Construction Project Management Plan Sydney Metro Sydenham to Bankstown Group 20
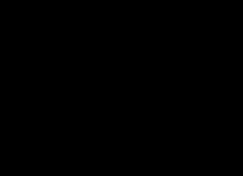
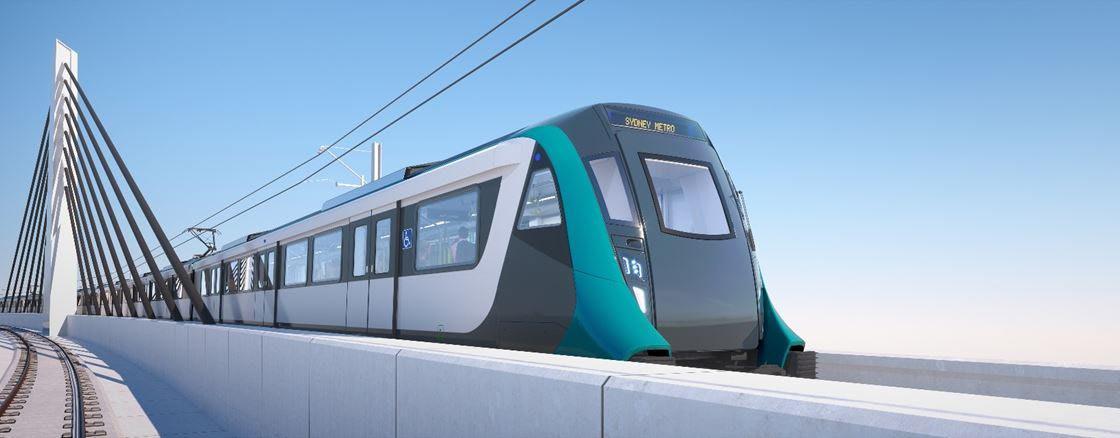
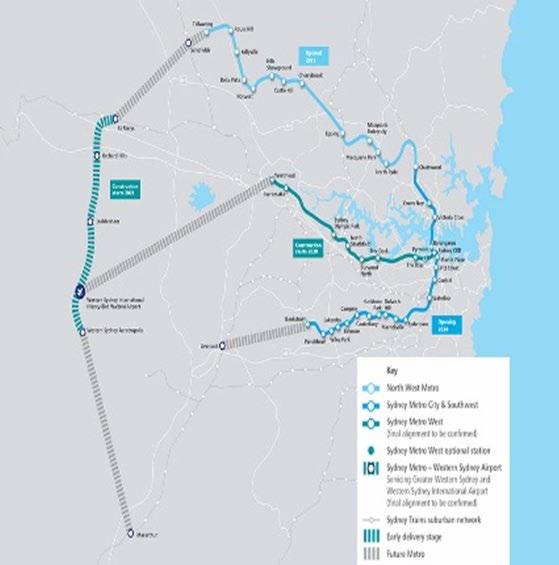
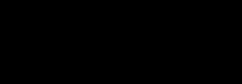
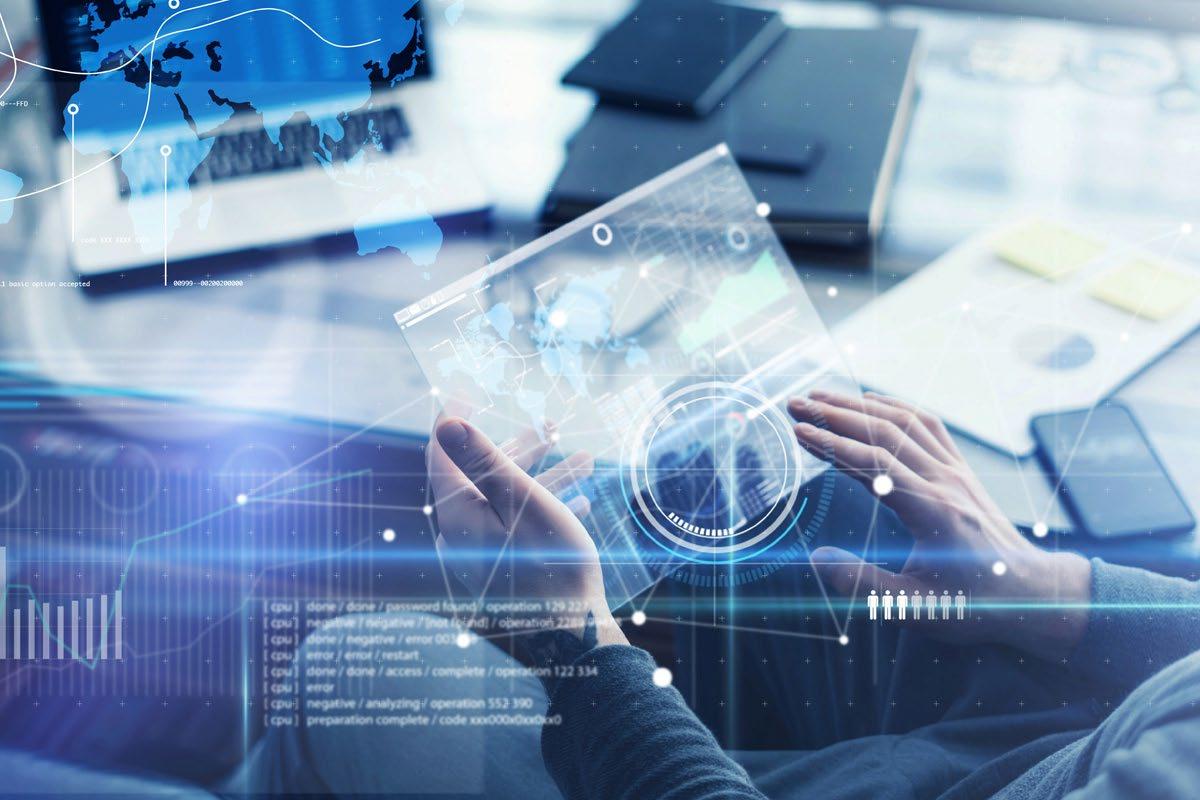

3 Revision History #Rev Date remarksRevised,Chapter/Section/Pageplusany by:Compiled ReviewerApprovals ManagerProject PM ManagerLine A 16/09/2021 Draft for Review Y.H. Y.Z. Y.Z. X.Z. B 07/10/2021 Updated following comments Y.H. Y.Z. Y.Z. H.Y. C 28/11/2021 Updated following comments Y.H. Y.Z. Y.Z. H.Y. This sheet records the version and a summary of approved changes to the document. If only a few revisions are made, only the new or revised pages may be issued. This document is the property of Group 20 and its issue is controlled. The information contained hereinmay not be disclosed in whole or in part, either verbally or in writing, without the prior consent of the Company. ApprovalsSeniorProject Engineer Signed: Y.H. . Date: . Project Manager Signed: Y.Z. . Date: . The issue and use of this Construction Project Management Plan (CPMP) is with my authority. All personnel employed on this project shall perform their duties in accordance with the requirements of this plan and in compliance with Sydney Metro Project requirements, any specific project procedures and associated instructions. All subsequent revisions and issue of this CPMP shall be completed by the authority of the Project Directorin consultation with the Construction Manager. NSW Constricton Manager Signed: Y.Z. . Date: .
4 Table of Content 1.0 Introduction and Overview ...................................................................................... 13 1.1 Introduction and Purpose ................................................................................................. 13 1.2 Application ......................................................................................................................... 14 1.3 Amendments ...................................................................................................................... 14 1.4 Authorisation ..................................................................................................................... 14 1.5 Glossary .............................................................................................................................. 14 1.6 Further Information ......................................................................................................... 15 2.0 Project Charter .......................................................................................................... 16 2.1 Purpose of Project Charter .............................................................................................. 16 2.2 Project Overview ............................................................................................................... 16 2.3 Justifications ...................................................................................................................... 17 2.4 Scope ................................................................................................................................... 18 2.4.1 Scope of works .................................................................................................................... 18 2.4.2 Objectives 19 2.4.3 Major Deliverables ..................................................................................................................... 20 2.5 Duration ............................................................................................................................. 21 2.5.1 Timeline ..................................................................................................................................... 21 2.5.2 Key Milestones 22 2.6 Budget Estimate................................................................................................................. 22 2.6.1 Funding Source .......................................................................................................................... 22 2.6.2 Estimate 22 2.7 Assumptions, Constrains and Risks ................................................................................ 23 2.7.1 Assumptions 23 2.7.2 Constrains .................................................................................................................................. 24 2.7.3 Risks 26 2.8 Team Organisation ............................................................................................................ 28 2.8.1 Team Roles and Responsibilities ............................................................................................... 28 2.8.2 Team Communication Plan 28 2.8.3 Team Risk Management Plan .................................................................................................... 29 3.0 Project Scope Management Plan ............................................................................. 30 3.1 Scope Definition ................................................................................................................. 31
5 3.2 Project Scope Statement ................................................................................................... 32 3.3 WBS .................................................................................................................................... 42 3.4 WBS Dictionary ................................................................................................................. 43 3.5 Project Scope Validation and Verification Process ........................................................ 46 3.6 Project Monitoring and Control System ......................................................................... 47 3.7 Scope Change Management Process ............................................................................... 47 4.0 Project Schedule Management Plan ........................................................................ 50 4.1 Project scheduling methodology ...................................................................................... 51 4.1.1 Scheduling Method 51 4.1.2 Organizational Procedure Links................................................................................................. 52 4.1.3 Scheduling Tool 52 4.1.4 Level of Accuracy ...................................................................................................................... 52 4.1.5 Units of Measurement 52 4.2 Activity identification process .......................................................................................... 53 4.2.1 Project Structure and Approach ................................................................................................. 53 4.2.2 Work Package Decomposition 53 4.3 Activity sequencing method.............................................................................................. 54 4.3.1 Relationship Types 54 4.3.2 Dependency Determination........................................................................................................ 55 4.3.3 Lead and Lag 55 4.4 Estimating activity duration method ............................................................................... 55 4.4.1 Activity Duration Estimation Methodology............................................................................... 55 4.4.2 Approaches Adopted in Sydney Metro Southwest Construction Project 56 4.5 Schedule baseline (up to level 3)....................................................................................... 63 4.5.1 Units of Measurement 63 4.5.2 Project Working Days and Calendar .......................................................................................... 63 4.5.3 Surrounding Areas Impact on Working Times 63 4.5.4 Schedule baseline ....................................................................................................................... 65 4.6 Schedule monitoring and control ..................................................................................... 67 4.6.1 Schedule Progress Collection Process 67 4.6.2 Schedule Progress Measurements .............................................................................................. 67 4.6.3 Schedule Reporting Format ....................................................................................................... 67 4.6.4 Schedule Variance Analysis and Control 68 5.0 Project Cost and Financial Management Plan ....................................................... 71
6 5.1 Cost Management Roles and Responsibilities ................................................................ 71 5.2. Cost Estimation and Budget Determination Methods ................................................. 74 5.2.1 Cost Estimation .......................................................................................................................... 74 5.2.2. Budget Determination Methods 74 5.3 Cost Breakdown Structure ............................................................................................... 75 5.4. Cost Baseline and Cash Flow Diagram .......................................................................... 77 5.4.1. Management Reserve 77 5.4.2. Cost Baseline ............................................................................................................................ 77 5.4.3. Cash flow Diagram 79 5.5 Cost Performance Measurement (Earned Value Management)................................... 80 5.5.1 Earned Value Curve of Sydney Metro Southwest Project ......................................................... 83 5.6 Cost Management Monitoring and Control ................................................................... 84 5.6.1 Work Performance Data and Information .................................................................................. 84 5.6.2 Cost Variance Response Process 84 5.7 Cost Baseline Change Control Process............................................................................ 88 6.0 Project Quality Management Plan........................................................................... 96 6.1 Quality Management Planning ........................................................................................ 96 6.1.1 Identify Roles and Responsibilities for QM team ...................................................................... 96 6.1.2 Quality Standards and Requirements 98 6.1.3 Procedure of Quality Planning ................................................................................................. 104 6.2 Manage Quality ............................................................................................................... 108 6.2.1 Tools and Techniques Applied to Manage Quality 108 6.2.2 Quality Checklist ..................................................................................................................... 109 6.2.3 Quality Metrics 112 6.3 Quality Assurance Process ............................................................................................. 113 6.4 Quality Control ................................................................................................................ 115 6.4.1 Quality Control Process 115 6.4.2 Control Quality Tools and Techniques: ................................................................................... 117 7.0 Project Resource Management Plan ...................................................................... 121 7.1 Organizational Breakdown Structure (OBS) ............................................................... 121 7.2 Roles and Responsibilities (5 roles) ............................................................................... 122 7.3 RACI Matrix .................................................................................................................... 125 7.4 Staff Acquisition and Release Plan ................................................................................ 132
7 7.4.1 Staff Acquisition Plan .............................................................................................................. 132 6.4.2 Staff Release Plan 135 7.5 HR Resource Calendar and HR Resource Histogram ................................................. 135 7.6 Machinery and Equipment Resource Histogram ......................................................... 140 7.7 Staff Induction and Training Plan, Performance Review, Staff Recognition and Rewards, Compliance, Equity and Safety ........................................................................... 142 7.7.1 Staff Induction and Training Plan ............................................................................................ 142 7.7.2 Performance Review 143 7.7.3 Staff Recognition and Rewards ................................................................................................ 144 8.0 Project Risk Management Plan .............................................................................. 147 8.1 Plan Risk Management ................................................................................................... 147 8.1.1 Methodologies 147 8.1.2 Roles and Responsibilities ....................................................................................................... 148 8.1.3 Risk Management Budget and Timing 149 8.2 Risk Identification ........................................................................................................... 150 8.2.1 Tools and Techniques Applied 150 8.2.2 Risk Breakdown Structure ....................................................................................................... 154 8.3 Qualitative Risk Analysis................................................................................................ 159 8.3.1 Definition of Probability and Impact 159 8.3.2 Probability and Impact Matrix ................................................................................................. 162 8.4 Quantitative Risk Analysis ............................................................................................. 164 8.4.1 Monte Carlo Simulation Introduction 164 8.4.2 Total Risk Contingency Reserve Estimation by MCS ............................................................. 164 8.5 Risk Response Plan ......................................................................................................... 169 8.5.1 Risk Response Strategies ......................................................................................................... 169 8.5.2 Risk Register 171 8.5.3 Risk Action Plan with Expectations ......................................................................................... 174 8.6 Risk Monitoring and Controlling .................................................................................. 176 8.6.1. Tools and techniques 176 9.0 Project Procurement Management Plan ............................................................... 178 9.1 Procurement Methodologies........................................................................................... 178 9.2 Procurement Process Diagram ...................................................................................... 179 9.3 Procurement Information Table .................................................................................... 180 9.4 Hire or buy analysis/make or buy analysis ................................................................... 181
8 9.4.1 Direct and indirect costs ........................................................................................................... 181 9.4.2. Business strategy 181 9.5 Contract Type Selection.................................................................................................. 183 9.5.1 Project Delivery Method .......................................................................................................... 183 9.5.2 Contract Price Type Selection 188 9.6 Source Selection Criteria ................................................................................................ 189 9.7 Procurement metrics to evaluate and select sellers, vendors, or subcontractors ...... 191 9.7.1. EOI Evaluation 191 9.7.2. Non Price Evaluation .............................................................................................................. 193 9.7.3. Overall Evaluation 193 9.8 Procurement controlling process and contract administration .................................. 195 9.8.1 Procurement controlling process .............................................................................................. 195 9.8.2 Contract administration 195 9.9 Procurement closing process .......................................................................................... 196 10.0 Project Communication Management Plan ........................................................ 197 10.1 Communications Matrix ............................................................................................... 197 10.2 Project Meeting Guideline ............................................................................................ 198 10.3 Project Reporting Procedure (Schedule and Template for Reports) ....................... 198 10.4 Project Management Information System (PMIS) .................................................... 199 10.5 Template for Project Work Performance Report ...................................................... 200 10.6 Glossary of Common Terminologies in the CPMP .................................................... 203 11.0 Project Stakeholder Management Plan ............................................................... 206 11.1 Stakeholder Analysis (Identification/Stakeholder Register) ..................................... 207 11.2 Stakeholder Analysis (Power/Interest Matrix) ........................................................... 210 11.3 Stakeholder Analysis (Engagement Analysis) ............................................................ 213 11.4 Control Stakeholder Engagement................................................................................ 215 11.4.1 Monitor (Inspect) Stakeholder Engagement: ......................................................................... 216 11.4.2 Control (Correct) Stakeholder Engagement 216 12.0 Project Change Control Management Plan ........................................................ 217 12.1 Change management process ....................................................................................... 218 12.2 Change request review .................................................................................................. 219 12.2.1 Change Request Form ............................................................................................................ 219 12.2.2 Change Request Log: 220
9 12.3 Change control board ................................................................................................... 220 13.0 Project Health, Safety and Security Management Plan ............................... 221 13.1 Strategies of Work, Health and Safety Management................................................. 221 13.2 General guidelines of WHS Responsibilities for Contractors ................................... 222 13.3 Methodologies of Safety Management......................................................................... 223 13.3.1 Checklists ............................................................................................................................... 223 13.3.2 Construction Induction and Safety Training 223 13.3.3 Licenses/Certifications/Registrations/Permits ....................................................................... 223 13.3.4 Supervision and Control 223 13.3.5 First Aid Team ....................................................................................................................... 223 13.4 Evaluation of Safety Performance 223 14.0 Construction Environmental Management Plan................................................ 224 14.1 CEMP Structure Overview .......................................................................................... 225 14.2 Scope of Proposed Environmental Management Work ............................................ 226 14.2.1 CEMP Framework High Level Objectives and Targets ........................................................ 226 14.2.2 Responsibilities and Authorities 226 14.3 Project Environmental Management Planning .......................................................... 228 14.3.1 Legal and Compliance Requirements 228 14.3.2 Standards and Codes .............................................................................................................. 229 14.3.3 Health, Safety and Environmental Management System 230 14.3.4 Environmental Policy ............................................................................................................. 230 14.3.5 Environmental Management Flowchart associated with Responsibilities 231 14.4 Project Environmental Management Executing ........................................................ 231 14.4.1 Environmental Risk Assessment and Control 231 14.4.2 Training, Awareness and Competence 232 14.4.3 Environmental Management System Audit 234 14.5 Project Environmental Management Monitoring and Controlling ......................... 234 14.5.1 Environmental Control Map .................................................................................................. 234 14.5.2 Site Shutdown Plan 236 14.6 Monitoring and Measurement ..................................................................................... 236 14.6.1 Environmental Monitoring ..................................................................................................... 236 14.6.2 Monthly Project Environmental System ................................................................................ 237 Conclusion and Recommendation................................................................................ 238
10 Conclusion .............................................................................................................................. 238 Recommendations ................................................................................................................. 241 Reference: ....................................................................................................................... 242 Appendix......................................................................................................................... 245 Appendix A: Normal Distribution and Standard Normal Distribution........................... 245 Appendix B: The Probability Table for a Normal Distribution ....................................... 247 Appendix C Quality Standards Further Explanation ....................................................... 248 APPENDIX D: FEMA From Template .............................................................................. 251 Appendix E: Sydney Metro Risk Identification Checklist ................................................ 252 Appendix F: The Calculation Process of Monte Carlo Simulation .................................. 254 Appendix G: Total Cost Estimation and Comparison ....................................................... 264 Appendix I: Risk Register .................................................................................................... 268 Appendix J: Legal and Other Requirements(Examples Listed) ....................................... 271 Appendix K: Health, Safety and Environmental System(HSEMS) ................................. 274 Appendix L: Environmental Policy ..................................................................................... 276 Figure and Table List: Figure 1:Location of Sydney Metro Southwest Line (Sydney Metro,2018) 16 Figure 2:Sydney's Rail Congestion ............................................................................................................. 18 Figure 3: Sydney Metro Sydenham to Bankstown Schedule (Submissions and Preferred infrastructure report, June 2018) 21 Figure 4: Southwest Metro Project Timeline (Southwest Metro Project Update, November 2020) 21 Figure 5: Heavy Vehicle Access Route Details for Access 1(Sydenham Metro Upgrade Construction Traffic Management Plan Revision 19, 2021) ............................................................................................ 25 Figure 6:Heritage items within Marrickville and platform 1 & 2 (Sydenham to Bankstown Environmental Impact Statement, June 2018) 26 Figure 7: Work Packages of Sydney City & Southwest Metro Project (Sydney Metro, 2018) 32 Figure 8: Delivery Requirements Gate 3 Possession (Sydenham Metro upgrade Construction Traffic Management Plan Revision19, 2021) 38 Figure 9: Heavy Vehicle Access Route Details for Access 1 (Sydenham Metro upgrade Construction Traffic Management Plan Revision 19, 2021) ............................................................................................ 39 Figure 10: Heritage items within Marrickville and platform 1 & 2 (Sydenham to Bankstown Environmental Impact Statemen, June 2018) 40 Figure 11: Filters in SmartPlant Construction enable users to find material and equipment availability. (Factors Affecting Construction Labour Productivity, n.d) 57 Figure 12: Typical railway construction activities and tools applied.......................................................... 57 Figure 13: The 3D model can be filtered in SmartPlant Construction due to two different work packages occurring in the same area at the same time, highlighting any labour inefficiencies.(Factors Affecting Construction Labour Productivity, n.d) 58 Figure 14: Project Financial Management Organizational Structure .......................................................... 71
11 Figure 15: Cost Breakdown Structure (CBS) of Sydney Metro Southwest Line........................................ 76 Figure 16: Overall Budget Structure of the Sydney Metro Southwest Line ............................................... 77 Figure 17:Interest Rate in Australia (Reserve Bank of Australia, 2021) 78 Figure 18: Inflation Rate Compared to the Previous Year (Statista, 2021) 78 Figure 19: Average AUD/USD Exchange Rate (Macrotrends, 2021) 79 Figure 20: Cash Flow Diagram of Sydney Metro Southwest Line ............................................................. 80 Figure 21: Earned Value Curves ................................................................................................................. 83 Figure 22: Earned Value Curve of Sydney Metro Southwest 83 Figure 23: PoC trends (Project Life Cycle Economics: Cost Estimation, Management and Effectiveness in Construction Projects, 2015) ....................................................................................................................... 85 Figure 24: Cost Variance Process ............................................................................................................... 86 Figure 25: Cost Control Procedure 95 Figure 26: Platform Fall Requirements 104 Figure 27: Types of Customers ................................................................................................................. 105 Figure 28: Cost of Quality (PMI, 2017, pg.283) ....................................................................................... 109 Figure 29: Lift Installation Onsite Checklist (WorkSafe Victoria, 2017) 111 Figure 30: Checklist of Quality Management 112 Figure 31: Examples of Quality Metrics ................................................................................................... 112 Figure 32: Quality Assurance Cycle ......................................................................................................... 116 Figure 33: Sydney Metro Quality Control Flowchart 117 Figure 34: Control Chart & Action Plan (Lucid Content Team, n.d.) 118 Figure 35: Ishikawa Diagram for Schedule Delay (Özdemir, 2010) 119 Figure 36: Organizational Breakdown Structure ...................................................................................... 121 Figure 37: Acquire Project Team: Inputs, Tools & Techniques, and Outputs .......................................... 134 Figure 38: Acquire Project Team Data Flow Diagram 134 Figure 39: Human Resource Histogram 139 Figure 40: Machinery Histogram .............................................................................................................. 141 Figure 41: Risk Management Process (ISO 31000, 2018) ........................................................................ 148 Figure 42: FTA for claims of individuals and organisations 152 Figure 43: Probability distribution of total risk contingency reserve 167 Figure 44: Cumulative probability curve of total contingency reserve ..................................................... 167 Figure 45: Risk contingency ranked by effect on total contingency cost ................................................. 168 Figure 46: Procurement Process for Head Contractor .............................................................................. 179 Figure 47: Identifying strategic, core and outstanding potential 182 Figure 48: Project criteria and delivery method matrix 186 Figure 49:Spectrum of distributed contract risks 188 Figure 50: Comparison of two risk contingency probability distribution in terms of two price types. 189 Figure 51: For each criterion, scores will be awarded on a descending scale, i.e., the most merit attracting the highest score, lesser merit attracting a lesser score and equal merit attracting an equal score. .......... 197 Figure 52: Example of Project Meeting Table .......................................................................................... 198 Figure 53: Sydney Metro Southwest Stakeholder Power/Interest Matrix 211 Figure 54: CEMP Framework Overview 225 Figure 55: Environmental Management Flowchart .................................................................................. 231 Figure 56: Environmental Control Map of Cantebury Station.................................................................. 235 Figure 57: Environmental Control Map of Bankstown Station ................................................................ 236
12 Table 1: Key Milestones Across Project Lifecycle ..................................................................................... 22 Table 2: Typical Unit of Measures in Sydney Metro Southwest Project .................................................... 59 Table 3: The Output of Duration Calculation 60 Table 4: The outcome of PERT example calculation of Sydney Metro Southwest 62 Table 5: Schedule Reporting Format 68 Table 6: Control Threshold Variance.......................................................................................................... 69 Table 7: Cost Variance Control Thresholds ................................................................................................ 87 Table 8: The Common Standards Used in Sydney Projects Associated with Work Packages 99 Table 9: Audit Information (Sydney Metro, 2018) 114 Table 10: Audit attendance register (Quality Assurance Log) .................................................................. 115 Table 11: Hazard identified list in Sydney Metro Project......................................................................... 153 Table 12: High Level Category of RBS 154 Table 13: RBS of Sydney Metro Project Sydenham to Bankstown 154 Table 14: Likelihood table ........................................................................................................................ 159 Table 15: Consequence table .................................................................................................................... 160 Table 16: Risk Analysis Table 163 Table 17: Three point estimation calculation table 165 Table 18: The output statistics data of MCS for 10,000 iterations ........................................................... 166 Table 19: Statistic outcome table .............................................................................................................. 166 Table 20: Risk Reporting Standards 176 Table 21: Financial value for money comparison 184 Table 22: Template of performance report for Sydney Metro Southwest project 201 Table 23: Project Performance and Measures of Sydney Metro Southwest Project ................................. 201 Table 24: Whole Stakeholder List ............................................................................................................ 212 Table 25: Stakeholder engagement matrix 214 Table 26: CEMF High Level Objectives and Targets 226 Table 27:Relevant Standards .................................................................................................................... 229 Table 28: Proposed Training ..................................................................................................................... 232
document namely
20
controlling
construction project management subsidiaries plans are integrated in this CPMP: • Project Charter • Project Scope Management Plan with Work Breakdown Structure (WBS) • Project Schedule Management Plan with Schedule Baseline • Project Cost and Financial Management Plan with Cost Baseline • Project Quality Management Plan • Project Resource Management Plan with RACI Matrix • Project Risk Management Plan • Project Procurement Management Plan • Project Communication Management Plan • Project Stakeholder Management Plan • Project Change Control Management Plan • Project Work, Health and Safety (WHS) Management Plan
This Construction Project Management Plan is developed by Group Construction in order to provide extensive guidance and support for the and phases of the Sydney Metro Southwest Project - Sydenham to TheBankstown.following
The purpose of the Construction Project Management Plan (CPMP) is to establish a formal procedure for defining, preparing, integrating and coordinating various planning activities and management tools involved in the Sydney Metro Sydenham to Bankstown. The aims of this plan include, but are not limited to, defining the work tasks of each entity involved in the project; clarifying the relationship between different work tasks and the individual personnel that are performing those tasks; making decisions about which methods and technologies will be adopted to bring about the successful completion of the overall project; providing a comprehensive assessment of all resources required to complete this construction; and integrating subsidiary project management plans to arrive at a timeline, budget and other requirements for the Sydney Metro Southwest Project.
planning, execution,
(CPMP)
Planning Company
13 1.0 Introduction and Overview 1.1 Introduction and Purpose
14 1.2 Application The Construction Project Management Plan (CPMP) and subsidiary project management plans are developed primarily as communication tools to the team and key stakeholders. These plans become the ‘Project Procedure’ for the mentioned project and the contents should be understood and implemented by the project team leaders and members. This document intends to satisfy the Sydney Metro contractual requirement for the implementation of a CPMP, whilst at the same time, satisfying the Group 20 internal requirements for implementing the procedure. 1.3 Amendments Please refer to Revision History. 1.4 Authorisation For the due management of this project, all project personnel concerned with management shall be fully familiar with the Sydney Metro Project requirements and all activities. All activities shall be performed in accordance with the requirements to deliver the development project of Sydney Metro Southwest Sydenham to Bankstown. 1.5AcronymGlossaryDefinition Acronym Definition AC Actual Cost ITB Invitation to Bid AS Australian Standard KPI Key Performance Indicator ASHRAE American Society for Heating, Refrigerating, and Air conditioning Engineers MCS Monte Carlo Simulaiton BAC Budget at Completion OBS Organisational breakdown structure BCA Building Code of Australia PERT Program Evaluation and Review Technique BCR Baseline Change Request PM Project Manager CBD Central Business District PMIS Project Management Information System CBS Cost Breakdown Structure PPE Personal Protective Equipment CCB Change Control Board PR Procurement Request CM Construction Manager PV Planned Value CPI Cost Performance Index QA Quality Assurance CPM Critical Path Method QC Quality Control CPMP Construction Project Management Plan RBS Risk Breakdown Structure CV Cost Variation RMP Risk Management Plan EAC Estimated Cost at Completion SF Start to Finish ETC Estimate to Completion SOW Statement of Work
15 EV Earned Value SPI Schedule Performance Index EVM Earned Value Management SS Start to Start FF Finish to Finish SV Schedule Variance FS Finish to Start TCPI To Complete Performance Index HR Human Resources WBS Work Breakdown Structure 1.6 Further Information The project overview, justifications, scope, expected duration, budget estimate and critical risk factors are detailed listed in the next section, Project Charter.
2.0 Project Charter
2.1 Purpose of Project Charter
2.2 Project Overview
As the second half of the Sydney City & Southwest Project Metro Project, the southwest metro line will be built based on the T3 Bankstown Line, upgrading all 11 stations and railway in between Sydenham and Bankstown to metro standards, expanding the train facility in Marrickville, and upgrading the power system from Campsie to Canterbury. The project was approved in Dec 2018, and the metro services are expected to be in operation in 2024. The estimated total budget for all work packages involved in the southwest line is around 2.55 billion. (Sydney Metro, 2021)
16
Figure 1:Location of Sydney Metro Southwest Line (Sydney Metro,2018)
Besides, it also outlines how we are going to manage the team during the project development process in the future.
As shown in figure 1, the southwest line is an east west metro line, which is the second half of the City & Southwest Line of Sydney Metro.
This charter is to provide a basic understanding of the Sydney Metro Project: Sydenham to Bankstown line, including the reasons to initiate the project, scope of works and deliverables, project timeline and milestones, expected budget, constraints, major risks and assumptions.
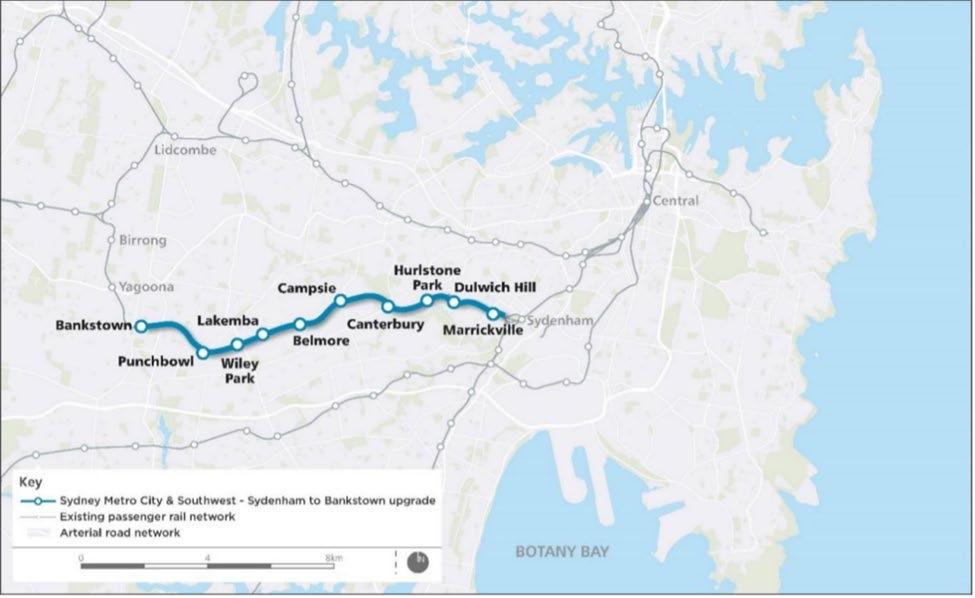
17 2.3 Justifications
Currently, there is a bottleneck for the existing rail network. The T3 Bankstown trains sometimes disrupt the travelling of T2 and T8 trains at central station as shown in the figure below, which may lead to further congestion in wider areas. However, by moving Bankstown Line services to the new standalone metro system, the problem can be easily solved. And the metro services address the issue of increasing demand in travelling between CBD and Western Sydney. In addition, Sydney Metro provides more frequent train services compared to traditional trains -- a train at least every four minutes. Therefore, passengers can turn up and go, no longer need to check the timetable. The new trains will give passengers a safer, faster, and more comfortable travelling experience, and the upgraded stations will provide more support to the disabled and elder passengers. (Sydney Metro, 2021) On the other hand, the value of this project is not only the transport service itself, but also a large number of new job opportunities, accelerating the development and growth of Western Sydney. It strengthens the link from the CBD to the future key suburbs like Bankstown and Liverpool, attracting more people to move to the inner area to reduce the burden of the east suburbs, which improves the living quality of Sydney residents.Thus, it is a sustainable infrastructure development as it brings many benefits from social, economic, and even environmental perspectives.
The project involves upgrading 11 train stations and the railway system to Sydney Metro standards, and also infrastructure services such as the trains facility in Marrickville and the power system along the corridor. For train station upgrades, the detailed scope of works may vary station by station. However, the majority of work packages are common, especially for the 9 stations in between Marrickville and Punchbowl. For example, construction is required to minimize the distance in height between Sydney Metro platforms and Metro Trains; new platform screen doors will be installed; and installing new lifts and paving works will be carried out to improve the accessibility for the disabled.
18 Figure 2:Sydney's Rail https://www.sydneymetro.info/citysouthwest/sydenham-Congestionbankstown 2.4 2.4.1ScopeScope of works

19
● To complete the project on time and within budget.
● Ensure prompt communications among project team members and external stakeholders and shareholders.
● To ensure the quality of work through implementing quality assurance and control processes.
● Provide a safe working environment for all workers on site with the assistance of experienced WHS professionals.
● Provide a transport system that is able to satisfy long term demand
● Ensure the health and safety of all present and future stakeholders, such as neighborhoods, inspection teams, end users, etc.
● Integrate the high efficient metro system to the whole rail system in Sydney to improve the travelling experience to passengers.
2.4.2
● To improve the efficiency of project delivery by minimizing the waste of resources.
Regarding the upgrade of the railway system, it is not only about replacing tracks, but also including upgrades of the operation and control system, communication system, signaling system, Finally,etc. the relevant infrastructure works are to ensure the capacity of support services. They are mainly grouped into the line wide work package. Apart from the works mentioned above, obviously, enabling works such as site preparation and demolition, are also very important to the success of a project. Please refer to the scope management plan for the complete list of the scope and some further information. Objectives
The objectives of the Sydenham to Bankstown Upgrade Project are as follows:
•
New Train Station and service building construction (including mechanical, electrical, and building fit-out). Installing platform screen doors to keep passengers and objects away from the platform's edge. Relocating services, seats, and bins on the platform. Construction of footings/foundations for new staircase and elevator shafts, both within and outside the platform area. Installation of anti throw screens and stairwells. Installation of fixtures, lights, and CCTV cameras in construction-affected areas. Provision of new kerbside and bike parking areas.
20 2.4.3 Major Deliverables The following table presents the major deliverables that need to be achieved in order to satisfy the project’s objectives (SYDENHAM TO BANKSTOWN SUBMISSIONS REPORT,2018). Major Deliverable Deliverable Description
Upgraded Power System
• Fit out (connection to the electrical network for substation).
• Piling and site excavation for in ground services, as well as earthworks to produce a level site.
Upgraded Railway System
•needs.Removing
• Ensuring that the current rail drainage system is in favorable working order.
Stations •
• Building, repairing, and welding new rails to sleepers.
•
• Prefabricated segments used to assemble buildings on site.
•
• Installing overhead wiring for rolling stock.
• Placing ballast and sleepers on the formation, tamping and profiling the ballast around the sleepers to a smooth alignment.
• Constructing maintenance sheds.
•
• Track alignment and overhead wiring along the line adjusted to satisfy Sydney Metro, Sydney Trains and freight operational old fastenings, rail, and sleepers.
•
• Trenching activities to link to the overhead wire structures.
Train Facility Expansion
• Expansion of the existing maintenance facility, including the installation of sheds and rooms.
•
•
• Modify some existing roads.
Erecting five new traction substations to power the metro trains.
• Advanced signalling technology is installed to support safe operations (ensure that trains stop at the cracked location, control train speed, initiate the opening and closing of train and platform screen doors).
21 2.5 2.5.1DurationTimeline The overall timeline of Sydney Metro Sydenham to Bankstown upgrading: Figure 3: Sydney Metro Sydenham to Bankstown Schedule (Submissions and Preferred infrastructure report, June 2018) Thehttp://majorprojects.planning.nsw.gov.au/index.pl?action=view_job&job_id=8256SouthwestMetroprojecttimelineisshownasfollows:Figure4:SouthwestMetroProjectTimeline(SouthwestMetroProjectUpdate,November 2020) https://www.sydneymetro.info/sites/default/files/document library/Southwest_Metro_Newsletter_Nov Theember_2020.pdfSydenham to Bankstown component of Sydney Metro City & Southwest is the upgrade of the more than 125 year old T3 Bankstown Line between Sydenham and Bankstown to metro
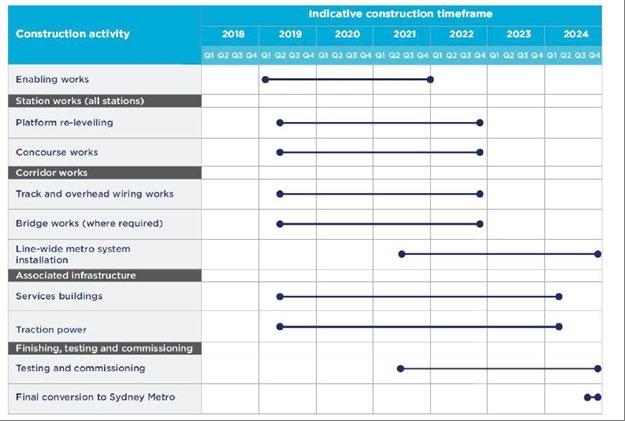

The table 1 below lists the high-level Key Milestones of the project and their estimated completion timeframe.
The Sydenham to Bankstown component delivery phase has now received all of its funding. Total Asset Management (TAM), Rebuilding NSW, and UrbanGrowth NSW and LAHC are its funding sources (Sydney Metro Final Business Case Summary, 2016).
2.6.1 Funding Source
22 standards. It involves the conversion of the rail corridor and upgrades to the 11 existing stations.
Southwest Metro received project approval in December 2018. In 2019, early works will be carried out before the start of substantial construction to establish key construction sites and provide protection to the public where required. Some site establishment works such as heritage protection, site traffic control, scaffolding instalment, vegetation removal and transport network adjustment are expected to be done during 2020. Major construction, including station upgrades and corridor works, will commence in late 2020 and early 2021 2.5.2 Key Milestones
Table 1: Key Milestones Across Project Lifecycle Key Milestones Estimated Completion Timeframe
2.6.2 Estimate
The estimated cost baseline for Sydenham to Bankstown upgrade is assumed as $2.552 billion AU dollars, which means that the indirect cost, escalation and activity contingency reserve are taken into account. Plus the management reserve, which accounts for 10% of the cost baseline ($255.2 million), the overall budget is $2.8 billion. The final budget value may vary due to continuous fine
After modifying project charter and getting approval, this project approaches the end of initiation phase 17th April 2018 Reaching the end of planning phase when purchasing and contracting are achieved. 20th November 2018 Fulfilling external work such as paving and landscaping and overbridge work at respective stations then reaching the end of constructing phase. 5th January 2024 Conducting integrated change and control 15th August 2018 Site clean up and deliverables of Sydney Metro Southwest Line handover 20th November 2024 2.6 Budget Estimate
Sufficient funds, cost payment allocation and project contingencies have been allowed for every stage of the project duration within the overall budget.
• Adequate site investigations have been undertaken in the early work stages of the project to identify existing site constraints that may affect the scope of work.
2.7 Assumptions, Constrains and Risks 2.7.1 Assumptions
•
The scope of works for the project is defined in the Project Brief for all stages of works.
• Days of delay due to the extreme weather will be calculated based on the average historical
•data.The cost and schedule contingency in a risk analysis will be assumed rationally and be explained by using an example with Monte Carlo Simulation analysis in this report.
• Construction hours: Monday to Friday 7 am to 6 pm and Saturday 8 am to 5 pm.
The exchange rate is assumed to be fixed in a steady range.
•
• Contingency reserve determination relies on the Monte Carlo Simulation which is conducted in risk analysis and the basic cost risk value is assumed reasonably correspond to the cost breakdown structure.
•
The whole project would be delivered within the approved budget $2.552 billion.
•
• Current construction market and major political conditions will not change, ending up having no impact on this project.
The project design team and selected contractor have the essential knowledge, appropriate experience, capability and capacity to deliver the project.
•
23 tuning and optimisation involving the key contracts awarded, due to the huge scope of the Sydney Metro City & Southwest project. The contracts will be awarded to different companies regarding various construction activities. The detailed Cost Breakdown Structure will be thoroughly dissected in the Cost Management Plan (Section 5.3).
•
•
All applications and certificates have been approved for construction.
The construction and upgrading work at Sydenham station is assumed to be included in the Sydenham to Bankstown line as a part of Sydney Metro City & Southwest.
24 2.7.2
Site Constraints: The T3 Bankstown Line and freight tracks operated by ARTC (Australian Rail Track Corporation) will remain operational for the majority of the construction period. Therefore, to ensure the station and infrastructure upgrade works can be conducted efficiently and safely, accommodating the works that cannot be undertaken when trains are operating, EIS Technical Paper 1 presented a Temporary Transport Strategy (TTS) which outlined the approach for the use of replacement bus
The project is restricted to the scope developed and documented in the approved Business Case and Project Brief. Budget There will be no increase in financing expected at the initiation stage of the project. The whole project team tends to monitor the cost closely to ensure the project expenditure is in accordance with the set budget, namely $2.8 billion AU dollars. The delivery of metro infrastructure will be undertaken by Sydney Metro and not funded by local councils.
Scope:Constrains
The approved planning phase program indicated a completion date by the end of 2024. The project team is committed to delivering the project corresponding to the key milestone dates.
Resources: All the financial, human and material resources are allocated to the project appropriately, which facilitate the successful delivery of the project. In respect of the material sourced from a domestic area or other countries, the price will remain within a reasonable range where to fluctuate. Quality: The quality and design of the project are associated with the functional requirements and project objectives developed by the consultant team with stakeholder approvals.
Time and schedule: This project will be requested that no work be undertaken after 10 pm, before 7am or after hours on weekends, including the movement of heavy vehicles.
25 services for periods when train was not able to run. This allows the construction work to be conducted during rail possession periods, when trains are not operating. As outlined in TTS, there are three further construction period scenarios that have been considered: ● The additional weekend possessions ● The night-time weekday possessions ● Where up to three stations are closed concurrently, for up to months. Also, heavy construction vehicles would be restricted to the specific designated road network to get access in or out the construction site. For example, figure 5 displays the key traffic routes for construction vehicles in Marrickville site. Figure 5: Heavy Vehicle Access Route Details for Access 1(Sydenham Metro Upgrade Construction Traffic Management Plan Revision 19, 2021 https://sydenhamstationupgrade.com/sydenhamstationupgrade/)
Heritage: There are heritage constraints to the project. All 11 stations in the project area are heritage listed. Three stations on the State Heritage Register (SHR) - Marrickville (SHR1186) Canterbury (SHR1109) and Belmore (SHR 1081) - all listed as Railway Station Groups. The main potential physical impacts to non Aboriginal heritage would occur during the construction phase. The Heritage Assessment has argued that all SHR stations would continue to meet the threshold for State significance and the building within the Listed Group the platform buildings- would be retained and more visible.
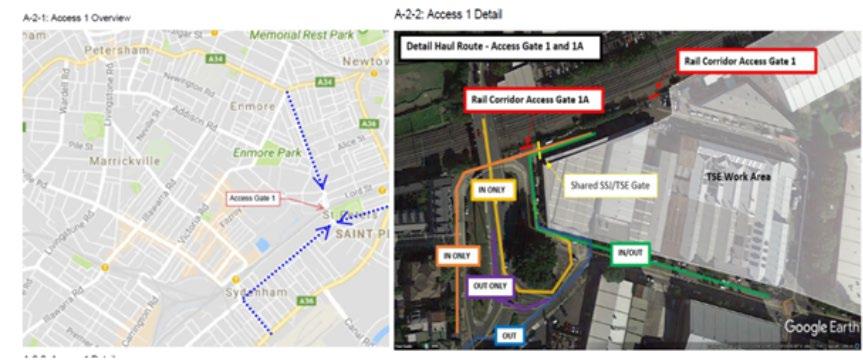
26 For example, at Marrickville Station, the existing platform would be straightened and extended to the east, and heritage station buildings on platforms 1 and 2 would be retained (Figure 6). Figure 6:Heritage items within Marrickville and platform 1 & 2 (Sydenham to Bankstown Environmental Impact Statement, June 2018) http://majorprojects.planning.nsw.gov.au/index.pl?action=view_job&job_id=8256 2.7.3 Risks Risk Mitigation

27 Poor construction traffic causing ● Provide additional commuter parking increased congestion and delays ● Commit to Sydney Metro to modify and improve intersection performance at the location by integrating construction traffic management plans. Excessive deformation and damage ● Adequate investigation when interfacing existing structure and equipment ● Using BIM to detect structure conflicts (Design and Technical) ● Employ skilful and experienced labours Noise and vibration as sleep ● An acoustic shed may be constructed over the disturbance during the night excavation to reduce noise impacts (Environmental) ● A noise barrier or hoarding will be built around the site Non Aboriginal heritage (Potential ● Consider the detailed design once those SHR items for impacts to items listed in State are confirmed, which retain the significance of those Heritage Register) items. (Legal and Heritage) ● Commit to the preparation of heritage interpretation plan Impacts on community ● Set a high-quality fence infrastructure located near the ● By designing an improved site layout planproject (Schedule)area ● A good preparation for surrounding structures and infrastructure investigation Hydrology, flooding and water ● Design new trunk drainage infrastructure quality (Changes in surface water ● Provide detention basinflows due to construction activities) (Environmental)Damagetotheexisting ● Conduct complete and thorough investigation of the infrastructure and services designated area
28 (Cost) ● Protection for the service area like encasing the pipeline ● Employ standard working procedure WHS risk due to the COVID 19 Strictly follow the safe instructions and rules displayed (WHS) by the government and encourage all employees to get fully vaccinated promptly 2.8 Team Organisation 2.8.1 Team Roles and Responsibilities Name Roles Responsibilities Y.Z. Construction Manager Responsible for overseeing the entirety of the project from start to finish. Y.H. Quantity Surveyor Responsible for estimating the costs, materials, and labour needed to complete a project. H.Y. Architect Responsible for envisioning the client’s needs and developing a creative solution. T.Z. WHS Manager Responsible for ensuring the construction project site has followed the safety regulations and codes of practice X.Z. Risk Manager Responsible for the project risk management and advice risk policies and process, monitor and control related risks during project execution. 2.8.2 Team Communication Plan Communication Communication Description Audiences Frequency Objective Platform
29 Weekly Tutorial Moodle, Bb Complete tutorial Team Weekly Activities Collaborate, questions by working in a members Google Docs team, present weekly tutorial works to receive feedback from tutors and submit the completed tutorial activity via Moodle Information WeChat Group A communication tool for Team Daily Updates Chat team members to keep in members touch Group Microsoft Teams Weekly Teams meetings Team Weekly Case Based Video to discuss the progress members Project Conferencing and challenge of the assignment Project Status Email Contact with tutor and Team As needed Updates lecturer for clarification or members assistance 2.8.3 Team Risk Management Plan Potential Risk Possible Causes Mitigation Strategies
30 Disagreement in some points Not clearly stating a proper Arrange weekly progress of views ground rules updates and regular meetings via Teams. Unfair or unequal contribution Personal reasons or poor Allocate team roles and communication among responsibilities equally. If teammates necessary, contact the Lecturer/Tutor for assistance. Overdue Poor time management, Establish a comprehensive lack of communication and team communication plan to scheduling track the progress. Set specific deadlines for each milestone of the project. 3.0 Project Scope Management Plan
• Southwest Metro Corridor After the completion of the project, passengers can enjoy the brand-new air-conditioned metro trains and increased train frequency at peak hours a train at least every four minutes at each station. In addition, they can have a safer and more convenient travelling experience with the upgrades of train stations including but not limited to, newly installed platform screen doors, minimal gaps between platforms and trains, accessible train stations with lifts for all stops. Apart from these, another important point is, the train stops at all local stations, thus, there is no need to wait for the right train.
The upgrade project also alleviate the congestion risk with T2 and T8 in the central station as the metro is a standalone system. It helps to fulfil the increasing demand, provides many job opportunities, accelerates the development of Western Sydney.
• Enabling Works.
31 3.1
As the second half of the Sydney City & Southwest Metro Project (one of the three lines of Sydney Metro), the Sydenham to Bankstown Upgrade Project (Sydney Southwest Metro Line) is a mega infrastructure project with an expected cost of $2.8 billion Australian dollars. It will be built based on the existing Sydney Train railway T3 Bankstown Line, upgrading all train stations and rail systems between Sydenham and Bankstown to metro standards, and providing associated infrastructure. The traditional T3 Sydney Train will continue to serve the area west beyond Bankstown.
• Trains, Systems, Operations and Maintenance (partial).
• Line-Wide (partial).
Because the project involves a huge amount of work, the Sydney Metro project is divided into different work packages for tendering as shown in the figure 7. Please refer to later sections for further details.
• Stations Upgrades (Sydenham, Marrickville, Canterbury and Lakemba Station, Dulwich Hill, Campsie and Punchbowl Station, Hurlstone Park, Belmore, Wiley Park, and Bankstown)
Scope Definition
The Sydney Southwest Metro Line Project covers 11 stations with a length of 13.5 km, which is consisting of:
32 Figure 7: Work Packages of Sydney City & Southwest Metro Project (Sydney Metro, 2018) 3.2 Project Scope Statement Project Title Sydney Metro Sydenham to Bankstown
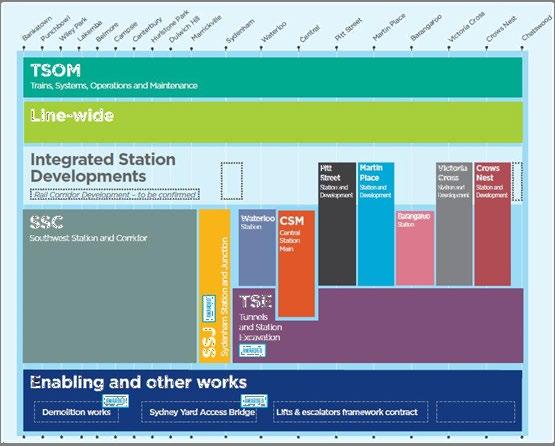
33 Date prepared 4/6/2017 Client Transport for NSW Project Deliverables: • Upgrades of 11 train stations according to metro standards • Installation of Sydney Metro rail systems, adjustment of existing Sydney Trains rail systems • Improvement of rail corridor fencing and noise walls • A new stabling facility for Sydney Metro trains • New traction substations • Upgrade of existing bridges/underpasses that cross the rail corridor Scope of Works: 1. Enabling Works: • Utility and geotechnical investigations • Site establishment activities • Transport network adjustments • Building and vegetation removals, e.g., section huts, trees, etc. • Installation of a combined services route trough • Embankment stabilization activities • Installation of some corridor boundary fencing 2. Station Works: 2.1 Bankstown Station Works: • Construction of a new at grade crossing between the Sydney Trains and Sydney Metro platforms, • Construction of new plazas at entrances on both sides of the rail corridor, • Construction of a new Sydney Metro ‘up’ platform to the east of the new at grade • Construction of a new canopy connecting the new station entrance with both the existing station platforms and the Sydney Metro platforms,
34 • Widening and maintenance of the rail bridge overpass connecting North Terrace and South Terrace, • Installation of track and rail infrastructure, and • Landscaping and installation of street furniture. 2.2 Southwest Metro Station Upgrades (Marrickville, Canterbury and Lakemba Station, Dulwich Hill, Campsie and Punchbowl Station, Hurlstone Park, Belmore and Wiley Park): • Re-levelling of platforms • Construction and installation of new lifts • Installation of platform screen doors • Installation of emergency egress ramps • Refurbishment / Repurposing of station buildings on platforms and/or at station entrances • Signage and wayfinding installation • Enhancements to footpaths, paving and lighting in the vicinity of station entrances • Landscaping and installation of street furniture 2.3 Sydenham Station and Junction Works • Upgrading of Platforms 1 and 2 to Sydney Metro standards, • Reconfiguration of existing track and rail systems to segregate the Sydney Trains T3 Bankstown Line and the goods line, • Installation of Sydney Metro rail systems, • Erection of a new second concourse over the station with lifts and stairs to each platform, • Straightening of the Sydney Metro platforms and platform screen doors, • Adjustments to the Sydenham Pit and Drainage Pumping Station, and • Construction of two new station entrances at Burrows Road and Railway Parade. 3. Trains, Systems, Operations and Maintenance: • Control and communications systems • Radio communications • Trains and signalling for the Sydney Metro City and the Sydney Metro Southwest sections • Platform screen doors and platform edge barriers on the Sydney Metro City section 4. Line Wide:
• All scope of works and project deliverables will complete in compliance with all quality standards outlined in the quality management plan, and are aligned with all Australian standards, Building Code of Australia, local council regulations and contractual Theobligations.project is subject to legislative environmental compliance requirements associated with: Environmental Planning and Assessment Act 1979(NSW)
The project will be handed over to the Sydney Metro for operation upon completion of construction and commissioning. The following acceptance criteria is what the Jonn Holland and Laing O’Rourke Australia Construction Pty Ltd Joint Venture as the project main contractor, will attain throughout the whole construction project cycle.
o
35 • Construction of the Sydney Metro Trains Facility (South) and associated stabling works • Lighting, low and high voltage power supply • Construction of electrical substations and services buildings • Station control systems, overhead line, and traction supply 5. Southwest Metro Corridor: • Installation of services in the combined services route trough, • Installation of segregation and corridor security fencing, • Construction of retaining walls and associated earthwork activities, • Removing existing fastenings, rail and sleepers, • Installation of new track, • Maintenance of existing track drainage, and • Bridge works. (Sydney Metro, 2018; Sydney Metro, 2021)
Project Acceptance Criteria:
• The completion of the project will be in accordance with the approved drawings, specifications, and other documentation encompassed in the contract which ensure customer needs and the objectives of this project can be satisfied.
o Protection of the Environment Operations Act 1997 (NSW)
The completion of the project is within the established schedule and set budget $2.552 billion to optimise the efficiency and effectiveness of the project
The adjustment and upgrading of the existing rail corridor in the west part of the Bankstown station is not included in the scope of the construction work.
•
The delivery of the project will comply with the City & Southwest CSSI planning approval requirements consisting of Conditions of Approval (CoAs) and Revised Environmental Mitigation Measures (REMMs) allocated to each stage of the project.
•
• There will be no increase in financing expected at the initiation stage of the project. The whole project team tends to monitor the cost in order to ensure the project expenditure is in accordance with the set budget, namely $2.8 billion AU dollars.
The delivery of metro infrastructure will be undertaken by Sydney Metro and not funded by local councils.
Resources:
Project Exclusion:
• The approved planning phase program indicated a completion date by the end of 2024. The project team is committed to deliver the project corresponding to the key milestone dates.
• Tunnelling construction in Marrickville dive site near the Sydenham station included in Sydney Metro southwest is excluded from the scope of Sydney Metro Sydenham to Bankstown line.
36 •
Project Constraints: Scope:
Time and schedule:
• This project will be requested that no work be undertaken after 10 pm, before 7am or after hours on weekends, including the movement of heavy vehicles.
• In the event of a change to stage scope of works, the stage’s applicable Construction Environmental Management Plan and sub plans will be reviewed and updated as required according to the relevance of the applicable Conditions of Approval and Revised Environmental Mitigation Measures to the stage.
• The project is restricted to the scope developed and documented in the approved Business Case and project Brief.
Budge:
Vehicle Route (figure 8): Vehicles will only access and exit site using the route shown in blue.
37
SiteRailConstraints:andSitePossession:
• Where up to three stations are closed concurrently, for up to months.
• Minimum 90% materials purchased must be sourced within Australia.
• The quality and design of the project correspond to the functional requirements, enabling design objectives, customer needs, safety and sustainability guideline.
• All metro property must be fully protected during construction of the development and all site work including clearances to metro tracks and protection reserves must comply with the relevant TfNSW standards relating to air space, external developments and tunnels.
All the financial, human and material resources are allocated to the project appropriately, which facilitate the successful delivery of the project. In respect of the material sourced from a domestic area or other country, the price will remain within a reasonable range where to fluctuate.
The T3 Bankstown Line and freight tracks operated by ARTC (Australian Rail Track Corporation) will remain operational for the majority of the construction period. Therefore, to ensure the station and infrastructure upgrade works can complete efficiently and safely, accommodating the works that cannot be undertaken when trains are operating, EIS Technical Paper 1 presented a Temporary Transport Strategy (TTS) which outlined the approach for the use of replacement bus services for periods when train will not be able to run. This allows the construction work to be conducted during rail possession periods, when trains are not operating.
• The additional weekend possessions
Quality and Construction work:
• The night-time weekday possessions
•
As outlined in TTS, there are three further construction period scenarios that have been considered:
38 Figure 8: Delivery Requirements Gate 3 – Possession (Sydenham Metro upgrade Construction Traffic Management Plan Revision19, https://sydenhamstationupgrade.com/sydenhamstationupgrade/2021) Site Traffic Access: Deliveries for works on site such as Heavy Construction Plant (beam and girder deliveries, precast deliveries, tower crane deliveries) associated with heavy construction vehicles would be restricted to the specific designated road network. For example, figure 9 displays the key traffic routes for construction vehicles in Marrickville site.
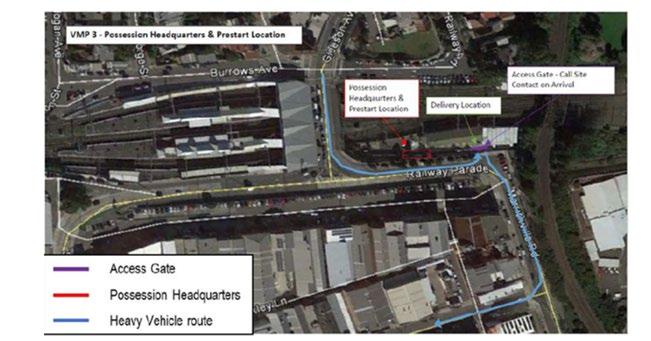
Safety:
39 Figure 9: Heavy Vehicle Access Route Details for Access 1 (Sydenham Metro upgrade Construction Traffic Management Plan Revision 19, 2021 https://sydenhamstationupgrade.com/sydenhamstationupgrade/)
For example, at Marrickville Station, the existing platform would be straightened and extended to the east, and heritage station buildings on platform 1 and 2 would be retained (Figure 10).
• All construction activities of the project carried out on metro property must be in compliance with the requirement of the relevant authorities and legislation including workplace health and safety (WHS). Heritage: There are heritage constraints to the project. All 11 stations in the project area are heritage listed. Three stations on the State Heritage Register (SHR) - Marrickville (SHR1186) Canterbury (SHR1109) and Belmore (SHR 1081) - all listed as Railway Station Groups. The main potential physical impacts to non Aboriginal heritage would occur during the construction phase. The Heritage Assessment has argued that all SHR stations would continue to meet the threshold for State significance and the building within the Listed Group the platform buildings- would be retained and more visible.
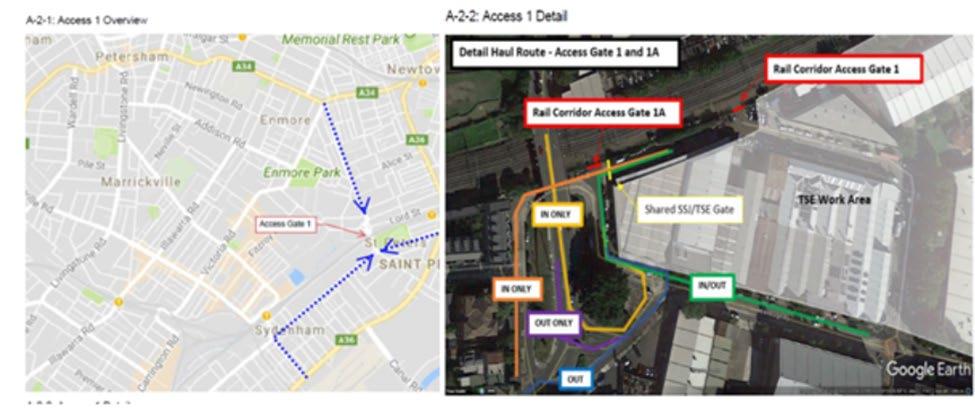
40 Figure 10: Heritage items within Marrickville and platform 1 & 2 (Sydenham to Bankstown Environmental Impact Statemen, June 2018 https://sydenhamstationupgrade.com/sydenhamstationupgrade) ASSUMPTIONS: • The scope of works for the project is defined in the Project Brief for all stages of works. • All applications and certificates have been approved for construction. • Sufficient funds, cost payment allocation and project contingencies have been allowed for every stage of the project duration within the overall budget. • The whole project would be delivered within the approved budget $2.552 billion.
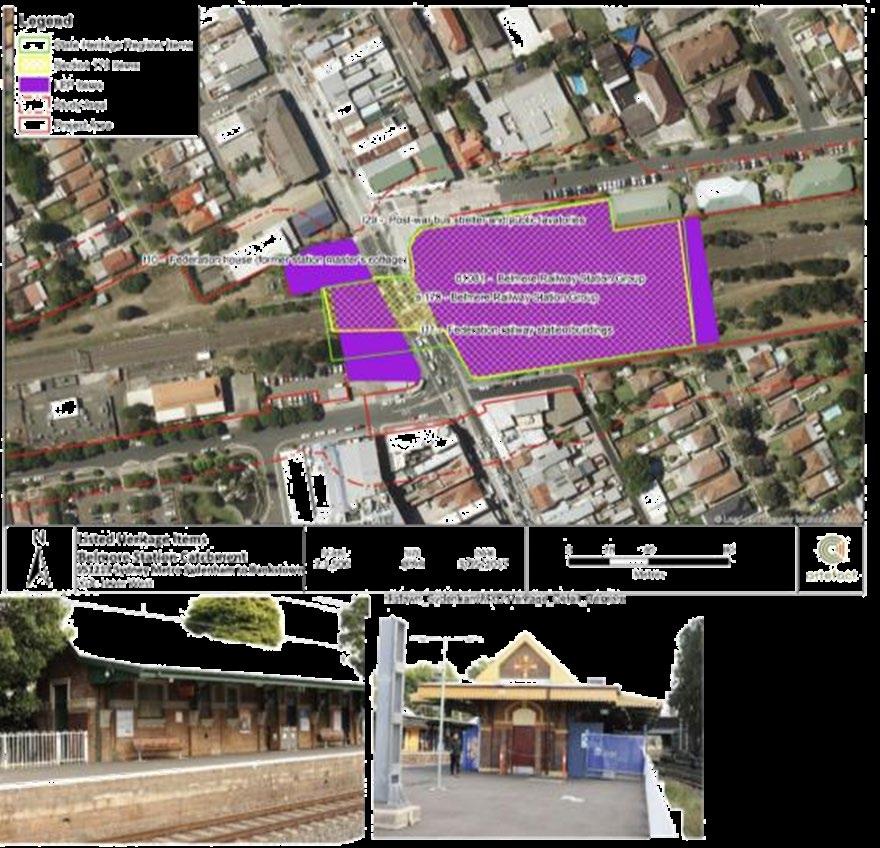
•
Dependency Linkage: The commencement of reconfiguration, installation and upgrading work at Sydenham station is linked to the completion of the tunnelling work at Marrickville Dive Site near the north part of Sydenham station.
The project design team and selected contractor have the essential knowledge, appropriate experience, capability and capacity to deliver the project.
Adequate site investigations have been undertaken in the early work stages of the project to identify existing site constraints that may affect the scope of work
•
Current construction market and major political conditions will not change, ending up having no impact on this project.
•
•
Days of delay due to the extreme weather will be calculated based on the average historical •data.The cost and schedule contingency in a risk analysis will be assumed rationally and be explained by using an example with Monte Carlo Simulation analysis in this report.
•
•
The exchange rate is assumed to be fixed in a steady range.
The construction and upgrading work at Sydenham station is assumed to be included in the Sydenham to Bankstown line as a part of Sydney Metro City & Southwest.
41 •
•
Contingency reserve determination relies on the Monte Carlo Simulation which is conducted in risk analysis and the basic cost risk value is assumed reasonably correspond to the cost breakdown structure.
Construction hours: Monday to Friday 7 am to 6 pm and Saturday 8 am to 5 pm.
42 3.3 WBS
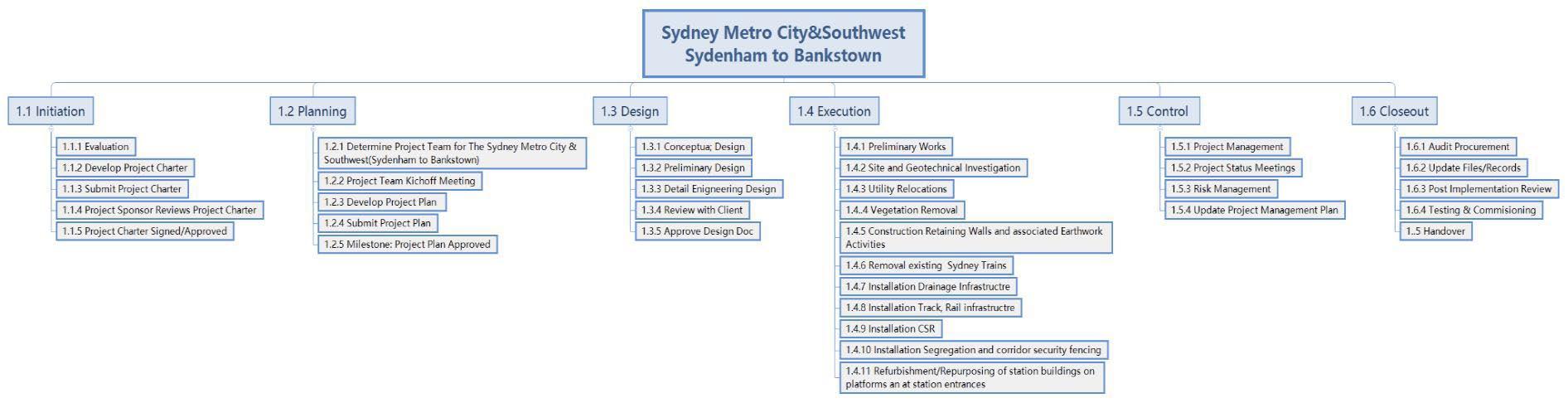
43 3.4 WBS Dictionary WBS ID 1.3.2 Date Started 29th November 2018 Work Package Name Site Preparation (Including all stations) Date Finished 22nd July 2021 Description These early works are typically carried out before the start of substantial construction to establish key construction site and provide protection to the public where required. Budget $50 million + GST Assumptions and Constrains ▪ Duration for rail and site possession ▪ The duration of site preparation incorporates all 11 stations preparation throughout the whole construction life cycle ▪ All station site areas are heritage listed Activities 1 Install site environment management and traffic control according to the construction environment plan. 2 Establishing construction compounds and work sites 3 Temporary or permanent power, water and other utilities supplying to construction site within work area. 4 Relocating, adjusting and protecting utilities and services affected by the project. 5 The removal of buildings and structures where required. 6 Vegetation clearance within the rail corridor Quality and Technical Requirements Adhere to ▪ AS 4191:2015 Portable traffic signal systems ▪ AS 1742.2-2009 Manual of uniform traffic control devices ▪ AS 4970-2009 Protection of trees on development site Acceptance Criteria ▪ The project is subject to legislative environmental compliance requirements associated with Protection of the Environment Operations Act 1997 (NSW) ▪ Meets quality and technical requirements ▪ Building within the Heritage Listed Group the platform buildings- would be retained and more visible.
44 WBS ID 1.3.11 Date Started 17th January 2019 Work Package Name Railway track and overhead wiring works Date Finished 29th February 2022 Description Following a detailed design and project plan, this work package would involve changes to the existing track. Also, work to upgrade, replace track and supporting infrastructure along the rail corridor need to be undertaken. Budget $750 million + GST Assumptions and Constrains ▪ Duration for rail and site possession ▪ Materials such as railway steel are sourced from Australia Activities 1 The removal of old fastenings, rail and sleepers 2 Laying the new rails 3 The placement of ballast and sleeper on the formation 4 Tamping and profiling the ballast around the sleepers Fixing and welding the rails to sleepers 5 Installing cable and equipment such as electrical system Installing overhead wiring for rolling stock(railway vehicles) 6 Mainternance of existing track drainage Quality and Technical Requirements Adhere to ▪ AS 7635:2013 Track Geometry ▪ AS 7639:2013 Track Structure and Support ▪ AS 1085.17: 2021 Railway track material, Part 17: Steel sleepers ▪ AS 7508: 2017 Track Forces and Stresses ▪ AS 1085.1:2019 Railway Track Material, Part 1: Steel Rails ▪ AS 1085.3-2002 Railway track material Part 3: Sleeper plates Acceptance Criteria ▪ The project is subject to legislative environmental compliance requirements associated with Protection of the Environment Operations Act 1997 (NSW) ▪ Meets quality and technical requirements ▪ Final inspections by Quantity Manager, Project Engineer and Project Manager
45 WBS ID 1.3.13 Date Started 17th January 2019 Work Package Name Bridge works Date Finished 29th September 2022 Description Most bridges would be able to remain partially open to traffic while installing new traffic barrier and anti throw screen. Budget $70 million + GST Assumptions and Constrains ▪ Duration for rail and site possession ▪ Materials such as anti throw screen are sourced from Australia and precast. Activities 1 Close bridge lanes and footpath based on requirements 2 Existing parapets being removed down to the existing bridge slab. 3 Precast parapet sections being positioned with the use of cranes and fixed to the bridge deck. Prefabricated anti-throw screen is ready to install. 4 The installation of bridge protection measures. 5 Bridge lanes and footpaths reopen to traffic. Quality and Technical Requirements Adhere to ▪ AS 5100.2:2017 Bridge design, Part 2: Design loads ▪ AS 5100.4: 2017 Bridge design, Part 4: Bearings and deck joints ▪ AS 5100.8:2017 Bridge design, Part 8: Rehabilitation and strengthening of existing bridges Acceptance Criteria ▪ The project is subject to legislative environmental compliance requirements associated with Protection of the Environment Operations Act 1997 (NSW) ▪ Meets quality and technical requirements ▪ Final inspections by Quantity Manager, Project Engineer and Project Manager
Diverse materials’ quantities are taken from the comprehensive drawings, forming the bill of materials (BOM). The number within the scope of work is then compared to the corresponding materials onsite. The outcome determines whether the work and deliverables fulfil the requirements and formal acceptance criteria for the product.
The figure above illustrates the detailed Scope Validation and Verification Process for this project. Inspections help ensure that all stage’s milestones are met. For example, quantity measurements are adopted in the metro upgrade project to verify installed material quantities.
The Sydney Metro Sydenham to Bankstown Upgrade Project has well defined scope (as shown in Section 2.2 PSS) and the scope validation process takes place in three phases.
46 3.5
Project Scope Validation and Verification Process
The process of formalizing acceptance of completed project deliverables is scope validation.
When the project is authorized at the end of the concept phase, the first phase begins. The construction contractors are not involved in this process as the contract has not been awarded. However, the eventual outcome is a preliminary scope of work and a contract that describes what will be delivered in general. The definition phase follows, during which ample plans and specifications are created to establish the baseline criteria for scope, budget and schedule. The final phase, project acceptance, should be done appropriately and in compliance with the contract. Before moving on to the next phase, each of these phases should be recognized by a formalized verification process (Project Management Institute, 2016).
For the deliverables successfully accepted, they are officially signed off by the sponsors (Total Asset Management, Rebuilding NSW, and Urban Growth NSW and LAHC). After all the
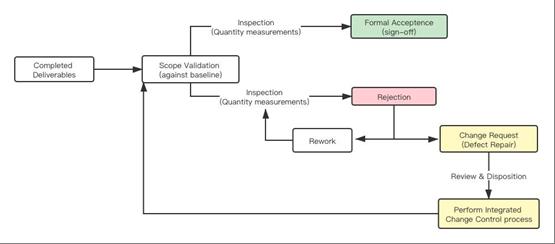
3.7 Scope Change Management Process
Changes to the scope are very likely to happen in large scale construction projects, not an exception in the Sydney Metro Sydenham to Bankstown. However, these modifications must be managed properly in order to avoid scope creep, which has been defined as “the uncontrolled expansion to product or project scope without adjustments to time, cost, and resources.” (Project Management Institute, 2017). It can be considered as an undesirable attribute towards
Monitoring and Control System is critical to ensure that the scope baseline is upheld throughout the duration of the overall project with minimal disruptions caused by inevitable changes. In order to monitor the project scope baseline, WBS Dictionaries as a tool that the project manager would utilize, which could support Work Breakdown Structure (WBS) by detailing all information regarding the deliverables (scheduling and the activities involved). (Project Management Institute, 2017).
47 deliverables are formally accepted, the project will be passed on to the Close Project or Phase Inprocedure.themeanwhile, the completed deliverables that have not been formally accepted, as well as the reasons for their non acceptance, are documented. Depending on different situations, the contractors may be entailed to redo the construction work. Otherwise, a change request for defect rectification may be required for those deliverables. The Change Requests are then processed through the Perform Integrated Change Control process for review and disposition (Project Management Institute, 2017).
In Sydney Metro Sydenham to Bankstown, the WBS dictionary is the principal tool used to compare the project actual work being performed against what should be completed. The WBS contains specific details for each work package including description, milestones/due dates, interdependent activities, budget, constraints, activity list, quality requirements and acceptance criteria. To be able to monitor and control the scope during the Sydney Metro Southwest, the project manager and construction team will be required to manage the modifications of the scope efficiently by employing an online database to report any changes to the baseline effectively and efficiently. It could enable all team members and stakeholders associated with the Sydney Metro Southwest project to be informed and leave sufficient revisions and updates to the scope and work activities.
3.6 Project Monitoring and Control System
Thedeliverables.ScopeChange
1.follows:Identify change items: Recognize variations within the project.
2. Evaluate and propose changes: Assess the identified differences and analyse the possible impacts, submitting the request report to the manager. The manager enters it into the changelog.
3. Approve change requests: All confirmed modifications shall go through into the approval process, and the proposed change requests should also be sent to the client, who would make the final decision for the indicated changes (may accept or reject).
4. Implement the change request: If the change request is accepted, the change will be executed. If the change request is rejected, consultations are needed with all members of the team before further Changesactions.tothe project scope will affect all aspects of the project life cycle, such as the performance, schedule, and budget. Therefore, controls must be fully considered alongside other factors within the project scope change, particularly control of events, cost holes and quality. Moreover, a Scope Change Request (SCR) form is also required to be completed for all scope changes for approval or rejection. In order to complete the SCR, the following scope change control flow chart shows some key steps of project scope management in Sydney Metro Southwest, which will be further used and adhered to:
Management Process for the Sydney Metro Southwest Project is listed as
48 the overall project scope; therefore, a scope change management process has been prepared for Sydney Metro. The construction phase of Sydney Metro Southwest may be impacted by several uncertainties’ factors, including unexpected soil instability, extended severe weather and COVID 19 pandemic. As a result, the Scope Change Management Plan with the Change Control Form and Change Control Board, are important to keep the process on track and record the modifications to manage the overall project effectively and efficiently with minimal disruptions to primary
49
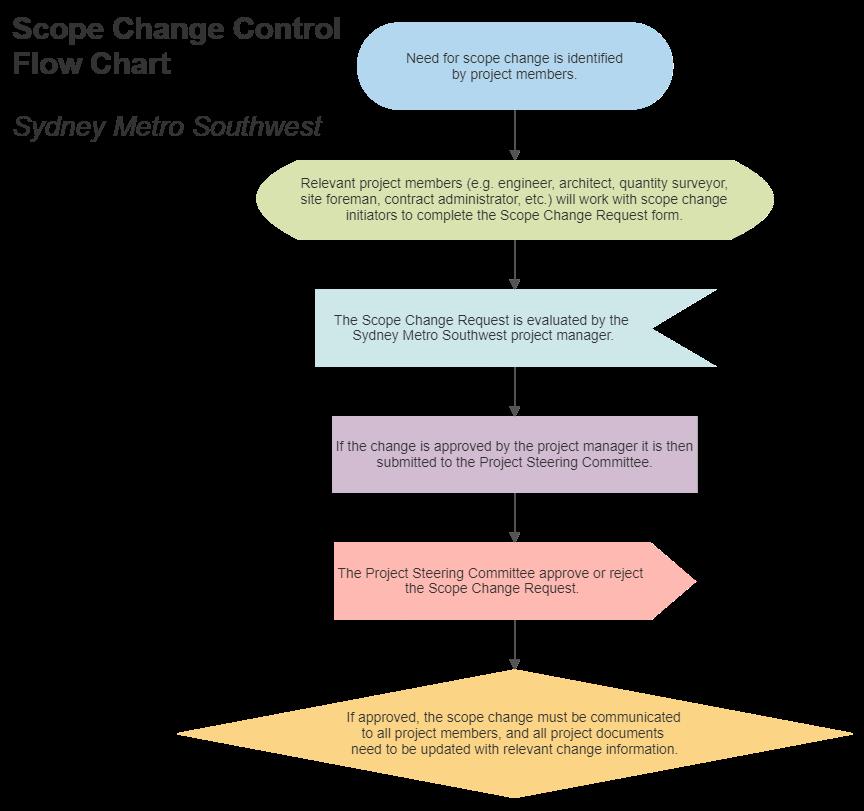
- During the construction process, make appropriate decisions for the implementation and realization of project goals.
- Ensure that the project is completed on time and that all subcontractors and project teams comply with all quality standards and management plans.
- Communicate with the project manager and process manager on time to ensure that the project goals are met on schedule.
The roles and responsibilities for the development of the project schedule are shown below:
Roles Responsibilities Schedule manager - Design and develop project plans - Supervise and manage the progress process, and conduct all related internal audits - Record project schedules and maintain a database of tasks and their status - Record all new information in the database and provide scheduled reports for contract coordination and reporting purposes - Work with project manag ers and field engineers to develop and update weekly short interval schedules
- Let stakeholders understand the project timetable and deadline.
Project Manager During the entire project construction period, supervise whether the entire team's work is proceeding in accordance with the project schedule.
50 4.0
- The construction project manager is responsible for formulating, implementing, and managing the overall project schedule process.
- Pay attention to the project's progress to ensure that the work of each stage is completed on time. Help the overall process of the project to be completed faster.
- Identify potential project schedule delays and facilitate timely intervention.
The Project Schedule Management Plan maps out the approach to the development of the project schedules and the delivery of the project in accordance with the project schedule. The plan specifies the proposed methodologies and tools to be used in monitoring and controlling the project schedule and approved baseline schedule.
ManagerConstruction The construction manager supervises the daily on site process of the project on behalf of the team on site.
Project Schedule Management Plan
In response to any project requirements that affect procurement In the process of project development, ensure that thecontract is accurately executed and satisfied.
Architecture - Design and draft the project's construction plan and get confirmation from the customer and the construction staff.
The contract manager will be responsible for the overall procurement of goods and services to complete the project.
51
- Confirm that the contract meets all quality standards.
- Ensure that the design drawings and construction detail documents comply with quality control and can be completed on Visittime.and review the construction site to ensure that the project meets local environmental and safety requirements.
Contracts Manager
4.1
In the Sydney Metro Sydenham to Bankstown project, the Critical Path Method (CPM) is adopted, which is a common method in construction management projects. By summing up the time duration of each task in the critical path, this analysis can determine the expected entire construction period and completion date of the overall project. This method decomposes the construction process into a step-by-step format to make sure that projected delivery schedules in the process are recorded, in order to minimize the risk of time overruns. Besides, it could provide a clear outline between the project's critical and non critical tasks to ensure when accidents happen, appropriate response actions could be taken immediately
4.1.1 Scheduling Method
- During the project construction process, communicate with the project team regularly to solve project problems and provide new design solutions in time.
The renewal or renewal of the relevant contract will affect the plans of multiple internal stakeholders. It is necessary to ensure the timeliness of the progress of the contract to avoid affecting the progress of the project.
Assist the project manager to ensure that the specific work plan and timetable of the project proposal are feasible and that these standards can be maintained and correctly implemented at all stages of construction. Project scheduling methodology
Schedule Management refers to the procedure of forming the policies, processes, and documentation for managing, planning, improving, executing, thus controlling the whole project timeline. It could be noticed that the complexity of the scheduling management in construction projects, as a series of activities in a project could happen simultaneously.
4.1.3
including: • Planning and Scheduling • Project Timeline View • Collaboration • Reporting • Resource Management • Multiple Projects ▪ Different Views 4.1.4 Level of Accuracy
52 4.1.2 Organizational Procedure Links
Tool
has lots of useful features (Furnival,
The Sydney Metro Southwest project is a large scale infrastructure project, and there are inevitably various uncontrollable factors that may affect the schedule efficiency of the project and lead to budget overrun. The project manager should consider the impact of these incidents on the progress of the overall project. Furthermore, the acceptable range used in determining realistic activity duration estimates is set between plus and minus 10%.
In the Sydney Metro project, The Work Breakdown Structure (WBS) can be considered as the organised process links which decompose stage works into smaller components, which are more manageable. This helps the project manager and project team to identify and manage the project work effectively, keeping the planned activities consistent. Scheduling
It is extremely important for the project manager to understand scope creep, pressure on the schedule, and the necessity for cost control, especially for large scale construction projects. Hence, Microsoft Project, as one of the most effective tools for scheduling and cost control, has been utilized in the Sydney Metro Southwest project. Microsoft Project is a communication tool that could provide the construction project management team with a road map for project execution, and it is also a software for productively managing time deadlines and minimizing cost Microsoftoverruns.Project 2018),
4.1.5 Units of Measurement ▪ ProjectWeeksduration:MonthsQuartersYears
According to the Scope Management Plan, the Sydney Metro Southwest project's construction work between Sydenham and Bankstown would be upgraded to metro standards. The T3 Bankstown Line and ARTC (Australian Rail Track Corporation) freight tracks will stay operating for most of the construction period. The work at each station will be planned, scheduled, and managed as a separate project. Each site's work is autonomous and unaffected by the progress of other sites' work, which can resolve variations in each location's unique scope and time and enable work to be readjusted according to the individual constraints of various places.
Project Structure and Approach
53 ▪ Cost:AUD$ ▪ Dimensions:mm(millimeter)m(Meter)sqm(SquareMeter)H(Hectare)A(Acre) ▪ Weight/Mass:Tons(Tonnes)Kgs(Kilograms) ▪ Volumem2 (Meter Square) m3 (Meter Cubed) 4.2 Activity identification process 4.2.1
The engineering project schedule must be further subdivided into the work packages defined in the WBS dictionary and contained in the WBS. Decomposing the construction work of each site results in the creation of a distinct work breakdown structure and WBS dictionary to explain the projects of each site adequately. The work packages are broken down into smaller, more manageable chunks, thus establishing a foundation for project schedule planning and construction activity monitoring. On the other hand, excessive decomposition of the project work schedule will complicate ongoing construction planning and monitoring, should also be avoided.
4.2.2 Work Package Decomposition
All the activities need to be sequenced as per the dependencies. Activity sequencing method is a process that demonstrates how activities are sorted and reflects their interdependencies. This approach requires an accurate calculation of the proposed activities that may occur within the Sydney Metro project with a determination of the most effective and rational sequence.
Furthermore, the project manager must assist the project team in subdividing the entire work schedule to increase the likelihood of project success. Activity sequencing method
The
Start
54
The
The
4.3.1
The
For the Sydney Metro Sydenham to Bankstown, Precedence Diagram Method (PDM) would be used at the beginning of project development. This method can effectively record and display information about the relationship between activities using the following four predecessors: to Start: The first activity must be started firstly, and then the next activity can be started Start to Finish: The predecessor activity must start before the successor activity is completed Finish to Start: Before a new activity begins, the previous activity should be completed
Sequencing also needs understanding and recognizing the multiple relationships between these activities in order to determine their importance and perform a successful outcome. This method can effectively record and display information regarding the position in the Sydney Metro Southwest project schedule. The specific details are shown as follows. duration of each activity early start dates late start dates The early finish dates late finish dates Relationship Types
4.3
The dependencies in the Sydney Metro Southwest project are classified into the 4 attributes below: Mandatory dependencies Discretionary dependencies External dependencies Internal dependencies
For the more complicated relationship between two activities whereby there is a period imposed on each, in this case, the precedence cannot be described in the four categories above. Therefore, the terminology of “lead” and “lag” is further introduced, which acquires the features below: Lead: The amount of time that the following activity can start prior to the finish of its preceding activity. The lead enables the occurrence of overlapping. Lag: The amount of time predefined in schedule in which it regulates that the following activity cannot start until this period of time passes after its preceding activity finishes.
The previous activity must be completed before the successors complete their activities
4.3.3 Lead and Lag
According to Uher (2003), estimating activity duration is the process of calculating the number of each individual period in construction corresponding to the unique activity required to be completed in the project. The approaches to estimate are more likely to be affected by the specific construction project, construction site and particular condition under consideration.
55 Finish to Finish:
4.4.1 Activity Duration Estimation Methodology
4.4 Estimating activity duration method
The appropriate dependency would be determined according to a comprehensive analysis of the complicated connections among each activity within the overall Sydney Metro project. Under some circumstances, two attributes may be applied concurrently.
4.3.2 Dependency Determination
56 The accuracy of the time estimated is subject to the availability of historical data, anticipated resource, relevant informed information such as design drawings, associated work to be performed and the effectiveness of approach adopted, and the capability of risk management. The duration estimation methods which tend to be employed in the construction project include: ● Expert Judgement (team’s past experience) ● Analogous Estimating (historical records) ● Parametric Estimating ● Three point Estimating ● Group Decision Making Techniques ● Published Estimating Data A schedule risk contingency will be allowed for all specific activity duration estimated to alleviate the influence of project uncertainties. And this will be elaborated in the risk management plan. 4.4.2 Approaches Adopted in Sydney Metro Southwest Construction Project In this stage, our team decides to perform activity duration estimation via three widely used approaches, namely analogous estimating, parametric estimating and three point estimating also known as PERT analysis. 4.4.2.1 Analogous estimating
Adjustment factor: As shown in figure11, users can filter materials and equipment in the 3D model in SmartPlant to visualise if the material or equipment in this activity is needed, which have not been used in previous construction activities.
By utilising the similar previous project data, the future activity duration estimation can be achieved when locality and some other unique factors are considered. In this report our team will reasonably choose partial activity similar to the Sydney Metro Sydenham to Bankstown line to estimate the duration with some adjustment factor adding to the amount.
Figure 11: Filters in SmartPlant Construction enable users to find material and equipment availability. (Factors Affecting Construction Labour Productivity, n.d) Error! Hyperlink reference not valid.As shown in figure 12 and 13, in the new construction project like in railway construction and rehabilitation some working package are prone to be congested in the same area at the same time. Using SmartPlant Construction enables the labour factor to be seen by team members. Therefore, they can encompass the 25% labour inefficiency factor into duration calculation.
Figure 12: Typical railway construction activities and tools applied
57
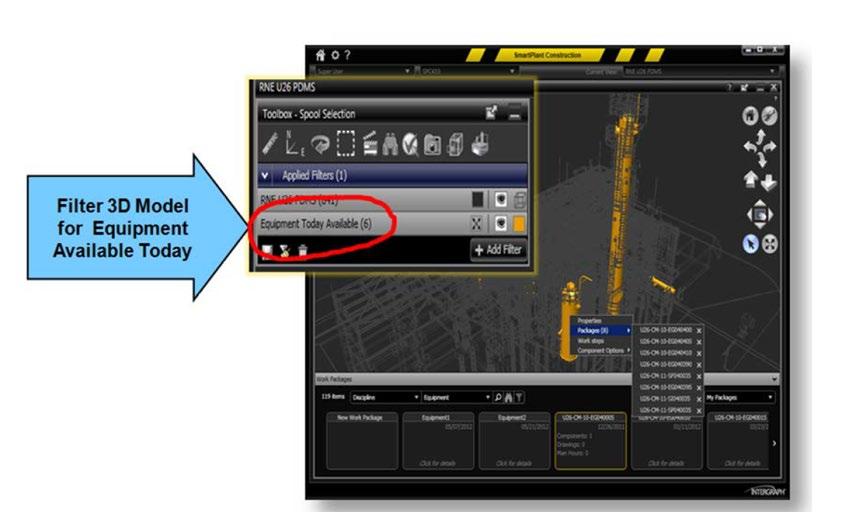
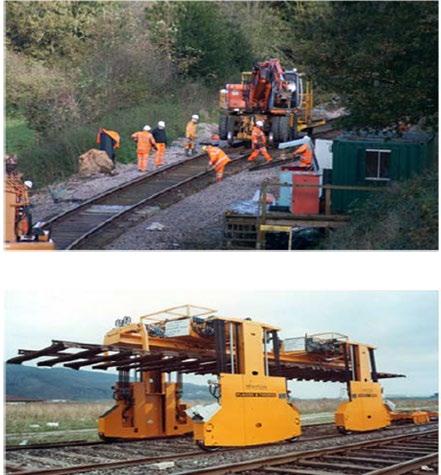
58 Figure 13: The 3D model can be filtered in SmartPlant Construction due to two different work packages occurring in the same area at the same time, highlighting any labour inefficiencies.(Factors Affecting Construction Labour Productivity, n.d) https://www.intergraph.com › global › documents 4.4.2.2 Parametric Estimation Parametric estimating method is another method could be embraced in the estimation of activity duration. This method pushes the work to be drilled down into the unit rate and depends heavily upon the resource usage for execution of a given activity in terms of labour-hour estimated by using productivity rates and appropriate job management adjustment factor. According to Uhe (2003), there are two methods for calculating the duration shown below: (1) Construction activity duration is determined by: ● Quantity of work ● Number of persons ● Productivity rate (labour hours / unit) ● Adjustment factor (2)Equation:Construction activity duration is determined by
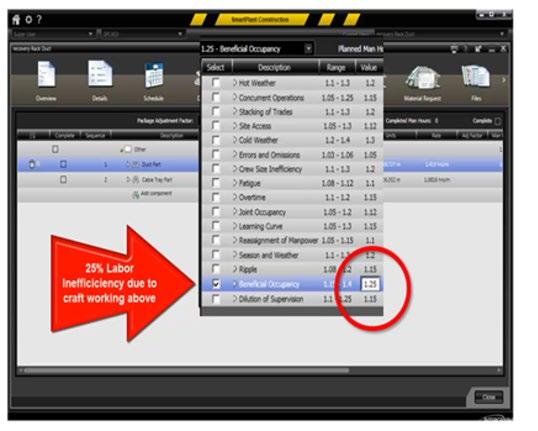

59 ● Quantity of work ● Daily output rate of resources Therefore:Equation: Total project duration= Example of specific activity in Sydney Metro project: Table 2: Typical Unit of Measures in Sydney Metro Southwest Project Unit Type Typical Elements metre(m2)Square (Concrete slab, formwork, roofing, ceiling, stairs) for new concourse Door screen metre(m3)Cubic Concrete slab, brick wall, excavation for in ground pit, conduit and separator tank and substation. Tonnes Rail structural steel, ballast Per unit item Sleeper, Lift Length (metre) Drainage pump, cable Some excavations for all required area across the whole lines: The output of calculation is summarised in table 3 below
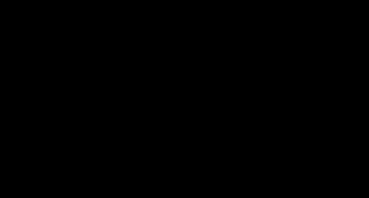
60 Table 3: The Output of Duration Calculation Activity Quantity Unit RateProductivity hrsworkingTotal sizeCrew no.Resources (days)DurationActivity separate)wholesotruckforExcavationwaterandforth(theline 2250m3 m3 4 hrs/m3labour 9000 hrs 3 excavators3 300 days
4.4.2.3
Uher (2003) states that unlike the PDM or parametric estimation where a single duration is estimated for each activity, PERT considers three duration estimates for each construction activity in this project as following:
This activity duration is included in the duration of site preparation extracted from timeline. This method could provide a preliminary guide for the activity duration but is restricted to the relevant quantity available and reasonable assumptions, which is not suitable for the entire project. Therefore, this report also introduces the three-point estimation. Three Point Estimation (PERT Analysis)
Optimistic () which is the minimum estimated duration that may occur in the best case scenario on that specific construction activity --Most likely ( ) which the duration estimated can be achieved in the most likely scenario
Pessimistic ( ) which is the maximum duration estimated that may occur in the worst case scenario on the specific construction activity From these three estimate durations, the expected duration value of the specific activity ( ) can be calculated by:
All the method like Precedence Diagram Method (PDM) or parametric estimation are assumed to be utilised when the duration of construction activities remain the same and are non variable along the duration of the entire project from start to finish. This is not realistic and practical. Therefore, the three point (PERT) estimation applied introduces the uncertainty into the estimation of the construction activity duration in the schedule management.




61
At this stage, the probability of duration to complete the project (X) is calculated by assuming that the probability distribution of the total project duration is normal distribution (Appendix A for the detailed explanation of Normal Distribution).
The normal variable (X) can be standardised into Z, which , a standard random variable, and is used to denote the distribution.
By utilising a simple statistical analysis which converts the normal distribution into standard normal distribution Z-value, we can calculate and find the specific activity duration of critical path with a corresponding probability P-value. (APPENDIX B)
Expected Duration (Mean Value):
Also, the Standard Deviation:
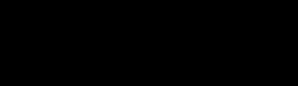
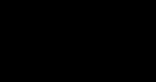


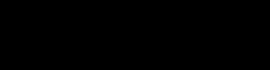
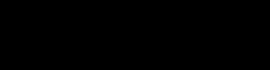

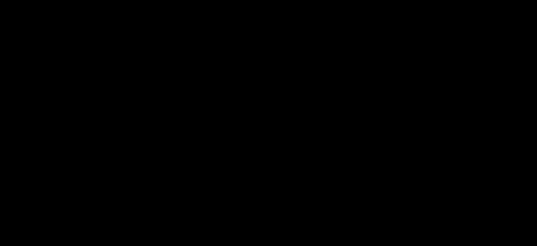
62 Example of specific activity: ( Assuming that partial site preparation included excavation can be separated in two activities) Table 4: The outcome of PERT example calculation of Sydney Metro Southwest excavatoin(andpreparationSite the whole lines) (days) (days) (days) (days) S( )(days) ()(days)levelConfidenceP-90 A( excavationDetailed) 250 295 310 290 10 302.8 B( levellingSite preparationand) 590 630 650 626.7 10 639.5 The outcome of calculation is shown above (table 4) Activity A: With 90% confidence level, Z score is 1.28 (Extracted from the probability table for Normal Therefore,Distribution)the Activity A duration would be 302.8 days with 90% confidence level. The expression in diagram is illustrated bellow:





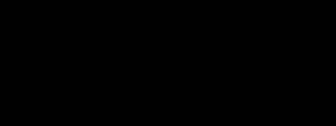
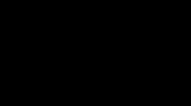
Activity B: The process of the calculation is almost the same with Activity A. Therefore, with 90% confidence level, the activity B duration would be 639.5 days.
Partial site preparation (including excavation) duration= Activity A+ Activity B= 942.3 days with 90% confidence level. This activity duration is included in the duration of site preparation extracted from timeline.
4.5.1 Units of Measurement
63
According to the assumptions of this report, construction working hours will be from 7am to 6 pm weekdays and be from 8am to 5pm on Saturdays through all construction life cycle in this project. Additionally, there will be an hour for lunch in working days.
4.5.3 Surrounding Areas Impact on Working Times
Given that the demand for T3 Bankstown lines remains ongoing, some construction works such as bridge works and corridor works would need to be undertaken during rail possession periods
The shade area represents the P 90 confidence level, which in this report we have 90% chance to complete the activity A within 302.8 days.
4.5 Schedule baseline (up to level 3)
4.5.2 Project Working Days and Calendar
Project activities will be measured in working days. All dimensions measurements tend to be made in metric values, and these values will be maintained to and consistent with the units mentioned in the part 4.1.5 of this report.
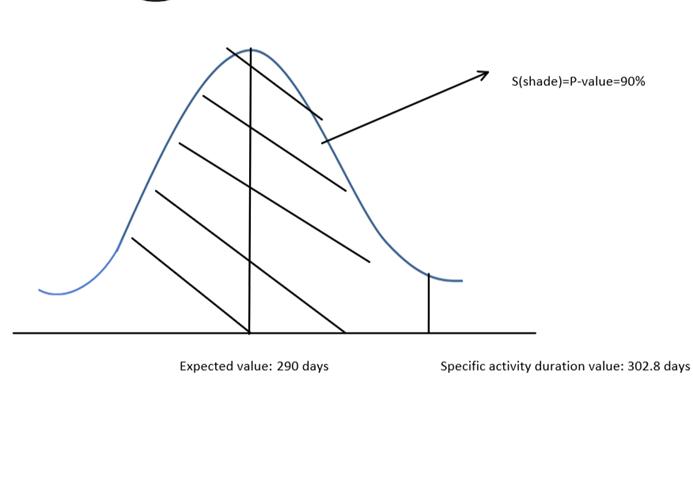
64 when trains are not operating, to ensure that works are conducted as efficiently as possible, and that worker safety would be maintained. During each possession period like standard weekend possessions when the rail lines are closed and school holiday possessions when less traffic on the surrounding road network would assist the efficient operation of rail replacement bus services, alternative transport arrangements would be implemented to ensure the train services can continue. The possession period is responsible for the impact on partial working hours associated with Sydney Metro project and will be managed by local council accordingly.
In the event of unforeseen change or significant departures from the working hours, the project team will apply for Extension of Time (EOT) in accordance with the contract requirements, catering for the acceptable schedule risk contingency.
65 4.5.4 Schedule baseline
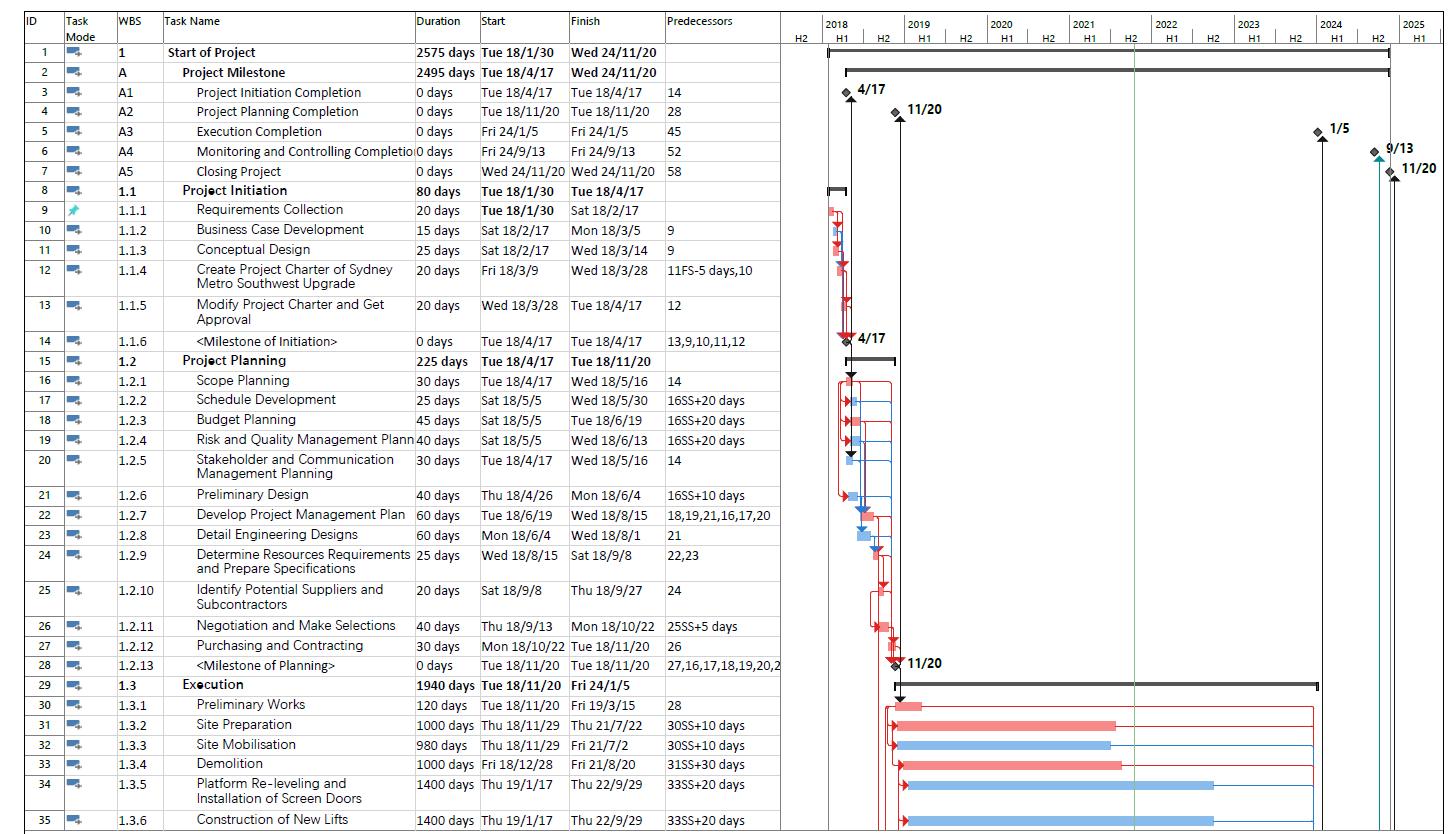
66
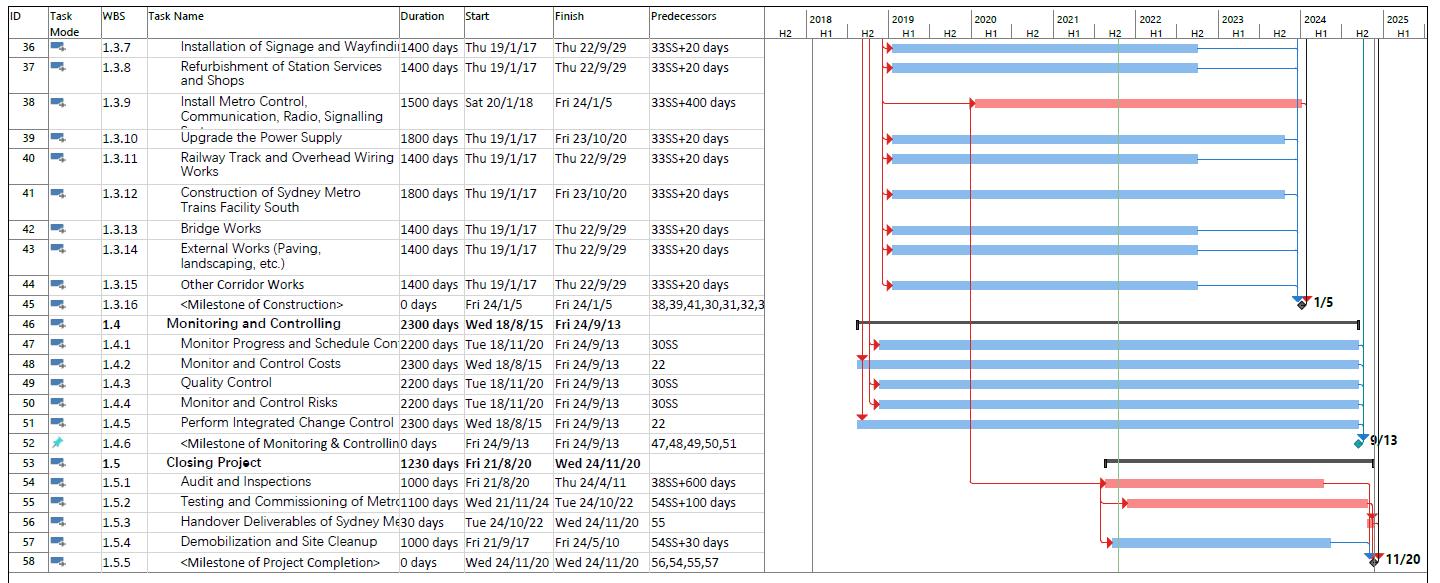
Proportion
4.6.1
67 4.6 Schedule monitoring and control
The practice of monitoring the status of project operations in order to update project progress and manage deviations to the schedule baseline in order to meet the plan is known as schedule controlling. The main objective of this procedure is to help stakeholders easily recognize deviations from the plan and take corrective and preventive actions to reduce risk. Schedule Progress Collection Process
On a monthly basis, project team members enter activity and progress updates into Primavera P6 (the online project scheduling tool designated for the Sydney Metro project). The data is checked by the functional manager to ensure that the information supplied is accurate. The Project Scheduler confirms that the month's updates are complete and discusses the results with the Project Manager. Any input errors will be reported to the functional managers so that the project team member can rectify them promptly. Schedule Progress Measurements
4.6.2
4.6.3 Schedule
Throughout the project life cycle, the following scheduled reports will be generated at the appropriate time intervals:
The Sydney Metro project will measure schedule performance using Schedule Variance (SV) and Schedule Performance Index (SPI). Furthermore, the project teams also track two supplementary data to improve the accuracy of estimation. of Tasks Completed on Time Calculates the percentage of tasks that are completed on time or ahead of schedule. Percentage of Tasks Performed on Budget (Effort) Calculates the percentage of tasks completed within their allocated time budget. Reporting Format
68 Table 5: Schedule Reporting Format Report Type Periodicity ResponsibleParties Content Resource Task Lists and Work Packages Weekly ManagerProject Establish individual resource task lists and work packages available online and communicate to project team members using the scheduling tool. ReportScheduleProject Fortnightly SchedulerProject Prepare a schedule progress report for presentation at the project status meeting. BaselineScheduleMaster (Gantt Upchart)to level 3 Monthly SchedulerProject Prepare a revised schedule Gantt chart for the project status meeting. Sponsor Project Report Every two months ManagerProject Prepare a Sponsor project status report for the Project Sponsor to review. 4.6.4 Schedule Variance Analysis and Control MS Project is adopted to accurately measure schedule variation. Usage of software will also help change certain activity related parameters and readily derive their impacts on critical path and project completion dates. For monitoring schedule performance, variance thresholds are defined as the amount of deviation that can be tolerated before taking action. In this project, thresholds are expressed as days of deviation from the schedule baseline plan's specifications. The project's agreed upon schedule variance thresholds are explained below (table 6).
amountDelay(Days)
impactedPath Action needed
>6 pathcriticalNon
>5 pathCritical
A serious warning level establishes. The project team keep close monitor to avoid the non-critical path turning into critical path.
<=6 pathcriticalNon
<2 pathCritical The team assembles to evaluate whether the adjustment is needed. Keep the delay under control to prevent further deterioration.
Corresponding professionals and consultants take immediate analysis. Prompt corrective actions have to be taken in place. The change request is needed when corrective actions are unrealistic or inefficient. pathCritical Prompt corrective actions have to be taken in place.
A warning signal emerges. This delay has been marked for further monitoring and evaluation. Update site logs every two days. If a team member believes a schedule modification is required, the Project Manager and the rest of the team assemble to discuss and evaluate the adjustment. The project team assesses which tasks are impacted, calculates the variation, and creates a list of potential. If the Project Manager determines that any modification exceeds the set thresholds or bounds, a change request will be sent to the Change Control Board (CCB). The Project Manager and Project Scheduler record the result of the schedule change request, keep the documents in the project repository, adjust the schedule to reflect the approved change and communicate the change and its implications to all stakeholders. A separate change request is filed for examination and approval if the project team believes a schedule re baseline is required. Before being actionable, change requests must go through the Perform Integrated Change Control process.
2~5
69 Table 6: Control Threshold Variance
Crashing is utilised in the work packages that cannot be carried out in parallel in this project, such as 1.3.4 Demolition and 1.3.5 Platform Re leveling and Installation of Screen Doors in WBS Fast tracking only works when tasks can be overlapped to reduce the critical path project duration. For example, 1.3.5 Platform Re leveling and Installation of Screen Doors with 1.3.6 Construction of New Lifts can be performed in parallel for at least a portion of their duration. However, when the schedule is accelerated, using leads usually demands more coordination efforts between the activities involved and raises quality risk. Therefore, close and more frequent monitoring will be applied in the compressed schedule plan.
Crashing is the compression technique utilised for the Project with the availability of more funding and the need to complete the project sooner than intended. Crashing aims to increase the project's resources to reduce the planned duration of project tasks (Project Management Institute, 2017). Additional resources are given specifically to the tasks connected with the project's critical pathway (e.g., additional resources, provided overtime, or monetary compensation).
70 4.6.4.1
Schedule Compression Techniques When scope changes are not necessitated, two strategies are used to compress schedules: fast tracking and crashing.
The development of these roles and responsibilities within the cost management process, allowing for the delineation of expectations. In addition to the breakdown of each role, their specific responsibilities are listed as follows:
71 5.0
5.1 Cost Management Roles and Responsibilities
Project Cost and Financial Management Plan
As an integral construction management component of the Sydney Metro Sydenham to Bankstown, cost management plays various roles with respective responsibilities to enable adherence to the scope and budget of the overall public transport project. Hence, it is crucial to understand the roles, responsibilities, and work methods to perform effective cost management and allocation, further improving the capacity to control project expenses.
The following figure illustrates the organizational relationship of project financial management for the Sydney Metro Southwest.
Figure 14: Project Financial Management Organizational Structure
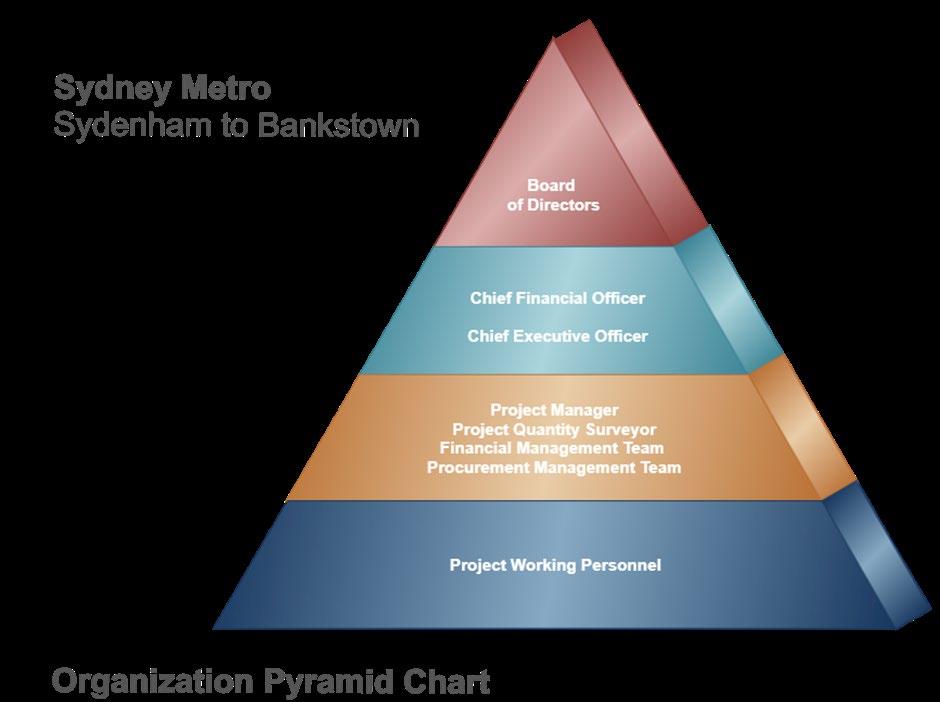
● Responsible for reviewing budget for the construction work with material requirements, establishing practices for how to manage funds, and ensuring these policies are followed on track.
Board of Directors
● Approve project plans and changes in execution.
● Chief Financial Officer provides accounting oversight and management for the Sydney Metro project.
● Work closely with the project manager and quantity surveyor to communicate and update financial information.
72
Cost
Chief Executive Officer (CEO)
Project Manager
● Responsible for the economic and technical compliance requirements of the construction contracts of the Sydney Metro project.
● In order to effectively manage the project’s financial performance, a CEO should also establish timely and accurate recording and reporting systems, obtain treasury management skills, plan project business growth, and familiarize with governance and controls.
● For the financial aspect, supervise the overall cost management process and establish appropriate budget control methods.
● Sign and approve project closeout at the final stage.
● Responsible for approving project plans with specific budgets and establishing management reserves for Sydney Metro.
Chief Financial Officer (CFO)
● Express written approval of various project requirements and qualification criteria.
RolesManagement Responsibilities
● Responsible for overseeing the operations of the entire Sydney Metro Southwest Project, from development, construction to operation, and only reports to the board of directors.
(Rosvold, 2016)
● Select appropriate project managers and other key personnel to assist with staffing.
● Examine structural drawings and specifications and liaise with clients and other professional consultants to deliver projects.
Project SurveyorQuantity
● Amend, update and reconcile Cost Reports.
73
● Responsible for the calculation and pricing of estimates and cost plans, measuring quantities for variations, and producing financial forecasts for the overall Sydney Metro project.
Financial Management Team
● Organize and recommend cooperative suppliers for projects and holding evaluation meetings to appoint ideal suppliers for Sydney Metro.
● Ability to maximize the use of appropriate software and technology, e.g., MS Office; MS Project and Cost X.
● Provide overall supervision of financial activities within the project, including the use of funds under the regulations, the implementation of plans, the acquisition of various income, expenses and other financial activities, and submit the implementation status to the project manager.
● Responsible for the accounting work of the project and formulates the cost management approach of the Sydney Metro project.
ManagementProcurement Team
● Ensure all procurement activities are conducted in accordance with relevant State laws, regulations, and internal company rules to avoid procurement risks.
● Responsible for standardizing internal procurement processes, reducing intermediate links, improving the efficiency of procurement funds, and minimizing procurement costs.
● Coordinate the work of all project departments, complete the tasks of the directors and report on time.
● Analogous Estimating Analogous estimation compares the actual cost of a project to the costs of previously completed similar projects. This approach has a low cost and a low quasi accuracy, and it is frequently used for approximate estimation when information is limited.
In order to estimate the amount of cost required to complete the project work, the detailed scope of work of the project needs to be defined, including the project description. The Sydney Metro Southwest primarily consists of building on the T3 Bankstown line and upgrading all 11 stations and tracks between Sydenham and Bankstown to subway standards. The work breakdown structure is used to outline all of the tasks that must be completed. The second step is to determine the time period required to complete the project. The project will start in 2018 and is expected to complete in 2024. All activities are listed on the activity list, which aids in the development of a network diagram and the formation of a work schedule.
To implement cost control, the cost must be estimated in advance The cost estimate for the Sydney Metro southwest is based on the proposed conceptual design and data collected from similar projects. The cost estimate is not very precise due to the limits of the compendiary design and the availability of correct data, but the cost management team will update all the data in the cost management plan when the detailed design plan is released. Some fundamental estimate approaches are as follows:
5.2.2. Budget Determination Methods
5.2.1 Cost Estimation
74 5.2. Cost Estimation and Budget Determination Methods
Cost estimation refers to the cost of all resources used for the project, including direct and indirect costs. Direct costs include all costs directly connected to project production, such as equipment, materials, human resources, team travel expenses, wages, and recognition. Indirect costs include taxes, fringe benefits, general sales and administration (GSA), or general administration (GA). When calculating project costs, particular classifications such as finance charges, contingency costs, and inflation allowances should be considered as well.
● Bottom Up Estimating Bottom up estimation is a method of estimating the cost of each activity and work package, so this estimation method is usually used in conjunction with a work breakdown structure (WBS). In the Sydney Metro Project, this method will be utilised for estimating high level working
By accounting for uncertainty and risk in the calculation, three point estimating enhances the accuracy of single point cost estimation. It is suggested that the Beta estimate approach be used to construct the Sydney Metro southwest project. The Beta distribution is a weighted average, which gives greater weight to the most likely estimate and helps to enhance estimate accuracy.
75 packages (Level 1 and 2). The advantage of this method is that it can estimate the cost of a single work package or activity to the specified details to provide a detailed cost budget.
● Three point estimating
5.3
Beta Distribution (PERT): E = (O + 4M + P) / 6 ● Monte Carlo Simulation (MCS)
This tool is particularly used to study the behaviour of stochastic systems and is one of the methods applied on many large scale construction projects. For example, in NSW any project more than $10 million including contingency, from a cost perspective, this methodology tends to be employed to define the contingency. In this report, MCS will be utilised to generate the Sydney Metro Project contingency. Further explanation and calculation will be demonstrated in Quantitative Risk Analysis as part of risk management plan
Cost Breakdown Structure
The Cost Breakdown Structure (CBS) is a hierarchical depiction of various costs in the project (figure15). The costs of the components in the Work Breakdown Structure (WBS) are represented by the Cost Breakdown Structure. By developing a structure for imposing measurable cost controls, the CBS is a mapping tool in managing the project lifecycle, particularly the financial components of the project. It is worth noting that the total cost ($2.552 billion) in figure 15 includes all items in the cost baseline, which means that the indirect cost, escalation and activity contingency reserve are distributed evenly among each work package. The detailed Cost Baseline will be thoroughly dissected in the next section.
76 Figure 15: Cost Breakdown Structure (CBS) of Sydney Metro Southwest Line
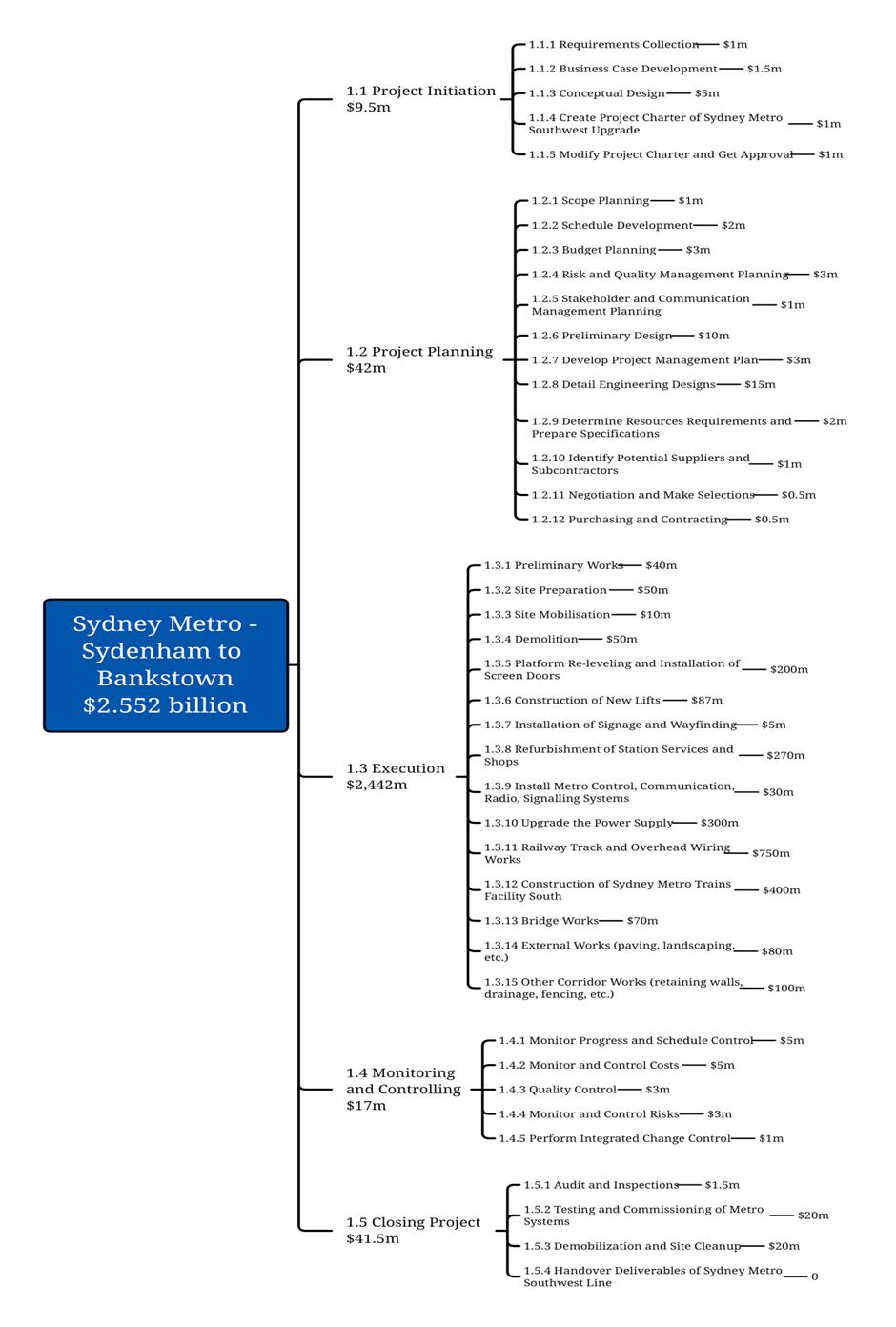
77 5.4. Cost Baseline and Cash-Flow Diagram
The overall budget structure of the Sydney Metro Southwest Line is depicted in the diagram below (figure 16).
Figure 16: Overall Budget Structure of the Sydney Metro Southwest Line
The total cost baseline of budget is determined by using Monte Carlo Simulation and the specific calculation is referred to Appendix G
The Management Reserve is estimated as 10% of the cost Baseline, which is $255.2m (Lee, 2020). 5.4.2. Cost Baseline
The causes of cost escalation analysed in this project are the fluctuation of interest rate, inflation rate and exchange rate. From figure 17, it is noticeable that from 2017 to nowadays, the interest rate dropped rapidly and inched ever closer to 0%.
5.4.1. Management Reserve
The Cost Baseline is a time phased project cost estimate that has been approved and can only be amended through formal change control procedures. It serves as a benchmark against which actual results can be compared. The Cost Baseline is created by aggregating all of the approved budgets for the various scheduled activities, which includes direct cost, indirect cost, escalation and contingency reserve. Their respective proportions among the Cost Baseline are listed in figure 5.4.2.116Cost Escalation
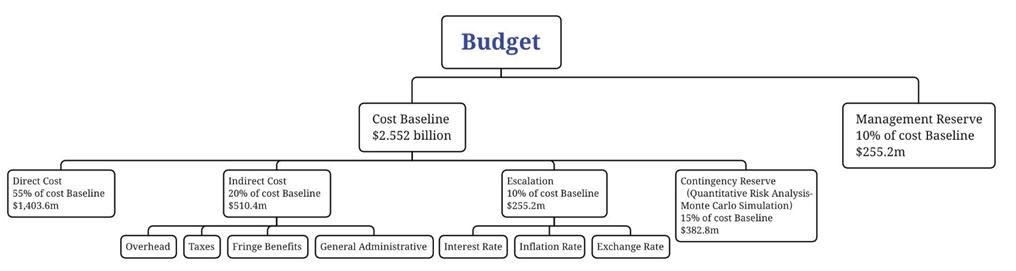
Figure 17:Interest Rate in Australia (Reserve Bank of Australia, 2021)
The inflation rate compared to the previous year has decreased from 2% to 0.87% between 2017 and 2020, and it is predicted to increase to 2.24% in 2024 (figure 18).
78
Figure 18: Inflation Rate Compared to the Previous Year (Statista, 2021)

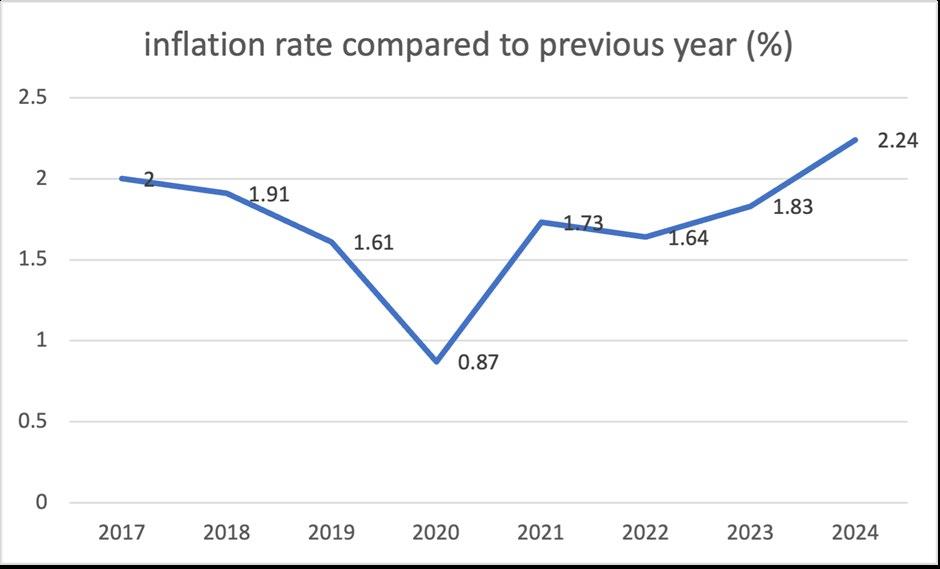
The contingency reserve is derived from the quantitative risk analysis Monte Carlo Simulation (MCS) in this project report. Further explanation and calculation are referred to the Risk Management Plan for the exhaustive simulation process. 5.4.3. Cash flow Diagram
Figure 19: Average AUD/USD Exchange Rate (Macrotrends, 2021)
According to the figures above and based on the analysis regarding previously similar projects, the predicted escalation accounts for 10% of the Cost Baseline. 5.4.2.2. Contingency Reserve
79 And the average AUD/USD exchange rate is displayed in figure 19
Because the cost estimations that make up the cost baseline are directly linked to the schedule activities, a Cash flow Diagram, which is commonly shown as an S curve, can be created (figure 20).
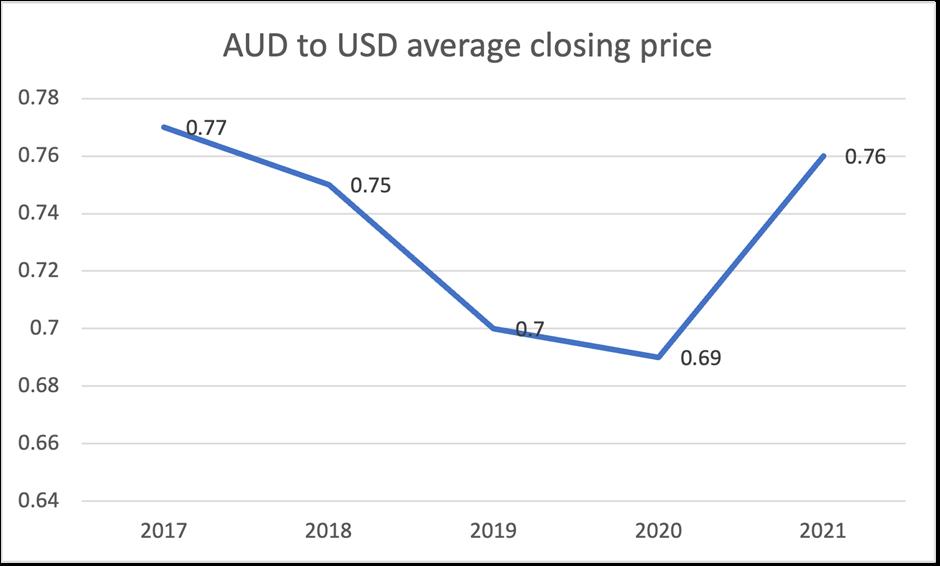
Several different tools can be utilized to measure the cost performance of the Sydney Metro project. The most common being Earned Value Measurement indicators which can be used by senior project directors to measure and control costs at detailed work levels. By utilising this method, the project management team can positively assess and measure the performance and progress of Sydney Metro Southwest, providing the advantage of maintaining a cost baseline throughout the project and implementing changes to alleviate any budget or schedule issues.
Sydney Metro Sydenham to Bankstown employs the following earned value techniques to determine the performance of the project, which will be updated as progress payments are received and will be forecasted into an S curve chart and reported to clients and senior management at regular monthly meetings.
Cash Flow Diagram of Sydney Metro Southwest Line 5.5 Cost Performance Measurement (Earned Value Management)
80 Figure 20:
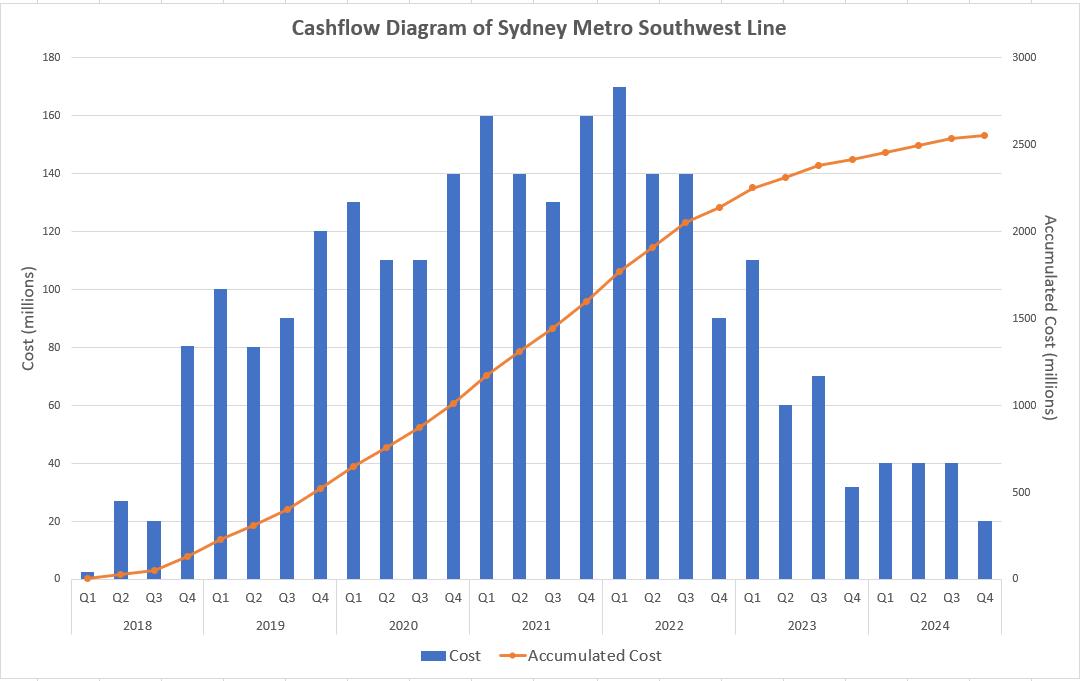
Work (ACWP)Performed--AC Cumulated
Earned
A measure of physical progress of works expressed by cumulated planned cost of works actually done related to time, it is also called Value. Cost of amount payable for works done related to time. planned cost of the whole project, it equals BCWS at the planned finish.
Budget Completionat (BAC) Total
The baseline for the analysis, cumulated planned costs related to time of their
Schedule Variance (SV) =BCWPSV BCWS
A measure of deviation between the actual progress and the planned progress. Though it is interpreted as time deviation, it is expressed in money units. In other words, it is the difference between the planned cost of works that have been done and planned cost of works that should have been done by the reporting date. If negative, it indicates a delay.
incurrence. Budgeted Cost of Work (BCWP)PerformedEV
Actual
81 Input BudgeteddataCost of Works (BCWS)ScheduledPV
Project DurationTime(T) Planned duration of the project Project status indicators CompletePercentage =BCWP/BACPC Cost Variance (CV) =ACWPCV BCWP
A measure of deviation between planned and actual cost of works done until the date of recording progress in money units. If negative, it indicates that the project is over budget.
Variance
A value of cost performance index that is to be maintained from now on if the project is to be completed to budget. In other words, TCPI is a proportion between the remaining work (expressed in terms of budgeted costs) and the money left from the budget Completionat (VAC) Is a project management and analysis tool used for projecting the difference between the initial budget and the most recent budget estimate. The following figure presents the basis of the Earned Value project control. The analysis requires the above inputs.
Earned Value “forecasting” parameters Estimate Completionat (EAC) =BAC+CVBCWP)/PF=ACWP+(BAC=BAC/CPIEAC
To PerformanceComplete
(TCPI) ACWP)BCWP)/(BAC=(BACTCPI
Is calculated at the date of reporting progress to serve as an estimate of the effect of deviations cumulated from the project’s start on the total project cost, so it informs how much the project is going to be in the end, if the cost performance index CPI stays the same Index
=BACVAC EAC
Compares the planned cost of works done with planned cost of works planned; if less than 1, it indicates a delay.
82 Cost IndexPerformed(CPI) =BCWP/ACWPCPI Compares the planned and actual value of works done, if less than 1, it indicates that the project has consumed more money than planned, if greater than 1, there have been savings. PerformedSchedule Index (SPI) =BCWP/BCWSSPI
83 Figure 21: Earned Value Curves 5.5.1 Earned Value Curve of Sydney Metro Southwest Project With regard to the abovementioned assumptions, earned value curve will be formed based on a reasonable estimation with a current time that is 2018 Q3. Figure 22: Earned Value Curve of Sydney Metro Southwest

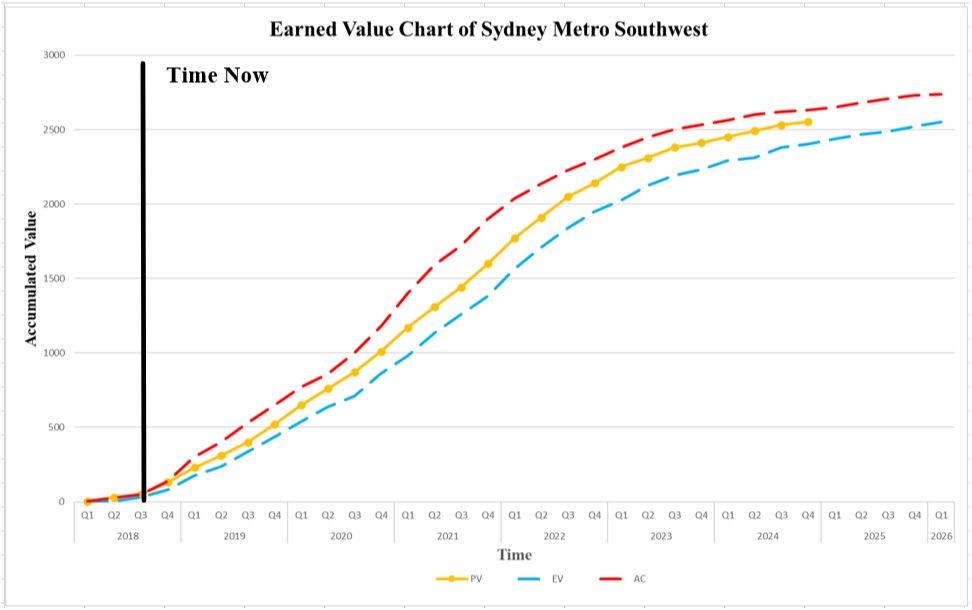
● Ensuring the Sydney Metro project cost expenditures do not exceed the authorised funding by period, by WBS component, by activity, and in total for the project.
The first cost control technique applied in the Sydney Metro Project is PoC metrics (the percentage of completion). Pica (2015, p.120) argues that the PoC (the percentage of completion) is applied as a metric, which demonstrates what activities have already been accomplished to give managers an indication of performance and trends for construction
● Monitoring work performance against funds expended.
Variance in the work performed and the cost of the work is evaluated at the work package level and control account level. In this report, earned value analysis (CPI, CV, SV, EAC) and the percentage of completion method (PoC) are documented for inclusion in work performance reports, which are utilised to detect cost variance.
● Monitoring cost performance to ascertain variances from the approved cost baseline.
● Informing appropriate stakeholders of all approved changes and associated cost deviations.
5.6.2.1 The Percentage of Completion as a Metric of Project Control
84 5.6
Cost Management Monitoring and Control
5.6.1 Work Performance Data and Information
5.6.2 Cost Variance Response Process
During the cost control process, a work performance information report is an important document for effective cost monitoring and control. The work performance information includes information on how the project work is performing compared to the cost baseline.
According to Project Management Institute (2017, p257), cost control is the process of monitoring the status of the project to update the project costs and managing changes to the cost baseline. This process is performed throughout the project. It basically involves analysing the relationship between the consumption of project funds and the work being accomplished for such expenditures. The key to effective cost control is the management of the approved cost baseline (shown in the previous part).
Thecontracts.PoCcalculation is carried out using the cost to cost formula:
Project control mainly includes:
85
the PoC trend against time is also an indicator of the cost control quality and reliability, which points to the cost variance (figure 23).
Figure 23: PoC trends (Project Life Cycle Economics: Cost Estimation, Management and Effectiveness in Construction Projects, 2015)
PoC diagram (a) is regular and (b) is irregular. Therefore, there are some adjustments needed to be adopted to address variance when the situation (b) occurs.
Furthermore, the revenue might be incorrect and overestimated in t0 and thus allocating a part of them in t1 period by reducing the PoC in t1 is necessary.
PoC takes into account the actual costs and cost estimation to finish. According to this approach, it will also be possible to calculate partial revenues and profit or losses during the entire project life cycle. After the PoC is calculated, the total project revenues ( R ) are multiplied by the PoC to calculate the revenues relevant to a period t1
5.6.2.2 Adjustment against the Cost Variance during Project Execution
Despite the accuracy of estimation and the sound approach adopted, supported by management judgement, imprecise evaluation may take place, which will affect the estimated total costs. Indicator for cost variance If , then and the actual costs are updated on an actual basis and are not affected. It indicates that the PoC was higher than the correct one at period t0 (Pica, 2015, Additionally,p.132).


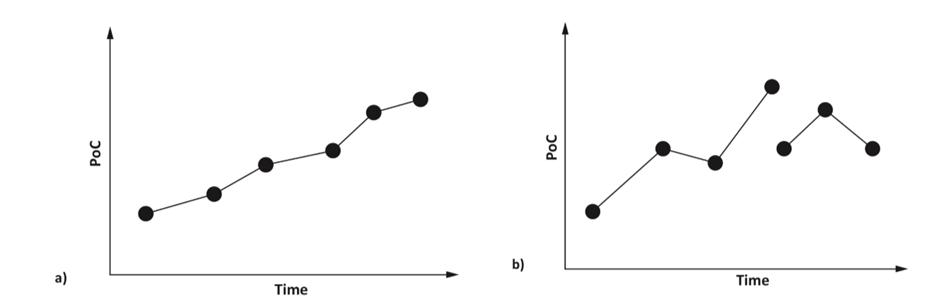
In addition to PoC metrics, EVA (Earned Value Analysis) is another major technique to embrace during the cost control process. EVA integrates the scope baseline with the cost baseline and schedule baseline to form the performance measurement baseline. EVM develops and monitors three key dimensions mentioned in the last section for each work package and control account, namely PV, EV and AC. Performance measurement Cost performance index (CPI) tends to be considered as the most critical EVA metric and measures the cost efficiency for the work completed (PMBOK®GUIDE, 2017, p.263). Also, schedule performance index (SPI) is sometimes utilised in conjunction with CPI, measuring how efficiently the project team accomplishing the work.
24:
Control Thresholds Based on the performance measure, the control thresholds for the Sydney Metro Project are summarised in Table 7:
Cost Variance Response Process
86
Figure Cost Variance Process 5.6.2.3 Earned Value Analysis in Cost Variance Response
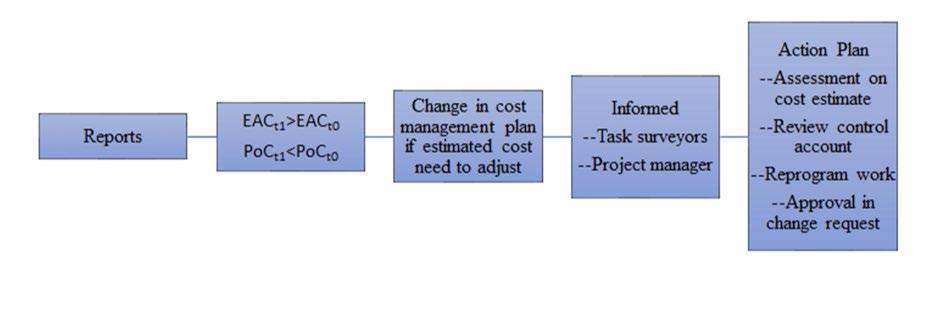
87 Table 7:
Cost Variance Control Thresholds
When >1, this means that this project is under planned cost, which means that the cost at specific work package is smaller than the original budget. If , this project is considered as a cost overrun one. Nevertheless, if CPI falls into the green condition, it indicates that this project is performing well and in a good state. However, if >1 and reaches the red condition threshold, it indicates that some errors have existed in cost estimation and the relevant cost control team needs to put effort into corrective action. Notifying the change control board and project sponsor by the project manager within a certain period is necessary. Through corrective action, it is reasonable to adjust the project performance to the desired level. As for the SPI, the explanation and analysis process are similar to the CPI. Consequently, the cost variance response process is summarised below as a flow chart.
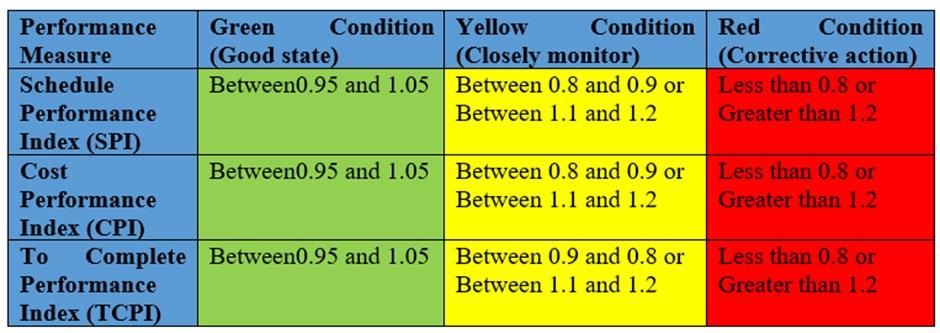

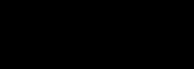

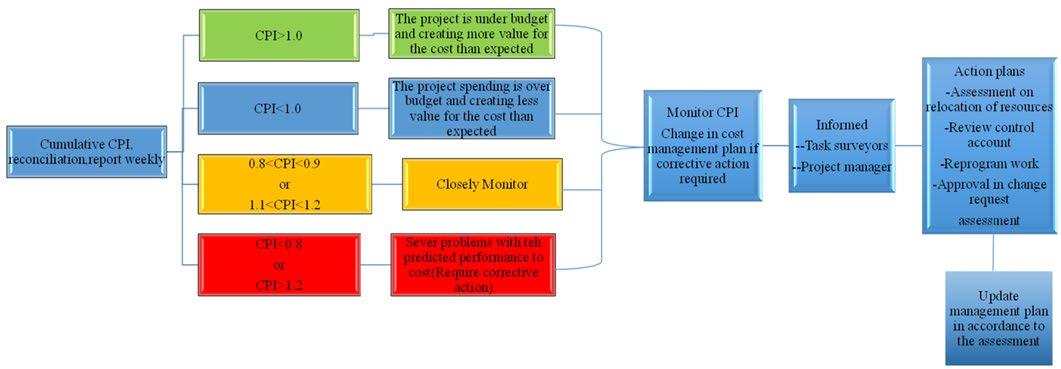
88 5.7 Cost Baseline Change Control Process This procedure applies to the entire life cycle of the Sydney Metro project. This procedure must be followed for any baseline change that crosses the change control thresholds defined in the Sydney Metro Project Execution Plan. Changing project cost control is subjected to the Cost Variance Response. In short, a Baseline Change Request (BCR) is required whenever there is a change in: ● Scope of Work ● Stakeholder Responsibilities ● Schedule ● Budget ● Funding Cost Baseline Change Process Details Step 1: Initiate Change Request (Responsibility: Site Office, Project Office, System Manager, Control Account Manager, Project Control Team) Step 2: Prepare Preliminary Briefing to CCB (Cost Control Board) (Responsibility: Site Office, Project Office, System Manager, Control Account Manager, Project Control Team) Topic required to be addressed: ● Summary of what change is requested in the drat Baseline Change Request Form ● Background information ● Describe the key problem ● Describe the proposed solution to the problem ● What is the impact of the change (technical, schedule, key milestones, cost, resources, funding) ● Any other details pertinent to the proposed change request – what else may be involved or impacted that will help the Change Control Board in their decision-making process. Step 3: Proceed (Responsibility: Cost Change Control Board)
● Request the draft Baseline Change Request Form and proposed change briefing content be revised based on specific instructions from the Change Control Board (identify what needs to be updated). When this occurs, the process returns to step 2.
Step 5: Assign BCR (Baseline Change Request) Number and Create Log Entry (Responsibility: Project Control Team) Once the draft Baseline Change Request has been approved by the Change Control Board, the request is assigned a unique Baseline Change Request number and is entered into the Change Control Log database. The cost change form is shown below.
● Decline the proposed change request. The Baseline Change Request Form moves to Step 4 in the process.
89
At this stage the Cost Change Control Board can do one of two things:
Step 4: Revise Briefing (Responsibility: System Manager, Cost Control Account Manager and Control Team) Once the change request is declined: ● When this occurs, the change control process stops. There is no change request to process.
● Approve the proposed change. The Baseline Change Request Form moves to Step 5 in the process.
90
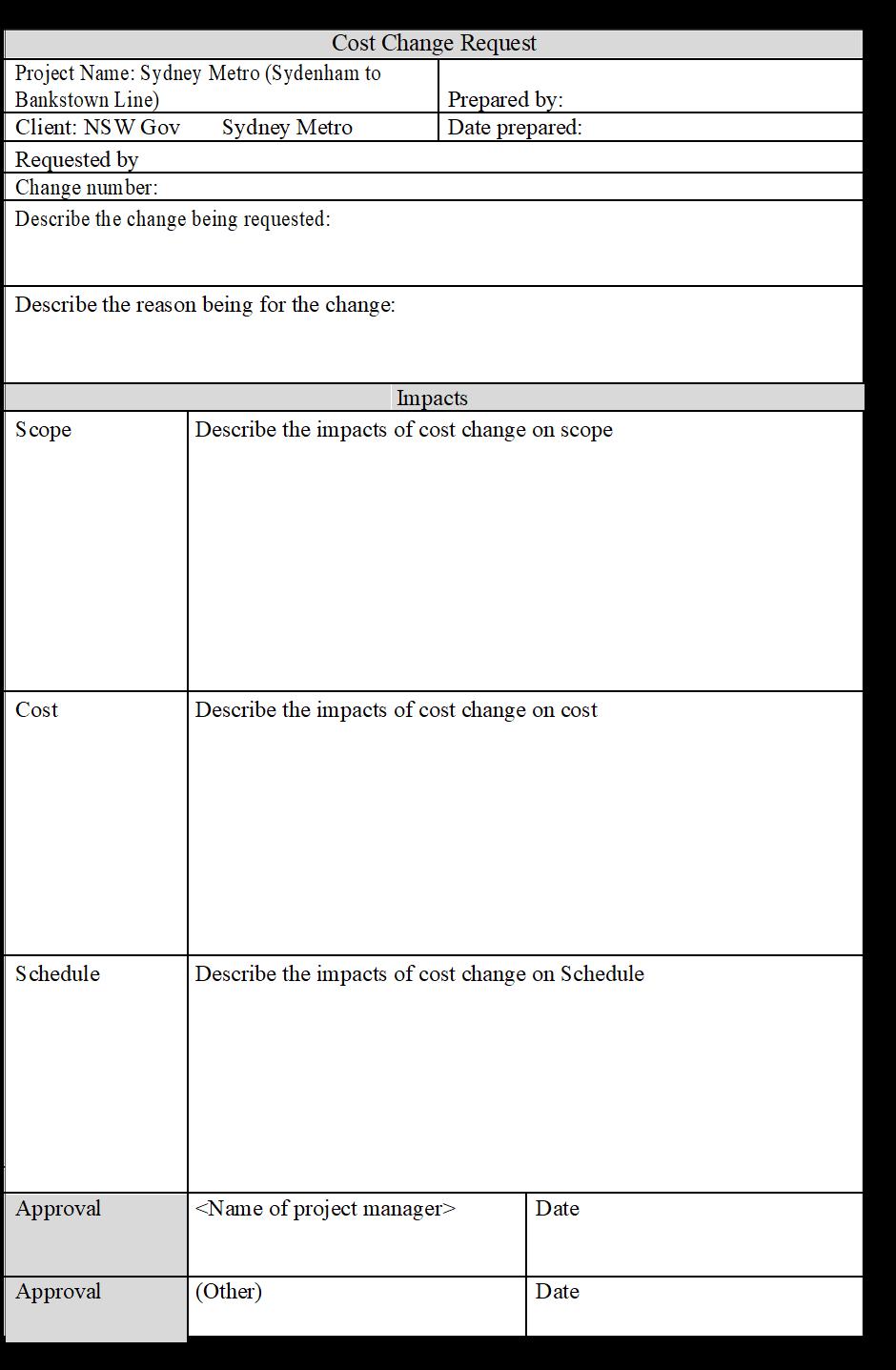
The originator of the Baseline Change Request updates the request form with the more accurate assessment of the impact of the change request from the project control team (schedule, cost, and technical).
91
Step 9: Present BCR to CCB (Responsibility: System Manager, Cost Control Account Manager and Control Team)
The originator of the request is responsible for preparing the content of the final presentation of the change request to the Change Control Board.
Step 6: Create Offline Cost Data (Responsibility: Project Cost Control Team)
Step 8: Prepare Final Briefing to CCB (Responsibility: System Manager, Cost Control Account Manager and Control Team)
The originator of the request is responsible for presenting the content of the change request form to the Change Control Board.
Based on the initial Baseline Change Request Form contents, the project control team assesses the impact of the change to the schedule and cost baselines. This what if analysis is performed in a separate, offline cost/schedule database.
Step 11: Rework BCR? (Responsibility: System Manager, Cost Control Account Manager and Control Team) When the Change Control Board declines the proposed change request, they can do one of two things: ● Reject the proposed change request. When this occurs, the change control process moves to Step 12.
● Request the Baseline Change Request Form and proposed change briefing content be revised based on specific instructions from the Change Control Board (identify what needs to be updated). When this occurs, the process returns to Step 7.
Step 7: Update BCR (Baseline Change Request) with Delta Cost Data (Responsibility: System Manager, Cost Control Account Manager and Control Team)
Step 10: Recommend for Approval? (Responsibility: Change Control Board)
Step 12: Remove BCR from Log (Responsibility: Project Cost Control Team)
Once the Baseline Change Request has been approved by the Change Control Board, the board assesses who is authorized to approve the changes. This approval is based on who originated the request and the scope of the request.
Step13: Determine Required Signature Level (Responsibility: Project Cost Control Team)
The appropriate approving party or parties sign the Baseline Change Request Form and return it to the Change Control Board.
Step15 Implement BCR and Update Log Once the Baseline Change Request Form is signed, the Change Control Log database is updated to note the date the form was signed and when the changes were implemented in the schedule and cost baselines. The Change Control Log database notes any summary level changes to the project (total costs, management reserve/contingency) as a result of the change request.
When a change control request is rejected, the Change Control Log database must be updated.
The Baseline Change Request is deleted from the Change Control Log database and the process stops.
The Major Process is depicted as a flowchart shown below: (The flowchart is referred to the Project Management Plan generated by Stanford Synchrotron Radiation Laboratory)
Step14: Sign BCR (Responsibility: Site Office, Project Office, System Manager)
92
93
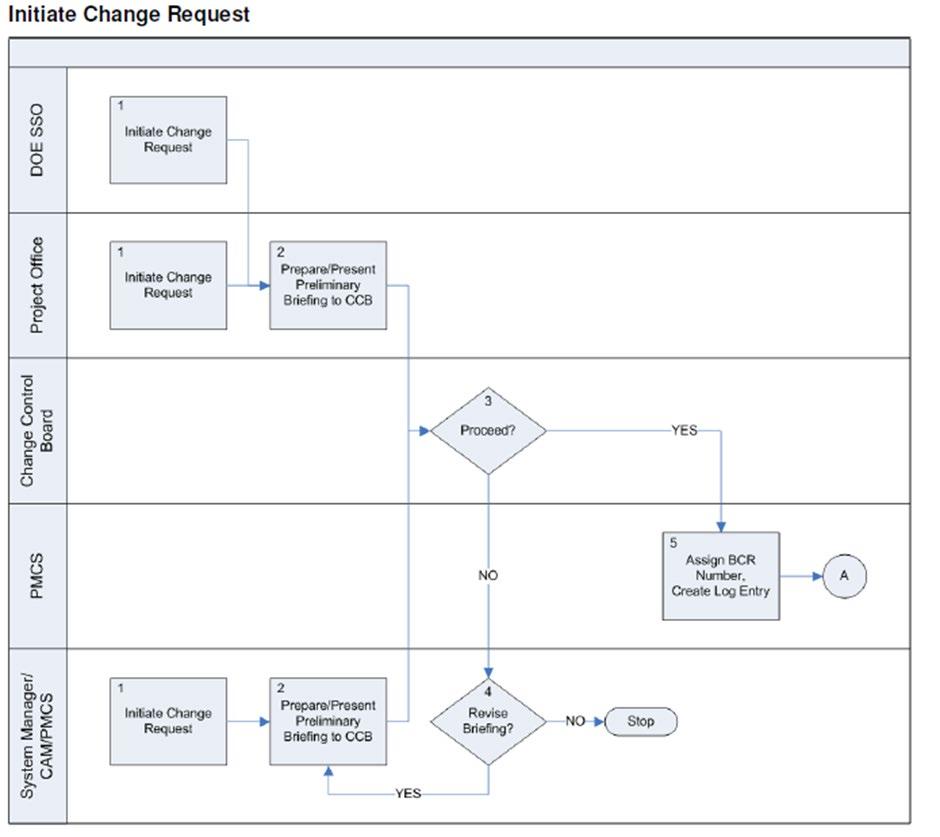
94
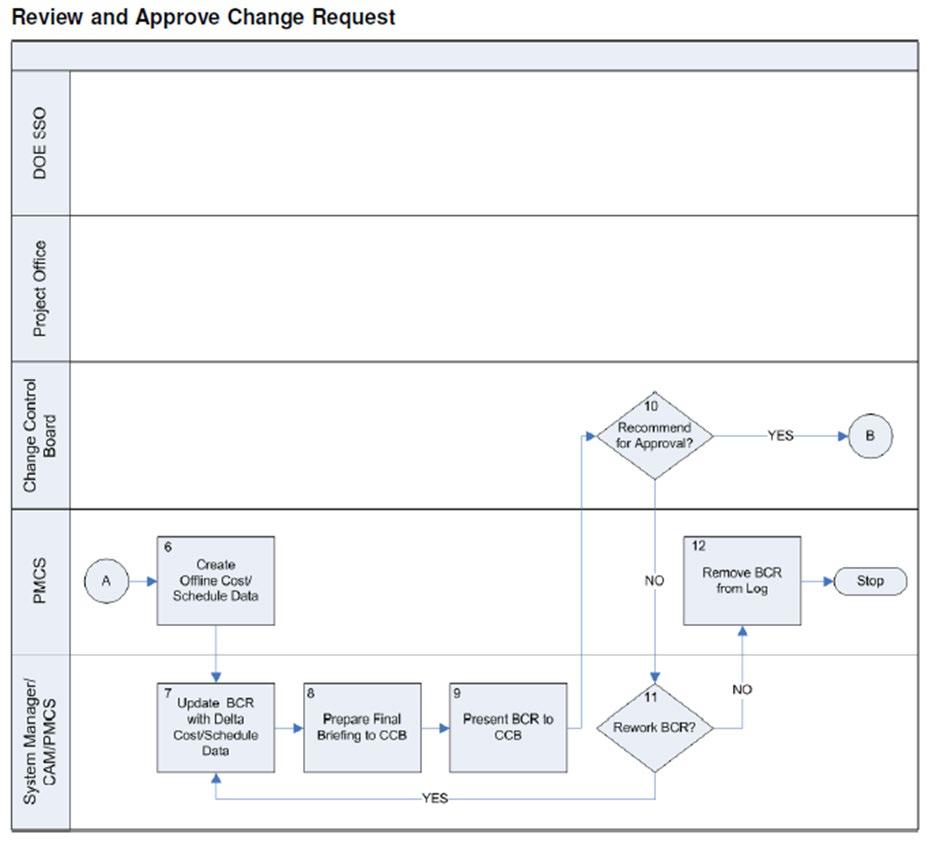
95 Figure 25: Cost Control https://silo.tips/download/patriciaProceduremast lcls project controls manager mark reichanadter lcls deputy projec

96 6.0 Project Quality Management Plan 6.1 Quality Management Planning 6.1.1 Identify Roles and Responsibilities for QM team Roles Quality Responsibility Level tInvolvemenof ManagerProject During the implementation phase, monitor if the project's quality is up to standard in accordance with the requirements. Pay close attention to quality issues during the project implementation phase, quality issues during the completion process, and quality issues that extend beyond the first set. Help standard goods attain higher quality. Little need to decrease rework. Extreme ManagerQuality Ensure the vendor's quality system is evaluated. Ensure that all quality requirements are met and provide feedback to consumers when faults arise. Manage trade monitoring, measurement, and evaluation on a regular basis. Hold a quarterly management review meeting. Track the product throughout the implementation process to ensure that every step is completed correctly. Inspect the goods at all stages and produce reports to document any production issues. Conduct a thorough record examination of the completed product to ensure that it meets industry and business requirements. Eliminate subpar items and figure out what's causing the product problems ExtremeHigh ManagerSite Communicate with the Project Manager and the Quality Manager Supervise the operation of the whole project during the construction phase to ensure that it is completed on schedule, within budget, and achieves the project's quality objectives. Ensure that the project is completed on schedule and that all subcontractors and project teams adhere to all quality standards and management plans. Utilize all funds and resources to the fullest extent while avoiding project flaws. Responsible for the implementation of quality assurance and reporting any defective items to the High
97 project manager and quality management. Reports to both the Project Engineer and the Site Manager. Ensure that all structural and technical operations on site satisfy project quality requirements. If any flaws are discovered throughout the building process, attempt to resolve them as soon as possible. Responsible for professional specialized quality management work during the project procurement and construction process, as well as managing Trades to guarantee optimum quality is reached.
Low-Med InspectorQuality
orAdministratContract
Med
High Med EngineerSupervision
EngineerSite
Ascertain that the contract satisfies all quality standards. All quality concerns should be reported to the project manager. Take part in project meetings and evaluations. Low
Coordinates with the Site Manager to ensure that quality standards are met. In charge of the specific execution of professional supervision Examine the construction contractor's plans, applications, and modifications. Report to the site manager on a regular basis on the implementation of professional supervision activity. Create a supervision diary based on the project's particular implementation; gather, summarize, and arrange data; and assist in the production of the monthly report. Supervises all material testing activities and reports directly to the superior. In charge of inspecting and testing building projects. Responsible for gathering and sorting quality inspection and evaluation data, as well as helping the quality manager in performing outstanding quality management. In charge of monitoring rectification implementation and supervising the construction crew. Directly report to the construction quality manager. High
98 6.1.2 Quality Standards and Requirements Planning quality management defines the process of identifying quality requirements and standards for the project’s deliverables and documenting how the project will demonstrate compliance with quality requirements and standards. Rumane (2018, p122) states that quality standards are the key to any conformity assessment activity, which are used to ensure that a product or system meets specifications and requirements. The standard setting is one of the first issues in developing quality assurance systems and serves as a reference base to justify the adequacy of a quality system, covering all the activities leading to the finished products. 6.1.2.1 Standards Organisations There are many well known organisations that produce standards in the quality field and those standards will be employed in Sydney Metro Project: ● International Organisation for Standardisation (ISO) ● International Electrotechnical Commission (IEC) ● American Society for Heating, Refrigerating, and Air Conditioning Engineers (ASHRAE) ● AS/NZS Australian Standard/ New Zealand Standard ● Building Code of Australia (BCA) ● The Australian Institute of Refrigeration, Air conditioning and Heating (AIRAH) 6.1.2.2 Quality Standard Applied in Respective Working Activity in Sydney Metro Project In this report, the construction stage and its relevant working activities of Sydney Metro Project are extracted, and associated standards applied to them are demonstrated in Table 8.
99 Table 8: The Common Standards Used in Sydney Projects Associated with Work Packages No.WBS Activity Name Section Related Standards (example) 1.3.2 Site preparation clearanceVegetationcontrol,Traffic AS 4191:2015 Portable traffic signal ASsystems1742.2 2009 Manual of uniform traffic control devices AS 4970 2009 Protection of trees on development site 1.3.3 Demolition Removal of structures AS 1576 1974 Code of practice for metal ASscaffolding2601 1991 The demolition of ISOstructures16369:2007 Elevating work platforms Mast climbing work platforms ISO 17723 1:2019 PPE ensembles for undertaking hazardous materials response activities 1.3.4 excavation(detailed)Site Excavation ISO 18400 103:2017 Soil quality sampling-part 103: Safety ISO 11272: 2017 Soil quality Determination of dry bulk density AS ISO 7135: 2021 Earth-moving machinery Hydraulic excavator terminology and commercial specification ISO 8643:2017 Earth moving machinery Hydraulic excavator and backhoe loader lowering control device Requirements and IECtests 60151 18:1968 Measurement of the electrical properties of electronic tubes and ASvalves.7638:2013 Railway Earthworks 1.3.5 Construction of footings for new stairs and lift shafts balustrade.stairs,Concrete, AS 3610: 2018 Formwork for concrete, Part 1: Specifications AS 3600:2018 Concrete structures ISO 21573 2:2020 Building construction
100 machinery and equipment Concrete AS/NZSpumps 4671:2019 Steel for the reinforcement of concrete AS 1012.3.1:2014 Methods of testing concrete, Method 3.1: Determination of properties related to the consistency of concrete Slump test AS 5100 Crowd loading requirements AS BCA1428.1(2001)clauseD2.17 1.3.6 Platform re levelling & finishes and installation of anti throw screen and glazing screen doors construction,Platformdoors,Screen ISO 3009:2003 Fire resistance tests Elements of building construction Glazed RailelementsInfrastructure Corporation, CSI 031, Engineering Works in the Vicinity of Platforms and Structure Footings AS/NZS 4586: 1999 Resistance Classification of New Pedestrian Surface HBMaterials197:1999 An introductory Guide to the Slip Resistance of Pedestrian Surface ISOMaterials10077 1:2006 Thermal performance of windows, doors and shutters Calculation of thermal transmittance Part1: TestingGeneralstandard: ASNZS 4284:2008 1.3.7 Installation of new lift Lift, AS 1735.12:2020 Lifts, escalators and moving walks, Part 12: Facilities for persons with disabilities (EN 81 70: 2018, Builmod)ding Code of Australia and where relevant, Station Guidelines for Fire and Life Safety in the Construction of the Underground Railway Facilities (SGFLS) AS 1428.2 1992 Design for access and mobility, Part 2: Enhanced and additional
101 requirements Buildings and facilities 1.3.8 Installation of signage, lighting, and CCTV CCTVSignage, AS 4806.2 2006 Closed circuit television (CCTV), Part 1: Management and ASoperation4806.2 2006 Closed circuit television (CCTV), Part 2: Application guidelines AS 7632:2015 Railway Infrastructure Signage 1.3.9 Refurbishment and installation of station HVAC services conditioningsystem,ventilationhandlingAirair AS 4254.1 Ductwork for air handling systems in buildings Flexible ducts AS 4254.1 Ductwork for air handling systems in buildings-Rigid ducts AS 1668.2-1976 SAA Mechanical ventilation and air conditioning code Part2 Ventilation requirements AS 2913 2000 Evaporative air conditioning equipment AS 1668.1:2015 The use of ventilation and air conditioning in buildings, Part1: Fire and smoke control in buildings ISO 19659 2:2020 Railway applications Heating, ventilation and air conditioning systems for rolling stock Part2: Thermal AIRAHcomfort Application Manuals, notably ASHRAEDA09 Handbooks NSW Health Regulations relating to health, amenity, safety, noise, pollution controls, relating to air conditioning system 1.3.10 Install, upgrade and connect electrical network for substation and power supply neelectricalsubstation,converters,powerElectronictwork IEC 62590: 2019 Railway Application Fixed installations Electronic power converters for substations IEC 62590: 2019 Railway Application Fixed installations Traction transformers
102 IEC 62236 5:2018 RLV Railway Applications Electromagnetic Compatibility Part 5: Emission and immunity of fixed power supply installations and apparatus. IEC 62497 2:2010 Railway Applications Insulation coordination Part2: Over voltages and related protection 1.3.11 Railway Track work ♦ removal of old rails, fastenings, and sleepers ♦ laying the new rails ♦ placement of ballast and sleepers on the formation ♦ tamping and profiling the ballast around the sleepers Track work, Steel AS 7635:2013 Track Geometry AS 7639:2013 Track Structure and ASSupport1085.17:2021 Railway track material, Part 17: Steel sleepers AS 7508: 2017 Track Forces and Stresses AS 1085.1:2019 Railway Track Material, Part 1: Steel Rails AS 1085.3 2002 Railway track material Part 3: Sleeper plates 1.3.12 Construction of south line facility (Installing cable, signalling, overhead wiring, electrical system and track drainage cable,wiring,Overhead IEC 60570:1995 Electrical supply track systems for luminaires IEC TR 62263:2005 Live Working Guidelines for the installation and maintenance of optical fibre cables on overhead power lines AS 7637:2014 Hydrology and Hydraulics 1.3.13 Bridge work structuresOverbridge AS 5100.2:2017 Bridge design, Part 2: Design loads AS 5100.4: 2017 Bridge design, Part 4: Bearings and deck joints AS 5100.8:2017 Bridge design, Part 8: Rehabilitation and strengthening of existing bridges 1.3.14 External Works (Landscaping, paving) landscapingsoftpavement,Asphalt,andhard AS/NZS 3661.2:1994 Slip resistance of pedestrian surface, Part 2: Guide to the reduction of slip hazards AS 1428.1:2021 Design for access and mobility, Part 1: General requirements for access new building work
103 AS 1428.2 1992 Design for access and mobility, Part 2: Enhanced and additional requirements—Buildings and facilities HB 197:1999 An introductory guide to the slip resistance of pedestrian surface materials
As prescribed by the BCA, Australian Standards specifications, design loadings will need to address train derailment, floor loadings, wind loadings, air pressures, seismic loadings, crowd loadings and collision loadings.
● Platform edge and corresponding rail alignment must be level in the longitudinal direction.
● Ponding of water on the platform surface is unacceptable. The specific resolutions of platform structure, sub base, surface falls, drainage, and finish are required.
Example: Task 1.3.6 Platform re levelling & finishes and installation of anti throw screen and glazing screen doors
There is a work activity extracted from table above as an example for further perception of quality standard. And other examples for further description please refer to the Appendix C.
The safety of the platform surface is paramount. Refer to Figure 26, critical requirements are:
Platform Finishes
1)Structural Design
● The platform cross section must have a minimum of 1:100 and a maximum 1:40 fall from the platform edge to the centre of the platform. The longitudinal gradient of the platform should also be considered in determining the platform cross fall.
● The platform surface must be slip resistant in both wet and dry conditions as set out in the relevant slip resistant standards AS/NZS 4586, AS/NZS 4663 and HB 197.
104 Figure 26: Platform Fall https://www.transport.nsw.gov.au/system/files/media/asa_standards/2020/esbRequirements 003.pdf 6.1.3 Procedure of Quality Planning Quality planning is a structured process for developing products (both goods and services) that ensures that customer needs are met by the result. The tools and methods of quality planning are incorporated along with the technological tools for the particular product being developed and delivered.
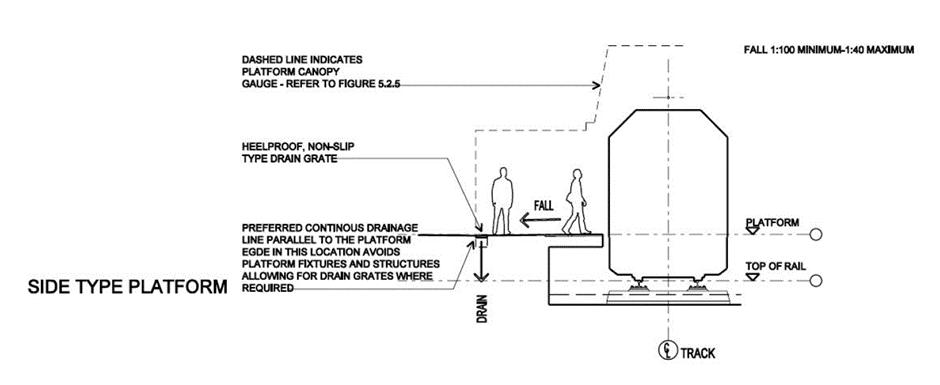
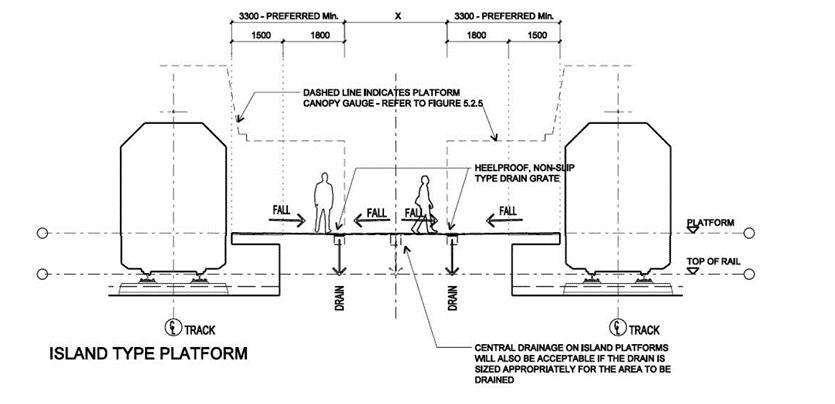
105 The process of planning quality management Step 1: Establish the Project The following activities are associated with establishing a quality planning project: • Identify which projects are required to fulfil the organization’s strategy • Prepare a mission statement for each project • Basis for establishing quality goals • Establish a team to carry out the project • Plan the project Step 2: Identify the Customers Figure 27: Types of https://tohproblemkyahai.com/theCustomers quality planning process/ External Customers ♦ The purchaser
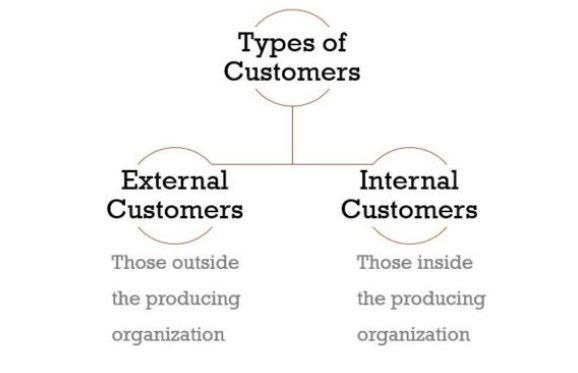

106 ♦ The end user/ultimate customer ♦ Merchants ♦ Processors ♦ Suppliers ♦ Original equipment manufacturers (OEMs) Internal Customers ♦ Identifying the internal customers requires some analysis because many of these relationships tend to be informal, resulting in a hazy perception of who the customers are and how they will be affected ♦ Effectiveness in meeting the needs of these internal customers can have a major impact on serving the external customers Step 3: Discover Customer Needs The third step of quality planning is to discover the needs of both internal and external customers. Some of the key activities required for effective discovery of customer needs include: ♦ Plan to collect customers’ needs. • Customer surveys, Routine communication • Tracking customer complaints, Customer meetings ♦ Collect a list of customers’ needs in their language. • Must be stated in terms of benefits sought ♦ Analyse and prioritize customers’ needs. • Organizing, consolidating, and prioritizing the list of needs for both internal and external customers ♦ Translate their needs into “our” language. • A common language facilitates efficient communication ♦ Establish units of measurement and sensors.
107 Step 4: Develop the Product There are six major activities in this step: ♦ Group together related customer needs ♦ Determine methods for identifying product features ♦ Select high level product features and goals ♦ Develop detailed product features and goals ♦ Optimize product features and goals ♦ Set and publish final product design Step 5: Develop the Process The eleven major activities involved in developing a process are: ♦ Review product goals ♦ Identify operating conditions ♦ Collect known information on alternate processes ♦ Select general process design ♦ Identify process features and goals ♦ Identify detailed process features and goals ♦ Design for critical factors and human error ♦ Optimize process features and goals ♦ Establish process capability ♦ Set and publish final process features and goals ♦ Set and publish final process design Step 6: Develop the Control and Transfer to Operations There are seven major activities in this step: ♦ Identify controls needed
As shown in the diagram below, there are four types of cost of quality (COQ) in the project.
2. Benchmarking By comparing with similar projects such as other lines in Sydney Metro or metro projects in other regions, best practices to potential quality risks, efficient management methods, effective solutions to common issues, and good ways to measure the performance can be identified.
3. Analysis of Cost of Quality
Besides, the main contractors are all tier 1 companies with many excellent professionals and specialists. (Duboudin, 2021; WSP, 2017; RPS, n.d.)
By analyzing the cost and the benefit of different schemes, the team can effectively ensure the conformance and rectify the nonconformance at a low cost and in a high quality. (PMI, 2017, pg.282 283) a) Prevention Costs: costs related to the prevention of poor quality in the products, deliverables, or services of the project.
1. Expert Judgement Experts can give a lot of useful advice to secure the success of projects. We seek helps from different entities with extended knowledge and abundant experience. For examples, a consortium of cost consultancy Turner & Townsend, Deloitte and risk consultancy HKA are involved to oversee the development. WSP is also engaged as a technical advisor to solve complex engineering problems, and RPS is coordinated with in major packages procurement.
To ensure the quality of works in Sydney Metro Southwest Line Upgrades, a variety of tools and techniques are adopted throughout the project.
108 ♦ Design feedback loop ♦ Optimize self control and self inspection ♦ Establish audit ♦ Demonstrate process capability and controllability ♦ Plan for transfer to operations ♦ Implement the plan and validate the transfer 6.2 Manage Quality 6.2.1 Tools and Techniques Applied to Manage Quality
6.2.2 Quality Checklist
c) Failure costs (internal/external): costs related to nonconformance of the products, deliverables, or services to the needs or expectations of the stakeholders.
Figure 28: Cost of Quality (PMI, 2017, pg.283)
109
b) Appraisal costs: costs related to evaluating, measuring, auditing, and testing the products, deliverables, or services of the project.
A quality checklist of a component or deliverable is a structured tool, specific to each component, which outlines a set of steps to be carried out to verify that the acceptance criteria described in the project scope statement are met (PMI, 2016, pg. 76) In Sydney metro project, each work package should have a specific checklist. Figure 29 is an example regarding the lift installation job. In addition, figure 30 shows a general quality management checklist to secure the overall quality management

110
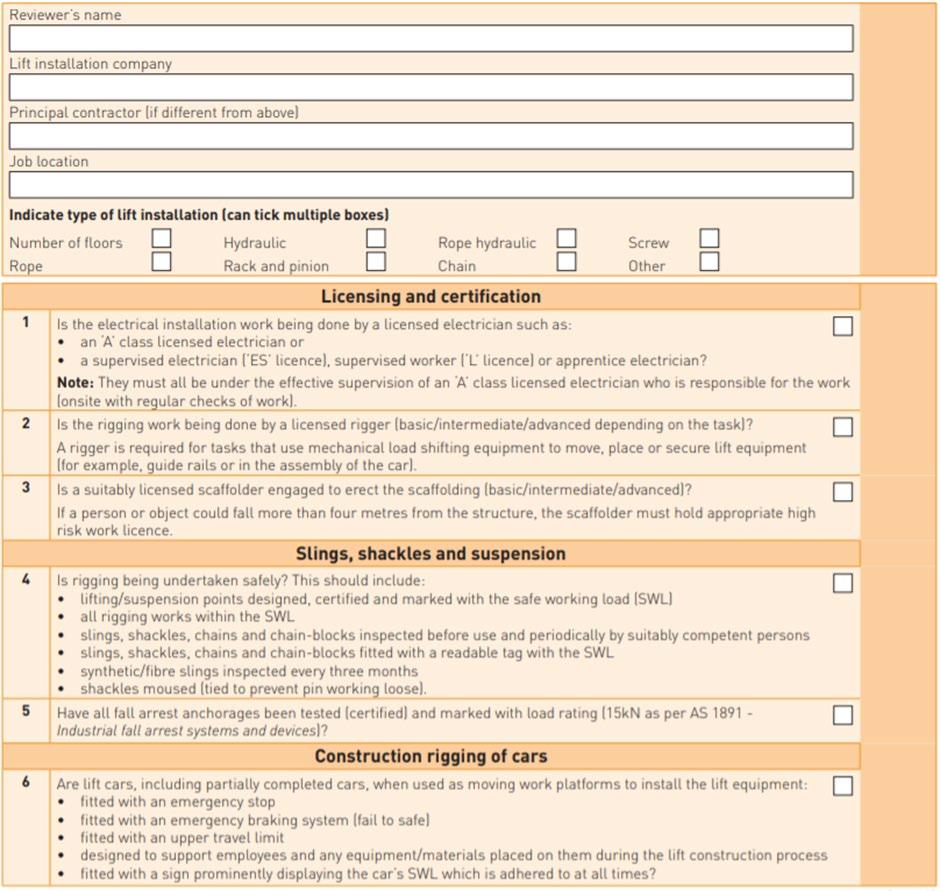
111 Figure 29: Lift Installation Onsite Checklist (WorkSafe Victoria, 2017)
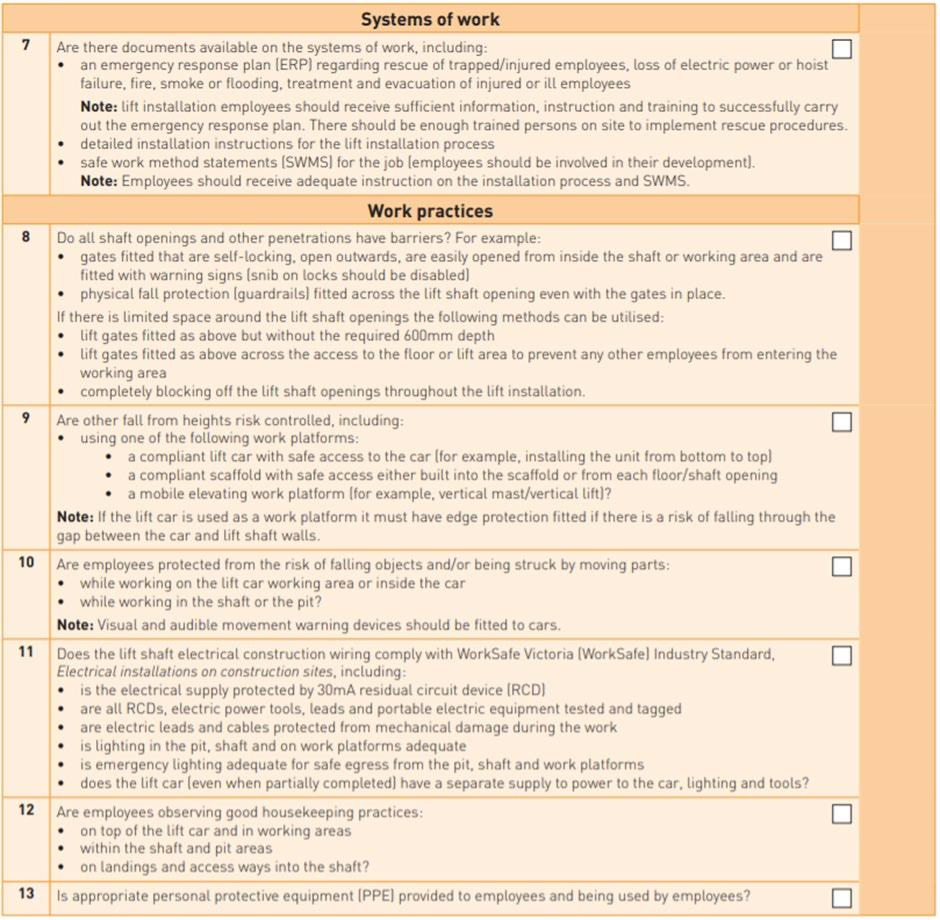
112 Figure 30: Checklist of Quality Management 6.2.3 Quality Metrics Quality metrics make the project quality performance measurable. Here below are some common metrics in construction projects that will also be used in Sydney metro project. Figure 31: Examples of Quality Metrics A quality metrics develops a detailed description about a project or product attribute and how Quality Metrics Formula First Pass Yield units which meet specifications without any rework or repair / total units Defects per Unit number of defects identified on all units / total number of units Rework Factortotal cost of rework / actual construction cost Material Wasteactual amount of materials waste / total amount of material used On-Time Delivery Rate numbers of on-time delivery/ total numbers of the delivery made Mean Time to Repair (MTTR) total downtime caused by defects / total number of defects Complaint Frequency number of complaints received in a certain period (etc. per month)
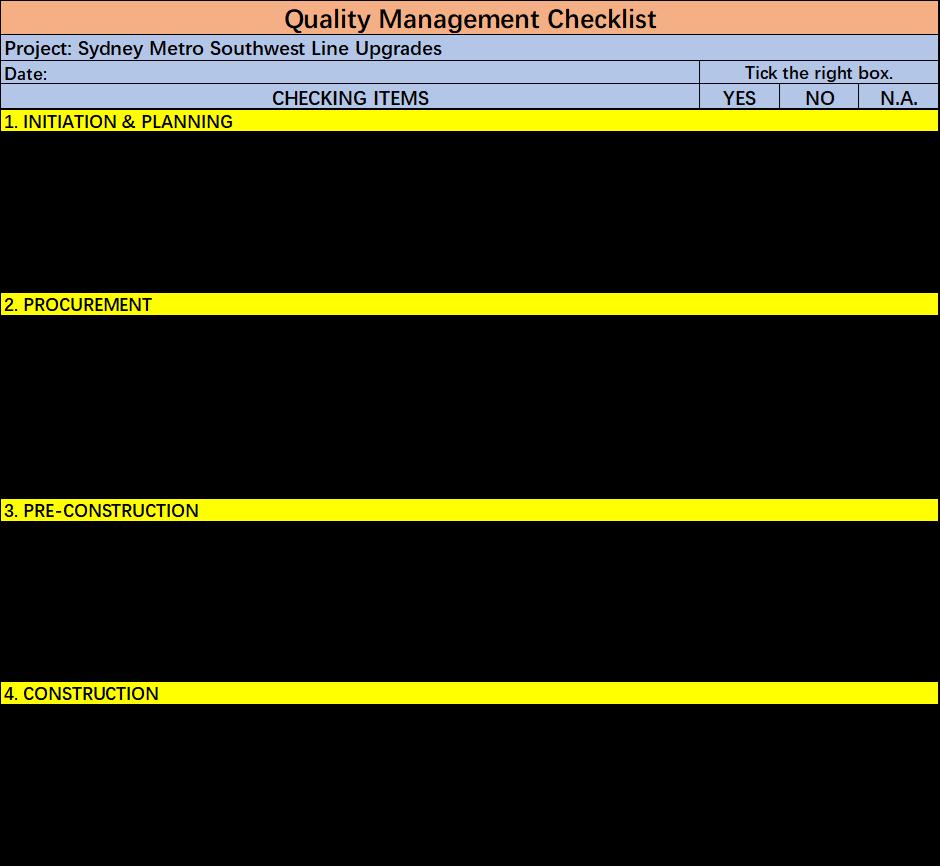
113 the Control Quality process tends to verify compliance to it. Percentage of tasks completed on time, cost performance measured by CPI, failure rate, number of defects identified per day and so forth all can act as quality metrics. In this section, a quality metrics template corresponding to a specific task activity is demonstrated below. QUALITY METRICS PROJECT DETAILS PROJECT No: xxxx FULLDATE:PROJECT NAME: Sydney Metro Project (Sydenham to Bankstown) PROJECT MANAGER: xxx PROJECT SPONSOR: xxx IDWBS Task name Item Method of Measurement Metrics samplingStatistical Reference 1.3.6 screenofInstalmentplatformdoor doorscreenPlatform Wind pressure load test and squeezing load (PAtestingcombinationandN/m) impactforcethe(mm)deformationDoorunderresultantofload 12.83mmisdeformationMaximum12.50mm 4284:2008AS/NZS 6.3 Quality Assurance Process Sydney Metro Southwest Line creates and documents an auditing mechanism to ensure that it is following the contract technical specification requirements. The auditing system will be utilised to determine whether or not the QA system is effective. Audits will be carried out by qualified and well trained employees who are familiar with the QA system, as well as auditing methods and methodologies. The objectivity and impartiality of the audit process will be ensured by the selection of auditors and the conduct of audits. The QA personnel designated are not permitted to act as independent auditors. The auditing system will encompass all actions that affect construction quality. The audit findings will be documented and communicated to the onsite supervisor. All non conformance problems discovered during the audit will be re audited to ensure that the appropriate organization's
114 corrective actions were effective. During the construction of this project, audits will be done on a regular basis. During the audit, the following significant systems, reports, information and records will be reviewed, accessed, or sighted (Table 9): Table 9: Audit Information (Sydney Metro, 2018) Systems Documentation/Information/Records Compliance Tracking for Preliminary 40% design. Planning Approvals Compliance Tracking Working. Engineering Assurance Register (Exported from Statutorydatabase).Planning Report. Condition reports (references the documents that address requirement for Station Design and Precinct Plans) Meeting key design drivers. Design Report Architectural. DDA Report (Disability Discrimination Act). Building Code of Australia (BCA) Report. Sustainability Report. Flood Management Addendum – Incorporating Sydney Water Requirements and Potential Design Options. Heritage IntegratedStrategy.Design Report. Internal planning and compliance reviews. Internal Comment register (Interdisciplinary Design ConsolidatedRegister). Comments Register. Environment and Sustainability Working Group minutes.
City of Sydney Meeting Attendance
115 Constructability Planning and Environmental Constraint. Planning Approvals Compliance Tracking. External stakeholders, independent reviews. Integrated Design Report (DRP Minutes and External Comments Register contained within appendices). External Comments Register - (in Integrated Design Report appendices).
Record.
A periodic inspection by the site supervisor/engineer is required to ensure that the construction is of high quality. The checks should primarily be carried out by filling out the attached proforma (Table 10) for each item at the following stages:
(1) Beginning of each new item of work. (2) Once a week (or sooner if the activity is being completed at a higher rate) for each relevant item. The in-charge Engineer may also elect to do the examination more frequently (3) In addition, supervisors/engineers should refer to the check lists throughout their daily or routine supervision/ inspection/ site visits to ensure strict adherence to quality control methods.
Table 10: Audit attendance register (Quality Assurance Log) 6.4 Quality Control 6.4.1 Quality Control Process
The standards for quality control of Sydney Metro Southwest are set out based on AS/NZS ISO 9001:2016 (Quality management systems - Requirements), which include determining the project-specific measures that would be implemented for this project to monitor quality specifications alongside the project scope objects. During the construction phase, the items to be inspected must be determined before assessing the conventional quality control procedures. Also, techniques must be implemented to identify and quantify any performance of a good or

116 service that does not satisfy the specific standard requirements. The quality planning and quality assurance process would be continuously reviewed and updated as necessary throughout the whole project lifecycle. This may involve the application of a third party quality audit. All quality requirements and milestones should be incorporated into a project quality register or matrix, which must be included in the project quality management plan. The project quality management plan must detail the definitions and instructions on the utilisation of FDRs, NCRs, CVNs, ORs, and Submittals on the Sydney Metro Project. Moreover, it would be specific for each work package and item within Level 3 of the WBS. Additional quality requirements may be further introduced into the project quality requirements upon client specification, specifically for highly complex areas of the stage or design.
The overall quality control process implemented in the Sydney Metro Southwest Project is illustrated in the below flowchart:
The below diagram shows where the Quality Control process sits in the Quality Assurance cycle (Hellgren, 2013): Figure 32: Quality Assurance Cycle Quality Control can be implemented in both products and services in the construction industry, while it is implemented by testing and inspecting during the manufacturing process of producing a product before the final product is released. In services, the installation is tested and inspected throughout the rough in and fit off phases before commissioning.
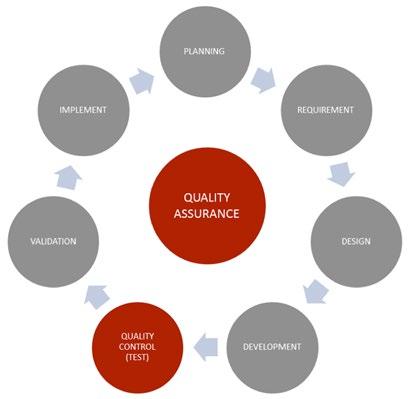
117 Figure 33: Sydney Metro Quality Control Flowchart Specifically, the six processes are listed as follows: ● 1. Project Start-Up Quality Control Meeting All Project Manager, Stakeholders, Quality Manager and project teams are required to attend the meeting to pre set standards and procedures for the follow up quality control process. ● 2. Continuous Quality Control Project Manager requires to ensure the regular quality process is carried out throughout the construction phase. ● 3. Make Necessary Updates and Adjustments Throughout the project life cycle, the Quality Manager and project team members can make necessary updates. ● 4. Quality Process Review Conduct regular quality process reviews throughout the project lifecycle. ● 5. Final Inspection and Checking Final inspection aims to confirm the completion of the construction and guarantee that all the works are consistent with drawings or specifications. ● 6. Quality Control Log Use a standard project quality control log to ensure the work conforms to drawings and specifications of the Sydney Metro project. 6.4.2 Control Quality Tools and Techniques: In Sydney Metro, there are 4 main tools that would be utilized in quality controlling, listed as follows: • Control Chart (Shewhart Chart):
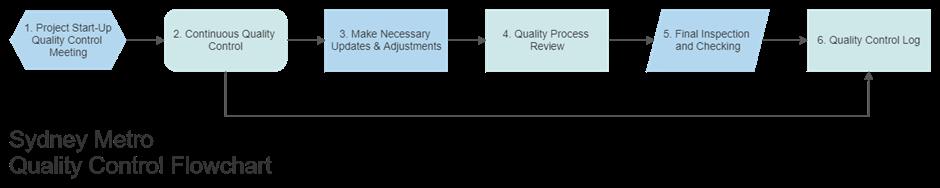
118
The Control Chart and Action Plan below can be used in conjunction in the Sydney Metro project to optimize processes, increase quality, and stop variation in its tracks.
Figure 34: Control Chart & Action Plan (Lucid Content Team, n.d.)
• Cause and Effect Diagram (also known as Ishikawa or Fishbone Diagram): It describes several potential causes of an effect or problem and organizes ideas into useful Forcategories.instance, the Ishikawa Diagram of categories and factors that cause schedule delays are shown below:
It's a statistical process control chart, which is one of several graphical tools typically used in quality control analysis to understand how a process changes over time.
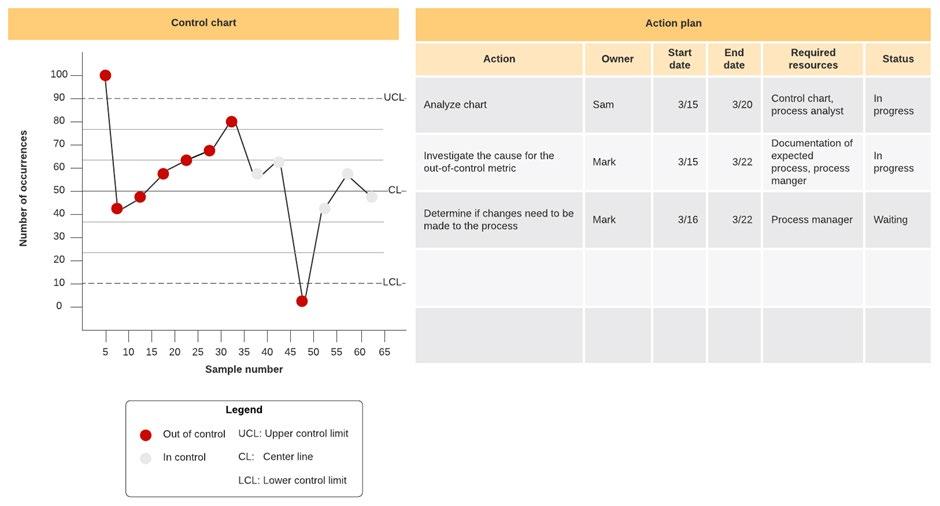
119 Figure 35: Ishikawa Diagram for Schedule Delay (Özdemir, 2010) • Check Sheets Form: It’s a method for data collection and analysis, organized and prepared; a generic tool that can be adapted for a wide range of purposes. The Check Sheets Form is shown below. #Ref Date DescriptionIssue Defect Type ActionsRectifications Status • Quality Control Log: It is used to research how over time a process shifts, by comparing current information with the previously acceptable limits. It provides answers to questions as to whether the variance of the mechanism is stable (in control) or variable (out of control, driven by unique causes of variation).
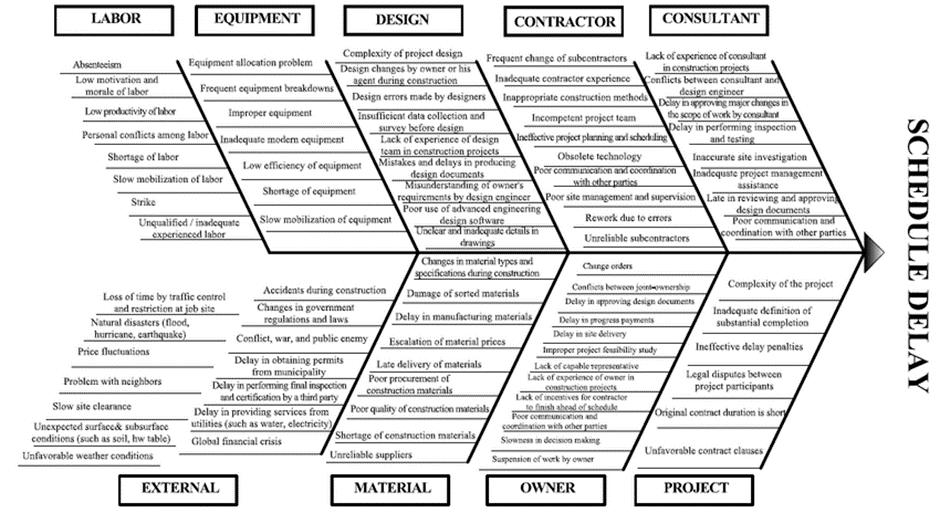
120 The Quality Control Log is shown below. #Ref Date Deliverable tRequiremen esMeasurActual Y/Nble?Accepta onmendatiRecom dResolveDate reSignatu
121 7.0 Project Resource Management Plan 7.1 Organizational Breakdown Structure (OBS) As can be seen in the figure 38, the Organizational Breakdown Structure displays departments involved in the Sydney Metro Southwest Line Project. It focusses on the head office members that directly work in the project. Figure 36: Organizational Breakdown Structure
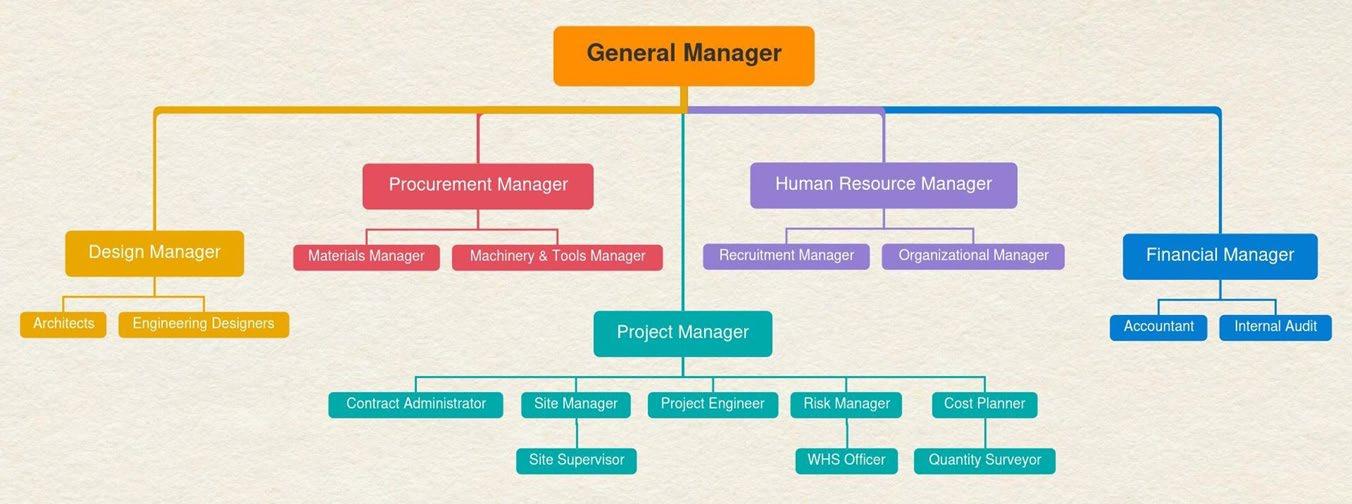
●
resources,project'sbindingprojectAtbudget,projectsprojectscontrolling,monitoring,andclosingtoensurethattheseareontime,onandwithinscope.thesametime,themanagermakesdecisionsontheproduct,schedule,andactivities. ● Leadership ● Communication ● Time management ● Problem solving ● Risk management ● Negotiation skills ● Technical skills officerFinancial ● Supervise and
●
122 7.2 Roles and Responsibilities (5 roles) Roles Responsibility Authority Skills ManagerProject ● Introduce the overall situation of project coordination and the specific management plan of the construction project tothe project sponsor. ● Assign the related activities of project management to the project sponsor to ensure that all objectives are met. ● In the project's entire life cycle, he is fully responsible for the successful launch, planning, design, execution, monitoring and control, and termination of the project. ● Fully responsible for the integration, communication and cooperation between project delivery team improvingmembers,effectivelythepossibility of project success. ● For the development of the project, formulate the project management plan and project cost plan in advance. ● Fully responsible for project development, maintenance and compliance with processes, procedures and standards.
●
● A qualificationaccountingformal ● Interpersonal skills ● Ability communicateto ● Financial reporting ● Analytical ability ● skillsProblem-solving ● Knowledge of digital tools ● Management
The project manager plays a leading role in planning, executing, company/projectmanagefinance. Work closely with the construction manager to ensure that the overall project cost is within budget. Before the start of the project, based on drawings and other documents, plus estimates of time, cost, materials and labour, an estimate of the overall project cost is proposed. Consult with engineers, architects, contractors and The Financial Officer is responsible for the planning, management,implementation,and operation of the company's financial activities. At the same time, it is necessary to track cash flow and update financial planning on time, analyze the company's financial advantages disadvantages,andand propose corrective measures.
●
●
123 subcontractors to change and adjust cost estimates. As the project develops, timely record, control, forecast and report all financial progress and matters, evaluate the cost effectiveness of products, projects or services, and formulate financial strategies. Mainly responsible for the daily on site operation of the construction project, managing on-site progress and all on site related issues. Try to solve the problems on the site to ensure that the project construction might be completed within the specified time and budget of the project. Check and prepare on site reports and regularly report the construction manager's progress via telephone and written reports. Responsible for managing the communication between all parties involved in the on site development of the project. Assist in the analysis and evaluation of project drawings andconduct safety inspections to ensure that the on site procedures meet the requirements. Find problems in project drawings in time and facilitate communication with architects. Participate in quality control management, emp The site manager is responsible for preparing the site before the construction, including arranging the site and organizing activities. At the same time, the site manager plans the overall budget and process arrangements for the project and ensures that they can be delivered on time. knowledge regulations.methodsbuildingand Manage all construction standard contracts to ensure the safety of contracts and proposals. Invite and process bids, prepare and prepare bid documentsand list of bidders. Prepare contract documents, manage the contract change
●
●
●
●
● skillscommunicationGood ● Problem solving skills ● Decision making ability ● awarenessCommercial ● Ability to motivate others ● skillsTeamworking ● Good
●
●
●
rAdministratoContract ●
experience ManagerSite ●
●
The contract administrator formulates, negotiates, and evaluates company contracts on behalf of the project organization. They are responsible for ensuring that both parties comply with the terms of the contract and that all Understand the legal contractrelatedrequirementstothe Pay attention to details and be able to spot errors
of
●
●
●
●
●
● Strong analytical and skillsorganizational ● Excellent reading
●
●
Architects create designs for new projects,constructionrenovation, and redevelopment. Use professional architectural knowledge and high level drawing skills to design a fully functional, safe, sustainable, and beautiful building. Design skills and knowledge. Knowledge of building construction.and To be thorough and pay attention to detail. Thinking and reasoning skills. Customer service skills. Excellent skills.communicationverbal ● Analyticalthinkingskills. The ability to use your initiative.
●
●
●
skillscomprehensionlanguage ●
contracts
● Ability executenegotiateeffectivelytoandcontracts ● skillscommunicationExcellent(oralandwritten)
●
●
124 procedure and analyze the potential risks the contract change may bring to the company. Report the status of contract execution and contract changesto the contract manager on time. Explain the contract terms to stakeholders to ensure the accuracy and appropriateness of the contract text and attachments and comply with legal and policy requirements. comply with local and federal laws. and Ability to work with teams at all levels of organizationthe
●
Architect ● Design and draft the project's construction plan and get confirmation from the customer and the construction staff. During the communicateconstructionprojectprocess,withthe project team regularly to solve project problems and provide new design solutions in time. Ensure that the design drawings and construction detail documents comply with quality control and can becompleted on time. Visit and review the construction site to ensure that the project meets local environmental and safety requirements. Assist the project manager to ensure that the specific work plan and timetable of the project proposal are feasible and that these standards can be maintained and correctly implemented at all stages of construction.
●
Project Management Institute (2013, p261) states that RACI, which represents the project resources assigned to each work package, is employed to illustrate the connections between work activities and project team members. When a project team consists of internal and external resources, this RACI matrix has an edge on ensuring clear assignment of roles and responsibilities.
125 7.3 RACI Matrix
● Consulted: The people who provide information for the project and with whom there is two way communication. This is usually several people, often subject matter experts.
● Responsible: The person who does the work to achieve the task. They have responsibility for getting the work done or decision made.
● Informed: The people kept informed of progress and with whom there is one way communication. These are people that are affected by the outcome of the tasks, so need to be kept up to date. A=Accountable C=Consulted I=Informed
The RACI matrix is created in this Resource Management Plan in a work package level, and this will go through some detailed unit work tasks associated with their higher-level working package.
In this Resource Management Plan, specific roles and responsibilities established are to support project human resource management process and control over the life cycle of the project.
R=Responsible
● Accountable: The person who is accountable for the correct and thorough completion of the task, which makes the final decision and has the ultimate ownership.
126 Role PackagesWork Project Manager Project irectorD Designer Procurement Manager Contract Administrator Quantity Surveyor Financial Manager OfficeLegal Construction Manager Project Engineer ManagerRisk ManagerSite Construction Services Engineer Facility Manager Foreman/ Supervisor WHSSite Manager 1.0 Project Initiation CollectionRequirements1.1 R A CI/ I/C I I I I I I/C I I C I I C Business1.2 DevelopmentCase R R C I I I R/C I I C C I C C I C DesignConceptual1.3 A I/A R I I I I IC/ I C I I C C I I Project1.4 CreationCharter R R C I/C I C/I I/C C I C I I C C I I Modify1.5 Project Charter and Get Approval R R/A /CI I/C I C/I I I I C/I I I I/C I I I
127 2.0 Project Planning Scope2.1 Planning R A C C/I I I/C I I I C I I C I I I/C DevelopmentSchedule2.2 R A C C I C/I I CI/ I C I I C I I I Budget2.3 Planning R R/A C I/C I R R I I C I I C I I I/C Risk2.4 PlanningQualityand R A C R I C/I I I I C R I C I I I Stakeholder2.5 PlanCommunicationand R R/A I C I I I I I I I I I I I C/I DesignPreliminary2.6 I A R C/I I I I I I C I I C I I C DesignEngineeringDetailed2.7 I A C I I I I I I R I I R I I C
128 SpecificationandRequirementsResource2.8 R A C R I I I I I C I I C I I C/I Purchasing2.9 Contractingand R A I R R I I CI/ I I I I I I I I 3.0 Construction WorksPreliminary3.1 A I C I I C/I I CI/ R C I R C I I R Site3.2 Preparation A I C I I C/I I I R C I R C R R C/I Demolition3.3 and Excavation A I C I I C/I I I R C I R C R R C/I Platform3.4 relevelling and Screen InstallationDoors A I C C/I I C/I I I R C I R C I R C/I
129 Construction3.5 of footings for new stairs and lift shafts A I C C/I I C/I I I R C I R C I R C/I NewConstruction3.6Lifts A I C C I C/I I I R C I R R I/C R C/I Installation3.7 of CommunicationMetroWayfinding,Signage,Control A I C C I C/I I I R C I R R I R C HVACofandRefurbishment3.8InstallationStationservices A I C I I C/I I I R C I R R/C I R C/I powerNetworkElectrical3.9andsupply A I C I I I I I R C I R R/C I R C/I
130 Railway3.10 Track Work A I C C/I I C/I I I R C I R C C R C Construction3.11 of South drainageandoverheadFacilityLinee.g.wiringtrack A I C I I C/I I I R C I R R/C C R C Bridge3.12 Work A I C I I C/I I I R C I R C I R C Landscaping)andWorks(PavingExternal3.13 A I C I I C/I I IC/ R C I R I I R C 4.0 Monitoring and Controlling ProgressMonitor4.1 and Schedule R A I I I C/I I I C/I C/I R R I I R I Monitor4.2 and Control Cost R A I C/I I R I/C I C/I C R C I I I C/I
131 Quality4.3 Control R A C R I C I IC/ R C I R I R R C Monitor4.4 and Control Risks R A I C I I I I C/I C R R I I R R ChangeIntegratedPerform4.5Control R A C C/I I C/I C/I IC/ I C I I C I I C 5.0 Project Closure Audit5.1 Inspectionand R A I I I C I C R C I R C I R C Testing5.2 Commissioningand R A I I I I I C R C I R C I I I DeliverablesHandover5.3 of Sydney Metro R A I I I I I I C I I I I I I I upandDemobilisation5.4SiteClean- R A C I I C I C R C I R C R R C
The methods of staffing acquisition in the Sydney Metro Sydenham to Bankstown are listed as follows: ● Pre Assessment: Choose suitable experts within the industry to form a specific human resources advisor team to conduct a consultation to determine the roles and positions required for the Sydney Metro Southwest project.
132
According to the Sydney Metro Sydenham to Bankstown Infrastructure Report (2018), the construction of this project will create thousands of job opportunities in surrounding areas. Moreover, the New South Wales Government has advocated and stipulated those residents of Southwestern Sydney and participants in related industries have priority employment opportunities. Therefore, the infrastructure project of Sydney Metro Sydenham to Bankstown can provide nearby employment opportunities for certain groups of people, thereby increasing the local employment rate.
7.4 Staff Acquisition and Release Plan
7.4.1 Staff Acquisition Plan
Acquire Project Team is the process of confirming human resource availability and obtaining the team necessary to complete project activities (Project Management Institute, 2013). For the Sydney Metro Southwest, numerous resources will be adopted for staffing management with the aim to deliver the project satisfying the budget, time and quality requirements. According to the various roles that are required to be recruited, construction firms will employ a range of different recruitment methods to hire employees for the Sydney Metro Sydenham to Bankstown. Staff acquisition will begin with the development of the project schedule and allocating resources based on that timeline. The construction project manager will determine the minimum qualifications, salary, working hours and other job responsibilities expected by diverse recruitment positions based on previous project experience and data analysis with the human resources manager. After they have communicated and reached a consensus, the project can issue a notice to commence recruiting. Where possible, project personnel will be first sourced from within the organization or from construction teams and subcontractors who had previously worked with. The reason for this is the familiarity and existing working relationships are beneficial for the project and the team as a whole.
133 ●
Internal Recruitment: It is the process of acquiring internal personnel for Sydney Metro Sydenham to Bankstown. The candidates for recruitment will be selected from other departments within the organization. Senior executives will first communicate with the human resources department, including preferred employees and compensation or bonuses after job modifications. Then, the HR manager would decide on suitable employees as job candidates and communicate and negotiate with them in detail. When they agree to transfer their positions and join the construction of Sydney Metro Southwest, they will be offered the jobs. Recruitment: This method will occur when no suitable candidate can be found through internal recruitment. The HR manager will then contact the external recruitment agency and provide recruitment conditions of the Sydney Metro project. Then the agency will assist in recruiting suitable workers according to the project requirements. However, external recruitment also has several unforeseeable uncertainties. Thus, the senior management team is expected to supervise the overall recruiting process for the Sydney Metro Southwest.
● Salary payments ● Dates and scheduling ● Roles and responsibilities ● Milestones and expectations ● Contract length durations
● External
When acquiring new personnel for Sydney Metro Southwest, the following factors will also be sought after and taken into consideration when adding personnel to the project team, a negotiation process will be undertaken between two parties, and the following aspects will be further addressed and confirmed:
seriously: ● Previous professional experience ● Personal characteristics ● Availability ● Interests In addition,
This negotiation process is extremely critical for Sydney Metro Sydenham to Bankstown in ensuring that recruitment and acquisition result in all parties on clear terms and can help further prevent disagreements between working relationships and disputes later in the project. According to Project Management Institute (2013), the key benefit of staff acquisition consists of outlining and guiding the team selection and responsibility assignment to obtain a successful team. The inputs, tools and techniques, and outputs of this process are depicted in Figure 37, while Figure 38 depicts the data flow diagram of the process.
Figure 37: Acquire Project Team: Inputs, Tools & Techniques, and Outputs Figure 38: Acquire Project Team Data Flow Diagram
134
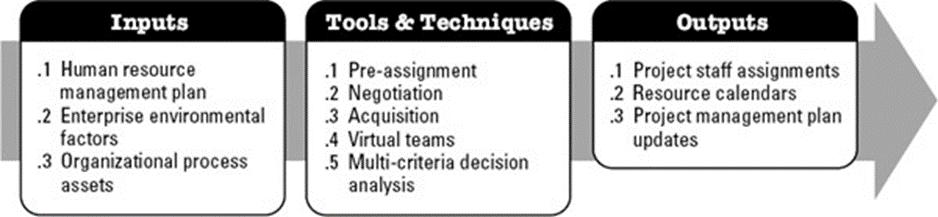
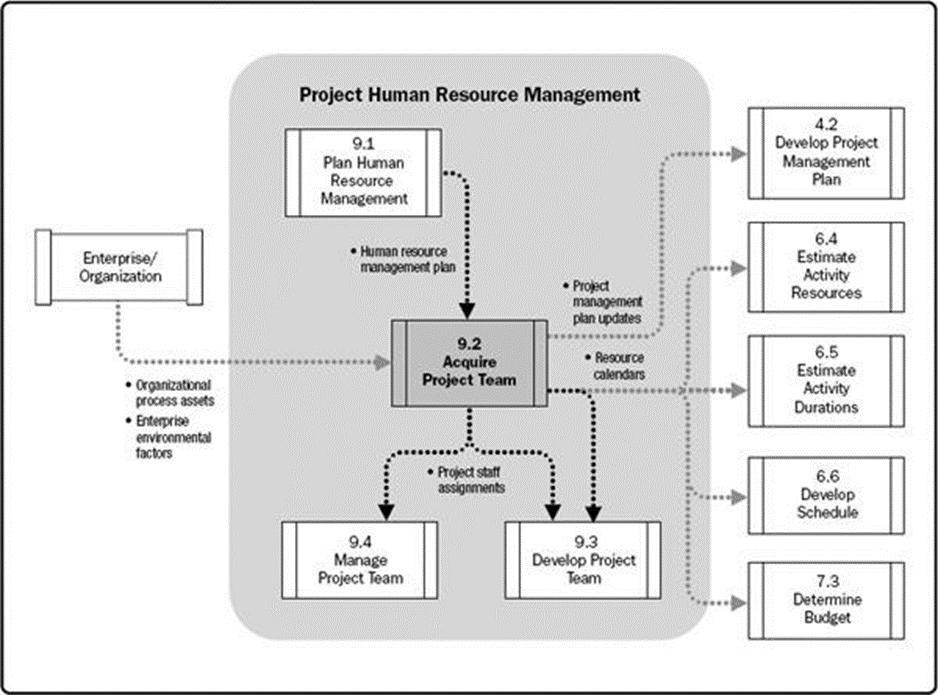
A resource calendar applied in this resource management is to identify the working days, the normal business hours when each resource is available. This human resource calendar comprises an important part of the staffing management plan documenting the information about human resources being potentially available during planned working activity periods, which is employed to estimate resource utilization. Human Resource Calendar
The proposed human resource calendar for Sydney Metro Project is illustrated below.
7.5 HR Resource Calendar and HR Resource Histogram
135 6.4.2 Staff Release Plan
In Sydney Metro Sydenham to Bankstown, it is equally necessary to release resources as it is to acquire them for the project, which enables cost and uncertainty reduction for employment activities in the future. In order to successfully achieve this objective in the project, certainty and rigidity in the agreements and contracts need to be signed by incoming construction personnel.
Given these facts, contracts will be firstly made with staff under the assumption of the project running on time, with personnel contracted for the period of time where their works would be carried out. Then, these contracts will feature agreements surrounding the change of dates of works, with extra room for contract extensions and appropriate pay considerations if these are to occur. Upon completion of their duties and contract, the staff will be finally released from the Sydney Metro project, with the potential for future employment on other future stages.
136
137
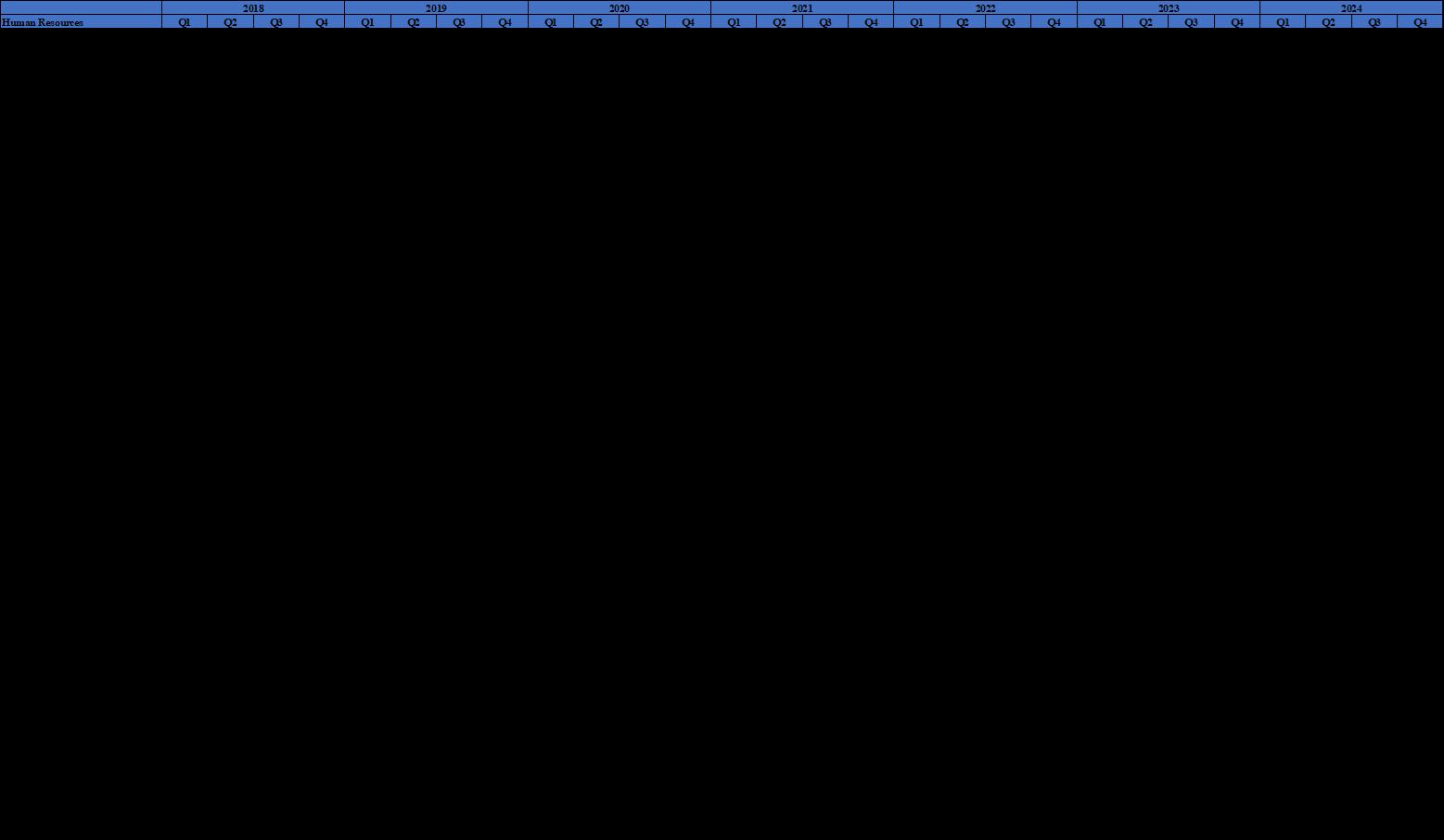
period
Histogram
cycle. The histogram generated by Excel
illustrated
Human Resource
HR resource histogram is created
This based on extracted from the resource calendar It displays that corresponding human resources are more likely to be available during that designated and how those HR resources distribute throughout the whole project life is below.
the information
138
139 Figure 39: Human Resource Histogram
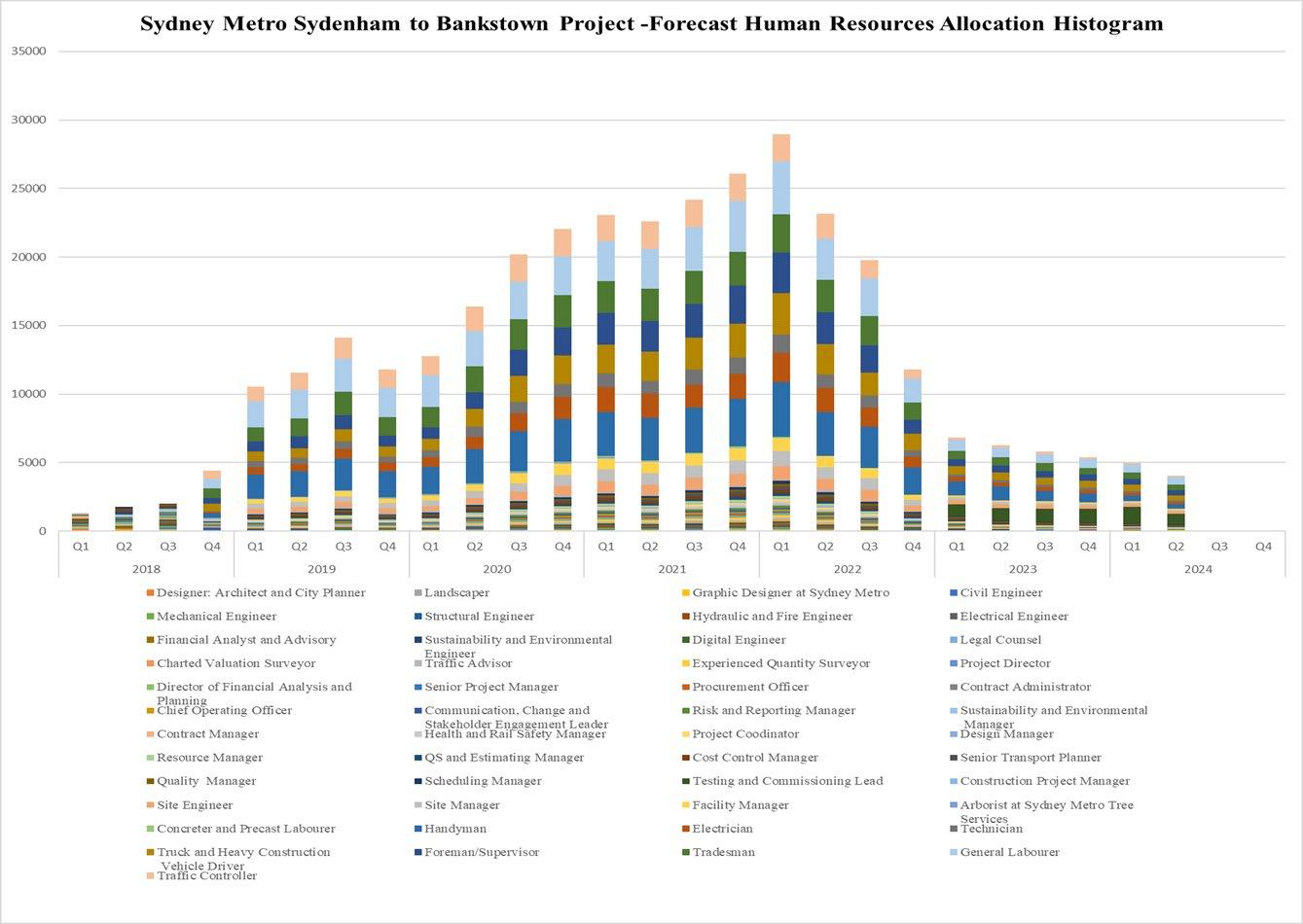
For projects located in the city center, the time for machines and equipment to and from the site (low noise) should be limited as follows:
➔
Monday to Friday: Between 7 am and 7 pm Saturday: Between 7 am and 5 pm ➔ Sundays and public holidays: Restrict all possible noisy construction activities
However, if the mechanical equipment is noisy, it should be restricted as follows: Monday to Friday: Between 8 am and 5 pm ➔ Saturday: Between 8 am and 1 pm
➔
At other times, other debris projects may be allowed, such as closing streets to erect towers. However, these construction plans need to be evaluated one by one, approved in writing, and subject to noise standards.
140 7.6
Machinery and Equipment Resource Histogram
➔
➔
When the project is located elsewhere in the local government area, the time for machines and equipment to and from the site (low noise) should be limited as follows: Monday to Friday: Between 7:30 am and 5:30 pm ➔ Saturday: Between 7:30 am and 3:30 pm ➔ Sundays and public holidays: Restrict all possible noisy construction activities
141 Figure 40: Machinery Histogram
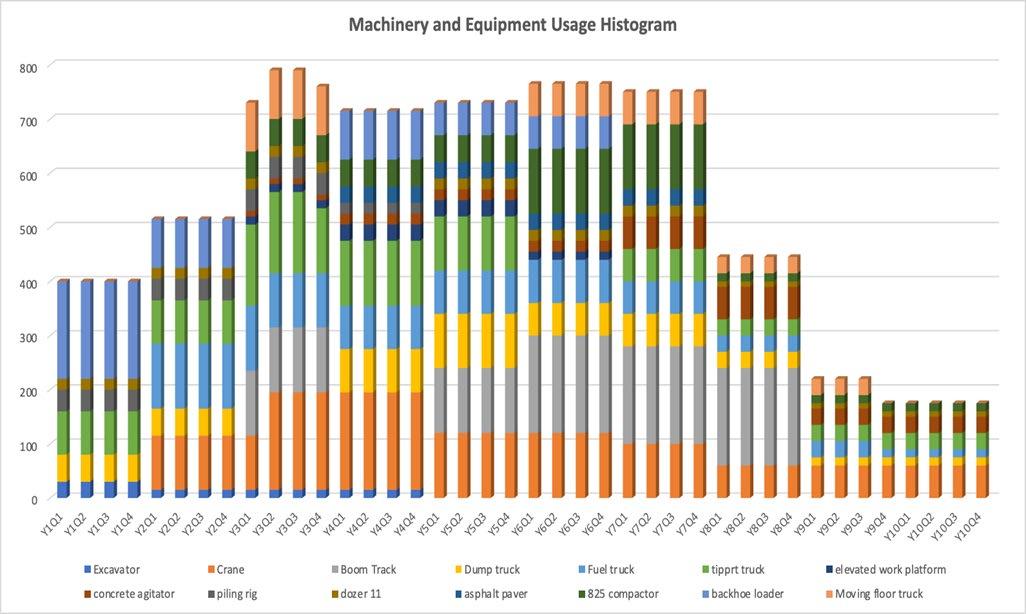
7.7.1.2
7.7.1.3
Any worker doing construction work in NSW must complete an approved construction safety awareness training course and obtain a "Construction Induction" (White) card, according to WorkCover NSW. All staff working at or visiting the Sydney Metro site must possess this card. Failure to do so may result in the person being requested to leave the construction site area immediately, and WorkCover NSW may take enforcement action.
The General Safety Induction Program for Sydney Metro is aimed to:
Start up Meetings & Site Inductions
All contractors, subcontractors, and their workers working on the Sydney Metro construction must attend a General Safety Induction training course. Sydney Metro facilitates this introduction, which must be completed every two years. The contractor will be unable to access the sites if the induction is not accomplished. The induction will conclude with an assessment. A passing grade of 85% is required to receive a Sydney Metro Contractor Safety Induction Card. This personal card is valid for two years and must be carried at all times while onsite.
The Contractor must attend a site induction that covers the following topics: ● Review and explanation of the Work Health and Safety Guidelines ● Specific site hazards and requirements. When site conditions have altered dramatically or when personnel status has changed, refresher site inductions will be required. The Sydney Metro Group Induction form should be used to keep track of these site inductions, and once completed, it should be forwarded to the Sydney Metro Responsible Officer.
Construction Induction General Construction Induction Training
Contractor Work Health & Safety Induction Program
142 7.7 Staff Induction and Training Plan, Performance Review, Staff Recognition and Rewards, Compliance, Equity and Safety 7.7.1 Staff Induction and Training Plan 7.7.1.1
Prior to the start of work, the Contractor's representatives and the Sydney Metro Responsible Officer shall undertake start up meetings to ensure that all parties are fully informed of the requirements and undertakings (Sydney Metro, 2018).
7.7.2 Performance Review
● At the first 30, 60 and 90 days of a new employee's tenure, provide a "mini version" of the Performance Review.
● Provide a “mini version” of the Performance Review at the first 30, 60 and 90 days of a new employee’s tenure. This evaluation may not be as thorough as an annual review, but it informs a new employee about their accomplishments early on and prepares them for what will become an annual event.
● Include a discussion of expectations for performance and behaviour. If the employee has deviated from what is expected or from his or her own previous positive "standards," the leader should make this effort extremely evident.
● Provide a complete, precise and consistent safety message to all contractors, sub contractors and their employees.
● Ensure that all staff members, customers and visitors are secured and kept away from various hazards.
Facts, actual and credible examples, and first hand observations are all important to bring together at the Performance Review (Humphrey, 2019). The following aspects need to be noted in executing the Performance Review:
● Make a few good observations as well as some remarks regarding areas that need to be addressed.
● Encourage the employee to ask questions about any concerns or any need for clarification. Encourage open discussion of those areas that the employee might feel differently than what was noted on the Performance Review.
● Hold the Performance Review in private to allow and reinforce privacy, as well as to create a comfortable environment.
143 ● Ensure that all contractors, sub contractors and their employees undertaking work recognize specific safety requirements and are able to work safely on all sites.
The Performance Review should, at the minimum, include the following areas:
(Technical skills; task related skills and knowledge; behaviour with co workers, leaders, clients and vendors; problem solving skills; attitude and willingness to grow; attendance history and adherence to corporate standards.)
7.7.3 Staff Recognition and Rewards Rewards are awards granted to employees on the basis of tasks performed, which meet or surpass the project's initial goals (Nani & Apraku, 2016).
● The employee's future effort, which is linked to all the above, must be addressed. Setting improvement goals and devising an action plan to achieve them are both part of this process.
● Include a succinct but clear action plan that further drives goal achievement. This endeavour should specify the activity that the employee will take, the leadership support that will be provided, and the resources that will be required.
● Observed "negatives" or "improvement opportunities" that must be addressed, fixed, and improved.
● The employee should be given the opportunity to "self assess." While the same Performance Review document that the leader uses can be supplied to the employee, it does not have to be the exact same document.
144
● Involve the employee in a proactive goal setting endeavour. Goals might be technical, attitudinal, or behavioural in nature, but they must be developed individually for each employee.
● Past performance and productive positives from the previous Performance Review should be highlighted so that both the employee and the senior leader can identify how far the worker has progressed.
● Specific aspects of the employee's performance that will be evaluated and examined.
PromotionPromotionisthe
Fringe benefits
7.7.3.3
145
Basic pay Basic pay (often referred to as basic salary) is practiced in rewarding performance. It is the most generally recognized and motivating reward for completing a construction task. Sydney Metro is working to create and strengthen a good basic wage system.
7.7.3.1
term used to describe a move within an organisation to a position with more responsibility and, presumably, prominence. Employee behaviour is influenced by promotion opportunities, which encourages employees to develop higher talents to progress (Prasad, 2001).
7.7.3.2
Increased basic pay, monitory allowances and other financial benefits are generally connected with higher positions. 7.7.3.4
A fringe benefit is a set of different rewards provided by a business to influence employee performance that are tax free if certain requirements are met. Health insurance, life insurance, education reimbursement, childcare, and personal use of a company owned vehicle are examples of fringe benefits (Booth and Frank, 1999). Despite the fact that these are not considered additional money paid to the employee, the employee's expenses have been decreased.
7.7.3.5
Verbal Praise
Compliance and Equity Sydney Metro Sydenham to Bankstown is dedicated to fostering a diverse and inclusive workforce, as well as enhancing employment outcomes, retention rates, development opportunities, and career advancement for all employees. The project aims to increase the number of women in leadership positions as well as the participation of Aboriginal and Torres Strait Islander people in the workforce.
Verbal praise is a means of showing admiration or approval for someone. Every employee enjoys receiving some verbal appreciation from their superiors in front of their coworkers. This reward system is intertwined with the concept of recognition. It confirms that the employee is performing a good job and is valued as an asset to the team.
Sydney
146
focuses on the following topics: ● Women in leadership positions ● Aboriginal involvement ● LGBTI (lesbian, gay, bisexual, transgender, and intersex) inclusion ● Workplace flexibility ● Disability inclusion
Sydney Metro aspires to create a workforce structure that reflects the variety of the NSW population. A diverse workforce can benefit the organisation by bringing a wide range of talents experiences to the table, which can lead to innovations. The diversity of Sydney Metro's personnel is reported in compliance with the reporting requirements of the NSW Public Service Commission. Metro introduced the 'we.SydneyMetro' programme from 2018, which aims to eliminate conscious and unconscious prejudices in the workplace by giving practical tools and support systems, as well as creating more inclusive teams. The programme
and
147 8.0 Project Risk Management Plan 8.1 Plan Risk Management 8.1.1 Methodologies
The risk is an inevitable topic in any project. There are numerous tools, techniques and methods to deal with them, while it is important to figure out the right ones to maximize the efficiency and effectiveness of the risk management of Sydney Metro Project. For example, to make a complete list of all main risks involved in different project stages, checklists summarized from similar projects which also involves upgrading the train system to the metro system are referenced. Besides, tools such as Failure Mode and Effect Analysis, Fault Tree Analysis, and Probability and Consequence Analysis, are utilized to further analyze and evaluate risks. When allocating contingency on risks, Three Point Estimate coupled with Monte Carlo Simulation is chosen to assist decisions. Please note that the budget for foreseeable risks is included in the cost baseline as the contingency reserve, while the management reserve is for the unforeseeable events – which are not considered as ‘risks’ in the context of the Sydney Metro project. Even though there are always some differences in methodologies for the risk management from project to project, the basic risk management process is extracted from the standard in the industry named ISO 31000: Risk Management Guidelines (2018). Although depicted as sequential in figure 41, the actual procedure will be carried out in a systematic and iterative manner. RMP's goal is to give suggestions to all stakeholders for establishing and implementing a thorough risk management strategy. It will integrate stakeholder perspectives, specialist expertise, historical data and additional investigation. Because risk transfer or avoid chances are limited during the construction process, it is advantageous to decrease the severity of as many risks as feasible. Potential hazards will be properly identified, analysed, and assessed, allowing for the prompt implementation of appropriate risk mitigation strategies. And these risks are conveyed and consulted concurrently, as well as continuously monitored and examined on a regular basis. Finally, assigning the contingency reserve to cost and schedule in order to manage the risk's probable pessimistic consequences when risk treatment is not feasible and the residual risk remains unacceptable.
148 Figure 41: Risk Management Process (ISO 31000, 2018) 8.1.2 Roles and Responsibilities
Risk Manager: Develop a general risk management process for the organization; Establish the level of risk the company are willing to take and figure out the proper contingency level; plan and distribute the risk budget; conduct policy and compliance audits; develop response measures; compile risk reports.
Project Manager: Authorize the implementation of risk response plans; assist the risk manager by coordinating team members to take corresponding actions for risks; make decisions on the priority of risks; review risk reports.
Risk Analyst: Perform risk analysis and evaluation through qualitative and quantitative methods; analyze root causes of risks to assist the development of response measures.
Design Manager: Minimize design risks, ensure the structural stability and compliance of the design.
Site Foreman: Minimize risks caused by improper handling of materials or improper operation of equipment; identify and report potential safety hazards to site manager or project manager.
Site Engineer & Site Manager: Minimize construction risks on site, especially from the perspective of quality.
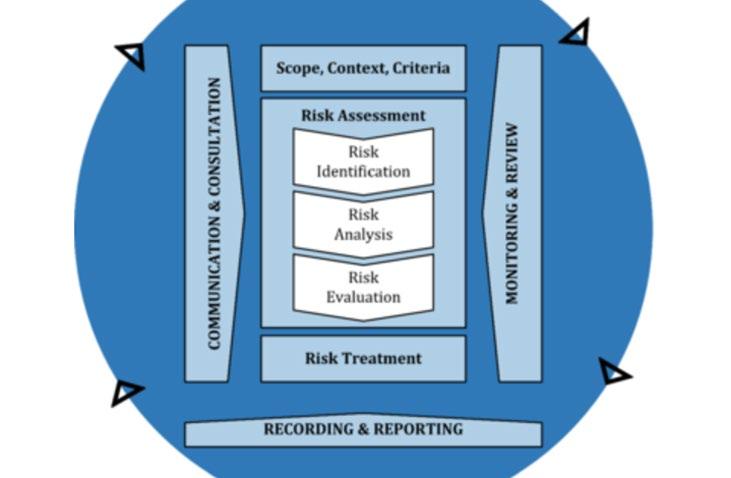
8.1.3 Risk Management Budget and Timing
In fact, the risk management is carried on throughout the entire project life cycle. However, the frequency of different departments or management roles of reviewing risks and taking responsive actions can be different. Please refer to the risk monitoring and controlling section and future documents for more information.
According to previous cost management section, a total budget of 382.8 million is assigned for the risk management, which accounts for 15% of the cost baseline. It is a ratio higher than the average construction contingency (5 10%) because the Sydney Metro is an extremely large scale infrastructure project which will last for many years. And a large share of the total risk budget is expected to be allocated to work packages in the planning and the construction phases as they are the stages in which most risks happen. In the section of Quantitative Risk Analysis, the method used for determining the contingency for each risk will be discussed in detail.
Contract Administrator & Procurement Manager: Manage contractual risks and procurement risks; ensure smooth cooperation with suppliers and subcontractors.
149 WHS Manager: manage site inspections; organize WHS trainings; hold regular safety meetings.
A sample Failure Mode and Effect Analysis form for identifying risk applied in Sydney Metro project is shown below:
8.2.1 Tools and Techniques Applied • Failure Mode and Effect Analysis (FMEA)
150 8.2 Risk Identification
Basically, risk identification entails a set of processes to ensure that the list of identified risks is comprehensive, and it is necessary to understand what source of the risk is before risk identification and that could be the root reason causing the risk. This RMP will conduct risk identification by going through a series of qualitative method such as Checklist, Failure Mode, Effect Analysis (FMEA), Ishikawa (fishbone method). In this process, risk manager, project manager and integrated project team are asked to identify project risks in their area of responsibility.
According to Juran (2018), Failure Mode, Effect Analysis gives insight into the reliability of systems by looking at the components and their comparative reliabilities. In this RMP of Sydney Metro, FEMA as a systematic method is to identify possible failures that pose the risk for a process, product, and service of different project work packages. As a tool, FEMA is one of the most effective low risk techniques for predicting risks and identifying the most cost effective solutions for preventing problems. Furthermore, the analysis is a bottom up approach, working from the components to the whole system, which assists manager to recognise and track risk items of each activity. It is important to document and assess all changes that occur which affect quality and reliability. There is a FEMA template applied for risk identification (shown in Appendix D)
151 System: Underground services of rail corridor Subsystem (Components): Underground electrical cable and drainage, sewer pipe Drawing No:1 FEMA No: 1 Rev No: 1 FAILURE MODES AND EFFECT ANALYSIS(FEMA) Sheet: One Of: One Prepared by: Site Engineer Date: 08/03/19 Reviewed by: Safety Supervisor Date: 08/03/19 Approved by: Safety Manager Date: 08/03/19 General Description Hazard Cause/Effect Corrective Action Description ModeFailure Cause of Failure Effect of Failure Subsystem/Systemon OccurrenceofProbability Severity Occurrenceof MeasureControllingPossible and Remarks Resolution drainagepipes,cables,Electricalsewer Contact cablepipedamageutilitiesundergroundwithandtheand andexcavationInappropriatedigging Pipe burst electrocutionfatalityelectricityhighLeakageundfloodsflowing,continuouswithandwaterthechannelerthecorridorofloworvoltagecausesby 0.04 Critical ▪ First engagementrefer and drawing as per site excavation plan ▪ Seek information about undergroundthe utilities and check for the same excavationbefore ▪ Use hand digging initially undergroundtill facility located if drawings not available Get fully investigationsite and avoid influence zone
Fault Tree Analysis (FTA)
The example for FTA applied on claim risk during construction is shown in figure 44. for claims individuals
Figure 42: FTA
•
and ent_of_Urban_Tunnel_Projectshttps://www.researchgate.net/publication/269337001_Risk_Identification_and_Fault_Tree_Developmorganisations
According to Olaga (2012, p 29), FTA is a technique aiming to identify and analyse the causes and the probable undesired event. The top event corresponds to a particular failure mode of the system and the fault tree provides a concise, orderly and graphical model displaying the various combinations of possible occurrences within the system, giving rise to a predetermined critical output event. This tool gives an edge in conducting root cause investigation after the recognition of any risk event, resembling the fishbone method.
152
of
• Checklist Checklists have been developed usually from experience, either as a result of a previous risk assessment or as a result of past failures. The checklist (shown in table 11) utilised in this RMP is developed by Sydney Metro railway construction engineers. They created this list depending upon the previous experience about the completed part of the whole Sydney Metro Project.
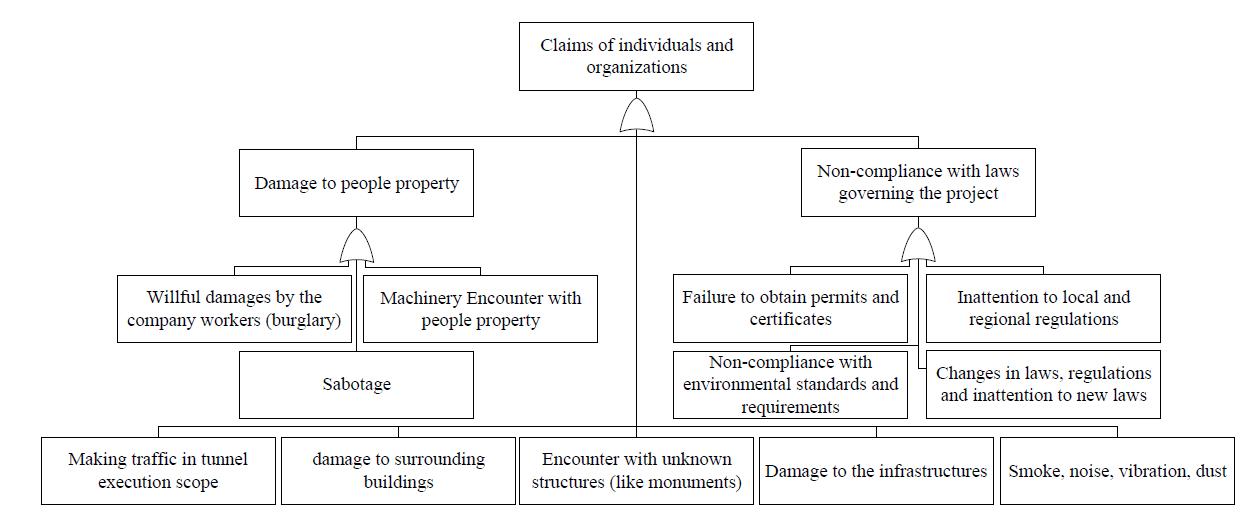
153 Table 11: Hazard identified list in Sydney Metro Project Thehttps://www.sydneymetro.info/article/southwest-metro-upgrade-updatewholechecklistwillbepresentedin Appendix E.
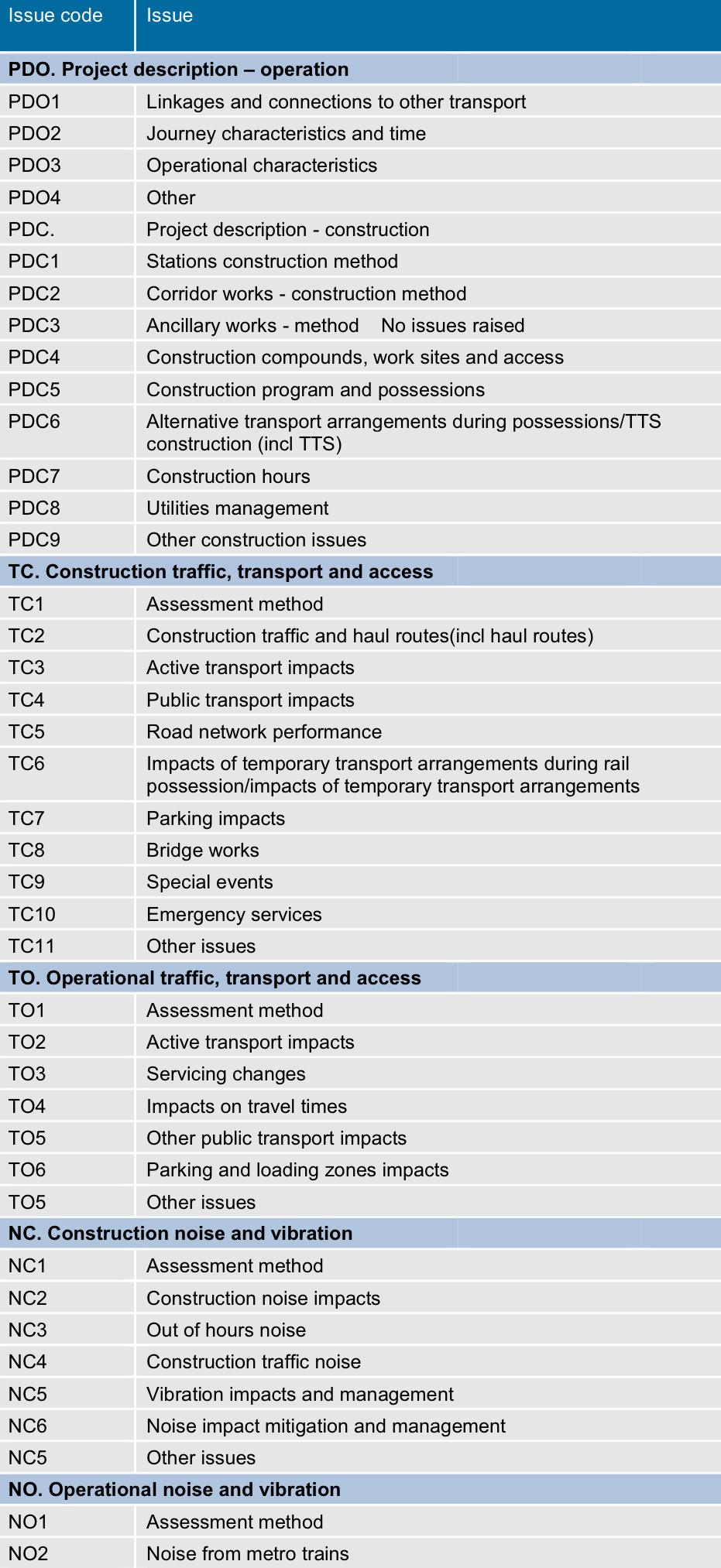
154 8.2.2 Risk Breakdown Structure Through the tools applied above, different types of identified risks in Sydney Metro Project can be divided into two main categories and 11 discrete groups according to the nature and areas of the project where might happen (table 12). A hierarchical breakdown of risk is provided by this RBS, which lower level 2 associated with detailed risk is structurally contained within the upper-risk level 1(table 13). This RBS will be updated regularly by risk management team as the construction proceeds progressively. Table 12: High Level Category of RBS External Risks Internal Risks Legal risks Project management risks Political risks Design risks Economic risks Human factor risks Environmental risks WHS risks Social risks Construction risks Contractual risks Table 13: RBS of Sydney Metro Project Sydenham to Bankstown RBS Level 0 RBS Level 1 RBS Level 2 Sydney ProjectBankstownSydenhamMetrotoRisks 1.0 Internal Risks 1.1 Project Management Risks 1.1.1 Unrealistic project plan and 1.1.2scheduleAdditional scope of works 1.1.3 Delay in providing design drawing and specification 1.1.4 Misunderstanding of drawings, specifications, and requirements 1.1.5 The variance between contract and actual quantities 1.1.6 Material not conforming to the 1.1.7specificationsInsufficient control over schedule and budget change
155 1.1.8 Poor supervision and design coordination 1.2 Design Risks 1.2.1 Defective design and design 1.2.2error Design drawings fail to be supplied on time 1.2.3 Inadequate investigation on site and soil condition 1.2.4 Design change 1.2.5 Heritage consideration 1.2.6 Station and track features 1.2.7 Ancillary facilities 1.3 Human Factor Risks 1.3.1 Poor communication and bad relationship among team members 1.3.2 Lack of technical labour 1.3.3 Lack of skill in workers 1.3.4 Low efficiency and 1.3.5productivityLabour cost increased 1.3.6 Low morale and poor human structure 1.4 WHS Risks 1.4.1Workers on site without PPE and not following safety procedures (lack of education for workers) 1.4.2 Car accident and getting injuries during vehicle manoeuvre 1.4.3 Working around electrical equipment and plant 1.4.4 Working with hazardous materials, tools and equipment 1.4.5 Fallen electrical wires and equipment
156 1.5 Construction Risks 1.5.1 Delay of supply of materials like rail tracks 1.5.2 Delay of equipment delivery 1.5.3 Excessive deformation and damage when interfacing existing built structures 1.5.4 Failure of equipment and tools 1.5.5 Insufficient supply or damage of 1.5.141.5.13routes1.5.12work1.5.11engineerlower1.5.10installationlaying,1.5.9management1.5.8servicesinfrastructure1.5.71.5.6resourceSiteaccessibilityDamagetotheexistinglikeundergroundPoorsiteorganisationandConstructiondefect(e.g.,railliftinstallationorscreendoorWeakimplementationandthecapacityofsupervisionConstructionpossessionandsiteaccessConstructiontrafficandhaulParkingimpactBridgeworks 1.6 Contractual Risks 1.6.1 Not achieve client 1.6.2requirementsMismanagement of contract and 1.6.3procurementMishapand extra cost involved in procurement
157 1.6.4 Poor communication with vendors, subcontractors and suppliers and conflict among 1.6.5stakeholdersDocumentation ambiguity 2.0 External Risks 2.1 Legal Risks 2.1.1 National Construction Code and standard change 2.1.2 Planning and constriction 2.1.3approvalsConstruction act and law 2.2 Political Risks 2.2.1 Change in the government 2.3 Economic Risks 2.3.1 Inflation 2.3.2 Fluctuation in exchange rate 2.3.3 Fluctuation in interest rate 2.3.4 Price change of personnel, materials, and equipment 2.3.5 Construction market condition 2.3.6 Tariffs added to importing goods 2.4 Environmental Risks 2.4.1 Inclement weather 2.4.2 Operating in flood prone area result in flooding impact on project 2.4.3infrastructurePollution complaint 2.4.4 Soil contamination 2.4.5 Vegetation damage and visual 2.4.5impactWater quality and air quality 2.5 Social Risks 2.5.1 Localised adverse airborne noise impact on human health 2.5.2 Vibration from surface works exceeding human comfort
158 2.5.3 Deterioration of traffic performance on surrounding road network due construction 2.5.4 Change to interchange arrangement at Sydenham to Bankstown line for customer commuting around Sydney Train 2.5.5servicesRestricted access to the facilities around station 2.5.6 Closure of the rail line between Sydenham and Bankstown for final conversion to metro, testing and 2.5.7commission.Impact to State Listed Heritage items and their values of conservation area during 2.5.8constructionOperation impact on community infrastructure 2.5.9 Community and amenity impacts
Likelihood and consequence matrix which is an estimating technique of qualitative risk analysis depends on a score for a range of probabilities and the different levels of impact. By doing this analysis, the likelihood table, consequence table, risk matrix will be established. Definition of Probability and Impact Probability When it comes to probability, there is no need to worry about specifying an exact value for the probability. The method is to enable the likelihood to fall within the bounds which divide the scale into five levels: Almost Certain (AC), Likely(L), Possible (P), Unlikely(U), Rare(R) and create likelihood table (table 14) Table 14: Likelihood table Score Rating
Description
159 8.3
Qualitative Risk Analysis
3
In this RMP, qualitative risk analysis will be employed when assess the identified risks initially
1
4
The analysis relies on the non numerical data to perform analysis and focuses on the impacts or consequences of each risk on the project objectives namely time, WHS and cost, etc
2
5 (Almost Certain) P(X)>90%(AC) The event is expected to occur in most situations during time of activity or the whole Sydney Metro Project(10 or more times per year) (Likely) 75%<P(X)<90%(L) This event has happened before and will probably occur occasionally again during time of activity or the whole Sydney Metro Project(1 to10 times per year) (Possible) 50%<P(X)<75%(P) The event is more likely to occur than not occur of activity or the whole Sydney Metro Project (once per year) (Unlikely) 25%<P(X)<50%(U) The event is less likely to occur than not occur of activity or the whole Sydney Metro Project (once every 1 to 10 years) (Rare) 10%<P(X)<25%(R) This event may only occur in exceptional situation and not expected to occur during time of Sydney Metro project (once every 10 to 100 years)
8.3.1
8.3.1.1
160 8.3.1.2 Consequence Table The impacts reflect consequences on certain project objectives. When it comes to impact scale, it is very project specific and depends on the project objectives. In this RMP, a consequence table based on four main project objectives: cost, time, WHS and Environmental & Social factor. The scale of impact will be classified into: Severe, Major, Moderate, Minor and Insignificant associated score ranging from 5 to 1 (table 15). Table 15: Consequence table Score Rating Objective Definition corresponding to Sydney Metro Project 5 Severe Cost Budget increase or unit production increase > e.g.,12% Rail track work and overhead wiring work cost increase>$90,000,000 or Total budget increase>$306,240,000 Schedule Slippage on project critical path and project schedule milestone fails to be met WHS Fatality in an accident of project construction e.g., Being electrocuted during corridor work SocialEnvironmental& ▪ Long term (6 to 12 months) and irreversible large scale environmental and social impact ▪ Extensive remediation required ▪ Severe disruptions or long term impact on stakeholders or customers 4 Major Cost Budget increase or unit production increase e.g.,<10%Rail track work and overhead wiring work cost increase>$75,000,000 or Total budget increase>$255,200,000 Schedule 3 4 month slippage on project critical path and associated high extra expense WHS Emergency medical services required to treat injury SocialEnvironmental& ▪ Medium term (between 3 to 6 months) and potentially irreversible impacts ▪ Considerable remediation required ▪ Major impact or disruption on stakeholders or customers 3 Moderate Cost Budget increase or unit production increase < 5%
161 e.g., Rail track work and overhead wiring work cost increase>$37,500,000 or Total budget increase>$127,60,000 Schedule 1 2 month slippage on project critical path and project is able to back on track WHS Injury results in person to receive medical treatment SocialEnvironmental& ▪ Medium term (between 1 to 3 months), reversible and well-contained impacts ▪ Minor remedial action required ▪ Moderate impact or disruption on stakeholders or customers 2 Minor Cost Budget increase or unit production increase < 1% e.g., Rail track work and overhead wiring work cost increase>$7,500,000 or Total budget increase>$25,520,000 Schedule < 1 month slippage and no impact on critical path WHS First aid required on site to treat injury SocialEnvironmental& ▪ Short term (less than 1 month), reversible or minor impacts that are within environmental regulatory limits and within site boundaries ▪ Minor or short-term impact on stakeholders or customers 1 Insignificant Cost Minimal financial impact which can be covered by daily operation cost Schedule Minimal impact on project schedule WHS No action needed SocialEnvironmental& ▪ No appreciable or noticeable changes to the environment ▪ Negligible impact to environment, stakeholders, or customers
By perform determine
162 8.3.2 Probability and Impact Matrix This is where combines the scale from likelihood table with the impact scale from consequence table to generate a matric to reflect the severity of the event, which is classified into Very High, High, Medium and Low. In this report, red colour represents very high level risks, orange colour represents high level risks, yellow represents medium level risks, and green represents the low-level risks. Likelihood Consequences Severe (5) Major (4) Moderate (3) Minor (2) (1)Insignificant Almost (AC)(5)Certain Very High Very High Very High High Medium Likely (L) (4) Very High Very High High Medium Medium Possible(P)(3) Very High High Medium Medium Low Unlikely(U)(2) High Medium Medium Low Low Rare(R)(1) Medium Medium Low Low Low
a deep analysis to
the value of contingency reserve (part of total contingency reserve as an example) by conducting quantitative risk analysis.
employing probability and impact matrix developed in qualitative analysis which provides a rapid and initial review of project risks, this Risk Management Report prioritises top 10 risks identified (Shown in table 16 below). After risks of Sydney Metro Project are identified and prioritised by qualitive risk analysis, this report will
163 Table 16: Risk Analysis Table Risk IDRBS Risk CategoryRisk Description Root Cause(s) ObjectiveProbability Consequence Risk Score(1-25)Rating (L*I) 1.2.1 Design Re-design leading to delaywork and cost incresase defective design and design error Time 3 4 1.4.5WHS Being electrocuted and bystruckequipment reslulting in fatality Fallen electrical wires and equipment due to unsafe storage and insufficientsitesafework WHS 3 5 1.4.4WHS A serious injury due to conductorelectricitylikematerialswithworkhazardousortoolsscaffolding,gases Lack siteinadequatehuamanknoledge,Untrainedofresource,supervision WHS 3 4 1.5.3Connstruction Excessive deformation damageand interfacingwhenexisting built structure Incompetent worker and insufficient site workengineering Cost 3 3 1.5.7Consstruction Damage to the existing orinfrastructureunderground utilities Inappropriate digging or dueexcavationtothe shortage of site information or bad drawing or investigation Cost 4 4 1.5.9Construction Construction defect occuring in rail laying,lift installation Inadequate knowledge of worker, material quality constructionproblem,tool issue Cost 3 5 1.6.1Contract Not achieve requirementsclient Inaccurate colllection of requirement Schedule/Cost2 4 2.4.4Environment Soil Contamination and damagevegetation Inaccurate initial andmeasuringbadsite investigation Cost 2 5 1.1.4Management Inaccurate early causeestimatewrong schedule, budget, work process and wrong procurement Misunderstanding of specificationsdrawings and requirements. communicationPoor Cost 2 5 2.3.4Economic Price change of equipmentmaterialspersonnel,and Unexpected change of conditionmarket Cost 2 5 Risk Identification Risk Analysis
The quantitative risk analysis provides a numerical and sophisticated estimate of the overall effect of risk on the objectives of the project. In this section of Risk Management Plan, the Three-Point Estimate Method will be utilised coupled with Monte Carlo Simulation (MCS) to quantify risk contingency reserve This will grant plan users a deeper understanding of how the total contingency reserve of $383m is determined.
Quantitative Risk Analysis
Assumption: All the cost and time values are set aligning with and referring to the Cost Management Plan of Sydney Metro Project. This will give a justification value assumption. Additionally, all the work package activities will approach to the normal distribution.
And there are two risk items extracted from the top 10 risk identification table as an example which act as variables for calculation and simulation to give an insight into the calculation procedure of the whole MCS (Appendix F).
The initial calculation of mean value and standard deviation of those risk before running MCS and their first simulation is shown in table 17.
164 8.4
8.4.2 Total Risk Contingency Reserve Estimation by MCS 8.4.2.1 Three-point Estimation Before conducting MCS, three point estimation will be used to generate expected value and standard deviation of those identified risk contingency cost. In this part of risk management plan, all risk item identified will be represented by the work package code.
8.4.1 Monte Carlo Simulation Introduction Douglas & Georage (2014) claim that Monte Carlo Simulation (MSC) is a tool that can be used to study the behaviour of systems that have probabilistic input and give probabilistic output data. MCS is particularly suitable when the stochastic problem is difficult to solve directly As for the cost contingency estimating of the Sydney Metro Southwest Project, this report will run this model for 10,000 iterations and each iteration will represent a scenario likely to happen in the real world. Therefore, harnessing this information makes it possible for the cost engineer or risk manager to decide the whole contingency reserve.
First Simulation
table
$2,439,987.00$3,000,000.00$3,876,903.0065%
$189,076.00$250,000.00$329,876.0078%
1.1.5 $120,000.00$150,000.00$200,000.0050%
1.2.4 $400,000.00$450,000.00$522,987.0075%
1.3.2 $7,000,000.00$7,500,000.00$8,000,000.0075% $5,625,000.00$166,666.671.28$5,838,333.33$5,479,364.47 1.3.3 $1,123,008.00$1,500,000.00$1,923,809.0045% $678,511.28$133,466.831.28$849,348.82$620,882.97 1.3.4 $990,808.00$1,000,000.00$2,103,020.0070%
1.1.3 $545,789.00$1,000,000.00$1,789,056.00 80%
1.2.3 $380,000.00$450,000.00$540,000.00 75%
1.1.1 $100,000.00$150,000.00 $210,000.0035% $53,083.33$18,333.331.28$76,550.00$67,548.93 1.1.2 $91,333.33$26,666.671.28$125,466.67$45,861.74 $844,646.00$207,211.171.28$1,109,876.29 $759,100.63 $228,000.0050% $77,602.83$20,794.331.28$104,219.58$87,613.06 $76,666.67$13,333.331.28$93,733.33$76,353.34 1.2.1 $139,333.33$20,000.001.28$164,933.33$110,131.55 1.2.2 $272,113.33$30,166.671.28$310,726.67$295,853.55 $340,000.00$26,666.671.28$374,133.33$317,857.58 $340,373.38$20,497.831.28$366,610.60$370,016.09 1.2.5 $197,463.76$23,466.671.28$227,501.09$212,200.12 1.2.6 $1,158,435.18 1.2.7 $294,748.13$16,500.001.28$315,868.13$280,778.26 1.2.8 $1,984,329.75$239,486.001.28$2,290,871.83$2,312,555.62 1.2.9 $234,587.00$300,000.00$367,356.0085% $255,275.26$22,128.171.28$283,599.31$221,562.28 1.2.10 $119,837.00$150,000.00$218,395.0023% $35,965.56$16,426.331.28$56,991.27$53,421.12 1.2.11 $67,983.00$75,000.00$84,321.0020% $15,076.80$2,723.001.28$18,562.24$13,926.89 1.2.12 $66,463.00$75,000.00$85,000.00 30% $22,573.15$3,089.501.28$26,527.71$20,965.54 1.3.1 $5,287,094.00$6,000,000.00$6,987,312.0085%$5,138,874.18$283,369.671.28$5,501,587.36$5,272,122.14 1.5.31.5.21.5.11.4.51.4.41.4.31.4.21.4.11.3.15$22,980,456.00$25,000,000.00$28,974,234.0055%$13,929,179.92$998,963.001.281.3.14$9,764,024.00$12,000,000.00$16,342,090.0069%$8,522,203.11$1,096,344.331.28$9,925,523.861.3.13$3,208,432.00$10,500,000.00$17,490,045.0070%$7,314,822.32$2,380,268.831.28$10,361,566.421.3.12$73,098,000.00$80,000,000.00$86,785,098.0065%$51,987,335.62$2,281,183.001.281.3.11$120,300,445.00$187,500,000.00$258,907,345.0065%$122,330,843.92$23,101,150.001.3.10$51,879,201.00$60,000,000.00$68,991,234.0065%$39,094,297.13$2,852,005.501.281.3.91.3.8$46,012,321.00$54,000,000.00$61,092,011.0080%$43,080,577.60$2,513,281.671.281.3.71.3.61.3.5$33,093,874.00$40,000,000.00$48,756,909.0058%$23,378,909.02$2,610,505.831.28$26,720,356.49$20,580,326.45$827,613.27$185,368.671.28$1,064,885.16$850,549.71$6,095,493.00$13,050,000.00$22,102,000.0085%$11,389,644.84$2,667,751.171.28$14,804,366.34$11,215,741.74$683,908.00$750,000.00$834,099.0045%$338,850.53$25,031.831.28$370,891.27$328,133.54$46,297,578.13$43,425,584.62$6,654,000.00$7,500,000.00$8,502,134.0070%$5,268,215.63$308,022.331.28$5,662,484.22$5,115,182.79$42,744,864.17$38,639,015.451.28$151,900,315.92$160,485,471.74$54,907,249.86$49,021,258.95$5,703,735.52$7,398,592.92$15,207,852.56$12,872,947.74$700,000.00$750,000.00$792,543.0040%$299,502.87$15,423.831.28$319,245.37$304,736.78$435,987.00$1,000,000.00$1,759,354.0065%$671,161.94$220,561.171.28$953,480.24$904,886.07$138,900.00$1,800,000.00$2,478,050.0080%$1,308,926.67$389,858.331.28$1,807,945.33$1,926,335.27$1,245,988.00$1,800,000.00$2,346,987.0024%$431,719.00$183,499.831.28$666,598.79$690,905.67$120,000.00$200,000.00$300,000.0020%$40,666.67$30,000.001.28$79,066.67$43,012.20$173,098.00$225,000.00$286,012.0059%$133,645.82$18,819.001.28$157,734.14$144,954.62$3,498,000.00$4,000,000.00$4,454,093.0086%$3,433,133.33$159,348.831.28$3,637,099.84$3,191,268.80$2,254,098.00$3,000,000.00$3,682,012.0049%$1,464,782.32$237,985.671.28$1,769,403.97$1,355,415.65
Table 17: Three
When the three-point estimate is achieved and required variables (expected value & standard deviation) are obtained, this probabilistic approach Monte Carlo Simulation will be conducted. Accordingly, this simulation will be conducted by using a computer generally. This report performs 10000 runs of MCS. 8.4.2.2 Real Simulation by Computer for Total Risk Contingency Estimation By applying Excel @ Risk 8, the performing of Monte Carlo Simulation for 10,000 realisations being set as the number of repeated simulation runs can be automatically achieved. Then the statistics table and the curve of probability distribution of the total risk contingency estimation of Sydney Metro Southwest project is obtained in table 18, figure 42 and 43, accordingly.
$200,000.00$250,000.00$320,000.0055%
Best case(a) Most Likely(m) Worst Case(b) P(x) Probability of contingencyrisk Expected =P(x)*(a+4m+b)/6Value SD=(b-a)/6 Z-ScoreCL-P90 CostCL-P90Value
165 point estimation calculation
$310,000.00$400,000.00$491,000.00 68%
$155,000.00$225,000.00$315,000.0040%
$987,475.00$1,500,000.00$2,239,876.00 75%$1,153,418.88$208,733.501.28$1,420,597.76
$410,876.00$450,000.00$509,876.0065%
1.1.4 $103,234.00$150,000.00
ItemContingencyRiskCode
166 The whole statistics table generated from this simulation is shown in table 18. Table 18: The output statistics data of MCS for 10,000 iterations The main outcome of simulation can be extracted from the whole table and is demonstrated in table 19. Table 19: Statistic outcome table Statistics Total cost contingency of two risk items chosen Mean $352,882,164.47 St.Dev $23,878,064.52 Min $255,118,727.42 Max $451,321,356.20 P(X<$352,854,396.57) 50% P(X<$383,553,402.58) 90%

Figure 43: Probability distribution of total risk contingency reserve
167
The probability distribution of total risk contingency estimation is shown below:
Figure 44: Cumulative probability curve of total contingency reserve
These two bell shape curves feature the possible total contingency values on the X axis and the level of confidence on the Y axis. The probability distribution presents the most probable value of the distribution by a confidence level of 90%, which is between $313.6 million and $391.91 million. By analysing these two diagrams and statistics table, it can be noted that with
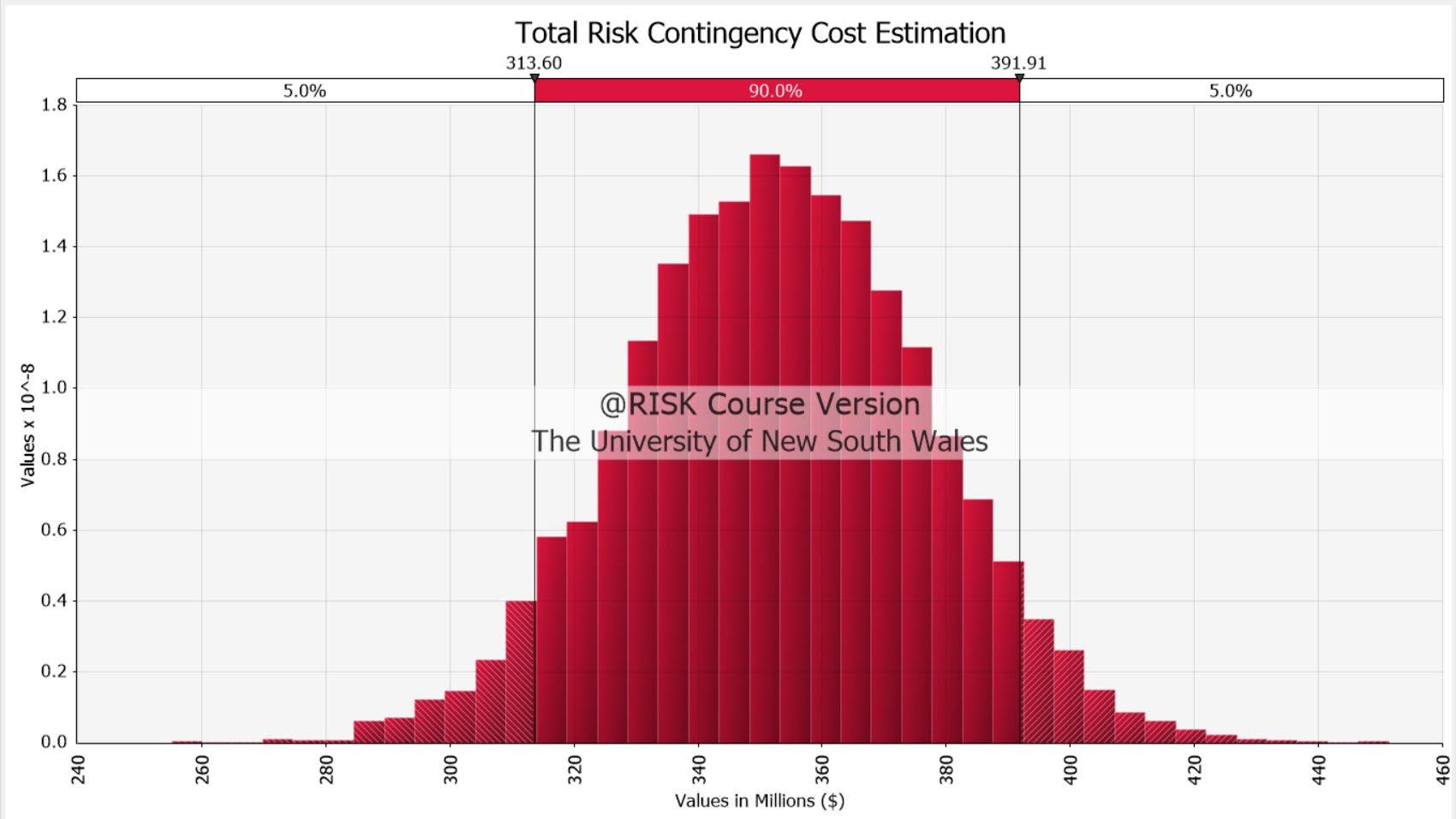
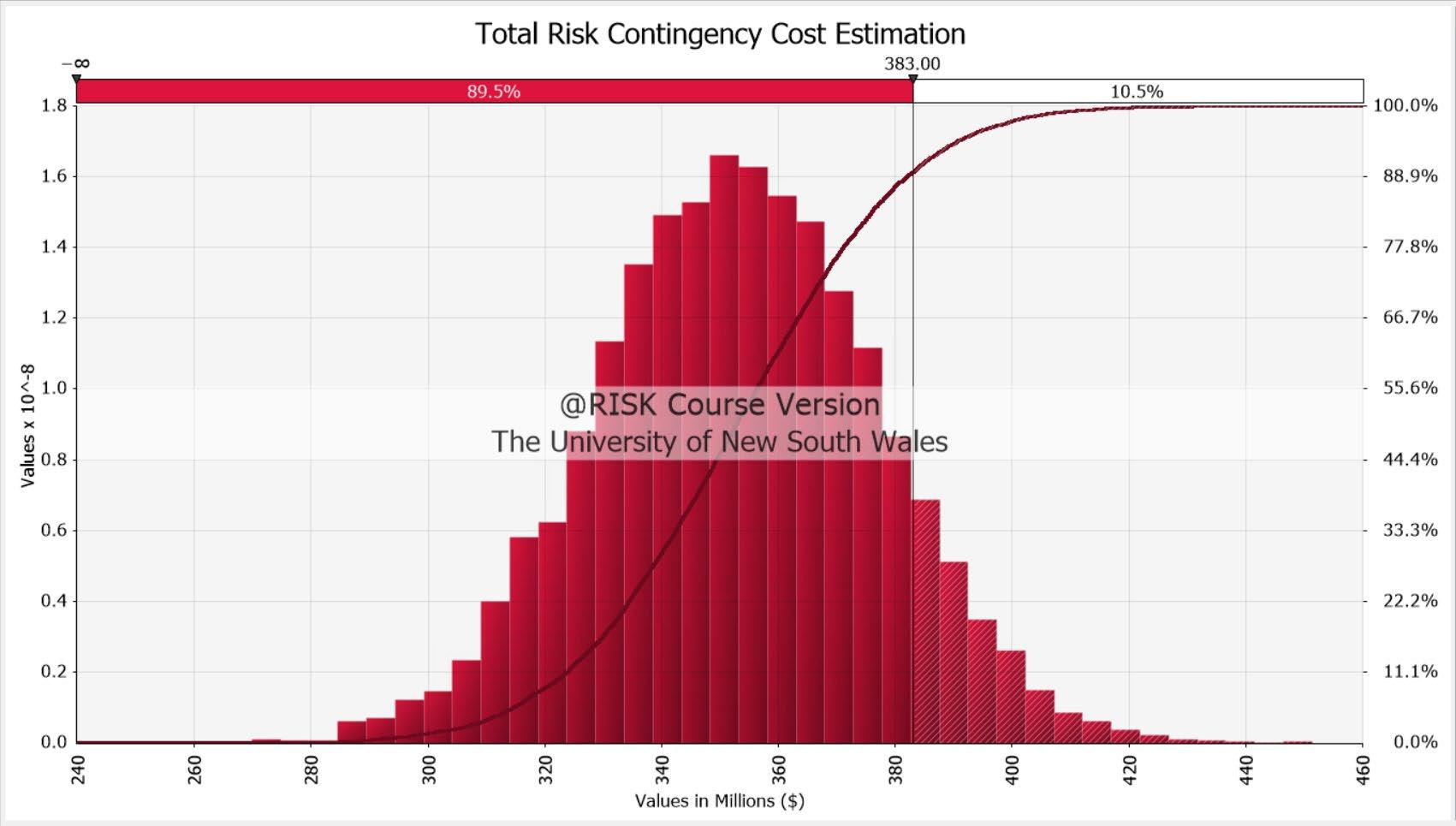
When 10,000 scenarios simulation for all risk contingency items of Sydney Metro Southwest Project runed, the result that reflects the probability distribution of contingency estimation and the degree of coverage corresponding to each value of allocated contingency enables the management team to get a deeper understanding of the aggregate effect of specific risks affecting the Sydney Metro Southwest Project.
Sensitivity Analysis
Figure 45: Risk contingency ranked by effect on total contingency cost This tornado graph illustrates the key driver in this model affecting the total risk contingency. It indicates that the work package 1.3.11 has the significant impact on total contingency reserve determination of Sydney Metro Southwest Project.
168 a confidence level of around 90%, the total contingency cost is equal to $383,553,402.58. This indicates that the total contingency cost amount of $383,553,402.58 covers the total obtained risk with the chance up to 90% and there will only be 10% chance to result in the total contingency cost more than $383,553,402.58.
Therefore, in this risk management plan, the total contingency reserve of $383 million is determined to cover the risk contingency generated from Sydney Metro Southwest project.

• Termination of the project if the risk is intolerable
A risk response/action plan is put in place when either the current controls are ineffective or require further improvements, or when no controls exist at all. However, having no controls is unlikely in such a large-scale government infrastructure context.
Transfer Strategy
This strategy is selected when a risk is identified as a critical risk with high impact to the project. The objective of the strategy is to shift all or some ownership of this risk to a third party who will then become responsible for the outcome of the risk. This may be used when the current team responsible for the risk lacks resources or tools to deal with the risk, thus transferring it to another party with a higher level of expertise in that specific area. Although transferring of risks shifts the responsibility to another party, the risk is not eliminated and still needs to be carefully monitored by the project management team in case new risks arise from it, e.g., the receiving party cannot handle the risk. This strategy is achieved by:
The risk response plan would comprise one or more actions that remedy identified issues or control weaknesses. When recording the treatment on the risk register, the description should detail who is doing what and what they are responsible for. This treatment plan may be generated from various business processes related to the Sydney Metro Project, including business plans, audit reports, action plans or simply in the risk register.
8.5.1 Risk Response Strategies
8.5 Risk Response Plan
169
• Changing the scope or design of the activity/work package in order to eliminate the risk occurring completely • Replacing the activity or action with a lower construction hazard impact
This strategy is adopted when a risk is identified as catastrophic or critical and would have a major impact on the overall project. The objective of the strategy is to completely eliminate the risk and its impact from ever affecting the project. It is best to try to find the threat early in order to put the avoid strategy into effect as early as possible. This strategy can be performed by:
Avoid Strategy:
170 • Contractually transferring the risk to a third party through subcontracting • Insurance, performance bonds and warranties
This strategy will be used when the impact and likelihood of the risk are inconsiderable, and the impact on the project is negligible. This strategy aims to identify risks and take no action before the risk occurs. This strategy is usually used when no other suitable strategy can alleviate or avoid the risk.
The strategy is realized in the following ways: Act early to reduce the likelihood Reduce complexity/use familiar solutions Allocate more resources and workforce to the identified risks
This strategy is recommended when the risk is identified as low to medium risk. It aims to reduce the possibility and consequences of the risk thus reduce the risk to an acceptable level.
•
•
•
• Choose more reliable subcontractors, suppliers, and distributors
• Reduce the complexity of tasks and work packages
• Prepare emergency reserves to deal with and manage risks
• Acknowledge the risk and prepare to act before the risk occurs
Mitigate Strategy
The specific risk response strategy is selected and adapted according to the overall level and priority in the risk matrix, as shown in figure below. Usually, higher-level risks would be avoided or transferred, whereas lower level risks would be mitigated or accepted. When choosing the most suitable risk response strategy for a hazard event, it is critical to not only consider the Probability and Impact of the risk occurring but also apply past project experience and professional expertise to decide.
The strategy usually includes:
• Absorb risks through daily operating costs, timetables, or manpower
Acceptance Strategy
By creating a risk level assessment for the risks that may occur in the project, risk response measures and strategies can be determined in advance to reduce the impact of risks on the project in actual operations.
3. Risks category. In most cases, the risk categories are divided into internal and external 4.causes.Potential risk owner. If a potential risk liability has been identified during the risk identification and analysis process, it should be recorded in the risk register.
The risk register accurately records risk identification, assessment, response, and monitoring.
When the risk identification process is completed, the content of the risk register may include:
2. Risk description. Describe and define each risk accurately and ensure that there is no ambiguity when using it. Structured risk description can describe in detail the characteristics of all aspects of the threat itself.
171 Severe Major Moderate Minor Insignificant CertainAlmost Avoid Avoid TransferMitigate/ MitigateTransfer/ Mitigate Likely MitigateAvoid/ MitigateAvoid/ MitigateTransfer/ Mitigate Mitigate Possible TransferMitigate/Avoid/ MitigateTransfer/ MitigateTransfer/ Mitigate Accept unlikely MitigateTransfer/ TransferMitigate/ Mitigate Accept Accept Rare Mitigate Mitigate Accept Accept Accept
5. Risk response checklist. Suppose the potential risk response measures can be analysed during the risk identification process. In that case, they will be recorded in the risk register, and this list can be used to determine the planned risk response process.
1. List of identified risks. In the risk register, each project risk is assigned a unique identification number.
8.5.2 Risk Register
172 Therefore, a risk register was established for Sydney Metro Sydenham to Bankstown Project to document the findings of the risk assessment process. The risk register contains details of impact pathways, their consequences, planned controls inherent in the Project Description, an initial risk assessment, additional treatment measures, and the revised risk assessment (residual risk). Sometimes it may be appropriate to record treatments in a separate plan or schedule cross referenced to the risk register Possible format contents for the risk register are outlined below. Risk Identification and Definition Unique Identifier Risk Name Originator Date ExplanationDefinition and amplification including assessment of existing controls and their effectiveness Risk Analysis and Evaluation Likelihood Consequences eg cost/ time/ function/ performance Overall Risk Level Priority Proximity when it might occur in the project Related Risks sharing sources and or consequences, treatment failure Disposition Reject/Accept/Treat Date Disposition Reject/Accept/Treat Date Treatment Risk Owner Budget Approach Reduce consequences/Avoid/Transferlikelihood/Reduce Effectiveness measure Likelihood of residual risk Consequences of residual risk Overall residual risk level Priority Work item reference Scheduled completion Eventuating Indicator Contingency Plan required/ reference
The risk register example of the Sydney Metro Southwest Project is attached in reviewed and updated risk assessment during the writing of their impact and as such the final risk register has changed to match the final impact
Appendix I. Technical specialists
their
173 Reviews and Monitoring Risk Owner Budget Approach Reduce consequences/Avoid/Transferlikelihood/Reduce Effectiveness measure Work item reference Scheduled completion Eventuating Indicator Contingency required/referencePlan Risk Status Post Implementation Review Risk Eventuated Consequences
assessments,
assessments.
174 8.5.3 Risk Action Plan with Expectations The Risk Action Plan provides a consistent structure that is applied across all Management Plans on the Sydney Metro Southwest Project. The expected high level outcomes achieved as part of Risk Treatment and Communication for managing this function on the Project has been illustrated in the following table. Expectations How will we meet the Expectation? requirements)(Minimum contributorKeyResponsible/ Deliverables Treatment options are recordedselectedassessed,andfor each risk in the Risk Register Treatment Options For each risk, options will be reviewed, and actions agreed on to reduce the risk or capitalise on the Treatmentsopportunity.will be recorded with the risk owner accountable for the action being implemented. The residual risk rating will be evaluated and recorded. Untreated risks will be escalated to the Project Director by the Risk Manager. Risk Owner ManagerRisk Risks Treatmentrecordedtreatmentshaveplans The treatments for high-risk work are based on ‘hard controls’ Hard Controls Hard controls will be used for high-risk work. Risk Owner Task Owner Hard controls
175 Treatment actions are implemented by the due date Implementation of treatments Actions documented in the treatment area of the Risk Register will be regularly reported and closed out by the due date. Untreated risks will be escalated to the Project Director by the Risk Manager. Risk Owner Task Owner ManagerRisk actionsTreatmentclose out by due dates Risks treatmentsand communicatedare to affected personnel and captured in the Risk Register Communication Risks and treatments are communicated to affected personnel through established communication mechanisms and captured in the Risk Register Risk Owner riskCommunicatedregister Treatments are monitored effectivenessfor Monitoring During the project, risk treatments will be monitored for effectiveness, reviewed and reported. Risk Owner reporteffectivenessTreatment Residual risks are transferred communicatedand to new risk owners Risk Transfer During the completion and handover stage, identify risks and include them in handover documentation. Any open residual risk needs to be transferred to the appropriate stakeholder. Risk ManagerCompletionsOwner documentationHandover
176 8.6 Risk Monitoring and Controlling To ensure that the process design, implementation and outputs are of the highest quality and effectiveness, monitoring and controlling are carried out throughout the Sydney Metro project life cycle. All activities in the risk management process should be evaluated and analysed on a regular basis. And these must be consistently documented and reported, which will improve relationships with stakeholders, particularly those in charge of risk management operations. The following risk reporting standards define roles and responsibilities, as well as reporting frequency (table 20). Table 20: Risk Reporting Standards Report Report by Report to Frequency Risk Report MembersExecutiveManager,Project Project Director Minimum monthly Risk Register ManagerProject RepresentativePrincipal Continuously updated as required Risk Assessment Report OwnersRisk Project MembersTeam Keep up with the latest danger register Risk Management Status Report (process, partakers and residual risks) ManagerRiskManager,Project CommitteeAssurance As continuouslyrequired, updated ‘Intolerable’ Risks (high severity level) emerge ManagerRisk Project Director Within 24 hours ‘Undesirable but tolerable’ level Risks (Medium severity level) emerge ManagerRisk Project Director Within 3 days 8.6.1. Tools and techniques 8.6.1.1. Risk audit Risk audits are conducted by project managers to assess the efficacy of risk responses and evaluate whether adjustments are required. The team not only assesses and documents the risk response's effectiveness in preventing, transferring, or minimizing risk. They also examine the
for
that
It is used for monitoring overall project cost and schedule performance against a baseline plan. There is more uncertainty and risk when the variations are increasing. Risk identification and analysis should be updated if there are significant deviations. risk events may occur as the project advances, having a positive or negative influence on cost or schedule contingency reserves. Reserve analysis compares available reserves to the level of risk that is still present at the time to evaluate whether reserves are enough. management processes, engage all team members and appropriate purpose these minutes include risks, decisions and action items.
8.6.1.4. Meetings • To facilitate the risk
stakeholders in meetings. • Distribute an agenda with a clearly stated
177 procedures for identifying, assessing, responding to, and controlling risks. Risk audits are performed during the whole project life cycle to control risk. 8.6.1.2. Variance and trend analysis
8.6.1.3. Reserve Evaluation Some
sessions. • Use the right tools and procedures. • Disseminate meeting
9.1
178 9.0
Project Procurement Management Plan Procurement Methodologies
Considering the complexity of Sydney Metro Southwest Line Upgrade Project, the job has been divided into many contract packages to ensure works can be done by the most capable and suitable entities. The delivery method and contract price type should be decided case by case, however, in most cases, Design & Construct contract will be adopted to ensure the consistency between the design and the engineering work. And Lump Sum pricing method is ideal to lower the risk of cost overrun. On the other hand, we can use incentivized target cost contract for those work packages with unclear scope. In addition, some procurement advisors or consulting companies with adequate experience in infrastructure industry and good reputation will be approached to perfect the processes, methods and evaluation criteria. It is worth noting that centralized contracting method is adopted since Sydney Metro CBD Line and Sydney Metro West Line are under development at the same time. It is more efficient to ask a procurement manager to manage the same type of resource in different projects in the same portfolio, which is also beneficial to the final integration of metro lines. Please refer to later sections and future documents for the finalization of procurement and pricing methods.
179 9.2 Procurement Process Diagram Figure 46: Procurement Process for Head Contractor
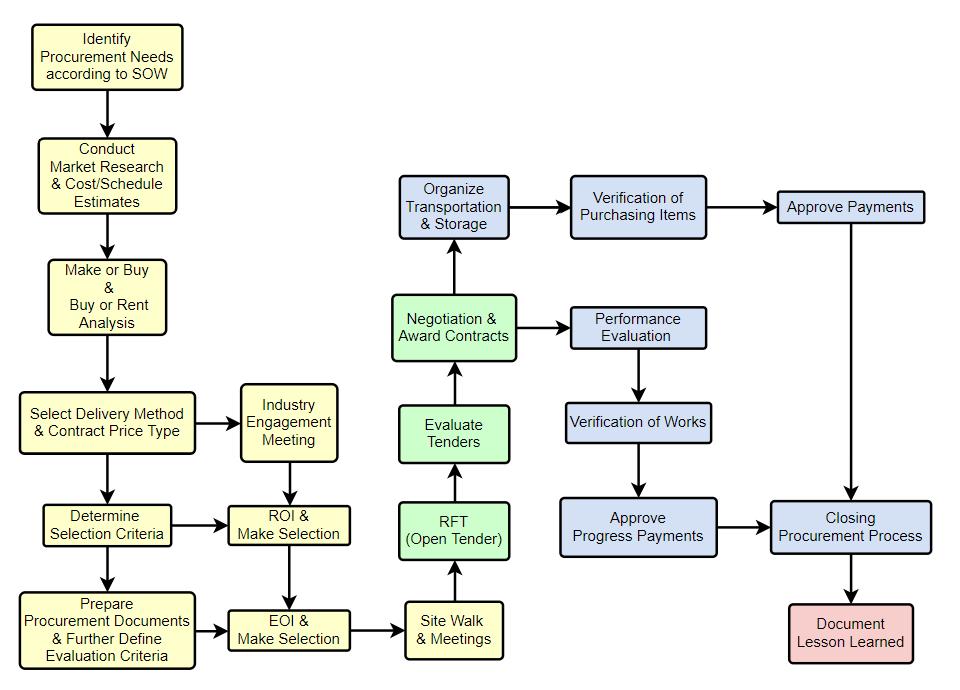
180 9.3 Procurement Information Table
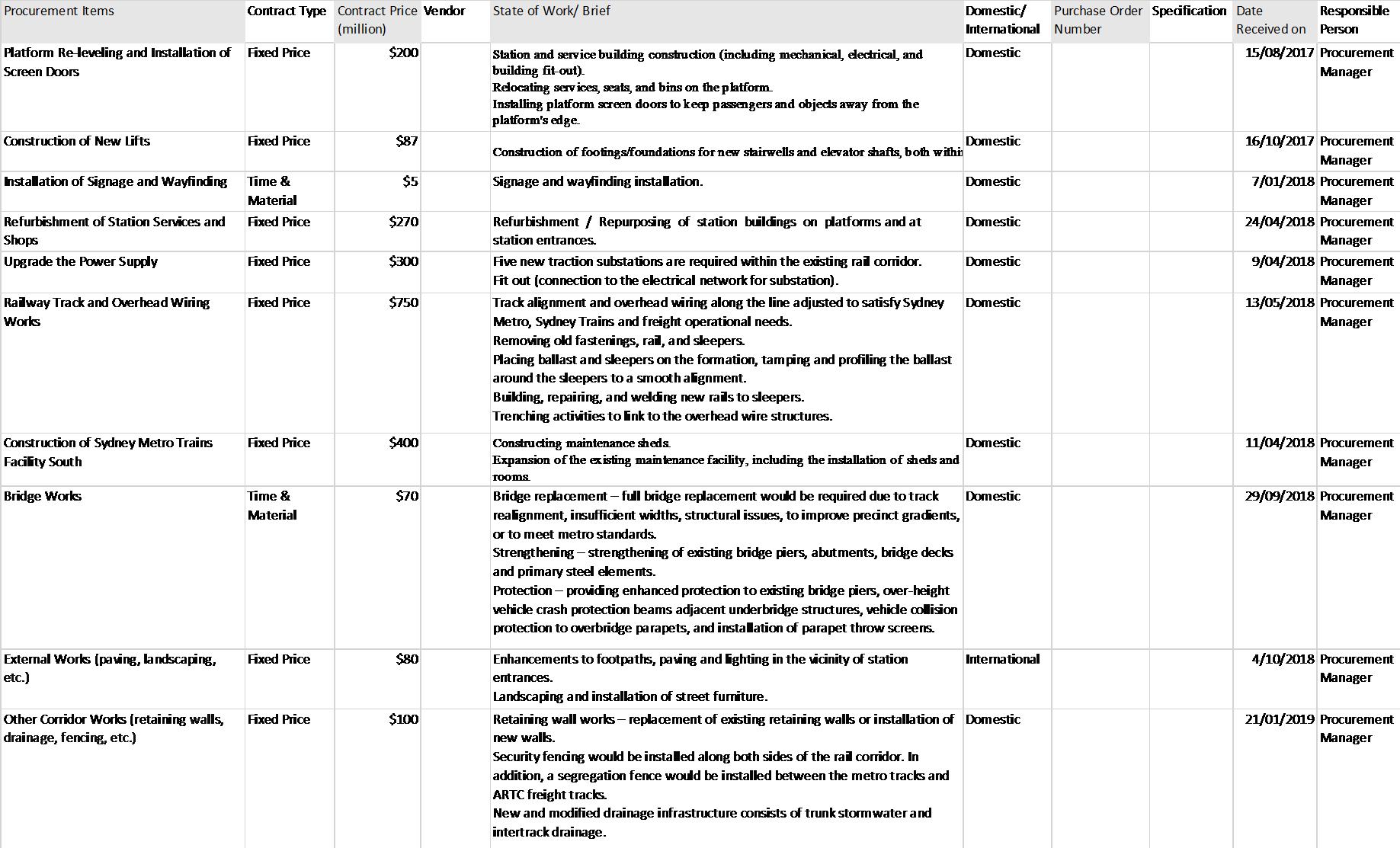
Hire or buy analysis/make or buy analysis
A make-or-buy analysis is used to decide whether project work or deliverables should be completed by the project team or purchased from outside sources. Sydney Metro's current resource allocation, employees' skills and talents, the need for independent or specialized expertise, and the desire to avoid expanding permanent employment obligations are factors to consider in the make-or-buy decision. It also entails assessing the risks associated with each buy-or-make choice.
• the expenses of scrapping or fixing non conforming components, as well as warranty and product liability costs if they are detected during the inspection process.
As a result, a high risk component (such as the construction of lifts) may be best left to a company with specific competence in making them. Purchasing high-risk components rather than manufacturing them in-house is one form of risk response strategy (transferring).
• the expenses of warranty/product liability claims/lawsuits if non-conforming components are not identified during the inspection process and passed on to the customer.
9.4.2. Business strategy
9.4
9.4.1 Direct and indirect costs
Indirect costs arise as a result of the training required for team members who will use it and the need for technology upgrades. Another indirect cost is the cost incurred if the component's quality does not meet criteria, whether such specifications are imposed by the company's control limitations or the government restrictions (Rowley, 2013). Non conformance expenses may include the following:
Business strategy includes the strategic importance to the company of the product or service that is being considered for outsourcing, as well as the process, technologies or skills required to make the product or deliver the service (Figure 47). These considerations must be made not
181
Both direct and indirect costs should be taken into account when comparing producing the component in house with outsourcing the work packages. The direct costs are those of making or acquiring the product, while the indirect costs are the support costs for the product. For instance, the implementation of fully automated trains and other forms of autonomous operation in rail operations has resulted in the new workplace and job designs, as well as new skill requirements. The ability to employ communications technology and massive data created by wireless signalling and sensors for predictive monitoring and maintenance systems is now a necessity. (Australian Industry Standards, 2017).
•
182 only in light of the existing competitive environment, but also in anticipation of how the environment may develop in the future. If the construction activity doesn’t have much future competitive advantage or potential oncoming technologies, Sydney Metro will not invest much manpower, resources and capital into the work package. In addition to this, if its core criticality ranking is low, the procurement procedure will commence to employ the most suitable
When a product or a service is vital to a Sydney Metro’s performance or is regarded as a core activity, it's usually preferable to adopt in house skills. For example, the Metro Control, Communication, Radio and Signalling Systems will be installed by the team members. Third party manufacture, for example, would be a mistake if a product is time sensitive or subject to frequent design modifications. Conversely, outsourcing is a good choice for companies looking to: Reduce costs Gain flexibility to adjust output in response to changing demand Phase out management of paperwork or training Supervise fewer workers Gain access to a new process or network technologies Leverage external expertise
•
Figuresubcontractor.47:Identifying strategic, core and outstanding potential
•
•
•
•
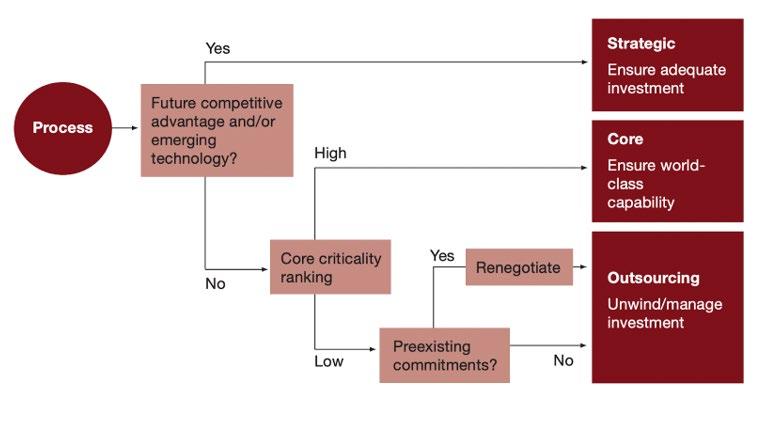
These contract package associated with their scope can be identified as:
● Trains, Systems and Operations and Maintenance (TSOM package)
183 9.5 Contract Type Selection 9.5.1 Project Delivery Method
Theworks)works include bridge and non station civil works, station works, services buildings and facilities, electrical works, cable and services routing and track with other rail infrastructure.
● Platform Screen Doors and Mechanical Gap Fillers
● Line wide package This involves track services, station control systems, overhead line, and electrical sub stations
● Southwest Metro Packages (Station upgrade packages and main works contract for corridor
This contract package involves major upgrade work to the existing rail system and reconfiguration of existing track and rail system to segregate the T3 Bankstown Line and goods line.
The team will procure the platform screen doors (PSDs) and mechanical gap fillers (MGFs) for Sydney Metro Southwest.
9.5.1.1 Basic Contract Packages and Scope of Sydney Metro Project
This project is divided into and delivered in several major contract packages in line with Sydney Metro Project Delivery Strategy and meeting the Australian and NSW Government’s strategic planning and policy goals. Therefore, it indicates that the SSC (Southwest Station and Corridor works) contract would be delivered in a series of contracts instead of a single design and construct contract.
This comprises the operation and maintenance of the rest part of 66km metro lines and 11 stations from Sydenham to Bankstown and delivery of core rail and communication systems.
● Sydenham Station and Junction (SSJ) package
● Lifts and Escalators
When it comes to selecting a project delivery method for Sydney Metro Project (Sydenham to Bankstown Southwest Line), this procurement management plan will conduct it based on the purpose of satisfying project scope and requirements.
● Building and Management Control System (BMCS) It involves design, supply, installing test and commission the BMCS forming part of each Foundation Infrastructure Works.
The delivery method selected in Sydney Metro Project is PPP and D&C delivery method.
9.5.1.2 Evaluation on Delivery Method
● Public Private Partnerships (PPP) The relationship between head contractor and the InvestopediaGovernment (2021) states that public private partnerships involve collaboration between a government agency and a private sector company that can be used to finance, build, and operate projects, such as public transportation networks, which give some edges on project delivery. It allows large scale government projects to be completed with private funding, technology and innovation of public sector, enabling the project to be completed on time and within budget. As for the Sydney Metro Project, OTS2 PPP will be determined as the main contract type for TSOM package. In this procurement management plan, another delivery strategy alternative to OTS2 PPP was used by Sydney Metro as the ultimate quantitative value for money test (Table21).
Table 21: Financial value for money comparison
The contract is awarded to a private partner to both design and build a facility or a piece of infrastructure that delivers the performance specification in the PPP contract. This type of
The scope involves design, supply and installation of the lifts and escalators equipment for the Project including 70 lifts and 130 escalators.
184
● Design and Construct the relationship between head contractor and subcontractors
The financial value for money analysis of the OTS2 PPP at financial indicates a forecast saving of $185.7m in NPC.
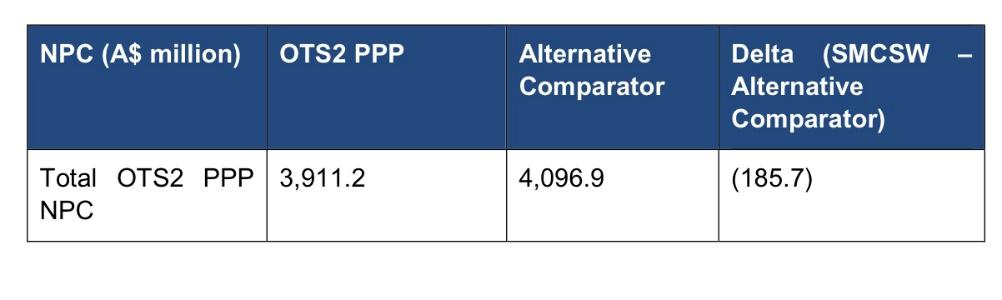
185 partnership can reduce time, save money, provide stronger guarantees (as the work is with a single entity rather than a consortium) and allocate additional project risk to the private sector.
Some common features of Design & Construct can be summarised and illustrated below:
Ashttps://www.roads.org.au/Policy/Capacity/Presentations-and-reportsthemaincharacteristicscanbeseenabove,itcanbearguedthat
Additionally, a series of factors required to be taken into account in scope management such as time, cost, quality and risk can be identified as evaluation criteria assisting Sydney Metro Project Management team to decide which contract type should be chosen.
D&C contract has an advantage in terms of tender cost as client or head contractor needs to compensate the sellers.
Therefore, D&C is suitable for the infrastructure project to a large extent when encountering the problem of contract type selection.
Comprehensive Factors
AccordingTenderingtoRoads
Cost of
Australia (2017), 52% of infrastructure projects examined in a survey were tendered under a design & construct model, of which 20 D&C projects examined as part of the survey and three of them were international projects.
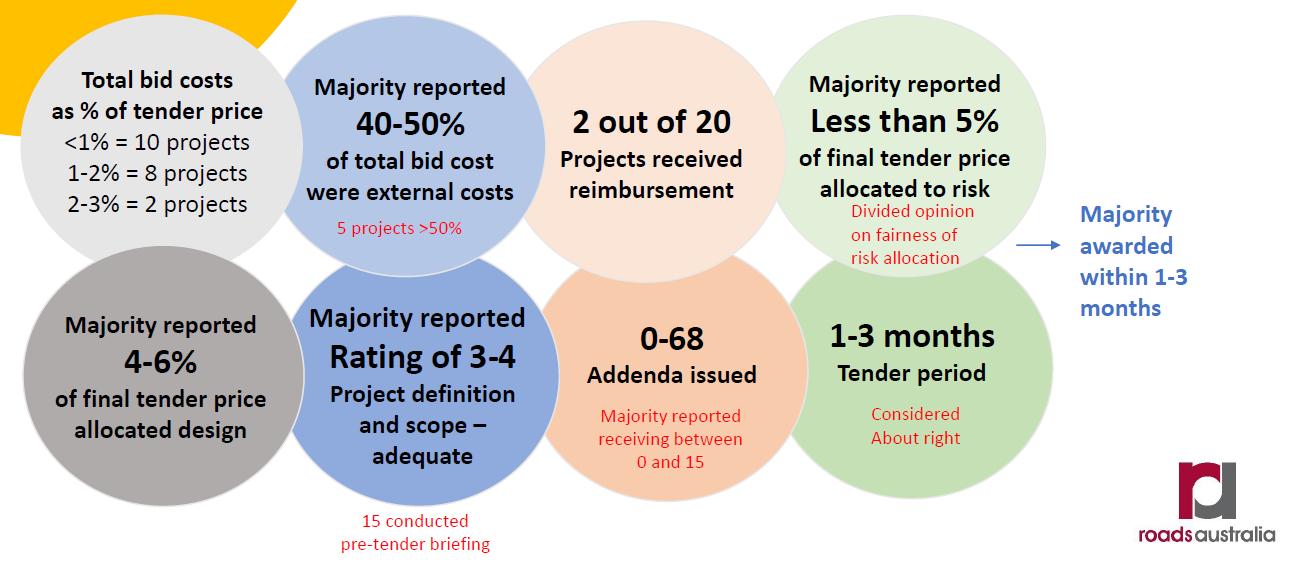
186 An evaluation table (figure 48) extracted from previous project will be utilised in this Sydney Metro project to examine several types of contracts. Figure 48: Project criteria and delivery method matrix
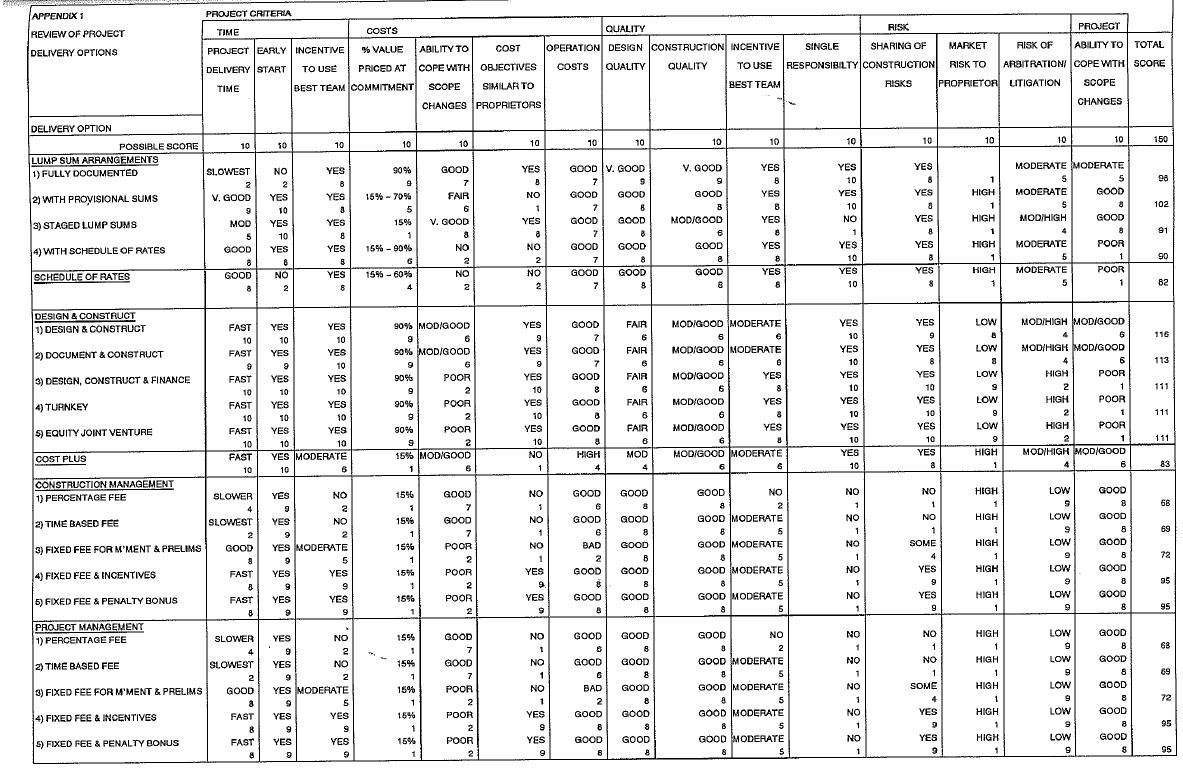
187 According to the table shown above, D&C delivery method receive the highest score and it allows the contractor to bring together valuable specialists to incorporate their own knowledge on latest construction technologies and materials to ensure project innovation. Consequently, D&C delivery method will act as the main contract type of Sydney Metro Project Southwest Line. Additionally, some other contract types like Construct Only will also be utilised in this 9.5.1.3project.Specific Contracts of Sydney Metro Project Southwest OTS2 PPP: The public sector parties to the contract: Sydney Metro and the NSW Treasurer The main private sector parties: NRT CSW Pty Ltd, MTR Corporation (UK) NRT Ltd, Plenary Investments (NRT) Pty Ltd, LNWR Pty Ltd, Marubeni NRT Investment Pty Ltd and CDP Infrastructures Group III Inc. The core contractors: MTR Corporation (Sydney) SMCSW Pty Limited and Metro Trains Sydney Pty Ltd. 1)TSOM package Trains, Systems and Operations and Maintenance also known as OTS2 PPP (OTS2 Project Deed) D&C contracts 1) Sydney Metro City & Southwest Sydenham Station and Junction Works Incentivised Target Cost Contract (SSJ Contract) 2)Sydney Metro City& Southwest Line wide Works Incentivised Target Cost Contract D&C Contracts and Construct Only Mixture 1) SSC (Southwest Stations and Corridor works) ▪ Station upgraded contracts (Dulwich Hill, Campsie and Punchbowl stations, Hurlstone Park, Belmore and Wiley Park stations) Construct only Contract ▪ Station upgraded contracts (Marrickville, Canterbury and Lakemba stations) Construct only Contract ▪ Bankstown and main corridor work contract
Figure Spectrum of distributed contract risks
49:
According to the spectrum of distributed contract risks, Fixed Price Type tends to result in a higher risk being posed to seller’s side. It indicates that when buyer signs a lump sum contract with vendor, a large proportion of risk will be transferred to seller’s side.
Lump Sum price including FPIF price type which is the most common type of contract in the world will be selected as this project’s contract price type.
Furthermore, based on the assumption in cost management plan, the cost contingency of the procurement with respect to two different price types will be calculated and in this procurement management plan Monte Carlo Simulation for this cost contingency calculation will run for 10,000 iterations. And the outcome can be generated by utilising Excel @Risk and demonstrated in figure 50.
188 2) Sydney Metro City& Southwest, Southwest Metro, Mechanical Gap Fillers (MGF) and Platform Screen Doors(PSD) Product Proving Deed 3)Sydney Metro City& Southwest Lifts and Escalators Framework Contract 4) Sydney Metro City& Southwest Building Management and Control System Framework Contract. 9.5.2 Contract Price Type Selection
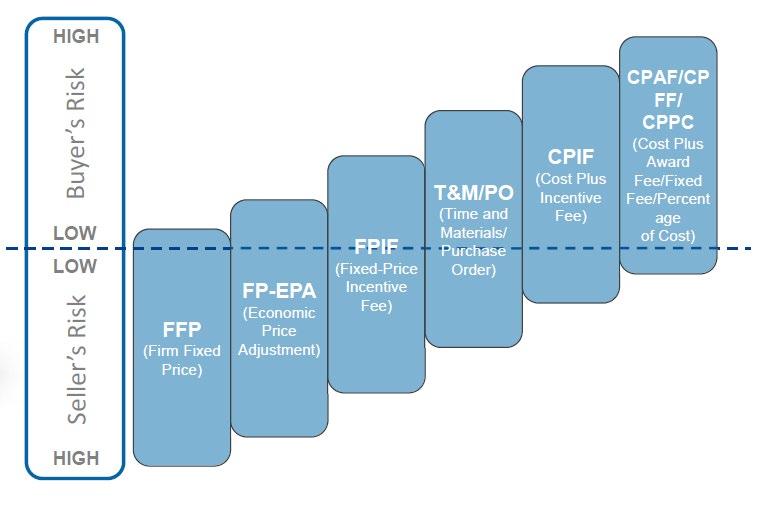
Sydney Metro Southwest Project procurement success is subject to the value for money in the procurement of products and services in an ideal way supporting the project per se strategic, operational and financial objectives. Therefore, all the procurement activities will take the money value into consideration. This enables Sydney Metro Southwest project management team to decide to incorporate some criteria such as supplier technical, experience, performance history and sustainability criteria into tender guideline.
The red bell shape represents the lump sum price type and the blue one represents the cost plus price type. This indicates that lump sum price contract will only have 5% chance to generate contingency cost more than $1.820m. Compared to lump sum price, cost plus price will have 81.3% chance to generate contingency cost more than $1.820m. Therefore, through quantitative analysis, lump sum price type finally will be the suitable contract price method employed in the Sydney Metro Southwest Project. Selection Criteria
9.6 Source
Figure 50: Comparison of two risk contingency probability distribution in terms of two price types.
189
The Evaluation Criteria for selected bid packages will be established prior to the release of Request for Quotation (RFQ) to suppliers. And this is established in collaboration with all relevant stakeholders. This Evaluation form is a document which is used to measure the project’s significance with a criterion governed by a set of standards. This will enable performance, proposal or any alternatives to be assessed thus assisting users to make a decision.
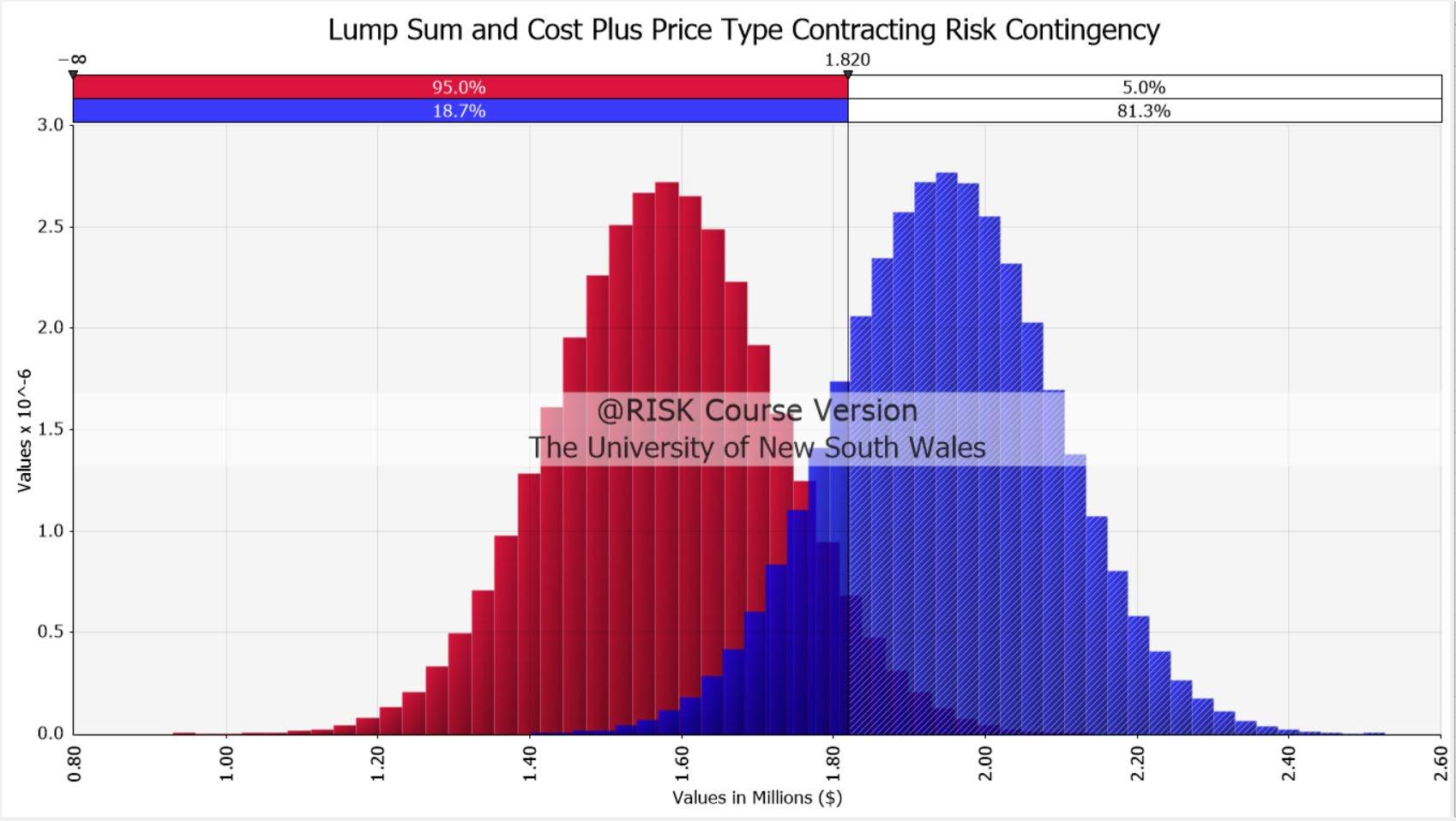
190 Evaluation Area: Key Evaluation Question: Weighting A Commercial: 1.Price/Total Cost 3.Employee2.CapabilityIndustrialandrelated 20% B Health Safety and Environmental Criteria 1.The ManagementCultural2.Environmentalhealthbusinessesparticipatingoccupational,andsafetyControlHeritage 20% C Quality Criteria 1.Quality 3.QualityChecklist2.QualityManagementAssuranceMetricsandControlCriteria 20% D Technical and Experience Criteria 1.How was the experience of participating agencies (inspector and internal 2.Experiencestakeholders) with similar projects 20% E Stakeholder Criteria 1.Stakeholder Management 2.StakeholderPlan Register 20% A maximum score of 5 for a criterion will only be awarded if it fully complies with the specific requirement of the criterion. Each Evaluation Objective has been weighted in order to ensure that sufficient emphasis is given to the certain important functions based on user’s understanding of the requirements. Weight Description 0 None - Feature is not important 1 Low - Feature is of low importance 2 Average - Feature would be nice in the tool, maybe a future requirement 3 Medium - Feature should be present in tool or a workaround available 4 High - Feature must be present in the tool - A success factor 5 Critical - Feature is considered a critical success factor
1.2 The composition and experience of the tender’s team proposed to engage effectively with the Sydney Metro Project and its representative(s) during the subsequent tendering process.
Assessment Criteria Rating • No response provided 0 •
The tender has assembled a team whose key members’ experience in cooperative tender processes, negotiations and development of tender documents – as presented in the applicant’s Submission – is judged acceptable. 33
1 –
34 – 66
To
9.7.1. EOI Evaluation 1.1
Tender has demonstrated moderate experience on previous similar projects, and satisfactory performance is indicated in referee reports & referee checks. 66
Procurement metrics to evaluate and select sellers, vendors, or subcontractors
1 –
•
Tender has demonstrated minimal experience on previous similar projects and referees’ reports indicate that performance is acceptable. 33
The tender evaluation of parties engaged within the project will be done through numerous stages and phases to ensure the most capable and best suited sellers, vendors and subcontractors are selected for Sydney Metro Sydenham to Bankstown. The tendering will be divided into three main categories, including EOI, Non-Price and Price evaluations for contractors and suppliers being price-sensitive items and non-price sensitive items. calculate the rating the following tables will be implemented for the Sydney Metro Project. Evidence of the tender’s experience and performance on contracts of a similar project in Australia.
•
Tender has demonstrated extensive experience on previous similar projects, and good past performance is confirmed by referee reports & referee checks. 100
•
The tender has assembled a team whose key members’ experience in cooperative tender processes, negotiations and development of tender documents – based on the evidence in the tender’s Submission – is judged as good to very good.
67 –
34 –
191 9.7
Assessment Criteria Rating • No response provided 0 •
•
The tender has provided assurances in its application that it is committed to meeting the timetable and that it has the ability to carry out the required work without impeding its other commitments. 33
–
•
–
67 –
The tender has proposed a project team whose mix of key members and sub contractors whose experience in project management, resource coordination and construction of works of a similar nature to the one required is considered as good. 66
The tender has proposed a project team whose mix of key members and sub-contractors with experience in project management, resource coordination and construction of works of a similar nature to the one required is considered as superior and also may have been demonstrated on previous engagements with Sydney Metro.
34 66
The tender has clearly demonstrated that it is committed to meeting the timetable and that its resource base is such that it has the ability to carry out the required work without impeding his other commitments. 100
•
192 •
The tender has proposed a project delivery team whose mix of key members and sub-contractors – as presented in the tender’s Submission – is considered acceptable. 33
No response provided 0
34 –
The tender has assembled a team whose key members’ experience in cooperative tender processes, negotiations and development of tender documents – based on the evidence in the tender’s Submission – is judged as superior and also may have been demonstrated on previous engagements with Sydney Metro. 100 1.3 The make up of the tender’s construction delivery team, including the key personnel and major sub contractors, proposed in the case of the applicant winning the tender for the proposed work.
Assessment Criteria
•
The tender has demonstrated that it not only is committed to the meeting the timetable but that its resource base is such that it has the ability to carry out the required work without impeding its other commitments.
•
Rating •
67 –
1 –
67 100 1.4 The tender’s commitment to and capability in meeting the Sydney Metro Project’s procurement process timetable contained in the Briefing Document.
•
1 –
Assessment Criteria Rating No response provided 0
•
193 9.7.2. Non-Price Evaluation Non-Price Evaluation Tenderer No. Category Item Max Score Weighting Scored Weighted Score 2.1 Safety WH&S Management Plan 100 40% 2.2 WH&S Staff 100 30% 2.3 History of WH&S Incidents and Procedures 100 30% 3.1 Time Schedule& Programme Start Date 100 40% 3.2 Programme Detail 100 20% 3.3 Programme Completion Date 100 40% 4.1 Quality Quality Management Plan 100 35% 4.2 Proposed Buildability 100 35% 4.3 Project Quality References 100 30% 5.1 Project Team Project Team Members 100 30% 5.2 Company History and Values 100 40% 5.3 Resource Allocation 100 30% 6.1 Sustainability Environmental & Sustainability Management Plan 100 50% 6.2 Sustainability Initiatives Proposed 100 25% 6.3 Greenstar Methodology 100 25% 7.1 Company Company Diversity and Cultural Embracement 100 30% 7.2 Company History and Values 100 30% 7.3 Company Financial Position 100 40% 9.7.3. Overall Evaluation The combined evaluated score is adding the sections of the standard and non-price related evaluation worth a total of 50%, with the submitted tender price which is also worth 50%. Combined, these will form the final tender evaluation score to benchmark against competitors.
194 For each criterion, scores will be awarded on a descending scale, i.e., the most merit attracting the highest score, lesser merit attracting a lesser score and equal merit attracting an equal score. Total Evaluation Tenderer 1 Tenderer 2 Tenderer 3 No. Category Item Max Score Weighting Scored WeightedScore Scored WeightedScore Scored WeightedScore 1 EOI Experience 100 5% Engagement 100 5% Key personnel 100 5% Commitment 100 5% 2 Non-Price Safety 100 5% 3 Time & Schedule 100 5% 4 Quality 100 5% 5 Project Team 100 5% 6 Sustainability 100 5% 7 Company 100 5% 8 Price Tender Price 100 50% 9 Total CombinedTenderEvaluatedScore 100 100%
9.8.1 Procurement controlling process
• Track
accepted • Measure outputs • Harmonizing
• Approve changes • Take corrective action 9.8.2
• Monitor progress • Execute plans • Verifying
Project contract management is the systematic work of managing the execution of the contract, ensuring that both parties of the contract fulfill the terms of the contract, and coordinating the relationship between contract execution and project execution. Contract management is the realization stage of project procurement management and the core of project management. Contract management may include the bidding phase and the post-construction phase. When creating a contract, there may be errors, disputes, and poor communication. The job of the contract administrator is to monitor what is happening and develop the best version of the contract. The contract
Project procurement management refers to a series of planning, organization, control, and coordination work for obtaining qualified goods, materials, and services. Project procurement management usually includes six tasks: initial procurement, procurement, urging, inspection, transportation and handover, and closing services. Controlled procurement is the process of managing procurement relationships, monitoring contract performance, and changing and correcting contracts as appropriate.
Procurement controlling process and contract administration
The procurement control process can be specifically combined with the following project processes: the scope by accepting the result costs and ensure payments are made against the work that has been both verified and contractual deliverables with the schedule Contract administration
The main benefit of this process is to ensure that the performance of the buyer and seller complies with the procurement requirements stipulated in the legal agreement. At the same time, in controlling the procurement process, the project team needs to update any project management plan components or other project documents to maintain adequate and up to date records, which including project management plans, job performance information, performance reports, approved change requests, and of course contracts.
195 9.8
196 administrator is the intermediary handling all subcontractor communications, payments, disputes, and contract changes. The contract administrator will be responsible for: • Managing disputes • Providing contract updates • Coordinating with different departments, such as the legal team • Making fair, impartial decisions • Analysing risks • Setting quality standards • Communicating expectations • Setting meeting 9.9 Procurement closing process
Closing the procurement phase is a necessary process to complete each purchase. The main benefit of this process is that it records and documents related agreements for future reference.
5. Update reports and records: Ensure that all documents related to the Sydney Metro project are fully recorded, and the records can be easily retrieved in the management system. The documents include the contract, the documents submitted by the seller, financial information, inspection results, and the final contract report.
2. Negotiated settlement: The claim is required when a defect is found in the project during the inspection. The claim is two way, and only the actual economic loss or exemplary damage can be claimed from the other party. In construction projects, inspections involve walkthroughs of the buyer and the contractor to the site to ensure mutual understanding of the work in progress.
3. Financial closure : According to the contract's payment terms and the final workload, the Sydney Metro will be settled following the prescribed procedures.
4. Procurement audit: a structured review of the procurement process of Sydney Metro.
The following tasks need to be included in the closing procurement phase:
1. Product verification: This includes checking whether the Sydney Metro project has reached the stakeholders' standards and has completed all the project deliverables satisfactorily. Once the contractor has completed all requirements following its contract, CA will close the transaction as agreed with the project manager.
Response to Community Complaints Sydney
Neighborhood,Shareholders,
197 10.0 Project Communication Management Plan 10.1 Communications Matrix
7/24
Budget
Frequency Delivery Vehicle Progress of Work Sydney
Whoever
Here below is merely an example of the communication matrix adopted by the Sydney Metro project.
Safety Hazards on Site identify the Potential Hazard PM, Site Manager or any other stakeholders Inform the responsible person to make decisions on mitigation actions; remind the potential victim in time. Daily Message, Orals, Body Language Metro CommunicationsProjectteam Neighborhood, the Public Keep the complainant informed of the process and response from relevant department. oactivitiesconstructionwhenareccurring telephone call, email Figure 51: For each criterion, scores will be awarded on a descending scale, i.e., the most merit attracting the highest score, lesser merit attracting a lesser score and equal merit attracting an equal score.
CommunicationDeliverables Sender / Facilitator Target Audience Objective
As Sydney Metro Southwest Line Upgrade is a complex large scale infrastructure project, which means there will be numerous stakeholders and shareholders, the communication management involves a large amount of work. To avoid any omission of key communication deliverables, the communication requirements will be identified by different project stages and also by different areas including scope, cost, schedule, quality, safety, environmental impact, social impact, procurement, human resource, shareholders, etc. Please refer to future supplementary document for the complete version of communication matrix. / Expectation Metro the Public Share the information of construction progress or unexpected changes to the construction program. Report, Newsletter, Sydney WebsiteMetro with revevant experts Project Team Inform the person who is in charge of the execution of the solution scheme. Weekly Meetings Usage QS, Accountant PM, CFO, Shareholders Report the analysis result of project expenses. Report
Monthly
Solutions of Design / Engineering / Technical Issues PM
Monthly
teamCommunicationsProject
Report the project progress and any delays / unsolvable technical issues / significant work failures came across, identify the causes, discuss the jobs and actions taken in the next working period. Discuss status of change orders in progress. Weekly
Project Meeting Guideline
Design Meetings, Procurement Meetings, Quality Meetings, Safety Meetings, Cost Control Meetings, Community Information Sessions, Disputes Resolution Meetings… Figure 52: Example of Project Meeting Table
and managerProject Weekly/Monthly
To achieve high efficiency in meetings, it is very important to make sure all participants are clear about the objectives of the meeting as well as their roles in it. The table below provides a format of the project meeting guideline. Remember to register any meeting in the table beforehand.
Project reports are required for all stages of the entire construction cycle until all scheduled tasks complete. Project reports include regular collection and analysis of actual data so that relevant personnel and stakeholders can understand and communicate project progress and performance compared with the baselines. At the same time, it can predict the project's future development based on the received status report and progress measurement. The team availability report shows the workload of each team member so that adjustments can be made at any time to make intelligent resource decisions for the project. PMO Provides a clear overall perspective to help project managers and stakeholders fully understand the progress, status, and changes of the project, and make decisions on future action plans based on the current status.
198 10.2
Daily Doorknock Meetings Sydney
Discuss the potential impacts of Sydney Metro with highly impacted stakeholders. Before the start of activitiesconstruction PM teamrolesforfromRepresentativesTransportNSW,keyinproject
Project Status Meetings
10.3 Project Reporting Procedure (Schedule and Template for Reports)
2 ReportStatusProject
Reinforce safety basics, focus on high-risk scenarios and to inform workers about changes of site conditions that may have occurred since their last shift. Metro BusinessesResidents, in local area
No Typereportof Responsible Frequency Contents/Purpose Attendance 1 ReportAvailableTeam ManagerProject Daily
directorateProjectsponsorProject Frequency / Site Supervisor Workers
Type of Meeting Chaired by Attendees Objective
Tool Box Meetings Site Manager
o Project
o Project
199 3 ReportHealthProject PMO and managerProject Weekly
The risk assessment report identifies and categorizes the risks that may occur, which helps prioritize the problems before the risk destroys the project's success and suppresses the risks in the bud.
PMO and managerProject Weekly
6 PMO and managerProject Monthly
10.4
o Project scope
o Project workflow management o Critical work
directorateProjectsponsorProject PMO and managerProject Monthly
directorateProjectsponsorProject
4 AssessmentRisk
The project health report provides a high level snapshot of the project status. Let the team members and stakeholders know what is going on as planned, what is behind, and what is overdue.
ReportBaseline
5 ReportTrackingTime
The system will be implemented for the following: management plan report budget and cost management definition path
directorateProjectsponsorProject
In constructing the Sydney Metro, the project management information system will be used to collect, integrate, and manage project documents and project processes. PMIS is a centralized storage centre for all basic project information. At the same time, PMIS can follow everything within the scope of the project, including project plans, project schedules, costs, and time. Quality and risk management. This online operation based management information software can communicate with external parties and stakeholders on time, providing a powerful platform for automated workflow, bid management, problem management, and digital operation and maintenance manual management. The project manager will be responsible for system setup, management, and ensuring the regular operation of the system.
Project Management Information System (PMIS)
The time tracking report can better track the team's actual time on project tasks to better track the project estimates. This helps to detect potential budget overruns before they happen and provides insights for future project estimates.
analysis o Project schedule analysis and management o Project safety report and management o Project quality report and management
The baseline report compares the original timetable with the actual project timetable and can show how delays in the project will affect the entire project timetable.
directorateProjectsponsorProject
200 o Project performance review and management o Project historical data management o Contract administration o Reporting and auditing o Distribution of related documents o BIM system management
For the Sydney Metro project, stakeholders will upload existing documents to PMIS. Every relevant staff member can easily access all documents in this system, including project specifications, project drawings, BIM models, related contracts, reports, and progressive evolution, which can better help the staff get familiar with and understand the project before the construction. At the same time, on the PMIS system, all documents can be reviewed and modified, and all modifications will be automatically tracked and recorded by the system, which can effectively strengthen the communication between staff and relevant stakeholders, improve work efficiency, and provide an effective communication platform and reduce the risk of misunderstandings.
10.5 Template for Project Work Performance Report
Monitoring the status of the work is essential to the success of the project. Regular reporting of work performance helps the project team understand whether the project is executed as planned or deviated from the original plan. Project performance reports provide a clear overall perspective, which can help project managers and stakeholders fully understand the progress, status, and changes of the project, and make decisions about future action plans based on the current status. If the project progress is being executed according to the plan, the project team and stakeholders will be satisfied; otherwise, they must alter the future course of action to get the project on track.
The well prepared and comprehensive performance report of Sydney Metro Southwest Project tends to incorporate earned value analysis, cost and schedule performance index, and quality measurement. Also, this report will include project risk summaries through applying contingency estimation, top risk item identification, project critical path and milestones marked, project change requests, trend forecast, variance from the baseline and so forth.
A project performance dashboard for the reporting period makes it possible for stakeholders to track and target current work situation. Two dashboard template of performance report for Sydney Metro Southwest project is demonstrated below:
201 Table 22: Template of performance report for Sydney Metro Southwest project This table below is an illustration of the dashboard information template extracted from other management plan of the Sydney Metro Southwest Project, which will be utilised for project performance reporting (Reporting time 2018 Q3). Table 23: Project Performance and Measures of Sydney Metro Southwest Project Project Performance and Measures of Sydney Metro Southwest Project Financial Cash Flow Earned Value Chart
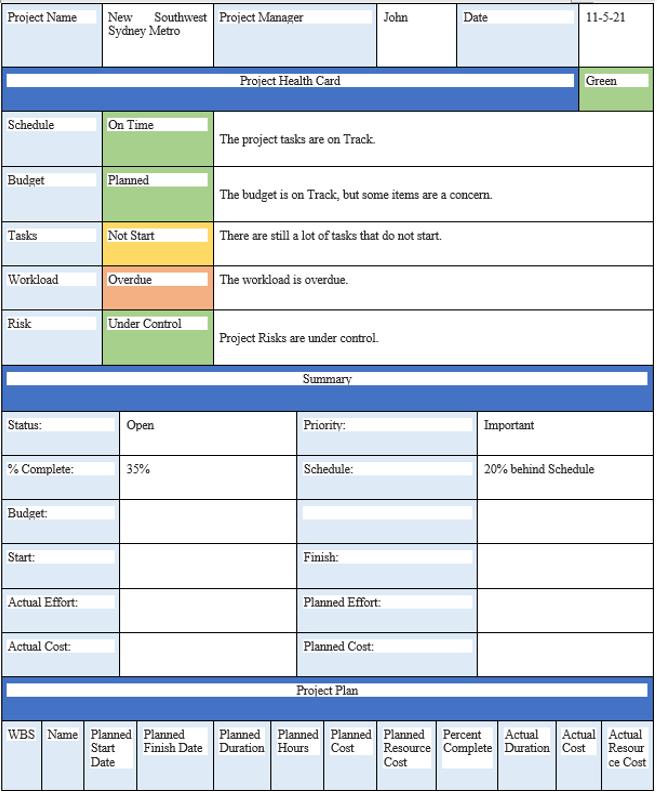
202 Schedule Overview Top Risk Prioritising Contingency Reserve Estimation Risk Contingency Ranked (Sensitivity Analysis)
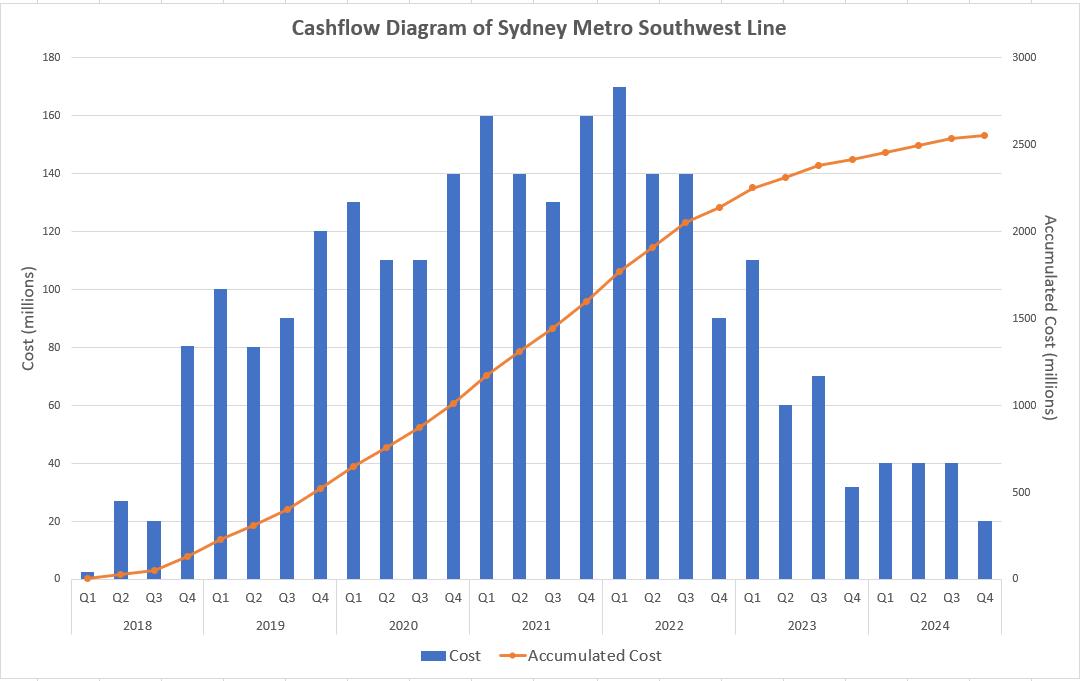
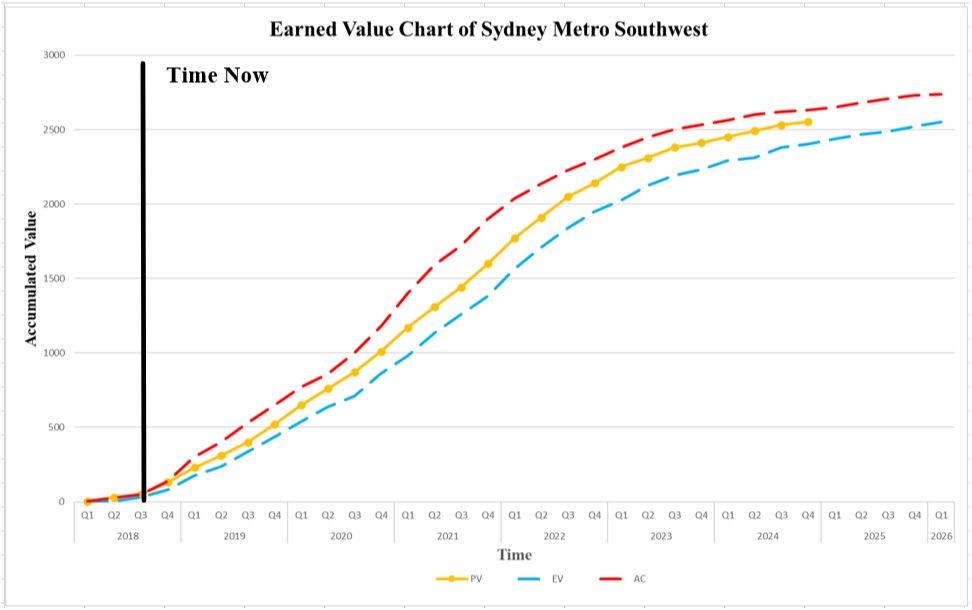
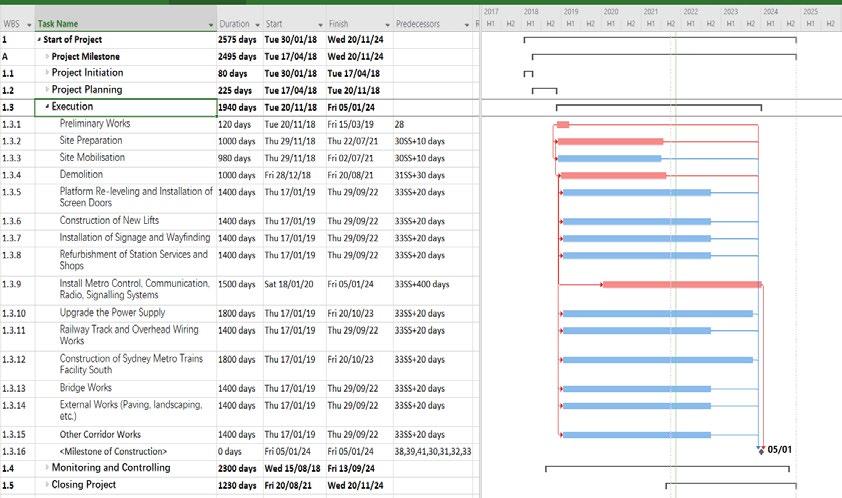
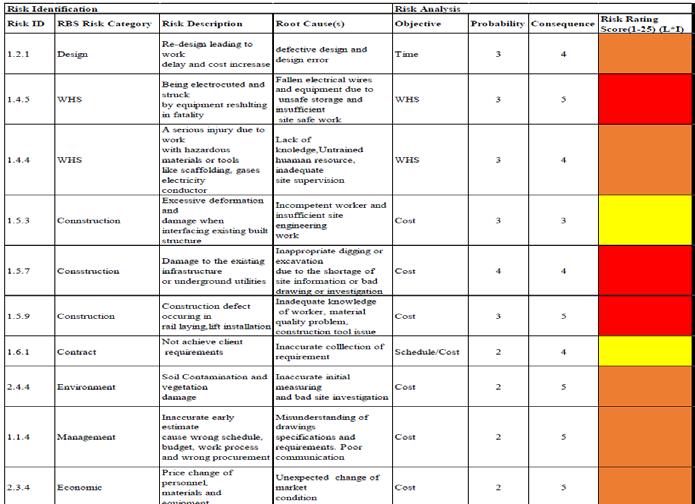
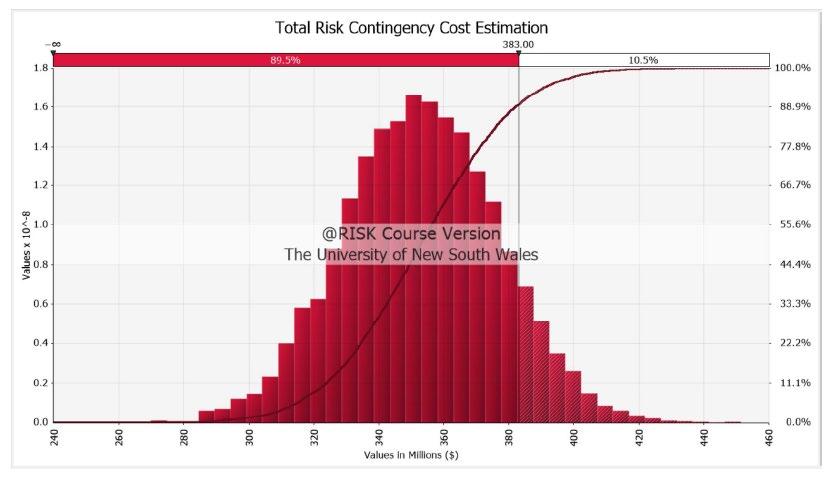
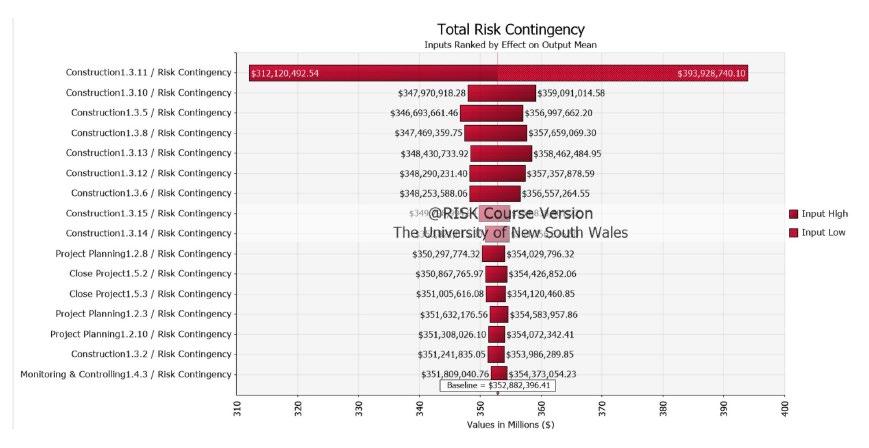
Earned value
Activity
The sum of work package estimates, contingency reserve, and other associated costs by which project performance is assessed. A formal change control process is necessary to change the cost baseline.
The Cost variance of a project is its earned value minus its actual cost. A negative cost variance indicates that a project is running over budget. A positive cost variance indicates that a project is running below budget.
Integrated change control
The specific requirements expected of project deliverables. To be formally accepted, deliverables must meet all acceptance criteria.
Cost variance
Cost baseline
The hierarchical breaking down of project deliverables into smaller components that are easier to plan and manage.
The smallest unit of work necessary to complete a project work package (which includes multiple activities). Time, resources, and finances are required to complete each activity.
This term represents the costs and schedules approved at the start of the project. They use baselines as a basis for monitoring and evaluating performance.
203
Acceptance criteria
Baseline
Configuration Configuration of a product involves shaping its functions and characteristics to make it suitable for customer use.
Cost of quality
The cost associated with ensuring project quality. This cost may mean the difference between unacceptable and acceptable project results.
Cost performance index (CPI) A cost performance index measures the cost efficiency of a project by calculating the ratio of earned value to actual cost.
10.6 Glossary of Common Terminologies in the CPMP
Decomposition
A concept used to gauge project schedule and cost performance. Portions of the project budget are assigned to components of the work breakdown structure, and successful completion of a work breakdown structure component is understood as value earned through work.
Here is a selected list of terminologies mentioned in this report which may be confusing to readers.
The coordination of changes throughout all aspects of a project, including scope, budget, and schedule.
204
(See also three point estimating) Quality assurance
A hierarchical list of resources needed for project work, classified by type and function.
Resource calendar
Precedence diagramming method (PDM) The process of constructing a project schedule network diagram. It illustrates the logical relationships between project activities and shows the order in which they must be performed by using nodes to represent activities and arrows to show dependencies. PDM also indicates early and late start and finish dates, as well as activity durations.
Program Evaluation and Review Technique (PERT) PERT is a statistical method used to analyse activity and project durations. PERT networks are typically illustrated with activity on arrow diagrams. The method makes use of optimistic, pessimistic, and most likely durations to estimate expected durations for project activities and to determine float times, early and late start dates, and critical paths.
Resource breakdown structure
Quantitative risk analysis
A set of practices designed to monitor processes and provide confidence that result in deliverables meeting quality expectations. It may involve quality audits and the stipulated use of best practices. Quality control
A project management technique that subjectively analyses risk probability and impact. The risks are categorized on a probability and impact matrix, and those deemed significant may undergo a quantitative risk analysis.
The use of standardized practices to ensure that deliverables meet stakeholder expectations. It involves not only the definition and identification of unacceptable results but also the management of processes to optimize results.
A resource calendar indicates resource availability, usually by shift, over a period of time.
Key performance indicator (KPI) A Key performance indicator is a metric for measuring project success. Key performance indicators are established before project execution begins.
Qualitative risk analysis
The mathematical analysis of risk probability and impact. In project management, it is not a substitute for qualitative risk analysis. Instead, quantitative analysis is conducted after qualitative analysis and assesses risks that qualitative analysis has identified as significant.
Schedule performance index (SPI) The ratio of earned value to planned value at a given point in time. It shows whether a project is running to schedule. An SPI lower than one indicates the project is behind schedule. An SPI higher than one indicates the project is ahead of schedule.
A schedule baseline is the original project schedule approved by the project team, sponsor, and stakeholders by which performance is assessed. Schedule baselines are generally inflexible, though alteration of a schedule baseline via a formal change control process may be allowed.
Three point estimating
205
The set of requirements, expectations, and work packages approved as project deliverables. It is used to guide and assess project performance.
A superset of estimating techniques that use averages (or weighted averages) of most likely, optimistic, and pessimistic costs, and duration estimates to form final estimates.
Task In project management, a task is a unit of work or activity needed for progress towards project goals. Typically, a task must be completed by a set deadline. Tasks may be further broken down into assignments or subtasks.
Scope baseline
Schedule baseline
S Curve analysis
Scope creep Scope creep refers to gradual changes in project scope that occur without a formal scope change procedure. Scope creep is considered negative since unapproved changes in scope affect cost and schedule but do not allow complementary revisions to cost and schedule estimates.
Risk register
The amount and type of risk an organization is willing to accept in anticipation of gains. It is not the same as risk tolerance, which is the amount of variation in performance measures that an organization is willing to accept.
Risk appetite
An s curve tracks cumulative financial or labor costs. S Curve analysis is used to compare a project’s cumulative costs at any given point with a cumulative cost baseline created during the planning phase. It allows project managers and sponsors to assess performance and progress.
Work package The work packages of a project are its lowest level deliverables. They are detailed in a work breakdown structure dictionary.
A risk register, or risk log, is a tool used to chronicle risky situations and risk responses as they arise.
206 11.0 Project Stakeholder Management Plan
Sydney Metro is implementing a comprehensive community and stakeholder consultation program for Sydney Metro, to engage proactively with local communities and critical stakeholders (Sydney Metro, 2018) Therefore, this Stakeholder Management Plan aims to document a well defined engagement and management strategy for key stakeholders within the Sydney Metro Sydenham to Bankstown (Southwest) project. This plan is essential to create and maintain a positive relationship with project stakeholders and will help to map out stakeholder needs, requirements and impacts to better support their interests. Stakeholder management should be implemented throughout the entire project lifecycle and updated as required 11.1 Stakeholder Analysis (Identification/Stakeholder Register)
The below table identifies, assesses, and classifies all major stakeholders that have an interest or may be affected by the Sydney Metro Southwest project. This document should be updated regularly as emerging stakeholders are identified or information regarding current stakeholders changes
207
External 5 Suppliers Refer to supplier lists Includes
High
WHS RiskSiteEngineersArchitectureLegalProcurementFinancePeopleOfficersandCultureTeamTeamTeamandDesignEngineersManagementTeam Directly
High Low Contact as required responsible for the delivery of the Sydney Metro Southwest project.
High High Daily Project should be set early during the planning stage and engagementregularwill be required throughout the development process of Sydney Metro Southwest project. High Regular up dates of activities.major planning and development of Sydney Metro Southwest
inspections
External Australian Government 8 Department andRegionalInfrastructure,ofDevelopmentCities GPOBox 594 Canberra ACT 260 Ph: 1800 075 001 Government body involved in the
High High Will be informed on progressprojecton a weekly basis. Major issues and concerns will require communication.prompt Manager Responsible in overseeing and managing the entire Sydney Metro Southwest project. Involved in decisions around all aspects of the project including the project’s budget, schedule, methods, resources, and contracts.
Manager Internal 7 End user N/A The client and end users’ expectations
project. It sets out andbuildingenvironmentalinsurance,andcodeguidelinesregulations. High High Monthly meeting External NSW Government 9 Department of Planning Environmentand Locked Bag 5022 Parramatta NSW 2124 Ph: 1300 305 695 High Low Monthly meeting External 10 Transport for NSW PO Box HaymarketK659NSW 1240 Ph: (02) 8202 2200 Low High Monthly meeting External 11 Roads and Maritime Services Locked Bag 928 North Sydney NSW 2059 Ph: 13 22 13 / 13 27 01 (traffic) Low Low Monthly meeting External
Internal 3 Project
updates to Site Engineers and
High High Will be informed on progressprojecton a weekly basis. Major issues and concerns will require communication.prompt Team involved in the development of the Sydney Metro Southwest project. High High Will be informed on progressprojecton a weekly basis. Major issues and concerns will require communication.prompt will be consulted for their area of expertise or for necessary and audits during the construction phases of Sydney Metro Sydenham to Bankstown High High Meetings as required. all material for the construction of the Sydney Metro Southwest project.
suppliers
Internal 2 Project
Internal 4 External Auditors/Consultants/Inspectors Refer to list of external consultants Stakeholders
208 Identification Assessment Classification ID Organisation / role in Project Contact information (postal address/phone, etc.) Requirements and expectations Influence Interest needsCommunication Classification Sydney Metro Sydenham to Bankstown (Southwest) 1 Board of Directors
External 6 Contractors Subcontractorsand Refer to list of contractors and subcontractors Directly
209 12 NSW ProtectionEnvironmentAuthority Locked Bag 5022 Parramatta NSW 2124 Ph: 131 555 Local Government 13 Inner West Council PO Box Petersham14NSW 2049 Ph: (02) 9392 5000 The project falls within these council boundaries. Construction must comply with all beIssueslifecyclethroughoutRegularrequirements.councilengagementtheprojectwillberequired.andconcernsmustaddressedwithpriority. High High Monthly meeting External 14 BankstownCanterbury Council PO Box Bankstown8 NSW 1885 Ph: 9707 9000 High High Monthly meeting External 15 Sydney Coordination Office PO Box 588 North Ryde, BC NSW 1670 Ph: 1800 019 989 High High Monthly meeting External Other Agencies 16 Australian Rail Track Corporation PO Box 10343 Gouger Ph:AdelaideStreetSA50001800732761 Provides Sydney Metro Sydenham to Bankstown with access to rail for businesses and producers. Low High Contact as required External 17 Greater CommissionSydney PO Box Parramatta257NSW 2124 Ph: (02) 8289 6200 Coordinates and aligns planning for Sydney Metro Southwest project, and has a direct reporting line to the NSW Government, as an agency under the Department of Premier and Cabinet. Low High Contact as required External Peak Bodies 18 Engineers Australia 11 National Circuit Barton ACT 2600 Ph: (02) 6270 6555 Provides professionalsknowledgespecialisedandtosupport the Sydney Metro Southwest project performance. Low Low Contact as required External 19 Warren Centre for Advanced Engineering Room 530 Computer Science Building The University of Sydney NSW 2006 Ph: (02) 9351 3576 Low Low Contact as required External Industry Associations 20 Marrickville Chamber of Commerce PO Box Marrickville766 NSW 1475 Ph: (02) 9572 6287 Various associationsindustrywill be engaged in the strategies.raiseMetromanagementcommunicationstakeholderofSydneySouthwestprojecttoconcernsandshare Low Low Contact as required External 21 NSW CouncilProperty 11 Barrack Street Sydney NSW 2000 Ph: (02) 9033 1900 Low Low Contact as required External 22 PartnershipsInfrastructureAustralia PO Box R1771 Royal Exchange NSW 1225 Ph: (02) 9152 6000 Low Low Contact as required External 23 Sydney Business Suite 2, L23, 45 Clarence St Sydney NSW 2000 Ph: (02) 9350 8119 Low Low Contact as required External 24 Business Western Sydney Suite P1, Podium 2, 4 Parramatta Square 12 Darcy ParramattaStreetNSW 2150 Ph: 02 9466 4406 Low Low Contact as required External Utility Providers 25 Quenos Gate 3 Denison Street Botany NSW 2019 Ph: (03) 9258 7333 / (03) 9258 7333 (emergency) In Sydney Metro Sydenham to Bankstown, these services will provide necessary utility services during the construction phase as well as delivering services during the infrastructures use. Low Low Stakeholders only need to phases.requiredcontactedbeduringproject External 26 Sydney Water PO Box Parramatta399NSW 2124 Ph: 13 20 92 / 13 20 90 (leaks and faults) Low Low External 27 TransGrid 180 Thomas Street Sydney NSW 2000 Ph: (02) 9284 3000 Low Low External 28 Ausgrid GPO Box 4009 Sydney NSW 2001 Ph: 13 13 65 / 13 13 88 (emergency) Low Low External Community and Interest Groups
The Sydney Metro Southwest project will directly impact local users and thus stakeholders must be kept up to date on project progress. Regular engagement throughout the entire project lifecycle is Membersrequired. are invited to contact Sydney Metro to raise issues or concerns. Feedback will be further discussed and issues managed promptly.
[Low Interest, High Power]: Stakeholders with low interest high power are capable of derailing the project over seemingly minor issues. Therefore, the project management team should keep them satisfied.
[High Interest, Low Power]: Stakeholders with high interest and low power tends to exert a strong influence on project per se, which is conducive to and support the development of
External 30 Broader communitySydney Contact via online forum
[High Interest, High Power]: Stakeholders with high interest and high power will affect the project significantly. They are allowed to participate in all project meeting and interest related activities. They need to be managed closely and fully engaged via quality communication as regular basis.
High High forumandinformationviaCommunicationToll-freelineviaonline 02 9663 8539 Landowners/Employers are invited to active participate in the project consultation on heritage. communicationConstantisrequired.
External 31 Indigenous stakeholdersAustralian
11.2 Stakeholder Analysis (Power/Interest Matrix)
29 Local Badgerys Creek residents businessesand Contact via online forum
External 32 Committee for Sydney PO Box R323 Royal Exchange NSW
High High forumandinformationviaCommunicationToll-freelineviaonline
External
External Major Landowners/Employers 33 Australian Turf Club Ph:
The stakeholder power and interest matrix for Sydney Metro Southwest Project will be created relying on the power that stakeholders exert over this project and the interest which stakeholders express in this project. This matric will facilitate the identification and grouping of those relevant stakeholders, enabling management team to recognise the degree of their concern and level of involvement. Consequently, different strategies can be generated to cope with different problem which is more likely to be posed by respective stakeholder group.
Generally, all the Sydney Metro Southwest stakeholders can be grouped into:
High High forumandinformationviaCommunicationToll-freelineviaonline
210
High High forumandinformationviaCommunicationToll-freelineviaonline Contact via online forum stakeholders will be engaged to preserves local heritage on site. All project staff will undertake cultural awareness training.
Aboriginal
High High forumandinformationviaCommunicationToll-freelineviaonline 1225 (02) 8320
Ph:
6750
[Low Interest, Low Power]: Project management team is more likely to put less effort on the engagement with these stakeholders. They will be monitored via some effective passive engagement Basedmethod.on the methodology stated above, the stakeholder power and interest matrix is created and demonstrated as figure53: With respect to those grouped stakeholders falling in four respective quadrants, the whole stakeholder list will be referred to table 24 which is created aligning with stakeholder register.
211 Sydney Metro Project. Therefore, they need to be kept informed through frequent, efficient, and effective communication.
Figure 53: Sydney Metro Southwest Stakeholder Power/Interest Matrix

212 Table 24: Whole Stakeholder List ID Key Community(Subcontractor,StakeholdersAuthority,andetc.) Power Interest Manage Strategy Sydney Metro Sydenham to Bankstown (Southwest) 1 Board of Directors High High Manage Closely 2 Project Manager High High Manage Closely 3 Project Team (Financial Team, Procurement Team, Legal Team, Architecture Design Team, Engineers, Quantity Surveyors, Site Engineers, Risk Management Team and etc.) High High Manage Closely 4 External Consultants/ Auditors/ Inspectors High High Manage Closely 5 Suppliers High Low Keep Satisfied 6 Contractors High High Manage Closely 7 Subcontractors Low High Keep Infromed 8 End User High High Manage Closely Australian Government 9 Department of Infrastructure, Regional Development and Cities High High Manage Closely NSW Government 10 Department of Planning and Environment High low Keep Satisfied 11 Transport NSW High High Manage Closely 12 Roads and Maritime Services High Low Keep Satisfied 13 NSW Environment Protection Authority High Low Keep Satisfied Local Government 14 Inner West Council High High Manage Closely 15 Canterbury Bankstown Council High High Manage Closely 16 Sydney Coordination Office High High Manage Closely Other Agencies 17 Australian Rail Track Corporation Low High Keep Informed 18 Greater Sydney Commission Low High Keep Informed Peak Bodies 19 Engineers Australia Low Low Monitor 20 Warren Centre for Advanced Engineering Low Low Monitor Industry Associations 21 Marrickville Chamber of Commerce Low Low Monitor 22 NSW Property Council Low Low Monitor 23 Infrastructure Partnerships Australia Low Low Monitor
According to PMBOK GUIDE 6th Edition (2017), to fulfil project stakeholder’s requirements, address issues and facilitate the involvement of appropriate stakeholders, stakeholder engagement will be employed as a process to communicate and work with stakeholders. This process gives an edge in minimising the stakeholder impediment to project progress and fostering support.
The engagement level of stakeholders can be classified into:
▪ Supportive: stakeholders are aware of the project and its potentials and supportive to change
▪ Unaware: stakeholders are unaware of the potential and impacts of the project
▪ Resistant: stakeholders are aware of the project and potential impacts but resist to any changes. They may be unsupportive of the project outcome.
Managing stakeholder engagement for the Sydney Metro Southwest project will utilise the stakeholder engagement assessment matrix created according to the information provider by stakeholder register, ensuring the clear understanding of the stakeholder’s objective, benefit from and attitude towards the Sydney Metro Southwest project. This allows management team to develop a customised plan and take an individualised course of action to make a positive interaction among stakeholders. The probability of project success eventually has a tendency to increase. As for the stakeholder engagement matrix, it achieves the comparison between the current engagement levels of stakeholders and the desired engagement levels demanded for successful project delivery.
213 24 Sydney Business Low Low Monitor 25 Business Western Sydney Low Low Monitor Utility Providers 26 Quenos High Low Keep Satisfied 27 Sydney Water High Low Keep Satisfied 28 TransGrid High Low Keep Satisfied 29 Ausgrid High Low Keep Satisfied Community and Interest Groups 30 Local Badgerys Creek residents and businesses High High Manage Closely 31 Broader Sydney community High High Manage Closely 32 Indigenous Australian stakeholders High High Manage Closely 33 Committee for Sydney High High Manage Closely Major Landowners/Employers 34 Australian Turf Club High High Manage Closely 11.3 Stakeholder Analysis (Engagement Analysis)
▪ Neutral: stakeholders are aware of project, but neither supportive nor unsupportive
214 ▪ Leading: stakeholders are not only support the project but also more likely to engage in promoting the success of it. C and D will be used in this matrix representing the current engagement level of each stakeholder and desired engagement level, respectively. Therefore, the stakeholder engagement matrix of Sydney Metro Southwest is formed as table 25: Table 25: Stakeholder engagement matrix ID Key Community(Subcontractor,StakeholdersAuthority,andetc.) Unaware Resistant Neutral Supportive Leading Sydney Metro Sydenham to Bankstown (Southwest) 1 Board of Directors C, D 2 Project Manager C, D 3 Project Team (Financial Team, Procurement Team, Legal Team, Architecture Design Team, Engineers, Quantity Surveyors, Site Engineers, Risk Management Team and etc.) C, D 4 External Auditors/Consultants/Inspectors C 5 Suppliers C D 6 Contractors C, D 7 Subcontractors C D 8 End User C D Australian Government 9 Department of Infrastructure, Regional Development and Cities C, D NSW Government 10 Department of Planning and Environment C D 11 Transport NSW C, D 12 Roads and Maritime Services C D 13 NSW Environment Protection Authority C D Local Government 14 Inner West Council C, D 15 Canterbury Bankstown Council C, D 16 Sydney Coordination Office C, D Other Agencies 17 Australian Rail Track Corporation C D 18 Greater Sydney Commission C D Peak Bodies
215 19 Engineers Australia C D 20 Warren Centre for Advanced Engineering C D Industry Associations 21 Marrickville Chamber of Commerce C D 22 NSW Property Council C D 23 Infrastructure Partnerships Australia C D 24 Sydney Business C D 25 Business Western Sydney C D Utility Providers 26 Quenos C D 27 Sydney Water C D 28 TransGrid C D 29 Ausgrid C D Community and Interest Groups 30 Local Badgerys Creek residents and businesses C, D 31 Broader Sydney community C D 32 Indigenous Australian stakeholders C D 33 Committee for Sydney C, D Major Landowners/Employers 34 Australian Turf Club C D 11.4 Control Stakeholder Engagement Stakeholders are critical to Sydney Metro’s success. The efficiency and efficacy of engagement initiatives can be maintained and improved by monitoring and controlling stakeholder involvement. Stakeholder engagement monitoring and controlling entails more than just responding to complaints.
• Identify and fix concerns in a timely manner. If a stakeholder's complaint has progressed to the point where the project manager needs to document and address it, do so as quickly as possible. Occasionally, this results in a request for a change to the timeline, scope, or resources.
• Resolve stakeholder issues before they escalate. Conduct one-on-one interactions with specific stakeholders to make sure they understand corresponding issues (e.g., why certain deliverables cannot be achieved in the set timeframe, why their workers are required for specified periods of time). A lot of time and effort will be saved if concerns can be addressed before they become problems.
• Actively manage stakeholder expectations throughout the project's life cycle. Stakeholders’ feedback can assist the designing, construction and operation process. The project management plan and project documentation are written records that detail every facet of the project. These are a desirable way to keep expectations in check.
11.4.2.2
11.4.2.1
♦ Root
Complaint log: this is used to examine customer complaints. Consultations with Stakeholders
♦
♦ Alternate
216 • Keep track of stakeholder engagement. Throughout the project lifetime, communicating and engaging with stakeholders to meet their needs/expectations, addressing issues as they arise, and ensuring appropriate engagement in project activities. 11.4.1 Monitor (Inspect) Stakeholder Engagement: The Stakeholder Management Plan is always used to evaluate the Stakeholder Engagement inspection. Keep a copy of this handy and accessible. Verify that the project's Stakeholder Engagement activities are effective in achieving the following goals: • Managing Expectations of Stakeholders • Gaining a better grasp of the requirements and expectations of stakeholders Cultivating stakeholder support • Addressing developing concerns before they escalate • Increasing stakeholder satisfaction to the greatest extent possible The following are the useful tools for monitoring stakeholder engagement: • Stakeholder satisfaction survey: to collect input on the project's level of satisfaction. (e.g., In what way is this project meeting (or not meeting) stakeholders’ expectations.)
11.4.2 Control (Correct) Stakeholder Engagement Changes are required when monitoring reveals that Stakeholder Engagement is not sufficiently effective. Data Analysis tools: Stakeholder data Analysis and Representation: to determine whose interests should be taken into account more. (Power Interest grid, Stakeholder prioritization) Cause Analysis: to discover the fundamental reasons for a problem Solution Analyses: evaluation of alternate solutions to find the one most suitable Decision Making tools
•
217 ♦ Multi Criteria Data Analysis: leads to selecting an alternate by using weighted criteria ♦ Voting: relevant Stakeholders vote openly or by secret ballot ♦ Communications Skills such as feedback and presentation skills ♦ Interpersonal and Team skills. 12.0 Project Change Control Management Plan During the project development, there will always be new challenges and better ways of doing things, such as changes in project scope, budget, time, and personnel. Change management is a systematic
method that guides the realization of changes in projects and organizations. The project change control management plan helps the project avoid unnecessary changes. At the same time, the change process needs to be carefully planned and implemented before starting the change process. During the change process, it is necessary to track and record the necessary information from the beginning of the project to the delivery process, ensuring the thorough and smooth implementation of the change and generating expectations Impact. In addition, in project change control management, it is necessary to ensure that every change that occurs during the construction process is fully defined, reviewed, and approved before implementation and that all relevant personnel has understood these changes.
12.1 Change management process
Step 1. Identification the change request
218
Change requests for this project will occur in various links in the project cycle, such as schedule, budget, scope, and design. These changes may affect the project baseline, so the project manager must review any approvals and communicate them to relevant stakeholders to confirm the implementation of the required actions.
The change request process is as follows:
This project change control management plan of New Western Sydney Metro will be outlining the detailed plan including Change Management Processes, Change Request Review and Change Control Board.
The change management process is important in all construction projects. Various changes usually occur during the construction process. An orderly and effective process is established to track the submission of change requests, evaluate change requests, approve change requests, and implement change requests.
Step 2. Analysis of Change Requests and associated reporting
First, it is necessary to confirm the reasons for the need to change, determine the changes to the project, and evaluate the affected people and sponsors. The new change plan needs to be specific, measurable, and achievable.
Step 3. Approval or rejection of Change Requests
The change plan may have a significant impact on the current organization or project. It is necessary to evaluate all identified changes and analyze all possible impacts on the business or related stakeholders. At this stage, it is necessary to submit a change request form to the change manager formally, and the change manager will enter the request into the change request log.
All change requests in the change request log will need to go through a formal approval process. If all interested parties agree to the change request, the change request will be sent to the customer
Part 1: For use by individuals submitting change requests.
Part 2: For project managers to record their initial impact analysis of the requested changes.
1.) SUBMITTER GENERAL INFORMATION Change Request NO: Type of Change Request: Enhancement Defect Other Submitter Name: Brief Description: Date Submitted: Date Priority:Required: Low Medium High Mandatory
This process is to test whether the change brings better results to the project. In the implementation phase, monitoring and management of data confirm whether the change process has brought better results.
If the change request is rejected, the applicant and the team will be notified of the reason. Whether it is approved or rejected, the change manager must record all necessary information.
Step 4. Implement the change request
12.2.1 Change Request Form
The relevant project personnel of the new Sydney Metro must fill out a change request form when requesting a change. The change request form is part of the change management process, which can help the project manager better record every change request. At the same time, the project manager can use the change request form to identify the operability of the change request and whether it can bring better to the project Benefit.
Step 5. Tracking changes
219 who made the final decision on the change, and they will make the final approval for the process and may accept/approve the change or reject the change.
The following change application form award is used for the new Sydney Metro project to identify all changes, implement the formal change approval process, and monitor the effects of the implementation changes. This form will be submitted to the Change Control Board.
The form is divided into two parts.
12.2 Change request review
When the change request is officially approved, the change request will be communicated to the submitter of the change request, and changes will be made according to the submitted application.
220 Reason for Change: Intended AttachmentsComments:AssumptionsOutcome(s):andNotes:orReferences Yes No Link: Approval Signature Date Signed 2.) PROJECT MANAGER INITIAL ANALYSIS Hour Impact: [#hrs] Duration Impact: [#dys] Schedule Impact: [WBS] Cost Impact: [Cost] ApprovalRecommendations:Comments:Signature [Approval Signature] Date Signed [mm/dd/yyyy] 12.2.2 Change Request Log: The change request log is used to record all change requests received during the new Sydney Metro project's life cycle, which helps track the change request decision, whether through implementation or rejected request. By monitoring the status of each change request received, the project manager can better control the project scope, budget, schedule, and quality requirements. Change Request Management Log NameProject NumberProject ManagerProject OwnerProject No.Change TypeChange DescriptionChange Status Priority Assigned SubmittedDate ResolutionExpected Action Impact Comments 12.3 Change control board The change control committee is a group of stakeholders responsible for controlling project changes by reviewing, evaluating, and approving or rejecting proposed change requests. All members of the CCB must vote for the change request to be approved. Without the approval of the change control committee, the project change will not be implemented. If more information is required for a particular change request, the request will be returned to the requester for more information. The following table is used by the Change Control Board (CCB) to record their final decision on the requested change. CHANGE CONTROL BOARD DECISION Decision: Approved Approved with Conditions Rejected More Info Decision Date: Decision Explanation: Conditions: Approval Signature Date Signed
Design Consultant Team As a member of CCB, the design manager is solely responsible for reviewing any change requests related to the project design.
Roles Responsibilities
Project Manager - As the chairperson of the CCB, the project manager makes the final decision on the change request
Site Manager As a CCB member, the site manager will provide more practical experience to confirm the rationality of the project change request.
Project Sponsor As a member of CCB, project funders have the right to approve or reject changes in the allocation of funds and changes in the planned budget
- Conduct feasibility studies on design related change requests to evaluate the constructability of design changes - Provide an initial assessment of the advisory membership change request - When submitting the change request form, provide all applicable information in as much detail as possible
- Review and evaluate project performance reports
- Approve or reject any event schedule changes
The following table illustrates the list of change control committees and their roles and responsibilities:
13.1 Strategies of Work, Health and Safety Management
- Review and record all change requests from the project community and stakeholders - Perform analysis of initial risks, cost changes, schedule changes, and scope changes - Monitor construction progress - Control the scope of project construction - Submit updated completed work and cost, quality, and risk reports to project stakeholders
- Be prepared to resolve issues related to the submitted change request, if necessary, provide feedback and suggest the impact of the change
- Monitor and supervise construction progress
13.0 Project Health, Safety and Security Management Plan
221
“Work, Health and Safety” (WHS) is always the most important aspect in Australian construction projects. Sydney Metro has commitment with our delivery partners, which is to ensure everyone goes home safe at the end of the day, and the work environment should not damage the health no matter in the short run or in the long run.
Contractors, sub contractors and their employees who are engaged to undertake work in Sydney Metro Southwest Line Upgrade must comply with all statutory requirements in relation to Work Health and Safety as well as organizational work safety management requirements. The Contractor must, so far as is practicable, provide and maintain a working environment in which people are not exposed to hazards. In particular, Contractors shall: Understand their Work Health and Safety responsibilities. Ensure the health and safety of themselves. Avoid risking the health and safety of any other person. Adhere to all statutory requirements; the requirements outlined in this document; their own WHS policies and procedures. Provide sub contractors and employees with information, instruction, training and supervision to enable them to work in a safe manner. Ensure that all new personnel on site complete an induction to enable them to work. Accept directions related to safe working practices, the requirement to wear appropriate personal protective equipment (PPE) and the use of safety equipment. Provide adequate protective clothing and equipment to their subcontractors’ and employees where
13.2 General guidelines of WHS Responsibilities for Contractors
Apart from what have been mentioned above, here we also would like to emphasize that we put high attention to the silica dust, which is one of the largest risks to workers’ health. The control measures include minimizing concrete cutting on site by using more precast concrete modules, installation of remote control misting system and water cannons towards the cutting area, installation of advanced ventilation system, adoption of wet vac system to clean the working area, provision of boot washers and high grade PPE, monitoring silica dust by sampling pumps and adjusting work practices if any problem is Lastly,identified.weneed
222
to emphasize that it is a basic requirement to meet legal regulations and industry codes in safety work, such as Work Health and Safety Act 2011 (Cth) and Work Health and Safety Regulations 2017 (Cth).
To achieve a satisfactory WHS management, we have a robust audit and review process to verify that work is done in a safe way, and benchmark and review our management systems to continually improve health and safety performance. Besides, we use digital models to simulate construction activities to foresee potential safety risks on site and take preventive or mitigative actions in advance. In addition, we try to use more lightweight plants and trucks in construction, which are more friendly to workers and less likely to cause accidents.
Provide
Provide
Keep
Licenses/Certifications/Registrations are essential qualifications of workers, materials, plants, equipment, vehicles. Permits are usually for construction activities with high risk or significant influence, which is to check if the site condition and the preparation are ready for the work. Please refer to supplementary documents for specific requirements.
Ensure
13.3.1 Checklists
13.4 Evaluation of Safety Performance
It is a widely used tools in construction management, especially when you want to identify risks and validate works. In safety management, checklists are mostly used for identifying safety hazards, checking the alignment with safety manuals and adoption of protective or preventive measures.
Ensure workers obtained white card and get proper training before the start of work. Works should be done in a safe manner. All staffs should be familiar with the emergency response plan and safety reporting requirements.
13.3 Methodologies of Safety Management
13.3.3
Provide
13.3.4 Supervision and Control WHS manager, site manager, foreman should work together to ensure the work safety.
There are some indicators to measure or predict the safety performance. We can take proactive actions when we come across unsatisfactory results of leading indicators and adopt reactive solutions when we detect unsatisfactory lagging indicators in monitoring and review of works. Here below are some examples of indicators.
13.3.2 Construction Induction and Safety Training
Licenses/Certifications/Registrations/Permits
13.3.5 First Aid Team Ensure there are enough first aiders on site. Make sure the first aid office is available during the construction.
Ensure
223 hazards cannot be eliminated. their work site is maintained in a safe condition for themselves and others. documented evidence that they, their subcontractors and employees have all the necessary licenses/insurances for the work they are about to perform. risk assessments and safe work method statements for any work they are about to perform. the responsible officer fully informed of any activities that pose or may potentially pose a hazard to the safety or wellbeing of any person. the WHS plan and emergency plan are well prepared and maintained. Conduct internal job safe analysis periodically. Safe Work Method Statement and inspection reports.
224 Percentage of workers passing WHS knowledge Test Average Response Time to Safety Hazards. Injury Frequency & Severity. Frequency of Near Misses. Workers’ Compensation Claims. Fatality Rate 14.0 Construction Environmental Management Plan This Construction Environmental Management Plan (CEMP) and associated Sub plans have been prepared to comply with the requirements of the planning approval SSI 8256, contract requirements for
This framework will be in accordance with the Sydney Metro City & Southwest Sydenham to Bankstown Staging Report Biodiversity, Groundwater, Air Quality and Waste and Spoil are included within the CEMP as ERAPs (Procedures).
225 environmental management, relevant environmental legislation and other environmental obligations associated with the project.
The construction environmental framework(figure54)illustrates the relationship between relevant statutory requirements and approval documentation and plans.
Figure 54: CEMP Framework Overview
This CEMP has been developed to ensure that construction work considers aspects of environmental protection within the context of compliance with contractual, legal and other environmental requirements including the Conditions of Approval, Revised Environmental Mitigation Measures and Construction Environmental Management Framework.
The CEMP is intended to ensure that positive and negative effects on the environment are assessed as they relate to organisational stakeholders including those described in Laing O’Rourke’s (LOR) Health, Safety and Environmental Management System (HSEMS).
14.1 CEMP Structure Overview
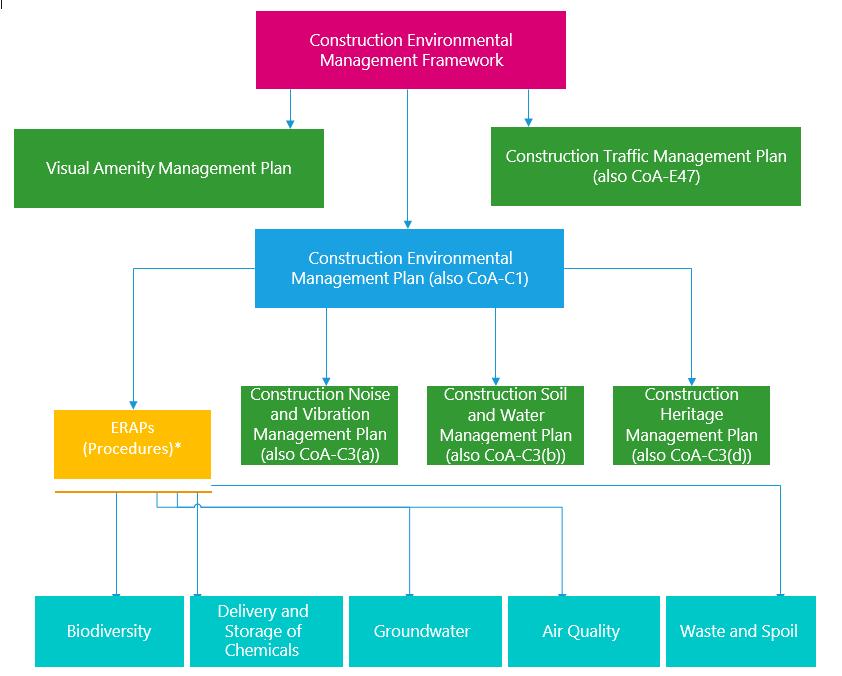
226 14.2 Scope of Proposed Environmental Management Work 14.2.1 CEMP Framework High Level Objectives and Targets High level objectives and targets for this project are based on the CEMF are listed in Table 26 Table 26: CEMF High Level Objectives and Targets Objective Targets Reporting Monitoring/ Compliance with the Minister for Planning’s Project Planning Approval and all permits and licences Full compliance with the planning approval, all permits and licences TrackingComplianceProgram Implementation of the performance andmeasurescommitmentsoutcomes,andmitigationspecifiedintheEISSPIR. Full compliance with the performance outcomes, commitments and mitigation measures specified in the EIS and SPIR. TrackingComplianceProgram Leadership proactively manage performanceenvironmental Leadership attendance rate at environmental inspections at 80% Actual vs. planned attendance at planned environmental awareness training at 80% (excludes tool boxes and inductions) Inspection reports attendanceTraining sheets Quality of relationships with Representative,Environmental EPA official and Heritage Council Score from quarterly survey with Environmental Representative, EPA official and Heritage Council (as applicable) is greater than 65% on a rolling average Survey report 14.2.2 Responsibilities and Authorities Roles Key Responsibilities and Authorities Project Director (Project Leader) ▪Reports to senior management within John Holland and Laing O’Rourke •Ensure that internal audits of the system are conducted •Review audit corrective actions and take action as necessary to ensure timely close out of issues •Authorise expenditure on environmental issues within limits of authority •Resolve major issues which cannot be resolved by the Project Manager Must complete corporate and project induction covering environmental responsibilities and LORs’ environmental management system •Approve and implement the CEMP •Ensure that the CEMP is effectively implemented and maintained •Appoint/nominate and provide support for the Environmental Manager ▪Report to senior management on the performance of the system and environmental breaches Manager)(ConstructionManagerProject •Reports to the Project Director •Support the Project Director in environmental matters as required •Oversight of environmental requirements for design and construction •Must complete corporate and project induction covering environmental responsibilities and LORs’ environmental management system.
227 •Supervise all site construction activities and personnel by ensuring that they meet environmental and other requirements •Organise and manage site plant, labour and temporary materials •Ensure that site environmental controls are properly maintained and provide support for the Environmental Manager •Report all environmental incidents O’RourkeLaing RegionalHollandLeader/JohnHSE •Provide environmental support to the project team •Coordinate internal audits ManagerEnvironmentalProject •Reports to the Project Director •Ensure that the CEMP is effectively established, implemented and maintained at the project level •Ensure all project personnel are aware of the CEMP and their responsibilities •Ensure compliance with all relevant statutes, regulations, rules, procedures, standards and policies •Ensure that all personnel on site receive appropriate environmental induction and training and are aware of their environmental responsibilities under relevant legislation and the contract •Report to the Project Director on the performance of the system and improvement opportunities •Provide support to the project team to enable them to meet their environmental •Ensurecommitmentsthatenvironmental records and files are collected and maintained •Regular compliance checking as required by this CEMP •Liaise directly with the Independent Environment Representative as required and where appropriate to facilitate any environmental management requirements, including those identified within the Planning Approvals. The Project Environmental Manager will be the primary contractor contact for the Independent Environmental Representative •Must have tertiary qualifications in environmental engineering / science along with relevant experience working in environmental management roles in Australia. Infrastructure Sustainability Accredited Professional preferred ManagerRelationsandCommunicationStakeholder •Leadership and management of the Communications, Stakeholder and Community Relations Team •Build and maintain effective working relationship with TfNSW’s representative and Stakeholder and Community Liaison team •Develops and oversees the implementation of the CCS and subplans •Responsible for a stakeholder and community relations induction and training program for all personnel involved in the performance of the project •Approves the Communications, Stakeholder and Community Relations team roles, role descriptions and responsibilities •Ensures the Community Communications Strategy and key activities are integrated into the project schedule •Attends the TfNSW led Communications Management Control Group and reports on activities, strategies and issues PlaceCommunityManager •Build and maintain effective working relationship with community, businesses, and stakeholders
228 •Support the successful delivery of the project’s Community Communication’s Strategy and •ImplementationrequirementsoftheCommunity Communications Strategy and any relevant •EstablishSub-plans effective working relationships with local stakeholder to support the effective delivery of the project •Required to be on call 24 hours based on the team rotation to respond to enquiries and complaints. •Review, approve and oversee the development and distribution of all notification, newsletter, social media, photography, and other communication material. CoordinatorTrainingProject •Develop a Training Needs Analysis to identify relevant environmental training for all contractor (and subcontractor, where appropriate) personnel •Develop environmental training materials in consultation with the Project Environmental Manager Subcontractor • Comply with all legal, contractual requirements and this CEMP •Comply with site environmental requirements •Comply with management / supervisory directions •Participate in induction and training as directed •Report all •Environmentalincidentsqualifications as required by contract •Must complete project induction covering environmental responsibilities and LORs’ environmental management system. 14.3 Project Environmental Management Planning 14.3.1 Legal and Compliance Requirements Mandatory compliance obligations and requirements relevant to the project are summarised below. The Compliance Obligations Environmental System Requirement LOR’s HSEMS outlines the process LOR uses to determine legal and other mandatory requirements.
• City and Southwest – Sydenham to Bankstown Compliance Monitoring and Reporting Program Report (Sydney Metro, 2019).
• Sydney Metro City & Southwest – Sydenham to Bankstown Upgrade Staging Report (Sydney Metro, 2019).
The Overarching Stakeholder and Community Involvement Plan (Sydney Metro Community Consultation Strategy (CCS));
•
The Sydney Metro Southwest Project will be carried out in accordance with the following consents;
The Sydney Metro City & Southwest – Sydenham to Bankstown – State Significant Infrastructure Assessment (SSI 8256), dated 12th December 2018
The Sydney Metro Construction Environmental Management Framework v3.2;
• Department’s Guideline for the Preparation of Environmental Management Plans.
The Sydney Metro Construction Noise and Vibration Strategy (including out-of-hour works protocol)
Full details of the relevant legislative instruments are provided in Appendix J 14.3.2 Standards and Codes
Table 27:Relevant Standards Standard/Guideline Relevant Authority ISO 14001:2015 Environmental Management Systems – Requirements with Guidelines for use DPIE Guideline for the Preparation of Environmental Management Plans (Department of Infrastructure, Planning and Natural Resources, 2001) DPIE Interim Construction Noise Guidelines (Department of Environment and Climate Change, 2009) EPA Managing Urban Stormwater: Soil and Construction (Landcom, 2008) EPA/DPIE AS4282:1997 Control of the Obtrusive Effect of Outdoor Lighting Australian Standards Waste Classification Guidelines (Department of Environment, Climate Change and Water, 2008) EPA AS 1742.3 Manual of uniform traffic control devices Part 3: Traffic control for works on roads RMS (TfNSW) RMS Traffic Control at Worksites Manual RMS (TfNSW)
229
•
•
•
•
•
The environmental publications, standards, codes of practice and guidelines included in Table 27 are relevant to Sydney Metro Southwest Project and are referenced throughout this Plan.
•
The Sydney Metro City & Southwest – Sydenham to Bankstown – Submissions and Preferred Infrastructure Report June 2018;
The Sydney Metro City & Southwest – Sydenham to Bankstown – Instrument of Approval, dated 12th December 2018
The Sydney Metro City & Southwest – Sydenham to Bankstown - Environmental Impact Statement , dated 7th September 2017;
An outline of the LOR HSEMS is provided in Appendix K 14.3.4 Environmental Policy
The HSEMS is available to access via https://nextgearsms.com. The system includes three core environmental components: System Requirements, Environmental Primary Standards and Severe Environmental Risk protocols.
The Company is currently certified (No. 4749) with SciQual(Appendix K)
230 Australian and New Zealand Guidelines for Fresh and Marine Water Quality EPA
This Plan references relevant parts of the Company’s environmental management system and incorporates the additional elements necessary to satisfy the client’s environmental system requirements.
A Joint Venture (JV) Environmental Policy has been produced for the project. The Policy states in Appendix L Sydney Metro Environmental&Sustainability Policy(SM SE MM 102) will be referred to Appendix L
All works carried out on the site (including works carried out by sub contractors and others) will be in accordance Clientwith: requirements as detailed in the Contract LOR’s environmental requirements, as detailed in the HSEMS ISO 14001:2015 Environmental Management System LOR’s compliance obligations including mandatory and voluntary requirements.
AS/ NZS 1940: 2017 - The Storage and Handling of Flammable and Combustible Liquids Australian Standards 14.3.3 Health, Safety and Environmental Management System
The environmental policy differs from the quality policy in that it dictates how construction activities should be conducted from a environmental perspective. And this also includes the degree to which the performing organization’s management is committee to social responsibility and environmental conservation issues.
LOR maintains an industry leading HSEMS that is applied across all operations and is accredited by Sci Qual International to ISO 14001:2015 Environmental Management Systems – Requirements with Guidance for Use
231 14.3.5 Environmental Management Flowchart associated with Responsibilities Figure 55: Environmental Management Flowchart 14.4 Project Environmental Management Executing 14.4.1 Environmental Risk Assessment and Control The Risk Register established outlines the environmental aspects that need to be assessed and effectively managed to meet LOR’s environmental obligations with respect to the context of the organisation and
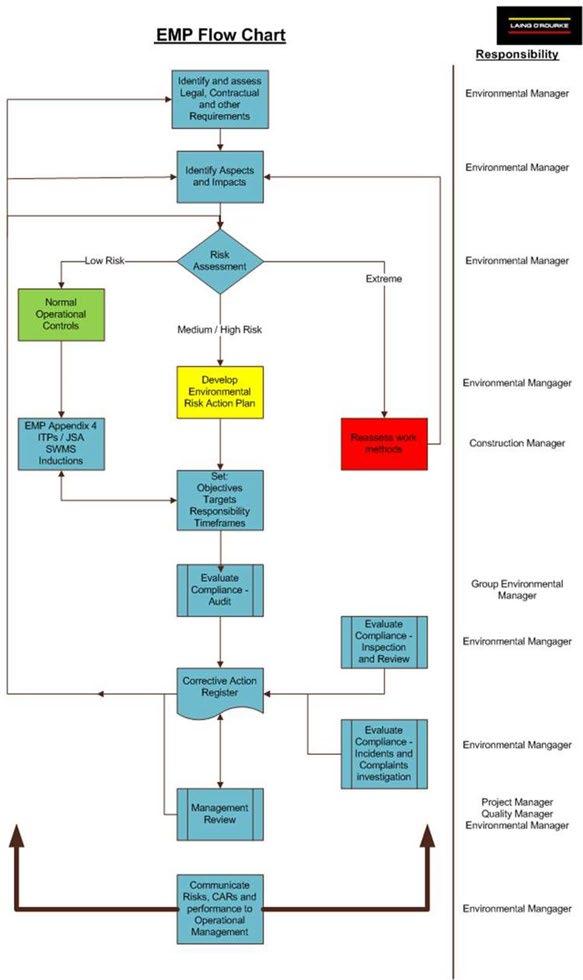
The Project Environmental Manager will establish a schedule of environmental training in conjunction with the development of this CEMP. Training in high risk aspects shall be undertaken as the project progresses. The proposed training as identified through the Training Needs Analysis (produced by the Project Training Coordinator) is presented in Table 28 below. The training shall be scheduled to reflect the requirements of the construction program.Table28:
Personnel Required Timing
232 its projects. The register is to be used to inform the development of the project- specific aspects and impacts register and associated risk and opportunity assessment.
14.4.2 Training, Awareness and Competence
Requirements for training, awareness and competence for environmental aspects and impacts are outlined in System Requirement Onboarding, Training, Induction and Verification of Competency (VOC) and this management plan. All employees will receive suitable environmental induction / training to ensure that they are aware of their responsibilities and are competent to carry out the work.Environmental requirements will be explained to employees during site induction and on-going training via toolbox meetings, briefings, notifications and the like. Training in the operation and implementation of LOR HSEMS shall be provided for all operational staff.
Leadership • Effective leadership • HSEMS
Project wide environmental risks and opportunities are assessed in the project's Risk and Opportunity Register. This register which Site specific environmental aspects and impacts have been identified and assessed in Project Risk Register Appendix I. Project risk and opportunity assessments must be reviewed and updated as the project progresses and as a minimum as part of the CEMP management review. The project's Risk and Opportunity Register must be maintained on a monthly basis or as required and must include project wide environmental risks and opportunities.
Aspect Training Inclusion / Frequency/Means Management basis
Proposed Training
Frontline Leadership Modules – ongoing
233 Emergency Spill Response • Use and location of spill kits • Spill control • Emergency response procedures • Presentation and assessment • Spill response drill • Identification of hydraulic hose fatigue ManagementpersonnelOperational Project Induction Project Toolbox Talks Erosion SedimentandControl • Standard erosion and sediment controls from the Landcom 'Blue Book' • Implementation of controls on site • Erosion and Sediment Control Plans ManagementpersonnelOperational Project Induction Project Toolbox Talks AwarenessHeritage • Stop works and reporting protocols for discovery of previously unknown heritage and archaeological items • Identification of heritage items/areas zonesarchaeologicalandmanagement ManagementpersonnelOperational Project Induction Project Toolbox Talks Protocol posted on message boards AwarenessContamination • Contamination status of site • Stop works protocols for unidentified asbestos,contaminationpotential(hydrocarbons,etc) ManagementpersonnelOperational Project Induction Project Toolbox Talks Protocol distributed to workers and posted on message boards LegalEnvironmentalObligations • POEO Act and other project requirements • Applicable fines and prosecutions ManagementpersonnelOperational Project Induction Project Toolbox Talks Energy ResourceandUsage • Awareness training of energy and resource efficiency in the workplace office/compoundincludingand site initiatives such as harvesting rainwater for dust suppression instead of potable mains water and use of bio fuels ManagementpersonnelOperational Project Induction Project Toolbox Talks Community / AwarenessStakeholder • Adjacent community and Project involvement • Relevant Project stakeholders • Accepted behaviours • Approved hours of work ManagementpersonnelOperational Project Induction Project Toolbox Talks Biodiversity • Wildlife status of project and surrounds • Stop work and reporting protocols for injured wildlife,trees and vegetation • Measures to stop feral animals coming to site ManagementpersonnelOperational Project Induction Project Toolbox Talks Noise and Vibration • Work hours personnelOperational Project Induction Project Toolbox Talks
The project Environmental Control Maps (ECMs) are prepared to assist in the planning and delivery of the project. It is specific to the site or work area and outlines the location of protection measures, monitoring requirements, conditions of approval and environmentally sensitive areas. It is the practical application of the proposed control measures.
14.4.3
The project ECM may include but not limited to:
Location of site offices
Environmental Management System Audit
The worksite layout and boundary, including entry/exit points and internal roads and clearing Locationlimitsofadjoining
14.5.1 Environmental Control Map
Vegetation and trees to be protected
234
Location of known heritage (indigenous and non indigenous) items
Auditing of the project HSEMS will be carried out in accordance with the System Requirement Compliance, Review and Assurance. The audit will evaluate compliance with this CEMP and associated documentation including legal, contractual and other requirements.The audits will be conducted by either the LOR Environment Leader (or delegate), the John Holland Regional Manager (or delegate) or the Project Quality Manager It is expected that the project will be audited within 3 months of commencing on site and approximately every 6 months thereafter and in accordance with the Audit Schedule. The relevant HSE Leader, in consultation with the project leadership team, will decide on the frequency, scope and timing of project/site audits.An audit report will be issued to management for action. Actions will be followed up for close out of actions within 1 month of the issue of the audit report.Audits shall be captured within the Assurance application in Impact. Actions associated with audits shall also be logged in the Assurance application in Impact.
14.5 Project Environmental Management Monitoring and Controlling
Location of worksite waste management facilities
Hours of work applicable to the worksite (including deliveries and any restrictions on high noise generating activities).
land use and nearest noise sensitive receivers
Location and type of sediment and erosion control measures, including size / capacity of detention basins and wheel wash facilities
Location of spill containment and clean up equipment
Location of environmentally sensitive areas (e.g. threatened species, critical habitat, contaminated areas, heritage zones, etc.)
235 Location of stormwater drainage and watercourses leading to / from the worksite Specific environmental management requirements from licenses, approvals or permit conditions There are two ECM of southwest line stations(Canterbury and Bankstown) as an example shown below:Figure56: Environmental Control Map of Cantebury Station
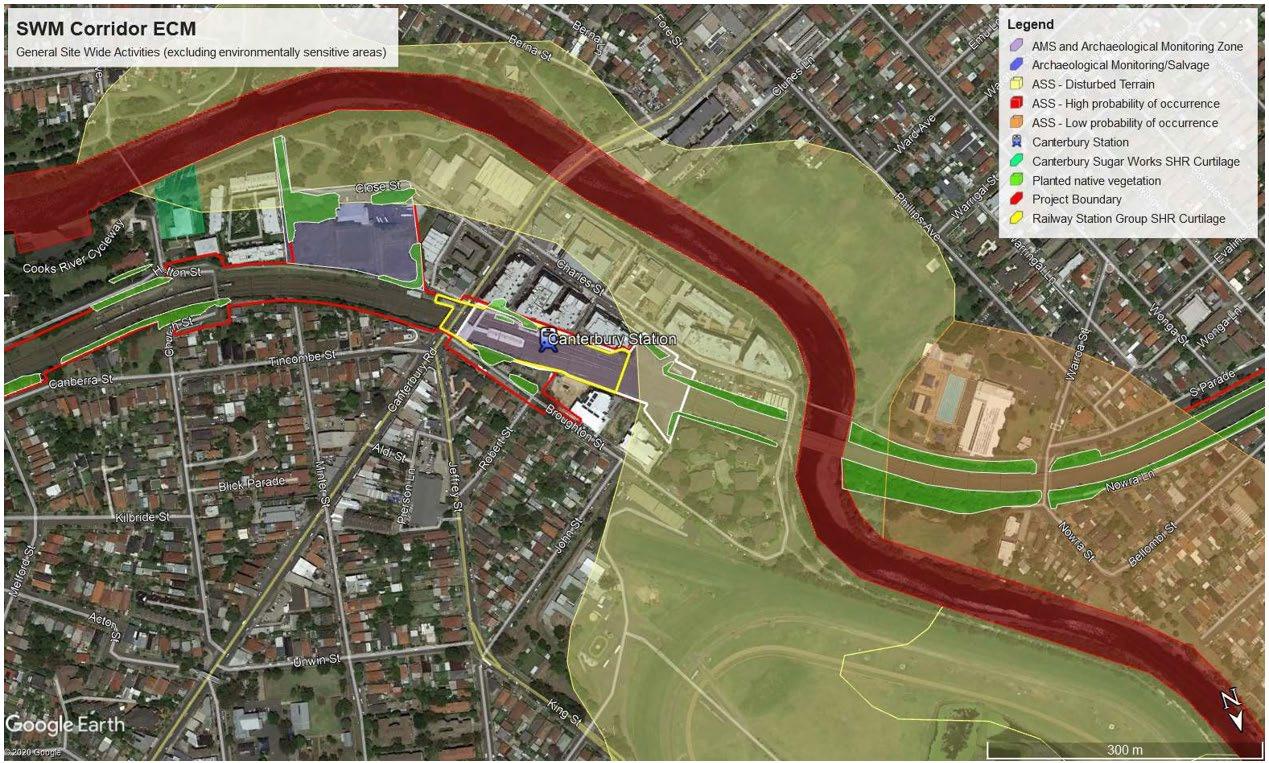
236 Figure 57: Environmental Control Map of Bankstown Station
Site shutdown periods must be planned and coordinated to ensure the risk of environmental impact is minimised. Shutdown periods are considered to be any period in which construction activities are not planned to take place on the site for more than 3 consecutive days. This includes public holiday and Rostered Day Off (RDO) periods. Site shutdown planning must be undertaken in accordance with System Requirement Environmental Planning. Planning activities must ensure that inspections, resources and contingency measures are agreed and implemented for the shutdown period. This is to be documented in a specific Shutdown Go Pack.
14.5.2 Site Shutdown Plan
14.6.1 Environmental Monitoring
14.6 Monitoring and Measurement
Key characteristics of the project operations and activities which have a significant impact on the environment will be regularly monitored and measured. This will include:recording of information to track performance monitoring operational controls level of conformance with objectives and targets
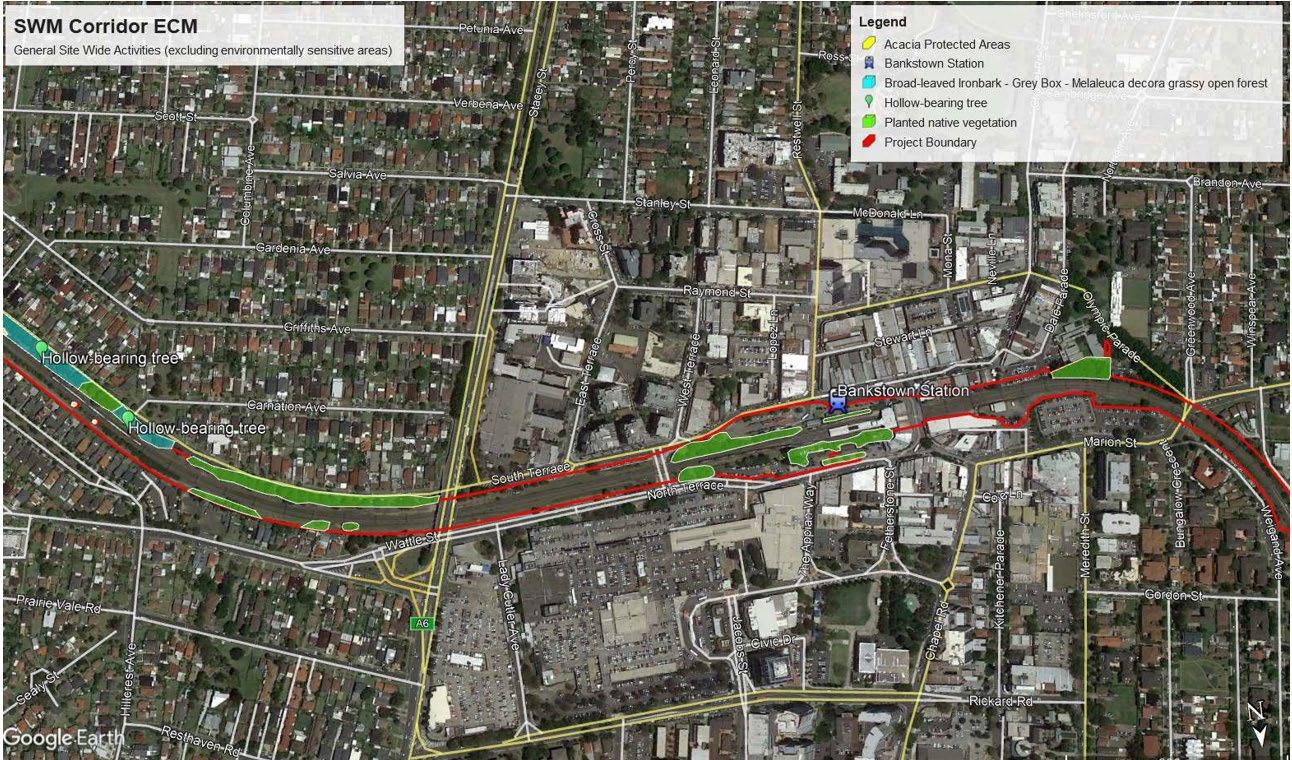
Monthly Conditions
237
relevant regulatory agencies) • Procedures to
(based
Monthly Waste
Quarterly
mitigation
System Requirement Criteria Frequency SER Program Program implemented and actions complete Monthly onimplementatiinspectionSite Site
The Management Site Safety and Environment Inspection Report will be completed each week by the project’s Supervisors to monitor environmental issues on site. The reports will be issued to the Project Leader/ Site Manager for review and signing. Construction Monitoring Program data (including dates of when the data will be obtained) frequency of results to the Planning Secretary and identify and implement measures on results)
monitoring
and location of monitoring • Details of reporting
The
(including
• Details of consultation 14.6.2 Monthly Project Environmental System
Monthly ProgramMonitoringEnvironmental
On a monthly basis, the project will assess the performance and implementation of the project environmental system through the project Environmental System Self-check. Outcomes of the project environmental system self-check are to be retained in the project records. inspections have been completed in accordance with the environmental management plan requirements. Event management Environmental incidents have been reviewed, investigations completed and actions closed out. Environmental monitoring has been completed and reviewed for compliance. Non compliances have been actioned and closed out management Project waste management register is up to date including spoil management and disposal of Approval tracking Conditions of approval compliance matrix has been reviewed and updated demonstrating compliance with conditions Environmental licence compliance has been reviewed and reporting completed as nominated.
Monthly
The Environmental Inspection Report will be used to monitor environmental issues on site and issued to the Project Leader. The report will be completed on a weekly basis. The Environmental Inspection Report may be updated for Project specific risks.
Quarterly LicencesEnvironmental
• Details of all monitoring to be undertaken • The parameters,
will include: • Details of baseline
To be specificlly, the subsidiary project management plans with detailed sections include: • Project Charter • Project Scope Management Plan • Project Scope Definition • Project Scope Statement (PSS) • Work Breakdown Structure (3 levels) • WBS Dictionary (1 Dictionary) • Project Scope Validation and Verification Process • Project Monitoring and Control system • Scope Change Management Process • Project Schedule Management Plan • Project scheduling methodology • Activity identification process • Estimate activity duration method • Activity sequencing method • Schedule baseline • Schedule monitoring and control • Project Cost and Financial Management Plan • Cost estimation and budget determination methods • Cost Breakdown Structure • Cash flow diagram or cost baseline • Cost management roles and responsibilities • Cost performance measurement (earned value management) • Cost variance response process • Cost change control process • Project Quality Management Plan
Recommendation
Project key stakeholders and team members are encouraged to apply this CPMP to serve as solutions to any management issues with specific management plans, protocols, processes and tools for all aspects regarding the Sydney Metro Southwest project. This CPMP covers various aspects of how the project will be planned, executed, and controlled. Tools, techniques and methodologies also provided as this document is also made as a guidance purposes for the appointed contractor for the construction of Sydney Metro Sydenham to Bankstown.
are
This document namely Construction Project Management Plan (CPMP) has been created by Group 20 Construction Planning Company to provide a thorough, well researched and extensive guideline detailing all the information for the management, planning and execution of Sydney Metro - Sydenham to Bankstown, part of Australia’s biggest public transport project.
Conclusion and
238
Conclusion
239 • Quality Planning (Identify Roles and Responsibilities for QM team) • Quality Planning (Quality Standards, Processes, Procedures, Tools, Quality Metrics and Checklists) • Quality Assurance Process • Quality Control Process • Project Resource Management Plan • Organisational Breakdown Structure (OBS) • Roles and Responsibilities • RACI Matrix • Staff Acquisition and Release Plan • HR Resource Calendar and HR Resource Histogram • Machinery and Equipment Resource Histogram • Staff Induction and Training Plan, Performance Review, Staff Recognition and Rewards, Compliance, Equity and Safety • Project Risk Management Plan • Risk Management Methodology • Risk Identification Process and Categories (Risk Breakdown Structure) • Definition of Risk Probability and Impact/Probability and Impact Matrix • Risk Response Plan • Risk Control Process • Risk Register • Project Procurement Management Plan • Procurement methodologies • Procurement process diagram • Designated responsible organisation (DRO) log or package list • Hire or buy analysis/make or buy analysis • Contract type selection • Source selection criteria • Procurement metrics to evaluate and select sellers, vendors or subcontractors • Procurement controlling process and contract administration • Procurement closing process • Project Communication Management Plan • Communications Requirement • Communications Matrix • Communications Tools and Technologies • Project management Information System (PMIS) • Template for Project Performance Report • Project Stakeholder Management Plan • Stakeholder Analysis (Identification/Stakeholder Register) • Stakeholder Analysis (Power/Interest Matrix) • Stakeholder Analysis (Engagement Analysis) • Control Stakeholder Engagement • Project Change Control Management Plan • Project Work, Health and Safety (WHS) Management Plan
• improved CCTV surveillance, platform screen doors, and platforms level with train floors;
• safe and efficient connections during the peak and non peak periods between key centres along the T3 Bankstown Line; and
• Delivery of an upgrade and convert all 11 stations between Sydenham and Bankstown to metro standards;
And, the benefits after the complation of the Sydeny Metro Sydenham to Bankstown, including
240
These management plans allow the construction team members to be able to identify any issues throughout the project lifecycle within the Sydney Metro Sydenham to Bankstown and come to this Construction Project Management Plan (CPMP) for reference. All necessary diagrams, documents and forms (e.g. Risk Register), are attached in the Appendices to this CPMP. Any changes to the scope, baseline plans, or risk management must be updated immediately in this plan and communicated constantly to all key project stakeholders. This document is to be used as a formal document for project management throughout the entire project, therefore highlighting its importance that all related construction project personnel are familiar with this Meanwhile,CPMP.
• Facility opened by the agreed date.
The key success factors for the Sydney Metro Southwest project are:
• an air conditioned metro train every four minutes in the peak;
• less time spent waiting due to higher frequency services;
• Project meets budget; and
• fully accessible stations including lifts;
understanding principle project deliverables, schedules, baselines, safety management protocols and quality control processes will also ensure the Sydney Metro Southwest project is delivered to the client smoothly, achieving the highest quality possible and aiming to be performed on budget, and schedule.
• all trains stopping at all local stations no waiting for the right train;
• Project meets all legislative regulations and requirements;
• reduced travel times to key employment and education precincts.
This Construction Project Management Plan (CPMP) should be used as the formal document for any management issues or concerns that arise. It is Sydney Metro and the delivery partners recommendation that this project would be undertaken and commenced immediately in order for the operation of Sydney Metro Sydenham to Bankstown to start operation in 2024.
Moreover, in order to achieve the best performance and construction possible, it is recommended that the subsidiary project management plans in this document also adhere to the suggestions and feedback from the New South Wales Government and the Local Community, which also needed to regular review with internal/external audits involvements to ensure a high quality of construction and a well organised project management process.
Recommendations
Besides, this Construction Project Management Plan (CPMP) should be informed by all project personnel in order to allow for the Sydney Metro Southwest Project (Sydenham to Bankstown) to be performed with the highest quality possible. Furthermore, this CPMP should also be monitored, updated and communicated with various project stakeholders regularly throughout the entire project lifecycle of the Sydney Metro Southwest Project. Any changes or amendments will be noted in the Revision History at the cover page of this document. And it is recommended that this Plan will be updated bi annually at minimum, though also at any time as a direct result of:
• Changes in design or construction sequence, staging, methodology or resourcing,
• The status and progress of the works activities
241
• Changes directed by Sydney Metro Representative under the contract Any reviews/changes resulting in the delay in Practical Completion Date, or Reduction in Margin Dollar Value > 5%, or change in legal/commercial obligations will require approval (sign off) from Senior Management. The Project Manager should be also responsible for reviewing the Project program on a monthly basis to ensure that the current program is not being compromised and to take remedial action if current performance is not achieving the program milestones. They will also have the opportunity to highlight any key concerns or aspects of the progress of the program at weekly site meetings or toolbox talks.
• Changes to access to site, and
242 Reference: Australian and New Zealand Infrastructure Pipeline (2021). Project Sydney MetroInfrastructure Pipeline. Retrieved BONG.(2019).CPB%20andmetro#:~:text=The%20NSW%20Government%20awarded%20a,venture%20comprising%20https://infrastructurepipeline.org/project/sydneyfrom%20UGL QUALITY OBSERVATION / AUDIT - GENERAL CHECKLIST. Retrieved from: https://idoc.pub/download/general-quality checklist in-construction-x4e6j7mw09n3 Duboudin, T. (2021). Sydney Metro awards oversight contract. Retrieved from: https://www.railjournal.com/passenger/metros/sydney metro awards-oversight-contract/ Furnival, S. (2018). 7 Microsoft Project Features You Need to Use. Retrieved from Özdemir,historicalMacrotrends,a-control-VariationLucidBusinessLecturesLee,https://reqtest.com/testingHellgren,https://www.sherweb.com/blog/office-365/o365-7-microsoft-project-features/M.(2013).QualityAssurancevsQualityControl.Retrievedfrom-blog/quality-assurance-vs-quality-control/B,(2020).BLDG3023ConstructionBusinessStrategyandEntrepreneurship2&3EnvironmentalScanning-Week6:ProfitandCostManagement,andDevelopment.ContentTeam.ControlChart:AKeyToolforEnsuringQualityandMinimizing|LucidchartBlog.Retrievedfromhttps://www.lucidchart.com/blog/how-to-make-chart(2021).Australian-USDollarExchangeRate(AUDUSD)-HistoricalChart,Retrievedfromhttps://www.macrotrends.net/2551/australian-us-dollar-exchange-ratechartM.(2010). A probabilistic schedule delay analysis in construction projects by using fuzzy logic incorporated with relative importance index (RII) method [M.S. - Master of Science]. Middle East Technical University. Pica,M.(2015). Project Life Cycle Economics: Cost Estimation, Management and Effectiveness in Construction Projects. Surrey, England. Gower Publishing Limited. Project Management Institute. (2017). A guide to the Project Management Body of Knowledge (PMBOK guide) (Sixth edition). Newtown Square, Pennsylvania USA: Project Management Institute, Inc. Project Management Institute. (2016). Construction Extension to the PMBOK® Guide. Reserve Bank of Australia, (2021). Interest Rate in Australia. Retrieved from https://tradingeconomics.com/australia/interest rate
Sydneyhttp://majorprojects.planning.nsw.gov.au/index.pl?action=view_job&job_id=8256fromMetro(2018)
Sydenham to Bankstown Submissions and Preferred Infrastructure Report. NSW Government Transport for NSW. Retrieved http://majorprojects.planning.nsw.gov.au/index.pl?action=view_job&job_id=8256from Sydney Metro- Southwest Metro Upgrade Update, (2021). Retrieved from: https://www.sydneymetro.info/article/southwest-metro-upgrade-update Sydenham to Bankstown Rail Link | Sydney Metro. (2021). Retrieved from: Sydneyhttps://www.sydneymetro.info/citysouthwest/sydenham-bankstownMetro.(2021). Sydenham to Bankstown Upgrade – Staging Report (5th ed.).
Rumane,A,R.https://www.rpsgroup.com/projects/sydney-metro/(2018).
SydneylibrarySouthwestSydneyss%20Cahttps://www.sydneymetro.info/sites/default/files/Sydney%20Metro%20CSW%20Businefrom:se%20Summary.pdfMetro,(2018).IndependentEnvironmentalAuditonSydneyMetroCityand–DesignFinalReport.Retrievedfromhttps://www.sydneymetro.info/document-Metro(2018)
243 Rosvold, S. (2016). 4 Things Your CEO Needs To Know For Sound Financial Management. Retrieved from https://businessfinancialconsulting.com/what-your-ceo must-know-aboutfinancial management/ RPS. (n.d.). Projects Sydney Metro. Retrieved from:
Quality Management in Construction Projects. Second Edition.Boca Raton, America. Talor&Francis Group,LLC CRC Press. Siddiqui, I.A. (2014). Quality Assurance Plan (Civil Work). Retrieved https://www.researchgate.net/publication/260715118_Quality_Assurance_Plan_Civil_Workfrom Southwest Metro project update, (November 2020). Retrieved from Statista,library/Southwest_Metro_Newsletter_Novhttps://www.sydneymetro.info/sites/default/files/document-ember_2020.pdf(2021).InflationRateComparedtothePreviousYear. Retrieved from https://www.statista.com/statistics/271845/inflation rate in australia/ Sydney Metro, (2016). Final Business Case Summary. Retrieved
Sydenham to Bankstown Environmental Impact Statement. NSW Government Transport for NSW. Retrieved
244 Sydney Metro. (2018). Industry briefing. Retrieved Sydneylibrary/Sydney_Metro_Industry_Briefing_April_2018.pdft-https://www.sydneymetro.info/sites/default/files/documenfromMetro.(2018). Sydenham to Bankstown, Submissions and Preferred Infrastructure Report. (p. Appendix B - Preferred project description). Sydney Metro. (n.d.). Sydenham to Bankstown Rail Link. Retrieved from Sydneyhttps://www.sydneymetro.info/citysouthwest/sydenham-bankstownMetro(2021).SydenhamMetroUpgrade-ConstructionTraffic Management Plan Revision 19, Retrieved Thomas,https://sydenhamstationupgrade.com/sydenhamstationupgrade/fromE,Uher.(2003). Programming and Scheduling Techniques. Sydney, Australia: University of New South Wakes Press. WORKSAFE VICTORIA (2017). DOMESTIC LIFT INSTALLATION – ONSITE CHECKLIST. Retrieved from: https://www.mbav.com.au/sites/default/files/ISBN Domestic lift WSP.installation-onsite-checklist-2017-06.pdf(2017).SydneyMetroCity&Southwest. Retrieved from: https://www.wsp.com/en AU/projects/sydney-metro city-and-southwest
Also, the normal distribution density function can be depicted as a Bell Shape shown as TFigurefigure1:1:hearea of the shadow represents the probabilities associated with a normal distribution. When people try to solve the issue in real world with normal distribution, the practice is to transform the normal random variable into standard normal random variable, being widely available in computer packages.
In Normal Distribution, a random variable X with probability density function which is: , The parameters of this function And the expected value and standard deviation are , respectively. , this is used to denote the distribution.
A: Normal Distribution and Standard Normal Distribution
245 Appendix Appendix
Therefore, the normal variable X can be standardised into Z, which
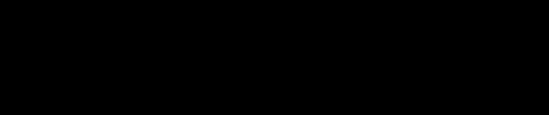
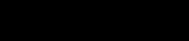
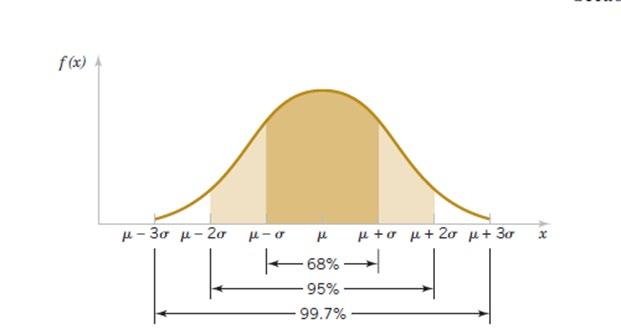
The standard normal distribution density distribution can be defined as: And the probability relating to the standard normal distribution is the shaded area (figure 3): Therefore, for an example, the probability P(Z≤1.5) equals the value of Figure 3:
Figure 2:
246 , a standard random variable, and is used to denote the distribution (figure 2).
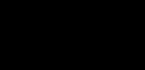
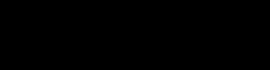

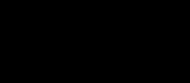


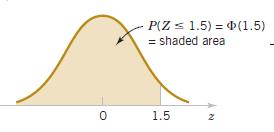
247 Appendix B: The Probability Table for a Normal Distribution
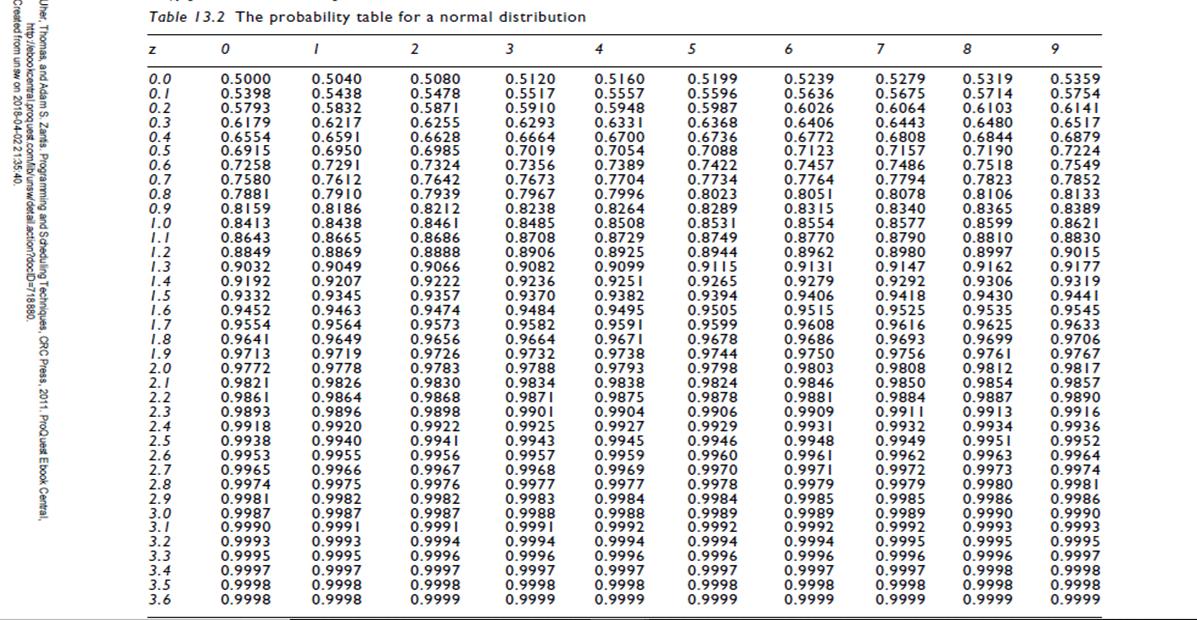
248 Appendix C Quality Standards Further Explanation There are two working tasks extracted from Table 8 from Quality Management Plan as examples to perceive associated standards. Example 1: Task 1.3.5 Construction of footings for new stairs and lift shafts Stairs and Balustrades 1)Stair Width Stair Width should: ● Accommodate normal passenger movement in two directions where prefers that a 600630mm width for comfort between handrails ● Provide a centre double handrail if the stair width is over 2 metres as per BCA clause D2.17 2) Stair Flight ● Where height of stairs rise above 5.3 m a minimum of 2 mid landings are required ● Provide minimum stair landings 1500mm long ● Where a stair is required to have more than 36 risers in total a straight stair is preferred to ensure good passenger orientation and comprehensibility. Additional landings should be provided at every 13-14 risers to enable more regular rest points Refer to Figure 4 Figure 4: Typical Stair Flight Section https://www.transport.nsw.gov.au/system/files/media/asa_standards/2020/esb-003.pdf
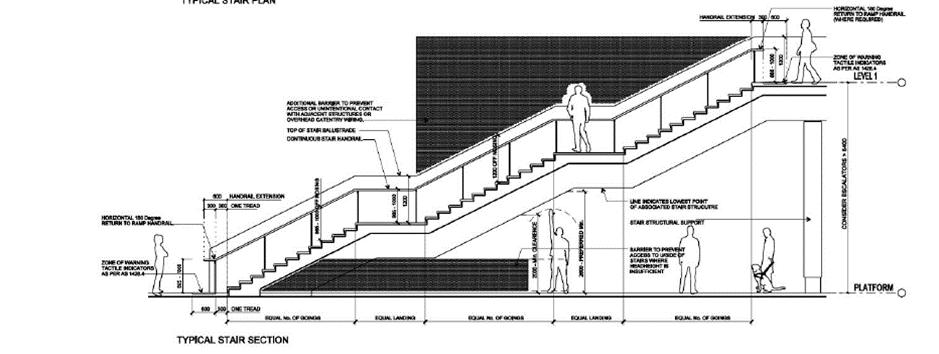
249 3)Stair StandardDetailsrequires a stair going and riser dimension of Goings: 300mm Risers:150mm ● Open risers are not permitted ● A solid barrier in the vertical plane and no gaps in the horizontal plane is required to prevent objects from falling off the edge of stairs or ramps ● No slip luminance contrasting nosing vertical 25 50mm and horizontal 50 75mm with permanent colour (not a painted finished) ● Kerb upstand or extended balustrading at the edge of stairs to prevent objects falling off the edge of stairs to the platform. Refer to the Figure 5 Figure5: Typical Stair https://www.transport.nsw.gov.au/system/files/media/asa_standards/2020/esbDetail 003.pdf Example 2: 1.3.13 Bridge work Collision protection and robustness requirements Lift structures: 1)is wholly within earth filled platform walls complying with ESC 350 Platforms and Retaining Walls, the lift structure shall be designed for the following:
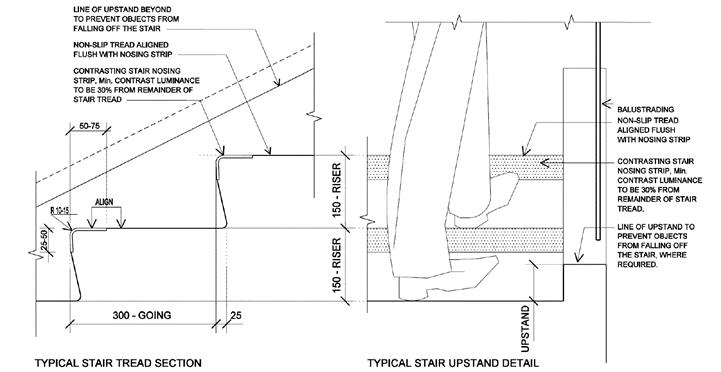
250 ♦ a force of 200kN applied in the horizontal direction and at a level (between adjacent rail level and 2m above rail level) to produce the greatest effect. ♦ a force of 100kN applied in the horizontal direction and at a level (between adjacent rail level and 3m above rail level) to produce the greatest effect. 2)is outside (wholly or partially) the platform walls (but within the rail corridor) ♦ is within 10m of the centreline of the nearest track, then the lift structure shall be designed for a minimum collision load of 500kN in accordance with AS 5100.2Bridge Design Design loads CI.10.4; or ♦ the lift structure location and structure are such that the risk of damage to an adjacent overbridge, to the extent that the overbridge could collapse. Then collision protection walls shall be provided to the lift structure or overbridge support.
251 APPENDIX D: FEMA From Template https://www.hsdl.org/?view&did=455178
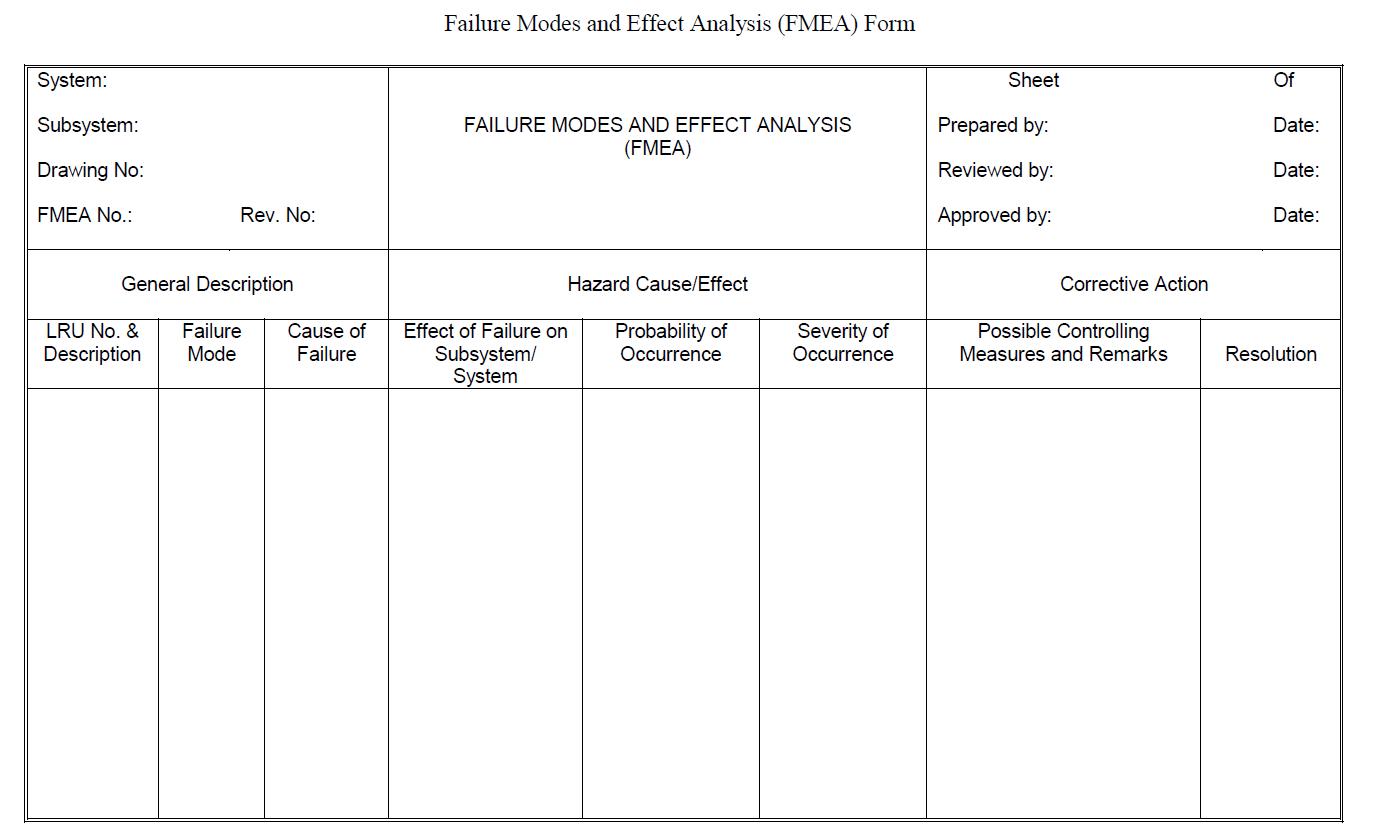
252 Appendix E: Sydney Metro Risk Identification Checklist
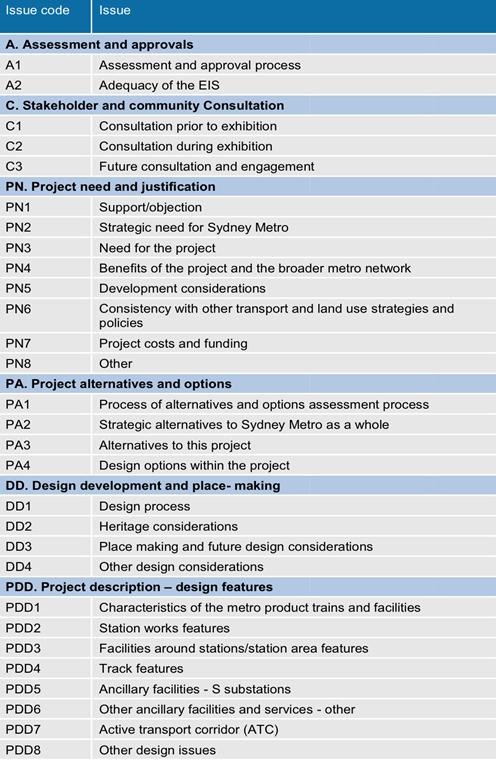
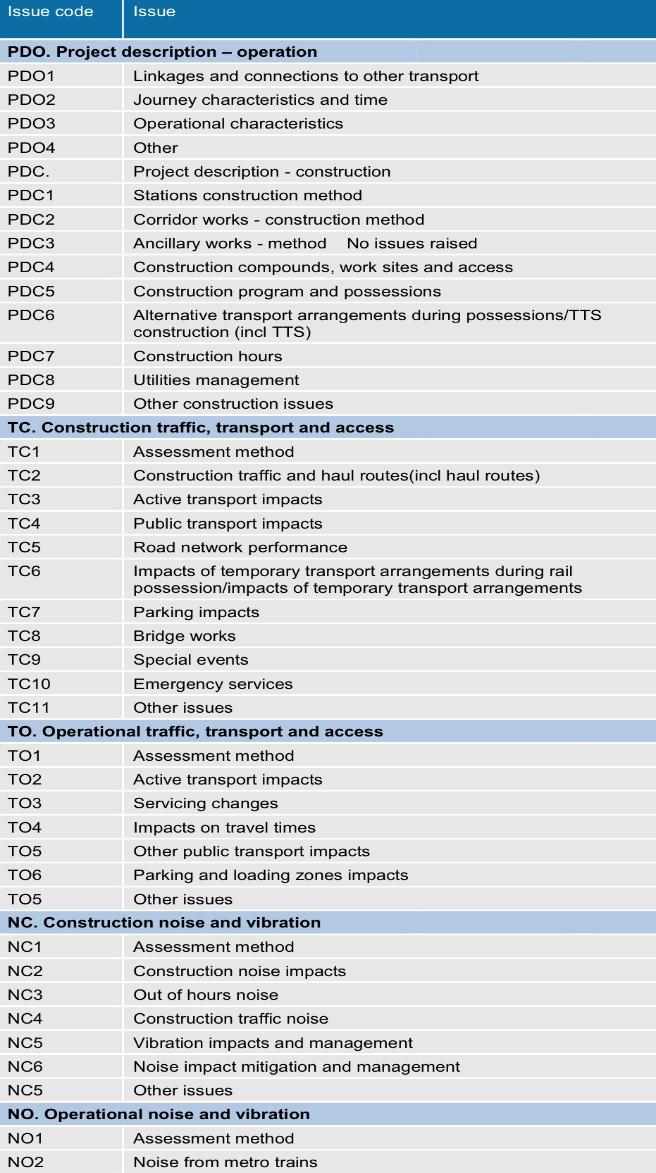
253
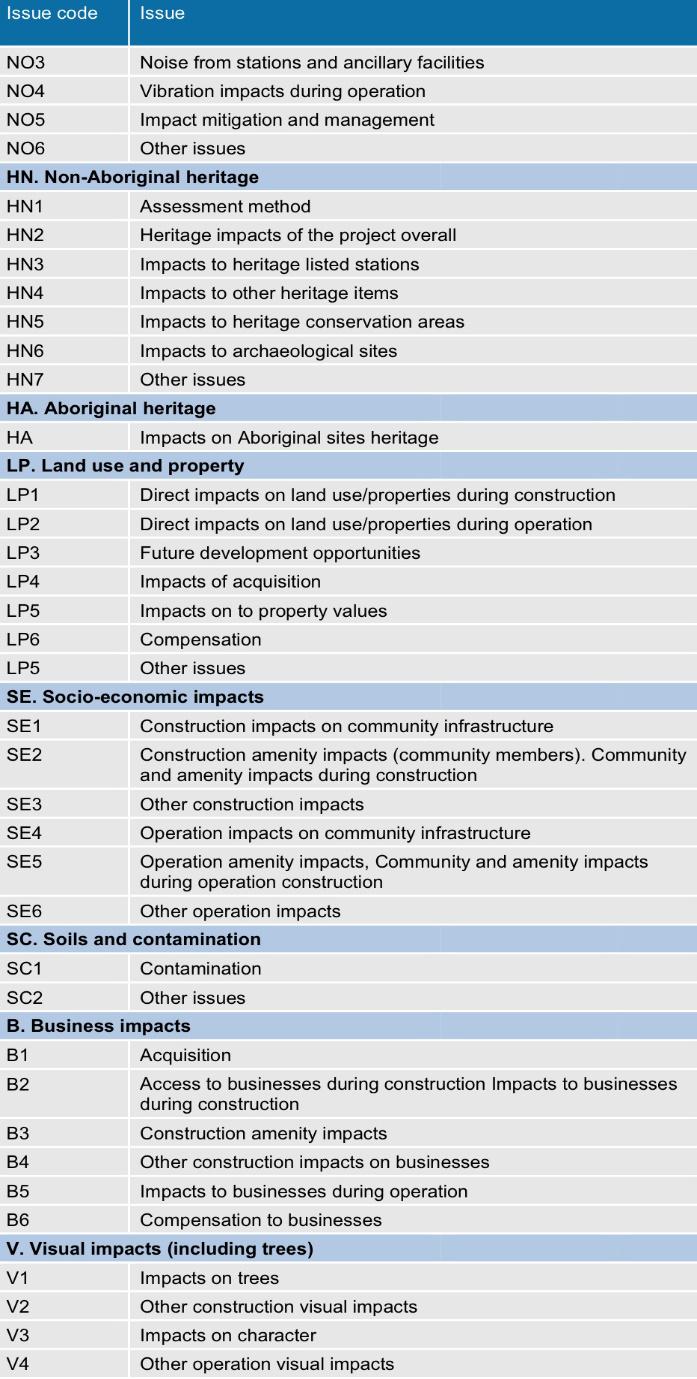
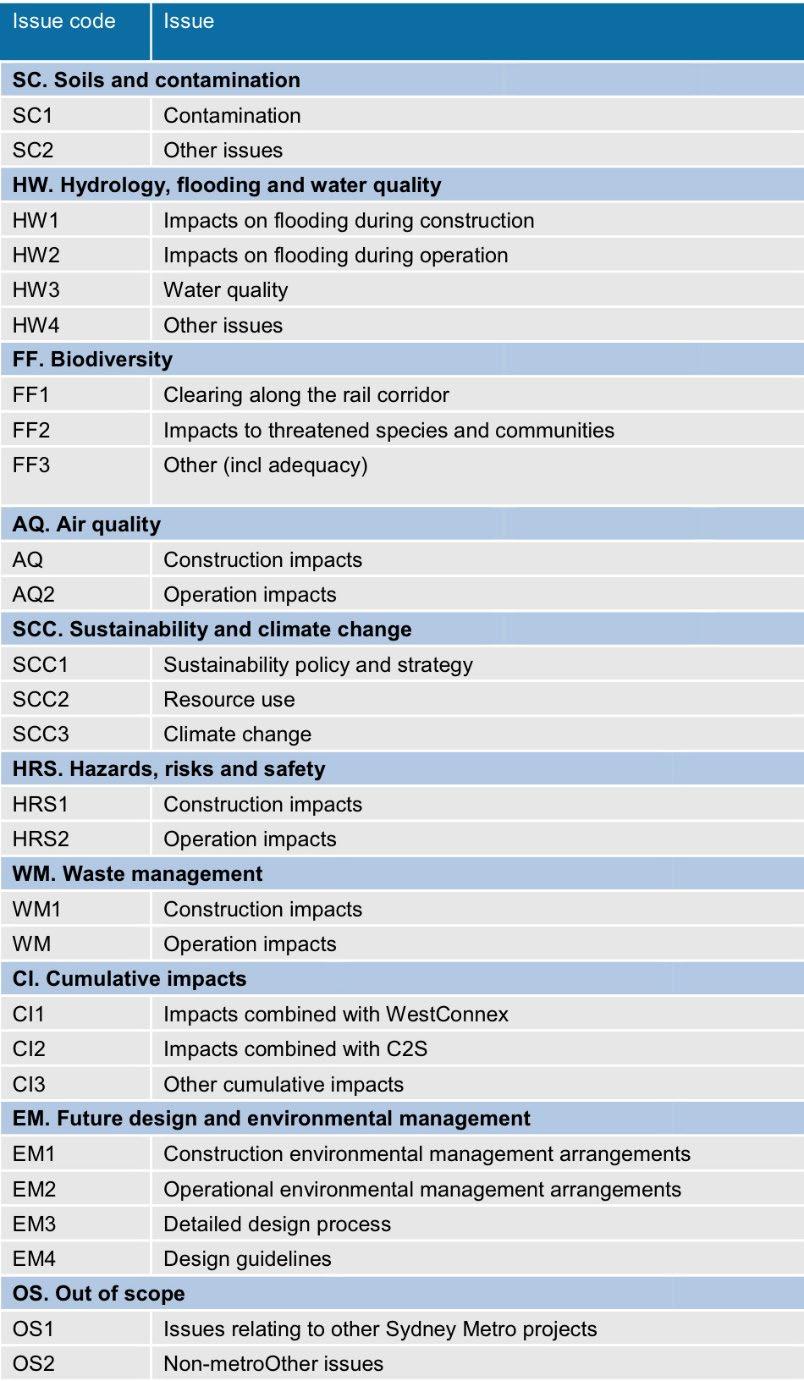
Contingency risk item used in this example: Cost contingency risk: (1) 1.5.7 Damage to the existing infrastructure and underground utilities; Cost Contingency A (2) 1.5.9 Construction defect in track work: Cost Contingency B
254 Appendix F: The Calculation Process of Monte Carlo Simulation
From these three estimate cost contingency, the expected cost value of the specific activity ( )can be calculated by:
Pessimistic( ) which is the maximum cost estimated that may occur in the worst case scenario on the specific construction activity
Three Point Estimate Three point cost estimates:
Optimistic ( ) which is the minimum estimated cost that may occur in the best case scenario on that specific construction activity
Expected Cost Contingency (Mean Value): = Also, the Standard Deviation: At this stage, each of these two cost items and the sum of the separate cost items distribution will approximate to a normal distribution (Appendix A), a simple statistical analysis using standard normal variate Z value can then be used to find P value
Most likely ( ) which the cost estimated can be achieved in the most likely scenario





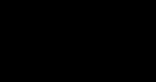
255 As for the Z-value and standard normal variable equation can be referred to Schedule Management Plan. Contingency Cost descriptionRisk Best case a(dollars) (dollars)LikelyMost m (dollars)CaseWorst b contingencyofProbabilityP(x)risk P(x)(aValue=Expected+4m+b)/6* aSD=(b-)/6 P50econfidencwithZ-scocelevel P90econfidencwithZ-scorelevel P50eConfidenclevel P90eConfidencLevel Cost A $6,794,603 $9,066,000 0$12,046,02 85% $7,806,488 $875,236 0 1.28 $7,806,488 $8,926,790 Cost B 0$55,098,00 0$67,500,00 1$82,503,23 75% $50,950,154 9$4,567,53 0 1.28 4$50,950,15 4$56,796,60 Total $65,723,394 P-90CL Therefore, for these two risks, totally there will be 90% chance to generate cost contingency of $65,723,394.
256 When the three point estimate is achieved, the probabilistic approach MCS will be conducted. As for the cost contingency estimating of the Sydney Metro Project, this report will run this model for 10,000 iterations and each iteration will represent a scenario likely to happen in the real world. Accordingly, this simulation will be conducted by using a computer generally. The three point estimate outcome that this report requires to perform MCS is shown below Cost Contingency A Cost Contingency B Mean Value (Expected Cost Contingency) $7,806,488 $50,950,154 St.Dev $875,236 $4,567,539 Monte Carlo Simulation Algorithm Step: 1)Generate random numbers for each of input variables The random number can be used to represent the countless scenario of real world. Standard uniform random numbers can be generated by using Mersenne Twister http://www.math.sci.hiroshima-u.ac.jp/m-mat/MT/emt.html
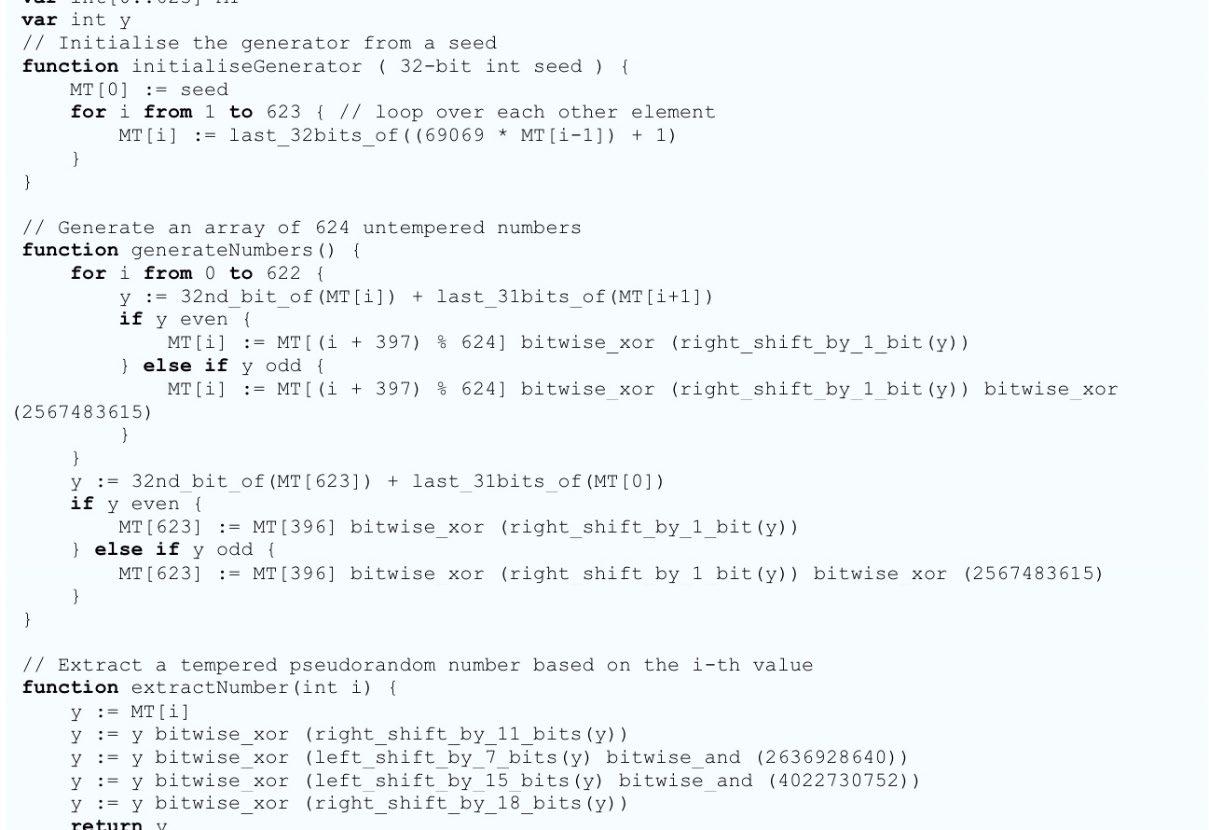
257 Random number list example can be seen in Appendix H Probability Distribution Random numbers for probability distributions other than the uniform distribution are usually determined through some form of transformation from the standard uniform distribution. Box-Muller Method Applied to Normal Distribution Normal distribution is the distribution function chosen for each work package variable of Sydney Metro Project. The Box Muller method involving a polar transformation can calculate two standard normal random numbers (Z1 and Z2) from two standard uniform random numbers (U1 and U2) Z1 and Z2 are the Z-value 2)Carry out a deterministic analysis using the inputs from above In this calculation example, we will conduct this simulation with 20 iterations based on the input of three point estimate outcome and deliver a concept of MCS to people. The output of three-pointCostestimateContingency A Cost Contingency B Mean Value (Expected Cost Contingency) $7,806,488 $50,950,154 St. Dev $875,236 $4,567,539 The random number extracted from random digit table are 0.94737 and 0.66612 Therefore, the calculation for iteration 1 would be:
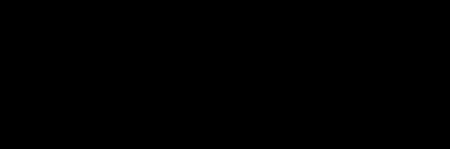
258 The normal distribution variable X can be standardised into Z, which is Z-value We assume all work package variables are statistically independent and the two risk items A and B are statistically independent Therefore: 3)Repeat first two stages many times By using Excel, the following table give the calculation for 20 iteration/realisations:
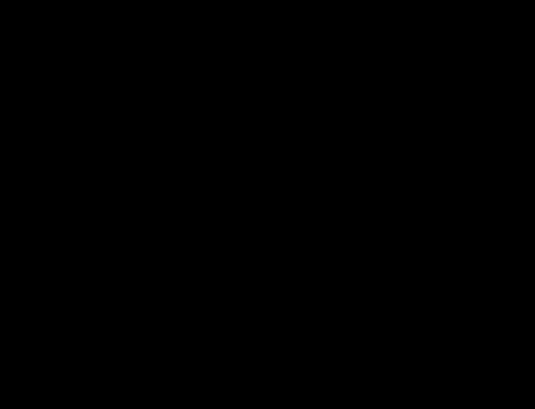
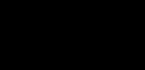
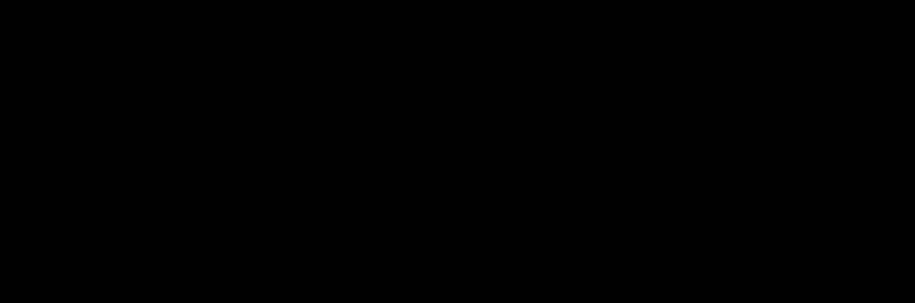
259 Realisation U1U2 Z1Z2 Cost Contingency ACost Contingency BTotal 200.414150.225580.202931.31220$7,984,102.38$56,943,684.61$64,927,786.99190.64930.941070.86638-0.33631$8,564,777.62$49,414,066.32$57,978,843.95180.17190.60906-1.45300-1.18764$6,534,773.05$45,525,568.13$52,060,341.19170.788040.56406-0.63507-0.27038$7,250,654.78$49,715,201.18$56,965,855.96160.033370.72573-0.39612-2.57746$7,459,790.24$39,177,517.76$46,637,308.00150.59160.116340.762850.68404$8,474,159.79$54,074,539.12$62,548,698.91140.114490.40531-1.724221.16688$6,297,388.21$56,279,905.46$62,577,293.67130.61130.011590.989510.07219$8,672,540.15$51,279,864.74$59,952,404.89120.751170.900350.61297-0.44329$8,342,984.27$48,925,387.38$57,268,371.65110.91080.777550.07445-0.42582$7,871,653.58$49,005,216.93$56,876,870.52100.276850.808120.57234-1.49699$8,307,420.88$44,112,584.14$52,420,005.0290.584570.4539-0.993060.29597$6,937,329.40$52,301,996.85$59,239,326.2580.138630.000221.987940.00275$9,546,400.37$50,962,705.26$60,509,105.6370.005460.111082.473272.07450$9,971,184.39$60,425,502.69$70,396,687.0860.778690.57805-0.62395-0.33313$7,260,387.16$49,428,575.84$56,688,963.0050.467240.176960.546471.10598$8,284,782.15$56,001,757.34$64,286,539.5040.66070.26179-0.067380.90795$7,747,511.98$55,097,243.82$62,844,755.8030.315670.882391.12249-1.02281$8,788,931.48$46,278,446.88$55,067,378.3720.307120.997081.53631-0.02819$9,151,119.08$50,821,396.75$59,972,515.8310.947370.66612-0.16539-0.28421$7,661,729.51$49,652,007.94$57,313,737.45Contingency
260 4)Collect relevant statistics on the required outputs The probability that the total contingency of these two risk items will be less than $64,000,000 can be obtained by determining the proportion of realisations where this occurs. It occurs in realisations 1,2,3,4,6,8,9,10,11,12,13,14,15,16,17,18, and19 so the probability of the contingency under $64,00,000 is 85%. The mean for the expected contingency cost on the project is $58,526,639.48 And other statistic outputs are summarised in the table below: Statistics Total cost contingency of two risk items chosen Mean $58,526,639.48 St.Dev $5,218,174.18 Min $46,637,308.00 Max $70,396,687.08 P(X<$64,000,000) 85% The contingency value probability distribution also can be created by selecting those 20iteration outcome calculated by hand. Figure 6: Two Risk Contingency Probability Distribution (20 simulations)
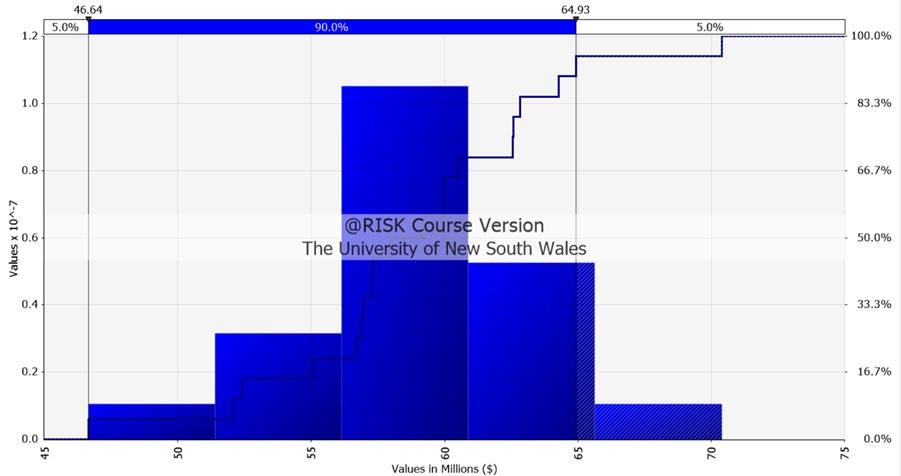
261 Real Simulation by Computer for Two Risk Contingency By applying Excel @Risk 8, the performing of Monte Carlo Simulation for 10,000 realisations being set as the number of repeated simulation runs can be automatically achieved. (This process performed by computer is the same with the 20 simulations above) The whole statistics table generated from this simulation is shown in table 1. Table 1: The output statistics data of MCS for 10,000 iterations The main outcome of simulation can be extracted from the whole table and is demonstrated in table 2. Table 2: Statistic outcome table Statistics Total cost contingency of two risk items chosen Mean $58,827,444.25 St.Dev $4,652,086.56 Min $42,054,788.57 Max $76,788,304.38 P(X<$58,819,225.69) 50% P(X<$64,767,084.37) 90%
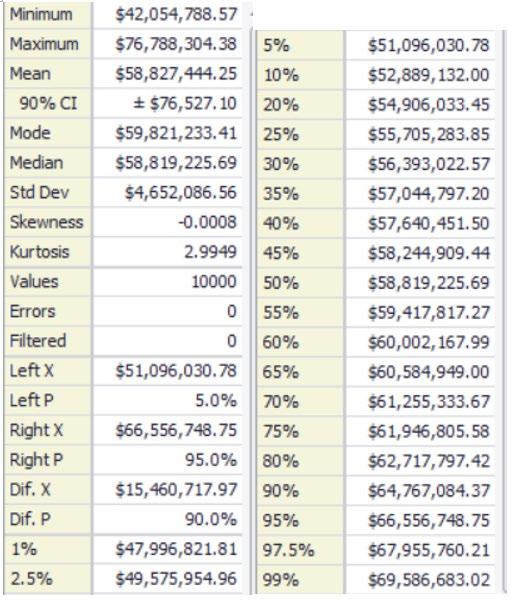
262 According to the table, the expected total cost contingency of those two risk items is $58,827,444.25. For these two risk items, there will be 50% chance to generate cost contingency under $58,819,225.69 and 90% chance to generate cost contingency under $64,767,084.37 on the Sydney Metro Project. The bell shaped curve of the probability distribution of cost contingency derived from 10,000 simulations shown in figure 7 and 8 are also obtained from MSC run. Figure 7: Cost Contingency Value and Probability Distribution Figure 8: Cumulative Cost Contingency Value and Probability Distribution

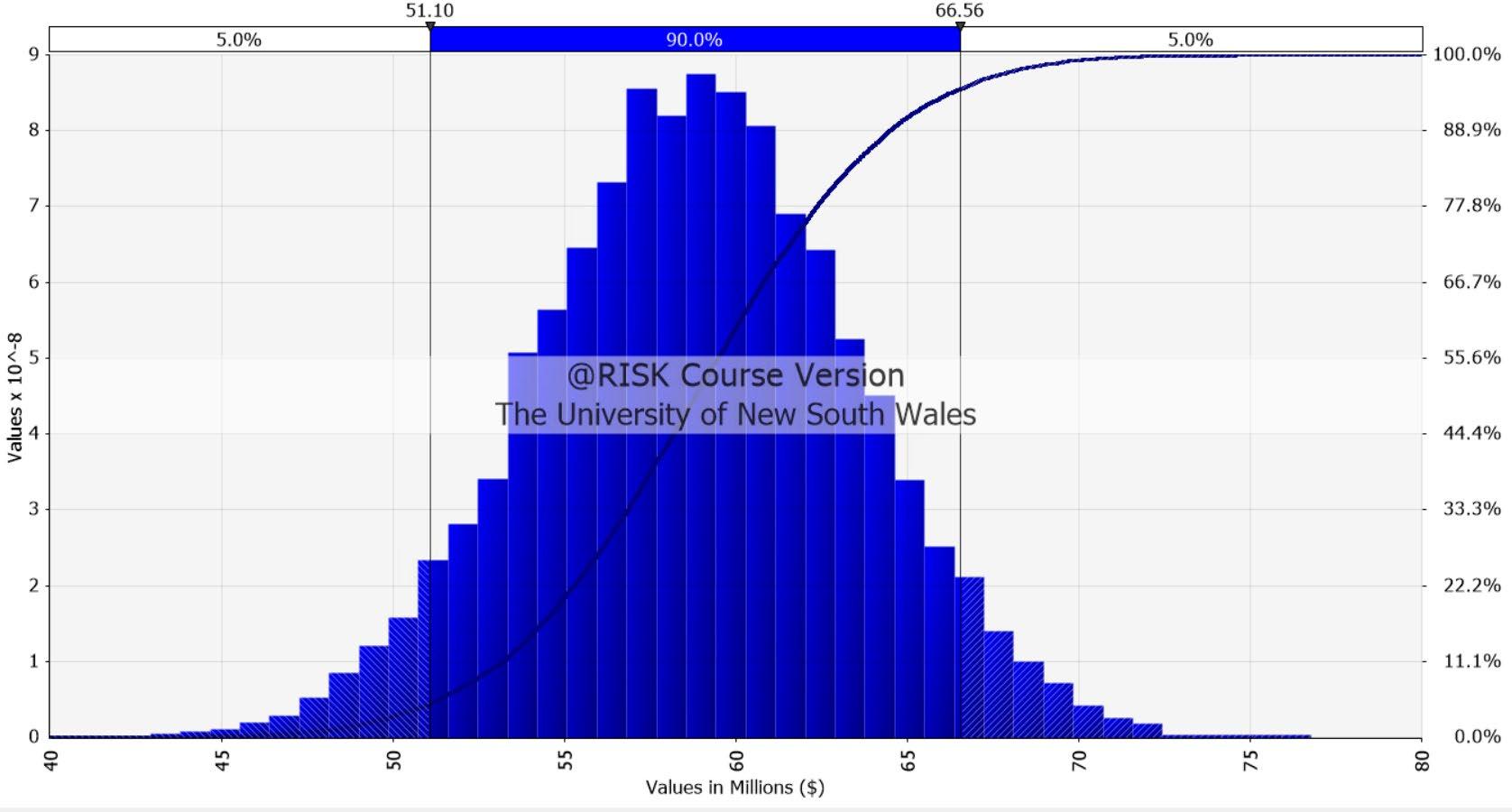
From the curve, indicates that this project has the capability of achieving those cost contingency under $66,556,748.75 with a 95% confidence level and there will be only 5% chance to generate cost contingency more than $66,556,748.75.
263
it
distribution
264 Appendix G: Total Cost Estimation and Comparison Initial calculation for all work package cost of mean value and standard deviation. By using 10000 runs Monte Carlo Simulation in computer, statistics and probability distribution are obtained. Cost Code Best case(a) Most Likely(m) Worst Case(b) Expected =(a+4m+b)/6Value SD=(b-a)/6 First Simulation 1.1.1 $602,456.00$1,000,000.00$1,698,234.00$1,050,115.00$182,629.67$965,504.56 1.1.2 1.5.3$15,043,989.00$20,000,000.00$24,564,859.00$19,934,808.00$1,586,811.67$19,906,378.221.5.2$14,909,808.00$20,000,000.00$26,987,767.00$20,316,262.50$2,012,993.17$18,425,103.751.5.1$902,899.00$1,500,000.00$2,098,787.00$1,500,281.00$199,314.67$1,538,809.611.4.5$677,098.00$1,000,000.00$1,500,212.00$1,029,551.67$137,185.67$1,093,203.061.4.4$2,475,869.00$3,000,000.00$3,567,965.00$3,007,305.67$182,016.00$3,283,335.251.4.3$2,234,987.00$3,000,000.00$3,790,999.00$3,004,331.00$259,335.33$2,840,035.271.4.2$4,784,123.00$5,000,000.00$5,364,988.00$5,024,851.83$96,810.83$4,973,522.751.4.1$4,312,456.00$5,000,000.00$5,895,786.00$5,034,707.00$263,888.33$4,988,689.031.3.15$76,832,456.00$100,000,000.00$143,098,475.00$103,321,821.83$11,044,336.50$91,314,036.681.3.14$71,000,000.00$80,000,000.00$89,000,000.00$80,000,000.00$3,000,000.00$79,184,009.271.3.13$61,234,987.00$70,000,000.00$76,098,312.00$69,555,549.83$2,477,220.83$73,497,141.331.3.12$334,123,049.00$395,000,000.00$479,576,345.00$398,949,899.00$24,242,216.00$368,889,643.031.3.11$712,345,086.00$750,000,000.00$785,023,483.00$749,561,428.17$12,113,066.17$748,812,126.501.3.10$240,194,589.00$300,000,000.00$356,000,345.00$299,365,822.33$19,300,959.33$297,285,327.251.3.9$23,000,000.00$30,000,000.00$38,909,444.00$30,318,240.67$2,651,574.00$31,205,127.031.3.8$220,498,000.00$270,000,000.00$315,890,567.00$269,398,094.50$15,898,761.17$284,394,875.551.3.7$3,989,000.00$5,000,000.00$6,345,890.00$5,055,815.00$392,815.00$4,795,151.631.3.6$80,111,222.00$87,000,000.00$96,666,666.00$87,462,981.33$2,759,240.67$86,783,187.991.3.5$167,987,000.00$200,000,000.00$245,008,909.00$202,165,984.83$12,836,984.83$192,534,281.511.3.4$42,998,442.00$50,000,000.00$59,485,756.00$50,414,033.00$2,747,885.67$50,018,876.471.3.3$7,989,808.00$10,000,000.00$13,987,343.00$10,329,525.17$999,589.17$10,168,390.551.3.2$47,400,000.00$50,000,000.00$54,908,657.00$50,384,776.17$1,251,442.83$48,447,074.691.3.1$37,983,459.00$40,000,000.00$43,897,432.00$40,313,481.83$985,662.17$41,194,715.561.2.12$470,998.00$500,000.00$589,098.00$510,016.00$19,683.33$500,117.621.2.11$449,987.00$500,000.00$547,890.00$499,646.17$16,317.17$513,599.091.2.10$598,567.00$1,000,000.00$1,675,987.00$1,045,759.00$179,570.00$1,133,684.801.2.9$1,703,984.00$2,000,000.00$2,439,245.00$2,023,871.50$122,543.50$2,143,771.631.2.8$8,800,000.00$15,000,000.00$21,000,000.00$14,966,666.67$2,033,333.33$14,850,787.991.2.7$2,703,857.00$3,000,000.00$3,394,865.00$3,016,453.67$115,168.00$2,713,966.191.2.6$5,897,645.00$10,000,000.00$14,000,000.00$9,982,940.83$1,350,392.50$10,874,627.541.2.5$560,987.00$1,000,000.00$1,402,900.00$993,981.17$140,318.83$1,005,146.001.2.4$2,549,837.00$3,000,000.00$3,685,374.00$3,039,201.83$189,256.17$3,120,514.531.2.3$2,723,458.00$3,000,000.00$3,786,453.00$3,084,985.17$177,165.83$2,940,118.671.2.2$1,586,784.00$2,000,000.00$2,432,987.00$2,003,295.17$141,033.83$1,989,038.201.2.1$423,987.00$1,000,000.00$1,698,423.00$1,020,401.67$212,406.00$1,385,544.961.1.5$689,132.00$1,000,000.00$1,500,000.00$1,031,522.00$135,144.67$904,927.681.1.41.1.3$4,602,000.00$5,000,000.00$5,798,243.00$5,066,707.17$199,373.83$4,849,977.02$980,354.00$1,500,000.00$2,012,475.00$1,498,804.83$172,020.17$1,310,284.21$598,756.00$1,000,000.00$1,498,567.00$1,016,220.50$149,968.50$910,829.46
It indicated that the cost amount of $2,552m is more likely to cover the total project cost including contingency reserve with the coverage level up to 90%.
The probability distribution comparison between total cost estimation including risk contingency and total cost estimating without risk consideration is shown next.
265

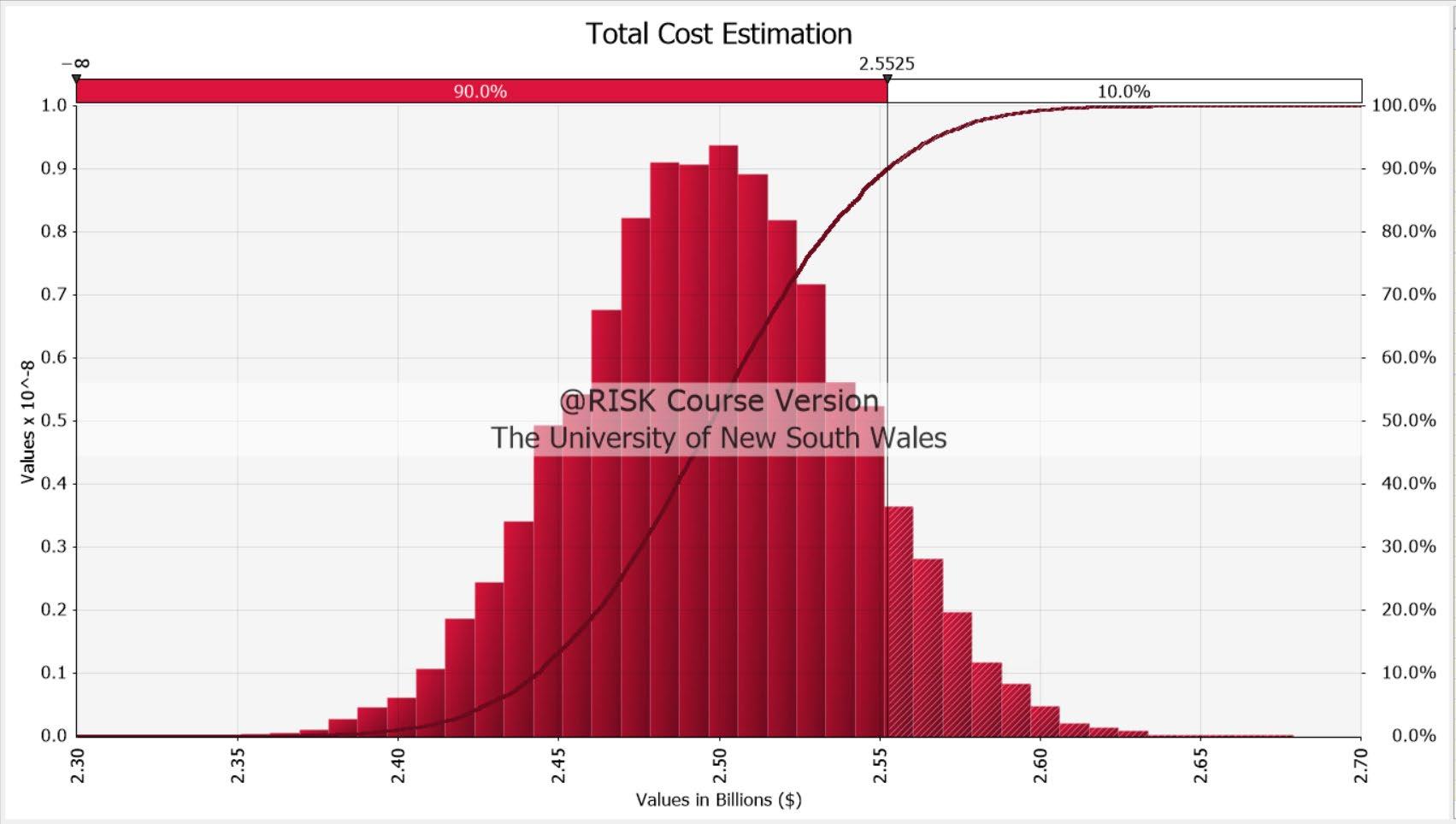
266
By analysing the probability distribution curve, it can be noted that the risk effect on the cost of whole Sydney Metro Southwest project. It means that there will be 0% chance to generate total project cost under $2,310m when the risk contingency factor is taken into account in this project.
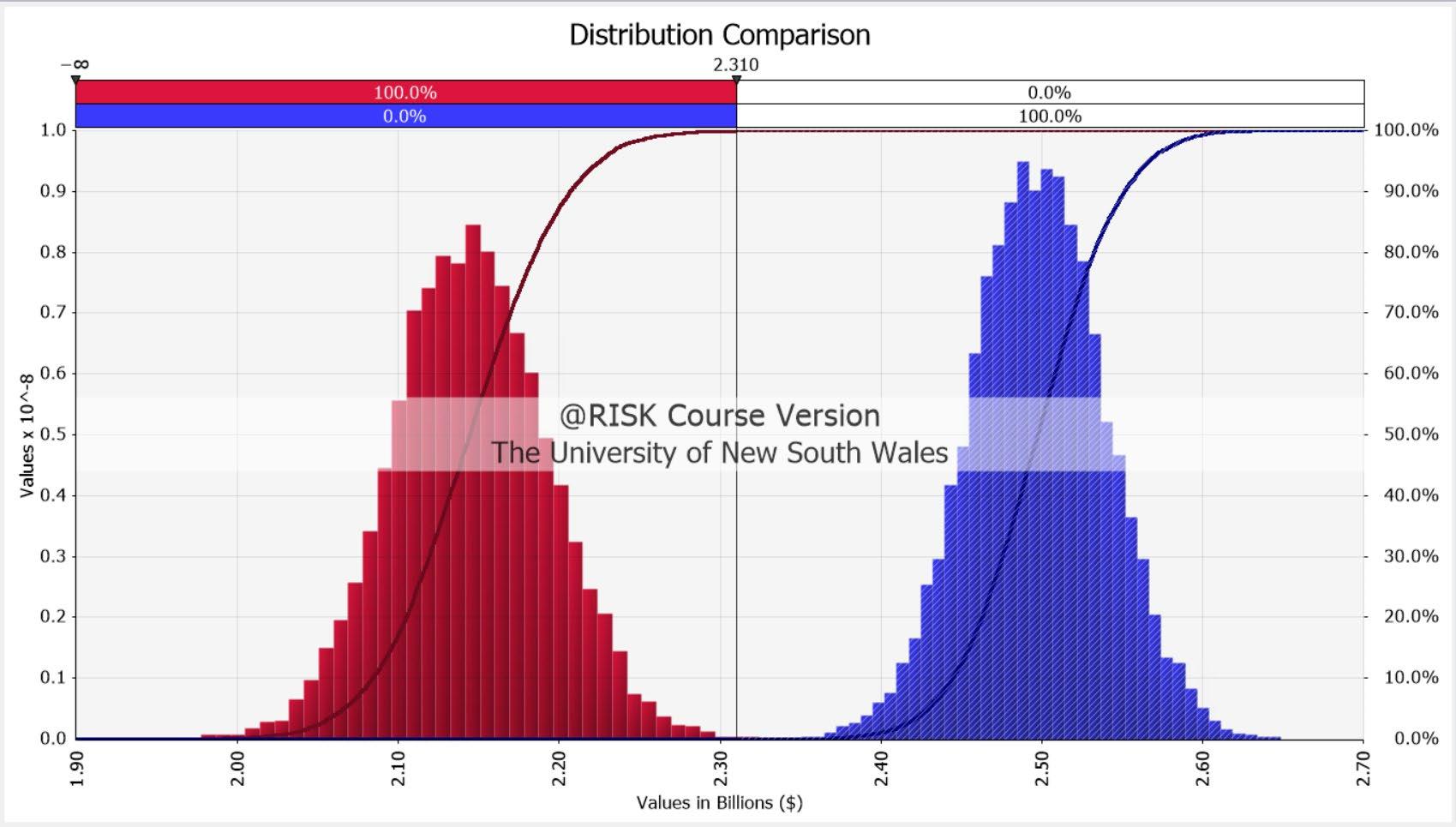
267 Appendix H: Random Digits:
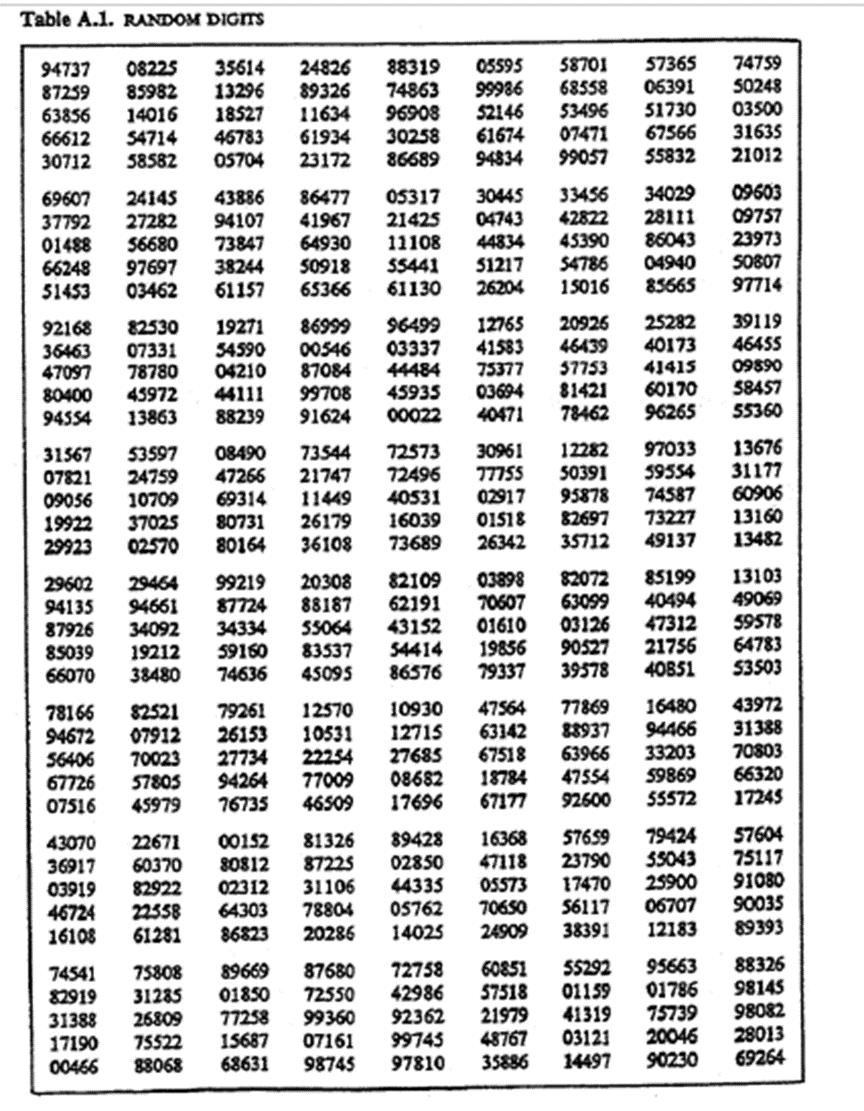
268 Appendix I: Risk Register

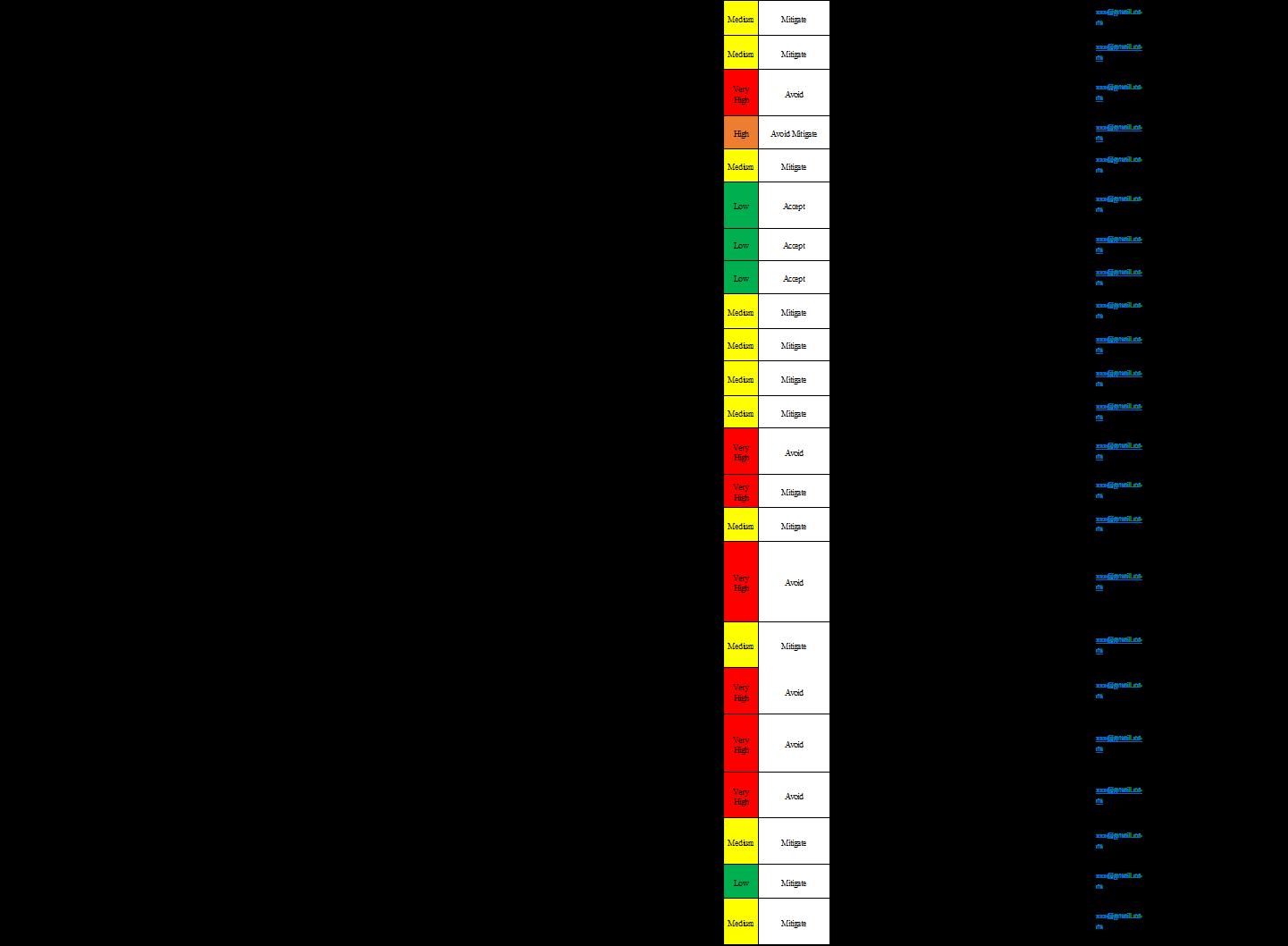
270
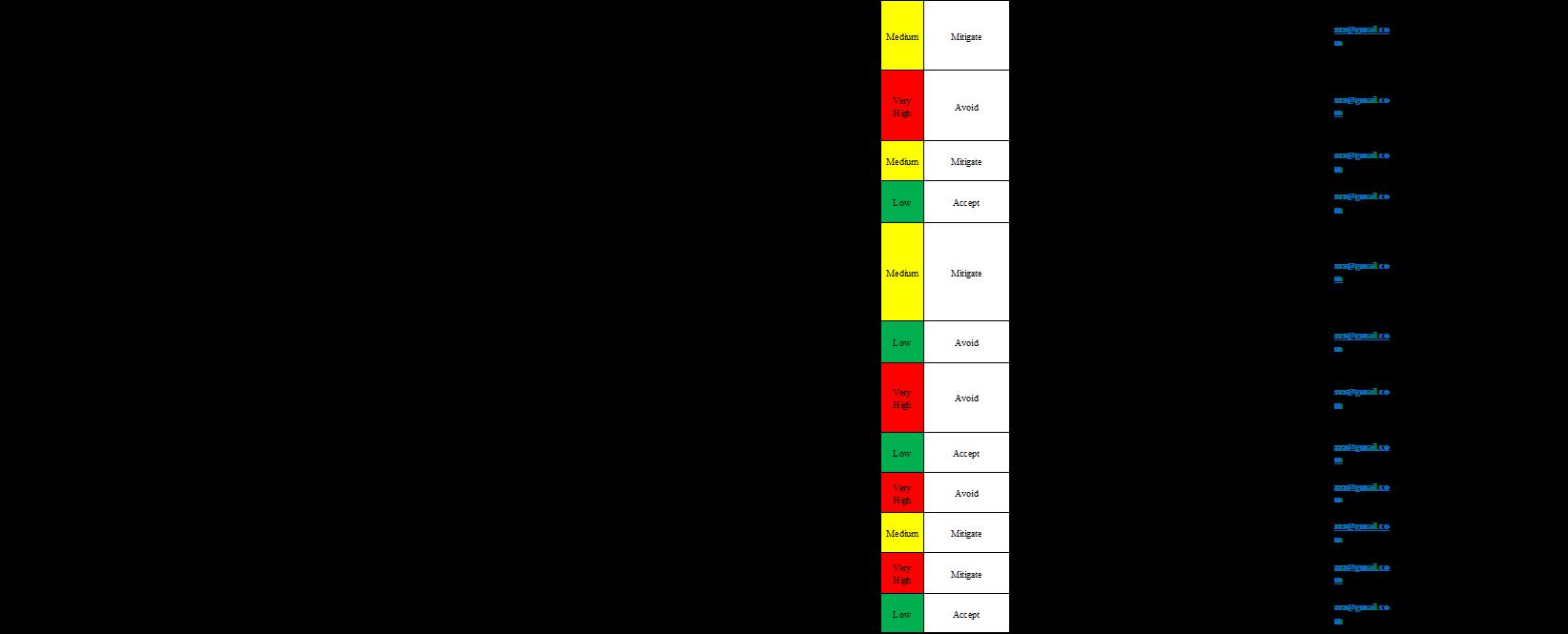
Medium Relevance This act governs Road Occupancy Licences (ROL) that will be required for works on and round roads. An ROL cannot be refused to carry out works required under an SSI approval as per Section 115ZH of the EP&A Act.
The project is approved under Part 5.1 of the EP&A Act.
271 Appendix J: Legal and Other Requirements(Examples Listed) Legal and Other Requirements Summary of Obligations
The Local Government Act and Local Government (General) Regulation provide a legal framework for an environmentally responsible system of Local Government including theresponsibility to administer various regulatory systems (e.g. Environmental Planning, Development Consents and Conditions of Approval). No Relevance
Environmental Planning and Assessment Act 1979 (EP&A Act) This Act establishes a system of environmental planning and assessment of developmentproposals for the State. High Relevance The development consent conditions and obligations are incorporated into the JHLOR’sspecificationdocumentsCEMP.
This Act is of little relevance to SMC as it has been determined significant” cultural and natural resources, protected wildlife and protected plants withoutApproval. not to trigger the provisions of the Act.
Notesand
Environmental Planning Legislation
Relevance to the Project / System
Local Government Act 1993 Local Government (General) Regulation 2005
This Act and Regulation primarily provide for such things as the opening and closing of public roads, identification of road boundaries and road widening, road levels, classification of public roads, road work, protection of public road and regulation of traffic, regulation of work, structuresand activities.
Soil Conservation Act 1938 This Act makes provision for the conservation of soil resources, farm water resources and the mitigation of erosion. The Act is binding on the Crown, however the Crown is not liable for prosecution. The Act provides for notification in the government gazette catchments where erosion is liable to cause degradation of rivers; lakes etc. (i.e. protected land). No Relevance This Act has low relevance as the SMC site is not located within “protected land”. Further, such notification has not been given tothe owner of the land.
Environment Protection and Biodiversity Conservation Act 1999(Cwth) The main purpose of this Act is to provide for the protection of the environment especially thoseaspects that are of national environmental importance and to promote ecological sustainable development. The Act binds the Crown. Do not take, use, keep or interfere with “nationally No Relevance
Roads Act 1993 Roads Regulation 2018
Fire Control Legislation
National Greenhouse and Energy Reporting Act
1979 The Land and Environment Court is constituted under this Act. The jurisdiction of the Court is divided into numerous classes. The relevant classes for the project covers matter such as the prosecution for offences under various environmental legislation and to appeal against conditionsof approvals, permits or orders.
Laing O’Rourke Australia and John Holland are registered entities under this Act. As such, where Laing O’Rourke or John Holland has Operational Control,the Scope 1 and Scope 2 emissions associated with the project must be reported. This includes the collation and reporting of subcontractors site emissions.
272 Land and Environment Court Act
This Act provides for a process to investigate and remediate land that has been contaminated and presents a significant risk of harm to human health. Section 60 of the Act is a “Duty to ReportContamination”. This duty applies to owners of land and persons who become aware their activities have contaminated the land.
Low Relevance The relevance of this Act would only apply to work under the contract if JHLOR were prosecuted for an EnvironmentalOffence.
Corporations emitting more than 50kT of carbon dioxide equivalent units are required to registerand report their Scope 1 and Scope 2 emissions for all Facilities in which they have OperationalControl. Facilities emitting more than 25kT of carbon dioxide equivalent units must register and report Scope 1 and Scope 2 emissions.
Contaminated Land ManagementAct 1997
Rural Fires Act 1997
Low Relevance The SMC project site and surrounding areas are within bushfire prone determined land.
Hazardous Legislation
Substances
Contaminated Land Legislation
Medium Relevance The relevance of this Act to the contractor will be in the event suspected or contaminatedpotentiallygroundis found during construction activities.
This Act is intended to prevent, mitigate and suppress bush and other fires. It places a duty on JHLOR as the occupier of the site to extinguish fires during bush fire danger periods or if unable to do so notify appropriate firefighting authorities of the existence of the fire and its location.
2007
High Relevance
Greenhouse Gas (GHG) Emissions
Environmentally Hazardous Chemicals Act 1985
This Act prohibits the manufacturing, processing, keeping, distributing, conveying, using, selling or disposing of an environmental hazardous substance or waste (prescribed activity) except under the provisions of a chemical control or a licence. The EPA is required to prepare inventoriesof environmentally hazardous substances and declared chemical wastes.
Low Relevance
Australian Heritage Council (Consequential & Transitional Provisions) Act 2003 Australian Heritage Council Act2003 (Cwth) The Australian Heritage Council (Consequential and Transitional Provisions) Act 2003 repealed the Australian Heritage Commission Act 1975. The Australian Heritage Council Act 2003 establishes the Australian Heritage Council. The Council is required to identify places to be included in the National Estate and to maintain a Register of the National Estate of places. No Relevance The site is not on Register of the National Estate of places.
Dangerous Goods (Road and Rail Transport) Act 2008
Aboriginal and Torres Strait Islander Heritage Protection Act1984 (Cwth) This Act provides for the preservation and protection from injury or desecration to areas and objects of particular significance to Aboriginals. Areas and objects can be protected by MinisterialDeclaration and it is then and offence to contravene such a declaration. No Relevance No areas or objects within the works site have been identified asbeing subject to such a declaration and this Act is of little relevance to the project.
273
Depending on the quantities being transported, the Act outlines specific requirements for including appropriate placards on the transport vehicle, emergency procedures, PPE, manifest documentation and fire extinguishers. High Relevance The relevance of the Act is in respect to the transport of dangerous good to & from the site. The project will require the use of a variety of dangerous goods. JHLOR will need to reviewand ensure Dangerous Goods requirements are addressed where transported by its vehicles, plant and equipment.
It is not anticipated any environmentally hazardous substances or declared chemical waste will be used or stored on the site. The Act therefore has little relevance to the site other than being aware of the existenceof registers of declared chemical wastes and environmentally hazardous substances.
The purpose of this Act is to regulate the transport of Dangerous Goods by road and rail in orderto promote public safety and protect property and the environment. The transport of DangerousGoods is required to be appropriately licensed (both vehicle and driver).
Other Legislation
274 Appendix K: Health, Safety and Environmental System(HSEMS) The subcontractor company is certified with SciQual An outline of the LOR HSEMS is provided below.
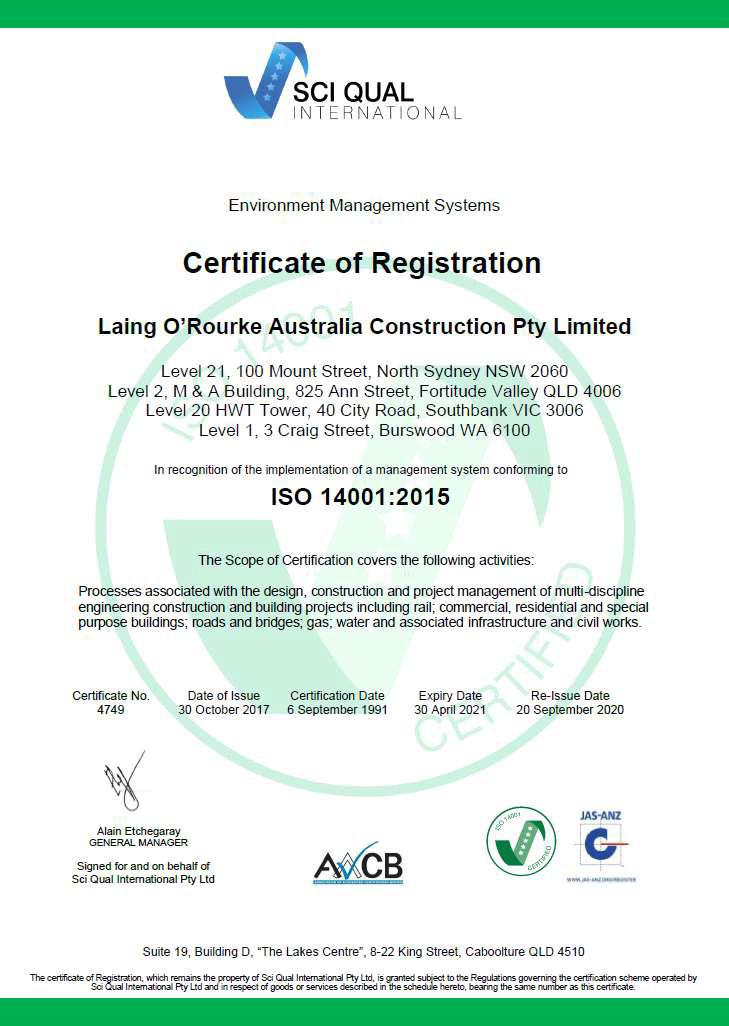
275
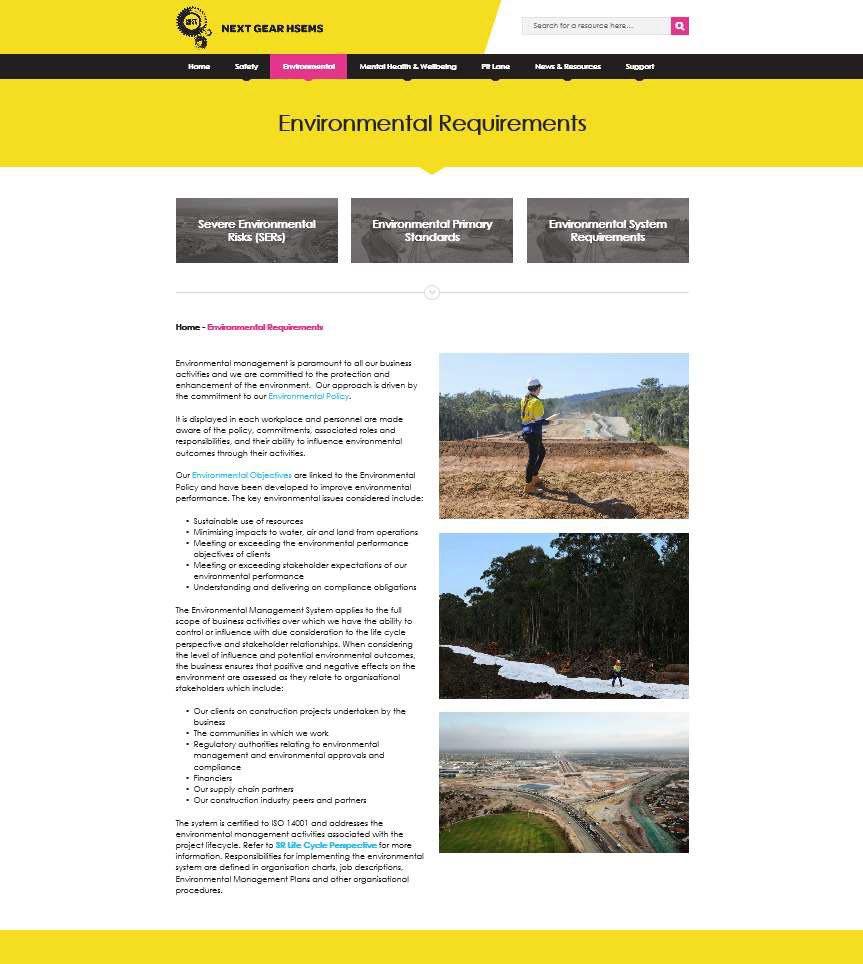
276 Appendix L: Environmental Policy A Joint Venture (JV) Environmental Policy has been produced for the project. The Policy states the following;
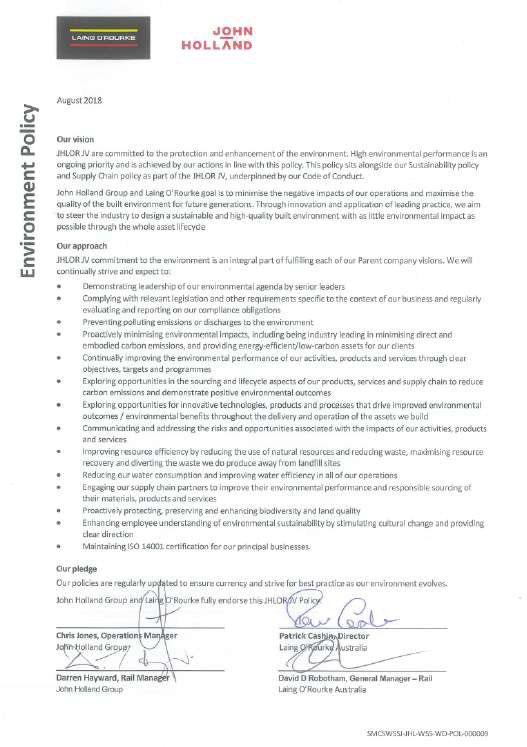
277 Sydney Metro Environmental&Sustainability Policy:

278