamente coordinata ad un intervallo di impostazione della velocità sensorless elevato di 1:40”.
Inoltre l’efficienza energetica dell’unità di azionamento MOVIGEAR® classic è ben al di sopra delle specifiche standard per la classe di efficienza IE5 e, se combinata con MOVITRAC® advanced, anche al di sopra dell’efficienza del sistema IES2.
Efficienza non significa solo però solo risparmio di energia, ma anche riduzione della complessità: il personale addetto sia alla messa in servizio che alla manutenzione non deve essere gravato, ad esempio, da interfacce non necessarie. Ciò significa che ogni azionamento deve essere pronto per l’uso solo con la specifica del setpoint tramite Profinet, subito dopo l’installazione elettrica. Poiché il convertitore MOVITRAC® advanced è dotato di un Web Server integrato per scopi diagnostici, il personale addetto alla manutenzione può accedere in maniera semplice alla pagina di diagnostica di qualsiasi azionamento con qualsiasi browser Web senza strumenti software specifici. Ma non solo.
Il concetto di salvaguardia della qualità del prodotto imbottigliato non può prescindere dalla massima pulizia e igiene di tutte le parti che direttamente o indirettamente vengono a contatto con l’acqua: diventa pertanto necessario installare tecnologie di azionamento che siano in grado di soddisfare i più elevati requisiti di igiene e sicurezza, per facilitare la pulizia e per aumentare la durata dell’azionamento in ambienti umidi e soggetti a sanificazione, in modo da garantire prestazioni più affidabili e durature.
I sistemi di trasporto dell’intero impianto richiedono un totale di 108 azionamenti.
Già da anni Krones utilizza MOVIGEAR® classic di SEW-Eurodrive in quanto unità di azionamento particolarmente efficiente, flessibili, semplici ma anche sicuri, sviluppati dalla multinazionale tedesca grazie al sistema modulare per l’automazione MOVI-C®. MOVIGEAR® sono unità di azionamento estremamente efficienti perché abbattono il consumo energetico: l’elevato livello di rendimento grazie alla classificazione di efficienza IE5 del motore, li rende una soluzione di azionamento innovativa e sostenibile, rispetto ai sistemi esistenti e disponibili in commercio.
La flessibilità è dovuta sia alla compattezza e alla forma costruttiva universale, oltre che alla loro capacità di sovraccarico (comportante una riduzione del numero di varianti necessarie, con conseguente ottimizzazione dei costi di gestione in magazzino). Infine sono anche di semplice e rapida installazione. Queste caratteristiche rendono
MOVIGEAR® classic particolarmente indicati nell’industria alimentare e delle bevande nei quali sono richieste un livello di efficienza energetica e prestazioni elevate, in spazi ridotti. Inoltre la struttura liscia della superficie di MOVIGEAR® impedisce che vi aderisca lo sporco e facilita la pulizia degli impianti; per via del raffreddamento in superficie non sono richiesti ventole, né ventilatori addizionali: ciò significa che lo sporco non viene aspirato dal sistema e pertanto germi e batteri non vengono diffusi dai vortici d’aria. È stato impiegato anche il nuovo inverter MOVITRAC® advanced: soluzione che punta su compattezza, flessibilità e semplicità di implementazione di sistemi di controllo. Un inverter tuttofare pensato per applicazioni di intralogistica e movimentazione – come nastri trasportatori, elevatori e pallettizzatori – adatto a tutti i settori e in questo specifico utilizzo al food & beverage.
Ideale per controllare e monitorare motori AC sincroni e asincroni, con o senza encoder (a media/bassa accuratezza), motori con tecnologia LSPM e motori lineari, l’unità
MOVITRAC® advanced può essere impiegata in un’incredibile varietà di aree di applicazione, grazie a un considerevole range di potenza da 0,25 a 315 kW e una capacità di sovraccarico del 150%.
Un’adattabilità potenziata a sua volta dalla flessibilità dell’interfaccia di comunicazione integrata, che consente il collegamento dell’inverter a sistemi di controllo di uso comune. Diverse le tecnologie di collegamento possibili grazie alla molteplicità delle linee offerte: PROFINET, EtherNet/IPTM, EtherCAT® / SBusPLUS, Modus TCP, EtherCAT®/CiA402 o POWERLINK/ CiA402.
L’inverter compatto della gamma di SEWEurodrive offre vantaggi anche in termini di rapidità di parametrizzazione, semplicità di utilizzo, adattabilità degli strumenti e flessibilità funzionale. Targhetta elettronica e impiego di moduli software preconfigurati MOVIKIT® – nati per implementare funzioni di base, quali la modulazione della velocità, il posizionamento e il controllo del
movimento – permettono un considerevole risparmio nelle tempistiche di engineering e di messa in servizio.
Ulteriore vantaggio sta nella semplicità di manutenzione dell’inverter MOVITRAC® advanced: la sostituzione del dispositivo può essere eseguita in modo semplice, senza l’uso di un PC, grazie al modulo di memoria estraibile in cui sono salvati tutti i dati del dispositivo. Inoltre, il tuttofare di casa SEWEURODRIVE offre diverse opzioni grazie alla sua adattabilità nel collegamento a sistemi di controllo di uso comune e alla possibilità di utilizzare numerosi protocolli fieldbus.
Il risultato di questa stretta collaborazione può essere riassunto con queste poche parole espresse da Paolo Colombo, Industry Consultant Beverage di SEW-Eurodrive Italia: “Garantiamo sempre professionalità e competenza ai nostri clienti. Grazie alla collaudata unità di azionamento MOVIGEAR classic e all’innovativo convertitore di frequenza MOVITRAC advanced, perfettamente abbinati, Krones ha realizzato un impianto completamente equipaggiato con soluzioni SEWEurodrive che, per flessibilità e sicurezza, hanno convinto anche Acqua Minerale di Calizzano. La costruzione compatta, la semplificazione della messa in servizio e della manutenzione, nonché l’elevata efficienza e affidabilità sono stati gli argomenti chiave per la riuscita del progetto”. “Sul fronte dell’efficienza e della sostenibilità degli impianti per l’imbottigliamento – conclude Angelo Nan - abbiamo tra le nostre missioni principali, quella di creare un futuro sostenibile; per questo siamo costantemente impegnati non solo nel cercare di ridurre l’utilizzo della plastica all’interno dei nostri processi ma anche nell’impiego di nuove tecnologie che garantiscano una riduzione dei consumi elettrici ed un utilizzo dell’energia più efficiente. Grazie a soluzioni all’avanguardia, che partono dall’efficienza dei motori, appartenenti alla classe di risparmio energetico IE5, fino a un pacchetto esplicitamente dedicato all’efficientamento dell’impianto, il consumo energetico viene ottimizzato per una produzione veramente green”.
Leister è conosciuta a livello mondiale per le sue tecnologie di lavorazione della plastica; oltre alle apparecchiature per la saldatura ad aria calda e a infrarossi e per il calore di processo, l’azienda fornisce anche soluzioni all’avanguardia per la saldatura laser della plastica. Queste sono apprezzate in una vasta gamma di segmenti industriali: automobilistico, medicale, sensoristica ed elettronica, nonché tecnologia dei microsistemi.
Con [X]M matrice modale ottenuta raccogliendo gli n autovettori, ovvero i modi di vibrare corrispondenti alle pulsazioni
Si possono disaccoppiare le varie matrici che, diventando diagonali, rendono i calcoli molto più agevoli, trasformando il sistema sotto riportato in una serie di equazioni risolvibili singolarmente.
Uno degli ultimi sviluppi dell’azienda è BASIC S, un sistema laser raffreddato ad aria progettato per essere integrato nelle linee e nelle celle di produzione. Il suo design intelligente e funzionale ne consente l’utilizzo in una grande varietà di applicazioni. Abbiamo parlato di questa soluzione con Johannes Eckstädt, Product Manager di Leister.
In generale, le vibrazioni vengono distinte in deterministiche, descrivibili mediante opportune relazioni matematiche, e casuali, il cui andamento non è prevedibile, motivo per cui vengono considerate come disturbi o rumore.
Perché vogliamo migliorare proprio le vi brazioni?
BASIC, nelle sue diverse versioni, è dotato di una serie di opzioni: potrebbe elencare le principali e spiegare come contribuiscono a migliorare le prestazioni?
Questo fenomeno, insieme agli urti, concorre al catti vo funzi onamento ed al precoce deterioramento delle macchine e delle strutture, nonché all’inquinamento acustico dell’ambiente circostante. Anche la salute dell’uomo ne è influenzata negativamente, con conseguenze sempre più oggetto di attenzione da parte dei responsabili preposti alla sicurezza.
BASIC S sta riscuotendo successo tra i clienti. Potrebbe descriverci le sue caratteristiche originali e gli aspetti che hanno fatto ottenere a questo prodotto un’accoglienza calorosa sul mercato? Le aziende clienti apprezzano il BASIC S per molte ragioni: è facile da integrare in qualsiasi processo produttivo, è flessibile e poco costoso. I parametri di saldatura possono essere facilmente regolati tramite Web-HMI su un laptop collegato o direttamente sull’unità BASIC S utilizzando il suo display.
prossime fiere per aumentarne la notorietà sui mercati internazionali, e in particolare in Italia?
Per cominciare, presenteremo il concetto di base di BASIC S/M/L alla fiera K di Düsseldorf, in Germania, e ne sveleremo le caratteristiche in dettaglio.
Come già spiegato nell’articolo Lo smorzamento delle vibrazioni nelle macchine utensili | Blog RW Italia le vibrazioni nelle macchine utensili sono dovute principalmente a tre fattori :
squi l i bri degl i al beri rotanti, come quello di trasmissione che collega il motore al mandrino, passando dai giunti e dalle ruote di trasmissione; difetti dimensioonali di alcuni componenti che costituiscono gli azionamenti; un ingaggio intermittente fra l’utensile ed il pezzo da lavorare.
L’intero sistema M/L si basa su una costruzione modulare: si scelgono solo le parti necessarie. L’unità principale, il laser e l’ottica sono fondamentali per il processo di saldatura e costituiscono quindi la configurazione di base di un sistema M/L BASIC. L’unità principale garantisce la sicurezza e il controllo degli altri componenti. Tra le altre unità funzionali, il sistema può essere ampliato con un’unità di movimento e un’unità di serraggio, ma sono tutte opzionali.
Le vibrazioni autoindotte e rigenerative
Le nostre unità standard hanno una configurazione predefinita, ma il sistema può essere adattato e personalizzato in base alle esigenze specifiche dei clienti.
BASIC S si distingue anche per l’innovativo sistema di raffreddamento: sviluppato internamente da Leister, garantisce una maggiore durata del modulo laser. A differenza di altri sistemi, il raffreddamento Leister mantiene il modulo laser sempre alla sua temperatura ottimale.
Tutti questi eventi generano delle forze periodiche che vengono convertite in vibrazioni forzate , che raramente causano problemi, e vibrazioni autoindotte , note anche come chatter, che sono uno dei limiti più importanti alla produttività dei processi di lavorazione. Già nel 1907 Taylor definì il chatter come “il problema più oscuro e delicato che si affronta nella lavorazione meccanica”. Esse si manifestano con l ’ aumento del l a vel oci tà di lavorazione, parametro molto importante per incrementare il rendimento delle macchine o durante il processo di finitura dei componenti; la diretta conseguenza è la generazione di asperità molto evidenti di geometria particolare sulla superficie del componente, causandone spesso lo scarto. I modelli matematici di Arnold o di tipo B (ampiamente analizzati nell’articolo https://blog.rw italia.it/smorzamento vibrazioni macchine utensili) constatano che questo fenomeno dipenda dalla lunghezza e dalla profondità del taglio, dallo smorzamento dell’utensile e da un fattore relativo alla forza.
Sulla scia del successo ottenuto dal BASIC S, state pianificando il lancio dei Sistemi M e L. Quali elementi li distinguono dalla versione S?
Come BASIC S, anche BASIC M e L sono entrambi sistemi facilmente integrabili, progettati per essere inseriti in una linea di produzione. Tuttavia, mentre il BASIC S è costituito da un laser e da un’ottica, con il BASIC M questa
L’elenco delle unità che lavorano all’interno del sistema M/L continuerà a crescere nei prossimi anni. Il nostro obiettivo è quello di adottare tutte le caratteristiche e i moduli che abbiamo attualmente nella nostra workstation.
Offriamo anche un’ampia gamma di funzioni per il controllo della qualità, per garantire al
Oltre a BASIC M/L, presenteremo MAXI, un sistema di saldatura laser per plastica chiavi in mano. MAXI sarà mostrato per la prima volta al pubblico; sarà dotato di un robot e di un tavolo rotante che simulerà la saldatura dei fanali posteriori con l’ottica GLOBO. In quanto “ prossima grande novità” per Leister, BASIC M/L sarà una parte importante delle nostre esposizioni del prossimo anno. In Italia stiamo pianificando di esporre al MECSPE di Bologna o al PLAST di Milano - forse anche a entrambi. Stiamo anche valutando la possibilità di organizzare un evento interno con un distributore italiano di macchine per la pressofusione.
Con l’uscita di nuove unità a intervalli frequenti, la BASIC S/M/L sarà a lungo protagonista di fiere ed eventi internazionali.
Come si inserisce BASIC M/L in un ambiente di produzione moderno?
La flessibilità dell’hardware e del processo soddisfa le esigenze dei clienti di oggi.
Siamo in grado di gestire sistemi di produzione caotici e siamo pronti a comunicare con i più moderni sistemi di produzione.
Il BASIC M/L è inoltre progettato per essere facilmente esteso a nuove unità e alle funzionalità dell’industria 4.0 / IOT in futuro.
Scanner Optic LQuelli che un tempo erano gli encoder, semplici componenti magnetici o ottici, oggi si sono evoluti per diventare vere e proprie periferiche intelligenti in grado di fornire accurate informazioni di angolo o posi zionamento attraverso protocolli di comunicazione dedicati. Soprattutto negli ultimi 15 anni sono arrivate nel mercato le nuove generazioni di prodotto che, grazie allo sviluppo delle tecnologie magnetiche, ottiche e microelettroniche, hanno fatto diventare gli encoder apparecchiature complesse. Come sempre accade l’evoluzione tecnologica di un pro dotto apre spazi per l’introduzione di nuove idee o ottimizzazioni e implementazioni ulteriori di prodotti esistenti. È in questo ambito che si posizionano i nuovi prodotti Flux distribuiti da Servotecnica. Gli encoder di posizionamento o misuratori di angolo della rappresentata combinano le caratteristiche di assenza di isteresi ed elevata precisione, tipiche di un encoder ottico, con la robustezza di un encoder induttivo e le ampie tolleranze di un encoder magnetico. Questo è possibile grazie
alle caratteristiche della tecno logia GMI (Giant Magneto Impedence) utilizzata in questi encoder assolutamente innovativi. L’utilizzo di questa tecnologia per le misure di posizionamento mas simizza l’interazione tra la soluzione magnetica e quella induttiva. Questa è un’innovazione attraverso la quale Flux è in grado di progettare e costruire encoder rivoluzionari con caratteristiche uniche e perfor mance d’avanguardia. Sono disponibili in tre differenti famiglie: il GMI angle encoder che garantisce alte performance, il GMI rotary encoder il più versatile, l’Inductive Rotary Encoder la soluzione più compatta. La particolare geometria degli encoder Flux, e le sue ridotte dimensioni assiali li rendono adatti ad essere integrati in molte applicazioni, tra cui la robotica, i macchinari per l’industria dei semiconduttori, medicale, le macchine utensili e le teste ottiche mobili. Per informazioni: www.servotecnica.com
Leister, multinazionale svizzera leader nella progettazione e realizzazione di soluzioni innovative per la lavorazione della plastica, è da sempre attenta all’aspetto della sosteni bilità ambientale; i reparti di progettazione lavorano per fornire soluzioni più efficienti e leggere a parità di prestazioni, per assicu rare il minor consumo possibile di energia e risorse. Un numero elevato e crescente di pistole ad aria calda e saldatrici automatiche Leister e Weldy, dalle numerose applicazioni in diversi settori industriali e in aziende di produzione e commerciali in tutto il mondo, sono disponibili con la funzionalità Eco Mode. Come funziona e quali vantaggi comporta? Soffianti e saldatrici Leister e Weldy sono utilizzate in ambiti diversi, dall’ingegneria civile alle pavimentazioni, dalla impermeabilizzazione di coperture e piscine alle applicazioni tessili tecniche, come al realizzazione di banner promozionali e teloni per camion, fino alle applicazioni per il set tore del trasporto e dell’elettronica: leggere e maneggevoli, sono parte inte grante del lavoro quotidiano per un elevato numero di operatori professionali. La crescente centralità delle tematiche ambientali ha fatto sì che la mag gior parte di questi operatori abbia mostrato interesse per soluzioni improntate al risparmi energetico, esigenza che Leister è stata la prima a soddisfare proprio con l’introduzione dell’Eco Mode, attivabile su tutte le soluzioni manuali con interfaccia digitale Leister e Weldy già dal 2019. La modalità Eco Mode è attivabile dal menu di configurazione; l’ap parecchio rileva ogni pausa nelle operazioni e riduce automaticamente la velocità del motore della soffiante aria, risparmiando così il 40% di energia. Oltre all’indubbio effetto positivo sull’ambiente, Eco Mode apporta anche vantaggi in termini di maggior sicurezza degli operatori e di risparmio, aspetti tenuti in grande considerazione dai progettisti
Leister. A titolo esemplificativo un’azienda che utilizzi 10 Solano AT con ECO Mode attivata risparmierà circa 1.700 euro all’anno rispetto all’utilizzo senza questa modalità (calcolo fatto ipotizzando 1 turno lavorativo da 8 ore), por tando gli apparecchi a ripagarsi in poco tempo. Questo senza contare l’ulteriore risparmio dovuto al minor riscaldamento dell’ambiente di lavoro e di conseguenza alla minor necessità di utilizzare climatizzatori per mantenere una temperatura accettabile. Oltre al con sumo energetico, anche l’usura dei soffianti si riduce: gli apparecchi durano almeno il 10% in più e gli interventi di manutenzione diventano meno frequenti, con ulteriori risvolti positivi su ambiente e struttura dei costi. Utilizzando Eco Mode si contribuisce inoltre a contenere l’inquinamento acustico all’interno dell’ambiente di lavoro: la rumorosità si riduce del 50% quando interviene Eco Mode, con un gran beneficio in termini di comfort degli operatori. L’elettroutensile poi rimane sempre disponibile e pronto all’uso: il sensore di accelerazione inserito nell’elettroutensile rileva immediatamente il movimento di ripresa del lavoro e in pochi istanti è in grado di passare dalla modalità ECO al pieno regime. I prodotti disponibili con la funzionalità Eco Mode comprendono numerosi best-seller dell’azienda sia a livello di elettroutensili manuali, come le pistole ad aria calda Solano AT e Triac AT, sia a livello di saldatrici automatiche come Uniroof 700, Unifloor 500 e Comet 700. Che si tratti di lavorare in cantiere o all’interno della propria area pro duttiva, Eco Mode offre alle aziende una risposta efficace alla sfida del rispetto ambientale e dei costi sempre più alti dell’energia. Maggiori informazioni sulla modalità Eco Mode sono disponibili nel video sul sito Leister: https://www.leister.com/it/Stories/2022-02-15-LAGEco-Mode
Flex Fix di Kemmer è un sistema mono tagliente per troncatura che assicura elevate prestazioni grazie all’innovativo sistema di fissaggio e all’inserto realizzato con un elevato volume di metallo duro. Pensato per la troncatura di grandi dia metri fino a 100 mm, il sistema Flex Fix comprende utensili monoblocco, lame, cartucce modulari Grip Lock e utensili o lame con refrigerazione interna ad alta pressione.
Peculiarità del sistema Flex Fix è il posizionamento a 0° dell’in serto, che permette di mantenere costante l’altezza del tagliente durante le lavorazioni. Grazie ad un accurato studio della distri buzione delle forze, il serraggio dell’inserto aumenta proporzio nalmente all’aumentare dell’avanzamento, assicurando a questo
sistema Kemmer sempre le massime presta zioni durante l’intero ciclo di lavorazione.
La speciale chiave AWF16 fornita gratui tamente in dotazione consente una rapida e sicura sostituzione dell’inserto minimiz zando i tempi dell’operazione.
Sono disponibili numerose geometrie e gradi per la troncatura di materiali ISO P, M, K, N ed S, con inserti dallo spessore 2 a 4 mm nelle versioni neutra e angolata (destra e sinistra).
Fino al 25 novembre, Sorma propone l’acquisto di 10 inserti e 1 utensile a condizioni estremamente vantaggiose. Un’occa sione da non perdere per quanti sono alla ricerca di un sistema di troncatura altamente efficiente. Per maggiori dettagli, inqua drare il codice QR per scaricare il volantino della promozione
OMRON ha lanciato un nuovo calcolatore del ROI per supportare il processo di valutazione di un investimento in robot collaborativi e mobili, che comprende anche le opportunità di leasing facili e con venienti, ideali per le piccole e medie imprese (PMI).
Il calcolatore del ROI di OMRON offre, alle aziende che stanno valutando di investire in robot mobili o collaborativi, una panoramica rapida e semplice del ritorno sugli investimenti basato su dati reali. Consente agli utenti di stimare il numero di mesi necessari per rag giungere il pareggio dell’investimento, tenendo conto dell’inflazione e degli adeguamenti dei tassi d’interesse in funzione delle condizioni di mercato.
I robot mobili e i cobot sono facili da implementare e trasportare, il che li rende un alleato vantaggioso per ottenere una maggiore fles sibilità nella produzione. Possono inoltre contribuire a un ambiente di lavoro più sicuro, collaborando con i colleghi umani per il solleva mento o il trasporto di prodotti e materiali.
Tuttavia, molte piccole e medie imprese (PMI) non possono permet tersi l’investimento di capitale iniziale di tali tecnologie. OMRON offre opzioni di leasing progettate per semplificare la vita dei pro duttori che desiderano sviluppare le loro flotte di robot mobili o col laborativi (cobot), mantenendo bassi i costi di investimento iniziali. Eduardo de Robbio, Strategic Business Development Manager di OMRON, ha osservato: “Durante la pandemia, abbiamo assistito a un aumento della necessità di produzione di volumi ridotti e alta mente diversificati, unito a una carenza di lavoratori in molti settori.
Ciò ha portato a un maggior numero di posizioni aperte sia per gli
operatori, sia per i robot. Oltre alle opzioni di leasing flessibili, vole vamo offrire ai nostri clienti uno strumento di calcolo del ROI di facile utilizzo per supportare il loro processo decisionale”.
Una volta inseriti i dati relativi alle operazioni correnti e selezionati il tipo e il numero di robot, il calcolatore del ROI fornisce una chiara panoramica chiara del periodo di ammortamento, della percentuale ROI e del valore attuale netto (VAN), che mostra la stima attualizzata del valore totale dei flussi di cassa futuri.
Una decisione chiave per il cliente è come finanziare un nuovo inve stimento. Il calcolatore del ROI di OMRON offre due opzioni tipi che: l’opzione Capex tradizionale con pagamento totale all’inizio, e l’opzione Opex con leasing, con pagamenti dilazionati in 3-5 anni. De Robbio ha proseguito: “I robot possono occuparsi di compiti ripetitivi e garantire operazioni flessibili, accurate ed efficienti, con sentendo ai colleghi umani di concentrarsi su questioni critiche per l’azienda e su attività creative”. Per quanto riguarda l’aspetto fonda mentale del ROI, la manodopera umana viene assegnata a compiti a maggior valore aggiunto, il che sarà assolutamente essenziale per i produttori in futuro. Inoltre, l’automazione può bilanciare la carenza di personale esperto nel mercato del lavoro”.
Per informazioni: www.industrial.omron.it
Eaton presenta il sistema xModular, la più recente novità nel suo portfolio di sistemi critici che porta innovazione, integrazione e una nuova dimensione digitale alla progettazione, all’implemen tazione e al funzionamento dei data center.
Il nuovo sistema xModular di Eaton riduce la complessità del pro getto, della costruzione in loco e del coordinamento. Ciò consente di ottenere tempi di costruzione inferiori a quelli dei metodi tradi zionali e di ridefinire la tecnologia e il modo di pensare all’infra struttura. Inoltre, Eaton offre elevati livelli di customer experience grazie alla competenza sviluppata in termini di progettazione del sistema, qualità, flessibilità, sicurezza, installazione, test e messa in servizio e risponde all’esigenza dei clienti di ottenere più rapi damente sviluppo, scalabilità e sostenibilità.
Il nuovo sistema xModular include la tecnologia UPS Eaton Ener gyAwareTM. Grazie a un UPS grid-interactive, la rete elettrica di un’unità data center xModular è in grado di agire da Risorsa di Energia Distribuita (DER) e di fornire all’operatore di rete ser vizi fondamentali, quali l’accelerazione e l’eliminazione dei rischi legati all’adozione delle rinnovabili. Questo supera di gran lunga molti dei tradizionali sforzi fatti in termini di sostenibilità della progettazione dell’infrastruttura e delle operation. L’integrazione di un software per il monitoraggio dell’energia elet trica e la gestione dell’infrastruttura sicure a livello informatico, in loco o da remoto, offre poi agli utenti la sicurezza di ottenere visibilità e comando completi per la loro infrastruttura critica. “L’economia sta diventando sempre più digitalizzata, pertanto la necessità delle strutture di ospitare infrastrutture di calcolo e digitali è in continua crescita. Che si tratti di un data center, di una rete IT locale o di una rete di telecomunicazione, tutte queste infrastrutture devono poter trovare un modo più economico,
veloce, flessibile e sicuro per ospitare le apparecchiature digitali. Il sistema xModular e la strategia go-to-market rispondono a queste necessità indipendentemente dal tipo di applicazione o di cliente”, ha dichiarato Karina Rigby, president, Critical Systems, Electrical Sector di Eaton EMEA.
Eaton si occupa dell’intero modulo e delle prestazioni del sistema e, in qualità di leader di mercato nella produzione di quadri elettrici, apparecchiature per la distribuzione dell’energia e UPS, ricopre una posizione strategica per ottimizzare, integrare e modularizzare l’energia. Oltre a interessare gli aspetti relativi all’infrastruttura (grey space), xModular può essere configurato per fornire ampio spazio anche all’apparecchiatura IT di calcolo (white space). Tale spazio è progettato secondo i requisiti elettrici, di raffreddamento, di comando e di sicurezza, fornendo un sistema all-in-one. Il partner program xModular di Eaton sfrutta inoltre i vantaggi offerti dalla collaborazione con le migliori aziende del settore tec nologia e servizi. “Come alternativa alle limitazioni legate ad un tipo di progettazione o ai costi legati a soluzioni su misura, xMo dular offre una serie di design adatti a diverse applicazioni e aree geografiche. Questo lo rende unico sul mercato, fornendo la fles sibilità di cui i clienti hanno davvero bisogno” ha spiegato Ciarán Forde, Data Centre market segment manager di Eaton EMEA. Grazie a una vasta esperienza nel settore elettrico e a elevate competenze nel project management, nei servizi sul campo e nell’assistenza post-vendita, Eaton garantisce la gestione dell’in tero ciclo di vita del prodotto. Con oltre 2.000 service engineer e innumerevoli progetti completati a livello globale in ambito data center, Eaton è in grado di fornire una tecnologia e un’assistenza di altissimo livello.
Per informazioni: www.eaton.com
Ct Meca amplia la propria gamma di elementi di manovra con la serie di volantini interamente in inox per rispondere alle esigenze particolari dell’industria agroalimentare, medicale e chimica. I volantini pieni in inox 304 con impugnatura girevole sono pro posti da diametro 76mm a 254mm. I volantini a razze da 100 a 200mm di diametro sono in inox 316 e sono proposti con o senza impugnatura girevole e scanalatura per la chiavetta. Questi modelli completano la nostra ampia gamma di volantini in poliammide o alluminio: a razze, pieni, con o senza impugnatura. Su alcuni modelli l’impugnatura è disponibile come accessorio. Numerosi modelli sono proposti in pronta consegna.
Per informazioni: www.ctmeca.com
TURCK BANNERTurck Banner ha ampliato le funzionalità delle sue interfacce RFID IP67 con la specifica AutoID Companion V. 1.01 per OPC UA e con la modalità bus HF.
Mentre il server OPC UA con la specifica AutoID Companion V. 1.01 garantisce una comunicazione diretta senza problemi con sistemi MES, PLC, ERP o cloud, la modalità bus HF di Turck Banner offre vantaggi in termini di costi per applicazioni con molti punti di lettura.
Gli utenti beneficiano anche del quasi nullo impegno per l’integrazione richiesto per i sistemi HF e UHF.
L’aggiornamento del firmware trasforma il TBENL5-4RFID-8DXP-OPC-UA nel primo modulo RFID con server OPC UA integrato a supportare la modalità bus HF di Turck Banner, che consente di collegare fino a 32 dispositivi di lettura/scrittura HF a ogni singolo ingresso RFID.
Con quattro canali RFID per modulo, significa che è possibile acquisire e parametrizzare a livello centrale fino a 128 punti di lettura.
Il nuovo firmware consente anche la lettura continua dei dati utente UID/EPC o RFID. In questo modo, un sistema MES o SAP può ad esempio ricevere o elaborare i dati in qualsiasi momento come messaggio di evento senza eseguire un metodo.
L’attivazione avviene tramite l’impostazione di una varia bile che rimane attiva anche dopo un reset dell’alimen tazione, in modo che il sistema RFID possa continuare a fornire dati in modo affidabile anche dopo un’interru zione dell’alimentazione.
Il nuovo server web, con una guida utente ottimizzata e un design intuitivo, consente di configurare via web il server OPC UA, compresi i parametri UHF, e fornisce strumenti UHF per testare la lettura dei tag. Per informazioni: www.turckbanner.it
CT MECAIl nuovo sensore i.Sense TR.B permette di monitorare le condizioni delle catene portacavi triflex R in applicazioni tridimensionali. Da tempo ormai, i robot sono diventati parte integrante della produ zione industriale e, sulla scia della digitalizzazione, continuano a crescere gli ambiti di utilizzo. Saldatura, verniciatura, brasatura o pallettizza zione... I robot industriali si caratterizzano per il loro funzionamento dinamico. Una catena portacavi flessibile come la triflex R igus permette di guidare i cavi in tutta sicurezza nei movimenti tridimensionali del robot. Per rilevare in tempo reale eventuali rotture della catena dovute a carichi estremi ed evitare guasti imprevisti alla macchina, igus presenta i.Sense TR.B, il primo sistema al mondo per il monitoraggio delle rot ture su catene portacavi 3D.
Miglioramento dell’efficienza energetica e dei materiali, soluzione ai colli di bottiglia lungo la supply-chain grazie alla produzione locale e risoluzione del problema di carenza di manodopera: secondo l’indice delle tendenze 2022 rilasciato dalla fiera Automatica, manifestazione di riferimento per il settore dell’automazione, sono queste le risposte più frequenti alla domanda sul perché i robot industriali siano così impor tanti per l’economia tedesca. Tuttavia, perché un robot industriale possa funzionare in modo affidabile, è fondamentale predisporre una guida sicura dei cavi. Sui robot, i cavi devono sopportare numerosi cicli di flessione e carichi dovuti a torsione e tensione. Con triflex R, igus ha svi luppato una catena portacavi rotonda con un raggio di curvatura definito ideale per l’uso sui robot industriali, al fine di proteggere i cavi anche durante i movimenti dinamici di rotazione e di oscillazione. La rottura di una catena può avere conseguenze disastrose: i tempi di inattività, i
fermi di produzione e i ritardi nelle consegne costano tempo e denaro. igus, specialista di motion plastics, ha sviluppato una soluzione nuova ed economica per individuare tempestivamente eventuali rotture nella catena e prevenire i costosi danni associati. Stiamo parlando di i.Sense TR.B - un sistema di monitoraggio della rottura per le catene portacavi tridimensionali triflex R.
Con i.Sense TR.B, il nuovo dispositivo i.Sense smart plastics igus, è possibile monitorare eventuali rotture anche in applicazioni dinamiche tridimensionali. Con i.Sense TR.B, i clienti potranno incrementare la sicurezza dei loro sistemi robotici a fronte di un investimento decisa mente contenuto. Il sensore i.Sense TR.B è collegato direttamente al PLC del cliente, senza costi di software supplementari. In caso di rot tura di una maglia, il sistema rileva una variazione nella lunghezza del cavetto installato nella catena, inviando un segnale digitale al sistema di controllo. Il rilevamento istantaneo delle rotture permette di intra prendere interventi di manutenzione immediati, evitando fermi non pianificati e guasti estesi in caso di rotture delle singole maglie. “In particolare nel settore automotive dove abbiamo volumi di produzione elevati, qualsiasi interruzione non pianificata può causare ingenti costi, anche di svariate centinaia di migliaia di euro. Per questo il monitorag gio in tempo reale dello stato del sistema di alimentazione nei robot industriali offre un notevole valore aggiunto” spiega Richard Habering, Responsabile della Business Unit smart plastics presso igus GmbH.
Grazie ai numerosi test eseguiti nel più grande laboratorio di prova del set tore, igus è nelle condizioni di appor tare continue ottimizzazioni per offrire prodotti sempre migliori sia in termini di qualità che di durata d’esercizio.
Oggi - per guidare e proteggere i cavi robot, aumentandone sensibilmente la durata utile - igus propone di installare il nuovo sensore i.Sense TR.B sulle catene portacavi robot della serie triflex R (catene caratterizzate da un elevato assorbimento della forza di trazione).
Il monitoraggio delle condizioni attraverso il sensore TR.B aumenta la sostenibilità della manutenzione, evi tando la sostituzione superflua o pre matura dei prodotti. In caso di rotture alla catena, dopo l’arresto di emergenza del sistema, il sensore è riutilizzabile. Per informazioni: www.igus.it
n. 7 Ottobre 2022 www.meccanica-automazione.com
Redazione Direttore Responsabile Giorgio Albonetti
Coordinamento Editoriale Area Industry Marco Tenaglia –marco.tenaglia@quine.it – cel. 3298490024
Direttore tecnico Chiara Tagliaferri
Segreteria di Redazione Cristina Gualdoni cristina.gualdoni@quine.it – cel. 3477623887
Hanno collaborato a questo numero Andrea Mazzoleni, Patrizia Ricci, Eleonora Segafredo
Pubblicità Ufficio Traffico Elena Genitoni e.genitoni@lswr.it – tel. 0289293962
Servizio abbonamenti abbonamenti.quine@lswr.it Abbonamento annuale € 49,99 Costo copia singola € 7,07 (presso l’editore)
Produzione Antonio Iovene | Procurement Specialist a.iovene@lswr.it | Cell. 349.1811231
Grafica e Fotolito: Fabio Castiglioni Stampa: Aziende Grafiche Printing Srl Peschiera Borromeo (MI)
Registrazione del Tribunale di Milano n. 653 del 21.09.2005.
Iscrizione al R.O.C. n. 12191 del 29/10/2005 Tutti gli articoli pubblicati su m&a meccanica &automazione sono redatti sotto la responsabilità degli Autori. La pubblicazione o la ristampa degli articoli deve essere autorizzata per iscritto dall’Editore. Ai sensi dell’art. 13 del D.Lgs. 196/03, dati di tutti i lettori saranno trattati sia manualmente sia con strumenti informatici e saranno utilizzati per l’invio di questa e di altre pubblicazioni e di materiale informativo e promozionale. Le modalità di trattamento saranno conformi a quanto previsto dall’art. 11 D.Lgs. 196/03. I dati potrebbero essere comunicati a soggetti con i quali Quine S.r.l. intrattiene rapporti contrattuali necessari per l’invio delle copie della rivista. Il titolare del trattamento dei dati è Quine S.r.l. - via Spadolini, 7 - 20141 Milano Tel +39 02 864105 Fax +39 02 72016740, al quale il lettore si potrà rivolgere per chiedere l’aggiornamento, l’integrazione, la cancellazione e ogni altra operazione di cui all’art. 7 D.Lgs. 196/03.
Ai sensi dell’art. 13 Regolamento Europeo per la Protezione dei Dati Personali 679/2016 di seguito GDPR, i dati di tutti lettori saranno trattati sia manualmente, sia con strumenti informatici e saranno utilizzati per l’invio di questa e di altre pubblicazioni e di materiale informativo e promozionale. Le modalità di trattamento saranno conformi a quanto previsto dagli art. 5-6-7 del GDPR. I dati potranno essere comunicati a soggetti con i quali Edra S.p.A. intrattiene rapporti contrattuali necessari per l’invio delle copie della rivista. Il titolare del trattamento dei dati è Edra S.p.A., Via G. Spadolini 7 - 20141 Milano, al quale il lettore si potrà rivolgere per chiedere l’aggiornamento, l’integrazione, la cancellazione e ogni altra operazione di cui agli articoli 15-21 del GDPR.
Testata associata
ABB 82 AFIL 74 ASSTEL 8 Baumer 64 Bosch Rexroth 66 Cognex 67 Ct Meca 94 Eaton 92 Ericsson 8 Euroblech 26 Fastener Fair Italy 24 Gefran 13 Gefran 68 igus 69-96 Krones 84 Leister 88-90 Lovato Electric 8 MADE 16 Mewa 20 MiR 30 Mitsubishi Electric 10 Nidec 12 OML 10 Omron 78-91 R+W 70 Renishaw 44 Sandvik Coromant 37-48 Schneider Electric 71 Schunk 22 Servotecnica 90 Sew-Eurodrive 84 Siemens 72 smc 14 Soraluce 50 Sorma 91 Studer 54 Synergon 56 Terranova Instruments 11 Tork 18 Tornos 58 Turk Banner 94 Valve World Expo 32 AMC 93 Atomat 65 Comoli Ferrari 28 Dkc 19 DMG MORI 4 Fastener Fair Italy 9 Gom 11 Ifp 13 Ige-xao 77 igus 3 Losma 47 Mikron 95 MMC II COP Pei 53 Pilz 73 Pirate Rocket IV COP Renishaw 81 Romani Components I COP Soraluce 15 Sorma 7 Topsolid 35 Tork 25 UCIMU 40