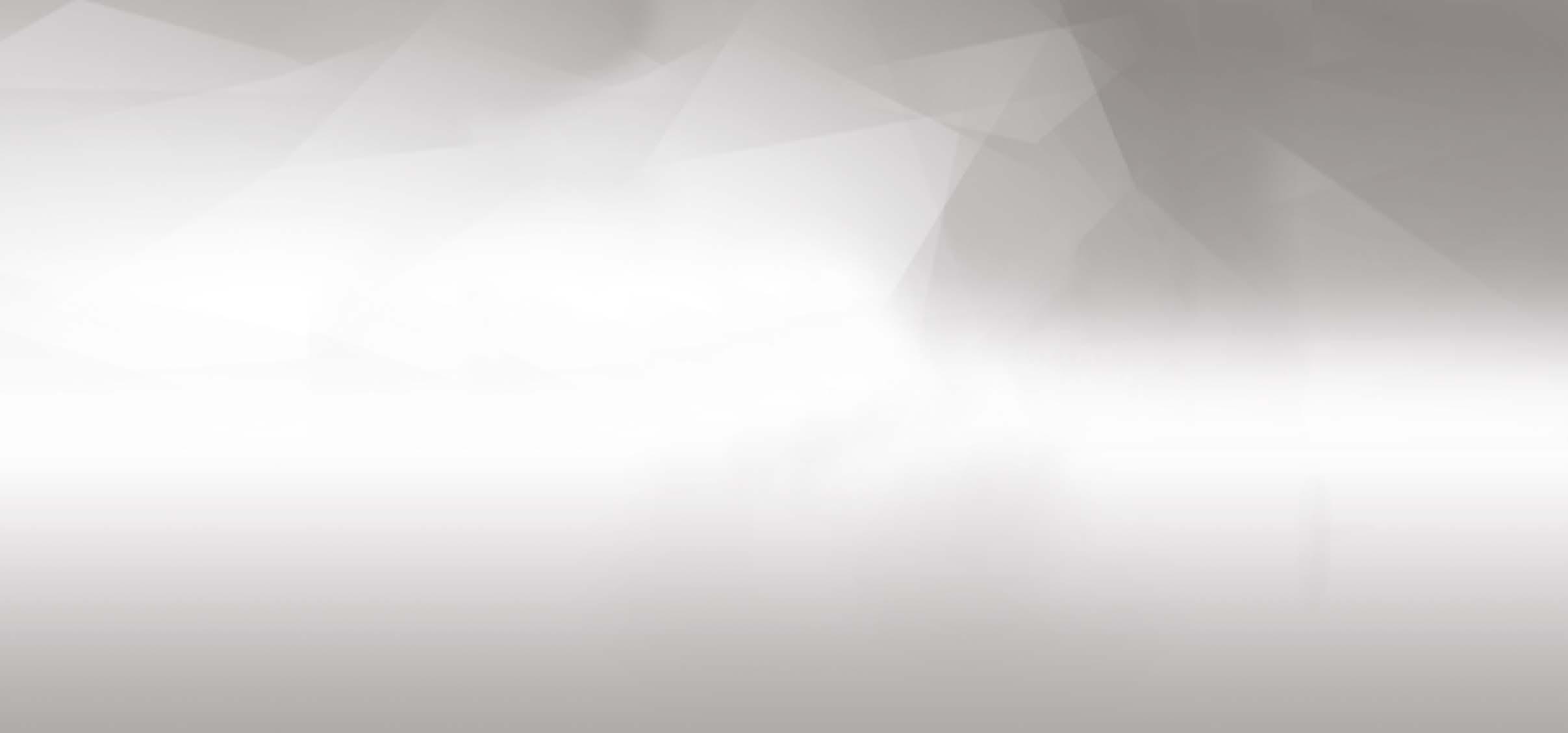
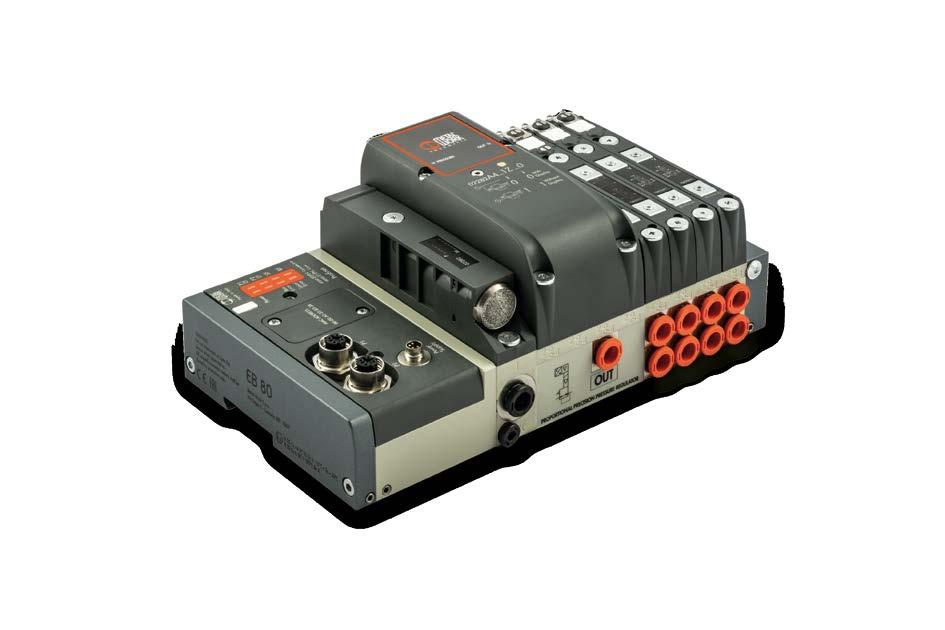

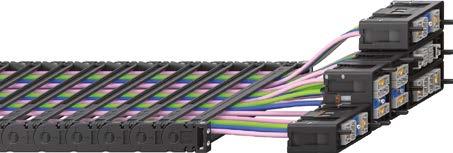


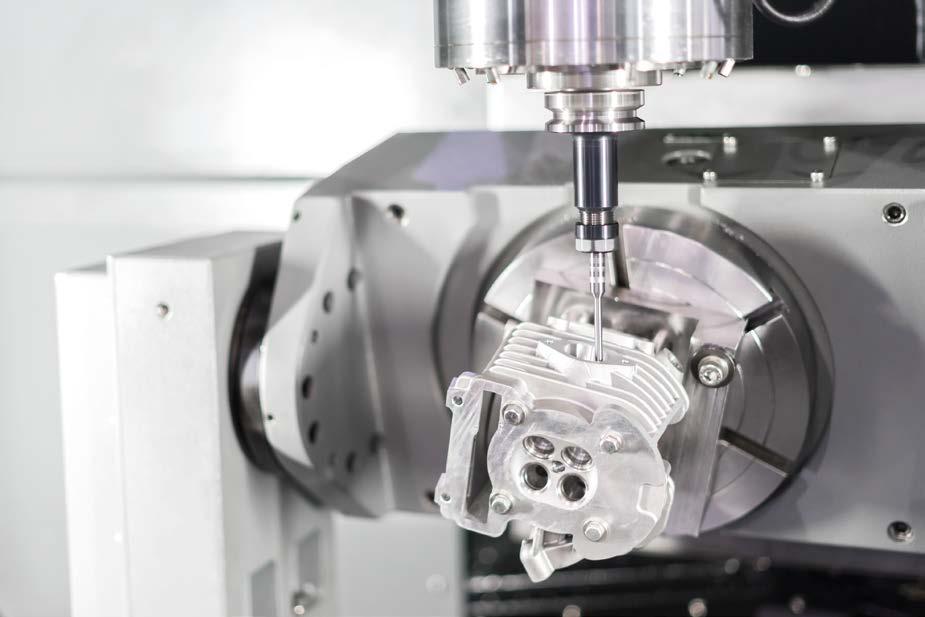
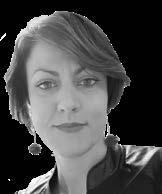
Si può dire che l’ascesa del computer e dell’automazione siano stati, storicamente, elementi cardine della terza rivoluzione industriale. Tecnologie e sistemi di automazione sono certamente ascrivibili come i grandi protagonisti della svolta produttiva avvenuta tra gli anni 50 e 90. E da allora non si sono più fermati. Messi in relazione e collaborazione con le altre tecnologie 4.0 continuano ad evolversi e ad adattarsi restando protagonisti indiscussi della attuale quarta rivoluzione industriale. Come potrete leggere nelle pagine della rivista, lungi dall’adagiarsi sugli allori, mossi dalla volontà di dare risposte a sfide sempre più competitive, i produttori e sviluppatori di queste tecnologie stanno evolvendo con rapidità e flessibilità ponendo sul mercato prodotti e soluzioni sempre nuovi e d’avanguardia.
Ed è proprio per continuare ad essere leader del progresso e del cambiamento positivo, che più recentemente stanno puntando ad un ulteriore svolta di paradigma, allineandosi ai tre pilasti di Industry 5.0 ovvero umano-centrismo, resilienza e sostenibilità.
Ed arrivo al mio consueto cauto monito. A tutta questa rapidissima ed entusiasmante evoluzione per consentire il consolidamento del nuovo, non credete debba essere applicata una giusta variabile tempo? Mettere l’uomo al centro della tecnologia non dovrebbe voler dire anche un po’ questo? La storia, tanto quanto i cambiamenti epocali innescati dalle rivoluzioni industriali, ci invita a rispettare i ritmi umani e i tempi necessari all’apprendimento. Prima di considerare già archiviata la quarta rivoluzione industriale occorrerebbe
ragionare un po’ di più sul tempo di penetrazione e sedimentazione della conoscenza e cultura tecnologica, tanto nel tessuto industriale quanto in quello sociale ed educativo.
Cito un esempio. Anche se tra addetti ai lavori sapevamo bene che già a partire dalla fine degli anni 90 la quarta rivoluzione industriale era già realtà ci sono voluti altri dieci anni per vederla consolidata. Oggi non possiamo dimenticare che meno di un quarto di generazione è sicuramente un tempo enorme per le evoluzioni di mercato, ma forse decisamente poco per le capacità di apprendimento umane. Identità, competenze, saperi e trasformazione, hanno bisogno di un tempo di metabolizzazione e giusti linguaggi di comunicazione.
Lasciamo perdere l’ignoranza blablaista diventata dilagante negli ultimi anni, gli infelici errori classificatori fatti anche ad alti livelli, non facciamo prevalere la forma sui contenuti, non ci facciamo confondere. Continuiamo a cavalcare la transizione 4.0, prendiamo come riferimento lo stato dell’arte della tecnologia, poniamo maggiore attenzione agli impatti delle nostre scelte e ai bisogni dell’uomo cercando di favorire un rapporto più equilibrato tra le tecnologie sempre più intelligenti e gli esseri umani.
chiara.tagliaferri@cnr.itEDITORIALE
5 Storia tecnologica e apprendimento
CALEIDOSCOPIO
8 News e novità
PANORAMA
12 Soluzioni ITDR le cinque funzionalità chiave
16 Sostenibilità del settore macchine utensili
20 Moulding Expo 2023 ventata di aria nuova
24 Oltre 25 anni di collaborazione e benefici
26 Saldatura della plastica
30 La responsabilità sociale valore fondamentale
32 Saldatura robotizzata
FOCUS ON
35 Lo stato dell’arte del CNC
STORIA DI COPERTINA
40 Metal work specialisti in pneumatica
DOSSIER CENTRI DI LAVORO
45 Centri di lavoro no limits!
48 Nuova serie GT 3000 precisa, robusta e compatta
50 DMU 40 lavorazione completa e versatile in poco spazio
52 “Apriamo gli occhi all’innovazione del futuro”
54 C12 il centro di lavorazione più compatto della high-performance-line di Hermle
56 Tank 1000 evo flessibilità nella lavorazione di lotti di piccole dimensioni
58 RMI-OE l’interfacci di ultima generazione per un futuro digitale
60 Corodrill 860 la punta in metallo duro integrale per l’innovazione nella produzione
62 Una nuova gamma di centri di lavoro per il massello
SPECIALE CONTROLLI NUMERICI
RICERCA E INNOVAZIONE
78 Soluzioni lean e integrate
IN FABBRICA
82 Da cliente a partner storico
86 Produzione di Kebab ad alta velocità Non più fermi macchina
PRISMA
Prodotti
Interroll ha disegnato il futuro dell’intralogistica con l’innovativo concetto di piattaforma. Qualità, semplicità di funzionamento e di design, risparmio energetico e sostenibilità. Per ogni peso, per ogni mercato, per ogni esigenza.
interroll.it
MindSphere World – Associazione che promuove la digitalizzazione dell’industria – prosegue con gli appuntamenti di incontro e confronto tra esperti di settore a supporto della divulgazione di una corretta cultura digitale per l’Industry 4.0. Dopo il successo di Macchine Connesse, il 04 aprile presso Expo Fiere Piacenza, si terrà “Macchine Protette – non c’è più safety senza cybersecurity”: una giornata dedicata alla sicurezza informatica e alla sua interconnessione con la sicurezza fisica degli asset produttivi.
L’evento risponde alla necessità preponderante di proteggere gli impianti industriali ed i relativi sistemi di gestione, in considerazione degli attacchi cyber subiti di recente da diverse aziende a livello nazionale. Lo scopo, dunque,
è quello di portare case study e best practices che possano fornire soluzioni e approcci vincenti per imprenditori, costruttori di macchine o impianti, system integrator e utilizzatori finali. A Macchine Protette, attraverso il contributo di professionisti provenienti dal mondo accademico, istituzionale e dell’industria, si toccheranno temi tecnici, legali e normativi per una visione completa della cybersecurity in ambito industriale.
L’apertura dei lavori sarà alle ore 09.45 con la plenaria “Dare senso alla sicurezza”. Un momento di approfondimento sull’importanza della formazione e delle competenze interne necessarie a garantire la sicurezza degli impianti, sempre più interconnessi e legati all’uso dei dati digitali. La
giornata proseguirà con quattro sessioni di confronto che ospiteranno speaker di rilievo - tra cui delegati di ANIPLA, ISA – Global Security Alliance, UCIMA, UCIMU e l’Università di Genova.
Tutti gli interventi saranno a cura di delegati di associazioni, accademici, aziende di consulenza ed industrie leader del settore costruzione e vendita di macchine e impianti. I partecipanti che lo desiderano potranno incontrare durante le pause del convegno gli esperti associati MindSphere World che hanno curato l’organizzazione - H-ON Consulting, ITCore e Siemens - per scambiare idee e consigli in tema di cybersecurity industriale. Per informazioni: Macchineprotette.io
Il piano di espansione strategica di CMZ procede a spron battuto verso i diversi obiettivi proposti, il più recente dei quali è l’apertura della nuova filiale danese. CMZ Danimarca inizia la sua attività per rafforzare la sua presenza nel paese. È un segno tangibile della crescita di cui l’azienda è protagonista negli ultimi anni, con il chiaro obiettivo di superare la soglia dei 100 milioni di euro di fatturato annuo. La Danimarca è un mercato interessante con un notevole potenziale di crescita, che CMZ ha sempre avuto nel mirino. La chiusura di quello che era stato finora il distributore ufficiale in Danimarca, Maskingruppen AS, ha accelerato i piani per il mercato danese e si è trasformata in un’opportunità commerciale fondamentale per il gruppo. Nicolaj Søndergaard (nella foto), ex dipendente dell’ormai scomparso Maskingruppen, guiderà il team commerciale come responsabile in prima linea. La sua vasta esperienza nel settore e la sua profonda conoscenza del mercato sono il suo miglior biglietto da visita. Con questa mossa tattica CMZ intende espandere la propria quota di mercato in Danimarca offrendo un servizio più diretto e personalizzato
ai propri clienti. Questi ultimi avranno a disposizione un servizio di assistenza post-vendita vicino, professionale e diretto da parte del proprio reparto post-vendita locale, focalizzato a fornire una risposta diretta a tutte le loro esigenze. Nuovi orizzonti Neoprec, l’ultimo impianto di lavorazione meccanica messo in funzione da CMZ, ha permesso all’azienda di espandere la propria capacità produttiva. La fine del 2022 è stata segnata da cifre di fatturato vicine ai 100 milioni di euro. La gamma di prodotti è sempre più orientata a soddisfare le esigenze di qualsiasi tipo di cliente: lavorazione di pezzi di grandi dimensioni, tornitura e alta produzione... In termini di apertura dei mercati e di pari passo con la crescita sostenuta della capacità di fabbricazione, CMZ sta consolidando la sua presenza in paesi come gli Stati Uniti e la Turchia senza perdere di vista il suo mercato per eccellenza: l’Europa. L’apertura di CMZ Danimarca diventa quindi un aspetto fondamentale per l’azienda, rafforzandone i piani di crescita e le capacità.
Eni e Commonwealth Fusion System, spinout del Massachusetts Institute of Technology, hanno firmato un nuovo accordo di cooperazione con l’obiettivo di accelerare l’industrializzazione dell’energia da fusione. CFS ha intrapreso il percorso più veloce per la commercializzazione dell’energia da fusione. Nel settembre 2021, CFS ha raggiunto un traguardo importante con il successo del test su un magnete con tecnologia superconduttiva HTS (HighTemperature Superconductors), il magnete più potente del suo genere al mondo, che assicurerà il confinamento del plasma nel processo di fusione magnetica e che potrà contribuire al raggiungimento dell’energia netta da fusione in un futuro impianto dimostrativo. La strada intrapresa da CFS con il supporto di Eni è caratterizzata da un approccio pragmatico e progressivo finalizzato ad ottenere l’applicazione industriale della tecnologia della fusione a confinamento magnetico nel prossimo decennio. SPARC, che punta ad essere il primo impianto pilota a confinamento magnetico al mondo a produzione netta di energia da fusione, è in costruzione e sarà operativo entro il 2025. Si prevede che SPARC, a sua volta, farà da banco di prova per lo sviluppo di ARC: la prima centrale elettrica industriale da fusione in grado di immettere elettricità in rete, che dovrebbe essere operativa nei primi anni del 2030. L’Amministratore Delegato di Eni, Claudio Descalzi, ha commentato: “Vedremo realizzata la prima centrale elettrica di CFS basata sulla fusione a confinamento magnetico all’inizio del prossimo decennio, avendo poi davanti a noi quasi vent’anni per diffondere la tecnologia e raggiungere gli obiettivi di transizione energetica al 2050. Questo vorrà dire disporre a livello industriale di una tecnologia in grado di fornire grandi quantità di energia senza alcuna emissione di gas serra prodotta in modo sicuro, pulito e virtualmente inesauribile fornendo un contributo sostanziale alla transizione energetica. Per questo siamo di fronte a una potenziale svolta tecnologica epocale. Da diversi anni Eni sta ponendo la leadership tecnologica, con un approccio di neutralità e diversificazione, alla base del proprio percorso di decarbonizzazione. Consapevoli del grande valore strategico di questa tecnologia e della solidità di CFS, fin dal 2018 Eni ha investito nella società ed è stata la prima azienda energetica ad impegnarsi concretamente in questo settore. Oggi rafforziamo ulteriormente questa collaborazione con le nostre competenze ed esperienza con l’obiettivo di accelerare il più possibile il percorso di industrializzazione della fusione”.
Datalogic Spa, leader tecnologico globale nei mercati dell’acquisizione automatica dei dati e dell’automazione di fabbrica, aggiunge un altro importante tassello al suo percorso di crescita con il conseguimento della prestigiosa certificazione SA8000. Datalogic ha infatti implementato un sistema di gestione a garanzia del rispetto dei requisiti dello standard internazionale sulla responsabilità sociale dell’organizzazione e della sua catena di fornitura. “Sono particolarmente orgogliosa del riconoscimento ottenuto a testimonianza del nostro impegno nello sviluppo sostenibile, con particolare attenzione alle tematiche sociali. Aver ottenuto questa prestigiosa certificazione ci consente la corretta gestione e il costante monitoraggio di tutte le attività che abbiamo portato avanti in questi anni per migliorare le condizioni dei nostri lavoratori,” spiega la Dott.ssa Volta, amministratore delegato del Gruppo. “Dalla salute e sicurezza sul lavoro, alla non discriminazione, allo sviluppo, valorizzazione, formazione e crescita. Tematiche importanti e imprescindibili per creare valore nel lungo termine, su cui continueremo ad investire anche in futuro.” In Datalogic l’ascolto costante delle esigenze del personale è una pratica consolidata, che ha come obiettivo primario quello di arricchire l’esperienza lavorativa e garantire la soddisfazione dei dipendenti, requisito imprescindibile per il successo di un’azienda. A seguito di una recente attività di ascolto interno, sono state avviate molte iniziative per migliorare ulteriormente l’ambiente e accrescere i benefit riservati ai dipendenti. Tra le nuove iniziative, alcune hanno lo scopo di bilanciare l’equilibrio tra vita personale
e professionale, ad esempio attraverso l’ampliamento della flessibilità in ingresso e uscita, lo smart-working e i servizi salva-tempo (come l’internal delivery point e la cena take-away). Altre azioni intendono rafforzare i principi di sostenibilità aziendale, quali, ad esempio, l’eliminazione delle bottiglie di plastica grazie all’introduzione di distributori d’acqua e la consegna di borracce a tutti i dipendenti. Sono inoltre previsti ulteriori programmi a supporto della genitorialità (borse di studio per i figli meritevoli, buoni acquisto per i libri scolastici, ecc.) e attività informative mirate a offrire gli strumenti per poter fruire al meglio dei benefit (tra cui l’assicurazione medico-sanitaria, il bonus per l’asilo nido e l’integrazione della maternità facoltativa). Il programma di sviluppo continuo delle persone rappresenta un focus di estrema rilevanza per il Gruppo. La recente introduzione di una nuova offerta formativa volta a rafforzare le competenze tecniche e soft, progettata e realizzata a supporto dei percorsi di carriera, sottolinea ulteriormente l’attenzione dell’azienda alla crescita delle proprie persone. PRESS RELEASE www.datalogic.com Datalogic Confidential Internal “I più di 3.000 dipendenti in tutto il mondo costituiscono il nostro principale vantaggio competitivo, e in quanto tali meritano il massimo impegno nell’assicurare loro condizioni di lavoro ottimali. È fondamentale che le persone possano esprimere appieno il proprio potenziale, anche attraverso la formazione interna, le esperienze internazionali, la collaborazione con università e altri istituti,” conclude la Dott.ssa Valentina Volta.
S2E Solutions 2 Enterprise, società di consulenza che opera in ambito business technology, annuncia la nomina di Luca Pellizzari quale direttore responsabile per la ricerca e sviluppo.
Il suo ruolo chiave sarà quello di assicurare un costante coordinamento con l’Innovation Committee di S2E sull’evoluzione dei mercati e delle tecnologie, attuali e in sviluppo, con l’obiettivo di anticipare e di accelerare le evoluzioni previste nelle strategie di crescita di S2E. In tal modo, Pellizzari contribuirà al processo di continua creazione di valore attraverso decisioni, comportamenti e modelli istituzionali, nel rispetto del codice etico di S2E. Nel corso di una carriera trentennale diversificata, Pellizzari ha ricoperto posizioni di top management, operative
e commerciali in diversi settori quali telecomunicazioni, sicurezza pubblica, biometria ed energia in aree come tecnologie, servizi e infrastrutture. Tra le aziende in cui ha operato citiamo A2A, Lucent Technologies, Nec Italia, Nokia Siemens Networks, Telecom Italia. Con una esperienza globale, lavorando in USA, Germania, Spagna, Regno Unito, Belgio, Arabia Saudita, Giappone e Italia, e occupandosi di aspetti sia strategici sia operativi, Pellizzari ha sviluppato un forte focus sulla generazione di guadagni sostenibili in termini di ricavi/EBITDA. “Sono orgoglioso di entrare in una azienda votata all’innovazione come S2E, andando a ricoprire una ruolo chiave per conquistare e mantenere una posizione di riferimento in un mercato dinamico e complesso come quello in cui opera
l’azienda.” - dichiara Pellizzari - “Sono convinto che le mie esperienze e le competenze che ho sviluppato mi permetteranno di dare un forte contributo al successo di S2E”.
“Nel corso della sua carriera Luca ha dimostrato notevoli capacità di problem solving, con una spiccata abilità nel risolvere problemi tecnologici e nel trovare soluzioni innovative a fronte di esigenze tecnologiche complesse.”
- commenta Marco Salerni Direttore Generale di S2E - “Il suo arrivo aumenta la nostra competitività e la nostra capacità di progettare e costruire soluzioni efficaci per i nostri clienti”.
Il nostro filo conduttore è “Fresare meglio”. Ogni problema che riusciamo a risolvere, ogni modifica e ogni ottimizzazione che apportiamo contribuisce a rendere il risultato migliore, più preciso e disponibile più velocemente. Non per noi, ma per il successo dei nostri clienti, che con i nostri centri di lavorazione ottengono i risultati migliori.
www.hermle-italia.it
LA SICUREZZA INCENTRATA SULLE IDENTITÀ SARÀ SULLA BOCCA DI TUTTI NEL 2023. NEGLI ULTIMI ANNI LE AZIENDE SONO PASSATE A MODELLI PIÙ FLESSIBILI PER ADATTARSI ALLA COSÌ
DETTA EPOCA DELLA “NUOVA NORMALITÀ”. IL RISULTATO?
GLI AMBIENTI CLOUD IBRIDI SONO SEMPRE PIÙ DIFFUSI. di Cristina Gualdoni
Il mondo del lavoro ha continuato la strada verso la digitalizzazione, come dimostra l’ampia gamma di tecnologie, soluzioni, applicazioni e dispositivi innovativi che offrono diversi vantaggi operativi e produttivi. D’altro canto, però, le valutazioni in termini di sicurezza di questa transizione sono state un po’ complesse. Il passaggio al cloud implica infatti la scomparsa del perimetro di rete tradizionale e le aziende si trovano a dover gestire ambienti con identità ibride e caratterizzati da una serie infinita di potenziali punti di accesso da difendere. È emersa una preoccupazione
chiave tra molte aziende: come impedire agli utenti malintenzionati di spostarsi liberamente tra gli ambienti on-premise basati su Active Directory (AD) e quelli cloud incentrati su Azure AD.
Il motivo principale per cui molte realtà hanno sviluppato gli ambienti ibridi non era rappresentato dalla sicurezza, ma piuttosto da un’esigenza operativa in risposta alla pandemia. Il risultato è che ora molte di quelle aziende stanno cercando di colmare a posteriori i gap nella sicurezza, anche se purtroppo non è un obiettivo semplice. Quando si parla di minacce che puntano ad AD, che si tratti di prevenire,
rilevare, risolvere o ripristinare, le sfide riguardano l’intero ciclo di vita di un attacco ad AD.
Per questo molte aziende temono di non avere le competenze per rispondere a tali sfide nell’attuale scenario delle minacce. Grazie a un sondaggio effettuato da Semperis, che ha coinvolto i responsabili IT e della sicurezza di oltre 50 aziende, abbiamo scoperto che solo un terzo (33%) di queste era fiducioso sulla sua capacità di prevenire gli attacchi ad AD on-premise, mentre poco più di un quarto (27%) si è detto sicuro di poter contrastare gli attacchi ad Azure AD.
Questi dati sono preoccupanti, soprattutto visto che i sistemi di gestione delle identità rappresentano ormai un obiettivo chiave degli utenti malintenzionati.
Si stima che AD venga sfruttato in 9 attacchi informatici su 10. Si evidenzia come l’uso dannoso delle credenziali sia la tecnica principale scelta per le violazioni. Non è un caso se gli utenti malintenzionati sostenuti da governi nazionali che scelgono come target AD e l’infrastruttura delle identità raggiungano risultati pazzeschi.
È da specificare che gli ambienti ibridi non spariranno, in quanto, non solo AD è il principale strumento di archiviazione per il 90% delle aziende al mondo, ma solo il 3% delle organizzazioni eseguirà una migrazione completa da AD on-premise a un servizio basato su cloud entro il 2025.
Per tali ragioni, oltre ad aver indicato la difesa dei sistemi di gestione delle identità come uno dei trend chiave per la sicurezza informatica del 2022, è stato ideata
anche una categoria del tutto nuova: le soluzioni ITDR (Identity Threat Detection and Response).
È ovvio che le aziende sanno di dover proteggere meglio i propri sistemi di gestione delle identità.
Purtroppo, più di tre quarti degli intervistati (77%) hanno ammesso che le conseguenze probabilmente sarebbero gravi o critiche se un attacco mettesse fuori uso AD. Solo il 32% si è detto “molto fiducioso” rispetto alla capacità di ripristino dopo un attacco ad AD.
In una fase in cui le aziende cercano di dare una svolta rispetto alle minacce ad AD, le soluzioni ITDR ideate appositamente per proteggere i sistemi di gestione delle identità sono quindi diventate una priorità. Del resto, le organizzazioni sono in cerca di diversi metodi per difendere e ripristinare i propri ambienti ibridi. Ecco alcuni dei requisiti più importanti di una soluzione ITDR secondo i partecipanti al sondaggio.
1. Ripristino di AD rapido e automatico
Il sondaggio mostra come, in caso di un attacco informatico che metta fuori gioco
AD, una netta maggioranza (77%) delle aziende subirebbe conseguenze serie (dispone di una soluzione di ripristino di emergenza generale ma non di una specifica per AD) o critiche (dovrebbe procedere a un ripristino manuale tramite backup che richiederebbe giorni o settimane). Perciò, la possibilità di un ripristino automatico e rapido, nel giro di ore, anziché di giorni o settimane, è una delle priorità chiave per chi cerca una soluzione ITDR.
2. Rilevamento degli attacchi che aggirano gli strumenti tradizionali Tra le preoccupazioni principali legate alla protezione di AD, gli intervistati hanno indicato anche il mancato rilevamento degli attacchi da parte degli strumenti di monitoraggio tradizionali. Le organizzazioni sono alla ricerca di soluzioni che ricorrono a diverse fonti di dati, incluso il flusso di replica di AD, per individuare e limitare gli effetti degli attacchi avanzati.
3. Maggiore trasparenza in AD e Azure AD
Rilevare gli attacchi che passano da AD on-premise ad Azure AD, e viceversa, è
emerso come uno dei maggiori timori delle aziende che gestiscono ambienti ibridi. Infatti, solo un terzo dei partecipanti al sondaggio ha detto di sentirsi molto fiducioso rispetto alla capacità di prevenire o risolvere un attacco ad AD on-premise. Quando si parla di Azure AD, tale percezione è solo del 27%. Le aziende hanno bisogno di soluzioni che forniscano maggiore trasparenza sulle attività relative agli ambienti sia AD che Azure AD.
4. Individuazione di vulnerabilità e configurazioni errate già esistenti Dato il numero di attacchi che sfruttano le vulnerabilità di AD pressoché ogni giorno, le aziende sono comprensibilmente preoccupate rispetto alla valutazione dei propri ambienti alla ricerca di falle che gli utenti malintenzionati potrebbero sfruttare. Del resto, identificarle è il primo passo per migliorare la sicurezza. Un programma di manutenzione a lungo termine implica la verifica costante del livello di protezione delle identità per isolare i punti deboli, un aspetto che le aziende ricercano nelle soluzioni ITDR.
5. Correzione automatica Spesso, non appena gli utenti malintenzionati hanno infettato il sistema con il malware, gli attacchi informatici avvengono alla velocità della luce. Pertanto la correzione automatica è fondamentale per evitare che un exploit ottenga privilegi avanzati o addirittura prenda il controllo della rete. Nel celebre attacco NotPetya del 2017 al gigante delle spedizioni marittime Maersk, l’intera rete dell’azienda è stata compromessa in pochi minuti. Gli intervistati hanno indicato la capacità di correzione automatica delle modifiche dannose, al fine di impedire la rapida diffusione degli attacchi, come funzionalità più importante. Seguono poi il monitoraggio e la correlazione delle modifiche tra AD on-premise e Azure AD. Risposta ai diversi requisiti con una strategia multilivello
È evidente come le aziende vogliano soluzioni in grado di gestire le minacce prima, durante e dopo un attacco che sfrutta le identità.
Il ripristino rapido da un evento di questo genere è essenziale. Anche la possibili-
tà di reagire alle minacce è altrettanto importante perché le aziende vogliono risolvere le loro vulnerabilità e bloccare immediatamente gli utenti malintenzionati. Sono necessarie una serie di capacità che includono le valutazioni del livello di sicurezza, il monitoraggio in tempo reale, la correzione automatica delle minacce rilevate e un backup e un ripristino rapidi di una foresta AD.
Quando valutano le soluzioni ITDR, le aziende dovrebbero quindi scegliere quelle che forniscono una difesa stratificata e completa, in grado di offrire una protezione ottimale dei loro ambienti ibridi.
Qr code: È possibile scaricare il sondaggio completo e saperne di più sulle possibili soluzioni ITDR
Vi presentiamo la vostra nuova alleata: la gamma Swiss DT di ultima generazione. Superate le vostre stesse aspe ative, aumentate il vostro vantaggio competitivo e approfi ate di una soluzione che si evolve in base alla vostra strategia aziendale.
La gamma è composta da sei confi gurazioni di macchine S e HP che possono lavorare barre di 13, 26, 32 e 38 mm di diametro.
UCIMU PRESENTA IL PRIMO BILANCIO NEL COMPARTO DEI BENI DI INVESTIMENTO. È LA PRIMA ASSOCIAZIONE, IN ITALIA E IN EUROPA, AD AVERLO REALIZZATO a
Èstato presentato, nel corso di un incontro aperto alla partecipazione di imprese, mondo del credito, istituzioni e stampa, il primo Bilancio di Sostenibilità dedicato al settore delle macchine utensili, realizzato da UCIMU-SISTEMI PER PRODURRE, l’associazione dei costruttori italiani di macchine utensili, robot e automazione, in collaborazione con ALTIS, Alta Scuola Impresa e Società dell’Università Cattolica del Sacro Cuore.
“La sostenibilità è un campo estremamente proficuo per le aziende perché non solo permette di migliorare i rapporti con i propri stakeholder ma offre anche la possibilità di reinventarsi e allinearsi con lo scenario normativo europeo, il quale sottolinea l’importanza sempre maggiore della diffusione delle buone pratiche ESG. Di fronte a questo Bilancio, si può affermare che già un buon numero di pratiche in linea con i criteri ESG è stato introdotto. Nel comparto dei beni di investimento,
UCIMU-SISTEMI PER PRODURRE
è la prima associazione, in Italia e in Europa, ad aver realizzato il Bilancio di sostenibilità di settore. Un risultato che ci rende senza dubbio molto orgogliosi: il prossimo step sarà quello di formalizzare questo processo ed estenderlo ad una platea di aziende più ampia. A tal fine UCIMU continuerà con l’attività di formazione e supporto alle associate avviata negli ultimi anni”, ha affermato Barbara Colombo, Presidente UCIMU-SISTEMI PER PRODURRE, che ha aperto i lavori insieme a Vito Moramarco, Direttore di ALTIS Università Cattolica. Stella Gubelli, AD di ALTIS
Advisory Srl Società Benefit, Spinoff dell’Università Cattolica del Sacro Cuore, ha poi illustrato i contenuti e le principali evidenze emerse dallo studio: “Il progetto sviluppato con UCIMU vuole favorire nelle aziende associate l’avvio di percorsi di miglioramento basati su una valutazione ESG oggettiva e orientati agli ambiti di sostenibilità rilevanti per il settore. Crediamo
sia, questo, il modo più efficace per accompagnare le imprese ad affrontare le sfide e cogliere le opportunità”. Durante la tavola rotonda moderata da Mauro Bellini, Direttore Responsabile di ESG360.it, sono state riportate le testimonianze di Barbara Colombo, AD di Ficep, Massimo Carboniero, AD e Contitolare di Omera, e Andrea Portosa, Responsabile Area Acquisti di Rosa Ermando, quali rappresentanti di tre imprese del settore che hanno stilato il loro primo bilancio di sostenibilità; di Natale Schettini, Responsabile Governo del Credito, Banco BPM, Carolina Lonetti, Chief Export Finance & Internationalization Officer SIMEST, Marco Cantalamessa, Chief Marketing & CEO Staff Officer SIMEST, che hanno evidenziato la crescente rilevanza dei criteri ESG nella valutazione di richieste di finanziamento per attività di sviluppo e crescita dell’azienda; di Maurizio Bellosta, AD di Rubinetterie Bellosta e Vicepresidente AVR, che ha sottolineato quanto, nella scelta di un fornitore, sia determinante l’approccio alla sostenibilità
che pone nello svolgimento della sua attività. A chiudere i lavori è stata Patrizia Ghiringhelli, Vicepresidente UCIMU e Coordinatrice del Comitato Marchio UCIMU.
Il Bilancio di Sostenibilità fa riferimento all’anno 2021 ed è stato redatto sulla base delle risposte al questionario indirizzato alle imprese associate con Marchio UCIMU . Delle 66 imprese concessionarie del Marchio UCIMU hanno risposto 53. Il questionario di valutazione predisposto da UCIMU in collaborazione con ALTIS è stato costruito secondo un’analisi di materialità, ovvero focalizzando l’attenzione sugli ambiti di sostenibilità maggiormente influenzati dall’attività delle aziende del settore. In altre parole, le aree ESG oggetto di valutazione sono state scelte, a partire da 11 obiettivi dell’Agenda ONU 2030, perché più coerenti rispetto al business delle imprese della macchina utensile.
I risultati contenuti nel Report vengono qui presentati secondo i tre grandi ambiti in cui si dispiega l’attività di impresa rispetto ai criteri di sostenibilità: ambientale, economico e sociale.
Per il settore il tema dell’economia circolare (SDG 12) è un indiscusso ambito di eccellenza, tanto che il 62% delle imprese intervistate ha implementato buone pratiche. Quasi la totalità delle aziende, il 98%, esegue la raccolta differenziata dei rifiuti; il 76% ha definito i propri obiettivi in materia di riduzione degli scarti e dei rifiuti prodotti, il 50% si serve di materie prime provenienti da riciclo.
Dal punto di vista delle emissioni di anidride carbonica (SDG 13), le imprese del settore devono invece ancora configurare il loro operato. Infatti, solo il 33% delle rispondenti ha definito obiettivi legati alla riduzione della CO2 e, ancor meno, l’11% delle imprese ha formalizzato questi obiettivi in un documento ufficiale.
Tra le attività che rientrano nel pacchetto di buone pratiche rispetto all’obiettivo
Il settore si muove bene sul fronte della sostenibilità: la metà delle aziende con Marchio UCIMU dichiara di avere in programma, nel prossimo triennio, la pubblicazione di un Report di Sostenibilità (48%) e la redazione di un Piano Strategico (54%). Obiettivi di breve-medio periodo per le imprese del comparto sono: una maggiore formalizzazione di policy e processi e l’attuazione di iniziative di comunicazione mirata.
13, solo il 9% delle aziende intervistate ha preso in considerazione lo sviluppo di azioni di compensazione i cui costi di realizzazione sarebbero decisamente contenuti, considerato il basso impatto ambientale che, per loro natura, hanno le imprese di questo settore.
In un settore ad alto contenuto di tecnologia e specializzazione, ove l’innovazione risulta centrale per la competitività dell’offerta, il capitale umano e, quindi, la formazione di qualità (SDG 4) dei collaboratori sono tra gli asset intangibili più importanti. Il 92% delle aziende dichiara di aver impostato o adottato un sistema di gestione per rispondere alle esigenze formative dei dipendenti. L’87% ha definito obiettivi formativi per i propri collaboratori, di questi più della metà (54%) sono obiettivi formalizzati. Inoltre, il 63% delle aziende dichiara di erogare formazione su competenze trasversali oltre che su materie tecniche e l’82% dichiara di aver adottato procedure di valutazione delle performance del personale.
Forte anche l’impegno delle aziende per lo sviluppo sostenibile del territorio e della comunità (SDG 11): il 68% delle imprese dimostra di essere consapevole del proprio ruolo di propulsore di crescita attraverso, ad esempio, l’erogazione di contributi economici a supporto di enti locali e dei giovani talenti.
Tra gli ambiti di miglioramento, quello relativo alla diversità e alle pari opportunità (SDG 5), rispetto al quale occorre lavorare sull’implementazione di politiche volte a una maggiore inclusività, sia delle presenze femminili, sia dei giovani, in un settore tradizionalmente maschile. Ad oggi la forza lavoro è prevalentemente di genere
maschile (86%). I giovani rappresentano una parte davvero minimale rispetto al totale degli addetti: il 77% delle persone che operano nelle aziende del comparto ha più di 30 anni. Solo il 22% delle imprese dispone di una politica o di un comitato per la valorizzazione della diversità e per la promozione delle pari opportunità.
Detto questo, tra le buone pratiche adottate dalle aziende in tema di pari opportunità e diversità si contano l’implementazione di una policy più inclusiva, la creazione di asili nido aziendali e azioni di accompagnamento alla maternità.
Infine, occorre che le imprese investano maggiormente nella governance della sostenibilità (SDG 16) e nella formalizzazione delle proprie iniziative:
infatti, solo il 30% comunica i temi ESG attraverso una sezione dedicata nel proprio sito e solo il 4% ha formalizzato questa procedura attraverso la stesura di un documento di rendicontazione quale è il Bilancio di Sostenibilità.
Sostenibilità economica
Nel campo dell’innovazione (SDG 9), dal digitale alla sicurezza informatica, le imprese sono fortemente orientate allo sviluppo di tecnologie innovative ed efficienti, in grado di ridurre lo spreco di risorse, favorire modelli di consumo più sostenibili e assicurare maggiore produttività alle aziende clienti. I risultati dell’indagine ci dicono, infatti, che il 91% delle imprese ha definito una strategia o obiettivi futuri in materia di digitalizzazione, automazione e industria
4.0. Tra le buone pratiche più diffuse vi è quella relativa allo sviluppo di progetti di digitalizzazione e di comunicazione con i prodotti installati per consentirne, in accordo con il cliente, il monitoraggio continuo e prevederne le esigenze di manutenzione. Tutto ciò significa, infatti, riduzione dei tempi di produzione e dei fermi macchina, oltre che corretto utilizzo delle risorse. Attività, queste, che contribuiscono al miglioramento della competitività dell’azienda.
Sul fronte della Ricerca e Sviluppo: il 72% delle aziende ha definito una strategia o obiettivi futuri orientati alla riduzione degli impatti ambientali dei prodotti. La quasi totalità delle intervistate assicura di servirsi dello strumento dell’etichettatura o di quello della formazione per istruire i clienti sul
corretto utilizzo delle macchine (91%) e sullo smaltimento delle stesse a fine ciclo vita (72%).
In generale, dal Bilancio di Sostenibilità 2021 emerge una diffusa mancanza di formalizzazione dei processi: nonostante il 64% delle aziende abbia definito strategie e obiettivi, solo il 24% lo ha fatto in maniera formalizzata. La percentuale relativa alla gestione e monitoraggio dei percorsi sostenibili, seppur più alta (39% in modo formalizzato), rimane al di sotto della metà. D’altra parte, i risultati del Report mettono in luce la necessità per le imprese del settore di consolidare la loro attitudine a “comunicare la sostenibilità” attraverso l’implementazione di pratiche aziendali ad hoc.
“DOPO QUATTRO ANNI DI PAUSA, QUEST’ANNO RIUNIREMO I COSTRUTTORI DI UTENSILI, MODELLI E STAMPI E I LORO FORNITORI SOTTO UN UNICO TETTO, FACENDO INCONTRARE I MIGLIORI OPERATORI DEL SETTORE CON I LORO
CLIENTI”, AFFERMA FLORIAN NIETHAMMER, RESPONSABILE FIERE ED EVENTI DI MESSE STUTTGART
A cura della redazione
La Moulding Expo aprirà i battenti a Stoccarda dal 13 al 16 giugno 2023. Per la prima volta, la fiera internazionale per la costruzione di utensili, modelli e stampi si svolgerà nell’L-Bank Forum (padiglione 1) di Messe Stuttgart. Essendo il padiglione più grande del sito fieristico, insieme alla galleria circostante e all’area del foyer, offre una superficie totale di quasi tre padiglioni standard.
Attualmente, 300 espositori si sono già registrati per la Moulding Expo.
“In qualità di organizzatori della fiera, siamo soddisfatti del forte consenso e del profondo attaccamento delle aziende espositrici nei confronti del loro luogo di incontro di settore, la Moulding Expo. Questo è un segnale forte in tempi di aumento dei prezzi dell’energia e delle materie prime, che stanno mettendo a dura prova tante aziende in modi molto
diversi”, afferma Roland Bleinroth, Direttore Generale di Messe Stuttgart.
Nuove imprese: una ventata
d’aria fresca
Tra le imprese registrate molte partecipano per la prima volta. Ad esempio la Alfred Konrad Veith GmbH & Co. KG. “Consideriamo la Moulding Expo un’importante fiera regionale e nazionale per la costruzione
di utensili, modelli e stampi e per la lavorazione delle materie plastiche. Partecipiamo alla Moulding Expo per presentare la nostra azienda e i nostri prodotti e rivolgerci così a nuovi clienti”, afferma Zeljko Zinic, procuratore/ responsabile del settore vendite di Alfred Konrad Veith GmbH & Co. KG. Anche SCHRÖTER MODELLUND FORMENBAU esporrà per la prima volta alla Moulding Expo: “Le fiere sono sempre state un fattore importante per il nostro contatto diretto con i clienti. Pertanto, è logico per noi partecipare alla Moulding Expo. Il fattore decisivo per la nostra partecipazione alla Moulding Expo è l’ampia offerta e la versatilità della fiera. Siamo lieti di poter presentare servizi e prodotti innovativi nonché il nostro pezzo forte, un prototipo di elicottero monoposto del nostro cliente FlyNow Aviation”, afferma Maximilian Lörzel, Direttore Generale e titolare di SCHRÖTER
MODELL - UND FORMENBAU GMBH.
L’importanza che la manifestazione rappresenta per l’industria europea degli utensili, dei modelli e degli stampi si riflette nel carattere internazionale delle aziende espositrici. Oltre il 30% degli espositori proviene da altri Paesi europei. Quest’anno sono particolarmente rappresentati Portogallo, Turchia, Svizzera e Italia.
Un esempio su tutte l’italiana PROMAC: “La Moulding Expo è di importanza
strategica per noi, poiché la fiera si svolge nel cuore dell’industria europea. Alla Moulding Expo presentiamo sistemi di automazione come i sistemi di cambio pallet e i sistemi di cambio accessori che consentono cicli di lavoro non presidiati”, rivela Alberto Cattelan, Sales Manager dell’azienda.Anche per Punto Stampi la Moulding Expo è di grande importanza. “Lavoriamo da sempre ed esclusivamente come fornitori del mercato europeo. Partecipare per la prima volta alla Moulding Expo ci dà l’opportunità di incontrare e ampliare la nostra cerchia di clienti e anche di fornitori”, riassume Christiane Taschner, Project / Export Management di Punto Stampi s.r.l..
I preparativi si intensificano I preparativi per la Moulding Expo sono a pieno regime e anche le aziende espositrici si stanno preparando per la loro partecipazione alla fiera. Numerose piccole e medie imprese si sono presentate per la prima volta alla fiera in stand comuni, così ad esempio la Lercher Werkzeugbau und Kunststoffspritzguss. “Una piattaforma di presentazione con un formato europeo è più che benvenuta per il nostro settore. La partecipazione allo stand comune della VDWF offre un’ottima opportunità per presentarci per la prima volta alla Moulding Expo”, afferma Dominik Lercher, Direttore Generale del settore tecnico della Lercher Werkzeugbau und Kunststoffspritzguss. Gli interessati
possono scoprire quali prodotti e servizi l’azienda esporrà alla Moulding Expo ancora prima dell’inizio della fiera.
“Con la Sneak Preview della Moulding Expo è possibile farsi una prima idea dei fornitori più interessanti e fare una preselezione per la propria visita in fiera, in modo da sfruttare al meglio il tempo a disposizione”, aggiunge Lercher.
Tutte le anteprime di alcune aziende espositrici sono disponibili online: www.moulding-expo.com/sneak-preview
La fiera internazionale per la costruzione di utensili, modelli e stampi è divisa in diverse aree espositive. Al centro dell’attenzione si trova la costruzione di utensili, modelli e stampi finalizzata agli utenti con le sue attrezzature per lo stampaggio a iniezione, la pressofusione, la foggiatura, la costruzione di dime e attrezzature. Inoltre in fiera sono presenti anche fornitori di sistemi e servizi per tutti gli aspetti della tecnologia delle materie plastiche e della lavorazione dei metalli: dai produttori di macchine utensili ai fornitori di materiali, fornitori di canali caldi, fornitori di attrezzature di misurazione e di collaudo, produttori di utensili per la lavorazione fino alle software house.
L’INDUSTRIA DELLE MATERIE PLASTICHE E DELLE GOMMA
TORNA PROTAGONISTA A MILANO DAL 5 ALL’8 SETTEMBRE DOPO LA PAUSA CAUSATA DALLA PANDEMIA a cura della redazione
Sono 500 gli espositori diretti che hanno aderito alla fase early bird chiusa il 10 dicembre, con 34mila metri quadri prenotati; dati che rafforzano la prospettiva di una mostra sempre più ricca di proposte innovative grazie a professionisti e imprese provenienti da tutto il mondo. Fin dalle prime battute, l’edizione 2023 di PLAST si conferma quindi un successo, rafforzato dai tre saloni-satellite dedicati ad altrettante filiere d’eccellenza nel settore, cioè RUBBER, 3D PLAST e PLAST-MAT, a dimostrazione della dinamicità di un mercato che esprime valori estremamente positivi.
Nucleo portante della mostra è il segmento dei macchinari, delle attrezzature ausiliarie, degli stampi per la lavorazione della plastica e della gomma, un settore che rappresenta un’importante realtà nell’industria manifatturiera italiana, con oltre 400 aziende. Per tale comparto, il centro studi MECS dell’Associazione di categoria Amaplast stima un bilancio sostanzialmente favorevole per il 2022 - dopo il rimbalzo
registrato nel 2021, anno archiviato con incrementi a doppia cifra per tutti gli indicatori - a conferma della sua capacità di assorbire i contraccolpi delle gravi criticità che si sono manifestate e sovrapposte nell’ultimo triennio. Infatti, la produzione complessiva dovrebbe raggiungere la soglia dei 4,5 miliardi di euro, con un incremento di un punto percentuale rispetto al 2021: si tratta di una variazione contenuta che però consolida il recupero messo a segno lo scorso anno, superando anche di due punti il valore del 2019 (pre-pandemia).
Risultano ancora in crescita, seppure di misura, entrambe le componenti della domanda: da un lato le esportazioni – che assorbono il 70% circa della produzione – mostrano un aumento del 2% circa, fino a superare nuovamente i 3 miliardi, dall’altro il mercato interno segna un +1%, anche in funzione di importazioni in progressione del 5%. In base alla più recente indagine congiunturale svolta tra gli associati Amaplast, si è verificata una progressiva attenuazione della crescita nel corso di quest’anno. Sia sul mercato interno sia all’estero si è osservato un rallentamento più marcato per i macchinari mentre le vendite e le commesse in entrata di ricambistica hanno mantenuto una crescita. I costruttori italiani auspicano che in chiusura di periodo la raccolta ordini torni più sostenuta, anche grazie all’ “effetto-K”, con la mostra di Düsseldorf che potrebbe contribuire a sbloccare investimenti rimasti precedentemente in stand-by. Gli imprenditori sono però cauti, alla luce dei venti di guerra e delle turbolenze economiche che caratterizzano lo scenario globale.
Volgendo lo sguardo al 2023 è verosimile attendersi un ripiego di tutti gli indicatori di settore, con una flessione peraltro contenuta a pochi punti percentuali. Del resto, anche le previsioni di CONFINDUSTRIA sull’andamento dell’economia italiana nel suo complesso indicano una crescita bassa o negativa, a fronte di un tasso di inflazione ancora elevato, soprattutto a causa degli alti costi energetici.
Centri di tornitura mono e bimandrino, plurimandrino e a fantina mobile
CENTRI DI TORNITURA E FRESATURA INDEX SERIE G200.2
INDEX G200.2 a 3 torrette, con tre assi Y e un asse B, mandrino di fresatura addizionale e cambio utensile a 6 posizioni.
La macchina è Industry 4.0 Ready grazie al controllo C200-sl su base SIEMENS S840D sl arricchito dalle funzionalità del sistema XPanel della INDEX.
Passaggio barra D65 – Torretta 1 con assi X, Z, Y e B - Torrette 2 e 3 con assi X, Z e Y
I torni a doppio mandrino TTL di CMZ montano le guide lineari a rulli Serie RA di NSK per agevolare il movimento fra le torrette e le teste portamandrino
IL COSTRUTTORE DI TORNI SPAGNOLO CMZ DA OLTRE UN QUARTO DI SECOLO HA STRETTO UNA COLLABORAZIONE TECNOLOGICA AD ALTO LIVELLO CON NSK, AZIENDA SPECIALIZZATA IN SOLUZIONI DI MOTO LINEARE E CUSCINETTI a cura della redazione
CMZ è un’azienda a gestione familiare con una storia di oltre 75 anni nella produzione di torni. Negli ultimi tre decenni l’azienda spagnola si è costantemente evoluta siglando partnership con fornitori di primo livello come NSK, che offre un contributo importante alla costruzione di oltre 500 macchine ogni anno. La collaborazione tra le due aziende
è cominciata nel 1996 con la serie di torni TBI: fu quella la prima macchina a utilizzare viti a ricircolazione di sfere di NSK, caratterizzate dalla ricircolazione esterna delle sfere e da molte altre funzionalità adattate alle macchine utensili. Questo ha presto convinto CMZ che NSK offriva la tecnologia più adatta ai propri torni, cominciando a utilizzare esclusivamente le viti a ricircolazione di sfere della casa giapponese.
Nel 2000 CMZ ha lanciato la serie di torni TL, che rappresentava un grande balzo tecnologico grazie, da un lato, alla tecnologia della torretta che sostituiva la vecchia elettromeccanica con la nuova tecnologia dei servocontrolli. L’azienda spagnola sperimentò una testa di nuova concezione dotata di motore integrato. Per aumentare la rigidità e ottenere un design compatto, l’azienda cominciò a utilizzare i
cuscinetti a due corone di rulli cilindrici di NSK, abbinati a cuscinetti a sfere a contatto obliquo BTR per assorbire i carichi radiali. Questa scelta portò grandi vantaggi per quanto riguarda le prestazioni della testa alle alte velocità. ROBUST BAR e BTR sono le serie di cuscinetti a rulli ad alte prestazioni specificamente per i torni di ultima generazione realizzate da NSK per offrire le massime prestazioni con minime oscillazioni di temperature e garantire una precisione elevata. Per soddisfare le richieste specifiche dei clienti, questi cuscinetti vengono proposti con contatti obliqui a 30° o 40° e possono contenere elementi volventi in ceramica per le applicazioni che richiedono velocità più elevate. Le teste di CMZ richiedono un processo di assemblaggio preciso. L’azienda ha costruito la prima camera bianca nello stabilimento di Zaldibar nel 2000 e, successivamente, ne ha realizzata una seconda nell’impianto di Seuner. All’interno delle camere bianche, l’aria deve essere trattata in modo specifico per garantire il corretto assemblaggio di questo tipo di testa, controllando la temperatura e l’umidità pressurizzazione per espellere polvere e altre particelle, in conformit normativa ISO Classe 8.
Un’altra innovazione da cui CMZ trae beneficio è la vite a ricircolazione di sfere di NSK con raffreddamento della chiocciola, che definisce nuovi standard di precisione e velocità nelle macchine utensili. I vantaggi in termini di adeguamento dei costi, compattezza del design e semplificazione del sistema portano miglioramenti importanti rispetto al raffreddamento ad albero cavo. Questi vantaggi favoriscono anche il controllo della temperatura alle alte velocità per mantenere una precisione micrometrica, requisito fondamentale per le moderne macchine utensili. Inoltre, il sistema consente un raffreddamento efficace del mandrino. Quando ha sviluppato la serie TD di
macchine per applicazioni di tornitura su larga scala, CMZ ha incorporato le viti a ricircolazione di sfere di NSK con raffreddamento della chiocciola negli assi che eseguono movimenti più ripetitivi, dove la generazione di calore potrebbe causare imprecisioni nelle lavorazioni di tornitura. Grazie a questa concezione, il catalogo di prodotti di CMZ offre oggi torni in grado di lavorare a livelli di precisione più elevati su pezzi di grandi dimensioni.
CMZ ha la certezza che NSK è in grado di rispondere a tutte le sue esigenze di sviluppo, grazie alla stretta interazione con gli uffici tecnici in Giappone. Questo canale di comunicazione consente all’azienda spagnola di essere sempre aggiornata sulle innovazioni tecnologiche, come le guide lineari a rulli dotate di speciali sistemi anti-contaminazione e i modelli più avanzati di viti a ricircolazione di sfere e cuscinetti.
Fra le ultime macchine lanciate da CMZ sul mercato, infatti, c’è il tornio CNC a doppio mandrino serie TTL, che ben testimonia la collaborazione fra CMZ e NSK. Questo modello ad alta produttività utilizza le guide lineari
di movimenti fra le torrette e le teste dei mandrini, azionate da motori sincroni. NSK ha sviluppato una serie di guide lineari dotate del rivoluzionario sistema di lubrificazione K1, che eroga olio per tutta la vita della macchina, offrendo una soluzione sostenibile ed ecologica che risponde alle aspettative di CMZ. Attualmente l’azienda costruisce circa 100 torni della serie TTL ogni anno. Un altro progetto in corso e che ben testimonia la partnership tra le due la digitalizzazione. Anche una priorità per le due aziende, in particolare per quanto riguarda il consumo di olio. Le soluzioni di NSK sono dotate di sistemi di protezione e lubrificazione che non devono mai essere sostituiti, assicurando una drastica riduzione del consumo di olio.
CMZ e NSK stanno valutando diverse soluzioni per ridurre al minimo gli sprechi nei progetti dei torni recenti realizzati dall’azienda. Come per tutti i progetti di sviluppo degli ultimi 25 anni e oltre, NSK continuer à ad assistere CMZ nella sua ambizione di essere all’avanguardia del mercato. La partnership fra le due solida, fondata su fiducia e comprensione reciproche.
UN 2022 DINAMICO E DI SUCCESSO NONOSTANTE LA COMPLESSITÀ DEGLI
SCENARI MACROECONOMICI QUELLO CHE HA VISTO PROTAGONISTA LEISTER, PONENDO COSÌ LE BASI PER UN 2023 INTERESSANTE E FRUTTUOSO di E.S.
Bilancio positivo e buone prospettive per il 2023 questi sono gli scenari che si presentano per la saldatura della plastica e il calore di processo. Ne abbiamo parlato con Paolo Possa, General Manager di Leister Technologies Italial, filiale italiana della multinazionale svizzera che da oltre
70 anni fornisce soluzioni innovative per gli operatori professionali in diversi segmenti, dall’edilizia ai macchinari industriali.
Il 2022 è stato caratterizzato da un inizio decisamente brillante per la maggior parte settori industriali, ma l’entusiasmo in alcuni casi è
stato mitigato da un successivo rallentamento e dalle dinamiche inflattive. Per Leister com’è andata? Nell’insieme siamo comunque soddisfatti del lavoro fatto e dei risultati raggiunti. È stato un anno non banale per la nostra azienda, con diversi elementi favorevoli che ci hanno consentito di offrire sempre
maggior valore ai nostri clienti, ma anche importanti sfide che hanno ostacolato il nostro lavoro.
Tra gli elementi favorevoli possiamo certamente includere il contesto macroeconomico, caratterizzato da un generale sostegno alla crescita e che ha determinato nei 12 mesi del 2022 una crescita dell’economia italiana vicino ai 4 punti percentuali. Leister fornisce soluzioni in diversi mercati, e i due principali, ovvero la fornitura di elementi di tecnologia per il settore dei macchinari industriali e la fornitura di elettroutensili per il settore delle costruzioni, in particolare per l’impermeabilizzazione, hanno beneficiato di questo “vento” a favore. Tra gli elementi a favore segnaliamo inoltre alcune iniziative ed alcuni investimenti fatti dall’azienda e che hanno portato a benefici fin da subito. Abbiamo realizzato uno showroom dedicato al settore dei teloni e tessuti tecnici, dove finalmente i nostri clienti hanno potuto conoscere SEAMTEK, l’innovativa saldatrice stazionaria a cuneo caldo, caratterizzata da bassissimo consumo di energia elettrica e con un PLC che la rende facilmente configurabile per gli standard Industria 4.0. Sempre nel 2022 abbiamo lanciato nel mercato italiano diverse novità di prodotto tra cui UNIROOF 700, saldatrice dedicata a chi opera nell’ambito dell’impermeabilizzazione di coperture industriali e che grazie ad un sistema di controllo “intelligente” è in grado di supportare l’operatore nel massimizzare la qualità delle saldature su tetti. Chiamato “Monitor Welding Assistant” questo sistema agisce da vero e proprio assistente sul campo, sempre vigile e pronto a segnalare all’operatore, sia acusticamente che tramite indicazioni a display, eventuali scostamenti dai corretti parametri di saldatura. In ultimo voglio ricordare anche il 2022 come l’anno in cui siamo tornati ad incontrare in presenza i nostri clienti dopo i due anni della pandemia che ci avevano forzato ad un lungo “letargo” nella relazione commerciale. Siamo tornati a visitare i nostri clienti in cantiere o presso le loro sedi, ma siamo anche tornati ad essere presenti nelle fiere dei
numerosi settori dove Leister fornisce tecnologia, da MECSPE ad Ipack-IMA, da Forum Piscine ad ECOMONDO.
La logistica quest’anno è stata una nota dolente per molte aziende industriali: come ha fatto fronte ai problemi di approvvigionamento la Casa madre, e che riflessi hanno avuto gli accorgimenti adottati sulla puntualità delle consegne e del servizio per Leister Italia?
Le difficoltà di approvvigionamento di materiali, in particolare di schede elettroniche, hanno costituito il principale elemento di sfida del 2022 per la nostra organizzazione. La Casa Madre svizzera aveva creato fin dal 2021 una task force per seguire le situazioni più critiche e valutare le misure più opportune a seconda della situazione, ma il top delle sfide alle catene di fornitura si è verificato nell’anno appena chiuso. In alcuni casi si è intervenuto supportando i fornitori anche nel reperimento sul mercato internazionale di materie prime e componentistica. In
altri casi è stato necessario attivare nuovi fornitori nell’ottica di ricercare puntualità nei tempi di consegna e qualità adeguati agli standard definiti dall’azienda. In altri ancora si è preferito ritardare il lancio di nuovi prodotti per non aggiungere ulteriori difficoltà.
Va anche segnalato che in diversi casi le difficoltà di approvvigionamento sono state conseguenza di elementi positivi; Leister è una multinazionale che opera a livello globale e per diversi prodotti le criticità sono state la conseguenza di volumi cresciuti a livello globale ben al di sopra di quanto immaginabile dopo l’anno particolare del 2020. Guardando ora al 2023 l’aspettativa è di un graduale ritorno alla normalità passati i primi mesi del nuovo anno. Sia noi che lavoriamo a diretto contatto col cliente finale, ma anche chi opera nella logistica e nella produzione, non ne vediamo l’ora!
Nei segmenti principali che trattate, plastic welding e process heat, quali fra le soluzioni che proponete hanno riscosso maggior successo quest’anno?
In ambito saldatura della plastica, oltre alla saldatrice automatica UNIROOF 700 di cui abbiamo già parlato, sono da segnalare la sorella minore UNIROOF 300, e la saldatrice semi-automatica UNIDRIVE 500.
UNIROOF 300 per chi realizza piscine è l’aiuto che da tanti anni gli installatori di piscine chiedevano; finalmente esiste una soluzione per saldare comodi, stando in piedi (quindi senza affaticare schiena e ginocchia), con la qualità che la piscina richiede e ad un prezzo accessibile.
UNIDRIVE 500 è attrezzo versatile, in grado di saldare verticali o trasversalmente su tegoli, e altre applicazioni con velocità più che doppia rispetto alla saldatura manuale, problemsolver in un gran numero di situazioni, sia in ambito coperture, realizzazione di vasche o di piscine, ma anche in opere di ingegneria civile (applicazione waterstop).
Senza dimenticare SOLANO AT, pistola ad aria calda fiore all’occhiello di Leister, che grazie alla funzione ECO-MODE è in grado di consumare energia elettrica solo quando serve, a vantaggio di comfort
nell’ambiente di lavoro nonché della bolletta elettrica.
Se parliamo di efficienza energetica e di uso intelligente della risorsa energia dobbiamo assolutamente citare anche i pannelli ad Infrarosso Krelus. Qui siamo nell’ambito delle soluzioni offerte da Leister per il calore di processo e i pannelli Krelus sono una soluzione che sta trovando sempre più impiego nell’industria, per due motivi principalmente:
sono caratterizzati da altissima efficienza energetica (fino al 90% dell’energia utilizzata si traduce in effetto utile sul materiale da scaldare); hanno una bassissima inerzia termica (accensione e spegnimento in tempi rapidissimi, a beneficio di sicurezza e di riduzione tempi per avviamento impianto).
La forte attenzione a ridurre i consumi da un lato e la ricerca di fonti alternative al gas per il calore di processo dall’altro hanno dato forte impulso a questa soluzione negli ultimi anni, e in modo particolare nel 2022.
Avete iniziato a proporre le soluzioni
Laser Plastic Welding, com’è stata l’accoglienza finora?
Leister produce sistemi per la saldatura delle materie plastiche con tecnologia
Laser da oltre 20 anni e in alcuni paesi ed industrie, Germania per esempio, e settori come il medicale, l’automotive oppure l’industria elettronica, ha trovato accoglienza estremamente favorevole. Qualità e ripetibilità elevata del processo, assenza pressoché totale di bave o polveri a fine saldatura sono tra le principali ragioni di questo successo.
Noi siamo partiti più tardi dei colleghi tedeschi e abbiamo cominciato a investire con una certa continuità per sviluppare il mercato locale solo in anni recenti. Dopo una prima presenza con saldatrice laser alla fiera Plast 2015, è solo dal 2019 che abbiamo trovato in MECSPE la fiera ideale per promuovere questa tecnologia. In generale l’accoglienza è buona, sia da parte di progettisti che di aziende, e cresce di anno in anno il numero di progetti che seguiamo. C’è comunque ancora tanto da fare per far conoscere la
saldatura Laser di materiali plastici in Italia e concretizzare tutto il potenziale che la tecnologia offre.
Quali novità sono previste per il 2023?
Il 2023 è da poco iniziato e la prima novità rispetto al 2022 sembra essere data proprio dalla macroeconomia.
Gli esperti sembrano dirci che il 2023 sarà caratterizzato da un’economia in progressivo “raffreddamento”, a causa della crescita di inflazione e tassi di interesse e al protrarsi del conflitto in Ucraina. Niente più quindi il vento in poppa del 2022 ma quantomeno un ridimensionamento dello stesso è quello che leggiamo da qualche mese a questa
parte su quotidiani economici e siti specializzati. Al momento le previsioni dicono che la crescita dell’economia del nostro paese si attesterà intorno al +0,40,5% e che quindi le aziende si dovranno accontentare dopo gli ultimi due anni di forte impulso.
A prescindere da come andrà in generale l’economia, quello che noi nel nostro piccolo faremo come azienda sarà di mantenere il forte impegno a tornare sul mercato con incontri in presenza e con la partecipazione a fiere di settore. Quest’anno a Milano tornerà dopo diversi anni la fiera PLAST, evento triennale dedicato all’industria delle materie plastiche e della gomma, così
come tornerà ITMA, la principale fiera per quanto riguarda l’industria tessile e le tecnologie collegate, fiera annuale ma itinerante che mancava dal contesto italiano da quasi una decade. Come da tradizione avremo anche interessanti novità di prodotto da presentare, tra tutti citiamo un innovativo saldatore manuale partner nel lavoro di tutti i giorni per chi si occupa di carpenteria plastica, e l’aggiornamento di due saldatrici automatiche che hanno fatto la storia nella saldatura dei teli in PVC spalmato e nella saldatura dei manti sintetici per impermeabilizzazione.
Lavoreremo inoltre a rendere il nostro
negozio online www.leistershop. it ancora più ricco ed interessante. A poco meno di due anni dalla sua nascita il sito si è affermato come valido supporto per l’acquisto di tutti quegli articoli che noi definiamo “non problematici”, principalmente accessori, ricambi e piccoli elettroutensili come le pistole ad aria calda e i saldatori manuali, ma abbiamo ancora tanto spazio di miglioramento come “negozianti virtuali”. Per il 2023 contiamo di rendere ancora più interessante il nostro negozio online, con notizie sempre aggiornate sulle nostre iniziative, racconti dal campo di nuove applicazioni e, perché no, anche
con qualche offerta commerciale. In attesa di ulteriori novità, come potrebbe essere l’integrazione dell’online shop all’interno del sito “istituzionale” www. leister.com, progetto a cui la nostra Casa Madre sta lavorando e che coniugherebbe il top in termini di informazioni tecniche con il negozio virtuale disponibile h24, 7 giorni su 7. Ultimo ma non meno importante quest’anno ricorre il decimo anno da quando Leister Italia è stata fondata. Stiamo lavorando ad una serie di iniziative per raccontare questi 10 anni di lavoro al servizio dei nostri clienti e contiamo a breve di dare maggiori dettagli su quanto “bolle in pentola”.
Nello stabilimento tedesco Mewa di Immenhausen vengono prodotti 31 panni al secondo (@ Mewa)
PRODURRE IN EUROPA NON SIGNIFICA SOLO DIMINUIRE I PROBLEMI LOGISTICI, MA HA
ANCHE UNA FORTE RILEVANZA SOCIALE. PER QUESTO MEWA PRODUCE I PANNI NEL
PROPRIO STABILIMENTO TEDESCO a cura della redazione
La pandemia ha mostrato in modo evidente la fragilità dei sistemi logistici dell’economia globalizzata. Molte aziende hanno pertanto dovuto stravolgere le loro modalità di fornitura e riorganizzare l’ubicazione geografica dei loro siti produttivi. In questo senso, riportare la produzione in Europa non significa solo eliminare i potenziali problemi di capacità produttiva: qui gioca un ruolo rilevante anche l’aspetto sociale. Mentre infatti l’ambiente di lavoro nelle fabbriche europee soddisfa le elevate aspettative del XXI secolo in termini sociali, altrettanto non avviene necessariamente in altri continenti.
In seguito alla pandemia, si è verificata una carenza di forniture e di capacità produttive in quasi tutti i settori industriali. Per le aziende meno dipendenti dalla produzione dei Paesi dell’Estremo Oriente, ora tornare a crescere risulta più semplice. Il fornitore tedesco di servizi tessili Mewa
produce i panni per la pulizia industriale in Germania, in un proprio stabilimento. In questo modo l’azienda risponde anche ai requisiti di responsabilità sociale: è infatti facile monitorare anche le condizioni di lavoro e i salari dei fornitori.
In Mewa la responsabilità riveste una grande importanza, non solo nei confronti dell’ambiente, ma anche verso i dipendenti e i clienti, in termini di standard sociali, di sicurezza sul lavoro e di prodotti e servizi innovativi facilmente accessibili.
I clienti Mewa attribuiscono un grande valore alla sostenibilità e alla responsabilità sociale: quando scelgono i servizi Mewa possono essere sicuri di aver soddisfatto le aspettative dei propri consumatori.
Il fondatore di Mewa, Hermann Gebauer, ebbe un’idea rivoluzionaria all’inizio del XX secolo: offrire alle imprese e agli artigiani panni per pulire le macchine, ritirarli dopo l’uso, lavarli e riconsegnarli puliti, pronti per essere riutilizzati. Con questo obiettivo fondò in Sassonia la Mewa, acronimo
di “Mechanische Weberei Altstadt”, un’azienda che già più di cento anni fa rispondeva al principio della conservazione delle risorse.
Con il suo sistema di panni, oggi Mewa è leader di mercato in Europa. Ogni giorno, più di 2,8 milioni di persone utilizzano un panno Mewa per pulire macchine e attrezzature in moltissime aziende di diversi settori. In 21 Paesi i panni Mewa vengono ritirati dai clienti e poi riconsegnati puliti. Nello stabilimento tedesco Mewa di Immenhausen si producono quasi 105 milioni di panni all’anno. I filati e tutte le materie prime utilizzate provengono da fabbriche in cui vengono controllate le condizioni di lavoro e il rispetto degli standard sociali.
In questo caso, il “Made in Germany” non è solo sinonimo di qualità dei panni, ma anche di responsabilità sociale, fattore che svolge un ruolo determinante anche in una dimensione più allargata, nei rapporti di collaborazione con i fornitori.
INTEGRARE LA ROBOTICA NEI PROCESSI DI SALDATURA IN MODO FLESSIBILE, SALVASPAZIO E CONVENIENTE: QUESTO L’OBIETTIVO YASKAWA di Cristina Gualdoni
L’ottimizzazione dei processi, il risparmio in tempi di lavorazione e costi assumono oramai un ruolo fondamentale per qualsiasi lavorazione. Molti imprenditori si trovano così a valutare continue strategie di miglioramento dei propri flussi produttivi. Nella loro apparente semplicità, le isole robotizzate rappresentano a questo proposito un nuovo modo di lavorare che può essere applicato a qualsiasi settore produttivo: dall’assemblaggio, alla manipolazione, all’asservimento macchina, fino ad arrivare alla saldatura. Ma che cos’è esattamente un’isola robotizzata? Per prima cosa è un insieme di macchine organizzate all’interno di una cella di lavoro automatica in cui sono installati uno o più robot programmabili, il cui scopo è quello di massimizzare,
velocizzare e semplificare la lavorazione, raggiungendo elevati standard qualitativi. Questi sistemi di automazione sono caratterizzati da un livello di autonomia molto elevato e i robot possono coprire più turni senza l’intervento dell’uomo, quindi, anche se possono rappresentare un importante investimento iniziale, consentono di avere un veloce ritorno sull’investimento. Inoltre, le isole robotizzate sono molto flessibili e la loro capacità di adattamento è data proprio dalle possibili combinazioni robot-macchina che si possono realizzare all’interno della cella. I robot industriali integrabili all’interno di un’isola possono essere di diverse tipologie e solitamente si scelgono in base agli oggetti da manipolare, dagli spazi disponibili, al tipo di lavorazione da effettuare, al macchinario su cui si vanno a implementare e al tipo di performance che si vogliono ottenere.
Per quanto riguarda la saldatura l’impiego di queste celle è sempre più diffuso. La saldatura robotizzata non è altro che il connubio di due distinte tecnologie: la saldatura e la robotica; queste, insieme, permettono l’automazione di un processo altrimenti demandato totalmente alla manualità dell’operatore e al rischio di errore. Per queste operazioni si utilizzano normalmente robot antropomorfi alle cui estremità si monta l’apparato di saldatura. Yaskawa Italia vanta un’ampia esperienza nel campo della saldatura, tanto da essere considerata il centro di eccellenza di Yaskawa in Europa per la saldatura a punti. Ma l’impegno dell’azienda è notevole anche nella saldatura ad arco.
Ne sono un esempio le Celle ArcWorld RS Mini e ArcWorld HS Micro, che si collocano perfettamente all’interno di una filosofia che punta all’ottimizzazio-
ne del processo di saldatura attraverso il risparmio di tempo e costi. Su questo secondo versante, la standardizzazione gioca un ruolo fondamentale: è vero che le soluzioni, soprattutto quelle destinate a rispondere a esigenze di lavorazione più particolari, sono spesso custom, ma questa customizzazione viene realizzata a partire da prodotti e celle standard. Solo così si può ottenere un’efficienza di costo veramente importante per i clienti e una più rapida disponibilità delle soluzioni, riducendo anche i tempi di sviluppo e avvio delle applicazioni.
Le celle ArcWorld RS Mini e ArcWorld HS Micro colpiscono a prima vista per l’ingombro ridotto - 2,3 mq per le prime e 1,4 mq per le seconde. Ciò nonostante, consentono di ottenere elevate prestazioni in termini sia di produttività sia di qualità e precisione della lavorazione. Un ruolo fondamentale all’interno della cella è rappresentato dai robot. All’interno di ArcWorld RS Mini e ArcWorld HS Micro trova posto MOTOMAN
AR900, robot a sei assi nato per rispondere alle elevate esigenze delle applicazioni di saldatura ad arco, con una capacità di carico di 7 kg e una finitura facile da pulire. È dotato di una selezione
di funzioni di programmazione avanzate per massimizzare qualità e velocità della saldatura. Inoltre, per incrementare l’output ottenibile, la soluzione ArcWorld RS Mini adotta una porta girevole con doppia tavola di saldatura preforata che permette il caricamento in tempo mascherato. Queste caratteristiche, insieme alla rapidità di cambio formato, rendono le celle ArcWorld una valida soluzione per sostituire o integrare saldatura manuale di pezzi di medie e piccole dimensioni, ad esempio per il premontaggio dei
componenti prima della saldatura in una cella robotica più grande.
Yaskawa ha progettato tutto per favorire un rapido rientro dell’investimento, attraverso una veloce messa in servizio e un’elevata produttività. Le celle si presentano infatti come soluzioni plug&play già complete di tutto ciò che serve a gestire il processo di saldatura: il sistema infatti non richiede più una progettazione accurata dei singoli componenti e si presta ad essere facilmente spostato e riposizionato in caso di necessità. Non da ultimo, le celle sono progettate con un occhio di riguardo all’ergonomia, in termini di altezza di carico/scarico, fruibilità tramite carroponte e protezione antiabbagliamento. Per quanto riguarda la facilità di utilizzo indubbiamente l’uso di una cella di saldatura robotizzata favorisce la semplificazione delle attività, ma non può sopperire al background di esperienza di saldatura dell’operatore. L’uomo continua a far la differenza, risultando indispensabili per prendere alcune decisioni non delegabili al sistema robotizzato, quali ad esempio la scelta dei gas più adatti o l’identificazione di eventuali procedure particolari da seguire. Per questo motivo Yaskawa offre all’interno dei propri corsi di formazione dei focus sul processo di saldatura nei suoi aspetti più tradizionali. Resta comunque innegabile la capacità delle celle robotiche di ridurre la complessità dei processi. Sono infatti sempre più diffusi sistemi di saldatura anche per quelle realtà che si trovano a gestire lotti piccoli ed estremamente variabili.
DISPLAY LCD WIDESCREEN A COLORI
ANALISI FINO ALLA 63° ARMONICA DI TENSIONI E CORRENTI
ELEVATA ACCURATEZZA DELLE MISURE
DIAGRAMMA POLARE
COMUNICAZIONE INTEGRATA
LOGICA PLC
CONFIGURAZIONE NFC
ESPANDIBILITA’ PER INTEGRAZIONE CON SEGNALI DI CAMPO
WEB SERVER
STATISTICHE SECONDO EN 50160
MEMORIA INTEGRATA
10 LINGUE
www.LovatoElectric.com
Il controllo numerico di ultima generazione M8V offre grande precisione, velocità e rappresenta la soluzione ideale per qualsiasi tipologia di macchine, dalle più semplici alle più complesse
a cura della redazione
I CNC M8V offrono anche la funzionalità
DRC (Direct Robot Control)
che consente agli operatori di macchine utensili di programmare rapidamente i robot direttamente dal pannello CNC, senza competenze specialistiche
I CONTROLLER PER LAVORAZIONI CNC M8V DI MITSUBISHI ELECTRIC FORNISCONO PRESTAZIONI ALL’AVANGUARDIA COMBINATE CON UN’INFRASTRUTTURA INTUITIVA E DI FACILE UTILIZZO. INOLTRE, RAPPRESENTANO L’EVOLUZIONE DELLA TECNOLOGIA CNC IN OTTICA INDUSTRY 4.0, POICHÉ DISPONGONO DI WI-FI INTEGRATO E SONO STATI SVILUPPATI PER SUPPORTARE LE STRATEGIE MIRATE ALLA TRASFORMAZIONE DIGITALE E ABILITARE LE APPLICAZIONI DI SMART MANUFACTURING
Nella fabbrica moderna è fondamentale che il controllo numerico sia interconnesso e capace di interfacciarsi coi sistemi complessi aziendali, per permettere alla macchina di essere parte integrante del processo produttivo.
I nuovi controller per lavorazioni CNC M8V di Mitsubishi Electric rappresentano l’evoluzione della tecnologia CNC in ottica Industry 4.0, poiché dispongono di Wi-Fi integrato e sono stati sviluppati per supportare le strategie mirate alla trasformazione digitale e abilitare le applicazioni di smart manufacturing. Grazie al collegamento diretto alle reti WLAN, la
serie M8V è un fattore abilitante chiave per ambienti IIoT (Industrial Internet of Things) mirati alla produzione ‘smart’ basata sui dati. Il design originale che garantisce l’immunità dai disturbi sulla rete permette agli utenti di azionare e monitorare le macchine utensili CNC con affidabilità e in sicurezza ovunque e in qualsiasi momento tramite dispositivi connessi, come i tablet.
Precisione e velocità
Il controllo numerico di ultima generazione M8V offre grande precisione e velocità e rappresenta lo stato dell’arte del CNC. La combinazione tra la CPU RISC-64 Bit dedicata, l’innovativa tecnologia di
controllo della traiettoria (OMR-CC) e il controllo automatico del carico di taglio aiuta le aziende a minimizzare i tempi di lavorazione beneficiando di una grande accuratezza. Queste caratteristiche consentono di creare prodotti di alta qualità riducendo i tempi di ciclo almeno dell’11% rispetto ai modelli precedenti, abbassando inoltre gli errori di percorso del 15%. Le applicazioni di lavorazione dei metalli possono inoltre beneficiare di un elevato numero di assi per i centri di lavorazione e i sistemi di tornitura, nonché di capacità di elaborazione dei segmenti fini raddoppiate, che possono arrivare a 540 chilo-blocchi al minuto.
La serie M8V trova applicazione in tutti i settori, dall’ Automotive al Medicale,
fino all’Aerospace. Rappresenta la soluzione ideale per qualsiasi tipologia di macchine, dalle più semplici alle più complesse, come per esempio i transfer o le multispindle o per tutte quelle macchine che richiedono lavorazioni di elevate precisioni e velocità su 5 assi interpolati, come quelle del comparto degli stampi. La serie M8V integra anche nuove funzionalità appositamente studiate per rispondere anche alle esigenze di nuovi mercati, come quello delle macchine per la lavorazione laser, un settore in forte crescita. Per questo, sono state aggiunte nuove funzioni come la fly-cut che consente di sincronizzare la sorgente del laser con il movimento degli assi riducendo i tempi-ciclo.
Un altro elemento distintivo di questa serie di controller CNC è la facilità d’uso. L’interfaccia con pannello interattivo supporta i gesti multi-touch a 4 punti di contatto, offrendo così all’utente un’esperienza d’uso analoga all’utilizzo di uno smartphone. La programmazione è semplificata e razionalizzata grazie alla procedura guidata Job Lathe che guida gli utenti all’installazione e alla configurazione. Inoltre, lo schermo di grandi dimensioni del nuovo display da 19”, che va ad aggiungersi a quelli da 8,4, 10,4 e 15 pollici, migliora la visibilità e rende più flessibile la progettazione del pannello operatore.
I CNC M8V, come tutti i controlli numerici della serie M8 di Mitsubishi Electric, offrono anche la funzionalità DRC (Direct Robot Control), che consente agli operatori di macchine utensili di programmare rapidamente i robot direttamente dal pannello CNC, senza competenze specialistiche. La semplicità di utilizzo, di configurazione e di connessione è l’elemento distintivo di questa funzionalità sviluppata dalla multinazionale giapponese, oltre alla
possibilità di mantenere invariata la logica della macchina.
Le fabbriche di domani utilizzeranno conoscenze basate sui dati per creare sistemi cyber-fisici che accresceranno la flessibilità, l’efficienza e la produttività. Il primo passo nella creazione di applicazioni intelligenti per la lavorazione del metallo è l’adozione di macchine CNC avanzate, in grado di generare e raccogliere dati sui processi eseguiti, sullo stato dell’unità e dei suoi componenti nonché sull’efficienza globale dell’apparecchiatura (OEE, Overall Equipment Effectiveness).
dati a un’ampia gamma di sistemi tramite il protocollo di comunicazione OPC UA per generare conoscenza. Inoltre, la programmazione è semplificata grazie alla procedura guidata Job Lathe. Una delle piattaforme chiave che può essere facilmente abbinata a questo connettore per migliorare l’efficienza delle strutture produttive è NC Machine Tool Optimizer. Questo software è in grado di interpretare le informazioni ricevute da diverse macchine utensili dotate di qualsiasi unità CNC e di NC Machine Tool Connector per mettere a disposizione una piattaforma intuitiva per la visualizzazione e il monitoraggio dei processi. Consente, quindi, agli utenti di prendere decisioni basate sui dati per migliorare la produzione, massimizzando inoltre la visibilità e l’accessibilità in tutta la fabbrica.
Il nuovo software NC Machine Tool Connector di Mitsubishi Electric contribuisce alla creazione delle basi per una smart factory interconnessa con un investimento minimo ed è in grado di raccogliere dati da qualsiasi macchina CNC, a prescindere dalla marca. Consente di trasferire efficacemente le informazioni ai sistemi di livello superiore, senza dover tenere conto dei diversi protocolli di comunicazione specifici dei produttori. Il software raccoglie i dati sui dispositivi di produzione e su PLC dai controller di qualsiasi macchina CNC, incluse le soluzioni legacy. Si avvale quindi dell’interfaccia umati per inviare questi
Alla propria linea di controlli numerici affidabili, performanti e interconnessi, Mitsubishi Electric affianca un eccellente servizio di assistenza tecnica, operativo in tutto il mondo con una presenza capillare. Un team qualificato di tecnici esperti sul campo e un servizio telefonico gratuito permettono tempi di intervento strettissimi. Inoltre, Mitsubishi Electric è in grado di garantire una disponibilità dei pezzi di ricambio in 24 ore, un magazzino di parti anche per macchine molto vecchie (con oltre 30 anni di vita), oltre alla retrocompatibilità. E’ disponibile anche il servizio Smart Remote Service, che permette di superare tutte le distanze consentendo agli operatori del supporto tecnico di effettuare la manutenzione da remoto con soluzioni di assistenza multi-dispositivo per smartphone, tablet e occhiali intelligenti. In questo modo il supporto tecnico ai clienti diventa ancora più capillare e tempestivo, permettendo di individuare rapidamente eventuali errori ed evitando ripetute visite in loco, con un notevole risparmio di tempi e costi.
WORKSHOP TECNICO SCIENTIFICI CORSI DI FORMAZIONE
AGGIORNAMENTI
FAQ | ESPOSIZIONE
ww w gns.iis.i t
Le GNS - Giornate Nazionali di Saldatura da oltre 24 anni offrono un significativo momento di aggiornamento professionale per progettisti, coordinatori e ispettori di saldatura, tecnici e utilizzatori di impianti e strutture saldate, responsabili di produzione, ricercatori e per tutte le figure professionali che operano nel settore della fabbricazione dei prodotti saldati.
MEDIA PARTNERS
Le soluzioni Yaskawa ArcWorld RS Mini e HS Micro offrono un'opzione flessibile, pratica e conveniente per integrare la robotica nei processi di saldatura. Ideali per sostituire o integrare la saldatura manuale, come il pre-assemblaggio prima della saldatura definitiva. Con la nostra serie ArcWorld è possibile raddoppiare l'output, con metà del tempo di preparazione e una facilità di movimentazione eccezionale. Complete di robot, controller e saldatrice (a scelta), le celle ArcWorld rappresentano il futuro della saldatura robotica.
Contatta i nostri esperti e scopri di più su arcworld.eu
II flussimetri sono dispositivi sempre più richiesti nelle applicazioni industriali ed utilizzati per misurare la portata di aria compressa in varie zone di un impianto pneumatico. Questi dispositivi possono essere impiegati per controllare un singolo elemento oppure l’intero impianto, piuttosto che per monitorare le perdite o per dosare un volume preciso di aria o gas inerti.
La serie FLUX comprende la versione miniaturizzata FLUX 0, presente in due modelli, per portate fino a 50 Nl/min e per portate fino a 200 Nl/min. Questi modelli vengono tipicamente montati in varie sezioni della macchina o dell’impianto e servono a rilevare piccole perdite (o la loro deviazione nel tempo), piuttosto che a dosare con precisione piccole quantità di fluido. Il FLUX 0 è dotato di un display a tre colori che permette di visualizzare e di impostare numerose funzioni. Dispone di 2 uscite digitali ed una analogica, ognuna delle quali può essere impostata liberamente per misurare la portata istantanea, la portata cumulata o la pressione, quindi possono svolgere la funzione di flussimetro, flussostato, manometro o pressostato. Le taglie superiori misurano portate fino a 2.000 Nl/min (FLUX 1) e 4.000 Nl/min (FLUX 2). Questi dispositivi, tipicamente montati sulle calate dell’impianto o all’in-
gresso delle macchine, sono costituite da un robusto corpo in alluminio anodizzato con filetti d’ingresso e uscita da G ½” (FLUX 1) e G 1” (FLUX2), sul quale è montata l’elettronica per la misurazione ed il controllo. All’ingresso è montato un dispositivo di linearizzazione del flusso che garantisce un’ottima precisione di misura; possono essere montati con qualsiasi orientamento ed è possibile ruotare lo schermo di 90° 180° e 270° in tal modo la lettura dei dati risulta essere sempre comoda. I flussimetri FLUX 1 e 2 possono essere utilizzati singolarmente o inseriti in un gruppo di trattamento aria della Serie Syntesi. Sono disponibili nelle versioni con o senza display, sempre con connettore M12 per
Metal Work, nata nel 1967 come ditta individuale per la produzione di innesti rapidi per aria compressa, è oggi l’azienda italiana specializzata nella produzione di componenti pneumatici per l’automazione industriale. Negli anni l’azienda ha ampliato la propria struttura produttiva e commerciale fino a divenire una delle più significative real tà nel settore della pneumatica per automazione, con una gamma di prodotti che si articola su cinque linee: attuatori, valvole, gruppi trattamento aria, raccordi e componenti per manipolazione, raccolta in un catalogo di oltre 1700 pagine. Attualmente lavorano negli stabilimenti di Concesio (BS) più di 500 dipendenti, mentre la struttura commerciale italiana ed estera è composta da oltre 800 persone. La distribuzione e l’assistenza sono affidate alle 50 filiali, tra Italia e estero.
Dal 1992 Metal Work è certificata secondo la ISO 9001. Alla certificazione del sistema di qualità, si è aggiunta nel 2000 quella del sistema di gestione ambientale secondo la norma ISO 14001. A queste, nel 2007 Metal Work, per garantire un Sistema di Gestione della Sicurezza e Salute dei Lavoratori, ha applicato la norma inglese OHSAS 18001, per poi passare nel 2019 alla ISO 45001. Tutte le certificazioni sopra citate sono state rilasciate dall›ente certificatore tedesco DEKRA ITS, accreditato dal TGA. Dal 2016 Metal Work è anche certificata Elite, il progetto di Borsa Italiana realizzato in collaborazione con il Ministero dell’Economia e delle Finanze, Confindustria e ABI, pensato per accompagnare e sostenere la crescita delle PMI.
l’alimentazione e la gestione dei segnali. I dispositivi possono essere alimentati con tensione variabile tra 12 VDC (-10%) e 24 VDC (+30%). Le versioni con display dispongono anche di un trasduttore di pressione e temperatura che, grazie all’algoritmo implementato nel software del dispositivo, consente minimizzare l’errore di misura all’interno del range di temperatura indicato a catalogo. Tutte le versioni hanno un grado di protezione IP65.
Su display vengono visualizzati i valori di portata, pressione, temperatura oltre ai grafici delle grandezze istantanee e cumulate. Viene inoltre calcolato e visualizzato il valore di potenza elettrica utilizzata per produrre il flusso misurato.
Dal punto di vista della comunicazione sono disponibili un’uscita digitale PNP - configurabile sul valore di portata, di pressione o di consumo totale - ed un’uscita analogica settabile in tensione (0-10 VDC) o in corrente (4-20 mA). Sono disponibili anche versioni con interfaccia IO-Link con caratteristiche analoghe. Anche i FLUX 1 e 2 possono quindi essere utilizzati come flussimetro, flussostato, manometro o pressostato. Anche le nuove taglie sono idonee all’utilizzo con aria compressa o gas inerti.
La novità più importante relativa alla
Serie FLUX, taglia 1 e 2, riguarda il rilascio delle versioni Wireless che sono in grado di comunicare con reti Ethernet (tramite protocollo di comunicazione MQTT) e dispositivi mobili, quali smartphone e tablet con connessione Bluetooth® attraverso un’APP dedicata sviluppata da Metal Work. Tramite l’APP, oltre a visualizzare le grandezze misurate, è possibile modificare tutte le impostazioni dei flussimetri e visualizzarne in tempo reale i valori misurati. In questo modo i nostri FLUX possono essere configurati e monitorati senza la necessità di un collegamento fisico.
L’APP Metal Work FluxUp, consente infatti il collegamento via Bluetooth®, da smartphone, ai flussimetri Metal Work della serie FLUX 1 e 2, dotati di interfaccia Wireless. Tramite Metal Work FluxUp è possibile visualizzare in tempo reale, tutti i dati rilevati da FLUX ed impostare tutti i parametri di funzionamento.
E’ inoltre disponibile la funzione Charts per la visualizzazione dei grafici dei valori sal-
vati di portata e pressione: in questo modo è possibile visualizzare i dati rilevati nelle ultime 24 ore, ad intervalli di 2 minuti. Le versioni Wireless di FLUX 1 e 2, consentono la connessione ad una rete Ethernet Wi-Fi®, tramite un Access point oppure un Gateway, per monitorare ed acquisire tutte le grandezze misurate del gas in esame. A tale scopo viene utilizzato il protocollo di comunicazione MQTT, standard molto diffuso per questo tipo di applicazioni. I nostri FLUX sono quindi compatibili con tutti i
sistemi avanzati di raccolta ed elaborazione dati diagnostici e predittivi.
La raccolta dei dati dal campo consente di effettuare una diagnosi predittiva dell’impianto: permette di mantenere sempre sotto controllo i parametri operativi e di ottimizzare il funzionamento delle macchine e dell’impianto pneumatico; consente di individuare le perdite al fine di evitare gli sprechi energetici. Il software può essere implementato con funzioni di analisi che consentono il controllo dell’efficienza macchine nonché dell’andamento dei consumi e previsione a lungo termine (valutazione miglioramento impianto).
Una volta impostati i parametri applicativi, ogni singolo FLUX sarà in grado di monitorare il tratto specifico dell’impianto in cui è installato, inviando al gestore di sistema i dati di consumo energetico nonché eventuali allarmi di esubero dovuti a perdite eccessive o rotture.
La connessione da remoto consente sia un controllo continuo che una verifica periodica e fornisce il grande vantaggio di facilitare il collegamento anche a punti difficilmente raggiungibili quali, ad esempio, gli attacchi delle calate dell’impianto oppure le zone interne a macchine complesse, anche durante le fasi di lavoro.
Installando più dispositivi sulla rete pneumatica aziendale, sarà inoltre possibile realizzare una rete di punti di controllo e, mediante specifici algoritmi di AI, monitorare lo stato dell’impianto e pianificare gli interventi di manutenzione alle macchine e alle tubazioni di collegamento. In questo ambito, Metal Work sta lavorando anche allo sviluppo di algoritmi predittivi basati su tecniche di Machine Learning integrate con esperienze dirette sul campo e testate nei nostri laboratori.
SOLUZIONI PRODUTTIVE SEMPRE PIÙ VERSATILI E ALTAMENTE PRODUTTIVE, CONFIGURABILI ED AFFIDABILI, IN GRADO DI ASSICURARE LAVORAZIONI ANCORA PIÙ EFFICIENTI, PRECISE E FLESSIBILI CON IL GIUSTO RAPPORTO QUALITÀ-PREZZO
L’inarrestabile trend verso una sempre maggiore complessità dei pezzi richiesti aumenta il fabbisogno di soluzioni di produzione estremamente versatili. I costruttori di macchine utensili sono quindi spinti verso la produzione di centri di lavoro completi, che consentano un’elevata produttività e permettano di rispondere efficacemente alle richieste del mercato.
Quando si parla di centri di lavorazione, in sostanza si fa riferimento a quelle macchine utensili che partendo da un blocco di metallo, attraverso le operazioni di fresatura, tornitura e foratura realizzano un pezzo dalla forma complessa.
I centri di lavoro, identificati con la sigla MC, dall’inglese Machining Center, sono macchine CNC multiasse dedicate alla lavorazione completa di svariati componenti che possono tornire
o fresare e forare, cambiando gli utensili automaticamente. Quindi si parla di una macchina utensile dotata di controllo numerico che riesce a eseguire più di un’operazione meccanica con un solo set-up su più di una superfice dello stesso pezzo di lavoro.
Con l’acronimo FMC - Flexible Manufacturing Cell, si intendono invece le celle di produzione flessibile, ovvero sistemi formati da centri di lavoro collegati da un trasporto dei pezzi automatico.
Per definizione, quindi, i centri di lavoro sono delle macchine multifunzionali che permettono con grande flessibilità di adempiere ad un elevato numero di operazioni meccaniche, quali ad esempio, fresatura, alesatura, filettatura e foratura, grazie
alla possibilità di disporre di un elevato numero di utensili a magazzino.
In base alla configurazione, al numero di assi, alle dimensioni dell’area di lavoro, alla posizione del mandrino e degli optional presenti, abbiamo diverse tipologie di centri di lavoro. Tuttavia le due più importanti macro-categorie si caratterizzano per il posizionamento dell’asse del mandrino. In base ad esso, si distinguono centri di lavoro verticali e centri di lavoro orizzontali. In un MC orizzontale, il mandrino dell’utensile è montato orizzontalmente, cioè parallelamente al pavimento, mentre nei sistemi verticali il mandrino è in posizione verticale e il pezzo viene lavorato dall’alto, permettendo all’operatore di maneggiare agevolmente i pezzi. Entrambi hanno vantaggi e svantaggi. Tra i vantaggi, ad esempio, nel caso di quelli in cui il mandrino è orizzontale, è possibile effettuare tagli con un’inclinazione ridotta, in particolare sui lati del pezzo. Inoltre, questo modello è particolarmente adatto alla fresatura di scanalature e alla lavorazione di superfici piane così come alla lavorazione di pezzi di grandi dimensioni con geometrie complesse. È in grado di cambiare automaticamente il pezzo in lavorazione attraverso i pallet, un vantaggio in caso di produzione in serie. Nei centri di lavorazione orizzontali, i trucioli prodotti durante la lavorazione cadono spontaneamente dal tavolo e non devono essere soffiati o lavati via, come avviene nei centri verticali.
Nei centri di lavoro che dispongono di un mandrino verticale, invece, gli utensili eseguono il taglio sulla parte superiore del pezzo. Questa tipologia di macchine permette di lavorare su pezzi di grandi dimensioni e su tutti i lati senza l’intervento di un operatore.
Determinata la classificazione principale, occorre considerare altri fattori nella scelta di un centro di lavoro. È importante definire dimensionalmente quella che è l’area di lavoro o campo operativo, determinata dalle dimensioni della zona di operatività del mandrino in funzione degli assi di traslazione x,y e z. Le dimensioni degli assi influiscono infatti sulla dimensione max dei pezzi da lavorare e sul tipo di lavorazioni che si possono effettuare. Per quanto riguarda le caratteristiche dei modelli più richiesti dal mercato, oltre alla precisione, una delle tendenze più attuali è quella della compattezza delle macchine, per venire incontro alle esigenze dei clienti che richiedono superfici di installazione sempre più ridotte. Sono sempre di più gli operatori che richiedono un’estrema versatilità della macchina a fronte di un design salvaspazio, con un minor ingombro della stessa. Negli ultimi anni è cresciuta anche la richiesta di macchine a 5 assi, in grado di gestire grossi volumi di truciolo asportato, senza nessun compromesso in termini di precisione e di affidabilità. Una crescita che è dovuta alla necessità di lavorare pezzi meccanici anche complessi, riducendo al contempo al minimo il numero di riposizionamenti durante il ciclo di lavoro. Per realizzare pezzi con forme geometriche complesse, senza costosi tempi di arresto e di conversione, l’utensile da taglio deve essere mobile su cinque assi: sui tre assi lineari X, Y e Z e sui due assi di rotazione A e B che si spostano per interpolazione in modo simultaneo lungo tutta la superficie del pezzo.
Quando non si ha la necessità di eseguire più interpolazioni nello stesso momento è possibile utilizzare macchine dotate di funzionalità multi-asse con configurazioni 4+1 oppure 3+2 dove i movimenti degli assi rotanti si combinano per eseguire operazioni di fresatura lungo gli assi lineari.
La possibilità di eseguire operazioni così complesse rende i centri di lavorazione a 5 assi estremamente versatili e adatti per lavorazioni nel settore aerospaziale, dell’automotive, in quello sportivo e medicale per realizzare protesi per articolazioni umane.
Il principale vantaggio legato all’utilizzo di centri di lavoro 5 assi è rappresentato dalla possibilità di lavorare pezzi con superfici complesse sfruttando un unico programma CNC e un solo set-up di macchina senza la necessità di dover riposizionare il pezzo più volte.
Tempi di elaborazione minori e cicli di lavoro ridotti si traducono, all’atto pratico, nell’incremento del livello di produttività.
Con l’avvento di Industry 4.0 e lo sviluppo dell’Internet of Things (IoT), i centri di lavoro si sono adattati alle esigenze di una produzione connessa, sono diventati sempre più sofisticati e, ormai, dotati di sensori (di velocità, di temperatura, ecc.) in grado di trasmettere in real time i dati raccolti, sulla base dei quali elaborare informazioni utili per migliorare la produzione e ridurre il rischio di guasti e fermi macchina, attraverso una manutenzione di tipo predittivo. Ulteriori vantaggi derivano anche dalla possibilità di controllare le lavorazioni da remoto così come di usufruire di segnali di allerta, 24 ore su 24 e 7 giorni su 7, in caso di problemi.
La crescente attenzione verso processi di produzione più sostenibili ed ecologici, sia in termini di energetici che di materie prime, negli anni più recenti, ha indirizzato la produzione su centri di lavorazione che consumano meno energia e hanno un minore impatto ambientale, favorendo le tecnologie per il recupero dell’energia delle macchine. In alcuni modelli, la velocità dell’utensile, così come le vibrazioni e il calore generati dalla macchina, vengono sfruttati come fonti di energia per alimentare i sensori, evitando sprechi di natura energetica. Da ultimo, ma non meno importante, è lo sviluppo dei centri di lavorazione ibridi che, oggi, devono il loro nome non solo al fatto che combinano sia tornitura che fresatura, ma anche, in certi casi, anche la lavorazione e la stampa 3D (produzione additiva) in una sola macchina.
Le macchine utensili ibride aiutano a ridurre i cicli di produzione e ad aumentare l’efficienza produttiva. Offrono anche la possibilità di creare pezzi con forme che nessun’altra macchina sarebbe in grado di realizzare. E, naturalmente, poiché sono in grado di effettuare il lavoro di più macchine, rappresentano anche una soluzione salvaspazio.
Tutte queste caratteristiche sono importanti e vanno considerate nella scelta del centro di lavoro: in funzione del tipo di produzione e delle lavorazioni necessarie, occorrerà indirizzare la propria ricerca verso l’esatta tipologia di centro di lavoro in grado di soddisfare non solo le proprie esigenze ma di adattarsi velocemente alle mutevoli richieste del mercato.
IL CENTRO GT3000 ASSICURA UNA PRECISIONE E UNA DINAMICA SUPERIORI CHE LO
RENDONO INDICATO SOPRATTUTTO PER IL SETTORE DEGLI STAMPI, MA ANCHE PER CHI OPERA NEL COMPARTO DELLA MECCANICA DI PRECISIONE
FFondata nel 1966, C.B. Ferrari ha da poco compiuto 56 anni, caratterizzati da continue sfide tecnologiche, alla costante ricerca dell’innovazione e al continuo incremento delle prestazioni dei propri prodotti.
Nata nel mondo delle macchine per stampi (produzione di punzoni, matrici e particolari complessi), C.B. Ferrari ha perfezionato la propria offerta in questo settore con modelli di macchine a 5 assi, da sempre particolarmente apprezzate principalmente dai produttori di stampi: per plastica, gomma o lamiera dei numerosi settori quali, automotive, elettrodomestici, giocattoli, bottiglie, ecc. ed anche dai produttori di particolari di precisione ed attrezzature.
Grazie ad un know-how acquisito in più di 50 anni di attività e ad un installato di oltre 4500 macchine ed impianti nel mondo in settori chiave quali l’aerospaziale, gli stampi e le attrezzature, il medicale, l’automobilistico, la meccanica di precisione e l’energia, l’azienda ha acquisito solide fondamenta con cui supportare i clienti
nel continuo incremento di produttività e marginalità. L’impiego delle più avanzate tecnologie progettuali, produttive e di controllo qualità, consente ai prodotti C.B. FERRARI di assicurare prestazioni al vertice del settore.
Dopo l’introduzione sul mercato dei modelli GT1200, GT1600 e GT2000, C.B. Ferrari ha deciso di ampliare la serie dei centri evoluti ad alta velocità e precisione a montante mobile, con il modello GT3000.
Il nuovo modello, del tipo a montante mobile, ha un design moderno e presenta un cubo di lavoro molto ampio, con le corse di 3000 mm per l’asse longitudinale, 920 mm per l’asse trasversale e 1000 mm per l’asse verticale. L’avanzamento rapido degli assi è pari a 50 m/min.
La sua precisione e l’elevata dinamica dei movimenti di lavoro, la rendono particolarmente indicata per il settore degli stampi, della meccanica di precisione e per lavorazioni che richiedono elevata accuratezza con alti gradi di finitura superficiale.
Due configurazioni del centro di lavoro per la versione a 5 assi
Il modello GT3000 può essere configurato a 3, 4 o 5 assi continui. Nella versione a 5 assi sono previste due configurazioni distinte: la
Le macchine della serie GT PRO sono centri di lavoro a montante mobile caratterizzate da un innovativo design ed una grande area di lavoro. Le ampie corse degli assi longitudinali (1200, 2000 e 3000 mm) pongono queste macchine al più alto livello della loro categoria. Sono realizzate con strutture in ghisa, sottoposte ad un trattamento di normalizzazione della durata di almeno 58 ore per eliminare qualsiasi tipo di tensione interna. I tre modelli GT1200, GT2000 e GT3000 possono essere configurati con 3, 4 o 5 assi controllati. Sono disponibili in due versioni: con tavola fissa o con tavola girevole.
prima con gli assi rotativi a posizionamento meccanico e la seconda con assi torque che permettono di eseguire le lavorazioni a 5 assi continui. La piattaforma della tavola con diametro 1000 mm è annegata tra due semitavole oppure affiancata da una semitavola sagomata. In tutte due i casi, il piano di lavoro è perfettamente allineato sullo stesso piano, per permettere di eseguire facilmente l’esecuzione di lavorazioni a 3 o a 4 assi, di pezzi lunghi quanto tutta la corsa della macchina. In aggiunta, è possibile avere l’opzione tornitura con la tavola girevole nelle versioni a 150 o 450 rpm di velocità di rotazione.
Per quello che riguarda la motorizzazione del mandrino, è possibile scegliere tra differenti tipi di elettromandrini di produzione C.B. Ferrari: a 9000, 16.000, 20.000, 24.000 RPM con attacco HSK A63/ISO V40 e HSK T63 per tornitura, oppure da 10.000 RPM con attacco HSK A100. È possibile scegliere tra differenti tipi di magazzini utensili: la versione più semplice, a 30 utensili a ruota mobile oppure a 40, 60, 80 o 120 utensili a catena con braccio di scambio. Sono previste diverse opzioni tra le quali evidenziamo la sonda controllo pezzo 3D, l’apparecchio par la taratura degli utensili meccanico o Laser e l’impianto di refrigerazione via mandrino a 75 BAR. Su tutta la serie GT sono applicate le righe assolute ed encoder Heidenhain ed il Controllo Numerico di ultima generazione Heidenhain TNC 640 HSCI oppure Siemens 840 D sl o il nuovo Sinumerik ONE, che permettono alla macchina di raggiungere le migliori performance, sia in termini di velocità di esecuzione, che di precisione sui 5 assi.
La serie GT è dotata del Controllo Numerico di ultima generazione Heidenhain Heidenhain TNC 640 HSCI oppure Siemens 840 D sl o il nuovo Sinumerik ONE.
UN RAPPORTO QUALITÀ-PREZZO IMBATTIBILE
Le macchine universali compatte ed economiche per la lavorazione simultanea a 5 assi godono di un’alta priorità in numerosi settori industriali. Presentata in anteprima mondiale sul palcoscenico della tradizionale open house di Pfronten, che ha aperto le porte ai visitatori dal 30 gennaio all’11 febbraio 2023, la nuova DMU 40 di DMG Mori risponde esplicitamente alla necessità del settore entrylevel di soluzioni produttive versatili per la lavorazione completa, attestata dalle oltre 10.000 macchine vendute della DMU 50 di terza generazione.
La DMU 40 si basa sul concetto della DMU 50 di terza
generazione e presenta i migliori componenti della sua categoria, dai mandrini agli azionamenti diretti nell’asse X e Y, passando per i componenti Best-in-Class, oltre alla predisposizione per la produzione automatizzata con PH 150 o Robo2Go. Le tre macchine base DMU 40, DMU 40 PLUS e DMU 40 PRO soddisfano le esigenze individuali della clientela, garantendo anche la massima precisione nella gamma dei µm. In breve: la DMU 40 offre tutti i vantaggi della DMU 50 di terza generazione al prezzo entry-level più vantaggioso nel segmento di mercato della lavorazione simultanea a 5 assi.
Il design salvaspazio con una larghezza della macchina inferiore a due metri e l’ampia zona lavoro con corse di 550 x 450 x 420 mm fanno della DMU 40 il completamento ideale delle realtà produttive più anguste. Durante lo sviluppo di questa macchina, DMG MORI ha posto l’accento sull’elevata stabilità. Il basamento monopezzo in ghisa grigia, le slitte Y e Z ottimizzate dal punto di vista geometrico e il mandrino Inline con serraggio idraulico assicurano un’elevata rigidità, che è la base per ottenere risultati di lavorazione ottimali. Inoltre, il magazzino utensili dispone di un sistema di connessione ottimizzato, che esercita un’influenza minore sulla geometria della macchina. Le viti a ricircolo di sfere ad azionamento diretto negli assi X e Y migliorano la qualità delle superfici lavorate. Per garantire una lavorazione simultanea a 5 assi il più versatile possibile, DMG MORI ha integrato anche sulla DMU 40 la comprovata tavola rotobasculante della DMU 50 di terza generazione. E non solo: il campo di brandeggio dell’asse B, che va da -35° a 110°, conferisce alla macchina una flessibilità ancora maggiore.
Il design ergonomico della DMU 40 offre un’accessibilità ottimale alla zona lavoro. L’altezza di carico della tavola è di 800 mm con una distanza ridotta tra l’operatore e il centro della tavola. L’ampia finestra e l’illuminazione ottimizzata offrono una visibilità perfetta nella zona lavoro ed il carico in macchina è possibile mediante gru fino al centro della tavola. In opzione, è disponibile il carico del magazzino utensili dalla zona anteriore.
Con i migliori componenti della sua categoria, dai mandrini agli azionamenti diretti, la DMU 40 è la soluzione ideale per i settori più esigenti
macchine
DMG MORI ha concepito la DMU 40 in tre diverse macchine base per soddisfare le diverse esigenze di produzione. La dotazione di serie include già il mandrino Inline con velocità di rotazione di 12.000 giri/min, il magazzino utensili da 24 posti e la tavola rotobasculante a 5 assi integrata. Il modello base soddisfa già, infatti, i requisiti della lavorazione simultanea a 5 assi. La DMU 40 PLUS è dotata di un mandrino inlineMASTER con velocità di 15.000 giri/min e di un magazzino utensili con 30 posti. I sistemi di misura corsa diretti assoluti e il raffreddamento passivo di tutti i componenti principali
per mezzo di scambiatori di calore ampliano ulteriormente la gamma di lavorazione. La DMU 40 PRO raggiunge la massima precisione di posizionamento pari a 5 µm secondo la norma ISO 230-2. I suoi componenti principali dispongono di un sistema di raffreddamento attivo ed è, inoltre, presente un mandrino SpeedMASTER con velocità di rotazione di 20.000 giri/min.
In qualità di pioniere nell’automazione delle macchine utensili, DMG MORI ha tenuto in debita considerazione anche quest’aspetto nello sviluppo della DMU 40. Il modello universale può essere ampliato, in opzione, con il sistema di gestione pallet PH 150 o con il Robo2Go Milling. Ciò consente ai clienti una produzione flessibile e autonoma anche nei turni non presidiati di notte e nei fine settimana.
MACCHINE A 4 E 5 ASSI ALTAMENTE PRODUTTIVE, CONFIGURABILI ED AFFIDABILI PER LAVORAZIONI ANCORA PIÙ
EFFICIENTI, PRECISE E FLESSIBILI CON IL GIUSTO RAPPORTO QUALITÀ-PREZZO
FFondata a Nürtingen in Germania nel 1894 come piccola impresa artigianale, oggi il gruppo HELLER si estende in tutto il mondo, impiegando più di 2.500 persone, ed è in grado di sviluppare e produrre macchine utensili CNC all’avanguardia e sistemi di produzione per applicazioni e lavorazioni di metalli ed altri materiali. Grazie a 5 plant di produzione – due dei quali in Europa e gli altri tre presenti in Asia, Nord e Sud America –l’azienda assicura una fornitura affidabile ai clienti di molti settori diversi; inoltre, le 30 filiali di vendita e assistenza con partner di assistenza qualificati fanno sì che HELLER sia rappresentata in tutto il mondo. La gamma di prodotti HELLER comprende centri di lavorazione a 4 e 5 assi, centri di fresatura/tornitura, macchine speciali e di processo, macchine per la lavorazione di alberi a gomito e a camme e moduli di rivestimento. Il portafoglio è completato da una gamma modulare di servizi e da un’ampia serie di soluzioni per la digitalizzazione e l’automazione della produzione. Abbiamo chiesto ad Alessio Pedoni, Amministratore Delegato di HELLER Italia, quali sono le esigenze del settore in termini di lavorazioni, automazione e digitalizzazione.
Le macchine più diffuse in Italia sono i centri di lavoro orizzontali standard a 4 assi, con una crescita decisa di macchine a 5 assi della serie HF e di macchine di grosse dimensioni.
Le aziende italiane che si rivolgono a HELLER devono poter contare su macchine in grado di gestire grossi volumi di truciolo asportato, senza nessun compromesso in termini di precisione e di affidabilità.
“La crescita dei centri di lavoro HF – spiega Pedoni - risponde senz’altro alla necessità di lavorare pezzi meccanici anche complessi riducendo nel contempo al minimo il numero di riposizionamenti durante il ciclo di lavoro. Mentre la crescita delle macchine con elevate corse degli assi e ampie aree di lavoro, rispecchia la crescita di HELLER nel settore del macchinario industriale e delle macchine agricole, dove è necessario lavorare componenti quali telai e basamenti”.
Le macchine HELLER nascono già come prodotti meccatronici, con una rilevante dotazione di software di controllo del processo produttivo. Inoltre, da sempre HELLER ha sposato l’idea dell’automazione come leva in grado di incrementare la produttività, l’affidabilità e la ripetibilità dei processi di produzione e la qualità del prodotto finito.
“Le soluzioni di automazione HELLER – spiega Pedonisono concetti che sviluppiamo appositamente per ogni specifica produzione. Analizziamo tutte le esigenze ed elaboriamo una soluzione con la quale ottenere il massimo valore aggiunto.
Le nostre soluzioni ‘made by HELLER’, ovvero prodotte e fornite da un unico brand, sono molteplici: dal sistema RZ con cella robotizzata, al sistema con magazzino/container rotante
RSP –FLEX, passando inoltre dalla collaborazione con aziende Leader nel settore dell’automazione, per soddisfare realmente ogni richiesta”.
La cella robotizzata RZ HELLER consiste nell’automazione robot per la gestione dei pezzi direttamente nella stazione di carico del centro di lavoro. Il sistema provvede, per mezzo di una pinza, al carico/scarico dei pezzi nel punto zero del pallet, riconoscendo anche eventuali bloccaggi del pezzo nella morsa del robot.
Il meccanismo di cambio pallet del centro di lavoro provvede poi al trasferimento del pallet correttamente caricato nella zona mandrino.
Il container RSP [Rund-SPeicher] - FLEX invece è composto da più moduli, meccanismo grazie al quale si rende possibile la configurazione del container a proprio piacimento, con una o più stazioni di carico posizionabili nelle posizioni preferite.
Il sistema a design modulare permette di configurare il pallet container come meglio si addice alle proprie necessità: il modulo di stoccaggio permette una postazione pallet per ogni livello; il modulo di carico prevede solamente la stazione operativa di attrezzaggio; infine il modulo dedicato al pannello elettrico prevede postazioni di stoccaggio per i soli livelli superiori al primo, per un totale di 3 livelli.
Assistenza e manutenzione: un team service di prima classe
Heller offre un servizio di assistenza completo, sia in loco, sia in remoto. “Ci teniamo particolarmente alla tempistica di intervento e, a tal fine, abbiamo effettuato una mappatura dell’Italia in modo da assicurare una copertura adeguata del territorio. In questo modo, per gli interventi di manutenzione che richiedono la presenza di un tecnico, non sarà necessario attendere la sua partenza dalla nostra sede di Verona, ma sarà già geograficamente vicino al nostro cliente. In questo modo i vantaggi sono importanti: tempistica ridotta di
intervento ed ulteriore riduzione dei costi per il cliente”, precisa Pedoni. “Il team Service di HELLER Italia è sinonimo di servizi di 1° classe: sempre vicino, sempre disponibile, rapidamente sul posto: con tecnici di massima competenza formati al 100% da HELLER - non ci appoggiamo a realtà esterne -, interveniamo anche su richiesta con personale specializzato proveniente da altre filiali o dalla sede principale”.
Grazie ad una hot-line sempre attiva con una persona dedicata, la consulenza HELLER per ordini di ricambi, richieste di riparazione o domande tecniche è rapida ed efficace. “Essendo tutto prodotto internamente, disponiamo di oltre 40.000 pezzi di ricambio nel magazzino centrale. In qualità di partner affidabile, vogliamo garantire la produttività e la disponibilità, rimanendo al fianco dei nostri clienti durante l’intero ciclo di vita della macchina”, aggiunge Pedoni.
In un prossimo futuro, HELLER Italia punta sugli eventi in presenza, sia con la partecipazione alle principali fiere di settore sul territorio italiano, sia mettendo a disposizione la sede produttiva in Germania per offrire Open House dedicati sia per settore che per specifiche lavorazioni. In tal senso, a maggio 2023, HELLER Italia organizza il primo Technology Day interamente svolto in sede centrale a Nürtingen esclusivamente per le Aziende italiane che intendono partecipare. Un’occasione unica per tutti i clienti italiani di poter visionare dal vivo gli stabilimenti produttivi del gruppo, le macchine in funzione con cutting-test dedicati e tutte le nuove tecnologie innovative di lavorazione. Altri progetti saranno sviluppati per ulteriori ‘Open Day’ dislocati sul territorio italiano, da nord a sud, in modo da poter raggiungere tutti i clienti e potenziali interessati, ed offrire un servizio di esposizione dedicato per settore e per territorio geografico.
COMPATTA, PRECISA, DINAMICA, LA C12 GARANTISCE MASSIMA EFFICIENZA
NONOSTANTE UNA MINORE SUPERFICIE DI ALLESTIMENTO
Progettato per la lavorazione di pezzi cubici fino a 100 kg di peso, il nuovo centro di lavorazione a 5 assi Hermle C12 viene incontro alle esigenze dei clienti che richiedono superfici di installazione sempre più ridotte, completando la gamma di prodotti Hermle nel segmento inferiore, senza avere nulla in meno rispetto ai modelli più grandi.
Oltre che per la compattezza, la macchina si distingue per le competenze chiave di Hermle quali precisione, durevolezza e naturalmente dinamismo. Le corse di lavoro di 350-440-330 mm negli assi X-Y-Z offrono i migliori presupposti per una lavorazione a 5 assi simultanei/su 5 lati con rapidi e accelerazioni fino a 50 m/ min e 8 m/s2
La tavola roto-basculante CN, provvista di un azionamento
torque nell’asse C, offre un campo di basculamento di +/- 115°, consentendo così anche sottosquadri complessi.
Per quanto concerne il mandrino è possibile optare tra 5 diverse soluzioni da 12000 a 42000 giri/min con attacco SK 40/HSK A63/HSK A50/HSK E40. Si ha a disposizione il numero di giri appropriato per pressoché tutti i campi di applicazione. Anche la protezione anticollisione brevettata di Hermle per mandrini fino a 18000 giri/min è stata nuovamente integrata.
Il clou della C12 è il magazzino utensili, in grado di contenere 71 utensili su un doppio livello senza necessitare di ulteriore superficie di appoggio rispetto all’anello standard da 36 posti.
Il raddoppio della capacità è ottenuto posizionando due anelli uno sopra l’altro nel bancale della macchina. Un piccolo sistema di handling sposta gli utensili tra gli anelli in maniera rapida e affidabile, in modo tale che il successivo utensile da utilizzare sia sempre pronto.
In merito alle soluzioni di automazione, la C 12 può essere dotata di un cambio pallet PW 100 o di un sistema robotizzato RS 05. Installati sul lato sinistro, entrambi i sistemi sono accanto alla macchina e utilizzano l’accesso attraverso la spalla laterale sinistra della zona di lavoro.
RS 05-2, 2a generazione del sistema robotizzato compatto
Ai centri di lavorazione Hermle può ora essere adattata frontalmente (C250, C400 e C32) o anche lateralmente (C12 e C22) la 2a generazione dell’RS 05.
Con un ingombro di appena 2 m2, il sistema robotizzato è estremamente compatto e, in base all’applicazione specifica, può essere dotato dei più svariati moduli magazzini. Per esempio viene proposto con matrice semplice, magazzino con cinque cassetti telescopici e ripiano per matrici, magazzino pallet o anche come sistema Kanban. La modularità si pone al primo posto in assoluto. Grazie a un accesso ottimizzato per l’operatore, è possibile raggiungere tanto la zona di lavoro quanto il magazzino per compiere lavori manuali di regolazione o prova. Il robot può eseguire il cambio di pezzi grezzi/lavorati e anche pallet fino a 10 kg di peso. Esso viene utilizzato anche per la movimentazione delle matrici da e nei vari magazzini in quanto con un dispositivo di spinta e trazione, adattato alla pinza, estrae le matrici dal magazzino
o le reinserisce. Infine, il robot può essere dotato di una pinza semplice o doppia e possiede anche un’unità di soffiaggio aggiuntiva per la pulizia del dispositivo di serraggio.
HACS, il software di automazione targato Hermle Con l’HACS (abbreviazione di Hermle AutomationControl-System) Hermle offre un proprio software di automazione. L’HACS viene utilizzato con successo già da molto tempo nei sistemi di cambio pallet e handling, così come negli impianti robotizzati di Hermle.
Un quadro di comando aggiuntivo orientabile è stato adattato al posto di attrezzaggio. L’interfaccia utente semplice e intuitiva, comandabile mediante “drag & drop”, facilita l’impiego quotidiano nella produzione. L’operatore ha in ogni momento una panoramica dei compiti ancora da svolgere. Ciò garantisce una produzione il più possibile priva di inconvenienti. La struttura chiara e semplice del sistema aiuta a evitare di commettere errori. Il sistema HACS è pienamente integrato nel suo ambiente di lavoro. Il software intuitivo fornisce in un solo colpo d’occhio tutti i dati rilevanti, sia nel posto di attrezzaggio sia sull’unità di comando della macchina: per esempio panoramica del sistema, piani di lavoro, pallet, diagramma di flusso, compiti e tabella utensili. Tutti i nuovi pezzi preparati vengono inseriti automaticamente nel diagramma di flusso. Attraverso la definizione di ordini è possibile influenzare in qualsiasi momento la priorità e la sequenza di lavorazione. Con la GRP (abbreviazione di interfaccia grafica per la programmazione dei robot), i più svariati tipi di pezzi grezzi vengono posizionati sulle matrici con semplici valori di immissione in modo da ottimizzare gli spazi. Grazie alla GRP integrata nello SmartPad a sfioramento, anche le procedure dei robot e l’inserimento dei pezzi nel rispettivo dispositivo di serraggio della macchina sono eseguiti con grande rapidità sulla base dei requisiti specifici.
Hermle offre un proprio software di automazione: Hermle AutomationControl-System pienamente integrato nell’ambiente di lavoro
Ai centri di lavoro Hermle può essere adattato RS 05-2, la 2a generazione del sistema robotizzato compattoCON UNA DOTAZIONE DIGITALE COMPLETA E PIATTAFORME SOFTWARE PER LA SUPERVISIONE, LA DIAGNOSTICA E LA MANUTENZIONE PREDITTIVA, IL NUOVO
CENTRO DI LAVORO ORIZZONTALE DI MCM APRE A NUOVE OPPORTUNITÀ APPLICATIVE
SSeguendo il medesimo percorso evolutivo che ha interessato negli anni passati la linea Clock, che oggi comprende i tre modelli Clock EVO 800, 1000 e 1200 a 4 e 5 assi, il nuovo Tank 1000 EVO amplia la gamma TANK, storica linea di macchine MCM, con un nuovo modello di taglia inferiore rispetto a quelli preesistenti e avvia il processo di restyling della serie Tank, che interesserà via via tutti gli altri modelli.
La nuova linea Tank EVO, che racchiude più di 40 anni di know-how tecnologico di MCM, sarà disponibile in versione a 5 assi, configurabile anche per lavorazioni in Multitasking come tornitura e rettifica.
Con il nuovo Tank 1000 EVO verranno messe a disposizione dei clienti di ogni settore le capacità e le features che negli anni l’azienda ha sviluppato per un comparto high-demanding come quello Aerospace. Le caratteristiche del nuovo centro di lavoro orizzontale aprono, infatti, a nuove opportunità applicative con soluzioni adatte alla meccanica generale, alla modelleria e alla
stampistica, dove le dimensioni dei componenti e i volumi di lavoro sono più contenuti, ma in cui sono richieste flessibilità e lavorazioni con più assi coordinati in simultanea.
Le caratteristiche della nuova Tank 1000 EVO
Tank 1000 EVO è una macchina per lavorazioni a 5 assi con un’elevata portata sulla tavola e disponibile con due tipologie di testa differenti. La testa tiltante come asse A, che consente di avere un set di lavoro in asse negativo molto significativo; la doppia motorizzazione nella struttura della testa offre un ottimale comportamento in operazioni di tornitura e rettifica. La testa tiltante come asse B consente, invece, di eseguire lavorazioni di sculpturing e modelling, più legate a settori come quello degli stampi. Elettromandrini ad alte prestazioni, inoltre, sono stati progettati per mantenere costante la precisione di lavorazione nel tempo.
Tutti gli assi lineari sono dotati di un sistema di misura diretto
tramite righe ottiche di alta precisione, mentre gli assi rotativi sono dotati di sistemi di misura assoluti realizzati tramite encoder di grandi dimensioni per contenere al massimo il possibile errore angolare.
Lo studio di analisi FEM delle masse in movimento ha portato MCM ad ottimizzare la struttura della nuova Tank 1000 EVO, conferendole massima rigidità e precisione costante, ottenendo al contempo dinamiche superiori, accelerazioni e velocità più elevate anche in caso di lavorazioni con un peso su pallet in macchina fino a 2.500 kg. Rilevante è anche la riduzione ottenuta nei consumi energetici. La struttura solida della macchina si compone di basamento, montante dell’asse X e colonna dell’asse Y. Il posizionamento sul doppio livello delle guide dell’asse X garantisce rigidità e resistenza alla spinta nelle lavorazioni pesanti. Le dimensioni complessive e l’altezza della macchina sono state ridotte di circa il 25%, nonostante il volume di lavoro sia aumentato.
Il sistema a Multipallet è dotato di movimento verticale per gestire due livelli di stoccaggio. Un’ampia disponibilità di pallet ed un adeguato numero di utensili nei magazzini modulari assicurano un’elevata occupazione oraria, migliorando efficienza e produttività. La capacità di pallet va da 9 a 15 (opzionale) espandibile anche in after-sales. Rapidi ritorni d’investimento e gestione di importanti volumi produttivi composti da lotti medio piccoli, sono i vantaggi dei sistemi d’automazione Multipallet ed FMS di MCM, nei quali tutte le macchine della nuova linea Tank EVO sono integrabili.
Configurabile anche per lavorazioni in multitasking, come tornitura e rettifica, Tank 1000 EVO si presenta con una dotazione digitale completa, con piattaforme software per la supervisione, la diagnostica e la manutenzione predittiva - jFMX e jFRX, prodotti da MCE Solutions, la divisone informatica di MCM, concretizzando flessibilità ed efficienza produttiva.
MIA | MCM Intelligent Automation
MIA | MCM Intelligent Automation riunisce tutto il know-how delle soluzioni di automazione che negli anni l’azienda ha progettato e realizzato, dando l’avvio a una nuova fase di metodologie di progettazione, produzione e montaggio, a tutto vantaggio dell’affidabilità dei sistemi MCM.
Da sempre l’automazione è un elemento importante nel DNA di MCM, che la considera come un tassello fondamentale nell’offerta delle proprie soluzioni. Questo approccio di MCM è la risposta giusta alle esigenze manifestate dai mercati, ossia poter disporre di una flessibilità sempre maggiore che consenta di gestire e abilitare il cambio di serie di componenti e di generare volumi importanti costituiti da lotti sempre più piccoli e variegati.
Nella proposta di MIA | MCM Intelligent Automation è racchiusa tutta l’esperienza che l’azienda ha accumulato nei suoi 40 anni di vita, declinata in diverse opzioni sui centri di lavoro: si va dagli FMS (Flexible Manufacturing Systems) con manipolazione lineare, alle soluzioni multipallet, fino ad arrivare a versioni che prevedono la manipolazione diretta del pezzo mediante l’adozione di robot. L’integrazione di più sistemi è una peculiarità resa possibile dalle soluzioni “aperte” di MCM, in cui l’automazione consente di integrare anche macchinari appartenenti a cicli produttivi differenti. Questa razionalizzazione delle competenze in automazione, con la riduzione dell’impatto ambientale e dei consumi energetici dei sistemi, prosegue il percorso evolutivo in ambito di ecosostenibilità.
JFMX e JFRX, lo smart manufacturing secondo MCM
Sin dalla sua fondazione, MCM ha riconosciuto il ruolo dell’Information Technology come elemento fondamentale per l’integrazione tecnologica, includendolo da subito nella propria offerta. MCE è la divisione IT di MCM, fondata nel 1986 per concepire e sviluppare una serie progressiva di servizi software dedicati alla supervisione della produzione e organizzati nelle suite ‘jFMX’. L’architettura del supervisore jFMX, esclusivo MCM, è strutturata su diversi livelli al fine di gestire le crescenti complessità di impianti e di informazioni, fino al possibile coordinamento e gestione centralizzata dell’intero workshop. Per vincere non solo la sfida legata alla produzione, ma anche quella dell’analisi dei dati, MCM ha intrapreso e concretizzato progetti che sfruttano la grande quantità di informazioni presente nei propri sistemi flessibili di produzione. Nella proposta di gestione degli impianti, già ricca di funzionalità di supervisione della produzione a vari livelli, MCM ha infatti introdotto un nuovo sistema di monitoraggio costituito da differenti sensori e dal dispositivo hardware jNODE FR, su cui la società ha implementato in completa autonomia la piattaforma jFRX per la raccolta ad alta frequenza e l’aggregazione dei dati macchina, grazie ai quali è possibile creare nuovi servizi, pensati per migliorare l’esperienza del cliente e la disponibilità della macchina. In tal senso, collaborando con clienti chiave, MCM ha sviluppato un sistema per la manutenzione predittiva che sfrutta il concetto di “fingerprint”, ogni macchina viene periodicamente sollecitata con un test a vuoto predefinito, e un software “DataAnalyzer”, sviluppato in collaborazione con il Politecnico di Milano.
RMI-QE è il sistema di ispezione a trasmissione radio per macchine utensili di ultima generazione di Renishaw, leader mondiale nelle tecnologie di misura; una delle molteplici soluzioni di smart factory per il controllo dei processi proposte dall’azienda e progettate per aiutare le officine a ottimizzare le proprie capacità produttive.
Il sistema include un’interfaccia radio RMI-QE ultracompatta che utilizza un protocollo di comunicazione avanzato. Inoltre, sono stati apportati importanti aggiornamenti sull’intera gamma di sonde a trasmissione radio. Le nuove funzionalità garantiscono un significativo incremento della durata delle batterie, un’impostazione del sistema più semplice rispetto al passato e la possibilità di una diagnostica remota su tutta la gamma dei tastatori radio.
L’interfaccia RMI-QE viene installata all’interno della macchina, è dotata di un protocollo di comunicazione aggiornato ed è già predisposta per supportare i sensori e i dispositivi smart di ultima generazione sviluppati da Renishaw.
Grazie a una versione aggiornata del consolidato sistema a spettro diffuso con salto di frequenza (FHSS - frequency hopping spread spectrum) da 2.4 GHz, il sistema risulta conforme alle normative radio internazionali e funziona in modo affidabile anche in ambienti con un gran numero di segnali radio. L’interfaccia è ideale per applicazioni in cui non è possibile garantire una linea visiva fra la sonda e il ricevitore, come ad esempio nei centri di lavoro 5 assi e macchine multi-tasking di tornitura/fresatura.
inoltre adatto all’installazione su centri di lavoro con tavole rotanti o
con cambio pallet, perché consente di gestire fino a quattro diverse sonde di presetting utensili o ispezione pezzo sulla stessa macchina CNC.
Grazie al suo design ultracompatto, assicura un’eccellente flessibilità di montaggio e garantisce piena compatibilità con le versioni precedenti.
Da sempre, gli utenti Renishaw hanno la possibilità di configurare manualmente le impostazioni delle sonde radio per adattarle alle condizioni di lavoro delle loro macchine, opzione che risulta particolarmente utile quando si lavora ad alta velocità o in presenza di forti vibrazioni. Ora il processo è stato ulteriormente semplificato. Con la rivoluzionaria tecnologia Opti-Logic™, accessibile tramite la nuova app Probe Setup, è possibile configurare le impostazioni della sonda direttamente dallo smartphone. Le opzioni selezionabili vengono visualizzate sullo schermo dello smartphone e trasferite alla sonda tramite un sistema di comunicazione bidirezionale. Questa funzione semplifica notevolmente il processo di configurazione e consente di effettuare controlli diagnostici a distanza, utilizzando applicazioni molto comuni come email, iMessage®, WhatsApp, LINE e WeChat.
Attenzione all’ambiente
Gli aggiornamenti all’elettronica della sonda e al sistema di trasmissione radio hanno permesso di aumentare la durata delle batterie del 400%. Questo significa che, con un utilizzo standard, la batteria di una nuova sonda abbinata a RMI-QE può durare fino a 5 anni. Le migliorie appena citate, implementate recentemente anche alle sonde a trasmissione ottica OMP40 e OSP60, dimostrano l’impegno di Renishaw nel realizzare prodotti con un impatto ambientale ridotto, riducendo i materiali di consumo”.
L’ultima generazione di sistemi di ispezione a trasmissione radio Renishaw, consente di svolgere operazioni di presetting, rilevamento dell’integrità degli utensili, impostazione e verifica dei pezzi in maniera automatica e affidabile. Integrando questi metodi di controllo nei processi produttivi si possono ottenere tutti i dati necessari per migliorare in modo significativo la produttività, ottimizzare l’utilizzo delle macchine e ridurre la necessità di supervisione e di interventi degli operatori.
serraggio di 1.000 pezzi differenti attrezzamento veloce grazie agli adattamenti per interno ed esterno senza necessità di regolazioni il mandrino di serraggio rimane sulla macchina
CONCEPITA PER OPERAZIONI DI FORATURA RAPIDE E SENZA PROBLEMI, CORODRILL® 860
MASSIMIZZA LA PRODUTTIVITÀ GRAZIE ALL’ELEVATA EFFICIENZA DI TAGLIO DEL METALLO
LLa progettazione per la producibilità (DFM - Design For Manufacturability) è un processo che permette di progettare e sviluppare prodotti che possono essere realizzati in maniera più facile, efficiente ed economicamente conveniente. Per i clienti di Sandvik Coromant, questo significa ottenere un costo per componente favorevole nella lavorazione di componenti (o un buon costo per foro nelle applicazioni di foratura e maschiatura). Ognuno di questi obiettivi richiede utensili da taglio estremamente affidabili e ad elevata produttività.
Il maggior livello di globalizzazione delle catene di approvvigionamento, l’aumento della domanda di prodotti personalizzati e la mobilità elettrica, i cui componenti sono più vari e sempre più spesso realizzati in materiali tenaci come acciai debolmente legati, Inconel e alluminio, influiscono sull’evoluzione del concetto di progettazione per la producibilità.
Le soluzioni di attrezzamento avanzate possono fare la
differenza nell’ambito della progettazione per la producibilità (DFM) nel passaggio dal modello CAD (Computer Aided Design) al componente, attraverso tre fasi di produzione: la fase CAD>mandrino, in cui si utilizzano modelli CAD e CAM (Computer Aided Manufacturing), compresa la simulazione di esatte repliche digitali, per preparare un’operazione di lavorazione e ottimizzare l’attrezzamento, il pezzo da lavorare e i parametri di lavorazione; la fase mandrino, ovvero l’operazione di lavorazione effettiva; la fase mandrino>componente, dove si valutano la qualità e la finitura del componente finale.
Indipendentemente dal settore, la finitura e altre caratteristiche, come l’integrità superficiale del foro, sono di primaria importanza. Una migliore qualità del foro può prevenire il guasto del componente — e dipende in larga misura dai processi di lavorazione adottati per la lavorazione o la finitura dei fori.
Il design della punta è particolarmente importante al fine di
produrre fori di qualità migliore. Ecco perché le geometrie del tagliente sono in continua evoluzione: rispettare i più elevati standard di produzione e qualità del componente è fondamentale. Anche l’utilizzo di refrigerante è importante, per ridurre l’accumulo di calore nell’utensile. Ed è qui che gli specialisti di Sandvik Coromant possono rivestire un ruolo essenziale nel sostenere i clienti.
Sandvik Coromant lavora al fianco dei clienti per raccogliere tutte le opportune informazioni sul loro progetto di lavorazione e stabilirne i requisiti.
Nella fase CAD>mandrino, gli specialisti di Sandvik Coromant possono esaminare e decodificare i processi del cliente, compresi i modelli CAD e CAM utilizzati e sviluppare un prototipo di utensile la mattina per averlo pronto al collaudo nell’area R&S nel pomeriggio. Prima dell’avvento del digitale, questo processo avrebbe richiesto lo scambio ripetuto di disegni e progetti, arrivando a durare fino a sei settimane. Oggi, avere la capacità di fornire prototipi nel giro di un giorno è rivoluzionario per Sandvik Coromant.
Maggiore durata utensile
Sandvik Coromant mette a disposizione una gamma di prodotti per sostenere i clienti nella produzione di componenti, anche quelli destinati alla mobilità elettrica. Questi includono CoroDrill® 860, una punta in metallo duro integrale concepita per operazioni di foratura rapide e prive di problemi che massimizza la produttività mediante un’elevata efficienza di taglio del metallo. L’utensile è disponibile in varie geometrie, tra cui la geometria 860-MM per materiali in acciaio inossidabile a truciolo lungo come quelli austenitici, superaustenitici, ferritici e duplex.
Poi c’è CoroDrill® 860GM, che si è dimostrata utile ai costruttori automotive nella foratura di blocchi motore, casse, flange e collettori. Oltre all’automotive e alla meccanica generale, questa punta è adatta anche a tutte le applicazioni in cui la qualità del foro è fondamentale — come spesso accade nel settore aerospaziale, Oil & Gas, nucleare e delle energie rinnovabili.
La punta 860-GM ha fornito risultati straordinari a numerosi clienti, tra cui un costruttore automotive
in Corea. L’operazione del cliente di Sandvik Coromant prevedeva la realizzazione di fori passanti in un lotto di connettori per trasmissioni automotive. L’obiettivo era praticare otto fori passanti da 8.2 mm (0.32”) di diametro in ciascun componente, con una profondità di 10 mm (0.39”). In un confronto tra le due punte, la soluzione esistente è stata in grado di produrre 200 componenti, per un totale di 1600 fori, con una velocità di taglio (Vc) di 80 m/ min (3102 giri/min) e un avanzamento (Vf) di 381 mm/min. Con CoroDrill® 860-GM, invece, sono stati prodotti 2300 componenti (18400 fori) con un valore Vc di 100 m/min (3878 giri/min) e un valore Vf di 814 mm/min.
Complessivamente, CoroDrill® 860-GM ha offerto un aumento della durata utensile del 1150%, un traguardo straordinario. Questo risultato è stato accompagnato da un aumento della produttività che ha contribuito a ridurre notevolmente il costo per componente.
La maschiatura, ossia l’operazione che crea un filetto all’interno del foro, è importante almeno tanto quanto la realizzazione di fori lisci. Per questo Sandvik Coromant mette a disposizione le soluzioni CoroTap® 100, 200, 300 e 400, ognuna ottimizzata per applicazioni diverse. Per analizzare qualche esempio, CoroTap® 100 è una gamma di maschi con scanalatura diritta ottimizzata per i materiali ISO K, ISO N e ISO H a truciolo corto. CoroTap® 400, invece, è un maschio a rullare ad alta velocità che non prevede la formazione di trucioli ed è adatto alla lavorazione di fori passanti e ciechi su acciaio, acciaio inossidabile e alluminio. La scelta del cliente dipenderà dai requisiti della propria applicazione.
A marzo 2023, Sandvik Coromant ha presentato anche le soluzioni CoroTap® 100-N e CoroTap® 400-N, progettate per agevolare i clienti nella maschiatura dell’alluminio, un’operazione sempre più importante nei processi di produzione.
Per il momento, le prestazioni degli utensili Sandvik Coromant dimostrano che gli utensili studiati per agevolare le operazioni di foratura e filettatura su vari materiali saranno fondamentali per aiutare i costruttori a produrre componenti più leggeri, variegati e di minori dimensioni. Non solo le officine meccaniche possono progettare e sviluppare tali componenti in maniera più facile ed economicamente efficiente, ma possono garantire che la progettazione per la producibilità (DFM) continui a essere una priorità lungo l’intero processo di produzione — innovando così con efficienza.
AL CENTRO DEI NUOVI MODELLI ACCORD 500 E ACCORD 600 E DELL’UPGRADE DI MORBIDELLI M200, LA NECESSITÀ DEL CLIENTE DI RIAPPROPRIARSI DEL PROPRIO TEMPO, GUADAGNANDO IN PRODUTTIVITÀ, MANTENENDO ALTI LIVELLI DI QUALITÀ DI FINITURA
SCM cambia le “regole del gioco” nella lavorazione di porte, finestre, scale ed elementi in massello. According to wood (Secondo il legno), il claim scelto da SCM per il lancio della sua nuova gamma di centri di lavoro per il massello, esprime l’obiettivo di SCM di fornire un’ampia varietà di soluzioni tecnologiche ancora più efficienti e performanti, ma soprattutto “progettate dal legno” perché dotate di caratteristiche tecniche e prestazioni totalmente in linea con le sfide del mercato.
Al tempo stesso, According richiama ad accord: una lunga storia di successi e know-how come quella dell’omonima gamma di centri di lavoro per la fresatura e la foratura del massello di SCM, punto di riferimento per il settore da 15 anni. La stessa gamma da oggi si amplia e si rinnova in un’ottica del tutto nuova, strategica, per stare al passo con i tempi e dare giusto valore al tempo dei clienti, ottimizzando e velocizzando i loro processi produttivi, ma garantendo al contempo un’elevata qualità di finitura.
Proprio il tempo è il fattore-chiave che più ha guidato la rivoluzione dei centri di lavoro SCM. Ogni caratteristica tecnica è studiata per ridurre i tempi nelle fasi più cruciali per ogni produttore del settore: dalla programmazione al set-up della macchina, dal processo di lavorazione alla manutenzione. “Abbiamo voluto dare al cliente, che si trova ad affrontare problematiche sempre più complesse nella lavorazione del massello, una risposta da specialisti che individuasse la soluzione più puntuale per ogni specifica richiesta.
Queste nuove tecnologie semplificano notevolmente il lavoro quotidiano degli operatori, lo rendono più efficiente e consentono quindi un migliore ritorno dell’investimento”, sottolinea il Business Manager dei Centri di Lavoro di SCM Bruno Di Napoli.
Nuovi centri di lavoro accord 500/600
SCM aumenta la produttività del 30% rispetto agli standard di mercato grazie alla struttura “gantry” a telaio chiuso che, in continuità con il progetto accord, consente di ottenere robustezza e precisione anche alle massime velocità di avanzamento e nelle lavorazioni più impegnative.
Incrementata ulteriormente anche la velocità di fresatura che ora supera i 15 metri al minuto con il nuovo gruppo operatore a 5 assi KPX con elettromandrino Hiteco da 17 Kw, studiato per consentire sempre in modo veloce e accurato anche le operazioni più complesse.
Anche i tempi di ciclo produttivo vengono estremamente ridotti con l’esclusivo gruppo BRC-S, ancora più flessibile e compatto, che permette di realizzare tutte le lavorazioni di taglio, fresatura e foratura tipiche dei componenti di finestre.
Un’altra novità di rilievo sono gli oltre 100 utensili sempre a disposizione e rapidamente pronti all’uso con il nuovo magazzino Caddy 35, esclusivo sia per capienza che per struttura perché integrato all’interno del centro di lavoro senza aumentare l’ingombro della macchina.
La gestione degli utensili è poi ulteriormente ottimizzata e semplificata dal nuovo software Maestro Power TMS integrato alla suite Maestro di SCM. Grazie a questo programma che massimizza la capacità del magazzino ed ottimizza la programmazione, l’operatore non deve più perdere tempo ed energie per cercare l’utensile più adatto: è il software ad individuare e indicare la posizione giusta dell’utensile nel magazzino nell’ottica di minimizzare i tempi di lavorazione.
La pulizia dell’ambiente è un altro tema cruciale nella lavorazione del massello e per rispondere a questa problematica SCM ha studiato un nuovo convogliatore trucioli posizionato automaticamente in funzione del programma di lavorazione, in modo da avere la massima efficienza di aspirazione in ogni condizione.
Il progetto According to Wood viene proposto al mercato attraverso una gamma che permette di soddisfare appieno le varie esigenze produttive.
Accord 500 coniuga tradizione, semplicità e compattezza, senza rinunciare all’alta tecnologia: tutta la potenza al servizio del legno sviluppata dal nuovo gruppo operatore a 5 assi con elettromandrino da 17 kW, con la possibilità di scegliere una configurazione Pro-Space senza protezioni perimetrali, ideale per chi non ha grandi spazi a disposizione. Accord 600 rappresenta la soluzione progettuale che non prevede compromessi sulle prestazioni: con l’obiettivo di ridurre al massimo i tempi di produzione in qualsiasi settore applicativo, presenta un nuovissimo gruppo operatore iper-performante dotato di ben 3 unità indipendenti. Gli elettromandrini 4 assi e JQX 5 assi, rispettivamente da 21 e 13.5 kW, con magazzini on-board indipendenti, consentono un cambio utensile in tempo mascherato anche durante le lavorazioni del gruppo anteriore indipendente, con BRC-S o testa a forare a seconda delle esigenze.
Il tutto votato al risparmio di tempo, il concetto protagonista assoluto dell’intera gamma.
L’upgrade del centro di lavoro “all-in-one technology” morbidelli m200
La gamma morbidelli m200, punto di riferimento per i centri di lavoro CNC a livello mondiale, conferma le caratteristiche tecniche più apprezzate dal mercato, come la sua struttura solida, il passaggio pezzo da 250mm, il 5 assi Prisma KT ed il piano FlexMatic che consentono di gestire non solo tutti i tipi di lavorazione per il pannello, ma anche quelli per il legno massello.
Oggi questo centro di lavoro si arricchisce anche di nuove prestazioni, ideali soprattutto per la produzione di elementi di finestre.
Riduzione dei tempi ciclo con il piano FlexMatic che
diventa ancora più flessibile con i suoi movimenti che avvengono contemporaneamente sotto la gestione del software Maestro CNC di SCM. Oltre a questo, il sistema di tenuta del pezzo è stato reso ancora più performante grazie al morsetto MULTIGRIP, studiato per la lavorazione specifica di elementi di serramento, che permette di posizionare e bloccare i pezzi di lavoro in modo rapido ed affidabile.
Importanti novità anche per il gruppo operatore JQX che si arricchisce di un innovativo convogliatore trucioli studiato appositamente per ottenere la massima pulizia anche in presenza di grosse asportazioni. Esso è gestito da CN non solo in rotazione, seguendo il percorso delle lavorazioni, ma anche in posizione verticale: ciò permette al convogliatore di posizionarsi sempre esattamente di fronte al getto del truciolo per captarlo nel miglior modo possibile. A conferma dell’attenzione al mondo del serramento, anche su morbidelli m200 troviamo il nuovo gruppo BRC-S che permette di eseguire tagli di lama e forature e fresature orizzontali nel minor tempo possibile, lasciando al mandrino a 5 assi solo le principali operazioni di profilatura e tenonatura.
CAPACITÀ DI RACCOLTA E TRASMISSIONE DATI DI MACCHINA E DI PROCESSO, DIGITALIZZAZIONE E INTEGRAZIONE IOT SONO I REQUISITI ESSENZIALI DEI CNC 4.0 di Patrizia Ricci
NNel corso degli ultimi anni, i mercati hanno richiesto al settore delle macchine utensili di eseguire lavorazioni meccaniche con prestazioni sempre più spinte, maggiore velocità e produttività, qualità e precisioni sempre più elevate, con livelli di sicurezza e flessibilità sempre crescenti. Queste richieste hanno determinato una parallela e naturale evoluzione delle tecnologie di controllo del CNC, deputato all’esecuzione delle lavorazioni meccaniche, verso una progressiva digitalizzazione. Nelle smart factory, grazie al loro impiego, ogni azione delle macchine viene decisa e controllata tramite un software integrato, da cui deriva l’acronimo CNC, ovvero “controllo numerico computerizzato”. Oggi, i CNC rappresentano il cuore di quella che è la fabbrica guidata dal flusso trasparente dei dati, la soluzione e lo strumento ideali per far fronte alle difficoltà delle aziende determinate dall’approvvigionamento delle materie prime e di tutte quelle criticità che caratterizzano lo scenario dei mercati globali.
I moderni controlli numerici si contraddistinguono per l’approccio votato alla versatilità: si tratta di piattaforme hardware dalle alte prestazioni sulle quali è installato un software completo, per coprire i più disparati settori, e al tempo stesso totalmente adattabile. Questa flessibilità costituisce il valore aggiunto riconosciuto dal mercato, perché permette di trovare una risposta per ogni genere di macchina (per metallo, vetro, marmo o legno) e tipo di operazione (rettifica, tornitura, fresatura, alesatura, taglio laser o plasma...). Le soluzioni disponibili si differenziano proprio per la loro capacità di soddisfare più ambiti applicativi e per il loro essere modulari e ampiamente configurabili e scalabili per un controllo sicuro delle macchine utensili. Queste caratteristiche permettono agli OEM di standardizzare una singola architettura CNC, ottimizzata per costi e prestazioni, per una vasta tipologia di macchine: da quelle piccole, con pochi assi, ai grandi centri di produzione multi celle, anche con centinaia di assi e mandrini. In tal modo, l’architettura aperta della piattaforma può ridurre sensibilmente i costi di sviluppo e di supporto e velocizzare il tempo di introduzione dei prodotti sul mercato. Per garantire una ancor maggiore versatilità, prestazioni dinamiche e precisione, queste piattaforme sono dotate di hardware che comprendono azionamenti digitali con sicurezza integrata, moduli PLC di sicurezza, moduli di ingresso e uscita sicuri e pannelli operatore multi processore con touch screen. I software di supporto dovrebbero includere sistemi operativi di precisione e PLC di automation, interfaccia uomo-macchina completamente personalizzabile (HMI), architetture di sicurezza integrate e complete di funzioni di lavorazione opzionali e simulatore 3D per la verifica di parti del programma e per la visualizzazione dei processi di lavorazione.
Ma cosa si intende con tecnologia CNC?
CNC è l’acronimo di Computer Numerical Control ed è un tipo di tecnologia che, inserita all’interno della macchina, le permette di muoversi seguendo un preimpostato programma di lavoro. Grazie al dispositivo digitale interno, è possibile conservare in memoria le funzioni eseguite durante la lavorazione. Tenere traccia delle operazioni, permette di adattare la macchina in base alle esigenze produttive. A differenza dei robot, non essendo in grado di adattarsi a mutamenti dell’ambiente e di reagire ad eventuali imprevisti, ostacoli improvvisi e collisioni, le macchine a tecnologia CNC necessitano del controllo di un operatore, che pur non essendo indispensabile per il suo corretto funzionamento, può esercitare una supervisione utile per impostare il programma di lavorazione, preparare i materiali da manipolare e intervenire in caso di malfunzionamenti.
La tecnologia CNC, attraverso l’impostazione di software CAM (Computer-Aided Manufacturing), CAD (Computer-Aided Design) e CNC, viene impiegata nelle lavorazioni ad alta precisione, in quelle che necessitano di tempi lunghi e in quelle che richiedono velocità, flessibilità, adattabilità, ripetizione, coadiuvando l’operatore ed evitando errori di distrazione derivanti da processi lunghi e ripetitivi.
In effetti, l’evoluzione del CNC muove i primi passi con l’introduzione del PLC, il Controllore Logico Programmabile integrato. All’inizio, infatti, i CNC, ovvero quelle che altro non erano se non macchine calcolatori nate per la gestione dei movimenti degli assi, non erano dotate di PLC. Questi controller possono automatizzare un processo specifico, una funzione della macchina o persino un’intera linea di produzione e, quindi, consentono al CNC di gestire in modo più completo le macchine utensili, incrementandone la funzionalità e flessibilità. La possibilità di assolvere a lavorazioni sempre più complesse, invece, è stata garantita dallo sviluppo delle cinematiche a 5 assi; un passaggio, quello dai 3 ai 5 assi con algoritmi dedicati, significativo perché consente di lavorare profili pezzo tra i più complessi, particolarmente utilizzati nei settori aerospaziale, dell’automotive, in particolare quello sportivo, degli stampi
e medicale, aumentando la produttività grazie a tempi di elaborazione e di ciclo ridotti. L’ultimo step del processo evolutivo, in ottica 4.0, ci porta da un controllo numerico di tipo stand-alone ad un CNC interconnesso responsabile della centralità della macchina utensile all’interno del processo produttivo e protagonista dello scambio di dati e informazioni con il mondo interno ed esterno all’ambiente di fabbrica, sulla base del quale vengono prese le decisioni sui processi produttivi. Oggi, i moderni CNC sono sempre più user-friendly e interattivi, capaci di gestire la macchina e di integrarsi nei sistemi IoT che proliferano in ambienti di fabbrica data-driven sempre più digitali e connessi, sempre più aperti, dove, grazie all’Intelligenza Artificiale, è possibile avere maggiore produttività e flessibilità, un costante monitoraggio di sistemi e consumi che garantiscono un uso più responsabile e sostenibile delle risorse.
A garantire che il CNC possa assolvere a queste funzioni, oltre all’aumento delle prestazioni hardware, c’è la parte software, determinante nel processo di evoluzione del controllo CNC.
È infatti il software, sempre più intelligente, che raccoglie i dati dai numerosi sensori installati sulle macchine e trasmette al CNC le informazioni sulla base delle quali cambiare in automatico i parametri delle lavorazioni per ottimizzare i processi e assicurare una maggiore flessibilità. Spetta, infatti, alle piattaforme software dotate di intelligenza artificiale e algoritmi di machine learning il compito di aggregare dati in modo strutturale e di analizzarli per restituire in real time informazioni legate a produttività, qualità superficiale del pezzo e manutenzione predittiva di processi e macchinari, facendo comunicare reparti IT e OT all’interno dell’azienda e mettendo a disposizione dei team manager i dati del controllo numerico, dei drive e dei PLC.
L’impiego del CNC consente di aumentare o ottimizzare la produzione in funzione delle richieste del mercato, ridurre i tempi passivi, anche quelli di montaggio e smontaggio, e adattare velocemente la produzione a molte variabili, grazie alla possibilità di programmare le lavorazioni e la gestione dei costi in funzione delle specifiche esigenze e dei lotti da realizzare. Diventa quindi più facile per un’azienda
M8V è il nuovo CNC interconnesso per lo Smart Manufacturing. Il livello evoluto, la praticità di utilizzo multitouch, le numerose nuove funzioni avanzate e la connettività wi-fi incorporata per la prima volta in un CNC, sono stati pensati per essere parte integrante del processo produttivo e per supportare ogni tipo di lavorazione con requisiti di precisione e velocità estreme. Il controllo numerico si evolve a supporto dello Smart Manufacturing e degli ambienti IIoT in fabbrica. M8V renderà possibile il futuro delle lavorazioni.
accettare una commessa con piccoli numeri o gestirne un’altra con grandi quantitativi di pezzi da produrre. Inoltre l’impiego di queste soluzioni intelligenti garantisce un elevato miglioramento della qualità del prodotto finale e una riduzione considerevole degli scarti e dei possibili errori.
A stretto contatto dell’automazione: digitalizzazione e integrazione IoT
Essendo inseriti in contesti di automazione sempre più sofisticati, per i fornitori di CNC, abilitare la gestione anche di altre parti dell’ecosistema di automazione è un plus ormai inevitabile. In tal senso, alcuni sistemi CNC sono progettati in modo da assolvere a tale esigenza in modo autonomo e indipendente dal controllore principale, sulla base delle stesse strutture hardware e software dei CNC dell’azienda produttrice. Altri, invece, sono in grado di dialogare sfruttando i protocolli di comunicazione più comuni con tutti i prodotti per automazione presenti, anche di differenti fornitori, dalla parte di elettromeccanica ai robot, gli inverter e il motion control. Interfacciandosi con tutti i device presenti, i CNC consentono la loro programmazione direttamente dal proprio pannello CNC di controllo, senza particolari difficoltà o competenze specialistiche. Proporre quindi soluzioni integrate per il controllo dei vari aspetti dell’automazione aziendale è diventato un requisito fondamentale ed essenziale. L’interfaccia verso i robot consente al controllo di gestire, ad esempio, le attività di
handing per carico/scarico dei pezzi e nel machining. Tutto con un unico CNC, che grazie ad una flessibilità sempre più spinta consente sia la gestione di una pinza su robot che quella di una testa additive, laddove richiesto, nelle lavorazioni di difficile esecuzione con i metodi tradizionali. Prestazioni sempre maggiori necessitano tuttavia di una dotazione hardware sempre più potente in grado di sviluppare algoritmi sempre più dinamici e adattivi. Lo stesso vale anche per la possibilità, offerta dalle moderne macchine utensili, di combinare più lavorazioni sulla stessa macchina, sommando alle tradizionali lavorazioni di fresatura, cicli di tornitura e rettifica. Con l’incremento delle velocità, la riduzione dei tempi di attrezzaggio, fissaggio e manipolazione pezzi e la ricerca di soluzioni multitasking che integrino processi di foratura, fresatura e rettifica in un solo sistema, crescono anche le necessità di tempi e livelli di elaborazione più spinti, al pari del volume dei dati trasmessi. Ciò comporta che i CNC più evoluti offrano anche una maggiore versatilità e potenza.
Infine, un altro aspetto fondamentale nella scelta di un CNC risiede nella sua ergonomia e facilità d’uso. Questi due aspetti guidano i processi di innovazione dei CNC più evoluti e moderni. In particolar modo, la facilità di programmazione realizzata mediante testiere fisiche di elevata qualità e schermi touch sempre più user friendly con interfacce HMI personalizzabili sono le caratteristiche più richieste dal mercato. Al pari delle applicazioni di remote
desktop manager grazie alle quali è possibile connettere tra loro i vari reparti aziendali coinvolti nella produzione e agevolare lo scambio dati. Le HMI completamente personalizzabili, permettono agli OEM di aggiungere valore alle loro macchine, grazie ad un’ergonomia migliorata.
Al giorno d’oggi non esiste macchina utensile che non sia connessa al mondo della fabbrica digitale. La totale apertura dei CNC di ultima generazione, in grado di dialogare con tutti i sistemi presenti sul mercato e di rilevare tutti i dati utili all’azienda per il controllo della produzione e dei consumi, consente alle aziende di realizzare un notevole risparmio in termini di energia e materie prime e di intraprendere produzioni sostenibili. Maggiore è la quantità di dati che il CNC sarà in grado di raccogliere e trasmettere, migliore e più corretta sarà l’interpretazione degli stessi, più efficiente e precisa la manutenzione e la previsione di possibili malfunzionamenti in un’ottica di manutenzione predittiva.
La tecnologia del gemello digitale si sta rapidamente affermando nel settore industriale come uno dei modi più convenienti per accelerare lo sviluppo di prodotti, processi e servizi. Nei prodotti di automazione quali le macchine utensili, il digital twin è un modello virtuale che utilizza la simulazione, l’acquisizione/analisi dei dati in tempo reale e
le tecniche di apprendimento della macchina per fornire una valutazione completa delle prestazioni dinamiche della stessa prima di costruire un prototipo fisico. Un legame stretto caratterizza anche CNC e digital twin. I programmi parziali scritti manualmente o generati da CAM possono essere verificati e ottimizzati facilmente e velocemente, usando dei software di simulazione grafica, disponibili su un PC offline. Alternativamente, il software può girare direttamente sul pannello operatore e interagire con l’unità CNC della macchina per simulare parti del programma, sia prima del funzionamento o simultaneamente, con un’elaborazione parziale. In questo modo, gli utilizzatori possono visualizzare il percorso del punto centrale dell’utensile, simulare l’asportazione di materiale e verificare le possibilità di collisione. La possibilità di simulare tutte le lavorazioni che la macchina utensile sarà in grado di eseguire in modo sicuro, con una chiara stima dei tempi e dei costi, consentendo anche di prevenire collisioni accidentali, costituisce un reale vantaggio per i clienti che possono fare offerte più mirate per i pezzi finiti. Per ricavare il gemello digitale della macchina utensile, il CNC deve possedere dei requisiti specifici in termini di grafica 3D che rendano possibile la simulazione della macchina e delle sue lavorazioni. Infine grazie al digital twin di cui sono dotate le tecnologie CNC è possibile attuare un controllo immediato sul pezzo, sulle sue dimensioni e caratteristiche, e se necessario intervenire immediatamente sul processo di lavorazione simulato evitando di andare in produzione con un pezzo destinato allo scarto.
La collaborazione fra le aziende risale ai tempi della nascita di S.EL.ME.C. La gamma dei prodotti impiegati di quest’ultima, che va dal profilato alle apparecchiature elettroniche, ha spesso richiesto la consulenza di Bosch Rexroth per quanto riguarda l’avvitatura industriale, anche di tipo wireless, per gli assemblaggi automatizzati. Ma uno degli ultimi progetti realizzati con Bosch Rexroth è la servo pressa elettrica, progettata ad hoc per essere installata su un impianto di motori ad alta velocità di impiego automotive in Slovacchia, un prodotto costruito “allo stato dell’arte”. Il cliente finale ha avuto la necessità di effettuare un assemblaggio per interferenza, oltre che un incollaggio, sistema che ha richiesto l’implementazione di un componente con parametri ben determinati di corsa di accoppiamento e forza di accoppiamento. Inoltre, tutti i dati della pressatura dovevano essere salvati ed era necessario inserire finestre di controllo sul grafico di pressatura. S.EL.ME.C. si è rivolta ancora una volta a Bosch Rexroth per richiedere lo Smart Function Kit for Pressing, la soluzione ideale per un gran numero di applicazioni di pressatura e piantaggio per forze comprese fra i 2 e i 30 kN. Il kit modulare integra componenti elettrici e meccanici con il software, creando così la base perfetta per una pressa elettrica affidabile, disponibile in tempi brevi, semplice e immediata da utilizzare per l’utente finale - visto che inserire i parametri sulle presse spesso si rivela un’operazione complessa - e affidabile nel tempo, perché questa macchina opera a ritmi molto elevati: un ciclo di pressatura ogni 55 secondi. Dal punto di vista delle dimensioni, viste le forze in gioco, la macchina doveva essere di piccola taglia, riuscendo a garantire allo stesso tempo una potenza paragonabile a quella di presse con capacità maggiori. Le caratteristiche elettroniche del prodotto di Bosch Rexroth hanno fin da subito convinto sia S.EL.ME.C. sia il cliente finale, vantando un’interfaccia utente HTML 5, ovvero un’interfaccia visualizzabile su un comune browser web, poiché tutte le macchine S.EL. ME.C. possiedono un computer a bordo per essere immediatamente fruibili per l’utente finale. Un altro punto di forza è la possibilità di esportare dati nel formato JSON, presente nativamente sul prodotto Rexroth, che nell’ambito dei big data è tra i più utilizzati per l’esportazione di grandi moli di dati eterogenei. Da non sottovalutare anche l’utilizzo di componentistica elettronica ed elettromeccanica Bosch Rexroth, come il motore dell’azionamento e del controllo, componenti che si erano già rivelati all’altezza, per affidabilità ed efficienza, nelle passate collaborazioni. Dall’inizio del progetto alla finalizzazione del collaudo, è trascorso solo un anno, considerando anche una pausa dovuta
alla pandemia. La servo pressa di ultima generazione, dal punto di vista della dissipazione energetica e dell’ingombro, offre grandi vantaggi grazie ad un motore brushless super compatto. Per concludere, l’interfaccia HTML 5 dà la possibilità di individuare rapidamente i prodotti difettosi o un eventuale malfunzionamento della macchina, evitando i fermi macchine, il dispendio di energie e lo spreco di risorse materiali per la sostenibilità ambientale. “S.EL.ME.C e Bosch Rexroth collaborano da tanto tempo. In questo ultimo progetto a fare la differenza non sono stati soltanto i componenti efficienti e all’avanguardia, ma anche l’assistenza ricevuta in fase di commissioning, soprattutto quando si sono presentate difficoltà causate dal difficile periodo storico in cui abbiamo lavorato insieme, la pandemia. L’azienda è stata al nostro fianco e siamo soddisfatti del risultato finale” ha dichiarato Ottorino Odoardi, R&D Manager di S.EL.ME.C. Siamo fieri di aver collaborato con S.EL.ME.C, una realtà internazionale importante. Per la progettazione e l’implementazione delle macchine, ci siamo messi in gioco per realizzare soluzioni sempre più sfidanti e complesse. Sappiamo che insieme potremo andare ancora più lontano” ha dichiarato Stefano Balansino, Head of Sales Product Management Linear Motion Technology di Bosch Rexroth.
Oltre quarant’anni di vita votati all’innovazione nei controlli numerici e azionamenti sono il biglietto da visita di D.Electron, azienda fiorentina che è cresciuta divenendo un punto di riferimento nel settore della progettazione e costruzione di CN destinati ai centri di lavoro. Competenza, innovazione, collaborazione e servizio sono i quattro punti cardinali chiave per la storia di D.Electron. Una storia votata all’innovazione nel campo dei controlli numerici e degli azionamenti, ponendosi col CNC Z32 come partner per l’industria manifatturiera italiana e internazionale, forte del know-how maturato nel comparto della meccanica al servizio della clientela. Le configurazioni del sistema di controllo Z32 D.Electron ruotano attorno a una Unità Centrale che contiene il sistema operativo FlorenZ ed il software del controllo numerico. L’unità centrale è collegata ad una scheda che instrada i pacchetti d’informazioni dalle periferiche concentrate o distribuite e gli azionamenti digitali ZStar2 verso il controllo numerico e viceversa, il bus di comunicazione è in fibra ottica ed il protocollo è proprietario.
Il CNC Z32 D.Electron può gestire fino a 32 assi digitali e 16 tramite riferimento analogico oltre che 25 nodi distribuiti di periferiche I/O ognuno basato fino a 8 schede di acquisizione. Le schede possono essere da 16 o 32 IN oppure OUT digitali, riferimenti analogici, encoder, ecc. Il controllo può gestire fino a 6 canali di interpolazione. Svariate le possibilità di fornitura di soluzioni per l’interfaccia uomo macchina, dal compatto All-in-one Z32C15 al PC panel per soluzioni full-touch OST22.
Il contatto diretto con costruttori di macchine utensili ed integratori di sistemi ha favorito lo sviluppo di strumenti software tali da accompagnare il tecnico step by step verso la messa in servizio degli assi ed eventuali operazioni di service.
Nell’Unità Centrale è preinstallata la suite software “Z32 for windows” che contiene una ricca dotazione di applicazioni: ZETA, l’interfaccia operatore del CNC; ZFlash, il tool di programmazione a bordo macchina; Z32Info, che esegue il backup ed il ripristino dei dati del sistema ed il software per il teleservice.
Nella suite sono presenti anche gli strumenti per configurare il sistema e renderlo operativo: AXIS-Tune controlla il corretto cablaggio dell’hardware e dei servomotori asse della macchina. I parametri che definiscono elettricamente i servomotori e i trasduttori di posizione sono preinstallati nel configuratore Tarat
e organizzati in liste. Alla prima messa in servizio si procede col check delle connessioni elettriche di potenza e di segnale tra il servomotore e sistema di controllo. Eseguite le verifiche di connessione, il tecnico inizia la messa a punto dell’asse. Il primo passo è definire i valori dei parametri della maglia di corrente e, per eseguire i calcoli necessari, in ingresso alla maglia AXIS-Tune applica un riferimento di corrente con forma d’onda a gradino ampia al 30% della corrente massima. Il servomotore esegue movimenti impercettibili sui quali si calcola la risposta migliore. I valori dei guadagni della maglia di corrente sono immediatamente visibili, attivi e acquisiti come taratura dell’asse, non occorre salvare dati ed elaborarli con altri strumenti o men che meno copiarli manualmente in altri campi o pagine. Successivamente il tecnico passa alla taratura della maglia di velocità. Anche in questo caso viene applicato un riferimento di velocità la cui forma d’onda è di tipo a gradino.
I movimenti del motore sono più ampi rispetto a quelli fatti per la maglia di corrente e AXIS-Tune se ne serve per rilevare l’inerzia meccanica dell’asse vista dal motore. La taratura G125 è una procedura automatica di tuning eseguita sfruttando uno degli strumenti per la gestione dell’alta velocità che sono a disposizione sia del tecnico installatore sia del programmatore dei cicli di lavoro. Il tecnico definisce velocità e corsa dell’asse mosso dalla G125 al fine di ridurre gli errori d’inseguimento della risposta e individuare le migliori condizioni di moto introducendo automaticamente le correzioni dei parametri necessarie all’ottimizzazione della dinamica del sistema.
La funzione G125 è potente, semplice da usare e permette anche all’utente finale della macchina di avere prestazioni ottimali nelle zone più critiche dell’area di lavoro specie se la macchina ha condizioni dinamiche che possono cambiare in virtù della configurazione oppure della posizione assunta dagli assi.
Il test finale è detto Maglia di Posizione ed è eseguito su tutta la corsa dell’asse che si sta mettendo in servizio. Analizzando i dati rilevati, questo test ha lo scopo di individuare possibili impuntamenti meccanici o non uniformità permettendo così ai tecnici di porvi rimedio. Infine, per individuare eventuali errori geometrici all’inversione dell’asse, si procede con un test del cerchio. Si tratta di uno degli strumenti della gestione dell’alta velocità chiamato Test G113X KA1 ed è assimilabile a una sorta di test di ballbar.
Il 2022 per il gruppo Fagor Automation ha rappresentato un anno molto proficuo per quanto riguarda il lancio di nuovi prodotti ed in particolar modo la nuova piattaforma denominata CNC Elite, con interfaccia totalmente rinnovata, e con la nuova famiglia di azionamenti Quercus. La piattaforma Elite è ancora più intuitiva, semplice e interattiva. Grazie ad una serie di strumenti moderni insieme alla consulenza di designer di spicco, è nato un prodotto mai realizzato fino ad oggi da Fagor a partire dal linguaggio HTML5, utilizzato per lo sviluppo HMI, che permette l’interfacciamento del CNC a tutti i tipi di dispositivi come smartphone, tablet, ecc. Infatti la famiglia Elite, relativamente al tema Industry 4.0, offre una serie di soluzioni e funzionalità necessarie a soddisfare i requisiti, per quanto riguarda il mercato italiano, richiesti dalle leggi fiscali che si sono via via evolute negli anni. In aggiunta, Fagor offre un software sviluppato ad hoc che permette l’estrazione dei dati necessari alla richiesta individuale dell’applicazione e li converte nei formati desiderati dal processo produttivo.
Parallelamente, la nuova famiglia di azionamenti digitali Quercus di ultimissima generazione, che lavorano su bus di campo Ethernet - Sercos III, consente di avere una qualità di movimento e precisione tali da soddisfare le esigenze di macchinari applicati in ambiti ad alta tecnologia. Questo nuovo sistema viene fornito con una serie di eccezionali nuove
caratteristiche, a partire dalla memoria di grandi dimensioni e alla possibilità di ampliarla attraverso chiavetta USB o flash CFast, con le quali eseguire part program. Oltre a ciò, grazie ad una postazione di lavoro virtuale, vi è a disposizione un simulatore CNC, scaricabile dal sito web aziendale, per simulare completamente il comportamento del macchinario considerando gli effettivi avanzamenti, velocità, ecc.
I campi d’utilizzo del simulatore spaziano dalla formazione tecnica per programmatori e operatori, all’editing/Simulazione nei reparti di progettazione per determinare una stima dei tempi di lavorazione, fino alle esigenze di centri di formazione a distanza. Nella piattaforma Elite è stato dato ampio risalto al mondo della connettività, infatti, sia che parliamo di I4.0 che di mere esigenze legate alla connessione alla rete aziendale, il CNC ha a bordo tutte le dotazioni HW e Sw atte a soddisfare qualsivoglia esigenza di condivisione dati. Un classico esempio è quello di Telessistenza, dove da una postazione remota un tecnico, in maniera sicura, può connettersi al CNC per diagnosticare e risolvere i problemi che in quel momento la macchina potrebbe avere. Questo potente strumento non solo consente al tecnico di ottimizzare il tuning di assi e mandrini ma anche modificare PLC, parametri, programmi ecc. Seguendo l’impegno verso l’ambiente, protezione e sostenibilità, Fagor ha
adottato una manualistica digitale presente a bordo di ogni sistema ed in particolar modo nella piattaforma Elite, che funge da documentazione tecnica. Ogni CNC ha una libreria incorporata con tutta la gamma di manuali, richiamabile attraverso un apposito soft key denominato “Help”. Oltre alla qualità del prodotto Elite, la filiale italiana ha sviluppato anche un particolare approccio verso gli end user che la casa madre basca ha poi adottato e replicato in altre aree di mercato. Si tratta di Fagor For You, il Club riservato ai clienti di Fagor Automation. Questo Club, che rimarca la vicinanza dell’azienda ai suoi clienti, permette di usufruire di servizi dedicati, offerte e vantaggi esclusivi pensati in forma personalizzata per ogni azienda.
L’obiettivo è accompagnare il socio prima, durante e dopo l’acquisto dei prodotti di Fagor Automation stabilendo un rapporto diretto e continuativo che consenta di mantener lo aggiornato sulle novità e sui servizi offerti.
Fagor For You è di fatto un Club, coordinato dal Sig. Rosario Oldani, che garantisce un canale di comunicazione attivo da parte nostra, orientato al cliente finale offrendo help line telefonica, informazioni aggiornate, visite di supervisione. Si tratta di un servizio che oltre a garantire una serie di vantaggi e un costante aggiornamento sulle novità per l’end user ci permette di fidelizzare il cliente, e avvantaggia anche i costruttori di macchine che ricevono un canale di feedback sul risultato finale del loro lavoro e sulla soddisfazione dei loro clienti. I servizi del Club non sostituiscono quelli già previsti dalle classiche attività di assistenza tecnica, ma vanno ad affiancarsi secondo modalità più personalizzate; sono in primis rivolti agli utilizzatori di macchine ma non mancano adesioni da parte di retrofittatori, system integrator, costruttori di macchine utensili e softwaristi, cioè quei profili professionali che si trovano a interagire con gli end user.
Fidia è un’azienda innovatrice nel settore dell’automazione fin dalla sua nascita a metà degli anni ’70 con la progettazione del primo CNC applicato ad una fresatrice di uno storico costruttore Italiano di macchine utensili di allora. Quella aziendale è la storia di come la tecnologia del CNC, applicata alla fresatura di forme complesse, si sia evoluta, passando dall’utilizzo del PDP11, il padre dei moderni microprocessori, agli attuali processori Intel di ultima generazione. La stessa tecnologia che da oltre 30 anni Fidia ha messo a disposizione dei suoi centri di fresatura ad alta velocità a 5 assi.
L’architettura del CNC FIDIA
I CNC FIDIA, nC19, C20 e C20 Vision (con doppio monitor), sono caratterizzati da un’architettura a doppio processore. Lato operatore, l’hardware è su base standard PC e sistema operativo Windows-10, con processore Intel Core i3, nel caso di nC19, oppure i7 per C20 e C20 Vision. L’utilizzo di software e hardware standardizzato rende i CNC Fidia facilmente manutenibili ed aggiornabili con indubbi benefici in termini di contenimento di costi e miglioramento delle prestazioni. L’interfaccia operatore del CNC FIDIA sfrutta appieno i plus dei monitor Touch-Screen con un approccio facile ed intuitivo a tutti i parametri di settaggio della macchina fresatrice.
Le lavorazioni a 5 assi
I CNC FIDIA offrono soluzioni tra le più innovative e performanti disponibili oggi sul mercato per le lavorazioni di fresatura ad Alta Velocità a 5-assi, in particolare per i settori automotive ed aerospaziale. È possibile eseguire qualsiasi lavorazione in modo efficace attraverso un’ampia gamma di funzioni che sia l’operatore macchina sia il responsabile dell’ufficio CAM possono decidere di utilizzare per ottenere la
massima flessibilità in ogni condizione di impiego. Parliamo di Velocity Five V5™-Plus: la tecnologia di controllo delle traiettorie con gestione dinamica dei parametri (DYNA) alla stregua, facendo un parallelo automobilistico, degli assetti “Eco”, “Standard”, “Sport” disponibili su molte vetture, in cui, in funzione della precisione della lavorazione si possono migliorare la qualità delle superfici lavorate o anche solo ridurre i tempi medi di esecuzione in macchina dei percorsi. Nelle lavorazioni a 5 assi, la funzione RTCP (Rotation Tool Center Point) permette di programmare i movimenti della macchina ragionando sulla sola posizione dell’utensile sul pezzo e lasciando al CNC FIDIA tutti i calcoli e le correzioni necessarie affinchè, in funzione della lunghezza dell’utensile, il posizionamento sul pezzo venga rispettato. Il CNC FIDIA mette sempre a disposizione dell’operatore un asse aggiuntivo (virtuale) dato dall’orientamento a 5 assi dell’utensile e gestibile alla stregua degli assi fisici X,Y,Z e rotativi. Parliamo dell’asse HW, Hand-Wheel, utilizzabile con estrema semplicità anche solo per inserire in tempo reale offset positivi (di distacco dalla superficie) o negativi (di avvicinamento alla superficie) durante l’esecuzione del percorso in macchina. La funzione TCPhs (hyper smooth) disponibile nelle lavorazioni a 5 assi, attenua potenziali movimenti bruschi indotti nelle compensazioni RTCP con ripercussioni positive sulla superficie del pezzo e sugli organi meccanici della macchina utensile in ragione della loro trasformazione in movimenti fluidi e morbidi.
Ancor più nelle lavorazioni a 5 assi, gioca un ruolo fondamentale la meccanica di tutti gli assi macchina in ottica di precisione e di qualità della superficie fresata. Per questo motivo FIDIA ha progettato e messo a disposizione dei suoi CNC lo strumento HMS™ (Head Measuring System) che impiega 3 sensori di posizione ad alta precisione per acquisire i dati sulla posizione reale della macchina successivamente utilizzati dal CNC per correggere automaticamente gli errori geometrici ed i parametri RTCP.
L’anticollisione secondo FIDIA FIDIA, unica nel settore, ha sviluppato ViMill® un potente software di anticollisione, coperto da brevetto, disponibile sui CNC top di gamma C20 Vision. ViMill® incorpora il modello 3D della macchina, il grezzo da lavorare e gli utensili che verranno utilizzati. Al momento dell’esecuzione di un percorso, simula in tempo reale tutti i movimenti richiesti controllandone preventivamente la correttezza e bloccandone così l’esecuzione fisica in macchina nel caso rilevamento di potenziali collisioni. ViMill® opera in simbiosi con il CNC FIDIA con il quale condivide tutti i parametri attivi istantaneamente. ViMill® controlla anche tutti i potenziali movimenti da
volantino o da singola linea di programma dell’operatore inibendo tutti quelli potenzialmente a rischio.
Industria 4.0: il futuro è adesso Gli incentivi messi in campo dal Governo in ottica di nuovi investimenti fin dall’anno 2017, hanno permesso di incasellare sotto il cappello dell’Industria 4.0 quanto FIDIA aveva già sviluppato e reso disponibile a tutti i suoi utenti. In particolare, i CNC
FIDIA collegati ad una rete ethernet, sono tutti potenzialmente accessibili dalla sua rete di Assistenza Tecnica attraverso il software di TELESERVICE. In questo modo, all’occorrenza e da remoto, è possibile accedere il CNC per una verifica dei parametri, il controllo dello stato di servizio e, se necessario, procedere all’aggiornamento del software. Un altro aspetto imprescindibile in ottica I4.0 è rappresentato dal monitoraggio continuo
della macchina utensile con conseguente raccolta di informazioni in relazione all’andamento delle commesse, ai fermi macchina, ed alla sua manutenzione preventiva. MachineMonitor è il software FIDIA che permette tutto questo raccogliendo tutti i dati sensibili che vengono quindi resi disponibili e piattaforme esterne attraverso server e protocolli standard di accesso al CNC da remoto.
Più compatto, più potente e con molte più possibilità in termini di applicazioni, grazie al suo design compatto, iTENDO² può sostituire perfettamente i portautensili standard e può quindi fare la differenza anche in produzioni di serie
iTENDO² rileva eventuali anomalie nel processo di asportazione come ad esempio vibrazioni eccessive, segni da vibrazione o se un utensile sta per rompersi. Dotato di sensore, batteria e unità di trasmissione, il portautensile intelligente monitora le vibrazioni sull’utensile: se le condizioni del tagliente o dell’utensile cambiano, è in grado di reagire in tempo reale, prevenendo così danni al pezzo o all’utensile.
Già il suo predecessore iTENDO eccelleva in vari campi di applicazione in termini di fresatura classica, svasatura o microasportazione, ma la nuova versione iTENDO² apre ora le porte a molte altre possibilità. Con una velocità incrementata, di massimo 30.000 giri/min, trova spazio in numerose applicazioni nel settore aerospaziale, nella lavorazione del vetro, nell’industria automotive e nella tecnologia medicale. Dà prova delle sue capacità anche in lavorazioni di serie complesse. Grazie all’ingombro ottimizzato, può sostituire perfettamente i portautensili standard, evitando così di dover riprogrammare la macchina. L’ingombro, infatti, resta lo stesso rispetto ai portautensili standard.
Il nuovo iTENDO² è disponibile nella versione TENDO HSK-A 63 con un diametro di 20, lunghezza 90. Diametri di serraggio inferiori possono essere bloccati ricorrendo a bussole di riduzione.
Tre pacchetti per ogni grado di complessità
Per favorire il passaggio a questa
tecnologia in modo semplice, Il portautensile intelligente iTENDO2 è disponibile in tre diversi pacchetti, ognuno dei quali è destinato a offrire una soluzione adeguata ad ogni uso e grado di complessità nella gestione dei dati.
Il portautensile nella versione base iTENDO2 pad invia i dati registrati direttamente al tablet in dotazione. Con l’app, l’utente può richiamare tutti i dati importanti direttamente sul dispositivo e utilizzarli per l’impostazione dei parametri e le analisi dei trend. In questo modo l’attenzione è focalizzata sulla trasparenza dei processi e sulla loro ottimizzazione in modo da evitare vibrazioni. Ciò si traduce non solo in superfici migliori, ma anche in una vita utile degli utensili sensibilmente prolungata.
Nella variante iTENDO2 easy connect può, invece, trasferire i valori rilevati ad altri sistemi tramite interfaccia analogica. Nella versione iTENDO2 pro, disponibile in futuro, potrà inviare i dati anche direttamente al sistema di controllo della macchina.
Tutte le varianti consentono un upgrade: è possibile iniziare a testare la tecnologia con la variante base con tablet. Dopo aver provato i vantaggi del portautensile intelligente, è possibile passare allo step successivo relativo alla gestione dei dati, per realizzare un monitoraggio automatizzato dei processi sempre più complesso.
Dal 2019 alla fiera di Hannover – anno in cui è stato presentato sul mercato il nuovo controllo numerico nativo digitale – Siemens si è posta l’obiettivo di unire in un unico CN il mondo digitale con quello reale e ad oggi, è possibile affermare che il 90% del suo portfolio clienti OEMs ha migrato a Sinumerik ONE totalmente o ne ha pianificato la migrazione.
“Le richieste dei nostri clienti sono rivolte al nostro CNC nativo digitale, Sinumerik ONE – spiega Cosma Vellere, Business Development Machine Tool System Manager di Siemens – e sono dettate in particolare dall’esigenza crescente di far parte della trasformazione digitale. Avere a disposizione strumenti che supportino gli end-users a combinare il mondo reale con quello digitale, è infatti fondamentale per raggiungere un sistema di fabbrica sempre più sostenibile”.
Siemens è al fianco dei clienti per aiutarli a rispondere ai propri obiettivi di sostenibilità e ad accelerare il proprio percorso di trasformazione digitale, fornendo tecnologie in grado di reinventare le aziende e le industrie.
Il portfolio software di Siemens si basa su tre pilastri fondamentali, tutti e tre orientati allo “Smart”:
Rendere una macchina utensile “smart” significa renderla più produttiva, flessibile e in grado di fornire al momento giusto le informazioni necessarie per prendere decisioni e intervenire.
La mancanza di trasparenza di dati sui cicli produttivi, sommata all’inconsistenza dei dati attuali disponibili, rende necessaria per la maggior parte delle aziende italiane la raccolta e la
gestione di dati puntuali realmente provenienti dalle macchine in produzione. Siemens offre Mcenter, la piattaforma SW basata su architettura aperta, modulare e connettibile con tutte le macchine utensili. Integrata con l’infrastruttura IT esistente, Mcenter permette di avere visibilità sui dati delle singole macchine utensili, aumentandone così la produttività e centralizzando tutte le operazioni, da un unico server centrale, per:
Manage MyResources /Tools
• Panoramica dello stato degli utensili di tutte le macchine
• Lista degli utensili caricati/scaricati
• Registrazione di parametri del singolo utensile
• Tracciabilità e calcolo lista utensili necessaria per il part program
• Interfaccia per i presetting utensili presenti sul mercato
Manage MyResources /Programs
• Assegnazione di un part program per la specifica macchina utensile
• Carico e scarico di part program, lista utensili, disegni CAD e
documentazione
• Tracciabilità del part program inviato e ricevuto, con funzione di comparazione
• Trasferimento diretto nel direttorio di lavoro del CNC Analyze MyPerformance /OEE
• Visualizzazione e grafica dei principali parametri per il calcolo dell’OEE:
• Disponibilità, efficienza e qualità – parametrizzabili con formule libere
• Trasparenza tra pianificato e realmente prodotto
• Evidenza dei “colli di bottiglia” in produttività e relativa risoluzione
• Modi operativi del CNC (manuale-semiautomaticoautomatico)
• Allarmi, descrizione e statistiche
• Personalizzazione grafica su segnali “focus”
Il Sinumerik ONE, primo CNC nativo digitale, si compone di 8 differenti livelli di gemello digitale.
Il gemello digitale di una macchina utensile permette di simulare accuratamente il comportamento della macchina reale nella sua interezza e nelle effettive condizioni operative, permettendo di testare i part-program in ufficio, lasciando la macchina reale in produzione, aumentando la produttività.
• Il gemello digitale permette la simulazione grafica del part-program, verificando la collisione utensile/mandrino pezzo segnalando l’eventuale blocco/blocchi programma di collisione avvenuta, fornendo un report dettagliato, oltre che un tempo di esecuzione programma fedele alla macchina utensile in quanto è presente sia il PLC macchina che l’interpolatore del CNC reale. Il tempo calcolato in simulazione può così essere utilizzato per offerte mirate a terzisti.
Smart Shopfloor
Allargando la visuale dalla singola macchina all’intera officina, emergono molte altre opportunità per aumentare efficienza e produttività, attraverso:
Manage MyMachines
• Visualizzazione grafica delle singole macchine con dettaglio dell’intera officina
• Macchina in produzione/stop /manutenzione
• Macchina in allarme, con storico degli allarmi precedenti per identificare eventuali ricorrenze
Manage MyMachines /Remote
• Accessibilità da remoto per interventi di service e/o supporto alla programmazione
Analyze MyMachine /Condition
• Visualizzazione risposta dinamica della macchina utensile, con possibilità di confronto grafici e pianificazione interventi di manutenzione per non bloccare la produttività.
BLUETECHHUB, POLO BRESCIANO DELL’ADVANCED MANUFACTURING E DELL’AUTOMAZIONE, È IL FIORE ALL’OCCHIELLO DELLE BUFFOLI INDUSTRIES, OFFRENDO SOLUZIONI INTEGRATE PER LA LAVORAZIONE MECCANICA PER ASPORTAZIONE, AUTOMAZIONE ROBOTIZZATA, ACCESSORI PER MACCHINE UTENSILI, CONTROLLO NUMERICO, SISTEMI DI MANIFATTURA ADDITIVA, REALTÀ AUMENTATA E INTELLIGENZA ARTIFICIALE di Stefano Baron – Buffoli Industries; Andrea Mazzoleni - AFIL
IIl gruppo Buffoli, presente in Italia, Europa, Nord America e Asia con 180 dipendenti, offre su scala globale un’ampia gamma di soluzioni, spesso brevettate, e servizi volti a raggiungere gli obiettivi di eccellenza operativa. È composto da una dozzina di aziende, ciascuna dotata di uno specifico know-how all’interno del vasto settore del manufacturing.
La forza della tecnologia su cui le aziende si stanno concentrando oggi non risiede nelle tecnologie singolarmente. Il valore deriva da come le aziende integrano la tecnologia per trasformare il business e il modo in cui si lavora, le aziende di BlueTechHub lavorano con questo obiettivo.
L’azienda principale del gruppo è Buffoli Transfer, che si occupa, come si intuisce dal nome, della produzione di “macchine transfer”: grandi impianti che rappresentano lo stato dell’arte delle macchine utensili. I sistemi transfer sono macchine che combinano più stazioni di lavorazione, ciascuna con uno o più mandrini. Il pezzo, normalmente fisso, può essere portato in rotazione anche in ogni stazione.
Il tutto spesso comprende anche dei robot o dei sistemi asserviti per il carico, il riposizionamento, lo scarico e la palletizzazione dei pezzi. La suddivisione delle fasi di lavorazione su più stazioni determina radicalmente la configurazione delle macchine transfer dovendone integrare il processo di lavoro, tanto che essa viene comprata tipicamente come soluzione a un problema produttivo (famiglie di pezzi). Per offrire maggiore versatilità, particolarmente in presenza di volumi produttivi più contenuti, l’azienda propone anche FMC o multicentri. Queste soluzioni flessibili a tre o più mandrini sono l’oggetto di questo articolo.
Nell’ambito dei Centri di lavoro, Buffoli, tradizionalmente legata a soluzioni transfer rotativi propone il medesimo concetto su celle flessibili di lavorazione multimandrino che consentono la lavorazione completamente automatica di componenti complessi,
dal pezzo grezzo a quello finito con un’unica macchina. Il processo di carico / riposizionamento / scarico, privo di impatto sul tempo di ciclo, riduce al minimo i tempi di fermo e incrementa la produttività.
Non si tratta di una soluzione per grandissime serie: gli obbiettivi sono la rapidità e l’economia di riattrezzaggio, unite ad una spiccata versatilità di impiego e modularità costruttiva. L’approccio modulare permette di realizzare macchine con elementi collaudati e quindi con maggiore affidabilità. La maggiore standardizzazione si riflette positivamente in ridotti tempi di consegna.
VERTI-CENTER è disponibile in due versioni base, la prima è equipaggiata con 3 centri di lavoro disposti attorno ad una tavola rotante a 4 stazioni, la seconda con 5 centri di lavoro e 6 stazioni. Elevate potenze specifiche in un ingombro compatto di soli 8 x 6 m e un consumo energetico ridotto sono i fattori fondamentali per raggiungere la migliore densità produttiva.
La struttura base della macchina è costituita da una cellula monolitica elettrosaldata in acciaio/polimero, a garanzia di rigidezza e stabilità dimensionale; l’intrinseca ermeticità porta benefici anche all’ambiente di lavoro con il confinamento dei fumi, del lubrorefrigerante e la riduzione delle emissioni acustiche.
I centri di lavoro integrano il cambio automatico dell’utensile (ATC) con prelievo diretto dai relativi magazzini utensili, ciascuno con capacità fino a 24 postazioni. L’assenza di cinematismi di trasferimento utensile garantisce un alto livello di affidabilità. Il sistema di refrigerazione forzata ad alta pressione è un equipaggiamento standard.
La completa integrazione di sistemi di automazione robotica, controllo dimensionale, ispezione con visione artificiale intelligente, lavaggio, protezione anti-ossidante ed eventuale packing sono ulteriori servizi resi disponibili ai clienti. Essi sono frutto dell’esperienza del gruppo e sono realizzati interamente grazie alle competenze delle
varie società della galassia Buffoli in una visione sistemica.
Grazie all’utilizzo delle tecnologie Internet of Things (IoT), viene offerto un accesso completo alle macchine e ai sensori di impianto, sfruttando i dati e le informazioni generati per migliorare la produttività.
VERTI-CENTER è adattabile a esigenze personalizzate. È possibile infatti attrezzare queste macchine con diverse tipologie di mandrino, attrezzature di bloccaggio pezzo e in configurazione a 4 o 5 assi. La stazione di carico ampiamente dimensionata consente la realizzazione di soluzioni di automazione estremamente produttive.
Partner nei cambiamenti
Mentre gli investimenti nella produzione intelligente stanno aumentando, molti progetti non riescono ad essere implementati con successo. La forza della tecnologia su cui le aziende si stanno concentrando oggi (digital twin, piattaforma IoT, realtà virtuale ed aumentata, intelligenza artificiale, analisi predittiva e altro) non risiede nelle tecnologie singolarmente. Il valore deriva da come le aziende integrano la tecnologia per trasformare il business e il modo in cui si lavora.
L’automazione dei processi non deve essere una soluzione “uguale per tutti” per gestire le operazioni critiche del settore.
Buffoli Industries offre un’ampia gamma di soluzioni con metodi e tecnologie che salvaguardano le operazioni e soddisfano i requisiti economici e prestazionali del cliente. Si tratta di soluzioni scalabili, flessibili e facili da integrare. Tutto questo aiuta l’organizzazione ad aumentare la produttività, ridurre i costi e il consumo energetico e a migliorare la sicurezza. La vasta esperienza nei processi aiuta i clienti a migliorare l’efficacia operativa e a ottenere un’elevata disponibilità.
Può essere utile avere un partner che
conosce il vostro settore operativo, i vostri punti di forza, i vostri sistemi e i vostri obiettivi operativi. L’esperienza acquisita dagli esperti Buffoli nelle applicazioni di una varietà di settori (idraulico, elettrico, automotive, sicurezza, gas, elettrodomestici) permette di avere conversazioni utili e rilevanti. Che desideriate fare un piccolo passo avanti o una vera e propria rivoluzione, Buffoli mette al vostro servizio la propria esperienza e una gamma di soluzioni ottimizzate per le vostre esigenze.
AFIL – Associazione Fabbrica Intelligente Lombardia – è il cluster tecnologico per il manifatturiero avanzato ufficialmente riconosciuto da Regione Lombardia. Attraverso le Strategic Communities, ovvero gruppi di lavoro formati da grandi imprese, PMI, start-up, associazioni, università e centri di ricerca che lavorano su tematiche strategiche per il manifatturiero lombardo, AFIL accompagna i suoi associati in un percorso collaborativo di crescita attraverso incontri tematici, workshop, webinar, matchmaking, missioni internazionali, favorendo lo sviluppo di progettualità di filiera e promuovendo la R&I anche a livello interregionale.
Le Strategic Communities di AFIL ad oggi sono 6: De- and Remanufacturing for Circular Economy, Digital Transformation, Advanced Polymers, Additive Manufacturing, Secure and Sustainable Food Manufacturing e Smart Components. Coloro che volessero ricevere maggiori informazioni sulle attività di AFIL sono pregati di scrivere ad andrea.mazzoleni@afil.it.
Per associarsi ad AFIL visitare www.afil.it
Cella flessibile (FMC) con processo di lavorazione sequenziale disponibile in versione a 4 o 5 assi con tavola sospesa ad asse verticale, equipaggiata con centri di lavoro ad alte prestazioni in grado di rispondere ai requisiti più rigorosi in termini di complessità dei pezzi e gestione dei lotti di prodotto
LE MACCHINE UTENSILI TREVISAN MACCHINE UTENSILI E I GIUNTI ROTANTI JOHNSON-FLUITEN
HANNO IN COMUNE PROCESSI PRODUTTIVI SVOLTI IN MASSIMA PARTE INTERNAMENTE CHE GARANTISCONO UN CONTROLLO TOTALE E PRESTAZIONI ECCELLENTI: UNA VISIONE CONDIVISA ALLA BASE DELLA FRUTTUOSA COLLABORAZIONE FRA LE DUE AZIENDE di C.G.
Da 60 anni Trevisan Macchine Utensili è un nome conosciuto e apprezzato in tutto il mondo per l’affidabilità e precisione delle sue soluzioni per l’industria meccanica. Fra le caratteristiche dell’offerta che hanno decretato il successo dell’azienda vanno sicuramente ricordate
la capacità di personalizzare le soluzioni in base alle richieste dei clienti e l’efficienza e puntualità del servizio di assistenza.
I centri di lavoro, le linee di tornitura e le macchine speciali di Trevisan Macchine Utensili sono stati acquistati da aziende operanti in moti campi , dall’industria energetica al comparto agricolo, passando per il settore spaziale, aeronautico, navale,
automotive, meccanico e oil & gas, distinguendosi in tutti i casi per le ottime prestazioni e il contributo decisivo alla competitività dei processi produttivi nelle realtà che li hanno scelti.
Il successo dell’azienda è determinato dalla capacità di raggiungere l’eccellenza in tutte le fasi del processo produttivo, dalla progettazione alla realizzazione: la maggior
{!}$ = [4]%! {x}
Con [X]M matrice modale ottenuta raccogliendo gli n autovettori, ovvero i modi di vibrare corrispondenti alle pulsazioni ωni trovate.
Si possono disaccoppiare le varie matrici che, diventando diagonali, rendono i calcoli molto più agevoli, trasformando il sistema sotto riportato in una serie di equazioni risolvibili singolarmente.
[5]$ {!}$ + [& ]$ {!}$ + [*]$ {! }$ = [4]% ' {, }
In generale, le vibrazioni vengono distinte in deterministiche, descrivibili mediante opportune relazioni matematiche, e casuali, il cui andamento non è prevedibile, motivo per cui vengono considerate come disturbi o rumore.
Perché vogliamo migliorare proprio le vi brazioni?
parte delle lavorazioni meccaniche, le finiture, il controllo qualità, l’assemblaggio e il collaudo sono effettuate internamente, garantendo una totale conformità di ogni aspetto agli elevati standard richiesti dalle aziende clienti.
Questo fenomeno, insieme agli urti, concorre al catti vo funzi onamento ed al precoce deterioramento delle macchine e delle strutture, nonché all’inquinamento acustico dell’ambiente circostante. Anche la salute dell’uomo ne è influenzata negativamente, con conseguenze sempre più oggetto di attenzione da parte dei responsabili preposti alla sicurezza.
Un accurato controllo dei componenti
surriscaldi e per consentire una lavorazione uniforme. Per far arrivare il lubrificante fino all’utensile occorre un giunto rotante, la cui resistenza e tenuta devono assicurare un apporto constante di fluido, nelle giuste quantità e solo dove occorre, in tutte le fasi della lavorazione.
Come già spiegato nell’articolo Lo smorzamento delle vibrazioni nelle macchine utensili | Blog RWItalia le vibrazioni nelle macchine utensili sono dovute principalmente a tre fattori :
- squi l i bri degl i al beri rotanti, come quello di trasmissione che collega il motore al mandrino, passando dai giunti e dalle ruote di trasmissione;
- difetti dimensioonali di alcuni componenti che costituiscono gli azionamenti;
Con queste premesse è logico aspettarsi l’applicazione di standard elevatissimi anche per la selezione dei componenti speciali che però devono essere acquistati da aziende specialistiche.
- un ingaggio intermittente fra l’utensile ed il pezzo da lavorare.
Le vibrazioni autoindotte e rigenerative
Fra questi rientrano i giunti rotanti, fondamentali nelle macchine utensili: il calore sviluppato durante la lavorazione richiede che l’utensile sia lubrificato adeguatamente per evitare che si
Molti anni or sono, Trevisan Macchine Utensili, decise di testare alternative ai giunti che utilizzava abitualmente: la ricerca delle soluzioni disponibili sul mercato condusse l’azienda verso JohnsonFluiten, che da oltre vent’anni progetta e produce giunti rotanti per applicazioni con acqua, vapore, olio e fluidi refrigeranti.
Efficienti e versatili
Tutti questi eventi generano delle forze periodiche che vengono convertite in vibrazioni forzate , che raramente causano problemi, e vibrazioni autoindotte , note anche come chatter, che sono uno dei limiti più importanti alla produttività dei processi di lavorazione. Già nel 1907 Taylor definì il chatter come “il problema più oscuro e delicato che si affronta nella lavorazione meccanica”. , parametro molto importante per incrementare il rendimento delle macchine o durante il processo di finitura dei componenti; la diretta conseguenza è la generazione di asperità molto evidenti di geometria particolare sulla superficie del componente, causandone spesso lo scarto. I modelli matematici di Arnold o di tipo B italia.it/smorzamento-vibrazioni-macchineo dipenda dalla lunghezza e dalla profondità del taglio,
Fra le caratteristiche della produzione Trevisan Macchine Utensili, che permettono di fornire soluzioni performanti ad aziende di tutti i segmenti industriali, va sicuramente ricordata l’attenta progettazione, in grado di unire un elevato grado di personalizzazione dell’impianto finito con una relativa standardizzazione della componentistica, che consente un’efficiente gestione del magazzino.
I giunti Johnson-Fluiten sono infatti particolarmente versatili: a differenza della maggior parte dei giunti sul mercato, che si adattano al variare di una sola condizione operativa (velocità, pressione, temperatura o tipo di fluido), queste soluzioni sono utilizzabili in tutte le condizioni, grazie alla speciale tenuta meccanica. Questo semplifica notevolmente diversi aspetti del processo produttivo e gestionale, riducendo notevolmente il numero di referenze che è necessario tenere a magazzino, con vantaggi per la logistica e la produttività
“ I tecnici Johnson-Fluiten si sono mostrati convinti della validità delle loro soluzioni, che ci hanno fatto provare senza impegno…
Ed abbiamo subito convenuto che avevano ragione: al di là delle minime difficoltà implicite in qualunque cambiamento di componenti, che abbiamo per altro superato rapidamente con l’aiuto del fornitore, le prestazioni si sono subito rivelate brillanti, del tutto all’altezza delle aspettative.”
Rossella Trevisan, titolare Trevisan Macchine Utensili
mettere a frutto.
In particolare, il componente scelto per la maggior parte dei progetti è un giunto rotante Serie G, nella versione GFLA con attacco radiale, particolarmente adatto per applicazioni ad alta dinamica con l’impiego di liquidi lubrorefrigeranti. La lavorazione speciale delle facce di tenuta in carburo di silicio rende questi giunti particolarmente resistenti all’usura e agli shock termici, mentre il sistema di tenuta a labirinto garantisce un’efficiente protezione dei cuscinetti a sfere da eventuali trafilamenti.
Il componente non richiede alcuna manutenzione e ha una durata molto elevata, caratteristica fondamentale per ridurre la necessità di interventi e particolarmente apprezzata da chi,
esporta macchinari in tutto il mondo e comprensibilmente adotta ogni cautela per evitare che siano necessarie onerose trasferte per manutenerli.
I giunti Serie G permettono di ridurre al minimo vibrazioni, coppia di attrito e perdite di carico, consentendo un andamento costante della lavorazione, ottimizzando l’efficienza e quindi la competitività della produzione.
L’importanza del servizio
La perfetta tenuta, l’affidabilità e la resistenza dei giunti rotanti JohsnonFluiten non sono le sole caratteristiche
alla base di questa lunga collaborazione. Come tutti i clienti di Johnson-Fluiten anche Trevisan Macchine Utensili ha infatti avuto modo di apprezzare gli elementi che compongono il servizio pre e post-vendita. In particolare, la preparazione dei tecnici di JohnsonFluiten si traduce in un servizio di consulenza, che anche nel caso di Trevisan Machine Tools è stato prestato senza alcun impegno sin dal primo contatto. La capacità di ascolto e comprensione delle esigenze del cliente ha permesso ai tecnici di ottenere le informazioni giuste per proporre la soluzione più adatta in tempi brevi; l’esperienza e conoscenza dei settori applicativi sono ala base della sicurezza con la quale Johnson-Fluiten ha potuto garantire il reperimento del giunto rotante ottimale per le esigenze della produzione. “La massima disponibilità dei tecnici, la puntualità delle consegne e il supporto costante dimostrato in questi anni sono importanti quanto la qualità dei prodotti nel determinare l’ottimo rapporto con Johnson-Fluiten; il nostro rapporto è destinato a proseguire ancora per molto tempo con reciproca soddisfazione”, ha commentato ancora Rossella Trevisan.
“Cerchiamo di utilizzare per quanto possibile gli stessi giunti rotanti per tutte le nostre soluzioni, che sono molte e spaziano dai centri di lavoro per la lavorazione di piccoli pezzi ai macchinari oversize, dalle linee di tornitura alle soluzioni speciali… Trovare un unico giunto che si adatti alle diverse situazioni che si presentano a fronte di una così ampia gamma di macchinari non è banale, ma le soluzioni Johnson-Fluiten hanno dimostrato di possedere questa caratteristica.”
Rossella Trevisan, titolare Trevisan Macchine Utensili che Trevisan Macchine Utensili ha saputo apprezzare eGiunto Rotante La sede Trevisan Macchine Utensili
I RIGOROSI STANDARD IGIENICI E LE DIFFICOLTÀ NELLA MANIPOLAZIONE DEI PRODOTTI
RENDONO L’AUTOMAZIONE DELLA PRODUZIONE ALIMENTARE UNA DELLE PIÙ GRANDI SFIDE. L’AZIENDA PINTRO HA IDEATO UNA NUOVA SOLUZIONE: IL SISTEMA PICK & SKEWER
COMPLETAMENTE AUTOMATIZZATO PER LA PREPARAZIONE DI KEBAB GRAZIE AI ROBOT STÄUBLI a cura della redazione
Shashlik, souvlaki, kebab e satay – tutte variazioni sul tema della carne allo spiedo –godono di grande popolarità tra i consumatori. La forza lavoro di 160 persone nello stabilimento di produzione di Beltaste N.V. a Morahalom, nel sud dell’Ungheria, produce principalmente shish kebab. Agli occhi
degli esperti di automazione è considerato un pioniere del “Food Processing 4.0”, ovvero la quarta generazione della tecnologia di produzione. Questo perché la prima macchina di infilzamento completamente automatica al mondo è stata commissionata lì, un anno e mezzo fa, e Beltaste ne ha installata una seconda. Per capire come funziona «ad occhio
nudo» il sistema completamente automatizzato Pick & Skewer, è necessaria la massima concentrazione, poiché il processo funziona a una velocità formidabile. Gli ingredienti vengono alimentati su due nastri trasportatori nel punto centrale della linea di produzione, con carne impanata, cruda o marinata su un binario e cipolle, peperoni, pomodorini
migliorasse la qualità, ma non abbiamo trovato nulla di adatto. Quando abbiamo visto il Pick & Skewer, siamo stati immediatamente conquistati. Abbiamo creduto nel concetto e abbiamo avuto fiducia nello sviluppatore e nel produttore”.
Con [X]M matrice modale ottenuta raccogliendo gli n autovettori, ovvero i modi di vibrare corrispondenti alle pulsazioni ωni trovate.
Cinque robot infilzano 15.000 ingredienti all’ora
Si possono disaccoppiare le varie matrici che, diventando diagonali, rendono i calcoli molto più agevoli, trasformando il sistema sotto riportato in una serie di equazioni risolvibili singolarmente.
I robot sono guidati da sistemi di visione e si muovono in base alle ricette memorizzate nel sistema di controllo. In tal modo, non sono solo veloci, ma anche versatili. “Generalmente variamo la ricetta ogni 16-20 ore. Se questo comporta un cambio pinze e ci vogliono solo cinque minuti grazie ai sistemi di cambio rapido”, afferma Muyshondt.
[5]$ {!}$ + [& ]$ {!}$ + [*]$ {! }$ = [4]% ' {, }
In generale, le vibrazioni vengono distinte in deterministiche, descrivibili mediante opportune relazioni matematiche, e casuali, il cui andamento non è prevedibile, motivo per cui vengono considerate come disturbi o rumore.
Il sistema è stato sviluppato dalla società belga PINTRO bv. Il suo nome è una forma semplificata della frase inglese “pin through”. Dal 2007, questa filiale del produttore di attrezzature speciali SMO bv produce macchinari per la produzione manuale o semiautomatica di kebab.
Perché vogliamo migliorare proprio le vi brazioni?
Gli ingegneri PINTRO hanno utilizzato tutta la loro esperienza nello sviluppo delle pinze. Il risultato è una combinazione di pinze meccaniche e a vuoto che prelevano più ingredienti diversi in un unico passaggio e poi li forano con precisione millimetrica, diversamente non sarebbe possibile raggiungere l’alto livello di prestazioni.
Questo fenomeno, insieme agli urti, concorre al catti vo funzi onamento ed al precoce deterioramento delle macchine e delle strutture, nonché all’inquinamento acustico dell’ambiente circostante. Anche la salute dell’uomo ne è influenzata negativamente, con conseguenze sempre più oggetto di attenzione da parte dei responsabili preposti alla sicurezza.
Come già spiegato nell’articolo Lo smorzamento delle vibrazioni nelle macchine utensili | Blog RWItalia le vibrazioni nelle macchine utensili sono dovute principalmente a tre fattori :
- squi l i bri degl i al beri rotanti, come quello di trasmissione che collega il motore al mandrino, passando dai giunti e dalle ruote di trasmissione;
- difetti dimensioonali di alcuni componenti che costituiscono gli azionamenti;
- un ingaggio intermittente fra l’utensile ed il pezzo da lavorare.
Il Pick & Skewer ha permesso un salto di qualità alla produzione completamente automatizzata di kebab, anche su larga scala. A seconda dell’output desiderato, un minimo di due e un massimo di cinque robot scelgono tutti gli ingredienti e li tengono pronti per lo spiedo. Beltaste ha optato per la versione con cinque robot top di gamma Stäubli TX2-60L HE. Poiché un robot a sei assi è in grado di prelevare e infilare fino a 3.000 ingredienti separati all’ora, il sistema raggiunge una produttività massima di 15.000 ingredienti. 10 ingredienti per spiedino, equivale a 1.500 kebab all’ora.
Le vibrazioni autoindotte e rigenerative
o qualsiasi altra cosa la ricetta richieda dall’altra. Posizionati a lato del sistema ci sono i meccanismi in cui gli ingredienti sono separati e tenuti pronti per lo skewering orizzontale.
Il compito dei robot Stäubli è quello di afferrare gli ingredienti e assicurarsi che lo spiedino li fori esattamente attraverso il loro centro. I kebab finiti vengono quindi convogliati alla stazione di confezionamento. Il sistema Beltaste produce tra 1.000 e 1.200 shish kebab all’ora senza l’intervento umano. E ognuno è di alta qualità.
Ogni robot produce il suo kebab completo individuale in pochi secondi. La posizione esatta di ogni singolo ingrediente è continuamente monitorata dai sistemi di elaborazione delle immagini. Pieter Weyens, responsabile di PINTRO: “I robot Stäubli montati a soffitto afferrano e posizionano ogni ingrediente con una precisione di ± 0,1 mm. Il posizionamento e l’allineamento precisi non sono gli unici criteri che contano qui. È anche importante che i kebab sembrino fatti a mano”.
Tutti questi eventi generano delle forze periodiche che vengono convertite in che raramente causano problemi, e uno dei limiti più importanti alla produttività dei processi di lavorazione. Già nel 1907 Taylor definì il chatter come “il problema più oscuro e delicato che si affronta nella lavorazione meccanica”. Esse si manifestano con l ’ aumen incrementare il rendimento delle macchine o durante il processo di finitura dei componenti; la diretta conseguenza è la generazione di asperità molto evidenti di geome superficie del componente, causandone spesso lo scarto. I modelli matematici di Arnold o di tipo B (ampiamente analizzati nell’articolo https://blog.rw utensili) constatano che questo fenomen dallo smorzamento dell’utensile e da un fattore relativo alla forza.
È stato proprio questo livello di performance che ha spinto il senior management di Beltaste a investire nel primo sistema Pick & Skewer al mondo. Come spiega Leon Muyshondt, Chief Technology Officer di Beltaste a Morahalom, “Abbiamo passato anni a cercare una soluzione che aumentasse la produttività e allo stesso tempo
L’igiene come fattore decisivo
Oltre alla velocità e precisione, anche l’igiene e la possibilità di lavaggio hanno giocato un ruolo chiave nella selezione del robot. Le procedure di pulizia sono massicce, come descrive Muyshondt: “Due volte al giorno, eseguiamo un ciclo automatico di pulizia e disinfezione degli utensili, che richiede un minuto e mezzo ogni volta. Dopo ogni turno, l’attrezzatura viene accuratamente pulita e disinfettata: prima viene applicata la schiuma, quindi viene irrorata con acqua calda tramite una lancia da 40 bar – e questo include i robot.” La versione HE (ambiente umido) del robot Stäubli TX2 a sei assi è impermeabile e quindi assolutamente adeguata a questo requisito. Il braccio è completamente incapsulato e resiste alla pulizia senza alcuna compromissione della funzione. Anche i processi di pulizia frequenti e intensivi, come quelli prevalenti nell’industria farmaceutica e alimentare, non portano ad alcuna riduzione della durata. Inoltre, i robot HE sono progettati per funzionare anche in ambienti sensibili. Il loro design igienico compatibile con il lavaggio è considerato unico.
I robot utilizzati nel sistema di spiedatura sono inoltre lubrificati con olio NSF
H1 per uso alimentare. “I robot sono sottoposti a un carico di lavoro pesante, perché eseguono molti movimenti rapidi e delicati. Quindi il lubrificante deve essere efficiente e allo stesso tempo soddisfare i requisiti dell’industria alimentare”, afferma Muyshondt. L’olio H1 che Stäubli ha sviluppato in collaborazione con un affermato produttore di lubrificanti soddisfa perfettamente questi criteri.
La coordinazione tra l’elaborazione delle immagini e i movimenti del robot, a questa velocità e con la precisione richiesta, chiede anche requisiti elevati del controller del robot. Questa è un altro punto in cui le macchine ottengono il massimo punteggio: i controller Stäubli CS9 sono noti per le loro elevate prestazioni e anche per l’eccellente connettività. Un ulteriore vantaggio è la loro semplicità di programmazione.
Per gli utenti del Pick & Skewer è ancora più elementare, spiega Muyshondt: “Il dipendente seleziona semplicemente una ricetta, carica gli ingredienti e preme il pulsante di avvio lavoro, fatto!” Mentre la produzione di kebab è in esecuzione, gli ingredienti possono essere aggiunti.
I sistemi di elaborazione delle immagini supervisionano anche il controllo di qualità di ogni singolo spiedino.
Nel Pick & Skewer, PINTRO ha sviluppato una novità “mondiale” per l’industria alimentare, eliminando gli ostacoli più duri incontrarti lungo il percorso, ad esempio col design delle pinze che raccolgono e posizionano fette di cipolla e pomodorini a velocità così alta per poter essere vista ad occhio nudo. Poiché il sistema gestisce carne cruda, l’intero processo deve essere eseguito nelle più rigorose condizioni igieniche il che, per fortuna, non è un problema per i robot Stäubli HE.
Dal punto di vista dei primi utilizzatori, il concetto offre chiari vantaggi. Muyshondt è entusiasta: “La qualità dei kebab è costantemente alta. Gli ingredienti sono infilzati con precisione e abbiamo una libera scelta degli ingredienti. I tempi di pulizia e disinfezione sono estremamente brevi e i robot possono essere lavati contemporaneamente. Questo è il futuro della produzione di kebab”. Con la prima linea Pick & Skewer che ha avuto un enorme successo, una seconda è recentemente entrata in funzione presso lo stabilimento di Beltaste in Ungheria.
DEI CUSCINETTI NELLA TESTA DEGLI UGELLI SPRUZZATORI ASSERVITI A MACCHINE DI RIVESTIMENTO, IL PIÙ GRANDE PRODUTTORE MONDIALE DI BEVANDE SI È RIVOLTO AGLI ESPERTI DI NSK a cura della redazione
Con [X]M matrice modale ottenuta raccogliendo gli n autovettori, ovvero i modi di vibrare corrispondenti alle pulsazioni ωni trovate.
Si possono disaccoppiare le varie matrici che, diventando diagonali, rendono i calcoli molto più agevoli, trasformando il sistema sotto riportato in una serie di equazioni risolvibili singolarmente.
industria alimentare e delle bevande è estremamente esigente, soprattutto perché i fermi delle linee di produzione possono rivelarsi molto costosi in tutti i tipi di applicazioni. Non fa eccezione la produzione di lattine di alluminio per bibite, bevande isotoniche e alcoliche, in particolare quando si parla del più grande produttore mondiale di bevande. Ripetuti cedimenti dei cuscinetti montati sul mandrino che aziona gli ugelli spruzzatori delle macchine per il rivestimento delle lattine causavano gravi interruzioni della produzione e tempi morti estremamente costosi su una linea di produzione per grandi volumi. L’azienda ha quindi incaricato NSK di risolvere il problema.
L’Le vibrazioni autoindotte e rigenerative
fuoriuscita del grasso, espulso dall’aria ad alta pressione utilizzata nel processo produttivo. Le tenute dei cuscinetti erano inadeguate a prevenire questo effetto indesiderato.
Tutti questi eventi generano delle forze periodiche che vengono convertite in vibrazioni forzate , che raramente causano problemi, e vibrazioni autoindotte , note anche come chatter, che sono uno dei limiti più importanti alla produttività dei processi di lavorazione. Già nel 1907 Taylor definì il chatter come “il problema più oscuro e delicato che si affronta nella lavorazione meccanica”. Esse si manifestano con l ’ aumento del l a vel oci tà di lavorazione , parametro molto importante per incrementare il rendimento delle macchine o durante il processo di finitura dei componenti; la diretta conseguenza è la generazione di asperità molto evidenti di geometria particolare sulla superficie del componente, causandone spesso lo scarto. I modelli matematici di Arnold o di tipo B (ampiamente analizzati nell’articolo https://blog.rw-italia.it/smorzamento-vibrazioni-macchineutensili) constatano che questo fenomeno dipenda dalla lunghezza e dalla profondità del taglio, dallo smorzamento dell’utensile e da un fattore relativo alla forza.
I tecnici esperti di NSK hanno condotto un’analisi approfondita dell’applicazione, ispezionando accuratamente i cuscinetti e il lubrificante. L’attività ha evidenziato che i cuscinetti si grippavano a causa della
Nell’ambito di una proposta completa a valore aggiunto, NSK ha raccomandato l’adozione dei propri cuscinetti radiali rigidi a sfere con tenute non striscianti serie VV e geometria di gioco interno C3. Offrendo prestazioni elevate
in ambienti contaminati, questa configurazione innovativa garantisce una tenuta efficace senza aumentare l’attrito o le temperature di esercizio. In particolare, il labbro non strisciante riduce la resistenza nel cuscinetto, garantendo un vantaggio importante nelle applicazioni in cui la coppia resistente è un fattore critico. La soluzione di NSK ha garantito un’eccellente ritenzione del grasso, consentendo al tempo stesso all’aria compressa ad alta pressione di fluire attraverso il cuscinetto, come richiesto dalle procedure operative dell’impianto. Ma, soprattutto, la fabbrica di lattine ha ottenuto un notevole incremento della durata dei cuscinetti, da 7 a 110 giorni, dopo i quali viene effettuata la manutenzione ordinaria. Il cliente beneficia cos ì di una maggiore durata dei cuscinetti, unita a un aumento della produttivit à e una riduzione dei costi di manutenzione, con un risparmio annuale quantificato in 240.000 Euro.
Eaton, leader a livello globale nella gestione dell’energia, presenta i nuovi relè di controllo easyE4, notevolmente migliorati, per ampliare la gamma di possibili applicazioni e soddisfare i crescenti requisiti di sicurezza informatica. Aggiornati rispetto alla versione precedente, i nuovi relè di controllo easyE4 di Eaton includono una comunicazione Ethernet significativamente più veloce, una memoria estesa e una trasmissione dati crittografata, che rendono l’implementazione delle attività di regolazione e controllo ancora più sicura e user-friendly. Inoltre, il nuovo controllore offre maggiore memoria e un MAC (Media Access Control) Ethernet integrato, a sostituzione di quello separato. Ciò rende easyE4 ancora più potente e pone le basi per ulteriori espansioni funzionali, in programma nel prossimo futuro.
Con l’aggiornamento, Eaton introduce anche un nuovo certificato per connessioni sicure tra il server Web di easyE4 e il browser, nonché una nuova versione (V2) del protocollo easyProtocol utilizzato per trasferire il programma. Grazie alla comunicazione crittografata SSL/TLS, i dati vengono trasmessi in modo sicuro senza essere letti da persone non autorizzate. Allo stesso tempo, la memoria del programma è stata più che triplicata, raggiungendo i 128 kB. Ciò consente programmi clienti più complessi, semplificando al contempo l’utilizzo dei popolari blocchi utente.
Inoltre, grazie a un importante aggiornamento delle funzioni, i blocchi utente ora sono accessibili tramite una cartella di archivio e possono quindi essere facilmente utilizzati anche in altri progetti senza onerose operazioni di esportazione/ importazione. Per analizzare da vicino cosa sta succedendo esattamente al loro interno, i blocchi utenti possono essere aperti in simulazione per visualizzarne lo stato.
Un’ulteriore innovazione riguarda i miglioramenti nel data logger e nella lettura dei file di log. Non è più necessario arrestare il programma per valutare i valori misurati: tale operazione può essere portata a termine anche nel cosiddetto stato “run”, cioè durante il funzionamento in corso. Mentre in precedenza l’accesso al data logger era possibile solo direttamente sul rispettivo relè di controllo, ora i dati possono essere comodamente letti tramite il server web integrato (e quindi tramite la rete aziendale), anche senza una licenza easySoft.
La modularità è uno dei grandi vantaggi di easyE4: anche il supporto per i moduli di espansione opzionali in easySoft è stato ulteriormente migliorato. Ora la stessa estensione può essere gestita all’interno di un unico programma, anche se l’applicazione comprende più macchine di diverse dimensioni, ciascuna con un differente numero di moduli di estensione. “Affidabili e versatili, i nuovi relè di controllo easyE4 sono stati creati specificamente per l’implementazione del comando e della regolazione di diverse applicazioni in maniera efficiente, flessibile e semplice. Oltre a essere facili da utilizzare, i dispositivi easyE4 sono anche semplici da programmare e sono quindi particolarmente adatti per la costruzione di macchine o nelle applicazioni di automazione di edifici”, ha spiegato Luca Vismara, Product Manager Drives di Eaton Italia. Per maggiori informazioni eaton.com
Una soluzione igus che ottimizza il collegamento di cavi elettrici, cavi in fibra ottica e tubi pneumatici riducendo dell’80% i tempi di installazione.
Module Connect è l’innovativo connettore plug-in compatto e modulare progettato da igus – specialista delle motion plastics - per il collegamento di cavi elettrici, cavi in fibra ottica e tubi pneumatici. Una soluzione che agevola notevolmente la predisposizione di numerosi cavi in catene portacavi, ideale per situazioni in cui lo spazio è limitato. Un sistema che offre all‘utente la possibilità di configurare l‘interfaccia su misura, scegliendo tra i 180 componenti disponibili nello shop online Module Connect. Il sistema modulare è stato sviluppato per offrire una pratica
alternativa all’impiego di diversi singoli connettori. Come spiega intrinsecamente il nome stesso, Module Connect consente ai clienti di combinare i plug-in più adatti alle singole necessità, collegando connettori e alloggiamenti per ottenere la combinazione perfetta, anche in termini di larghezze e altezze, dando vita a un modulo personalizzato e compatto. “Inoltre, Module Connect è un’interfaccia pronta per il collegamento che permette all’utente di ridurre dell’80% i tempi di installazione”, spiega Roberto Scaccabarozzi, Product Manager readycable e readychain presso igus Italia.
Per consentire agli utenti di progettare liberamente la propria interfaccia personalizzata, igus infatti offre la possibilità di selezionare nello shop online i singoli componenti tra le 180
proposte della gamma Module Connect. Un’offerta in costante ampliamento che, oltre ai set predefiniti con tre o quattro ingressi, comprende alloggiamenti di ogni tipo, meccanismi di bloccaggio, moduli e contatti per cavi elettrici, dati o tubi pneumatici. Grazie a questo adattatore, il sistema modulare si trasforma in un’unica interfaccia, riducendo il tempo di montaggio dell’80%. Esempio pratico: un utente vuole inserire 16 cavi in una catena portacavi e renderli innestabili. Nel Module Connect entrano quattro innesti diversi. Combinando quattro moduli Module Connect, il cliente può predisporre la sua interfaccia personalizzata. Mentre, con un sistema convenzionale avrebbe dovuto installare, collegare e serrare i singoli connettori nell’impianto. “Se consideriamo tutte queste varie fasi di lavoro, dall’installazione al riempimento delle catene portacavi fino alla regolazione delle sporgenze e alla posa dei cavi, occorre un tempo di montaggio di diverse ore”, spiega Markus Hüffel, responsabile readychain presso igus GmbH. “Grazie all’adattatore Module
Connect, l’intero assemblaggio è innestabile. Perciò viene collegato e serrato in un’unica volta, con una sola operazione. L’autocodifica del Module Connect permette inoltre di evitare gli errori di collegamento. In questo modo riduciamo il tempo di installazione da diverse ore ad alcuni minuti.” Anche in caso di manutenzione, l’operatore potrà semplicemente scollegare la
catena portacavi dall’adattatore, ricollegare un sistema di alimentazione preassemblato per rimettere direttamente in funzione la macchina o l’impianto.
Un collegamento sicuro e affidabile
Gli accessori integrati nell’alloggiamento, come gli elementi per il bloccaggio e per il fissaggio dei cavi, garantiscono la massima affidabilità e una connessione sicura, anche a fronte di decine di migliaia di movimenti. Gli alloggiamenti del sistema Module Connect sono realizzati in plastica ad alte prestazioni rinforzata con fibre e sono contraddistinti da un peso inferiore del 50% rispetto ai classici connettori rettangolari. L’adattatore Module Connect permette di collegare il connettore plug-in alla catena portacavi per formare un insieme robusto e sicuro. Una soluzione che si presta anche al retrofitting di sistemi di alimentazione già esistenti.
Design premiato
L’adattatore Module Connect è un prodotto che non convince solo clienti e utenti, ma ha conquistato anche la giuria del German Design Award 2020. Nella categoria Excellent Product Design l’adattatore è stato premiato dal Consiglio internazionale del design.
OMRON ha lanciato una nuova soluzione di pallettizzazione per i robot collaborativi, in risposta all’esigenza di processi di produzione più flessibili e tempi di programmazione ridotti. La soluzione di pallettizzazione con cobot basata su PLC è creata sul machine controller modulare serie NX1 di OMRON, dotato di uno speciale blocco funzione per la pallettizzazione.
Le soluzioni di pallettizzazione con robot collaborativi possono essere inserite in spazi ridotti e consentono a operatori e cobot di lavorare fianco a fianco in tutta sicurezza, senza l’aggiunta di recinzioni, liberando al contempo gli operatori da operazioni di sollevamento gravose e ripetitive. I pallettizzatori cobot sono quindi sempre più richiesti in molti settori e applicazioni di fine linea. Per semplificare e velocizzare la programmazione di queste applicazioni, OMRON ha lanciato una nuova soluzione di pallettizzazione con cobot.
Le funzionalità principali della soluzione, basate sul machine controller NX di OMRON con un unico blocco funzione, includono una rapida definizione degli schemi di pallet, una facile e dettagliata configurazione e la calibrazione tramite apprendimento, nonché una dashboard di produzione completa. La flessibilità della soluzione consente una semplice
INNODISK
espansione e l’integrazione di funzionalità aggiuntive. Il machine controller NX comunica direttamente con il controllore del cobot e gestisce senza problemi i diversi dispositivi di ingresso e di uscita e gli strumenti necessari per una soluzione di pallettizzazione, quali pinze, pilastri, nastri trasportatori, componenti di sicurezza, sensori, e servomotori. Ciò consente di eseguire il sequenziamento completo dal PLC. Questa soluzione può essere collegata a un’interfaccia uomo-macchina per il funzionamento.
“Una delle principali sfide attuali per le applicazioni di pallettizzazione è la complessità legata alla programmazione dei diversi schemi di pallet. Questa soluzione riduce significativamente i tempi di programmazione e semplifica le modifiche per gli operatori”, ha commentato Fernando Vaquerizo, Fixed and Cobots Product Marketing Manager di OMRON Europe. “Sono molto entusiasta di questa soluzione sviluppata in collaborazione con il nostro Automation Center di Barcellona. Abbiamo sfruttato al massimo l’ampia esperienza applicativa accumulata dai nostri ingegneri nel corso degli anni”, ha concluso Vaquerizo.
Informazioni su OMRON Corporation
L’industria del 5G è in piena espansione, in particolare nella tecnologia di networking slicing, che ha consentito lo sviluppo di un’architettura di trasmissione efficiente per le reti 5G. Il network slicing consente ai gestori di creare più reti per soddisfare i requisiti differenziati di capacità di rete di clienti diversi, ma comporta anche nuove sfide di archiviazione dei dati per il settore. Per aiutare i clienti a superare gli ostacoli dell›archiviazione e dell›accesso ai dati in ambienti industriali difficili, Innodisk, fornitore globale leader di storage flash di livello industriale, ha lanciato la linea più completa di soluzioni di storage di livello industriale. In risposta ai requisiti di lettura e scrittura ad alta resistenza generati dai dispositivi IoT e dall’edge computing AI, Innodisk ha introdotto la tecnologia iSLC brevettata di nuova generazione con la sua esclusiva innovazione tecnologica del firmware. Combinando la flash NAND 3D TLC BiCS5 a 112 strati, la nuova tecnologia migliora le prestazioni di archiviazione industriale e raggiunge i 100.000 cicli P/E, il valore più elevato del settore. Rispetto alle tradizionali Flash NAND TLC 3D, ciò estende la durata di 33 volte. Inoltre, poiché molte reti 5G, infrastrutture 5G e applicazioni per città intelligenti sono implementate in condizioni esterne difficili o in ambienti operativi 24 ore su 24, 7 giorni su 7, come il pagamento elettronico intelligente basato sull›ispezione visiva AI e ANPR, Innodisk sfrutta la sua capacità di integrazione hardware- software per incorporare le tecnologie firmware nella serie iSLC. Con l’esclusivo firmware iData Guard e iPower Guard di Innodisk, la transizione dei dati può essere condotta in ambienti instabili ed essere protetta per ottenere stabilità ed esperienza ottimali per le opportunità di business di reti 5G, smart city e applicazioni AIoT. La serie iSLC Innodisk supporta le interfacce SATA e PCIe e fornisce varie specifiche dimensionali, nonché modelli di temperatura standard e industriali ad ampio range. Ora, le serie SATA SSD 3IE7 e PCIe 4IG2-P sono già disponibili sul mercato e le serie PCIe 3IE6 e PCIe 4IE3 saranno presto lanciate nel secondo trimestre del 2023. I clienti di diversi settori possono quindi trovare soluzioni ideali grazie alla gamma completa e di alta qualità dell’offerta Innodisk. Informazioni su Innodisk.com
HAINBUCH, specialista delle soluzioni di bloccaggio pezzi sulle macchine utensili propone una serie di dispositivi di bloccaggio che sono in grado di aumentare la flessibilità della macchina utensile e di abbattere in maniera considerevole i tempi di attrezzaggio della stessa.
HAINBUCH System è un sistema modulare che prevede una attrezzatura di base che viene scelta in base al tipo e alla dimensione della macchina sulla quale verrà montata e che utilizza delle pinze per poter serrare i pezzi sul loro profilo esterno. Dette attrezzature di base, che esistono sia con azionamento manuale, idraulico o meccanico, possono essere montate sia su macchine nelle quali il sistema di bloccaggio va in rotazione, come torni, rettifiche, dentatrici, etc., oppure su macchine dove l’attrezzatura rimane statica, come ad esempio i centri di lavoro verticali, orizzontali, a tre o più assi, macchine transfer etc.
Il cambio della pinza da un diametro all’altro avviene in pochi secondi e in tutta sicurezza grazie ad un apposito attrezzo di cambio che può essere manuale o pneumatico.
Nel caso nel quale il particolare da bloccare dovesse avere una misura superiore al limite massimo della pinza, allora è possibile inserire al posto della stessa un modulo
che trasforma l’attrezzo di base in un vero e proprio mandrino autocentrante a due o a tre griffe che ne aumenta la capacità di bloccaggio, inoltre è possibile, sempre inserendo l’ apposito modulo di adattamento, trasformare l’attrezzatura di base da bloccaggio da diametro esterno ad una da diametro interno tramite delle bussole ad espansione, completano l’offerta degli adattamenti anche un modulo magnetico, una contropunta con trascinatore frontale e un’ alloggiamento per il cono Morse. Queste trasformazioni avvengono in maniera semplice, richiedono solo pochi minuti e non hanno la necessità di ulteriori regolazioni di centraggio.
Le attrezzature di base, siano esse destinate all’uso statico che dinamico, hanno la possibilità di montare, sempre in brevissimo tempo, dei sistemi che fungono da riferimento per la posizione del pezzo da lavorare garantendo precisioni di ripetibilità elevatissime.
Un altro grande vantaggio di questi sistemi modulari è che gli adattatori, a parità di
taglia, sono intercambiabili tra le varie attrezzature di base presenti in azienda, sia statiche che rotanti.
La rapidità del cambio tra una attrezzatura di bloccaggio e un’altra conferisce enorme versatilità alla macchina utensile, consentendole di produrre in maniera redditizia anche piccoli lotti. La riduzione dei tempi di attrezzaggio e il conseguente massiccio abbattimento dei costi di fermo macchina consentono il rientro dell’investimento in un breve lasso di tempo.
Completano il quadro l’affidabilità e la necessità di una manutenzione ridotta che fanno di queste attrezzature dei veri strumenti per il risparmio del tempo.
Il tema della compatibilità elettromagnetica (EMC) sta diventando sempre più centrale nelle Smart Factory, in virtù della crescente interconnessione di macchine e sistemi. In questo contesto, le interferenze elettromagnetiche possono infatti portare rapidamente a malfunzionamenti nell’intero sistema e, di conseguenza, un’attenzione particolare viene rivolta alla scelta di componenti ottimizzati in ottica EMC. Per soddisfare queste esigenze, LAPP, leader nello sviluppo e produzione di soluzioni integrate nella tecnologia di connessione e cablaggio, ha ideato l’innovativa tecnologia brevettata zeroCM® (CommonMode).
A seconda delle applicazioni, LAPP propone soluzioni per ridurre o eliminare le interferenze. Tre in particolare le tipologie di schermatura adottate da LAPP per i suoi cavi. La più comune prevede l’utilizzo di una calza in rame stagnato tra guaina e conduttori, con un livello di copertura di circa l’80%. In presenza di frequenze di funzionamento elevate, la seconda tipologia ottimale è quella con foglio di alluminio laminato. Inoltre, i cavi spesso presentano diverse tipologie di schermatura contemporaneamente. È il caso di ÖLFLEX®
SERVO 2XSLCH-JB, che combina le due configurazioni sopra menzionate. Entrando più nel merito dei cavi dati, particolarmente soggetti a interferenze, è possibile indivi-
duare un ulteriore metodo per ridurre gli effetti delle interferenze elettromagnetiche, in cui le anime del cavo sono twistate a coppie, affinché gli effetti di campo si compensino. Declinazione concreta è il cavo di rete ETHERLINE® Cat 6a H 4x2xAWG22/1, il quale è dotato di una schermatura con calza di rame stagnato sul cordato totale dei cavi e a nastro di alluminio sulle singole coppie.
ÖLFLEX® SERVO FD zeroCM completa l’offerta LAPP. Progettato come cavo di collegamento tra convertitore di frequenza e motore, è stato completamente riprogettato: i tre conduttori di potenza sono ora cordati simmetricamente, mentre il conduttore di protezione è avvolto in senso opposto. L’isolamento dei conduttori in polietilene o polipropilene “attenua” i picchi di tensione. Infine, la sua struttura inedita permette di ottimizzare il cavo in ottica EMC, raggiungendo il 100% di simmetria elettromagnetica, a garanzia di una notevole riduzione delle interferenze sulla trasmissione dei dati e delle correnti parassite nei cuscinetti motore.
La tecnologia zeroCM® non elimina la causa delle interferenze elettromagnetiche, ma gestisce uno dei punti chiave attraverso il quale l’interferenza entra nel sistema. In specifico, da un lato, l’inusuale design del cavo assicura una riduzione delle correnti di
compensazione dell’80% all’uscita del convertitore di frequenza e su percorsi paralleli, con presenza di cavi dati. Dall’altro, la riduzione delle perdite di energia nel cavo permette di installare cavi di lunghezze maggiori, mantenendo il convertitore entro i suoi limiti EMC previsti. Inoltre, ulteriori vantaggi sono la riduzione dei costi, in quanto non risulta più necessaria una complessa tecnologia di filtraggio e una stabilità del sistema superiore. Sebbene il nuovo cavo possa apparire insolito, l’installazione si rivela semplificata rispetto ai cavi simmetrici con conduttore di terra suddiviso in tre parti.
“La richiesta di soluzioni ottimizzate EMC è in aumento, come risultato del crescente impiego di soluzioni di connettività nelle fabbriche intelligenti” dichiara Simone Albrizio, Product Marketing Manager di LAPP, che prosegue “Finora il problema della compatibilità elettromagnetica è stato affrontato mediante l’impiego di schermature, la tecnologia di ultima generazione zeroCM® apre invece le porte a nuove possibilità nella progettazione dei cavi, all’insegna di prestazioni sempre più elevate anche in termini di protezione da interferenze EMI. Il focus di LAPP sarà di ampliare la gamma di prodotti zeroCM®, con particolare riguardo ai cavi ibridi”. Per informazioni www.lappitalia.com
n.3 Aprile 2023
www.meccanica-automazione.com
Redazione Direttore Responsabile
Giorgio Albonetti
Coordinamento Editoriale Area Industry
Marco Tenaglia –marco.tenaglia@quine.it – cel. 3298490024
Direttore tecnico
Chiara Tagliaferri
Segreteria di Redazione
Cristina Gualdoni
cristina.gualdoni@quine.it – cel. 3477623887
Hanno collaborato a questo numero
Patrizia Ricci, Eleonora Segafredo, Stefano Baron, Andrea Mazzoleni
Pubblicità Costantino Cialfi | Direttore Commerciale c.cialfi@lswr.it - tel. +39 3466705086
Elena Genitoni | Ufficio Traffico e.genitoni@lswr.it – tel. 0289293962
Servizio abbonamenti abbonamenti.quine@lswr.it
Abbonamento annuale € 49,99
Costo copia singola € 7,07 (presso l’editore)
Produzione Antonio Iovene | Procurement Specialist
a.iovene@lswr.it | Cell. 349.1811231
Grafica e Fotolito: Fabio Castiglioni
Stampa: Aziende Grafiche Printing Srl
Peschiera Borromeo (MI)
Registrazione del Tribunale di Milano n. 653 del 21.09.2005.
Iscrizione al R.O.C. n. 12191 del 29/10/2005 Tutti gli articoli pubblicati su m&a meccanica &automazione sono redatti sotto la responsabilità degli Autori. La pubblicazione o la ristampa degli articoli deve essere autorizzata per iscritto dall’Editore. Ai sensi dell’art. 13 del D.Lgs. 196/03, dati di tutti i lettori saranno trattati sia manualmente sia con strumenti informatici e saranno utilizzati per l’invio di questa e di altre pubblicazioni e di materiale informativo e promozionale. Le modalità di trattamento saranno conformi a quanto previsto dall’art. 11 D.Lgs. 196/03. I dati potrebbero essere comunicati a soggetti con i quali Quine S.r.l. intrattiene rapporti contrattuali necessari per l’invio delle copie della rivista. Il titolare del trattamento dei dati è Quine S.r.l. - via Spadolini, 7 - 20141 Milano Tel +39 02 864105 Fax +39 02 72016740, al quale il lettore si potrà rivolgere per chiedere l’aggiornamento, l’integrazione, la cancellazione e ogni altra operazione di cui all’art. 7 D.Lgs. 196/03.
Ai sensi dell’art. 13 Regolamento Europeo per la Protezione dei Dati Personali 679/2016 di seguito GDPR, i dati di tutti lettori saranno trattati sia manualmente, sia con strumenti informatici e saranno utilizzati per l’invio di questa e di altre pubblicazioni e di materiale informativo e promozionale. Le modalità di trattamento saranno conformi a quanto previsto dagli art. 5-6-7 del GDPR. I dati potranno essere comunicati a soggetti con i quali Edra S.p.A. intrattiene rapporti contrattuali necessari per l’invio delle copie della rivista. Il titolare del trattamento dei dati è Edra S.p.A., Via G. Spadolini 7 - 20141 Milano, al quale il lettore si potrà rivolgere per chiedere l’aggiornamento, l’integrazione, la cancellazione e ogni altra operazione di cui agli articoli 15-21 del GDPR.
Testata associata